Detailed Analysis of Construction Changes: Upper West Side Project
VerifiedAdded on 2023/04/05
|4
|1112
|194
Report
AI Summary
This report provides a detailed analysis of the construction changes made to the Upper West Side project. The project involved modifications to the car park screen, junction walls, and glazing. Initially, the car park screen was designed with an aluminum box fixed to the slab, later replaced with a small...
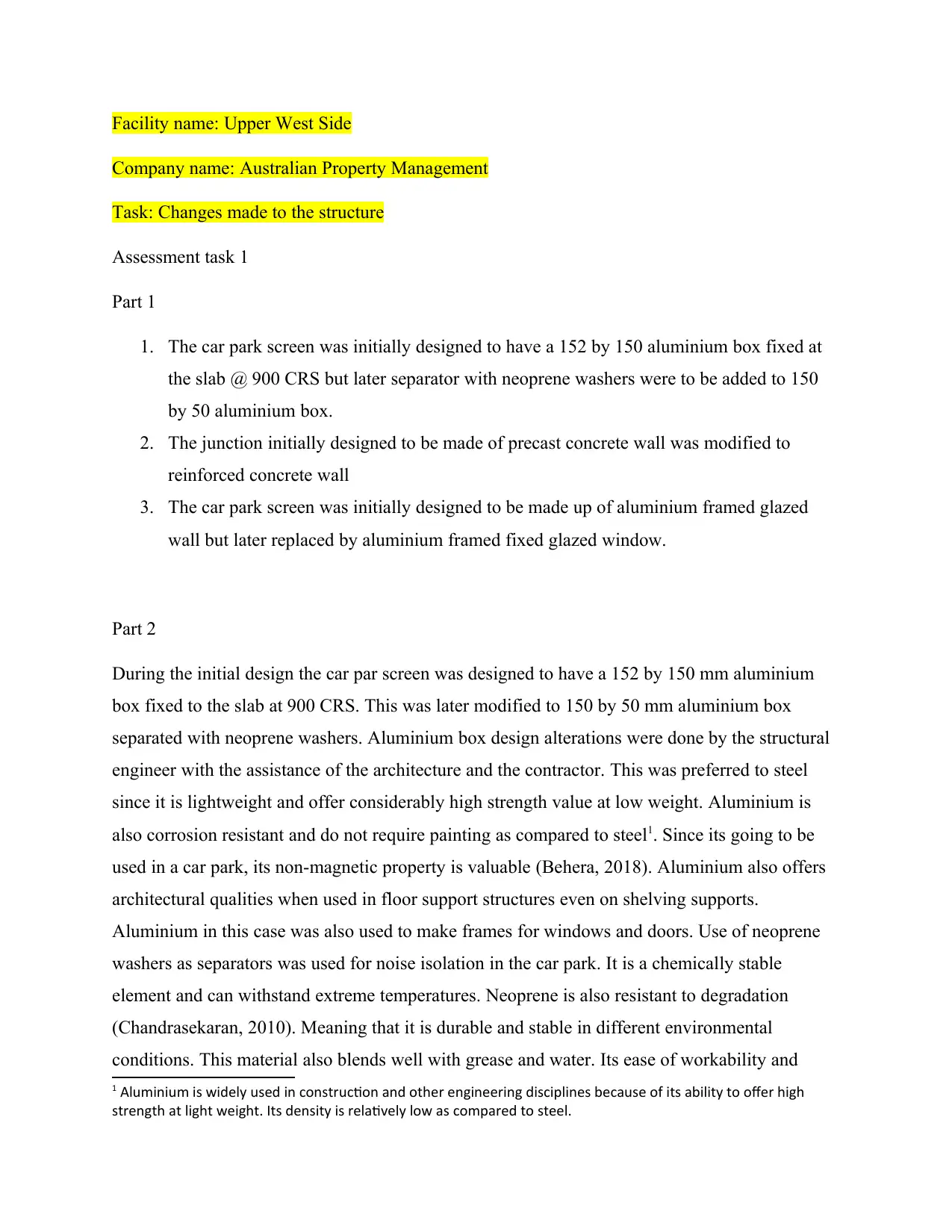
Facility name: Upper West Side
Company name: Australian Property Management
Task: Changes made to the structure
Assessment task 1
Part 1
1. The car park screen was initially designed to have a 152 by 150 aluminium box fixed at
the slab @ 900 CRS but later separator with neoprene washers were to be added to 150
by 50 aluminium box.
