Health and Safety Report: Buncefield Oil Terminal Accident Analysis
VerifiedAdded on 2022/08/19
|13
|3161
|15
Report
AI Summary
This report provides a comprehensive analysis of the Buncefield oil terminal fire, one of the largest fire accidents in the oil and gas industry. It examines the health and safety issues, including technology failures like the malfunctioning ATG and IHLS, poor management systems, failure of hazardous identification, and lack of corporate leadership. The report details the accident's impact on the downstream oil industry, including loss of fuel, storage problems, and effects on buyers. It also explores relevant health and safety theories like HAZOP and FMEA, comparing them to the Buncefield case to highlight shortcomings in risk management. The report concludes with recommendations for the Buncefield Oil Terminal Company to prevent similar accidents in the future. The study covers the causes, impacts, and proposed solutions to enhance safety measures in the oil and gas sector, emphasizing the importance of proactive risk management and a strong safety culture.
Contribute Materials
Your contribution can guide someone’s learning journey. Share your
documents today.
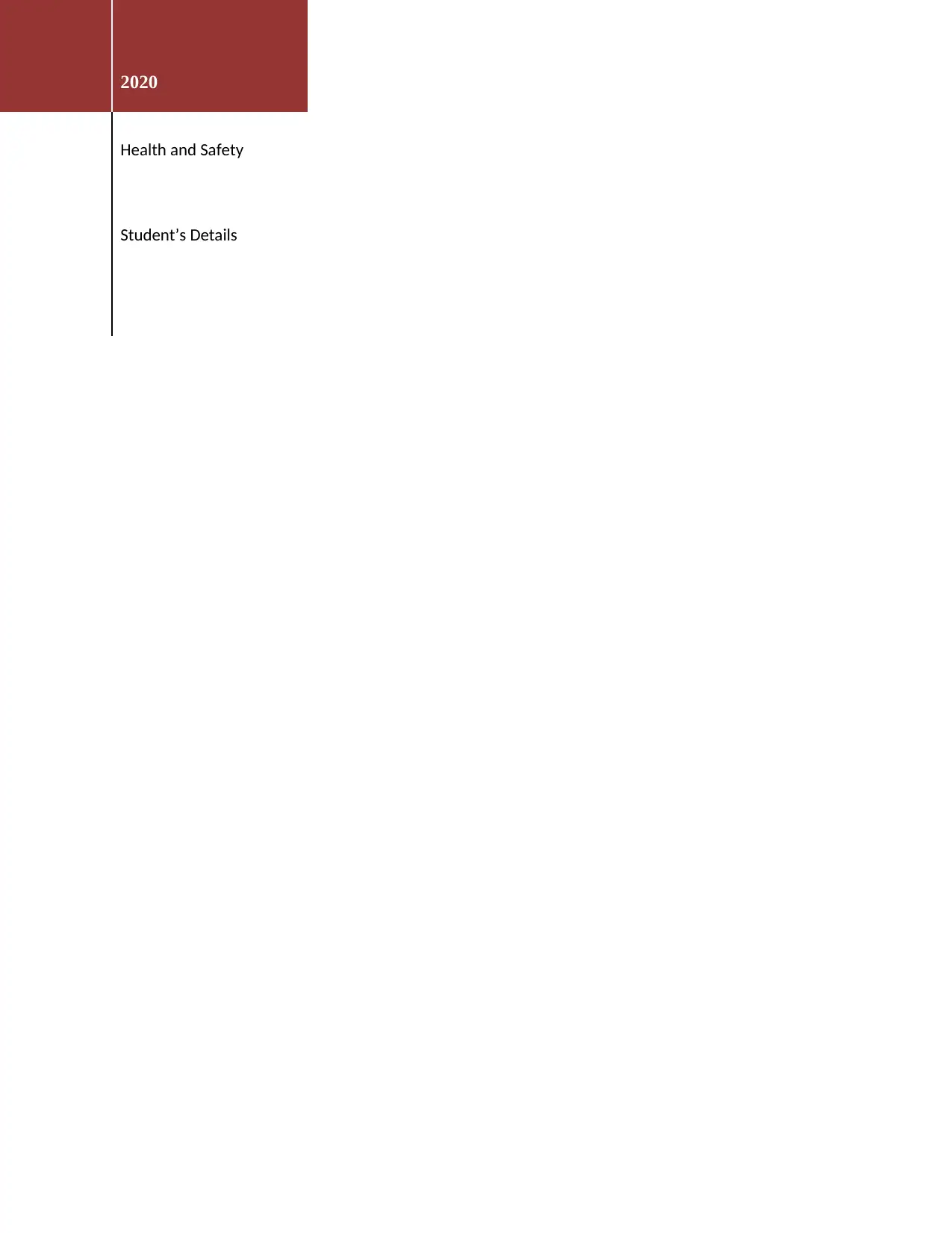
2020
Health and Safety
Student’s Details
Health and Safety
Student’s Details
Secure Best Marks with AI Grader
Need help grading? Try our AI Grader for instant feedback on your assignments.
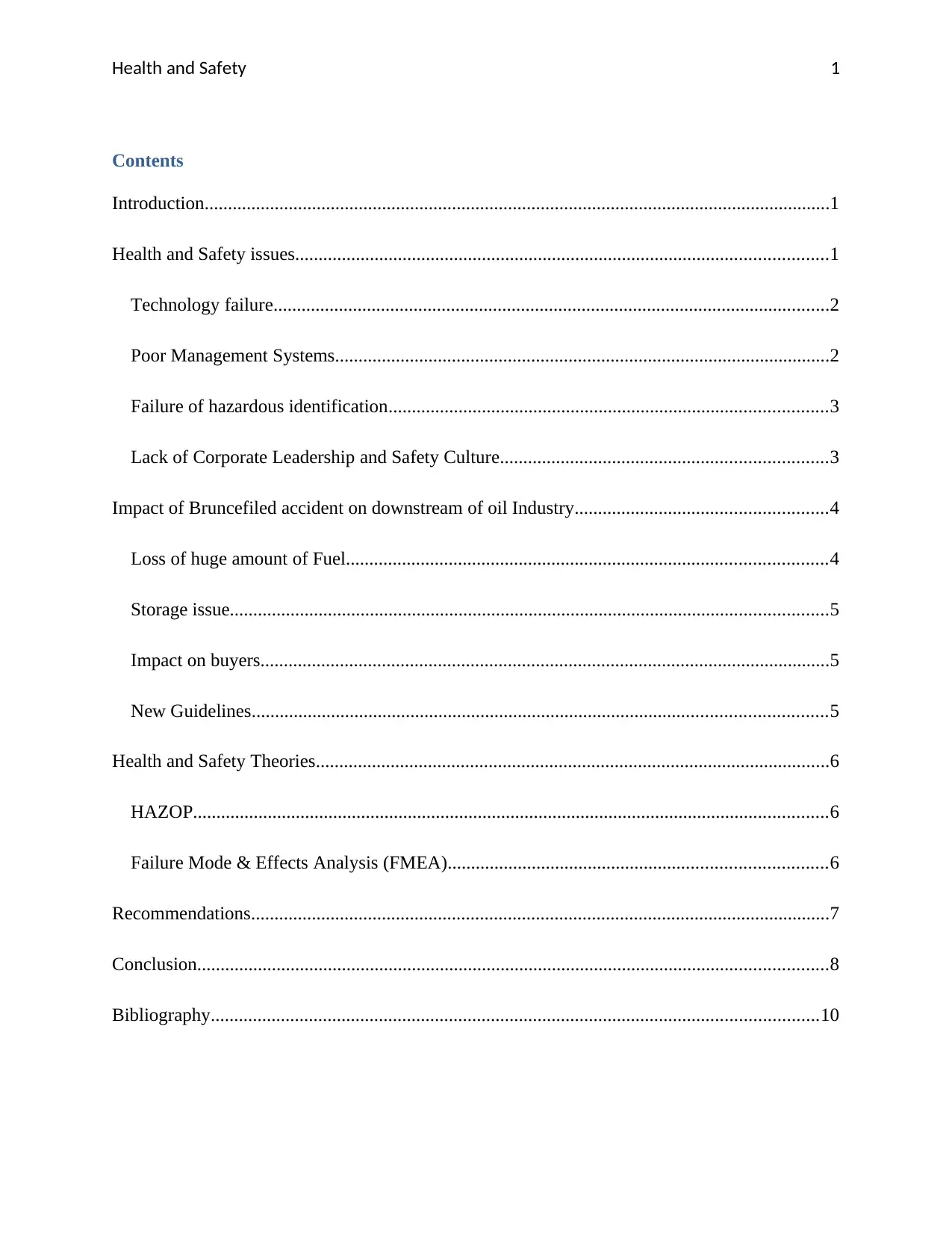
Health and Safety 1
Contents
Introduction......................................................................................................................................1
Health and Safety issues..................................................................................................................1
Technology failure.......................................................................................................................2
Poor Management Systems..........................................................................................................2
Failure of hazardous identification..............................................................................................3
Lack of Corporate Leadership and Safety Culture......................................................................3
Impact of Bruncefiled accident on downstream of oil Industry......................................................4
Loss of huge amount of Fuel.......................................................................................................4
Storage issue................................................................................................................................5
Impact on buyers..........................................................................................................................5
New Guidelines...........................................................................................................................5
Health and Safety Theories..............................................................................................................6
HAZOP........................................................................................................................................6
Failure Mode & Effects Analysis (FMEA).................................................................................6
Recommendations............................................................................................................................7
Conclusion.......................................................................................................................................8
Bibliography..................................................................................................................................10
Contents
Introduction......................................................................................................................................1
Health and Safety issues..................................................................................................................1
Technology failure.......................................................................................................................2
Poor Management Systems..........................................................................................................2
Failure of hazardous identification..............................................................................................3
Lack of Corporate Leadership and Safety Culture......................................................................3
Impact of Bruncefiled accident on downstream of oil Industry......................................................4
Loss of huge amount of Fuel.......................................................................................................4
Storage issue................................................................................................................................5
