CPCCBC4010B Assessment 6: Building Demolition and Construction Plan
VerifiedAdded on  2021/06/17
|40
|6766
|220
Report
AI Summary
This report outlines a comprehensive plan for the demolition of a building, addressing legislative and planning requirements, and emphasizing safe work practices, particularly when dealing with asbestos-containing materials. It details a step-by-step approach, including risk management, demolition work plans, and hazard control measures. The report also covers structural load assessments, illustrating load paths and the application of wind, dead, and live loads. Furthermore, it researches and lists the Building Code of Australia requirements for various zones, including bushfire (medium risk), high wind, and earthquake areas. The report emphasizes compliance with relevant Australian Standards and Codes, such as AS4801, and provides insights into the requirements of different building zones. The report also covers the removal of trees and provides a detailed plan for the demolition process.
Contribute Materials
Your contribution can guide someone’s learning journey. Share your
documents today.
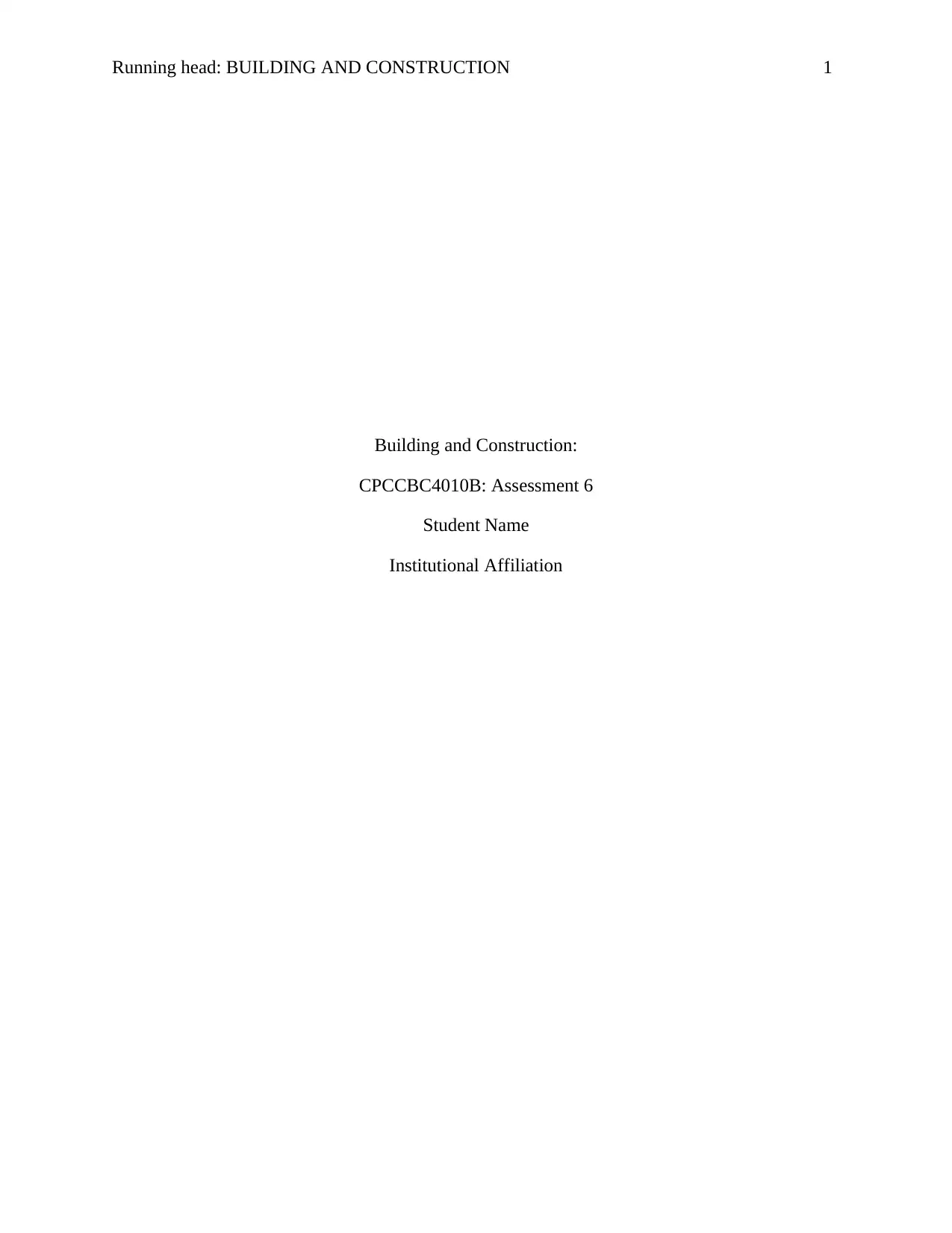
Running head: BUILDING AND CONSTRUCTION 1
Building and Construction:
CPCCBC4010B: Assessment 6
Student Name
Institutional Affiliation
Building and Construction:
CPCCBC4010B: Assessment 6
Student Name
Institutional Affiliation
Secure Best Marks with AI Grader
Need help grading? Try our AI Grader for instant feedback on your assignments.
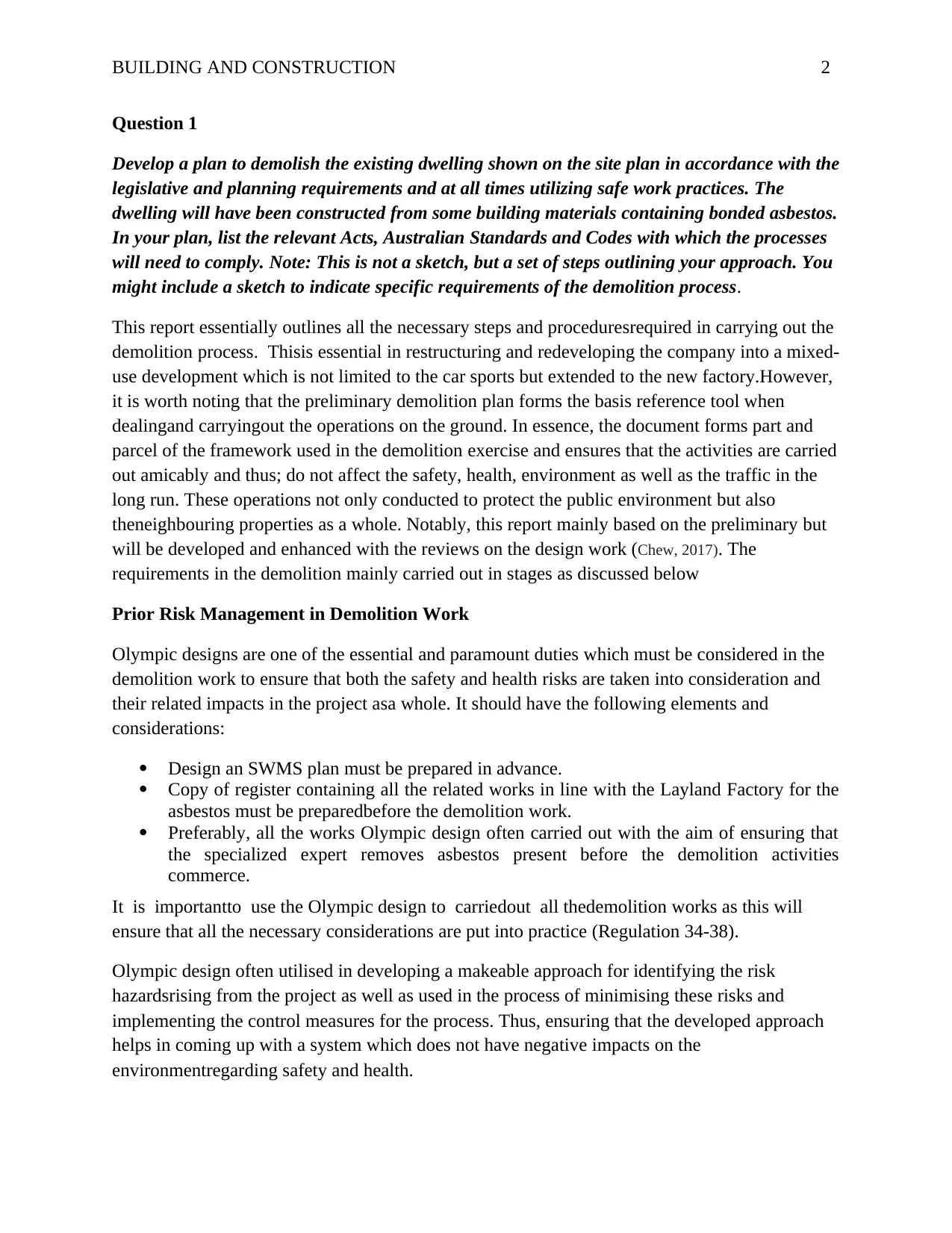
BUILDING AND CONSTRUCTION 2
Question 1
Develop a plan to demolish the existing dwelling shown on the site plan in accordance with the
legislative and planning requirements and at all times utilizing safe work practices. The
dwelling will have been constructed from some building materials containing bonded asbestos.
In your plan, list the relevant Acts, Australian Standards and Codes with which the processes
will need to comply. Note: This is not a sketch, but a set of steps outlining your approach. You
might include a sketch to indicate specific requirements of the demolition process.
This report essentially outlines all the necessary steps and proceduresrequired in carrying out the
demolition process. Thisis essential in restructuring and redeveloping the company into a mixed-
use development which is not limited to the car sports but extended to the new factory.However,
it is worth noting that the preliminary demolition plan forms the basis reference tool when
dealingand carryingout the operations on the ground. In essence, the document forms part and
parcel of the framework used in the demolition exercise and ensures that the activities are carried
out amicably and thus; do not affect the safety, health, environment as well as the traffic in the
long run. These operations not only conducted to protect the public environment but also
theneighbouring properties as a whole. Notably, this report mainly based on the preliminary but
will be developed and enhanced with the reviews on the design work (Chew, 2017). The
requirements in the demolition mainly carried out in stages as discussed below
Prior Risk Management in Demolition Work
Olympic designs are one of the essential and paramount duties which must be considered in the
demolition work to ensure that both the safety and health risks are taken into consideration and
their related impacts in the project asa whole. It should have the following elements and
considerations:
ï‚· Design an SWMS plan must be prepared in advance.
ï‚· Copy of register containing all the related works in line with the Layland Factory for the
asbestos must be preparedbefore the demolition work.
ï‚· Preferably, all the works Olympic design often carried out with the aim of ensuring that
the specialized expert removes asbestos present before the demolition activities
commerce.
It is importantto use the Olympic design to carriedout all thedemolition works as this will
ensure that all the necessary considerations are put into practice (Regulation 34-38).
Olympic design often utilised in developing a makeable approach for identifying the risk
hazardsrising from the project as well as used in the process of minimising these risks and
implementing the control measures for the process. Thus, ensuring that the developed approach
helps in coming up with a system which does not have negative impacts on the
environmentregarding safety and health.
Question 1
Develop a plan to demolish the existing dwelling shown on the site plan in accordance with the
legislative and planning requirements and at all times utilizing safe work practices. The
dwelling will have been constructed from some building materials containing bonded asbestos.
In your plan, list the relevant Acts, Australian Standards and Codes with which the processes
will need to comply. Note: This is not a sketch, but a set of steps outlining your approach. You
might include a sketch to indicate specific requirements of the demolition process.
This report essentially outlines all the necessary steps and proceduresrequired in carrying out the
demolition process. Thisis essential in restructuring and redeveloping the company into a mixed-
use development which is not limited to the car sports but extended to the new factory.However,
it is worth noting that the preliminary demolition plan forms the basis reference tool when
dealingand carryingout the operations on the ground. In essence, the document forms part and
parcel of the framework used in the demolition exercise and ensures that the activities are carried
out amicably and thus; do not affect the safety, health, environment as well as the traffic in the
long run. These operations not only conducted to protect the public environment but also
theneighbouring properties as a whole. Notably, this report mainly based on the preliminary but
will be developed and enhanced with the reviews on the design work (Chew, 2017). The
requirements in the demolition mainly carried out in stages as discussed below
Prior Risk Management in Demolition Work
Olympic designs are one of the essential and paramount duties which must be considered in the
demolition work to ensure that both the safety and health risks are taken into consideration and
their related impacts in the project asa whole. It should have the following elements and
considerations:
ï‚· Design an SWMS plan must be prepared in advance.
ï‚· Copy of register containing all the related works in line with the Layland Factory for the
asbestos must be preparedbefore the demolition work.
ï‚· Preferably, all the works Olympic design often carried out with the aim of ensuring that
the specialized expert removes asbestos present before the demolition activities
commerce.
It is importantto use the Olympic design to carriedout all thedemolition works as this will
ensure that all the necessary considerations are put into practice (Regulation 34-38).
Olympic design often utilised in developing a makeable approach for identifying the risk
hazardsrising from the project as well as used in the process of minimising these risks and
implementing the control measures for the process. Thus, ensuring that the developed approach
helps in coming up with a system which does not have negative impacts on the
environmentregarding safety and health.
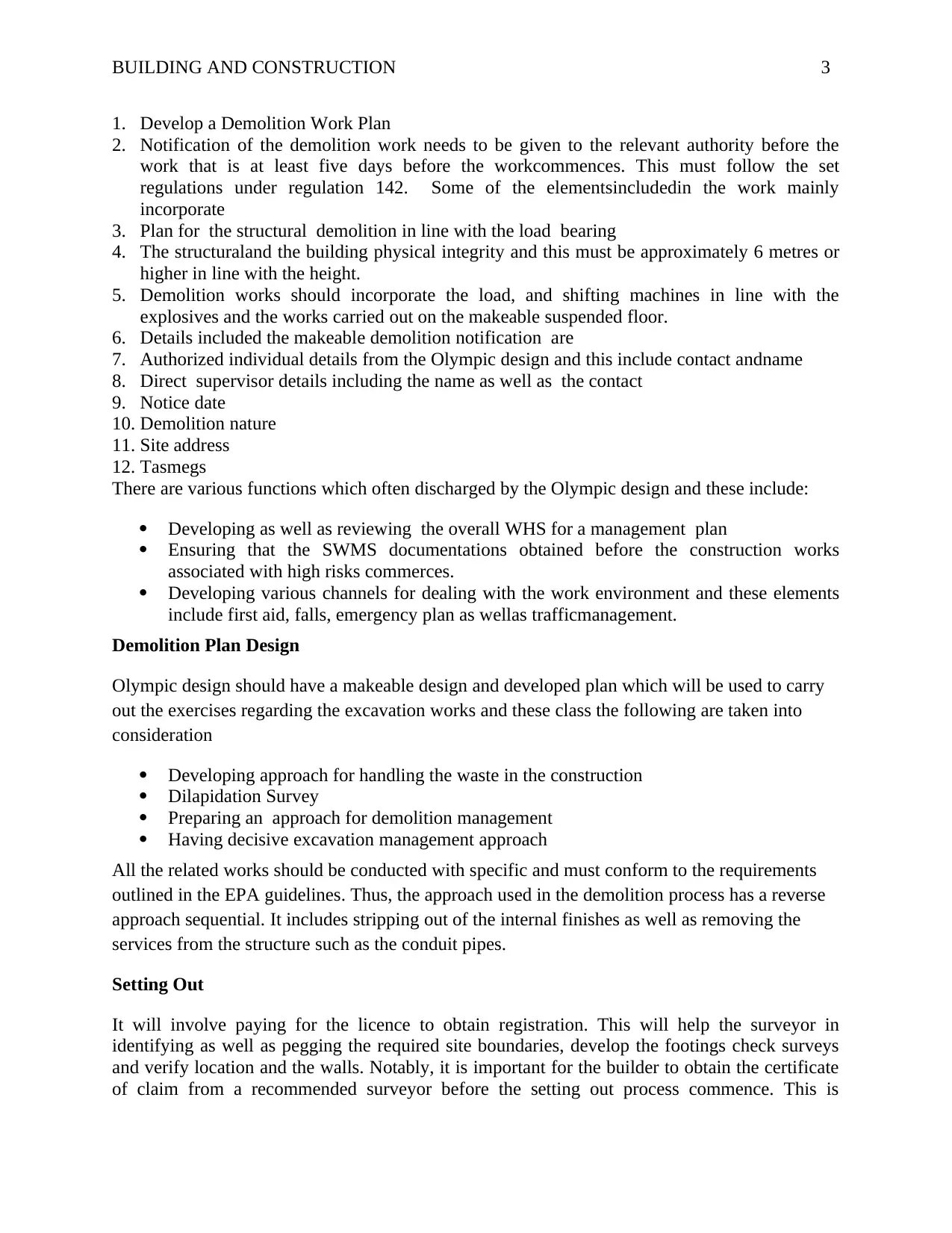
BUILDING AND CONSTRUCTION 3
1. Develop a Demolition Work Plan
2. Notification of the demolition work needs to be given to the relevant authority before the
work that is at least five days before the workcommences. This must follow the set
regulations under regulation 142. Some of the elementsincludedin the work mainly
incorporate
3. Plan for the structural demolition in line with the load bearing
4. The structuraland the building physical integrity and this must be approximately 6 metres or
higher in line with the height.
5. Demolition works should incorporate the load, and shifting machines in line with the
explosives and the works carried out on the makeable suspended floor.
6. Details included the makeable demolition notification are
7. Authorized individual details from the Olympic design and this include contact andname
8. Direct supervisor details including the name as well as the contact
9. Notice date
10. Demolition nature
11. Site address
12. Tasmegs
There are various functions which often discharged by the Olympic design and these include:
ï‚· Developing as well as reviewing the overall WHS for a management plan
ï‚· Ensuring that the SWMS documentations obtained before the construction works
associated with high risks commerces.
ï‚· Developing various channels for dealing with the work environment and these elements
include first aid, falls, emergency plan as wellas trafficmanagement.
Demolition Plan Design
Olympic design should have a makeable design and developed plan which will be used to carry
out the exercises regarding the excavation works and these class the following are taken into
consideration
ï‚· Developing approach for handling the waste in the construction
ï‚· Dilapidation Survey
ï‚· Preparing an approach for demolition management
ï‚· Having decisive excavation management approach
All the related works should be conducted with specific and must conform to the requirements
outlined in the EPA guidelines. Thus, the approach used in the demolition process has a reverse
approach sequential. It includes stripping out of the internal finishes as well as removing the
services from the structure such as the conduit pipes.
Setting Out
It will involve paying for the licence to obtain registration. This will help the surveyor in
identifying as well as pegging the required site boundaries, develop the footings check surveys
and verify location and the walls. Notably, it is important for the builder to obtain the certificate
of claim from a recommended surveyor before the setting out process commence. This is
1. Develop a Demolition Work Plan
2. Notification of the demolition work needs to be given to the relevant authority before the
work that is at least five days before the workcommences. This must follow the set
regulations under regulation 142. Some of the elementsincludedin the work mainly
incorporate
3. Plan for the structural demolition in line with the load bearing
4. The structuraland the building physical integrity and this must be approximately 6 metres or
higher in line with the height.
5. Demolition works should incorporate the load, and shifting machines in line with the
explosives and the works carried out on the makeable suspended floor.
6. Details included the makeable demolition notification are
7. Authorized individual details from the Olympic design and this include contact andname
8. Direct supervisor details including the name as well as the contact
9. Notice date
10. Demolition nature
11. Site address
12. Tasmegs
There are various functions which often discharged by the Olympic design and these include:
ï‚· Developing as well as reviewing the overall WHS for a management plan
ï‚· Ensuring that the SWMS documentations obtained before the construction works
associated with high risks commerces.
ï‚· Developing various channels for dealing with the work environment and these elements
include first aid, falls, emergency plan as wellas trafficmanagement.
Demolition Plan Design
Olympic design should have a makeable design and developed plan which will be used to carry
out the exercises regarding the excavation works and these class the following are taken into
consideration
ï‚· Developing approach for handling the waste in the construction
ï‚· Dilapidation Survey
ï‚· Preparing an approach for demolition management
ï‚· Having decisive excavation management approach
All the related works should be conducted with specific and must conform to the requirements
outlined in the EPA guidelines. Thus, the approach used in the demolition process has a reverse
approach sequential. It includes stripping out of the internal finishes as well as removing the
services from the structure such as the conduit pipes.
Setting Out
It will involve paying for the licence to obtain registration. This will help the surveyor in
identifying as well as pegging the required site boundaries, develop the footings check surveys
and verify location and the walls. Notably, it is important for the builder to obtain the certificate
of claim from a recommended surveyor before the setting out process commence. This is
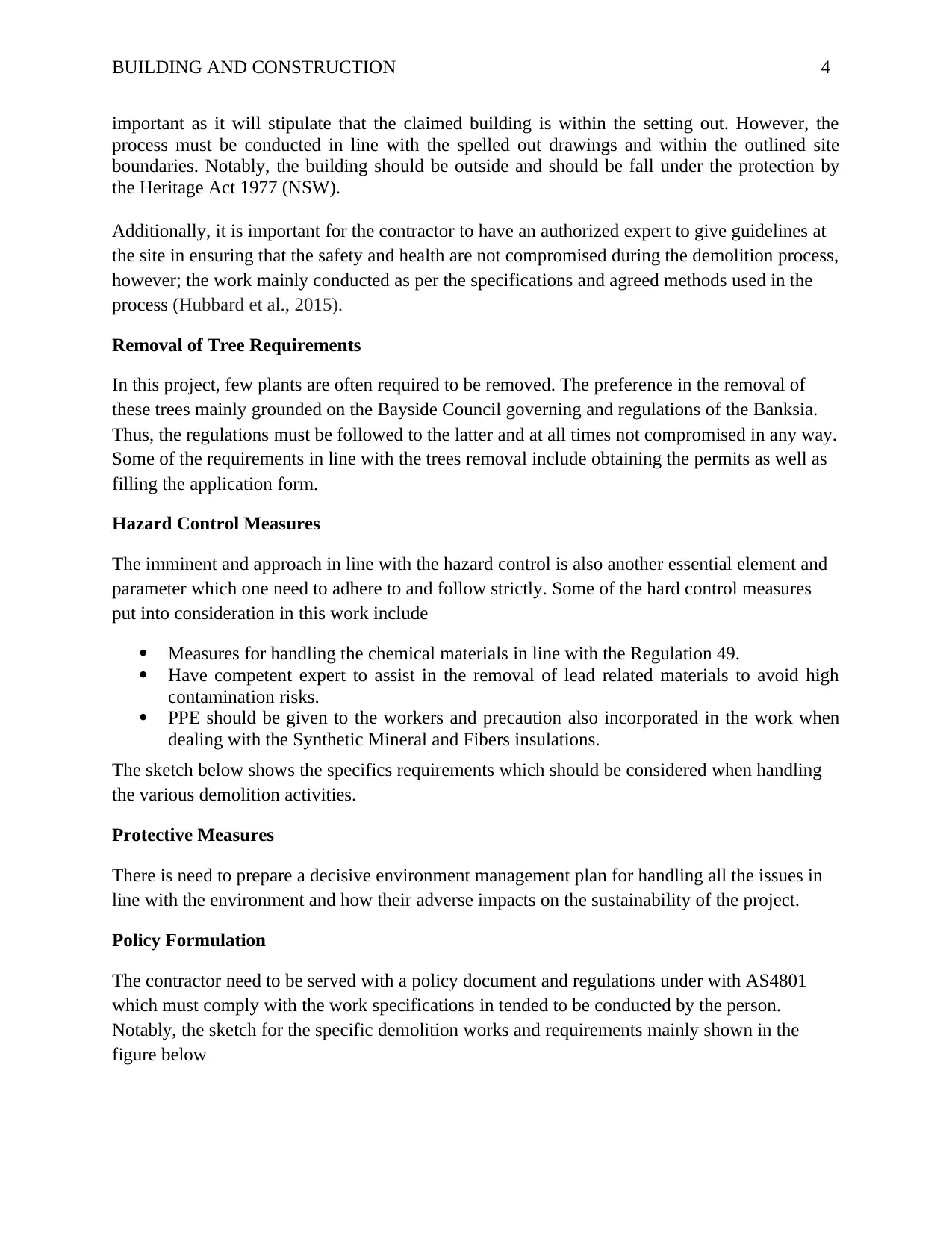
BUILDING AND CONSTRUCTION 4
important as it will stipulate that the claimed building is within the setting out. However, the
process must be conducted in line with the spelled out drawings and within the outlined site
boundaries. Notably, the building should be outside and should be fall under the protection by
the Heritage Act 1977 (NSW).
Additionally, it is important for the contractor to have an authorized expert to give guidelines at
the site in ensuring that the safety and health are not compromised during the demolition process,
however; the work mainly conducted as per the specifications and agreed methods used in the
process (Hubbard et al., 2015).
Removal of Tree Requirements
In this project, few plants are often required to be removed. The preference in the removal of
these trees mainly grounded on the Bayside Council governing and regulations of the Banksia.
Thus, the regulations must be followed to the latter and at all times not compromised in any way.
Some of the requirements in line with the trees removal include obtaining the permits as well as
filling the application form.
Hazard Control Measures
The imminent and approach in line with the hazard control is also another essential element and
parameter which one need to adhere to and follow strictly. Some of the hard control measures
put into consideration in this work include
ï‚· Measures for handling the chemical materials in line with the Regulation 49.
ï‚· Have competent expert to assist in the removal of lead related materials to avoid high
contamination risks.
ï‚· PPE should be given to the workers and precaution also incorporated in the work when
dealing with the Synthetic Mineral and Fibers insulations.
The sketch below shows the specifics requirements which should be considered when handling
the various demolition activities.
Protective Measures
There is need to prepare a decisive environment management plan for handling all the issues in
line with the environment and how their adverse impacts on the sustainability of the project.
Policy Formulation
The contractor need to be served with a policy document and regulations under with AS4801
which must comply with the work specifications in tended to be conducted by the person.
Notably, the sketch for the specific demolition works and requirements mainly shown in the
figure below
important as it will stipulate that the claimed building is within the setting out. However, the
process must be conducted in line with the spelled out drawings and within the outlined site
boundaries. Notably, the building should be outside and should be fall under the protection by
the Heritage Act 1977 (NSW).
Additionally, it is important for the contractor to have an authorized expert to give guidelines at
the site in ensuring that the safety and health are not compromised during the demolition process,
however; the work mainly conducted as per the specifications and agreed methods used in the
process (Hubbard et al., 2015).
Removal of Tree Requirements
In this project, few plants are often required to be removed. The preference in the removal of
these trees mainly grounded on the Bayside Council governing and regulations of the Banksia.
Thus, the regulations must be followed to the latter and at all times not compromised in any way.
Some of the requirements in line with the trees removal include obtaining the permits as well as
filling the application form.
Hazard Control Measures
The imminent and approach in line with the hazard control is also another essential element and
parameter which one need to adhere to and follow strictly. Some of the hard control measures
put into consideration in this work include
ï‚· Measures for handling the chemical materials in line with the Regulation 49.
ï‚· Have competent expert to assist in the removal of lead related materials to avoid high
contamination risks.
ï‚· PPE should be given to the workers and precaution also incorporated in the work when
dealing with the Synthetic Mineral and Fibers insulations.
The sketch below shows the specifics requirements which should be considered when handling
the various demolition activities.
Protective Measures
There is need to prepare a decisive environment management plan for handling all the issues in
line with the environment and how their adverse impacts on the sustainability of the project.
Policy Formulation
The contractor need to be served with a policy document and regulations under with AS4801
which must comply with the work specifications in tended to be conducted by the person.
Notably, the sketch for the specific demolition works and requirements mainly shown in the
figure below
Secure Best Marks with AI Grader
Need help grading? Try our AI Grader for instant feedback on your assignments.
