Arden University BUS5002D Business Processes Case Study Analysis
VerifiedAdded on 2022/12/05
|15
|3335
|95
Case Study
AI Summary
This case study analyzes business processes, quality management approaches, and project management principles within the context of Starbucks and McDonald's. The assignment begins by identifying various quality management approaches, including lean production and total quality manag...
Read More
Contribute Materials
Your contribution can guide someone’s learning journey. Share your
documents today.
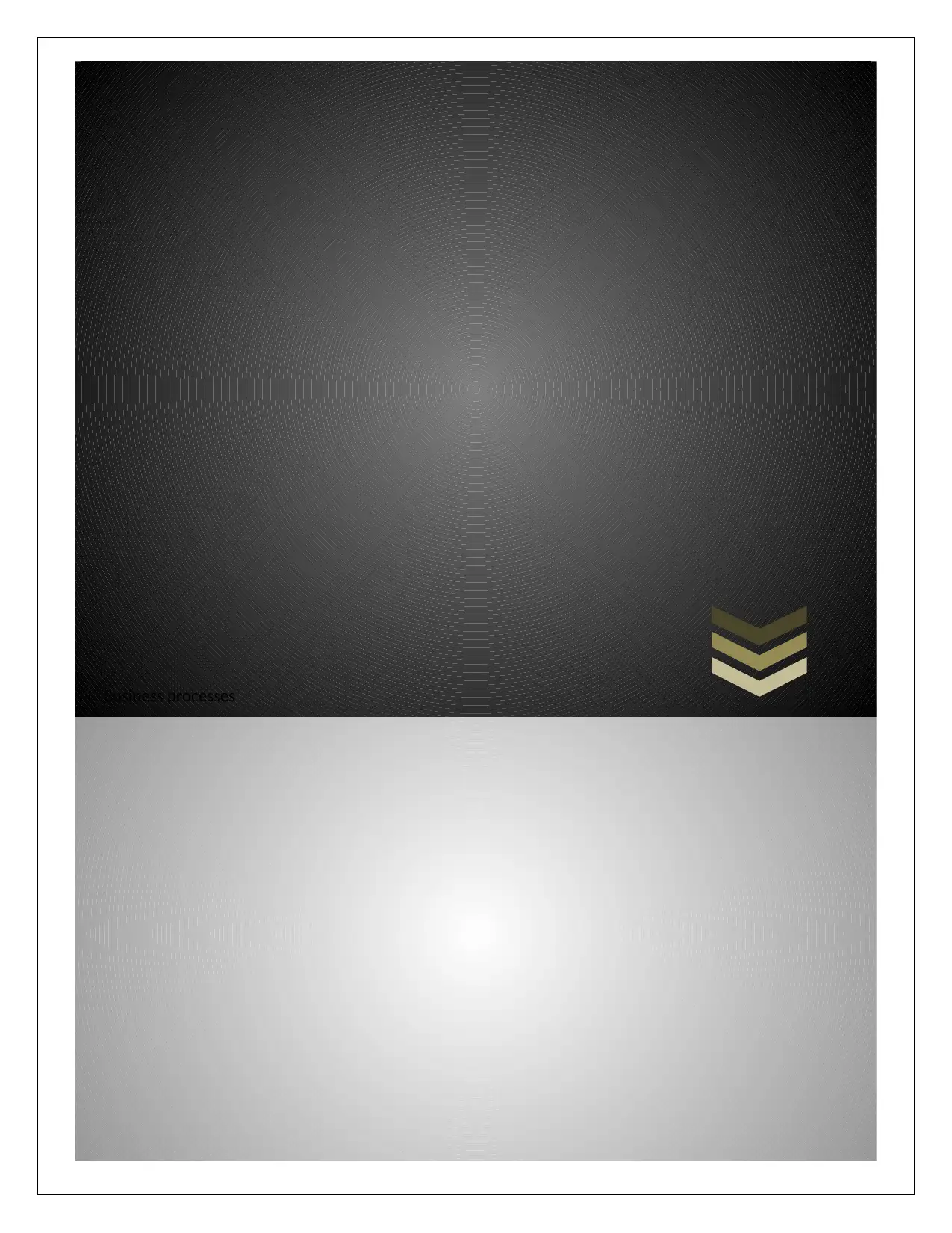
Business processes
Secure Best Marks with AI Grader
Need help grading? Try our AI Grader for instant feedback on your assignments.
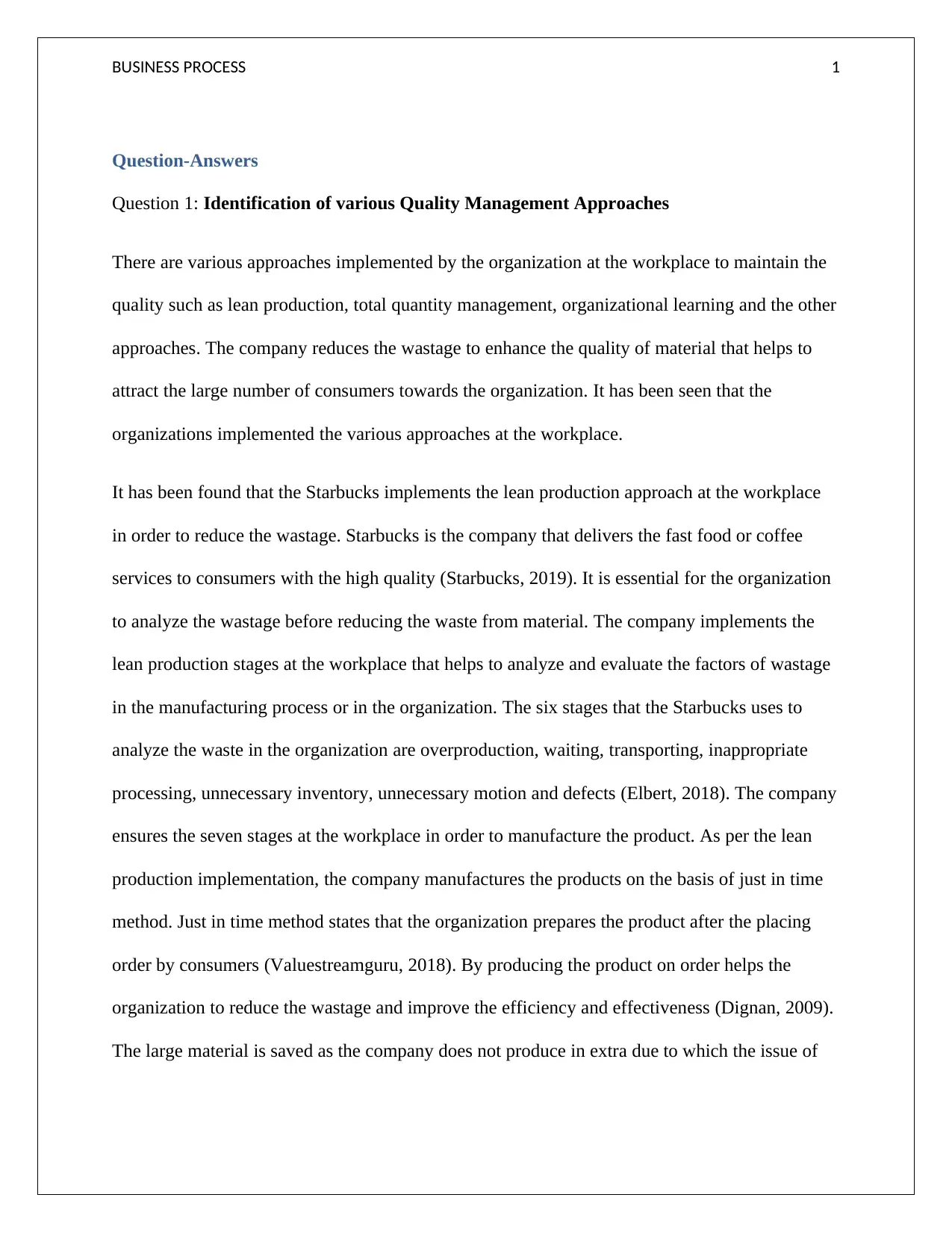
BUSINESS PROCESS 1
Question-Answers
Question 1: Identification of various Quality Management Approaches
There are various approaches implemented by the organization at the workplace to maintain the
quality such as lean production, total quantity management, organizational learning and the other
approaches. The company reduces the wastage to enhance the quality of material that helps to
attract the large number of consumers towards the organization. It has been seen that the
organizations implemented the various approaches at the workplace.
It has been found that the Starbucks implements the lean production approach at the workplace
in order to reduce the wastage. Starbucks is the company that delivers the fast food or coffee
services to consumers with the high quality (Starbucks, 2019). It is essential for the organization
to analyze the wastage before reducing the waste from material. The company implements the
lean production stages at the workplace that helps to analyze and evaluate the factors of wastage
in the manufacturing process or in the organization. The six stages that the Starbucks uses to
analyze the waste in the organization are overproduction, waiting, transporting, inappropriate
processing, unnecessary inventory, unnecessary motion and defects (Elbert, 2018). The company
ensures the seven stages at the workplace in order to manufacture the product. As per the lean
production implementation, the company manufactures the products on the basis of just in time
method. Just in time method states that the organization prepares the product after the placing
order by consumers (Valuestreamguru, 2018). By producing the product on order helps the
organization to reduce the wastage and improve the efficiency and effectiveness (Dignan, 2009).
The large material is saved as the company does not produce in extra due to which the issue of
Question-Answers
Question 1: Identification of various Quality Management Approaches
There are various approaches implemented by the organization at the workplace to maintain the
quality such as lean production, total quantity management, organizational learning and the other
approaches. The company reduces the wastage to enhance the quality of material that helps to
attract the large number of consumers towards the organization. It has been seen that the
organizations implemented the various approaches at the workplace.
It has been found that the Starbucks implements the lean production approach at the workplace
in order to reduce the wastage. Starbucks is the company that delivers the fast food or coffee
services to consumers with the high quality (Starbucks, 2019). It is essential for the organization
to analyze the wastage before reducing the waste from material. The company implements the
lean production stages at the workplace that helps to analyze and evaluate the factors of wastage
in the manufacturing process or in the organization. The six stages that the Starbucks uses to
analyze the waste in the organization are overproduction, waiting, transporting, inappropriate
processing, unnecessary inventory, unnecessary motion and defects (Elbert, 2018). The company
ensures the seven stages at the workplace in order to manufacture the product. As per the lean
production implementation, the company manufactures the products on the basis of just in time
method. Just in time method states that the organization prepares the product after the placing
order by consumers (Valuestreamguru, 2018). By producing the product on order helps the
organization to reduce the wastage and improve the efficiency and effectiveness (Dignan, 2009).
