Case Study Analysis: Boeing's Production, Lean Thinking, and Change
VerifiedAdded on 2020/02/05
|12
|3941
|1229
Case Study
AI Summary
This case study examines Boeing's transformation of its production system, focusing on the implementation of lean thinking and its impact on competitive advantage. The study begins by evaluating the changes in Boeing's production processes, highlighting the shift away from a traditional rigid culture to a more efficient and collaborative environment. The 'Move to the Lake' strategy, which involved relocating engineers and office workers to the manufacturing plant floor, is analyzed as a key driver of cultural change and improved communication. The case study explores the benefits of lean thinking, including waste reduction, improved competency levels, and the incorporation of new ideas. It emphasizes the importance of lean synchronization in maintaining low costs and attracting customers. The analysis also discusses how Boeing fostered a positive work culture, improved employee motivation, and enhanced collaboration, ultimately leading to increased productivity, quality, and competitiveness. The study concludes by underscoring the significance of continuous improvement and trust within the organization to achieve its goals.
Contribute Materials
Your contribution can guide someone’s learning journey. Share your
documents today.
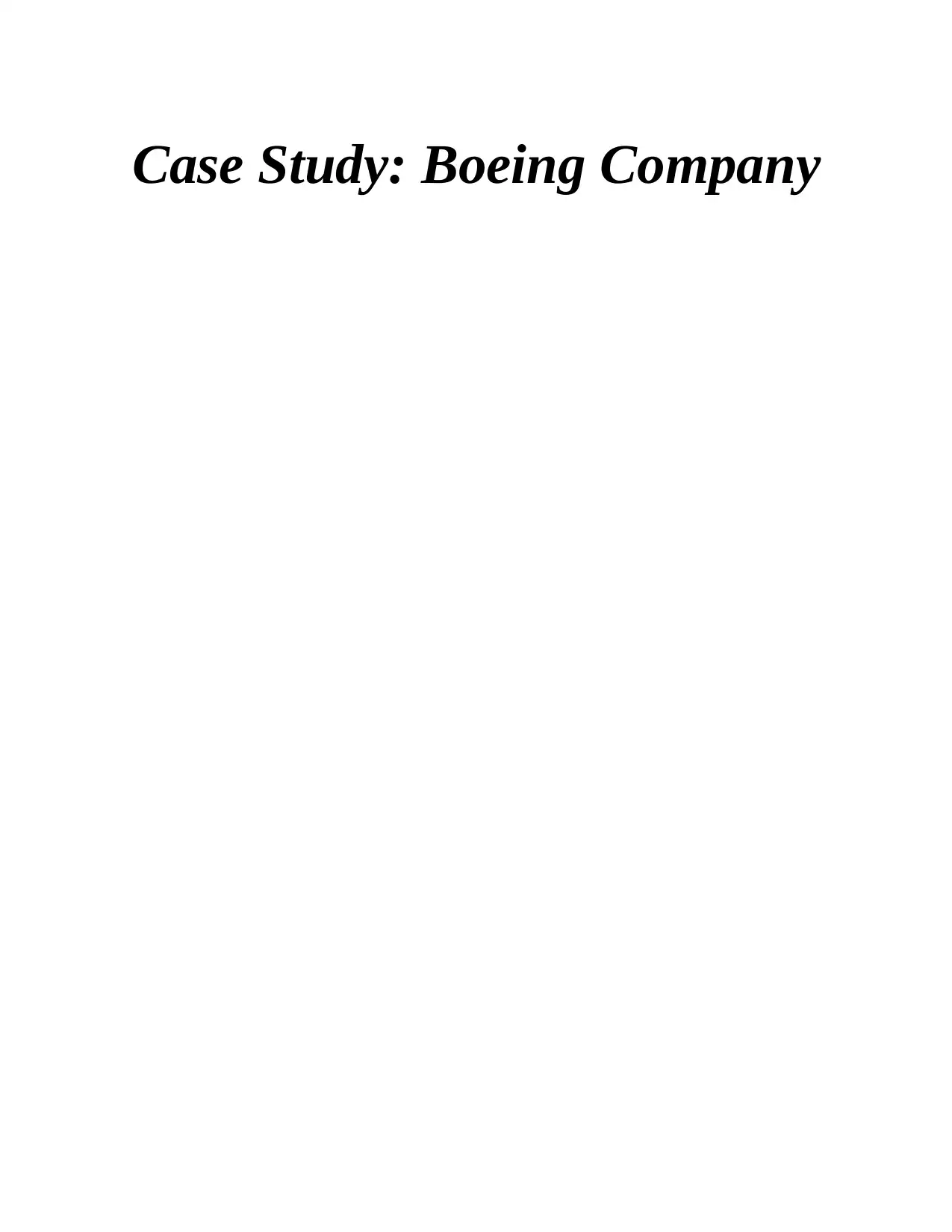
Case Study: Boeing Company
Secure Best Marks with AI Grader
Need help grading? Try our AI Grader for instant feedback on your assignments.
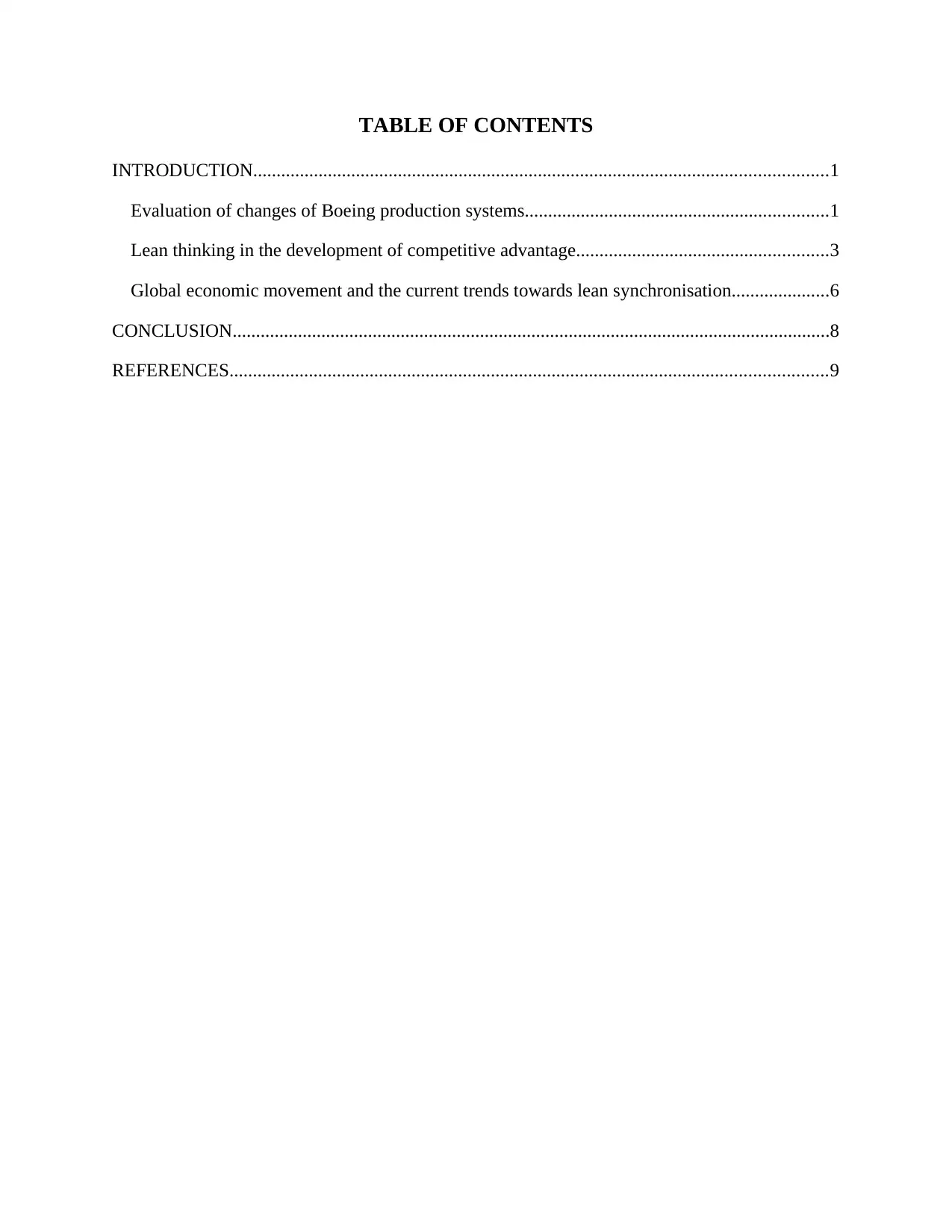
TABLE OF CONTENTS
INTRODUCTION...........................................................................................................................1
Evaluation of changes of Boeing production systems.................................................................1
Lean thinking in the development of competitive advantage......................................................3
Global economic movement and the current trends towards lean synchronisation.....................6
CONCLUSION................................................................................................................................8
REFERENCES................................................................................................................................9
INTRODUCTION...........................................................................................................................1
Evaluation of changes of Boeing production systems.................................................................1
Lean thinking in the development of competitive advantage......................................................3
Global economic movement and the current trends towards lean synchronisation.....................6
CONCLUSION................................................................................................................................8
REFERENCES................................................................................................................................9
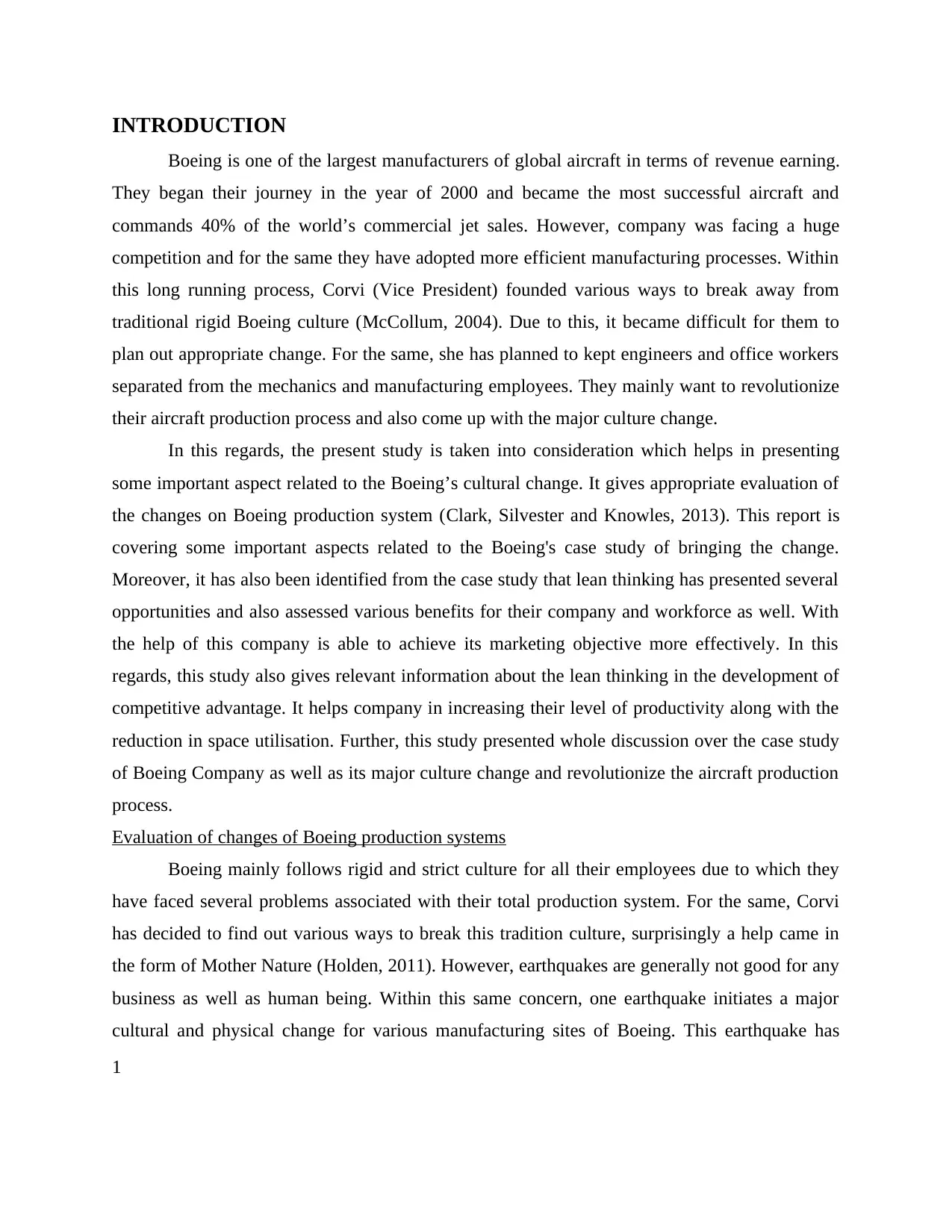
INTRODUCTION
Boeing is one of the largest manufacturers of global aircraft in terms of revenue earning.
They began their journey in the year of 2000 and became the most successful aircraft and
commands 40% of the world’s commercial jet sales. However, company was facing a huge
competition and for the same they have adopted more efficient manufacturing processes. Within
this long running process, Corvi (Vice President) founded various ways to break away from
traditional rigid Boeing culture (McCollum, 2004). Due to this, it became difficult for them to
plan out appropriate change. For the same, she has planned to kept engineers and office workers
separated from the mechanics and manufacturing employees. They mainly want to revolutionize
their aircraft production process and also come up with the major culture change.
In this regards, the present study is taken into consideration which helps in presenting
some important aspect related to the Boeing’s cultural change. It gives appropriate evaluation of
the changes on Boeing production system (Clark, Silvester and Knowles, 2013). This report is
covering some important aspects related to the Boeing's case study of bringing the change.
