Freight Forwarding: Client Report on ACFS Port Logistics Services
VerifiedAdded on 2022/08/12
|6
|1098
|28
Report
AI Summary
This email report, written by a student for an importer client, evaluates the services offered by ACFS Port Logistics, a container logistics operator in Australia. The report addresses the client's concerns about paper-based systems, manual order picking, and order errors. It details ACFS's warehouse size, classification (air-conditioned/food grade), operating systems with remote access, cargo receipt processes, racking systems, and order fulfillment procedures. The report highlights the benefits of ACFS's services, including its large warehouse, food-grade capabilities, and efficient turnaround times, with the aim of making the client's customers satisfied. The report also provides references to support the information presented.
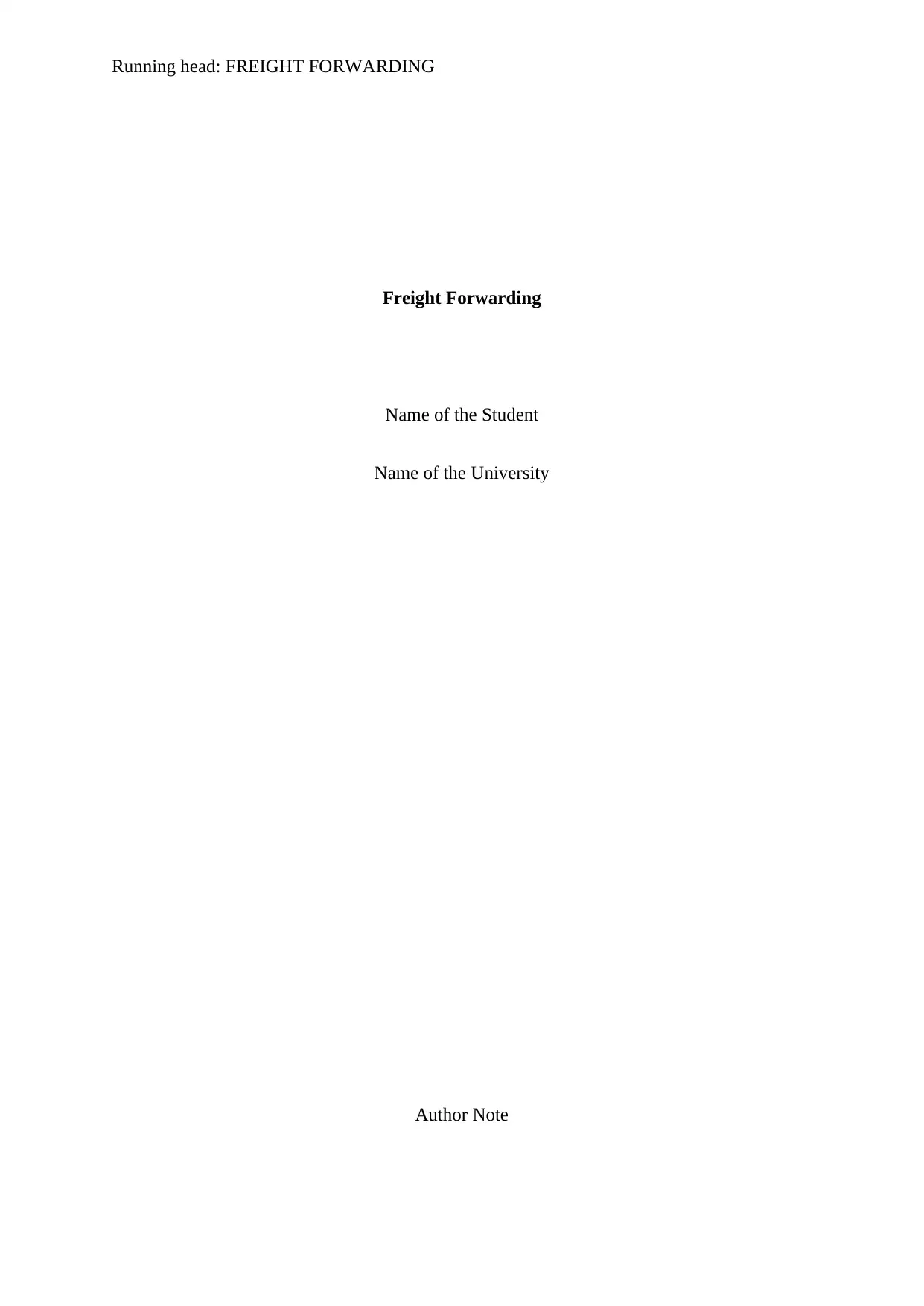
Running head: FREIGHT FORWARDING
Freight Forwarding
Name of the Student
Name of the University
Author Note
Freight Forwarding
Name of the Student
Name of the University
Author Note
Secure Best Marks with AI Grader
Need help grading? Try our AI Grader for instant feedback on your assignments.
