Comprehensive Analysis of Cost Reduction in Aircraft Engine Production
VerifiedAdded on  2020/05/11
|8
|1782
|138
AI Summary
The project focused on reducing the cost of manufacturing aircraft engines without compromising quality or fuel efficiency. Hiranmay Dash led a team to implement design-to-cost methods and provided training for DFSS procedures while managing key performance indicators (KPI) for Design To Cost (DTC) initiatives across India. The effort culminated in successfully developing a methodology that reduced production costs, earning recognition with an annual award for DTC initiatives.
Contribute Materials
Your contribution can guide someone’s learning journey. Share your
documents today.
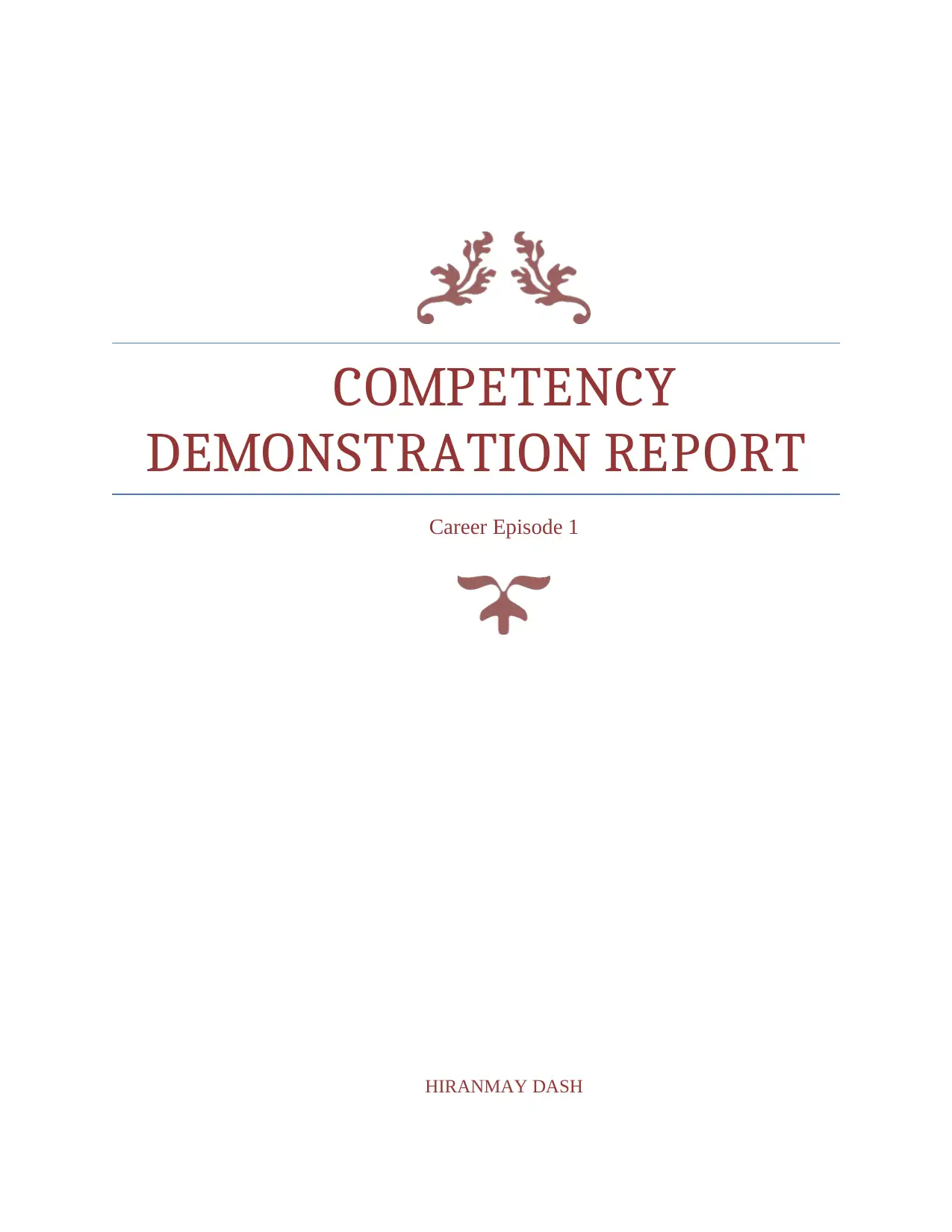
COMPETENCY
DEMONSTRATION REPORT
Career Episode 1
HIRANMAY DASH
DEMONSTRATION REPORT
Career Episode 1
HIRANMAY DASH
Secure Best Marks with AI Grader
Need help grading? Try our AI Grader for instant feedback on your assignments.