Impact on buyers..........................................................................................................................5
New Guidelines...........................................................................................................................5
Health and Safety Theories..............................................................................................................6
HAZOP........................................................................................................................................6
Failure Mode & Effects Analysis (FMEA).................................................................................6
Recommendations............................................................................................................................7
Conclusion.......................................................................................................................................8
Bibliography..................................................................................................................................10
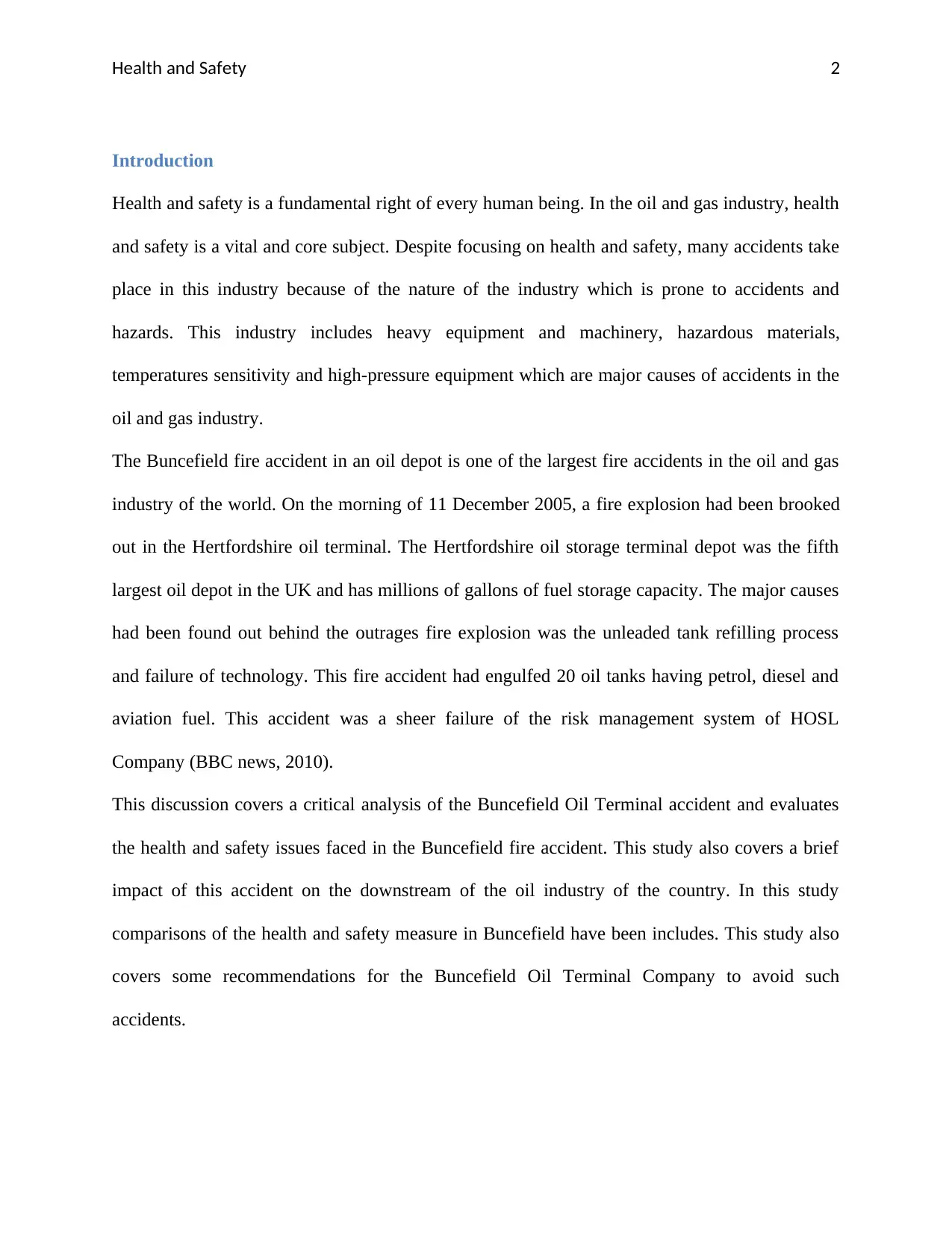
Health and Safety 2
Introduction
Health and safety is a fundamental right of every human being. In the oil and gas industry, health
and safety is a vital and core subject. Despite focusing on health and safety, many accidents take
place in this industry because of the nature of the industry which is prone to accidents and
hazards. This industry includes heavy equipment and machinery, hazardous materials,
temperatures sensitivity and high-pressure equipment which are major causes of accidents in the
oil and gas industry.
The Buncefield fire accident in an oil depot is one of the largest fire accidents in the oil and gas
industry of the world. On the morning of 11 December 2005, a fire explosion had been brooked
out in the Hertfordshire oil terminal. The Hertfordshire oil storage terminal depot was the fifth
largest oil depot in the UK and has millions of gallons of fuel storage capacity. The major causes
had been found out behind the outrages fire explosion was the unleaded tank refilling process
and failure of technology. This fire accident had engulfed 20 oil tanks having petrol, diesel and
aviation fuel. This accident was a sheer failure of the risk management system of HOSL
Company (BBC news, 2010).
This discussion covers a critical analysis of the Buncefield Oil Terminal accident and evaluates
the health and safety issues faced in the Buncefield fire accident. This study also covers a brief
impact of this accident on the downstream of the oil industry of the country. In this study
comparisons of the health and safety measure in Buncefield have been includes. This study also
covers some recommendations for the Buncefield Oil Terminal Company to avoid such
accidents.
Introduction
Health and safety is a fundamental right of every human being. In the oil and gas industry, health
and safety is a vital and core subject. Despite focusing on health and safety, many accidents take
place in this industry because of the nature of the industry which is prone to accidents and
hazards. This industry includes heavy equipment and machinery, hazardous materials,
temperatures sensitivity and high-pressure equipment which are major causes of accidents in the
oil and gas industry.
The Buncefield fire accident in an oil depot is one of the largest fire accidents in the oil and gas
industry of the world. On the morning of 11 December 2005, a fire explosion had been brooked
out in the Hertfordshire oil terminal. The Hertfordshire oil storage terminal depot was the fifth
largest oil depot in the UK and has millions of gallons of fuel storage capacity. The major causes
had been found out behind the outrages fire explosion was the unleaded tank refilling process
and failure of technology. This fire accident had engulfed 20 oil tanks having petrol, diesel and
aviation fuel. This accident was a sheer failure of the risk management system of HOSL
Company (BBC news, 2010).
This discussion covers a critical analysis of the Buncefield Oil Terminal accident and evaluates
the health and safety issues faced in the Buncefield fire accident. This study also covers a brief
impact of this accident on the downstream of the oil industry of the country. In this study
comparisons of the health and safety measure in Buncefield have been includes. This study also
covers some recommendations for the Buncefield Oil Terminal Company to avoid such
accidents.
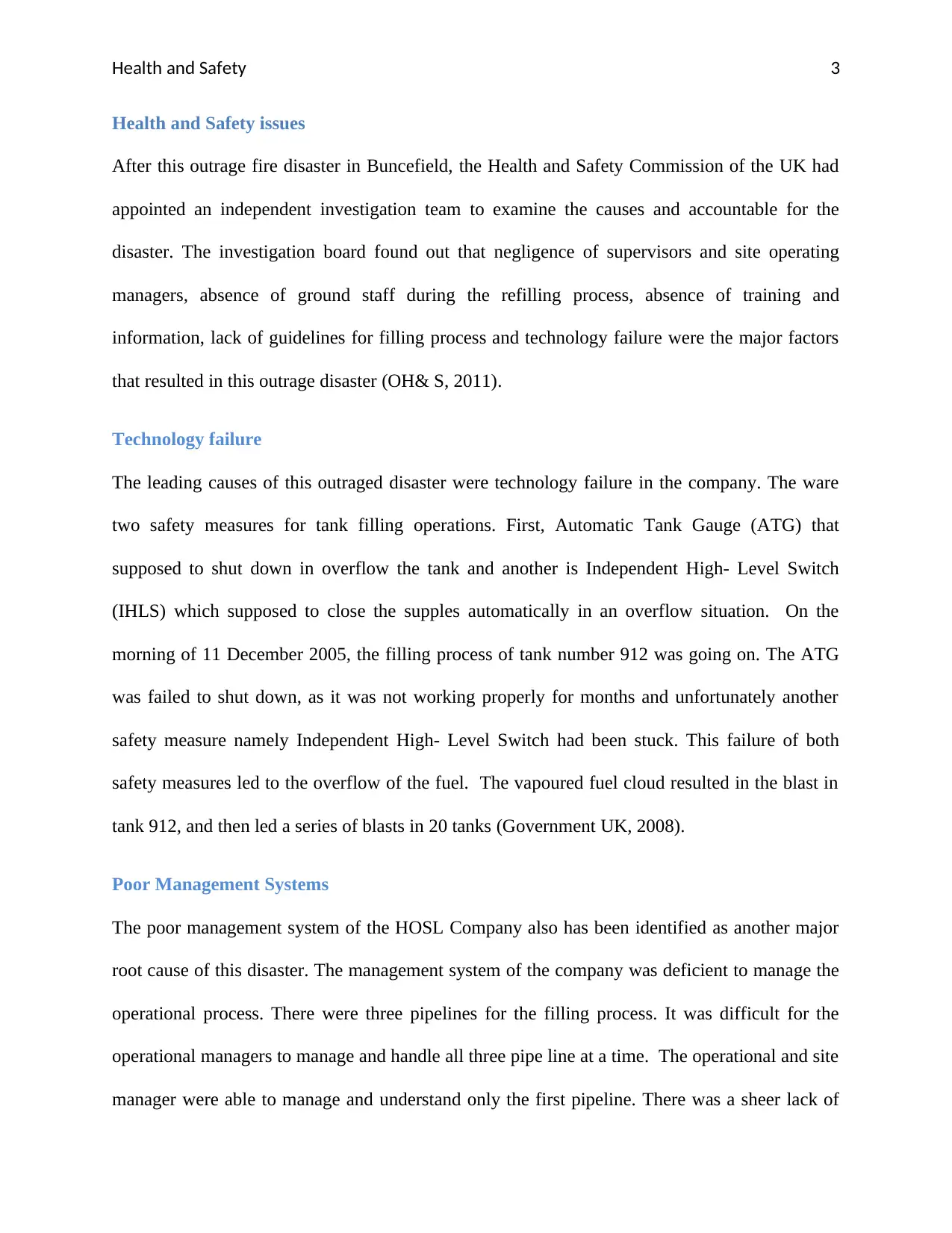
Health and Safety 3
Health and Safety issues
After this outrage fire disaster in Buncefield, the Health and Safety Commission of the UK had
appointed an independent investigation team to examine the causes and accountable for the
disaster. The investigation board found out that negligence of supervisors and site operating
managers, absence of ground staff during the refilling process, absence of training and
information, lack of guidelines for filling process and technology failure were the major factors
that resulted in this outrage disaster (OH& S, 2011).
