Business Operations: Transformation, Strategies, and Influences
VerifiedAdded on 2021/03/26
|10
|2774
|76
Report
AI Summary
This document provides a comprehensive overview of business operations, encompassing the transformation of inputs into outputs and the strategic role of operations management in achieving a competitive advantage. It details the importance of effective operations management in increasing productivity, reducing costs, and improving quality. The report explores the interdependence of operations with other key business functions, the influence of globalization and technology, and the significance of quality expectations and cost-based competition. It also examines government policies, legal regulations, and environmental sustainability. The report outlines operations processes, including inputs, transformed and transforming resources, and the influence of volume, variation, and visibility on operations. It discusses sequencing and scheduling tools, technology, task design, and process layout. The document also covers outputs, customer service, and operations strategies such as design and development, and supply chain management, including logistics and e-commerce. Finally, it highlights performance objectives like quality, speed, dependability, flexibility, customization, and cost, providing a thorough understanding of business operations.
Contribute Materials
Your contribution can guide someone’s learning journey. Share your
documents today.
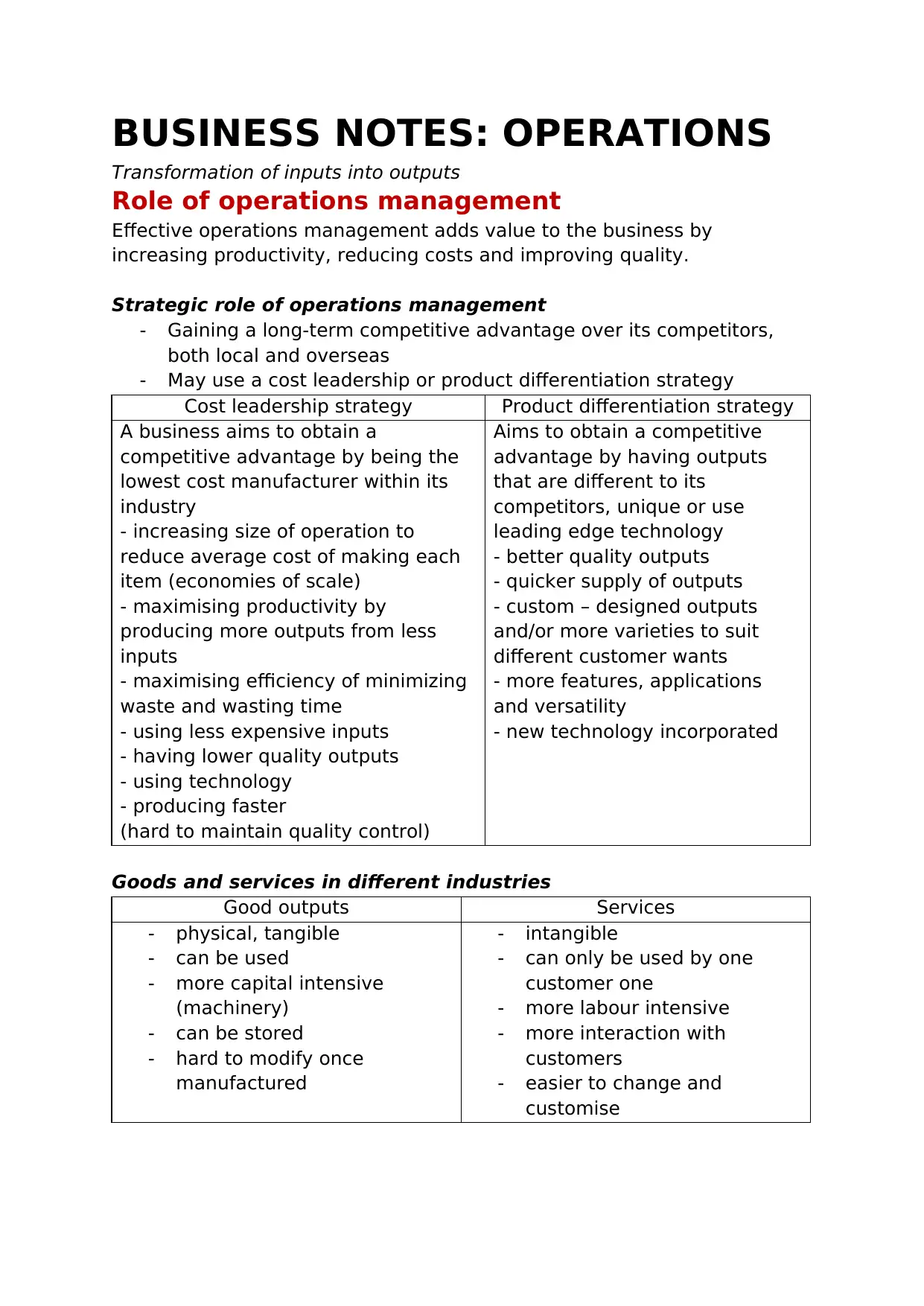
BUSINESS NOTES: OPERATIONS
Transformation of inputs into outputs
Role of operations management
Effective operations management adds value to the business by
increasing productivity, reducing costs and improving quality.
Strategic role of operations management
- Gaining a long-term competitive advantage over its competitors,
both local and overseas
- May use a cost leadership or product differentiation strategy
Cost leadership strategy Product differentiation strategy
A business aims to obtain a
competitive advantage by being the
lowest cost manufacturer within its
industry
- increasing size of operation to
reduce average cost of making each
item (economies of scale)
- maximising productivity by
producing more outputs from less
inputs
- maximising efficiency of minimizing
waste and wasting time
- using less expensive inputs
- having lower quality outputs
- using technology
- producing faster
(hard to maintain quality control)
Aims to obtain a competitive
advantage by having outputs
that are different to its
competitors, unique or use
leading edge technology
- better quality outputs
- quicker supply of outputs
- custom – designed outputs
and/or more varieties to suit
different customer wants
- more features, applications
and versatility
- new technology incorporated
Goods and services in different industries
Good outputs Services
- physical, tangible
- can be used
- more capital intensive
(machinery)
- can be stored
- hard to modify once
manufactured
- intangible
- can only be used by one
customer one
- more labour intensive
- more interaction with
customers
- easier to change and
customise
Transformation of inputs into outputs
Role of operations management
Effective operations management adds value to the business by
increasing productivity, reducing costs and improving quality.
Strategic role of operations management
- Gaining a long-term competitive advantage over its competitors,
both local and overseas
- May use a cost leadership or product differentiation strategy
Cost leadership strategy Product differentiation strategy
A business aims to obtain a
competitive advantage by being the
lowest cost manufacturer within its
industry
- increasing size of operation to
reduce average cost of making each
item (economies of scale)
- maximising productivity by
producing more outputs from less
inputs
- maximising efficiency of minimizing
waste and wasting time
- using less expensive inputs
- having lower quality outputs
- using technology
- producing faster
(hard to maintain quality control)
Aims to obtain a competitive
advantage by having outputs
that are different to its
competitors, unique or use
leading edge technology
- better quality outputs
- quicker supply of outputs
- custom – designed outputs
and/or more varieties to suit
different customer wants
- more features, applications
and versatility
- new technology incorporated
Goods and services in different industries
Good outputs Services
- physical, tangible
- can be used
- more capital intensive
(machinery)
- can be stored
- hard to modify once
manufactured
- intangible
- can only be used by one
customer one
- more labour intensive
- more interaction with
customers
- easier to change and
customise
Secure Best Marks with AI Grader
Need help grading? Try our AI Grader for instant feedback on your assignments.
