Detailed Report: Implementing Autonomous Maintenance in Engineering
VerifiedAdded on 2023/06/04
|19
|4272
|298
Report
AI Summary
This report, prepared by a student, delves into the concept of Autonomous Maintenance (AM) within the framework of Total Productive Maintenance (TPM). It begins with an introduction to AM, defining it from the perspectives of multiple scholars, and outlines its core functions and objectives within an organization. The report then describes the methodology for conducting AM training, emphasizing the importance of operator education and skill development. A significant portion is dedicated to proposing an AM development program, detailing initial preparation steps such as team formation, time frame establishment, and equipment selection. The execution process is explained, covering preliminary cleaning, removal of pollution sources, inspection and control procedures, and the establishment of lubrication standards. Furthermore, the report addresses task transfer between maintenance teams and proposes an improvement plan incorporating the SMED strategy and Kaizen method to enhance the maintenance system. Finally, it evaluates the implications of the proposed plan, assessing how the strategies will positively impact the organization. The report provides a comprehensive overview of AM implementation and its benefits in enhancing equipment efficiency and overall productivity.
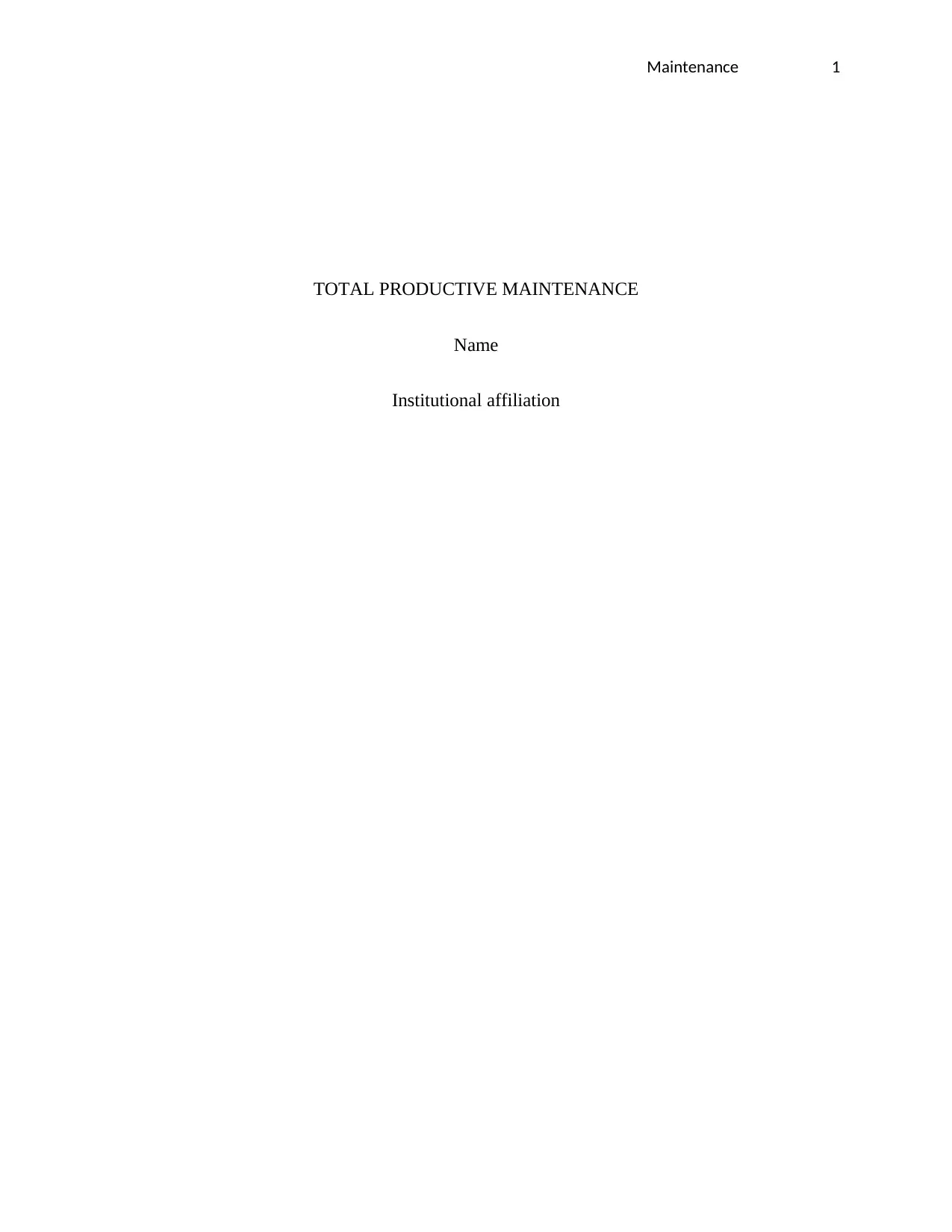
Maintenance 1
TOTAL PRODUCTIVE MAINTENANCE
Name
Institutional affiliation
TOTAL PRODUCTIVE MAINTENANCE
Name
Institutional affiliation
Secure Best Marks with AI Grader
Need help grading? Try our AI Grader for instant feedback on your assignments.
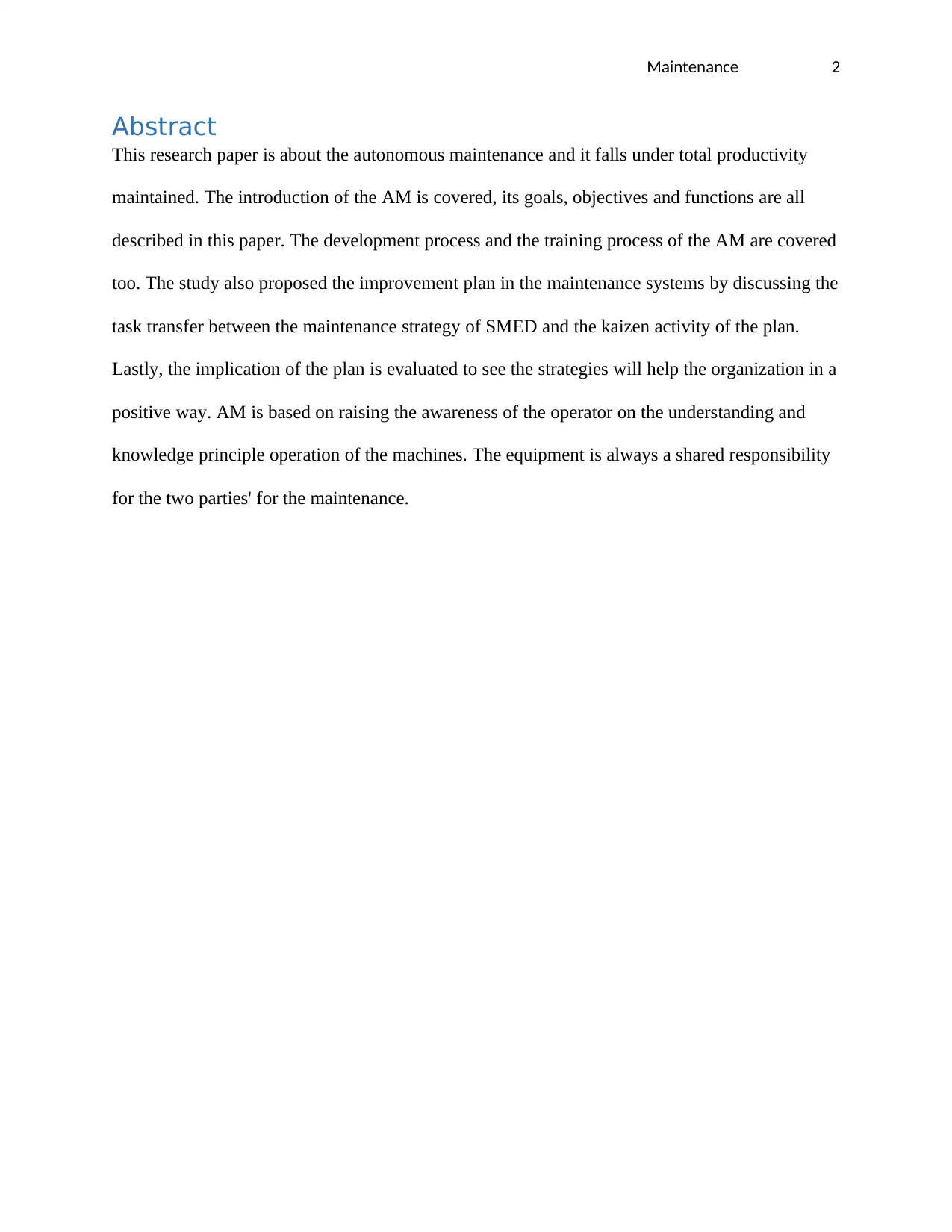
Maintenance 2
Abstract
This research paper is about the autonomous maintenance and it falls under total productivity
maintained. The introduction of the AM is covered, its goals, objectives and functions are all
described in this paper. The development process and the training process of the AM are covered
too. The study also proposed the improvement plan in the maintenance systems by discussing the
task transfer between the maintenance strategy of SMED and the kaizen activity of the plan.
Lastly, the implication of the plan is evaluated to see the strategies will help the organization in a
positive way. AM is based on raising the awareness of the operator on the understanding and
knowledge principle operation of the machines. The equipment is always a shared responsibility
for the two parties' for the maintenance.
Abstract
This research paper is about the autonomous maintenance and it falls under total productivity
maintained. The introduction of the AM is covered, its goals, objectives and functions are all
described in this paper. The development process and the training process of the AM are covered
too. The study also proposed the improvement plan in the maintenance systems by discussing the
task transfer between the maintenance strategy of SMED and the kaizen activity of the plan.
Lastly, the implication of the plan is evaluated to see the strategies will help the organization in a
positive way. AM is based on raising the awareness of the operator on the understanding and
knowledge principle operation of the machines. The equipment is always a shared responsibility
for the two parties' for the maintenance.
