ALPINA Automobile Manufacturing: Operations Management Report
VerifiedAdded on 2020/03/02
|19
|6181
|72
Report
AI Summary
This report analyzes the operations management of ALPINA, a medium-sized automobile manufacturer, focusing on key performance objectives such as cost, quality, dependability, speed, and flexibility. It examines the challenges posed by customization demands and regulatory requirements. The...
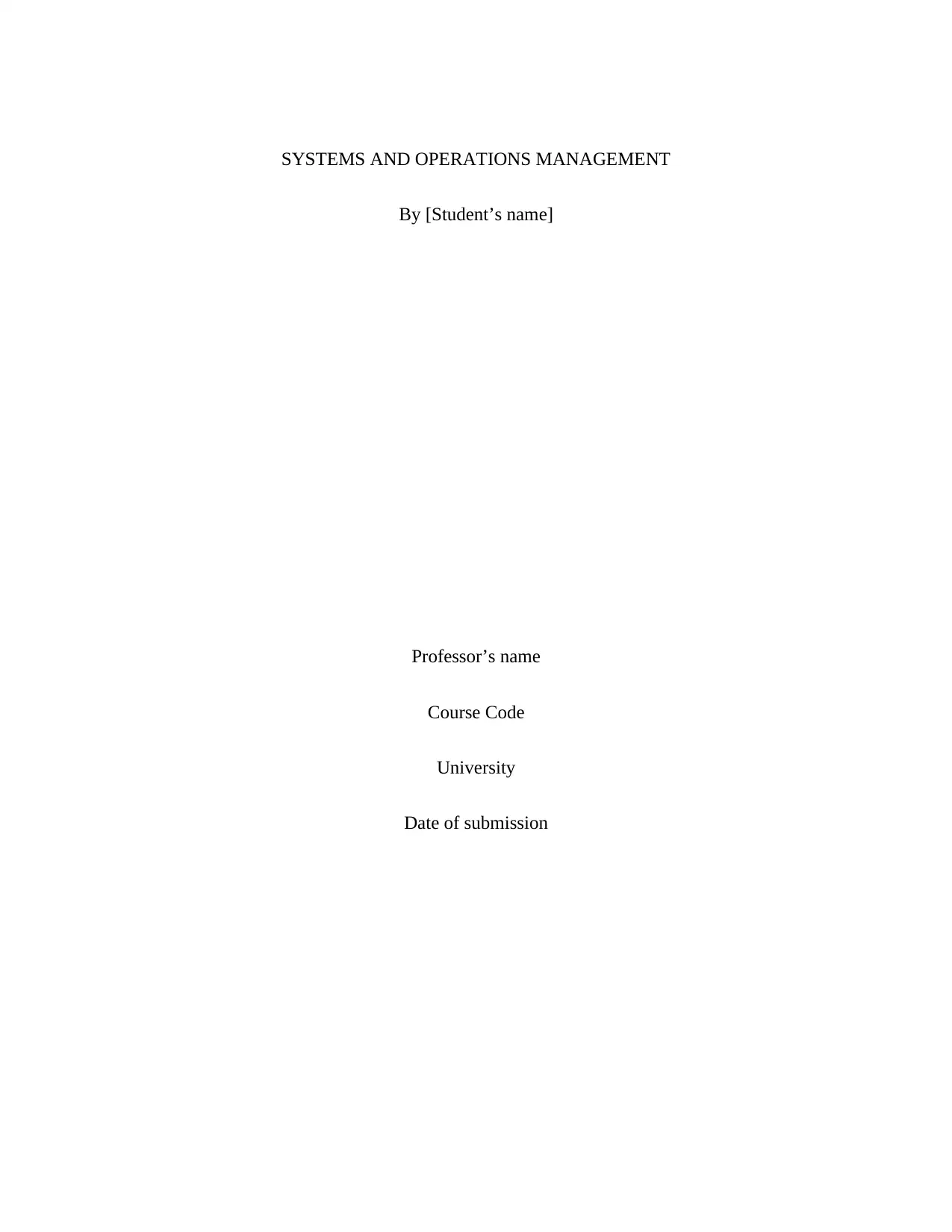
SYSTEMS AND OPERATIONS MANAGEMENT
By [Student’s name]
Professor’s name
Course Code
University
Date of submission
By [Student’s name]
Professor’s name
Course Code
University
Date of submission
Secure Best Marks with AI Grader
Need help grading? Try our AI Grader for instant feedback on your assignments.
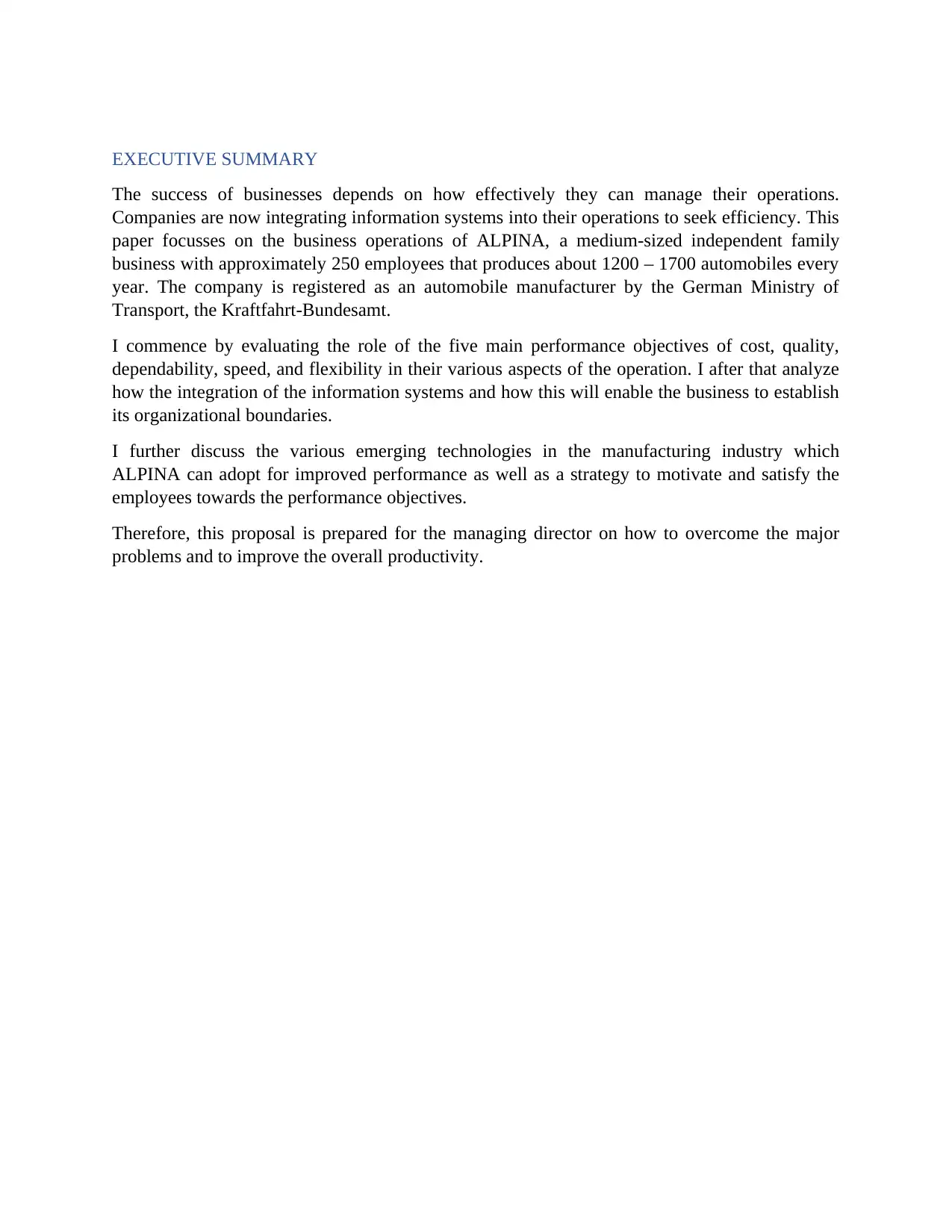
EXECUTIVE SUMMARY
The success of businesses depends on how effectively they can manage their operations.
Companies are now integrating information systems into their operations to seek efficiency. This
paper focusses on the business operations of ALPINA, a medium-sized independent family
business with approximately 250 employees that produces about 1200 – 1700 automobiles every
year. The company is registered as an automobile manufacturer by the German Ministry of
Transport, the Kraftfahrt-Bundesamt.
I commence by evaluating the role of the five main performance objectives of cost, quality,
dependability, speed, and flexibility in their various aspects of the operation. I after that analyze
how the integration of the information systems and how this will enable the business to establish
its organizational boundaries.
I further discuss the various emerging technologies in the manufacturing industry which
ALPINA can adopt for improved performance as well as a strategy to motivate and satisfy the
employees towards the performance objectives.
Therefore, this proposal is prepared for the managing director on how to overcome the major
problems and to improve the overall productivity.
The success of businesses depends on how effectively they can manage their operations.
Companies are now integrating information systems into their operations to seek efficiency. This
paper focusses on the business operations of ALPINA, a medium-sized independent family
business with approximately 250 employees that produces about 1200 – 1700 automobiles every
year. The company is registered as an automobile manufacturer by the German Ministry of
Transport, the Kraftfahrt-Bundesamt.
I commence by evaluating the role of the five main performance objectives of cost, quality,
dependability, speed, and flexibility in their various aspects of the operation. I after that analyze
how the integration of the information systems and how this will enable the business to establish
its organizational boundaries.
I further discuss the various emerging technologies in the manufacturing industry which
ALPINA can adopt for improved performance as well as a strategy to motivate and satisfy the
employees towards the performance objectives.
Therefore, this proposal is prepared for the managing director on how to overcome the major
problems and to improve the overall productivity.
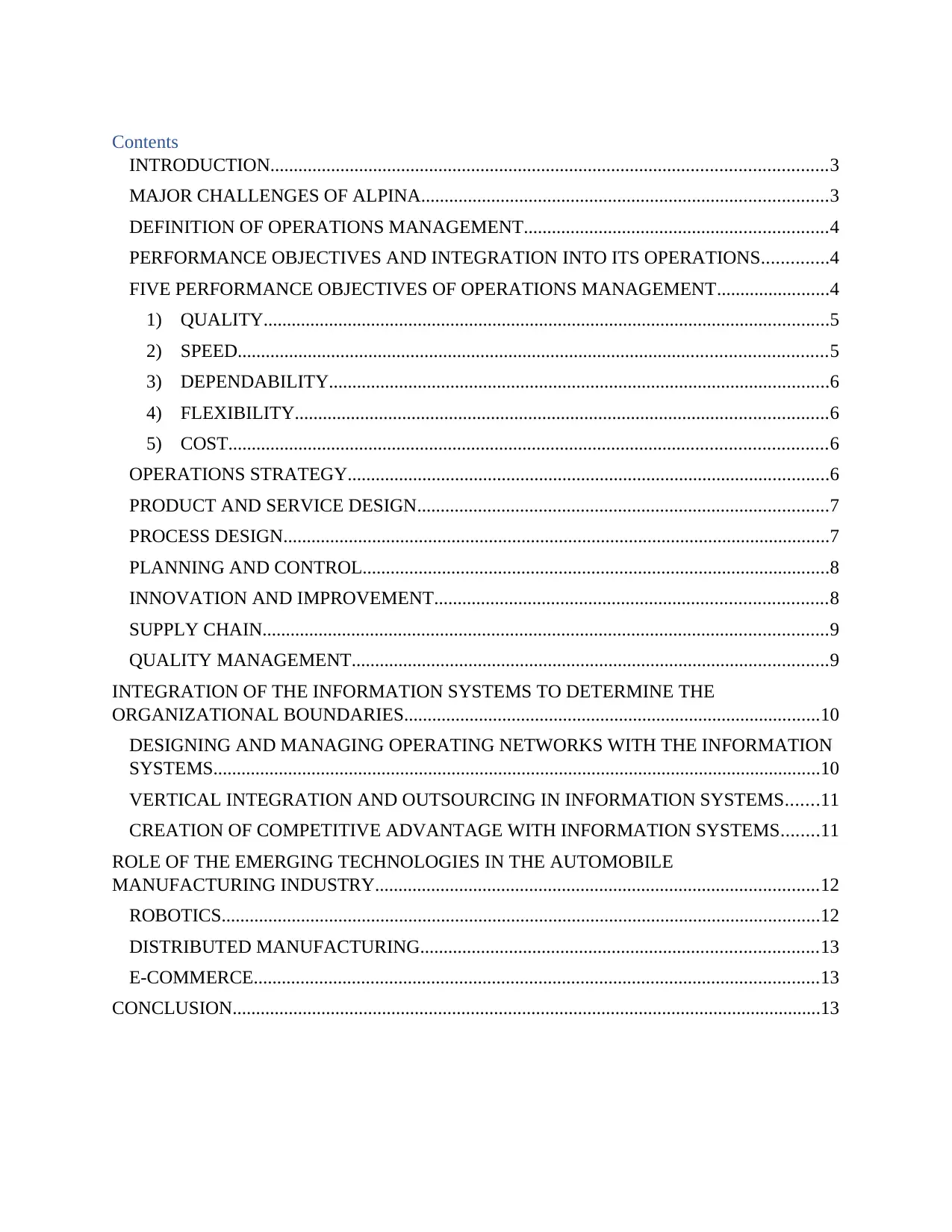
Contents
INTRODUCTION.......................................................................................................................3
MAJOR CHALLENGES OF ALPINA.......................................................................................3
DEFINITION OF OPERATIONS MANAGEMENT.................................................................4
PERFORMANCE OBJECTIVES AND INTEGRATION INTO ITS OPERATIONS..............4
FIVE PERFORMANCE OBJECTIVES OF OPERATIONS MANAGEMENT........................4
1) QUALITY.........................................................................................................................5
2) SPEED..............................................................................................................................5
3) DEPENDABILITY...........................................................................................................6
4) FLEXIBILITY..................................................................................................................6
5) COST................................................................................................................................6
OPERATIONS STRATEGY.......................................................................................................6
PRODUCT AND SERVICE DESIGN........................................................................................7
PROCESS DESIGN.....................................................................................................................7
PLANNING AND CONTROL....................................................................................................8
INNOVATION AND IMPROVEMENT....................................................................................8
SUPPLY CHAIN.........................................................................................................................9
QUALITY MANAGEMENT......................................................................................................9
INTEGRATION OF THE INFORMATION SYSTEMS TO DETERMINE THE
ORGANIZATIONAL BOUNDARIES.........................................................................................10
DESIGNING AND MANAGING OPERATING NETWORKS WITH THE INFORMATION
SYSTEMS..................................................................................................................................10
VERTICAL INTEGRATION AND OUTSOURCING IN INFORMATION SYSTEMS.......11
CREATION OF COMPETITIVE ADVANTAGE WITH INFORMATION SYSTEMS........11
ROLE OF THE EMERGING TECHNOLOGIES IN THE AUTOMOBILE
MANUFACTURING INDUSTRY...............................................................................................12
ROBOTICS................................................................................................................................12
DISTRIBUTED MANUFACTURING.....................................................................................13
E-COMMERCE.........................................................................................................................13
CONCLUSION..............................................................................................................................13
INTRODUCTION.......................................................................................................................3
MAJOR CHALLENGES OF ALPINA.......................................................................................3
DEFINITION OF OPERATIONS MANAGEMENT.................................................................4
PERFORMANCE OBJECTIVES AND INTEGRATION INTO ITS OPERATIONS..............4
FIVE PERFORMANCE OBJECTIVES OF OPERATIONS MANAGEMENT........................4
1) QUALITY.........................................................................................................................5
2) SPEED..............................................................................................................................5
3) DEPENDABILITY...........................................................................................................6
4) FLEXIBILITY..................................................................................................................6
5) COST................................................................................................................................6
OPERATIONS STRATEGY.......................................................................................................6
PRODUCT AND SERVICE DESIGN........................................................................................7
PROCESS DESIGN.....................................................................................................................7
PLANNING AND CONTROL....................................................................................................8
INNOVATION AND IMPROVEMENT....................................................................................8
SUPPLY CHAIN.........................................................................................................................9
QUALITY MANAGEMENT......................................................................................................9
INTEGRATION OF THE INFORMATION SYSTEMS TO DETERMINE THE
ORGANIZATIONAL BOUNDARIES.........................................................................................10
DESIGNING AND MANAGING OPERATING NETWORKS WITH THE INFORMATION
SYSTEMS..................................................................................................................................10
VERTICAL INTEGRATION AND OUTSOURCING IN INFORMATION SYSTEMS.......11
CREATION OF COMPETITIVE ADVANTAGE WITH INFORMATION SYSTEMS........11
ROLE OF THE EMERGING TECHNOLOGIES IN THE AUTOMOBILE
MANUFACTURING INDUSTRY...............................................................................................12
ROBOTICS................................................................................................................................12
DISTRIBUTED MANUFACTURING.....................................................................................13
E-COMMERCE.........................................................................................................................13
CONCLUSION..............................................................................................................................13
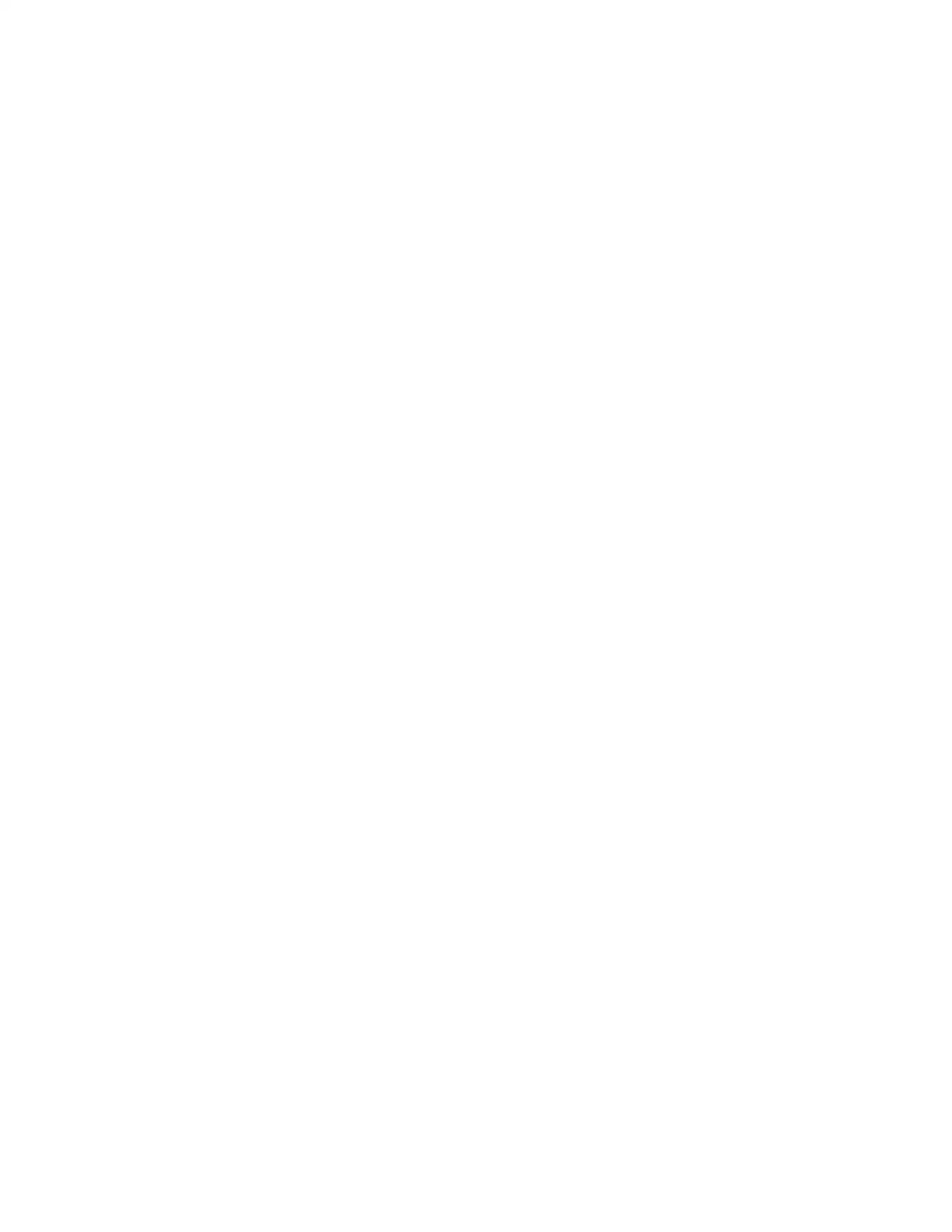
Secure Best Marks with AI Grader
Need help grading? Try our AI Grader for instant feedback on your assignments.
