BSBWHS605: Analysis and Recommendations for WHS Management System
VerifiedAdded on 2023/06/12
|12
|2489
|257
Report
AI Summary
This report analyzes the effectiveness of a newly implemented WHS management system framework at Pitstop Pty Ltd. Data collected after implementation revealed that the system failed to meet the set expectations, with injury and health problem incidents remaining critically high. The analysis identifies lack of awareness, insufficient training, lack of technical knowledge, skills audit deficiencies, and employee unwillingness as key contributing factors. The report proposes mandatory training sessions, skills audits, and surveillance to address these issues. Ultimately, the report concludes that both employees and managers must take more proactive roles in adhering to and enforcing WHS guidelines to improve workplace health and safety. Desklib offers a range of study tools and past papers to support students in understanding and applying these concepts.
Contribute Materials
Your contribution can guide someone’s learning journey. Share your
documents today.
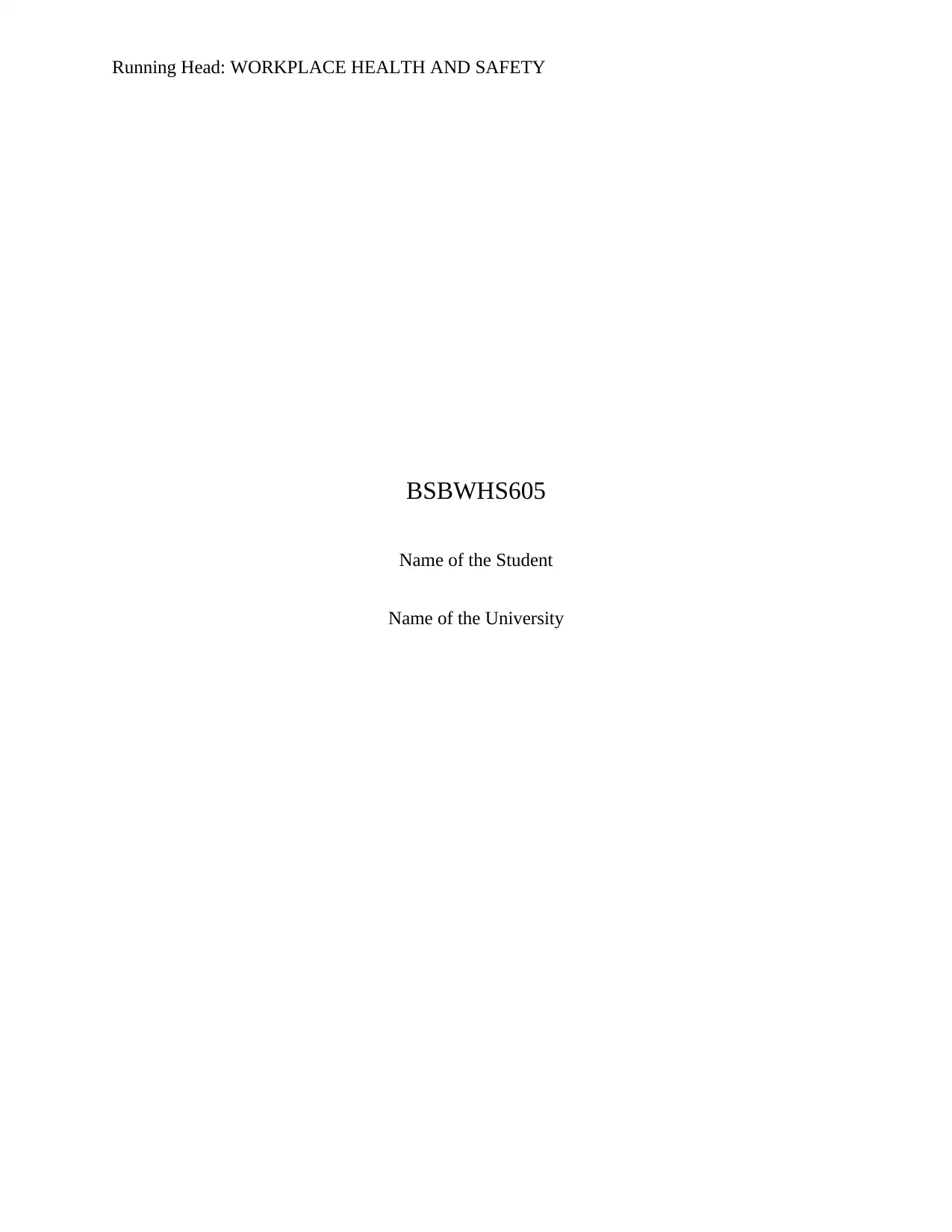
Running Head: WORKPLACE HEALTH AND SAFETY
BSBWHS605
Name of the Student
Name of the University
BSBWHS605
Name of the Student
Name of the University
Secure Best Marks with AI Grader
Need help grading? Try our AI Grader for instant feedback on your assignments.
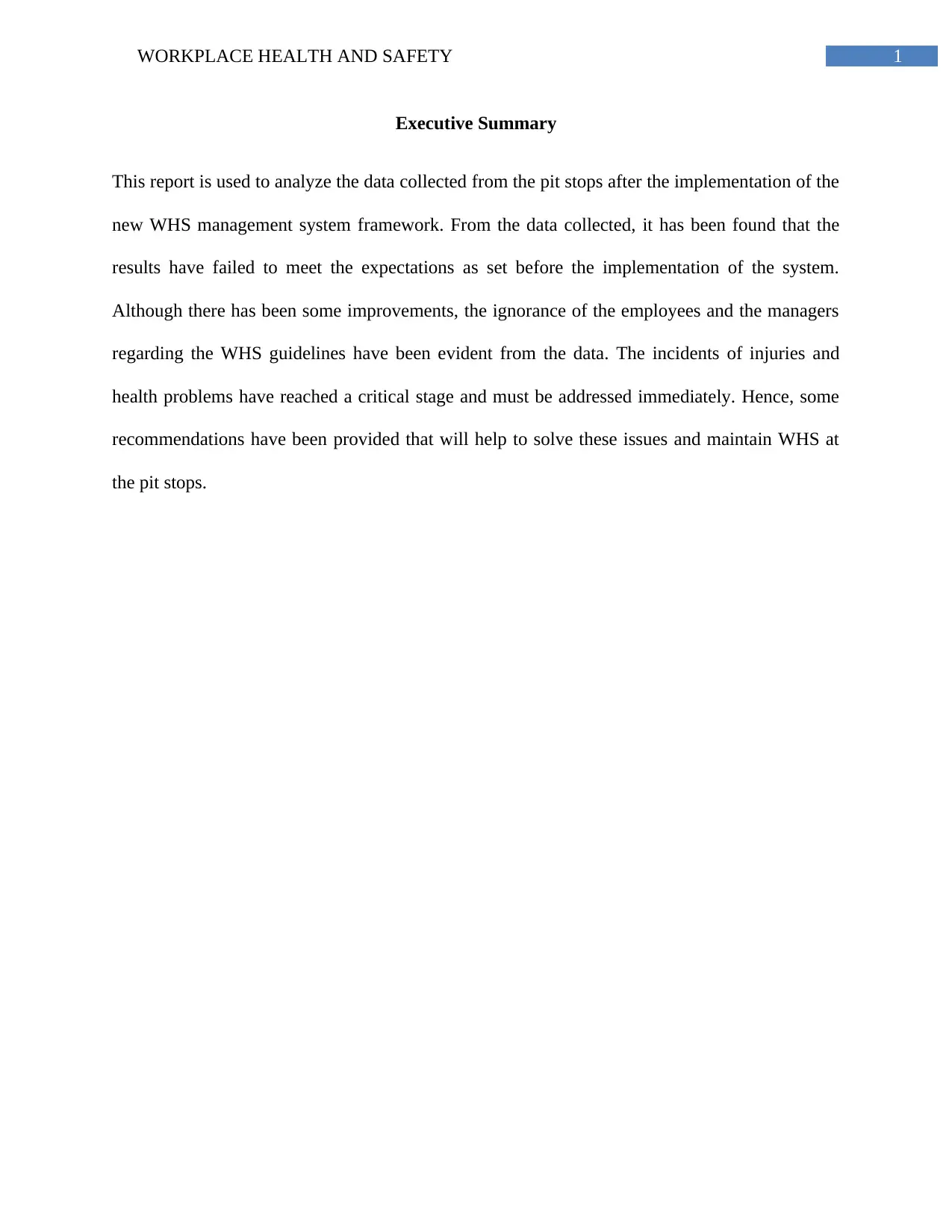
1WORKPLACE HEALTH AND SAFETY
Executive Summary
This report is used to analyze the data collected from the pit stops after the implementation of the
new WHS management system framework. From the data collected, it has been found that the
results have failed to meet the expectations as set before the implementation of the system.
