Business Accounting Report: Costing Methods for Sewing Easy Ltd.
VerifiedAdded on 2021/05/30
|15
|3157
|29
Report
AI Summary
This report provides a comprehensive analysis of activity-based costing (ABC) compared to traditional costing methods within the context of Sewing Easy Ltd., a sewing machine manufacturer. The report begins by calculating the cost per unit for two sewing machine models using the traditional co...
Read More
Contribute Materials
Your contribution can guide someone’s learning journey. Share your
documents today.
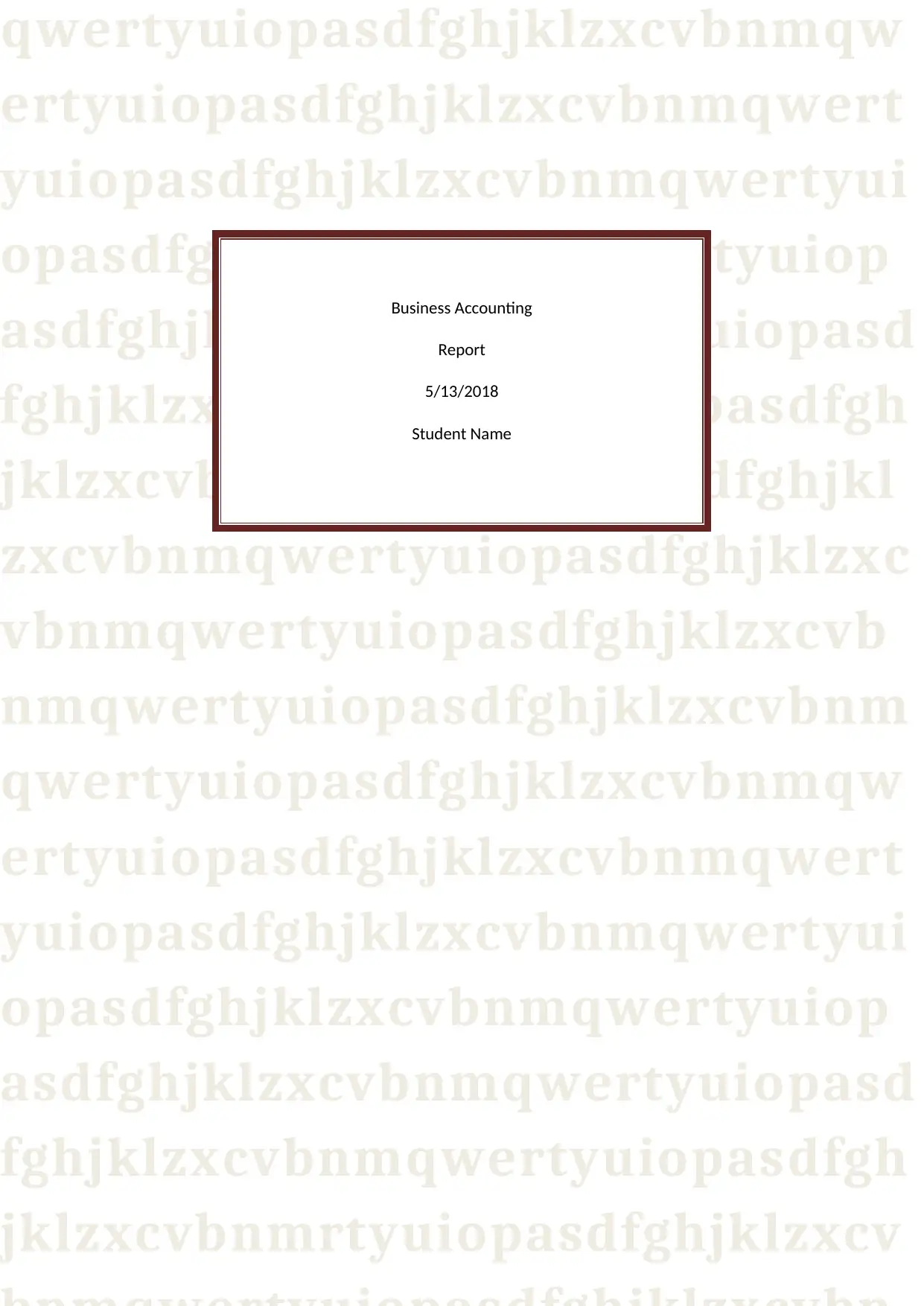
qwertyuiopasdfghjklzxcvbnmqw
ertyuiopasdfghjklzxcvbnmqwert
yuiopasdfghjklzxcvbnmqwertyui
opasdfghjklzxcvbnmqwertyuiop
asdfghjklzxcvbnmqwertyuiopasd
fghjklzxcvbnmqwertyuiopasdfgh
jklzxcvbnmqwertyuiopasdfghjkl
zxcvbnmqwertyuiopasdfghjklzxc
vbnmqwertyuiopasdfghjklzxcvb
nmqwertyuiopasdfghjklzxcvbnm
qwertyuiopasdfghjklzxcvbnmqw
ertyuiopasdfghjklzxcvbnmqwert
yuiopasdfghjklzxcvbnmqwertyui
opasdfghjklzxcvbnmqwertyuiop
asdfghjklzxcvbnmqwertyuiopasd
fghjklzxcvbnmqwertyuiopasdfgh
jklzxcvbnmrtyuiopasdfghjklzxcv
Business Accounting
Report
5/13/2018
Student Name
ertyuiopasdfghjklzxcvbnmqwert
yuiopasdfghjklzxcvbnmqwertyui
opasdfghjklzxcvbnmqwertyuiop
asdfghjklzxcvbnmqwertyuiopasd
fghjklzxcvbnmqwertyuiopasdfgh
jklzxcvbnmqwertyuiopasdfghjkl
zxcvbnmqwertyuiopasdfghjklzxc
vbnmqwertyuiopasdfghjklzxcvb
nmqwertyuiopasdfghjklzxcvbnm
qwertyuiopasdfghjklzxcvbnmqw
ertyuiopasdfghjklzxcvbnmqwert
yuiopasdfghjklzxcvbnmqwertyui
opasdfghjklzxcvbnmqwertyuiop
asdfghjklzxcvbnmqwertyuiopasd
fghjklzxcvbnmqwertyuiopasdfgh
jklzxcvbnmrtyuiopasdfghjklzxcv
Business Accounting
Report
5/13/2018
Student Name
Secure Best Marks with AI Grader
Need help grading? Try our AI Grader for instant feedback on your assignments.
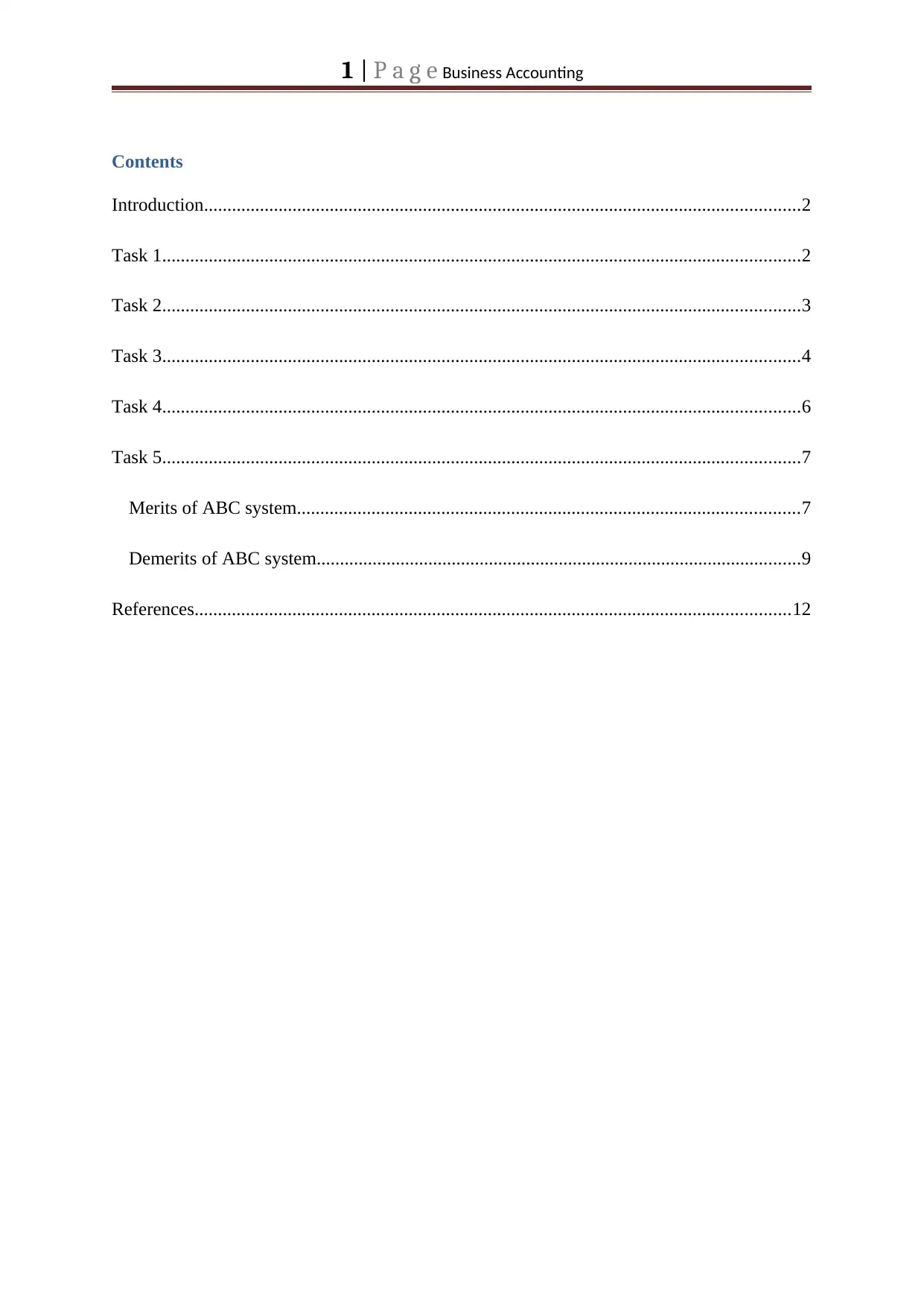
1 | P a g e Business Accounting
Contents
Introduction................................................................................................................................2
Task 1.........................................................................................................................................2
Task 2.........................................................................................................................................3
Task 3.........................................................................................................................................4
Task 4.........................................................................................................................................6
Task 5.........................................................................................................................................7
Merits of ABC system............................................................................................................7
Demerits of ABC system........................................................................................................9
References................................................................................................................................12
Contents
Introduction................................................................................................................................2
Task 1.........................................................................................................................................2
Task 2.........................................................................................................................................3
Task 3.........................................................................................................................................4
Task 4.........................................................................................................................................6
Task 5.........................................................................................................................................7
Merits of ABC system............................................................................................................7
Demerits of ABC system........................................................................................................9
References................................................................................................................................12
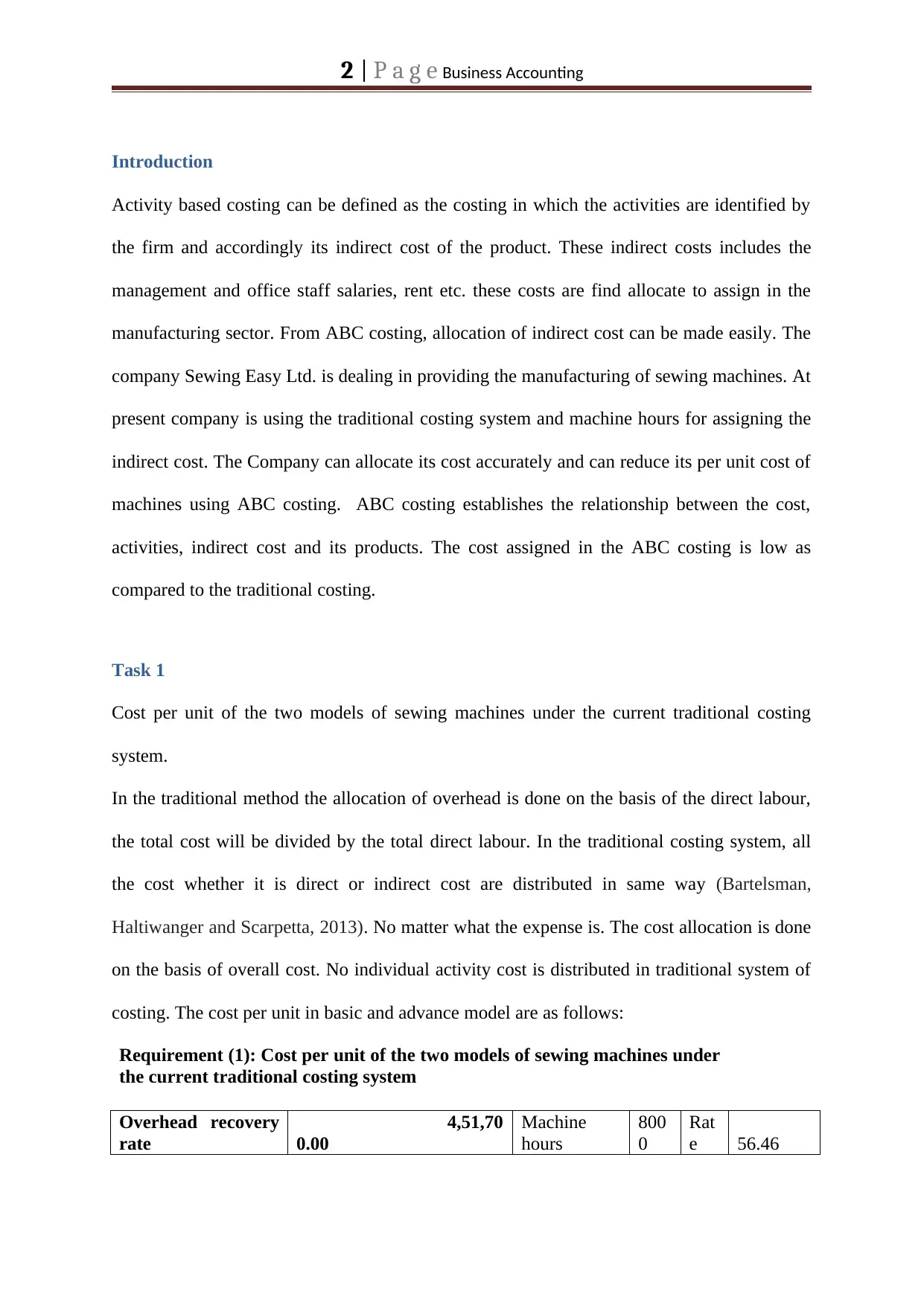
2 | P a g e Business Accounting
Introduction
Activity based costing can be defined as the costing in which the activities are identified by
the firm and accordingly its indirect cost of the product. These indirect costs includes the