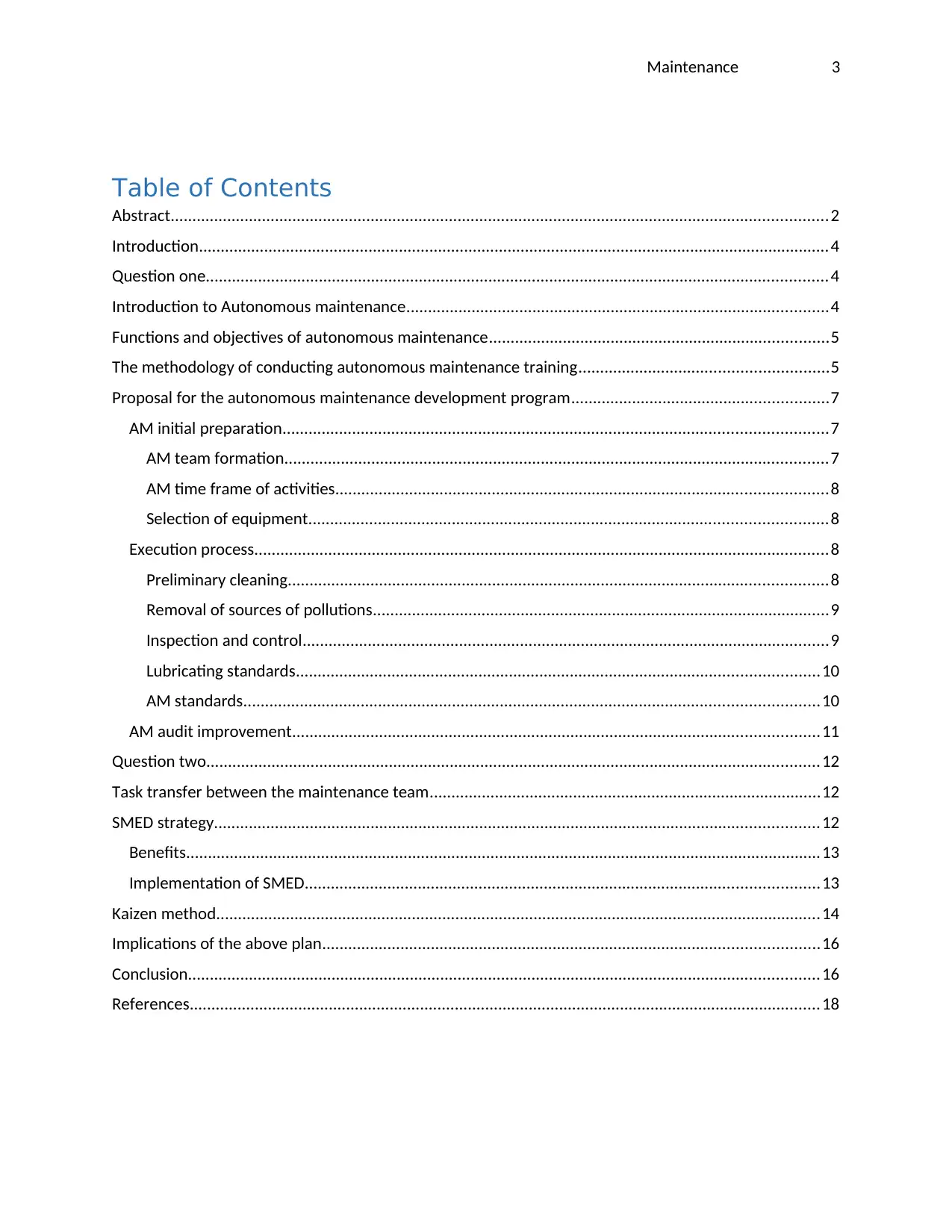
Maintenance 3
Table of Contents
Abstract.......................................................................................................................................................2
Introduction.................................................................................................................................................4
Question one...............................................................................................................................................4
Introduction to Autonomous maintenance.................................................................................................4
Functions and objectives of autonomous maintenance..............................................................................5
The methodology of conducting autonomous maintenance training.........................................................5
Proposal for the autonomous maintenance development program...........................................................7
AM initial preparation.............................................................................................................................7
AM team formation.............................................................................................................................7
AM time frame of activities.................................................................................................................8
Selection of equipment.......................................................................................................................8
Execution process....................................................................................................................................8
Preliminary cleaning............................................................................................................................8
Removal of sources of pollutions.........................................................................................................9
Inspection and control.........................................................................................................................9
Lubricating standards........................................................................................................................10
AM standards....................................................................................................................................10
AM audit improvement.........................................................................................................................11
Question two.............................................................................................................................................12
Task transfer between the maintenance team..........................................................................................12
SMED strategy...........................................................................................................................................12
Benefits..................................................................................................................................................13
Implementation of SMED......................................................................................................................13
Kaizen method...........................................................................................................................................14
Implications of the above plan..................................................................................................................16
Conclusion.................................................................................................................................................16
References.................................................................................................................................................18
Table of Contents
Abstract.......................................................................................................................................................2
Introduction.................................................................................................................................................4
Question one...............................................................................................................................................4
Introduction to Autonomous maintenance.................................................................................................4
Functions and objectives of autonomous maintenance..............................................................................5
The methodology of conducting autonomous maintenance training.........................................................5
Proposal for the autonomous maintenance development program...........................................................7
AM initial preparation.............................................................................................................................7
AM team formation.............................................................................................................................7
AM time frame of activities.................................................................................................................8
Selection of equipment.......................................................................................................................8
Execution process....................................................................................................................................8
Preliminary cleaning............................................................................................................................8
Removal of sources of pollutions.........................................................................................................9
Inspection and control.........................................................................................................................9
Lubricating standards........................................................................................................................10
AM standards....................................................................................................................................10
AM audit improvement.........................................................................................................................11
Question two.............................................................................................................................................12
Task transfer between the maintenance team..........................................................................................12
SMED strategy...........................................................................................................................................12
Benefits..................................................................................................................................................13
Implementation of SMED......................................................................................................................13
Kaizen method...........................................................................................................................................14
Implications of the above plan..................................................................................................................16
Conclusion.................................................................................................................................................16
References.................................................................................................................................................18
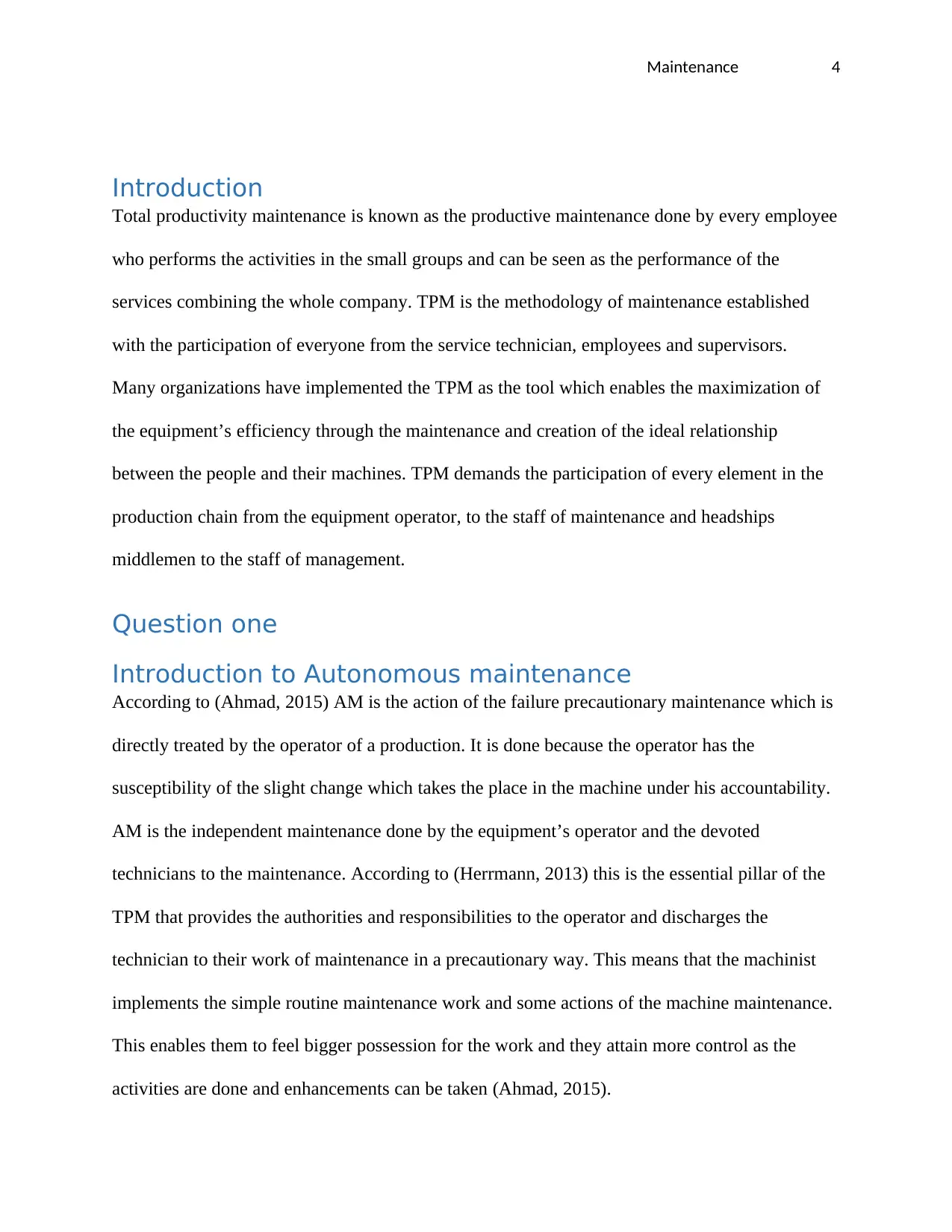
Maintenance 4
Introduction
Total productivity maintenance is known as the productive maintenance done by every employee
who performs the activities in the small groups and can be seen as the performance of the
services combining the whole company. TPM is the methodology of maintenance established
with the participation of everyone from the service technician, employees and supervisors.
Many organizations have implemented the TPM as the tool which enables the maximization of
the equipment’s efficiency through the maintenance and creation of the ideal relationship
between the people and their machines. TPM demands the participation of every element in the
production chain from the equipment operator, to the staff of maintenance and headships
middlemen to the staff of management.
Question one
Introduction to Autonomous maintenance
According to (Ahmad, 2015) AM is the action of the failure precautionary maintenance which is
directly treated by the operator of a production. It is done because the operator has the
susceptibility of the slight change which takes the place in the machine under his accountability.
AM is the independent maintenance done by the equipment’s operator and the devoted
technicians to the maintenance. According to (Herrmann, 2013) this is the essential pillar of the
TPM that provides the authorities and responsibilities to the operator and discharges the
technician to their work of maintenance in a precautionary way. This means that the machinist
implements the simple routine maintenance work and some actions of the machine maintenance.
This enables them to feel bigger possession for the work and they attain more control as the
activities are done and enhancements can be taken (Ahmad, 2015).
Introduction
Total productivity maintenance is known as the productive maintenance done by every employee
who performs the activities in the small groups and can be seen as the performance of the
services combining the whole company. TPM is the methodology of maintenance established
with the participation of everyone from the service technician, employees and supervisors.
Many organizations have implemented the TPM as the tool which enables the maximization of
the equipment’s efficiency through the maintenance and creation of the ideal relationship
between the people and their machines. TPM demands the participation of every element in the
production chain from the equipment operator, to the staff of maintenance and headships
middlemen to the staff of management.
Question one
Introduction to Autonomous maintenance
According to (Ahmad, 2015) AM is the action of the failure precautionary maintenance which is
directly treated by the operator of a production. It is done because the operator has the
susceptibility of the slight change which takes the place in the machine under his accountability.
AM is the independent maintenance done by the equipment’s operator and the devoted
technicians to the maintenance. According to (Herrmann, 2013) this is the essential pillar of the
TPM that provides the authorities and responsibilities to the operator and discharges the
technician to their work of maintenance in a precautionary way. This means that the machinist
implements the simple routine maintenance work and some actions of the machine maintenance.
This enables them to feel bigger possession for the work and they attain more control as the
activities are done and enhancements can be taken (Ahmad, 2015).
Secure Best Marks with AI Grader
Need help grading? Try our AI Grader for instant feedback on your assignments.
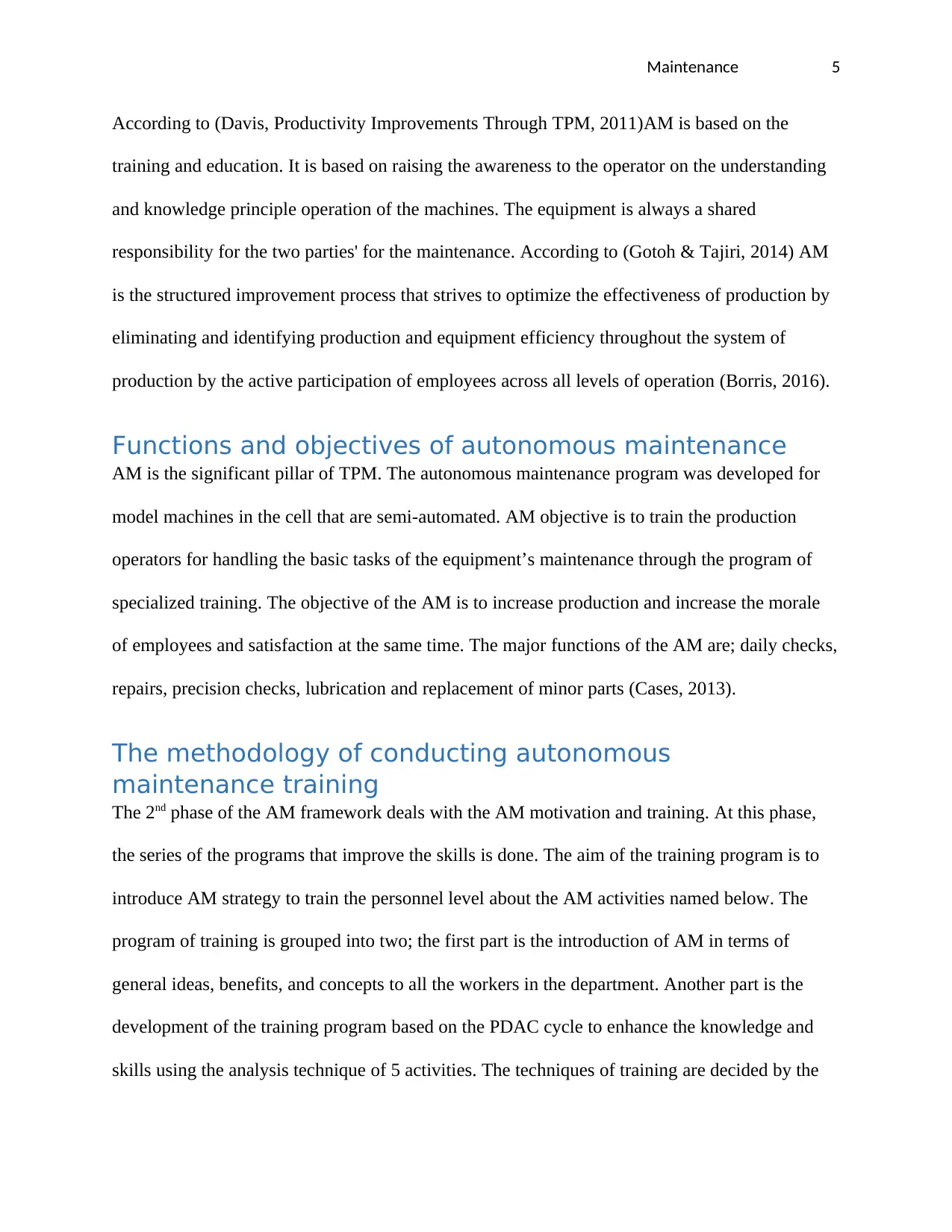
Maintenance 5
According to (Davis, Productivity Improvements Through TPM, 2011)AM is based on the
training and education. It is based on raising the awareness to the operator on the understanding
and knowledge principle operation of the machines. The equipment is always a shared
responsibility for the two parties' for the maintenance. According to (Gotoh & Tajiri, 2014) AM
is the structured improvement process that strives to optimize the effectiveness of production by
eliminating and identifying production and equipment efficiency throughout the system of
production by the active participation of employees across all levels of operation (Borris, 2016).
Functions and objectives of autonomous maintenance
AM is the significant pillar of TPM. The autonomous maintenance program was developed for
model machines in the cell that are semi-automated. AM objective is to train the production
operators for handling the basic tasks of the equipment’s maintenance through the program of
specialized training. The objective of the AM is to increase production and increase the morale
of employees and satisfaction at the same time. The major functions of the AM are; daily checks,
repairs, precision checks, lubrication and replacement of minor parts (Cases, 2013).
The methodology of conducting autonomous
maintenance training
The 2nd phase of the AM framework deals with the AM motivation and training. At this phase,
the series of the programs that improve the skills is done. The aim of the training program is to
introduce AM strategy to train the personnel level about the AM activities named below. The
program of training is grouped into two; the first part is the introduction of AM in terms of
general ideas, benefits, and concepts to all the workers in the department. Another part is the
development of the training program based on the PDAC cycle to enhance the knowledge and
skills using the analysis technique of 5 activities. The techniques of training are decided by the
According to (Davis, Productivity Improvements Through TPM, 2011)AM is based on the
training and education. It is based on raising the awareness to the operator on the understanding
and knowledge principle operation of the machines. The equipment is always a shared
responsibility for the two parties' for the maintenance. According to (Gotoh & Tajiri, 2014) AM
is the structured improvement process that strives to optimize the effectiveness of production by
eliminating and identifying production and equipment efficiency throughout the system of
production by the active participation of employees across all levels of operation (Borris, 2016).
Functions and objectives of autonomous maintenance
AM is the significant pillar of TPM. The autonomous maintenance program was developed for
model machines in the cell that are semi-automated. AM objective is to train the production
operators for handling the basic tasks of the equipment’s maintenance through the program of
specialized training. The objective of the AM is to increase production and increase the morale
of employees and satisfaction at the same time. The major functions of the AM are; daily checks,
repairs, precision checks, lubrication and replacement of minor parts (Cases, 2013).
