ACC200 - Evaluating Costing Methods for Fantori Ltd Sewing Machines
VerifiedAdded on 2023/04/21
|12
|2572
|72
Report
AI Summary
This report analyzes Fantori Ltd's current traditional costing method and compares it with activity-based costing (ABC) to understand why a foreign buyer is only interested in the advanced sewing machine model. The analysis includes detailed computations of unit costs for both basic and advanced models under both costing methods. The report also constructs income statements under each costing approach to highlight the impact on profitability. It discusses the importance of accurate product pricing, the reasons for under-application or over-application of overheads, and provides recommendations for managing these issues. The report concludes that the traditional costing method under-prices the advanced model and over-prices the basic model, leading to skewed sales patterns and profit loss. Switching to ABC is recommended for better decision-making and profitability.
Contribute Materials
Your contribution can guide someone’s learning journey. Share your
documents today.
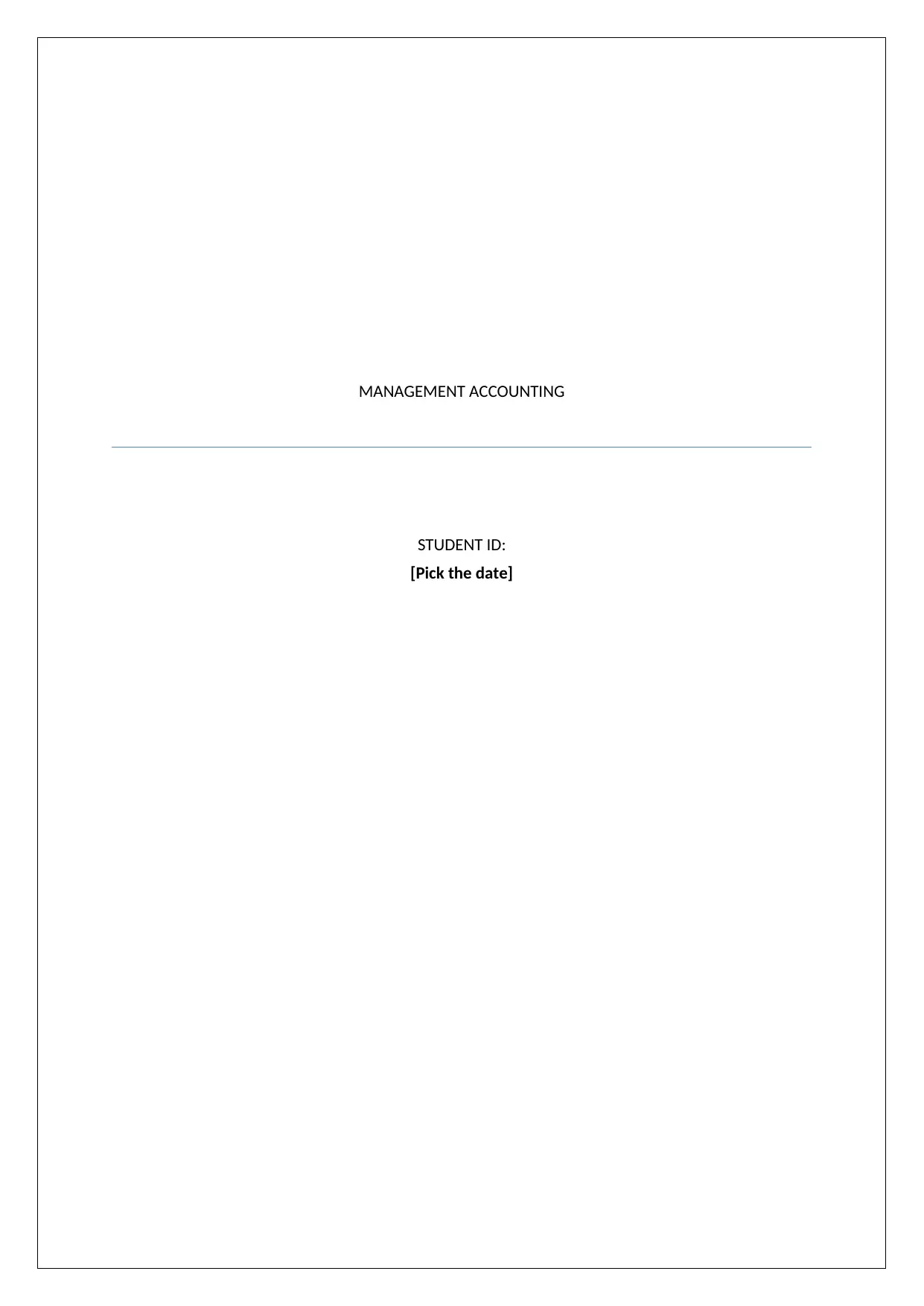
MANAGEMENT ACCOUNTING
STUDENT ID:
[Pick the date]
STUDENT ID:
[Pick the date]
Secure Best Marks with AI Grader
Need help grading? Try our AI Grader for instant feedback on your assignments.
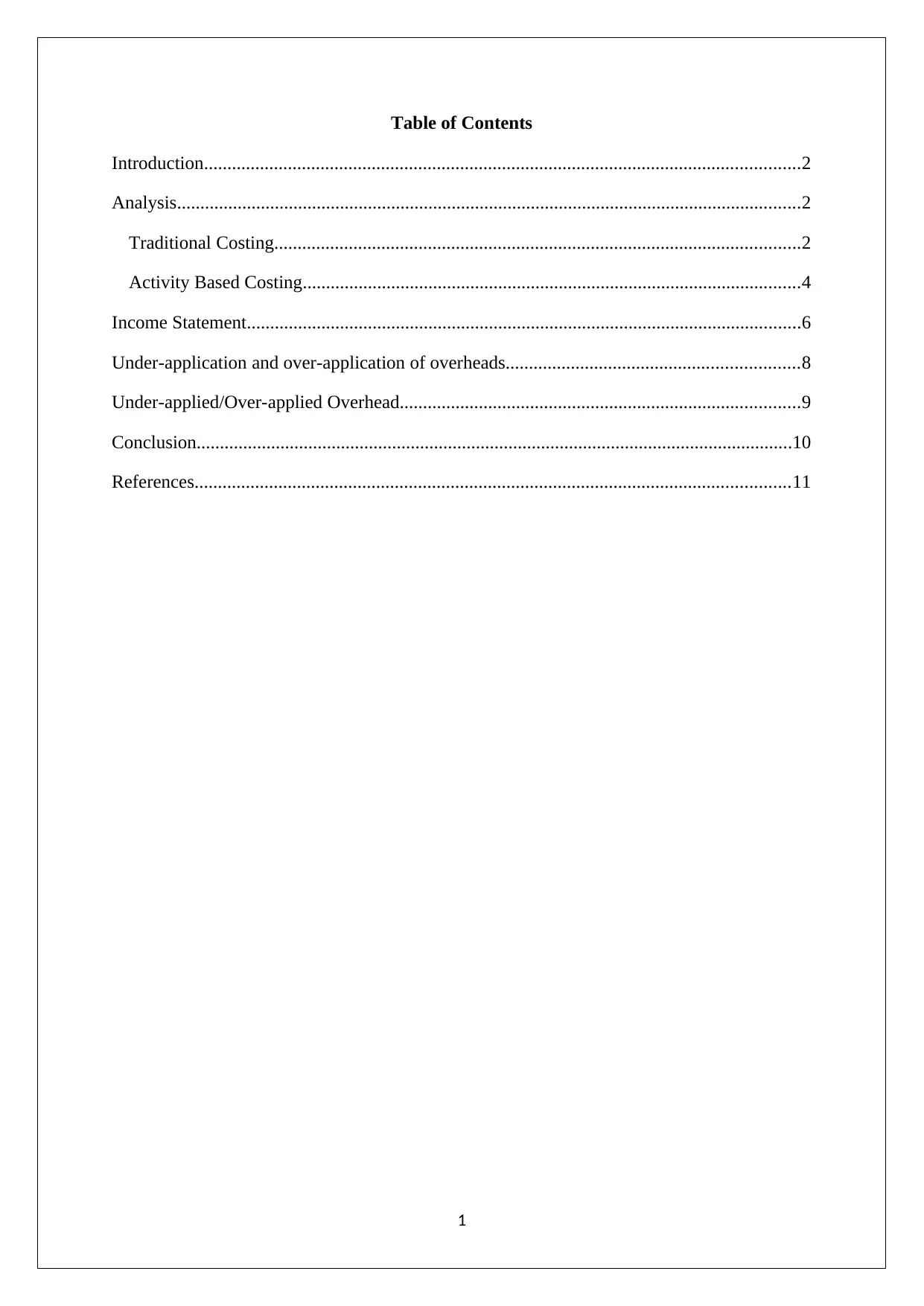
Table of Contents
Introduction................................................................................................................................2
Analysis......................................................................................................................................2
Traditional Costing.................................................................................................................2
Activity Based Costing...........................................................................................................4
Income Statement.......................................................................................................................6
Under-application and over-application of overheads...............................................................8
Under-applied/Over-applied Overhead......................................................................................9
Conclusion................................................................................................................................10
References................................................................................................................................11
1
Introduction................................................................................................................................2
Analysis......................................................................................................................................2
Traditional Costing.................................................................................................................2
Activity Based Costing...........................................................................................................4
Income Statement.......................................................................................................................6
Under-application and over-application of overheads...............................................................8
Under-applied/Over-applied Overhead......................................................................................9
Conclusion................................................................................................................................10