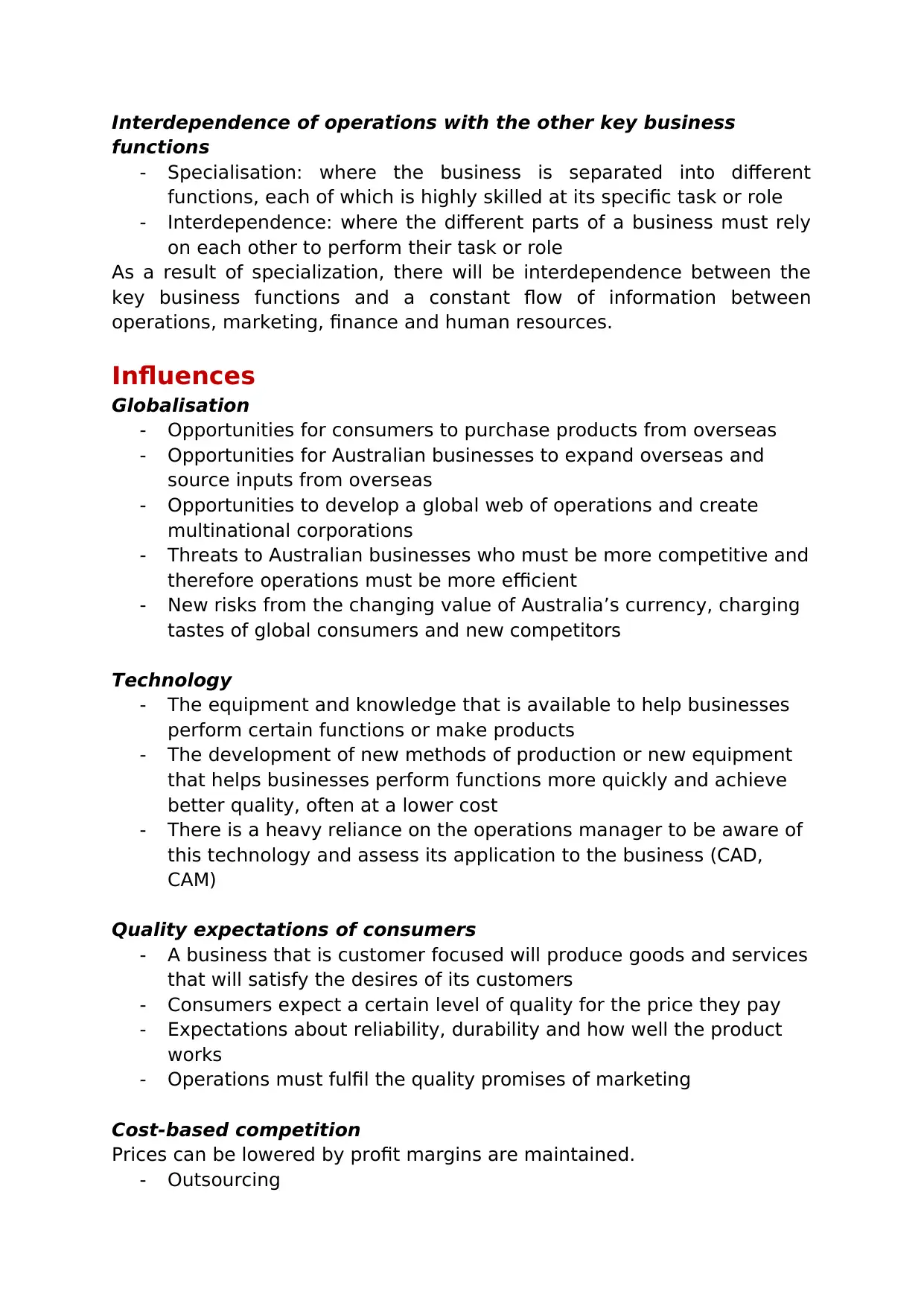
Interdependence of operations with the other key business
functions
- Specialisation: where the business is separated into different
functions, each of which is highly skilled at its specific task or role
- Interdependence: where the different parts of a business must rely
on each other to perform their task or role
As a result of specialization, there will be interdependence between the
key business functions and a constant flow of information between
operations, marketing, finance and human resources.
Influences
Globalisation
- Opportunities for consumers to purchase products from overseas
- Opportunities for Australian businesses to expand overseas and
source inputs from overseas
- Opportunities to develop a global web of operations and create
multinational corporations
- Threats to Australian businesses who must be more competitive and
therefore operations must be more efficient
- New risks from the changing value of Australia’s currency, charging
tastes of global consumers and new competitors
Technology
- The equipment and knowledge that is available to help businesses
perform certain functions or make products
- The development of new methods of production or new equipment
that helps businesses perform functions more quickly and achieve
better quality, often at a lower cost
- There is a heavy reliance on the operations manager to be aware of
this technology and assess its application to the business (CAD,
CAM)
Quality expectations of consumers
- A business that is customer focused will produce goods and services
that will satisfy the desires of its customers
- Consumers expect a certain level of quality for the price they pay
- Expectations about reliability, durability and how well the product
works
- Operations must fulfil the quality promises of marketing
Cost-based competition
Prices can be lowered by profit margins are maintained.
- Outsourcing
functions
- Specialisation: where the business is separated into different
functions, each of which is highly skilled at its specific task or role
- Interdependence: where the different parts of a business must rely
on each other to perform their task or role
As a result of specialization, there will be interdependence between the
key business functions and a constant flow of information between
operations, marketing, finance and human resources.
Influences
Globalisation
- Opportunities for consumers to purchase products from overseas
- Opportunities for Australian businesses to expand overseas and
source inputs from overseas
- Opportunities to develop a global web of operations and create
multinational corporations
- Threats to Australian businesses who must be more competitive and
therefore operations must be more efficient
- New risks from the changing value of Australia’s currency, charging
tastes of global consumers and new competitors
Technology
- The equipment and knowledge that is available to help businesses
perform certain functions or make products
- The development of new methods of production or new equipment
that helps businesses perform functions more quickly and achieve
better quality, often at a lower cost
- There is a heavy reliance on the operations manager to be aware of
this technology and assess its application to the business (CAD,
CAM)
Quality expectations of consumers
- A business that is customer focused will produce goods and services
that will satisfy the desires of its customers
- Consumers expect a certain level of quality for the price they pay
- Expectations about reliability, durability and how well the product
works
- Operations must fulfil the quality promises of marketing
Cost-based competition
Prices can be lowered by profit margins are maintained.