The large material is saved as the company does not produce in extra due to which the issue of
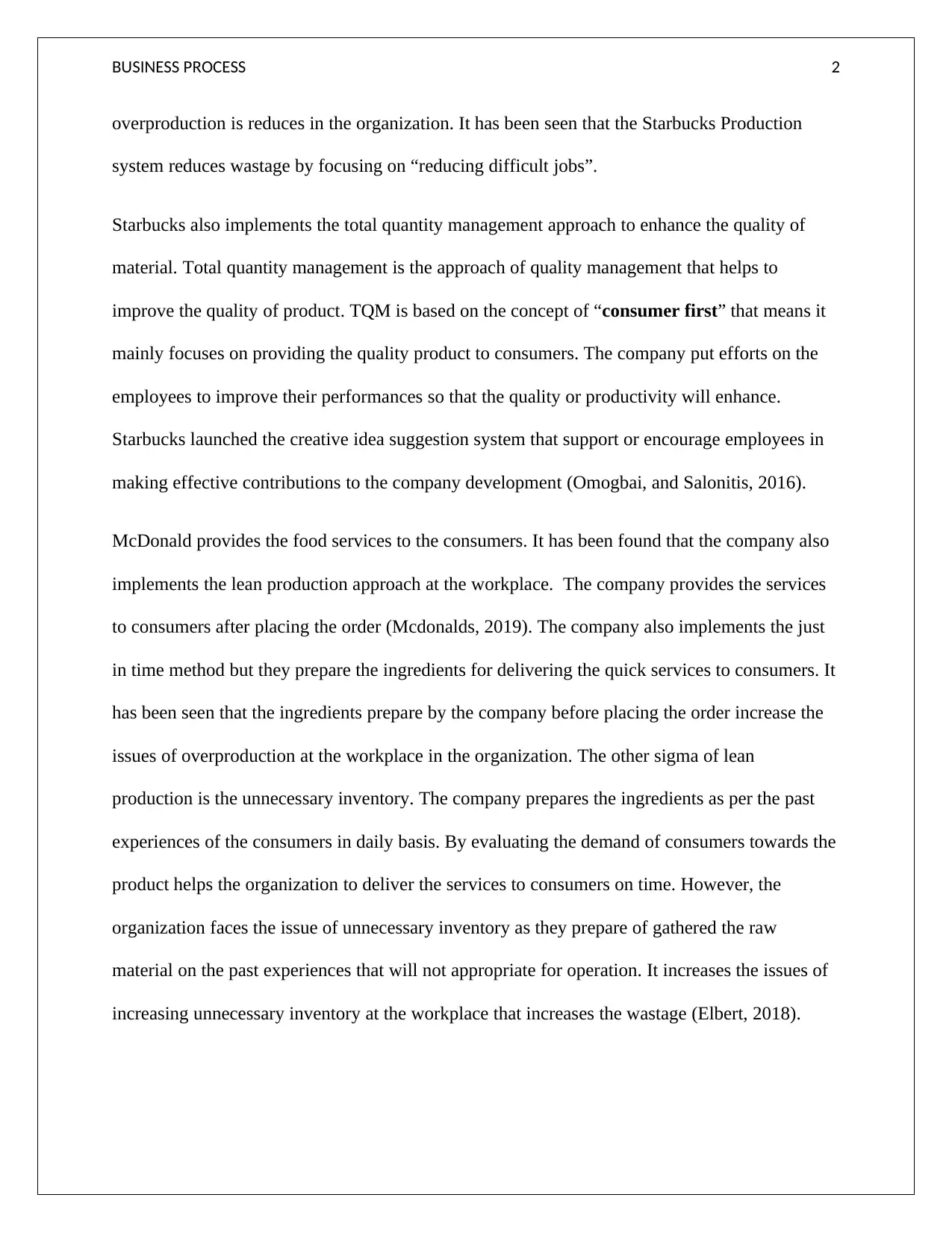
BUSINESS PROCESS 2
overproduction is reduces in the organization. It has been seen that the Starbucks Production
system reduces wastage by focusing on “reducing difficult jobs”.
Starbucks also implements the total quantity management approach to enhance the quality of
material. Total quantity management is the approach of quality management that helps to
improve the quality of product. TQM is based on the concept of “consumer first” that means it
mainly focuses on providing the quality product to consumers. The company put efforts on the
employees to improve their performances so that the quality or productivity will enhance.
Starbucks launched the creative idea suggestion system that support or encourage employees in
making effective contributions to the company development (Omogbai, and Salonitis, 2016).
McDonald provides the food services to the consumers. It has been found that the company also
implements the lean production approach at the workplace. The company provides the services
to consumers after placing the order (Mcdonalds, 2019). The company also implements the just
in time method but they prepare the ingredients for delivering the quick services to consumers. It
has been seen that the ingredients prepare by the company before placing the order increase the
issues of overproduction at the workplace in the organization. The other sigma of lean
production is the unnecessary inventory. The company prepares the ingredients as per the past
experiences of the consumers in daily basis. By evaluating the demand of consumers towards the
product helps the organization to deliver the services to consumers on time. However, the
organization faces the issue of unnecessary inventory as they prepare of gathered the raw
material on the past experiences that will not appropriate for operation. It increases the issues of
increasing unnecessary inventory at the workplace that increases the wastage (Elbert, 2018).
overproduction is reduces in the organization. It has been seen that the Starbucks Production
system reduces wastage by focusing on “reducing difficult jobs”.
Starbucks also implements the total quantity management approach to enhance the quality of
material. Total quantity management is the approach of quality management that helps to
improve the quality of product. TQM is based on the concept of “consumer first” that means it
mainly focuses on providing the quality product to consumers. The company put efforts on the
employees to improve their performances so that the quality or productivity will enhance.
Starbucks launched the creative idea suggestion system that support or encourage employees in
making effective contributions to the company development (Omogbai, and Salonitis, 2016).
McDonald provides the food services to the consumers. It has been found that the company also
implements the lean production approach at the workplace. The company provides the services
to consumers after placing the order (Mcdonalds, 2019). The company also implements the just
in time method but they prepare the ingredients for delivering the quick services to consumers. It
has been seen that the ingredients prepare by the company before placing the order increase the
issues of overproduction at the workplace in the organization. The other sigma of lean
production is the unnecessary inventory. The company prepares the ingredients as per the past
experiences of the consumers in daily basis. By evaluating the demand of consumers towards the
product helps the organization to deliver the services to consumers on time. However, the
organization faces the issue of unnecessary inventory as they prepare of gathered the raw
material on the past experiences that will not appropriate for operation. It increases the issues of
increasing unnecessary inventory at the workplace that increases the wastage (Elbert, 2018).
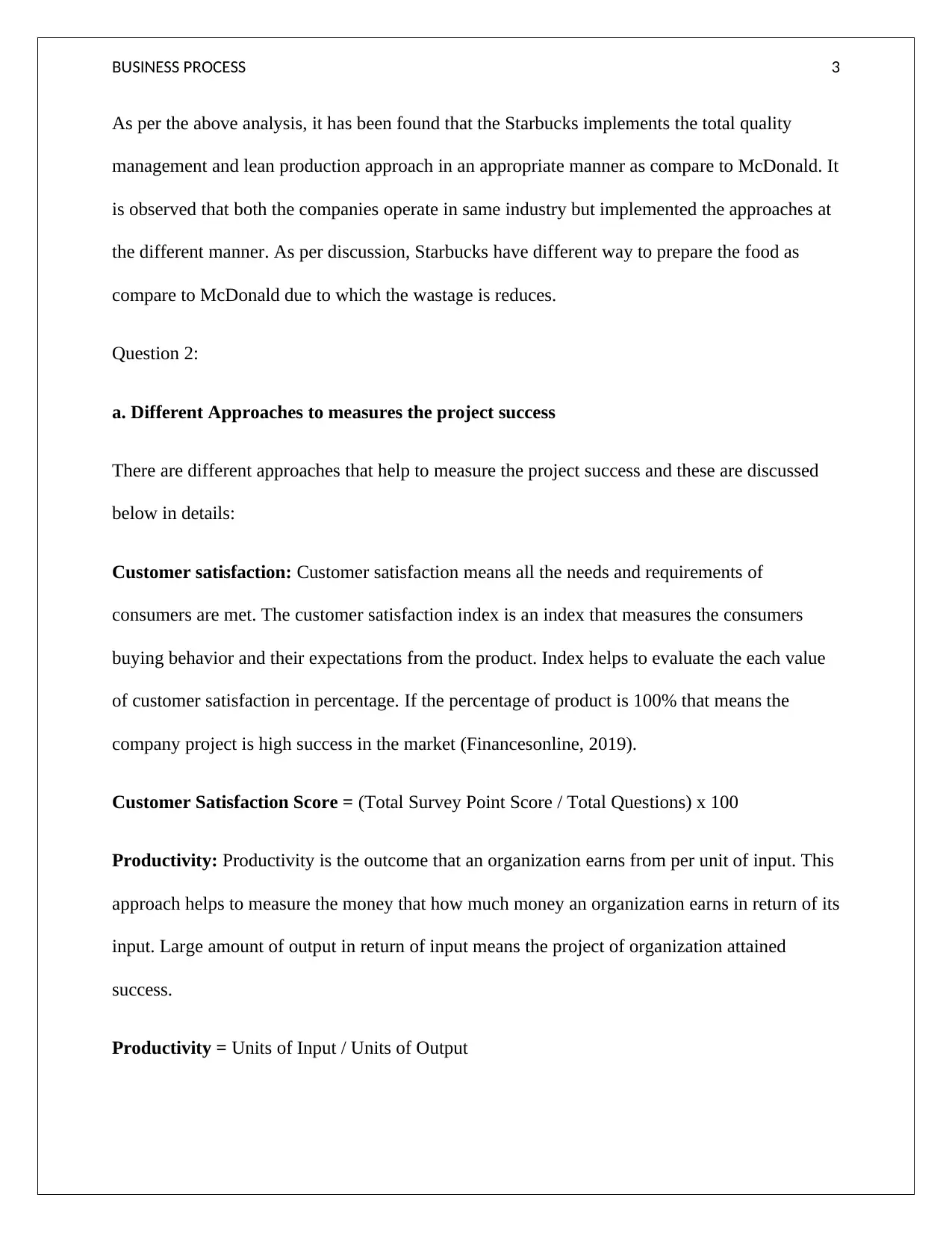
BUSINESS PROCESS 3
As per the above analysis, it has been found that the Starbucks implements the total quality
management and lean production approach in an appropriate manner as compare to McDonald. It
is observed that both the companies operate in same industry but implemented the approaches at
the different manner. As per discussion, Starbucks have different way to prepare the food as
compare to McDonald due to which the wastage is reduces.
Question 2:
a. Different Approaches to measures the project success
There are different approaches that help to measure the project success and these are discussed
below in details:
Customer satisfaction: Customer satisfaction means all the needs and requirements of
consumers are met. The customer satisfaction index is an index that measures the consumers
buying behavior and their expectations from the product. Index helps to evaluate the each value
of customer satisfaction in percentage. If the percentage of product is 100% that means the
company project is high success in the market (Financesonline, 2019).
Customer Satisfaction Score = (Total Survey Point Score / Total Questions) x 100
Productivity: Productivity is the outcome that an organization earns from per unit of input. This
approach helps to measure the money that how much money an organization earns in return of its
input. Large amount of output in return of input means the project of organization attained
success.
