Managing Business Activities: Nissan Motor UK Limited Analysis
VerifiedAdded on 2024/05/17
|27
|4276
|187
Report
AI Summary
This report evaluates the management of business activities within Nissan Motor Manufacturing UK Limited, focusing on the interrelationship between different processes and functions. It justifies the methodology for mapping processes to organizational goals and assesses the outputs and quality gateways within the operations department. The report designs operational plans using Management by Objectives (MBO), sets SMART objectives, and discusses implementing systems like Gantt charts to achieve these objectives efficiently. It also explores quality management systems like Total Quality Management and ISO 9000, and recommends improvements across organizational functions. Finally, the report addresses health and safety regulations, risk assessments, and policy reviews to ensure workplace compliance and safety within Nissan.
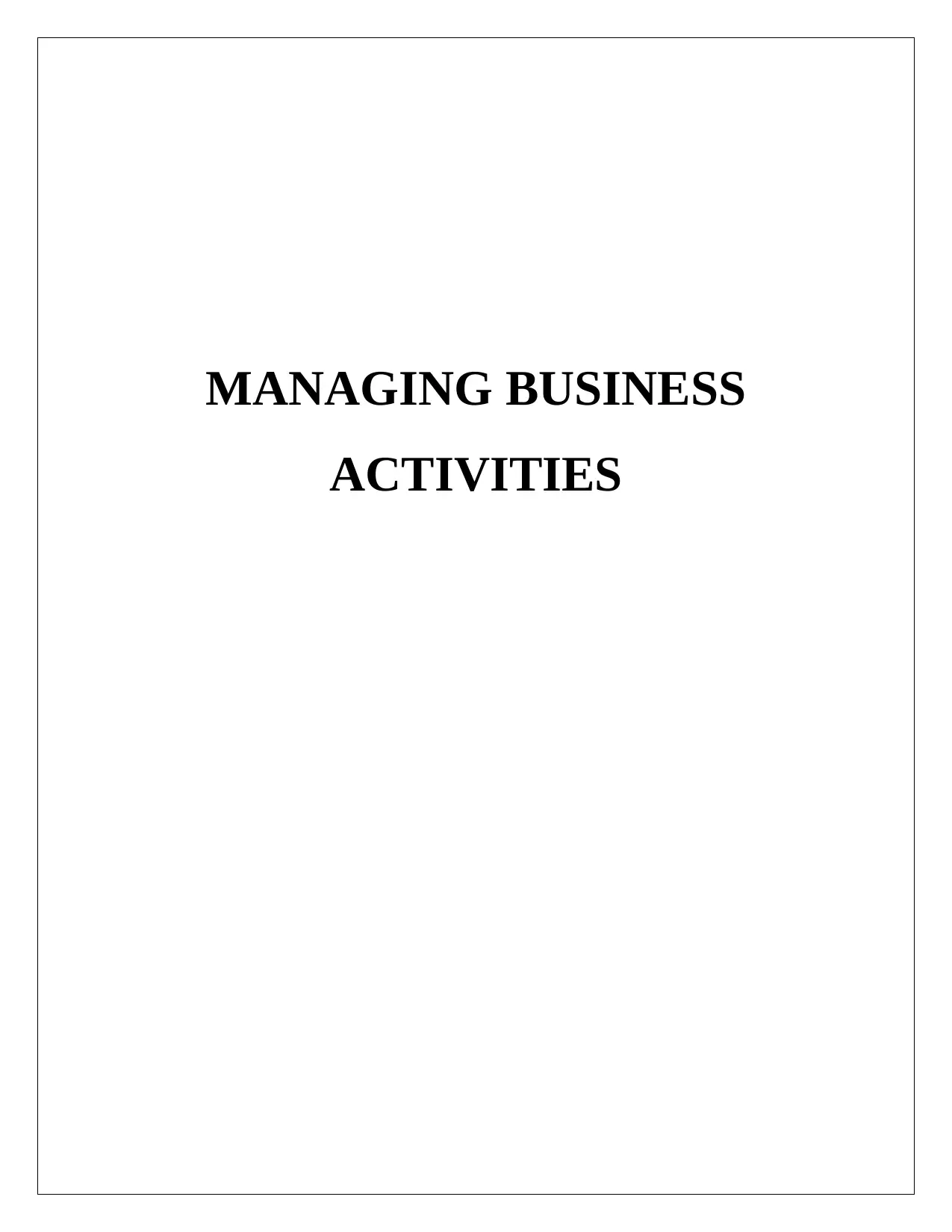
MANAGING BUSINESS
ACTIVITIES
ACTIVITIES
Secure Best Marks with AI Grader
Need help grading? Try our AI Grader for instant feedback on your assignments.
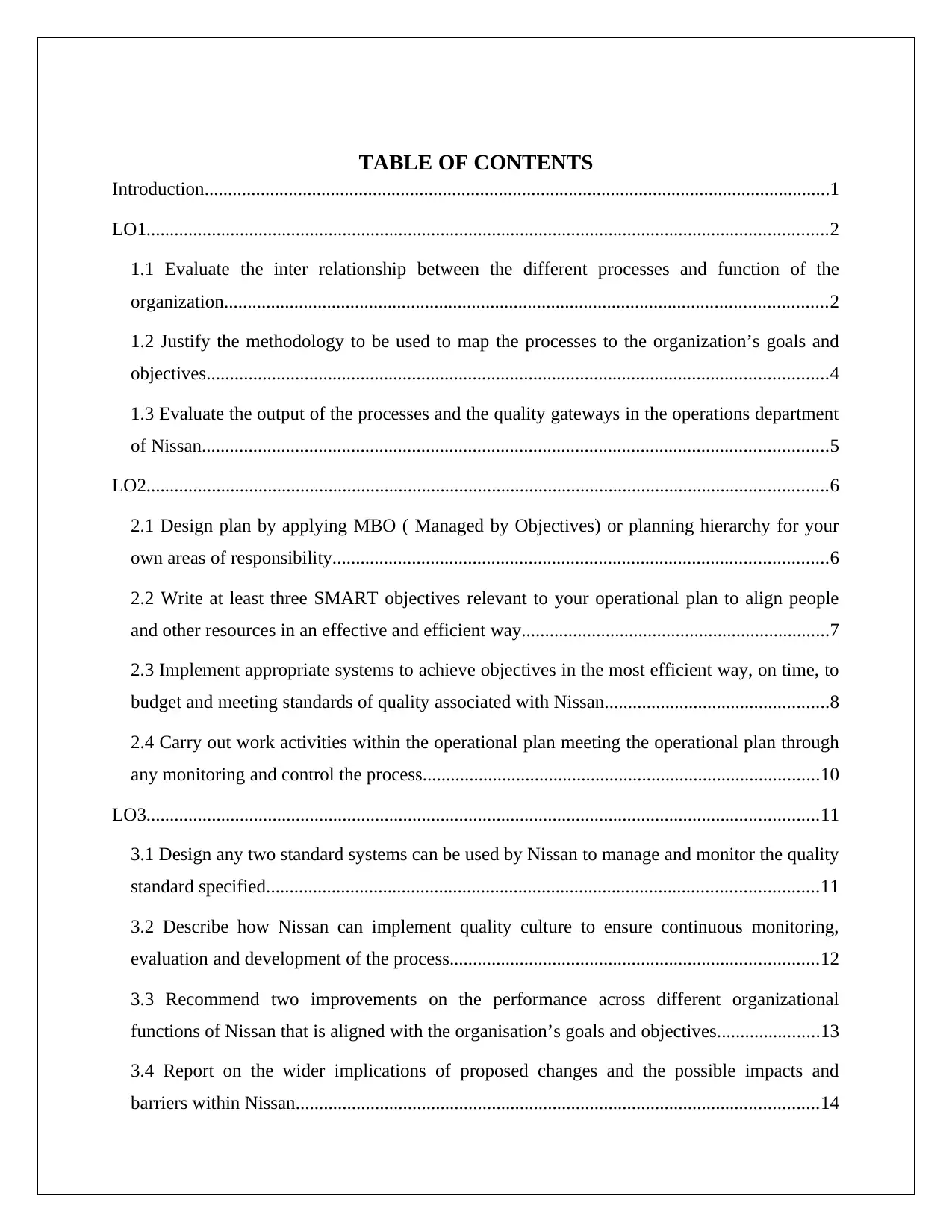
TABLE OF CONTENTS
Introduction......................................................................................................................................1
LO1..................................................................................................................................................2
1.1 Evaluate the inter relationship between the different processes and function of the
organization.................................................................................................................................2
1.2 Justify the methodology to be used to map the processes to the organization’s goals and
objectives.....................................................................................................................................4
1.3 Evaluate the output of the processes and the quality gateways in the operations department
of Nissan......................................................................................................................................5
LO2..................................................................................................................................................6
2.1 Design plan by applying MBO ( Managed by Objectives) or planning hierarchy for your
own areas of responsibility..........................................................................................................6
2.2 Write at least three SMART objectives relevant to your operational plan to align people
and other resources in an effective and efficient way..................................................................7
2.3 Implement appropriate systems to achieve objectives in the most efficient way, on time, to
budget and meeting standards of quality associated with Nissan................................................8
2.4 Carry out work activities within the operational plan meeting the operational plan through
any monitoring and control the process.....................................................................................10
LO3................................................................................................................................................11
3.1 Design any two standard systems can be used by Nissan to manage and monitor the quality
standard specified......................................................................................................................11
3.2 Describe how Nissan can implement quality culture to ensure continuous monitoring,
evaluation and development of the process...............................................................................12
3.3 Recommend two improvements on the performance across different organizational
functions of Nissan that is aligned with the organisation’s goals and objectives......................13
3.4 Report on the wider implications of proposed changes and the possible impacts and
barriers within Nissan................................................................................................................14
Introduction......................................................................................................................................1
LO1..................................................................................................................................................2
1.1 Evaluate the inter relationship between the different processes and function of the
organization.................................................................................................................................2
1.2 Justify the methodology to be used to map the processes to the organization’s goals and
objectives.....................................................................................................................................4
1.3 Evaluate the output of the processes and the quality gateways in the operations department
of Nissan......................................................................................................................................5
LO2..................................................................................................................................................6
2.1 Design plan by applying MBO ( Managed by Objectives) or planning hierarchy for your
own areas of responsibility..........................................................................................................6
2.2 Write at least three SMART objectives relevant to your operational plan to align people
and other resources in an effective and efficient way..................................................................7
2.3 Implement appropriate systems to achieve objectives in the most efficient way, on time, to
budget and meeting standards of quality associated with Nissan................................................8
2.4 Carry out work activities within the operational plan meeting the operational plan through
any monitoring and control the process.....................................................................................10
LO3................................................................................................................................................11
3.1 Design any two standard systems can be used by Nissan to manage and monitor the quality
standard specified......................................................................................................................11
3.2 Describe how Nissan can implement quality culture to ensure continuous monitoring,
evaluation and development of the process...............................................................................12
3.3 Recommend two improvements on the performance across different organizational
functions of Nissan that is aligned with the organisation’s goals and objectives......................13
3.4 Report on the wider implications of proposed changes and the possible impacts and
barriers within Nissan................................................................................................................14
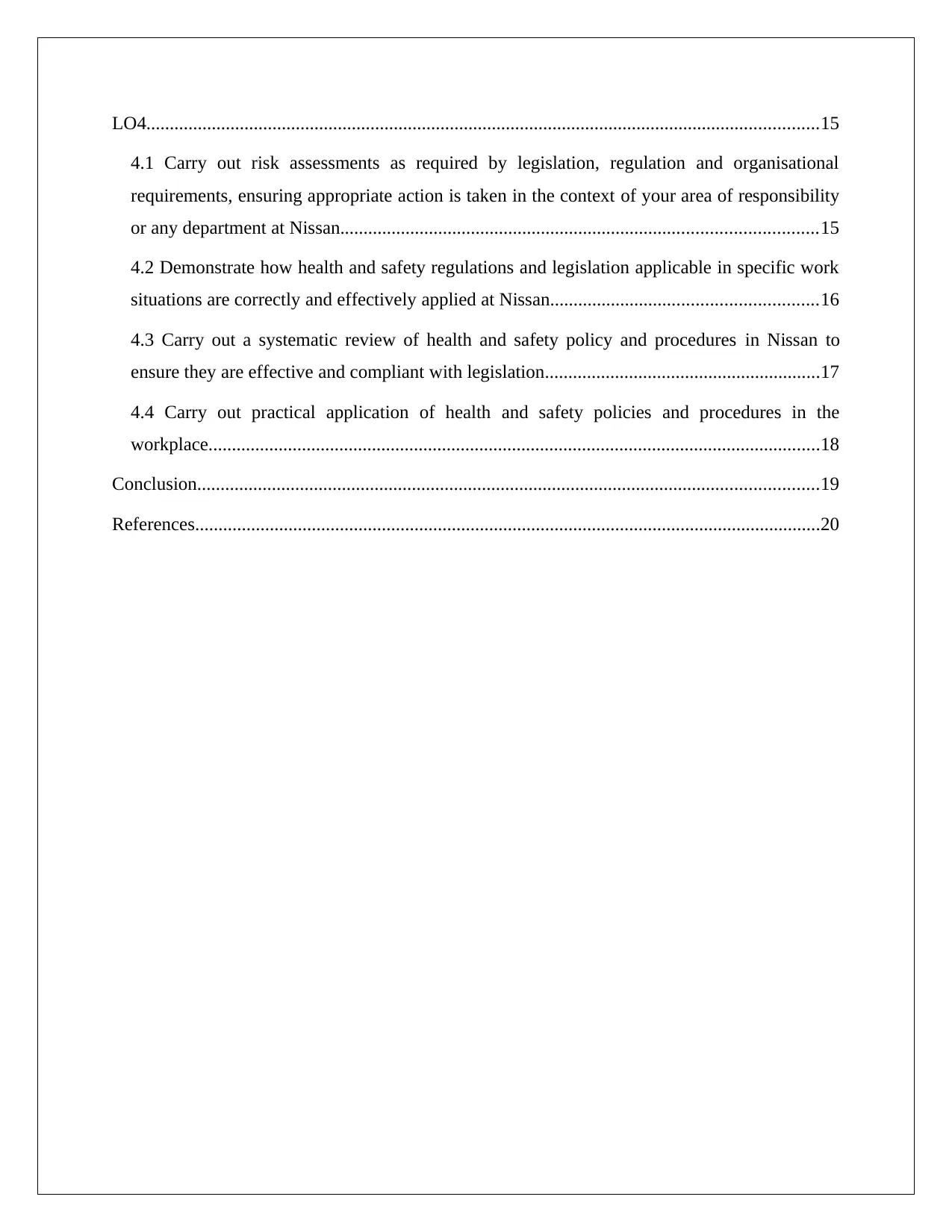
LO4................................................................................................................................................15
4.1 Carry out risk assessments as required by legislation, regulation and organisational
requirements, ensuring appropriate action is taken in the context of your area of responsibility
or any department at Nissan......................................................................................................15
4.2 Demonstrate how health and safety regulations and legislation applicable in specific work
situations are correctly and effectively applied at Nissan.........................................................16
4.3 Carry out a systematic review of health and safety policy and procedures in Nissan to
ensure they are effective and compliant with legislation...........................................................17
4.4 Carry out practical application of health and safety policies and procedures in the
workplace...................................................................................................................................18
Conclusion.....................................................................................................................................19
References......................................................................................................................................20
4.1 Carry out risk assessments as required by legislation, regulation and organisational
requirements, ensuring appropriate action is taken in the context of your area of responsibility
or any department at Nissan......................................................................................................15
4.2 Demonstrate how health and safety regulations and legislation applicable in specific work
situations are correctly and effectively applied at Nissan.........................................................16
4.3 Carry out a systematic review of health and safety policy and procedures in Nissan to
ensure they are effective and compliant with legislation...........................................................17
4.4 Carry out practical application of health and safety policies and procedures in the
workplace...................................................................................................................................18
Conclusion.....................................................................................................................................19
References......................................................................................................................................20
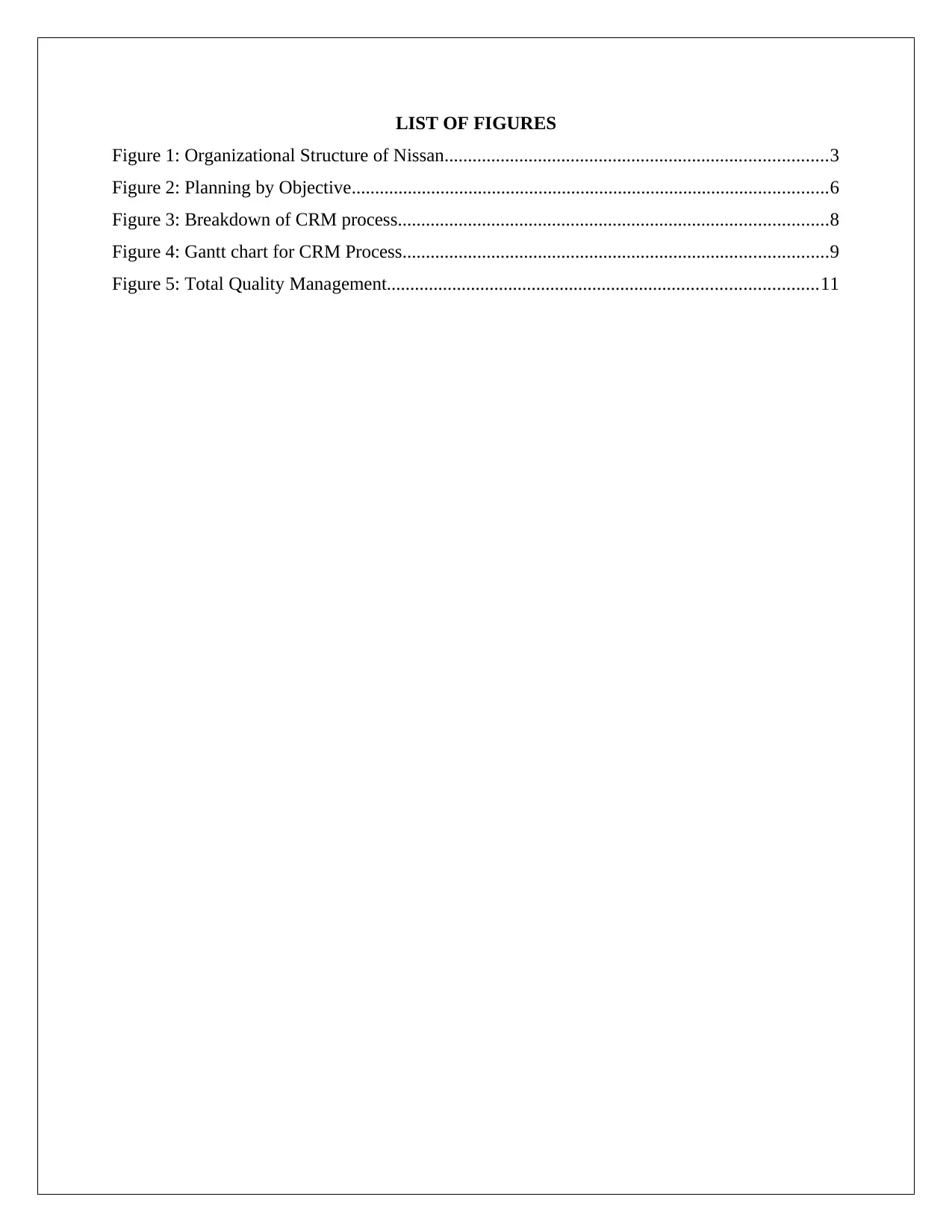
LIST OF FIGURES
Figure 1: Organizational Structure of Nissan..................................................................................3
Figure 2: Planning by Objective......................................................................................................6
Figure 3: Breakdown of CRM process............................................................................................8
Figure 4: Gantt chart for CRM Process...........................................................................................9
Figure 5: Total Quality Management............................................................................................11
Figure 1: Organizational Structure of Nissan..................................................................................3
Figure 2: Planning by Objective......................................................................................................6
Figure 3: Breakdown of CRM process............................................................................................8
Figure 4: Gantt chart for CRM Process...........................................................................................9
Figure 5: Total Quality Management............................................................................................11
Secure Best Marks with AI Grader
Need help grading? Try our AI Grader for instant feedback on your assignments.