References................................................................................................................................11
1
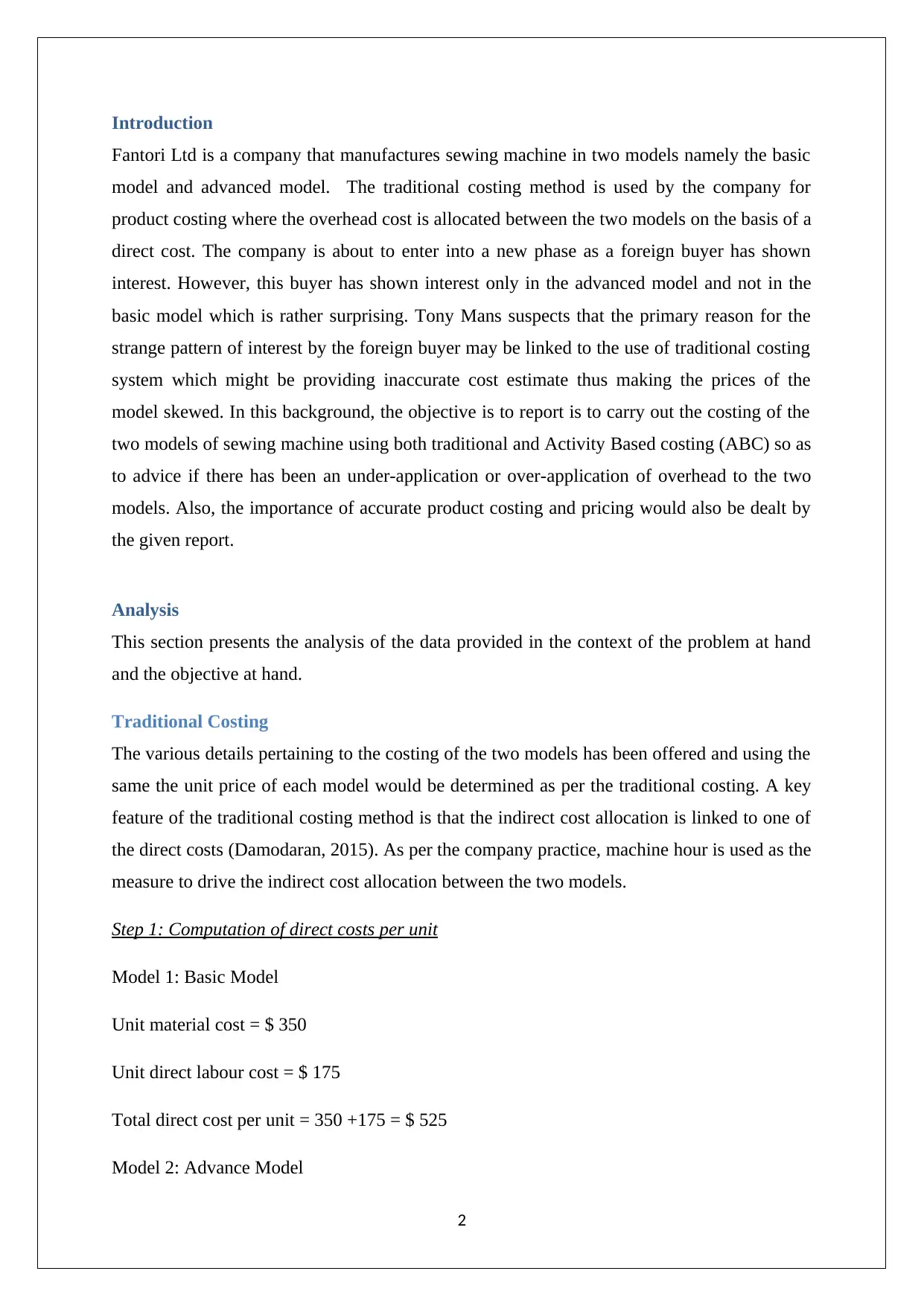
Introduction
Fantori Ltd is a company that manufactures sewing machine in two models namely the basic
model and advanced model. The traditional costing method is used by the company for
product costing where the overhead cost is allocated between the two models on the basis of a
direct cost. The company is about to enter into a new phase as a foreign buyer has shown
interest. However, this buyer has shown interest only in the advanced model and not in the
basic model which is rather surprising. Tony Mans suspects that the primary reason for the
strange pattern of interest by the foreign buyer may be linked to the use of traditional costing
system which might be providing inaccurate cost estimate thus making the prices of the
model skewed. In this background, the objective is to report is to carry out the costing of the
two models of sewing machine using both traditional and Activity Based costing (ABC) so as
to advice if there has been an under-application or over-application of overhead to the two
models. Also, the importance of accurate product costing and pricing would also be dealt by
the given report.
Analysis
This section presents the analysis of the data provided in the context of the problem at hand
and the objective at hand.
Traditional Costing
The various details pertaining to the costing of the two models has been offered and using the
same the unit price of each model would be determined as per the traditional costing. A key
feature of the traditional costing method is that the indirect cost allocation is linked to one of
the direct costs (Damodaran, 2015). As per the company practice, machine hour is used as the
measure to drive the indirect cost allocation between the two models.
Step 1: Computation of direct costs per unit
Model 1: Basic Model
Unit material cost = $ 350
Unit direct labour cost = $ 175
Total direct cost per unit = 350 +175 = $ 525
Model 2: Advance Model
2
Fantori Ltd is a company that manufactures sewing machine in two models namely the basic
model and advanced model. The traditional costing method is used by the company for
product costing where the overhead cost is allocated between the two models on the basis of a
direct cost. The company is about to enter into a new phase as a foreign buyer has shown
interest. However, this buyer has shown interest only in the advanced model and not in the
basic model which is rather surprising. Tony Mans suspects that the primary reason for the
strange pattern of interest by the foreign buyer may be linked to the use of traditional costing
system which might be providing inaccurate cost estimate thus making the prices of the
model skewed. In this background, the objective is to report is to carry out the costing of the
two models of sewing machine using both traditional and Activity Based costing (ABC) so as
to advice if there has been an under-application or over-application of overhead to the two
models. Also, the importance of accurate product costing and pricing would also be dealt by
the given report.
Analysis
This section presents the analysis of the data provided in the context of the problem at hand
and the objective at hand.
Traditional Costing
The various details pertaining to the costing of the two models has been offered and using the
same the unit price of each model would be determined as per the traditional costing. A key
feature of the traditional costing method is that the indirect cost allocation is linked to one of
the direct costs (Damodaran, 2015). As per the company practice, machine hour is used as the
measure to drive the indirect cost allocation between the two models.
