Comprehensive Analysis of Advanced Measurement Systems and Equipment
VerifiedAdded on 2022/08/15
|12
|2437
|14
Report
AI Summary
This report provides a comprehensive overview of advanced measurement systems and equipment, focusing on their applications in an industrial context. It begins with an introduction to measurement techniques and their evolution, highlighting the importance of accuracy and automation. The report then delves into specific types of equipment, including sensors and transducers, coordinated measuring machines (CMMs), and surface measuring machines, detailing their operating principles, characteristics, and performance. The report also discusses common error sources in CMMs and methods for calibration, as well as the evaluation and reduction of measurement uncertainty using the GUM approach. The report concludes by emphasizing the significance of these techniques in improving measurement capabilities and making informed decisions regarding equipment selection. The report provides a good understanding of the principles of advanced measurement system and data analysis and abilities to apply them to solve practical problems related to advanced measurement system and data analysis.
Contribute Materials
Your contribution can guide someone’s learning journey. Share your
documents today.
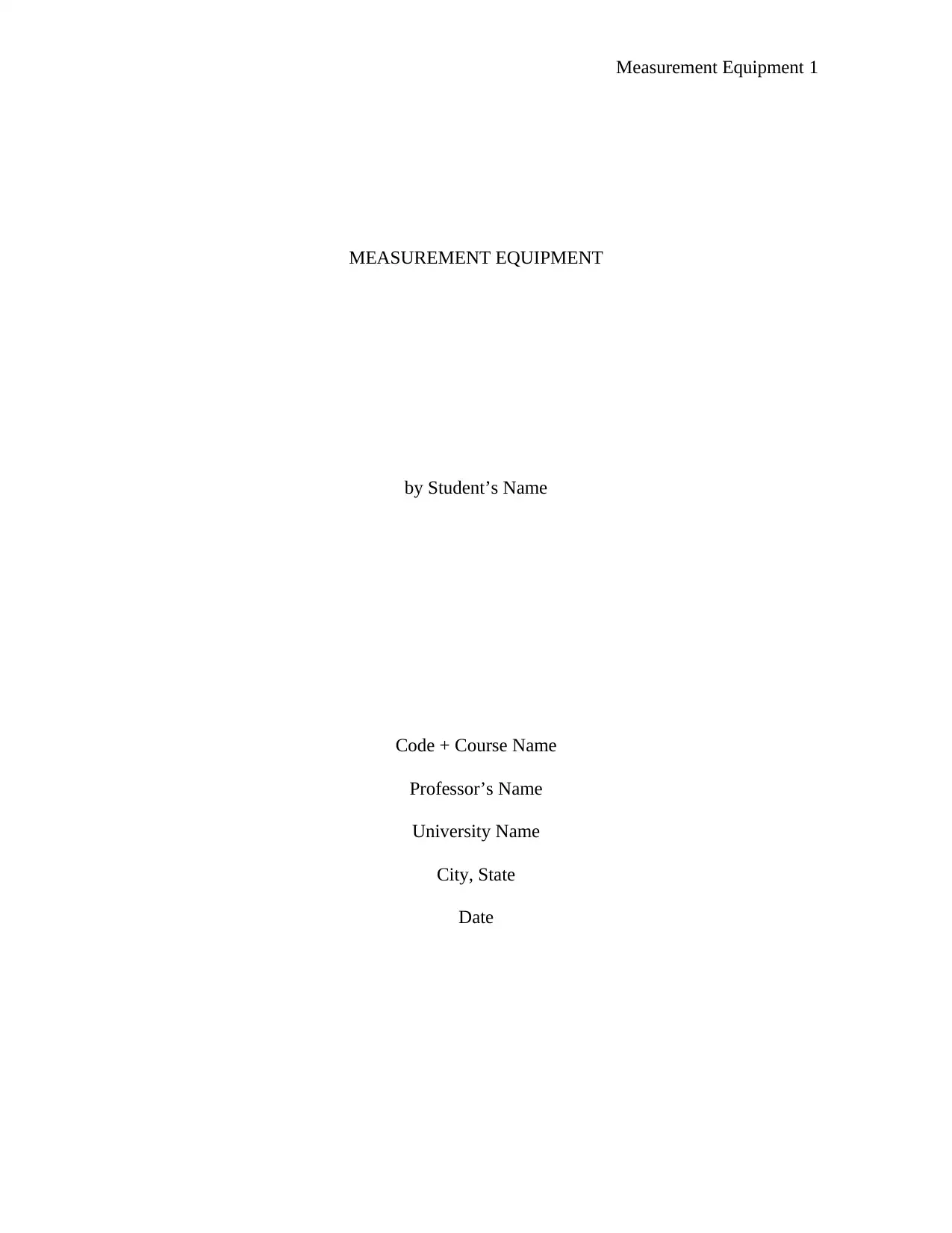
Measurement Equipment 1
MEASUREMENT EQUIPMENT
by Student’s Name
Code + Course Name
Professor’s Name
University Name
City, State
Date
MEASUREMENT EQUIPMENT
by Student’s Name
Code + Course Name
Professor’s Name
University Name
City, State
Date
Secure Best Marks with AI Grader
Need help grading? Try our AI Grader for instant feedback on your assignments.
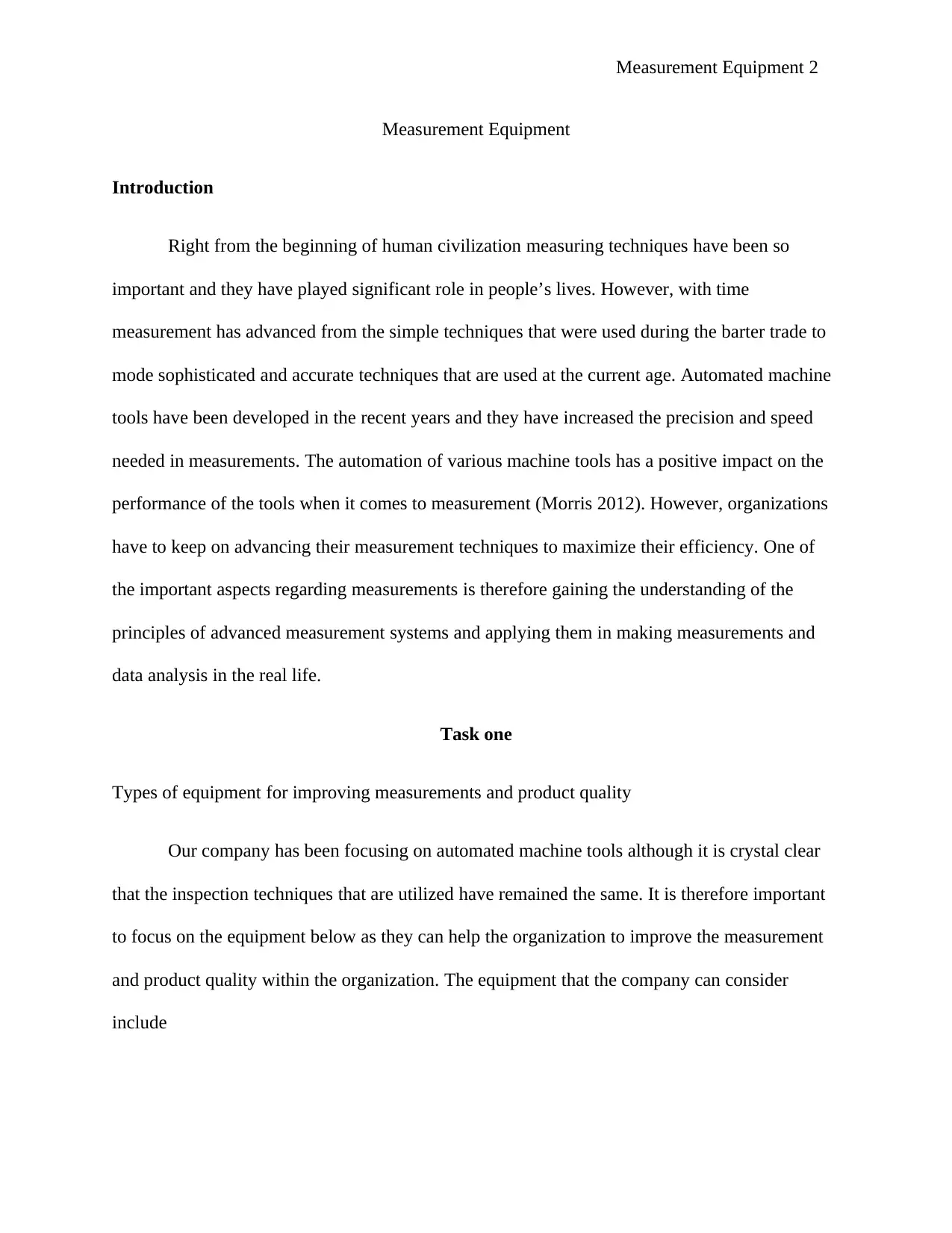
Measurement Equipment 2
Measurement Equipment
Introduction
Right from the beginning of human civilization measuring techniques have been so
important and they have played significant role in people’s lives. However, with time
measurement has advanced from the simple techniques that were used during the barter trade to
mode sophisticated and accurate techniques that are used at the current age. Automated machine
tools have been developed in the recent years and they have increased the precision and speed
needed in measurements. The automation of various machine tools has a positive impact on the
performance of the tools when it comes to measurement (Morris 2012). However, organizations
have to keep on advancing their measurement techniques to maximize their efficiency. One of
the important aspects regarding measurements is therefore gaining the understanding of the
principles of advanced measurement systems and applying them in making measurements and
data analysis in the real life.