- Outsourcing
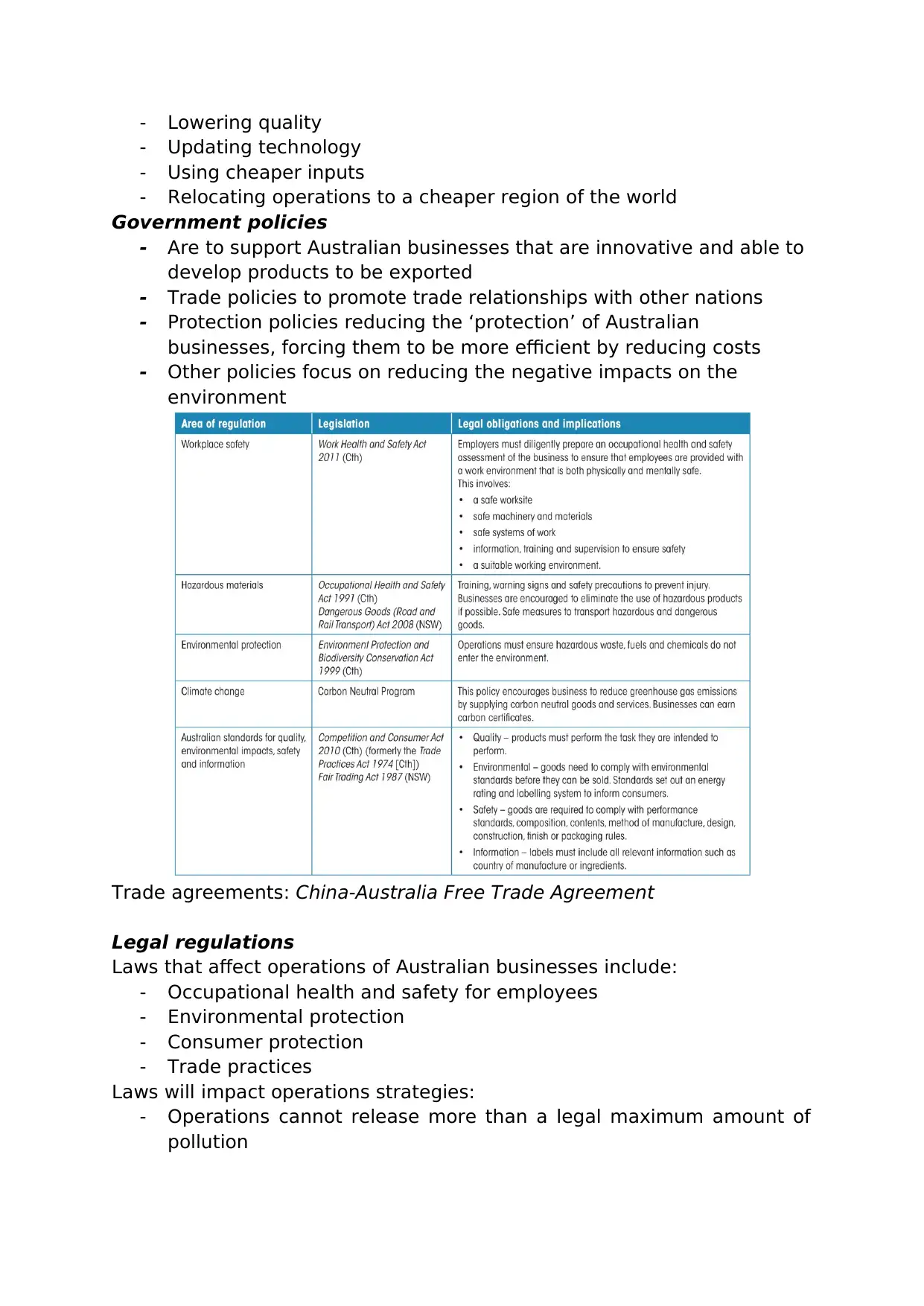
- Lowering quality
- Updating technology
- Using cheaper inputs
- Relocating operations to a cheaper region of the world
Government policies
- Are to support Australian businesses that are innovative and able to
develop products to be exported
- Trade policies to promote trade relationships with other nations
- Protection policies reducing the ‘protection’ of Australian
businesses, forcing them to be more efficient by reducing costs
- Other policies focus on reducing the negative impacts on the
environment
Trade agreements: China-Australia Free Trade Agreement
Legal regulations
Laws that affect operations of Australian businesses include:
- Occupational health and safety for employees
- Environmental protection
- Consumer protection
- Trade practices
Laws will impact operations strategies:
- Operations cannot release more than a legal maximum amount of
pollution
- Updating technology
- Using cheaper inputs
- Relocating operations to a cheaper region of the world
Government policies
- Are to support Australian businesses that are innovative and able to
develop products to be exported
- Trade policies to promote trade relationships with other nations
- Protection policies reducing the ‘protection’ of Australian
businesses, forcing them to be more efficient by reducing costs
- Other policies focus on reducing the negative impacts on the
environment
Trade agreements: China-Australia Free Trade Agreement
Legal regulations
Laws that affect operations of Australian businesses include:
- Occupational health and safety for employees
- Environmental protection
- Consumer protection
- Trade practices
Laws will impact operations strategies:
- Operations cannot release more than a legal maximum amount of
pollution
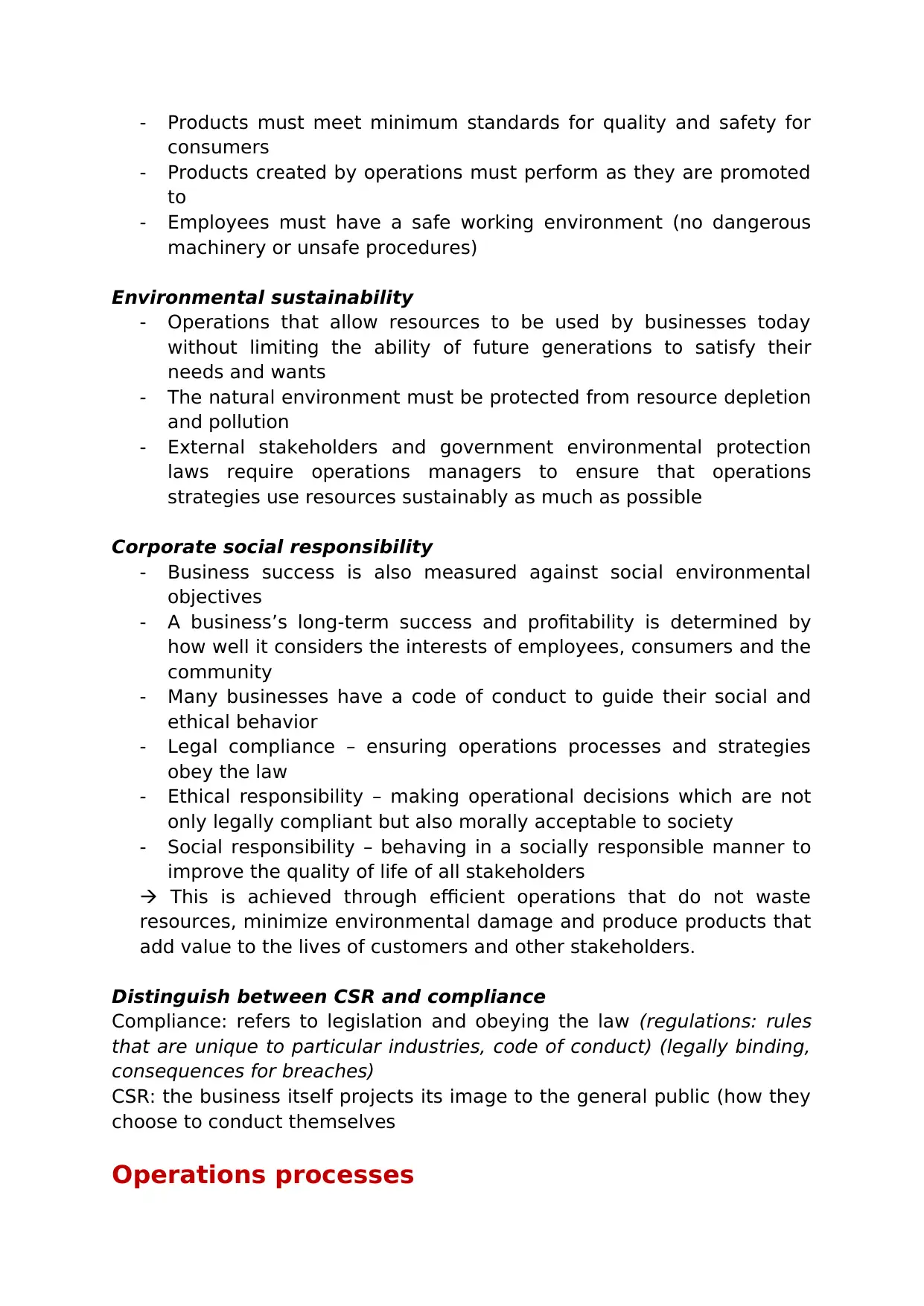
- Products must meet minimum standards for quality and safety for
consumers
- Products created by operations must perform as they are promoted
to
- Employees must have a safe working environment (no dangerous
machinery or unsafe procedures)
Environmental sustainability
- Operations that allow resources to be used by businesses today
without limiting the ability of future generations to satisfy their
needs and wants
- The natural environment must be protected from resource depletion
and pollution
- External stakeholders and government environmental protection
laws require operations managers to ensure that operations
strategies use resources sustainably as much as possible
Corporate social responsibility
- Business success is also measured against social environmental
objectives
- A business’s long-term success and profitability is determined by
how well it considers the interests of employees, consumers and the
community
- Many businesses have a code of conduct to guide their social and
ethical behavior
- Legal compliance – ensuring operations processes and strategies
obey the law
- Ethical responsibility – making operational decisions which are not
only legally compliant but also morally acceptable to society
- Social responsibility – behaving in a socially responsible manner to
improve the quality of life of all stakeholders
This is achieved through efficient operations that do not waste
resources, minimize environmental damage and produce products that
add value to the lives of customers and other stakeholders.
