Detailed Technical Report: Aircraft Engine Lubrication and Air Systems
VerifiedAdded on 2023/01/30
|3
|1707
|55
Report
AI Summary
This technical report examines the function and operation of aircraft engine lubrication and internal air systems. It begins with the principles of engine lubrication, emphasizing the role of oil in reducing friction and wear, and the different types of friction encountered in engines. The report details the functions of engine oil, including friction reduction, cushioning, cooling, sealing, and cleaning. It then describes the two main circulatory systems: the pressure relief valve system and the full flow control system, including their components and operation. The report further explores the components of the engine lubrication system, such as the oil tank, oil pump, turbine oil filters, and oil jets, explaining their roles and importance in maintaining engine performance and longevity. The report provides a comprehensive overview of these critical systems.
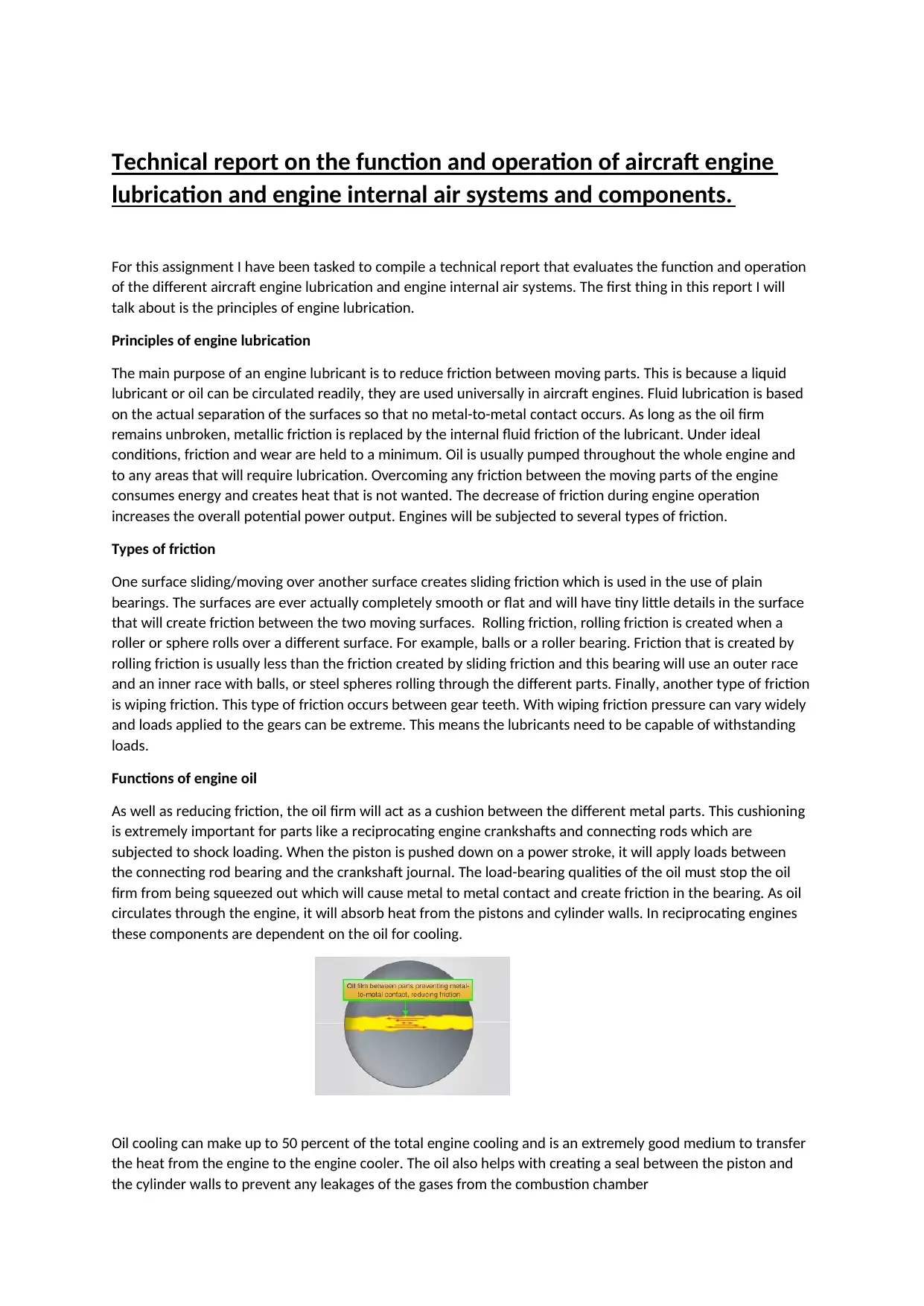
Technical report on the function and operation of aircraft engine
lubrication and engine internal air systems and components.