The methodology of conducting autonomous
maintenance training
The 2nd phase of the AM framework deals with the AM motivation and training. At this phase,
the series of the programs that improve the skills is done. The aim of the training program is to
introduce AM strategy to train the personnel level about the AM activities named below. The
program of training is grouped into two; the first part is the introduction of AM in terms of
general ideas, benefits, and concepts to all the workers in the department. Another part is the
development of the training program based on the PDAC cycle to enhance the knowledge and
skills using the analysis technique of 5 activities. The techniques of training are decided by the
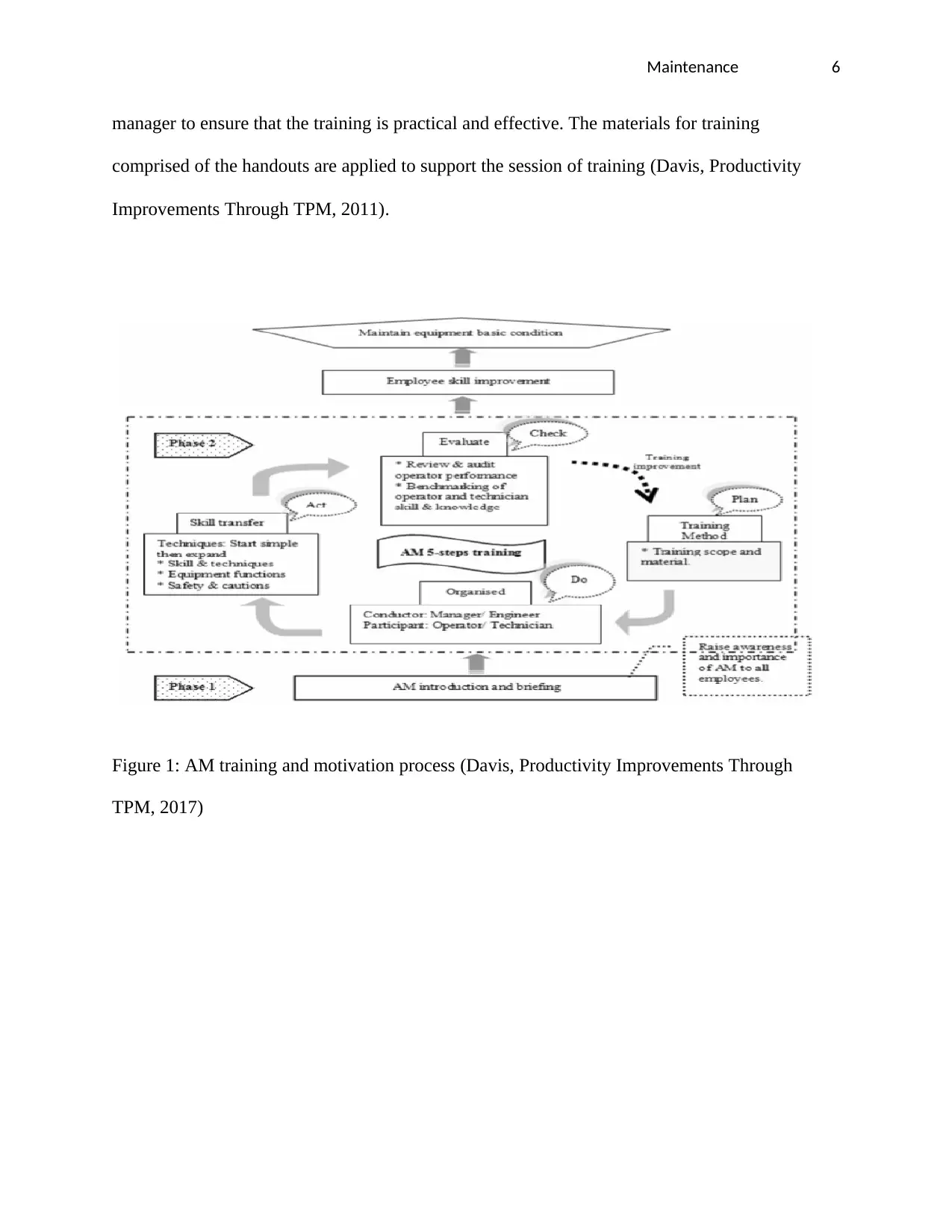
Maintenance 6
manager to ensure that the training is practical and effective. The materials for training
comprised of the handouts are applied to support the session of training (Davis, Productivity
Improvements Through TPM, 2011).
Figure 1: AM training and motivation process (Davis, Productivity Improvements Through
TPM, 2017)
manager to ensure that the training is practical and effective. The materials for training
comprised of the handouts are applied to support the session of training (Davis, Productivity
Improvements Through TPM, 2011).
Figure 1: AM training and motivation process (Davis, Productivity Improvements Through
TPM, 2017)
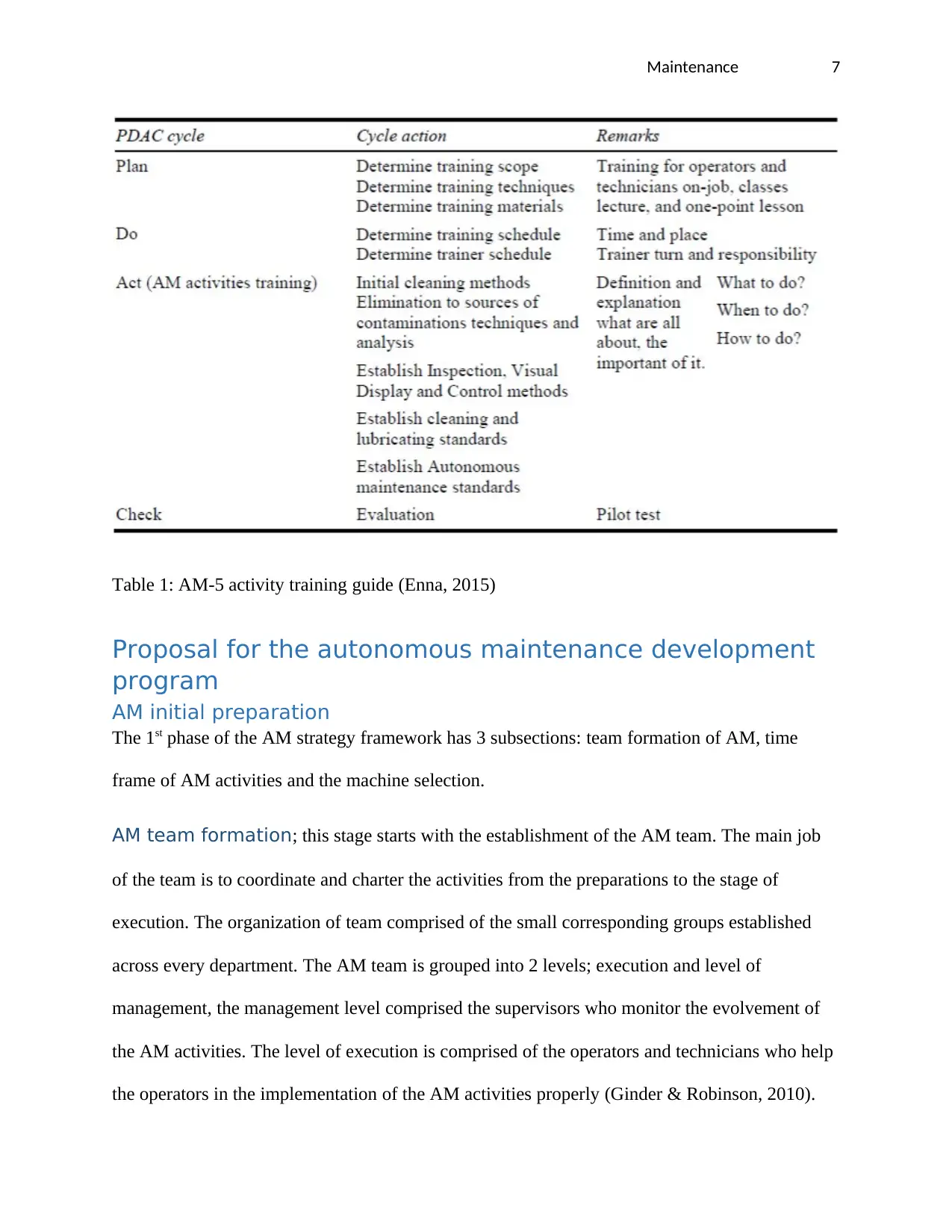
Maintenance 7
Table 1: AM-5 activity training guide (Enna, 2015)
Proposal for the autonomous maintenance development
program
AM initial preparation
The 1st phase of the AM strategy framework has 3 subsections: team formation of AM, time
frame of AM activities and the machine selection.
AM team formation; this stage starts with the establishment of the AM team. The main job
of the team is to coordinate and charter the activities from the preparations to the stage of
execution. The organization of team comprised of the small corresponding groups established
across every department. The AM team is grouped into 2 levels; execution and level of
management, the management level comprised the supervisors who monitor the evolvement of
the AM activities. The level of execution is comprised of the operators and technicians who help
the operators in the implementation of the AM activities properly (Ginder & Robinson, 2010).
Table 1: AM-5 activity training guide (Enna, 2015)
Proposal for the autonomous maintenance development
program
AM initial preparation
The 1st phase of the AM strategy framework has 3 subsections: team formation of AM, time
frame of AM activities and the machine selection.
AM team formation; this stage starts with the establishment of the AM team. The main job
of the team is to coordinate and charter the activities from the preparations to the stage of
execution. The organization of team comprised of the small corresponding groups established
across every department. The AM team is grouped into 2 levels; execution and level of
management, the management level comprised the supervisors who monitor the evolvement of
the AM activities. The level of execution is comprised of the operators and technicians who help
the operators in the implementation of the AM activities properly (Ginder & Robinson, 2010).
Paraphrase This Document
Need a fresh take? Get an instant paraphrase of this document with our AI Paraphraser
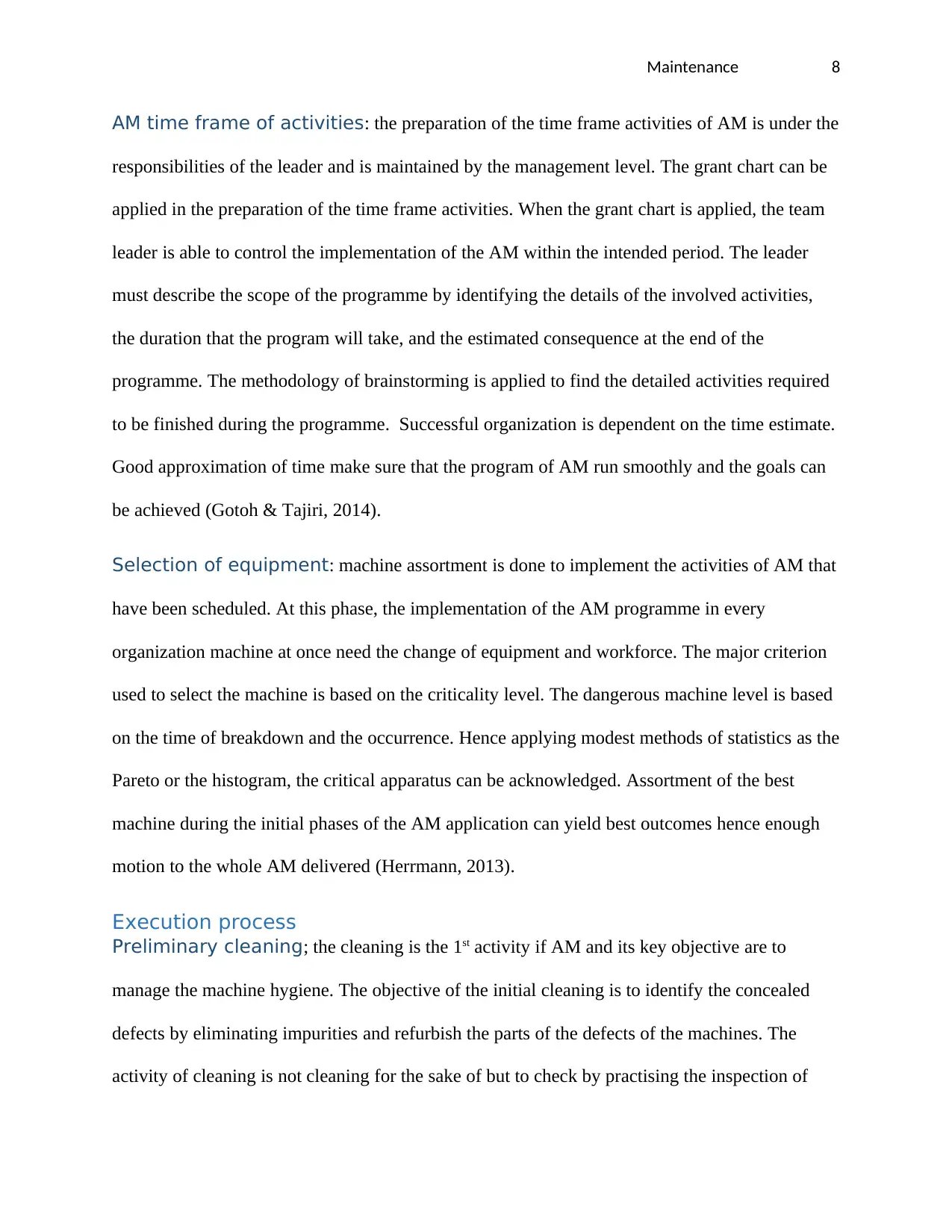
Maintenance 8
AM time frame of activities: the preparation of the time frame activities of AM is under the
responsibilities of the leader and is maintained by the management level. The grant chart can be
applied in the preparation of the time frame activities. When the grant chart is applied, the team
leader is able to control the implementation of the AM within the intended period. The leader
must describe the scope of the programme by identifying the details of the involved activities,
the duration that the program will take, and the estimated consequence at the end of the
programme. The methodology of brainstorming is applied to find the detailed activities required
to be finished during the programme. Successful organization is dependent on the time estimate.
