Wittgenstein Pty Ltd: Accounting for Managers Report & Analysis
VerifiedAdded on 2020/10/04
|10
|2543
|24
Report
AI Summary
This report presents a comprehensive analysis of accounting for managers, focusing on the creation and evaluation of a master budget for Wittgenstein Pty Ltd. The report meticulously constructs key budgetary components including sales, production, direct material purchases, direct labor, manufacturing overhead, ending finished goods inventory, cost of goods sold, budgeted income statement, and cash budget. Part A provides a detailed breakdown of each budget, while Part B addresses the implications of alternate electricity production equipment and its potential impact on direct and manufacturing costs. Part C evaluates the variances between budgeted and actual figures, highlighting areas of financial performance and inefficiency. Finally, Part D explores the impact of employee behavior and organizational structure on financial outcomes. The conclusion summarizes the key findings and recommendations for improved financial management and decision-making within the company.
Contribute Materials
Your contribution can guide someone’s learning journey. Share your
documents today.
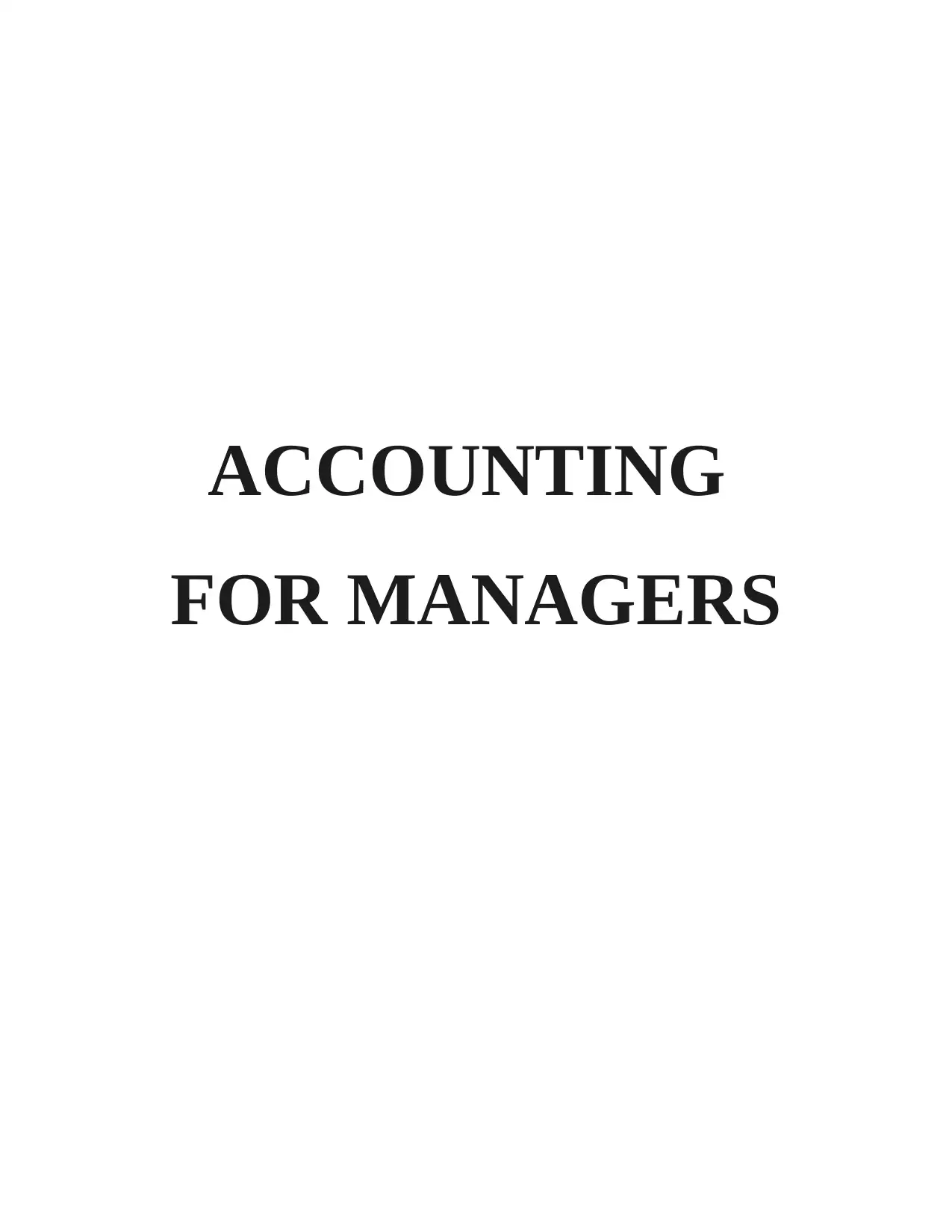
ACCOUNTING
FOR MANAGERS
FOR MANAGERS
Secure Best Marks with AI Grader
Need help grading? Try our AI Grader for instant feedback on your assignments.
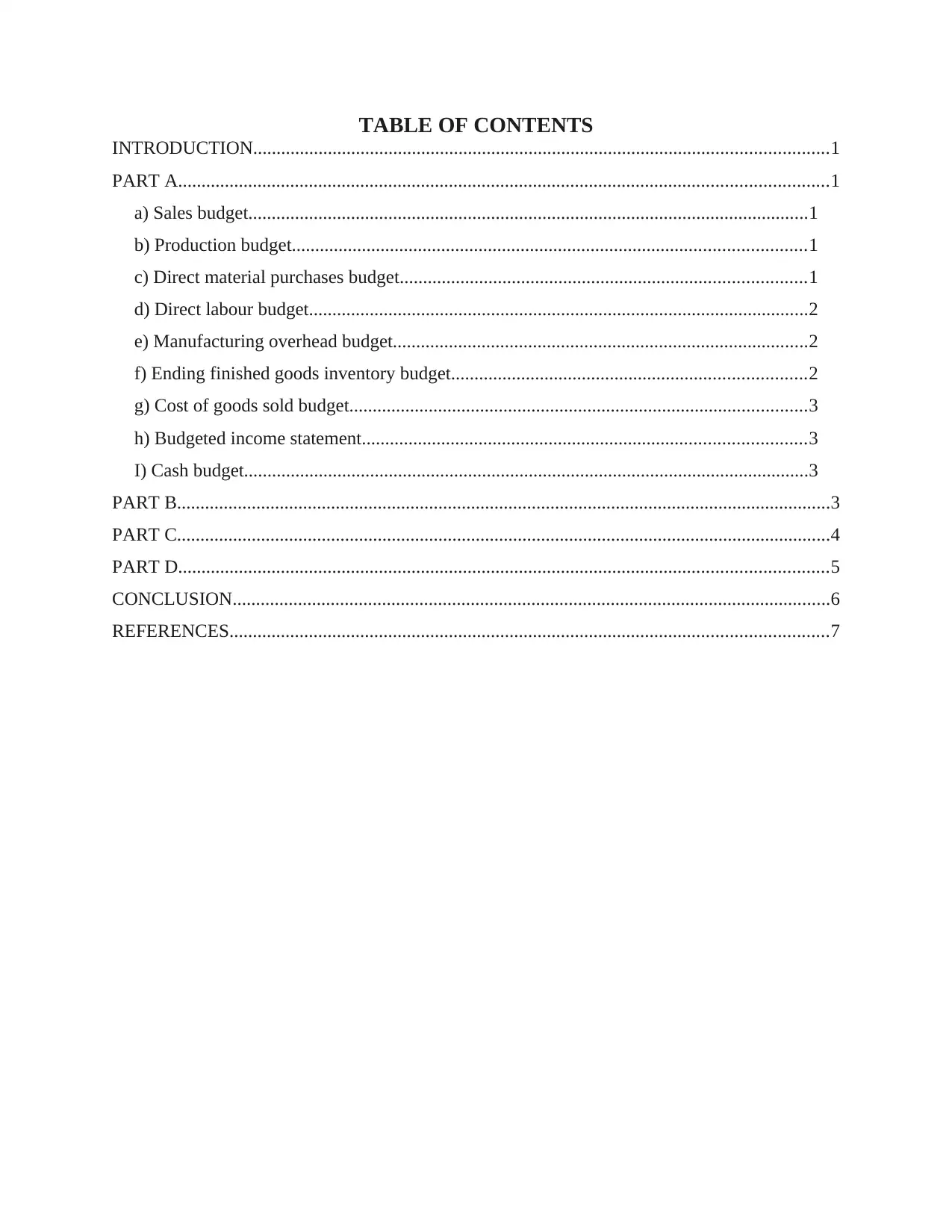
TABLE OF CONTENTS
INTRODUCTION...........................................................................................................................1
PART A...........................................................................................................................................1
a) Sales budget........................................................................................................................1
b) Production budget..............................................................................................................1
c) Direct material purchases budget.......................................................................................1
d) Direct labour budget...........................................................................................................2
e) Manufacturing overhead budget.........................................................................................2
f) Ending finished goods inventory budget............................................................................2
g) Cost of goods sold budget..................................................................................................3
h) Budgeted income statement...............................................................................................3
I) Cash budget.........................................................................................................................3
PART B............................................................................................................................................3
PART C............................................................................................................................................4
PART D...........................................................................................................................................5
CONCLUSION................................................................................................................................6
REFERENCES................................................................................................................................7
INTRODUCTION...........................................................................................................................1
PART A...........................................................................................................................................1
