Cost Accounting Report: Job, Process, ABC Costing, Overhead Analysis
VerifiedAdded on 2023/06/08
|11
|1740
|109
Report
AI Summary
This report delves into the core concepts of cost accounting, providing a comprehensive overview of various costing methods. It begins by defining accountancy and its role in business, then explores the differences between job costing and process costing, illustrating their applicability through real-world examples like architect firms and oil refineries. The report then calculates the cost of goods manufactured, including direct materials, direct labor, and manufacturing overhead. It proceeds to analyze traditional costing versus ABC costing, calculating overhead rates and cost per unit under both methods, and determining which method overvalues the amount and why. The report includes journal entries for various transactions, such as material purchases, labor costs, and depreciation. Finally, it discusses the application of ABC and traditional costing, highlighting the benefits of ABC in improving operational efficiency and profitability, and concludes by summarizing the key findings and emphasizing the importance of accurate cost allocation in modern business environments. The report utilizes formulas, calculations, and real-world examples to illustrate the concepts, providing a clear understanding of cost accounting principles.
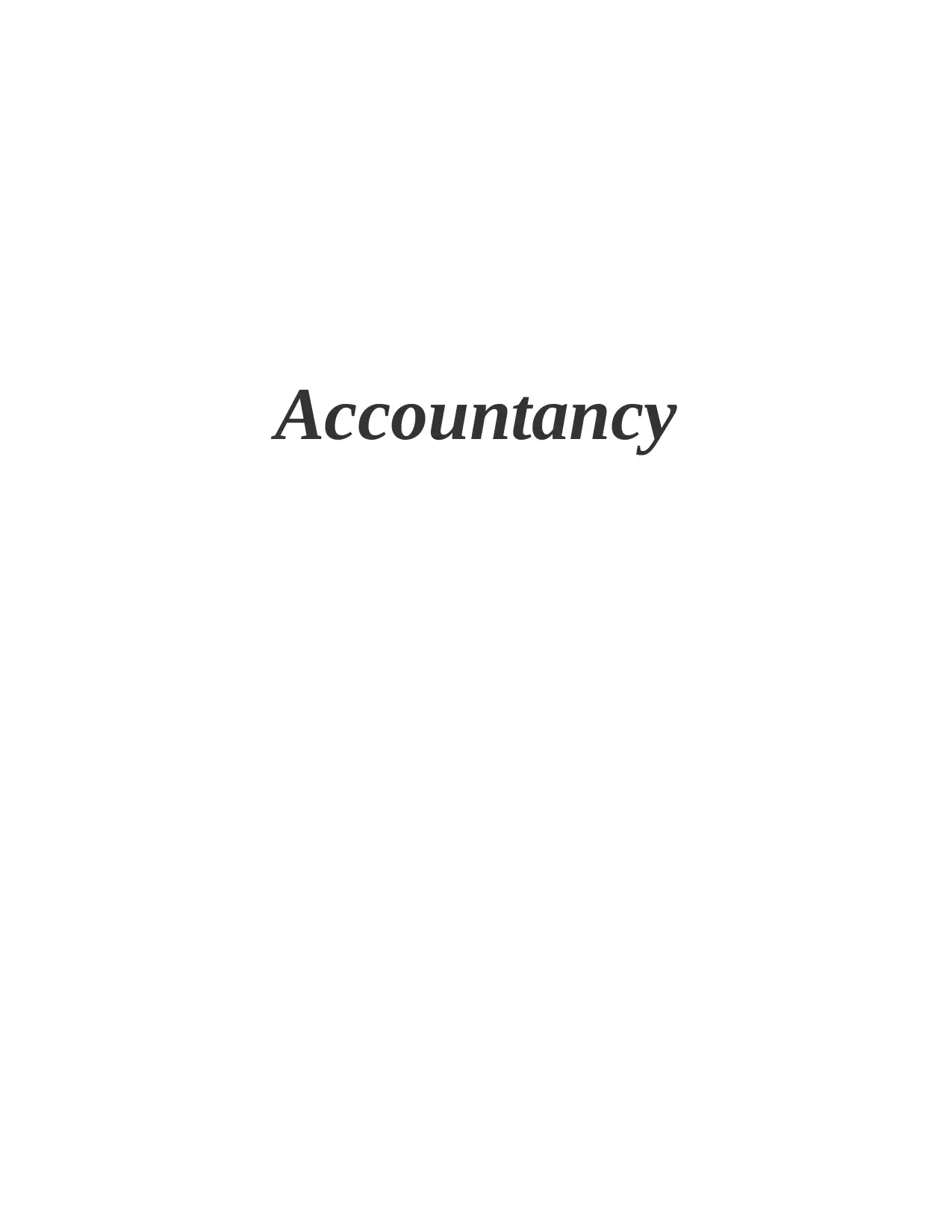
Accountancy
Secure Best Marks with AI Grader
Need help grading? Try our AI Grader for instant feedback on your assignments.
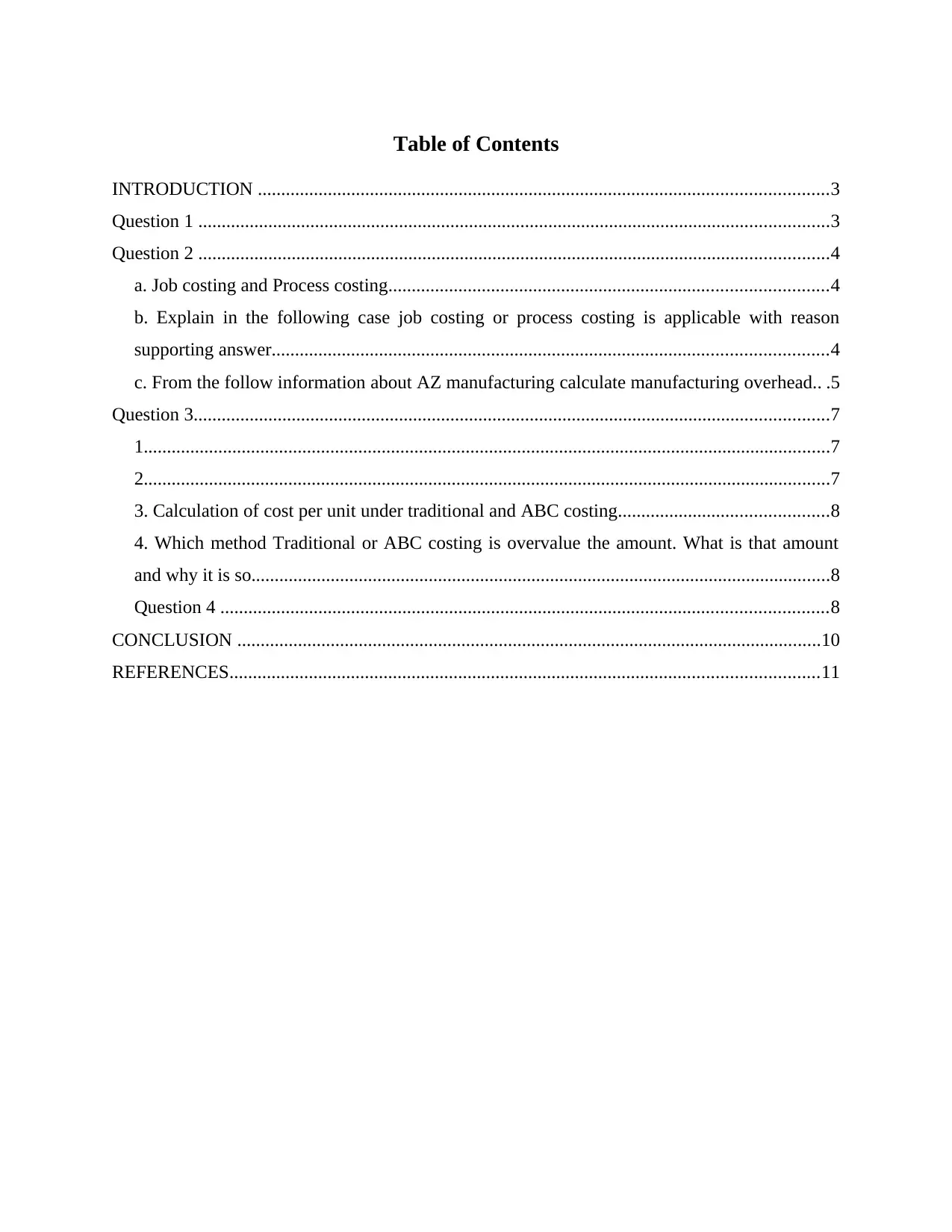
Table of Contents
INTRODUCTION ..........................................................................................................................3
Question 1 .......................................................................................................................................3
Question 2 .......................................................................................................................................4
a. Job costing and Process costing..............................................................................................4
b. Explain in the following case job costing or process costing is applicable with reason
supporting answer.......................................................................................................................4
c. From the follow information about AZ manufacturing calculate manufacturing overhead.. .5
Question 3........................................................................................................................................7
1...................................................................................................................................................7
2...................................................................................................................................................7
3. Calculation of cost per unit under traditional and ABC costing.............................................8
4. Which method Traditional or ABC costing is overvalue the amount. What is that amount
and why it is so............................................................................................................................8
Question 4 ..................................................................................................................................8
CONCLUSION .............................................................................................................................10
