Analysis of Process Improvement Strategies in Cleveland Clinic's SPD
VerifiedAdded on 2023/01/19
|8
|2203
|51
Report
AI Summary
This report analyzes the application of strategic management techniques to improve the Surgical Processing Department (SPD) at Cleveland Clinic. The report details the implementation of Six Sigma, Lean management, PDCA (Plan-Do-Check-Adjust), and FMEA (Failure Mode and Effects Analysis) t...
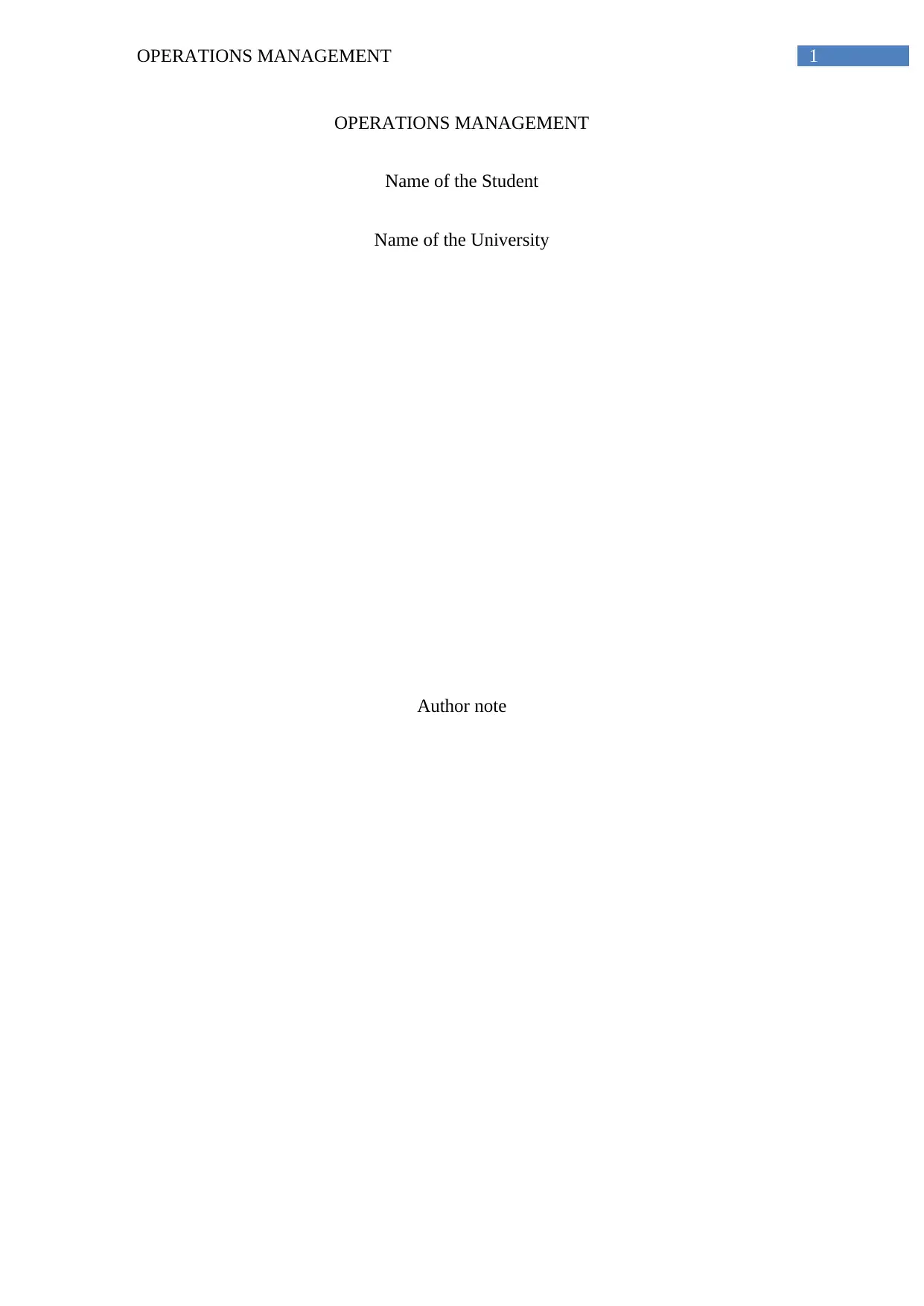
1OPERATIONS MANAGEMENT
OPERATIONS MANAGEMENT
Name of the Student
Name of the University
Author note
OPERATIONS MANAGEMENT
Name of the Student
Name of the University
Author note
Paraphrase This Document
Need a fresh take? Get an instant paraphrase of this document with our AI Paraphraser
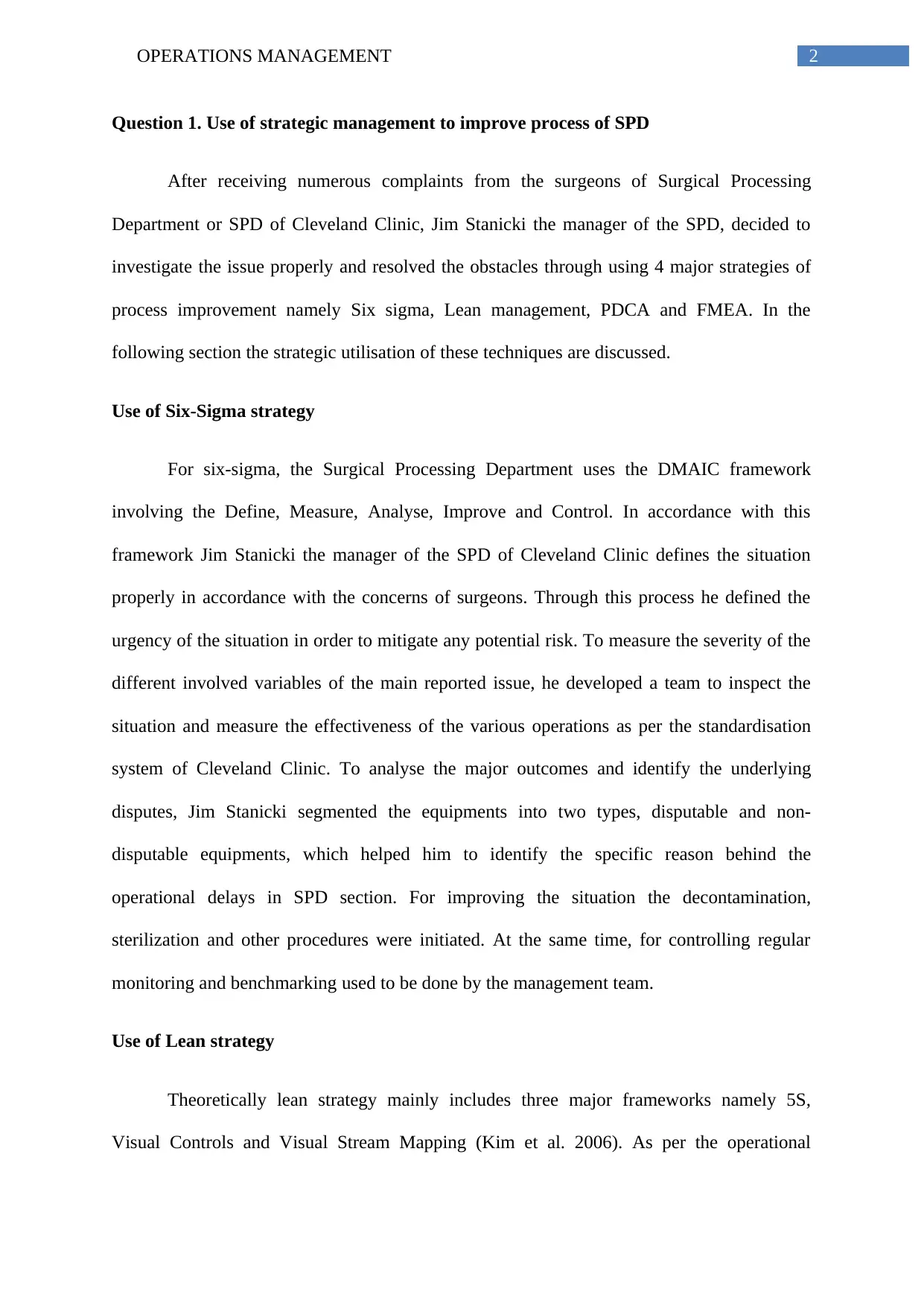
2OPERATIONS MANAGEMENT
Question 1. Use of strategic management to improve process of SPD
After receiving numerous complaints from the surgeons of Surgical Processing
Department or SPD of Cleveland Clinic, Jim Stanicki the manager of the SPD, decided to
investigate the issue properly and resolved the obstacles through using 4 major strategies of
process improvement namely Six sigma, Lean management, PDCA and FMEA. In the
following section the strategic utilisation of these techniques are discussed.
Use of Six-Sigma strategy
For six-sigma, the Surgical Processing Department uses the DMAIC framework
involving the Define, Measure, Analyse, Improve and Control. In accordance with this
framework Jim Stanicki the manager of the SPD of Cleveland Clinic defines the situation
properly in accordance with the concerns of surgeons. Through this process he defined the
urgency of the situation in order to mitigate any potential risk. To measure the severity of the
different involved variables of the main reported issue, he developed a team to inspect the
situation and measure the effectiveness of the various operations as per the standardisation
system of Cleveland Clinic. To analyse the major outcomes and identify the underlying
disputes, Jim Stanicki segmented the equipments into two types, disputable and non-