For this assignment I have been tasked to compile a technical report that evaluates the function and operation
of the different aircraft engine lubrication and engine internal air systems. The first thing in this report I will
talk about is the principles of engine lubrication.
Principles of engine lubrication
The main purpose of an engine lubricant is to reduce friction between moving parts. This is because a liquid
lubricant or oil can be circulated readily, they are used universally in aircraft engines. Fluid lubrication is based
on the actual separation of the surfaces so that no metal-to-metal contact occurs. As long as the oil firm
remains unbroken, metallic friction is replaced by the internal fluid friction of the lubricant. Under ideal
conditions, friction and wear are held to a minimum. Oil is usually pumped throughout the whole engine and
to any areas that will require lubrication. Overcoming any friction between the moving parts of the engine
consumes energy and creates heat that is not wanted. The decrease of friction during engine operation
increases the overall potential power output. Engines will be subjected to several types of friction.
Types of friction
One surface sliding/moving over another surface creates sliding friction which is used in the use of plain
bearings. The surfaces are ever actually completely smooth or flat and will have tiny little details in the surface
that will create friction between the two moving surfaces. Rolling friction, rolling friction is created when a
roller or sphere rolls over a different surface. For example, balls or a roller bearing. Friction that is created by
rolling friction is usually less than the friction created by sliding friction and this bearing will use an outer race
and an inner race with balls, or steel spheres rolling through the different parts. Finally, another type of friction
is wiping friction. This type of friction occurs between gear teeth. With wiping friction pressure can vary widely
and loads applied to the gears can be extreme. This means the lubricants need to be capable of withstanding
loads.
Functions of engine oil
As well as reducing friction, the oil firm will act as a cushion between the different metal parts. This cushioning
is extremely important for parts like a reciprocating engine crankshafts and connecting rods which are
subjected to shock loading. When the piston is pushed down on a power stroke, it will apply loads between
the connecting rod bearing and the crankshaft journal. The load-bearing qualities of the oil must stop the oil
firm from being squeezed out which will cause metal to metal contact and create friction in the bearing. As oil
circulates through the engine, it will absorb heat from the pistons and cylinder walls. In reciprocating engines
these components are dependent on the oil for cooling.
Oil cooling can make up to 50 percent of the total engine cooling and is an extremely good medium to transfer
the heat from the engine to the engine cooler. The oil also helps with creating a seal between the piston and
the cylinder walls to prevent any leakages of the gases from the combustion chamber
lubrication and engine internal air systems and components.
For this assignment I have been tasked to compile a technical report that evaluates the function and operation
of the different aircraft engine lubrication and engine internal air systems. The first thing in this report I will
talk about is the principles of engine lubrication.