Task one
Types of equipment for improving measurements and product quality
Our company has been focusing on automated machine tools although it is crystal clear
that the inspection techniques that are utilized have remained the same. It is therefore important
to focus on the equipment below as they can help the organization to improve the measurement
and product quality within the organization. The equipment that the company can consider
include
Measurement Equipment
Introduction
Right from the beginning of human civilization measuring techniques have been so
important and they have played significant role in people’s lives. However, with time
measurement has advanced from the simple techniques that were used during the barter trade to
mode sophisticated and accurate techniques that are used at the current age. Automated machine
tools have been developed in the recent years and they have increased the precision and speed
needed in measurements. The automation of various machine tools has a positive impact on the
performance of the tools when it comes to measurement (Morris 2012). However, organizations
have to keep on advancing their measurement techniques to maximize their efficiency. One of
the important aspects regarding measurements is therefore gaining the understanding of the
principles of advanced measurement systems and applying them in making measurements and
data analysis in the real life.
Task one
Types of equipment for improving measurements and product quality
Our company has been focusing on automated machine tools although it is crystal clear
that the inspection techniques that are utilized have remained the same. It is therefore important
to focus on the equipment below as they can help the organization to improve the measurement
and product quality within the organization. The equipment that the company can consider
include
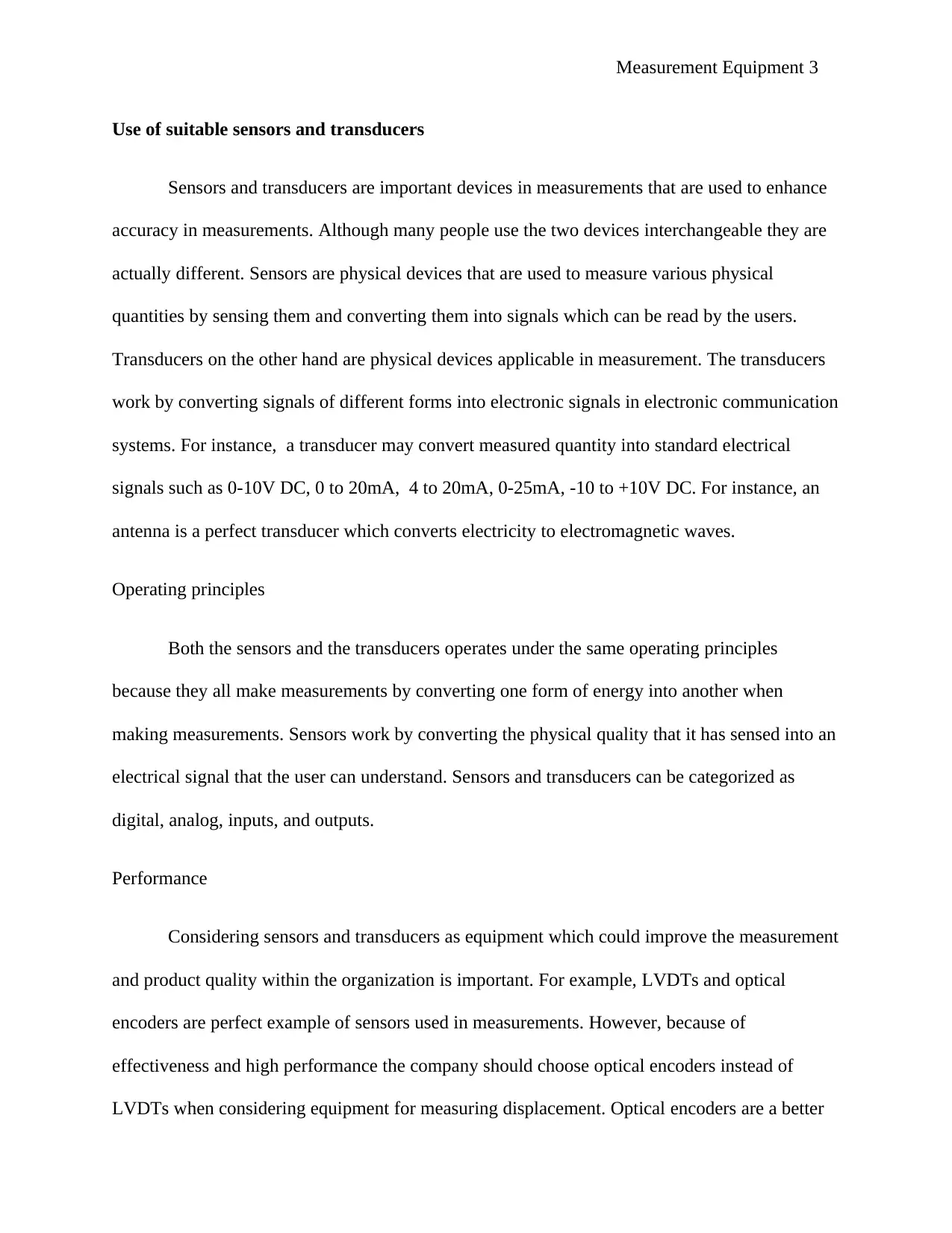
Measurement Equipment 3
Use of suitable sensors and transducers
Sensors and transducers are important devices in measurements that are used to enhance
accuracy in measurements. Although many people use the two devices interchangeable they are
actually different. Sensors are physical devices that are used to measure various physical
quantities by sensing them and converting them into signals which can be read by the users.
Transducers on the other hand are physical devices applicable in measurement. The transducers
work by converting signals of different forms into electronic signals in electronic communication
systems. For instance, a transducer may convert measured quantity into standard electrical
signals such as 0-10V DC, 0 to 20mA, 4 to 20mA, 0-25mA, -10 to +10V DC. For instance, an
antenna is a perfect transducer which converts electricity to electromagnetic waves.
Operating principles
Both the sensors and the transducers operates under the same operating principles
because they all make measurements by converting one form of energy into another when
making measurements. Sensors work by converting the physical quality that it has sensed into an
electrical signal that the user can understand. Sensors and transducers can be categorized as
digital, analog, inputs, and outputs.
Performance
Considering sensors and transducers as equipment which could improve the measurement
and product quality within the organization is important. For example, LVDTs and optical
encoders are perfect example of sensors used in measurements. However, because of
effectiveness and high performance the company should choose optical encoders instead of
LVDTs when considering equipment for measuring displacement. Optical encoders are a better
Use of suitable sensors and transducers
Sensors and transducers are important devices in measurements that are used to enhance
accuracy in measurements. Although many people use the two devices interchangeable they are
actually different. Sensors are physical devices that are used to measure various physical
quantities by sensing them and converting them into signals which can be read by the users.
Transducers on the other hand are physical devices applicable in measurement. The transducers
work by converting signals of different forms into electronic signals in electronic communication
systems. For instance, a transducer may convert measured quantity into standard electrical
signals such as 0-10V DC, 0 to 20mA, 4 to 20mA, 0-25mA, -10 to +10V DC. For instance, an
antenna is a perfect transducer which converts electricity to electromagnetic waves.
Operating principles
Both the sensors and the transducers operates under the same operating principles
because they all make measurements by converting one form of energy into another when
making measurements. Sensors work by converting the physical quality that it has sensed into an
electrical signal that the user can understand. Sensors and transducers can be categorized as
digital, analog, inputs, and outputs.