Good approximation of time make sure that the program of AM run smoothly and the goals can
be achieved (Gotoh & Tajiri, 2014).
Selection of equipment: machine assortment is done to implement the activities of AM that
have been scheduled. At this phase, the implementation of the AM programme in every
organization machine at once need the change of equipment and workforce. The major criterion
used to select the machine is based on the criticality level. The dangerous machine level is based
on the time of breakdown and the occurrence. Hence applying modest methods of statistics as the
Pareto or the histogram, the critical apparatus can be acknowledged. Assortment of the best
machine during the initial phases of the AM application can yield best outcomes hence enough
motion to the whole AM delivered (Herrmann, 2013).
Execution process
Preliminary cleaning; the cleaning is the 1st activity if AM and its key objective are to
manage the machine hygiene. The objective of the initial cleaning is to identify the concealed
defects by eliminating impurities and refurbish the parts of the defects of the machines. The
activity of cleaning is not cleaning for the sake of but to check by practising the inspection of
AM time frame of activities: the preparation of the time frame activities of AM is under the
responsibilities of the leader and is maintained by the management level. The grant chart can be
applied in the preparation of the time frame activities. When the grant chart is applied, the team
leader is able to control the implementation of the AM within the intended period. The leader
must describe the scope of the programme by identifying the details of the involved activities,
the duration that the program will take, and the estimated consequence at the end of the
programme. The methodology of brainstorming is applied to find the detailed activities required
to be finished during the programme. Successful organization is dependent on the time estimate.
Good approximation of time make sure that the program of AM run smoothly and the goals can
be achieved (Gotoh & Tajiri, 2014).
Selection of equipment: machine assortment is done to implement the activities of AM that
have been scheduled. At this phase, the implementation of the AM programme in every
organization machine at once need the change of equipment and workforce. The major criterion
used to select the machine is based on the criticality level. The dangerous machine level is based
on the time of breakdown and the occurrence. Hence applying modest methods of statistics as the
Pareto or the histogram, the critical apparatus can be acknowledged. Assortment of the best
machine during the initial phases of the AM application can yield best outcomes hence enough
motion to the whole AM delivered (Herrmann, 2013).
Execution process
Preliminary cleaning; the cleaning is the 1st activity if AM and its key objective are to
manage the machine hygiene. The objective of the initial cleaning is to identify the concealed
defects by eliminating impurities and refurbish the parts of the defects of the machines. The
activity of cleaning is not cleaning for the sake of but to check by practising the inspection of
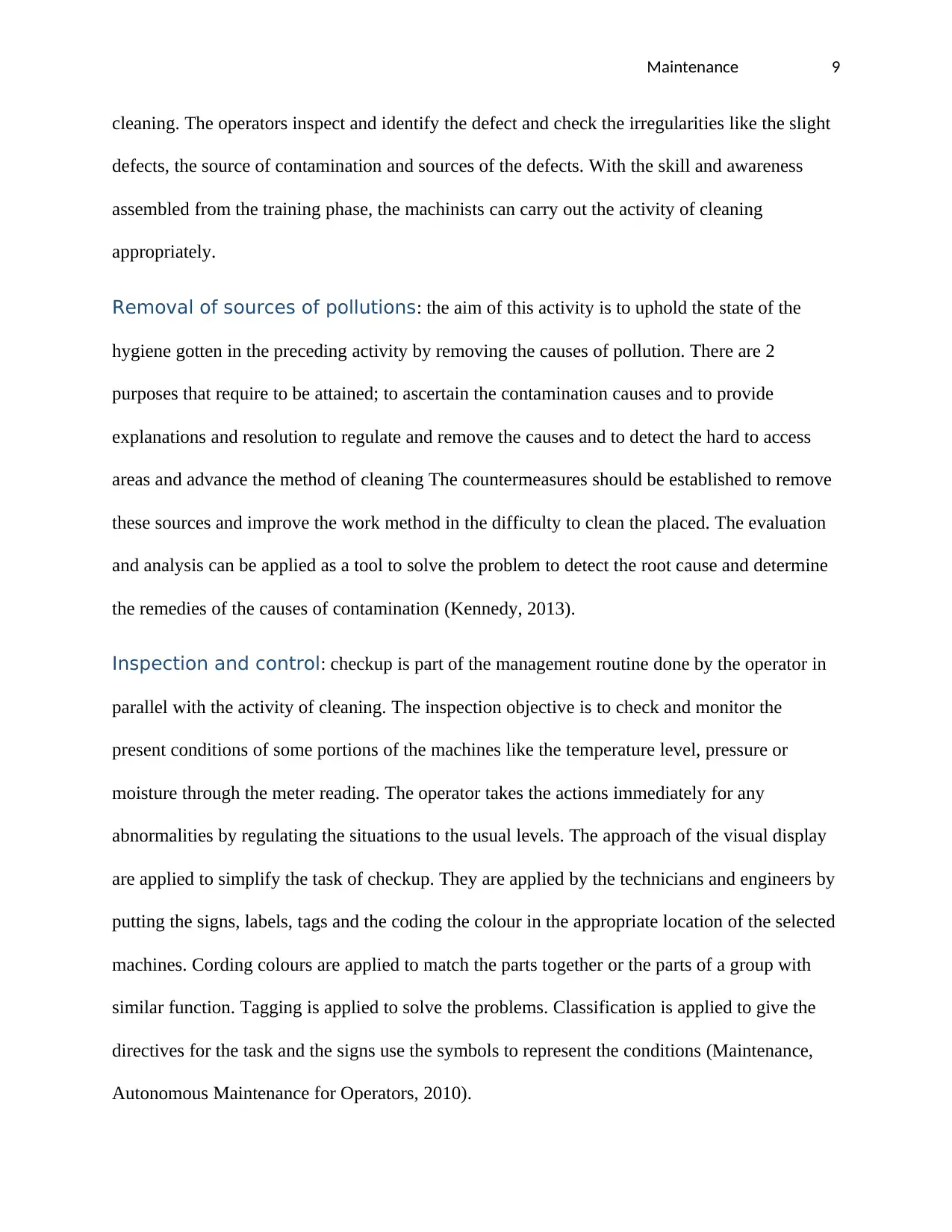
Maintenance 9
cleaning. The operators inspect and identify the defect and check the irregularities like the slight
defects, the source of contamination and sources of the defects. With the skill and awareness
assembled from the training phase, the machinists can carry out the activity of cleaning
appropriately.
Removal of sources of pollutions: the aim of this activity is to uphold the state of the
hygiene gotten in the preceding activity by removing the causes of pollution. There are 2
purposes that require to be attained; to ascertain the contamination causes and to provide
explanations and resolution to regulate and remove the causes and to detect the hard to access
areas and advance the method of cleaning The countermeasures should be established to remove
these sources and improve the work method in the difficulty to clean the placed. The evaluation
and analysis can be applied as a tool to solve the problem to detect the root cause and determine
the remedies of the causes of contamination (Kennedy, 2013).
Inspection and control: checkup is part of the management routine done by the operator in
parallel with the activity of cleaning. The inspection objective is to check and monitor the
present conditions of some portions of the machines like the temperature level, pressure or
moisture through the meter reading. The operator takes the actions immediately for any
abnormalities by regulating the situations to the usual levels. The approach of the visual display
are applied to simplify the task of checkup. They are applied by the technicians and engineers by
putting the signs, labels, tags and the coding the colour in the appropriate location of the selected
machines. Cording colours are applied to match the parts together or the parts of a group with
similar function. Tagging is applied to solve the problems. Classification is applied to give the
directives for the task and the signs use the symbols to represent the conditions (Maintenance,
Autonomous Maintenance for Operators, 2010).
cleaning. The operators inspect and identify the defect and check the irregularities like the slight
defects, the source of contamination and sources of the defects. With the skill and awareness
assembled from the training phase, the machinists can carry out the activity of cleaning
appropriately.
Removal of sources of pollutions: the aim of this activity is to uphold the state of the
hygiene gotten in the preceding activity by removing the causes of pollution. There are 2
purposes that require to be attained; to ascertain the contamination causes and to provide
explanations and resolution to regulate and remove the causes and to detect the hard to access
areas and advance the method of cleaning The countermeasures should be established to remove
these sources and improve the work method in the difficulty to clean the placed. The evaluation
and analysis can be applied as a tool to solve the problem to detect the root cause and determine
the remedies of the causes of contamination (Kennedy, 2013).
Inspection and control: checkup is part of the management routine done by the operator in
parallel with the activity of cleaning. The inspection objective is to check and monitor the
present conditions of some portions of the machines like the temperature level, pressure or
moisture through the meter reading. The operator takes the actions immediately for any
abnormalities by regulating the situations to the usual levels. The approach of the visual display
are applied to simplify the task of checkup. They are applied by the technicians and engineers by
putting the signs, labels, tags and the coding the colour in the appropriate location of the selected
machines. Cording colours are applied to match the parts together or the parts of a group with
similar function. Tagging is applied to solve the problems. Classification is applied to give the
directives for the task and the signs use the symbols to represent the conditions (Maintenance,
Autonomous Maintenance for Operators, 2010).
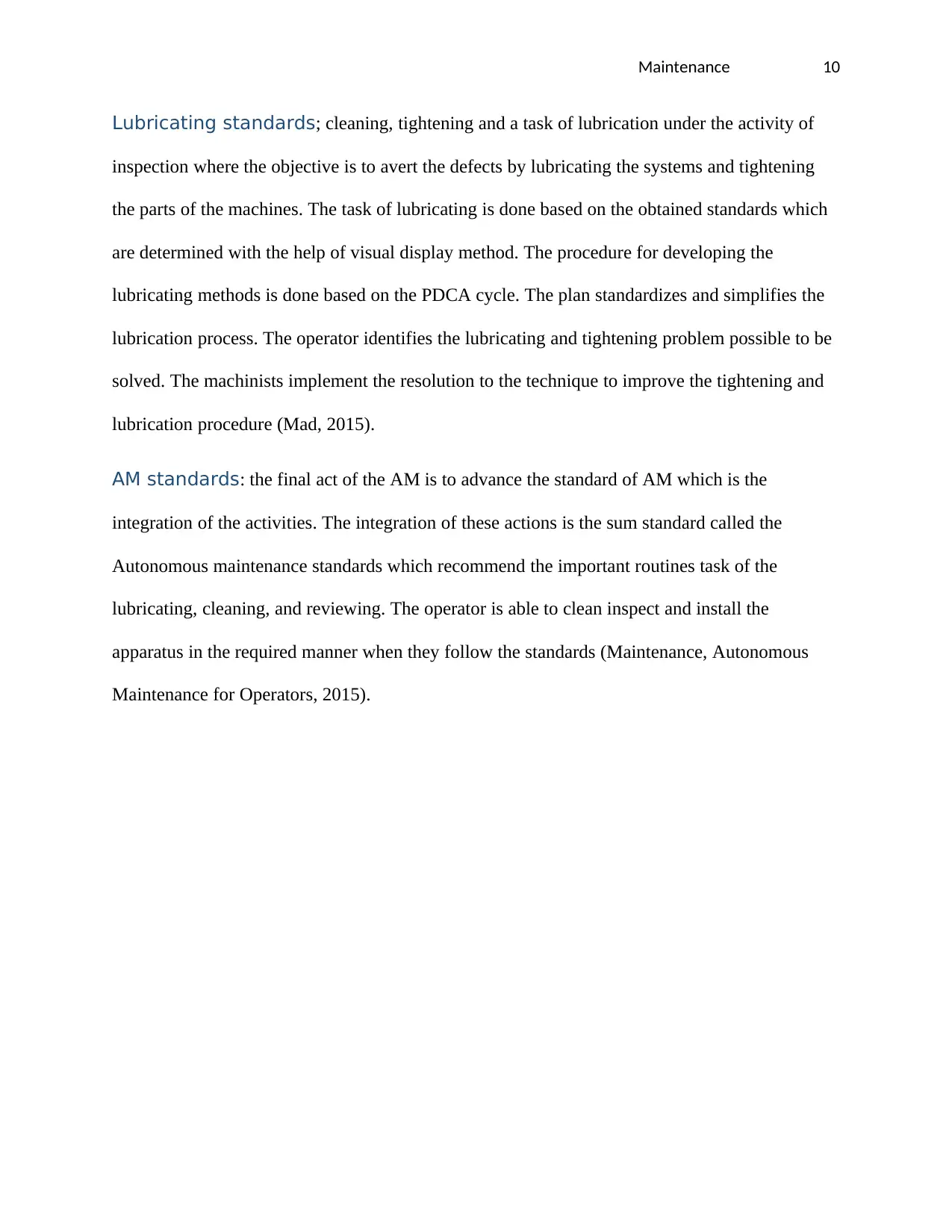
Maintenance 10
Lubricating standards; cleaning, tightening and a task of lubrication under the activity of
inspection where the objective is to avert the defects by lubricating the systems and tightening
the parts of the machines. The task of lubricating is done based on the obtained standards which
are determined with the help of visual display method. The procedure for developing the
lubricating methods is done based on the PDCA cycle. The plan standardizes and simplifies the
lubrication process. The operator identifies the lubricating and tightening problem possible to be
solved. The machinists implement the resolution to the technique to improve the tightening and
lubrication procedure (Mad, 2015).
AM standards: the final act of the AM is to advance the standard of AM which is the
integration of the activities. The integration of these actions is the sum standard called the
Autonomous maintenance standards which recommend the important routines task of the
lubricating, cleaning, and reviewing. The operator is able to clean inspect and install the
apparatus in the required manner when they follow the standards (Maintenance, Autonomous
Maintenance for Operators, 2015).
