Cleanroom Validation Report: ISO Standards and Risk Assessment
VerifiedAdded on 2022/09/08
|10
|2204
|18
Report
AI Summary
This report provides a comprehensive overview of a cleanroom validation project. It begins with an introduction highlighting the importance of cleanroom validation for achieving compliance and ensuring operational efficiency, particularly focusing on ISO 14544-1 standards. The report then outline...
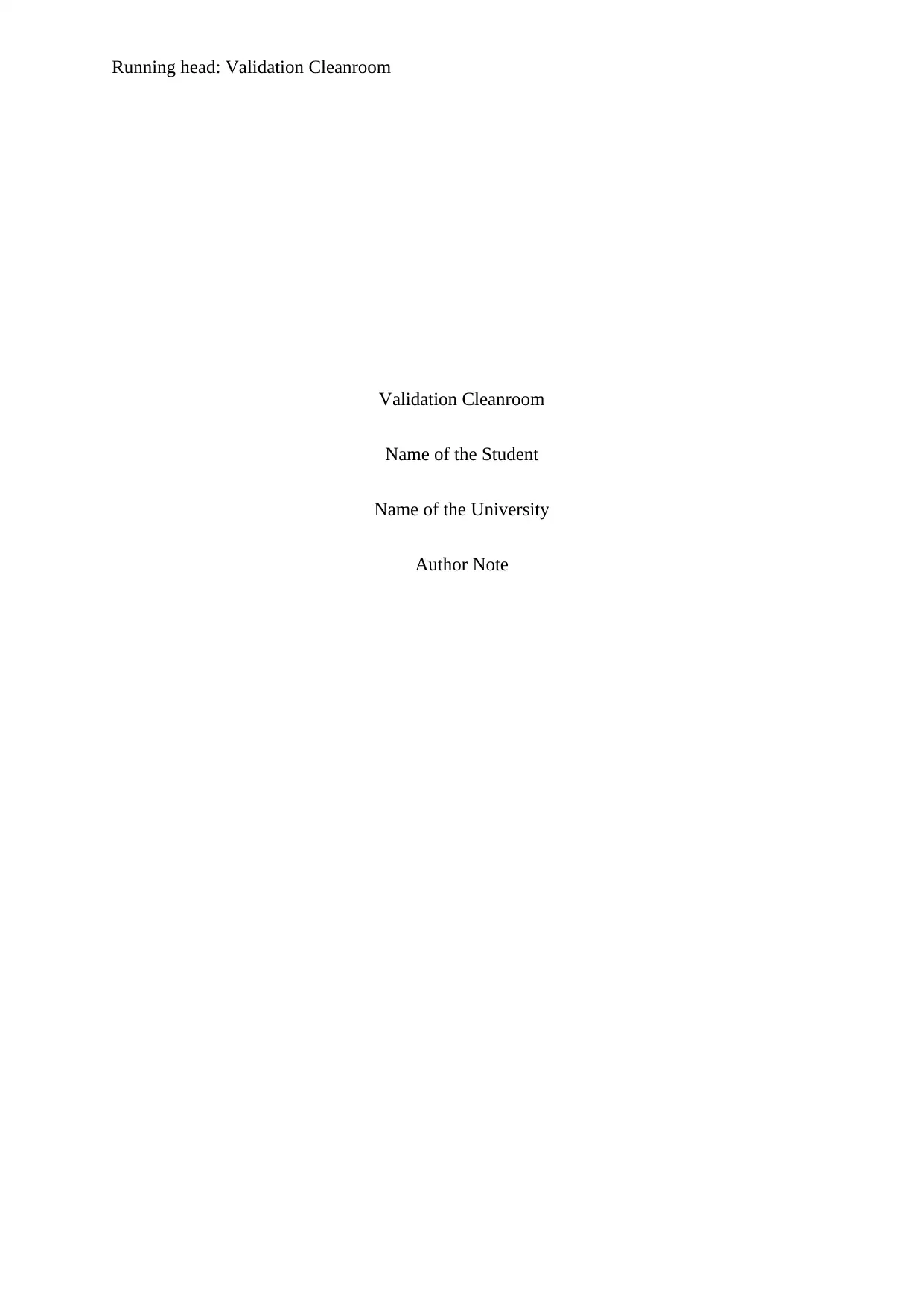
Running head: Validation Cleanroom
Validation Cleanroom
Name of the Student
Name of the University
Author Note
Validation Cleanroom
Name of the Student
Name of the University
Author Note
Paraphrase This Document
Need a fresh take? Get an instant paraphrase of this document with our AI Paraphraser
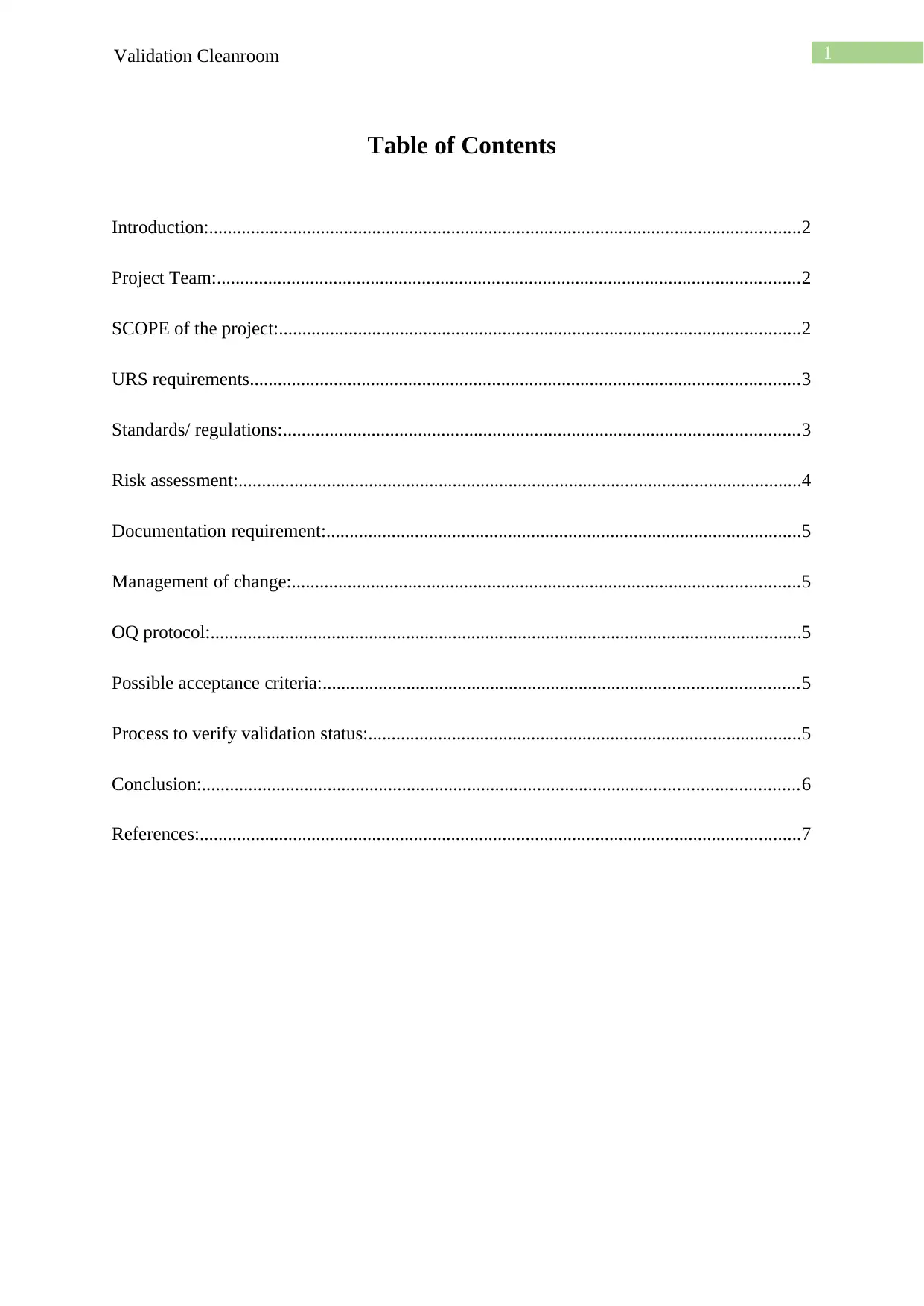
Validation Cleanroom 1
Table of Contents
Introduction:...............................................................................................................................2
Project Team:.............................................................................................................................2
SCOPE of the project:................................................................................................................2
URS requirements......................................................................................................................3
Standards/ regulations:...............................................................................................................3
Risk assessment:.........................................................................................................................4
Documentation requirement:......................................................................................................5
Management of change:.............................................................................................................5
OQ protocol:...............................................................................................................................5
Possible acceptance criteria:......................................................................................................5
Process to verify validation status:.............................................................................................5
Conclusion:................................................................................................................................6
References:.................................................................................................................................7
Table of Contents
Introduction:...............................................................................................................................2
Project Team:.............................................................................................................................2
SCOPE of the project:................................................................................................................2
URS requirements......................................................................................................................3
Standards/ regulations:...............................................................................................................3
Risk assessment:.........................................................................................................................4
Documentation requirement:......................................................................................................5
Management of change:.............................................................................................................5
OQ protocol:...............................................................................................................................5
Possible acceptance criteria:......................................................................................................5