Performance
Considering sensors and transducers as equipment which could improve the measurement
and product quality within the organization is important. For example, LVDTs and optical
encoders are perfect example of sensors used in measurements. However, because of
effectiveness and high performance the company should choose optical encoders instead of
LVDTs when considering equipment for measuring displacement. Optical encoders are a better
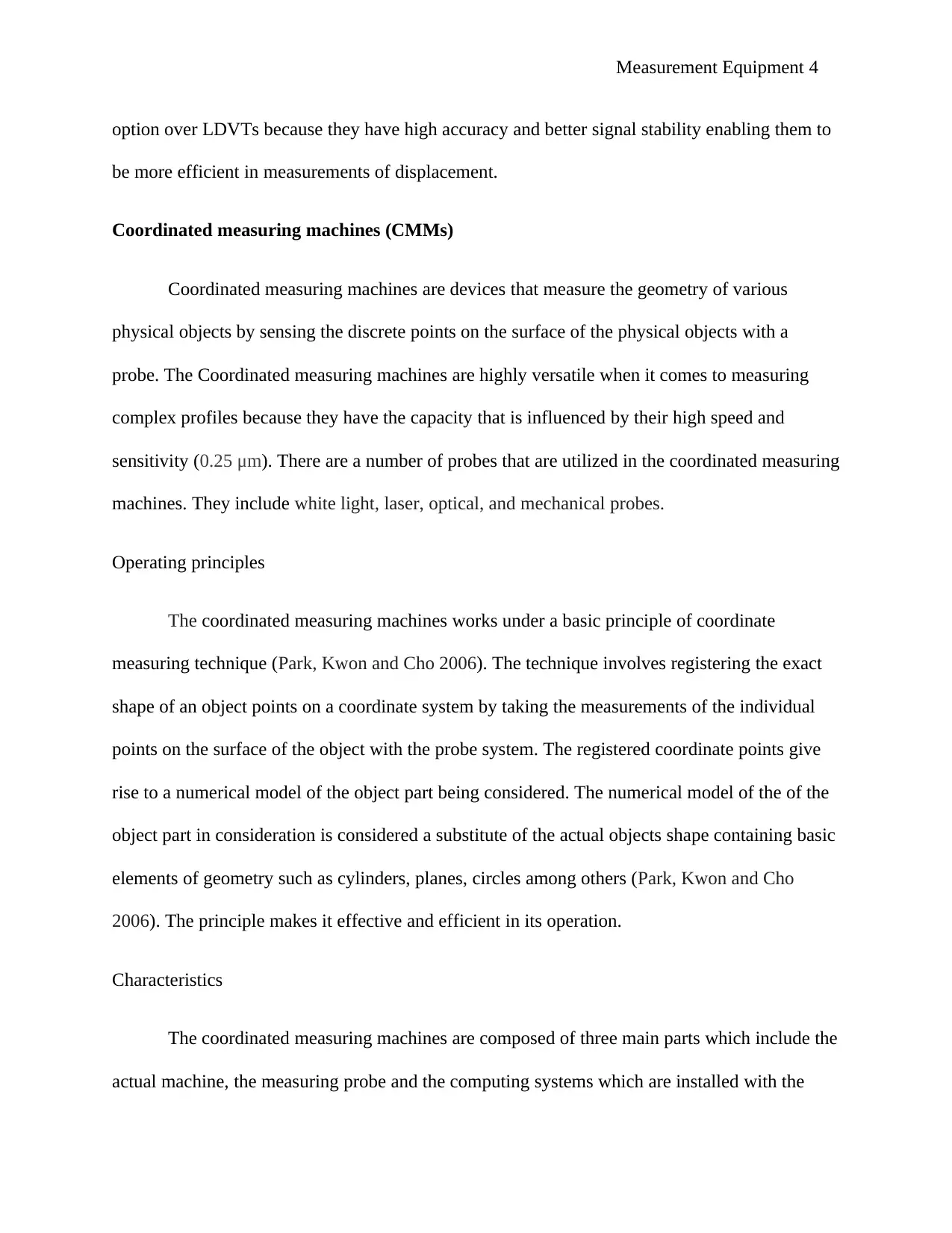
Measurement Equipment 4
option over LDVTs because they have high accuracy and better signal stability enabling them to
be more efficient in measurements of displacement.
Coordinated measuring machines (CMMs)
Coordinated measuring machines are devices that measure the geometry of various
physical objects by sensing the discrete points on the surface of the physical objects with a
probe. The Coordinated measuring machines are highly versatile when it comes to measuring
complex profiles because they have the capacity that is influenced by their high speed and
sensitivity (0.25 μm). There are a number of probes that are utilized in the coordinated measuring
machines. They include white light, laser, optical, and mechanical probes.
Operating principles
The coordinated measuring machines works under a basic principle of coordinate
measuring technique (Park, Kwon and Cho 2006). The technique involves registering the exact
shape of an object points on a coordinate system by taking the measurements of the individual
points on the surface of the object with the probe system. The registered coordinate points give
rise to a numerical model of the object part being considered. The numerical model of the of the
object part in consideration is considered a substitute of the actual objects shape containing basic
elements of geometry such as cylinders, planes, circles among others (Park, Kwon and Cho
2006). The principle makes it effective and efficient in its operation.
Characteristics
The coordinated measuring machines are composed of three main parts which include the
actual machine, the measuring probe and the computing systems which are installed with the
option over LDVTs because they have high accuracy and better signal stability enabling them to
be more efficient in measurements of displacement.
Coordinated measuring machines (CMMs)
Coordinated measuring machines are devices that measure the geometry of various
physical objects by sensing the discrete points on the surface of the physical objects with a
probe. The Coordinated measuring machines are highly versatile when it comes to measuring
complex profiles because they have the capacity that is influenced by their high speed and
sensitivity (0.25 μm). There are a number of probes that are utilized in the coordinated measuring
machines. They include white light, laser, optical, and mechanical probes.
Operating principles
The coordinated measuring machines works under a basic principle of coordinate
measuring technique (Park, Kwon and Cho 2006). The technique involves registering the exact
shape of an object points on a coordinate system by taking the measurements of the individual
points on the surface of the object with the probe system. The registered coordinate points give
rise to a numerical model of the object part being considered. The numerical model of the of the
object part in consideration is considered a substitute of the actual objects shape containing basic
elements of geometry such as cylinders, planes, circles among others (Park, Kwon and Cho
2006). The principle makes it effective and efficient in its operation.
Characteristics
The coordinated measuring machines are composed of three main parts which include the
actual machine, the measuring probe and the computing systems which are installed with the
Secure Best Marks with AI Grader
Need help grading? Try our AI Grader for instant feedback on your assignments.
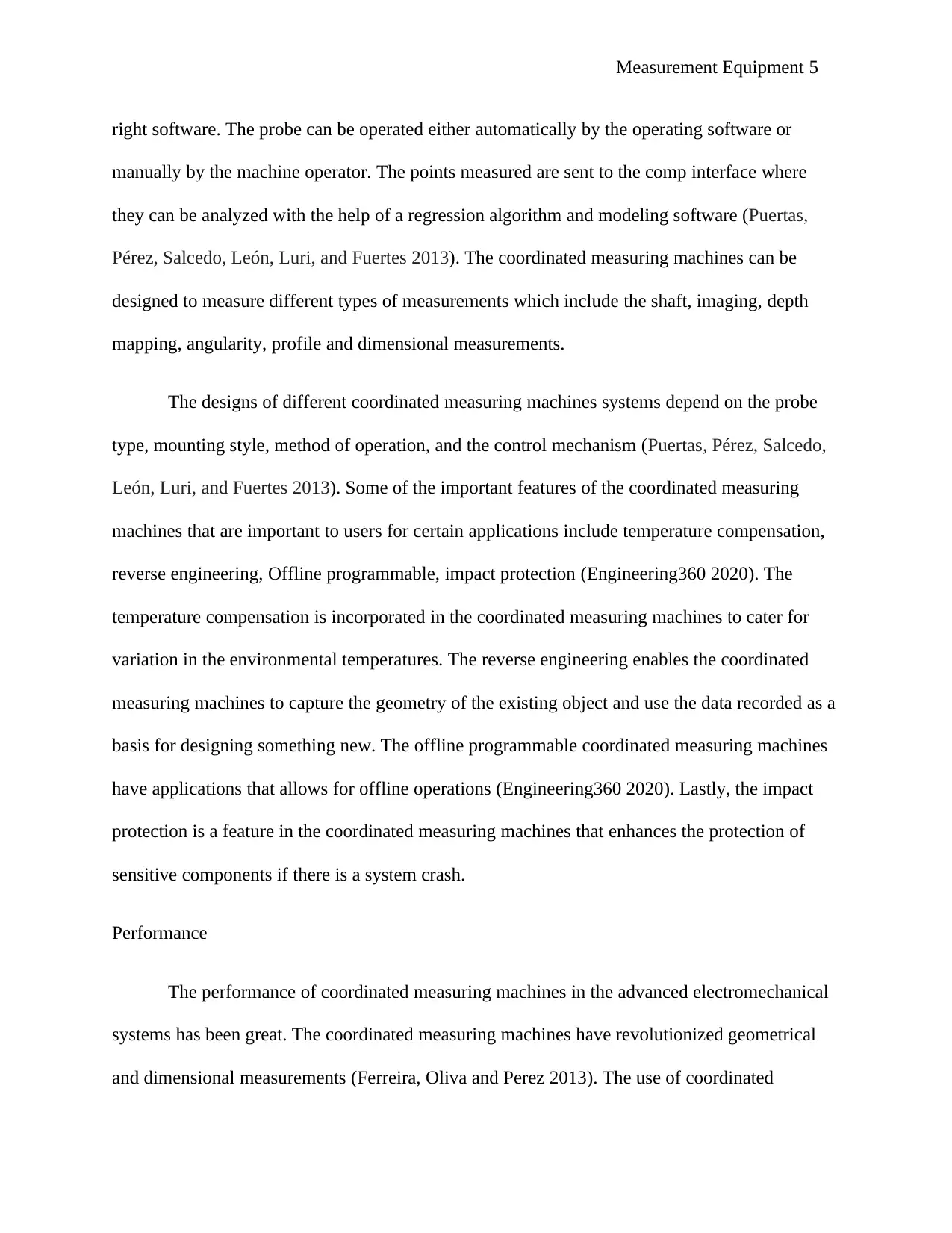
Measurement Equipment 5
right software. The probe can be operated either automatically by the operating software or
manually by the machine operator. The points measured are sent to the comp interface where
they can be analyzed with the help of a regression algorithm and modeling software (Puertas,
Pérez, Salcedo, León, Luri, and Fuertes 2013). The coordinated measuring machines can be
designed to measure different types of measurements which include the shaft, imaging, depth
mapping, angularity, profile and dimensional measurements.