Lubricating standards; cleaning, tightening and a task of lubrication under the activity of
inspection where the objective is to avert the defects by lubricating the systems and tightening
the parts of the machines. The task of lubricating is done based on the obtained standards which
are determined with the help of visual display method. The procedure for developing the
lubricating methods is done based on the PDCA cycle. The plan standardizes and simplifies the
lubrication process. The operator identifies the lubricating and tightening problem possible to be
solved. The machinists implement the resolution to the technique to improve the tightening and
lubrication procedure (Mad, 2015).
AM standards: the final act of the AM is to advance the standard of AM which is the
integration of the activities. The integration of these actions is the sum standard called the
Autonomous maintenance standards which recommend the important routines task of the
lubricating, cleaning, and reviewing. The operator is able to clean inspect and install the
apparatus in the required manner when they follow the standards (Maintenance, Autonomous
Maintenance for Operators, 2015).
Secure Best Marks with AI Grader
Need help grading? Try our AI Grader for instant feedback on your assignments.
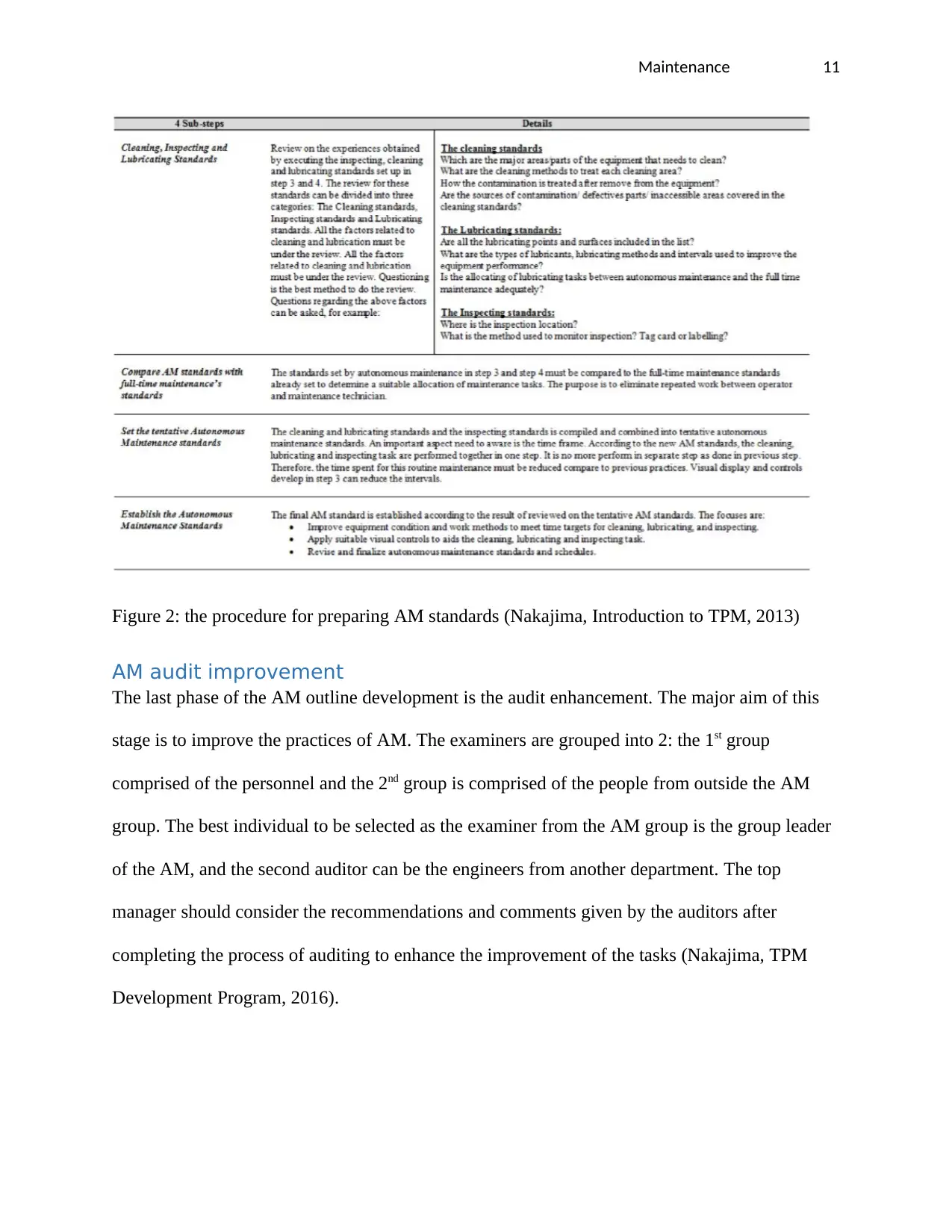
Maintenance 11
Figure 2: the procedure for preparing AM standards (Nakajima, Introduction to TPM, 2013)
AM audit improvement
The last phase of the AM outline development is the audit enhancement. The major aim of this
stage is to improve the practices of AM. The examiners are grouped into 2: the 1st group
comprised of the personnel and the 2nd group is comprised of the people from outside the AM
group. The best individual to be selected as the examiner from the AM group is the group leader
of the AM, and the second auditor can be the engineers from another department. The top
manager should consider the recommendations and comments given by the auditors after
completing the process of auditing to enhance the improvement of the tasks (Nakajima, TPM
Development Program, 2016).
Figure 2: the procedure for preparing AM standards (Nakajima, Introduction to TPM, 2013)
AM audit improvement
The last phase of the AM outline development is the audit enhancement. The major aim of this
stage is to improve the practices of AM. The examiners are grouped into 2: the 1st group
comprised of the personnel and the 2nd group is comprised of the people from outside the AM
group. The best individual to be selected as the examiner from the AM group is the group leader
of the AM, and the second auditor can be the engineers from another department. The top
manager should consider the recommendations and comments given by the auditors after
completing the process of auditing to enhance the improvement of the tasks (Nakajima, TPM
Development Program, 2016).
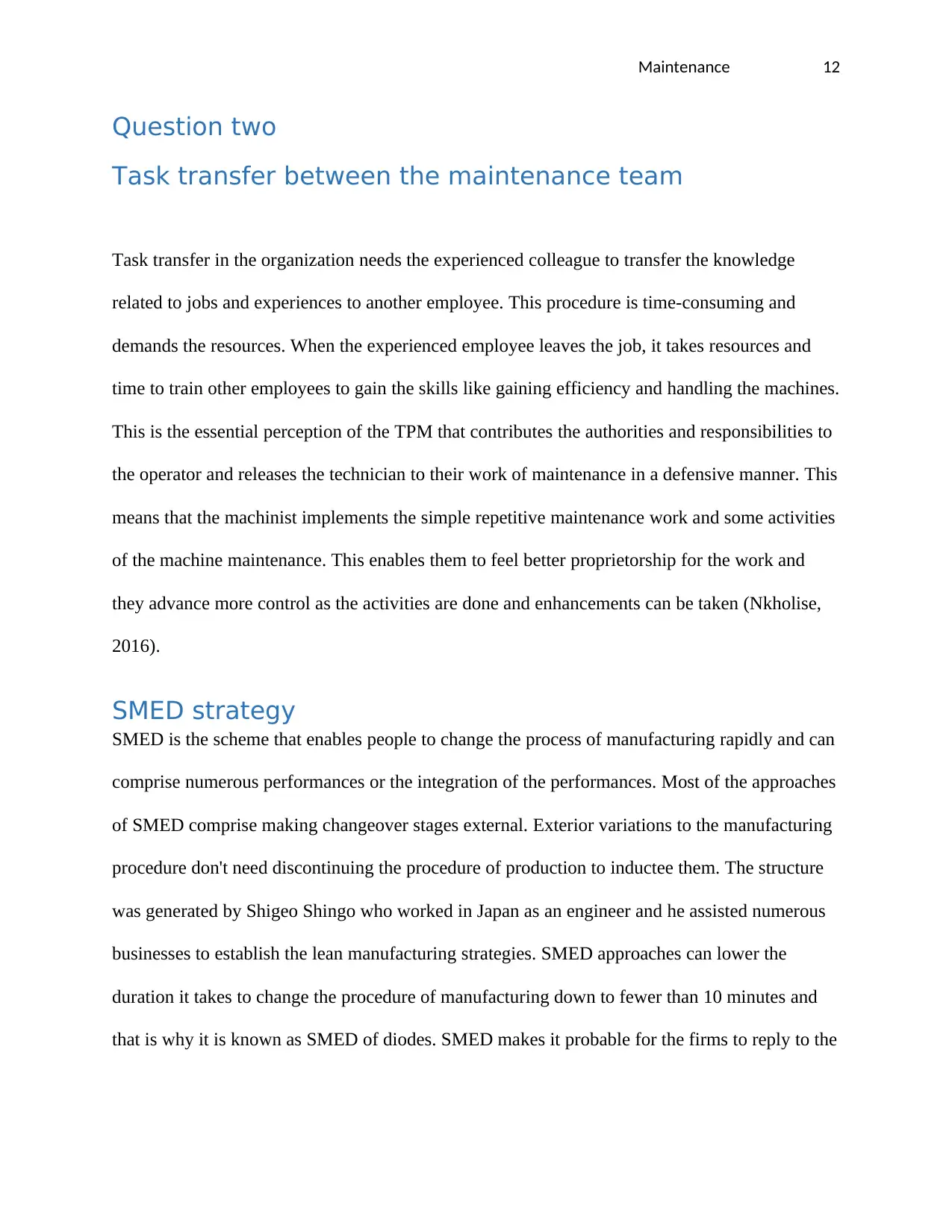
Maintenance 12
Question two
Task transfer between the maintenance team
Task transfer in the organization needs the experienced colleague to transfer the knowledge
related to jobs and experiences to another employee. This procedure is time-consuming and
demands the resources. When the experienced employee leaves the job, it takes resources and
time to train other employees to gain the skills like gaining efficiency and handling the machines.
This is the essential perception of the TPM that contributes the authorities and responsibilities to
the operator and releases the technician to their work of maintenance in a defensive manner. This
means that the machinist implements the simple repetitive maintenance work and some activities
of the machine maintenance. This enables them to feel better proprietorship for the work and
they advance more control as the activities are done and enhancements can be taken (Nkholise,
2016).
SMED strategy
SMED is the scheme that enables people to change the process of manufacturing rapidly and can
comprise numerous performances or the integration of the performances. Most of the approaches
of SMED comprise making changeover stages external. Exterior variations to the manufacturing
procedure don't need discontinuing the procedure of production to inductee them. The structure
was generated by Shigeo Shingo who worked in Japan as an engineer and he assisted numerous
businesses to establish the lean manufacturing strategies. SMED approaches can lower the
duration it takes to change the procedure of manufacturing down to fewer than 10 minutes and
that is why it is known as SMED of diodes. SMED makes it probable for the firms to reply to the
Question two
Task transfer between the maintenance team
Task transfer in the organization needs the experienced colleague to transfer the knowledge
related to jobs and experiences to another employee. This procedure is time-consuming and
demands the resources. When the experienced employee leaves the job, it takes resources and
time to train other employees to gain the skills like gaining efficiency and handling the machines.
This is the essential perception of the TPM that contributes the authorities and responsibilities to
the operator and releases the technician to their work of maintenance in a defensive manner. This
means that the machinist implements the simple repetitive maintenance work and some activities
of the machine maintenance. This enables them to feel better proprietorship for the work and
they advance more control as the activities are done and enhancements can be taken (Nkholise,
2016).
SMED strategy
SMED is the scheme that enables people to change the process of manufacturing rapidly and can
comprise numerous performances or the integration of the performances. Most of the approaches
of SMED comprise making changeover stages external. Exterior variations to the manufacturing
procedure don't need discontinuing the procedure of production to inductee them. The structure
was generated by Shigeo Shingo who worked in Japan as an engineer and he assisted numerous
businesses to establish the lean manufacturing strategies. SMED approaches can lower the
duration it takes to change the procedure of manufacturing down to fewer than 10 minutes and
that is why it is known as SMED of diodes. SMED makes it probable for the firms to reply to the
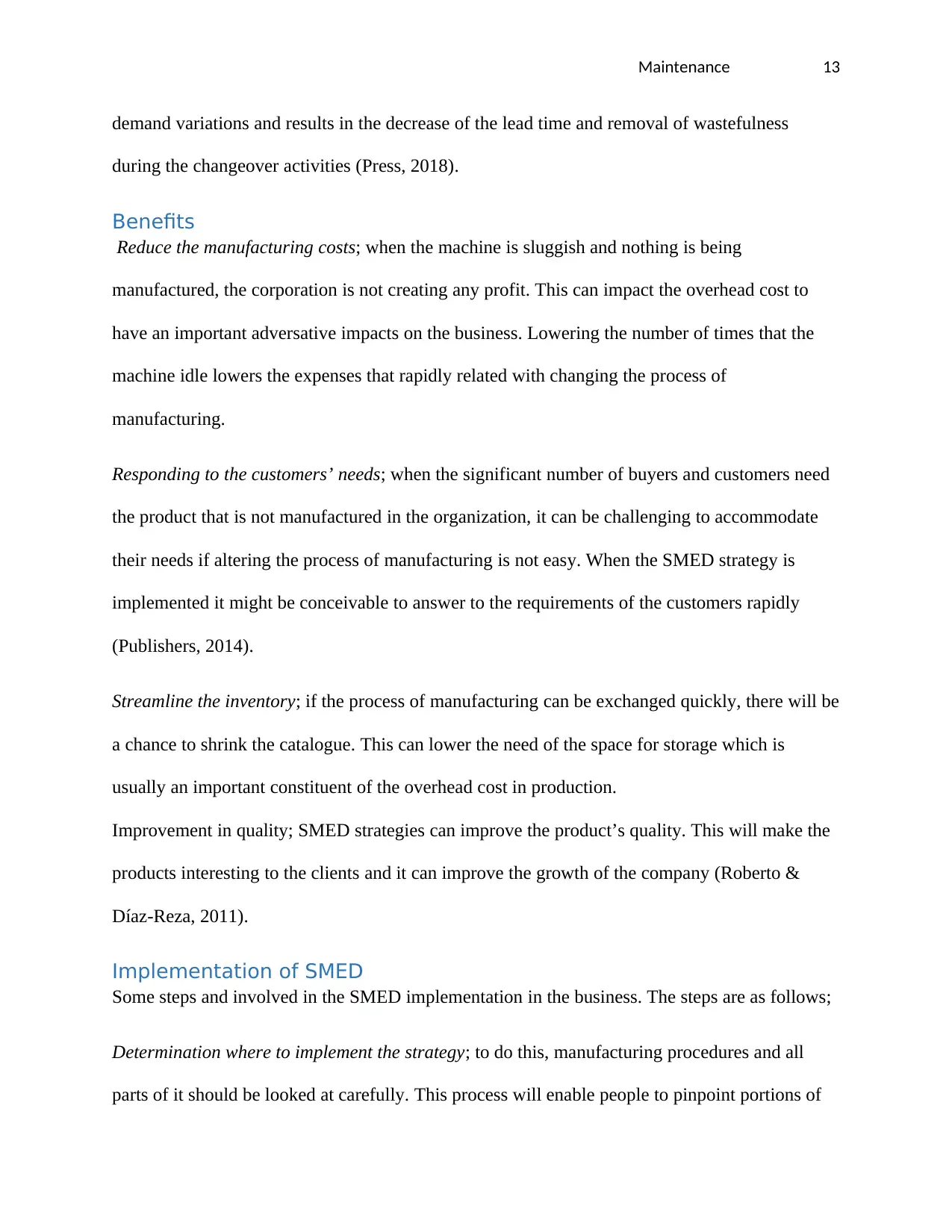
Maintenance 13
demand variations and results in the decrease of the lead time and removal of wastefulness
during the changeover activities (Press, 2018).