2. The junction initially designed to be made of precast concrete wall was modified to
reinforced concrete wall
3. The car park screen was initially designed to be made up of aluminium framed glazed
wall but later replaced by aluminium framed fixed glazed window.
Part 2
During the initial design the car par screen was designed to have a 152 by 150 mm aluminium
box fixed to the slab at 900 CRS. This was later modified to 150 by 50 mm aluminium box
separated with neoprene washers. Aluminium box design alterations were done by the structural
engineer with the assistance of the architecture and the contractor. This was preferred to steel
since it is lightweight and offer considerably high strength value at low weight. Aluminium is
also corrosion resistant and do not require painting as compared to steel1. Since its going to be
used in a car park, its non-magnetic property is valuable (Behera, 2018). Aluminium also offers
architectural qualities when used in floor support structures even on shelving supports.
Aluminium in this case was also used to make frames for windows and doors. Use of neoprene
washers as separators was used for noise isolation in the car park. It is a chemically stable
element and can withstand extreme temperatures. Neoprene is also resistant to degradation
(Chandrasekaran, 2010). Meaning that it is durable and stable in different environmental
conditions. This material also blends well with grease and water. Its ease of workability and
1 Aluminium is widely used in construction and other engineering disciplines because of its ability to offer high
strength at light weight. Its density is relatively low as compared to steel.
Company name: Australian Property Management
Task: Changes made to the structure
Assessment task 1
Part 1
1. The car park screen was initially designed to have a 152 by 150 aluminium box fixed at
the slab @ 900 CRS but later separator with neoprene washers were to be added to 150
by 50 aluminium box.
2. The junction initially designed to be made of precast concrete wall was modified to
reinforced concrete wall
3. The car park screen was initially designed to be made up of aluminium framed glazed
wall but later replaced by aluminium framed fixed glazed window.
Part 2
During the initial design the car par screen was designed to have a 152 by 150 mm aluminium
box fixed to the slab at 900 CRS. This was later modified to 150 by 50 mm aluminium box
separated with neoprene washers. Aluminium box design alterations were done by the structural
engineer with the assistance of the architecture and the contractor. This was preferred to steel
since it is lightweight and offer considerably high strength value at low weight. Aluminium is
also corrosion resistant and do not require painting as compared to steel1. Since its going to be
used in a car park, its non-magnetic property is valuable (Behera, 2018). Aluminium also offers
architectural qualities when used in floor support structures even on shelving supports.
Aluminium in this case was also used to make frames for windows and doors. Use of neoprene
washers as separators was used for noise isolation in the car park. It is a chemically stable
element and can withstand extreme temperatures. Neoprene is also resistant to degradation
(Chandrasekaran, 2010). Meaning that it is durable and stable in different environmental
conditions. This material also blends well with grease and water. Its ease of workability and
1 Aluminium is widely used in construction and other engineering disciplines because of its ability to offer high
strength at light weight. Its density is relatively low as compared to steel.