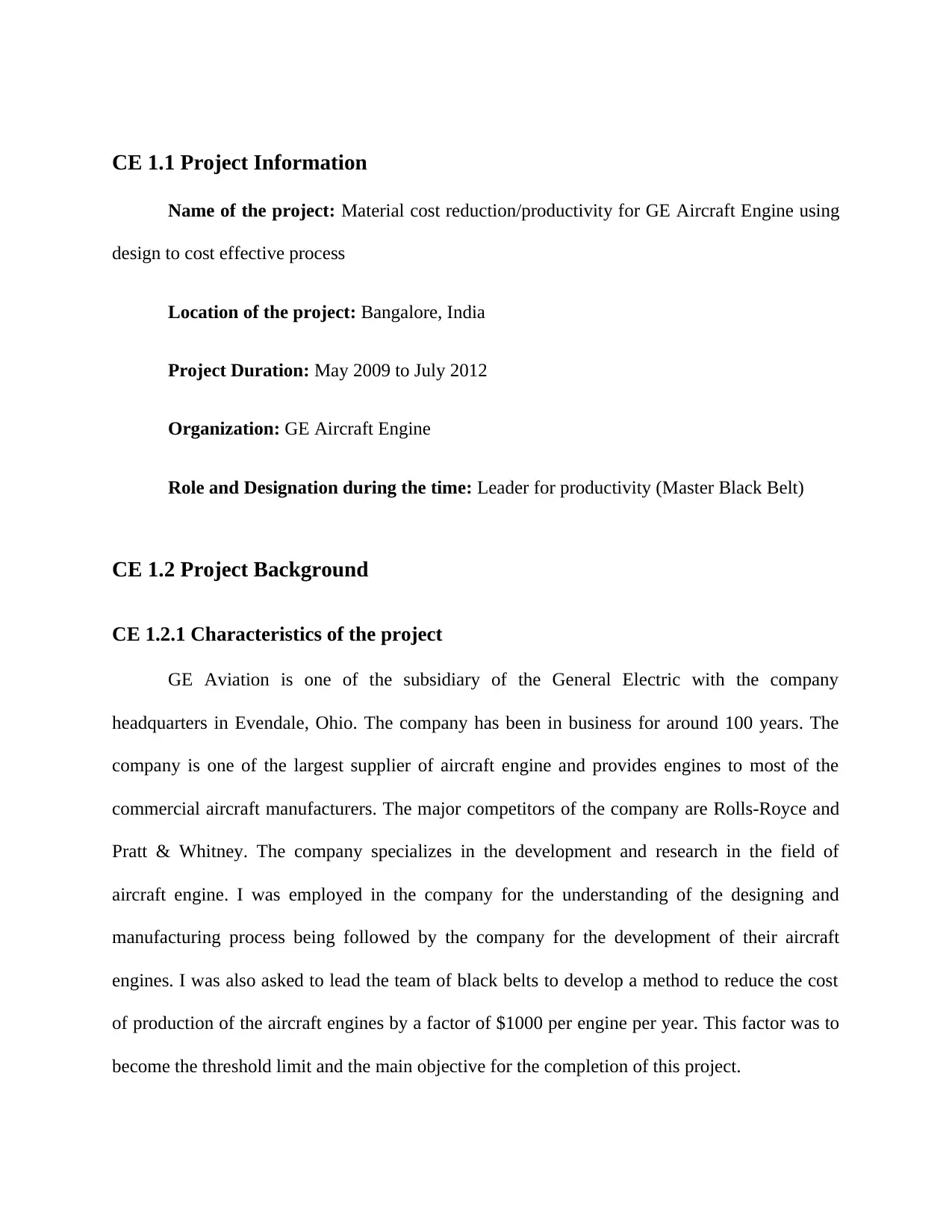
CE 1.1 Project Information
Name of the project: Material cost reduction/productivity for GE Aircraft Engine using
design to cost effective process
Location of the project: Bangalore, India
Project Duration: May 2009 to July 2012
Organization: GE Aircraft Engine
Role and Designation during the time: Leader for productivity (Master Black Belt)
CE 1.2 Project Background
CE 1.2.1 Characteristics of the project
GE Aviation is one of the subsidiary of the General Electric with the company
headquarters in Evendale, Ohio. The company has been in business for around 100 years. The
company is one of the largest supplier of aircraft engine and provides engines to most of the
commercial aircraft manufacturers. The major competitors of the company are Rolls-Royce and
Pratt & Whitney. The company specializes in the development and research in the field of
aircraft engine. I was employed in the company for the understanding of the designing and
manufacturing process being followed by the company for the development of their aircraft
engines. I was also asked to lead the team of black belts to develop a method to reduce the cost
of production of the aircraft engines by a factor of $1000 per engine per year. This factor was to
become the threshold limit and the main objective for the completion of this project.
Name of the project: Material cost reduction/productivity for GE Aircraft Engine using
design to cost effective process
Location of the project: Bangalore, India
Project Duration: May 2009 to July 2012
Organization: GE Aircraft Engine
Role and Designation during the time: Leader for productivity (Master Black Belt)
CE 1.2 Project Background
CE 1.2.1 Characteristics of the project
GE Aviation is one of the subsidiary of the General Electric with the company
headquarters in Evendale, Ohio. The company has been in business for around 100 years. The
company is one of the largest supplier of aircraft engine and provides engines to most of the
commercial aircraft manufacturers. The major competitors of the company are Rolls-Royce and
Pratt & Whitney. The company specializes in the development and research in the field of
aircraft engine. I was employed in the company for the understanding of the designing and
manufacturing process being followed by the company for the development of their aircraft
engines. I was also asked to lead the team of black belts to develop a method to reduce the cost
of production of the aircraft engines by a factor of $1000 per engine per year. This factor was to
become the threshold limit and the main objective for the completion of this project.
