INFO498: Club IT Inventory Management System - A Detailed Case Study
VerifiedAdded on 2023/04/21
|10
|1784
|277
Case Study
AI Summary
This case study delves into the inventory management challenges faced by Club IT, a downtown music venue. The study identifies problems related to inaccurate inventory counts, inefficient processes, and a lack of system automation. A fishbone diagram highlights key contributing factors such as issues with people, methods, materials, and machinery. The project scope focuses on using inventory information to control costs and prioritize inventory turnover. Fact-finding is conducted using questionnaires to gather data from employees. The current inventory management process is mapped to identify areas for improvement. The study outlines both functional and non-functional requirements for a new inventory management system to address the identified issues. The report concludes with a bibliography of relevant sources. Desklib provides students access to this and many other solved assignments and past papers.
Contribute Materials
Your contribution can guide someone’s learning journey. Share your
documents today.
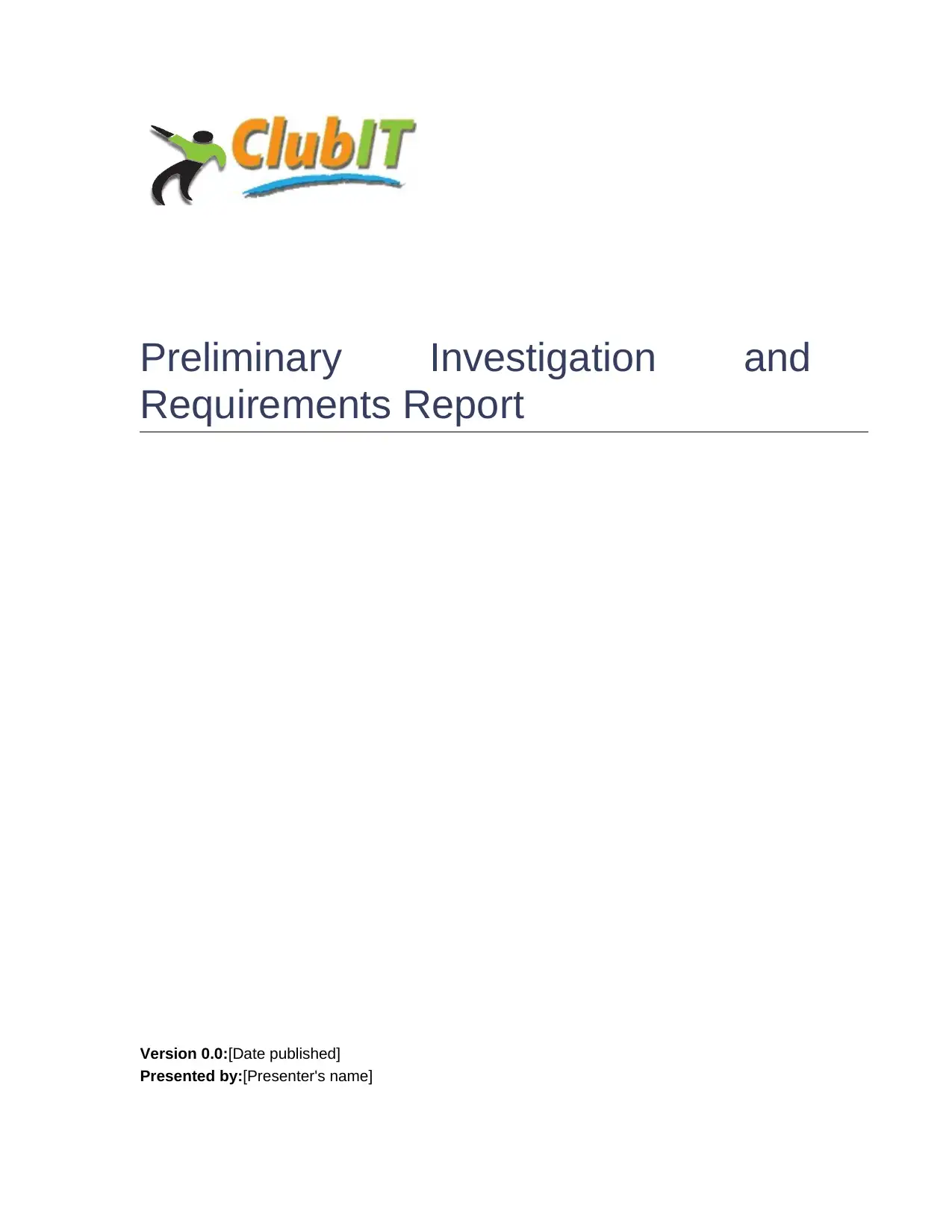
Preliminary Investigation and
Requirements Report
Version 0.0:[Date published]
Presented by:[Presenter's name]
Requirements Report
Version 0.0:[Date published]
Presented by:[Presenter's name]
Secure Best Marks with AI Grader
Need help grading? Try our AI Grader for instant feedback on your assignments.
