ACC203 Assignment: Managerial Accounting and Cost Analysis Report
VerifiedAdded on 2022/10/03
|9
|1893
|15
Homework Assignment
AI Summary
This document presents a comprehensive solution to a managerial accounting assignment. The assignment focuses on analyzing the operational efficiency of Flying Airlines. The solution includes a detailed cost analysis for a loader truck replacement decision, comparing the costs of using the existing truck versus replacing it with a new one. It also addresses cost classification, categorizing various costs into prime, period, overhead, and conversion costs. Furthermore, the solution explores overhead allocation, calculating predetermined overhead rates based on direct labor hours, direct labor costs, machine hours, and direct material costs. The assignment also involves calculating applied overhead and determining whether overhead is under or over applied. The solution provides step-by-step calculations and explanations, making it a valuable resource for students studying managerial accounting. This assignment is contributed by a student to be published on the website Desklib. Desklib is a platform which provides all the necessary AI based study tools for students.
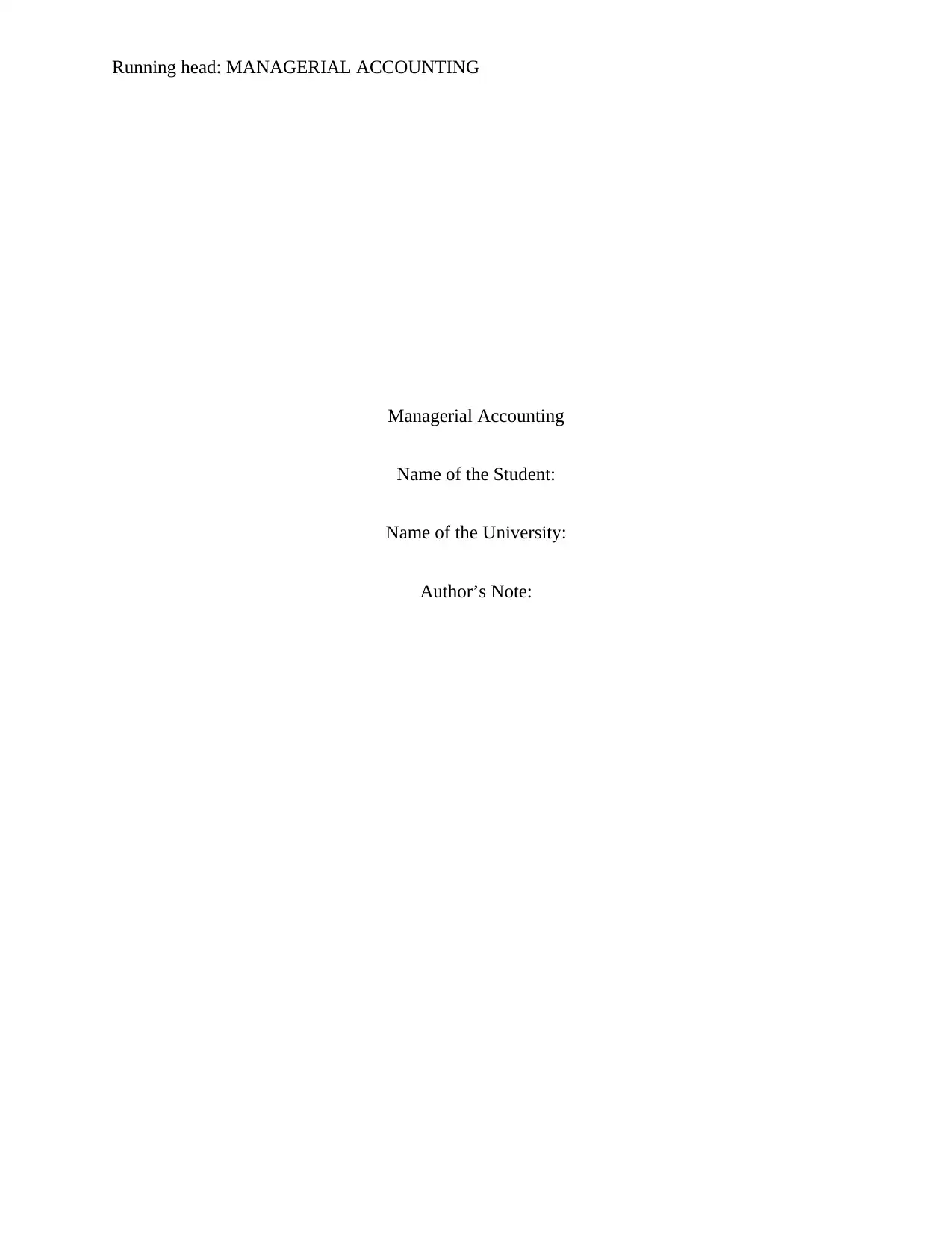
Running head: MANAGERIAL ACCOUNTING
Managerial Accounting
Name of the Student:
Name of the University:
Author’s Note:
Managerial Accounting
Name of the Student:
Name of the University:
Author’s Note:
Paraphrase This Document
Need a fresh take? Get an instant paraphrase of this document with our AI Paraphraser
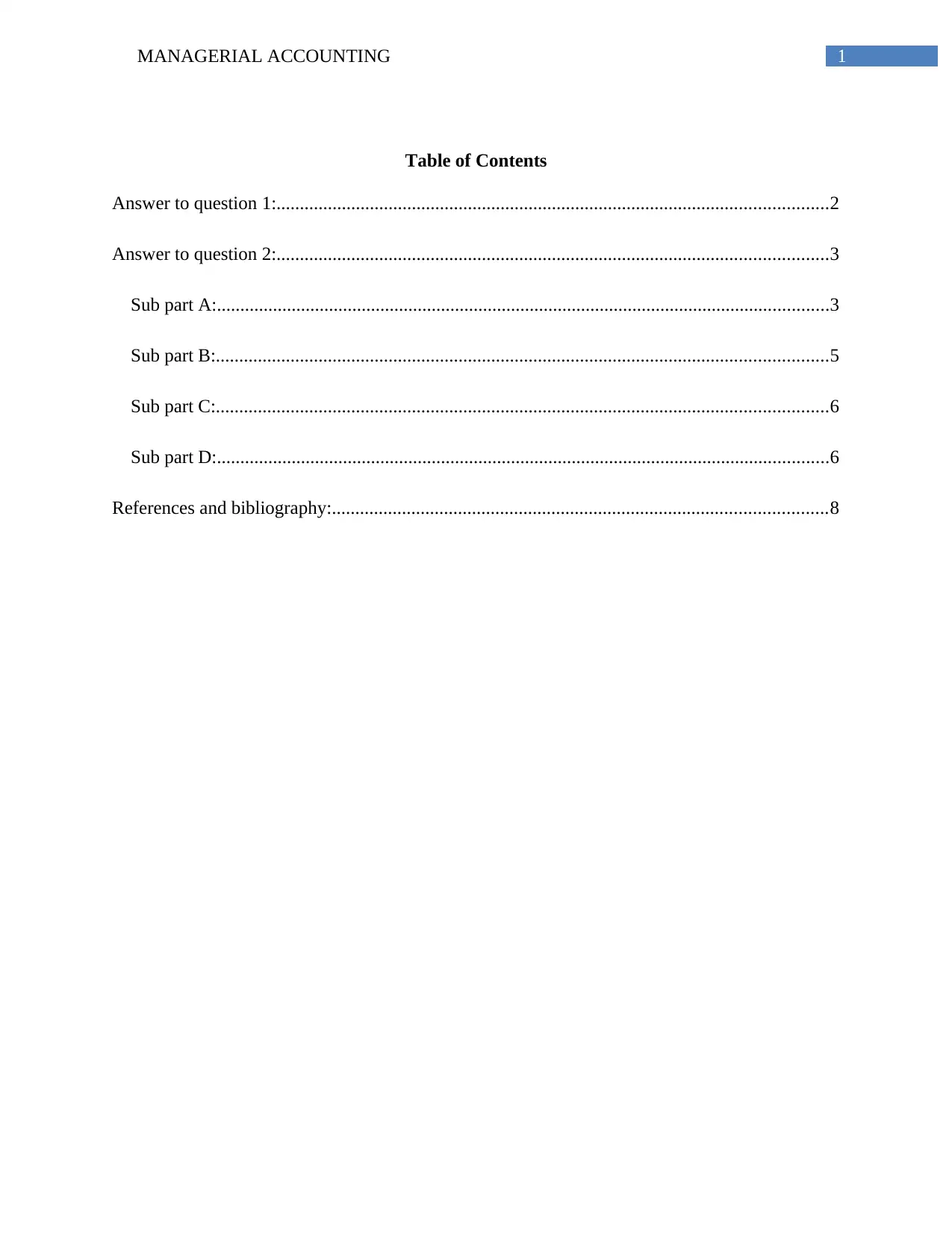
1MANAGERIAL ACCOUNTING
Table of Contents
Answer to question 1:......................................................................................................................2
Answer to question 2:......................................................................................................................3
Sub part A:...................................................................................................................................3
Sub part B:...................................................................................................................................5
Sub part C:...................................................................................................................................6
Sub part D:...................................................................................................................................6
References and bibliography:..........................................................................................................8
Table of Contents