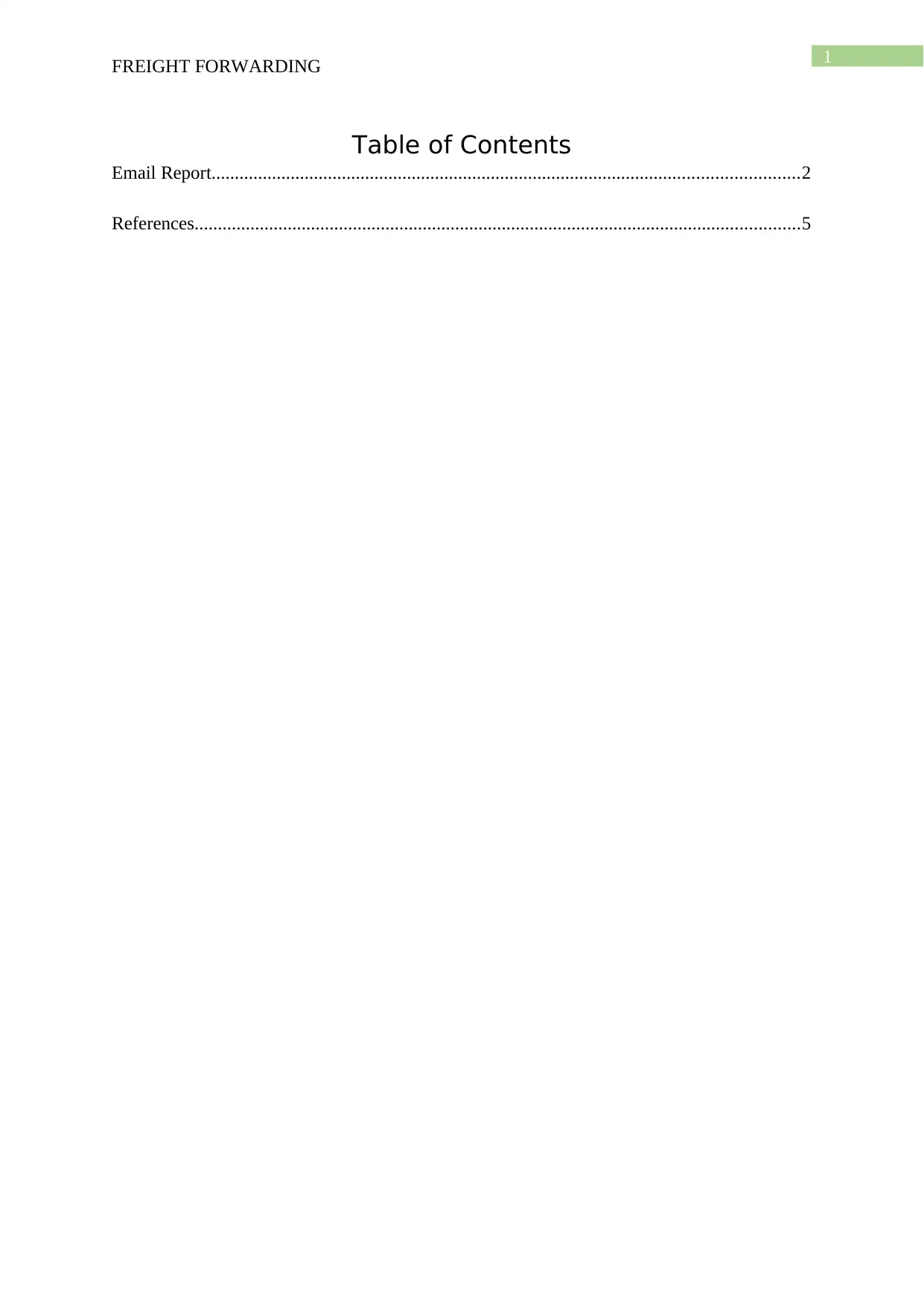
1
FREIGHT FORWARDING
Table of Contents
Email Report..............................................................................................................................2
References..................................................................................................................................5
FREIGHT FORWARDING
Table of Contents
Email Report..............................................................................................................................2
