Final Report: Performance Analysis of a 4-Stroke Combustion Engine
VerifiedAdded on 2022/12/02
|26
|10560
|268
Report
AI Summary
This report presents a comprehensive performance analysis of a 4-stroke combustion engine. It begins with an introduction to internal combustion engines, their significance in energy development, and the technical background of 4-stroke engines, including intake, compression, power, and exhaust strokes. The report then delves into the performance analysis, comparing air-fuel ratios and detailing the experimental setup used. The results and discussion section analyzes the engine's performance based on the experimental data, followed by a conclusion summarizing the key findings and suggestions for future work. The report also includes a literature review covering various aspects of internal combustion engines, including fuel injection parameters and the historical development of these engines, and the report also includes figures and tables to support the findings. The study aims to characterize and parameterize the output of internal combustion engines to understand the factors influencing their functionality.
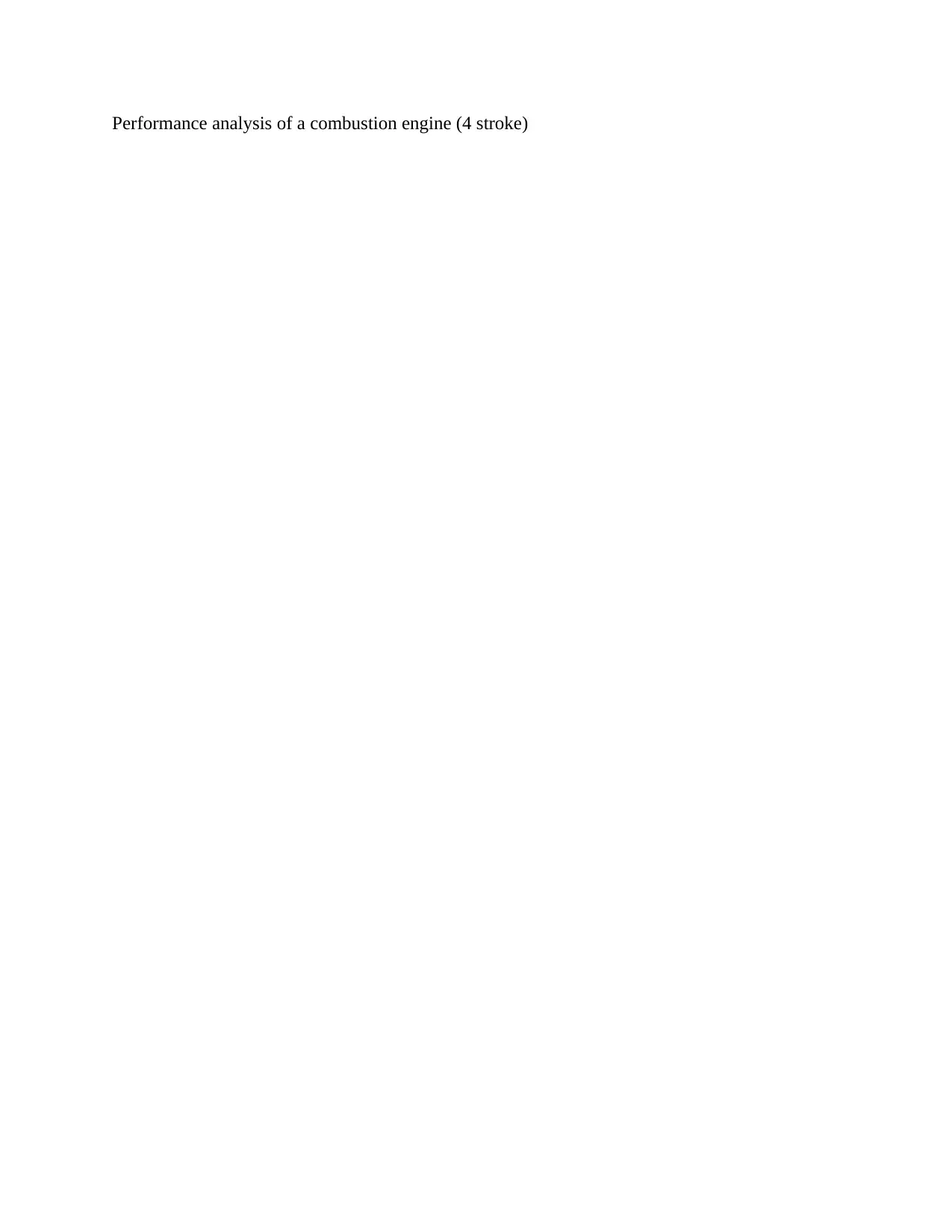
Performance analysis of a combustion engine (4 stroke)
Secure Best Marks with AI Grader
Need help grading? Try our AI Grader for instant feedback on your assignments.
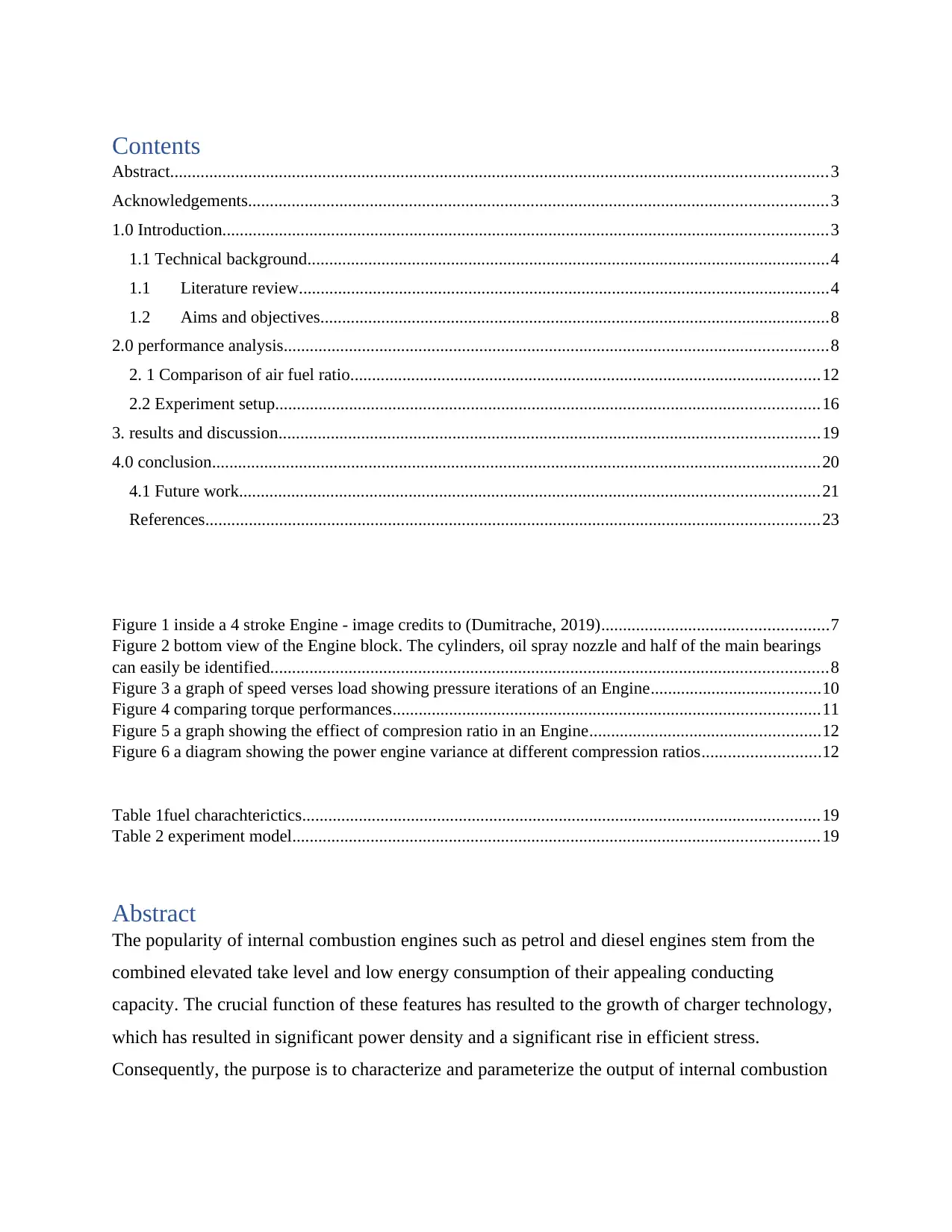
Contents
Abstract.......................................................................................................................................................3
Acknowledgements.....................................................................................................................................3
1.0 Introduction...........................................................................................................................................3
1.1 Technical background........................................................................................................................4
1.1 Literature review..........................................................................................................................4
1.2 Aims and objectives.....................................................................................................................8
2.0 performance analysis.............................................................................................................................8
2. 1 Comparison of air fuel ratio............................................................................................................12
2.2 Experiment setup.............................................................................................................................16
3. results and discussion............................................................................................................................19
4.0 conclusion............................................................................................................................................20
4.1 Future work.....................................................................................................................................21
References.............................................................................................................................................23
Figure 1 inside a 4 stroke Engine - image credits to (Dumitrache, 2019)....................................................7
Figure 2 bottom view of the Engine block. The cylinders, oil spray nozzle and half of the main bearings
can easily be identified................................................................................................................................8
Figure 3 a graph of speed verses load showing pressure iterations of an Engine.......................................10
Figure 4 comparing torque performances..................................................................................................11
Figure 5 a graph showing the effiect of compresion ratio in an Engine.....................................................12
Figure 6 a diagram showing the power engine variance at different compression ratios...........................12
Table 1fuel charachterictics.......................................................................................................................19
Table 2 experiment model.........................................................................................................................19
Abstract
The popularity of internal combustion engines such as petrol and diesel engines stem from the
combined elevated take level and low energy consumption of their appealing conducting
capacity. The crucial function of these features has resulted to the growth of charger technology,
which has resulted in significant power density and a significant rise in efficient stress.
Consequently, the purpose is to characterize and parameterize the output of internal combustion
Abstract.......................................................................................................................................................3
Acknowledgements.....................................................................................................................................3
1.0 Introduction...........................................................................................................................................3
1.1 Technical background........................................................................................................................4
1.1 Literature review..........................................................................................................................4
1.2 Aims and objectives.....................................................................................................................8
2.0 performance analysis.............................................................................................................................8
2. 1 Comparison of air fuel ratio............................................................................................................12
2.2 Experiment setup.............................................................................................................................16
3. results and discussion............................................................................................................................19
4.0 conclusion............................................................................................................................................20
4.1 Future work.....................................................................................................................................21
References.............................................................................................................................................23
Figure 1 inside a 4 stroke Engine - image credits to (Dumitrache, 2019)....................................................7
Figure 2 bottom view of the Engine block. The cylinders, oil spray nozzle and half of the main bearings
can easily be identified................................................................................................................................8
Figure 3 a graph of speed verses load showing pressure iterations of an Engine.......................................10
Figure 4 comparing torque performances..................................................................................................11
Figure 5 a graph showing the effiect of compresion ratio in an Engine.....................................................12
Figure 6 a diagram showing the power engine variance at different compression ratios...........................12
Table 1fuel charachterictics.......................................................................................................................19
Table 2 experiment model.........................................................................................................................19
Abstract
The popularity of internal combustion engines such as petrol and diesel engines stem from the
combined elevated take level and low energy consumption of their appealing conducting
capacity. The crucial function of these features has resulted to the growth of charger technology,
which has resulted in significant power density and a significant rise in efficient stress.
Consequently, the purpose is to characterize and parameterize the output of internal combustion
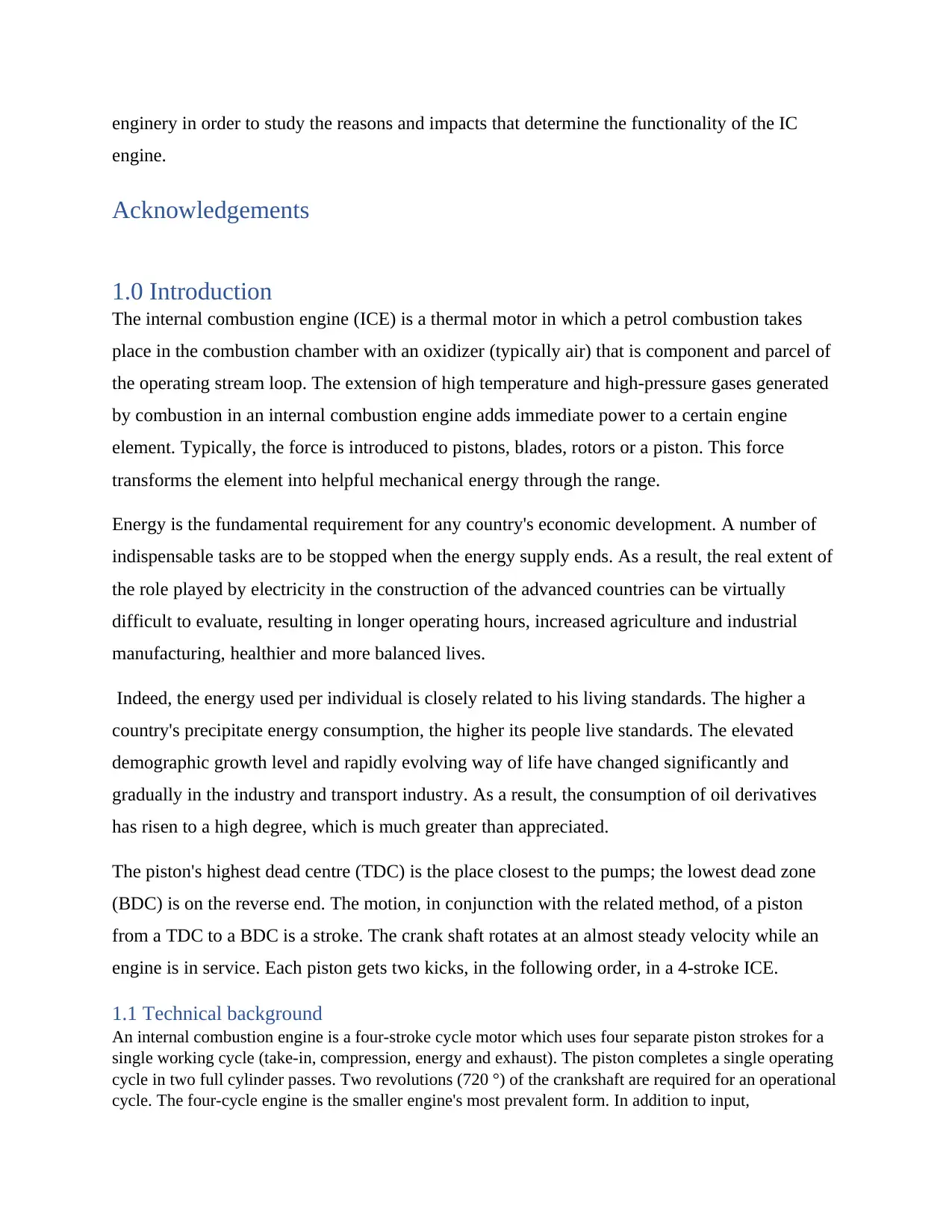
enginery in order to study the reasons and impacts that determine the functionality of the IC
engine.
Acknowledgements
1.0 Introduction
The internal combustion engine (ICE) is a thermal motor in which a petrol combustion takes
place in the combustion chamber with an oxidizer (typically air) that is component and parcel of
the operating stream loop. The extension of high temperature and high-pressure gases generated
by combustion in an internal combustion engine adds immediate power to a certain engine
element. Typically, the force is introduced to pistons, blades, rotors or a piston. This force
transforms the element into helpful mechanical energy through the range.
Energy is the fundamental requirement for any country's economic development. A number of
indispensable tasks are to be stopped when the energy supply ends. As a result, the real extent of
the role played by electricity in the construction of the advanced countries can be virtually
difficult to evaluate, resulting in longer operating hours, increased agriculture and industrial
manufacturing, healthier and more balanced lives.
Indeed, the energy used per individual is closely related to his living standards. The higher a
country's precipitate energy consumption, the higher its people live standards. The elevated
demographic growth level and rapidly evolving way of life have changed significantly and
gradually in the industry and transport industry. As a result, the consumption of oil derivatives
has risen to a high degree, which is much greater than appreciated.
The piston's highest dead centre (TDC) is the place closest to the pumps; the lowest dead zone
(BDC) is on the reverse end. The motion, in conjunction with the related method, of a piston
from a TDC to a BDC is a stroke. The crank shaft rotates at an almost steady velocity while an
engine is in service. Each piston gets two kicks, in the following order, in a 4-stroke ICE.
1.1 Technical background
An internal combustion engine is a four-stroke cycle motor which uses four separate piston strokes for a
single working cycle (take-in, compression, energy and exhaust). The piston completes a single operating
cycle in two full cylinder passes. Two revolutions (720 °) of the crankshaft are required for an operational
cycle. The four-cycle engine is the smaller engine's most prevalent form. In addition to input,
engine.
Acknowledgements
1.0 Introduction
The internal combustion engine (ICE) is a thermal motor in which a petrol combustion takes
place in the combustion chamber with an oxidizer (typically air) that is component and parcel of
the operating stream loop. The extension of high temperature and high-pressure gases generated
by combustion in an internal combustion engine adds immediate power to a certain engine
element. Typically, the force is introduced to pistons, blades, rotors or a piston. This force
transforms the element into helpful mechanical energy through the range.
Energy is the fundamental requirement for any country's economic development. A number of
indispensable tasks are to be stopped when the energy supply ends. As a result, the real extent of
the role played by electricity in the construction of the advanced countries can be virtually
difficult to evaluate, resulting in longer operating hours, increased agriculture and industrial
manufacturing, healthier and more balanced lives.
Indeed, the energy used per individual is closely related to his living standards. The higher a
country's precipitate energy consumption, the higher its people live standards. The elevated
demographic growth level and rapidly evolving way of life have changed significantly and
gradually in the industry and transport industry. As a result, the consumption of oil derivatives
has risen to a high degree, which is much greater than appreciated.
The piston's highest dead centre (TDC) is the place closest to the pumps; the lowest dead zone
(BDC) is on the reverse end. The motion, in conjunction with the related method, of a piston
from a TDC to a BDC is a stroke. The crank shaft rotates at an almost steady velocity while an
engine is in service. Each piston gets two kicks, in the following order, in a 4-stroke ICE.
1.1 Technical background
An internal combustion engine is a four-stroke cycle motor which uses four separate piston strokes for a
single working cycle (take-in, compression, energy and exhaust). The piston completes a single operating
cycle in two full cylinder passes. Two revolutions (720 °) of the crankshaft are required for an operational
cycle. The four-cycle engine is the smaller engine's most prevalent form. In addition to input,
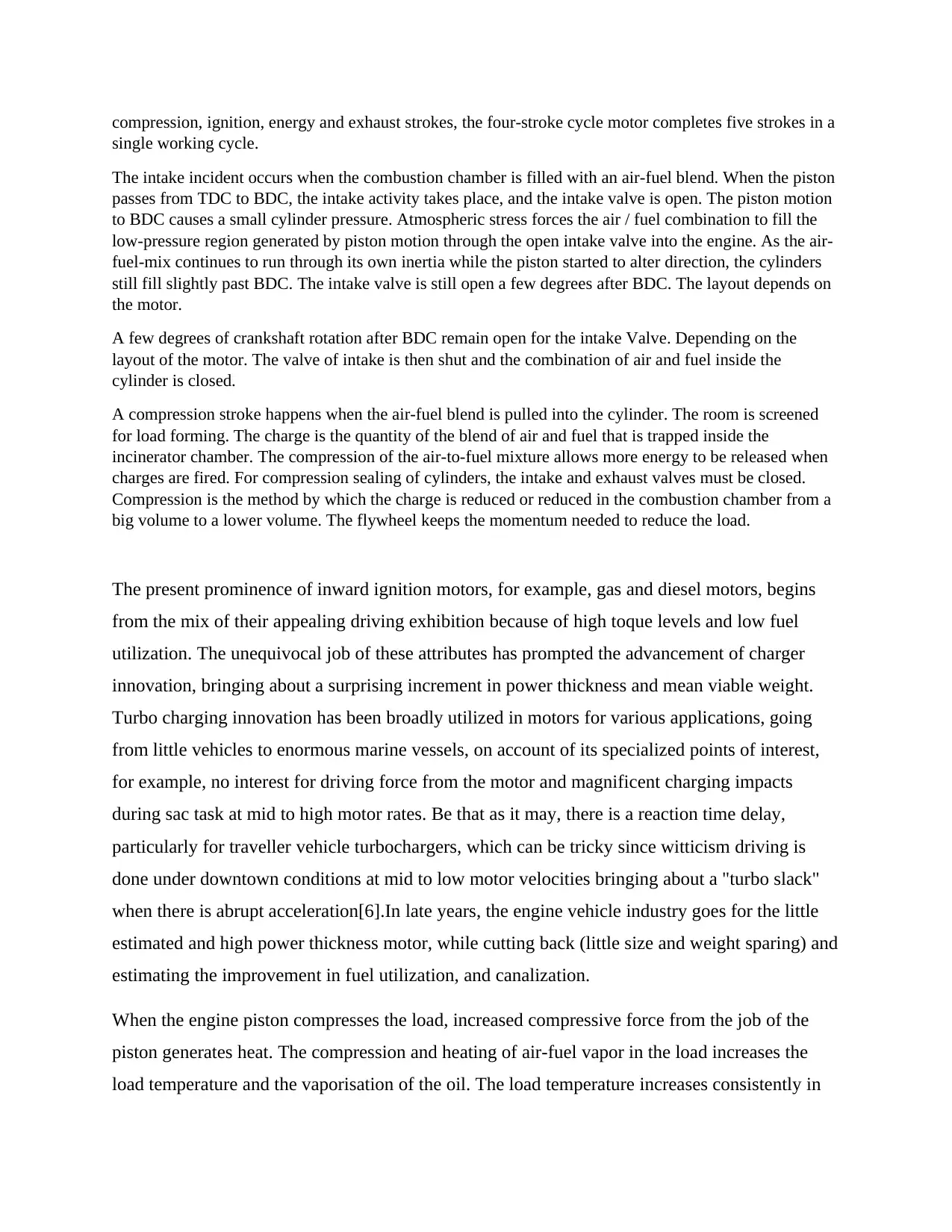
compression, ignition, energy and exhaust strokes, the four-stroke cycle motor completes five strokes in a
single working cycle.
The intake incident occurs when the combustion chamber is filled with an air-fuel blend. When the piston
passes from TDC to BDC, the intake activity takes place, and the intake valve is open. The piston motion
to BDC causes a small cylinder pressure. Atmospheric stress forces the air / fuel combination to fill the
low-pressure region generated by piston motion through the open intake valve into the engine. As the air-
fuel-mix continues to run through its own inertia while the piston started to alter direction, the cylinders
still fill slightly past BDC. The intake valve is still open a few degrees after BDC. The layout depends on
the motor.
A few degrees of crankshaft rotation after BDC remain open for the intake Valve. Depending on the
layout of the motor. The valve of intake is then shut and the combination of air and fuel inside the
cylinder is closed.
A compression stroke happens when the air-fuel blend is pulled into the cylinder. The room is screened
for load forming. The charge is the quantity of the blend of air and fuel that is trapped inside the
incinerator chamber. The compression of the air-to-fuel mixture allows more energy to be released when
charges are fired. For compression sealing of cylinders, the intake and exhaust valves must be closed.
Compression is the method by which the charge is reduced or reduced in the combustion chamber from a
big volume to a lower volume. The flywheel keeps the momentum needed to reduce the load.
The present prominence of inward ignition motors, for example, gas and diesel motors, begins
from the mix of their appealing driving exhibition because of high toque levels and low fuel
utilization. The unequivocal job of these attributes has prompted the advancement of charger
innovation, bringing about a surprising increment in power thickness and mean viable weight.