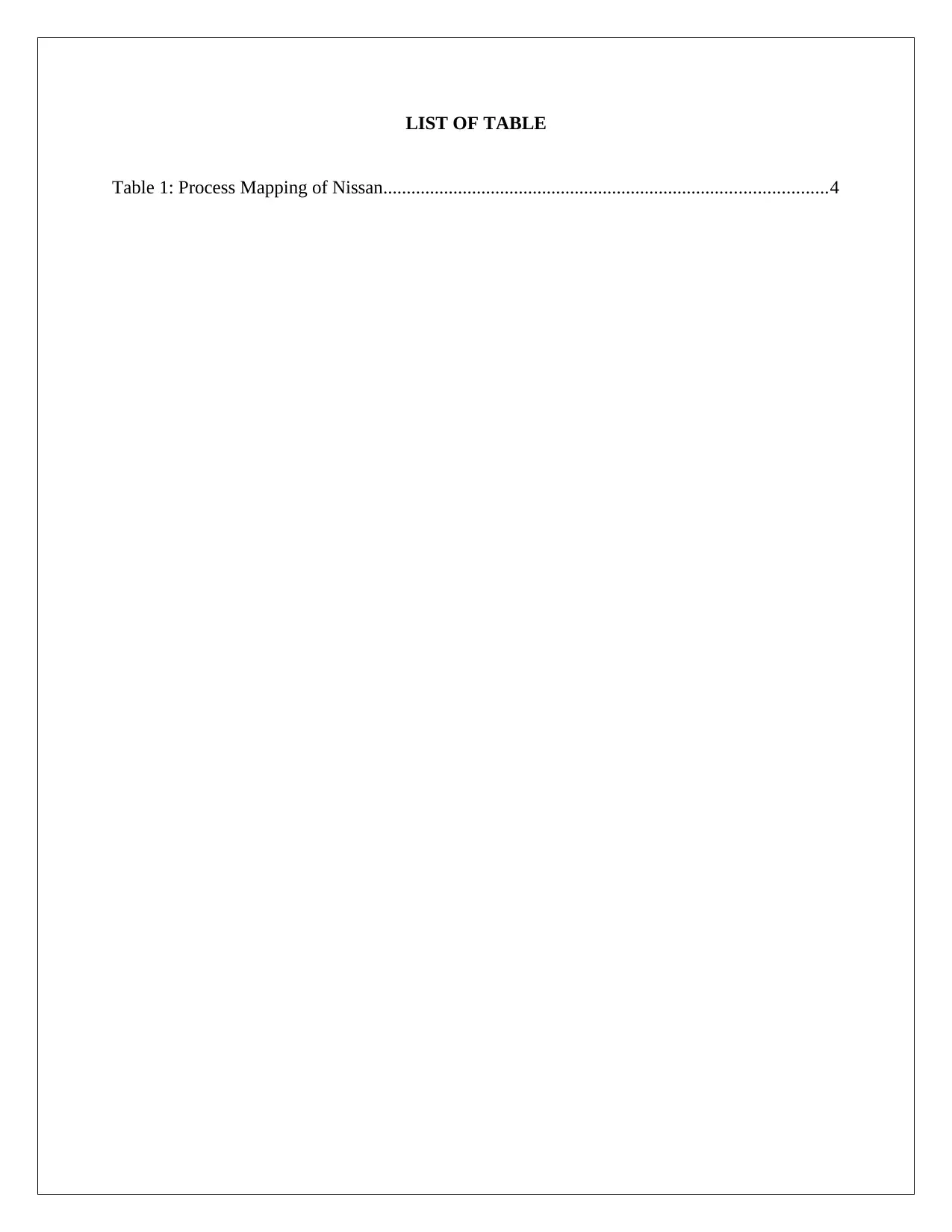
LIST OF TABLE
Table 1: Process Mapping of Nissan...............................................................................................4
Table 1: Process Mapping of Nissan...............................................................................................4
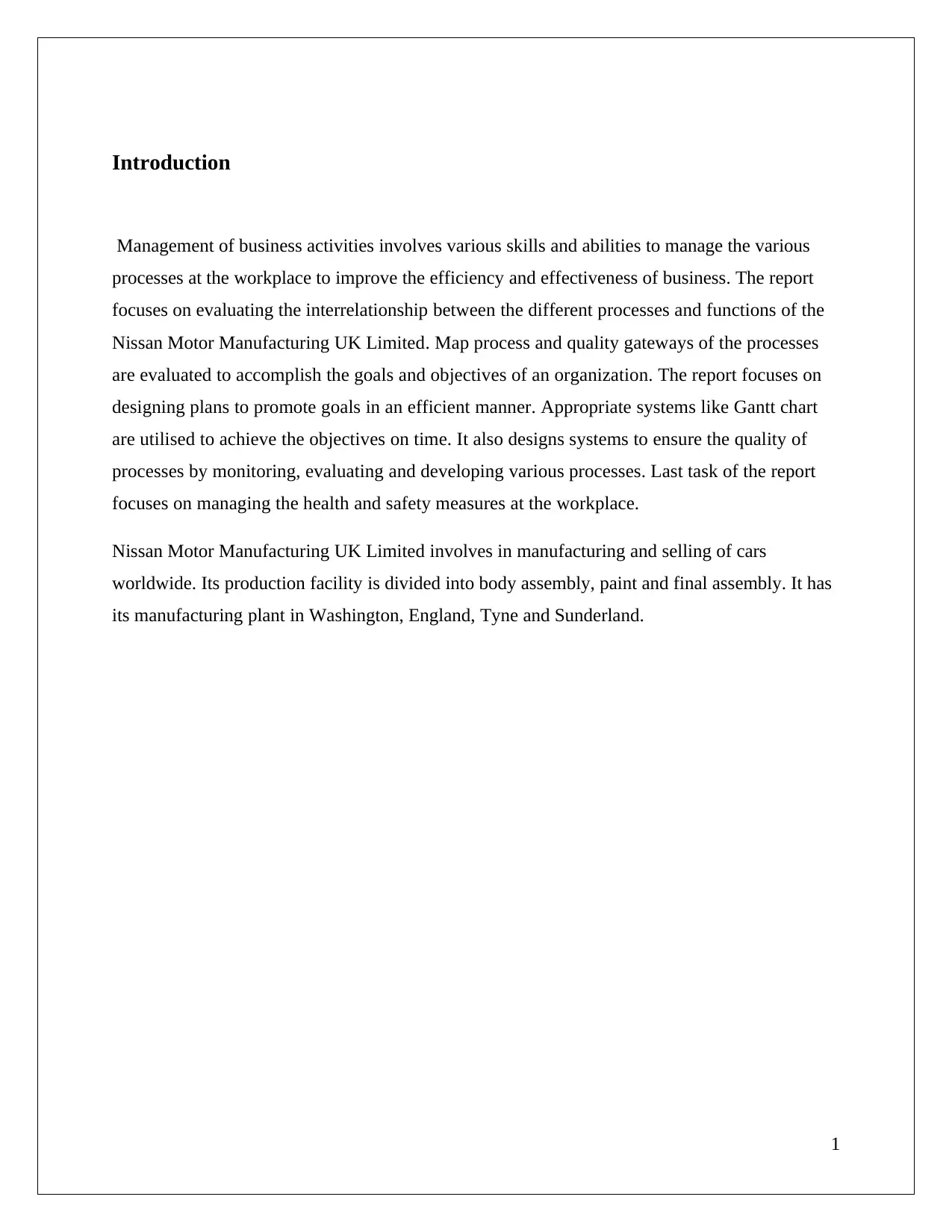
Introduction
Management of business activities involves various skills and abilities to manage the various
processes at the workplace to improve the efficiency and effectiveness of business. The report
focuses on evaluating the interrelationship between the different processes and functions of the
Nissan Motor Manufacturing UK Limited. Map process and quality gateways of the processes
are evaluated to accomplish the goals and objectives of an organization. The report focuses on
designing plans to promote goals in an efficient manner. Appropriate systems like Gantt chart
are utilised to achieve the objectives on time. It also designs systems to ensure the quality of
processes by monitoring, evaluating and developing various processes. Last task of the report
focuses on managing the health and safety measures at the workplace.
Nissan Motor Manufacturing UK Limited involves in manufacturing and selling of cars
worldwide. Its production facility is divided into body assembly, paint and final assembly. It has
its manufacturing plant in Washington, England, Tyne and Sunderland.
1
Management of business activities involves various skills and abilities to manage the various
processes at the workplace to improve the efficiency and effectiveness of business. The report
focuses on evaluating the interrelationship between the different processes and functions of the
Nissan Motor Manufacturing UK Limited. Map process and quality gateways of the processes
are evaluated to accomplish the goals and objectives of an organization. The report focuses on
designing plans to promote goals in an efficient manner. Appropriate systems like Gantt chart
are utilised to achieve the objectives on time. It also designs systems to ensure the quality of
processes by monitoring, evaluating and developing various processes. Last task of the report
focuses on managing the health and safety measures at the workplace.
Nissan Motor Manufacturing UK Limited involves in manufacturing and selling of cars
worldwide. Its production facility is divided into body assembly, paint and final assembly. It has
its manufacturing plant in Washington, England, Tyne and Sunderland.
1
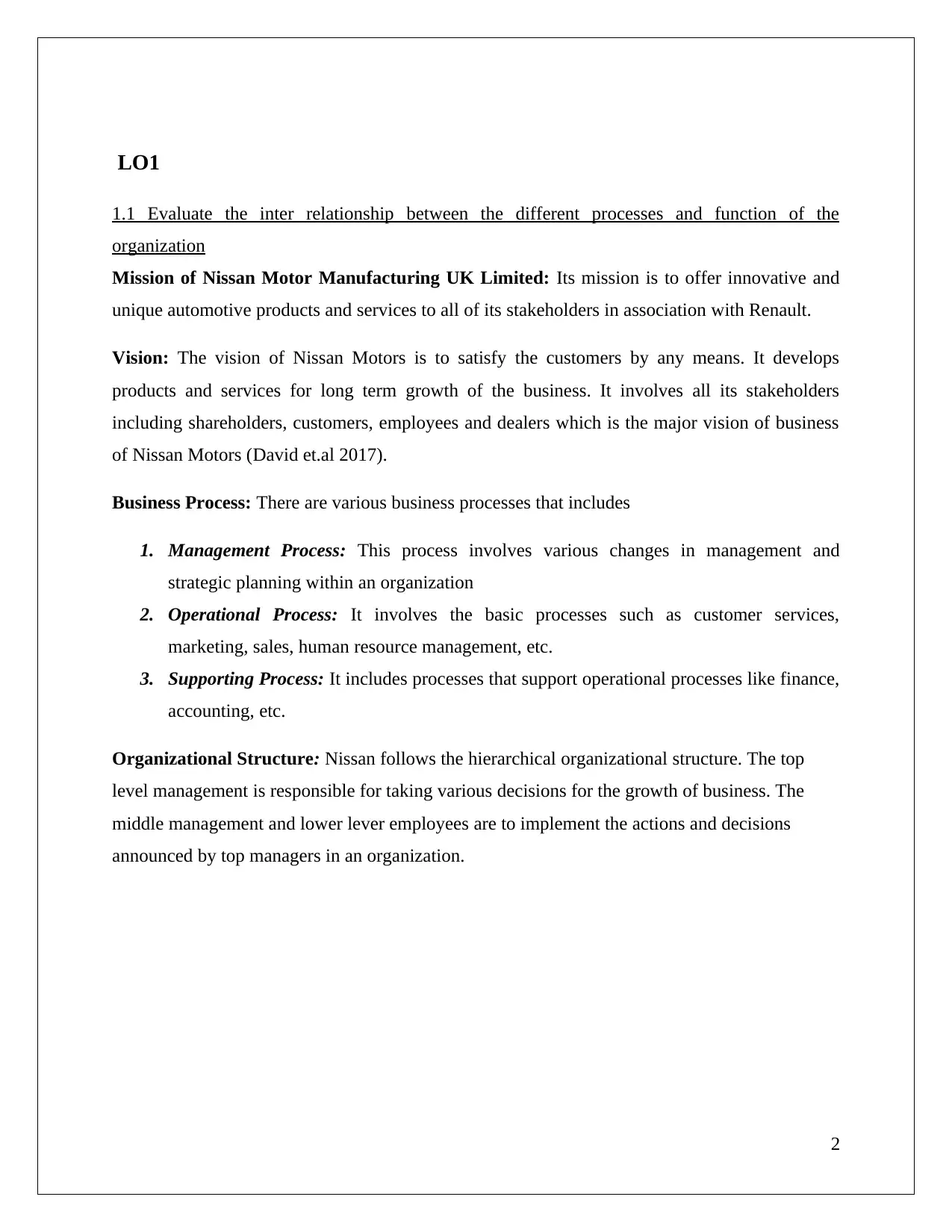
LO1
1.1 Evaluate the inter relationship between the different processes and function of the
organization
Mission of Nissan Motor Manufacturing UK Limited: Its mission is to offer innovative and
unique automotive products and services to all of its stakeholders in association with Renault.
Vision: The vision of Nissan Motors is to satisfy the customers by any means. It develops
products and services for long term growth of the business. It involves all its stakeholders
including shareholders, customers, employees and dealers which is the major vision of business
of Nissan Motors (David et.al 2017).
Business Process: There are various business processes that includes
1. Management Process: This process involves various changes in management and
strategic planning within an organization
2. Operational Process: It involves the basic processes such as customer services,
marketing, sales, human resource management, etc.
3. Supporting Process: It includes processes that support operational processes like finance,
accounting, etc.
