Project Quality Manual for Concrete Trade - BSBPMG505A, Blue Mountains
VerifiedAdded on 2022/09/08
|20
|4655
|15
Report
AI Summary
This document is a comprehensive concrete trade quality manual prepared by a student for a construction project, likely the Blue Mountains TAFE project. It outlines a quality control system for concrete supply, placement, and finishing, referencing ISO 9000 and AS standards. The manual covers various aspects, including formwork (material quality, installation, storage, and inspection), reinforcement steel (quality, tolerances, storage, installation sequence, and inspection), and concrete (material quality, testing, handling, placing, finishing, curing techniques, tolerances, and non-conformance). The manual emphasizes the importance of a supportive team, regular updates, and detailed documentation, including management records, quality control documents, and electronic records. Key staff roles and responsibilities are defined, along with controlling documents, test and inspection plans, and checklists for monitoring. The report emphasizes adherence to specifications, quality control procedures, and the use of Australian Standards to ensure client satisfaction.
Contribute Materials
Your contribution can guide someone’s learning journey. Share your
documents today.
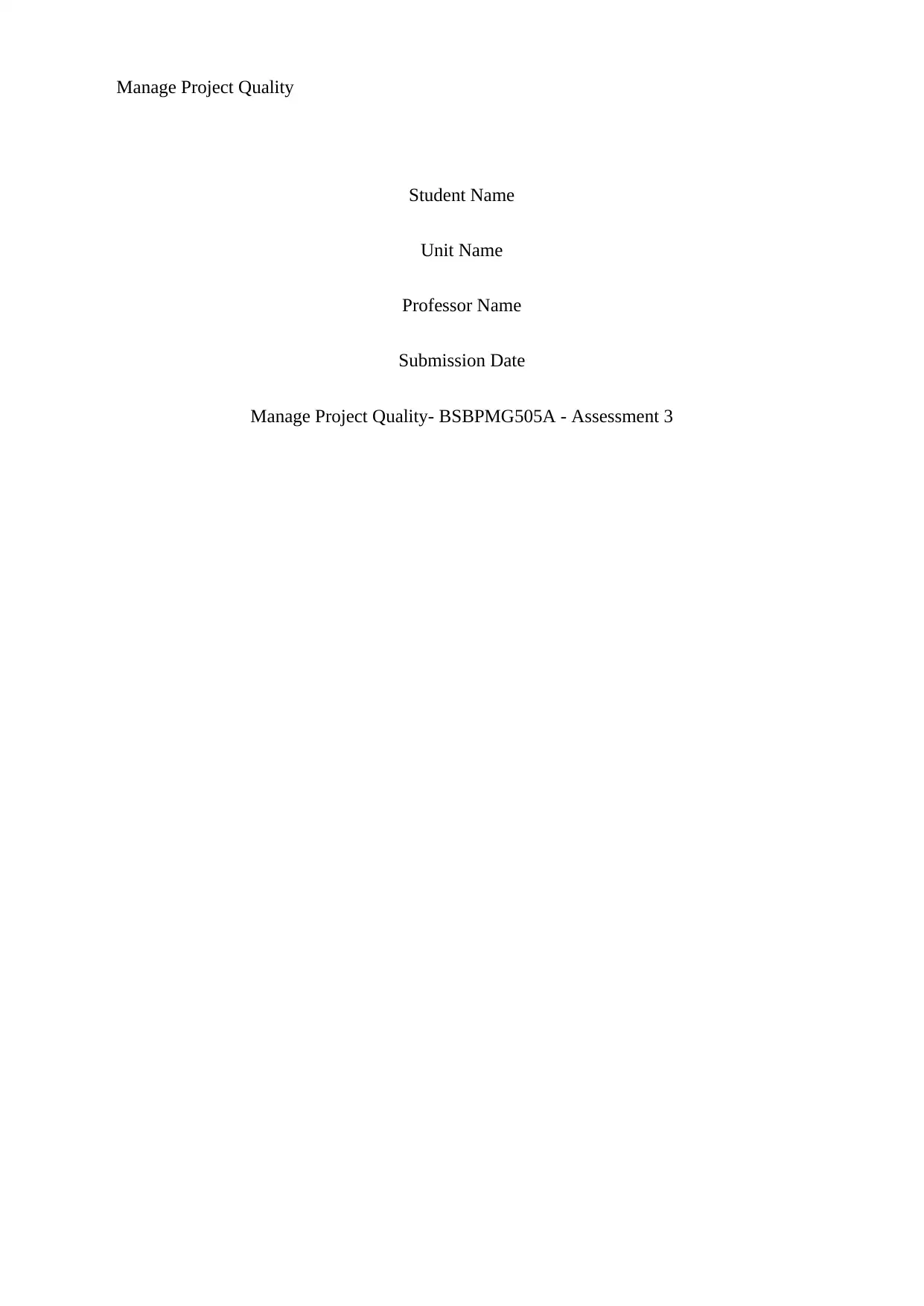
Manage Project Quality
Student Name
Unit Name
Professor Name
Submission Date
Manage Project Quality- BSBPMG505A - Assessment 3
Student Name
Unit Name
Professor Name
Submission Date
Manage Project Quality- BSBPMG505A - Assessment 3
Secure Best Marks with AI Grader
Need help grading? Try our AI Grader for instant feedback on your assignments.
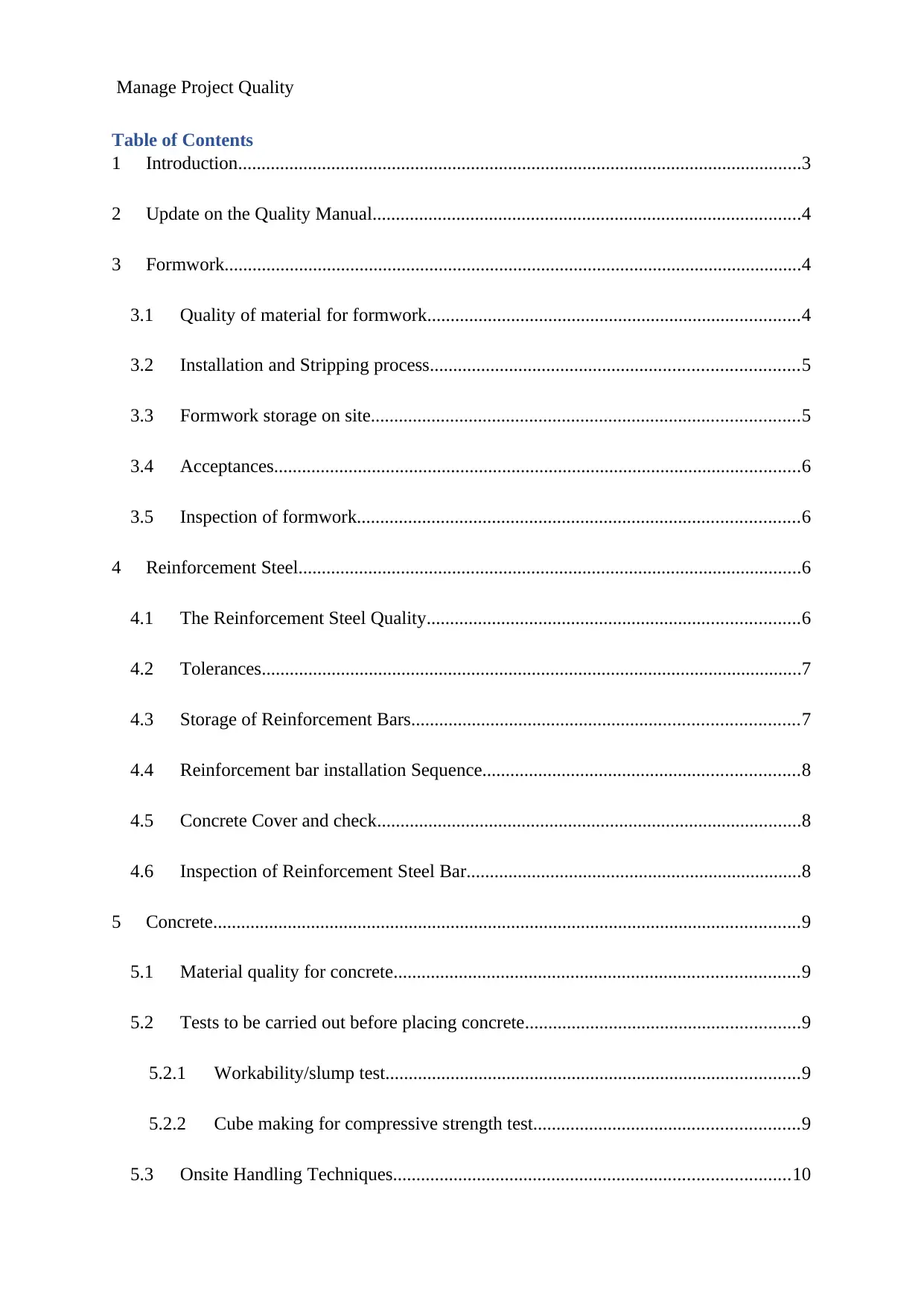
Manage Project Quality
Table of Contents
1 Introduction.........................................................................................................................3
2 Update on the Quality Manual............................................................................................4
3 Formwork............................................................................................................................4
3.1 Quality of material for formwork................................................................................4
3.2 Installation and Stripping process...............................................................................5
3.3 Formwork storage on site............................................................................................5
3.4 Acceptances.................................................................................................................6
3.5 Inspection of formwork...............................................................................................6
4 Reinforcement Steel............................................................................................................6
4.1 The Reinforcement Steel Quality................................................................................6
4.2 Tolerances....................................................................................................................7
4.3 Storage of Reinforcement Bars...................................................................................7
4.4 Reinforcement bar installation Sequence....................................................................8
4.5 Concrete Cover and check...........................................................................................8
4.6 Inspection of Reinforcement Steel Bar........................................................................8
5 Concrete..............................................................................................................................9
5.1 Material quality for concrete.......................................................................................9
5.2 Tests to be carried out before placing concrete...........................................................9
5.2.1 Workability/slump test.........................................................................................9
5.2.2 Cube making for compressive strength test.........................................................9
5.3 Onsite Handling Techniques.....................................................................................10
Table of Contents
1 Introduction.........................................................................................................................3
2 Update on the Quality Manual............................................................................................4
3 Formwork............................................................................................................................4
3.1 Quality of material for formwork................................................................................4
3.2 Installation and Stripping process...............................................................................5
3.3 Formwork storage on site............................................................................................5
3.4 Acceptances.................................................................................................................6
3.5 Inspection of formwork...............................................................................................6
4 Reinforcement Steel............................................................................................................6
4.1 The Reinforcement Steel Quality................................................................................6
4.2 Tolerances....................................................................................................................7
4.3 Storage of Reinforcement Bars...................................................................................7
4.4 Reinforcement bar installation Sequence....................................................................8
4.5 Concrete Cover and check...........................................................................................8
4.6 Inspection of Reinforcement Steel Bar........................................................................8
5 Concrete..............................................................................................................................9
5.1 Material quality for concrete.......................................................................................9
5.2 Tests to be carried out before placing concrete...........................................................9
5.2.1 Workability/slump test.........................................................................................9
5.2.2 Cube making for compressive strength test.........................................................9
5.3 Onsite Handling Techniques.....................................................................................10
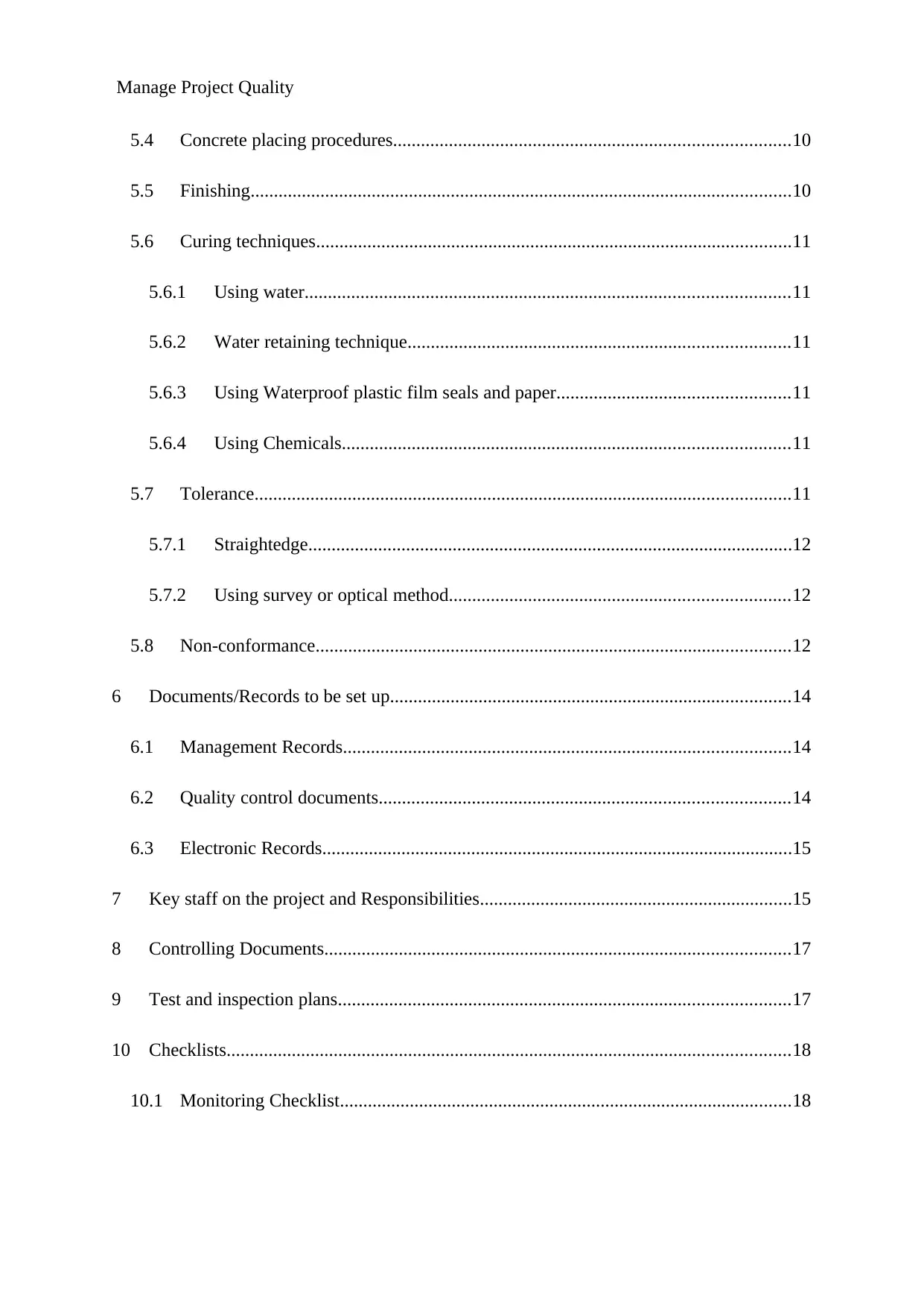
Manage Project Quality
5.4 Concrete placing procedures.....................................................................................10
5.5 Finishing....................................................................................................................10
5.6 Curing techniques......................................................................................................11
5.6.1 Using water........................................................................................................11
5.6.2 Water retaining technique..................................................................................11
5.6.3 Using Waterproof plastic film seals and paper..................................................11
5.6.4 Using Chemicals................................................................................................11
5.7 Tolerance...................................................................................................................11
5.7.1 Straightedge........................................................................................................12
5.7.2 Using survey or optical method.........................................................................12
5.8 Non-conformance......................................................................................................12
6 Documents/Records to be set up......................................................................................14
6.1 Management Records................................................................................................14
6.2 Quality control documents........................................................................................14
6.3 Electronic Records.....................................................................................................15
7 Key staff on the project and Responsibilities...................................................................15
8 Controlling Documents....................................................................................................17
9 Test and inspection plans.................................................................................................17
10 Checklists.........................................................................................................................18