Process to verify validation status:.............................................................................................5
Conclusion:................................................................................................................................6
References:.................................................................................................................................7

2Validation Cleanroom
Introduction:
The purpose of this paper is to make a report on validation cleanroom project. The
validation cleanroom is very much important part to achieve the compliance of cleanroom.
As well as in addition to the validation, that is prior to the operation, more work on validation
is very much needed at the time of operation for ensuring that a cleanroom is continuing to
meet the class parameters of ISO. The cleanrooms have been validated by the validation
agencies who are third parties. This can entail inspection thoroughly as well as various tests.
The cleanroom has been certified to a special class that indicate the control level of it, to a
class of ISO14544-1.
Project Team:
The validation is having several phases that is starting with the qualification of design
and ending with the final certification. Some of the tests can be performed in the phases
including velocity testing and airflow volume. The project team will work with for accessing
the needs of the clients. It is used to build the custom testing schedule (Díaz et al., 2014). The
project team must consider the ISO standard or GMP requirements. They validate the needs
of the frequency. It includes annual as well as interim testing. They consider the URS, risk
assessment and monitoring plan.
SCOPE of the project:
If a tester performs the cleanroom testing continuously then it can help to identify any
harmful resources. It assures the regulatory client to control the environment. It is used to
meet the ISO parameters. If the cleanroom testing does not have any current validation
process then it limits are set out in ISO 14644-1: 2015 (Kaur, Singh & Seth, 2013). It ensures
sufficient protection to the critical resources. The Scope can define by the risk assessment of
Introduction:
The purpose of this paper is to make a report on validation cleanroom project. The
validation cleanroom is very much important part to achieve the compliance of cleanroom.
As well as in addition to the validation, that is prior to the operation, more work on validation
is very much needed at the time of operation for ensuring that a cleanroom is continuing to
meet the class parameters of ISO. The cleanrooms have been validated by the validation
agencies who are third parties. This can entail inspection thoroughly as well as various tests.
The cleanroom has been certified to a special class that indicate the control level of it, to a
class of ISO14544-1.
Project Team:
The validation is having several phases that is starting with the qualification of design
and ending with the final certification. Some of the tests can be performed in the phases
including velocity testing and airflow volume. The project team will work with for accessing
the needs of the clients. It is used to build the custom testing schedule (Díaz et al., 2014). The
project team must consider the ISO standard or GMP requirements. They validate the needs
of the frequency. It includes annual as well as interim testing. They consider the URS, risk
assessment and monitoring plan.
SCOPE of the project:
If a tester performs the cleanroom testing continuously then it can help to identify any
harmful resources. It assures the regulatory client to control the environment. It is used to
meet the ISO parameters. If the cleanroom testing does not have any current validation
process then it limits are set out in ISO 14644-1: 2015 (Kaur, Singh & Seth, 2013). It ensures
sufficient protection to the critical resources. The Scope can define by the risk assessment of
⊘ This is a preview!⊘
Do you want full access?
Subscribe today to unlock all pages.