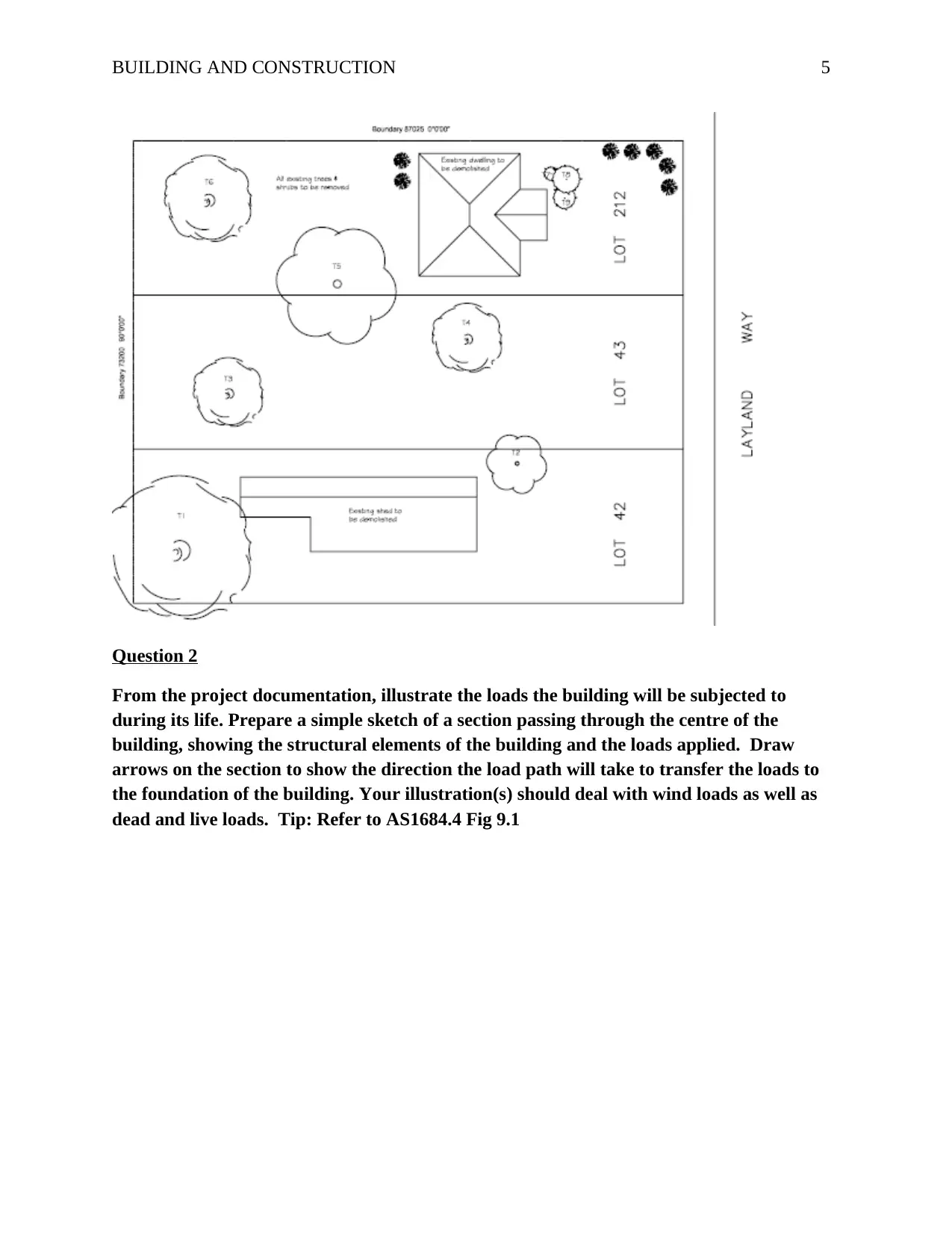
BUILDING AND CONSTRUCTION 5
Question 2
From the project documentation, illustrate the loads the building will be subjected to
during its life. Prepare a simple sketch of a section passing through the centre of the
building, showing the structural elements of the building and the loads applied. Draw
arrows on the section to show the direction the load path will take to transfer the loads to
the foundation of the building. Your illustration(s) should deal with wind loads as well as
dead and live loads. Tip: Refer to AS1684.4 Fig 9.1
Question 2
From the project documentation, illustrate the loads the building will be subjected to
during its life. Prepare a simple sketch of a section passing through the centre of the
building, showing the structural elements of the building and the loads applied. Draw
arrows on the section to show the direction the load path will take to transfer the loads to
the foundation of the building. Your illustration(s) should deal with wind loads as well as
dead and live loads. Tip: Refer to AS1684.4 Fig 9.1
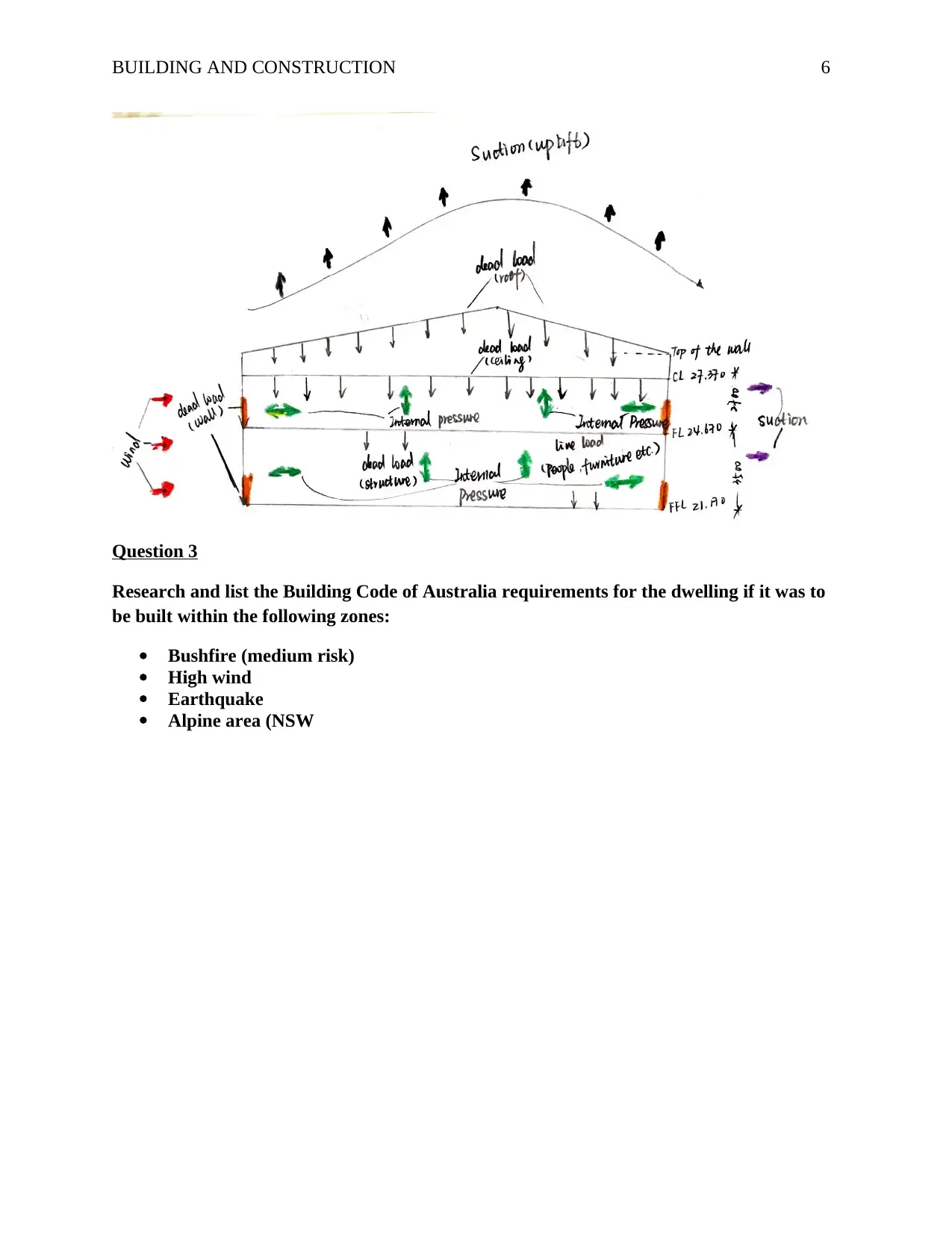
BUILDING AND CONSTRUCTION 6
Question 3
Research and list the Building Code of Australia requirements for the dwelling if it was to
be built within the following zones:
ï‚· Bushfire (medium risk)
ï‚· High wind
ï‚· Earthquake
ï‚· Alpine area (NSW
Question 3
Research and list the Building Code of Australia requirements for the dwelling if it was to
be built within the following zones:
ï‚· Bushfire (medium risk)
ï‚· High wind
ï‚· Earthquake
ï‚· Alpine area (NSW
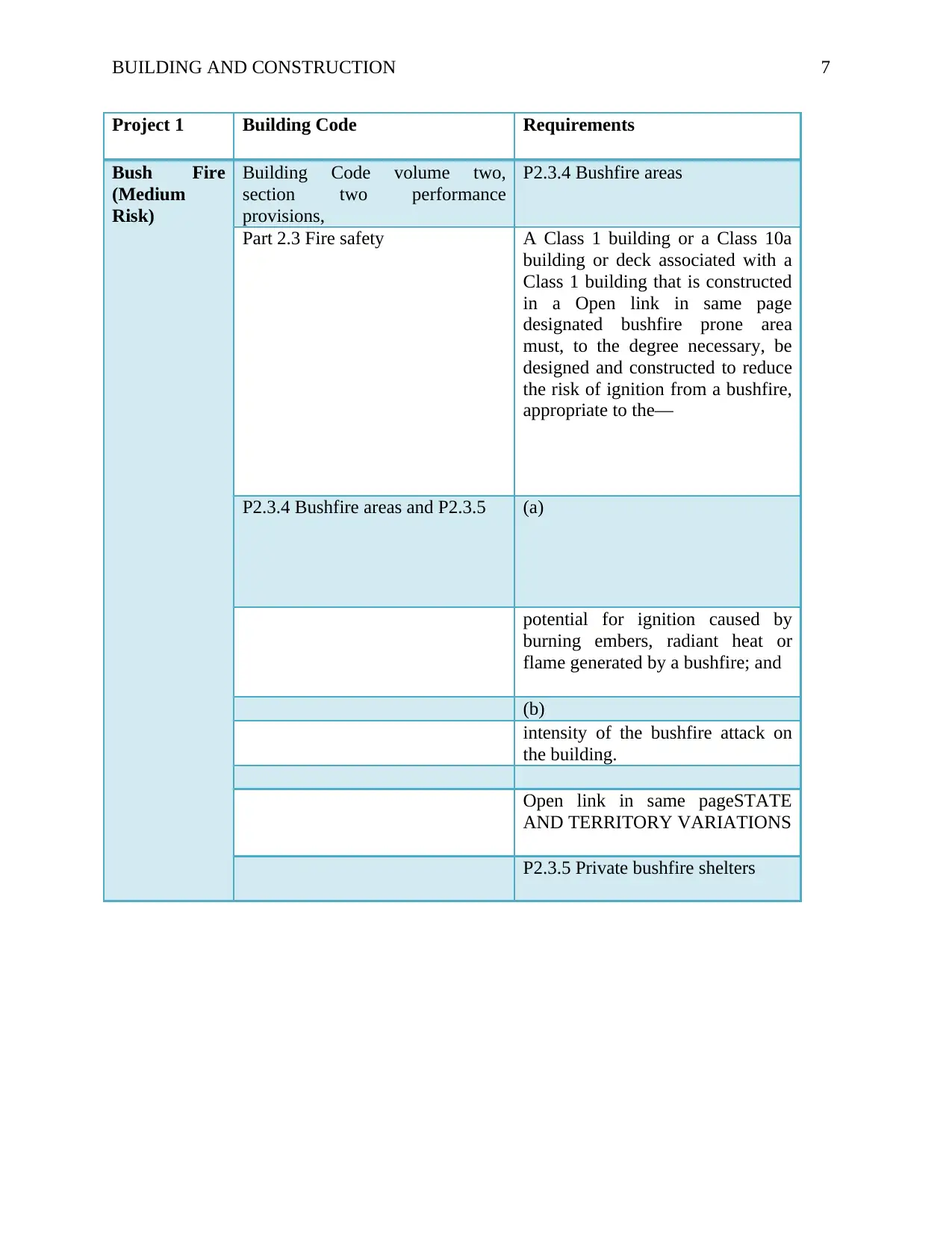
BUILDING AND CONSTRUCTION 7
Project 1 Building Code Requirements
Bush Fire
(Medium
Risk)
Building Code volume two,
section two performance
provisions,
P2.3.4 Bushfire areas
Part 2.3 Fire safety A Class 1 building or a Class 10a
building or deck associated with a
Class 1 building that is constructed
in a Open link in same page
designated bushfire prone area
must, to the degree necessary, be
designed and constructed to reduce
the risk of ignition from a bushfire,
appropriate to the—
P2.3.4 Bushfire areas and P2.3.5 (a)
potential for ignition caused by
burning embers, radiant heat or
flame generated by a bushfire; and
(b)
intensity of the bushfire attack on
the building.
Open link in same pageSTATE
AND TERRITORY VARIATIONS
P2.3.5 Private bushfire shelters
Project 1 Building Code Requirements
Bush Fire
(Medium
Risk)
Building Code volume two,
section two performance
provisions,
P2.3.4 Bushfire areas
Part 2.3 Fire safety A Class 1 building or a Class 10a
building or deck associated with a
Class 1 building that is constructed
in a Open link in same page
designated bushfire prone area
must, to the degree necessary, be
designed and constructed to reduce
the risk of ignition from a bushfire,
appropriate to the—
P2.3.4 Bushfire areas and P2.3.5 (a)
potential for ignition caused by
burning embers, radiant heat or
flame generated by a bushfire; and
(b)
intensity of the bushfire attack on
the building.
Open link in same pageSTATE
AND TERRITORY VARIATIONS
P2.3.5 Private bushfire shelters
Paraphrase This Document
Need a fresh take? Get an instant paraphrase of this document with our AI Paraphraser
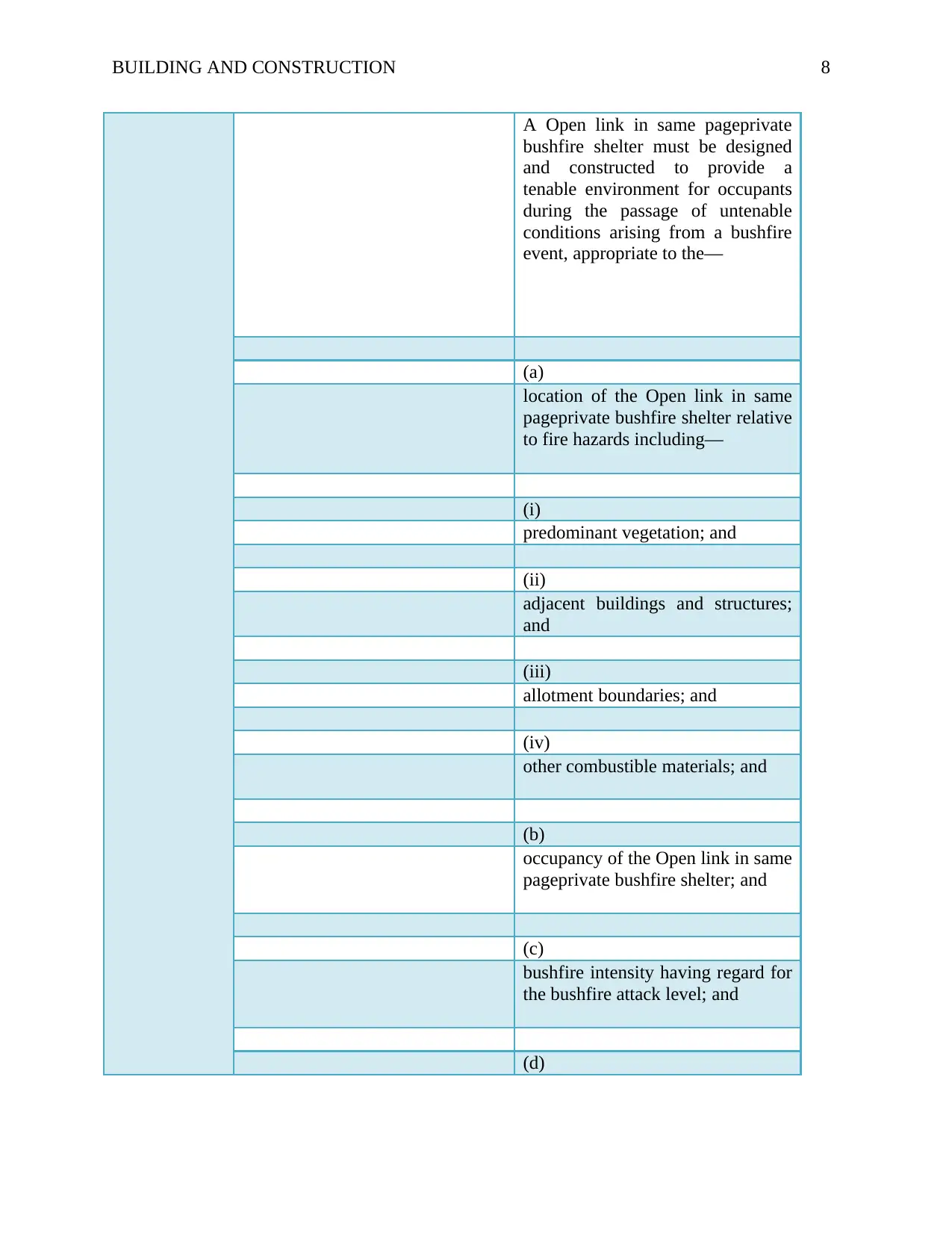
BUILDING AND CONSTRUCTION 8
A Open link in same pageprivate
bushfire shelter must be designed
and constructed to provide a
tenable environment for occupants
during the passage of untenable
conditions arising from a bushfire
event, appropriate to the—
(a)
location of the Open link in same
pageprivate bushfire shelter relative
to fire hazards including—
(i)
predominant vegetation; and
(ii)
adjacent buildings and structures;
and
(iii)
allotment boundaries; and
(iv)
other combustible materials; and
(b)
occupancy of the Open link in same
pageprivate bushfire shelter; and
(c)
bushfire intensity having regard for
the bushfire attack level; and
(d)
A Open link in same pageprivate
bushfire shelter must be designed
and constructed to provide a
tenable environment for occupants
during the passage of untenable
conditions arising from a bushfire
event, appropriate to the—
(a)
location of the Open link in same
pageprivate bushfire shelter relative
to fire hazards including—
(i)
predominant vegetation; and
(ii)
adjacent buildings and structures;
and
(iii)
allotment boundaries; and
(iv)
other combustible materials; and
(b)
occupancy of the Open link in same
pageprivate bushfire shelter; and
(c)
bushfire intensity having regard for
the bushfire attack level; and
(d)
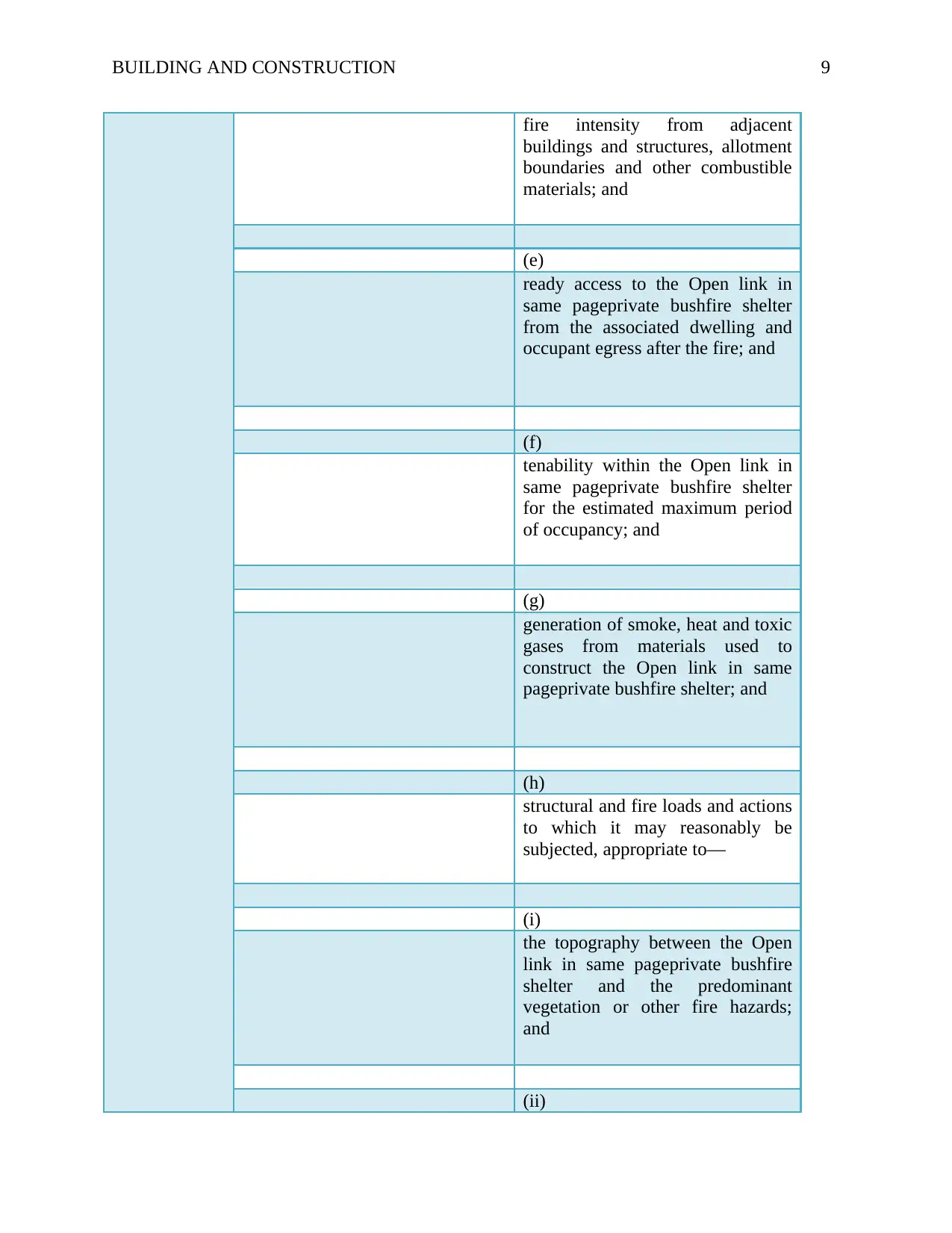
BUILDING AND CONSTRUCTION 9
fire intensity from adjacent
buildings and structures, allotment
boundaries and other combustible
materials; and
(e)
ready access to the Open link in
same pageprivate bushfire shelter
from the associated dwelling and
occupant egress after the fire; and
(f)
tenability within the Open link in
same pageprivate bushfire shelter
for the estimated maximum period
of occupancy; and
(g)
generation of smoke, heat and toxic
gases from materials used to
construct the Open link in same
pageprivate bushfire shelter; and
(h)
structural and fire loads and actions
to which it may reasonably be
subjected, appropriate to—
(i)
the topography between the Open
link in same pageprivate bushfire
shelter and the predominant
vegetation or other fire hazards;
and
(ii)
fire intensity from adjacent
buildings and structures, allotment
boundaries and other combustible
materials; and
(e)
ready access to the Open link in
same pageprivate bushfire shelter
from the associated dwelling and
occupant egress after the fire; and
(f)
tenability within the Open link in
same pageprivate bushfire shelter
for the estimated maximum period
of occupancy; and
(g)
generation of smoke, heat and toxic
gases from materials used to
construct the Open link in same
pageprivate bushfire shelter; and
(h)
structural and fire loads and actions
to which it may reasonably be
subjected, appropriate to—
(i)
the topography between the Open
link in same pageprivate bushfire
shelter and the predominant
vegetation or other fire hazards;
and
(ii)
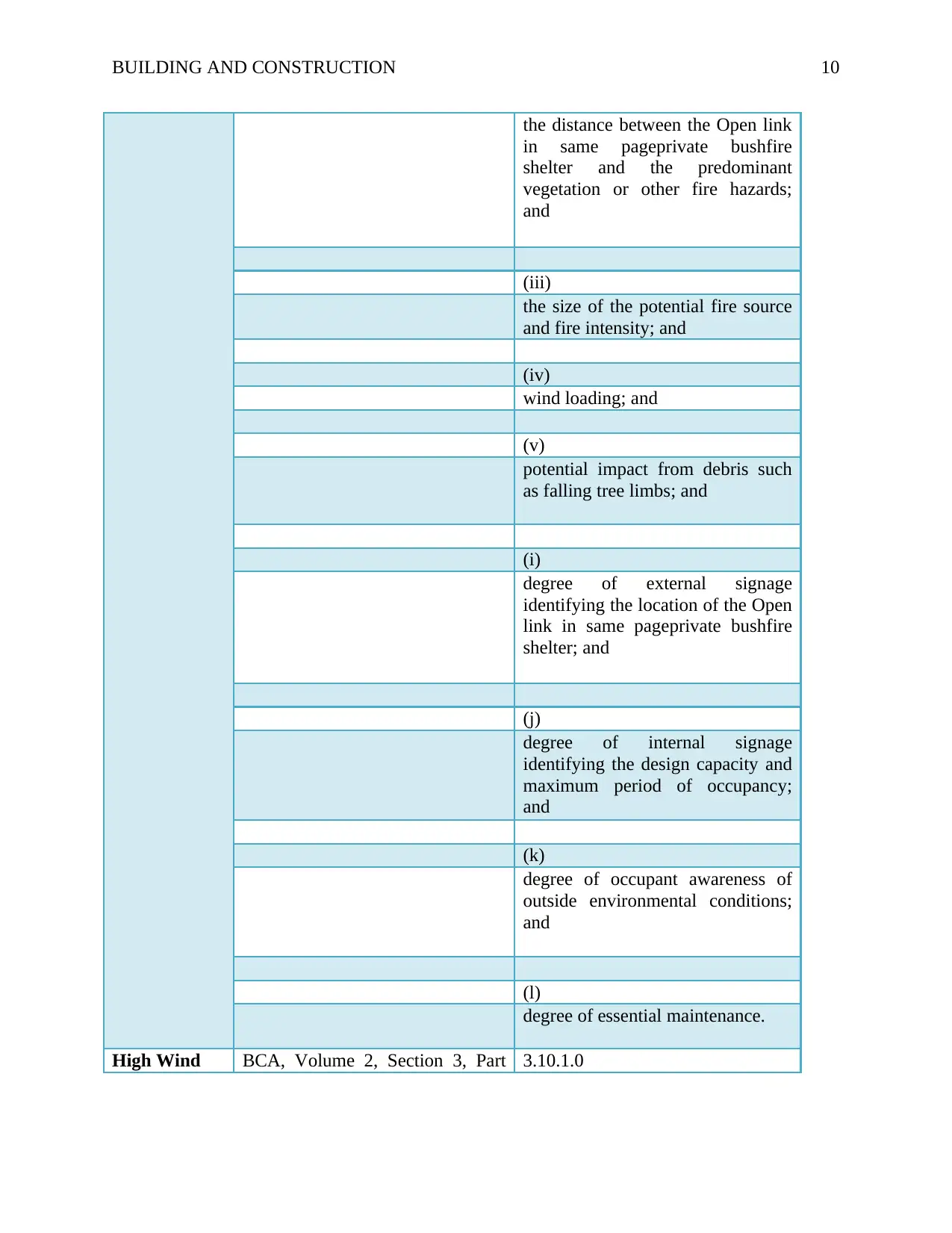
BUILDING AND CONSTRUCTION 10
the distance between the Open link
in same pageprivate bushfire
shelter and the predominant
vegetation or other fire hazards;
and
(iii)
the size of the potential fire source
and fire intensity; and
(iv)
wind loading; and
(v)
potential impact from debris such
as falling tree limbs; and
(i)
degree of external signage
identifying the location of the Open
link in same pageprivate bushfire
shelter; and
(j)
degree of internal signage
identifying the design capacity and
maximum period of occupancy;
and
(k)
degree of occupant awareness of
outside environmental conditions;
and
(l)
degree of essential maintenance.