The designs of different coordinated measuring machines systems depend on the probe
type, mounting style, method of operation, and the control mechanism (Puertas, Pérez, Salcedo,
León, Luri, and Fuertes 2013). Some of the important features of the coordinated measuring
machines that are important to users for certain applications include temperature compensation,
reverse engineering, Offline programmable, impact protection (Engineering360 2020). The
temperature compensation is incorporated in the coordinated measuring machines to cater for
variation in the environmental temperatures. The reverse engineering enables the coordinated
measuring machines to capture the geometry of the existing object and use the data recorded as a
basis for designing something new. The offline programmable coordinated measuring machines
have applications that allows for offline operations (Engineering360 2020). Lastly, the impact
protection is a feature in the coordinated measuring machines that enhances the protection of
sensitive components if there is a system crash.
Performance
The performance of coordinated measuring machines in the advanced electromechanical
systems has been great. The coordinated measuring machines have revolutionized geometrical
and dimensional measurements (Ferreira, Oliva and Perez 2013). The use of coordinated
right software. The probe can be operated either automatically by the operating software or
manually by the machine operator. The points measured are sent to the comp interface where
they can be analyzed with the help of a regression algorithm and modeling software (Puertas,
Pérez, Salcedo, León, Luri, and Fuertes 2013). The coordinated measuring machines can be
designed to measure different types of measurements which include the shaft, imaging, depth
mapping, angularity, profile and dimensional measurements.
The designs of different coordinated measuring machines systems depend on the probe
type, mounting style, method of operation, and the control mechanism (Puertas, Pérez, Salcedo,
León, Luri, and Fuertes 2013). Some of the important features of the coordinated measuring
machines that are important to users for certain applications include temperature compensation,
reverse engineering, Offline programmable, impact protection (Engineering360 2020). The
temperature compensation is incorporated in the coordinated measuring machines to cater for
variation in the environmental temperatures. The reverse engineering enables the coordinated
measuring machines to capture the geometry of the existing object and use the data recorded as a
basis for designing something new. The offline programmable coordinated measuring machines
have applications that allows for offline operations (Engineering360 2020). Lastly, the impact
protection is a feature in the coordinated measuring machines that enhances the protection of
sensitive components if there is a system crash.
Performance
The performance of coordinated measuring machines in the advanced electromechanical
systems has been great. The coordinated measuring machines have revolutionized geometrical
and dimensional measurements (Ferreira, Oliva and Perez 2013). The use of coordinated
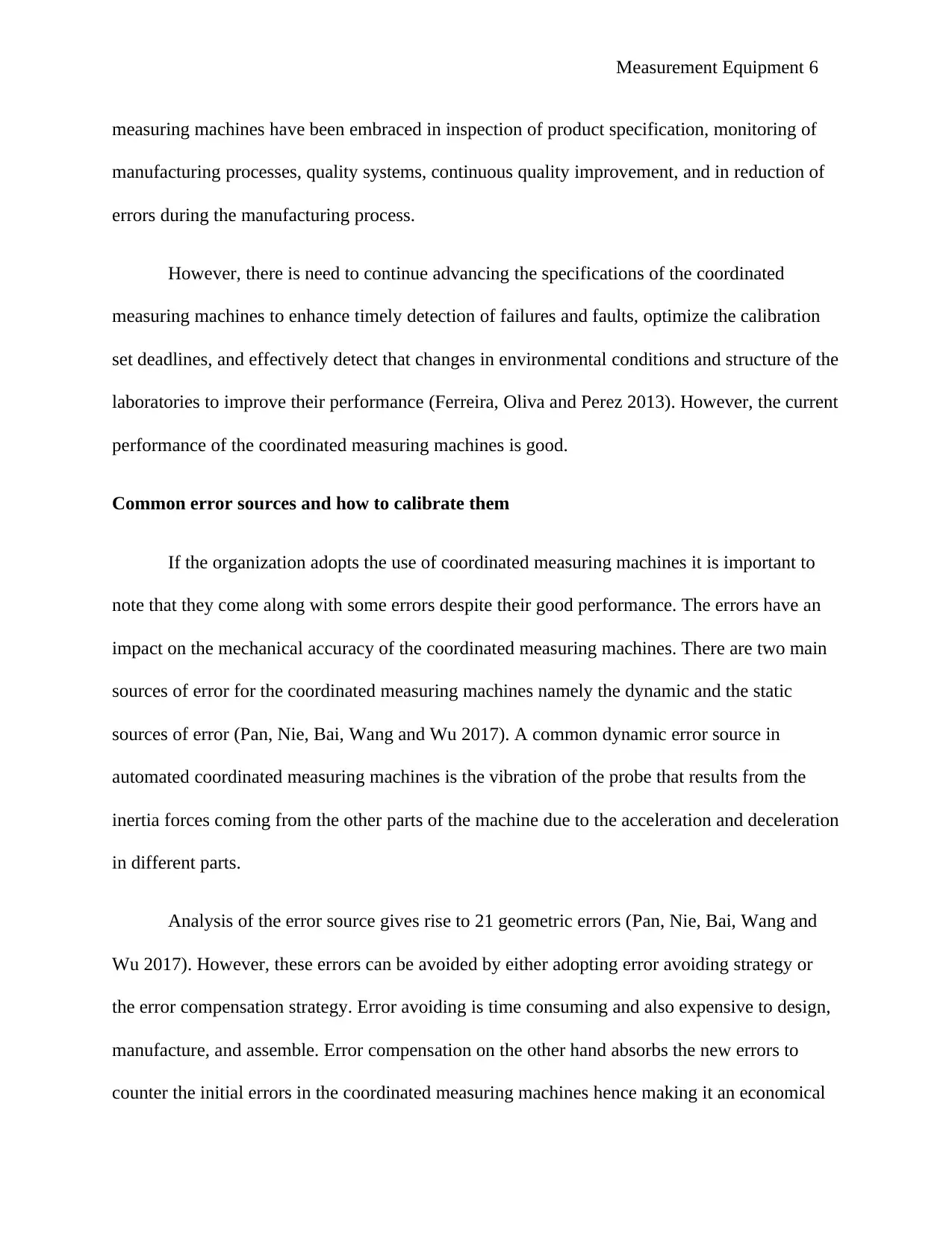
Measurement Equipment 6
measuring machines have been embraced in inspection of product specification, monitoring of
manufacturing processes, quality systems, continuous quality improvement, and in reduction of
errors during the manufacturing process.
However, there is need to continue advancing the specifications of the coordinated
measuring machines to enhance timely detection of failures and faults, optimize the calibration
set deadlines, and effectively detect that changes in environmental conditions and structure of the
laboratories to improve their performance (Ferreira, Oliva and Perez 2013). However, the current
performance of the coordinated measuring machines is good.
Common error sources and how to calibrate them
If the organization adopts the use of coordinated measuring machines it is important to
note that they come along with some errors despite their good performance. The errors have an
impact on the mechanical accuracy of the coordinated measuring machines. There are two main
sources of error for the coordinated measuring machines namely the dynamic and the static
sources of error (Pan, Nie, Bai, Wang and Wu 2017). A common dynamic error source in
automated coordinated measuring machines is the vibration of the probe that results from the
inertia forces coming from the other parts of the machine due to the acceleration and deceleration
in different parts.
