Report: Analysis of Costing Methods in Management Accounting
VerifiedAdded on  2022/08/21
|9
|2224
|28
Report
AI Summary
This report provides a comprehensive analysis of costing methods in management accounting, comparing traditional and activity-based costing approaches within a coffee business context. It begins by calculating the predetermined overhead rate using traditional costing, then determines product costs and selling prices for Kona and Malaysian coffee. The report then delves into activity-based costing, calculating cost driver rates and allocating overheads based on various activities such as purchasing, material handling, and packaging. A detailed comparison of product costs derived from both methods reveals significant differences, with the report explaining the reasons for these variations. Finally, the report determines the selling prices for both coffee types using activity-based costing, taking into account a 30% profit margin. The conclusion summarizes the key findings, highlighting the strengths and weaknesses of each costing method and their impact on pricing and profitability.
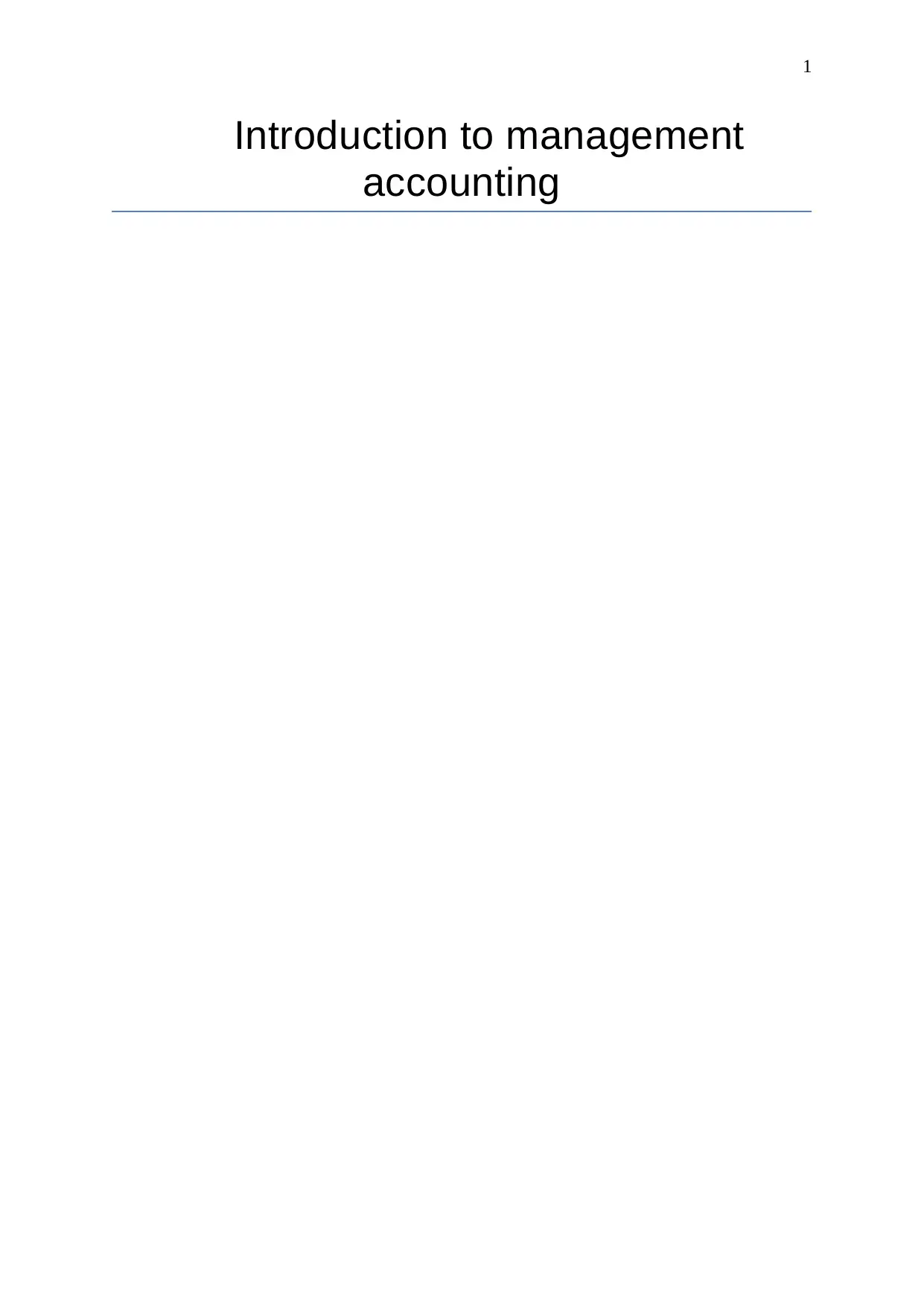
1
Introduction to management
accounting
Introduction to management
accounting
Secure Best Marks with AI Grader
Need help grading? Try our AI Grader for instant feedback on your assignments.
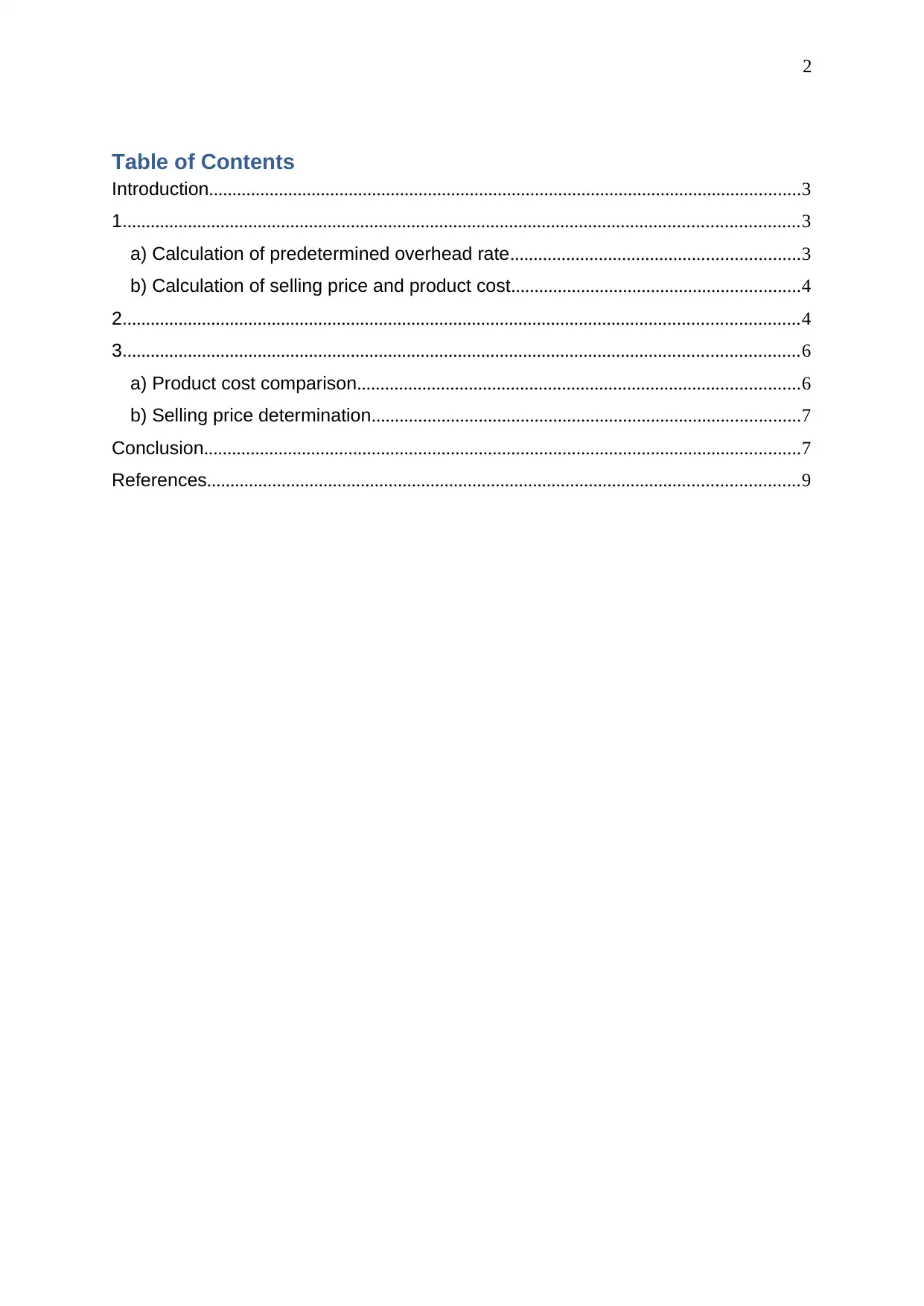
2
Table of Contents
Introduction...............................................................................................................................3
1.................................................................................................................................................3
a) Calculation of predetermined overhead rate..............................................................3
b) Calculation of selling price and product cost..............................................................4
2.................................................................................................................................................4
3.................................................................................................................................................6
a) Product cost comparison...............................................................................................6
b) Selling price determination............................................................................................7
Conclusion................................................................................................................................7