Although there has been some improvements, the ignorance of the employees and the managers
regarding the WHS guidelines have been evident from the data. The incidents of injuries and
health problems have reached a critical stage and must be addressed immediately. Hence, some
recommendations have been provided that will help to solve these issues and maintain WHS at
the pit stops.
Executive Summary
This report is used to analyze the data collected from the pit stops after the implementation of the
new WHS management system framework. From the data collected, it has been found that the
results have failed to meet the expectations as set before the implementation of the system.
Although there has been some improvements, the ignorance of the employees and the managers
regarding the WHS guidelines have been evident from the data. The incidents of injuries and
health problems have reached a critical stage and must be addressed immediately. Hence, some
recommendations have been provided that will help to solve these issues and maintain WHS at
the pit stops.
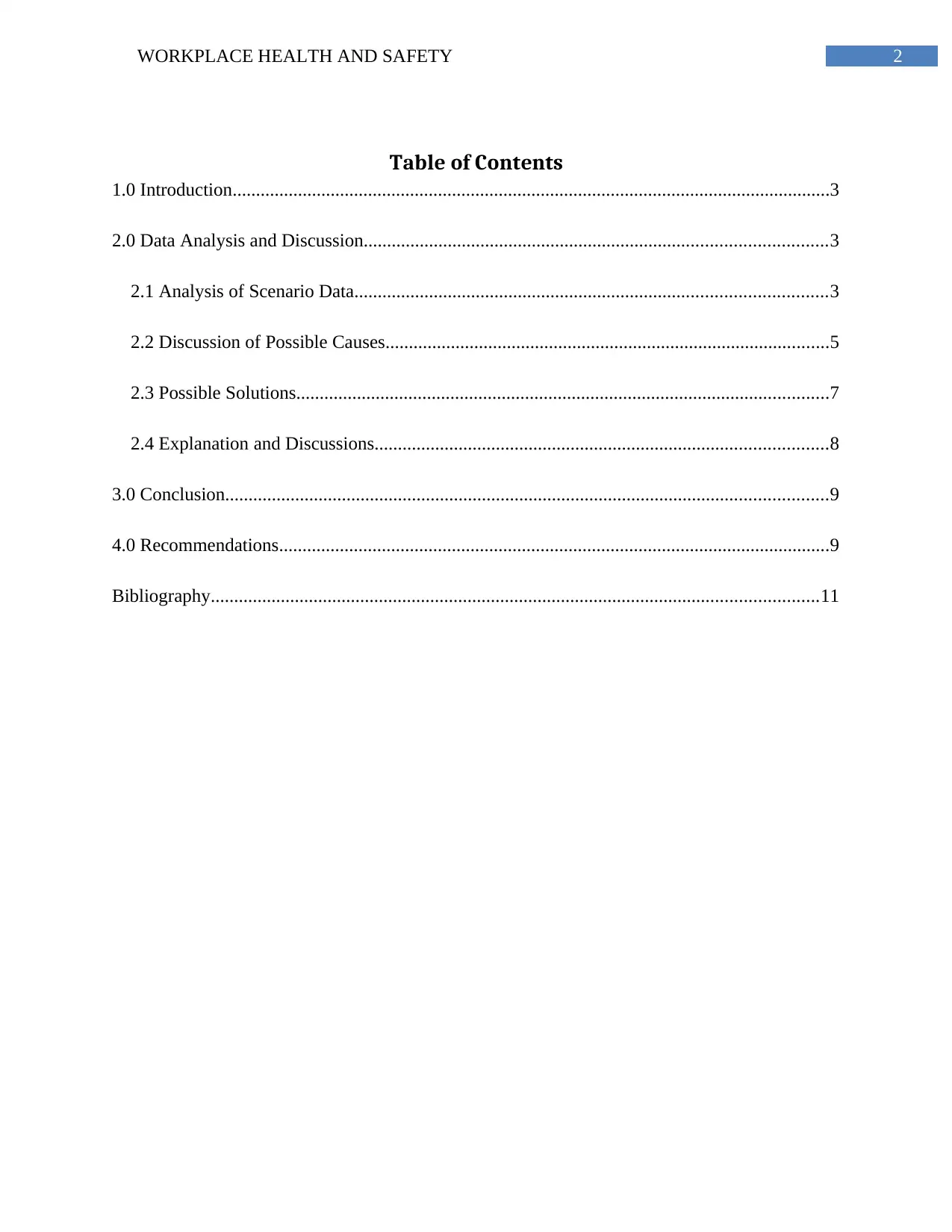
2WORKPLACE HEALTH AND SAFETY
Table of Contents
1.0 Introduction................................................................................................................................3
2.0 Data Analysis and Discussion...................................................................................................3
2.1 Analysis of Scenario Data.....................................................................................................3
2.2 Discussion of Possible Causes...............................................................................................5
2.3 Possible Solutions..................................................................................................................7
2.4 Explanation and Discussions.................................................................................................8
3.0 Conclusion.................................................................................................................................9
4.0 Recommendations......................................................................................................................9
Bibliography..................................................................................................................................11
Table of Contents
1.0 Introduction................................................................................................................................3
2.0 Data Analysis and Discussion...................................................................................................3
2.1 Analysis of Scenario Data.....................................................................................................3
2.2 Discussion of Possible Causes...............................................................................................5
2.3 Possible Solutions..................................................................................................................7
2.4 Explanation and Discussions.................................................................................................8
3.0 Conclusion.................................................................................................................................9
4.0 Recommendations......................................................................................................................9
Bibliography..................................................................................................................................11
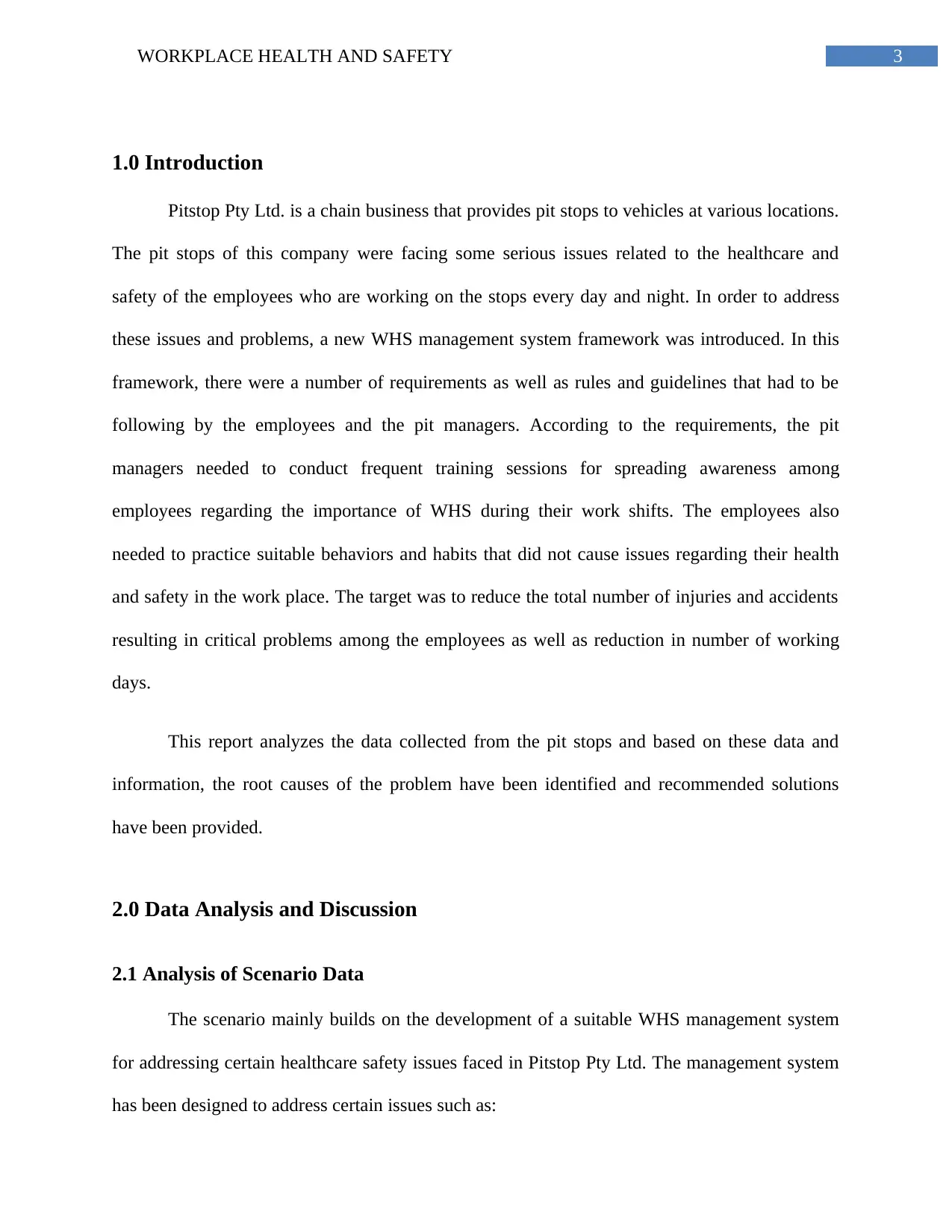
3WORKPLACE HEALTH AND SAFETY
1.0 Introduction
Pitstop Pty Ltd. is a chain business that provides pit stops to vehicles at various locations.