management and office staff salaries, rent etc. these costs are find allocate to assign in the
manufacturing sector. From ABC costing, allocation of indirect cost can be made easily. The
company Sewing Easy Ltd. is dealing in providing the manufacturing of sewing machines. At
present company is using the traditional costing system and machine hours for assigning the
indirect cost. The Company can allocate its cost accurately and can reduce its per unit cost of
machines using ABC costing. ABC costing establishes the relationship between the cost,
activities, indirect cost and its products. The cost assigned in the ABC costing is low as
compared to the traditional costing.
Task 1
Cost per unit of the two models of sewing machines under the current traditional costing
system.
In the traditional method the allocation of overhead is done on the basis of the direct labour,
the total cost will be divided by the total direct labour. In the traditional costing system, all
the cost whether it is direct or indirect cost are distributed in same way (Bartelsman,
Haltiwanger and Scarpetta, 2013). No matter what the expense is. The cost allocation is done
on the basis of overall cost. No individual activity cost is distributed in traditional system of
costing. The cost per unit in basic and advance model are as follows:
Requirement (1): Cost per unit of the two models of sewing machines under
the current traditional costing system
Overhead recovery
rate
4,51,70
0.00
Machine
hours
800
0
Rat
e 56.46
Introduction
Activity based costing can be defined as the costing in which the activities are identified by
the firm and accordingly its indirect cost of the product. These indirect costs includes the
management and office staff salaries, rent etc. these costs are find allocate to assign in the
manufacturing sector. From ABC costing, allocation of indirect cost can be made easily. The
company Sewing Easy Ltd. is dealing in providing the manufacturing of sewing machines. At
present company is using the traditional costing system and machine hours for assigning the
indirect cost. The Company can allocate its cost accurately and can reduce its per unit cost of
machines using ABC costing. ABC costing establishes the relationship between the cost,
activities, indirect cost and its products. The cost assigned in the ABC costing is low as
compared to the traditional costing.
Task 1
Cost per unit of the two models of sewing machines under the current traditional costing
system.
In the traditional method the allocation of overhead is done on the basis of the direct labour,
the total cost will be divided by the total direct labour. In the traditional costing system, all
the cost whether it is direct or indirect cost are distributed in same way (Bartelsman,
Haltiwanger and Scarpetta, 2013). No matter what the expense is. The cost allocation is done
on the basis of overall cost. No individual activity cost is distributed in traditional system of
costing. The cost per unit in basic and advance model are as follows:
Requirement (1): Cost per unit of the two models of sewing machines under
the current traditional costing system
Overhead recovery
rate
4,51,70
0.00
Machine
hours
800
0
Rat
e 56.46
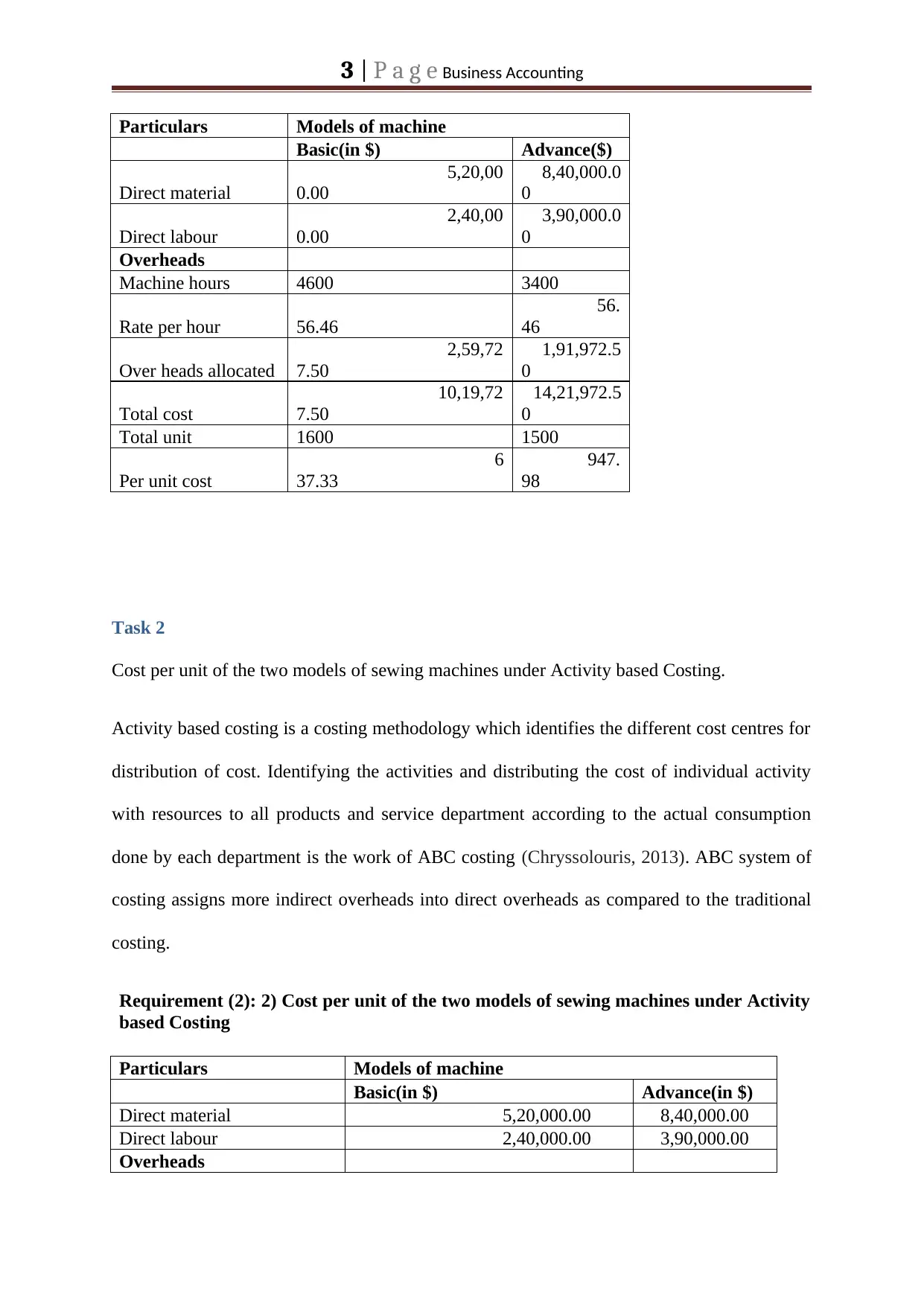
3 | P a g e Business Accounting
Particulars Models of machine
Basic(in $) Advance($)
Direct material
5,20,00
0.00
8,40,000.0
0
Direct labour
2,40,00
0.00
3,90,000.0
0
Overheads
Machine hours 4600 3400
Rate per hour 56.46
56.
46
Over heads allocated
2,59,72
7.50
1,91,972.5
0
Total cost
10,19,72
7.50
14,21,972.5
0
Total unit 1600 1500
Per unit cost
6
37.33
947.
98
Task 2
Cost per unit of the two models of sewing machines under Activity based Costing.
Activity based costing is a costing methodology which identifies the different cost centres for
distribution of cost. Identifying the activities and distributing the cost of individual activity
with resources to all products and service department according to the actual consumption
done by each department is the work of ABC costing (Chryssolouris, 2013). ABC system of
costing assigns more indirect overheads into direct overheads as compared to the traditional
costing.
Requirement (2): 2) Cost per unit of the two models of sewing machines under Activity
based Costing
Particulars Models of machine
Basic(in $) Advance(in $)
Direct material 5,20,000.00 8,40,000.00
Direct labour 2,40,000.00 3,90,000.00
Overheads
Particulars Models of machine
Basic(in $) Advance($)
Direct material
5,20,00
0.00
8,40,000.0
0
Direct labour
2,40,00
0.00
3,90,000.0
0
Overheads
Machine hours 4600 3400
Rate per hour 56.46
56.