a) Sales budget........................................................................................................................1
b) Production budget..............................................................................................................1
c) Direct material purchases budget.......................................................................................1
d) Direct labour budget...........................................................................................................2
e) Manufacturing overhead budget.........................................................................................2
f) Ending finished goods inventory budget............................................................................2
g) Cost of goods sold budget..................................................................................................3
h) Budgeted income statement...............................................................................................3
I) Cash budget.........................................................................................................................3
PART B............................................................................................................................................3
PART C............................................................................................................................................4
PART D...........................................................................................................................................5
CONCLUSION................................................................................................................................6
REFERENCES................................................................................................................................7
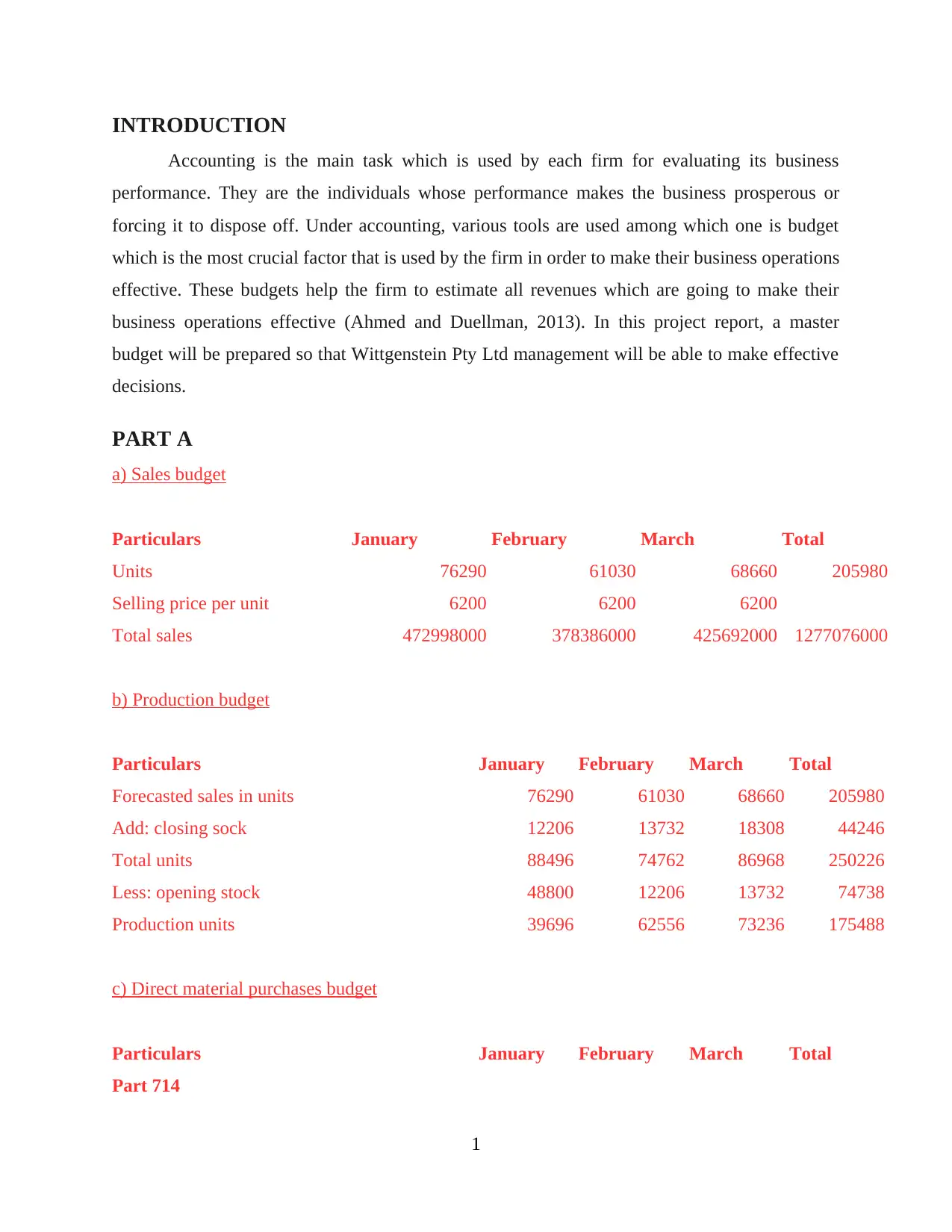
INTRODUCTION
Accounting is the main task which is used by each firm for evaluating its business
performance. They are the individuals whose performance makes the business prosperous or
forcing it to dispose off. Under accounting, various tools are used among which one is budget
which is the most crucial factor that is used by the firm in order to make their business operations
effective. These budgets help the firm to estimate all revenues which are going to make their
business operations effective (Ahmed and Duellman, 2013). In this project report, a master
budget will be prepared so that Wittgenstein Pty Ltd management will be able to make effective
decisions.
PART A
a) Sales budget
Particulars January February March Total
Units 76290 61030 68660 205980
Selling price per unit 6200 6200 6200
Total sales 472998000 378386000 425692000 1277076000
b) Production budget
Particulars January February March Total
Forecasted sales in units 76290 61030 68660 205980
Add: closing sock 12206 13732 18308 44246
Total units 88496 74762 86968 250226
Less: opening stock 48800 12206 13732 74738
Production units 39696 62556 73236 175488
c) Direct material purchases budget
Particulars January February March Total
Part 714
1
Accounting is the main task which is used by each firm for evaluating its business
performance. They are the individuals whose performance makes the business prosperous or
forcing it to dispose off. Under accounting, various tools are used among which one is budget
which is the most crucial factor that is used by the firm in order to make their business operations
effective. These budgets help the firm to estimate all revenues which are going to make their
business operations effective (Ahmed and Duellman, 2013). In this project report, a master
budget will be prepared so that Wittgenstein Pty Ltd management will be able to make effective
decisions.
