Applied Problem Solving in a Logistics Workspace - LOG3091M Report
VerifiedAdded on 2020/06/04
|20
|6069
|119
Report
AI Summary
This report delves into applied problem-solving within a logistics workspace, focusing on the challenges and methodologies used in supply chain management. It explores various aspects, including the integration of customer priorities and supply chain skills, the role of logistics in the flow ...
Read More
Contribute Materials
Your contribution can guide someone’s learning journey. Share your
documents today.
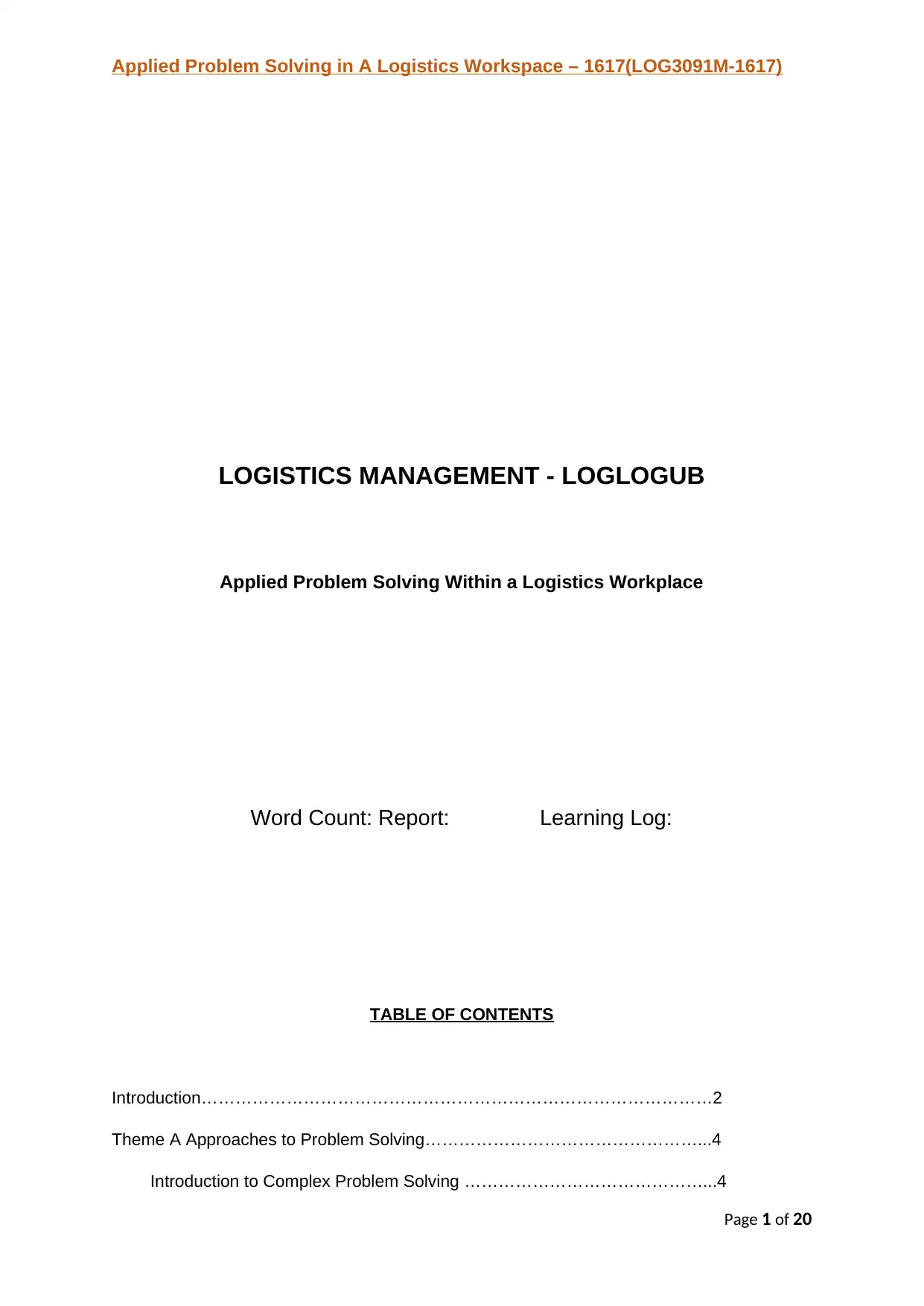
Applied Problem Solving in A Logistics Workspace – 1617(LOG3091M-1617)
LOGISTICS MANAGEMENT - LOGLOGUB
Applied Problem Solving Within a Logistics Workplace
Word Count: Report: Learning Log:
TABLE OF CONTENTS
Introduction………………………………………………………………………………2
Theme A Approaches to Problem Solving…………………………………………...4
Introduction to Complex Problem Solving ……………………………………...4
Page 1 of 20
LOGISTICS MANAGEMENT - LOGLOGUB
Applied Problem Solving Within a Logistics Workplace
Word Count: Report: Learning Log:
TABLE OF CONTENTS
Introduction………………………………………………………………………………2
Theme A Approaches to Problem Solving…………………………………………...4
Introduction to Complex Problem Solving ……………………………………...4
Page 1 of 20
Secure Best Marks with AI Grader
Need help grading? Try our AI Grader for instant feedback on your assignments.
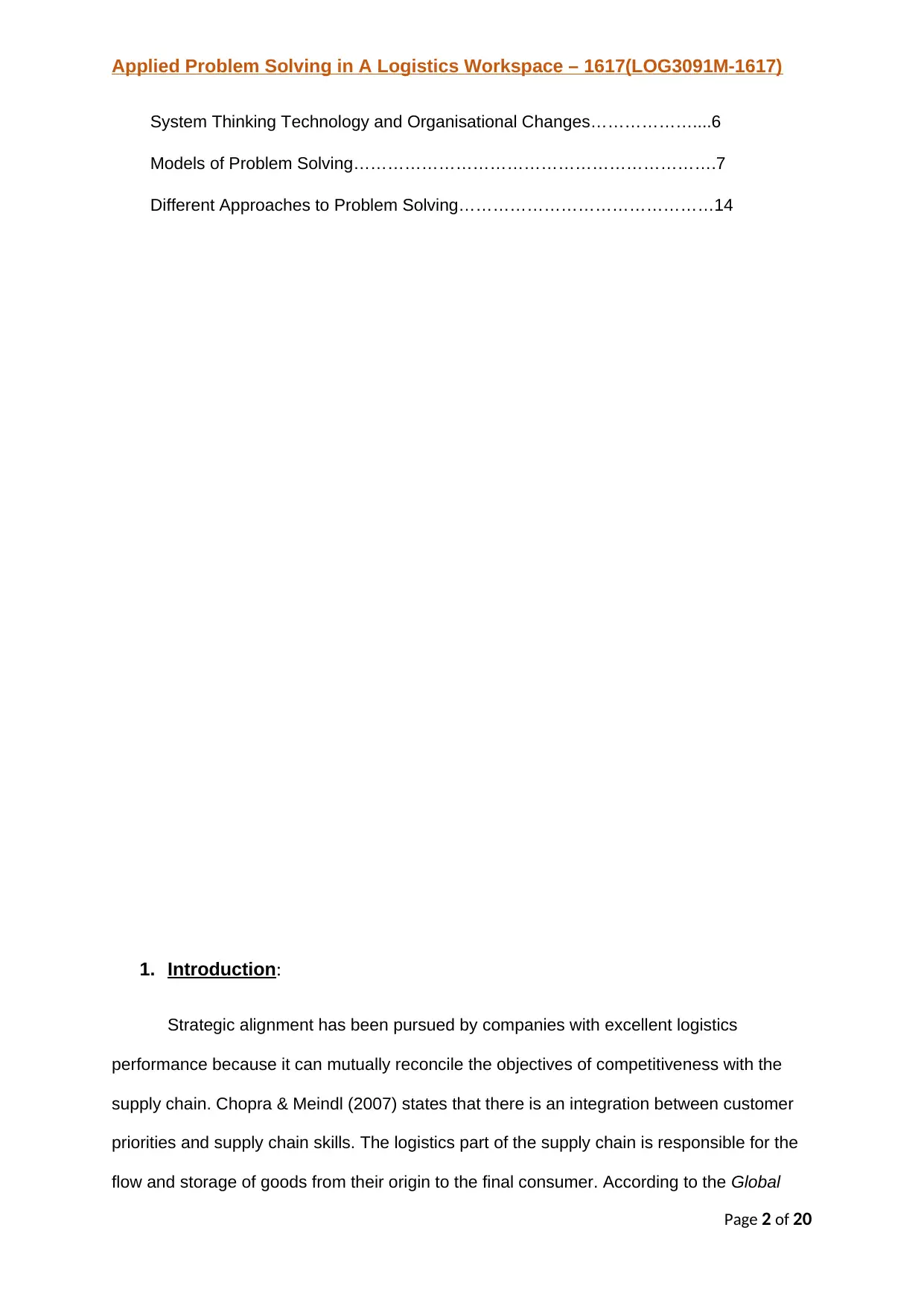
Applied Problem Solving in A Logistics Workspace – 1617(LOG3091M-1617)
System Thinking Technology and Organisational Changes………………....6
Models of Problem Solving……………………………………………………….7
Different Approaches to Problem Solving………………………………………14
1. Introduction:
Strategic alignment has been pursued by companies with excellent logistics
performance because it can mutually reconcile the objectives of competitiveness with the
supply chain. Chopra & Meindl (2007) states that there is an integration between customer
priorities and supply chain skills. The logistics part of the supply chain is responsible for the
flow and storage of goods from their origin to the final consumer. According to the Global
Page 2 of 20
System Thinking Technology and Organisational Changes………………....6
Models of Problem Solving……………………………………………………….7
Different Approaches to Problem Solving………………………………………14
1. Introduction:
Strategic alignment has been pursued by companies with excellent logistics
performance because it can mutually reconcile the objectives of competitiveness with the
supply chain. Chopra & Meindl (2007) states that there is an integration between customer
priorities and supply chain skills. The logistics part of the supply chain is responsible for the
flow and storage of goods from their origin to the final consumer. According to the Global
Page 2 of 20
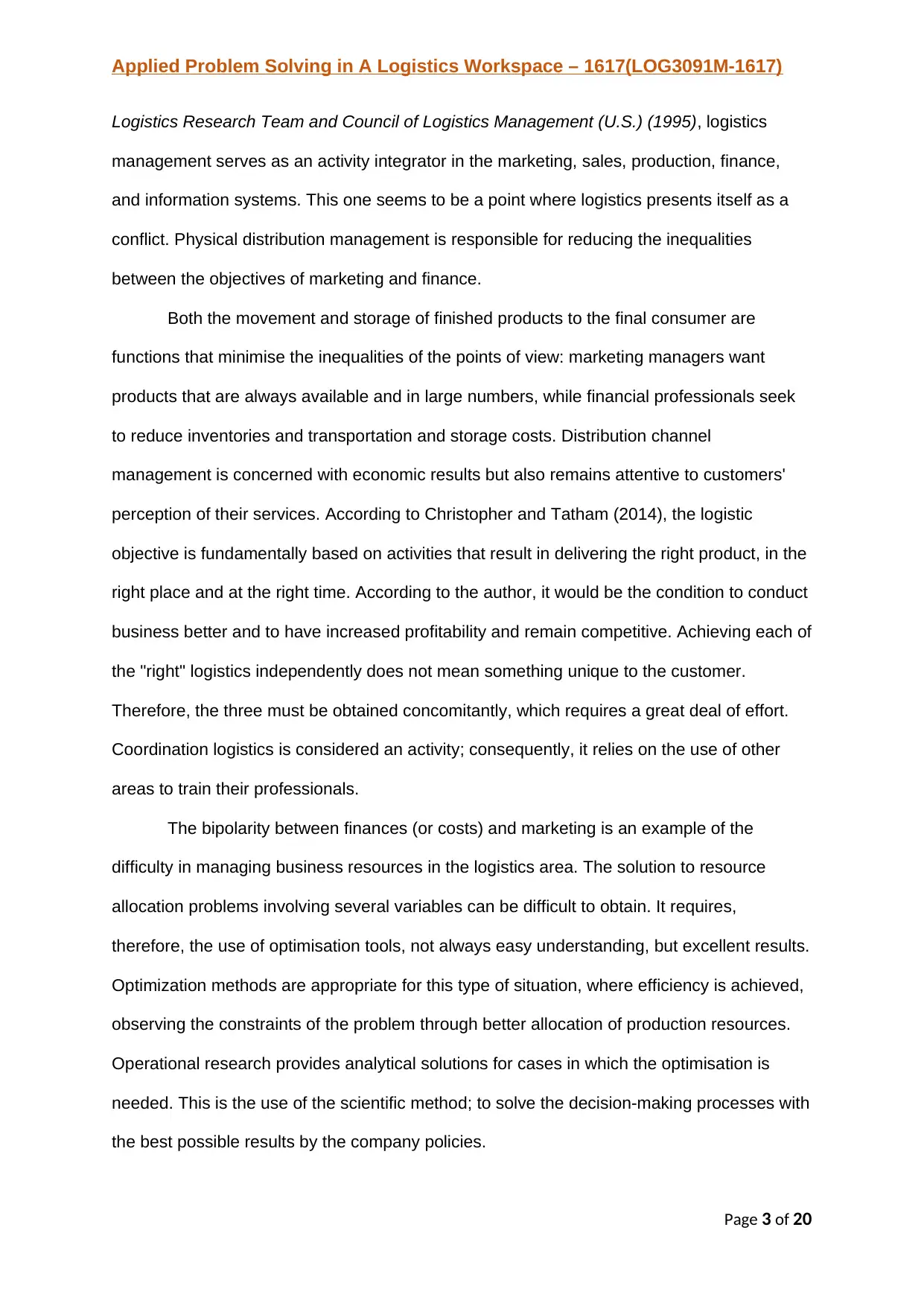
Applied Problem Solving in A Logistics Workspace – 1617(LOG3091M-1617)
Logistics Research Team and Council of Logistics Management (U.S.) (1995), logistics
management serves as an activity integrator in the marketing, sales, production, finance,
and information systems. This one seems to be a point where logistics presents itself as a
conflict. Physical distribution management is responsible for reducing the inequalities
between the objectives of marketing and finance.
Both the movement and storage of finished products to the final consumer are
functions that minimise the inequalities of the points of view: marketing managers want
products that are always available and in large numbers, while financial professionals seek
to reduce inventories and transportation and storage costs. Distribution channel
management is concerned with economic results but also remains attentive to customers'
perception of their services. According to Christopher and Tatham (2014), the logistic
objective is fundamentally based on activities that result in delivering the right product, in the
right place and at the right time. According to the author, it would be the condition to conduct
business better and to have increased profitability and remain competitive. Achieving each of
the "right" logistics independently does not mean something unique to the customer.
Therefore, the three must be obtained concomitantly, which requires a great deal of effort.
Coordination logistics is considered an activity; consequently, it relies on the use of other
areas to train their professionals.
The bipolarity between finances (or costs) and marketing is an example of the
difficulty in managing business resources in the logistics area. The solution to resource
allocation problems involving several variables can be difficult to obtain. It requires,
therefore, the use of optimisation tools, not always easy understanding, but excellent results.
Optimization methods are appropriate for this type of situation, where efficiency is achieved,
observing the constraints of the problem through better allocation of production resources.
Operational research provides analytical solutions for cases in which the optimisation is
needed. This is the use of the scientific method; to solve the decision-making processes with
the best possible results by the company policies.
Page 3 of 20
Logistics Research Team and Council of Logistics Management (U.S.) (1995), logistics
management serves as an activity integrator in the marketing, sales, production, finance,
and information systems. This one seems to be a point where logistics presents itself as a
conflict. Physical distribution management is responsible for reducing the inequalities
between the objectives of marketing and finance.