Turbo charging innovation has been broadly utilized in motors for various applications, going
from little vehicles to enormous marine vessels, on account of its specialized points of interest,
for example, no interest for driving force from the motor and magnificent charging impacts
during sac task at mid to high motor rates. Be that as it may, there is a reaction time delay,
particularly for traveller vehicle turbochargers, which can be tricky since witticism driving is
done under downtown conditions at mid to low motor velocities bringing about a "turbo slack"
when there is abrupt acceleration[6].In late years, the engine vehicle industry goes for the little
estimated and high power thickness motor, while cutting back (little size and weight sparing) and
estimating the improvement in fuel utilization, and canalization.
When the engine piston compresses the load, increased compressive force from the job of the
piston generates heat. The compression and heating of air-fuel vapor in the load increases the
load temperature and the vaporisation of the oil. The load temperature increases consistently in
single working cycle.
The intake incident occurs when the combustion chamber is filled with an air-fuel blend. When the piston
passes from TDC to BDC, the intake activity takes place, and the intake valve is open. The piston motion
to BDC causes a small cylinder pressure. Atmospheric stress forces the air / fuel combination to fill the
low-pressure region generated by piston motion through the open intake valve into the engine. As the air-
fuel-mix continues to run through its own inertia while the piston started to alter direction, the cylinders
still fill slightly past BDC. The intake valve is still open a few degrees after BDC. The layout depends on
the motor.
A few degrees of crankshaft rotation after BDC remain open for the intake Valve. Depending on the
layout of the motor. The valve of intake is then shut and the combination of air and fuel inside the
cylinder is closed.
A compression stroke happens when the air-fuel blend is pulled into the cylinder. The room is screened
for load forming. The charge is the quantity of the blend of air and fuel that is trapped inside the
incinerator chamber. The compression of the air-to-fuel mixture allows more energy to be released when
charges are fired. For compression sealing of cylinders, the intake and exhaust valves must be closed.
Compression is the method by which the charge is reduced or reduced in the combustion chamber from a
big volume to a lower volume. The flywheel keeps the momentum needed to reduce the load.
The present prominence of inward ignition motors, for example, gas and diesel motors, begins
from the mix of their appealing driving exhibition because of high toque levels and low fuel
utilization. The unequivocal job of these attributes has prompted the advancement of charger
innovation, bringing about a surprising increment in power thickness and mean viable weight.
Turbo charging innovation has been broadly utilized in motors for various applications, going
from little vehicles to enormous marine vessels, on account of its specialized points of interest,
for example, no interest for driving force from the motor and magnificent charging impacts
during sac task at mid to high motor rates. Be that as it may, there is a reaction time delay,
particularly for traveller vehicle turbochargers, which can be tricky since witticism driving is
done under downtown conditions at mid to low motor velocities bringing about a "turbo slack"
when there is abrupt acceleration[6].In late years, the engine vehicle industry goes for the little
estimated and high power thickness motor, while cutting back (little size and weight sparing) and
estimating the improvement in fuel utilization, and canalization.
When the engine piston compresses the load, increased compressive force from the job of the
piston generates heat. The compression and heating of air-fuel vapor in the load increases the
load temperature and the vaporisation of the oil. The load temperature increases consistently in
Secure Best Marks with AI Grader
Need help grading? Try our AI Grader for instant feedback on your assignments.
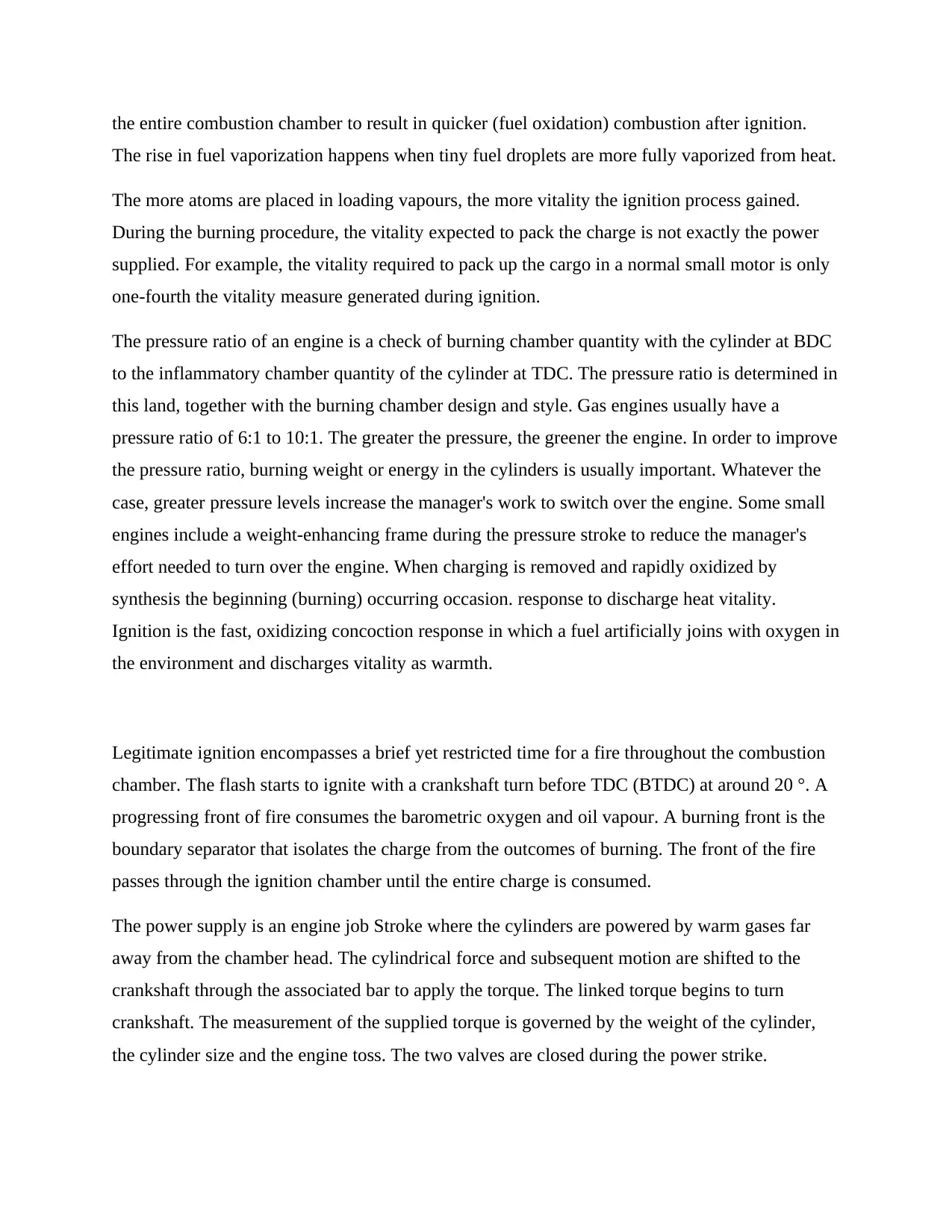
the entire combustion chamber to result in quicker (fuel oxidation) combustion after ignition.
The rise in fuel vaporization happens when tiny fuel droplets are more fully vaporized from heat.
The more atoms are placed in loading vapours, the more vitality the ignition process gained.
During the burning procedure, the vitality expected to pack the charge is not exactly the power
supplied. For example, the vitality required to pack up the cargo in a normal small motor is only
one-fourth the vitality measure generated during ignition.
The pressure ratio of an engine is a check of burning chamber quantity with the cylinder at BDC
to the inflammatory chamber quantity of the cylinder at TDC. The pressure ratio is determined in
this land, together with the burning chamber design and style. Gas engines usually have a
pressure ratio of 6:1 to 10:1. The greater the pressure, the greener the engine. In order to improve
the pressure ratio, burning weight or energy in the cylinders is usually important. Whatever the
case, greater pressure levels increase the manager's work to switch over the engine. Some small
engines include a weight-enhancing frame during the pressure stroke to reduce the manager's
effort needed to turn over the engine. When charging is removed and rapidly oxidized by
synthesis the beginning (burning) occurring occasion. response to discharge heat vitality.
Ignition is the fast, oxidizing concoction response in which a fuel artificially joins with oxygen in
the environment and discharges vitality as warmth.
Legitimate ignition encompasses a brief yet restricted time for a fire throughout the combustion
chamber. The flash starts to ignite with a crankshaft turn before TDC (BTDC) at around 20 °. A
progressing front of fire consumes the barometric oxygen and oil vapour. A burning front is the
boundary separator that isolates the charge from the outcomes of burning. The front of the fire
passes through the ignition chamber until the entire charge is consumed.
The power supply is an engine job Stroke where the cylinders are powered by warm gases far
away from the chamber head. The cylindrical force and subsequent motion are shifted to the
crankshaft through the associated bar to apply the torque. The linked torque begins to turn
crankshaft. The measurement of the supplied torque is governed by the weight of the cylinder,
the cylinder size and the engine toss. The two valves are closed during the power strike.
The rise in fuel vaporization happens when tiny fuel droplets are more fully vaporized from heat.
The more atoms are placed in loading vapours, the more vitality the ignition process gained.
During the burning procedure, the vitality expected to pack the charge is not exactly the power
supplied. For example, the vitality required to pack up the cargo in a normal small motor is only
one-fourth the vitality measure generated during ignition.
The pressure ratio of an engine is a check of burning chamber quantity with the cylinder at BDC
to the inflammatory chamber quantity of the cylinder at TDC. The pressure ratio is determined in
this land, together with the burning chamber design and style. Gas engines usually have a
pressure ratio of 6:1 to 10:1. The greater the pressure, the greener the engine. In order to improve
the pressure ratio, burning weight or energy in the cylinders is usually important. Whatever the
case, greater pressure levels increase the manager's work to switch over the engine. Some small
engines include a weight-enhancing frame during the pressure stroke to reduce the manager's
effort needed to turn over the engine. When charging is removed and rapidly oxidized by
synthesis the beginning (burning) occurring occasion. response to discharge heat vitality.
Ignition is the fast, oxidizing concoction response in which a fuel artificially joins with oxygen in
the environment and discharges vitality as warmth.
Legitimate ignition encompasses a brief yet restricted time for a fire throughout the combustion
chamber. The flash starts to ignite with a crankshaft turn before TDC (BTDC) at around 20 °. A
progressing front of fire consumes the barometric oxygen and oil vapour. A burning front is the
boundary separator that isolates the charge from the outcomes of burning. The front of the fire
passes through the ignition chamber until the entire charge is consumed.
The power supply is an engine job Stroke where the cylinders are powered by warm gases far
away from the chamber head. The cylindrical force and subsequent motion are shifted to the
crankshaft through the associated bar to apply the torque. The linked torque begins to turn
crankshaft. The measurement of the supplied torque is governed by the weight of the cylinder,
the cylinder size and the engine toss. The two valves are closed during the power strike.
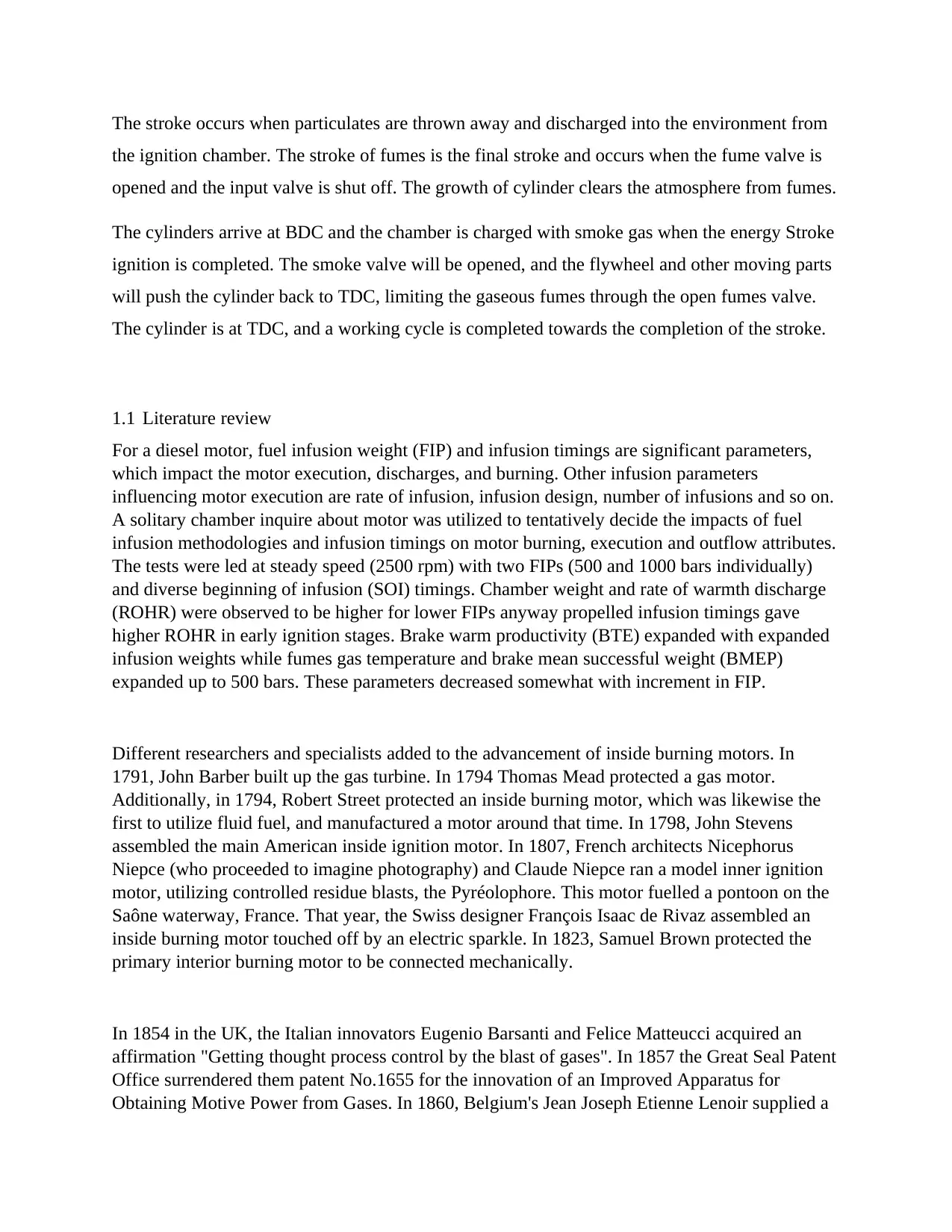
The stroke occurs when particulates are thrown away and discharged into the environment from
the ignition chamber. The stroke of fumes is the final stroke and occurs when the fume valve is
opened and the input valve is shut off. The growth of cylinder clears the atmosphere from fumes.
The cylinders arrive at BDC and the chamber is charged with smoke gas when the energy Stroke
ignition is completed. The smoke valve will be opened, and the flywheel and other moving parts
will push the cylinder back to TDC, limiting the gaseous fumes through the open fumes valve.
The cylinder is at TDC, and a working cycle is completed towards the completion of the stroke.
1.1 Literature review
For a diesel motor, fuel infusion weight (FIP) and infusion timings are significant parameters,
which impact the motor execution, discharges, and burning. Other infusion parameters
influencing motor execution are rate of infusion, infusion design, number of infusions and so on.
A solitary chamber inquire about motor was utilized to tentatively decide the impacts of fuel
infusion methodologies and infusion timings on motor burning, execution and outflow attributes.
The tests were led at steady speed (2500 rpm) with two FIPs (500 and 1000 bars individually)
and diverse beginning of infusion (SOI) timings. Chamber weight and rate of warmth discharge
(ROHR) were observed to be higher for lower FIPs anyway propelled infusion timings gave
higher ROHR in early ignition stages. Brake warm productivity (BTE) expanded with expanded
infusion weights while fumes gas temperature and brake mean successful weight (BMEP)
expanded up to 500 bars. These parameters decreased somewhat with increment in FIP.
Different researchers and specialists added to the advancement of inside burning motors. In
1791, John Barber built up the gas turbine. In 1794 Thomas Mead protected a gas motor.
Additionally, in 1794, Robert Street protected an inside burning motor, which was likewise the
first to utilize fluid fuel, and manufactured a motor around that time. In 1798, John Stevens
assembled the main American inside ignition motor. In 1807, French architects Nicephorus
Niepce (who proceeded to imagine photography) and Claude Niepce ran a model inner ignition
motor, utilizing controlled residue blasts, the Pyréolophore. This motor fuelled a pontoon on the
Saône waterway, France. That year, the Swiss designer François Isaac de Rivaz assembled an
inside burning motor touched off by an electric sparkle. In 1823, Samuel Brown protected the
primary interior burning motor to be connected mechanically.
In 1854 in the UK, the Italian innovators Eugenio Barsanti and Felice Matteucci acquired an
affirmation "Getting thought process control by the blast of gases". In 1857 the Great Seal Patent
Office surrendered them patent No.1655 for the innovation of an Improved Apparatus for
Obtaining Motive Power from Gases. In 1860, Belgium's Jean Joseph Etienne Lenoir supplied a
the ignition chamber. The stroke of fumes is the final stroke and occurs when the fume valve is
opened and the input valve is shut off. The growth of cylinder clears the atmosphere from fumes.
The cylinders arrive at BDC and the chamber is charged with smoke gas when the energy Stroke
ignition is completed. The smoke valve will be opened, and the flywheel and other moving parts
will push the cylinder back to TDC, limiting the gaseous fumes through the open fumes valve.
The cylinder is at TDC, and a working cycle is completed towards the completion of the stroke.
1.1 Literature review
For a diesel motor, fuel infusion weight (FIP) and infusion timings are significant parameters,
which impact the motor execution, discharges, and burning. Other infusion parameters
influencing motor execution are rate of infusion, infusion design, number of infusions and so on.
A solitary chamber inquire about motor was utilized to tentatively decide the impacts of fuel
infusion methodologies and infusion timings on motor burning, execution and outflow attributes.
The tests were led at steady speed (2500 rpm) with two FIPs (500 and 1000 bars individually)
and diverse beginning of infusion (SOI) timings. Chamber weight and rate of warmth discharge
(ROHR) were observed to be higher for lower FIPs anyway propelled infusion timings gave
higher ROHR in early ignition stages. Brake warm productivity (BTE) expanded with expanded
infusion weights while fumes gas temperature and brake mean successful weight (BMEP)
expanded up to 500 bars. These parameters decreased somewhat with increment in FIP.
Different researchers and specialists added to the advancement of inside burning motors. In
1791, John Barber built up the gas turbine. In 1794 Thomas Mead protected a gas motor.
Additionally, in 1794, Robert Street protected an inside burning motor, which was likewise the
first to utilize fluid fuel, and manufactured a motor around that time. In 1798, John Stevens
assembled the main American inside ignition motor. In 1807, French architects Nicephorus
Niepce (who proceeded to imagine photography) and Claude Niepce ran a model inner ignition
motor, utilizing controlled residue blasts, the Pyréolophore. This motor fuelled a pontoon on the
Saône waterway, France. That year, the Swiss designer François Isaac de Rivaz assembled an
inside burning motor touched off by an electric sparkle. In 1823, Samuel Brown protected the
primary interior burning motor to be connected mechanically.
In 1854 in the UK, the Italian innovators Eugenio Barsanti and Felice Matteucci acquired an
affirmation "Getting thought process control by the blast of gases". In 1857 the Great Seal Patent
Office surrendered them patent No.1655 for the innovation of an Improved Apparatus for
Obtaining Motive Power from Gases. In 1860, Belgium's Jean Joseph Etienne Lenoir supplied a
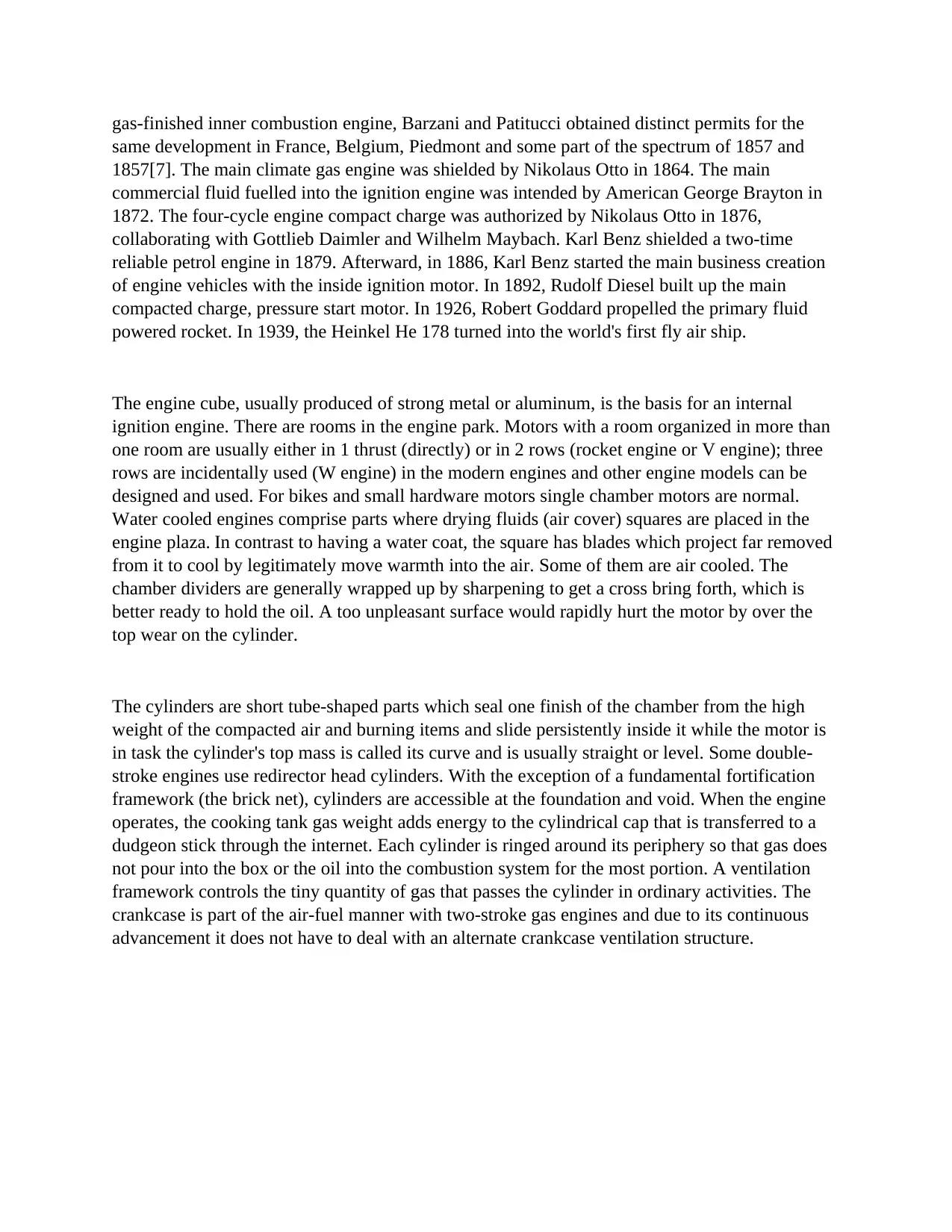
gas-finished inner combustion engine, Barzani and Patitucci obtained distinct permits for the
same development in France, Belgium, Piedmont and some part of the spectrum of 1857 and
1857[7]. The main climate gas engine was shielded by Nikolaus Otto in 1864. The main
commercial fluid fuelled into the ignition engine was intended by American George Brayton in
1872. The four-cycle engine compact charge was authorized by Nikolaus Otto in 1876,
collaborating with Gottlieb Daimler and Wilhelm Maybach. Karl Benz shielded a two-time
reliable petrol engine in 1879. Afterward, in 1886, Karl Benz started the main business creation
of engine vehicles with the inside ignition motor. In 1892, Rudolf Diesel built up the main
compacted charge, pressure start motor. In 1926, Robert Goddard propelled the primary fluid
powered rocket. In 1939, the Heinkel He 178 turned into the world's first fly air ship.