References..................................................................................................................................5
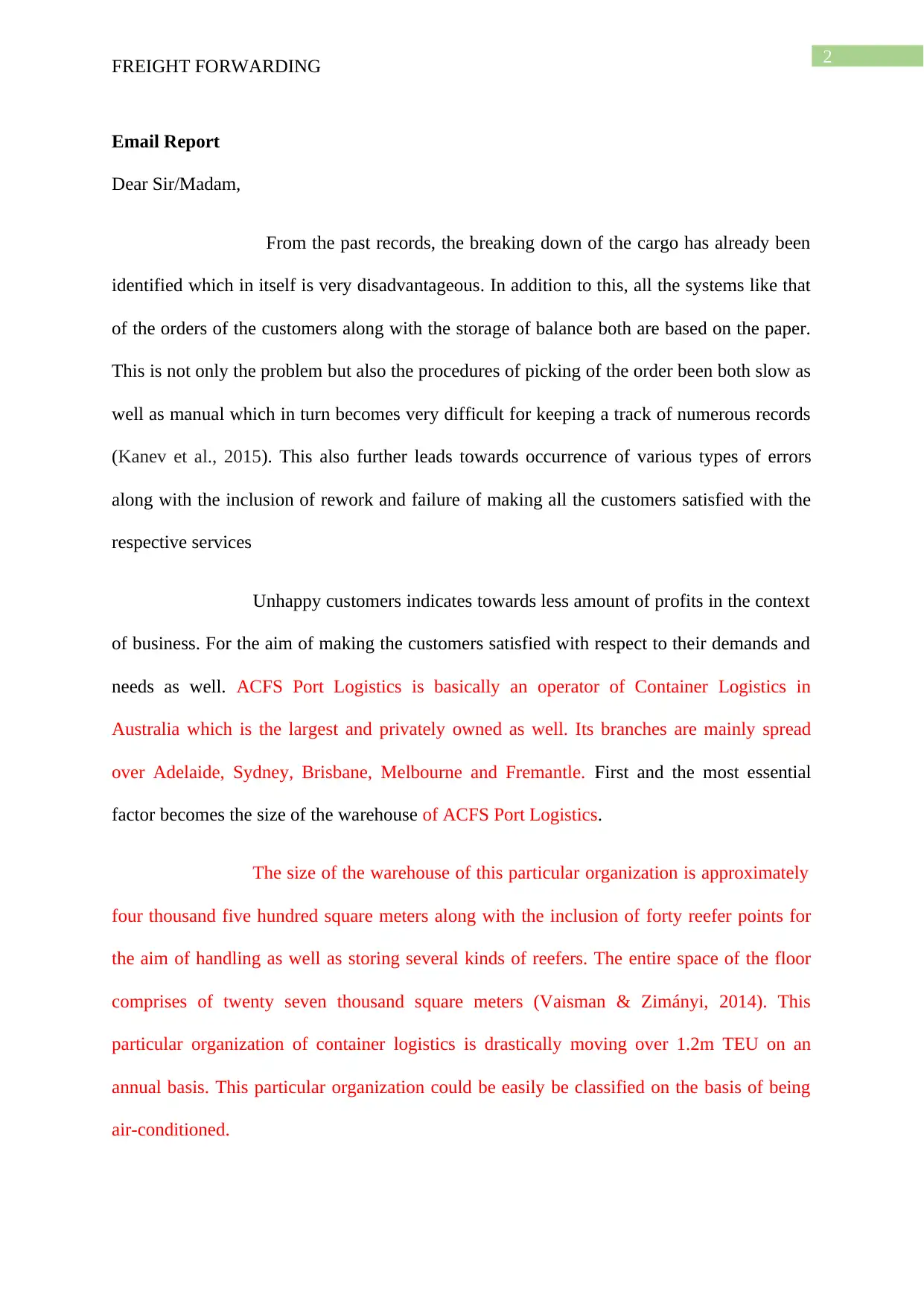
2
FREIGHT FORWARDING
Email Report
Dear Sir/Madam,
From the past records, the breaking down of the cargo has already been
identified which in itself is very disadvantageous. In addition to this, all the systems like that
of the orders of the customers along with the storage of balance both are based on the paper.