10.1 Monitoring Checklist.................................................................................................18
5.4 Concrete placing procedures.....................................................................................10
5.5 Finishing....................................................................................................................10
5.6 Curing techniques......................................................................................................11
5.6.1 Using water........................................................................................................11
5.6.2 Water retaining technique..................................................................................11
5.6.3 Using Waterproof plastic film seals and paper..................................................11
5.6.4 Using Chemicals................................................................................................11
5.7 Tolerance...................................................................................................................11
5.7.1 Straightedge........................................................................................................12
5.7.2 Using survey or optical method.........................................................................12
5.8 Non-conformance......................................................................................................12
6 Documents/Records to be set up......................................................................................14
6.1 Management Records................................................................................................14
6.2 Quality control documents........................................................................................14
6.3 Electronic Records.....................................................................................................15
7 Key staff on the project and Responsibilities...................................................................15
8 Controlling Documents....................................................................................................17
9 Test and inspection plans.................................................................................................17
10 Checklists.........................................................................................................................18
10.1 Monitoring Checklist.................................................................................................18
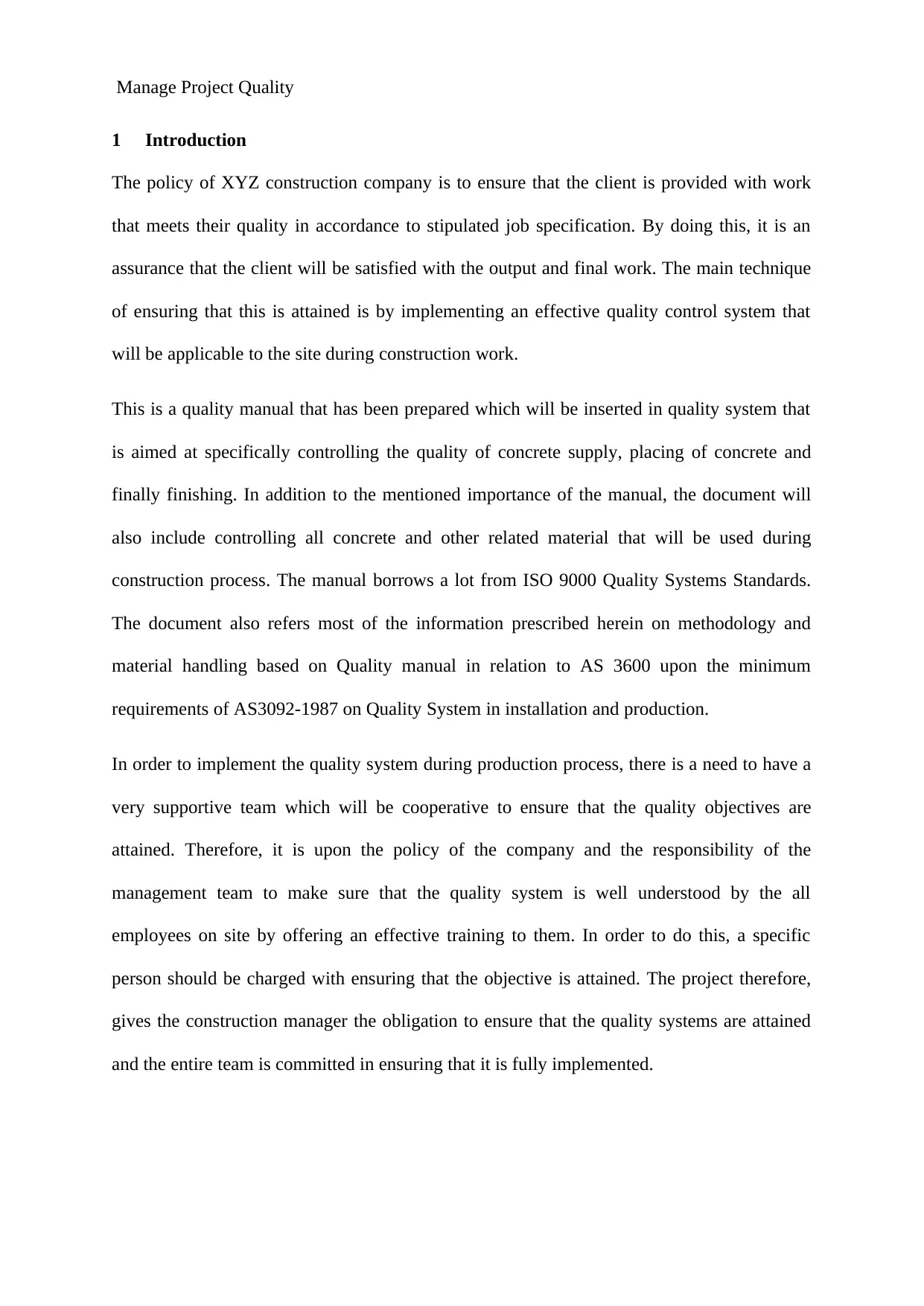
Manage Project Quality
1 Introduction
The policy of XYZ construction company is to ensure that the client is provided with work
that meets their quality in accordance to stipulated job specification. By doing this, it is an
assurance that the client will be satisfied with the output and final work. The main technique
of ensuring that this is attained is by implementing an effective quality control system that
will be applicable to the site during construction work.
This is a quality manual that has been prepared which will be inserted in quality system that
is aimed at specifically controlling the quality of concrete supply, placing of concrete and
finally finishing. In addition to the mentioned importance of the manual, the document will
also include controlling all concrete and other related material that will be used during
construction process. The manual borrows a lot from ISO 9000 Quality Systems Standards.
The document also refers most of the information prescribed herein on methodology and
material handling based on Quality manual in relation to AS 3600 upon the minimum
requirements of AS3092-1987 on Quality System in installation and production.
In order to implement the quality system during production process, there is a need to have a
very supportive team which will be cooperative to ensure that the quality objectives are
attained. Therefore, it is upon the policy of the company and the responsibility of the
management team to make sure that the quality system is well understood by the all
employees on site by offering an effective training to them. In order to do this, a specific
person should be charged with ensuring that the objective is attained. The project therefore,
gives the construction manager the obligation to ensure that the quality systems are attained
and the entire team is committed in ensuring that it is fully implemented.
1 Introduction
The policy of XYZ construction company is to ensure that the client is provided with work
that meets their quality in accordance to stipulated job specification. By doing this, it is an
assurance that the client will be satisfied with the output and final work. The main technique
of ensuring that this is attained is by implementing an effective quality control system that
will be applicable to the site during construction work.
This is a quality manual that has been prepared which will be inserted in quality system that
is aimed at specifically controlling the quality of concrete supply, placing of concrete and
finally finishing. In addition to the mentioned importance of the manual, the document will
also include controlling all concrete and other related material that will be used during
construction process. The manual borrows a lot from ISO 9000 Quality Systems Standards.
The document also refers most of the information prescribed herein on methodology and
material handling based on Quality manual in relation to AS 3600 upon the minimum
requirements of AS3092-1987 on Quality System in installation and production.
In order to implement the quality system during production process, there is a need to have a
very supportive team which will be cooperative to ensure that the quality objectives are
attained. Therefore, it is upon the policy of the company and the responsibility of the
management team to make sure that the quality system is well understood by the all
employees on site by offering an effective training to them. In order to do this, a specific
person should be charged with ensuring that the objective is attained. The project therefore,
gives the construction manager the obligation to ensure that the quality systems are attained
and the entire team is committed in ensuring that it is fully implemented.
Secure Best Marks with AI Grader
Need help grading? Try our AI Grader for instant feedback on your assignments.
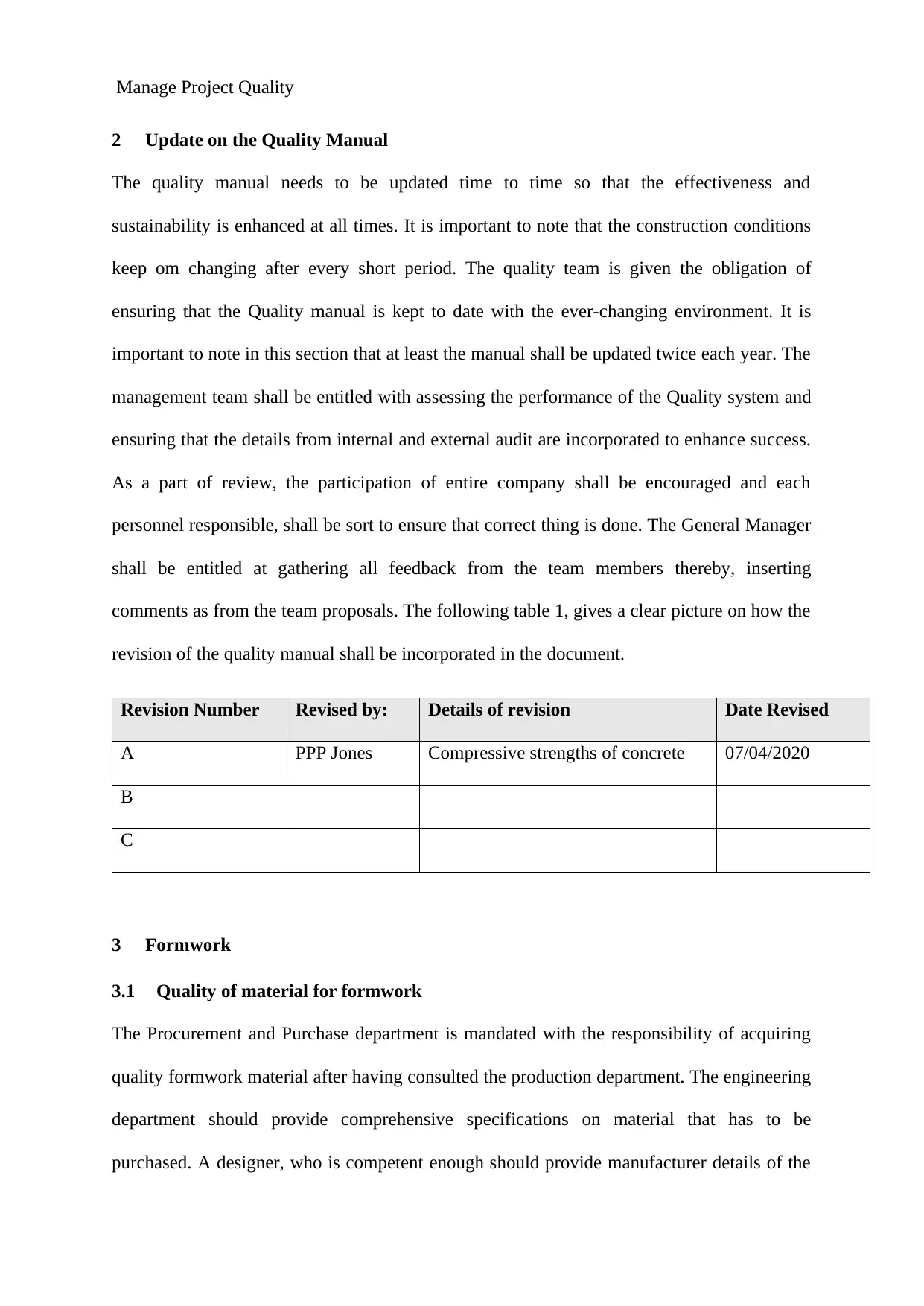
Manage Project Quality
2 Update on the Quality Manual
The quality manual needs to be updated time to time so that the effectiveness and
sustainability is enhanced at all times. It is important to note that the construction conditions
keep om changing after every short period. The quality team is given the obligation of
ensuring that the Quality manual is kept to date with the ever-changing environment. It is
important to note in this section that at least the manual shall be updated twice each year. The
management team shall be entitled with assessing the performance of the Quality system and
ensuring that the details from internal and external audit are incorporated to enhance success.
As a part of review, the participation of entire company shall be encouraged and each
personnel responsible, shall be sort to ensure that correct thing is done. The General Manager
shall be entitled at gathering all feedback from the team members thereby, inserting
comments as from the team proposals. The following table 1, gives a clear picture on how the
revision of the quality manual shall be incorporated in the document.
Revision Number Revised by: Details of revision Date Revised
A PPP Jones Compressive strengths of concrete 07/04/2020
B
C
3 Formwork
3.1 Quality of material for formwork
The Procurement and Purchase department is mandated with the responsibility of acquiring
quality formwork material after having consulted the production department. The engineering
department should provide comprehensive specifications on material that has to be
purchased. A designer, who is competent enough should provide manufacturer details of the
2 Update on the Quality Manual
The quality manual needs to be updated time to time so that the effectiveness and
sustainability is enhanced at all times. It is important to note that the construction conditions
keep om changing after every short period. The quality team is given the obligation of
ensuring that the Quality manual is kept to date with the ever-changing environment. It is
important to note in this section that at least the manual shall be updated twice each year. The
management team shall be entitled with assessing the performance of the Quality system and
ensuring that the details from internal and external audit are incorporated to enhance success.
As a part of review, the participation of entire company shall be encouraged and each
personnel responsible, shall be sort to ensure that correct thing is done. The General Manager
shall be entitled at gathering all feedback from the team members thereby, inserting
comments as from the team proposals. The following table 1, gives a clear picture on how the
revision of the quality manual shall be incorporated in the document.