disputable equipments, which helped him to identify the specific reason behind the
operational delays in SPD section. For improving the situation the decontamination,
sterilization and other procedures were initiated. At the same time, for controlling regular
monitoring and benchmarking used to be done by the management team.
Use of Lean strategy
Theoretically lean strategy mainly includes three major frameworks namely 5S,
Visual Controls and Visual Stream Mapping (Kim et al. 2006). As per the operational
Question 1. Use of strategic management to improve process of SPD
After receiving numerous complaints from the surgeons of Surgical Processing
Department or SPD of Cleveland Clinic, Jim Stanicki the manager of the SPD, decided to
investigate the issue properly and resolved the obstacles through using 4 major strategies of
process improvement namely Six sigma, Lean management, PDCA and FMEA. In the
following section the strategic utilisation of these techniques are discussed.
Use of Six-Sigma strategy
For six-sigma, the Surgical Processing Department uses the DMAIC framework
involving the Define, Measure, Analyse, Improve and Control. In accordance with this
framework Jim Stanicki the manager of the SPD of Cleveland Clinic defines the situation
properly in accordance with the concerns of surgeons. Through this process he defined the
urgency of the situation in order to mitigate any potential risk. To measure the severity of the
different involved variables of the main reported issue, he developed a team to inspect the
situation and measure the effectiveness of the various operations as per the standardisation
system of Cleveland Clinic. To analyse the major outcomes and identify the underlying
disputes, Jim Stanicki segmented the equipments into two types, disputable and non-
disputable equipments, which helped him to identify the specific reason behind the
operational delays in SPD section. For improving the situation the decontamination,
sterilization and other procedures were initiated. At the same time, for controlling regular
monitoring and benchmarking used to be done by the management team.