Step 1: Computation of direct costs per unit
Model 1: Basic Model
Unit material cost = $ 350
Unit direct labour cost = $ 175
Total direct cost per unit = 350 +175 = $ 525
Model 2: Advance Model
2
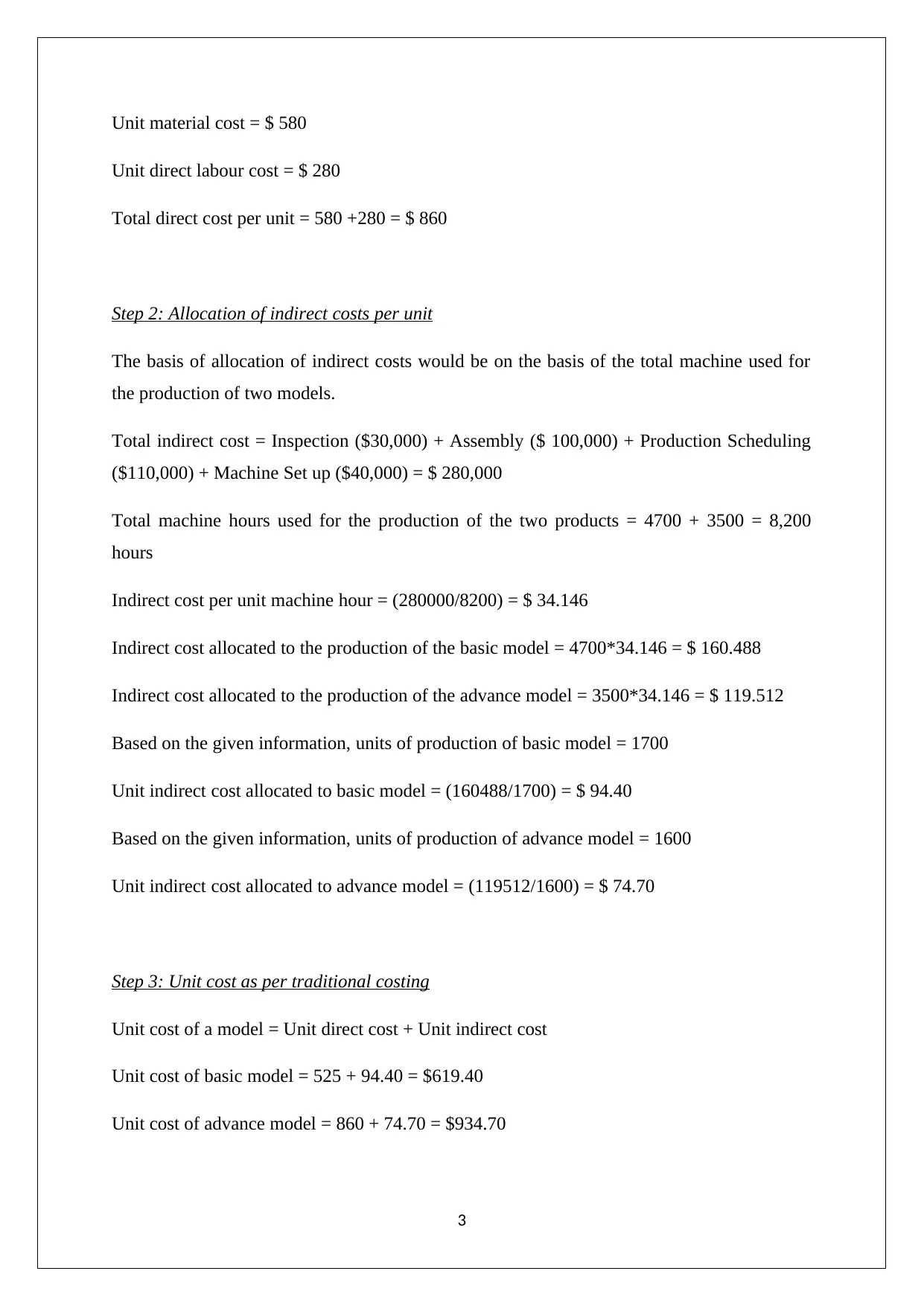
Unit material cost = $ 580
Unit direct labour cost = $ 280
Total direct cost per unit = 580 +280 = $ 860
Step 2: Allocation of indirect costs per unit
The basis of allocation of indirect costs would be on the basis of the total machine used for
the production of two models.
Total indirect cost = Inspection ($30,000) + Assembly ($ 100,000) + Production Scheduling
($110,000) + Machine Set up ($40,000) = $ 280,000
Total machine hours used for the production of the two products = 4700 + 3500 = 8,200
hours
Indirect cost per unit machine hour = (280000/8200) = $ 34.146
Indirect cost allocated to the production of the basic model = 4700*34.146 = $ 160.488
Indirect cost allocated to the production of the advance model = 3500*34.146 = $ 119.512
Based on the given information, units of production of basic model = 1700
Unit indirect cost allocated to basic model = (160488/1700) = $ 94.40
Based on the given information, units of production of advance model = 1600
Unit indirect cost allocated to advance model = (119512/1600) = $ 74.70
Step 3: Unit cost as per traditional costing
Unit cost of a model = Unit direct cost + Unit indirect cost
Unit cost of basic model = 525 + 94.40 = $619.40
Unit cost of advance model = 860 + 74.70 = $934.70
3
Unit direct labour cost = $ 280
Total direct cost per unit = 580 +280 = $ 860
Step 2: Allocation of indirect costs per unit
The basis of allocation of indirect costs would be on the basis of the total machine used for
the production of two models.
Total indirect cost = Inspection ($30,000) + Assembly ($ 100,000) + Production Scheduling
($110,000) + Machine Set up ($40,000) = $ 280,000
Total machine hours used for the production of the two products = 4700 + 3500 = 8,200
hours
Indirect cost per unit machine hour = (280000/8200) = $ 34.146
Indirect cost allocated to the production of the basic model = 4700*34.146 = $ 160.488
Indirect cost allocated to the production of the advance model = 3500*34.146 = $ 119.512
Based on the given information, units of production of basic model = 1700
Unit indirect cost allocated to basic model = (160488/1700) = $ 94.40
Based on the given information, units of production of advance model = 1600
Unit indirect cost allocated to advance model = (119512/1600) = $ 74.70
Step 3: Unit cost as per traditional costing
Unit cost of a model = Unit direct cost + Unit indirect cost
Unit cost of basic model = 525 + 94.40 = $619.40
Unit cost of advance model = 860 + 74.70 = $934.70
3
Secure Best Marks with AI Grader
Need help grading? Try our AI Grader for instant feedback on your assignments.
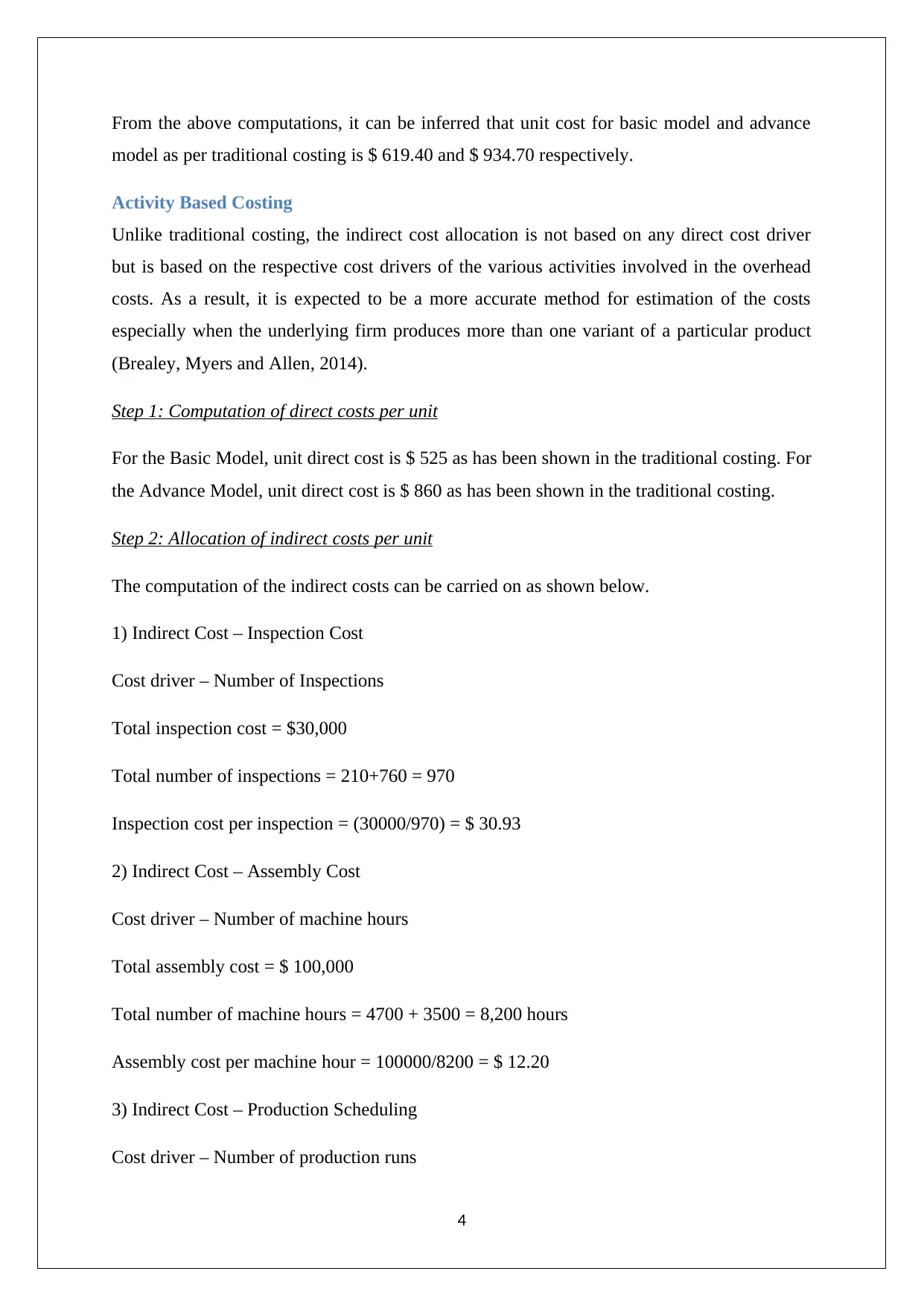
From the above computations, it can be inferred that unit cost for basic model and advance
model as per traditional costing is $ 619.40 and $ 934.70 respectively.