Trusted by 1+ million students worldwide
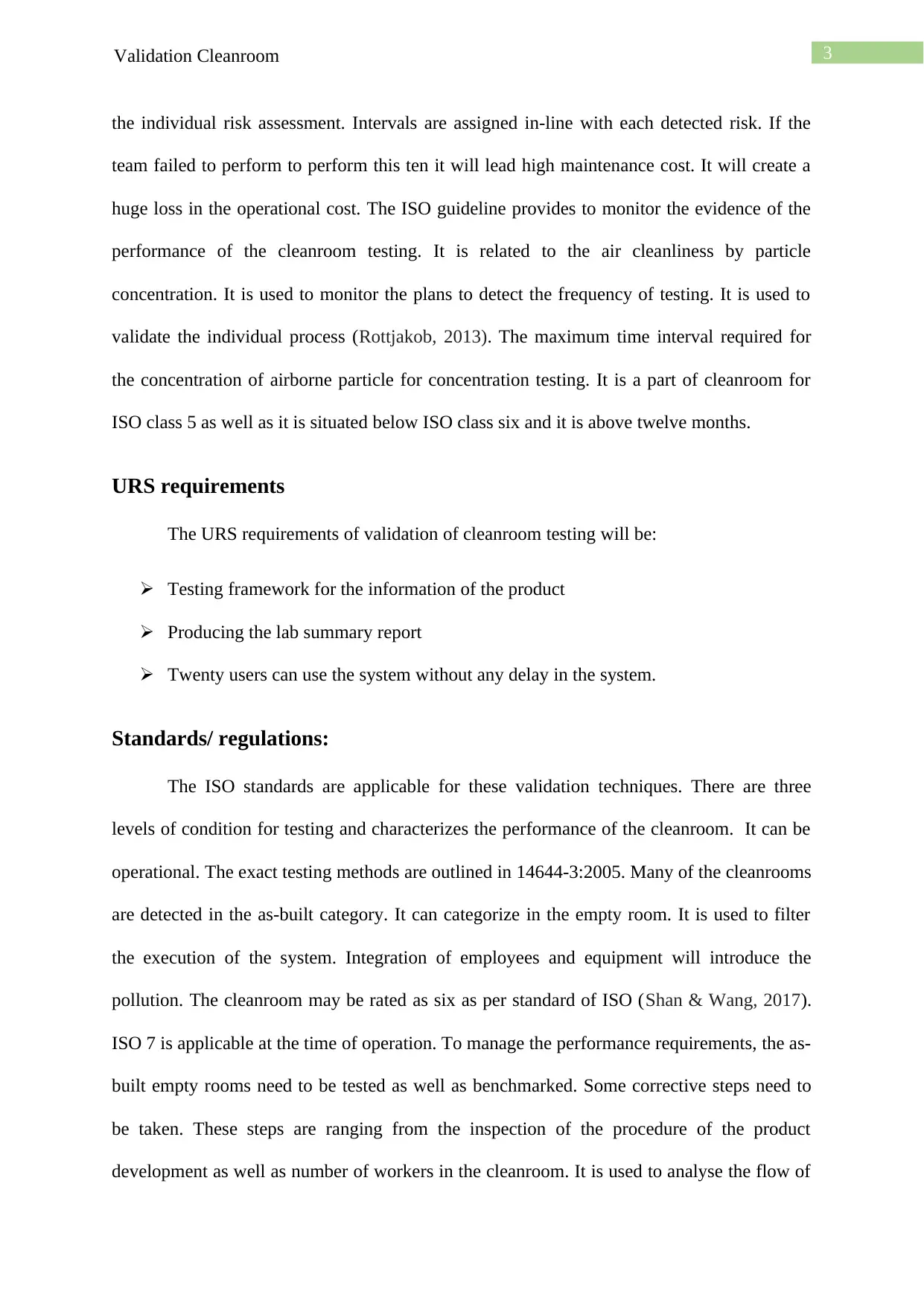
3Validation Cleanroom
the individual risk assessment. Intervals are assigned in-line with each detected risk. If the
team failed to perform to perform this ten it will lead high maintenance cost. It will create a
huge loss in the operational cost. The ISO guideline provides to monitor the evidence of the
performance of the cleanroom testing. It is related to the air cleanliness by particle
concentration. It is used to monitor the plans to detect the frequency of testing. It is used to
validate the individual process (Rottjakob, 2013). The maximum time interval required for
the concentration of airborne particle for concentration testing. It is a part of cleanroom for
ISO class 5 as well as it is situated below ISO class six and it is above twelve months.
URS requirements
The URS requirements of validation of cleanroom testing will be:
Testing framework for the information of the product
Producing the lab summary report
Twenty users can use the system without any delay in the system.
Standards/ regulations:
The ISO standards are applicable for these validation techniques. There are three
levels of condition for testing and characterizes the performance of the cleanroom. It can be
operational. The exact testing methods are outlined in 14644-3:2005. Many of the cleanrooms
are detected in the as-built category. It can categorize in the empty room. It is used to filter
the execution of the system. Integration of employees and equipment will introduce the
pollution. The cleanroom may be rated as six as per standard of ISO (Shan & Wang, 2017).
ISO 7 is applicable at the time of operation. To manage the performance requirements, the as-
built empty rooms need to be tested as well as benchmarked. Some corrective steps need to
be taken. These steps are ranging from the inspection of the procedure of the product
development as well as number of workers in the cleanroom. It is used to analyse the flow of
the individual risk assessment. Intervals are assigned in-line with each detected risk. If the
team failed to perform to perform this ten it will lead high maintenance cost. It will create a
huge loss in the operational cost. The ISO guideline provides to monitor the evidence of the
performance of the cleanroom testing. It is related to the air cleanliness by particle
concentration. It is used to monitor the plans to detect the frequency of testing. It is used to
validate the individual process (Rottjakob, 2013). The maximum time interval required for
the concentration of airborne particle for concentration testing. It is a part of cleanroom for
ISO class 5 as well as it is situated below ISO class six and it is above twelve months.
URS requirements
The URS requirements of validation of cleanroom testing will be:
Testing framework for the information of the product
Producing the lab summary report
Twenty users can use the system without any delay in the system.
Standards/ regulations:
The ISO standards are applicable for these validation techniques. There are three
levels of condition for testing and characterizes the performance of the cleanroom. It can be
operational. The exact testing methods are outlined in 14644-3:2005. Many of the cleanrooms
are detected in the as-built category. It can categorize in the empty room. It is used to filter
the execution of the system. Integration of employees and equipment will introduce the
pollution. The cleanroom may be rated as six as per standard of ISO (Shan & Wang, 2017).
ISO 7 is applicable at the time of operation. To manage the performance requirements, the as-
built empty rooms need to be tested as well as benchmarked. Some corrective steps need to
be taken. These steps are ranging from the inspection of the procedure of the product
development as well as number of workers in the cleanroom. It is used to analyse the flow of
Paraphrase This Document
Need a fresh take? Get an instant paraphrase of this document with our AI Paraphraser
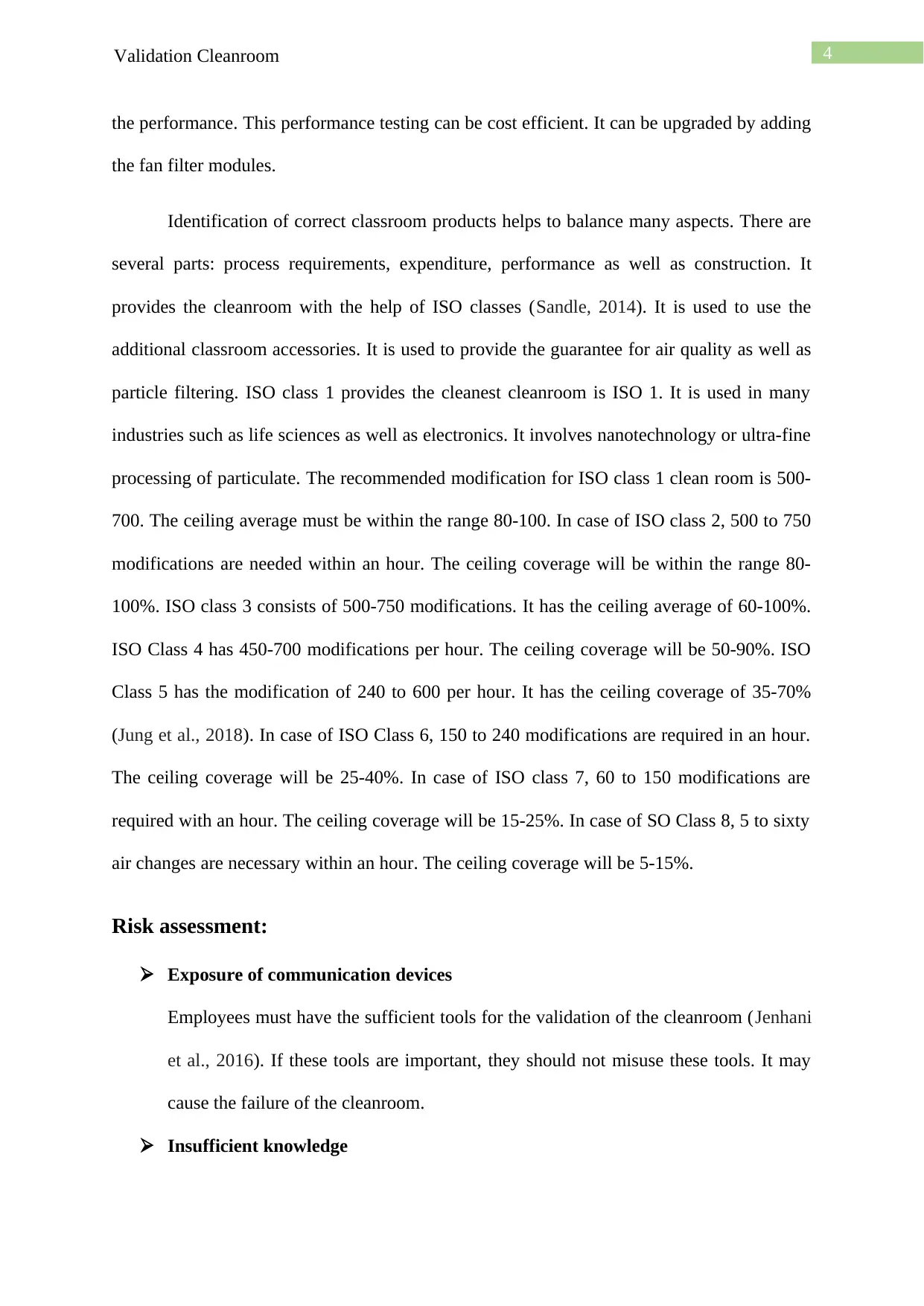
4Validation Cleanroom
the performance. This performance testing can be cost efficient. It can be upgraded by adding
the fan filter modules.