Organizational Structure: Nissan follows the hierarchical organizational structure. The top
level management is responsible for taking various decisions for the growth of business. The
middle management and lower lever employees are to implement the actions and decisions
announced by top managers in an organization.
2
1.1 Evaluate the inter relationship between the different processes and function of the
organization
Mission of Nissan Motor Manufacturing UK Limited: Its mission is to offer innovative and
unique automotive products and services to all of its stakeholders in association with Renault.
Vision: The vision of Nissan Motors is to satisfy the customers by any means. It develops
products and services for long term growth of the business. It involves all its stakeholders
including shareholders, customers, employees and dealers which is the major vision of business
of Nissan Motors (David et.al 2017).
Business Process: There are various business processes that includes
1. Management Process: This process involves various changes in management and
strategic planning within an organization
2. Operational Process: It involves the basic processes such as customer services,
marketing, sales, human resource management, etc.
3. Supporting Process: It includes processes that support operational processes like finance,
accounting, etc.
Organizational Structure: Nissan follows the hierarchical organizational structure. The top
level management is responsible for taking various decisions for the growth of business. The
middle management and lower lever employees are to implement the actions and decisions
announced by top managers in an organization.
2
Paraphrase This Document
Need a fresh take? Get an instant paraphrase of this document with our AI Paraphraser
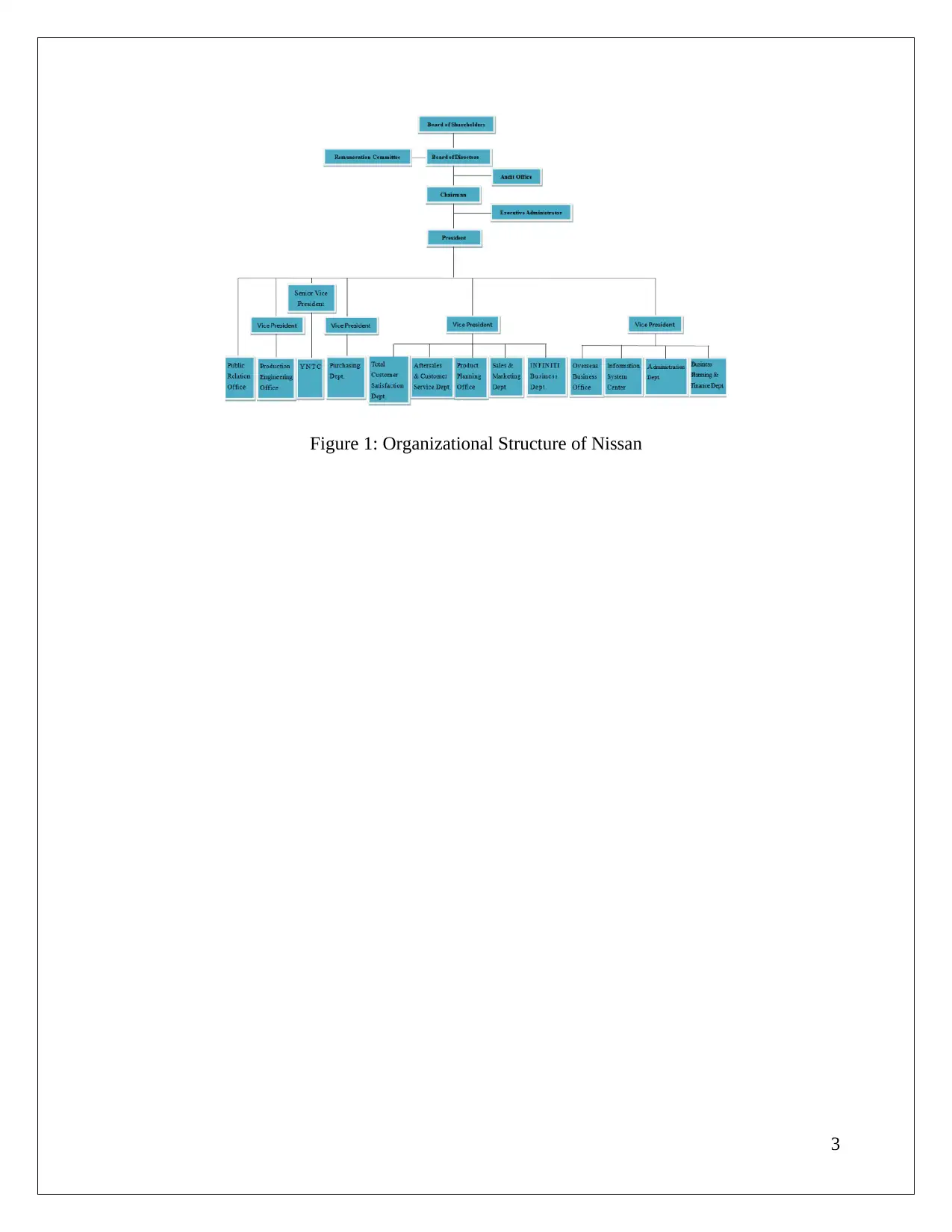
Figure 1: Organizational Structure of Nissan
3
3
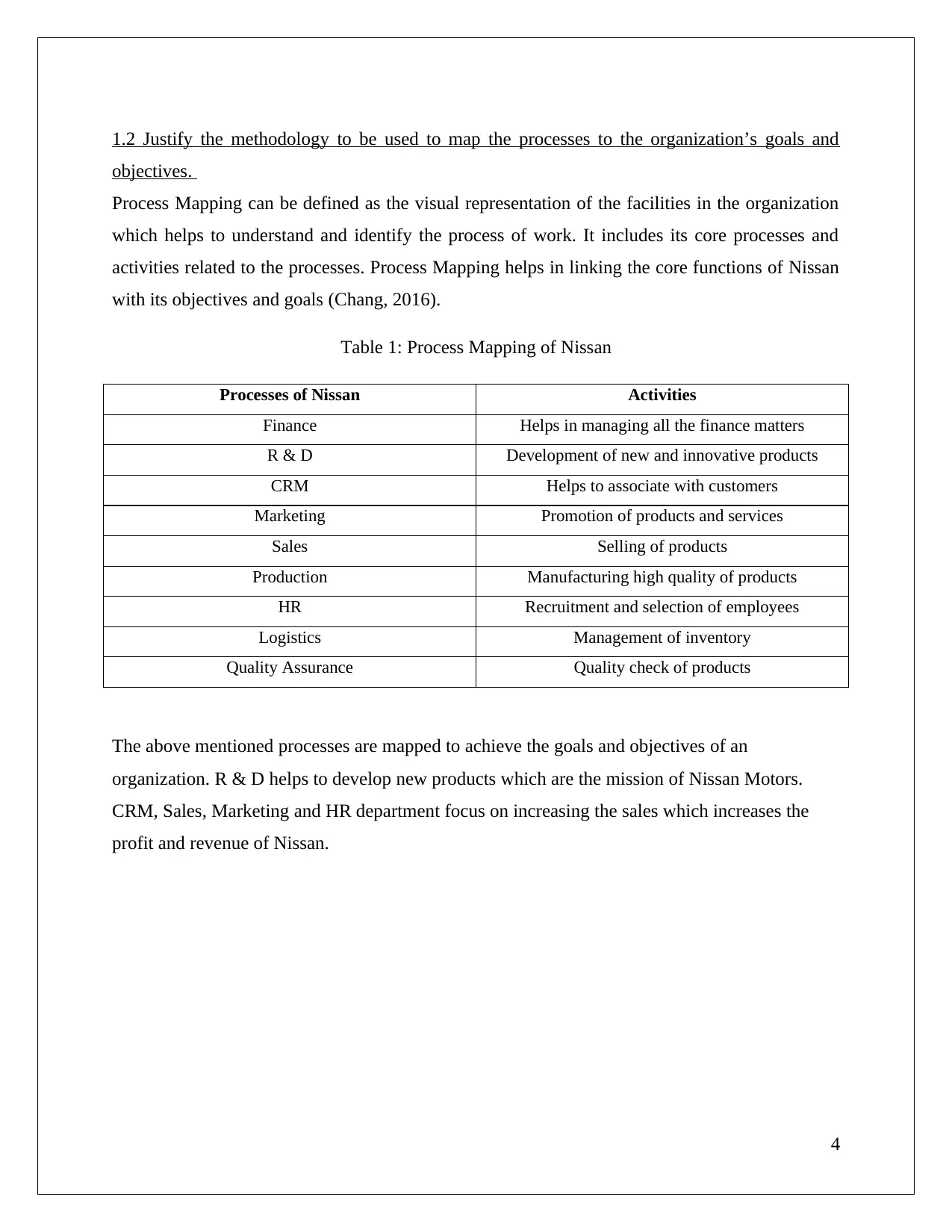
1.2 Justify the methodology to be used to map the processes to the organization’s goals and
objectives.
Process Mapping can be defined as the visual representation of the facilities in the organization
which helps to understand and identify the process of work. It includes its core processes and
activities related to the processes. Process Mapping helps in linking the core functions of Nissan
with its objectives and goals (Chang, 2016).
Table 1: Process Mapping of Nissan
Processes of Nissan Activities
Finance Helps in managing all the finance matters
R & D Development of new and innovative products
CRM Helps to associate with customers
Marketing Promotion of products and services
Sales Selling of products
Production Manufacturing high quality of products
HR Recruitment and selection of employees
Logistics Management of inventory
Quality Assurance Quality check of products
The above mentioned processes are mapped to achieve the goals and objectives of an
organization. R & D helps to develop new products which are the mission of Nissan Motors.
CRM, Sales, Marketing and HR department focus on increasing the sales which increases the
profit and revenue of Nissan.
4
objectives.
Process Mapping can be defined as the visual representation of the facilities in the organization
which helps to understand and identify the process of work. It includes its core processes and
activities related to the processes. Process Mapping helps in linking the core functions of Nissan
with its objectives and goals (Chang, 2016).
Table 1: Process Mapping of Nissan
Processes of Nissan Activities
Finance Helps in managing all the finance matters
R & D Development of new and innovative products
CRM Helps to associate with customers
Marketing Promotion of products and services
Sales Selling of products
Production Manufacturing high quality of products
HR Recruitment and selection of employees
Logistics Management of inventory
Quality Assurance Quality check of products
The above mentioned processes are mapped to achieve the goals and objectives of an
organization. R & D helps to develop new products which are the mission of Nissan Motors.
CRM, Sales, Marketing and HR department focus on increasing the sales which increases the
profit and revenue of Nissan.
4
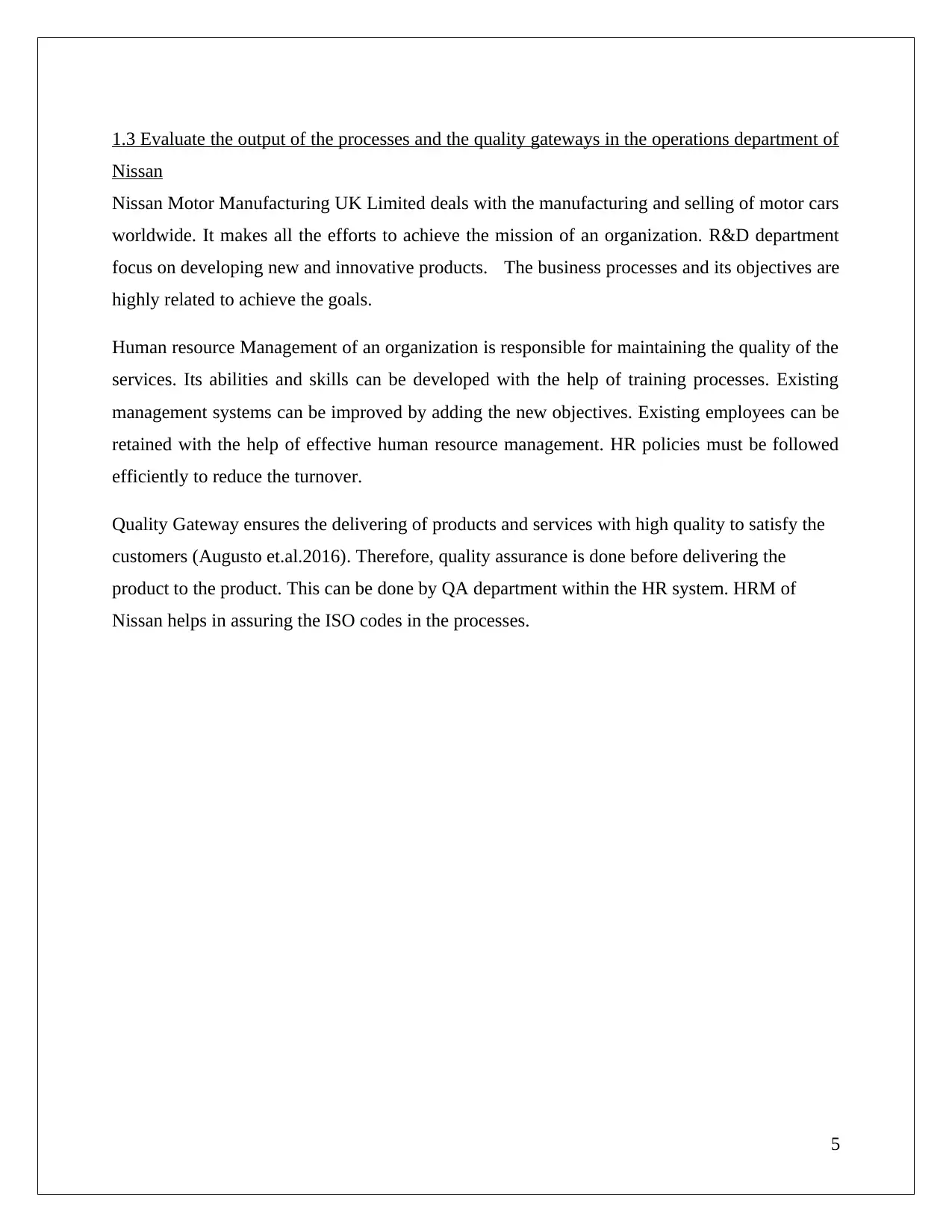
1.3 Evaluate the output of the processes and the quality gateways in the operations department of
Nissan
Nissan Motor Manufacturing UK Limited deals with the manufacturing and selling of motor cars
worldwide. It makes all the efforts to achieve the mission of an organization. R&D department
focus on developing new and innovative products. The business processes and its objectives are
highly related to achieve the goals.
Human resource Management of an organization is responsible for maintaining the quality of the
services. Its abilities and skills can be developed with the help of training processes. Existing
management systems can be improved by adding the new objectives. Existing employees can be
retained with the help of effective human resource management. HR policies must be followed
efficiently to reduce the turnover.
Quality Gateway ensures the delivering of products and services with high quality to satisfy the
customers (Augusto et.al.2016). Therefore, quality assurance is done before delivering the
product to the product. This can be done by QA department within the HR system. HRM of
Nissan helps in assuring the ISO codes in the processes.
5
Nissan
Nissan Motor Manufacturing UK Limited deals with the manufacturing and selling of motor cars
worldwide. It makes all the efforts to achieve the mission of an organization. R&D department
focus on developing new and innovative products. The business processes and its objectives are
highly related to achieve the goals.
Human resource Management of an organization is responsible for maintaining the quality of the
services. Its abilities and skills can be developed with the help of training processes. Existing
management systems can be improved by adding the new objectives. Existing employees can be
retained with the help of effective human resource management. HR policies must be followed
efficiently to reduce the turnover.
Quality Gateway ensures the delivering of products and services with high quality to satisfy the
customers (Augusto et.al.2016). Therefore, quality assurance is done before delivering the
product to the product. This can be done by QA department within the HR system. HRM of
Nissan helps in assuring the ISO codes in the processes.
5
Secure Best Marks with AI Grader
Need help grading? Try our AI Grader for instant feedback on your assignments.