This is not only the problem but also the procedures of picking of the order been both slow as
well as manual which in turn becomes very difficult for keeping a track of numerous records
(Kanev et al., 2015). This also further leads towards occurrence of various types of errors
along with the inclusion of rework and failure of making all the customers satisfied with the
respective services
Unhappy customers indicates towards less amount of profits in the context
of business. For the aim of making the customers satisfied with respect to their demands and
needs as well. ACFS Port Logistics is basically an operator of Container Logistics in
Australia which is the largest and privately owned as well. Its branches are mainly spread
over Adelaide, Sydney, Brisbane, Melbourne and Fremantle. First and the most essential
factor becomes the size of the warehouse of ACFS Port Logistics.
The size of the warehouse of this particular organization is approximately
four thousand five hundred square meters along with the inclusion of forty reefer points for
the aim of handling as well as storing several kinds of reefers. The entire space of the floor
comprises of twenty seven thousand square meters (Vaisman & Zimányi, 2014). This
particular organization of container logistics is drastically moving over 1.2m TEU on an
annual basis. This particular organization could be easily be classified on the basis of being
air-conditioned.
FREIGHT FORWARDING
Email Report
Dear Sir/Madam,
From the past records, the breaking down of the cargo has already been
identified which in itself is very disadvantageous. In addition to this, all the systems like that
of the orders of the customers along with the storage of balance both are based on the paper.
This is not only the problem but also the procedures of picking of the order been both slow as
well as manual which in turn becomes very difficult for keeping a track of numerous records
(Kanev et al., 2015). This also further leads towards occurrence of various types of errors
along with the inclusion of rework and failure of making all the customers satisfied with the
respective services
Unhappy customers indicates towards less amount of profits in the context
of business. For the aim of making the customers satisfied with respect to their demands and
needs as well. ACFS Port Logistics is basically an operator of Container Logistics in
Australia which is the largest and privately owned as well. Its branches are mainly spread
over Adelaide, Sydney, Brisbane, Melbourne and Fremantle. First and the most essential
factor becomes the size of the warehouse of ACFS Port Logistics.
The size of the warehouse of this particular organization is approximately
four thousand five hundred square meters along with the inclusion of forty reefer points for
the aim of handling as well as storing several kinds of reefers. The entire space of the floor
comprises of twenty seven thousand square meters (Vaisman & Zimányi, 2014). This