Activity Based Costing
Unlike traditional costing, the indirect cost allocation is not based on any direct cost driver
but is based on the respective cost drivers of the various activities involved in the overhead
costs. As a result, it is expected to be a more accurate method for estimation of the costs
especially when the underlying firm produces more than one variant of a particular product
(Brealey, Myers and Allen, 2014).
Step 1: Computation of direct costs per unit
For the Basic Model, unit direct cost is $ 525 as has been shown in the traditional costing. For
the Advance Model, unit direct cost is $ 860 as has been shown in the traditional costing.
Step 2: Allocation of indirect costs per unit
The computation of the indirect costs can be carried on as shown below.
1) Indirect Cost – Inspection Cost
Cost driver – Number of Inspections
Total inspection cost = $30,000
Total number of inspections = 210+760 = 970
Inspection cost per inspection = (30000/970) = $ 30.93
2) Indirect Cost – Assembly Cost
Cost driver – Number of machine hours
Total assembly cost = $ 100,000
Total number of machine hours = 4700 + 3500 = 8,200 hours
Assembly cost per machine hour = 100000/8200 = $ 12.20
3) Indirect Cost – Production Scheduling
Cost driver – Number of production runs
4
model as per traditional costing is $ 619.40 and $ 934.70 respectively.
Activity Based Costing
Unlike traditional costing, the indirect cost allocation is not based on any direct cost driver
but is based on the respective cost drivers of the various activities involved in the overhead
costs. As a result, it is expected to be a more accurate method for estimation of the costs
especially when the underlying firm produces more than one variant of a particular product
(Brealey, Myers and Allen, 2014).
Step 1: Computation of direct costs per unit
For the Basic Model, unit direct cost is $ 525 as has been shown in the traditional costing. For
the Advance Model, unit direct cost is $ 860 as has been shown in the traditional costing.
Step 2: Allocation of indirect costs per unit
The computation of the indirect costs can be carried on as shown below.
1) Indirect Cost – Inspection Cost
Cost driver – Number of Inspections
Total inspection cost = $30,000
Total number of inspections = 210+760 = 970
Inspection cost per inspection = (30000/970) = $ 30.93
2) Indirect Cost – Assembly Cost
Cost driver – Number of machine hours
Total assembly cost = $ 100,000
Total number of machine hours = 4700 + 3500 = 8,200 hours
Assembly cost per machine hour = 100000/8200 = $ 12.20
3) Indirect Cost – Production Scheduling
Cost driver – Number of production runs
4
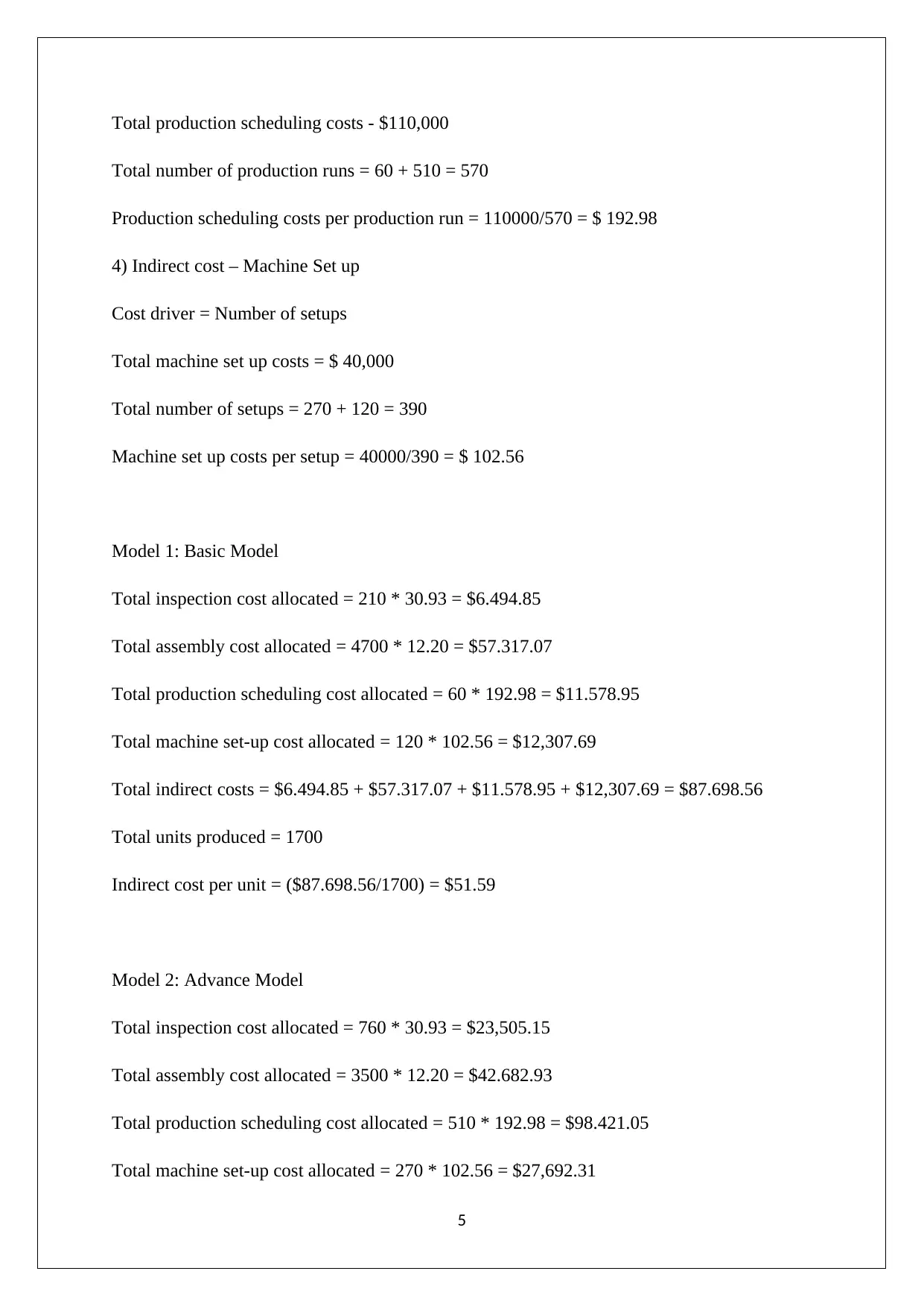
Total production scheduling costs - $110,000
Total number of production runs = 60 + 510 = 570
Production scheduling costs per production run = 110000/570 = $ 192.98
4) Indirect cost – Machine Set up
Cost driver = Number of setups
Total machine set up costs = $ 40,000
Total number of setups = 270 + 120 = 390
Machine set up costs per setup = 40000/390 = $ 102.56
Model 1: Basic Model
Total inspection cost allocated = 210 * 30.93 = $6.494.85
Total assembly cost allocated = 4700 * 12.20 = $57.317.07
Total production scheduling cost allocated = 60 * 192.98 = $11.578.95
Total machine set-up cost allocated = 120 * 102.56 = $12,307.69
Total indirect costs = $6.494.85 + $57.317.07 + $11.578.95 + $12,307.69 = $87.698.56
Total units produced = 1700
Indirect cost per unit = ($87.698.56/1700) = $51.59
Model 2: Advance Model
Total inspection cost allocated = 760 * 30.93 = $23,505.15
Total assembly cost allocated = 3500 * 12.20 = $42.682.93
Total production scheduling cost allocated = 510 * 192.98 = $98.421.05
Total machine set-up cost allocated = 270 * 102.56 = $27,692.31
5
