National College of Ireland: Business Process Management TQM Report
VerifiedAdded on  2022/08/22
|12
|2736
|19
Report
AI Summary
This report delves into the application of Business Process Management (BPM) and Total Quality Management (TQM) within the context of two distinct companies: Ford and McDonald's. It begins by defining BPM and highlighting its significance in enhancing corporate performance through the optimization of business processes, which in turn impacts costs and revenue. The report then explores the concept of TQM, emphasizing its role in improving overall business quality and customer satisfaction. The core of the report analyzes the implementation of TQM in Ford and McDonald's, comparing and contrasting their approaches. It examines the challenges faced during implementation, such as inefficient management, resource constraints, and employee involvement, and how both companies overcame them. The report also outlines the benefits of TQM, including improved operational activities, problem-solving methodologies (like Ford's 8D process), and the achievement of customer-centric goals. It concludes by underscoring the importance of TQM as a modern management tool for sustainable business success.
Contribute Materials
Your contribution can guide someone’s learning journey. Share your
documents today.
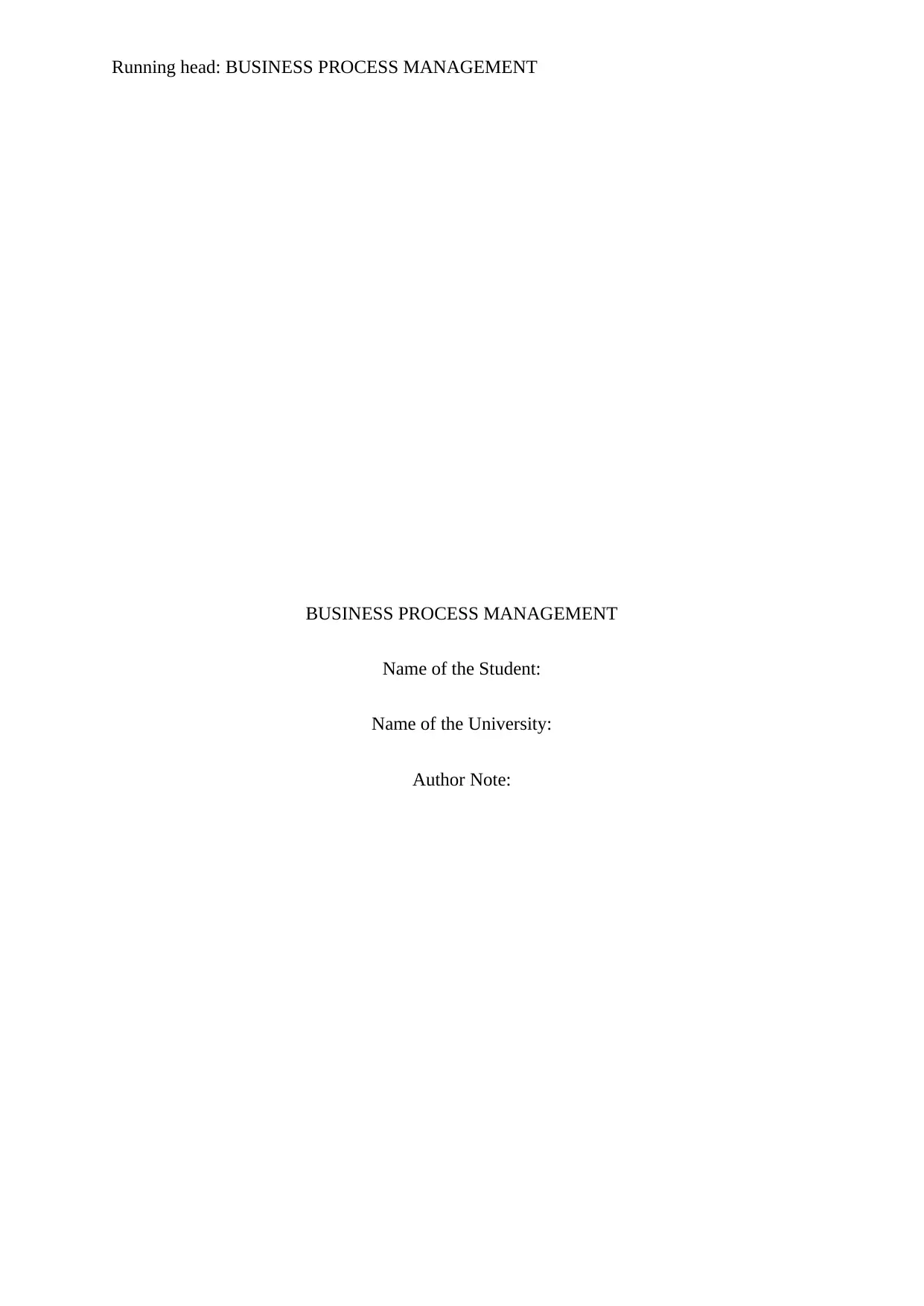
Running head: BUSINESS PROCESS MANAGEMENT
BUSINESS PROCESS MANAGEMENT
Name of the Student:
Name of the University:
Author Note:
BUSINESS PROCESS MANAGEMENT
Name of the Student:
Name of the University:
Author Note:
Secure Best Marks with AI Grader
Need help grading? Try our AI Grader for instant feedback on your assignments.
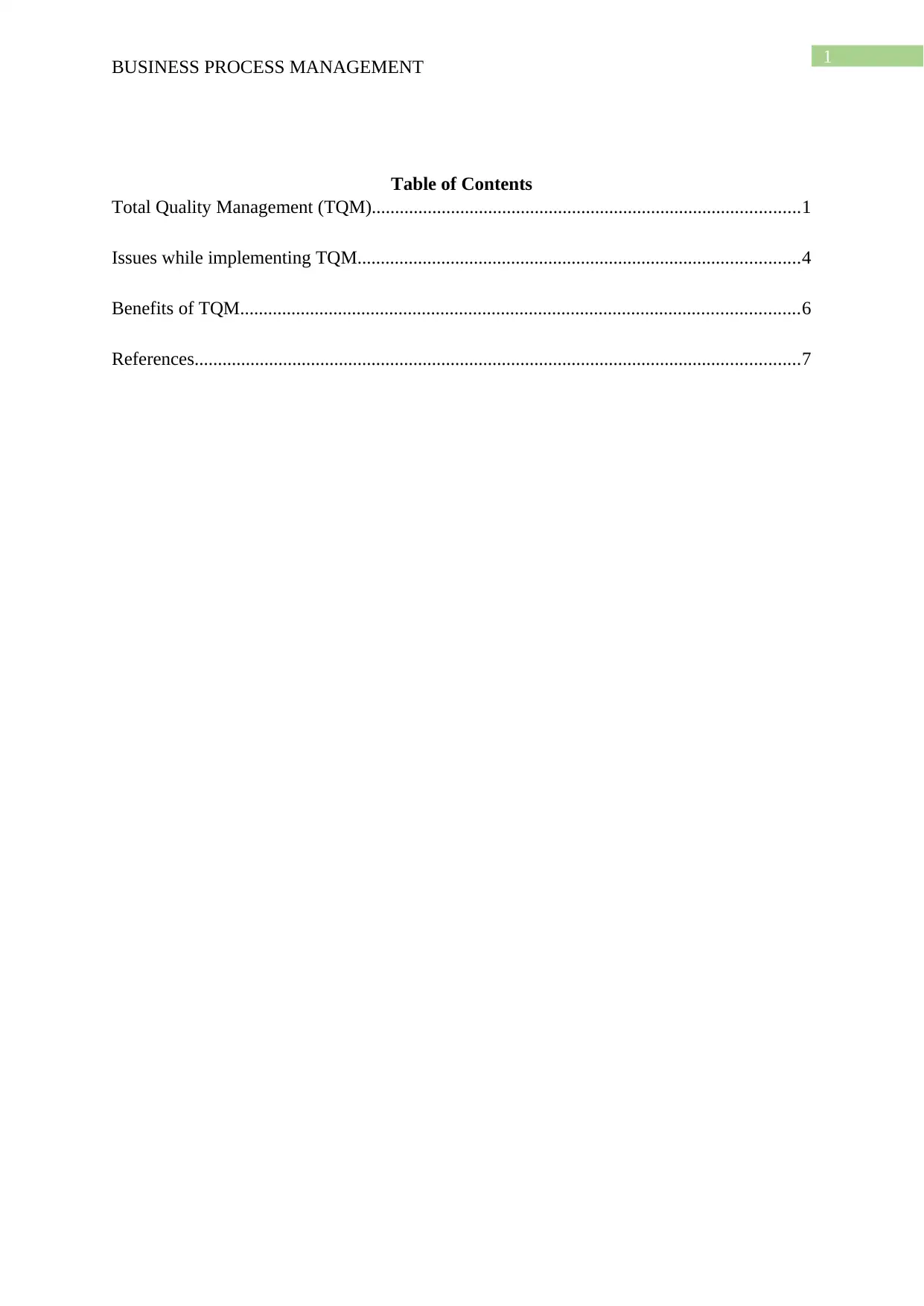
1
BUSINESS PROCESS MANAGEMENT
Table of Contents
Total Quality Management (TQM)............................................................................................1
Issues while implementing TQM...............................................................................................4
Benefits of TQM........................................................................................................................6
References..................................................................................................................................7
BUSINESS PROCESS MANAGEMENT
Table of Contents
Total Quality Management (TQM)............................................................................................1
Issues while implementing TQM...............................................................................................4
Benefits of TQM........................................................................................................................6
References..................................................................................................................................7
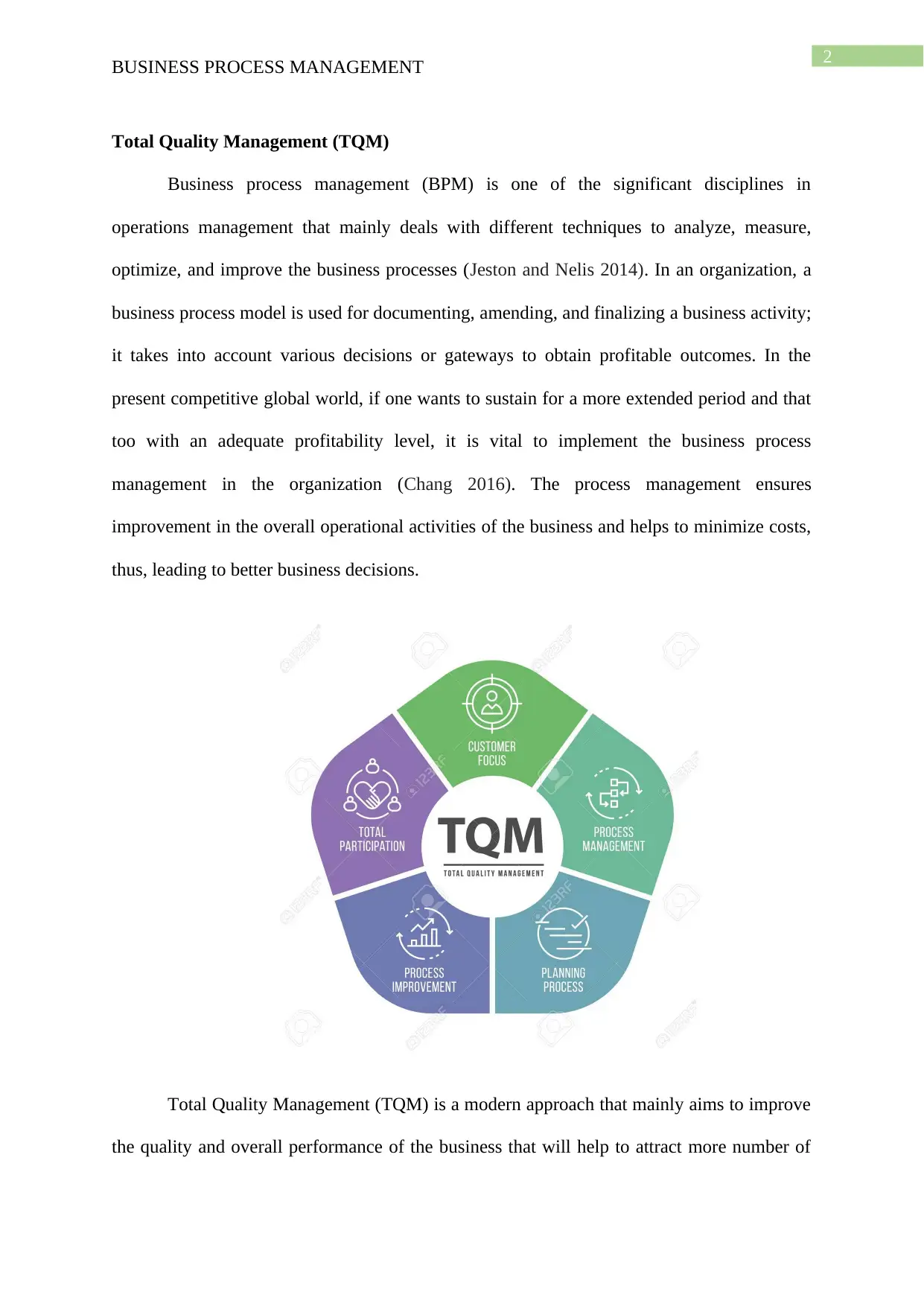
2
BUSINESS PROCESS MANAGEMENT
Total Quality Management (TQM)
Business process management (BPM) is one of the significant disciplines in
operations management that mainly deals with different techniques to analyze, measure,
optimize, and improve the business processes (Jeston and Nelis 2014). In an organization, a
business process model is used for documenting, amending, and finalizing a business activity;
it takes into account various decisions or gateways to obtain profitable outcomes. In the