particular organization of container logistics is drastically moving over 1.2m TEU on an
annual basis. This particular organization could be easily be classified on the basis of being
air-conditioned.
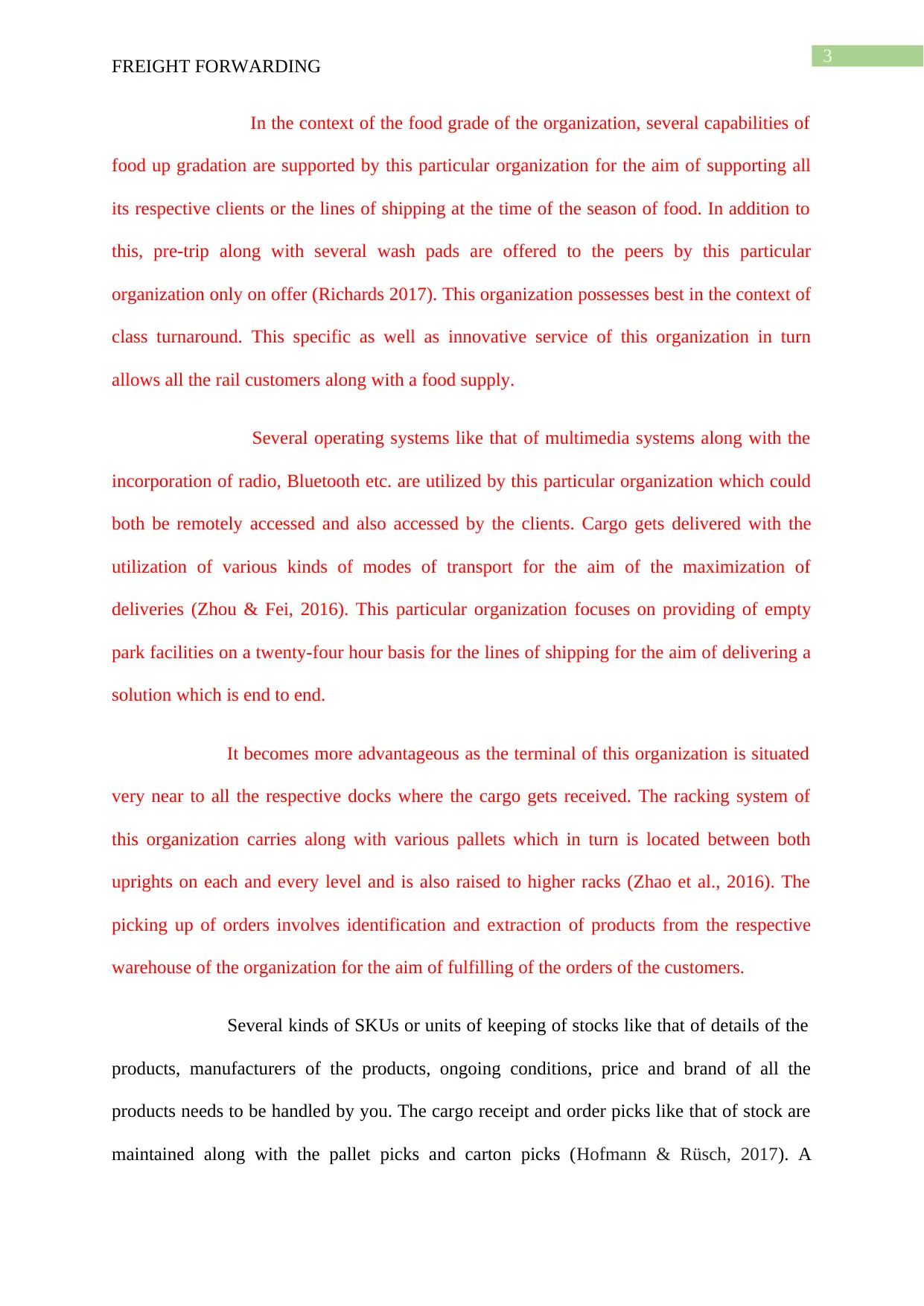
3
FREIGHT FORWARDING
In the context of the food grade of the organization, several capabilities of
food up gradation are supported by this particular organization for the aim of supporting all
its respective clients or the lines of shipping at the time of the season of food. In addition to
this, pre-trip along with several wash pads are offered to the peers by this particular
organization only on offer (Richards 2017). This organization possesses best in the context of
class turnaround. This specific as well as innovative service of this organization in turn
allows all the rail customers along with a food supply.
Several operating systems like that of multimedia systems along with the
incorporation of radio, Bluetooth etc. are utilized by this particular organization which could
both be remotely accessed and also accessed by the clients. Cargo gets delivered with the
utilization of various kinds of modes of transport for the aim of the maximization of
deliveries (Zhou & Fei, 2016). This particular organization focuses on providing of empty
park facilities on a twenty-four hour basis for the lines of shipping for the aim of delivering a
solution which is end to end.
It becomes more advantageous as the terminal of this organization is situated
very near to all the respective docks where the cargo gets received. The racking system of
this organization carries along with various pallets which in turn is located between both
uprights on each and every level and is also raised to higher racks (Zhao et al., 2016). The
picking up of orders involves identification and extraction of products from the respective
warehouse of the organization for the aim of fulfilling of the orders of the customers.
Several kinds of SKUs or units of keeping of stocks like that of details of the
products, manufacturers of the products, ongoing conditions, price and brand of all the
products needs to be handled by you. The cargo receipt and order picks like that of stock are
maintained along with the pallet picks and carton picks (Hofmann & Rüsch, 2017). A
FREIGHT FORWARDING
In the context of the food grade of the organization, several capabilities of
food up gradation are supported by this particular organization for the aim of supporting all
its respective clients or the lines of shipping at the time of the season of food. In addition to
this, pre-trip along with several wash pads are offered to the peers by this particular
organization only on offer (Richards 2017). This organization possesses best in the context of
class turnaround. This specific as well as innovative service of this organization in turn
allows all the rail customers along with a food supply.