Identification of correct classroom products helps to balance many aspects. There are
several parts: process requirements, expenditure, performance as well as construction. It
provides the cleanroom with the help of ISO classes (Sandle, 2014). It is used to use the
additional classroom accessories. It is used to provide the guarantee for air quality as well as
particle filtering. ISO class 1 provides the cleanest cleanroom is ISO 1. It is used in many
industries such as life sciences as well as electronics. It involves nanotechnology or ultra-fine
processing of particulate. The recommended modification for ISO class 1 clean room is 500-
700. The ceiling average must be within the range 80-100. In case of ISO class 2, 500 to 750
modifications are needed within an hour. The ceiling coverage will be within the range 80-
100%. ISO class 3 consists of 500-750 modifications. It has the ceiling average of 60-100%.
ISO Class 4 has 450-700 modifications per hour. The ceiling coverage will be 50-90%. ISO
Class 5 has the modification of 240 to 600 per hour. It has the ceiling coverage of 35-70%
(Jung et al., 2018). In case of ISO Class 6, 150 to 240 modifications are required in an hour.
The ceiling coverage will be 25-40%. In case of ISO class 7, 60 to 150 modifications are
required with an hour. The ceiling coverage will be 15-25%. In case of SO Class 8, 5 to sixty
air changes are necessary within an hour. The ceiling coverage will be 5-15%.
Risk assessment:
Exposure of communication devices
Employees must have the sufficient tools for the validation of the cleanroom (Jenhani
et al., 2016). If these tools are important, they should not misuse these tools. It may
cause the failure of the cleanroom.
Insufficient knowledge
the performance. This performance testing can be cost efficient. It can be upgraded by adding
the fan filter modules.
Identification of correct classroom products helps to balance many aspects. There are
several parts: process requirements, expenditure, performance as well as construction. It
provides the cleanroom with the help of ISO classes (Sandle, 2014). It is used to use the
additional classroom accessories. It is used to provide the guarantee for air quality as well as
particle filtering. ISO class 1 provides the cleanest cleanroom is ISO 1. It is used in many
industries such as life sciences as well as electronics. It involves nanotechnology or ultra-fine
processing of particulate. The recommended modification for ISO class 1 clean room is 500-
700. The ceiling average must be within the range 80-100. In case of ISO class 2, 500 to 750
modifications are needed within an hour. The ceiling coverage will be within the range 80-
100%. ISO class 3 consists of 500-750 modifications. It has the ceiling average of 60-100%.
ISO Class 4 has 450-700 modifications per hour. The ceiling coverage will be 50-90%. ISO
Class 5 has the modification of 240 to 600 per hour. It has the ceiling coverage of 35-70%
(Jung et al., 2018). In case of ISO Class 6, 150 to 240 modifications are required in an hour.
The ceiling coverage will be 25-40%. In case of ISO class 7, 60 to 150 modifications are
required with an hour. The ceiling coverage will be 15-25%. In case of SO Class 8, 5 to sixty
air changes are necessary within an hour. The ceiling coverage will be 5-15%.
Risk assessment:
Exposure of communication devices
Employees must have the sufficient tools for the validation of the cleanroom (Jenhani
et al., 2016). If these tools are important, they should not misuse these tools. It may
cause the failure of the cleanroom.
