Boeing 737 Production System Report
VerifiedAdded on 2020/01/28
|11
|3270
|201
Report
AI Summary
This report analyzes the changes in Boeing's 737 production system, focusing on the reasons behind these changes and the resulting waste reduction. It utilizes relevant theories like lean management and Six Sigma to assess the impact of these changes. The report explores the competitive benefits and limitations of lean thinking in the context of Boeing's operations, considering the impact of current economic trends on Boeing's strategies. The analysis includes a discussion of waste reduction before and after the changes, highlighting the effectiveness of lean synchronization in improving efficiency and productivity. The report concludes by summarizing the key findings and their implications for Boeing's overall operational strategy.
Contribute Materials
Your contribution can guide someone’s learning journey. Share your
documents today.
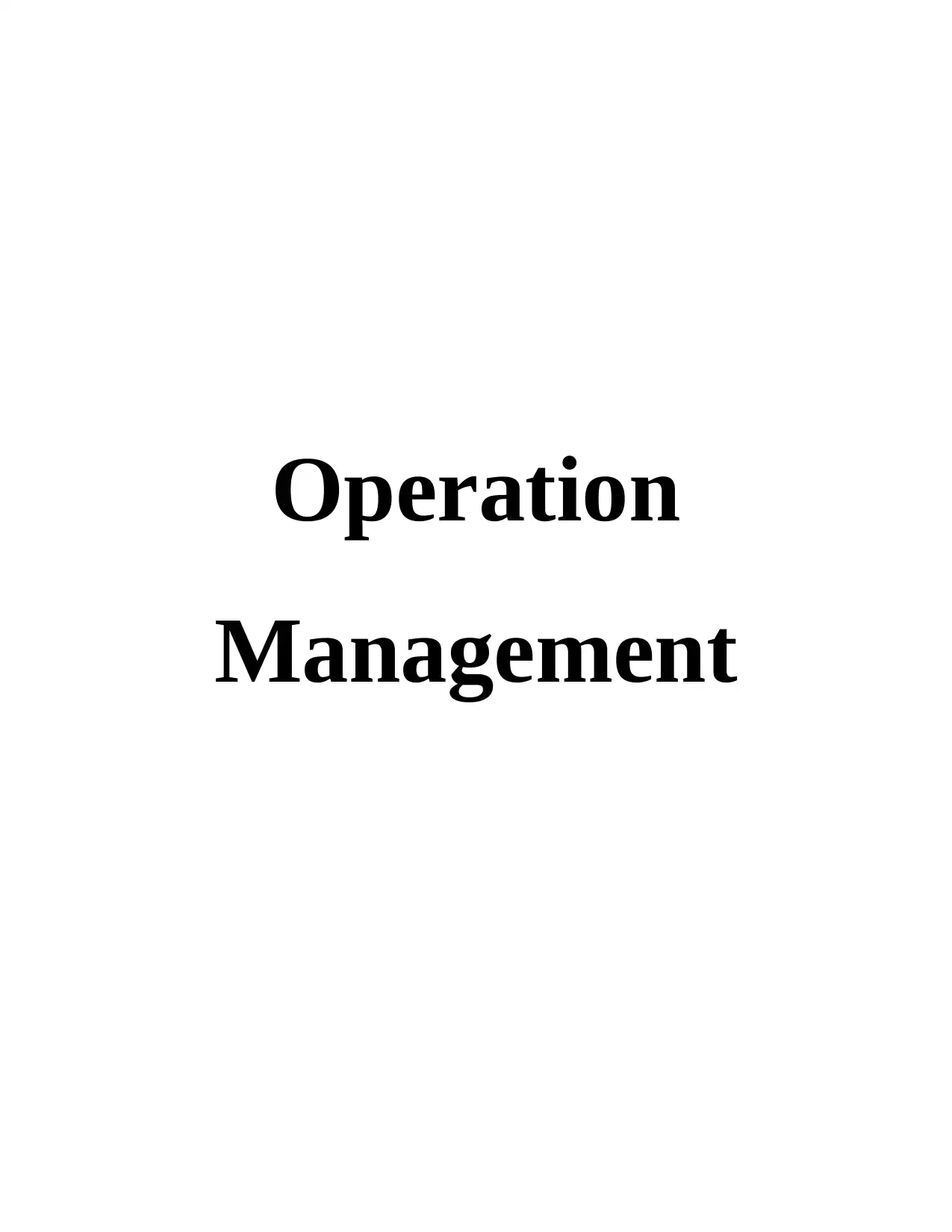
Operation
Management
Management
Secure Best Marks with AI Grader
Need help grading? Try our AI Grader for instant feedback on your assignments.
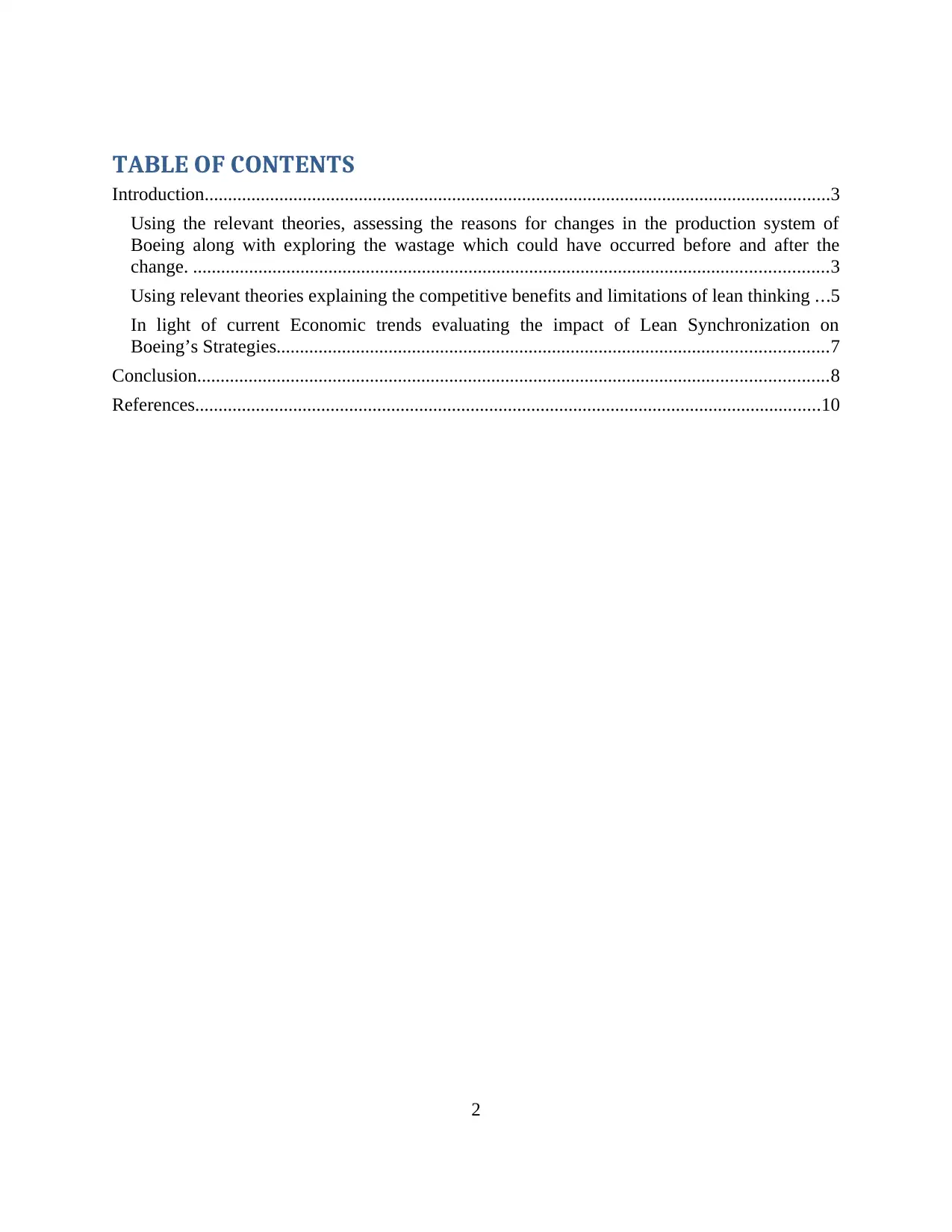
TABLE OF CONTENTS
Introduction......................................................................................................................................3
Using the relevant theories, assessing the reasons for changes in the production system of
Boeing along with exploring the wastage which could have occurred before and after the
change. ........................................................................................................................................3
Using relevant theories explaining the competitive benefits and limitations of lean thinking ...5
In light of current Economic trends evaluating the impact of Lean Synchronization on
Boeing’s Strategies......................................................................................................................7
Conclusion.......................................................................................................................................8
References......................................................................................................................................10
2
Introduction......................................................................................................................................3
Using the relevant theories, assessing the reasons for changes in the production system of
Boeing along with exploring the wastage which could have occurred before and after the
change. ........................................................................................................................................3
Using relevant theories explaining the competitive benefits and limitations of lean thinking ...5
In light of current Economic trends evaluating the impact of Lean Synchronization on
Boeing’s Strategies......................................................................................................................7
Conclusion.......................................................................................................................................8
References......................................................................................................................................10
2
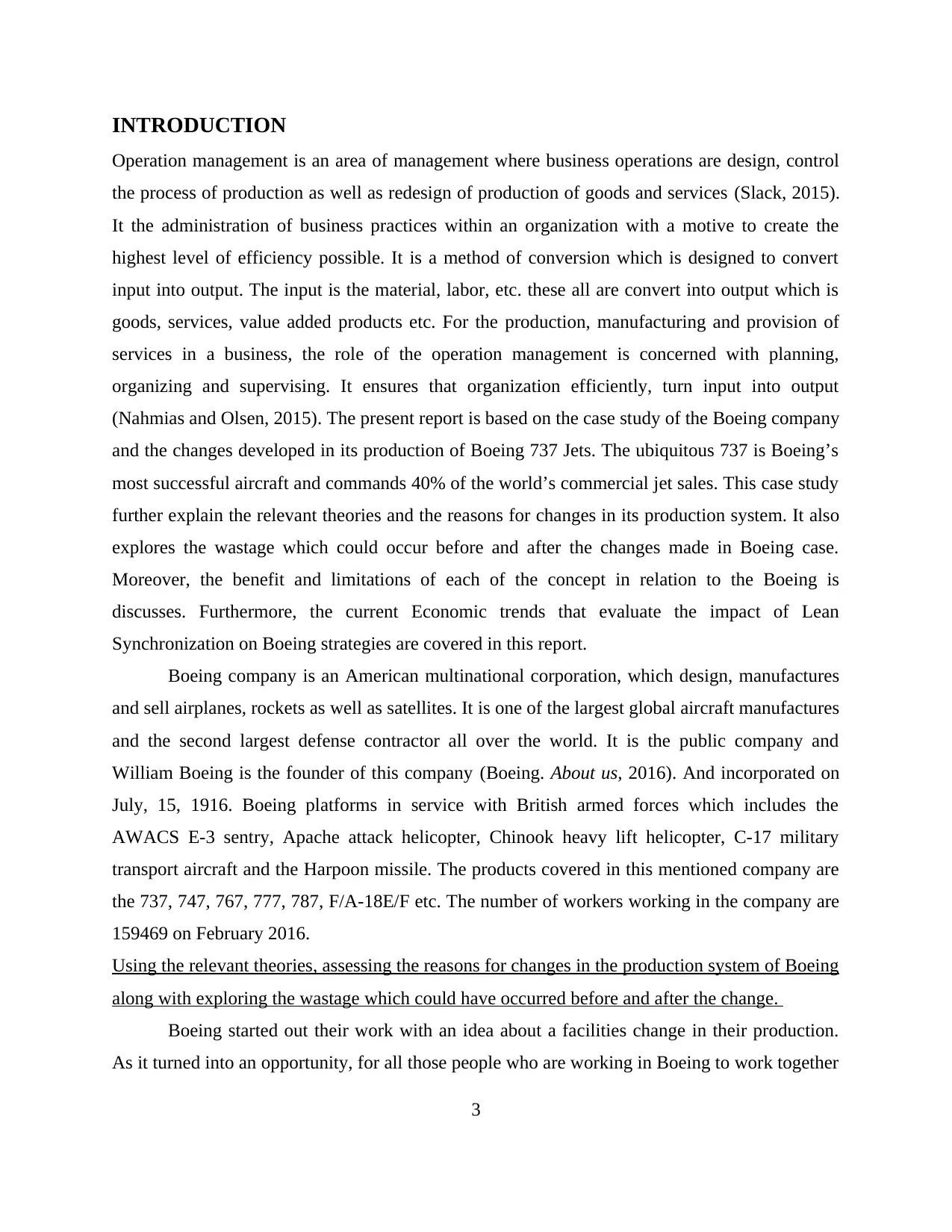
INTRODUCTION
Operation management is an area of management where business operations are design, control
the process of production as well as redesign of production of goods and services (Slack, 2015).
It the administration of business practices within an organization with a motive to create the
highest level of efficiency possible. It is a method of conversion which is designed to convert
input into output. The input is the material, labor, etc. these all are convert into output which is
goods, services, value added products etc. For the production, manufacturing and provision of
services in a business, the role of the operation management is concerned with planning,
organizing and supervising. It ensures that organization efficiently, turn input into output
(Nahmias and Olsen, 2015). The present report is based on the case study of the Boeing company