References...............................................................................................................................9
Table of Contents
Introduction...............................................................................................................................3
1.................................................................................................................................................3
a) Calculation of predetermined overhead rate..............................................................3
b) Calculation of selling price and product cost..............................................................4
2.................................................................................................................................................4
3.................................................................................................................................................6
a) Product cost comparison...............................................................................................6
b) Selling price determination............................................................................................7
Conclusion................................................................................................................................7
References...............................................................................................................................9
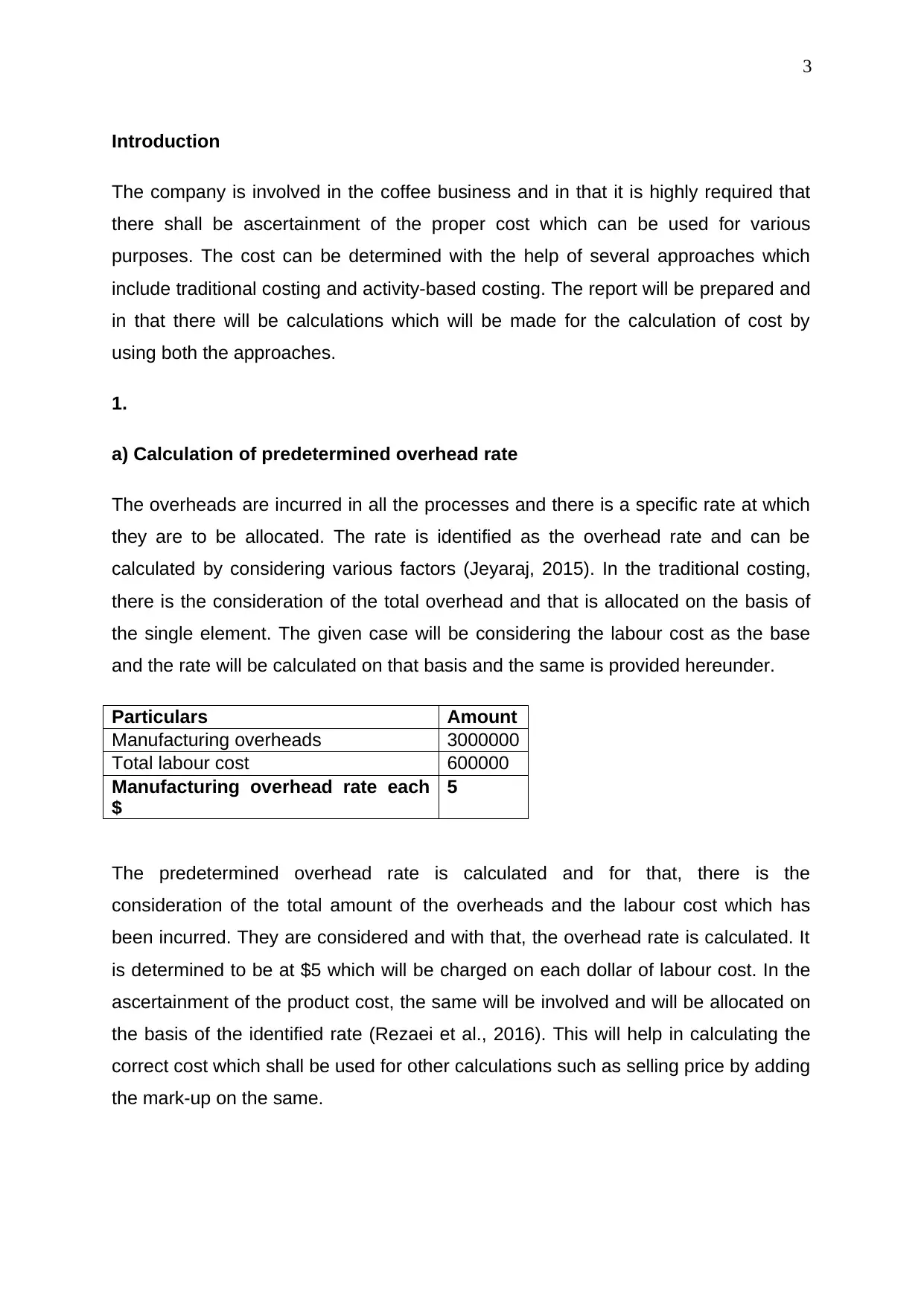
3
Introduction
The company is involved in the coffee business and in that it is highly required that
there shall be ascertainment of the proper cost which can be used for various
purposes. The cost can be determined with the help of several approaches which
include traditional costing and activity-based costing. The report will be prepared and
in that there will be calculations which will be made for the calculation of cost by
using both the approaches.
1.
a) Calculation of predetermined overhead rate
The overheads are incurred in all the processes and there is a specific rate at which
they are to be allocated. The rate is identified as the overhead rate and can be
calculated by considering various factors (Jeyaraj, 2015). In the traditional costing,
there is the consideration of the total overhead and that is allocated on the basis of
the single element. The given case will be considering the labour cost as the base
and the rate will be calculated on that basis and the same is provided hereunder.
