In-Depth Analysis of Honda's Business Operations and Reliability
VerifiedAdded on 2023/06/12
|22
|4108
|93
Report
AI Summary
This report provides a comprehensive analysis of Honda Motor Co. Ltd.'s business operations and reliability strategies. It begins with a company description, highlighting Honda's mission, key performance indicators (KPIs), and operational philosophies. The report includes a flowchart illustrating the interrelation of various manufacturing and processing functions, followed by an affinity diagram identifying key factors such as customer satisfaction and efficient manufacturing. A detailed table outlines consumer requirements ('Whats') and the required processes ('Hows'), which are then used to construct a House of Quality (HOQ) for Honda's processes. The report also covers Honda's information collection system, emphasizing market analysis and social media-based research. It concludes with performance importance graph and recommendations for improving Honda's operational efficiency and reliability. Desklib provides access to similar solved assignments and study tools for students.
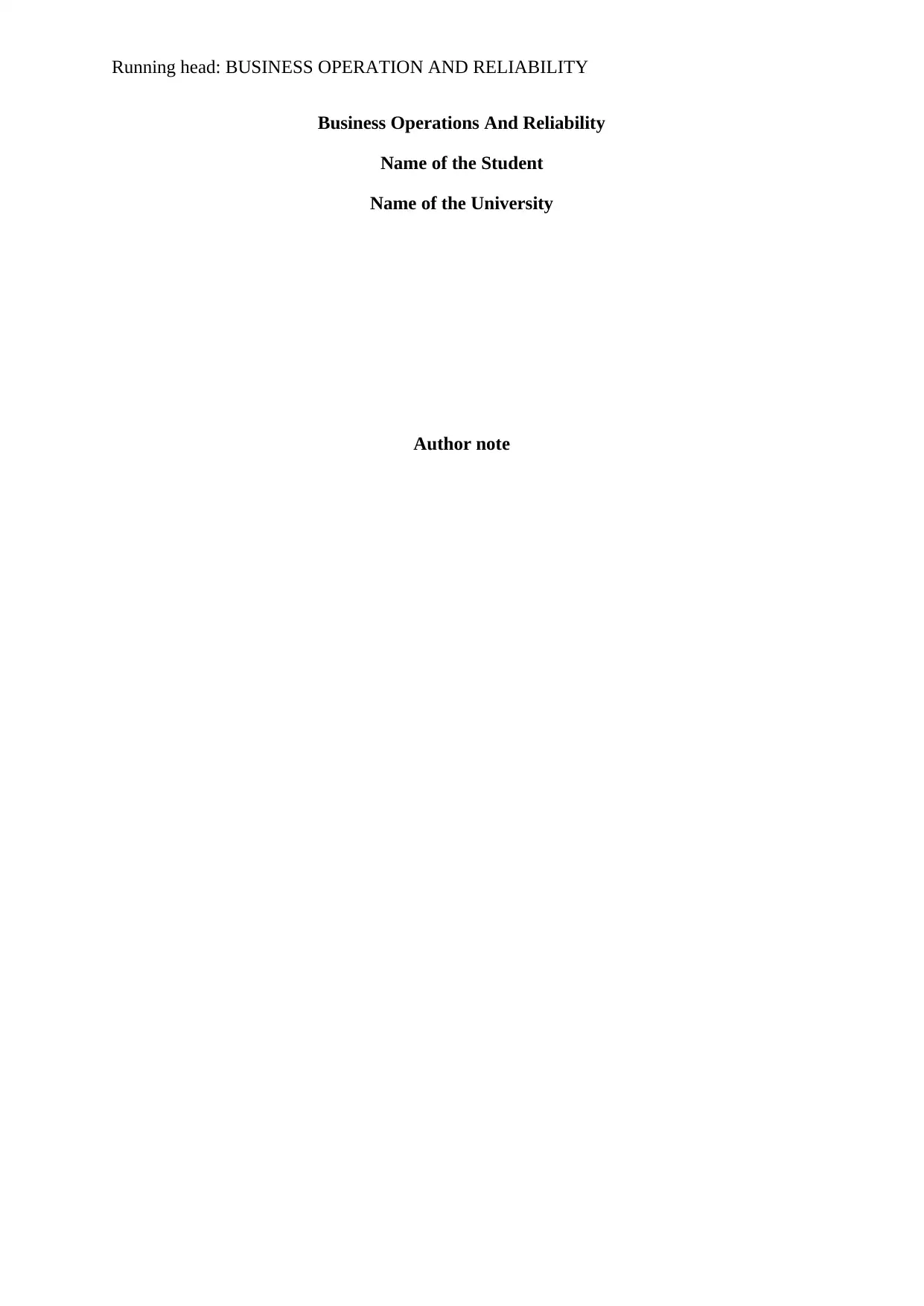
Running head: BUSINESS OPERATION AND RELIABILITY
Business Operations And Reliability
Name of the Student
Name of the University
Author note
Business Operations And Reliability
Name of the Student
Name of the University
Author note
Paraphrase This Document
Need a fresh take? Get an instant paraphrase of this document with our AI Paraphraser
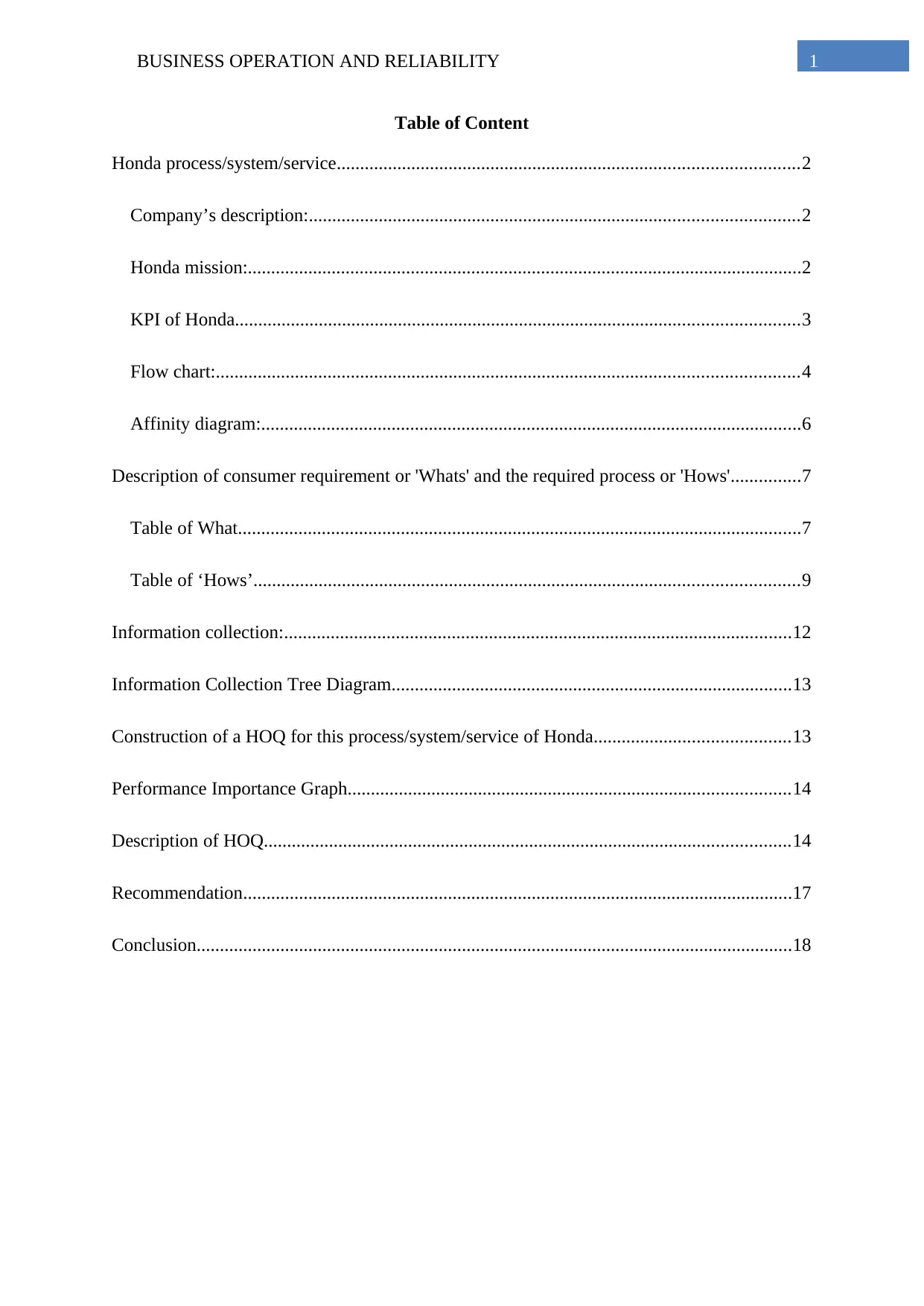
1BUSINESS OPERATION AND RELIABILITY
Table of Content
Honda process/system/service...................................................................................................2
Company’s description:.........................................................................................................2
Honda mission:.......................................................................................................................2
KPI of Honda.........................................................................................................................3
Flow chart:.............................................................................................................................4
Affinity diagram:....................................................................................................................6
Description of consumer requirement or 'Whats' and the required process or 'Hows'...............7
Table of What.........................................................................................................................7
Table of ‘Hows’.....................................................................................................................9
Information collection:.............................................................................................................12
Information Collection Tree Diagram......................................................................................13
Construction of a HOQ for this process/system/service of Honda..........................................13
Performance Importance Graph...............................................................................................14
Description of HOQ.................................................................................................................14
Recommendation......................................................................................................................17
Conclusion................................................................................................................................18
Table of Content
Honda process/system/service...................................................................................................2
Company’s description:.........................................................................................................2
Honda mission:.......................................................................................................................2
KPI of Honda.........................................................................................................................3
Flow chart:.............................................................................................................................4
Affinity diagram:....................................................................................................................6
Description of consumer requirement or 'Whats' and the required process or 'Hows'...............7
Table of What.........................................................................................................................7
Table of ‘Hows’.....................................................................................................................9
Information collection:.............................................................................................................12
Information Collection Tree Diagram......................................................................................13
Construction of a HOQ for this process/system/service of Honda..........................................13
Performance Importance Graph...............................................................................................14
Description of HOQ.................................................................................................................14
Recommendation......................................................................................................................17
Conclusion................................................................................................................................18
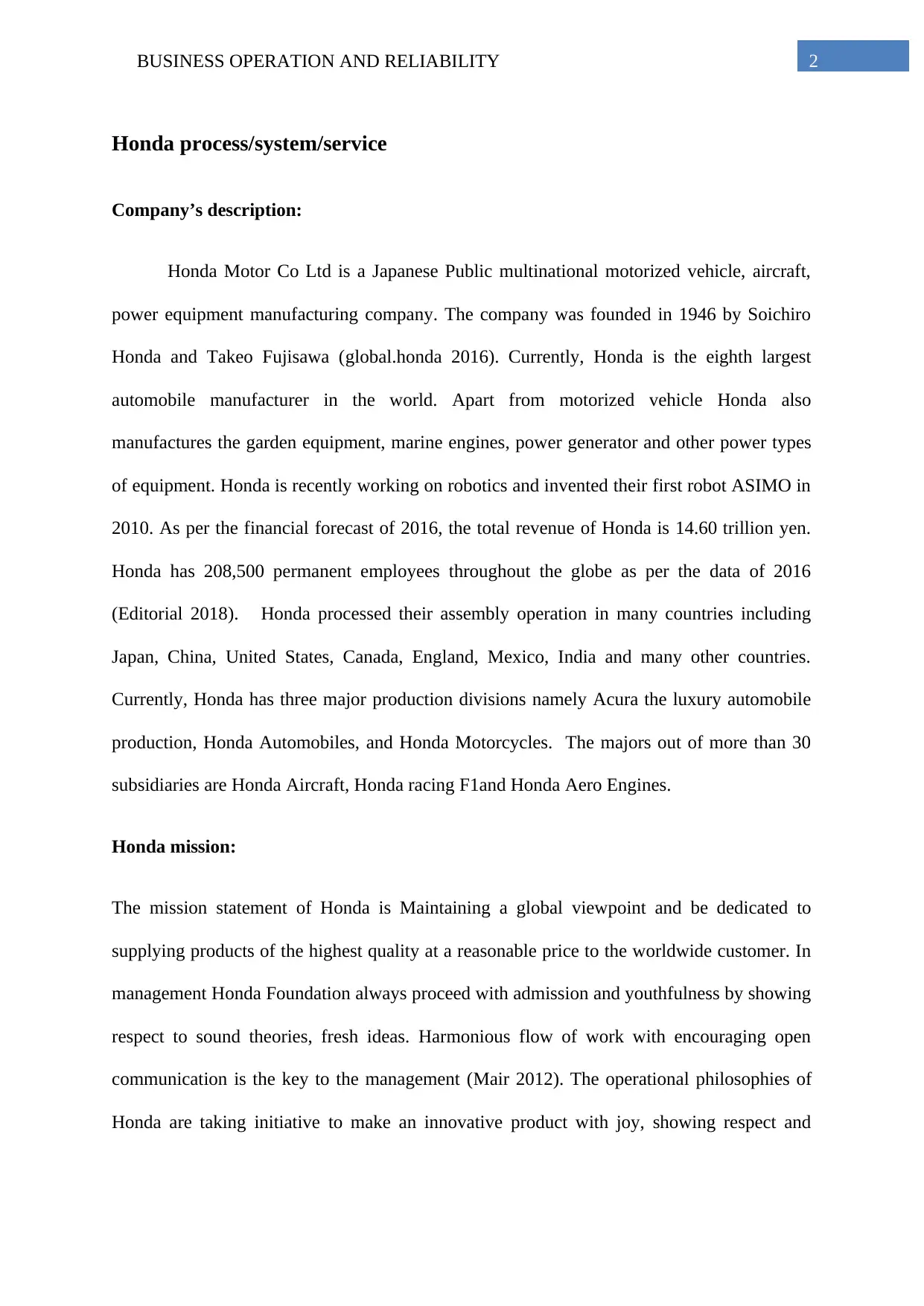
2BUSINESS OPERATION AND RELIABILITY
Honda process/system/service
Company’s description:
Honda Motor Co Ltd is a Japanese Public multinational motorized vehicle, aircraft,
power equipment manufacturing company. The company was founded in 1946 by Soichiro
Honda and Takeo Fujisawa (global.honda 2016). Currently, Honda is the eighth largest
automobile manufacturer in the world. Apart from motorized vehicle Honda also
manufactures the garden equipment, marine engines, power generator and other power types
of equipment. Honda is recently working on robotics and invented their first robot ASIMO in
2010. As per the financial forecast of 2016, the total revenue of Honda is 14.60 trillion yen.
Honda has 208,500 permanent employees throughout the globe as per the data of 2016
(Editorial 2018). Honda processed their assembly operation in many countries including
Japan, China, United States, Canada, England, Mexico, India and many other countries.
Currently, Honda has three major production divisions namely Acura the luxury automobile
production, Honda Automobiles, and Honda Motorcycles. The majors out of more than 30
subsidiaries are Honda Aircraft, Honda racing F1and Honda Aero Engines.