and the changes developed in its production of Boeing 737 Jets. The ubiquitous 737 is Boeing’s
most successful aircraft and commands 40% of the world’s commercial jet sales. This case study
further explain the relevant theories and the reasons for changes in its production system. It also
explores the wastage which could occur before and after the changes made in Boeing case.
Moreover, the benefit and limitations of each of the concept in relation to the Boeing is
discusses. Furthermore, the current Economic trends that evaluate the impact of Lean
Synchronization on Boeing strategies are covered in this report.
Boeing company is an American multinational corporation, which design, manufactures
and sell airplanes, rockets as well as satellites. It is one of the largest global aircraft manufactures
and the second largest defense contractor all over the world. It is the public company and
William Boeing is the founder of this company (Boeing. About us, 2016). And incorporated on
July, 15, 1916. Boeing platforms in service with British armed forces which includes the
AWACS E-3 sentry, Apache attack helicopter, Chinook heavy lift helicopter, C-17 military
transport aircraft and the Harpoon missile. The products covered in this mentioned company are
the 737, 747, 767, 777, 787, F/A-18E/F etc. The number of workers working in the company are
159469 on February 2016.
Using the relevant theories, assessing the reasons for changes in the production system of Boeing
along with exploring the wastage which could have occurred before and after the change.
Boeing started out their work with an idea about a facilities change in their production.
As it turned into an opportunity, for all those people who are working in Boeing to work together
3
Operation management is an area of management where business operations are design, control
the process of production as well as redesign of production of goods and services (Slack, 2015).
It the administration of business practices within an organization with a motive to create the
highest level of efficiency possible. It is a method of conversion which is designed to convert
input into output. The input is the material, labor, etc. these all are convert into output which is
goods, services, value added products etc. For the production, manufacturing and provision of
services in a business, the role of the operation management is concerned with planning,
organizing and supervising. It ensures that organization efficiently, turn input into output
(Nahmias and Olsen, 2015). The present report is based on the case study of the Boeing company
and the changes developed in its production of Boeing 737 Jets. The ubiquitous 737 is Boeing’s
most successful aircraft and commands 40% of the world’s commercial jet sales. This case study
further explain the relevant theories and the reasons for changes in its production system. It also
explores the wastage which could occur before and after the changes made in Boeing case.
Moreover, the benefit and limitations of each of the concept in relation to the Boeing is
discusses. Furthermore, the current Economic trends that evaluate the impact of Lean
Synchronization on Boeing strategies are covered in this report.
Boeing company is an American multinational corporation, which design, manufactures
and sell airplanes, rockets as well as satellites. It is one of the largest global aircraft manufactures
and the second largest defense contractor all over the world. It is the public company and
William Boeing is the founder of this company (Boeing. About us, 2016). And incorporated on
July, 15, 1916. Boeing platforms in service with British armed forces which includes the
AWACS E-3 sentry, Apache attack helicopter, Chinook heavy lift helicopter, C-17 military
transport aircraft and the Harpoon missile. The products covered in this mentioned company are
the 737, 747, 767, 777, 787, F/A-18E/F etc. The number of workers working in the company are
159469 on February 2016.
Using the relevant theories, assessing the reasons for changes in the production system of Boeing
along with exploring the wastage which could have occurred before and after the change.
Boeing started out their work with an idea about a facilities change in their production.