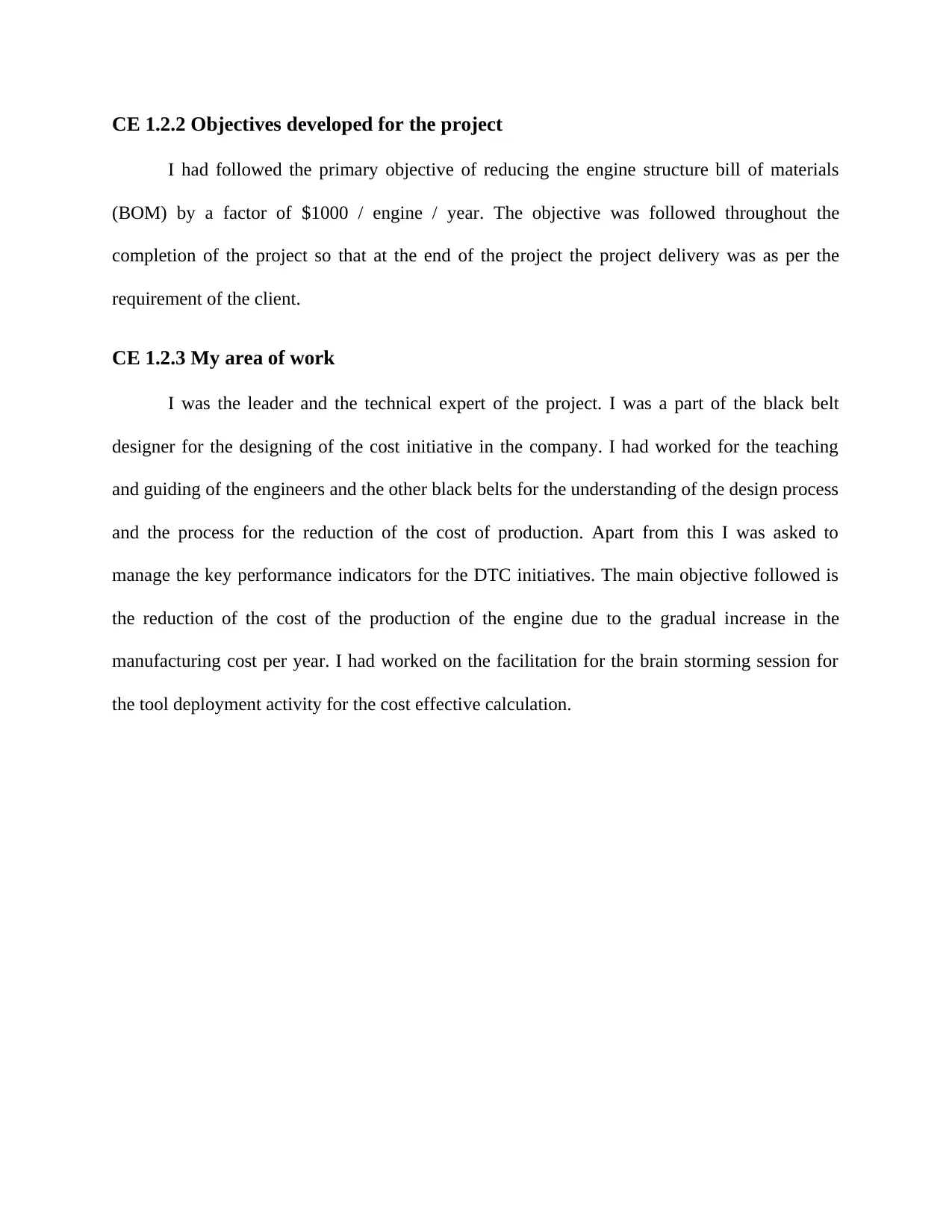
CE 1.2.2 Objectives developed for the project
I had followed the primary objective of reducing the engine structure bill of materials
(BOM) by a factor of $1000 / engine / year. The objective was followed throughout the
completion of the project so that at the end of the project the project delivery was as per the
requirement of the client.
CE 1.2.3 My area of work
I was the leader and the technical expert of the project. I was a part of the black belt
designer for the designing of the cost initiative in the company. I had worked for the teaching
and guiding of the engineers and the other black belts for the understanding of the design process
and the process for the reduction of the cost of production. Apart from this I was asked to
manage the key performance indicators for the DTC initiatives. The main objective followed is
the reduction of the cost of the production of the engine due to the gradual increase in the
manufacturing cost per year. I had worked on the facilitation for the brain storming session for
the tool deployment activity for the cost effective calculation.
I had followed the primary objective of reducing the engine structure bill of materials
(BOM) by a factor of $1000 / engine / year. The objective was followed throughout the
completion of the project so that at the end of the project the project delivery was as per the
requirement of the client.
CE 1.2.3 My area of work
I was the leader and the technical expert of the project. I was a part of the black belt
designer for the designing of the cost initiative in the company. I had worked for the teaching
and guiding of the engineers and the other black belts for the understanding of the design process
and the process for the reduction of the cost of production. Apart from this I was asked to
manage the key performance indicators for the DTC initiatives. The main objective followed is
the reduction of the cost of the production of the engine due to the gradual increase in the
manufacturing cost per year. I had worked on the facilitation for the brain storming session for
the tool deployment activity for the cost effective calculation.