Insufficient knowledge
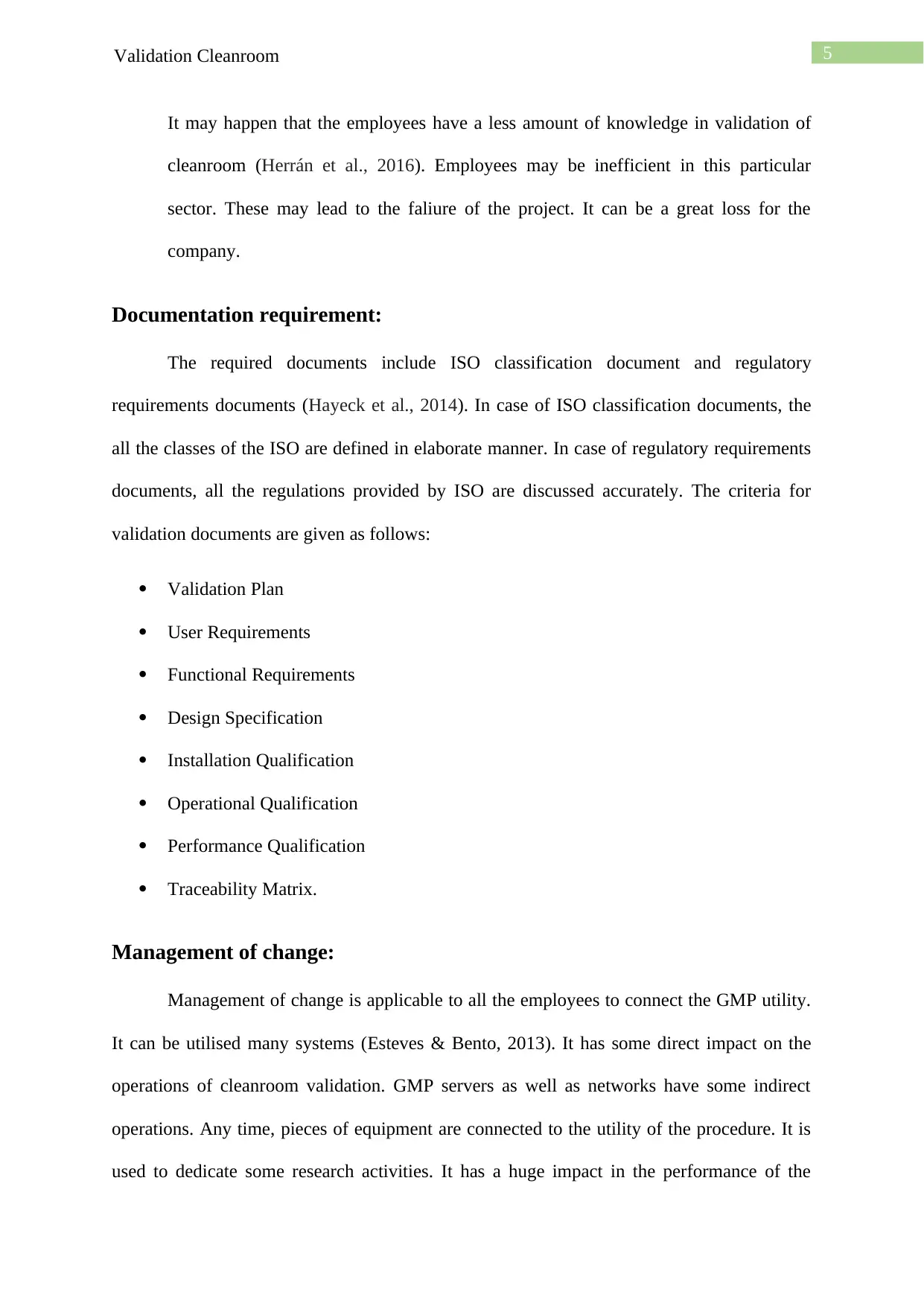
5Validation Cleanroom
It may happen that the employees have a less amount of knowledge in validation of
cleanroom (Herrán et al., 2016). Employees may be inefficient in this particular
sector. These may lead to the faliure of the project. It can be a great loss for the
company.
Documentation requirement:
The required documents include ISO classification document and regulatory
requirements documents (Hayeck et al., 2014). In case of ISO classification documents, the
all the classes of the ISO are defined in elaborate manner. In case of regulatory requirements
documents, all the regulations provided by ISO are discussed accurately. The criteria for
validation documents are given as follows:
Validation Plan
User Requirements
Functional Requirements
Design Specification
Installation Qualification
Operational Qualification
Performance Qualification
Traceability Matrix.
Management of change:
Management of change is applicable to all the employees to connect the GMP utility.
It can be utilised many systems (Esteves & Bento, 2013). It has some direct impact on the
operations of cleanroom validation. GMP servers as well as networks have some indirect
operations. Any time, pieces of equipment are connected to the utility of the procedure. It is
used to dedicate some research activities. It has a huge impact in the performance of the
It may happen that the employees have a less amount of knowledge in validation of
cleanroom (Herrán et al., 2016). Employees may be inefficient in this particular
sector. These may lead to the faliure of the project. It can be a great loss for the
company.
Documentation requirement:
The required documents include ISO classification document and regulatory
requirements documents (Hayeck et al., 2014). In case of ISO classification documents, the
all the classes of the ISO are defined in elaborate manner. In case of regulatory requirements
documents, all the regulations provided by ISO are discussed accurately. The criteria for
validation documents are given as follows:
Validation Plan
User Requirements
Functional Requirements
Design Specification
Installation Qualification
Operational Qualification
Performance Qualification
Traceability Matrix.
Management of change:
Management of change is applicable to all the employees to connect the GMP utility.
It can be utilised many systems (Esteves & Bento, 2013). It has some direct impact on the
operations of cleanroom validation. GMP servers as well as networks have some indirect
operations. Any time, pieces of equipment are connected to the utility of the procedure. It is
used to dedicate some research activities. It has a huge impact in the performance of the
⊘ This is a preview!⊘
Do you want full access?
Subscribe today to unlock all pages.

Trusted by 1+ million students worldwide
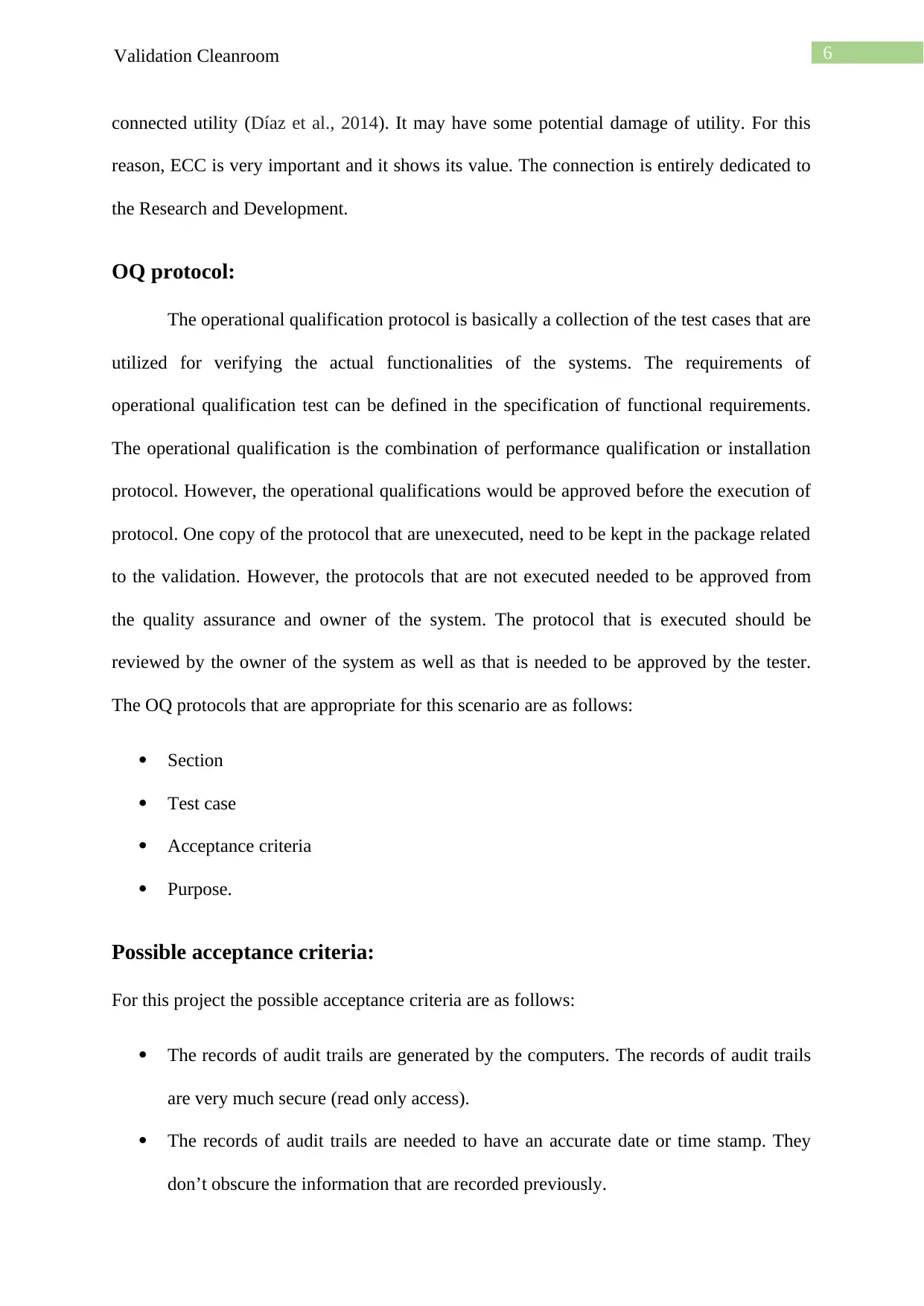
6Validation Cleanroom
connected utility (Díaz et al., 2014). It may have some potential damage of utility. For this
reason, ECC is very important and it shows its value. The connection is entirely dedicated to
the Research and Development.