Both the movement and storage of finished products to the final consumer are
functions that minimise the inequalities of the points of view: marketing managers want
products that are always available and in large numbers, while financial professionals seek
to reduce inventories and transportation and storage costs. Distribution channel
management is concerned with economic results but also remains attentive to customers'
perception of their services. According to Christopher and Tatham (2014), the logistic
objective is fundamentally based on activities that result in delivering the right product, in the
right place and at the right time. According to the author, it would be the condition to conduct
business better and to have increased profitability and remain competitive. Achieving each of
the "right" logistics independently does not mean something unique to the customer.
Therefore, the three must be obtained concomitantly, which requires a great deal of effort.
Coordination logistics is considered an activity; consequently, it relies on the use of other
areas to train their professionals.
The bipolarity between finances (or costs) and marketing is an example of the
difficulty in managing business resources in the logistics area. The solution to resource
allocation problems involving several variables can be difficult to obtain. It requires,
therefore, the use of optimisation tools, not always easy understanding, but excellent results.
Optimization methods are appropriate for this type of situation, where efficiency is achieved,
observing the constraints of the problem through better allocation of production resources.
Operational research provides analytical solutions for cases in which the optimisation is
needed. This is the use of the scientific method; to solve the decision-making processes with
the best possible results by the company policies.
Page 3 of 20
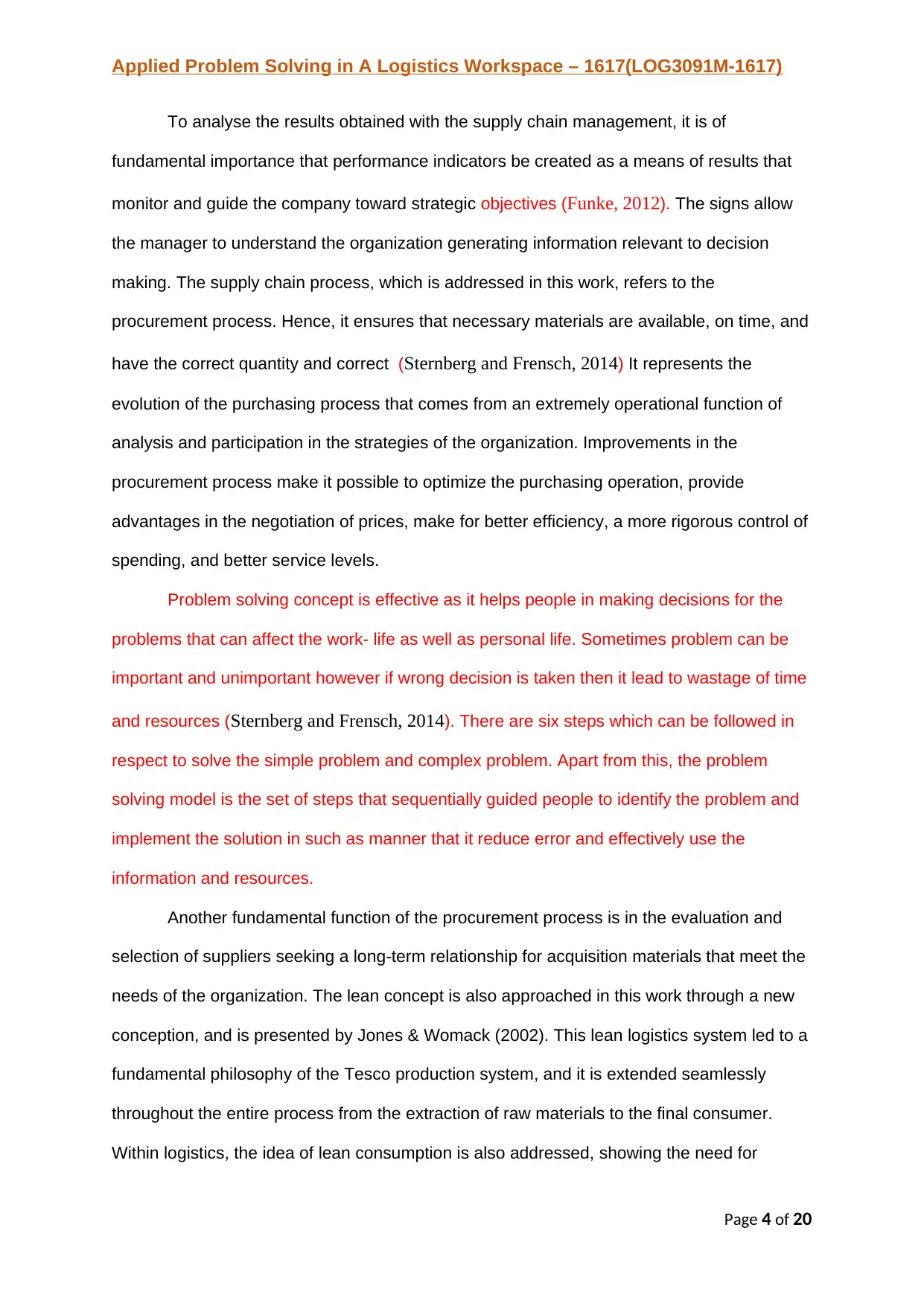
Applied Problem Solving in A Logistics Workspace – 1617(LOG3091M-1617)
To analyse the results obtained with the supply chain management, it is of
fundamental importance that performance indicators be created as a means of results that
monitor and guide the company toward strategic objectives (Funke, 2012). The signs allow
the manager to understand the organization generating information relevant to decision
making. The supply chain process, which is addressed in this work, refers to the
procurement process. Hence, it ensures that necessary materials are available, on time, and
have the correct quantity and correct (Sternberg and Frensch, 2014) It represents the
evolution of the purchasing process that comes from an extremely operational function of
analysis and participation in the strategies of the organization. Improvements in the
procurement process make it possible to optimize the purchasing operation, provide
advantages in the negotiation of prices, make for better efficiency, a more rigorous control of
spending, and better service levels.
Problem solving concept is effective as it helps people in making decisions for the
problems that can affect the work- life as well as personal life. Sometimes problem can be
important and unimportant however if wrong decision is taken then it lead to wastage of time
and resources (Sternberg and Frensch, 2014). There are six steps which can be followed in
respect to solve the simple problem and complex problem. Apart from this, the problem
solving model is the set of steps that sequentially guided people to identify the problem and
implement the solution in such as manner that it reduce error and effectively use the
information and resources.
Another fundamental function of the procurement process is in the evaluation and
selection of suppliers seeking a long-term relationship for acquisition materials that meet the
needs of the organization. The lean concept is also approached in this work through a new
conception, and is presented by Jones & Womack (2002). This lean logistics system led to a
fundamental philosophy of the Tesco production system, and it is extended seamlessly
throughout the entire process from the extraction of raw materials to the final consumer.
Within logistics, the idea of lean consumption is also addressed, showing the need for
Page 4 of 20
To analyse the results obtained with the supply chain management, it is of
fundamental importance that performance indicators be created as a means of results that
monitor and guide the company toward strategic objectives (Funke, 2012). The signs allow
the manager to understand the organization generating information relevant to decision
making. The supply chain process, which is addressed in this work, refers to the
procurement process. Hence, it ensures that necessary materials are available, on time, and
have the correct quantity and correct (Sternberg and Frensch, 2014) It represents the
evolution of the purchasing process that comes from an extremely operational function of
analysis and participation in the strategies of the organization. Improvements in the
procurement process make it possible to optimize the purchasing operation, provide
advantages in the negotiation of prices, make for better efficiency, a more rigorous control of
spending, and better service levels.
Problem solving concept is effective as it helps people in making decisions for the
problems that can affect the work- life as well as personal life. Sometimes problem can be
important and unimportant however if wrong decision is taken then it lead to wastage of time
and resources (Sternberg and Frensch, 2014). There are six steps which can be followed in
respect to solve the simple problem and complex problem. Apart from this, the problem
solving model is the set of steps that sequentially guided people to identify the problem and
implement the solution in such as manner that it reduce error and effectively use the
information and resources.
Another fundamental function of the procurement process is in the evaluation and
selection of suppliers seeking a long-term relationship for acquisition materials that meet the
needs of the organization. The lean concept is also approached in this work through a new
conception, and is presented by Jones & Womack (2002). This lean logistics system led to a
fundamental philosophy of the Tesco production system, and it is extended seamlessly
throughout the entire process from the extraction of raw materials to the final consumer.
Within logistics, the idea of lean consumption is also addressed, showing the need for
Page 4 of 20
Secure Best Marks with AI Grader
Need help grading? Try our AI Grader for instant feedback on your assignments.
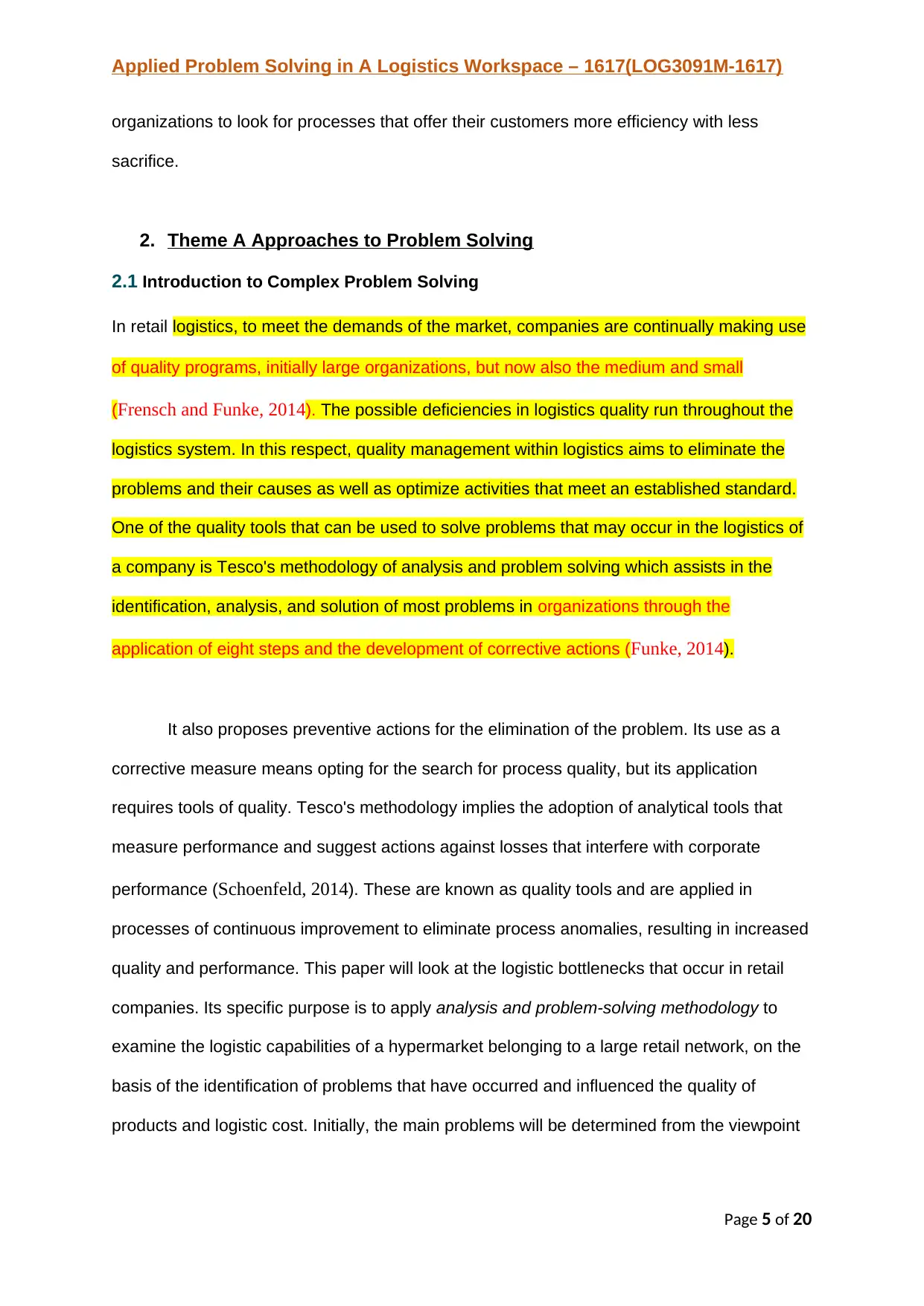
Applied Problem Solving in A Logistics Workspace – 1617(LOG3091M-1617)
organizations to look for processes that offer their customers more efficiency with less
sacrifice.
2. Theme A Approaches to Problem Solving
2.1 Introduction to Complex Problem Solving
In retail logistics, to meet the demands of the market, companies are continually making use
of quality programs, initially large organizations, but now also the medium and small
(Frensch and Funke, 2014). The possible deficiencies in logistics quality run throughout the
logistics system. In this respect, quality management within logistics aims to eliminate the
problems and their causes as well as optimize activities that meet an established standard.
One of the quality tools that can be used to solve problems that may occur in the logistics of
a company is Tesco's methodology of analysis and problem solving which assists in the
identification, analysis, and solution of most problems in organizations through the
application of eight steps and the development of corrective actions (Funke, 2014).
It also proposes preventive actions for the elimination of the problem. Its use as a
corrective measure means opting for the search for process quality, but its application
requires tools of quality. Tesco's methodology implies the adoption of analytical tools that
measure performance and suggest actions against losses that interfere with corporate
performance (Schoenfeld, 2014). These are known as quality tools and are applied in
processes of continuous improvement to eliminate process anomalies, resulting in increased
quality and performance. This paper will look at the logistic bottlenecks that occur in retail
companies. Its specific purpose is to apply analysis and problem-solving methodology to
examine the logistic capabilities of a hypermarket belonging to a large retail network, on the
basis of the identification of problems that have occurred and influenced the quality of
products and logistic cost. Initially, the main problems will be determined from the viewpoint
Page 5 of 20
organizations to look for processes that offer their customers more efficiency with less
sacrifice.
2. Theme A Approaches to Problem Solving
2.1 Introduction to Complex Problem Solving
In retail logistics, to meet the demands of the market, companies are continually making use
of quality programs, initially large organizations, but now also the medium and small
(Frensch and Funke, 2014). The possible deficiencies in logistics quality run throughout the
logistics system. In this respect, quality management within logistics aims to eliminate the
problems and their causes as well as optimize activities that meet an established standard.
One of the quality tools that can be used to solve problems that may occur in the logistics of
a company is Tesco's methodology of analysis and problem solving which assists in the
identification, analysis, and solution of most problems in organizations through the
application of eight steps and the development of corrective actions (Funke, 2014).