Revision Number Revised by: Details of revision Date Revised
A PPP Jones Compressive strengths of concrete 07/04/2020
B
C
3 Formwork
3.1 Quality of material for formwork
The Procurement and Purchase department is mandated with the responsibility of acquiring
quality formwork material after having consulted the production department. The engineering
department should provide comprehensive specifications on material that has to be
purchased. A designer, who is competent enough should provide manufacturer details of the
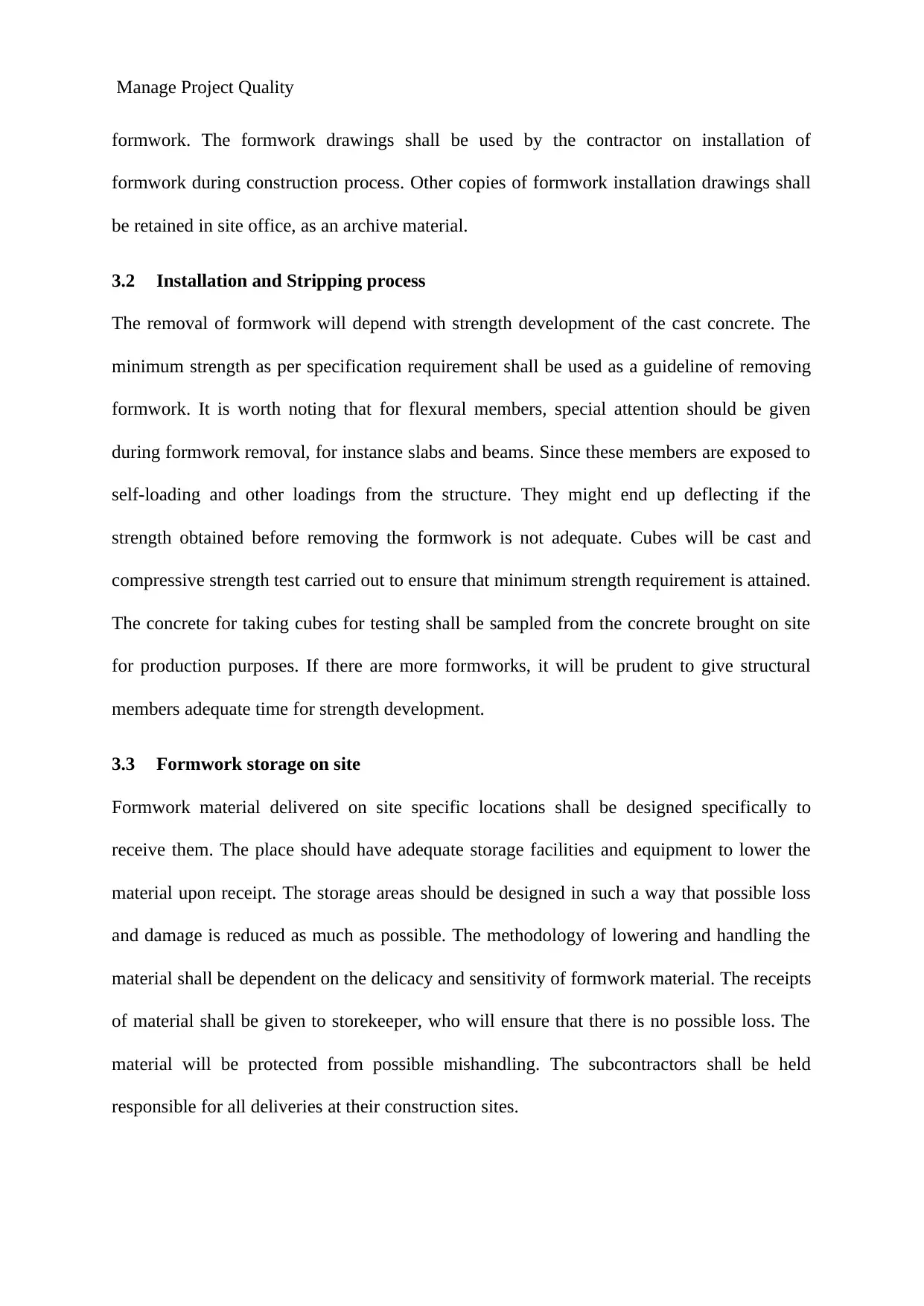
Manage Project Quality
formwork. The formwork drawings shall be used by the contractor on installation of
formwork during construction process. Other copies of formwork installation drawings shall
be retained in site office, as an archive material.
3.2 Installation and Stripping process
The removal of formwork will depend with strength development of the cast concrete. The
minimum strength as per specification requirement shall be used as a guideline of removing
formwork. It is worth noting that for flexural members, special attention should be given
during formwork removal, for instance slabs and beams. Since these members are exposed to
self-loading and other loadings from the structure. They might end up deflecting if the
strength obtained before removing the formwork is not adequate. Cubes will be cast and
compressive strength test carried out to ensure that minimum strength requirement is attained.
The concrete for taking cubes for testing shall be sampled from the concrete brought on site
for production purposes. If there are more formworks, it will be prudent to give structural
members adequate time for strength development.
3.3 Formwork storage on site
Formwork material delivered on site specific locations shall be designed specifically to
receive them. The place should have adequate storage facilities and equipment to lower the
material upon receipt. The storage areas should be designed in such a way that possible loss
and damage is reduced as much as possible. The methodology of lowering and handling the
material shall be dependent on the delicacy and sensitivity of formwork material. The receipts
of material shall be given to storekeeper, who will ensure that there is no possible loss. The
material will be protected from possible mishandling. The subcontractors shall be held
responsible for all deliveries at their construction sites.
formwork. The formwork drawings shall be used by the contractor on installation of
formwork during construction process. Other copies of formwork installation drawings shall
be retained in site office, as an archive material.
3.2 Installation and Stripping process
The removal of formwork will depend with strength development of the cast concrete. The
minimum strength as per specification requirement shall be used as a guideline of removing
formwork. It is worth noting that for flexural members, special attention should be given
during formwork removal, for instance slabs and beams. Since these members are exposed to
self-loading and other loadings from the structure. They might end up deflecting if the
strength obtained before removing the formwork is not adequate. Cubes will be cast and
compressive strength test carried out to ensure that minimum strength requirement is attained.
The concrete for taking cubes for testing shall be sampled from the concrete brought on site
for production purposes. If there are more formworks, it will be prudent to give structural
members adequate time for strength development.
3.3 Formwork storage on site
Formwork material delivered on site specific locations shall be designed specifically to
receive them. The place should have adequate storage facilities and equipment to lower the
material upon receipt. The storage areas should be designed in such a way that possible loss
and damage is reduced as much as possible. The methodology of lowering and handling the
material shall be dependent on the delicacy and sensitivity of formwork material. The receipts
of material shall be given to storekeeper, who will ensure that there is no possible loss. The
material will be protected from possible mishandling. The subcontractors shall be held
responsible for all deliveries at their construction sites.
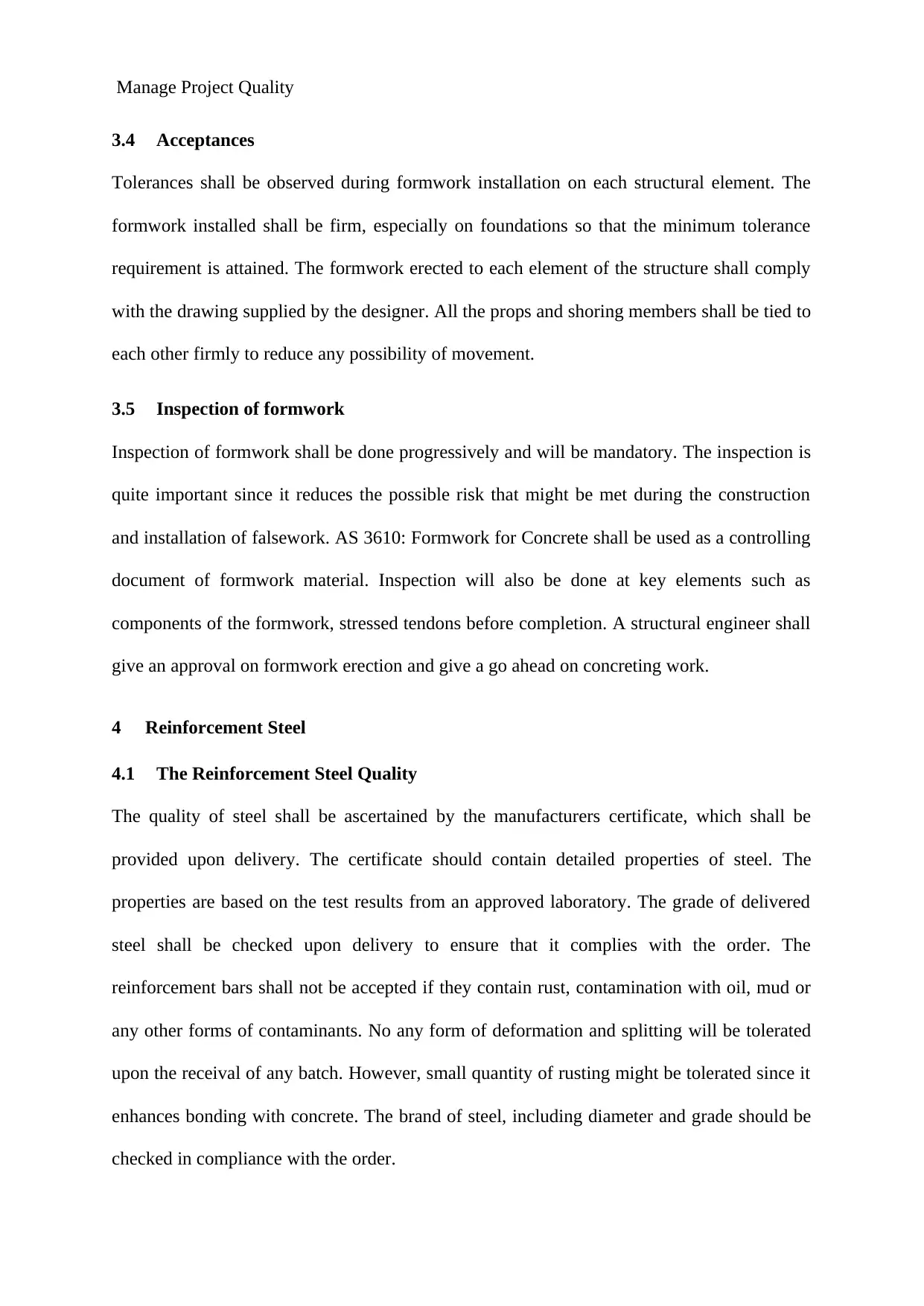
Manage Project Quality
3.4 Acceptances
Tolerances shall be observed during formwork installation on each structural element. The
formwork installed shall be firm, especially on foundations so that the minimum tolerance
requirement is attained. The formwork erected to each element of the structure shall comply
with the drawing supplied by the designer. All the props and shoring members shall be tied to
each other firmly to reduce any possibility of movement.
3.5 Inspection of formwork
Inspection of formwork shall be done progressively and will be mandatory. The inspection is
quite important since it reduces the possible risk that might be met during the construction
and installation of falsework. AS 3610: Formwork for Concrete shall be used as a controlling
document of formwork material. Inspection will also be done at key elements such as
components of the formwork, stressed tendons before completion. A structural engineer shall
give an approval on formwork erection and give a go ahead on concreting work.
4 Reinforcement Steel
4.1 The Reinforcement Steel Quality
The quality of steel shall be ascertained by the manufacturers certificate, which shall be
provided upon delivery. The certificate should contain detailed properties of steel. The
properties are based on the test results from an approved laboratory. The grade of delivered
steel shall be checked upon delivery to ensure that it complies with the order. The
reinforcement bars shall not be accepted if they contain rust, contamination with oil, mud or
any other forms of contaminants. No any form of deformation and splitting will be tolerated
upon the receival of any batch. However, small quantity of rusting might be tolerated since it
enhances bonding with concrete. The brand of steel, including diameter and grade should be
checked in compliance with the order.
3.4 Acceptances
Tolerances shall be observed during formwork installation on each structural element. The
formwork installed shall be firm, especially on foundations so that the minimum tolerance
requirement is attained. The formwork erected to each element of the structure shall comply
with the drawing supplied by the designer. All the props and shoring members shall be tied to
each other firmly to reduce any possibility of movement.
3.5 Inspection of formwork
Inspection of formwork shall be done progressively and will be mandatory. The inspection is
quite important since it reduces the possible risk that might be met during the construction
and installation of falsework. AS 3610: Formwork for Concrete shall be used as a controlling
document of formwork material. Inspection will also be done at key elements such as
components of the formwork, stressed tendons before completion. A structural engineer shall
give an approval on formwork erection and give a go ahead on concreting work.
4 Reinforcement Steel
4.1 The Reinforcement Steel Quality
The quality of steel shall be ascertained by the manufacturers certificate, which shall be
provided upon delivery. The certificate should contain detailed properties of steel. The
properties are based on the test results from an approved laboratory. The grade of delivered
steel shall be checked upon delivery to ensure that it complies with the order. The
reinforcement bars shall not be accepted if they contain rust, contamination with oil, mud or
any other forms of contaminants. No any form of deformation and splitting will be tolerated
upon the receival of any batch. However, small quantity of rusting might be tolerated since it
enhances bonding with concrete. The brand of steel, including diameter and grade should be
checked in compliance with the order.
Paraphrase This Document
Need a fresh take? Get an instant paraphrase of this document with our AI Paraphraser
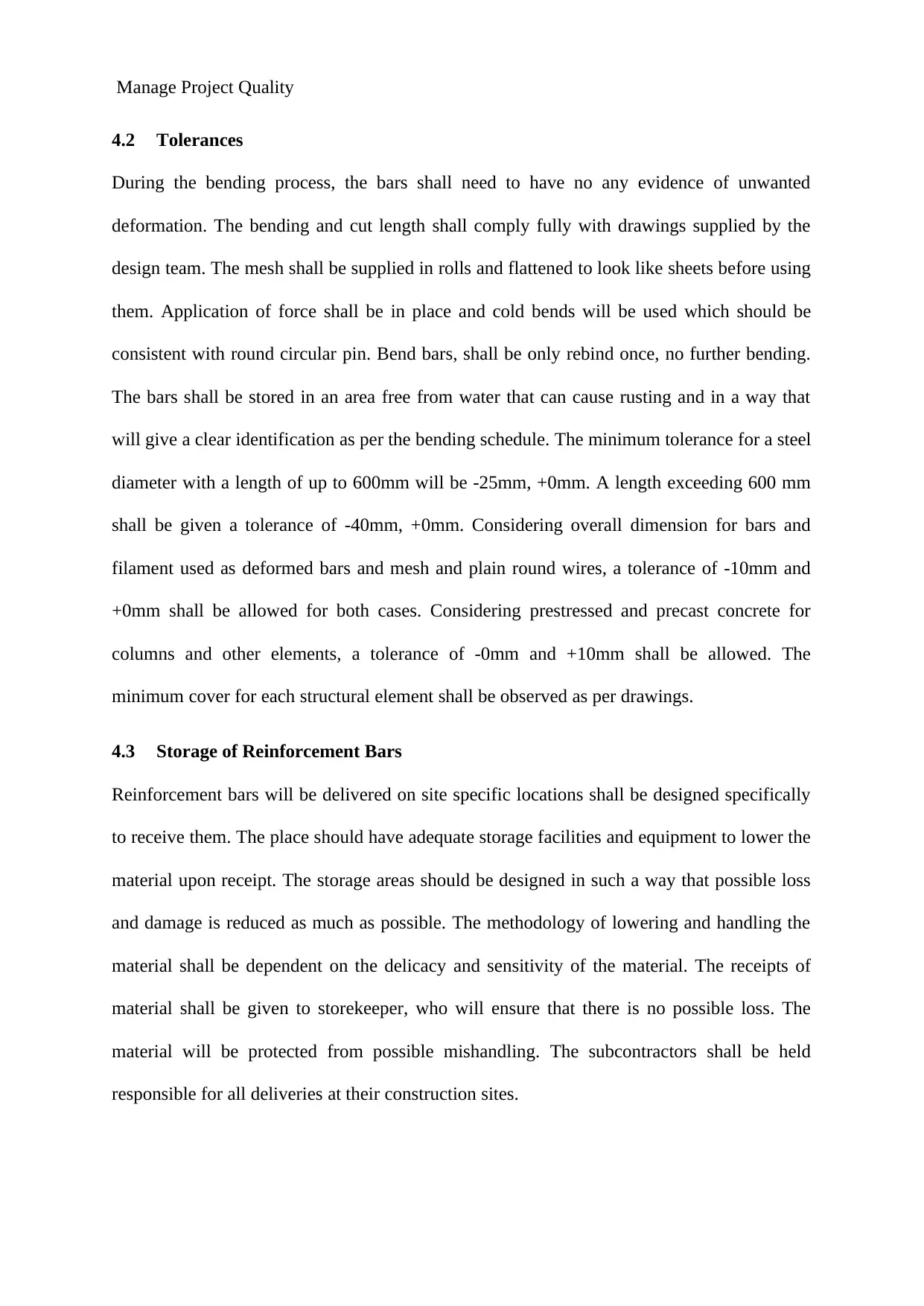
Manage Project Quality
4.2 Tolerances
During the bending process, the bars shall need to have no any evidence of unwanted
deformation. The bending and cut length shall comply fully with drawings supplied by the
design team. The mesh shall be supplied in rolls and flattened to look like sheets before using
them. Application of force shall be in place and cold bends will be used which should be
consistent with round circular pin. Bend bars, shall be only rebind once, no further bending.
