ENAR12014: Project Management Report on Australian Mining Automation
VerifiedAdded on 2022/09/18
|15
|2679
|29
Report
AI Summary
This report provides a comprehensive overview of coal mining in Australia, focusing on the historical context, technological advancements, and the impact of automation on safety, productivity, and sustainability. The report begins with an executive summary and introduction that highlights the role of mining in Australia, particularly coal, and the shift towards automation in response to safety concerns and the need for sustainable practices. The report then delves into the evolution of coal mining, discussing the transition from manual to automated processes, including longwall mining, automated haul trucks, and drilling equipment. It explores the benefits of these technologies, such as increased efficiency, reduced costs, and improved worker safety. The report also examines the importance of sensors and data analysis in optimizing mining operations, including the use of risk assessment matrices and hazard inventory tables. Furthermore, it addresses the concept of sustainable mining, emphasizing the need for environmentally friendly practices and adherence to regulations. The report concludes with recommendations for the broader adoption of automation in the mining sector and highlights the importance of awareness and education to reduce risks and enhance productivity. Finally, the report includes figures, tables, and references to support the findings and analysis.
Contribute Materials
Your contribution can guide someone’s learning journey. Share your
documents today.
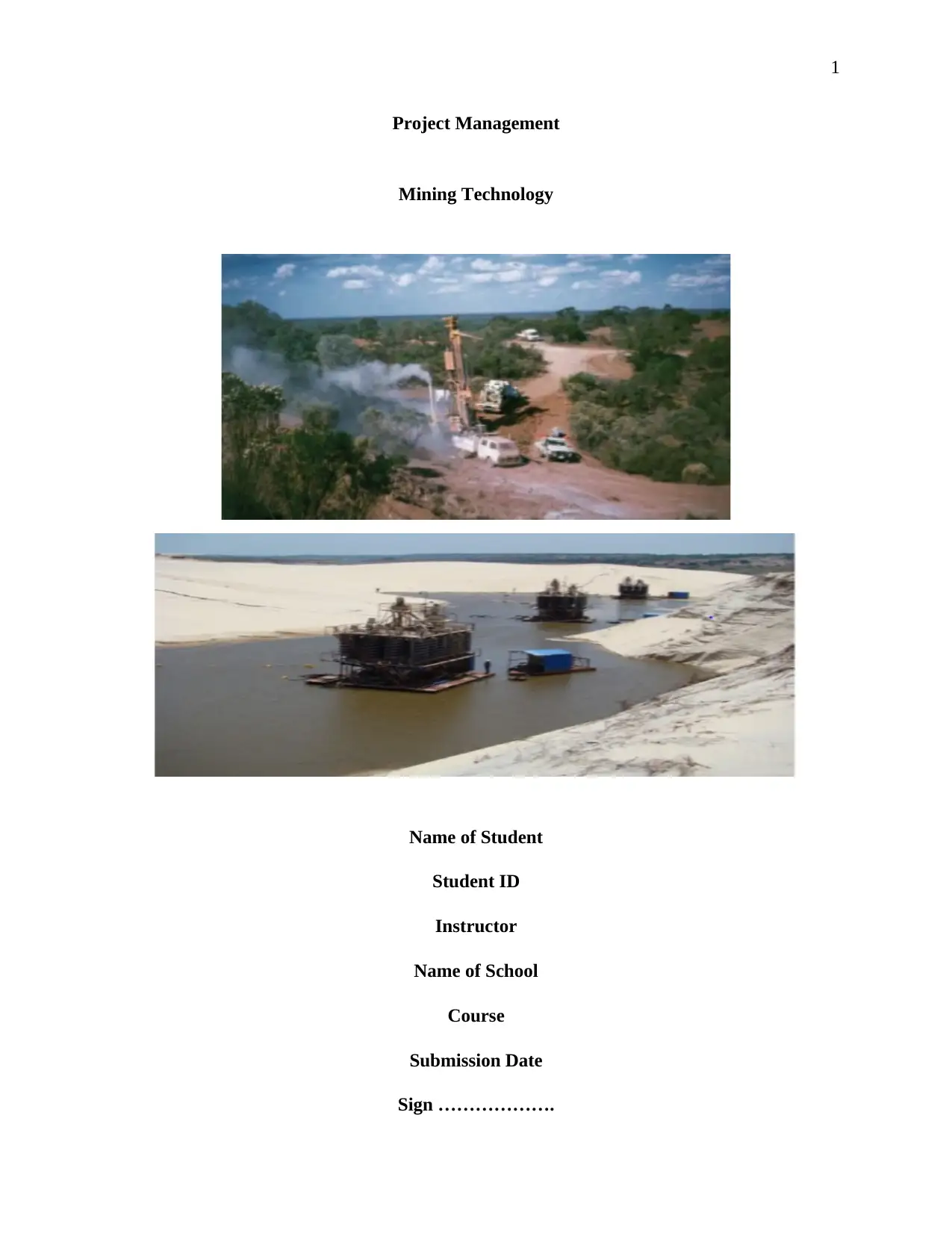
1
Project Management
Mining Technology
Name of Student
Student ID
Instructor
Name of School
Course
Submission Date
Sign ……………….
Project Management
Mining Technology
Name of Student
Student ID
Instructor
Name of School
Course
Submission Date
Sign ……………….
Secure Best Marks with AI Grader
Need help grading? Try our AI Grader for instant feedback on your assignments.
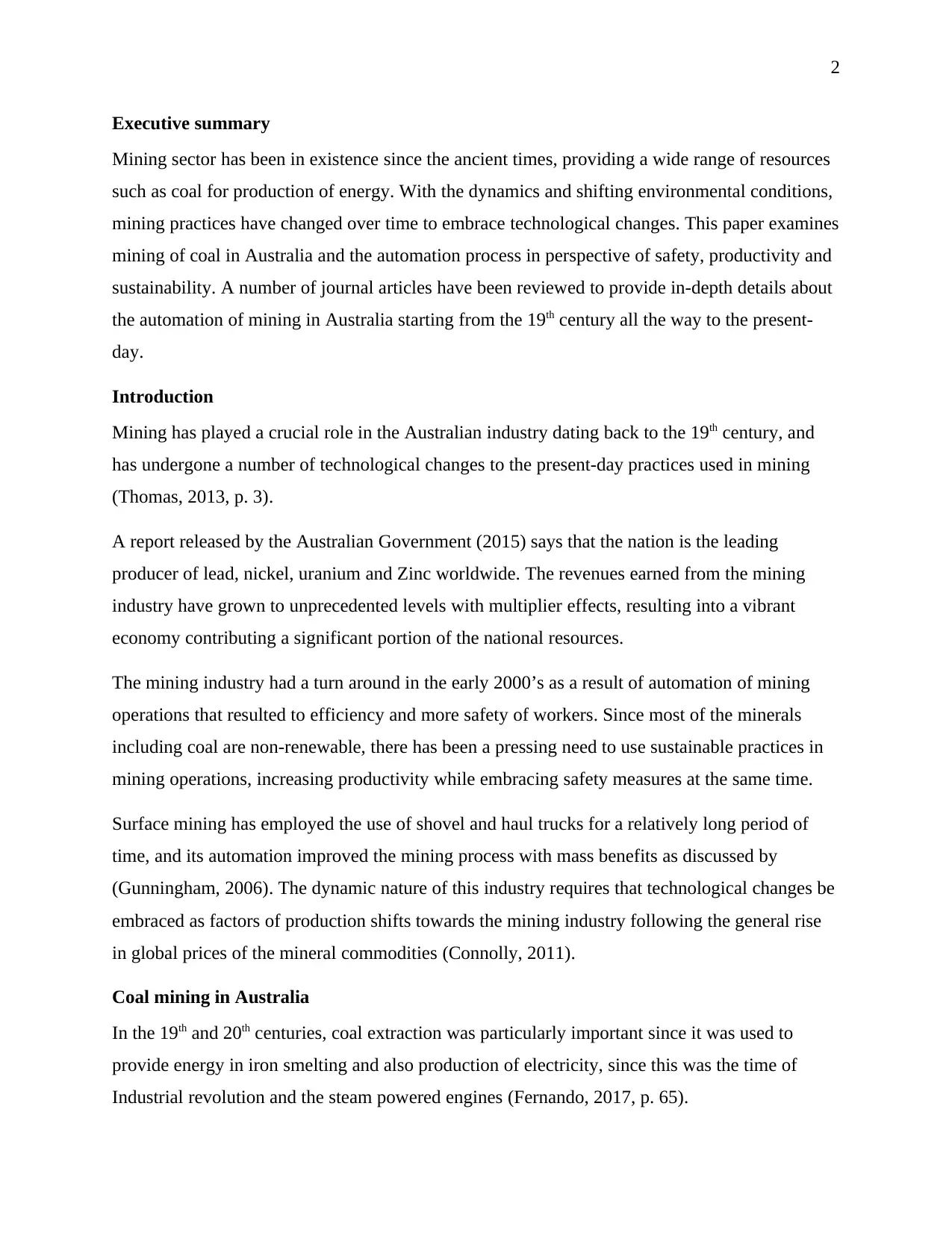
2
Executive summary
Mining sector has been in existence since the ancient times, providing a wide range of resources
such as coal for production of energy. With the dynamics and shifting environmental conditions,
mining practices have changed over time to embrace technological changes. This paper examines
mining of coal in Australia and the automation process in perspective of safety, productivity and
sustainability. A number of journal articles have been reviewed to provide in-depth details about
the automation of mining in Australia starting from the 19th century all the way to the present-
day.
Introduction
Mining has played a crucial role in the Australian industry dating back to the 19th century, and
has undergone a number of technological changes to the present-day practices used in mining
(Thomas, 2013, p. 3).
A report released by the Australian Government (2015) says that the nation is the leading
producer of lead, nickel, uranium and Zinc worldwide. The revenues earned from the mining
industry have grown to unprecedented levels with multiplier effects, resulting into a vibrant
economy contributing a significant portion of the national resources.
The mining industry had a turn around in the early 2000’s as a result of automation of mining
operations that resulted to efficiency and more safety of workers. Since most of the minerals
including coal are non-renewable, there has been a pressing need to use sustainable practices in
mining operations, increasing productivity while embracing safety measures at the same time.
Surface mining has employed the use of shovel and haul trucks for a relatively long period of
time, and its automation improved the mining process with mass benefits as discussed by
(Gunningham, 2006). The dynamic nature of this industry requires that technological changes be
embraced as factors of production shifts towards the mining industry following the general rise
in global prices of the mineral commodities (Connolly, 2011).
