Assessment of Chemical Hazards and Management in Chemical Industry
VerifiedAdded on 2022/11/18
|16
|3814
|1
Report
AI Summary
This report critically analyzes chemical hazards in the chemical industry, focusing on their impact on workers. The report begins with an executive summary, followed by an introduction outlining the significance of chemical hazards in the workplace. It then examines the occupational demography of the industry and conducts a thorough risk assessment, identifying hazards such as respiratory complications, skin and eye damage, and explosions. Legal requirements and ethical considerations, including REACH regulations and industrial chemical acts, are discussed, emphasizing the importance of worker protection and training. A literature review synthesizes existing research on chemical hazards and management strategies. The report proposes a comprehensive management plan addressing hazard control through source reduction, exposure path mitigation, and employee protection. The plan includes training, engineering controls, and the provision of personal protective equipment (PPE). The conclusion reiterates the importance of prioritizing the control of chemical hazards to ensure employee safety. Finally, the report includes a detailed reference list.
Contribute Materials
Your contribution can guide someone’s learning journey. Share your
documents today.
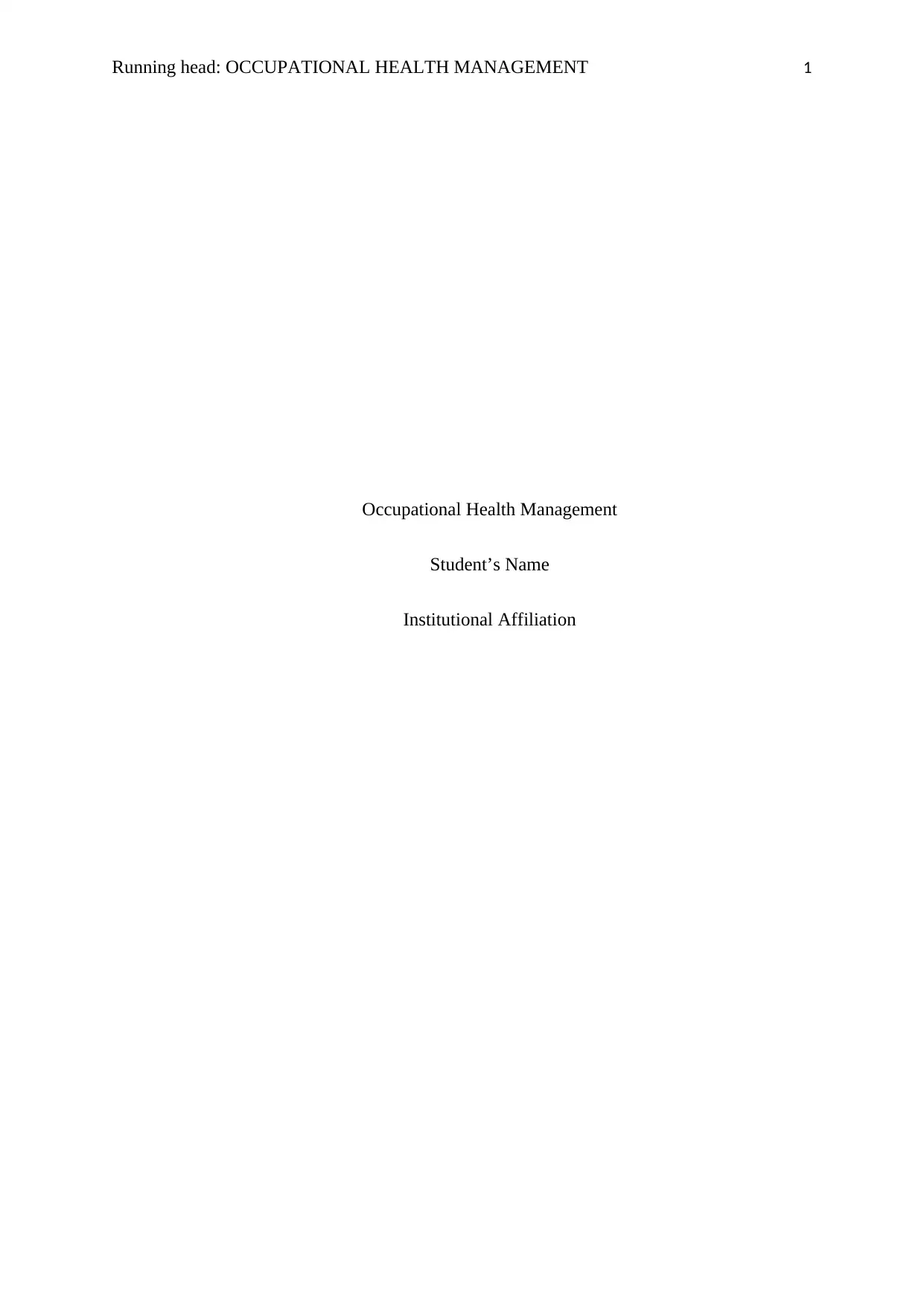
Running head: OCCUPATIONAL HEALTH MANAGEMENT 1
Occupational Health Management
Student’s Name
Institutional Affiliation
Occupational Health Management
Student’s Name
Institutional Affiliation
Secure Best Marks with AI Grader
Need help grading? Try our AI Grader for instant feedback on your assignments.
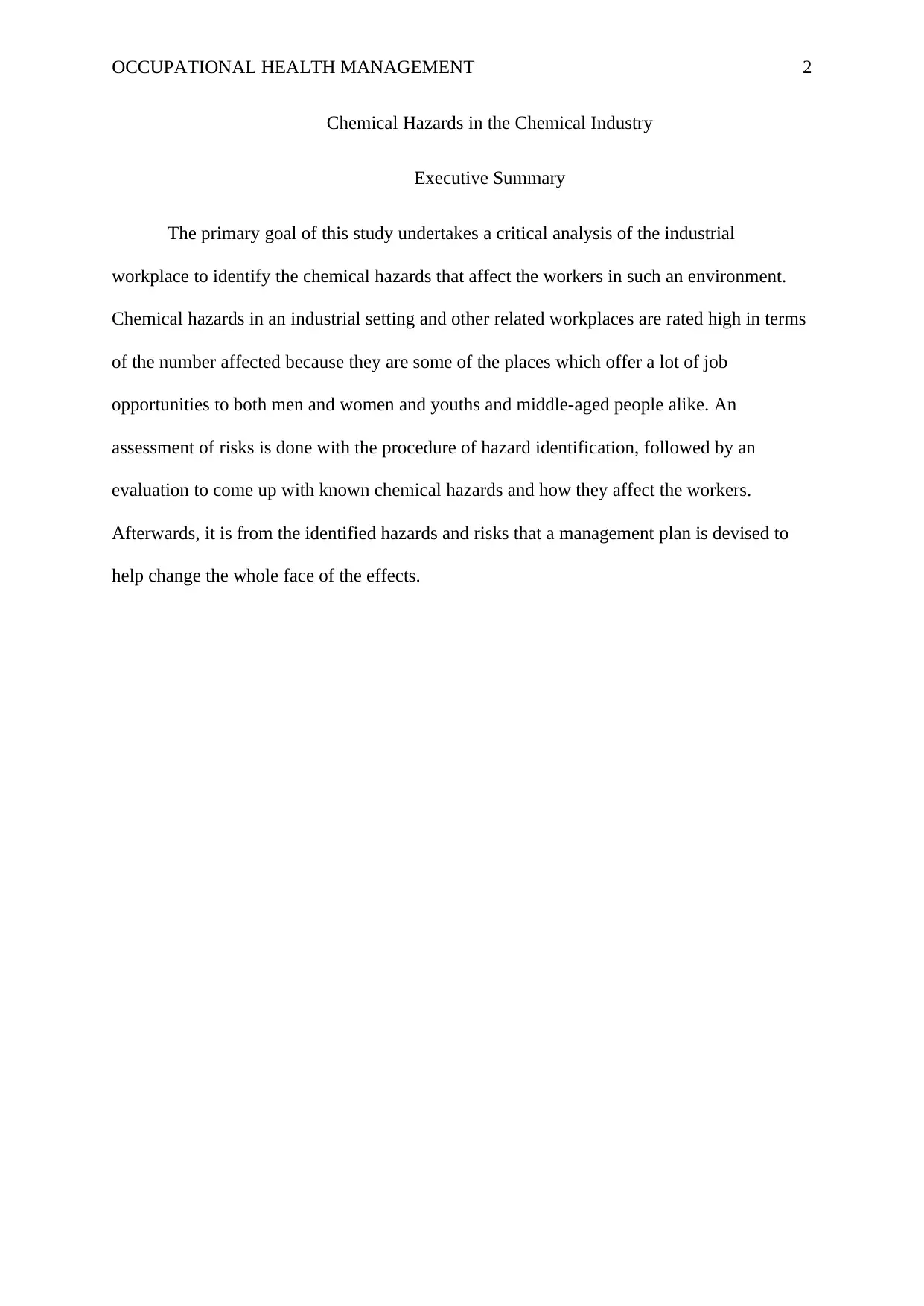
OCCUPATIONAL HEALTH MANAGEMENT 2
Chemical Hazards in the Chemical Industry
Executive Summary
The primary goal of this study undertakes a critical analysis of the industrial
workplace to identify the chemical hazards that affect the workers in such an environment.
Chemical hazards in an industrial setting and other related workplaces are rated high in terms
of the number affected because they are some of the places which offer a lot of job
opportunities to both men and women and youths and middle-aged people alike. An
assessment of risks is done with the procedure of hazard identification, followed by an
evaluation to come up with known chemical hazards and how they affect the workers.
Afterwards, it is from the identified hazards and risks that a management plan is devised to
help change the whole face of the effects.
Chemical Hazards in the Chemical Industry
Executive Summary
The primary goal of this study undertakes a critical analysis of the industrial
workplace to identify the chemical hazards that affect the workers in such an environment.
Chemical hazards in an industrial setting and other related workplaces are rated high in terms
of the number affected because they are some of the places which offer a lot of job
opportunities to both men and women and youths and middle-aged people alike. An
assessment of risks is done with the procedure of hazard identification, followed by an
evaluation to come up with known chemical hazards and how they affect the workers.
Afterwards, it is from the identified hazards and risks that a management plan is devised to
help change the whole face of the effects.