Particulars Amount
Manufacturing overheads 3000000
Total labour cost 600000
Manufacturing overhead rate each
$
5
The predetermined overhead rate is calculated and for that, there is the
consideration of the total amount of the overheads and the labour cost which has
been incurred. They are considered and with that, the overhead rate is calculated. It
is determined to be at $5 which will be charged on each dollar of labour cost. In the
ascertainment of the product cost, the same will be involved and will be allocated on
the basis of the identified rate (Rezaei et al., 2016). This will help in calculating the
correct cost which shall be used for other calculations such as selling price by adding
the mark-up on the same.
Introduction
The company is involved in the coffee business and in that it is highly required that
there shall be ascertainment of the proper cost which can be used for various
purposes. The cost can be determined with the help of several approaches which
include traditional costing and activity-based costing. The report will be prepared and
in that there will be calculations which will be made for the calculation of cost by
using both the approaches.
1.
a) Calculation of predetermined overhead rate
The overheads are incurred in all the processes and there is a specific rate at which
they are to be allocated. The rate is identified as the overhead rate and can be
calculated by considering various factors (Jeyaraj, 2015). In the traditional costing,
there is the consideration of the total overhead and that is allocated on the basis of
the single element. The given case will be considering the labour cost as the base
and the rate will be calculated on that basis and the same is provided hereunder.
Particulars Amount
Manufacturing overheads 3000000
Total labour cost 600000
Manufacturing overhead rate each
$
5
The predetermined overhead rate is calculated and for that, there is the
consideration of the total amount of the overheads and the labour cost which has
been incurred. They are considered and with that, the overhead rate is calculated. It
is determined to be at $5 which will be charged on each dollar of labour cost. In the
ascertainment of the product cost, the same will be involved and will be allocated on
the basis of the identified rate (Rezaei et al., 2016). This will help in calculating the
correct cost which shall be used for other calculations such as selling price by adding
the mark-up on the same.
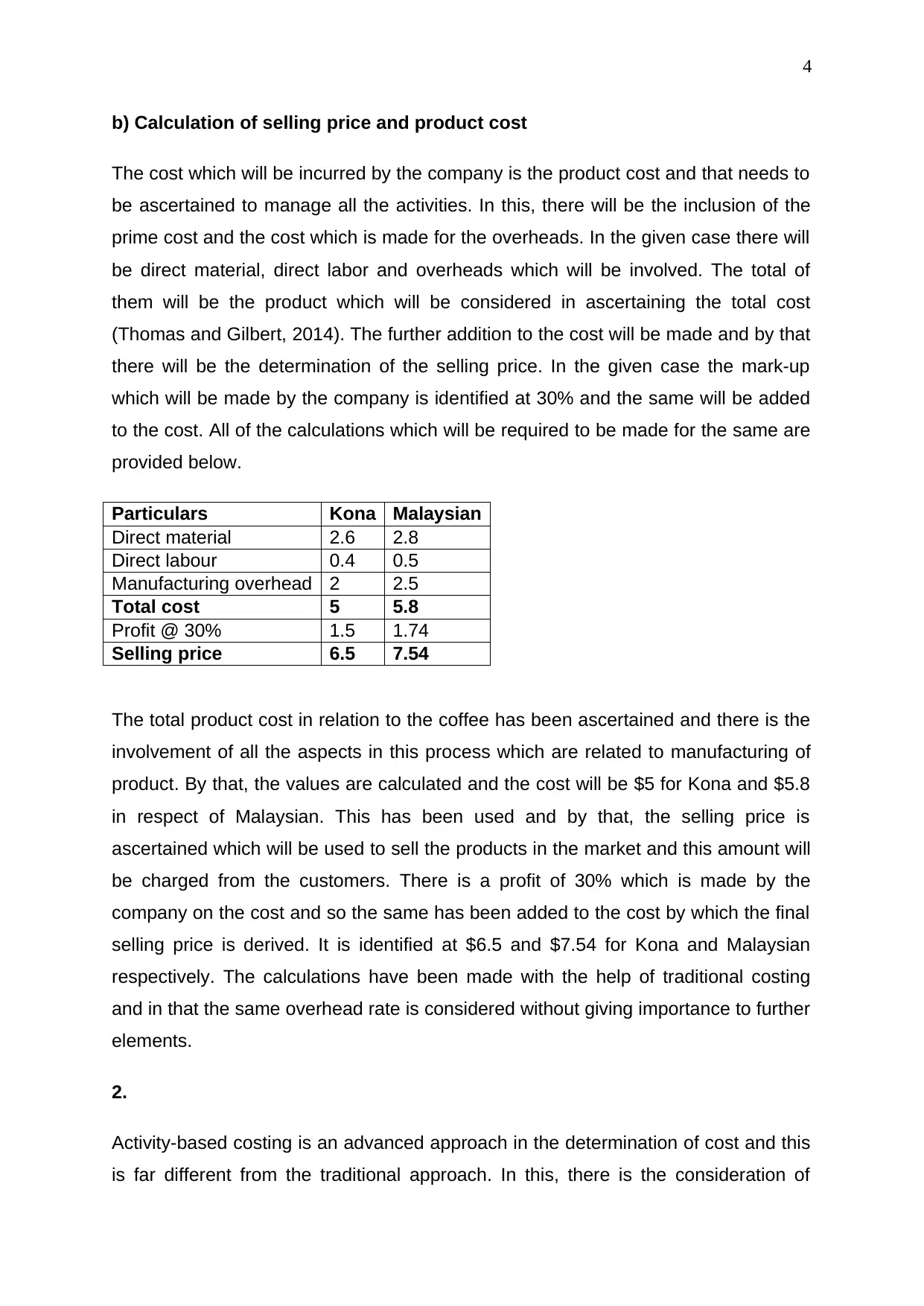
4
b) Calculation of selling price and product cost
The cost which will be incurred by the company is the product cost and that needs to
be ascertained to manage all the activities. In this, there will be the inclusion of the
prime cost and the cost which is made for the overheads. In the given case there will
be direct material, direct labor and overheads which will be involved. The total of
them will be the product which will be considered in ascertaining the total cost
(Thomas and Gilbert, 2014). The further addition to the cost will be made and by that
there will be the determination of the selling price. In the given case the mark-up
which will be made by the company is identified at 30% and the same will be added
to the cost. All of the calculations which will be required to be made for the same are
provided below.
Particulars Kona Malaysian
Direct material 2.6 2.8
Direct labour 0.4 0.5
Manufacturing overhead 2 2.5
Total cost 5 5.8
Profit @ 30% 1.5 1.74
Selling price 6.5 7.54
The total product cost in relation to the coffee has been ascertained and there is the
involvement of all the aspects in this process which are related to manufacturing of
product. By that, the values are calculated and the cost will be $5 for Kona and $5.8
in respect of Malaysian. This has been used and by that, the selling price is
ascertained which will be used to sell the products in the market and this amount will
be charged from the customers. There is a profit of 30% which is made by the
company on the cost and so the same has been added to the cost by which the final
selling price is derived. It is identified at $6.5 and $7.54 for Kona and Malaysian
respectively. The calculations have been made with the help of traditional costing
and in that the same overhead rate is considered without giving importance to further
elements.
