Contractual Procedures and Procurement for Construction Report
VerifiedAdded on 2021/04/21
|30
|12023
|152
Report
AI Summary
This report delves into the multifaceted world of contractual procedures and procurement within the construction and built environment sector. It begins by outlining critical client needs in construction projects, encompassing functionality, safety, quality, speed, cost, risk mitigation, aesthetics, sustain...
Read More
Contribute Materials
Your contribution can guide someone’s learning journey. Share your
documents today.
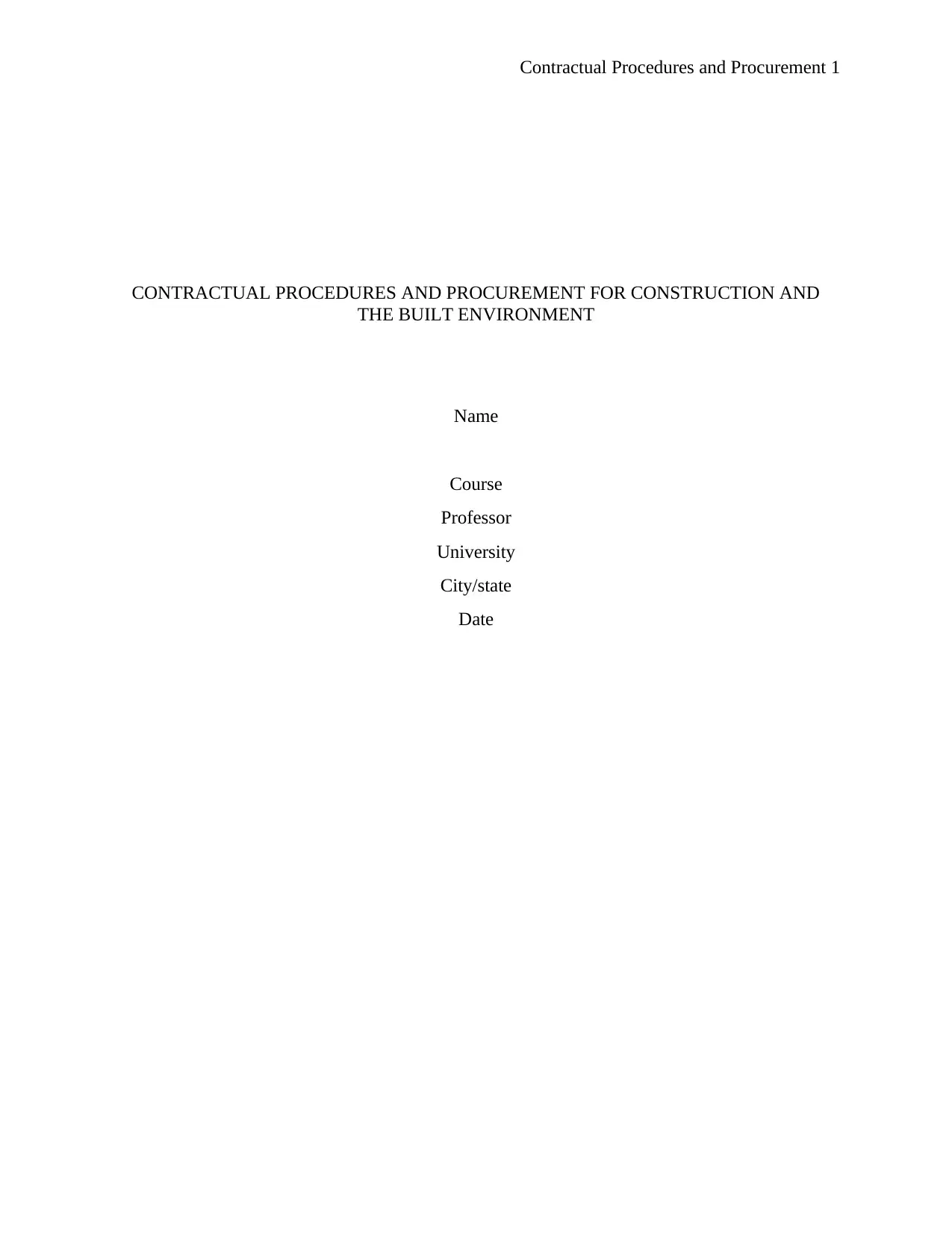
Contractual Procedures and Procurement 1
CONTRACTUAL PROCEDURES AND PROCUREMENT FOR CONSTRUCTION AND
THE BUILT ENVIRONMENT
Name
Course
Professor
University
City/state
Date
CONTRACTUAL PROCEDURES AND PROCUREMENT FOR CONSTRUCTION AND
THE BUILT ENVIRONMENT
Name
Course
Professor
University
City/state
Date
Secure Best Marks with AI Grader
Need help grading? Try our AI Grader for instant feedback on your assignments.