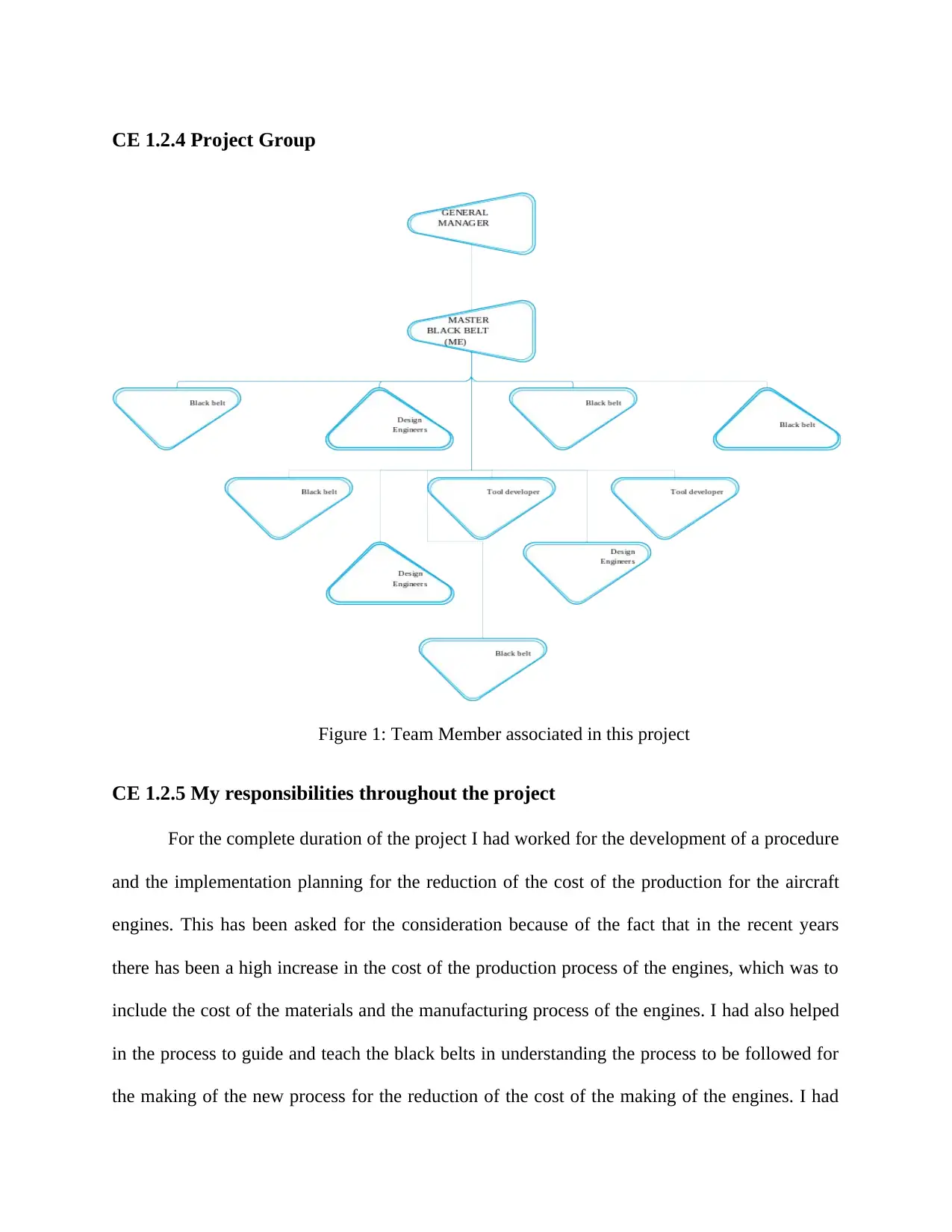
CE 1.2.4 Project Group
Figure 1: Team Member associated in this project
CE 1.2.5 My responsibilities throughout the project
For the complete duration of the project I had worked for the development of a procedure
and the implementation planning for the reduction of the cost of the production for the aircraft
engines. This has been asked for the consideration because of the fact that in the recent years
there has been a high increase in the cost of the production process of the engines, which was to
include the cost of the materials and the manufacturing process of the engines. I had also helped
in the process to guide and teach the black belts in understanding the process to be followed for
the making of the new process for the reduction of the cost of the making of the engines. I had
Figure 1: Team Member associated in this project
CE 1.2.5 My responsibilities throughout the project
For the complete duration of the project I had worked for the development of a procedure
and the implementation planning for the reduction of the cost of the production for the aircraft
engines. This has been asked for the consideration because of the fact that in the recent years
there has been a high increase in the cost of the production process of the engines, which was to
include the cost of the materials and the manufacturing process of the engines. I had also helped
in the process to guide and teach the black belts in understanding the process to be followed for
the making of the new process for the reduction of the cost of the making of the engines. I had
Secure Best Marks with AI Grader
Need help grading? Try our AI Grader for instant feedback on your assignments.
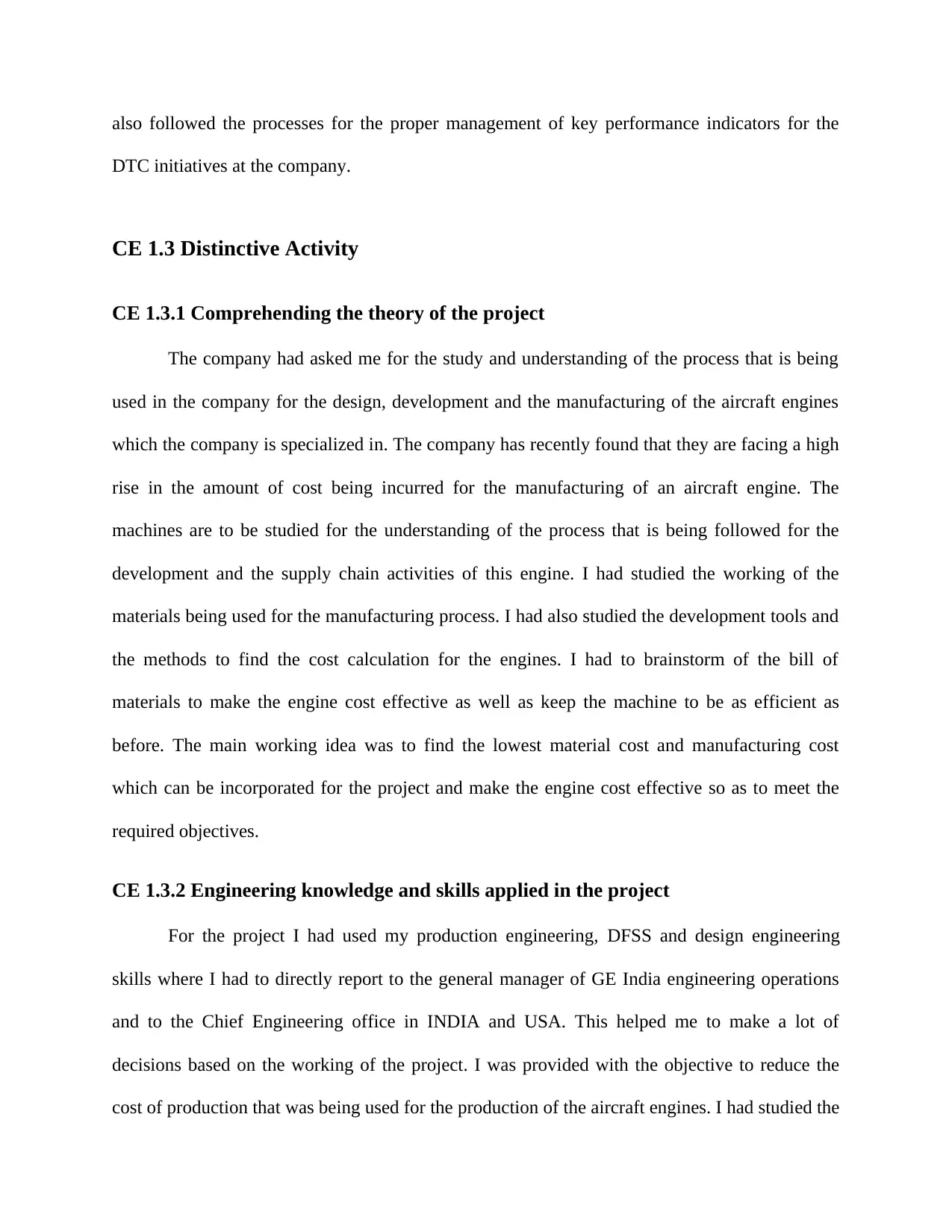
also followed the processes for the proper management of key performance indicators for the
DTC initiatives at the company.
CE 1.3 Distinctive Activity
CE 1.3.1 Comprehending the theory of the project
The company had asked me for the study and understanding of the process that is being
used in the company for the design, development and the manufacturing of the aircraft engines
which the company is specialized in. The company has recently found that they are facing a high
rise in the amount of cost being incurred for the manufacturing of an aircraft engine. The