Moreover, it has also been identified from the case study that lean thinking has presented several
opportunities and also assessed various benefits for their company and workforce as well. With
the help of this company is able to achieve its marketing objective more effectively. In this
regards, this study also gives relevant information about the lean thinking in the development of
competitive advantage. It helps company in increasing their level of productivity along with the
reduction in space utilisation. Further, this study presented whole discussion over the case study
of Boeing Company as well as its major culture change and revolutionize the aircraft production
process.
Evaluation of changes of Boeing production systems
Boeing mainly follows rigid and strict culture for all their employees due to which they
have faced several problems associated with their total production system. For the same, Corvi
has decided to find out various ways to break this tradition culture, surprisingly a help came in
the form of Mother Nature (Holden, 2011). However, earthquakes are generally not good for any
business as well as human being. Within this same concern, one earthquake initiates a major
cultural and physical change for various manufacturing sites of Boeing. This earthquake has
1
Boeing is one of the largest manufacturers of global aircraft in terms of revenue earning.
They began their journey in the year of 2000 and became the most successful aircraft and
commands 40% of the world’s commercial jet sales. However, company was facing a huge
competition and for the same they have adopted more efficient manufacturing processes. Within
this long running process, Corvi (Vice President) founded various ways to break away from
traditional rigid Boeing culture (McCollum, 2004). Due to this, it became difficult for them to
plan out appropriate change. For the same, she has planned to kept engineers and office workers
separated from the mechanics and manufacturing employees. They mainly want to revolutionize
their aircraft production process and also come up with the major culture change.
In this regards, the present study is taken into consideration which helps in presenting
some important aspect related to the Boeing’s cultural change. It gives appropriate evaluation of
the changes on Boeing production system (Clark, Silvester and Knowles, 2013). This report is
covering some important aspects related to the Boeing's case study of bringing the change.
Moreover, it has also been identified from the case study that lean thinking has presented several
opportunities and also assessed various benefits for their company and workforce as well. With
the help of this company is able to achieve its marketing objective more effectively. In this
regards, this study also gives relevant information about the lean thinking in the development of
competitive advantage. It helps company in increasing their level of productivity along with the
reduction in space utilisation. Further, this study presented whole discussion over the case study
of Boeing Company as well as its major culture change and revolutionize the aircraft production
process.
Evaluation of changes of Boeing production systems
Boeing mainly follows rigid and strict culture for all their employees due to which they
have faced several problems associated with their total production system. For the same, Corvi
has decided to find out various ways to break this tradition culture, surprisingly a help came in
the form of Mother Nature (Holden, 2011). However, earthquakes are generally not good for any
business as well as human being. Within this same concern, one earthquake initiates a major
cultural and physical change for various manufacturing sites of Boeing. This earthquake has
1
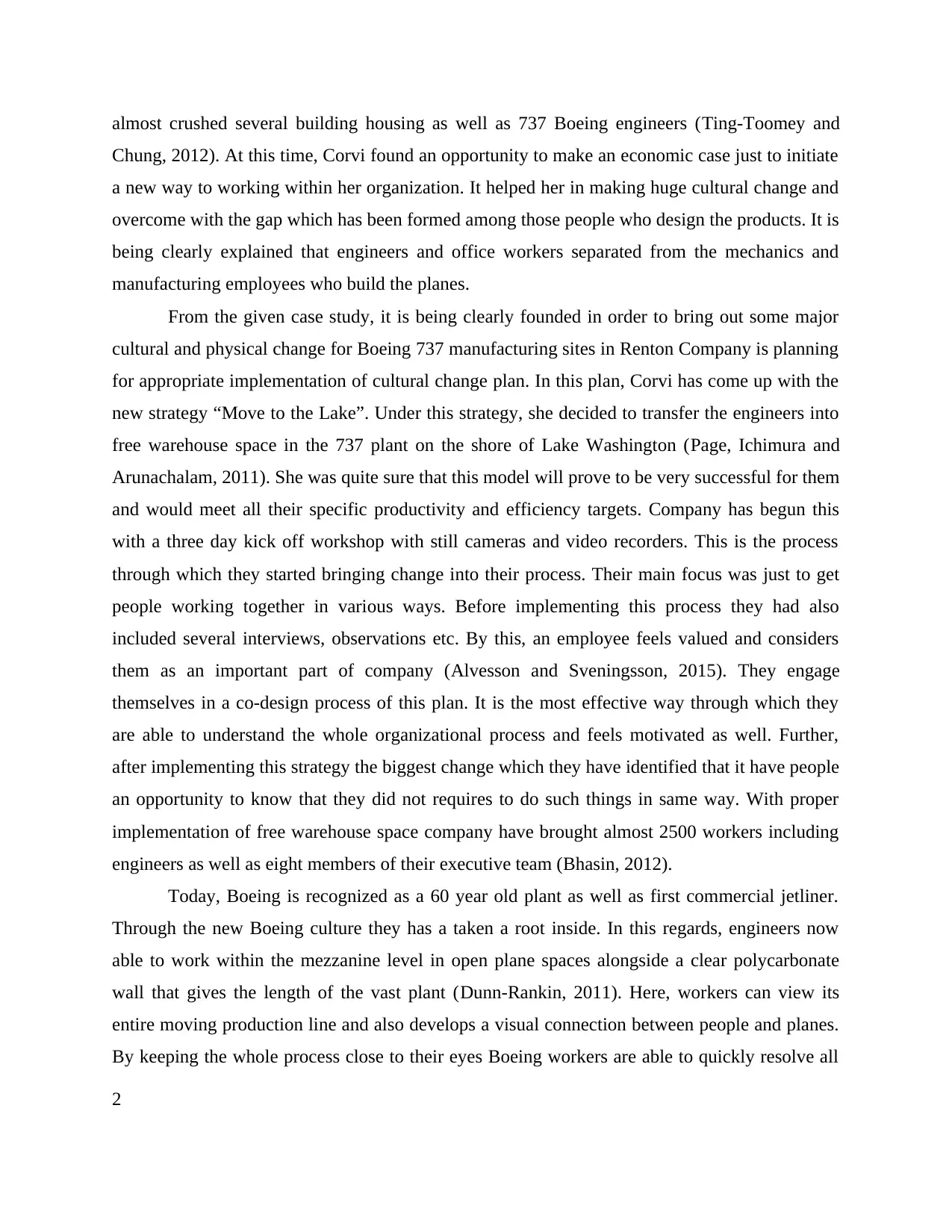
almost crushed several building housing as well as 737 Boeing engineers (Ting-Toomey and
Chung, 2012). At this time, Corvi found an opportunity to make an economic case just to initiate
a new way to working within her organization. It helped her in making huge cultural change and
overcome with the gap which has been formed among those people who design the products. It is
being clearly explained that engineers and office workers separated from the mechanics and
manufacturing employees who build the planes.