Technology failure
The leading causes of this outraged disaster were technology failure in the company. The ware
two safety measures for tank filling operations. First, Automatic Tank Gauge (ATG) that
supposed to shut down in overflow the tank and another is Independent High- Level Switch
(IHLS) which supposed to close the supples automatically in an overflow situation. On the
morning of 11 December 2005, the filling process of tank number 912 was going on. The ATG
was failed to shut down, as it was not working properly for months and unfortunately another
safety measure namely Independent High- Level Switch had been stuck. This failure of both
safety measures led to the overflow of the fuel. The vapoured fuel cloud resulted in the blast in
tank 912, and then led a series of blasts in 20 tanks (Government UK, 2008).
Poor Management Systems
The poor management system of the HOSL Company also has been identified as another major
root cause of this disaster. The management system of the company was deficient to manage the
operational process. There were three pipelines for the filling process. It was difficult for the
operational managers to manage and handle all three pipe line at a time. The operational and site
manager were able to manage and understand only the first pipeline. There was a sheer lack of
Health and Safety issues
After this outrage fire disaster in Buncefield, the Health and Safety Commission of the UK had
appointed an independent investigation team to examine the causes and accountable for the
disaster. The investigation board found out that negligence of supervisors and site operating
managers, absence of ground staff during the refilling process, absence of training and
information, lack of guidelines for filling process and technology failure were the major factors
that resulted in this outrage disaster (OH& S, 2011).
Technology failure
The leading causes of this outraged disaster were technology failure in the company. The ware
two safety measures for tank filling operations. First, Automatic Tank Gauge (ATG) that
supposed to shut down in overflow the tank and another is Independent High- Level Switch
(IHLS) which supposed to close the supples automatically in an overflow situation. On the
morning of 11 December 2005, the filling process of tank number 912 was going on. The ATG
was failed to shut down, as it was not working properly for months and unfortunately another
safety measure namely Independent High- Level Switch had been stuck. This failure of both
safety measures led to the overflow of the fuel. The vapoured fuel cloud resulted in the blast in
tank 912, and then led a series of blasts in 20 tanks (Government UK, 2008).
Poor Management Systems
The poor management system of the HOSL Company also has been identified as another major
root cause of this disaster. The management system of the company was deficient to manage the
operational process. There were three pipelines for the filling process. It was difficult for the
operational managers to manage and handle all three pipe line at a time. The operational and site
manager were able to manage and understand only the first pipeline. There was a sheer lack of
Secure Best Marks with AI Grader
Need help grading? Try our AI Grader for instant feedback on your assignments.
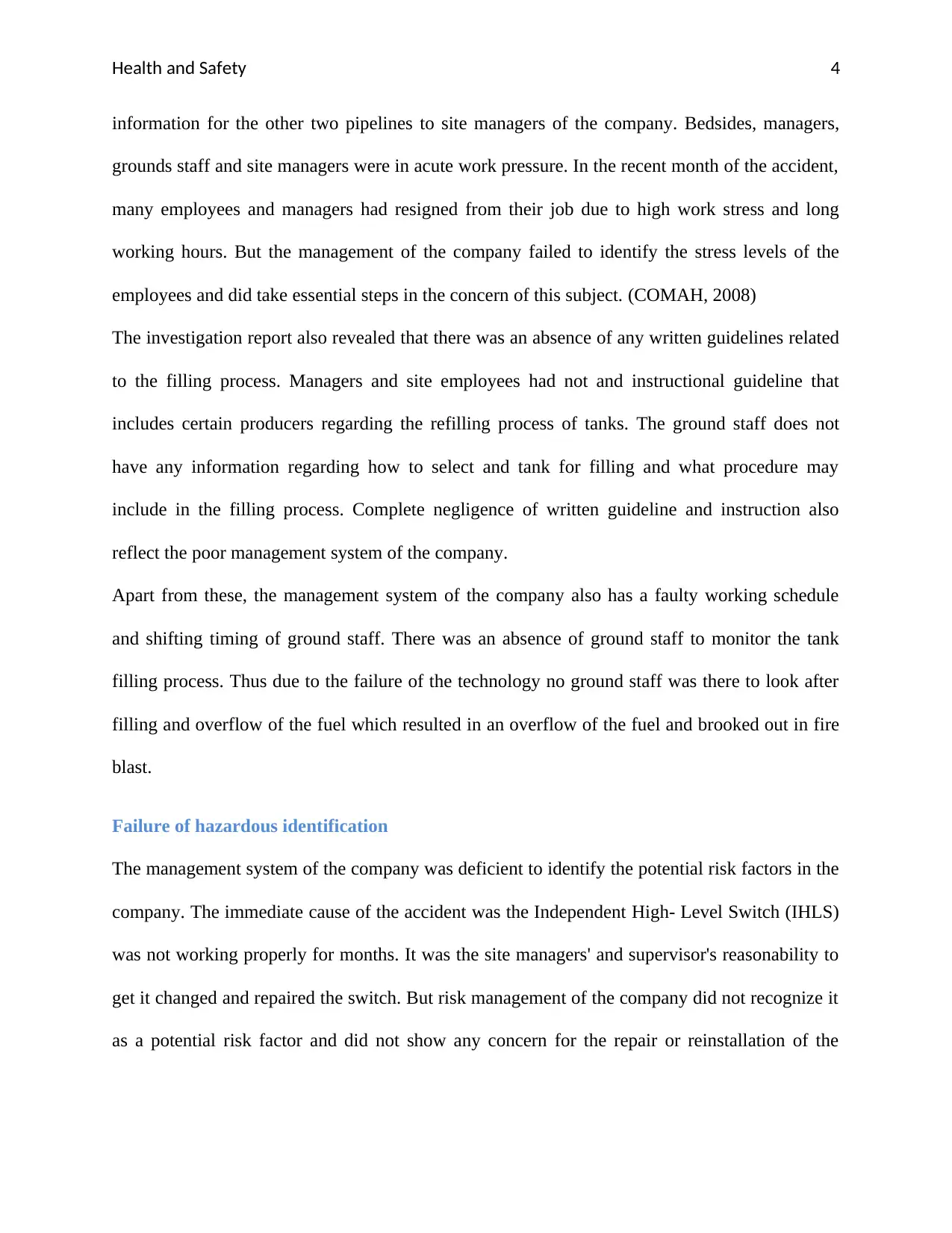
Health and Safety 4
information for the other two pipelines to site managers of the company. Bedsides, managers,
grounds staff and site managers were in acute work pressure. In the recent month of the accident,
many employees and managers had resigned from their job due to high work stress and long
working hours. But the management of the company failed to identify the stress levels of the
employees and did take essential steps in the concern of this subject. (COMAH, 2008)
The investigation report also revealed that there was an absence of any written guidelines related
to the filling process. Managers and site employees had not and instructional guideline that
includes certain producers regarding the refilling process of tanks. The ground staff does not
have any information regarding how to select and tank for filling and what procedure may
include in the filling process. Complete negligence of written guideline and instruction also
reflect the poor management system of the company.
Apart from these, the management system of the company also has a faulty working schedule
and shifting timing of ground staff. There was an absence of ground staff to monitor the tank
filling process. Thus due to the failure of the technology no ground staff was there to look after
filling and overflow of the fuel which resulted in an overflow of the fuel and brooked out in fire
blast.
Failure of hazardous identification
The management system of the company was deficient to identify the potential risk factors in the
company. The immediate cause of the accident was the Independent High- Level Switch (IHLS)
was not working properly for months. It was the site managers' and supervisor's reasonability to
get it changed and repaired the switch. But risk management of the company did not recognize it
as a potential risk factor and did not show any concern for the repair or reinstallation of the
information for the other two pipelines to site managers of the company. Bedsides, managers,
grounds staff and site managers were in acute work pressure. In the recent month of the accident,
many employees and managers had resigned from their job due to high work stress and long
working hours. But the management of the company failed to identify the stress levels of the
employees and did take essential steps in the concern of this subject. (COMAH, 2008)
The investigation report also revealed that there was an absence of any written guidelines related
to the filling process. Managers and site employees had not and instructional guideline that
includes certain producers regarding the refilling process of tanks. The ground staff does not
have any information regarding how to select and tank for filling and what procedure may
include in the filling process. Complete negligence of written guideline and instruction also
reflect the poor management system of the company.
Apart from these, the management system of the company also has a faulty working schedule
and shifting timing of ground staff. There was an absence of ground staff to monitor the tank
filling process. Thus due to the failure of the technology no ground staff was there to look after
filling and overflow of the fuel which resulted in an overflow of the fuel and brooked out in fire
blast.