Use of Lean strategy
Theoretically lean strategy mainly includes three major frameworks namely 5S,
Visual Controls and Visual Stream Mapping (Kim et al. 2006). As per the operational
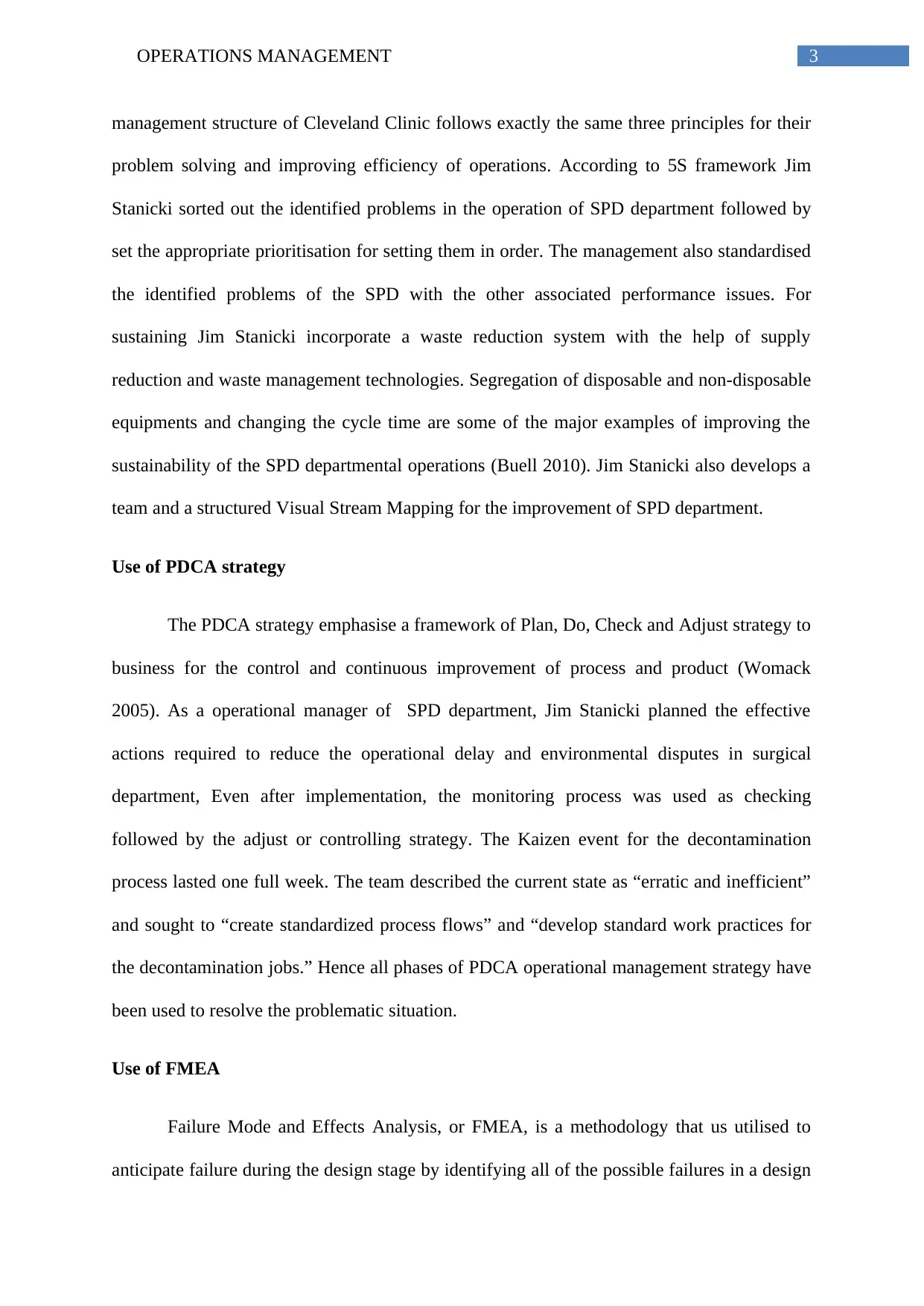
3OPERATIONS MANAGEMENT
management structure of Cleveland Clinic follows exactly the same three principles for their
problem solving and improving efficiency of operations. According to 5S framework Jim
Stanicki sorted out the identified problems in the operation of SPD department followed by
set the appropriate prioritisation for setting them in order. The management also standardised
the identified problems of the SPD with the other associated performance issues. For
sustaining Jim Stanicki incorporate a waste reduction system with the help of supply
reduction and waste management technologies. Segregation of disposable and non-disposable
equipments and changing the cycle time are some of the major examples of improving the
sustainability of the SPD departmental operations (Buell 2010). Jim Stanicki also develops a
team and a structured Visual Stream Mapping for the improvement of SPD department.
Use of PDCA strategy
The PDCA strategy emphasise a framework of Plan, Do, Check and Adjust strategy to
business for the control and continuous improvement of process and product (Womack
2005). As a operational manager of SPD department, Jim Stanicki planned the effective
actions required to reduce the operational delay and environmental disputes in surgical
department, Even after implementation, the monitoring process was used as checking
followed by the adjust or controlling strategy. The Kaizen event for the decontamination
process lasted one full week. The team described the current state as “erratic and inefficient”
and sought to “create standardized process flows” and “develop standard work practices for
the decontamination jobs.” Hence all phases of PDCA operational management strategy have
been used to resolve the problematic situation.