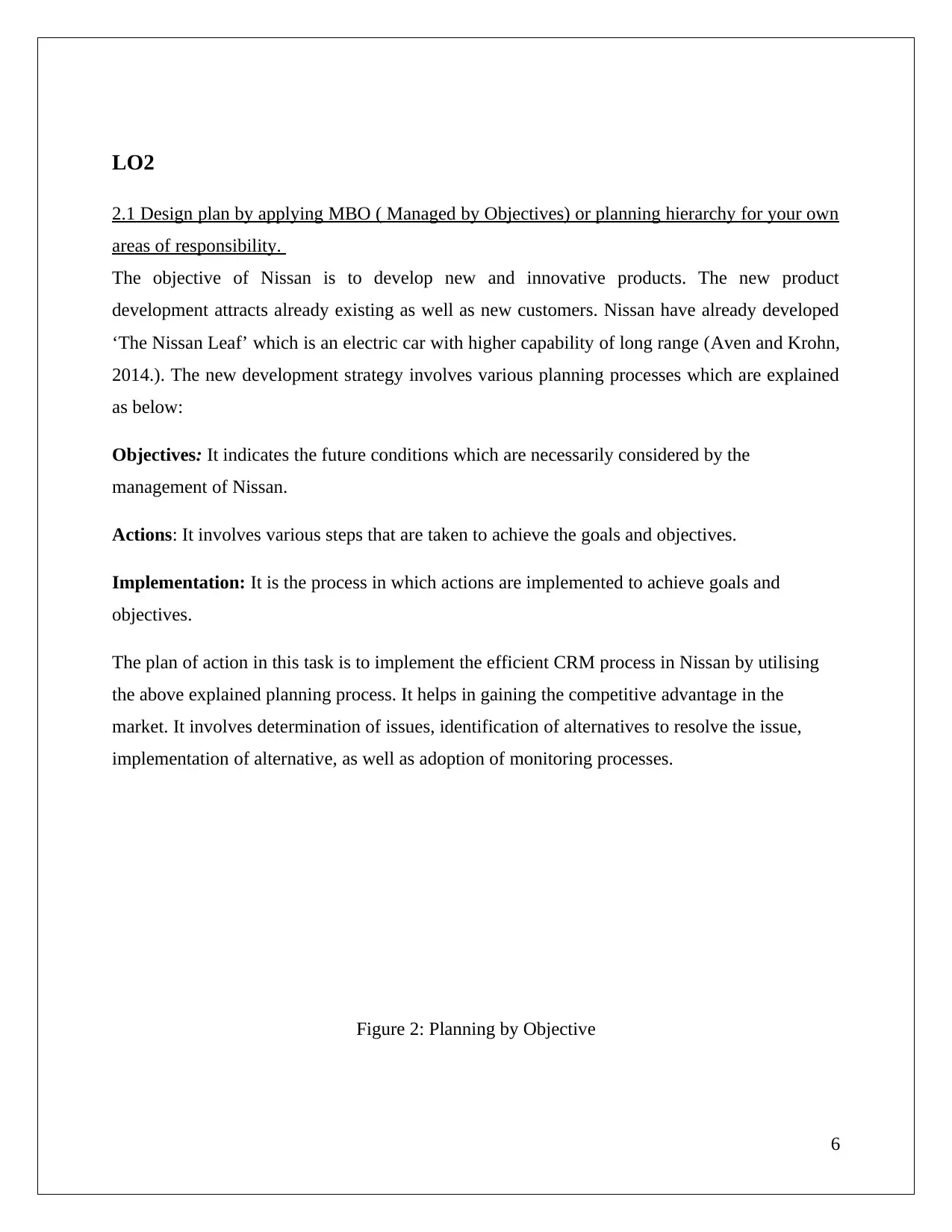
LO2
2.1 Design plan by applying MBO ( Managed by Objectives) or planning hierarchy for your own
areas of responsibility.
The objective of Nissan is to develop new and innovative products. The new product
development attracts already existing as well as new customers. Nissan have already developed
‘The Nissan Leaf’ which is an electric car with higher capability of long range (Aven and Krohn,
2014.). The new development strategy involves various planning processes which are explained
as below:
Objectives: It indicates the future conditions which are necessarily considered by the
management of Nissan.
Actions: It involves various steps that are taken to achieve the goals and objectives.
Implementation: It is the process in which actions are implemented to achieve goals and
objectives.
The plan of action in this task is to implement the efficient CRM process in Nissan by utilising
the above explained planning process. It helps in gaining the competitive advantage in the
market. It involves determination of issues, identification of alternatives to resolve the issue,
implementation of alternative, as well as adoption of monitoring processes.
Figure 2: Planning by Objective
6
2.1 Design plan by applying MBO ( Managed by Objectives) or planning hierarchy for your own
areas of responsibility.
The objective of Nissan is to develop new and innovative products. The new product
development attracts already existing as well as new customers. Nissan have already developed
‘The Nissan Leaf’ which is an electric car with higher capability of long range (Aven and Krohn,
2014.). The new development strategy involves various planning processes which are explained
as below:
Objectives: It indicates the future conditions which are necessarily considered by the
management of Nissan.
Actions: It involves various steps that are taken to achieve the goals and objectives.
Implementation: It is the process in which actions are implemented to achieve goals and
objectives.
The plan of action in this task is to implement the efficient CRM process in Nissan by utilising
the above explained planning process. It helps in gaining the competitive advantage in the
market. It involves determination of issues, identification of alternatives to resolve the issue,
implementation of alternative, as well as adoption of monitoring processes.
Figure 2: Planning by Objective
6
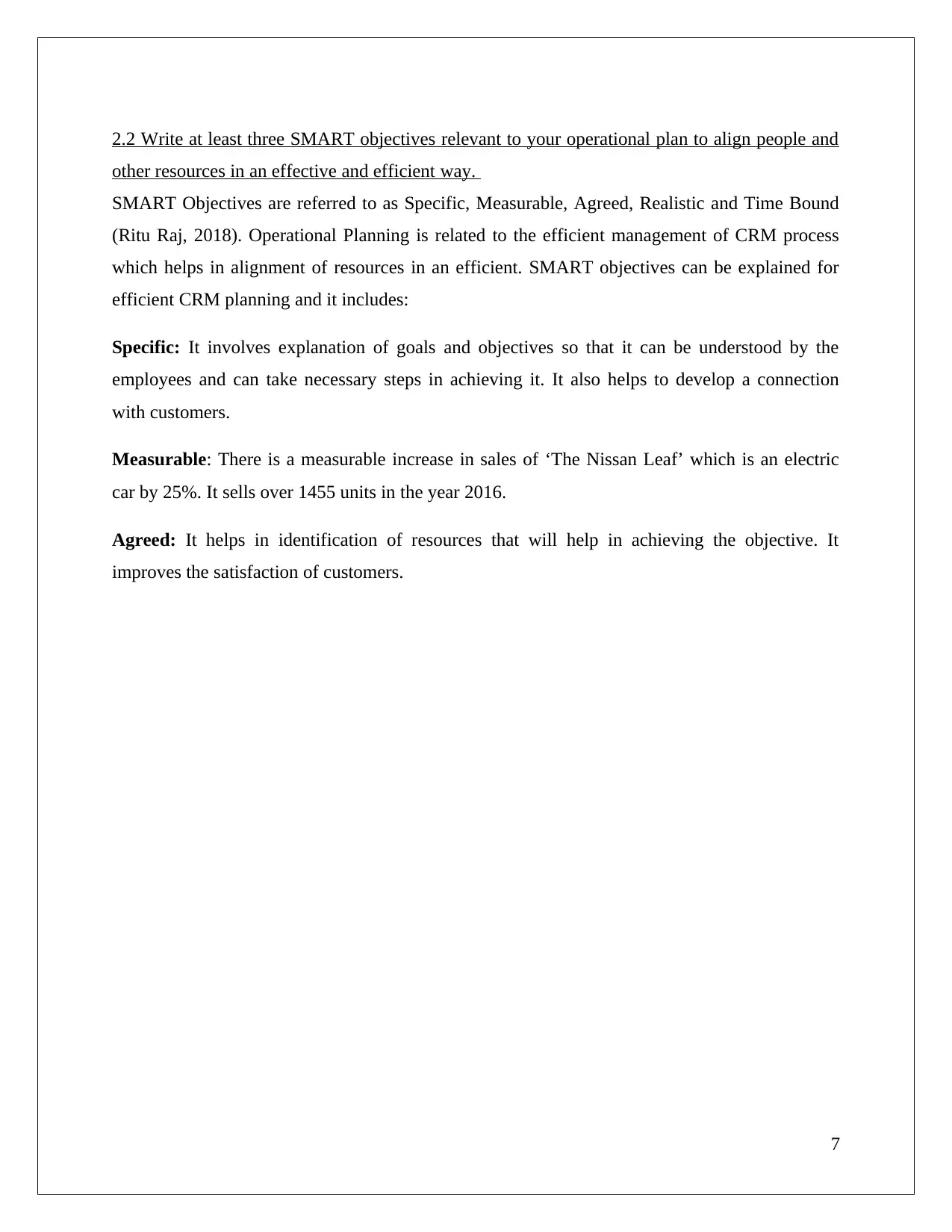
2.2 Write at least three SMART objectives relevant to your operational plan to align people and
other resources in an effective and efficient way.
SMART Objectives are referred to as Specific, Measurable, Agreed, Realistic and Time Bound
(Ritu Raj, 2018). Operational Planning is related to the efficient management of CRM process
which helps in alignment of resources in an efficient. SMART objectives can be explained for
efficient CRM planning and it includes:
Specific: It involves explanation of goals and objectives so that it can be understood by the
employees and can take necessary steps in achieving it. It also helps to develop a connection
with customers.
Measurable: There is a measurable increase in sales of ‘The Nissan Leaf’ which is an electric
car by 25%. It sells over 1455 units in the year 2016.
Agreed: It helps in identification of resources that will help in achieving the objective. It
improves the satisfaction of customers.
7
other resources in an effective and efficient way.
SMART Objectives are referred to as Specific, Measurable, Agreed, Realistic and Time Bound
(Ritu Raj, 2018). Operational Planning is related to the efficient management of CRM process
which helps in alignment of resources in an efficient. SMART objectives can be explained for
efficient CRM planning and it includes:
Specific: It involves explanation of goals and objectives so that it can be understood by the
employees and can take necessary steps in achieving it. It also helps to develop a connection
with customers.
Measurable: There is a measurable increase in sales of ‘The Nissan Leaf’ which is an electric
car by 25%. It sells over 1455 units in the year 2016.
Agreed: It helps in identification of resources that will help in achieving the objective. It
improves the satisfaction of customers.
7
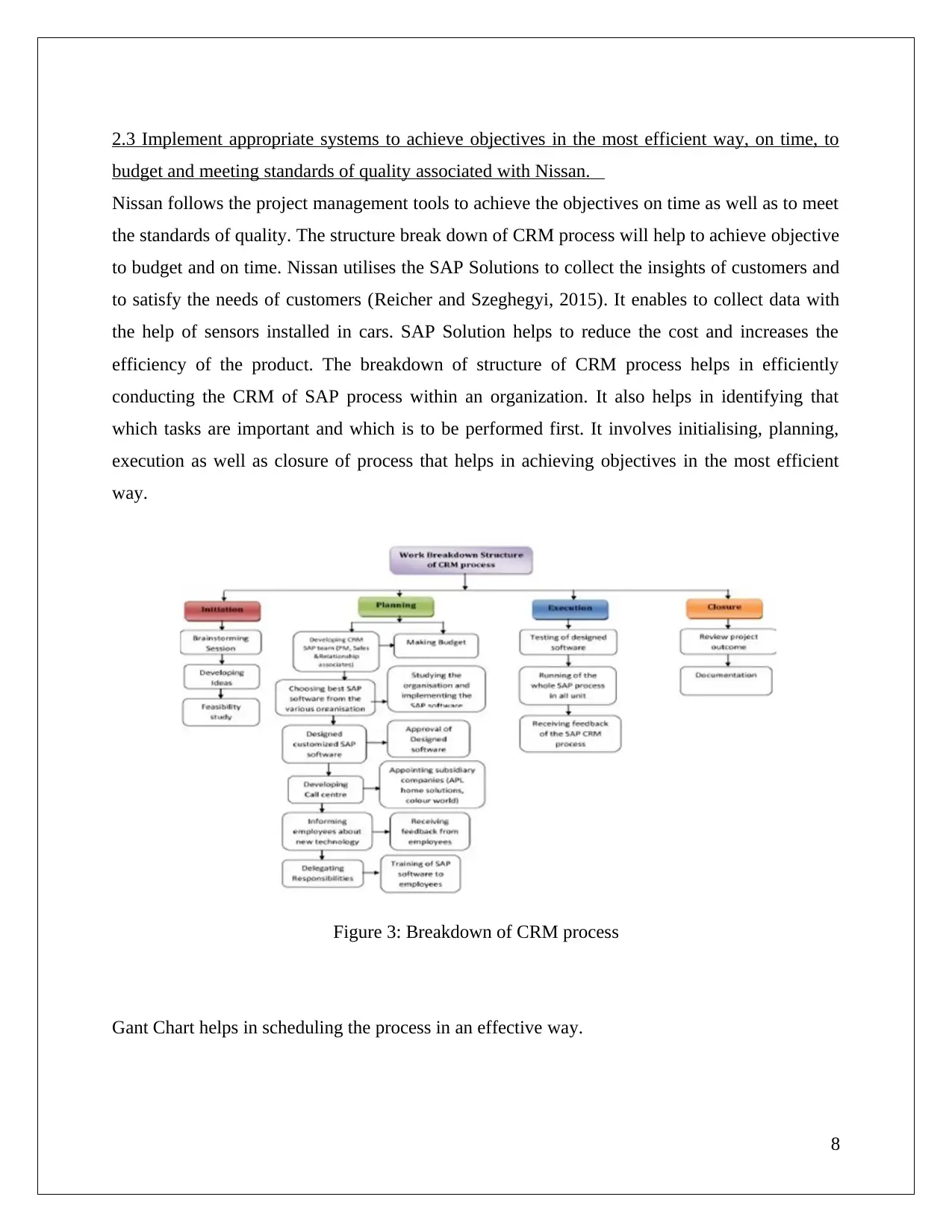
2.3 Implement appropriate systems to achieve objectives in the most efficient way, on time, to
budget and meeting standards of quality associated with Nissan.
Nissan follows the project management tools to achieve the objectives on time as well as to meet
the standards of quality. The structure break down of CRM process will help to achieve objective
to budget and on time. Nissan utilises the SAP Solutions to collect the insights of customers and
to satisfy the needs of customers (Reicher and Szeghegyi, 2015). It enables to collect data with
the help of sensors installed in cars. SAP Solution helps to reduce the cost and increases the
efficiency of the product. The breakdown of structure of CRM process helps in efficiently
conducting the CRM of SAP process within an organization. It also helps in identifying that
which tasks are important and which is to be performed first. It involves initialising, planning,
execution as well as closure of process that helps in achieving objectives in the most efficient
way.
Figure 3: Breakdown of CRM process
Gant Chart helps in scheduling the process in an effective way.
8
budget and meeting standards of quality associated with Nissan.
Nissan follows the project management tools to achieve the objectives on time as well as to meet
the standards of quality. The structure break down of CRM process will help to achieve objective
to budget and on time. Nissan utilises the SAP Solutions to collect the insights of customers and
to satisfy the needs of customers (Reicher and Szeghegyi, 2015). It enables to collect data with
the help of sensors installed in cars. SAP Solution helps to reduce the cost and increases the
efficiency of the product. The breakdown of structure of CRM process helps in efficiently
conducting the CRM of SAP process within an organization. It also helps in identifying that
which tasks are important and which is to be performed first. It involves initialising, planning,
execution as well as closure of process that helps in achieving objectives in the most efficient
way.
Figure 3: Breakdown of CRM process
Gant Chart helps in scheduling the process in an effective way.