Total number of production runs = 60 + 510 = 570
Production scheduling costs per production run = 110000/570 = $ 192.98
4) Indirect cost – Machine Set up
Cost driver = Number of setups
Total machine set up costs = $ 40,000
Total number of setups = 270 + 120 = 390
Machine set up costs per setup = 40000/390 = $ 102.56
Model 1: Basic Model
Total inspection cost allocated = 210 * 30.93 = $6.494.85
Total assembly cost allocated = 4700 * 12.20 = $57.317.07
Total production scheduling cost allocated = 60 * 192.98 = $11.578.95
Total machine set-up cost allocated = 120 * 102.56 = $12,307.69
Total indirect costs = $6.494.85 + $57.317.07 + $11.578.95 + $12,307.69 = $87.698.56
Total units produced = 1700
Indirect cost per unit = ($87.698.56/1700) = $51.59
Model 2: Advance Model
Total inspection cost allocated = 760 * 30.93 = $23,505.15
Total assembly cost allocated = 3500 * 12.20 = $42.682.93
Total production scheduling cost allocated = 510 * 192.98 = $98.421.05
Total machine set-up cost allocated = 270 * 102.56 = $27,692.31
5
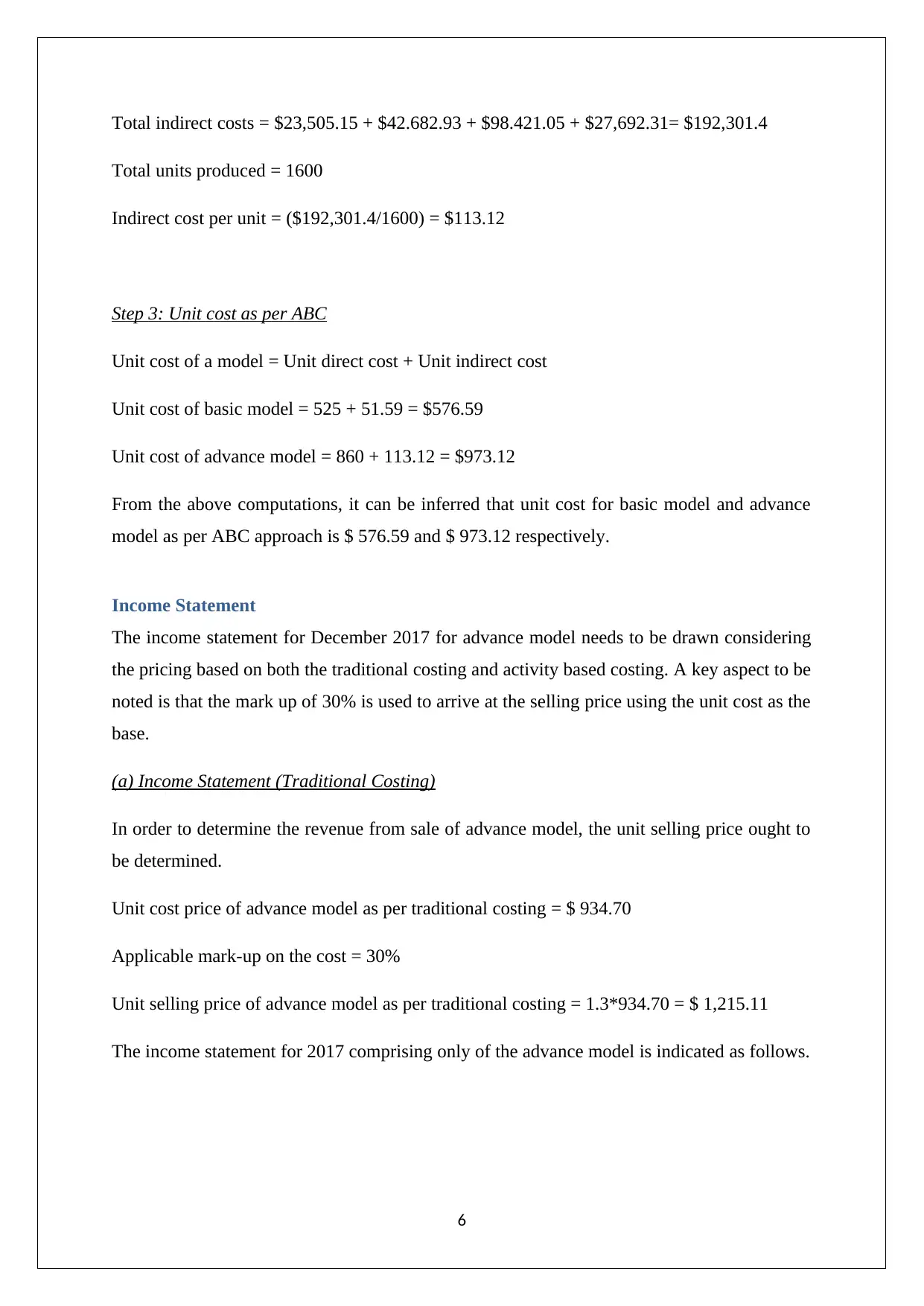
Total indirect costs = $23,505.15 + $42.682.93 + $98.421.05 + $27,692.31= $192,301.4
Total units produced = 1600
Indirect cost per unit = ($192,301.4/1600) = $113.12
Step 3: Unit cost as per ABC
Unit cost of a model = Unit direct cost + Unit indirect cost
Unit cost of basic model = 525 + 51.59 = $576.59
Unit cost of advance model = 860 + 113.12 = $973.12
From the above computations, it can be inferred that unit cost for basic model and advance
model as per ABC approach is $ 576.59 and $ 973.12 respectively.
Income Statement
The income statement for December 2017 for advance model needs to be drawn considering
the pricing based on both the traditional costing and activity based costing. A key aspect to be
noted is that the mark up of 30% is used to arrive at the selling price using the unit cost as the
base.
(a) Income Statement (Traditional Costing)
In order to determine the revenue from sale of advance model, the unit selling price ought to
be determined.
Unit cost price of advance model as per traditional costing = $ 934.70
Applicable mark-up on the cost = 30%
Unit selling price of advance model as per traditional costing = 1.3*934.70 = $ 1,215.11
The income statement for 2017 comprising only of the advance model is indicated as follows.
6
Total units produced = 1600
Indirect cost per unit = ($192,301.4/1600) = $113.12
Step 3: Unit cost as per ABC
Unit cost of a model = Unit direct cost + Unit indirect cost
Unit cost of basic model = 525 + 51.59 = $576.59
Unit cost of advance model = 860 + 113.12 = $973.12
From the above computations, it can be inferred that unit cost for basic model and advance
model as per ABC approach is $ 576.59 and $ 973.12 respectively.
Income Statement
The income statement for December 2017 for advance model needs to be drawn considering
the pricing based on both the traditional costing and activity based costing. A key aspect to be
noted is that the mark up of 30% is used to arrive at the selling price using the unit cost as the
base.
(a) Income Statement (Traditional Costing)
In order to determine the revenue from sale of advance model, the unit selling price ought to
be determined.
Unit cost price of advance model as per traditional costing = $ 934.70
Applicable mark-up on the cost = 30%
Unit selling price of advance model as per traditional costing = 1.3*934.70 = $ 1,215.11
The income statement for 2017 comprising only of the advance model is indicated as follows.
6
Paraphrase This Document
Need a fresh take? Get an instant paraphrase of this document with our AI Paraphraser
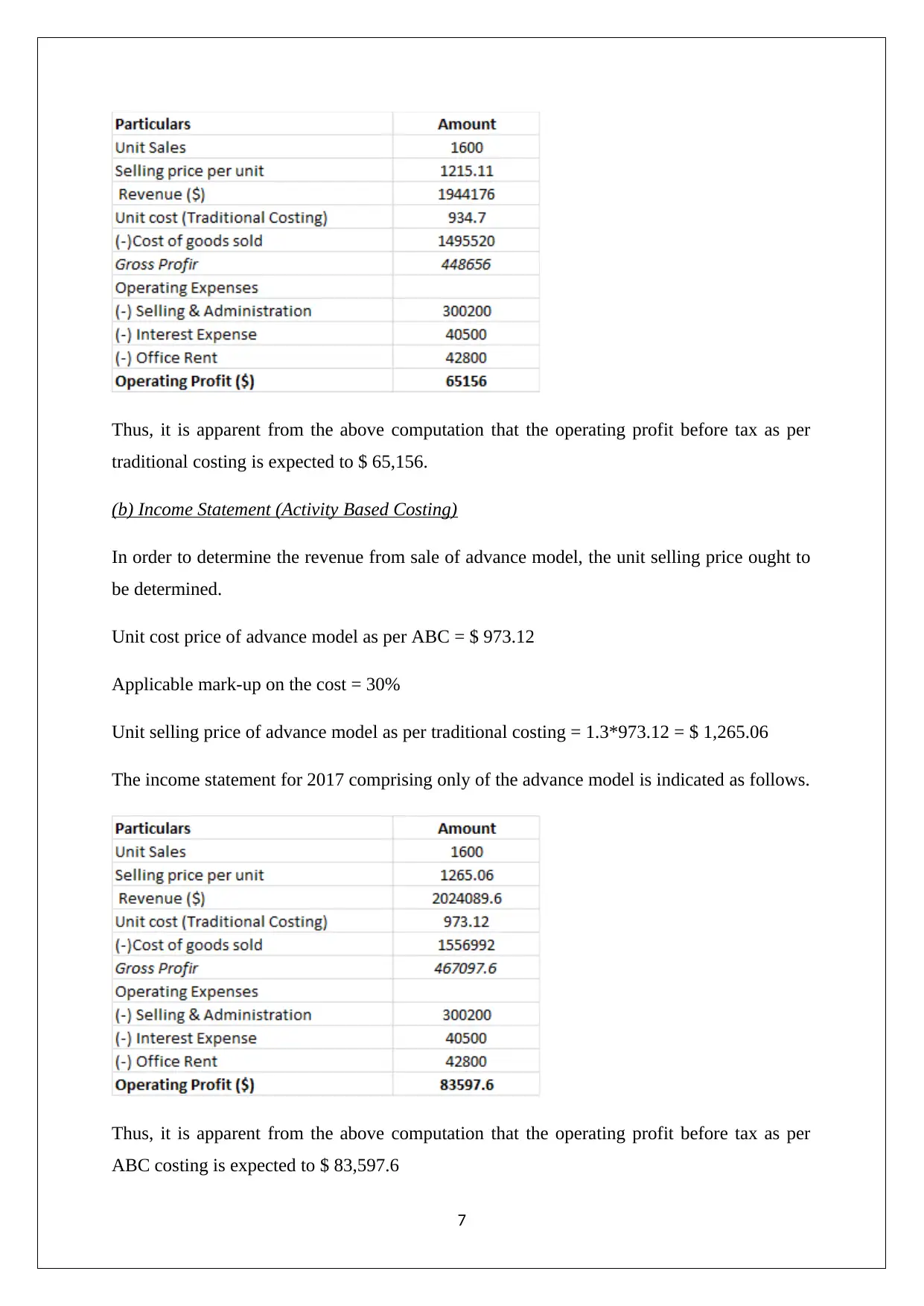
Thus, it is apparent from the above computation that the operating profit before tax as per
traditional costing is expected to $ 65,156.