Use of FMEA
Failure Mode and Effects Analysis, or FMEA, is a methodology that us utilised to
anticipate failure during the design stage by identifying all of the possible failures in a design
management structure of Cleveland Clinic follows exactly the same three principles for their
problem solving and improving efficiency of operations. According to 5S framework Jim
Stanicki sorted out the identified problems in the operation of SPD department followed by
set the appropriate prioritisation for setting them in order. The management also standardised
the identified problems of the SPD with the other associated performance issues. For
sustaining Jim Stanicki incorporate a waste reduction system with the help of supply
reduction and waste management technologies. Segregation of disposable and non-disposable
equipments and changing the cycle time are some of the major examples of improving the
sustainability of the SPD departmental operations (Buell 2010). Jim Stanicki also develops a
team and a structured Visual Stream Mapping for the improvement of SPD department.
Use of PDCA strategy
The PDCA strategy emphasise a framework of Plan, Do, Check and Adjust strategy to
business for the control and continuous improvement of process and product (Womack
2005). As a operational manager of SPD department, Jim Stanicki planned the effective
actions required to reduce the operational delay and environmental disputes in surgical
department, Even after implementation, the monitoring process was used as checking
followed by the adjust or controlling strategy. The Kaizen event for the decontamination
process lasted one full week. The team described the current state as “erratic and inefficient”
and sought to “create standardized process flows” and “develop standard work practices for
the decontamination jobs.” Hence all phases of PDCA operational management strategy have
been used to resolve the problematic situation.
Use of FMEA
Failure Mode and Effects Analysis, or FMEA, is a methodology that us utilised to
anticipate failure during the design stage by identifying all of the possible failures in a design
⊘ This is a preview!⊘
Do you want full access?
Subscribe today to unlock all pages.

Trusted by 1+ million students worldwide
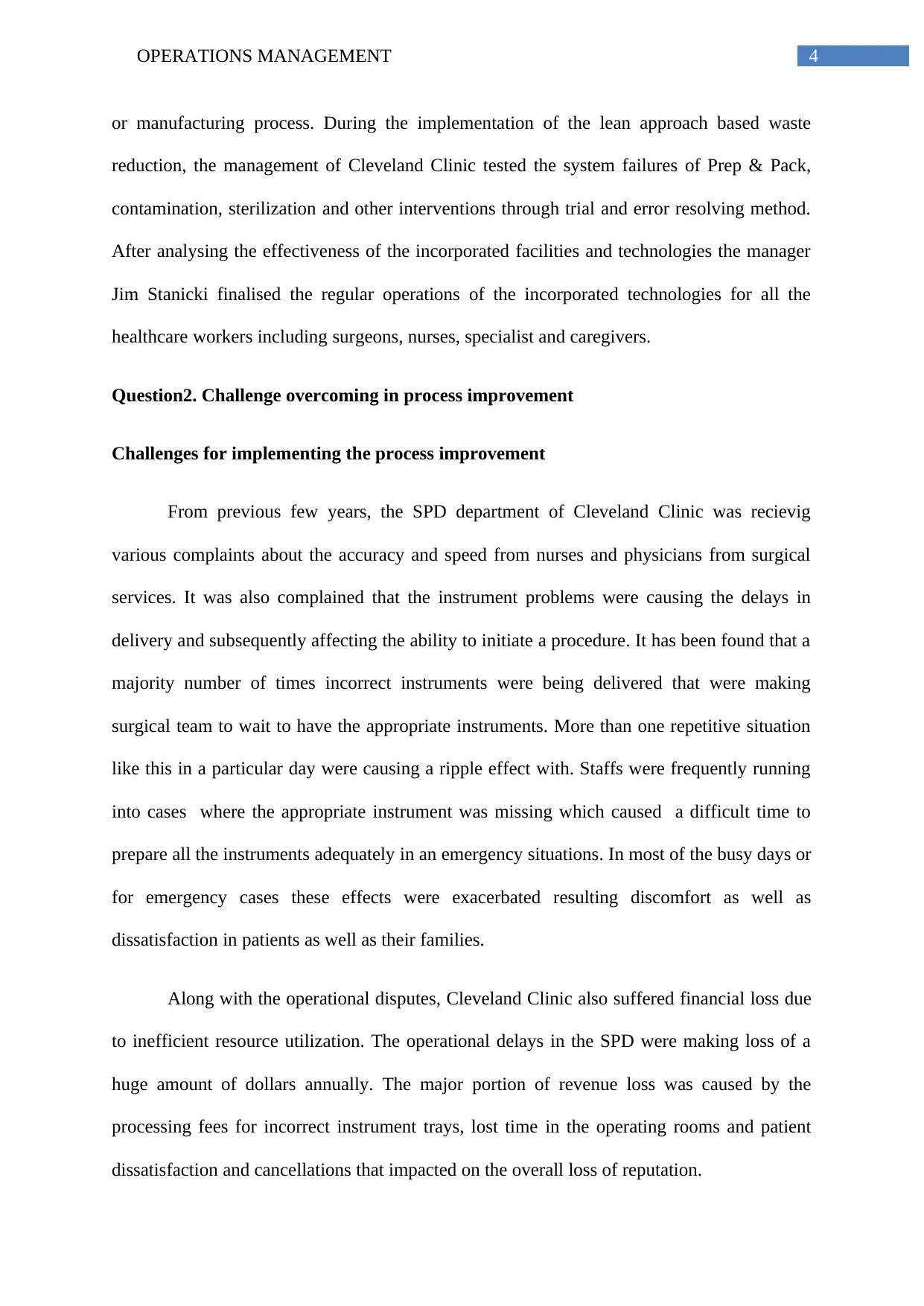
4OPERATIONS MANAGEMENT
or manufacturing process. During the implementation of the lean approach based waste
reduction, the management of Cleveland Clinic tested the system failures of Prep & Pack,
contamination, sterilization and other interventions through trial and error resolving method.
After analysing the effectiveness of the incorporated facilities and technologies the manager
Jim Stanicki finalised the regular operations of the incorporated technologies for all the
healthcare workers including surgeons, nurses, specialist and caregivers.