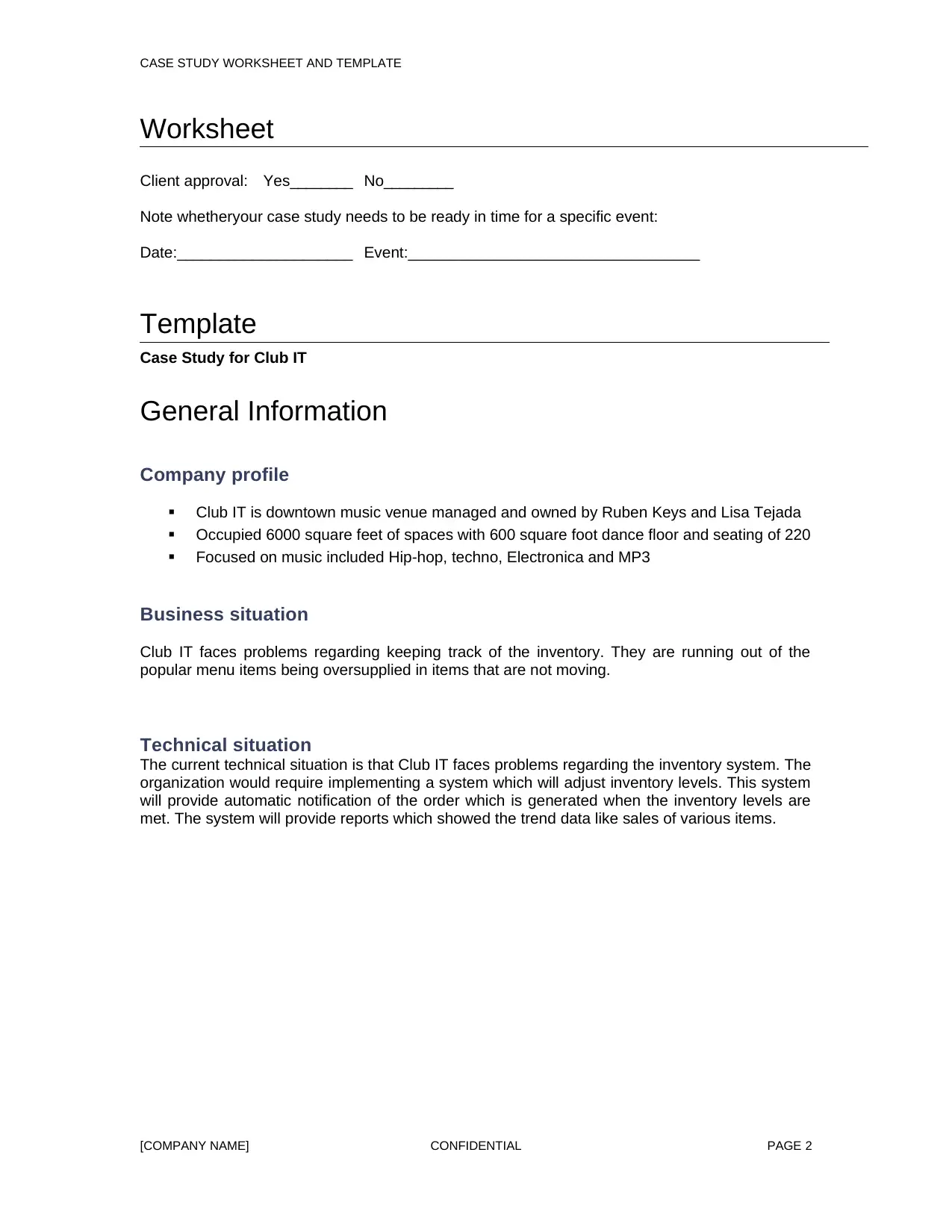
CASE STUDY WORKSHEET AND TEMPLATE
Worksheet
Client approval: Yes________ No_________
Note whetheryour case study needs to be ready in time for a specific event:
Date:_____________________ Event:__________________________________
Template
Case Study for Club IT
General Information
Company profile
Club IT is downtown music venue managed and owned by Ruben Keys and Lisa Tejada
Occupied 6000 square feet of spaces with 600 square foot dance floor and seating of 220
Focused on music included Hip-hop, techno, Electronica and MP3
Business situation
Club IT faces problems regarding keeping track of the inventory. They are running out of the
popular menu items being oversupplied in items that are not moving.
Technical situation
The current technical situation is that Club IT faces problems regarding the inventory system. The
organization would require implementing a system which will adjust inventory levels. This system
will provide automatic notification of the order which is generated when the inventory levels are
met. The system will provide reports which showed the trend data like sales of various items.
[COMPANY NAME] CONFIDENTIAL PAGE 2
Worksheet
Client approval: Yes________ No_________
Note whetheryour case study needs to be ready in time for a specific event:
Date:_____________________ Event:__________________________________
Template
Case Study for Club IT
General Information
Company profile
Club IT is downtown music venue managed and owned by Ruben Keys and Lisa Tejada
Occupied 6000 square feet of spaces with 600 square foot dance floor and seating of 220
Focused on music included Hip-hop, techno, Electronica and MP3
Business situation
Club IT faces problems regarding keeping track of the inventory. They are running out of the
popular menu items being oversupplied in items that are not moving.
Technical situation
The current technical situation is that Club IT faces problems regarding the inventory system. The
organization would require implementing a system which will adjust inventory levels. This system
will provide automatic notification of the order which is generated when the inventory levels are
met. The system will provide reports which showed the trend data like sales of various items.
[COMPANY NAME] CONFIDENTIAL PAGE 2