machines are to be studied for the understanding of the process that is being followed for the
development and the supply chain activities of this engine. I had studied the working of the
materials being used for the manufacturing process. I had also studied the development tools and
the methods to find the cost calculation for the engines. I had to brainstorm of the bill of
materials to make the engine cost effective as well as keep the machine to be as efficient as
before. The main working idea was to find the lowest material cost and manufacturing cost
which can be incorporated for the project and make the engine cost effective so as to meet the
required objectives.
CE 1.3.2 Engineering knowledge and skills applied in the project
For the project I had used my production engineering, DFSS and design engineering
skills where I had to directly report to the general manager of GE India engineering operations
and to the Chief Engineering office in INDIA and USA. This helped me to make a lot of
decisions based on the working of the project. I was provided with the objective to reduce the
cost of production that was being used for the production of the aircraft engines. I had studied the
DTC initiatives at the company.
CE 1.3 Distinctive Activity
CE 1.3.1 Comprehending the theory of the project
The company had asked me for the study and understanding of the process that is being
used in the company for the design, development and the manufacturing of the aircraft engines
which the company is specialized in. The company has recently found that they are facing a high
rise in the amount of cost being incurred for the manufacturing of an aircraft engine. The
machines are to be studied for the understanding of the process that is being followed for the
development and the supply chain activities of this engine. I had studied the working of the
materials being used for the manufacturing process. I had also studied the development tools and
the methods to find the cost calculation for the engines. I had to brainstorm of the bill of
materials to make the engine cost effective as well as keep the machine to be as efficient as
before. The main working idea was to find the lowest material cost and manufacturing cost
which can be incorporated for the project and make the engine cost effective so as to meet the
required objectives.