Productivity = Units of Input / Units of Output
As per the above analysis, it has been found that the Starbucks implements the total quality
management and lean production approach in an appropriate manner as compare to McDonald. It
is observed that both the companies operate in same industry but implemented the approaches at
the different manner. As per discussion, Starbucks have different way to prepare the food as
compare to McDonald due to which the wastage is reduces.
Question 2:
a. Different Approaches to measures the project success
There are different approaches that help to measure the project success and these are discussed
below in details:
Customer satisfaction: Customer satisfaction means all the needs and requirements of
consumers are met. The customer satisfaction index is an index that measures the consumers
buying behavior and their expectations from the product. Index helps to evaluate the each value
of customer satisfaction in percentage. If the percentage of product is 100% that means the
company project is high success in the market (Financesonline, 2019).
Customer Satisfaction Score = (Total Survey Point Score / Total Questions) x 100
Productivity: Productivity is the outcome that an organization earns from per unit of input. This
approach helps to measure the money that how much money an organization earns in return of its
input. Large amount of output in return of input means the project of organization attained
success.
Productivity = Units of Input / Units of Output
Secure Best Marks with AI Grader
Need help grading? Try our AI Grader for instant feedback on your assignments.
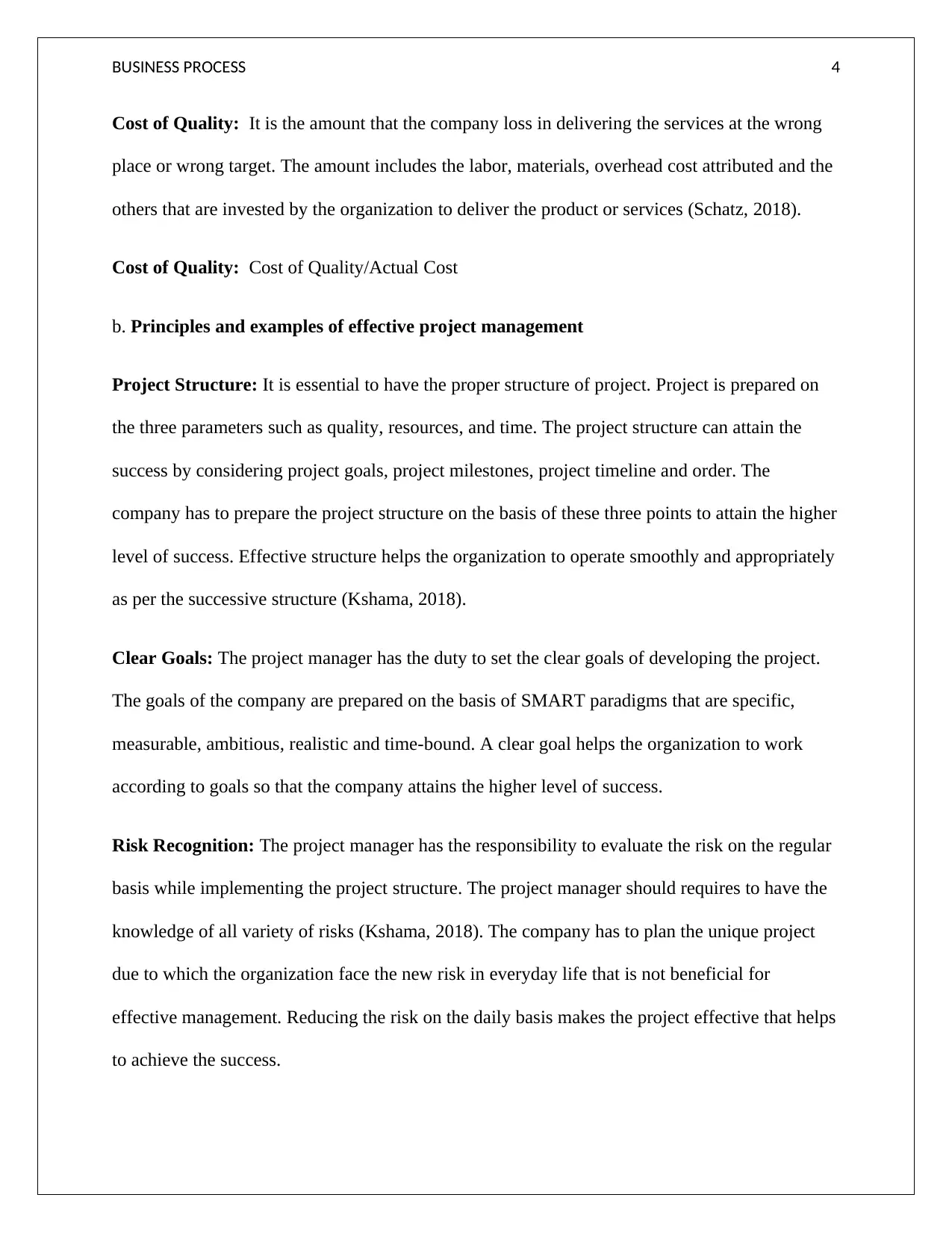
BUSINESS PROCESS 4
Cost of Quality: It is the amount that the company loss in delivering the services at the wrong
place or wrong target. The amount includes the labor, materials, overhead cost attributed and the
others that are invested by the organization to deliver the product or services (Schatz, 2018).
Cost of Quality: Cost of Quality/Actual Cost
b. Principles and examples of effective project management
Project Structure: It is essential to have the proper structure of project. Project is prepared on
the three parameters such as quality, resources, and time. The project structure can attain the
success by considering project goals, project milestones, project timeline and order. The
company has to prepare the project structure on the basis of these three points to attain the higher
level of success. Effective structure helps the organization to operate smoothly and appropriately
as per the successive structure (Kshama, 2018).
Clear Goals: The project manager has the duty to set the clear goals of developing the project.
The goals of the company are prepared on the basis of SMART paradigms that are specific,
measurable, ambitious, realistic and time-bound. A clear goal helps the organization to work
according to goals so that the company attains the higher level of success.
Risk Recognition: The project manager has the responsibility to evaluate the risk on the regular
basis while implementing the project structure. The project manager should requires to have the
knowledge of all variety of risks (Kshama, 2018). The company has to plan the unique project
due to which the organization face the new risk in everyday life that is not beneficial for
effective management. Reducing the risk on the daily basis makes the project effective that helps
to achieve the success.
Cost of Quality: It is the amount that the company loss in delivering the services at the wrong
place or wrong target. The amount includes the labor, materials, overhead cost attributed and the
others that are invested by the organization to deliver the product or services (Schatz, 2018).
Cost of Quality: Cost of Quality/Actual Cost
b. Principles and examples of effective project management
Project Structure: It is essential to have the proper structure of project. Project is prepared on
the three parameters such as quality, resources, and time. The project structure can attain the
success by considering project goals, project milestones, project timeline and order. The
company has to prepare the project structure on the basis of these three points to attain the higher
level of success. Effective structure helps the organization to operate smoothly and appropriately
as per the successive structure (Kshama, 2018).
Clear Goals: The project manager has the duty to set the clear goals of developing the project.
The goals of the company are prepared on the basis of SMART paradigms that are specific,
measurable, ambitious, realistic and time-bound. A clear goal helps the organization to work
according to goals so that the company attains the higher level of success.
Risk Recognition: The project manager has the responsibility to evaluate the risk on the regular
basis while implementing the project structure. The project manager should requires to have the
knowledge of all variety of risks (Kshama, 2018). The company has to plan the unique project
due to which the organization face the new risk in everyday life that is not beneficial for
effective management. Reducing the risk on the daily basis makes the project effective that helps
to achieve the success.
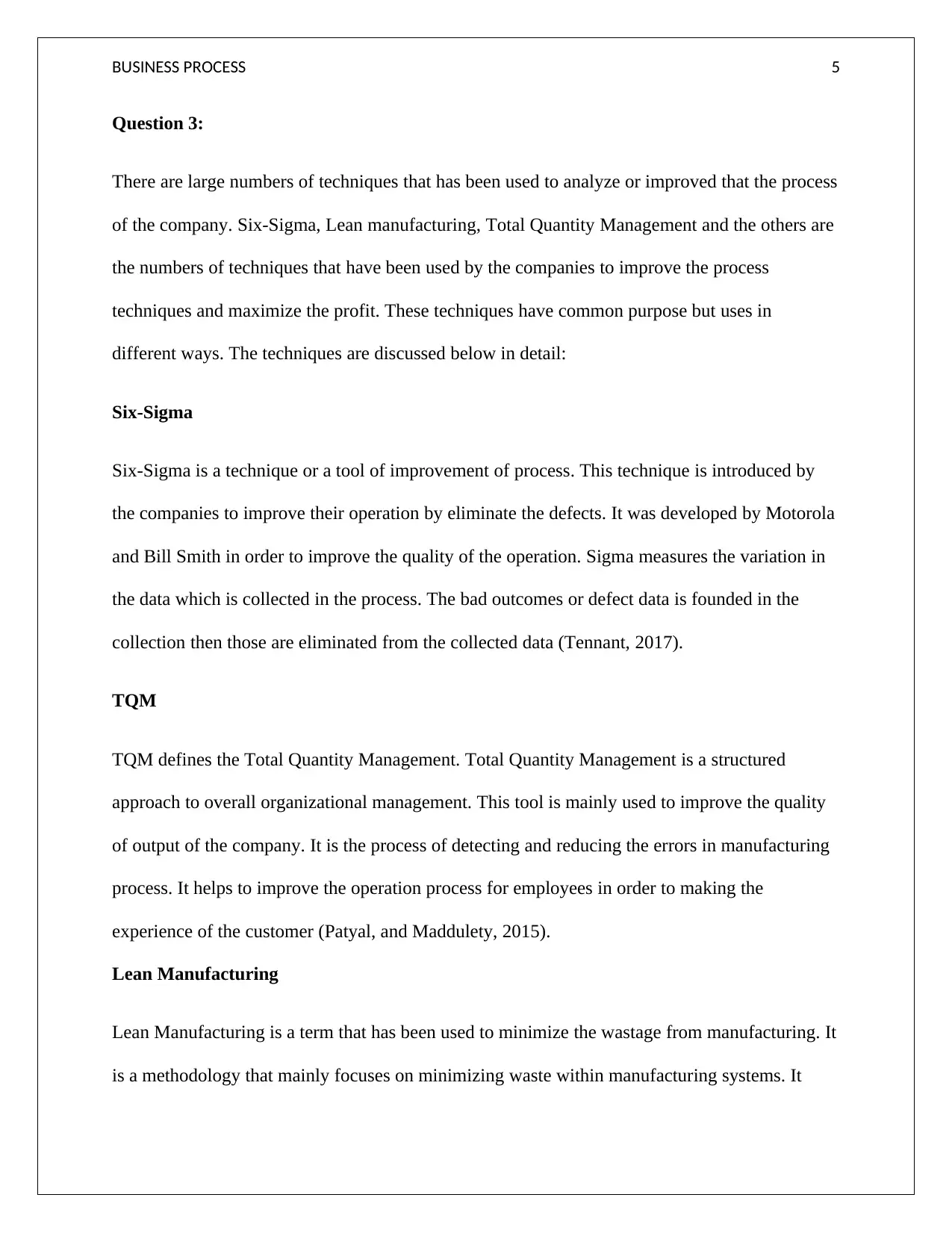
BUSINESS PROCESS 5
Question 3:
There are large numbers of techniques that has been used to analyze or improved that the process
of the company. Six-Sigma, Lean manufacturing, Total Quantity Management and the others are
the numbers of techniques that have been used by the companies to improve the process
techniques and maximize the profit. These techniques have common purpose but uses in
different ways. The techniques are discussed below in detail:
Six-Sigma
Six-Sigma is a technique or a tool of improvement of process. This technique is introduced by
the companies to improve their operation by eliminate the defects. It was developed by Motorola
and Bill Smith in order to improve the quality of the operation. Sigma measures the variation in
the data which is collected in the process. The bad outcomes or defect data is founded in the
collection then those are eliminated from the collected data (Tennant, 2017).