PART A
a) Sales budget
Particulars January February March Total
Units 76290 61030 68660 205980
Selling price per unit 6200 6200 6200
Total sales 472998000 378386000 425692000 1277076000
b) Production budget
Particulars January February March Total
Forecasted sales in units 76290 61030 68660 205980
Add: closing sock 12206 13732 18308 44246
Total units 88496 74762 86968 250226
Less: opening stock 48800 12206 13732 74738
Production units 39696 62556 73236 175488
c) Direct material purchases budget
Particulars January February March Total
Part 714
1
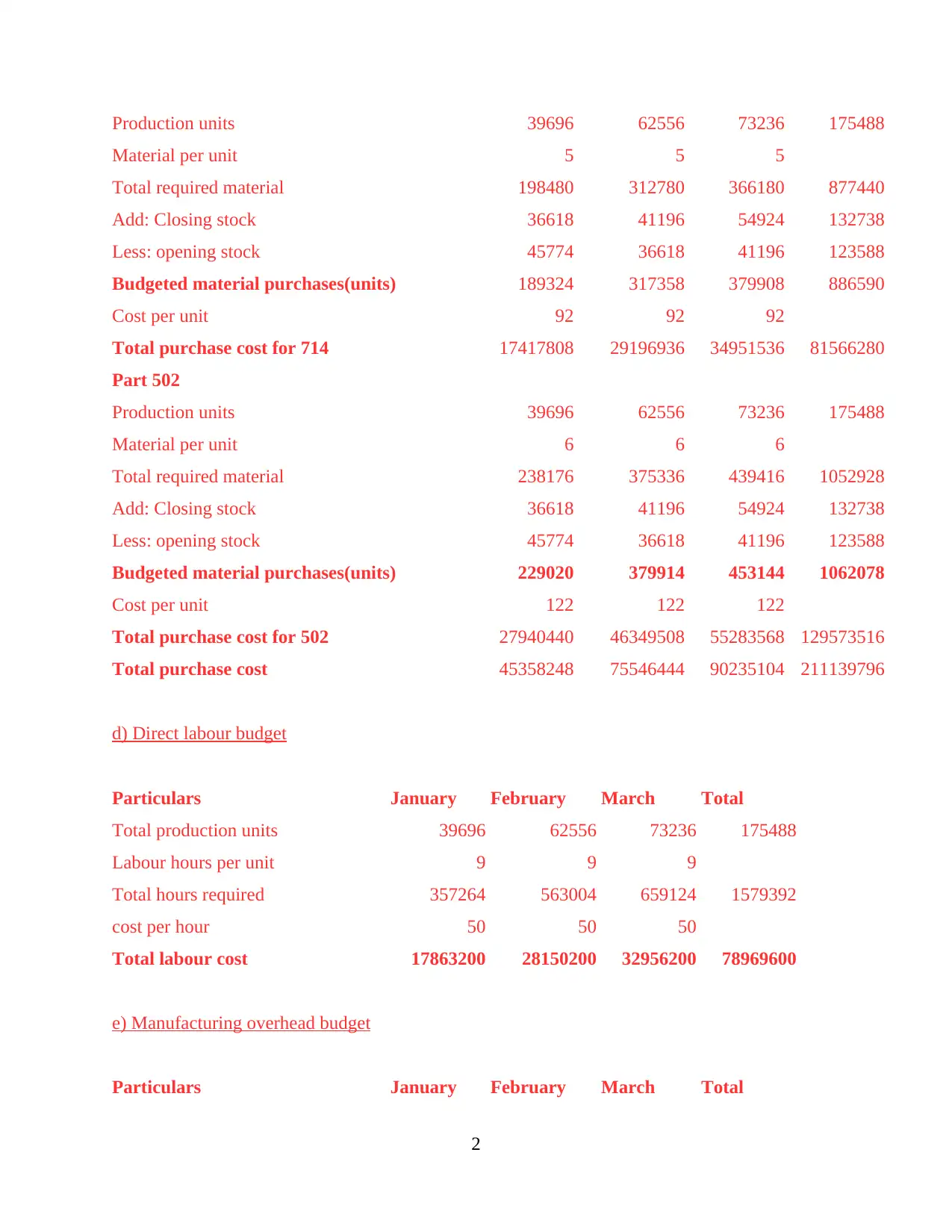
Production units 39696 62556 73236 175488
Material per unit 5 5 5
Total required material 198480 312780 366180 877440
Add: Closing stock 36618 41196 54924 132738
Less: opening stock 45774 36618 41196 123588
Budgeted material purchases(units) 189324 317358 379908 886590
Cost per unit 92 92 92
Total purchase cost for 714 17417808 29196936 34951536 81566280
Part 502
Production units 39696 62556 73236 175488
Material per unit 6 6 6
Total required material 238176 375336 439416 1052928
Add: Closing stock 36618 41196 54924 132738
Less: opening stock 45774 36618 41196 123588
Budgeted material purchases(units) 229020 379914 453144 1062078
Cost per unit 122 122 122
Total purchase cost for 502 27940440 46349508 55283568 129573516
Total purchase cost 45358248 75546444 90235104 211139796
d) Direct labour budget
Particulars January February March Total
Total production units 39696 62556 73236 175488
Labour hours per unit 9 9 9
Total hours required 357264 563004 659124 1579392
cost per hour 50 50 50
Total labour cost 17863200 28150200 32956200 78969600
e) Manufacturing overhead budget
Particulars January February March Total
2
Material per unit 5 5 5
Total required material 198480 312780 366180 877440
Add: Closing stock 36618 41196 54924 132738
Less: opening stock 45774 36618 41196 123588
Budgeted material purchases(units) 189324 317358 379908 886590
Cost per unit 92 92 92
Total purchase cost for 714 17417808 29196936 34951536 81566280
Part 502
Production units 39696 62556 73236 175488
Material per unit 6 6 6
Total required material 238176 375336 439416 1052928
Add: Closing stock 36618 41196 54924 132738
Less: opening stock 45774 36618 41196 123588
Budgeted material purchases(units) 229020 379914 453144 1062078
Cost per unit 122 122 122
Total purchase cost for 502 27940440 46349508 55283568 129573516
Total purchase cost 45358248 75546444 90235104 211139796
d) Direct labour budget
Particulars January February March Total
Total production units 39696 62556 73236 175488
Labour hours per unit 9 9 9
Total hours required 357264 563004 659124 1579392
cost per hour 50 50 50
Total labour cost 17863200 28150200 32956200 78969600
e) Manufacturing overhead budget
Particulars January February March Total
2
Secure Best Marks with AI Grader
Need help grading? Try our AI Grader for instant feedback on your assignments.