Honda mission:
The mission statement of Honda is Maintaining a global viewpoint and be dedicated to
supplying products of the highest quality at a reasonable price to the worldwide customer. In
management Honda Foundation always proceed with admission and youthfulness by showing
respect to sound theories, fresh ideas. Harmonious flow of work with encouraging open
communication is the key to the management (Mair 2012). The operational philosophies of
Honda are taking initiative to make an innovative product with joy, showing respect and
Honda process/system/service
Company’s description:
Honda Motor Co Ltd is a Japanese Public multinational motorized vehicle, aircraft,
power equipment manufacturing company. The company was founded in 1946 by Soichiro
Honda and Takeo Fujisawa (global.honda 2016). Currently, Honda is the eighth largest
automobile manufacturer in the world. Apart from motorized vehicle Honda also
manufactures the garden equipment, marine engines, power generator and other power types
of equipment. Honda is recently working on robotics and invented their first robot ASIMO in
2010. As per the financial forecast of 2016, the total revenue of Honda is 14.60 trillion yen.
Honda has 208,500 permanent employees throughout the globe as per the data of 2016
(Editorial 2018). Honda processed their assembly operation in many countries including
Japan, China, United States, Canada, England, Mexico, India and many other countries.
Currently, Honda has three major production divisions namely Acura the luxury automobile
production, Honda Automobiles, and Honda Motorcycles. The majors out of more than 30
subsidiaries are Honda Aircraft, Honda racing F1and Honda Aero Engines.
Honda mission:
The mission statement of Honda is Maintaining a global viewpoint and be dedicated to
supplying products of the highest quality at a reasonable price to the worldwide customer. In
management Honda Foundation always proceed with admission and youthfulness by showing
respect to sound theories, fresh ideas. Harmonious flow of work with encouraging open
communication is the key to the management (Mair 2012). The operational philosophies of
Honda are taking initiative to make an innovative product with joy, showing respect and
You're viewing a preview
Unlock full access by subscribing today!
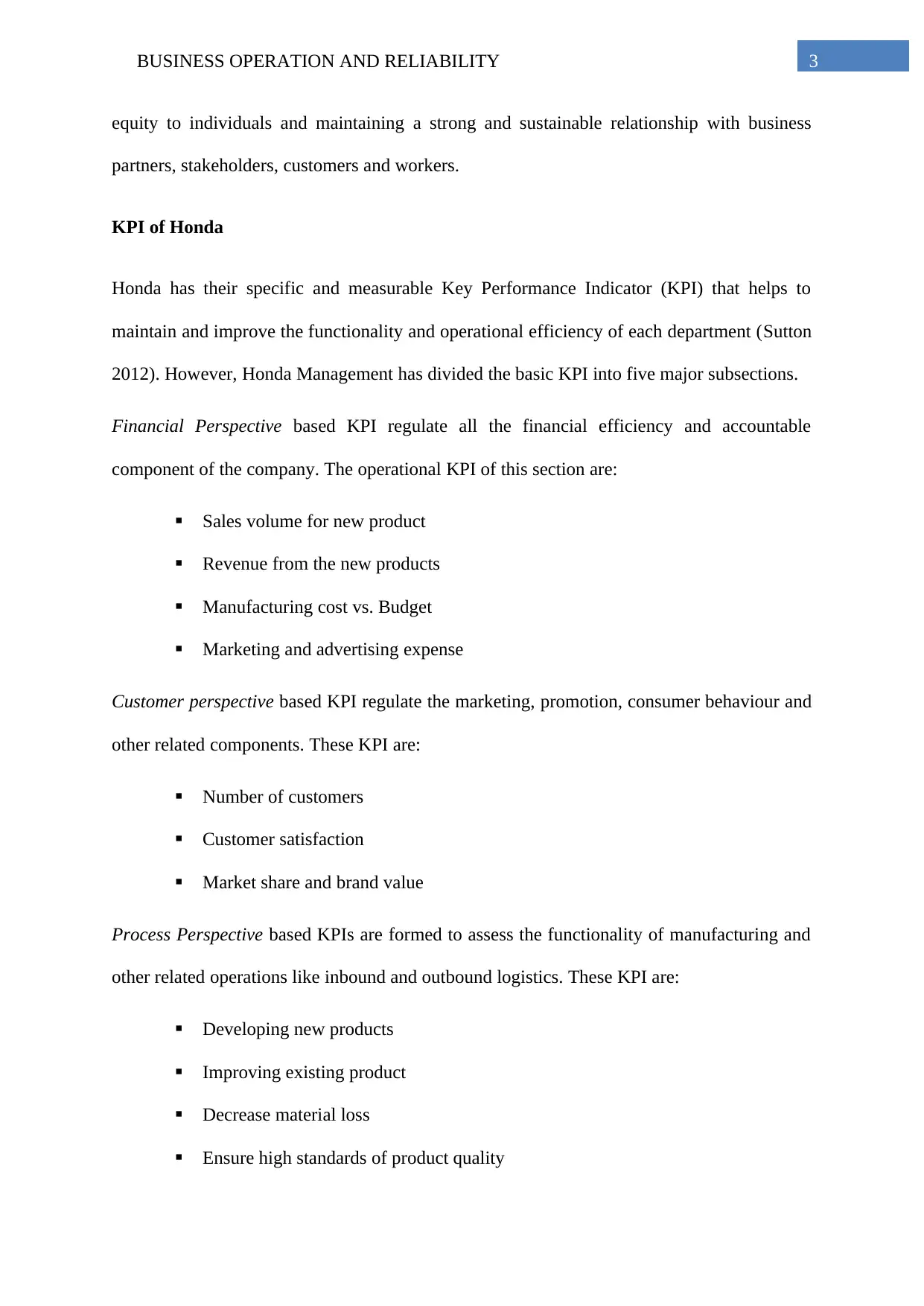
3BUSINESS OPERATION AND RELIABILITY
equity to individuals and maintaining a strong and sustainable relationship with business
partners, stakeholders, customers and workers.
KPI of Honda
Honda has their specific and measurable Key Performance Indicator (KPI) that helps to
maintain and improve the functionality and operational efficiency of each department (Sutton
2012). However, Honda Management has divided the basic KPI into five major subsections.
Financial Perspective based KPI regulate all the financial efficiency and accountable
component of the company. The operational KPI of this section are:
Sales volume for new product
Revenue from the new products
Manufacturing cost vs. Budget
Marketing and advertising expense
Customer perspective based KPI regulate the marketing, promotion, consumer behaviour and
other related components. These KPI are:
Number of customers
Customer satisfaction
Market share and brand value
Process Perspective based KPIs are formed to assess the functionality of manufacturing and
other related operations like inbound and outbound logistics. These KPI are:
Developing new products
Improving existing product
Decrease material loss
Ensure high standards of product quality
equity to individuals and maintaining a strong and sustainable relationship with business
partners, stakeholders, customers and workers.
KPI of Honda
Honda has their specific and measurable Key Performance Indicator (KPI) that helps to
maintain and improve the functionality and operational efficiency of each department (Sutton
2012). However, Honda Management has divided the basic KPI into five major subsections.
Financial Perspective based KPI regulate all the financial efficiency and accountable
component of the company. The operational KPI of this section are:
Sales volume for new product
Revenue from the new products
Manufacturing cost vs. Budget
Marketing and advertising expense
Customer perspective based KPI regulate the marketing, promotion, consumer behaviour and
other related components. These KPI are:
Number of customers
Customer satisfaction
Market share and brand value
Process Perspective based KPIs are formed to assess the functionality of manufacturing and
other related operations like inbound and outbound logistics. These KPI are:
Developing new products
Improving existing product
Decrease material loss
Ensure high standards of product quality
Paraphrase This Document
Need a fresh take? Get an instant paraphrase of this document with our AI Paraphraser
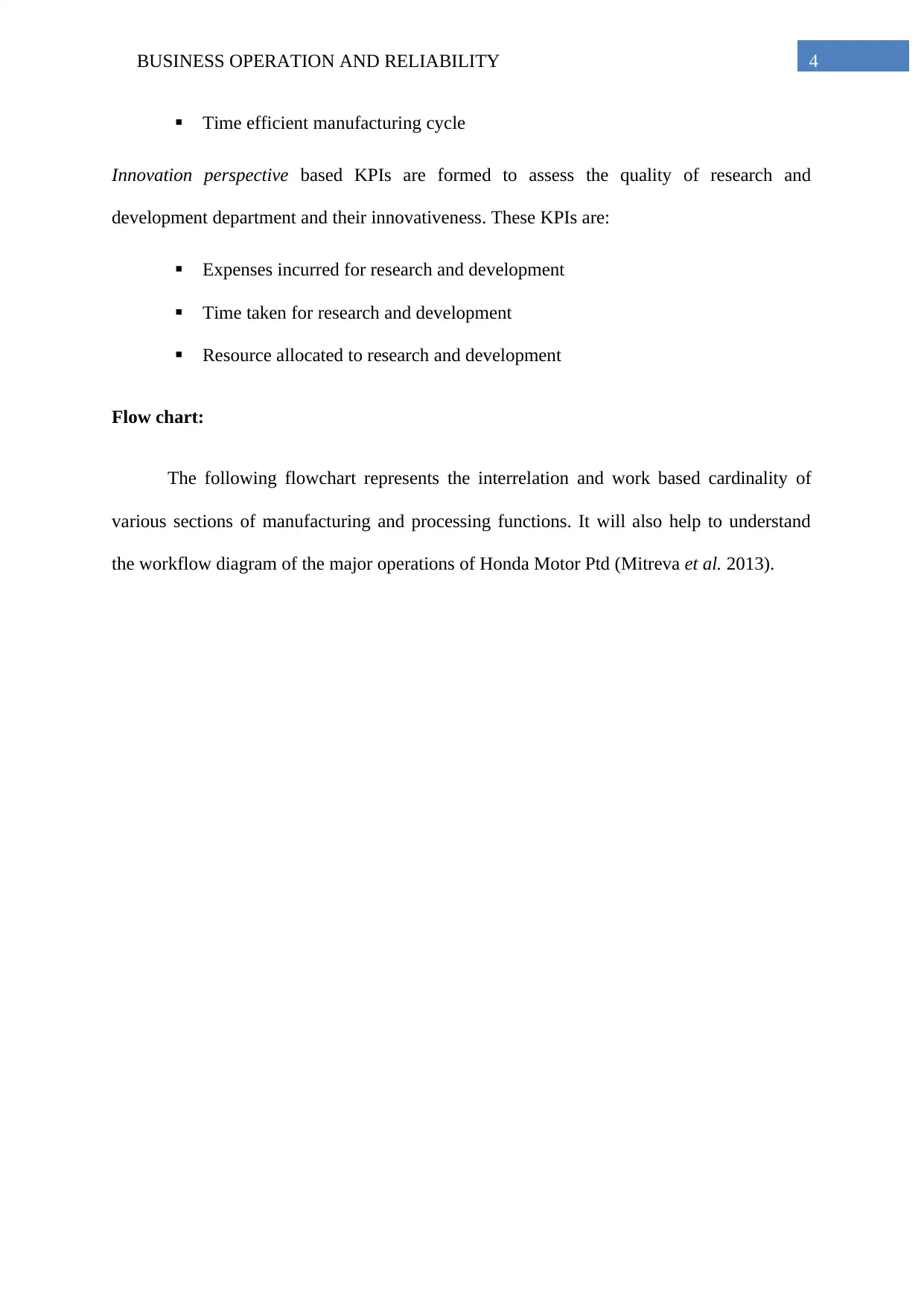
4BUSINESS OPERATION AND RELIABILITY
Time efficient manufacturing cycle
Innovation perspective based KPIs are formed to assess the quality of research and
development department and their innovativeness. These KPIs are:
Expenses incurred for research and development
Time taken for research and development
Resource allocated to research and development
Flow chart:
The following flowchart represents the interrelation and work based cardinality of
various sections of manufacturing and processing functions. It will also help to understand
the workflow diagram of the major operations of Honda Motor Ptd (Mitreva et al. 2013).
Time efficient manufacturing cycle
Innovation perspective based KPIs are formed to assess the quality of research and
development department and their innovativeness. These KPIs are:
Expenses incurred for research and development
Time taken for research and development
Resource allocated to research and development
Flow chart:
The following flowchart represents the interrelation and work based cardinality of
various sections of manufacturing and processing functions. It will also help to understand
the workflow diagram of the major operations of Honda Motor Ptd (Mitreva et al. 2013).
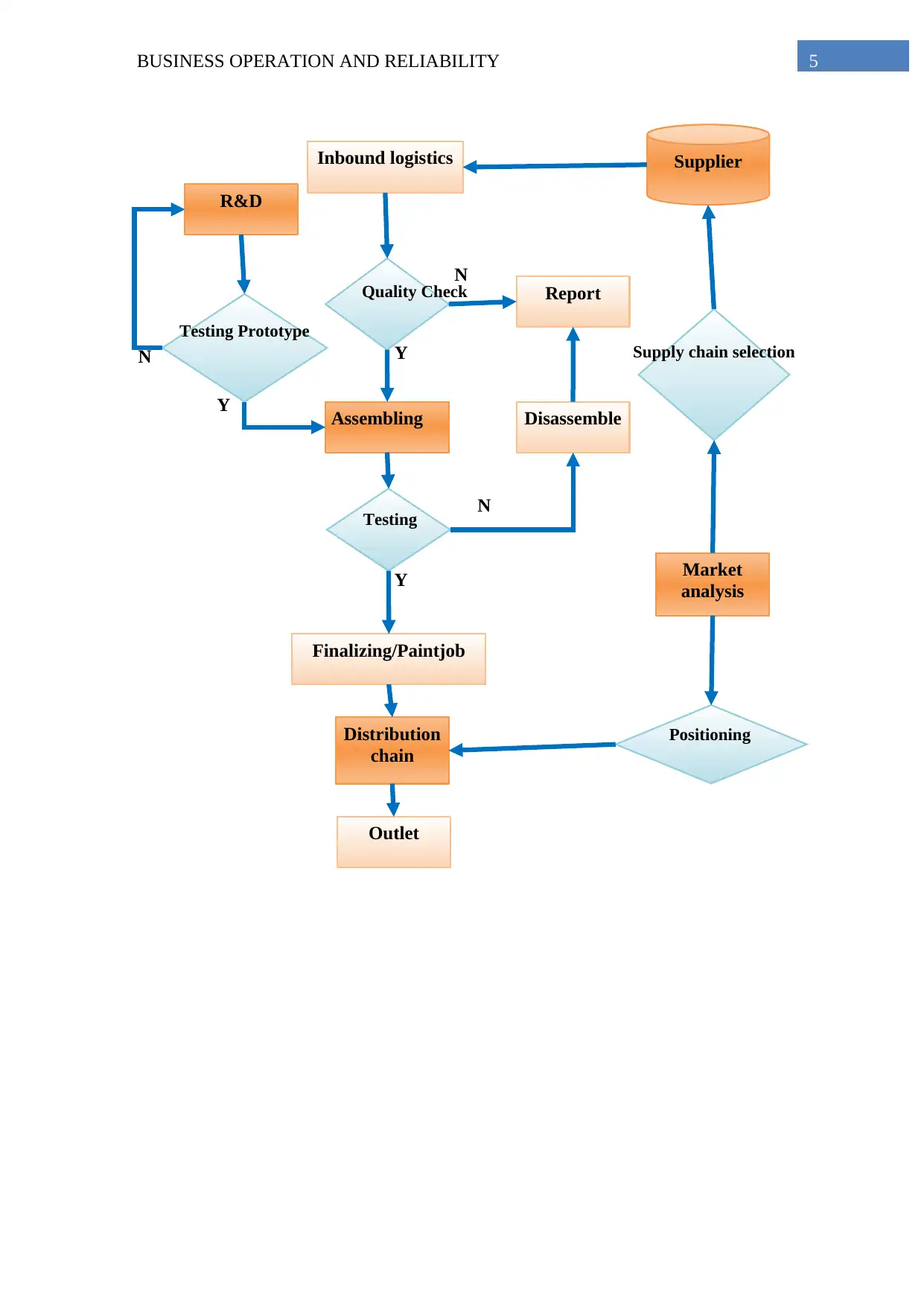
5BUSINESS OPERATION AND RELIABILITY
Inbound logistics
DisassembleAssembling
Finalizing/Paintjob
Distribution
chain
Quality Check Report
Testing
R&D
Testing Prototype
Market
analysis
Positioning
Outlet
Y
Y
N
N
N
Y Supply chain selection
Supplier
Inbound logistics
DisassembleAssembling
Finalizing/Paintjob
Distribution
chain
Quality Check Report
Testing
R&D
Testing Prototype
Market
analysis
Positioning
Outlet
Y
Y
N
N
N
Y Supply chain selection
Supplier
You're viewing a preview
Unlock full access by subscribing today!