Distinguish between CSR and compliance
Compliance: refers to legislation and obeying the law (regulations: rules
that are unique to particular industries, code of conduct) (legally binding,
consequences for breaches)
CSR: the business itself projects its image to the general public (how they
choose to conduct themselves
Operations processes
consumers
- Products created by operations must perform as they are promoted
to
- Employees must have a safe working environment (no dangerous
machinery or unsafe procedures)
Environmental sustainability
- Operations that allow resources to be used by businesses today
without limiting the ability of future generations to satisfy their
needs and wants
- The natural environment must be protected from resource depletion
and pollution
- External stakeholders and government environmental protection
laws require operations managers to ensure that operations
strategies use resources sustainably as much as possible
Corporate social responsibility
- Business success is also measured against social environmental
objectives
- A business’s long-term success and profitability is determined by
how well it considers the interests of employees, consumers and the
community
- Many businesses have a code of conduct to guide their social and
ethical behavior
- Legal compliance – ensuring operations processes and strategies
obey the law
- Ethical responsibility – making operational decisions which are not
only legally compliant but also morally acceptable to society
- Social responsibility – behaving in a socially responsible manner to
improve the quality of life of all stakeholders
This is achieved through efficient operations that do not waste
resources, minimize environmental damage and produce products that
add value to the lives of customers and other stakeholders.
Distinguish between CSR and compliance
Compliance: refers to legislation and obeying the law (regulations: rules
that are unique to particular industries, code of conduct) (legally binding,
consequences for breaches)
CSR: the business itself projects its image to the general public (how they
choose to conduct themselves
Operations processes
Secure Best Marks with AI Grader
Need help grading? Try our AI Grader for instant feedback on your assignments.

Inputs
Transformed resources
Inputs that are charged and converted into something, such as a
component to be used as an input by another business or a finished good
or service.
- Materials: raw ingredients, components, parts and supplies
- Information: about how to produce, technical knowledge, analysis of
performance
- Customers: become satisfied and have an improved quality of life
Transforming resources
Resources that remain in the business and are applied to the inputs to
change them to add value. They are not used up.
These include:
- Human resources: mental and physical labour of employees who
apply their knowledge, skills and effort
- Facilities: building, land, equipment and technology (non-current
assets)
Transformation processes
Those activities that determine how value will be added
Influence of the 4Vs
- Volume: number of products or services that operations needs to
produce
- Variation: the number of different models and varieties that
operations needs to create
- Variation in demand: the change in demand overtime; operations
needs to be flexible to increase or decrease output
- Visibility to customers: the degree to which customers can see the
operations in action
influence the type of production:
- Sob: producing individual unique outputs
- Batch: producing in groups or bundles
- Flow: production that is continuous
influence the combination of labout and/or equipment used in
production
(ex: more technology and machinery will be used for high-volume output)
Sequencing and scheduling tools
Are used to identify all steps in the operations process and organize them
into the most efficient order to complete. This may be called task analysis.
1. Gantt charts
Transformed resources
Inputs that are charged and converted into something, such as a
component to be used as an input by another business or a finished good
or service.
- Materials: raw ingredients, components, parts and supplies
- Information: about how to produce, technical knowledge, analysis of
performance
- Customers: become satisfied and have an improved quality of life
Transforming resources
Resources that remain in the business and are applied to the inputs to
change them to add value. They are not used up.
These include:
- Human resources: mental and physical labour of employees who
apply their knowledge, skills and effort
- Facilities: building, land, equipment and technology (non-current
assets)
Transformation processes
Those activities that determine how value will be added
Influence of the 4Vs
- Volume: number of products or services that operations needs to
produce
- Variation: the number of different models and varieties that
operations needs to create
- Variation in demand: the change in demand overtime; operations
needs to be flexible to increase or decrease output
- Visibility to customers: the degree to which customers can see the
operations in action
influence the type of production:
- Sob: producing individual unique outputs
- Batch: producing in groups or bundles
- Flow: production that is continuous
influence the combination of labout and/or equipment used in
production
(ex: more technology and machinery will be used for high-volume output)
Sequencing and scheduling tools
Are used to identify all steps in the operations process and organize them
into the most efficient order to complete. This may be called task analysis.
1. Gantt charts
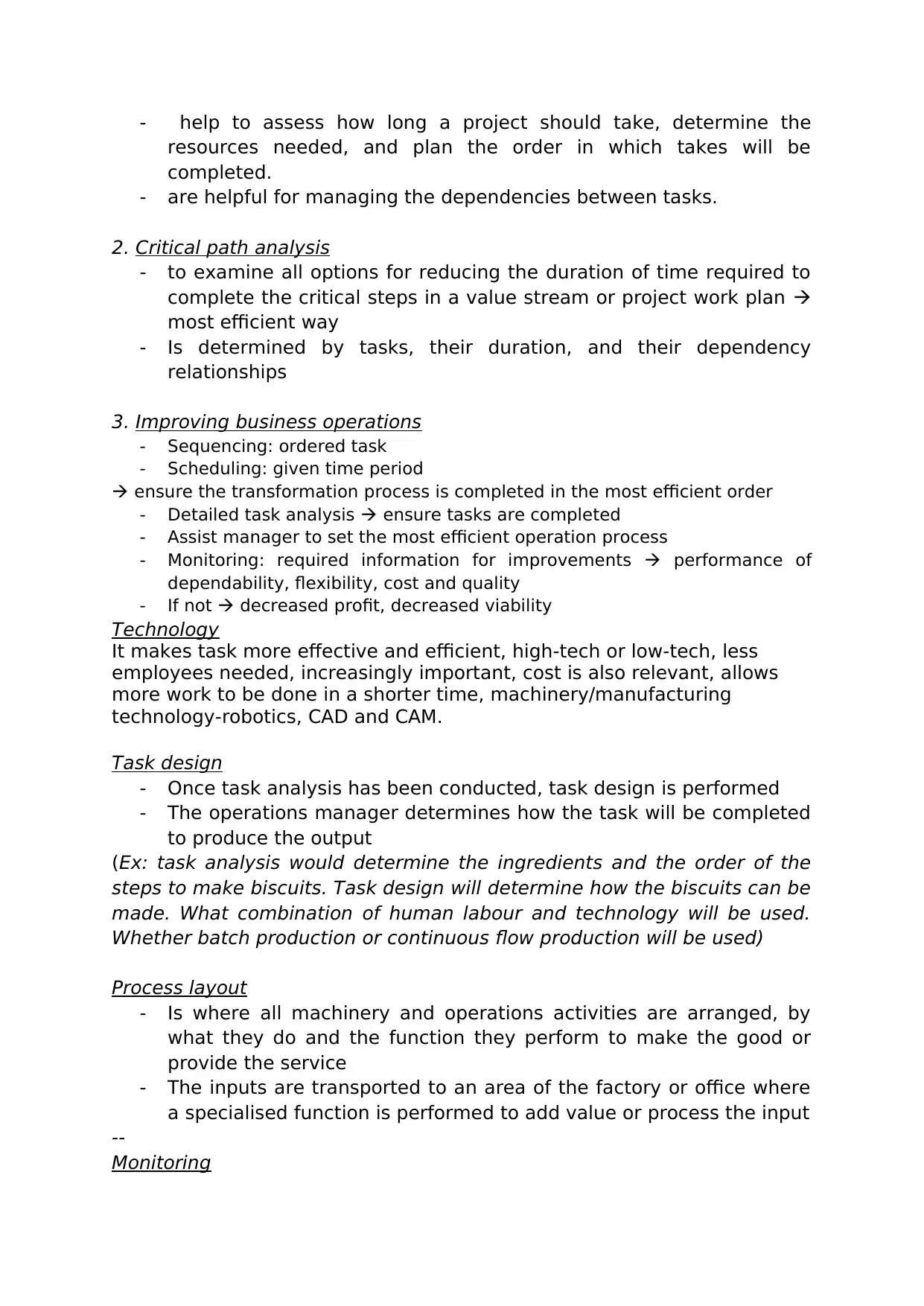
- help to assess how long a project should take, determine the
resources needed, and plan the order in which takes will be
completed.