It also proposes preventive actions for the elimination of the problem. Its use as a
corrective measure means opting for the search for process quality, but its application
requires tools of quality. Tesco's methodology implies the adoption of analytical tools that
measure performance and suggest actions against losses that interfere with corporate
performance (Schoenfeld, 2014). These are known as quality tools and are applied in
processes of continuous improvement to eliminate process anomalies, resulting in increased
quality and performance. This paper will look at the logistic bottlenecks that occur in retail
companies. Its specific purpose is to apply analysis and problem-solving methodology to
examine the logistic capabilities of a hypermarket belonging to a large retail network, on the
basis of the identification of problems that have occurred and influenced the quality of
products and logistic cost. Initially, the main problems will be determined from the viewpoint
Page 5 of 20
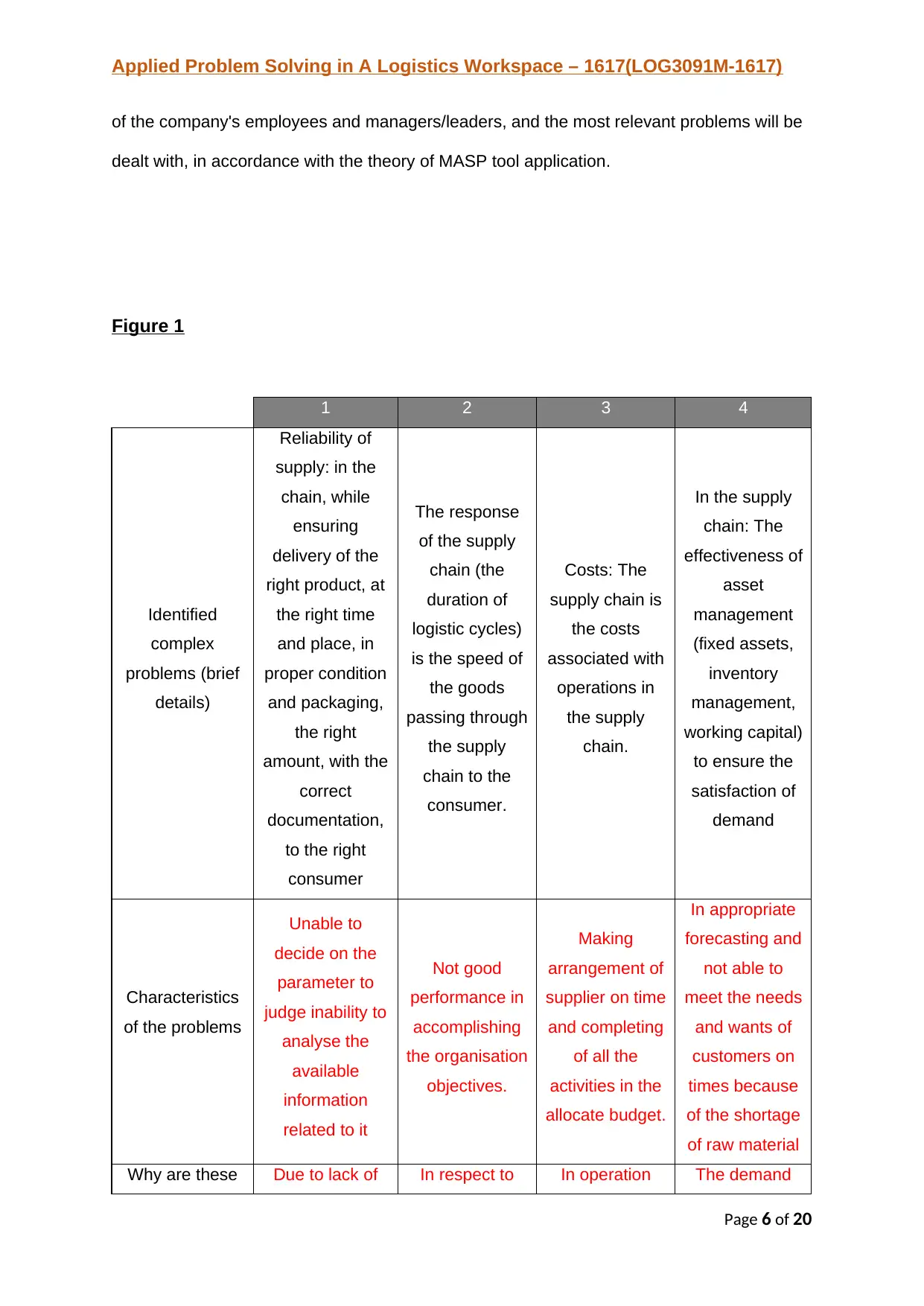
Applied Problem Solving in A Logistics Workspace – 1617(LOG3091M-1617)
of the company's employees and managers/leaders, and the most relevant problems will be
dealt with, in accordance with the theory of MASP tool application.
Figure 1
1 2 3 4
Identified
complex
problems (brief
details)
Reliability of
supply: in the
chain, while
ensuring
delivery of the
right product, at
the right time
and place, in
proper condition
and packaging,
the right
amount, with the
correct
documentation,
to the right
consumer
The response
of the supply
chain (the
duration of
logistic cycles)
is the speed of
the goods
passing through
the supply
chain to the
consumer.
Costs: The
supply chain is
the costs
associated with
operations in
the supply
chain.
In the supply
chain: The
effectiveness of
asset
management
(fixed assets,
inventory
management,
working capital)
to ensure the
satisfaction of
demand
Characteristics
of the problems
Unable to
decide on the
parameter to
judge inability to
analyse the
available
information
related to it
Not good
performance in
accomplishing
the organisation
objectives.
Making
arrangement of
supplier on time
and completing
of all the
activities in the
allocate budget.
In appropriate
forecasting and
not able to
meet the needs
and wants of
customers on
times because
of the shortage
of raw material
Why are these Due to lack of In respect to In operation The demand
Page 6 of 20
of the company's employees and managers/leaders, and the most relevant problems will be
dealt with, in accordance with the theory of MASP tool application.
Figure 1
1 2 3 4
Identified
complex
problems (brief
details)
Reliability of
supply: in the
chain, while
ensuring
delivery of the
right product, at
the right time
and place, in
proper condition
and packaging,
the right
amount, with the
correct
documentation,
to the right
consumer
The response
of the supply
chain (the
duration of
logistic cycles)
is the speed of
the goods
passing through
the supply
chain to the
consumer.
Costs: The
supply chain is
the costs
associated with
operations in
the supply
chain.
In the supply
chain: The
effectiveness of
asset
management
(fixed assets,
inventory
management,
working capital)
to ensure the
satisfaction of
demand
Characteristics
of the problems
Unable to
decide on the
parameter to
judge inability to
analyse the
available
information
related to it
Not good
performance in
accomplishing
the organisation
objectives.
Making
arrangement of
supplier on time
and completing
of all the
activities in the
allocate budget.
In appropriate
forecasting and
not able to
meet the needs
and wants of
customers on
times because
of the shortage
of raw material
Why are these Due to lack of In respect to In operation The demand
Page 6 of 20
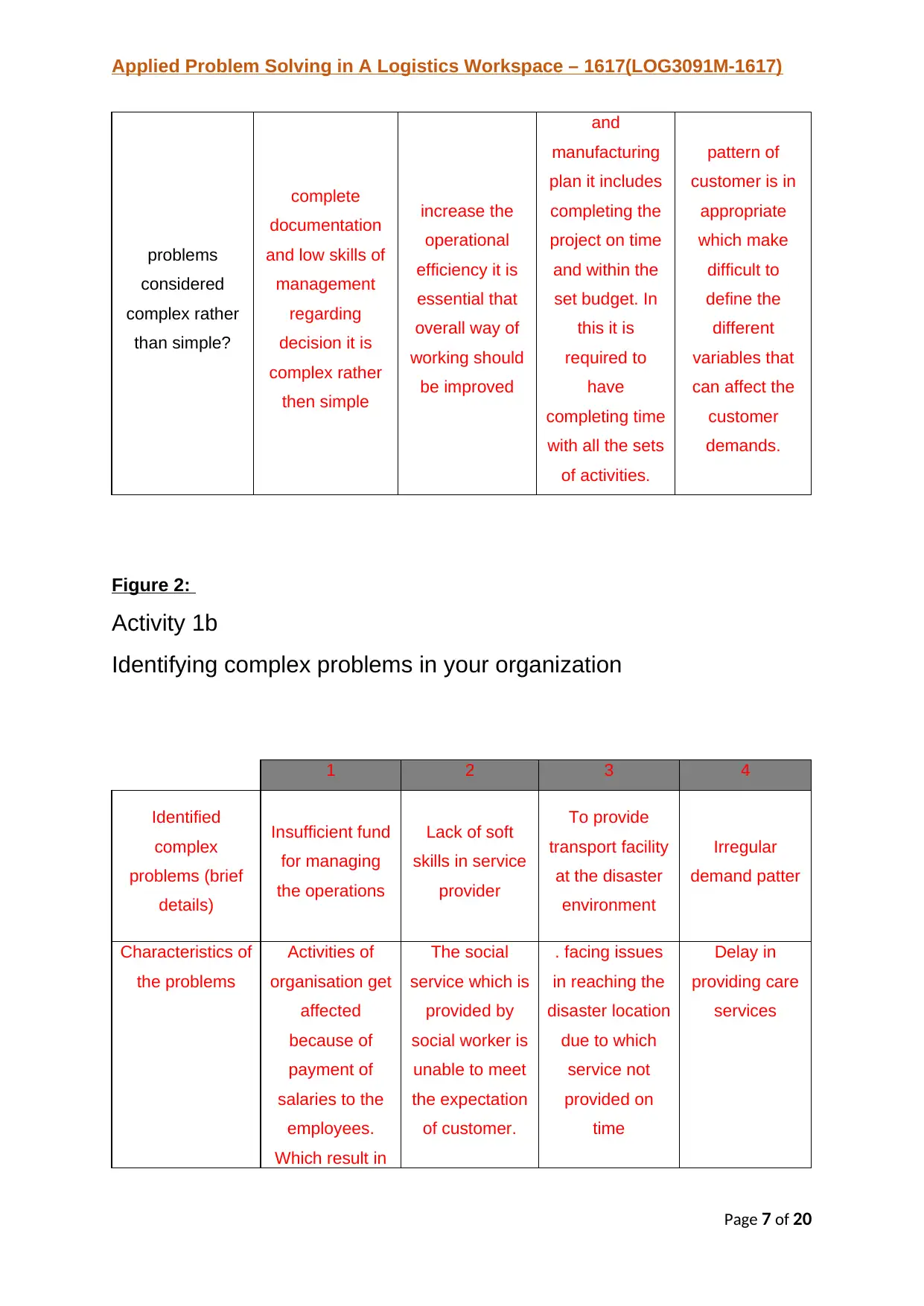
Applied Problem Solving in A Logistics Workspace – 1617(LOG3091M-1617)
problems
considered
complex rather
than simple?
complete
documentation
and low skills of
management
regarding
decision it is
complex rather
then simple
increase the
operational
efficiency it is
essential that
overall way of
working should
be improved
and
manufacturing
plan it includes
completing the
project on time
and within the
set budget. In
this it is
required to
have
completing time
with all the sets
of activities.
pattern of
customer is in
appropriate
which make
difficult to
define the
different
variables that
can affect the
customer
demands.
Figure 2:
Activity 1b
Identifying complex problems in your organization
1 2 3 4
Identified
complex
problems (brief
details)
Insufficient fund
for managing
the operations
Lack of soft
skills in service
provider
To provide
transport facility
at the disaster
environment
Irregular
demand patter
Characteristics of
the problems
Activities of
organisation get
affected
because of
payment of
salaries to the
employees.
Which result in
The social
service which is
provided by
social worker is
unable to meet
the expectation
of customer.
. facing issues
in reaching the
disaster location
due to which
service not
provided on
time
Delay in
providing care
services
Page 7 of 20
problems
considered
complex rather
than simple?
complete
documentation
and low skills of
management
regarding
decision it is
complex rather
then simple
increase the
operational
efficiency it is
essential that
overall way of
working should
be improved
and
manufacturing
plan it includes
completing the
project on time
and within the
set budget. In
this it is
required to
have
completing time
with all the sets
of activities.
pattern of
customer is in
appropriate
which make
difficult to
define the
different
variables that
can affect the
customer
demands.
Figure 2:
Activity 1b
Identifying complex problems in your organization
1 2 3 4
Identified
complex
problems (brief
details)
Insufficient fund
for managing
the operations
Lack of soft
skills in service
provider
To provide
transport facility
at the disaster
environment
Irregular
demand patter
Characteristics of
the problems
Activities of
organisation get
affected
because of
payment of
salaries to the
employees.
Which result in
The social
service which is
provided by
social worker is
unable to meet
the expectation
of customer.
. facing issues
in reaching the
disaster location
due to which
service not
provided on
time
Delay in
providing care
services
Page 7 of 20
Paraphrase This Document
Need a fresh take? Get an instant paraphrase of this document with our AI Paraphraser
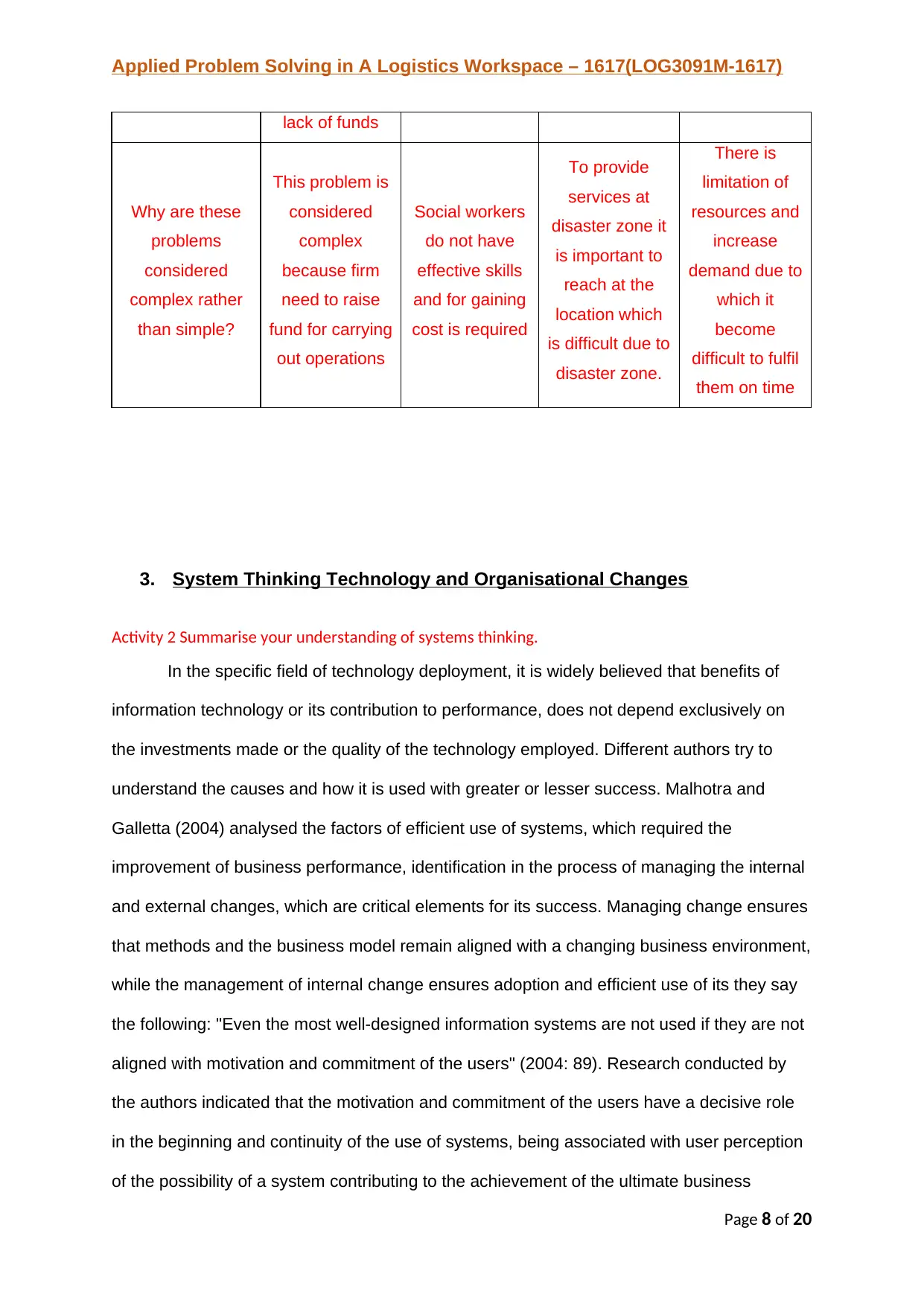
Applied Problem Solving in A Logistics Workspace – 1617(LOG3091M-1617)
lack of funds
Why are these
problems
considered
complex rather
than simple?
This problem is
considered
complex
because firm
need to raise
fund for carrying
out operations
Social workers
do not have
effective skills
and for gaining
cost is required
To provide
services at
disaster zone it
is important to
reach at the
location which
is difficult due to
disaster zone.
There is
limitation of
resources and
increase
demand due to
which it
become
difficult to fulfil
them on time
3. System Thinking Technology and Organisational Changes
Activity 2 Summarise your understanding of systems thinking.