2.
Activity-based costing is an advanced approach in the determination of cost and this
is far different from the traditional approach. In this, there is the consideration of
b) Calculation of selling price and product cost
The cost which will be incurred by the company is the product cost and that needs to
be ascertained to manage all the activities. In this, there will be the inclusion of the
prime cost and the cost which is made for the overheads. In the given case there will
be direct material, direct labor and overheads which will be involved. The total of
them will be the product which will be considered in ascertaining the total cost
(Thomas and Gilbert, 2014). The further addition to the cost will be made and by that
there will be the determination of the selling price. In the given case the mark-up
which will be made by the company is identified at 30% and the same will be added
to the cost. All of the calculations which will be required to be made for the same are
provided below.
Particulars Kona Malaysian
Direct material 2.6 2.8
Direct labour 0.4 0.5
Manufacturing overhead 2 2.5
Total cost 5 5.8
Profit @ 30% 1.5 1.74
Selling price 6.5 7.54
The total product cost in relation to the coffee has been ascertained and there is the
involvement of all the aspects in this process which are related to manufacturing of
product. By that, the values are calculated and the cost will be $5 for Kona and $5.8
in respect of Malaysian. This has been used and by that, the selling price is
ascertained which will be used to sell the products in the market and this amount will
be charged from the customers. There is a profit of 30% which is made by the
company on the cost and so the same has been added to the cost by which the final
selling price is derived. It is identified at $6.5 and $7.54 for Kona and Malaysian
respectively. The calculations have been made with the help of traditional costing
and in that the same overhead rate is considered without giving importance to further
elements.
2.
Activity-based costing is an advanced approach in the determination of cost and this
is far different from the traditional approach. In this, there is the consideration of
Secure Best Marks with AI Grader
Need help grading? Try our AI Grader for instant feedback on your assignments.
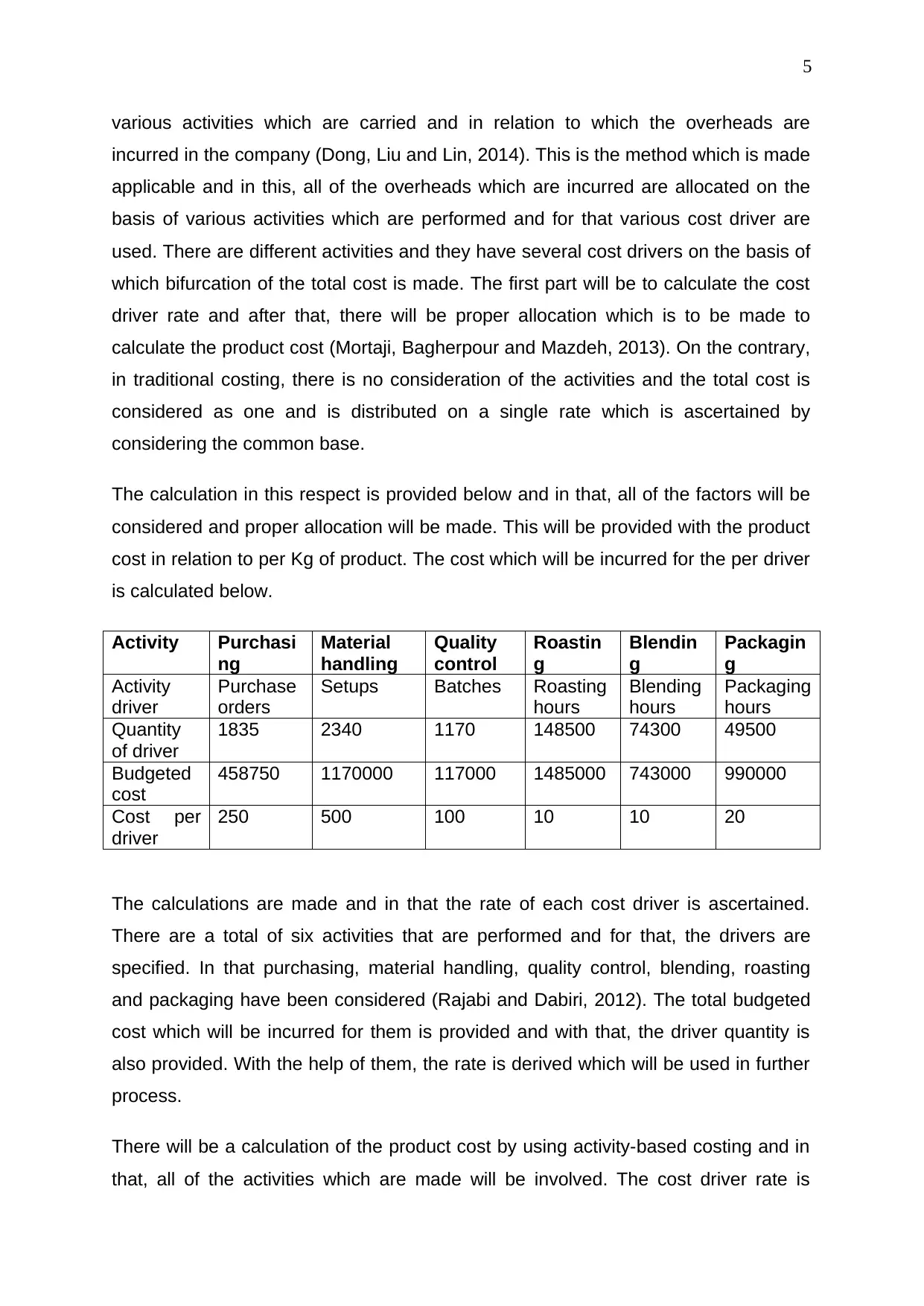
5
various activities which are carried and in relation to which the overheads are
incurred in the company (Dong, Liu and Lin, 2014). This is the method which is made
applicable and in this, all of the overheads which are incurred are allocated on the
basis of various activities which are performed and for that various cost driver are
used. There are different activities and they have several cost drivers on the basis of
which bifurcation of the total cost is made. The first part will be to calculate the cost
driver rate and after that, there will be proper allocation which is to be made to
calculate the product cost (Mortaji, Bagherpour and Mazdeh, 2013). On the contrary,
in traditional costing, there is no consideration of the activities and the total cost is
considered as one and is distributed on a single rate which is ascertained by
considering the common base.
The calculation in this respect is provided below and in that, all of the factors will be
considered and proper allocation will be made. This will be provided with the product
cost in relation to per Kg of product. The cost which will be incurred for the per driver
is calculated below.