Analysis of the error source gives rise to 21 geometric errors (Pan, Nie, Bai, Wang and
Wu 2017). However, these errors can be avoided by either adopting error avoiding strategy or
the error compensation strategy. Error avoiding is time consuming and also expensive to design,
manufacture, and assemble. Error compensation on the other hand absorbs the new errors to
counter the initial errors in the coordinated measuring machines hence making it an economical
measuring machines have been embraced in inspection of product specification, monitoring of
manufacturing processes, quality systems, continuous quality improvement, and in reduction of
errors during the manufacturing process.
However, there is need to continue advancing the specifications of the coordinated
measuring machines to enhance timely detection of failures and faults, optimize the calibration
set deadlines, and effectively detect that changes in environmental conditions and structure of the
laboratories to improve their performance (Ferreira, Oliva and Perez 2013). However, the current
performance of the coordinated measuring machines is good.
Common error sources and how to calibrate them
If the organization adopts the use of coordinated measuring machines it is important to
note that they come along with some errors despite their good performance. The errors have an
impact on the mechanical accuracy of the coordinated measuring machines. There are two main
sources of error for the coordinated measuring machines namely the dynamic and the static
sources of error (Pan, Nie, Bai, Wang and Wu 2017). A common dynamic error source in
automated coordinated measuring machines is the vibration of the probe that results from the
inertia forces coming from the other parts of the machine due to the acceleration and deceleration
in different parts.
Analysis of the error source gives rise to 21 geometric errors (Pan, Nie, Bai, Wang and
Wu 2017). However, these errors can be avoided by either adopting error avoiding strategy or
the error compensation strategy. Error avoiding is time consuming and also expensive to design,
manufacture, and assemble. Error compensation on the other hand absorbs the new errors to
counter the initial errors in the coordinated measuring machines hence making it an economical
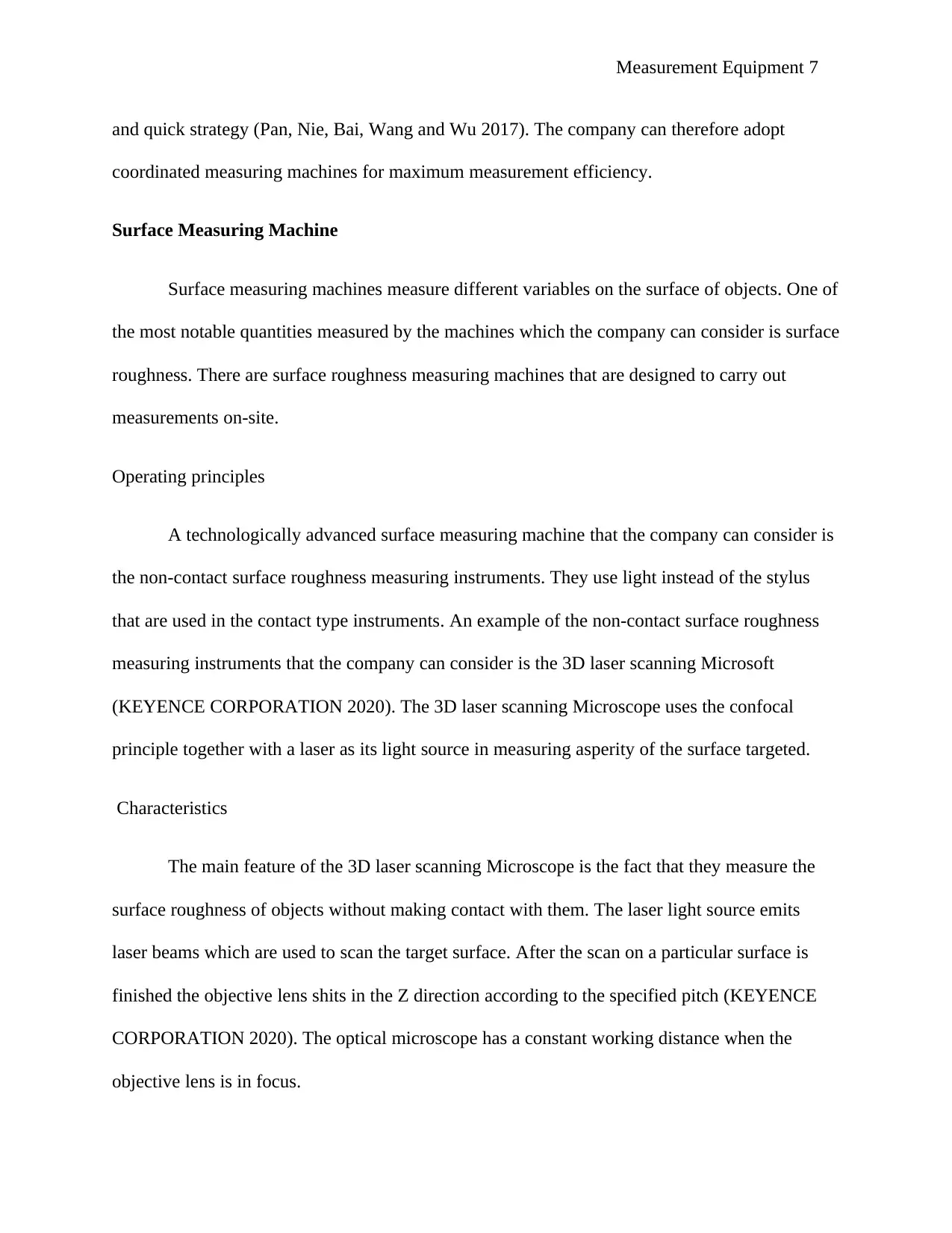
Measurement Equipment 7
and quick strategy (Pan, Nie, Bai, Wang and Wu 2017). The company can therefore adopt
coordinated measuring machines for maximum measurement efficiency.
Surface Measuring Machine
Surface measuring machines measure different variables on the surface of objects. One of
the most notable quantities measured by the machines which the company can consider is surface
roughness. There are surface roughness measuring machines that are designed to carry out
measurements on-site.
Operating principles
A technologically advanced surface measuring machine that the company can consider is
the non-contact surface roughness measuring instruments. They use light instead of the stylus
that are used in the contact type instruments. An example of the non-contact surface roughness
measuring instruments that the company can consider is the 3D laser scanning Microsoft
(KEYENCE CORPORATION 2020). The 3D laser scanning Microscope uses the confocal
principle together with a laser as its light source in measuring asperity of the surface targeted.
Characteristics
The main feature of the 3D laser scanning Microscope is the fact that they measure the
surface roughness of objects without making contact with them. The laser light source emits
laser beams which are used to scan the target surface. After the scan on a particular surface is
finished the objective lens shits in the Z direction according to the specified pitch (KEYENCE
CORPORATION 2020). The optical microscope has a constant working distance when the
objective lens is in focus.
and quick strategy (Pan, Nie, Bai, Wang and Wu 2017). The company can therefore adopt
coordinated measuring machines for maximum measurement efficiency.
Surface Measuring Machine
Surface measuring machines measure different variables on the surface of objects. One of
the most notable quantities measured by the machines which the company can consider is surface
roughness. There are surface roughness measuring machines that are designed to carry out
measurements on-site.
Operating principles
A technologically advanced surface measuring machine that the company can consider is
the non-contact surface roughness measuring instruments. They use light instead of the stylus
that are used in the contact type instruments. An example of the non-contact surface roughness
measuring instruments that the company can consider is the 3D laser scanning Microsoft
(KEYENCE CORPORATION 2020). The 3D laser scanning Microscope uses the confocal
principle together with a laser as its light source in measuring asperity of the surface targeted.
Characteristics
The main feature of the 3D laser scanning Microscope is the fact that they measure the
surface roughness of objects without making contact with them. The laser light source emits
laser beams which are used to scan the target surface. After the scan on a particular surface is
finished the objective lens shits in the Z direction according to the specified pitch (KEYENCE
CORPORATION 2020). The optical microscope has a constant working distance when the
objective lens is in focus.