The engine cube, usually produced of strong metal or aluminum, is the basis for an internal
ignition engine. There are rooms in the engine park. Motors with a room organized in more than
one room are usually either in 1 thrust (directly) or in 2 rows (rocket engine or V engine); three
rows are incidentally used (W engine) in the modern engines and other engine models can be
designed and used. For bikes and small hardware motors single chamber motors are normal.
Water cooled engines comprise parts where drying fluids (air cover) squares are placed in the
engine plaza. In contrast to having a water coat, the square has blades which project far removed
from it to cool by legitimately move warmth into the air. Some of them are air cooled. The
chamber dividers are generally wrapped up by sharpening to get a cross bring forth, which is
better ready to hold the oil. A too unpleasant surface would rapidly hurt the motor by over the
top wear on the cylinder.
The cylinders are short tube-shaped parts which seal one finish of the chamber from the high
weight of the compacted air and burning items and slide persistently inside it while the motor is
in task the cylinder's top mass is called its curve and is usually straight or level. Some double-
stroke engines use redirector head cylinders. With the exception of a fundamental fortification
framework (the brick net), cylinders are accessible at the foundation and void. When the engine
operates, the cooking tank gas weight adds energy to the cylindrical cap that is transferred to a
dudgeon stick through the internet. Each cylinder is ringed around its periphery so that gas does
not pour into the box or the oil into the combustion system for the most portion. A ventilation
framework controls the tiny quantity of gas that passes the cylinder in ordinary activities. The
crankcase is part of the air-fuel manner with two-stroke gas engines and due to its continuous
advancement it does not have to deal with an alternate crankcase ventilation structure.
same development in France, Belgium, Piedmont and some part of the spectrum of 1857 and
1857[7]. The main climate gas engine was shielded by Nikolaus Otto in 1864. The main
commercial fluid fuelled into the ignition engine was intended by American George Brayton in
1872. The four-cycle engine compact charge was authorized by Nikolaus Otto in 1876,
collaborating with Gottlieb Daimler and Wilhelm Maybach. Karl Benz shielded a two-time
reliable petrol engine in 1879. Afterward, in 1886, Karl Benz started the main business creation
of engine vehicles with the inside ignition motor. In 1892, Rudolf Diesel built up the main
compacted charge, pressure start motor. In 1926, Robert Goddard propelled the primary fluid
powered rocket. In 1939, the Heinkel He 178 turned into the world's first fly air ship.
The engine cube, usually produced of strong metal or aluminum, is the basis for an internal
ignition engine. There are rooms in the engine park. Motors with a room organized in more than
one room are usually either in 1 thrust (directly) or in 2 rows (rocket engine or V engine); three
rows are incidentally used (W engine) in the modern engines and other engine models can be
designed and used. For bikes and small hardware motors single chamber motors are normal.
Water cooled engines comprise parts where drying fluids (air cover) squares are placed in the
engine plaza. In contrast to having a water coat, the square has blades which project far removed
from it to cool by legitimately move warmth into the air. Some of them are air cooled. The
chamber dividers are generally wrapped up by sharpening to get a cross bring forth, which is
better ready to hold the oil. A too unpleasant surface would rapidly hurt the motor by over the
top wear on the cylinder.
The cylinders are short tube-shaped parts which seal one finish of the chamber from the high
weight of the compacted air and burning items and slide persistently inside it while the motor is
in task the cylinder's top mass is called its curve and is usually straight or level. Some double-
stroke engines use redirector head cylinders. With the exception of a fundamental fortification
framework (the brick net), cylinders are accessible at the foundation and void. When the engine
operates, the cooking tank gas weight adds energy to the cylindrical cap that is transferred to a
dudgeon stick through the internet. Each cylinder is ringed around its periphery so that gas does
not pour into the box or the oil into the combustion system for the most portion. A ventilation
framework controls the tiny quantity of gas that passes the cylinder in ordinary activities. The
crankcase is part of the air-fuel manner with two-stroke gas engines and due to its continuous
advancement it does not have to deal with an alternate crankcase ventilation structure.
Paraphrase This Document
Need a fresh take? Get an instant paraphrase of this document with our AI Paraphraser
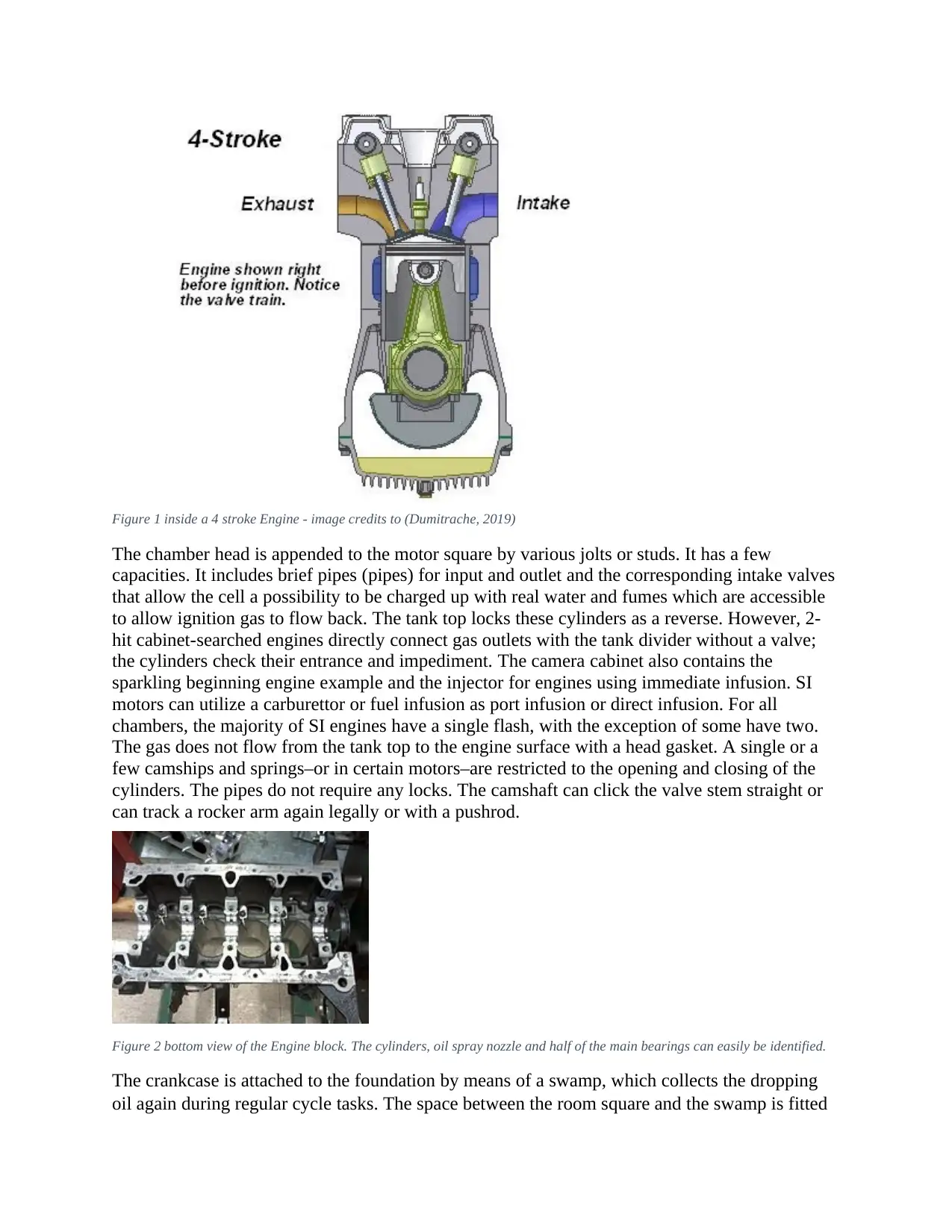
Figure 1 inside a 4 stroke Engine - image credits to (Dumitrache, 2019)
The chamber head is appended to the motor square by various jolts or studs. It has a few
capacities. It includes brief pipes (pipes) for input and outlet and the corresponding intake valves
that allow the cell a possibility to be charged up with real water and fumes which are accessible
to allow ignition gas to flow back. The tank top locks these cylinders as a reverse. However, 2-
hit cabinet-searched engines directly connect gas outlets with the tank divider without a valve;
the cylinders check their entrance and impediment. The camera cabinet also contains the
sparkling beginning engine example and the injector for engines using immediate infusion. SI
motors can utilize a carburettor or fuel infusion as port infusion or direct infusion. For all
chambers, the majority of SI engines have a single flash, with the exception of some have two.
The gas does not flow from the tank top to the engine surface with a head gasket. A single or a
few camships and springs–or in certain motors–are restricted to the opening and closing of the
cylinders. The pipes do not require any locks. The camshaft can click the valve stem straight or
can track a rocker arm again legally or with a pushrod.
Figure 2 bottom view of the Engine block. The cylinders, oil spray nozzle and half of the main bearings can easily be identified.
The crankcase is attached to the foundation by means of a swamp, which collects the dropping
oil again during regular cycle tasks. The space between the room square and the swamp is fitted
The chamber head is appended to the motor square by various jolts or studs. It has a few
capacities. It includes brief pipes (pipes) for input and outlet and the corresponding intake valves
that allow the cell a possibility to be charged up with real water and fumes which are accessible
to allow ignition gas to flow back. The tank top locks these cylinders as a reverse. However, 2-
hit cabinet-searched engines directly connect gas outlets with the tank divider without a valve;
the cylinders check their entrance and impediment. The camera cabinet also contains the
sparkling beginning engine example and the injector for engines using immediate infusion. SI
motors can utilize a carburettor or fuel infusion as port infusion or direct infusion. For all
chambers, the majority of SI engines have a single flash, with the exception of some have two.
The gas does not flow from the tank top to the engine surface with a head gasket. A single or a
few camships and springs–or in certain motors–are restricted to the opening and closing of the
cylinders. The pipes do not require any locks. The camshaft can click the valve stem straight or
can track a rocker arm again legally or with a pushrod.
Figure 2 bottom view of the Engine block. The cylinders, oil spray nozzle and half of the main bearings can easily be identified.
The crankcase is attached to the foundation by means of a swamp, which collects the dropping
oil again during regular cycle tasks. The space between the room square and the swamp is fitted
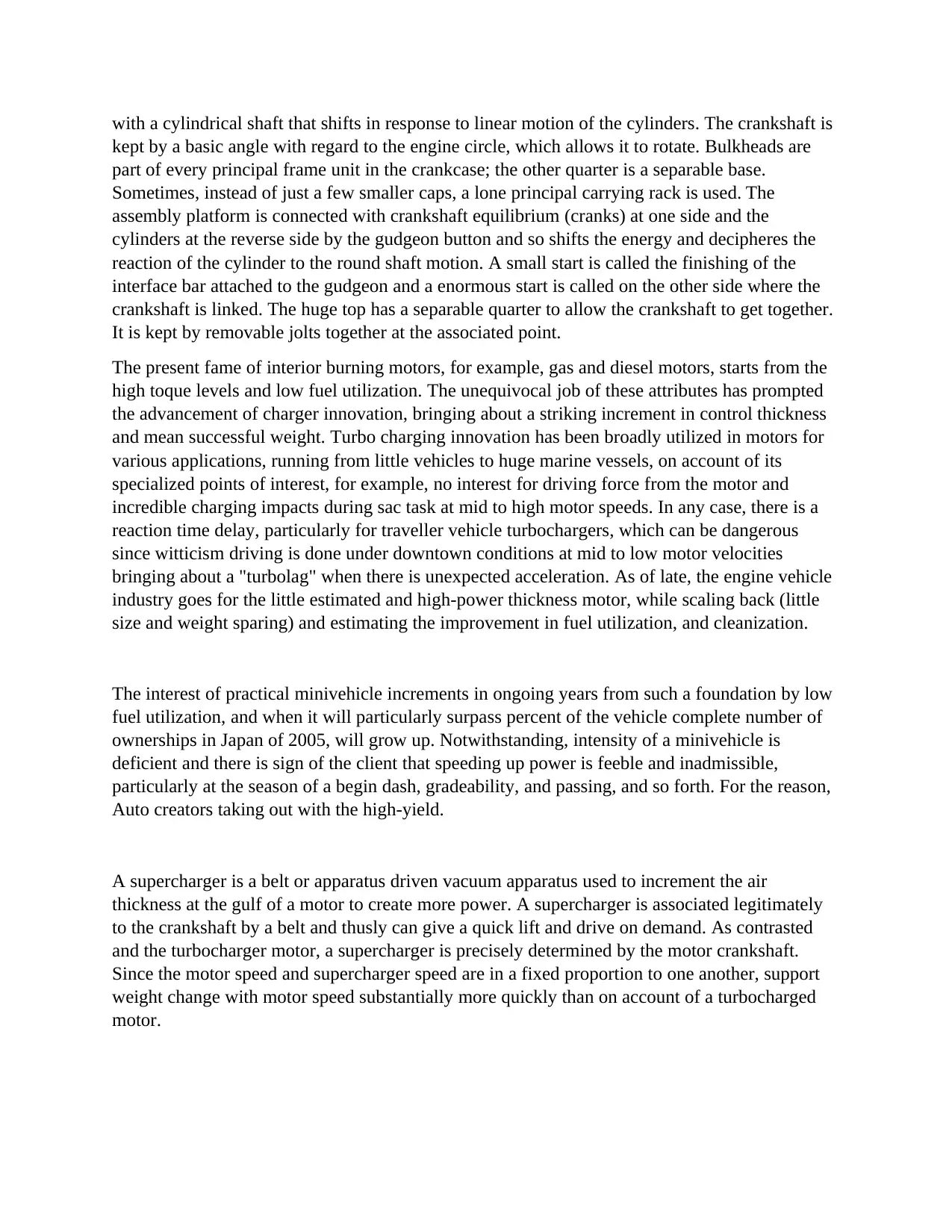
with a cylindrical shaft that shifts in response to linear motion of the cylinders. The crankshaft is
kept by a basic angle with regard to the engine circle, which allows it to rotate. Bulkheads are
part of every principal frame unit in the crankcase; the other quarter is a separable base.
Sometimes, instead of just a few smaller caps, a lone principal carrying rack is used. The
assembly platform is connected with crankshaft equilibrium (cranks) at one side and the
cylinders at the reverse side by the gudgeon button and so shifts the energy and decipheres the
reaction of the cylinder to the round shaft motion. A small start is called the finishing of the
interface bar attached to the gudgeon and a enormous start is called on the other side where the
crankshaft is linked. The huge top has a separable quarter to allow the crankshaft to get together.
It is kept by removable jolts together at the associated point.
The present fame of interior burning motors, for example, gas and diesel motors, starts from the
high toque levels and low fuel utilization. The unequivocal job of these attributes has prompted
the advancement of charger innovation, bringing about a striking increment in control thickness
and mean successful weight. Turbo charging innovation has been broadly utilized in motors for
various applications, running from little vehicles to huge marine vessels, on account of its
specialized points of interest, for example, no interest for driving force from the motor and
incredible charging impacts during sac task at mid to high motor speeds. In any case, there is a
reaction time delay, particularly for traveller vehicle turbochargers, which can be dangerous
since witticism driving is done under downtown conditions at mid to low motor velocities
bringing about a "turbolag" when there is unexpected acceleration. As of late, the engine vehicle
industry goes for the little estimated and high-power thickness motor, while scaling back (little
size and weight sparing) and estimating the improvement in fuel utilization, and cleanization.
The interest of practical minivehicle increments in ongoing years from such a foundation by low
fuel utilization, and when it will particularly surpass percent of the vehicle complete number of
ownerships in Japan of 2005, will grow up. Notwithstanding, intensity of a minivehicle is
deficient and there is sign of the client that speeding up power is feeble and inadmissible,
particularly at the season of a begin dash, gradeability, and passing, and so forth. For the reason,
Auto creators taking out with the high-yield.
A supercharger is a belt or apparatus driven vacuum apparatus used to increment the air
thickness at the gulf of a motor to create more power. A supercharger is associated legitimately
to the crankshaft by a belt and thusly can give a quick lift and drive on demand. As contrasted
and the turbocharger motor, a supercharger is precisely determined by the motor crankshaft.
Since the motor speed and supercharger speed are in a fixed proportion to one another, support
weight change with motor speed substantially more quickly than on account of a turbocharged
motor.
kept by a basic angle with regard to the engine circle, which allows it to rotate. Bulkheads are
part of every principal frame unit in the crankcase; the other quarter is a separable base.
Sometimes, instead of just a few smaller caps, a lone principal carrying rack is used. The
assembly platform is connected with crankshaft equilibrium (cranks) at one side and the
cylinders at the reverse side by the gudgeon button and so shifts the energy and decipheres the
reaction of the cylinder to the round shaft motion. A small start is called the finishing of the
interface bar attached to the gudgeon and a enormous start is called on the other side where the
crankshaft is linked. The huge top has a separable quarter to allow the crankshaft to get together.
It is kept by removable jolts together at the associated point.
The present fame of interior burning motors, for example, gas and diesel motors, starts from the
high toque levels and low fuel utilization. The unequivocal job of these attributes has prompted
the advancement of charger innovation, bringing about a striking increment in control thickness
and mean successful weight. Turbo charging innovation has been broadly utilized in motors for
various applications, running from little vehicles to huge marine vessels, on account of its
specialized points of interest, for example, no interest for driving force from the motor and
incredible charging impacts during sac task at mid to high motor speeds. In any case, there is a
reaction time delay, particularly for traveller vehicle turbochargers, which can be dangerous
since witticism driving is done under downtown conditions at mid to low motor velocities
bringing about a "turbolag" when there is unexpected acceleration. As of late, the engine vehicle
industry goes for the little estimated and high-power thickness motor, while scaling back (little
size and weight sparing) and estimating the improvement in fuel utilization, and cleanization.
The interest of practical minivehicle increments in ongoing years from such a foundation by low
fuel utilization, and when it will particularly surpass percent of the vehicle complete number of
ownerships in Japan of 2005, will grow up. Notwithstanding, intensity of a minivehicle is
deficient and there is sign of the client that speeding up power is feeble and inadmissible,
particularly at the season of a begin dash, gradeability, and passing, and so forth. For the reason,
Auto creators taking out with the high-yield.
A supercharger is a belt or apparatus driven vacuum apparatus used to increment the air
thickness at the gulf of a motor to create more power. A supercharger is associated legitimately
to the crankshaft by a belt and thusly can give a quick lift and drive on demand. As contrasted
and the turbocharger motor, a supercharger is precisely determined by the motor crankshaft.
Since the motor speed and supercharger speed are in a fixed proportion to one another, support
weight change with motor speed substantially more quickly than on account of a turbocharged
motor.
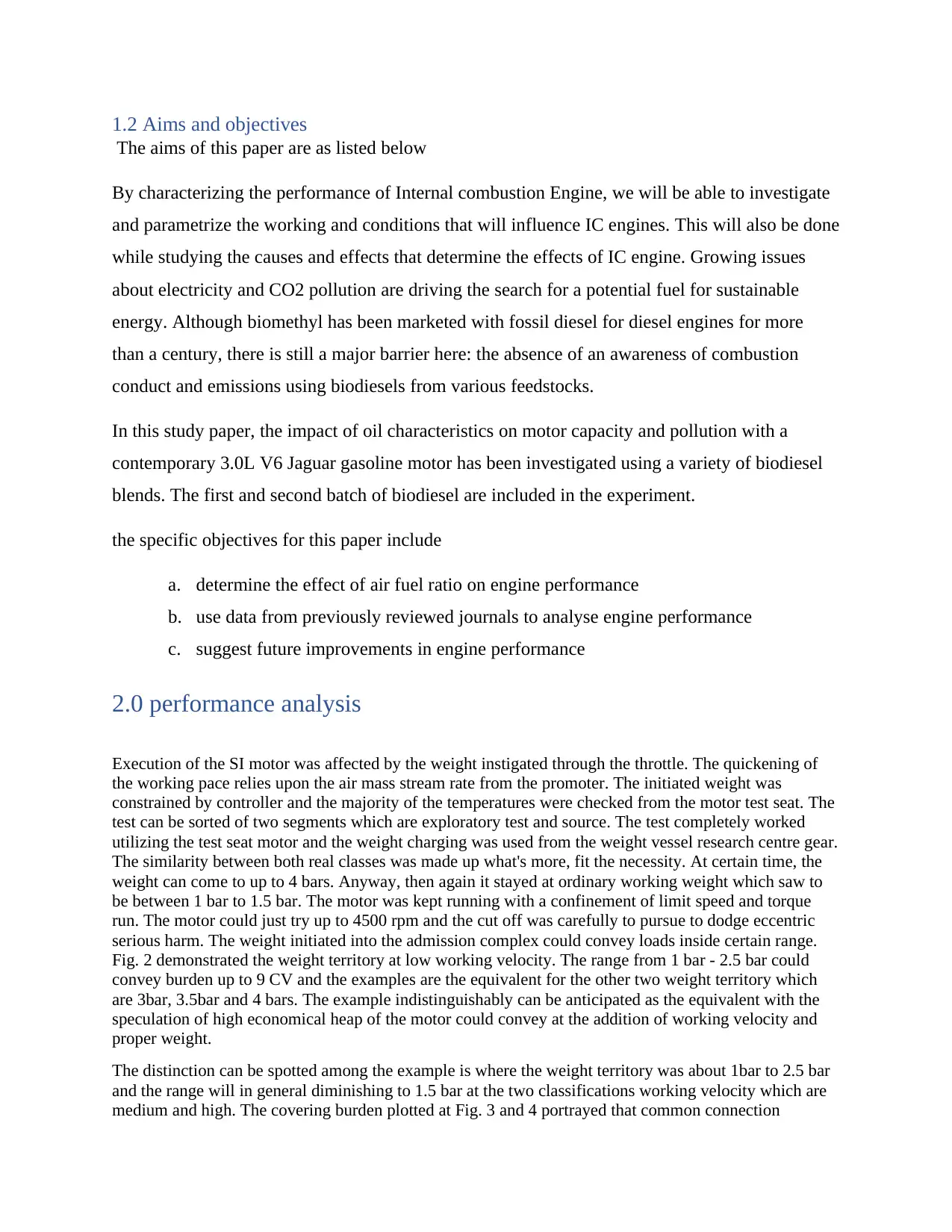
1.2 Aims and objectives
The aims of this paper are as listed below
By characterizing the performance of Internal combustion Engine, we will be able to investigate
and parametrize the working and conditions that will influence IC engines. This will also be done
while studying the causes and effects that determine the effects of IC engine. Growing issues
about electricity and CO2 pollution are driving the search for a potential fuel for sustainable
energy. Although biomethyl has been marketed with fossil diesel for diesel engines for more
than a century, there is still a major barrier here: the absence of an awareness of combustion
conduct and emissions using biodiesels from various feedstocks.
In this study paper, the impact of oil characteristics on motor capacity and pollution with a
contemporary 3.0L V6 Jaguar gasoline motor has been investigated using a variety of biodiesel
blends. The first and second batch of biodiesel are included in the experiment.
the specific objectives for this paper include
a. determine the effect of air fuel ratio on engine performance
b. use data from previously reviewed journals to analyse engine performance
c. suggest future improvements in engine performance
2.0 performance analysis
Execution of the SI motor was affected by the weight instigated through the throttle. The quickening of
the working pace relies upon the air mass stream rate from the promoter. The initiated weight was
constrained by controller and the majority of the temperatures were checked from the motor test seat. The
test can be sorted of two segments which are exploratory test and source. The test completely worked
utilizing the test seat motor and the weight charging was used from the weight vessel research centre gear.