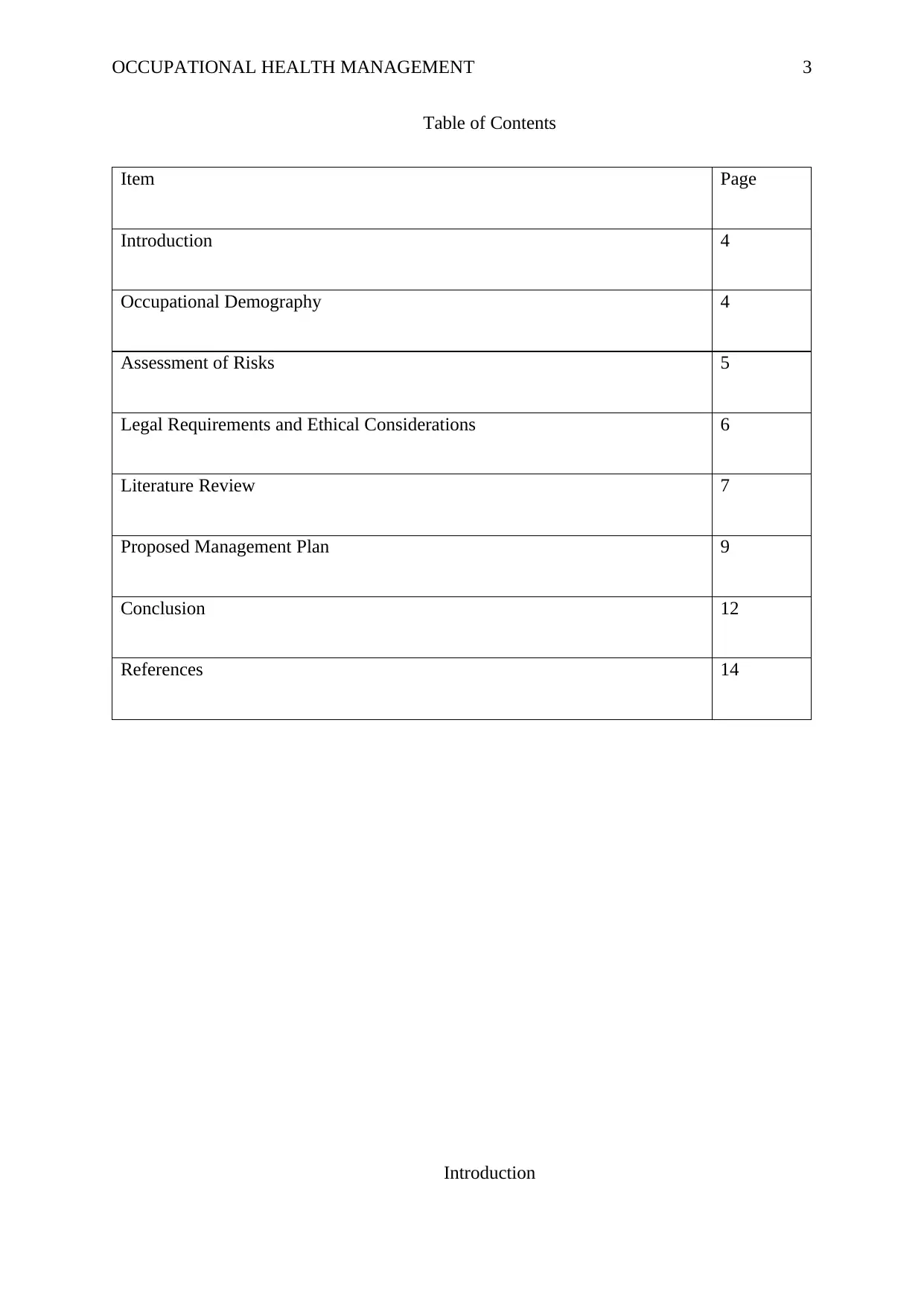
OCCUPATIONAL HEALTH MANAGEMENT 3
Table of Contents
Item Page
Introduction 4
Occupational Demography 4
Assessment of Risks 5
Legal Requirements and Ethical Considerations 6
Literature Review 7
Proposed Management Plan 9
Conclusion 12
References 14
Introduction
Table of Contents
Item Page
Introduction 4
Occupational Demography 4
Assessment of Risks 5
Legal Requirements and Ethical Considerations 6
Literature Review 7
Proposed Management Plan 9
Conclusion 12
References 14
Introduction
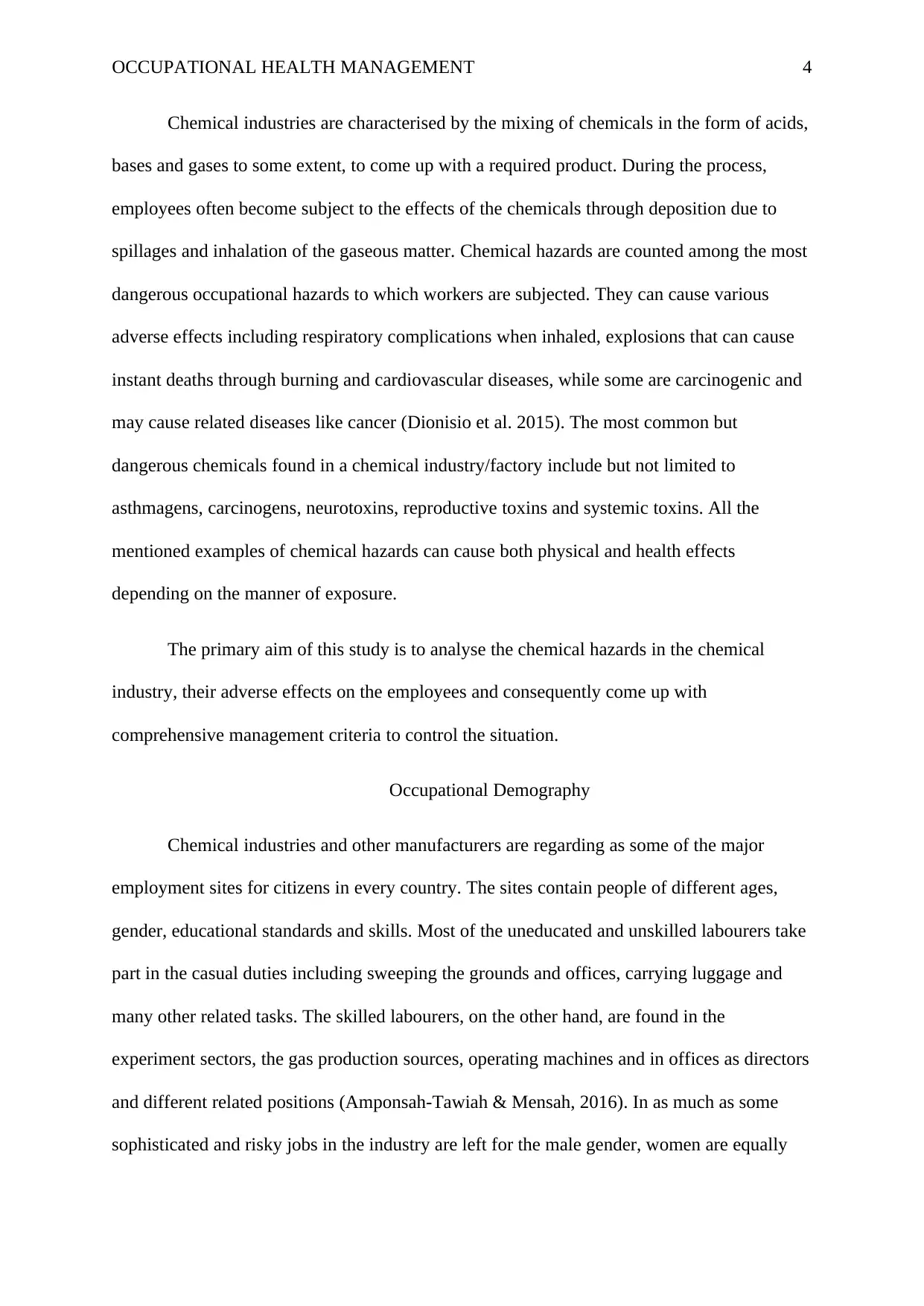
OCCUPATIONAL HEALTH MANAGEMENT 4
Chemical industries are characterised by the mixing of chemicals in the form of acids,
bases and gases to some extent, to come up with a required product. During the process,
employees often become subject to the effects of the chemicals through deposition due to
spillages and inhalation of the gaseous matter. Chemical hazards are counted among the most
dangerous occupational hazards to which workers are subjected. They can cause various
adverse effects including respiratory complications when inhaled, explosions that can cause
instant deaths through burning and cardiovascular diseases, while some are carcinogenic and
may cause related diseases like cancer (Dionisio et al. 2015). The most common but
dangerous chemicals found in a chemical industry/factory include but not limited to
asthmagens, carcinogens, neurotoxins, reproductive toxins and systemic toxins. All the
mentioned examples of chemical hazards can cause both physical and health effects
depending on the manner of exposure.
The primary aim of this study is to analyse the chemical hazards in the chemical
industry, their adverse effects on the employees and consequently come up with
comprehensive management criteria to control the situation.
Occupational Demography
Chemical industries and other manufacturers are regarding as some of the major
employment sites for citizens in every country. The sites contain people of different ages,
gender, educational standards and skills. Most of the uneducated and unskilled labourers take
part in the casual duties including sweeping the grounds and offices, carrying luggage and
many other related tasks. The skilled labourers, on the other hand, are found in the
experiment sectors, the gas production sources, operating machines and in offices as directors
and different related positions (Amponsah-Tawiah & Mensah, 2016). In as much as some
sophisticated and risky jobs in the industry are left for the male gender, women are equally
Chemical industries are characterised by the mixing of chemicals in the form of acids,
bases and gases to some extent, to come up with a required product. During the process,
employees often become subject to the effects of the chemicals through deposition due to
spillages and inhalation of the gaseous matter. Chemical hazards are counted among the most
dangerous occupational hazards to which workers are subjected. They can cause various
adverse effects including respiratory complications when inhaled, explosions that can cause
instant deaths through burning and cardiovascular diseases, while some are carcinogenic and
may cause related diseases like cancer (Dionisio et al. 2015). The most common but
dangerous chemicals found in a chemical industry/factory include but not limited to
asthmagens, carcinogens, neurotoxins, reproductive toxins and systemic toxins. All the
mentioned examples of chemical hazards can cause both physical and health effects
depending on the manner of exposure.
The primary aim of this study is to analyse the chemical hazards in the chemical
industry, their adverse effects on the employees and consequently come up with
comprehensive management criteria to control the situation.
Occupational Demography
Chemical industries and other manufacturers are regarding as some of the major
employment sites for citizens in every country. The sites contain people of different ages,
gender, educational standards and skills. Most of the uneducated and unskilled labourers take
part in the casual duties including sweeping the grounds and offices, carrying luggage and
many other related tasks. The skilled labourers, on the other hand, are found in the
experiment sectors, the gas production sources, operating machines and in offices as directors
and different related positions (Amponsah-Tawiah & Mensah, 2016). In as much as some
sophisticated and risky jobs in the industry are left for the male gender, women are equally
Secure Best Marks with AI Grader
Need help grading? Try our AI Grader for instant feedback on your assignments.
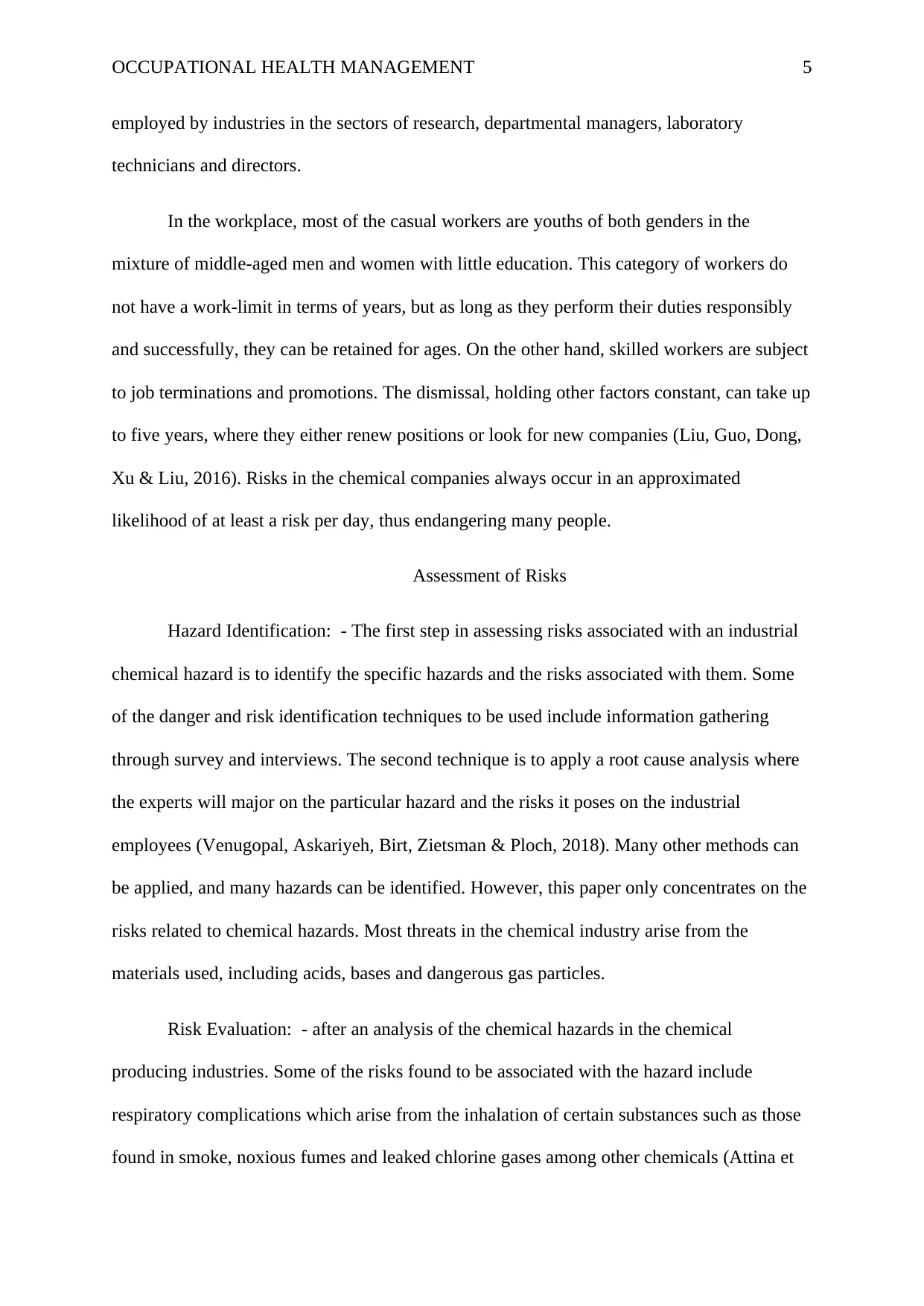
OCCUPATIONAL HEALTH MANAGEMENT 5
employed by industries in the sectors of research, departmental managers, laboratory
technicians and directors.