present competitive global world, if one wants to sustain for a more extended period and that
too with an adequate profitability level, it is vital to implement the business process
management in the organization (Chang 2016). The process management ensures
improvement in the overall operational activities of the business and helps to minimize costs,
thus, leading to better business decisions.
Total Quality Management (TQM) is a modern approach that mainly aims to improve
the quality and overall performance of the business that will help to attract more number of
BUSINESS PROCESS MANAGEMENT
Total Quality Management (TQM)
Business process management (BPM) is one of the significant disciplines in
operations management that mainly deals with different techniques to analyze, measure,
optimize, and improve the business processes (Jeston and Nelis 2014). In an organization, a
business process model is used for documenting, amending, and finalizing a business activity;
it takes into account various decisions or gateways to obtain profitable outcomes. In the
present competitive global world, if one wants to sustain for a more extended period and that
too with an adequate profitability level, it is vital to implement the business process
management in the organization (Chang 2016). The process management ensures
improvement in the overall operational activities of the business and helps to minimize costs,
thus, leading to better business decisions.
Total Quality Management (TQM) is a modern approach that mainly aims to improve
the quality and overall performance of the business that will help to attract more number of
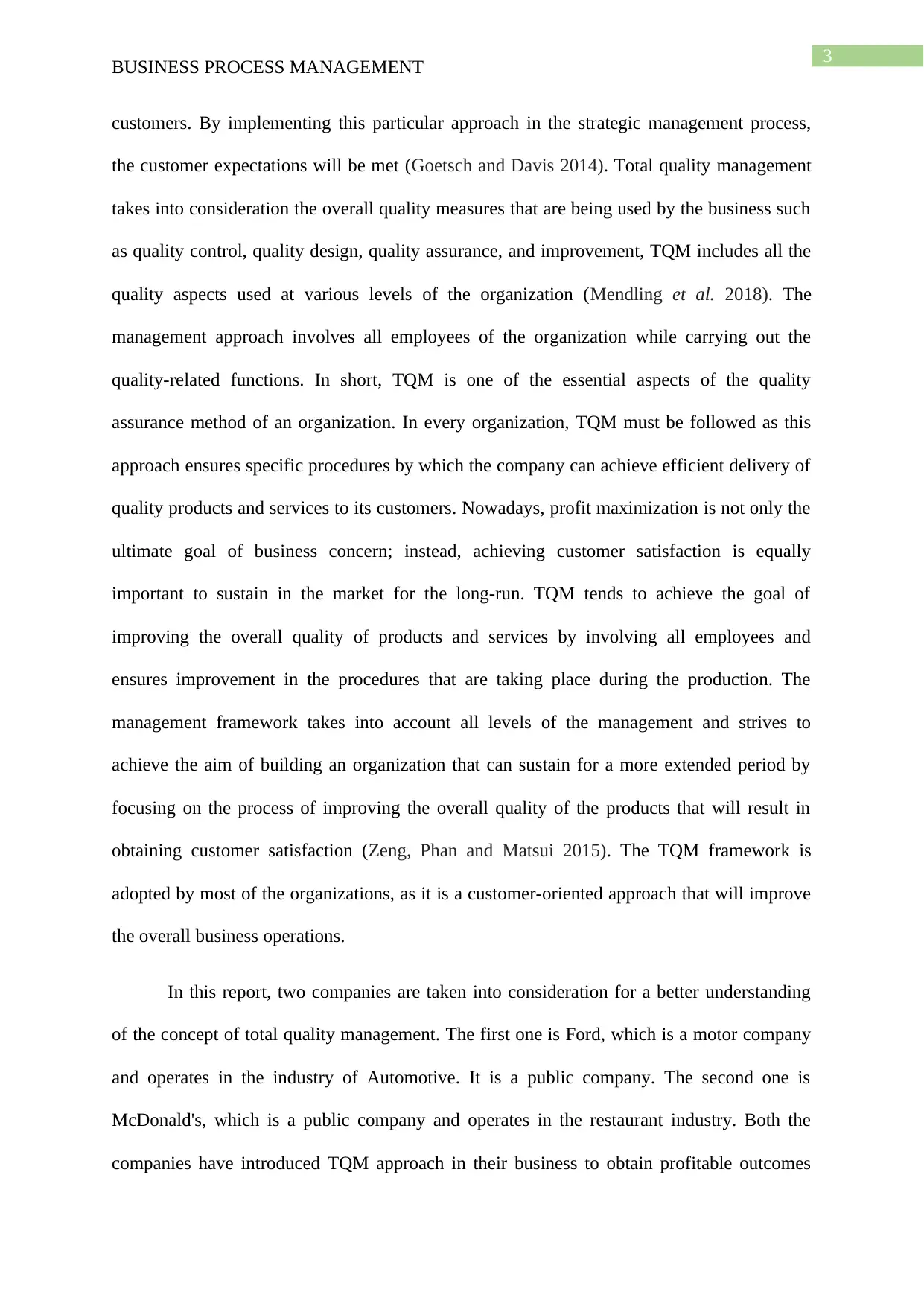
3
BUSINESS PROCESS MANAGEMENT
customers. By implementing this particular approach in the strategic management process,
the customer expectations will be met (Goetsch and Davis 2014). Total quality management
takes into consideration the overall quality measures that are being used by the business such
as quality control, quality design, quality assurance, and improvement, TQM includes all the
quality aspects used at various levels of the organization (Mendling et al. 2018). The
management approach involves all employees of the organization while carrying out the
quality-related functions. In short, TQM is one of the essential aspects of the quality
assurance method of an organization. In every organization, TQM must be followed as this
approach ensures specific procedures by which the company can achieve efficient delivery of
quality products and services to its customers. Nowadays, profit maximization is not only the
ultimate goal of business concern; instead, achieving customer satisfaction is equally
important to sustain in the market for the long-run. TQM tends to achieve the goal of
improving the overall quality of products and services by involving all employees and
ensures improvement in the procedures that are taking place during the production. The
management framework takes into account all levels of the management and strives to
achieve the aim of building an organization that can sustain for a more extended period by
focusing on the process of improving the overall quality of the products that will result in
obtaining customer satisfaction (Zeng, Phan and Matsui 2015). The TQM framework is
adopted by most of the organizations, as it is a customer-oriented approach that will improve
the overall business operations.