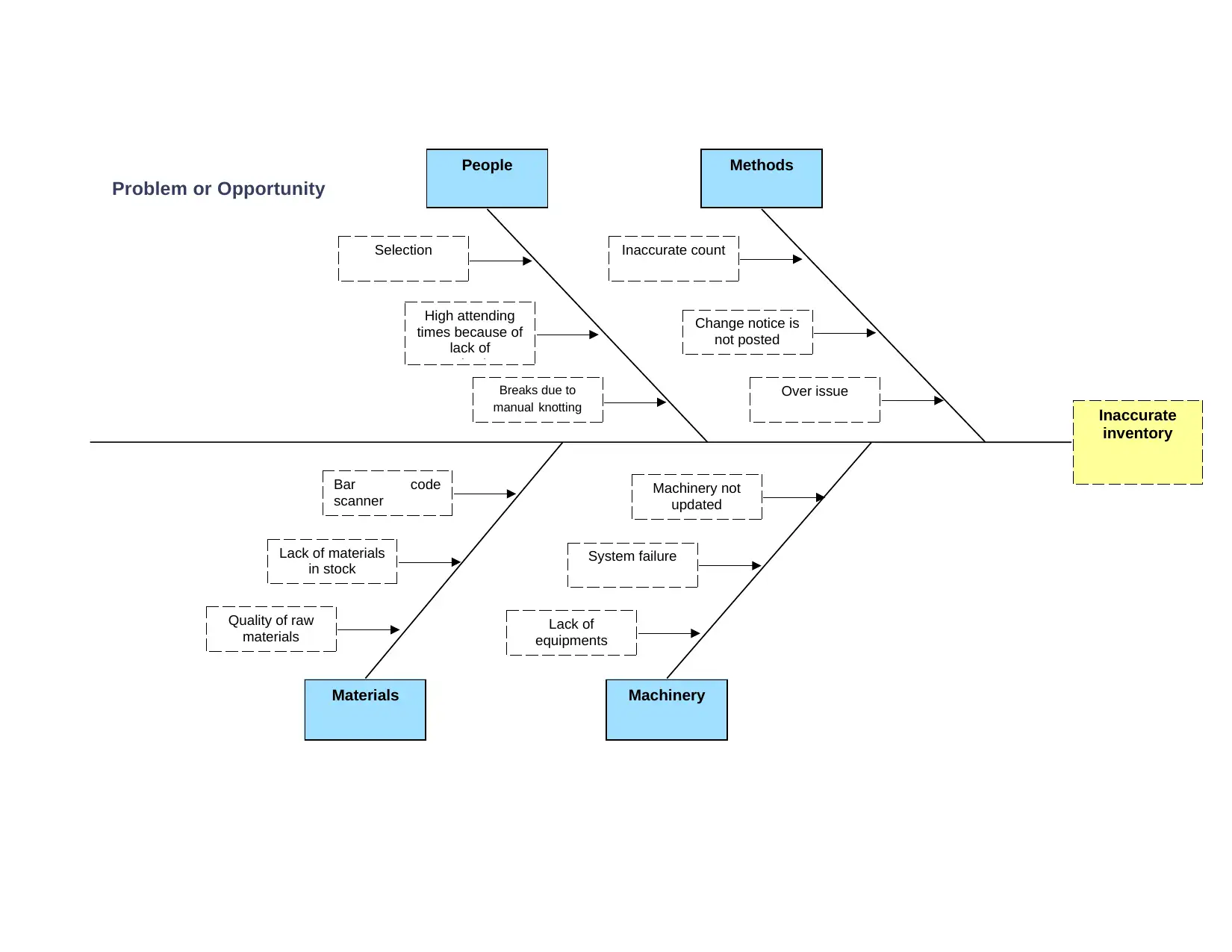
Problem or Opportunity
Selection
High attending
times because of
lack of
motivation
Breaks due to
manual knotting
Inaccurate count
Change notice is
not posted
Over issue
Machinery not
updated
System failure
Lack of
equipments
Bar code
scanner
Lack of materials
in stock
Quality of raw
materials
People Methods
Materials Machinery
Inaccurate
inventory
Selection
High attending
times because of
lack of
motivation
Breaks due to
manual knotting
Inaccurate count
Change notice is
not posted
Over issue
Machinery not
updated
System failure
Lack of
equipments
Bar code
scanner
Lack of materials
in stock
Quality of raw
materials
People Methods
Materials Machinery
Inaccurate
inventory
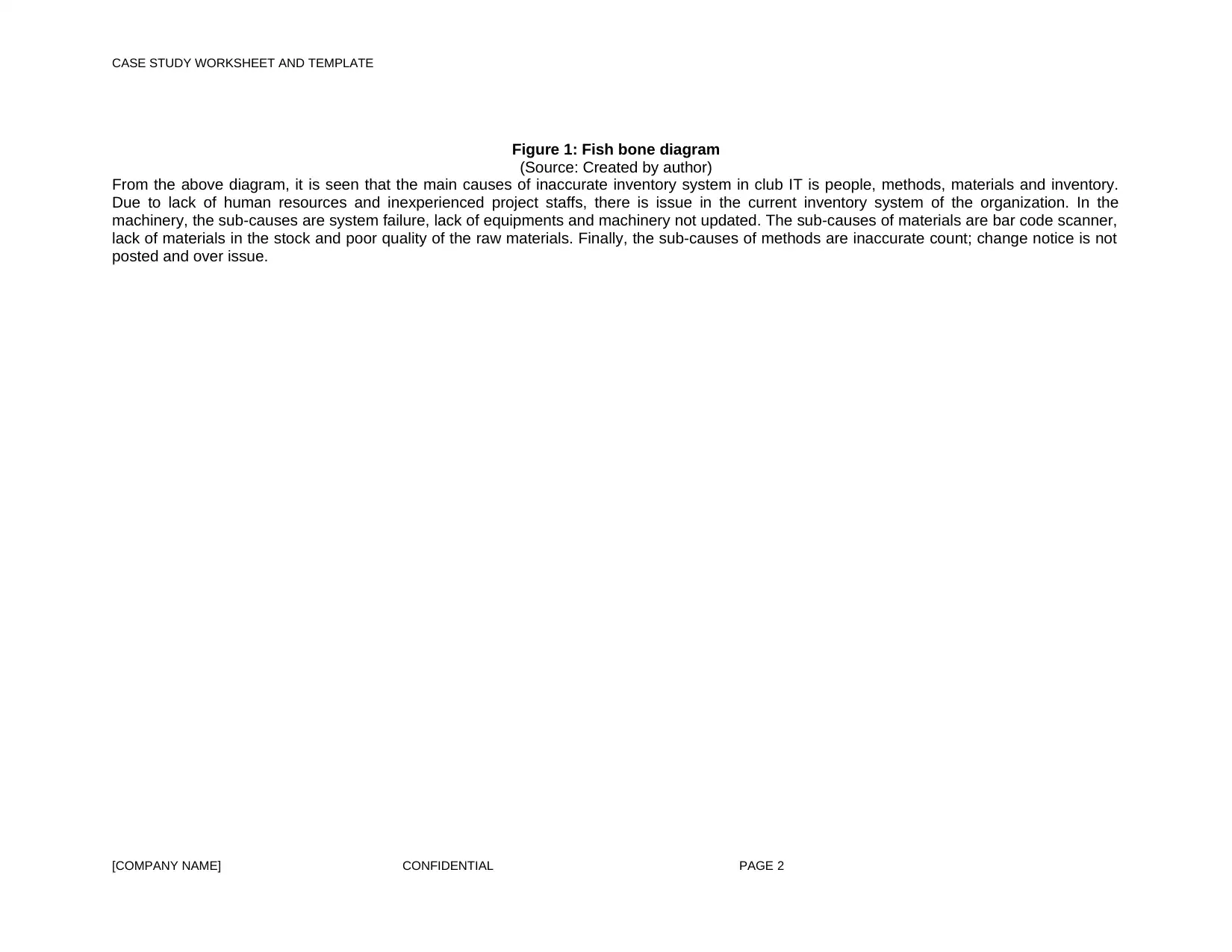
CASE STUDY WORKSHEET AND TEMPLATE
Figure 1: Fish bone diagram
(Source: Created by author)
From the above diagram, it is seen that the main causes of inaccurate inventory system in club IT is people, methods, materials and inventory.
Due to lack of human resources and inexperienced project staffs, there is issue in the current inventory system of the organization. In the
machinery, the sub-causes are system failure, lack of equipments and machinery not updated. The sub-causes of materials are bar code scanner,
lack of materials in the stock and poor quality of the raw materials. Finally, the sub-causes of methods are inaccurate count; change notice is not
posted and over issue.
[COMPANY NAME] CONFIDENTIAL PAGE 2
Figure 1: Fish bone diagram
(Source: Created by author)
From the above diagram, it is seen that the main causes of inaccurate inventory system in club IT is people, methods, materials and inventory.
Due to lack of human resources and inexperienced project staffs, there is issue in the current inventory system of the organization. In the
machinery, the sub-causes are system failure, lack of equipments and machinery not updated. The sub-causes of materials are bar code scanner,
lack of materials in the stock and poor quality of the raw materials. Finally, the sub-causes of methods are inaccurate count; change notice is not
posted and over issue.
[COMPANY NAME] CONFIDENTIAL PAGE 2
Secure Best Marks with AI Grader
Need help grading? Try our AI Grader for instant feedback on your assignments.
