Leadership and Ethics: Bryson Cable Warhead Cable Test Case Study
VerifiedAdded on 2019/09/20
|3
|1148
|125
Case Study
AI Summary
This case study examines the ethical challenges faced by Stanton Wong, the quality supervisor at Bryson Corporation's cable division. The central issue revolves around a directive from the plant manager, Harry Jackson, to disregard defects in a batch of warhead cables, which are critical components of missile fuse systems. The assignment requires an analysis of three ethical issues present in the case, supported by justifications. It further explores whether selling the faulty cable is right or wrong, supported by three ethical reasoning methods. Finally, the case study asks for three actionable solutions Stanton can take to resolve the identified ethical problems. The case highlights issues of leadership, ethical decision-making, and the potential consequences of compromising quality control in a military context.
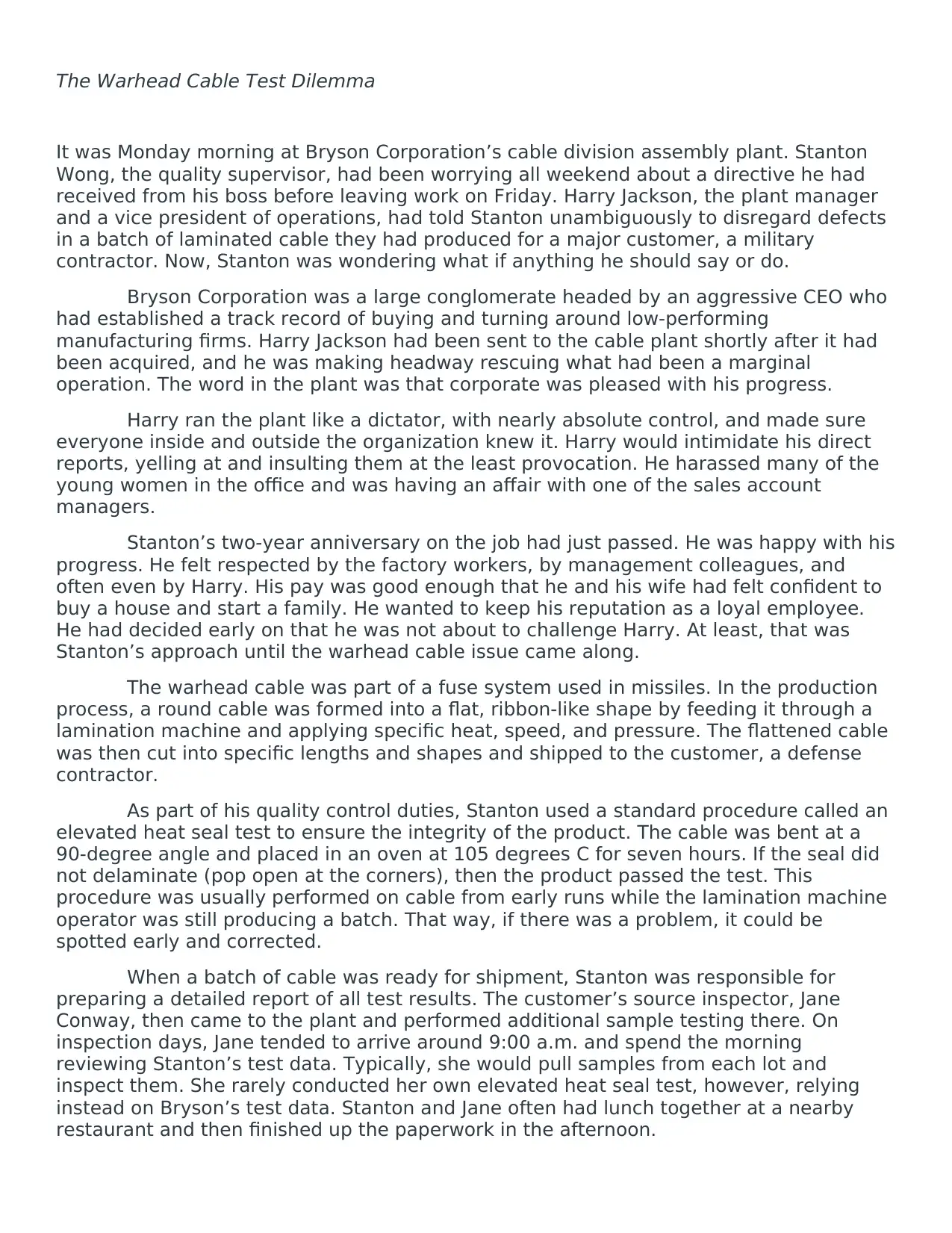
The Warhead Cable Test Dilemma
It was Monday morning at Bryson Corporation’s cable division assembly plant. Stanton
Wong, the quality supervisor, had been worrying all weekend about a directive he had
received from his boss before leaving work on Friday. Harry Jackson, the plant manager
and a vice president of operations, had told Stanton unambiguously to disregard defects
in a batch of laminated cable they had produced for a major customer, a military
contractor. Now, Stanton was wondering what if anything he should say or do.