In this report, two companies are taken into consideration for a better understanding
of the concept of total quality management. The first one is Ford, which is a motor company
and operates in the industry of Automotive. It is a public company. The second one is
McDonald's, which is a public company and operates in the restaurant industry. Both the
companies have introduced TQM approach in their business to obtain profitable outcomes
BUSINESS PROCESS MANAGEMENT
customers. By implementing this particular approach in the strategic management process,
the customer expectations will be met (Goetsch and Davis 2014). Total quality management
takes into consideration the overall quality measures that are being used by the business such
as quality control, quality design, quality assurance, and improvement, TQM includes all the
quality aspects used at various levels of the organization (Mendling et al. 2018). The
management approach involves all employees of the organization while carrying out the
quality-related functions. In short, TQM is one of the essential aspects of the quality
assurance method of an organization. In every organization, TQM must be followed as this
approach ensures specific procedures by which the company can achieve efficient delivery of
quality products and services to its customers. Nowadays, profit maximization is not only the
ultimate goal of business concern; instead, achieving customer satisfaction is equally
important to sustain in the market for the long-run. TQM tends to achieve the goal of
improving the overall quality of products and services by involving all employees and
ensures improvement in the procedures that are taking place during the production. The
management framework takes into account all levels of the management and strives to
achieve the aim of building an organization that can sustain for a more extended period by
focusing on the process of improving the overall quality of the products that will result in
obtaining customer satisfaction (Zeng, Phan and Matsui 2015). The TQM framework is
adopted by most of the organizations, as it is a customer-oriented approach that will improve
the overall business operations.
In this report, two companies are taken into consideration for a better understanding
of the concept of total quality management. The first one is Ford, which is a motor company
and operates in the industry of Automotive. It is a public company. The second one is
McDonald's, which is a public company and operates in the restaurant industry. Both the
companies have introduced TQM approach in their business to obtain profitable outcomes
Secure Best Marks with AI Grader
Need help grading? Try our AI Grader for instant feedback on your assignments.
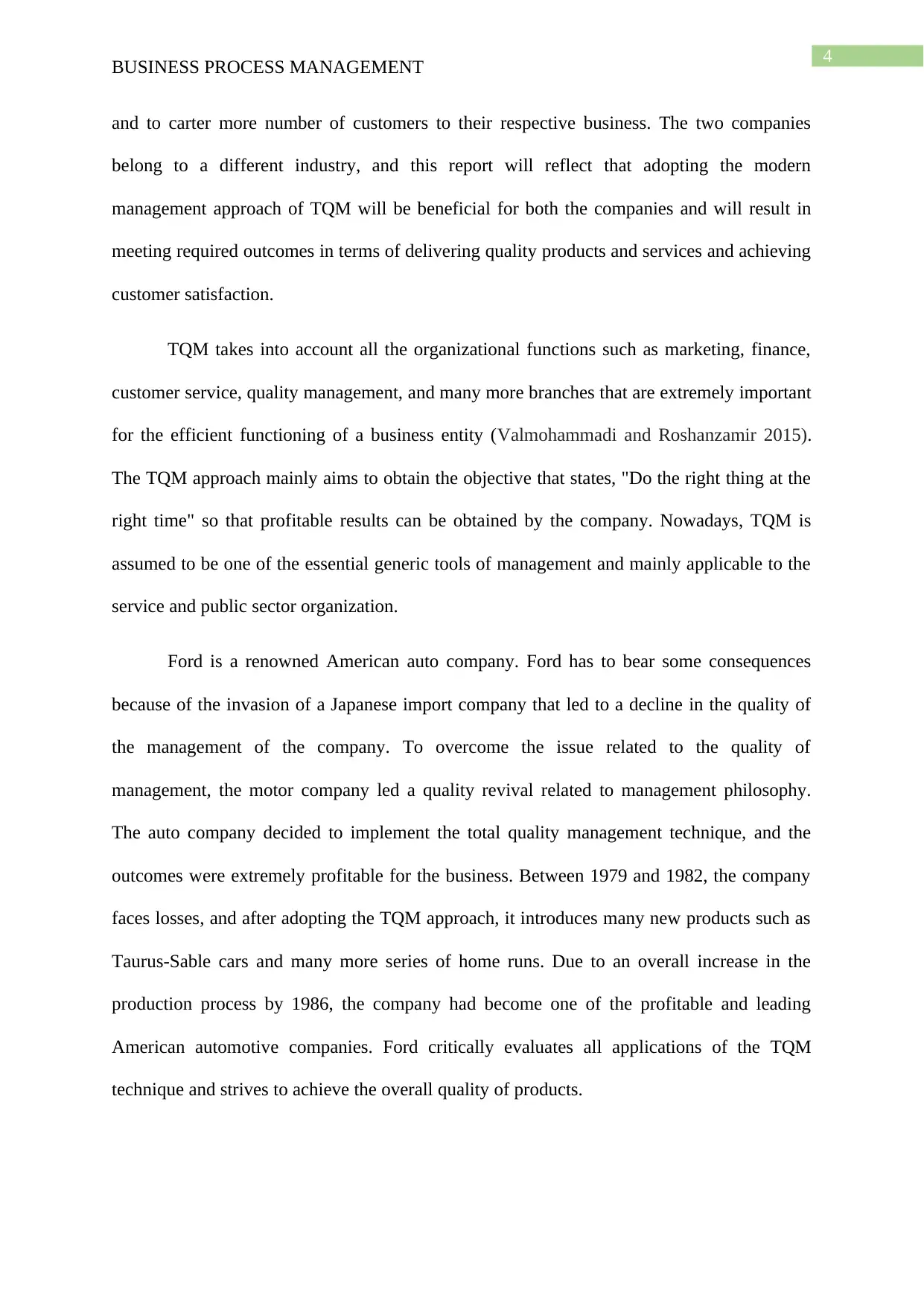
4
BUSINESS PROCESS MANAGEMENT
and to carter more number of customers to their respective business. The two companies
belong to a different industry, and this report will reflect that adopting the modern
management approach of TQM will be beneficial for both the companies and will result in
meeting required outcomes in terms of delivering quality products and services and achieving
customer satisfaction.
TQM takes into account all the organizational functions such as marketing, finance,
customer service, quality management, and many more branches that are extremely important
for the efficient functioning of a business entity (Valmohammadi and Roshanzamir 2015).
The TQM approach mainly aims to obtain the objective that states, "Do the right thing at the
right time" so that profitable results can be obtained by the company. Nowadays, TQM is
assumed to be one of the essential generic tools of management and mainly applicable to the
service and public sector organization.
Ford is a renowned American auto company. Ford has to bear some consequences
because of the invasion of a Japanese import company that led to a decline in the quality of
the management of the company. To overcome the issue related to the quality of
management, the motor company led a quality revival related to management philosophy.
The auto company decided to implement the total quality management technique, and the
outcomes were extremely profitable for the business. Between 1979 and 1982, the company
faces losses, and after adopting the TQM approach, it introduces many new products such as
Taurus-Sable cars and many more series of home runs. Due to an overall increase in the
production process by 1986, the company had become one of the profitable and leading
American automotive companies. Ford critically evaluates all applications of the TQM
technique and strives to achieve the overall quality of products.