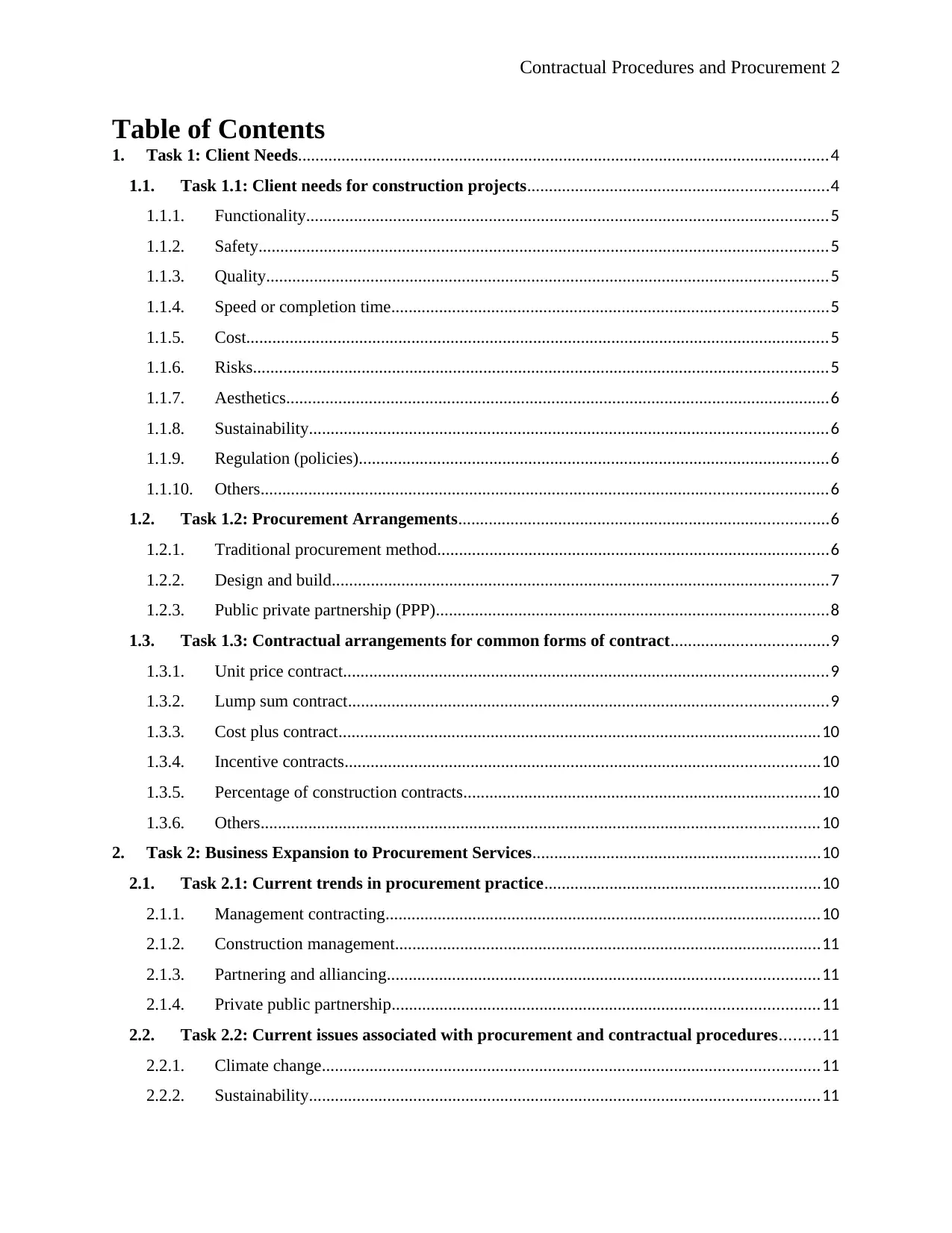
Contractual Procedures and Procurement 2
Table of Contents
1. Task 1: Client Needs..........................................................................................................................4
1.1. Task 1.1: Client needs for construction projects.....................................................................4
1.1.1. Functionality........................................................................................................................5
1.1.2. Safety...................................................................................................................................5
1.1.3. Quality.................................................................................................................................5
1.1.4. Speed or completion time....................................................................................................5
1.1.5. Cost......................................................................................................................................5
1.1.6. Risks....................................................................................................................................5
1.1.7. Aesthetics.............................................................................................................................6
1.1.8. Sustainability.......................................................................................................................6
1.1.9. Regulation (policies)............................................................................................................6
1.1.10. Others..................................................................................................................................6
1.2. Task 1.2: Procurement Arrangements.....................................................................................6
1.2.1. Traditional procurement method..........................................................................................6
1.2.2. Design and build..................................................................................................................7
1.2.3. Public private partnership (PPP)..........................................................................................8
1.3. Task 1.3: Contractual arrangements for common forms of contract....................................9
1.3.1. Unit price contract...............................................................................................................9
1.3.2. Lump sum contract..............................................................................................................9
1.3.3. Cost plus contract...............................................................................................................10
1.3.4. Incentive contracts.............................................................................................................10
1.3.5. Percentage of construction contracts..................................................................................10
1.3.6. Others................................................................................................................................10
2. Task 2: Business Expansion to Procurement Services..................................................................10
2.1. Task 2.1: Current trends in procurement practice...............................................................10
2.1.1. Management contracting....................................................................................................10
2.1.2. Construction management..................................................................................................11
2.1.3. Partnering and alliancing...................................................................................................11
2.1.4. Private public partnership..................................................................................................11