Answer to question 1:......................................................................................................................2
Answer to question 2:......................................................................................................................3
Sub part A:...................................................................................................................................3
Sub part B:...................................................................................................................................5
Sub part C:...................................................................................................................................6
Sub part D:...................................................................................................................................6
References and bibliography:..........................................................................................................8
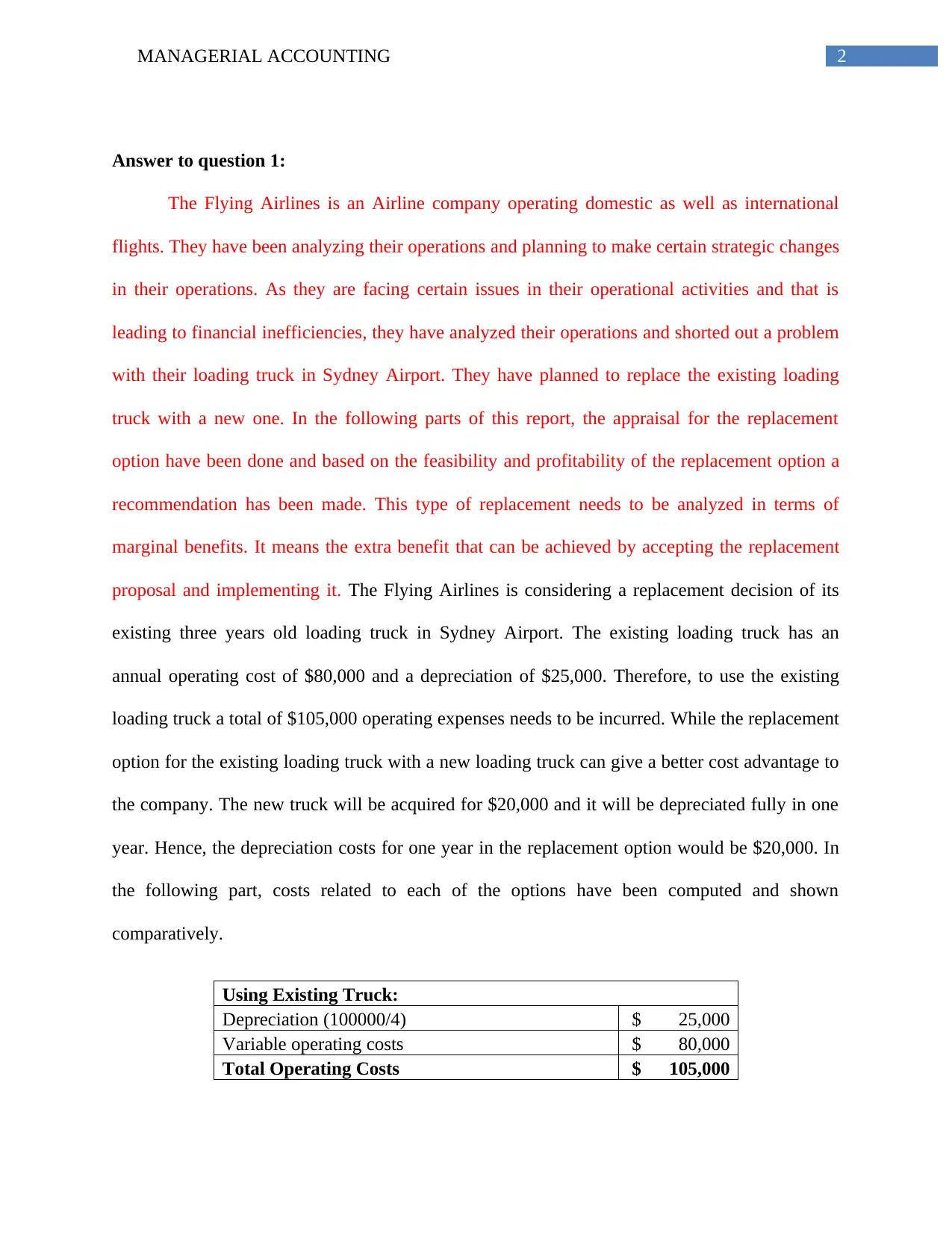
2MANAGERIAL ACCOUNTING
Answer to question 1:
The Flying Airlines is an Airline company operating domestic as well as international
flights. They have been analyzing their operations and planning to make certain strategic changes
in their operations. As they are facing certain issues in their operational activities and that is
leading to financial inefficiencies, they have analyzed their operations and shorted out a problem
with their loading truck in Sydney Airport. They have planned to replace the existing loading
truck with a new one. In the following parts of this report, the appraisal for the replacement
option have been done and based on the feasibility and profitability of the replacement option a
recommendation has been made. This type of replacement needs to be analyzed in terms of
marginal benefits. It means the extra benefit that can be achieved by accepting the replacement
proposal and implementing it. The Flying Airlines is considering a replacement decision of its
existing three years old loading truck in Sydney Airport. The existing loading truck has an
annual operating cost of $80,000 and a depreciation of $25,000. Therefore, to use the existing
loading truck a total of $105,000 operating expenses needs to be incurred. While the replacement
option for the existing loading truck with a new loading truck can give a better cost advantage to
the company. The new truck will be acquired for $20,000 and it will be depreciated fully in one
year. Hence, the depreciation costs for one year in the replacement option would be $20,000. In
the following part, costs related to each of the options have been computed and shown
comparatively.