In the workplace, most of the casual workers are youths of both genders in the
mixture of middle-aged men and women with little education. This category of workers do
not have a work-limit in terms of years, but as long as they perform their duties responsibly
and successfully, they can be retained for ages. On the other hand, skilled workers are subject
to job terminations and promotions. The dismissal, holding other factors constant, can take up
to five years, where they either renew positions or look for new companies (Liu, Guo, Dong,
Xu & Liu, 2016). Risks in the chemical companies always occur in an approximated
likelihood of at least a risk per day, thus endangering many people.
Assessment of Risks
Hazard Identification: - The first step in assessing risks associated with an industrial
chemical hazard is to identify the specific hazards and the risks associated with them. Some
of the danger and risk identification techniques to be used include information gathering
through survey and interviews. The second technique is to apply a root cause analysis where
the experts will major on the particular hazard and the risks it poses on the industrial
employees (Venugopal, Askariyeh, Birt, Zietsman & Ploch, 2018). Many other methods can
be applied, and many hazards can be identified. However, this paper only concentrates on the
risks related to chemical hazards. Most threats in the chemical industry arise from the
materials used, including acids, bases and dangerous gas particles.
Risk Evaluation: - after an analysis of the chemical hazards in the chemical
producing industries. Some of the risks found to be associated with the hazard include
respiratory complications which arise from the inhalation of certain substances such as those
found in smoke, noxious fumes and leaked chlorine gases among other chemicals (Attina et
employed by industries in the sectors of research, departmental managers, laboratory
technicians and directors.
In the workplace, most of the casual workers are youths of both genders in the
mixture of middle-aged men and women with little education. This category of workers do
not have a work-limit in terms of years, but as long as they perform their duties responsibly
and successfully, they can be retained for ages. On the other hand, skilled workers are subject
to job terminations and promotions. The dismissal, holding other factors constant, can take up
to five years, where they either renew positions or look for new companies (Liu, Guo, Dong,
Xu & Liu, 2016). Risks in the chemical companies always occur in an approximated
likelihood of at least a risk per day, thus endangering many people.
Assessment of Risks
Hazard Identification: - The first step in assessing risks associated with an industrial
chemical hazard is to identify the specific hazards and the risks associated with them. Some
of the danger and risk identification techniques to be used include information gathering
through survey and interviews. The second technique is to apply a root cause analysis where
the experts will major on the particular hazard and the risks it poses on the industrial
employees (Venugopal, Askariyeh, Birt, Zietsman & Ploch, 2018). Many other methods can
be applied, and many hazards can be identified. However, this paper only concentrates on the
risks related to chemical hazards. Most threats in the chemical industry arise from the
materials used, including acids, bases and dangerous gas particles.
Risk Evaluation: - after an analysis of the chemical hazards in the chemical
producing industries. Some of the risks found to be associated with the hazard include
respiratory complications which arise from the inhalation of certain substances such as those
found in smoke, noxious fumes and leaked chlorine gases among other chemicals (Attina et
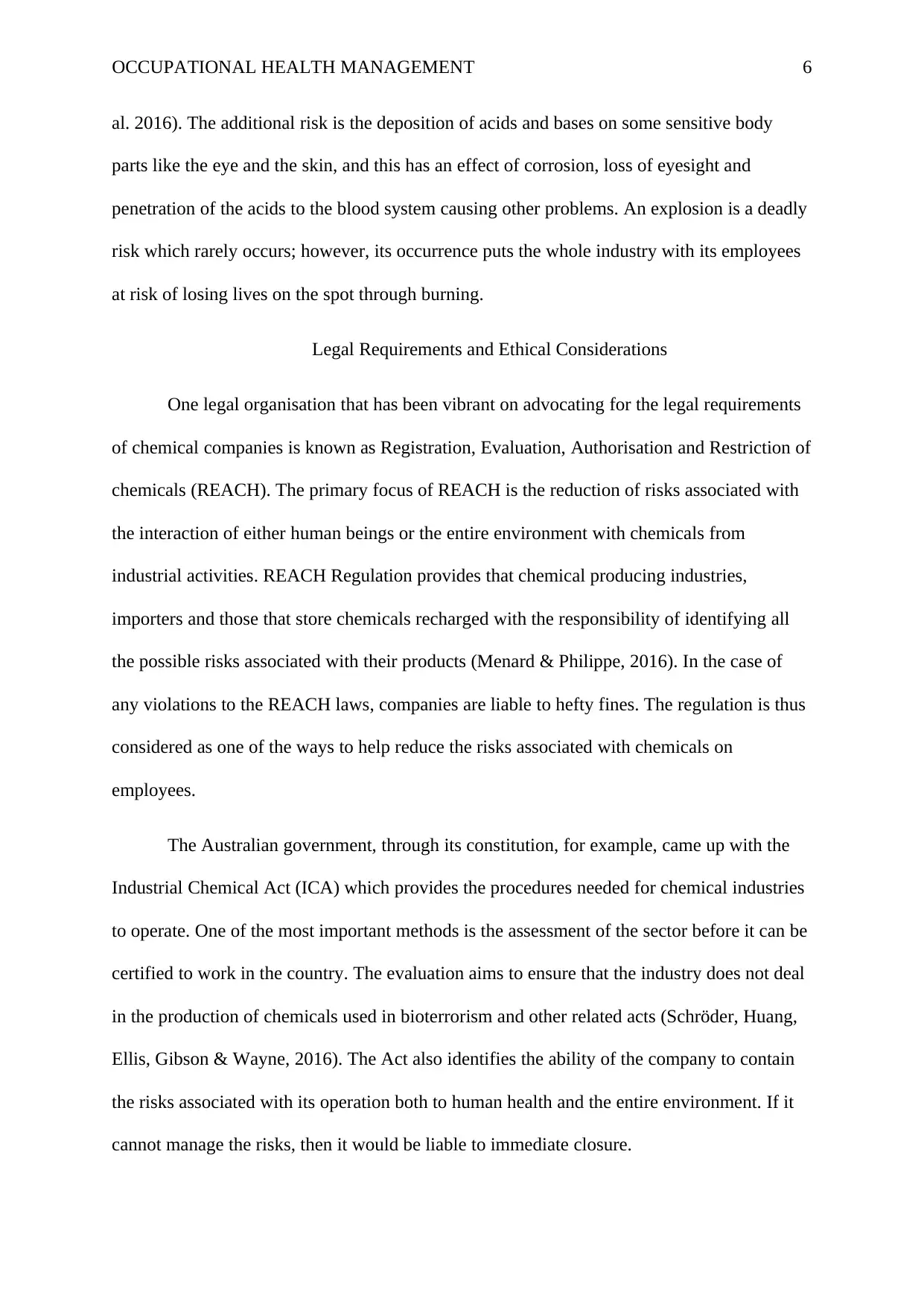
OCCUPATIONAL HEALTH MANAGEMENT 6
al. 2016). The additional risk is the deposition of acids and bases on some sensitive body
parts like the eye and the skin, and this has an effect of corrosion, loss of eyesight and
penetration of the acids to the blood system causing other problems. An explosion is a deadly
risk which rarely occurs; however, its occurrence puts the whole industry with its employees
at risk of losing lives on the spot through burning.
Legal Requirements and Ethical Considerations
One legal organisation that has been vibrant on advocating for the legal requirements
of chemical companies is known as Registration, Evaluation, Authorisation and Restriction of
chemicals (REACH). The primary focus of REACH is the reduction of risks associated with
the interaction of either human beings or the entire environment with chemicals from
industrial activities. REACH Regulation provides that chemical producing industries,
importers and those that store chemicals recharged with the responsibility of identifying all
the possible risks associated with their products (Menard & Philippe, 2016). In the case of
any violations to the REACH laws, companies are liable to hefty fines. The regulation is thus
considered as one of the ways to help reduce the risks associated with chemicals on
employees.
The Australian government, through its constitution, for example, came up with the
Industrial Chemical Act (ICA) which provides the procedures needed for chemical industries
to operate. One of the most important methods is the assessment of the sector before it can be
certified to work in the country. The evaluation aims to ensure that the industry does not deal
in the production of chemicals used in bioterrorism and other related acts (Schröder, Huang,
Ellis, Gibson & Wayne, 2016). The Act also identifies the ability of the company to contain
the risks associated with its operation both to human health and the entire environment. If it
cannot manage the risks, then it would be liable to immediate closure.
al. 2016). The additional risk is the deposition of acids and bases on some sensitive body
parts like the eye and the skin, and this has an effect of corrosion, loss of eyesight and
penetration of the acids to the blood system causing other problems. An explosion is a deadly
risk which rarely occurs; however, its occurrence puts the whole industry with its employees
at risk of losing lives on the spot through burning.
Legal Requirements and Ethical Considerations
One legal organisation that has been vibrant on advocating for the legal requirements
of chemical companies is known as Registration, Evaluation, Authorisation and Restriction of
chemicals (REACH). The primary focus of REACH is the reduction of risks associated with
the interaction of either human beings or the entire environment with chemicals from
industrial activities. REACH Regulation provides that chemical producing industries,
importers and those that store chemicals recharged with the responsibility of identifying all
the possible risks associated with their products (Menard & Philippe, 2016). In the case of
any violations to the REACH laws, companies are liable to hefty fines. The regulation is thus
considered as one of the ways to help reduce the risks associated with chemicals on
employees.
The Australian government, through its constitution, for example, came up with the
Industrial Chemical Act (ICA) which provides the procedures needed for chemical industries
to operate. One of the most important methods is the assessment of the sector before it can be
certified to work in the country. The evaluation aims to ensure that the industry does not deal
in the production of chemicals used in bioterrorism and other related acts (Schröder, Huang,
Ellis, Gibson & Wayne, 2016). The Act also identifies the ability of the company to contain
the risks associated with its operation both to human health and the entire environment. If it
cannot manage the risks, then it would be liable to immediate closure.