Failure of hazardous identification
The management system of the company was deficient to identify the potential risk factors in the
company. The immediate cause of the accident was the Independent High- Level Switch (IHLS)
was not working properly for months. It was the site managers' and supervisor's reasonability to
get it changed and repaired the switch. But risk management of the company did not recognize it
as a potential risk factor and did not show any concern for the repair or reinstallation of the
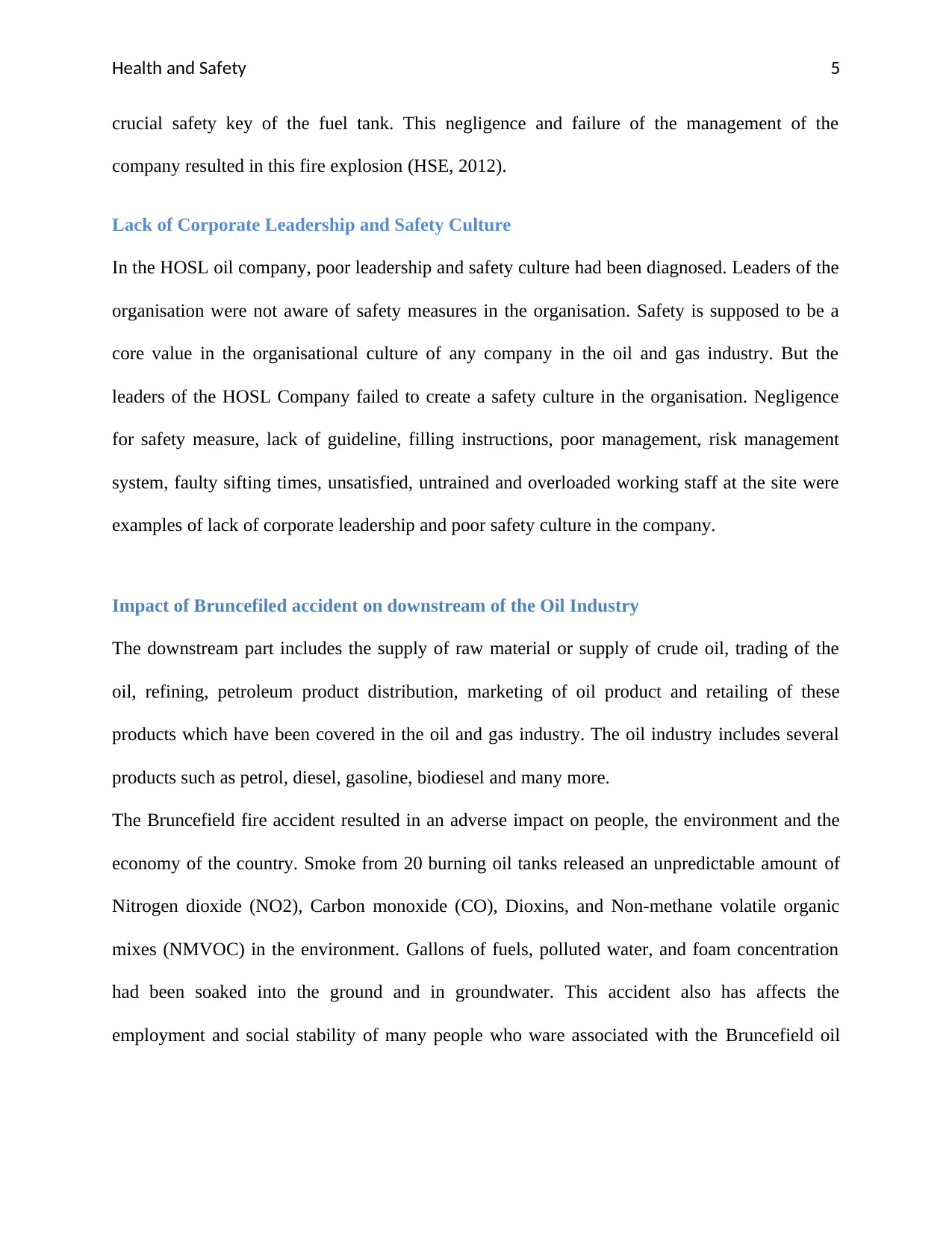
Health and Safety 5
crucial safety key of the fuel tank. This negligence and failure of the management of the
company resulted in this fire explosion (HSE, 2012).
Lack of Corporate Leadership and Safety Culture
In the HOSL oil company, poor leadership and safety culture had been diagnosed. Leaders of the
organisation were not aware of safety measures in the organisation. Safety is supposed to be a
core value in the organisational culture of any company in the oil and gas industry. But the
leaders of the HOSL Company failed to create a safety culture in the organisation. Negligence
for safety measure, lack of guideline, filling instructions, poor management, risk management
system, faulty sifting times, unsatisfied, untrained and overloaded working staff at the site were
examples of lack of corporate leadership and poor safety culture in the company.
Impact of Bruncefiled accident on downstream of the Oil Industry
The downstream part includes the supply of raw material or supply of crude oil, trading of the
oil, refining, petroleum product distribution, marketing of oil product and retailing of these
products which have been covered in the oil and gas industry. The oil industry includes several
products such as petrol, diesel, gasoline, biodiesel and many more.
The Bruncefield fire accident resulted in an adverse impact on people, the environment and the
economy of the country. Smoke from 20 burning oil tanks released an unpredictable amount of
Nitrogen dioxide (NO2), Carbon monoxide (CO), Dioxins, and Non-methane volatile organic
mixes (NMVOC) in the environment. Gallons of fuels, polluted water, and foam concentration
had been soaked into the ground and in groundwater. This accident also has affects the
employment and social stability of many people who ware associated with the Bruncefield oil
crucial safety key of the fuel tank. This negligence and failure of the management of the
company resulted in this fire explosion (HSE, 2012).
Lack of Corporate Leadership and Safety Culture
In the HOSL oil company, poor leadership and safety culture had been diagnosed. Leaders of the
organisation were not aware of safety measures in the organisation. Safety is supposed to be a
core value in the organisational culture of any company in the oil and gas industry. But the
leaders of the HOSL Company failed to create a safety culture in the organisation. Negligence
for safety measure, lack of guideline, filling instructions, poor management, risk management
system, faulty sifting times, unsatisfied, untrained and overloaded working staff at the site were
examples of lack of corporate leadership and poor safety culture in the company.
Impact of Bruncefiled accident on downstream of the Oil Industry
The downstream part includes the supply of raw material or supply of crude oil, trading of the
oil, refining, petroleum product distribution, marketing of oil product and retailing of these
products which have been covered in the oil and gas industry. The oil industry includes several
products such as petrol, diesel, gasoline, biodiesel and many more.
The Bruncefield fire accident resulted in an adverse impact on people, the environment and the
economy of the country. Smoke from 20 burning oil tanks released an unpredictable amount of
Nitrogen dioxide (NO2), Carbon monoxide (CO), Dioxins, and Non-methane volatile organic
mixes (NMVOC) in the environment. Gallons of fuels, polluted water, and foam concentration
had been soaked into the ground and in groundwater. This accident also has affects the
employment and social stability of many people who ware associated with the Bruncefield oil
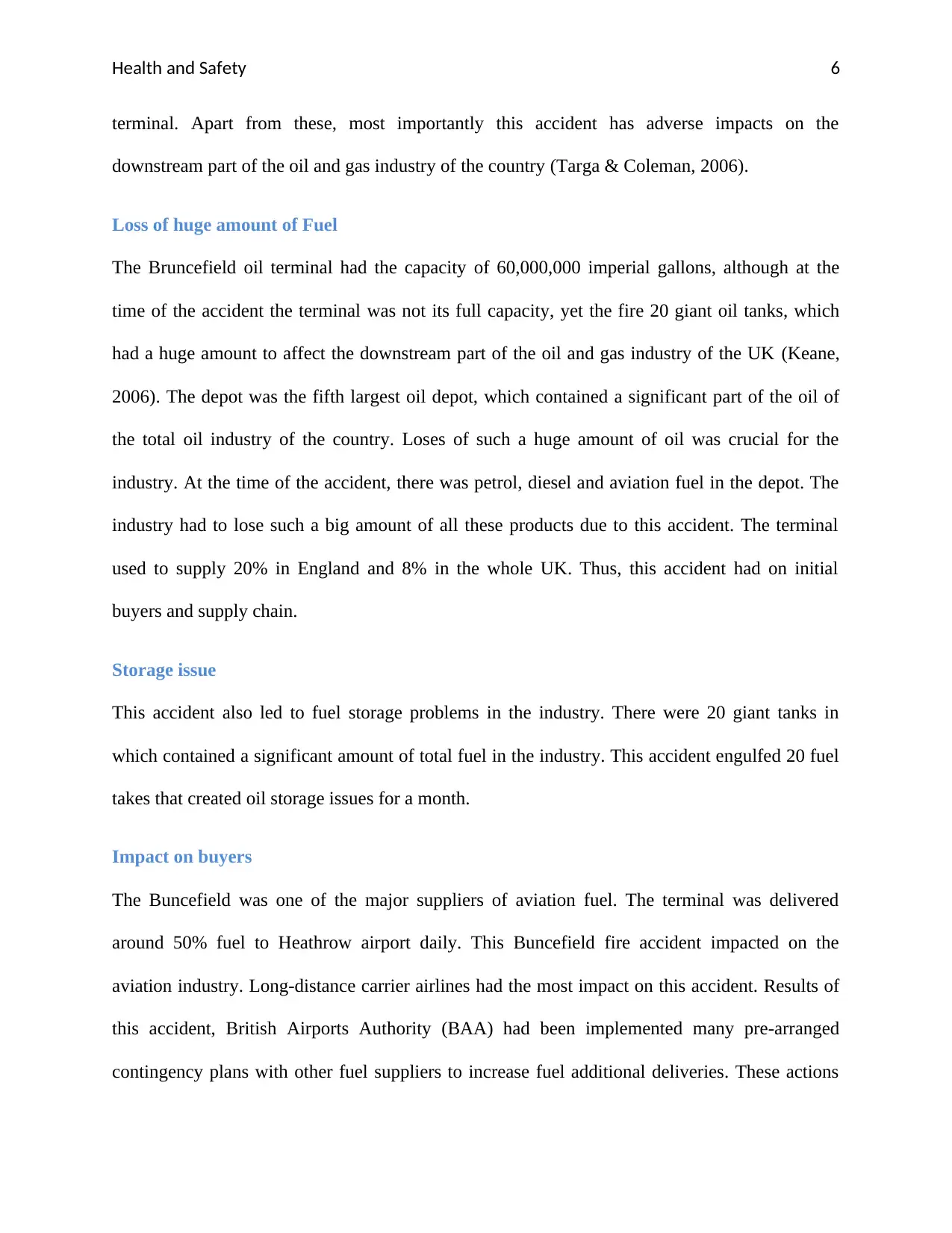
Health and Safety 6
terminal. Apart from these, most importantly this accident has adverse impacts on the
downstream part of the oil and gas industry of the country (Targa & Coleman, 2006).