In the specific field of technology deployment, it is widely believed that benefits of
information technology or its contribution to performance, does not depend exclusively on
the investments made or the quality of the technology employed. Different authors try to
understand the causes and how it is used with greater or lesser success. Malhotra and
Galletta (2004) analysed the factors of efficient use of systems, which required the
improvement of business performance, identification in the process of managing the internal
and external changes, which are critical elements for its success. Managing change ensures
that methods and the business model remain aligned with a changing business environment,
while the management of internal change ensures adoption and efficient use of its they say
the following: "Even the most well-designed information systems are not used if they are not
aligned with motivation and commitment of the users" (2004: 89). Research conducted by
the authors indicated that the motivation and commitment of the users have a decisive role
in the beginning and continuity of the use of systems, being associated with user perception
of the possibility of a system contributing to the achievement of the ultimate business
Page 8 of 20
lack of funds
Why are these
problems
considered
complex rather
than simple?
This problem is
considered
complex
because firm
need to raise
fund for carrying
out operations
Social workers
do not have
effective skills
and for gaining
cost is required
To provide
services at
disaster zone it
is important to
reach at the
location which
is difficult due to
disaster zone.
There is
limitation of
resources and
increase
demand due to
which it
become
difficult to fulfil
them on time
3. System Thinking Technology and Organisational Changes
Activity 2 Summarise your understanding of systems thinking.
In the specific field of technology deployment, it is widely believed that benefits of
information technology or its contribution to performance, does not depend exclusively on
the investments made or the quality of the technology employed. Different authors try to
understand the causes and how it is used with greater or lesser success. Malhotra and
Galletta (2004) analysed the factors of efficient use of systems, which required the
improvement of business performance, identification in the process of managing the internal
and external changes, which are critical elements for its success. Managing change ensures
that methods and the business model remain aligned with a changing business environment,
while the management of internal change ensures adoption and efficient use of its they say
the following: "Even the most well-designed information systems are not used if they are not
aligned with motivation and commitment of the users" (2004: 89). Research conducted by
the authors indicated that the motivation and commitment of the users have a decisive role
in the beginning and continuity of the use of systems, being associated with user perception
of the possibility of a system contributing to the achievement of the ultimate business
Page 8 of 20
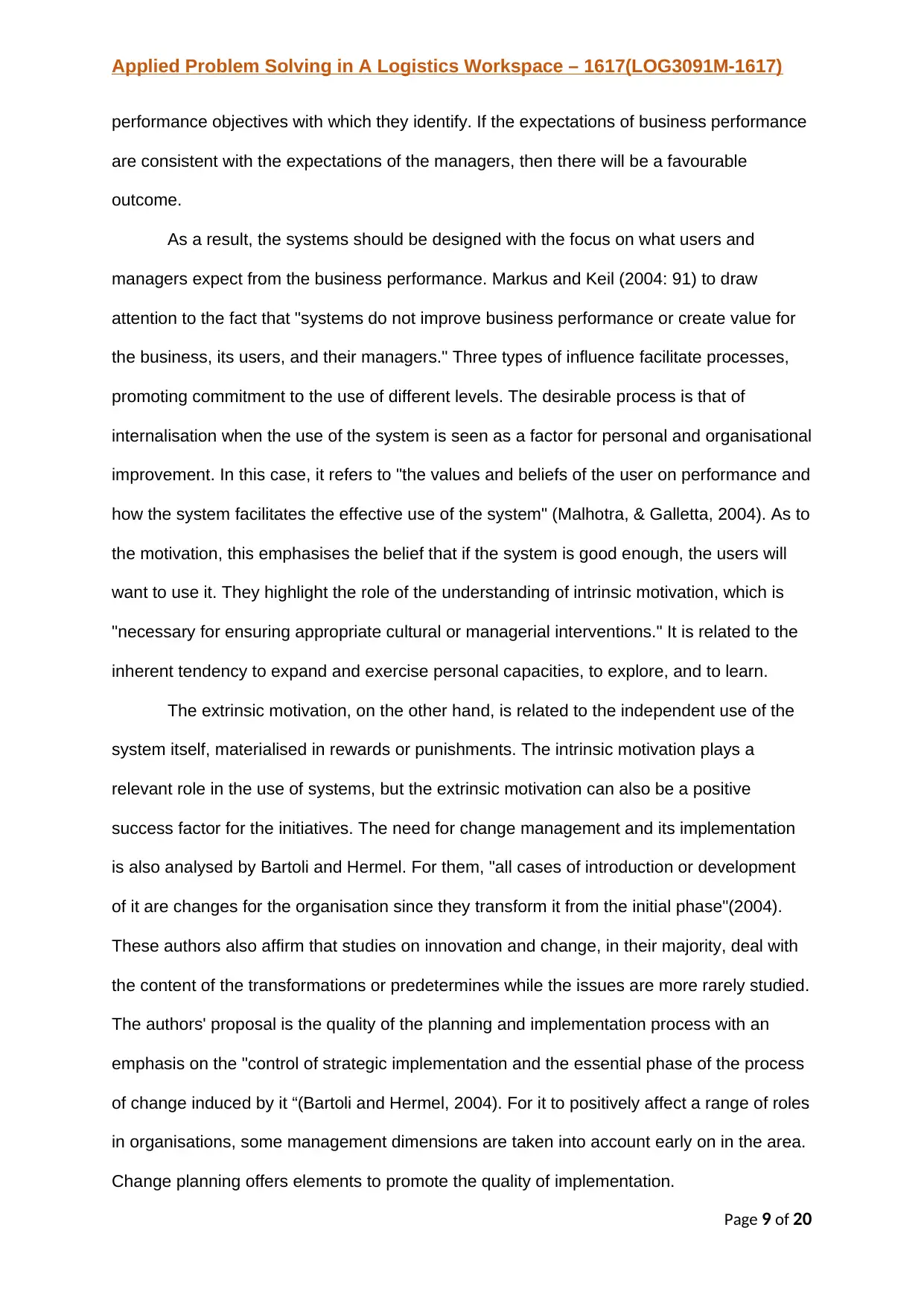
Applied Problem Solving in A Logistics Workspace – 1617(LOG3091M-1617)
performance objectives with which they identify. If the expectations of business performance
are consistent with the expectations of the managers, then there will be a favourable
outcome.
As a result, the systems should be designed with the focus on what users and
managers expect from the business performance. Markus and Keil (2004: 91) to draw
attention to the fact that "systems do not improve business performance or create value for
the business, its users, and their managers." Three types of influence facilitate processes,
promoting commitment to the use of different levels. The desirable process is that of
internalisation when the use of the system is seen as a factor for personal and organisational
improvement. In this case, it refers to "the values and beliefs of the user on performance and
how the system facilitates the effective use of the system" (Malhotra, & Galletta, 2004). As to
the motivation, this emphasises the belief that if the system is good enough, the users will
want to use it. They highlight the role of the understanding of intrinsic motivation, which is
"necessary for ensuring appropriate cultural or managerial interventions." It is related to the
inherent tendency to expand and exercise personal capacities, to explore, and to learn.
The extrinsic motivation, on the other hand, is related to the independent use of the
system itself, materialised in rewards or punishments. The intrinsic motivation plays a
relevant role in the use of systems, but the extrinsic motivation can also be a positive
success factor for the initiatives. The need for change management and its implementation
is also analysed by Bartoli and Hermel. For them, "all cases of introduction or development
of it are changes for the organisation since they transform it from the initial phase"(2004).
These authors also affirm that studies on innovation and change, in their majority, deal with
the content of the transformations or predetermines while the issues are more rarely studied.
The authors' proposal is the quality of the planning and implementation process with an
emphasis on the "control of strategic implementation and the essential phase of the process
of change induced by it “(Bartoli and Hermel, 2004). For it to positively affect a range of roles
in organisations, some management dimensions are taken into account early on in the area.
Change planning offers elements to promote the quality of implementation.
Page 9 of 20
performance objectives with which they identify. If the expectations of business performance
are consistent with the expectations of the managers, then there will be a favourable
outcome.
As a result, the systems should be designed with the focus on what users and
managers expect from the business performance. Markus and Keil (2004: 91) to draw
attention to the fact that "systems do not improve business performance or create value for
the business, its users, and their managers." Three types of influence facilitate processes,
promoting commitment to the use of different levels. The desirable process is that of
internalisation when the use of the system is seen as a factor for personal and organisational
improvement. In this case, it refers to "the values and beliefs of the user on performance and
how the system facilitates the effective use of the system" (Malhotra, & Galletta, 2004). As to
the motivation, this emphasises the belief that if the system is good enough, the users will
want to use it. They highlight the role of the understanding of intrinsic motivation, which is
"necessary for ensuring appropriate cultural or managerial interventions." It is related to the
inherent tendency to expand and exercise personal capacities, to explore, and to learn.
The extrinsic motivation, on the other hand, is related to the independent use of the
system itself, materialised in rewards or punishments. The intrinsic motivation plays a
relevant role in the use of systems, but the extrinsic motivation can also be a positive
success factor for the initiatives. The need for change management and its implementation
is also analysed by Bartoli and Hermel. For them, "all cases of introduction or development
of it are changes for the organisation since they transform it from the initial phase"(2004).
These authors also affirm that studies on innovation and change, in their majority, deal with
the content of the transformations or predetermines while the issues are more rarely studied.
The authors' proposal is the quality of the planning and implementation process with an
emphasis on the "control of strategic implementation and the essential phase of the process
of change induced by it “(Bartoli and Hermel, 2004). For it to positively affect a range of roles
in organisations, some management dimensions are taken into account early on in the area.
Change planning offers elements to promote the quality of implementation.
Page 9 of 20
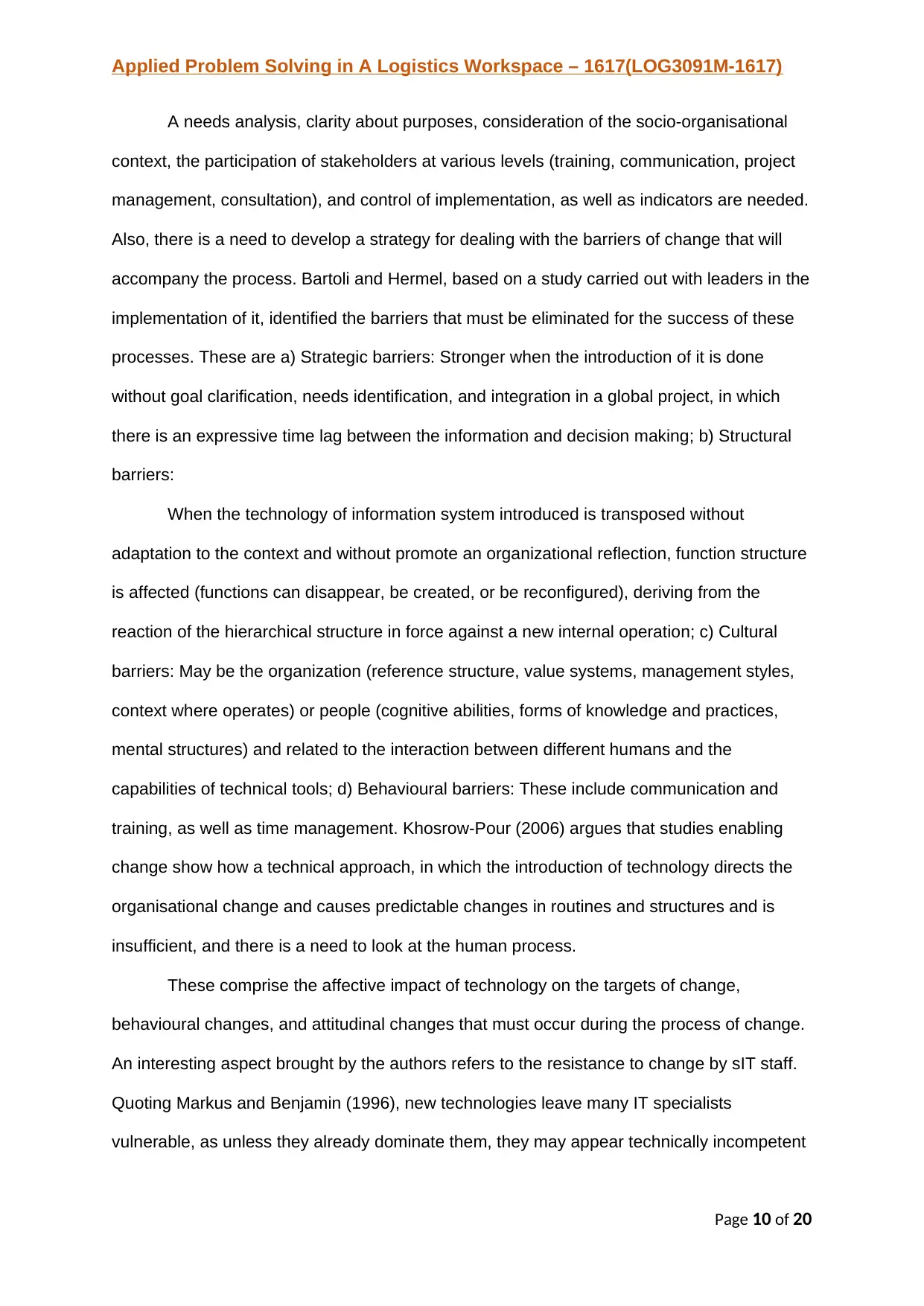
Applied Problem Solving in A Logistics Workspace – 1617(LOG3091M-1617)
A needs analysis, clarity about purposes, consideration of the socio-organisational
context, the participation of stakeholders at various levels (training, communication, project
management, consultation), and control of implementation, as well as indicators are needed.
Also, there is a need to develop a strategy for dealing with the barriers of change that will
accompany the process. Bartoli and Hermel, based on a study carried out with leaders in the
implementation of it, identified the barriers that must be eliminated for the success of these
processes. These are a) Strategic barriers: Stronger when the introduction of it is done
without goal clarification, needs identification, and integration in a global project, in which
there is an expressive time lag between the information and decision making; b) Structural
barriers:
When the technology of information system introduced is transposed without
adaptation to the context and without promote an organizational reflection, function structure
is affected (functions can disappear, be created, or be reconfigured), deriving from the
reaction of the hierarchical structure in force against a new internal operation; c) Cultural
barriers: May be the organization (reference structure, value systems, management styles,
context where operates) or people (cognitive abilities, forms of knowledge and practices,
mental structures) and related to the interaction between different humans and the
capabilities of technical tools; d) Behavioural barriers: These include communication and
training, as well as time management. Khosrow-Pour (2006) argues that studies enabling
change show how a technical approach, in which the introduction of technology directs the
organisational change and causes predictable changes in routines and structures and is
insufficient, and there is a need to look at the human process.
These comprise the affective impact of technology on the targets of change,
behavioural changes, and attitudinal changes that must occur during the process of change.
An interesting aspect brought by the authors refers to the resistance to change by sIT staff.
Quoting Markus and Benjamin (1996), new technologies leave many IT specialists
vulnerable, as unless they already dominate them, they may appear technically incompetent
Page 10 of 20
A needs analysis, clarity about purposes, consideration of the socio-organisational
context, the participation of stakeholders at various levels (training, communication, project
management, consultation), and control of implementation, as well as indicators are needed.
Also, there is a need to develop a strategy for dealing with the barriers of change that will
accompany the process. Bartoli and Hermel, based on a study carried out with leaders in the
implementation of it, identified the barriers that must be eliminated for the success of these
processes. These are a) Strategic barriers: Stronger when the introduction of it is done
without goal clarification, needs identification, and integration in a global project, in which
there is an expressive time lag between the information and decision making; b) Structural
barriers:
When the technology of information system introduced is transposed without
adaptation to the context and without promote an organizational reflection, function structure
is affected (functions can disappear, be created, or be reconfigured), deriving from the
reaction of the hierarchical structure in force against a new internal operation; c) Cultural
barriers: May be the organization (reference structure, value systems, management styles,
context where operates) or people (cognitive abilities, forms of knowledge and practices,
mental structures) and related to the interaction between different humans and the
capabilities of technical tools; d) Behavioural barriers: These include communication and
training, as well as time management. Khosrow-Pour (2006) argues that studies enabling
change show how a technical approach, in which the introduction of technology directs the
organisational change and causes predictable changes in routines and structures and is
insufficient, and there is a need to look at the human process.