Paraphrase This Document
Need a fresh take? Get an instant paraphrase of this document with our AI Paraphraser
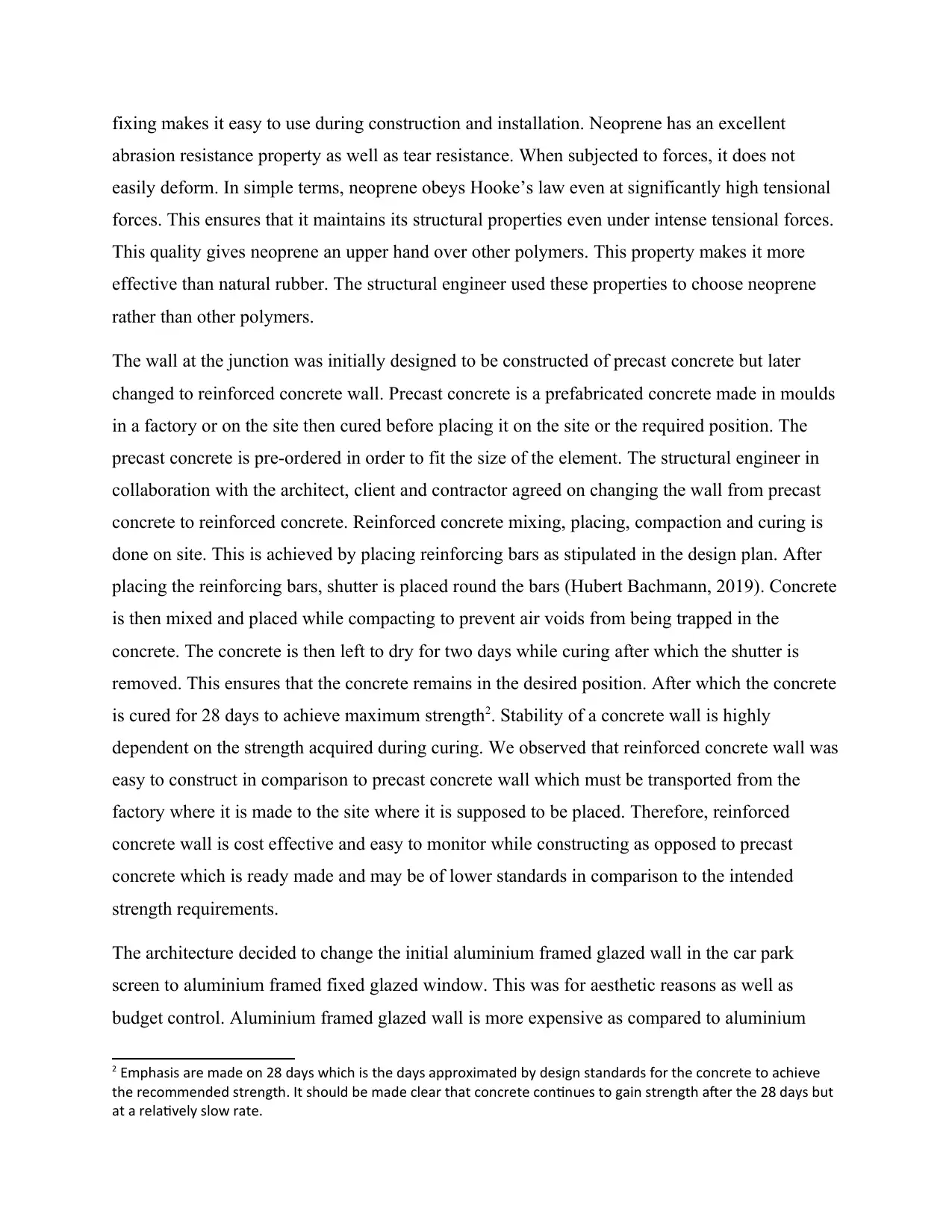
fixing makes it easy to use during construction and installation. Neoprene has an excellent
abrasion resistance property as well as tear resistance. When subjected to forces, it does not
easily deform. In simple terms, neoprene obeys Hooke’s law even at significantly high tensional
forces. This ensures that it maintains its structural properties even under intense tensional forces.
This quality gives neoprene an upper hand over other polymers. This property makes it more
effective than natural rubber. The structural engineer used these properties to choose neoprene
rather than other polymers.