CE 1.3.2 Engineering knowledge and skills applied in the project
For the project I had used my production engineering, DFSS and design engineering
skills where I had to directly report to the general manager of GE India engineering operations
and to the Chief Engineering office in INDIA and USA. This helped me to make a lot of
decisions based on the working of the project. I was provided with the objective to reduce the
cost of production that was being used for the production of the aircraft engines. I had studied the
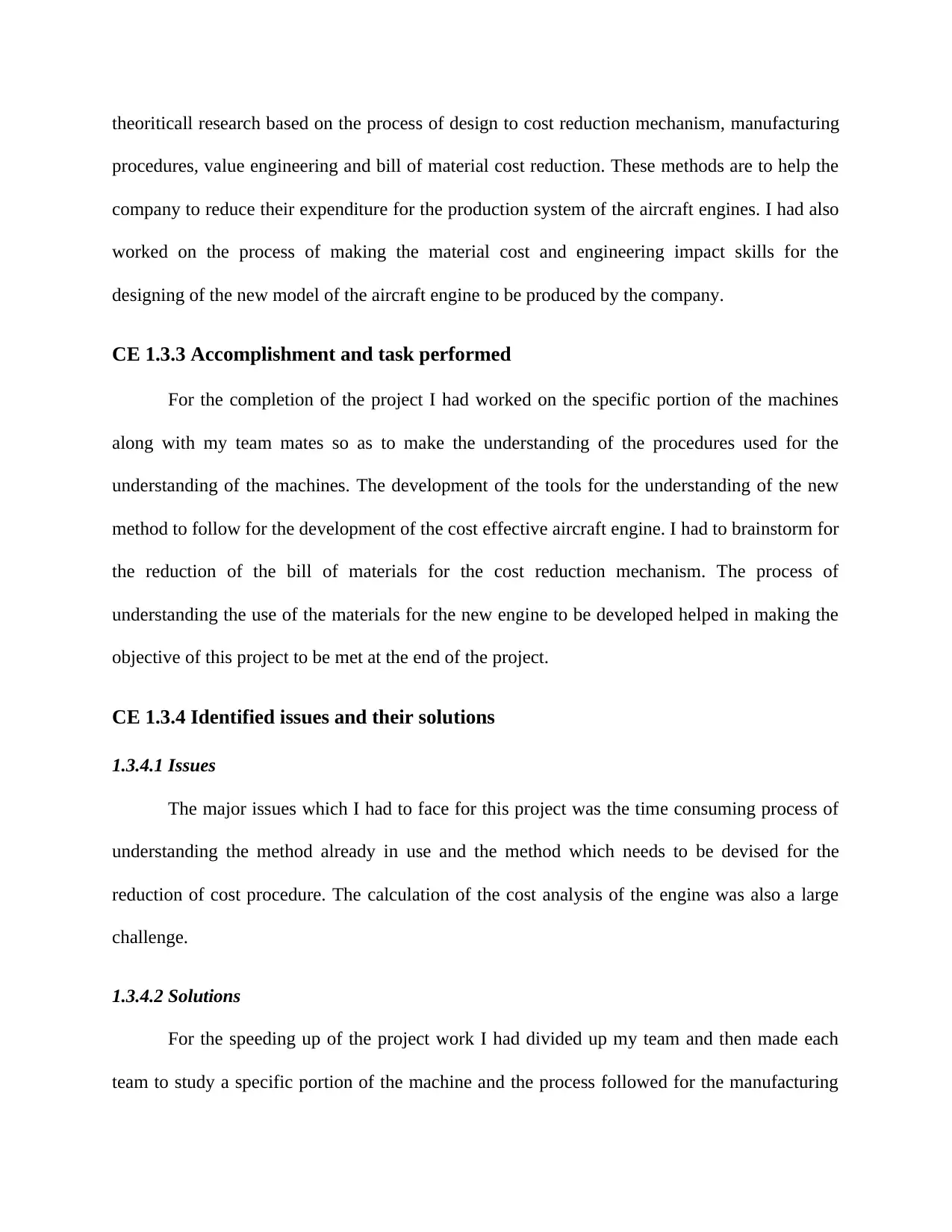
theoriticall research based on the process of design to cost reduction mechanism, manufacturing
procedures, value engineering and bill of material cost reduction. These methods are to help the
company to reduce their expenditure for the production system of the aircraft engines. I had also
worked on the process of making the material cost and engineering impact skills for the
designing of the new model of the aircraft engine to be produced by the company.
CE 1.3.3 Accomplishment and task performed
For the completion of the project I had worked on the specific portion of the machines
along with my team mates so as to make the understanding of the procedures used for the
understanding of the machines. The development of the tools for the understanding of the new
method to follow for the development of the cost effective aircraft engine. I had to brainstorm for
the reduction of the bill of materials for the cost reduction mechanism. The process of
understanding the use of the materials for the new engine to be developed helped in making the
objective of this project to be met at the end of the project.
CE 1.3.4 Identified issues and their solutions
1.3.4.1 Issues
The major issues which I had to face for this project was the time consuming process of
understanding the method already in use and the method which needs to be devised for the
reduction of cost procedure. The calculation of the cost analysis of the engine was also a large
challenge.
1.3.4.2 Solutions
For the speeding up of the project work I had divided up my team and then made each
team to study a specific portion of the machine and the process followed for the manufacturing
procedures, value engineering and bill of material cost reduction. These methods are to help the
company to reduce their expenditure for the production system of the aircraft engines. I had also
worked on the process of making the material cost and engineering impact skills for the
designing of the new model of the aircraft engine to be produced by the company.
CE 1.3.3 Accomplishment and task performed
For the completion of the project I had worked on the specific portion of the machines
along with my team mates so as to make the understanding of the procedures used for the
understanding of the machines. The development of the tools for the understanding of the new
method to follow for the development of the cost effective aircraft engine. I had to brainstorm for
the reduction of the bill of materials for the cost reduction mechanism. The process of
understanding the use of the materials for the new engine to be developed helped in making the
objective of this project to be met at the end of the project.
CE 1.3.4 Identified issues and their solutions
1.3.4.1 Issues
The major issues which I had to face for this project was the time consuming process of
understanding the method already in use and the method which needs to be devised for the
reduction of cost procedure. The calculation of the cost analysis of the engine was also a large
challenge.