These comprise the affective impact of technology on the targets of change,
behavioural changes, and attitudinal changes that must occur during the process of change.
An interesting aspect brought by the authors refers to the resistance to change by sIT staff.
Quoting Markus and Benjamin (1996), new technologies leave many IT specialists
vulnerable, as unless they already dominate them, they may appear technically incompetent
Page 10 of 20
Secure Best Marks with AI Grader
Need help grading? Try our AI Grader for instant feedback on your assignments.
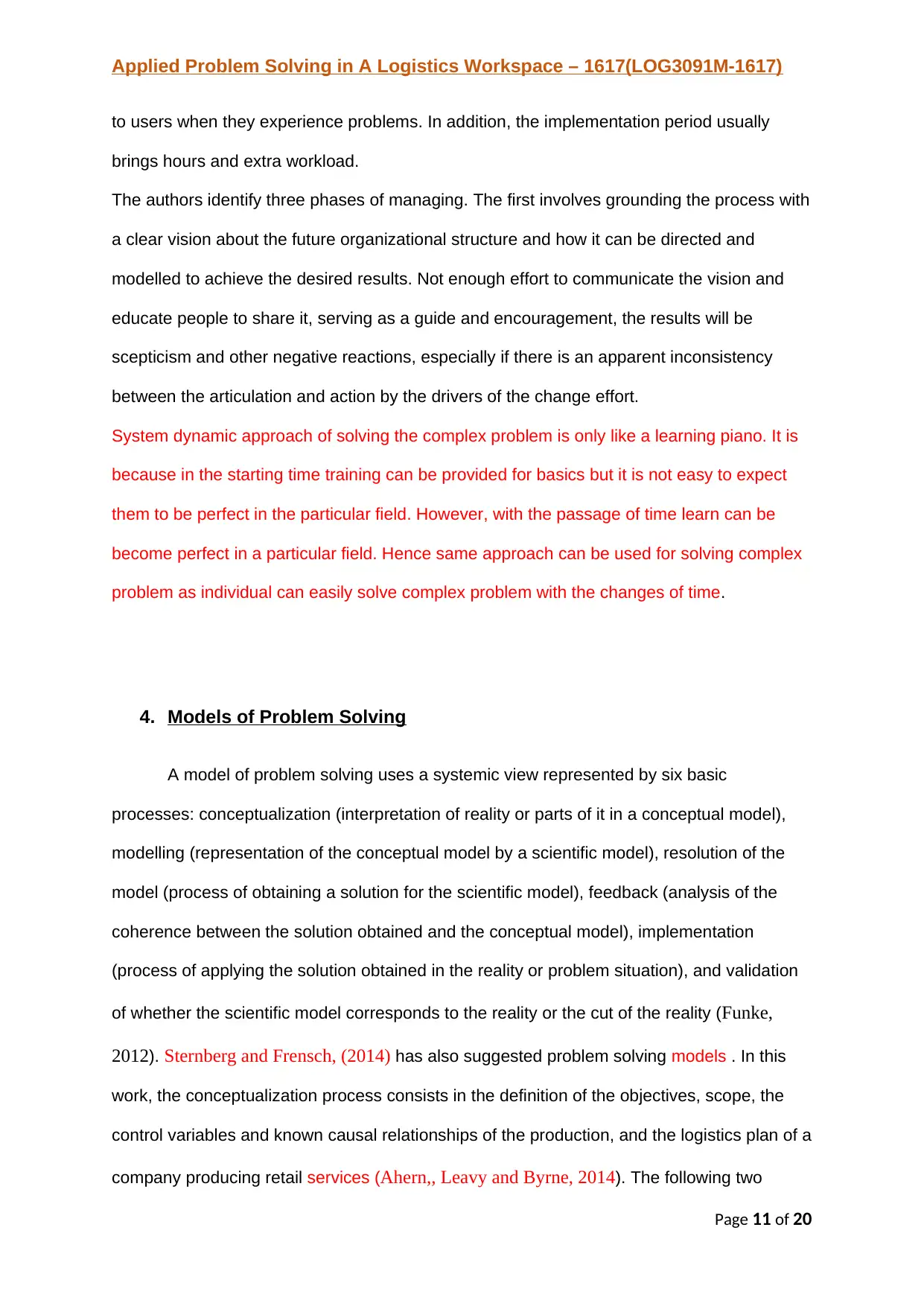
Applied Problem Solving in A Logistics Workspace – 1617(LOG3091M-1617)
to users when they experience problems. In addition, the implementation period usually
brings hours and extra workload.
The authors identify three phases of managing. The first involves grounding the process with
a clear vision about the future organizational structure and how it can be directed and
modelled to achieve the desired results. Not enough effort to communicate the vision and
educate people to share it, serving as a guide and encouragement, the results will be
scepticism and other negative reactions, especially if there is an apparent inconsistency
between the articulation and action by the drivers of the change effort.
System dynamic approach of solving the complex problem is only like a learning piano. It is
because in the starting time training can be provided for basics but it is not easy to expect
them to be perfect in the particular field. However, with the passage of time learn can be
become perfect in a particular field. Hence same approach can be used for solving complex
problem as individual can easily solve complex problem with the changes of time.
4. Models of Problem Solving
A model of problem solving uses a systemic view represented by six basic
processes: conceptualization (interpretation of reality or parts of it in a conceptual model),
modelling (representation of the conceptual model by a scientific model), resolution of the
model (process of obtaining a solution for the scientific model), feedback (analysis of the
coherence between the solution obtained and the conceptual model), implementation
(process of applying the solution obtained in the reality or problem situation), and validation
of whether the scientific model corresponds to the reality or the cut of the reality (Funke,
2012). Sternberg and Frensch, (2014) has also suggested problem solving models . In this
work, the conceptualization process consists in the definition of the objectives, scope, the
control variables and known causal relationships of the production, and the logistics plan of a
company producing retail services (Ahern,, Leavy and Byrne, 2014). The following two
Page 11 of 20
to users when they experience problems. In addition, the implementation period usually
brings hours and extra workload.
The authors identify three phases of managing. The first involves grounding the process with
a clear vision about the future organizational structure and how it can be directed and
modelled to achieve the desired results. Not enough effort to communicate the vision and
educate people to share it, serving as a guide and encouragement, the results will be
scepticism and other negative reactions, especially if there is an apparent inconsistency
between the articulation and action by the drivers of the change effort.
System dynamic approach of solving the complex problem is only like a learning piano. It is
because in the starting time training can be provided for basics but it is not easy to expect
them to be perfect in the particular field. However, with the passage of time learn can be
become perfect in a particular field. Hence same approach can be used for solving complex
problem as individual can easily solve complex problem with the changes of time.
4. Models of Problem Solving
A model of problem solving uses a systemic view represented by six basic
processes: conceptualization (interpretation of reality or parts of it in a conceptual model),
modelling (representation of the conceptual model by a scientific model), resolution of the
model (process of obtaining a solution for the scientific model), feedback (analysis of the
coherence between the solution obtained and the conceptual model), implementation
(process of applying the solution obtained in the reality or problem situation), and validation
of whether the scientific model corresponds to the reality or the cut of the reality (Funke,
2012). Sternberg and Frensch, (2014) has also suggested problem solving models . In this
work, the conceptualization process consists in the definition of the objectives, scope, the
control variables and known causal relationships of the production, and the logistics plan of a
company producing retail services (Ahern,, Leavy and Byrne, 2014). The following two
Page 11 of 20
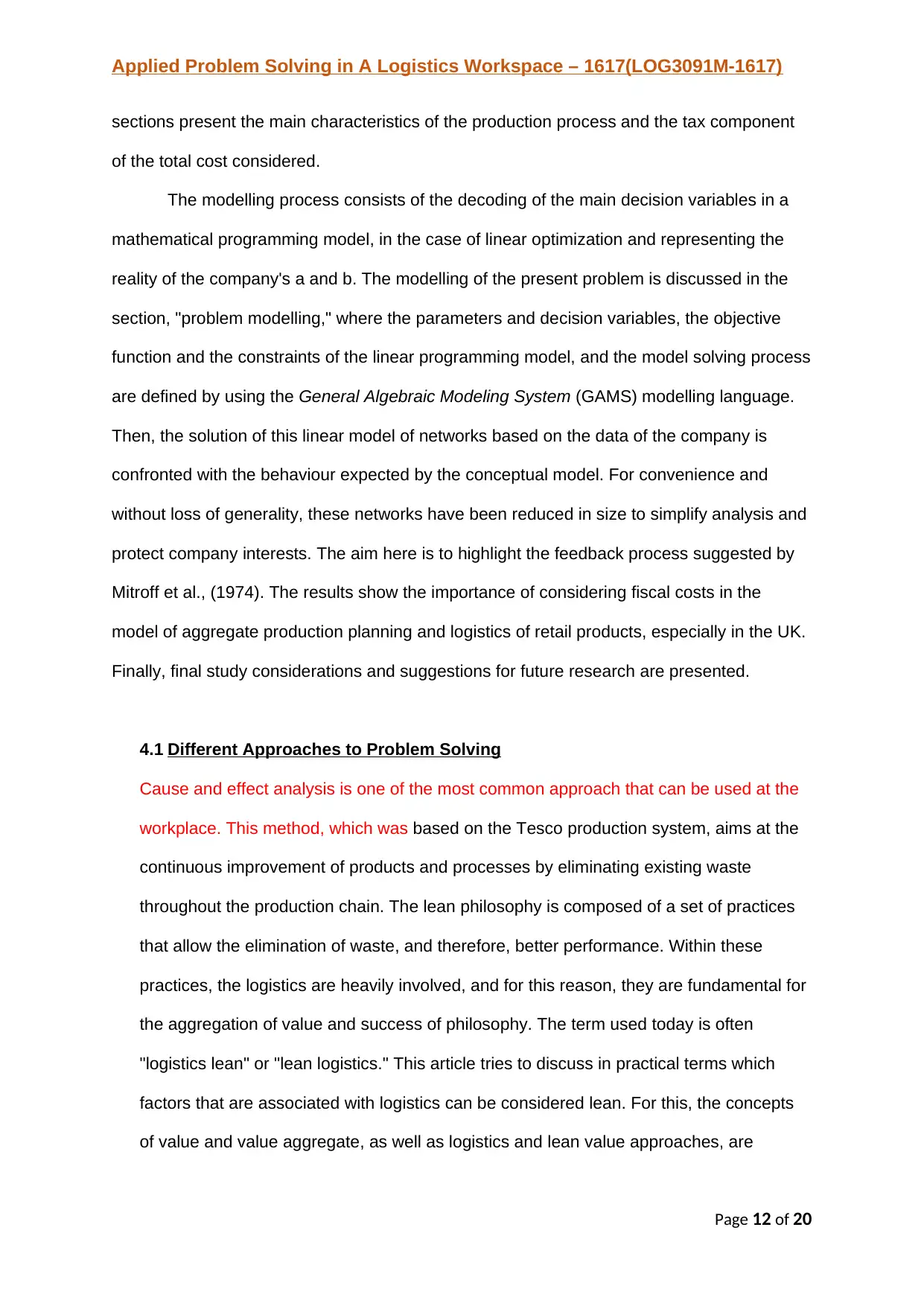
Applied Problem Solving in A Logistics Workspace – 1617(LOG3091M-1617)
sections present the main characteristics of the production process and the tax component
of the total cost considered.
The modelling process consists of the decoding of the main decision variables in a
mathematical programming model, in the case of linear optimization and representing the
reality of the company's a and b. The modelling of the present problem is discussed in the
section, "problem modelling," where the parameters and decision variables, the objective
function and the constraints of the linear programming model, and the model solving process
are defined by using the General Algebraic Modeling System (GAMS) modelling language.
Then, the solution of this linear model of networks based on the data of the company is
confronted with the behaviour expected by the conceptual model. For convenience and
without loss of generality, these networks have been reduced in size to simplify analysis and
protect company interests. The aim here is to highlight the feedback process suggested by
Mitroff et al., (1974). The results show the importance of considering fiscal costs in the
model of aggregate production planning and logistics of retail products, especially in the UK.
Finally, final study considerations and suggestions for future research are presented.
4.1 Different Approaches to Problem Solving
Cause and effect analysis is one of the most common approach that can be used at the
workplace. This method, which was based on the Tesco production system, aims at the
continuous improvement of products and processes by eliminating existing waste
throughout the production chain. The lean philosophy is composed of a set of practices
that allow the elimination of waste, and therefore, better performance. Within these
practices, the logistics are heavily involved, and for this reason, they are fundamental for
the aggregation of value and success of philosophy. The term used today is often
"logistics lean" or "lean logistics." This article tries to discuss in practical terms which
factors that are associated with logistics can be considered lean. For this, the concepts
of value and value aggregate, as well as logistics and lean value approaches, are
Page 12 of 20
sections present the main characteristics of the production process and the tax component
of the total cost considered.
The modelling process consists of the decoding of the main decision variables in a
mathematical programming model, in the case of linear optimization and representing the
reality of the company's a and b. The modelling of the present problem is discussed in the
section, "problem modelling," where the parameters and decision variables, the objective
function and the constraints of the linear programming model, and the model solving process
are defined by using the General Algebraic Modeling System (GAMS) modelling language.
Then, the solution of this linear model of networks based on the data of the company is
confronted with the behaviour expected by the conceptual model. For convenience and
without loss of generality, these networks have been reduced in size to simplify analysis and
protect company interests. The aim here is to highlight the feedback process suggested by
Mitroff et al., (1974). The results show the importance of considering fiscal costs in the
model of aggregate production planning and logistics of retail products, especially in the UK.
Finally, final study considerations and suggestions for future research are presented.