Activity Purchasi
ng
Material
handling
Quality
control
Roastin
g
Blendin
g
Packagin
g
Activity
driver
Purchase
orders
Setups Batches Roasting
hours
Blending
hours
Packaging
hours
Quantity
of driver
1835 2340 1170 148500 74300 49500
Budgeted
cost
458750 1170000 117000 1485000 743000 990000
Cost per
driver
250 500 100 10 10 20
The calculations are made and in that the rate of each cost driver is ascertained.
There are a total of six activities that are performed and for that, the drivers are
specified. In that purchasing, material handling, quality control, blending, roasting
and packaging have been considered (Rajabi and Dabiri, 2012). The total budgeted
cost which will be incurred for them is provided and with that, the driver quantity is
also provided. With the help of them, the rate is derived which will be used in further
process.
There will be a calculation of the product cost by using activity-based costing and in
that, all of the activities which are made will be involved. The cost driver rate is
various activities which are carried and in relation to which the overheads are
incurred in the company (Dong, Liu and Lin, 2014). This is the method which is made
applicable and in this, all of the overheads which are incurred are allocated on the
basis of various activities which are performed and for that various cost driver are
used. There are different activities and they have several cost drivers on the basis of
which bifurcation of the total cost is made. The first part will be to calculate the cost
driver rate and after that, there will be proper allocation which is to be made to
calculate the product cost (Mortaji, Bagherpour and Mazdeh, 2013). On the contrary,
in traditional costing, there is no consideration of the activities and the total cost is
considered as one and is distributed on a single rate which is ascertained by
considering the common base.
The calculation in this respect is provided below and in that, all of the factors will be
considered and proper allocation will be made. This will be provided with the product
cost in relation to per Kg of product. The cost which will be incurred for the per driver
is calculated below.
Activity Purchasi
ng
Material
handling
Quality
control
Roastin
g
Blendin
g
Packagin
g
Activity
driver
Purchase
orders
Setups Batches Roasting
hours
Blending
hours
Packaging
hours
Quantity
of driver
1835 2340 1170 148500 74300 49500
Budgeted
cost
458750 1170000 117000 1485000 743000 990000
Cost per
driver
250 500 100 10 10 20
The calculations are made and in that the rate of each cost driver is ascertained.
There are a total of six activities that are performed and for that, the drivers are
specified. In that purchasing, material handling, quality control, blending, roasting
and packaging have been considered (Rajabi and Dabiri, 2012). The total budgeted
cost which will be incurred for them is provided and with that, the driver quantity is
also provided. With the help of them, the rate is derived which will be used in further
process.
There will be a calculation of the product cost by using activity-based costing and in
that, all of the activities which are made will be involved. The cost driver rate is
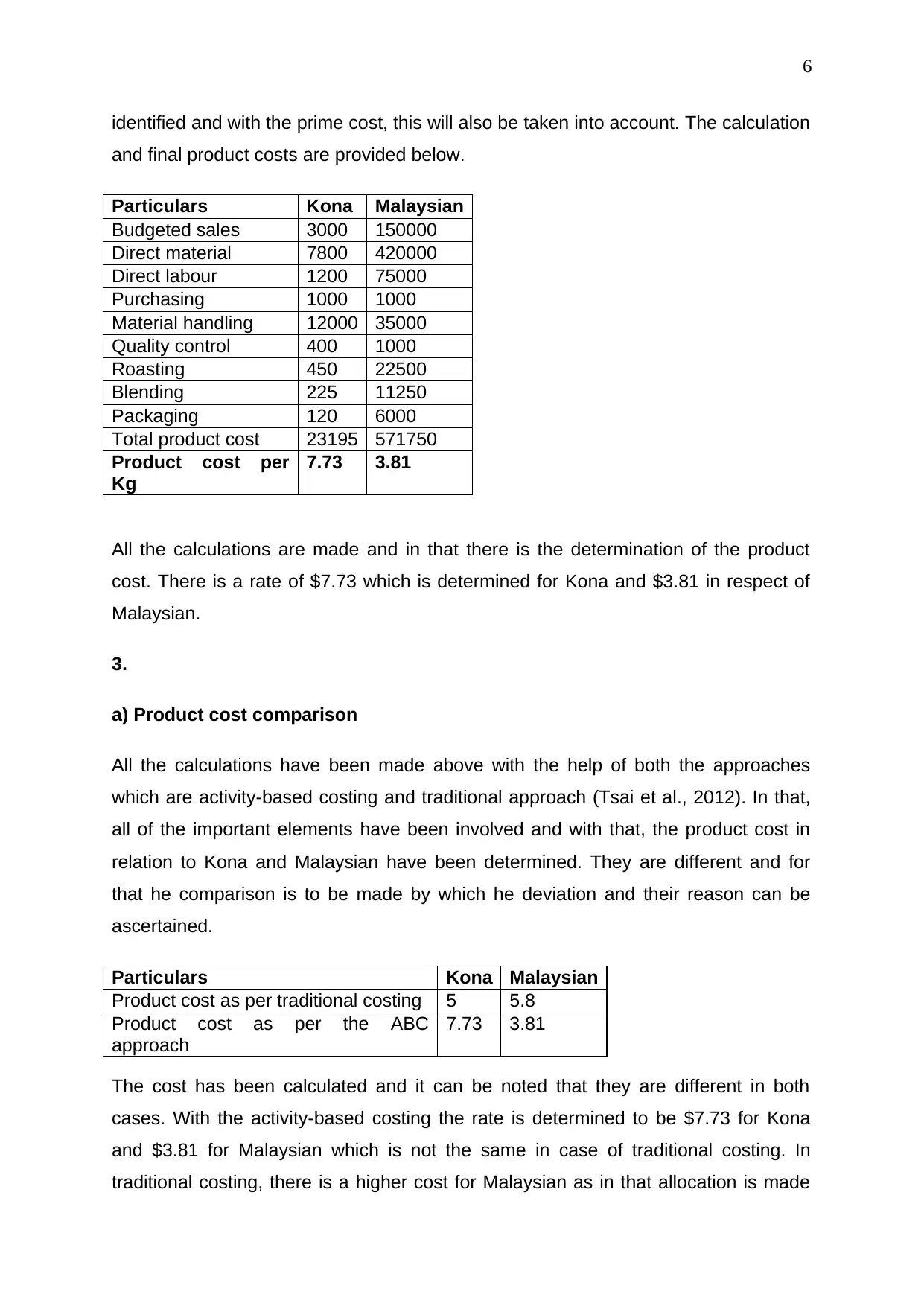
6
identified and with the prime cost, this will also be taken into account. The calculation
and final product costs are provided below.
Particulars Kona Malaysian
Budgeted sales 3000 150000
Direct material 7800 420000
Direct labour 1200 75000
Purchasing 1000 1000
Material handling 12000 35000
Quality control 400 1000
Roasting 450 22500
Blending 225 11250
Packaging 120 6000
Total product cost 23195 571750
Product cost per
Kg
7.73 3.81
All the calculations are made and in that there is the determination of the product
cost. There is a rate of $7.73 which is determined for Kona and $3.81 in respect of
Malaysian.