The bars shall be stored in an area free from water that can cause rusting and in a way that
will give a clear identification as per the bending schedule. The minimum tolerance for a steel
diameter with a length of up to 600mm will be -25mm, +0mm. A length exceeding 600 mm
shall be given a tolerance of -40mm, +0mm. Considering overall dimension for bars and
filament used as deformed bars and mesh and plain round wires, a tolerance of -10mm and
+0mm shall be allowed for both cases. Considering prestressed and precast concrete for
columns and other elements, a tolerance of -0mm and +10mm shall be allowed. The
minimum cover for each structural element shall be observed as per drawings.
4.3 Storage of Reinforcement Bars
Reinforcement bars will be delivered on site specific locations shall be designed specifically
to receive them. The place should have adequate storage facilities and equipment to lower the
material upon receipt. The storage areas should be designed in such a way that possible loss
and damage is reduced as much as possible. The methodology of lowering and handling the
material shall be dependent on the delicacy and sensitivity of the material. The receipts of
material shall be given to storekeeper, who will ensure that there is no possible loss. The
material will be protected from possible mishandling. The subcontractors shall be held
responsible for all deliveries at their construction sites.
4.2 Tolerances
During the bending process, the bars shall need to have no any evidence of unwanted
deformation. The bending and cut length shall comply fully with drawings supplied by the
design team. The mesh shall be supplied in rolls and flattened to look like sheets before using
them. Application of force shall be in place and cold bends will be used which should be
consistent with round circular pin. Bend bars, shall be only rebind once, no further bending.
The bars shall be stored in an area free from water that can cause rusting and in a way that
will give a clear identification as per the bending schedule. The minimum tolerance for a steel
diameter with a length of up to 600mm will be -25mm, +0mm. A length exceeding 600 mm
shall be given a tolerance of -40mm, +0mm. Considering overall dimension for bars and
filament used as deformed bars and mesh and plain round wires, a tolerance of -10mm and
+0mm shall be allowed for both cases. Considering prestressed and precast concrete for
columns and other elements, a tolerance of -0mm and +10mm shall be allowed. The
minimum cover for each structural element shall be observed as per drawings.
4.3 Storage of Reinforcement Bars
Reinforcement bars will be delivered on site specific locations shall be designed specifically
to receive them. The place should have adequate storage facilities and equipment to lower the
material upon receipt. The storage areas should be designed in such a way that possible loss
and damage is reduced as much as possible. The methodology of lowering and handling the
material shall be dependent on the delicacy and sensitivity of the material. The receipts of
material shall be given to storekeeper, who will ensure that there is no possible loss. The
material will be protected from possible mishandling. The subcontractors shall be held
responsible for all deliveries at their construction sites.
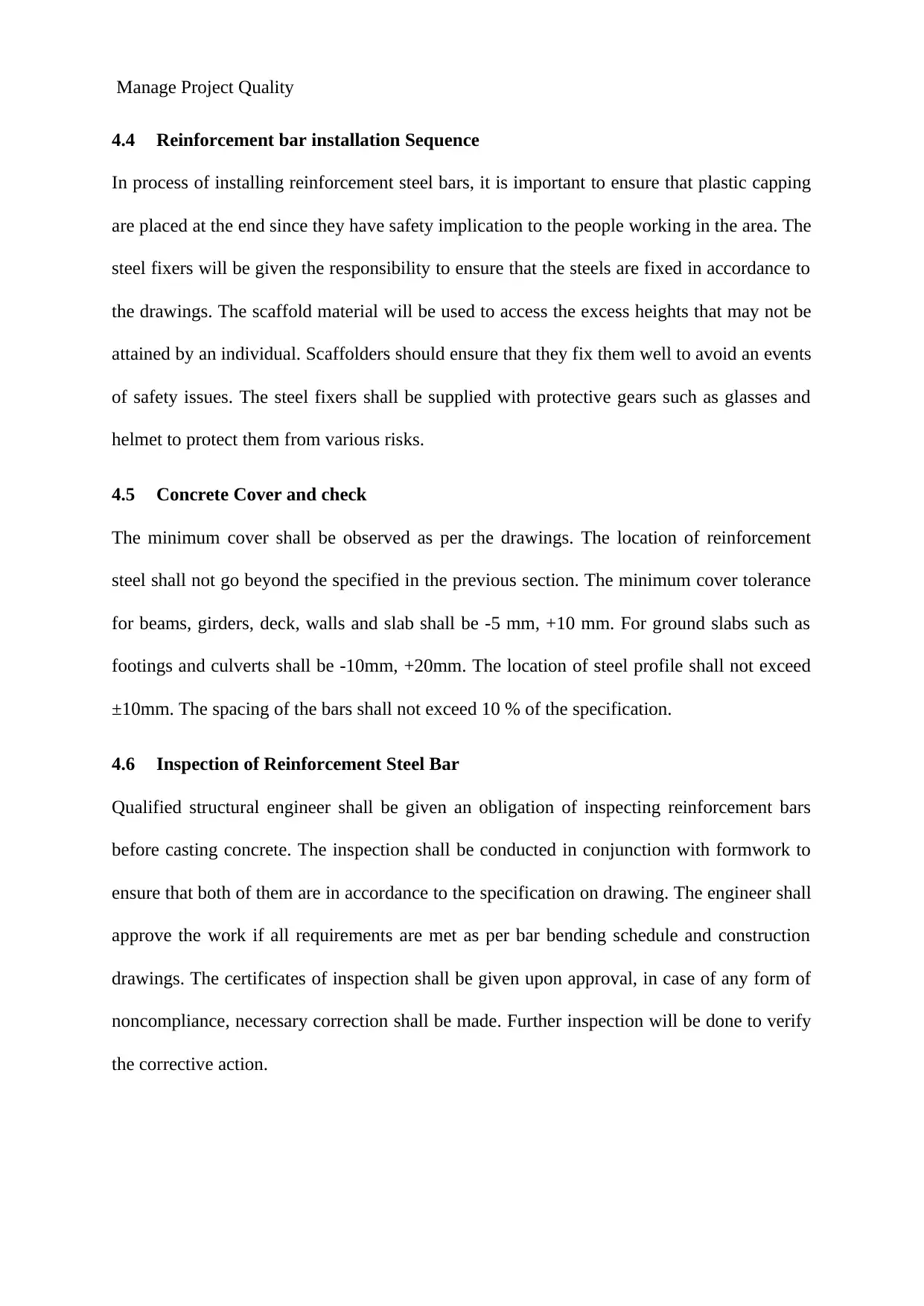
Manage Project Quality
4.4 Reinforcement bar installation Sequence
In process of installing reinforcement steel bars, it is important to ensure that plastic capping
are placed at the end since they have safety implication to the people working in the area. The
steel fixers will be given the responsibility to ensure that the steels are fixed in accordance to
the drawings. The scaffold material will be used to access the excess heights that may not be
attained by an individual. Scaffolders should ensure that they fix them well to avoid an events
of safety issues. The steel fixers shall be supplied with protective gears such as glasses and
helmet to protect them from various risks.
4.5 Concrete Cover and check
The minimum cover shall be observed as per the drawings. The location of reinforcement
steel shall not go beyond the specified in the previous section. The minimum cover tolerance
for beams, girders, deck, walls and slab shall be -5 mm, +10 mm. For ground slabs such as
footings and culverts shall be -10mm, +20mm. The location of steel profile shall not exceed
±10mm. The spacing of the bars shall not exceed 10 % of the specification.
4.6 Inspection of Reinforcement Steel Bar
Qualified structural engineer shall be given an obligation of inspecting reinforcement bars
before casting concrete. The inspection shall be conducted in conjunction with formwork to
ensure that both of them are in accordance to the specification on drawing. The engineer shall
approve the work if all requirements are met as per bar bending schedule and construction
drawings. The certificates of inspection shall be given upon approval, in case of any form of
noncompliance, necessary correction shall be made. Further inspection will be done to verify
the corrective action.
4.4 Reinforcement bar installation Sequence
In process of installing reinforcement steel bars, it is important to ensure that plastic capping
are placed at the end since they have safety implication to the people working in the area. The
steel fixers will be given the responsibility to ensure that the steels are fixed in accordance to
the drawings. The scaffold material will be used to access the excess heights that may not be
attained by an individual. Scaffolders should ensure that they fix them well to avoid an events
of safety issues. The steel fixers shall be supplied with protective gears such as glasses and
helmet to protect them from various risks.
4.5 Concrete Cover and check
The minimum cover shall be observed as per the drawings. The location of reinforcement
steel shall not go beyond the specified in the previous section. The minimum cover tolerance
for beams, girders, deck, walls and slab shall be -5 mm, +10 mm. For ground slabs such as
footings and culverts shall be -10mm, +20mm. The location of steel profile shall not exceed
±10mm. The spacing of the bars shall not exceed 10 % of the specification.
4.6 Inspection of Reinforcement Steel Bar
Qualified structural engineer shall be given an obligation of inspecting reinforcement bars
before casting concrete. The inspection shall be conducted in conjunction with formwork to
ensure that both of them are in accordance to the specification on drawing. The engineer shall
approve the work if all requirements are met as per bar bending schedule and construction
drawings. The certificates of inspection shall be given upon approval, in case of any form of
noncompliance, necessary correction shall be made. Further inspection will be done to verify
the corrective action.
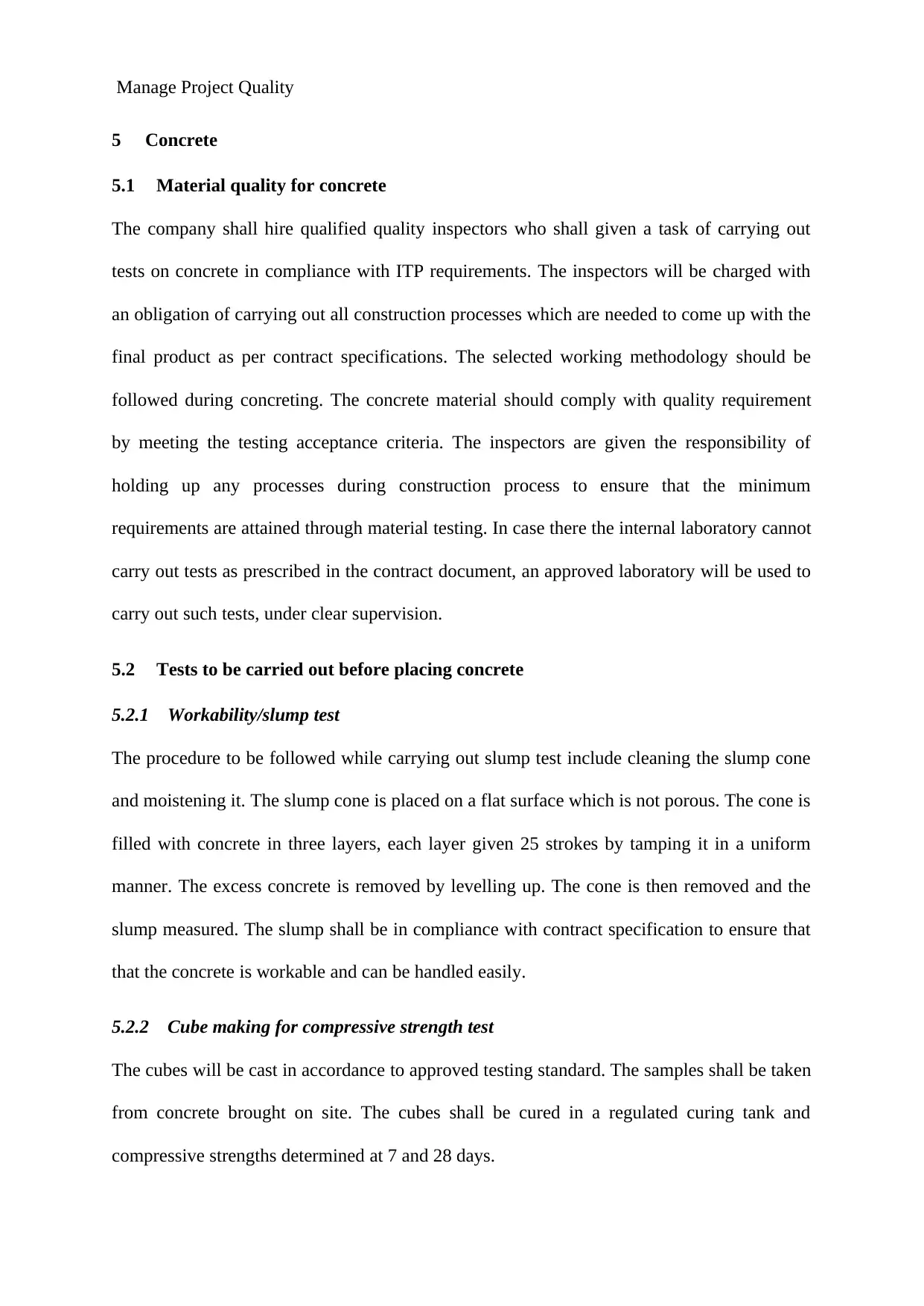
Manage Project Quality
5 Concrete
5.1 Material quality for concrete
The company shall hire qualified quality inspectors who shall given a task of carrying out
tests on concrete in compliance with ITP requirements. The inspectors will be charged with
an obligation of carrying out all construction processes which are needed to come up with the
final product as per contract specifications. The selected working methodology should be
followed during concreting. The concrete material should comply with quality requirement
by meeting the testing acceptance criteria. The inspectors are given the responsibility of
holding up any processes during construction process to ensure that the minimum
requirements are attained through material testing. In case there the internal laboratory cannot
carry out tests as prescribed in the contract document, an approved laboratory will be used to
carry out such tests, under clear supervision.
5.2 Tests to be carried out before placing concrete
5.2.1 Workability/slump test
The procedure to be followed while carrying out slump test include cleaning the slump cone
and moistening it. The slump cone is placed on a flat surface which is not porous. The cone is
filled with concrete in three layers, each layer given 25 strokes by tamping it in a uniform
manner. The excess concrete is removed by levelling up. The cone is then removed and the
slump measured. The slump shall be in compliance with contract specification to ensure that
that the concrete is workable and can be handled easily.