4.1 Different Approaches to Problem Solving
Cause and effect analysis is one of the most common approach that can be used at the
workplace. This method, which was based on the Tesco production system, aims at the
continuous improvement of products and processes by eliminating existing waste
throughout the production chain. The lean philosophy is composed of a set of practices
that allow the elimination of waste, and therefore, better performance. Within these
practices, the logistics are heavily involved, and for this reason, they are fundamental for
the aggregation of value and success of philosophy. The term used today is often
"logistics lean" or "lean logistics." This article tries to discuss in practical terms which
factors that are associated with logistics can be considered lean. For this, the concepts
of value and value aggregate, as well as logistics and lean value approaches, are
Page 12 of 20
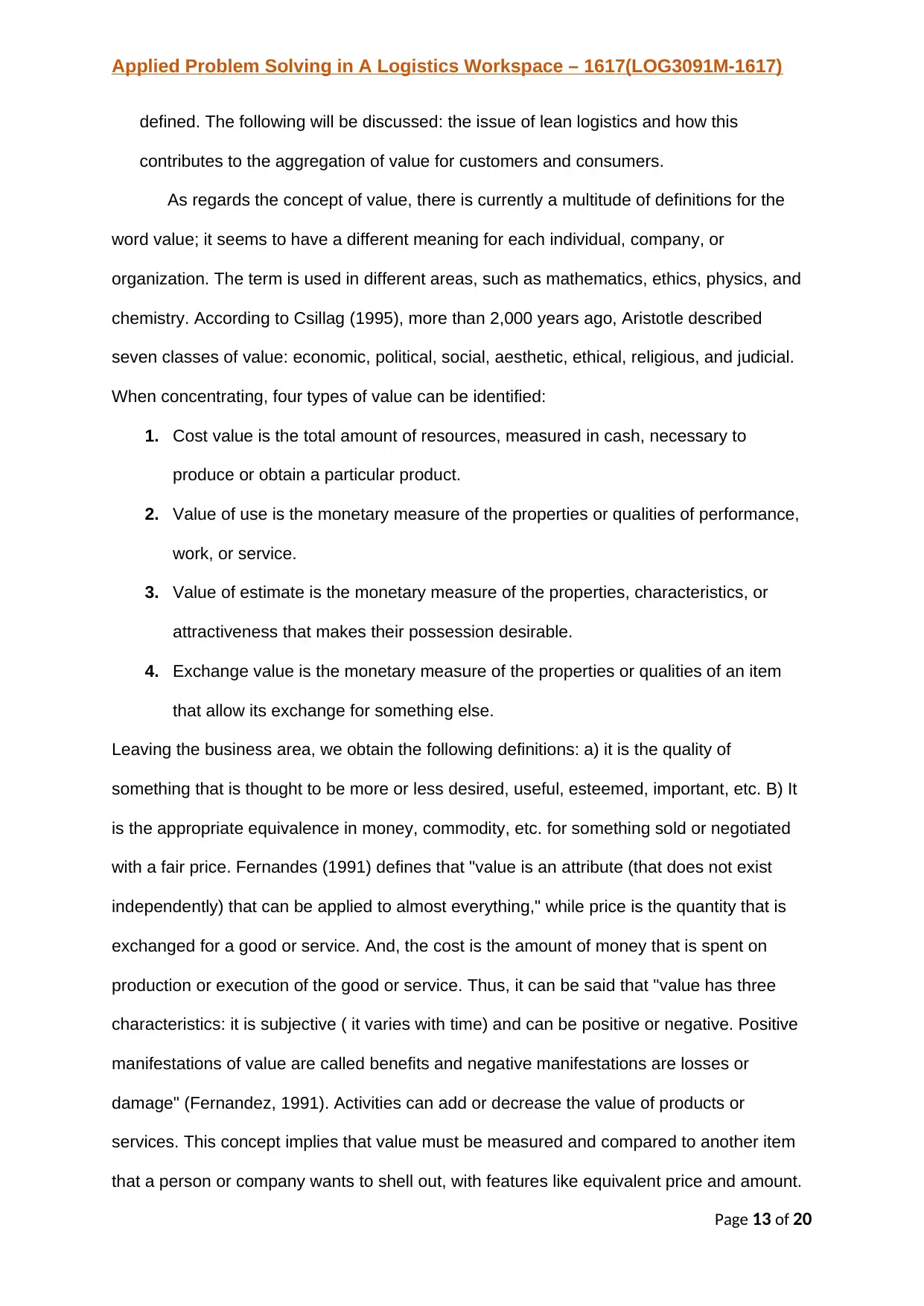
Applied Problem Solving in A Logistics Workspace – 1617(LOG3091M-1617)
defined. The following will be discussed: the issue of lean logistics and how this
contributes to the aggregation of value for customers and consumers.
As regards the concept of value, there is currently a multitude of definitions for the
word value; it seems to have a different meaning for each individual, company, or
organization. The term is used in different areas, such as mathematics, ethics, physics, and
chemistry. According to Csillag (1995), more than 2,000 years ago, Aristotle described
seven classes of value: economic, political, social, aesthetic, ethical, religious, and judicial.
When concentrating, four types of value can be identified:
1. Cost value is the total amount of resources, measured in cash, necessary to
produce or obtain a particular product.
2. Value of use is the monetary measure of the properties or qualities of performance,
work, or service.
3. Value of estimate is the monetary measure of the properties, characteristics, or
attractiveness that makes their possession desirable.
4. Exchange value is the monetary measure of the properties or qualities of an item
that allow its exchange for something else.
Leaving the business area, we obtain the following definitions: a) it is the quality of
something that is thought to be more or less desired, useful, esteemed, important, etc. B) It
is the appropriate equivalence in money, commodity, etc. for something sold or negotiated
with a fair price. Fernandes (1991) defines that "value is an attribute (that does not exist
independently) that can be applied to almost everything," while price is the quantity that is
exchanged for a good or service. And, the cost is the amount of money that is spent on
production or execution of the good or service. Thus, it can be said that "value has three
characteristics: it is subjective ( it varies with time) and can be positive or negative. Positive
manifestations of value are called benefits and negative manifestations are losses or
damage" (Fernandez, 1991). Activities can add or decrease the value of products or
services. This concept implies that value must be measured and compared to another item
that a person or company wants to shell out, with features like equivalent price and amount.
Page 13 of 20
defined. The following will be discussed: the issue of lean logistics and how this
contributes to the aggregation of value for customers and consumers.
As regards the concept of value, there is currently a multitude of definitions for the
word value; it seems to have a different meaning for each individual, company, or
organization. The term is used in different areas, such as mathematics, ethics, physics, and
chemistry. According to Csillag (1995), more than 2,000 years ago, Aristotle described
seven classes of value: economic, political, social, aesthetic, ethical, religious, and judicial.
When concentrating, four types of value can be identified:
1. Cost value is the total amount of resources, measured in cash, necessary to
produce or obtain a particular product.
2. Value of use is the monetary measure of the properties or qualities of performance,
work, or service.
3. Value of estimate is the monetary measure of the properties, characteristics, or
attractiveness that makes their possession desirable.
4. Exchange value is the monetary measure of the properties or qualities of an item
that allow its exchange for something else.
Leaving the business area, we obtain the following definitions: a) it is the quality of
something that is thought to be more or less desired, useful, esteemed, important, etc. B) It
is the appropriate equivalence in money, commodity, etc. for something sold or negotiated
with a fair price. Fernandes (1991) defines that "value is an attribute (that does not exist
independently) that can be applied to almost everything," while price is the quantity that is
exchanged for a good or service. And, the cost is the amount of money that is spent on
production or execution of the good or service. Thus, it can be said that "value has three
characteristics: it is subjective ( it varies with time) and can be positive or negative. Positive
manifestations of value are called benefits and negative manifestations are losses or
damage" (Fernandez, 1991). Activities can add or decrease the value of products or
services. This concept implies that value must be measured and compared to another item
that a person or company wants to shell out, with features like equivalent price and amount.
Page 13 of 20
Paraphrase This Document
Need a fresh take? Get an instant paraphrase of this document with our AI Paraphraser
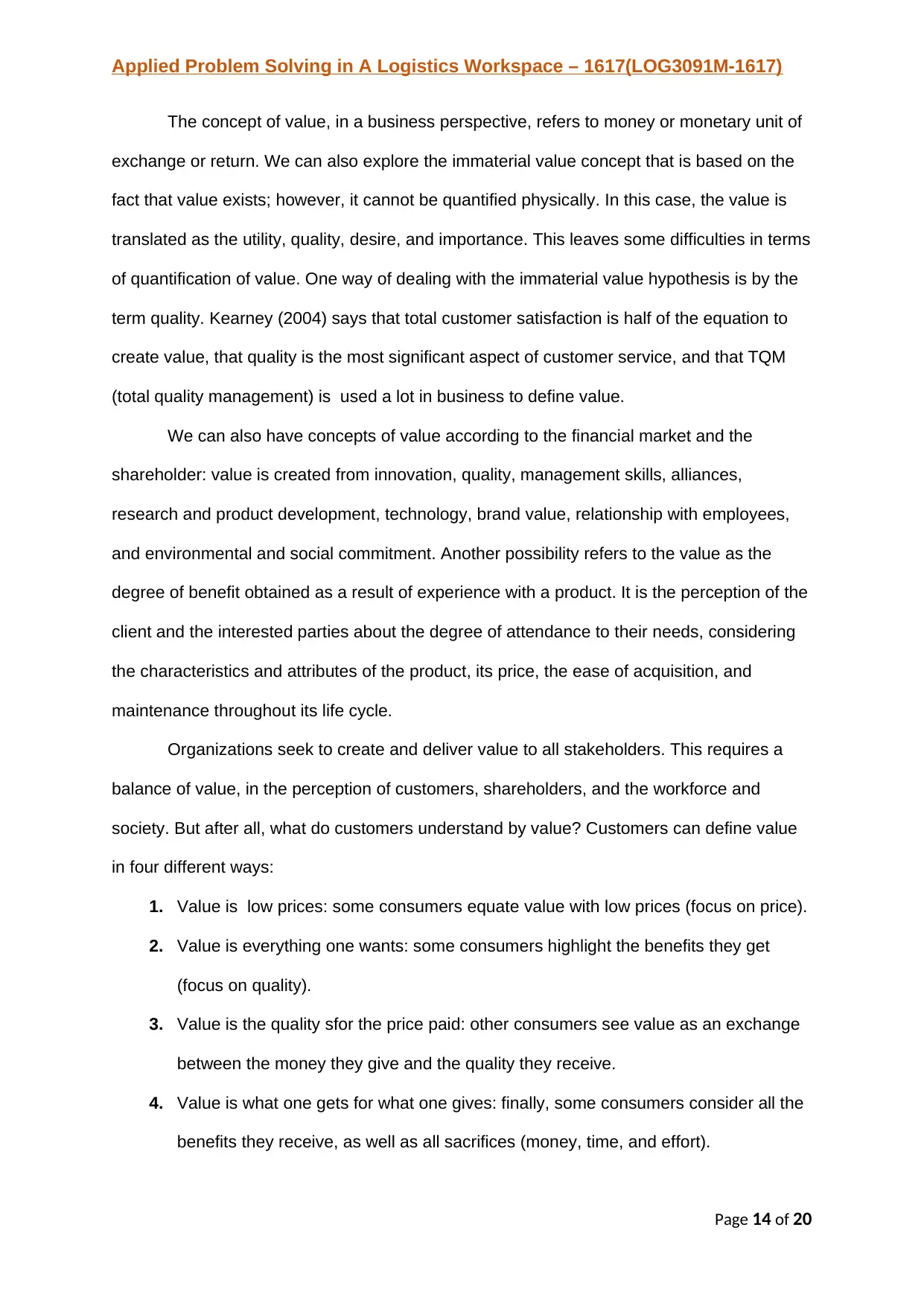
Applied Problem Solving in A Logistics Workspace – 1617(LOG3091M-1617)
The concept of value, in a business perspective, refers to money or monetary unit of
exchange or return. We can also explore the immaterial value concept that is based on the
fact that value exists; however, it cannot be quantified physically. In this case, the value is
translated as the utility, quality, desire, and importance. This leaves some difficulties in terms
of quantification of value. One way of dealing with the immaterial value hypothesis is by the
term quality. Kearney (2004) says that total customer satisfaction is half of the equation to
create value, that quality is the most significant aspect of customer service, and that TQM
(total quality management) is used a lot in business to define value.
We can also have concepts of value according to the financial market and the
shareholder: value is created from innovation, quality, management skills, alliances,
research and product development, technology, brand value, relationship with employees,
and environmental and social commitment. Another possibility refers to the value as the
degree of benefit obtained as a result of experience with a product. It is the perception of the
client and the interested parties about the degree of attendance to their needs, considering
the characteristics and attributes of the product, its price, the ease of acquisition, and
maintenance throughout its life cycle.
Organizations seek to create and deliver value to all stakeholders. This requires a
balance of value, in the perception of customers, shareholders, and the workforce and
society. But after all, what do customers understand by value? Customers can define value
in four different ways:
1. Value is low prices: some consumers equate value with low prices (focus on price).
2. Value is everything one wants: some consumers highlight the benefits they get
(focus on quality).
3. Value is the quality sfor the price paid: other consumers see value as an exchange
between the money they give and the quality they receive.
4. Value is what one gets for what one gives: finally, some consumers consider all the
benefits they receive, as well as all sacrifices (money, time, and effort).
Page 14 of 20
The concept of value, in a business perspective, refers to money or monetary unit of
exchange or return. We can also explore the immaterial value concept that is based on the
fact that value exists; however, it cannot be quantified physically. In this case, the value is
translated as the utility, quality, desire, and importance. This leaves some difficulties in terms
of quantification of value. One way of dealing with the immaterial value hypothesis is by the
term quality. Kearney (2004) says that total customer satisfaction is half of the equation to
create value, that quality is the most significant aspect of customer service, and that TQM
(total quality management) is used a lot in business to define value.
We can also have concepts of value according to the financial market and the
shareholder: value is created from innovation, quality, management skills, alliances,
research and product development, technology, brand value, relationship with employees,
and environmental and social commitment. Another possibility refers to the value as the
degree of benefit obtained as a result of experience with a product. It is the perception of the
client and the interested parties about the degree of attendance to their needs, considering
the characteristics and attributes of the product, its price, the ease of acquisition, and
maintenance throughout its life cycle.
Organizations seek to create and deliver value to all stakeholders. This requires a
balance of value, in the perception of customers, shareholders, and the workforce and
society. But after all, what do customers understand by value? Customers can define value
in four different ways:
1. Value is low prices: some consumers equate value with low prices (focus on price).
2. Value is everything one wants: some consumers highlight the benefits they get
(focus on quality).
3. Value is the quality sfor the price paid: other consumers see value as an exchange
between the money they give and the quality they receive.
4. Value is what one gets for what one gives: finally, some consumers consider all the
benefits they receive, as well as all sacrifices (money, time, and effort).
Page 14 of 20
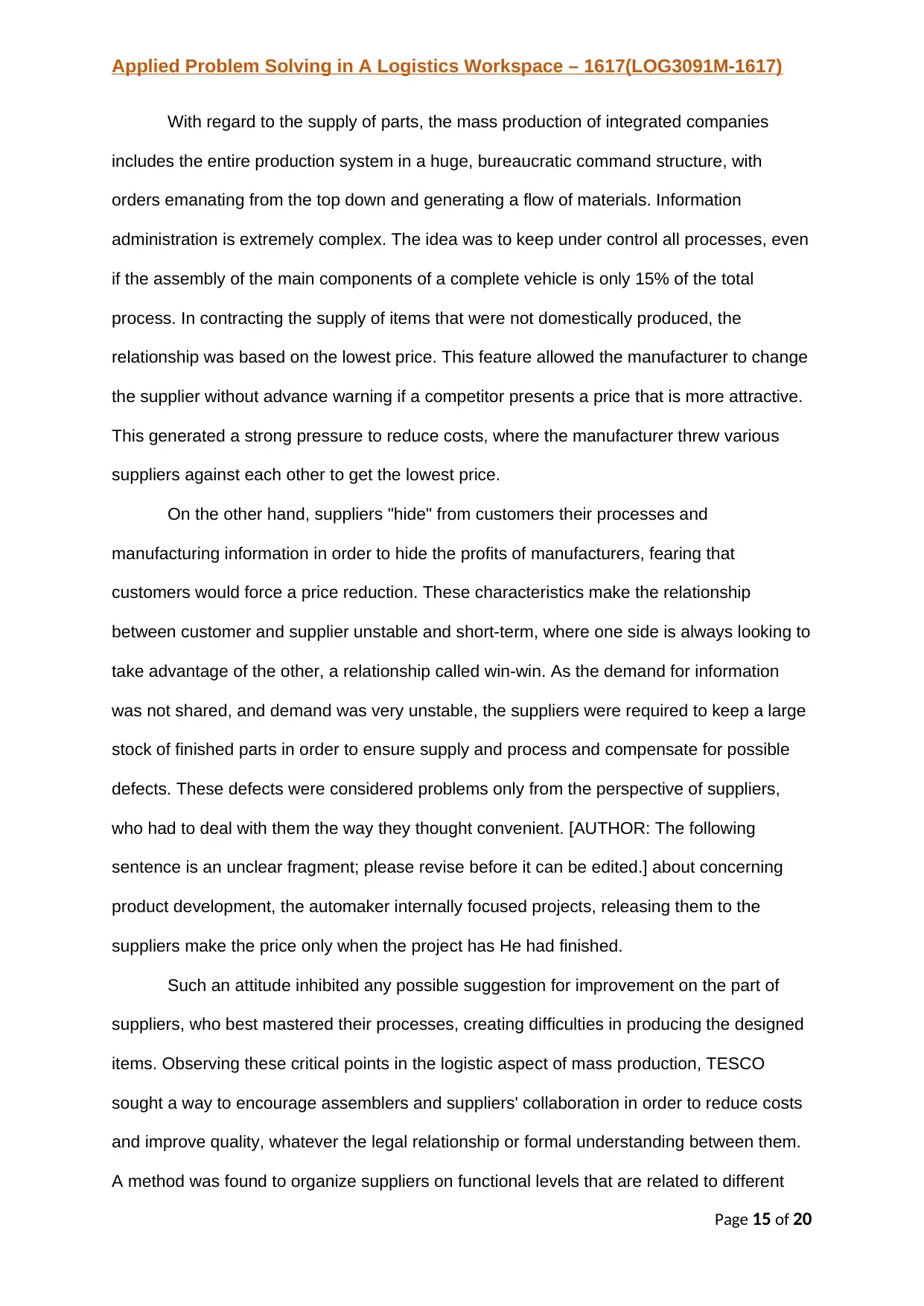
Applied Problem Solving in A Logistics Workspace – 1617(LOG3091M-1617)
With regard to the supply of parts, the mass production of integrated companies
includes the entire production system in a huge, bureaucratic command structure, with
orders emanating from the top down and generating a flow of materials. Information
administration is extremely complex. The idea was to keep under control all processes, even
if the assembly of the main components of a complete vehicle is only 15% of the total
process. In contracting the supply of items that were not domestically produced, the
relationship was based on the lowest price. This feature allowed the manufacturer to change
the supplier without advance warning if a competitor presents a price that is more attractive.