Coal mining in Australia
In the 19th and 20th centuries, coal extraction was particularly important since it was used to
provide energy in iron smelting and also production of electricity, since this was the time of
Industrial revolution and the steam powered engines (Fernando, 2017, p. 65).
Executive summary
Mining sector has been in existence since the ancient times, providing a wide range of resources
such as coal for production of energy. With the dynamics and shifting environmental conditions,
mining practices have changed over time to embrace technological changes. This paper examines
mining of coal in Australia and the automation process in perspective of safety, productivity and
sustainability. A number of journal articles have been reviewed to provide in-depth details about
the automation of mining in Australia starting from the 19th century all the way to the present-
day.
Introduction
Mining has played a crucial role in the Australian industry dating back to the 19th century, and
has undergone a number of technological changes to the present-day practices used in mining
(Thomas, 2013, p. 3).
A report released by the Australian Government (2015) says that the nation is the leading
producer of lead, nickel, uranium and Zinc worldwide. The revenues earned from the mining
industry have grown to unprecedented levels with multiplier effects, resulting into a vibrant
economy contributing a significant portion of the national resources.
The mining industry had a turn around in the early 2000’s as a result of automation of mining
operations that resulted to efficiency and more safety of workers. Since most of the minerals
including coal are non-renewable, there has been a pressing need to use sustainable practices in
mining operations, increasing productivity while embracing safety measures at the same time.
Surface mining has employed the use of shovel and haul trucks for a relatively long period of
time, and its automation improved the mining process with mass benefits as discussed by
(Gunningham, 2006). The dynamic nature of this industry requires that technological changes be
embraced as factors of production shifts towards the mining industry following the general rise
in global prices of the mineral commodities (Connolly, 2011).
Coal mining in Australia
In the 19th and 20th centuries, coal extraction was particularly important since it was used to
provide energy in iron smelting and also production of electricity, since this was the time of
Industrial revolution and the steam powered engines (Fernando, 2017, p. 65).
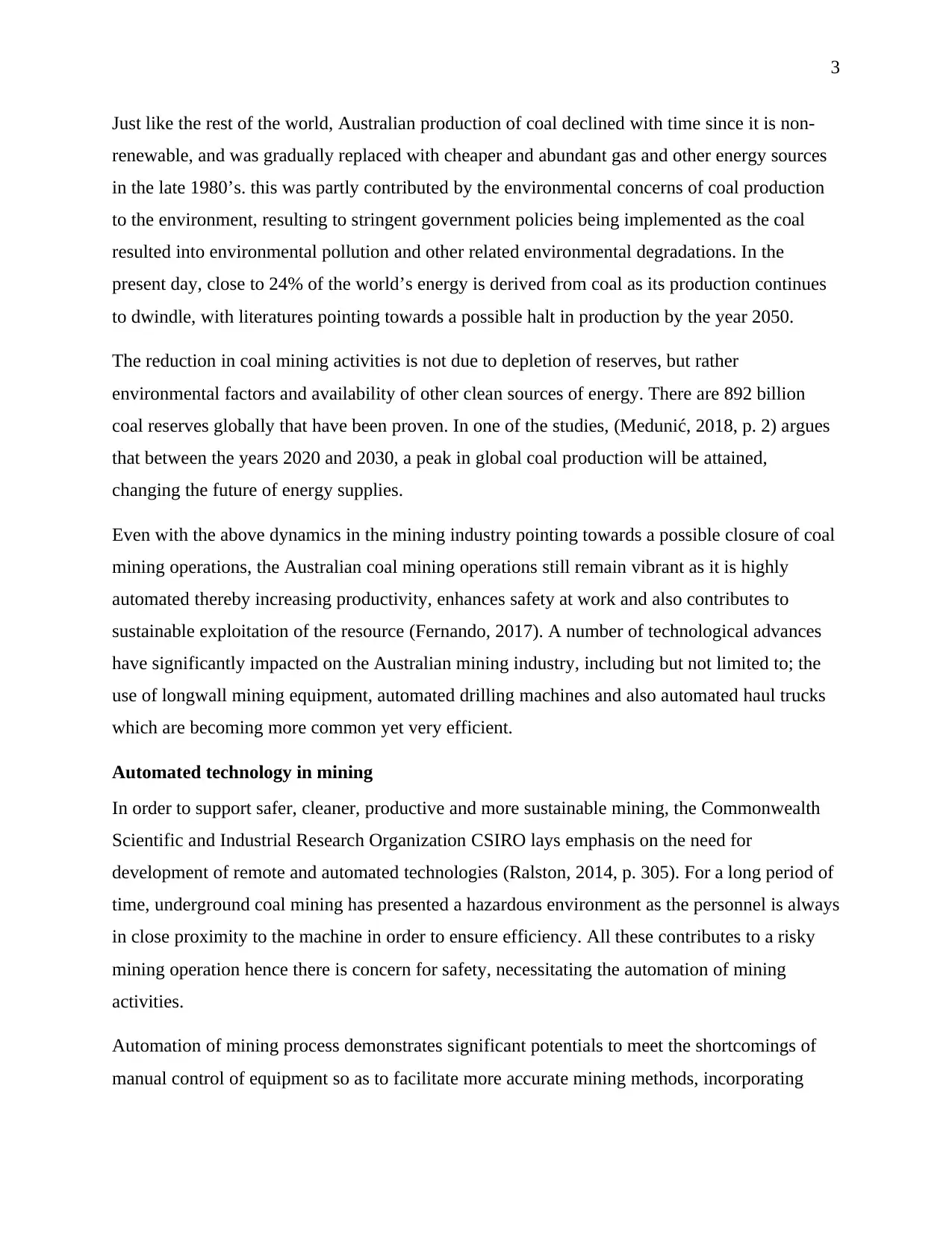
3
Just like the rest of the world, Australian production of coal declined with time since it is non-
renewable, and was gradually replaced with cheaper and abundant gas and other energy sources
in the late 1980’s. this was partly contributed by the environmental concerns of coal production
to the environment, resulting to stringent government policies being implemented as the coal
resulted into environmental pollution and other related environmental degradations. In the
present day, close to 24% of the world’s energy is derived from coal as its production continues
to dwindle, with literatures pointing towards a possible halt in production by the year 2050.
The reduction in coal mining activities is not due to depletion of reserves, but rather
environmental factors and availability of other clean sources of energy. There are 892 billion
coal reserves globally that have been proven. In one of the studies, (Medunić, 2018, p. 2) argues
that between the years 2020 and 2030, a peak in global coal production will be attained,
changing the future of energy supplies.
Even with the above dynamics in the mining industry pointing towards a possible closure of coal
mining operations, the Australian coal mining operations still remain vibrant as it is highly
automated thereby increasing productivity, enhances safety at work and also contributes to
sustainable exploitation of the resource (Fernando, 2017). A number of technological advances
have significantly impacted on the Australian mining industry, including but not limited to; the
use of longwall mining equipment, automated drilling machines and also automated haul trucks
which are becoming more common yet very efficient.
Automated technology in mining
In order to support safer, cleaner, productive and more sustainable mining, the Commonwealth
Scientific and Industrial Research Organization CSIRO lays emphasis on the need for
development of remote and automated technologies (Ralston, 2014, p. 305). For a long period of
time, underground coal mining has presented a hazardous environment as the personnel is always
in close proximity to the machine in order to ensure efficiency. All these contributes to a risky
mining operation hence there is concern for safety, necessitating the automation of mining
activities.
Automation of mining process demonstrates significant potentials to meet the shortcomings of
manual control of equipment so as to facilitate more accurate mining methods, incorporating
Just like the rest of the world, Australian production of coal declined with time since it is non-
renewable, and was gradually replaced with cheaper and abundant gas and other energy sources
in the late 1980’s. this was partly contributed by the environmental concerns of coal production
to the environment, resulting to stringent government policies being implemented as the coal
resulted into environmental pollution and other related environmental degradations. In the
present day, close to 24% of the world’s energy is derived from coal as its production continues
to dwindle, with literatures pointing towards a possible halt in production by the year 2050.
The reduction in coal mining activities is not due to depletion of reserves, but rather
environmental factors and availability of other clean sources of energy. There are 892 billion
coal reserves globally that have been proven. In one of the studies, (Medunić, 2018, p. 2) argues
that between the years 2020 and 2030, a peak in global coal production will be attained,
changing the future of energy supplies.
Even with the above dynamics in the mining industry pointing towards a possible closure of coal
mining operations, the Australian coal mining operations still remain vibrant as it is highly
automated thereby increasing productivity, enhances safety at work and also contributes to
sustainable exploitation of the resource (Fernando, 2017). A number of technological advances
have significantly impacted on the Australian mining industry, including but not limited to; the
use of longwall mining equipment, automated drilling machines and also automated haul trucks
which are becoming more common yet very efficient.
Automated technology in mining
In order to support safer, cleaner, productive and more sustainable mining, the Commonwealth
Scientific and Industrial Research Organization CSIRO lays emphasis on the need for
development of remote and automated technologies (Ralston, 2014, p. 305). For a long period of
time, underground coal mining has presented a hazardous environment as the personnel is always
in close proximity to the machine in order to ensure efficiency. All these contributes to a risky
mining operation hence there is concern for safety, necessitating the automation of mining
activities.