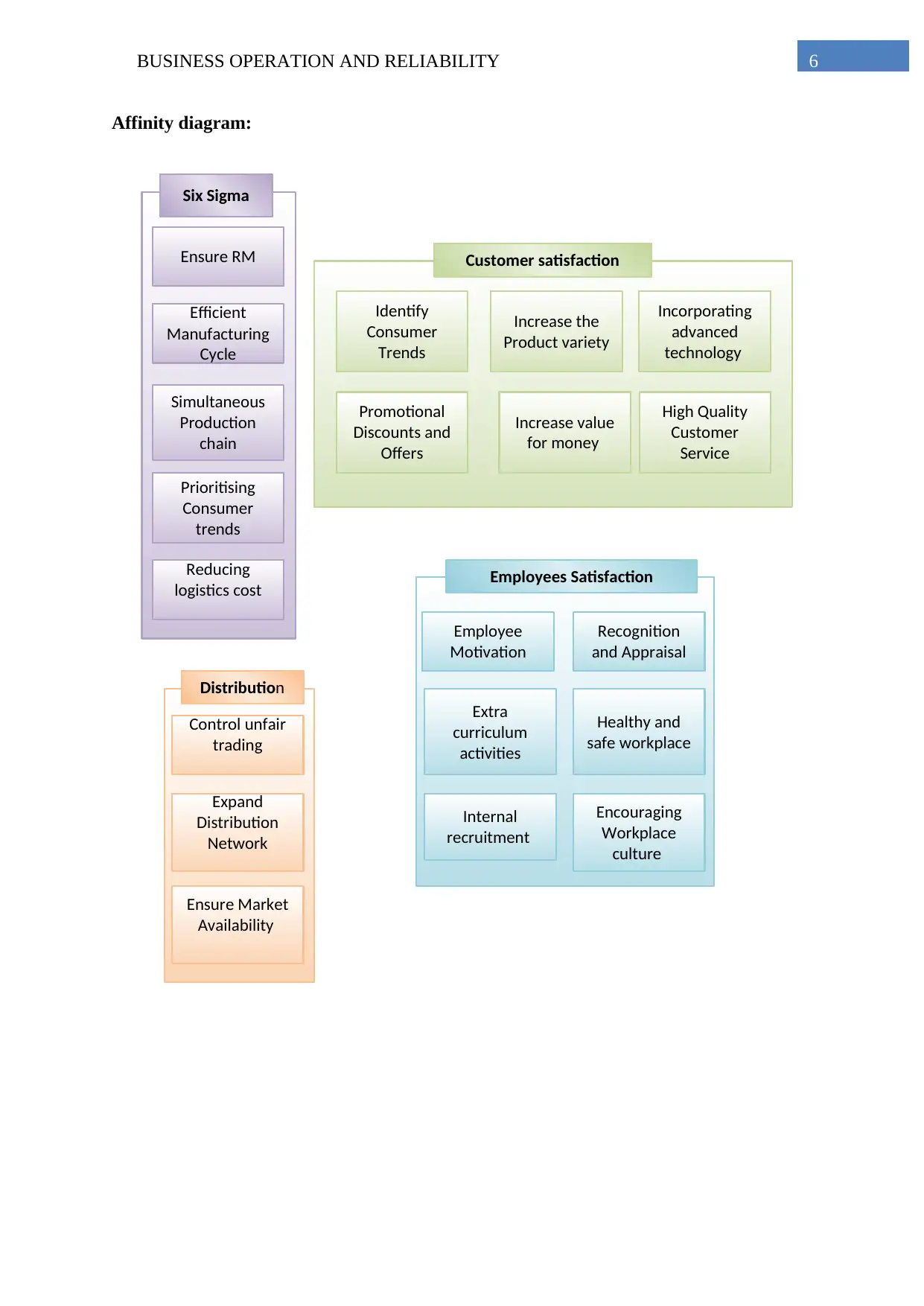
6BUSINESS OPERATION AND RELIABILITY
Ensure RM
Efficient
Manufacturing
Cycle
Reducing
logistics cost
Simultaneous
Production
chain
Six Sigma
Prioritising
Consumer
trends
Identify
Consumer
Trends
Customer satisfaction
Increase the
Product variety
Incorporating
advanced
technology
Promotional
Discounts and
Offers
Increase value
for money
High Quality
Customer
Service
Employee
Motivation
Employees Satisfaction
Extra
curriculum
activities
Recognition
and Appraisal
Internal
recruitment
Healthy and
safe workplace
Encouraging
Workplace
culture
Control unfair
trading
Distribution
Expand
Distribution
Network
Ensure Market
Availability
Affinity diagram:
Ensure RM
Efficient
Manufacturing
Cycle
Reducing
logistics cost
Simultaneous
Production
chain
Six Sigma
Prioritising
Consumer
trends
Identify
Consumer
Trends
Customer satisfaction
Increase the
Product variety
Incorporating
advanced
technology
Promotional
Discounts and
Offers
Increase value
for money
High Quality
Customer
Service
Employee
Motivation
Employees Satisfaction
Extra
curriculum
activities
Recognition
and Appraisal
Internal
recruitment
Healthy and
safe workplace
Encouraging
Workplace
culture
Control unfair
trading
Distribution
Expand
Distribution
Network
Ensure Market
Availability
Affinity diagram:
Paraphrase This Document
Need a fresh take? Get an instant paraphrase of this document with our AI Paraphraser
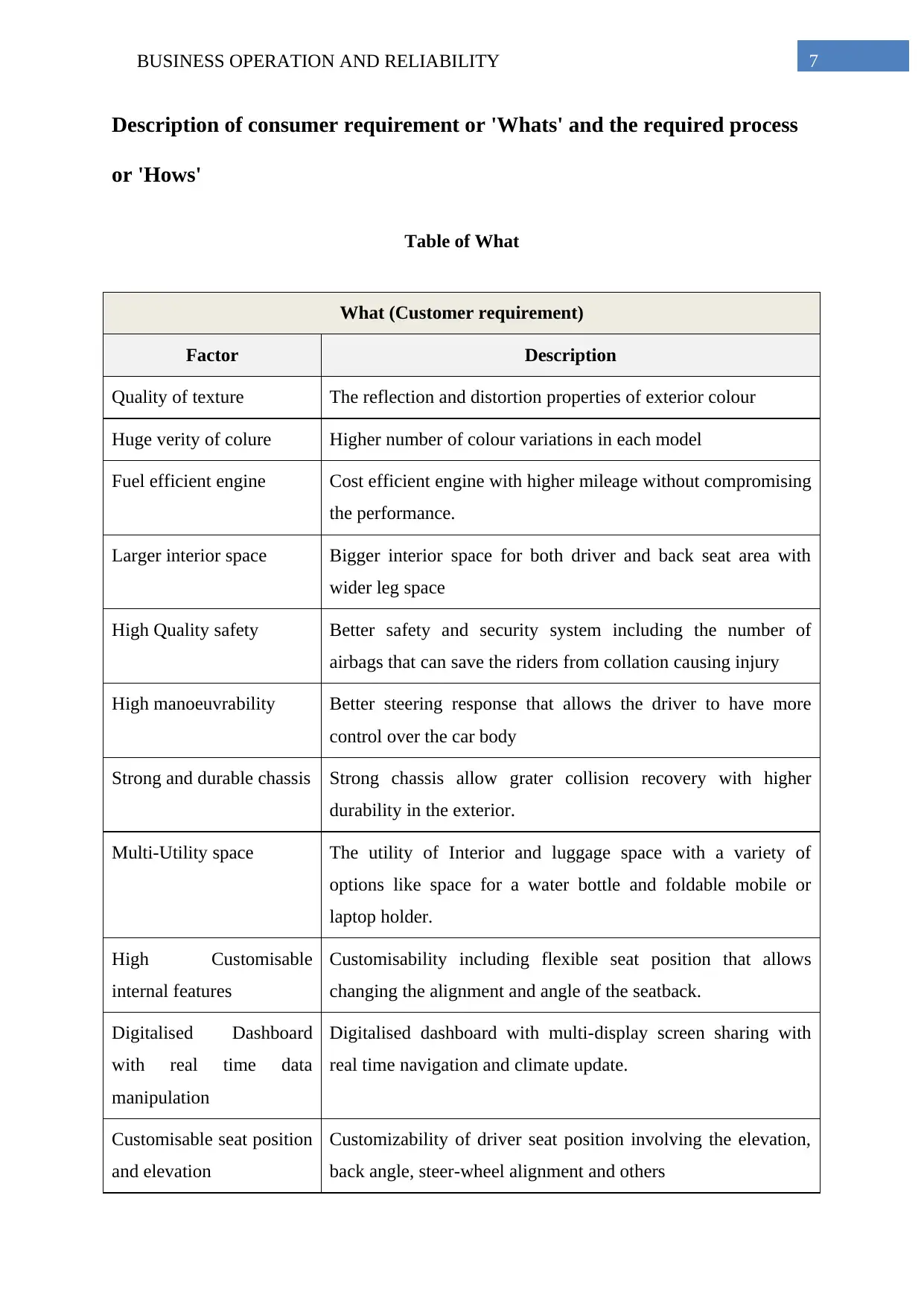
7BUSINESS OPERATION AND RELIABILITY
Description of consumer requirement or 'Whats' and the required process
or 'Hows'
Table of What
What (Customer requirement)
Factor Description
Quality of texture The reflection and distortion properties of exterior colour
Huge verity of colure Higher number of colour variations in each model
Fuel efficient engine Cost efficient engine with higher mileage without compromising
the performance.
Larger interior space Bigger interior space for both driver and back seat area with
wider leg space
High Quality safety Better safety and security system including the number of
airbags that can save the riders from collation causing injury
High manoeuvrability Better steering response that allows the driver to have more
control over the car body
Strong and durable chassis Strong chassis allow grater collision recovery with higher
durability in the exterior.
Multi-Utility space The utility of Interior and luggage space with a variety of
options like space for a water bottle and foldable mobile or
laptop holder.
High Customisable
internal features
Customisability including flexible seat position that allows
changing the alignment and angle of the seatback.
Digitalised Dashboard
with real time data
manipulation
Digitalised dashboard with multi-display screen sharing with
real time navigation and climate update.
Customisable seat position
and elevation
Customizability of driver seat position involving the elevation,
back angle, steer-wheel alignment and others
Description of consumer requirement or 'Whats' and the required process
or 'Hows'
Table of What
What (Customer requirement)
Factor Description
Quality of texture The reflection and distortion properties of exterior colour
Huge verity of colure Higher number of colour variations in each model
Fuel efficient engine Cost efficient engine with higher mileage without compromising
the performance.
Larger interior space Bigger interior space for both driver and back seat area with
wider leg space
High Quality safety Better safety and security system including the number of
airbags that can save the riders from collation causing injury
High manoeuvrability Better steering response that allows the driver to have more
control over the car body
Strong and durable chassis Strong chassis allow grater collision recovery with higher
durability in the exterior.
Multi-Utility space The utility of Interior and luggage space with a variety of
options like space for a water bottle and foldable mobile or
laptop holder.
High Customisable
internal features
Customisability including flexible seat position that allows
changing the alignment and angle of the seatback.
Digitalised Dashboard
with real time data
manipulation
Digitalised dashboard with multi-display screen sharing with
real time navigation and climate update.
Customisable seat position
and elevation
Customizability of driver seat position involving the elevation,
back angle, steer-wheel alignment and others
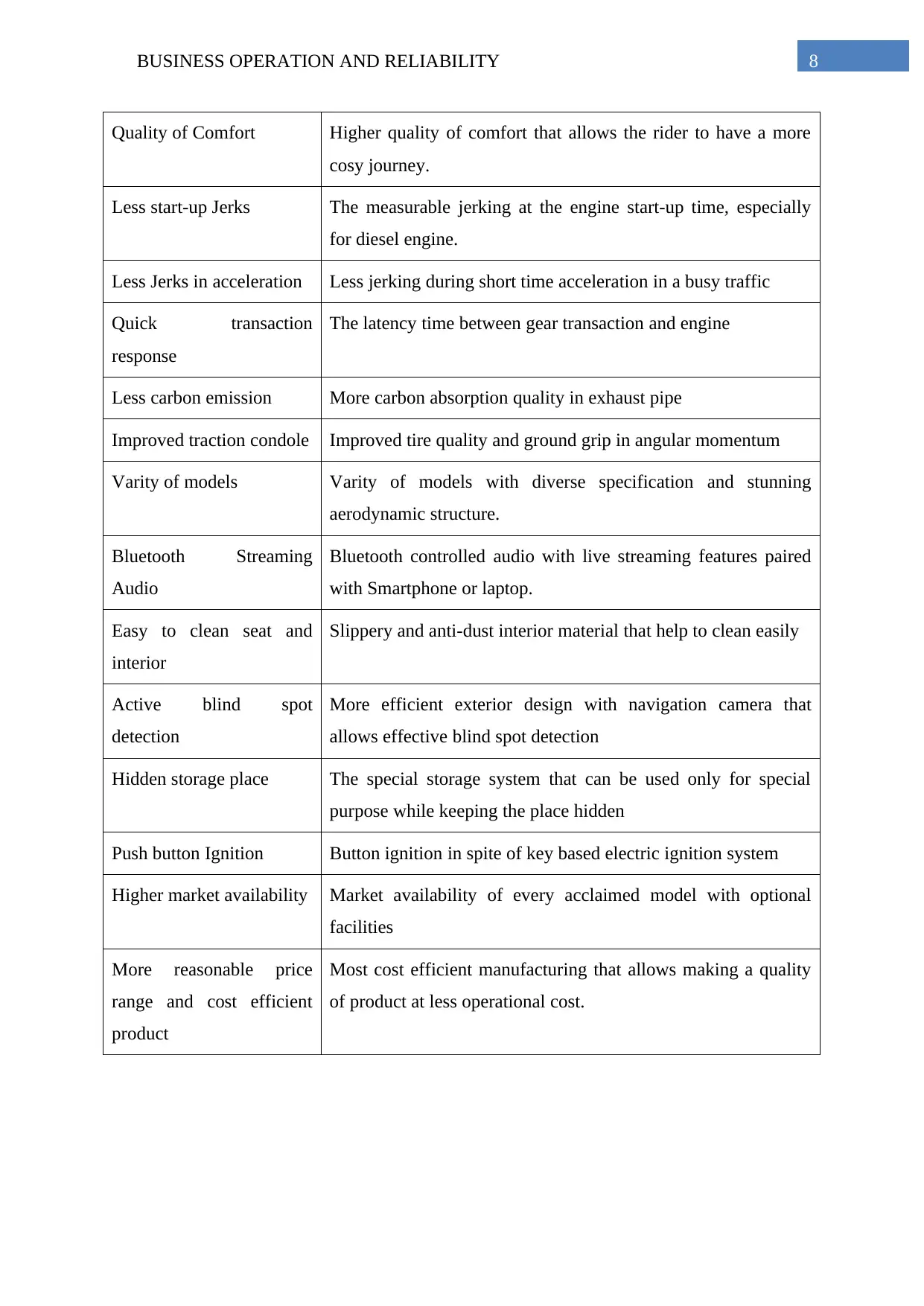
8BUSINESS OPERATION AND RELIABILITY
Quality of Comfort Higher quality of comfort that allows the rider to have a more
cosy journey.