REFERENCES..............................................................................................................................11
INTRODUCTION ..........................................................................................................................3
Question 1 .......................................................................................................................................3
Question 2 .......................................................................................................................................4
a. Job costing and Process costing..............................................................................................4
b. Explain in the following case job costing or process costing is applicable with reason
supporting answer.......................................................................................................................4
c. From the follow information about AZ manufacturing calculate manufacturing overhead.. .5
Question 3........................................................................................................................................7
1...................................................................................................................................................7
2...................................................................................................................................................7
3. Calculation of cost per unit under traditional and ABC costing.............................................8
4. Which method Traditional or ABC costing is overvalue the amount. What is that amount
and why it is so............................................................................................................................8
Question 4 ..................................................................................................................................8
CONCLUSION .............................................................................................................................10
REFERENCES..............................................................................................................................11
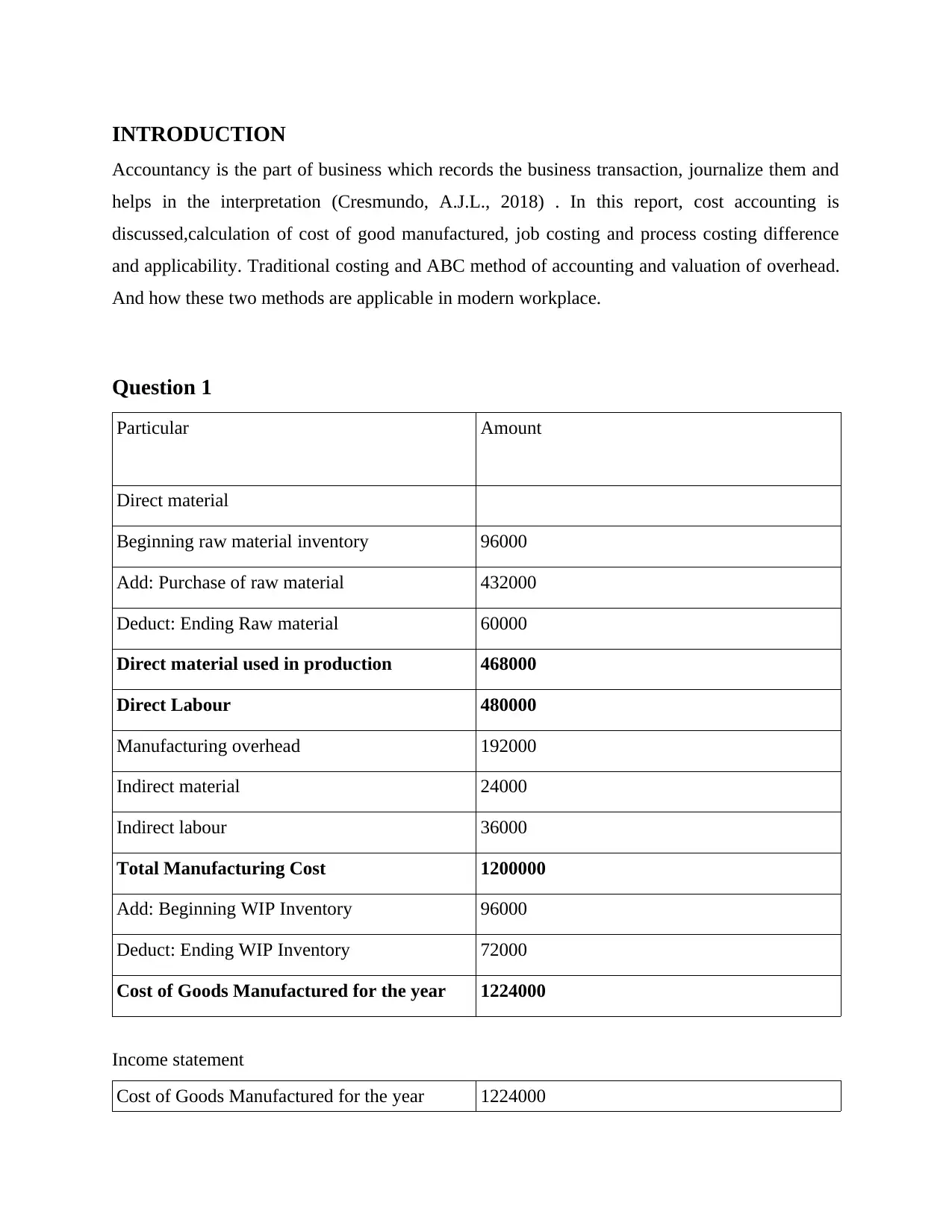
INTRODUCTION
Accountancy is the part of business which records the business transaction, journalize them and
helps in the interpretation (Cresmundo, A.J.L., 2018) . In this report, cost accounting is
discussed,calculation of cost of good manufactured, job costing and process costing difference
and applicability. Traditional costing and ABC method of accounting and valuation of overhead.
And how these two methods are applicable in modern workplace.
Question 1
Particular Amount
Direct material
Beginning raw material inventory 96000
Add: Purchase of raw material 432000
Deduct: Ending Raw material 60000
Direct material used in production 468000
Direct Labour 480000
Manufacturing overhead 192000
Indirect material 24000
Indirect labour 36000
Total Manufacturing Cost 1200000
Add: Beginning WIP Inventory 96000
Deduct: Ending WIP Inventory 72000
Cost of Goods Manufactured for the year 1224000
Income statement
Cost of Goods Manufactured for the year 1224000
Accountancy is the part of business which records the business transaction, journalize them and
helps in the interpretation (Cresmundo, A.J.L., 2018) . In this report, cost accounting is
discussed,calculation of cost of good manufactured, job costing and process costing difference
and applicability. Traditional costing and ABC method of accounting and valuation of overhead.
And how these two methods are applicable in modern workplace.