The pit stops of this company were facing some serious issues related to the healthcare and
safety of the employees who are working on the stops every day and night. In order to address
these issues and problems, a new WHS management system framework was introduced. In this
framework, there were a number of requirements as well as rules and guidelines that had to be
following by the employees and the pit managers. According to the requirements, the pit
managers needed to conduct frequent training sessions for spreading awareness among
employees regarding the importance of WHS during their work shifts. The employees also
needed to practice suitable behaviors and habits that did not cause issues regarding their health
and safety in the work place. The target was to reduce the total number of injuries and accidents
resulting in critical problems among the employees as well as reduction in number of working
days.
This report analyzes the data collected from the pit stops and based on these data and
information, the root causes of the problem have been identified and recommended solutions
have been provided.
2.0 Data Analysis and Discussion
2.1 Analysis of Scenario Data
The scenario mainly builds on the development of a suitable WHS management system
for addressing certain healthcare safety issues faced in Pitstop Pty Ltd. The management system
has been designed to address certain issues such as:
1.0 Introduction
Pitstop Pty Ltd. is a chain business that provides pit stops to vehicles at various locations.
The pit stops of this company were facing some serious issues related to the healthcare and
safety of the employees who are working on the stops every day and night. In order to address
these issues and problems, a new WHS management system framework was introduced. In this
framework, there were a number of requirements as well as rules and guidelines that had to be
following by the employees and the pit managers. According to the requirements, the pit
managers needed to conduct frequent training sessions for spreading awareness among
employees regarding the importance of WHS during their work shifts. The employees also
needed to practice suitable behaviors and habits that did not cause issues regarding their health
and safety in the work place. The target was to reduce the total number of injuries and accidents
resulting in critical problems among the employees as well as reduction in number of working
days.
This report analyzes the data collected from the pit stops and based on these data and
information, the root causes of the problem have been identified and recommended solutions
have been provided.
2.0 Data Analysis and Discussion
2.1 Analysis of Scenario Data
The scenario mainly builds on the development of a suitable WHS management system
for addressing certain healthcare safety issues faced in Pitstop Pty Ltd. The management system
has been designed to address certain issues such as:
Secure Best Marks with AI Grader
Need help grading? Try our AI Grader for instant feedback on your assignments.
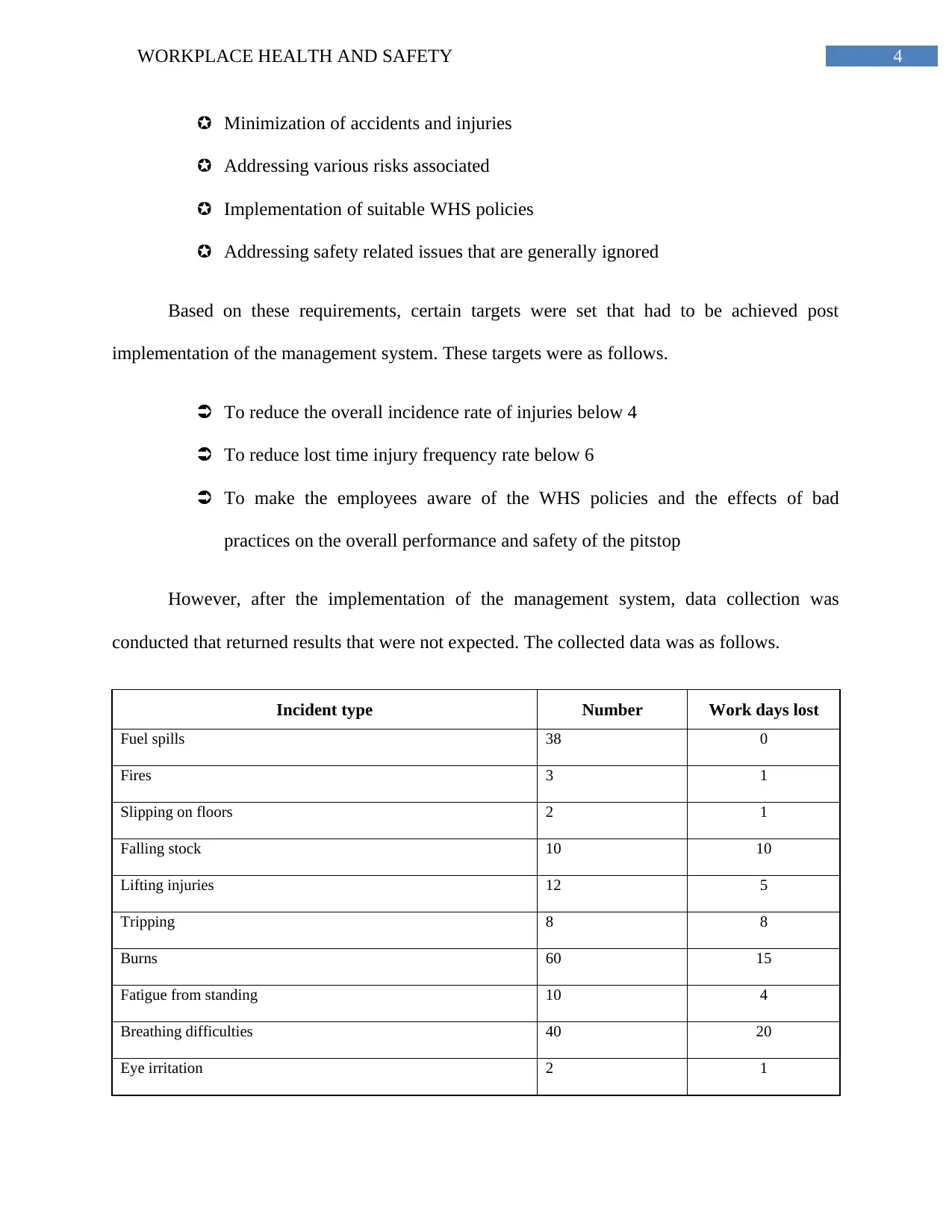
4WORKPLACE HEALTH AND SAFETY
Minimization of accidents and injuries
Addressing various risks associated
Implementation of suitable WHS policies
Addressing safety related issues that are generally ignored
Based on these requirements, certain targets were set that had to be achieved post
implementation of the management system. These targets were as follows.
To reduce the overall incidence rate of injuries below 4
To reduce lost time injury frequency rate below 6
To make the employees aware of the WHS policies and the effects of bad
practices on the overall performance and safety of the pitstop
However, after the implementation of the management system, data collection was
conducted that returned results that were not expected. The collected data was as follows.
Incident type Number Work days lost
Fuel spills 38 0
Fires 3 1
Slipping on floors 2 1
Falling stock 10 10
Lifting injuries 12 5
Tripping 8 8
Burns 60 15
Fatigue from standing 10 4
Breathing difficulties 40 20
Eye irritation 2 1
Minimization of accidents and injuries
Addressing various risks associated
Implementation of suitable WHS policies
Addressing safety related issues that are generally ignored
Based on these requirements, certain targets were set that had to be achieved post
implementation of the management system. These targets were as follows.