OQ protocol:
The operational qualification protocol is basically a collection of the test cases that are
utilized for verifying the actual functionalities of the systems. The requirements of
operational qualification test can be defined in the specification of functional requirements.
The operational qualification is the combination of performance qualification or installation
protocol. However, the operational qualifications would be approved before the execution of
protocol. One copy of the protocol that are unexecuted, need to be kept in the package related
to the validation. However, the protocols that are not executed needed to be approved from
the quality assurance and owner of the system. The protocol that is executed should be
reviewed by the owner of the system as well as that is needed to be approved by the tester.
The OQ protocols that are appropriate for this scenario are as follows:
Section
Test case
Acceptance criteria
Purpose.
Possible acceptance criteria:
For this project the possible acceptance criteria are as follows:
The records of audit trails are generated by the computers. The records of audit trails
are very much secure (read only access).
The records of audit trails are needed to have an accurate date or time stamp. They
don’t obscure the information that are recorded previously.
connected utility (Díaz et al., 2014). It may have some potential damage of utility. For this
reason, ECC is very important and it shows its value. The connection is entirely dedicated to
the Research and Development.
OQ protocol:
The operational qualification protocol is basically a collection of the test cases that are
utilized for verifying the actual functionalities of the systems. The requirements of
operational qualification test can be defined in the specification of functional requirements.
The operational qualification is the combination of performance qualification or installation
protocol. However, the operational qualifications would be approved before the execution of
protocol. One copy of the protocol that are unexecuted, need to be kept in the package related
to the validation. However, the protocols that are not executed needed to be approved from
the quality assurance and owner of the system. The protocol that is executed should be
reviewed by the owner of the system as well as that is needed to be approved by the tester.
The OQ protocols that are appropriate for this scenario are as follows:
Section
Test case
Acceptance criteria
Purpose.
Possible acceptance criteria:
For this project the possible acceptance criteria are as follows:
The records of audit trails are generated by the computers. The records of audit trails
are very much secure (read only access).
The records of audit trails are needed to have an accurate date or time stamp. They
don’t obscure the information that are recorded previously.
Paraphrase This Document
Need a fresh take? Get an instant paraphrase of this document with our AI Paraphraser
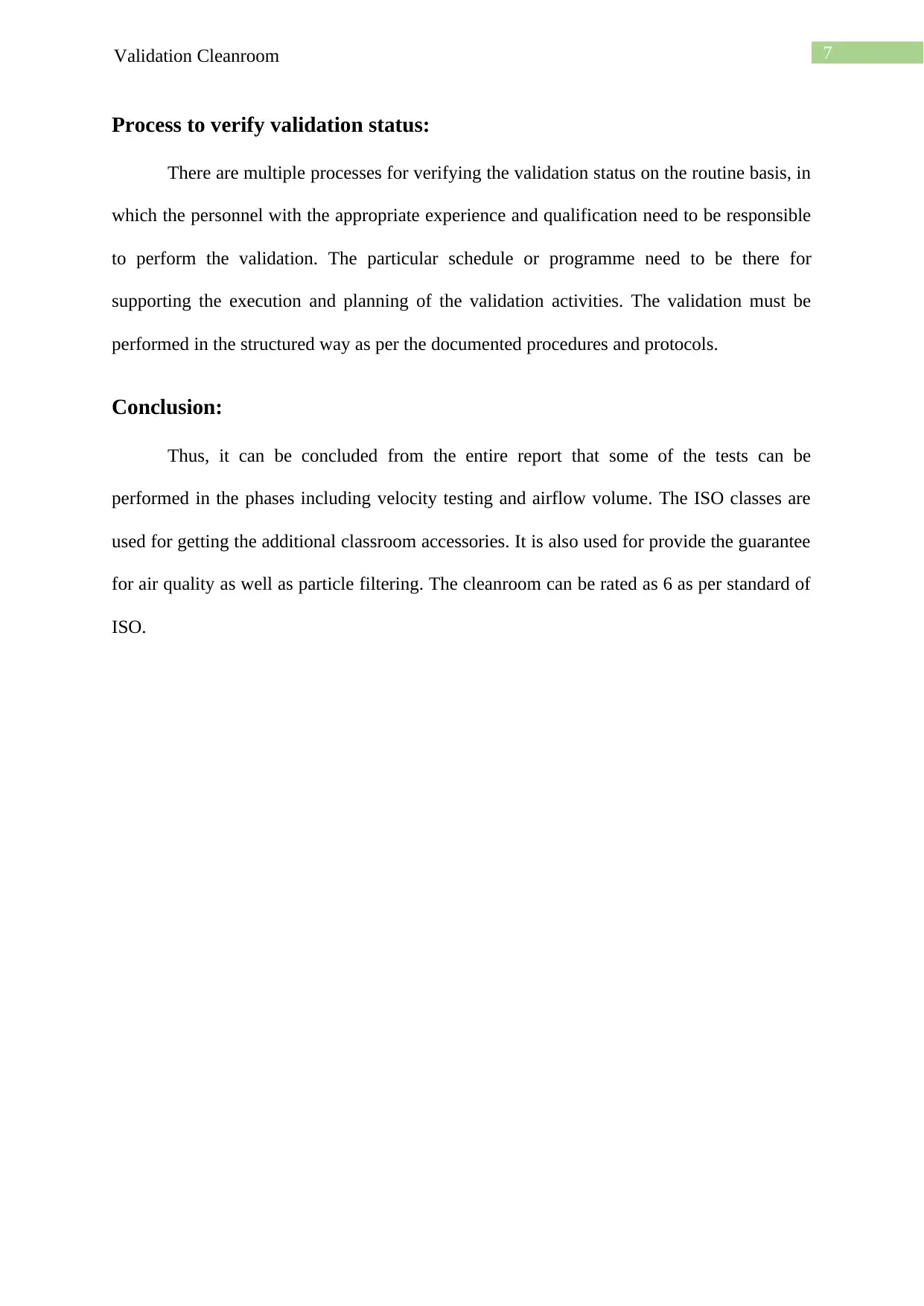
7Validation Cleanroom
Process to verify validation status:
There are multiple processes for verifying the validation status on the routine basis, in
which the personnel with the appropriate experience and qualification need to be responsible
to perform the validation. The particular schedule or programme need to be there for
supporting the execution and planning of the validation activities. The validation must be
performed in the structured way as per the documented procedures and protocols.