As it turned into an opportunity, for all those people who are working in Boeing to work together
3
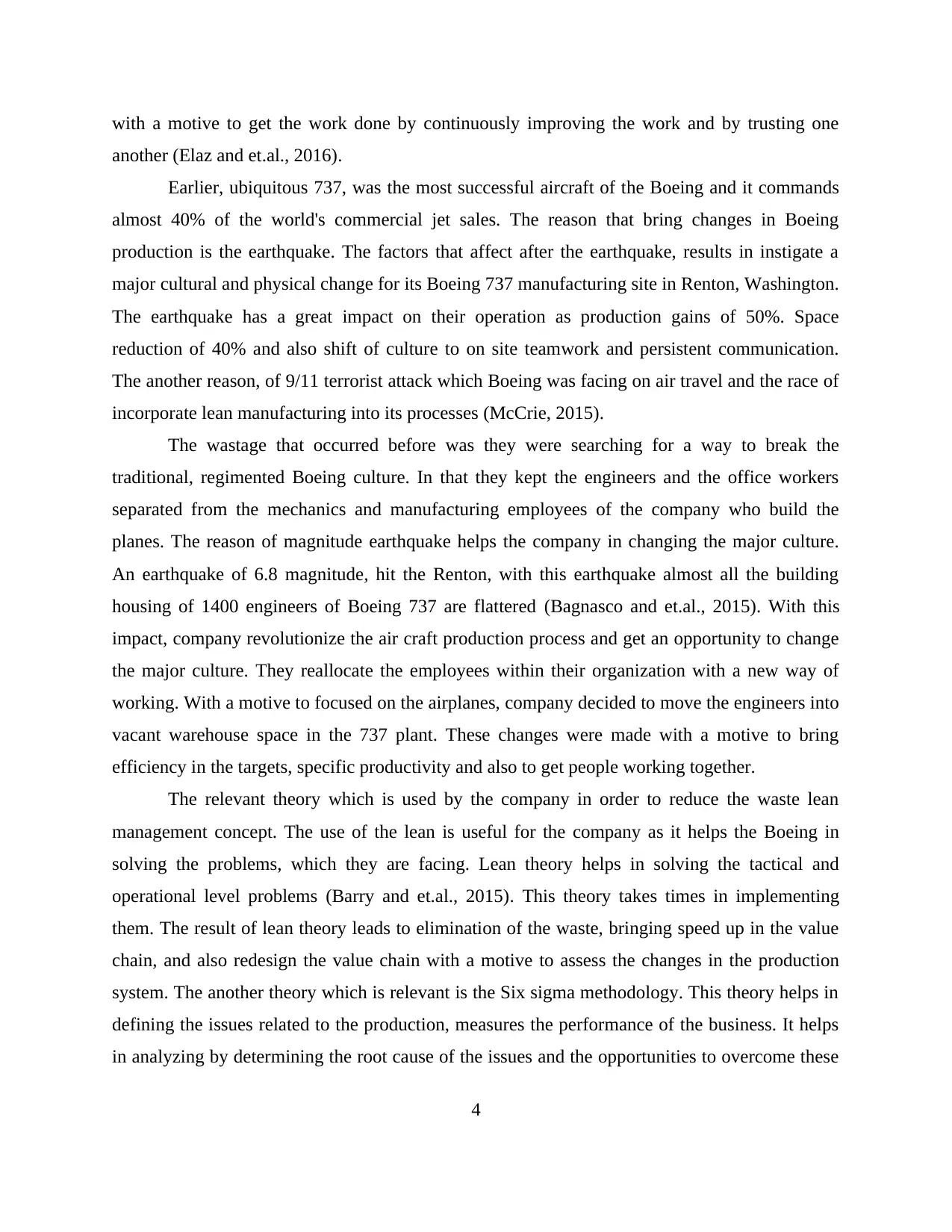
with a motive to get the work done by continuously improving the work and by trusting one
another (Elaz and et.al., 2016).
Earlier, ubiquitous 737, was the most successful aircraft of the Boeing and it commands
almost 40% of the world's commercial jet sales. The reason that bring changes in Boeing
production is the earthquake. The factors that affect after the earthquake, results in instigate a
major cultural and physical change for its Boeing 737 manufacturing site in Renton, Washington.
The earthquake has a great impact on their operation as production gains of 50%. Space
reduction of 40% and also shift of culture to on site teamwork and persistent communication.
The another reason, of 9/11 terrorist attack which Boeing was facing on air travel and the race of
incorporate lean manufacturing into its processes (McCrie, 2015).
The wastage that occurred before was they were searching for a way to break the
traditional, regimented Boeing culture. In that they kept the engineers and the office workers
separated from the mechanics and manufacturing employees of the company who build the
planes. The reason of magnitude earthquake helps the company in changing the major culture.
An earthquake of 6.8 magnitude, hit the Renton, with this earthquake almost all the building
housing of 1400 engineers of Boeing 737 are flattered (Bagnasco and et.al., 2015). With this
impact, company revolutionize the air craft production process and get an opportunity to change
the major culture. They reallocate the employees within their organization with a new way of
working. With a motive to focused on the airplanes, company decided to move the engineers into
vacant warehouse space in the 737 plant. These changes were made with a motive to bring
efficiency in the targets, specific productivity and also to get people working together.
The relevant theory which is used by the company in order to reduce the waste lean
management concept. The use of the lean is useful for the company as it helps the Boeing in
solving the problems, which they are facing. Lean theory helps in solving the tactical and
operational level problems (Barry and et.al., 2015). This theory takes times in implementing
them. The result of lean theory leads to elimination of the waste, bringing speed up in the value
chain, and also redesign the value chain with a motive to assess the changes in the production
system. The another theory which is relevant is the Six sigma methodology. This theory helps in
defining the issues related to the production, measures the performance of the business. It helps
in analyzing by determining the root cause of the issues and the opportunities to overcome these
4
another (Elaz and et.al., 2016).
Earlier, ubiquitous 737, was the most successful aircraft of the Boeing and it commands
almost 40% of the world's commercial jet sales. The reason that bring changes in Boeing
production is the earthquake. The factors that affect after the earthquake, results in instigate a
major cultural and physical change for its Boeing 737 manufacturing site in Renton, Washington.
The earthquake has a great impact on their operation as production gains of 50%. Space
reduction of 40% and also shift of culture to on site teamwork and persistent communication.
The another reason, of 9/11 terrorist attack which Boeing was facing on air travel and the race of
incorporate lean manufacturing into its processes (McCrie, 2015).
The wastage that occurred before was they were searching for a way to break the
traditional, regimented Boeing culture. In that they kept the engineers and the office workers
separated from the mechanics and manufacturing employees of the company who build the
planes. The reason of magnitude earthquake helps the company in changing the major culture.
An earthquake of 6.8 magnitude, hit the Renton, with this earthquake almost all the building
housing of 1400 engineers of Boeing 737 are flattered (Bagnasco and et.al., 2015). With this
impact, company revolutionize the air craft production process and get an opportunity to change
the major culture. They reallocate the employees within their organization with a new way of
working. With a motive to focused on the airplanes, company decided to move the engineers into
vacant warehouse space in the 737 plant. These changes were made with a motive to bring
efficiency in the targets, specific productivity and also to get people working together.
The relevant theory which is used by the company in order to reduce the waste lean
management concept. The use of the lean is useful for the company as it helps the Boeing in
solving the problems, which they are facing. Lean theory helps in solving the tactical and
operational level problems (Barry and et.al., 2015). This theory takes times in implementing
them. The result of lean theory leads to elimination of the waste, bringing speed up in the value
chain, and also redesign the value chain with a motive to assess the changes in the production
system. The another theory which is relevant is the Six sigma methodology. This theory helps in
defining the issues related to the production, measures the performance of the business. It helps
in analyzing by determining the root cause of the issues and the opportunities to overcome these
4
Secure Best Marks with AI Grader
Need help grading? Try our AI Grader for instant feedback on your assignments.