Using Existing Truck:
Depreciation (100000/4) $ 25,000
Variable operating costs $ 80,000
Total Operating Costs $ 105,000
Answer to question 1:
The Flying Airlines is an Airline company operating domestic as well as international
flights. They have been analyzing their operations and planning to make certain strategic changes
in their operations. As they are facing certain issues in their operational activities and that is
leading to financial inefficiencies, they have analyzed their operations and shorted out a problem
with their loading truck in Sydney Airport. They have planned to replace the existing loading
truck with a new one. In the following parts of this report, the appraisal for the replacement
option have been done and based on the feasibility and profitability of the replacement option a
recommendation has been made. This type of replacement needs to be analyzed in terms of
marginal benefits. It means the extra benefit that can be achieved by accepting the replacement
proposal and implementing it. The Flying Airlines is considering a replacement decision of its
existing three years old loading truck in Sydney Airport. The existing loading truck has an
annual operating cost of $80,000 and a depreciation of $25,000. Therefore, to use the existing
loading truck a total of $105,000 operating expenses needs to be incurred. While the replacement
option for the existing loading truck with a new loading truck can give a better cost advantage to
the company. The new truck will be acquired for $20,000 and it will be depreciated fully in one
year. Hence, the depreciation costs for one year in the replacement option would be $20,000. In
the following part, costs related to each of the options have been computed and shown
comparatively.
Using Existing Truck:
Depreciation (100000/4) $ 25,000
Variable operating costs $ 80,000
Total Operating Costs $ 105,000
You're viewing a preview
Unlock full access by subscribing today!
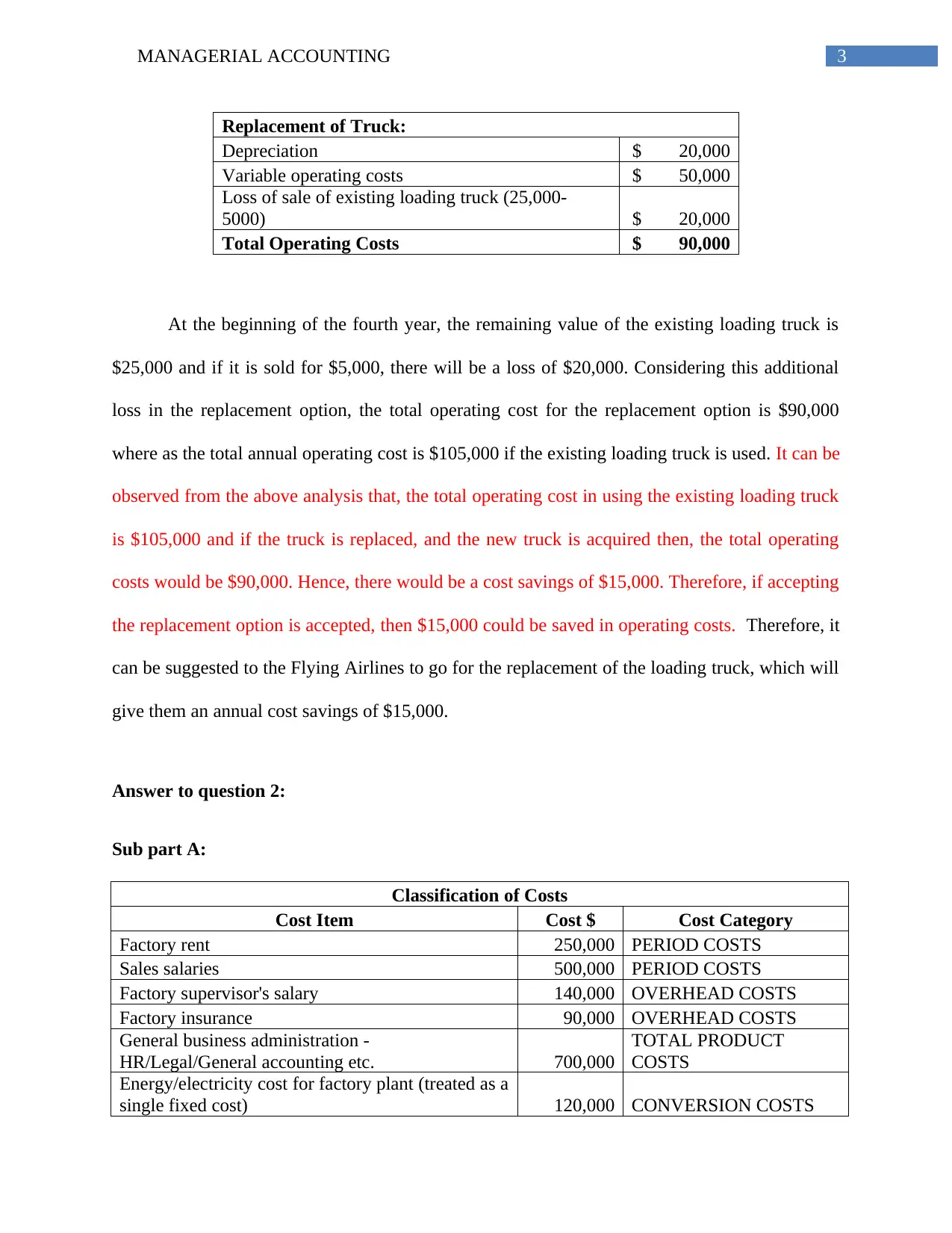
3MANAGERIAL ACCOUNTING
Replacement of Truck:
Depreciation $ 20,000
Variable operating costs $ 50,000
Loss of sale of existing loading truck (25,000-
5000) $ 20,000
Total Operating Costs $ 90,000
At the beginning of the fourth year, the remaining value of the existing loading truck is
$25,000 and if it is sold for $5,000, there will be a loss of $20,000. Considering this additional
loss in the replacement option, the total operating cost for the replacement option is $90,000
where as the total annual operating cost is $105,000 if the existing loading truck is used. It can be
observed from the above analysis that, the total operating cost in using the existing loading truck
is $105,000 and if the truck is replaced, and the new truck is acquired then, the total operating
costs would be $90,000. Hence, there would be a cost savings of $15,000. Therefore, if accepting
the replacement option is accepted, then $15,000 could be saved in operating costs. Therefore, it
can be suggested to the Flying Airlines to go for the replacement of the loading truck, which will
give them an annual cost savings of $15,000.