BUSINESS PROCESS MANAGEMENT
and to carter more number of customers to their respective business. The two companies
belong to a different industry, and this report will reflect that adopting the modern
management approach of TQM will be beneficial for both the companies and will result in
meeting required outcomes in terms of delivering quality products and services and achieving
customer satisfaction.
TQM takes into account all the organizational functions such as marketing, finance,
customer service, quality management, and many more branches that are extremely important
for the efficient functioning of a business entity (Valmohammadi and Roshanzamir 2015).
The TQM approach mainly aims to obtain the objective that states, "Do the right thing at the
right time" so that profitable results can be obtained by the company. Nowadays, TQM is
assumed to be one of the essential generic tools of management and mainly applicable to the
service and public sector organization.
Ford is a renowned American auto company. Ford has to bear some consequences
because of the invasion of a Japanese import company that led to a decline in the quality of
the management of the company. To overcome the issue related to the quality of
management, the motor company led a quality revival related to management philosophy.
The auto company decided to implement the total quality management technique, and the
outcomes were extremely profitable for the business. Between 1979 and 1982, the company
faces losses, and after adopting the TQM approach, it introduces many new products such as
Taurus-Sable cars and many more series of home runs. Due to an overall increase in the
production process by 1986, the company had become one of the profitable and leading
American automotive companies. Ford critically evaluates all applications of the TQM
technique and strives to achieve the overall quality of products.
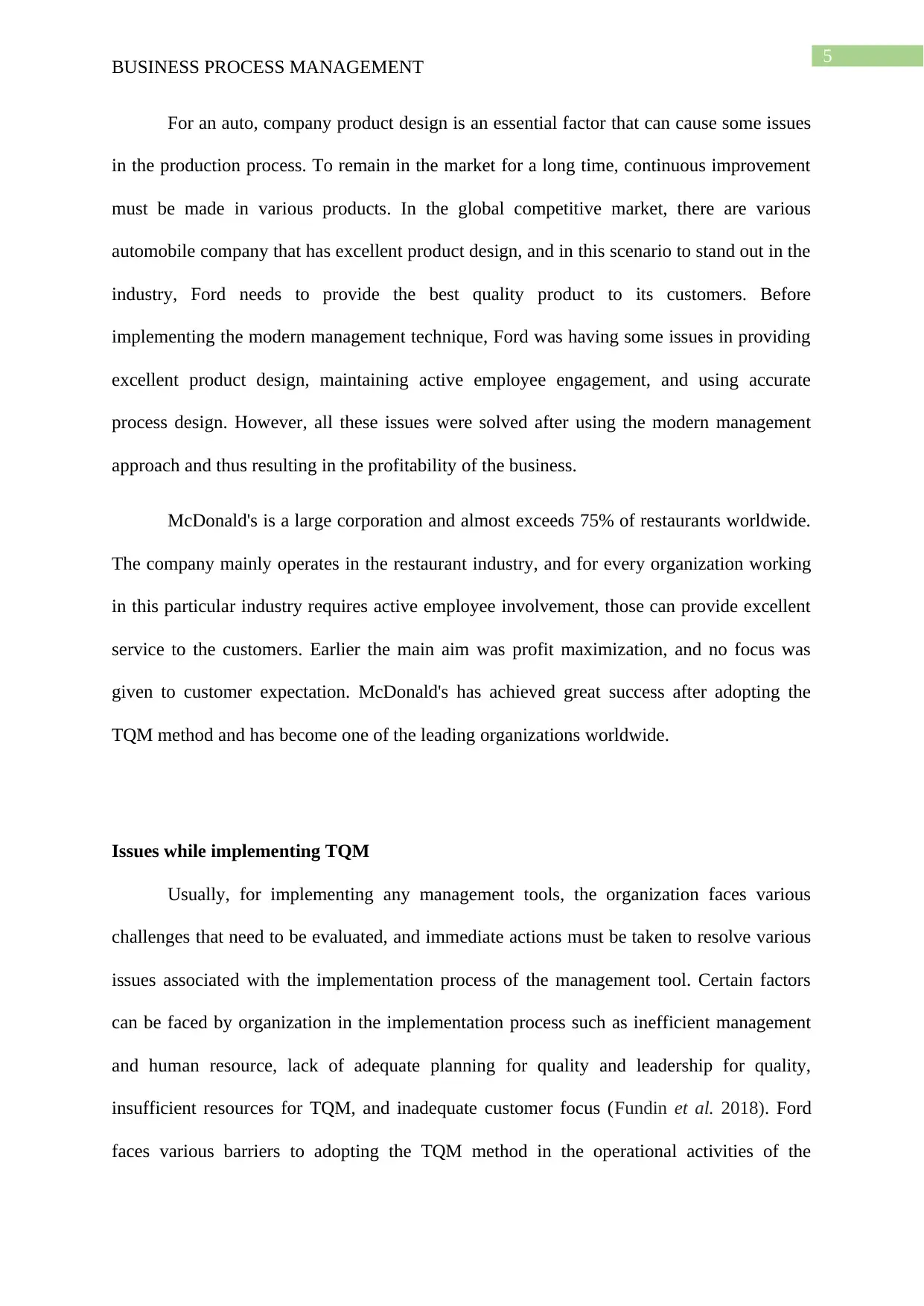
5
BUSINESS PROCESS MANAGEMENT
For an auto, company product design is an essential factor that can cause some issues
in the production process. To remain in the market for a long time, continuous improvement
must be made in various products. In the global competitive market, there are various
automobile company that has excellent product design, and in this scenario to stand out in the
industry, Ford needs to provide the best quality product to its customers. Before
implementing the modern management technique, Ford was having some issues in providing
excellent product design, maintaining active employee engagement, and using accurate
process design. However, all these issues were solved after using the modern management
approach and thus resulting in the profitability of the business.
McDonald's is a large corporation and almost exceeds 75% of restaurants worldwide.
The company mainly operates in the restaurant industry, and for every organization working
in this particular industry requires active employee involvement, those can provide excellent
service to the customers. Earlier the main aim was profit maximization, and no focus was
given to customer expectation. McDonald's has achieved great success after adopting the
TQM method and has become one of the leading organizations worldwide.
Issues while implementing TQM
Usually, for implementing any management tools, the organization faces various
challenges that need to be evaluated, and immediate actions must be taken to resolve various
issues associated with the implementation process of the management tool. Certain factors
can be faced by organization in the implementation process such as inefficient management
and human resource, lack of adequate planning for quality and leadership for quality,
insufficient resources for TQM, and inadequate customer focus (Fundin et al. 2018). Ford
faces various barriers to adopting the TQM method in the operational activities of the
BUSINESS PROCESS MANAGEMENT
For an auto, company product design is an essential factor that can cause some issues
in the production process. To remain in the market for a long time, continuous improvement
must be made in various products. In the global competitive market, there are various
automobile company that has excellent product design, and in this scenario to stand out in the
industry, Ford needs to provide the best quality product to its customers. Before
implementing the modern management technique, Ford was having some issues in providing
excellent product design, maintaining active employee engagement, and using accurate
process design. However, all these issues were solved after using the modern management
approach and thus resulting in the profitability of the business.
McDonald's is a large corporation and almost exceeds 75% of restaurants worldwide.
The company mainly operates in the restaurant industry, and for every organization working
in this particular industry requires active employee involvement, those can provide excellent
service to the customers. Earlier the main aim was profit maximization, and no focus was
given to customer expectation. McDonald's has achieved great success after adopting the
TQM method and has become one of the leading organizations worldwide.