The similarity between both real classes was made up what's more, fit the necessity. At certain time, the
weight can come to up to 4 bars. Anyway, then again it stayed at ordinary working weight which saw to
be between 1 bar to 1.5 bar. The motor was kept running with a confinement of limit speed and torque
run. The motor could just try up to 4500 rpm and the cut off was carefully to pursue to dodge eccentric
serious harm. The weight initiated into the admission complex could convey loads inside certain range.
Fig. 2 demonstrated the weight territory at low working velocity. The range from 1 bar - 2.5 bar could
convey burden up to 9 CV and the examples are the equivalent for the other two weight territory which
are 3bar, 3.5bar and 4 bars. The example indistinguishably can be anticipated as the equivalent with the
speculation of high economical heap of the motor could convey at the addition of working velocity and
proper weight.
The distinction can be spotted among the example is where the weight territory was about 1bar to 2.5 bar
and the range will in general diminishing to 1.5 bar at the two classifications working velocity which are
medium and high. The covering burden plotted at Fig. 3 and 4 portrayed that common connection
The aims of this paper are as listed below
By characterizing the performance of Internal combustion Engine, we will be able to investigate
and parametrize the working and conditions that will influence IC engines. This will also be done
while studying the causes and effects that determine the effects of IC engine. Growing issues
about electricity and CO2 pollution are driving the search for a potential fuel for sustainable
energy. Although biomethyl has been marketed with fossil diesel for diesel engines for more
than a century, there is still a major barrier here: the absence of an awareness of combustion
conduct and emissions using biodiesels from various feedstocks.
In this study paper, the impact of oil characteristics on motor capacity and pollution with a
contemporary 3.0L V6 Jaguar gasoline motor has been investigated using a variety of biodiesel
blends. The first and second batch of biodiesel are included in the experiment.
the specific objectives for this paper include
a. determine the effect of air fuel ratio on engine performance
b. use data from previously reviewed journals to analyse engine performance
c. suggest future improvements in engine performance
2.0 performance analysis
Execution of the SI motor was affected by the weight instigated through the throttle. The quickening of
the working pace relies upon the air mass stream rate from the promoter. The initiated weight was
constrained by controller and the majority of the temperatures were checked from the motor test seat. The
test can be sorted of two segments which are exploratory test and source. The test completely worked
utilizing the test seat motor and the weight charging was used from the weight vessel research centre gear.
The similarity between both real classes was made up what's more, fit the necessity. At certain time, the
weight can come to up to 4 bars. Anyway, then again it stayed at ordinary working weight which saw to
be between 1 bar to 1.5 bar. The motor was kept running with a confinement of limit speed and torque
run. The motor could just try up to 4500 rpm and the cut off was carefully to pursue to dodge eccentric
serious harm. The weight initiated into the admission complex could convey loads inside certain range.
Fig. 2 demonstrated the weight territory at low working velocity. The range from 1 bar - 2.5 bar could
convey burden up to 9 CV and the examples are the equivalent for the other two weight territory which
are 3bar, 3.5bar and 4 bars. The example indistinguishably can be anticipated as the equivalent with the
speculation of high economical heap of the motor could convey at the addition of working velocity and
proper weight.
The distinction can be spotted among the example is where the weight territory was about 1bar to 2.5 bar
and the range will in general diminishing to 1.5 bar at the two classifications working velocity which are
medium and high. The covering burden plotted at Fig. 3 and 4 portrayed that common connection
Secure Best Marks with AI Grader
Need help grading? Try our AI Grader for instant feedback on your assignments.
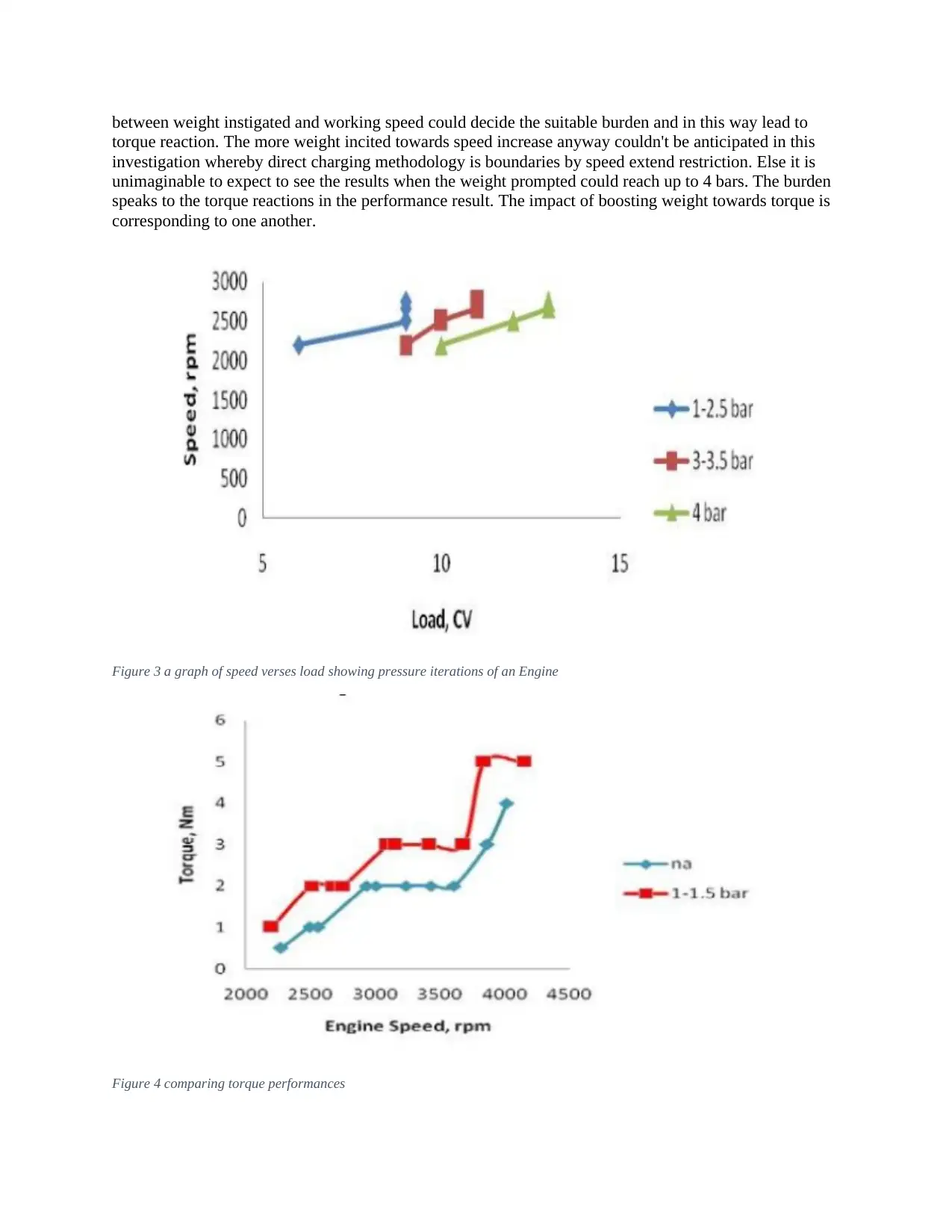
between weight instigated and working speed could decide the suitable burden and in this way lead to
torque reaction. The more weight incited towards speed increase anyway couldn't be anticipated in this
investigation whereby direct charging methodology is boundaries by speed extend restriction. Else it is
unimaginable to expect to see the results when the weight prompted could reach up to 4 bars. The burden
speaks to the torque reactions in the performance result. The impact of boosting weight towards torque is
corresponding to one another.
Figure 3 a graph of speed verses load showing pressure iterations of an Engine
Figure 4 comparing torque performances
torque reaction. The more weight incited towards speed increase anyway couldn't be anticipated in this
investigation whereby direct charging methodology is boundaries by speed extend restriction. Else it is
unimaginable to expect to see the results when the weight prompted could reach up to 4 bars. The burden
speaks to the torque reactions in the performance result. The impact of boosting weight towards torque is
corresponding to one another.
Figure 3 a graph of speed verses load showing pressure iterations of an Engine
Figure 4 comparing torque performances
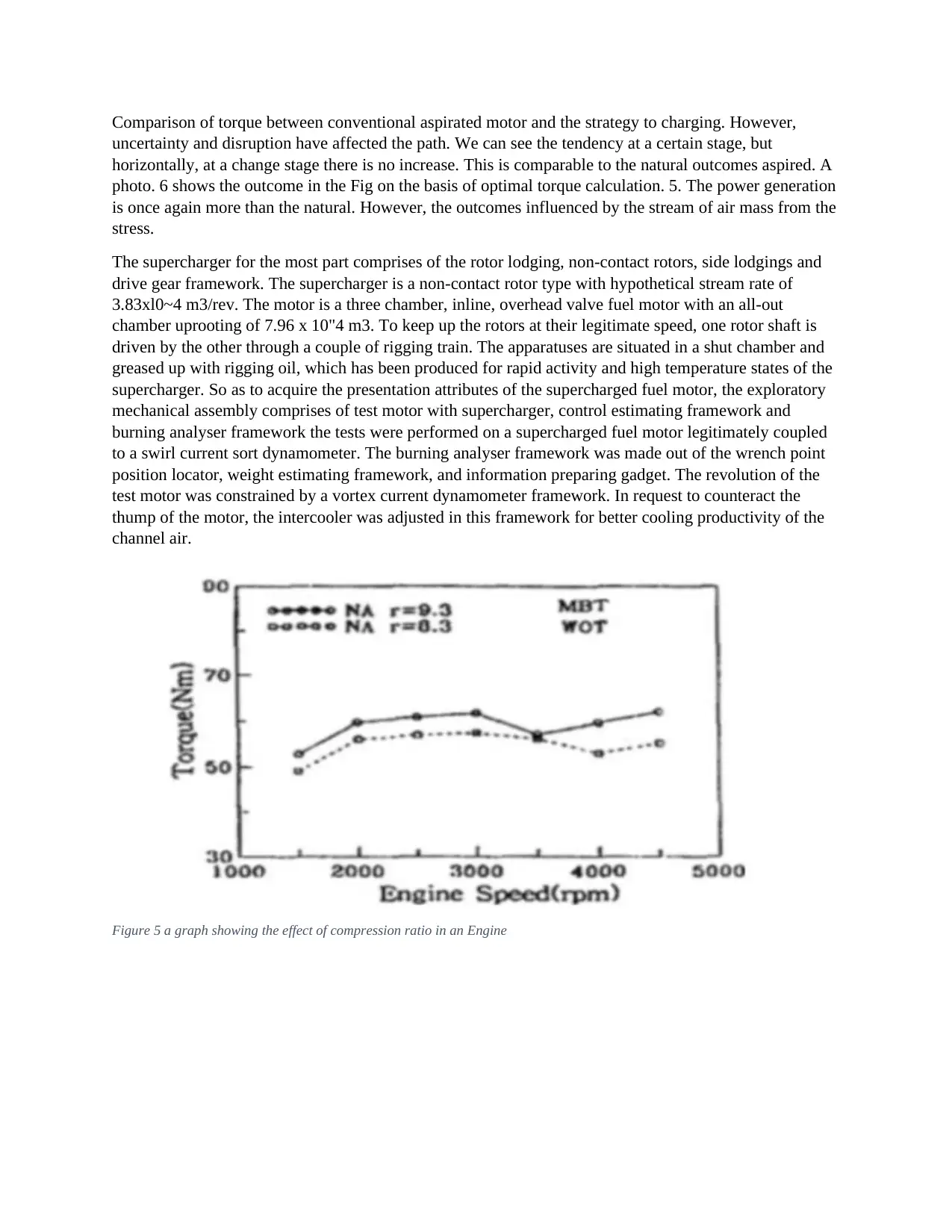
Comparison of torque between conventional aspirated motor and the strategy to charging. However,
uncertainty and disruption have affected the path. We can see the tendency at a certain stage, but
horizontally, at a change stage there is no increase. This is comparable to the natural outcomes aspired. A
photo. 6 shows the outcome in the Fig on the basis of optimal torque calculation. 5. The power generation
is once again more than the natural. However, the outcomes influenced by the stream of air mass from the
stress.
The supercharger for the most part comprises of the rotor lodging, non-contact rotors, side lodgings and
drive gear framework. The supercharger is a non-contact rotor type with hypothetical stream rate of
3.83xl0~4 m3/rev. The motor is a three chamber, inline, overhead valve fuel motor with an all-out
chamber uprooting of 7.96 x 10"4 m3. To keep up the rotors at their legitimate speed, one rotor shaft is
driven by the other through a couple of rigging train. The apparatuses are situated in a shut chamber and
greased up with rigging oil, which has been produced for rapid activity and high temperature states of the
supercharger. So as to acquire the presentation attributes of the supercharged fuel motor, the exploratory
mechanical assembly comprises of test motor with supercharger, control estimating framework and
burning analyser framework the tests were performed on a supercharged fuel motor legitimately coupled
to a swirl current sort dynamometer. The burning analyser framework was made out of the wrench point
position locator, weight estimating framework, and information preparing gadget. The revolution of the
test motor was constrained by a vortex current dynamometer framework. In request to counteract the
thump of the motor, the intercooler was adjusted in this framework for better cooling productivity of the
channel air.
Figure 5 a graph showing the effect of compression ratio in an Engine
uncertainty and disruption have affected the path. We can see the tendency at a certain stage, but
horizontally, at a change stage there is no increase. This is comparable to the natural outcomes aspired. A
photo. 6 shows the outcome in the Fig on the basis of optimal torque calculation. 5. The power generation
is once again more than the natural. However, the outcomes influenced by the stream of air mass from the
stress.
The supercharger for the most part comprises of the rotor lodging, non-contact rotors, side lodgings and
drive gear framework. The supercharger is a non-contact rotor type with hypothetical stream rate of
3.83xl0~4 m3/rev. The motor is a three chamber, inline, overhead valve fuel motor with an all-out
chamber uprooting of 7.96 x 10"4 m3. To keep up the rotors at their legitimate speed, one rotor shaft is
driven by the other through a couple of rigging train. The apparatuses are situated in a shut chamber and
greased up with rigging oil, which has been produced for rapid activity and high temperature states of the
supercharger. So as to acquire the presentation attributes of the supercharged fuel motor, the exploratory
mechanical assembly comprises of test motor with supercharger, control estimating framework and
burning analyser framework the tests were performed on a supercharged fuel motor legitimately coupled
to a swirl current sort dynamometer. The burning analyser framework was made out of the wrench point
position locator, weight estimating framework, and information preparing gadget. The revolution of the
test motor was constrained by a vortex current dynamometer framework. In request to counteract the
thump of the motor, the intercooler was adjusted in this framework for better cooling productivity of the
channel air.
Figure 5 a graph showing the effect of compression ratio in an Engine
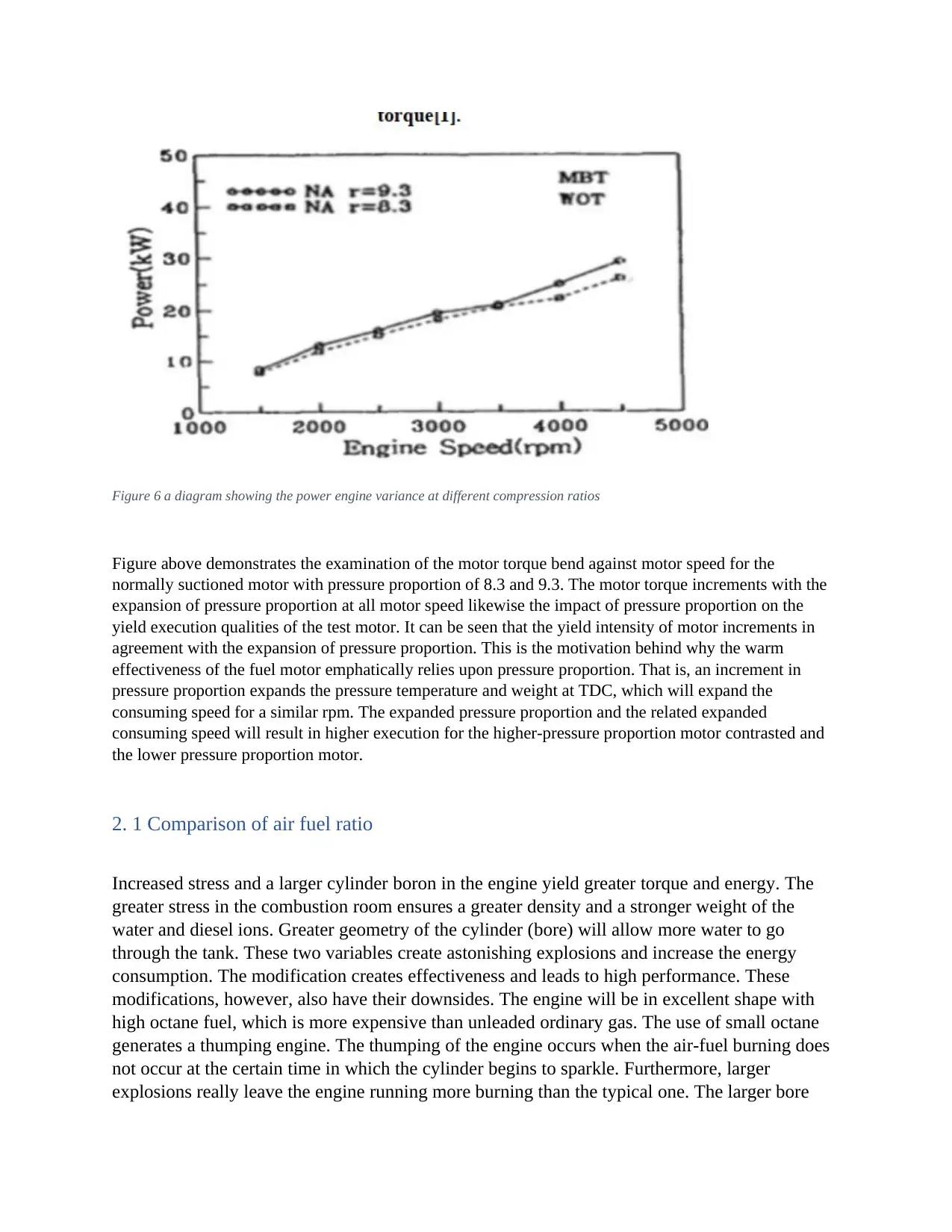
Figure 6 a diagram showing the power engine variance at different compression ratios
Figure above demonstrates the examination of the motor torque bend against motor speed for the
normally suctioned motor with pressure proportion of 8.3 and 9.3. The motor torque increments with the
expansion of pressure proportion at all motor speed likewise the impact of pressure proportion on the
yield execution qualities of the test motor. It can be seen that the yield intensity of motor increments in
agreement with the expansion of pressure proportion. This is the motivation behind why the warm
effectiveness of the fuel motor emphatically relies upon pressure proportion. That is, an increment in
pressure proportion expands the pressure temperature and weight at TDC, which will expand the
consuming speed for a similar rpm. The expanded pressure proportion and the related expanded
consuming speed will result in higher execution for the higher-pressure proportion motor contrasted and
the lower pressure proportion motor.
2. 1 Comparison of air fuel ratio
Increased stress and a larger cylinder boron in the engine yield greater torque and energy. The
greater stress in the combustion room ensures a greater density and a stronger weight of the
water and diesel ions. Greater geometry of the cylinder (bore) will allow more water to go
through the tank. These two variables create astonishing explosions and increase the energy
consumption. The modification creates effectiveness and leads to high performance. These
modifications, however, also have their downsides. The engine will be in excellent shape with
high octane fuel, which is more expensive than unleaded ordinary gas. The use of small octane
generates a thumping engine. The thumping of the engine occurs when the air-fuel burning does
not occur at the certain time in which the cylinder begins to sparkle. Furthermore, larger
explosions really leave the engine running more burning than the typical one. The larger bore
Figure above demonstrates the examination of the motor torque bend against motor speed for the
normally suctioned motor with pressure proportion of 8.3 and 9.3. The motor torque increments with the
expansion of pressure proportion at all motor speed likewise the impact of pressure proportion on the
yield execution qualities of the test motor. It can be seen that the yield intensity of motor increments in
agreement with the expansion of pressure proportion. This is the motivation behind why the warm
effectiveness of the fuel motor emphatically relies upon pressure proportion. That is, an increment in
pressure proportion expands the pressure temperature and weight at TDC, which will expand the
consuming speed for a similar rpm. The expanded pressure proportion and the related expanded
consuming speed will result in higher execution for the higher-pressure proportion motor contrasted and
the lower pressure proportion motor.
2. 1 Comparison of air fuel ratio
Increased stress and a larger cylinder boron in the engine yield greater torque and energy. The
greater stress in the combustion room ensures a greater density and a stronger weight of the
water and diesel ions. Greater geometry of the cylinder (bore) will allow more water to go
through the tank. These two variables create astonishing explosions and increase the energy
consumption. The modification creates effectiveness and leads to high performance. These
modifications, however, also have their downsides. The engine will be in excellent shape with
high octane fuel, which is more expensive than unleaded ordinary gas. The use of small octane
generates a thumping engine. The thumping of the engine occurs when the air-fuel burning does
not occur at the certain time in which the cylinder begins to sparkle. Furthermore, larger
explosions really leave the engine running more burning than the typical one. The larger bore
Paraphrase This Document
Need a fresh take? Get an instant paraphrase of this document with our AI Paraphraser
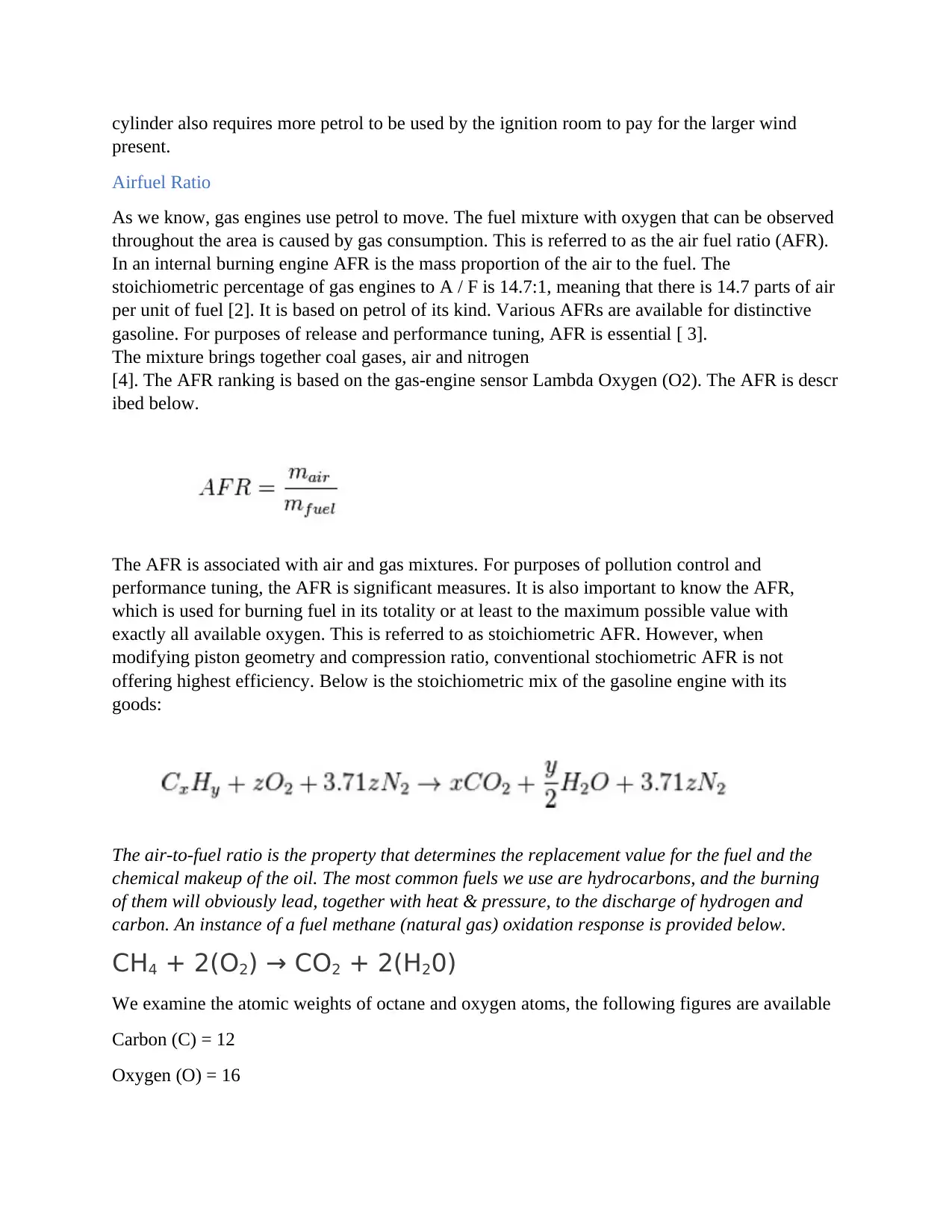
cylinder also requires more petrol to be used by the ignition room to pay for the larger wind
present.