8
Paraphrase This Document
Need a fresh take? Get an instant paraphrase of this document with our AI Paraphraser
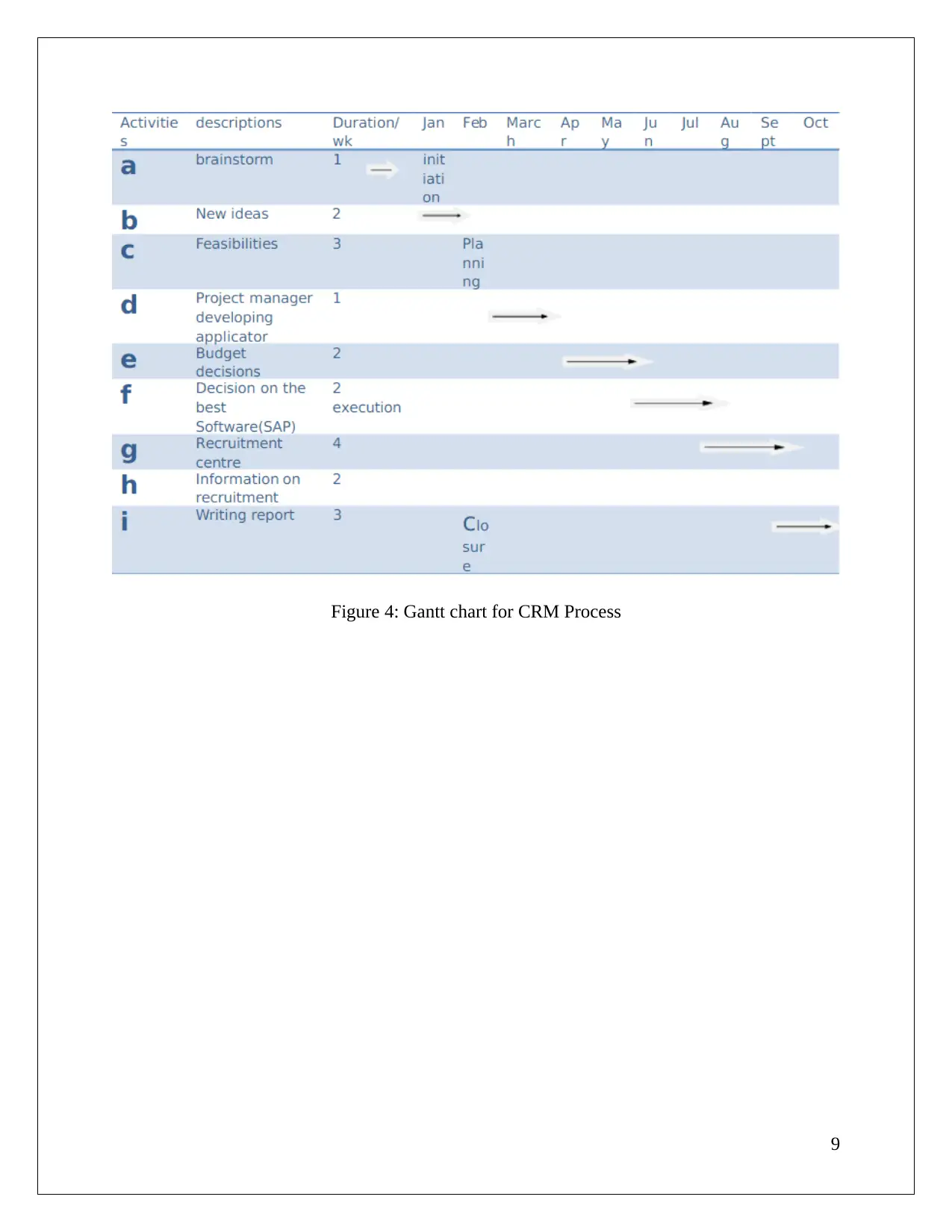
Figure 4: Gantt chart for CRM Process
9
9
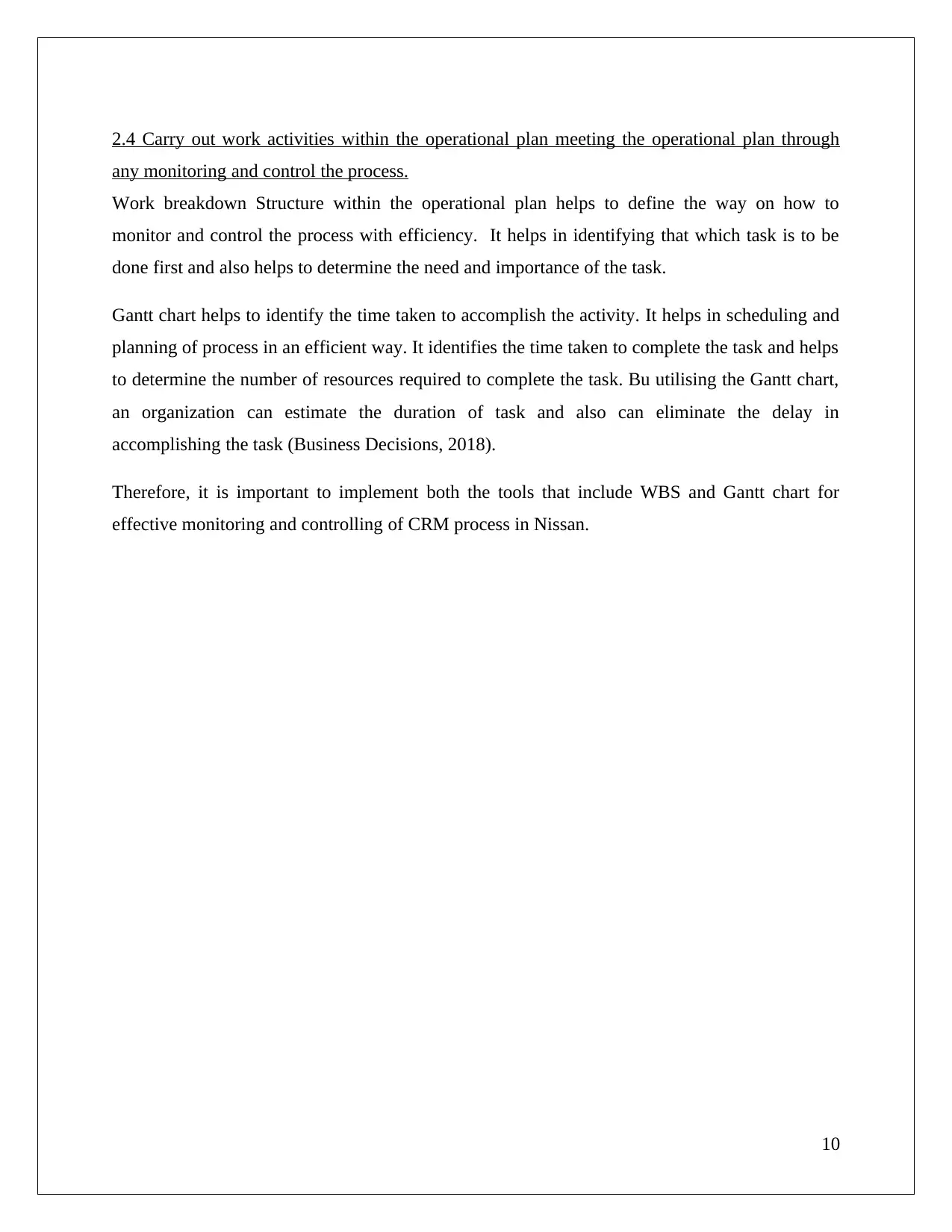
2.4 Carry out work activities within the operational plan meeting the operational plan through
any monitoring and control the process.
Work breakdown Structure within the operational plan helps to define the way on how to
monitor and control the process with efficiency. It helps in identifying that which task is to be
done first and also helps to determine the need and importance of the task.
Gantt chart helps to identify the time taken to accomplish the activity. It helps in scheduling and
planning of process in an efficient way. It identifies the time taken to complete the task and helps
to determine the number of resources required to complete the task. Bu utilising the Gantt chart,
an organization can estimate the duration of task and also can eliminate the delay in
accomplishing the task (Business Decisions, 2018).
Therefore, it is important to implement both the tools that include WBS and Gantt chart for
effective monitoring and controlling of CRM process in Nissan.
10
any monitoring and control the process.
Work breakdown Structure within the operational plan helps to define the way on how to
monitor and control the process with efficiency. It helps in identifying that which task is to be
done first and also helps to determine the need and importance of the task.
Gantt chart helps to identify the time taken to accomplish the activity. It helps in scheduling and
planning of process in an efficient way. It identifies the time taken to complete the task and helps
to determine the number of resources required to complete the task. Bu utilising the Gantt chart,
an organization can estimate the duration of task and also can eliminate the delay in
accomplishing the task (Business Decisions, 2018).
Therefore, it is important to implement both the tools that include WBS and Gantt chart for
effective monitoring and controlling of CRM process in Nissan.
10
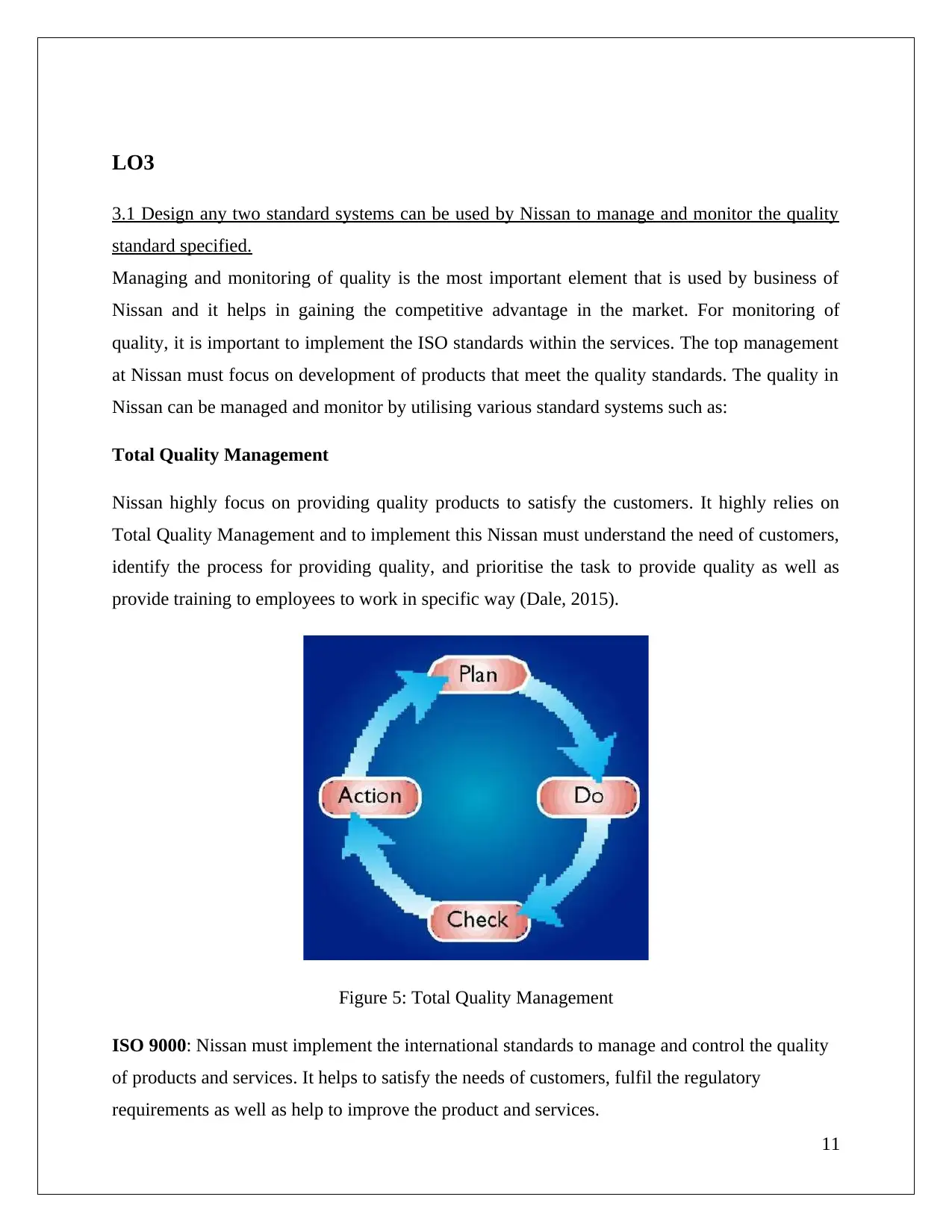
LO3
3.1 Design any two standard systems can be used by Nissan to manage and monitor the quality
standard specified.
Managing and monitoring of quality is the most important element that is used by business of
Nissan and it helps in gaining the competitive advantage in the market. For monitoring of
quality, it is important to implement the ISO standards within the services. The top management
at Nissan must focus on development of products that meet the quality standards. The quality in
Nissan can be managed and monitor by utilising various standard systems such as:
Total Quality Management
Nissan highly focus on providing quality products to satisfy the customers. It highly relies on
Total Quality Management and to implement this Nissan must understand the need of customers,
identify the process for providing quality, and prioritise the task to provide quality as well as
provide training to employees to work in specific way (Dale, 2015).
Figure 5: Total Quality Management
ISO 9000: Nissan must implement the international standards to manage and control the quality
of products and services. It helps to satisfy the needs of customers, fulfil the regulatory
requirements as well as help to improve the product and services.
11
3.1 Design any two standard systems can be used by Nissan to manage and monitor the quality
standard specified.
Managing and monitoring of quality is the most important element that is used by business of
Nissan and it helps in gaining the competitive advantage in the market. For monitoring of
quality, it is important to implement the ISO standards within the services. The top management
at Nissan must focus on development of products that meet the quality standards. The quality in
Nissan can be managed and monitor by utilising various standard systems such as:
Total Quality Management
Nissan highly focus on providing quality products to satisfy the customers. It highly relies on
Total Quality Management and to implement this Nissan must understand the need of customers,
identify the process for providing quality, and prioritise the task to provide quality as well as
provide training to employees to work in specific way (Dale, 2015).
Figure 5: Total Quality Management
ISO 9000: Nissan must implement the international standards to manage and control the quality
of products and services. It helps to satisfy the needs of customers, fulfil the regulatory
requirements as well as help to improve the product and services.
11
Secure Best Marks with AI Grader
Need help grading? Try our AI Grader for instant feedback on your assignments.
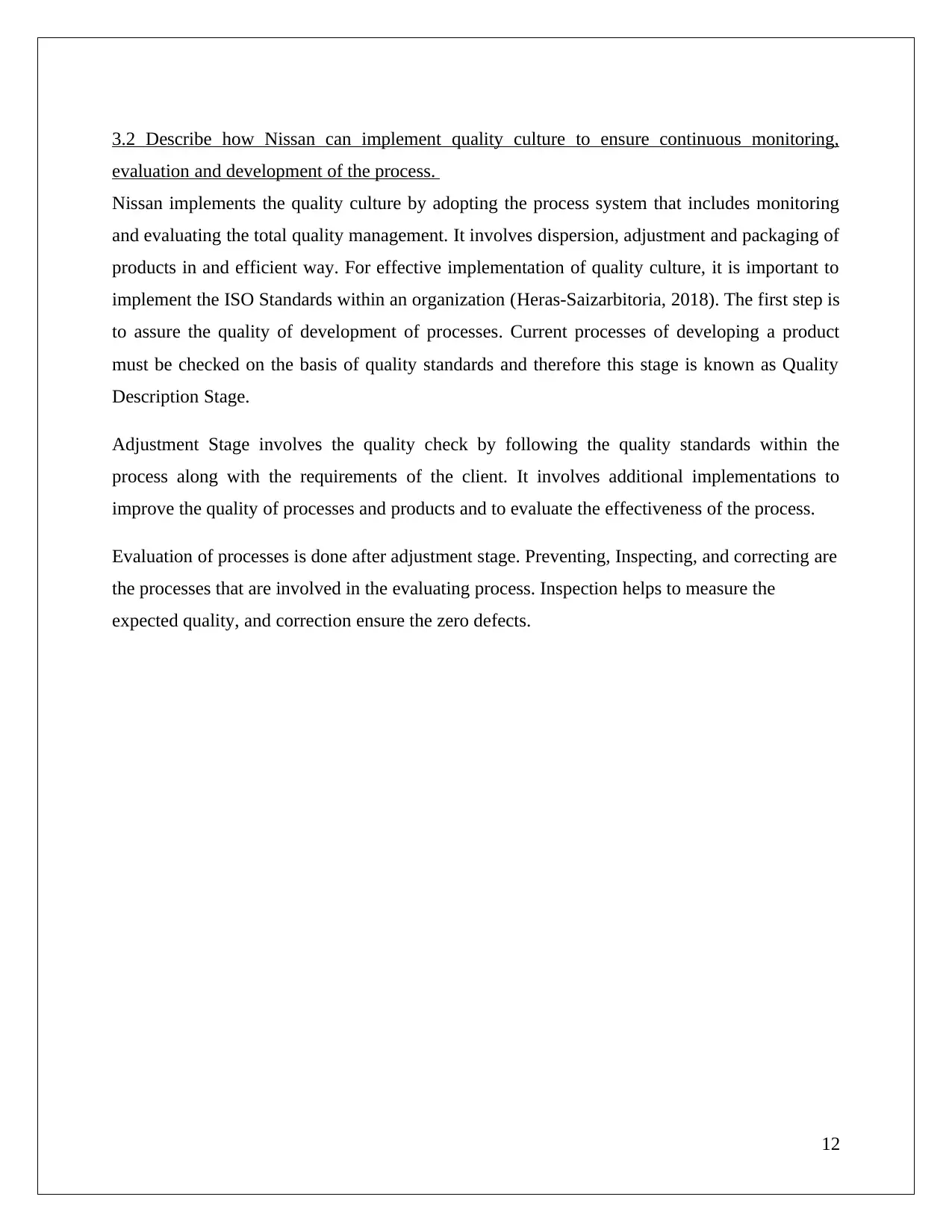
3.2 Describe how Nissan can implement quality culture to ensure continuous monitoring,
evaluation and development of the process.
Nissan implements the quality culture by adopting the process system that includes monitoring
and evaluating the total quality management. It involves dispersion, adjustment and packaging of
products in and efficient way. For effective implementation of quality culture, it is important to
implement the ISO Standards within an organization (Heras-Saizarbitoria, 2018). The first step is
to assure the quality of development of processes. Current processes of developing a product
must be checked on the basis of quality standards and therefore this stage is known as Quality
Description Stage.
Adjustment Stage involves the quality check by following the quality standards within the
process along with the requirements of the client. It involves additional implementations to
improve the quality of processes and products and to evaluate the effectiveness of the process.
Evaluation of processes is done after adjustment stage. Preventing, Inspecting, and correcting are
the processes that are involved in the evaluating process. Inspection helps to measure the
expected quality, and correction ensure the zero defects.
12
evaluation and development of the process.