Conclusion:
Thus, it can be concluded from the entire report that some of the tests can be
performed in the phases including velocity testing and airflow volume. The ISO classes are
used for getting the additional classroom accessories. It is also used for provide the guarantee
for air quality as well as particle filtering. The cleanroom can be rated as 6 as per standard of
ISO.
Process to verify validation status:
There are multiple processes for verifying the validation status on the routine basis, in
which the personnel with the appropriate experience and qualification need to be responsible
to perform the validation. The particular schedule or programme need to be there for
supporting the execution and planning of the validation activities. The validation must be
performed in the structured way as per the documented procedures and protocols.
Conclusion:
Thus, it can be concluded from the entire report that some of the tests can be
performed in the phases including velocity testing and airflow volume. The ISO classes are
used for getting the additional classroom accessories. It is also used for provide the guarantee
for air quality as well as particle filtering. The cleanroom can be rated as 6 as per standard of
ISO.
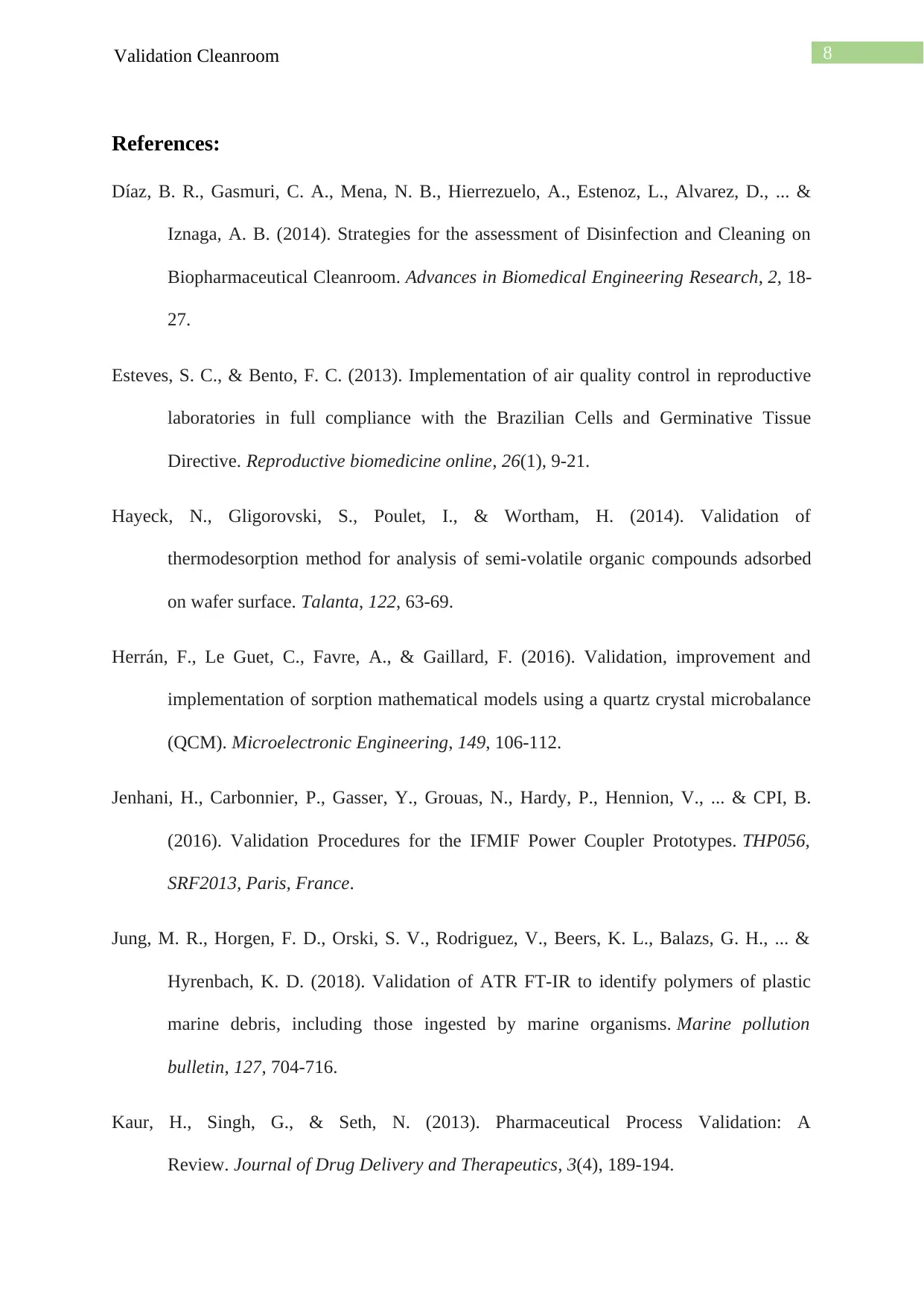
8Validation Cleanroom
References:
Díaz, B. R., Gasmuri, C. A., Mena, N. B., Hierrezuelo, A., Estenoz, L., Alvarez, D., ... &
Iznaga, A. B. (2014). Strategies for the assessment of Disinfection and Cleaning on
Biopharmaceutical Cleanroom. Advances in Biomedical Engineering Research, 2, 18-
27.
Esteves, S. C., & Bento, F. C. (2013). Implementation of air quality control in reproductive
laboratories in full compliance with the Brazilian Cells and Germinative Tissue
Directive. Reproductive biomedicine online, 26(1), 9-21.
Hayeck, N., Gligorovski, S., Poulet, I., & Wortham, H. (2014). Validation of
thermodesorption method for analysis of semi-volatile organic compounds adsorbed
on wafer surface. Talanta, 122, 63-69.
Herrán, F., Le Guet, C., Favre, A., & Gaillard, F. (2016). Validation, improvement and
implementation of sorption mathematical models using a quartz crystal microbalance
(QCM). Microelectronic Engineering, 149, 106-112.
Jenhani, H., Carbonnier, P., Gasser, Y., Grouas, N., Hardy, P., Hennion, V., ... & CPI, B.
(2016). Validation Procedures for the IFMIF Power Coupler Prototypes. THP056,
SRF2013, Paris, France.
Jung, M. R., Horgen, F. D., Orski, S. V., Rodriguez, V., Beers, K. L., Balazs, G. H., ... &
Hyrenbach, K. D. (2018). Validation of ATR FT-IR to identify polymers of plastic
marine debris, including those ingested by marine organisms. Marine pollution
bulletin, 127, 704-716.
Kaur, H., Singh, G., & Seth, N. (2013). Pharmaceutical Process Validation: A
Review. Journal of Drug Delivery and Therapeutics, 3(4), 189-194.