To reduce the overall incidence rate of injuries below 4
To reduce lost time injury frequency rate below 6
To make the employees aware of the WHS policies and the effects of bad
practices on the overall performance and safety of the pitstop
However, after the implementation of the management system, data collection was
conducted that returned results that were not expected. The collected data was as follows.
Incident type Number Work days lost
Fuel spills 38 0
Fires 3 1
Slipping on floors 2 1
Falling stock 10 10
Lifting injuries 12 5
Tripping 8 8
Burns 60 15
Fatigue from standing 10 4
Breathing difficulties 40 20
Eye irritation 2 1
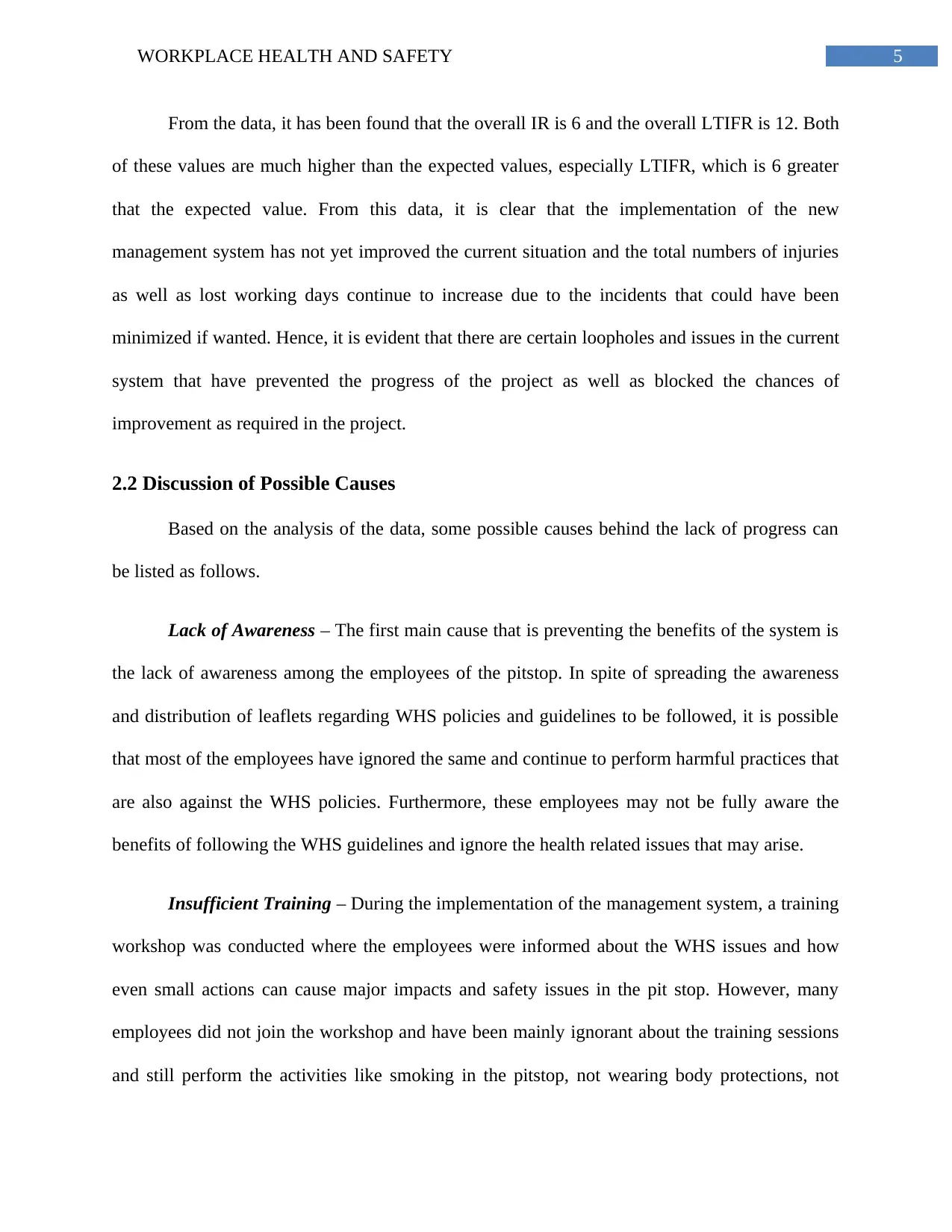
5WORKPLACE HEALTH AND SAFETY
From the data, it has been found that the overall IR is 6 and the overall LTIFR is 12. Both
of these values are much higher than the expected values, especially LTIFR, which is 6 greater
that the expected value. From this data, it is clear that the implementation of the new
management system has not yet improved the current situation and the total numbers of injuries
as well as lost working days continue to increase due to the incidents that could have been
minimized if wanted. Hence, it is evident that there are certain loopholes and issues in the current
system that have prevented the progress of the project as well as blocked the chances of
improvement as required in the project.
2.2 Discussion of Possible Causes
Based on the analysis of the data, some possible causes behind the lack of progress can
be listed as follows.
Lack of Awareness – The first main cause that is preventing the benefits of the system is
the lack of awareness among the employees of the pitstop. In spite of spreading the awareness
and distribution of leaflets regarding WHS policies and guidelines to be followed, it is possible
that most of the employees have ignored the same and continue to perform harmful practices that
are also against the WHS policies. Furthermore, these employees may not be fully aware the
benefits of following the WHS guidelines and ignore the health related issues that may arise.
Insufficient Training – During the implementation of the management system, a training
workshop was conducted where the employees were informed about the WHS issues and how
even small actions can cause major impacts and safety issues in the pit stop. However, many
employees did not join the workshop and have been mainly ignorant about the training sessions
and still perform the activities like smoking in the pitstop, not wearing body protections, not
From the data, it has been found that the overall IR is 6 and the overall LTIFR is 12. Both
of these values are much higher than the expected values, especially LTIFR, which is 6 greater
that the expected value. From this data, it is clear that the implementation of the new
management system has not yet improved the current situation and the total numbers of injuries
as well as lost working days continue to increase due to the incidents that could have been
minimized if wanted. Hence, it is evident that there are certain loopholes and issues in the current
system that have prevented the progress of the project as well as blocked the chances of
improvement as required in the project.
2.2 Discussion of Possible Causes
Based on the analysis of the data, some possible causes behind the lack of progress can
be listed as follows.
Lack of Awareness – The first main cause that is preventing the benefits of the system is
the lack of awareness among the employees of the pitstop. In spite of spreading the awareness
and distribution of leaflets regarding WHS policies and guidelines to be followed, it is possible
that most of the employees have ignored the same and continue to perform harmful practices that
are also against the WHS policies. Furthermore, these employees may not be fully aware the
benefits of following the WHS guidelines and ignore the health related issues that may arise.