High Wind BCA, Volume 2, Section 3, Part 3.10.1.0
the distance between the Open link
in same pageprivate bushfire
shelter and the predominant
vegetation or other fire hazards;
and
(iii)
the size of the potential fire source
and fire intensity; and
(iv)
wind loading; and
(v)
potential impact from debris such
as falling tree limbs; and
(i)
degree of external signage
identifying the location of the Open
link in same pageprivate bushfire
shelter; and
(j)
degree of internal signage
identifying the design capacity and
maximum period of occupancy;
and
(k)
degree of occupant awareness of
outside environmental conditions;
and
(l)
degree of essential maintenance.
High Wind BCA, Volume 2, Section 3, Part 3.10.1.0
Secure Best Marks with AI Grader
Need help grading? Try our AI Grader for instant feedback on your assignments.

BUILDING AND CONSTRUCTION 11
3.10.1 Performance Requirement Open
link in same pageP2.1.1 is satisfied
for a building constructed in
a Open link in same pagehigh wind
area if it complies with one or
more of the following, as
appropriate:
(a)
Masonry:
(i)
AS 3700.
(ii)
AS 4773 Parts 1 and 2.
(b)
The Northern Territory
Deemed-to-Comply Standards
Manual.
(c)
Timber:
(i)
AS 1684.2.
(ii)
AS 1684.3.
(d)
Steel:
(i)
Steel framing:
AS 4100.
(ii)
Cold-formed steel
structures: AS 4600.
(iii)
Residential and low-
rise steel framing: NASH Standard
– Residential and Low-Rise Steel
Framing, Part 1 or Part 2.
(e)
Glazed assemblies:
(i)
3.10.1 Performance Requirement Open
link in same pageP2.1.1 is satisfied
for a building constructed in
a Open link in same pagehigh wind
area if it complies with one or
more of the following, as
appropriate:
(a)
Masonry:
(i)
AS 3700.
(ii)
AS 4773 Parts 1 and 2.
(b)
The Northern Territory
Deemed-to-Comply Standards
Manual.
(c)
Timber:
(i)
AS 1684.2.
(ii)
AS 1684.3.
(d)
Steel:
(i)
Steel framing:
AS 4100.
(ii)
Cold-formed steel
structures: AS 4600.
(iii)
Residential and low-
rise steel framing: NASH Standard
– Residential and Low-Rise Steel
Framing, Part 1 or Part 2.
(e)
Glazed assemblies:
(i)
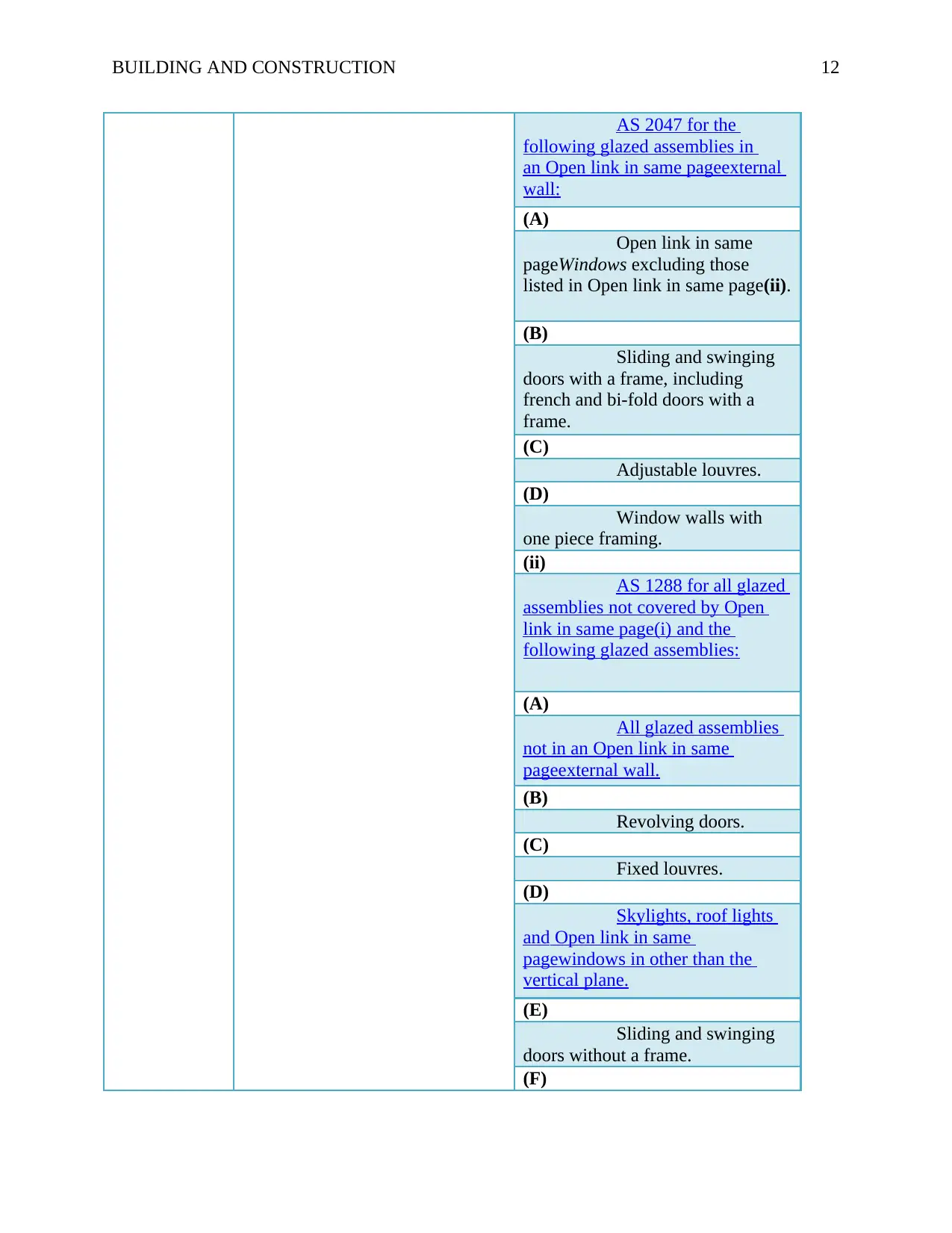
BUILDING AND CONSTRUCTION 12
AS 2047 for the
following glazed assemblies in
an Open link in same pageexternal
wall:
(A)
Open link in same
pageWindows excluding those
listed in Open link in same page(ii).
(B)
Sliding and swinging
doors with a frame, including
french and bi-fold doors with a
frame.
(C)
Adjustable louvres.
(D)
Window walls with
one piece framing.
(ii)
AS 1288 for all glazed
assemblies not covered by Open
link in same page(i) and the
following glazed assemblies:
(A)
All glazed assemblies
not in an Open link in same
pageexternal wall.
(B)
Revolving doors.
(C)
Fixed louvres.
(D)
Skylights, roof lights
and Open link in same
pagewindows in other than the
vertical plane.
(E)
Sliding and swinging
doors without a frame.
(F)
AS 2047 for the
following glazed assemblies in
an Open link in same pageexternal
wall:
(A)
Open link in same
pageWindows excluding those
listed in Open link in same page(ii).
(B)
Sliding and swinging
doors with a frame, including
french and bi-fold doors with a
frame.
(C)
Adjustable louvres.
(D)
Window walls with
one piece framing.
(ii)
AS 1288 for all glazed
assemblies not covered by Open
link in same page(i) and the
following glazed assemblies:
(A)
All glazed assemblies
not in an Open link in same
pageexternal wall.
(B)
Revolving doors.
(C)
Fixed louvres.
(D)
Skylights, roof lights
and Open link in same
pagewindows in other than the
vertical plane.
(E)
Sliding and swinging
doors without a frame.
(F)
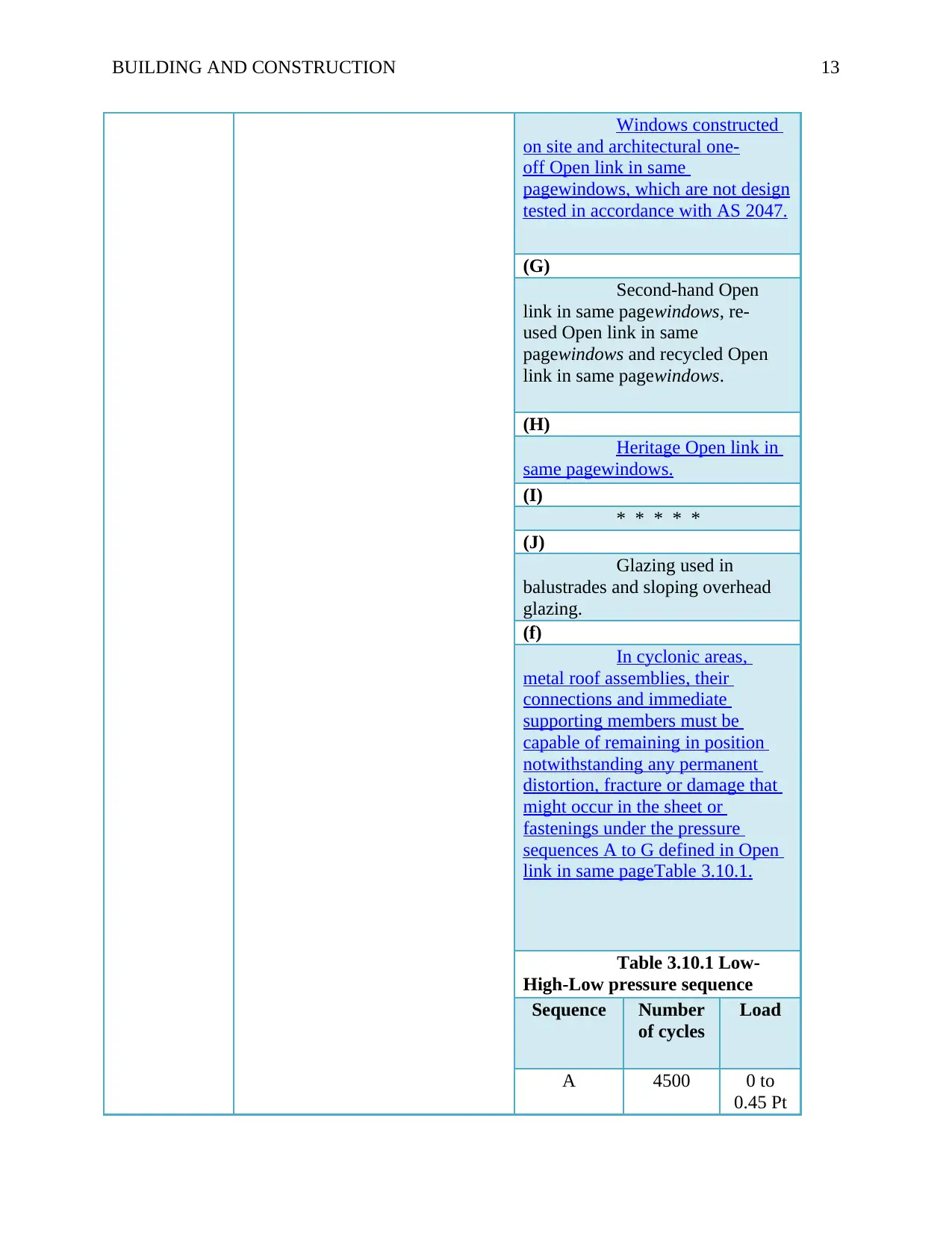
BUILDING AND CONSTRUCTION 13
Windows constructed
on site and architectural one-
off Open link in same
pagewindows, which are not design
tested in accordance with AS 2047.
(G)
Second-hand Open
link in same pagewindows, re-
used Open link in same
pagewindows and recycled Open
link in same pagewindows.
(H)
Heritage Open link in
same pagewindows.
(I)
* * * * *
(J)
Glazing used in
balustrades and sloping overhead
glazing.
(f)
In cyclonic areas,
metal roof assemblies, their
connections and immediate
supporting members must be
capable of remaining in position
notwithstanding any permanent
distortion, fracture or damage that
might occur in the sheet or
fastenings under the pressure
sequences A to G defined in Open
link in same pageTable 3.10.1.
Table 3.10.1 Low-
High-Low pressure sequence
Sequence Number
of cycles
Load
A 4500 0 to
0.45 Pt
Windows constructed
on site and architectural one-
off Open link in same
pagewindows, which are not design
tested in accordance with AS 2047.
(G)
Second-hand Open
link in same pagewindows, re-
used Open link in same
pagewindows and recycled Open
link in same pagewindows.
(H)
Heritage Open link in
same pagewindows.
(I)
* * * * *
(J)
Glazing used in
balustrades and sloping overhead
glazing.
(f)
In cyclonic areas,
metal roof assemblies, their
connections and immediate
supporting members must be
capable of remaining in position
notwithstanding any permanent
distortion, fracture or damage that
might occur in the sheet or
fastenings under the pressure
sequences A to G defined in Open
link in same pageTable 3.10.1.
Table 3.10.1 Low-
High-Low pressure sequence
Sequence Number
of cycles
Load
A 4500 0 to
0.45 Pt
Paraphrase This Document
Need a fresh take? Get an instant paraphrase of this document with our AI Paraphraser
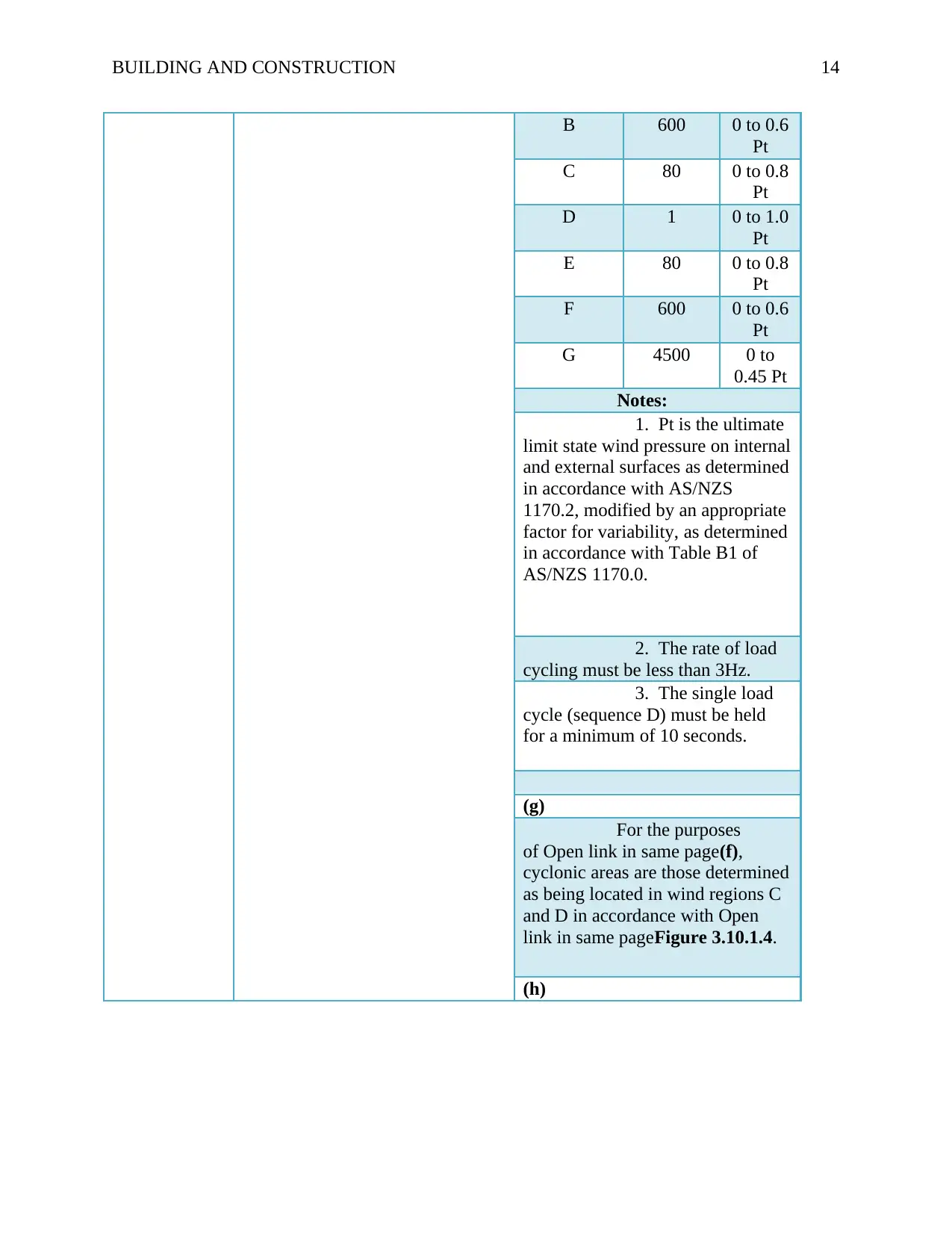
BUILDING AND CONSTRUCTION 14
B 600 0 to 0.6
Pt
C 80 0 to 0.8
Pt
D 1 0 to 1.0
Pt
E 80 0 to 0.8
Pt
F 600 0 to 0.6
Pt
G 4500 0 to
0.45 Pt
Notes:
1. Pt is the ultimate
limit state wind pressure on internal
and external surfaces as determined
in accordance with AS/NZS
1170.2, modified by an appropriate
factor for variability, as determined
in accordance with Table B1 of
AS/NZS 1170.0.
2. The rate of load
cycling must be less than 3Hz.
3. The single load
cycle (sequence D) must be held
for a minimum of 10 seconds.
(g)
For the purposes
of Open link in same page(f),
cyclonic areas are those determined
as being located in wind regions C
and D in accordance with Open
link in same pageFigure 3.10.1.4.
(h)
B 600 0 to 0.6
Pt
C 80 0 to 0.8
Pt
D 1 0 to 1.0
Pt
E 80 0 to 0.8
Pt
F 600 0 to 0.6
Pt
G 4500 0 to
0.45 Pt
Notes:
1. Pt is the ultimate
limit state wind pressure on internal
and external surfaces as determined
in accordance with AS/NZS
1170.2, modified by an appropriate
factor for variability, as determined
in accordance with Table B1 of
AS/NZS 1170.0.
2. The rate of load
cycling must be less than 3Hz.
3. The single load
cycle (sequence D) must be held
for a minimum of 10 seconds.
(g)
For the purposes
of Open link in same page(f),
cyclonic areas are those determined
as being located in wind regions C
and D in accordance with Open
link in same pageFigure 3.10.1.4.
(h)
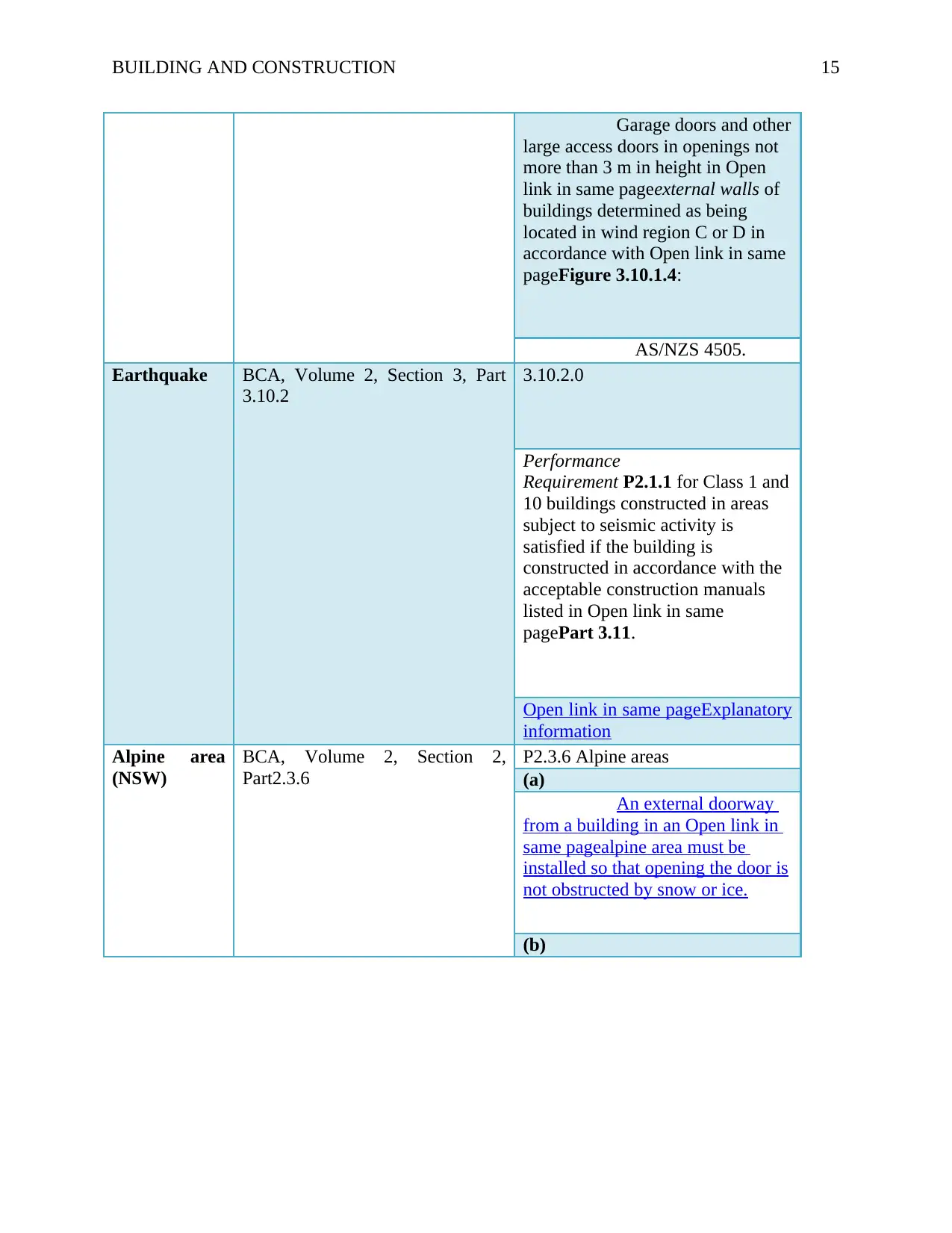
BUILDING AND CONSTRUCTION 15
Garage doors and other
large access doors in openings not
more than 3 m in height in Open
link in same pageexternal walls of
buildings determined as being
located in wind region C or D in
accordance with Open link in same
pageFigure 3.10.1.4:
AS/NZS 4505.
Earthquake BCA, Volume 2, Section 3, Part
3.10.2
3.10.2.0
Performance
Requirement P2.1.1 for Class 1 and
10 buildings constructed in areas
subject to seismic activity is
satisfied if the building is
constructed in accordance with the
acceptable construction manuals
listed in Open link in same
pagePart 3.11.
Open link in same pageExplanatory
information
Alpine area
(NSW)
BCA, Volume 2, Section 2,
Part2.3.6
P2.3.6 Alpine areas
(a)
An external doorway
from a building in an Open link in
same pagealpine area must be
installed so that opening the door is
not obstructed by snow or ice.
(b)
Garage doors and other
large access doors in openings not
more than 3 m in height in Open
link in same pageexternal walls of
buildings determined as being
located in wind region C or D in
accordance with Open link in same
pageFigure 3.10.1.4:
AS/NZS 4505.
Earthquake BCA, Volume 2, Section 3, Part
3.10.2
3.10.2.0
Performance
Requirement P2.1.1 for Class 1 and
10 buildings constructed in areas
subject to seismic activity is
satisfied if the building is
constructed in accordance with the
acceptable construction manuals
listed in Open link in same
pagePart 3.11.
Open link in same pageExplanatory
information
Alpine area
(NSW)
BCA, Volume 2, Section 2,
Part2.3.6
P2.3.6 Alpine areas
(a)
An external doorway
from a building in an Open link in
same pagealpine area must be
installed so that opening the door is
not obstructed by snow or ice.
(b)
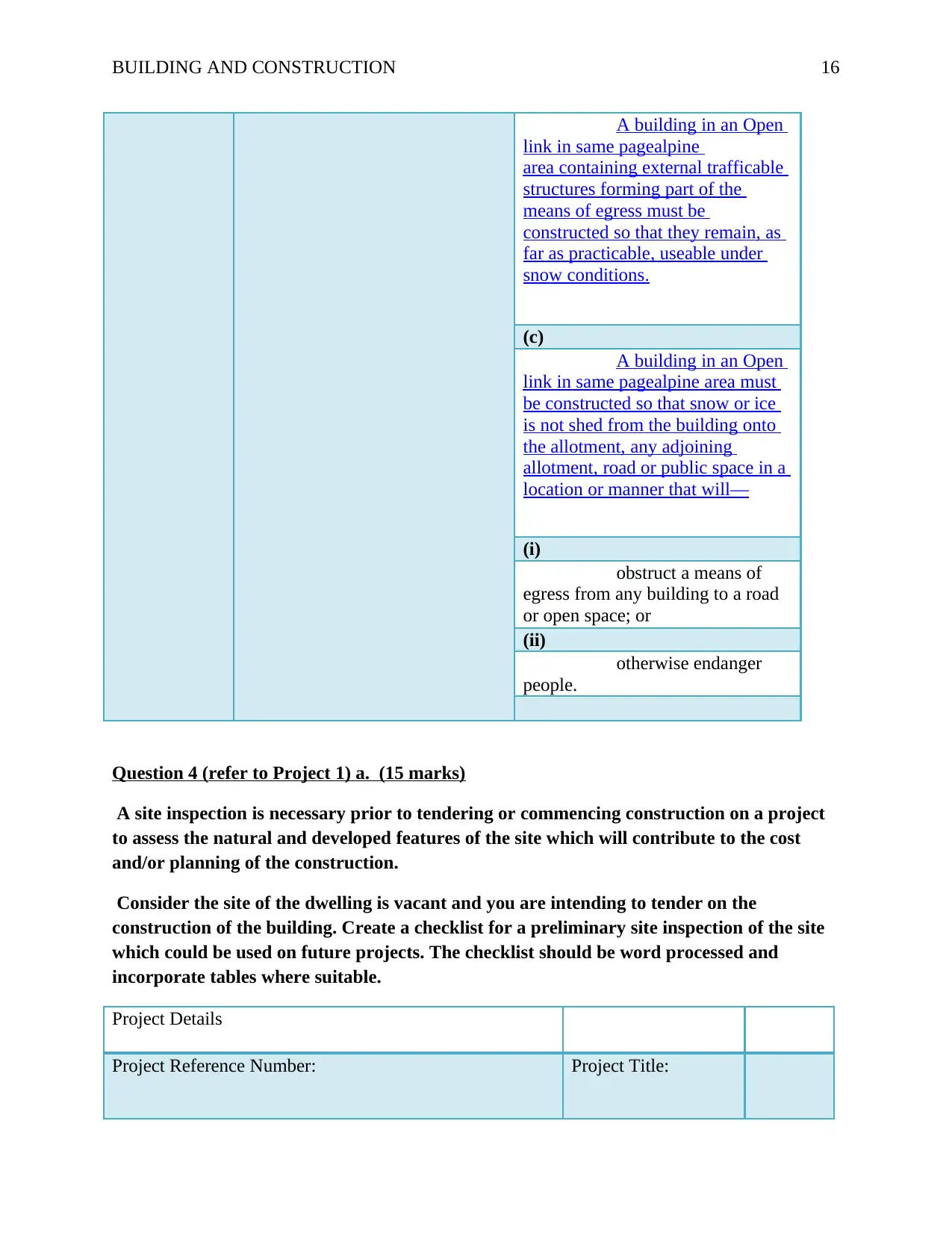
BUILDING AND CONSTRUCTION 16
A building in an Open
link in same pagealpine
area containing external trafficable
structures forming part of the
means of egress must be
constructed so that they remain, as
far as practicable, useable under
snow conditions.