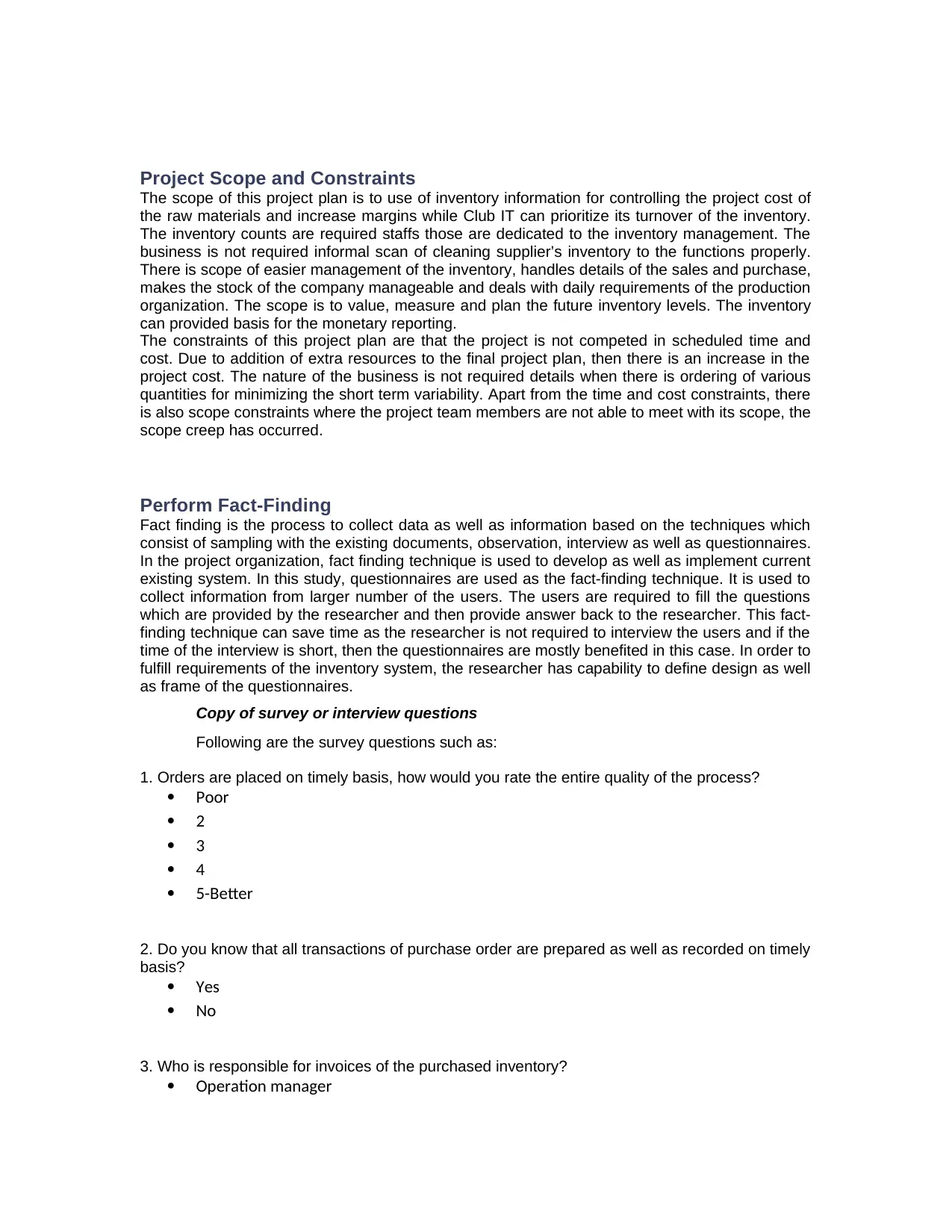
Project Scope and Constraints
The scope of this project plan is to use of inventory information for controlling the project cost of
the raw materials and increase margins while Club IT can prioritize its turnover of the inventory.
The inventory counts are required staffs those are dedicated to the inventory management. The
business is not required informal scan of cleaning supplier’s inventory to the functions properly.
There is scope of easier management of the inventory, handles details of the sales and purchase,
makes the stock of the company manageable and deals with daily requirements of the production
organization. The scope is to value, measure and plan the future inventory levels. The inventory
can provided basis for the monetary reporting.
The constraints of this project plan are that the project is not competed in scheduled time and
cost. Due to addition of extra resources to the final project plan, then there is an increase in the
project cost. The nature of the business is not required details when there is ordering of various
quantities for minimizing the short term variability. Apart from the time and cost constraints, there
is also scope constraints where the project team members are not able to meet with its scope, the
scope creep has occurred.
Perform Fact-Finding
Fact finding is the process to collect data as well as information based on the techniques which
consist of sampling with the existing documents, observation, interview as well as questionnaires.
In the project organization, fact finding technique is used to develop as well as implement current
existing system. In this study, questionnaires are used as the fact-finding technique. It is used to
collect information from larger number of the users. The users are required to fill the questions
which are provided by the researcher and then provide answer back to the researcher. This fact-
finding technique can save time as the researcher is not required to interview the users and if the
time of the interview is short, then the questionnaires are mostly benefited in this case. In order to
fulfill requirements of the inventory system, the researcher has capability to define design as well
as frame of the questionnaires.
Copy of survey or interview questions
Following are the survey questions such as:
1. Orders are placed on timely basis, how would you rate the entire quality of the process?
Poor
2
3
4
5-Better
2. Do you know that all transactions of purchase order are prepared as well as recorded on timely
basis?
Yes
No
3. Who is responsible for invoices of the purchased inventory?
Operation manager
The scope of this project plan is to use of inventory information for controlling the project cost of
the raw materials and increase margins while Club IT can prioritize its turnover of the inventory.
The inventory counts are required staffs those are dedicated to the inventory management. The
business is not required informal scan of cleaning supplier’s inventory to the functions properly.
There is scope of easier management of the inventory, handles details of the sales and purchase,
makes the stock of the company manageable and deals with daily requirements of the production
organization. The scope is to value, measure and plan the future inventory levels. The inventory
can provided basis for the monetary reporting.
The constraints of this project plan are that the project is not competed in scheduled time and
cost. Due to addition of extra resources to the final project plan, then there is an increase in the
project cost. The nature of the business is not required details when there is ordering of various
quantities for minimizing the short term variability. Apart from the time and cost constraints, there
is also scope constraints where the project team members are not able to meet with its scope, the
scope creep has occurred.
Perform Fact-Finding
Fact finding is the process to collect data as well as information based on the techniques which
consist of sampling with the existing documents, observation, interview as well as questionnaires.
In the project organization, fact finding technique is used to develop as well as implement current
existing system. In this study, questionnaires are used as the fact-finding technique. It is used to
collect information from larger number of the users. The users are required to fill the questions
which are provided by the researcher and then provide answer back to the researcher. This fact-
finding technique can save time as the researcher is not required to interview the users and if the
time of the interview is short, then the questionnaires are mostly benefited in this case. In order to
fulfill requirements of the inventory system, the researcher has capability to define design as well
as frame of the questionnaires.
Copy of survey or interview questions
Following are the survey questions such as:
1. Orders are placed on timely basis, how would you rate the entire quality of the process?
Poor
2
3
4
5-Better
2. Do you know that all transactions of purchase order are prepared as well as recorded on timely
basis?