Automation of mining process demonstrates significant potentials to meet the shortcomings of
manual control of equipment so as to facilitate more accurate mining methods, incorporating
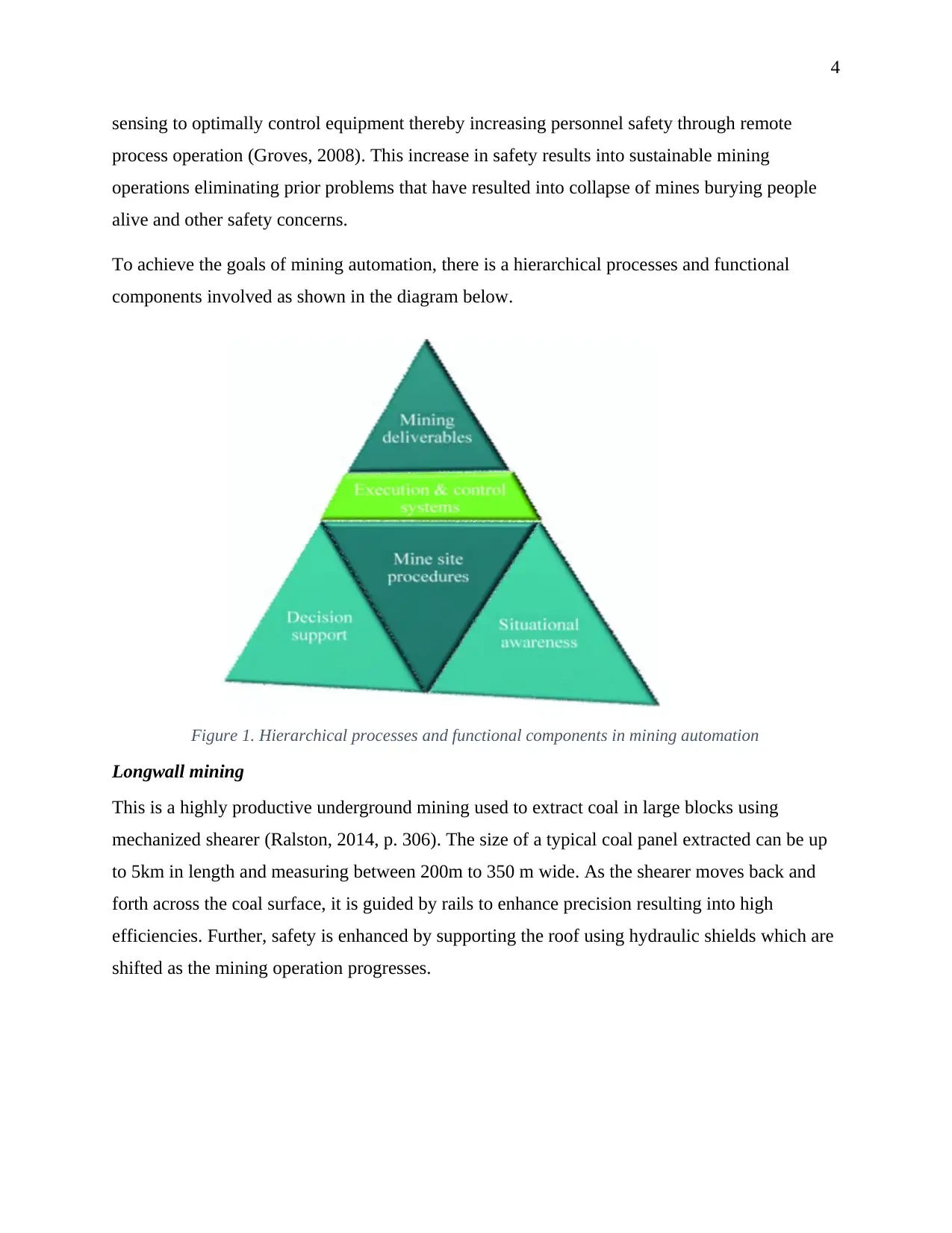
4
sensing to optimally control equipment thereby increasing personnel safety through remote
process operation (Groves, 2008). This increase in safety results into sustainable mining
operations eliminating prior problems that have resulted into collapse of mines burying people
alive and other safety concerns.
To achieve the goals of mining automation, there is a hierarchical processes and functional
components involved as shown in the diagram below.
Figure 1. Hierarchical processes and functional components in mining automation
Longwall mining
This is a highly productive underground mining used to extract coal in large blocks using
mechanized shearer (Ralston, 2014, p. 306). The size of a typical coal panel extracted can be up
to 5km in length and measuring between 200m to 350 m wide. As the shearer moves back and
forth across the coal surface, it is guided by rails to enhance precision resulting into high
efficiencies. Further, safety is enhanced by supporting the roof using hydraulic shields which are
shifted as the mining operation progresses.
sensing to optimally control equipment thereby increasing personnel safety through remote
process operation (Groves, 2008). This increase in safety results into sustainable mining
operations eliminating prior problems that have resulted into collapse of mines burying people
alive and other safety concerns.
To achieve the goals of mining automation, there is a hierarchical processes and functional
components involved as shown in the diagram below.
Figure 1. Hierarchical processes and functional components in mining automation
Longwall mining
This is a highly productive underground mining used to extract coal in large blocks using
mechanized shearer (Ralston, 2014, p. 306). The size of a typical coal panel extracted can be up
to 5km in length and measuring between 200m to 350 m wide. As the shearer moves back and
forth across the coal surface, it is guided by rails to enhance precision resulting into high
efficiencies. Further, safety is enhanced by supporting the roof using hydraulic shields which are
shifted as the mining operation progresses.
Secure Best Marks with AI Grader
Need help grading? Try our AI Grader for instant feedback on your assignments.
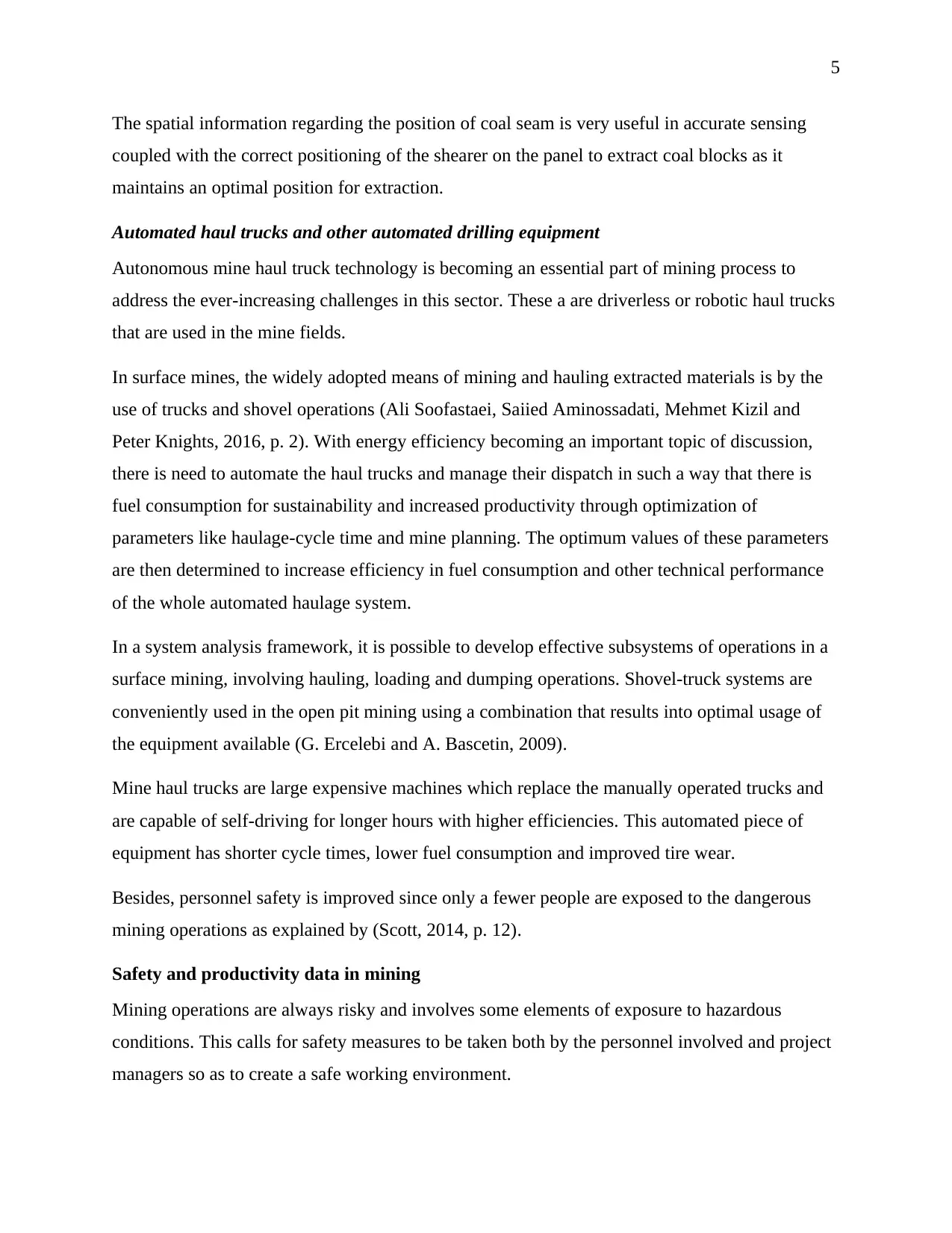
5
The spatial information regarding the position of coal seam is very useful in accurate sensing
coupled with the correct positioning of the shearer on the panel to extract coal blocks as it
maintains an optimal position for extraction.
Automated haul trucks and other automated drilling equipment
Autonomous mine haul truck technology is becoming an essential part of mining process to
address the ever-increasing challenges in this sector. These a are driverless or robotic haul trucks
that are used in the mine fields.
In surface mines, the widely adopted means of mining and hauling extracted materials is by the
use of trucks and shovel operations (Ali Soofastaei, Saiied Aminossadati, Mehmet Kizil and
Peter Knights, 2016, p. 2). With energy efficiency becoming an important topic of discussion,
there is need to automate the haul trucks and manage their dispatch in such a way that there is
fuel consumption for sustainability and increased productivity through optimization of
parameters like haulage-cycle time and mine planning. The optimum values of these parameters
are then determined to increase efficiency in fuel consumption and other technical performance
of the whole automated haulage system.
In a system analysis framework, it is possible to develop effective subsystems of operations in a
surface mining, involving hauling, loading and dumping operations. Shovel-truck systems are
conveniently used in the open pit mining using a combination that results into optimal usage of
the equipment available (G. Ercelebi and A. Bascetin, 2009).
Mine haul trucks are large expensive machines which replace the manually operated trucks and
are capable of self-driving for longer hours with higher efficiencies. This automated piece of
equipment has shorter cycle times, lower fuel consumption and improved tire wear.
Besides, personnel safety is improved since only a fewer people are exposed to the dangerous
mining operations as explained by (Scott, 2014, p. 12).
Safety and productivity data in mining
Mining operations are always risky and involves some elements of exposure to hazardous
conditions. This calls for safety measures to be taken both by the personnel involved and project
managers so as to create a safe working environment.
The spatial information regarding the position of coal seam is very useful in accurate sensing
coupled with the correct positioning of the shearer on the panel to extract coal blocks as it
maintains an optimal position for extraction.
Automated haul trucks and other automated drilling equipment
Autonomous mine haul truck technology is becoming an essential part of mining process to
address the ever-increasing challenges in this sector. These a are driverless or robotic haul trucks
that are used in the mine fields.