TQM
TQM defines the Total Quantity Management. Total Quantity Management is a structured
approach to overall organizational management. This tool is mainly used to improve the quality
of output of the company. It is the process of detecting and reducing the errors in manufacturing
process. It helps to improve the operation process for employees in order to making the
experience of the customer (Patyal, and Maddulety, 2015).
Lean Manufacturing
Lean Manufacturing is a term that has been used to minimize the wastage from manufacturing. It
is a methodology that mainly focuses on minimizing waste within manufacturing systems. It
Question 3:
There are large numbers of techniques that has been used to analyze or improved that the process
of the company. Six-Sigma, Lean manufacturing, Total Quantity Management and the others are
the numbers of techniques that have been used by the companies to improve the process
techniques and maximize the profit. These techniques have common purpose but uses in
different ways. The techniques are discussed below in detail:
Six-Sigma
Six-Sigma is a technique or a tool of improvement of process. This technique is introduced by
the companies to improve their operation by eliminate the defects. It was developed by Motorola
and Bill Smith in order to improve the quality of the operation. Sigma measures the variation in
the data which is collected in the process. The bad outcomes or defect data is founded in the
collection then those are eliminated from the collected data (Tennant, 2017).
TQM
TQM defines the Total Quantity Management. Total Quantity Management is a structured
approach to overall organizational management. This tool is mainly used to improve the quality
of output of the company. It is the process of detecting and reducing the errors in manufacturing
process. It helps to improve the operation process for employees in order to making the
experience of the customer (Patyal, and Maddulety, 2015).
Lean Manufacturing
Lean Manufacturing is a term that has been used to minimize the wastage from manufacturing. It
is a methodology that mainly focuses on minimizing waste within manufacturing systems. It
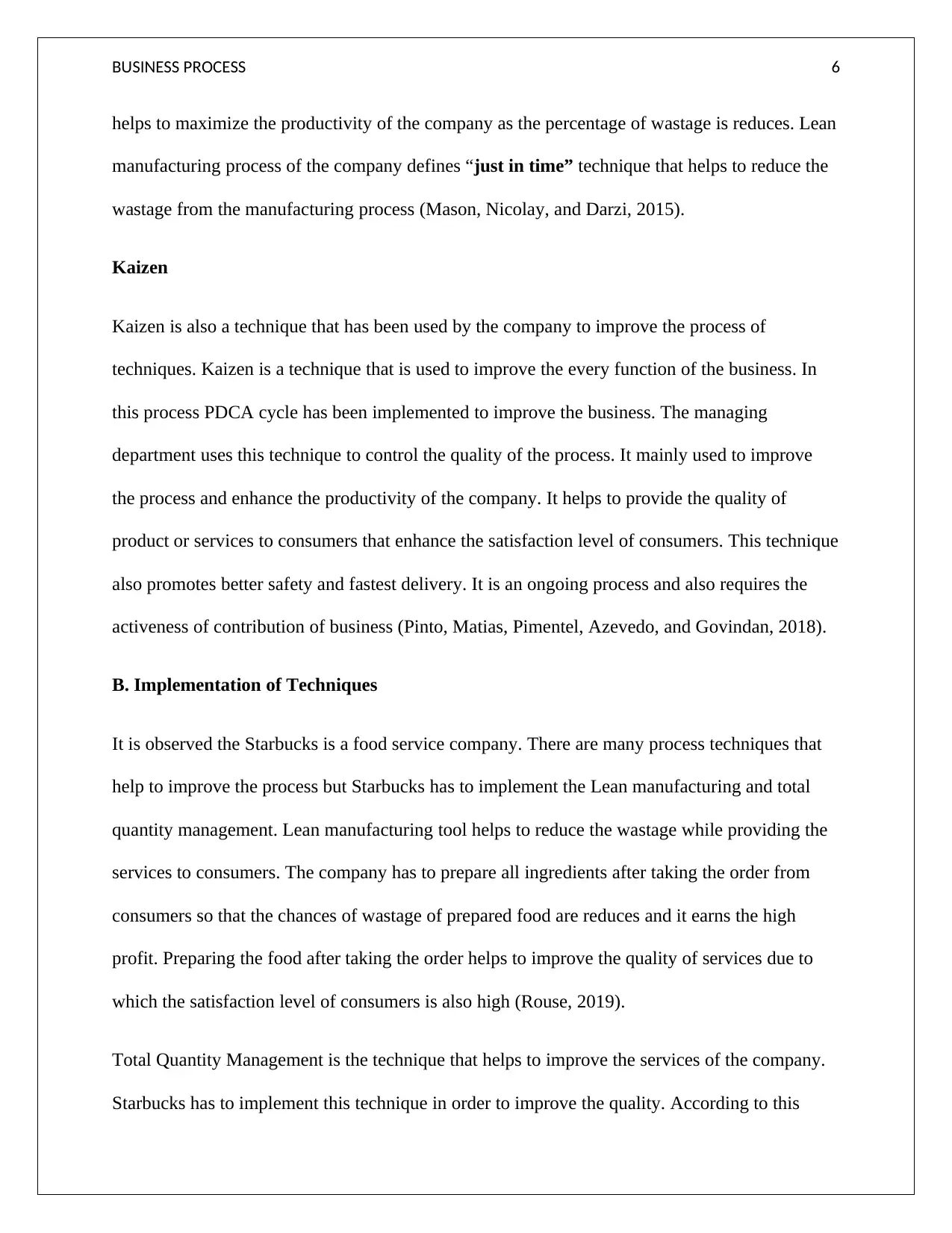
BUSINESS PROCESS 6
helps to maximize the productivity of the company as the percentage of wastage is reduces. Lean
manufacturing process of the company defines “just in time” technique that helps to reduce the
wastage from the manufacturing process (Mason, Nicolay, and Darzi, 2015).
Kaizen
Kaizen is also a technique that has been used by the company to improve the process of
techniques. Kaizen is a technique that is used to improve the every function of the business. In
this process PDCA cycle has been implemented to improve the business. The managing
department uses this technique to control the quality of the process. It mainly used to improve
the process and enhance the productivity of the company. It helps to provide the quality of
product or services to consumers that enhance the satisfaction level of consumers. This technique
also promotes better safety and fastest delivery. It is an ongoing process and also requires the
activeness of contribution of business (Pinto, Matias, Pimentel, Azevedo, and Govindan, 2018).
B. Implementation of Techniques
It is observed the Starbucks is a food service company. There are many process techniques that
help to improve the process but Starbucks has to implement the Lean manufacturing and total
quantity management. Lean manufacturing tool helps to reduce the wastage while providing the
services to consumers. The company has to prepare all ingredients after taking the order from
consumers so that the chances of wastage of prepared food are reduces and it earns the high
profit. Preparing the food after taking the order helps to improve the quality of services due to
which the satisfaction level of consumers is also high (Rouse, 2019).
Total Quantity Management is the technique that helps to improve the services of the company.
Starbucks has to implement this technique in order to improve the quality. According to this
helps to maximize the productivity of the company as the percentage of wastage is reduces. Lean
manufacturing process of the company defines “just in time” technique that helps to reduce the
wastage from the manufacturing process (Mason, Nicolay, and Darzi, 2015).
Kaizen
Kaizen is also a technique that has been used by the company to improve the process of
techniques. Kaizen is a technique that is used to improve the every function of the business. In
this process PDCA cycle has been implemented to improve the business. The managing
department uses this technique to control the quality of the process. It mainly used to improve
the process and enhance the productivity of the company. It helps to provide the quality of
product or services to consumers that enhance the satisfaction level of consumers. This technique
also promotes better safety and fastest delivery. It is an ongoing process and also requires the
activeness of contribution of business (Pinto, Matias, Pimentel, Azevedo, and Govindan, 2018).
B. Implementation of Techniques
It is observed the Starbucks is a food service company. There are many process techniques that
help to improve the process but Starbucks has to implement the Lean manufacturing and total
quantity management. Lean manufacturing tool helps to reduce the wastage while providing the
services to consumers. The company has to prepare all ingredients after taking the order from
consumers so that the chances of wastage of prepared food are reduces and it earns the high
profit. Preparing the food after taking the order helps to improve the quality of services due to
which the satisfaction level of consumers is also high (Rouse, 2019).
Total Quantity Management is the technique that helps to improve the services of the company.