Insufficient Training – During the implementation of the management system, a training
workshop was conducted where the employees were informed about the WHS issues and how
even small actions can cause major impacts and safety issues in the pit stop. However, many
employees did not join the workshop and have been mainly ignorant about the training sessions
and still perform the activities like smoking in the pitstop, not wearing body protections, not
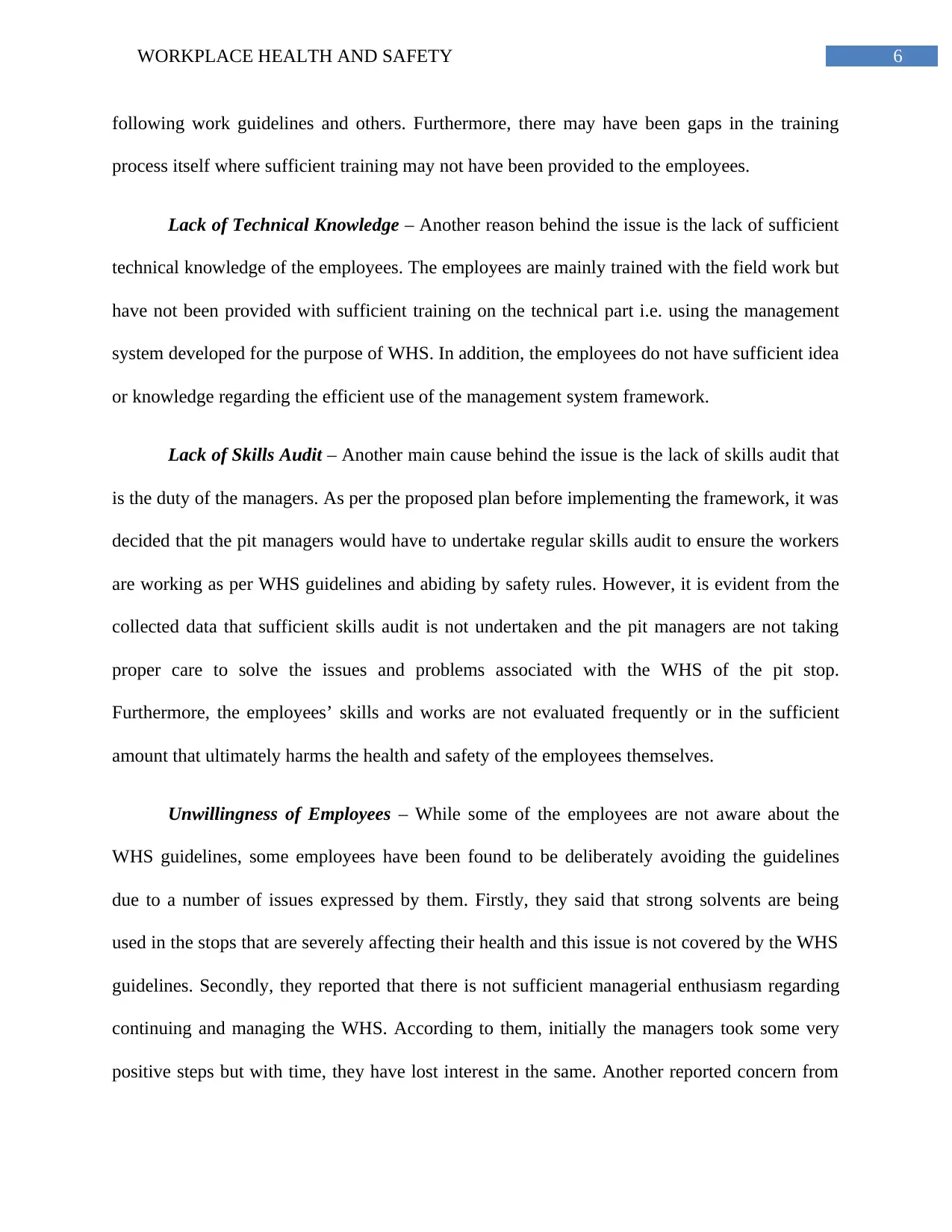
6WORKPLACE HEALTH AND SAFETY
following work guidelines and others. Furthermore, there may have been gaps in the training
process itself where sufficient training may not have been provided to the employees.
Lack of Technical Knowledge – Another reason behind the issue is the lack of sufficient
technical knowledge of the employees. The employees are mainly trained with the field work but
have not been provided with sufficient training on the technical part i.e. using the management
system developed for the purpose of WHS. In addition, the employees do not have sufficient idea
or knowledge regarding the efficient use of the management system framework.
Lack of Skills Audit – Another main cause behind the issue is the lack of skills audit that
is the duty of the managers. As per the proposed plan before implementing the framework, it was
decided that the pit managers would have to undertake regular skills audit to ensure the workers
are working as per WHS guidelines and abiding by safety rules. However, it is evident from the
collected data that sufficient skills audit is not undertaken and the pit managers are not taking
proper care to solve the issues and problems associated with the WHS of the pit stop.
Furthermore, the employees’ skills and works are not evaluated frequently or in the sufficient
amount that ultimately harms the health and safety of the employees themselves.
Unwillingness of Employees – While some of the employees are not aware about the
WHS guidelines, some employees have been found to be deliberately avoiding the guidelines
due to a number of issues expressed by them. Firstly, they said that strong solvents are being
used in the stops that are severely affecting their health and this issue is not covered by the WHS
guidelines. Secondly, they reported that there is not sufficient managerial enthusiasm regarding
continuing and managing the WHS. According to them, initially the managers took some very
positive steps but with time, they have lost interest in the same. Another reported concern from
following work guidelines and others. Furthermore, there may have been gaps in the training
process itself where sufficient training may not have been provided to the employees.
Lack of Technical Knowledge – Another reason behind the issue is the lack of sufficient
technical knowledge of the employees. The employees are mainly trained with the field work but
have not been provided with sufficient training on the technical part i.e. using the management
system developed for the purpose of WHS. In addition, the employees do not have sufficient idea
or knowledge regarding the efficient use of the management system framework.
Lack of Skills Audit – Another main cause behind the issue is the lack of skills audit that
is the duty of the managers. As per the proposed plan before implementing the framework, it was
decided that the pit managers would have to undertake regular skills audit to ensure the workers
are working as per WHS guidelines and abiding by safety rules. However, it is evident from the
collected data that sufficient skills audit is not undertaken and the pit managers are not taking
proper care to solve the issues and problems associated with the WHS of the pit stop.
Furthermore, the employees’ skills and works are not evaluated frequently or in the sufficient
amount that ultimately harms the health and safety of the employees themselves.
Unwillingness of Employees – While some of the employees are not aware about the
WHS guidelines, some employees have been found to be deliberately avoiding the guidelines
due to a number of issues expressed by them. Firstly, they said that strong solvents are being
used in the stops that are severely affecting their health and this issue is not covered by the WHS
guidelines. Secondly, they reported that there is not sufficient managerial enthusiasm regarding
continuing and managing the WHS. According to them, initially the managers took some very
positive steps but with time, they have lost interest in the same. Another reported concern from
Paraphrase This Document
Need a fresh take? Get an instant paraphrase of this document with our AI Paraphraser
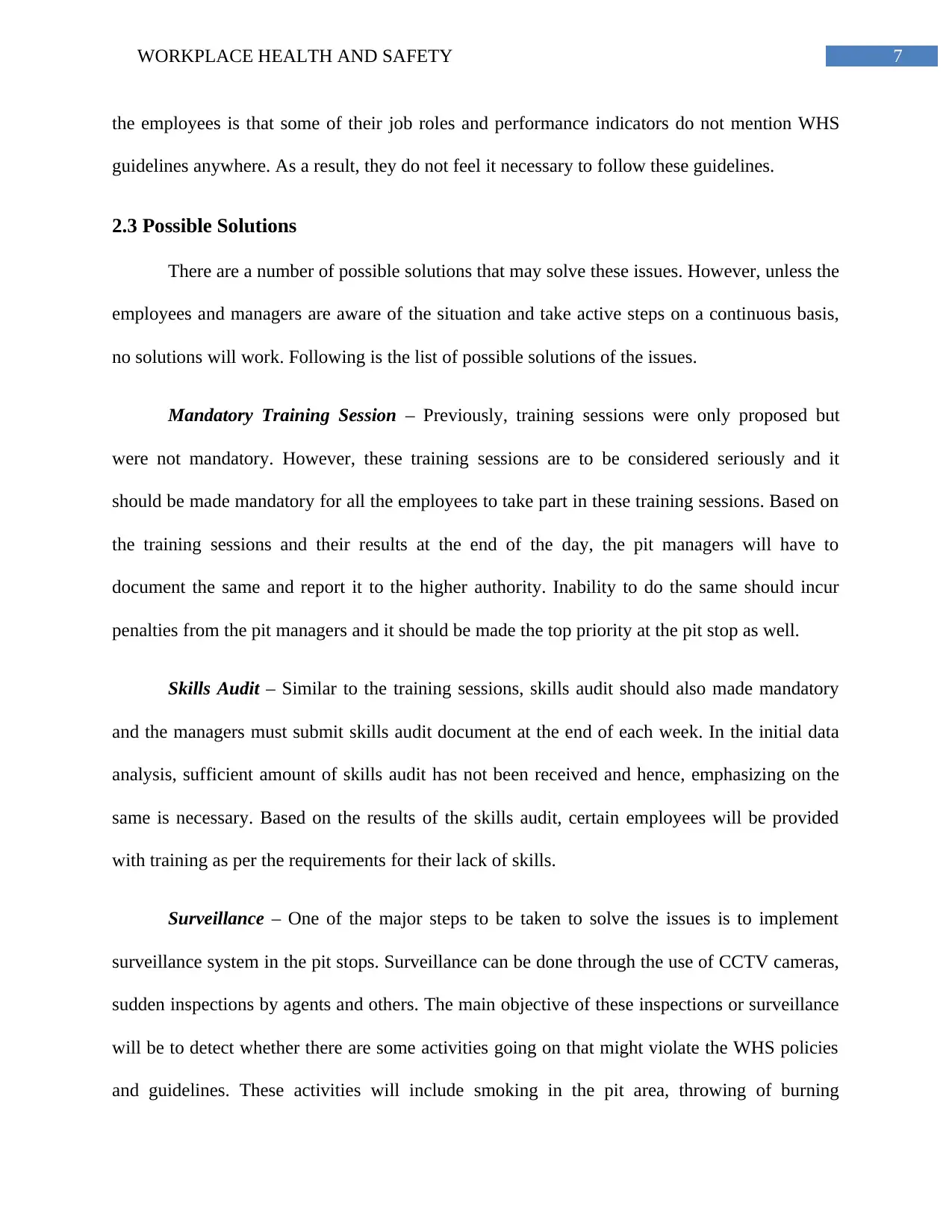
7WORKPLACE HEALTH AND SAFETY
the employees is that some of their job roles and performance indicators do not mention WHS
guidelines anywhere. As a result, they do not feel it necessary to follow these guidelines.