Nissan implements the quality culture by adopting the process system that includes monitoring
and evaluating the total quality management. It involves dispersion, adjustment and packaging of
products in and efficient way. For effective implementation of quality culture, it is important to
implement the ISO Standards within an organization (Heras-Saizarbitoria, 2018). The first step is
to assure the quality of development of processes. Current processes of developing a product
must be checked on the basis of quality standards and therefore this stage is known as Quality
Description Stage.
Adjustment Stage involves the quality check by following the quality standards within the
process along with the requirements of the client. It involves additional implementations to
improve the quality of processes and products and to evaluate the effectiveness of the process.
Evaluation of processes is done after adjustment stage. Preventing, Inspecting, and correcting are
the processes that are involved in the evaluating process. Inspection helps to measure the
expected quality, and correction ensure the zero defects.
12
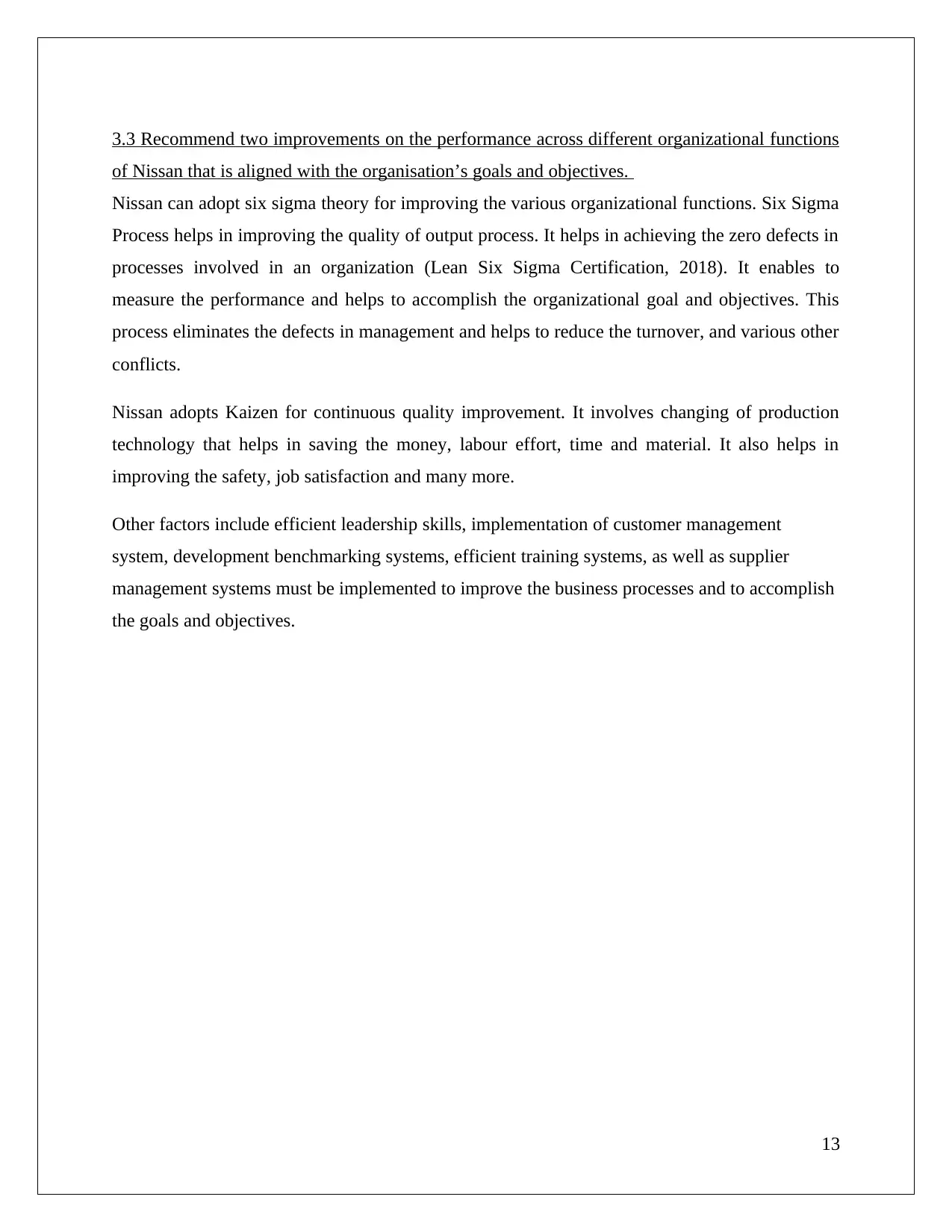
3.3 Recommend two improvements on the performance across different organizational functions
of Nissan that is aligned with the organisation’s goals and objectives.
Nissan can adopt six sigma theory for improving the various organizational functions. Six Sigma
Process helps in improving the quality of output process. It helps in achieving the zero defects in
processes involved in an organization (Lean Six Sigma Certification, 2018). It enables to
measure the performance and helps to accomplish the organizational goal and objectives. This
process eliminates the defects in management and helps to reduce the turnover, and various other
conflicts.
Nissan adopts Kaizen for continuous quality improvement. It involves changing of production
technology that helps in saving the money, labour effort, time and material. It also helps in
improving the safety, job satisfaction and many more.
Other factors include efficient leadership skills, implementation of customer management
system, development benchmarking systems, efficient training systems, as well as supplier
management systems must be implemented to improve the business processes and to accomplish
the goals and objectives.
13
of Nissan that is aligned with the organisation’s goals and objectives.
Nissan can adopt six sigma theory for improving the various organizational functions. Six Sigma
Process helps in improving the quality of output process. It helps in achieving the zero defects in
processes involved in an organization (Lean Six Sigma Certification, 2018). It enables to
measure the performance and helps to accomplish the organizational goal and objectives. This
process eliminates the defects in management and helps to reduce the turnover, and various other
conflicts.
Nissan adopts Kaizen for continuous quality improvement. It involves changing of production
technology that helps in saving the money, labour effort, time and material. It also helps in
improving the safety, job satisfaction and many more.
Other factors include efficient leadership skills, implementation of customer management
system, development benchmarking systems, efficient training systems, as well as supplier
management systems must be implemented to improve the business processes and to accomplish
the goals and objectives.
13
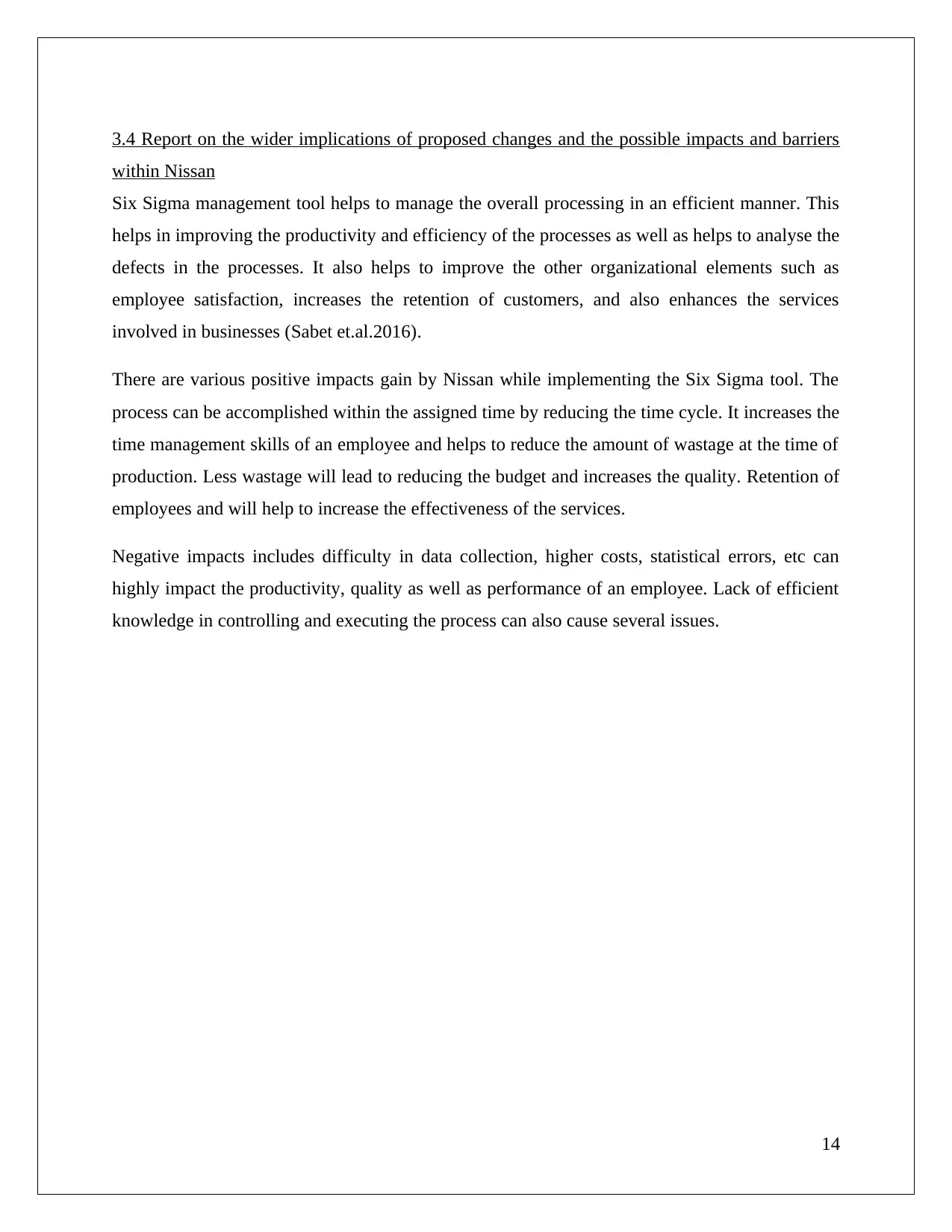
3.4 Report on the wider implications of proposed changes and the possible impacts and barriers
within Nissan
Six Sigma management tool helps to manage the overall processing in an efficient manner. This
helps in improving the productivity and efficiency of the processes as well as helps to analyse the
defects in the processes. It also helps to improve the other organizational elements such as
employee satisfaction, increases the retention of customers, and also enhances the services
involved in businesses (Sabet et.al.2016).
There are various positive impacts gain by Nissan while implementing the Six Sigma tool. The
process can be accomplished within the assigned time by reducing the time cycle. It increases the
time management skills of an employee and helps to reduce the amount of wastage at the time of
production. Less wastage will lead to reducing the budget and increases the quality. Retention of
employees and will help to increase the effectiveness of the services.
Negative impacts includes difficulty in data collection, higher costs, statistical errors, etc can
highly impact the productivity, quality as well as performance of an employee. Lack of efficient
knowledge in controlling and executing the process can also cause several issues.
14
within Nissan
Six Sigma management tool helps to manage the overall processing in an efficient manner. This
helps in improving the productivity and efficiency of the processes as well as helps to analyse the
defects in the processes. It also helps to improve the other organizational elements such as
employee satisfaction, increases the retention of customers, and also enhances the services
involved in businesses (Sabet et.al.2016).
There are various positive impacts gain by Nissan while implementing the Six Sigma tool. The
process can be accomplished within the assigned time by reducing the time cycle. It increases the
time management skills of an employee and helps to reduce the amount of wastage at the time of
production. Less wastage will lead to reducing the budget and increases the quality. Retention of
employees and will help to increase the effectiveness of the services.
Negative impacts includes difficulty in data collection, higher costs, statistical errors, etc can
highly impact the productivity, quality as well as performance of an employee. Lack of efficient
knowledge in controlling and executing the process can also cause several issues.
14
Paraphrase This Document
Need a fresh take? Get an instant paraphrase of this document with our AI Paraphraser

LO4
4.1 Carry out risk assessments as required by legislation, regulation and organisational
requirements, ensuring appropriate action is taken in the context of your area of responsibility or
any department at Nissan.
PESTEL Analysis can be done for carrying out the risk assessment in Nissan. The analysis can
be done by considering the below mentioned elements:
Political: Political issues include changes in government policies under which business is
operating its business, recruitment policies and many more can impact over the organization.
Economical: It includes recession, inflation rate; changes in exchange rates can have negative
and positive impact on recruitment processes.
Social: Change in social lifestyle influences the demand of human resources.
Technological: Advancement in technology needs proper training of employees.
Legal: Employment Acts and other legislations influence the various activities of businesses.
Environmental: Changing policies influence the operations of businesses in Nissan.
Risk factor can be eliminated by implementing the legislation laws, health and safety regulation,
measurement of fiscal policies, and following of employment act (Keith-Roach et.al.2015).
Organization must assess the risk factor and its impacts, establish the regulations and laws,
monitoring of activities and reviewing the output and results to identify the risk.
15
4.1 Carry out risk assessments as required by legislation, regulation and organisational
requirements, ensuring appropriate action is taken in the context of your area of responsibility or
any department at Nissan.
PESTEL Analysis can be done for carrying out the risk assessment in Nissan. The analysis can
be done by considering the below mentioned elements:
Political: Political issues include changes in government policies under which business is
operating its business, recruitment policies and many more can impact over the organization.
Economical: It includes recession, inflation rate; changes in exchange rates can have negative
and positive impact on recruitment processes.
Social: Change in social lifestyle influences the demand of human resources.
Technological: Advancement in technology needs proper training of employees.
Legal: Employment Acts and other legislations influence the various activities of businesses.
Environmental: Changing policies influence the operations of businesses in Nissan.
Risk factor can be eliminated by implementing the legislation laws, health and safety regulation,
measurement of fiscal policies, and following of employment act (Keith-Roach et.al.2015).
Organization must assess the risk factor and its impacts, establish the regulations and laws,
monitoring of activities and reviewing the output and results to identify the risk.
15
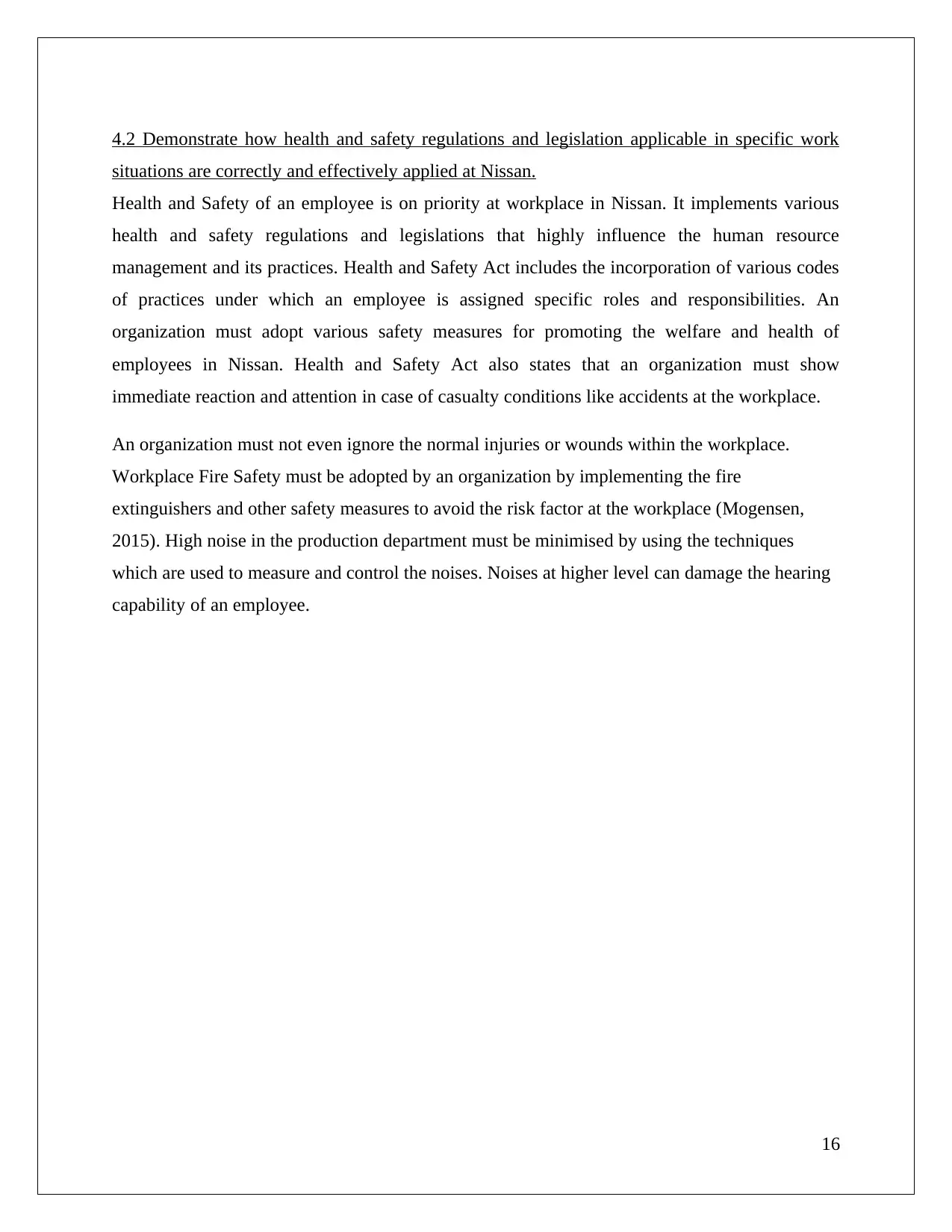
4.2 Demonstrate how health and safety regulations and legislation applicable in specific work
situations are correctly and effectively applied at Nissan.