3.
a) Product cost comparison
All the calculations have been made above with the help of both the approaches
which are activity-based costing and traditional approach (Tsai et al., 2012). In that,
all of the important elements have been involved and with that, the product cost in
relation to Kona and Malaysian have been determined. They are different and for
that he comparison is to be made by which he deviation and their reason can be
ascertained.
Particulars Kona Malaysian
Product cost as per traditional costing 5 5.8
Product cost as per the ABC
approach
7.73 3.81
The cost has been calculated and it can be noted that they are different in both
cases. With the activity-based costing the rate is determined to be $7.73 for Kona
and $3.81 for Malaysian which is not the same in case of traditional costing. In
traditional costing, there is a higher cost for Malaysian as in that allocation is made
identified and with the prime cost, this will also be taken into account. The calculation
and final product costs are provided below.
Particulars Kona Malaysian
Budgeted sales 3000 150000
Direct material 7800 420000
Direct labour 1200 75000
Purchasing 1000 1000
Material handling 12000 35000
Quality control 400 1000
Roasting 450 22500
Blending 225 11250
Packaging 120 6000
Total product cost 23195 571750
Product cost per
Kg
7.73 3.81
All the calculations are made and in that there is the determination of the product
cost. There is a rate of $7.73 which is determined for Kona and $3.81 in respect of
Malaysian.
3.
a) Product cost comparison
All the calculations have been made above with the help of both the approaches
which are activity-based costing and traditional approach (Tsai et al., 2012). In that,
all of the important elements have been involved and with that, the product cost in
relation to Kona and Malaysian have been determined. They are different and for
that he comparison is to be made by which he deviation and their reason can be
ascertained.
Particulars Kona Malaysian
Product cost as per traditional costing 5 5.8
Product cost as per the ABC
approach
7.73 3.81
The cost has been calculated and it can be noted that they are different in both
cases. With the activity-based costing the rate is determined to be $7.73 for Kona
and $3.81 for Malaysian which is not the same in case of traditional costing. In
traditional costing, there is a higher cost for Malaysian as in that allocation is made
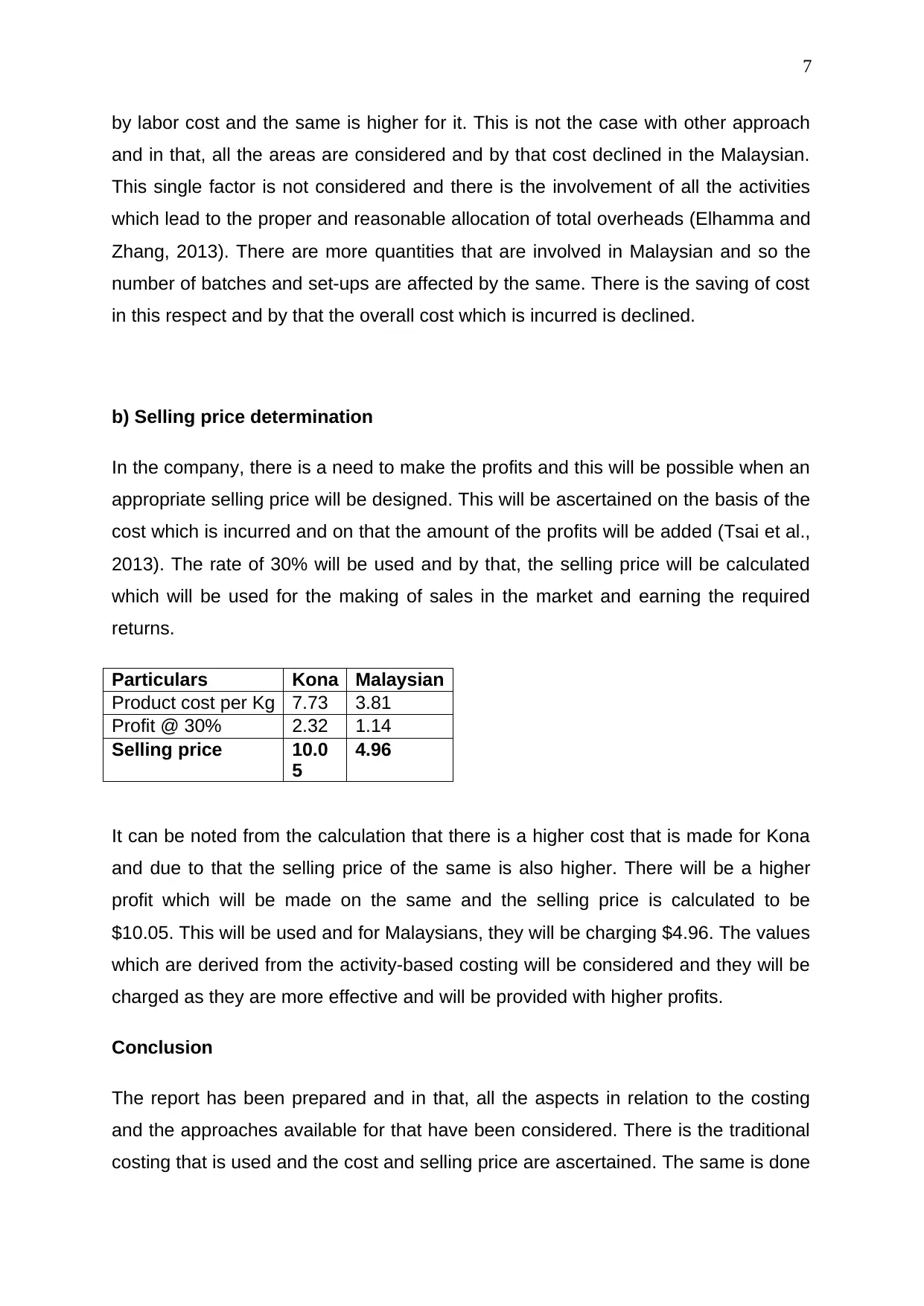
7
by labor cost and the same is higher for it. This is not the case with other approach
and in that, all the areas are considered and by that cost declined in the Malaysian.
This single factor is not considered and there is the involvement of all the activities
which lead to the proper and reasonable allocation of total overheads (Elhamma and
Zhang, 2013). There are more quantities that are involved in Malaysian and so the
number of batches and set-ups are affected by the same. There is the saving of cost
in this respect and by that the overall cost which is incurred is declined.
b) Selling price determination
In the company, there is a need to make the profits and this will be possible when an
appropriate selling price will be designed. This will be ascertained on the basis of the
cost which is incurred and on that the amount of the profits will be added (Tsai et al.,
2013). The rate of 30% will be used and by that, the selling price will be calculated
which will be used for the making of sales in the market and earning the required
returns.
Particulars Kona Malaysian
Product cost per Kg 7.73 3.81
Profit @ 30% 2.32 1.14
Selling price 10.0
5
4.96
It can be noted from the calculation that there is a higher cost that is made for Kona
and due to that the selling price of the same is also higher. There will be a higher
profit which will be made on the same and the selling price is calculated to be
$10.05. This will be used and for Malaysians, they will be charging $4.96. The values
which are derived from the activity-based costing will be considered and they will be
charged as they are more effective and will be provided with higher profits.