(c)
A building in an Open
link in same pagealpine area must
be constructed so that snow or ice
is not shed from the building onto
the allotment, any adjoining
allotment, road or public space in a
location or manner that will—
(i)
obstruct a means of
egress from any building to a road
or open space; or
(ii)
otherwise endanger
people.
Question 4 (refer to Project 1) a. (15 marks)
A site inspection is necessary prior to tendering or commencing construction on a project
to assess the natural and developed features of the site which will contribute to the cost
and/or planning of the construction.
Consider the site of the dwelling is vacant and you are intending to tender on the
construction of the building. Create a checklist for a preliminary site inspection of the site
which could be used on future projects. The checklist should be word processed and
incorporate tables where suitable.
Project Details
Project Reference Number: Project Title:
A building in an Open
link in same pagealpine
area containing external trafficable
structures forming part of the
means of egress must be
constructed so that they remain, as
far as practicable, useable under
snow conditions.
(c)
A building in an Open
link in same pagealpine area must
be constructed so that snow or ice
is not shed from the building onto
the allotment, any adjoining
allotment, road or public space in a
location or manner that will—
(i)
obstruct a means of
egress from any building to a road
or open space; or
(ii)
otherwise endanger
people.
Question 4 (refer to Project 1) a. (15 marks)
A site inspection is necessary prior to tendering or commencing construction on a project
to assess the natural and developed features of the site which will contribute to the cost
and/or planning of the construction.
Consider the site of the dwelling is vacant and you are intending to tender on the
construction of the building. Create a checklist for a preliminary site inspection of the site
which could be used on future projects. The checklist should be word processed and
incorporate tables where suitable.
Project Details
Project Reference Number: Project Title:
Secure Best Marks with AI Grader
Need help grading? Try our AI Grader for instant feedback on your assignments.
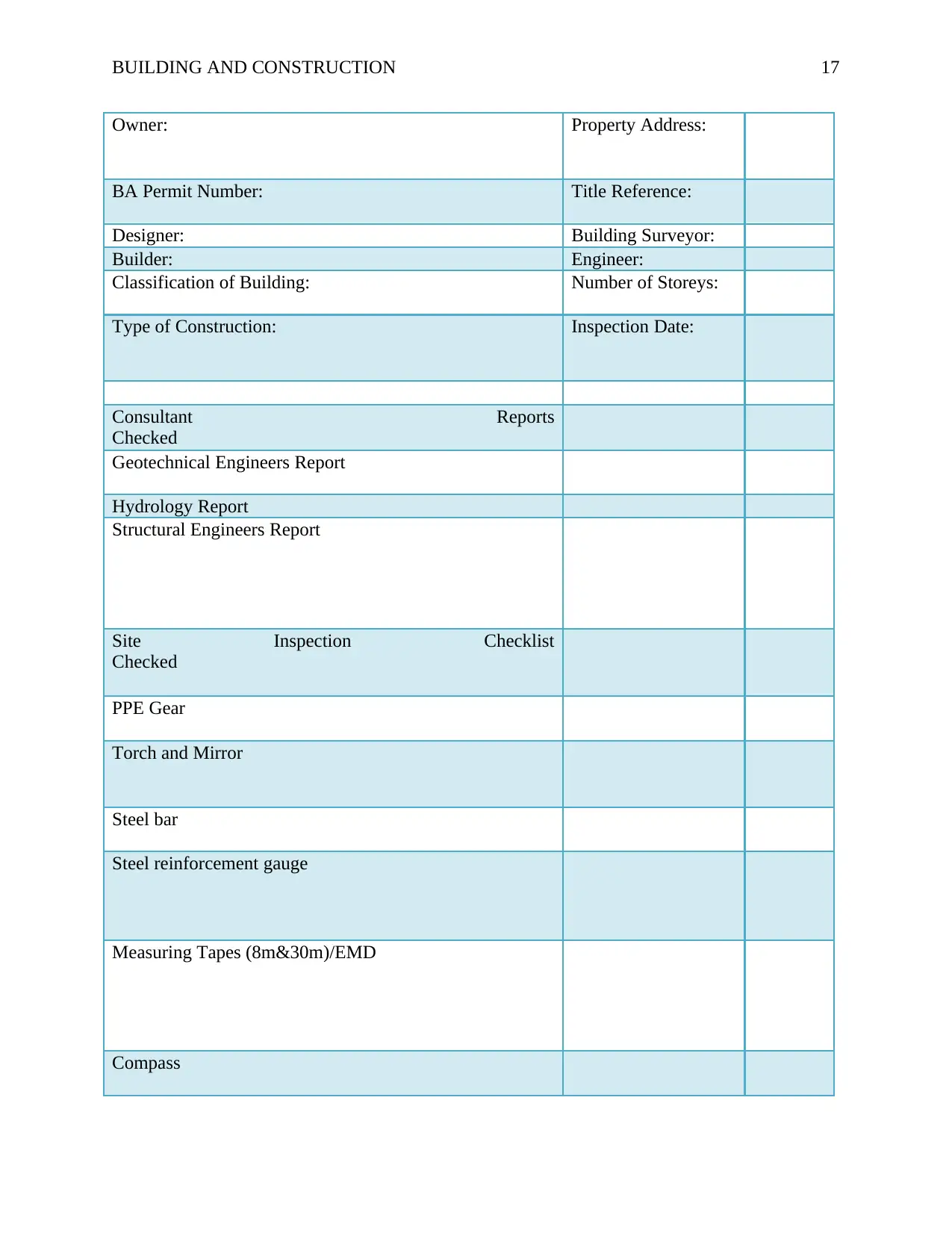
BUILDING AND CONSTRUCTION 17
Owner: Property Address:
BA Permit Number: Title Reference:
Designer: Building Surveyor:
Builder: Engineer:
Classification of Building: Number of Storeys:
Type of Construction: Inspection Date:
Consultant Reports
Checked
Geotechnical Engineers Report
Hydrology Report
Structural Engineers Report
Site Inspection Checklist
Checked
PPE Gear
Torch and Mirror
Steel bar
Steel reinforcement gauge
Measuring Tapes (8m&30m)/EMD
Compass
Owner: Property Address:
BA Permit Number: Title Reference:
Designer: Building Surveyor:
Builder: Engineer:
Classification of Building: Number of Storeys:
Type of Construction: Inspection Date:
Consultant Reports
Checked
Geotechnical Engineers Report
Hydrology Report
Structural Engineers Report
Site Inspection Checklist
Checked
PPE Gear
Torch and Mirror
Steel bar
Steel reinforcement gauge
Measuring Tapes (8m&30m)/EMD
Compass
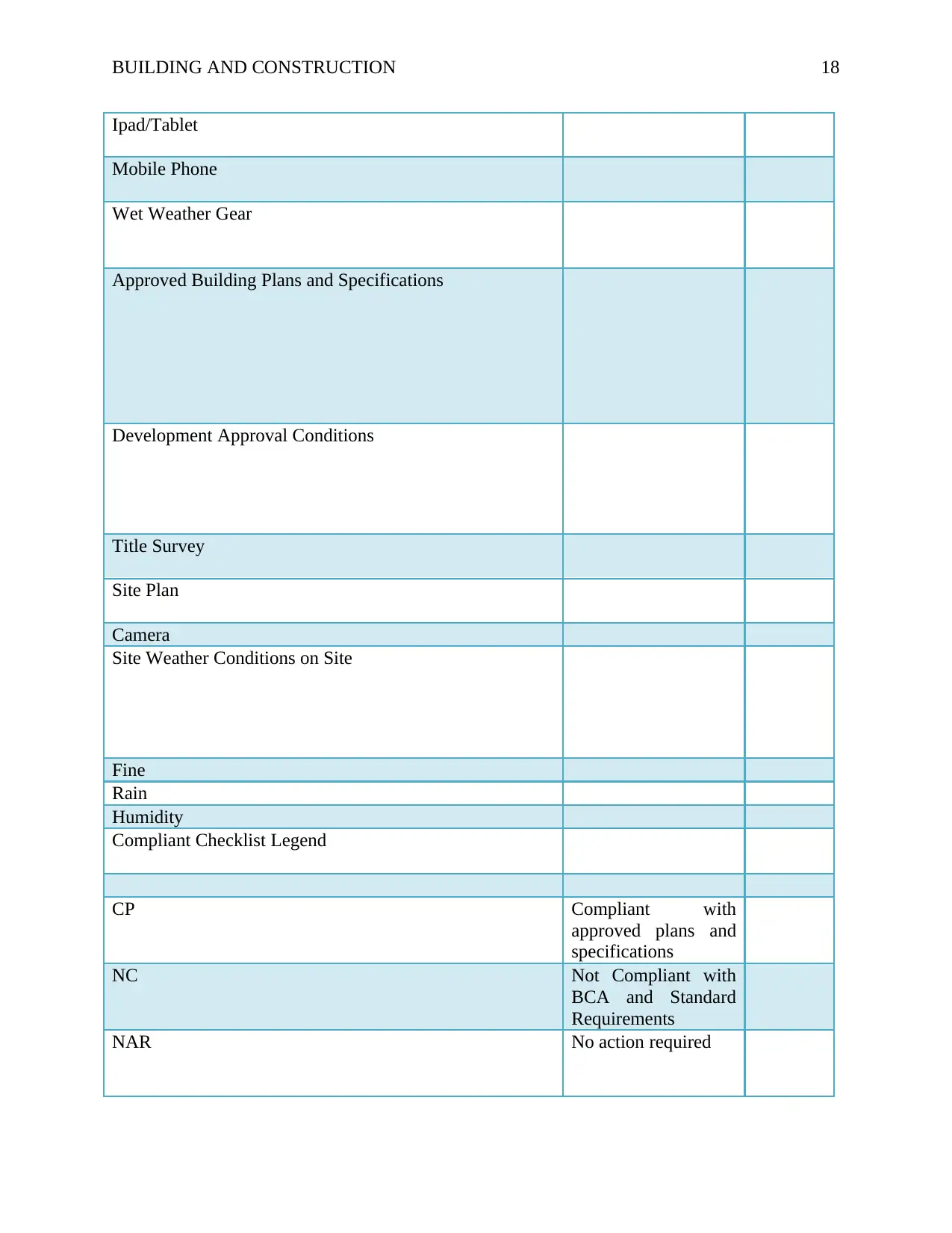
BUILDING AND CONSTRUCTION 18
Ipad/Tablet
Mobile Phone
Wet Weather Gear
Approved Building Plans and Specifications
Development Approval Conditions
Title Survey
Site Plan
Camera
Site Weather Conditions on Site
Fine
Rain
Humidity
Compliant Checklist Legend
CP Compliant with
approved plans and
specifications
NC Not Compliant with
BCA and Standard
Requirements
NAR No action required
Ipad/Tablet
Mobile Phone
Wet Weather Gear
Approved Building Plans and Specifications
Development Approval Conditions
Title Survey
Site Plan
Camera
Site Weather Conditions on Site
Fine
Rain
Humidity
Compliant Checklist Legend
CP Compliant with
approved plans and
specifications
NC Not Compliant with
BCA and Standard
Requirements
NAR No action required
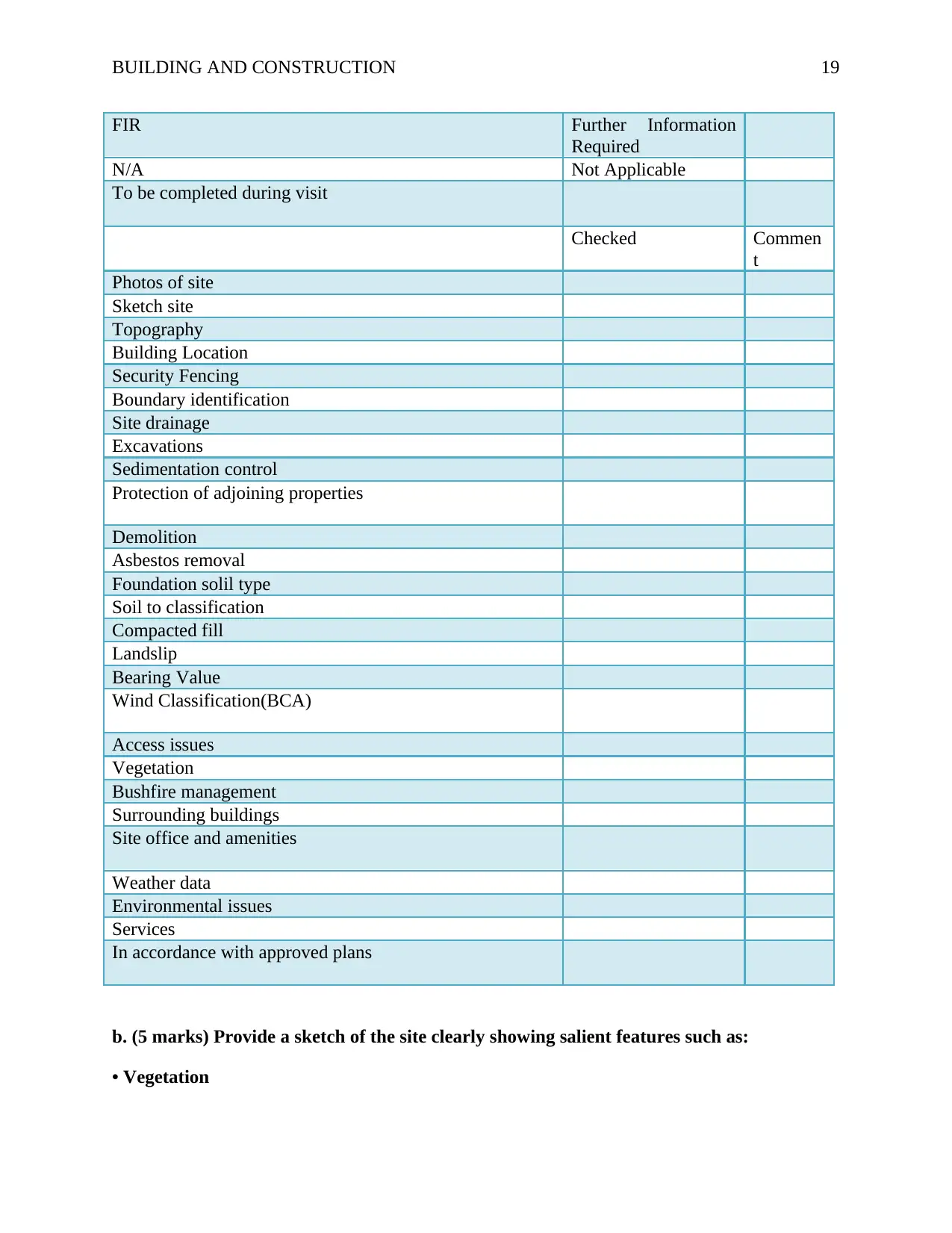
BUILDING AND CONSTRUCTION 19
FIR Further Information
Required
N/A Not Applicable
To be completed during visit
Checked Commen
t
Photos of site
Sketch site
Topography
Building Location
Security Fencing
Boundary identification
Site drainage
Excavations
Sedimentation control
Protection of adjoining properties
Demolition
Asbestos removal
Foundation solil type
Soil to classification
Compacted fill
Landslip
Bearing Value
Wind Classification(BCA)
Access issues
Vegetation
Bushfire management
Surrounding buildings
Site office and amenities
Weather data
Environmental issues
Services
In accordance with approved plans
b. (5 marks) Provide a sketch of the site clearly showing salient features such as:
• Vegetation
FIR Further Information
Required
N/A Not Applicable
To be completed during visit
Checked Commen
t
Photos of site
Sketch site
Topography
Building Location
Security Fencing
Boundary identification
Site drainage
Excavations
Sedimentation control
Protection of adjoining properties
Demolition
Asbestos removal
Foundation solil type
Soil to classification
Compacted fill
Landslip
Bearing Value
Wind Classification(BCA)
Access issues
Vegetation
Bushfire management
Surrounding buildings
Site office and amenities
Weather data
Environmental issues
Services
In accordance with approved plans
b. (5 marks) Provide a sketch of the site clearly showing salient features such as:
• Vegetation
Paraphrase This Document
Need a fresh take? Get an instant paraphrase of this document with our AI Paraphraser
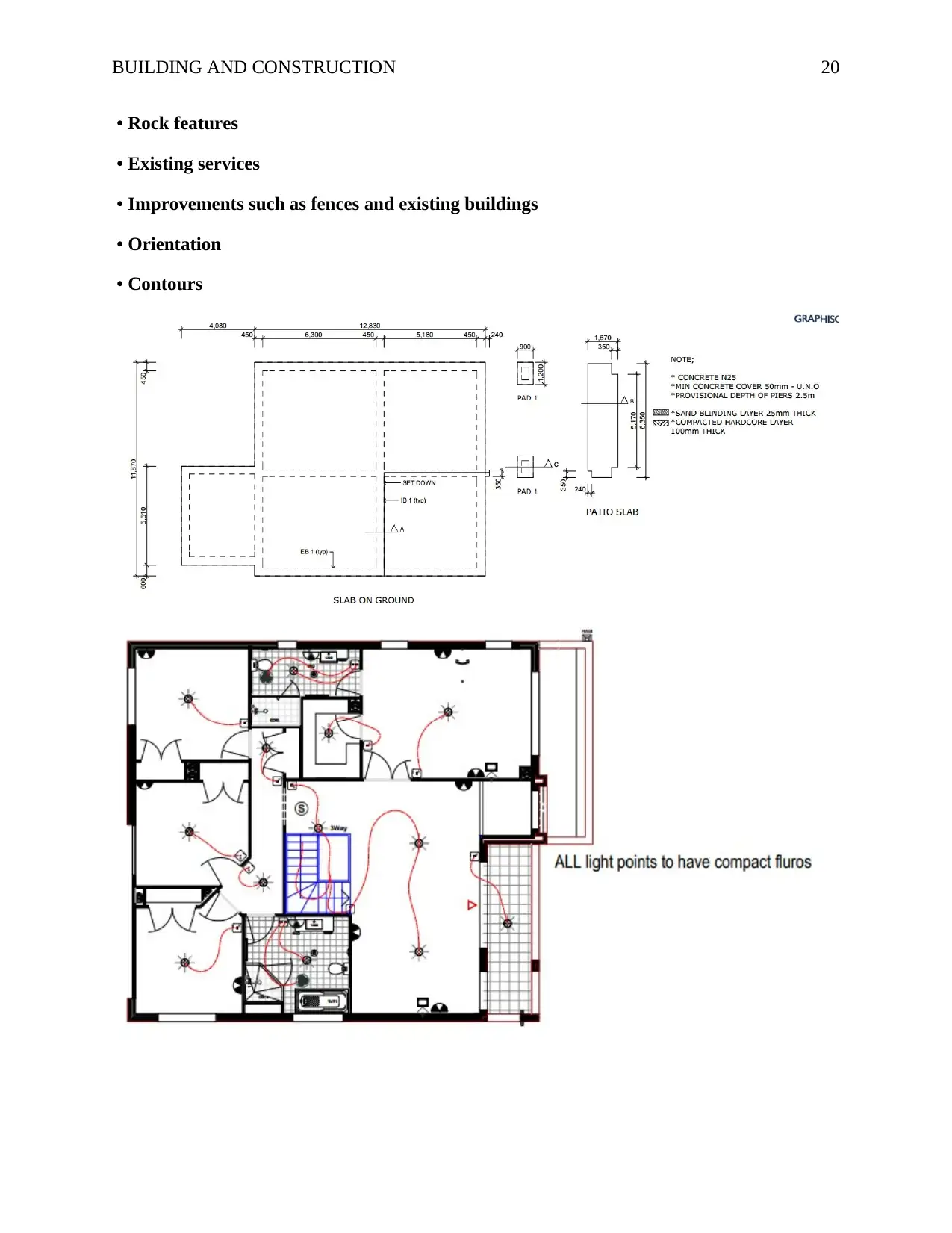
BUILDING AND CONSTRUCTION 20
• Rock features
• Existing services
• Improvements such as fences and existing buildings
• Orientation
• Contours
• Rock features
• Existing services
• Improvements such as fences and existing buildings
• Orientation
• Contours
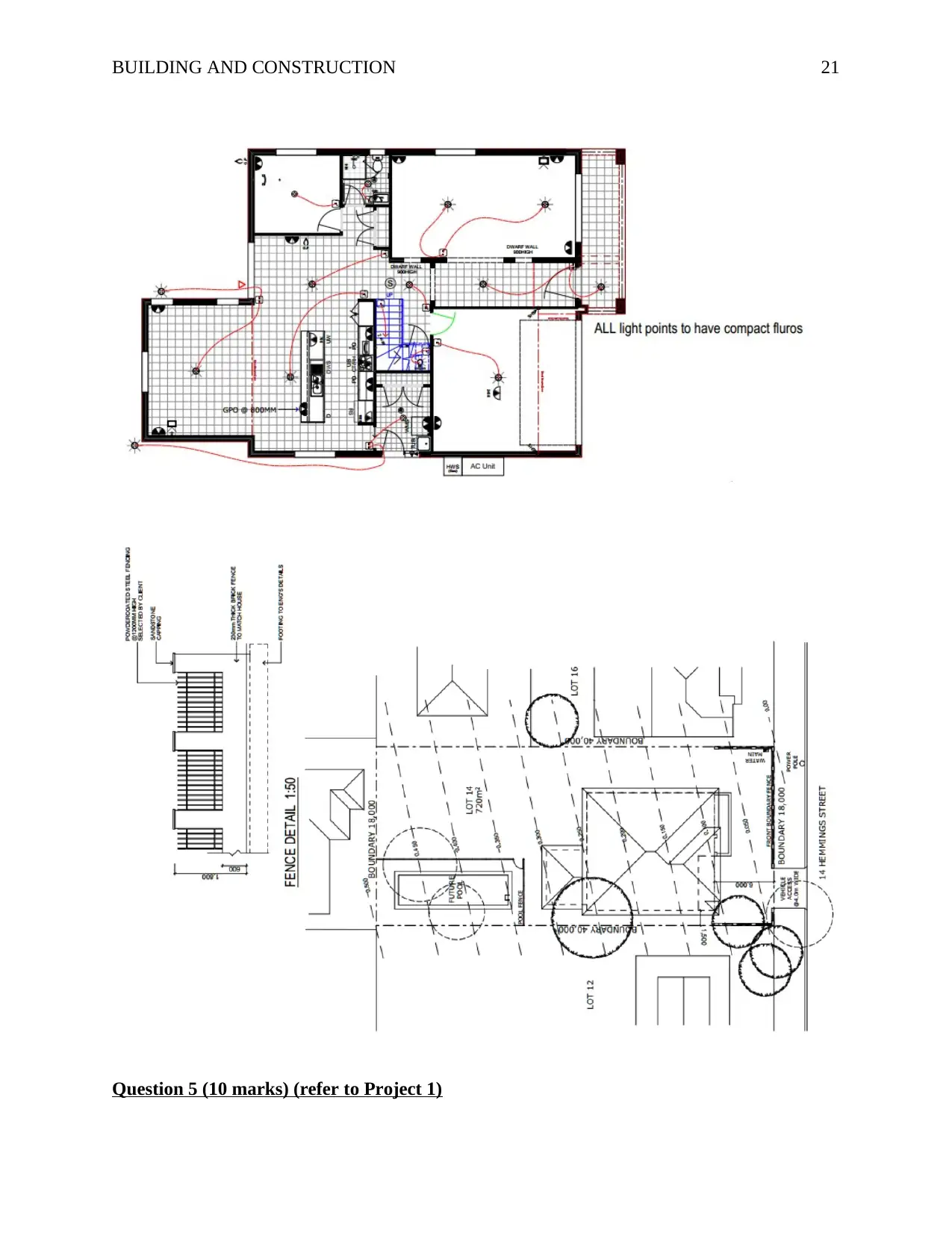
BUILDING AND CONSTRUCTION 21
Question 5 (10 marks) (refer to Project 1)
Question 5 (10 marks) (refer to Project 1)
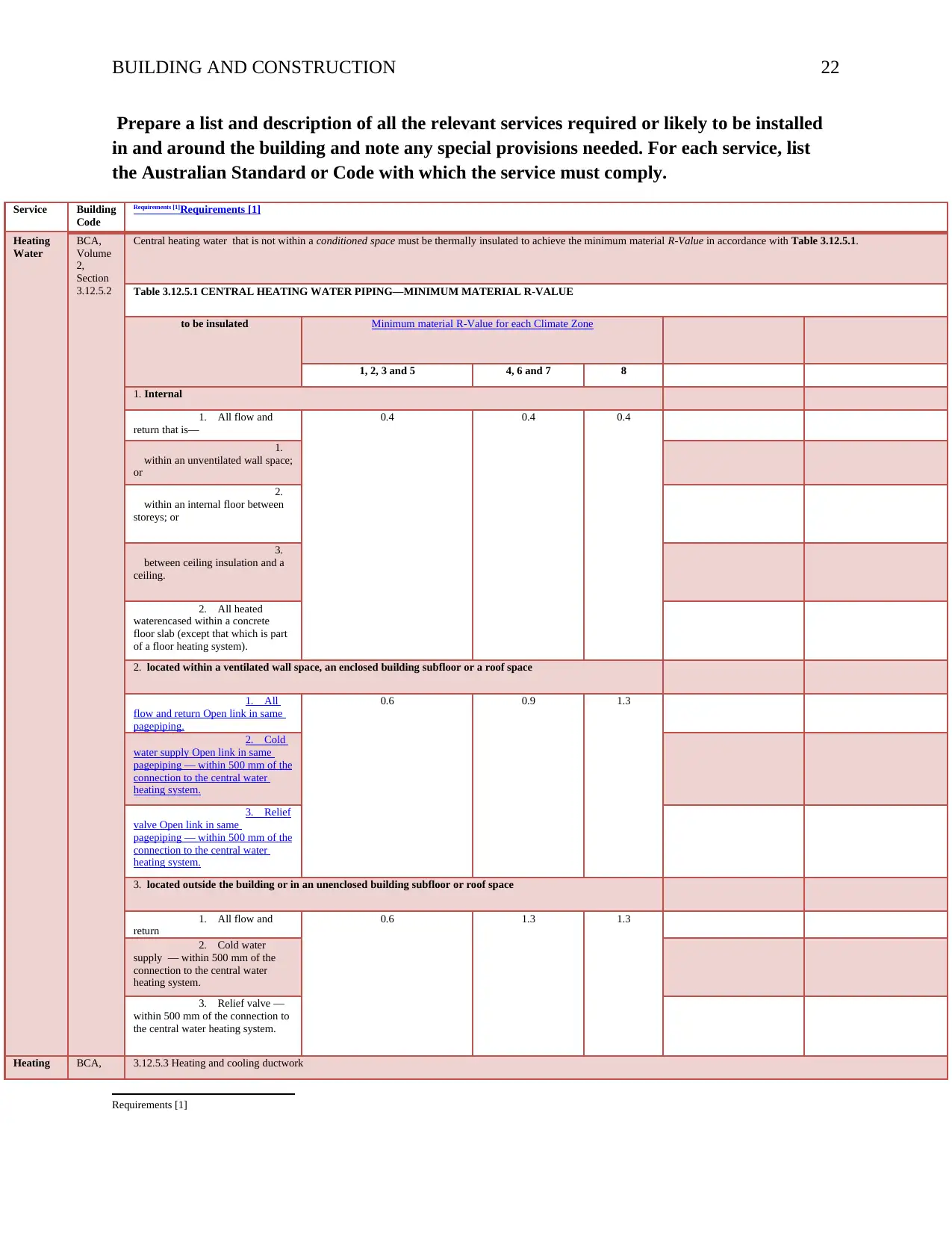
BUILDING AND CONSTRUCTION 22
Prepare a list and description of all the relevant services required or likely to be installed
in and around the building and note any special provisions needed. For each service, list
the Australian Standard or Code with which the service must comply.