Question 1
Particular Amount
Direct material
Beginning raw material inventory 96000
Add: Purchase of raw material 432000
Deduct: Ending Raw material 60000
Direct material used in production 468000
Direct Labour 480000
Manufacturing overhead 192000
Indirect material 24000
Indirect labour 36000
Total Manufacturing Cost 1200000
Add: Beginning WIP Inventory 96000
Deduct: Ending WIP Inventory 72000
Cost of Goods Manufactured for the year 1224000
Income statement
Cost of Goods Manufactured for the year 1224000
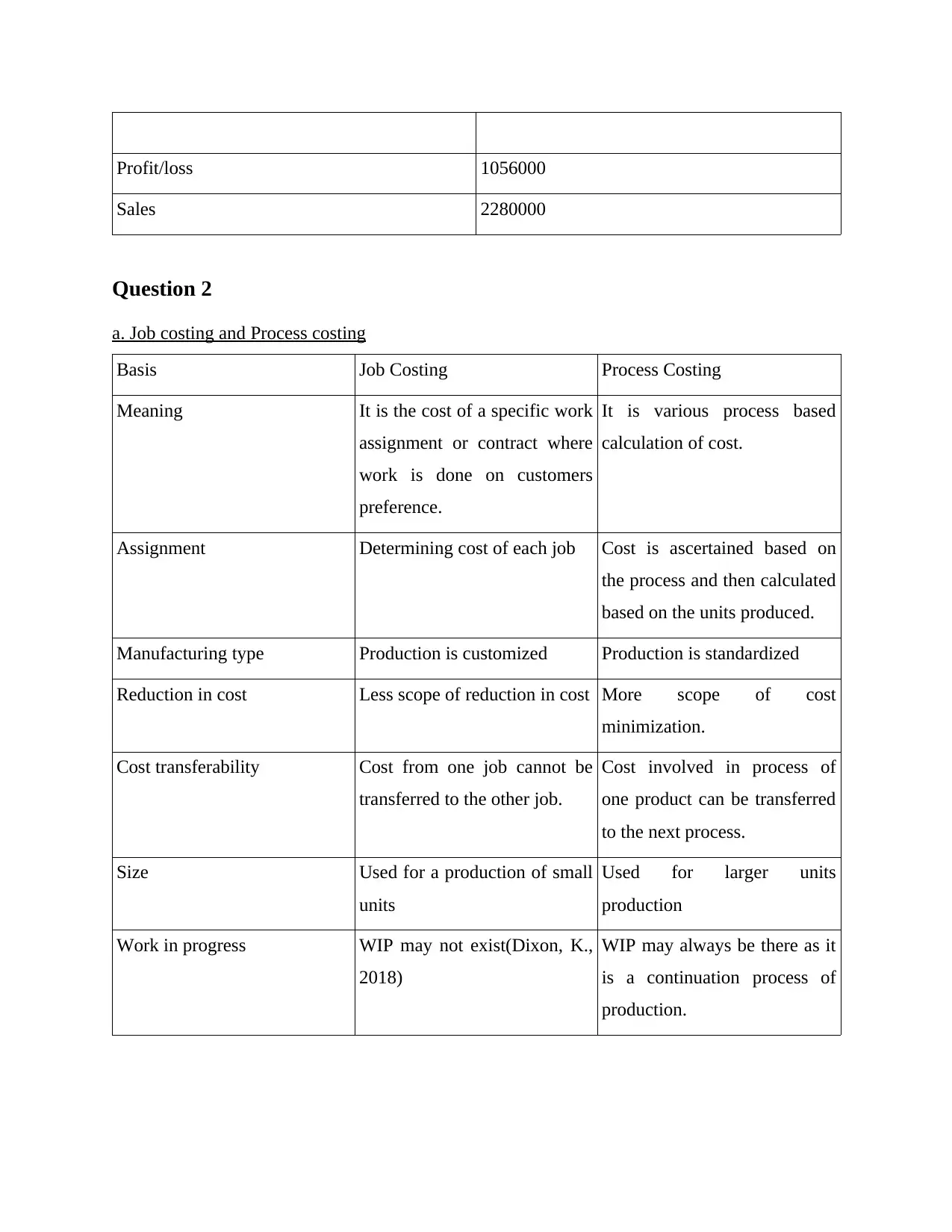
Profit/loss 1056000
Sales 2280000
Question 2
a. Job costing and Process costing
Basis Job Costing Process Costing
Meaning It is the cost of a specific work
assignment or contract where
work is done on customers
preference.
It is various process based
calculation of cost.
Assignment Determining cost of each job Cost is ascertained based on
the process and then calculated
based on the units produced.
Manufacturing type Production is customized Production is standardized
Reduction in cost Less scope of reduction in cost More scope of cost
minimization.
Cost transferability Cost from one job cannot be
transferred to the other job.
Cost involved in process of
one product can be transferred
to the next process.
Size Used for a production of small
units
Used for larger units
production
Work in progress WIP may not exist(Dixon, K.,
2018)
WIP may always be there as it
is a continuation process of
production.
Sales 2280000
Question 2
a. Job costing and Process costing
Basis Job Costing Process Costing
Meaning It is the cost of a specific work
assignment or contract where
work is done on customers
preference.
It is various process based
calculation of cost.
Assignment Determining cost of each job Cost is ascertained based on
the process and then calculated
based on the units produced.
Manufacturing type Production is customized Production is standardized
Reduction in cost Less scope of reduction in cost More scope of cost
minimization.
Cost transferability Cost from one job cannot be
transferred to the other job.
Cost involved in process of
one product can be transferred
to the next process.
Size Used for a production of small
units
Used for larger units
production
Work in progress WIP may not exist(Dixon, K.,
2018)
WIP may always be there as it
is a continuation process of
production.
Secure Best Marks with AI Grader
Need help grading? Try our AI Grader for instant feedback on your assignments.