Answer to question 2:
Sub part A:
Classification of Costs
Cost Item Cost $ Cost Category
Factory rent 250,000 PERIOD COSTS
Sales salaries 500,000 PERIOD COSTS
Factory supervisor's salary 140,000 OVERHEAD COSTS
Factory insurance 90,000 OVERHEAD COSTS
General business administration -
HR/Legal/General accounting etc. 700,000
TOTAL PRODUCT
COSTS
Energy/electricity cost for factory plant (treated as a
single fixed cost) 120,000 CONVERSION COSTS
Replacement of Truck:
Depreciation $ 20,000
Variable operating costs $ 50,000
Loss of sale of existing loading truck (25,000-
5000) $ 20,000
Total Operating Costs $ 90,000
At the beginning of the fourth year, the remaining value of the existing loading truck is
$25,000 and if it is sold for $5,000, there will be a loss of $20,000. Considering this additional
loss in the replacement option, the total operating cost for the replacement option is $90,000
where as the total annual operating cost is $105,000 if the existing loading truck is used. It can be
observed from the above analysis that, the total operating cost in using the existing loading truck
is $105,000 and if the truck is replaced, and the new truck is acquired then, the total operating
costs would be $90,000. Hence, there would be a cost savings of $15,000. Therefore, if accepting
the replacement option is accepted, then $15,000 could be saved in operating costs. Therefore, it
can be suggested to the Flying Airlines to go for the replacement of the loading truck, which will
give them an annual cost savings of $15,000.
Answer to question 2:
Sub part A:
Classification of Costs
Cost Item Cost $ Cost Category
Factory rent 250,000 PERIOD COSTS
Sales salaries 500,000 PERIOD COSTS
Factory supervisor's salary 140,000 OVERHEAD COSTS
Factory insurance 90,000 OVERHEAD COSTS
General business administration -
HR/Legal/General accounting etc. 700,000
TOTAL PRODUCT
COSTS
Energy/electricity cost for factory plant (treated as a
single fixed cost) 120,000 CONVERSION COSTS
Paraphrase This Document
Need a fresh take? Get an instant paraphrase of this document with our AI Paraphraser
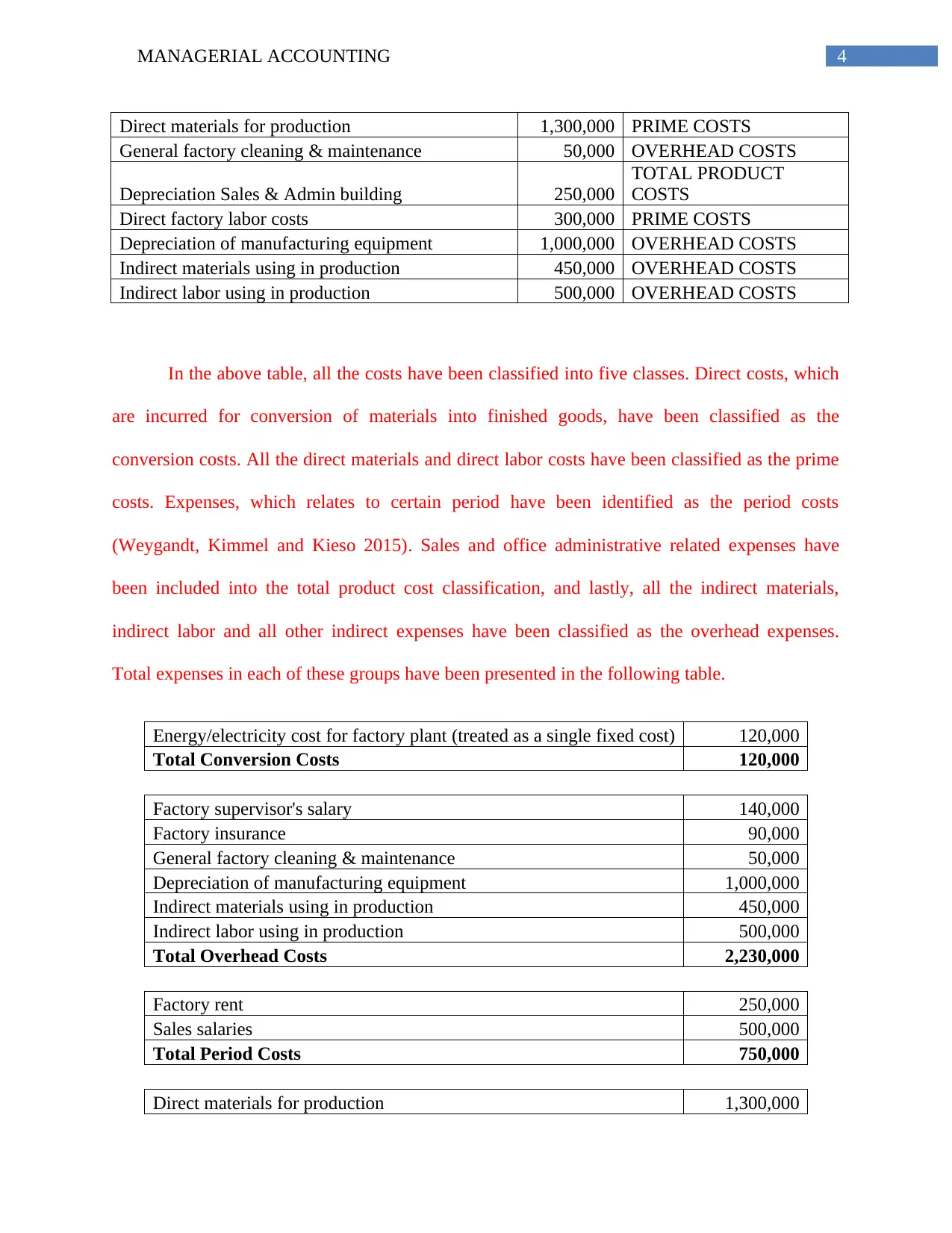
4MANAGERIAL ACCOUNTING
Direct materials for production 1,300,000 PRIME COSTS
General factory cleaning & maintenance 50,000 OVERHEAD COSTS
Depreciation Sales & Admin building 250,000
TOTAL PRODUCT
COSTS
Direct factory labor costs 300,000 PRIME COSTS
Depreciation of manufacturing equipment 1,000,000 OVERHEAD COSTS
Indirect materials using in production 450,000 OVERHEAD COSTS
Indirect labor using in production 500,000 OVERHEAD COSTS
In the above table, all the costs have been classified into five classes. Direct costs, which
are incurred for conversion of materials into finished goods, have been classified as the
conversion costs. All the direct materials and direct labor costs have been classified as the prime
costs. Expenses, which relates to certain period have been identified as the period costs
(Weygandt, Kimmel and Kieso 2015). Sales and office administrative related expenses have
been included into the total product cost classification, and lastly, all the indirect materials,
indirect labor and all other indirect expenses have been classified as the overhead expenses.
Total expenses in each of these groups have been presented in the following table.