Less start-up Jerks The measurable jerking at the engine start-up time, especially
for diesel engine.
Less Jerks in acceleration Less jerking during short time acceleration in a busy traffic
Quick transaction
response
The latency time between gear transaction and engine
Less carbon emission More carbon absorption quality in exhaust pipe
Improved traction condole Improved tire quality and ground grip in angular momentum
Varity of models Varity of models with diverse specification and stunning
aerodynamic structure.
Bluetooth Streaming
Audio
Bluetooth controlled audio with live streaming features paired
with Smartphone or laptop.
Easy to clean seat and
interior
Slippery and anti-dust interior material that help to clean easily
Active blind spot
detection
More efficient exterior design with navigation camera that
allows effective blind spot detection
Hidden storage place The special storage system that can be used only for special
purpose while keeping the place hidden
Push button Ignition Button ignition in spite of key based electric ignition system
Higher market availability Market availability of every acclaimed model with optional
facilities
More reasonable price
range and cost efficient
product
Most cost efficient manufacturing that allows making a quality
of product at less operational cost.
Quality of Comfort Higher quality of comfort that allows the rider to have a more
cosy journey.
Less start-up Jerks The measurable jerking at the engine start-up time, especially
for diesel engine.
Less Jerks in acceleration Less jerking during short time acceleration in a busy traffic
Quick transaction
response
The latency time between gear transaction and engine
Less carbon emission More carbon absorption quality in exhaust pipe
Improved traction condole Improved tire quality and ground grip in angular momentum
Varity of models Varity of models with diverse specification and stunning
aerodynamic structure.
Bluetooth Streaming
Audio
Bluetooth controlled audio with live streaming features paired
with Smartphone or laptop.
Easy to clean seat and
interior
Slippery and anti-dust interior material that help to clean easily
Active blind spot
detection
More efficient exterior design with navigation camera that
allows effective blind spot detection
Hidden storage place The special storage system that can be used only for special
purpose while keeping the place hidden
Push button Ignition Button ignition in spite of key based electric ignition system
Higher market availability Market availability of every acclaimed model with optional
facilities
More reasonable price
range and cost efficient
product
Most cost efficient manufacturing that allows making a quality
of product at less operational cost.
You're viewing a preview
Unlock full access by subscribing today!
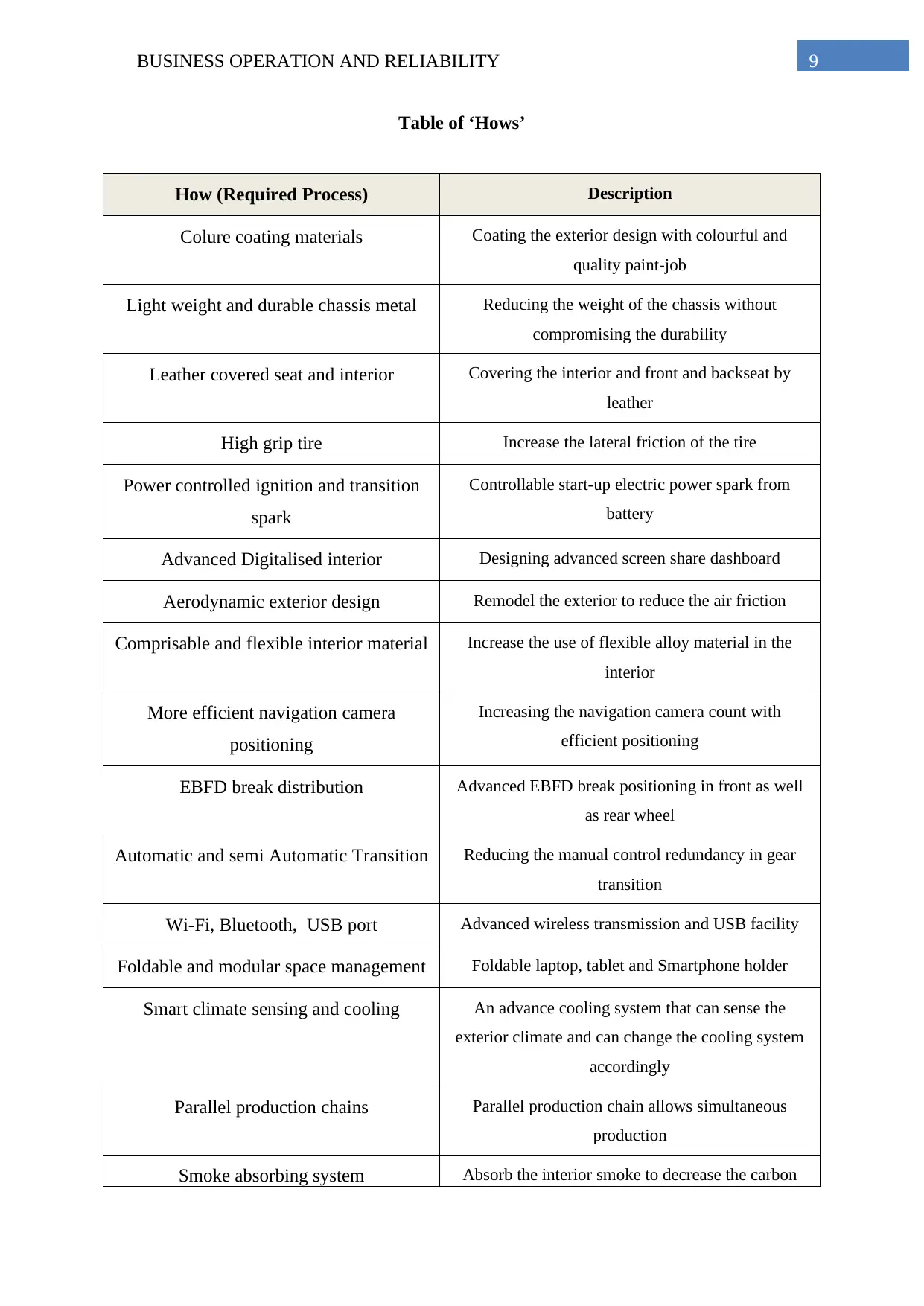
9BUSINESS OPERATION AND RELIABILITY
Table of ‘Hows’
How (Required Process) Description
Colure coating materials Coating the exterior design with colourful and
quality paint-job
Light weight and durable chassis metal Reducing the weight of the chassis without
compromising the durability
Leather covered seat and interior Covering the interior and front and backseat by
leather
High grip tire Increase the lateral friction of the tire
Power controlled ignition and transition
spark
Controllable start-up electric power spark from
battery
Advanced Digitalised interior Designing advanced screen share dashboard
Aerodynamic exterior design Remodel the exterior to reduce the air friction
Comprisable and flexible interior material Increase the use of flexible alloy material in the
interior
More efficient navigation camera
positioning
Increasing the navigation camera count with
efficient positioning
EBFD break distribution Advanced EBFD break positioning in front as well
as rear wheel
Automatic and semi Automatic Transition Reducing the manual control redundancy in gear
transition
Wi-Fi, Bluetooth, USB port Advanced wireless transmission and USB facility
Foldable and modular space management Foldable laptop, tablet and Smartphone holder
Smart climate sensing and cooling An advance cooling system that can sense the
exterior climate and can change the cooling system
accordingly
Parallel production chains Parallel production chain allows simultaneous
production
Smoke absorbing system Absorb the interior smoke to decrease the carbon
Table of ‘Hows’
How (Required Process) Description
Colure coating materials Coating the exterior design with colourful and
quality paint-job
Light weight and durable chassis metal Reducing the weight of the chassis without
compromising the durability
Leather covered seat and interior Covering the interior and front and backseat by
leather
High grip tire Increase the lateral friction of the tire
Power controlled ignition and transition
spark
Controllable start-up electric power spark from
battery
Advanced Digitalised interior Designing advanced screen share dashboard
Aerodynamic exterior design Remodel the exterior to reduce the air friction
Comprisable and flexible interior material Increase the use of flexible alloy material in the
interior
More efficient navigation camera
positioning
Increasing the navigation camera count with
efficient positioning
EBFD break distribution Advanced EBFD break positioning in front as well
as rear wheel
Automatic and semi Automatic Transition Reducing the manual control redundancy in gear
transition
Wi-Fi, Bluetooth, USB port Advanced wireless transmission and USB facility
Foldable and modular space management Foldable laptop, tablet and Smartphone holder
Smart climate sensing and cooling An advance cooling system that can sense the
exterior climate and can change the cooling system
accordingly
Parallel production chains Parallel production chain allows simultaneous
production
Smoke absorbing system Absorb the interior smoke to decrease the carbon
Paraphrase This Document
Need a fresh take? Get an instant paraphrase of this document with our AI Paraphraser
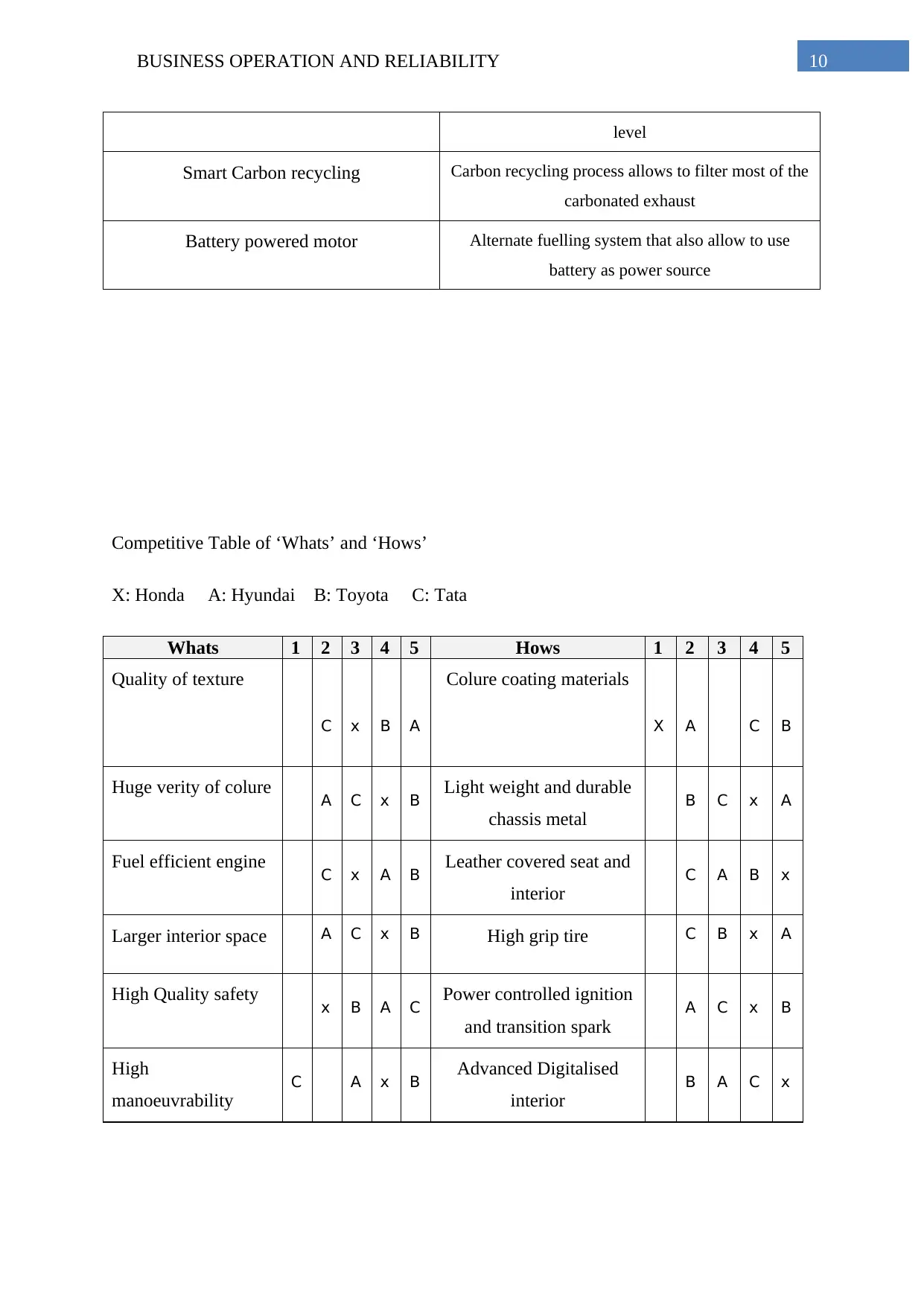
10BUSINESS OPERATION AND RELIABILITY
level
Smart Carbon recycling Carbon recycling process allows to filter most of the
carbonated exhaust
Battery powered motor Alternate fuelling system that also allow to use
battery as power source
Competitive Table of ‘Whats’ and ‘Hows’
X: Honda A: Hyundai B: Toyota C: Tata
Whats 1 2 3 4 5 Hows 1 2 3 4 5
Quality of texture
C x B A
Colure coating materials
X A C B
Huge verity of colure A C x B Light weight and durable
chassis metal
B C x A
Fuel efficient engine C x A B Leather covered seat and
interior
C A B x
Larger interior space A C x B High grip tire C B x A
High Quality safety x B A C Power controlled ignition
and transition spark
A C x B
High
manoeuvrability
C A x B Advanced Digitalised
interior
B A C x
level
Smart Carbon recycling Carbon recycling process allows to filter most of the
carbonated exhaust
Battery powered motor Alternate fuelling system that also allow to use
battery as power source
Competitive Table of ‘Whats’ and ‘Hows’
X: Honda A: Hyundai B: Toyota C: Tata
Whats 1 2 3 4 5 Hows 1 2 3 4 5
Quality of texture