Service Building
Code
Requirements [1]Requirements [1]
Heating
Water
BCA,
Volume
2,
Section
3.12.5.2
Central heating water that is not within a conditioned space must be thermally insulated to achieve the minimum material R-Value in accordance with Table 3.12.5.1.
Table 3.12.5.1 CENTRAL HEATING WATER PIPING—MINIMUM MATERIAL R-VALUE
to be insulated Minimum material R-Value for each Climate Zone
1, 2, 3 and 5 4, 6 and 7 8
1. Internal
1. All flow and
return that is—
0.4 0.4 0.4
1.
within an unventilated wall space;
or
2.
within an internal floor between
storeys; or
3.
between ceiling insulation and a
ceiling.
2. All heated
waterencased within a concrete
floor slab (except that which is part
of a floor heating system).
2. located within a ventilated wall space, an enclosed building subfloor or a roof space
1. All
flow and return Open link in same
pagepiping.
0.6 0.9 1.3
2. Cold
water supply Open link in same
pagepiping — within 500 mm of the
connection to the central water
heating system.
3. Relief
valve Open link in same
pagepiping — within 500 mm of the
connection to the central water
heating system.
3. located outside the building or in an unenclosed building subfloor or roof space
1. All flow and
return
0.6 1.3 1.3
2. Cold water
supply — within 500 mm of the
connection to the central water
heating system.
3. Relief valve —
within 500 mm of the connection to
the central water heating system.
Heating BCA, 3.12.5.3 Heating and cooling ductwork
Requirements [1]
Prepare a list and description of all the relevant services required or likely to be installed
in and around the building and note any special provisions needed. For each service, list
the Australian Standard or Code with which the service must comply.
Service Building
Code
Requirements [1]Requirements [1]
Heating
Water
BCA,
Volume
2,
Section
3.12.5.2
Central heating water that is not within a conditioned space must be thermally insulated to achieve the minimum material R-Value in accordance with Table 3.12.5.1.
Table 3.12.5.1 CENTRAL HEATING WATER PIPING—MINIMUM MATERIAL R-VALUE
to be insulated Minimum material R-Value for each Climate Zone
1, 2, 3 and 5 4, 6 and 7 8
1. Internal
1. All flow and
return that is—
0.4 0.4 0.4
1.
within an unventilated wall space;
or
2.
within an internal floor between
storeys; or
3.
between ceiling insulation and a
ceiling.
2. All heated
waterencased within a concrete
floor slab (except that which is part
of a floor heating system).
2. located within a ventilated wall space, an enclosed building subfloor or a roof space
1. All
flow and return Open link in same
pagepiping.
0.6 0.9 1.3
2. Cold
water supply Open link in same
pagepiping — within 500 mm of the
connection to the central water
heating system.
3. Relief
valve Open link in same
pagepiping — within 500 mm of the
connection to the central water
heating system.
3. located outside the building or in an unenclosed building subfloor or roof space
1. All flow and
return
0.6 1.3 1.3
2. Cold water
supply — within 500 mm of the
connection to the central water
heating system.
3. Relief valve —
within 500 mm of the connection to
the central water heating system.
Heating BCA, 3.12.5.3 Heating and cooling ductwork
Requirements [1]
Secure Best Marks with AI Grader
Need help grading? Try our AI Grader for instant feedback on your assignments.
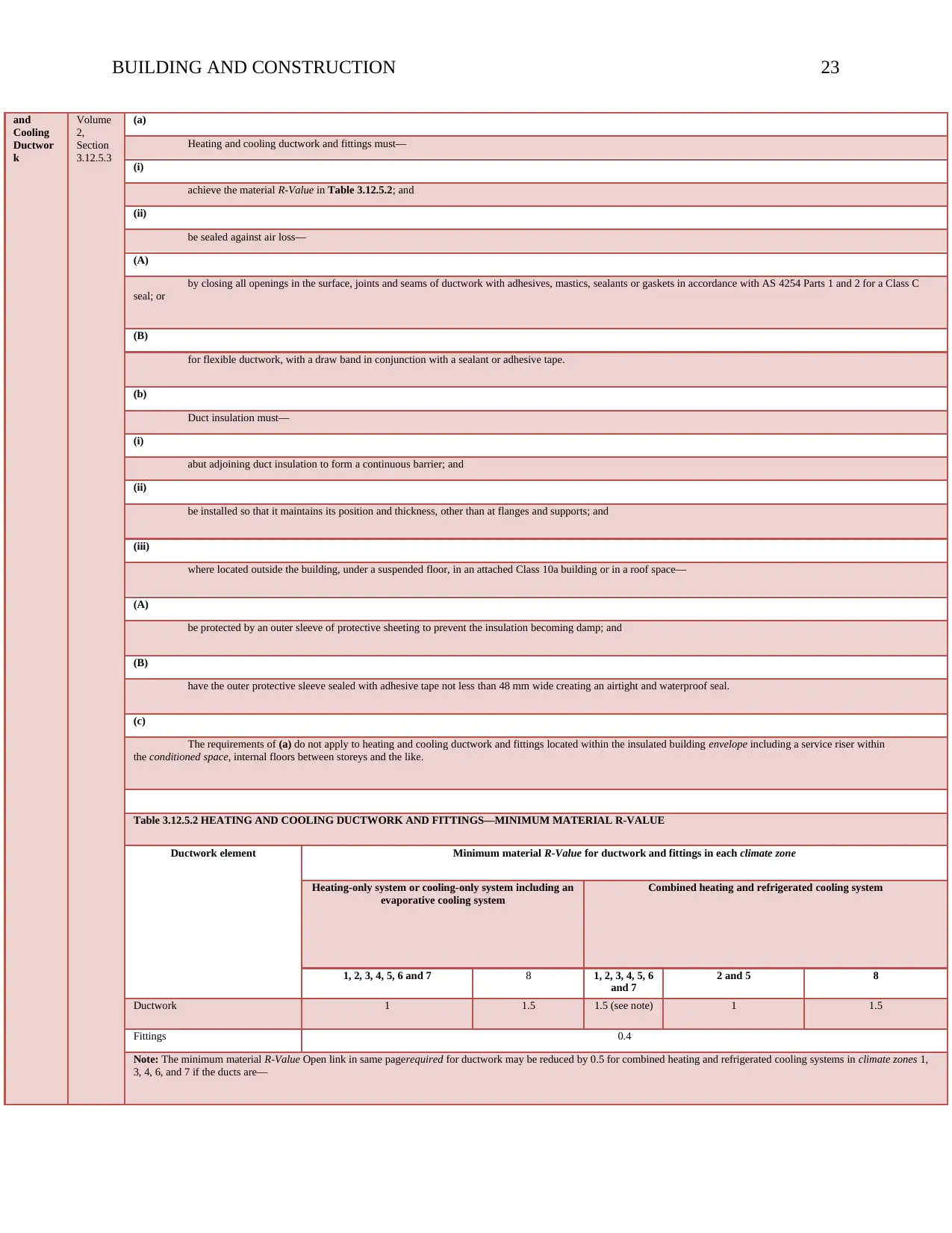
BUILDING AND CONSTRUCTION 23
and
Cooling
Ductwor
k
Volume
2,
Section
3.12.5.3
(a)
Heating and cooling ductwork and fittings must—
(i)
achieve the material R-Value in Table 3.12.5.2; and
(ii)
be sealed against air loss—
(A)
by closing all openings in the surface, joints and seams of ductwork with adhesives, mastics, sealants or gaskets in accordance with AS 4254 Parts 1 and 2 for a Class C
seal; or
(B)
for flexible ductwork, with a draw band in conjunction with a sealant or adhesive tape.
(b)
Duct insulation must—
(i)
abut adjoining duct insulation to form a continuous barrier; and
(ii)
be installed so that it maintains its position and thickness, other than at flanges and supports; and
(iii)
where located outside the building, under a suspended floor, in an attached Class 10a building or in a roof space—
(A)
be protected by an outer sleeve of protective sheeting to prevent the insulation becoming damp; and
(B)
have the outer protective sleeve sealed with adhesive tape not less than 48 mm wide creating an airtight and waterproof seal.
(c)
The requirements of (a) do not apply to heating and cooling ductwork and fittings located within the insulated building envelope including a service riser within
the conditioned space, internal floors between storeys and the like.
Table 3.12.5.2 HEATING AND COOLING DUCTWORK AND FITTINGS—MINIMUM MATERIAL R-VALUE
Ductwork element Minimum material R-Value for ductwork and fittings in each climate zone
Heating-only system or cooling-only system including an
evaporative cooling system
Combined heating and refrigerated cooling system
1, 2, 3, 4, 5, 6 and 7 8 1, 2, 3, 4, 5, 6
and 7
2 and 5 8
Ductwork 1 1.5 1.5 (see note) 1 1.5
Fittings 0.4
Note: The minimum material R-Value Open link in same pagerequired for ductwork may be reduced by 0.5 for combined heating and refrigerated cooling systems in climate zones 1,
3, 4, 6, and 7 if the ducts are—
and
Cooling
Ductwor
k
Volume
2,
Section
3.12.5.3
(a)
Heating and cooling ductwork and fittings must—
(i)
achieve the material R-Value in Table 3.12.5.2; and
(ii)
be sealed against air loss—
(A)
by closing all openings in the surface, joints and seams of ductwork with adhesives, mastics, sealants or gaskets in accordance with AS 4254 Parts 1 and 2 for a Class C
seal; or
(B)
for flexible ductwork, with a draw band in conjunction with a sealant or adhesive tape.
(b)
Duct insulation must—
(i)
abut adjoining duct insulation to form a continuous barrier; and
(ii)
be installed so that it maintains its position and thickness, other than at flanges and supports; and
(iii)
where located outside the building, under a suspended floor, in an attached Class 10a building or in a roof space—
(A)
be protected by an outer sleeve of protective sheeting to prevent the insulation becoming damp; and
(B)
have the outer protective sleeve sealed with adhesive tape not less than 48 mm wide creating an airtight and waterproof seal.
(c)
The requirements of (a) do not apply to heating and cooling ductwork and fittings located within the insulated building envelope including a service riser within
the conditioned space, internal floors between storeys and the like.
Table 3.12.5.2 HEATING AND COOLING DUCTWORK AND FITTINGS—MINIMUM MATERIAL R-VALUE
Ductwork element Minimum material R-Value for ductwork and fittings in each climate zone
Heating-only system or cooling-only system including an
evaporative cooling system
Combined heating and refrigerated cooling system
1, 2, 3, 4, 5, 6 and 7 8 1, 2, 3, 4, 5, 6
and 7
2 and 5 8
Ductwork 1 1.5 1.5 (see note) 1 1.5
Fittings 0.4
Note: The minimum material R-Value Open link in same pagerequired for ductwork may be reduced by 0.5 for combined heating and refrigerated cooling systems in climate zones 1,
3, 4, 6, and 7 if the ducts are—
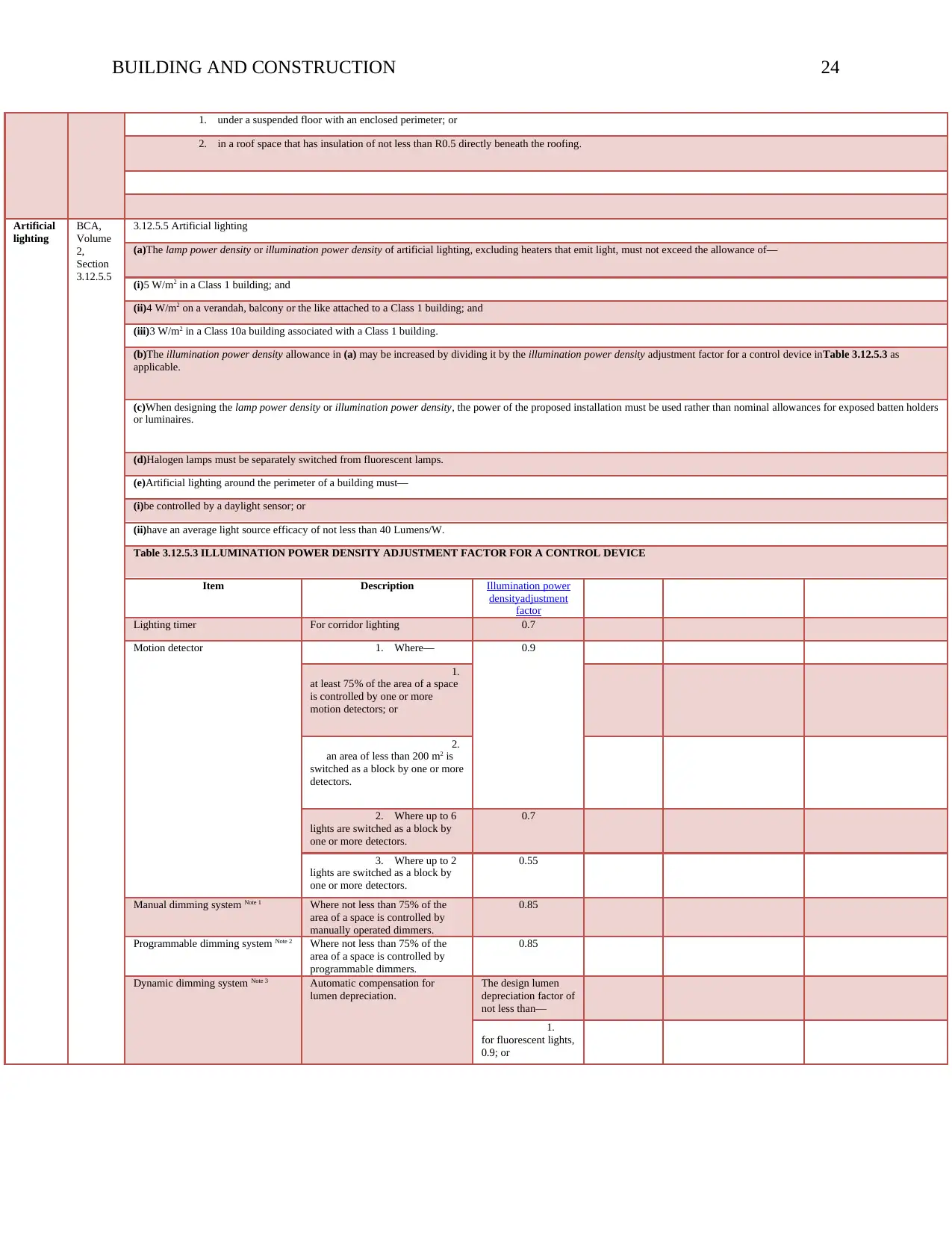
BUILDING AND CONSTRUCTION 24
1. under a suspended floor with an enclosed perimeter; or
2. in a roof space that has insulation of not less than R0.5 directly beneath the roofing.
Artificial
lighting
BCA,
Volume
2,
Section
3.12.5.5
3.12.5.5 Artificial lighting
(a)The lamp power density or illumination power density of artificial lighting, excluding heaters that emit light, must not exceed the allowance of—
(i)5 W/m2 in a Class 1 building; and
(ii)4 W/m2 on a verandah, balcony or the like attached to a Class 1 building; and
(iii)3 W/m2 in a Class 10a building associated with a Class 1 building.
(b)The illumination power density allowance in (a) may be increased by dividing it by the illumination power density adjustment factor for a control device inTable 3.12.5.3 as
applicable.
(c)When designing the lamp power density or illumination power density, the power of the proposed installation must be used rather than nominal allowances for exposed batten holders
or luminaires.
(d)Halogen lamps must be separately switched from fluorescent lamps.
(e)Artificial lighting around the perimeter of a building must—
(i)be controlled by a daylight sensor; or
(ii)have an average light source efficacy of not less than 40 Lumens/W.
Table 3.12.5.3 ILLUMINATION POWER DENSITY ADJUSTMENT FACTOR FOR A CONTROL DEVICE
Item Description Illumination power
densityadjustment
factor
Lighting timer For corridor lighting 0.7
Motion detector 1. Where— 0.9
1.
at least 75% of the area of a space
is controlled by one or more
motion detectors; or
2.
an area of less than 200 m2 is
switched as a block by one or more
detectors.
2. Where up to 6
lights are switched as a block by
one or more detectors.
0.7
3. Where up to 2
lights are switched as a block by
one or more detectors.
0.55
Manual dimming system Note 1 Where not less than 75% of the
area of a space is controlled by
manually operated dimmers.
0.85
Programmable dimming system Note 2 Where not less than 75% of the
area of a space is controlled by
programmable dimmers.
0.85
Dynamic dimming system Note 3 Automatic compensation for
lumen depreciation.
The design lumen
depreciation factor of
not less than—
1.
for fluorescent lights,
0.9; or
1. under a suspended floor with an enclosed perimeter; or
2. in a roof space that has insulation of not less than R0.5 directly beneath the roofing.
Artificial
lighting
BCA,
Volume
2,
Section
3.12.5.5
3.12.5.5 Artificial lighting
(a)The lamp power density or illumination power density of artificial lighting, excluding heaters that emit light, must not exceed the allowance of—
(i)5 W/m2 in a Class 1 building; and
(ii)4 W/m2 on a verandah, balcony or the like attached to a Class 1 building; and
(iii)3 W/m2 in a Class 10a building associated with a Class 1 building.
(b)The illumination power density allowance in (a) may be increased by dividing it by the illumination power density adjustment factor for a control device inTable 3.12.5.3 as
applicable.
(c)When designing the lamp power density or illumination power density, the power of the proposed installation must be used rather than nominal allowances for exposed batten holders
or luminaires.
(d)Halogen lamps must be separately switched from fluorescent lamps.
(e)Artificial lighting around the perimeter of a building must—
(i)be controlled by a daylight sensor; or
(ii)have an average light source efficacy of not less than 40 Lumens/W.
Table 3.12.5.3 ILLUMINATION POWER DENSITY ADJUSTMENT FACTOR FOR A CONTROL DEVICE
Item Description Illumination power
densityadjustment
factor
Lighting timer For corridor lighting 0.7
Motion detector 1. Where— 0.9
1.
at least 75% of the area of a space
is controlled by one or more
motion detectors; or
2.
an area of less than 200 m2 is
switched as a block by one or more
detectors.
2. Where up to 6
lights are switched as a block by
one or more detectors.
0.7
3. Where up to 2
lights are switched as a block by
one or more detectors.
0.55
Manual dimming system Note 1 Where not less than 75% of the
area of a space is controlled by
manually operated dimmers.
0.85
Programmable dimming system Note 2 Where not less than 75% of the
area of a space is controlled by
programmable dimmers.
0.85
Dynamic dimming system Note 3 Automatic compensation for
lumen depreciation.
The design lumen
depreciation factor of
not less than—
1.
for fluorescent lights,
0.9; or
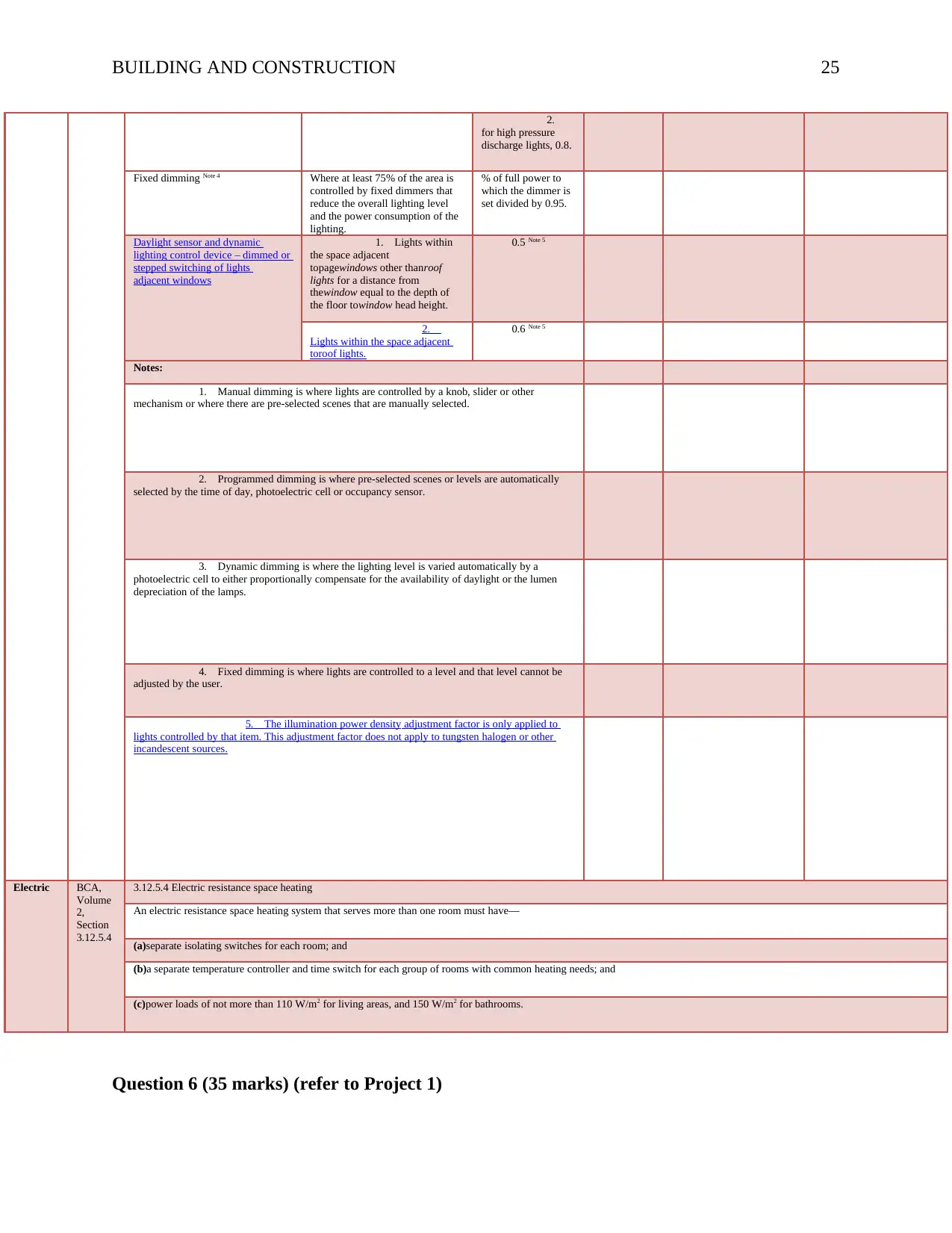
BUILDING AND CONSTRUCTION 25
2.
for high pressure
discharge lights, 0.8.
Fixed dimming Note 4 Where at least 75% of the area is
controlled by fixed dimmers that
reduce the overall lighting level
and the power consumption of the
lighting.
% of full power to
which the dimmer is
set divided by 0.95.
Daylight sensor and dynamic
lighting control device – dimmed or
stepped switching of lights
adjacent windows
1. Lights within
the space adjacent
topagewindows other thanroof
lights for a distance from
thewindow equal to the depth of
the floor towindow head height.
0.5 Note 5
2.
Lights within the space adjacent
toroof lights.
0.6 Note 5
Notes:
1. Manual dimming is where lights are controlled by a knob, slider or other
mechanism or where there are pre-selected scenes that are manually selected.
2. Programmed dimming is where pre-selected scenes or levels are automatically
selected by the time of day, photoelectric cell or occupancy sensor.
3. Dynamic dimming is where the lighting level is varied automatically by a
photoelectric cell to either proportionally compensate for the availability of daylight or the lumen
depreciation of the lamps.
4. Fixed dimming is where lights are controlled to a level and that level cannot be
adjusted by the user.
5. The illumination power density adjustment factor is only applied to
lights controlled by that item. This adjustment factor does not apply to tungsten halogen or other
incandescent sources.
Electric BCA,
Volume
2,
Section
3.12.5.4
3.12.5.4 Electric resistance space heating
An electric resistance space heating system that serves more than one room must have—
(a)separate isolating switches for each room; and
(b)a separate temperature controller and time switch for each group of rooms with common heating needs; and
(c)power loads of not more than 110 W/m2 for living areas, and 150 W/m2 for bathrooms.
Question 6 (35 marks) (refer to Project 1)
2.
for high pressure
discharge lights, 0.8.
Fixed dimming Note 4 Where at least 75% of the area is
controlled by fixed dimmers that
reduce the overall lighting level
and the power consumption of the
lighting.
% of full power to
which the dimmer is
set divided by 0.95.
Daylight sensor and dynamic
lighting control device – dimmed or
stepped switching of lights
adjacent windows
1. Lights within
the space adjacent
topagewindows other thanroof
lights for a distance from
thewindow equal to the depth of
the floor towindow head height.
0.5 Note 5
2.
Lights within the space adjacent
toroof lights.
0.6 Note 5
Notes:
1. Manual dimming is where lights are controlled by a knob, slider or other
mechanism or where there are pre-selected scenes that are manually selected.
2. Programmed dimming is where pre-selected scenes or levels are automatically
selected by the time of day, photoelectric cell or occupancy sensor.
3. Dynamic dimming is where the lighting level is varied automatically by a
photoelectric cell to either proportionally compensate for the availability of daylight or the lumen
depreciation of the lamps.
4. Fixed dimming is where lights are controlled to a level and that level cannot be
adjusted by the user.
5. The illumination power density adjustment factor is only applied to
lights controlled by that item. This adjustment factor does not apply to tungsten halogen or other
incandescent sources.
Electric BCA,
Volume
2,
Section
3.12.5.4
3.12.5.4 Electric resistance space heating
An electric resistance space heating system that serves more than one room must have—
(a)separate isolating switches for each room; and
(b)a separate temperature controller and time switch for each group of rooms with common heating needs; and
(c)power loads of not more than 110 W/m2 for living areas, and 150 W/m2 for bathrooms.