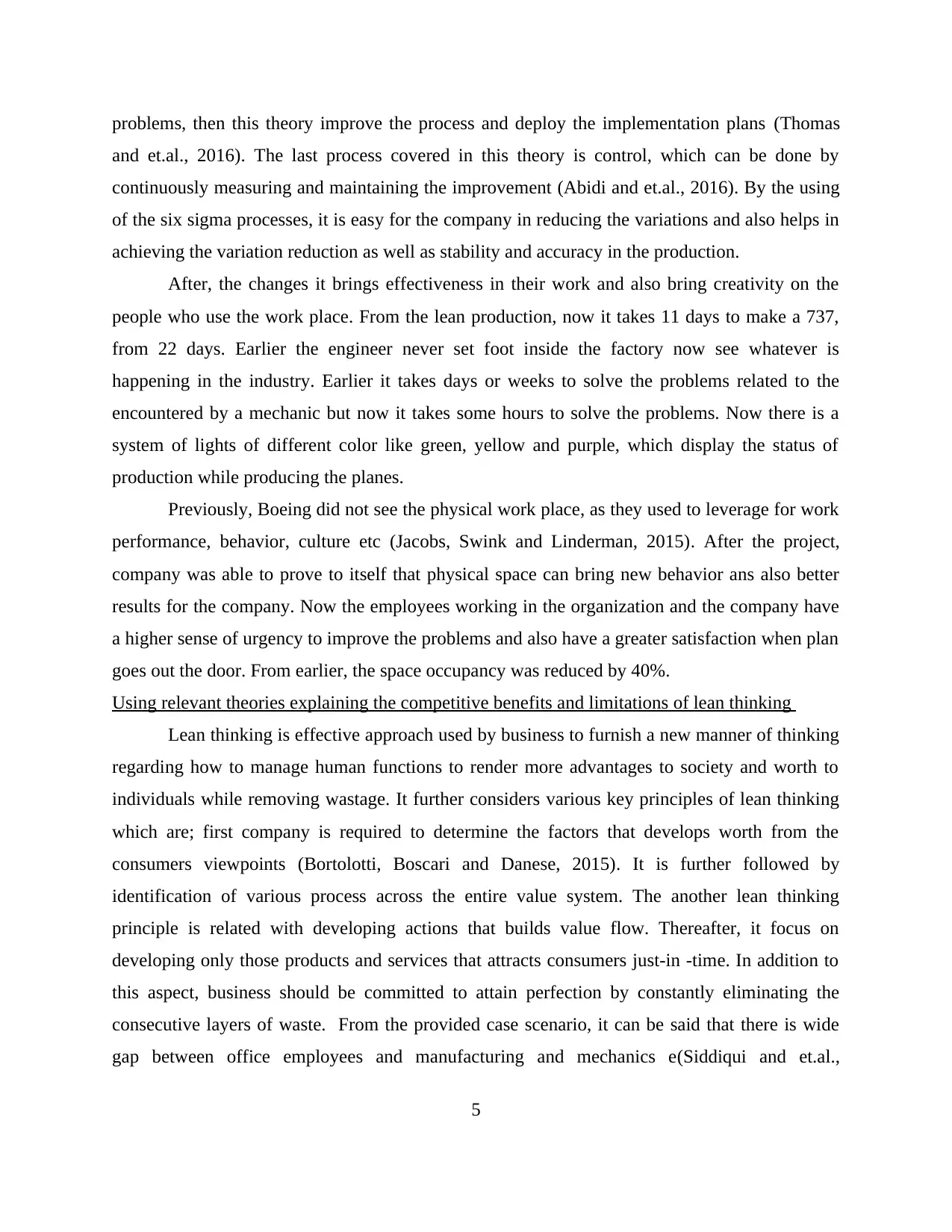
problems, then this theory improve the process and deploy the implementation plans (Thomas
and et.al., 2016). The last process covered in this theory is control, which can be done by
continuously measuring and maintaining the improvement (Abidi and et.al., 2016). By the using
of the six sigma processes, it is easy for the company in reducing the variations and also helps in
achieving the variation reduction as well as stability and accuracy in the production.
After, the changes it brings effectiveness in their work and also bring creativity on the
people who use the work place. From the lean production, now it takes 11 days to make a 737,
from 22 days. Earlier the engineer never set foot inside the factory now see whatever is
happening in the industry. Earlier it takes days or weeks to solve the problems related to the
encountered by a mechanic but now it takes some hours to solve the problems. Now there is a
system of lights of different color like green, yellow and purple, which display the status of
production while producing the planes.
Previously, Boeing did not see the physical work place, as they used to leverage for work
performance, behavior, culture etc (Jacobs, Swink and Linderman, 2015). After the project,
company was able to prove to itself that physical space can bring new behavior ans also better
results for the company. Now the employees working in the organization and the company have
a higher sense of urgency to improve the problems and also have a greater satisfaction when plan
goes out the door. From earlier, the space occupancy was reduced by 40%.
Using relevant theories explaining the competitive benefits and limitations of lean thinking
Lean thinking is effective approach used by business to furnish a new manner of thinking
regarding how to manage human functions to render more advantages to society and worth to
individuals while removing wastage. It further considers various key principles of lean thinking
which are; first company is required to determine the factors that develops worth from the
consumers viewpoints (Bortolotti, Boscari and Danese, 2015). It is further followed by
identification of various process across the entire value system. The another lean thinking
principle is related with developing actions that builds value flow. Thereafter, it focus on
developing only those products and services that attracts consumers just-in -time. In addition to
this aspect, business should be committed to attain perfection by constantly eliminating the
consecutive layers of waste. From the provided case scenario, it can be said that there is wide
gap between office employees and manufacturing and mechanics e(Siddiqui and et.al.,
5
and et.al., 2016). The last process covered in this theory is control, which can be done by
continuously measuring and maintaining the improvement (Abidi and et.al., 2016). By the using
of the six sigma processes, it is easy for the company in reducing the variations and also helps in
achieving the variation reduction as well as stability and accuracy in the production.
After, the changes it brings effectiveness in their work and also bring creativity on the
people who use the work place. From the lean production, now it takes 11 days to make a 737,
from 22 days. Earlier the engineer never set foot inside the factory now see whatever is
happening in the industry. Earlier it takes days or weeks to solve the problems related to the
encountered by a mechanic but now it takes some hours to solve the problems. Now there is a
system of lights of different color like green, yellow and purple, which display the status of
production while producing the planes.
Previously, Boeing did not see the physical work place, as they used to leverage for work
performance, behavior, culture etc (Jacobs, Swink and Linderman, 2015). After the project,
company was able to prove to itself that physical space can bring new behavior ans also better
results for the company. Now the employees working in the organization and the company have
a higher sense of urgency to improve the problems and also have a greater satisfaction when plan
goes out the door. From earlier, the space occupancy was reduced by 40%.
Using relevant theories explaining the competitive benefits and limitations of lean thinking
Lean thinking is effective approach used by business to furnish a new manner of thinking
regarding how to manage human functions to render more advantages to society and worth to
individuals while removing wastage. It further considers various key principles of lean thinking
which are; first company is required to determine the factors that develops worth from the
consumers viewpoints (Bortolotti, Boscari and Danese, 2015). It is further followed by
identification of various process across the entire value system. The another lean thinking
principle is related with developing actions that builds value flow. Thereafter, it focus on
developing only those products and services that attracts consumers just-in -time. In addition to
this aspect, business should be committed to attain perfection by constantly eliminating the
consecutive layers of waste. From the provided case scenario, it can be said that there is wide
gap between office employees and manufacturing and mechanics e(Siddiqui and et.al.,
5
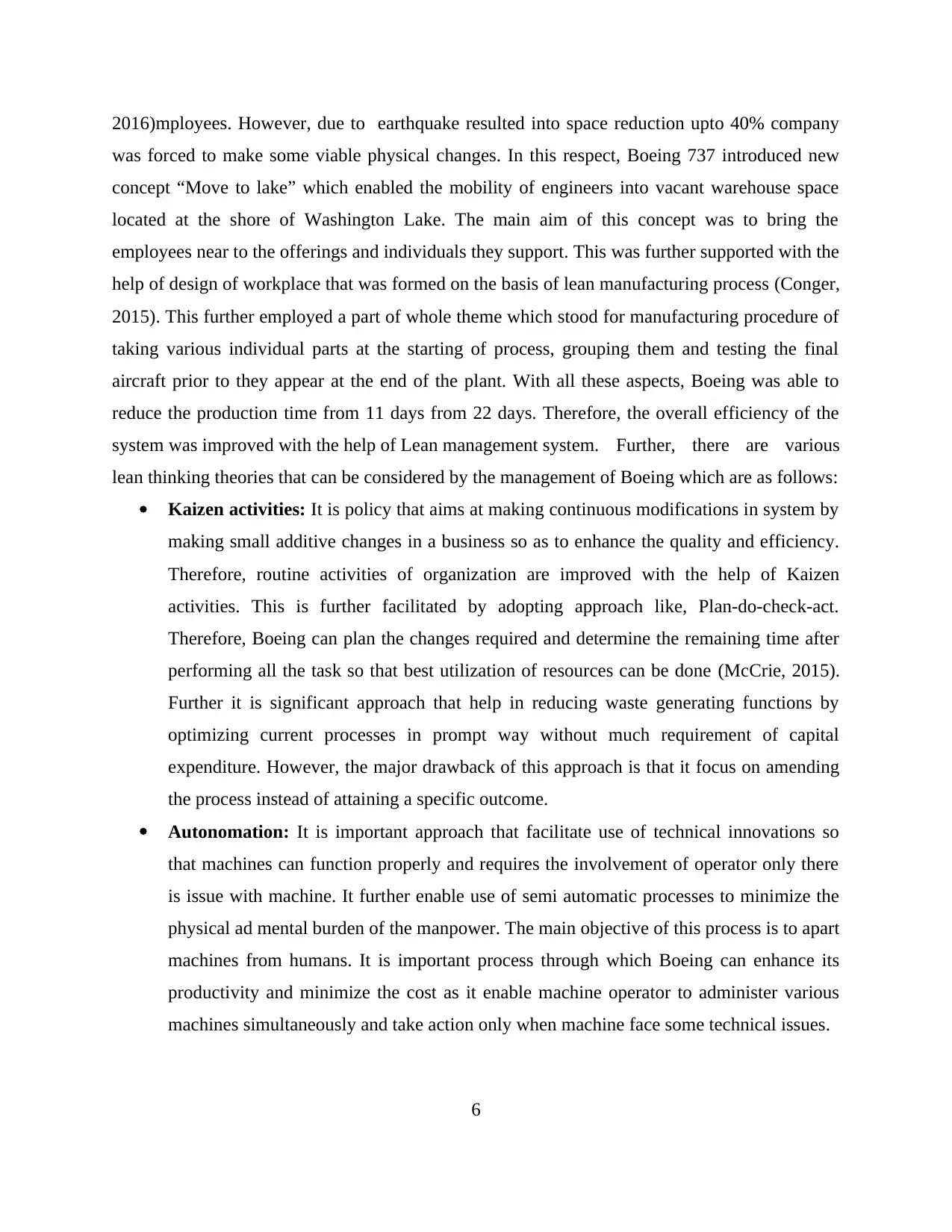
2016)mployees. However, due to earthquake resulted into space reduction upto 40% company
was forced to make some viable physical changes. In this respect, Boeing 737 introduced new
concept “Move to lake” which enabled the mobility of engineers into vacant warehouse space
located at the shore of Washington Lake. The main aim of this concept was to bring the
employees near to the offerings and individuals they support. This was further supported with the
help of design of workplace that was formed on the basis of lean manufacturing process (Conger,
2015). This further employed a part of whole theme which stood for manufacturing procedure of
taking various individual parts at the starting of process, grouping them and testing the final
aircraft prior to they appear at the end of the plant. With all these aspects, Boeing was able to
reduce the production time from 11 days from 22 days. Therefore, the overall efficiency of the
system was improved with the help of Lean management system. Further, there are various
lean thinking theories that can be considered by the management of Boeing which are as follows:
Kaizen activities: It is policy that aims at making continuous modifications in system by
making small additive changes in a business so as to enhance the quality and efficiency.