Principles of engine lubrication
The main purpose of an engine lubricant is to reduce friction between moving parts. This is because a liquid
lubricant or oil can be circulated readily, they are used universally in aircraft engines. Fluid lubrication is based
on the actual separation of the surfaces so that no metal-to-metal contact occurs. As long as the oil firm
remains unbroken, metallic friction is replaced by the internal fluid friction of the lubricant. Under ideal
conditions, friction and wear are held to a minimum. Oil is usually pumped throughout the whole engine and
to any areas that will require lubrication. Overcoming any friction between the moving parts of the engine
consumes energy and creates heat that is not wanted. The decrease of friction during engine operation
increases the overall potential power output. Engines will be subjected to several types of friction.
Types of friction
One surface sliding/moving over another surface creates sliding friction which is used in the use of plain
bearings. The surfaces are ever actually completely smooth or flat and will have tiny little details in the surface
that will create friction between the two moving surfaces. Rolling friction, rolling friction is created when a
roller or sphere rolls over a different surface. For example, balls or a roller bearing. Friction that is created by
rolling friction is usually less than the friction created by sliding friction and this bearing will use an outer race
and an inner race with balls, or steel spheres rolling through the different parts. Finally, another type of friction
is wiping friction. This type of friction occurs between gear teeth. With wiping friction pressure can vary widely
and loads applied to the gears can be extreme. This means the lubricants need to be capable of withstanding
loads.
Functions of engine oil
As well as reducing friction, the oil firm will act as a cushion between the different metal parts. This cushioning
is extremely important for parts like a reciprocating engine crankshafts and connecting rods which are
subjected to shock loading. When the piston is pushed down on a power stroke, it will apply loads between
the connecting rod bearing and the crankshaft journal. The load-bearing qualities of the oil must stop the oil
firm from being squeezed out which will cause metal to metal contact and create friction in the bearing. As oil
circulates through the engine, it will absorb heat from the pistons and cylinder walls. In reciprocating engines
these components are dependent on the oil for cooling.
Oil cooling can make up to 50 percent of the total engine cooling and is an extremely good medium to transfer
the heat from the engine to the engine cooler. The oil also helps with creating a seal between the piston and