C x B A
Colure coating materials
X A C B
Huge verity of colure A C x B Light weight and durable
chassis metal
B C x A
Fuel efficient engine C x A B Leather covered seat and
interior
C A B x
Larger interior space A C x B High grip tire C B x A
High Quality safety x B A C Power controlled ignition
and transition spark
A C x B
High
manoeuvrability
C A x B Advanced Digitalised
interior
B A C x
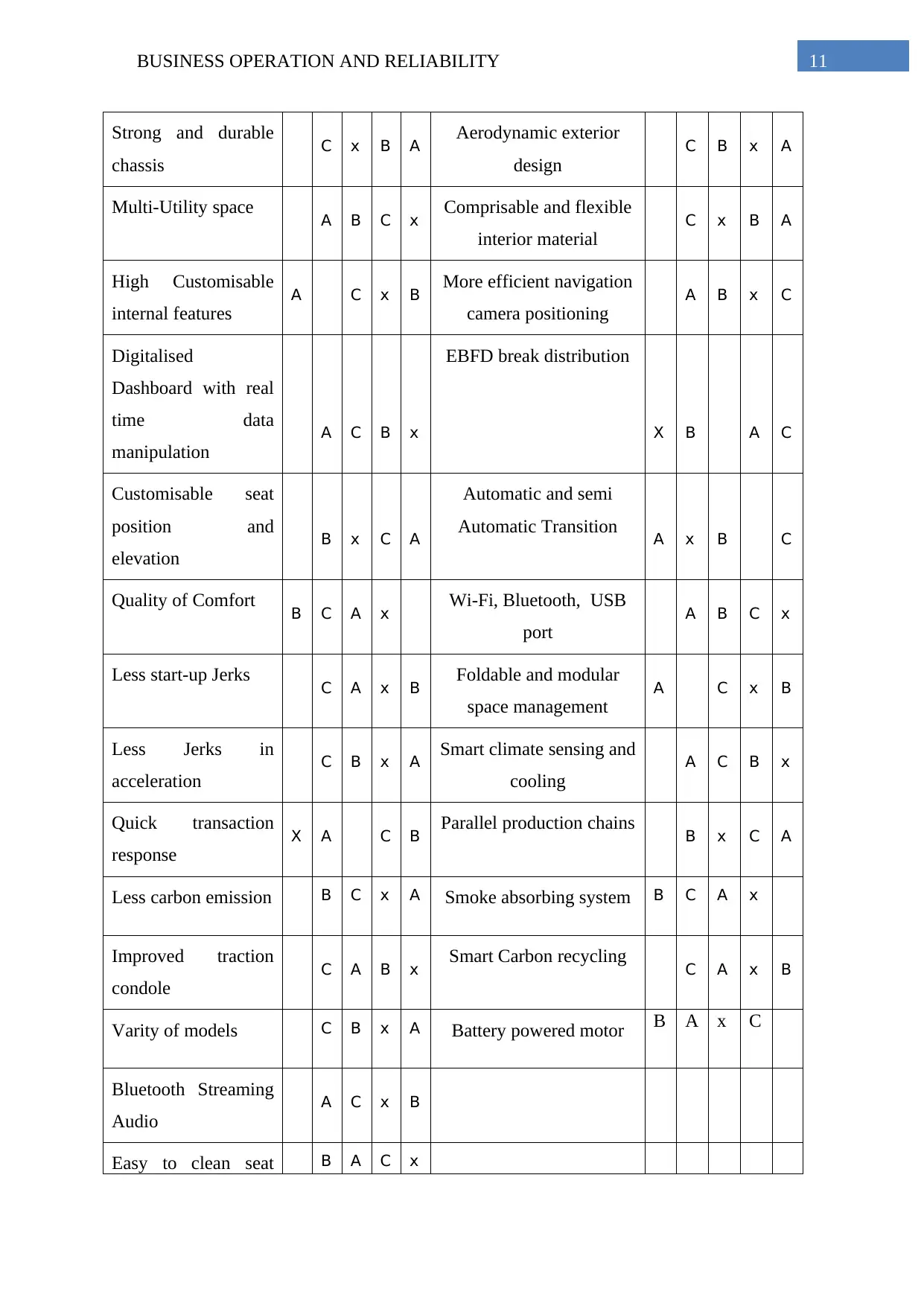
11BUSINESS OPERATION AND RELIABILITY
Strong and durable
chassis
C x B A Aerodynamic exterior
design
C B x A
Multi-Utility space A B C x Comprisable and flexible
interior material
C x B A
High Customisable
internal features
A C x B More efficient navigation
camera positioning
A B x C
Digitalised
Dashboard with real
time data
manipulation
A C B x
EBFD break distribution
X B A C
Customisable seat
position and
elevation
B x C A
Automatic and semi
Automatic Transition A x B C
Quality of Comfort B C A x Wi-Fi, Bluetooth, USB
port
A B C x
Less start-up Jerks C A x B Foldable and modular
space management
A C x B
Less Jerks in
acceleration
C B x A Smart climate sensing and
cooling
A C B x
Quick transaction
response
X A C B Parallel production chains B x C A
Less carbon emission B C x A Smoke absorbing system B C A x
Improved traction
condole
C A B x Smart Carbon recycling C A x B
Varity of models C B x A Battery powered motor B A x C
Bluetooth Streaming
Audio
A C x B
Easy to clean seat B A C x
Strong and durable
chassis
C x B A Aerodynamic exterior
design
C B x A
Multi-Utility space A B C x Comprisable and flexible
interior material
C x B A
High Customisable
internal features
A C x B More efficient navigation
camera positioning
A B x C
Digitalised
Dashboard with real
time data
manipulation
A C B x
EBFD break distribution
X B A C
Customisable seat
position and
elevation
B x C A
Automatic and semi
Automatic Transition A x B C
Quality of Comfort B C A x Wi-Fi, Bluetooth, USB
port
A B C x
Less start-up Jerks C A x B Foldable and modular
space management
A C x B
Less Jerks in
acceleration
C B x A Smart climate sensing and
cooling
A C B x
Quick transaction
response
X A C B Parallel production chains B x C A
Less carbon emission B C x A Smoke absorbing system B C A x
Improved traction
condole
C A B x Smart Carbon recycling C A x B
Varity of models C B x A Battery powered motor B A x C
Bluetooth Streaming
Audio
A C x B
Easy to clean seat B A C x
You're viewing a preview
Unlock full access by subscribing today!
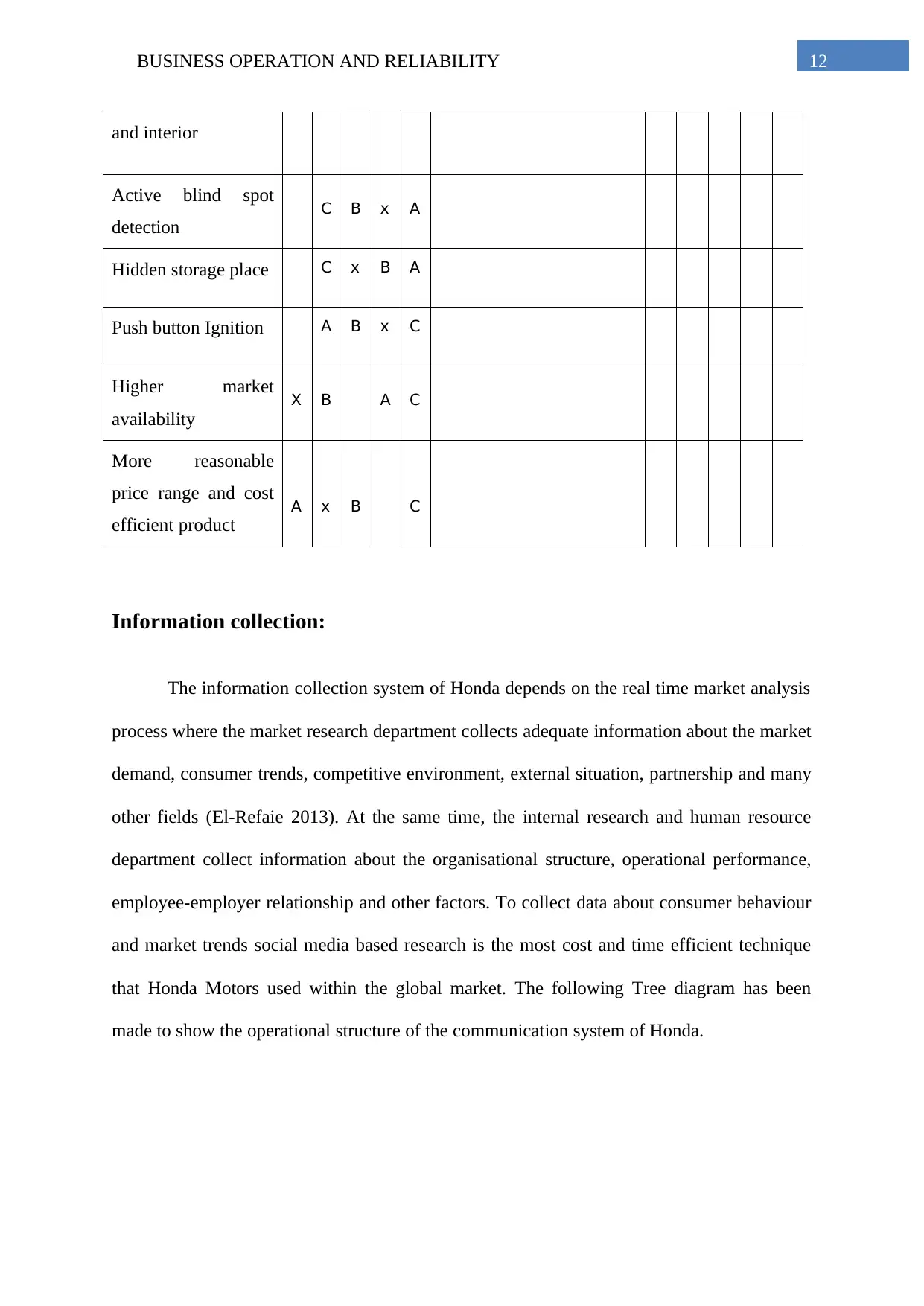
12BUSINESS OPERATION AND RELIABILITY
and interior
Active blind spot
detection
C B x A
Hidden storage place C x B A
Push button Ignition A B x C
Higher market
availability
X B A C
More reasonable
price range and cost
efficient product
A x B C
Information collection:
The information collection system of Honda depends on the real time market analysis
process where the market research department collects adequate information about the market
demand, consumer trends, competitive environment, external situation, partnership and many
other fields (El-Refaie 2013). At the same time, the internal research and human resource
department collect information about the organisational structure, operational performance,
employee-employer relationship and other factors. To collect data about consumer behaviour
and market trends social media based research is the most cost and time efficient technique
that Honda Motors used within the global market. The following Tree diagram has been
made to show the operational structure of the communication system of Honda.
and interior
Active blind spot
detection
C B x A
Hidden storage place C x B A
Push button Ignition A B x C
Higher market
availability
X B A C
More reasonable
price range and cost
efficient product
A x B C
Information collection:
The information collection system of Honda depends on the real time market analysis
process where the market research department collects adequate information about the market
demand, consumer trends, competitive environment, external situation, partnership and many
other fields (El-Refaie 2013). At the same time, the internal research and human resource
department collect information about the organisational structure, operational performance,
employee-employer relationship and other factors. To collect data about consumer behaviour
and market trends social media based research is the most cost and time efficient technique
that Honda Motors used within the global market. The following Tree diagram has been
made to show the operational structure of the communication system of Honda.
Paraphrase This Document
Need a fresh take? Get an instant paraphrase of this document with our AI Paraphraser
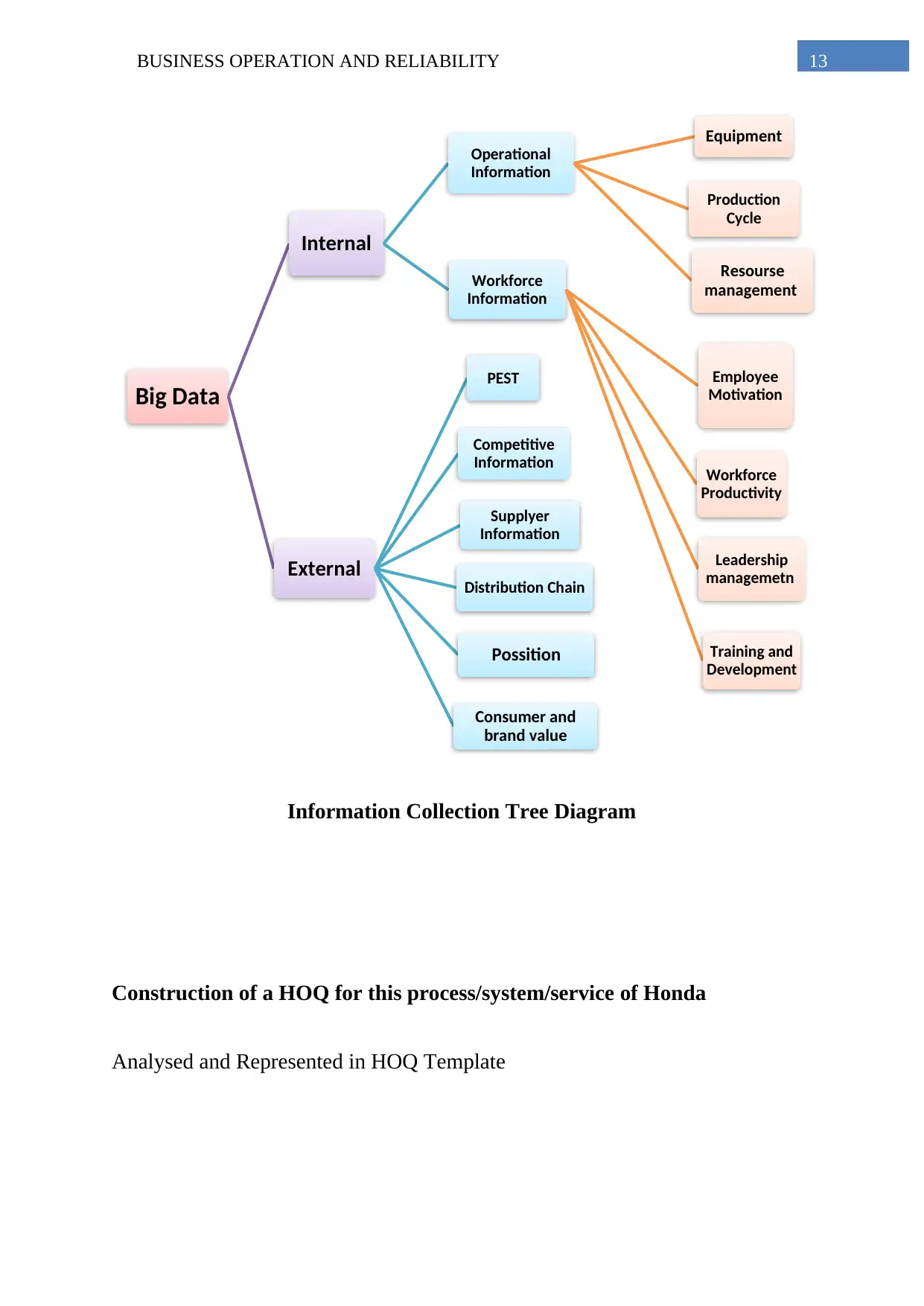
13BUSINESS OPERATION AND RELIABILITY
Information Collection Tree Diagram
Construction of a HOQ for this process/system/service of Honda
Analysed and Represented in HOQ Template
Big Data
Internal
Operational
Information
Equipment
Production
Cycle
Resourse
management
Workforce
Information
Employee
Motivation
Workforce
Productivity
Leadership
managemetn
Training and
Development
External
PEST
Competitive
Information
Supplyer
Information
Distribution Chain
Possition
Consumer and
brand value
Information Collection Tree Diagram
Construction of a HOQ for this process/system/service of Honda
Analysed and Represented in HOQ Template
Big Data
Internal
Operational
Information
Equipment
Production
Cycle
Resourse
management
Workforce
Information
Employee
Motivation
Workforce
Productivity
Leadership
managemetn
Training and
Development
External
PEST
Competitive
Information
Supplyer
Information
Distribution Chain
Possition
Consumer and
brand value

14BUSINESS OPERATION AND RELIABILITY
Performance Importance Graph
Performance Against
competitor
Low High
Value for money Engine performanceImportance to
Customer
High Vulnerable Strength
Digitalisation and advanced interior Parallel supply chain
Low Who Cares? Overkill
Interior clean-ability Use of leather
Description of HOQ
Consumer requirement:
The consumer requirement part focuses on the requirement or the demand of the consumers
from the company that should be prioritised during the production and other business
operation. In this analysis mainly 25 consumer requirements are enlisted within the consumer
requirement segment of House of Quality diagram. The reflection and distortion properties of
exterior colour with variations in each model are highly demanded. Cost efficient or fuel
efficient engine with higher mileage is another demanded properties (Frey 2012). Customer
also requires bigger and customisable interior space for both driver and back seat area with
wider leg space and hidden place. Higher safety and security are always the most highlighter
priority for automobile consumers. Strong and durable chassis with stunning exterior attract
the majority of customers. Advance digitalised dashboard with Bluetooth and USB facilities
are also widespread demands. Cost efficiency is another essential demand that regulates the
overall production operation of an automobile company (Goetsch and Davis, 2014).