- are helpful for managing the dependencies between tasks.
2. Critical path analysis
- to examine all options for reducing the duration of time required to
complete the critical steps in a value stream or project work plan
most efficient way
- Is determined by tasks, their duration, and their dependency
relationships
3. Improving business operations
- Sequencing: ordered task
- Scheduling: given time period
ensure the transformation process is completed in the most efficient order
- Detailed task analysis ensure tasks are completed
- Assist manager to set the most efficient operation process
- Monitoring: required information for improvements performance of
dependability, flexibility, cost and quality
- If not decreased profit, decreased viability
Technology
It makes task more effective and efficient, high-tech or low-tech, less
employees needed, increasingly important, cost is also relevant, allows
more work to be done in a shorter time, machinery/manufacturing
technology-robotics, CAD and CAM.
Task design
- Once task analysis has been conducted, task design is performed
- The operations manager determines how the task will be completed
to produce the output
(Ex: task analysis would determine the ingredients and the order of the
steps to make biscuits. Task design will determine how the biscuits can be
made. What combination of human labour and technology will be used.
Whether batch production or continuous flow production will be used)
Process layout
- Is where all machinery and operations activities are arranged, by
what they do and the function they perform to make the good or
provide the service
- The inputs are transported to an area of the factory or office where
a specialised function is performed to add value or process the input
--
Monitoring
resources needed, and plan the order in which takes will be
completed.
- are helpful for managing the dependencies between tasks.
2. Critical path analysis
- to examine all options for reducing the duration of time required to
complete the critical steps in a value stream or project work plan
most efficient way
- Is determined by tasks, their duration, and their dependency
relationships
3. Improving business operations
- Sequencing: ordered task
- Scheduling: given time period
ensure the transformation process is completed in the most efficient order
- Detailed task analysis ensure tasks are completed
- Assist manager to set the most efficient operation process
- Monitoring: required information for improvements performance of
dependability, flexibility, cost and quality
- If not decreased profit, decreased viability
Technology
It makes task more effective and efficient, high-tech or low-tech, less
employees needed, increasingly important, cost is also relevant, allows
more work to be done in a shorter time, machinery/manufacturing
technology-robotics, CAD and CAM.
Task design
- Once task analysis has been conducted, task design is performed
- The operations manager determines how the task will be completed
to produce the output
(Ex: task analysis would determine the ingredients and the order of the
steps to make biscuits. Task design will determine how the biscuits can be
made. What combination of human labour and technology will be used.
Whether batch production or continuous flow production will be used)
Process layout
- Is where all machinery and operations activities are arranged, by
what they do and the function they perform to make the good or
provide the service
- The inputs are transported to an area of the factory or office where
a specialised function is performed to add value or process the input
--
Monitoring
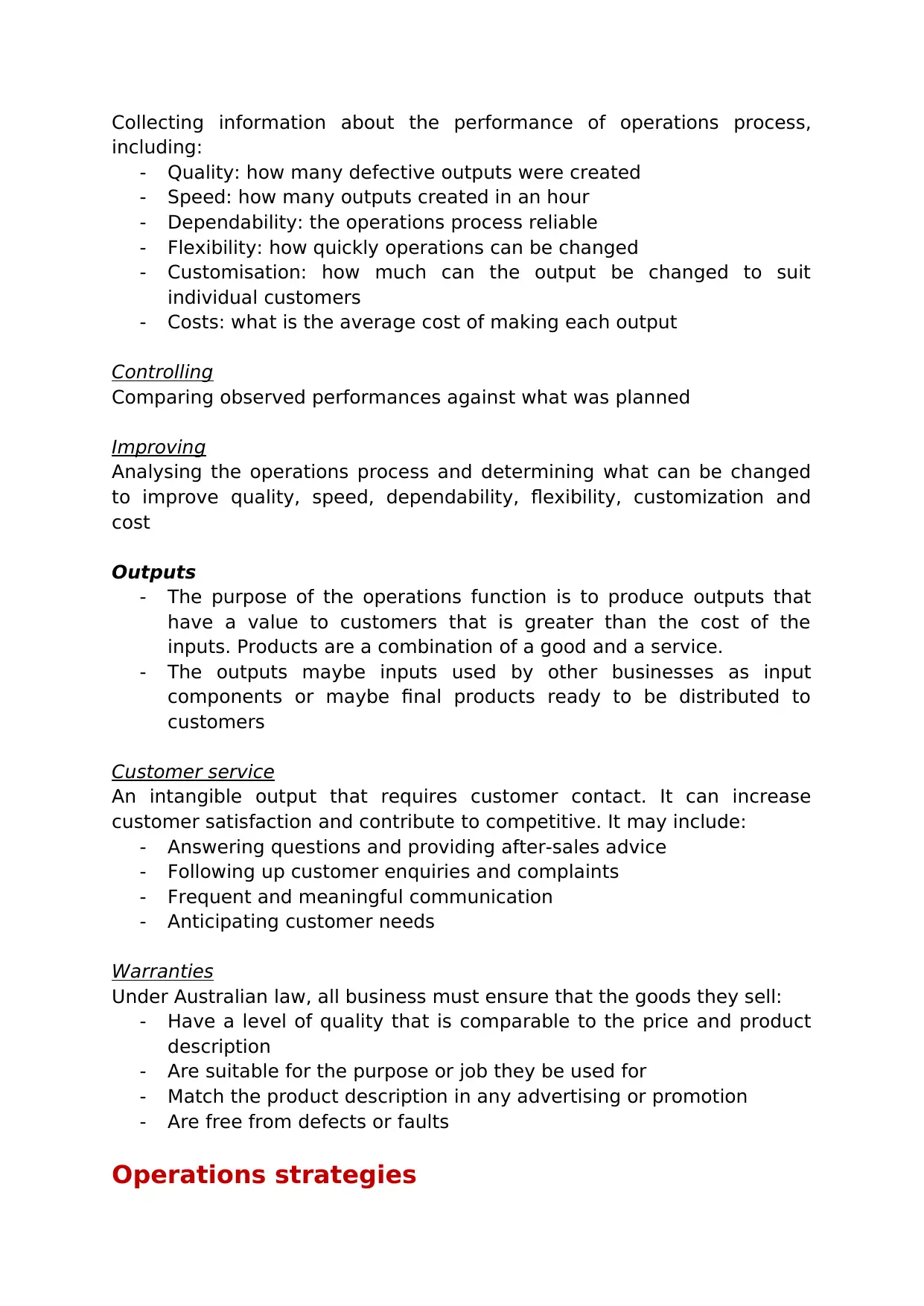
Collecting information about the performance of operations process,
including:
- Quality: how many defective outputs were created
- Speed: how many outputs created in an hour
- Dependability: the operations process reliable
- Flexibility: how quickly operations can be changed
- Customisation: how much can the output be changed to suit
individual customers
- Costs: what is the average cost of making each output
Controlling
Comparing observed performances against what was planned
Improving
Analysing the operations process and determining what can be changed
to improve quality, speed, dependability, flexibility, customization and
cost
Outputs
- The purpose of the operations function is to produce outputs that
have a value to customers that is greater than the cost of the
inputs. Products are a combination of a good and a service.