Therefore, routine activities of organization are improved with the help of Kaizen
activities. This is further facilitated by adopting approach like, Plan-do-check-act.
Therefore, Boeing can plan the changes required and determine the remaining time after
performing all the task so that best utilization of resources can be done (McCrie, 2015).
Further it is significant approach that help in reducing waste generating functions by
optimizing current processes in prompt way without much requirement of capital
expenditure. However, the major drawback of this approach is that it focus on amending
the process instead of attaining a specific outcome.
Autonomation: It is important approach that facilitate use of technical innovations so
that machines can function properly and requires the involvement of operator only there
is issue with machine. It further enable use of semi automatic processes to minimize the
physical ad mental burden of the manpower. The main objective of this process is to apart
machines from humans. It is important process through which Boeing can enhance its
productivity and minimize the cost as it enable machine operator to administer various
machines simultaneously and take action only when machine face some technical issues.
6
was forced to make some viable physical changes. In this respect, Boeing 737 introduced new
concept “Move to lake” which enabled the mobility of engineers into vacant warehouse space
located at the shore of Washington Lake. The main aim of this concept was to bring the
employees near to the offerings and individuals they support. This was further supported with the
help of design of workplace that was formed on the basis of lean manufacturing process (Conger,
2015). This further employed a part of whole theme which stood for manufacturing procedure of
taking various individual parts at the starting of process, grouping them and testing the final
aircraft prior to they appear at the end of the plant. With all these aspects, Boeing was able to
reduce the production time from 11 days from 22 days. Therefore, the overall efficiency of the
system was improved with the help of Lean management system. Further, there are various
lean thinking theories that can be considered by the management of Boeing which are as follows:
Kaizen activities: It is policy that aims at making continuous modifications in system by
making small additive changes in a business so as to enhance the quality and efficiency.
Therefore, routine activities of organization are improved with the help of Kaizen
activities. This is further facilitated by adopting approach like, Plan-do-check-act.
Therefore, Boeing can plan the changes required and determine the remaining time after
performing all the task so that best utilization of resources can be done (McCrie, 2015).
Further it is significant approach that help in reducing waste generating functions by
optimizing current processes in prompt way without much requirement of capital
expenditure. However, the major drawback of this approach is that it focus on amending
the process instead of attaining a specific outcome.
Autonomation: It is important approach that facilitate use of technical innovations so
that machines can function properly and requires the involvement of operator only there
is issue with machine. It further enable use of semi automatic processes to minimize the
physical ad mental burden of the manpower. The main objective of this process is to apart
machines from humans. It is important process through which Boeing can enhance its
productivity and minimize the cost as it enable machine operator to administer various
machines simultaneously and take action only when machine face some technical issues.
6
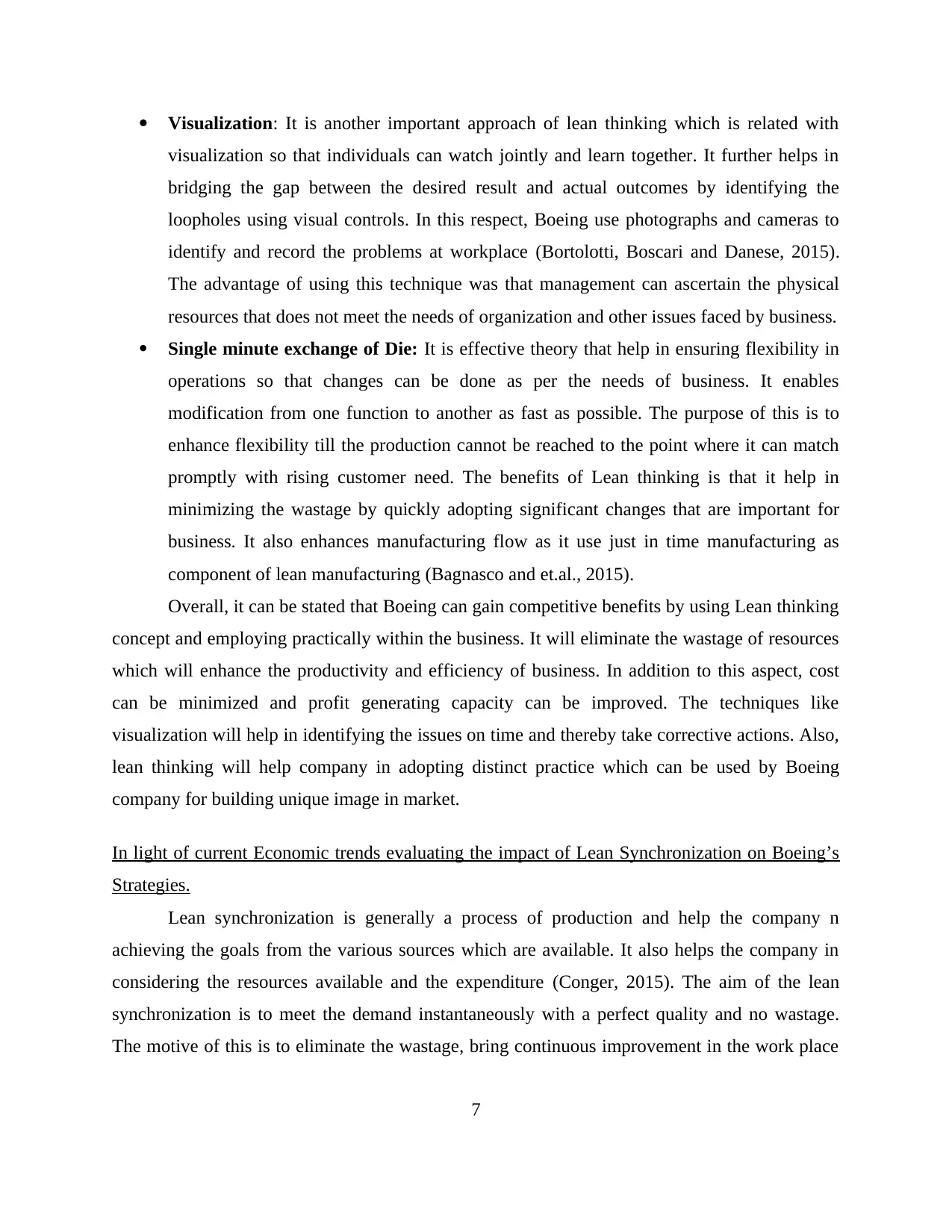
Visualization: It is another important approach of lean thinking which is related with
visualization so that individuals can watch jointly and learn together. It further helps in
bridging the gap between the desired result and actual outcomes by identifying the
loopholes using visual controls. In this respect, Boeing use photographs and cameras to
identify and record the problems at workplace (Bortolotti, Boscari and Danese, 2015).
The advantage of using this technique was that management can ascertain the physical
resources that does not meet the needs of organization and other issues faced by business.