Performance Importance Graph
Performance Against
competitor
Low High
Value for money Engine performanceImportance to
Customer
High Vulnerable Strength
Digitalisation and advanced interior Parallel supply chain
Low Who Cares? Overkill
Interior clean-ability Use of leather
Description of HOQ
Consumer requirement:
The consumer requirement part focuses on the requirement or the demand of the consumers
from the company that should be prioritised during the production and other business
operation. In this analysis mainly 25 consumer requirements are enlisted within the consumer
requirement segment of House of Quality diagram. The reflection and distortion properties of
exterior colour with variations in each model are highly demanded. Cost efficient or fuel
efficient engine with higher mileage is another demanded properties (Frey 2012). Customer
also requires bigger and customisable interior space for both driver and back seat area with
wider leg space and hidden place. Higher safety and security are always the most highlighter
priority for automobile consumers. Strong and durable chassis with stunning exterior attract
the majority of customers. Advance digitalised dashboard with Bluetooth and USB facilities
are also widespread demands. Cost efficiency is another essential demand that regulates the
overall production operation of an automobile company (Goetsch and Davis, 2014).
You're viewing a preview
Unlock full access by subscribing today!
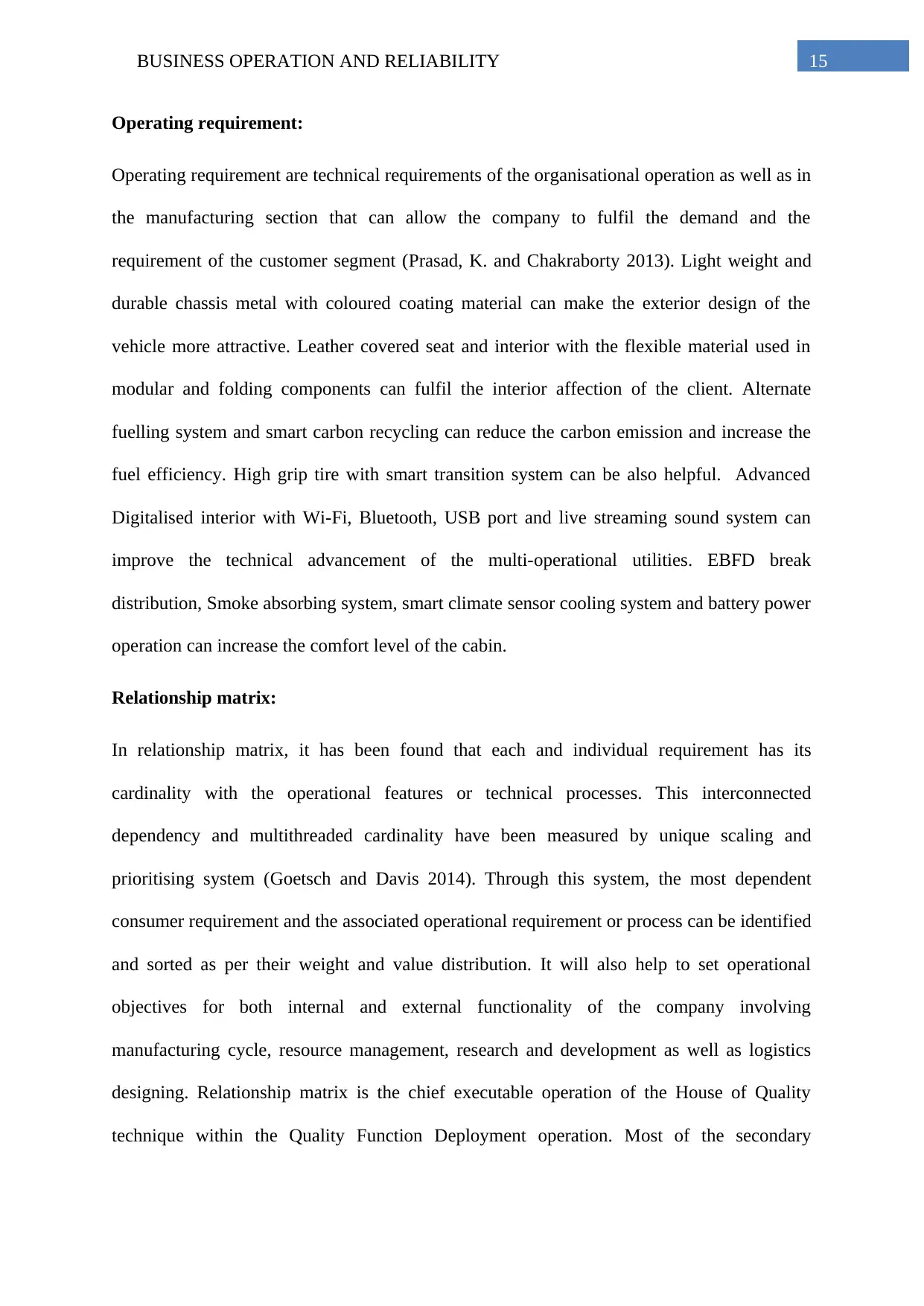
15BUSINESS OPERATION AND RELIABILITY
Operating requirement:
Operating requirement are technical requirements of the organisational operation as well as in
the manufacturing section that can allow the company to fulfil the demand and the
requirement of the customer segment (Prasad, K. and Chakraborty 2013). Light weight and
durable chassis metal with coloured coating material can make the exterior design of the
vehicle more attractive. Leather covered seat and interior with the flexible material used in
modular and folding components can fulfil the interior affection of the client. Alternate
fuelling system and smart carbon recycling can reduce the carbon emission and increase the
fuel efficiency. High grip tire with smart transition system can be also helpful. Advanced
Digitalised interior with Wi-Fi, Bluetooth, USB port and live streaming sound system can
improve the technical advancement of the multi-operational utilities. EBFD break
distribution, Smoke absorbing system, smart climate sensor cooling system and battery power
operation can increase the comfort level of the cabin.
Relationship matrix:
In relationship matrix, it has been found that each and individual requirement has its
cardinality with the operational features or technical processes. This interconnected
dependency and multithreaded cardinality have been measured by unique scaling and
prioritising system (Goetsch and Davis 2014). Through this system, the most dependent
consumer requirement and the associated operational requirement or process can be identified
and sorted as per their weight and value distribution. It will also help to set operational
objectives for both internal and external functionality of the company involving
manufacturing cycle, resource management, research and development as well as logistics
designing. Relationship matrix is the chief executable operation of the House of Quality
technique within the Quality Function Deployment operation. Most of the secondary
Operating requirement:
Operating requirement are technical requirements of the organisational operation as well as in
the manufacturing section that can allow the company to fulfil the demand and the
requirement of the customer segment (Prasad, K. and Chakraborty 2013). Light weight and
durable chassis metal with coloured coating material can make the exterior design of the
vehicle more attractive. Leather covered seat and interior with the flexible material used in
modular and folding components can fulfil the interior affection of the client. Alternate
fuelling system and smart carbon recycling can reduce the carbon emission and increase the
fuel efficiency. High grip tire with smart transition system can be also helpful. Advanced
Digitalised interior with Wi-Fi, Bluetooth, USB port and live streaming sound system can
improve the technical advancement of the multi-operational utilities. EBFD break
distribution, Smoke absorbing system, smart climate sensor cooling system and battery power
operation can increase the comfort level of the cabin.
Relationship matrix:
In relationship matrix, it has been found that each and individual requirement has its
cardinality with the operational features or technical processes. This interconnected
dependency and multithreaded cardinality have been measured by unique scaling and
prioritising system (Goetsch and Davis 2014). Through this system, the most dependent
consumer requirement and the associated operational requirement or process can be identified
and sorted as per their weight and value distribution. It will also help to set operational
objectives for both internal and external functionality of the company involving
manufacturing cycle, resource management, research and development as well as logistics
designing. Relationship matrix is the chief executable operation of the House of Quality
technique within the Quality Function Deployment operation. Most of the secondary
Paraphrase This Document
Need a fresh take? Get an instant paraphrase of this document with our AI Paraphraser
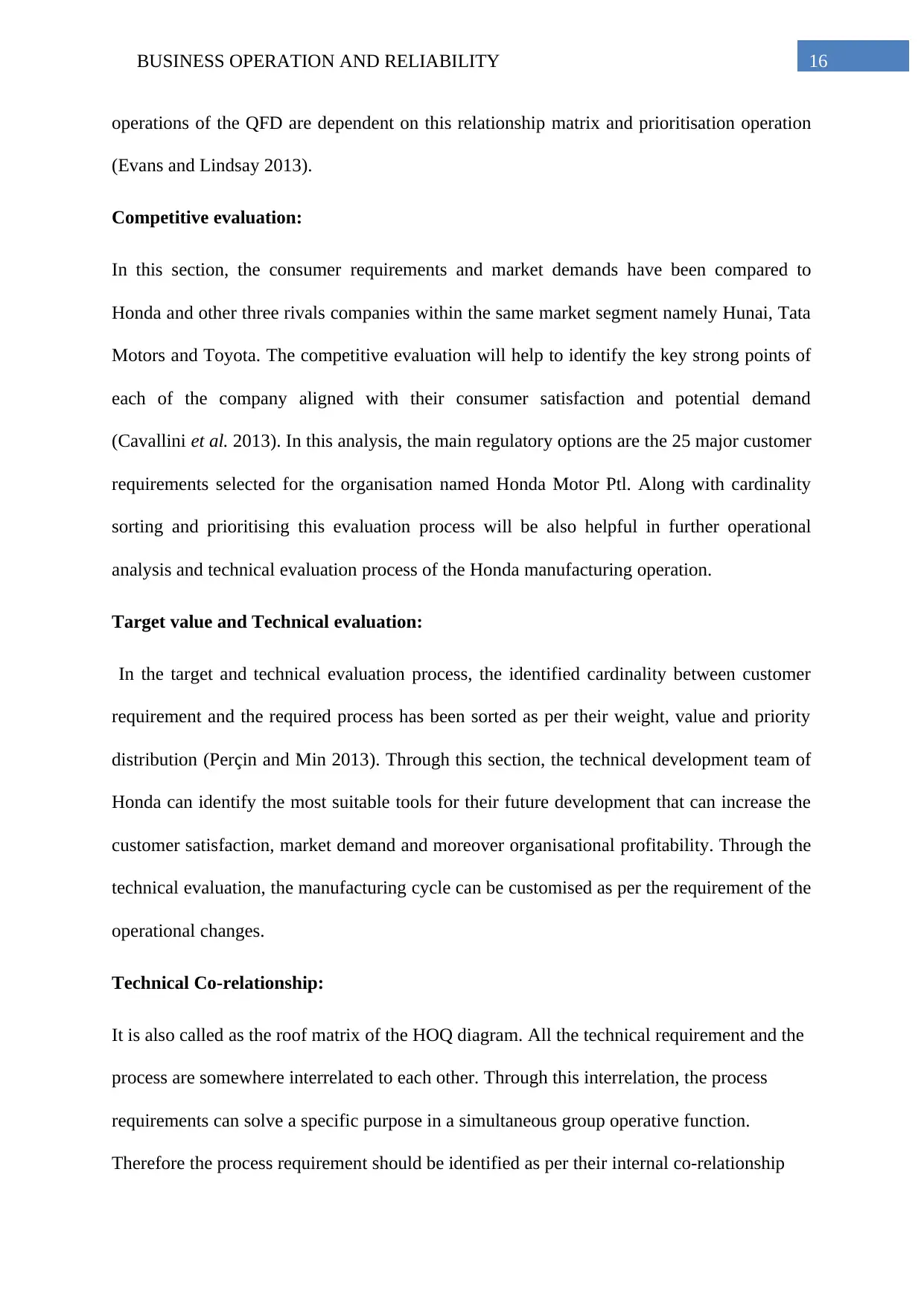
16BUSINESS OPERATION AND RELIABILITY
operations of the QFD are dependent on this relationship matrix and prioritisation operation
(Evans and Lindsay 2013).