Question 6 (35 marks) (refer to Project 1)
Paraphrase This Document
Need a fresh take? Get an instant paraphrase of this document with our AI Paraphraser
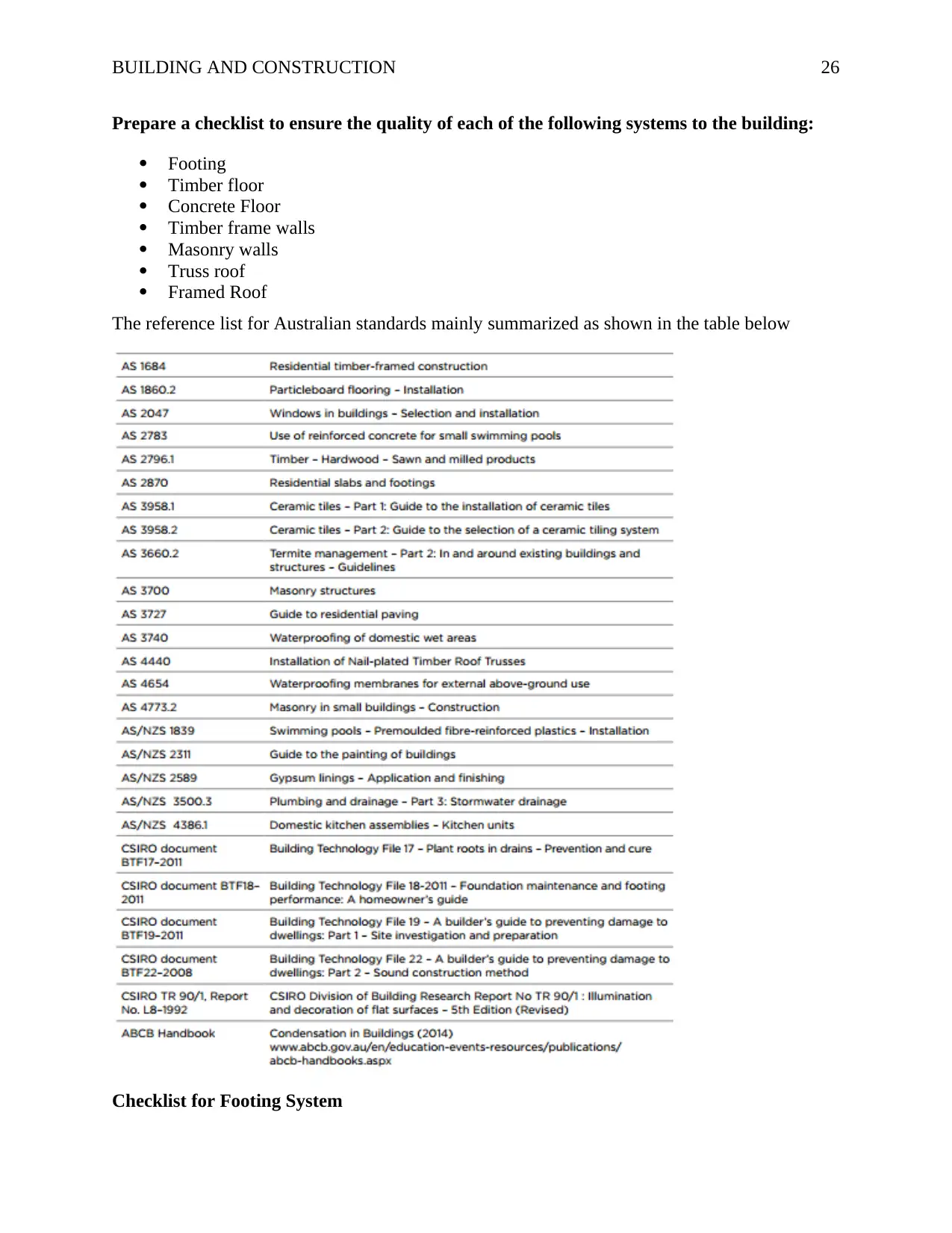
BUILDING AND CONSTRUCTION 26
Prepare a checklist to ensure the quality of each of the following systems to the building:
ï‚· Footing
ï‚· Timber floor
ï‚· Concrete Floor
ï‚· Timber frame walls
ï‚· Masonry walls
ï‚· Truss roof
ï‚· Framed Roof
The reference list for Australian standards mainly summarized as shown in the table below
Checklist for Footing System
Prepare a checklist to ensure the quality of each of the following systems to the building:
ï‚· Footing
ï‚· Timber floor
ï‚· Concrete Floor
ï‚· Timber frame walls
ï‚· Masonry walls
ï‚· Truss roof
ï‚· Framed Roof
The reference list for Australian standards mainly summarized as shown in the table below
Checklist for Footing System
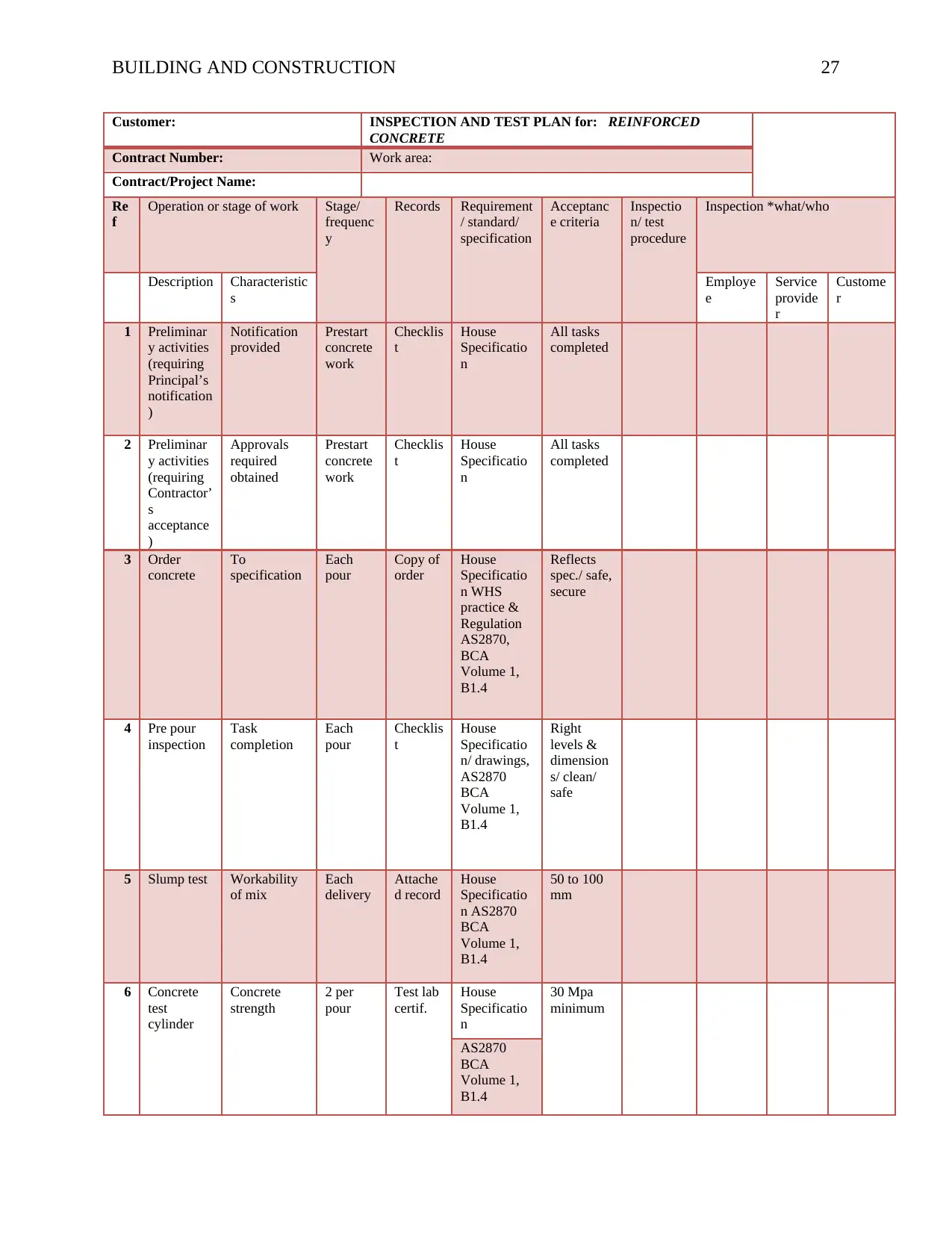
BUILDING AND CONSTRUCTION 27
Customer: INSPECTION AND TEST PLAN for: REINFORCED
CONCRETE
Contract Number: Work area:
Contract/Project Name:
Re
f
Operation or stage of work Stage/
frequenc
y
Records Requirement
/ standard/
specification
Acceptanc
e criteria
Inspectio
n/ test
procedure
Inspection *what/who
Description Characteristic
s
Employe
e
Service
provide
r
Custome
r
1 Preliminar
y activities
(requiring
Principal’s
notification
)
Notification
provided
Prestart
concrete
work
Checklis
t
House
Specificatio
n
All tasks
completed
2 Preliminar
y activities
(requiring
Contractor’
s
acceptance
)
Approvals
required
obtained
Prestart
concrete
work
Checklis
t
House
Specificatio
n
All tasks
completed
3 Order
concrete
To
specification
Each
pour
Copy of
order
House
Specificatio
n WHS
practice &
Regulation
AS2870,
BCA
Volume 1,
B1.4
Reflects
spec./ safe,
secure
4 Pre pour
inspection
Task
completion
Each
pour
Checklis
t
House
Specificatio
n/ drawings,
AS2870
BCA
Volume 1,
B1.4
Right
levels &
dimension
s/ clean/
safe
5 Slump test Workability
of mix
Each
delivery
Attache
d record
House
Specificatio
n AS2870
BCA
Volume 1,
B1.4
50 to 100
mm
6 Concrete
test
cylinder
Concrete
strength
2 per
pour
Test lab
certif.
House
Specificatio
n
30 Mpa
minimum
AS2870
BCA
Volume 1,
B1.4
Customer: INSPECTION AND TEST PLAN for: REINFORCED
CONCRETE
Contract Number: Work area:
Contract/Project Name:
Re
f
Operation or stage of work Stage/
frequenc
y
Records Requirement
/ standard/
specification
Acceptanc
e criteria
Inspectio
n/ test
procedure
Inspection *what/who
Description Characteristic
s
Employe
e
Service
provide
r
Custome
r
1 Preliminar
y activities
(requiring
Principal’s
notification
)
Notification
provided
Prestart
concrete
work
Checklis
t
House
Specificatio
n
All tasks
completed
2 Preliminar
y activities
(requiring
Contractor’
s
acceptance
)
Approvals
required
obtained
Prestart
concrete
work
Checklis
t
House
Specificatio
n
All tasks
completed
3 Order
concrete
To
specification
Each
pour
Copy of
order
House
Specificatio
n WHS
practice &
Regulation
AS2870,
BCA
Volume 1,
B1.4
Reflects
spec./ safe,
secure
4 Pre pour
inspection
Task
completion
Each
pour
Checklis
t
House
Specificatio
n/ drawings,
AS2870
BCA
Volume 1,
B1.4
Right
levels &
dimension
s/ clean/
safe
5 Slump test Workability
of mix
Each
delivery
Attache
d record
House
Specificatio
n AS2870
BCA
Volume 1,
B1.4
50 to 100
mm
6 Concrete
test
cylinder
Concrete
strength
2 per
pour
Test lab
certif.
House
Specificatio
n
30 Mpa
minimum
AS2870
BCA
Volume 1,
B1.4
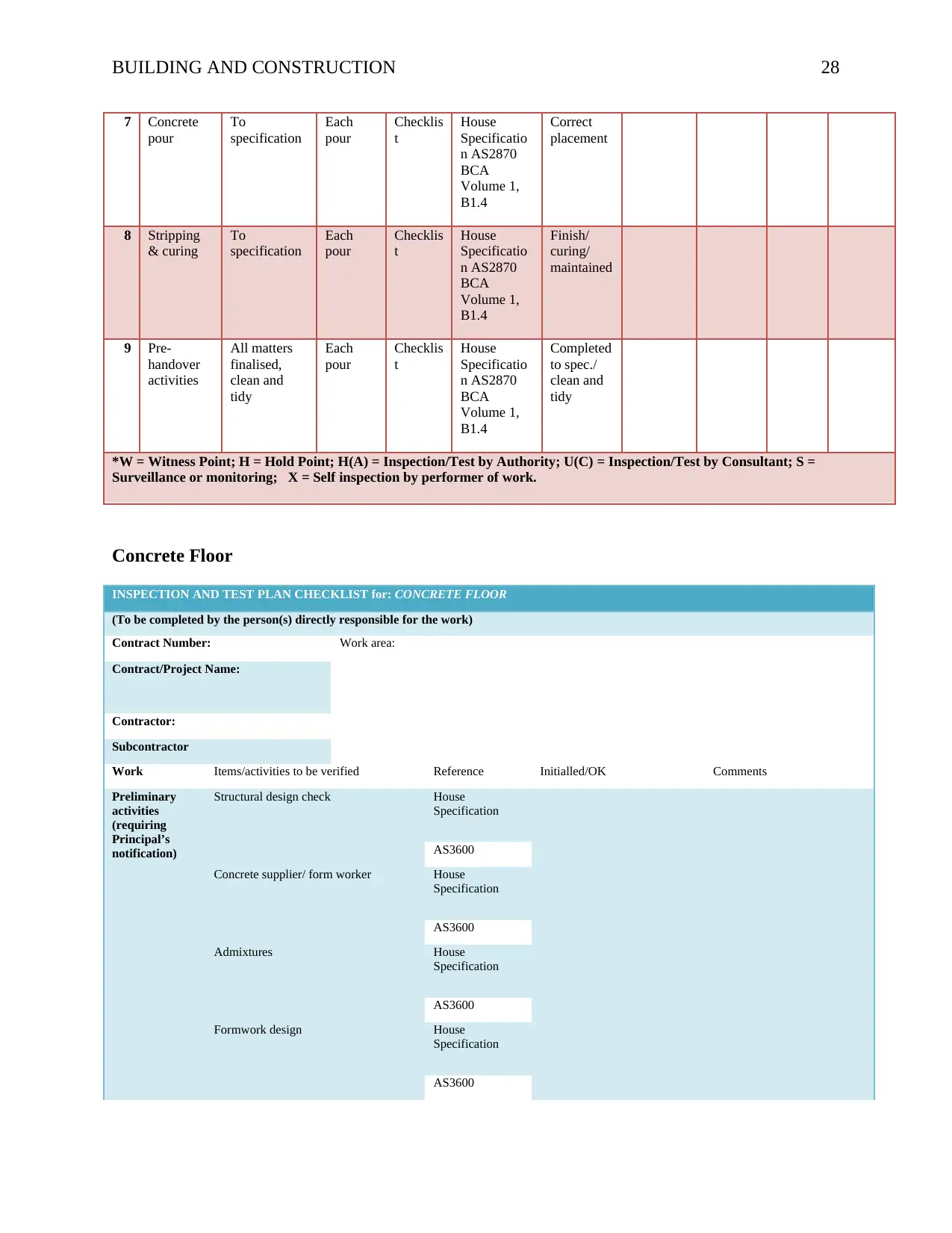
BUILDING AND CONSTRUCTION 28
7 Concrete
pour
To
specification
Each
pour
Checklis
t
House
Specificatio
n AS2870
BCA
Volume 1,
B1.4
Correct
placement
8 Stripping
& curing
To
specification
Each
pour
Checklis
t
House
Specificatio
n AS2870
BCA
Volume 1,
B1.4
Finish/
curing/
maintained
9 Pre-
handover
activities
All matters
finalised,
clean and
tidy
Each
pour
Checklis
t
House
Specificatio
n AS2870
BCA
Volume 1,
B1.4
Completed
to spec./
clean and
tidy
*W = Witness Point; H = Hold Point; H(A) = Inspection/Test by Authority; U(C) = Inspection/Test by Consultant; S =
Surveillance or monitoring; X = Self inspection by performer of work.
Concrete Floor
INSPECTION AND TEST PLAN CHECKLIST for: CONCRETE FLOOR
(To be completed by the person(s) directly responsible for the work)
Contract Number: Work area:
Contract/Project Name:
Contractor:
Subcontractor
Work Items/activities to be verified Reference Initialled/OK Comments
Preliminary
activities
(requiring
Principal’s
notification)
Structural design check House
Specification
AS3600
Concrete supplier/ form worker House
Specification
AS3600
Admixtures House
Specification
AS3600
Formwork design House
Specification
AS3600
7 Concrete
pour
To
specification
Each
pour
Checklis
t
House
Specificatio
n AS2870
BCA
Volume 1,
B1.4
Correct
placement
8 Stripping
& curing
To
specification
Each
pour
Checklis
t
House
Specificatio
n AS2870
BCA
Volume 1,
B1.4
Finish/
curing/
maintained
9 Pre-
handover
activities
All matters
finalised,
clean and
tidy
Each
pour
Checklis
t
House
Specificatio
n AS2870
BCA
Volume 1,
B1.4
Completed
to spec./
clean and
tidy
*W = Witness Point; H = Hold Point; H(A) = Inspection/Test by Authority; U(C) = Inspection/Test by Consultant; S =
Surveillance or monitoring; X = Self inspection by performer of work.
Concrete Floor
INSPECTION AND TEST PLAN CHECKLIST for: CONCRETE FLOOR
(To be completed by the person(s) directly responsible for the work)
Contract Number: Work area:
Contract/Project Name:
Contractor:
Subcontractor
Work Items/activities to be verified Reference Initialled/OK Comments
Preliminary
activities
(requiring
Principal’s
notification)
Structural design check House
Specification
AS3600
Concrete supplier/ form worker House
Specification
AS3600
Admixtures House
Specification
AS3600
Formwork design House
Specification
AS3600
Secure Best Marks with AI Grader
Need help grading? Try our AI Grader for instant feedback on your assignments.
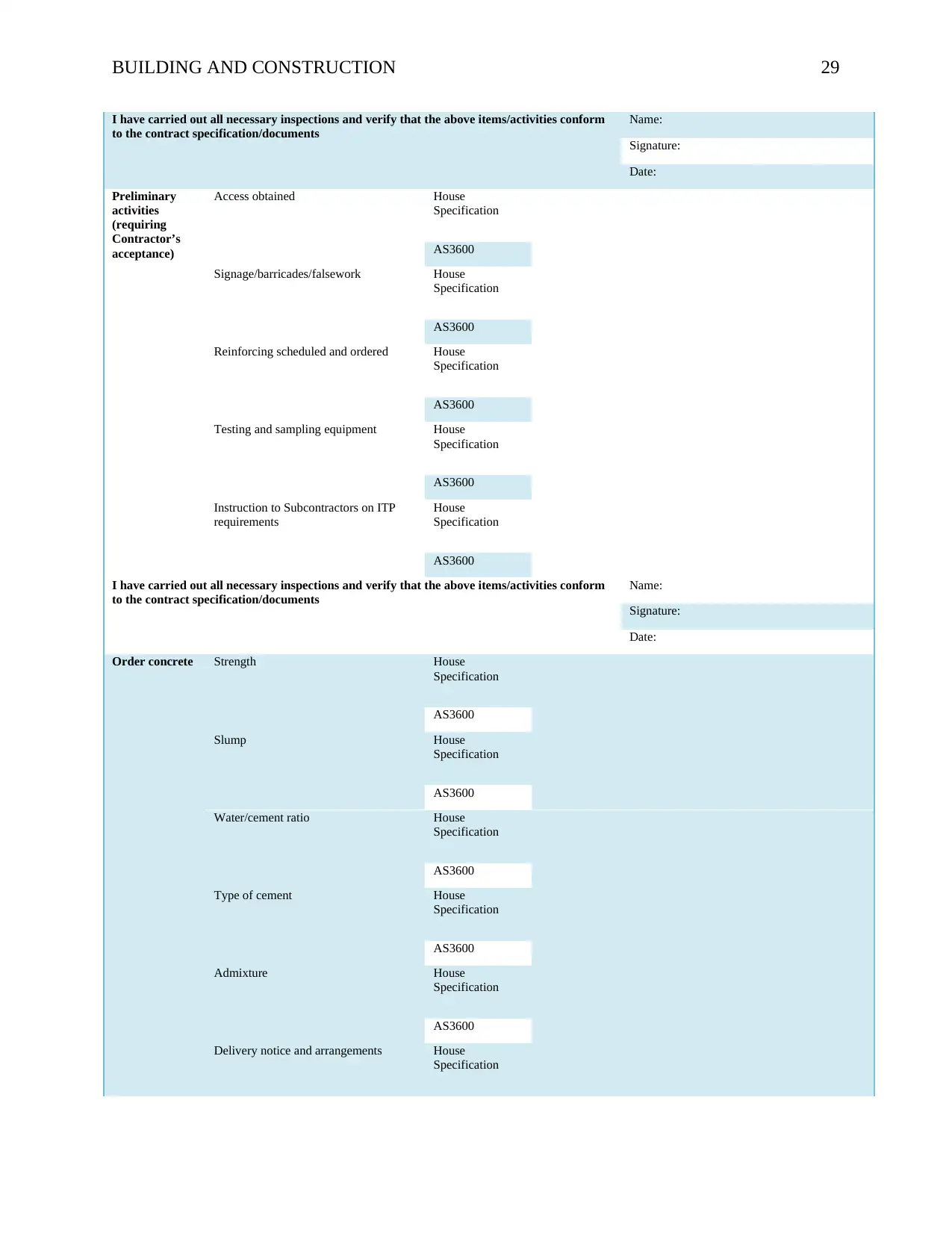
BUILDING AND CONSTRUCTION 29
I have carried out all necessary inspections and verify that the above items/activities conform
to the contract specification/documents
Name:
Signature:
Date:
Preliminary
activities
(requiring
Contractor’s
acceptance)
Access obtained House
Specification
AS3600
Signage/barricades/falsework House
Specification
AS3600
Reinforcing scheduled and ordered House
Specification
AS3600
Testing and sampling equipment House
Specification
AS3600
Instruction to Subcontractors on ITP
requirements
House
Specification
AS3600
I have carried out all necessary inspections and verify that the above items/activities conform
to the contract specification/documents
Name:
Signature:
Date:
Order concrete Strength House
Specification
AS3600
Slump House
Specification
AS3600
Water/cement ratio House
Specification
AS3600
Type of cement House
Specification
AS3600
Admixture House
Specification
AS3600
Delivery notice and arrangements House
Specification
I have carried out all necessary inspections and verify that the above items/activities conform
to the contract specification/documents
Name:
Signature:
Date:
Preliminary
activities
(requiring
Contractor’s
acceptance)
Access obtained House
Specification
AS3600
Signage/barricades/falsework House
Specification
AS3600
Reinforcing scheduled and ordered House
Specification
AS3600
Testing and sampling equipment House
Specification
AS3600
Instruction to Subcontractors on ITP
requirements
House
Specification
AS3600
I have carried out all necessary inspections and verify that the above items/activities conform
to the contract specification/documents
Name:
Signature:
Date:
Order concrete Strength House
Specification
AS3600
Slump House
Specification
AS3600
Water/cement ratio House
Specification
AS3600
Type of cement House
Specification
AS3600
Admixture House
Specification
AS3600
Delivery notice and arrangements House
Specification
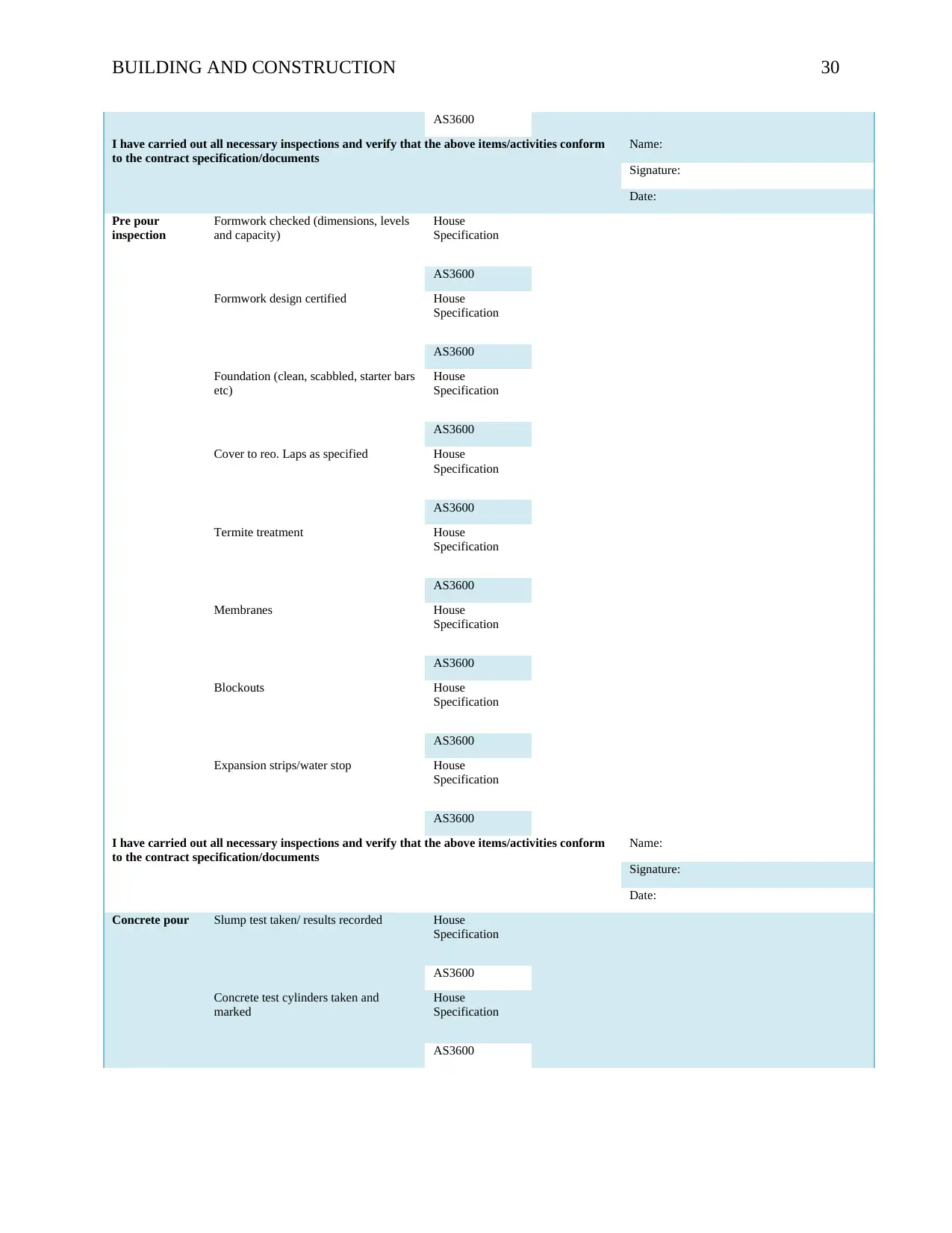
BUILDING AND CONSTRUCTION 30
AS3600
I have carried out all necessary inspections and verify that the above items/activities conform
to the contract specification/documents
Name:
Signature:
Date:
Pre pour
inspection
Formwork checked (dimensions, levels
and capacity)
House
Specification
AS3600
Formwork design certified House
Specification
AS3600
Foundation (clean, scabbled, starter bars
etc)
House
Specification
AS3600
Cover to reo. Laps as specified House
Specification
AS3600
Termite treatment House
Specification
AS3600
Membranes House
Specification
AS3600
Blockouts House
Specification
AS3600
Expansion strips/water stop House
Specification
AS3600
I have carried out all necessary inspections and verify that the above items/activities conform
to the contract specification/documents
Name:
Signature:
Date:
Concrete pour Slump test taken/ results recorded House
Specification
AS3600
Concrete test cylinders taken and
marked
House
Specification
AS3600
AS3600
I have carried out all necessary inspections and verify that the above items/activities conform
to the contract specification/documents
Name:
Signature:
Date:
Pre pour
inspection
Formwork checked (dimensions, levels
and capacity)
House
Specification
AS3600
Formwork design certified House
Specification
AS3600
Foundation (clean, scabbled, starter bars
etc)
House
Specification
AS3600
Cover to reo. Laps as specified House
Specification
AS3600
Termite treatment House
Specification
AS3600
Membranes House
Specification
AS3600
Blockouts House
Specification
AS3600
Expansion strips/water stop House