- The outputs maybe inputs used by other businesses as input
components or maybe final products ready to be distributed to
customers
Customer service
An intangible output that requires customer contact. It can increase
customer satisfaction and contribute to competitive. It may include:
- Answering questions and providing after-sales advice
- Following up customer enquiries and complaints
- Frequent and meaningful communication
- Anticipating customer needs
Warranties
Under Australian law, all business must ensure that the goods they sell:
- Have a level of quality that is comparable to the price and product
description
- Are suitable for the purpose or job they be used for
- Match the product description in any advertising or promotion
- Are free from defects or faults
Operations strategies
including:
- Quality: how many defective outputs were created
- Speed: how many outputs created in an hour
- Dependability: the operations process reliable
- Flexibility: how quickly operations can be changed
- Customisation: how much can the output be changed to suit
individual customers
- Costs: what is the average cost of making each output
Controlling
Comparing observed performances against what was planned
Improving
Analysing the operations process and determining what can be changed
to improve quality, speed, dependability, flexibility, customization and
cost
Outputs
- The purpose of the operations function is to produce outputs that
have a value to customers that is greater than the cost of the
inputs. Products are a combination of a good and a service.
- The outputs maybe inputs used by other businesses as input
components or maybe final products ready to be distributed to
customers
Customer service
An intangible output that requires customer contact. It can increase
customer satisfaction and contribute to competitive. It may include:
- Answering questions and providing after-sales advice
- Following up customer enquiries and complaints
- Frequent and meaningful communication
- Anticipating customer needs
Warranties
Under Australian law, all business must ensure that the goods they sell:
- Have a level of quality that is comparable to the price and product
description
- Are suitable for the purpose or job they be used for
- Match the product description in any advertising or promotion
- Are free from defects or faults
Operations strategies
Paraphrase This Document
Need a fresh take? Get an instant paraphrase of this document with our AI Paraphraser
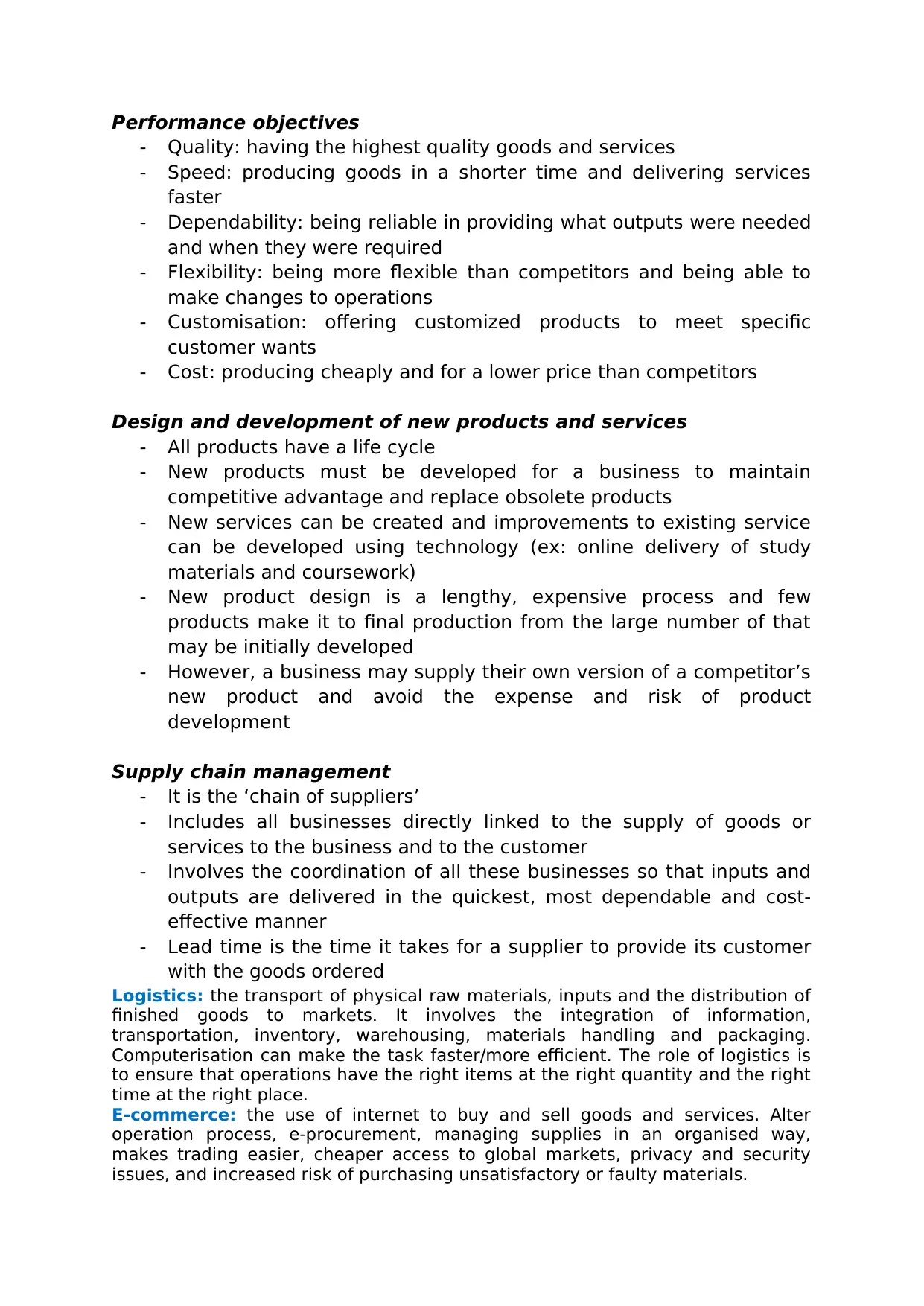
Performance objectives
- Quality: having the highest quality goods and services
- Speed: producing goods in a shorter time and delivering services
faster
- Dependability: being reliable in providing what outputs were needed
and when they were required
- Flexibility: being more flexible than competitors and being able to
make changes to operations
- Customisation: offering customized products to meet specific
customer wants
- Cost: producing cheaply and for a lower price than competitors
Design and development of new products and services
- All products have a life cycle
- New products must be developed for a business to maintain
competitive advantage and replace obsolete products
- New services can be created and improvements to existing service
can be developed using technology (ex: online delivery of study
materials and coursework)
- New product design is a lengthy, expensive process and few
products make it to final production from the large number of that
may be initially developed
- However, a business may supply their own version of a competitor’s
new product and avoid the expense and risk of product
development
Supply chain management
- It is the ‘chain of suppliers’
- Includes all businesses directly linked to the supply of goods or
services to the business and to the customer
- Involves the coordination of all these businesses so that inputs and
outputs are delivered in the quickest, most dependable and cost-
effective manner
- Lead time is the time it takes for a supplier to provide its customer
with the goods ordered
Logistics: the transport of physical raw materials, inputs and the distribution of
finished goods to markets. It involves the integration of information,
transportation, inventory, warehousing, materials handling and packaging.