The wall at the junction was initially designed to be constructed of precast concrete but later
changed to reinforced concrete wall. Precast concrete is a prefabricated concrete made in moulds
in a factory or on the site then cured before placing it on the site or the required position. The
precast concrete is pre-ordered in order to fit the size of the element. The structural engineer in
collaboration with the architect, client and contractor agreed on changing the wall from precast
concrete to reinforced concrete. Reinforced concrete mixing, placing, compaction and curing is
done on site. This is achieved by placing reinforcing bars as stipulated in the design plan. After
placing the reinforcing bars, shutter is placed round the bars (Hubert Bachmann, 2019). Concrete
is then mixed and placed while compacting to prevent air voids from being trapped in the
concrete. The concrete is then left to dry for two days while curing after which the shutter is
removed. This ensures that the concrete remains in the desired position. After which the concrete
is cured for 28 days to achieve maximum strength2. Stability of a concrete wall is highly
dependent on the strength acquired during curing. We observed that reinforced concrete wall was
easy to construct in comparison to precast concrete wall which must be transported from the
factory where it is made to the site where it is supposed to be placed. Therefore, reinforced
concrete wall is cost effective and easy to monitor while constructing as opposed to precast
concrete which is ready made and may be of lower standards in comparison to the intended
strength requirements.
The architecture decided to change the initial aluminium framed glazed wall in the car park
screen to aluminium framed fixed glazed window. This was for aesthetic reasons as well as
budget control. Aluminium framed glazed wall is more expensive as compared to aluminium
2 Emphasis are made on 28 days which is the days approximated by design standards for the concrete to achieve
the recommended strength. It should be made clear that concrete continues to gain strength after the 28 days but
at a relatively slow rate.
abrasion resistance property as well as tear resistance. When subjected to forces, it does not
easily deform. In simple terms, neoprene obeys Hooke’s law even at significantly high tensional
forces. This ensures that it maintains its structural properties even under intense tensional forces.
This quality gives neoprene an upper hand over other polymers. This property makes it more
effective than natural rubber. The structural engineer used these properties to choose neoprene
rather than other polymers.
The wall at the junction was initially designed to be constructed of precast concrete but later
changed to reinforced concrete wall. Precast concrete is a prefabricated concrete made in moulds
in a factory or on the site then cured before placing it on the site or the required position. The
precast concrete is pre-ordered in order to fit the size of the element. The structural engineer in
collaboration with the architect, client and contractor agreed on changing the wall from precast
concrete to reinforced concrete. Reinforced concrete mixing, placing, compaction and curing is
done on site. This is achieved by placing reinforcing bars as stipulated in the design plan. After
placing the reinforcing bars, shutter is placed round the bars (Hubert Bachmann, 2019). Concrete
is then mixed and placed while compacting to prevent air voids from being trapped in the
concrete. The concrete is then left to dry for two days while curing after which the shutter is
removed. This ensures that the concrete remains in the desired position. After which the concrete
is cured for 28 days to achieve maximum strength2. Stability of a concrete wall is highly
dependent on the strength acquired during curing. We observed that reinforced concrete wall was
easy to construct in comparison to precast concrete wall which must be transported from the
factory where it is made to the site where it is supposed to be placed. Therefore, reinforced
concrete wall is cost effective and easy to monitor while constructing as opposed to precast
concrete which is ready made and may be of lower standards in comparison to the intended
strength requirements.
The architecture decided to change the initial aluminium framed glazed wall in the car park
screen to aluminium framed fixed glazed window. This was for aesthetic reasons as well as
budget control. Aluminium framed glazed wall is more expensive as compared to aluminium
2 Emphasis are made on 28 days which is the days approximated by design standards for the concrete to achieve
the recommended strength. It should be made clear that concrete continues to gain strength after the 28 days but
at a relatively slow rate.