Loss of huge amount of Fuel
The Bruncefield oil terminal had the capacity of 60,000,000 imperial gallons, although at the
time of the accident the terminal was not its full capacity, yet the fire 20 giant oil tanks, which
had a huge amount to affect the downstream part of the oil and gas industry of the UK (Keane,
2006). The depot was the fifth largest oil depot, which contained a significant part of the oil of
the total oil industry of the country. Loses of such a huge amount of oil was crucial for the
industry. At the time of the accident, there was petrol, diesel and aviation fuel in the depot. The
industry had to lose such a big amount of all these products due to this accident. The terminal
used to supply 20% in England and 8% in the whole UK. Thus, this accident had on initial
buyers and supply chain.
Storage issue
This accident also led to fuel storage problems in the industry. There were 20 giant tanks in
which contained a significant amount of total fuel in the industry. This accident engulfed 20 fuel
takes that created oil storage issues for a month.
Impact on buyers
The Buncefield was one of the major suppliers of aviation fuel. The terminal was delivered
around 50% fuel to Heathrow airport daily. This Buncefield fire accident impacted on the
aviation industry. Long-distance carrier airlines had the most impact on this accident. Results of
this accident, British Airports Authority (BAA) had been implemented many pre-arranged
contingency plans with other fuel suppliers to increase fuel additional deliveries. These actions
terminal. Apart from these, most importantly this accident has adverse impacts on the
downstream part of the oil and gas industry of the country (Targa & Coleman, 2006).
Loss of huge amount of Fuel
The Bruncefield oil terminal had the capacity of 60,000,000 imperial gallons, although at the
time of the accident the terminal was not its full capacity, yet the fire 20 giant oil tanks, which
had a huge amount to affect the downstream part of the oil and gas industry of the UK (Keane,
2006). The depot was the fifth largest oil depot, which contained a significant part of the oil of
the total oil industry of the country. Loses of such a huge amount of oil was crucial for the
industry. At the time of the accident, there was petrol, diesel and aviation fuel in the depot. The
industry had to lose such a big amount of all these products due to this accident. The terminal
used to supply 20% in England and 8% in the whole UK. Thus, this accident had on initial
buyers and supply chain.
Storage issue
This accident also led to fuel storage problems in the industry. There were 20 giant tanks in
which contained a significant amount of total fuel in the industry. This accident engulfed 20 fuel
takes that created oil storage issues for a month.
Impact on buyers
The Buncefield was one of the major suppliers of aviation fuel. The terminal was delivered
around 50% fuel to Heathrow airport daily. This Buncefield fire accident impacted on the
aviation industry. Long-distance carrier airlines had the most impact on this accident. Results of
this accident, British Airports Authority (BAA) had been implemented many pre-arranged
contingency plans with other fuel suppliers to increase fuel additional deliveries. These actions
Paraphrase This Document
Need a fresh take? Get an instant paraphrase of this document with our AI Paraphraser
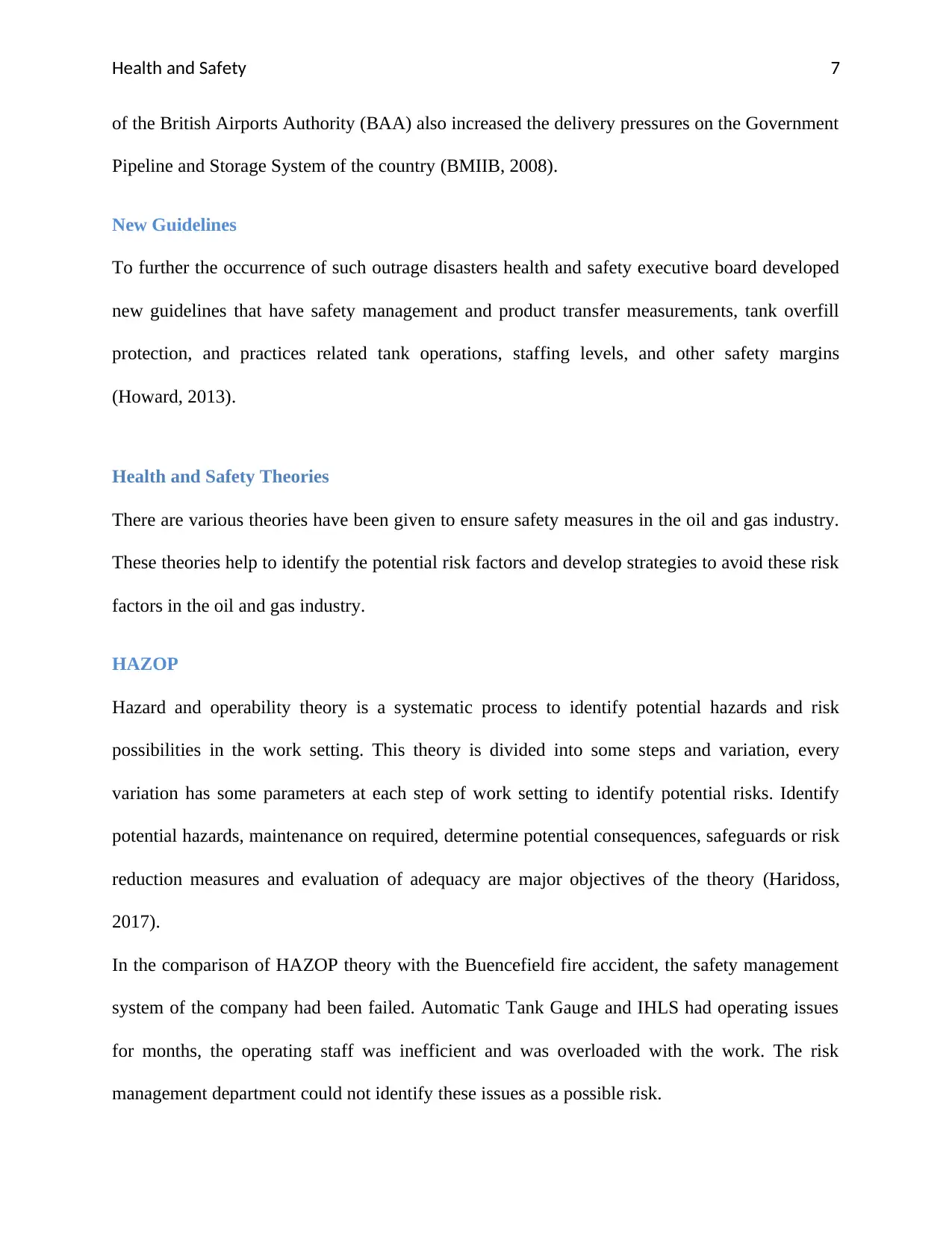
Health and Safety 7
of the British Airports Authority (BAA) also increased the delivery pressures on the Government
Pipeline and Storage System of the country (BMIIB, 2008).
New Guidelines
To further the occurrence of such outrage disasters health and safety executive board developed
new guidelines that have safety management and product transfer measurements, tank overfill
protection, and practices related tank operations, staffing levels, and other safety margins
(Howard, 2013).
Health and Safety Theories
There are various theories have been given to ensure safety measures in the oil and gas industry.
These theories help to identify the potential risk factors and develop strategies to avoid these risk
factors in the oil and gas industry.
HAZOP
Hazard and operability theory is a systematic process to identify potential hazards and risk
possibilities in the work setting. This theory is divided into some steps and variation, every
variation has some parameters at each step of work setting to identify potential risks. Identify
potential hazards, maintenance on required, determine potential consequences, safeguards or risk
reduction measures and evaluation of adequacy are major objectives of the theory (Haridoss,
2017).
In the comparison of HAZOP theory with the Buencefield fire accident, the safety management
system of the company had been failed. Automatic Tank Gauge and IHLS had operating issues
for months, the operating staff was inefficient and was overloaded with the work. The risk
management department could not identify these issues as a possible risk.
of the British Airports Authority (BAA) also increased the delivery pressures on the Government
Pipeline and Storage System of the country (BMIIB, 2008).
New Guidelines
To further the occurrence of such outrage disasters health and safety executive board developed
new guidelines that have safety management and product transfer measurements, tank overfill
protection, and practices related tank operations, staffing levels, and other safety margins
(Howard, 2013).
Health and Safety Theories
There are various theories have been given to ensure safety measures in the oil and gas industry.
These theories help to identify the potential risk factors and develop strategies to avoid these risk
factors in the oil and gas industry.
HAZOP
Hazard and operability theory is a systematic process to identify potential hazards and risk
possibilities in the work setting. This theory is divided into some steps and variation, every
variation has some parameters at each step of work setting to identify potential risks. Identify
potential hazards, maintenance on required, determine potential consequences, safeguards or risk
reduction measures and evaluation of adequacy are major objectives of the theory (Haridoss,
2017).
In the comparison of HAZOP theory with the Buencefield fire accident, the safety management
system of the company had been failed. Automatic Tank Gauge and IHLS had operating issues
for months, the operating staff was inefficient and was overloaded with the work. The risk
management department could not identify these issues as a possible risk.