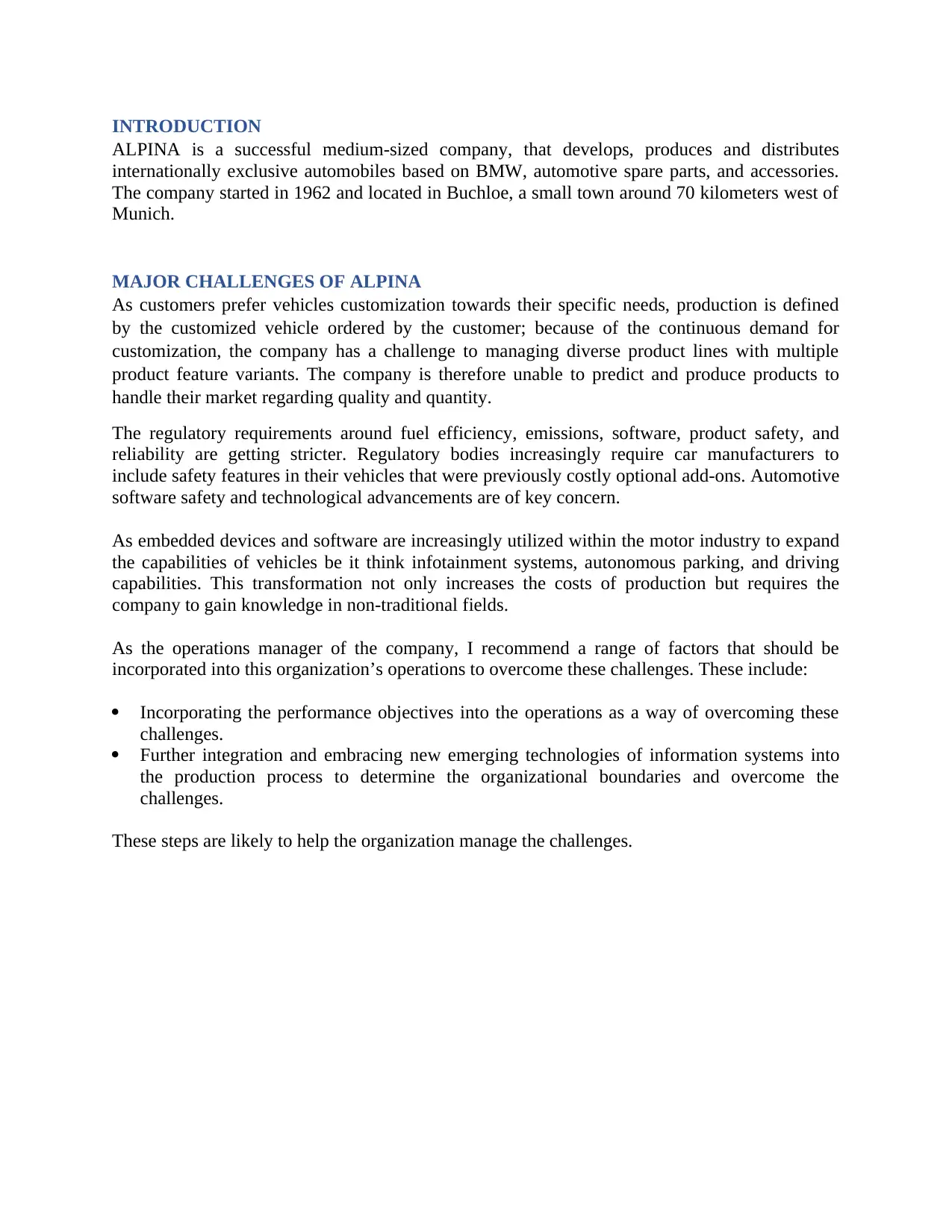
INTRODUCTION
ALPINA is a successful medium-sized company, that develops, produces and distributes
internationally exclusive automobiles based on BMW, automotive spare parts, and accessories.
The company started in 1962 and located in Buchloe, a small town around 70 kilometers west of
Munich.
MAJOR CHALLENGES OF ALPINA
As customers prefer vehicles customization towards their specific needs, production is defined
by the customized vehicle ordered by the customer; because of the continuous demand for
customization, the company has a challenge to managing diverse product lines with multiple
product feature variants. The company is therefore unable to predict and produce products to
handle their market regarding quality and quantity.
The regulatory requirements around fuel efficiency, emissions, software, product safety, and
reliability are getting stricter. Regulatory bodies increasingly require car manufacturers to
include safety features in their vehicles that were previously costly optional add-ons. Automotive
software safety and technological advancements are of key concern.
As embedded devices and software are increasingly utilized within the motor industry to expand
the capabilities of vehicles be it think infotainment systems, autonomous parking, and driving
capabilities. This transformation not only increases the costs of production but requires the
company to gain knowledge in non-traditional fields.
As the operations manager of the company, I recommend a range of factors that should be
incorporated into this organization’s operations to overcome these challenges. These include:
Incorporating the performance objectives into the operations as a way of overcoming these
challenges.
Further integration and embracing new emerging technologies of information systems into
the production process to determine the organizational boundaries and overcome the
challenges.
These steps are likely to help the organization manage the challenges.
ALPINA is a successful medium-sized company, that develops, produces and distributes
internationally exclusive automobiles based on BMW, automotive spare parts, and accessories.
The company started in 1962 and located in Buchloe, a small town around 70 kilometers west of
Munich.
MAJOR CHALLENGES OF ALPINA
As customers prefer vehicles customization towards their specific needs, production is defined
by the customized vehicle ordered by the customer; because of the continuous demand for
customization, the company has a challenge to managing diverse product lines with multiple
product feature variants. The company is therefore unable to predict and produce products to
handle their market regarding quality and quantity.
The regulatory requirements around fuel efficiency, emissions, software, product safety, and
reliability are getting stricter. Regulatory bodies increasingly require car manufacturers to
include safety features in their vehicles that were previously costly optional add-ons. Automotive
software safety and technological advancements are of key concern.
As embedded devices and software are increasingly utilized within the motor industry to expand
the capabilities of vehicles be it think infotainment systems, autonomous parking, and driving
capabilities. This transformation not only increases the costs of production but requires the
company to gain knowledge in non-traditional fields.
As the operations manager of the company, I recommend a range of factors that should be
incorporated into this organization’s operations to overcome these challenges. These include:
Incorporating the performance objectives into the operations as a way of overcoming these
challenges.
Further integration and embracing new emerging technologies of information systems into
the production process to determine the organizational boundaries and overcome the
challenges.
These steps are likely to help the organization manage the challenges.
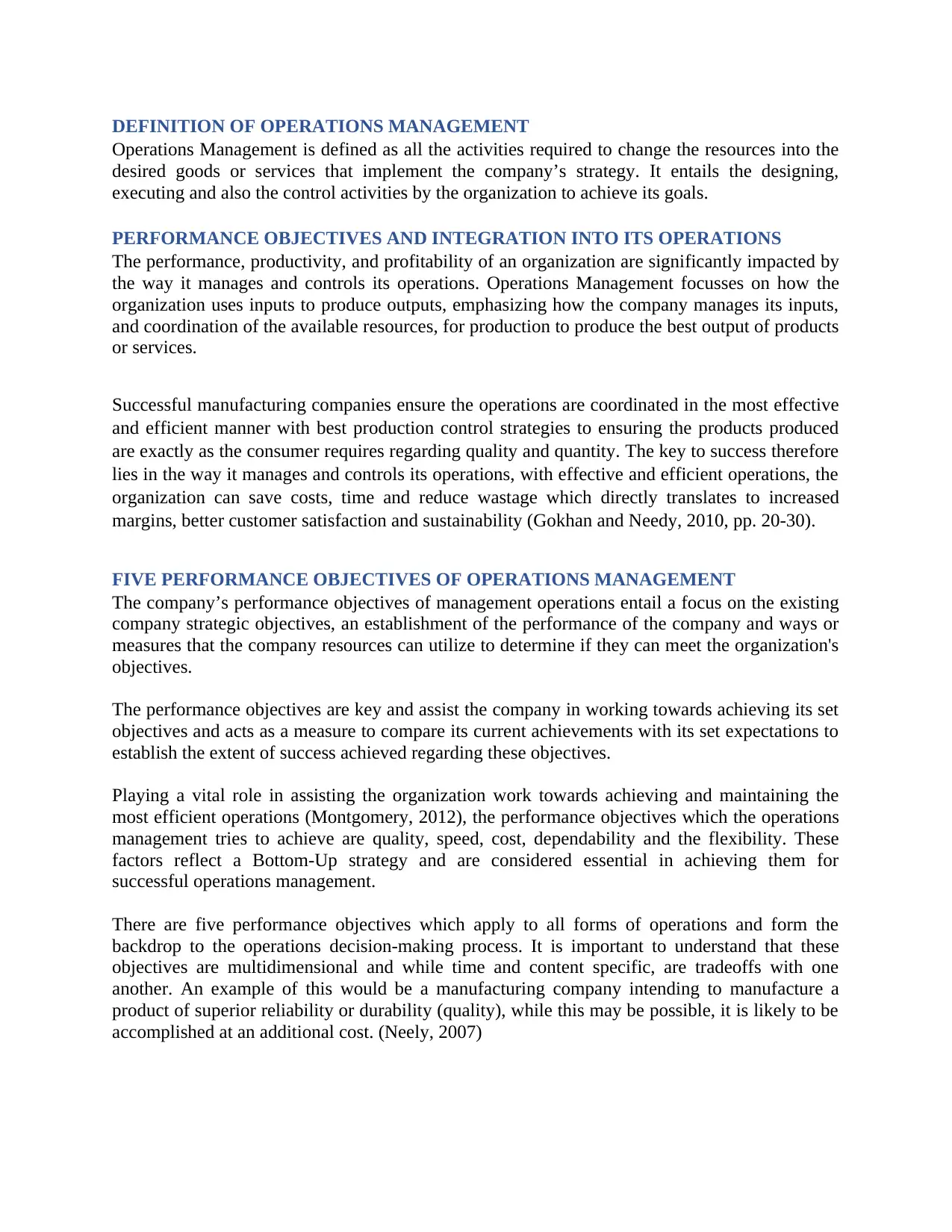
DEFINITION OF OPERATIONS MANAGEMENT
Operations Management is defined as all the activities required to change the resources into the
desired goods or services that implement the company’s strategy. It entails the designing,
executing and also the control activities by the organization to achieve its goals.
PERFORMANCE OBJECTIVES AND INTEGRATION INTO ITS OPERATIONS
The performance, productivity, and profitability of an organization are significantly impacted by
the way it manages and controls its operations. Operations Management focusses on how the
organization uses inputs to produce outputs, emphasizing how the company manages its inputs,
and coordination of the available resources, for production to produce the best output of products
or services.
Successful manufacturing companies ensure the operations are coordinated in the most effective
and efficient manner with best production control strategies to ensuring the products produced
are exactly as the consumer requires regarding quality and quantity. The key to success therefore
lies in the way it manages and controls its operations, with effective and efficient operations, the
organization can save costs, time and reduce wastage which directly translates to increased
margins, better customer satisfaction and sustainability (Gokhan and Needy, 2010, pp. 20-30).
FIVE PERFORMANCE OBJECTIVES OF OPERATIONS MANAGEMENT
The company’s performance objectives of management operations entail a focus on the existing
company strategic objectives, an establishment of the performance of the company and ways or
measures that the company resources can utilize to determine if they can meet the organization's
objectives.
The performance objectives are key and assist the company in working towards achieving its set
objectives and acts as a measure to compare its current achievements with its set expectations to
establish the extent of success achieved regarding these objectives.