Computerisation can make the task faster/more efficient. The role of logistics is
to ensure that operations have the right items at the right quantity and the right
time at the right place.
E-commerce: the use of internet to buy and sell goods and services. Alter
operation process, e-procurement, managing supplies in an organised way,
makes trading easier, cheaper access to global markets, privacy and security
issues, and increased risk of purchasing unsatisfactory or faulty materials.
- Quality: having the highest quality goods and services
- Speed: producing goods in a shorter time and delivering services
faster
- Dependability: being reliable in providing what outputs were needed
and when they were required
- Flexibility: being more flexible than competitors and being able to
make changes to operations
- Customisation: offering customized products to meet specific
customer wants
- Cost: producing cheaply and for a lower price than competitors
Design and development of new products and services
- All products have a life cycle
- New products must be developed for a business to maintain
competitive advantage and replace obsolete products
- New services can be created and improvements to existing service
can be developed using technology (ex: online delivery of study
materials and coursework)
- New product design is a lengthy, expensive process and few
products make it to final production from the large number of that
may be initially developed
- However, a business may supply their own version of a competitor’s
new product and avoid the expense and risk of product
development
Supply chain management
- It is the ‘chain of suppliers’
- Includes all businesses directly linked to the supply of goods or
services to the business and to the customer
- Involves the coordination of all these businesses so that inputs and
outputs are delivered in the quickest, most dependable and cost-
effective manner
- Lead time is the time it takes for a supplier to provide its customer
with the goods ordered
Logistics: the transport of physical raw materials, inputs and the distribution of
finished goods to markets. It involves the integration of information,
transportation, inventory, warehousing, materials handling and packaging.
Computerisation can make the task faster/more efficient. The role of logistics is
to ensure that operations have the right items at the right quantity and the right
time at the right place.
E-commerce: the use of internet to buy and sell goods and services. Alter
operation process, e-procurement, managing supplies in an organised way,
makes trading easier, cheaper access to global markets, privacy and security
issues, and increased risk of purchasing unsatisfactory or faulty materials.
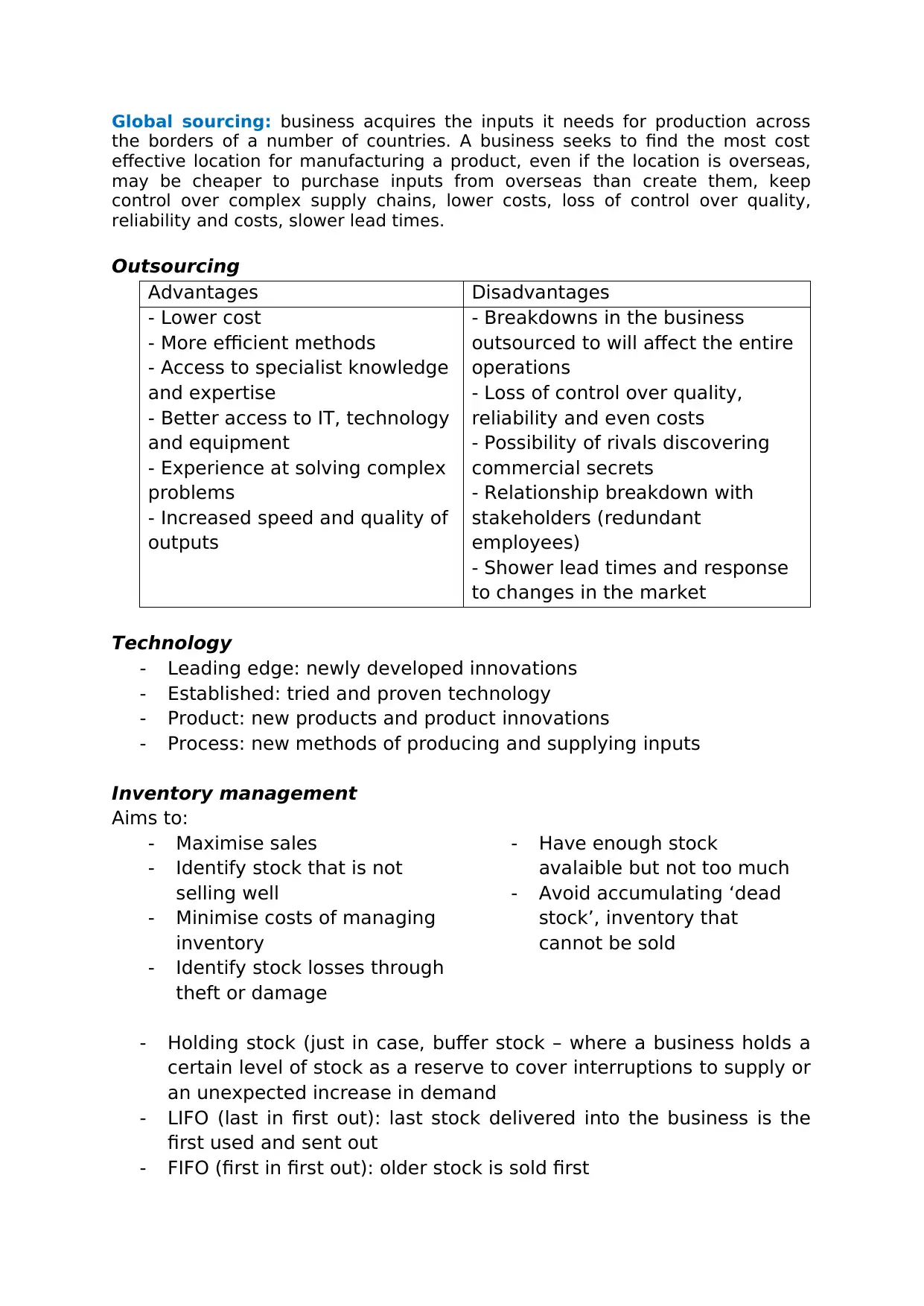
Global sourcing: business acquires the inputs it needs for production across
the borders of a number of countries. A business seeks to find the most cost
effective location for manufacturing a product, even if the location is overseas,
may be cheaper to purchase inputs from overseas than create them, keep
control over complex supply chains, lower costs, loss of control over quality,
reliability and costs, slower lead times.
Outsourcing
Advantages Disadvantages
- Lower cost
- More efficient methods
- Access to specialist knowledge
and expertise
- Better access to IT, technology
and equipment
- Experience at solving complex
problems
- Increased speed and quality of
outputs
- Breakdowns in the business
outsourced to will affect the entire
operations
- Loss of control over quality,
reliability and even costs
- Possibility of rivals discovering
commercial secrets
- Relationship breakdown with
stakeholders (redundant
employees)
- Shower lead times and response
to changes in the market
Technology
- Leading edge: newly developed innovations
- Established: tried and proven technology
- Product: new products and product innovations
- Process: new methods of producing and supplying inputs
Inventory management
Aims to:
- Maximise sales
- Identify stock that is not
selling well
- Minimise costs of managing
inventory
- Identify stock losses through
theft or damage
- Have enough stock
avalaible but not too much
- Avoid accumulating ‘dead
stock’, inventory that
cannot be sold
- Holding stock (just in case, buffer stock – where a business holds a
certain level of stock as a reserve to cover interruptions to supply or
an unexpected increase in demand
- LIFO (last in first out): last stock delivered into the business is the
first used and sent out
- FIFO (first in first out): older stock is sold first
the borders of a number of countries. A business seeks to find the most cost
effective location for manufacturing a product, even if the location is overseas,
may be cheaper to purchase inputs from overseas than create them, keep
control over complex supply chains, lower costs, loss of control over quality,
reliability and costs, slower lead times.