Benefits
Reduce the manufacturing costs; when the machine is sluggish and nothing is being
manufactured, the corporation is not creating any profit. This can impact the overhead cost to
have an important adversative impacts on the business. Lowering the number of times that the
machine idle lowers the expenses that rapidly related with changing the process of
manufacturing.
Responding to the customers’ needs; when the significant number of buyers and customers need
the product that is not manufactured in the organization, it can be challenging to accommodate
their needs if altering the process of manufacturing is not easy. When the SMED strategy is
implemented it might be conceivable to answer to the requirements of the customers rapidly
(Publishers, 2014).
Streamline the inventory; if the process of manufacturing can be exchanged quickly, there will be
a chance to shrink the catalogue. This can lower the need of the space for storage which is
usually an important constituent of the overhead cost in production.
Improvement in quality; SMED strategies can improve the product’s quality. This will make the
products interesting to the clients and it can improve the growth of the company (Roberto &
Díaz-Reza, 2011).
Implementation of SMED
Some steps and involved in the SMED implementation in the business. The steps are as follows;
Determination where to implement the strategy; to do this, manufacturing procedures and all
parts of it should be looked at carefully. This process will enable people to pinpoint portions of
demand variations and results in the decrease of the lead time and removal of wastefulness
during the changeover activities (Press, 2018).
Benefits
Reduce the manufacturing costs; when the machine is sluggish and nothing is being
manufactured, the corporation is not creating any profit. This can impact the overhead cost to
have an important adversative impacts on the business. Lowering the number of times that the
machine idle lowers the expenses that rapidly related with changing the process of
manufacturing.
Responding to the customers’ needs; when the significant number of buyers and customers need
the product that is not manufactured in the organization, it can be challenging to accommodate
their needs if altering the process of manufacturing is not easy. When the SMED strategy is
implemented it might be conceivable to answer to the requirements of the customers rapidly
(Publishers, 2014).
Streamline the inventory; if the process of manufacturing can be exchanged quickly, there will be
a chance to shrink the catalogue. This can lower the need of the space for storage which is
usually an important constituent of the overhead cost in production.
Improvement in quality; SMED strategies can improve the product’s quality. This will make the
products interesting to the clients and it can improve the growth of the company (Roberto &
Díaz-Reza, 2011).
Implementation of SMED
Some steps and involved in the SMED implementation in the business. The steps are as follows;
Determination where to implement the strategy; to do this, manufacturing procedures and all
parts of it should be looked at carefully. This process will enable people to pinpoint portions of
Paraphrase This Document
Need a fresh take? Get an instant paraphrase of this document with our AI Paraphraser
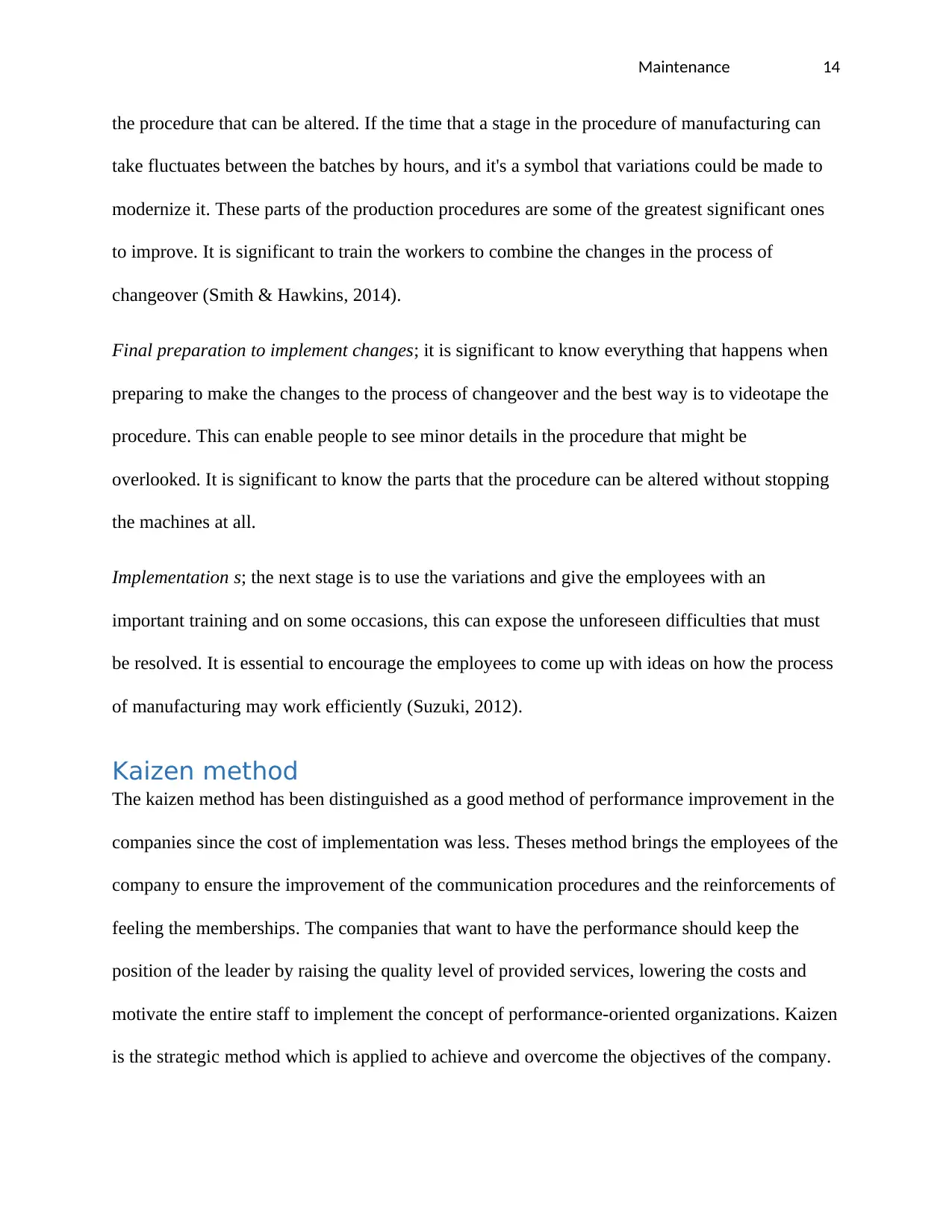
Maintenance 14
the procedure that can be altered. If the time that a stage in the procedure of manufacturing can
take fluctuates between the batches by hours, and it's a symbol that variations could be made to
modernize it. These parts of the production procedures are some of the greatest significant ones
to improve. It is significant to train the workers to combine the changes in the process of
changeover (Smith & Hawkins, 2014).
Final preparation to implement changes; it is significant to know everything that happens when
preparing to make the changes to the process of changeover and the best way is to videotape the
procedure. This can enable people to see minor details in the procedure that might be
overlooked. It is significant to know the parts that the procedure can be altered without stopping
the machines at all.
Implementation s; the next stage is to use the variations and give the employees with an
important training and on some occasions, this can expose the unforeseen difficulties that must
be resolved. It is essential to encourage the employees to come up with ideas on how the process
of manufacturing may work efficiently (Suzuki, 2012).
Kaizen method
The kaizen method has been distinguished as a good method of performance improvement in the
companies since the cost of implementation was less. Theses method brings the employees of the
company to ensure the improvement of the communication procedures and the reinforcements of
feeling the memberships. The companies that want to have the performance should keep the
position of the leader by raising the quality level of provided services, lowering the costs and
motivate the entire staff to implement the concept of performance-oriented organizations. Kaizen
is the strategic method which is applied to achieve and overcome the objectives of the company.
the procedure that can be altered. If the time that a stage in the procedure of manufacturing can
take fluctuates between the batches by hours, and it's a symbol that variations could be made to
modernize it. These parts of the production procedures are some of the greatest significant ones
to improve. It is significant to train the workers to combine the changes in the process of
changeover (Smith & Hawkins, 2014).
Final preparation to implement changes; it is significant to know everything that happens when
preparing to make the changes to the process of changeover and the best way is to videotape the
procedure. This can enable people to see minor details in the procedure that might be
overlooked. It is significant to know the parts that the procedure can be altered without stopping
the machines at all.
Implementation s; the next stage is to use the variations and give the employees with an
important training and on some occasions, this can expose the unforeseen difficulties that must
be resolved. It is essential to encourage the employees to come up with ideas on how the process
of manufacturing may work efficiently (Suzuki, 2012).
Kaizen method
The kaizen method has been distinguished as a good method of performance improvement in the
companies since the cost of implementation was less. Theses method brings the employees of the
company to ensure the improvement of the communication procedures and the reinforcements of
feeling the memberships. The companies that want to have the performance should keep the
position of the leader by raising the quality level of provided services, lowering the costs and
motivate the entire staff to implement the concept of performance-oriented organizations. Kaizen
is the strategic method which is applied to achieve and overcome the objectives of the company.
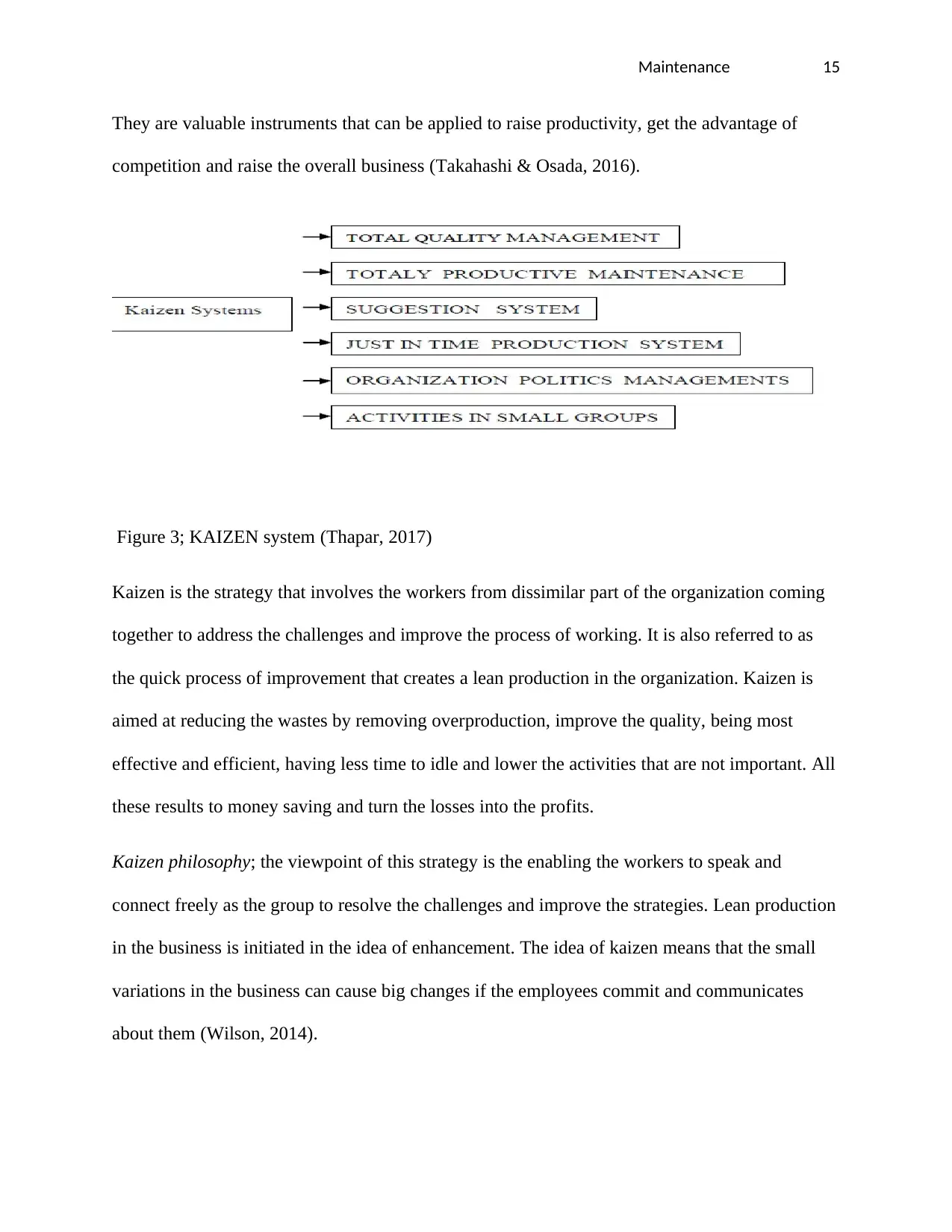
Maintenance 15
They are valuable instruments that can be applied to raise productivity, get the advantage of
competition and raise the overall business (Takahashi & Osada, 2016).