From the given case study, it is being clearly founded in order to bring out some major
cultural and physical change for Boeing 737 manufacturing sites in Renton Company is planning
for appropriate implementation of cultural change plan. In this plan, Corvi has come up with the
new strategy “Move to the Lake”. Under this strategy, she decided to transfer the engineers into
free warehouse space in the 737 plant on the shore of Lake Washington (Page, Ichimura and
Arunachalam, 2011). She was quite sure that this model will prove to be very successful for them
and would meet all their specific productivity and efficiency targets. Company has begun this
with a three day kick off workshop with still cameras and video recorders. This is the process
through which they started bringing change into their process. Their main focus was just to get
people working together in various ways. Before implementing this process they had also
included several interviews, observations etc. By this, an employee feels valued and considers
them as an important part of company (Alvesson and Sveningsson, 2015). They engage
themselves in a co-design process of this plan. It is the most effective way through which they
are able to understand the whole organizational process and feels motivated as well. Further,
after implementing this strategy the biggest change which they have identified that it have people
an opportunity to know that they did not requires to do such things in same way. With proper
implementation of free warehouse space company have brought almost 2500 workers including
engineers as well as eight members of their executive team (Bhasin, 2012).
Today, Boeing is recognized as a 60 year old plant as well as first commercial jetliner.
Through the new Boeing culture they has a taken a root inside. In this regards, engineers now
able to work within the mezzanine level in open plane spaces alongside a clear polycarbonate
wall that gives the length of the vast plant (Dunn-Rankin, 2011). Here, workers can view its
entire moving production line and also develops a visual connection between people and planes.
By keeping the whole process close to their eyes Boeing workers are able to quickly resolve all
2
Chung, 2012). At this time, Corvi found an opportunity to make an economic case just to initiate
a new way to working within her organization. It helped her in making huge cultural change and
overcome with the gap which has been formed among those people who design the products. It is
being clearly explained that engineers and office workers separated from the mechanics and
manufacturing employees who build the planes.
From the given case study, it is being clearly founded in order to bring out some major
cultural and physical change for Boeing 737 manufacturing sites in Renton Company is planning
for appropriate implementation of cultural change plan. In this plan, Corvi has come up with the
new strategy “Move to the Lake”. Under this strategy, she decided to transfer the engineers into
free warehouse space in the 737 plant on the shore of Lake Washington (Page, Ichimura and
Arunachalam, 2011). She was quite sure that this model will prove to be very successful for them
and would meet all their specific productivity and efficiency targets. Company has begun this
with a three day kick off workshop with still cameras and video recorders. This is the process
through which they started bringing change into their process. Their main focus was just to get
people working together in various ways. Before implementing this process they had also
included several interviews, observations etc. By this, an employee feels valued and considers
them as an important part of company (Alvesson and Sveningsson, 2015). They engage
themselves in a co-design process of this plan. It is the most effective way through which they
are able to understand the whole organizational process and feels motivated as well. Further,
after implementing this strategy the biggest change which they have identified that it have people
an opportunity to know that they did not requires to do such things in same way. With proper
implementation of free warehouse space company have brought almost 2500 workers including
engineers as well as eight members of their executive team (Bhasin, 2012).
Today, Boeing is recognized as a 60 year old plant as well as first commercial jetliner.
Through the new Boeing culture they has a taken a root inside. In this regards, engineers now
able to work within the mezzanine level in open plane spaces alongside a clear polycarbonate
wall that gives the length of the vast plant (Dunn-Rankin, 2011). Here, workers can view its
entire moving production line and also develops a visual connection between people and planes.
By keeping the whole process close to their eyes Boeing workers are able to quickly resolve all
2
Secure Best Marks with AI Grader
Need help grading? Try our AI Grader for instant feedback on your assignments.
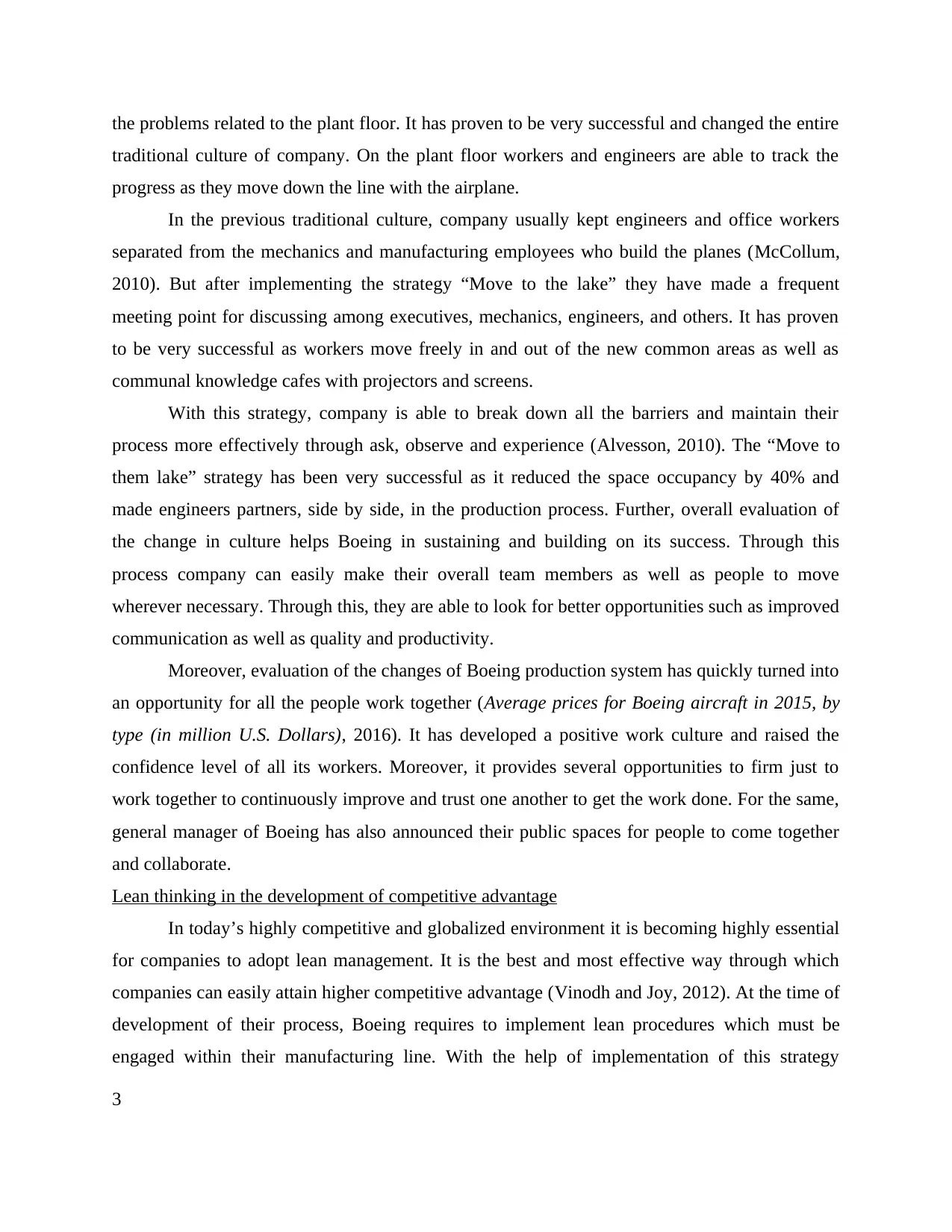
the problems related to the plant floor. It has proven to be very successful and changed the entire
traditional culture of company. On the plant floor workers and engineers are able to track the
progress as they move down the line with the airplane.
In the previous traditional culture, company usually kept engineers and office workers
separated from the mechanics and manufacturing employees who build the planes (McCollum,
2010). But after implementing the strategy “Move to the lake” they have made a frequent
meeting point for discussing among executives, mechanics, engineers, and others. It has proven
to be very successful as workers move freely in and out of the new common areas as well as
communal knowledge cafes with projectors and screens.
With this strategy, company is able to break down all the barriers and maintain their
process more effectively through ask, observe and experience (Alvesson, 2010). The “Move to
them lake” strategy has been very successful as it reduced the space occupancy by 40% and
made engineers partners, side by side, in the production process. Further, overall evaluation of
the change in culture helps Boeing in sustaining and building on its success. Through this
process company can easily make their overall team members as well as people to move
wherever necessary. Through this, they are able to look for better opportunities such as improved
communication as well as quality and productivity.
Moreover, evaluation of the changes of Boeing production system has quickly turned into
an opportunity for all the people work together (Average prices for Boeing aircraft in 2015, by
type (in million U.S. Dollars), 2016). It has developed a positive work culture and raised the
confidence level of all its workers. Moreover, it provides several opportunities to firm just to
work together to continuously improve and trust one another to get the work done. For the same,
general manager of Boeing has also announced their public spaces for people to come together
and collaborate.