the cylinder walls to prevent any leakages of the gases from the combustion chamber
Secure Best Marks with AI Grader
Need help grading? Try our AI Grader for instant feedback on your assignments.
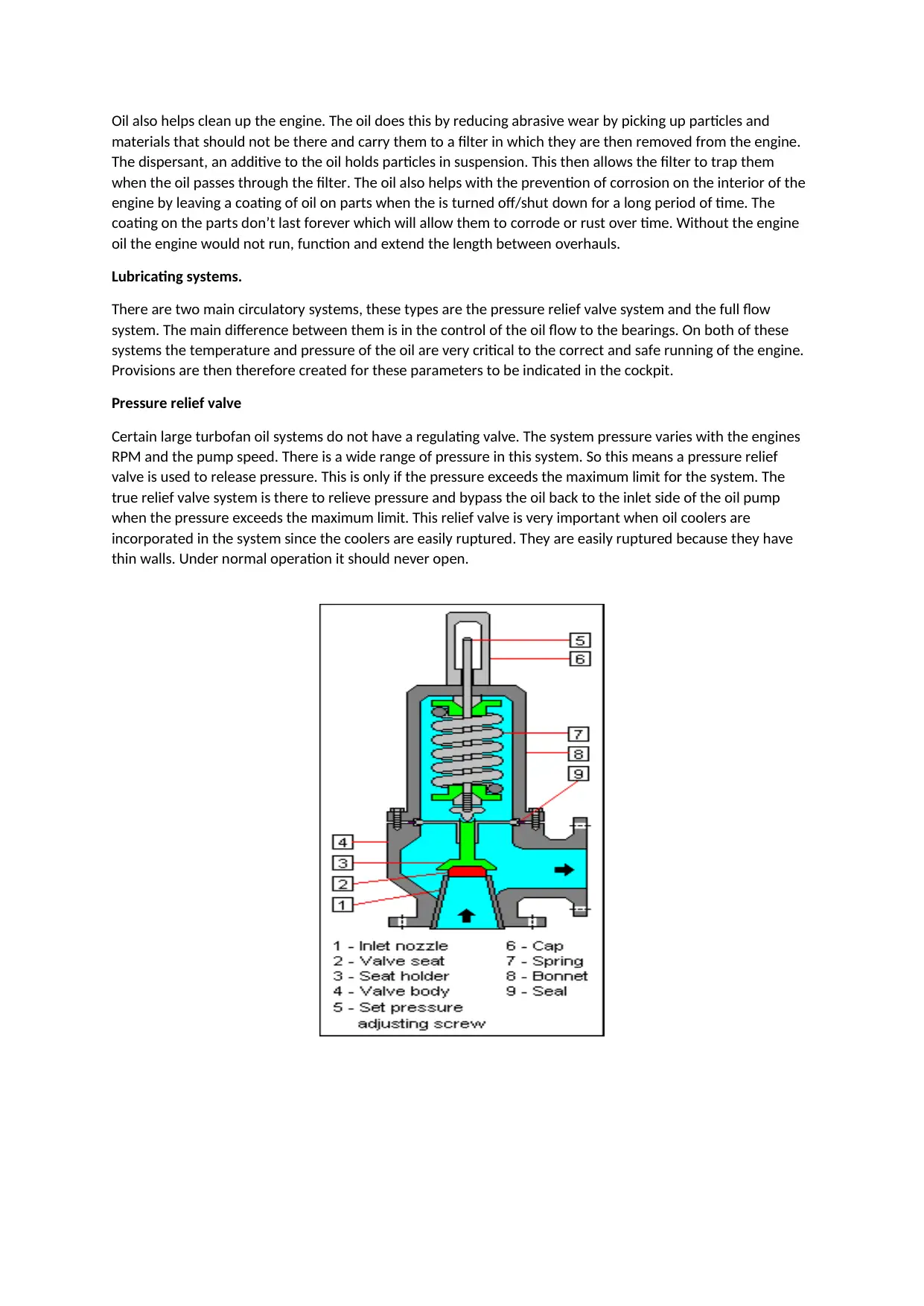
Oil also helps clean up the engine. The oil does this by reducing abrasive wear by picking up particles and
materials that should not be there and carry them to a filter in which they are then removed from the engine.
The dispersant, an additive to the oil holds particles in suspension. This then allows the filter to trap them
when the oil passes through the filter. The oil also helps with the prevention of corrosion on the interior of the
engine by leaving a coating of oil on parts when the is turned off/shut down for a long period of time. The
coating on the parts don’t last forever which will allow them to corrode or rust over time. Without the engine
oil the engine would not run, function and extend the length between overhauls.
Lubricating systems.
There are two main circulatory systems, these types are the pressure relief valve system and the full flow
system. The main difference between them is in the control of the oil flow to the bearings. On both of these
systems the temperature and pressure of the oil are very critical to the correct and safe running of the engine.
Provisions are then therefore created for these parameters to be indicated in the cockpit.
Pressure relief valve
Certain large turbofan oil systems do not have a regulating valve. The system pressure varies with the engines
RPM and the pump speed. There is a wide range of pressure in this system. So this means a pressure relief
valve is used to release pressure. This is only if the pressure exceeds the maximum limit for the system. The
true relief valve system is there to relieve pressure and bypass the oil back to the inlet side of the oil pump
when the pressure exceeds the maximum limit. This relief valve is very important when oil coolers are
incorporated in the system since the coolers are easily ruptured. They are easily ruptured because they have
thin walls. Under normal operation it should never open.
materials that should not be there and carry them to a filter in which they are then removed from the engine.
The dispersant, an additive to the oil holds particles in suspension. This then allows the filter to trap them
when the oil passes through the filter. The oil also helps with the prevention of corrosion on the interior of the
engine by leaving a coating of oil on parts when the is turned off/shut down for a long period of time. The
coating on the parts don’t last forever which will allow them to corrode or rust over time. Without the engine
oil the engine would not run, function and extend the length between overhauls.