Question2. Challenge overcoming in process improvement
Challenges for implementing the process improvement
From previous few years, the SPD department of Cleveland Clinic was recievig
various complaints about the accuracy and speed from nurses and physicians from surgical
services. It was also complained that the instrument problems were causing the delays in
delivery and subsequently affecting the ability to initiate a procedure. It has been found that a
majority number of times incorrect instruments were being delivered that were making
surgical team to wait to have the appropriate instruments. More than one repetitive situation
like this in a particular day were causing a ripple effect with. Staffs were frequently running
into cases where the appropriate instrument was missing which caused a difficult time to
prepare all the instruments adequately in an emergency situations. In most of the busy days or
for emergency cases these effects were exacerbated resulting discomfort as well as
dissatisfaction in patients as well as their families.
Along with the operational disputes, Cleveland Clinic also suffered financial loss due
to inefficient resource utilization. The operational delays in the SPD were making loss of a
huge amount of dollars annually. The major portion of revenue loss was caused by the
processing fees for incorrect instrument trays, lost time in the operating rooms and patient
dissatisfaction and cancellations that impacted on the overall loss of reputation.
or manufacturing process. During the implementation of the lean approach based waste
reduction, the management of Cleveland Clinic tested the system failures of Prep & Pack,
contamination, sterilization and other interventions through trial and error resolving method.
After analysing the effectiveness of the incorporated facilities and technologies the manager
Jim Stanicki finalised the regular operations of the incorporated technologies for all the
healthcare workers including surgeons, nurses, specialist and caregivers.
Question2. Challenge overcoming in process improvement
Challenges for implementing the process improvement
From previous few years, the SPD department of Cleveland Clinic was recievig
various complaints about the accuracy and speed from nurses and physicians from surgical
services. It was also complained that the instrument problems were causing the delays in
delivery and subsequently affecting the ability to initiate a procedure. It has been found that a
majority number of times incorrect instruments were being delivered that were making
surgical team to wait to have the appropriate instruments. More than one repetitive situation
like this in a particular day were causing a ripple effect with. Staffs were frequently running
into cases where the appropriate instrument was missing which caused a difficult time to
prepare all the instruments adequately in an emergency situations. In most of the busy days or
for emergency cases these effects were exacerbated resulting discomfort as well as
dissatisfaction in patients as well as their families.
Along with the operational disputes, Cleveland Clinic also suffered financial loss due
to inefficient resource utilization. The operational delays in the SPD were making loss of a
huge amount of dollars annually. The major portion of revenue loss was caused by the
processing fees for incorrect instrument trays, lost time in the operating rooms and patient
dissatisfaction and cancellations that impacted on the overall loss of reputation.
Paraphrase This Document
Need a fresh take? Get an instant paraphrase of this document with our AI Paraphraser
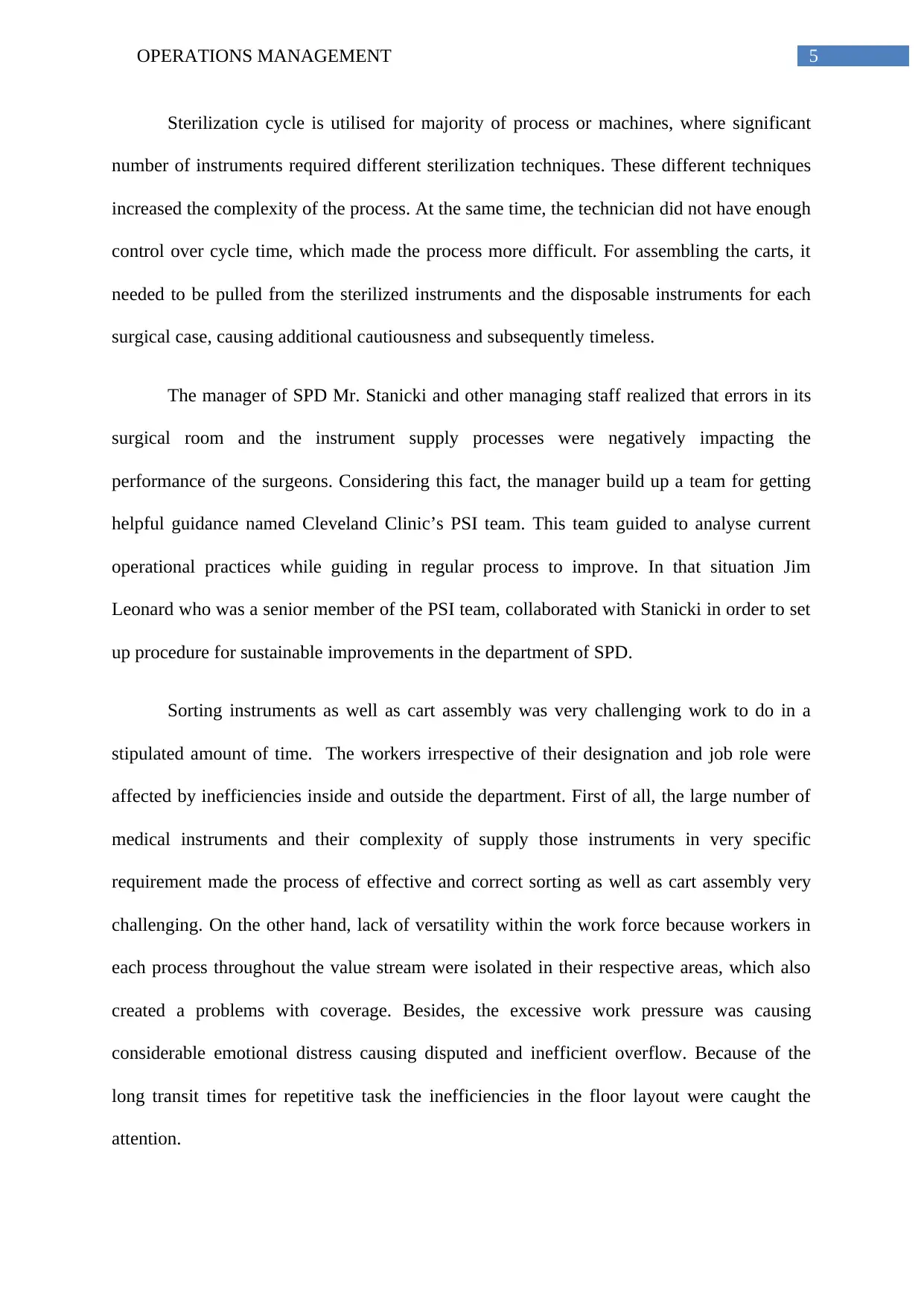
5OPERATIONS MANAGEMENT
Sterilization cycle is utilised for majority of process or machines, where significant
number of instruments required different sterilization techniques. These different techniques
increased the complexity of the process. At the same time, the technician did not have enough
control over cycle time, which made the process more difficult. For assembling the carts, it
needed to be pulled from the sterilized instruments and the disposable instruments for each
surgical case, causing additional cautiousness and subsequently timeless.