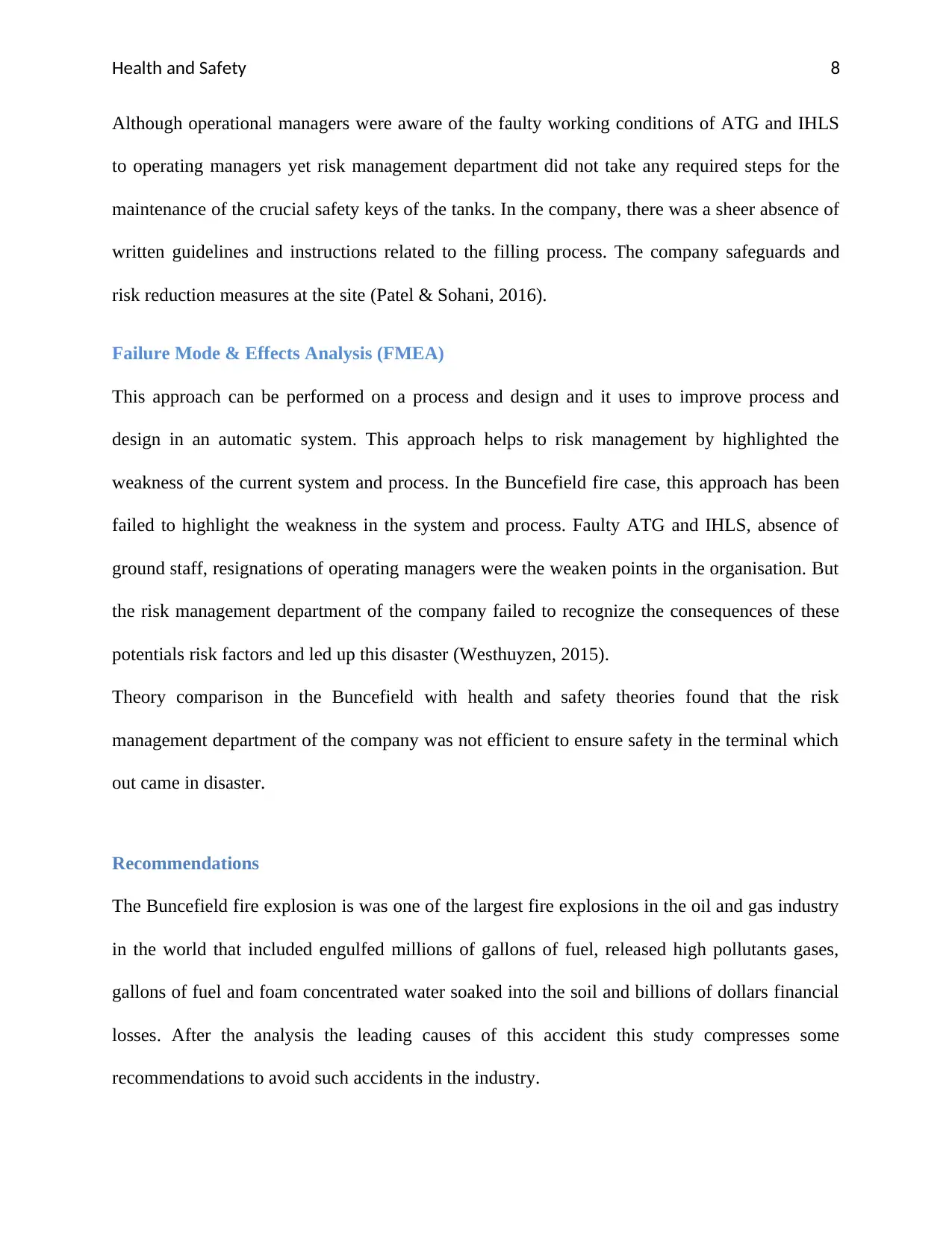
Health and Safety 8
Although operational managers were aware of the faulty working conditions of ATG and IHLS
to operating managers yet risk management department did not take any required steps for the
maintenance of the crucial safety keys of the tanks. In the company, there was a sheer absence of
written guidelines and instructions related to the filling process. The company safeguards and
risk reduction measures at the site (Patel & Sohani, 2016).
Failure Mode & Effects Analysis (FMEA)
This approach can be performed on a process and design and it uses to improve process and
design in an automatic system. This approach helps to risk management by highlighted the
weakness of the current system and process. In the Buncefield fire case, this approach has been
failed to highlight the weakness in the system and process. Faulty ATG and IHLS, absence of
ground staff, resignations of operating managers were the weaken points in the organisation. But
the risk management department of the company failed to recognize the consequences of these
potentials risk factors and led up this disaster (Westhuyzen, 2015).
Theory comparison in the Buncefield with health and safety theories found that the risk
management department of the company was not efficient to ensure safety in the terminal which
out came in disaster.
Recommendations
The Buncefield fire explosion is was one of the largest fire explosions in the oil and gas industry
in the world that included engulfed millions of gallons of fuel, released high pollutants gases,
gallons of fuel and foam concentrated water soaked into the soil and billions of dollars financial
losses. After the analysis the leading causes of this accident this study compresses some
recommendations to avoid such accidents in the industry.
Although operational managers were aware of the faulty working conditions of ATG and IHLS
to operating managers yet risk management department did not take any required steps for the
maintenance of the crucial safety keys of the tanks. In the company, there was a sheer absence of
written guidelines and instructions related to the filling process. The company safeguards and
risk reduction measures at the site (Patel & Sohani, 2016).
Failure Mode & Effects Analysis (FMEA)
This approach can be performed on a process and design and it uses to improve process and
design in an automatic system. This approach helps to risk management by highlighted the
weakness of the current system and process. In the Buncefield fire case, this approach has been
failed to highlight the weakness in the system and process. Faulty ATG and IHLS, absence of
ground staff, resignations of operating managers were the weaken points in the organisation. But
the risk management department of the company failed to recognize the consequences of these
potentials risk factors and led up this disaster (Westhuyzen, 2015).
Theory comparison in the Buncefield with health and safety theories found that the risk
management department of the company was not efficient to ensure safety in the terminal which
out came in disaster.
Recommendations
The Buncefield fire explosion is was one of the largest fire explosions in the oil and gas industry
in the world that included engulfed millions of gallons of fuel, released high pollutants gases,
gallons of fuel and foam concentrated water soaked into the soil and billions of dollars financial
losses. After the analysis the leading causes of this accident this study compresses some
recommendations to avoid such accidents in the industry.
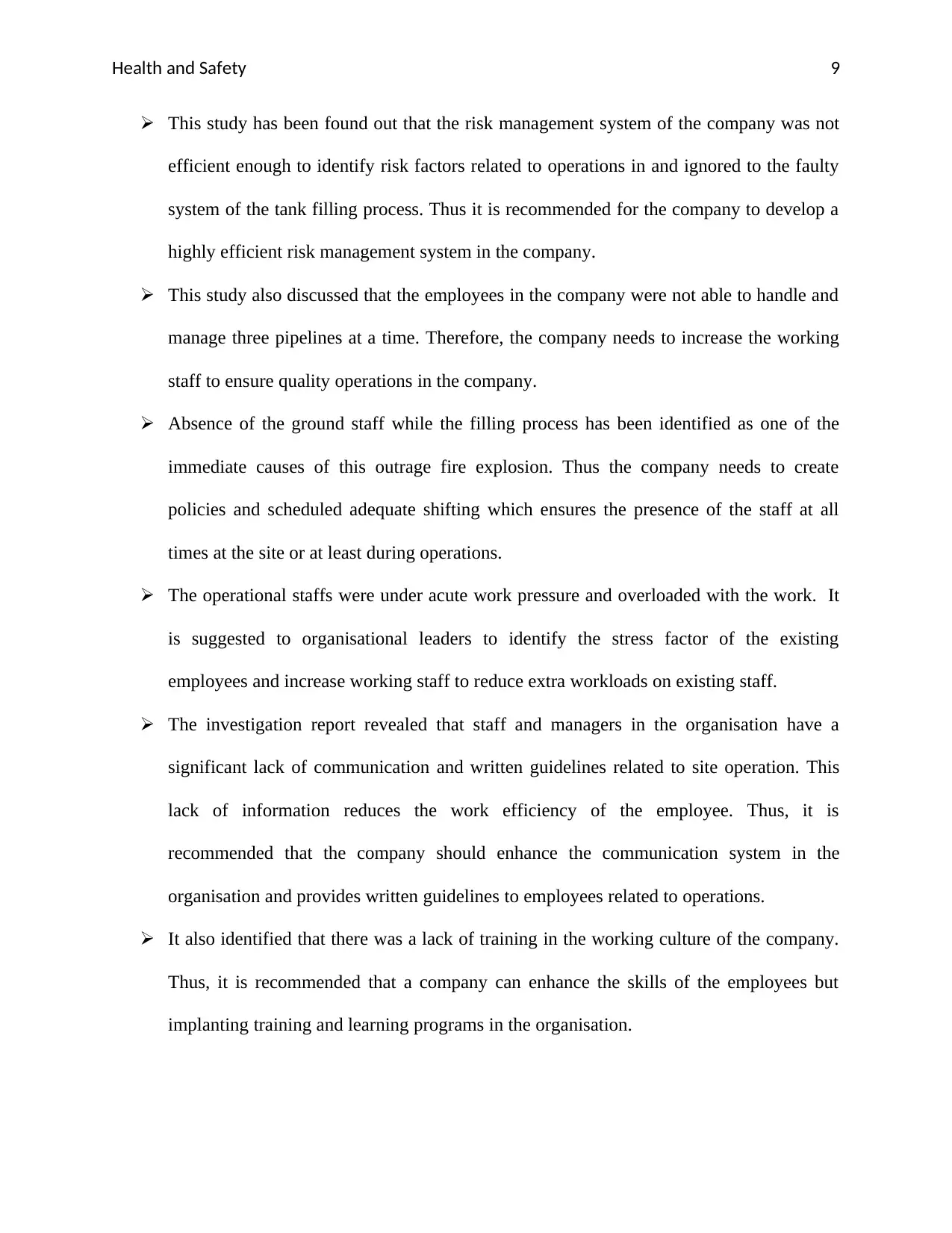
Health and Safety 9
This study has been found out that the risk management system of the company was not
efficient enough to identify risk factors related to operations in and ignored to the faulty
system of the tank filling process. Thus it is recommended for the company to develop a
highly efficient risk management system in the company.