References:
Díaz, B. R., Gasmuri, C. A., Mena, N. B., Hierrezuelo, A., Estenoz, L., Alvarez, D., ... &
Iznaga, A. B. (2014). Strategies for the assessment of Disinfection and Cleaning on
Biopharmaceutical Cleanroom. Advances in Biomedical Engineering Research, 2, 18-
27.
Esteves, S. C., & Bento, F. C. (2013). Implementation of air quality control in reproductive
laboratories in full compliance with the Brazilian Cells and Germinative Tissue
Directive. Reproductive biomedicine online, 26(1), 9-21.
Hayeck, N., Gligorovski, S., Poulet, I., & Wortham, H. (2014). Validation of
thermodesorption method for analysis of semi-volatile organic compounds adsorbed
on wafer surface. Talanta, 122, 63-69.
Herrán, F., Le Guet, C., Favre, A., & Gaillard, F. (2016). Validation, improvement and
implementation of sorption mathematical models using a quartz crystal microbalance
(QCM). Microelectronic Engineering, 149, 106-112.
Jenhani, H., Carbonnier, P., Gasser, Y., Grouas, N., Hardy, P., Hennion, V., ... & CPI, B.
(2016). Validation Procedures for the IFMIF Power Coupler Prototypes. THP056,
SRF2013, Paris, France.
Jung, M. R., Horgen, F. D., Orski, S. V., Rodriguez, V., Beers, K. L., Balazs, G. H., ... &
Hyrenbach, K. D. (2018). Validation of ATR FT-IR to identify polymers of plastic
marine debris, including those ingested by marine organisms. Marine pollution
bulletin, 127, 704-716.
Kaur, H., Singh, G., & Seth, N. (2013). Pharmaceutical Process Validation: A
Review. Journal of Drug Delivery and Therapeutics, 3(4), 189-194.
⊘ This is a preview!⊘
Do you want full access?
Subscribe today to unlock all pages.

Trusted by 1+ million students worldwide
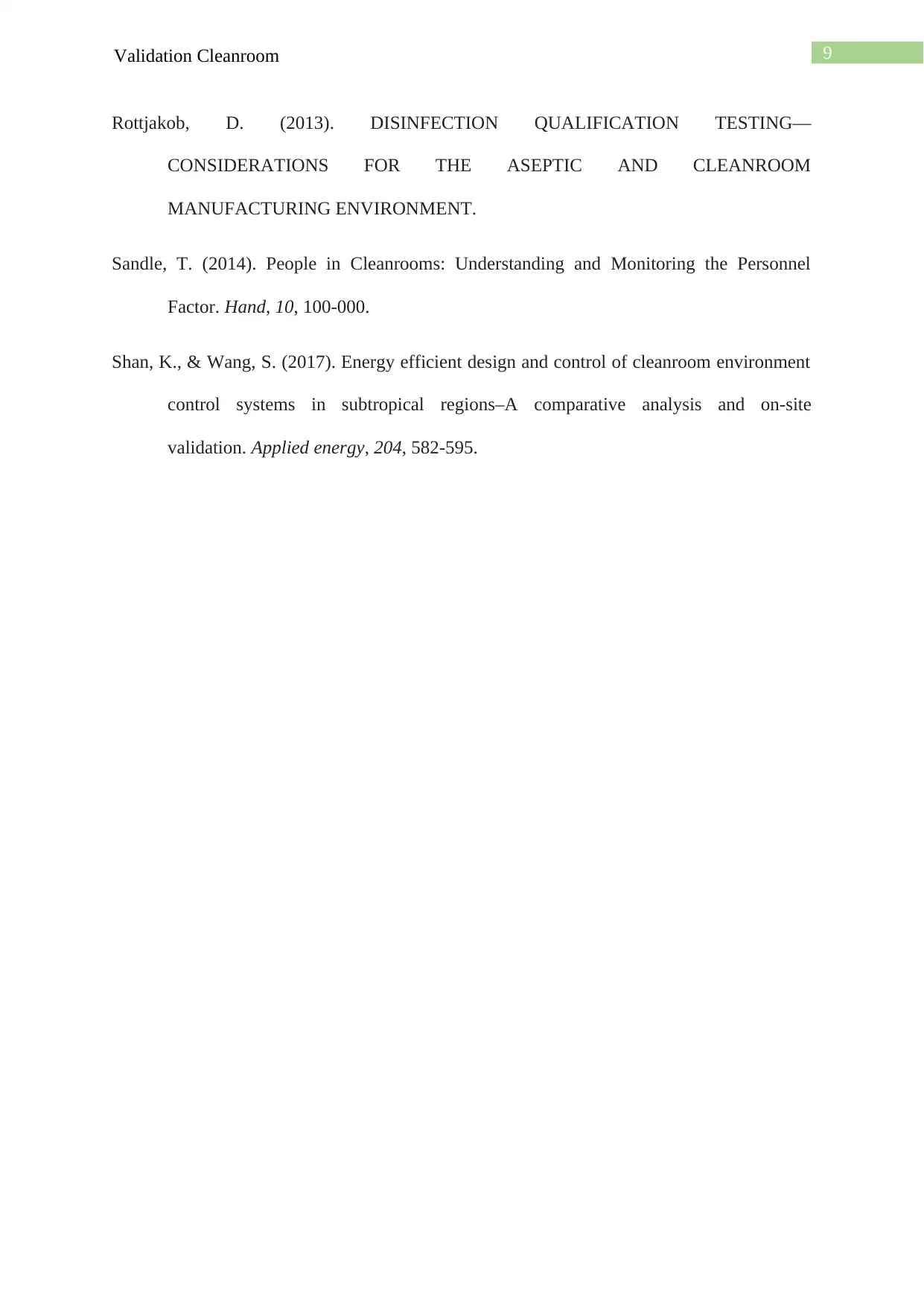
9Validation Cleanroom
Rottjakob, D. (2013). DISINFECTION QUALIFICATION TESTING—
CONSIDERATIONS FOR THE ASEPTIC AND CLEANROOM
MANUFACTURING ENVIRONMENT.
Sandle, T. (2014). People in Cleanrooms: Understanding and Monitoring the Personnel
Factor. Hand, 10, 100-000.
Shan, K., & Wang, S. (2017). Energy efficient design and control of cleanroom environment
control systems in subtropical regions–A comparative analysis and on-site
validation. Applied energy, 204, 582-595.
Rottjakob, D. (2013). DISINFECTION QUALIFICATION TESTING—
CONSIDERATIONS FOR THE ASEPTIC AND CLEANROOM
MANUFACTURING ENVIRONMENT.
Sandle, T. (2014). People in Cleanrooms: Understanding and Monitoring the Personnel
Factor. Hand, 10, 100-000.
Shan, K., & Wang, S. (2017). Energy efficient design and control of cleanroom environment
control systems in subtropical regions–A comparative analysis and on-site
validation. Applied energy, 204, 582-595.
1 out of 10
Related Documents

Your All-in-One AI-Powered Toolkit for Academic Success.
+13062052269
info@desklib.com
Available 24*7 on WhatsApp / Email
Unlock your academic potential
© 2024 | Zucol Services PVT LTD | All rights reserved.