Specification
AS3600
I have carried out all necessary inspections and verify that the above items/activities conform
to the contract specification/documents
Name:
Signature:
Date:
Concrete pour Slump test taken/ results recorded House
Specification
AS3600
Concrete test cylinders taken and
marked
House
Specification
AS3600
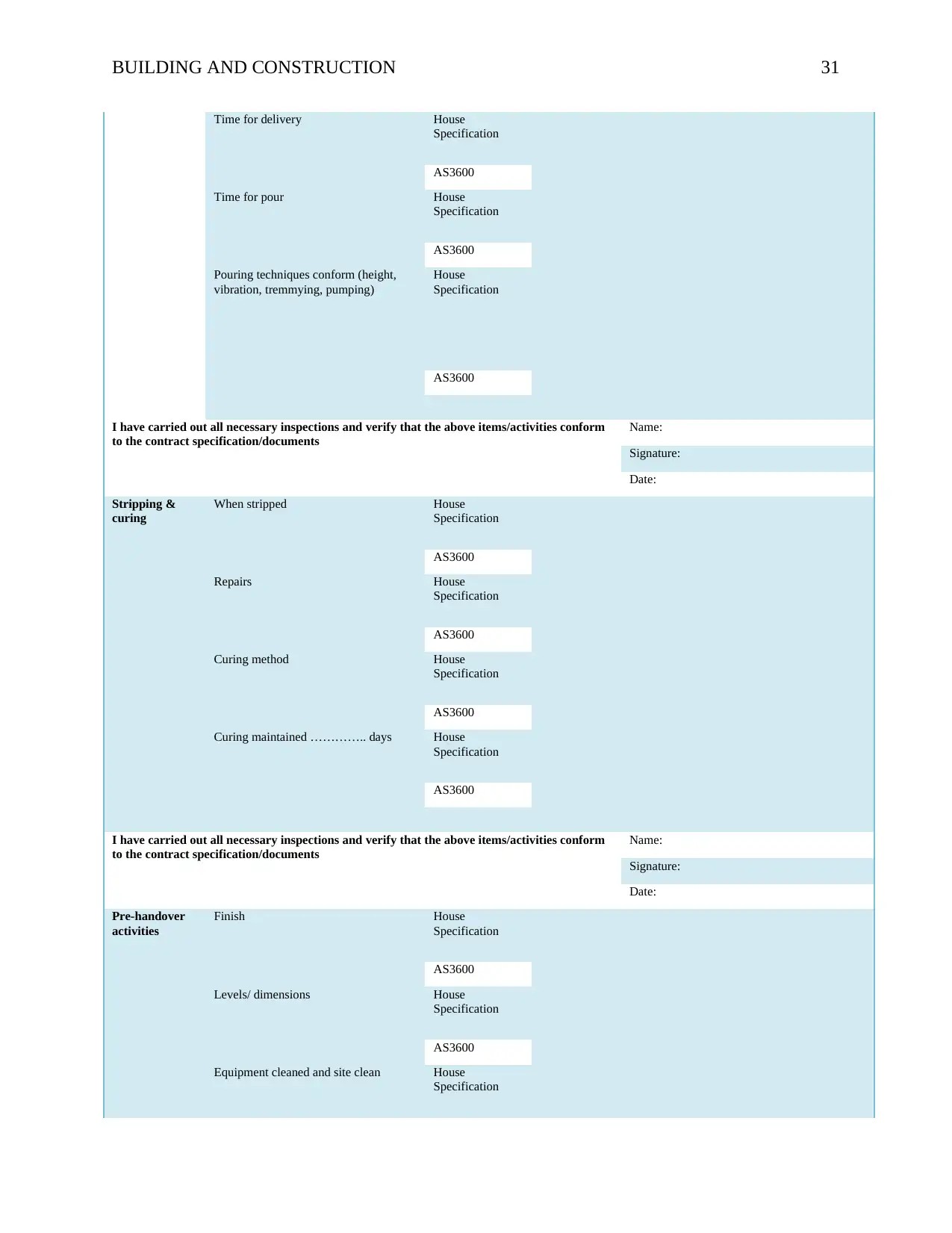
BUILDING AND CONSTRUCTION 31
Time for delivery House
Specification
AS3600
Time for pour House
Specification
AS3600
Pouring techniques conform (height,
vibration, tremmying, pumping)
House
Specification
AS3600
I have carried out all necessary inspections and verify that the above items/activities conform
to the contract specification/documents
Name:
Signature:
Date:
Stripping &
curing
When stripped House
Specification
AS3600
Repairs House
Specification
AS3600
Curing method House
Specification
AS3600
Curing maintained ………….. days House
Specification
AS3600
I have carried out all necessary inspections and verify that the above items/activities conform
to the contract specification/documents
Name:
Signature:
Date:
Pre-handover
activities
Finish House
Specification
AS3600
Levels/ dimensions House
Specification
AS3600
Equipment cleaned and site clean House
Specification
Time for delivery House
Specification
AS3600
Time for pour House
Specification
AS3600
Pouring techniques conform (height,
vibration, tremmying, pumping)
House
Specification
AS3600
I have carried out all necessary inspections and verify that the above items/activities conform
to the contract specification/documents
Name:
Signature:
Date:
Stripping &
curing
When stripped House
Specification
AS3600
Repairs House
Specification
AS3600
Curing method House
Specification
AS3600
Curing maintained ………….. days House
Specification
AS3600
I have carried out all necessary inspections and verify that the above items/activities conform
to the contract specification/documents
Name:
Signature:
Date:
Pre-handover
activities
Finish House
Specification
AS3600
Levels/ dimensions House
Specification
AS3600
Equipment cleaned and site clean House
Specification
Paraphrase This Document
Need a fresh take? Get an instant paraphrase of this document with our AI Paraphraser
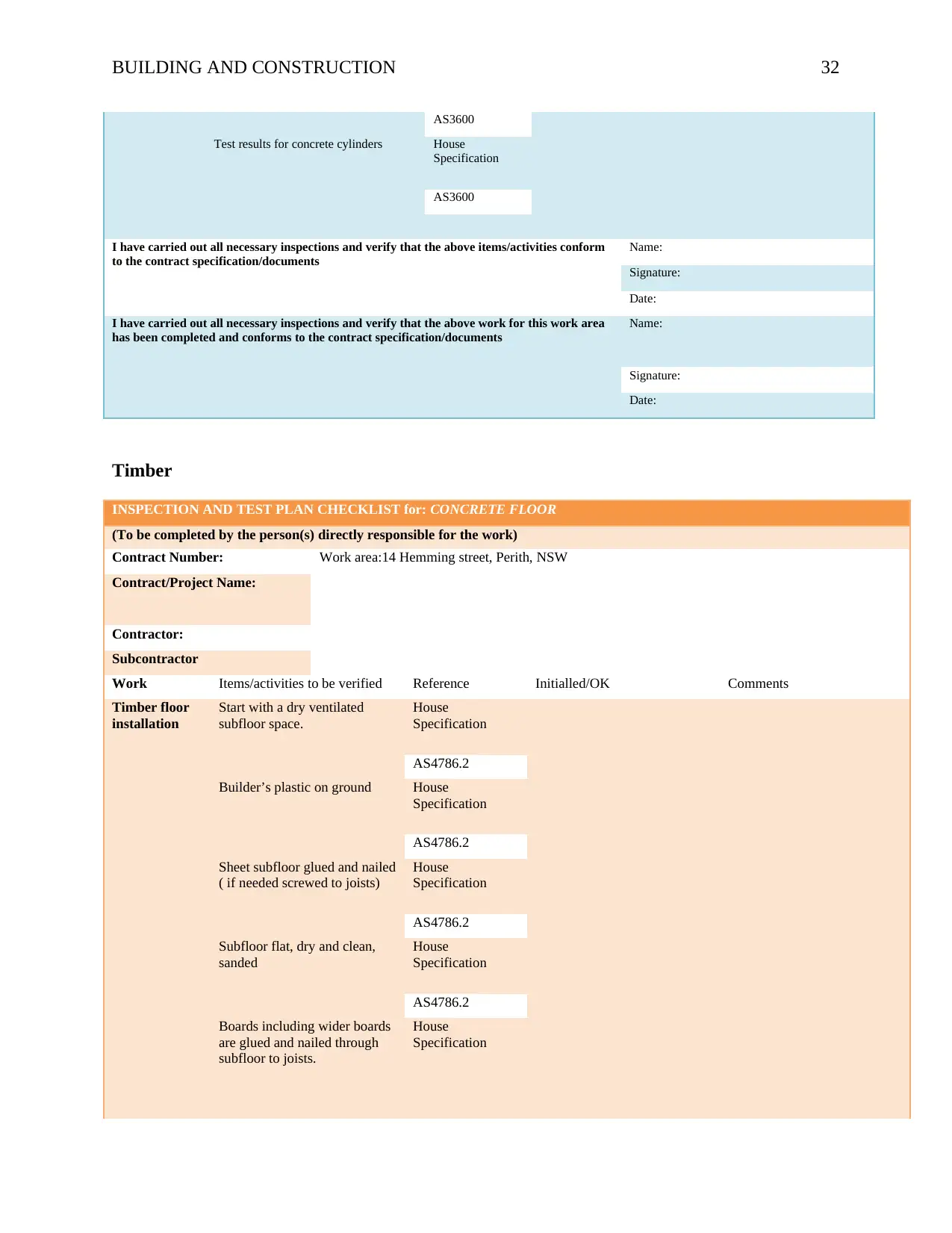
BUILDING AND CONSTRUCTION 32
AS3600
Test results for concrete cylinders House
Specification
AS3600
I have carried out all necessary inspections and verify that the above items/activities conform
to the contract specification/documents
Name:
Signature:
Date:
I have carried out all necessary inspections and verify that the above work for this work area
has been completed and conforms to the contract specification/documents
Name:
Signature:
Date:
Timber
INSPECTION AND TEST PLAN CHECKLIST for: CONCRETE FLOOR
(To be completed by the person(s) directly responsible for the work)
Contract Number: Work area:14 Hemming street, Perith, NSW
Contract/Project Name:
Contractor:
Subcontractor
Work Items/activities to be verified Reference Initialled/OK Comments
Timber floor
installation
Start with a dry ventilated
subfloor space.
House
Specification
AS4786.2
Builder’s plastic on ground House
Specification
AS4786.2
Sheet subfloor glued and nailed
( if needed screwed to joists)
House
Specification
AS4786.2
Subfloor flat, dry and clean,
sanded
House
Specification
AS4786.2
Boards including wider boards
are glued and nailed through
subfloor to joists.
House
Specification
AS3600
Test results for concrete cylinders House
Specification
AS3600
I have carried out all necessary inspections and verify that the above items/activities conform
to the contract specification/documents
Name:
Signature:
Date:
I have carried out all necessary inspections and verify that the above work for this work area
has been completed and conforms to the contract specification/documents
Name:
Signature:
Date:
Timber
INSPECTION AND TEST PLAN CHECKLIST for: CONCRETE FLOOR
(To be completed by the person(s) directly responsible for the work)
Contract Number: Work area:14 Hemming street, Perith, NSW
Contract/Project Name:
Contractor:
Subcontractor
Work Items/activities to be verified Reference Initialled/OK Comments
Timber floor
installation
Start with a dry ventilated
subfloor space.
House
Specification
AS4786.2
Builder’s plastic on ground House
Specification
AS4786.2
Sheet subfloor glued and nailed
( if needed screwed to joists)
House
Specification
AS4786.2
Subfloor flat, dry and clean,
sanded
House
Specification
AS4786.2
Boards including wider boards
are glued and nailed through
subfloor to joists.
House
Specification
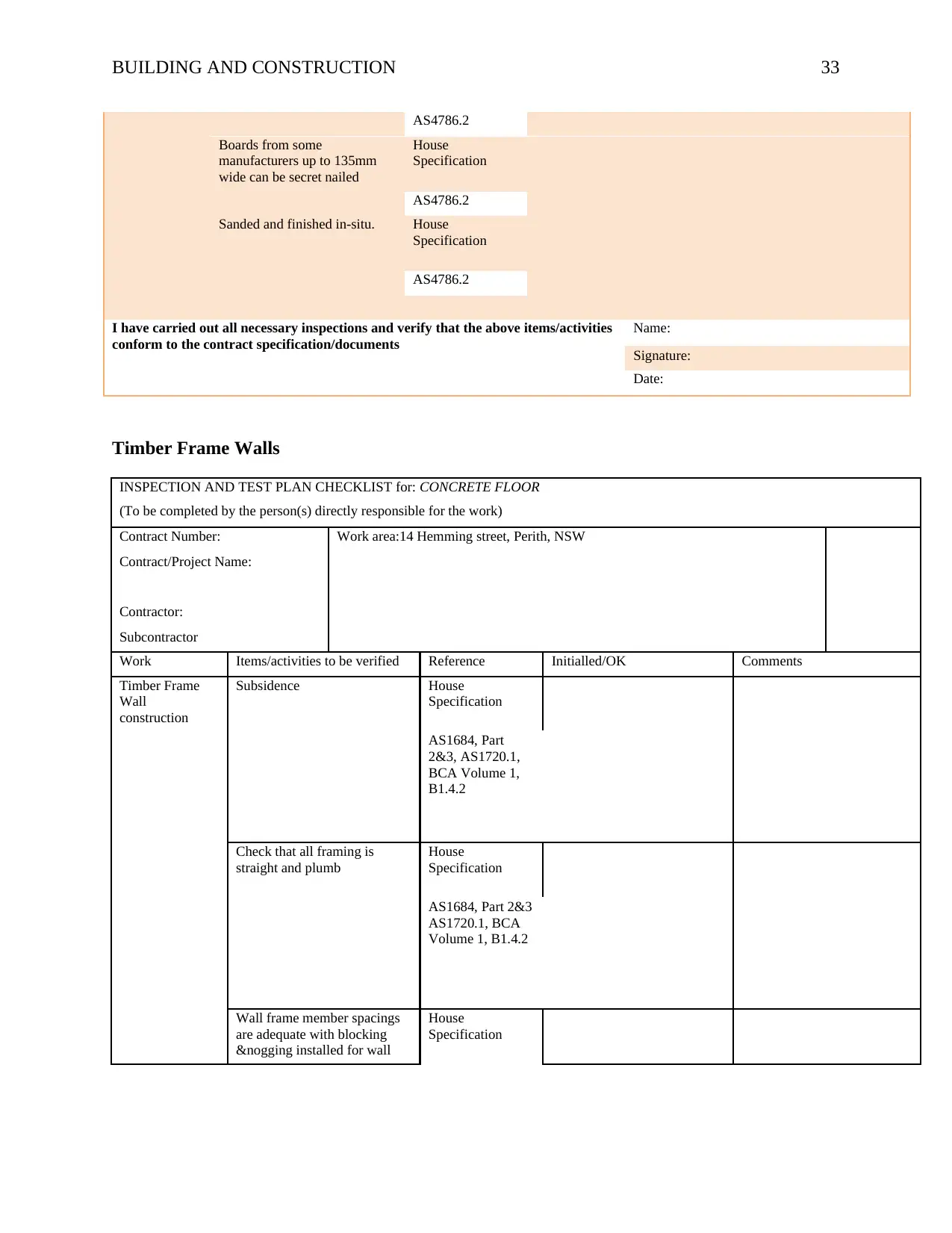
BUILDING AND CONSTRUCTION 33
AS4786.2
Boards from some
manufacturers up to 135mm
wide can be secret nailed
House
Specification
AS4786.2
Sanded and finished in-situ. House
Specification
AS4786.2
I have carried out all necessary inspections and verify that the above items/activities
conform to the contract specification/documents
Name:
Signature:
Date:
Timber Frame Walls
INSPECTION AND TEST PLAN CHECKLIST for: CONCRETE FLOOR
(To be completed by the person(s) directly responsible for the work)
Contract Number: Work area:14 Hemming street, Perith, NSW
Contract/Project Name:
Contractor:
Subcontractor
Work Items/activities to be verified Reference Initialled/OK Comments
Timber Frame
Wall
construction
Subsidence House
Specification
AS1684, Part
2&3, AS1720.1,
BCA Volume 1,
B1.4.2
Check that all framing is
straight and plumb
House
Specification
AS1684, Part 2&3
AS1720.1, BCA
Volume 1, B1.4.2
Wall frame member spacings
are adequate with blocking
&nogging installed for wall
House
Specification
AS4786.2
Boards from some
manufacturers up to 135mm
wide can be secret nailed
House
Specification
AS4786.2
Sanded and finished in-situ. House
Specification
AS4786.2
I have carried out all necessary inspections and verify that the above items/activities
conform to the contract specification/documents
Name:
Signature:
Date:
Timber Frame Walls
INSPECTION AND TEST PLAN CHECKLIST for: CONCRETE FLOOR
(To be completed by the person(s) directly responsible for the work)
Contract Number: Work area:14 Hemming street, Perith, NSW
Contract/Project Name:
Contractor:
Subcontractor
Work Items/activities to be verified Reference Initialled/OK Comments
Timber Frame
Wall
construction
Subsidence House
Specification
AS1684, Part
2&3, AS1720.1,
BCA Volume 1,
B1.4.2
Check that all framing is
straight and plumb
House
Specification
AS1684, Part 2&3
AS1720.1, BCA
Volume 1, B1.4.2
Wall frame member spacings
are adequate with blocking
&nogging installed for wall
House
Specification
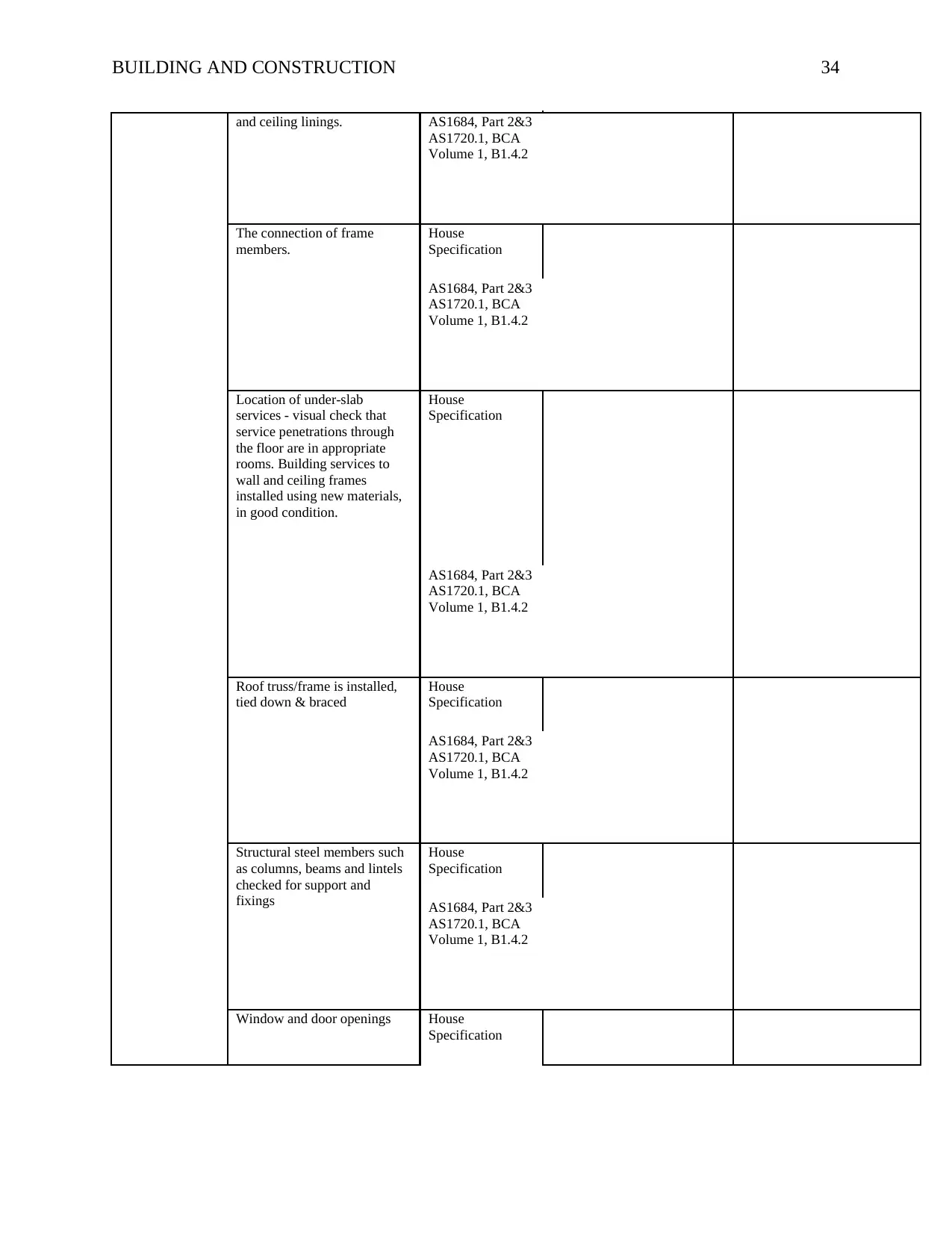
BUILDING AND CONSTRUCTION 34
and ceiling linings. AS1684, Part 2&3
AS1720.1, BCA
Volume 1, B1.4.2
The connection of frame
members.
House
Specification
AS1684, Part 2&3
AS1720.1, BCA
Volume 1, B1.4.2
Location of under-slab
services - visual check that
service penetrations through
the floor are in appropriate
rooms. Building services to
wall and ceiling frames
installed using new materials,
in good condition.
House
Specification
AS1684, Part 2&3
AS1720.1, BCA
Volume 1, B1.4.2
Roof truss/frame is installed,
tied down & braced
House
Specification
AS1684, Part 2&3
AS1720.1, BCA
Volume 1, B1.4.2
Structural steel members such
as columns, beams and lintels
checked for support and
fixings
House
Specification
AS1684, Part 2&3
AS1720.1, BCA
Volume 1, B1.4.2
Window and door openings House
Specification
and ceiling linings. AS1684, Part 2&3
AS1720.1, BCA
Volume 1, B1.4.2
The connection of frame
members.
House
Specification
AS1684, Part 2&3
AS1720.1, BCA
Volume 1, B1.4.2
Location of under-slab
services - visual check that
service penetrations through
the floor are in appropriate
rooms. Building services to
wall and ceiling frames
installed using new materials,
in good condition.
House
Specification
AS1684, Part 2&3
AS1720.1, BCA
Volume 1, B1.4.2
Roof truss/frame is installed,
tied down & braced
House
Specification
AS1684, Part 2&3
AS1720.1, BCA
Volume 1, B1.4.2
Structural steel members such
as columns, beams and lintels
checked for support and
fixings
House
Specification
AS1684, Part 2&3
AS1720.1, BCA
Volume 1, B1.4.2
Window and door openings House
Specification
Secure Best Marks with AI Grader
Need help grading? Try our AI Grader for instant feedback on your assignments.
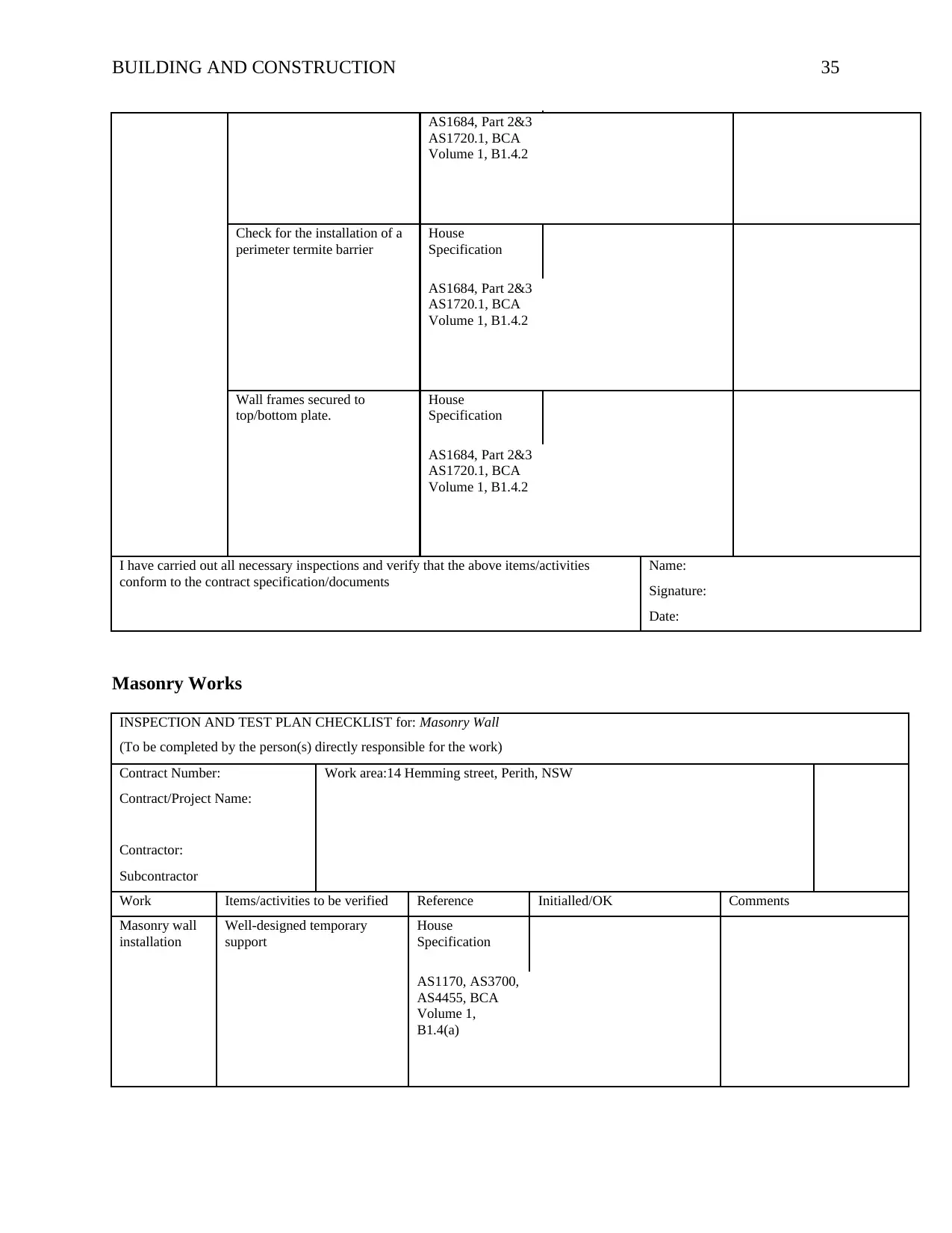
BUILDING AND CONSTRUCTION 35
AS1684, Part 2&3
AS1720.1, BCA
Volume 1, B1.4.2
Check for the installation of a
perimeter termite barrier
House
Specification
AS1684, Part 2&3
AS1720.1, BCA
Volume 1, B1.4.2
Wall frames secured to
top/bottom plate.
House
Specification
AS1684, Part 2&3
AS1720.1, BCA
Volume 1, B1.4.2
I have carried out all necessary inspections and verify that the above items/activities
conform to the contract specification/documents
Name:
Signature:
Date:
Masonry Works
INSPECTION AND TEST PLAN CHECKLIST for: Masonry Wall
(To be completed by the person(s) directly responsible for the work)
Contract Number: Work area:14 Hemming street, Perith, NSW
Contract/Project Name:
Contractor:
Subcontractor
Work Items/activities to be verified Reference Initialled/OK Comments
Masonry wall
installation
Well-designed temporary
support
House
Specification
AS1170, AS3700,
AS4455, BCA
Volume 1,
B1.4(a)
AS1684, Part 2&3
AS1720.1, BCA
Volume 1, B1.4.2
Check for the installation of a
perimeter termite barrier
House
Specification
AS1684, Part 2&3
AS1720.1, BCA
Volume 1, B1.4.2
Wall frames secured to
top/bottom plate.