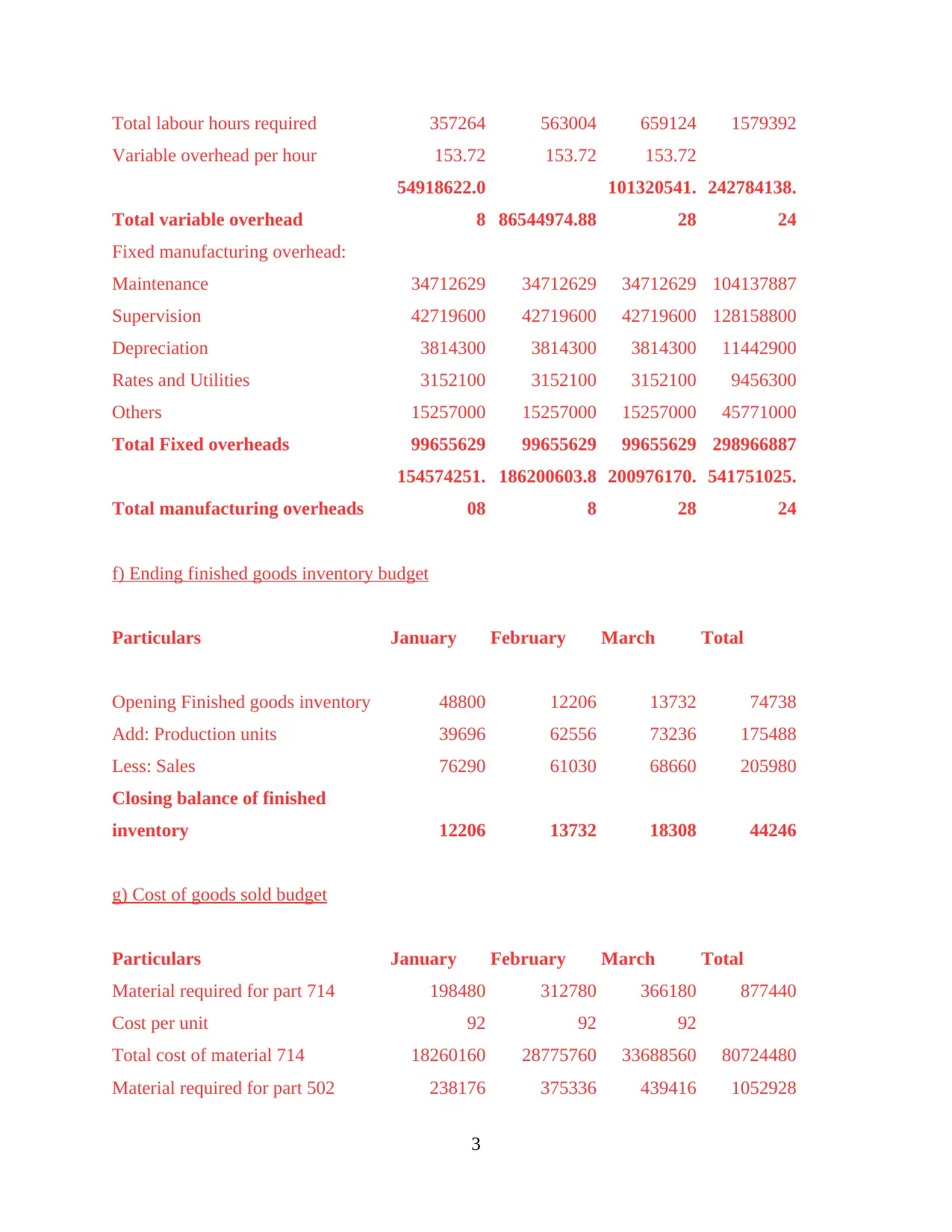
Total labour hours required 357264 563004 659124 1579392
Variable overhead per hour 153.72 153.72 153.72
Total variable overhead
54918622.0
8 86544974.88
101320541.
28
242784138.
24
Fixed manufacturing overhead:
Maintenance 34712629 34712629 34712629 104137887
Supervision 42719600 42719600 42719600 128158800
Depreciation 3814300 3814300 3814300 11442900
Rates and Utilities 3152100 3152100 3152100 9456300
Others 15257000 15257000 15257000 45771000
Total Fixed overheads 99655629 99655629 99655629 298966887
Total manufacturing overheads
154574251.
08
186200603.8
8
200976170.
28
541751025.
24
f) Ending finished goods inventory budget
Particulars January February March Total
Opening Finished goods inventory 48800 12206 13732 74738
Add: Production units 39696 62556 73236 175488
Less: Sales 76290 61030 68660 205980
Closing balance of finished
inventory 12206 13732 18308 44246
g) Cost of goods sold budget
Particulars January February March Total
Material required for part 714 198480 312780 366180 877440
Cost per unit 92 92 92
Total cost of material 714 18260160 28775760 33688560 80724480
Material required for part 502 238176 375336 439416 1052928
3
Variable overhead per hour 153.72 153.72 153.72
Total variable overhead
54918622.0
8 86544974.88
101320541.
28
242784138.
24
Fixed manufacturing overhead:
Maintenance 34712629 34712629 34712629 104137887
Supervision 42719600 42719600 42719600 128158800
Depreciation 3814300 3814300 3814300 11442900
Rates and Utilities 3152100 3152100 3152100 9456300
Others 15257000 15257000 15257000 45771000
Total Fixed overheads 99655629 99655629 99655629 298966887
Total manufacturing overheads
154574251.
08
186200603.8
8
200976170.
28
541751025.
24
f) Ending finished goods inventory budget
Particulars January February March Total
Opening Finished goods inventory 48800 12206 13732 74738
Add: Production units 39696 62556 73236 175488
Less: Sales 76290 61030 68660 205980
Closing balance of finished
inventory 12206 13732 18308 44246
g) Cost of goods sold budget
Particulars January February March Total
Material required for part 714 198480 312780 366180 877440
Cost per unit 92 92 92
Total cost of material 714 18260160 28775760 33688560 80724480
Material required for part 502 238176 375336 439416 1052928
3
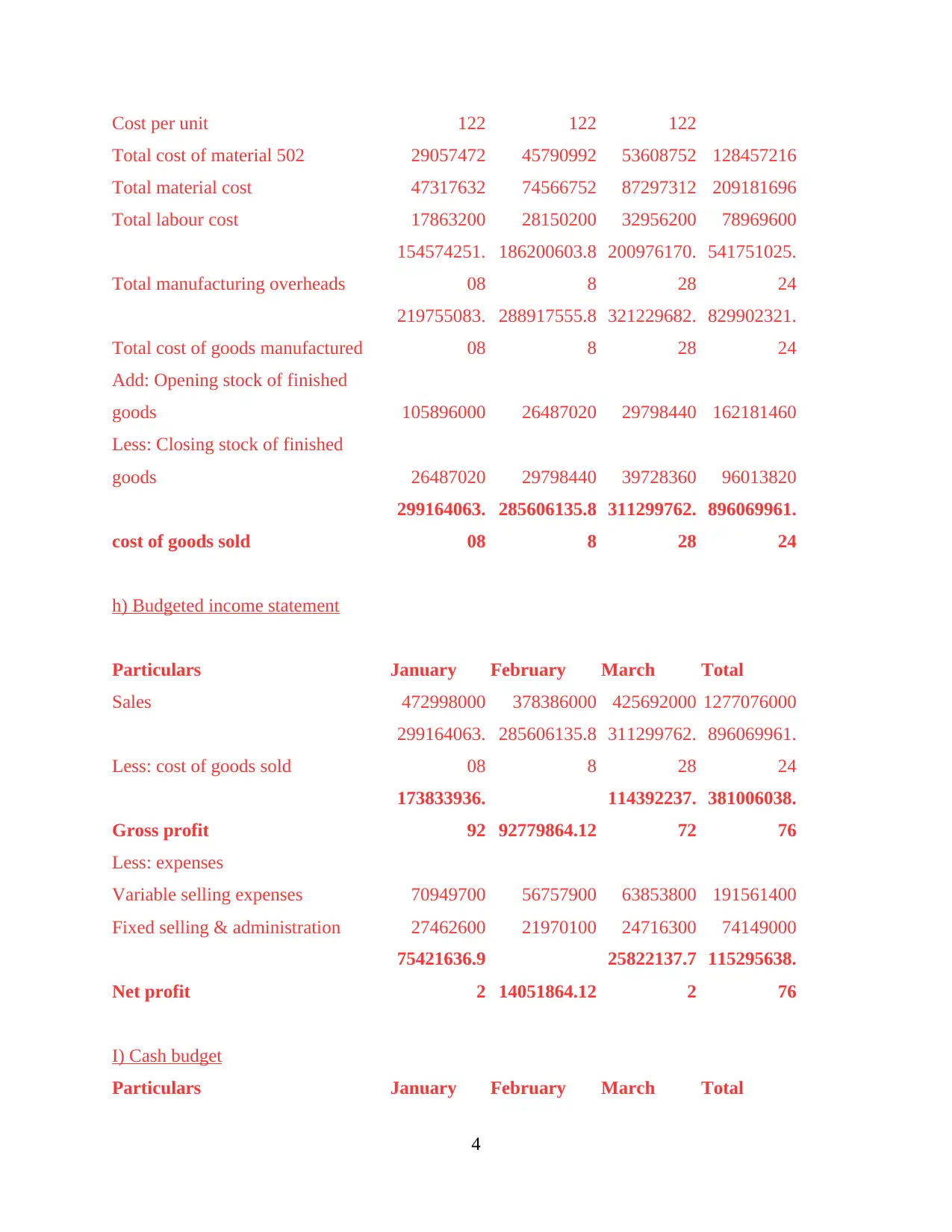
Cost per unit 122 122 122
Total cost of material 502 29057472 45790992 53608752 128457216
Total material cost 47317632 74566752 87297312 209181696
Total labour cost 17863200 28150200 32956200 78969600
Total manufacturing overheads
154574251.