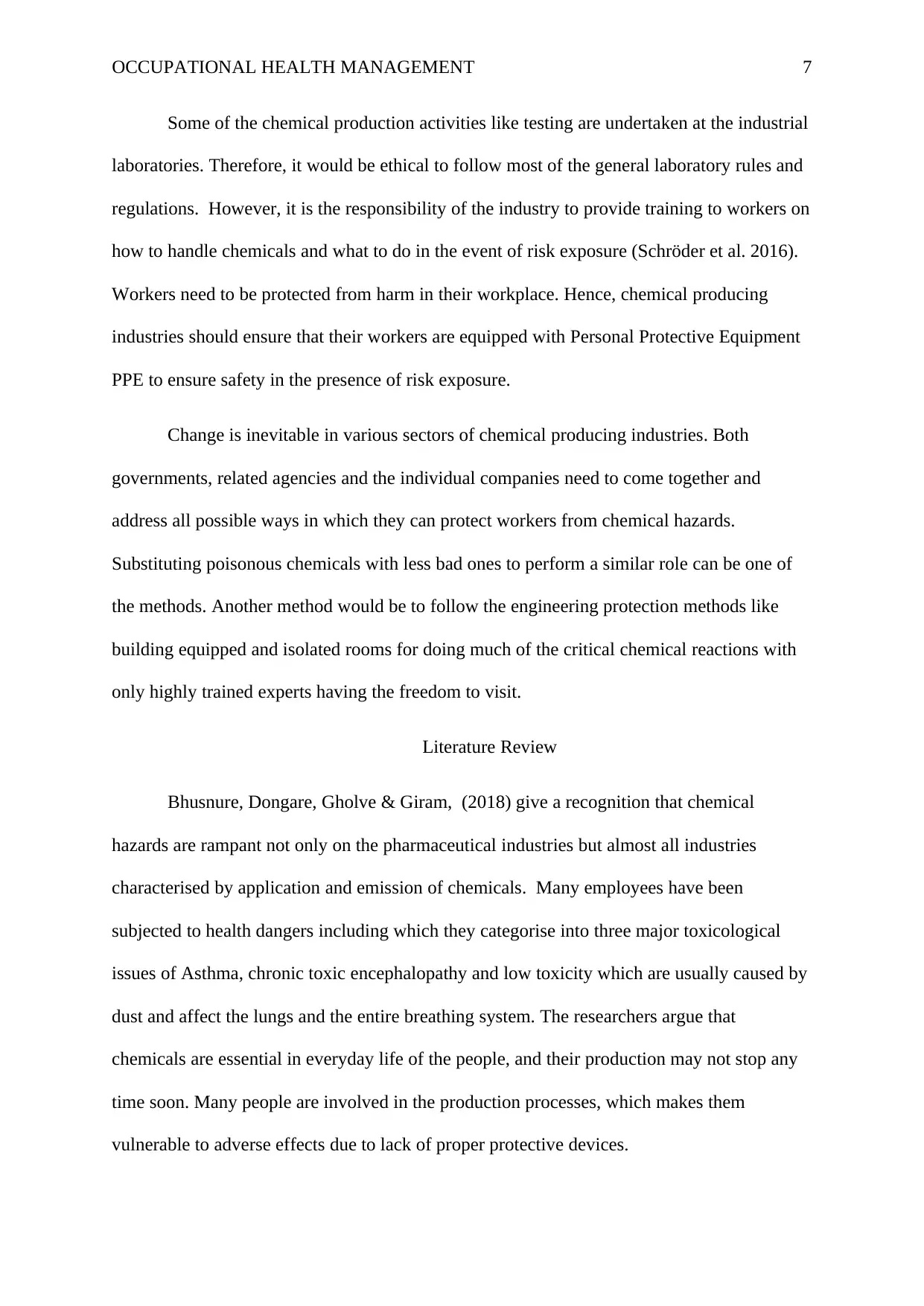
OCCUPATIONAL HEALTH MANAGEMENT 7
Some of the chemical production activities like testing are undertaken at the industrial
laboratories. Therefore, it would be ethical to follow most of the general laboratory rules and
regulations. However, it is the responsibility of the industry to provide training to workers on
how to handle chemicals and what to do in the event of risk exposure (Schröder et al. 2016).
Workers need to be protected from harm in their workplace. Hence, chemical producing
industries should ensure that their workers are equipped with Personal Protective Equipment
PPE to ensure safety in the presence of risk exposure.
Change is inevitable in various sectors of chemical producing industries. Both
governments, related agencies and the individual companies need to come together and
address all possible ways in which they can protect workers from chemical hazards.
Substituting poisonous chemicals with less bad ones to perform a similar role can be one of
the methods. Another method would be to follow the engineering protection methods like
building equipped and isolated rooms for doing much of the critical chemical reactions with
only highly trained experts having the freedom to visit.
Literature Review
Bhusnure, Dongare, Gholve & Giram, (2018) give a recognition that chemical
hazards are rampant not only on the pharmaceutical industries but almost all industries
characterised by application and emission of chemicals. Many employees have been
subjected to health dangers including which they categorise into three major toxicological
issues of Asthma, chronic toxic encephalopathy and low toxicity which are usually caused by
dust and affect the lungs and the entire breathing system. The researchers argue that
chemicals are essential in everyday life of the people, and their production may not stop any
time soon. Many people are involved in the production processes, which makes them
vulnerable to adverse effects due to lack of proper protective devices.
Some of the chemical production activities like testing are undertaken at the industrial
laboratories. Therefore, it would be ethical to follow most of the general laboratory rules and
regulations. However, it is the responsibility of the industry to provide training to workers on
how to handle chemicals and what to do in the event of risk exposure (Schröder et al. 2016).
Workers need to be protected from harm in their workplace. Hence, chemical producing
industries should ensure that their workers are equipped with Personal Protective Equipment
PPE to ensure safety in the presence of risk exposure.
Change is inevitable in various sectors of chemical producing industries. Both
governments, related agencies and the individual companies need to come together and
address all possible ways in which they can protect workers from chemical hazards.
Substituting poisonous chemicals with less bad ones to perform a similar role can be one of
the methods. Another method would be to follow the engineering protection methods like
building equipped and isolated rooms for doing much of the critical chemical reactions with
only highly trained experts having the freedom to visit.
Literature Review
Bhusnure, Dongare, Gholve & Giram, (2018) give a recognition that chemical
hazards are rampant not only on the pharmaceutical industries but almost all industries
characterised by application and emission of chemicals. Many employees have been
subjected to health dangers including which they categorise into three major toxicological
issues of Asthma, chronic toxic encephalopathy and low toxicity which are usually caused by
dust and affect the lungs and the entire breathing system. The researchers argue that
chemicals are essential in everyday life of the people, and their production may not stop any
time soon. Many people are involved in the production processes, which makes them
vulnerable to adverse effects due to lack of proper protective devices.
Paraphrase This Document
Need a fresh take? Get an instant paraphrase of this document with our AI Paraphraser
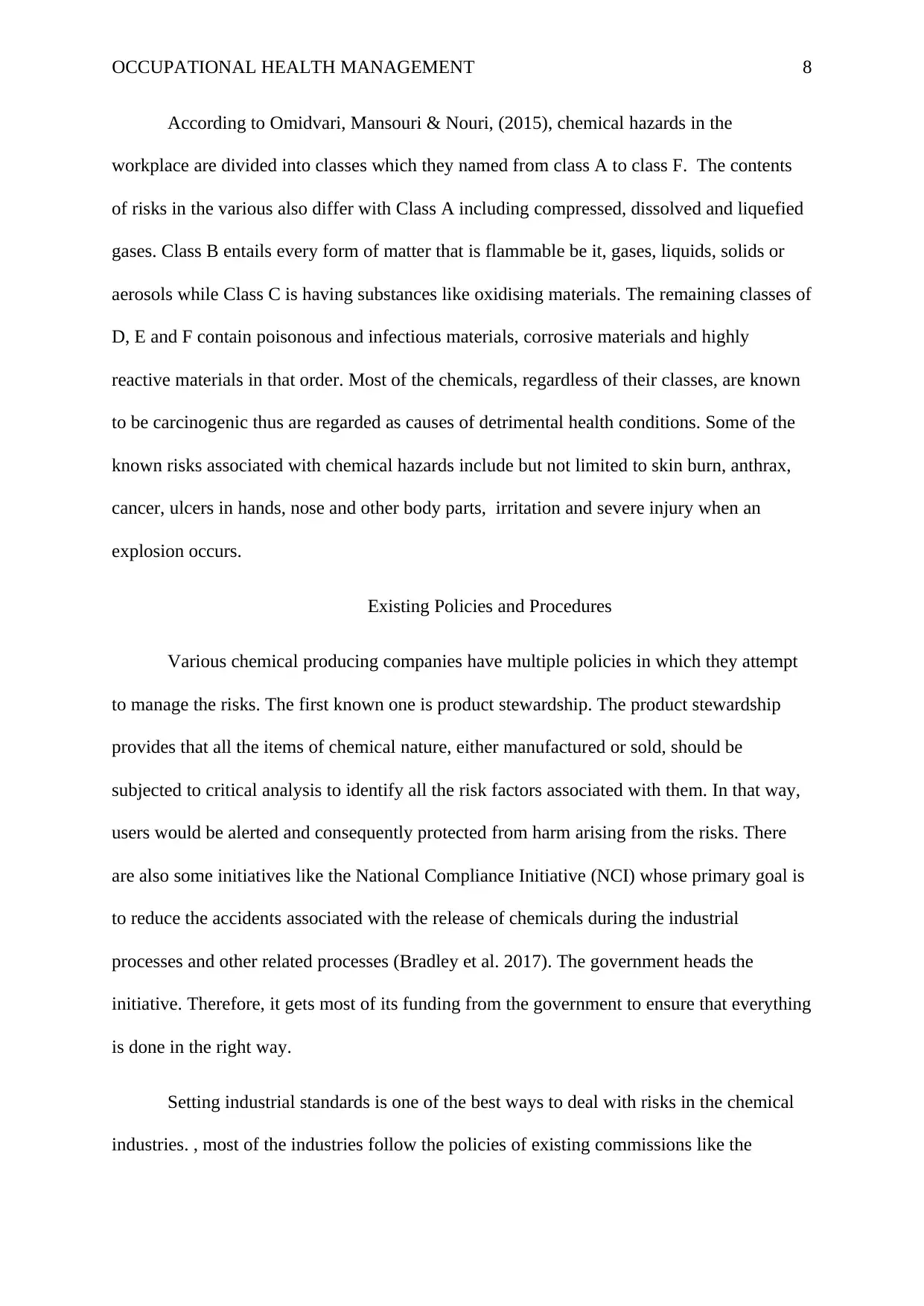
OCCUPATIONAL HEALTH MANAGEMENT 8
According to Omidvari, Mansouri & Nouri, (2015), chemical hazards in the
workplace are divided into classes which they named from class A to class F. The contents
of risks in the various also differ with Class A including compressed, dissolved and liquefied
gases. Class B entails every form of matter that is flammable be it, gases, liquids, solids or
aerosols while Class C is having substances like oxidising materials. The remaining classes of
D, E and F contain poisonous and infectious materials, corrosive materials and highly
reactive materials in that order. Most of the chemicals, regardless of their classes, are known
to be carcinogenic thus are regarded as causes of detrimental health conditions. Some of the
known risks associated with chemical hazards include but not limited to skin burn, anthrax,
cancer, ulcers in hands, nose and other body parts, irritation and severe injury when an
explosion occurs.
Existing Policies and Procedures
Various chemical producing companies have multiple policies in which they attempt
to manage the risks. The first known one is product stewardship. The product stewardship
provides that all the items of chemical nature, either manufactured or sold, should be
subjected to critical analysis to identify all the risk factors associated with them. In that way,
users would be alerted and consequently protected from harm arising from the risks. There
are also some initiatives like the National Compliance Initiative (NCI) whose primary goal is
to reduce the accidents associated with the release of chemicals during the industrial
processes and other related processes (Bradley et al. 2017). The government heads the
initiative. Therefore, it gets most of its funding from the government to ensure that everything
is done in the right way.
Setting industrial standards is one of the best ways to deal with risks in the chemical
industries. , most of the industries follow the policies of existing commissions like the
According to Omidvari, Mansouri & Nouri, (2015), chemical hazards in the
workplace are divided into classes which they named from class A to class F. The contents
of risks in the various also differ with Class A including compressed, dissolved and liquefied
gases. Class B entails every form of matter that is flammable be it, gases, liquids, solids or
aerosols while Class C is having substances like oxidising materials. The remaining classes of
D, E and F contain poisonous and infectious materials, corrosive materials and highly
reactive materials in that order. Most of the chemicals, regardless of their classes, are known
to be carcinogenic thus are regarded as causes of detrimental health conditions. Some of the
known risks associated with chemical hazards include but not limited to skin burn, anthrax,
cancer, ulcers in hands, nose and other body parts, irritation and severe injury when an
explosion occurs.