Bryson Corporation was a large conglomerate headed by an aggressive CEO who
had established a track record of buying and turning around low-performing
manufacturing firms. Harry Jackson had been sent to the cable plant shortly after it had
been acquired, and he was making headway rescuing what had been a marginal
operation. The word in the plant was that corporate was pleased with his progress.
Harry ran the plant like a dictator, with nearly absolute control, and made sure
everyone inside and outside the organization knew it. Harry would intimidate his direct
reports, yelling at and insulting them at the least provocation. He harassed many of the
young women in the office and was having an affair with one of the sales account
managers.
Stanton’s two-year anniversary on the job had just passed. He was happy with his
progress. He felt respected by the factory workers, by management colleagues, and
often even by Harry. His pay was good enough that he and his wife had felt confident to
buy a house and start a family. He wanted to keep his reputation as a loyal employee.
He had decided early on that he was not about to challenge Harry. At least, that was
Stanton’s approach until the warhead cable issue came along.
The warhead cable was part of a fuse system used in missiles. In the production
process, a round cable was formed into a flat, ribbon-like shape by feeding it through a
lamination machine and applying specific heat, speed, and pressure. The flattened cable
was then cut into specific lengths and shapes and shipped to the customer, a defense
contractor.
As part of his quality control duties, Stanton used a standard procedure called an
elevated heat seal test to ensure the integrity of the product. The cable was bent at a
90-degree angle and placed in an oven at 105 degrees C for seven hours. If the seal did
not delaminate (pop open at the corners), then the product passed the test. This
procedure was usually performed on cable from early runs while the lamination machine
operator was still producing a batch. That way, if there was a problem, it could be
spotted early and corrected.
When a batch of cable was ready for shipment, Stanton was responsible for
preparing a detailed report of all test results. The customer’s source inspector, Jane
Conway, then came to the plant and performed additional sample testing there. On
inspection days, Jane tended to arrive around 9:00 a.m. and spend the morning
reviewing Stanton’s test data. Typically, she would pull samples from each lot and
inspect them. She rarely conducted her own elevated heat seal test, however, relying
instead on Bryson’s test data. Stanton and Jane often had lunch together at a nearby
restaurant and then finished up the paperwork in the afternoon.
It was Monday morning at Bryson Corporation’s cable division assembly plant. Stanton
Wong, the quality supervisor, had been worrying all weekend about a directive he had
received from his boss before leaving work on Friday. Harry Jackson, the plant manager
and a vice president of operations, had told Stanton unambiguously to disregard defects
in a batch of laminated cable they had produced for a major customer, a military
contractor. Now, Stanton was wondering what if anything he should say or do.
Bryson Corporation was a large conglomerate headed by an aggressive CEO who
had established a track record of buying and turning around low-performing
manufacturing firms. Harry Jackson had been sent to the cable plant shortly after it had
been acquired, and he was making headway rescuing what had been a marginal
operation. The word in the plant was that corporate was pleased with his progress.
Harry ran the plant like a dictator, with nearly absolute control, and made sure
everyone inside and outside the organization knew it. Harry would intimidate his direct
reports, yelling at and insulting them at the least provocation. He harassed many of the
young women in the office and was having an affair with one of the sales account
managers.
Stanton’s two-year anniversary on the job had just passed. He was happy with his
progress. He felt respected by the factory workers, by management colleagues, and
often even by Harry. His pay was good enough that he and his wife had felt confident to
buy a house and start a family. He wanted to keep his reputation as a loyal employee.
He had decided early on that he was not about to challenge Harry. At least, that was
Stanton’s approach until the warhead cable issue came along.
The warhead cable was part of a fuse system used in missiles. In the production
process, a round cable was formed into a flat, ribbon-like shape by feeding it through a
lamination machine and applying specific heat, speed, and pressure. The flattened cable
was then cut into specific lengths and shapes and shipped to the customer, a defense
contractor.