The manager of SPD Mr. Stanicki and other managing staff realized that errors in its
surgical room and the instrument supply processes were negatively impacting the
performance of the surgeons. Considering this fact, the manager build up a team for getting
helpful guidance named Cleveland Clinic’s PSI team. This team guided to analyse current
operational practices while guiding in regular process to improve. In that situation Jim
Leonard who was a senior member of the PSI team, collaborated with Stanicki in order to set
up procedure for sustainable improvements in the department of SPD.
Sorting instruments as well as cart assembly was very challenging work to do in a
stipulated amount of time. The workers irrespective of their designation and job role were
affected by inefficiencies inside and outside the department. First of all, the large number of
medical instruments and their complexity of supply those instruments in very specific
requirement made the process of effective and correct sorting as well as cart assembly very
challenging. On the other hand, lack of versatility within the work force because workers in
each process throughout the value stream were isolated in their respective areas, which also
created a problems with coverage. Besides, the excessive work pressure was causing
considerable emotional distress causing disputed and inefficient overflow. Because of the
long transit times for repetitive task the inefficiencies in the floor layout were caught the
attention.
Sterilization cycle is utilised for majority of process or machines, where significant
number of instruments required different sterilization techniques. These different techniques
increased the complexity of the process. At the same time, the technician did not have enough
control over cycle time, which made the process more difficult. For assembling the carts, it
needed to be pulled from the sterilized instruments and the disposable instruments for each
surgical case, causing additional cautiousness and subsequently timeless.
The manager of SPD Mr. Stanicki and other managing staff realized that errors in its
surgical room and the instrument supply processes were negatively impacting the
performance of the surgeons. Considering this fact, the manager build up a team for getting
helpful guidance named Cleveland Clinic’s PSI team. This team guided to analyse current
operational practices while guiding in regular process to improve. In that situation Jim
Leonard who was a senior member of the PSI team, collaborated with Stanicki in order to set
up procedure for sustainable improvements in the department of SPD.
Sorting instruments as well as cart assembly was very challenging work to do in a
stipulated amount of time. The workers irrespective of their designation and job role were
affected by inefficiencies inside and outside the department. First of all, the large number of
medical instruments and their complexity of supply those instruments in very specific
requirement made the process of effective and correct sorting as well as cart assembly very
challenging. On the other hand, lack of versatility within the work force because workers in
each process throughout the value stream were isolated in their respective areas, which also
created a problems with coverage. Besides, the excessive work pressure was causing
considerable emotional distress causing disputed and inefficient overflow. Because of the
long transit times for repetitive task the inefficiencies in the floor layout were caught the
attention.

6OPERATIONS MANAGEMENT
Overcoming these obstacle
The most frequently found problems by Leonard and Stanicki in the SPD, are
“instrument delays” and “missing instruments.” After considering many process
improvement strategies, They decided that the lean approach could help to resolve those
issues. As the first step, proper analysis was done to create a current state value stream map,
which was basically an outline of the whole processes undertaken within the SPD considering
the time consumption as well. The recording session was developed to record the existing
layout of the SPD, to design the Current State Value Stream Map. According to this Value
Stream Map, the SPD process was comprised of four sequential sub-procedures namely
Decontamination, Prep & Pack, Sterilization, and Case Cart Assembly and Delivery. Through
measuring the start up to finish procedure by a SPD staff for each sample, the cycle times
were determined. To analyse the sub-procedures more critically Stanicki and Leonard
decided to hold Kaizen.
After this analysis and formulating solution, the management team redesigned the
process layout of the decontamination area which allowed them to reduce the cart breakdown
time by 63%. The walking time was also reduced as well, identified , by 56%
(My.clevelandclinic.org 2013). At the same time, all employees in the prep & pack area were
started to have very less difficulties to have decontaminated instruments while they re-
assembled sets. Previously they used to constantly walking back and forth for picking out the
right instruments for their sets. On the other hand the Prep & pack operators were assigned in
individual and specific instrument stations like colorectal surgery, neurological surgery and
others. After assigning a new staff in the workflow as material handler with the duty of
sorting the instruments out from the decontamination process while properly suppling to the
prep & pack operators, the efficiency was the system got improved significantly.