Airfuel Ratio
As we know, gas engines use petrol to move. The fuel mixture with oxygen that can be observed
throughout the area is caused by gas consumption. This is referred to as the air fuel ratio (AFR).
In an internal burning engine AFR is the mass proportion of the air to the fuel. The
stoichiometric percentage of gas engines to A / F is 14.7:1, meaning that there is 14.7 parts of air
per unit of fuel [2]. It is based on petrol of its kind. Various AFRs are available for distinctive
gasoline. For purposes of release and performance tuning, AFR is essential [ 3].
The mixture brings together coal gases, air and nitrogen
[4]. The AFR ranking is based on the gas-engine sensor Lambda Oxygen (O2). The AFR is descr
ibed below.
The AFR is associated with air and gas mixtures. For purposes of pollution control and
performance tuning, the AFR is significant measures. It is also important to know the AFR,
which is used for burning fuel in its totality or at least to the maximum possible value with
exactly all available oxygen. This is referred to as stoichiometric AFR. However, when
modifying piston geometry and compression ratio, conventional stochiometric AFR is not
offering highest efficiency. Below is the stoichiometric mix of the gasoline engine with its
goods:
The air-to-fuel ratio is the property that determines the replacement value for the fuel and the
chemical makeup of the oil. The most common fuels we use are hydrocarbons, and the burning
of them will obviously lead, together with heat & pressure, to the discharge of hydrogen and
carbon. An instance of a fuel methane (natural gas) oxidation response is provided below.
CH4 + 2(O2) → CO2 + 2(H20)
We examine the atomic weights of octane and oxygen atoms, the following figures are available
Carbon (C) = 12
Oxygen (O) = 16
present.
Airfuel Ratio
As we know, gas engines use petrol to move. The fuel mixture with oxygen that can be observed
throughout the area is caused by gas consumption. This is referred to as the air fuel ratio (AFR).
In an internal burning engine AFR is the mass proportion of the air to the fuel. The
stoichiometric percentage of gas engines to A / F is 14.7:1, meaning that there is 14.7 parts of air
per unit of fuel [2]. It is based on petrol of its kind. Various AFRs are available for distinctive
gasoline. For purposes of release and performance tuning, AFR is essential [ 3].
The mixture brings together coal gases, air and nitrogen
[4]. The AFR ranking is based on the gas-engine sensor Lambda Oxygen (O2). The AFR is descr
ibed below.
The AFR is associated with air and gas mixtures. For purposes of pollution control and
performance tuning, the AFR is significant measures. It is also important to know the AFR,
which is used for burning fuel in its totality or at least to the maximum possible value with
exactly all available oxygen. This is referred to as stoichiometric AFR. However, when
modifying piston geometry and compression ratio, conventional stochiometric AFR is not
offering highest efficiency. Below is the stoichiometric mix of the gasoline engine with its
goods:
The air-to-fuel ratio is the property that determines the replacement value for the fuel and the
chemical makeup of the oil. The most common fuels we use are hydrocarbons, and the burning
of them will obviously lead, together with heat & pressure, to the discharge of hydrogen and
carbon. An instance of a fuel methane (natural gas) oxidation response is provided below.
CH4 + 2(O2) → CO2 + 2(H20)
We examine the atomic weights of octane and oxygen atoms, the following figures are available
Carbon (C) = 12
Oxygen (O) = 16
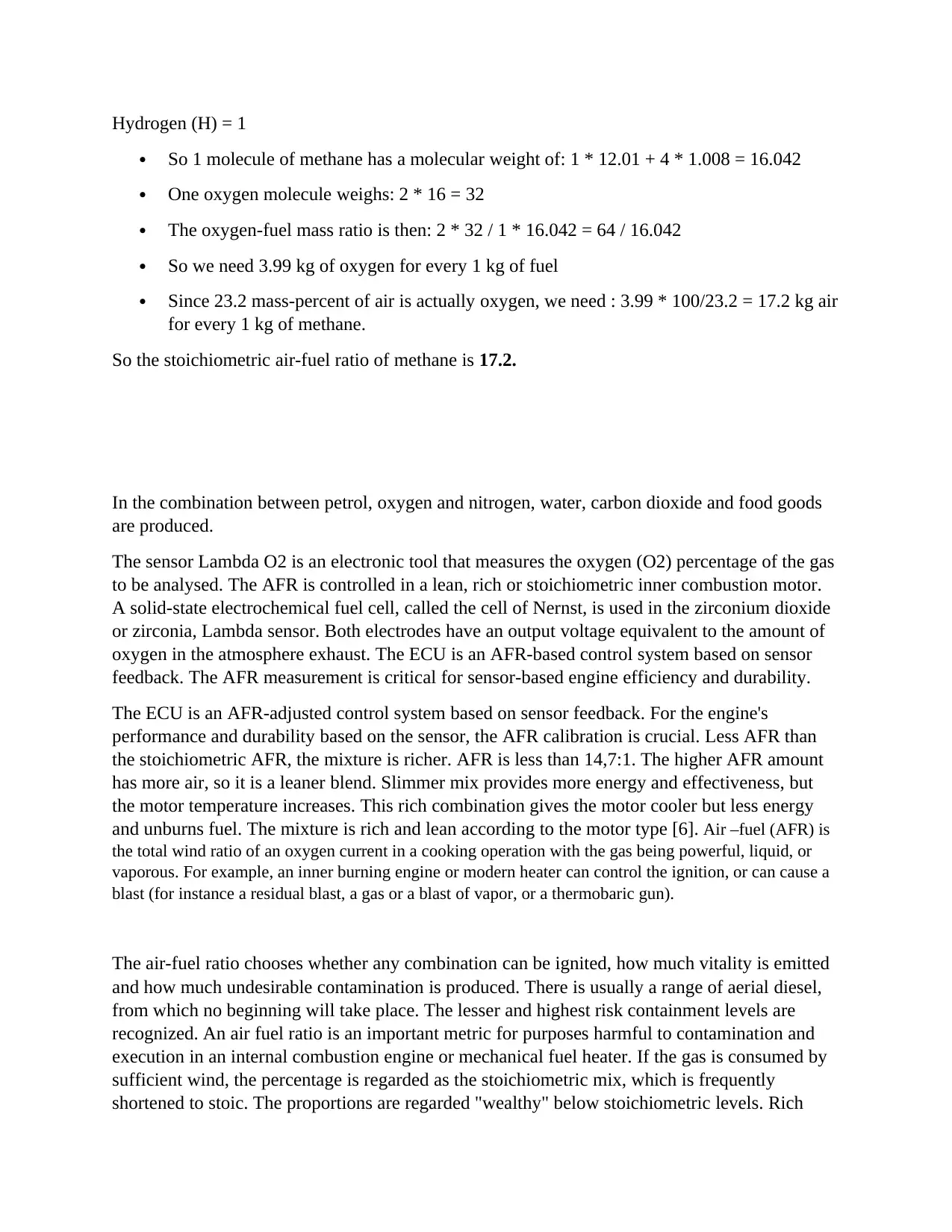
Hydrogen (H) = 1
So 1 molecule of methane has a molecular weight of: 1 * 12.01 + 4 * 1.008 = 16.042
One oxygen molecule weighs: 2 * 16 = 32
The oxygen-fuel mass ratio is then: 2 * 32 / 1 * 16.042 = 64 / 16.042
So we need 3.99 kg of oxygen for every 1 kg of fuel
Since 23.2 mass-percent of air is actually oxygen, we need : 3.99 * 100/23.2 = 17.2 kg air
for every 1 kg of methane.
So the stoichiometric air-fuel ratio of methane is 17.2.
In the combination between petrol, oxygen and nitrogen, water, carbon dioxide and food goods
are produced.
The sensor Lambda O2 is an electronic tool that measures the oxygen (O2) percentage of the gas
to be analysed. The AFR is controlled in a lean, rich or stoichiometric inner combustion motor.
A solid-state electrochemical fuel cell, called the cell of Nernst, is used in the zirconium dioxide
or zirconia, Lambda sensor. Both electrodes have an output voltage equivalent to the amount of
oxygen in the atmosphere exhaust. The ECU is an AFR-based control system based on sensor
feedback. The AFR measurement is critical for sensor-based engine efficiency and durability.
The ECU is an AFR-adjusted control system based on sensor feedback. For the engine's
performance and durability based on the sensor, the AFR calibration is crucial. Less AFR than
the stoichiometric AFR, the mixture is richer. AFR is less than 14,7:1. The higher AFR amount
has more air, so it is a leaner blend. Slimmer mix provides more energy and effectiveness, but
the motor temperature increases. This rich combination gives the motor cooler but less energy
and unburns fuel. The mixture is rich and lean according to the motor type [6]. Air –fuel (AFR) is
the total wind ratio of an oxygen current in a cooking operation with the gas being powerful, liquid, or
vaporous. For example, an inner burning engine or modern heater can control the ignition, or can cause a
blast (for instance a residual blast, a gas or a blast of vapor, or a thermobaric gun).
The air-fuel ratio chooses whether any combination can be ignited, how much vitality is emitted
and how much undesirable contamination is produced. There is usually a range of aerial diesel,
from which no beginning will take place. The lesser and highest risk containment levels are
recognized. An air fuel ratio is an important metric for purposes harmful to contamination and
execution in an internal combustion engine or mechanical fuel heater. If the gas is consumed by
sufficient wind, the percentage is regarded as the stoichiometric mix, which is frequently
shortened to stoic. The proportions are regarded "wealthy" below stoichiometric levels. Rich
So 1 molecule of methane has a molecular weight of: 1 * 12.01 + 4 * 1.008 = 16.042
One oxygen molecule weighs: 2 * 16 = 32
The oxygen-fuel mass ratio is then: 2 * 32 / 1 * 16.042 = 64 / 16.042
So we need 3.99 kg of oxygen for every 1 kg of fuel
Since 23.2 mass-percent of air is actually oxygen, we need : 3.99 * 100/23.2 = 17.2 kg air
for every 1 kg of methane.
So the stoichiometric air-fuel ratio of methane is 17.2.
In the combination between petrol, oxygen and nitrogen, water, carbon dioxide and food goods
are produced.
The sensor Lambda O2 is an electronic tool that measures the oxygen (O2) percentage of the gas
to be analysed. The AFR is controlled in a lean, rich or stoichiometric inner combustion motor.
A solid-state electrochemical fuel cell, called the cell of Nernst, is used in the zirconium dioxide
or zirconia, Lambda sensor. Both electrodes have an output voltage equivalent to the amount of
oxygen in the atmosphere exhaust. The ECU is an AFR-based control system based on sensor
feedback. The AFR measurement is critical for sensor-based engine efficiency and durability.
The ECU is an AFR-adjusted control system based on sensor feedback. For the engine's
performance and durability based on the sensor, the AFR calibration is crucial. Less AFR than
the stoichiometric AFR, the mixture is richer. AFR is less than 14,7:1. The higher AFR amount
has more air, so it is a leaner blend. Slimmer mix provides more energy and effectiveness, but
the motor temperature increases. This rich combination gives the motor cooler but less energy
and unburns fuel. The mixture is rich and lean according to the motor type [6]. Air –fuel (AFR) is
the total wind ratio of an oxygen current in a cooking operation with the gas being powerful, liquid, or
vaporous. For example, an inner burning engine or modern heater can control the ignition, or can cause a
blast (for instance a residual blast, a gas or a blast of vapor, or a thermobaric gun).
The air-fuel ratio chooses whether any combination can be ignited, how much vitality is emitted
and how much undesirable contamination is produced. There is usually a range of aerial diesel,
from which no beginning will take place. The lesser and highest risk containment levels are
recognized. An air fuel ratio is an important metric for purposes harmful to contamination and
execution in an internal combustion engine or mechanical fuel heater. If the gas is consumed by
sufficient wind, the percentage is regarded as the stoichiometric mix, which is frequently
shortened to stoic. The proportions are regarded "wealthy" below stoichiometric levels. Rich
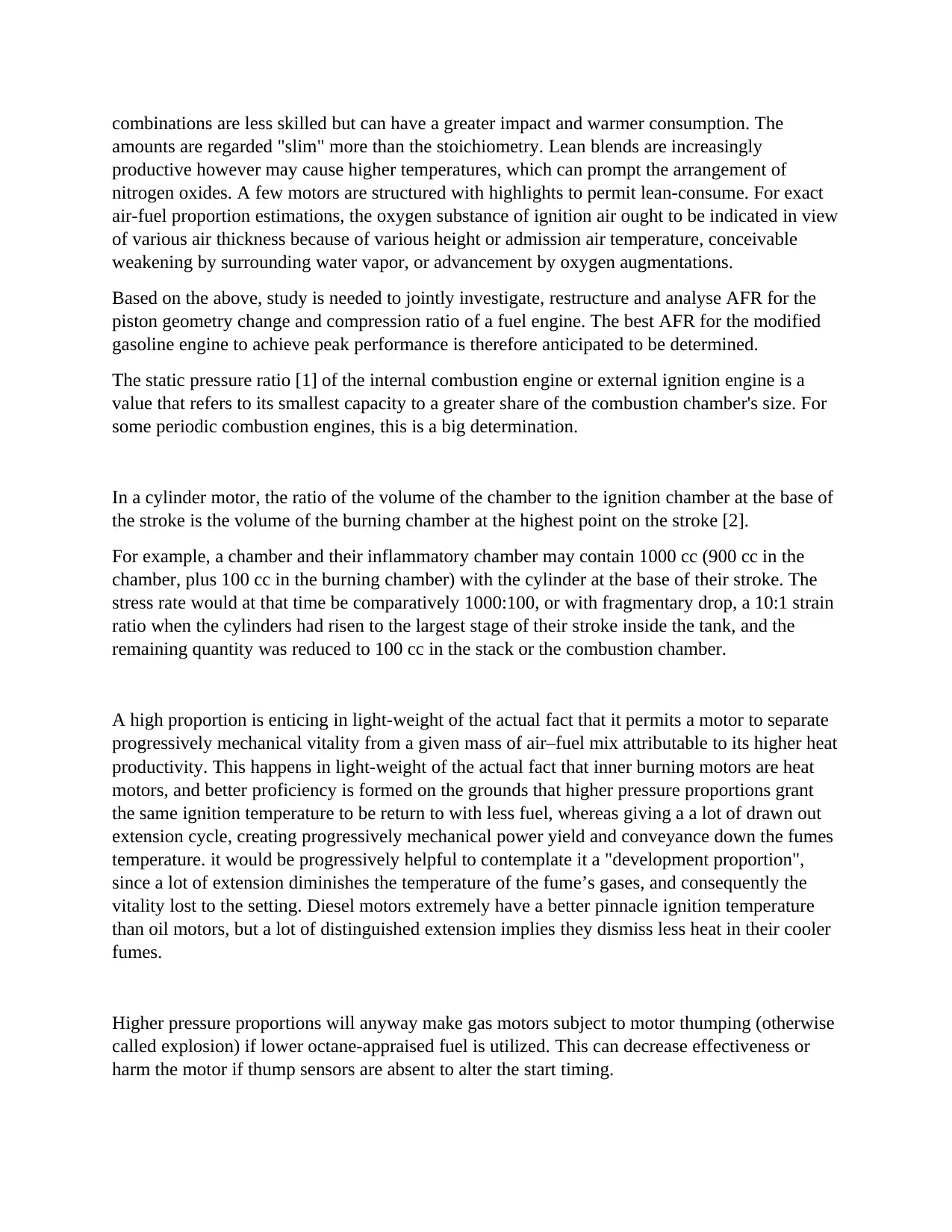
combinations are less skilled but can have a greater impact and warmer consumption. The
amounts are regarded "slim" more than the stoichiometry. Lean blends are increasingly
productive however may cause higher temperatures, which can prompt the arrangement of
nitrogen oxides. A few motors are structured with highlights to permit lean-consume. For exact
air-fuel proportion estimations, the oxygen substance of ignition air ought to be indicated in view
of various air thickness because of various height or admission air temperature, conceivable
weakening by surrounding water vapor, or advancement by oxygen augmentations.
Based on the above, study is needed to jointly investigate, restructure and analyse AFR for the
piston geometry change and compression ratio of a fuel engine. The best AFR for the modified
gasoline engine to achieve peak performance is therefore anticipated to be determined.
The static pressure ratio [1] of the internal combustion engine or external ignition engine is a
value that refers to its smallest capacity to a greater share of the combustion chamber's size. For
some periodic combustion engines, this is a big determination.
In a cylinder motor, the ratio of the volume of the chamber to the ignition chamber at the base of
the stroke is the volume of the burning chamber at the highest point on the stroke [2].
For example, a chamber and their inflammatory chamber may contain 1000 cc (900 cc in the
chamber, plus 100 cc in the burning chamber) with the cylinder at the base of their stroke. The
stress rate would at that time be comparatively 1000:100, or with fragmentary drop, a 10:1 strain
ratio when the cylinders had risen to the largest stage of their stroke inside the tank, and the
remaining quantity was reduced to 100 cc in the stack or the combustion chamber.
A high proportion is enticing in light-weight of the actual fact that it permits a motor to separate
progressively mechanical vitality from a given mass of air–fuel mix attributable to its higher heat
productivity. This happens in light-weight of the actual fact that inner burning motors are heat
motors, and better proficiency is formed on the grounds that higher pressure proportions grant
the same ignition temperature to be return to with less fuel, whereas giving a a lot of drawn out
extension cycle, creating progressively mechanical power yield and conveyance down the fumes
temperature. it would be progressively helpful to contemplate it a "development proportion",
since a lot of extension diminishes the temperature of the fume’s gases, and consequently the
vitality lost to the setting. Diesel motors extremely have a better pinnacle ignition temperature
than oil motors, but a lot of distinguished extension implies they dismiss less heat in their cooler
fumes.
Higher pressure proportions will anyway make gas motors subject to motor thumping (otherwise
called explosion) if lower octane-appraised fuel is utilized. This can decrease effectiveness or
harm the motor if thump sensors are absent to alter the start timing.
amounts are regarded "slim" more than the stoichiometry. Lean blends are increasingly
productive however may cause higher temperatures, which can prompt the arrangement of
nitrogen oxides. A few motors are structured with highlights to permit lean-consume. For exact
air-fuel proportion estimations, the oxygen substance of ignition air ought to be indicated in view
of various air thickness because of various height or admission air temperature, conceivable
weakening by surrounding water vapor, or advancement by oxygen augmentations.
Based on the above, study is needed to jointly investigate, restructure and analyse AFR for the
piston geometry change and compression ratio of a fuel engine. The best AFR for the modified
gasoline engine to achieve peak performance is therefore anticipated to be determined.
The static pressure ratio [1] of the internal combustion engine or external ignition engine is a
value that refers to its smallest capacity to a greater share of the combustion chamber's size. For
some periodic combustion engines, this is a big determination.
In a cylinder motor, the ratio of the volume of the chamber to the ignition chamber at the base of
the stroke is the volume of the burning chamber at the highest point on the stroke [2].
For example, a chamber and their inflammatory chamber may contain 1000 cc (900 cc in the
chamber, plus 100 cc in the burning chamber) with the cylinder at the base of their stroke. The
stress rate would at that time be comparatively 1000:100, or with fragmentary drop, a 10:1 strain
ratio when the cylinders had risen to the largest stage of their stroke inside the tank, and the
remaining quantity was reduced to 100 cc in the stack or the combustion chamber.
A high proportion is enticing in light-weight of the actual fact that it permits a motor to separate
progressively mechanical vitality from a given mass of air–fuel mix attributable to its higher heat
productivity. This happens in light-weight of the actual fact that inner burning motors are heat
motors, and better proficiency is formed on the grounds that higher pressure proportions grant
the same ignition temperature to be return to with less fuel, whereas giving a a lot of drawn out
extension cycle, creating progressively mechanical power yield and conveyance down the fumes
temperature. it would be progressively helpful to contemplate it a "development proportion",
since a lot of extension diminishes the temperature of the fume’s gases, and consequently the
vitality lost to the setting. Diesel motors extremely have a better pinnacle ignition temperature
than oil motors, but a lot of distinguished extension implies they dismiss less heat in their cooler
fumes.
Higher pressure proportions will anyway make gas motors subject to motor thumping (otherwise
called explosion) if lower octane-appraised fuel is utilized. This can decrease effectiveness or
harm the motor if thump sensors are absent to alter the start timing.
Secure Best Marks with AI Grader
Need help grading? Try our AI Grader for instant feedback on your assignments.
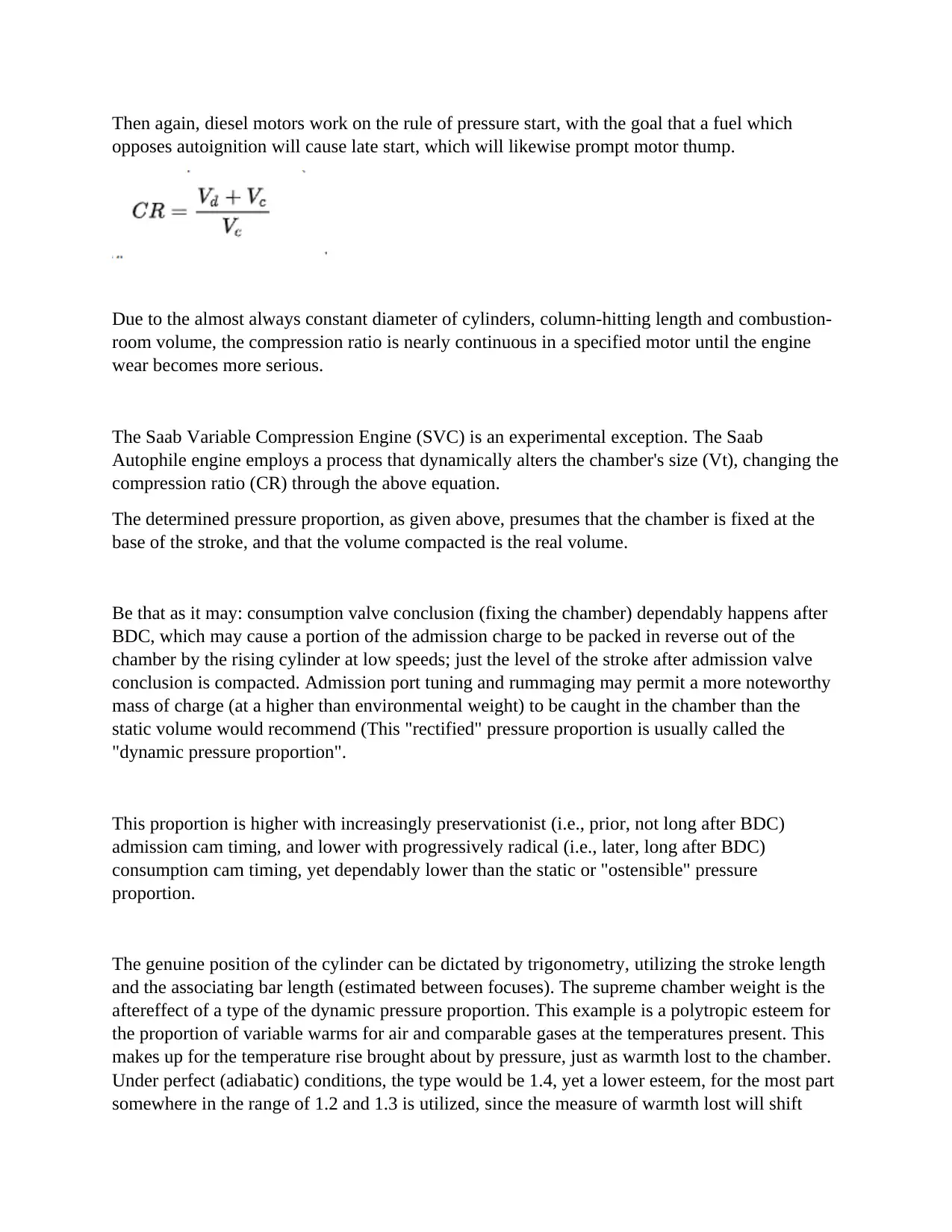
Then again, diesel motors work on the rule of pressure start, with the goal that a fuel which
opposes autoignition will cause late start, which will likewise prompt motor thump.