As part of his quality control duties, Stanton used a standard procedure called an
elevated heat seal test to ensure the integrity of the product. The cable was bent at a
90-degree angle and placed in an oven at 105 degrees C for seven hours. If the seal did
not delaminate (pop open at the corners), then the product passed the test. This
procedure was usually performed on cable from early runs while the lamination machine
operator was still producing a batch. That way, if there was a problem, it could be
spotted early and corrected.
When a batch of cable was ready for shipment, Stanton was responsible for
preparing a detailed report of all test results. The customer’s source inspector, Jane
Conway, then came to the plant and performed additional sample testing there. On
inspection days, Jane tended to arrive around 9:00 a.m. and spend the morning
reviewing Stanton’s test data. Typically, she would pull samples from each lot and
inspect them. She rarely conducted her own elevated heat seal test, however, relying
instead on Bryson’s test data. Stanton and Jane often had lunch together at a nearby
restaurant and then finished up the paperwork in the afternoon.
Secure Best Marks with AI Grader
Need help grading? Try our AI Grader for instant feedback on your assignments.
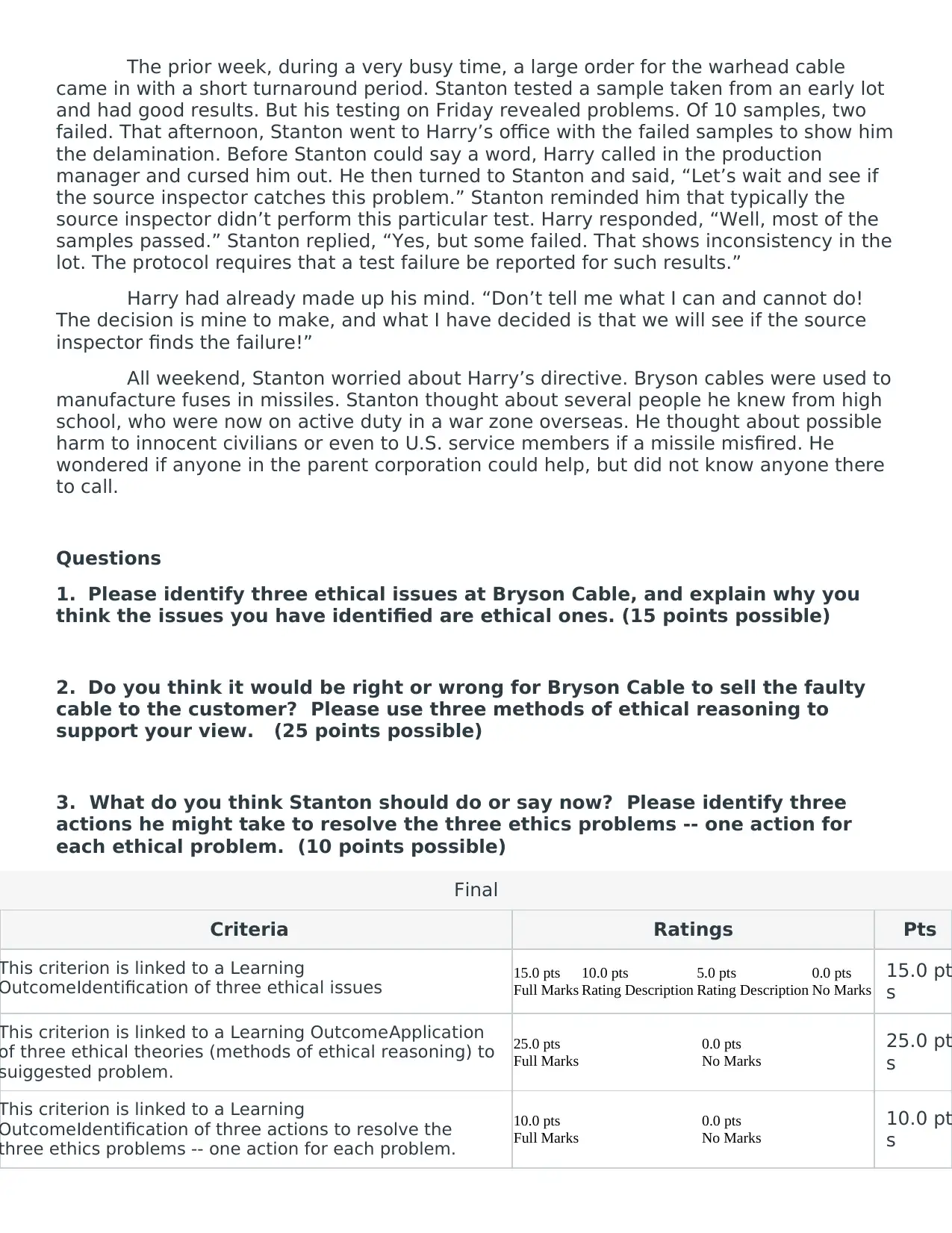
The prior week, during a very busy time, a large order for the warhead cable
came in with a short turnaround period. Stanton tested a sample taken from an early lot
and had good results. But his testing on Friday revealed problems. Of 10 samples, two
failed. That afternoon, Stanton went to Harry’s office with the failed samples to show him
the delamination. Before Stanton could say a word, Harry called in the production
manager and cursed him out. He then turned to Stanton and said, “Let’s wait and see if
the source inspector catches this problem.” Stanton reminded him that typically the
source inspector didn’t perform this particular test. Harry responded, “Well, most of the
samples passed.” Stanton replied, “Yes, but some failed. That shows inconsistency in the
lot. The protocol requires that a test failure be reported for such results.”