Paraphrase This Document
Need a fresh take? Get an instant paraphrase of this document with our AI Paraphraser
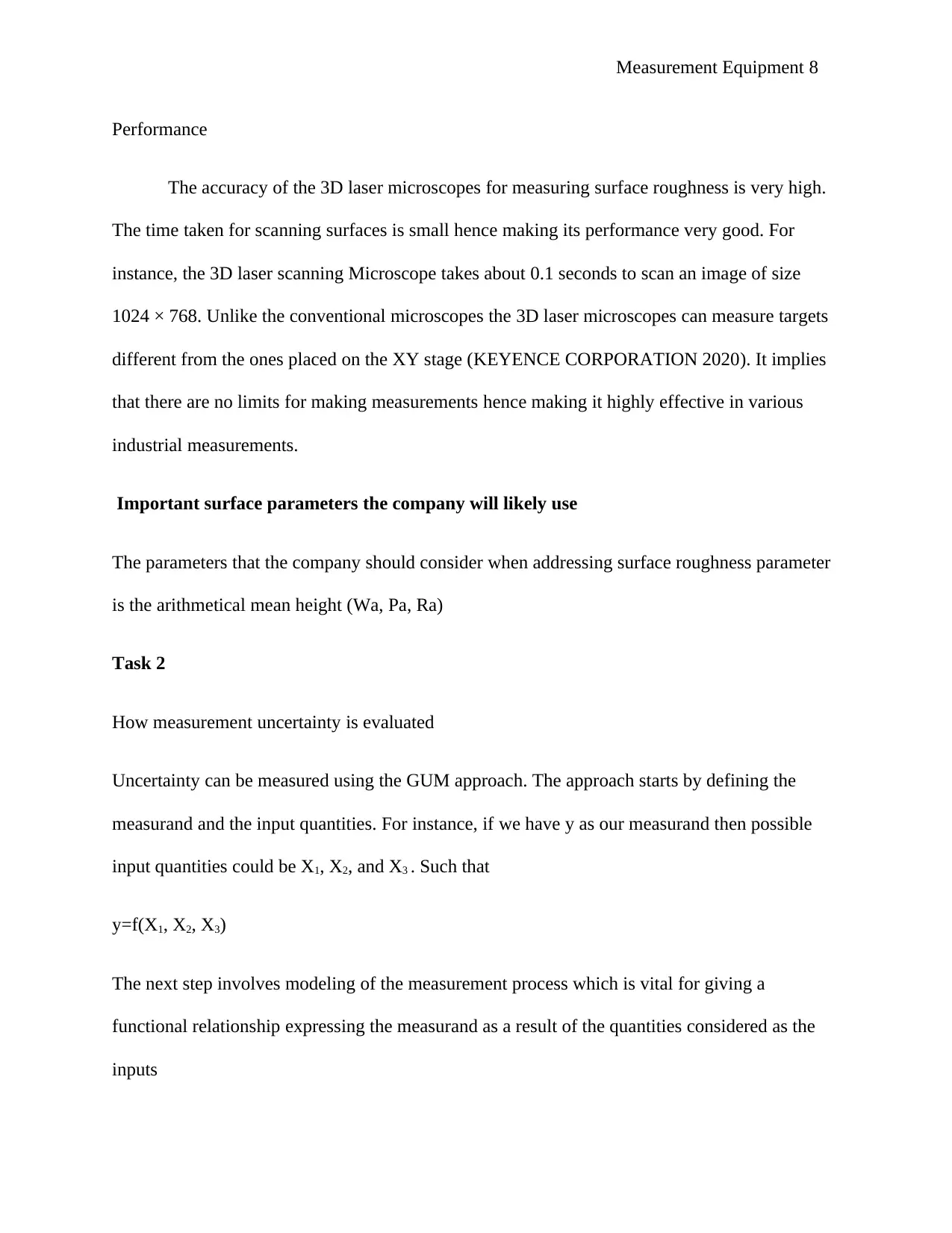
Measurement Equipment 8
Performance
The accuracy of the 3D laser microscopes for measuring surface roughness is very high.
The time taken for scanning surfaces is small hence making its performance very good. For
instance, the 3D laser scanning Microscope takes about 0.1 seconds to scan an image of size
1024 × 768. Unlike the conventional microscopes the 3D laser microscopes can measure targets
different from the ones placed on the XY stage (KEYENCE CORPORATION 2020). It implies
that there are no limits for making measurements hence making it highly effective in various
industrial measurements.
Important surface parameters the company will likely use
The parameters that the company should consider when addressing surface roughness parameter
is the arithmetical mean height (Wa, Pa, Ra)
Task 2
How measurement uncertainty is evaluated
Uncertainty can be measured using the GUM approach. The approach starts by defining the
measurand and the input quantities. For instance, if we have y as our measurand then possible
input quantities could be X1, X2, and X3 . Such that
y=f(X1, X2, X3)
The next step involves modeling of the measurement process which is vital for giving a
functional relationship expressing the measurand as a result of the quantities considered as the
inputs
Performance
The accuracy of the 3D laser microscopes for measuring surface roughness is very high.
The time taken for scanning surfaces is small hence making its performance very good. For
instance, the 3D laser scanning Microscope takes about 0.1 seconds to scan an image of size
1024 × 768. Unlike the conventional microscopes the 3D laser microscopes can measure targets
different from the ones placed on the XY stage (KEYENCE CORPORATION 2020). It implies
that there are no limits for making measurements hence making it highly effective in various
industrial measurements.
Important surface parameters the company will likely use
The parameters that the company should consider when addressing surface roughness parameter
is the arithmetical mean height (Wa, Pa, Ra)
Task 2
How measurement uncertainty is evaluated
Uncertainty can be measured using the GUM approach. The approach starts by defining the
measurand and the input quantities. For instance, if we have y as our measurand then possible
input quantities could be X1, X2, and X3 . Such that
y=f(X1, X2, X3)
The next step involves modeling of the measurement process which is vital for giving a
functional relationship expressing the measurand as a result of the quantities considered as the
inputs
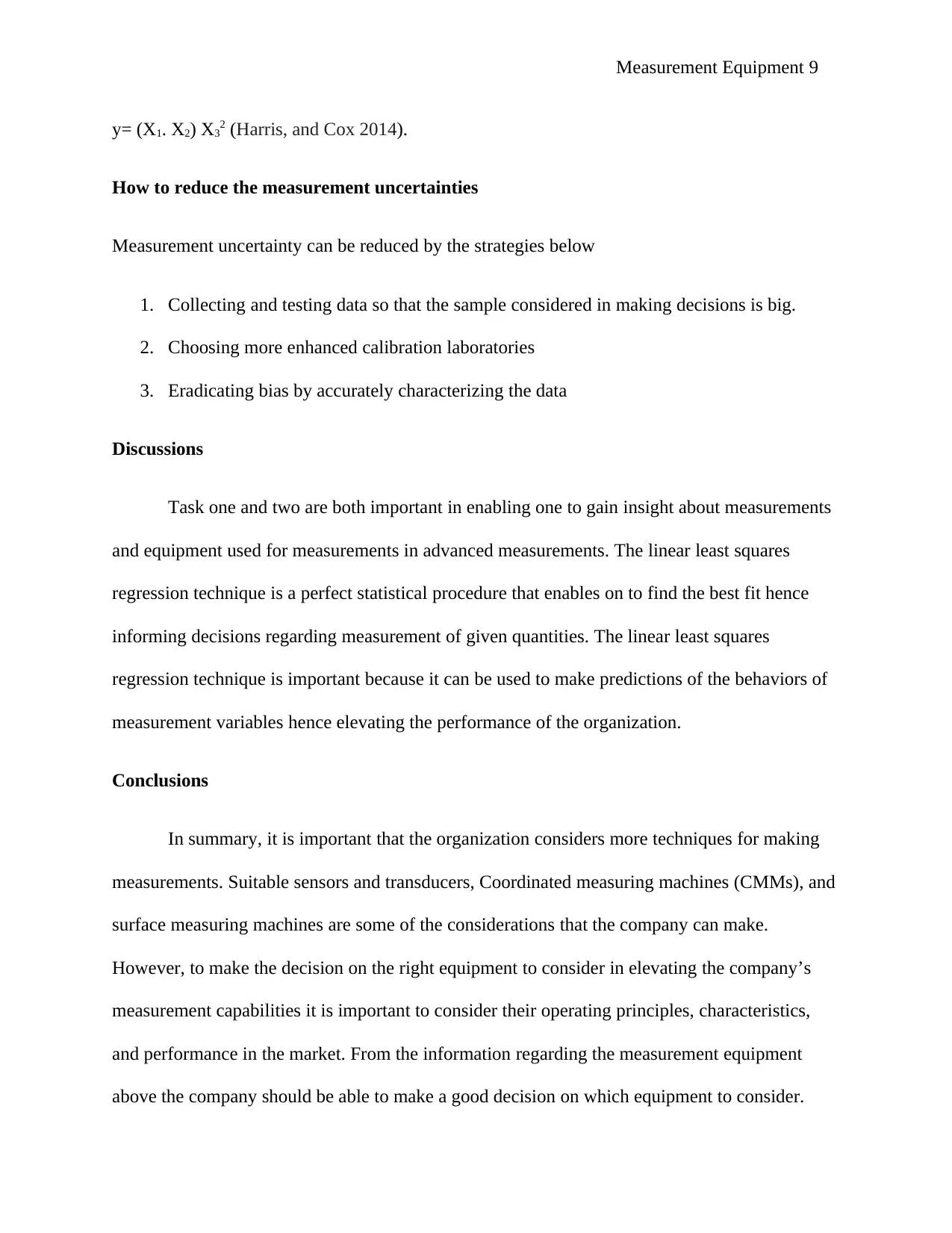
Measurement Equipment 9
y= (X1. X2) X32 (Harris, and Cox 2014).