In surface mines, the widely adopted means of mining and hauling extracted materials is by the
use of trucks and shovel operations (Ali Soofastaei, Saiied Aminossadati, Mehmet Kizil and
Peter Knights, 2016, p. 2). With energy efficiency becoming an important topic of discussion,
there is need to automate the haul trucks and manage their dispatch in such a way that there is
fuel consumption for sustainability and increased productivity through optimization of
parameters like haulage-cycle time and mine planning. The optimum values of these parameters
are then determined to increase efficiency in fuel consumption and other technical performance
of the whole automated haulage system.
In a system analysis framework, it is possible to develop effective subsystems of operations in a
surface mining, involving hauling, loading and dumping operations. Shovel-truck systems are
conveniently used in the open pit mining using a combination that results into optimal usage of
the equipment available (G. Ercelebi and A. Bascetin, 2009).
Mine haul trucks are large expensive machines which replace the manually operated trucks and
are capable of self-driving for longer hours with higher efficiencies. This automated piece of
equipment has shorter cycle times, lower fuel consumption and improved tire wear.
Besides, personnel safety is improved since only a fewer people are exposed to the dangerous
mining operations as explained by (Scott, 2014, p. 12).
Safety and productivity data in mining
Mining operations are always risky and involves some elements of exposure to hazardous
conditions. This calls for safety measures to be taken both by the personnel involved and project
managers so as to create a safe working environment.
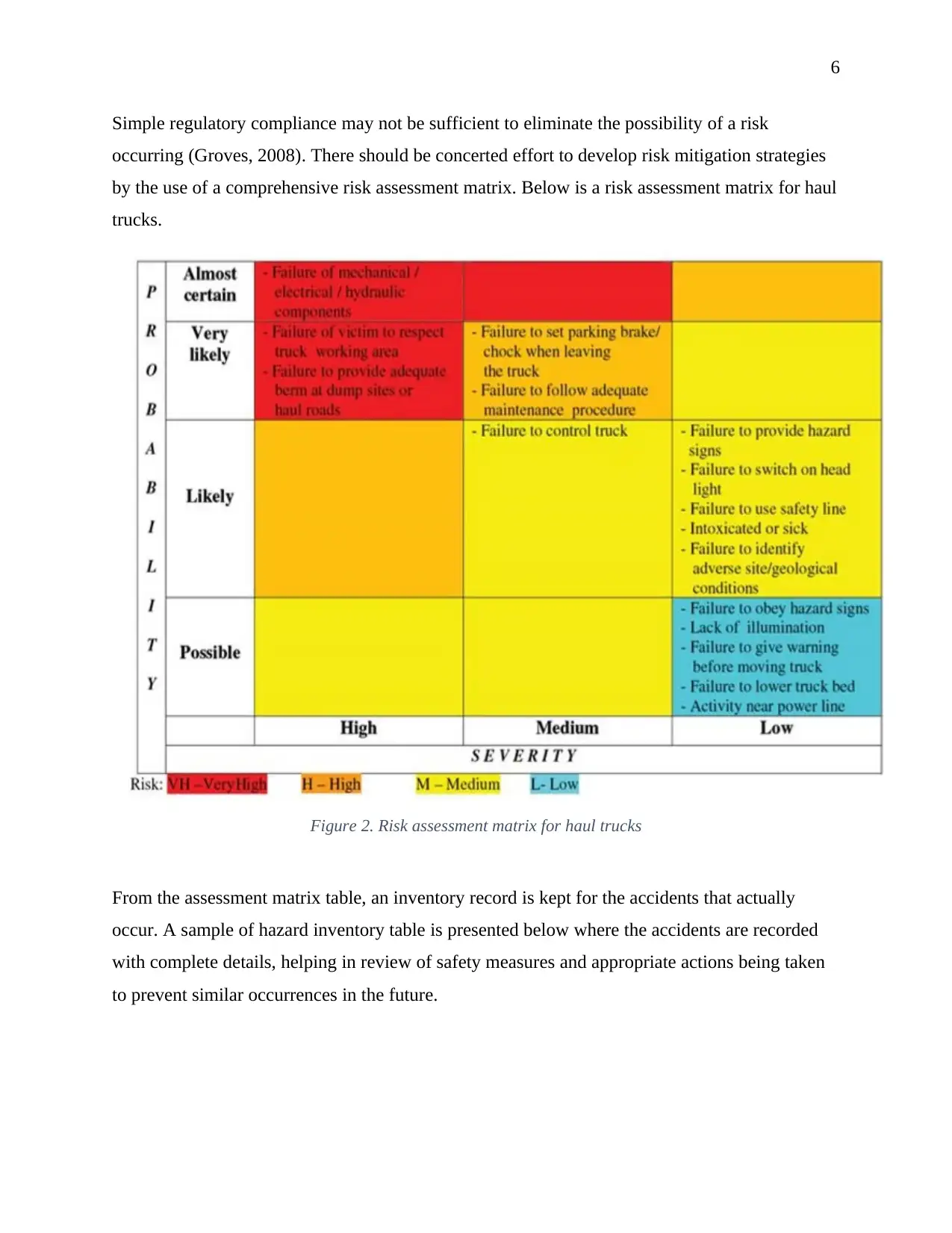
6
Simple regulatory compliance may not be sufficient to eliminate the possibility of a risk
occurring (Groves, 2008). There should be concerted effort to develop risk mitigation strategies
by the use of a comprehensive risk assessment matrix. Below is a risk assessment matrix for haul
trucks.
Figure 2. Risk assessment matrix for haul trucks
From the assessment matrix table, an inventory record is kept for the accidents that actually
occur. A sample of hazard inventory table is presented below where the accidents are recorded
with complete details, helping in review of safety measures and appropriate actions being taken
to prevent similar occurrences in the future.
Simple regulatory compliance may not be sufficient to eliminate the possibility of a risk
occurring (Groves, 2008). There should be concerted effort to develop risk mitigation strategies
by the use of a comprehensive risk assessment matrix. Below is a risk assessment matrix for haul
trucks.
Figure 2. Risk assessment matrix for haul trucks
From the assessment matrix table, an inventory record is kept for the accidents that actually
occur. A sample of hazard inventory table is presented below where the accidents are recorded
with complete details, helping in review of safety measures and appropriate actions being taken
to prevent similar occurrences in the future.
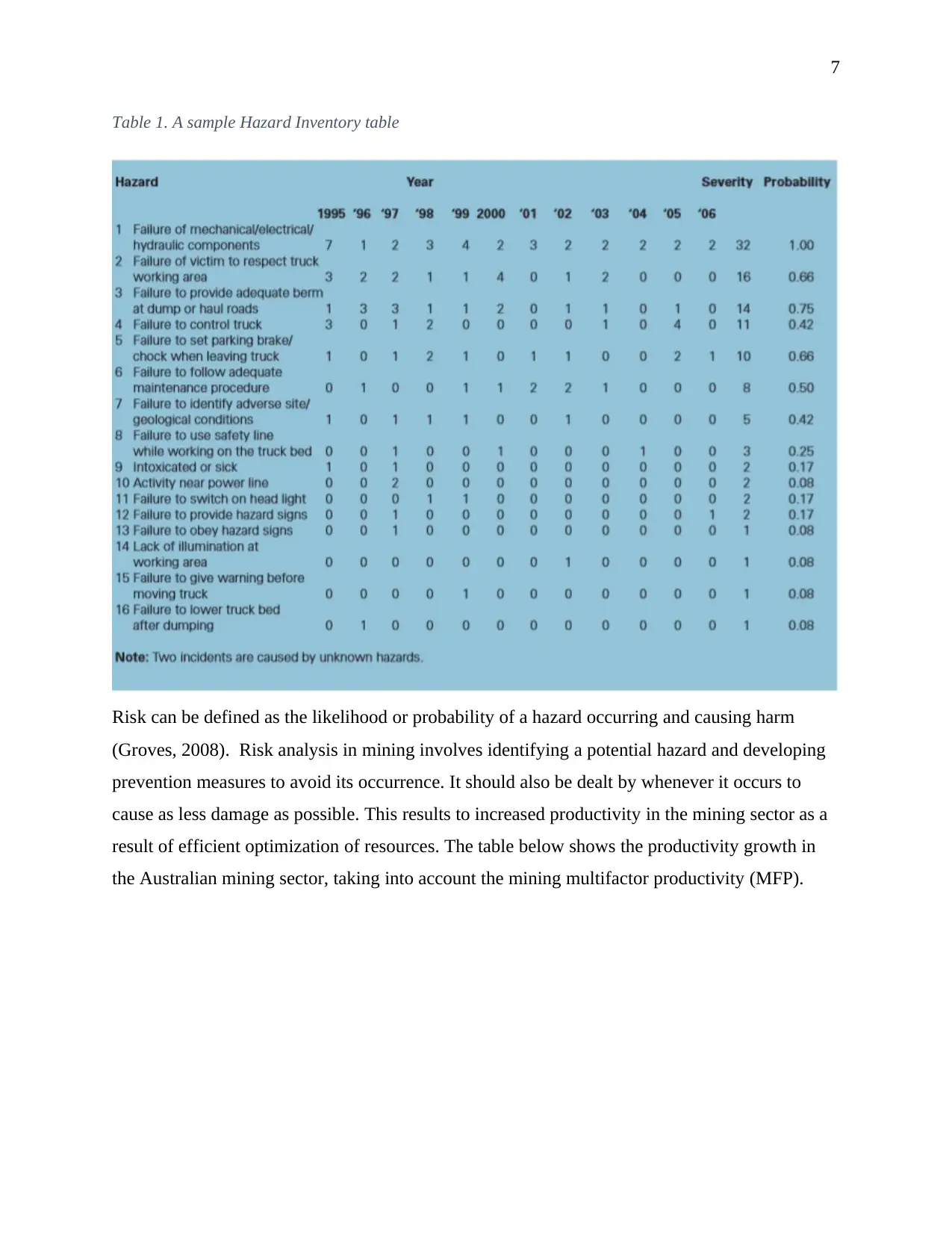
7
Table 1. A sample Hazard Inventory table
Risk can be defined as the likelihood or probability of a hazard occurring and causing harm
(Groves, 2008). Risk analysis in mining involves identifying a potential hazard and developing
prevention measures to avoid its occurrence. It should also be dealt by whenever it occurs to
cause as less damage as possible. This results to increased productivity in the mining sector as a
result of efficient optimization of resources. The table below shows the productivity growth in
the Australian mining sector, taking into account the mining multifactor productivity (MFP).