House
Specification
AS1684, Part 2&3
AS1720.1, BCA
Volume 1, B1.4.2
I have carried out all necessary inspections and verify that the above items/activities
conform to the contract specification/documents
Name:
Signature:
Date:
Masonry Works
INSPECTION AND TEST PLAN CHECKLIST for: Masonry Wall
(To be completed by the person(s) directly responsible for the work)
Contract Number: Work area:14 Hemming street, Perith, NSW
Contract/Project Name:
Contractor:
Subcontractor
Work Items/activities to be verified Reference Initialled/OK Comments
Masonry wall
installation
Well-designed temporary
support
House
Specification
AS1170, AS3700,
AS4455, BCA
Volume 1,
B1.4(a)
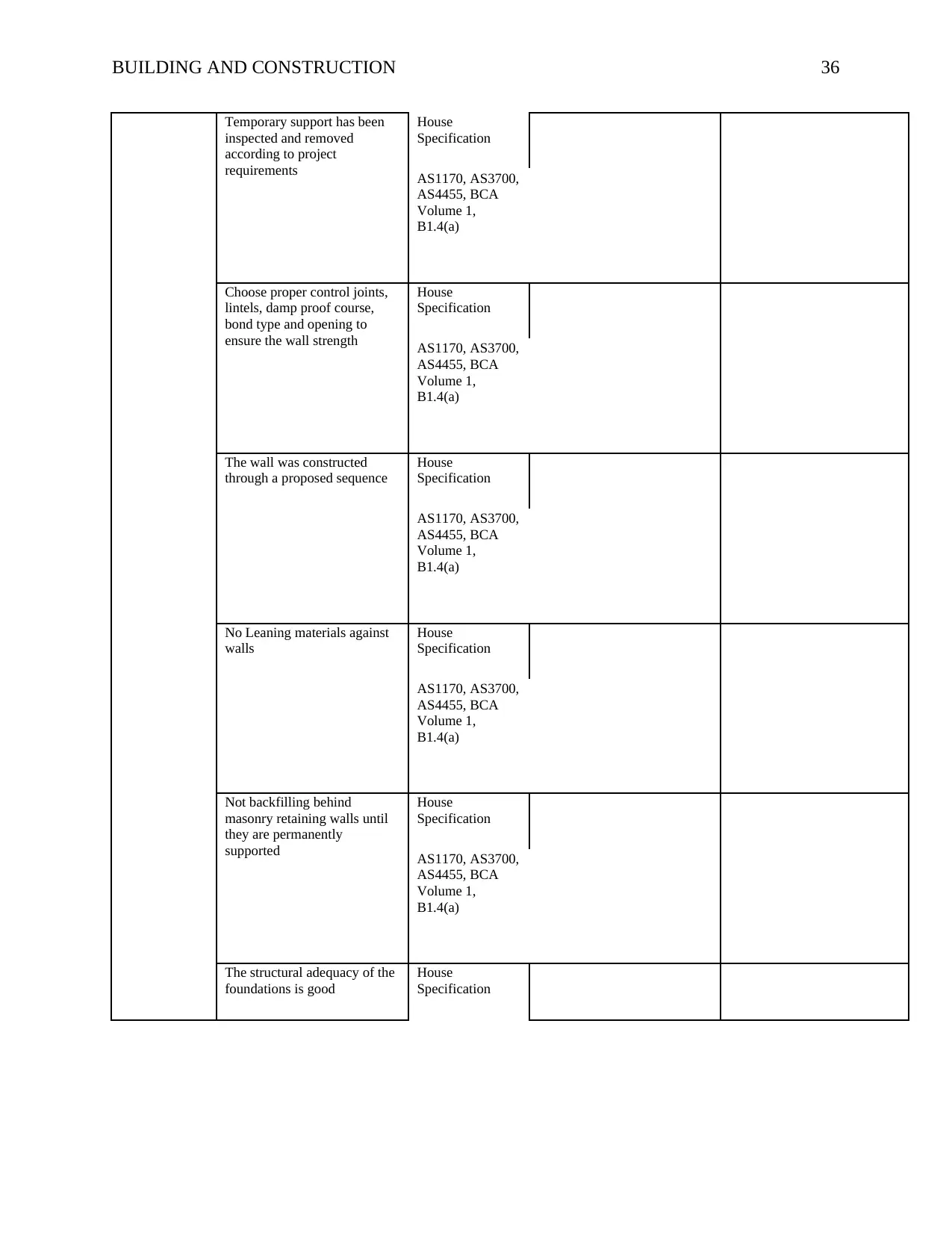
BUILDING AND CONSTRUCTION 36
Temporary support has been
inspected and removed
according to project
requirements
House
Specification
AS1170, AS3700,
AS4455, BCA
Volume 1,
B1.4(a)
Choose proper control joints,
lintels, damp proof course,
bond type and opening to
ensure the wall strength
House
Specification
AS1170, AS3700,
AS4455, BCA
Volume 1,
B1.4(a)
The wall was constructed
through a proposed sequence
House
Specification
AS1170, AS3700,
AS4455, BCA
Volume 1,
B1.4(a)
No Leaning materials against
walls
House
Specification
AS1170, AS3700,
AS4455, BCA
Volume 1,
B1.4(a)
Not backfilling behind
masonry retaining walls until
they are permanently
supported
House
Specification
AS1170, AS3700,
AS4455, BCA
Volume 1,
B1.4(a)
The structural adequacy of the
foundations is good
House
Specification
Temporary support has been
inspected and removed
according to project
requirements
House
Specification
AS1170, AS3700,
AS4455, BCA
Volume 1,
B1.4(a)
Choose proper control joints,
lintels, damp proof course,
bond type and opening to
ensure the wall strength
House
Specification
AS1170, AS3700,
AS4455, BCA
Volume 1,
B1.4(a)
The wall was constructed
through a proposed sequence
House
Specification
AS1170, AS3700,
AS4455, BCA
Volume 1,
B1.4(a)
No Leaning materials against
walls
House
Specification
AS1170, AS3700,
AS4455, BCA
Volume 1,
B1.4(a)
Not backfilling behind
masonry retaining walls until
they are permanently
supported
House
Specification
AS1170, AS3700,
AS4455, BCA
Volume 1,
B1.4(a)
The structural adequacy of the
foundations is good
House
Specification
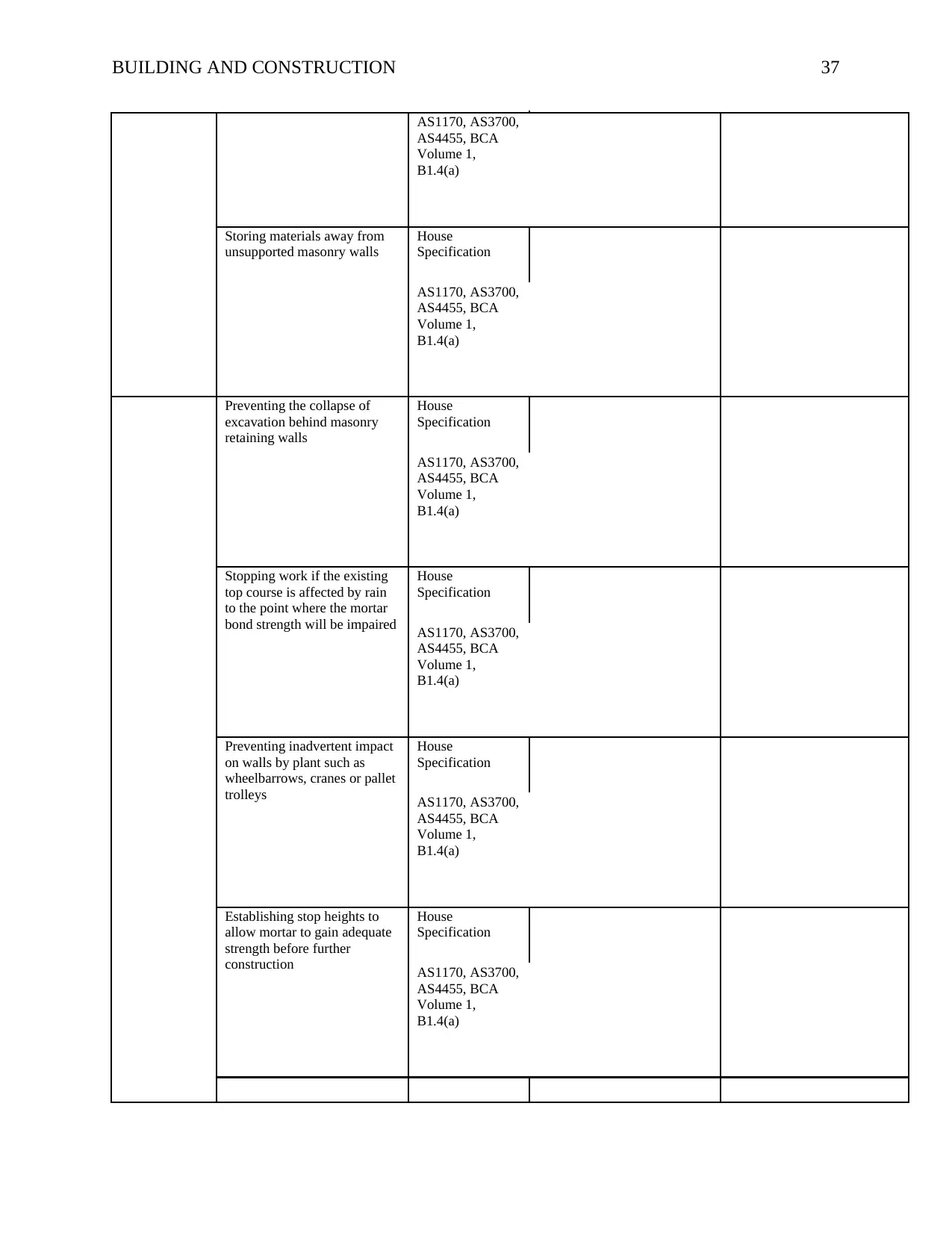
BUILDING AND CONSTRUCTION 37
AS1170, AS3700,
AS4455, BCA
Volume 1,
B1.4(a)
Storing materials away from
unsupported masonry walls
House
Specification
AS1170, AS3700,
AS4455, BCA
Volume 1,
B1.4(a)
Preventing the collapse of
excavation behind masonry
retaining walls
House
Specification
AS1170, AS3700,
AS4455, BCA
Volume 1,
B1.4(a)
Stopping work if the existing
top course is affected by rain
to the point where the mortar
bond strength will be impaired
House
Specification
AS1170, AS3700,
AS4455, BCA
Volume 1,
B1.4(a)
Preventing inadvertent impact
on walls by plant such as
wheelbarrows, cranes or pallet
trolleys
House
Specification
AS1170, AS3700,
AS4455, BCA
Volume 1,
B1.4(a)
Establishing stop heights to
allow mortar to gain adequate
strength before further
construction
House
Specification
AS1170, AS3700,
AS4455, BCA
Volume 1,
B1.4(a)
AS1170, AS3700,
AS4455, BCA
Volume 1,
B1.4(a)
Storing materials away from
unsupported masonry walls
House
Specification
AS1170, AS3700,
AS4455, BCA
Volume 1,
B1.4(a)
Preventing the collapse of
excavation behind masonry
retaining walls
House
Specification
AS1170, AS3700,
AS4455, BCA
Volume 1,
B1.4(a)
Stopping work if the existing
top course is affected by rain
to the point where the mortar
bond strength will be impaired
House
Specification
AS1170, AS3700,
AS4455, BCA
Volume 1,
B1.4(a)
Preventing inadvertent impact
on walls by plant such as
wheelbarrows, cranes or pallet
trolleys
House
Specification
AS1170, AS3700,
AS4455, BCA
Volume 1,
B1.4(a)
Establishing stop heights to
allow mortar to gain adequate
strength before further
construction
House
Specification
AS1170, AS3700,
AS4455, BCA
Volume 1,
B1.4(a)
Paraphrase This Document
Need a fresh take? Get an instant paraphrase of this document with our AI Paraphraser
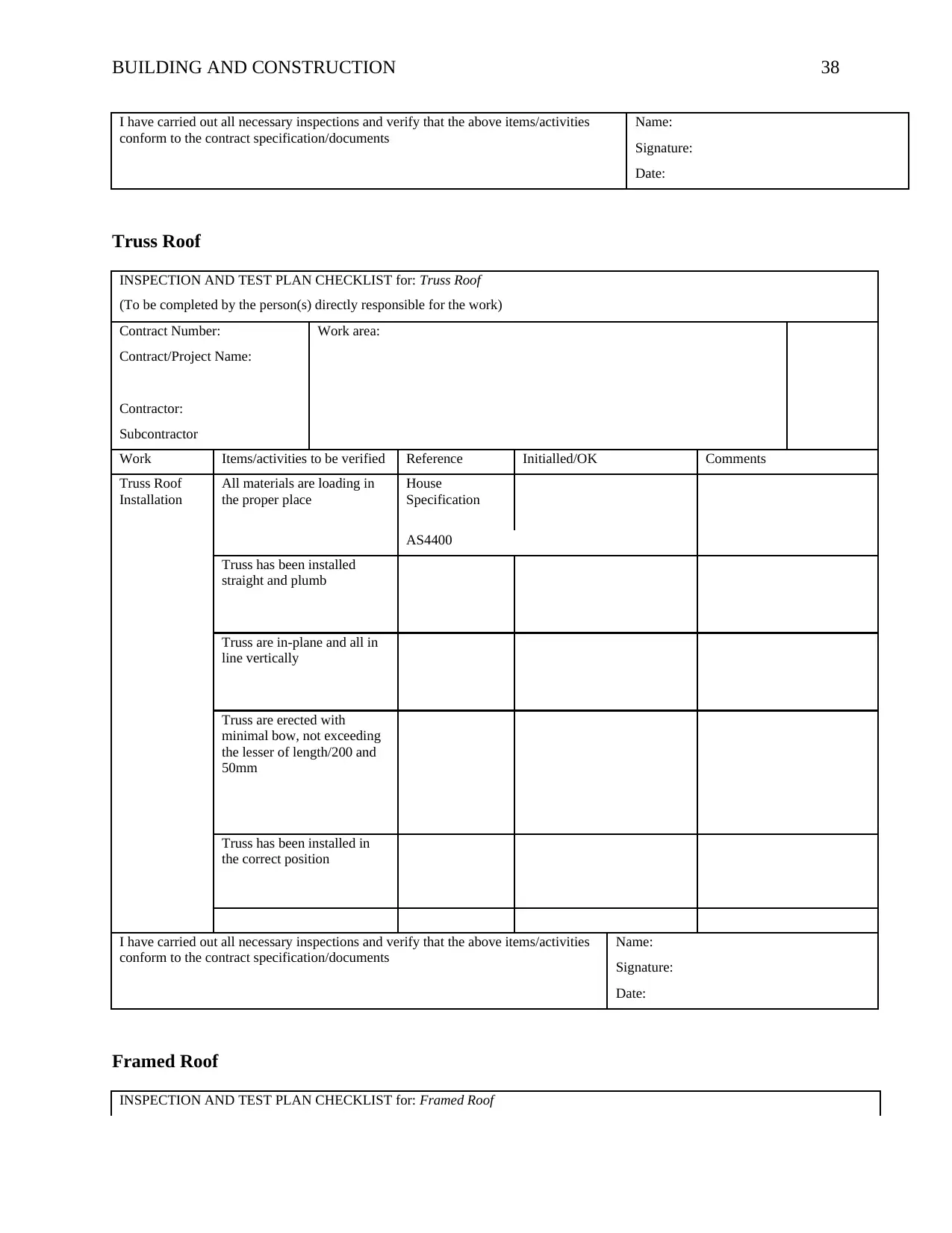
BUILDING AND CONSTRUCTION 38
I have carried out all necessary inspections and verify that the above items/activities
conform to the contract specification/documents
Name:
Signature:
Date:
Truss Roof
INSPECTION AND TEST PLAN CHECKLIST for: Truss Roof
(To be completed by the person(s) directly responsible for the work)
Contract Number: Work area:
Contract/Project Name:
Contractor:
Subcontractor
Work Items/activities to be verified Reference Initialled/OK Comments
Truss Roof
Installation
All materials are loading in
the proper place
House
Specification
AS4400
Truss has been installed
straight and plumb
Truss are in-plane and all in
line vertically
Truss are erected with
minimal bow, not exceeding
the lesser of length/200 and
50mm
Truss has been installed in
the correct position
I have carried out all necessary inspections and verify that the above items/activities
conform to the contract specification/documents
Name:
Signature:
Date:
Framed Roof
INSPECTION AND TEST PLAN CHECKLIST for: Framed Roof
I have carried out all necessary inspections and verify that the above items/activities
conform to the contract specification/documents
Name:
Signature:
Date:
Truss Roof
INSPECTION AND TEST PLAN CHECKLIST for: Truss Roof
(To be completed by the person(s) directly responsible for the work)
Contract Number: Work area:
Contract/Project Name:
Contractor:
Subcontractor
Work Items/activities to be verified Reference Initialled/OK Comments
Truss Roof
Installation
All materials are loading in
the proper place
House
Specification
AS4400
Truss has been installed
straight and plumb
Truss are in-plane and all in
line vertically
Truss are erected with
minimal bow, not exceeding
the lesser of length/200 and
50mm
Truss has been installed in
the correct position
I have carried out all necessary inspections and verify that the above items/activities
conform to the contract specification/documents
Name:
Signature:
Date:
Framed Roof
INSPECTION AND TEST PLAN CHECKLIST for: Framed Roof
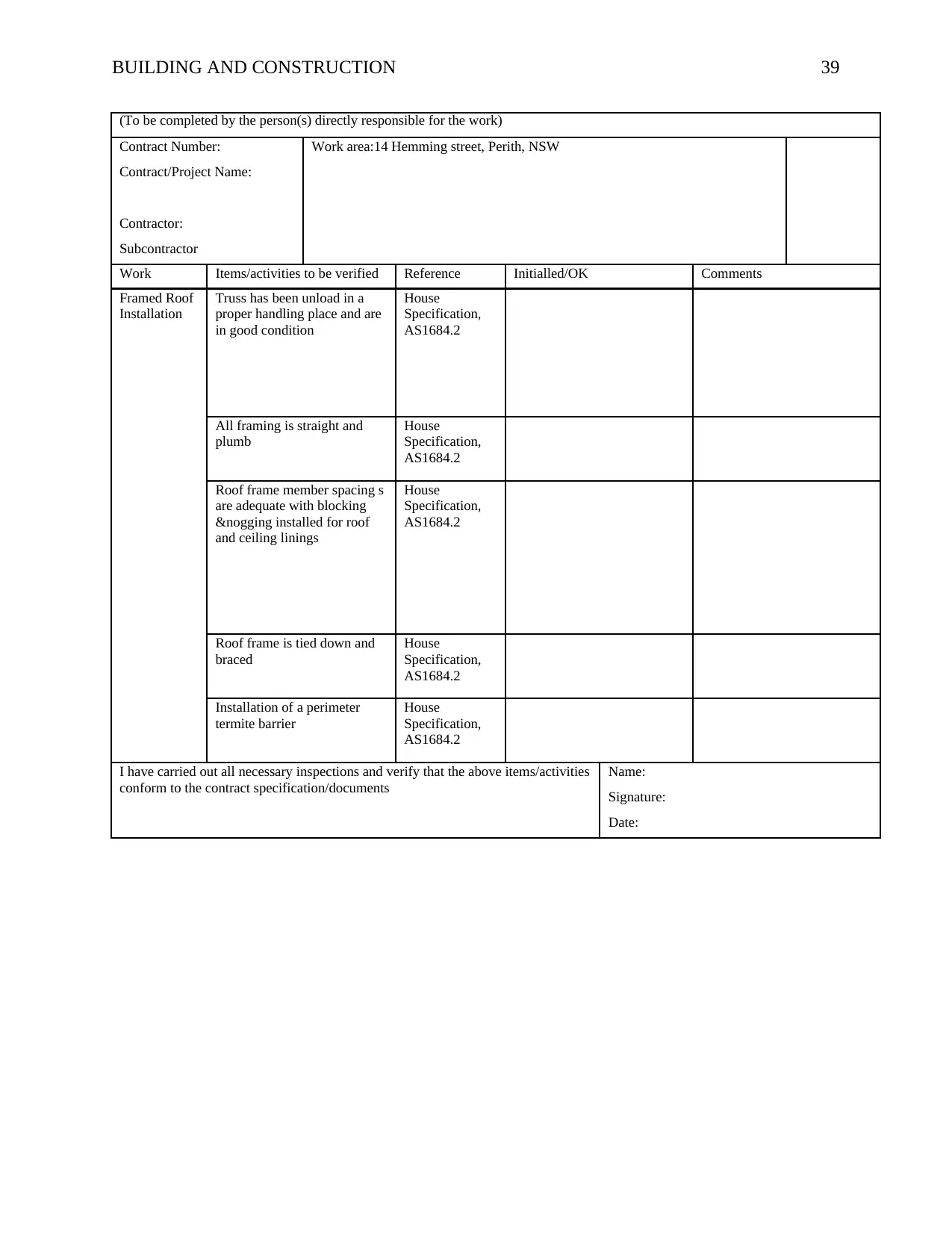
BUILDING AND CONSTRUCTION 39
(To be completed by the person(s) directly responsible for the work)
Contract Number: Work area:14 Hemming street, Perith, NSW
Contract/Project Name:
Contractor:
Subcontractor
Work Items/activities to be verified Reference Initialled/OK Comments
Framed Roof
Installation
Truss has been unload in a
proper handling place and are
in good condition
House
Specification,
AS1684.2
All framing is straight and
plumb
House
Specification,
AS1684.2
Roof frame member spacing s
are adequate with blocking
&nogging installed for roof
and ceiling linings
House
Specification,
AS1684.2
Roof frame is tied down and
braced
House
Specification,
AS1684.2
Installation of a perimeter
termite barrier
House
Specification,
AS1684.2
I have carried out all necessary inspections and verify that the above items/activities
conform to the contract specification/documents
Name:
Signature:
Date:
(To be completed by the person(s) directly responsible for the work)
Contract Number: Work area:14 Hemming street, Perith, NSW
Contract/Project Name:
Contractor:
Subcontractor
Work Items/activities to be verified Reference Initialled/OK Comments
Framed Roof
Installation
Truss has been unload in a
proper handling place and are
in good condition
House
Specification,
AS1684.2
All framing is straight and
plumb
House
Specification,
AS1684.2
Roof frame member spacing s
are adequate with blocking
&nogging installed for roof
and ceiling linings
House
Specification,
AS1684.2
Roof frame is tied down and
braced
House
Specification,
AS1684.2
Installation of a perimeter
termite barrier
House
Specification,
AS1684.2
I have carried out all necessary inspections and verify that the above items/activities
conform to the contract specification/documents
Name:
Signature:
Date:
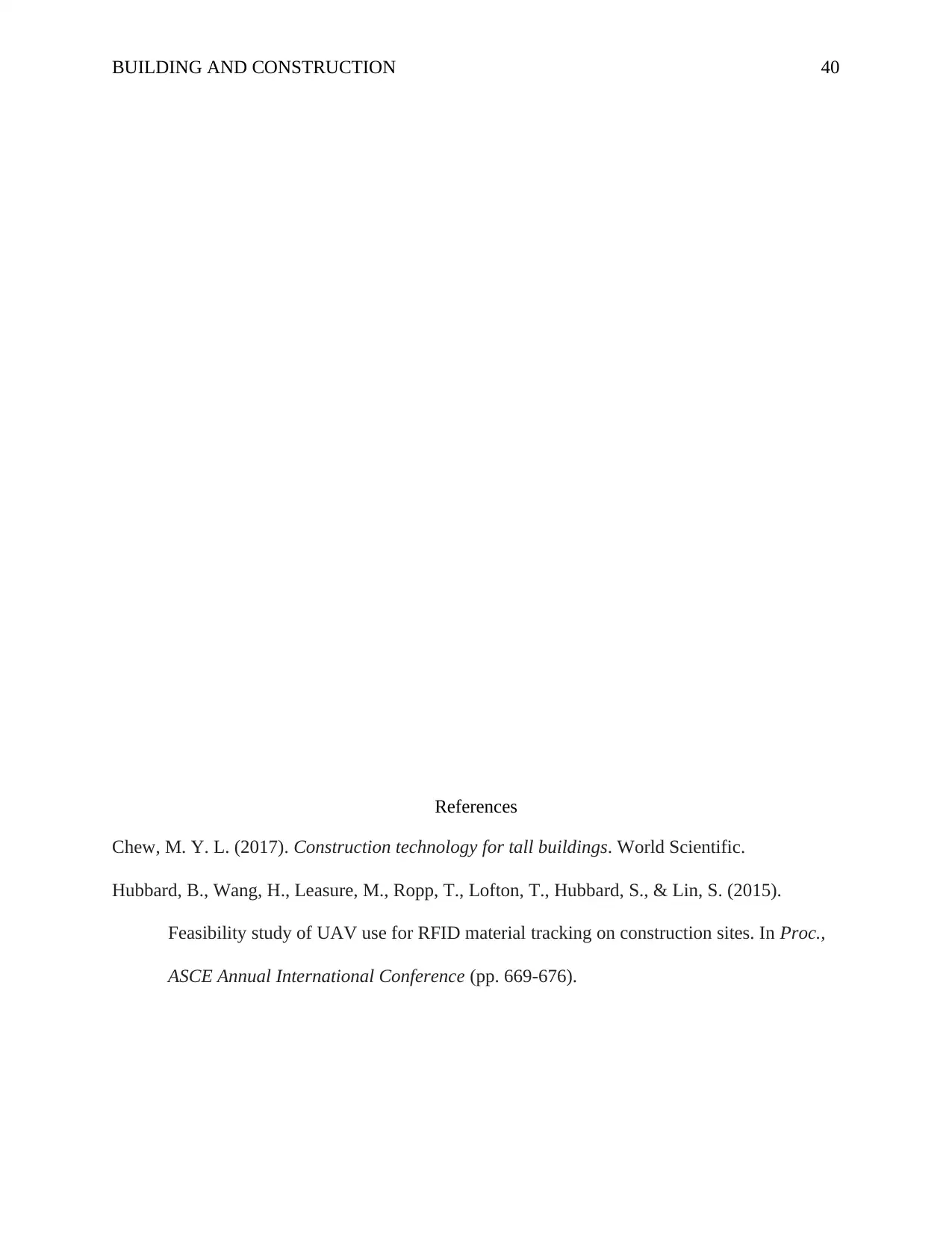
BUILDING AND CONSTRUCTION 40
References
Chew, M. Y. L. (2017). Construction technology for tall buildings. World Scientific.
Hubbard, B., Wang, H., Leasure, M., Ropp, T., Lofton, T., Hubbard, S., & Lin, S. (2015).
Feasibility study of UAV use for RFID material tracking on construction sites. In Proc.,
ASCE Annual International Conference (pp. 669-676).
References
Chew, M. Y. L. (2017). Construction technology for tall buildings. World Scientific.
Hubbard, B., Wang, H., Leasure, M., Ropp, T., Lofton, T., Hubbard, S., & Lin, S. (2015).
Feasibility study of UAV use for RFID material tracking on construction sites. In Proc.,
ASCE Annual International Conference (pp. 669-676).
1 out of 40
Related Documents

Your All-in-One AI-Powered Toolkit for Academic Success.
 +13062052269
info@desklib.com
Available 24*7 on WhatsApp / Email
Unlock your academic potential
© 2024  |  Zucol Services PVT LTD  |  All rights reserved.