Competitive evaluation:
In this section, the consumer requirements and market demands have been compared to
Honda and other three rivals companies within the same market segment namely Hunai, Tata
Motors and Toyota. The competitive evaluation will help to identify the key strong points of
each of the company aligned with their consumer satisfaction and potential demand
(Cavallini et al. 2013). In this analysis, the main regulatory options are the 25 major customer
requirements selected for the organisation named Honda Motor Ptl. Along with cardinality
sorting and prioritising this evaluation process will be also helpful in further operational
analysis and technical evaluation process of the Honda manufacturing operation.
Target value and Technical evaluation:
In the target and technical evaluation process, the identified cardinality between customer
requirement and the required process has been sorted as per their weight, value and priority
distribution (Perçin and Min 2013). Through this section, the technical development team of
Honda can identify the most suitable tools for their future development that can increase the
customer satisfaction, market demand and moreover organisational profitability. Through the
technical evaluation, the manufacturing cycle can be customised as per the requirement of the
operational changes.
Technical Co-relationship:
It is also called as the roof matrix of the HOQ diagram. All the technical requirement and the
process are somewhere interrelated to each other. Through this interrelation, the process
requirements can solve a specific purpose in a simultaneous group operative function.
Therefore the process requirement should be identified as per their internal co-relationship
operations of the QFD are dependent on this relationship matrix and prioritisation operation
(Evans and Lindsay 2013).
Competitive evaluation:
In this section, the consumer requirements and market demands have been compared to
Honda and other three rivals companies within the same market segment namely Hunai, Tata
Motors and Toyota. The competitive evaluation will help to identify the key strong points of
each of the company aligned with their consumer satisfaction and potential demand
(Cavallini et al. 2013). In this analysis, the main regulatory options are the 25 major customer
requirements selected for the organisation named Honda Motor Ptl. Along with cardinality
sorting and prioritising this evaluation process will be also helpful in further operational
analysis and technical evaluation process of the Honda manufacturing operation.
Target value and Technical evaluation:
In the target and technical evaluation process, the identified cardinality between customer
requirement and the required process has been sorted as per their weight, value and priority
distribution (Perçin and Min 2013). Through this section, the technical development team of
Honda can identify the most suitable tools for their future development that can increase the
customer satisfaction, market demand and moreover organisational profitability. Through the
technical evaluation, the manufacturing cycle can be customised as per the requirement of the
operational changes.
Technical Co-relationship:
It is also called as the roof matrix of the HOQ diagram. All the technical requirement and the
process are somewhere interrelated to each other. Through this interrelation, the process
requirements can solve a specific purpose in a simultaneous group operative function.
Therefore the process requirement should be identified as per their internal co-relationship
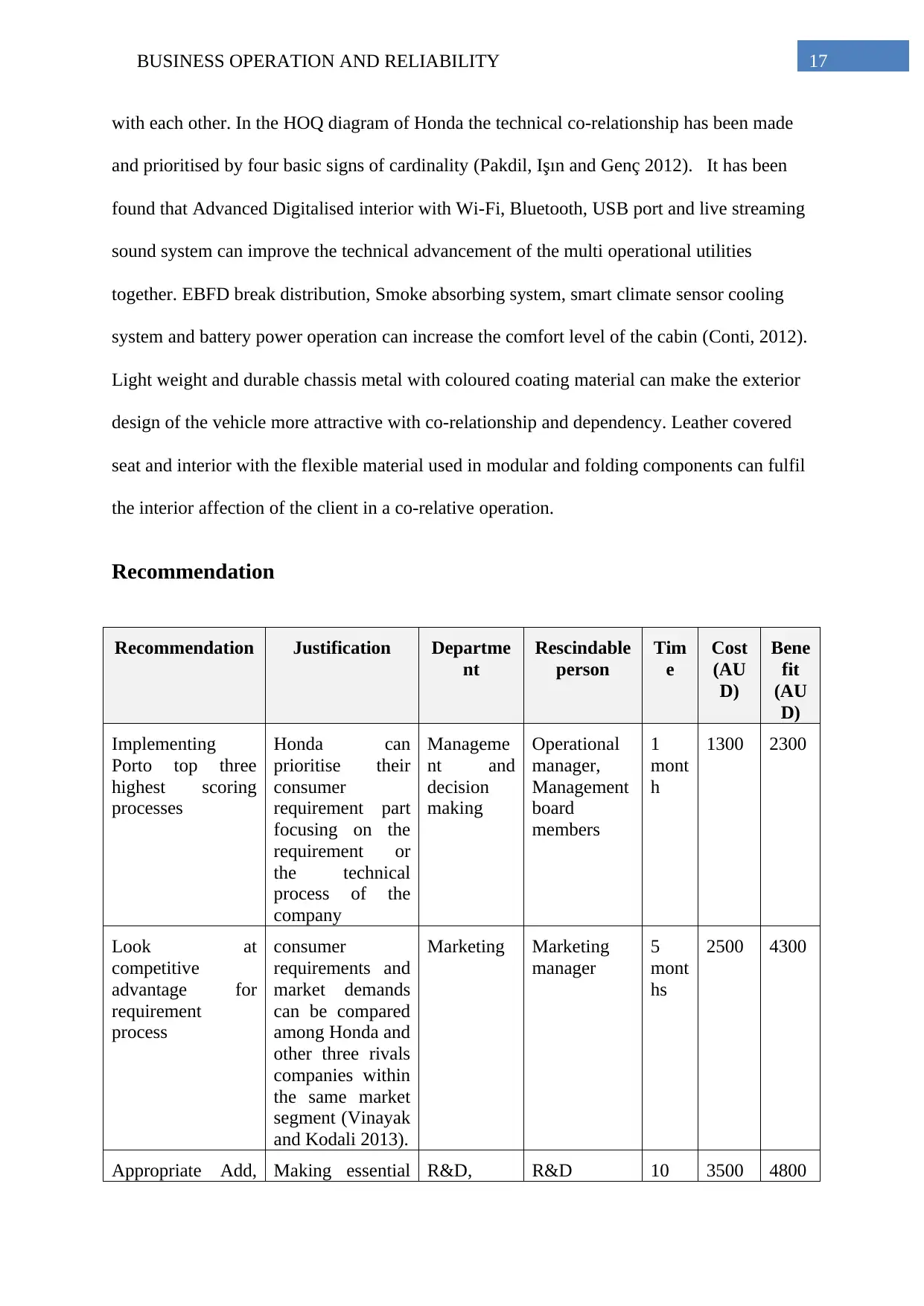
17BUSINESS OPERATION AND RELIABILITY
with each other. In the HOQ diagram of Honda the technical co-relationship has been made
and prioritised by four basic signs of cardinality (Pakdil, Işın and Genç 2012). It has been
found that Advanced Digitalised interior with Wi-Fi, Bluetooth, USB port and live streaming
sound system can improve the technical advancement of the multi operational utilities
together. EBFD break distribution, Smoke absorbing system, smart climate sensor cooling
system and battery power operation can increase the comfort level of the cabin (Conti, 2012).
Light weight and durable chassis metal with coloured coating material can make the exterior
design of the vehicle more attractive with co-relationship and dependency. Leather covered
seat and interior with the flexible material used in modular and folding components can fulfil
the interior affection of the client in a co-relative operation.
Recommendation
Recommendation Justification Departme
nt
Rescindable
person
Tim
e
Cost
(AU
D)
Bene
fit
(AU
D)
Implementing
Porto top three
highest scoring
processes
Honda can
prioritise their
consumer
requirement part
focusing on the
requirement or
the technical
process of the
company
Manageme
nt and
decision
making
Operational
manager,
Management
board
members
1
mont
h
1300 2300
Look at
competitive
advantage for
requirement
process
consumer
requirements and
market demands
can be compared
among Honda and
other three rivals
companies within
the same market
segment (Vinayak
and Kodali 2013).
Marketing Marketing
manager
5
mont
hs
2500 4300
Appropriate Add, Making essential R&D, R&D 10 3500 4800
with each other. In the HOQ diagram of Honda the technical co-relationship has been made
and prioritised by four basic signs of cardinality (Pakdil, Işın and Genç 2012). It has been
found that Advanced Digitalised interior with Wi-Fi, Bluetooth, USB port and live streaming
sound system can improve the technical advancement of the multi operational utilities
together. EBFD break distribution, Smoke absorbing system, smart climate sensor cooling
system and battery power operation can increase the comfort level of the cabin (Conti, 2012).
Light weight and durable chassis metal with coloured coating material can make the exterior
design of the vehicle more attractive with co-relationship and dependency. Leather covered
seat and interior with the flexible material used in modular and folding components can fulfil
the interior affection of the client in a co-relative operation.
Recommendation
Recommendation Justification Departme
nt
Rescindable
person
Tim
e
Cost
(AU
D)
Bene
fit
(AU
D)
Implementing
Porto top three
highest scoring
processes
Honda can
prioritise their
consumer
requirement part
focusing on the
requirement or
the technical
process of the
company
Manageme
nt and
decision
making
Operational
manager,
Management
board
members
1
mont
h
1300 2300
Look at
competitive
advantage for
requirement
process
consumer
requirements and
market demands
can be compared
among Honda and
other three rivals
companies within
the same market
segment (Vinayak
and Kodali 2013).
Marketing Marketing
manager
5
mont
hs
2500 4300
Appropriate Add, Making essential R&D, R&D 10 3500 4800
You're viewing a preview
Unlock full access by subscribing today!
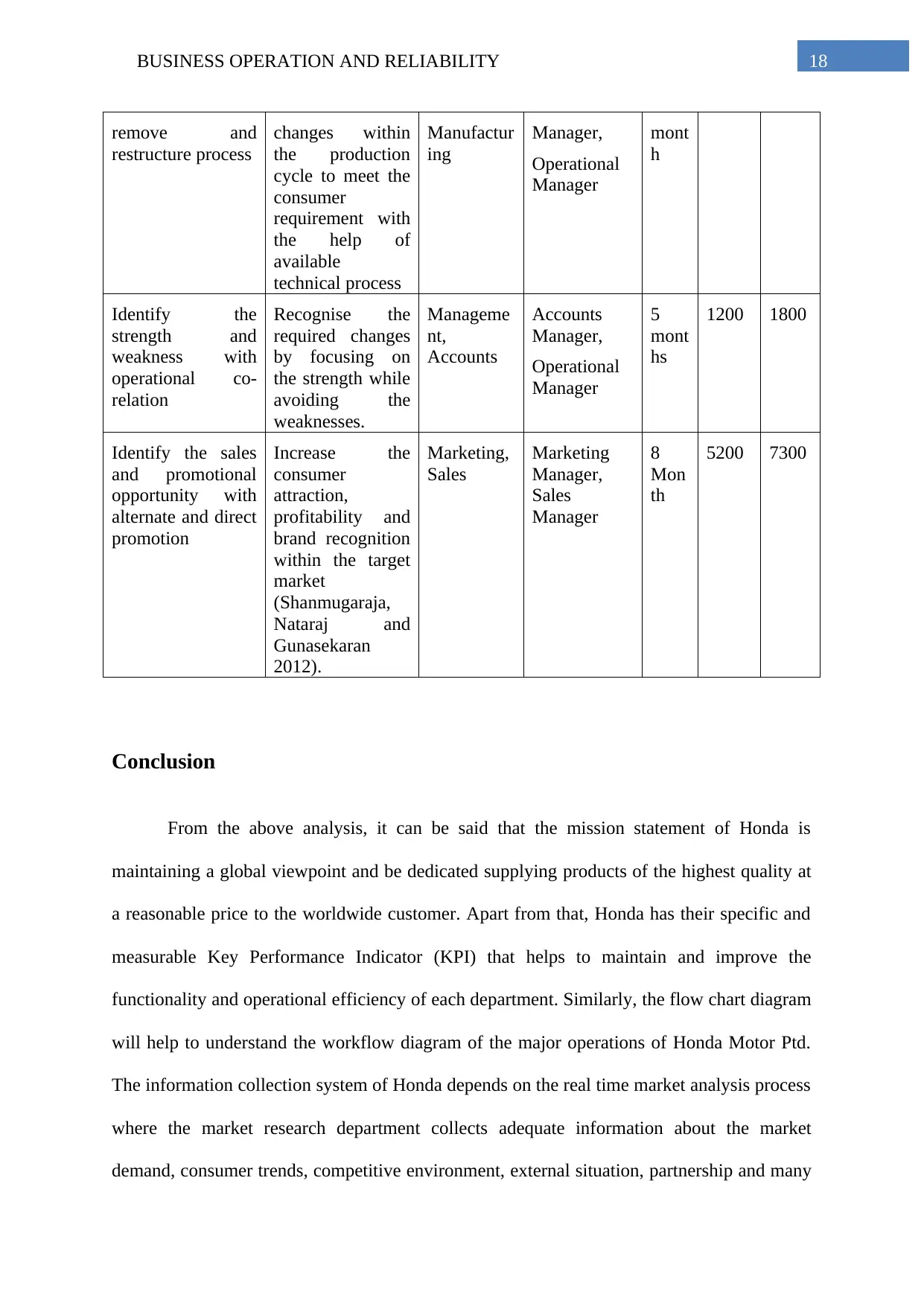
18BUSINESS OPERATION AND RELIABILITY
remove and
restructure process
changes within
the production
cycle to meet the
consumer
requirement with
the help of
available
technical process
Manufactur
ing
Manager,
Operational
Manager
mont
h
Identify the
strength and
weakness with
operational co-
relation
Recognise the
required changes
by focusing on
the strength while
avoiding the
weaknesses.
Manageme
nt,
Accounts
Accounts
Manager,
Operational
Manager
5
mont
hs
1200 1800
Identify the sales
and promotional
opportunity with
alternate and direct
promotion
Increase the
consumer
attraction,
profitability and
brand recognition
within the target
market
(Shanmugaraja,
Nataraj and
Gunasekaran
2012).
Marketing,
Sales
Marketing
Manager,
Sales
Manager
8
Mon
th
5200 7300
Conclusion
From the above analysis, it can be said that the mission statement of Honda is
maintaining a global viewpoint and be dedicated supplying products of the highest quality at
a reasonable price to the worldwide customer. Apart from that, Honda has their specific and
measurable Key Performance Indicator (KPI) that helps to maintain and improve the
functionality and operational efficiency of each department. Similarly, the flow chart diagram
will help to understand the workflow diagram of the major operations of Honda Motor Ptd.
The information collection system of Honda depends on the real time market analysis process
where the market research department collects adequate information about the market
demand, consumer trends, competitive environment, external situation, partnership and many
remove and
restructure process
changes within
the production
cycle to meet the
consumer
requirement with
the help of
available
technical process
Manufactur
ing
Manager,
Operational
Manager
mont
h
Identify the
strength and
weakness with
operational co-
relation
Recognise the
required changes
by focusing on
the strength while
avoiding the
weaknesses.
Manageme
nt,
Accounts
Accounts
Manager,
Operational
Manager
5
mont
hs
1200 1800
Identify the sales
and promotional
opportunity with
alternate and direct
promotion
Increase the
consumer
attraction,
profitability and
brand recognition
within the target
market
(Shanmugaraja,
Nataraj and
Gunasekaran
2012).