5.2.2 Cube making for compressive strength test
The cubes will be cast in accordance to approved testing standard. The samples shall be taken
from concrete brought on site. The cubes shall be cured in a regulated curing tank and
compressive strengths determined at 7 and 28 days.
5 Concrete
5.1 Material quality for concrete
The company shall hire qualified quality inspectors who shall given a task of carrying out
tests on concrete in compliance with ITP requirements. The inspectors will be charged with
an obligation of carrying out all construction processes which are needed to come up with the
final product as per contract specifications. The selected working methodology should be
followed during concreting. The concrete material should comply with quality requirement
by meeting the testing acceptance criteria. The inspectors are given the responsibility of
holding up any processes during construction process to ensure that the minimum
requirements are attained through material testing. In case there the internal laboratory cannot
carry out tests as prescribed in the contract document, an approved laboratory will be used to
carry out such tests, under clear supervision.
5.2 Tests to be carried out before placing concrete
5.2.1 Workability/slump test
The procedure to be followed while carrying out slump test include cleaning the slump cone
and moistening it. The slump cone is placed on a flat surface which is not porous. The cone is
filled with concrete in three layers, each layer given 25 strokes by tamping it in a uniform
manner. The excess concrete is removed by levelling up. The cone is then removed and the
slump measured. The slump shall be in compliance with contract specification to ensure that
that the concrete is workable and can be handled easily.
5.2.2 Cube making for compressive strength test
The cubes will be cast in accordance to approved testing standard. The samples shall be taken
from concrete brought on site. The cubes shall be cured in a regulated curing tank and
compressive strengths determined at 7 and 28 days.
Secure Best Marks with AI Grader
Need help grading? Try our AI Grader for instant feedback on your assignments.
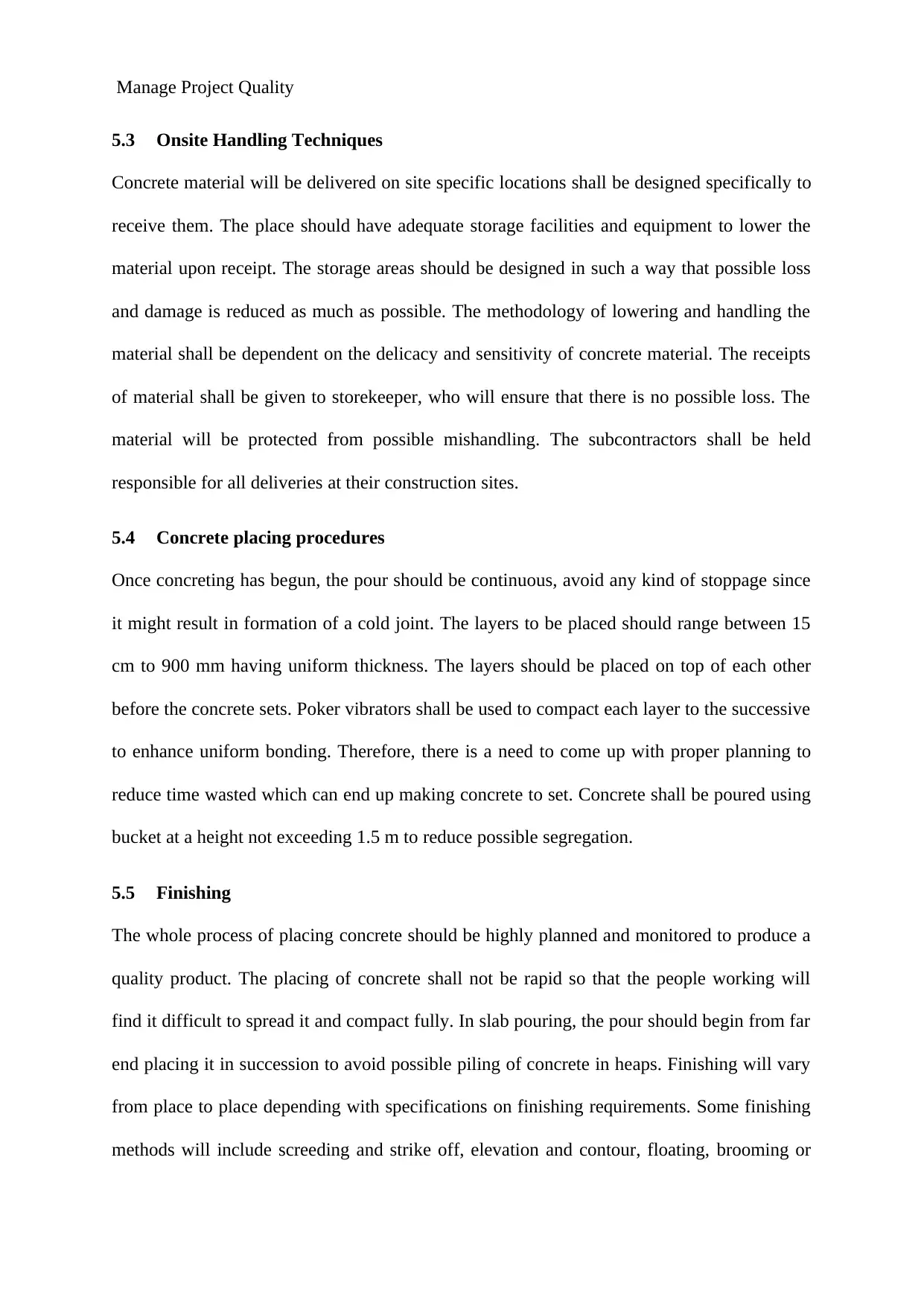
Manage Project Quality
5.3 Onsite Handling Techniques
Concrete material will be delivered on site specific locations shall be designed specifically to
receive them. The place should have adequate storage facilities and equipment to lower the
material upon receipt. The storage areas should be designed in such a way that possible loss
and damage is reduced as much as possible. The methodology of lowering and handling the
material shall be dependent on the delicacy and sensitivity of concrete material. The receipts
of material shall be given to storekeeper, who will ensure that there is no possible loss. The
material will be protected from possible mishandling. The subcontractors shall be held
responsible for all deliveries at their construction sites.
5.4 Concrete placing procedures
Once concreting has begun, the pour should be continuous, avoid any kind of stoppage since
it might result in formation of a cold joint. The layers to be placed should range between 15
cm to 900 mm having uniform thickness. The layers should be placed on top of each other
before the concrete sets. Poker vibrators shall be used to compact each layer to the successive
to enhance uniform bonding. Therefore, there is a need to come up with proper planning to
reduce time wasted which can end up making concrete to set. Concrete shall be poured using
bucket at a height not exceeding 1.5 m to reduce possible segregation.
5.5 Finishing
The whole process of placing concrete should be highly planned and monitored to produce a
quality product. The placing of concrete shall not be rapid so that the people working will
find it difficult to spread it and compact fully. In slab pouring, the pour should begin from far
end placing it in succession to avoid possible piling of concrete in heaps. Finishing will vary
from place to place depending with specifications on finishing requirements. Some finishing
methods will include screeding and strike off, elevation and contour, floating, brooming or
5.3 Onsite Handling Techniques
Concrete material will be delivered on site specific locations shall be designed specifically to
receive them. The place should have adequate storage facilities and equipment to lower the
material upon receipt. The storage areas should be designed in such a way that possible loss
and damage is reduced as much as possible. The methodology of lowering and handling the
material shall be dependent on the delicacy and sensitivity of concrete material. The receipts
of material shall be given to storekeeper, who will ensure that there is no possible loss. The
material will be protected from possible mishandling. The subcontractors shall be held
responsible for all deliveries at their construction sites.
5.4 Concrete placing procedures
Once concreting has begun, the pour should be continuous, avoid any kind of stoppage since
it might result in formation of a cold joint. The layers to be placed should range between 15
cm to 900 mm having uniform thickness. The layers should be placed on top of each other
before the concrete sets. Poker vibrators shall be used to compact each layer to the successive
to enhance uniform bonding. Therefore, there is a need to come up with proper planning to
reduce time wasted which can end up making concrete to set. Concrete shall be poured using
bucket at a height not exceeding 1.5 m to reduce possible segregation.
5.5 Finishing
The whole process of placing concrete should be highly planned and monitored to produce a
quality product. The placing of concrete shall not be rapid so that the people working will
find it difficult to spread it and compact fully. In slab pouring, the pour should begin from far
end placing it in succession to avoid possible piling of concrete in heaps. Finishing will vary
from place to place depending with specifications on finishing requirements. Some finishing
methods will include screeding and strike off, elevation and contour, floating, brooming or
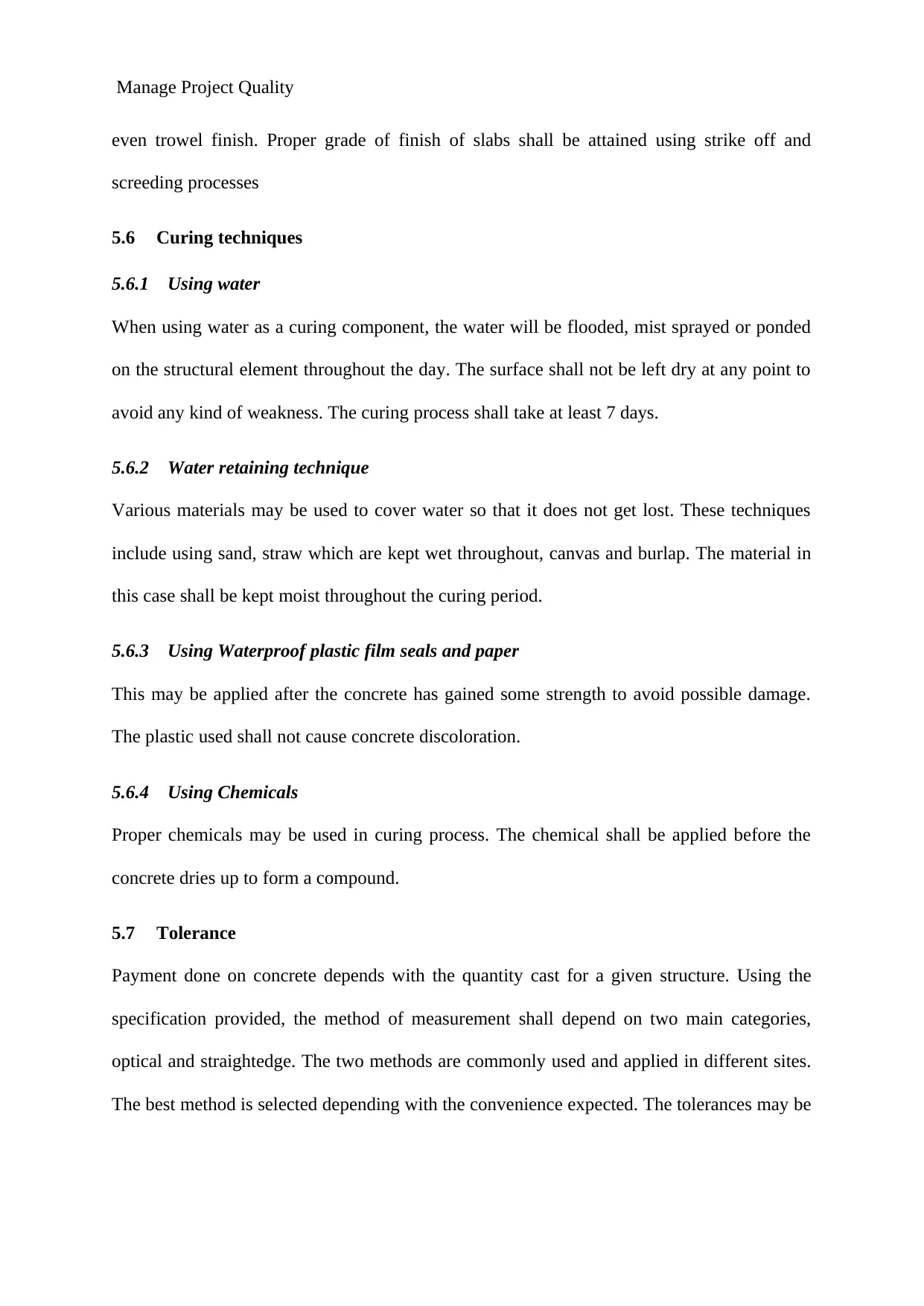
Manage Project Quality
even trowel finish. Proper grade of finish of slabs shall be attained using strike off and
screeding processes
5.6 Curing techniques
5.6.1 Using water
When using water as a curing component, the water will be flooded, mist sprayed or ponded
on the structural element throughout the day. The surface shall not be left dry at any point to
avoid any kind of weakness. The curing process shall take at least 7 days.
5.6.2 Water retaining technique
Various materials may be used to cover water so that it does not get lost. These techniques
include using sand, straw which are kept wet throughout, canvas and burlap. The material in
this case shall be kept moist throughout the curing period.
5.6.3 Using Waterproof plastic film seals and paper
This may be applied after the concrete has gained some strength to avoid possible damage.
The plastic used shall not cause concrete discoloration.
5.6.4 Using Chemicals
Proper chemicals may be used in curing process. The chemical shall be applied before the
concrete dries up to form a compound.
5.7 Tolerance
Payment done on concrete depends with the quantity cast for a given structure. Using the
specification provided, the method of measurement shall depend on two main categories,
optical and straightedge. The two methods are commonly used and applied in different sites.
The best method is selected depending with the convenience expected. The tolerances may be
even trowel finish. Proper grade of finish of slabs shall be attained using strike off and
screeding processes
5.6 Curing techniques
5.6.1 Using water
When using water as a curing component, the water will be flooded, mist sprayed or ponded
on the structural element throughout the day. The surface shall not be left dry at any point to
avoid any kind of weakness. The curing process shall take at least 7 days.
5.6.2 Water retaining technique
Various materials may be used to cover water so that it does not get lost. These techniques
include using sand, straw which are kept wet throughout, canvas and burlap. The material in
this case shall be kept moist throughout the curing period.
5.6.3 Using Waterproof plastic film seals and paper
This may be applied after the concrete has gained some strength to avoid possible damage.
The plastic used shall not cause concrete discoloration.
5.6.4 Using Chemicals
Proper chemicals may be used in curing process. The chemical shall be applied before the
concrete dries up to form a compound.
5.7 Tolerance
Payment done on concrete depends with the quantity cast for a given structure. Using the
specification provided, the method of measurement shall depend on two main categories,
optical and straightedge. The two methods are commonly used and applied in different sites.