Health and Safety of an employee is on priority at workplace in Nissan. It implements various
health and safety regulations and legislations that highly influence the human resource
management and its practices. Health and Safety Act includes the incorporation of various codes
of practices under which an employee is assigned specific roles and responsibilities. An
organization must adopt various safety measures for promoting the welfare and health of
employees in Nissan. Health and Safety Act also states that an organization must show
immediate reaction and attention in case of casualty conditions like accidents at the workplace.
An organization must not even ignore the normal injuries or wounds within the workplace.
Workplace Fire Safety must be adopted by an organization by implementing the fire
extinguishers and other safety measures to avoid the risk factor at the workplace (Mogensen,
2015). High noise in the production department must be minimised by using the techniques
which are used to measure and control the noises. Noises at higher level can damage the hearing
capability of an employee.
16
situations are correctly and effectively applied at Nissan.
Health and Safety of an employee is on priority at workplace in Nissan. It implements various
health and safety regulations and legislations that highly influence the human resource
management and its practices. Health and Safety Act includes the incorporation of various codes
of practices under which an employee is assigned specific roles and responsibilities. An
organization must adopt various safety measures for promoting the welfare and health of
employees in Nissan. Health and Safety Act also states that an organization must show
immediate reaction and attention in case of casualty conditions like accidents at the workplace.
An organization must not even ignore the normal injuries or wounds within the workplace.
Workplace Fire Safety must be adopted by an organization by implementing the fire
extinguishers and other safety measures to avoid the risk factor at the workplace (Mogensen,
2015). High noise in the production department must be minimised by using the techniques
which are used to measure and control the noises. Noises at higher level can damage the hearing
capability of an employee.
16
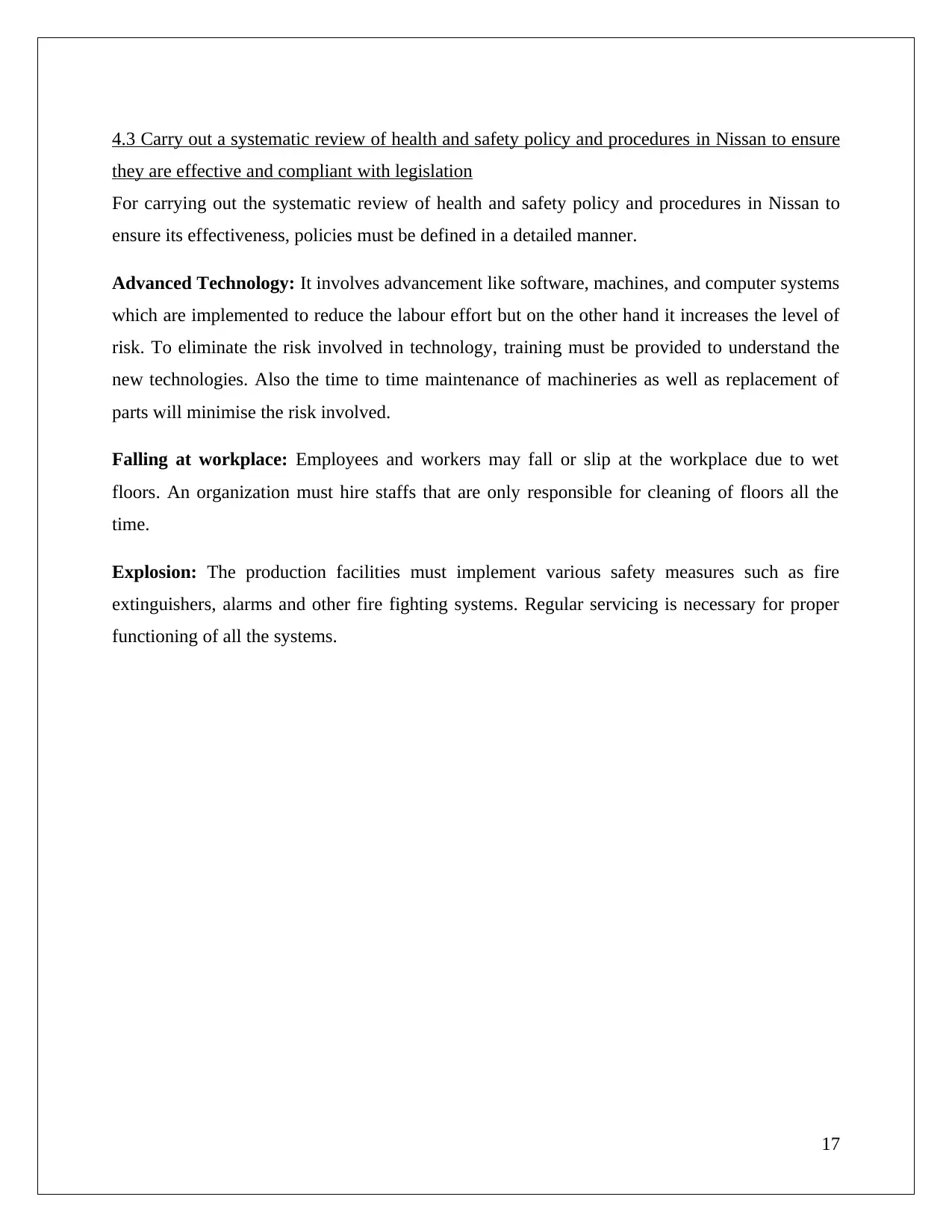
4.3 Carry out a systematic review of health and safety policy and procedures in Nissan to ensure
they are effective and compliant with legislation
For carrying out the systematic review of health and safety policy and procedures in Nissan to
ensure its effectiveness, policies must be defined in a detailed manner.
Advanced Technology: It involves advancement like software, machines, and computer systems
which are implemented to reduce the labour effort but on the other hand it increases the level of
risk. To eliminate the risk involved in technology, training must be provided to understand the
new technologies. Also the time to time maintenance of machineries as well as replacement of
parts will minimise the risk involved.
Falling at workplace: Employees and workers may fall or slip at the workplace due to wet
floors. An organization must hire staffs that are only responsible for cleaning of floors all the
time.
Explosion: The production facilities must implement various safety measures such as fire
extinguishers, alarms and other fire fighting systems. Regular servicing is necessary for proper
functioning of all the systems.
17
they are effective and compliant with legislation
For carrying out the systematic review of health and safety policy and procedures in Nissan to
ensure its effectiveness, policies must be defined in a detailed manner.
Advanced Technology: It involves advancement like software, machines, and computer systems
which are implemented to reduce the labour effort but on the other hand it increases the level of
risk. To eliminate the risk involved in technology, training must be provided to understand the
new technologies. Also the time to time maintenance of machineries as well as replacement of
parts will minimise the risk involved.
Falling at workplace: Employees and workers may fall or slip at the workplace due to wet
floors. An organization must hire staffs that are only responsible for cleaning of floors all the
time.
Explosion: The production facilities must implement various safety measures such as fire
extinguishers, alarms and other fire fighting systems. Regular servicing is necessary for proper
functioning of all the systems.
17
Secure Best Marks with AI Grader
Need help grading? Try our AI Grader for instant feedback on your assignments.
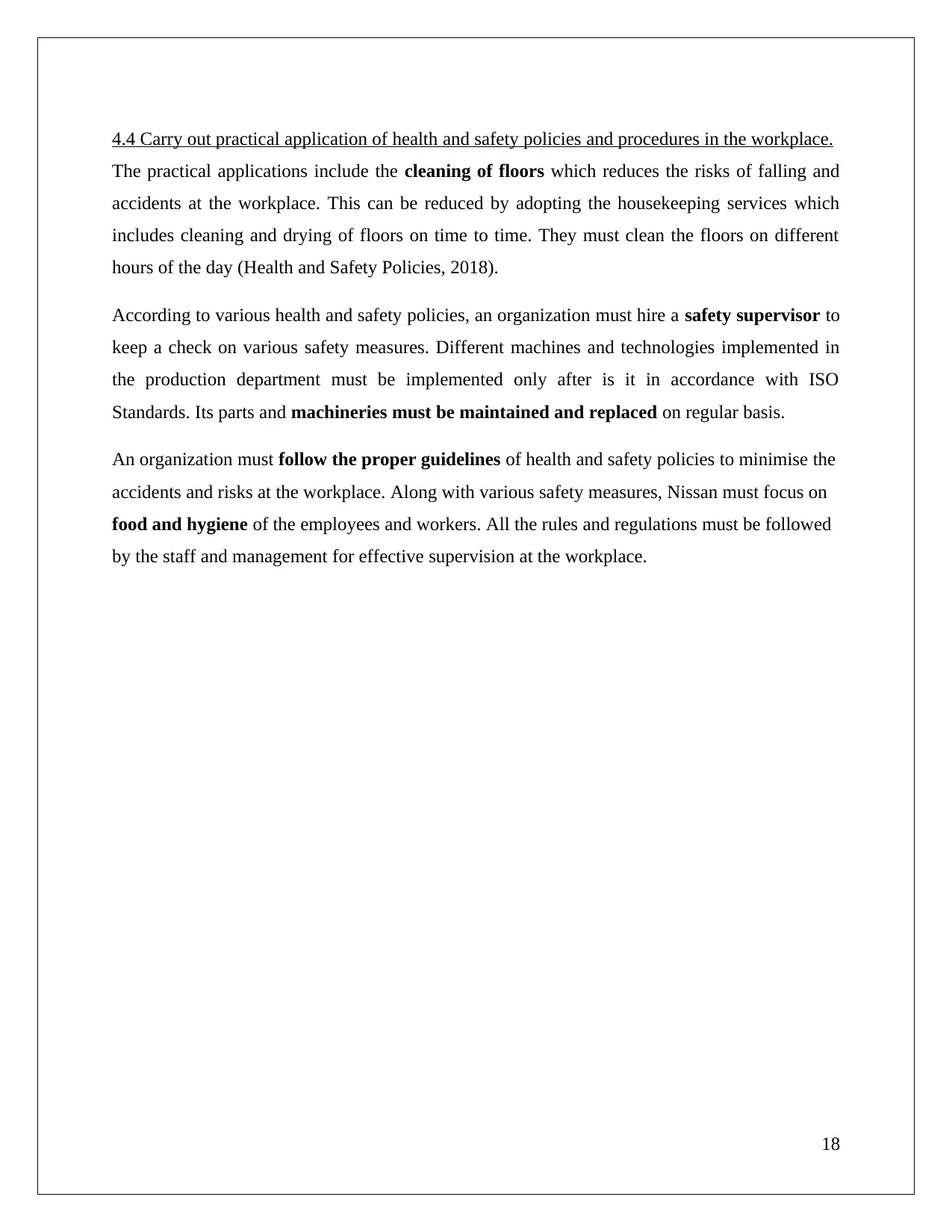
4.4 Carry out practical application of health and safety policies and procedures in the workplace.
The practical applications include the cleaning of floors which reduces the risks of falling and
accidents at the workplace. This can be reduced by adopting the housekeeping services which
includes cleaning and drying of floors on time to time. They must clean the floors on different
hours of the day (Health and Safety Policies, 2018).
According to various health and safety policies, an organization must hire a safety supervisor to
keep a check on various safety measures. Different machines and technologies implemented in
the production department must be implemented only after is it in accordance with ISO
Standards. Its parts and machineries must be maintained and replaced on regular basis.
An organization must follow the proper guidelines of health and safety policies to minimise the
accidents and risks at the workplace. Along with various safety measures, Nissan must focus on
food and hygiene of the employees and workers. All the rules and regulations must be followed
by the staff and management for effective supervision at the workplace.
18
The practical applications include the cleaning of floors which reduces the risks of falling and
accidents at the workplace. This can be reduced by adopting the housekeeping services which
includes cleaning and drying of floors on time to time. They must clean the floors on different
hours of the day (Health and Safety Policies, 2018).
According to various health and safety policies, an organization must hire a safety supervisor to
keep a check on various safety measures. Different machines and technologies implemented in
the production department must be implemented only after is it in accordance with ISO
Standards. Its parts and machineries must be maintained and replaced on regular basis.
An organization must follow the proper guidelines of health and safety policies to minimise the
accidents and risks at the workplace. Along with various safety measures, Nissan must focus on
food and hygiene of the employees and workers. All the rules and regulations must be followed
by the staff and management for effective supervision at the workplace.
18
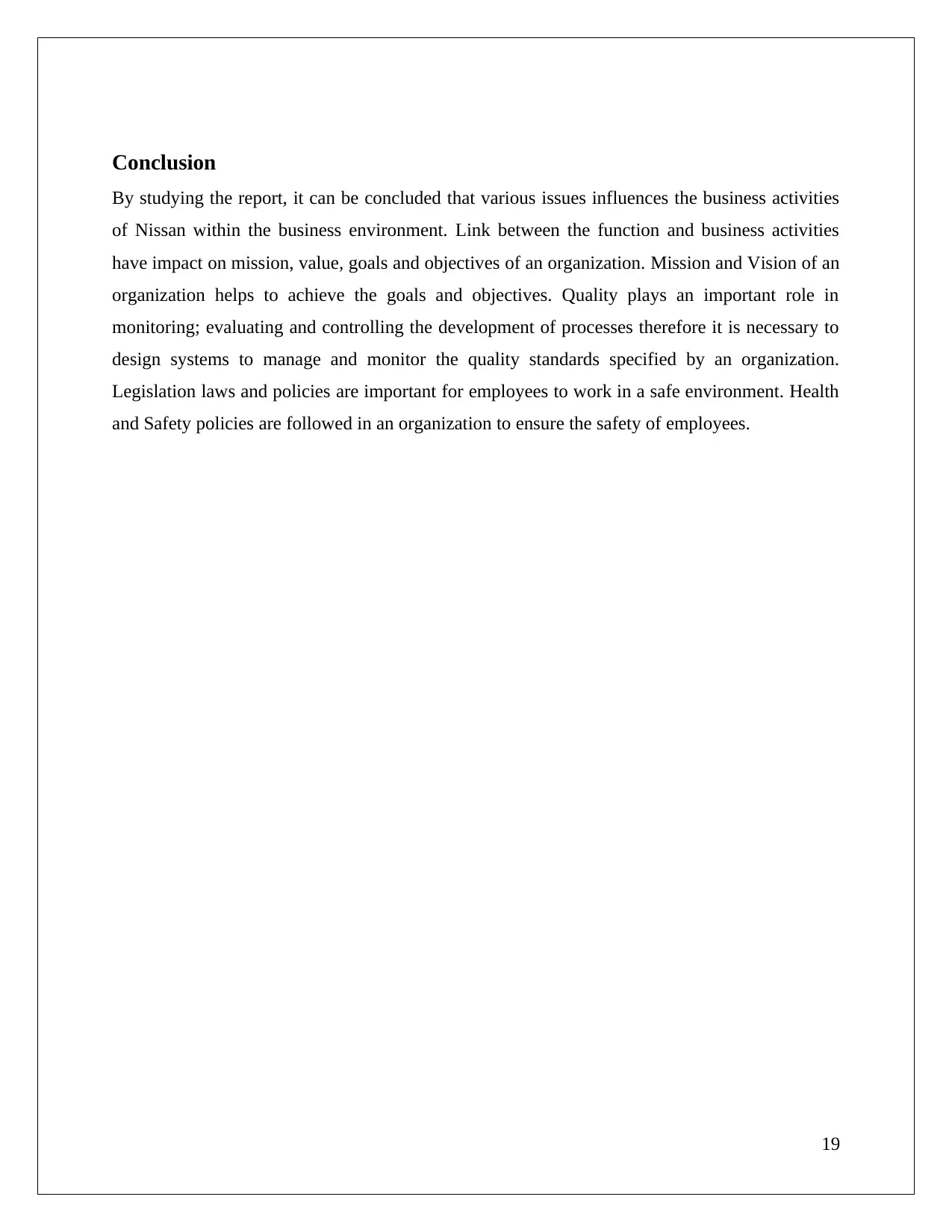
Conclusion
By studying the report, it can be concluded that various issues influences the business activities
of Nissan within the business environment. Link between the function and business activities
have impact on mission, value, goals and objectives of an organization. Mission and Vision of an
organization helps to achieve the goals and objectives. Quality plays an important role in
monitoring; evaluating and controlling the development of processes therefore it is necessary to
design systems to manage and monitor the quality standards specified by an organization.
Legislation laws and policies are important for employees to work in a safe environment. Health
and Safety policies are followed in an organization to ensure the safety of employees.
19
By studying the report, it can be concluded that various issues influences the business activities
of Nissan within the business environment. Link between the function and business activities
have impact on mission, value, goals and objectives of an organization. Mission and Vision of an
organization helps to achieve the goals and objectives. Quality plays an important role in
monitoring; evaluating and controlling the development of processes therefore it is necessary to
design systems to manage and monitor the quality standards specified by an organization.