Lean thinking in the development of competitive advantage
In today’s highly competitive and globalized environment it is becoming highly essential
for companies to adopt lean management. It is the best and most effective way through which
companies can easily attain higher competitive advantage (Vinodh and Joy, 2012). At the time of
development of their process, Boeing requires to implement lean procedures which must be
engaged within their manufacturing line. With the help of implementation of this strategy
3
traditional culture of company. On the plant floor workers and engineers are able to track the
progress as they move down the line with the airplane.
In the previous traditional culture, company usually kept engineers and office workers
separated from the mechanics and manufacturing employees who build the planes (McCollum,
2010). But after implementing the strategy “Move to the lake” they have made a frequent
meeting point for discussing among executives, mechanics, engineers, and others. It has proven
to be very successful as workers move freely in and out of the new common areas as well as
communal knowledge cafes with projectors and screens.
With this strategy, company is able to break down all the barriers and maintain their
process more effectively through ask, observe and experience (Alvesson, 2010). The “Move to
them lake” strategy has been very successful as it reduced the space occupancy by 40% and
made engineers partners, side by side, in the production process. Further, overall evaluation of
the change in culture helps Boeing in sustaining and building on its success. Through this
process company can easily make their overall team members as well as people to move
wherever necessary. Through this, they are able to look for better opportunities such as improved
communication as well as quality and productivity.
Moreover, evaluation of the changes of Boeing production system has quickly turned into
an opportunity for all the people work together (Average prices for Boeing aircraft in 2015, by
type (in million U.S. Dollars), 2016). It has developed a positive work culture and raised the
confidence level of all its workers. Moreover, it provides several opportunities to firm just to
work together to continuously improve and trust one another to get the work done. For the same,
general manager of Boeing has also announced their public spaces for people to come together
and collaborate.
Lean thinking in the development of competitive advantage
In today’s highly competitive and globalized environment it is becoming highly essential
for companies to adopt lean management. It is the best and most effective way through which
companies can easily attain higher competitive advantage (Vinodh and Joy, 2012). At the time of
development of their process, Boeing requires to implement lean procedures which must be
engaged within their manufacturing line. With the help of implementation of this strategy
3
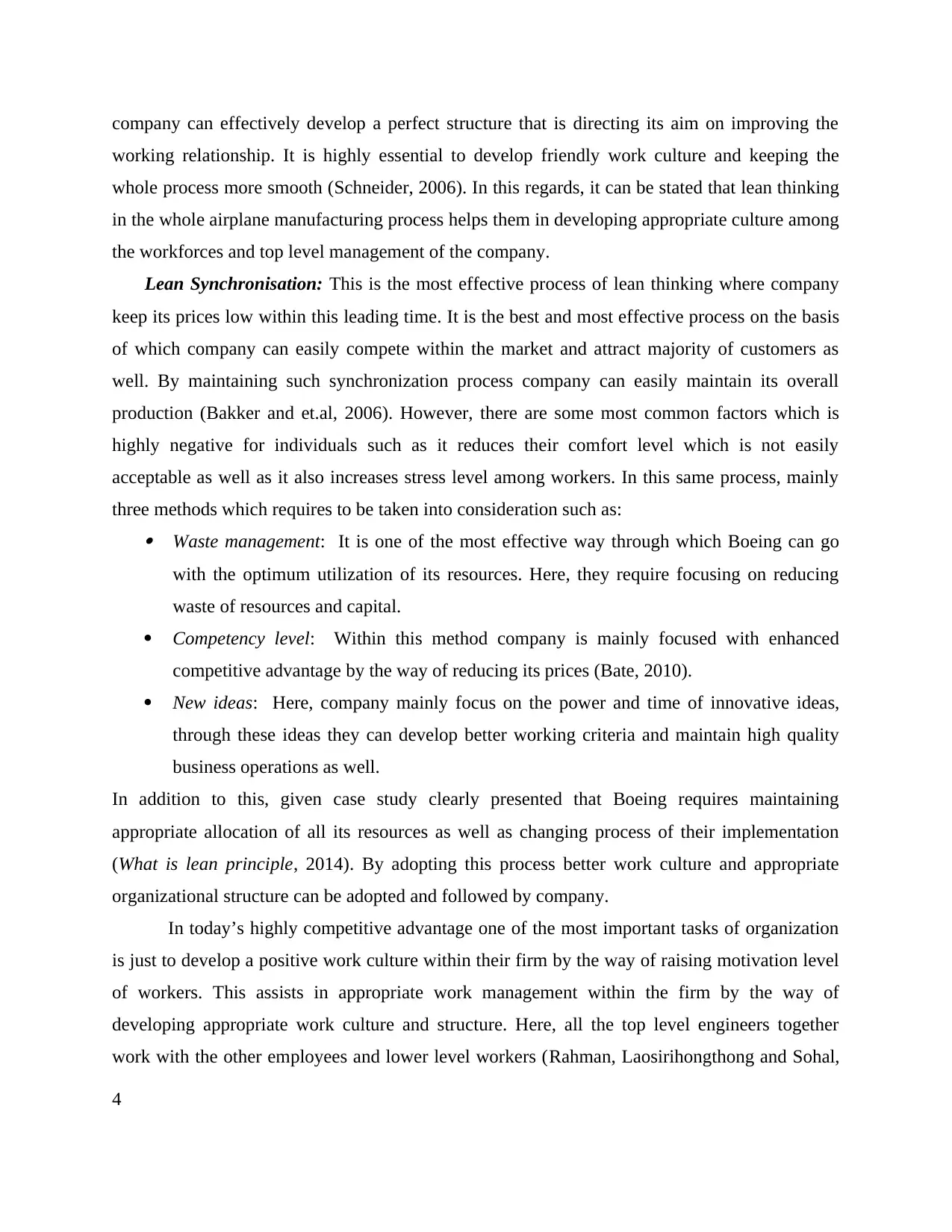
company can effectively develop a perfect structure that is directing its aim on improving the
working relationship. It is highly essential to develop friendly work culture and keeping the
whole process more smooth (Schneider, 2006). In this regards, it can be stated that lean thinking
in the whole airplane manufacturing process helps them in developing appropriate culture among
the workforces and top level management of the company.
Lean Synchronisation: This is the most effective process of lean thinking where company
keep its prices low within this leading time. It is the best and most effective process on the basis
of which company can easily compete within the market and attract majority of customers as
well. By maintaining such synchronization process company can easily maintain its overall
production (Bakker and et.al, 2006). However, there are some most common factors which is
highly negative for individuals such as it reduces their comfort level which is not easily
acceptable as well as it also increases stress level among workers. In this same process, mainly
three methods which requires to be taken into consideration such as: Waste management: It is one of the most effective way through which Boeing can go
with the optimum utilization of its resources. Here, they require focusing on reducing
waste of resources and capital.
Competency level: Within this method company is mainly focused with enhanced
competitive advantage by the way of reducing its prices (Bate, 2010).
New ideas: Here, company mainly focus on the power and time of innovative ideas,
through these ideas they can develop better working criteria and maintain high quality
business operations as well.
In addition to this, given case study clearly presented that Boeing requires maintaining
appropriate allocation of all its resources as well as changing process of their implementation
(What is lean principle, 2014). By adopting this process better work culture and appropriate
organizational structure can be adopted and followed by company.
In today’s highly competitive advantage one of the most important tasks of organization
is just to develop a positive work culture within their firm by the way of raising motivation level
of workers. This assists in appropriate work management within the firm by the way of
developing appropriate work culture and structure. Here, all the top level engineers together
work with the other employees and lower level workers (Rahman, Laosirihongthong and Sohal,
4
working relationship. It is highly essential to develop friendly work culture and keeping the
whole process more smooth (Schneider, 2006). In this regards, it can be stated that lean thinking
in the whole airplane manufacturing process helps them in developing appropriate culture among
the workforces and top level management of the company.
Lean Synchronisation: This is the most effective process of lean thinking where company
keep its prices low within this leading time. It is the best and most effective process on the basis
of which company can easily compete within the market and attract majority of customers as
well. By maintaining such synchronization process company can easily maintain its overall
production (Bakker and et.al, 2006). However, there are some most common factors which is
highly negative for individuals such as it reduces their comfort level which is not easily
acceptable as well as it also increases stress level among workers. In this same process, mainly
three methods which requires to be taken into consideration such as: Waste management: It is one of the most effective way through which Boeing can go
with the optimum utilization of its resources. Here, they require focusing on reducing
waste of resources and capital.
Competency level: Within this method company is mainly focused with enhanced
competitive advantage by the way of reducing its prices (Bate, 2010).
New ideas: Here, company mainly focus on the power and time of innovative ideas,
through these ideas they can develop better working criteria and maintain high quality
business operations as well.
In addition to this, given case study clearly presented that Boeing requires maintaining
appropriate allocation of all its resources as well as changing process of their implementation
(What is lean principle, 2014). By adopting this process better work culture and appropriate
organizational structure can be adopted and followed by company.