2.2. Task 2.2: Current issues associated with procurement and contractual procedures.........11
2.2.1. Climate change..................................................................................................................11
2.2.2. Sustainability.....................................................................................................................11
Table of Contents
1. Task 1: Client Needs..........................................................................................................................4
1.1. Task 1.1: Client needs for construction projects.....................................................................4
1.1.1. Functionality........................................................................................................................5
1.1.2. Safety...................................................................................................................................5
1.1.3. Quality.................................................................................................................................5
1.1.4. Speed or completion time....................................................................................................5
1.1.5. Cost......................................................................................................................................5
1.1.6. Risks....................................................................................................................................5
1.1.7. Aesthetics.............................................................................................................................6
1.1.8. Sustainability.......................................................................................................................6
1.1.9. Regulation (policies)............................................................................................................6
1.1.10. Others..................................................................................................................................6
1.2. Task 1.2: Procurement Arrangements.....................................................................................6
1.2.1. Traditional procurement method..........................................................................................6
1.2.2. Design and build..................................................................................................................7
1.2.3. Public private partnership (PPP)..........................................................................................8
1.3. Task 1.3: Contractual arrangements for common forms of contract....................................9
1.3.1. Unit price contract...............................................................................................................9
1.3.2. Lump sum contract..............................................................................................................9
1.3.3. Cost plus contract...............................................................................................................10
1.3.4. Incentive contracts.............................................................................................................10
1.3.5. Percentage of construction contracts..................................................................................10
1.3.6. Others................................................................................................................................10
2. Task 2: Business Expansion to Procurement Services..................................................................10
2.1. Task 2.1: Current trends in procurement practice...............................................................10
2.1.1. Management contracting....................................................................................................10
2.1.2. Construction management..................................................................................................11