46
Over heads allocated
2,59,72
7.50
1,91,972.5
0
Total cost
10,19,72
7.50
14,21,972.5
0
Total unit 1600 1500
Per unit cost
6
37.33
947.
98
Task 2
Cost per unit of the two models of sewing machines under Activity based Costing.
Activity based costing is a costing methodology which identifies the different cost centres for
distribution of cost. Identifying the activities and distributing the cost of individual activity
with resources to all products and service department according to the actual consumption
done by each department is the work of ABC costing (Chryssolouris, 2013). ABC system of
costing assigns more indirect overheads into direct overheads as compared to the traditional
costing.
Requirement (2): 2) Cost per unit of the two models of sewing machines under Activity
based Costing
Particulars Models of machine
Basic(in $) Advance(in $)
Direct material 5,20,000.00 8,40,000.00
Direct labour 2,40,000.00 3,90,000.00
Overheads
Secure Best Marks with AI Grader
Need help grading? Try our AI Grader for instant feedback on your assignments.
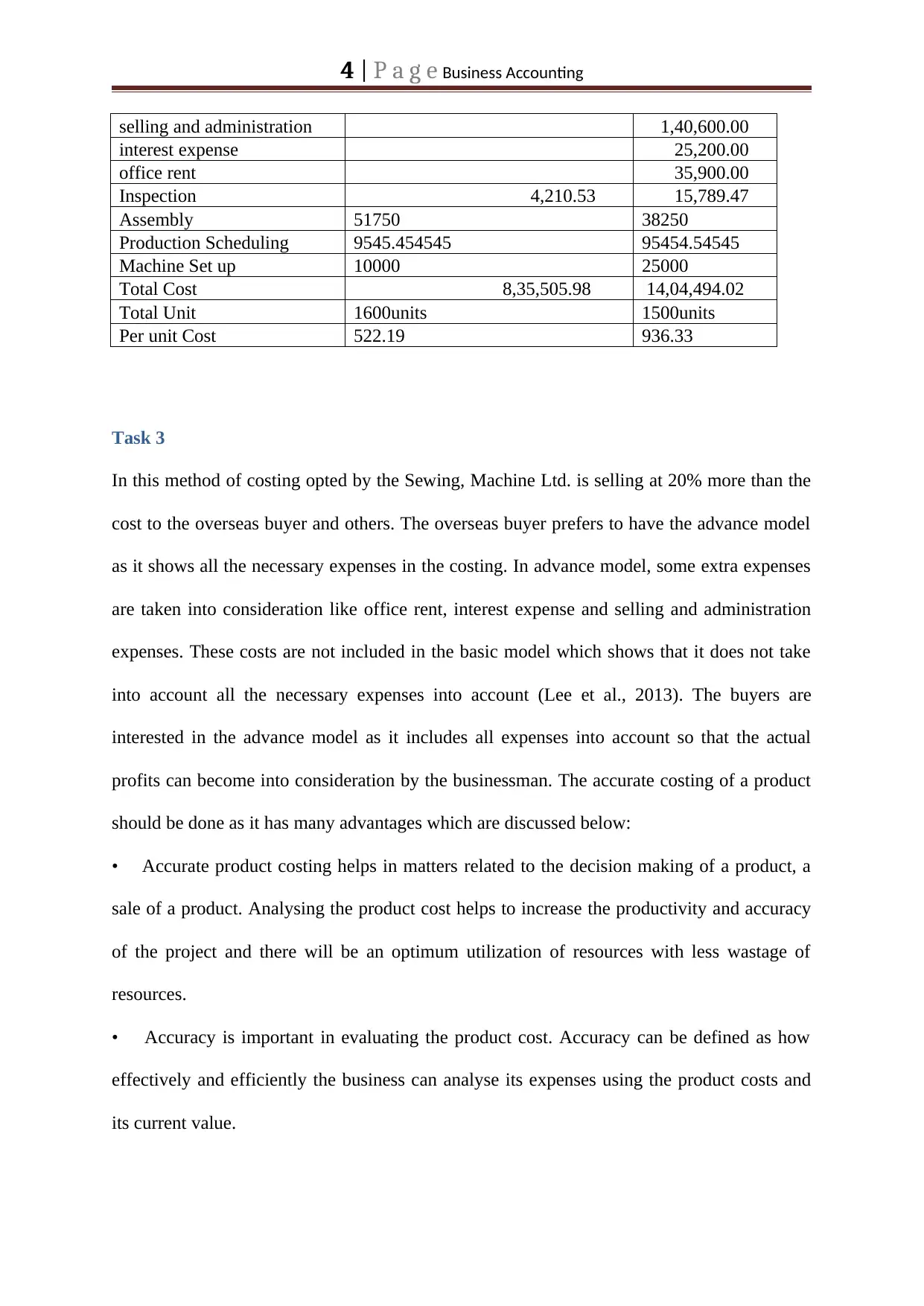
4 | P a g e Business Accounting
selling and administration 1,40,600.00
interest expense 25,200.00
office rent 35,900.00
Inspection 4,210.53 15,789.47
Assembly 51750 38250
Production Scheduling 9545.454545 95454.54545
Machine Set up 10000 25000
Total Cost 8,35,505.98 14,04,494.02
Total Unit 1600units 1500units
Per unit Cost 522.19 936.33
Task 3
In this method of costing opted by the Sewing, Machine Ltd. is selling at 20% more than the
cost to the overseas buyer and others. The overseas buyer prefers to have the advance model
as it shows all the necessary expenses in the costing. In advance model, some extra expenses
are taken into consideration like office rent, interest expense and selling and administration
expenses. These costs are not included in the basic model which shows that it does not take
into account all the necessary expenses into account (Lee et al., 2013). The buyers are
interested in the advance model as it includes all expenses into account so that the actual
profits can become into consideration by the businessman. The accurate costing of a product
should be done as it has many advantages which are discussed below:
• Accurate product costing helps in matters related to the decision making of a product, a
sale of a product. Analysing the product cost helps to increase the productivity and accuracy
of the project and there will be an optimum utilization of resources with less wastage of
resources.
• Accuracy is important in evaluating the product cost. Accuracy can be defined as how
effectively and efficiently the business can analyse its expenses using the product costs and
its current value.
selling and administration 1,40,600.00
interest expense 25,200.00
office rent 35,900.00
Inspection 4,210.53 15,789.47
Assembly 51750 38250
Production Scheduling 9545.454545 95454.54545
Machine Set up 10000 25000
Total Cost 8,35,505.98 14,04,494.02
Total Unit 1600units 1500units
Per unit Cost 522.19 936.33
Task 3
In this method of costing opted by the Sewing, Machine Ltd. is selling at 20% more than the
cost to the overseas buyer and others. The overseas buyer prefers to have the advance model
as it shows all the necessary expenses in the costing. In advance model, some extra expenses
are taken into consideration like office rent, interest expense and selling and administration
expenses. These costs are not included in the basic model which shows that it does not take
into account all the necessary expenses into account (Lee et al., 2013). The buyers are
interested in the advance model as it includes all expenses into account so that the actual
profits can become into consideration by the businessman. The accurate costing of a product
should be done as it has many advantages which are discussed below:
• Accurate product costing helps in matters related to the decision making of a product, a
sale of a product. Analysing the product cost helps to increase the productivity and accuracy
of the project and there will be an optimum utilization of resources with less wastage of
resources.
• Accuracy is important in evaluating the product cost. Accuracy can be defined as how
effectively and efficiently the business can analyse its expenses using the product costs and
its current value.
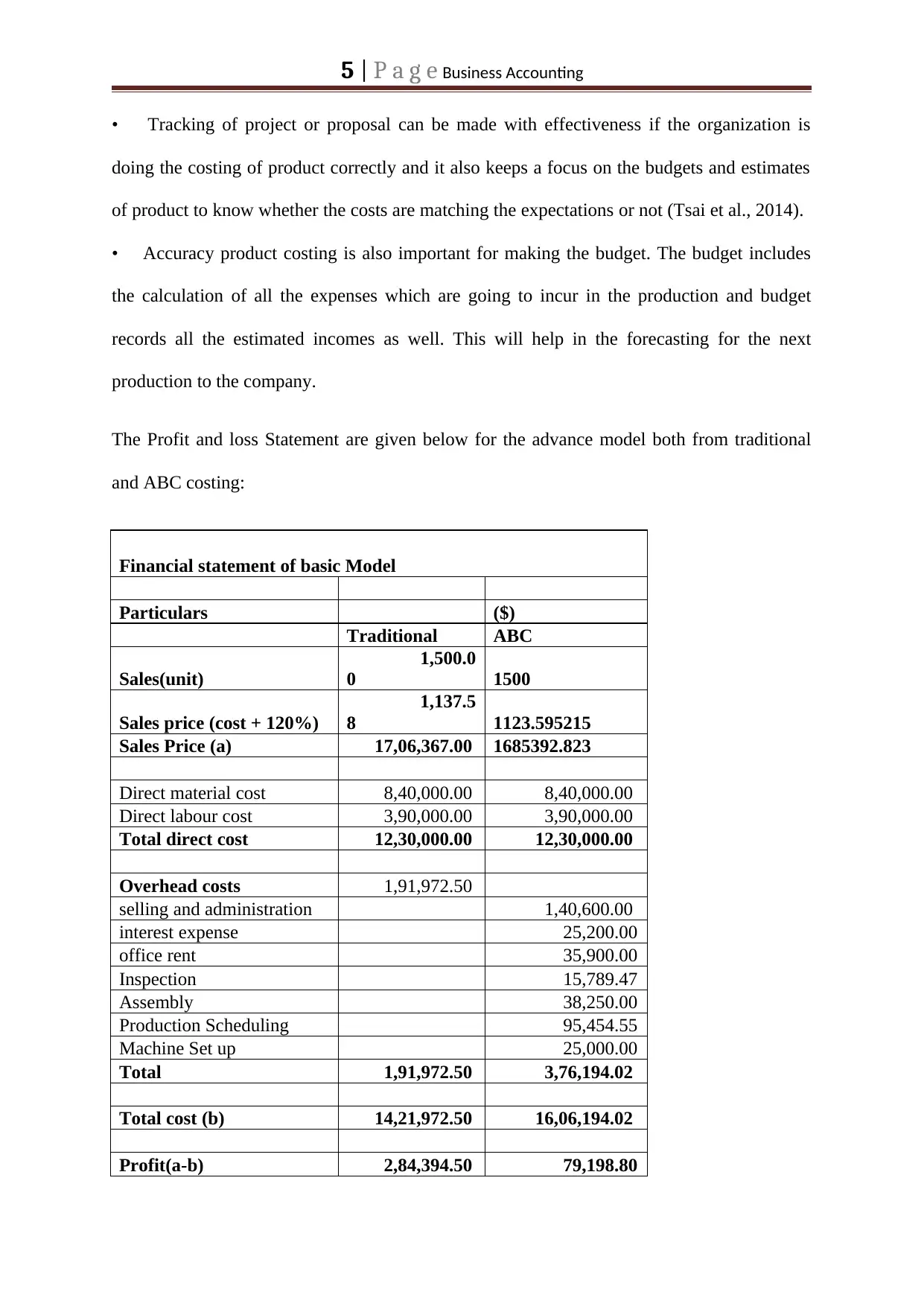
5 | P a g e Business Accounting
• Tracking of project or proposal can be made with effectiveness if the organization is
doing the costing of product correctly and it also keeps a focus on the budgets and estimates
of product to know whether the costs are matching the expectations or not (Tsai et al., 2014).