Existing Policies and Procedures
Various chemical producing companies have multiple policies in which they attempt
to manage the risks. The first known one is product stewardship. The product stewardship
provides that all the items of chemical nature, either manufactured or sold, should be
subjected to critical analysis to identify all the risk factors associated with them. In that way,
users would be alerted and consequently protected from harm arising from the risks. There
are also some initiatives like the National Compliance Initiative (NCI) whose primary goal is
to reduce the accidents associated with the release of chemicals during the industrial
processes and other related processes (Bradley et al. 2017). The government heads the
initiative. Therefore, it gets most of its funding from the government to ensure that everything
is done in the right way.
Setting industrial standards is one of the best ways to deal with risks in the chemical
industries. , most of the industries follow the policies of existing commissions like the
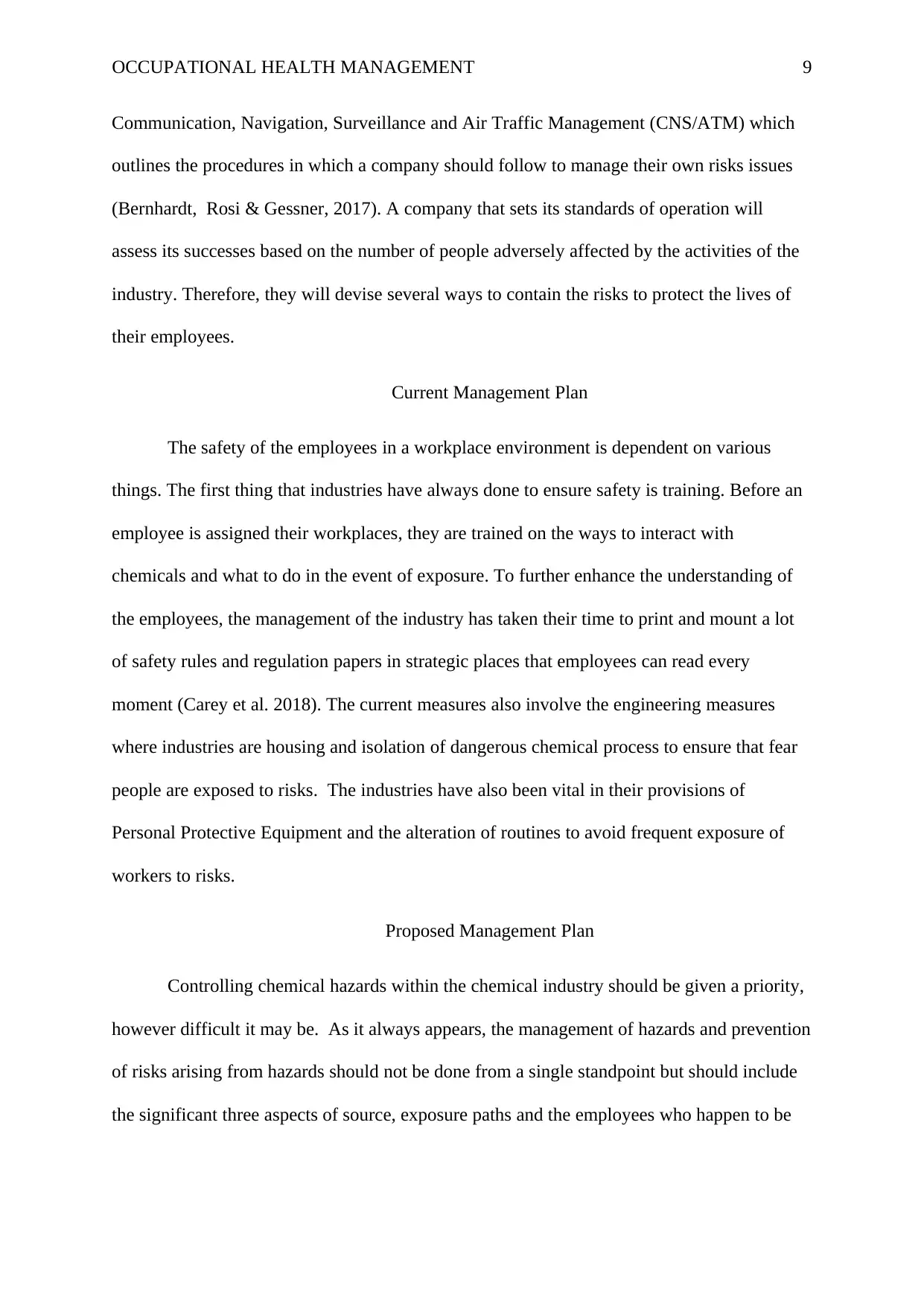
OCCUPATIONAL HEALTH MANAGEMENT 9
Communication, Navigation, Surveillance and Air Traffic Management (CNS/ATM) which
outlines the procedures in which a company should follow to manage their own risks issues
(Bernhardt, Rosi & Gessner, 2017). A company that sets its standards of operation will
assess its successes based on the number of people adversely affected by the activities of the
industry. Therefore, they will devise several ways to contain the risks to protect the lives of
their employees.
Current Management Plan
The safety of the employees in a workplace environment is dependent on various
things. The first thing that industries have always done to ensure safety is training. Before an
employee is assigned their workplaces, they are trained on the ways to interact with
chemicals and what to do in the event of exposure. To further enhance the understanding of
the employees, the management of the industry has taken their time to print and mount a lot
of safety rules and regulation papers in strategic places that employees can read every
moment (Carey et al. 2018). The current measures also involve the engineering measures
where industries are housing and isolation of dangerous chemical process to ensure that fear
people are exposed to risks. The industries have also been vital in their provisions of
Personal Protective Equipment and the alteration of routines to avoid frequent exposure of
workers to risks.
Proposed Management Plan
Controlling chemical hazards within the chemical industry should be given a priority,
however difficult it may be. As it always appears, the management of hazards and prevention
of risks arising from hazards should not be done from a single standpoint but should include
the significant three aspects of source, exposure paths and the employees who happen to be
Communication, Navigation, Surveillance and Air Traffic Management (CNS/ATM) which
outlines the procedures in which a company should follow to manage their own risks issues
(Bernhardt, Rosi & Gessner, 2017). A company that sets its standards of operation will
assess its successes based on the number of people adversely affected by the activities of the
industry. Therefore, they will devise several ways to contain the risks to protect the lives of
their employees.
Current Management Plan
The safety of the employees in a workplace environment is dependent on various
things. The first thing that industries have always done to ensure safety is training. Before an
employee is assigned their workplaces, they are trained on the ways to interact with
chemicals and what to do in the event of exposure. To further enhance the understanding of
the employees, the management of the industry has taken their time to print and mount a lot
of safety rules and regulation papers in strategic places that employees can read every
moment (Carey et al. 2018). The current measures also involve the engineering measures
where industries are housing and isolation of dangerous chemical process to ensure that fear
people are exposed to risks. The industries have also been vital in their provisions of
Personal Protective Equipment and the alteration of routines to avoid frequent exposure of
workers to risks.
Proposed Management Plan
Controlling chemical hazards within the chemical industry should be given a priority,
however difficult it may be. As it always appears, the management of hazards and prevention
of risks arising from hazards should not be done from a single standpoint but should include
the significant three aspects of source, exposure paths and the employees who happen to be
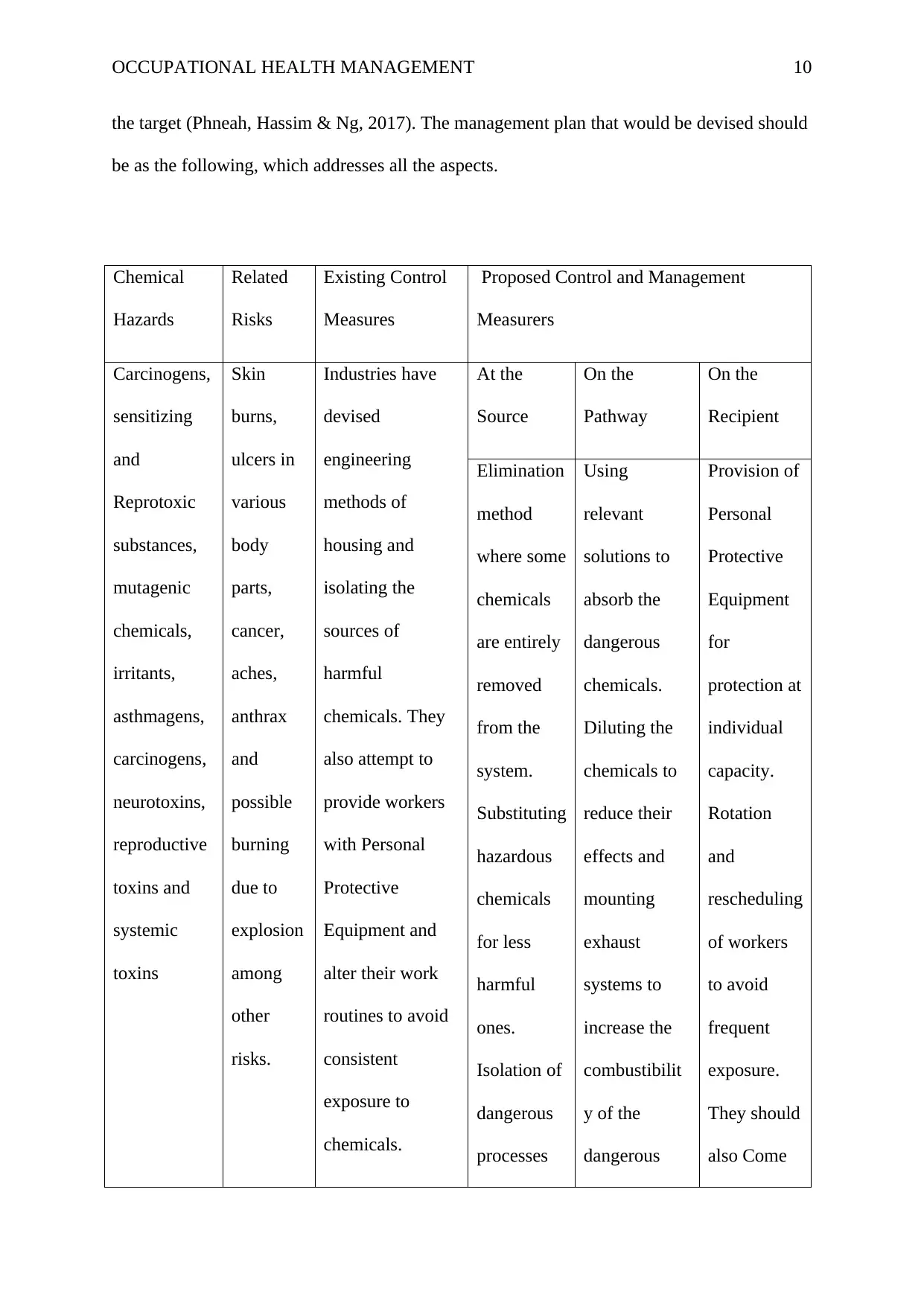
OCCUPATIONAL HEALTH MANAGEMENT 10
the target (Phneah, Hassim & Ng, 2017). The management plan that would be devised should
be as the following, which addresses all the aspects.
Chemical
Hazards
Related
Risks
Existing Control
Measures
Proposed Control and Management
Measurers
Carcinogens,
sensitizing
and
Reprotoxic
substances,
mutagenic
chemicals,
irritants,
asthmagens,
carcinogens,
neurotoxins,
reproductive
toxins and
systemic
toxins
Skin
burns,
ulcers in
various
body
parts,
cancer,
aches,
anthrax
and
possible
burning
due to
explosion
among
other
risks.