Conclusion
The report has been prepared and in that, all the aspects in relation to the costing
and the approaches available for that have been considered. There is the traditional
costing that is used and the cost and selling price are ascertained. The same is done
by labor cost and the same is higher for it. This is not the case with other approach
and in that, all the areas are considered and by that cost declined in the Malaysian.
This single factor is not considered and there is the involvement of all the activities
which lead to the proper and reasonable allocation of total overheads (Elhamma and
Zhang, 2013). There are more quantities that are involved in Malaysian and so the
number of batches and set-ups are affected by the same. There is the saving of cost
in this respect and by that the overall cost which is incurred is declined.
b) Selling price determination
In the company, there is a need to make the profits and this will be possible when an
appropriate selling price will be designed. This will be ascertained on the basis of the
cost which is incurred and on that the amount of the profits will be added (Tsai et al.,
2013). The rate of 30% will be used and by that, the selling price will be calculated
which will be used for the making of sales in the market and earning the required
returns.
Particulars Kona Malaysian
Product cost per Kg 7.73 3.81
Profit @ 30% 2.32 1.14
Selling price 10.0
5
4.96
It can be noted from the calculation that there is a higher cost that is made for Kona
and due to that the selling price of the same is also higher. There will be a higher
profit which will be made on the same and the selling price is calculated to be
$10.05. This will be used and for Malaysians, they will be charging $4.96. The values
which are derived from the activity-based costing will be considered and they will be
charged as they are more effective and will be provided with higher profits.
Conclusion
The report has been prepared and in that, all the aspects in relation to the costing
and the approaches available for that have been considered. There is the traditional
costing that is used and the cost and selling price are ascertained. The same is done
Paraphrase This Document
Need a fresh take? Get an instant paraphrase of this document with our AI Paraphraser
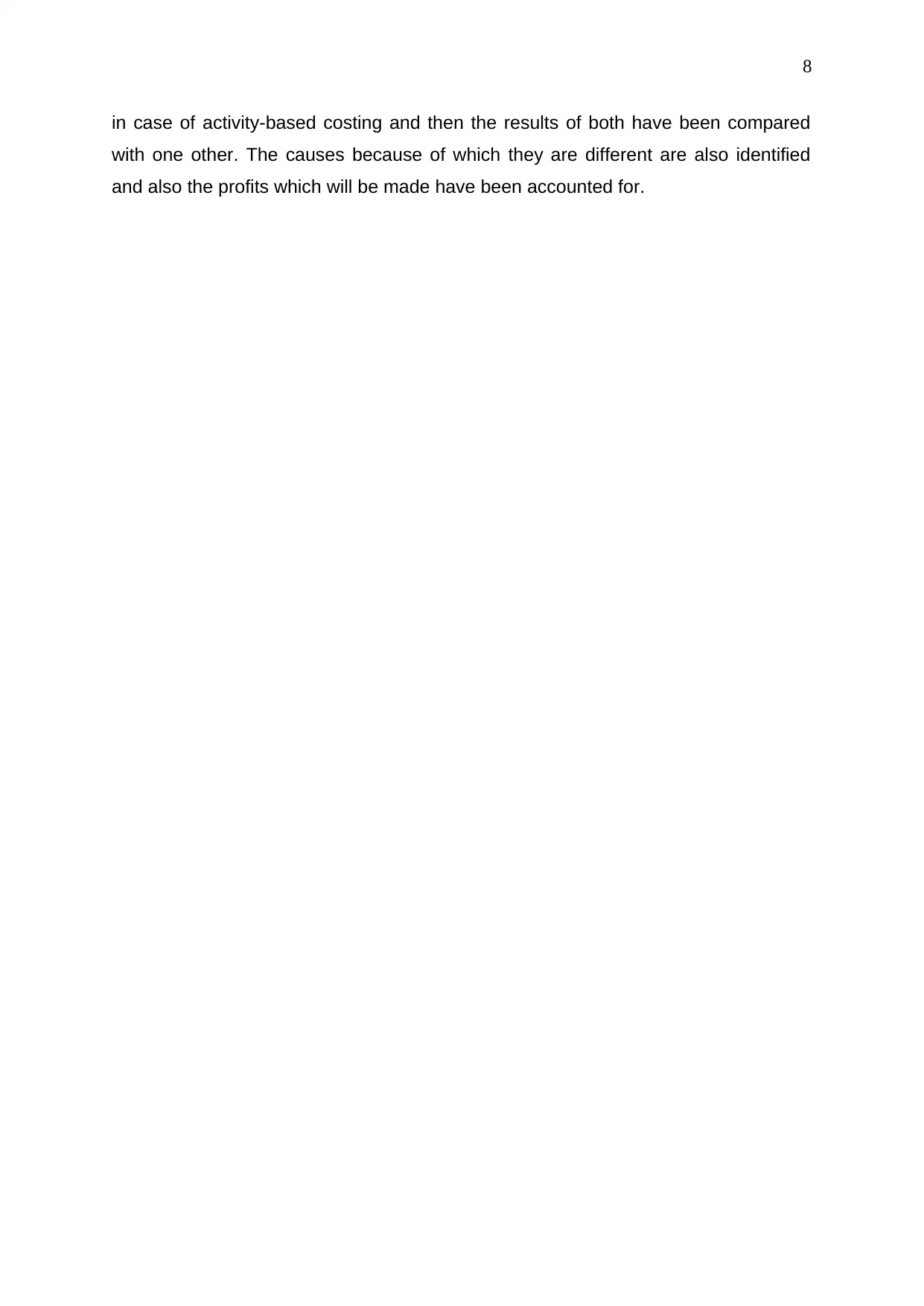
8
in case of activity-based costing and then the results of both have been compared
with one other. The causes because of which they are different are also identified
and also the profits which will be made have been accounted for.
in case of activity-based costing and then the results of both have been compared
with one other. The causes because of which they are different are also identified
and also the profits which will be made have been accounted for.