This generated a strong pressure to reduce costs, where the manufacturer threw various
suppliers against each other to get the lowest price.
On the other hand, suppliers "hide" from customers their processes and
manufacturing information in order to hide the profits of manufacturers, fearing that
customers would force a price reduction. These characteristics make the relationship
between customer and supplier unstable and short-term, where one side is always looking to
take advantage of the other, a relationship called win-win. As the demand for information
was not shared, and demand was very unstable, the suppliers were required to keep a large
stock of finished parts in order to ensure supply and process and compensate for possible
defects. These defects were considered problems only from the perspective of suppliers,
who had to deal with them the way they thought convenient. [AUTHOR: The following
sentence is an unclear fragment; please revise before it can be edited.] about concerning
product development, the automaker internally focused projects, releasing them to the
suppliers make the price only when the project has He had finished.
Such an attitude inhibited any possible suggestion for improvement on the part of
suppliers, who best mastered their processes, creating difficulties in producing the designed
items. Observing these critical points in the logistic aspect of mass production, TESCO
sought a way to encourage assemblers and suppliers' collaboration in order to reduce costs
and improve quality, whatever the legal relationship or formal understanding between them.
A method was found to organize suppliers on functional levels that are related to different
Page 15 of 20
With regard to the supply of parts, the mass production of integrated companies
includes the entire production system in a huge, bureaucratic command structure, with
orders emanating from the top down and generating a flow of materials. Information
administration is extremely complex. The idea was to keep under control all processes, even
if the assembly of the main components of a complete vehicle is only 15% of the total
process. In contracting the supply of items that were not domestically produced, the
relationship was based on the lowest price. This feature allowed the manufacturer to change
the supplier without advance warning if a competitor presents a price that is more attractive.
This generated a strong pressure to reduce costs, where the manufacturer threw various
suppliers against each other to get the lowest price.
On the other hand, suppliers "hide" from customers their processes and
manufacturing information in order to hide the profits of manufacturers, fearing that
customers would force a price reduction. These characteristics make the relationship
between customer and supplier unstable and short-term, where one side is always looking to
take advantage of the other, a relationship called win-win. As the demand for information
was not shared, and demand was very unstable, the suppliers were required to keep a large
stock of finished parts in order to ensure supply and process and compensate for possible
defects. These defects were considered problems only from the perspective of suppliers,
who had to deal with them the way they thought convenient. [AUTHOR: The following
sentence is an unclear fragment; please revise before it can be edited.] about concerning
product development, the automaker internally focused projects, releasing them to the
suppliers make the price only when the project has He had finished.
Such an attitude inhibited any possible suggestion for improvement on the part of
suppliers, who best mastered their processes, creating difficulties in producing the designed
items. Observing these critical points in the logistic aspect of mass production, TESCO
sought a way to encourage assemblers and suppliers' collaboration in order to reduce costs
and improve quality, whatever the legal relationship or formal understanding between them.
A method was found to organize suppliers on functional levels that are related to different
Page 15 of 20

Applied Problem Solving in A Logistics Workspace – 1617(LOG3091M-1617)
degrees of responsibility. First-tier suppliers participated fully in the development of the new
automobile and were encouraged to exchange ideas with other providers to improve the
design, resulting in fewer design changes. Tesco has turned supply operations into
companies, providing the first level almost independently, keeping part of its controlling
interest and financing the group providers. Second-tier suppliers were experts in making the
individual parts. They did not compete with each other and were grouped into associations,
and the suppliers were encouraged to work for other companies. These supplier
associations sought to unite the different suppliers to share information and discoveries that
improved their performance; therefore, they yielded the results for the whole group. They
were openly evaluated on their performance, and the results were compared to make
continuous improvements.
Tesco designated only one supplier per component, which avoided incompatibilities
among suppliers due to the standardization of the production process. There was also an
integrated team of engineers, between the supplier and the automaker, that provided a long-
term relationship. Unlike the conventional system, there was a cost reduction forecast,
providing the company's long-term learning curve and Kaizens. The target price for the
automobile was set, and the production steps were discussed with the suppliers to get a
price target with a reasonable profit margin for both the automaker and suppliers. But, the
reductions that would provide a cost below the target was created for the supplier to
encourage rapid and continuous improvements.
Thus, it was to replace the vicious circle of distrust between the parts of the circle
cooperation. The good relationship between the supplier and the customer made it possible
to pull the production, eliminating inventory and clearance and forcing people to anticipate
problems so thorderat they do not occur. This improvement in quality made it possible to
deliver the components directly to the production line and without inspection by the
automaker. Such procedure required a high degree of production levelling. It was necessary
to maintain control of the demand so that it is more stabilized. Tesco adopted an aggressive
system sale, which would ensure the control of demand (therefore, the assembly of cars)
Page 16 of 20
degrees of responsibility. First-tier suppliers participated fully in the development of the new
automobile and were encouraged to exchange ideas with other providers to improve the
design, resulting in fewer design changes. Tesco has turned supply operations into
companies, providing the first level almost independently, keeping part of its controlling
interest and financing the group providers. Second-tier suppliers were experts in making the
individual parts. They did not compete with each other and were grouped into associations,
and the suppliers were encouraged to work for other companies. These supplier
associations sought to unite the different suppliers to share information and discoveries that
improved their performance; therefore, they yielded the results for the whole group. They
were openly evaluated on their performance, and the results were compared to make
continuous improvements.
Tesco designated only one supplier per component, which avoided incompatibilities
among suppliers due to the standardization of the production process. There was also an
integrated team of engineers, between the supplier and the automaker, that provided a long-
term relationship. Unlike the conventional system, there was a cost reduction forecast,
providing the company's long-term learning curve and Kaizens. The target price for the
automobile was set, and the production steps were discussed with the suppliers to get a
price target with a reasonable profit margin for both the automaker and suppliers. But, the
reductions that would provide a cost below the target was created for the supplier to
encourage rapid and continuous improvements.
Thus, it was to replace the vicious circle of distrust between the parts of the circle
cooperation. The good relationship between the supplier and the customer made it possible
to pull the production, eliminating inventory and clearance and forcing people to anticipate
problems so thorderat they do not occur. This improvement in quality made it possible to
deliver the components directly to the production line and without inspection by the
automaker. Such procedure required a high degree of production levelling. It was necessary
to maintain control of the demand so that it is more stabilized. Tesco adopted an aggressive
system sale, which would ensure the control of demand (therefore, the assembly of cars)
Page 16 of 20
Secure Best Marks with AI Grader
Need help grading? Try our AI Grader for instant feedback on your assignments.
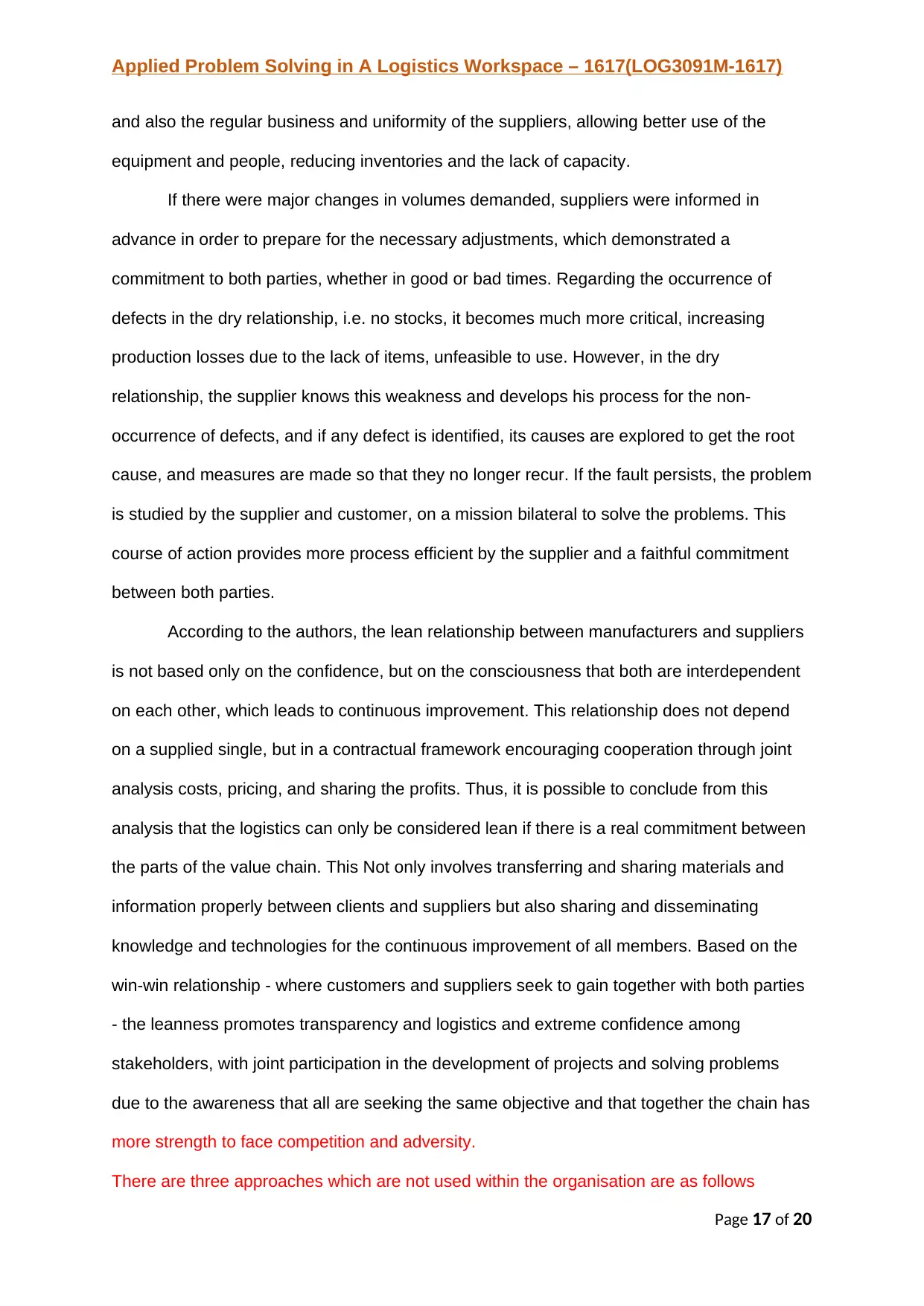
Applied Problem Solving in A Logistics Workspace – 1617(LOG3091M-1617)
and also the regular business and uniformity of the suppliers, allowing better use of the
equipment and people, reducing inventories and the lack of capacity.
If there were major changes in volumes demanded, suppliers were informed in
advance in order to prepare for the necessary adjustments, which demonstrated a
commitment to both parties, whether in good or bad times. Regarding the occurrence of
defects in the dry relationship, i.e. no stocks, it becomes much more critical, increasing
production losses due to the lack of items, unfeasible to use. However, in the dry
relationship, the supplier knows this weakness and develops his process for the non-
occurrence of defects, and if any defect is identified, its causes are explored to get the root
cause, and measures are made so that they no longer recur. If the fault persists, the problem
is studied by the supplier and customer, on a mission bilateral to solve the problems. This
course of action provides more process efficient by the supplier and a faithful commitment
between both parties.
According to the authors, the lean relationship between manufacturers and suppliers
is not based only on the confidence, but on the consciousness that both are interdependent
on each other, which leads to continuous improvement. This relationship does not depend
on a supplied single, but in a contractual framework encouraging cooperation through joint
analysis costs, pricing, and sharing the profits. Thus, it is possible to conclude from this
analysis that the logistics can only be considered lean if there is a real commitment between
the parts of the value chain. This Not only involves transferring and sharing materials and
information properly between clients and suppliers but also sharing and disseminating
knowledge and technologies for the continuous improvement of all members. Based on the
win-win relationship - where customers and suppliers seek to gain together with both parties
- the leanness promotes transparency and logistics and extreme confidence among
stakeholders, with joint participation in the development of projects and solving problems
due to the awareness that all are seeking the same objective and that together the chain has
more strength to face competition and adversity.
There are three approaches which are not used within the organisation are as follows
Page 17 of 20
and also the regular business and uniformity of the suppliers, allowing better use of the
equipment and people, reducing inventories and the lack of capacity.
If there were major changes in volumes demanded, suppliers were informed in
advance in order to prepare for the necessary adjustments, which demonstrated a
commitment to both parties, whether in good or bad times. Regarding the occurrence of
defects in the dry relationship, i.e. no stocks, it becomes much more critical, increasing
production losses due to the lack of items, unfeasible to use. However, in the dry
relationship, the supplier knows this weakness and develops his process for the non-
occurrence of defects, and if any defect is identified, its causes are explored to get the root
cause, and measures are made so that they no longer recur. If the fault persists, the problem
is studied by the supplier and customer, on a mission bilateral to solve the problems. This
course of action provides more process efficient by the supplier and a faithful commitment
between both parties.
According to the authors, the lean relationship between manufacturers and suppliers
is not based only on the confidence, but on the consciousness that both are interdependent
on each other, which leads to continuous improvement. This relationship does not depend
on a supplied single, but in a contractual framework encouraging cooperation through joint
analysis costs, pricing, and sharing the profits. Thus, it is possible to conclude from this
analysis that the logistics can only be considered lean if there is a real commitment between
the parts of the value chain. This Not only involves transferring and sharing materials and
information properly between clients and suppliers but also sharing and disseminating
knowledge and technologies for the continuous improvement of all members. Based on the
win-win relationship - where customers and suppliers seek to gain together with both parties
- the leanness promotes transparency and logistics and extreme confidence among
stakeholders, with joint participation in the development of projects and solving problems
due to the awareness that all are seeking the same objective and that together the chain has
more strength to face competition and adversity.