Figure 3; KAIZEN system (Thapar, 2017)
Kaizen is the strategy that involves the workers from dissimilar part of the organization coming
together to address the challenges and improve the process of working. It is also referred to as
the quick process of improvement that creates a lean production in the organization. Kaizen is
aimed at reducing the wastes by removing overproduction, improve the quality, being most
effective and efficient, having less time to idle and lower the activities that are not important. All
these results to money saving and turn the losses into the profits.
Kaizen philosophy; the viewpoint of this strategy is the enabling the workers to speak and
connect freely as the group to resolve the challenges and improve the strategies. Lean production
in the business is initiated in the idea of enhancement. The idea of kaizen means that the small
variations in the business can cause big changes if the employees commit and communicates
about them (Wilson, 2014).
They are valuable instruments that can be applied to raise productivity, get the advantage of
competition and raise the overall business (Takahashi & Osada, 2016).
Figure 3; KAIZEN system (Thapar, 2017)
Kaizen is the strategy that involves the workers from dissimilar part of the organization coming
together to address the challenges and improve the process of working. It is also referred to as
the quick process of improvement that creates a lean production in the organization. Kaizen is
aimed at reducing the wastes by removing overproduction, improve the quality, being most
effective and efficient, having less time to idle and lower the activities that are not important. All
these results to money saving and turn the losses into the profits.
Kaizen philosophy; the viewpoint of this strategy is the enabling the workers to speak and
connect freely as the group to resolve the challenges and improve the strategies. Lean production
in the business is initiated in the idea of enhancement. The idea of kaizen means that the small
variations in the business can cause big changes if the employees commit and communicates
about them (Wilson, 2014).
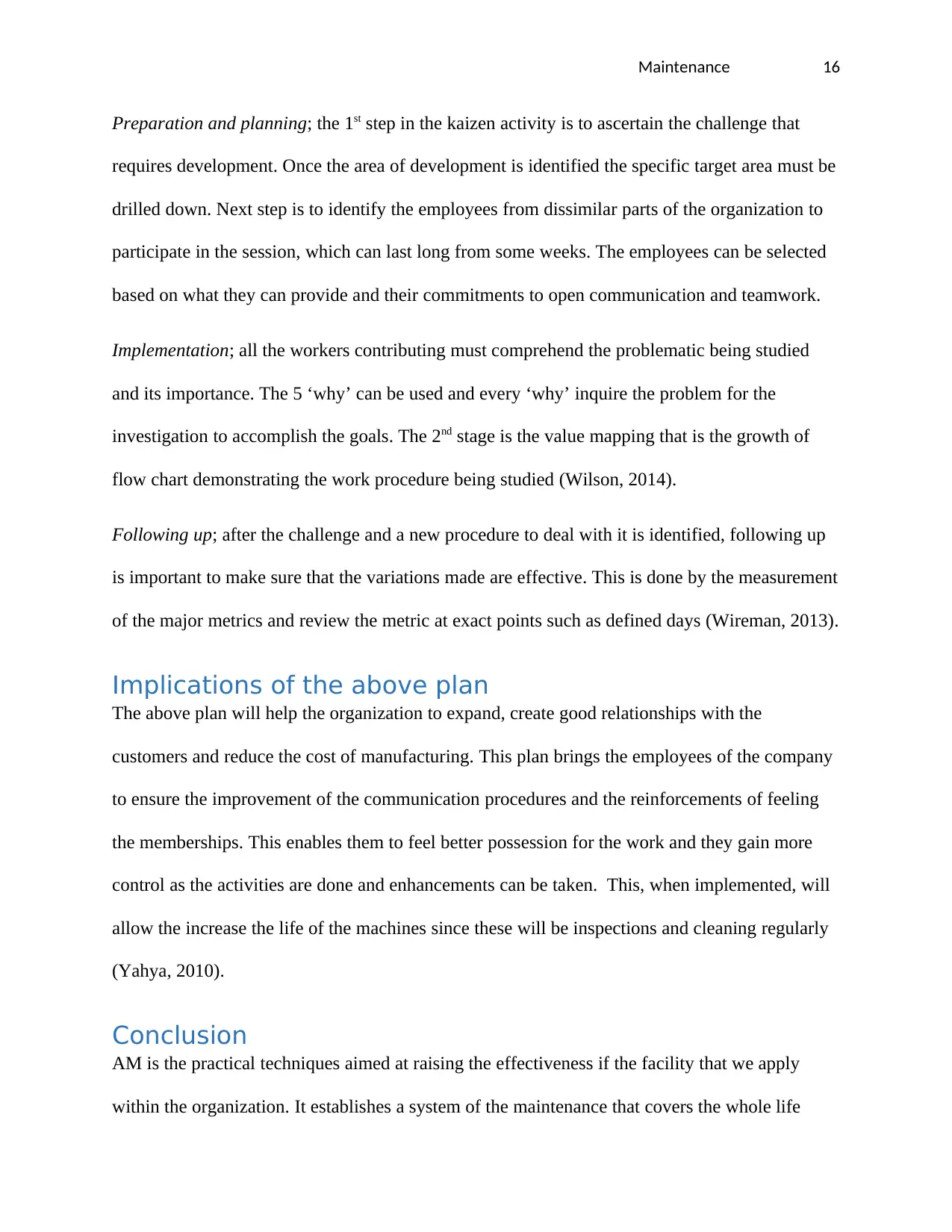
Maintenance 16
Preparation and planning; the 1st step in the kaizen activity is to ascertain the challenge that
requires development. Once the area of development is identified the specific target area must be
drilled down. Next step is to identify the employees from dissimilar parts of the organization to
participate in the session, which can last long from some weeks. The employees can be selected
based on what they can provide and their commitments to open communication and teamwork.
Implementation; all the workers contributing must comprehend the problematic being studied
and its importance. The 5 ‘why’ can be used and every ‘why’ inquire the problem for the
investigation to accomplish the goals. The 2nd stage is the value mapping that is the growth of
flow chart demonstrating the work procedure being studied (Wilson, 2014).
Following up; after the challenge and a new procedure to deal with it is identified, following up
is important to make sure that the variations made are effective. This is done by the measurement
of the major metrics and review the metric at exact points such as defined days (Wireman, 2013).
Implications of the above plan
The above plan will help the organization to expand, create good relationships with the
customers and reduce the cost of manufacturing. This plan brings the employees of the company
to ensure the improvement of the communication procedures and the reinforcements of feeling
the memberships. This enables them to feel better possession for the work and they gain more
control as the activities are done and enhancements can be taken. This, when implemented, will
allow the increase the life of the machines since these will be inspections and cleaning regularly
(Yahya, 2010).
Conclusion
AM is the practical techniques aimed at raising the effectiveness if the facility that we apply
within the organization. It establishes a system of the maintenance that covers the whole life
Preparation and planning; the 1st step in the kaizen activity is to ascertain the challenge that
requires development. Once the area of development is identified the specific target area must be
drilled down. Next step is to identify the employees from dissimilar parts of the organization to
participate in the session, which can last long from some weeks. The employees can be selected
based on what they can provide and their commitments to open communication and teamwork.
Implementation; all the workers contributing must comprehend the problematic being studied
and its importance. The 5 ‘why’ can be used and every ‘why’ inquire the problem for the
investigation to accomplish the goals. The 2nd stage is the value mapping that is the growth of
flow chart demonstrating the work procedure being studied (Wilson, 2014).
Following up; after the challenge and a new procedure to deal with it is identified, following up
is important to make sure that the variations made are effective. This is done by the measurement
of the major metrics and review the metric at exact points such as defined days (Wireman, 2013).
Implications of the above plan
The above plan will help the organization to expand, create good relationships with the
customers and reduce the cost of manufacturing. This plan brings the employees of the company
to ensure the improvement of the communication procedures and the reinforcements of feeling
the memberships. This enables them to feel better possession for the work and they gain more
control as the activities are done and enhancements can be taken. This, when implemented, will
allow the increase the life of the machines since these will be inspections and cleaning regularly
(Yahya, 2010).
Conclusion
AM is the practical techniques aimed at raising the effectiveness if the facility that we apply
within the organization. It establishes a system of the maintenance that covers the whole life
Secure Best Marks with AI Grader
Need help grading? Try our AI Grader for instant feedback on your assignments.
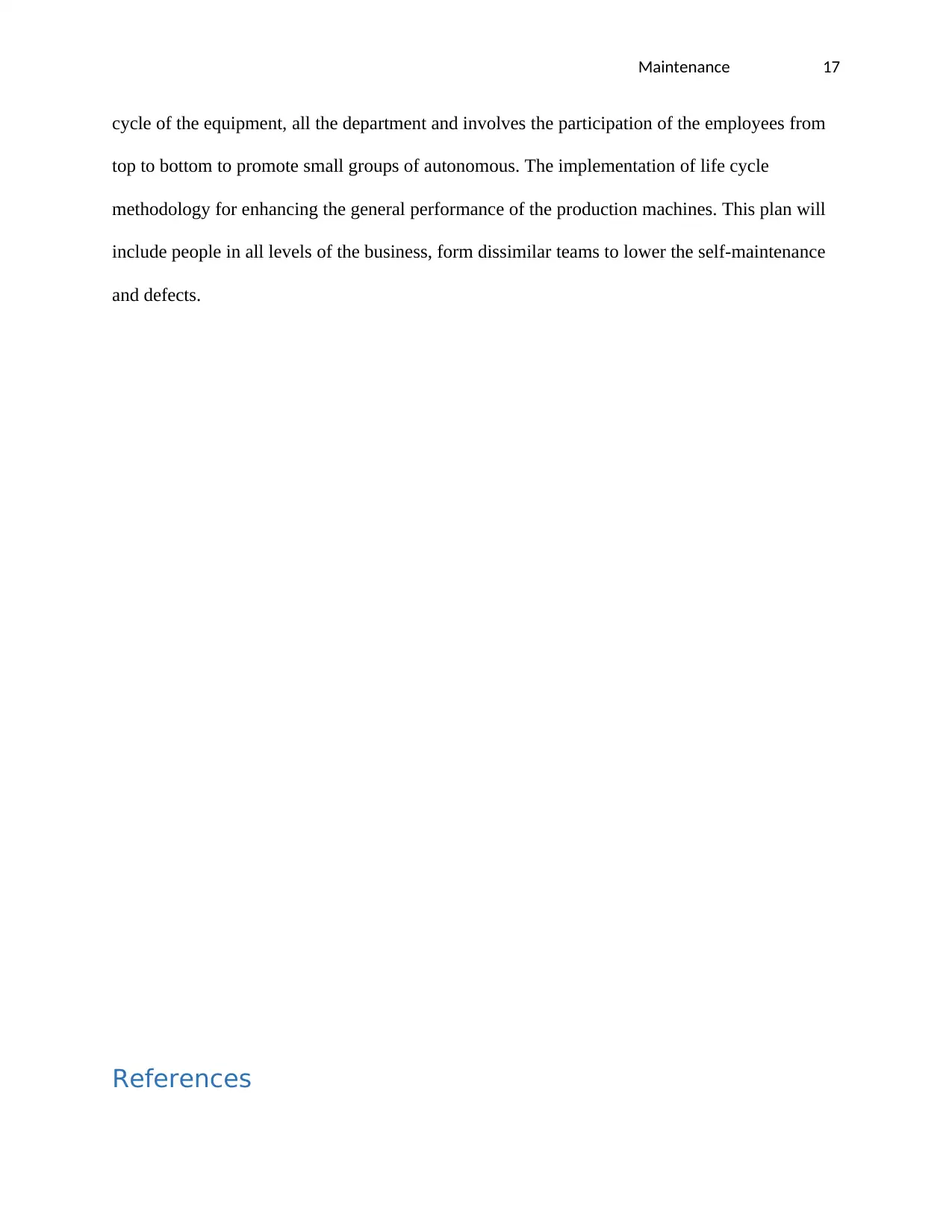
Maintenance 17
cycle of the equipment, all the department and involves the participation of the employees from
top to bottom to promote small groups of autonomous. The implementation of life cycle
methodology for enhancing the general performance of the production machines. This plan will
include people in all levels of the business, form dissimilar teams to lower the self-maintenance
and defects.
References
cycle of the equipment, all the department and involves the participation of the employees from
top to bottom to promote small groups of autonomous. The implementation of life cycle
methodology for enhancing the general performance of the production machines. This plan will
include people in all levels of the business, form dissimilar teams to lower the self-maintenance
and defects.