2.3 Possible Solutions
There are a number of possible solutions that may solve these issues. However, unless the
employees and managers are aware of the situation and take active steps on a continuous basis,
no solutions will work. Following is the list of possible solutions of the issues.
Mandatory Training Session – Previously, training sessions were only proposed but
were not mandatory. However, these training sessions are to be considered seriously and it
should be made mandatory for all the employees to take part in these training sessions. Based on
the training sessions and their results at the end of the day, the pit managers will have to
document the same and report it to the higher authority. Inability to do the same should incur
penalties from the pit managers and it should be made the top priority at the pit stop as well.
Skills Audit – Similar to the training sessions, skills audit should also made mandatory
and the managers must submit skills audit document at the end of each week. In the initial data
analysis, sufficient amount of skills audit has not been received and hence, emphasizing on the
same is necessary. Based on the results of the skills audit, certain employees will be provided
with training as per the requirements for their lack of skills.
Surveillance – One of the major steps to be taken to solve the issues is to implement
surveillance system in the pit stops. Surveillance can be done through the use of CCTV cameras,
sudden inspections by agents and others. The main objective of these inspections or surveillance
will be to detect whether there are some activities going on that might violate the WHS policies
and guidelines. These activities will include smoking in the pit area, throwing of burning
the employees is that some of their job roles and performance indicators do not mention WHS
guidelines anywhere. As a result, they do not feel it necessary to follow these guidelines.
2.3 Possible Solutions
There are a number of possible solutions that may solve these issues. However, unless the
employees and managers are aware of the situation and take active steps on a continuous basis,
no solutions will work. Following is the list of possible solutions of the issues.
Mandatory Training Session – Previously, training sessions were only proposed but
were not mandatory. However, these training sessions are to be considered seriously and it
should be made mandatory for all the employees to take part in these training sessions. Based on
the training sessions and their results at the end of the day, the pit managers will have to
document the same and report it to the higher authority. Inability to do the same should incur
penalties from the pit managers and it should be made the top priority at the pit stop as well.
Skills Audit – Similar to the training sessions, skills audit should also made mandatory
and the managers must submit skills audit document at the end of each week. In the initial data
analysis, sufficient amount of skills audit has not been received and hence, emphasizing on the
same is necessary. Based on the results of the skills audit, certain employees will be provided
with training as per the requirements for their lack of skills.
Surveillance – One of the major steps to be taken to solve the issues is to implement
surveillance system in the pit stops. Surveillance can be done through the use of CCTV cameras,
sudden inspections by agents and others. The main objective of these inspections or surveillance
will be to detect whether there are some activities going on that might violate the WHS policies
and guidelines. These activities will include smoking in the pit area, throwing of burning
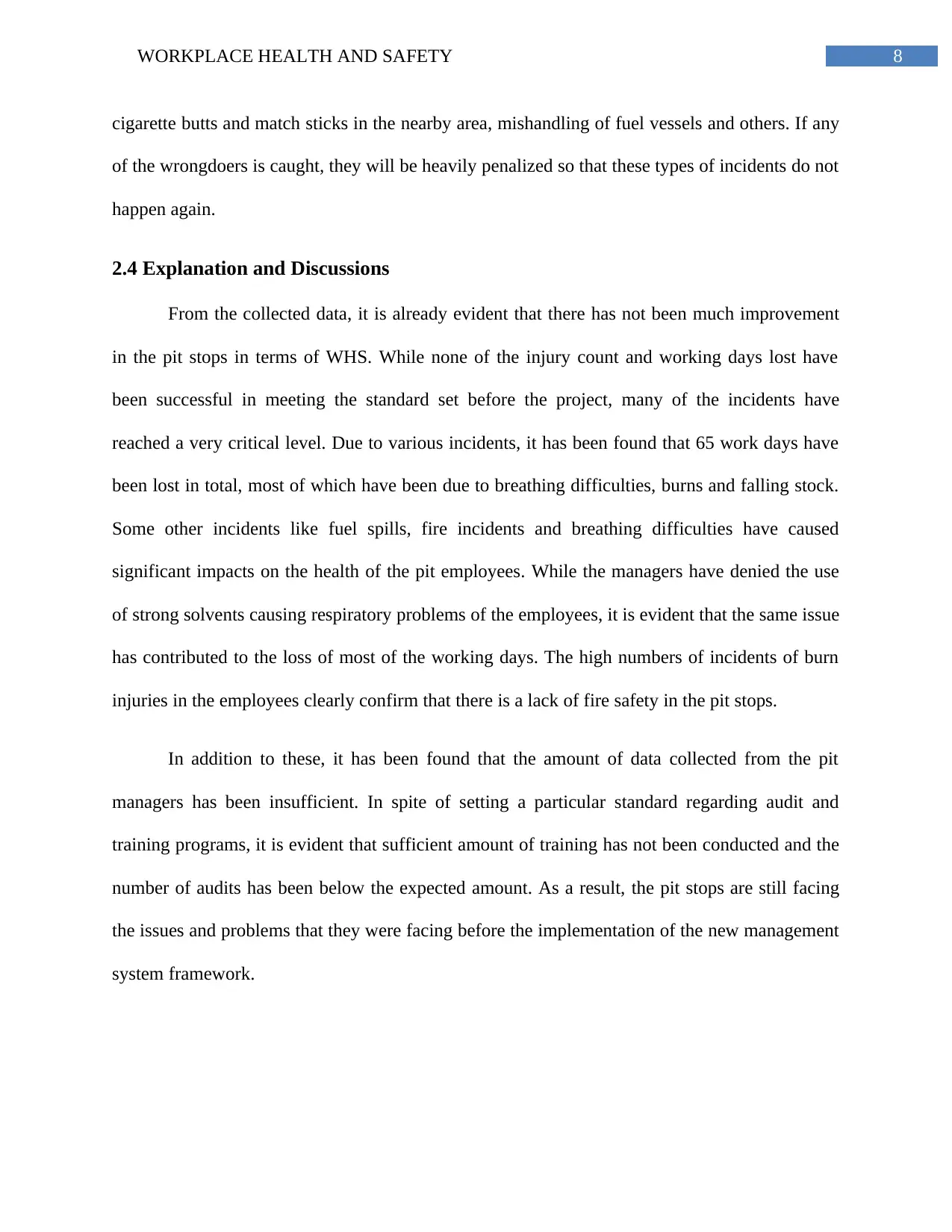
8WORKPLACE HEALTH AND SAFETY
cigarette butts and match sticks in the nearby area, mishandling of fuel vessels and others. If any
of the wrongdoers is caught, they will be heavily penalized so that these types of incidents do not
happen again.
2.4 Explanation and Discussions
From the collected data, it is already evident that there has not been much improvement
in the pit stops in terms of WHS. While none of the injury count and working days lost have
been successful in meeting the standard set before the project, many of the incidents have
reached a very critical level. Due to various incidents, it has been found that 65 work days have
been lost in total, most of which have been due to breathing difficulties, burns and falling stock.
Some other incidents like fuel spills, fire incidents and breathing difficulties have caused
significant impacts on the health of the pit employees. While the managers have denied the use
of strong solvents causing respiratory problems of the employees, it is evident that the same issue
has contributed to the loss of most of the working days. The high numbers of incidents of burn
injuries in the employees clearly confirm that there is a lack of fire safety in the pit stops.
In addition to these, it has been found that the amount of data collected from the pit
managers has been insufficient. In spite of setting a particular standard regarding audit and
training programs, it is evident that sufficient amount of training has not been conducted and the
number of audits has been below the expected amount. As a result, the pit stops are still facing
the issues and problems that they were facing before the implementation of the new management
system framework.
cigarette butts and match sticks in the nearby area, mishandling of fuel vessels and others. If any
of the wrongdoers is caught, they will be heavily penalized so that these types of incidents do not
happen again.