Starbucks has to implement this technique in order to improve the quality. According to this
Paraphrase This Document
Need a fresh take? Get an instant paraphrase of this document with our AI Paraphraser
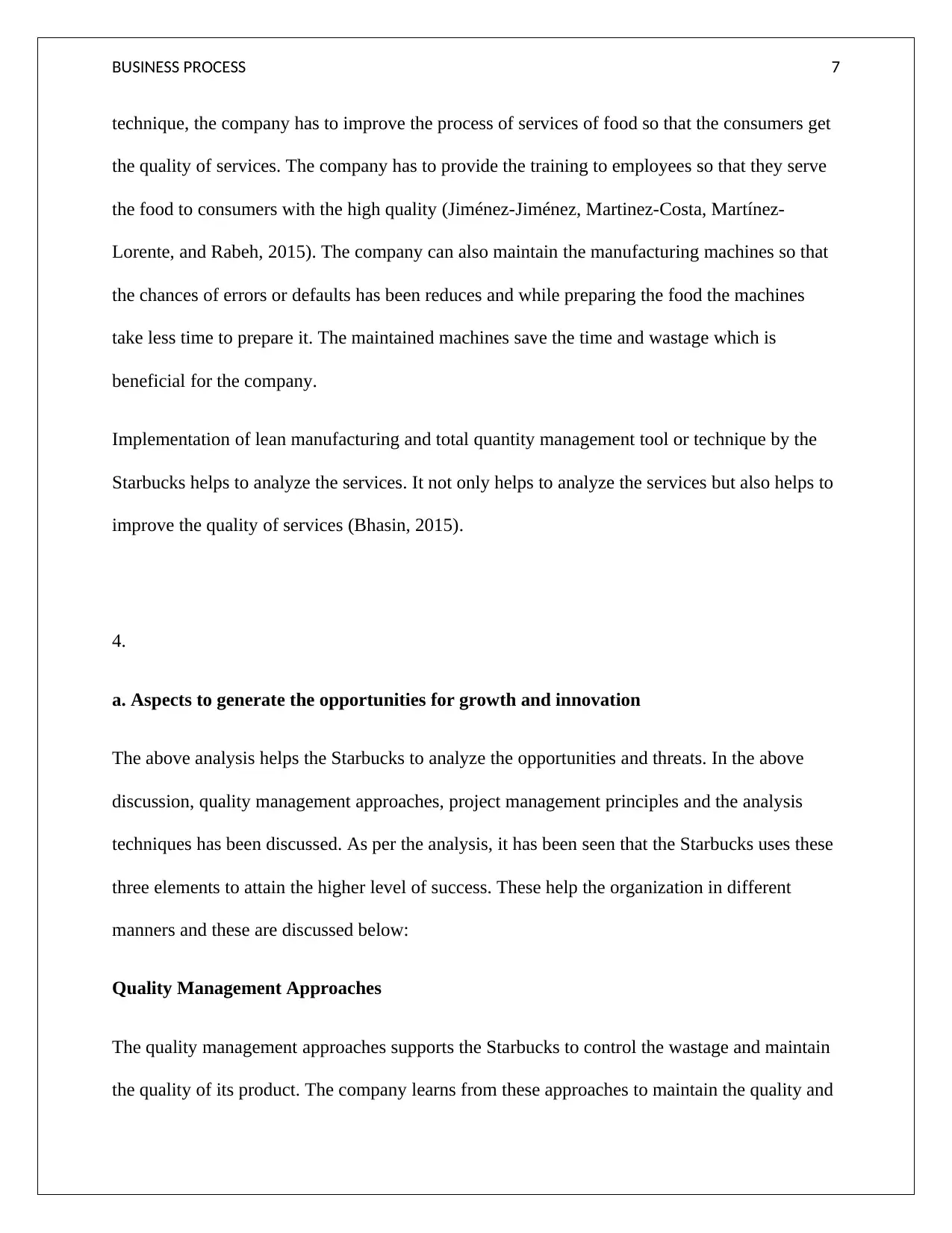
BUSINESS PROCESS 7
technique, the company has to improve the process of services of food so that the consumers get
the quality of services. The company has to provide the training to employees so that they serve
the food to consumers with the high quality (Jiménez-Jiménez, Martinez-Costa, Martínez-
Lorente, and Rabeh, 2015). The company can also maintain the manufacturing machines so that
the chances of errors or defaults has been reduces and while preparing the food the machines
take less time to prepare it. The maintained machines save the time and wastage which is
beneficial for the company.
Implementation of lean manufacturing and total quantity management tool or technique by the
Starbucks helps to analyze the services. It not only helps to analyze the services but also helps to
improve the quality of services (Bhasin, 2015).
4.
a. Aspects to generate the opportunities for growth and innovation
The above analysis helps the Starbucks to analyze the opportunities and threats. In the above
discussion, quality management approaches, project management principles and the analysis
techniques has been discussed. As per the analysis, it has been seen that the Starbucks uses these
three elements to attain the higher level of success. These help the organization in different
manners and these are discussed below:
Quality Management Approaches
The quality management approaches supports the Starbucks to control the wastage and maintain
the quality of its product. The company learns from these approaches to maintain the quality and
technique, the company has to improve the process of services of food so that the consumers get
the quality of services. The company has to provide the training to employees so that they serve
the food to consumers with the high quality (Jiménez-Jiménez, Martinez-Costa, Martínez-
Lorente, and Rabeh, 2015). The company can also maintain the manufacturing machines so that
the chances of errors or defaults has been reduces and while preparing the food the machines
take less time to prepare it. The maintained machines save the time and wastage which is
beneficial for the company.
Implementation of lean manufacturing and total quantity management tool or technique by the
Starbucks helps to analyze the services. It not only helps to analyze the services but also helps to
improve the quality of services (Bhasin, 2015).
4.
a. Aspects to generate the opportunities for growth and innovation
The above analysis helps the Starbucks to analyze the opportunities and threats. In the above
discussion, quality management approaches, project management principles and the analysis
techniques has been discussed. As per the analysis, it has been seen that the Starbucks uses these
three elements to attain the higher level of success. These help the organization in different
manners and these are discussed below:
Quality Management Approaches
The quality management approaches supports the Starbucks to control the wastage and maintain
the quality of its product. The company learns from these approaches to maintain the quality and
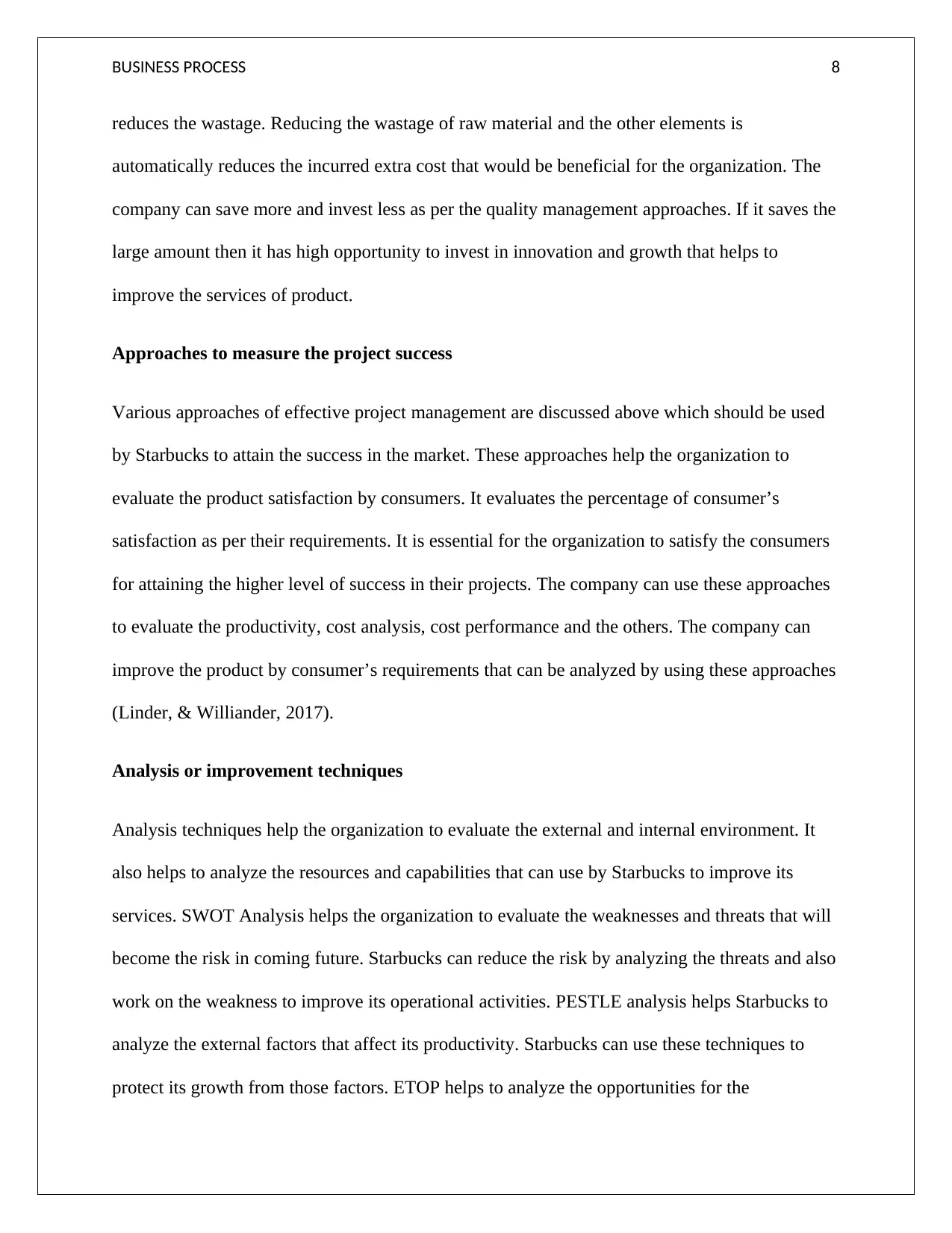
BUSINESS PROCESS 8
reduces the wastage. Reducing the wastage of raw material and the other elements is
automatically reduces the incurred extra cost that would be beneficial for the organization. The
company can save more and invest less as per the quality management approaches. If it saves the
large amount then it has high opportunity to invest in innovation and growth that helps to
improve the services of product.
Approaches to measure the project success
Various approaches of effective project management are discussed above which should be used
by Starbucks to attain the success in the market. These approaches help the organization to
evaluate the product satisfaction by consumers. It evaluates the percentage of consumer’s
satisfaction as per their requirements. It is essential for the organization to satisfy the consumers
for attaining the higher level of success in their projects. The company can use these approaches
to evaluate the productivity, cost analysis, cost performance and the others. The company can
improve the product by consumer’s requirements that can be analyzed by using these approaches
(Linder, & Williander, 2017).
Analysis or improvement techniques
Analysis techniques help the organization to evaluate the external and internal environment. It
also helps to analyze the resources and capabilities that can use by Starbucks to improve its
services. SWOT Analysis helps the organization to evaluate the weaknesses and threats that will
become the risk in coming future. Starbucks can reduce the risk by analyzing the threats and also
work on the weakness to improve its operational activities. PESTLE analysis helps Starbucks to
analyze the external factors that affect its productivity. Starbucks can use these techniques to
protect its growth from those factors. ETOP helps to analyze the opportunities for the
reduces the wastage. Reducing the wastage of raw material and the other elements is
automatically reduces the incurred extra cost that would be beneficial for the organization. The
company can save more and invest less as per the quality management approaches. If it saves the
large amount then it has high opportunity to invest in innovation and growth that helps to
improve the services of product.
Approaches to measure the project success
Various approaches of effective project management are discussed above which should be used
by Starbucks to attain the success in the market. These approaches help the organization to
evaluate the product satisfaction by consumers. It evaluates the percentage of consumer’s
satisfaction as per their requirements. It is essential for the organization to satisfy the consumers
for attaining the higher level of success in their projects. The company can use these approaches
to evaluate the productivity, cost analysis, cost performance and the others. The company can
improve the product by consumer’s requirements that can be analyzed by using these approaches
(Linder, & Williander, 2017).