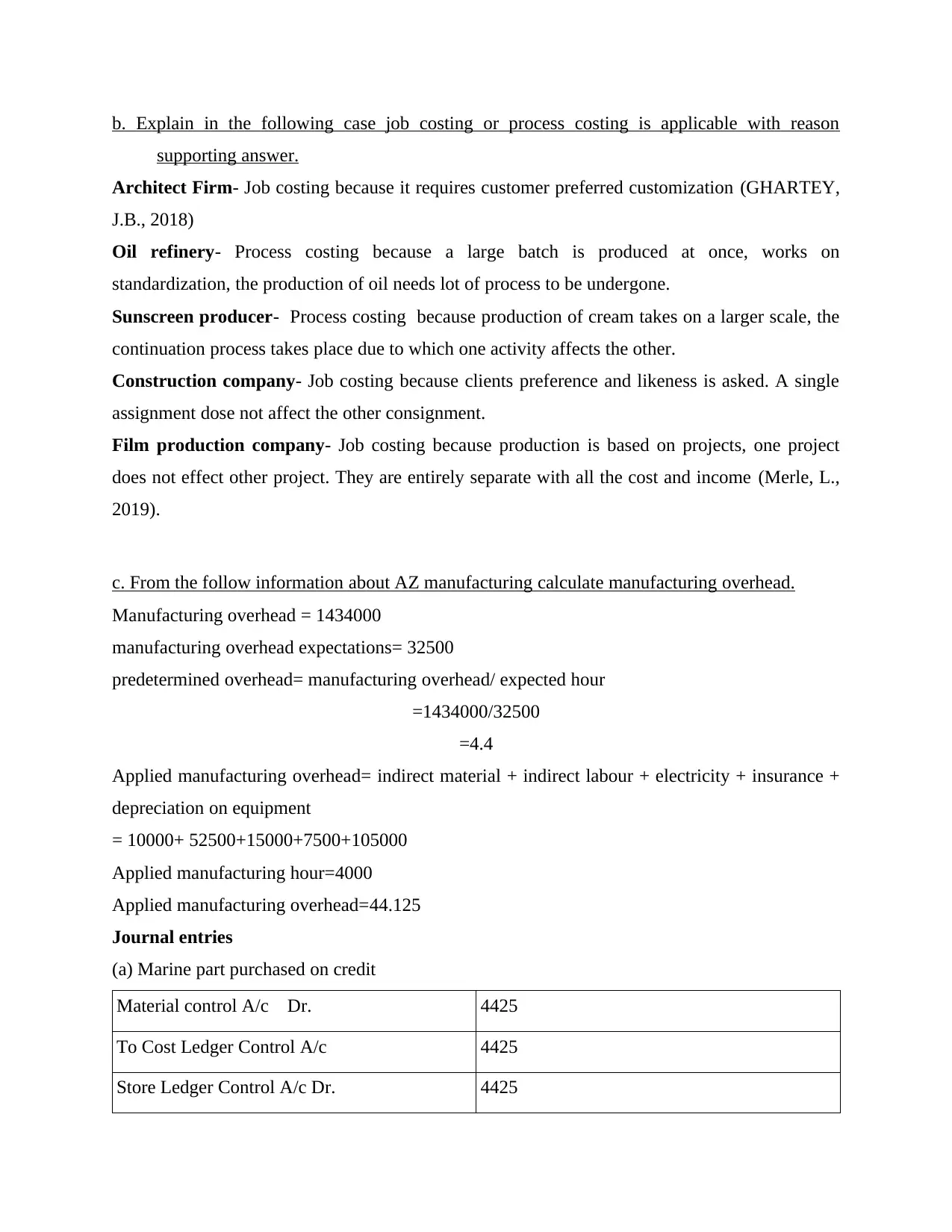
b. Explain in the following case job costing or process costing is applicable with reason
supporting answer.
Architect Firm- Job costing because it requires customer preferred customization (GHARTEY,
J.B., 2018)
Oil refinery- Process costing because a large batch is produced at once, works on
standardization, the production of oil needs lot of process to be undergone.
Sunscreen producer- Process costing because production of cream takes on a larger scale, the
continuation process takes place due to which one activity affects the other.
Construction company- Job costing because clients preference and likeness is asked. A single
assignment dose not affect the other consignment.
Film production company- Job costing because production is based on projects, one project
does not effect other project. They are entirely separate with all the cost and income (Merle, L.,
2019).
c. From the follow information about AZ manufacturing calculate manufacturing overhead.
Manufacturing overhead = 1434000
manufacturing overhead expectations= 32500
predetermined overhead= manufacturing overhead/ expected hour
=1434000/32500
=4.4
Applied manufacturing overhead= indirect material + indirect labour + electricity + insurance +
depreciation on equipment
= 10000+ 52500+15000+7500+105000
Applied manufacturing hour=4000
Applied manufacturing overhead=44.125
Journal entries
(a) Marine part purchased on credit
Material control A/c Dr. 4425
To Cost Ledger Control A/c 4425
Store Ledger Control A/c Dr. 4425
supporting answer.
Architect Firm- Job costing because it requires customer preferred customization (GHARTEY,
J.B., 2018)
Oil refinery- Process costing because a large batch is produced at once, works on
standardization, the production of oil needs lot of process to be undergone.
Sunscreen producer- Process costing because production of cream takes on a larger scale, the
continuation process takes place due to which one activity affects the other.
Construction company- Job costing because clients preference and likeness is asked. A single
assignment dose not affect the other consignment.
Film production company- Job costing because production is based on projects, one project
does not effect other project. They are entirely separate with all the cost and income (Merle, L.,
2019).
c. From the follow information about AZ manufacturing calculate manufacturing overhead.
Manufacturing overhead = 1434000
manufacturing overhead expectations= 32500
predetermined overhead= manufacturing overhead/ expected hour
=1434000/32500
=4.4
Applied manufacturing overhead= indirect material + indirect labour + electricity + insurance +