Table 1. A sample Hazard Inventory table
Risk can be defined as the likelihood or probability of a hazard occurring and causing harm
(Groves, 2008). Risk analysis in mining involves identifying a potential hazard and developing
prevention measures to avoid its occurrence. It should also be dealt by whenever it occurs to
cause as less damage as possible. This results to increased productivity in the mining sector as a
result of efficient optimization of resources. The table below shows the productivity growth in
the Australian mining sector, taking into account the mining multifactor productivity (MFP).
Paraphrase This Document
Need a fresh take? Get an instant paraphrase of this document with our AI Paraphraser
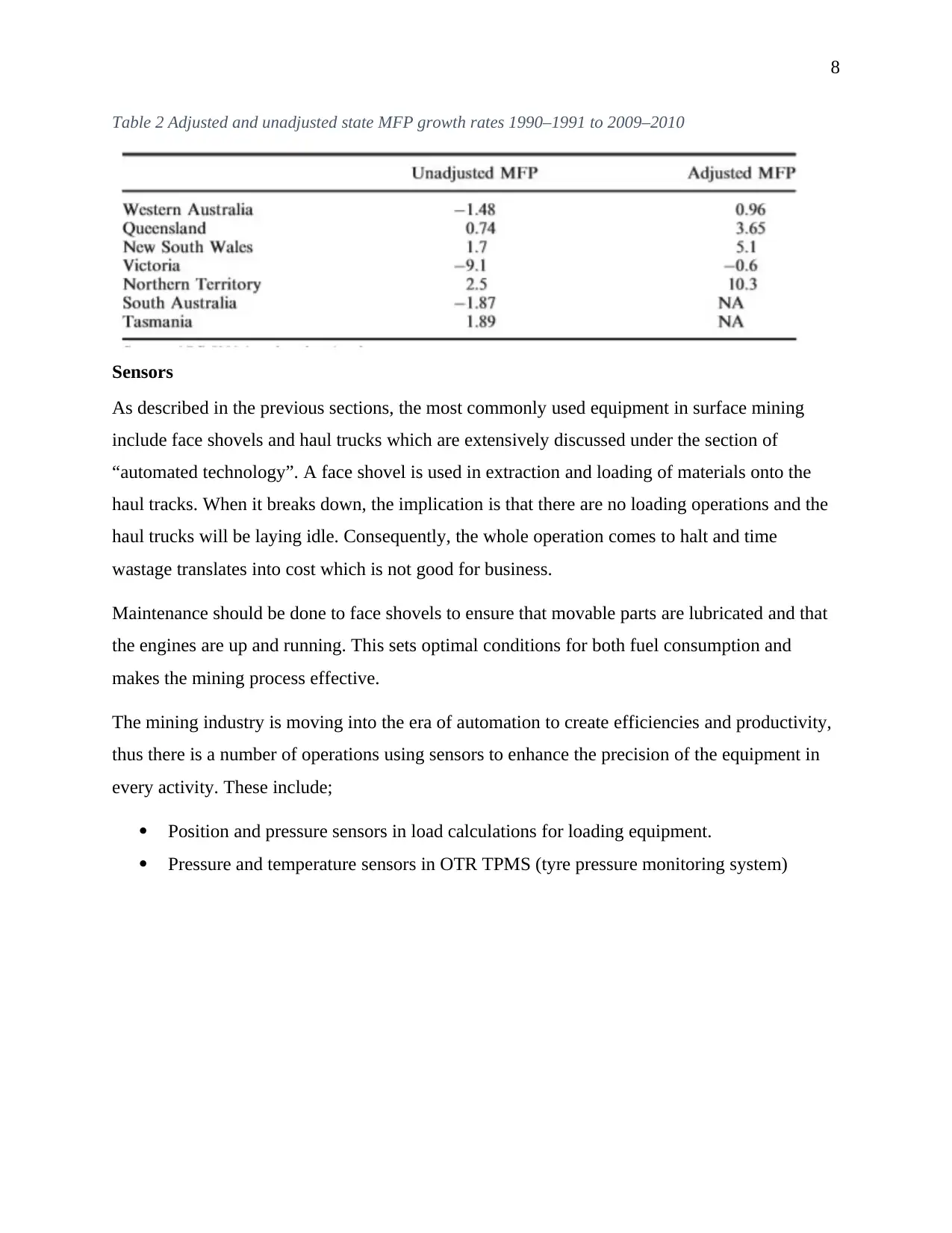
8
Table 2 Adjusted and unadjusted state MFP growth rates 1990–1991 to 2009–2010
Sensors
As described in the previous sections, the most commonly used equipment in surface mining
include face shovels and haul trucks which are extensively discussed under the section of
“automated technology”. A face shovel is used in extraction and loading of materials onto the
haul tracks. When it breaks down, the implication is that there are no loading operations and the
haul trucks will be laying idle. Consequently, the whole operation comes to halt and time
wastage translates into cost which is not good for business.
Maintenance should be done to face shovels to ensure that movable parts are lubricated and that
the engines are up and running. This sets optimal conditions for both fuel consumption and
makes the mining process effective.
The mining industry is moving into the era of automation to create efficiencies and productivity,
thus there is a number of operations using sensors to enhance the precision of the equipment in
every activity. These include;
Position and pressure sensors in load calculations for loading equipment.
Pressure and temperature sensors in OTR TPMS (tyre pressure monitoring system)
Table 2 Adjusted and unadjusted state MFP growth rates 1990–1991 to 2009–2010
Sensors
As described in the previous sections, the most commonly used equipment in surface mining
include face shovels and haul trucks which are extensively discussed under the section of
“automated technology”. A face shovel is used in extraction and loading of materials onto the
haul tracks. When it breaks down, the implication is that there are no loading operations and the
haul trucks will be laying idle. Consequently, the whole operation comes to halt and time
wastage translates into cost which is not good for business.
Maintenance should be done to face shovels to ensure that movable parts are lubricated and that
the engines are up and running. This sets optimal conditions for both fuel consumption and
makes the mining process effective.
The mining industry is moving into the era of automation to create efficiencies and productivity,
thus there is a number of operations using sensors to enhance the precision of the equipment in
every activity. These include;
Position and pressure sensors in load calculations for loading equipment.
Pressure and temperature sensors in OTR TPMS (tyre pressure monitoring system)
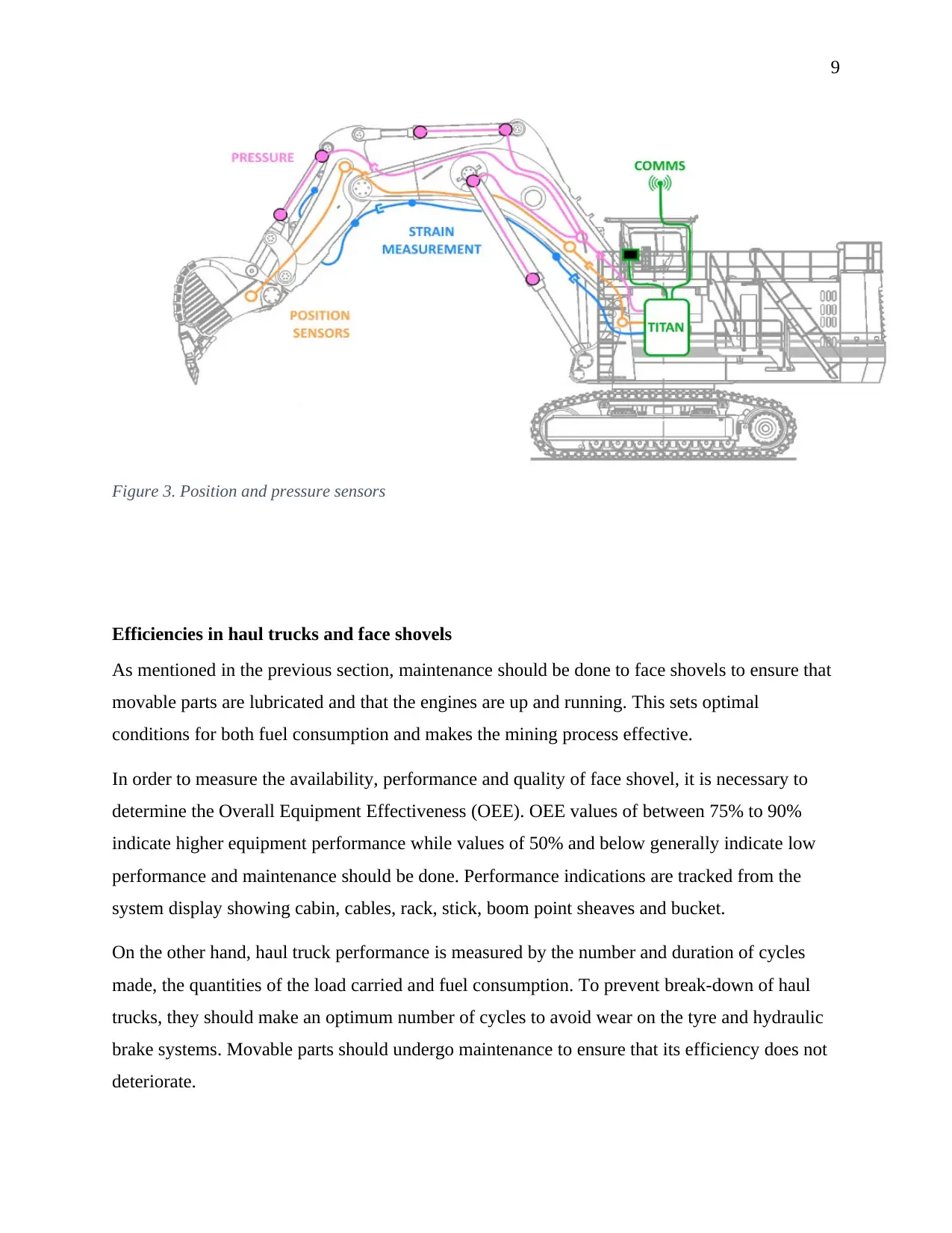
9
Figure 3. Position and pressure sensors
Efficiencies in haul trucks and face shovels
As mentioned in the previous section, maintenance should be done to face shovels to ensure that
movable parts are lubricated and that the engines are up and running. This sets optimal
conditions for both fuel consumption and makes the mining process effective.
In order to measure the availability, performance and quality of face shovel, it is necessary to
determine the Overall Equipment Effectiveness (OEE). OEE values of between 75% to 90%
indicate higher equipment performance while values of 50% and below generally indicate low
performance and maintenance should be done. Performance indications are tracked from the
system display showing cabin, cables, rack, stick, boom point sheaves and bucket.