2.1.3. Partnering and alliancing...................................................................................................11
2.1.4. Private public partnership..................................................................................................11
2.2. Task 2.2: Current issues associated with procurement and contractual procedures.........11
2.2.1. Climate change..................................................................................................................11
2.2.2. Sustainability.....................................................................................................................11
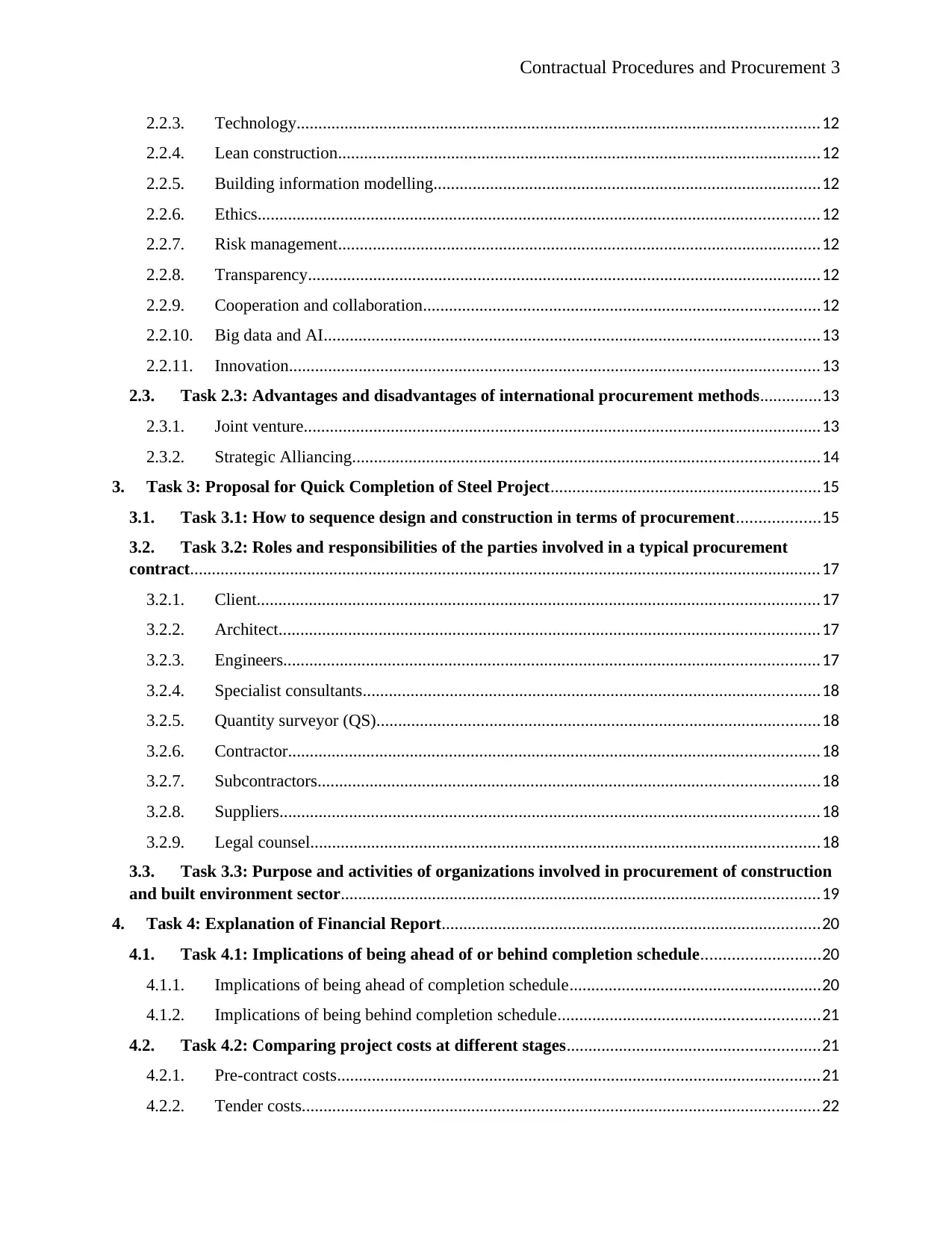
Contractual Procedures and Procurement 3
2.2.3. Technology........................................................................................................................12
2.2.4. Lean construction...............................................................................................................12
2.2.5. Building information modelling.........................................................................................12
2.2.6. Ethics.................................................................................................................................12
2.2.7. Risk management...............................................................................................................12
2.2.8. Transparency......................................................................................................................12
2.2.9. Cooperation and collaboration...........................................................................................12
2.2.10. Big data and AI..................................................................................................................13
2.2.11. Innovation..........................................................................................................................13
2.3. Task 2.3: Advantages and disadvantages of international procurement methods..............13
2.3.1. Joint venture.......................................................................................................................13
2.3.2. Strategic Alliancing...........................................................................................................14
3. Task 3: Proposal for Quick Completion of Steel Project..............................................................15
3.1. Task 3.1: How to sequence design and construction in terms of procurement...................15
3.2. Task 3.2: Roles and responsibilities of the parties involved in a typical procurement
contract.................................................................................................................................................17
3.2.1. Client.................................................................................................................................17
3.2.2. Architect............................................................................................................................17
3.2.3. Engineers...........................................................................................................................17
3.2.4. Specialist consultants.........................................................................................................18
3.2.5. Quantity surveyor (QS)......................................................................................................18
3.2.6. Contractor..........................................................................................................................18
3.2.7. Subcontractors...................................................................................................................18
3.2.8. Suppliers............................................................................................................................18
3.2.9. Legal counsel.....................................................................................................................18