Analysis or improvement techniques
Analysis techniques help the organization to evaluate the external and internal environment. It
also helps to analyze the resources and capabilities that can use by Starbucks to improve its
services. SWOT Analysis helps the organization to evaluate the weaknesses and threats that will
become the risk in coming future. Starbucks can reduce the risk by analyzing the threats and also
work on the weakness to improve its operational activities. PESTLE analysis helps Starbucks to
analyze the external factors that affect its productivity. Starbucks can use these techniques to
protect its growth from those factors. ETOP helps to analyze the opportunities for the
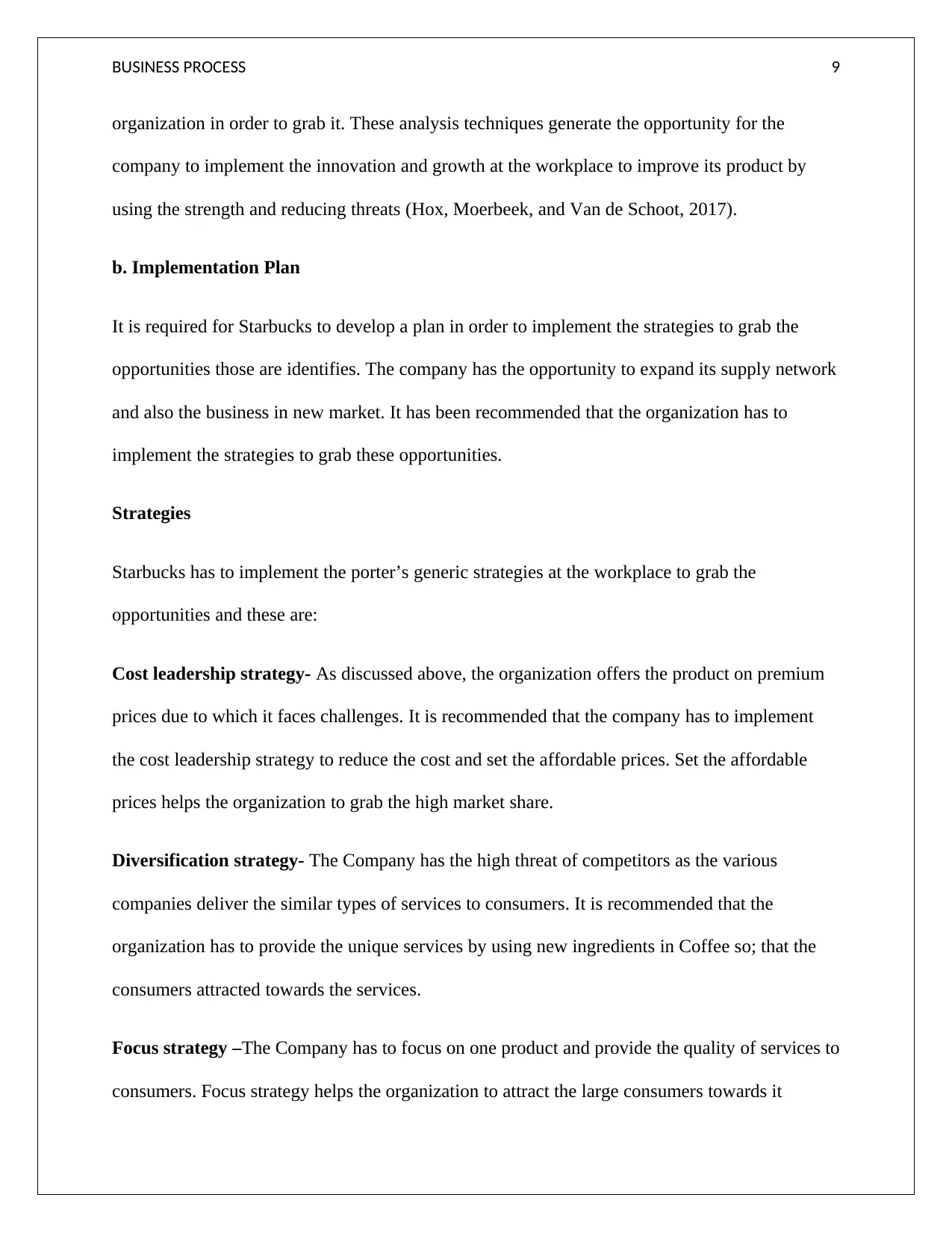
BUSINESS PROCESS 9
organization in order to grab it. These analysis techniques generate the opportunity for the
company to implement the innovation and growth at the workplace to improve its product by
using the strength and reducing threats (Hox, Moerbeek, and Van de Schoot, 2017).
b. Implementation Plan
It is required for Starbucks to develop a plan in order to implement the strategies to grab the
opportunities those are identifies. The company has the opportunity to expand its supply network
and also the business in new market. It has been recommended that the organization has to
implement the strategies to grab these opportunities.
Strategies
Starbucks has to implement the porter’s generic strategies at the workplace to grab the
opportunities and these are:
Cost leadership strategy- As discussed above, the organization offers the product on premium
prices due to which it faces challenges. It is recommended that the company has to implement
the cost leadership strategy to reduce the cost and set the affordable prices. Set the affordable
prices helps the organization to grab the high market share.
Diversification strategy- The Company has the high threat of competitors as the various
companies deliver the similar types of services to consumers. It is recommended that the
organization has to provide the unique services by using new ingredients in Coffee so; that the
consumers attracted towards the services.
Focus strategy –The Company has to focus on one product and provide the quality of services to
consumers. Focus strategy helps the organization to attract the large consumers towards it
organization in order to grab it. These analysis techniques generate the opportunity for the
company to implement the innovation and growth at the workplace to improve its product by
using the strength and reducing threats (Hox, Moerbeek, and Van de Schoot, 2017).
b. Implementation Plan
It is required for Starbucks to develop a plan in order to implement the strategies to grab the
opportunities those are identifies. The company has the opportunity to expand its supply network
and also the business in new market. It has been recommended that the organization has to
implement the strategies to grab these opportunities.
Strategies
Starbucks has to implement the porter’s generic strategies at the workplace to grab the
opportunities and these are:
Cost leadership strategy- As discussed above, the organization offers the product on premium
prices due to which it faces challenges. It is recommended that the company has to implement
the cost leadership strategy to reduce the cost and set the affordable prices. Set the affordable
prices helps the organization to grab the high market share.
Diversification strategy- The Company has the high threat of competitors as the various
companies deliver the similar types of services to consumers. It is recommended that the
organization has to provide the unique services by using new ingredients in Coffee so; that the
consumers attracted towards the services.
Focus strategy –The Company has to focus on one product and provide the quality of services to
consumers. Focus strategy helps the organization to attract the large consumers towards it
Secure Best Marks with AI Grader
Need help grading? Try our AI Grader for instant feedback on your assignments.
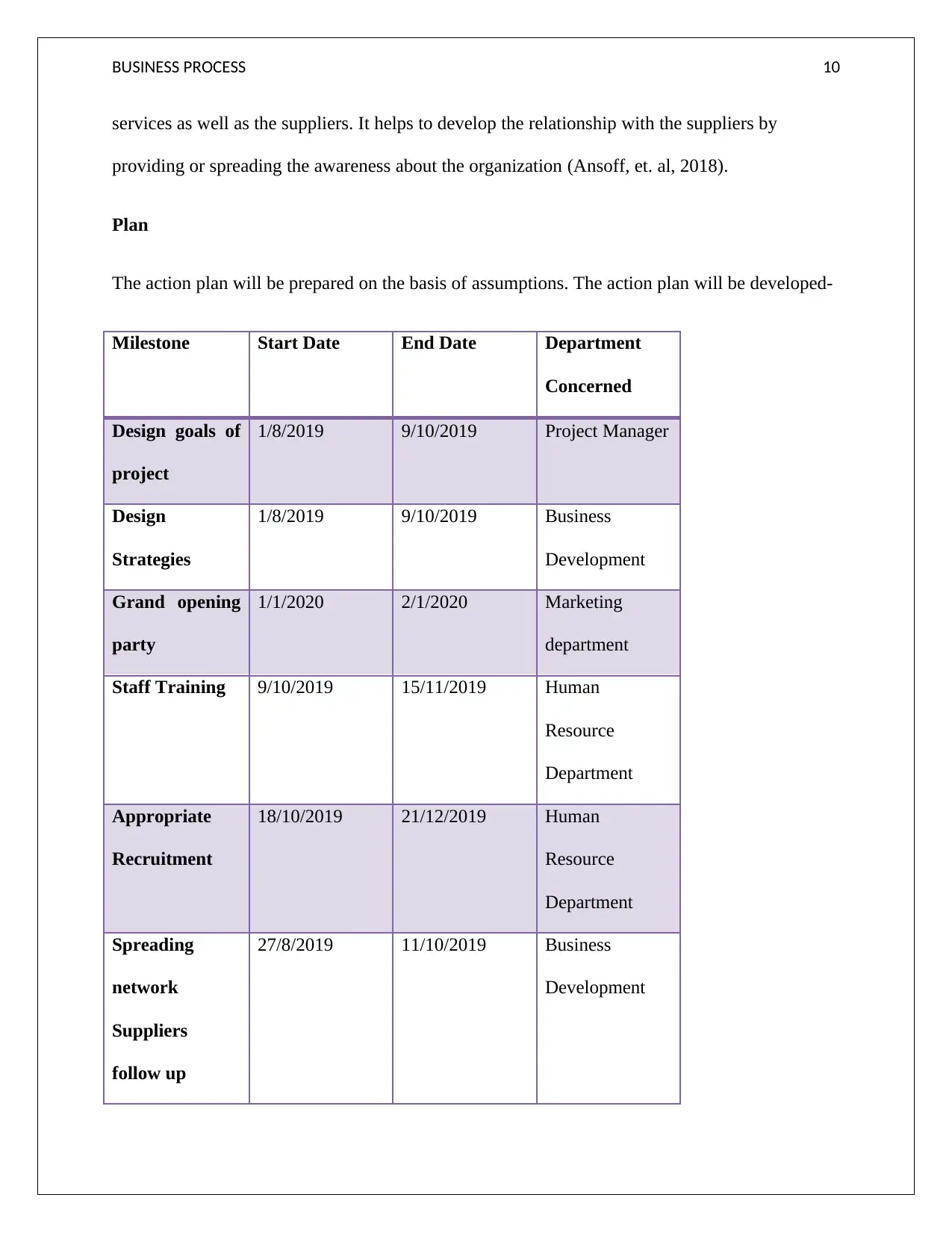
BUSINESS PROCESS 10
services as well as the suppliers. It helps to develop the relationship with the suppliers by
providing or spreading the awareness about the organization (Ansoff, et. al, 2018).
Plan
The action plan will be prepared on the basis of assumptions. The action plan will be developed-
Milestone Start Date End Date Department
Concerned
Design goals of
project
1/8/2019 9/10/2019 Project Manager
Design
Strategies
1/8/2019 9/10/2019 Business
Development
Grand opening
party
1/1/2020 2/1/2020 Marketing
department
Staff Training 9/10/2019 15/11/2019 Human
Resource
Department
Appropriate
Recruitment
18/10/2019 21/12/2019 Human
Resource
Department
Spreading
network
Suppliers
follow up
27/8/2019 11/10/2019 Business
Development
services as well as the suppliers. It helps to develop the relationship with the suppliers by
providing or spreading the awareness about the organization (Ansoff, et. al, 2018).