This study also discussed that the employees in the company were not able to handle and
manage three pipelines at a time. Therefore, the company needs to increase the working
staff to ensure quality operations in the company.
Absence of the ground staff while the filling process has been identified as one of the
immediate causes of this outrage fire explosion. Thus the company needs to create
policies and scheduled adequate shifting which ensures the presence of the staff at all
times at the site or at least during operations.
The operational staffs were under acute work pressure and overloaded with the work. It
is suggested to organisational leaders to identify the stress factor of the existing
employees and increase working staff to reduce extra workloads on existing staff.
The investigation report revealed that staff and managers in the organisation have a
significant lack of communication and written guidelines related to site operation. This
lack of information reduces the work efficiency of the employee. Thus, it is
recommended that the company should enhance the communication system in the
organisation and provides written guidelines to employees related to operations.
It also identified that there was a lack of training in the working culture of the company.
Thus, it is recommended that a company can enhance the skills of the employees but
implanting training and learning programs in the organisation.
This study has been found out that the risk management system of the company was not
efficient enough to identify risk factors related to operations in and ignored to the faulty
system of the tank filling process. Thus it is recommended for the company to develop a
highly efficient risk management system in the company.
This study also discussed that the employees in the company were not able to handle and
manage three pipelines at a time. Therefore, the company needs to increase the working
staff to ensure quality operations in the company.
Absence of the ground staff while the filling process has been identified as one of the
immediate causes of this outrage fire explosion. Thus the company needs to create
policies and scheduled adequate shifting which ensures the presence of the staff at all
times at the site or at least during operations.
The operational staffs were under acute work pressure and overloaded with the work. It
is suggested to organisational leaders to identify the stress factor of the existing
employees and increase working staff to reduce extra workloads on existing staff.
The investigation report revealed that staff and managers in the organisation have a
significant lack of communication and written guidelines related to site operation. This
lack of information reduces the work efficiency of the employee. Thus, it is
recommended that the company should enhance the communication system in the
organisation and provides written guidelines to employees related to operations.
It also identified that there was a lack of training in the working culture of the company.
Thus, it is recommended that a company can enhance the skills of the employees but
implanting training and learning programs in the organisation.
Secure Best Marks with AI Grader
Need help grading? Try our AI Grader for instant feedback on your assignments.
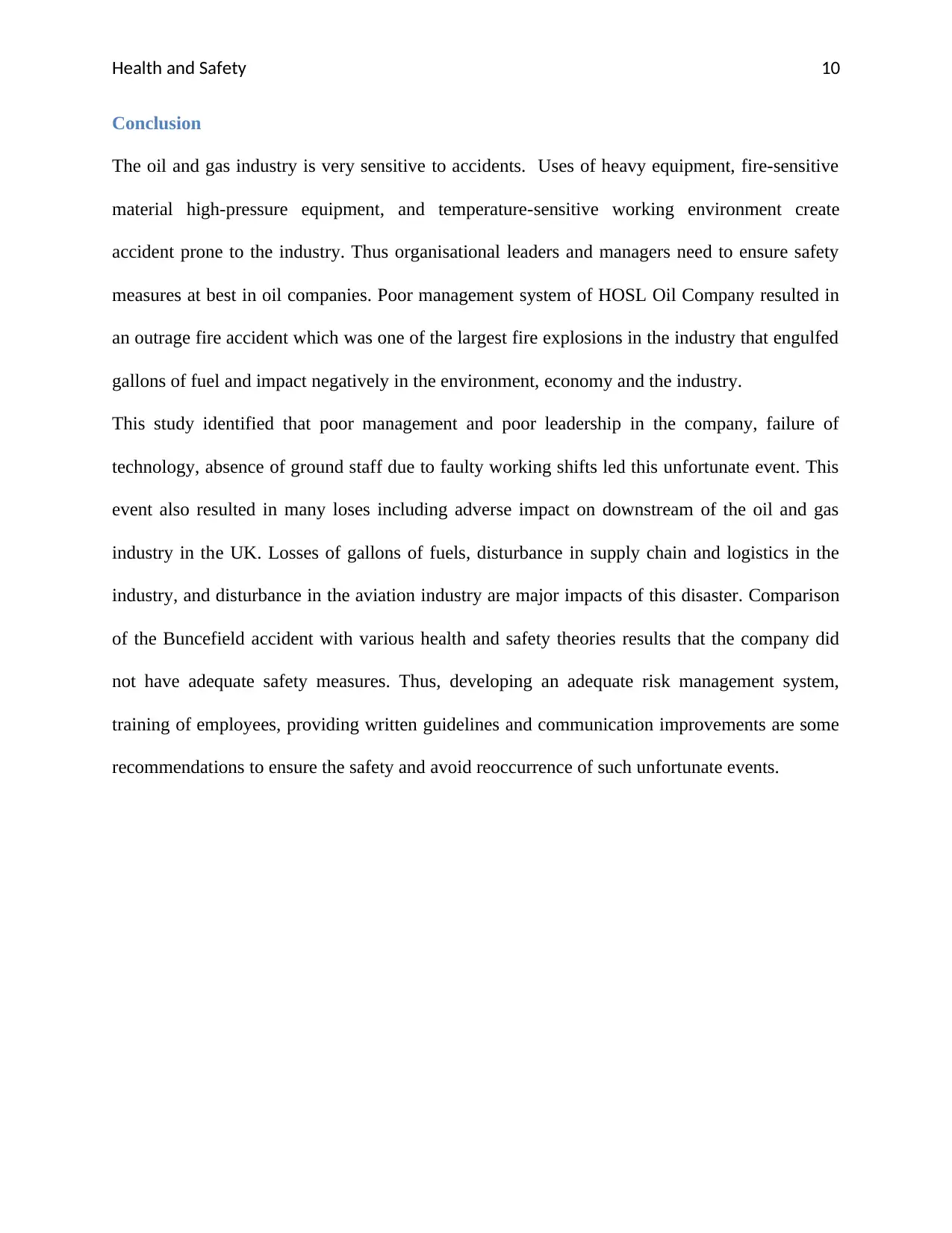
Health and Safety 10
Conclusion
The oil and gas industry is very sensitive to accidents. Uses of heavy equipment, fire-sensitive
material high-pressure equipment, and temperature-sensitive working environment create
accident prone to the industry. Thus organisational leaders and managers need to ensure safety
measures at best in oil companies. Poor management system of HOSL Oil Company resulted in
an outrage fire accident which was one of the largest fire explosions in the industry that engulfed
gallons of fuel and impact negatively in the environment, economy and the industry.
This study identified that poor management and poor leadership in the company, failure of
technology, absence of ground staff due to faulty working shifts led this unfortunate event. This
event also resulted in many loses including adverse impact on downstream of the oil and gas
industry in the UK. Losses of gallons of fuels, disturbance in supply chain and logistics in the
industry, and disturbance in the aviation industry are major impacts of this disaster. Comparison
of the Buncefield accident with various health and safety theories results that the company did
not have adequate safety measures. Thus, developing an adequate risk management system,
training of employees, providing written guidelines and communication improvements are some
recommendations to ensure the safety and avoid reoccurrence of such unfortunate events.
Conclusion
The oil and gas industry is very sensitive to accidents. Uses of heavy equipment, fire-sensitive
material high-pressure equipment, and temperature-sensitive working environment create
accident prone to the industry. Thus organisational leaders and managers need to ensure safety
measures at best in oil companies. Poor management system of HOSL Oil Company resulted in
an outrage fire accident which was one of the largest fire explosions in the industry that engulfed
gallons of fuel and impact negatively in the environment, economy and the industry.
This study identified that poor management and poor leadership in the company, failure of
technology, absence of ground staff due to faulty working shifts led this unfortunate event. This
event also resulted in many loses including adverse impact on downstream of the oil and gas
industry in the UK. Losses of gallons of fuels, disturbance in supply chain and logistics in the
industry, and disturbance in the aviation industry are major impacts of this disaster. Comparison
of the Buncefield accident with various health and safety theories results that the company did
not have adequate safety measures. Thus, developing an adequate risk management system,
training of employees, providing written guidelines and communication improvements are some
recommendations to ensure the safety and avoid reoccurrence of such unfortunate events.