3.3. Task 3.3: Purpose and activities of organizations involved in procurement of construction
and built environment sector..............................................................................................................19
4. Task 4: Explanation of Financial Report.......................................................................................20
4.1. Task 4.1: Implications of being ahead of or behind completion schedule...........................20
4.1.1. Implications of being ahead of completion schedule..........................................................20
4.1.2. Implications of being behind completion schedule............................................................21
4.2. Task 4.2: Comparing project costs at different stages..........................................................21
4.2.1. Pre-contract costs...............................................................................................................21
4.2.2. Tender costs.......................................................................................................................22
2.2.3. Technology........................................................................................................................12
2.2.4. Lean construction...............................................................................................................12
2.2.5. Building information modelling.........................................................................................12
2.2.6. Ethics.................................................................................................................................12
2.2.7. Risk management...............................................................................................................12
2.2.8. Transparency......................................................................................................................12
2.2.9. Cooperation and collaboration...........................................................................................12
2.2.10. Big data and AI..................................................................................................................13
2.2.11. Innovation..........................................................................................................................13
2.3. Task 2.3: Advantages and disadvantages of international procurement methods..............13
2.3.1. Joint venture.......................................................................................................................13
2.3.2. Strategic Alliancing...........................................................................................................14
3. Task 3: Proposal for Quick Completion of Steel Project..............................................................15
3.1. Task 3.1: How to sequence design and construction in terms of procurement...................15
3.2. Task 3.2: Roles and responsibilities of the parties involved in a typical procurement
contract.................................................................................................................................................17
3.2.1. Client.................................................................................................................................17
3.2.2. Architect............................................................................................................................17
3.2.3. Engineers...........................................................................................................................17
3.2.4. Specialist consultants.........................................................................................................18
3.2.5. Quantity surveyor (QS)......................................................................................................18
3.2.6. Contractor..........................................................................................................................18