Issues while implementing TQM
Usually, for implementing any management tools, the organization faces various
challenges that need to be evaluated, and immediate actions must be taken to resolve various
issues associated with the implementation process of the management tool. Certain factors
can be faced by organization in the implementation process such as inefficient management
and human resource, lack of adequate planning for quality and leadership for quality,
insufficient resources for TQM, and inadequate customer focus (Fundin et al. 2018). Ford
faces various barriers to adopting the TQM method in the operational activities of the
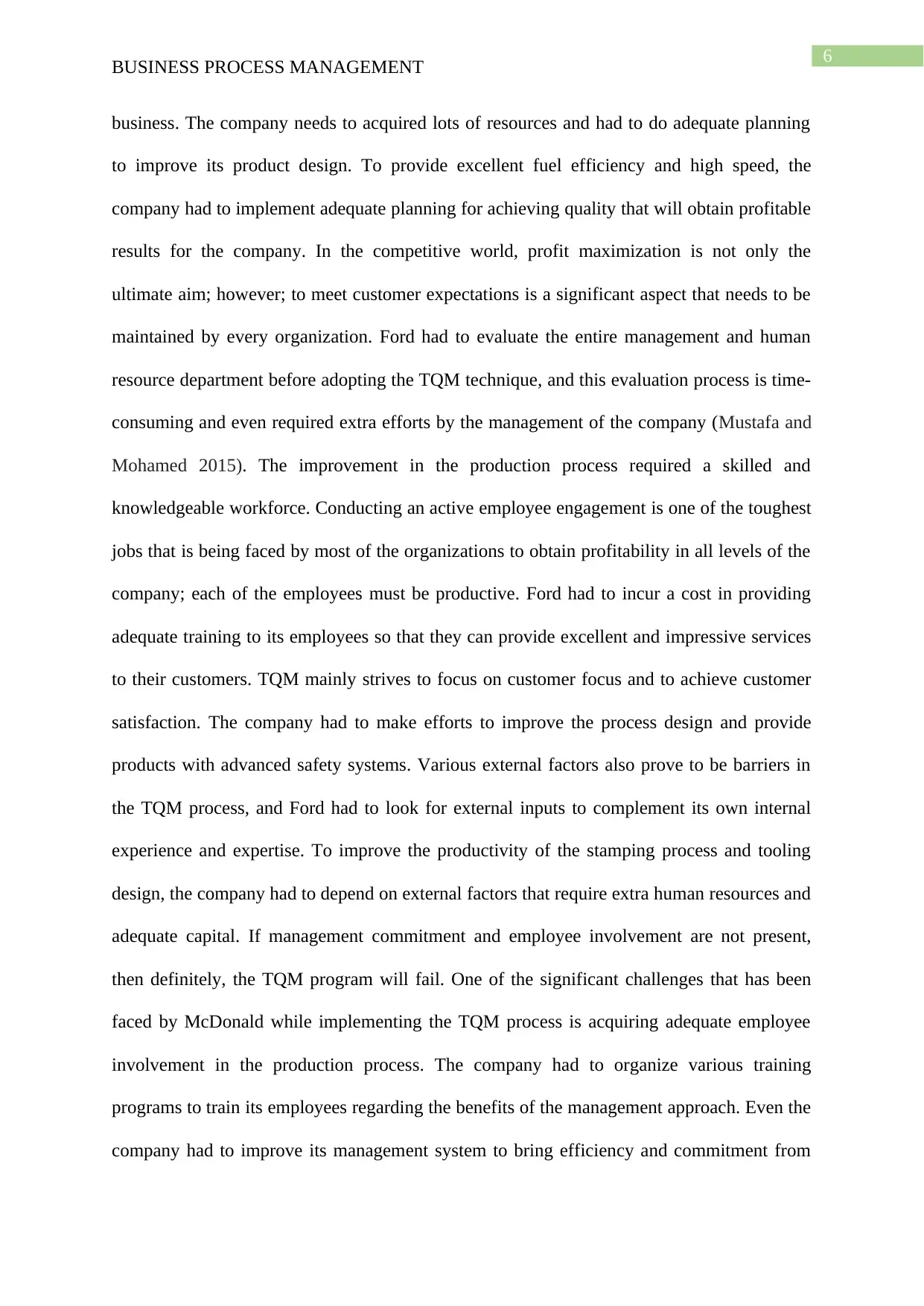
6
BUSINESS PROCESS MANAGEMENT
business. The company needs to acquired lots of resources and had to do adequate planning
to improve its product design. To provide excellent fuel efficiency and high speed, the
company had to implement adequate planning for achieving quality that will obtain profitable
results for the company. In the competitive world, profit maximization is not only the
ultimate aim; however; to meet customer expectations is a significant aspect that needs to be
maintained by every organization. Ford had to evaluate the entire management and human
resource department before adopting the TQM technique, and this evaluation process is time-
consuming and even required extra efforts by the management of the company (Mustafa and
Mohamed 2015). The improvement in the production process required a skilled and
knowledgeable workforce. Conducting an active employee engagement is one of the toughest
jobs that is being faced by most of the organizations to obtain profitability in all levels of the
company; each of the employees must be productive. Ford had to incur a cost in providing
adequate training to its employees so that they can provide excellent and impressive services
to their customers. TQM mainly strives to focus on customer focus and to achieve customer
satisfaction. The company had to make efforts to improve the process design and provide
products with advanced safety systems. Various external factors also prove to be barriers in
the TQM process, and Ford had to look for external inputs to complement its own internal
experience and expertise. To improve the productivity of the stamping process and tooling
design, the company had to depend on external factors that require extra human resources and
adequate capital. If management commitment and employee involvement are not present,
then definitely, the TQM program will fail. One of the significant challenges that has been
faced by McDonald while implementing the TQM process is acquiring adequate employee
involvement in the production process. The company had to organize various training
programs to train its employees regarding the benefits of the management approach. Even the
company had to improve its management system to bring efficiency and commitment from
BUSINESS PROCESS MANAGEMENT
business. The company needs to acquired lots of resources and had to do adequate planning
to improve its product design. To provide excellent fuel efficiency and high speed, the
company had to implement adequate planning for achieving quality that will obtain profitable
results for the company. In the competitive world, profit maximization is not only the
ultimate aim; however; to meet customer expectations is a significant aspect that needs to be
maintained by every organization. Ford had to evaluate the entire management and human
resource department before adopting the TQM technique, and this evaluation process is time-
consuming and even required extra efforts by the management of the company (Mustafa and
Mohamed 2015). The improvement in the production process required a skilled and
knowledgeable workforce. Conducting an active employee engagement is one of the toughest
jobs that is being faced by most of the organizations to obtain profitability in all levels of the
company; each of the employees must be productive. Ford had to incur a cost in providing
adequate training to its employees so that they can provide excellent and impressive services
to their customers. TQM mainly strives to focus on customer focus and to achieve customer
satisfaction. The company had to make efforts to improve the process design and provide
products with advanced safety systems. Various external factors also prove to be barriers in
the TQM process, and Ford had to look for external inputs to complement its own internal
experience and expertise. To improve the productivity of the stamping process and tooling
design, the company had to depend on external factors that require extra human resources and
adequate capital. If management commitment and employee involvement are not present,
then definitely, the TQM program will fail. One of the significant challenges that has been
faced by McDonald while implementing the TQM process is acquiring adequate employee
involvement in the production process. The company had to organize various training
programs to train its employees regarding the benefits of the management approach. Even the
company had to improve its management system to bring efficiency and commitment from
Paraphrase This Document
Need a fresh take? Get an instant paraphrase of this document with our AI Paraphraser
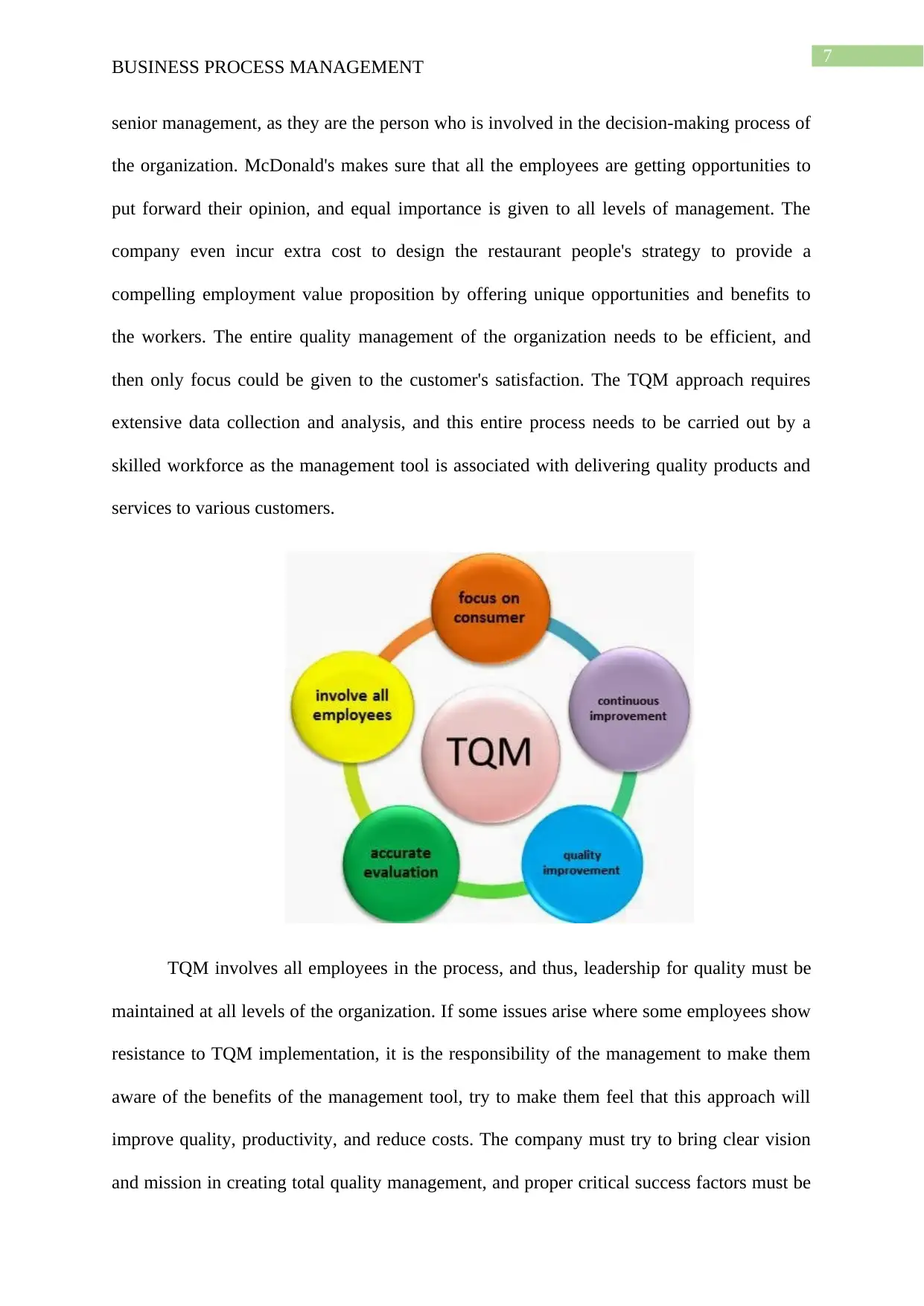
7
BUSINESS PROCESS MANAGEMENT
senior management, as they are the person who is involved in the decision-making process of
the organization. McDonald's makes sure that all the employees are getting opportunities to
put forward their opinion, and equal importance is given to all levels of management. The
company even incur extra cost to design the restaurant people's strategy to provide a
compelling employment value proposition by offering unique opportunities and benefits to
the workers. The entire quality management of the organization needs to be efficient, and
then only focus could be given to the customer's satisfaction. The TQM approach requires
extensive data collection and analysis, and this entire process needs to be carried out by a
skilled workforce as the management tool is associated with delivering quality products and
services to various customers.