Energy/electricity cost for factory plant (treated as a single fixed cost) 120,000
Total Conversion Costs 120,000
Factory supervisor's salary 140,000
Factory insurance 90,000
General factory cleaning & maintenance 50,000
Depreciation of manufacturing equipment 1,000,000
Indirect materials using in production 450,000
Indirect labor using in production 500,000
Total Overhead Costs 2,230,000
Factory rent 250,000
Sales salaries 500,000
Total Period Costs 750,000
Direct materials for production 1,300,000
Direct materials for production 1,300,000 PRIME COSTS
General factory cleaning & maintenance 50,000 OVERHEAD COSTS
Depreciation Sales & Admin building 250,000
TOTAL PRODUCT
COSTS
Direct factory labor costs 300,000 PRIME COSTS
Depreciation of manufacturing equipment 1,000,000 OVERHEAD COSTS
Indirect materials using in production 450,000 OVERHEAD COSTS
Indirect labor using in production 500,000 OVERHEAD COSTS
In the above table, all the costs have been classified into five classes. Direct costs, which
are incurred for conversion of materials into finished goods, have been classified as the
conversion costs. All the direct materials and direct labor costs have been classified as the prime
costs. Expenses, which relates to certain period have been identified as the period costs
(Weygandt, Kimmel and Kieso 2015). Sales and office administrative related expenses have
been included into the total product cost classification, and lastly, all the indirect materials,
indirect labor and all other indirect expenses have been classified as the overhead expenses.
Total expenses in each of these groups have been presented in the following table.
Energy/electricity cost for factory plant (treated as a single fixed cost) 120,000
Total Conversion Costs 120,000
Factory supervisor's salary 140,000
Factory insurance 90,000
General factory cleaning & maintenance 50,000
Depreciation of manufacturing equipment 1,000,000
Indirect materials using in production 450,000
Indirect labor using in production 500,000
Total Overhead Costs 2,230,000
Factory rent 250,000
Sales salaries 500,000
Total Period Costs 750,000
Direct materials for production 1,300,000
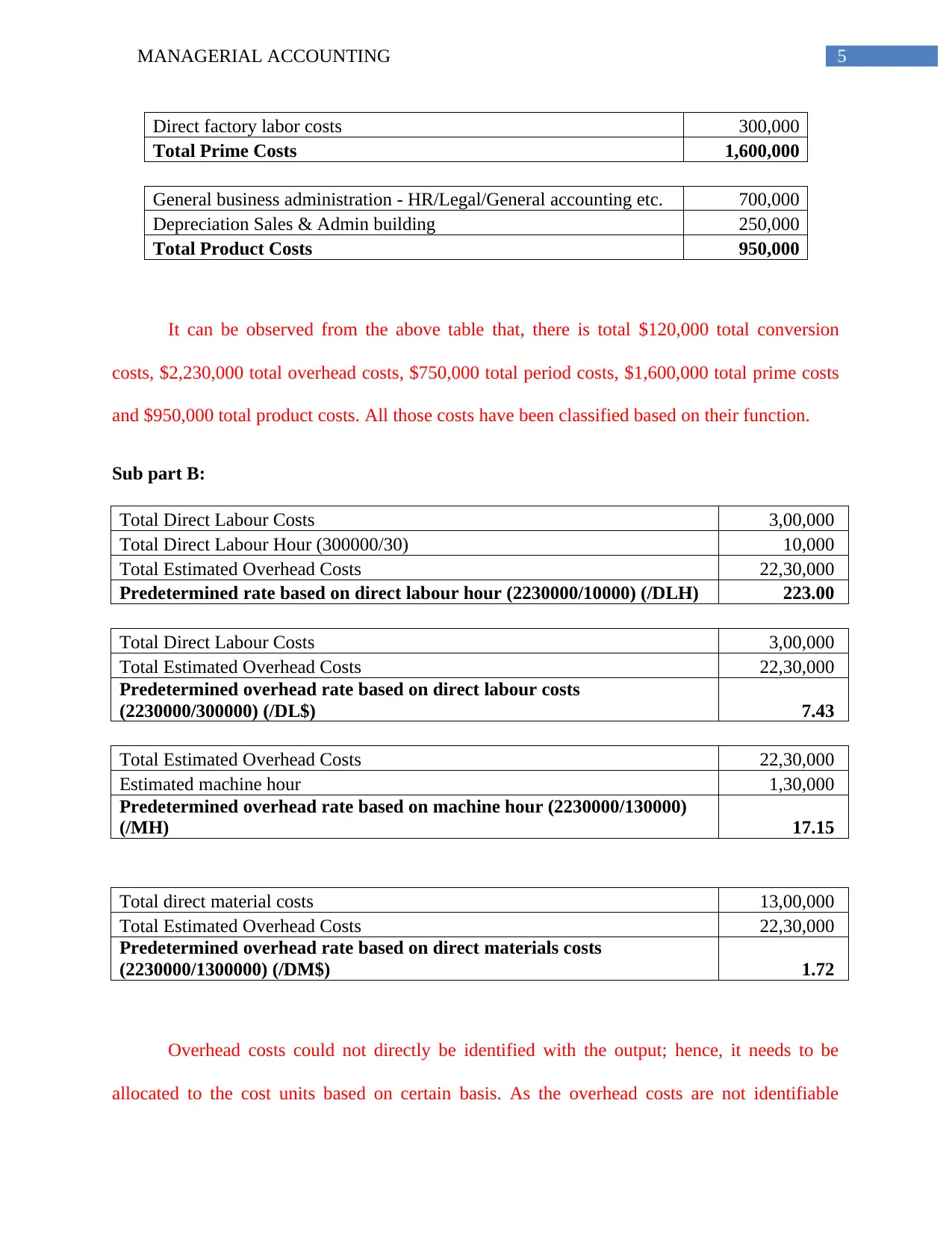
5MANAGERIAL ACCOUNTING
Direct factory labor costs 300,000
Total Prime Costs 1,600,000
General business administration - HR/Legal/General accounting etc. 700,000
Depreciation Sales & Admin building 250,000
Total Product Costs 950,000
It can be observed from the above table that, there is total $120,000 total conversion
costs, $2,230,000 total overhead costs, $750,000 total period costs, $1,600,000 total prime costs
and $950,000 total product costs. All those costs have been classified based on their function.
Sub part B:
Total Direct Labour Costs 3,00,000
Total Direct Labour Hour (300000/30) 10,000
Total Estimated Overhead Costs 22,30,000
Predetermined rate based on direct labour hour (2230000/10000) (/DLH) 223.00
Total Direct Labour Costs 3,00,000
Total Estimated Overhead Costs 22,30,000
Predetermined overhead rate based on direct labour costs
(2230000/300000) (/DL$) 7.43
Total Estimated Overhead Costs 22,30,000
Estimated machine hour 1,30,000
Predetermined overhead rate based on machine hour (2230000/130000)
(/MH) 17.15
Total direct material costs 13,00,000
Total Estimated Overhead Costs 22,30,000
Predetermined overhead rate based on direct materials costs
(2230000/1300000) (/DM$) 1.72
Overhead costs could not directly be identified with the output; hence, it needs to be
allocated to the cost units based on certain basis. As the overhead costs are not identifiable
Direct factory labor costs 300,000
Total Prime Costs 1,600,000
General business administration - HR/Legal/General accounting etc. 700,000
Depreciation Sales & Admin building 250,000
Total Product Costs 950,000
It can be observed from the above table that, there is total $120,000 total conversion
costs, $2,230,000 total overhead costs, $750,000 total period costs, $1,600,000 total prime costs
and $950,000 total product costs. All those costs have been classified based on their function.