Outsourcing
Advantages Disadvantages
- Lower cost
- More efficient methods
- Access to specialist knowledge
and expertise
- Better access to IT, technology
and equipment
- Experience at solving complex
problems
- Increased speed and quality of
outputs
- Breakdowns in the business
outsourced to will affect the entire
operations
- Loss of control over quality,
reliability and even costs
- Possibility of rivals discovering
commercial secrets
- Relationship breakdown with
stakeholders (redundant
employees)
- Shower lead times and response
to changes in the market
Technology
- Leading edge: newly developed innovations
- Established: tried and proven technology
- Product: new products and product innovations
- Process: new methods of producing and supplying inputs
Inventory management
Aims to:
- Maximise sales
- Identify stock that is not
selling well
- Minimise costs of managing
inventory
- Identify stock losses through
theft or damage
- Have enough stock
avalaible but not too much
- Avoid accumulating ‘dead
stock’, inventory that
cannot be sold
- Holding stock (just in case, buffer stock – where a business holds a
certain level of stock as a reserve to cover interruptions to supply or
an unexpected increase in demand
- LIFO (last in first out): last stock delivered into the business is the
first used and sent out
- FIFO (first in first out): older stock is sold first
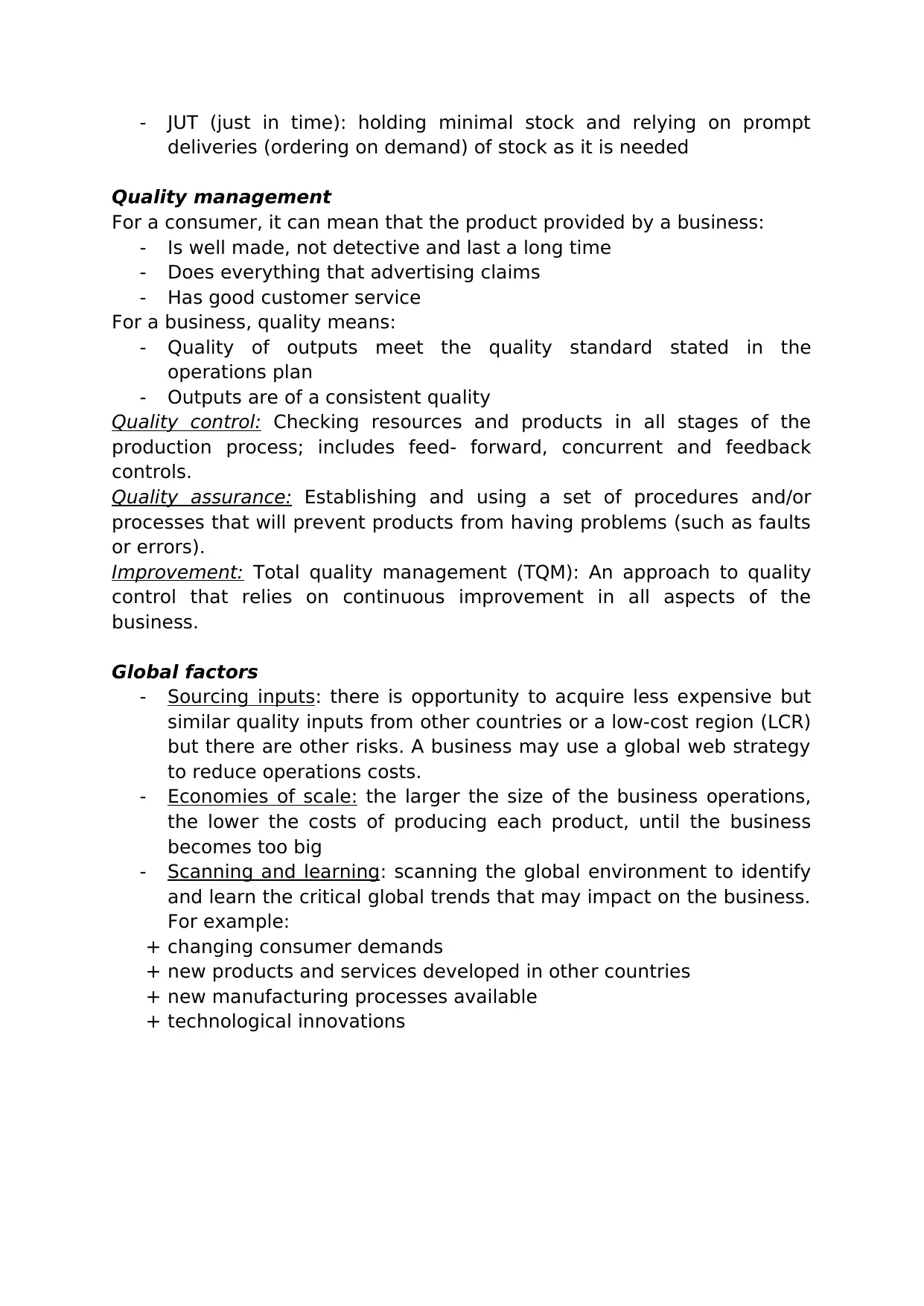
- JUT (just in time): holding minimal stock and relying on prompt
deliveries (ordering on demand) of stock as it is needed
Quality management
For a consumer, it can mean that the product provided by a business:
- Is well made, not detective and last a long time
- Does everything that advertising claims
- Has good customer service
For a business, quality means:
- Quality of outputs meet the quality standard stated in the
operations plan
- Outputs are of a consistent quality
Quality control: Checking resources and products in all stages of the
production process; includes feed- forward, concurrent and feedback
controls.
Quality assurance: Establishing and using a set of procedures and/or
processes that will prevent products from having problems (such as faults
or errors).
Improvement: Total quality management (TQM): An approach to quality
control that relies on continuous improvement in all aspects of the
business.
Global factors
- Sourcing inputs: there is opportunity to acquire less expensive but
similar quality inputs from other countries or a low-cost region (LCR)
but there are other risks. A business may use a global web strategy
to reduce operations costs.
- Economies of scale: the larger the size of the business operations,
the lower the costs of producing each product, until the business
becomes too big
- Scanning and learning: scanning the global environment to identify
and learn the critical global trends that may impact on the business.
For example:
+ changing consumer demands
+ new products and services developed in other countries
+ new manufacturing processes available
+ technological innovations
deliveries (ordering on demand) of stock as it is needed
Quality management
For a consumer, it can mean that the product provided by a business:
- Is well made, not detective and last a long time
- Does everything that advertising claims
- Has good customer service
For a business, quality means:
- Quality of outputs meet the quality standard stated in the
operations plan
- Outputs are of a consistent quality
Quality control: Checking resources and products in all stages of the
production process; includes feed- forward, concurrent and feedback
controls.
Quality assurance: Establishing and using a set of procedures and/or
processes that will prevent products from having problems (such as faults
or errors).
Improvement: Total quality management (TQM): An approach to quality
control that relies on continuous improvement in all aspects of the
business.
Global factors
- Sourcing inputs: there is opportunity to acquire less expensive but
similar quality inputs from other countries or a low-cost region (LCR)
but there are other risks. A business may use a global web strategy
to reduce operations costs.
- Economies of scale: the larger the size of the business operations,
the lower the costs of producing each product, until the business
becomes too big
- Scanning and learning: scanning the global environment to identify
and learn the critical global trends that may impact on the business.
For example:
+ changing consumer demands
+ new products and services developed in other countries
+ new manufacturing processes available
+ technological innovations
1 out of 10
Related Documents

Your All-in-One AI-Powered Toolkit for Academic Success.
+13062052269
info@desklib.com
Available 24*7 on WhatsApp / Email
Unlock your academic potential
© 2024 | Zucol Services PVT LTD | All rights reserved.