Yes
No
3. Who is responsible for invoices of the purchased inventory?
Operation manager
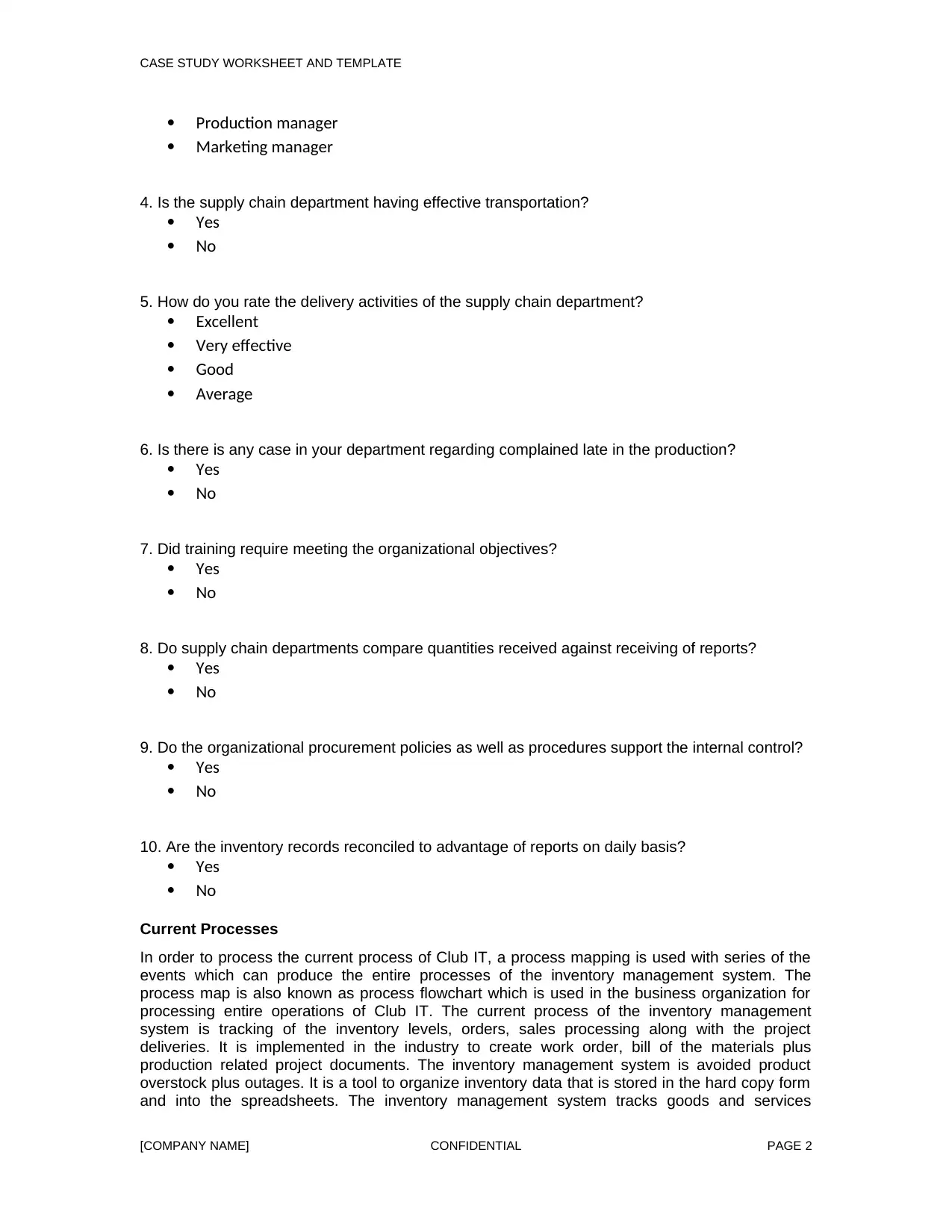
CASE STUDY WORKSHEET AND TEMPLATE
Production manager
Marketing manager
4. Is the supply chain department having effective transportation?
Yes
No
5. How do you rate the delivery activities of the supply chain department?
Excellent
Very effective
Good
Average
6. Is there is any case in your department regarding complained late in the production?
Yes
No
7. Did training require meeting the organizational objectives?
Yes
No
8. Do supply chain departments compare quantities received against receiving of reports?
Yes
No
9. Do the organizational procurement policies as well as procedures support the internal control?
Yes
No
10. Are the inventory records reconciled to advantage of reports on daily basis?
Yes
No
Current Processes
In order to process the current process of Club IT, a process mapping is used with series of the
events which can produce the entire processes of the inventory management system. The
process map is also known as process flowchart which is used in the business organization for
processing entire operations of Club IT. The current process of the inventory management
system is tracking of the inventory levels, orders, sales processing along with the project
deliveries. It is implemented in the industry to create work order, bill of the materials plus
production related project documents. The inventory management system is avoided product
overstock plus outages. It is a tool to organize inventory data that is stored in the hard copy form
and into the spreadsheets. The inventory management system tracks goods and services