• Accuracy product costing is also important for making the budget. The budget includes
the calculation of all the expenses which are going to incur in the production and budget
records all the estimated incomes as well. This will help in the forecasting for the next
production to the company.
The Profit and loss Statement are given below for the advance model both from traditional
and ABC costing:
Financial statement of basic Model
Particulars ($)
Traditional ABC
Sales(unit)
1,500.0
0 1500
Sales price (cost + 120%)
1,137.5
8 1123.595215
Sales Price (a) 17,06,367.00 1685392.823
Direct material cost 8,40,000.00 8,40,000.00
Direct labour cost 3,90,000.00 3,90,000.00
Total direct cost 12,30,000.00 12,30,000.00
Overhead costs 1,91,972.50
selling and administration 1,40,600.00
interest expense 25,200.00
office rent 35,900.00
Inspection 15,789.47
Assembly 38,250.00
Production Scheduling 95,454.55
Machine Set up 25,000.00
Total 1,91,972.50 3,76,194.02
Total cost (b) 14,21,972.50 16,06,194.02
Profit(a-b) 2,84,394.50 79,198.80
• Tracking of project or proposal can be made with effectiveness if the organization is
doing the costing of product correctly and it also keeps a focus on the budgets and estimates
of product to know whether the costs are matching the expectations or not (Tsai et al., 2014).
• Accuracy product costing is also important for making the budget. The budget includes
the calculation of all the expenses which are going to incur in the production and budget
records all the estimated incomes as well. This will help in the forecasting for the next
production to the company.
The Profit and loss Statement are given below for the advance model both from traditional
and ABC costing:
Financial statement of basic Model
Particulars ($)
Traditional ABC
Sales(unit)
1,500.0
0 1500
Sales price (cost + 120%)
1,137.5
8 1123.595215
Sales Price (a) 17,06,367.00 1685392.823
Direct material cost 8,40,000.00 8,40,000.00
Direct labour cost 3,90,000.00 3,90,000.00
Total direct cost 12,30,000.00 12,30,000.00
Overhead costs 1,91,972.50
selling and administration 1,40,600.00
interest expense 25,200.00
office rent 35,900.00
Inspection 15,789.47
Assembly 38,250.00
Production Scheduling 95,454.55
Machine Set up 25,000.00
Total 1,91,972.50 3,76,194.02
Total cost (b) 14,21,972.50 16,06,194.02
Profit(a-b) 2,84,394.50 79,198.80
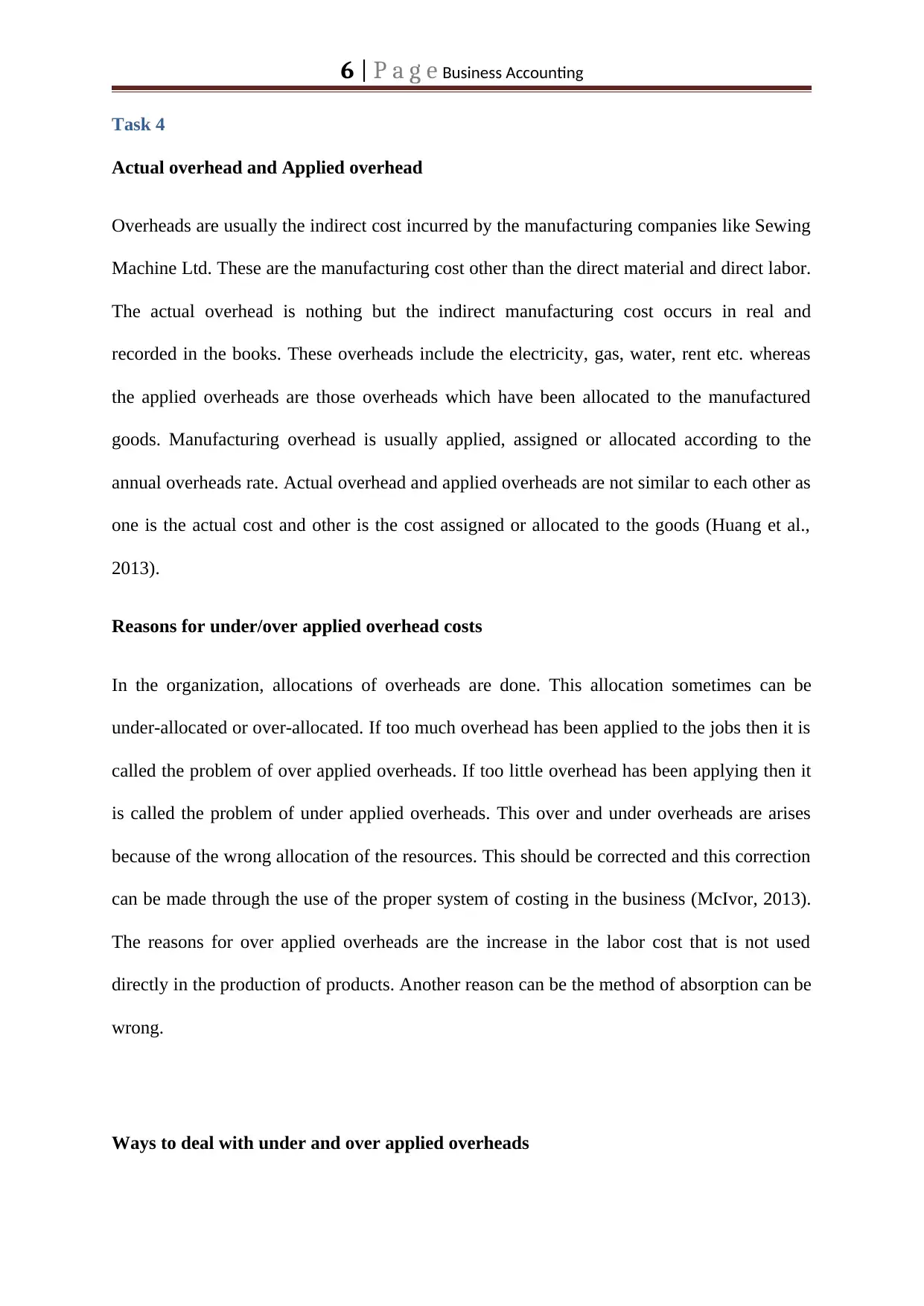
6 | P a g e Business Accounting
Task 4
Actual overhead and Applied overhead
Overheads are usually the indirect cost incurred by the manufacturing companies like Sewing
Machine Ltd. These are the manufacturing cost other than the direct material and direct labor.
The actual overhead is nothing but the indirect manufacturing cost occurs in real and
recorded in the books. These overheads include the electricity, gas, water, rent etc. whereas
the applied overheads are those overheads which have been allocated to the manufactured
goods. Manufacturing overhead is usually applied, assigned or allocated according to the
annual overheads rate. Actual overhead and applied overheads are not similar to each other as
one is the actual cost and other is the cost assigned or allocated to the goods (Huang et al.,
2013).
Reasons for under/over applied overhead costs
In the organization, allocations of overheads are done. This allocation sometimes can be
under-allocated or over-allocated. If too much overhead has been applied to the jobs then it is
called the problem of over applied overheads. If too little overhead has been applying then it
is called the problem of under applied overheads. This over and under overheads are arises
because of the wrong allocation of the resources. This should be corrected and this correction
can be made through the use of the proper system of costing in the business (McIvor, 2013).
The reasons for over applied overheads are the increase in the labor cost that is not used
directly in the production of products. Another reason can be the method of absorption can be
wrong.
Ways to deal with under and over applied overheads
Task 4
Actual overhead and Applied overhead
Overheads are usually the indirect cost incurred by the manufacturing companies like Sewing
Machine Ltd. These are the manufacturing cost other than the direct material and direct labor.
The actual overhead is nothing but the indirect manufacturing cost occurs in real and
recorded in the books. These overheads include the electricity, gas, water, rent etc. whereas
the applied overheads are those overheads which have been allocated to the manufactured
goods. Manufacturing overhead is usually applied, assigned or allocated according to the
annual overheads rate. Actual overhead and applied overheads are not similar to each other as
one is the actual cost and other is the cost assigned or allocated to the goods (Huang et al.,
2013).
Reasons for under/over applied overhead costs
In the organization, allocations of overheads are done. This allocation sometimes can be
under-allocated or over-allocated. If too much overhead has been applied to the jobs then it is
called the problem of over applied overheads. If too little overhead has been applying then it
is called the problem of under applied overheads. This over and under overheads are arises
because of the wrong allocation of the resources. This should be corrected and this correction
can be made through the use of the proper system of costing in the business (McIvor, 2013).
The reasons for over applied overheads are the increase in the labor cost that is not used
directly in the production of products. Another reason can be the method of absorption can be
wrong.
Ways to deal with under and over applied overheads
Paraphrase This Document
Need a fresh take? Get an instant paraphrase of this document with our AI Paraphraser
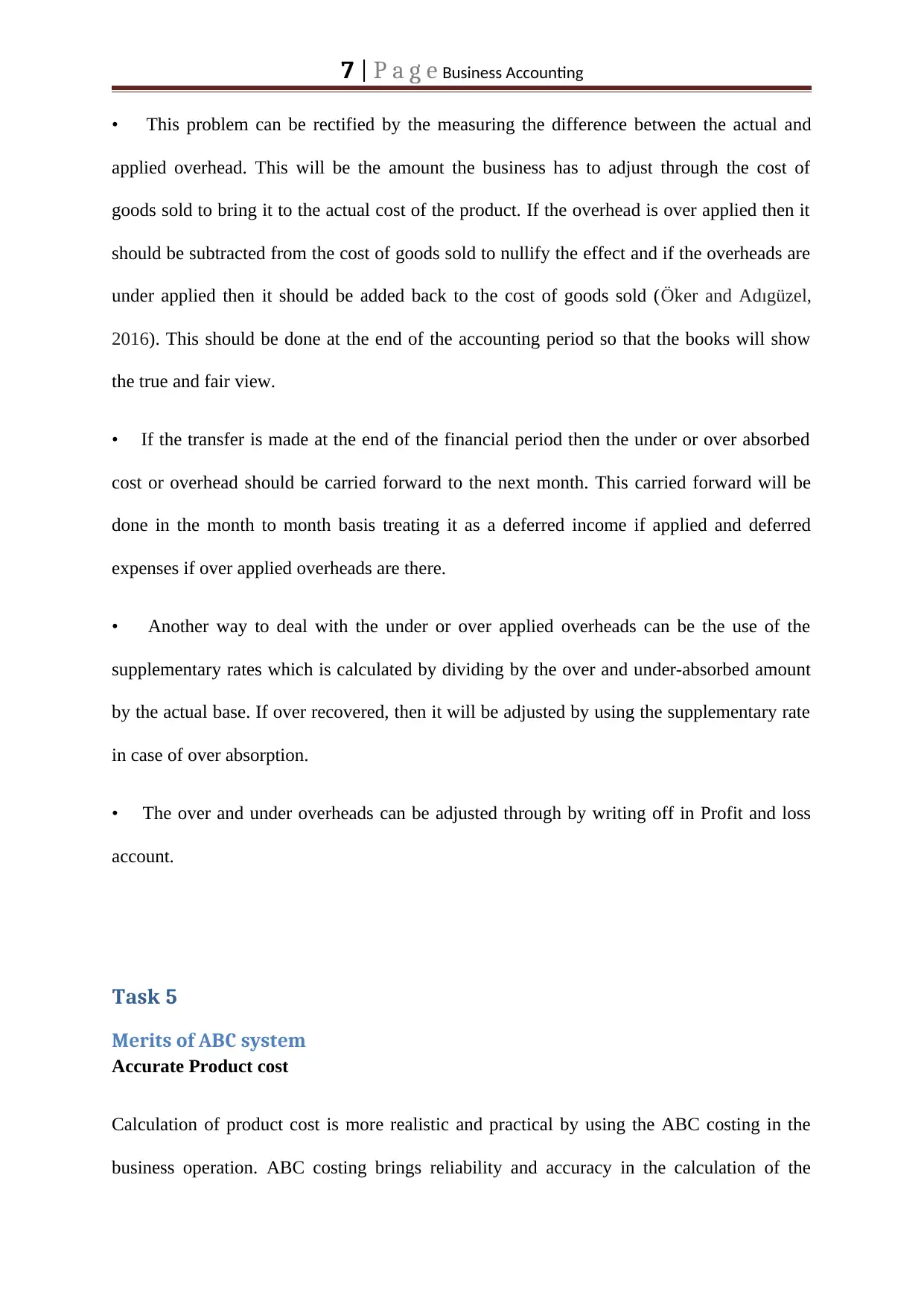
7 | P a g e Business Accounting
• This problem can be rectified by the measuring the difference between the actual and
applied overhead. This will be the amount the business has to adjust through the cost of
goods sold to bring it to the actual cost of the product. If the overhead is over applied then it
should be subtracted from the cost of goods sold to nullify the effect and if the overheads are
under applied then it should be added back to the cost of goods sold (Öker and Adıgüzel,
2016). This should be done at the end of the accounting period so that the books will show
the true and fair view.