Single minute exchange of Die: It is effective theory that help in ensuring flexibility in
operations so that changes can be done as per the needs of business. It enables
modification from one function to another as fast as possible. The purpose of this is to
enhance flexibility till the production cannot be reached to the point where it can match
promptly with rising customer need. The benefits of Lean thinking is that it help in
minimizing the wastage by quickly adopting significant changes that are important for
business. It also enhances manufacturing flow as it use just in time manufacturing as
component of lean manufacturing (Bagnasco and et.al., 2015).
Overall, it can be stated that Boeing can gain competitive benefits by using Lean thinking
concept and employing practically within the business. It will eliminate the wastage of resources
which will enhance the productivity and efficiency of business. In addition to this aspect, cost
can be minimized and profit generating capacity can be improved. The techniques like
visualization will help in identifying the issues on time and thereby take corrective actions. Also,
lean thinking will help company in adopting distinct practice which can be used by Boeing
company for building unique image in market.
In light of current Economic trends evaluating the impact of Lean Synchronization on Boeing’s
Strategies.
Lean synchronization is generally a process of production and help the company n
achieving the goals from the various sources which are available. It also helps the company in
considering the resources available and the expenditure (Conger, 2015). The aim of the lean
synchronization is to meet the demand instantaneously with a perfect quality and no wastage.
The motive of this is to eliminate the wastage, bring continuous improvement in the work place
7
visualization so that individuals can watch jointly and learn together. It further helps in
bridging the gap between the desired result and actual outcomes by identifying the
loopholes using visual controls. In this respect, Boeing use photographs and cameras to
identify and record the problems at workplace (Bortolotti, Boscari and Danese, 2015).
The advantage of using this technique was that management can ascertain the physical
resources that does not meet the needs of organization and other issues faced by business.
Single minute exchange of Die: It is effective theory that help in ensuring flexibility in
operations so that changes can be done as per the needs of business. It enables
modification from one function to another as fast as possible. The purpose of this is to
enhance flexibility till the production cannot be reached to the point where it can match
promptly with rising customer need. The benefits of Lean thinking is that it help in
minimizing the wastage by quickly adopting significant changes that are important for
business. It also enhances manufacturing flow as it use just in time manufacturing as
component of lean manufacturing (Bagnasco and et.al., 2015).
Overall, it can be stated that Boeing can gain competitive benefits by using Lean thinking
concept and employing practically within the business. It will eliminate the wastage of resources
which will enhance the productivity and efficiency of business. In addition to this aspect, cost
can be minimized and profit generating capacity can be improved. The techniques like
visualization will help in identifying the issues on time and thereby take corrective actions. Also,
lean thinking will help company in adopting distinct practice which can be used by Boeing
company for building unique image in market.
In light of current Economic trends evaluating the impact of Lean Synchronization on Boeing’s
Strategies.
Lean synchronization is generally a process of production and help the company n
achieving the goals from the various sources which are available. It also helps the company in
considering the resources available and the expenditure (Conger, 2015). The aim of the lean
synchronization is to meet the demand instantaneously with a perfect quality and no wastage.
The motive of this is to eliminate the wastage, bring continuous improvement in the work place
7
Paraphrase This Document
Need a fresh take? Get an instant paraphrase of this document with our AI Paraphraser
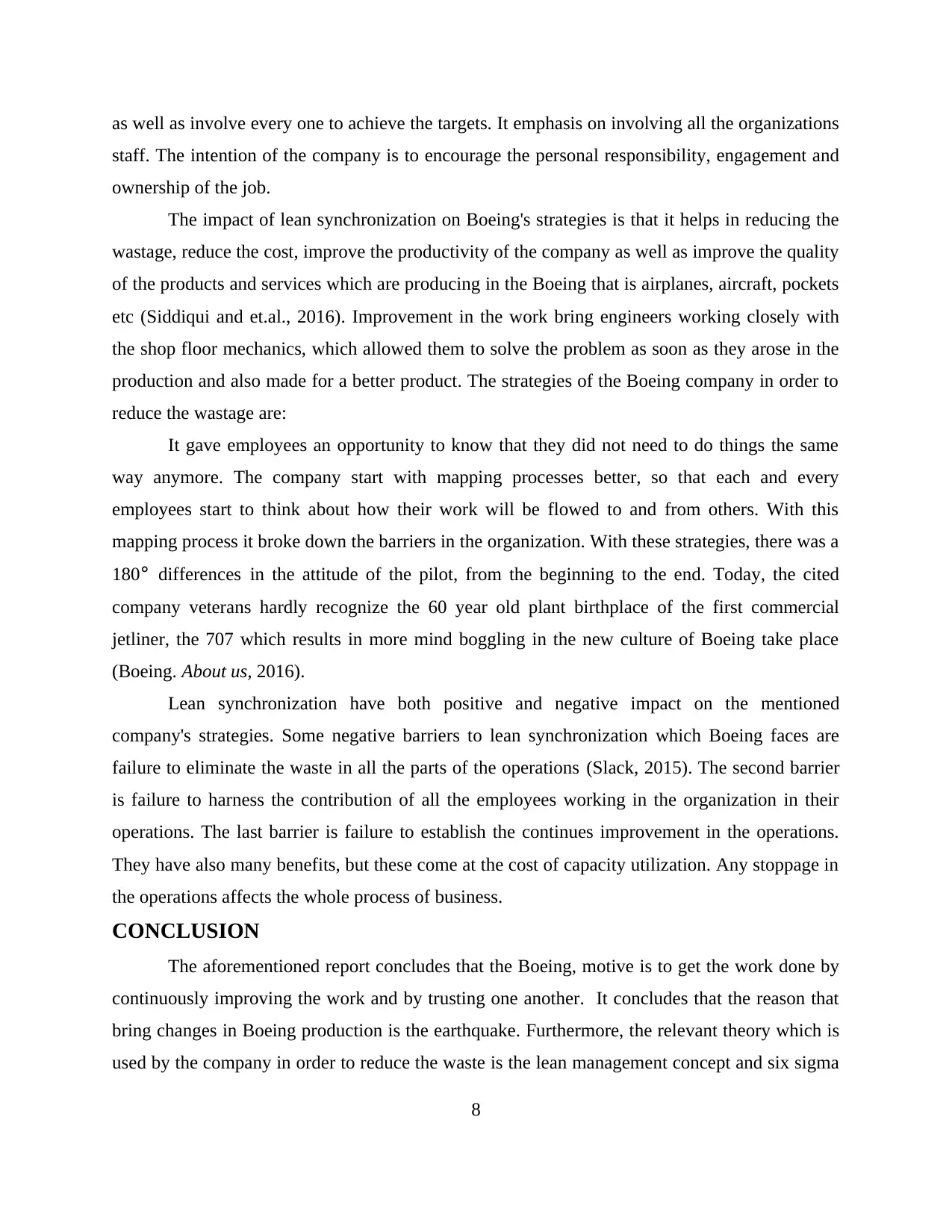
as well as involve every one to achieve the targets. It emphasis on involving all the organizations
staff. The intention of the company is to encourage the personal responsibility, engagement and
ownership of the job.
The impact of lean synchronization on Boeing's strategies is that it helps in reducing the
wastage, reduce the cost, improve the productivity of the company as well as improve the quality
of the products and services which are producing in the Boeing that is airplanes, aircraft, pockets
etc (Siddiqui and et.al., 2016). Improvement in the work bring engineers working closely with
the shop floor mechanics, which allowed them to solve the problem as soon as they arose in the
production and also made for a better product. The strategies of the Boeing company in order to
reduce the wastage are:
It gave employees an opportunity to know that they did not need to do things the same
way anymore. The company start with mapping processes better, so that each and every
employees start to think about how their work will be flowed to and from others. With this
mapping process it broke down the barriers in the organization. With these strategies, there was a
180° differences in the attitude of the pilot, from the beginning to the end. Today, the cited
company veterans hardly recognize the 60 year old plant birthplace of the first commercial
jetliner, the 707 which results in more mind boggling in the new culture of Boeing take place
(Boeing. About us, 2016).
Lean synchronization have both positive and negative impact on the mentioned
company's strategies. Some negative barriers to lean synchronization which Boeing faces are
failure to eliminate the waste in all the parts of the operations (Slack, 2015). The second barrier
is failure to harness the contribution of all the employees working in the organization in their
operations. The last barrier is failure to establish the continues improvement in the operations.
They have also many benefits, but these come at the cost of capacity utilization. Any stoppage in
the operations affects the whole process of business.
CONCLUSION
The aforementioned report concludes that the Boeing, motive is to get the work done by
continuously improving the work and by trusting one another. It concludes that the reason that
bring changes in Boeing production is the earthquake. Furthermore, the relevant theory which is
used by the company in order to reduce the waste is the lean management concept and six sigma
8
staff. The intention of the company is to encourage the personal responsibility, engagement and
ownership of the job.