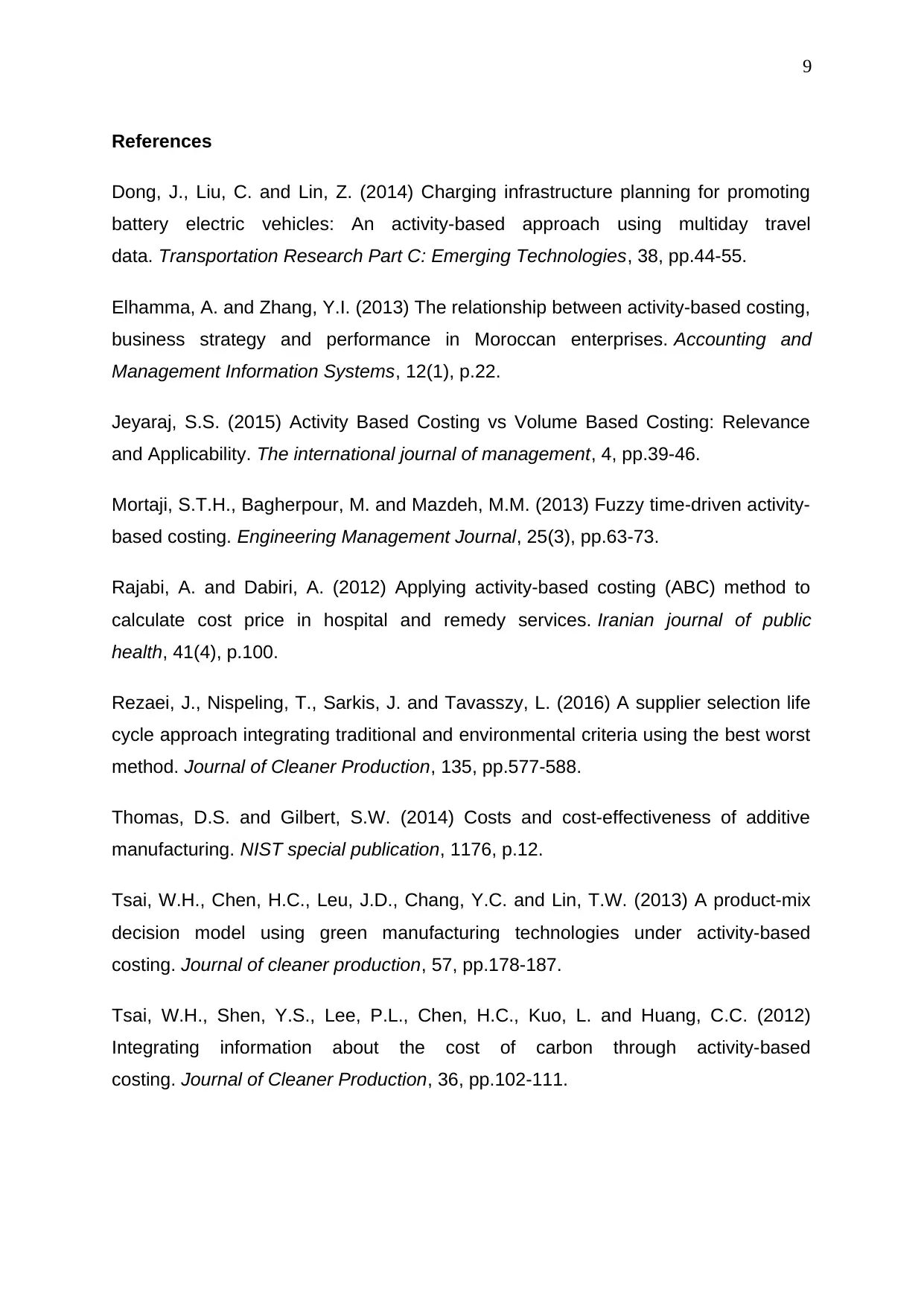
9
References
Dong, J., Liu, C. and Lin, Z. (2014) Charging infrastructure planning for promoting
battery electric vehicles: An activity-based approach using multiday travel
data. Transportation Research Part C: Emerging Technologies, 38, pp.44-55.
Elhamma, A. and Zhang, Y.I. (2013) The relationship between activity-based costing,
business strategy and performance in Moroccan enterprises. Accounting and
Management Information Systems, 12(1), p.22.
Jeyaraj, S.S. (2015) Activity Based Costing vs Volume Based Costing: Relevance
and Applicability. The international journal of management, 4, pp.39-46.
Mortaji, S.T.H., Bagherpour, M. and Mazdeh, M.M. (2013) Fuzzy time-driven activity-
based costing. Engineering Management Journal, 25(3), pp.63-73.
Rajabi, A. and Dabiri, A. (2012) Applying activity-based costing (ABC) method to
calculate cost price in hospital and remedy services. Iranian journal of public
health, 41(4), p.100.
Rezaei, J., Nispeling, T., Sarkis, J. and Tavasszy, L. (2016) A supplier selection life
cycle approach integrating traditional and environmental criteria using the best worst
method. Journal of Cleaner Production, 135, pp.577-588.
Thomas, D.S. and Gilbert, S.W. (2014) Costs and cost-effectiveness of additive
manufacturing. NIST special publication, 1176, p.12.
Tsai, W.H., Chen, H.C., Leu, J.D., Chang, Y.C. and Lin, T.W. (2013) A product-mix
decision model using green manufacturing technologies under activity-based
costing. Journal of cleaner production, 57, pp.178-187.
Tsai, W.H., Shen, Y.S., Lee, P.L., Chen, H.C., Kuo, L. and Huang, C.C. (2012)
Integrating information about the cost of carbon through activity-based
costing. Journal of Cleaner Production, 36, pp.102-111.
References
Dong, J., Liu, C. and Lin, Z. (2014) Charging infrastructure planning for promoting
battery electric vehicles: An activity-based approach using multiday travel
data. Transportation Research Part C: Emerging Technologies, 38, pp.44-55.
Elhamma, A. and Zhang, Y.I. (2013) The relationship between activity-based costing,
business strategy and performance in Moroccan enterprises. Accounting and
Management Information Systems, 12(1), p.22.
Jeyaraj, S.S. (2015) Activity Based Costing vs Volume Based Costing: Relevance
and Applicability. The international journal of management, 4, pp.39-46.
Mortaji, S.T.H., Bagherpour, M. and Mazdeh, M.M. (2013) Fuzzy time-driven activity-
based costing. Engineering Management Journal, 25(3), pp.63-73.
Rajabi, A. and Dabiri, A. (2012) Applying activity-based costing (ABC) method to
calculate cost price in hospital and remedy services. Iranian journal of public
health, 41(4), p.100.
Rezaei, J., Nispeling, T., Sarkis, J. and Tavasszy, L. (2016) A supplier selection life
cycle approach integrating traditional and environmental criteria using the best worst
method. Journal of Cleaner Production, 135, pp.577-588.
Thomas, D.S. and Gilbert, S.W. (2014) Costs and cost-effectiveness of additive
manufacturing. NIST special publication, 1176, p.12.
Tsai, W.H., Chen, H.C., Leu, J.D., Chang, Y.C. and Lin, T.W. (2013) A product-mix
decision model using green manufacturing technologies under activity-based
costing. Journal of cleaner production, 57, pp.178-187.
Tsai, W.H., Shen, Y.S., Lee, P.L., Chen, H.C., Kuo, L. and Huang, C.C. (2012)
Integrating information about the cost of carbon through activity-based
costing. Journal of Cleaner Production, 36, pp.102-111.
1 out of 9
Related Documents

Your All-in-One AI-Powered Toolkit for Academic Success.
 +13062052269
info@desklib.com
Available 24*7 on WhatsApp / Email
Unlock your academic potential
© 2024  |  Zucol Services PVT LTD  |  All rights reserved.