(b) Income Statement (Activity Based Costing)
In order to determine the revenue from sale of advance model, the unit selling price ought to
be determined.
Unit cost price of advance model as per ABC = $ 973.12
Applicable mark-up on the cost = 30%
Unit selling price of advance model as per traditional costing = 1.3*973.12 = $ 1,265.06
The income statement for 2017 comprising only of the advance model is indicated as follows.
Thus, it is apparent from the above computation that the operating profit before tax as per
ABC costing is expected to $ 83,597.6
7
traditional costing is expected to $ 65,156.
(b) Income Statement (Activity Based Costing)
In order to determine the revenue from sale of advance model, the unit selling price ought to
be determined.
Unit cost price of advance model as per ABC = $ 973.12
Applicable mark-up on the cost = 30%
Unit selling price of advance model as per traditional costing = 1.3*973.12 = $ 1,265.06
The income statement for 2017 comprising only of the advance model is indicated as follows.
Thus, it is apparent from the above computation that the operating profit before tax as per
ABC costing is expected to $ 83,597.6
7
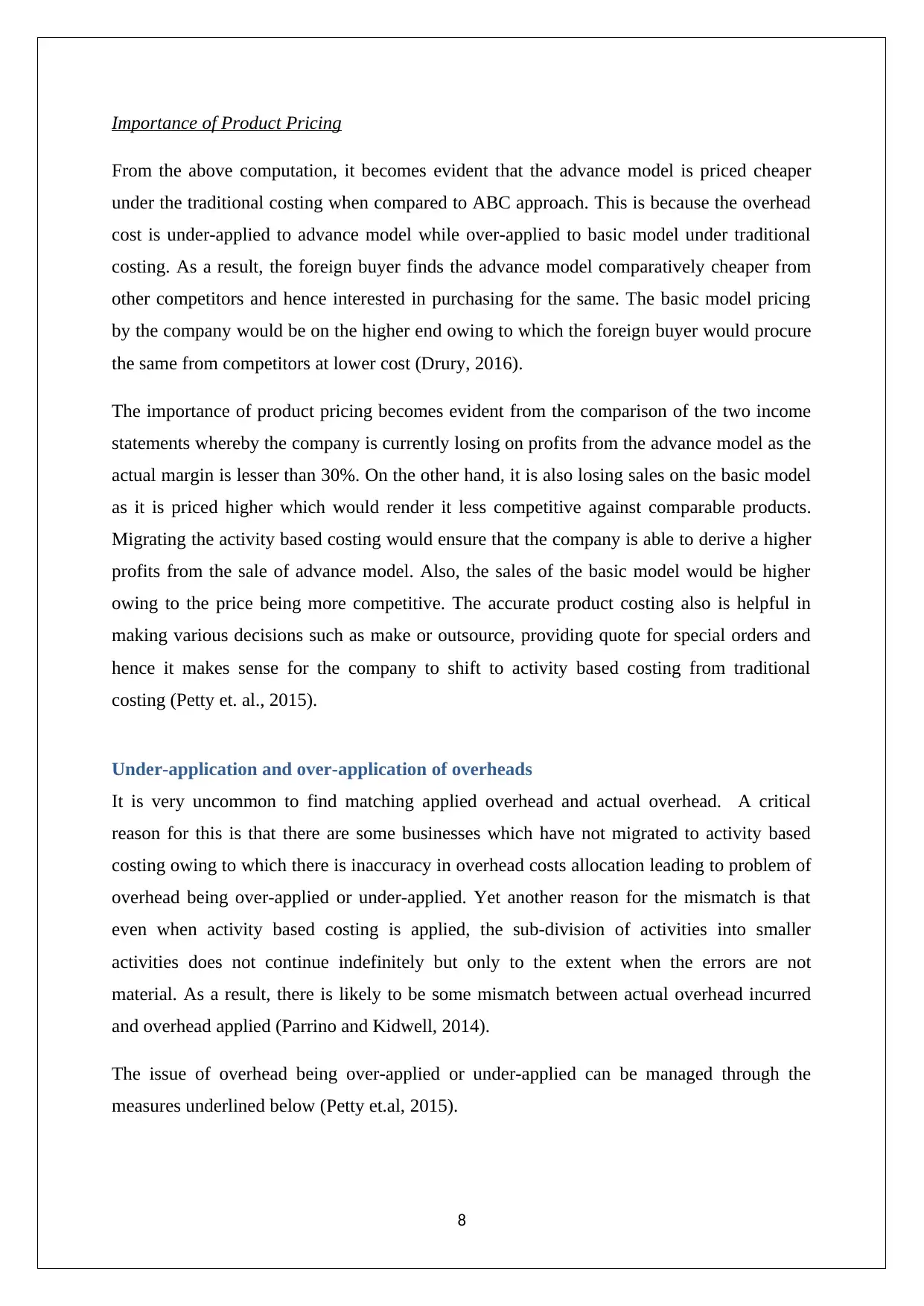
Importance of Product Pricing
From the above computation, it becomes evident that the advance model is priced cheaper
under the traditional costing when compared to ABC approach. This is because the overhead
cost is under-applied to advance model while over-applied to basic model under traditional
costing. As a result, the foreign buyer finds the advance model comparatively cheaper from
other competitors and hence interested in purchasing for the same. The basic model pricing
by the company would be on the higher end owing to which the foreign buyer would procure
the same from competitors at lower cost (Drury, 2016).
The importance of product pricing becomes evident from the comparison of the two income
statements whereby the company is currently losing on profits from the advance model as the
actual margin is lesser than 30%. On the other hand, it is also losing sales on the basic model
as it is priced higher which would render it less competitive against comparable products.
Migrating the activity based costing would ensure that the company is able to derive a higher
profits from the sale of advance model. Also, the sales of the basic model would be higher
owing to the price being more competitive. The accurate product costing also is helpful in
making various decisions such as make or outsource, providing quote for special orders and
hence it makes sense for the company to shift to activity based costing from traditional
costing (Petty et. al., 2015).
Under-application and over-application of overheads
It is very uncommon to find matching applied overhead and actual overhead. A critical
reason for this is that there are some businesses which have not migrated to activity based
costing owing to which there is inaccuracy in overhead costs allocation leading to problem of
overhead being over-applied or under-applied. Yet another reason for the mismatch is that
even when activity based costing is applied, the sub-division of activities into smaller
activities does not continue indefinitely but only to the extent when the errors are not
material. As a result, there is likely to be some mismatch between actual overhead incurred
and overhead applied (Parrino and Kidwell, 2014).
The issue of overhead being over-applied or under-applied can be managed through the
measures underlined below (Petty et.al, 2015).
8
From the above computation, it becomes evident that the advance model is priced cheaper
under the traditional costing when compared to ABC approach. This is because the overhead
cost is under-applied to advance model while over-applied to basic model under traditional
costing. As a result, the foreign buyer finds the advance model comparatively cheaper from
other competitors and hence interested in purchasing for the same. The basic model pricing
by the company would be on the higher end owing to which the foreign buyer would procure
the same from competitors at lower cost (Drury, 2016).
The importance of product pricing becomes evident from the comparison of the two income
statements whereby the company is currently losing on profits from the advance model as the
actual margin is lesser than 30%. On the other hand, it is also losing sales on the basic model
as it is priced higher which would render it less competitive against comparable products.
Migrating the activity based costing would ensure that the company is able to derive a higher
profits from the sale of advance model. Also, the sales of the basic model would be higher
owing to the price being more competitive. The accurate product costing also is helpful in
making various decisions such as make or outsource, providing quote for special orders and
hence it makes sense for the company to shift to activity based costing from traditional
costing (Petty et. al., 2015).
Under-application and over-application of overheads
It is very uncommon to find matching applied overhead and actual overhead. A critical
reason for this is that there are some businesses which have not migrated to activity based
costing owing to which there is inaccuracy in overhead costs allocation leading to problem of
overhead being over-applied or under-applied. Yet another reason for the mismatch is that
even when activity based costing is applied, the sub-division of activities into smaller
activities does not continue indefinitely but only to the extent when the errors are not
material. As a result, there is likely to be some mismatch between actual overhead incurred
and overhead applied (Parrino and Kidwell, 2014).