On the other hand, haul truck performance is measured by the number and duration of cycles
made, the quantities of the load carried and fuel consumption. To prevent break-down of haul
trucks, they should make an optimum number of cycles to avoid wear on the tyre and hydraulic
brake systems. Movable parts should undergo maintenance to ensure that its efficiency does not
deteriorate.
Figure 3. Position and pressure sensors
Efficiencies in haul trucks and face shovels
As mentioned in the previous section, maintenance should be done to face shovels to ensure that
movable parts are lubricated and that the engines are up and running. This sets optimal
conditions for both fuel consumption and makes the mining process effective.
In order to measure the availability, performance and quality of face shovel, it is necessary to
determine the Overall Equipment Effectiveness (OEE). OEE values of between 75% to 90%
indicate higher equipment performance while values of 50% and below generally indicate low
performance and maintenance should be done. Performance indications are tracked from the
system display showing cabin, cables, rack, stick, boom point sheaves and bucket.
On the other hand, haul truck performance is measured by the number and duration of cycles
made, the quantities of the load carried and fuel consumption. To prevent break-down of haul
trucks, they should make an optimum number of cycles to avoid wear on the tyre and hydraulic
brake systems. Movable parts should undergo maintenance to ensure that its efficiency does not
deteriorate.
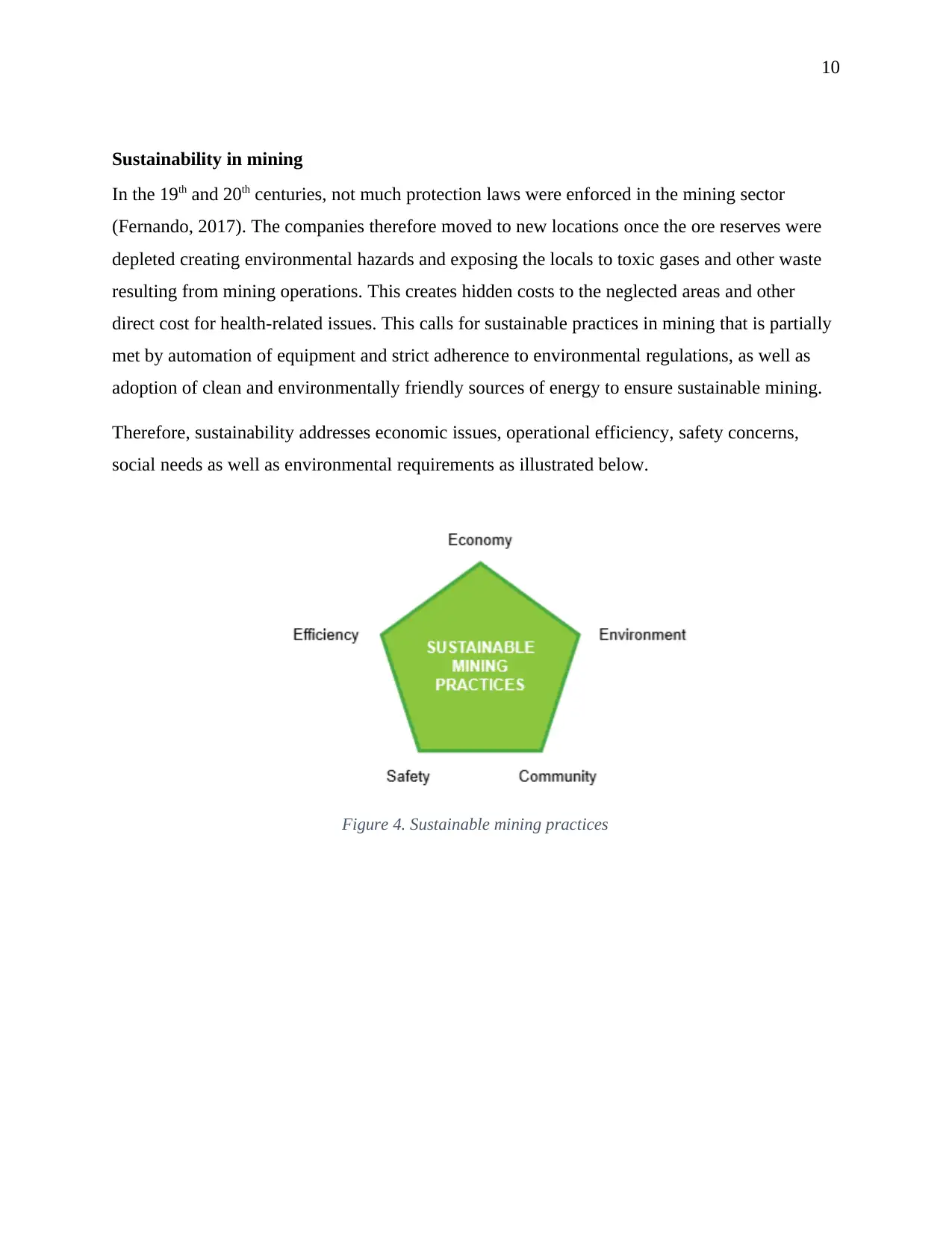
10
Sustainability in mining
In the 19th and 20th centuries, not much protection laws were enforced in the mining sector
(Fernando, 2017). The companies therefore moved to new locations once the ore reserves were
depleted creating environmental hazards and exposing the locals to toxic gases and other waste
resulting from mining operations. This creates hidden costs to the neglected areas and other
direct cost for health-related issues. This calls for sustainable practices in mining that is partially
met by automation of equipment and strict adherence to environmental regulations, as well as
adoption of clean and environmentally friendly sources of energy to ensure sustainable mining.
Therefore, sustainability addresses economic issues, operational efficiency, safety concerns,
social needs as well as environmental requirements as illustrated below.
Figure 4. Sustainable mining practices
Sustainability in mining
In the 19th and 20th centuries, not much protection laws were enforced in the mining sector
(Fernando, 2017). The companies therefore moved to new locations once the ore reserves were
depleted creating environmental hazards and exposing the locals to toxic gases and other waste
resulting from mining operations. This creates hidden costs to the neglected areas and other
direct cost for health-related issues. This calls for sustainable practices in mining that is partially
met by automation of equipment and strict adherence to environmental regulations, as well as
adoption of clean and environmentally friendly sources of energy to ensure sustainable mining.
Therefore, sustainability addresses economic issues, operational efficiency, safety concerns,
social needs as well as environmental requirements as illustrated below.
Figure 4. Sustainable mining practices
Secure Best Marks with AI Grader
Need help grading? Try our AI Grader for instant feedback on your assignments.
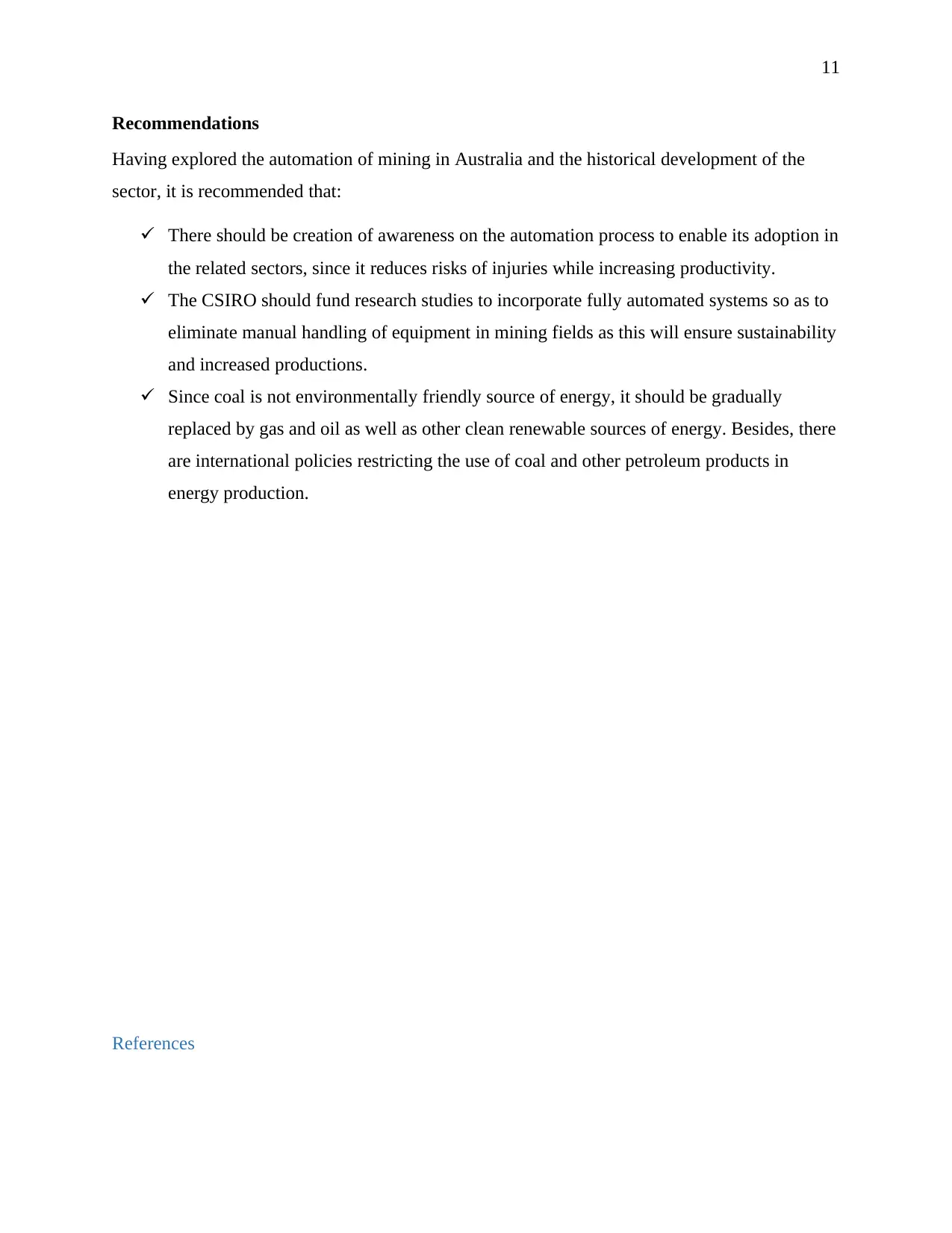
11
Recommendations
Having explored the automation of mining in Australia and the historical development of the
sector, it is recommended that:
There should be creation of awareness on the automation process to enable its adoption in
the related sectors, since it reduces risks of injuries while increasing productivity.