1.3.4.2 Solutions
For the speeding up of the project work I had divided up my team and then made each
team to study a specific portion of the machine and the process followed for the manufacturing
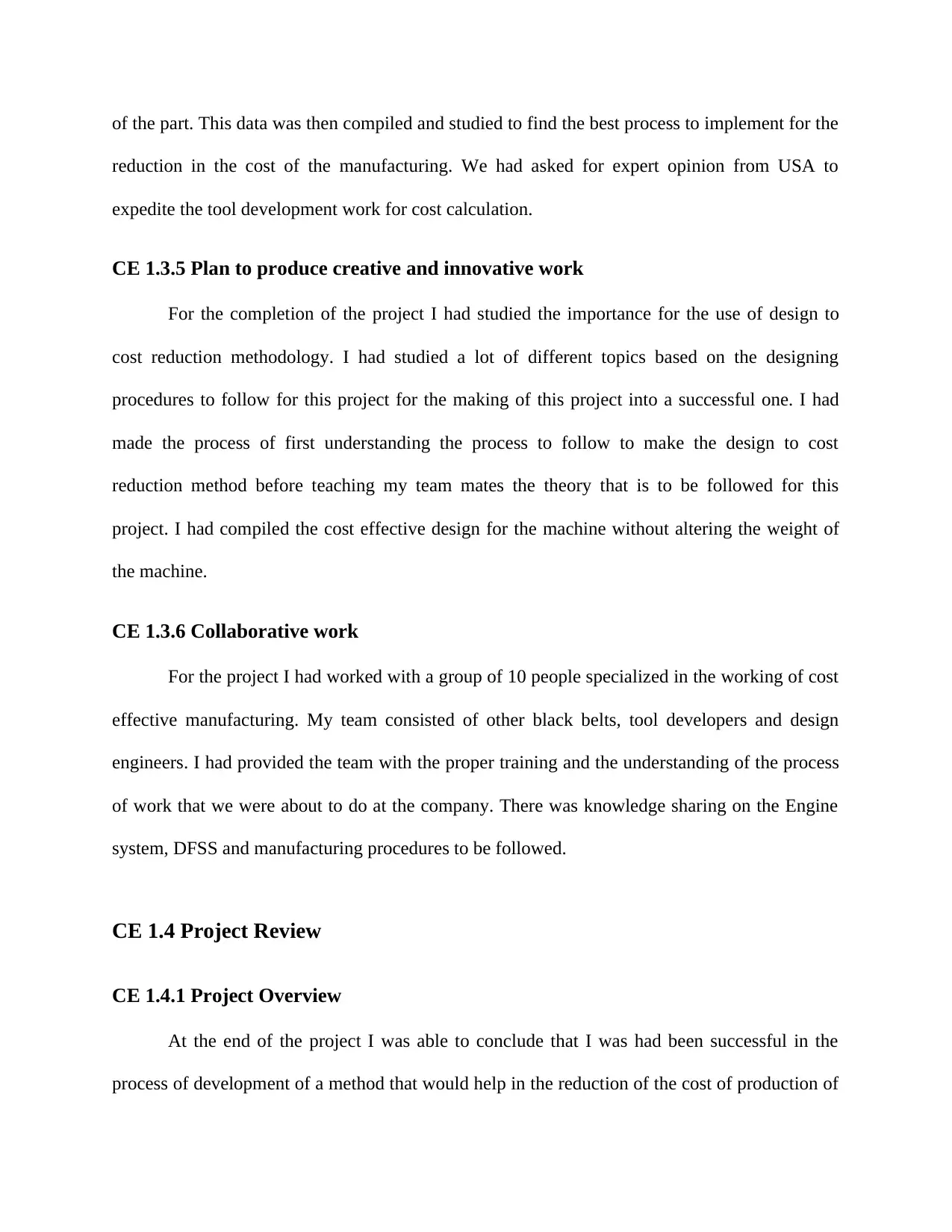
of the part. This data was then compiled and studied to find the best process to implement for the
reduction in the cost of the manufacturing. We had asked for expert opinion from USA to
expedite the tool development work for cost calculation.
CE 1.3.5 Plan to produce creative and innovative work
For the completion of the project I had studied the importance for the use of design to
cost reduction methodology. I had studied a lot of different topics based on the designing
procedures to follow for this project for the making of this project into a successful one. I had
made the process of first understanding the process to follow to make the design to cost
reduction method before teaching my team mates the theory that is to be followed for this
project. I had compiled the cost effective design for the machine without altering the weight of
the machine.
CE 1.3.6 Collaborative work
For the project I had worked with a group of 10 people specialized in the working of cost
effective manufacturing. My team consisted of other black belts, tool developers and design
engineers. I had provided the team with the proper training and the understanding of the process
of work that we were about to do at the company. There was knowledge sharing on the Engine
system, DFSS and manufacturing procedures to be followed.
CE 1.4 Project Review
CE 1.4.1 Project Overview
At the end of the project I was able to conclude that I was had been successful in the
process of development of a method that would help in the reduction of the cost of production of
reduction in the cost of the manufacturing. We had asked for expert opinion from USA to
expedite the tool development work for cost calculation.
CE 1.3.5 Plan to produce creative and innovative work
For the completion of the project I had studied the importance for the use of design to
cost reduction methodology. I had studied a lot of different topics based on the designing
procedures to follow for this project for the making of this project into a successful one. I had
made the process of first understanding the process to follow to make the design to cost
reduction method before teaching my team mates the theory that is to be followed for this
project. I had compiled the cost effective design for the machine without altering the weight of
the machine.
CE 1.3.6 Collaborative work
For the project I had worked with a group of 10 people specialized in the working of cost
effective manufacturing. My team consisted of other black belts, tool developers and design
engineers. I had provided the team with the proper training and the understanding of the process
of work that we were about to do at the company. There was knowledge sharing on the Engine
system, DFSS and manufacturing procedures to be followed.