Due to the almost always constant diameter of cylinders, column-hitting length and combustion-
room volume, the compression ratio is nearly continuous in a specified motor until the engine
wear becomes more serious.
The Saab Variable Compression Engine (SVC) is an experimental exception. The Saab
Autophile engine employs a process that dynamically alters the chamber's size (Vt), changing the
compression ratio (CR) through the above equation.
The determined pressure proportion, as given above, presumes that the chamber is fixed at the
base of the stroke, and that the volume compacted is the real volume.
Be that as it may: consumption valve conclusion (fixing the chamber) dependably happens after
BDC, which may cause a portion of the admission charge to be packed in reverse out of the
chamber by the rising cylinder at low speeds; just the level of the stroke after admission valve
conclusion is compacted. Admission port tuning and rummaging may permit a more noteworthy
mass of charge (at a higher than environmental weight) to be caught in the chamber than the
static volume would recommend (This "rectified" pressure proportion is usually called the
"dynamic pressure proportion".
This proportion is higher with increasingly preservationist (i.e., prior, not long after BDC)
admission cam timing, and lower with progressively radical (i.e., later, long after BDC)
consumption cam timing, yet dependably lower than the static or "ostensible" pressure
proportion.
The genuine position of the cylinder can be dictated by trigonometry, utilizing the stroke length
and the associating bar length (estimated between focuses). The supreme chamber weight is the
aftereffect of a type of the dynamic pressure proportion. This example is a polytropic esteem for
the proportion of variable warms for air and comparable gases at the temperatures present. This
makes up for the temperature rise brought about by pressure, just as warmth lost to the chamber.
Under perfect (adiabatic) conditions, the type would be 1.4, yet a lower esteem, for the most part
somewhere in the range of 1.2 and 1.3 is utilized, since the measure of warmth lost will shift
opposes autoignition will cause late start, which will likewise prompt motor thump.
Due to the almost always constant diameter of cylinders, column-hitting length and combustion-
room volume, the compression ratio is nearly continuous in a specified motor until the engine
wear becomes more serious.
The Saab Variable Compression Engine (SVC) is an experimental exception. The Saab
Autophile engine employs a process that dynamically alters the chamber's size (Vt), changing the
compression ratio (CR) through the above equation.
The determined pressure proportion, as given above, presumes that the chamber is fixed at the
base of the stroke, and that the volume compacted is the real volume.
Be that as it may: consumption valve conclusion (fixing the chamber) dependably happens after
BDC, which may cause a portion of the admission charge to be packed in reverse out of the
chamber by the rising cylinder at low speeds; just the level of the stroke after admission valve
conclusion is compacted. Admission port tuning and rummaging may permit a more noteworthy
mass of charge (at a higher than environmental weight) to be caught in the chamber than the
static volume would recommend (This "rectified" pressure proportion is usually called the
"dynamic pressure proportion".
This proportion is higher with increasingly preservationist (i.e., prior, not long after BDC)
admission cam timing, and lower with progressively radical (i.e., later, long after BDC)
consumption cam timing, yet dependably lower than the static or "ostensible" pressure
proportion.
The genuine position of the cylinder can be dictated by trigonometry, utilizing the stroke length
and the associating bar length (estimated between focuses). The supreme chamber weight is the
aftereffect of a type of the dynamic pressure proportion. This example is a polytropic esteem for
the proportion of variable warms for air and comparable gases at the temperatures present. This
makes up for the temperature rise brought about by pressure, just as warmth lost to the chamber.
Under perfect (adiabatic) conditions, the type would be 1.4, yet a lower esteem, for the most part
somewhere in the range of 1.2 and 1.3 is utilized, since the measure of warmth lost will shift
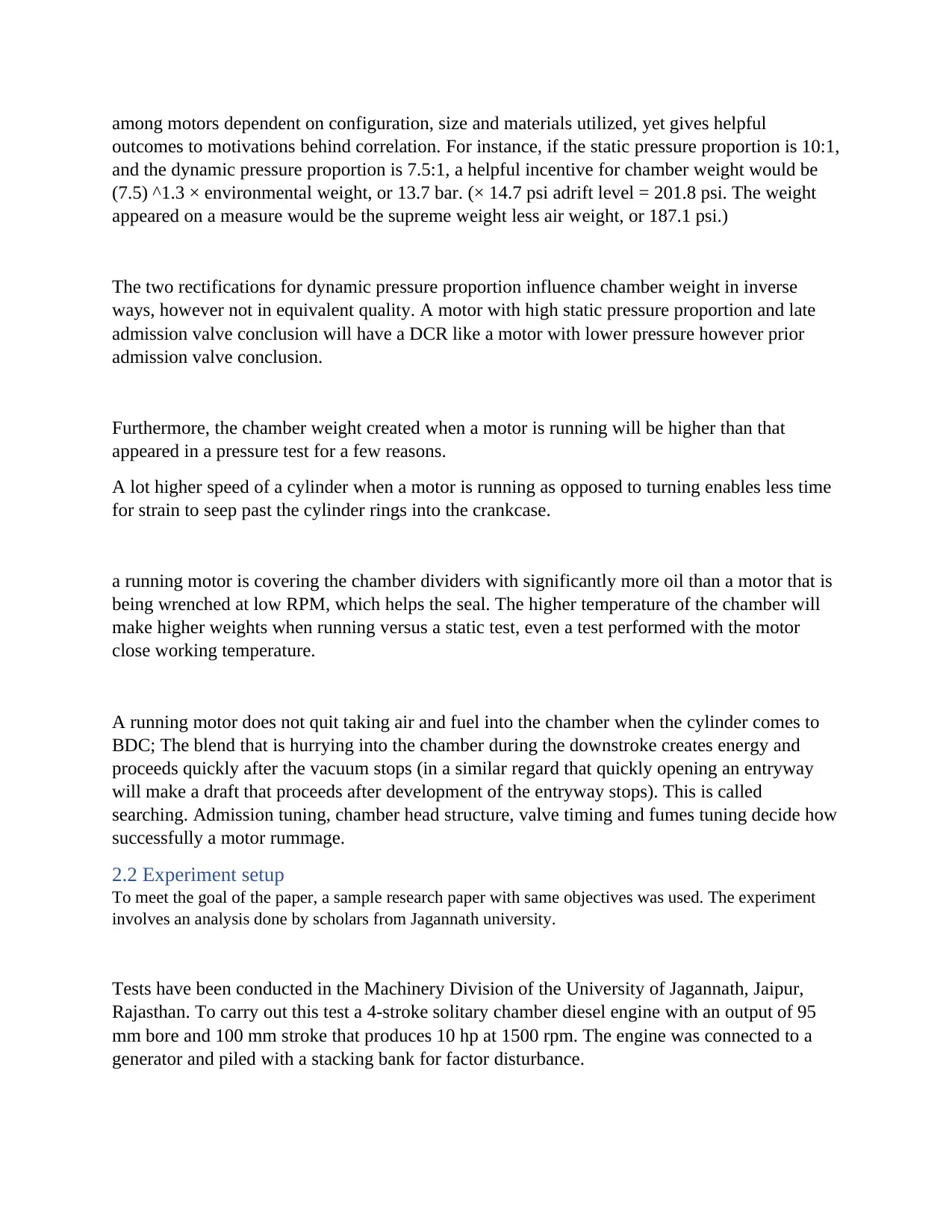
among motors dependent on configuration, size and materials utilized, yet gives helpful
outcomes to motivations behind correlation. For instance, if the static pressure proportion is 10:1,
and the dynamic pressure proportion is 7.5:1, a helpful incentive for chamber weight would be
(7.5) ^1.3 × environmental weight, or 13.7 bar. (× 14.7 psi adrift level = 201.8 psi. The weight
appeared on a measure would be the supreme weight less air weight, or 187.1 psi.)
The two rectifications for dynamic pressure proportion influence chamber weight in inverse
ways, however not in equivalent quality. A motor with high static pressure proportion and late
admission valve conclusion will have a DCR like a motor with lower pressure however prior
admission valve conclusion.
Furthermore, the chamber weight created when a motor is running will be higher than that
appeared in a pressure test for a few reasons.
A lot higher speed of a cylinder when a motor is running as opposed to turning enables less time
for strain to seep past the cylinder rings into the crankcase.
a running motor is covering the chamber dividers with significantly more oil than a motor that is
being wrenched at low RPM, which helps the seal. The higher temperature of the chamber will
make higher weights when running versus a static test, even a test performed with the motor
close working temperature.
A running motor does not quit taking air and fuel into the chamber when the cylinder comes to
BDC; The blend that is hurrying into the chamber during the downstroke creates energy and
proceeds quickly after the vacuum stops (in a similar regard that quickly opening an entryway
will make a draft that proceeds after development of the entryway stops). This is called
searching. Admission tuning, chamber head structure, valve timing and fumes tuning decide how
successfully a motor rummage.
2.2 Experiment setup
To meet the goal of the paper, a sample research paper with same objectives was used. The experiment
involves an analysis done by scholars from Jagannath university.
Tests have been conducted in the Machinery Division of the University of Jagannath, Jaipur,
Rajasthan. To carry out this test a 4-stroke solitary chamber diesel engine with an output of 95
mm bore and 100 mm stroke that produces 10 hp at 1500 rpm. The engine was connected to a
generator and piled with a stacking bank for factor disturbance.
outcomes to motivations behind correlation. For instance, if the static pressure proportion is 10:1,
and the dynamic pressure proportion is 7.5:1, a helpful incentive for chamber weight would be
(7.5) ^1.3 × environmental weight, or 13.7 bar. (× 14.7 psi adrift level = 201.8 psi. The weight
appeared on a measure would be the supreme weight less air weight, or 187.1 psi.)
The two rectifications for dynamic pressure proportion influence chamber weight in inverse
ways, however not in equivalent quality. A motor with high static pressure proportion and late
admission valve conclusion will have a DCR like a motor with lower pressure however prior
admission valve conclusion.
Furthermore, the chamber weight created when a motor is running will be higher than that
appeared in a pressure test for a few reasons.
A lot higher speed of a cylinder when a motor is running as opposed to turning enables less time
for strain to seep past the cylinder rings into the crankcase.
a running motor is covering the chamber dividers with significantly more oil than a motor that is
being wrenched at low RPM, which helps the seal. The higher temperature of the chamber will
make higher weights when running versus a static test, even a test performed with the motor
close working temperature.
A running motor does not quit taking air and fuel into the chamber when the cylinder comes to
BDC; The blend that is hurrying into the chamber during the downstroke creates energy and
proceeds quickly after the vacuum stops (in a similar regard that quickly opening an entryway
will make a draft that proceeds after development of the entryway stops). This is called
searching. Admission tuning, chamber head structure, valve timing and fumes tuning decide how
successfully a motor rummage.
2.2 Experiment setup
To meet the goal of the paper, a sample research paper with same objectives was used. The experiment
involves an analysis done by scholars from Jagannath university.
Tests have been conducted in the Machinery Division of the University of Jagannath, Jaipur,
Rajasthan. To carry out this test a 4-stroke solitary chamber diesel engine with an output of 95
mm bore and 100 mm stroke that produces 10 hp at 1500 rpm. The engine was connected to a
generator and piled with a stacking bank for factor disturbance.
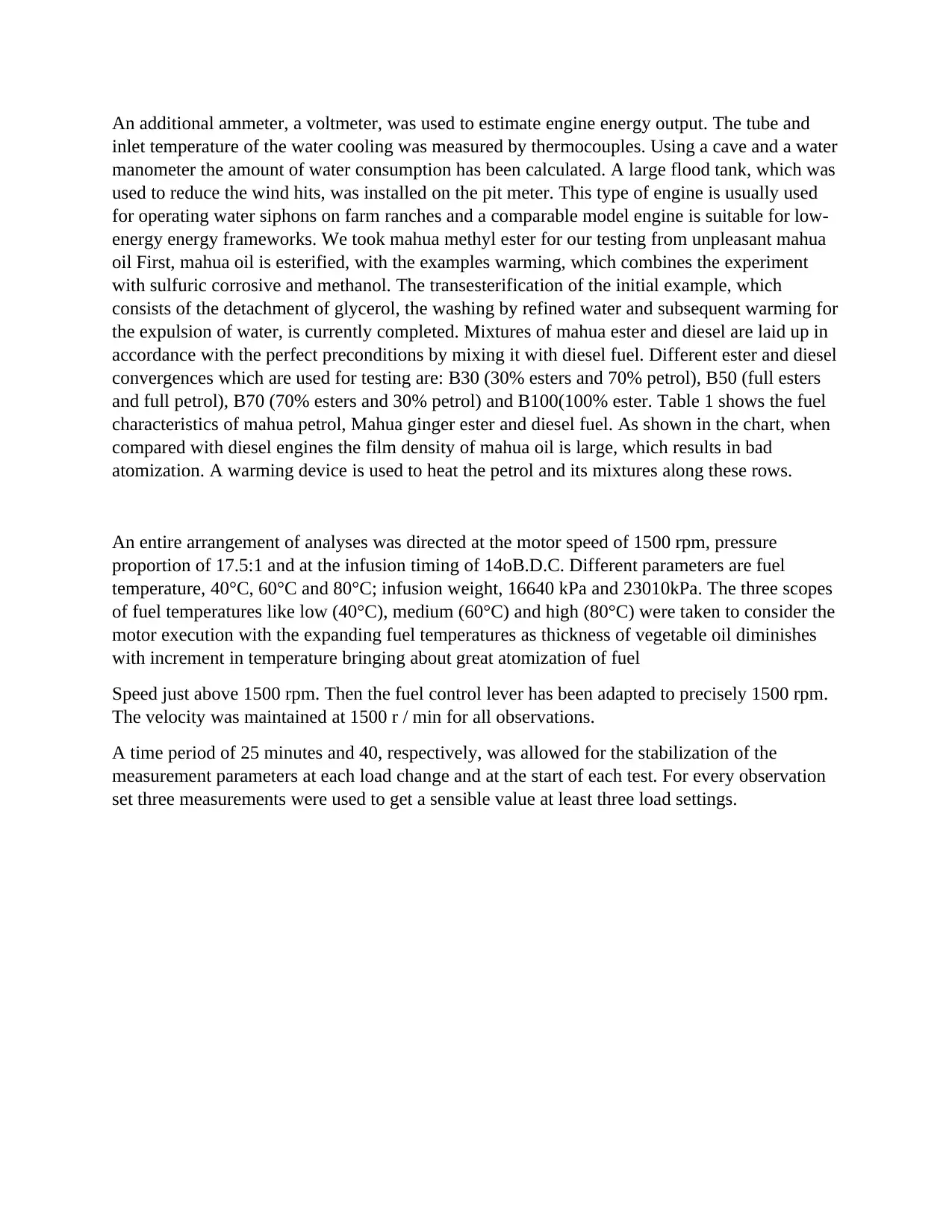
An additional ammeter, a voltmeter, was used to estimate engine energy output. The tube and
inlet temperature of the water cooling was measured by thermocouples. Using a cave and a water
manometer the amount of water consumption has been calculated. A large flood tank, which was
used to reduce the wind hits, was installed on the pit meter. This type of engine is usually used
for operating water siphons on farm ranches and a comparable model engine is suitable for low-
energy energy frameworks. We took mahua methyl ester for our testing from unpleasant mahua
oil First, mahua oil is esterified, with the examples warming, which combines the experiment
with sulfuric corrosive and methanol. The transesterification of the initial example, which
consists of the detachment of glycerol, the washing by refined water and subsequent warming for
the expulsion of water, is currently completed. Mixtures of mahua ester and diesel are laid up in
accordance with the perfect preconditions by mixing it with diesel fuel. Different ester and diesel
convergences which are used for testing are: B30 (30% esters and 70% petrol), B50 (full esters
and full petrol), B70 (70% esters and 30% petrol) and B100(100% ester. Table 1 shows the fuel
characteristics of mahua petrol, Mahua ginger ester and diesel fuel. As shown in the chart, when
compared with diesel engines the film density of mahua oil is large, which results in bad
atomization. A warming device is used to heat the petrol and its mixtures along these rows.
An entire arrangement of analyses was directed at the motor speed of 1500 rpm, pressure
proportion of 17.5:1 and at the infusion timing of 14oB.D.C. Different parameters are fuel
temperature, 40°C, 60°C and 80°C; infusion weight, 16640 kPa and 23010kPa. The three scopes
of fuel temperatures like low (40°C), medium (60°C) and high (80°C) were taken to consider the
motor execution with the expanding fuel temperatures as thickness of vegetable oil diminishes
with increment in temperature bringing about great atomization of fuel
Speed just above 1500 rpm. Then the fuel control lever has been adapted to precisely 1500 rpm.
The velocity was maintained at 1500 r / min for all observations.
A time period of 25 minutes and 40, respectively, was allowed for the stabilization of the
measurement parameters at each load change and at the start of each test. For every observation
set three measurements were used to get a sensible value at least three load settings.
inlet temperature of the water cooling was measured by thermocouples. Using a cave and a water
manometer the amount of water consumption has been calculated. A large flood tank, which was
used to reduce the wind hits, was installed on the pit meter. This type of engine is usually used
for operating water siphons on farm ranches and a comparable model engine is suitable for low-
energy energy frameworks. We took mahua methyl ester for our testing from unpleasant mahua
oil First, mahua oil is esterified, with the examples warming, which combines the experiment
with sulfuric corrosive and methanol. The transesterification of the initial example, which
consists of the detachment of glycerol, the washing by refined water and subsequent warming for
the expulsion of water, is currently completed. Mixtures of mahua ester and diesel are laid up in
accordance with the perfect preconditions by mixing it with diesel fuel. Different ester and diesel
convergences which are used for testing are: B30 (30% esters and 70% petrol), B50 (full esters
and full petrol), B70 (70% esters and 30% petrol) and B100(100% ester. Table 1 shows the fuel
characteristics of mahua petrol, Mahua ginger ester and diesel fuel. As shown in the chart, when
compared with diesel engines the film density of mahua oil is large, which results in bad
atomization. A warming device is used to heat the petrol and its mixtures along these rows.
An entire arrangement of analyses was directed at the motor speed of 1500 rpm, pressure
proportion of 17.5:1 and at the infusion timing of 14oB.D.C. Different parameters are fuel
temperature, 40°C, 60°C and 80°C; infusion weight, 16640 kPa and 23010kPa. The three scopes
of fuel temperatures like low (40°C), medium (60°C) and high (80°C) were taken to consider the
motor execution with the expanding fuel temperatures as thickness of vegetable oil diminishes
with increment in temperature bringing about great atomization of fuel
Speed just above 1500 rpm. Then the fuel control lever has been adapted to precisely 1500 rpm.
The velocity was maintained at 1500 r / min for all observations.
A time period of 25 minutes and 40, respectively, was allowed for the stabilization of the
measurement parameters at each load change and at the start of each test. For every observation
set three measurements were used to get a sensible value at least three load settings.