08
186200603.8
8
200976170.
28
541751025.
24
Total cost of goods manufactured
219755083.
08
288917555.8
8
321229682.
28
829902321.
24
Add: Opening stock of finished
goods 105896000 26487020 29798440 162181460
Less: Closing stock of finished
goods 26487020 29798440 39728360 96013820
cost of goods sold
299164063.
08
285606135.8
8
311299762.
28
896069961.
24
h) Budgeted income statement
Particulars January February March Total
Sales 472998000 378386000 425692000 1277076000
Less: cost of goods sold
299164063.
08
285606135.8
8
311299762.
28
896069961.
24
Gross profit
173833936.
92 92779864.12
114392237.
72
381006038.
76
Less: expenses
Variable selling expenses 70949700 56757900 63853800 191561400
Fixed selling & administration 27462600 21970100 24716300 74149000
Net profit
75421636.9
2 14051864.12
25822137.7
2
115295638.
76
I) Cash budget
Particulars January February March Total
4
Total cost of material 502 29057472 45790992 53608752 128457216
Total material cost 47317632 74566752 87297312 209181696
Total labour cost 17863200 28150200 32956200 78969600
Total manufacturing overheads
154574251.
08
186200603.8
8
200976170.
28
541751025.
24
Total cost of goods manufactured
219755083.
08
288917555.8
8
321229682.
28
829902321.
24
Add: Opening stock of finished
goods 105896000 26487020 29798440 162181460
Less: Closing stock of finished
goods 26487020 29798440 39728360 96013820
cost of goods sold
299164063.
08
285606135.8
8
311299762.
28
896069961.
24
h) Budgeted income statement
Particulars January February March Total
Sales 472998000 378386000 425692000 1277076000
Less: cost of goods sold
299164063.
08
285606135.8
8
311299762.
28
896069961.
24
Gross profit
173833936.
92 92779864.12
114392237.
72
381006038.
76
Less: expenses
Variable selling expenses 70949700 56757900 63853800 191561400
Fixed selling & administration 27462600 21970100 24716300 74149000
Net profit
75421636.9
2 14051864.12
25822137.7
2
115295638.
76
I) Cash budget
Particulars January February March Total
4
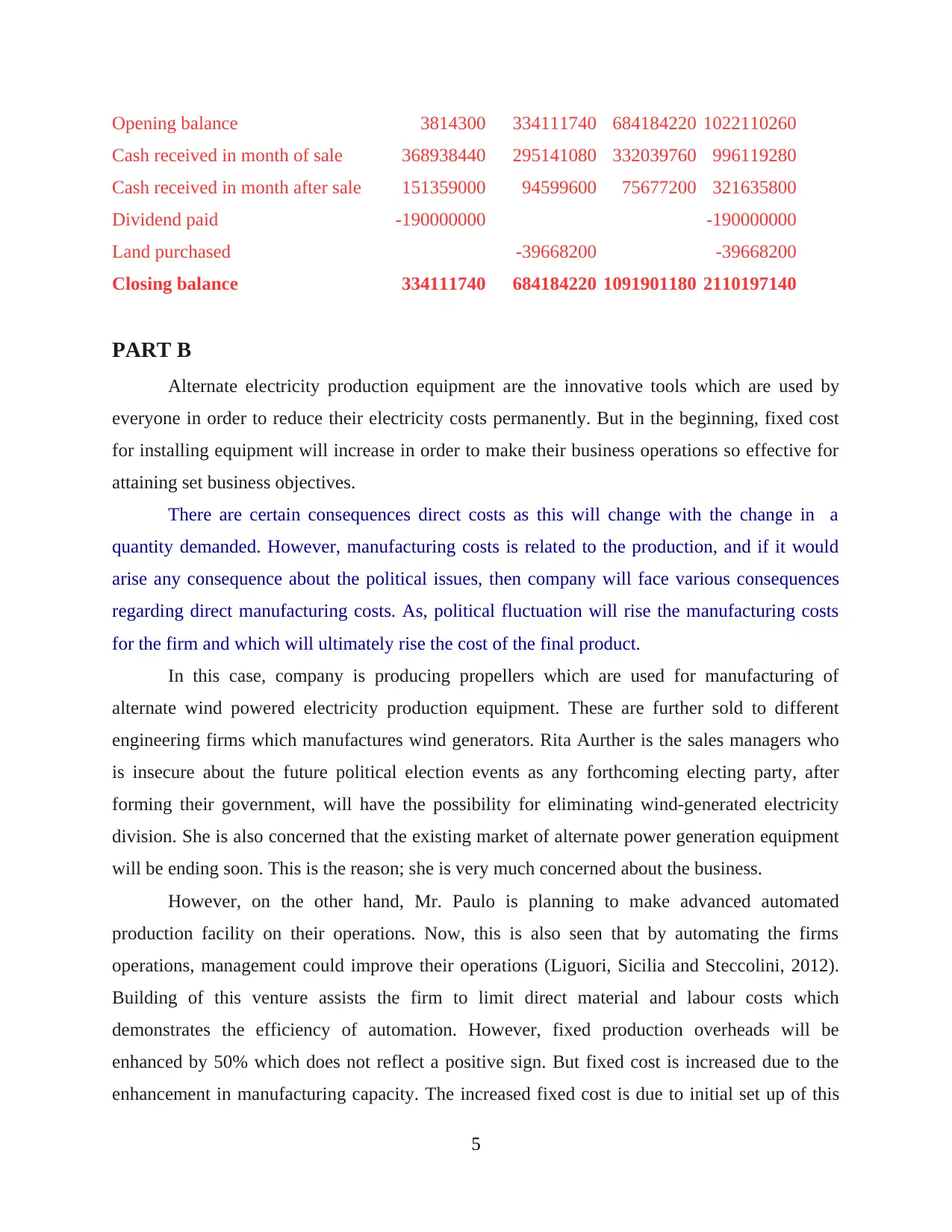
Opening balance 3814300 334111740 684184220 1022110260
Cash received in month of sale 368938440 295141080 332039760 996119280
Cash received in month after sale 151359000 94599600 75677200 321635800
Dividend paid -190000000 -190000000
Land purchased -39668200 -39668200
Closing balance 334111740 684184220 1091901180 2110197140
PART B
Alternate electricity production equipment are the innovative tools which are used by
everyone in order to reduce their electricity costs permanently. But in the beginning, fixed cost
for installing equipment will increase in order to make their business operations so effective for
attaining set business objectives.