Sub part B:
Total Direct Labour Costs 3,00,000
Total Direct Labour Hour (300000/30) 10,000
Total Estimated Overhead Costs 22,30,000
Predetermined rate based on direct labour hour (2230000/10000) (/DLH) 223.00
Total Direct Labour Costs 3,00,000
Total Estimated Overhead Costs 22,30,000
Predetermined overhead rate based on direct labour costs
(2230000/300000) (/DL$) 7.43
Total Estimated Overhead Costs 22,30,000
Estimated machine hour 1,30,000
Predetermined overhead rate based on machine hour (2230000/130000)
(/MH) 17.15
Total direct material costs 13,00,000
Total Estimated Overhead Costs 22,30,000
Predetermined overhead rate based on direct materials costs
(2230000/1300000) (/DM$) 1.72
Overhead costs could not directly be identified with the output; hence, it needs to be
allocated to the cost units based on certain basis. As the overhead costs are not identifiable
You're viewing a preview
Unlock full access by subscribing today!
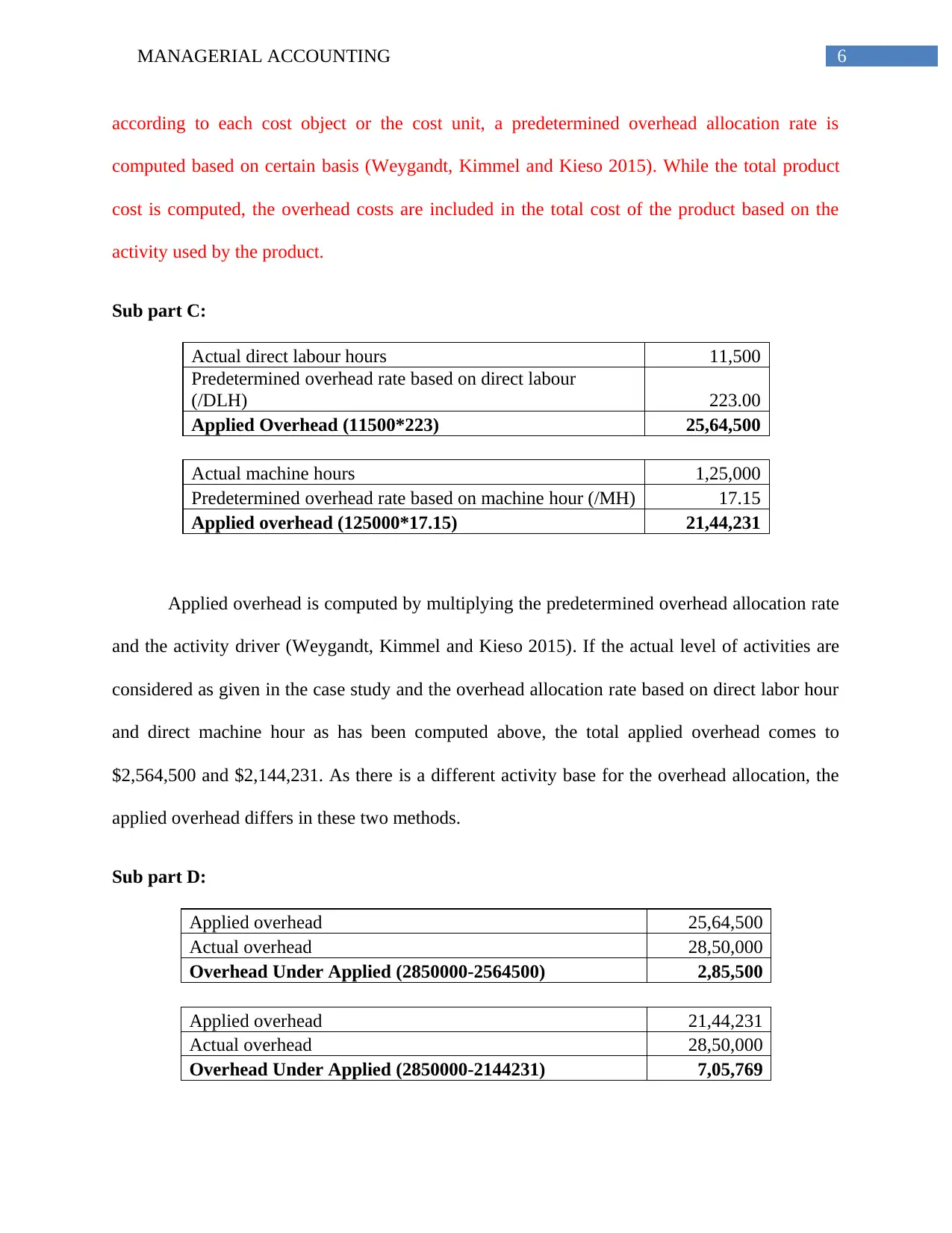
6MANAGERIAL ACCOUNTING
according to each cost object or the cost unit, a predetermined overhead allocation rate is
computed based on certain basis (Weygandt, Kimmel and Kieso 2015). While the total product
cost is computed, the overhead costs are included in the total cost of the product based on the
activity used by the product.
Sub part C:
Actual direct labour hours 11,500
Predetermined overhead rate based on direct labour
(/DLH) 223.00
Applied Overhead (11500*223) 25,64,500
Actual machine hours 1,25,000
Predetermined overhead rate based on machine hour (/MH) 17.15
Applied overhead (125000*17.15) 21,44,231
Applied overhead is computed by multiplying the predetermined overhead allocation rate
and the activity driver (Weygandt, Kimmel and Kieso 2015). If the actual level of activities are
considered as given in the case study and the overhead allocation rate based on direct labor hour
and direct machine hour as has been computed above, the total applied overhead comes to
$2,564,500 and $2,144,231. As there is a different activity base for the overhead allocation, the
applied overhead differs in these two methods.
Sub part D:
Applied overhead 25,64,500
Actual overhead 28,50,000
Overhead Under Applied (2850000-2564500) 2,85,500
Applied overhead 21,44,231
Actual overhead 28,50,000
Overhead Under Applied (2850000-2144231) 7,05,769
according to each cost object or the cost unit, a predetermined overhead allocation rate is
computed based on certain basis (Weygandt, Kimmel and Kieso 2015). While the total product
cost is computed, the overhead costs are included in the total cost of the product based on the
activity used by the product.