[COMPANY NAME] CONFIDENTIAL PAGE 2
Production manager
Marketing manager
4. Is the supply chain department having effective transportation?
Yes
No
5. How do you rate the delivery activities of the supply chain department?
Excellent
Very effective
Good
Average
6. Is there is any case in your department regarding complained late in the production?
Yes
No
7. Did training require meeting the organizational objectives?
Yes
No
8. Do supply chain departments compare quantities received against receiving of reports?
Yes
No
9. Do the organizational procurement policies as well as procedures support the internal control?
Yes
No
10. Are the inventory records reconciled to advantage of reports on daily basis?
Yes
No
Current Processes
In order to process the current process of Club IT, a process mapping is used with series of the
events which can produce the entire processes of the inventory management system. The
process map is also known as process flowchart which is used in the business organization for
processing entire operations of Club IT. The current process of the inventory management
system is tracking of the inventory levels, orders, sales processing along with the project
deliveries. It is implemented in the industry to create work order, bill of the materials plus
production related project documents. The inventory management system is avoided product
overstock plus outages. It is a tool to organize inventory data that is stored in the hard copy form
and into the spreadsheets. The inventory management system tracks goods and services
[COMPANY NAME] CONFIDENTIAL PAGE 2
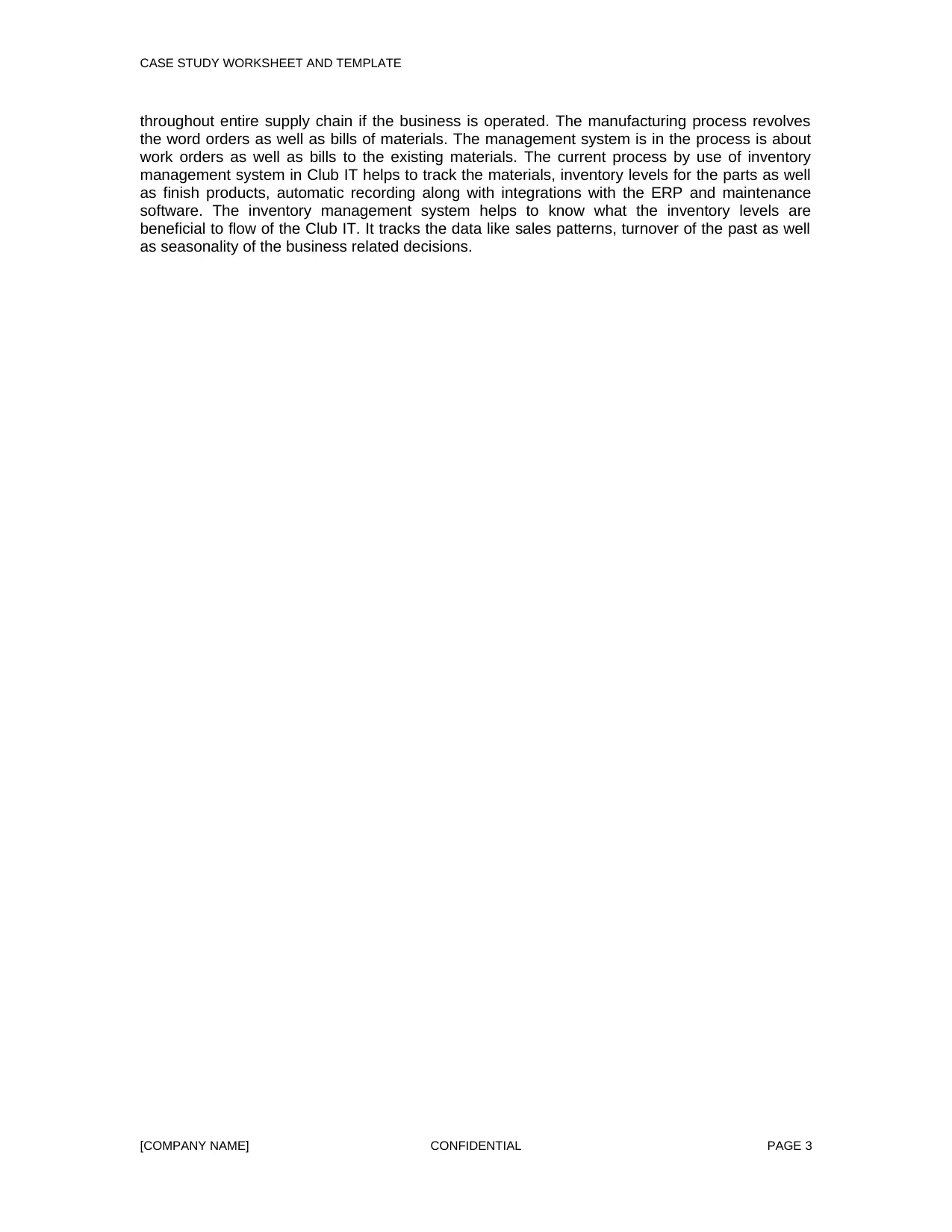
CASE STUDY WORKSHEET AND TEMPLATE
throughout entire supply chain if the business is operated. The manufacturing process revolves
the word orders as well as bills of materials. The management system is in the process is about
work orders as well as bills to the existing materials. The current process by use of inventory
management system in Club IT helps to track the materials, inventory levels for the parts as well
as finish products, automatic recording along with integrations with the ERP and maintenance
software. The inventory management system helps to know what the inventory levels are
beneficial to flow of the Club IT. It tracks the data like sales patterns, turnover of the past as well
as seasonality of the business related decisions.
[COMPANY NAME] CONFIDENTIAL PAGE 3
throughout entire supply chain if the business is operated. The manufacturing process revolves
the word orders as well as bills of materials. The management system is in the process is about