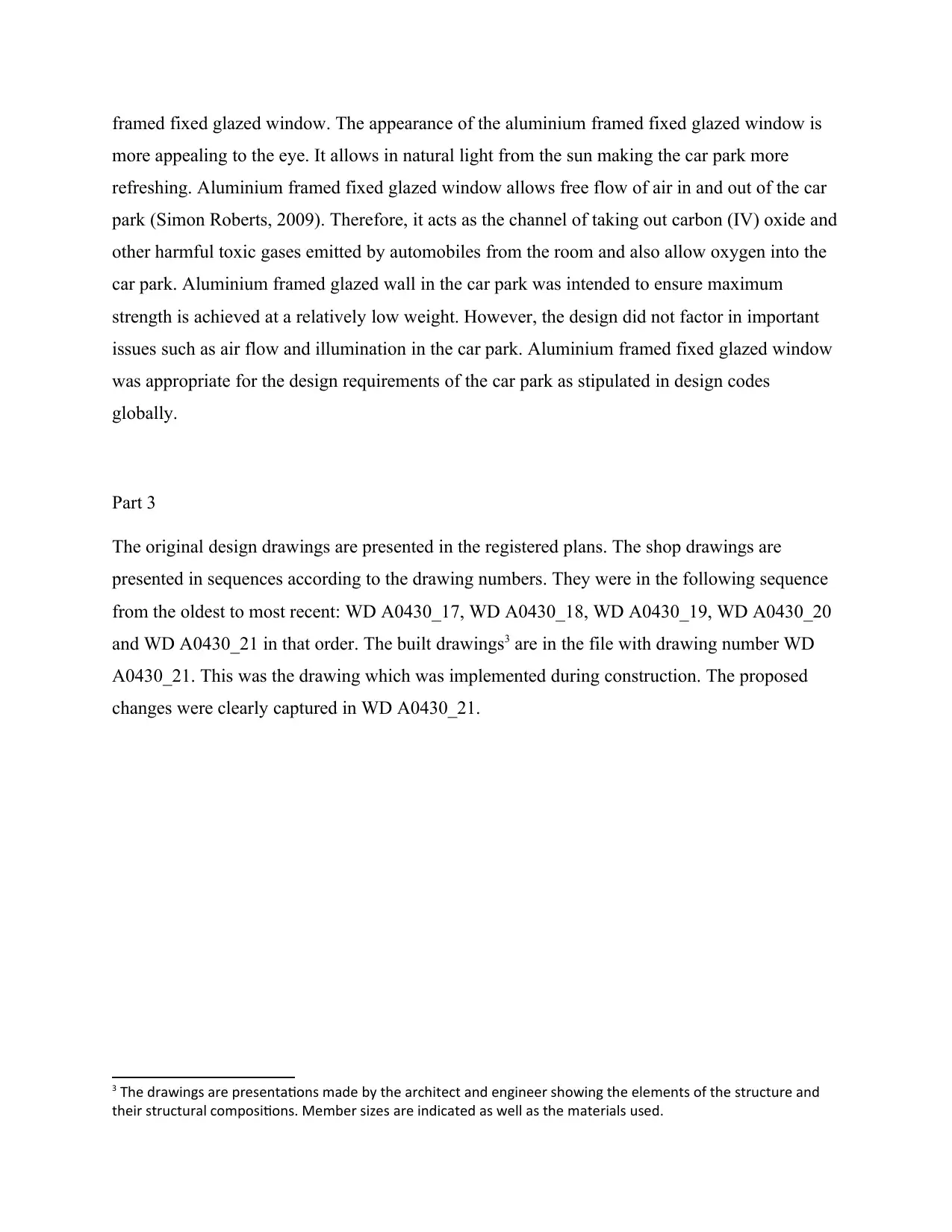
framed fixed glazed window. The appearance of the aluminium framed fixed glazed window is
more appealing to the eye. It allows in natural light from the sun making the car park more
refreshing. Aluminium framed fixed glazed window allows free flow of air in and out of the car
park (Simon Roberts, 2009). Therefore, it acts as the channel of taking out carbon (IV) oxide and
other harmful toxic gases emitted by automobiles from the room and also allow oxygen into the
car park. Aluminium framed glazed wall in the car park was intended to ensure maximum
strength is achieved at a relatively low weight. However, the design did not factor in important
issues such as air flow and illumination in the car park. Aluminium framed fixed glazed window
was appropriate for the design requirements of the car park as stipulated in design codes
globally.