There are three approaches which are not used within the organisation are as follows
Page 17 of 20
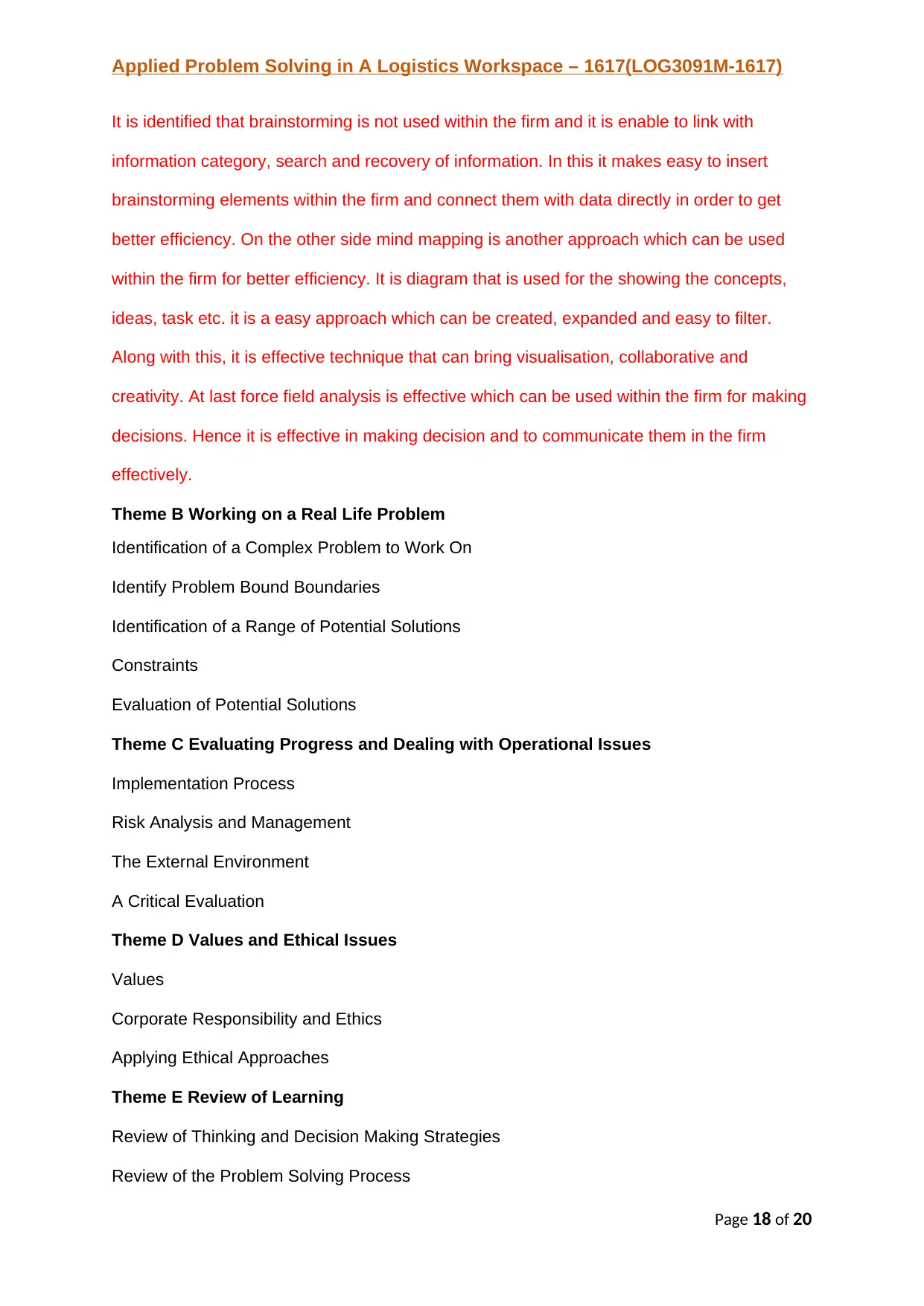
Applied Problem Solving in A Logistics Workspace – 1617(LOG3091M-1617)
It is identified that brainstorming is not used within the firm and it is enable to link with
information category, search and recovery of information. In this it makes easy to insert
brainstorming elements within the firm and connect them with data directly in order to get
better efficiency. On the other side mind mapping is another approach which can be used
within the firm for better efficiency. It is diagram that is used for the showing the concepts,
ideas, task etc. it is a easy approach which can be created, expanded and easy to filter.
Along with this, it is effective technique that can bring visualisation, collaborative and
creativity. At last force field analysis is effective which can be used within the firm for making
decisions. Hence it is effective in making decision and to communicate them in the firm
effectively.
Theme B Working on a Real Life Problem
Identification of a Complex Problem to Work On
Identify Problem Bound Boundaries
Identification of a Range of Potential Solutions
Constraints
Evaluation of Potential Solutions
Theme C Evaluating Progress and Dealing with Operational Issues
Implementation Process
Risk Analysis and Management
The External Environment
A Critical Evaluation
Theme D Values and Ethical Issues
Values
Corporate Responsibility and Ethics
Applying Ethical Approaches
Theme E Review of Learning
Review of Thinking and Decision Making Strategies
Review of the Problem Solving Process
Page 18 of 20
It is identified that brainstorming is not used within the firm and it is enable to link with
information category, search and recovery of information. In this it makes easy to insert
brainstorming elements within the firm and connect them with data directly in order to get
better efficiency. On the other side mind mapping is another approach which can be used
within the firm for better efficiency. It is diagram that is used for the showing the concepts,
ideas, task etc. it is a easy approach which can be created, expanded and easy to filter.
Along with this, it is effective technique that can bring visualisation, collaborative and
creativity. At last force field analysis is effective which can be used within the firm for making
decisions. Hence it is effective in making decision and to communicate them in the firm
effectively.
Theme B Working on a Real Life Problem
Identification of a Complex Problem to Work On
Identify Problem Bound Boundaries
Identification of a Range of Potential Solutions
Constraints
Evaluation of Potential Solutions
Theme C Evaluating Progress and Dealing with Operational Issues
Implementation Process
Risk Analysis and Management
The External Environment
A Critical Evaluation
Theme D Values and Ethical Issues
Values
Corporate Responsibility and Ethics
Applying Ethical Approaches
Theme E Review of Learning
Review of Thinking and Decision Making Strategies
Review of the Problem Solving Process
Page 18 of 20
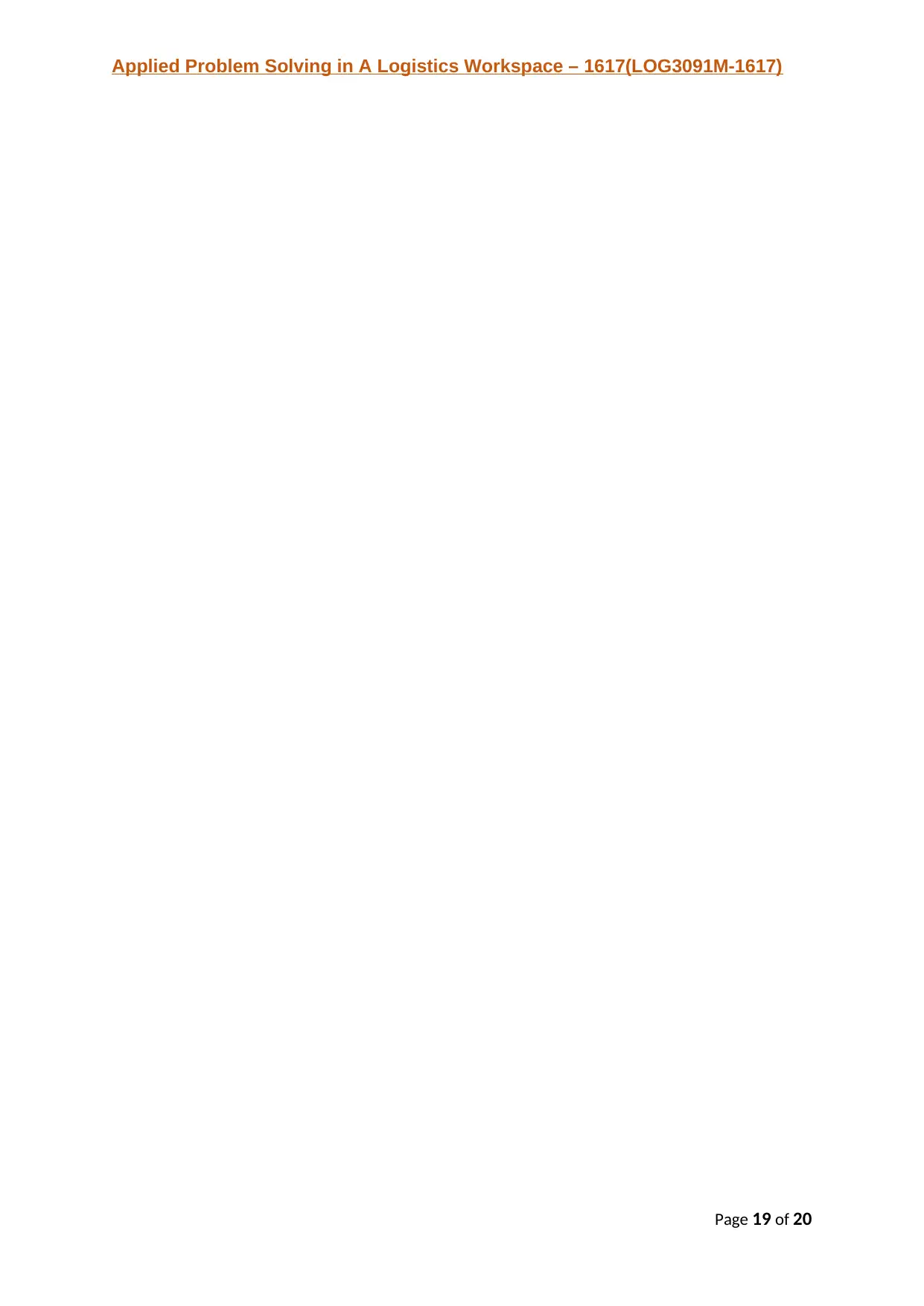
Applied Problem Solving in A Logistics Workspace – 1617(LOG3091M-1617)
Page 19 of 20
Page 19 of 20
Paraphrase This Document
Need a fresh take? Get an instant paraphrase of this document with our AI Paraphraser
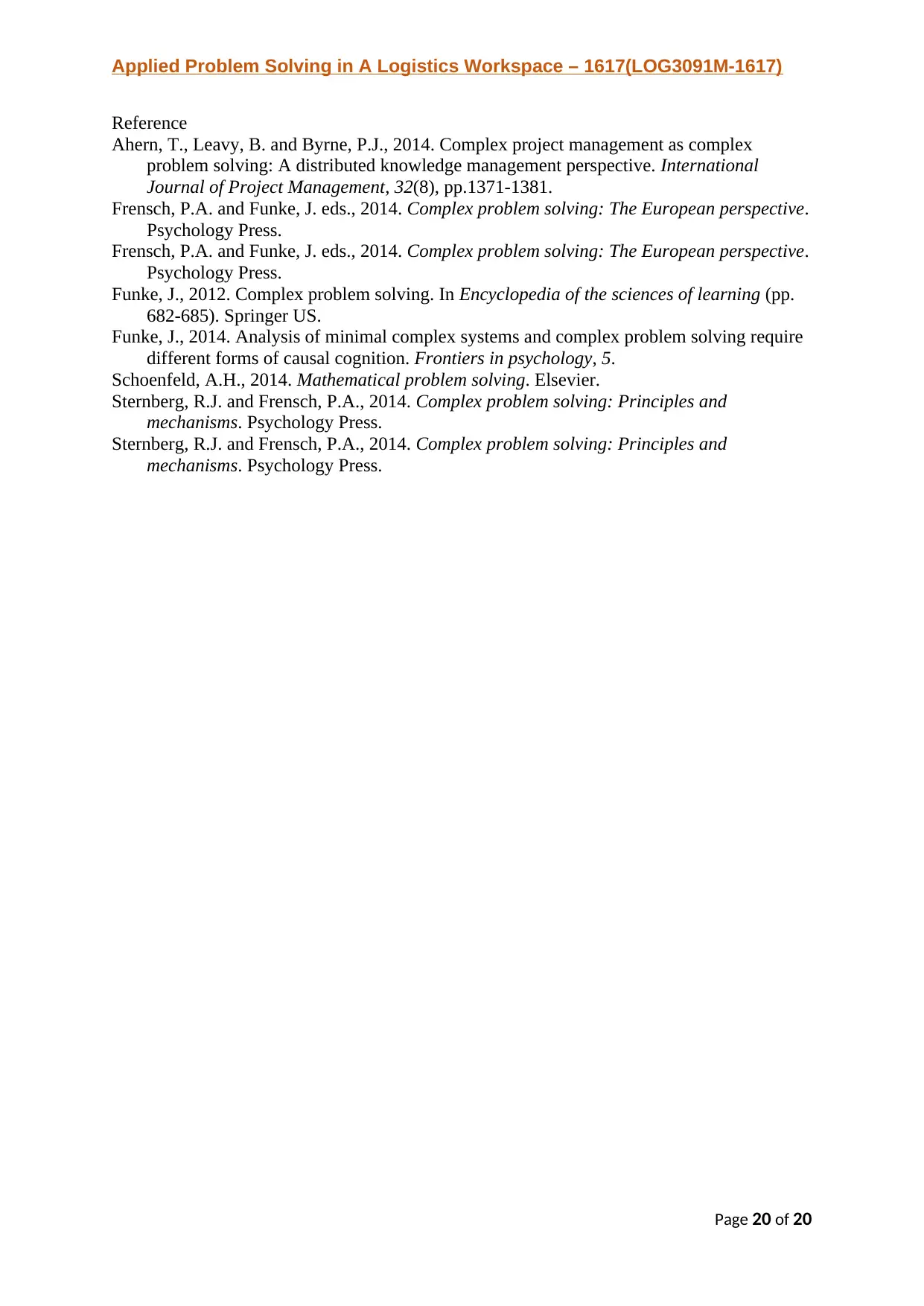
Applied Problem Solving in A Logistics Workspace – 1617(LOG3091M-1617)
Reference
Ahern, T., Leavy, B. and Byrne, P.J., 2014. Complex project management as complex
problem solving: A distributed knowledge management perspective. International
Journal of Project Management, 32(8), pp.1371-1381.
Frensch, P.A. and Funke, J. eds., 2014. Complex problem solving: The European perspective.
Psychology Press.
Frensch, P.A. and Funke, J. eds., 2014. Complex problem solving: The European perspective.
Psychology Press.
Funke, J., 2012. Complex problem solving. In Encyclopedia of the sciences of learning (pp.
682-685). Springer US.
Funke, J., 2014. Analysis of minimal complex systems and complex problem solving require
different forms of causal cognition. Frontiers in psychology, 5.
Schoenfeld, A.H., 2014. Mathematical problem solving. Elsevier.
Sternberg, R.J. and Frensch, P.A., 2014. Complex problem solving: Principles and
mechanisms. Psychology Press.
Sternberg, R.J. and Frensch, P.A., 2014. Complex problem solving: Principles and
mechanisms. Psychology Press.
Page 20 of 20
Reference
Ahern, T., Leavy, B. and Byrne, P.J., 2014. Complex project management as complex
problem solving: A distributed knowledge management perspective. International
Journal of Project Management, 32(8), pp.1371-1381.
Frensch, P.A. and Funke, J. eds., 2014. Complex problem solving: The European perspective.
Psychology Press.
Frensch, P.A. and Funke, J. eds., 2014. Complex problem solving: The European perspective.
Psychology Press.
Funke, J., 2012. Complex problem solving. In Encyclopedia of the sciences of learning (pp.
682-685). Springer US.
Funke, J., 2014. Analysis of minimal complex systems and complex problem solving require
different forms of causal cognition. Frontiers in psychology, 5.
Schoenfeld, A.H., 2014. Mathematical problem solving. Elsevier.
Sternberg, R.J. and Frensch, P.A., 2014. Complex problem solving: Principles and
mechanisms. Psychology Press.
Sternberg, R.J. and Frensch, P.A., 2014. Complex problem solving: Principles and
mechanisms. Psychology Press.
Page 20 of 20
1 out of 20
Related Documents

Your All-in-One AI-Powered Toolkit for Academic Success.
+13062052269
info@desklib.com
Available 24*7 on WhatsApp / Email
Unlock your academic potential
© 2024 | Zucol Services PVT LTD | All rights reserved.