TQM involves all employees in the process, and thus, leadership for quality must be
maintained at all levels of the organization. If some issues arise where some employees show
resistance to TQM implementation, it is the responsibility of the management to make them
aware of the benefits of the management tool, try to make them feel that this approach will
improve quality, productivity, and reduce costs. The company must try to bring clear vision
and mission in creating total quality management, and proper critical success factors must be
BUSINESS PROCESS MANAGEMENT
senior management, as they are the person who is involved in the decision-making process of
the organization. McDonald's makes sure that all the employees are getting opportunities to
put forward their opinion, and equal importance is given to all levels of management. The
company even incur extra cost to design the restaurant people's strategy to provide a
compelling employment value proposition by offering unique opportunities and benefits to
the workers. The entire quality management of the organization needs to be efficient, and
then only focus could be given to the customer's satisfaction. The TQM approach requires
extensive data collection and analysis, and this entire process needs to be carried out by a
skilled workforce as the management tool is associated with delivering quality products and
services to various customers.
TQM involves all employees in the process, and thus, leadership for quality must be
maintained at all levels of the organization. If some issues arise where some employees show
resistance to TQM implementation, it is the responsibility of the management to make them
aware of the benefits of the management tool, try to make them feel that this approach will
improve quality, productivity, and reduce costs. The company must try to bring clear vision
and mission in creating total quality management, and proper critical success factors must be
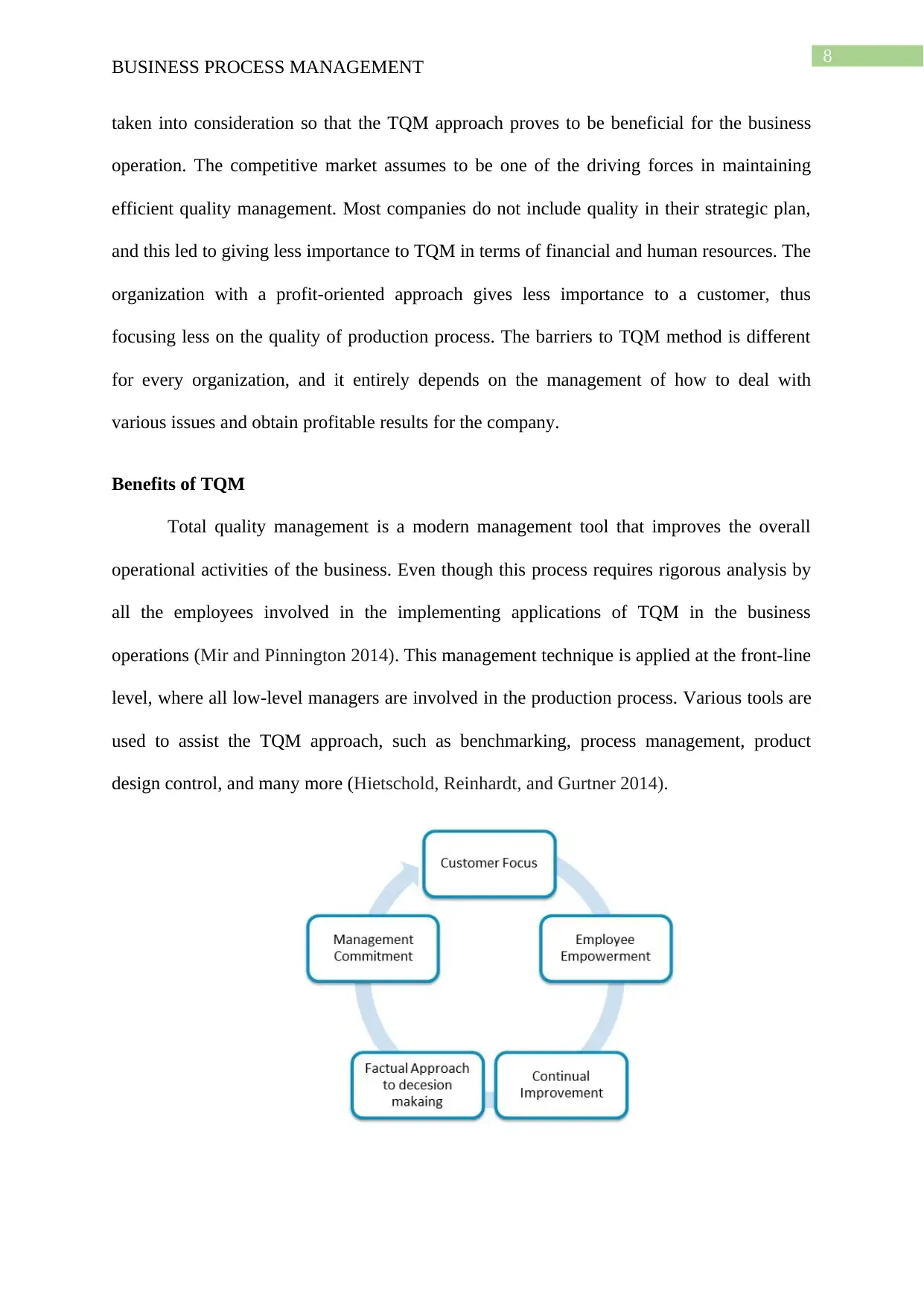
8
BUSINESS PROCESS MANAGEMENT
taken into consideration so that the TQM approach proves to be beneficial for the business
operation. The competitive market assumes to be one of the driving forces in maintaining
efficient quality management. Most companies do not include quality in their strategic plan,
and this led to giving less importance to TQM in terms of financial and human resources. The
organization with a profit-oriented approach gives less importance to a customer, thus
focusing less on the quality of production process. The barriers to TQM method is different
for every organization, and it entirely depends on the management of how to deal with
various issues and obtain profitable results for the company.
Benefits of TQM
Total quality management is a modern management tool that improves the overall
operational activities of the business. Even though this process requires rigorous analysis by
all the employees involved in the implementing applications of TQM in the business
operations (Mir and Pinnington 2014). This management technique is applied at the front-line
level, where all low-level managers are involved in the production process. Various tools are
used to assist the TQM approach, such as benchmarking, process management, product
design control, and many more (Hietschold, Reinhardt, and Gurtner 2014).
BUSINESS PROCESS MANAGEMENT
taken into consideration so that the TQM approach proves to be beneficial for the business
operation. The competitive market assumes to be one of the driving forces in maintaining
efficient quality management. Most companies do not include quality in their strategic plan,
and this led to giving less importance to TQM in terms of financial and human resources. The
organization with a profit-oriented approach gives less importance to a customer, thus
focusing less on the quality of production process. The barriers to TQM method is different
for every organization, and it entirely depends on the management of how to deal with
various issues and obtain profitable results for the company.
Benefits of TQM
Total quality management is a modern management tool that improves the overall
operational activities of the business. Even though this process requires rigorous analysis by
all the employees involved in the implementing applications of TQM in the business
operations (Mir and Pinnington 2014). This management technique is applied at the front-line
level, where all low-level managers are involved in the production process. Various tools are
used to assist the TQM approach, such as benchmarking, process management, product
design control, and many more (Hietschold, Reinhardt, and Gurtner 2014).