Overcoming these obstacle
The most frequently found problems by Leonard and Stanicki in the SPD, are
“instrument delays” and “missing instruments.” After considering many process
improvement strategies, They decided that the lean approach could help to resolve those
issues. As the first step, proper analysis was done to create a current state value stream map,
which was basically an outline of the whole processes undertaken within the SPD considering
the time consumption as well. The recording session was developed to record the existing
layout of the SPD, to design the Current State Value Stream Map. According to this Value
Stream Map, the SPD process was comprised of four sequential sub-procedures namely
Decontamination, Prep & Pack, Sterilization, and Case Cart Assembly and Delivery. Through
measuring the start up to finish procedure by a SPD staff for each sample, the cycle times
were determined. To analyse the sub-procedures more critically Stanicki and Leonard
decided to hold Kaizen.
After this analysis and formulating solution, the management team redesigned the
process layout of the decontamination area which allowed them to reduce the cart breakdown
time by 63%. The walking time was also reduced as well, identified , by 56%
(My.clevelandclinic.org 2013). At the same time, all employees in the prep & pack area were
started to have very less difficulties to have decontaminated instruments while they re-
assembled sets. Previously they used to constantly walking back and forth for picking out the
right instruments for their sets. On the other hand the Prep & pack operators were assigned in
individual and specific instrument stations like colorectal surgery, neurological surgery and
others. After assigning a new staff in the workflow as material handler with the duty of
sorting the instruments out from the decontamination process while properly suppling to the
prep & pack operators, the efficiency was the system got improved significantly.
⊘ This is a preview!⊘
Do you want full access?
Subscribe today to unlock all pages.

Trusted by 1+ million students worldwide

7OPERATIONS MANAGEMENT
Through reorganizing the supply room, making a streamline for supplies and placing
tape on the floor to outline assembly lanes for the carts, the cart assembly time was also
reduced significantly. On the other hand, after the remodelling the layout of sterilization
process, the team developed a “pull” system that allowed to change the location of loading
station while making to very close to prep & pack drop-off. A printer was also added in the
area that helped to decrease the time of gathering required printouts. Through widening the
aisles and relocating supplies, a 21% decrease in walking time was achieved, which also
reduce the stress level of the employees (Rinehart 2014).
Differences of challenges between service and manufacturing organisation
The operational challenges in manufacturing organisation are more tangible than the
service organisation. Hence, for being more tangible detection of physical disputes easier in
manufacturing enterprises (Chiarini 2014). However, in service proving enterprise
operational dilemmas are more difficult to find and resolved, because they are not easily
identifiable by physical inspection.
The operational challenges and faults are more human resource oriented in service
providing organisation. A service providing organisation needs to focus more on their current
workforce and their workflow. On the other hand, the challenges in major manufacturing
enterprise operation also include the inventory management and instrument based product life
cycle.
There are certain similarities in the challenges of manufacturing and service providing
enterprises as well. The cost control, and resultant impact on operational delay are same for
both these types of organisation (Erfan 2010). Moreover, both service providing and
manufacturing organisation needs to deal with customer loss, quality related ethical issues
because of their operational challenges.
Through reorganizing the supply room, making a streamline for supplies and placing
tape on the floor to outline assembly lanes for the carts, the cart assembly time was also
reduced significantly. On the other hand, after the remodelling the layout of sterilization
process, the team developed a “pull” system that allowed to change the location of loading
station while making to very close to prep & pack drop-off. A printer was also added in the
area that helped to decrease the time of gathering required printouts. Through widening the
aisles and relocating supplies, a 21% decrease in walking time was achieved, which also
reduce the stress level of the employees (Rinehart 2014).
Differences of challenges between service and manufacturing organisation
The operational challenges in manufacturing organisation are more tangible than the
service organisation. Hence, for being more tangible detection of physical disputes easier in
manufacturing enterprises (Chiarini 2014). However, in service proving enterprise
operational dilemmas are more difficult to find and resolved, because they are not easily
identifiable by physical inspection.
The operational challenges and faults are more human resource oriented in service
providing organisation. A service providing organisation needs to focus more on their current
workforce and their workflow. On the other hand, the challenges in major manufacturing
enterprise operation also include the inventory management and instrument based product life
cycle.
There are certain similarities in the challenges of manufacturing and service providing
enterprises as well. The cost control, and resultant impact on operational delay are same for
both these types of organisation (Erfan 2010). Moreover, both service providing and
manufacturing organisation needs to deal with customer loss, quality related ethical issues
because of their operational challenges.