References
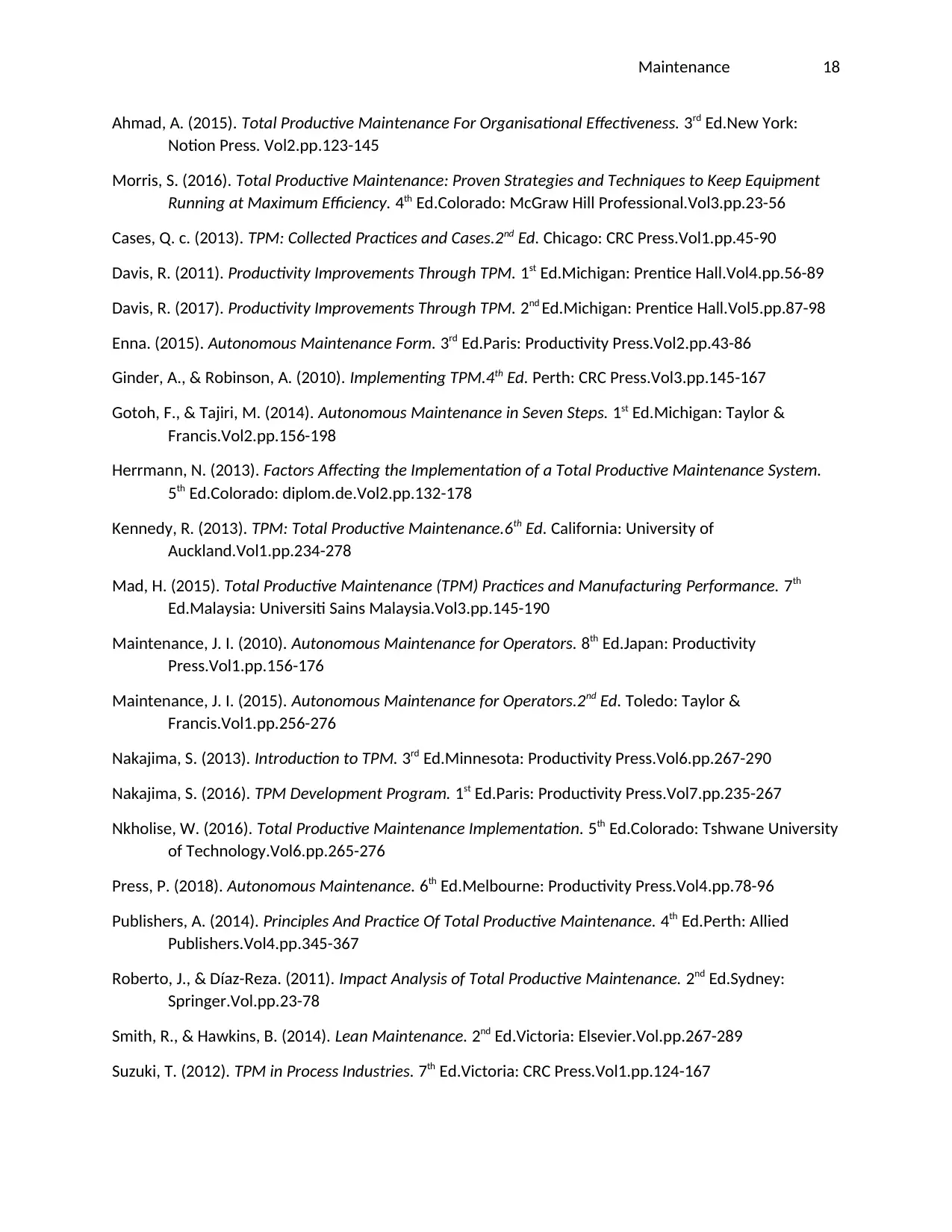
Maintenance 18
Ahmad, A. (2015). Total Productive Maintenance For Organisational Effectiveness. 3rd Ed.New York:
Notion Press. Vol2.pp.123-145
Morris, S. (2016). Total Productive Maintenance: Proven Strategies and Techniques to Keep Equipment
Running at Maximum Efficiency. 4th Ed.Colorado: McGraw Hill Professional.Vol3.pp.23-56
Cases, Q. c. (2013). TPM: Collected Practices and Cases.2nd Ed. Chicago: CRC Press.Vol1.pp.45-90
Davis, R. (2011). Productivity Improvements Through TPM. 1st Ed.Michigan: Prentice Hall.Vol4.pp.56-89
Davis, R. (2017). Productivity Improvements Through TPM. 2nd Ed.Michigan: Prentice Hall.Vol5.pp.87-98
Enna. (2015). Autonomous Maintenance Form. 3rd Ed.Paris: Productivity Press.Vol2.pp.43-86
Ginder, A., & Robinson, A. (2010). Implementing TPM.4th Ed. Perth: CRC Press.Vol3.pp.145-167
Gotoh, F., & Tajiri, M. (2014). Autonomous Maintenance in Seven Steps. 1st Ed.Michigan: Taylor &
Francis.Vol2.pp.156-198
Herrmann, N. (2013). Factors Affecting the Implementation of a Total Productive Maintenance System.
5th Ed.Colorado: diplom.de.Vol2.pp.132-178
Kennedy, R. (2013). TPM: Total Productive Maintenance.6th Ed. California: University of
Auckland.Vol1.pp.234-278
Mad, H. (2015). Total Productive Maintenance (TPM) Practices and Manufacturing Performance. 7th
Ed.Malaysia: Universiti Sains Malaysia.Vol3.pp.145-190
Maintenance, J. I. (2010). Autonomous Maintenance for Operators. 8th Ed.Japan: Productivity
Press.Vol1.pp.156-176
Maintenance, J. I. (2015). Autonomous Maintenance for Operators.2nd Ed. Toledo: Taylor &
Francis.Vol1.pp.256-276
Nakajima, S. (2013). Introduction to TPM. 3rd Ed.Minnesota: Productivity Press.Vol6.pp.267-290
Nakajima, S. (2016). TPM Development Program. 1st Ed.Paris: Productivity Press.Vol7.pp.235-267
Nkholise, W. (2016). Total Productive Maintenance Implementation. 5th Ed.Colorado: Tshwane University
of Technology.Vol6.pp.265-276
Press, P. (2018). Autonomous Maintenance. 6th Ed.Melbourne: Productivity Press.Vol4.pp.78-96
Publishers, A. (2014). Principles And Practice Of Total Productive Maintenance. 4th Ed.Perth: Allied
Publishers.Vol4.pp.345-367
Roberto, J., & Díaz-Reza. (2011). Impact Analysis of Total Productive Maintenance. 2nd Ed.Sydney:
Springer.Vol.pp.23-78
Smith, R., & Hawkins, B. (2014). Lean Maintenance. 2nd Ed.Victoria: Elsevier.Vol.pp.267-289
Suzuki, T. (2012). TPM in Process Industries. 7th Ed.Victoria: CRC Press.Vol1.pp.124-167
Ahmad, A. (2015). Total Productive Maintenance For Organisational Effectiveness. 3rd Ed.New York:
Notion Press. Vol2.pp.123-145
Morris, S. (2016). Total Productive Maintenance: Proven Strategies and Techniques to Keep Equipment
Running at Maximum Efficiency. 4th Ed.Colorado: McGraw Hill Professional.Vol3.pp.23-56
Cases, Q. c. (2013). TPM: Collected Practices and Cases.2nd Ed. Chicago: CRC Press.Vol1.pp.45-90
Davis, R. (2011). Productivity Improvements Through TPM. 1st Ed.Michigan: Prentice Hall.Vol4.pp.56-89
Davis, R. (2017). Productivity Improvements Through TPM. 2nd Ed.Michigan: Prentice Hall.Vol5.pp.87-98
Enna. (2015). Autonomous Maintenance Form. 3rd Ed.Paris: Productivity Press.Vol2.pp.43-86
Ginder, A., & Robinson, A. (2010). Implementing TPM.4th Ed. Perth: CRC Press.Vol3.pp.145-167
Gotoh, F., & Tajiri, M. (2014). Autonomous Maintenance in Seven Steps. 1st Ed.Michigan: Taylor &
Francis.Vol2.pp.156-198
Herrmann, N. (2013). Factors Affecting the Implementation of a Total Productive Maintenance System.
5th Ed.Colorado: diplom.de.Vol2.pp.132-178
Kennedy, R. (2013). TPM: Total Productive Maintenance.6th Ed. California: University of
Auckland.Vol1.pp.234-278
Mad, H. (2015). Total Productive Maintenance (TPM) Practices and Manufacturing Performance. 7th
Ed.Malaysia: Universiti Sains Malaysia.Vol3.pp.145-190
Maintenance, J. I. (2010). Autonomous Maintenance for Operators. 8th Ed.Japan: Productivity
Press.Vol1.pp.156-176
Maintenance, J. I. (2015). Autonomous Maintenance for Operators.2nd Ed. Toledo: Taylor &
Francis.Vol1.pp.256-276
Nakajima, S. (2013). Introduction to TPM. 3rd Ed.Minnesota: Productivity Press.Vol6.pp.267-290
Nakajima, S. (2016). TPM Development Program. 1st Ed.Paris: Productivity Press.Vol7.pp.235-267
Nkholise, W. (2016). Total Productive Maintenance Implementation. 5th Ed.Colorado: Tshwane University
of Technology.Vol6.pp.265-276
Press, P. (2018). Autonomous Maintenance. 6th Ed.Melbourne: Productivity Press.Vol4.pp.78-96
Publishers, A. (2014). Principles And Practice Of Total Productive Maintenance. 4th Ed.Perth: Allied
Publishers.Vol4.pp.345-367
Roberto, J., & Díaz-Reza. (2011). Impact Analysis of Total Productive Maintenance. 2nd Ed.Sydney:
Springer.Vol.pp.23-78
Smith, R., & Hawkins, B. (2014). Lean Maintenance. 2nd Ed.Victoria: Elsevier.Vol.pp.267-289
Suzuki, T. (2012). TPM in Process Industries. 7th Ed.Victoria: CRC Press.Vol1.pp.124-167
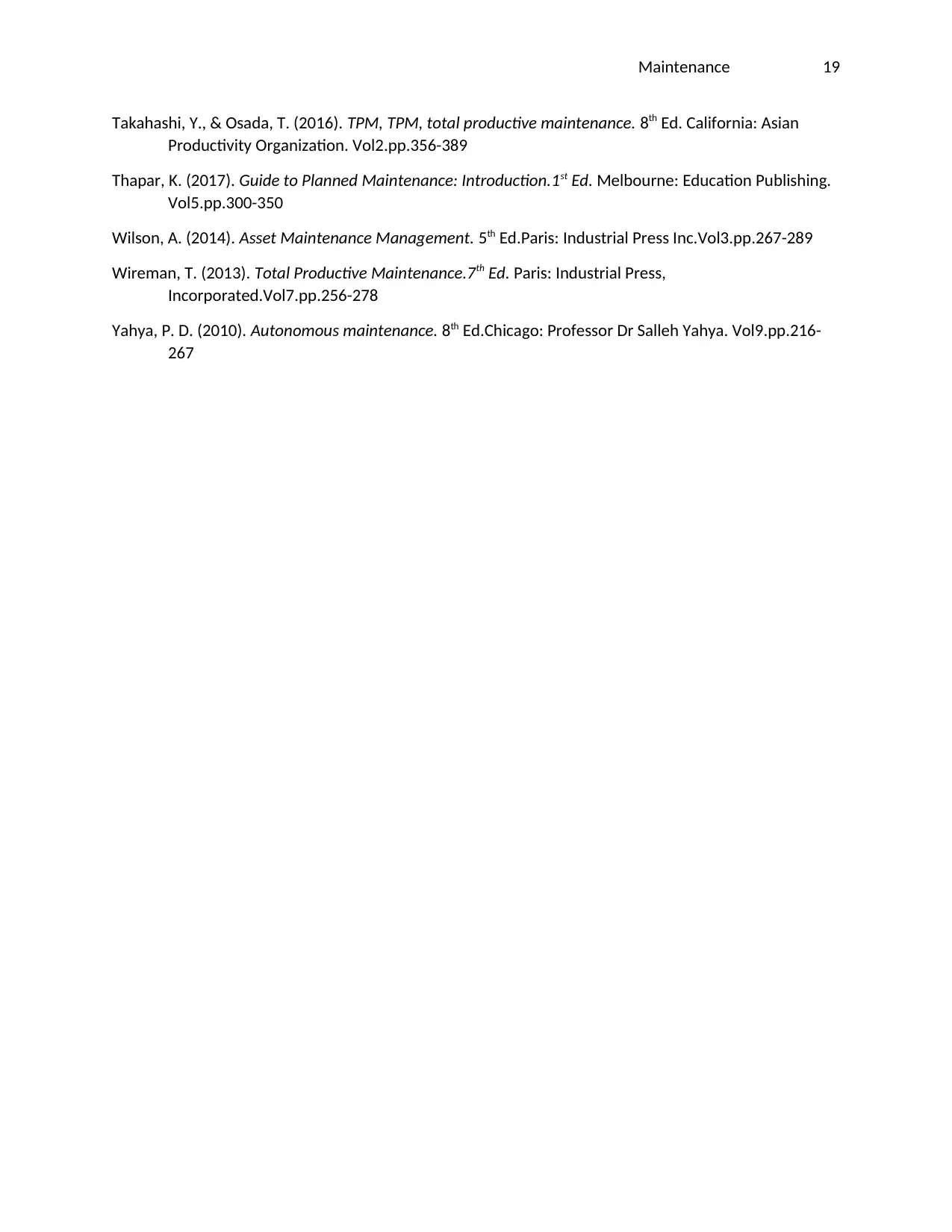
Maintenance 19
Takahashi, Y., & Osada, T. (2016). TPM, TPM, total productive maintenance. 8th Ed. California: Asian
Productivity Organization. Vol2.pp.356-389
Thapar, K. (2017). Guide to Planned Maintenance: Introduction.1st Ed. Melbourne: Education Publishing.
Vol5.pp.300-350
Wilson, A. (2014). Asset Maintenance Management. 5th Ed.Paris: Industrial Press Inc.Vol3.pp.267-289
Wireman, T. (2013). Total Productive Maintenance.7th Ed. Paris: Industrial Press,
Incorporated.Vol7.pp.256-278
Yahya, P. D. (2010). Autonomous maintenance. 8th Ed.Chicago: Professor Dr Salleh Yahya. Vol9.pp.216-
267
Takahashi, Y., & Osada, T. (2016). TPM, TPM, total productive maintenance. 8th Ed. California: Asian
Productivity Organization. Vol2.pp.356-389
Thapar, K. (2017). Guide to Planned Maintenance: Introduction.1st Ed. Melbourne: Education Publishing.
Vol5.pp.300-350
Wilson, A. (2014). Asset Maintenance Management. 5th Ed.Paris: Industrial Press Inc.Vol3.pp.267-289
Wireman, T. (2013). Total Productive Maintenance.7th Ed. Paris: Industrial Press,
Incorporated.Vol7.pp.256-278
Yahya, P. D. (2010). Autonomous maintenance. 8th Ed.Chicago: Professor Dr Salleh Yahya. Vol9.pp.216-
267
1 out of 19
Related Documents

Your All-in-One AI-Powered Toolkit for Academic Success.
+13062052269
info@desklib.com
Available 24*7 on WhatsApp / Email
Unlock your academic potential
© 2024 | Zucol Services PVT LTD | All rights reserved.