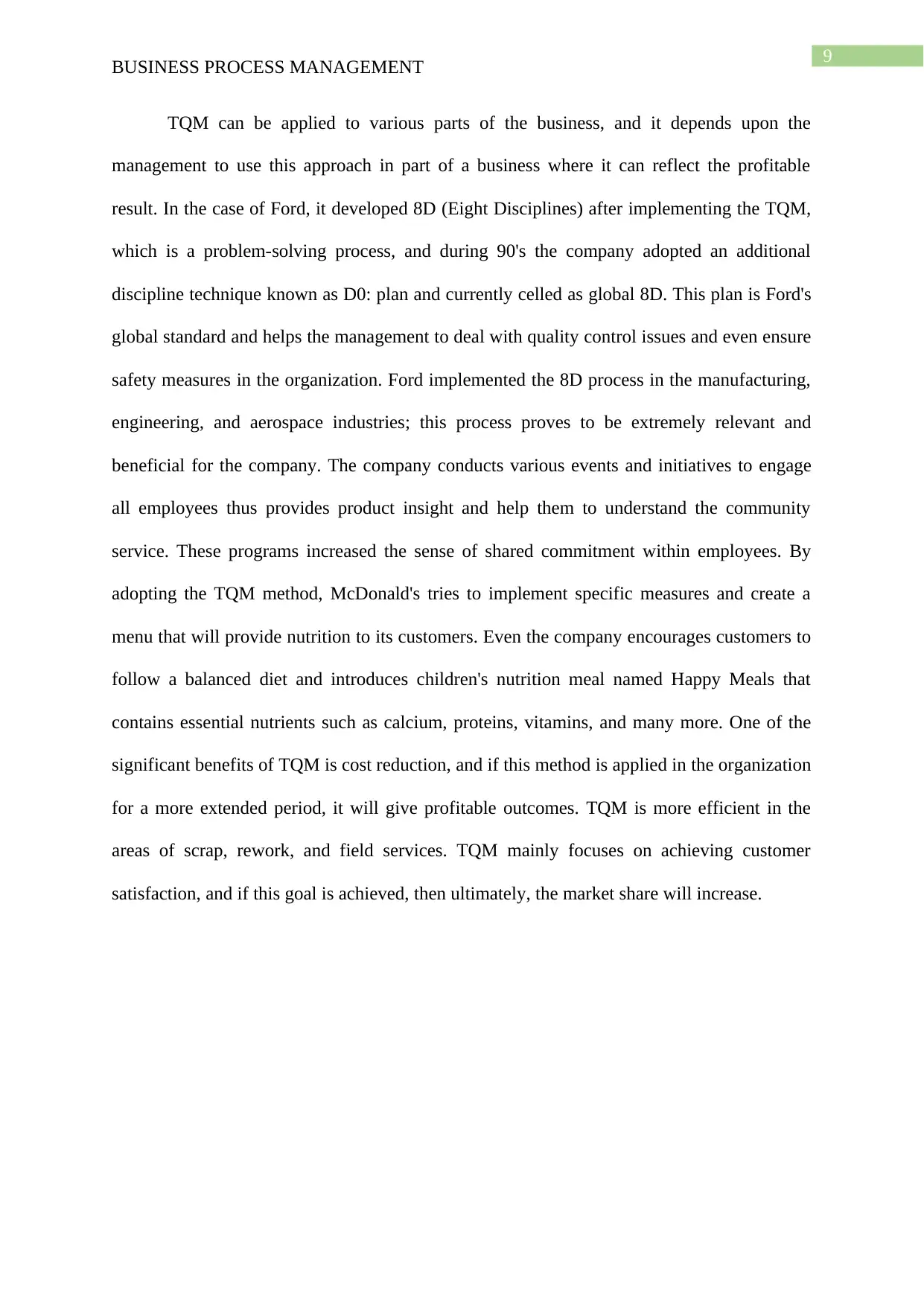
9
BUSINESS PROCESS MANAGEMENT
TQM can be applied to various parts of the business, and it depends upon the
management to use this approach in part of a business where it can reflect the profitable
result. In the case of Ford, it developed 8D (Eight Disciplines) after implementing the TQM,
which is a problem-solving process, and during 90's the company adopted an additional
discipline technique known as D0: plan and currently celled as global 8D. This plan is Ford's
global standard and helps the management to deal with quality control issues and even ensure
safety measures in the organization. Ford implemented the 8D process in the manufacturing,
engineering, and aerospace industries; this process proves to be extremely relevant and
beneficial for the company. The company conducts various events and initiatives to engage
all employees thus provides product insight and help them to understand the community
service. These programs increased the sense of shared commitment within employees. By
adopting the TQM method, McDonald's tries to implement specific measures and create a
menu that will provide nutrition to its customers. Even the company encourages customers to
follow a balanced diet and introduces children's nutrition meal named Happy Meals that
contains essential nutrients such as calcium, proteins, vitamins, and many more. One of the
significant benefits of TQM is cost reduction, and if this method is applied in the organization
for a more extended period, it will give profitable outcomes. TQM is more efficient in the
areas of scrap, rework, and field services. TQM mainly focuses on achieving customer
satisfaction, and if this goal is achieved, then ultimately, the market share will increase.
BUSINESS PROCESS MANAGEMENT
TQM can be applied to various parts of the business, and it depends upon the
management to use this approach in part of a business where it can reflect the profitable
result. In the case of Ford, it developed 8D (Eight Disciplines) after implementing the TQM,
which is a problem-solving process, and during 90's the company adopted an additional
discipline technique known as D0: plan and currently celled as global 8D. This plan is Ford's
global standard and helps the management to deal with quality control issues and even ensure
safety measures in the organization. Ford implemented the 8D process in the manufacturing,
engineering, and aerospace industries; this process proves to be extremely relevant and
beneficial for the company. The company conducts various events and initiatives to engage
all employees thus provides product insight and help them to understand the community
service. These programs increased the sense of shared commitment within employees. By
adopting the TQM method, McDonald's tries to implement specific measures and create a
menu that will provide nutrition to its customers. Even the company encourages customers to
follow a balanced diet and introduces children's nutrition meal named Happy Meals that
contains essential nutrients such as calcium, proteins, vitamins, and many more. One of the
significant benefits of TQM is cost reduction, and if this method is applied in the organization
for a more extended period, it will give profitable outcomes. TQM is more efficient in the
areas of scrap, rework, and field services. TQM mainly focuses on achieving customer
satisfaction, and if this goal is achieved, then ultimately, the market share will increase.
Secure Best Marks with AI Grader
Need help grading? Try our AI Grader for instant feedback on your assignments.
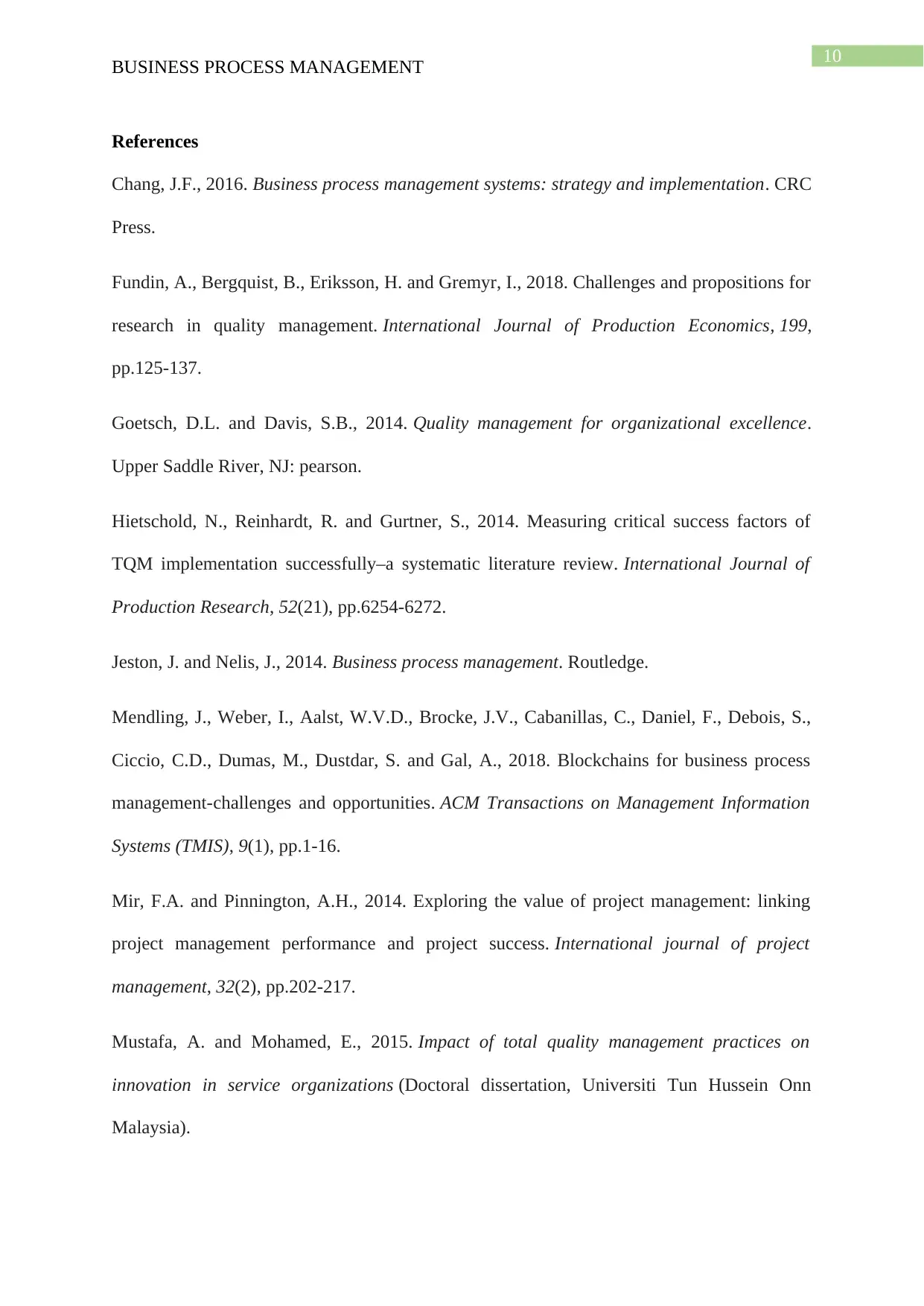
10
BUSINESS PROCESS MANAGEMENT
References
Chang, J.F., 2016. Business process management systems: strategy and implementation. CRC
Press.