Playing a vital role in assisting the organization work towards achieving and maintaining the
most efficient operations (Montgomery, 2012), the performance objectives which the operations
management tries to achieve are quality, speed, cost, dependability and the flexibility. These
factors reflect a Bottom-Up strategy and are considered essential in achieving them for
successful operations management.
There are five performance objectives which apply to all forms of operations and form the
backdrop to the operations decision-making process. It is important to understand that these
objectives are multidimensional and while time and content specific, are tradeoffs with one
another. An example of this would be a manufacturing company intending to manufacture a
product of superior reliability or durability (quality), while this may be possible, it is likely to be
accomplished at an additional cost. (Neely, 2007)
Operations Management is defined as all the activities required to change the resources into the
desired goods or services that implement the company’s strategy. It entails the designing,
executing and also the control activities by the organization to achieve its goals.
PERFORMANCE OBJECTIVES AND INTEGRATION INTO ITS OPERATIONS
The performance, productivity, and profitability of an organization are significantly impacted by
the way it manages and controls its operations. Operations Management focusses on how the
organization uses inputs to produce outputs, emphasizing how the company manages its inputs,
and coordination of the available resources, for production to produce the best output of products
or services.
Successful manufacturing companies ensure the operations are coordinated in the most effective
and efficient manner with best production control strategies to ensuring the products produced
are exactly as the consumer requires regarding quality and quantity. The key to success therefore
lies in the way it manages and controls its operations, with effective and efficient operations, the
organization can save costs, time and reduce wastage which directly translates to increased
margins, better customer satisfaction and sustainability (Gokhan and Needy, 2010, pp. 20-30).
FIVE PERFORMANCE OBJECTIVES OF OPERATIONS MANAGEMENT
The company’s performance objectives of management operations entail a focus on the existing
company strategic objectives, an establishment of the performance of the company and ways or
measures that the company resources can utilize to determine if they can meet the organization's
objectives.
The performance objectives are key and assist the company in working towards achieving its set
objectives and acts as a measure to compare its current achievements with its set expectations to
establish the extent of success achieved regarding these objectives.
Playing a vital role in assisting the organization work towards achieving and maintaining the
most efficient operations (Montgomery, 2012), the performance objectives which the operations
management tries to achieve are quality, speed, cost, dependability and the flexibility. These
factors reflect a Bottom-Up strategy and are considered essential in achieving them for
successful operations management.
There are five performance objectives which apply to all forms of operations and form the
backdrop to the operations decision-making process. It is important to understand that these
objectives are multidimensional and while time and content specific, are tradeoffs with one
another. An example of this would be a manufacturing company intending to manufacture a
product of superior reliability or durability (quality), while this may be possible, it is likely to be
accomplished at an additional cost. (Neely, 2007)
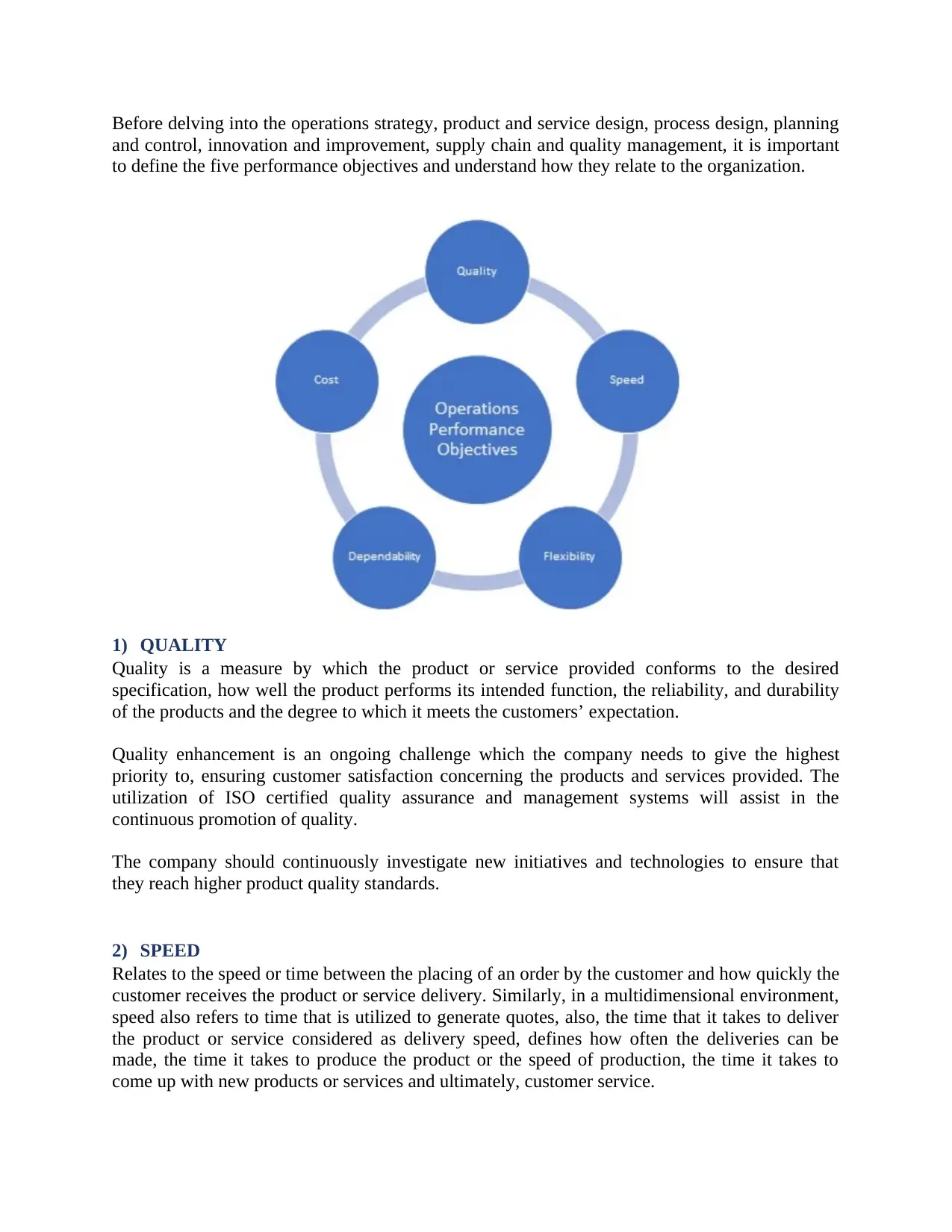
Before delving into the operations strategy, product and service design, process design, planning
and control, innovation and improvement, supply chain and quality management, it is important
to define the five performance objectives and understand how they relate to the organization.
1) QUALITY
Quality is a measure by which the product or service provided conforms to the desired
specification, how well the product performs its intended function, the reliability, and durability
of the products and the degree to which it meets the customers’ expectation.
Quality enhancement is an ongoing challenge which the company needs to give the highest
priority to, ensuring customer satisfaction concerning the products and services provided. The
utilization of ISO certified quality assurance and management systems will assist in the
continuous promotion of quality.
The company should continuously investigate new initiatives and technologies to ensure that
they reach higher product quality standards.
2) SPEED
Relates to the speed or time between the placing of an order by the customer and how quickly the
customer receives the product or service delivery. Similarly, in a multidimensional environment,
speed also refers to time that is utilized to generate quotes, also, the time that it takes to deliver
the product or service considered as delivery speed, defines how often the deliveries can be
made, the time it takes to produce the product or the speed of production, the time it takes to
come up with new products or services and ultimately, customer service.
and control, innovation and improvement, supply chain and quality management, it is important
to define the five performance objectives and understand how they relate to the organization.
1) QUALITY
Quality is a measure by which the product or service provided conforms to the desired
specification, how well the product performs its intended function, the reliability, and durability
of the products and the degree to which it meets the customers’ expectation.
Quality enhancement is an ongoing challenge which the company needs to give the highest
priority to, ensuring customer satisfaction concerning the products and services provided. The
utilization of ISO certified quality assurance and management systems will assist in the
continuous promotion of quality.
The company should continuously investigate new initiatives and technologies to ensure that
they reach higher product quality standards.
2) SPEED
Relates to the speed or time between the placing of an order by the customer and how quickly the
customer receives the product or service delivery. Similarly, in a multidimensional environment,
speed also refers to time that is utilized to generate quotes, also, the time that it takes to deliver
the product or service considered as delivery speed, defines how often the deliveries can be
made, the time it takes to produce the product or the speed of production, the time it takes to
come up with new products or services and ultimately, customer service.
Paraphrase This Document
Need a fresh take? Get an instant paraphrase of this document with our AI Paraphraser
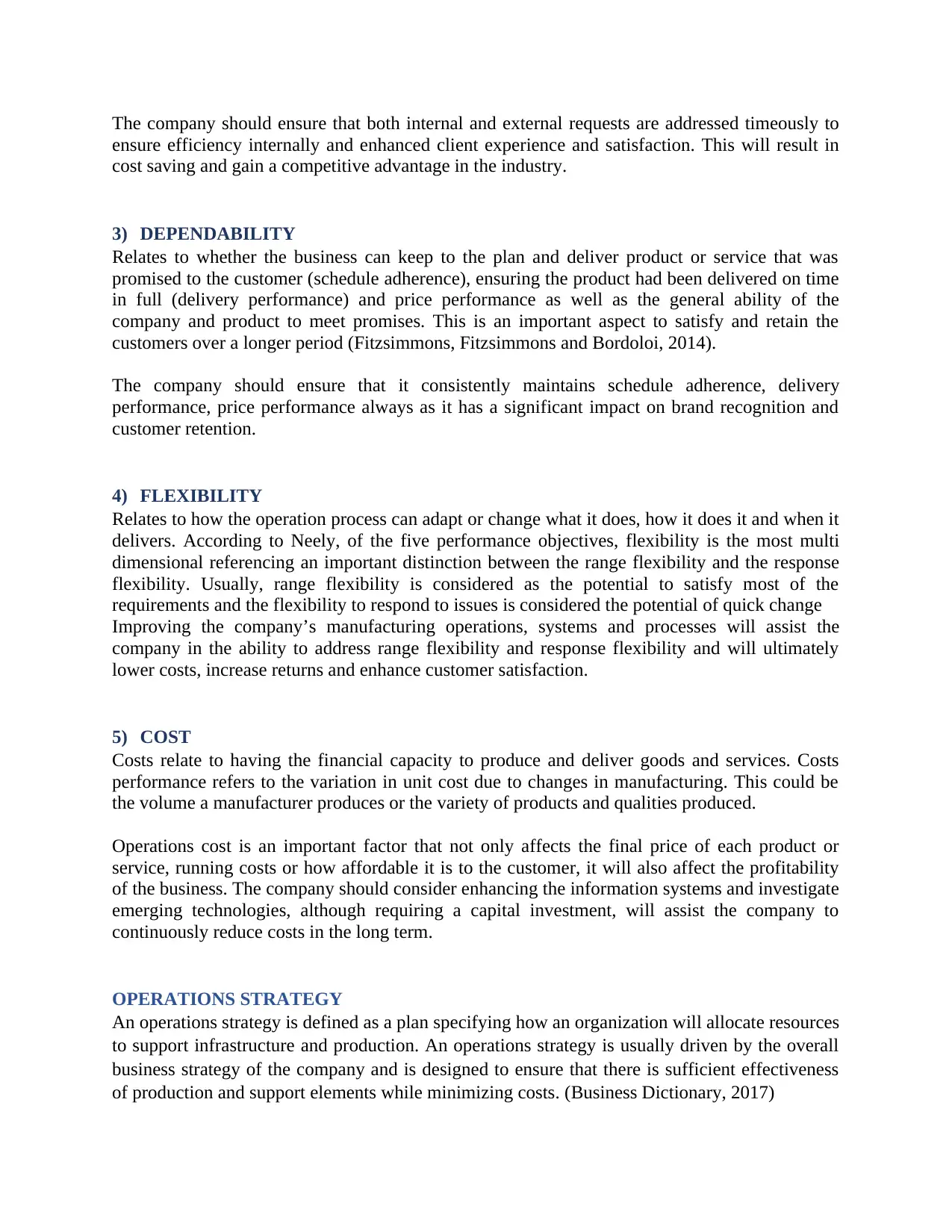
The company should ensure that both internal and external requests are addressed timeously to
ensure efficiency internally and enhanced client experience and satisfaction. This will result in
cost saving and gain a competitive advantage in the industry.
3) DEPENDABILITY
Relates to whether the business can keep to the plan and deliver product or service that was
promised to the customer (schedule adherence), ensuring the product had been delivered on time
in full (delivery performance) and price performance as well as the general ability of the
company and product to meet promises. This is an important aspect to satisfy and retain the
customers over a longer period (Fitzsimmons, Fitzsimmons and Bordoloi, 2014).
The company should ensure that it consistently maintains schedule adherence, delivery
performance, price performance always as it has a significant impact on brand recognition and
customer retention.
4) FLEXIBILITY
Relates to how the operation process can adapt or change what it does, how it does it and when it
delivers. According to Neely, of the five performance objectives, flexibility is the most multi
dimensional referencing an important distinction between the range flexibility and the response
flexibility. Usually, range flexibility is considered as the potential to satisfy most of the
requirements and the flexibility to respond to issues is considered the potential of quick change
Improving the company’s manufacturing operations, systems and processes will assist the
company in the ability to address range flexibility and response flexibility and will ultimately
lower costs, increase returns and enhance customer satisfaction.
5) COST
Costs relate to having the financial capacity to produce and deliver goods and services. Costs
performance refers to the variation in unit cost due to changes in manufacturing. This could be
the volume a manufacturer produces or the variety of products and qualities produced.
Operations cost is an important factor that not only affects the final price of each product or
service, running costs or how affordable it is to the customer, it will also affect the profitability
of the business. The company should consider enhancing the information systems and investigate
emerging technologies, although requiring a capital investment, will assist the company to
continuously reduce costs in the long term.
OPERATIONS STRATEGY
An operations strategy is defined as a plan specifying how an organization will allocate resources
to support infrastructure and production. An operations strategy is usually driven by the overall
business strategy of the company and is designed to ensure that there is sufficient effectiveness
of production and support elements while minimizing costs. (Business Dictionary, 2017)
ensure efficiency internally and enhanced client experience and satisfaction. This will result in
cost saving and gain a competitive advantage in the industry.
3) DEPENDABILITY
Relates to whether the business can keep to the plan and deliver product or service that was
promised to the customer (schedule adherence), ensuring the product had been delivered on time
in full (delivery performance) and price performance as well as the general ability of the
company and product to meet promises. This is an important aspect to satisfy and retain the
customers over a longer period (Fitzsimmons, Fitzsimmons and Bordoloi, 2014).
The company should ensure that it consistently maintains schedule adherence, delivery
performance, price performance always as it has a significant impact on brand recognition and
customer retention.
4) FLEXIBILITY
Relates to how the operation process can adapt or change what it does, how it does it and when it
delivers. According to Neely, of the five performance objectives, flexibility is the most multi
dimensional referencing an important distinction between the range flexibility and the response
flexibility. Usually, range flexibility is considered as the potential to satisfy most of the
requirements and the flexibility to respond to issues is considered the potential of quick change
Improving the company’s manufacturing operations, systems and processes will assist the
company in the ability to address range flexibility and response flexibility and will ultimately
lower costs, increase returns and enhance customer satisfaction.
5) COST
Costs relate to having the financial capacity to produce and deliver goods and services. Costs
performance refers to the variation in unit cost due to changes in manufacturing. This could be
the volume a manufacturer produces or the variety of products and qualities produced.
Operations cost is an important factor that not only affects the final price of each product or
service, running costs or how affordable it is to the customer, it will also affect the profitability
of the business. The company should consider enhancing the information systems and investigate
emerging technologies, although requiring a capital investment, will assist the company to
continuously reduce costs in the long term.