The CSIRO should fund research studies to incorporate fully automated systems so as to
eliminate manual handling of equipment in mining fields as this will ensure sustainability
and increased productions.
Since coal is not environmentally friendly source of energy, it should be gradually
replaced by gas and oil as well as other clean renewable sources of energy. Besides, there
are international policies restricting the use of coal and other petroleum products in
energy production.
References
Recommendations
Having explored the automation of mining in Australia and the historical development of the
sector, it is recommended that:
There should be creation of awareness on the automation process to enable its adoption in
the related sectors, since it reduces risks of injuries while increasing productivity.
The CSIRO should fund research studies to incorporate fully automated systems so as to
eliminate manual handling of equipment in mining fields as this will ensure sustainability
and increased productions.
Since coal is not environmentally friendly source of energy, it should be gradually
replaced by gas and oil as well as other clean renewable sources of energy. Besides, there
are international policies restricting the use of coal and other petroleum products in
energy production.
References
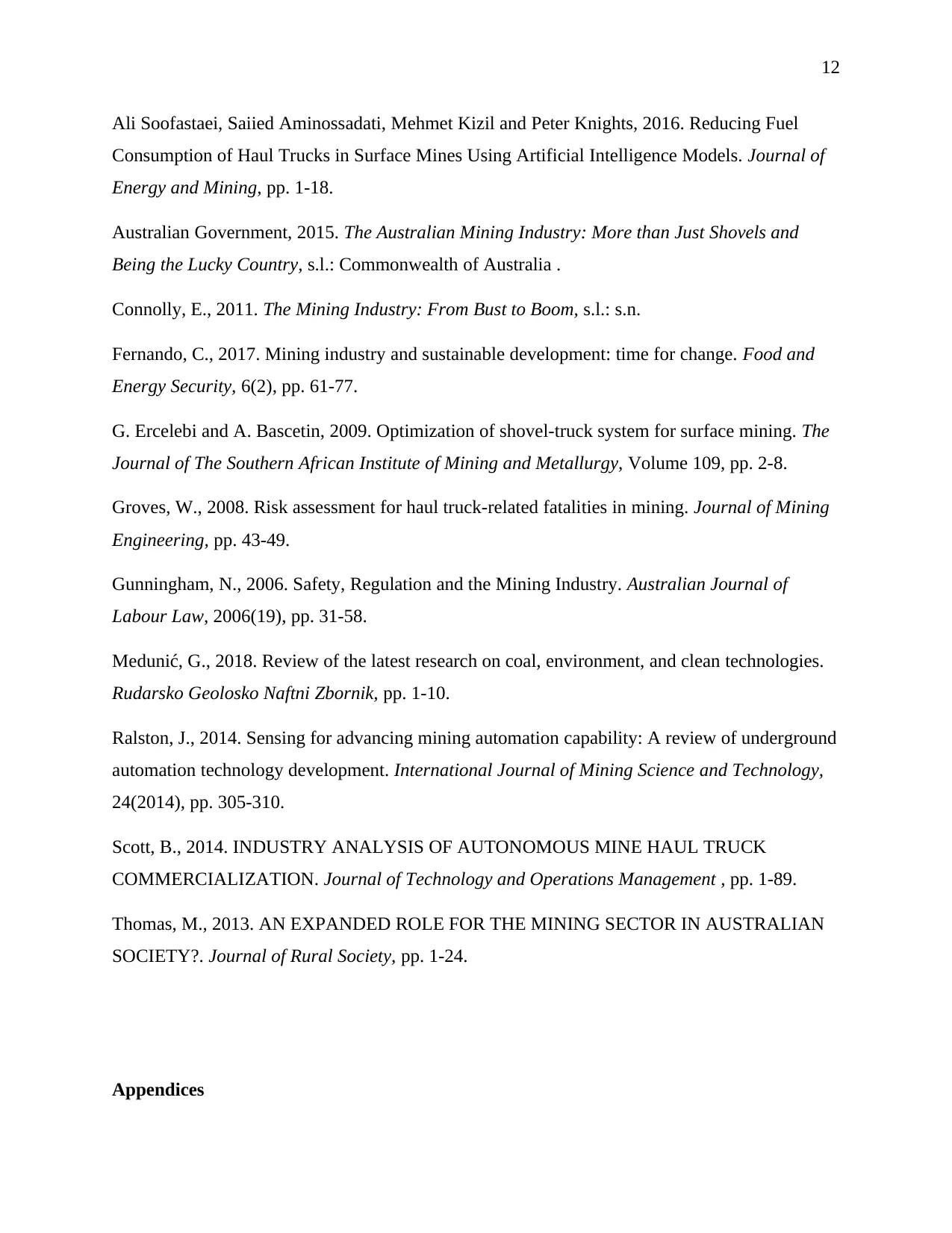
12
Ali Soofastaei, Saiied Aminossadati, Mehmet Kizil and Peter Knights, 2016. Reducing Fuel
Consumption of Haul Trucks in Surface Mines Using Artificial Intelligence Models. Journal of
Energy and Mining, pp. 1-18.
Australian Government, 2015. The Australian Mining Industry: More than Just Shovels and
Being the Lucky Country, s.l.: Commonwealth of Australia .
Connolly, E., 2011. The Mining Industry: From Bust to Boom, s.l.: s.n.
Fernando, C., 2017. Mining industry and sustainable development: time for change. Food and
Energy Security, 6(2), pp. 61-77.
G. Ercelebi and A. Bascetin, 2009. Optimization of shovel-truck system for surface mining. The
Journal of The Southern African Institute of Mining and Metallurgy, Volume 109, pp. 2-8.
Groves, W., 2008. Risk assessment for haul truck-related fatalities in mining. Journal of Mining
Engineering, pp. 43-49.
Gunningham, N., 2006. Safety, Regulation and the Mining Industry. Australian Journal of
Labour Law, 2006(19), pp. 31-58.
Medunić, G., 2018. Review of the latest research on coal, environment, and clean technologies.
Rudarsko Geolosko Naftni Zbornik, pp. 1-10.
Ralston, J., 2014. Sensing for advancing mining automation capability: A review of underground
automation technology development. International Journal of Mining Science and Technology,
24(2014), pp. 305-310.
Scott, B., 2014. INDUSTRY ANALYSIS OF AUTONOMOUS MINE HAUL TRUCK
COMMERCIALIZATION. Journal of Technology and Operations Management , pp. 1-89.
Thomas, M., 2013. AN EXPANDED ROLE FOR THE MINING SECTOR IN AUSTRALIAN
SOCIETY?. Journal of Rural Society, pp. 1-24.
Appendices
Ali Soofastaei, Saiied Aminossadati, Mehmet Kizil and Peter Knights, 2016. Reducing Fuel
Consumption of Haul Trucks in Surface Mines Using Artificial Intelligence Models. Journal of
Energy and Mining, pp. 1-18.
Australian Government, 2015. The Australian Mining Industry: More than Just Shovels and
Being the Lucky Country, s.l.: Commonwealth of Australia .
Connolly, E., 2011. The Mining Industry: From Bust to Boom, s.l.: s.n.
Fernando, C., 2017. Mining industry and sustainable development: time for change. Food and
Energy Security, 6(2), pp. 61-77.
G. Ercelebi and A. Bascetin, 2009. Optimization of shovel-truck system for surface mining. The
Journal of The Southern African Institute of Mining and Metallurgy, Volume 109, pp. 2-8.
Groves, W., 2008. Risk assessment for haul truck-related fatalities in mining. Journal of Mining
Engineering, pp. 43-49.
Gunningham, N., 2006. Safety, Regulation and the Mining Industry. Australian Journal of
Labour Law, 2006(19), pp. 31-58.
Medunić, G., 2018. Review of the latest research on coal, environment, and clean technologies.
Rudarsko Geolosko Naftni Zbornik, pp. 1-10.
Ralston, J., 2014. Sensing for advancing mining automation capability: A review of underground
automation technology development. International Journal of Mining Science and Technology,
24(2014), pp. 305-310.
Scott, B., 2014. INDUSTRY ANALYSIS OF AUTONOMOUS MINE HAUL TRUCK
COMMERCIALIZATION. Journal of Technology and Operations Management , pp. 1-89.
Thomas, M., 2013. AN EXPANDED ROLE FOR THE MINING SECTOR IN AUSTRALIAN
SOCIETY?. Journal of Rural Society, pp. 1-24.