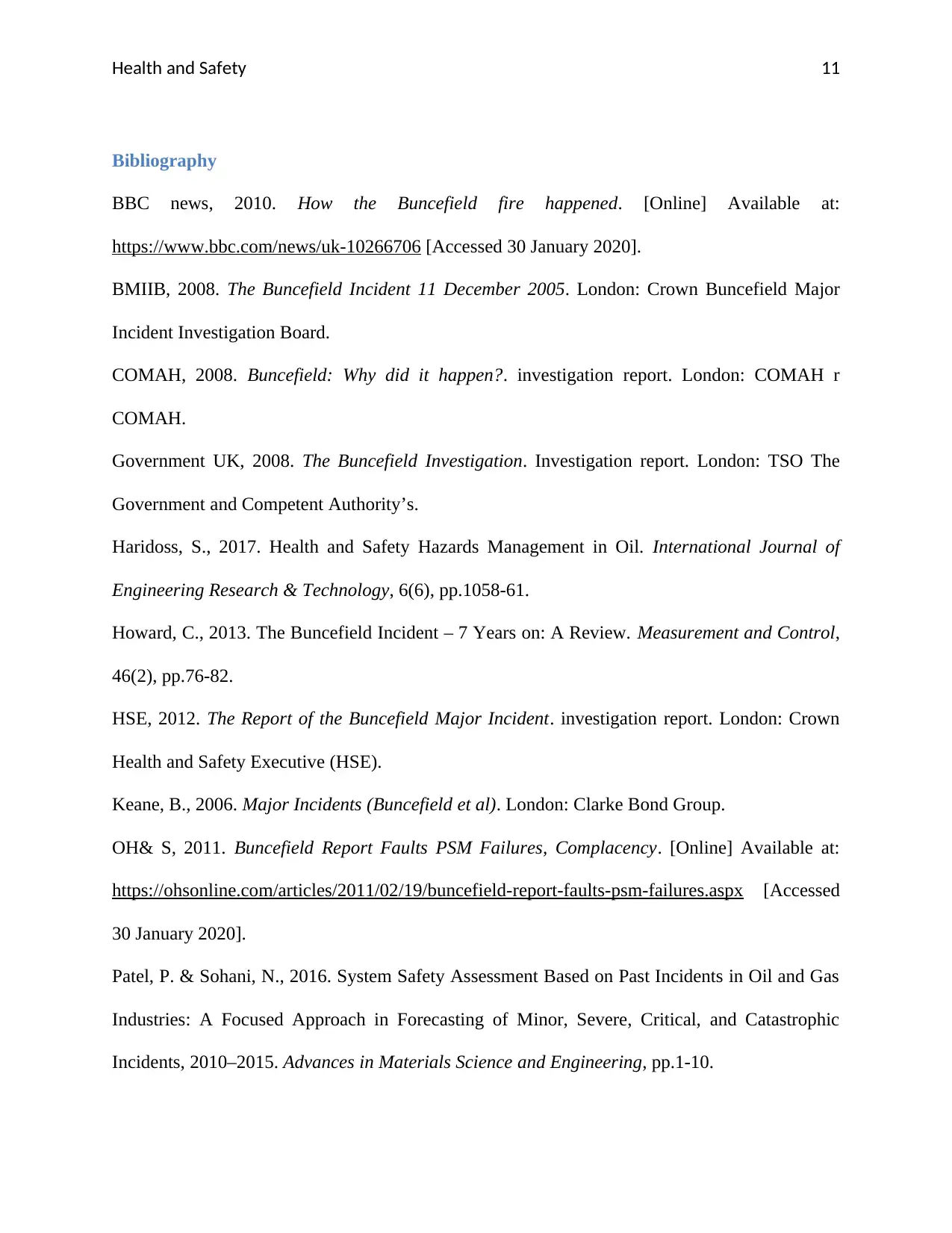
Health and Safety 11
Bibliography
BBC news, 2010. How the Buncefield fire happened. [Online] Available at:
https://www.bbc.com/news/uk-10266706 [Accessed 30 January 2020].
BMIIB, 2008. The Buncefield Incident 11 December 2005. London: Crown Buncefield Major
Incident Investigation Board.
COMAH, 2008. Buncefield: Why did it happen?. investigation report. London: COMAH r
COMAH.
Government UK, 2008. The Buncefield Investigation. Investigation report. London: TSO The
Government and Competent Authority’s.
Haridoss, S., 2017. Health and Safety Hazards Management in Oil. International Journal of
Engineering Research & Technology, 6(6), pp.1058-61.
Howard, C., 2013. The Buncefield Incident – 7 Years on: A Review. Measurement and Control,
46(2), pp.76-82.
HSE, 2012. The Report of the Buncefield Major Incident. investigation report. London: Crown
Health and Safety Executive (HSE).
Keane, B., 2006. Major Incidents (Buncefield et al). London: Clarke Bond Group.
OH& S, 2011. Buncefield Report Faults PSM Failures, Complacency. [Online] Available at:
https://ohsonline.com/articles/2011/02/19/buncefield-report-faults-psm-failures.aspx [Accessed
30 January 2020].
Patel, P. & Sohani, N., 2016. System Safety Assessment Based on Past Incidents in Oil and Gas
Industries: A Focused Approach in Forecasting of Minor, Severe, Critical, and Catastrophic
Incidents, 2010–2015. Advances in Materials Science and Engineering, pp.1-10.
Bibliography
BBC news, 2010. How the Buncefield fire happened. [Online] Available at:
https://www.bbc.com/news/uk-10266706 [Accessed 30 January 2020].
BMIIB, 2008. The Buncefield Incident 11 December 2005. London: Crown Buncefield Major
Incident Investigation Board.
COMAH, 2008. Buncefield: Why did it happen?. investigation report. London: COMAH r
COMAH.
Government UK, 2008. The Buncefield Investigation. Investigation report. London: TSO The
Government and Competent Authority’s.
Haridoss, S., 2017. Health and Safety Hazards Management in Oil. International Journal of
Engineering Research & Technology, 6(6), pp.1058-61.
Howard, C., 2013. The Buncefield Incident – 7 Years on: A Review. Measurement and Control,
46(2), pp.76-82.
HSE, 2012. The Report of the Buncefield Major Incident. investigation report. London: Crown
Health and Safety Executive (HSE).
Keane, B., 2006. Major Incidents (Buncefield et al). London: Clarke Bond Group.
OH& S, 2011. Buncefield Report Faults PSM Failures, Complacency. [Online] Available at:
https://ohsonline.com/articles/2011/02/19/buncefield-report-faults-psm-failures.aspx [Accessed
30 January 2020].
Patel, P. & Sohani, N., 2016. System Safety Assessment Based on Past Incidents in Oil and Gas
Industries: A Focused Approach in Forecasting of Minor, Severe, Critical, and Catastrophic
Incidents, 2010–2015. Advances in Materials Science and Engineering, pp.1-10.
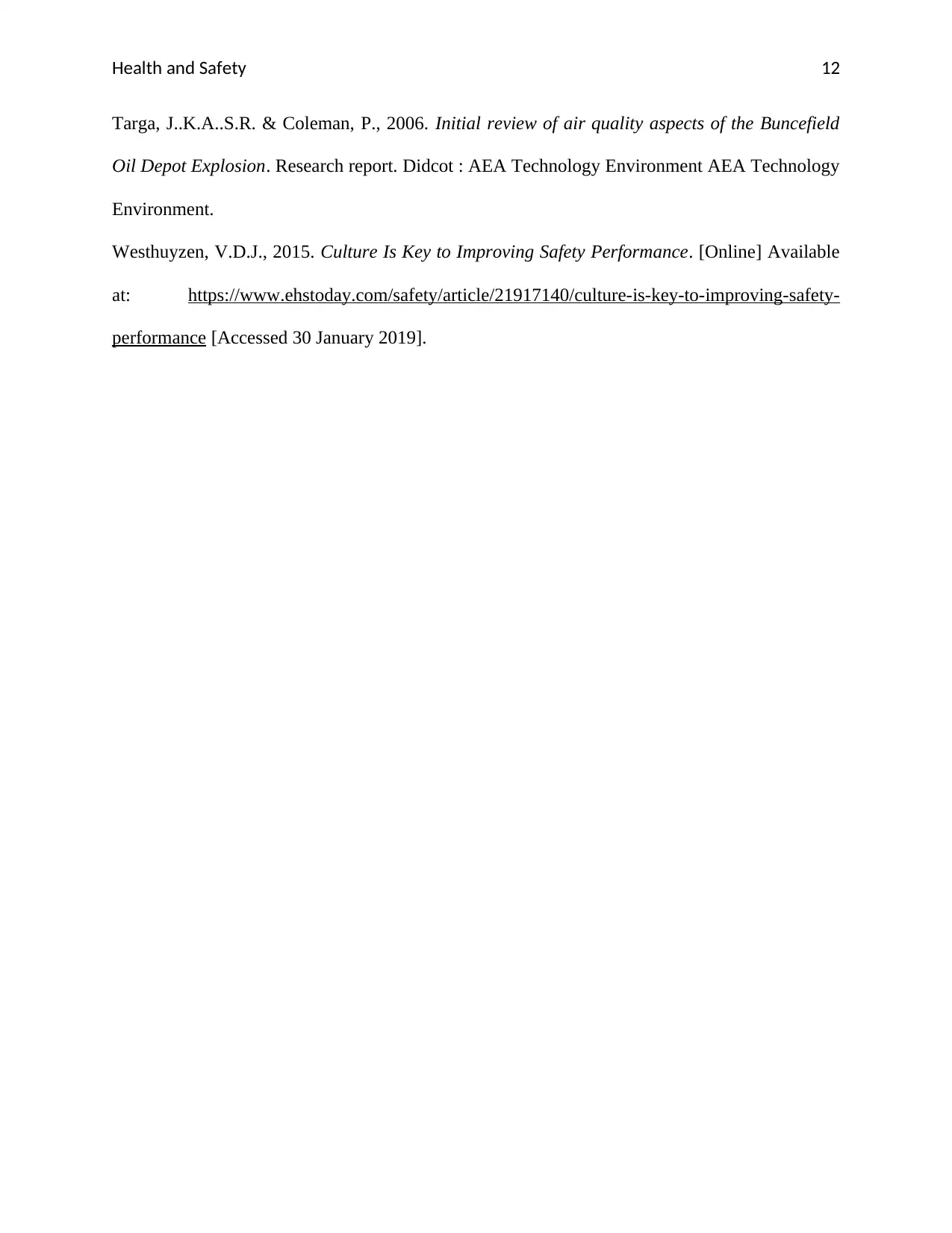
Health and Safety 12
Targa, J..K.A..S.R. & Coleman, P., 2006. Initial review of air quality aspects of the Buncefield
Oil Depot Explosion. Research report. Didcot : AEA Technology Environment AEA Technology
Environment.
Westhuyzen, V.D.J., 2015. Culture Is Key to Improving Safety Performance. [Online] Available
at: https://www.ehstoday.com/safety/article/21917140/culture-is-key-to-improving-safety-
performance [Accessed 30 January 2019].
Targa, J..K.A..S.R. & Coleman, P., 2006. Initial review of air quality aspects of the Buncefield
Oil Depot Explosion. Research report. Didcot : AEA Technology Environment AEA Technology
Environment.
Westhuyzen, V.D.J., 2015. Culture Is Key to Improving Safety Performance. [Online] Available
at: https://www.ehstoday.com/safety/article/21917140/culture-is-key-to-improving-safety-
performance [Accessed 30 January 2019].
1 out of 13
Related Documents

Your All-in-One AI-Powered Toolkit for Academic Success.
+13062052269
info@desklib.com
Available 24*7 on WhatsApp / Email
Unlock your academic potential
© 2024 | Zucol Services PVT LTD | All rights reserved.