Several operating systems like that of multimedia systems along with the
incorporation of radio, Bluetooth etc. are utilized by this particular organization which could
both be remotely accessed and also accessed by the clients. Cargo gets delivered with the
utilization of various kinds of modes of transport for the aim of the maximization of
deliveries (Zhou & Fei, 2016). This particular organization focuses on providing of empty
park facilities on a twenty-four hour basis for the lines of shipping for the aim of delivering a
solution which is end to end.
It becomes more advantageous as the terminal of this organization is situated
very near to all the respective docks where the cargo gets received. The racking system of
this organization carries along with various pallets which in turn is located between both
uprights on each and every level and is also raised to higher racks (Zhao et al., 2016). The
picking up of orders involves identification and extraction of products from the respective
warehouse of the organization for the aim of fulfilling of the orders of the customers.
Several kinds of SKUs or units of keeping of stocks like that of details of the
products, manufacturers of the products, ongoing conditions, price and brand of all the
products needs to be handled by you. The cargo receipt and order picks like that of stock are
maintained along with the pallet picks and carton picks (Hofmann & Rüsch, 2017). A
Secure Best Marks with AI Grader
Need help grading? Try our AI Grader for instant feedback on your assignments.
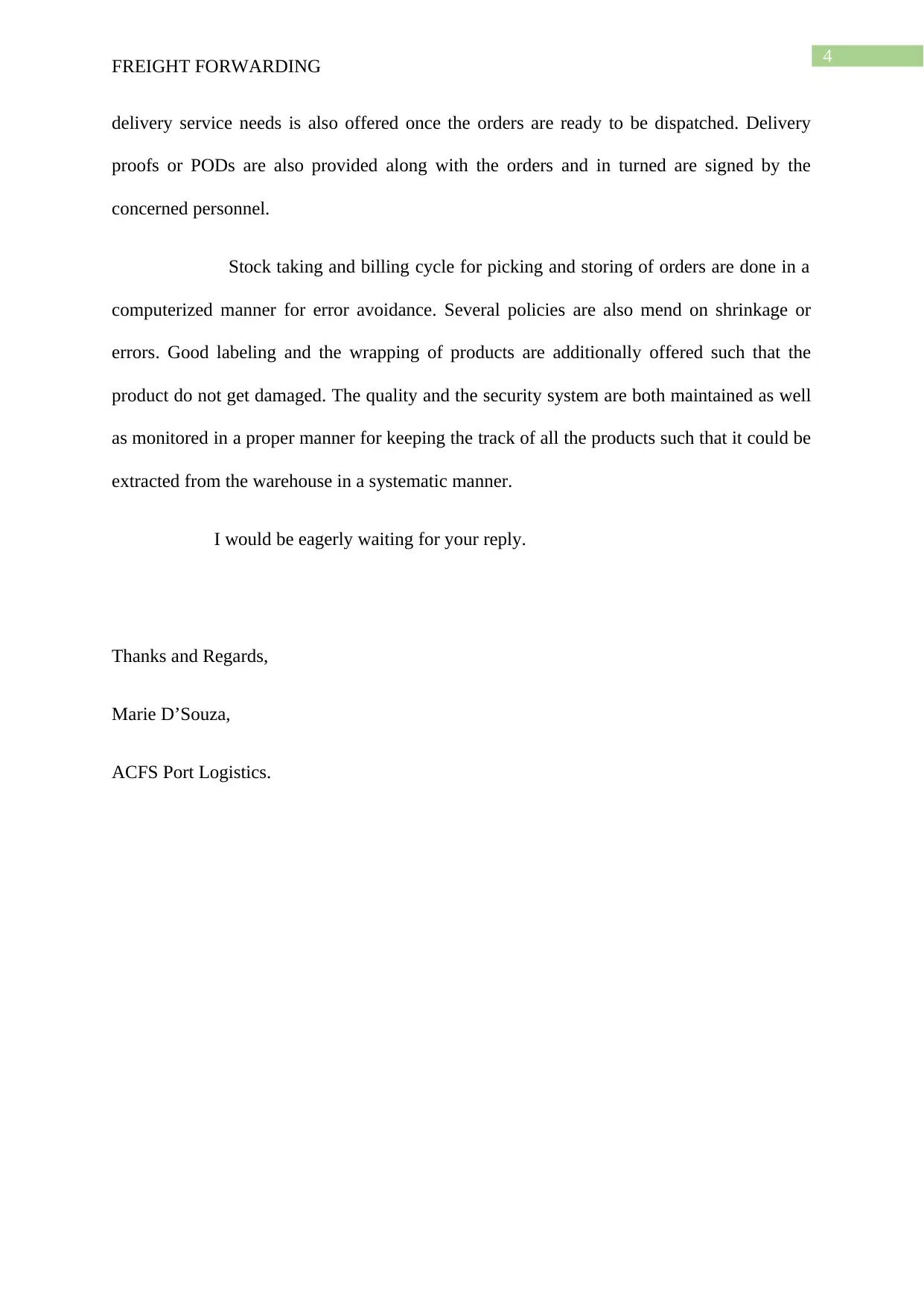
4
FREIGHT FORWARDING
delivery service needs is also offered once the orders are ready to be dispatched. Delivery
proofs or PODs are also provided along with the orders and in turned are signed by the
concerned personnel.