Lubricating systems.
There are two main circulatory systems, these types are the pressure relief valve system and the full flow
system. The main difference between them is in the control of the oil flow to the bearings. On both of these
systems the temperature and pressure of the oil are very critical to the correct and safe running of the engine.
Provisions are then therefore created for these parameters to be indicated in the cockpit.
Pressure relief valve
Certain large turbofan oil systems do not have a regulating valve. The system pressure varies with the engines
RPM and the pump speed. There is a wide range of pressure in this system. So this means a pressure relief
valve is used to release pressure. This is only if the pressure exceeds the maximum limit for the system. The
true relief valve system is there to relieve pressure and bypass the oil back to the inlet side of the oil pump
when the pressure exceeds the maximum limit. This relief valve is very important when oil coolers are
incorporated in the system since the coolers are easily ruptured. They are easily ruptured because they have
thin walls. Under normal operation it should never open.
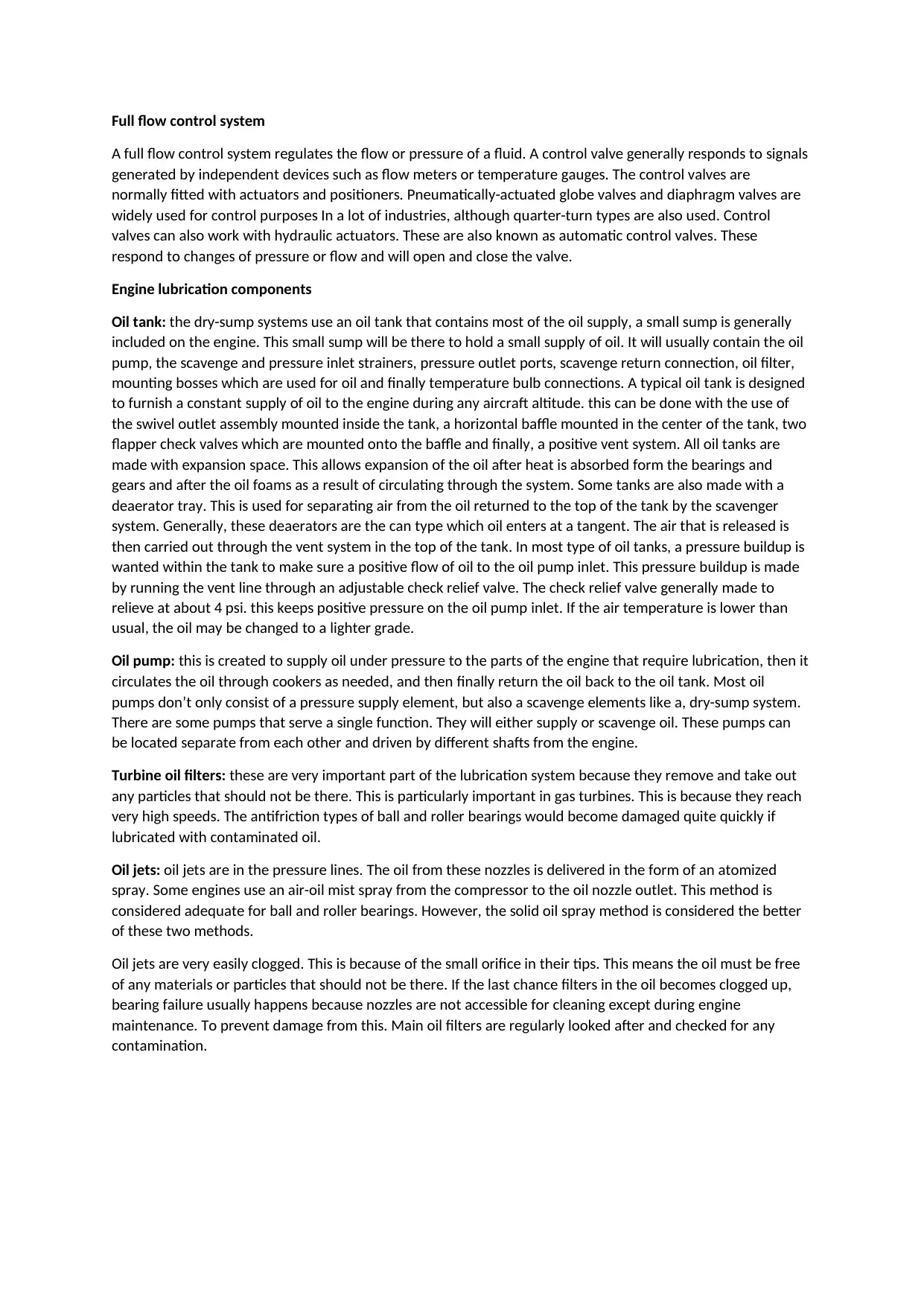
Full flow control system
A full flow control system regulates the flow or pressure of a fluid. A control valve generally responds to signals
generated by independent devices such as flow meters or temperature gauges. The control valves are
normally fitted with actuators and positioners. Pneumatically-actuated globe valves and diaphragm valves are
widely used for control purposes In a lot of industries, although quarter-turn types are also used. Control
valves can also work with hydraulic actuators. These are also known as automatic control valves. These
respond to changes of pressure or flow and will open and close the valve.
Engine lubrication components
Oil tank: the dry-sump systems use an oil tank that contains most of the oil supply, a small sump is generally
included on the engine. This small sump will be there to hold a small supply of oil. It will usually contain the oil
pump, the scavenge and pressure inlet strainers, pressure outlet ports, scavenge return connection, oil filter,
mounting bosses which are used for oil and finally temperature bulb connections. A typical oil tank is designed
to furnish a constant supply of oil to the engine during any aircraft altitude. this can be done with the use of