In today’s highly competitive advantage one of the most important tasks of organization
is just to develop a positive work culture within their firm by the way of raising motivation level
of workers. This assists in appropriate work management within the firm by the way of
developing appropriate work culture and structure. Here, all the top level engineers together
work with the other employees and lower level workers (Rahman, Laosirihongthong and Sohal,
4
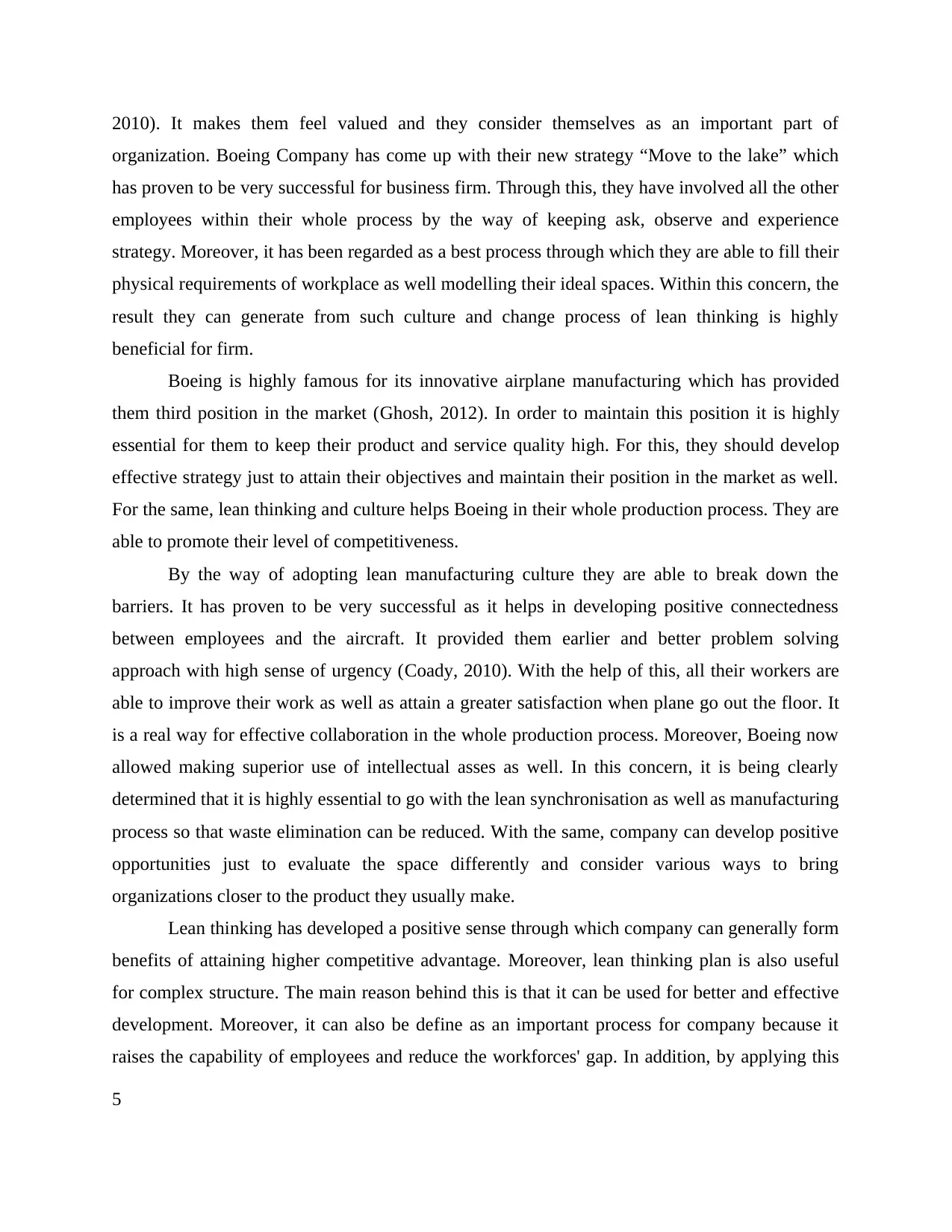
2010). It makes them feel valued and they consider themselves as an important part of
organization. Boeing Company has come up with their new strategy “Move to the lake” which
has proven to be very successful for business firm. Through this, they have involved all the other
employees within their whole process by the way of keeping ask, observe and experience
strategy. Moreover, it has been regarded as a best process through which they are able to fill their
physical requirements of workplace as well modelling their ideal spaces. Within this concern, the
result they can generate from such culture and change process of lean thinking is highly
beneficial for firm.
Boeing is highly famous for its innovative airplane manufacturing which has provided
them third position in the market (Ghosh, 2012). In order to maintain this position it is highly
essential for them to keep their product and service quality high. For this, they should develop
effective strategy just to attain their objectives and maintain their position in the market as well.
For the same, lean thinking and culture helps Boeing in their whole production process. They are
able to promote their level of competitiveness.
By the way of adopting lean manufacturing culture they are able to break down the
barriers. It has proven to be very successful as it helps in developing positive connectedness
between employees and the aircraft. It provided them earlier and better problem solving
approach with high sense of urgency (Coady, 2010). With the help of this, all their workers are
able to improve their work as well as attain a greater satisfaction when plane go out the floor. It
is a real way for effective collaboration in the whole production process. Moreover, Boeing now
allowed making superior use of intellectual asses as well. In this concern, it is being clearly
determined that it is highly essential to go with the lean synchronisation as well as manufacturing
process so that waste elimination can be reduced. With the same, company can develop positive
opportunities just to evaluate the space differently and consider various ways to bring
organizations closer to the product they usually make.
Lean thinking has developed a positive sense through which company can generally form
benefits of attaining higher competitive advantage. Moreover, lean thinking plan is also useful
for complex structure. The main reason behind this is that it can be used for better and effective
development. Moreover, it can also be define as an important process for company because it
raises the capability of employees and reduce the workforces' gap. In addition, by applying this
5
organization. Boeing Company has come up with their new strategy “Move to the lake” which
has proven to be very successful for business firm. Through this, they have involved all the other
employees within their whole process by the way of keeping ask, observe and experience
strategy. Moreover, it has been regarded as a best process through which they are able to fill their
physical requirements of workplace as well modelling their ideal spaces. Within this concern, the
result they can generate from such culture and change process of lean thinking is highly
beneficial for firm.
Boeing is highly famous for its innovative airplane manufacturing which has provided
them third position in the market (Ghosh, 2012). In order to maintain this position it is highly
essential for them to keep their product and service quality high. For this, they should develop
effective strategy just to attain their objectives and maintain their position in the market as well.
For the same, lean thinking and culture helps Boeing in their whole production process. They are
able to promote their level of competitiveness.
By the way of adopting lean manufacturing culture they are able to break down the
barriers. It has proven to be very successful as it helps in developing positive connectedness
between employees and the aircraft. It provided them earlier and better problem solving
approach with high sense of urgency (Coady, 2010). With the help of this, all their workers are
able to improve their work as well as attain a greater satisfaction when plane go out the floor. It
is a real way for effective collaboration in the whole production process. Moreover, Boeing now
allowed making superior use of intellectual asses as well. In this concern, it is being clearly
determined that it is highly essential to go with the lean synchronisation as well as manufacturing
process so that waste elimination can be reduced. With the same, company can develop positive
opportunities just to evaluate the space differently and consider various ways to bring
organizations closer to the product they usually make.
Lean thinking has developed a positive sense through which company can generally form
benefits of attaining higher competitive advantage. Moreover, lean thinking plan is also useful
for complex structure. The main reason behind this is that it can be used for better and effective
development. Moreover, it can also be define as an important process for company because it
raises the capability of employees and reduce the workforces' gap. In addition, by applying this
5
Paraphrase This Document
Need a fresh take? Get an instant paraphrase of this document with our AI Paraphraser
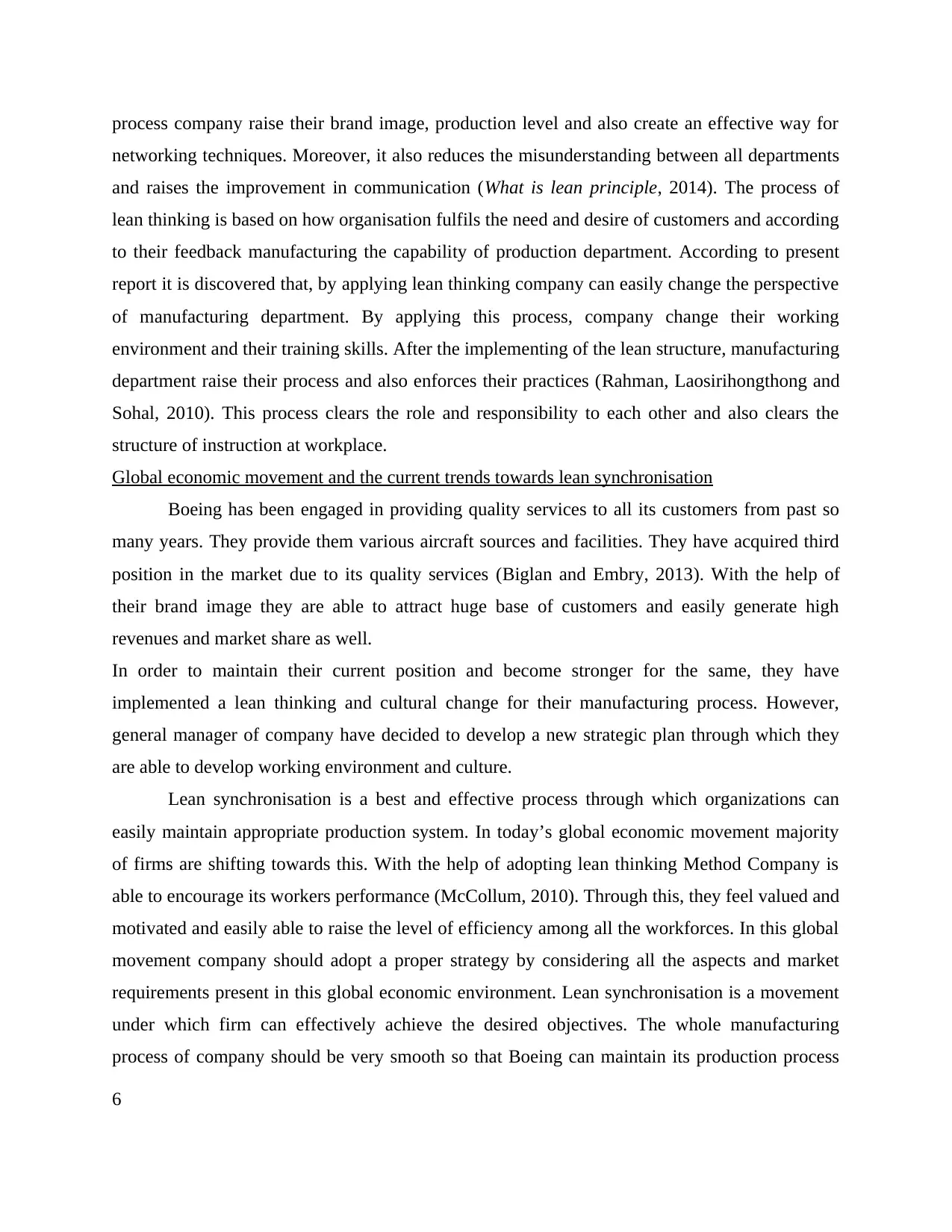
process company raise their brand image, production level and also create an effective way for
networking techniques. Moreover, it also reduces the misunderstanding between all departments
and raises the improvement in communication (What is lean principle, 2014). The process of
lean thinking is based on how organisation fulfils the need and desire of customers and according
to their feedback manufacturing the capability of production department. According to present
report it is discovered that, by applying lean thinking company can easily change the perspective
of manufacturing department. By applying this process, company change their working
environment and their training skills. After the implementing of the lean structure, manufacturing
department raise their process and also enforces their practices (Rahman, Laosirihongthong and
Sohal, 2010). This process clears the role and responsibility to each other and also clears the
structure of instruction at workplace.