The issue of overhead being over-applied or under-applied can be managed through the
measures underlined below (Petty et.al, 2015).
8
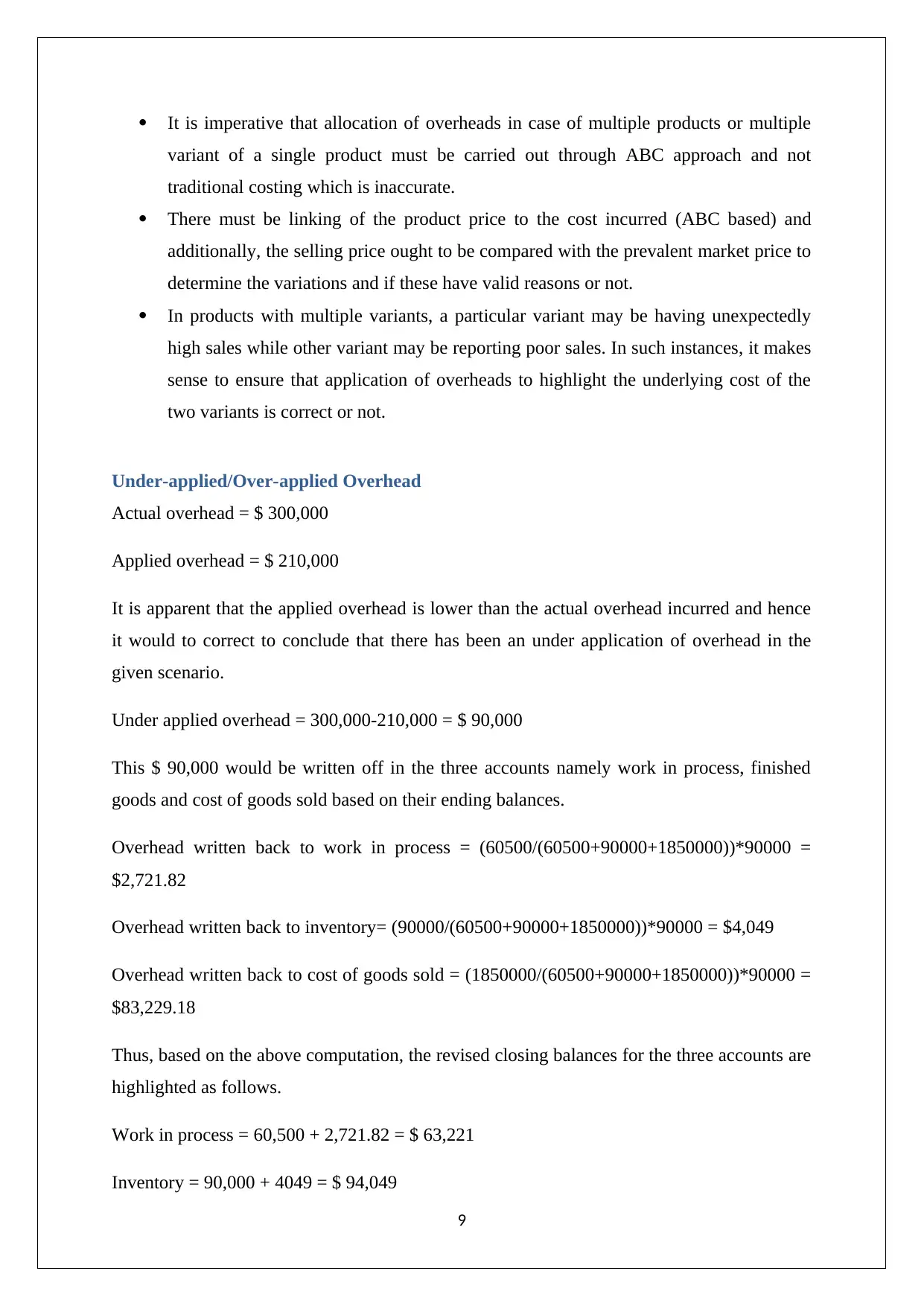
It is imperative that allocation of overheads in case of multiple products or multiple
variant of a single product must be carried out through ABC approach and not
traditional costing which is inaccurate.
There must be linking of the product price to the cost incurred (ABC based) and
additionally, the selling price ought to be compared with the prevalent market price to
determine the variations and if these have valid reasons or not.
In products with multiple variants, a particular variant may be having unexpectedly
high sales while other variant may be reporting poor sales. In such instances, it makes
sense to ensure that application of overheads to highlight the underlying cost of the
two variants is correct or not.
Under-applied/Over-applied Overhead
Actual overhead = $ 300,000
Applied overhead = $ 210,000
It is apparent that the applied overhead is lower than the actual overhead incurred and hence
it would to correct to conclude that there has been an under application of overhead in the
given scenario.
Under applied overhead = 300,000-210,000 = $ 90,000
This $ 90,000 would be written off in the three accounts namely work in process, finished
goods and cost of goods sold based on their ending balances.
Overhead written back to work in process = (60500/(60500+90000+1850000))*90000 =
$2,721.82
Overhead written back to inventory= (90000/(60500+90000+1850000))*90000 = $4,049
Overhead written back to cost of goods sold = (1850000/(60500+90000+1850000))*90000 =
$83,229.18
Thus, based on the above computation, the revised closing balances for the three accounts are
highlighted as follows.
Work in process = 60,500 + 2,721.82 = $ 63,221
Inventory = 90,000 + 4049 = $ 94,049
9
variant of a single product must be carried out through ABC approach and not
traditional costing which is inaccurate.
There must be linking of the product price to the cost incurred (ABC based) and
additionally, the selling price ought to be compared with the prevalent market price to
determine the variations and if these have valid reasons or not.
In products with multiple variants, a particular variant may be having unexpectedly
high sales while other variant may be reporting poor sales. In such instances, it makes
sense to ensure that application of overheads to highlight the underlying cost of the
two variants is correct or not.
Under-applied/Over-applied Overhead
Actual overhead = $ 300,000
Applied overhead = $ 210,000
It is apparent that the applied overhead is lower than the actual overhead incurred and hence
it would to correct to conclude that there has been an under application of overhead in the
given scenario.
Under applied overhead = 300,000-210,000 = $ 90,000
This $ 90,000 would be written off in the three accounts namely work in process, finished
goods and cost of goods sold based on their ending balances.
Overhead written back to work in process = (60500/(60500+90000+1850000))*90000 =
$2,721.82
Overhead written back to inventory= (90000/(60500+90000+1850000))*90000 = $4,049
Overhead written back to cost of goods sold = (1850000/(60500+90000+1850000))*90000 =
$83,229.18
Thus, based on the above computation, the revised closing balances for the three accounts are
highlighted as follows.
Work in process = 60,500 + 2,721.82 = $ 63,221
Inventory = 90,000 + 4049 = $ 94,049
9
Secure Best Marks with AI Grader
Need help grading? Try our AI Grader for instant feedback on your assignments.