There are certain consequences direct costs as this will change with the change in a
quantity demanded. However, manufacturing costs is related to the production, and if it would
arise any consequence about the political issues, then company will face various consequences
regarding direct manufacturing costs. As, political fluctuation will rise the manufacturing costs
for the firm and which will ultimately rise the cost of the final product.
In this case, company is producing propellers which are used for manufacturing of
alternate wind powered electricity production equipment. These are further sold to different
engineering firms which manufactures wind generators. Rita Aurther is the sales managers who
is insecure about the future political election events as any forthcoming electing party, after
forming their government, will have the possibility for eliminating wind-generated electricity
division. She is also concerned that the existing market of alternate power generation equipment
will be ending soon. This is the reason; she is very much concerned about the business.
However, on the other hand, Mr. Paulo is planning to make advanced automated
production facility on their operations. Now, this is also seen that by automating the firms
operations, management could improve their operations (Liguori, Sicilia and Steccolini, 2012).
Building of this venture assists the firm to limit direct material and labour costs which
demonstrates the efficiency of automation. However, fixed production overheads will be
enhanced by 50% which does not reflect a positive sign. But fixed cost is increased due to the
enhancement in manufacturing capacity. The increased fixed cost is due to initial set up of this
5
Cash received in month of sale 368938440 295141080 332039760 996119280
Cash received in month after sale 151359000 94599600 75677200 321635800
Dividend paid -190000000 -190000000
Land purchased -39668200 -39668200
Closing balance 334111740 684184220 1091901180 2110197140
PART B
Alternate electricity production equipment are the innovative tools which are used by
everyone in order to reduce their electricity costs permanently. But in the beginning, fixed cost
for installing equipment will increase in order to make their business operations so effective for
attaining set business objectives.
There are certain consequences direct costs as this will change with the change in a
quantity demanded. However, manufacturing costs is related to the production, and if it would
arise any consequence about the political issues, then company will face various consequences
regarding direct manufacturing costs. As, political fluctuation will rise the manufacturing costs
for the firm and which will ultimately rise the cost of the final product.
In this case, company is producing propellers which are used for manufacturing of
alternate wind powered electricity production equipment. These are further sold to different
engineering firms which manufactures wind generators. Rita Aurther is the sales managers who
is insecure about the future political election events as any forthcoming electing party, after
forming their government, will have the possibility for eliminating wind-generated electricity
division. She is also concerned that the existing market of alternate power generation equipment
will be ending soon. This is the reason; she is very much concerned about the business.
However, on the other hand, Mr. Paulo is planning to make advanced automated
production facility on their operations. Now, this is also seen that by automating the firms
operations, management could improve their operations (Liguori, Sicilia and Steccolini, 2012).
Building of this venture assists the firm to limit direct material and labour costs which
demonstrates the efficiency of automation. However, fixed production overheads will be
enhanced by 50% which does not reflect a positive sign. But fixed cost is increased due to the
enhancement in manufacturing capacity. The increased fixed cost is due to initial set up of this
5
Paraphrase This Document
Need a fresh take? Get an instant paraphrase of this document with our AI Paraphraser
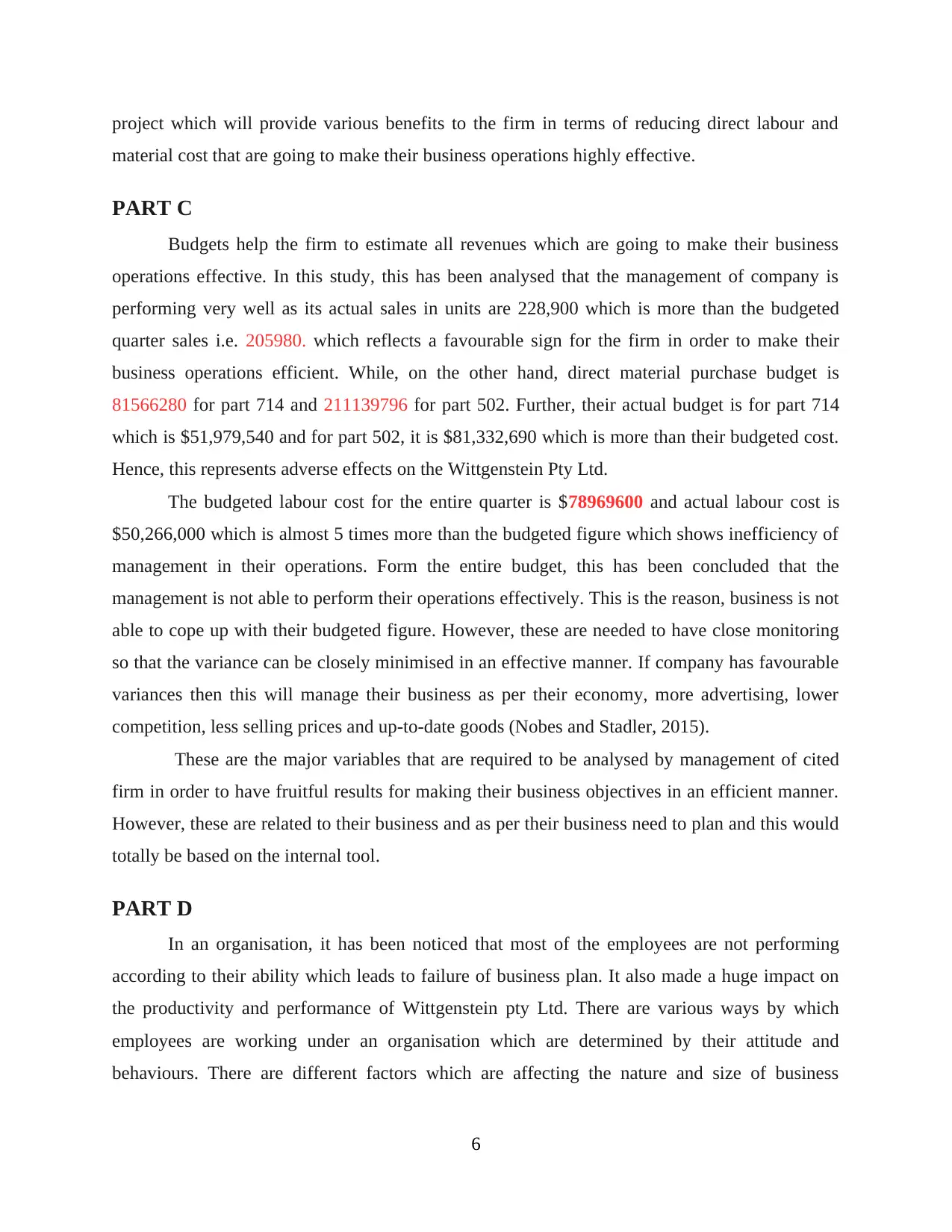
project which will provide various benefits to the firm in terms of reducing direct labour and
material cost that are going to make their business operations highly effective.