Appendices
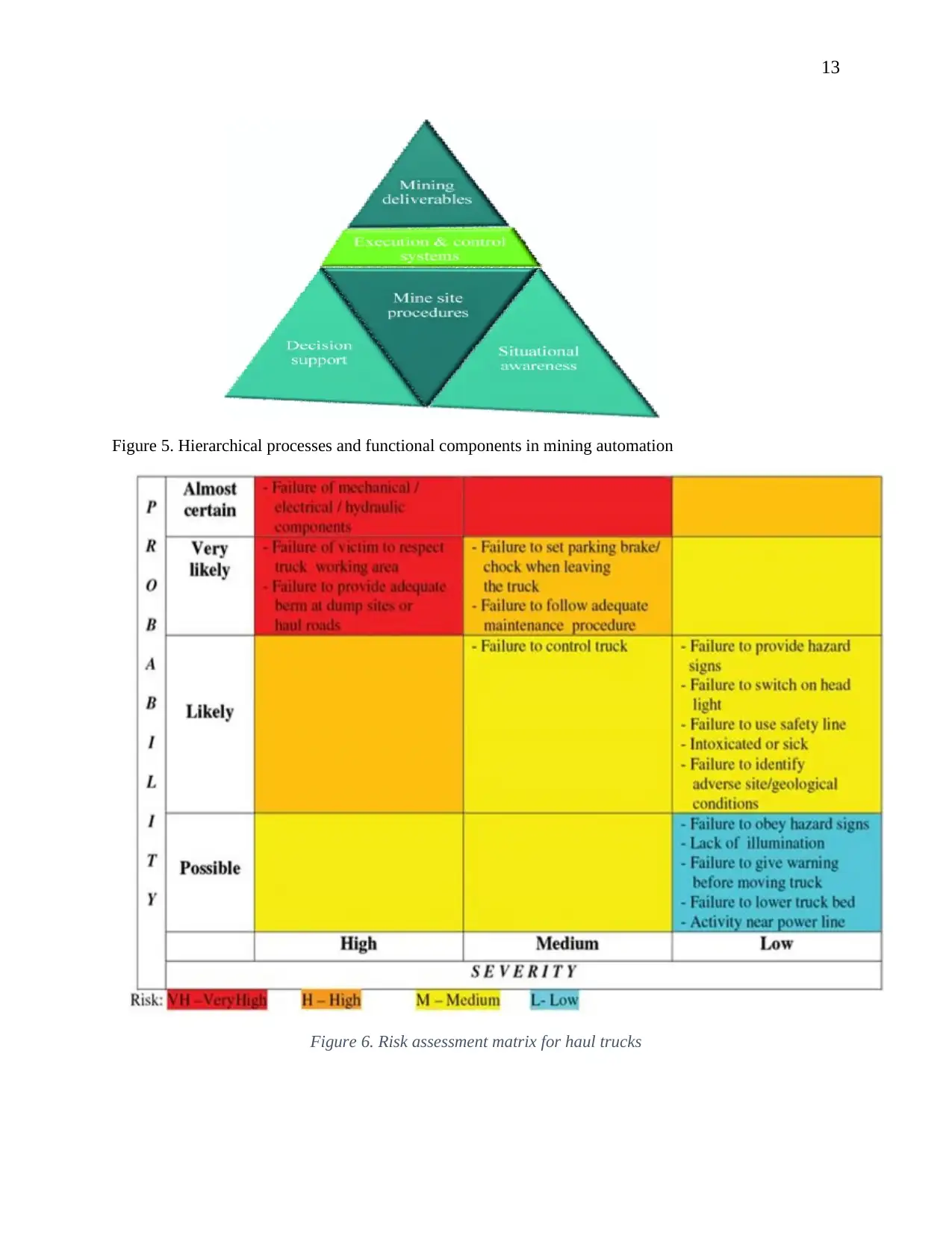
13
Figure 5. Hierarchical processes and functional components in mining automation
Figure 6. Risk assessment matrix for haul trucks
Figure 5. Hierarchical processes and functional components in mining automation
Figure 6. Risk assessment matrix for haul trucks
Paraphrase This Document
Need a fresh take? Get an instant paraphrase of this document with our AI Paraphraser
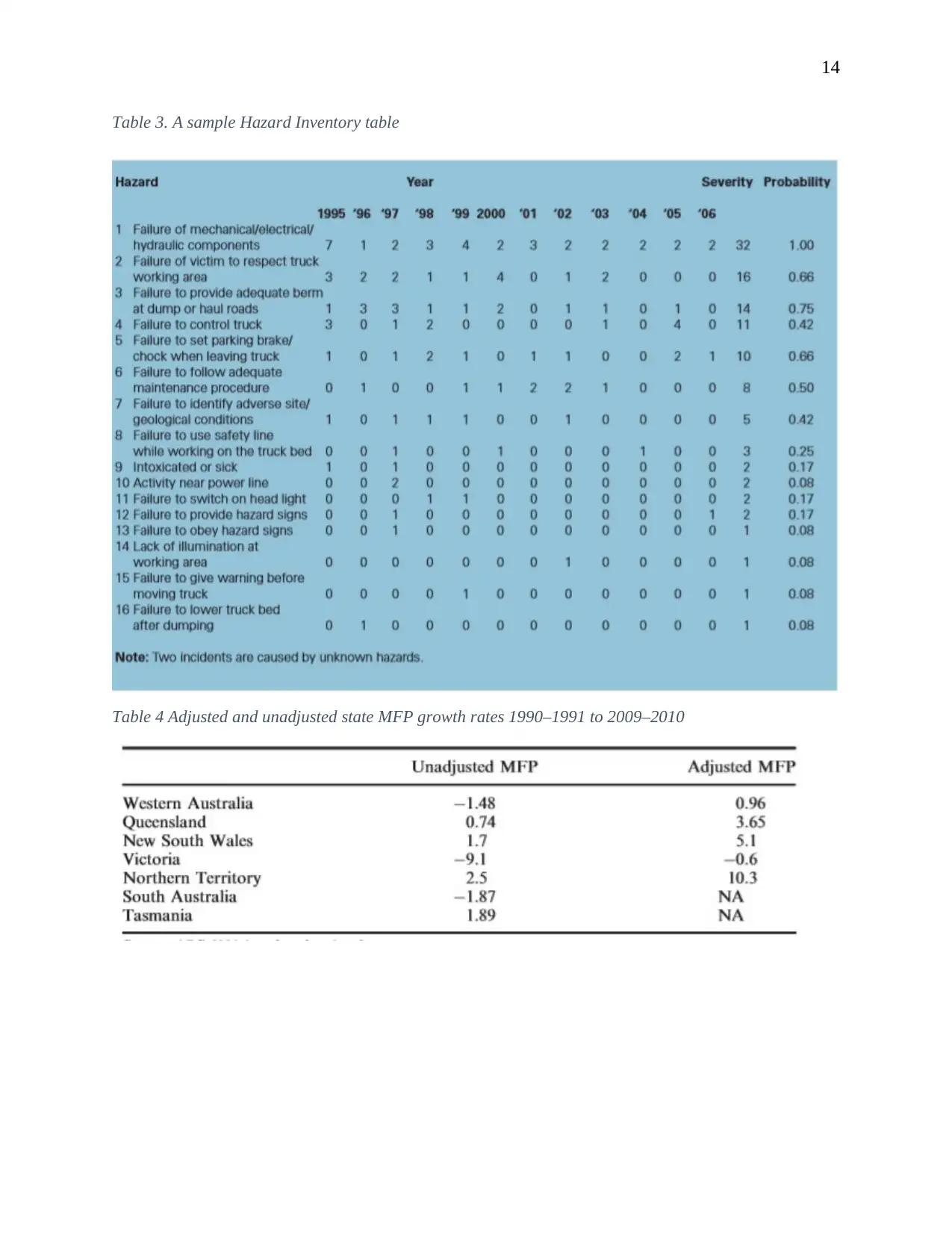
14
Table 3. A sample Hazard Inventory table
Table 4 Adjusted and unadjusted state MFP growth rates 1990–1991 to 2009–2010
Table 3. A sample Hazard Inventory table
Table 4 Adjusted and unadjusted state MFP growth rates 1990–1991 to 2009–2010
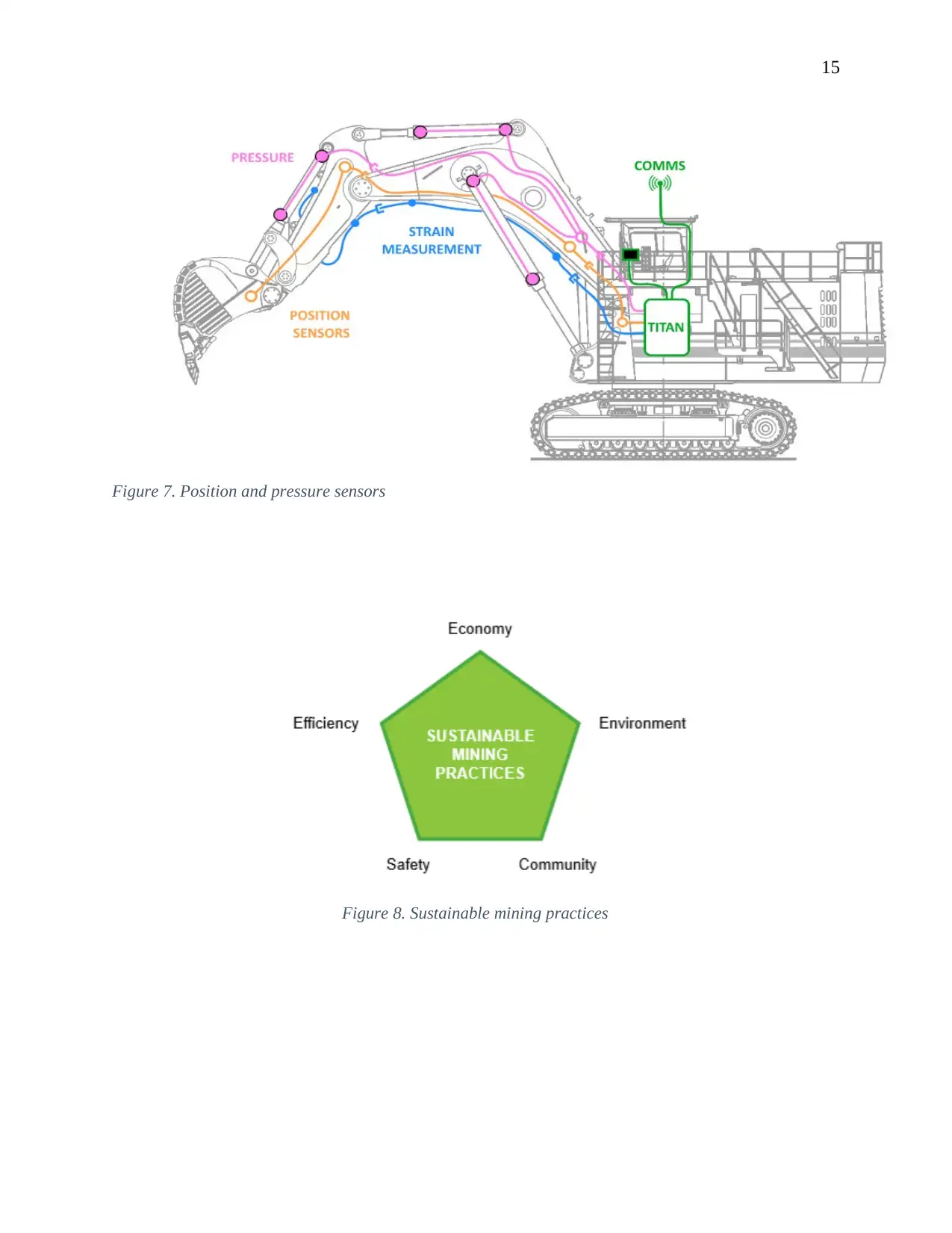
15
Figure 7. Position and pressure sensors
Figure 8. Sustainable mining practices
Figure 7. Position and pressure sensors
Figure 8. Sustainable mining practices
1 out of 15
Related Documents

Your All-in-One AI-Powered Toolkit for Academic Success.
+13062052269
info@desklib.com
Available 24*7 on WhatsApp / Email
Unlock your academic potential
© 2024 | Zucol Services PVT LTD | All rights reserved.