Part 3
The original design drawings are presented in the registered plans. The shop drawings are
presented in sequences according to the drawing numbers. They were in the following sequence
from the oldest to most recent: WD A0430_17, WD A0430_18, WD A0430_19, WD A0430_20
and WD A0430_21 in that order. The built drawings3 are in the file with drawing number WD
A0430_21. This was the drawing which was implemented during construction. The proposed
changes were clearly captured in WD A0430_21.
3 The drawings are presentations made by the architect and engineer showing the elements of the structure and
their structural compositions. Member sizes are indicated as well as the materials used.
more appealing to the eye. It allows in natural light from the sun making the car park more
refreshing. Aluminium framed fixed glazed window allows free flow of air in and out of the car
park (Simon Roberts, 2009). Therefore, it acts as the channel of taking out carbon (IV) oxide and
other harmful toxic gases emitted by automobiles from the room and also allow oxygen into the
car park. Aluminium framed glazed wall in the car park was intended to ensure maximum
strength is achieved at a relatively low weight. However, the design did not factor in important
issues such as air flow and illumination in the car park. Aluminium framed fixed glazed window
was appropriate for the design requirements of the car park as stipulated in design codes
globally.
Part 3
The original design drawings are presented in the registered plans. The shop drawings are
presented in sequences according to the drawing numbers. They were in the following sequence
from the oldest to most recent: WD A0430_17, WD A0430_18, WD A0430_19, WD A0430_20
and WD A0430_21 in that order. The built drawings3 are in the file with drawing number WD