OPERATIONS STRATEGY
An operations strategy is defined as a plan specifying how an organization will allocate resources
to support infrastructure and production. An operations strategy is usually driven by the overall
business strategy of the company and is designed to ensure that there is sufficient effectiveness
of production and support elements while minimizing costs. (Business Dictionary, 2017)
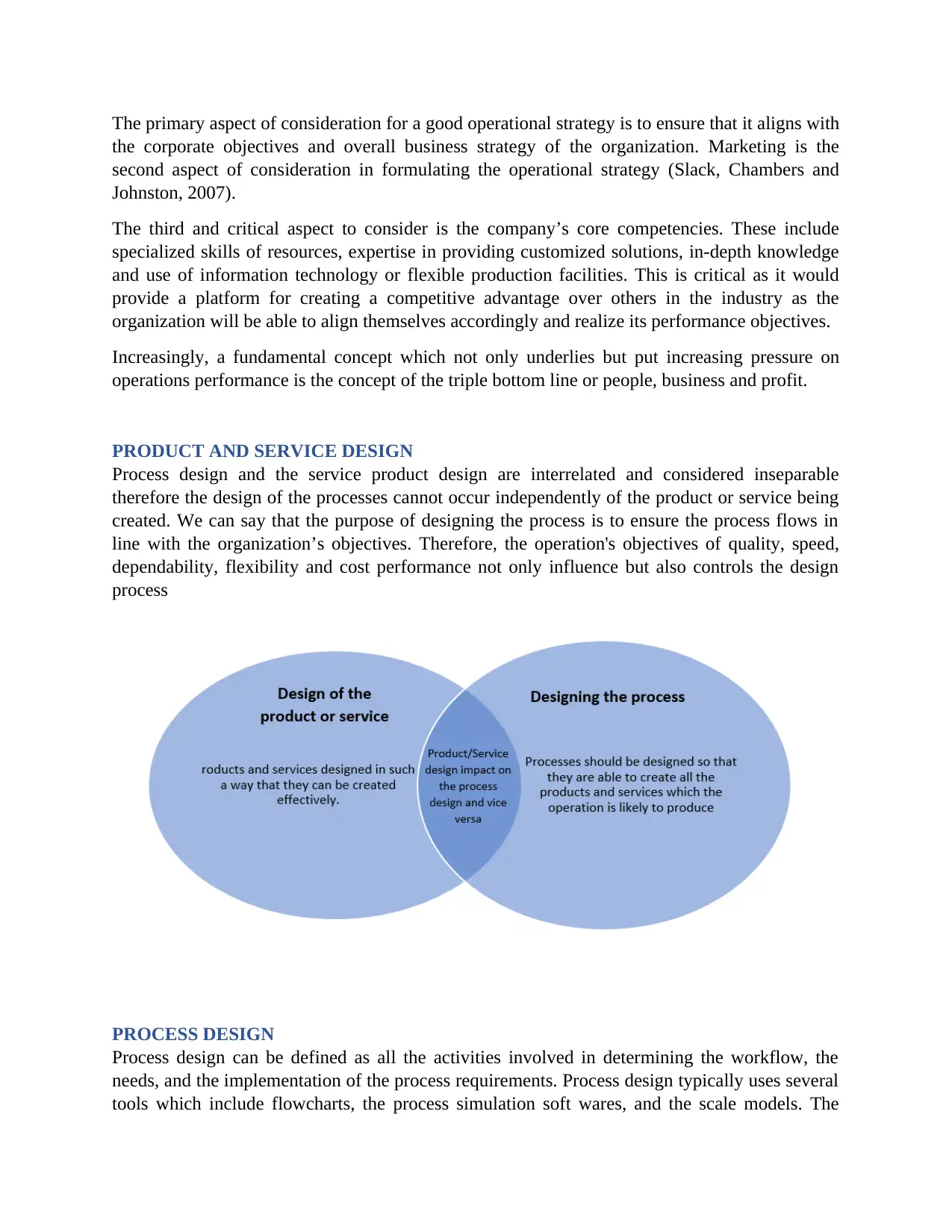
The primary aspect of consideration for a good operational strategy is to ensure that it aligns with
the corporate objectives and overall business strategy of the organization. Marketing is the
second aspect of consideration in formulating the operational strategy (Slack, Chambers and
Johnston, 2007).
The third and critical aspect to consider is the company’s core competencies. These include
specialized skills of resources, expertise in providing customized solutions, in-depth knowledge
and use of information technology or flexible production facilities. This is critical as it would
provide a platform for creating a competitive advantage over others in the industry as the
organization will be able to align themselves accordingly and realize its performance objectives.
Increasingly, a fundamental concept which not only underlies but put increasing pressure on
operations performance is the concept of the triple bottom line or people, business and profit.
PRODUCT AND SERVICE DESIGN
Process design and the service product design are interrelated and considered inseparable
therefore the design of the processes cannot occur independently of the product or service being
created. We can say that the purpose of designing the process is to ensure the process flows in
line with the organization’s objectives. Therefore, the operation's objectives of quality, speed,
dependability, flexibility and cost performance not only influence but also controls the design
process
PROCESS DESIGN
Process design can be defined as all the activities involved in determining the workflow, the
needs, and the implementation of the process requirements. Process design typically uses several
tools which include flowcharts, the process simulation soft wares, and the scale models. The
the corporate objectives and overall business strategy of the organization. Marketing is the
second aspect of consideration in formulating the operational strategy (Slack, Chambers and
Johnston, 2007).
The third and critical aspect to consider is the company’s core competencies. These include
specialized skills of resources, expertise in providing customized solutions, in-depth knowledge
and use of information technology or flexible production facilities. This is critical as it would
provide a platform for creating a competitive advantage over others in the industry as the
organization will be able to align themselves accordingly and realize its performance objectives.
Increasingly, a fundamental concept which not only underlies but put increasing pressure on
operations performance is the concept of the triple bottom line or people, business and profit.
PRODUCT AND SERVICE DESIGN
Process design and the service product design are interrelated and considered inseparable
therefore the design of the processes cannot occur independently of the product or service being
created. We can say that the purpose of designing the process is to ensure the process flows in
line with the organization’s objectives. Therefore, the operation's objectives of quality, speed,
dependability, flexibility and cost performance not only influence but also controls the design
process
PROCESS DESIGN
Process design can be defined as all the activities involved in determining the workflow, the
needs, and the implementation of the process requirements. Process design typically uses several
tools which include flowcharts, the process simulation soft wares, and the scale models. The
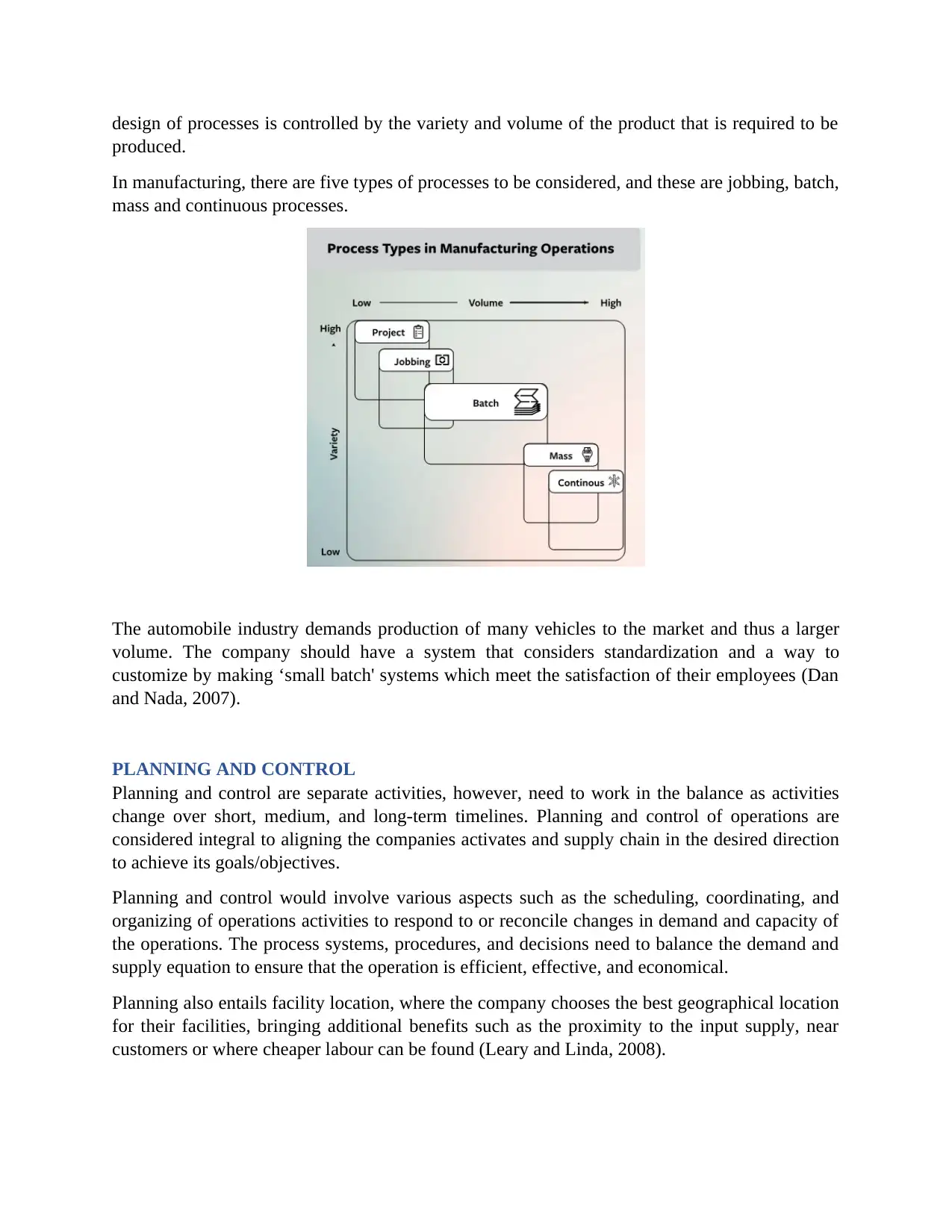
design of processes is controlled by the variety and volume of the product that is required to be
produced.
In manufacturing, there are five types of processes to be considered, and these are jobbing, batch,
mass and continuous processes.
The automobile industry demands production of many vehicles to the market and thus a larger
volume. The company should have a system that considers standardization and a way to
customize by making ‘small batch' systems which meet the satisfaction of their employees (Dan
and Nada, 2007).
PLANNING AND CONTROL
Planning and control are separate activities, however, need to work in the balance as activities
change over short, medium, and long-term timelines. Planning and control of operations are
considered integral to aligning the companies activates and supply chain in the desired direction
to achieve its goals/objectives.
Planning and control would involve various aspects such as the scheduling, coordinating, and
organizing of operations activities to respond to or reconcile changes in demand and capacity of
the operations. The process systems, procedures, and decisions need to balance the demand and
supply equation to ensure that the operation is efficient, effective, and economical.
Planning also entails facility location, where the company chooses the best geographical location
for their facilities, bringing additional benefits such as the proximity to the input supply, near
customers or where cheaper labour can be found (Leary and Linda, 2008).
produced.
In manufacturing, there are five types of processes to be considered, and these are jobbing, batch,
mass and continuous processes.
The automobile industry demands production of many vehicles to the market and thus a larger
volume. The company should have a system that considers standardization and a way to
customize by making ‘small batch' systems which meet the satisfaction of their employees (Dan
and Nada, 2007).
PLANNING AND CONTROL
Planning and control are separate activities, however, need to work in the balance as activities
change over short, medium, and long-term timelines. Planning and control of operations are
considered integral to aligning the companies activates and supply chain in the desired direction
to achieve its goals/objectives.
Planning and control would involve various aspects such as the scheduling, coordinating, and
organizing of operations activities to respond to or reconcile changes in demand and capacity of
the operations. The process systems, procedures, and decisions need to balance the demand and
supply equation to ensure that the operation is efficient, effective, and economical.
Planning also entails facility location, where the company chooses the best geographical location
for their facilities, bringing additional benefits such as the proximity to the input supply, near
customers or where cheaper labour can be found (Leary and Linda, 2008).
Secure Best Marks with AI Grader
Need help grading? Try our AI Grader for instant feedback on your assignments.
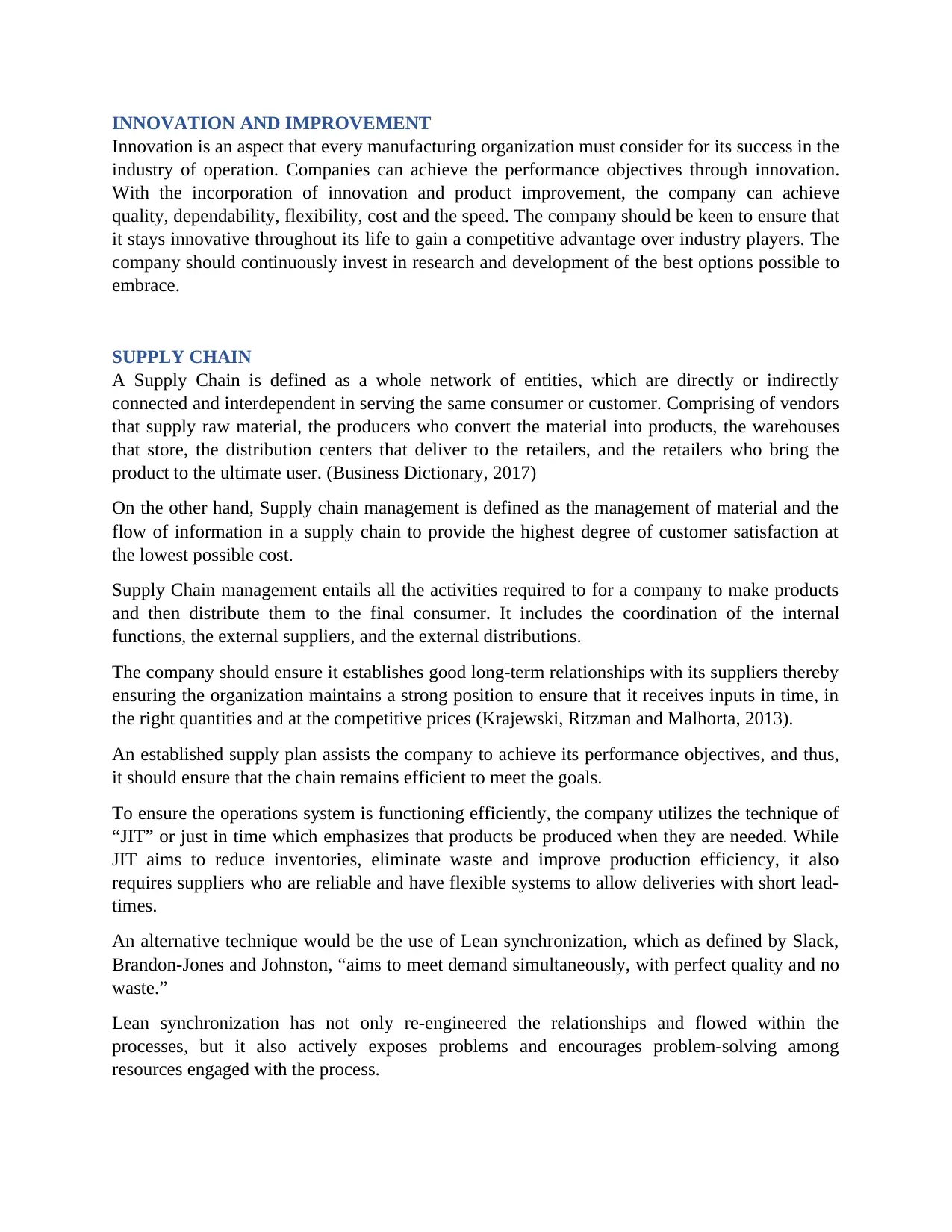
INNOVATION AND IMPROVEMENT
Innovation is an aspect that every manufacturing organization must consider for its success in the
industry of operation. Companies can achieve the performance objectives through innovation.
With the incorporation of innovation and product improvement, the company can achieve
quality, dependability, flexibility, cost and the speed. The company should be keen to ensure that
it stays innovative throughout its life to gain a competitive advantage over industry players. The
company should continuously invest in research and development of the best options possible to
embrace.