3.2.7. Subcontractors...................................................................................................................18
3.2.8. Suppliers............................................................................................................................18
3.2.9. Legal counsel.....................................................................................................................18
3.3. Task 3.3: Purpose and activities of organizations involved in procurement of construction
and built environment sector..............................................................................................................19
4. Task 4: Explanation of Financial Report.......................................................................................20
4.1. Task 4.1: Implications of being ahead of or behind completion schedule...........................20
4.1.1. Implications of being ahead of completion schedule..........................................................20
4.1.2. Implications of being behind completion schedule............................................................21
4.2. Task 4.2: Comparing project costs at different stages..........................................................21
4.2.1. Pre-contract costs...............................................................................................................21
4.2.2. Tender costs.......................................................................................................................22
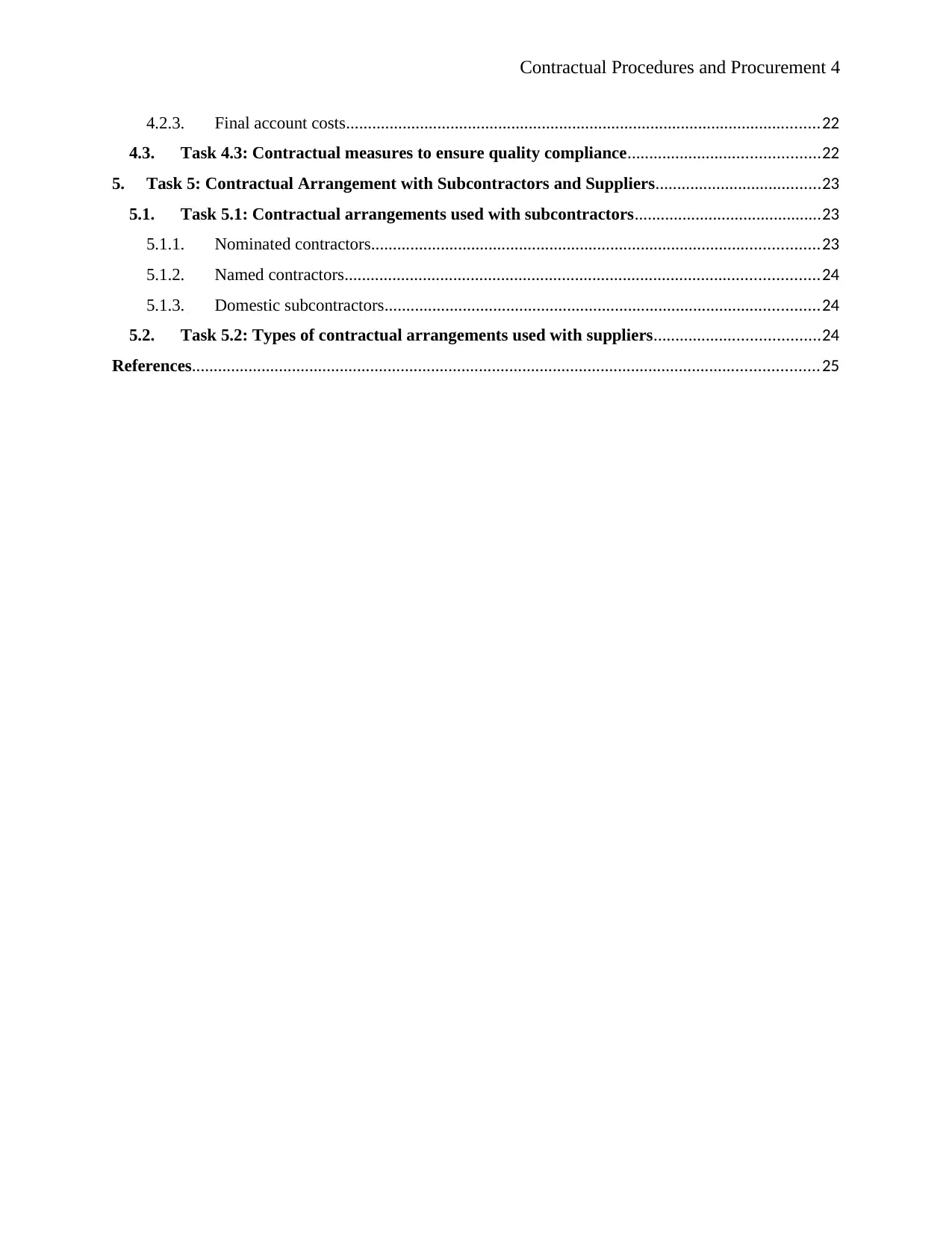
Contractual Procedures and Procurement 4
4.2.3. Final account costs.............................................................................................................22
4.3. Task 4.3: Contractual measures to ensure quality compliance............................................22
5. Task 5: Contractual Arrangement with Subcontractors and Suppliers......................................23
5.1. Task 5.1: Contractual arrangements used with subcontractors...........................................23
5.1.1. Nominated contractors.......................................................................................................23
5.1.2. Named contractors.............................................................................................................24
5.1.3. Domestic subcontractors....................................................................................................24
5.2. Task 5.2: Types of contractual arrangements used with suppliers......................................24
References................................................................................................................................................25
4.2.3. Final account costs.............................................................................................................22
4.3. Task 4.3: Contractual measures to ensure quality compliance............................................22
5. Task 5: Contractual Arrangement with Subcontractors and Suppliers......................................23
5.1. Task 5.1: Contractual arrangements used with subcontractors...........................................23
5.1.1. Nominated contractors.......................................................................................................23
5.1.2. Named contractors.............................................................................................................24
5.1.3. Domestic subcontractors....................................................................................................24
5.2. Task 5.2: Types of contractual arrangements used with suppliers......................................24
References................................................................................................................................................25
Secure Best Marks with AI Grader
Need help grading? Try our AI Grader for instant feedback on your assignments.