The best method is selected depending with the convenience expected. The tolerances may be
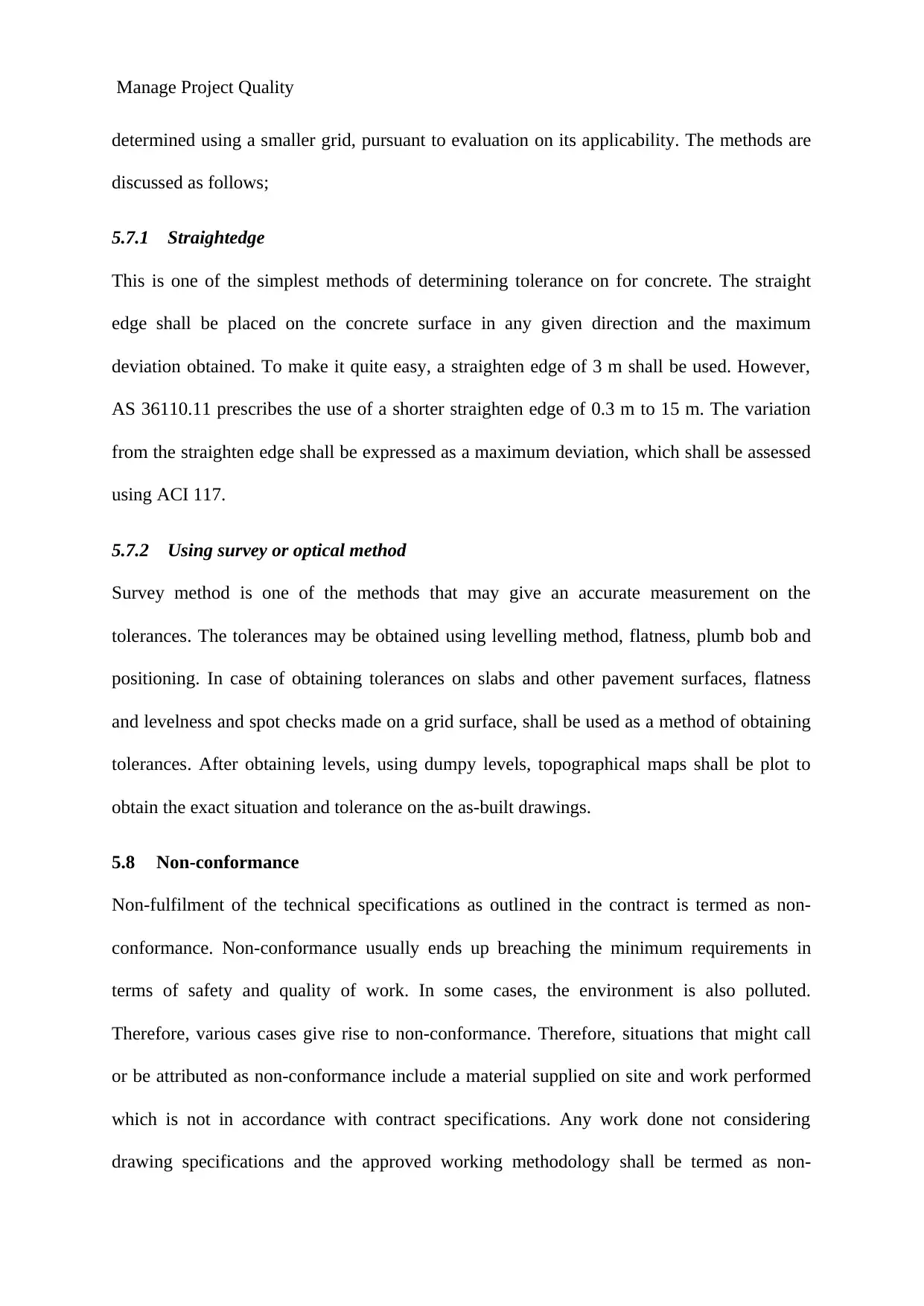
Manage Project Quality
determined using a smaller grid, pursuant to evaluation on its applicability. The methods are
discussed as follows;
5.7.1 Straightedge
This is one of the simplest methods of determining tolerance on for concrete. The straight
edge shall be placed on the concrete surface in any given direction and the maximum
deviation obtained. To make it quite easy, a straighten edge of 3 m shall be used. However,
AS 36110.11 prescribes the use of a shorter straighten edge of 0.3 m to 15 m. The variation
from the straighten edge shall be expressed as a maximum deviation, which shall be assessed
using ACI 117.
5.7.2 Using survey or optical method
Survey method is one of the methods that may give an accurate measurement on the
tolerances. The tolerances may be obtained using levelling method, flatness, plumb bob and
positioning. In case of obtaining tolerances on slabs and other pavement surfaces, flatness
and levelness and spot checks made on a grid surface, shall be used as a method of obtaining
tolerances. After obtaining levels, using dumpy levels, topographical maps shall be plot to
obtain the exact situation and tolerance on the as-built drawings.
5.8 Non-conformance
Non-fulfilment of the technical specifications as outlined in the contract is termed as non-
conformance. Non-conformance usually ends up breaching the minimum requirements in
terms of safety and quality of work. In some cases, the environment is also polluted.
Therefore, various cases give rise to non-conformance. Therefore, situations that might call
or be attributed as non-conformance include a material supplied on site and work performed
which is not in accordance with contract specifications. Any work done not considering
drawing specifications and the approved working methodology shall be termed as non-
determined using a smaller grid, pursuant to evaluation on its applicability. The methods are
discussed as follows;
5.7.1 Straightedge
This is one of the simplest methods of determining tolerance on for concrete. The straight
edge shall be placed on the concrete surface in any given direction and the maximum
deviation obtained. To make it quite easy, a straighten edge of 3 m shall be used. However,
AS 36110.11 prescribes the use of a shorter straighten edge of 0.3 m to 15 m. The variation
from the straighten edge shall be expressed as a maximum deviation, which shall be assessed
using ACI 117.
5.7.2 Using survey or optical method
Survey method is one of the methods that may give an accurate measurement on the
tolerances. The tolerances may be obtained using levelling method, flatness, plumb bob and
positioning. In case of obtaining tolerances on slabs and other pavement surfaces, flatness
and levelness and spot checks made on a grid surface, shall be used as a method of obtaining
tolerances. After obtaining levels, using dumpy levels, topographical maps shall be plot to
obtain the exact situation and tolerance on the as-built drawings.
5.8 Non-conformance
Non-fulfilment of the technical specifications as outlined in the contract is termed as non-
conformance. Non-conformance usually ends up breaching the minimum requirements in
terms of safety and quality of work. In some cases, the environment is also polluted.
Therefore, various cases give rise to non-conformance. Therefore, situations that might call
or be attributed as non-conformance include a material supplied on site and work performed
which is not in accordance with contract specifications. Any work done not considering
drawing specifications and the approved working methodology shall be termed as non-
Paraphrase This Document
Need a fresh take? Get an instant paraphrase of this document with our AI Paraphraser
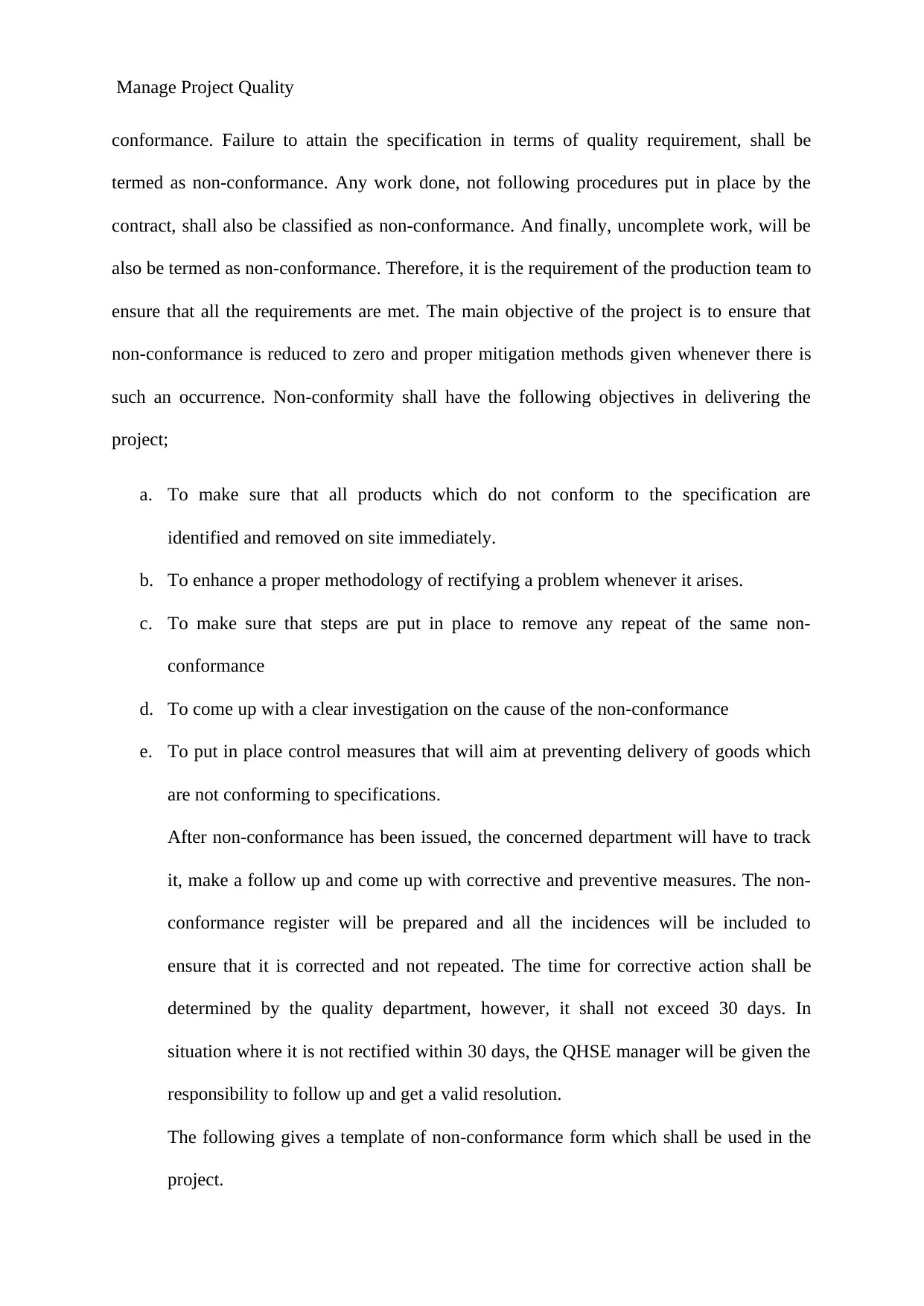
Manage Project Quality
conformance. Failure to attain the specification in terms of quality requirement, shall be
termed as non-conformance. Any work done, not following procedures put in place by the
contract, shall also be classified as non-conformance. And finally, uncomplete work, will be
also be termed as non-conformance. Therefore, it is the requirement of the production team to
ensure that all the requirements are met. The main objective of the project is to ensure that
non-conformance is reduced to zero and proper mitigation methods given whenever there is
such an occurrence. Non-conformity shall have the following objectives in delivering the
project;
a. To make sure that all products which do not conform to the specification are
identified and removed on site immediately.
b. To enhance a proper methodology of rectifying a problem whenever it arises.
c. To make sure that steps are put in place to remove any repeat of the same non-
conformance
d. To come up with a clear investigation on the cause of the non-conformance
e. To put in place control measures that will aim at preventing delivery of goods which
are not conforming to specifications.
After non-conformance has been issued, the concerned department will have to track
it, make a follow up and come up with corrective and preventive measures. The non-
conformance register will be prepared and all the incidences will be included to
ensure that it is corrected and not repeated. The time for corrective action shall be
determined by the quality department, however, it shall not exceed 30 days. In
situation where it is not rectified within 30 days, the QHSE manager will be given the
responsibility to follow up and get a valid resolution.
The following gives a template of non-conformance form which shall be used in the
project.
conformance. Failure to attain the specification in terms of quality requirement, shall be
termed as non-conformance. Any work done, not following procedures put in place by the
contract, shall also be classified as non-conformance. And finally, uncomplete work, will be
also be termed as non-conformance. Therefore, it is the requirement of the production team to
ensure that all the requirements are met. The main objective of the project is to ensure that
non-conformance is reduced to zero and proper mitigation methods given whenever there is
such an occurrence. Non-conformity shall have the following objectives in delivering the
project;
a. To make sure that all products which do not conform to the specification are
identified and removed on site immediately.
b. To enhance a proper methodology of rectifying a problem whenever it arises.
c. To make sure that steps are put in place to remove any repeat of the same non-
conformance
d. To come up with a clear investigation on the cause of the non-conformance
e. To put in place control measures that will aim at preventing delivery of goods which
are not conforming to specifications.
After non-conformance has been issued, the concerned department will have to track
it, make a follow up and come up with corrective and preventive measures. The non-
conformance register will be prepared and all the incidences will be included to
ensure that it is corrected and not repeated. The time for corrective action shall be
determined by the quality department, however, it shall not exceed 30 days. In
situation where it is not rectified within 30 days, the QHSE manager will be given the
responsibility to follow up and get a valid resolution.
The following gives a template of non-conformance form which shall be used in the
project.
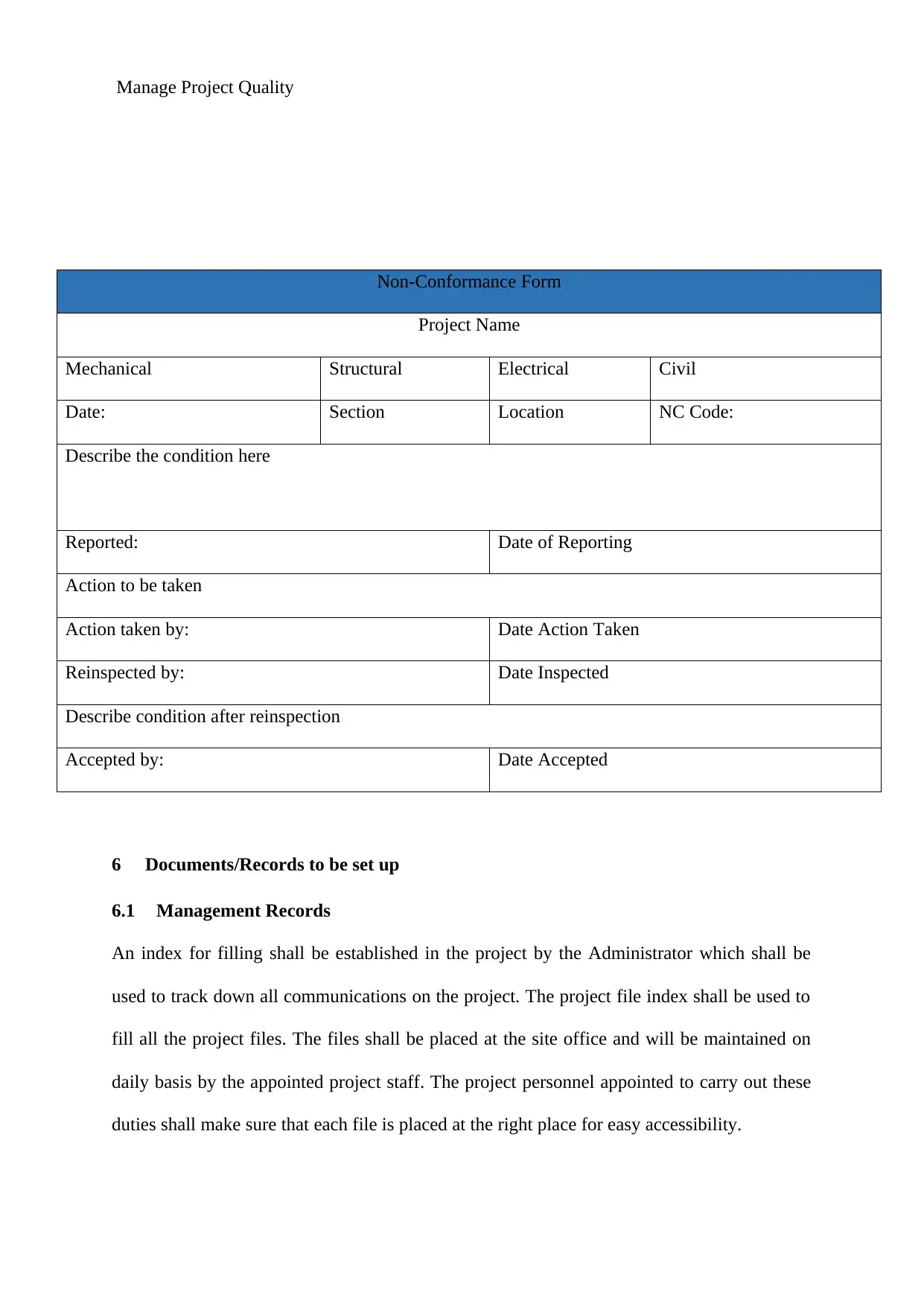
Manage Project Quality
Non-Conformance Form
Project Name
Mechanical Structural Electrical Civil
Date: Section Location NC Code:
Describe the condition here
Reported: Date of Reporting
Action to be taken
Action taken by: Date Action Taken
Reinspected by: Date Inspected
Describe condition after reinspection
Accepted by: Date Accepted
6 Documents/Records to be set up
6.1 Management Records
An index for filling shall be established in the project by the Administrator which shall be
used to track down all communications on the project. The project file index shall be used to
fill all the project files. The files shall be placed at the site office and will be maintained on
daily basis by the appointed project staff. The project personnel appointed to carry out these
duties shall make sure that each file is placed at the right place for easy accessibility.