Marketing,
Sales
Marketing
Manager,
Sales
Manager
8
Mon
th
5200 7300
Conclusion
From the above analysis, it can be said that the mission statement of Honda is
maintaining a global viewpoint and be dedicated supplying products of the highest quality at
a reasonable price to the worldwide customer. Apart from that, Honda has their specific and
measurable Key Performance Indicator (KPI) that helps to maintain and improve the
functionality and operational efficiency of each department. Similarly, the flow chart diagram
will help to understand the workflow diagram of the major operations of Honda Motor Ptd.
The information collection system of Honda depends on the real time market analysis process
where the market research department collects adequate information about the market
demand, consumer trends, competitive environment, external situation, partnership and many
Paraphrase This Document
Need a fresh take? Get an instant paraphrase of this document with our AI Paraphraser
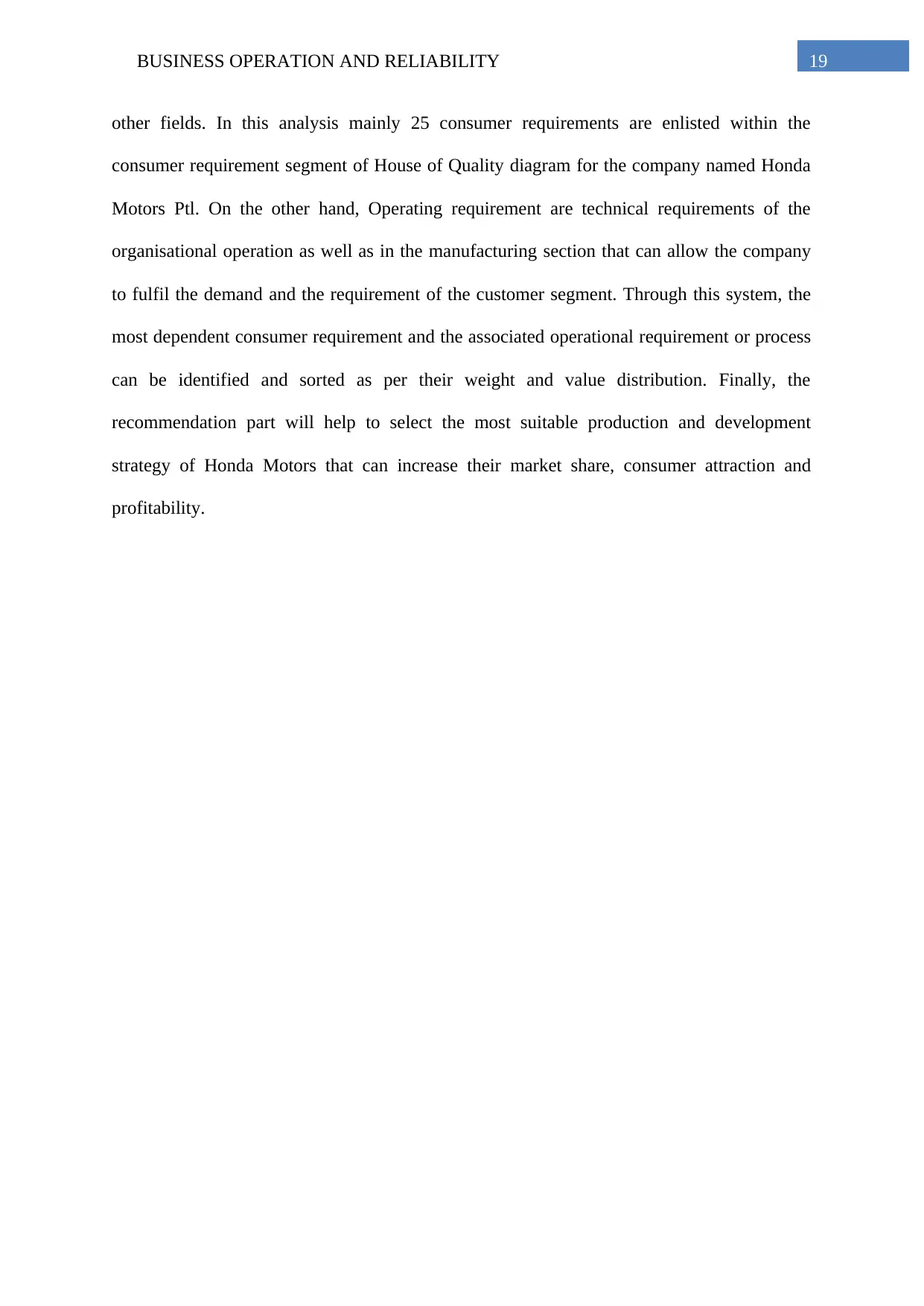
19BUSINESS OPERATION AND RELIABILITY
other fields. In this analysis mainly 25 consumer requirements are enlisted within the
consumer requirement segment of House of Quality diagram for the company named Honda
Motors Ptl. On the other hand, Operating requirement are technical requirements of the
organisational operation as well as in the manufacturing section that can allow the company
to fulfil the demand and the requirement of the customer segment. Through this system, the
most dependent consumer requirement and the associated operational requirement or process
can be identified and sorted as per their weight and value distribution. Finally, the
recommendation part will help to select the most suitable production and development
strategy of Honda Motors that can increase their market share, consumer attraction and
profitability.
other fields. In this analysis mainly 25 consumer requirements are enlisted within the
consumer requirement segment of House of Quality diagram for the company named Honda
Motors Ptl. On the other hand, Operating requirement are technical requirements of the
organisational operation as well as in the manufacturing section that can allow the company
to fulfil the demand and the requirement of the customer segment. Through this system, the
most dependent consumer requirement and the associated operational requirement or process
can be identified and sorted as per their weight and value distribution. Finally, the
recommendation part will help to select the most suitable production and development
strategy of Honda Motors that can increase their market share, consumer attraction and
profitability.
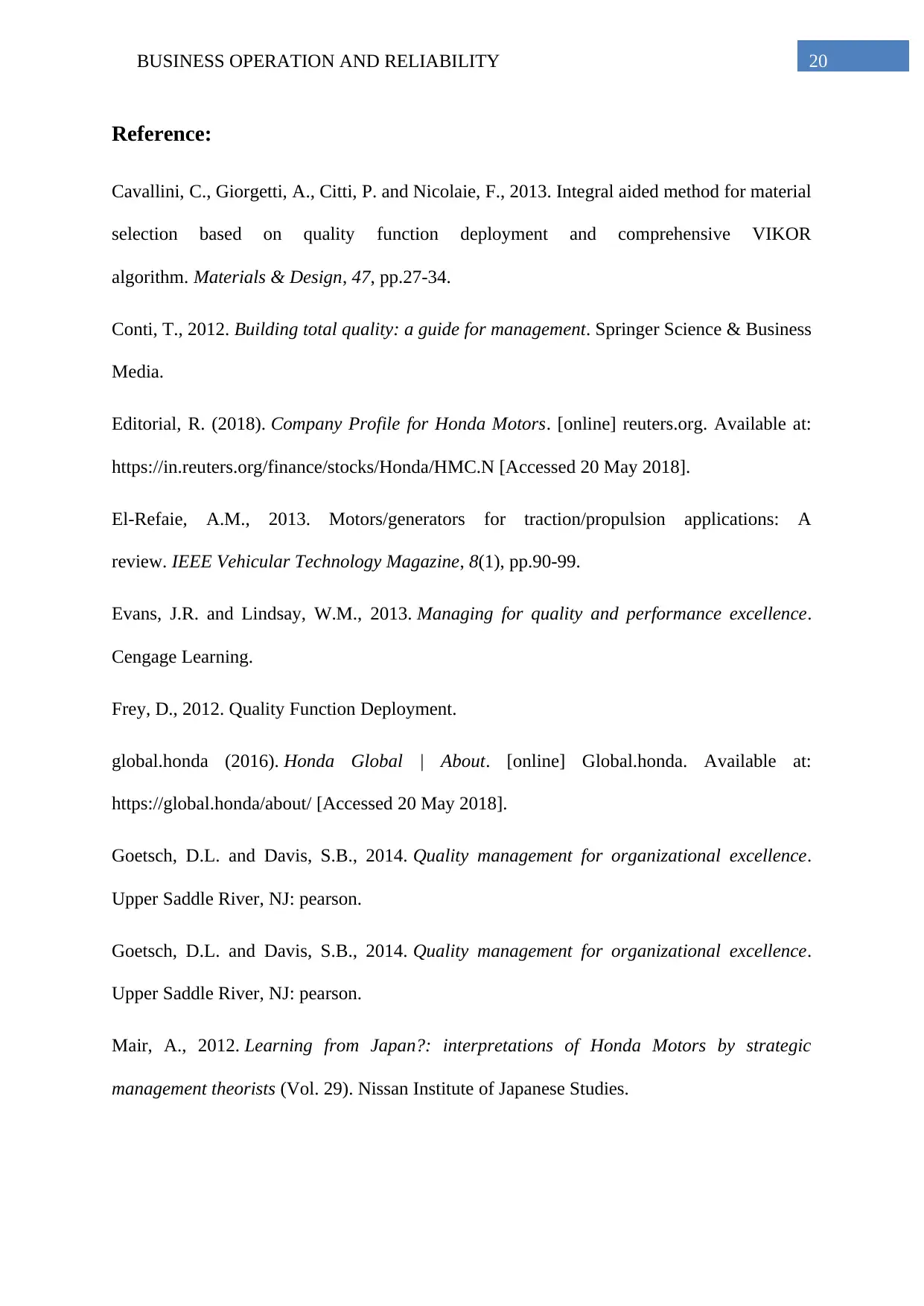
20BUSINESS OPERATION AND RELIABILITY
Reference:
Cavallini, C., Giorgetti, A., Citti, P. and Nicolaie, F., 2013. Integral aided method for material
selection based on quality function deployment and comprehensive VIKOR
algorithm. Materials & Design, 47, pp.27-34.
Conti, T., 2012. Building total quality: a guide for management. Springer Science & Business
Media.
Editorial, R. (2018). Company Profile for Honda Motors. [online] reuters.org. Available at:
https://in.reuters.org/finance/stocks/Honda/HMC.N [Accessed 20 May 2018].
El-Refaie, A.M., 2013. Motors/generators for traction/propulsion applications: A
review. IEEE Vehicular Technology Magazine, 8(1), pp.90-99.
Evans, J.R. and Lindsay, W.M., 2013. Managing for quality and performance excellence.
Cengage Learning.
Frey, D., 2012. Quality Function Deployment.
global.honda (2016). Honda Global | About. [online] Global.honda. Available at:
https://global.honda/about/ [Accessed 20 May 2018].
Goetsch, D.L. and Davis, S.B., 2014. Quality management for organizational excellence.
Upper Saddle River, NJ: pearson.
Goetsch, D.L. and Davis, S.B., 2014. Quality management for organizational excellence.
Upper Saddle River, NJ: pearson.
Mair, A., 2012. Learning from Japan?: interpretations of Honda Motors by strategic
management theorists (Vol. 29). Nissan Institute of Japanese Studies.
Reference:
Cavallini, C., Giorgetti, A., Citti, P. and Nicolaie, F., 2013. Integral aided method for material
selection based on quality function deployment and comprehensive VIKOR
algorithm. Materials & Design, 47, pp.27-34.
Conti, T., 2012. Building total quality: a guide for management. Springer Science & Business
Media.
Editorial, R. (2018). Company Profile for Honda Motors. [online] reuters.org. Available at:
https://in.reuters.org/finance/stocks/Honda/HMC.N [Accessed 20 May 2018].
El-Refaie, A.M., 2013. Motors/generators for traction/propulsion applications: A
review. IEEE Vehicular Technology Magazine, 8(1), pp.90-99.
Evans, J.R. and Lindsay, W.M., 2013. Managing for quality and performance excellence.
Cengage Learning.
Frey, D., 2012. Quality Function Deployment.
global.honda (2016). Honda Global | About. [online] Global.honda. Available at:
https://global.honda/about/ [Accessed 20 May 2018].
Goetsch, D.L. and Davis, S.B., 2014. Quality management for organizational excellence.
Upper Saddle River, NJ: pearson.
Goetsch, D.L. and Davis, S.B., 2014. Quality management for organizational excellence.
Upper Saddle River, NJ: pearson.
Mair, A., 2012. Learning from Japan?: interpretations of Honda Motors by strategic
management theorists (Vol. 29). Nissan Institute of Japanese Studies.
You're viewing a preview
Unlock full access by subscribing today!

21BUSINESS OPERATION AND RELIABILITY
Mitreva, E., Taskov, N., Kitanov, V., Filiposki, O. and Dzaleva, T., 2013. The Need for
Information System Design in Building a House of Quality. International Journal of Pure
and Applied Sciences and Technology, 16(1), p.26.
Pakdil, F., Işın, F.B. and Genç, H., 2012. A quality function deployment application using
qualitative and quantitative analysis in after sales services. Total Quality Management &
Business Excellence, 23(11-12), pp.1397-1411.
Perçin, S. and Min, H., 2013. A hybrid quality function deployment and fuzzy decision-
making methodology for the optimal selection of third-party logistics service
providers. International Journal of Logistics Research and Applications, 16(5), pp.380-397.
Prasad, K. and Chakraborty, S., 2013. A quality function deployment-based model for
materials selection. Materials & Design, 49, pp.525-535.
Shanmugaraja, M., Nataraj, M. and Gunasekaran, N., 2012. Six Sigma project selection via
quality function deployment. International Journal of Productivity and Quality
Management, 10(1), pp.85-111.
Sutton, J., 2012. The auto-component supply chain in China and India: A benchmarking
study.
Vinayak, K. and Kodali, R., 2013. Benchmarking the quality function deployment
models. Benchmarking: An International Journal, 20(6), pp.825-854.
Mitreva, E., Taskov, N., Kitanov, V., Filiposki, O. and Dzaleva, T., 2013. The Need for
Information System Design in Building a House of Quality. International Journal of Pure
and Applied Sciences and Technology, 16(1), p.26.
Pakdil, F., Işın, F.B. and Genç, H., 2012. A quality function deployment application using
qualitative and quantitative analysis in after sales services. Total Quality Management &
Business Excellence, 23(11-12), pp.1397-1411.
Perçin, S. and Min, H., 2013. A hybrid quality function deployment and fuzzy decision-
making methodology for the optimal selection of third-party logistics service
providers. International Journal of Logistics Research and Applications, 16(5), pp.380-397.
Prasad, K. and Chakraborty, S., 2013. A quality function deployment-based model for
materials selection. Materials & Design, 49, pp.525-535.
Shanmugaraja, M., Nataraj, M. and Gunasekaran, N., 2012. Six Sigma project selection via
quality function deployment. International Journal of Productivity and Quality
Management, 10(1), pp.85-111.
Sutton, J., 2012. The auto-component supply chain in China and India: A benchmarking
study.
Vinayak, K. and Kodali, R., 2013. Benchmarking the quality function deployment
models. Benchmarking: An International Journal, 20(6), pp.825-854.
1 out of 22
Related Documents

Your All-in-One AI-Powered Toolkit for Academic Success.
+13062052269
info@desklib.com
Available 24*7 on WhatsApp / Email
Unlock your academic potential
© 2024 | Zucol Services PVT LTD | All rights reserved.