The impact of lean synchronization on Boeing's strategies is that it helps in reducing the
wastage, reduce the cost, improve the productivity of the company as well as improve the quality
of the products and services which are producing in the Boeing that is airplanes, aircraft, pockets
etc (Siddiqui and et.al., 2016). Improvement in the work bring engineers working closely with
the shop floor mechanics, which allowed them to solve the problem as soon as they arose in the
production and also made for a better product. The strategies of the Boeing company in order to
reduce the wastage are:
It gave employees an opportunity to know that they did not need to do things the same
way anymore. The company start with mapping processes better, so that each and every
employees start to think about how their work will be flowed to and from others. With this
mapping process it broke down the barriers in the organization. With these strategies, there was a
180° differences in the attitude of the pilot, from the beginning to the end. Today, the cited
company veterans hardly recognize the 60 year old plant birthplace of the first commercial
jetliner, the 707 which results in more mind boggling in the new culture of Boeing take place
(Boeing. About us, 2016).
Lean synchronization have both positive and negative impact on the mentioned
company's strategies. Some negative barriers to lean synchronization which Boeing faces are
failure to eliminate the waste in all the parts of the operations (Slack, 2015). The second barrier
is failure to harness the contribution of all the employees working in the organization in their
operations. The last barrier is failure to establish the continues improvement in the operations.
They have also many benefits, but these come at the cost of capacity utilization. Any stoppage in
the operations affects the whole process of business.
CONCLUSION
The aforementioned report concludes that the Boeing, motive is to get the work done by
continuously improving the work and by trusting one another. It concludes that the reason that
bring changes in Boeing production is the earthquake. Furthermore, the relevant theory which is
used by the company in order to reduce the waste is the lean management concept and six sigma
8
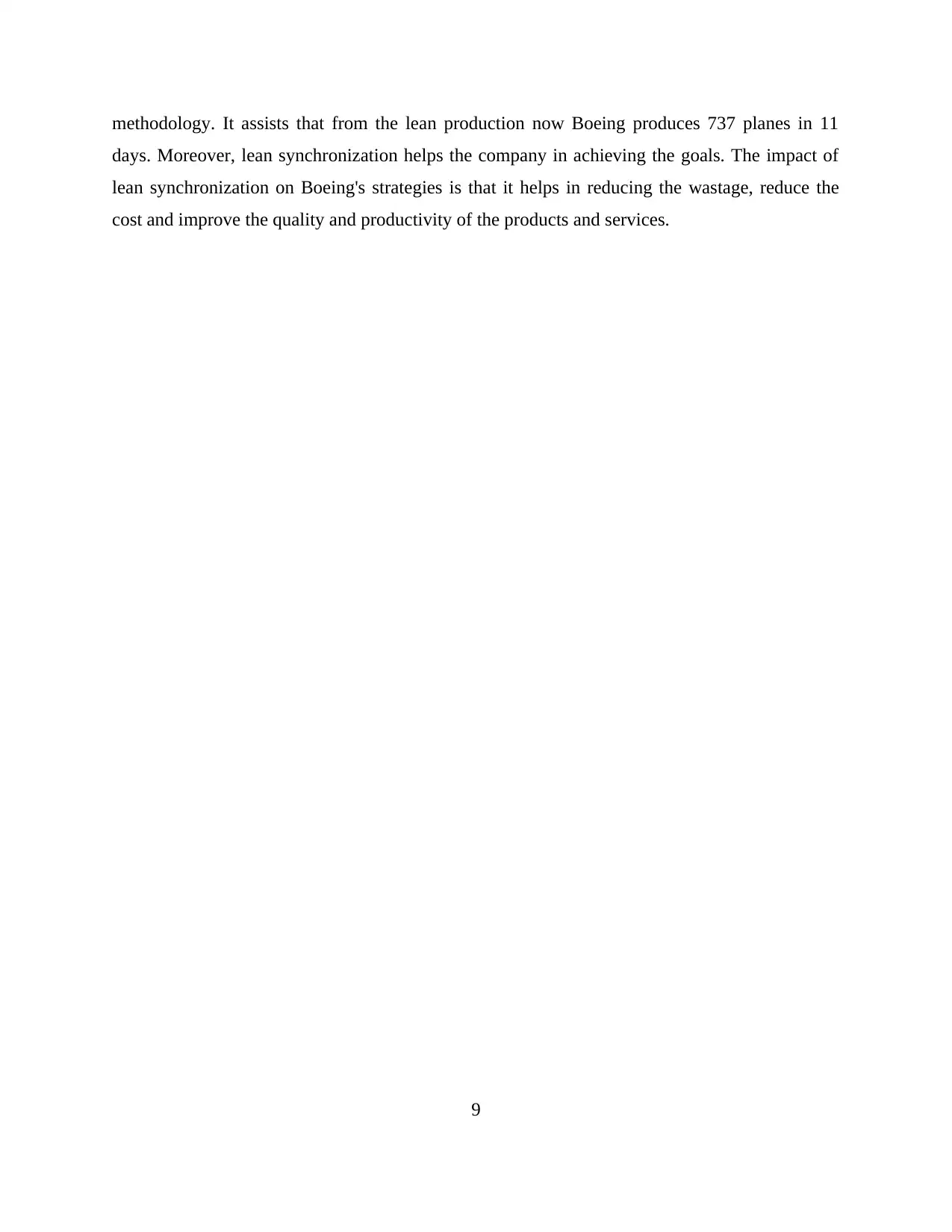
methodology. It assists that from the lean production now Boeing produces 737 planes in 11
days. Moreover, lean synchronization helps the company in achieving the goals. The impact of
lean synchronization on Boeing's strategies is that it helps in reducing the wastage, reduce the
cost and improve the quality and productivity of the products and services.
9
days. Moreover, lean synchronization helps the company in achieving the goals. The impact of
lean synchronization on Boeing's strategies is that it helps in reducing the wastage, reduce the
cost and improve the quality and productivity of the products and services.
9
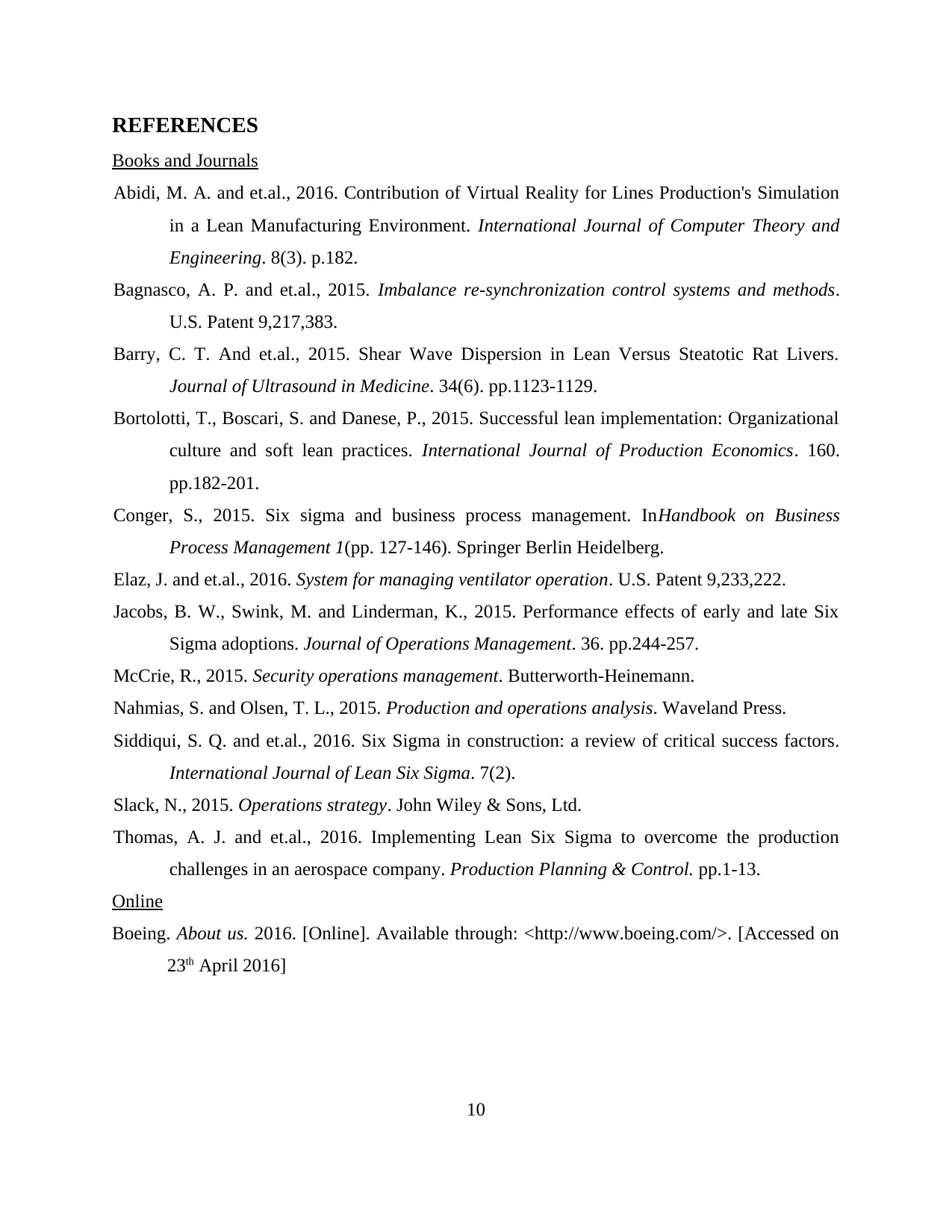
REFERENCES
Books and Journals
Abidi, M. A. and et.al., 2016. Contribution of Virtual Reality for Lines Production's Simulation
in a Lean Manufacturing Environment. International Journal of Computer Theory and
Engineering. 8(3). p.182.