SUPPLY CHAIN
A Supply Chain is defined as a whole network of entities, which are directly or indirectly
connected and interdependent in serving the same consumer or customer. Comprising of vendors
that supply raw material, the producers who convert the material into products, the warehouses
that store, the distribution centers that deliver to the retailers, and the retailers who bring the
product to the ultimate user. (Business Dictionary, 2017)
On the other hand, Supply chain management is defined as the management of material and the
flow of information in a supply chain to provide the highest degree of customer satisfaction at
the lowest possible cost.
Supply Chain management entails all the activities required to for a company to make products
and then distribute them to the final consumer. It includes the coordination of the internal
functions, the external suppliers, and the external distributions.
The company should ensure it establishes good long-term relationships with its suppliers thereby
ensuring the organization maintains a strong position to ensure that it receives inputs in time, in
the right quantities and at the competitive prices (Krajewski, Ritzman and Malhorta, 2013).
An established supply plan assists the company to achieve its performance objectives, and thus,
it should ensure that the chain remains efficient to meet the goals.
To ensure the operations system is functioning efficiently, the company utilizes the technique of
“JIT” or just in time which emphasizes that products be produced when they are needed. While
JIT aims to reduce inventories, eliminate waste and improve production efficiency, it also
requires suppliers who are reliable and have flexible systems to allow deliveries with short lead-
times.
An alternative technique would be the use of Lean synchronization, which as defined by Slack,
Brandon-Jones and Johnston, “aims to meet demand simultaneously, with perfect quality and no
waste.”
Lean synchronization has not only re-engineered the relationships and flowed within the
processes, but it also actively exposes problems and encourages problem-solving among
resources engaged with the process.
Innovation is an aspect that every manufacturing organization must consider for its success in the
industry of operation. Companies can achieve the performance objectives through innovation.
With the incorporation of innovation and product improvement, the company can achieve
quality, dependability, flexibility, cost and the speed. The company should be keen to ensure that
it stays innovative throughout its life to gain a competitive advantage over industry players. The
company should continuously invest in research and development of the best options possible to
embrace.
SUPPLY CHAIN
A Supply Chain is defined as a whole network of entities, which are directly or indirectly
connected and interdependent in serving the same consumer or customer. Comprising of vendors
that supply raw material, the producers who convert the material into products, the warehouses
that store, the distribution centers that deliver to the retailers, and the retailers who bring the
product to the ultimate user. (Business Dictionary, 2017)
On the other hand, Supply chain management is defined as the management of material and the
flow of information in a supply chain to provide the highest degree of customer satisfaction at
the lowest possible cost.
Supply Chain management entails all the activities required to for a company to make products
and then distribute them to the final consumer. It includes the coordination of the internal
functions, the external suppliers, and the external distributions.
The company should ensure it establishes good long-term relationships with its suppliers thereby
ensuring the organization maintains a strong position to ensure that it receives inputs in time, in
the right quantities and at the competitive prices (Krajewski, Ritzman and Malhorta, 2013).
An established supply plan assists the company to achieve its performance objectives, and thus,
it should ensure that the chain remains efficient to meet the goals.
To ensure the operations system is functioning efficiently, the company utilizes the technique of
“JIT” or just in time which emphasizes that products be produced when they are needed. While
JIT aims to reduce inventories, eliminate waste and improve production efficiency, it also
requires suppliers who are reliable and have flexible systems to allow deliveries with short lead-
times.
An alternative technique would be the use of Lean synchronization, which as defined by Slack,
Brandon-Jones and Johnston, “aims to meet demand simultaneously, with perfect quality and no
waste.”
Lean synchronization has not only re-engineered the relationships and flowed within the
processes, but it also actively exposes problems and encourages problem-solving among
resources engaged with the process.
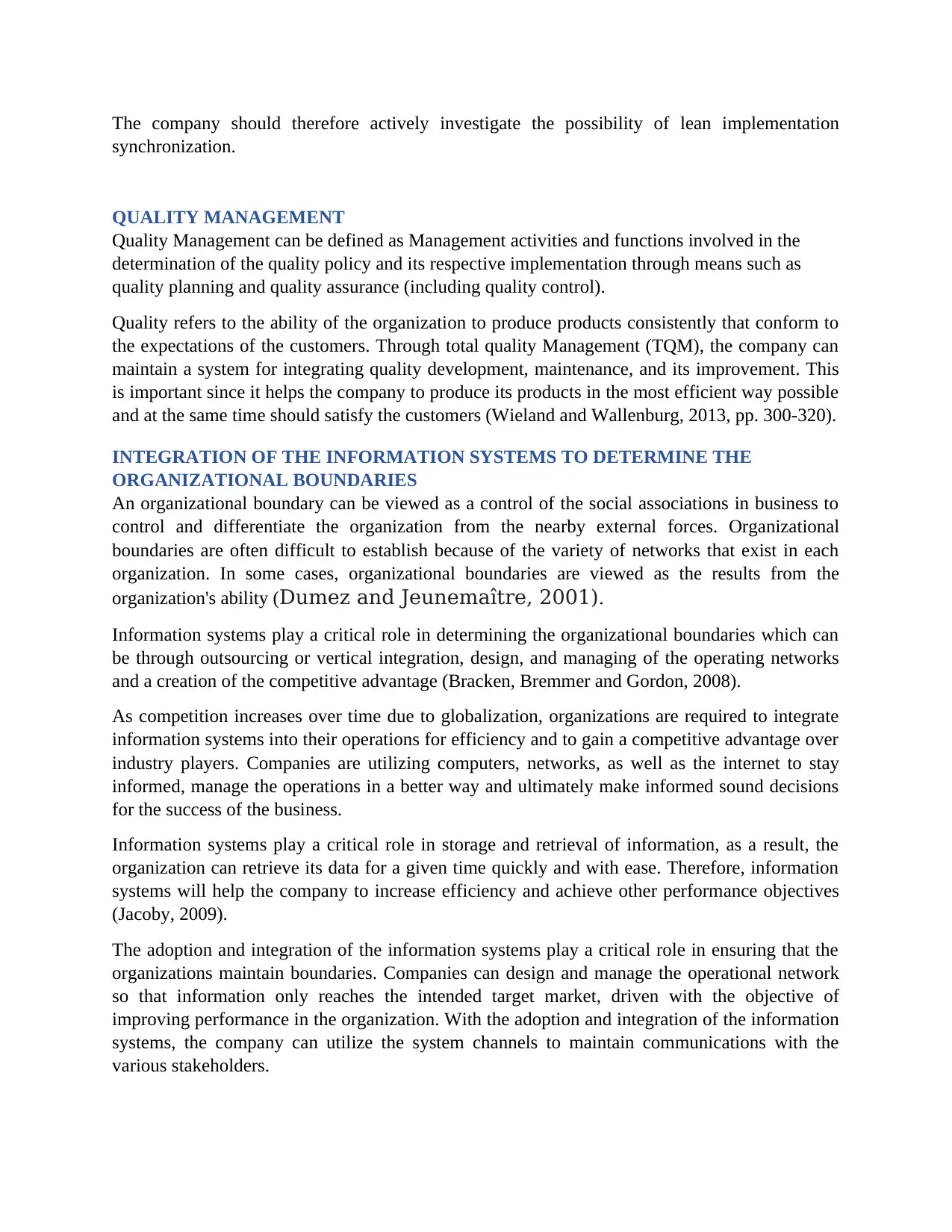
The company should therefore actively investigate the possibility of lean implementation
synchronization.
QUALITY MANAGEMENT
Quality Management can be defined as Management activities and functions involved in the
determination of the quality policy and its respective implementation through means such as
quality planning and quality assurance (including quality control).
Quality refers to the ability of the organization to produce products consistently that conform to
the expectations of the customers. Through total quality Management (TQM), the company can
maintain a system for integrating quality development, maintenance, and its improvement. This
is important since it helps the company to produce its products in the most efficient way possible
and at the same time should satisfy the customers (Wieland and Wallenburg, 2013, pp. 300-320).
INTEGRATION OF THE INFORMATION SYSTEMS TO DETERMINE THE
ORGANIZATIONAL BOUNDARIES
An organizational boundary can be viewed as a control of the social associations in business to
control and differentiate the organization from the nearby external forces. Organizational
boundaries are often difficult to establish because of the variety of networks that exist in each
organization. In some cases, organizational boundaries are viewed as the results from the
organization's ability (Dumez and Jeunemaître, 2001).
Information systems play a critical role in determining the organizational boundaries which can
be through outsourcing or vertical integration, design, and managing of the operating networks
and a creation of the competitive advantage (Bracken, Bremmer and Gordon, 2008).
As competition increases over time due to globalization, organizations are required to integrate
information systems into their operations for efficiency and to gain a competitive advantage over
industry players. Companies are utilizing computers, networks, as well as the internet to stay
informed, manage the operations in a better way and ultimately make informed sound decisions
for the success of the business.
Information systems play a critical role in storage and retrieval of information, as a result, the
organization can retrieve its data for a given time quickly and with ease. Therefore, information
systems will help the company to increase efficiency and achieve other performance objectives
(Jacoby, 2009).
The adoption and integration of the information systems play a critical role in ensuring that the
organizations maintain boundaries. Companies can design and manage the operational network
so that information only reaches the intended target market, driven with the objective of
improving performance in the organization. With the adoption and integration of the information
systems, the company can utilize the system channels to maintain communications with the
various stakeholders.
synchronization.
QUALITY MANAGEMENT
Quality Management can be defined as Management activities and functions involved in the
determination of the quality policy and its respective implementation through means such as
quality planning and quality assurance (including quality control).
Quality refers to the ability of the organization to produce products consistently that conform to
the expectations of the customers. Through total quality Management (TQM), the company can
maintain a system for integrating quality development, maintenance, and its improvement. This
is important since it helps the company to produce its products in the most efficient way possible
and at the same time should satisfy the customers (Wieland and Wallenburg, 2013, pp. 300-320).
INTEGRATION OF THE INFORMATION SYSTEMS TO DETERMINE THE
ORGANIZATIONAL BOUNDARIES
An organizational boundary can be viewed as a control of the social associations in business to
control and differentiate the organization from the nearby external forces. Organizational
boundaries are often difficult to establish because of the variety of networks that exist in each
organization. In some cases, organizational boundaries are viewed as the results from the
organization's ability (Dumez and Jeunemaître, 2001).
Information systems play a critical role in determining the organizational boundaries which can
be through outsourcing or vertical integration, design, and managing of the operating networks
and a creation of the competitive advantage (Bracken, Bremmer and Gordon, 2008).
As competition increases over time due to globalization, organizations are required to integrate
information systems into their operations for efficiency and to gain a competitive advantage over
industry players. Companies are utilizing computers, networks, as well as the internet to stay
informed, manage the operations in a better way and ultimately make informed sound decisions
for the success of the business.
Information systems play a critical role in storage and retrieval of information, as a result, the
organization can retrieve its data for a given time quickly and with ease. Therefore, information
systems will help the company to increase efficiency and achieve other performance objectives
(Jacoby, 2009).
The adoption and integration of the information systems play a critical role in ensuring that the
organizations maintain boundaries. Companies can design and manage the operational network
so that information only reaches the intended target market, driven with the objective of
improving performance in the organization. With the adoption and integration of the information
systems, the company can utilize the system channels to maintain communications with the
various stakeholders.
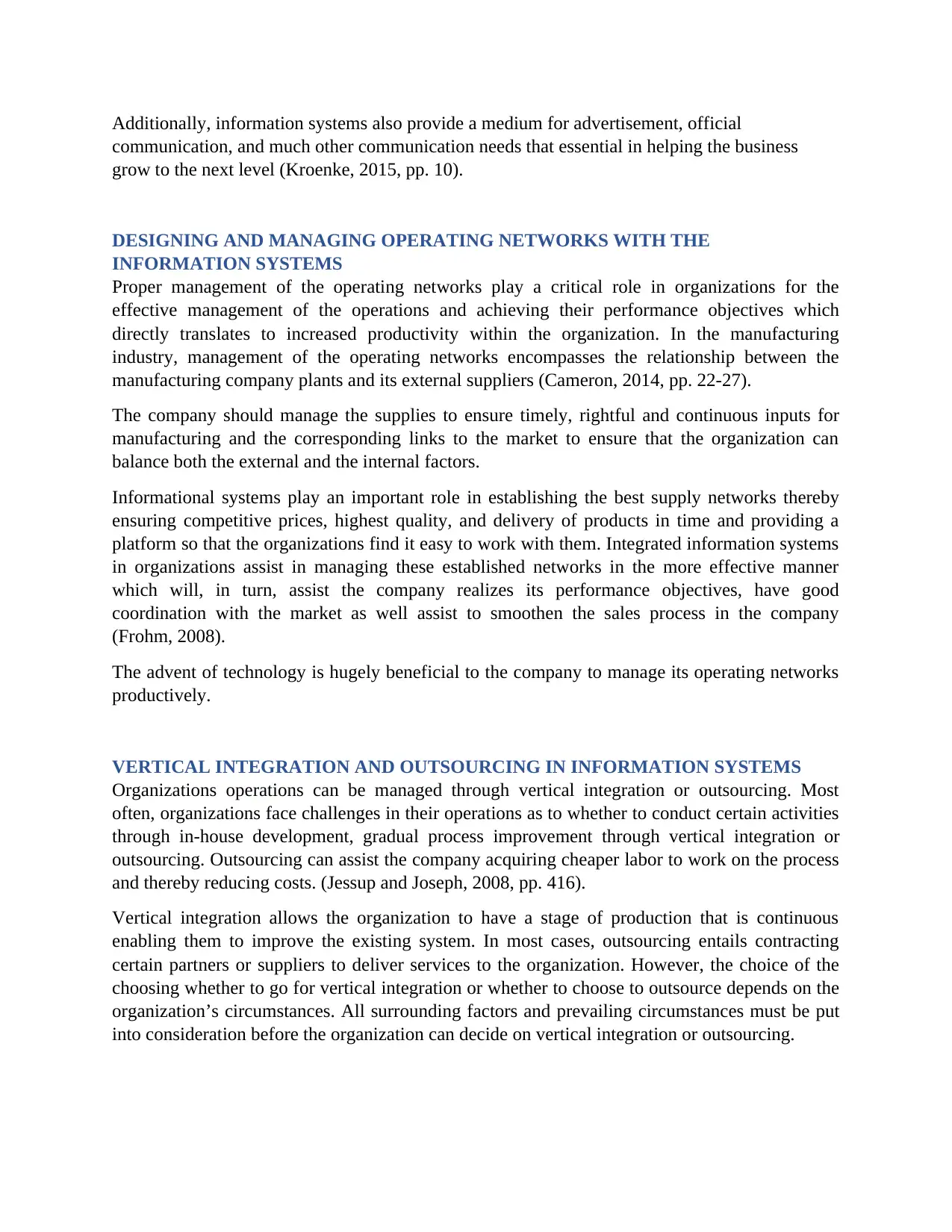
Additionally, information systems also provide a medium for advertisement, official
communication, and much other communication needs that essential in helping the business
grow to the next level (Kroenke, 2015, pp. 10).
DESIGNING AND MANAGING OPERATING NETWORKS WITH THE
INFORMATION SYSTEMS
Proper management of the operating networks play a critical role in organizations for the
effective management of the operations and achieving their performance objectives which
directly translates to increased productivity within the organization. In the manufacturing
industry, management of the operating networks encompasses the relationship between the
manufacturing company plants and its external suppliers (Cameron, 2014, pp. 22-27).
The company should manage the supplies to ensure timely, rightful and continuous inputs for
manufacturing and the corresponding links to the market to ensure that the organization can
balance both the external and the internal factors.
Informational systems play an important role in establishing the best supply networks thereby
ensuring competitive prices, highest quality, and delivery of products in time and providing a
platform so that the organizations find it easy to work with them. Integrated information systems
in organizations assist in managing these established networks in the more effective manner
which will, in turn, assist the company realizes its performance objectives, have good
coordination with the market as well assist to smoothen the sales process in the company
(Frohm, 2008).
The advent of technology is hugely beneficial to the company to manage its operating networks
productively.
VERTICAL INTEGRATION AND OUTSOURCING IN INFORMATION SYSTEMS
Organizations operations can be managed through vertical integration or outsourcing. Most
often, organizations face challenges in their operations as to whether to conduct certain activities
through in-house development, gradual process improvement through vertical integration or
outsourcing. Outsourcing can assist the company acquiring cheaper labor to work on the process
and thereby reducing costs. (Jessup and Joseph, 2008, pp. 416).