Non-Conformance Form
Project Name
Mechanical Structural Electrical Civil
Date: Section Location NC Code:
Describe the condition here
Reported: Date of Reporting
Action to be taken
Action taken by: Date Action Taken
Reinspected by: Date Inspected
Describe condition after reinspection
Accepted by: Date Accepted
6 Documents/Records to be set up
6.1 Management Records
An index for filling shall be established in the project by the Administrator which shall be
used to track down all communications on the project. The project file index shall be used to
fill all the project files. The files shall be placed at the site office and will be maintained on
daily basis by the appointed project staff. The project personnel appointed to carry out these
duties shall make sure that each file is placed at the right place for easy accessibility.
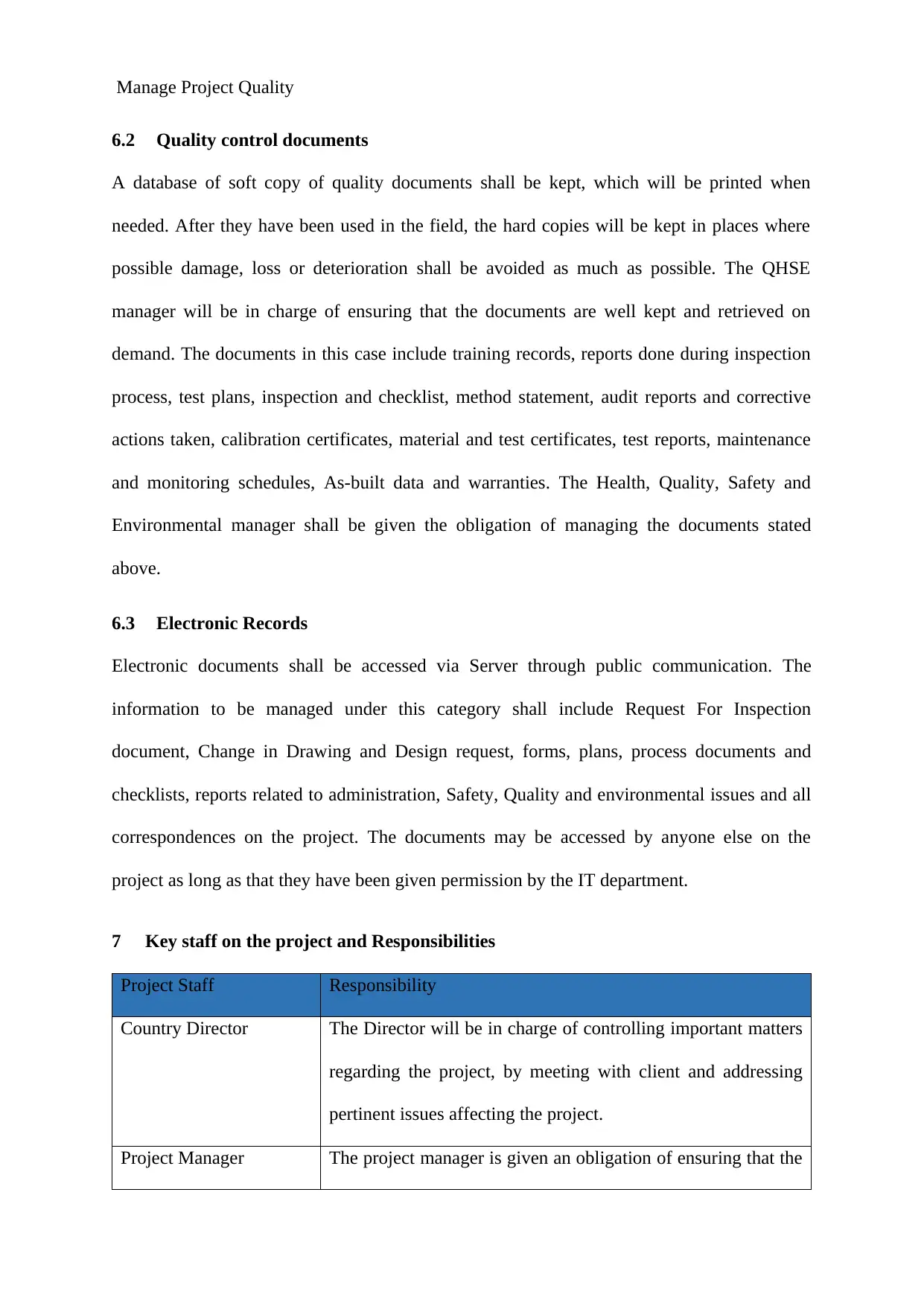
Manage Project Quality
6.2 Quality control documents
A database of soft copy of quality documents shall be kept, which will be printed when
needed. After they have been used in the field, the hard copies will be kept in places where
possible damage, loss or deterioration shall be avoided as much as possible. The QHSE
manager will be in charge of ensuring that the documents are well kept and retrieved on
demand. The documents in this case include training records, reports done during inspection
process, test plans, inspection and checklist, method statement, audit reports and corrective
actions taken, calibration certificates, material and test certificates, test reports, maintenance
and monitoring schedules, As-built data and warranties. The Health, Quality, Safety and
Environmental manager shall be given the obligation of managing the documents stated
above.
6.3 Electronic Records
Electronic documents shall be accessed via Server through public communication. The
information to be managed under this category shall include Request For Inspection
document, Change in Drawing and Design request, forms, plans, process documents and
checklists, reports related to administration, Safety, Quality and environmental issues and all
correspondences on the project. The documents may be accessed by anyone else on the
project as long as that they have been given permission by the IT department.
7 Key staff on the project and Responsibilities
Project Staff Responsibility
Country Director The Director will be in charge of controlling important matters
regarding the project, by meeting with client and addressing
pertinent issues affecting the project.
Project Manager The project manager is given an obligation of ensuring that the
6.2 Quality control documents
A database of soft copy of quality documents shall be kept, which will be printed when
needed. After they have been used in the field, the hard copies will be kept in places where
possible damage, loss or deterioration shall be avoided as much as possible. The QHSE
manager will be in charge of ensuring that the documents are well kept and retrieved on
demand. The documents in this case include training records, reports done during inspection
process, test plans, inspection and checklist, method statement, audit reports and corrective
actions taken, calibration certificates, material and test certificates, test reports, maintenance
and monitoring schedules, As-built data and warranties. The Health, Quality, Safety and
Environmental manager shall be given the obligation of managing the documents stated
above.
6.3 Electronic Records
Electronic documents shall be accessed via Server through public communication. The
information to be managed under this category shall include Request For Inspection
document, Change in Drawing and Design request, forms, plans, process documents and
checklists, reports related to administration, Safety, Quality and environmental issues and all
correspondences on the project. The documents may be accessed by anyone else on the
project as long as that they have been given permission by the IT department.
7 Key staff on the project and Responsibilities
Project Staff Responsibility
Country Director The Director will be in charge of controlling important matters
regarding the project, by meeting with client and addressing
pertinent issues affecting the project.
Project Manager The project manager is given an obligation of ensuring that the
Secure Best Marks with AI Grader
Need help grading? Try our AI Grader for instant feedback on your assignments.
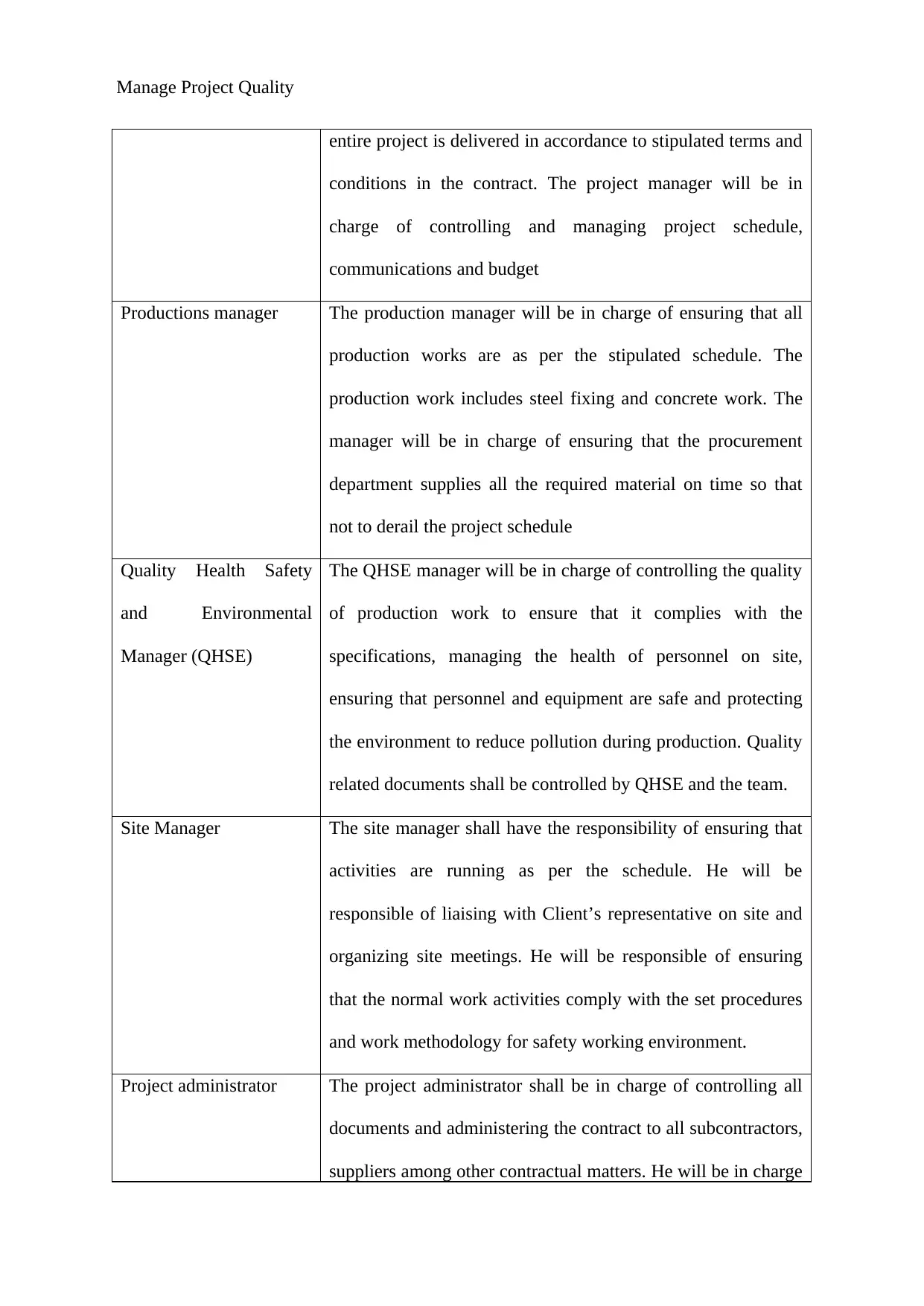
Manage Project Quality
entire project is delivered in accordance to stipulated terms and
conditions in the contract. The project manager will be in
charge of controlling and managing project schedule,
communications and budget
Productions manager The production manager will be in charge of ensuring that all
production works are as per the stipulated schedule. The
production work includes steel fixing and concrete work. The
manager will be in charge of ensuring that the procurement
department supplies all the required material on time so that
not to derail the project schedule
Quality Health Safety
and Environmental
Manager (QHSE)
The QHSE manager will be in charge of controlling the quality
of production work to ensure that it complies with the
specifications, managing the health of personnel on site,
ensuring that personnel and equipment are safe and protecting
the environment to reduce pollution during production. Quality
related documents shall be controlled by QHSE and the team.
Site Manager The site manager shall have the responsibility of ensuring that
activities are running as per the schedule. He will be
responsible of liaising with Client’s representative on site and
organizing site meetings. He will be responsible of ensuring
that the normal work activities comply with the set procedures
and work methodology for safety working environment.
Project administrator The project administrator shall be in charge of controlling all
documents and administering the contract to all subcontractors,
suppliers among other contractual matters. He will be in charge
entire project is delivered in accordance to stipulated terms and
conditions in the contract. The project manager will be in
charge of controlling and managing project schedule,
communications and budget
Productions manager The production manager will be in charge of ensuring that all
production works are as per the stipulated schedule. The
production work includes steel fixing and concrete work. The
manager will be in charge of ensuring that the procurement
department supplies all the required material on time so that
not to derail the project schedule
Quality Health Safety
and Environmental
Manager (QHSE)
The QHSE manager will be in charge of controlling the quality
of production work to ensure that it complies with the
specifications, managing the health of personnel on site,
ensuring that personnel and equipment are safe and protecting
the environment to reduce pollution during production. Quality
related documents shall be controlled by QHSE and the team.
Site Manager The site manager shall have the responsibility of ensuring that
activities are running as per the schedule. He will be
responsible of liaising with Client’s representative on site and
organizing site meetings. He will be responsible of ensuring
that the normal work activities comply with the set procedures
and work methodology for safety working environment.