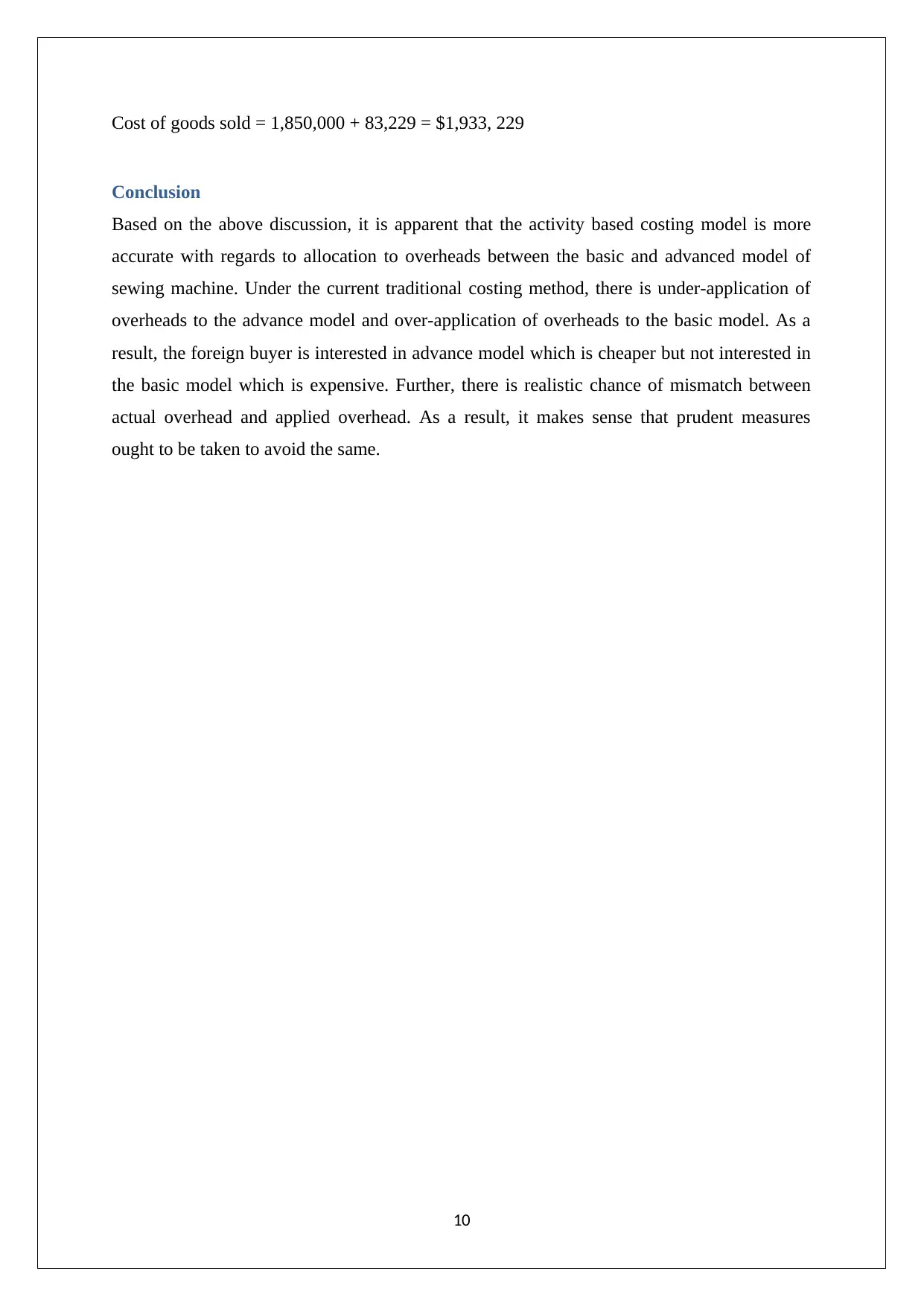
Cost of goods sold = 1,850,000 + 83,229 = $1,933, 229
Conclusion
Based on the above discussion, it is apparent that the activity based costing model is more
accurate with regards to allocation to overheads between the basic and advanced model of
sewing machine. Under the current traditional costing method, there is under-application of
overheads to the advance model and over-application of overheads to the basic model. As a
result, the foreign buyer is interested in advance model which is cheaper but not interested in
the basic model which is expensive. Further, there is realistic chance of mismatch between
actual overhead and applied overhead. As a result, it makes sense that prudent measures
ought to be taken to avoid the same.
10
Conclusion
Based on the above discussion, it is apparent that the activity based costing model is more
accurate with regards to allocation to overheads between the basic and advanced model of
sewing machine. Under the current traditional costing method, there is under-application of
overheads to the advance model and over-application of overheads to the basic model. As a
result, the foreign buyer is interested in advance model which is cheaper but not interested in
the basic model which is expensive. Further, there is realistic chance of mismatch between
actual overhead and applied overhead. As a result, it makes sense that prudent measures
ought to be taken to avoid the same.
10
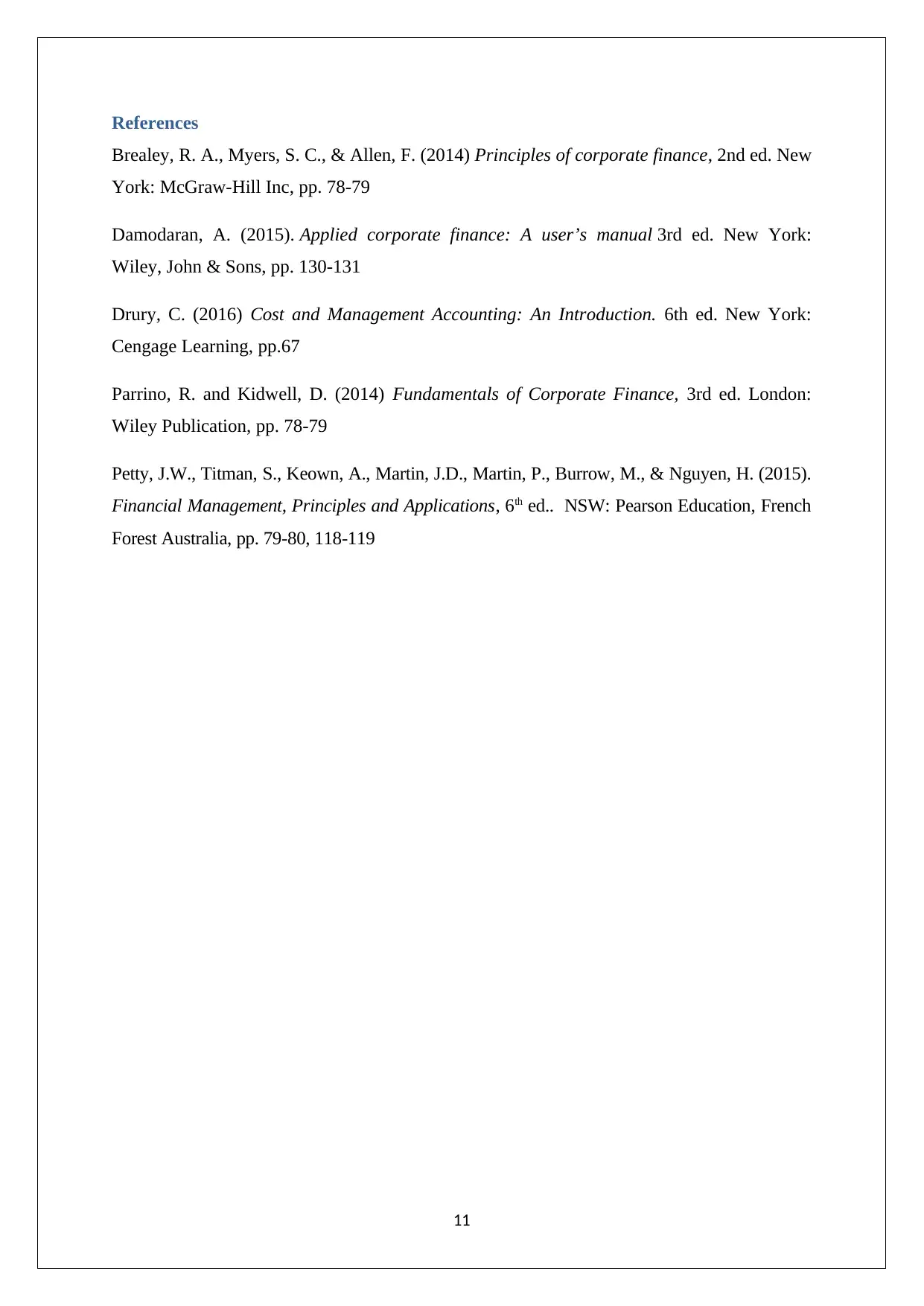
References
Brealey, R. A., Myers, S. C., & Allen, F. (2014) Principles of corporate finance, 2nd ed. New
York: McGraw-Hill Inc, pp. 78-79
Damodaran, A. (2015). Applied corporate finance: A user’s manual 3rd ed. New York:
Wiley, John & Sons, pp. 130-131
Drury, C. (2016) Cost and Management Accounting: An Introduction. 6th ed. New York:
Cengage Learning, pp.67
Parrino, R. and Kidwell, D. (2014) Fundamentals of Corporate Finance, 3rd ed. London:
Wiley Publication, pp. 78-79
Petty, J.W., Titman, S., Keown, A., Martin, J.D., Martin, P., Burrow, M., & Nguyen, H. (2015).
Financial Management, Principles and Applications, 6th ed.. NSW: Pearson Education, French
Forest Australia, pp. 79-80, 118-119
11
Brealey, R. A., Myers, S. C., & Allen, F. (2014) Principles of corporate finance, 2nd ed. New
York: McGraw-Hill Inc, pp. 78-79
Damodaran, A. (2015). Applied corporate finance: A user’s manual 3rd ed. New York:
Wiley, John & Sons, pp. 130-131
Drury, C. (2016) Cost and Management Accounting: An Introduction. 6th ed. New York:
Cengage Learning, pp.67
Parrino, R. and Kidwell, D. (2014) Fundamentals of Corporate Finance, 3rd ed. London:
Wiley Publication, pp. 78-79
Petty, J.W., Titman, S., Keown, A., Martin, J.D., Martin, P., Burrow, M., & Nguyen, H. (2015).
Financial Management, Principles and Applications, 6th ed.. NSW: Pearson Education, French
Forest Australia, pp. 79-80, 118-119
11
1 out of 12
Related Documents

Your All-in-One AI-Powered Toolkit for Academic Success.
+13062052269
info@desklib.com
Available 24*7 on WhatsApp / Email
Unlock your academic potential
© 2024 | Zucol Services PVT LTD | All rights reserved.