Fundin, A., Bergquist, B., Eriksson, H. and Gremyr, I., 2018. Challenges and propositions for
research in quality management. International Journal of Production Economics, 199,
pp.125-137.
Goetsch, D.L. and Davis, S.B., 2014. Quality management for organizational excellence.
Upper Saddle River, NJ: pearson.
Hietschold, N., Reinhardt, R. and Gurtner, S., 2014. Measuring critical success factors of
TQM implementation successfully–a systematic literature review. International Journal of
Production Research, 52(21), pp.6254-6272.
Jeston, J. and Nelis, J., 2014. Business process management. Routledge.
Mendling, J., Weber, I., Aalst, W.V.D., Brocke, J.V., Cabanillas, C., Daniel, F., Debois, S.,
Ciccio, C.D., Dumas, M., Dustdar, S. and Gal, A., 2018. Blockchains for business process
management-challenges and opportunities. ACM Transactions on Management Information
Systems (TMIS), 9(1), pp.1-16.
Mir, F.A. and Pinnington, A.H., 2014. Exploring the value of project management: linking
project management performance and project success. International journal of project
management, 32(2), pp.202-217.
Mustafa, A. and Mohamed, E., 2015. Impact of total quality management practices on
innovation in service organizations (Doctoral dissertation, Universiti Tun Hussein Onn
Malaysia).
BUSINESS PROCESS MANAGEMENT
References
Chang, J.F., 2016. Business process management systems: strategy and implementation. CRC
Press.
Fundin, A., Bergquist, B., Eriksson, H. and Gremyr, I., 2018. Challenges and propositions for
research in quality management. International Journal of Production Economics, 199,
pp.125-137.
Goetsch, D.L. and Davis, S.B., 2014. Quality management for organizational excellence.
Upper Saddle River, NJ: pearson.
Hietschold, N., Reinhardt, R. and Gurtner, S., 2014. Measuring critical success factors of
TQM implementation successfully–a systematic literature review. International Journal of
Production Research, 52(21), pp.6254-6272.
Jeston, J. and Nelis, J., 2014. Business process management. Routledge.
Mendling, J., Weber, I., Aalst, W.V.D., Brocke, J.V., Cabanillas, C., Daniel, F., Debois, S.,
Ciccio, C.D., Dumas, M., Dustdar, S. and Gal, A., 2018. Blockchains for business process
management-challenges and opportunities. ACM Transactions on Management Information
Systems (TMIS), 9(1), pp.1-16.
Mir, F.A. and Pinnington, A.H., 2014. Exploring the value of project management: linking
project management performance and project success. International journal of project
management, 32(2), pp.202-217.
Mustafa, A. and Mohamed, E., 2015. Impact of total quality management practices on
innovation in service organizations (Doctoral dissertation, Universiti Tun Hussein Onn
Malaysia).
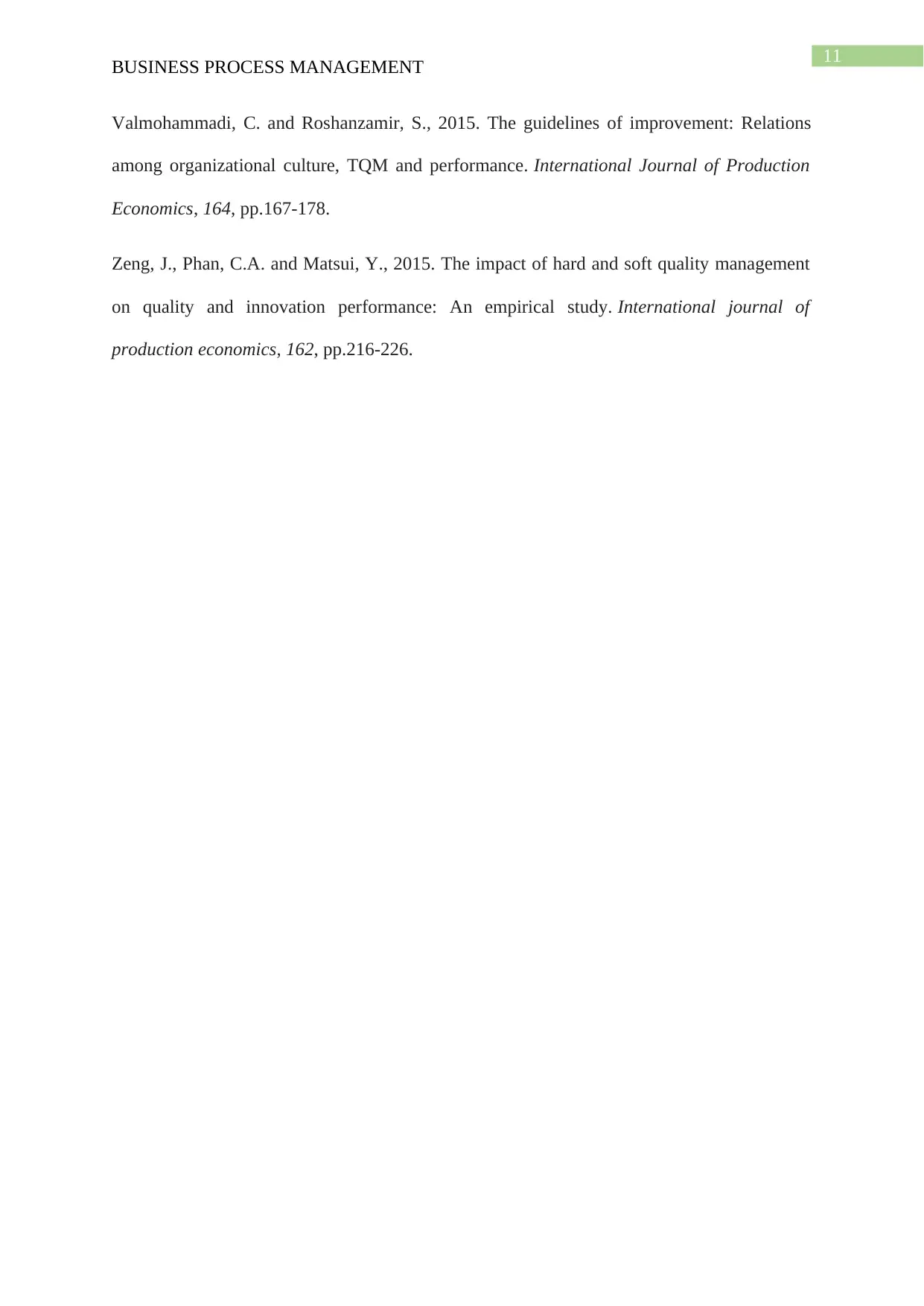
11
BUSINESS PROCESS MANAGEMENT
Valmohammadi, C. and Roshanzamir, S., 2015. The guidelines of improvement: Relations
among organizational culture, TQM and performance. International Journal of Production
Economics, 164, pp.167-178.
Zeng, J., Phan, C.A. and Matsui, Y., 2015. The impact of hard and soft quality management
on quality and innovation performance: An empirical study. International journal of
production economics, 162, pp.216-226.
BUSINESS PROCESS MANAGEMENT
Valmohammadi, C. and Roshanzamir, S., 2015. The guidelines of improvement: Relations
among organizational culture, TQM and performance. International Journal of Production
Economics, 164, pp.167-178.
Zeng, J., Phan, C.A. and Matsui, Y., 2015. The impact of hard and soft quality management
on quality and innovation performance: An empirical study. International journal of
production economics, 162, pp.216-226.
1 out of 12
Related Documents

Your All-in-One AI-Powered Toolkit for Academic Success.
 +13062052269
info@desklib.com
Available 24*7 on WhatsApp / Email
Unlock your academic potential
© 2024  |  Zucol Services PVT LTD  |  All rights reserved.