Global economic movement and the current trends towards lean synchronisation
Boeing has been engaged in providing quality services to all its customers from past so
many years. They provide them various aircraft sources and facilities. They have acquired third
position in the market due to its quality services (Biglan and Embry, 2013). With the help of
their brand image they are able to attract huge base of customers and easily generate high
revenues and market share as well.
In order to maintain their current position and become stronger for the same, they have
implemented a lean thinking and cultural change for their manufacturing process. However,
general manager of company have decided to develop a new strategic plan through which they
are able to develop working environment and culture.
Lean synchronisation is a best and effective process through which organizations can
easily maintain appropriate production system. In today’s global economic movement majority
of firms are shifting towards this. With the help of adopting lean thinking Method Company is
able to encourage its workers performance (McCollum, 2010). Through this, they feel valued and
motivated and easily able to raise the level of efficiency among all the workforces. In this global
movement company should adopt a proper strategy by considering all the aspects and market
requirements present in this global economic environment. Lean synchronisation is a movement
under which firm can effectively achieve the desired objectives. The whole manufacturing
process of company should be very smooth so that Boeing can maintain its production process
6
networking techniques. Moreover, it also reduces the misunderstanding between all departments
and raises the improvement in communication (What is lean principle, 2014). The process of
lean thinking is based on how organisation fulfils the need and desire of customers and according
to their feedback manufacturing the capability of production department. According to present
report it is discovered that, by applying lean thinking company can easily change the perspective
of manufacturing department. By applying this process, company change their working
environment and their training skills. After the implementing of the lean structure, manufacturing
department raise their process and also enforces their practices (Rahman, Laosirihongthong and
Sohal, 2010). This process clears the role and responsibility to each other and also clears the
structure of instruction at workplace.
Global economic movement and the current trends towards lean synchronisation
Boeing has been engaged in providing quality services to all its customers from past so
many years. They provide them various aircraft sources and facilities. They have acquired third
position in the market due to its quality services (Biglan and Embry, 2013). With the help of
their brand image they are able to attract huge base of customers and easily generate high
revenues and market share as well.
In order to maintain their current position and become stronger for the same, they have
implemented a lean thinking and cultural change for their manufacturing process. However,
general manager of company have decided to develop a new strategic plan through which they
are able to develop working environment and culture.
Lean synchronisation is a best and effective process through which organizations can
easily maintain appropriate production system. In today’s global economic movement majority
of firms are shifting towards this. With the help of adopting lean thinking Method Company is
able to encourage its workers performance (McCollum, 2010). Through this, they feel valued and
motivated and easily able to raise the level of efficiency among all the workforces. In this global
movement company should adopt a proper strategy by considering all the aspects and market
requirements present in this global economic environment. Lean synchronisation is a movement
under which firm can effectively achieve the desired objectives. The whole manufacturing
process of company should be very smooth so that Boeing can maintain its production process
6
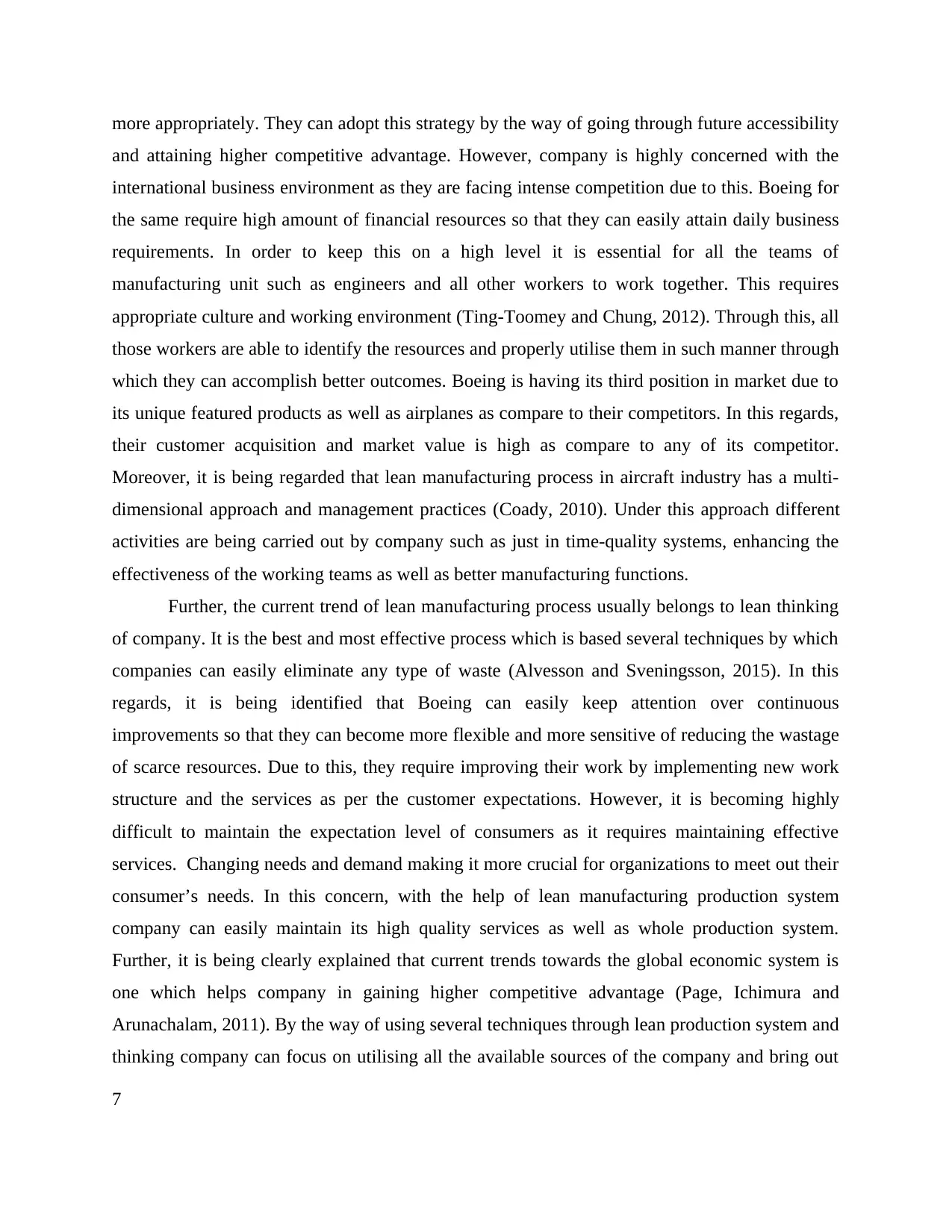
more appropriately. They can adopt this strategy by the way of going through future accessibility
and attaining higher competitive advantage. However, company is highly concerned with the
international business environment as they are facing intense competition due to this. Boeing for
the same require high amount of financial resources so that they can easily attain daily business
requirements. In order to keep this on a high level it is essential for all the teams of
manufacturing unit such as engineers and all other workers to work together. This requires
appropriate culture and working environment (Ting-Toomey and Chung, 2012). Through this, all
those workers are able to identify the resources and properly utilise them in such manner through
which they can accomplish better outcomes. Boeing is having its third position in market due to
its unique featured products as well as airplanes as compare to their competitors. In this regards,
their customer acquisition and market value is high as compare to any of its competitor.
Moreover, it is being regarded that lean manufacturing process in aircraft industry has a multi-
dimensional approach and management practices (Coady, 2010). Under this approach different
activities are being carried out by company such as just in time-quality systems, enhancing the
effectiveness of the working teams as well as better manufacturing functions.
Further, the current trend of lean manufacturing process usually belongs to lean thinking
of company. It is the best and most effective process which is based several techniques by which
companies can easily eliminate any type of waste (Alvesson and Sveningsson, 2015). In this
regards, it is being identified that Boeing can easily keep attention over continuous
improvements so that they can become more flexible and more sensitive of reducing the wastage
of scarce resources. Due to this, they require improving their work by implementing new work
structure and the services as per the customer expectations. However, it is becoming highly
difficult to maintain the expectation level of consumers as it requires maintaining effective
services. Changing needs and demand making it more crucial for organizations to meet out their
consumer’s needs. In this concern, with the help of lean manufacturing production system
company can easily maintain its high quality services as well as whole production system.
Further, it is being clearly explained that current trends towards the global economic system is
one which helps company in gaining higher competitive advantage (Page, Ichimura and
Arunachalam, 2011). By the way of using several techniques through lean production system and
thinking company can focus on utilising all the available sources of the company and bring out
7
and attaining higher competitive advantage. However, company is highly concerned with the
international business environment as they are facing intense competition due to this. Boeing for
the same require high amount of financial resources so that they can easily attain daily business
requirements. In order to keep this on a high level it is essential for all the teams of
manufacturing unit such as engineers and all other workers to work together. This requires
appropriate culture and working environment (Ting-Toomey and Chung, 2012). Through this, all
those workers are able to identify the resources and properly utilise them in such manner through
which they can accomplish better outcomes. Boeing is having its third position in market due to
its unique featured products as well as airplanes as compare to their competitors. In this regards,
their customer acquisition and market value is high as compare to any of its competitor.