Plan
The action plan will be prepared on the basis of assumptions. The action plan will be developed-
Milestone Start Date End Date Department
Concerned
Design goals of
project
1/8/2019 9/10/2019 Project Manager
Design
Strategies
1/8/2019 9/10/2019 Business
Development
Grand opening
party
1/1/2020 2/1/2020 Marketing
department
Staff Training 9/10/2019 15/11/2019 Human
Resource
Department
Appropriate
Recruitment
18/10/2019 21/12/2019 Human
Resource
Department
Spreading
network
Suppliers
follow up
27/8/2019 11/10/2019 Business
Development
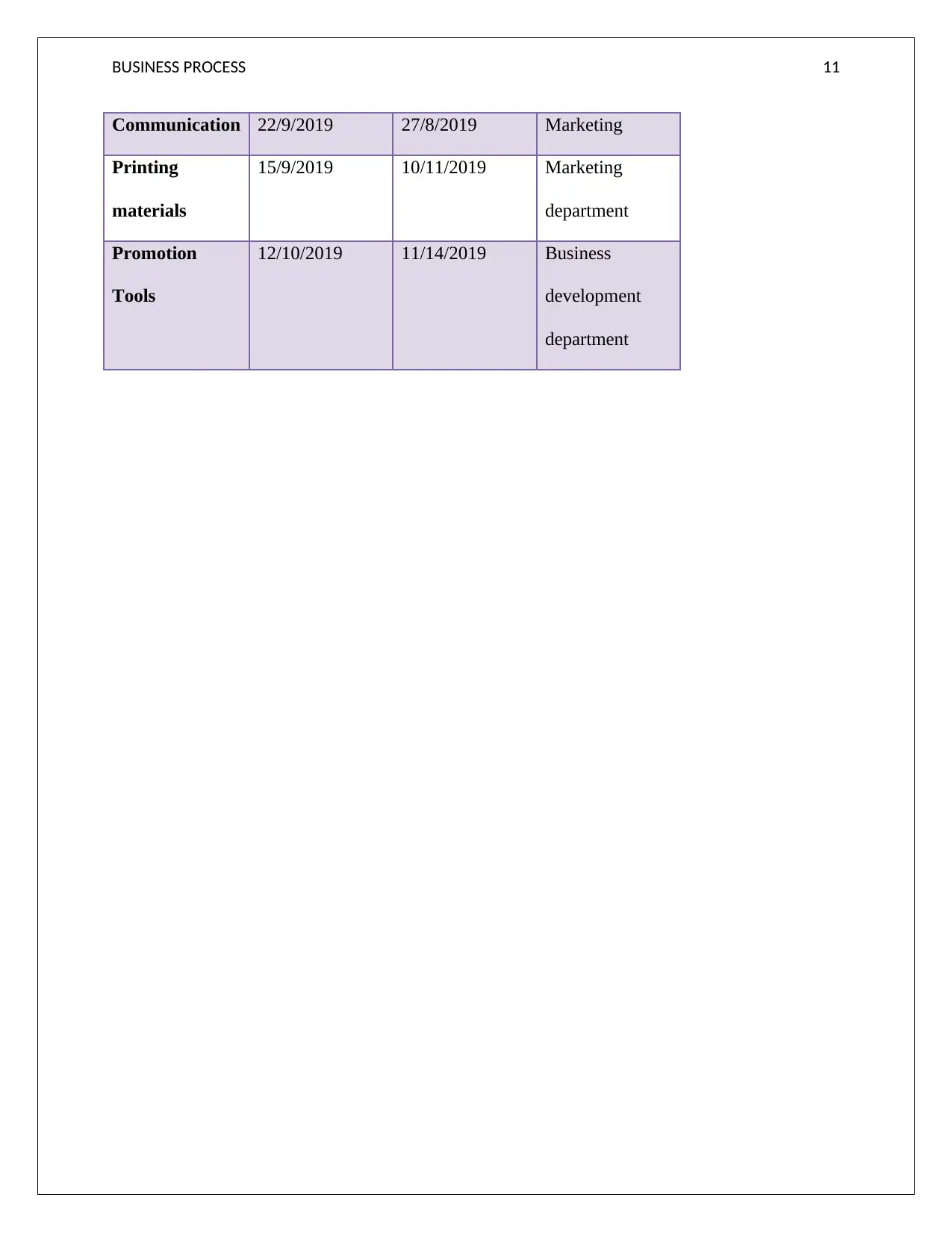
BUSINESS PROCESS 11
Communication 22/9/2019 27/8/2019 Marketing
Printing
materials
15/9/2019 10/11/2019 Marketing
department
Promotion
Tools
12/10/2019 11/14/2019 Business
development
department
Communication 22/9/2019 27/8/2019 Marketing
Printing
materials
15/9/2019 10/11/2019 Marketing
department
Promotion
Tools
12/10/2019 11/14/2019 Business
development
department
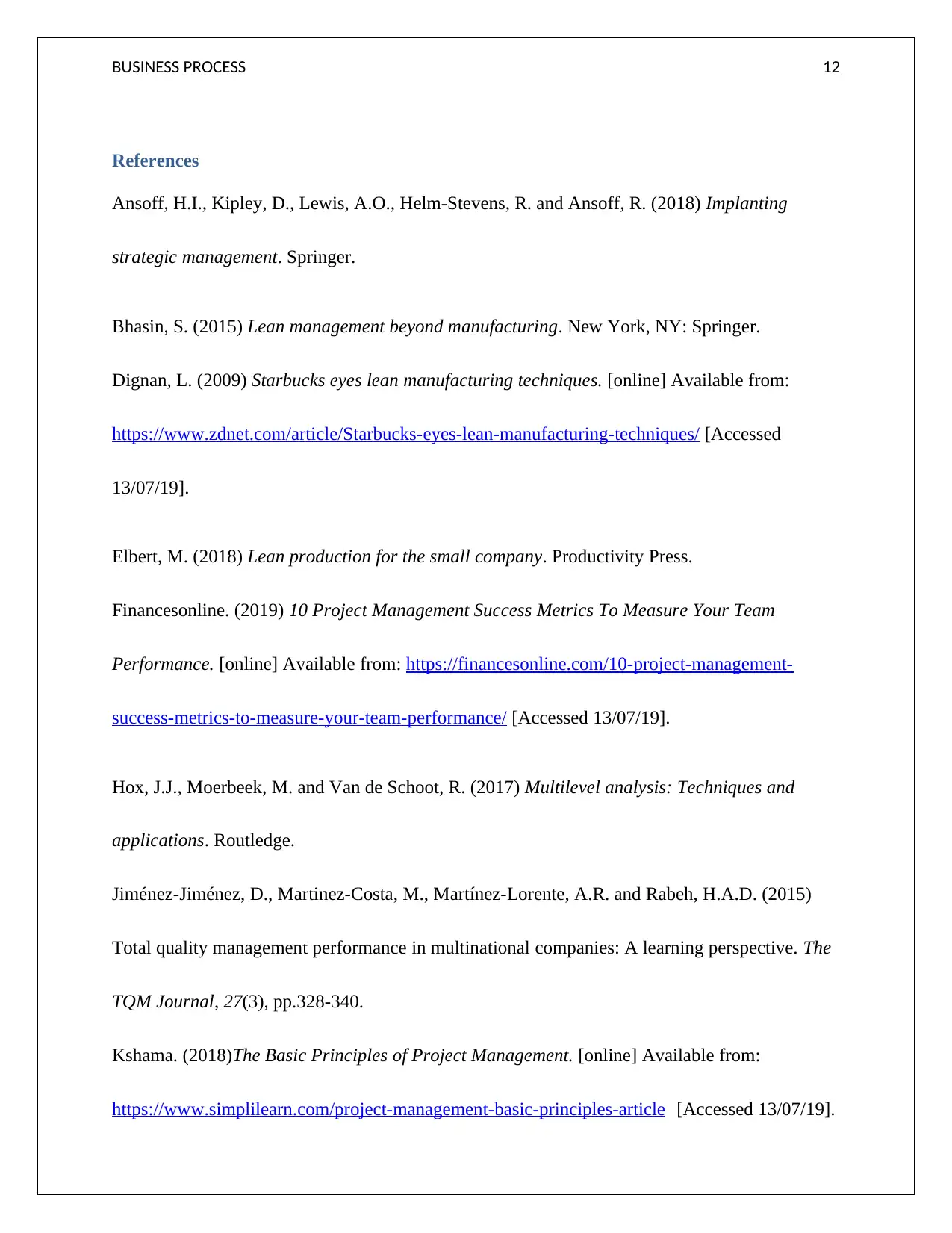
BUSINESS PROCESS 12
References
Ansoff, H.I., Kipley, D., Lewis, A.O., Helm-Stevens, R. and Ansoff, R. (2018) Implanting
strategic management. Springer.
Bhasin, S. (2015) Lean management beyond manufacturing. New York, NY: Springer.
Dignan, L. (2009) Starbucks eyes lean manufacturing techniques. [online] Available from:
https://www.zdnet.com/article/Starbucks-eyes-lean-manufacturing-techniques/ [Accessed
13/07/19].
Elbert, M. (2018) Lean production for the small company. Productivity Press.
Financesonline. (2019) 10 Project Management Success Metrics To Measure Your Team
Performance. [online] Available from: https://financesonline.com/10-project-management-
success-metrics-to-measure-your-team-performance/ [Accessed 13/07/19].
Hox, J.J., Moerbeek, M. and Van de Schoot, R. (2017) Multilevel analysis: Techniques and
applications. Routledge.
Jiménez-Jiménez, D., Martinez-Costa, M., Martínez-Lorente, A.R. and Rabeh, H.A.D. (2015)
Total quality management performance in multinational companies: A learning perspective. The
TQM Journal, 27(3), pp.328-340.
Kshama. (2018)The Basic Principles of Project Management. [online] Available from:
https://www.simplilearn.com/project-management-basic-principles-article [Accessed 13/07/19].
References
Ansoff, H.I., Kipley, D., Lewis, A.O., Helm-Stevens, R. and Ansoff, R. (2018) Implanting
strategic management. Springer.
Bhasin, S. (2015) Lean management beyond manufacturing. New York, NY: Springer.
Dignan, L. (2009) Starbucks eyes lean manufacturing techniques. [online] Available from:
https://www.zdnet.com/article/Starbucks-eyes-lean-manufacturing-techniques/ [Accessed
13/07/19].
Elbert, M. (2018) Lean production for the small company. Productivity Press.
Financesonline. (2019) 10 Project Management Success Metrics To Measure Your Team
Performance. [online] Available from: https://financesonline.com/10-project-management-
success-metrics-to-measure-your-team-performance/ [Accessed 13/07/19].
Hox, J.J., Moerbeek, M. and Van de Schoot, R. (2017) Multilevel analysis: Techniques and
applications. Routledge.
Jiménez-Jiménez, D., Martinez-Costa, M., Martínez-Lorente, A.R. and Rabeh, H.A.D. (2015)
Total quality management performance in multinational companies: A learning perspective. The
TQM Journal, 27(3), pp.328-340.
Kshama. (2018)The Basic Principles of Project Management. [online] Available from:
https://www.simplilearn.com/project-management-basic-principles-article [Accessed 13/07/19].