• If the transfer is made at the end of the financial period then the under or over absorbed
cost or overhead should be carried forward to the next month. This carried forward will be
done in the month to month basis treating it as a deferred income if applied and deferred
expenses if over applied overheads are there.
• Another way to deal with the under or over applied overheads can be the use of the
supplementary rates which is calculated by dividing by the over and under-absorbed amount
by the actual base. If over recovered, then it will be adjusted by using the supplementary rate
in case of over absorption.
• The over and under overheads can be adjusted through by writing off in Profit and loss
account.
Task 5
Merits of ABC system
Accurate Product cost
Calculation of product cost is more realistic and practical by using the ABC costing in the
business operation. ABC costing brings reliability and accuracy in the calculation of the
• This problem can be rectified by the measuring the difference between the actual and
applied overhead. This will be the amount the business has to adjust through the cost of
goods sold to bring it to the actual cost of the product. If the overhead is over applied then it
should be subtracted from the cost of goods sold to nullify the effect and if the overheads are
under applied then it should be added back to the cost of goods sold (Öker and Adıgüzel,
2016). This should be done at the end of the accounting period so that the books will show
the true and fair view.
• If the transfer is made at the end of the financial period then the under or over absorbed
cost or overhead should be carried forward to the next month. This carried forward will be
done in the month to month basis treating it as a deferred income if applied and deferred
expenses if over applied overheads are there.
• Another way to deal with the under or over applied overheads can be the use of the
supplementary rates which is calculated by dividing by the over and under-absorbed amount
by the actual base. If over recovered, then it will be adjusted by using the supplementary rate
in case of over absorption.
• The over and under overheads can be adjusted through by writing off in Profit and loss
account.
Task 5
Merits of ABC system
Accurate Product cost
Calculation of product cost is more realistic and practical by using the ABC costing in the
business operation. ABC costing brings reliability and accuracy in the calculation of the
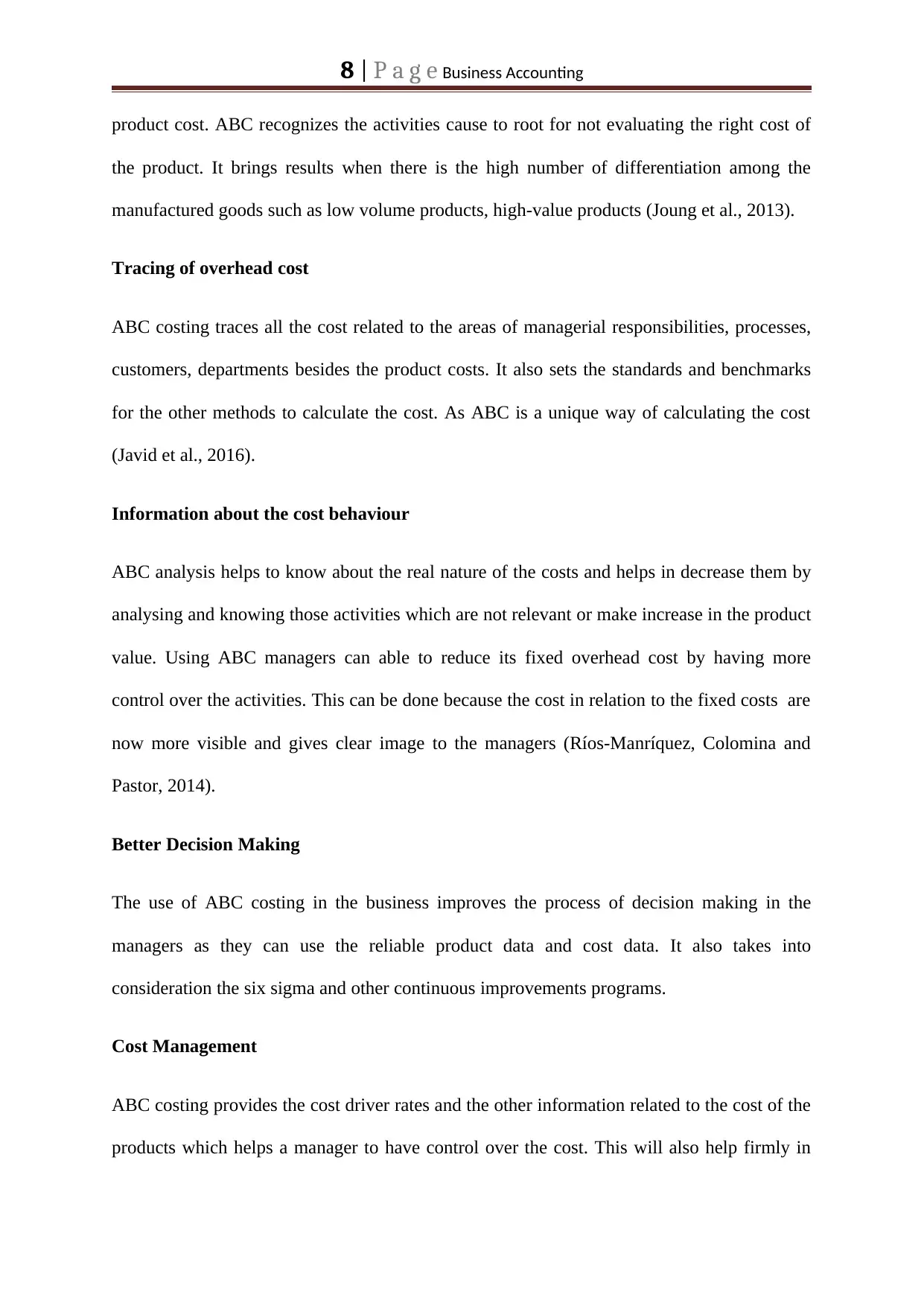
8 | P a g e Business Accounting
product cost. ABC recognizes the activities cause to root for not evaluating the right cost of
the product. It brings results when there is the high number of differentiation among the
manufactured goods such as low volume products, high-value products (Joung et al., 2013).
Tracing of overhead cost
ABC costing traces all the cost related to the areas of managerial responsibilities, processes,
customers, departments besides the product costs. It also sets the standards and benchmarks
for the other methods to calculate the cost. As ABC is a unique way of calculating the cost
(Javid et al., 2016).
Information about the cost behaviour
ABC analysis helps to know about the real nature of the costs and helps in decrease them by
analysing and knowing those activities which are not relevant or make increase in the product
value. Using ABC managers can able to reduce its fixed overhead cost by having more
control over the activities. This can be done because the cost in relation to the fixed costs are
now more visible and gives clear image to the managers (Ríos-Manríquez, Colomina and
Pastor, 2014).
Better Decision Making
The use of ABC costing in the business improves the process of decision making in the
managers as they can use the reliable product data and cost data. It also takes into
consideration the six sigma and other continuous improvements programs.
Cost Management
ABC costing provides the cost driver rates and the other information related to the cost of the
products which helps a manager to have control over the cost. This will also help firmly in
product cost. ABC recognizes the activities cause to root for not evaluating the right cost of
the product. It brings results when there is the high number of differentiation among the
manufactured goods such as low volume products, high-value products (Joung et al., 2013).
Tracing of overhead cost
ABC costing traces all the cost related to the areas of managerial responsibilities, processes,
customers, departments besides the product costs. It also sets the standards and benchmarks
for the other methods to calculate the cost. As ABC is a unique way of calculating the cost
(Javid et al., 2016).
Information about the cost behaviour
ABC analysis helps to know about the real nature of the costs and helps in decrease them by
analysing and knowing those activities which are not relevant or make increase in the product
value. Using ABC managers can able to reduce its fixed overhead cost by having more
control over the activities. This can be done because the cost in relation to the fixed costs are
now more visible and gives clear image to the managers (Ríos-Manríquez, Colomina and
Pastor, 2014).
Better Decision Making
The use of ABC costing in the business improves the process of decision making in the
managers as they can use the reliable product data and cost data. It also takes into
consideration the six sigma and other continuous improvements programs.