Stock taking and billing cycle for picking and storing of orders are done in a
computerized manner for error avoidance. Several policies are also mend on shrinkage or
errors. Good labeling and the wrapping of products are additionally offered such that the
product do not get damaged. The quality and the security system are both maintained as well
as monitored in a proper manner for keeping the track of all the products such that it could be
extracted from the warehouse in a systematic manner.
I would be eagerly waiting for your reply.
Thanks and Regards,
Marie D’Souza,
ACFS Port Logistics.
FREIGHT FORWARDING
delivery service needs is also offered once the orders are ready to be dispatched. Delivery
proofs or PODs are also provided along with the orders and in turned are signed by the
concerned personnel.
Stock taking and billing cycle for picking and storing of orders are done in a
computerized manner for error avoidance. Several policies are also mend on shrinkage or
errors. Good labeling and the wrapping of products are additionally offered such that the
product do not get damaged. The quality and the security system are both maintained as well
as monitored in a proper manner for keeping the track of all the products such that it could be
extracted from the warehouse in a systematic manner.
I would be eagerly waiting for your reply.
Thanks and Regards,
Marie D’Souza,
ACFS Port Logistics.
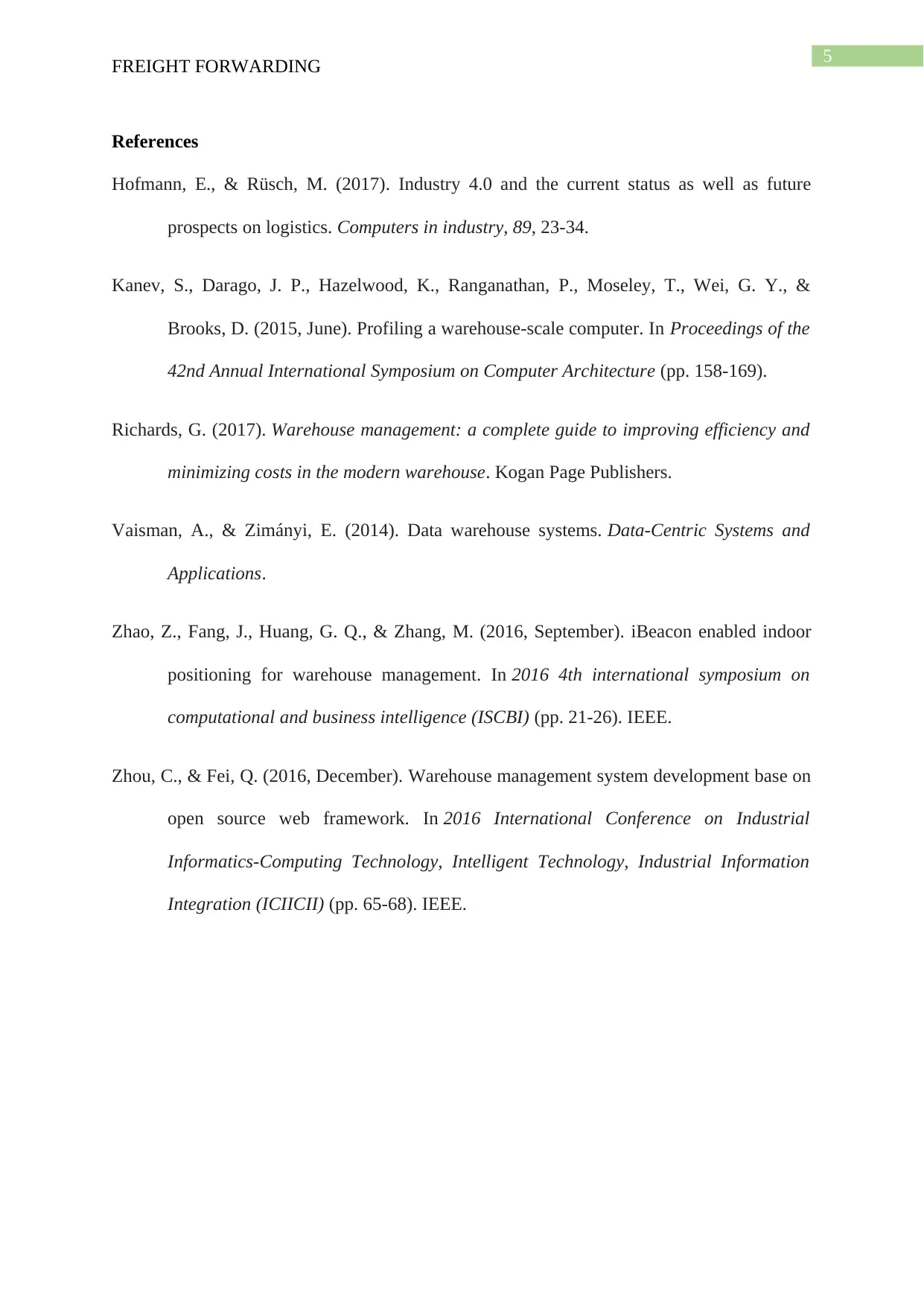
5
FREIGHT FORWARDING
References
Hofmann, E., & Rüsch, M. (2017). Industry 4.0 and the current status as well as future
prospects on logistics. Computers in industry, 89, 23-34.
Kanev, S., Darago, J. P., Hazelwood, K., Ranganathan, P., Moseley, T., Wei, G. Y., &
Brooks, D. (2015, June). Profiling a warehouse-scale computer. In Proceedings of the
42nd Annual International Symposium on Computer Architecture (pp. 158-169).
Richards, G. (2017). Warehouse management: a complete guide to improving efficiency and
minimizing costs in the modern warehouse. Kogan Page Publishers.