depreciation on equipment
= 10000+ 52500+15000+7500+105000
Applied manufacturing hour=4000
Applied manufacturing overhead=44.125
Journal entries
(a) Marine part purchased on credit
Material control A/c Dr. 4425
To Cost Ledger Control A/c 4425
Store Ledger Control A/c Dr. 4425
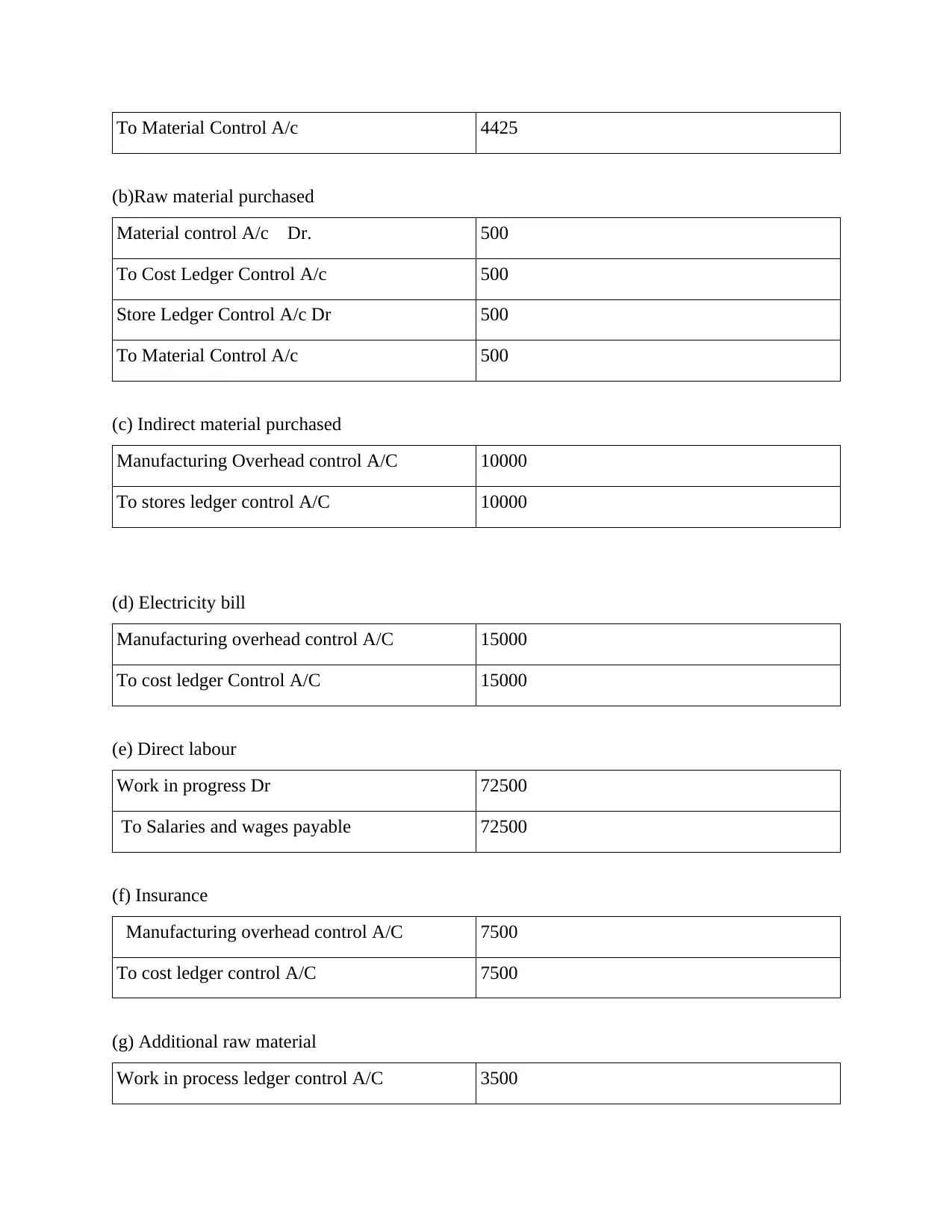
To Material Control A/c 4425
(b)Raw material purchased
Material control A/c Dr. 500
To Cost Ledger Control A/c 500
Store Ledger Control A/c Dr 500
To Material Control A/c 500
(c) Indirect material purchased
Manufacturing Overhead control A/C 10000
To stores ledger control A/C 10000
(d) Electricity bill
Manufacturing overhead control A/C 15000
To cost ledger Control A/C 15000
(e) Direct labour
Work in progress Dr 72500
To Salaries and wages payable 72500
(f) Insurance
Manufacturing overhead control A/C 7500
To cost ledger control A/C 7500
(g) Additional raw material
Work in process ledger control A/C 3500
(b)Raw material purchased
Material control A/c Dr. 500
To Cost Ledger Control A/c 500
Store Ledger Control A/c Dr 500
To Material Control A/c 500
(c) Indirect material purchased
Manufacturing Overhead control A/C 10000
To stores ledger control A/C 10000
(d) Electricity bill
Manufacturing overhead control A/C 15000
To cost ledger Control A/C 15000
(e) Direct labour
Work in progress Dr 72500
To Salaries and wages payable 72500
(f) Insurance
Manufacturing overhead control A/C 7500
To cost ledger control A/C 7500
(g) Additional raw material
Work in process ledger control A/C 3500
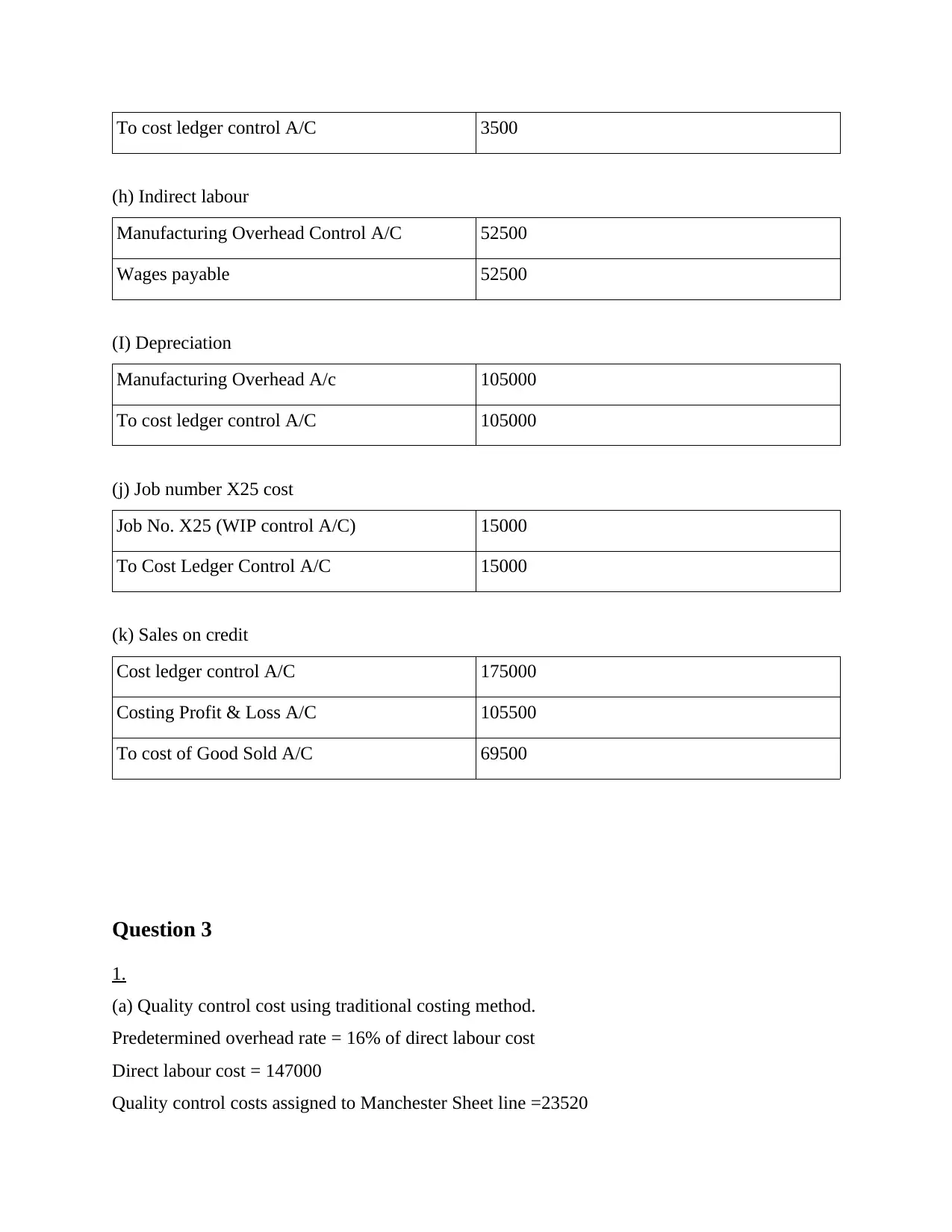
To cost ledger control A/C 3500
(h) Indirect labour
Manufacturing Overhead Control A/C 52500
Wages payable 52500
(I) Depreciation
Manufacturing Overhead A/c 105000
To cost ledger control A/C 105000
(j) Job number X25 cost
Job No. X25 (WIP control A/C) 15000
To Cost Ledger Control A/C 15000
(k) Sales on credit
Cost ledger control A/C 175000
Costing Profit & Loss A/C 105500
To cost of Good Sold A/C 69500
Question 3
1.
(a) Quality control cost using traditional costing method.
Predetermined overhead rate = 16% of direct labour cost
Direct labour cost = 147000
Quality control costs assigned to Manchester Sheet line =23520
(h) Indirect labour
Manufacturing Overhead Control A/C 52500
Wages payable 52500
(I) Depreciation
Manufacturing Overhead A/c 105000
To cost ledger control A/C 105000
(j) Job number X25 cost
Job No. X25 (WIP control A/C) 15000
To Cost Ledger Control A/C 15000
(k) Sales on credit
Cost ledger control A/C 175000
Costing Profit & Loss A/C 105500
To cost of Good Sold A/C 69500
Question 3
1.
(a) Quality control cost using traditional costing method.