A0430_21. This was the drawing which was implemented during construction. The proposed
changes were clearly captured in WD A0430_21.
3 The drawings are presentations made by the architect and engineer showing the elements of the structure and
their structural compositions. Member sizes are indicated as well as the materials used.
⊘ This is a preview!⊘
Do you want full access?
Subscribe today to unlock all pages.

Trusted by 1+ million students worldwide
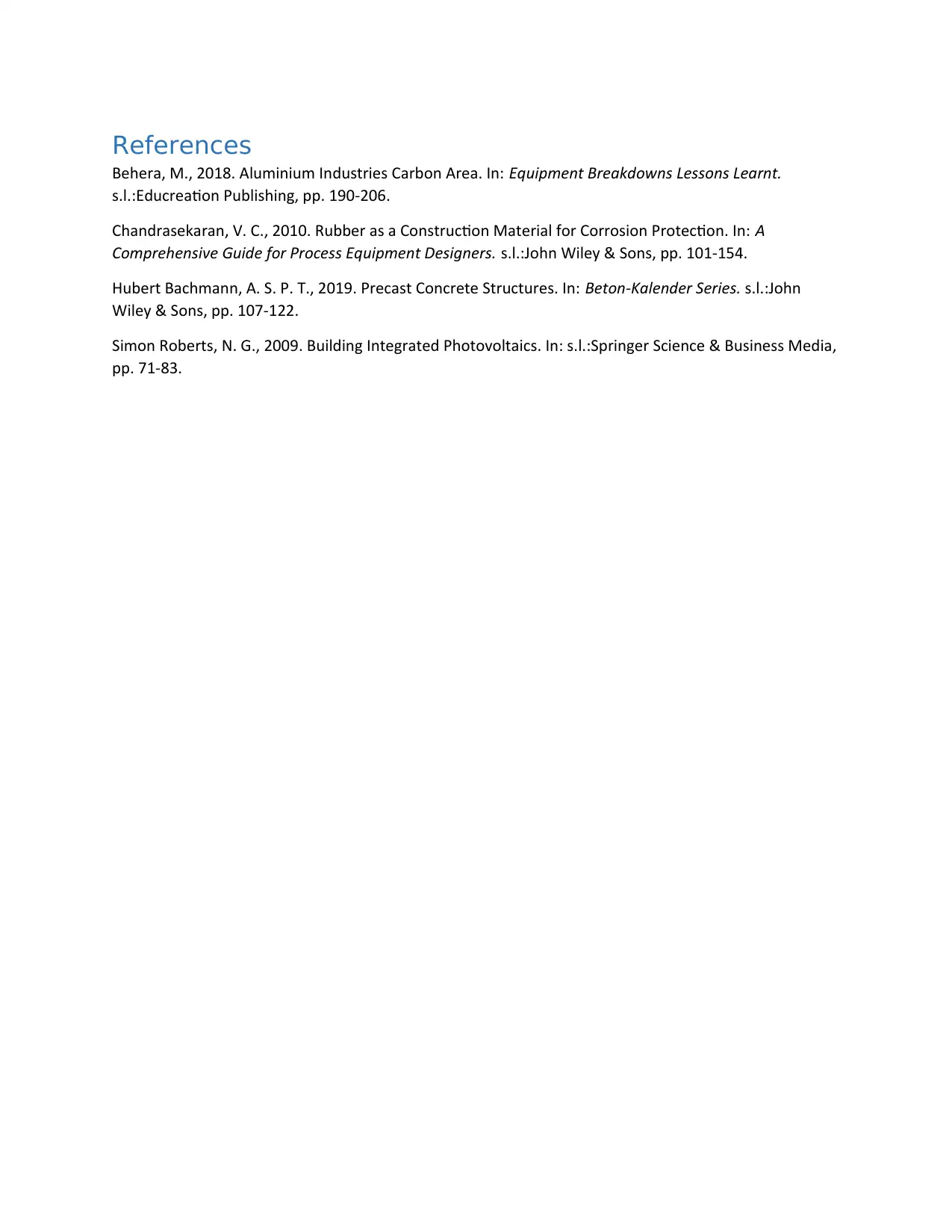
References
Behera, M., 2018. Aluminium Industries Carbon Area. In: Equipment Breakdowns Lessons Learnt.
s.l.:Educreation Publishing, pp. 190-206.
Chandrasekaran, V. C., 2010. Rubber as a Construction Material for Corrosion Protection. In: A
Comprehensive Guide for Process Equipment Designers. s.l.:John Wiley & Sons, pp. 101-154.
Hubert Bachmann, A. S. P. T., 2019. Precast Concrete Structures. In: Beton-Kalender Series. s.l.:John
Wiley & Sons, pp. 107-122.
Simon Roberts, N. G., 2009. Building Integrated Photovoltaics. In: s.l.:Springer Science & Business Media,
pp. 71-83.
Behera, M., 2018. Aluminium Industries Carbon Area. In: Equipment Breakdowns Lessons Learnt.
s.l.:Educreation Publishing, pp. 190-206.
Chandrasekaran, V. C., 2010. Rubber as a Construction Material for Corrosion Protection. In: A
Comprehensive Guide for Process Equipment Designers. s.l.:John Wiley & Sons, pp. 101-154.
Hubert Bachmann, A. S. P. T., 2019. Precast Concrete Structures. In: Beton-Kalender Series. s.l.:John
Wiley & Sons, pp. 107-122.
Simon Roberts, N. G., 2009. Building Integrated Photovoltaics. In: s.l.:Springer Science & Business Media,
pp. 71-83.
1 out of 4

Your All-in-One AI-Powered Toolkit for Academic Success.
+13062052269
info@desklib.com
Available 24*7 on WhatsApp / Email
Unlock your academic potential
© 2024 | Zucol Services PVT LTD | All rights reserved.