Bagnasco, A. P. and et.al., 2015. Imbalance re-synchronization control systems and methods.
U.S. Patent 9,217,383.
Barry, C. T. And et.al., 2015. Shear Wave Dispersion in Lean Versus Steatotic Rat Livers.
Journal of Ultrasound in Medicine. 34(6). pp.1123-1129.
Bortolotti, T., Boscari, S. and Danese, P., 2015. Successful lean implementation: Organizational
culture and soft lean practices. International Journal of Production Economics. 160.
pp.182-201.
Conger, S., 2015. Six sigma and business process management. InHandbook on Business
Process Management 1(pp. 127-146). Springer Berlin Heidelberg.
Elaz, J. and et.al., 2016. System for managing ventilator operation. U.S. Patent 9,233,222.
Jacobs, B. W., Swink, M. and Linderman, K., 2015. Performance effects of early and late Six
Sigma adoptions. Journal of Operations Management. 36. pp.244-257.
McCrie, R., 2015. Security operations management. Butterworth-Heinemann.
Nahmias, S. and Olsen, T. L., 2015. Production and operations analysis. Waveland Press.
Siddiqui, S. Q. and et.al., 2016. Six Sigma in construction: a review of critical success factors.
International Journal of Lean Six Sigma. 7(2).
Slack, N., 2015. Operations strategy. John Wiley & Sons, Ltd.
Thomas, A. J. and et.al., 2016. Implementing Lean Six Sigma to overcome the production
challenges in an aerospace company. Production Planning & Control. pp.1-13.
Online
Boeing. About us. 2016. [Online]. Available through: <http://www.boeing.com/>. [Accessed on
23th April 2016]
10
Books and Journals
Abidi, M. A. and et.al., 2016. Contribution of Virtual Reality for Lines Production's Simulation
in a Lean Manufacturing Environment. International Journal of Computer Theory and
Engineering. 8(3). p.182.
Bagnasco, A. P. and et.al., 2015. Imbalance re-synchronization control systems and methods.
U.S. Patent 9,217,383.
Barry, C. T. And et.al., 2015. Shear Wave Dispersion in Lean Versus Steatotic Rat Livers.
Journal of Ultrasound in Medicine. 34(6). pp.1123-1129.
Bortolotti, T., Boscari, S. and Danese, P., 2015. Successful lean implementation: Organizational
culture and soft lean practices. International Journal of Production Economics. 160.
pp.182-201.
Conger, S., 2015. Six sigma and business process management. InHandbook on Business
Process Management 1(pp. 127-146). Springer Berlin Heidelberg.
Elaz, J. and et.al., 2016. System for managing ventilator operation. U.S. Patent 9,233,222.
Jacobs, B. W., Swink, M. and Linderman, K., 2015. Performance effects of early and late Six
Sigma adoptions. Journal of Operations Management. 36. pp.244-257.
McCrie, R., 2015. Security operations management. Butterworth-Heinemann.
Nahmias, S. and Olsen, T. L., 2015. Production and operations analysis. Waveland Press.
Siddiqui, S. Q. and et.al., 2016. Six Sigma in construction: a review of critical success factors.
International Journal of Lean Six Sigma. 7(2).
Slack, N., 2015. Operations strategy. John Wiley & Sons, Ltd.
Thomas, A. J. and et.al., 2016. Implementing Lean Six Sigma to overcome the production
challenges in an aerospace company. Production Planning & Control. pp.1-13.
Online
Boeing. About us. 2016. [Online]. Available through: <http://www.boeing.com/>. [Accessed on
23th April 2016]
10
Secure Best Marks with AI Grader
Need help grading? Try our AI Grader for instant feedback on your assignments.
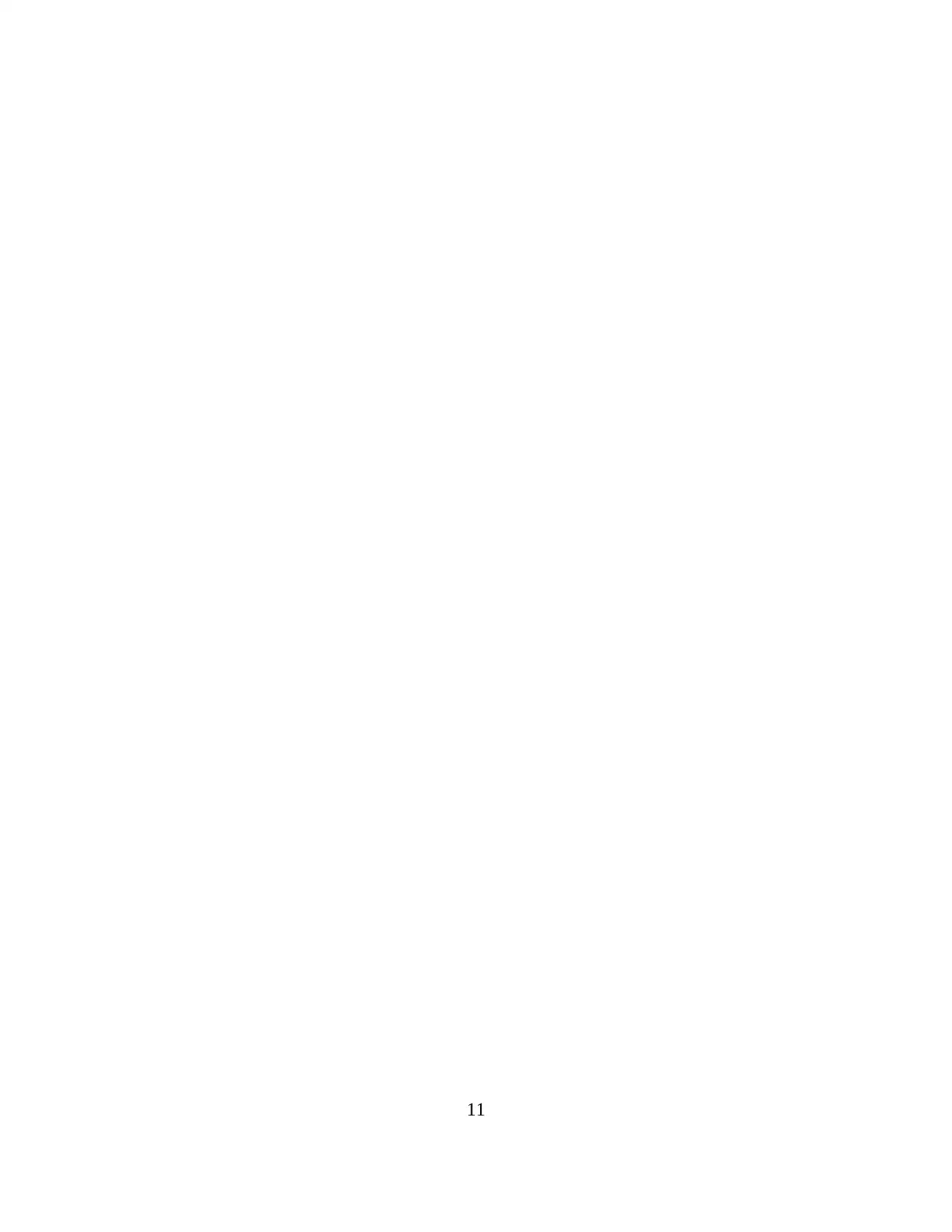
11
1 out of 11
Related Documents

Your All-in-One AI-Powered Toolkit for Academic Success.
+13062052269
info@desklib.com
Available 24*7 on WhatsApp / Email
Unlock your academic potential
© 2024 | Zucol Services PVT LTD | All rights reserved.