Predetermined overhead rate = 16% of direct labour cost
Direct labour cost = 147000
Quality control costs assigned to Manchester Sheet line =23520
Paraphrase This Document
Need a fresh take? Get an instant paraphrase of this document with our AI Paraphraser
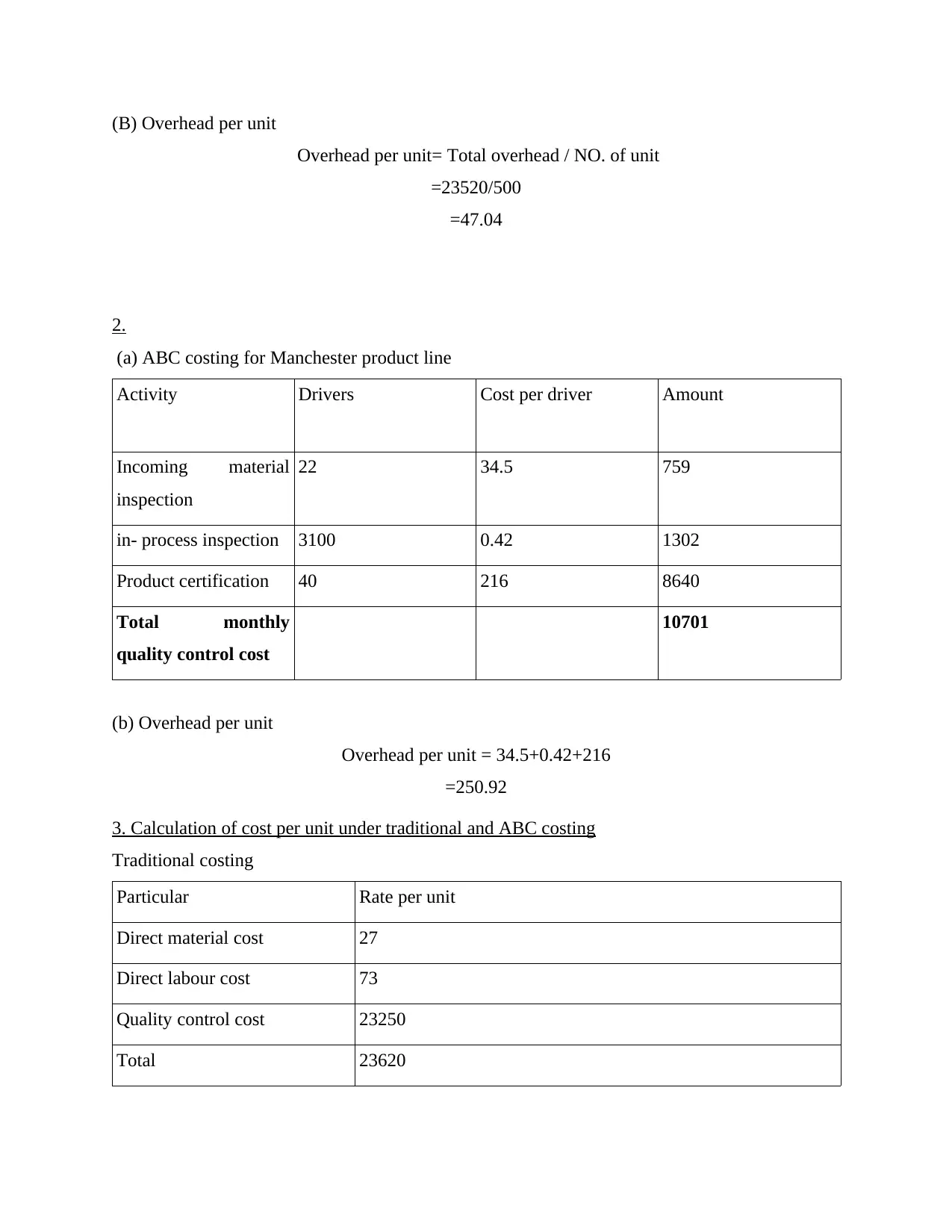
(B) Overhead per unit
Overhead per unit= Total overhead / NO. of unit
=23520/500
=47.04
2.
(a) ABC costing for Manchester product line
Activity Drivers Cost per driver Amount
Incoming material
inspection
22 34.5 759
in- process inspection 3100 0.42 1302
Product certification 40 216 8640
Total monthly
quality control cost
10701
(b) Overhead per unit
Overhead per unit = 34.5+0.42+216
=250.92
3. Calculation of cost per unit under traditional and ABC costing
Traditional costing
Particular Rate per unit
Direct material cost 27
Direct labour cost 73
Quality control cost 23250
Total 23620
Overhead per unit= Total overhead / NO. of unit
=23520/500
=47.04
2.
(a) ABC costing for Manchester product line
Activity Drivers Cost per driver Amount
Incoming material
inspection
22 34.5 759
in- process inspection 3100 0.42 1302
Product certification 40 216 8640
Total monthly
quality control cost
10701
(b) Overhead per unit
Overhead per unit = 34.5+0.42+216
=250.92
3. Calculation of cost per unit under traditional and ABC costing
Traditional costing
Particular Rate per unit
Direct material cost 27
Direct labour cost 73
Quality control cost 23250
Total 23620
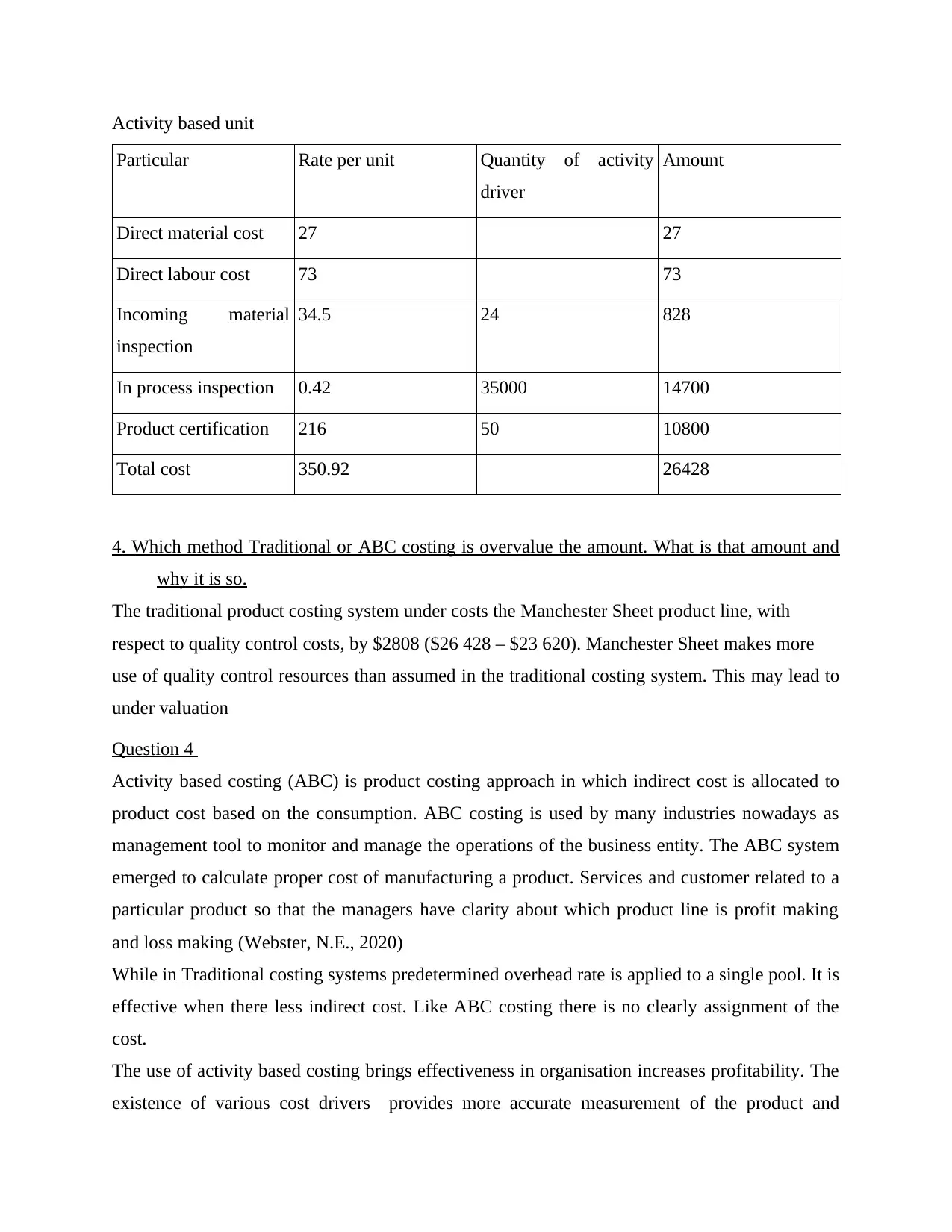
Activity based unit
Particular Rate per unit Quantity of activity
driver
Amount
Direct material cost 27 27
Direct labour cost 73 73
Incoming material
inspection
34.5 24 828
In process inspection 0.42 35000 14700
Product certification 216 50 10800
Total cost 350.92 26428
4. Which method Traditional or ABC costing is overvalue the amount. What is that amount and
why it is so.