the swivel outlet assembly mounted inside the tank, a horizontal baffle mounted in the center of the tank, two
flapper check valves which are mounted onto the baffle and finally, a positive vent system. All oil tanks are
made with expansion space. This allows expansion of the oil after heat is absorbed form the bearings and
gears and after the oil foams as a result of circulating through the system. Some tanks are also made with a
deaerator tray. This is used for separating air from the oil returned to the top of the tank by the scavenger
system. Generally, these deaerators are the can type which oil enters at a tangent. The air that is released is
then carried out through the vent system in the top of the tank. In most type of oil tanks, a pressure buildup is
wanted within the tank to make sure a positive flow of oil to the oil pump inlet. This pressure buildup is made
by running the vent line through an adjustable check relief valve. The check relief valve generally made to
relieve at about 4 psi. this keeps positive pressure on the oil pump inlet. If the air temperature is lower than
usual, the oil may be changed to a lighter grade.
Oil pump: this is created to supply oil under pressure to the parts of the engine that require lubrication, then it
circulates the oil through cookers as needed, and then finally return the oil back to the oil tank. Most oil
pumps don’t only consist of a pressure supply element, but also a scavenge elements like a, dry-sump system.
There are some pumps that serve a single function. They will either supply or scavenge oil. These pumps can
be located separate from each other and driven by different shafts from the engine.
Turbine oil filters: these are very important part of the lubrication system because they remove and take out
any particles that should not be there. This is particularly important in gas turbines. This is because they reach
very high speeds. The antifriction types of ball and roller bearings would become damaged quite quickly if
lubricated with contaminated oil.
Oil jets: oil jets are in the pressure lines. The oil from these nozzles is delivered in the form of an atomized
spray. Some engines use an air-oil mist spray from the compressor to the oil nozzle outlet. This method is
considered adequate for ball and roller bearings. However, the solid oil spray method is considered the better
of these two methods.