Vertical integration allows the organization to have a stage of production that is continuous
enabling them to improve the existing system. In most cases, outsourcing entails contracting
certain partners or suppliers to deliver services to the organization. However, the choice of the
choosing whether to go for vertical integration or whether to choose to outsource depends on the
organization’s circumstances. All surrounding factors and prevailing circumstances must be put
into consideration before the organization can decide on vertical integration or outsourcing.
communication, and much other communication needs that essential in helping the business
grow to the next level (Kroenke, 2015, pp. 10).
DESIGNING AND MANAGING OPERATING NETWORKS WITH THE
INFORMATION SYSTEMS
Proper management of the operating networks play a critical role in organizations for the
effective management of the operations and achieving their performance objectives which
directly translates to increased productivity within the organization. In the manufacturing
industry, management of the operating networks encompasses the relationship between the
manufacturing company plants and its external suppliers (Cameron, 2014, pp. 22-27).
The company should manage the supplies to ensure timely, rightful and continuous inputs for
manufacturing and the corresponding links to the market to ensure that the organization can
balance both the external and the internal factors.
Informational systems play an important role in establishing the best supply networks thereby
ensuring competitive prices, highest quality, and delivery of products in time and providing a
platform so that the organizations find it easy to work with them. Integrated information systems
in organizations assist in managing these established networks in the more effective manner
which will, in turn, assist the company realizes its performance objectives, have good
coordination with the market as well assist to smoothen the sales process in the company
(Frohm, 2008).
The advent of technology is hugely beneficial to the company to manage its operating networks
productively.
VERTICAL INTEGRATION AND OUTSOURCING IN INFORMATION SYSTEMS
Organizations operations can be managed through vertical integration or outsourcing. Most
often, organizations face challenges in their operations as to whether to conduct certain activities
through in-house development, gradual process improvement through vertical integration or
outsourcing. Outsourcing can assist the company acquiring cheaper labor to work on the process
and thereby reducing costs. (Jessup and Joseph, 2008, pp. 416).
Vertical integration allows the organization to have a stage of production that is continuous
enabling them to improve the existing system. In most cases, outsourcing entails contracting
certain partners or suppliers to deliver services to the organization. However, the choice of the
choosing whether to go for vertical integration or whether to choose to outsource depends on the
organization’s circumstances. All surrounding factors and prevailing circumstances must be put
into consideration before the organization can decide on vertical integration or outsourcing.
Paraphrase This Document
Need a fresh take? Get an instant paraphrase of this document with our AI Paraphraser
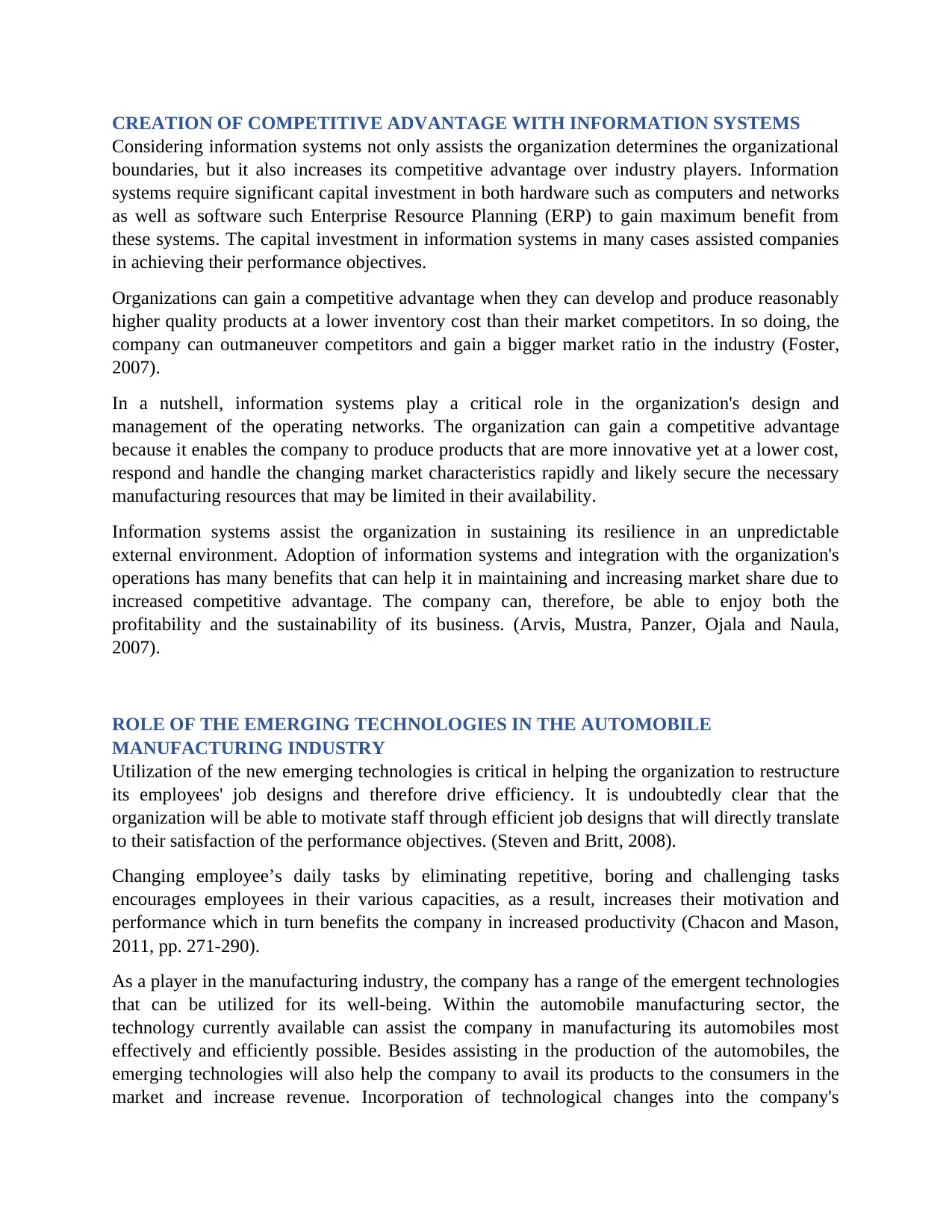
CREATION OF COMPETITIVE ADVANTAGE WITH INFORMATION SYSTEMS
Considering information systems not only assists the organization determines the organizational
boundaries, but it also increases its competitive advantage over industry players. Information
systems require significant capital investment in both hardware such as computers and networks
as well as software such Enterprise Resource Planning (ERP) to gain maximum benefit from
these systems. The capital investment in information systems in many cases assisted companies
in achieving their performance objectives.
Organizations can gain a competitive advantage when they can develop and produce reasonably
higher quality products at a lower inventory cost than their market competitors. In so doing, the
company can outmaneuver competitors and gain a bigger market ratio in the industry (Foster,
2007).
In a nutshell, information systems play a critical role in the organization's design and
management of the operating networks. The organization can gain a competitive advantage
because it enables the company to produce products that are more innovative yet at a lower cost,
respond and handle the changing market characteristics rapidly and likely secure the necessary
manufacturing resources that may be limited in their availability.
Information systems assist the organization in sustaining its resilience in an unpredictable
external environment. Adoption of information systems and integration with the organization's
operations has many benefits that can help it in maintaining and increasing market share due to
increased competitive advantage. The company can, therefore, be able to enjoy both the
profitability and the sustainability of its business. (Arvis, Mustra, Panzer, Ojala and Naula,
2007).
ROLE OF THE EMERGING TECHNOLOGIES IN THE AUTOMOBILE
MANUFACTURING INDUSTRY
Utilization of the new emerging technologies is critical in helping the organization to restructure
its employees' job designs and therefore drive efficiency. It is undoubtedly clear that the
organization will be able to motivate staff through efficient job designs that will directly translate
to their satisfaction of the performance objectives. (Steven and Britt, 2008).
Changing employee’s daily tasks by eliminating repetitive, boring and challenging tasks
encourages employees in their various capacities, as a result, increases their motivation and
performance which in turn benefits the company in increased productivity (Chacon and Mason,
2011, pp. 271-290).
As a player in the manufacturing industry, the company has a range of the emergent technologies
that can be utilized for its well-being. Within the automobile manufacturing sector, the
technology currently available can assist the company in manufacturing its automobiles most
effectively and efficiently possible. Besides assisting in the production of the automobiles, the
emerging technologies will also help the company to avail its products to the consumers in the
market and increase revenue. Incorporation of technological changes into the company's
Considering information systems not only assists the organization determines the organizational
boundaries, but it also increases its competitive advantage over industry players. Information
systems require significant capital investment in both hardware such as computers and networks
as well as software such Enterprise Resource Planning (ERP) to gain maximum benefit from
these systems. The capital investment in information systems in many cases assisted companies
in achieving their performance objectives.
Organizations can gain a competitive advantage when they can develop and produce reasonably
higher quality products at a lower inventory cost than their market competitors. In so doing, the
company can outmaneuver competitors and gain a bigger market ratio in the industry (Foster,
2007).
In a nutshell, information systems play a critical role in the organization's design and
management of the operating networks. The organization can gain a competitive advantage
because it enables the company to produce products that are more innovative yet at a lower cost,
respond and handle the changing market characteristics rapidly and likely secure the necessary
manufacturing resources that may be limited in their availability.
Information systems assist the organization in sustaining its resilience in an unpredictable
external environment. Adoption of information systems and integration with the organization's
operations has many benefits that can help it in maintaining and increasing market share due to
increased competitive advantage. The company can, therefore, be able to enjoy both the
profitability and the sustainability of its business. (Arvis, Mustra, Panzer, Ojala and Naula,
2007).
ROLE OF THE EMERGING TECHNOLOGIES IN THE AUTOMOBILE
MANUFACTURING INDUSTRY
Utilization of the new emerging technologies is critical in helping the organization to restructure
its employees' job designs and therefore drive efficiency. It is undoubtedly clear that the
organization will be able to motivate staff through efficient job designs that will directly translate
to their satisfaction of the performance objectives. (Steven and Britt, 2008).
Changing employee’s daily tasks by eliminating repetitive, boring and challenging tasks
encourages employees in their various capacities, as a result, increases their motivation and
performance which in turn benefits the company in increased productivity (Chacon and Mason,
2011, pp. 271-290).
As a player in the manufacturing industry, the company has a range of the emergent technologies
that can be utilized for its well-being. Within the automobile manufacturing sector, the
technology currently available can assist the company in manufacturing its automobiles most
effectively and efficiently possible. Besides assisting in the production of the automobiles, the
emerging technologies will also help the company to avail its products to the consumers in the
market and increase revenue. Incorporation of technological changes into the company's
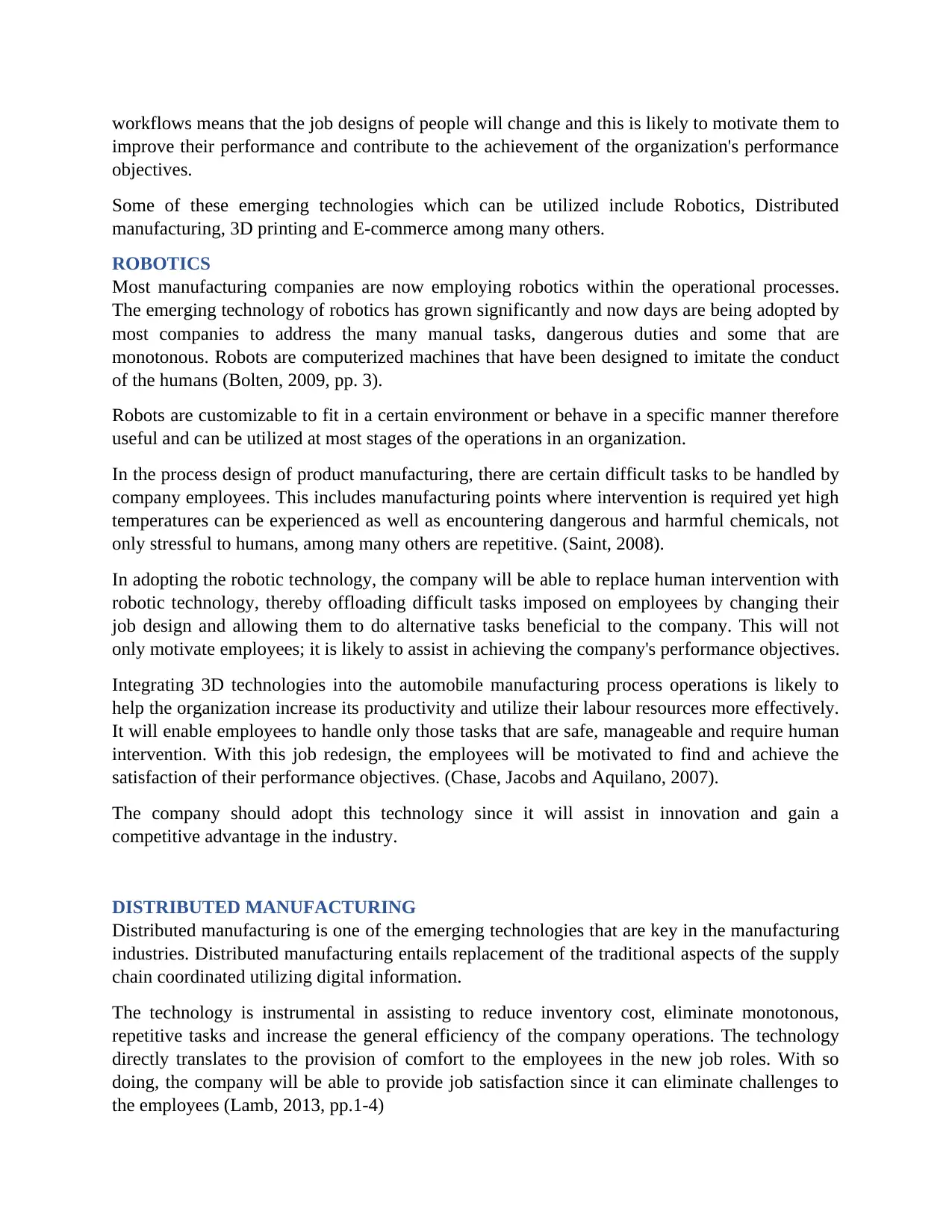
workflows means that the job designs of people will change and this is likely to motivate them to
improve their performance and contribute to the achievement of the organization's performance
objectives.
Some of these emerging technologies which can be utilized include Robotics, Distributed
manufacturing, 3D printing and E-commerce among many others.
ROBOTICS
Most manufacturing companies are now employing robotics within the operational processes.
The emerging technology of robotics has grown significantly and now days are being adopted by
most companies to address the many manual tasks, dangerous duties and some that are
monotonous. Robots are computerized machines that have been designed to imitate the conduct
of the humans (Bolten, 2009, pp. 3).
Robots are customizable to fit in a certain environment or behave in a specific manner therefore
useful and can be utilized at most stages of the operations in an organization.
In the process design of product manufacturing, there are certain difficult tasks to be handled by
company employees. This includes manufacturing points where intervention is required yet high
temperatures can be experienced as well as encountering dangerous and harmful chemicals, not
only stressful to humans, among many others are repetitive. (Saint, 2008).
In adopting the robotic technology, the company will be able to replace human intervention with
robotic technology, thereby offloading difficult tasks imposed on employees by changing their
job design and allowing them to do alternative tasks beneficial to the company. This will not
only motivate employees; it is likely to assist in achieving the company's performance objectives.
Integrating 3D technologies into the automobile manufacturing process operations is likely to
help the organization increase its productivity and utilize their labour resources more effectively.
It will enable employees to handle only those tasks that are safe, manageable and require human
intervention. With this job redesign, the employees will be motivated to find and achieve the
satisfaction of their performance objectives. (Chase, Jacobs and Aquilano, 2007).
The company should adopt this technology since it will assist in innovation and gain a
competitive advantage in the industry.
DISTRIBUTED MANUFACTURING
Distributed manufacturing is one of the emerging technologies that are key in the manufacturing
industries. Distributed manufacturing entails replacement of the traditional aspects of the supply
chain coordinated utilizing digital information.