work orders as well as bills to the existing materials. The current process by use of inventory
management system in Club IT helps to track the materials, inventory levels for the parts as well
as finish products, automatic recording along with integrations with the ERP and maintenance
software. The inventory management system helps to know what the inventory levels are
beneficial to flow of the Club IT. It tracks the data like sales patterns, turnover of the past as well
as seasonality of the business related decisions.
[COMPANY NAME] CONFIDENTIAL PAGE 3
Paraphrase This Document
Need a fresh take? Get an instant paraphrase of this document with our AI Paraphraser
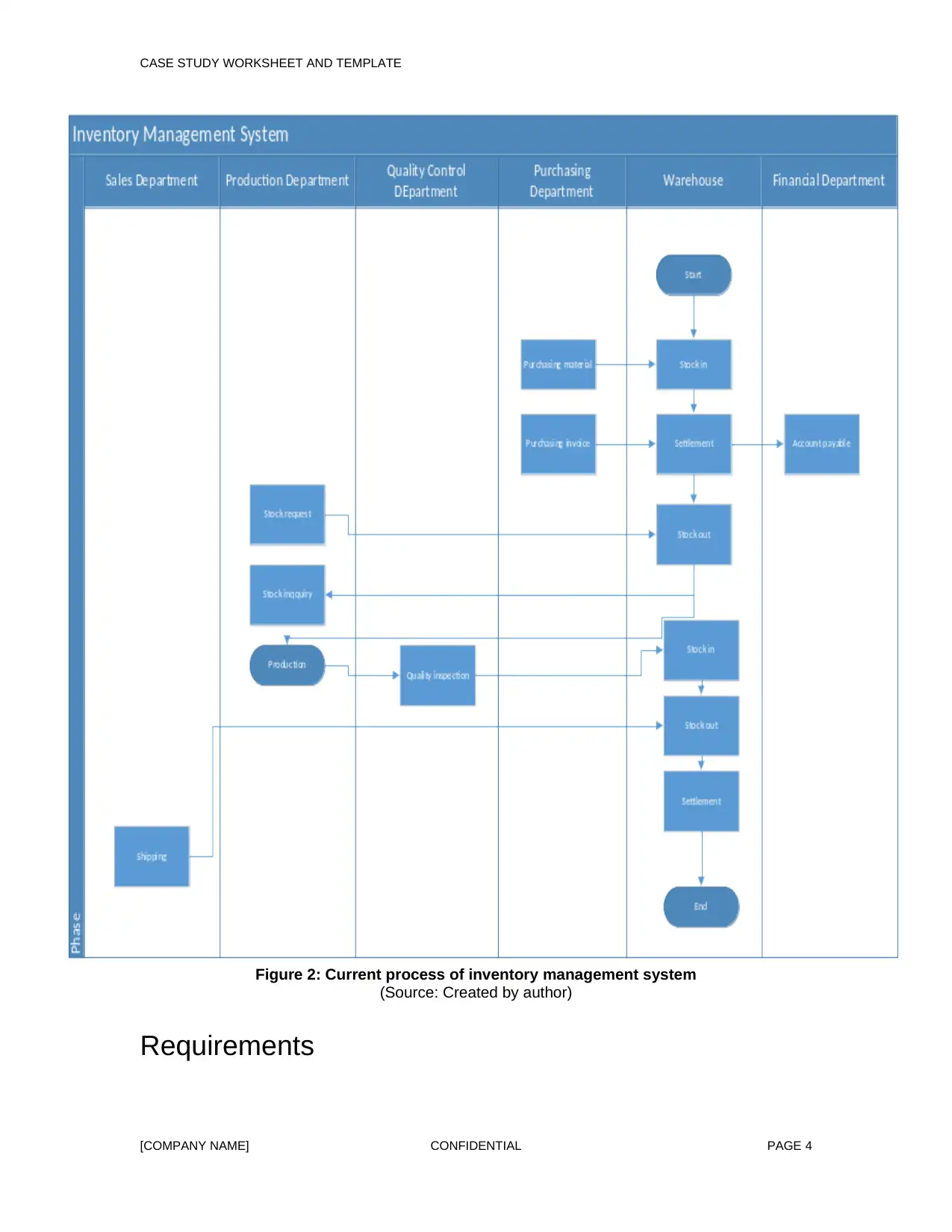
CASE STUDY WORKSHEET AND TEMPLATE
Figure 2: Current process of inventory management system
(Source: Created by author)
Requirements
[COMPANY NAME] CONFIDENTIAL PAGE 4
Figure 2: Current process of inventory management system
(Source: Created by author)
Requirements
[COMPANY NAME] CONFIDENTIAL PAGE 4
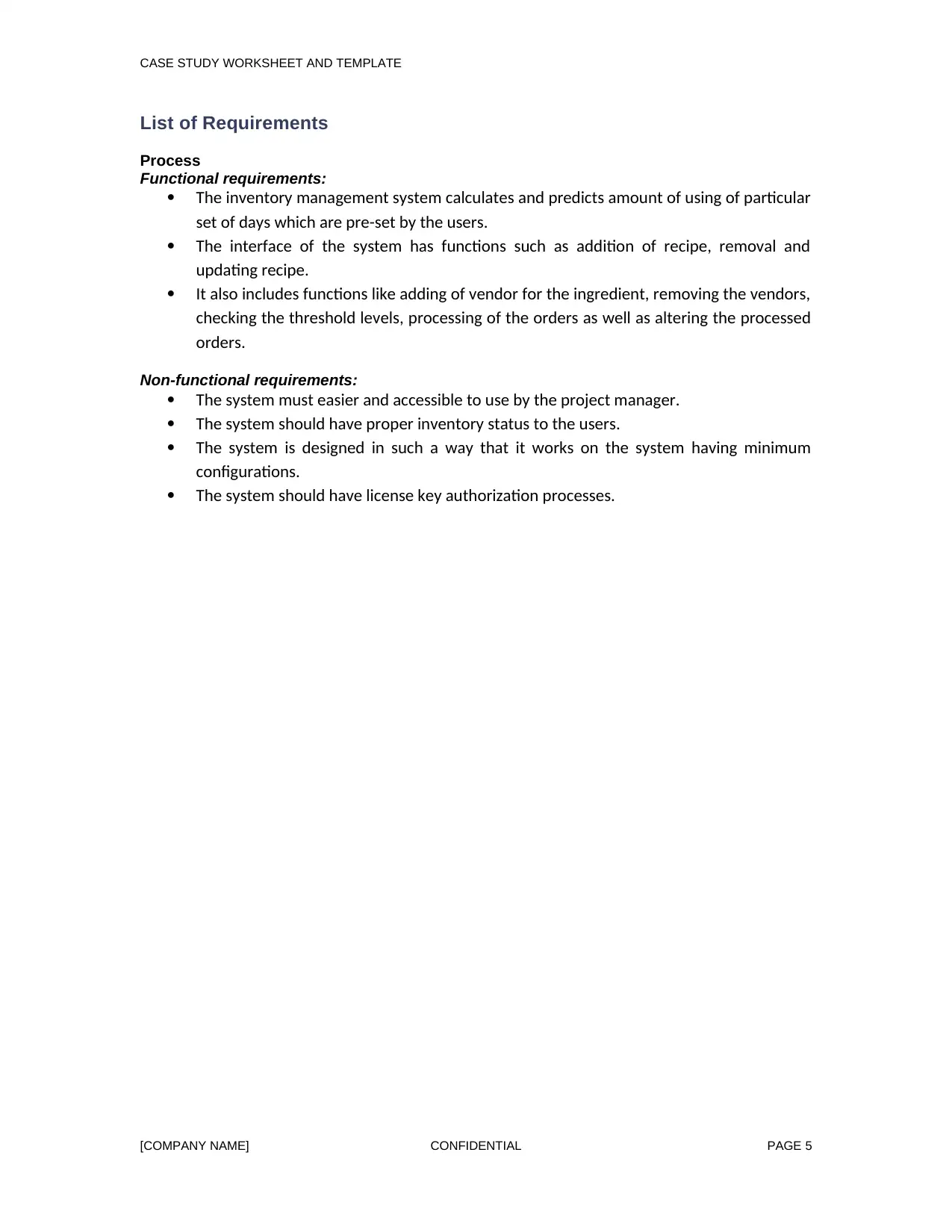
CASE STUDY WORKSHEET AND TEMPLATE
List of Requirements
Process
Functional requirements:
The inventory management system calculates and predicts amount of using of particular
set of days which are pre-set by the users.
The interface of the system has functions such as addition of recipe, removal and
updating recipe.
It also includes functions like adding of vendor for the ingredient, removing the vendors,
checking the threshold levels, processing of the orders as well as altering the processed
orders.
Non-functional requirements:
The system must easier and accessible to use by the project manager.
The system should have proper inventory status to the users.
The system is designed in such a way that it works on the system having minimum
configurations.
The system should have license key authorization processes.
[COMPANY NAME] CONFIDENTIAL PAGE 5
List of Requirements
Process
Functional requirements:
The inventory management system calculates and predicts amount of using of particular
set of days which are pre-set by the users.
The interface of the system has functions such as addition of recipe, removal and
updating recipe.
It also includes functions like adding of vendor for the ingredient, removing the vendors,
checking the threshold levels, processing of the orders as well as altering the processed
orders.
Non-functional requirements:
The system must easier and accessible to use by the project manager.
The system should have proper inventory status to the users.
The system is designed in such a way that it works on the system having minimum
configurations.
The system should have license key authorization processes.