Paraphrase This Document
Need a fresh take? Get an instant paraphrase of this document with our AI Paraphraser
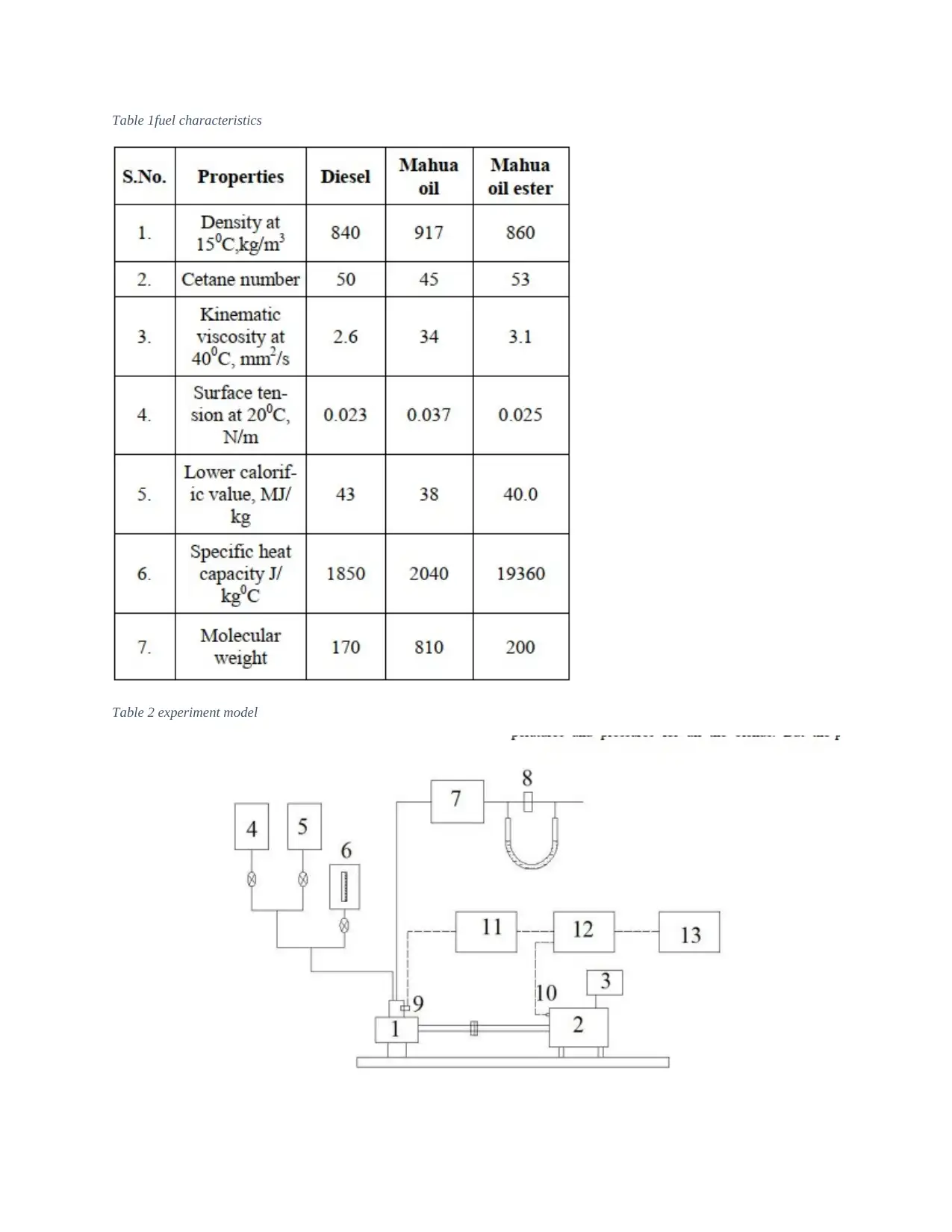
Table 1fuel characteristics
Table 2 experiment model
Table 2 experiment model
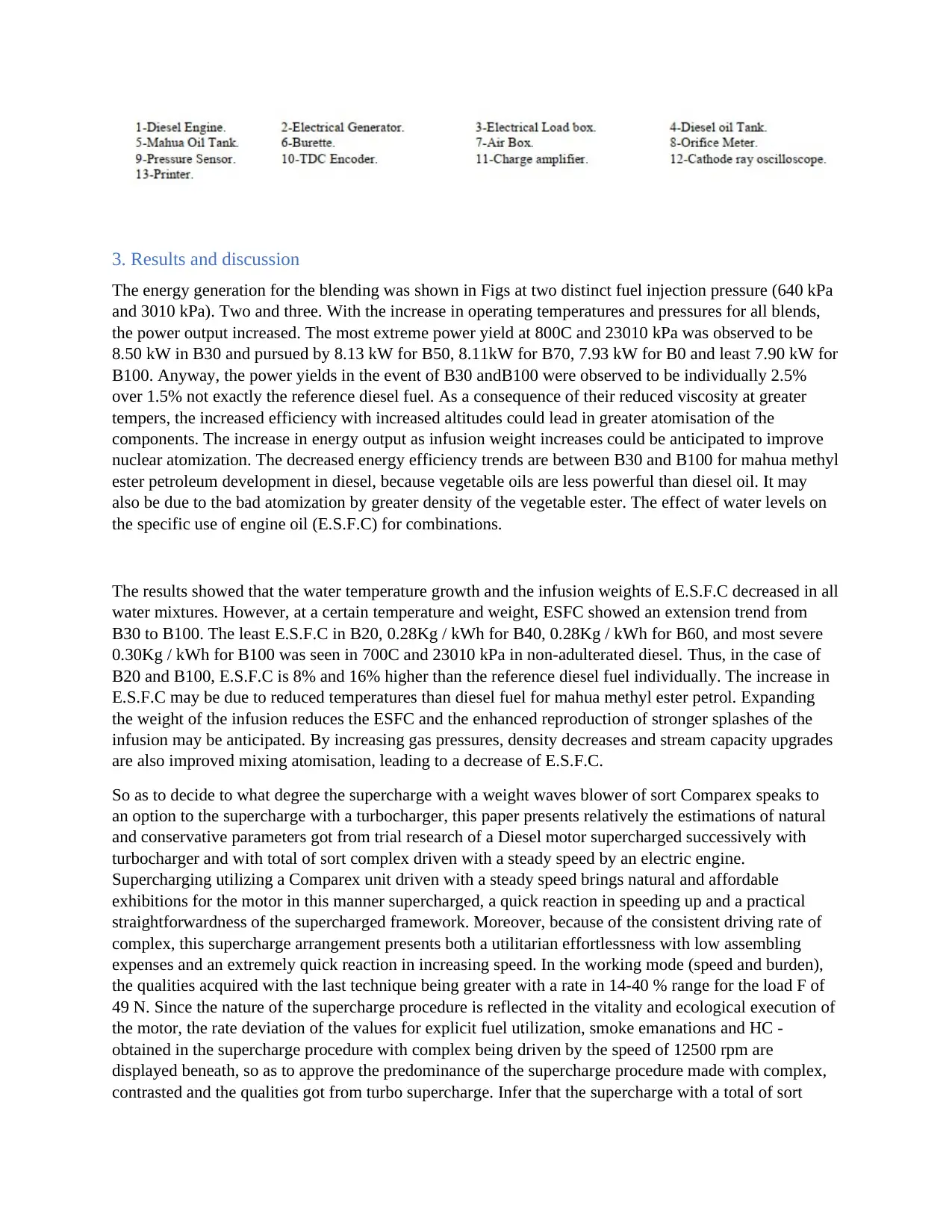
3. Results and discussion
The energy generation for the blending was shown in Figs at two distinct fuel injection pressure (640 kPa
and 3010 kPa). Two and three. With the increase in operating temperatures and pressures for all blends,
the power output increased. The most extreme power yield at 800C and 23010 kPa was observed to be
8.50 kW in B30 and pursued by 8.13 kW for B50, 8.11kW for B70, 7.93 kW for B0 and least 7.90 kW for
B100. Anyway, the power yields in the event of B30 andB100 were observed to be individually 2.5%
over 1.5% not exactly the reference diesel fuel. As a consequence of their reduced viscosity at greater
tempers, the increased efficiency with increased altitudes could lead in greater atomisation of the
components. The increase in energy output as infusion weight increases could be anticipated to improve
nuclear atomization. The decreased energy efficiency trends are between B30 and B100 for mahua methyl
ester petroleum development in diesel, because vegetable oils are less powerful than diesel oil. It may
also be due to the bad atomization by greater density of the vegetable ester. The effect of water levels on
the specific use of engine oil (E.S.F.C) for combinations.
The results showed that the water temperature growth and the infusion weights of E.S.F.C decreased in all
water mixtures. However, at a certain temperature and weight, ESFC showed an extension trend from
B30 to B100. The least E.S.F.C in B20, 0.28Kg / kWh for B40, 0.28Kg / kWh for B60, and most severe
0.30Kg / kWh for B100 was seen in 700C and 23010 kPa in non-adulterated diesel. Thus, in the case of
B20 and B100, E.S.F.C is 8% and 16% higher than the reference diesel fuel individually. The increase in
E.S.F.C may be due to reduced temperatures than diesel fuel for mahua methyl ester petrol. Expanding
the weight of the infusion reduces the ESFC and the enhanced reproduction of stronger splashes of the
infusion may be anticipated. By increasing gas pressures, density decreases and stream capacity upgrades
are also improved mixing atomisation, leading to a decrease of E.S.F.C.
So as to decide to what degree the supercharge with a weight waves blower of sort Comparex speaks to
an option to the supercharge with a turbocharger, this paper presents relatively the estimations of natural
and conservative parameters got from trial research of a Diesel motor supercharged successively with
turbocharger and with total of sort complex driven with a steady speed by an electric engine.
Supercharging utilizing a Comparex unit driven with a steady speed brings natural and affordable
exhibitions for the motor in this manner supercharged, a quick reaction in speeding up and a practical
straightforwardness of the supercharged framework. Moreover, because of the consistent driving rate of
complex, this supercharge arrangement presents both a utilitarian effortlessness with low assembling
expenses and an extremely quick reaction in increasing speed. In the working mode (speed and burden),
the qualities acquired with the last technique being greater with a rate in 14-40 % range for the load F of
49 N. Since the nature of the supercharge procedure is reflected in the vitality and ecological execution of
the motor, the rate deviation of the values for explicit fuel utilization, smoke emanations and HC -
obtained in the supercharge procedure with complex being driven by the speed of 12500 rpm are
displayed beneath, so as to approve the predominance of the supercharge procedure made with complex,
contrasted and the qualities got from turbo supercharge. Infer that the supercharge with a total of sort
The energy generation for the blending was shown in Figs at two distinct fuel injection pressure (640 kPa
and 3010 kPa). Two and three. With the increase in operating temperatures and pressures for all blends,
the power output increased. The most extreme power yield at 800C and 23010 kPa was observed to be
8.50 kW in B30 and pursued by 8.13 kW for B50, 8.11kW for B70, 7.93 kW for B0 and least 7.90 kW for
B100. Anyway, the power yields in the event of B30 andB100 were observed to be individually 2.5%
over 1.5% not exactly the reference diesel fuel. As a consequence of their reduced viscosity at greater
tempers, the increased efficiency with increased altitudes could lead in greater atomisation of the
components. The increase in energy output as infusion weight increases could be anticipated to improve
nuclear atomization. The decreased energy efficiency trends are between B30 and B100 for mahua methyl
ester petroleum development in diesel, because vegetable oils are less powerful than diesel oil. It may
also be due to the bad atomization by greater density of the vegetable ester. The effect of water levels on
the specific use of engine oil (E.S.F.C) for combinations.
The results showed that the water temperature growth and the infusion weights of E.S.F.C decreased in all
water mixtures. However, at a certain temperature and weight, ESFC showed an extension trend from
B30 to B100. The least E.S.F.C in B20, 0.28Kg / kWh for B40, 0.28Kg / kWh for B60, and most severe
0.30Kg / kWh for B100 was seen in 700C and 23010 kPa in non-adulterated diesel. Thus, in the case of
B20 and B100, E.S.F.C is 8% and 16% higher than the reference diesel fuel individually. The increase in
E.S.F.C may be due to reduced temperatures than diesel fuel for mahua methyl ester petrol. Expanding
the weight of the infusion reduces the ESFC and the enhanced reproduction of stronger splashes of the
infusion may be anticipated. By increasing gas pressures, density decreases and stream capacity upgrades
are also improved mixing atomisation, leading to a decrease of E.S.F.C.
So as to decide to what degree the supercharge with a weight waves blower of sort Comparex speaks to
an option to the supercharge with a turbocharger, this paper presents relatively the estimations of natural
and conservative parameters got from trial research of a Diesel motor supercharged successively with
turbocharger and with total of sort complex driven with a steady speed by an electric engine.
Supercharging utilizing a Comparex unit driven with a steady speed brings natural and affordable
exhibitions for the motor in this manner supercharged, a quick reaction in speeding up and a practical
straightforwardness of the supercharged framework. Moreover, because of the consistent driving rate of
complex, this supercharge arrangement presents both a utilitarian effortlessness with low assembling
expenses and an extremely quick reaction in increasing speed. In the working mode (speed and burden),
the qualities acquired with the last technique being greater with a rate in 14-40 % range for the load F of
49 N. Since the nature of the supercharge procedure is reflected in the vitality and ecological execution of
the motor, the rate deviation of the values for explicit fuel utilization, smoke emanations and HC -
obtained in the supercharge procedure with complex being driven by the speed of 12500 rpm are
displayed beneath, so as to approve the predominance of the supercharge procedure made with complex,
contrasted and the qualities got from turbo supercharge. Infer that the supercharge with a total of sort

complex, driven with a steady speed of 12500 rpm, for the researched working modes, gives the motor
improved (altogether, some of the time) vitality, economy and ecological exhibitions, contrasted and
those acquired from a similar motor however furnished with a turbocharger. It must be noted that during
tests of engines with a constant speed of 12500 rpm overloaded with complex the control usage of the
Comparex unit was too estimated with a normal value of around 1.86 per cent, which is a reduced energy
consumption for the super loading unit. Milburn, S. [5], The Diesel and flash starter motors have
developed a variable, favourable relocation supercharger (VPDSTM). Advantages include lower
outflows, better efficiencies and enhanced low velocity torque. M., M., J., Amnéus, P., and Mauss, F.[6].
J. The small indicated feasible mean weight achieved by the Homogenous Load Pressure Start (HCCI)
usually sucked limit future company use of the Homogenous load pressure begin concept.
4.0 conclusion
The reasonable strategies and new innovation that help in expanding the performance of the internal
ignition motors are as per the following:
Regenerative driving: When a vehicle or car is brewing, regenerative driving is the ideal approach for
controlling the effective vitality as warmth, when it is necessary to brake your vehicle (like on a descent).
This electromagnetic braking process is performed as small motors absorb vitality and make it battery
vital.
Variable Injection Timing: This is as of now utilized in Maritime motors. At low loads and speeds, the
infusion is progressed permitting same mean viable strain to be kept up. This not just builds the
proficiency of the motor as the search weight is kept up, it additionally takes into consideration lower
quality fuel to be scorched.
Variable valve timing: In this strategy the fumes and channel valves opening and shutting time can be
fluctuated, influencing the productivity of the motor. This strategy can build the proficiency by 4 to 5%.
Cutting off chambers: In huge motors in cruising or going downhill, half of the chambers can be cut off
along these lines diminishing fuel request. It is impossible on little motors as the motor would turn out to
be harsh.
The best strategy to Improve Internal Combustion Engine Efficiency .There is a lot of concern nowadays
about the capability of the inside start engine (ICE), and a huge amount of research is being done to
improve it. Nevertheless, what decisively is the profitability of the inward consuming engine and how
might we measure it? The effectiveness of any motor merely depends on the necessity of the gas which
allows for job per device and the output at the engine gate in the aftermath of all malfunctions. The fuel's
information energy can be derived from the engine mass and its calorific value. A brake dynamometer
can evaluate the output afterwards. Output / Input is just putting effectiveness. The traditional ICE is
small in its suitability of between 20 to 30%.
improved (altogether, some of the time) vitality, economy and ecological exhibitions, contrasted and
those acquired from a similar motor however furnished with a turbocharger. It must be noted that during
tests of engines with a constant speed of 12500 rpm overloaded with complex the control usage of the
Comparex unit was too estimated with a normal value of around 1.86 per cent, which is a reduced energy
consumption for the super loading unit. Milburn, S. [5], The Diesel and flash starter motors have
developed a variable, favourable relocation supercharger (VPDSTM). Advantages include lower
outflows, better efficiencies and enhanced low velocity torque. M., M., J., Amnéus, P., and Mauss, F.[6].
J. The small indicated feasible mean weight achieved by the Homogenous Load Pressure Start (HCCI)
usually sucked limit future company use of the Homogenous load pressure begin concept.
4.0 conclusion
The reasonable strategies and new innovation that help in expanding the performance of the internal
ignition motors are as per the following:
Regenerative driving: When a vehicle or car is brewing, regenerative driving is the ideal approach for
controlling the effective vitality as warmth, when it is necessary to brake your vehicle (like on a descent).
This electromagnetic braking process is performed as small motors absorb vitality and make it battery
vital.
Variable Injection Timing: This is as of now utilized in Maritime motors. At low loads and speeds, the
infusion is progressed permitting same mean viable strain to be kept up. This not just builds the
proficiency of the motor as the search weight is kept up, it additionally takes into consideration lower
quality fuel to be scorched.
Variable valve timing: In this strategy the fumes and channel valves opening and shutting time can be
fluctuated, influencing the productivity of the motor. This strategy can build the proficiency by 4 to 5%.
Cutting off chambers: In huge motors in cruising or going downhill, half of the chambers can be cut off
along these lines diminishing fuel request. It is impossible on little motors as the motor would turn out to
be harsh.
The best strategy to Improve Internal Combustion Engine Efficiency .There is a lot of concern nowadays
about the capability of the inside start engine (ICE), and a huge amount of research is being done to
improve it. Nevertheless, what decisively is the profitability of the inward consuming engine and how
might we measure it? The effectiveness of any motor merely depends on the necessity of the gas which
allows for job per device and the output at the engine gate in the aftermath of all malfunctions. The fuel's
information energy can be derived from the engine mass and its calorific value. A brake dynamometer
can evaluate the output afterwards. Output / Input is just putting effectiveness. The traditional ICE is
small in its suitability of between 20 to 30%.
Secure Best Marks with AI Grader
Need help grading? Try our AI Grader for instant feedback on your assignments.
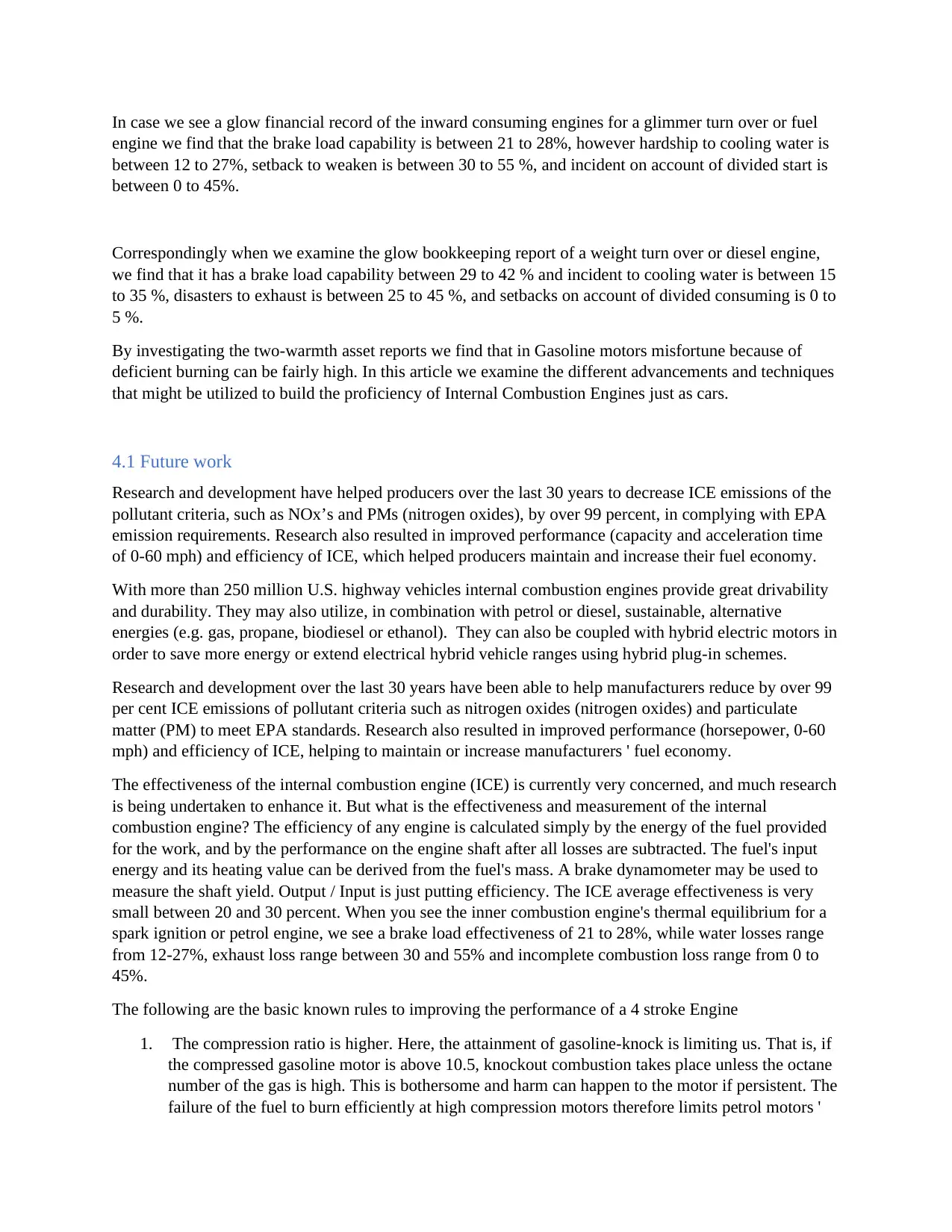
In case we see a glow financial record of the inward consuming engines for a glimmer turn over or fuel
engine we find that the brake load capability is between 21 to 28%, however hardship to cooling water is
between 12 to 27%, setback to weaken is between 30 to 55 %, and incident on account of divided start is
between 0 to 45%.
Correspondingly when we examine the glow bookkeeping report of a weight turn over or diesel engine,
we find that it has a brake load capability between 29 to 42 % and incident to cooling water is between 15
to 35 %, disasters to exhaust is between 25 to 45 %, and setbacks on account of divided consuming is 0 to
5 %.
By investigating the two-warmth asset reports we find that in Gasoline motors misfortune because of
deficient burning can be fairly high. In this article we examine the different advancements and techniques
that might be utilized to build the proficiency of Internal Combustion Engines just as cars.
4.1 Future work
Research and development have helped producers over the last 30 years to decrease ICE emissions of the
pollutant criteria, such as NOx’s and PMs (nitrogen oxides), by over 99 percent, in complying with EPA
emission requirements. Research also resulted in improved performance (capacity and acceleration time
of 0-60 mph) and efficiency of ICE, which helped producers maintain and increase their fuel economy.
With more than 250 million U.S. highway vehicles internal combustion engines provide great drivability
and durability. They may also utilize, in combination with petrol or diesel, sustainable, alternative
energies (e.g. gas, propane, biodiesel or ethanol). They can also be coupled with hybrid electric motors in
order to save more energy or extend electrical hybrid vehicle ranges using hybrid plug-in schemes.
Research and development over the last 30 years have been able to help manufacturers reduce by over 99
per cent ICE emissions of pollutant criteria such as nitrogen oxides (nitrogen oxides) and particulate
matter (PM) to meet EPA standards. Research also resulted in improved performance (horsepower, 0-60
mph) and efficiency of ICE, helping to maintain or increase manufacturers ' fuel economy.
The effectiveness of the internal combustion engine (ICE) is currently very concerned, and much research
is being undertaken to enhance it. But what is the effectiveness and measurement of the internal
combustion engine? The efficiency of any engine is calculated simply by the energy of the fuel provided
for the work, and by the performance on the engine shaft after all losses are subtracted. The fuel's input
energy and its heating value can be derived from the fuel's mass. A brake dynamometer may be used to
measure the shaft yield. Output / Input is just putting efficiency. The ICE average effectiveness is very
small between 20 and 30 percent. When you see the inner combustion engine's thermal equilibrium for a
spark ignition or petrol engine, we see a brake load effectiveness of 21 to 28%, while water losses range
from 12-27%, exhaust loss range between 30 and 55% and incomplete combustion loss range from 0 to
45%.
The following are the basic known rules to improving the performance of a 4 stroke Engine
1. The compression ratio is higher. Here, the attainment of gasoline-knock is limiting us. That is, if
the compressed gasoline motor is above 10.5, knockout combustion takes place unless the octane
number of the gas is high. This is bothersome and harm can happen to the motor if persistent. The
failure of the fuel to burn efficiently at high compression motors therefore limits petrol motors '
engine we find that the brake load capability is between 21 to 28%, however hardship to cooling water is
between 12 to 27%, setback to weaken is between 30 to 55 %, and incident on account of divided start is
between 0 to 45%.
Correspondingly when we examine the glow bookkeeping report of a weight turn over or diesel engine,
we find that it has a brake load capability between 29 to 42 % and incident to cooling water is between 15
to 35 %, disasters to exhaust is between 25 to 45 %, and setbacks on account of divided consuming is 0 to
5 %.
By investigating the two-warmth asset reports we find that in Gasoline motors misfortune because of
deficient burning can be fairly high. In this article we examine the different advancements and techniques
that might be utilized to build the proficiency of Internal Combustion Engines just as cars.
4.1 Future work
Research and development have helped producers over the last 30 years to decrease ICE emissions of the
pollutant criteria, such as NOx’s and PMs (nitrogen oxides), by over 99 percent, in complying with EPA
emission requirements. Research also resulted in improved performance (capacity and acceleration time
of 0-60 mph) and efficiency of ICE, which helped producers maintain and increase their fuel economy.
With more than 250 million U.S. highway vehicles internal combustion engines provide great drivability
and durability. They may also utilize, in combination with petrol or diesel, sustainable, alternative
energies (e.g. gas, propane, biodiesel or ethanol). They can also be coupled with hybrid electric motors in
order to save more energy or extend electrical hybrid vehicle ranges using hybrid plug-in schemes.
Research and development over the last 30 years have been able to help manufacturers reduce by over 99
per cent ICE emissions of pollutant criteria such as nitrogen oxides (nitrogen oxides) and particulate
matter (PM) to meet EPA standards. Research also resulted in improved performance (horsepower, 0-60
mph) and efficiency of ICE, helping to maintain or increase manufacturers ' fuel economy.