How to reduce the measurement uncertainties
Measurement uncertainty can be reduced by the strategies below
1. Collecting and testing data so that the sample considered in making decisions is big.
2. Choosing more enhanced calibration laboratories
3. Eradicating bias by accurately characterizing the data
Discussions
Task one and two are both important in enabling one to gain insight about measurements
and equipment used for measurements in advanced measurements. The linear least squares
regression technique is a perfect statistical procedure that enables on to find the best fit hence
informing decisions regarding measurement of given quantities. The linear least squares
regression technique is important because it can be used to make predictions of the behaviors of
measurement variables hence elevating the performance of the organization.
Conclusions
In summary, it is important that the organization considers more techniques for making
measurements. Suitable sensors and transducers, Coordinated measuring machines (CMMs), and
surface measuring machines are some of the considerations that the company can make.
However, to make the decision on the right equipment to consider in elevating the company’s
measurement capabilities it is important to consider their operating principles, characteristics,
and performance in the market. From the information regarding the measurement equipment
above the company should be able to make a good decision on which equipment to consider.
y= (X1. X2) X32 (Harris, and Cox 2014).
How to reduce the measurement uncertainties
Measurement uncertainty can be reduced by the strategies below
1. Collecting and testing data so that the sample considered in making decisions is big.
2. Choosing more enhanced calibration laboratories
3. Eradicating bias by accurately characterizing the data
Discussions
Task one and two are both important in enabling one to gain insight about measurements
and equipment used for measurements in advanced measurements. The linear least squares
regression technique is a perfect statistical procedure that enables on to find the best fit hence
informing decisions regarding measurement of given quantities. The linear least squares
regression technique is important because it can be used to make predictions of the behaviors of
measurement variables hence elevating the performance of the organization.
Conclusions
In summary, it is important that the organization considers more techniques for making
measurements. Suitable sensors and transducers, Coordinated measuring machines (CMMs), and
surface measuring machines are some of the considerations that the company can make.
However, to make the decision on the right equipment to consider in elevating the company’s
measurement capabilities it is important to consider their operating principles, characteristics,
and performance in the market. From the information regarding the measurement equipment
above the company should be able to make a good decision on which equipment to consider.
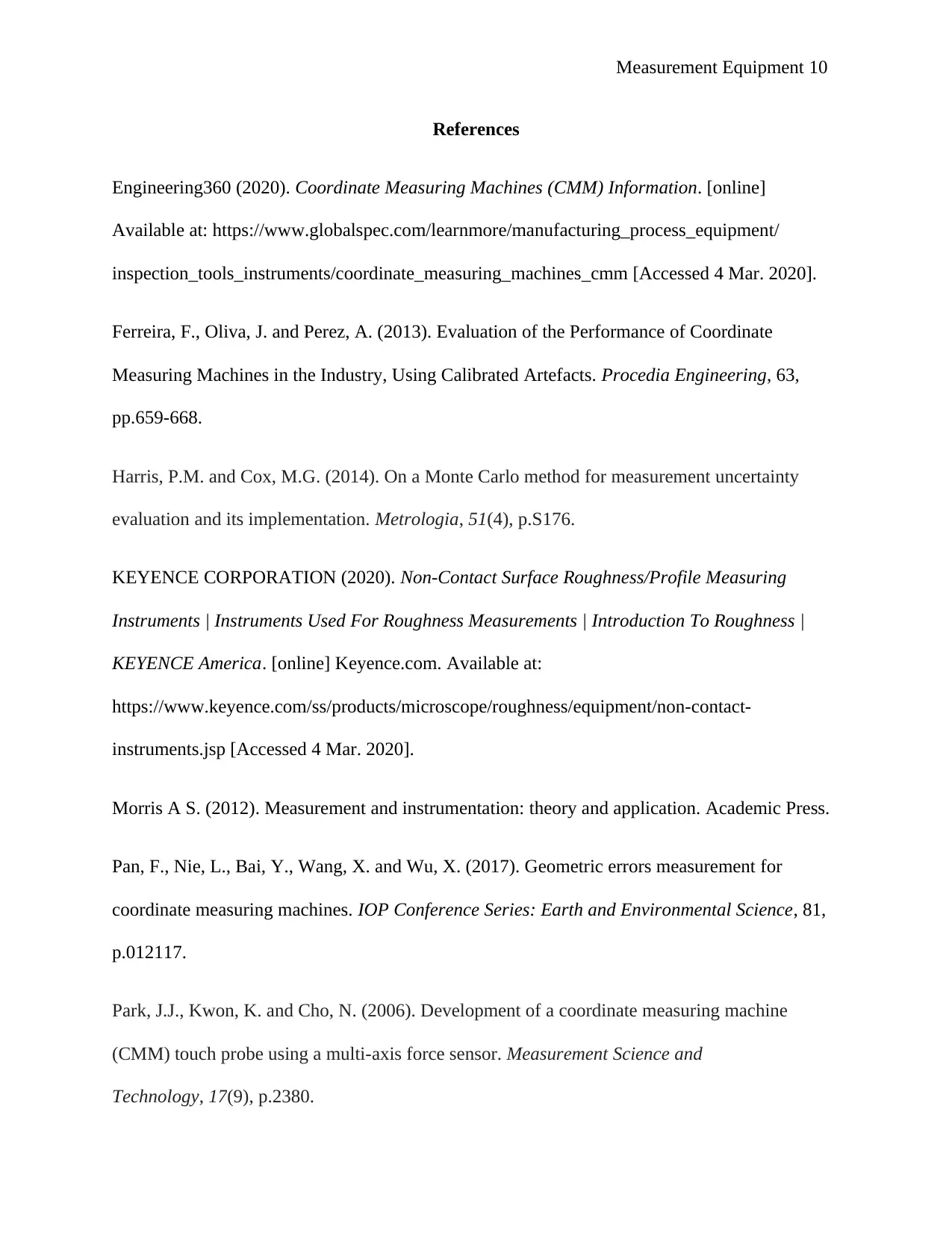
Measurement Equipment 10
References
Engineering360 (2020). Coordinate Measuring Machines (CMM) Information. [online]
Available at: https://www.globalspec.com/learnmore/manufacturing_process_equipment/
inspection_tools_instruments/coordinate_measuring_machines_cmm [Accessed 4 Mar. 2020].
Ferreira, F., Oliva, J. and Perez, A. (2013). Evaluation of the Performance of Coordinate
Measuring Machines in the Industry, Using Calibrated Artefacts. Procedia Engineering, 63,
pp.659-668.
Harris, P.M. and Cox, M.G. (2014). On a Monte Carlo method for measurement uncertainty
evaluation and its implementation. Metrologia, 51(4), p.S176.
KEYENCE CORPORATION (2020). Non-Contact Surface Roughness/Profile Measuring
Instruments | Instruments Used For Roughness Measurements | Introduction To Roughness |
KEYENCE America. [online] Keyence.com. Available at:
https://www.keyence.com/ss/products/microscope/roughness/equipment/non-contact-
instruments.jsp [Accessed 4 Mar. 2020].
Morris A S. (2012). Measurement and instrumentation: theory and application. Academic Press.
Pan, F., Nie, L., Bai, Y., Wang, X. and Wu, X. (2017). Geometric errors measurement for
coordinate measuring machines. IOP Conference Series: Earth and Environmental Science, 81,
p.012117.
Park, J.J., Kwon, K. and Cho, N. (2006). Development of a coordinate measuring machine
(CMM) touch probe using a multi-axis force sensor. Measurement Science and
Technology, 17(9), p.2380.
References
Engineering360 (2020). Coordinate Measuring Machines (CMM) Information. [online]
Available at: https://www.globalspec.com/learnmore/manufacturing_process_equipment/
inspection_tools_instruments/coordinate_measuring_machines_cmm [Accessed 4 Mar. 2020].
Ferreira, F., Oliva, J. and Perez, A. (2013). Evaluation of the Performance of Coordinate
Measuring Machines in the Industry, Using Calibrated Artefacts. Procedia Engineering, 63,
pp.659-668.
Harris, P.M. and Cox, M.G. (2014). On a Monte Carlo method for measurement uncertainty
evaluation and its implementation. Metrologia, 51(4), p.S176.
KEYENCE CORPORATION (2020). Non-Contact Surface Roughness/Profile Measuring
Instruments | Instruments Used For Roughness Measurements | Introduction To Roughness |
KEYENCE America. [online] Keyence.com. Available at:
https://www.keyence.com/ss/products/microscope/roughness/equipment/non-contact-
instruments.jsp [Accessed 4 Mar. 2020].
Morris A S. (2012). Measurement and instrumentation: theory and application. Academic Press.
Pan, F., Nie, L., Bai, Y., Wang, X. and Wu, X. (2017). Geometric errors measurement for
coordinate measuring machines. IOP Conference Series: Earth and Environmental Science, 81,
p.012117.