Cost Management
ABC costing provides the cost driver rates and the other information related to the cost of the
products which helps a manager to have control over the cost. This will also help firmly in
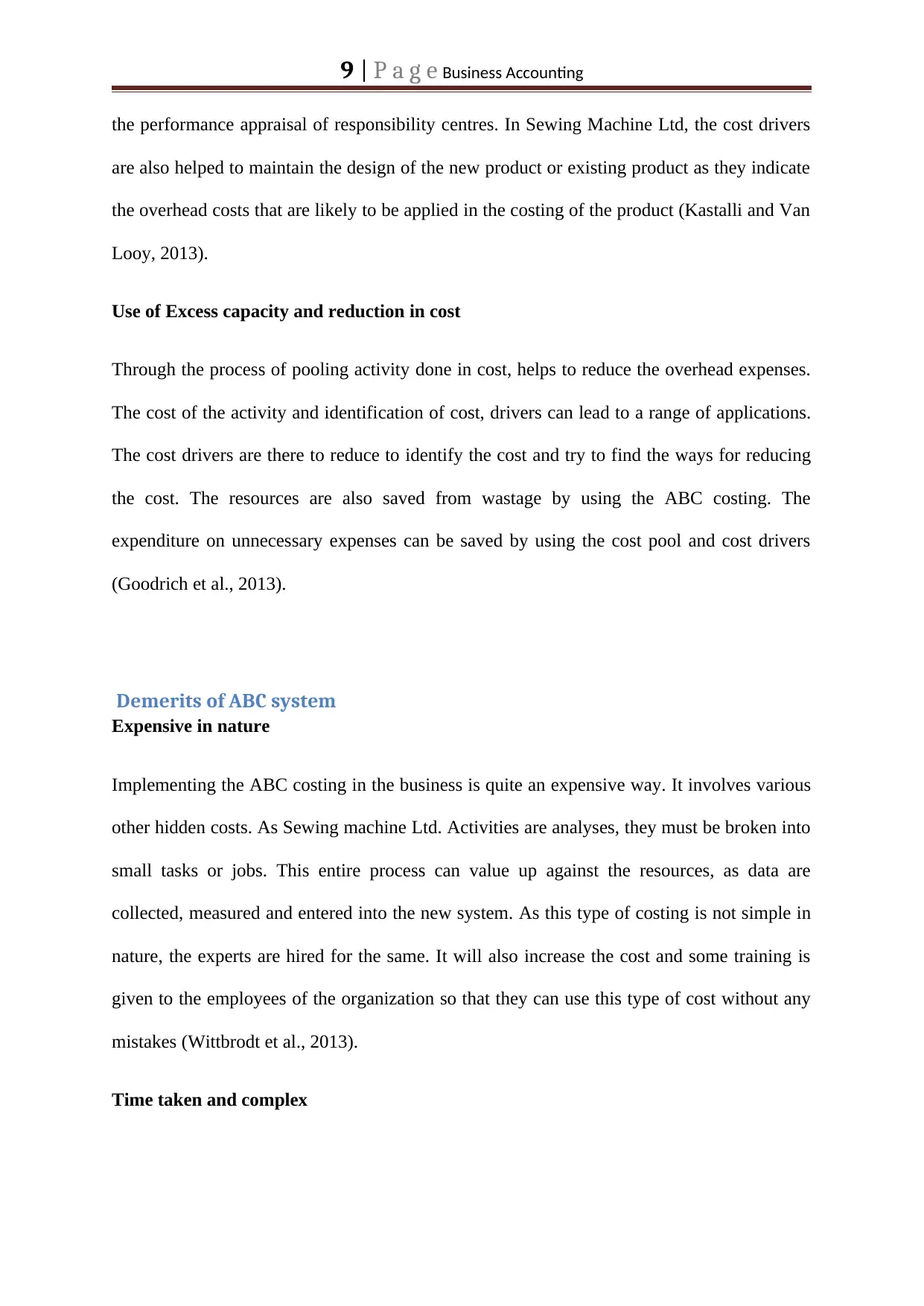
9 | P a g e Business Accounting
the performance appraisal of responsibility centres. In Sewing Machine Ltd, the cost drivers
are also helped to maintain the design of the new product or existing product as they indicate
the overhead costs that are likely to be applied in the costing of the product (Kastalli and Van
Looy, 2013).
Use of Excess capacity and reduction in cost
Through the process of pooling activity done in cost, helps to reduce the overhead expenses.
The cost of the activity and identification of cost, drivers can lead to a range of applications.
The cost drivers are there to reduce to identify the cost and try to find the ways for reducing
the cost. The resources are also saved from wastage by using the ABC costing. The
expenditure on unnecessary expenses can be saved by using the cost pool and cost drivers
(Goodrich et al., 2013).
Demerits of ABC system
Expensive in nature
Implementing the ABC costing in the business is quite an expensive way. It involves various
other hidden costs. As Sewing machine Ltd. Activities are analyses, they must be broken into
small tasks or jobs. This entire process can value up against the resources, as data are
collected, measured and entered into the new system. As this type of costing is not simple in
nature, the experts are hired for the same. It will also increase the cost and some training is
given to the employees of the organization so that they can use this type of cost without any
mistakes (Wittbrodt et al., 2013).
Time taken and complex
the performance appraisal of responsibility centres. In Sewing Machine Ltd, the cost drivers
are also helped to maintain the design of the new product or existing product as they indicate
the overhead costs that are likely to be applied in the costing of the product (Kastalli and Van
Looy, 2013).
Use of Excess capacity and reduction in cost
Through the process of pooling activity done in cost, helps to reduce the overhead expenses.
The cost of the activity and identification of cost, drivers can lead to a range of applications.
The cost drivers are there to reduce to identify the cost and try to find the ways for reducing
the cost. The resources are also saved from wastage by using the ABC costing. The
expenditure on unnecessary expenses can be saved by using the cost pool and cost drivers
(Goodrich et al., 2013).
Demerits of ABC system
Expensive in nature
Implementing the ABC costing in the business is quite an expensive way. It involves various
other hidden costs. As Sewing machine Ltd. Activities are analyses, they must be broken into
small tasks or jobs. This entire process can value up against the resources, as data are
collected, measured and entered into the new system. As this type of costing is not simple in
nature, the experts are hired for the same. It will also increase the cost and some training is
given to the employees of the organization so that they can use this type of cost without any
mistakes (Wittbrodt et al., 2013).
Time taken and complex
Secure Best Marks with AI Grader
Need help grading? Try our AI Grader for instant feedback on your assignments.
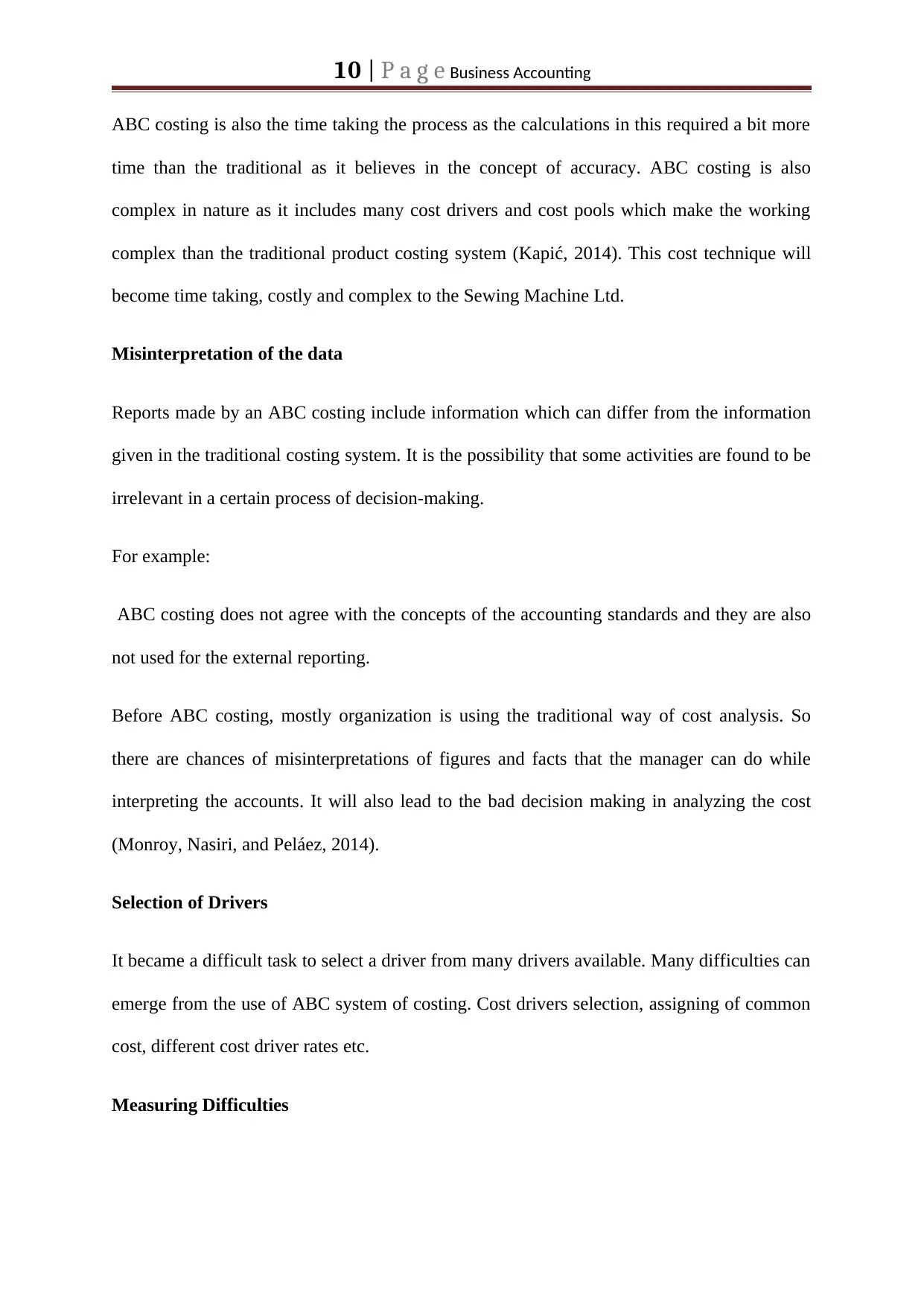
10 | P a g e Business Accounting
ABC costing is also the time taking the process as the calculations in this required a bit more
time than the traditional as it believes in the concept of accuracy. ABC costing is also
complex in nature as it includes many cost drivers and cost pools which make the working
complex than the traditional product costing system (Kapić, 2014). This cost technique will
become time taking, costly and complex to the Sewing Machine Ltd.
Misinterpretation of the data
Reports made by an ABC costing include information which can differ from the information
given in the traditional costing system. It is the possibility that some activities are found to be
irrelevant in a certain process of decision-making.
For example:
ABC costing does not agree with the concepts of the accounting standards and they are also
not used for the external reporting.
Before ABC costing, mostly organization is using the traditional way of cost analysis. So
there are chances of misinterpretations of figures and facts that the manager can do while
interpreting the accounts. It will also lead to the bad decision making in analyzing the cost
(Monroy, Nasiri, and Peláez, 2014).
Selection of Drivers
It became a difficult task to select a driver from many drivers available. Many difficulties can
emerge from the use of ABC system of costing. Cost drivers selection, assigning of common
cost, different cost driver rates etc.
Measuring Difficulties
ABC costing is also the time taking the process as the calculations in this required a bit more
time than the traditional as it believes in the concept of accuracy. ABC costing is also
complex in nature as it includes many cost drivers and cost pools which make the working
complex than the traditional product costing system (Kapić, 2014). This cost technique will
become time taking, costly and complex to the Sewing Machine Ltd.
Misinterpretation of the data
Reports made by an ABC costing include information which can differ from the information
given in the traditional costing system. It is the possibility that some activities are found to be
irrelevant in a certain process of decision-making.
For example:
ABC costing does not agree with the concepts of the accounting standards and they are also
not used for the external reporting.
Before ABC costing, mostly organization is using the traditional way of cost analysis. So
there are chances of misinterpretations of figures and facts that the manager can do while
interpreting the accounts. It will also lead to the bad decision making in analyzing the cost
(Monroy, Nasiri, and Peláez, 2014).
Selection of Drivers
It became a difficult task to select a driver from many drivers available. Many difficulties can
emerge from the use of ABC system of costing. Cost drivers selection, assigning of common
cost, different cost driver rates etc.