The technology is instrumental in assisting to reduce inventory cost, eliminate monotonous,
repetitive tasks and increase the general efficiency of the company operations. The technology
directly translates to the provision of comfort to the employees in the new job roles. With so
doing, the company will be able to provide job satisfaction since it can eliminate challenges to
the employees (Lamb, 2013, pp.1-4)
improve their performance and contribute to the achievement of the organization's performance
objectives.
Some of these emerging technologies which can be utilized include Robotics, Distributed
manufacturing, 3D printing and E-commerce among many others.
ROBOTICS
Most manufacturing companies are now employing robotics within the operational processes.
The emerging technology of robotics has grown significantly and now days are being adopted by
most companies to address the many manual tasks, dangerous duties and some that are
monotonous. Robots are computerized machines that have been designed to imitate the conduct
of the humans (Bolten, 2009, pp. 3).
Robots are customizable to fit in a certain environment or behave in a specific manner therefore
useful and can be utilized at most stages of the operations in an organization.
In the process design of product manufacturing, there are certain difficult tasks to be handled by
company employees. This includes manufacturing points where intervention is required yet high
temperatures can be experienced as well as encountering dangerous and harmful chemicals, not
only stressful to humans, among many others are repetitive. (Saint, 2008).
In adopting the robotic technology, the company will be able to replace human intervention with
robotic technology, thereby offloading difficult tasks imposed on employees by changing their
job design and allowing them to do alternative tasks beneficial to the company. This will not
only motivate employees; it is likely to assist in achieving the company's performance objectives.
Integrating 3D technologies into the automobile manufacturing process operations is likely to
help the organization increase its productivity and utilize their labour resources more effectively.
It will enable employees to handle only those tasks that are safe, manageable and require human
intervention. With this job redesign, the employees will be motivated to find and achieve the
satisfaction of their performance objectives. (Chase, Jacobs and Aquilano, 2007).
The company should adopt this technology since it will assist in innovation and gain a
competitive advantage in the industry.
DISTRIBUTED MANUFACTURING
Distributed manufacturing is one of the emerging technologies that are key in the manufacturing
industries. Distributed manufacturing entails replacement of the traditional aspects of the supply
chain coordinated utilizing digital information.
The technology is instrumental in assisting to reduce inventory cost, eliminate monotonous,
repetitive tasks and increase the general efficiency of the company operations. The technology
directly translates to the provision of comfort to the employees in the new job roles. With so
doing, the company will be able to provide job satisfaction since it can eliminate challenges to
the employees (Lamb, 2013, pp.1-4)
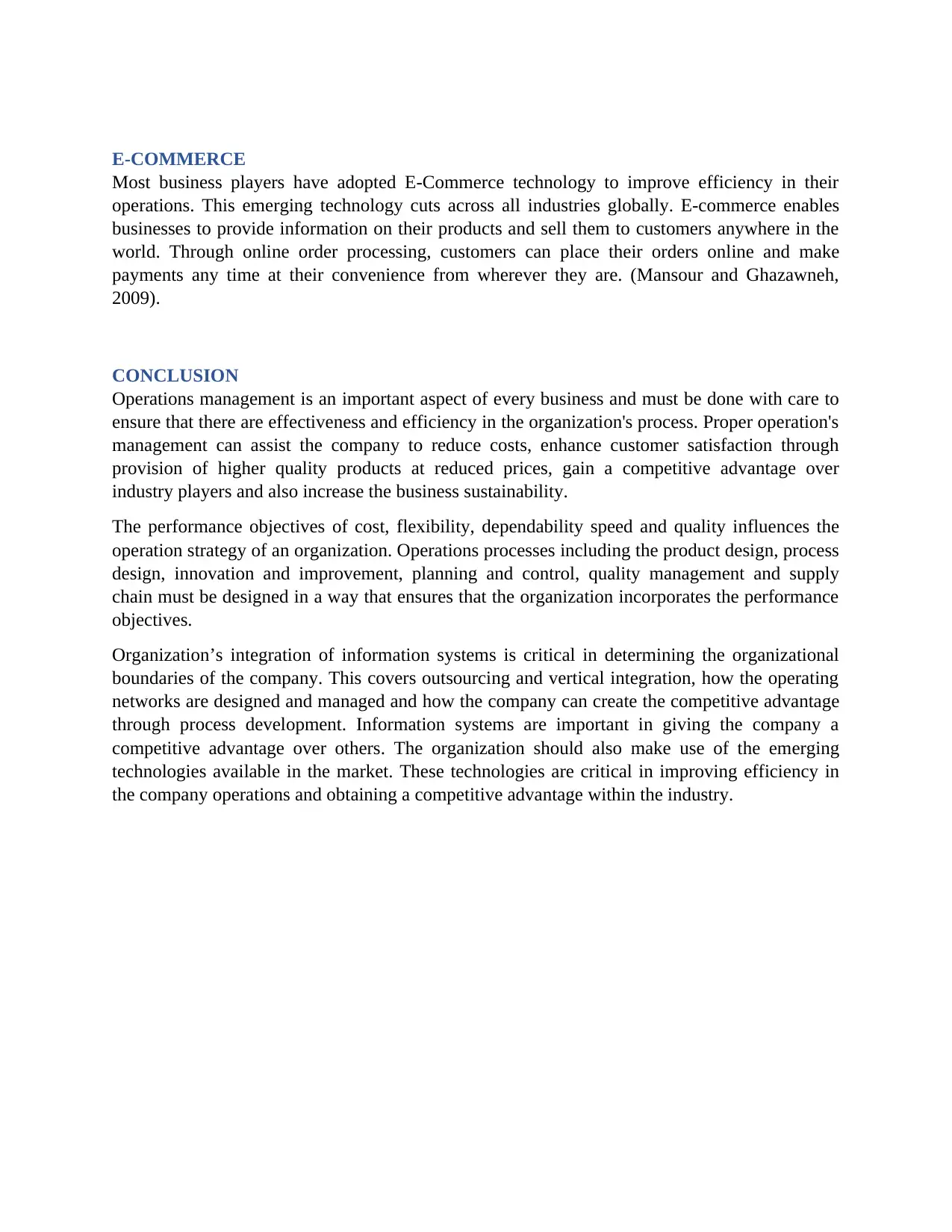
E-COMMERCE
Most business players have adopted E-Commerce technology to improve efficiency in their
operations. This emerging technology cuts across all industries globally. E-commerce enables
businesses to provide information on their products and sell them to customers anywhere in the
world. Through online order processing, customers can place their orders online and make
payments any time at their convenience from wherever they are. (Mansour and Ghazawneh,
2009).
CONCLUSION
Operations management is an important aspect of every business and must be done with care to
ensure that there are effectiveness and efficiency in the organization's process. Proper operation's
management can assist the company to reduce costs, enhance customer satisfaction through
provision of higher quality products at reduced prices, gain a competitive advantage over
industry players and also increase the business sustainability.
The performance objectives of cost, flexibility, dependability speed and quality influences the
operation strategy of an organization. Operations processes including the product design, process
design, innovation and improvement, planning and control, quality management and supply
chain must be designed in a way that ensures that the organization incorporates the performance
objectives.
Organization’s integration of information systems is critical in determining the organizational
boundaries of the company. This covers outsourcing and vertical integration, how the operating
networks are designed and managed and how the company can create the competitive advantage
through process development. Information systems are important in giving the company a
competitive advantage over others. The organization should also make use of the emerging
technologies available in the market. These technologies are critical in improving efficiency in
the company operations and obtaining a competitive advantage within the industry.
Most business players have adopted E-Commerce technology to improve efficiency in their
operations. This emerging technology cuts across all industries globally. E-commerce enables
businesses to provide information on their products and sell them to customers anywhere in the
world. Through online order processing, customers can place their orders online and make
payments any time at their convenience from wherever they are. (Mansour and Ghazawneh,
2009).
CONCLUSION
Operations management is an important aspect of every business and must be done with care to
ensure that there are effectiveness and efficiency in the organization's process. Proper operation's
management can assist the company to reduce costs, enhance customer satisfaction through
provision of higher quality products at reduced prices, gain a competitive advantage over
industry players and also increase the business sustainability.
The performance objectives of cost, flexibility, dependability speed and quality influences the
operation strategy of an organization. Operations processes including the product design, process
design, innovation and improvement, planning and control, quality management and supply
chain must be designed in a way that ensures that the organization incorporates the performance
objectives.
Organization’s integration of information systems is critical in determining the organizational
boundaries of the company. This covers outsourcing and vertical integration, how the operating
networks are designed and managed and how the company can create the competitive advantage
through process development. Information systems are important in giving the company a
competitive advantage over others. The organization should also make use of the emerging
technologies available in the market. These technologies are critical in improving efficiency in
the company operations and obtaining a competitive advantage within the industry.
Secure Best Marks with AI Grader
Need help grading? Try our AI Grader for instant feedback on your assignments.
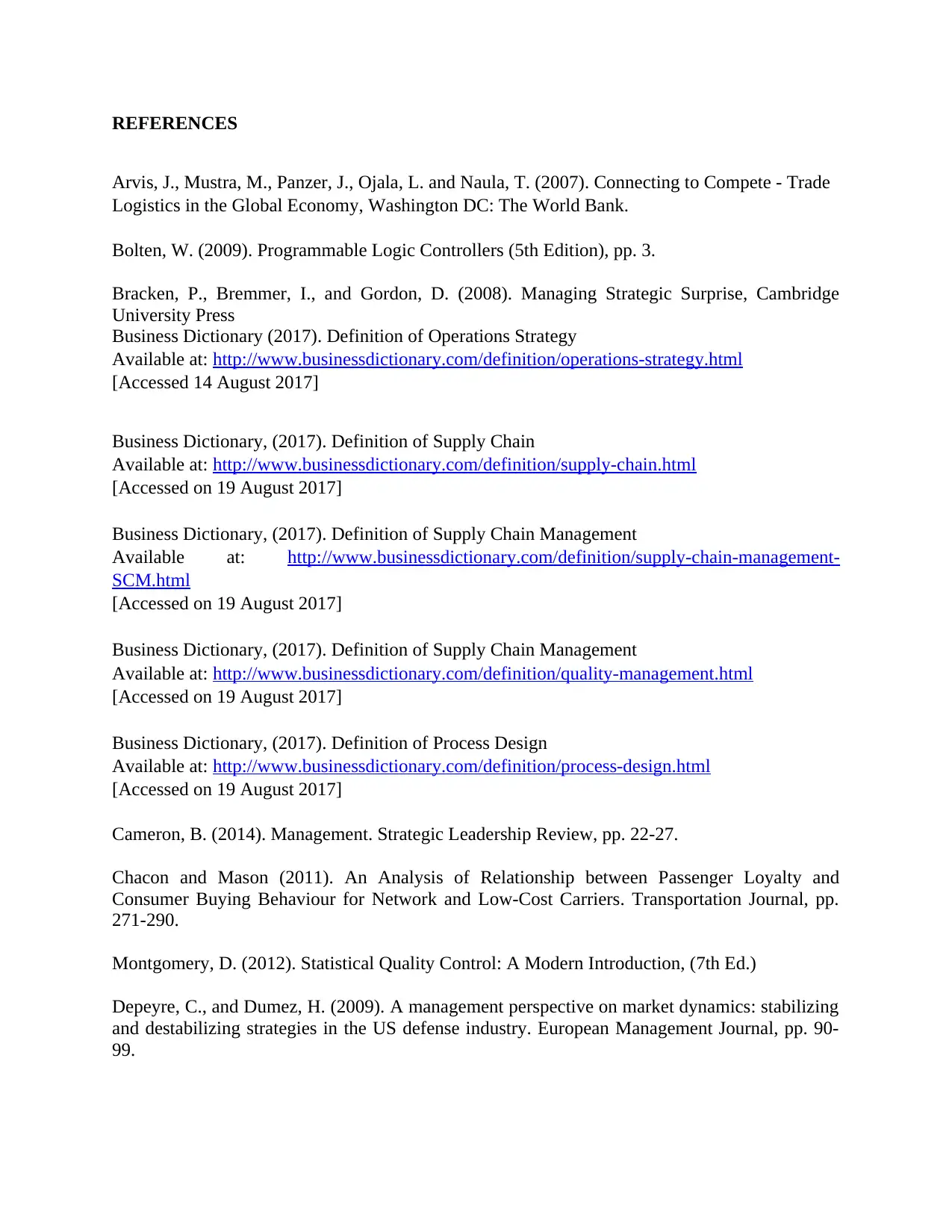
REFERENCES
Arvis, J., Mustra, M., Panzer, J., Ojala, L. and Naula, T. (2007). Connecting to Compete - Trade
Logistics in the Global Economy, Washington DC: The World Bank.
Bolten, W. (2009). Programmable Logic Controllers (5th Edition), pp. 3.
Bracken, P., Bremmer, I., and Gordon, D. (2008). Managing Strategic Surprise, Cambridge
University Press
Business Dictionary (2017). Definition of Operations Strategy
Available at: http://www.businessdictionary.com/definition/operations-strategy.html
[Accessed 14 August 2017]
Business Dictionary, (2017). Definition of Supply Chain
Available at: http://www.businessdictionary.com/definition/supply-chain.html
[Accessed on 19 August 2017]
Business Dictionary, (2017). Definition of Supply Chain Management
Available at: http://www.businessdictionary.com/definition/supply-chain-management-
SCM.html
[Accessed on 19 August 2017]
Business Dictionary, (2017). Definition of Supply Chain Management
Available at: http://www.businessdictionary.com/definition/quality-management.html
[Accessed on 19 August 2017]
Business Dictionary, (2017). Definition of Process Design
Available at: http://www.businessdictionary.com/definition/process-design.html
[Accessed on 19 August 2017]
Cameron, B. (2014). Management. Strategic Leadership Review, pp. 22-27.
Chacon and Mason (2011). An Analysis of Relationship between Passenger Loyalty and
Consumer Buying Behaviour for Network and Low-Cost Carriers. Transportation Journal, pp.
271-290.
Montgomery, D. (2012). Statistical Quality Control: A Modern Introduction, (7th Ed.)
Depeyre, C., and Dumez, H. (2009). A management perspective on market dynamics: stabilizing
and destabilizing strategies in the US defense industry. European Management Journal, pp. 90-
99.
Arvis, J., Mustra, M., Panzer, J., Ojala, L. and Naula, T. (2007). Connecting to Compete - Trade
Logistics in the Global Economy, Washington DC: The World Bank.
Bolten, W. (2009). Programmable Logic Controllers (5th Edition), pp. 3.
Bracken, P., Bremmer, I., and Gordon, D. (2008). Managing Strategic Surprise, Cambridge
University Press
Business Dictionary (2017). Definition of Operations Strategy
Available at: http://www.businessdictionary.com/definition/operations-strategy.html
[Accessed 14 August 2017]
Business Dictionary, (2017). Definition of Supply Chain
Available at: http://www.businessdictionary.com/definition/supply-chain.html
[Accessed on 19 August 2017]
Business Dictionary, (2017). Definition of Supply Chain Management
Available at: http://www.businessdictionary.com/definition/supply-chain-management-
SCM.html
[Accessed on 19 August 2017]
Business Dictionary, (2017). Definition of Supply Chain Management
Available at: http://www.businessdictionary.com/definition/quality-management.html
[Accessed on 19 August 2017]
Business Dictionary, (2017). Definition of Process Design
Available at: http://www.businessdictionary.com/definition/process-design.html
[Accessed on 19 August 2017]
Cameron, B. (2014). Management. Strategic Leadership Review, pp. 22-27.
Chacon and Mason (2011). An Analysis of Relationship between Passenger Loyalty and
Consumer Buying Behaviour for Network and Low-Cost Carriers. Transportation Journal, pp.
271-290.
Montgomery, D. (2012). Statistical Quality Control: A Modern Introduction, (7th Ed.)
Depeyre, C., and Dumez, H. (2009). A management perspective on market dynamics: stabilizing
and destabilizing strategies in the US defense industry. European Management Journal, pp. 90-
99.