Sub part C:
Actual direct labour hours 11,500
Predetermined overhead rate based on direct labour
(/DLH) 223.00
Applied Overhead (11500*223) 25,64,500
Actual machine hours 1,25,000
Predetermined overhead rate based on machine hour (/MH) 17.15
Applied overhead (125000*17.15) 21,44,231
Applied overhead is computed by multiplying the predetermined overhead allocation rate
and the activity driver (Weygandt, Kimmel and Kieso 2015). If the actual level of activities are
considered as given in the case study and the overhead allocation rate based on direct labor hour
and direct machine hour as has been computed above, the total applied overhead comes to
$2,564,500 and $2,144,231. As there is a different activity base for the overhead allocation, the
applied overhead differs in these two methods.
Sub part D:
Applied overhead 25,64,500
Actual overhead 28,50,000
Overhead Under Applied (2850000-2564500) 2,85,500
Applied overhead 21,44,231
Actual overhead 28,50,000
Overhead Under Applied (2850000-2144231) 7,05,769
Paraphrase This Document
Need a fresh take? Get an instant paraphrase of this document with our AI Paraphraser
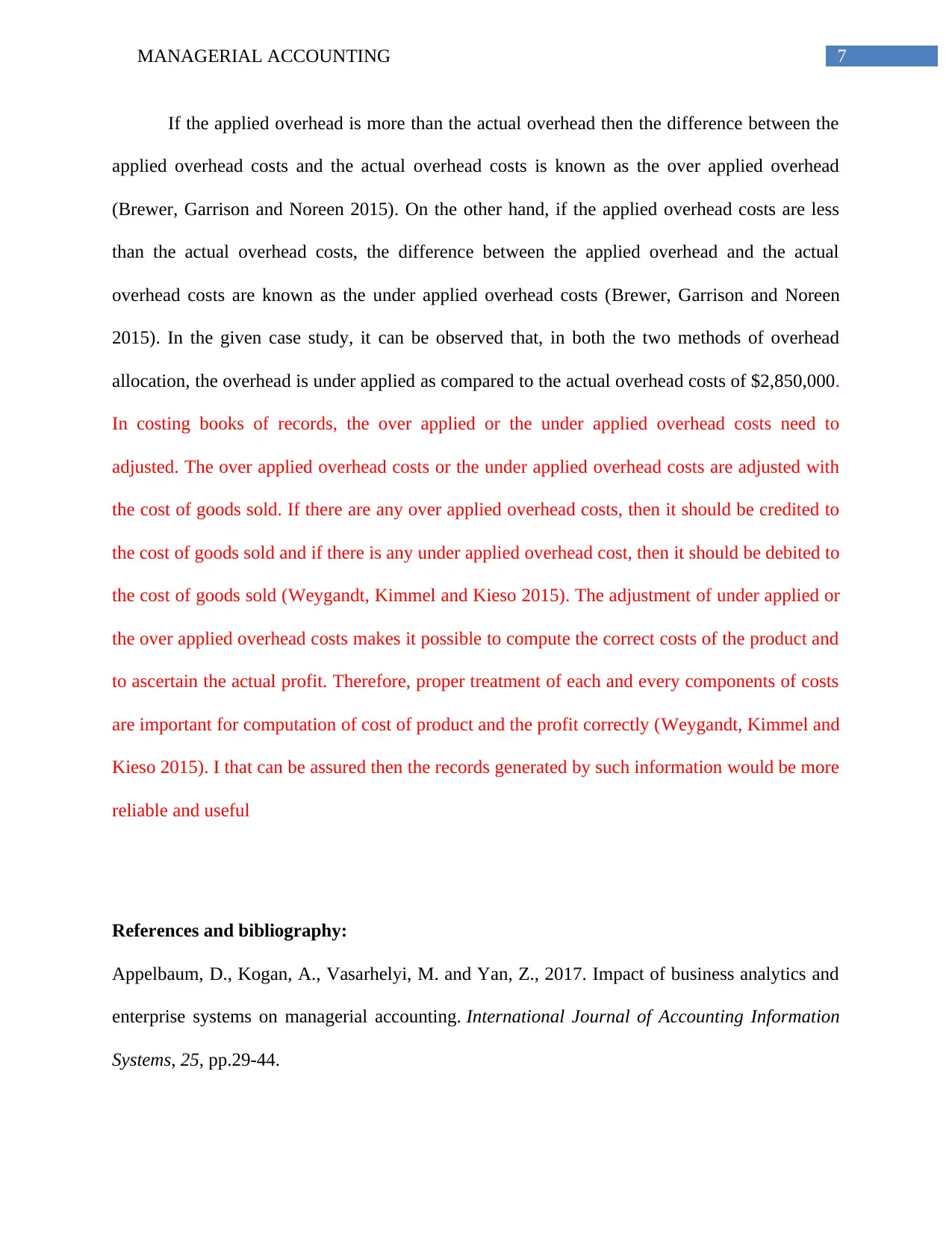
7MANAGERIAL ACCOUNTING
If the applied overhead is more than the actual overhead then the difference between the
applied overhead costs and the actual overhead costs is known as the over applied overhead
(Brewer, Garrison and Noreen 2015). On the other hand, if the applied overhead costs are less
than the actual overhead costs, the difference between the applied overhead and the actual
overhead costs are known as the under applied overhead costs (Brewer, Garrison and Noreen
2015). In the given case study, it can be observed that, in both the two methods of overhead
allocation, the overhead is under applied as compared to the actual overhead costs of $2,850,000.
In costing books of records, the over applied or the under applied overhead costs need to
adjusted. The over applied overhead costs or the under applied overhead costs are adjusted with
the cost of goods sold. If there are any over applied overhead costs, then it should be credited to
the cost of goods sold and if there is any under applied overhead cost, then it should be debited to
the cost of goods sold (Weygandt, Kimmel and Kieso 2015). The adjustment of under applied or
the over applied overhead costs makes it possible to compute the correct costs of the product and
to ascertain the actual profit. Therefore, proper treatment of each and every components of costs
are important for computation of cost of product and the profit correctly (Weygandt, Kimmel and
Kieso 2015). I that can be assured then the records generated by such information would be more
reliable and useful
References and bibliography:
Appelbaum, D., Kogan, A., Vasarhelyi, M. and Yan, Z., 2017. Impact of business analytics and
enterprise systems on managerial accounting. International Journal of Accounting Information
Systems, 25, pp.29-44.
If the applied overhead is more than the actual overhead then the difference between the
applied overhead costs and the actual overhead costs is known as the over applied overhead
(Brewer, Garrison and Noreen 2015). On the other hand, if the applied overhead costs are less
than the actual overhead costs, the difference between the applied overhead and the actual
overhead costs are known as the under applied overhead costs (Brewer, Garrison and Noreen
2015). In the given case study, it can be observed that, in both the two methods of overhead
allocation, the overhead is under applied as compared to the actual overhead costs of $2,850,000.