Harry had already made up his mind. “Don’t tell me what I can and cannot do!
The decision is mine to make, and what I have decided is that we will see if the source
inspector finds the failure!”
All weekend, Stanton worried about Harry’s directive. Bryson cables were used to
manufacture fuses in missiles. Stanton thought about several people he knew from high
school, who were now on active duty in a war zone overseas. He thought about possible
harm to innocent civilians or even to U.S. service members if a missile misfired. He
wondered if anyone in the parent corporation could help, but did not know anyone there
to call.
Questions
1. Please identify three ethical issues at Bryson Cable, and explain why you
think the issues you have identified are ethical ones. (15 points possible)
2. Do you think it would be right or wrong for Bryson Cable to sell the faulty
cable to the customer? Please use three methods of ethical reasoning to
support your view. (25 points possible)
3. What do you think Stanton should do or say now? Please identify three
actions he might take to resolve the three ethics problems -- one action for
each ethical problem. (10 points possible)
Final
Criteria Ratings Pts
This criterion is linked to a Learning
OutcomeIdentification of three ethical issues 15.0 pts
Full Marks
10.0 pts
Rating Description
5.0 pts
Rating Description
0.0 pts
No Marks
15.0 pt
s
This criterion is linked to a Learning OutcomeApplication
of three ethical theories (methods of ethical reasoning) to
suiggested problem.
25.0 pts
Full Marks
0.0 pts
No Marks
25.0 pt
s
This criterion is linked to a Learning
OutcomeIdentification of three actions to resolve the
three ethics problems -- one action for each problem.
10.0 pts
Full Marks
0.0 pts
No Marks
10.0 pt
s
came in with a short turnaround period. Stanton tested a sample taken from an early lot
and had good results. But his testing on Friday revealed problems. Of 10 samples, two
failed. That afternoon, Stanton went to Harry’s office with the failed samples to show him
the delamination. Before Stanton could say a word, Harry called in the production
manager and cursed him out. He then turned to Stanton and said, “Let’s wait and see if
the source inspector catches this problem.” Stanton reminded him that typically the
source inspector didn’t perform this particular test. Harry responded, “Well, most of the
samples passed.” Stanton replied, “Yes, but some failed. That shows inconsistency in the
lot. The protocol requires that a test failure be reported for such results.”
Harry had already made up his mind. “Don’t tell me what I can and cannot do!
The decision is mine to make, and what I have decided is that we will see if the source
inspector finds the failure!”
All weekend, Stanton worried about Harry’s directive. Bryson cables were used to
manufacture fuses in missiles. Stanton thought about several people he knew from high
school, who were now on active duty in a war zone overseas. He thought about possible
harm to innocent civilians or even to U.S. service members if a missile misfired. He
wondered if anyone in the parent corporation could help, but did not know anyone there
to call.
Questions
1. Please identify three ethical issues at Bryson Cable, and explain why you
think the issues you have identified are ethical ones. (15 points possible)
2. Do you think it would be right or wrong for Bryson Cable to sell the faulty
cable to the customer? Please use three methods of ethical reasoning to
support your view. (25 points possible)
3. What do you think Stanton should do or say now? Please identify three
actions he might take to resolve the three ethics problems -- one action for
each ethical problem. (10 points possible)
Final
Criteria Ratings Pts
This criterion is linked to a Learning
OutcomeIdentification of three ethical issues 15.0 pts
Full Marks
10.0 pts
Rating Description
5.0 pts
Rating Description
0.0 pts
No Marks
15.0 pt
s
This criterion is linked to a Learning OutcomeApplication
of three ethical theories (methods of ethical reasoning) to
suiggested problem.