Industries have
devised
engineering
methods of
housing and
isolating the
sources of
harmful
chemicals. They
also attempt to
provide workers
with Personal
Protective
Equipment and
alter their work
routines to avoid
consistent
exposure to
chemicals.
At the
Source
On the
Pathway
On the
Recipient
Elimination
method
where some
chemicals
are entirely
removed
from the
system.
Substituting
hazardous
chemicals
for less
harmful
ones.
Isolation of
dangerous
processes
Using
relevant
solutions to
absorb the
dangerous
chemicals.
Diluting the
chemicals to
reduce their
effects and
mounting
exhaust
systems to
increase the
combustibilit
y of the
dangerous
Provision of
Personal
Protective
Equipment
for
protection at
individual
capacity.
Rotation
and
rescheduling
of workers
to avoid
frequent
exposure.
They should
also Come
the target (Phneah, Hassim & Ng, 2017). The management plan that would be devised should
be as the following, which addresses all the aspects.
Chemical
Hazards
Related
Risks
Existing Control
Measures
Proposed Control and Management
Measurers
Carcinogens,
sensitizing
and
Reprotoxic
substances,
mutagenic
chemicals,
irritants,
asthmagens,
carcinogens,
neurotoxins,
reproductive
toxins and
systemic
toxins
Skin
burns,
ulcers in
various
body
parts,
cancer,
aches,
anthrax
and
possible
burning
due to
explosion
among
other
risks.
Industries have
devised
engineering
methods of
housing and
isolating the
sources of
harmful
chemicals. They
also attempt to
provide workers
with Personal
Protective
Equipment and
alter their work
routines to avoid
consistent
exposure to
chemicals.
At the
Source
On the
Pathway
On the
Recipient
Elimination
method
where some
chemicals
are entirely
removed
from the
system.
Substituting
hazardous
chemicals
for less
harmful
ones.
Isolation of
dangerous
processes
Using
relevant
solutions to
absorb the
dangerous
chemicals.
Diluting the
chemicals to
reduce their
effects and
mounting
exhaust
systems to
increase the
combustibilit
y of the
dangerous
Provision of
Personal
Protective
Equipment
for
protection at
individual
capacity.
Rotation
and
rescheduling
of workers
to avoid
frequent
exposure.
They should
also Come
Secure Best Marks with AI Grader
Need help grading? Try our AI Grader for instant feedback on your assignments.

OCCUPATIONAL HEALTH MANAGEMENT 11
and
redesigning
the
workplace
gases. up with
automatic
methods of
operations
to decrease
human
contacts
with
chemicals.
Communication of the Risk: - communicating the risk plan should first involve the
identification of the primary issue to be expressed. For this case, the central theme of
discussion is the exposure of employees of chemical industries to chemical hazards. In
addressing the proposed plan, the management of the industry, officials from the concerned
environmental agencies and concerned government department officials should be engaged in
a manner of the convention that takes 2-3 days to exhaustively elaborate the requirements of
successfully implementing the plan (Kanki, 2019).
Emergency Response: - Control programs are mostly designed to bar people from
getting into contacts with chemicals in the chemical industry. However, if the exposure has
occurred, and the victim is at risk, specific procedures should be followed. The first
procedure is the removal of the employee from the site of the exposure to avoid further
contamination. If the victim has collapsed and fainted, their normal status of health should be
restored through first aid and hospitalisation but away from the exposure site (Carbajo et al.
2015). The third and the last step is the decontamination of the skin and any place that came
and
redesigning
the
workplace
gases. up with
automatic
methods of
operations
to decrease
human
contacts
with
chemicals.
Communication of the Risk: - communicating the risk plan should first involve the
identification of the primary issue to be expressed. For this case, the central theme of
discussion is the exposure of employees of chemical industries to chemical hazards. In
addressing the proposed plan, the management of the industry, officials from the concerned
environmental agencies and concerned government department officials should be engaged in
a manner of the convention that takes 2-3 days to exhaustively elaborate the requirements of
successfully implementing the plan (Kanki, 2019).
Emergency Response: - Control programs are mostly designed to bar people from
getting into contacts with chemicals in the chemical industry. However, if the exposure has
occurred, and the victim is at risk, specific procedures should be followed. The first
procedure is the removal of the employee from the site of the exposure to avoid further
contamination. If the victim has collapsed and fainted, their normal status of health should be
restored through first aid and hospitalisation but away from the exposure site (Carbajo et al.
2015). The third and the last step is the decontamination of the skin and any place that came
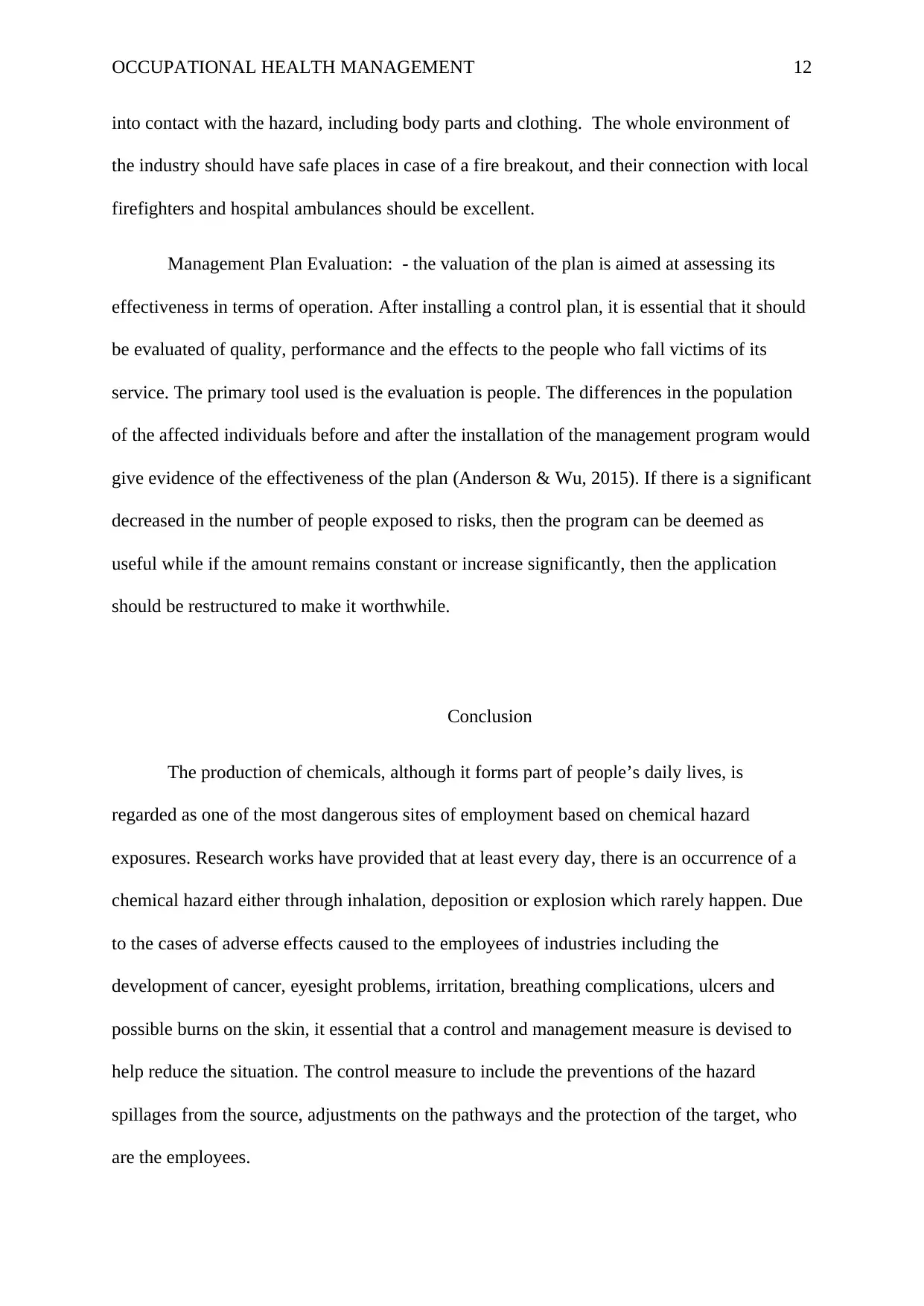
OCCUPATIONAL HEALTH MANAGEMENT 12
into contact with the hazard, including body parts and clothing. The whole environment of
the industry should have safe places in case of a fire breakout, and their connection with local
firefighters and hospital ambulances should be excellent.
Management Plan Evaluation: - the valuation of the plan is aimed at assessing its
effectiveness in terms of operation. After installing a control plan, it is essential that it should
be evaluated of quality, performance and the effects to the people who fall victims of its
service. The primary tool used is the evaluation is people. The differences in the population
of the affected individuals before and after the installation of the management program would
give evidence of the effectiveness of the plan (Anderson & Wu, 2015). If there is a significant
decreased in the number of people exposed to risks, then the program can be deemed as
useful while if the amount remains constant or increase significantly, then the application
should be restructured to make it worthwhile.
Conclusion
The production of chemicals, although it forms part of people’s daily lives, is
regarded as one of the most dangerous sites of employment based on chemical hazard
exposures. Research works have provided that at least every day, there is an occurrence of a
chemical hazard either through inhalation, deposition or explosion which rarely happen. Due
to the cases of adverse effects caused to the employees of industries including the
development of cancer, eyesight problems, irritation, breathing complications, ulcers and
possible burns on the skin, it essential that a control and management measure is devised to
help reduce the situation. The control measure to include the preventions of the hazard
spillages from the source, adjustments on the pathways and the protection of the target, who
are the employees.
into contact with the hazard, including body parts and clothing. The whole environment of
the industry should have safe places in case of a fire breakout, and their connection with local
firefighters and hospital ambulances should be excellent.
Management Plan Evaluation: - the valuation of the plan is aimed at assessing its
effectiveness in terms of operation. After installing a control plan, it is essential that it should
be evaluated of quality, performance and the effects to the people who fall victims of its
service. The primary tool used is the evaluation is people. The differences in the population
of the affected individuals before and after the installation of the management program would
give evidence of the effectiveness of the plan (Anderson & Wu, 2015). If there is a significant
decreased in the number of people exposed to risks, then the program can be deemed as
useful while if the amount remains constant or increase significantly, then the application
should be restructured to make it worthwhile.
Conclusion
The production of chemicals, although it forms part of people’s daily lives, is
regarded as one of the most dangerous sites of employment based on chemical hazard
exposures. Research works have provided that at least every day, there is an occurrence of a
chemical hazard either through inhalation, deposition or explosion which rarely happen. Due
to the cases of adverse effects caused to the employees of industries including the
development of cancer, eyesight problems, irritation, breathing complications, ulcers and
possible burns on the skin, it essential that a control and management measure is devised to
help reduce the situation. The control measure to include the preventions of the hazard
spillages from the source, adjustments on the pathways and the protection of the target, who
are the employees.