CE 1.4 Project Review
CE 1.4.1 Project Overview
At the end of the project I was able to conclude that I was had been successful in the
process of development of a method that would help in the reduction of the cost of production of
Paraphrase This Document
Need a fresh take? Get an instant paraphrase of this document with our AI Paraphraser
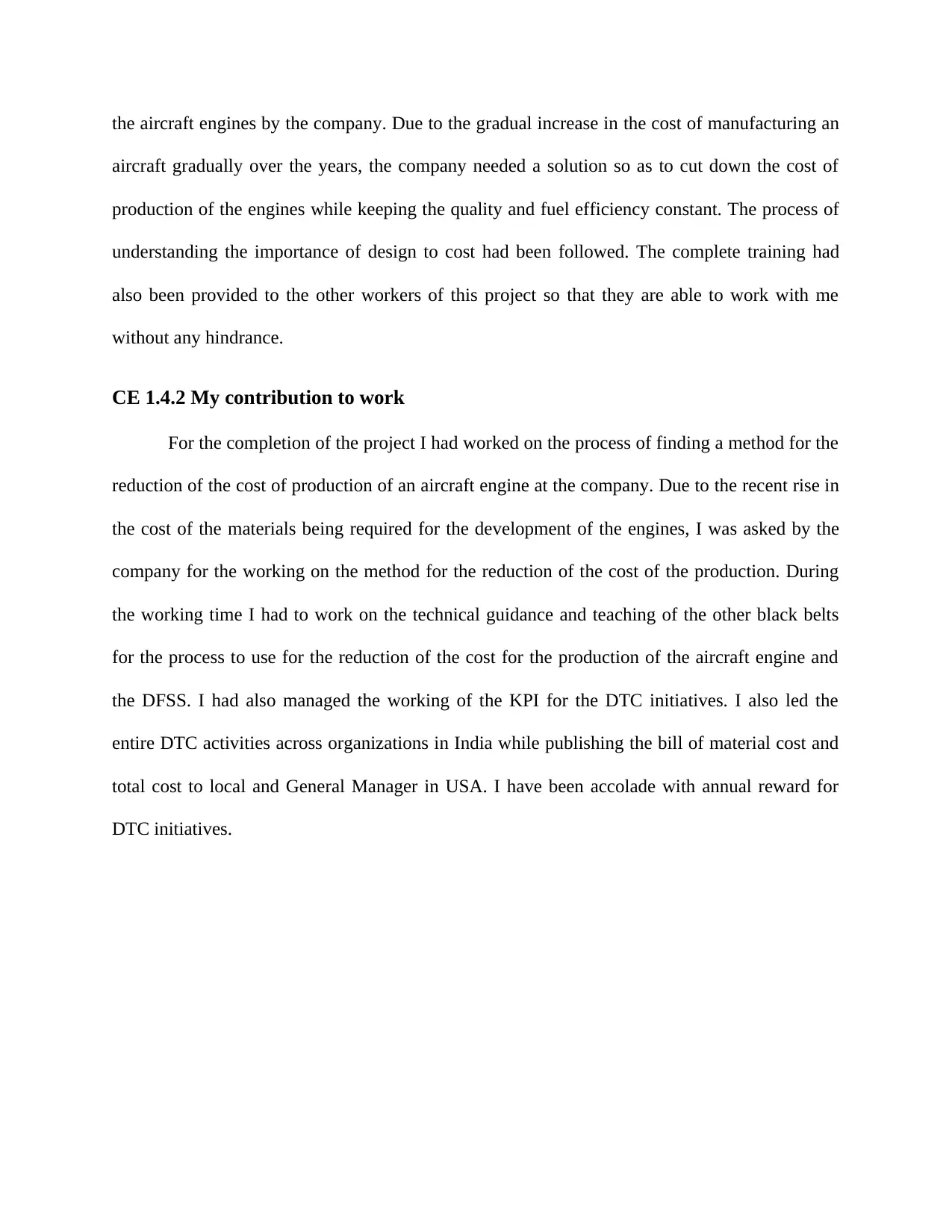
the aircraft engines by the company. Due to the gradual increase in the cost of manufacturing an
aircraft gradually over the years, the company needed a solution so as to cut down the cost of
production of the engines while keeping the quality and fuel efficiency constant. The process of
understanding the importance of design to cost had been followed. The complete training had
also been provided to the other workers of this project so that they are able to work with me
without any hindrance.
CE 1.4.2 My contribution to work
For the completion of the project I had worked on the process of finding a method for the
reduction of the cost of production of an aircraft engine at the company. Due to the recent rise in
the cost of the materials being required for the development of the engines, I was asked by the
company for the working on the method for the reduction of the cost of the production. During
the working time I had to work on the technical guidance and teaching of the other black belts
for the process to use for the reduction of the cost for the production of the aircraft engine and
the DFSS. I had also managed the working of the KPI for the DTC initiatives. I also led the
entire DTC activities across organizations in India while publishing the bill of material cost and
total cost to local and General Manager in USA. I have been accolade with annual reward for
DTC initiatives.
aircraft gradually over the years, the company needed a solution so as to cut down the cost of
production of the engines while keeping the quality and fuel efficiency constant. The process of
understanding the importance of design to cost had been followed. The complete training had
also been provided to the other workers of this project so that they are able to work with me
without any hindrance.
CE 1.4.2 My contribution to work
For the completion of the project I had worked on the process of finding a method for the
reduction of the cost of production of an aircraft engine at the company. Due to the recent rise in
the cost of the materials being required for the development of the engines, I was asked by the
company for the working on the method for the reduction of the cost of the production. During
the working time I had to work on the technical guidance and teaching of the other black belts
for the process to use for the reduction of the cost for the production of the aircraft engine and
the DFSS. I had also managed the working of the KPI for the DTC initiatives. I also led the
entire DTC activities across organizations in India while publishing the bill of material cost and
total cost to local and General Manager in USA. I have been accolade with annual reward for
DTC initiatives.
1 out of 8
Related Documents

Your All-in-One AI-Powered Toolkit for Academic Success.
 +13062052269
info@desklib.com
Available 24*7 on WhatsApp / Email
Unlock your academic potential
© 2024  |  Zucol Services PVT LTD  |  All rights reserved.