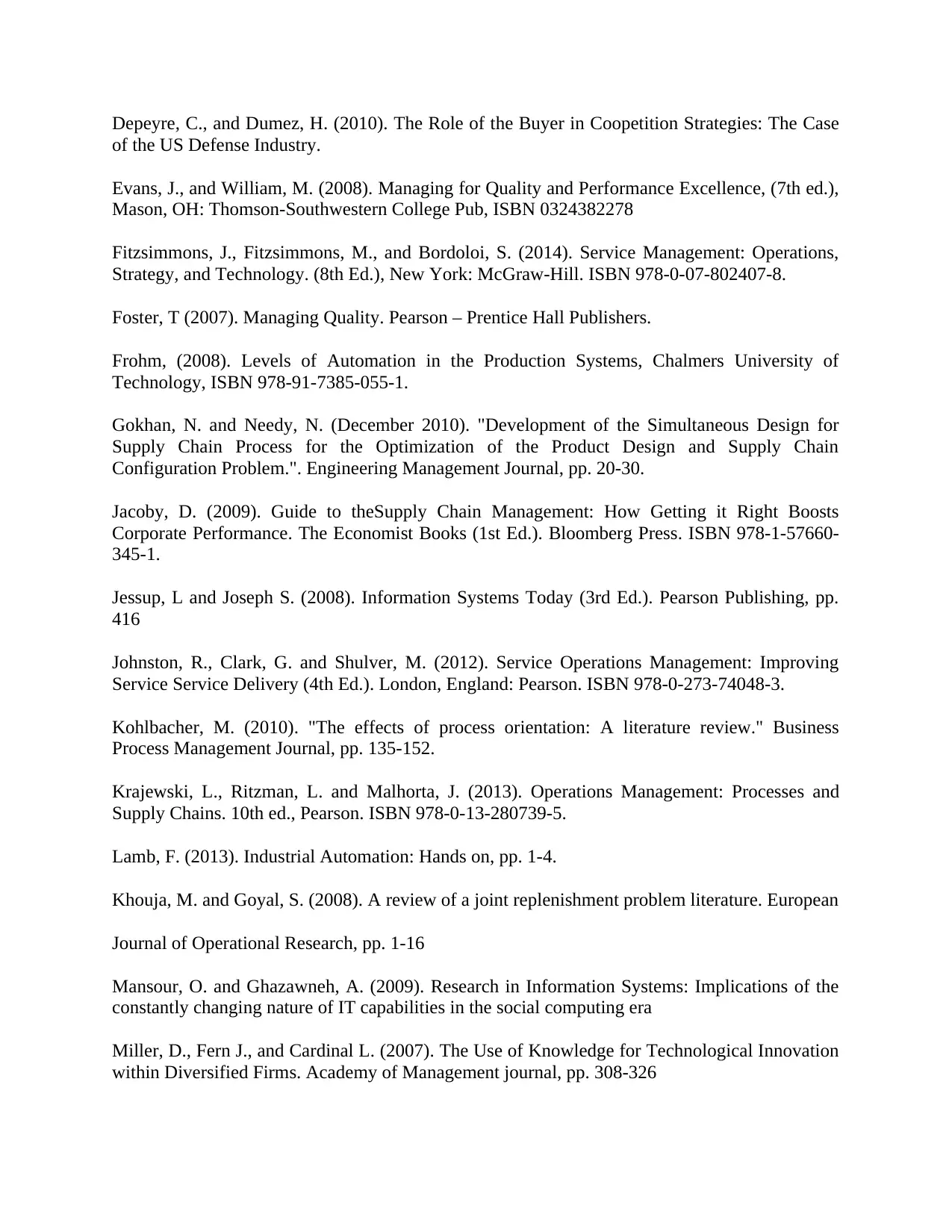
Depeyre, C., and Dumez, H. (2010). The Role of the Buyer in Coopetition Strategies: The Case
of the US Defense Industry.
Evans, J., and William, M. (2008). Managing for Quality and Performance Excellence, (7th ed.),
Mason, OH: Thomson-Southwestern College Pub, ISBN 0324382278
Fitzsimmons, J., Fitzsimmons, M., and Bordoloi, S. (2014). Service Management: Operations,
Strategy, and Technology. (8th Ed.), New York: McGraw-Hill. ISBN 978-0-07-802407-8.
Foster, T (2007). Managing Quality. Pearson – Prentice Hall Publishers.
Frohm, (2008). Levels of Automation in the Production Systems, Chalmers University of
Technology, ISBN 978-91-7385-055-1.
Gokhan, N. and Needy, N. (December 2010). "Development of the Simultaneous Design for
Supply Chain Process for the Optimization of the Product Design and Supply Chain
Configuration Problem.". Engineering Management Journal, pp. 20-30.
Jacoby, D. (2009). Guide to theSupply Chain Management: How Getting it Right Boosts
Corporate Performance. The Economist Books (1st Ed.). Bloomberg Press. ISBN 978-1-57660-
345-1.
Jessup, L and Joseph S. (2008). Information Systems Today (3rd Ed.). Pearson Publishing, pp.
416
Johnston, R., Clark, G. and Shulver, M. (2012). Service Operations Management: Improving
Service Service Delivery (4th Ed.). London, England: Pearson. ISBN 978-0-273-74048-3.
Kohlbacher, M. (2010). "The effects of process orientation: A literature review." Business
Process Management Journal, pp. 135-152.
Krajewski, L., Ritzman, L. and Malhorta, J. (2013). Operations Management: Processes and
Supply Chains. 10th ed., Pearson. ISBN 978-0-13-280739-5.
Lamb, F. (2013). Industrial Automation: Hands on, pp. 1-4.
Khouja, M. and Goyal, S. (2008). A review of a joint replenishment problem literature. European
Journal of Operational Research, pp. 1-16
Mansour, O. and Ghazawneh, A. (2009). Research in Information Systems: Implications of the
constantly changing nature of IT capabilities in the social computing era
Miller, D., Fern J., and Cardinal L. (2007). The Use of Knowledge for Technological Innovation
within Diversified Firms. Academy of Management journal, pp. 308-326
of the US Defense Industry.
Evans, J., and William, M. (2008). Managing for Quality and Performance Excellence, (7th ed.),
Mason, OH: Thomson-Southwestern College Pub, ISBN 0324382278
Fitzsimmons, J., Fitzsimmons, M., and Bordoloi, S. (2014). Service Management: Operations,
Strategy, and Technology. (8th Ed.), New York: McGraw-Hill. ISBN 978-0-07-802407-8.
Foster, T (2007). Managing Quality. Pearson – Prentice Hall Publishers.
Frohm, (2008). Levels of Automation in the Production Systems, Chalmers University of
Technology, ISBN 978-91-7385-055-1.
Gokhan, N. and Needy, N. (December 2010). "Development of the Simultaneous Design for
Supply Chain Process for the Optimization of the Product Design and Supply Chain
Configuration Problem.". Engineering Management Journal, pp. 20-30.
Jacoby, D. (2009). Guide to theSupply Chain Management: How Getting it Right Boosts
Corporate Performance. The Economist Books (1st Ed.). Bloomberg Press. ISBN 978-1-57660-
345-1.
Jessup, L and Joseph S. (2008). Information Systems Today (3rd Ed.). Pearson Publishing, pp.
416
Johnston, R., Clark, G. and Shulver, M. (2012). Service Operations Management: Improving
Service Service Delivery (4th Ed.). London, England: Pearson. ISBN 978-0-273-74048-3.
Kohlbacher, M. (2010). "The effects of process orientation: A literature review." Business
Process Management Journal, pp. 135-152.
Krajewski, L., Ritzman, L. and Malhorta, J. (2013). Operations Management: Processes and
Supply Chains. 10th ed., Pearson. ISBN 978-0-13-280739-5.
Lamb, F. (2013). Industrial Automation: Hands on, pp. 1-4.
Khouja, M. and Goyal, S. (2008). A review of a joint replenishment problem literature. European
Journal of Operational Research, pp. 1-16
Mansour, O. and Ghazawneh, A. (2009). Research in Information Systems: Implications of the
constantly changing nature of IT capabilities in the social computing era
Miller, D., Fern J., and Cardinal L. (2007). The Use of Knowledge for Technological Innovation
within Diversified Firms. Academy of Management journal, pp. 308-326
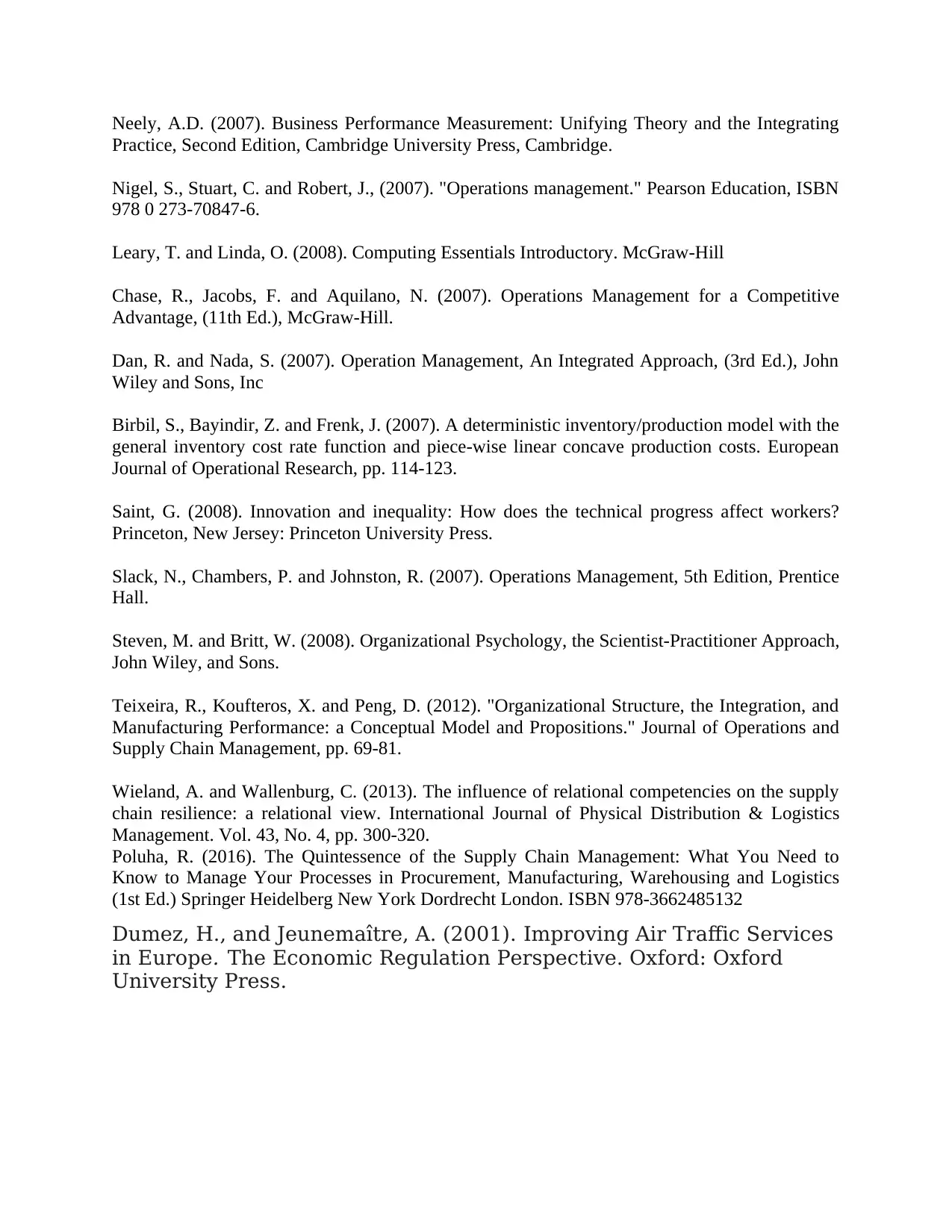
Neely, A.D. (2007). Business Performance Measurement: Unifying Theory and the Integrating
Practice, Second Edition, Cambridge University Press, Cambridge.
Nigel, S., Stuart, C. and Robert, J., (2007). "Operations management." Pearson Education, ISBN
978 0 273-70847-6.
Leary, T. and Linda, O. (2008). Computing Essentials Introductory. McGraw-Hill
Chase, R., Jacobs, F. and Aquilano, N. (2007). Operations Management for a Competitive
Advantage, (11th Ed.), McGraw-Hill.
Dan, R. and Nada, S. (2007). Operation Management, An Integrated Approach, (3rd Ed.), John
Wiley and Sons, Inc
Birbil, S., Bayindir, Z. and Frenk, J. (2007). A deterministic inventory/production model with the
general inventory cost rate function and piece-wise linear concave production costs. European
Journal of Operational Research, pp. 114-123.
Saint, G. (2008). Innovation and inequality: How does the technical progress affect workers?
Princeton, New Jersey: Princeton University Press.
Slack, N., Chambers, P. and Johnston, R. (2007). Operations Management, 5th Edition, Prentice
Hall.
Steven, M. and Britt, W. (2008). Organizational Psychology, the Scientist-Practitioner Approach,
John Wiley, and Sons.
Teixeira, R., Koufteros, X. and Peng, D. (2012). "Organizational Structure, the Integration, and
Manufacturing Performance: a Conceptual Model and Propositions." Journal of Operations and
Supply Chain Management, pp. 69-81.
Wieland, A. and Wallenburg, C. (2013). The influence of relational competencies on the supply
chain resilience: a relational view. International Journal of Physical Distribution & Logistics
Management. Vol. 43, No. 4, pp. 300-320.
Poluha, R. (2016). The Quintessence of the Supply Chain Management: What You Need to
Know to Manage Your Processes in Procurement, Manufacturing, Warehousing and Logistics
(1st Ed.) Springer Heidelberg New York Dordrecht London. ISBN 978-3662485132
Dumez, H., and Jeunemaître, A. (2001). Improving Air Traffic Services
in Europe. The Economic Regulation Perspective. Oxford: Oxford
University Press.
Practice, Second Edition, Cambridge University Press, Cambridge.
Nigel, S., Stuart, C. and Robert, J., (2007). "Operations management." Pearson Education, ISBN
978 0 273-70847-6.
Leary, T. and Linda, O. (2008). Computing Essentials Introductory. McGraw-Hill
Chase, R., Jacobs, F. and Aquilano, N. (2007). Operations Management for a Competitive
Advantage, (11th Ed.), McGraw-Hill.
Dan, R. and Nada, S. (2007). Operation Management, An Integrated Approach, (3rd Ed.), John
Wiley and Sons, Inc
Birbil, S., Bayindir, Z. and Frenk, J. (2007). A deterministic inventory/production model with the
general inventory cost rate function and piece-wise linear concave production costs. European
Journal of Operational Research, pp. 114-123.
Saint, G. (2008). Innovation and inequality: How does the technical progress affect workers?
Princeton, New Jersey: Princeton University Press.
Slack, N., Chambers, P. and Johnston, R. (2007). Operations Management, 5th Edition, Prentice
Hall.
Steven, M. and Britt, W. (2008). Organizational Psychology, the Scientist-Practitioner Approach,
John Wiley, and Sons.
Teixeira, R., Koufteros, X. and Peng, D. (2012). "Organizational Structure, the Integration, and
Manufacturing Performance: a Conceptual Model and Propositions." Journal of Operations and
Supply Chain Management, pp. 69-81.
Wieland, A. and Wallenburg, C. (2013). The influence of relational competencies on the supply
chain resilience: a relational view. International Journal of Physical Distribution & Logistics
Management. Vol. 43, No. 4, pp. 300-320.
Poluha, R. (2016). The Quintessence of the Supply Chain Management: What You Need to
Know to Manage Your Processes in Procurement, Manufacturing, Warehousing and Logistics
(1st Ed.) Springer Heidelberg New York Dordrecht London. ISBN 978-3662485132
Dumez, H., and Jeunemaître, A. (2001). Improving Air Traffic Services
in Europe. The Economic Regulation Perspective. Oxford: Oxford
University Press.
1 out of 19
Related Documents

Your All-in-One AI-Powered Toolkit for Academic Success.
+13062052269
info@desklib.com
Available 24*7 on WhatsApp / Email
Unlock your academic potential
© 2024 | Zucol Services PVT LTD | All rights reserved.