2.4 Explanation and Discussions
From the collected data, it is already evident that there has not been much improvement
in the pit stops in terms of WHS. While none of the injury count and working days lost have
been successful in meeting the standard set before the project, many of the incidents have
reached a very critical level. Due to various incidents, it has been found that 65 work days have
been lost in total, most of which have been due to breathing difficulties, burns and falling stock.
Some other incidents like fuel spills, fire incidents and breathing difficulties have caused
significant impacts on the health of the pit employees. While the managers have denied the use
of strong solvents causing respiratory problems of the employees, it is evident that the same issue
has contributed to the loss of most of the working days. The high numbers of incidents of burn
injuries in the employees clearly confirm that there is a lack of fire safety in the pit stops.
In addition to these, it has been found that the amount of data collected from the pit
managers has been insufficient. In spite of setting a particular standard regarding audit and
training programs, it is evident that sufficient amount of training has not been conducted and the
number of audits has been below the expected amount. As a result, the pit stops are still facing
the issues and problems that they were facing before the implementation of the new management
system framework.
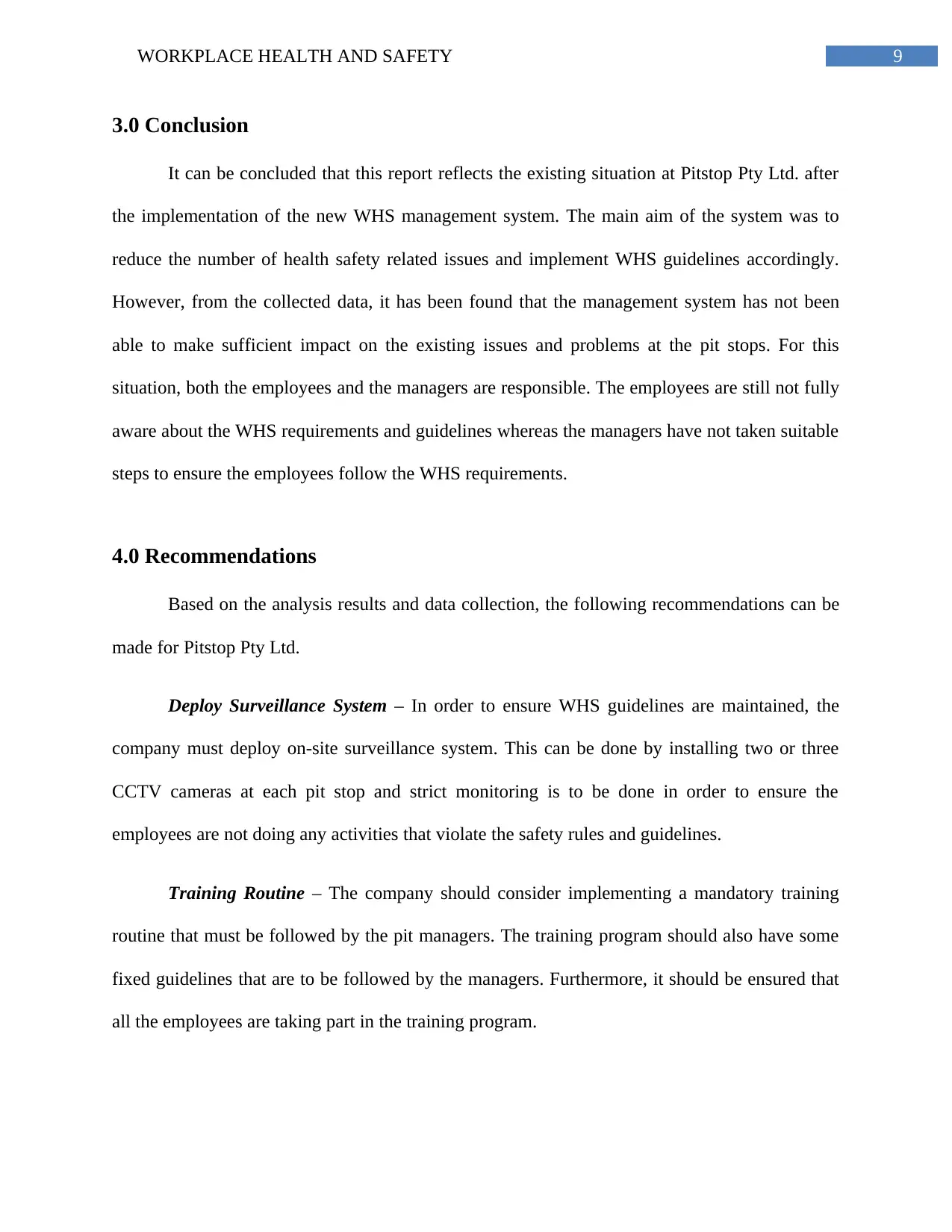
9WORKPLACE HEALTH AND SAFETY
3.0 Conclusion
It can be concluded that this report reflects the existing situation at Pitstop Pty Ltd. after
the implementation of the new WHS management system. The main aim of the system was to
reduce the number of health safety related issues and implement WHS guidelines accordingly.
However, from the collected data, it has been found that the management system has not been
able to make sufficient impact on the existing issues and problems at the pit stops. For this
situation, both the employees and the managers are responsible. The employees are still not fully
aware about the WHS requirements and guidelines whereas the managers have not taken suitable
steps to ensure the employees follow the WHS requirements.
4.0 Recommendations
Based on the analysis results and data collection, the following recommendations can be
made for Pitstop Pty Ltd.
Deploy Surveillance System – In order to ensure WHS guidelines are maintained, the
company must deploy on-site surveillance system. This can be done by installing two or three
CCTV cameras at each pit stop and strict monitoring is to be done in order to ensure the
employees are not doing any activities that violate the safety rules and guidelines.
Training Routine – The company should consider implementing a mandatory training
routine that must be followed by the pit managers. The training program should also have some
fixed guidelines that are to be followed by the managers. Furthermore, it should be ensured that
all the employees are taking part in the training program.
3.0 Conclusion
It can be concluded that this report reflects the existing situation at Pitstop Pty Ltd. after
the implementation of the new WHS management system. The main aim of the system was to
reduce the number of health safety related issues and implement WHS guidelines accordingly.
However, from the collected data, it has been found that the management system has not been
able to make sufficient impact on the existing issues and problems at the pit stops. For this
situation, both the employees and the managers are responsible. The employees are still not fully
aware about the WHS requirements and guidelines whereas the managers have not taken suitable
steps to ensure the employees follow the WHS requirements.
4.0 Recommendations
Based on the analysis results and data collection, the following recommendations can be
made for Pitstop Pty Ltd.
Deploy Surveillance System – In order to ensure WHS guidelines are maintained, the
company must deploy on-site surveillance system. This can be done by installing two or three
CCTV cameras at each pit stop and strict monitoring is to be done in order to ensure the
employees are not doing any activities that violate the safety rules and guidelines.
Training Routine – The company should consider implementing a mandatory training
routine that must be followed by the pit managers. The training program should also have some
fixed guidelines that are to be followed by the managers. Furthermore, it should be ensured that
all the employees are taking part in the training program.
Secure Best Marks with AI Grader
Need help grading? Try our AI Grader for instant feedback on your assignments.