PART C
Budgets help the firm to estimate all revenues which are going to make their business
operations effective. In this study, this has been analysed that the management of company is
performing very well as its actual sales in units are 228,900 which is more than the budgeted
quarter sales i.e. 205980. which reflects a favourable sign for the firm in order to make their
business operations efficient. While, on the other hand, direct material purchase budget is
81566280 for part 714 and 211139796 for part 502. Further, their actual budget is for part 714
which is $51,979,540 and for part 502, it is $81,332,690 which is more than their budgeted cost.
Hence, this represents adverse effects on the Wittgenstein Pty Ltd.
The budgeted labour cost for the entire quarter is $78969600 and actual labour cost is
$50,266,000 which is almost 5 times more than the budgeted figure which shows inefficiency of
management in their operations. Form the entire budget, this has been concluded that the
management is not able to perform their operations effectively. This is the reason, business is not
able to cope up with their budgeted figure. However, these are needed to have close monitoring
so that the variance can be closely minimised in an effective manner. If company has favourable
variances then this will manage their business as per their economy, more advertising, lower
competition, less selling prices and up-to-date goods (Nobes and Stadler, 2015).
These are the major variables that are required to be analysed by management of cited
firm in order to have fruitful results for making their business objectives in an efficient manner.
However, these are related to their business and as per their business need to plan and this would
totally be based on the internal tool.
PART D
In an organisation, it has been noticed that most of the employees are not performing
according to their ability which leads to failure of business plan. It also made a huge impact on
the productivity and performance of Wittgenstein pty Ltd. There are various ways by which
employees are working under an organisation which are determined by their attitude and
behaviours. There are different factors which are affecting the nature and size of business
6
material cost that are going to make their business operations highly effective.
PART C
Budgets help the firm to estimate all revenues which are going to make their business
operations effective. In this study, this has been analysed that the management of company is
performing very well as its actual sales in units are 228,900 which is more than the budgeted
quarter sales i.e. 205980. which reflects a favourable sign for the firm in order to make their
business operations efficient. While, on the other hand, direct material purchase budget is
81566280 for part 714 and 211139796 for part 502. Further, their actual budget is for part 714
which is $51,979,540 and for part 502, it is $81,332,690 which is more than their budgeted cost.
Hence, this represents adverse effects on the Wittgenstein Pty Ltd.
The budgeted labour cost for the entire quarter is $78969600 and actual labour cost is
$50,266,000 which is almost 5 times more than the budgeted figure which shows inefficiency of
management in their operations. Form the entire budget, this has been concluded that the
management is not able to perform their operations effectively. This is the reason, business is not
able to cope up with their budgeted figure. However, these are needed to have close monitoring
so that the variance can be closely minimised in an effective manner. If company has favourable
variances then this will manage their business as per their economy, more advertising, lower
competition, less selling prices and up-to-date goods (Nobes and Stadler, 2015).
These are the major variables that are required to be analysed by management of cited
firm in order to have fruitful results for making their business objectives in an efficient manner.
However, these are related to their business and as per their business need to plan and this would
totally be based on the internal tool.
PART D
In an organisation, it has been noticed that most of the employees are not performing
according to their ability which leads to failure of business plan. It also made a huge impact on
the productivity and performance of Wittgenstein pty Ltd. There are various ways by which
employees are working under an organisation which are determined by their attitude and
behaviours. There are different factors which are affecting the nature and size of business
6
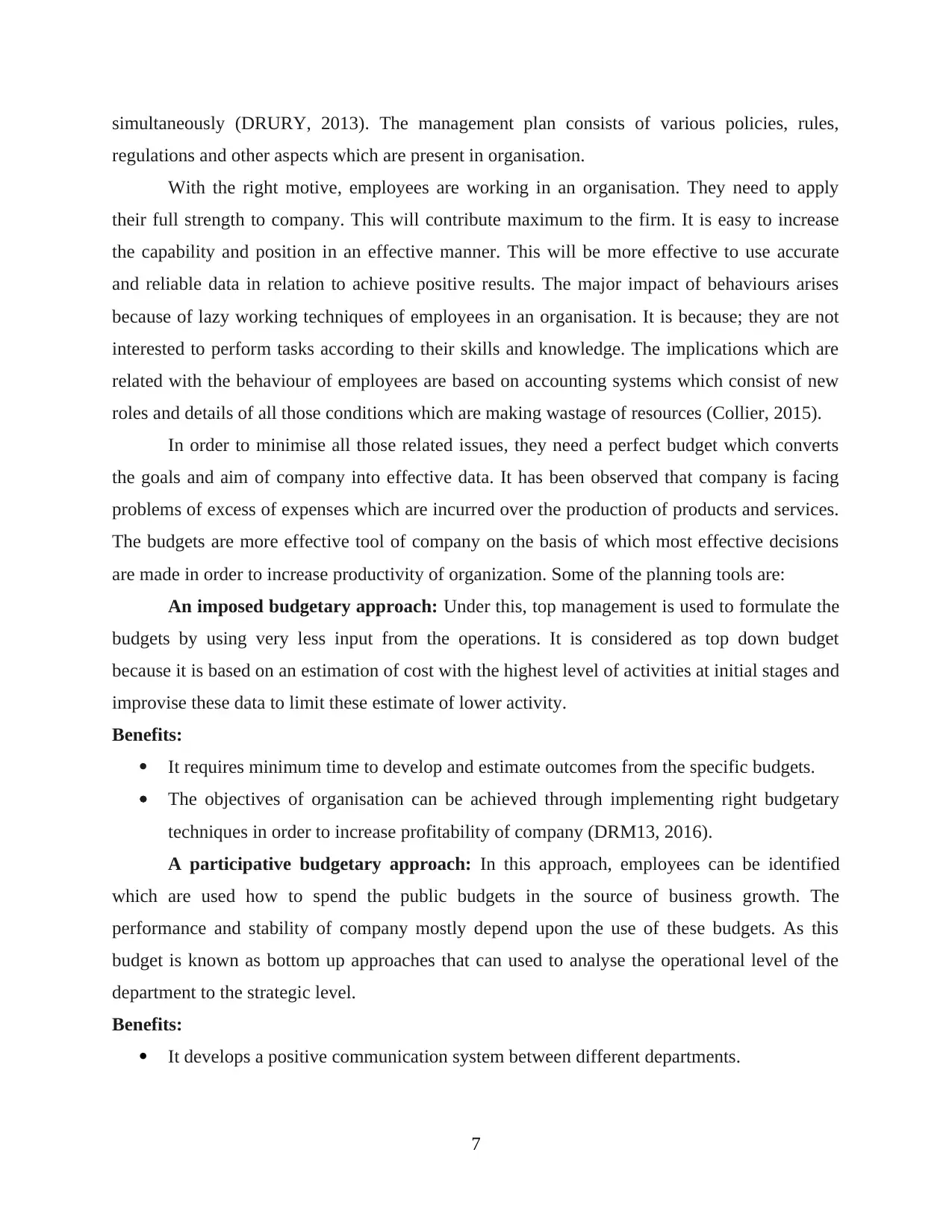
simultaneously (DRURY, 2013). The management plan consists of various policies, rules,
regulations and other aspects which are present in organisation.
With the right motive, employees are working in an organisation. They need to apply
their full strength to company. This will contribute maximum to the firm. It is easy to increase
the capability and position in an effective manner. This will be more effective to use accurate
and reliable data in relation to achieve positive results. The major impact of behaviours arises
because of lazy working techniques of employees in an organisation. It is because; they are not
interested to perform tasks according to their skills and knowledge. The implications which are
related with the behaviour of employees are based on accounting systems which consist of new
roles and details of all those conditions which are making wastage of resources (Collier, 2015).