In costing books of records, the over applied or the under applied overhead costs need to
adjusted. The over applied overhead costs or the under applied overhead costs are adjusted with
the cost of goods sold. If there are any over applied overhead costs, then it should be credited to
the cost of goods sold and if there is any under applied overhead cost, then it should be debited to
the cost of goods sold (Weygandt, Kimmel and Kieso 2015). The adjustment of under applied or
the over applied overhead costs makes it possible to compute the correct costs of the product and
to ascertain the actual profit. Therefore, proper treatment of each and every components of costs
are important for computation of cost of product and the profit correctly (Weygandt, Kimmel and
Kieso 2015). I that can be assured then the records generated by such information would be more
reliable and useful
References and bibliography:
Appelbaum, D., Kogan, A., Vasarhelyi, M. and Yan, Z., 2017. Impact of business analytics and
enterprise systems on managerial accounting. International Journal of Accounting Information
Systems, 25, pp.29-44.
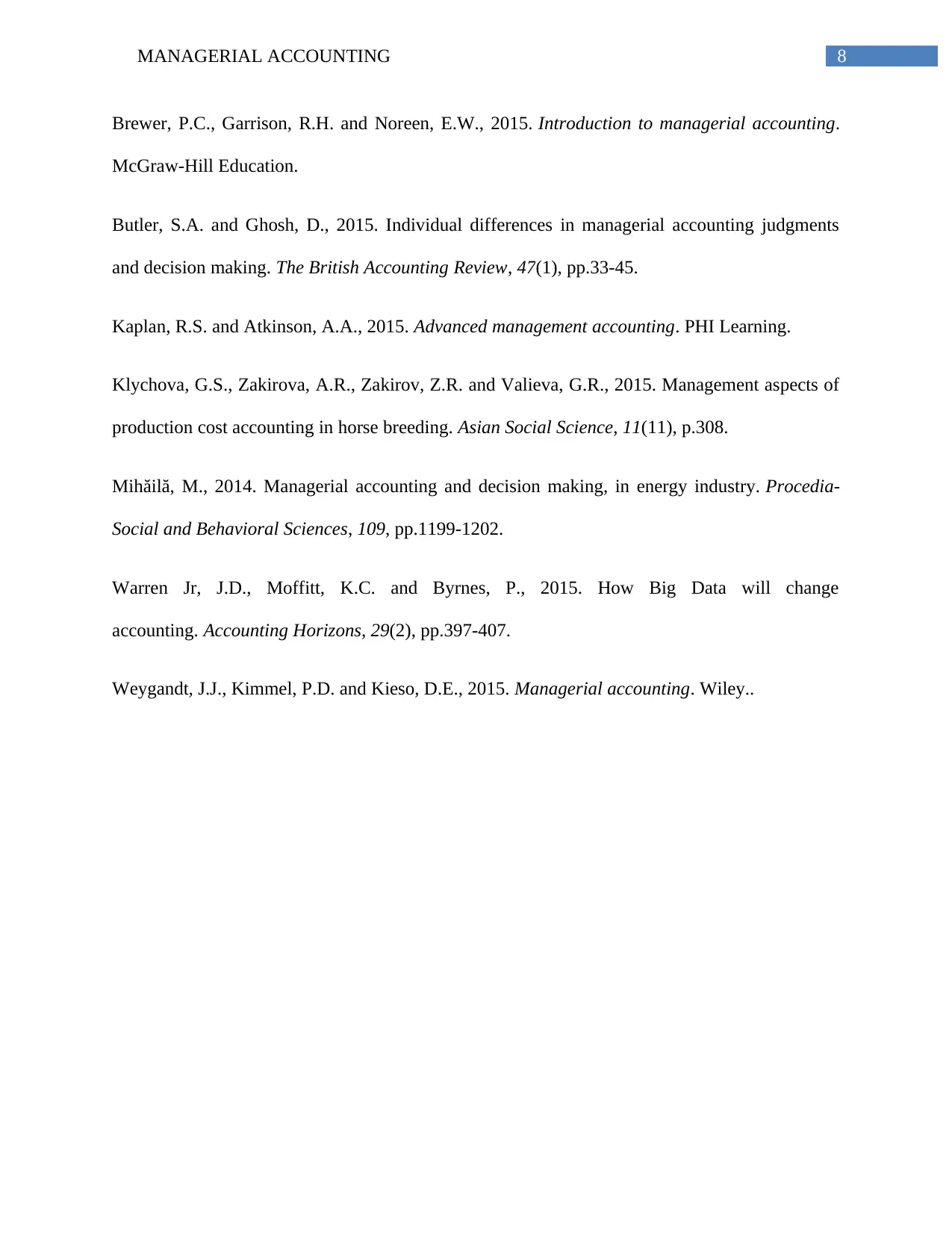
8MANAGERIAL ACCOUNTING
Brewer, P.C., Garrison, R.H. and Noreen, E.W., 2015. Introduction to managerial accounting.
McGraw-Hill Education.
Butler, S.A. and Ghosh, D., 2015. Individual differences in managerial accounting judgments
and decision making. The British Accounting Review, 47(1), pp.33-45.
Kaplan, R.S. and Atkinson, A.A., 2015. Advanced management accounting. PHI Learning.
Klychova, G.S., Zakirova, A.R., Zakirov, Z.R. and Valieva, G.R., 2015. Management aspects of
production cost accounting in horse breeding. Asian Social Science, 11(11), p.308.
Mihăilă, M., 2014. Managerial accounting and decision making, in energy industry. Procedia-
Social and Behavioral Sciences, 109, pp.1199-1202.
Warren Jr, J.D., Moffitt, K.C. and Byrnes, P., 2015. How Big Data will change
accounting. Accounting Horizons, 29(2), pp.397-407.
Weygandt, J.J., Kimmel, P.D. and Kieso, D.E., 2015. Managerial accounting. Wiley..
Brewer, P.C., Garrison, R.H. and Noreen, E.W., 2015. Introduction to managerial accounting.
McGraw-Hill Education.
Butler, S.A. and Ghosh, D., 2015. Individual differences in managerial accounting judgments
and decision making. The British Accounting Review, 47(1), pp.33-45.
Kaplan, R.S. and Atkinson, A.A., 2015. Advanced management accounting. PHI Learning.
Klychova, G.S., Zakirova, A.R., Zakirov, Z.R. and Valieva, G.R., 2015. Management aspects of
production cost accounting in horse breeding. Asian Social Science, 11(11), p.308.
Mihăilă, M., 2014. Managerial accounting and decision making, in energy industry. Procedia-
Social and Behavioral Sciences, 109, pp.1199-1202.
Warren Jr, J.D., Moffitt, K.C. and Byrnes, P., 2015. How Big Data will change
accounting. Accounting Horizons, 29(2), pp.397-407.
Weygandt, J.J., Kimmel, P.D. and Kieso, D.E., 2015. Managerial accounting. Wiley..
You're viewing a preview
Unlock full access by subscribing today!
1 out of 9
Related Documents

Your All-in-One AI-Powered Toolkit for Academic Success.
+13062052269
info@desklib.com
Available 24*7 on WhatsApp / Email
Unlock your academic potential
© 2024 | Zucol Services PVT LTD | All rights reserved.