The effectiveness of the internal combustion engine (ICE) is currently very concerned, and much research
is being undertaken to enhance it. But what is the effectiveness and measurement of the internal
combustion engine? The efficiency of any engine is calculated simply by the energy of the fuel provided
for the work, and by the performance on the engine shaft after all losses are subtracted. The fuel's input
energy and its heating value can be derived from the fuel's mass. A brake dynamometer may be used to
measure the shaft yield. Output / Input is just putting efficiency. The ICE average effectiveness is very
small between 20 and 30 percent. When you see the inner combustion engine's thermal equilibrium for a
spark ignition or petrol engine, we see a brake load effectiveness of 21 to 28%, while water losses range
from 12-27%, exhaust loss range between 30 and 55% and incomplete combustion loss range from 0 to
45%.
The following are the basic known rules to improving the performance of a 4 stroke Engine
1. The compression ratio is higher. Here, the attainment of gasoline-knock is limiting us. That is, if
the compressed gasoline motor is above 10.5, knockout combustion takes place unless the octane
number of the gas is high. This is bothersome and harm can happen to the motor if persistent. The
failure of the fuel to burn efficiently at high compression motors therefore limits petrol motors '
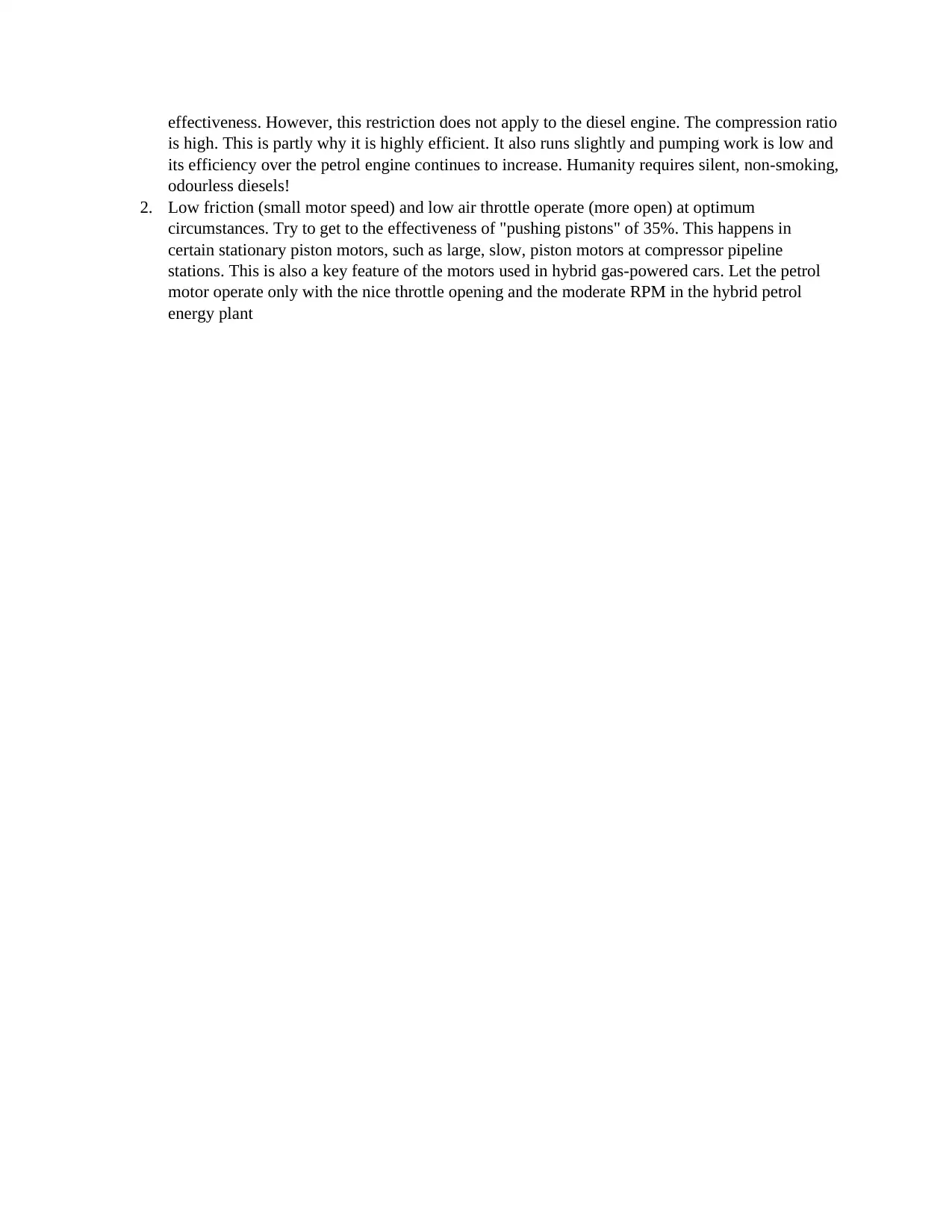
effectiveness. However, this restriction does not apply to the diesel engine. The compression ratio
is high. This is partly why it is highly efficient. It also runs slightly and pumping work is low and
its efficiency over the petrol engine continues to increase. Humanity requires silent, non-smoking,
odourless diesels!
2. Low friction (small motor speed) and low air throttle operate (more open) at optimum
circumstances. Try to get to the effectiveness of "pushing pistons" of 35%. This happens in
certain stationary piston motors, such as large, slow, piston motors at compressor pipeline
stations. This is also a key feature of the motors used in hybrid gas-powered cars. Let the petrol
motor operate only with the nice throttle opening and the moderate RPM in the hybrid petrol
energy plant
is high. This is partly why it is highly efficient. It also runs slightly and pumping work is low and
its efficiency over the petrol engine continues to increase. Humanity requires silent, non-smoking,
odourless diesels!
2. Low friction (small motor speed) and low air throttle operate (more open) at optimum
circumstances. Try to get to the effectiveness of "pushing pistons" of 35%. This happens in
certain stationary piston motors, such as large, slow, piston motors at compressor pipeline
stations. This is also a key feature of the motors used in hybrid gas-powered cars. Let the petrol
motor operate only with the nice throttle opening and the moderate RPM in the hybrid petrol
energy plant
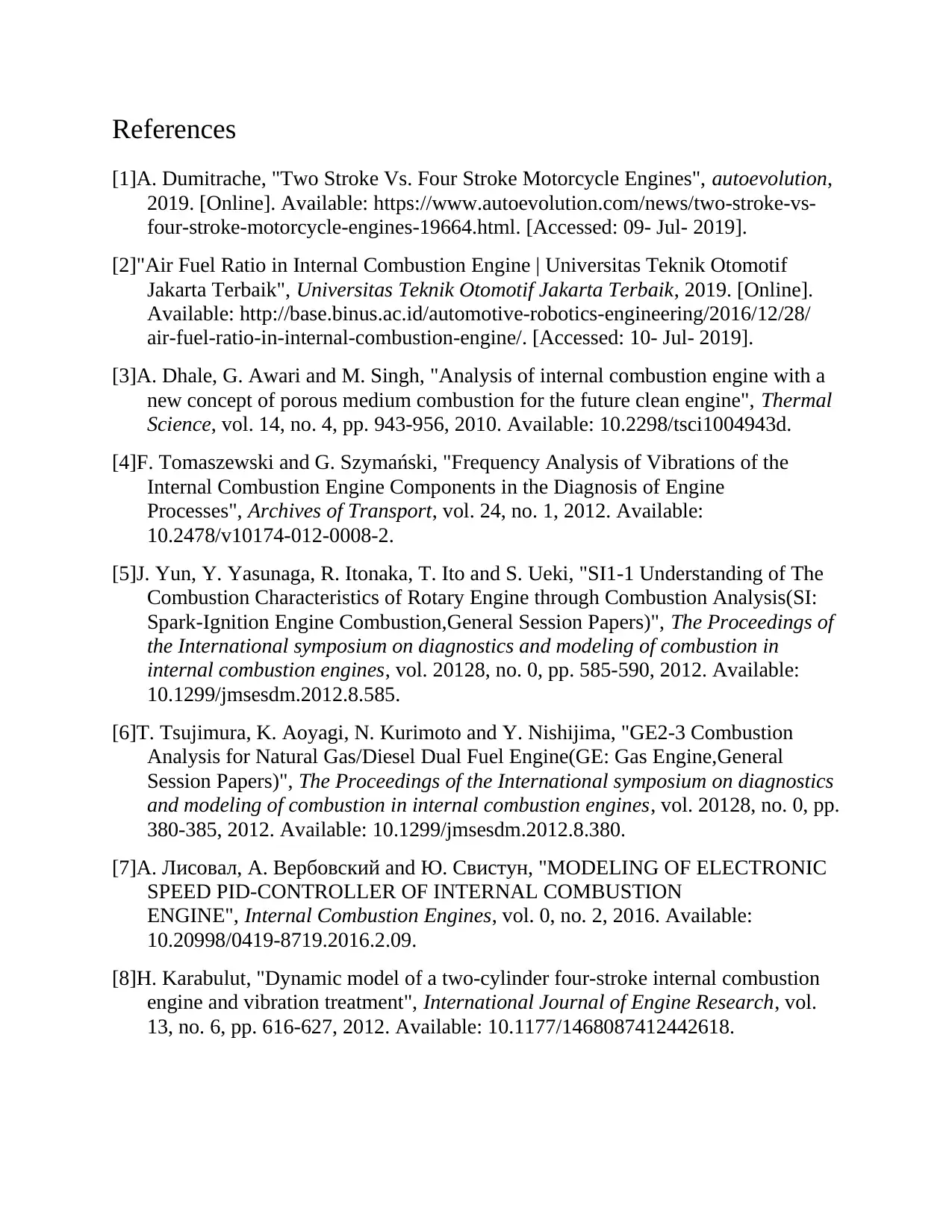
References
[1]A. Dumitrache, "Two Stroke Vs. Four Stroke Motorcycle Engines", autoevolution,
2019. [Online]. Available: https://www.autoevolution.com/news/two-stroke-vs-
four-stroke-motorcycle-engines-19664.html. [Accessed: 09- Jul- 2019].
[2]"Air Fuel Ratio in Internal Combustion Engine | Universitas Teknik Otomotif
Jakarta Terbaik", Universitas Teknik Otomotif Jakarta Terbaik, 2019. [Online].
Available: http://base.binus.ac.id/automotive-robotics-engineering/2016/12/28/
air-fuel-ratio-in-internal-combustion-engine/. [Accessed: 10- Jul- 2019].
[3]A. Dhale, G. Awari and M. Singh, "Analysis of internal combustion engine with a
new concept of porous medium combustion for the future clean engine", Thermal
Science, vol. 14, no. 4, pp. 943-956, 2010. Available: 10.2298/tsci1004943d.
[4]F. Tomaszewski and G. Szymański, "Frequency Analysis of Vibrations of the
Internal Combustion Engine Components in the Diagnosis of Engine
Processes", Archives of Transport, vol. 24, no. 1, 2012. Available:
10.2478/v10174-012-0008-2.
[5]J. Yun, Y. Yasunaga, R. Itonaka, T. Ito and S. Ueki, "SI1-1 Understanding of The
Combustion Characteristics of Rotary Engine through Combustion Analysis(SI:
Spark-Ignition Engine Combustion,General Session Papers)", The Proceedings of
the International symposium on diagnostics and modeling of combustion in
internal combustion engines, vol. 20128, no. 0, pp. 585-590, 2012. Available:
10.1299/jmsesdm.2012.8.585.
[6]T. Tsujimura, K. Aoyagi, N. Kurimoto and Y. Nishijima, "GE2-3 Combustion
Analysis for Natural Gas/Diesel Dual Fuel Engine(GE: Gas Engine,General
Session Papers)", The Proceedings of the International symposium on diagnostics
and modeling of combustion in internal combustion engines, vol. 20128, no. 0, pp.
380-385, 2012. Available: 10.1299/jmsesdm.2012.8.380.
[7]А. Лисовал, А. Вербовский and Ю. Свистун, "MODELING OF ELECTRONIC
SPEED PID-CONTROLLER OF INTERNAL COMBUSTION
ENGINE", Internal Combustion Engines, vol. 0, no. 2, 2016. Available:
10.20998/0419-8719.2016.2.09.
[8]H. Karabulut, "Dynamic model of a two-cylinder four-stroke internal combustion
engine and vibration treatment", International Journal of Engine Research, vol.
13, no. 6, pp. 616-627, 2012. Available: 10.1177/1468087412442618.
[1]A. Dumitrache, "Two Stroke Vs. Four Stroke Motorcycle Engines", autoevolution,
2019. [Online]. Available: https://www.autoevolution.com/news/two-stroke-vs-
four-stroke-motorcycle-engines-19664.html. [Accessed: 09- Jul- 2019].
[2]"Air Fuel Ratio in Internal Combustion Engine | Universitas Teknik Otomotif
Jakarta Terbaik", Universitas Teknik Otomotif Jakarta Terbaik, 2019. [Online].
Available: http://base.binus.ac.id/automotive-robotics-engineering/2016/12/28/
air-fuel-ratio-in-internal-combustion-engine/. [Accessed: 10- Jul- 2019].
[3]A. Dhale, G. Awari and M. Singh, "Analysis of internal combustion engine with a
new concept of porous medium combustion for the future clean engine", Thermal
Science, vol. 14, no. 4, pp. 943-956, 2010. Available: 10.2298/tsci1004943d.
[4]F. Tomaszewski and G. Szymański, "Frequency Analysis of Vibrations of the
Internal Combustion Engine Components in the Diagnosis of Engine
Processes", Archives of Transport, vol. 24, no. 1, 2012. Available:
10.2478/v10174-012-0008-2.
[5]J. Yun, Y. Yasunaga, R. Itonaka, T. Ito and S. Ueki, "SI1-1 Understanding of The
Combustion Characteristics of Rotary Engine through Combustion Analysis(SI:
Spark-Ignition Engine Combustion,General Session Papers)", The Proceedings of
the International symposium on diagnostics and modeling of combustion in
internal combustion engines, vol. 20128, no. 0, pp. 585-590, 2012. Available:
10.1299/jmsesdm.2012.8.585.
[6]T. Tsujimura, K. Aoyagi, N. Kurimoto and Y. Nishijima, "GE2-3 Combustion
Analysis for Natural Gas/Diesel Dual Fuel Engine(GE: Gas Engine,General
Session Papers)", The Proceedings of the International symposium on diagnostics
and modeling of combustion in internal combustion engines, vol. 20128, no. 0, pp.
380-385, 2012. Available: 10.1299/jmsesdm.2012.8.380.
[7]А. Лисовал, А. Вербовский and Ю. Свистун, "MODELING OF ELECTRONIC
SPEED PID-CONTROLLER OF INTERNAL COMBUSTION
ENGINE", Internal Combustion Engines, vol. 0, no. 2, 2016. Available:
10.20998/0419-8719.2016.2.09.
[8]H. Karabulut, "Dynamic model of a two-cylinder four-stroke internal combustion
engine and vibration treatment", International Journal of Engine Research, vol.
13, no. 6, pp. 616-627, 2012. Available: 10.1177/1468087412442618.
Paraphrase This Document
Need a fresh take? Get an instant paraphrase of this document with our AI Paraphraser
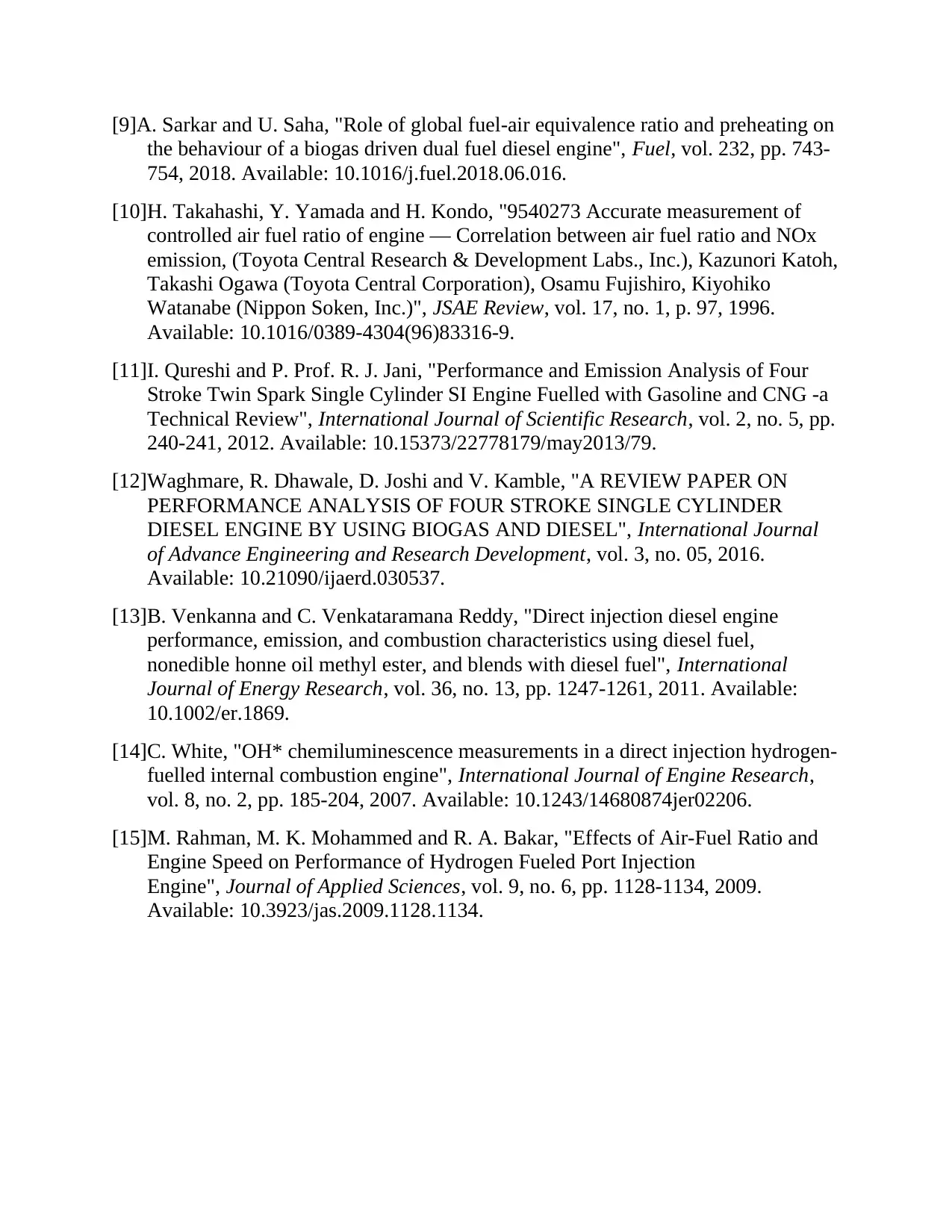
[9]A. Sarkar and U. Saha, "Role of global fuel-air equivalence ratio and preheating on
the behaviour of a biogas driven dual fuel diesel engine", Fuel, vol. 232, pp. 743-
754, 2018. Available: 10.1016/j.fuel.2018.06.016.
[10]H. Takahashi, Y. Yamada and H. Kondo, "9540273 Accurate measurement of
controlled air fuel ratio of engine — Correlation between air fuel ratio and NOx
emission, (Toyota Central Research & Development Labs., Inc.), Kazunori Katoh,
Takashi Ogawa (Toyota Central Corporation), Osamu Fujishiro, Kiyohiko
Watanabe (Nippon Soken, Inc.)", JSAE Review, vol. 17, no. 1, p. 97, 1996.
Available: 10.1016/0389-4304(96)83316-9.
[11]I. Qureshi and P. Prof. R. J. Jani, "Performance and Emission Analysis of Four
Stroke Twin Spark Single Cylinder SI Engine Fuelled with Gasoline and CNG -a
Technical Review", International Journal of Scientific Research, vol. 2, no. 5, pp.
240-241, 2012. Available: 10.15373/22778179/may2013/79.
[12]Waghmare, R. Dhawale, D. Joshi and V. Kamble, "A REVIEW PAPER ON
PERFORMANCE ANALYSIS OF FOUR STROKE SINGLE CYLINDER
DIESEL ENGINE BY USING BIOGAS AND DIESEL", International Journal
of Advance Engineering and Research Development, vol. 3, no. 05, 2016.
Available: 10.21090/ijaerd.030537.
[13]B. Venkanna and C. Venkataramana Reddy, "Direct injection diesel engine
performance, emission, and combustion characteristics using diesel fuel,
nonedible honne oil methyl ester, and blends with diesel fuel", International
Journal of Energy Research, vol. 36, no. 13, pp. 1247-1261, 2011. Available:
10.1002/er.1869.
[14]C. White, "OH* chemiluminescence measurements in a direct injection hydrogen-
fuelled internal combustion engine", International Journal of Engine Research,
vol. 8, no. 2, pp. 185-204, 2007. Available: 10.1243/14680874jer02206.
[15]M. Rahman, M. K. Mohammed and R. A. Bakar, "Effects of Air-Fuel Ratio and
Engine Speed on Performance of Hydrogen Fueled Port Injection
Engine", Journal of Applied Sciences, vol. 9, no. 6, pp. 1128-1134, 2009.
Available: 10.3923/jas.2009.1128.1134.
the behaviour of a biogas driven dual fuel diesel engine", Fuel, vol. 232, pp. 743-
754, 2018. Available: 10.1016/j.fuel.2018.06.016.
[10]H. Takahashi, Y. Yamada and H. Kondo, "9540273 Accurate measurement of
controlled air fuel ratio of engine — Correlation between air fuel ratio and NOx
emission, (Toyota Central Research & Development Labs., Inc.), Kazunori Katoh,
Takashi Ogawa (Toyota Central Corporation), Osamu Fujishiro, Kiyohiko
Watanabe (Nippon Soken, Inc.)", JSAE Review, vol. 17, no. 1, p. 97, 1996.
Available: 10.1016/0389-4304(96)83316-9.
[11]I. Qureshi and P. Prof. R. J. Jani, "Performance and Emission Analysis of Four
Stroke Twin Spark Single Cylinder SI Engine Fuelled with Gasoline and CNG -a
Technical Review", International Journal of Scientific Research, vol. 2, no. 5, pp.
240-241, 2012. Available: 10.15373/22778179/may2013/79.
[12]Waghmare, R. Dhawale, D. Joshi and V. Kamble, "A REVIEW PAPER ON
PERFORMANCE ANALYSIS OF FOUR STROKE SINGLE CYLINDER
DIESEL ENGINE BY USING BIOGAS AND DIESEL", International Journal
of Advance Engineering and Research Development, vol. 3, no. 05, 2016.
Available: 10.21090/ijaerd.030537.
[13]B. Venkanna and C. Venkataramana Reddy, "Direct injection diesel engine
performance, emission, and combustion characteristics using diesel fuel,
nonedible honne oil methyl ester, and blends with diesel fuel", International
Journal of Energy Research, vol. 36, no. 13, pp. 1247-1261, 2011. Available:
10.1002/er.1869.
[14]C. White, "OH* chemiluminescence measurements in a direct injection hydrogen-
fuelled internal combustion engine", International Journal of Engine Research,
vol. 8, no. 2, pp. 185-204, 2007. Available: 10.1243/14680874jer02206.
[15]M. Rahman, M. K. Mohammed and R. A. Bakar, "Effects of Air-Fuel Ratio and
Engine Speed on Performance of Hydrogen Fueled Port Injection
Engine", Journal of Applied Sciences, vol. 9, no. 6, pp. 1128-1134, 2009.
Available: 10.3923/jas.2009.1128.1134.
1 out of 26

Your All-in-One AI-Powered Toolkit for Academic Success.
+13062052269
info@desklib.com
Available 24*7 on WhatsApp / Email
Unlock your academic potential
© 2024 | Zucol Services PVT LTD | All rights reserved.