[COMPANY NAME] CONFIDENTIAL PAGE 5
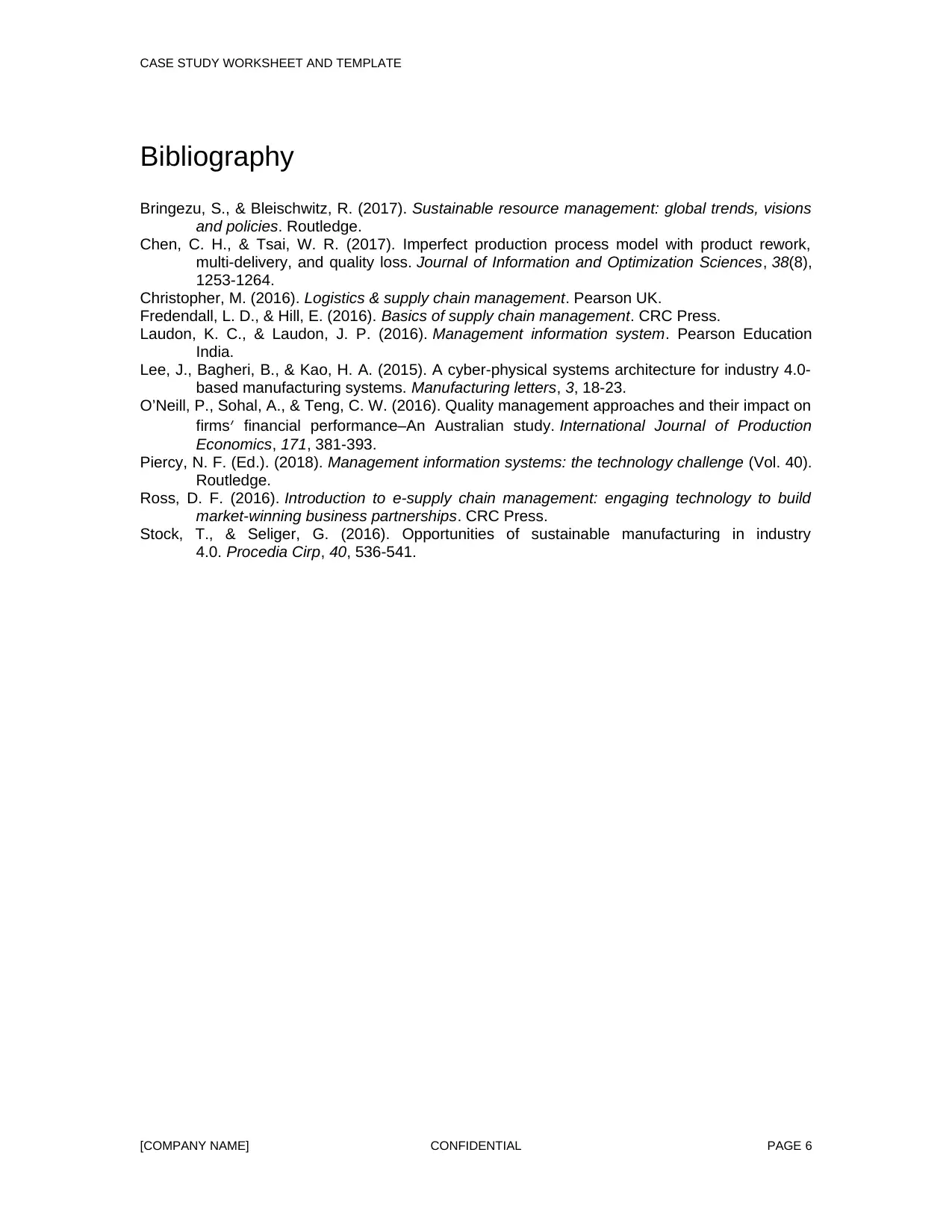
CASE STUDY WORKSHEET AND TEMPLATE
Bibliography
Bringezu, S., & Bleischwitz, R. (2017). Sustainable resource management: global trends, visions
and policies. Routledge.
Chen, C. H., & Tsai, W. R. (2017). Imperfect production process model with product rework,
multi-delivery, and quality loss. Journal of Information and Optimization Sciences, 38(8),
1253-1264.
Christopher, M. (2016). Logistics & supply chain management. Pearson UK.
Fredendall, L. D., & Hill, E. (2016). Basics of supply chain management. CRC Press.
Laudon, K. C., & Laudon, J. P. (2016). Management information system. Pearson Education
India.
Lee, J., Bagheri, B., & Kao, H. A. (2015). A cyber-physical systems architecture for industry 4.0-
based manufacturing systems. Manufacturing letters, 3, 18-23.
O’Neill, P., Sohal, A., & Teng, C. W. (2016). Quality management approaches and their impact on
firms׳ financial performance–An Australian study. International Journal of Production
Economics, 171, 381-393.
Piercy, N. F. (Ed.). (2018). Management information systems: the technology challenge (Vol. 40).
Routledge.
Ross, D. F. (2016). Introduction to e-supply chain management: engaging technology to build
market-winning business partnerships. CRC Press.
Stock, T., & Seliger, G. (2016). Opportunities of sustainable manufacturing in industry
4.0. Procedia Cirp, 40, 536-541.
[COMPANY NAME] CONFIDENTIAL PAGE 6
Bibliography
Bringezu, S., & Bleischwitz, R. (2017). Sustainable resource management: global trends, visions
and policies. Routledge.
Chen, C. H., & Tsai, W. R. (2017). Imperfect production process model with product rework,
multi-delivery, and quality loss. Journal of Information and Optimization Sciences, 38(8),
1253-1264.
Christopher, M. (2016). Logistics & supply chain management. Pearson UK.
Fredendall, L. D., & Hill, E. (2016). Basics of supply chain management. CRC Press.
Laudon, K. C., & Laudon, J. P. (2016). Management information system. Pearson Education
India.
Lee, J., Bagheri, B., & Kao, H. A. (2015). A cyber-physical systems architecture for industry 4.0-
based manufacturing systems. Manufacturing letters, 3, 18-23.
O’Neill, P., Sohal, A., & Teng, C. W. (2016). Quality management approaches and their impact on
firms׳ financial performance–An Australian study. International Journal of Production
Economics, 171, 381-393.
Piercy, N. F. (Ed.). (2018). Management information systems: the technology challenge (Vol. 40).
Routledge.
Ross, D. F. (2016). Introduction to e-supply chain management: engaging technology to build
market-winning business partnerships. CRC Press.
Stock, T., & Seliger, G. (2016). Opportunities of sustainable manufacturing in industry
4.0. Procedia Cirp, 40, 536-541.
[COMPANY NAME] CONFIDENTIAL PAGE 6
1 out of 10

Your All-in-One AI-Powered Toolkit for Academic Success.
+13062052269
info@desklib.com
Available 24*7 on WhatsApp / Email
Unlock your academic potential
© 2024 | Zucol Services PVT LTD | All rights reserved.