25.0 pts
Full Marks
0.0 pts
No Marks
25.0 pt
s
This criterion is linked to a Learning
OutcomeIdentification of three actions to resolve the
three ethics problems -- one action for each problem.
10.0 pts
Full Marks
0.0 pts
No Marks
10.0 pt
s
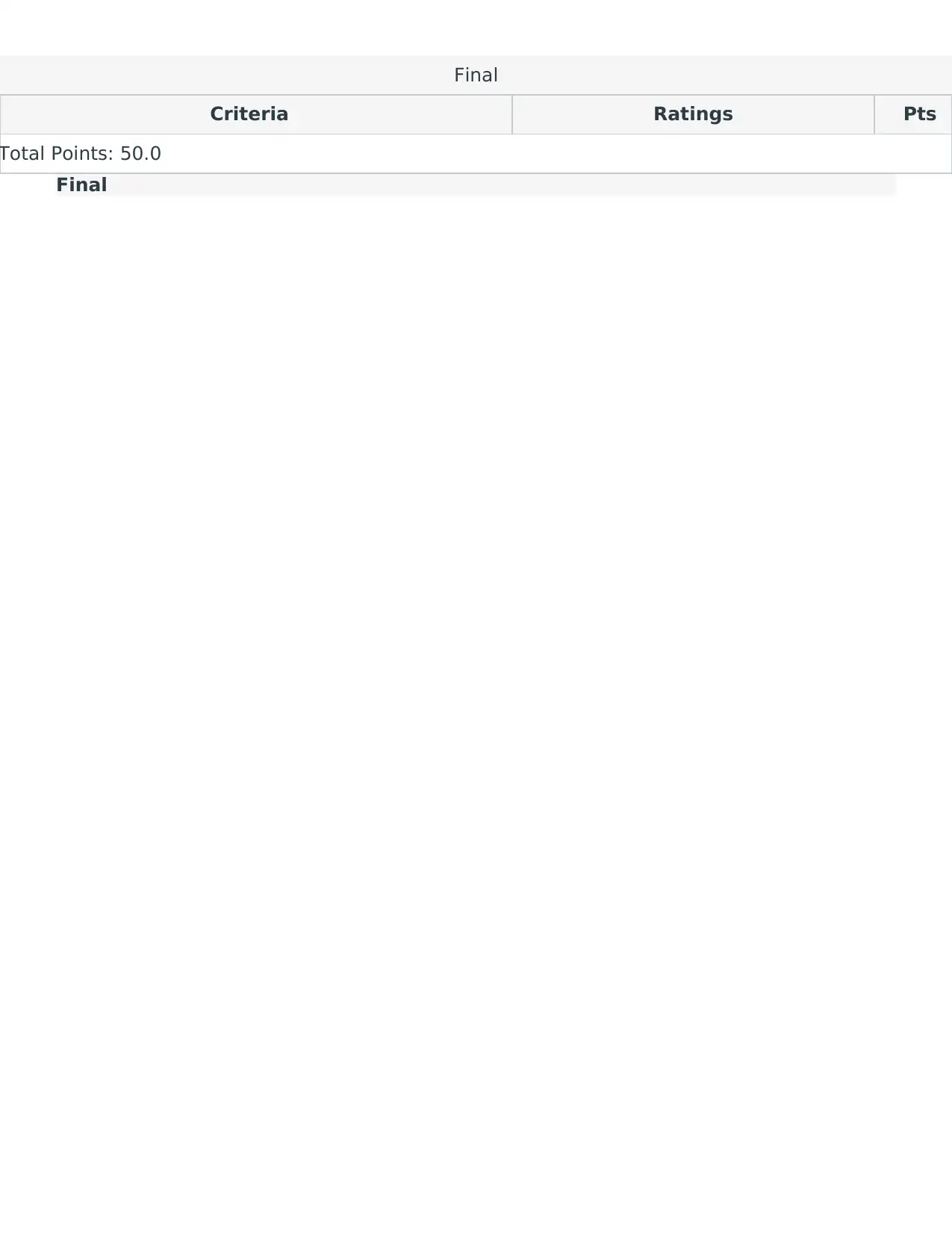
Final
Criteria Ratings Pts
Total Points: 50.0
Final
Criteria Ratings Pts
Total Points: 50.0
Final
1 out of 3

Your All-in-One AI-Powered Toolkit for Academic Success.
+13062052269
info@desklib.com
Available 24*7 on WhatsApp / Email
Unlock your academic potential
© 2024 | Zucol Services PVT LTD | All rights reserved.