The traditional product costing system under costs the Manchester Sheet product line, with
respect to quality control costs, by $2808 ($26 428 – $23 620). Manchester Sheet makes more
use of quality control resources than assumed in the traditional costing system. This may lead to
under valuation
Question 4
Activity based costing (ABC) is product costing approach in which indirect cost is allocated to
product cost based on the consumption. ABC costing is used by many industries nowadays as
management tool to monitor and manage the operations of the business entity. The ABC system
emerged to calculate proper cost of manufacturing a product. Services and customer related to a
particular product so that the managers have clarity about which product line is profit making
and loss making (Webster, N.E., 2020)
While in Traditional costing systems predetermined overhead rate is applied to a single pool. It is
effective when there less indirect cost. Like ABC costing there is no clearly assignment of the
cost.
The use of activity based costing brings effectiveness in organisation increases profitability. The
existence of various cost drivers provides more accurate measurement of the product and
Particular Rate per unit Quantity of activity
driver
Amount
Direct material cost 27 27
Direct labour cost 73 73
Incoming material
inspection
34.5 24 828
In process inspection 0.42 35000 14700
Product certification 216 50 10800
Total cost 350.92 26428
4. Which method Traditional or ABC costing is overvalue the amount. What is that amount and
why it is so.
The traditional product costing system under costs the Manchester Sheet product line, with
respect to quality control costs, by $2808 ($26 428 – $23 620). Manchester Sheet makes more
use of quality control resources than assumed in the traditional costing system. This may lead to
under valuation
Question 4
Activity based costing (ABC) is product costing approach in which indirect cost is allocated to
product cost based on the consumption. ABC costing is used by many industries nowadays as
management tool to monitor and manage the operations of the business entity. The ABC system
emerged to calculate proper cost of manufacturing a product. Services and customer related to a
particular product so that the managers have clarity about which product line is profit making
and loss making (Webster, N.E., 2020)
While in Traditional costing systems predetermined overhead rate is applied to a single pool. It is
effective when there less indirect cost. Like ABC costing there is no clearly assignment of the
cost.
The use of activity based costing brings effectiveness in organisation increases profitability. The
existence of various cost drivers provides more accurate measurement of the product and
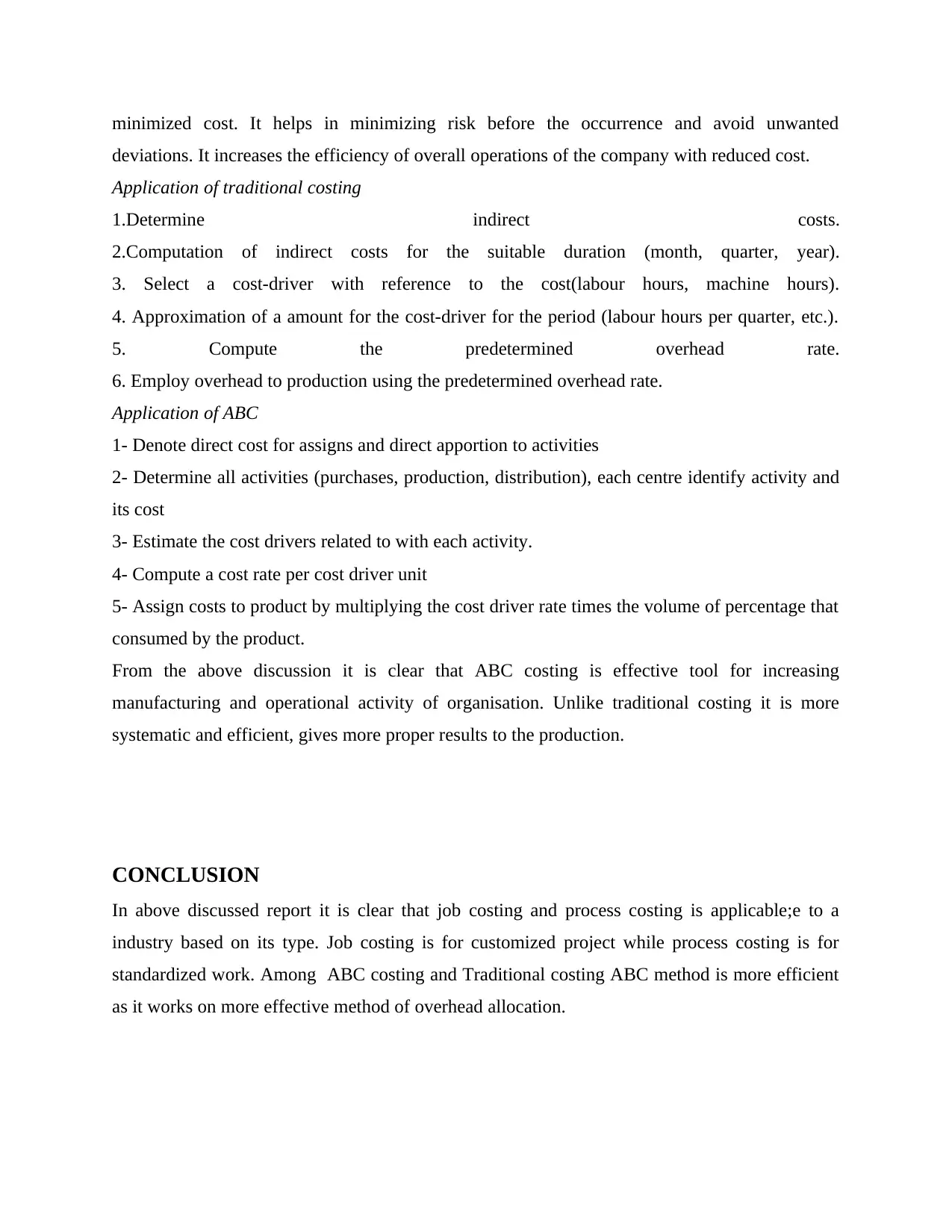
minimized cost. It helps in minimizing risk before the occurrence and avoid unwanted
deviations. It increases the efficiency of overall operations of the company with reduced cost.
Application of traditional costing
1.Determine indirect costs.
2.Computation of indirect costs for the suitable duration (month, quarter, year).
3. Select a cost-driver with reference to the cost(labour hours, machine hours).
4. Approximation of a amount for the cost-driver for the period (labour hours per quarter, etc.).
5. Compute the predetermined overhead rate.
6. Employ overhead to production using the predetermined overhead rate.
Application of ABC
1- Denote direct cost for assigns and direct apportion to activities
2- Determine all activities (purchases, production, distribution), each centre identify activity and
its cost
3- Estimate the cost drivers related to with each activity.
4- Compute a cost rate per cost driver unit
5- Assign costs to product by multiplying the cost driver rate times the volume of percentage that
consumed by the product.
From the above discussion it is clear that ABC costing is effective tool for increasing
manufacturing and operational activity of organisation. Unlike traditional costing it is more
systematic and efficient, gives more proper results to the production.