Paraphrase This Document
Need a fresh take? Get an instant paraphrase of this document with our AI Paraphraser
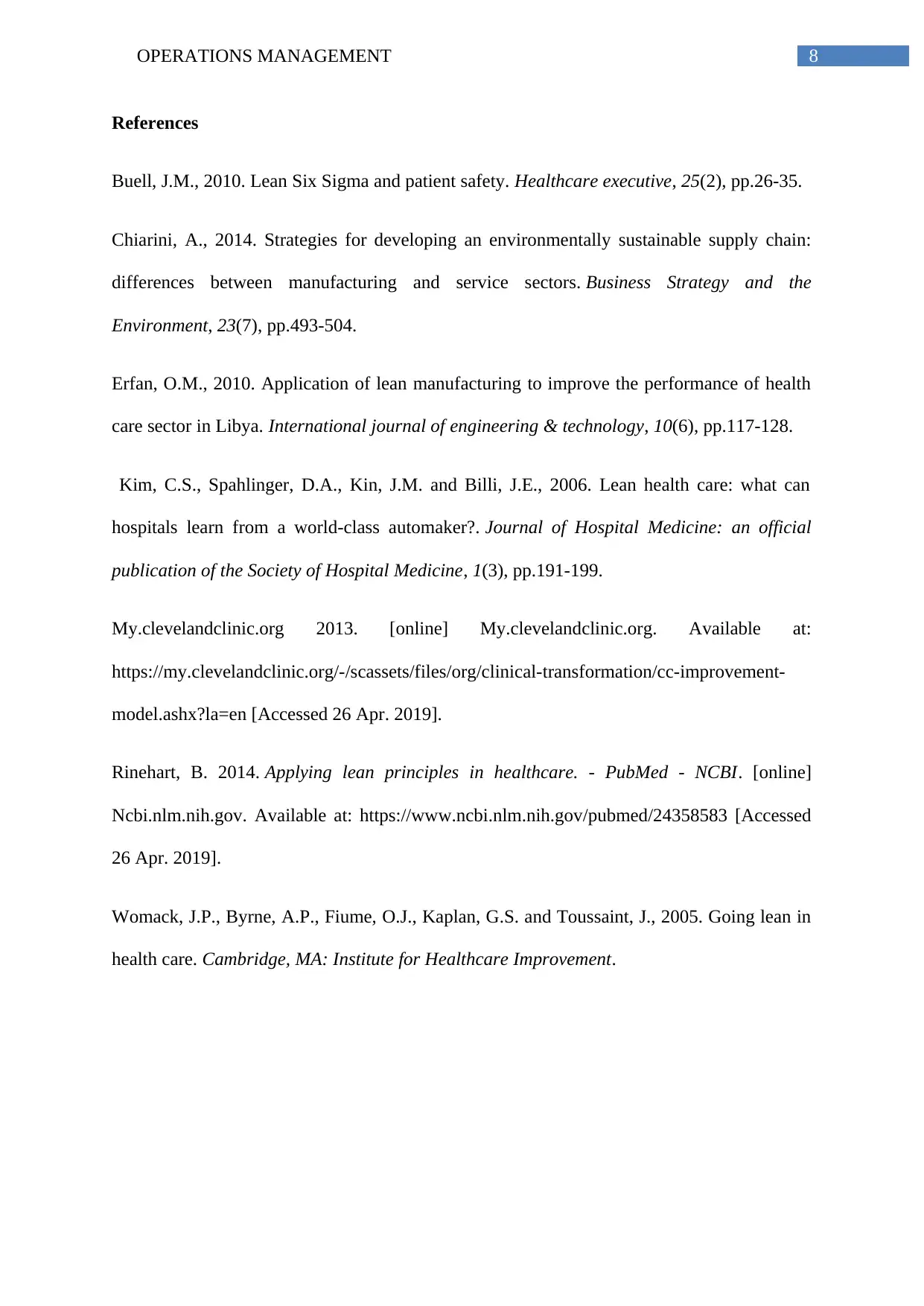
8OPERATIONS MANAGEMENT
References
Buell, J.M., 2010. Lean Six Sigma and patient safety. Healthcare executive, 25(2), pp.26-35.
Chiarini, A., 2014. Strategies for developing an environmentally sustainable supply chain:
differences between manufacturing and service sectors. Business Strategy and the
Environment, 23(7), pp.493-504.
Erfan, O.M., 2010. Application of lean manufacturing to improve the performance of health
care sector in Libya. International journal of engineering & technology, 10(6), pp.117-128.
Kim, C.S., Spahlinger, D.A., Kin, J.M. and Billi, J.E., 2006. Lean health care: what can
hospitals learn from a world‐class automaker?. Journal of Hospital Medicine: an official
publication of the Society of Hospital Medicine, 1(3), pp.191-199.
My.clevelandclinic.org 2013. [online] My.clevelandclinic.org. Available at:
https://my.clevelandclinic.org/-/scassets/files/org/clinical-transformation/cc-improvement-
model.ashx?la=en [Accessed 26 Apr. 2019].
Rinehart, B. 2014. Applying lean principles in healthcare. - PubMed - NCBI. [online]
Ncbi.nlm.nih.gov. Available at: https://www.ncbi.nlm.nih.gov/pubmed/24358583 [Accessed
26 Apr. 2019].
Womack, J.P., Byrne, A.P., Fiume, O.J., Kaplan, G.S. and Toussaint, J., 2005. Going lean in
health care. Cambridge, MA: Institute for Healthcare Improvement.
References
Buell, J.M., 2010. Lean Six Sigma and patient safety. Healthcare executive, 25(2), pp.26-35.
Chiarini, A., 2014. Strategies for developing an environmentally sustainable supply chain:
differences between manufacturing and service sectors. Business Strategy and the
Environment, 23(7), pp.493-504.
Erfan, O.M., 2010. Application of lean manufacturing to improve the performance of health
care sector in Libya. International journal of engineering & technology, 10(6), pp.117-128.
Kim, C.S., Spahlinger, D.A., Kin, J.M. and Billi, J.E., 2006. Lean health care: what can
hospitals learn from a world‐class automaker?. Journal of Hospital Medicine: an official
publication of the Society of Hospital Medicine, 1(3), pp.191-199.
My.clevelandclinic.org 2013. [online] My.clevelandclinic.org. Available at:
https://my.clevelandclinic.org/-/scassets/files/org/clinical-transformation/cc-improvement-
model.ashx?la=en [Accessed 26 Apr. 2019].
Rinehart, B. 2014. Applying lean principles in healthcare. - PubMed - NCBI. [online]
Ncbi.nlm.nih.gov. Available at: https://www.ncbi.nlm.nih.gov/pubmed/24358583 [Accessed
26 Apr. 2019].
Womack, J.P., Byrne, A.P., Fiume, O.J., Kaplan, G.S. and Toussaint, J., 2005. Going lean in
health care. Cambridge, MA: Institute for Healthcare Improvement.
1 out of 8
Related Documents

Your All-in-One AI-Powered Toolkit for Academic Success.
+13062052269
info@desklib.com
Available 24*7 on WhatsApp / Email
Unlock your academic potential
© 2024 | Zucol Services PVT LTD | All rights reserved.