Paraphrase This Document
Need a fresh take? Get an instant paraphrase of this document with our AI Paraphraser
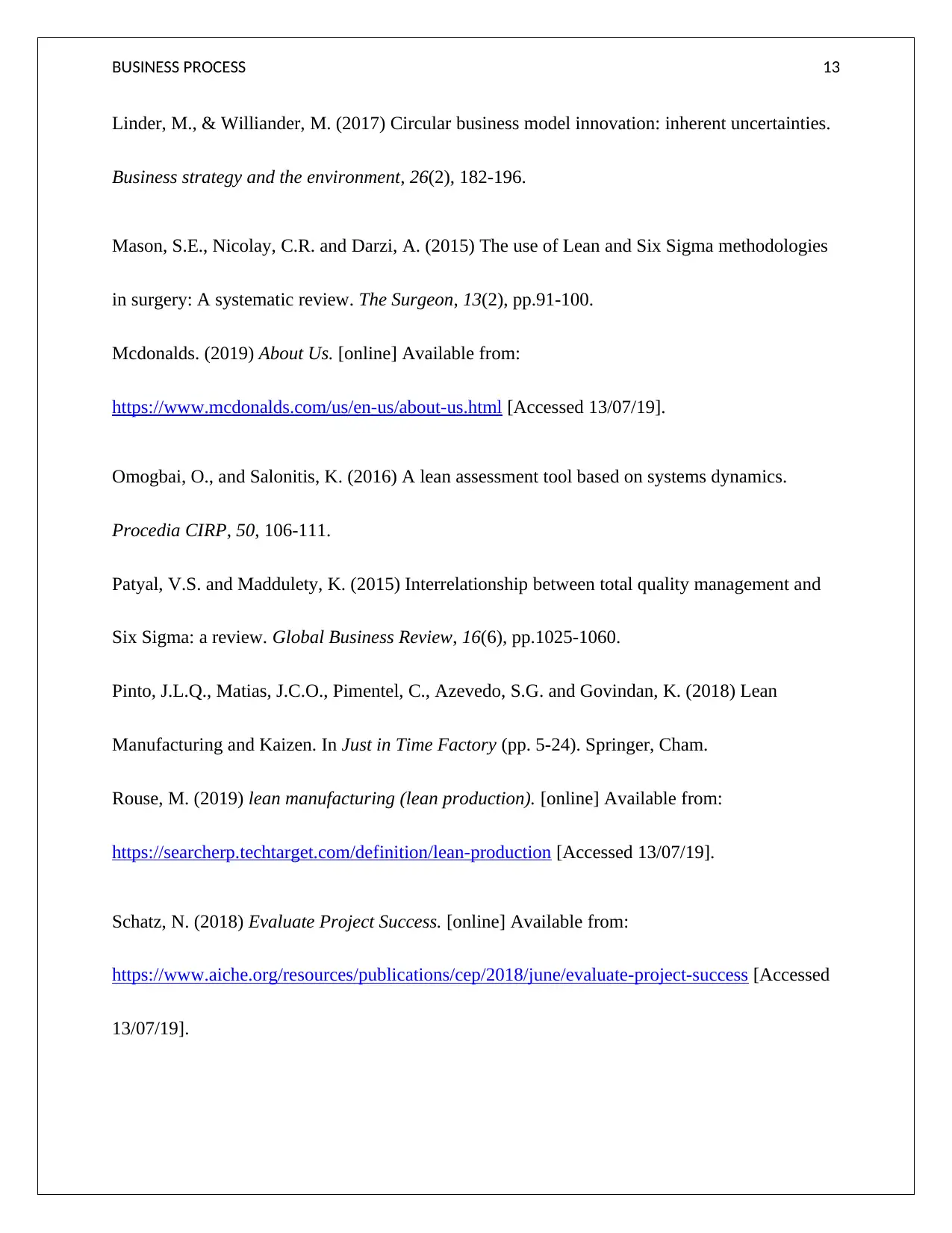
BUSINESS PROCESS 13
Linder, M., & Williander, M. (2017) Circular business model innovation: inherent uncertainties.
Business strategy and the environment, 26(2), 182-196.
Mason, S.E., Nicolay, C.R. and Darzi, A. (2015) The use of Lean and Six Sigma methodologies
in surgery: A systematic review. The Surgeon, 13(2), pp.91-100.
Mcdonalds. (2019) About Us. [online] Available from:
https://www.mcdonalds.com/us/en-us/about-us.html [Accessed 13/07/19].
Omogbai, O., and Salonitis, K. (2016) A lean assessment tool based on systems dynamics.
Procedia CIRP, 50, 106-111.
Patyal, V.S. and Maddulety, K. (2015) Interrelationship between total quality management and
Six Sigma: a review. Global Business Review, 16(6), pp.1025-1060.
Pinto, J.L.Q., Matias, J.C.O., Pimentel, C., Azevedo, S.G. and Govindan, K. (2018) Lean
Manufacturing and Kaizen. In Just in Time Factory (pp. 5-24). Springer, Cham.
Rouse, M. (2019) lean manufacturing (lean production). [online] Available from:
https://searcherp.techtarget.com/definition/lean-production [Accessed 13/07/19].
Schatz, N. (2018) Evaluate Project Success. [online] Available from:
https://www.aiche.org/resources/publications/cep/2018/june/evaluate-project-success [Accessed
13/07/19].
Linder, M., & Williander, M. (2017) Circular business model innovation: inherent uncertainties.
Business strategy and the environment, 26(2), 182-196.
Mason, S.E., Nicolay, C.R. and Darzi, A. (2015) The use of Lean and Six Sigma methodologies
in surgery: A systematic review. The Surgeon, 13(2), pp.91-100.
Mcdonalds. (2019) About Us. [online] Available from:
https://www.mcdonalds.com/us/en-us/about-us.html [Accessed 13/07/19].
Omogbai, O., and Salonitis, K. (2016) A lean assessment tool based on systems dynamics.
Procedia CIRP, 50, 106-111.
Patyal, V.S. and Maddulety, K. (2015) Interrelationship between total quality management and
Six Sigma: a review. Global Business Review, 16(6), pp.1025-1060.
Pinto, J.L.Q., Matias, J.C.O., Pimentel, C., Azevedo, S.G. and Govindan, K. (2018) Lean
Manufacturing and Kaizen. In Just in Time Factory (pp. 5-24). Springer, Cham.
Rouse, M. (2019) lean manufacturing (lean production). [online] Available from:
https://searcherp.techtarget.com/definition/lean-production [Accessed 13/07/19].
Schatz, N. (2018) Evaluate Project Success. [online] Available from:
https://www.aiche.org/resources/publications/cep/2018/june/evaluate-project-success [Accessed
13/07/19].
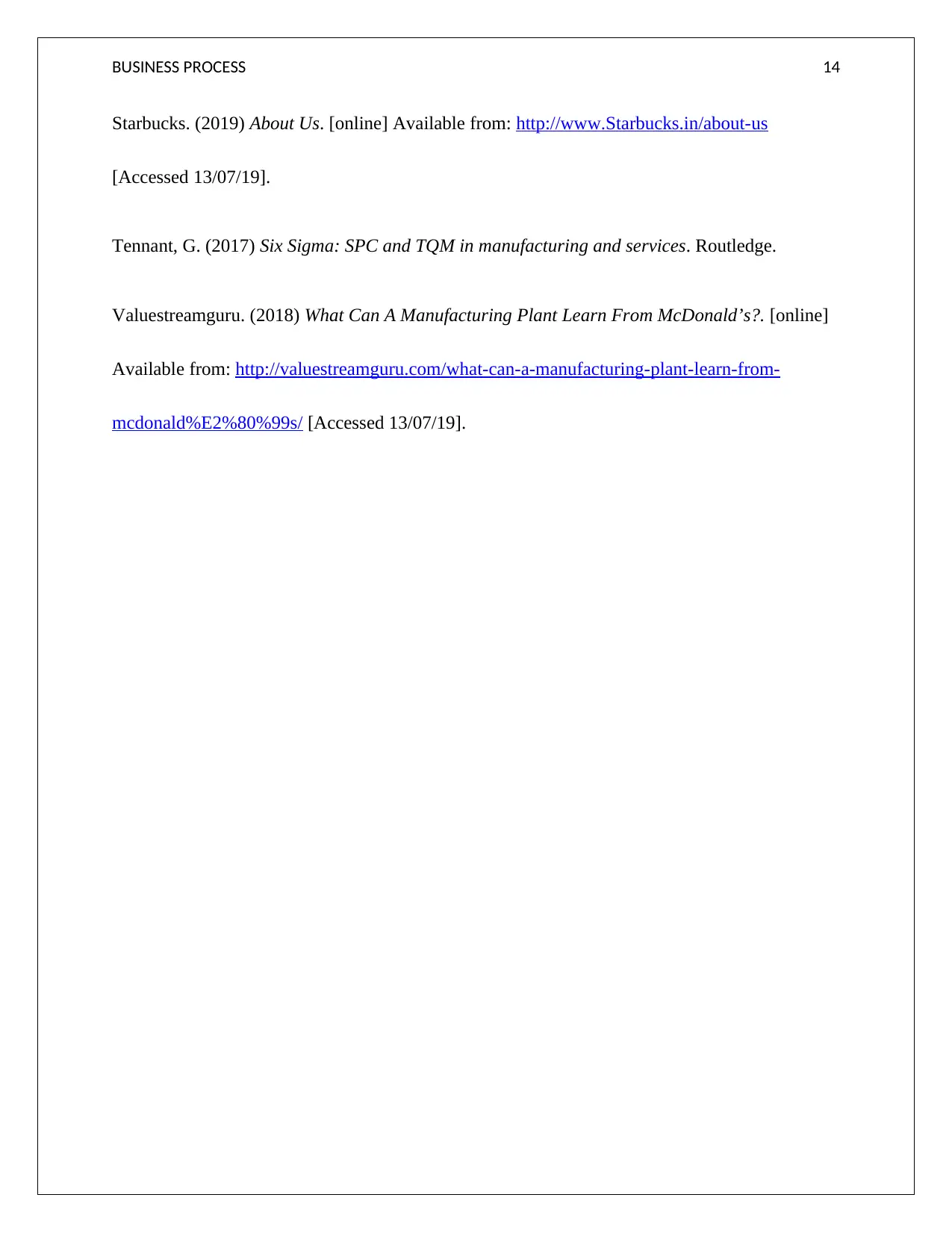
BUSINESS PROCESS 14
Starbucks. (2019) About Us. [online] Available from: http://www.Starbucks.in/about-us
[Accessed 13/07/19].
Tennant, G. (2017) Six Sigma: SPC and TQM in manufacturing and services. Routledge.
Valuestreamguru. (2018) What Can A Manufacturing Plant Learn From McDonald’s?. [online]
Available from: http://valuestreamguru.com/what-can-a-manufacturing-plant-learn-from-
mcdonald%E2%80%99s/ [Accessed 13/07/19].
Starbucks. (2019) About Us. [online] Available from: http://www.Starbucks.in/about-us
[Accessed 13/07/19].
Tennant, G. (2017) Six Sigma: SPC and TQM in manufacturing and services. Routledge.
Valuestreamguru. (2018) What Can A Manufacturing Plant Learn From McDonald’s?. [online]
Available from: http://valuestreamguru.com/what-can-a-manufacturing-plant-learn-from-
mcdonald%E2%80%99s/ [Accessed 13/07/19].
1 out of 15
Related Documents

Your All-in-One AI-Powered Toolkit for Academic Success.
+13062052269
info@desklib.com
Available 24*7 on WhatsApp / Email
Unlock your academic potential
© 2024 | Zucol Services PVT LTD | All rights reserved.