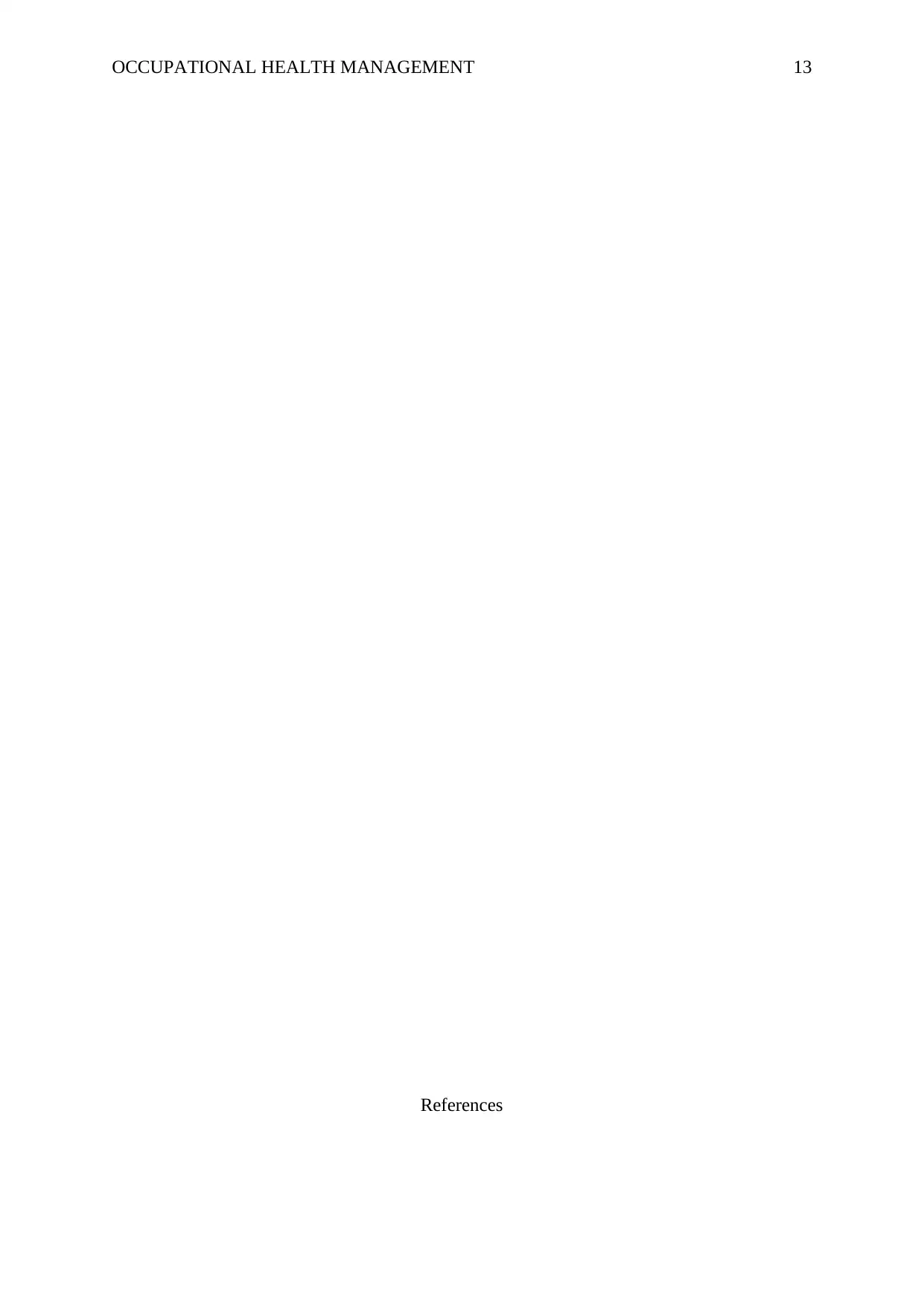
OCCUPATIONAL HEALTH MANAGEMENT 13
References
References
Paraphrase This Document
Need a fresh take? Get an instant paraphrase of this document with our AI Paraphraser
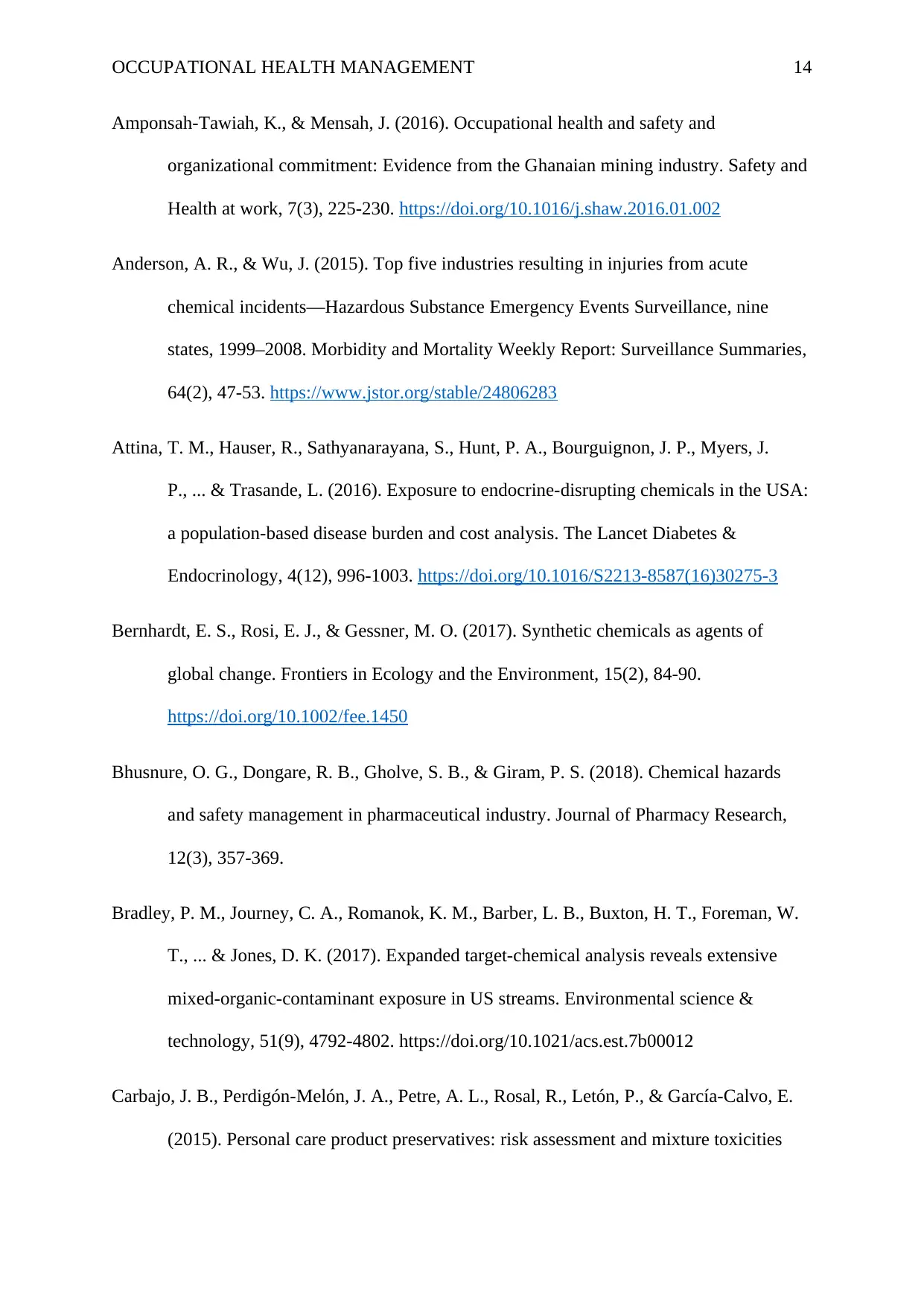
OCCUPATIONAL HEALTH MANAGEMENT 14
Amponsah-Tawiah, K., & Mensah, J. (2016). Occupational health and safety and
organizational commitment: Evidence from the Ghanaian mining industry. Safety and
Health at work, 7(3), 225-230. https://doi.org/10.1016/j.shaw.2016.01.002
Anderson, A. R., & Wu, J. (2015). Top five industries resulting in injuries from acute
chemical incidents—Hazardous Substance Emergency Events Surveillance, nine
states, 1999–2008. Morbidity and Mortality Weekly Report: Surveillance Summaries,
64(2), 47-53. https://www.jstor.org/stable/24806283
Attina, T. M., Hauser, R., Sathyanarayana, S., Hunt, P. A., Bourguignon, J. P., Myers, J.
P., ... & Trasande, L. (2016). Exposure to endocrine-disrupting chemicals in the USA:
a population-based disease burden and cost analysis. The Lancet Diabetes &
Endocrinology, 4(12), 996-1003. https://doi.org/10.1016/S2213-8587(16)30275-3
Bernhardt, E. S., Rosi, E. J., & Gessner, M. O. (2017). Synthetic chemicals as agents of
global change. Frontiers in Ecology and the Environment, 15(2), 84-90.
https://doi.org/10.1002/fee.1450
Bhusnure, O. G., Dongare, R. B., Gholve, S. B., & Giram, P. S. (2018). Chemical hazards
and safety management in pharmaceutical industry. Journal of Pharmacy Research,
12(3), 357-369.
Bradley, P. M., Journey, C. A., Romanok, K. M., Barber, L. B., Buxton, H. T., Foreman, W.
T., ... & Jones, D. K. (2017). Expanded target-chemical analysis reveals extensive
mixed-organic-contaminant exposure in US streams. Environmental science &
technology, 51(9), 4792-4802. https://doi.org/10.1021/acs.est.7b00012
Carbajo, J. B., Perdigón-Melón, J. A., Petre, A. L., Rosal, R., Letón, P., & García-Calvo, E.
(2015). Personal care product preservatives: risk assessment and mixture toxicities
Amponsah-Tawiah, K., & Mensah, J. (2016). Occupational health and safety and
organizational commitment: Evidence from the Ghanaian mining industry. Safety and
Health at work, 7(3), 225-230. https://doi.org/10.1016/j.shaw.2016.01.002
Anderson, A. R., & Wu, J. (2015). Top five industries resulting in injuries from acute
chemical incidents—Hazardous Substance Emergency Events Surveillance, nine
states, 1999–2008. Morbidity and Mortality Weekly Report: Surveillance Summaries,
64(2), 47-53. https://www.jstor.org/stable/24806283
Attina, T. M., Hauser, R., Sathyanarayana, S., Hunt, P. A., Bourguignon, J. P., Myers, J.
P., ... & Trasande, L. (2016). Exposure to endocrine-disrupting chemicals in the USA:
a population-based disease burden and cost analysis. The Lancet Diabetes &
Endocrinology, 4(12), 996-1003. https://doi.org/10.1016/S2213-8587(16)30275-3
Bernhardt, E. S., Rosi, E. J., & Gessner, M. O. (2017). Synthetic chemicals as agents of
global change. Frontiers in Ecology and the Environment, 15(2), 84-90.
https://doi.org/10.1002/fee.1450
Bhusnure, O. G., Dongare, R. B., Gholve, S. B., & Giram, P. S. (2018). Chemical hazards
and safety management in pharmaceutical industry. Journal of Pharmacy Research,
12(3), 357-369.
Bradley, P. M., Journey, C. A., Romanok, K. M., Barber, L. B., Buxton, H. T., Foreman, W.
T., ... & Jones, D. K. (2017). Expanded target-chemical analysis reveals extensive
mixed-organic-contaminant exposure in US streams. Environmental science &
technology, 51(9), 4792-4802. https://doi.org/10.1021/acs.est.7b00012
Carbajo, J. B., Perdigón-Melón, J. A., Petre, A. L., Rosal, R., Letón, P., & García-Calvo, E.