CONCLUSION
In above discussed report it is clear that job costing and process costing is applicable;e to a
industry based on its type. Job costing is for customized project while process costing is for
standardized work. Among ABC costing and Traditional costing ABC method is more efficient
as it works on more effective method of overhead allocation.
deviations. It increases the efficiency of overall operations of the company with reduced cost.
Application of traditional costing
1.Determine indirect costs.
2.Computation of indirect costs for the suitable duration (month, quarter, year).
3. Select a cost-driver with reference to the cost(labour hours, machine hours).
4. Approximation of a amount for the cost-driver for the period (labour hours per quarter, etc.).
5. Compute the predetermined overhead rate.
6. Employ overhead to production using the predetermined overhead rate.
Application of ABC
1- Denote direct cost for assigns and direct apportion to activities
2- Determine all activities (purchases, production, distribution), each centre identify activity and
its cost
3- Estimate the cost drivers related to with each activity.
4- Compute a cost rate per cost driver unit
5- Assign costs to product by multiplying the cost driver rate times the volume of percentage that
consumed by the product.
From the above discussion it is clear that ABC costing is effective tool for increasing
manufacturing and operational activity of organisation. Unlike traditional costing it is more
systematic and efficient, gives more proper results to the production.
CONCLUSION
In above discussed report it is clear that job costing and process costing is applicable;e to a
industry based on its type. Job costing is for customized project while process costing is for
standardized work. Among ABC costing and Traditional costing ABC method is more efficient
as it works on more effective method of overhead allocation.
Secure Best Marks with AI Grader
Need help grading? Try our AI Grader for instant feedback on your assignments.
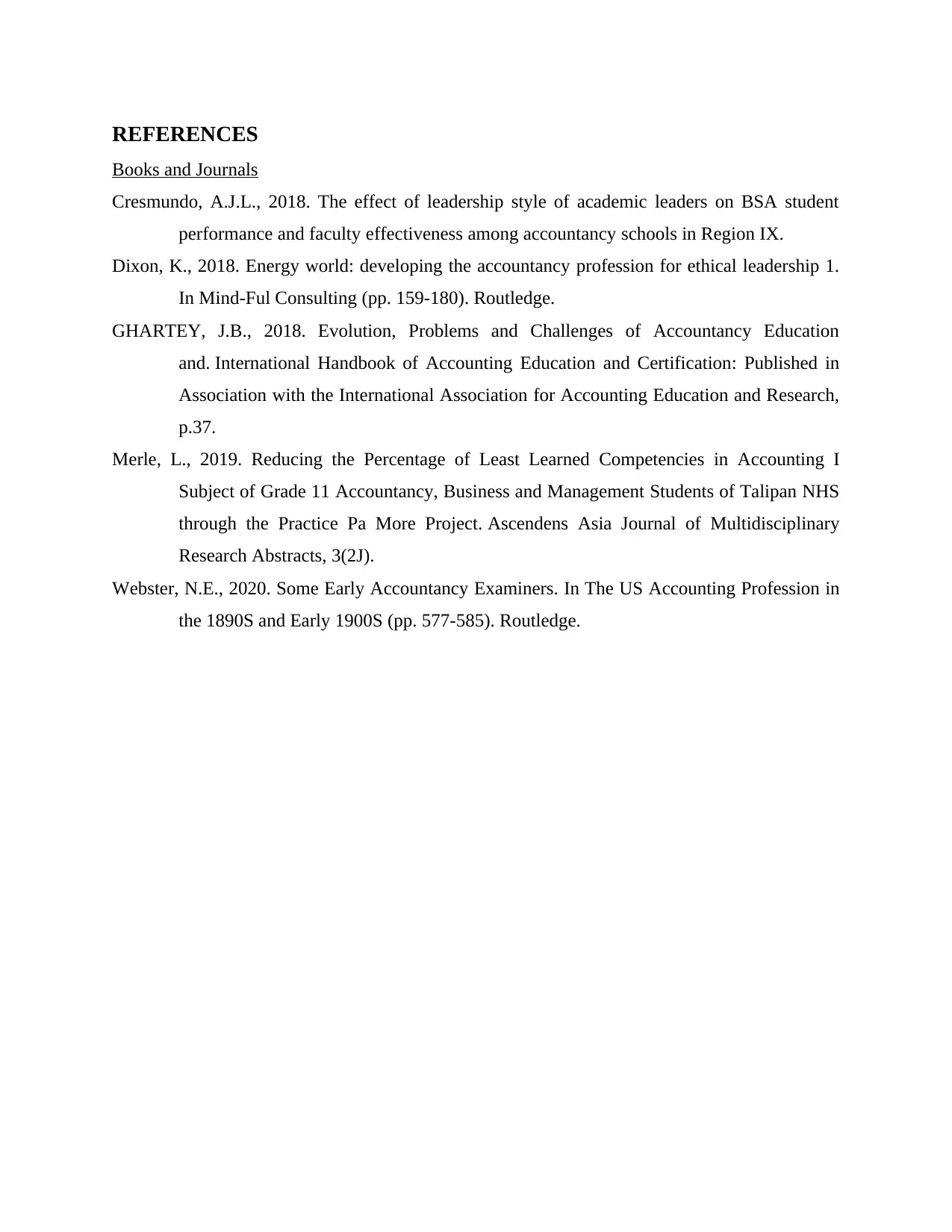
REFERENCES
Books and Journals
Cresmundo, A.J.L., 2018. The effect of leadership style of academic leaders on BSA student
performance and faculty effectiveness among accountancy schools in Region IX.
Dixon, K., 2018. Energy world: developing the accountancy profession for ethical leadership 1.
In Mind-Ful Consulting (pp. 159-180). Routledge.
GHARTEY, J.B., 2018. Evolution, Problems and Challenges of Accountancy Education
and. International Handbook of Accounting Education and Certification: Published in
Association with the International Association for Accounting Education and Research,
p.37.
Merle, L., 2019. Reducing the Percentage of Least Learned Competencies in Accounting I
Subject of Grade 11 Accountancy, Business and Management Students of Talipan NHS
through the Practice Pa More Project. Ascendens Asia Journal of Multidisciplinary
Research Abstracts, 3(2J).
Webster, N.E., 2020. Some Early Accountancy Examiners. In The US Accounting Profession in
the 1890S and Early 1900S (pp. 577-585). Routledge.
Books and Journals
Cresmundo, A.J.L., 2018. The effect of leadership style of academic leaders on BSA student
performance and faculty effectiveness among accountancy schools in Region IX.
Dixon, K., 2018. Energy world: developing the accountancy profession for ethical leadership 1.
In Mind-Ful Consulting (pp. 159-180). Routledge.
GHARTEY, J.B., 2018. Evolution, Problems and Challenges of Accountancy Education
and. International Handbook of Accounting Education and Certification: Published in
Association with the International Association for Accounting Education and Research,
p.37.
Merle, L., 2019. Reducing the Percentage of Least Learned Competencies in Accounting I
Subject of Grade 11 Accountancy, Business and Management Students of Talipan NHS
through the Practice Pa More Project. Ascendens Asia Journal of Multidisciplinary
Research Abstracts, 3(2J).
Webster, N.E., 2020. Some Early Accountancy Examiners. In The US Accounting Profession in
the 1890S and Early 1900S (pp. 577-585). Routledge.
1 out of 11
Related Documents

Your All-in-One AI-Powered Toolkit for Academic Success.
+13062052269
info@desklib.com
Available 24*7 on WhatsApp / Email
Unlock your academic potential
© 2024 | Zucol Services PVT LTD | All rights reserved.