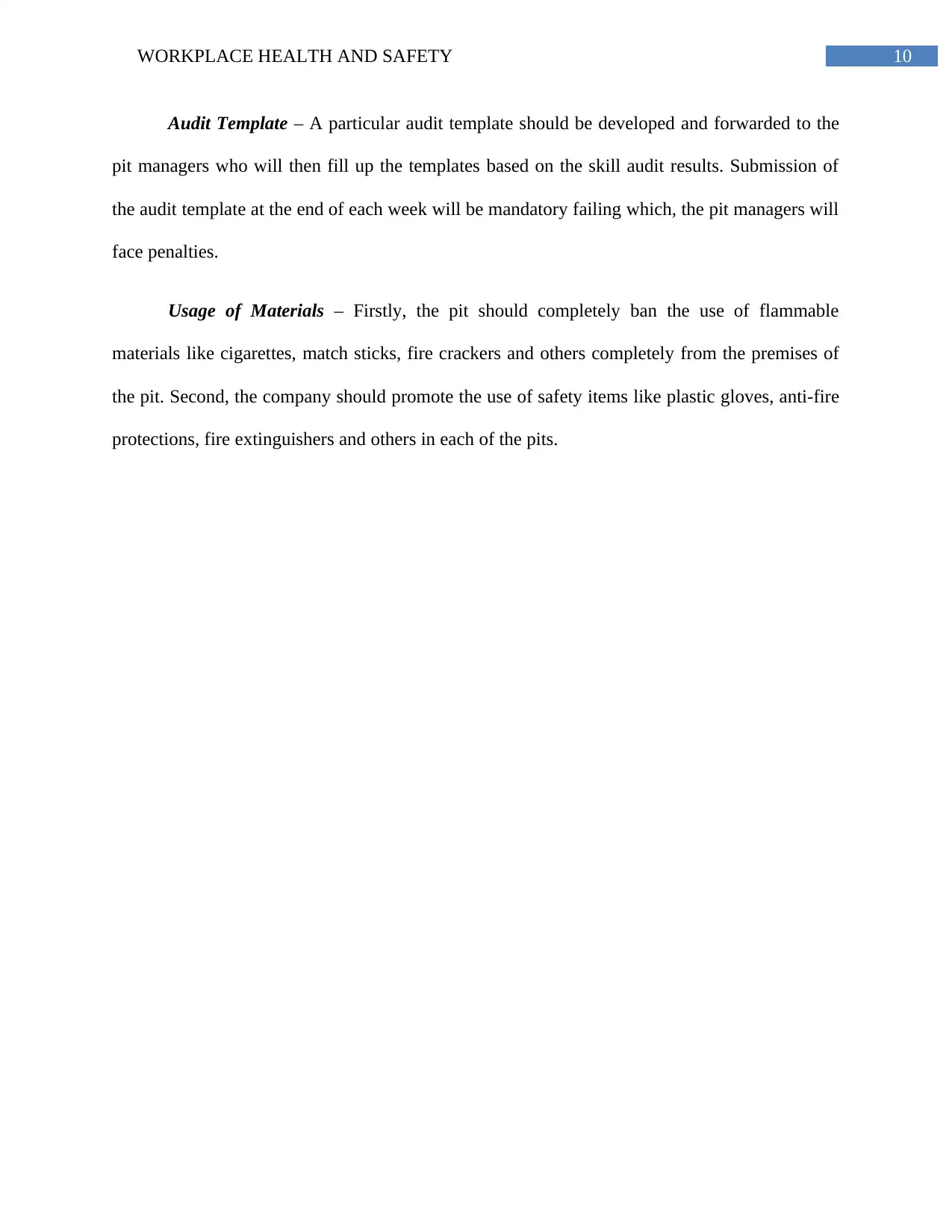
10WORKPLACE HEALTH AND SAFETY
Audit Template – A particular audit template should be developed and forwarded to the
pit managers who will then fill up the templates based on the skill audit results. Submission of
the audit template at the end of each week will be mandatory failing which, the pit managers will
face penalties.
Usage of Materials – Firstly, the pit should completely ban the use of flammable
materials like cigarettes, match sticks, fire crackers and others completely from the premises of
the pit. Second, the company should promote the use of safety items like plastic gloves, anti-fire
protections, fire extinguishers and others in each of the pits.
Audit Template – A particular audit template should be developed and forwarded to the
pit managers who will then fill up the templates based on the skill audit results. Submission of
the audit template at the end of each week will be mandatory failing which, the pit managers will
face penalties.
Usage of Materials – Firstly, the pit should completely ban the use of flammable
materials like cigarettes, match sticks, fire crackers and others completely from the premises of
the pit. Second, the company should promote the use of safety items like plastic gloves, anti-fire
protections, fire extinguishers and others in each of the pits.
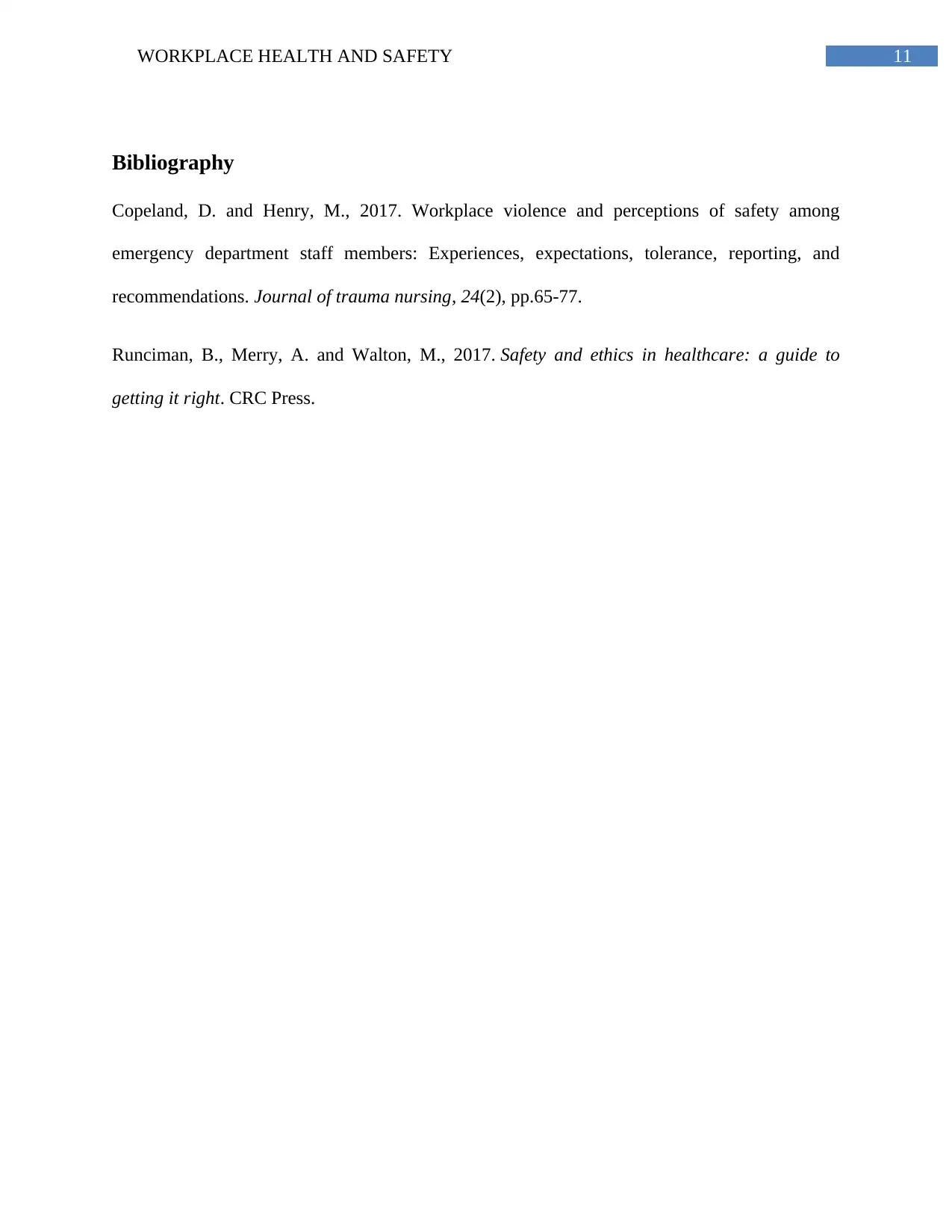
11WORKPLACE HEALTH AND SAFETY
Bibliography
Copeland, D. and Henry, M., 2017. Workplace violence and perceptions of safety among
emergency department staff members: Experiences, expectations, tolerance, reporting, and
recommendations. Journal of trauma nursing, 24(2), pp.65-77.
Runciman, B., Merry, A. and Walton, M., 2017. Safety and ethics in healthcare: a guide to
getting it right. CRC Press.
Bibliography
Copeland, D. and Henry, M., 2017. Workplace violence and perceptions of safety among
emergency department staff members: Experiences, expectations, tolerance, reporting, and
recommendations. Journal of trauma nursing, 24(2), pp.65-77.
Runciman, B., Merry, A. and Walton, M., 2017. Safety and ethics in healthcare: a guide to
getting it right. CRC Press.
1 out of 12
Related Documents

Your All-in-One AI-Powered Toolkit for Academic Success.
+13062052269
info@desklib.com
Available 24*7 on WhatsApp / Email
Unlock your academic potential
© 2024 | Zucol Services PVT LTD | All rights reserved.