In order to minimise all those related issues, they need a perfect budget which converts
the goals and aim of company into effective data. It has been observed that company is facing
problems of excess of expenses which are incurred over the production of products and services.
The budgets are more effective tool of company on the basis of which most effective decisions
are made in order to increase productivity of organization. Some of the planning tools are:
An imposed budgetary approach: Under this, top management is used to formulate the
budgets by using very less input from the operations. It is considered as top down budget
because it is based on an estimation of cost with the highest level of activities at initial stages and
improvise these data to limit these estimate of lower activity.
Benefits:
It requires minimum time to develop and estimate outcomes from the specific budgets.
The objectives of organisation can be achieved through implementing right budgetary
techniques in order to increase profitability of company (DRM13, 2016).
A participative budgetary approach: In this approach, employees can be identified
which are used how to spend the public budgets in the source of business growth. The
performance and stability of company mostly depend upon the use of these budgets. As this
budget is known as bottom up approaches that can used to analyse the operational level of the
department to the strategic level.
Benefits:
It develops a positive communication system between different departments.
7
regulations and other aspects which are present in organisation.
With the right motive, employees are working in an organisation. They need to apply
their full strength to company. This will contribute maximum to the firm. It is easy to increase
the capability and position in an effective manner. This will be more effective to use accurate
and reliable data in relation to achieve positive results. The major impact of behaviours arises
because of lazy working techniques of employees in an organisation. It is because; they are not
interested to perform tasks according to their skills and knowledge. The implications which are
related with the behaviour of employees are based on accounting systems which consist of new
roles and details of all those conditions which are making wastage of resources (Collier, 2015).
In order to minimise all those related issues, they need a perfect budget which converts
the goals and aim of company into effective data. It has been observed that company is facing
problems of excess of expenses which are incurred over the production of products and services.
The budgets are more effective tool of company on the basis of which most effective decisions
are made in order to increase productivity of organization. Some of the planning tools are:
An imposed budgetary approach: Under this, top management is used to formulate the
budgets by using very less input from the operations. It is considered as top down budget
because it is based on an estimation of cost with the highest level of activities at initial stages and
improvise these data to limit these estimate of lower activity.
Benefits:
It requires minimum time to develop and estimate outcomes from the specific budgets.
The objectives of organisation can be achieved through implementing right budgetary
techniques in order to increase profitability of company (DRM13, 2016).
A participative budgetary approach: In this approach, employees can be identified
which are used how to spend the public budgets in the source of business growth. The
performance and stability of company mostly depend upon the use of these budgets. As this
budget is known as bottom up approaches that can used to analyse the operational level of the
department to the strategic level.
Benefits:
It develops a positive communication system between different departments.
7
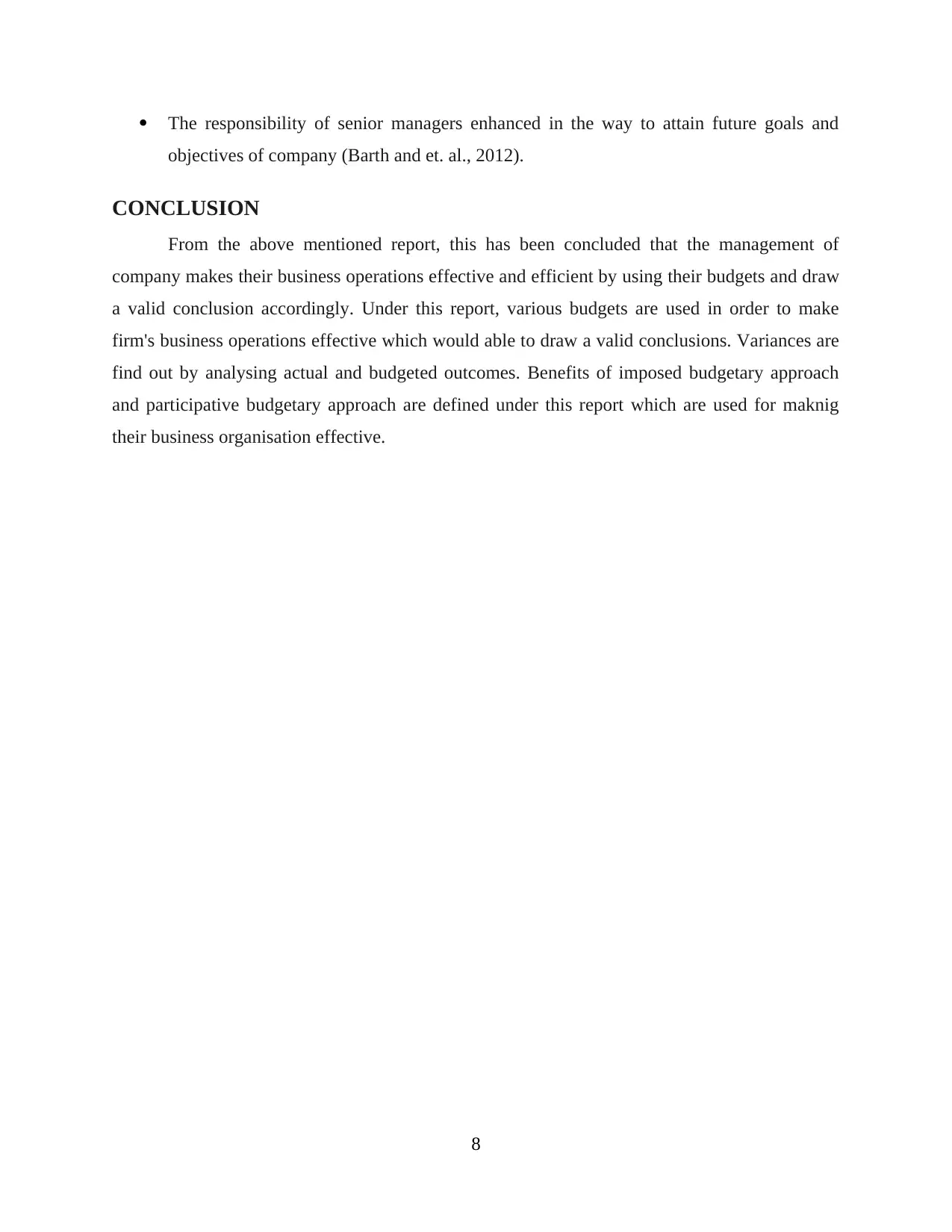
The responsibility of senior managers enhanced in the way to attain future goals and
objectives of company (Barth and et. al., 2012).
CONCLUSION
From the above mentioned report, this has been concluded that the management of
company makes their business operations effective and efficient by using their budgets and draw
a valid conclusion accordingly. Under this report, various budgets are used in order to make
firm's business operations effective which would able to draw a valid conclusions. Variances are
find out by analysing actual and budgeted outcomes. Benefits of imposed budgetary approach
and participative budgetary approach are defined under this report which are used for maknig
their business organisation effective.
8
objectives of company (Barth and et. al., 2012).
CONCLUSION
From the above mentioned report, this has been concluded that the management of
company makes their business operations effective and efficient by using their budgets and draw
a valid conclusion accordingly. Under this report, various budgets are used in order to make
firm's business operations effective which would able to draw a valid conclusions. Variances are
find out by analysing actual and budgeted outcomes. Benefits of imposed budgetary approach
and participative budgetary approach are defined under this report which are used for maknig
their business organisation effective.
8
1 out of 10
Related Documents

Your All-in-One AI-Powered Toolkit for Academic Success.
+13062052269
info@desklib.com
Available 24*7 on WhatsApp / Email
Unlock your academic potential
© 2024 | Zucol Services PVT LTD | All rights reserved.