Legislation laws and policies are important for employees to work in a safe environment. Health
and Safety policies are followed in an organization to ensure the safety of employees.
19
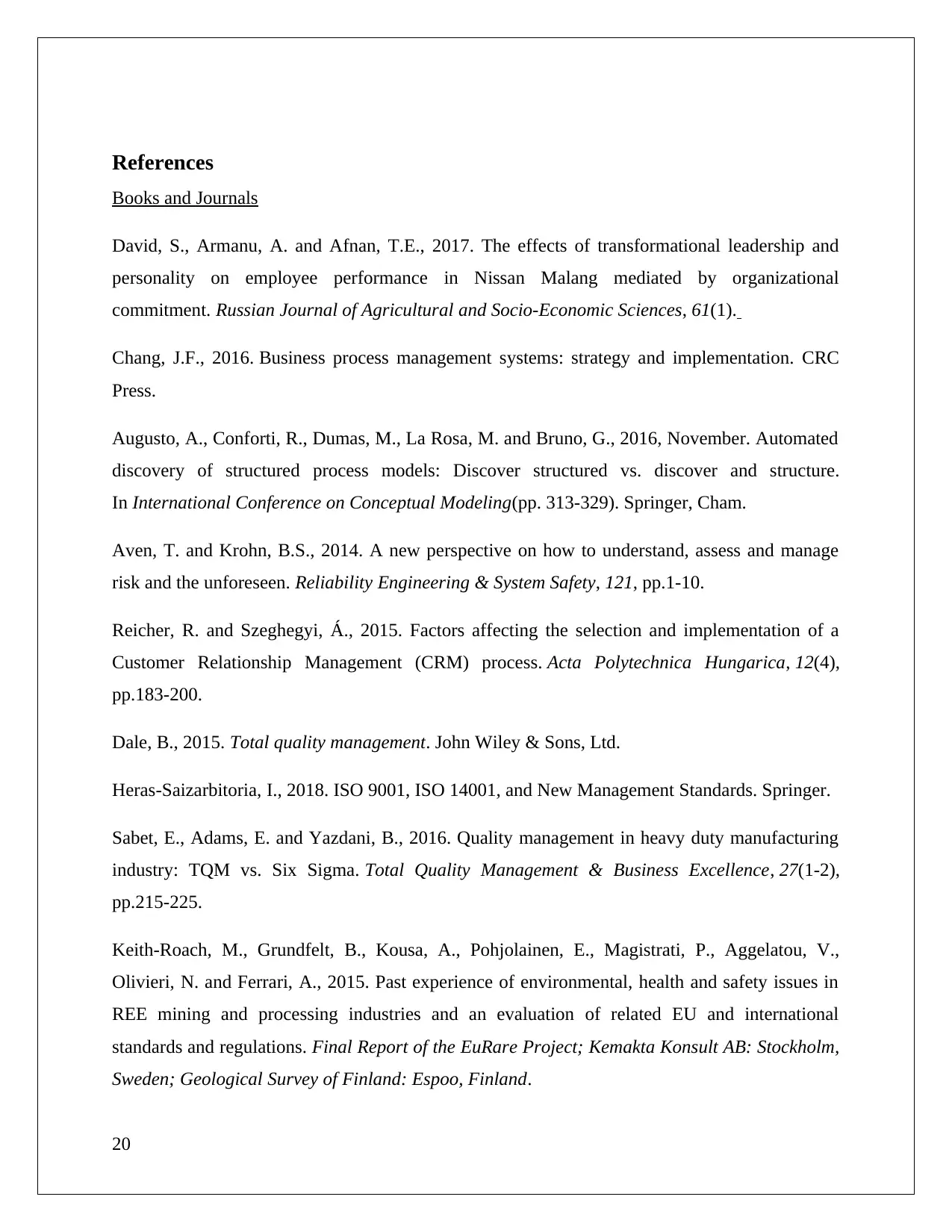
References
Books and Journals
David, S., Armanu, A. and Afnan, T.E., 2017. The effects of transformational leadership and
personality on employee performance in Nissan Malang mediated by organizational
commitment. Russian Journal of Agricultural and Socio-Economic Sciences, 61(1).
Chang, J.F., 2016. Business process management systems: strategy and implementation. CRC
Press.
Augusto, A., Conforti, R., Dumas, M., La Rosa, M. and Bruno, G., 2016, November. Automated
discovery of structured process models: Discover structured vs. discover and structure.
In International Conference on Conceptual Modeling(pp. 313-329). Springer, Cham.
Aven, T. and Krohn, B.S., 2014. A new perspective on how to understand, assess and manage
risk and the unforeseen. Reliability Engineering & System Safety, 121, pp.1-10.
Reicher, R. and Szeghegyi, Á., 2015. Factors affecting the selection and implementation of a
Customer Relationship Management (CRM) process. Acta Polytechnica Hungarica, 12(4),
pp.183-200.
Dale, B., 2015. Total quality management. John Wiley & Sons, Ltd.
Heras-Saizarbitoria, I., 2018. ISO 9001, ISO 14001, and New Management Standards. Springer.
Sabet, E., Adams, E. and Yazdani, B., 2016. Quality management in heavy duty manufacturing
industry: TQM vs. Six Sigma. Total Quality Management & Business Excellence, 27(1-2),
pp.215-225.
Keith-Roach, M., Grundfelt, B., Kousa, A., Pohjolainen, E., Magistrati, P., Aggelatou, V.,
Olivieri, N. and Ferrari, A., 2015. Past experience of environmental, health and safety issues in
REE mining and processing industries and an evaluation of related EU and international
standards and regulations. Final Report of the EuRare Project; Kemakta Konsult AB: Stockholm,
Sweden; Geological Survey of Finland: Espoo, Finland.
20
Books and Journals
David, S., Armanu, A. and Afnan, T.E., 2017. The effects of transformational leadership and
personality on employee performance in Nissan Malang mediated by organizational
commitment. Russian Journal of Agricultural and Socio-Economic Sciences, 61(1).
Chang, J.F., 2016. Business process management systems: strategy and implementation. CRC
Press.
Augusto, A., Conforti, R., Dumas, M., La Rosa, M. and Bruno, G., 2016, November. Automated
discovery of structured process models: Discover structured vs. discover and structure.
In International Conference on Conceptual Modeling(pp. 313-329). Springer, Cham.
Aven, T. and Krohn, B.S., 2014. A new perspective on how to understand, assess and manage
risk and the unforeseen. Reliability Engineering & System Safety, 121, pp.1-10.
Reicher, R. and Szeghegyi, Á., 2015. Factors affecting the selection and implementation of a
Customer Relationship Management (CRM) process. Acta Polytechnica Hungarica, 12(4),
pp.183-200.
Dale, B., 2015. Total quality management. John Wiley & Sons, Ltd.
Heras-Saizarbitoria, I., 2018. ISO 9001, ISO 14001, and New Management Standards. Springer.
Sabet, E., Adams, E. and Yazdani, B., 2016. Quality management in heavy duty manufacturing
industry: TQM vs. Six Sigma. Total Quality Management & Business Excellence, 27(1-2),
pp.215-225.
Keith-Roach, M., Grundfelt, B., Kousa, A., Pohjolainen, E., Magistrati, P., Aggelatou, V.,
Olivieri, N. and Ferrari, A., 2015. Past experience of environmental, health and safety issues in
REE mining and processing industries and an evaluation of related EU and international
standards and regulations. Final Report of the EuRare Project; Kemakta Konsult AB: Stockholm,
Sweden; Geological Survey of Finland: Espoo, Finland.
20
Paraphrase This Document
Need a fresh take? Get an instant paraphrase of this document with our AI Paraphraser
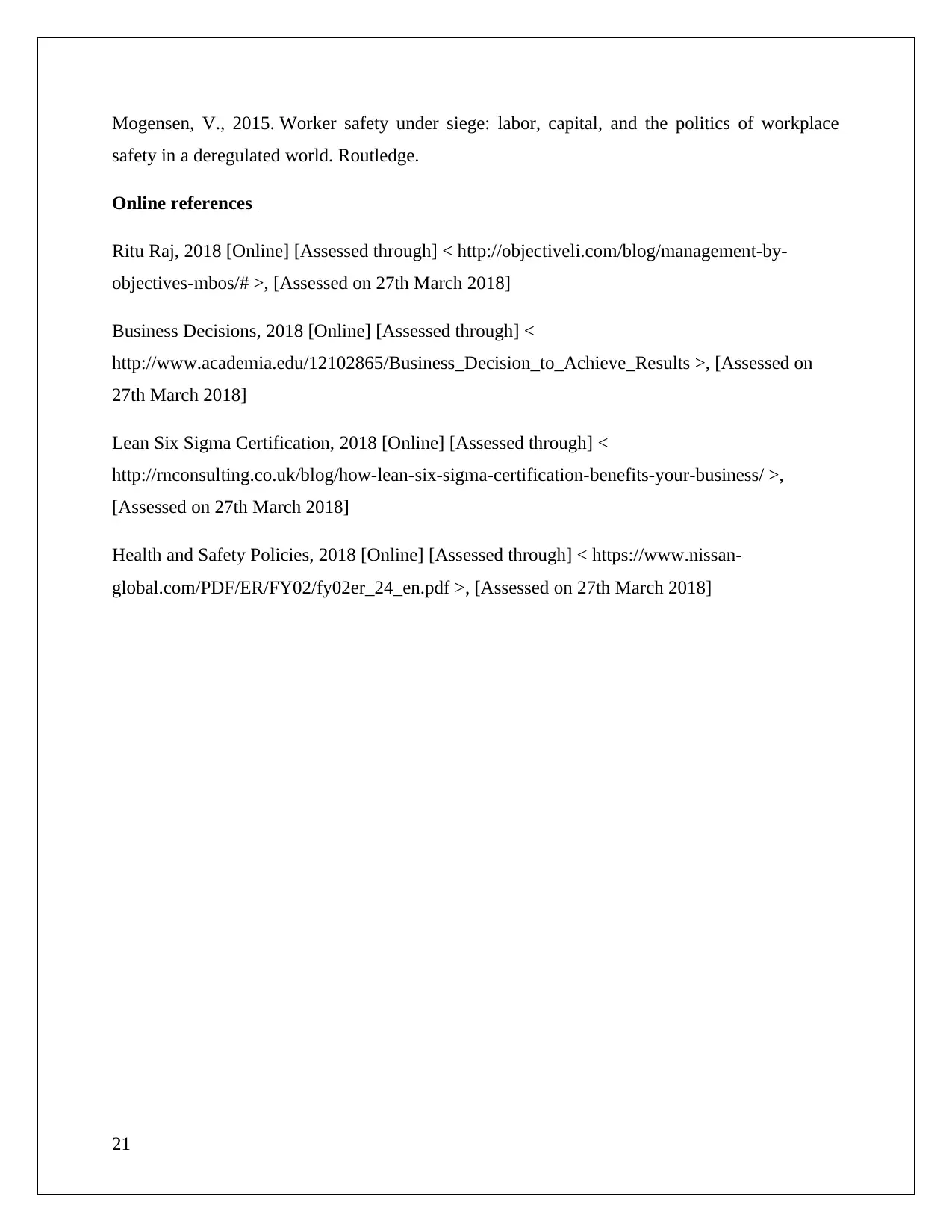
Mogensen, V., 2015. Worker safety under siege: labor, capital, and the politics of workplace
safety in a deregulated world. Routledge.
Online references
Ritu Raj, 2018 [Online] [Assessed through] < http://objectiveli.com/blog/management-by-
objectives-mbos/# >, [Assessed on 27th March 2018]
Business Decisions, 2018 [Online] [Assessed through] <
http://www.academia.edu/12102865/Business_Decision_to_Achieve_Results >, [Assessed on
27th March 2018]
Lean Six Sigma Certification, 2018 [Online] [Assessed through] <
http://rnconsulting.co.uk/blog/how-lean-six-sigma-certification-benefits-your-business/ >,
[Assessed on 27th March 2018]
Health and Safety Policies, 2018 [Online] [Assessed through] < https://www.nissan-
global.com/PDF/ER/FY02/fy02er_24_en.pdf >, [Assessed on 27th March 2018]
21
safety in a deregulated world. Routledge.
Online references
Ritu Raj, 2018 [Online] [Assessed through] < http://objectiveli.com/blog/management-by-
objectives-mbos/# >, [Assessed on 27th March 2018]
Business Decisions, 2018 [Online] [Assessed through] <
http://www.academia.edu/12102865/Business_Decision_to_Achieve_Results >, [Assessed on
27th March 2018]
Lean Six Sigma Certification, 2018 [Online] [Assessed through] <
http://rnconsulting.co.uk/blog/how-lean-six-sigma-certification-benefits-your-business/ >,
[Assessed on 27th March 2018]
Health and Safety Policies, 2018 [Online] [Assessed through] < https://www.nissan-
global.com/PDF/ER/FY02/fy02er_24_en.pdf >, [Assessed on 27th March 2018]
21
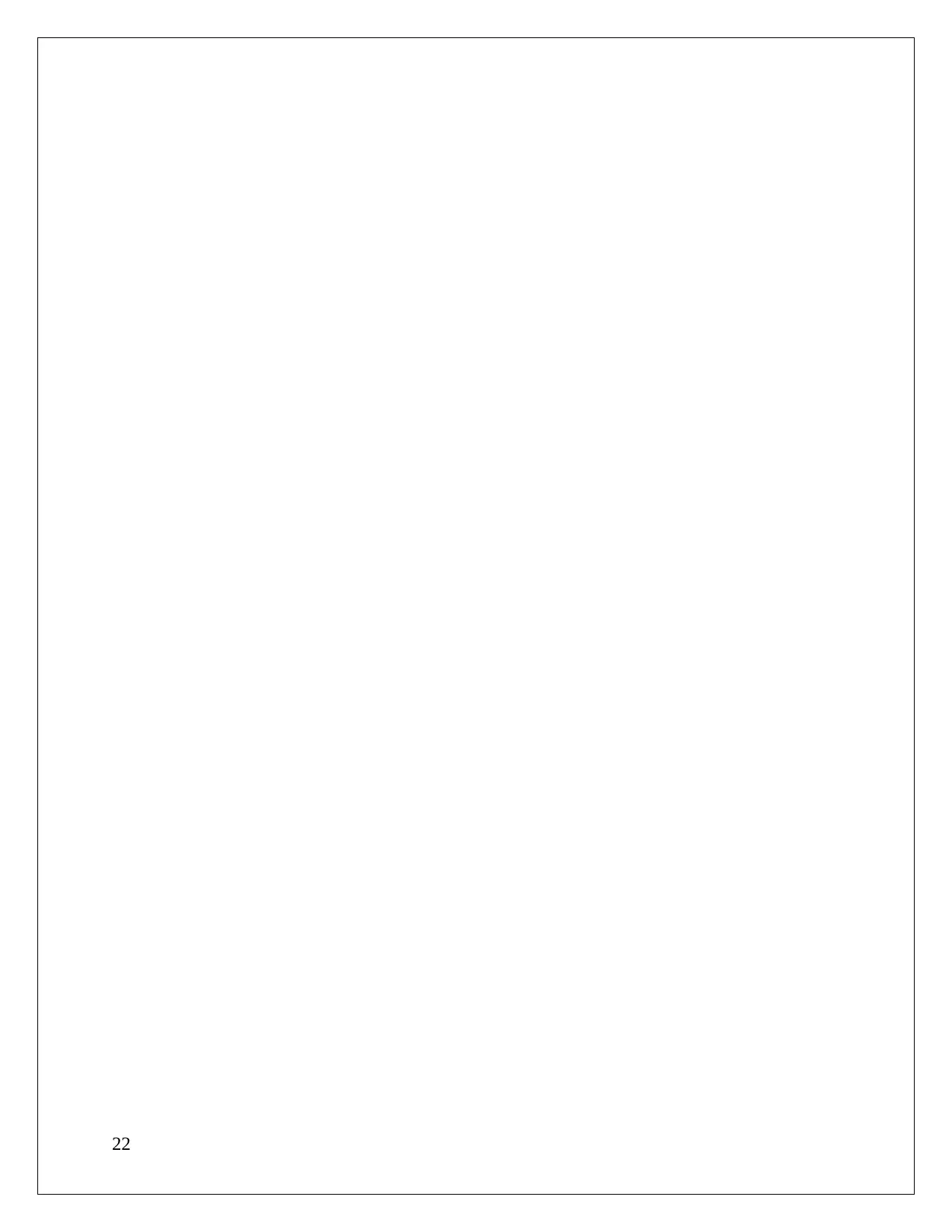
22
1 out of 27
Related Documents

Your All-in-One AI-Powered Toolkit for Academic Success.
+13062052269
info@desklib.com
Available 24*7 on WhatsApp / Email
Unlock your academic potential
© 2024 | Zucol Services PVT LTD | All rights reserved.