Measuring Difficulties
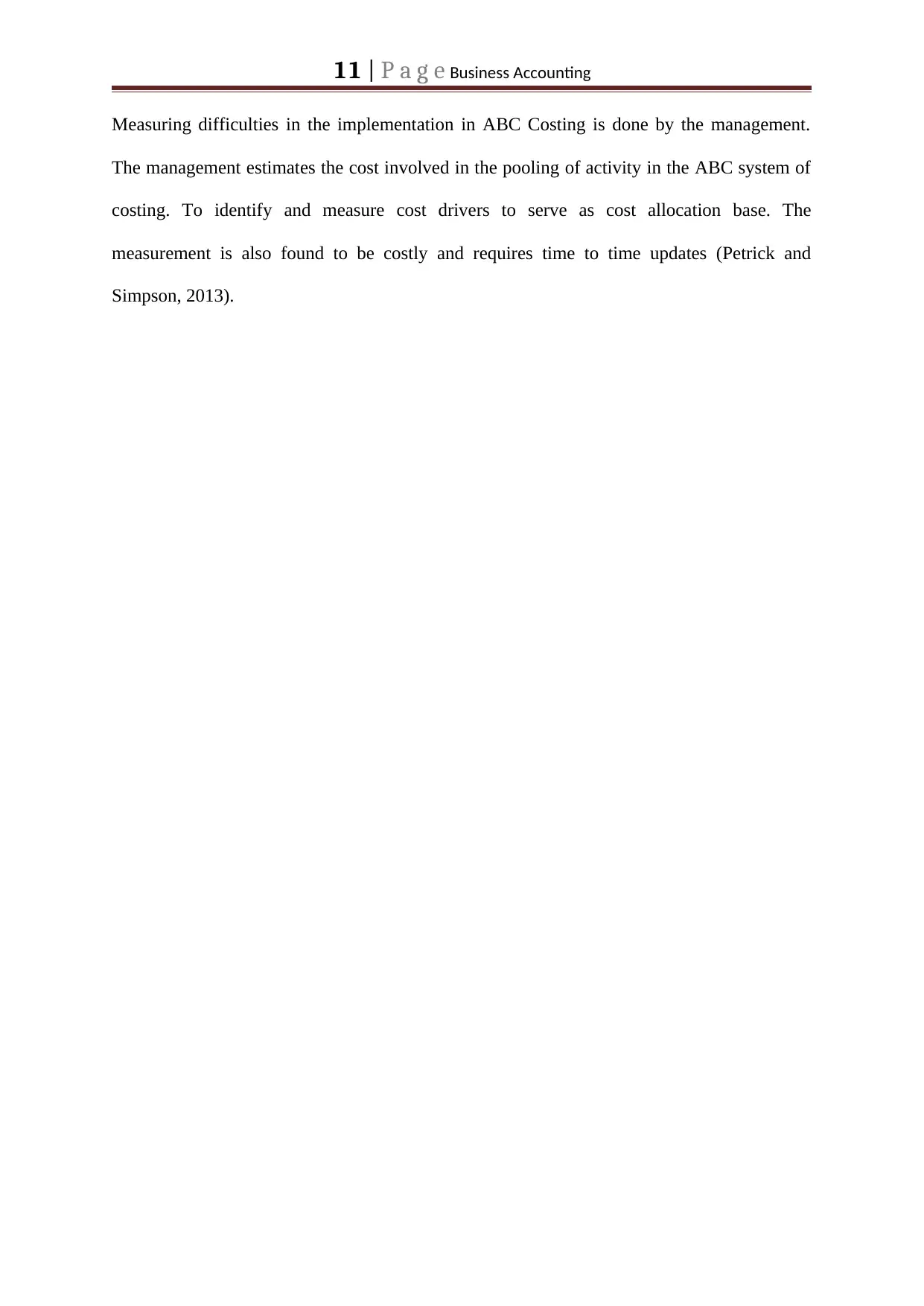
11 | P a g e Business Accounting
Measuring difficulties in the implementation in ABC Costing is done by the management.
The management estimates the cost involved in the pooling of activity in the ABC system of
costing. To identify and measure cost drivers to serve as cost allocation base. The
measurement is also found to be costly and requires time to time updates (Petrick and
Simpson, 2013).
Measuring difficulties in the implementation in ABC Costing is done by the management.
The management estimates the cost involved in the pooling of activity in the ABC system of
costing. To identify and measure cost drivers to serve as cost allocation base. The
measurement is also found to be costly and requires time to time updates (Petrick and
Simpson, 2013).
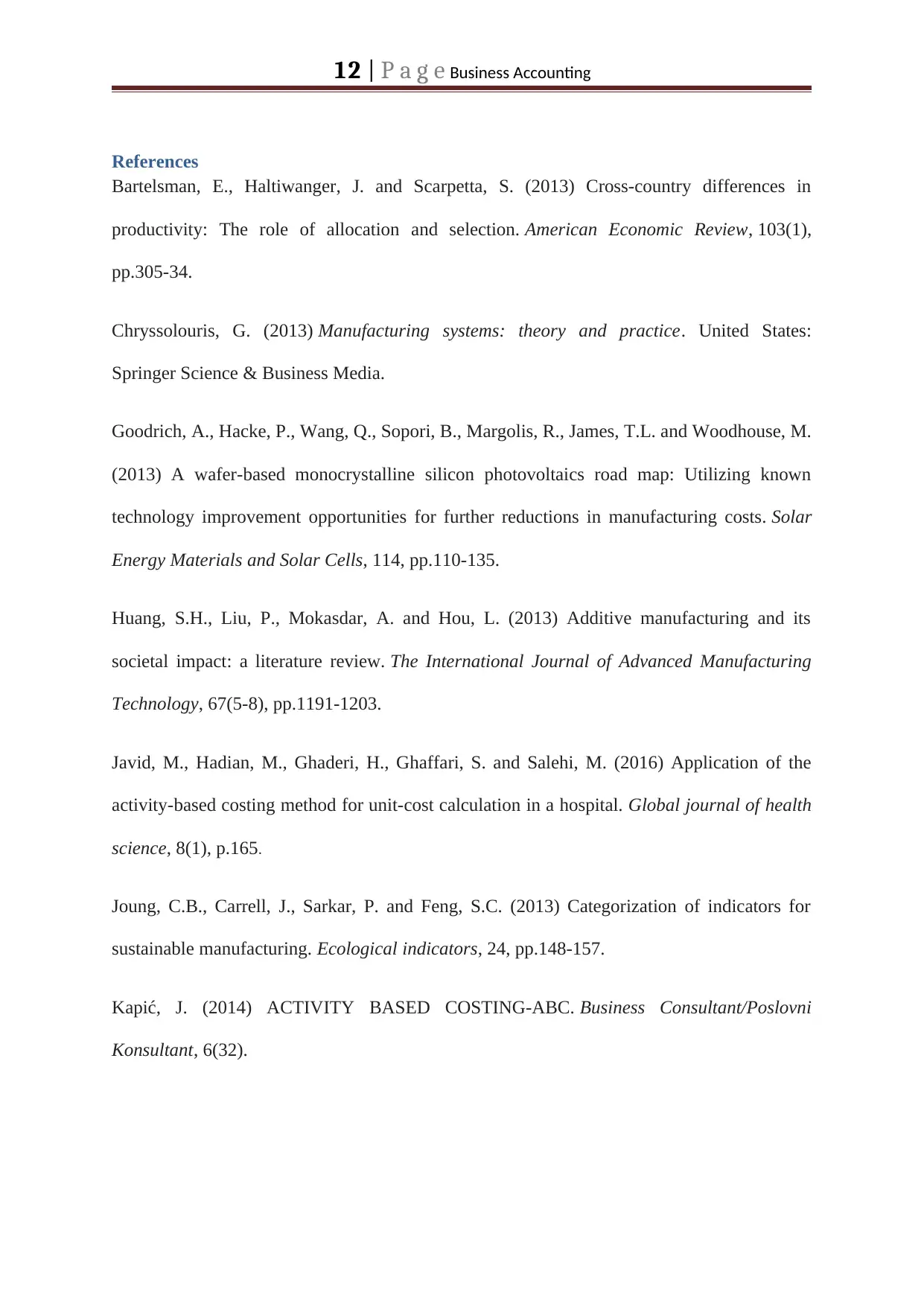
12 | P a g e Business Accounting
References
Bartelsman, E., Haltiwanger, J. and Scarpetta, S. (2013) Cross-country differences in
productivity: The role of allocation and selection. American Economic Review, 103(1),
pp.305-34.
Chryssolouris, G. (2013) Manufacturing systems: theory and practice. United States:
Springer Science & Business Media.
Goodrich, A., Hacke, P., Wang, Q., Sopori, B., Margolis, R., James, T.L. and Woodhouse, M.
(2013) A wafer-based monocrystalline silicon photovoltaics road map: Utilizing known
technology improvement opportunities for further reductions in manufacturing costs. Solar
Energy Materials and Solar Cells, 114, pp.110-135.
Huang, S.H., Liu, P., Mokasdar, A. and Hou, L. (2013) Additive manufacturing and its
societal impact: a literature review. The International Journal of Advanced Manufacturing
Technology, 67(5-8), pp.1191-1203.
Javid, M., Hadian, M., Ghaderi, H., Ghaffari, S. and Salehi, M. (2016) Application of the
activity-based costing method for unit-cost calculation in a hospital. Global journal of health
science, 8(1), p.165.
Joung, C.B., Carrell, J., Sarkar, P. and Feng, S.C. (2013) Categorization of indicators for
sustainable manufacturing. Ecological indicators, 24, pp.148-157.
Kapić, J. (2014) ACTIVITY BASED COSTING-ABC. Business Consultant/Poslovni
Konsultant, 6(32).
References
Bartelsman, E., Haltiwanger, J. and Scarpetta, S. (2013) Cross-country differences in
productivity: The role of allocation and selection. American Economic Review, 103(1),
pp.305-34.
Chryssolouris, G. (2013) Manufacturing systems: theory and practice. United States:
Springer Science & Business Media.
Goodrich, A., Hacke, P., Wang, Q., Sopori, B., Margolis, R., James, T.L. and Woodhouse, M.
(2013) A wafer-based monocrystalline silicon photovoltaics road map: Utilizing known
technology improvement opportunities for further reductions in manufacturing costs. Solar
Energy Materials and Solar Cells, 114, pp.110-135.
Huang, S.H., Liu, P., Mokasdar, A. and Hou, L. (2013) Additive manufacturing and its
societal impact: a literature review. The International Journal of Advanced Manufacturing
Technology, 67(5-8), pp.1191-1203.
Javid, M., Hadian, M., Ghaderi, H., Ghaffari, S. and Salehi, M. (2016) Application of the
activity-based costing method for unit-cost calculation in a hospital. Global journal of health
science, 8(1), p.165.
Joung, C.B., Carrell, J., Sarkar, P. and Feng, S.C. (2013) Categorization of indicators for
sustainable manufacturing. Ecological indicators, 24, pp.148-157.
Kapić, J. (2014) ACTIVITY BASED COSTING-ABC. Business Consultant/Poslovni
Konsultant, 6(32).