Oil jets are very easily clogged. This is because of the small orifice in their tips. This means the oil must be free
of any materials or particles that should not be there. If the last chance filters in the oil becomes clogged up,
bearing failure usually happens because nozzles are not accessible for cleaning except during engine
maintenance. To prevent damage from this. Main oil filters are regularly looked after and checked for any
contamination.
A full flow control system regulates the flow or pressure of a fluid. A control valve generally responds to signals
generated by independent devices such as flow meters or temperature gauges. The control valves are
normally fitted with actuators and positioners. Pneumatically-actuated globe valves and diaphragm valves are
widely used for control purposes In a lot of industries, although quarter-turn types are also used. Control
valves can also work with hydraulic actuators. These are also known as automatic control valves. These
respond to changes of pressure or flow and will open and close the valve.
Engine lubrication components
Oil tank: the dry-sump systems use an oil tank that contains most of the oil supply, a small sump is generally
included on the engine. This small sump will be there to hold a small supply of oil. It will usually contain the oil
pump, the scavenge and pressure inlet strainers, pressure outlet ports, scavenge return connection, oil filter,
mounting bosses which are used for oil and finally temperature bulb connections. A typical oil tank is designed
to furnish a constant supply of oil to the engine during any aircraft altitude. this can be done with the use of
the swivel outlet assembly mounted inside the tank, a horizontal baffle mounted in the center of the tank, two
flapper check valves which are mounted onto the baffle and finally, a positive vent system. All oil tanks are
made with expansion space. This allows expansion of the oil after heat is absorbed form the bearings and
gears and after the oil foams as a result of circulating through the system. Some tanks are also made with a
deaerator tray. This is used for separating air from the oil returned to the top of the tank by the scavenger
system. Generally, these deaerators are the can type which oil enters at a tangent. The air that is released is
then carried out through the vent system in the top of the tank. In most type of oil tanks, a pressure buildup is
wanted within the tank to make sure a positive flow of oil to the oil pump inlet. This pressure buildup is made
by running the vent line through an adjustable check relief valve. The check relief valve generally made to
relieve at about 4 psi. this keeps positive pressure on the oil pump inlet. If the air temperature is lower than
usual, the oil may be changed to a lighter grade.
Oil pump: this is created to supply oil under pressure to the parts of the engine that require lubrication, then it
circulates the oil through cookers as needed, and then finally return the oil back to the oil tank. Most oil
pumps don’t only consist of a pressure supply element, but also a scavenge elements like a, dry-sump system.
There are some pumps that serve a single function. They will either supply or scavenge oil. These pumps can
be located separate from each other and driven by different shafts from the engine.
Turbine oil filters: these are very important part of the lubrication system because they remove and take out
any particles that should not be there. This is particularly important in gas turbines. This is because they reach
very high speeds. The antifriction types of ball and roller bearings would become damaged quite quickly if
lubricated with contaminated oil.
Oil jets: oil jets are in the pressure lines. The oil from these nozzles is delivered in the form of an atomized
spray. Some engines use an air-oil mist spray from the compressor to the oil nozzle outlet. This method is
considered adequate for ball and roller bearings. However, the solid oil spray method is considered the better
of these two methods.
Oil jets are very easily clogged. This is because of the small orifice in their tips. This means the oil must be free
of any materials or particles that should not be there. If the last chance filters in the oil becomes clogged up,
bearing failure usually happens because nozzles are not accessible for cleaning except during engine
maintenance. To prevent damage from this. Main oil filters are regularly looked after and checked for any
contamination.
1 out of 3

Your All-in-One AI-Powered Toolkit for Academic Success.
+13062052269
info@desklib.com
Available 24*7 on WhatsApp / Email
Unlock your academic potential
© 2024 | Zucol Services PVT LTD | All rights reserved.