(2015). Personal care product preservatives: risk assessment and mixture toxicities
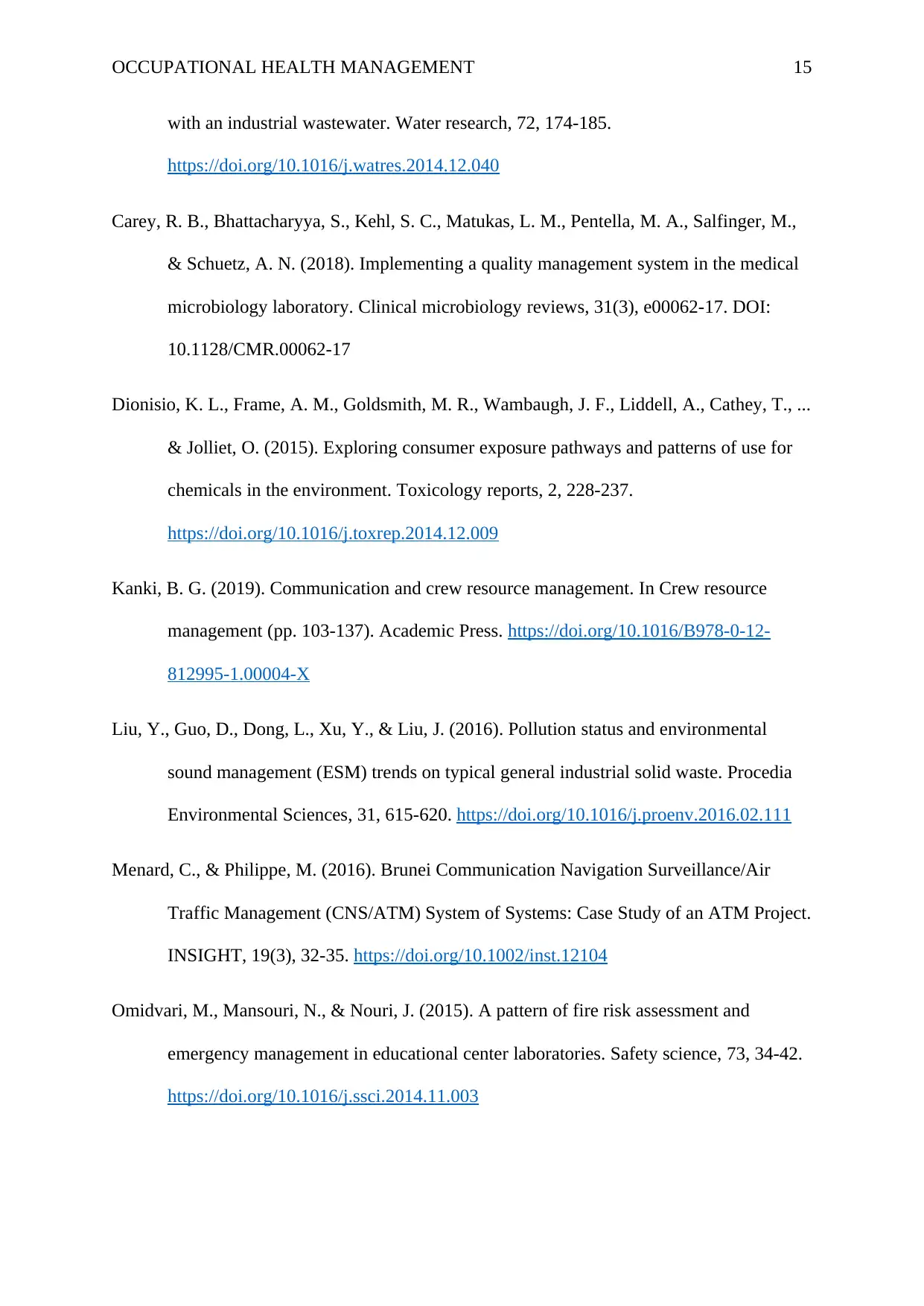
OCCUPATIONAL HEALTH MANAGEMENT 15
with an industrial wastewater. Water research, 72, 174-185.
https://doi.org/10.1016/j.watres.2014.12.040
Carey, R. B., Bhattacharyya, S., Kehl, S. C., Matukas, L. M., Pentella, M. A., Salfinger, M.,
& Schuetz, A. N. (2018). Implementing a quality management system in the medical
microbiology laboratory. Clinical microbiology reviews, 31(3), e00062-17. DOI:
10.1128/CMR.00062-17
Dionisio, K. L., Frame, A. M., Goldsmith, M. R., Wambaugh, J. F., Liddell, A., Cathey, T., ...
& Jolliet, O. (2015). Exploring consumer exposure pathways and patterns of use for
chemicals in the environment. Toxicology reports, 2, 228-237.
https://doi.org/10.1016/j.toxrep.2014.12.009
Kanki, B. G. (2019). Communication and crew resource management. In Crew resource
management (pp. 103-137). Academic Press. https://doi.org/10.1016/B978-0-12-
812995-1.00004-X
Liu, Y., Guo, D., Dong, L., Xu, Y., & Liu, J. (2016). Pollution status and environmental
sound management (ESM) trends on typical general industrial solid waste. Procedia
Environmental Sciences, 31, 615-620. https://doi.org/10.1016/j.proenv.2016.02.111
Menard, C., & Philippe, M. (2016). Brunei Communication Navigation Surveillance/Air
Traffic Management (CNS/ATM) System of Systems: Case Study of an ATM Project.
INSIGHT, 19(3), 32-35. https://doi.org/10.1002/inst.12104
Omidvari, M., Mansouri, N., & Nouri, J. (2015). A pattern of fire risk assessment and
emergency management in educational center laboratories. Safety science, 73, 34-42.
https://doi.org/10.1016/j.ssci.2014.11.003
with an industrial wastewater. Water research, 72, 174-185.
https://doi.org/10.1016/j.watres.2014.12.040
Carey, R. B., Bhattacharyya, S., Kehl, S. C., Matukas, L. M., Pentella, M. A., Salfinger, M.,
& Schuetz, A. N. (2018). Implementing a quality management system in the medical
microbiology laboratory. Clinical microbiology reviews, 31(3), e00062-17. DOI:
10.1128/CMR.00062-17
Dionisio, K. L., Frame, A. M., Goldsmith, M. R., Wambaugh, J. F., Liddell, A., Cathey, T., ...
& Jolliet, O. (2015). Exploring consumer exposure pathways and patterns of use for
chemicals in the environment. Toxicology reports, 2, 228-237.
https://doi.org/10.1016/j.toxrep.2014.12.009
Kanki, B. G. (2019). Communication and crew resource management. In Crew resource
management (pp. 103-137). Academic Press. https://doi.org/10.1016/B978-0-12-
812995-1.00004-X
Liu, Y., Guo, D., Dong, L., Xu, Y., & Liu, J. (2016). Pollution status and environmental
sound management (ESM) trends on typical general industrial solid waste. Procedia
Environmental Sciences, 31, 615-620. https://doi.org/10.1016/j.proenv.2016.02.111
Menard, C., & Philippe, M. (2016). Brunei Communication Navigation Surveillance/Air
Traffic Management (CNS/ATM) System of Systems: Case Study of an ATM Project.
INSIGHT, 19(3), 32-35. https://doi.org/10.1002/inst.12104
Omidvari, M., Mansouri, N., & Nouri, J. (2015). A pattern of fire risk assessment and
emergency management in educational center laboratories. Safety science, 73, 34-42.
https://doi.org/10.1016/j.ssci.2014.11.003
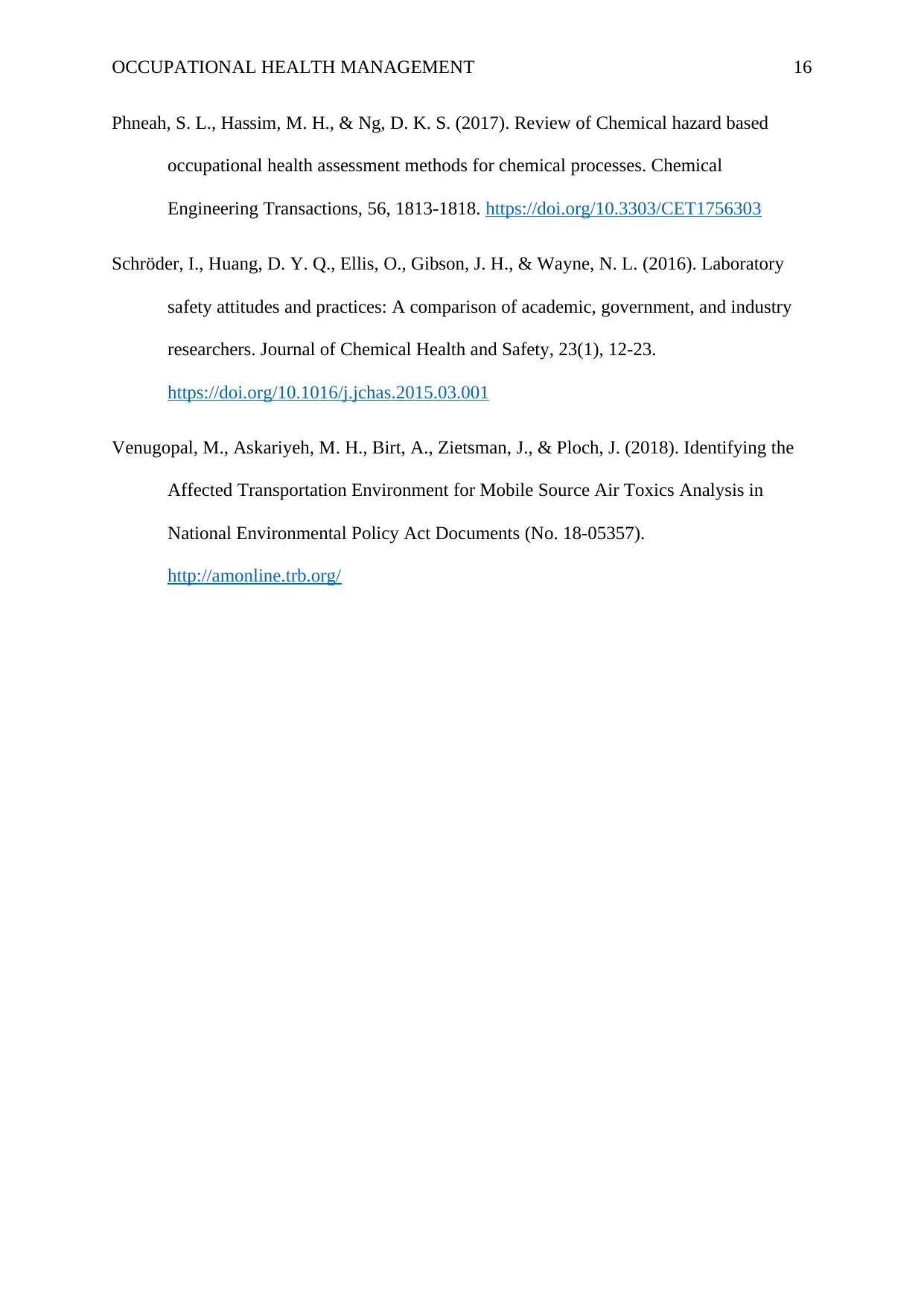
OCCUPATIONAL HEALTH MANAGEMENT 16
Phneah, S. L., Hassim, M. H., & Ng, D. K. S. (2017). Review of Chemical hazard based
occupational health assessment methods for chemical processes. Chemical
Engineering Transactions, 56, 1813-1818. https://doi.org/10.3303/CET1756303
Schröder, I., Huang, D. Y. Q., Ellis, O., Gibson, J. H., & Wayne, N. L. (2016). Laboratory
safety attitudes and practices: A comparison of academic, government, and industry
researchers. Journal of Chemical Health and Safety, 23(1), 12-23.
https://doi.org/10.1016/j.jchas.2015.03.001
Venugopal, M., Askariyeh, M. H., Birt, A., Zietsman, J., & Ploch, J. (2018). Identifying the
Affected Transportation Environment for Mobile Source Air Toxics Analysis in
National Environmental Policy Act Documents (No. 18-05357).
http://amonline.trb.org/
Phneah, S. L., Hassim, M. H., & Ng, D. K. S. (2017). Review of Chemical hazard based
occupational health assessment methods for chemical processes. Chemical
Engineering Transactions, 56, 1813-1818. https://doi.org/10.3303/CET1756303
Schröder, I., Huang, D. Y. Q., Ellis, O., Gibson, J. H., & Wayne, N. L. (2016). Laboratory
safety attitudes and practices: A comparison of academic, government, and industry
researchers. Journal of Chemical Health and Safety, 23(1), 12-23.
https://doi.org/10.1016/j.jchas.2015.03.001
Venugopal, M., Askariyeh, M. H., Birt, A., Zietsman, J., & Ploch, J. (2018). Identifying the
Affected Transportation Environment for Mobile Source Air Toxics Analysis in
National Environmental Policy Act Documents (No. 18-05357).
http://amonline.trb.org/
1 out of 16
Related Documents

Your All-in-One AI-Powered Toolkit for Academic Success.
+13062052269
info@desklib.com
Available 24*7 on WhatsApp / Email
Unlock your academic potential
© 2024 | Zucol Services PVT LTD | All rights reserved.