Paraphrase This Document
Need a fresh take? Get an instant paraphrase of this document with our AI Paraphraser
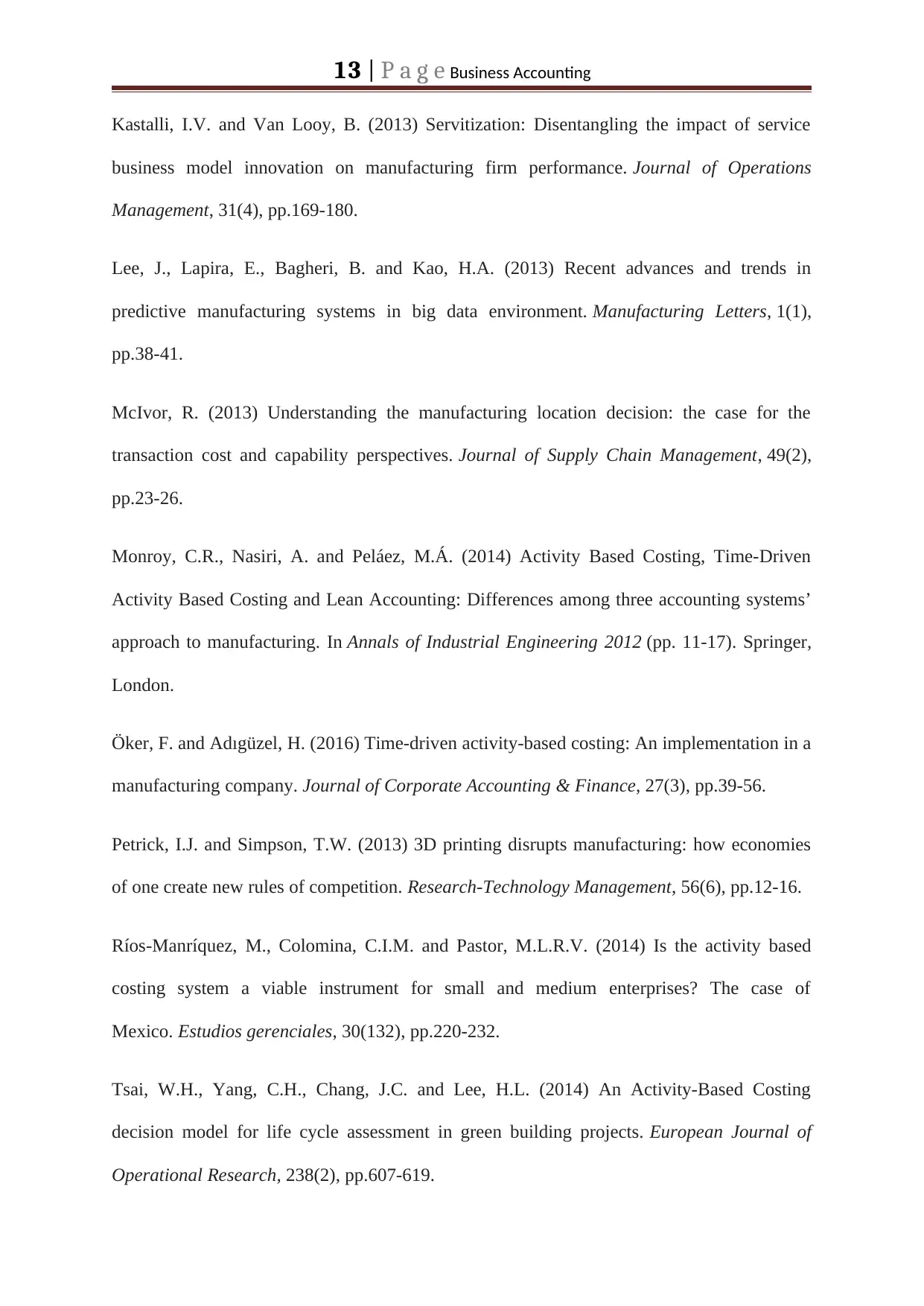
13 | P a g e Business Accounting
Kastalli, I.V. and Van Looy, B. (2013) Servitization: Disentangling the impact of service
business model innovation on manufacturing firm performance. Journal of Operations
Management, 31(4), pp.169-180.
Lee, J., Lapira, E., Bagheri, B. and Kao, H.A. (2013) Recent advances and trends in
predictive manufacturing systems in big data environment. Manufacturing Letters, 1(1),
pp.38-41.
McIvor, R. (2013) Understanding the manufacturing location decision: the case for the
transaction cost and capability perspectives. Journal of Supply Chain Management, 49(2),
pp.23-26.
Monroy, C.R., Nasiri, A. and Peláez, M.Á. (2014) Activity Based Costing, Time-Driven
Activity Based Costing and Lean Accounting: Differences among three accounting systems’
approach to manufacturing. In Annals of Industrial Engineering 2012 (pp. 11-17). Springer,
London.
Öker, F. and Adıgüzel, H. (2016) Time‐driven activity‐based costing: An implementation in a
manufacturing company. Journal of Corporate Accounting & Finance, 27(3), pp.39-56.
Petrick, I.J. and Simpson, T.W. (2013) 3D printing disrupts manufacturing: how economies
of one create new rules of competition. Research-Technology Management, 56(6), pp.12-16.
Ríos-Manríquez, M., Colomina, C.I.M. and Pastor, M.L.R.V. (2014) Is the activity based
costing system a viable instrument for small and medium enterprises? The case of
Mexico. Estudios gerenciales, 30(132), pp.220-232.
Tsai, W.H., Yang, C.H., Chang, J.C. and Lee, H.L. (2014) An Activity-Based Costing
decision model for life cycle assessment in green building projects. European Journal of
Operational Research, 238(2), pp.607-619.
Kastalli, I.V. and Van Looy, B. (2013) Servitization: Disentangling the impact of service
business model innovation on manufacturing firm performance. Journal of Operations
Management, 31(4), pp.169-180.
Lee, J., Lapira, E., Bagheri, B. and Kao, H.A. (2013) Recent advances and trends in
predictive manufacturing systems in big data environment. Manufacturing Letters, 1(1),
pp.38-41.
McIvor, R. (2013) Understanding the manufacturing location decision: the case for the
transaction cost and capability perspectives. Journal of Supply Chain Management, 49(2),
pp.23-26.
Monroy, C.R., Nasiri, A. and Peláez, M.Á. (2014) Activity Based Costing, Time-Driven
Activity Based Costing and Lean Accounting: Differences among three accounting systems’
approach to manufacturing. In Annals of Industrial Engineering 2012 (pp. 11-17). Springer,
London.
Öker, F. and Adıgüzel, H. (2016) Time‐driven activity‐based costing: An implementation in a
manufacturing company. Journal of Corporate Accounting & Finance, 27(3), pp.39-56.
Petrick, I.J. and Simpson, T.W. (2013) 3D printing disrupts manufacturing: how economies
of one create new rules of competition. Research-Technology Management, 56(6), pp.12-16.
Ríos-Manríquez, M., Colomina, C.I.M. and Pastor, M.L.R.V. (2014) Is the activity based
costing system a viable instrument for small and medium enterprises? The case of
Mexico. Estudios gerenciales, 30(132), pp.220-232.
Tsai, W.H., Yang, C.H., Chang, J.C. and Lee, H.L. (2014) An Activity-Based Costing
decision model for life cycle assessment in green building projects. European Journal of
Operational Research, 238(2), pp.607-619.
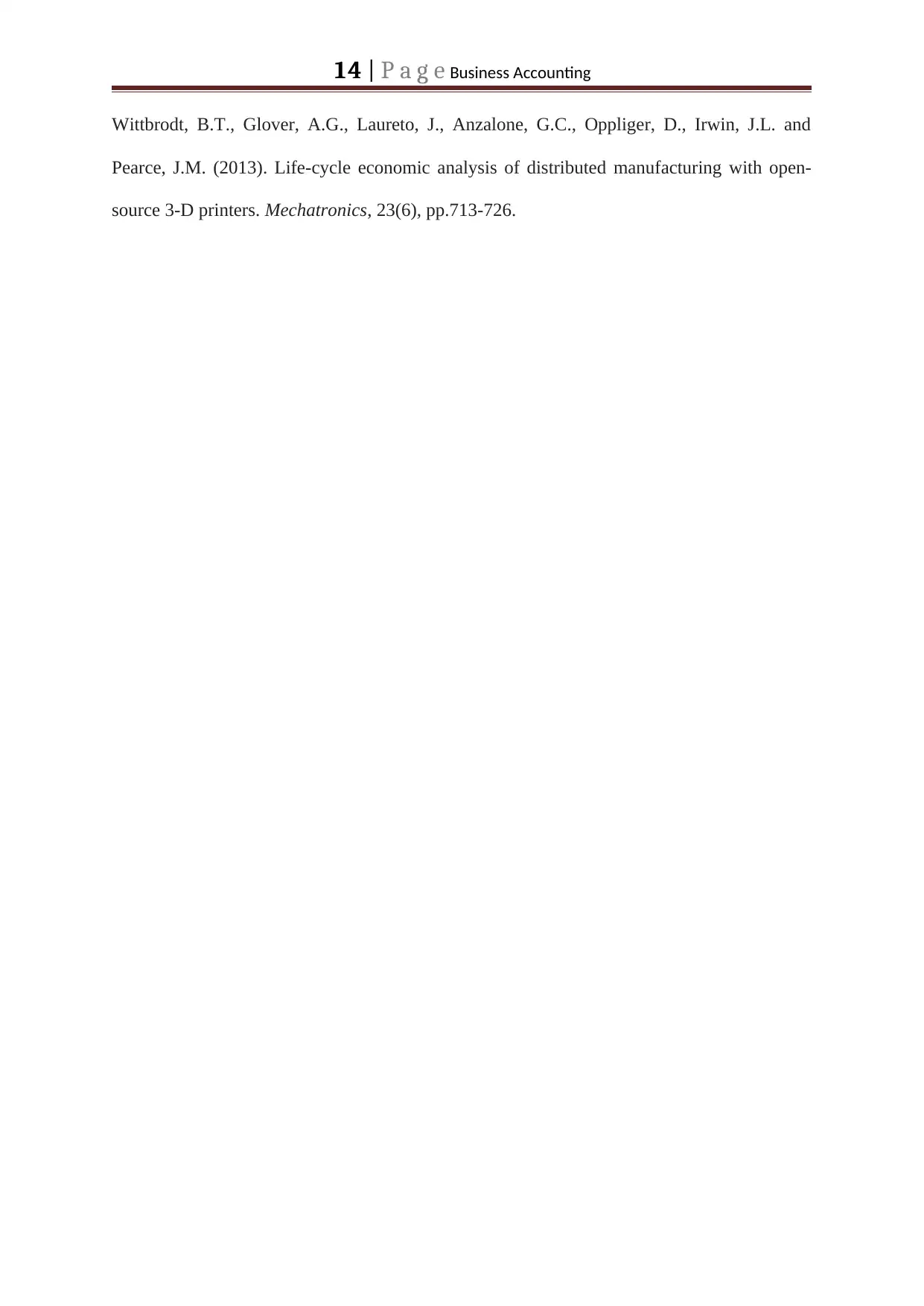
14 | P a g e Business Accounting
Wittbrodt, B.T., Glover, A.G., Laureto, J., Anzalone, G.C., Oppliger, D., Irwin, J.L. and
Pearce, J.M. (2013). Life-cycle economic analysis of distributed manufacturing with open-
source 3-D printers. Mechatronics, 23(6), pp.713-726.
Wittbrodt, B.T., Glover, A.G., Laureto, J., Anzalone, G.C., Oppliger, D., Irwin, J.L. and
Pearce, J.M. (2013). Life-cycle economic analysis of distributed manufacturing with open-
source 3-D printers. Mechatronics, 23(6), pp.713-726.
1 out of 15
Related Documents

Your All-in-One AI-Powered Toolkit for Academic Success.
+13062052269
info@desklib.com
Available 24*7 on WhatsApp / Email
Unlock your academic potential
© 2024 | Zucol Services PVT LTD | All rights reserved.