Vaisman, A., & Zimányi, E. (2014). Data warehouse systems. Data-Centric Systems and
Applications.
Zhao, Z., Fang, J., Huang, G. Q., & Zhang, M. (2016, September). iBeacon enabled indoor
positioning for warehouse management. In 2016 4th international symposium on
computational and business intelligence (ISCBI) (pp. 21-26). IEEE.
Zhou, C., & Fei, Q. (2016, December). Warehouse management system development base on
open source web framework. In 2016 International Conference on Industrial
Informatics-Computing Technology, Intelligent Technology, Industrial Information
Integration (ICIICII) (pp. 65-68). IEEE.
FREIGHT FORWARDING
References
Hofmann, E., & Rüsch, M. (2017). Industry 4.0 and the current status as well as future
prospects on logistics. Computers in industry, 89, 23-34.
Kanev, S., Darago, J. P., Hazelwood, K., Ranganathan, P., Moseley, T., Wei, G. Y., &
Brooks, D. (2015, June). Profiling a warehouse-scale computer. In Proceedings of the
42nd Annual International Symposium on Computer Architecture (pp. 158-169).
Richards, G. (2017). Warehouse management: a complete guide to improving efficiency and
minimizing costs in the modern warehouse. Kogan Page Publishers.
Vaisman, A., & Zimányi, E. (2014). Data warehouse systems. Data-Centric Systems and
Applications.
Zhao, Z., Fang, J., Huang, G. Q., & Zhang, M. (2016, September). iBeacon enabled indoor
positioning for warehouse management. In 2016 4th international symposium on
computational and business intelligence (ISCBI) (pp. 21-26). IEEE.
Zhou, C., & Fei, Q. (2016, December). Warehouse management system development base on
open source web framework. In 2016 International Conference on Industrial
Informatics-Computing Technology, Intelligent Technology, Industrial Information
Integration (ICIICII) (pp. 65-68). IEEE.
1 out of 6

Your All-in-One AI-Powered Toolkit for Academic Success.
+13062052269
info@desklib.com
Available 24*7 on WhatsApp / Email
Unlock your academic potential
© 2024 | Zucol Services PVT LTD | All rights reserved.