Moreover, it is being regarded that lean manufacturing process in aircraft industry has a multi-
dimensional approach and management practices (Coady, 2010). Under this approach different
activities are being carried out by company such as just in time-quality systems, enhancing the
effectiveness of the working teams as well as better manufacturing functions.
Further, the current trend of lean manufacturing process usually belongs to lean thinking
of company. It is the best and most effective process which is based several techniques by which
companies can easily eliminate any type of waste (Alvesson and Sveningsson, 2015). In this
regards, it is being identified that Boeing can easily keep attention over continuous
improvements so that they can become more flexible and more sensitive of reducing the wastage
of scarce resources. Due to this, they require improving their work by implementing new work
structure and the services as per the customer expectations. However, it is becoming highly
difficult to maintain the expectation level of consumers as it requires maintaining effective
services. Changing needs and demand making it more crucial for organizations to meet out their
consumer’s needs. In this concern, with the help of lean manufacturing production system
company can easily maintain its high quality services as well as whole production system.
Further, it is being clearly explained that current trends towards the global economic system is
one which helps company in gaining higher competitive advantage (Page, Ichimura and
Arunachalam, 2011). By the way of using several techniques through lean production system and
thinking company can focus on utilising all the available sources of the company and bring out
7
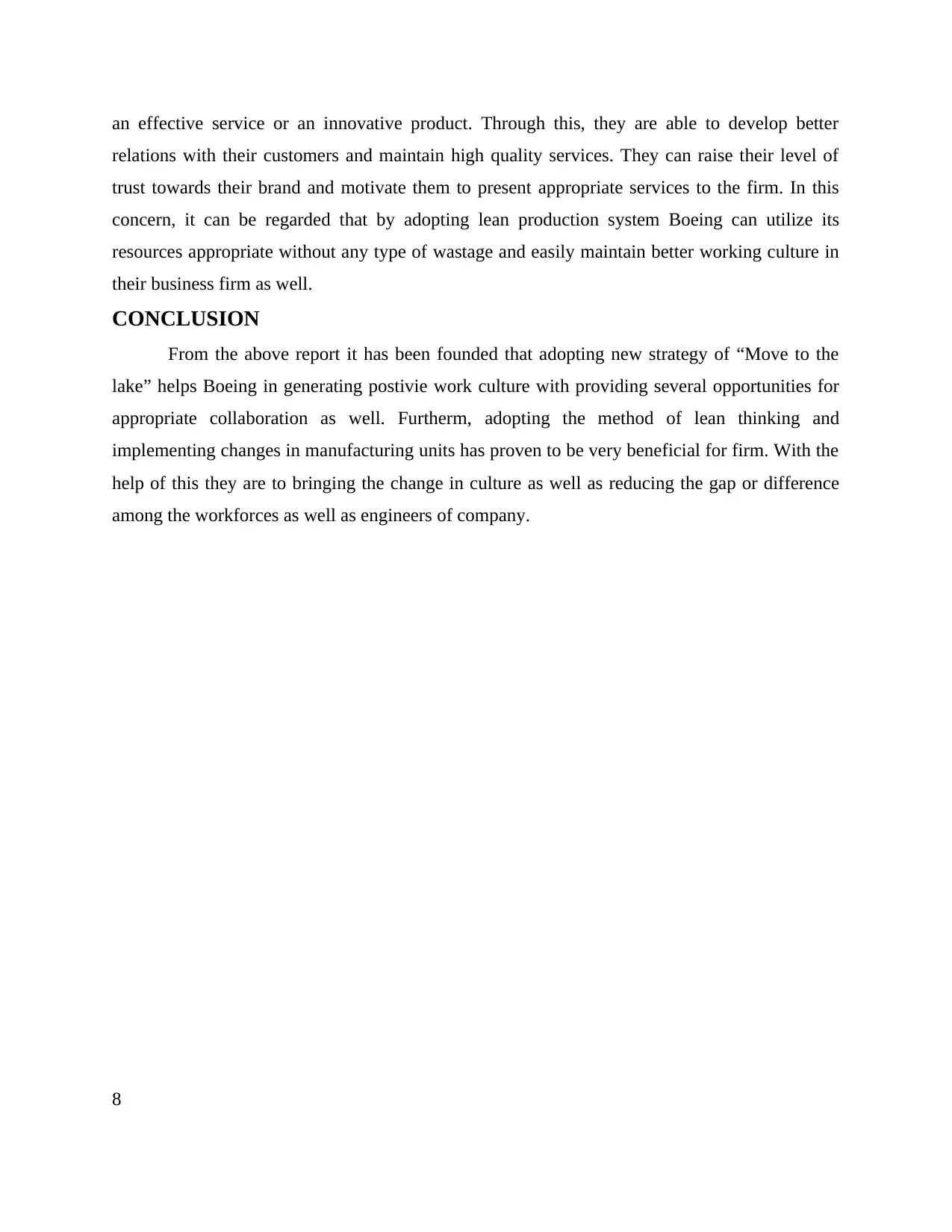
an effective service or an innovative product. Through this, they are able to develop better
relations with their customers and maintain high quality services. They can raise their level of
trust towards their brand and motivate them to present appropriate services to the firm. In this
concern, it can be regarded that by adopting lean production system Boeing can utilize its
resources appropriate without any type of wastage and easily maintain better working culture in
their business firm as well.
CONCLUSION
From the above report it has been founded that adopting new strategy of “Move to the
lake” helps Boeing in generating postivie work culture with providing several opportunities for
appropriate collaboration as well. Furtherm, adopting the method of lean thinking and
implementing changes in manufacturing units has proven to be very beneficial for firm. With the
help of this they are to bringing the change in culture as well as reducing the gap or difference
among the workforces as well as engineers of company.
8
relations with their customers and maintain high quality services. They can raise their level of
trust towards their brand and motivate them to present appropriate services to the firm. In this
concern, it can be regarded that by adopting lean production system Boeing can utilize its
resources appropriate without any type of wastage and easily maintain better working culture in
their business firm as well.
CONCLUSION
From the above report it has been founded that adopting new strategy of “Move to the
lake” helps Boeing in generating postivie work culture with providing several opportunities for
appropriate collaboration as well. Furtherm, adopting the method of lean thinking and
implementing changes in manufacturing units has proven to be very beneficial for firm. With the
help of this they are to bringing the change in culture as well as reducing the gap or difference
among the workforces as well as engineers of company.
8
Secure Best Marks with AI Grader
Need help grading? Try our AI Grader for instant feedback on your assignments.
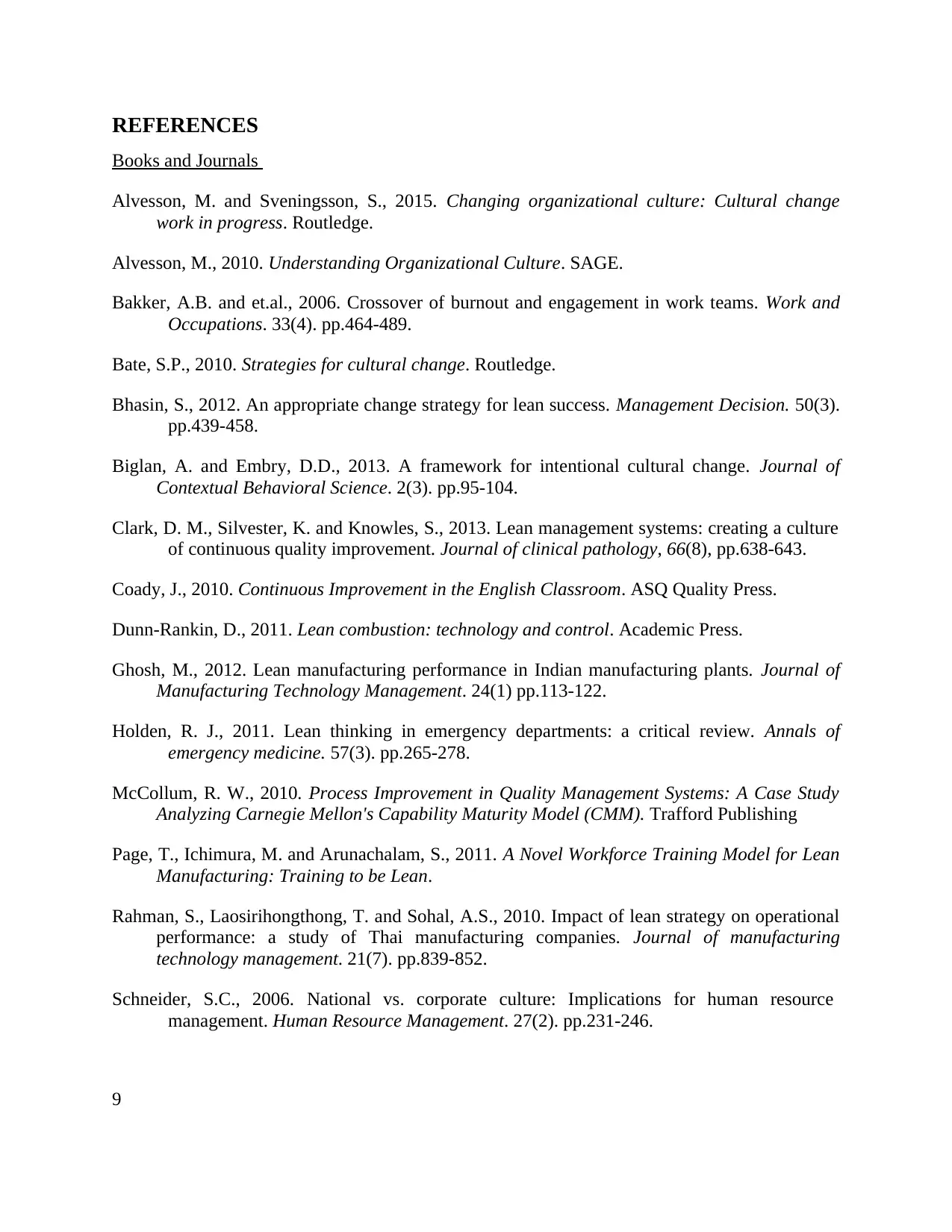
REFERENCES
Books and Journals
Alvesson, M. and Sveningsson, S., 2015. Changing organizational culture: Cultural change
work in progress. Routledge.