Project administrator The project administrator shall be in charge of controlling all
documents and administering the contract to all subcontractors,
suppliers among other contractual matters. He will be in charge
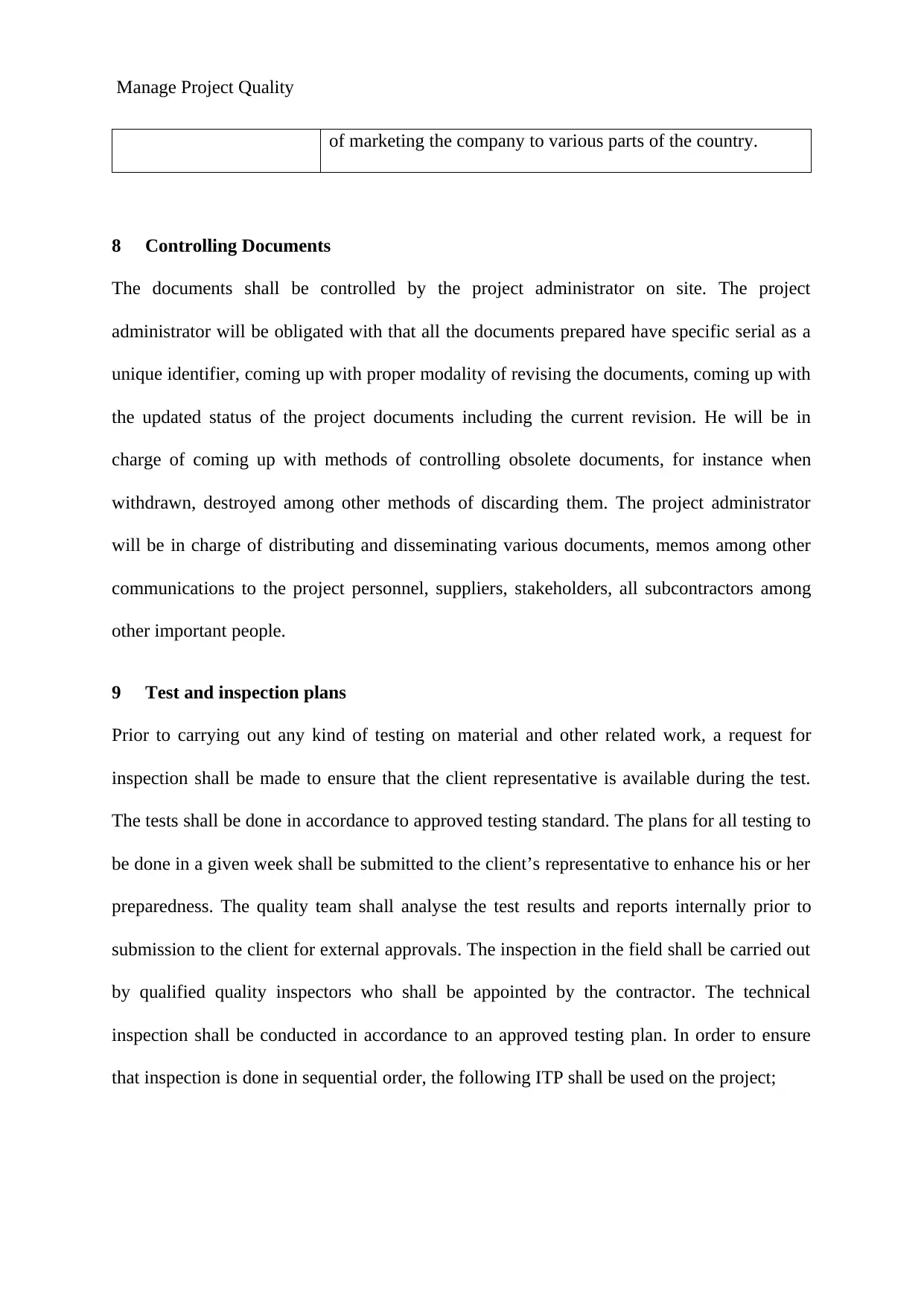
Manage Project Quality
of marketing the company to various parts of the country.
8 Controlling Documents
The documents shall be controlled by the project administrator on site. The project
administrator will be obligated with that all the documents prepared have specific serial as a
unique identifier, coming up with proper modality of revising the documents, coming up with
the updated status of the project documents including the current revision. He will be in
charge of coming up with methods of controlling obsolete documents, for instance when
withdrawn, destroyed among other methods of discarding them. The project administrator
will be in charge of distributing and disseminating various documents, memos among other
communications to the project personnel, suppliers, stakeholders, all subcontractors among
other important people.
9 Test and inspection plans
Prior to carrying out any kind of testing on material and other related work, a request for
inspection shall be made to ensure that the client representative is available during the test.
The tests shall be done in accordance to approved testing standard. The plans for all testing to
be done in a given week shall be submitted to the client’s representative to enhance his or her
preparedness. The quality team shall analyse the test results and reports internally prior to
submission to the client for external approvals. The inspection in the field shall be carried out
by qualified quality inspectors who shall be appointed by the contractor. The technical
inspection shall be conducted in accordance to an approved testing plan. In order to ensure
that inspection is done in sequential order, the following ITP shall be used on the project;
of marketing the company to various parts of the country.
8 Controlling Documents
The documents shall be controlled by the project administrator on site. The project
administrator will be obligated with that all the documents prepared have specific serial as a
unique identifier, coming up with proper modality of revising the documents, coming up with
the updated status of the project documents including the current revision. He will be in
charge of coming up with methods of controlling obsolete documents, for instance when
withdrawn, destroyed among other methods of discarding them. The project administrator
will be in charge of distributing and disseminating various documents, memos among other
communications to the project personnel, suppliers, stakeholders, all subcontractors among
other important people.
9 Test and inspection plans
Prior to carrying out any kind of testing on material and other related work, a request for
inspection shall be made to ensure that the client representative is available during the test.
The tests shall be done in accordance to approved testing standard. The plans for all testing to
be done in a given week shall be submitted to the client’s representative to enhance his or her
preparedness. The quality team shall analyse the test results and reports internally prior to
submission to the client for external approvals. The inspection in the field shall be carried out
by qualified quality inspectors who shall be appointed by the contractor. The technical
inspection shall be conducted in accordance to an approved testing plan. In order to ensure
that inspection is done in sequential order, the following ITP shall be used on the project;
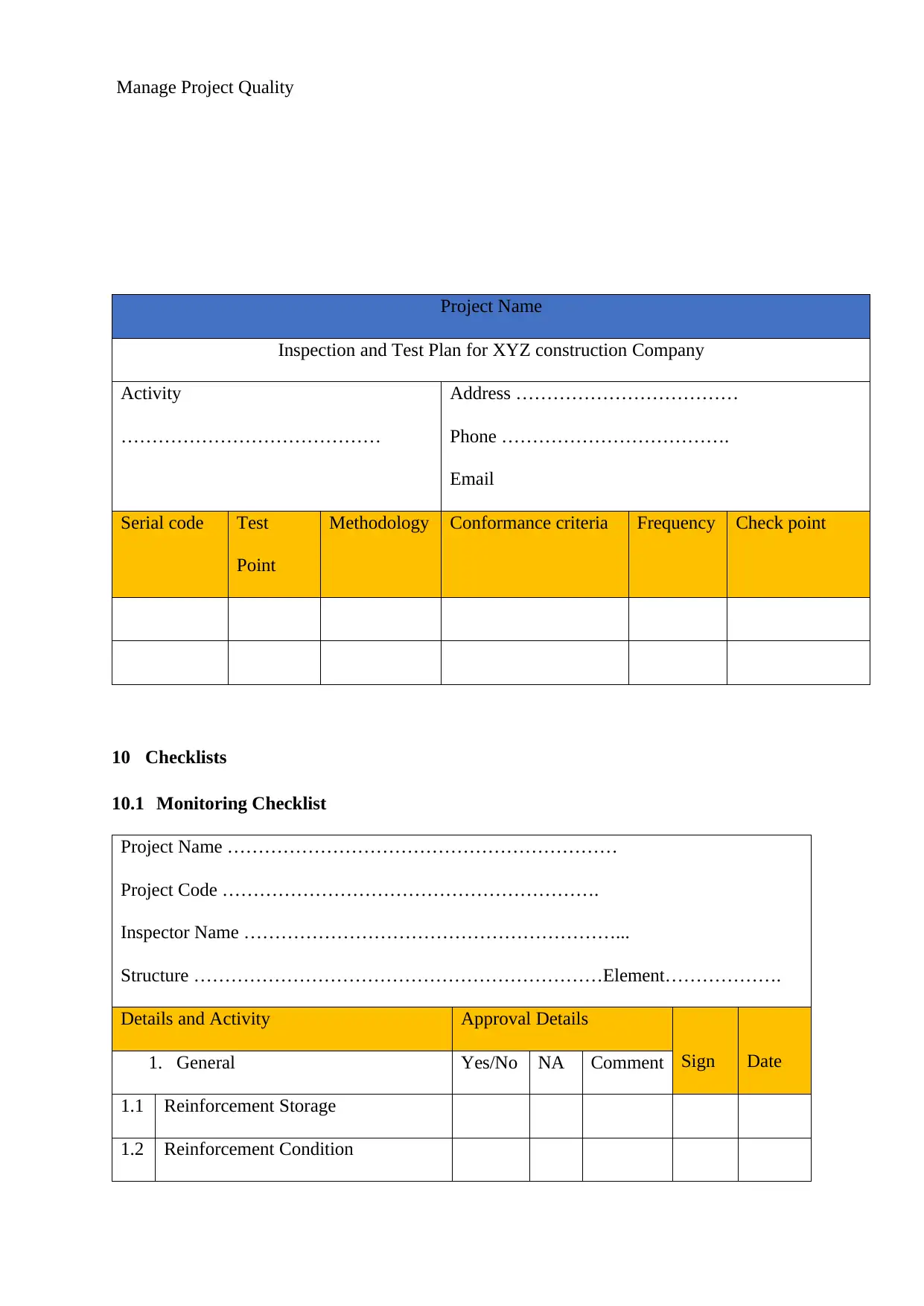
Manage Project Quality
Project Name
Inspection and Test Plan for XYZ construction Company
Activity
……………………………………
Address ………………………………
Phone ……………………………….
Email
Serial code Test
Point
Methodology Conformance criteria Frequency Check point
10 Checklists
10.1 Monitoring Checklist
Project Name ………………………………………………………
Project Code …………………………………………………….
Inspector Name ……………………………………………………...
Structure …………………………………………………………Element……………….
Details and Activity Approval Details
Sign Date1. General Yes/No NA Comment
1.1 Reinforcement Storage
1.2 Reinforcement Condition
Project Name
Inspection and Test Plan for XYZ construction Company
Activity
……………………………………
Address ………………………………
Phone ……………………………….
Serial code Test
Point
Methodology Conformance criteria Frequency Check point
10 Checklists
10.1 Monitoring Checklist
Project Name ………………………………………………………
Project Code …………………………………………………….
Inspector Name ……………………………………………………...
Structure …………………………………………………………Element……………….
Details and Activity Approval Details
Sign Date1. General Yes/No NA Comment
1.1 Reinforcement Storage
1.2 Reinforcement Condition
Paraphrase This Document
Need a fresh take? Get an instant paraphrase of this document with our AI Paraphraser
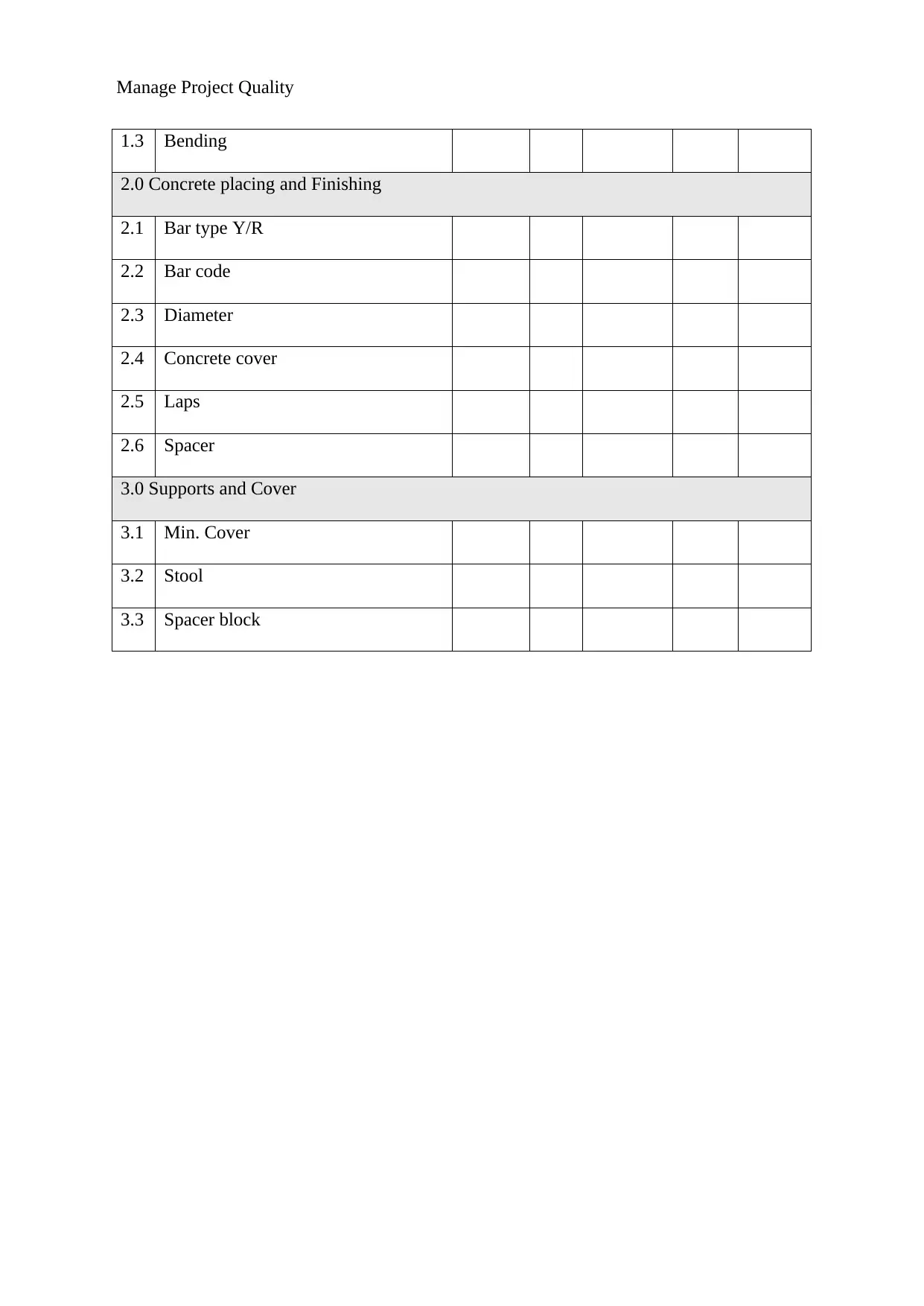
Manage Project Quality
1.3 Bending
2.0 Concrete placing and Finishing
2.1 Bar type Y/R
2.2 Bar code
2.3 Diameter
2.4 Concrete cover
2.5 Laps
2.6 Spacer
3.0 Supports and Cover
3.1 Min. Cover
3.2 Stool
3.3 Spacer block
1.3 Bending
2.0 Concrete placing and Finishing
2.1 Bar type Y/R
2.2 Bar code
2.3 Diameter
2.4 Concrete cover
2.5 Laps
2.6 Spacer
3.0 Supports and Cover
3.1 Min. Cover
3.2 Stool
3.3 Spacer block
1 out of 20
Related Documents

Your All-in-One AI-Powered Toolkit for Academic Success.
+13062052269
info@desklib.com
Available 24*7 on WhatsApp / Email
Unlock your academic potential
© 2024 | Zucol Services PVT LTD | All rights reserved.