Park, J.J., Kwon, K. and Cho, N. (2006). Development of a coordinate measuring machine
(CMM) touch probe using a multi-axis force sensor. Measurement Science and
Technology, 17(9), p.2380.
Secure Best Marks with AI Grader
Need help grading? Try our AI Grader for instant feedback on your assignments.
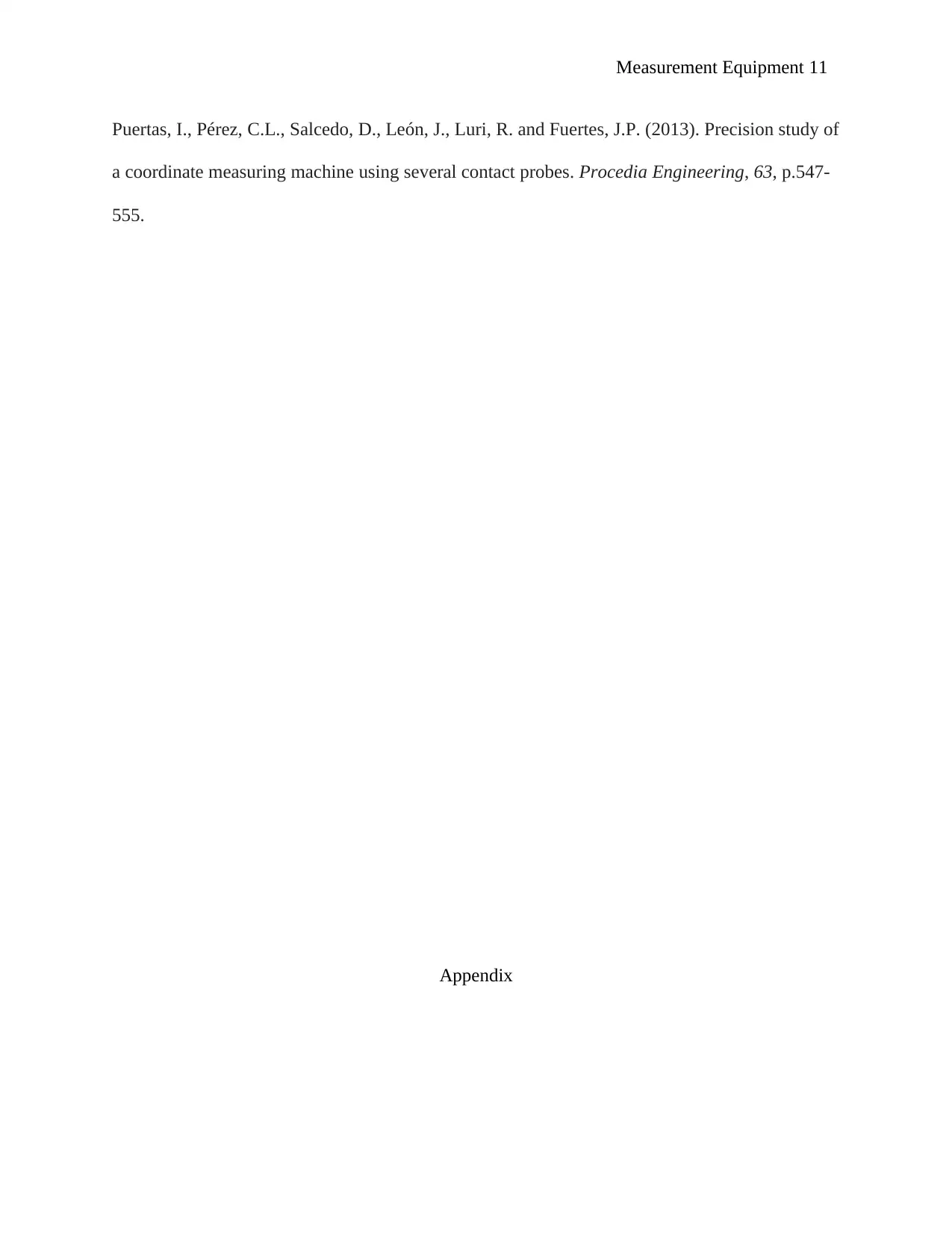
Measurement Equipment 11
Puertas, I., Pérez, C.L., Salcedo, D., León, J., Luri, R. and Fuertes, J.P. (2013). Precision study of
a coordinate measuring machine using several contact probes. Procedia Engineering, 63, p.547-
555.
Appendix
Puertas, I., Pérez, C.L., Salcedo, D., León, J., Luri, R. and Fuertes, J.P. (2013). Precision study of
a coordinate measuring machine using several contact probes. Procedia Engineering, 63, p.547-
555.
Appendix
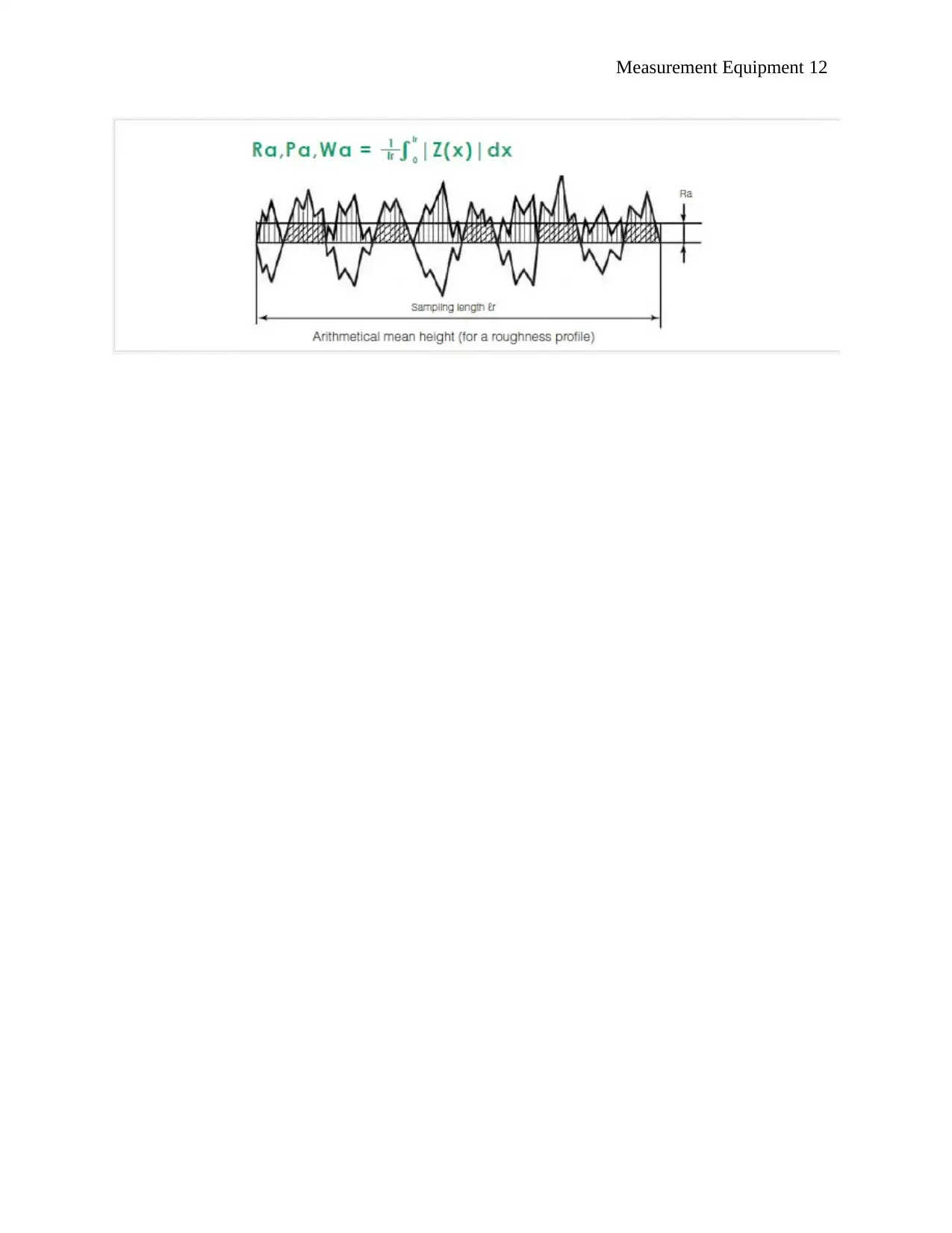
Measurement Equipment 12
1 out of 12
Related Documents

Your All-in-One AI-Powered Toolkit for Academic Success.
+13062052269
info@desklib.com
Available 24*7 on WhatsApp / Email
Unlock your academic potential
© 2024 | Zucol Services PVT LTD | All rights reserved.