Alvesson, M., 2010. Understanding Organizational Culture. SAGE.
Bakker, A.B. and et.al., 2006. Crossover of burnout and engagement in work teams. Work and
Occupations. 33(4). pp.464-489.
Bate, S.P., 2010. Strategies for cultural change. Routledge.
Bhasin, S., 2012. An appropriate change strategy for lean success. Management Decision. 50(3).
pp.439-458.
Biglan, A. and Embry, D.D., 2013. A framework for intentional cultural change. Journal of
Contextual Behavioral Science. 2(3). pp.95-104.
Clark, D. M., Silvester, K. and Knowles, S., 2013. Lean management systems: creating a culture
of continuous quality improvement. Journal of clinical pathology, 66(8), pp.638-643.
Coady, J., 2010. Continuous Improvement in the English Classroom. ASQ Quality Press.
Dunn-Rankin, D., 2011. Lean combustion: technology and control. Academic Press.
Ghosh, M., 2012. Lean manufacturing performance in Indian manufacturing plants. Journal of
Manufacturing Technology Management. 24(1) pp.113-122.
Holden, R. J., 2011. Lean thinking in emergency departments: a critical review. Annals of
emergency medicine. 57(3). pp.265-278.
McCollum, R. W., 2010. Process Improvement in Quality Management Systems: A Case Study
Analyzing Carnegie Mellon's Capability Maturity Model (CMM). Trafford Publishing
Page, T., Ichimura, M. and Arunachalam, S., 2011. A Novel Workforce Training Model for Lean
Manufacturing: Training to be Lean.
Rahman, S., Laosirihongthong, T. and Sohal, A.S., 2010. Impact of lean strategy on operational
performance: a study of Thai manufacturing companies. Journal of manufacturing
technology management. 21(7). pp.839-852.
Schneider, S.C., 2006. National vs. corporate culture: Implications for human resource
management. Human Resource Management. 27(2). pp.231-246.
9
Books and Journals
Alvesson, M. and Sveningsson, S., 2015. Changing organizational culture: Cultural change
work in progress. Routledge.
Alvesson, M., 2010. Understanding Organizational Culture. SAGE.
Bakker, A.B. and et.al., 2006. Crossover of burnout and engagement in work teams. Work and
Occupations. 33(4). pp.464-489.
Bate, S.P., 2010. Strategies for cultural change. Routledge.
Bhasin, S., 2012. An appropriate change strategy for lean success. Management Decision. 50(3).
pp.439-458.
Biglan, A. and Embry, D.D., 2013. A framework for intentional cultural change. Journal of
Contextual Behavioral Science. 2(3). pp.95-104.
Clark, D. M., Silvester, K. and Knowles, S., 2013. Lean management systems: creating a culture
of continuous quality improvement. Journal of clinical pathology, 66(8), pp.638-643.
Coady, J., 2010. Continuous Improvement in the English Classroom. ASQ Quality Press.
Dunn-Rankin, D., 2011. Lean combustion: technology and control. Academic Press.
Ghosh, M., 2012. Lean manufacturing performance in Indian manufacturing plants. Journal of
Manufacturing Technology Management. 24(1) pp.113-122.
Holden, R. J., 2011. Lean thinking in emergency departments: a critical review. Annals of
emergency medicine. 57(3). pp.265-278.
McCollum, R. W., 2010. Process Improvement in Quality Management Systems: A Case Study
Analyzing Carnegie Mellon's Capability Maturity Model (CMM). Trafford Publishing
Page, T., Ichimura, M. and Arunachalam, S., 2011. A Novel Workforce Training Model for Lean
Manufacturing: Training to be Lean.
Rahman, S., Laosirihongthong, T. and Sohal, A.S., 2010. Impact of lean strategy on operational
performance: a study of Thai manufacturing companies. Journal of manufacturing
technology management. 21(7). pp.839-852.
Schneider, S.C., 2006. National vs. corporate culture: Implications for human resource
management. Human Resource Management. 27(2). pp.231-246.
9
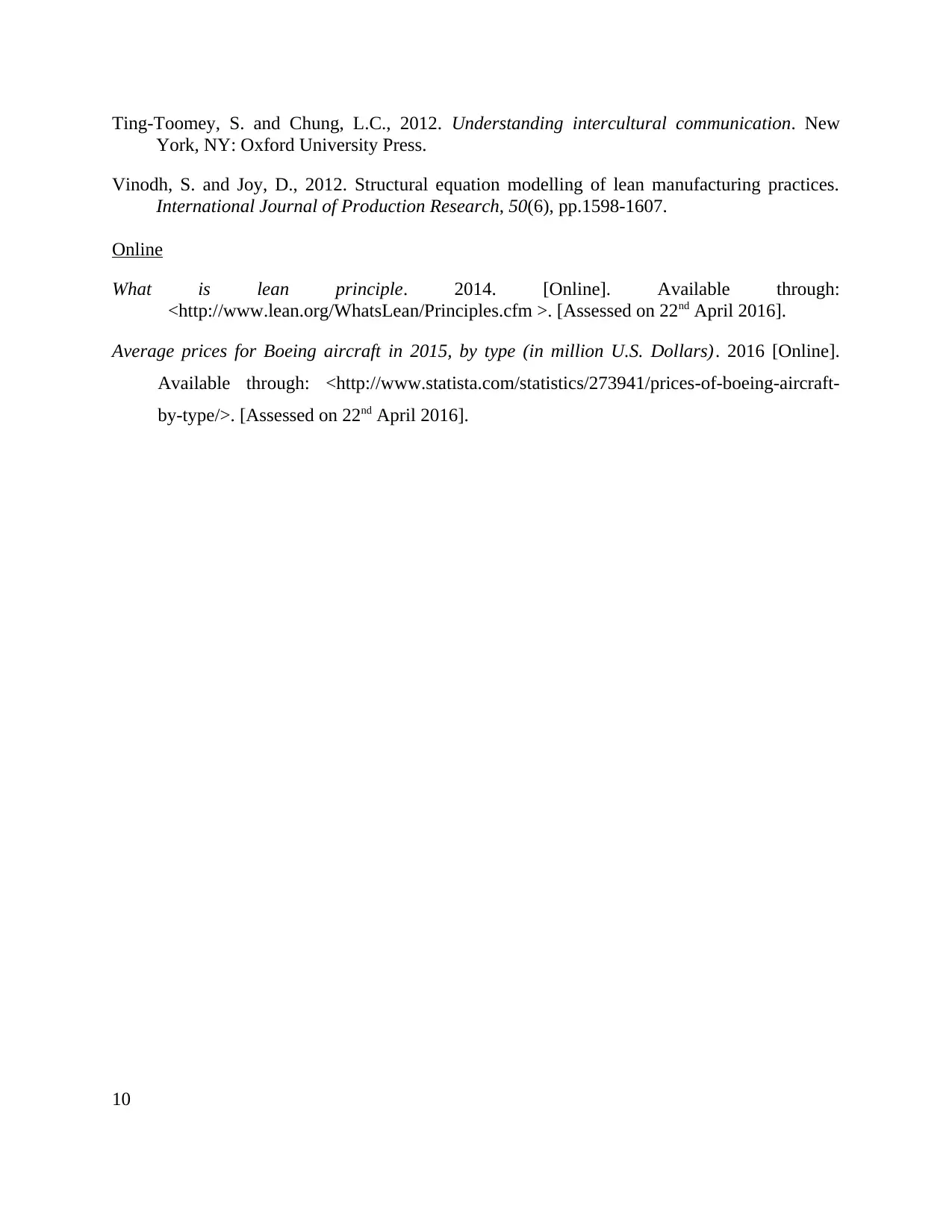
Ting-Toomey, S. and Chung, L.C., 2012. Understanding intercultural communication. New
York, NY: Oxford University Press.
Vinodh, S. and Joy, D., 2012. Structural equation modelling of lean manufacturing practices.
International Journal of Production Research, 50(6), pp.1598-1607.
Online
What is lean principle. 2014. [Online]. Available through:
<http://www.lean.org/WhatsLean/Principles.cfm >. [Assessed on 22nd April 2016].
Average prices for Boeing aircraft in 2015, by type (in million U.S. Dollars). 2016 [Online].
Available through: <http://www.statista.com/statistics/273941/prices-of-boeing-aircraft-
by-type/>. [Assessed on 22nd April 2016].
10
York, NY: Oxford University Press.
Vinodh, S. and Joy, D., 2012. Structural equation modelling of lean manufacturing practices.
International Journal of Production Research, 50(6), pp.1598-1607.
Online
What is lean principle. 2014. [Online]. Available through:
<http://www.lean.org/WhatsLean/Principles.cfm >. [Assessed on 22nd April 2016].
Average prices for Boeing aircraft in 2015, by type (in million U.S. Dollars). 2016 [Online].
Available through: <http://www.statista.com/statistics/273941/prices-of-boeing-aircraft-
by-type/>. [Assessed on 22nd April 2016].
10
1 out of 12
Related Documents

Your All-in-One AI-Powered Toolkit for Academic Success.
+13062052269
info@desklib.com
Available 24*7 on WhatsApp / Email
Unlock your academic potential
© 2024 | Zucol Services PVT LTD | All rights reserved.