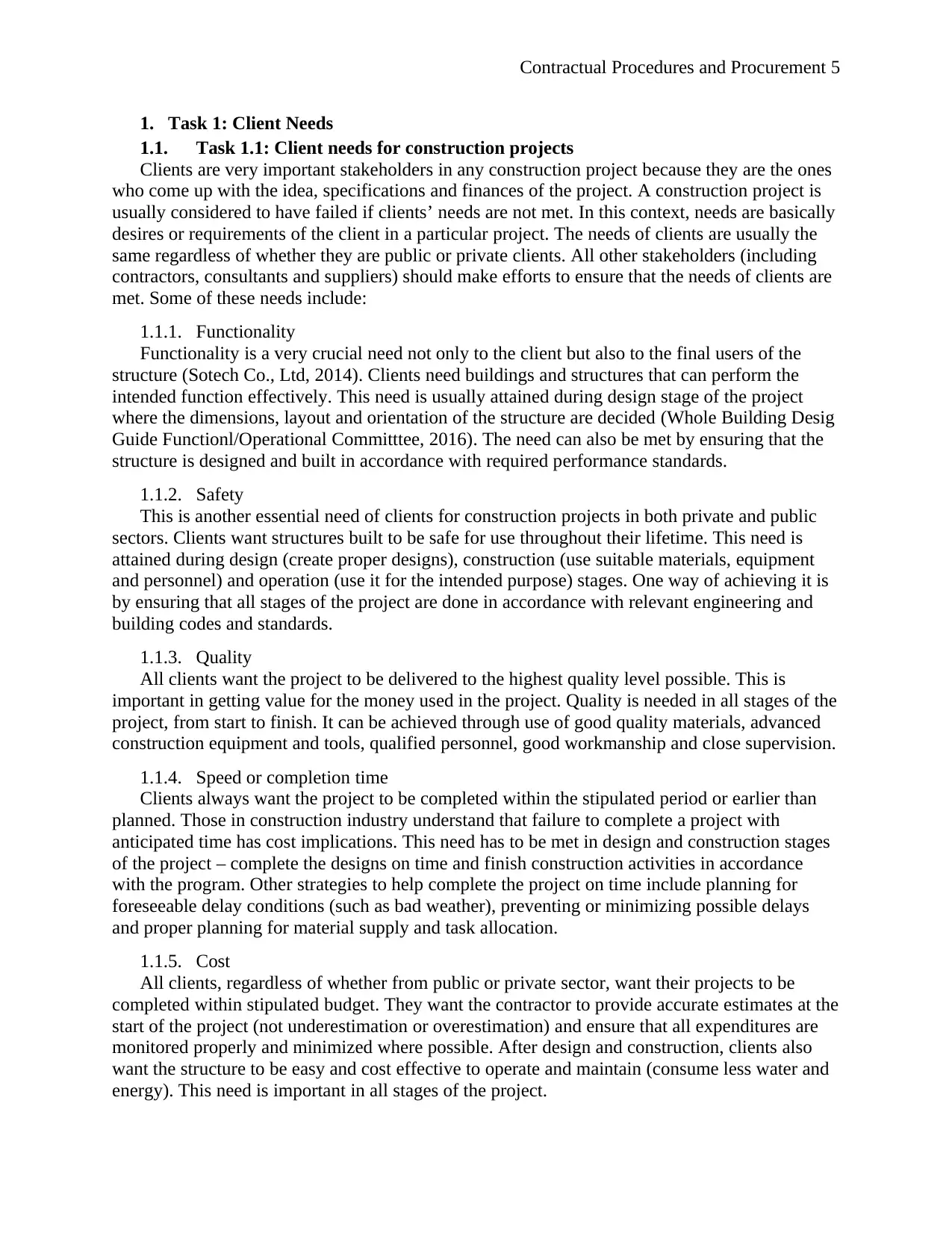
Contractual Procedures and Procurement 5
1. Task 1: Client Needs
1.1. Task 1.1: Client needs for construction projects
Clients are very important stakeholders in any construction project because they are the ones
who come up with the idea, specifications and finances of the project. A construction project is
usually considered to have failed if clients’ needs are not met. In this context, needs are basically
desires or requirements of the client in a particular project. The needs of clients are usually the
same regardless of whether they are public or private clients. All other stakeholders (including
contractors, consultants and suppliers) should make efforts to ensure that the needs of clients are
met. Some of these needs include:
1.1.1. Functionality
Functionality is a very crucial need not only to the client but also to the final users of the
structure (Sotech Co., Ltd, 2014). Clients need buildings and structures that can perform the
intended function effectively. This need is usually attained during design stage of the project
where the dimensions, layout and orientation of the structure are decided (Whole Building Desig
Guide Functionl/Operational Committtee, 2016). The need can also be met by ensuring that the
structure is designed and built in accordance with required performance standards.
1.1.2. Safety
This is another essential need of clients for construction projects in both private and public
sectors. Clients want structures built to be safe for use throughout their lifetime. This need is
attained during design (create proper designs), construction (use suitable materials, equipment
and personnel) and operation (use it for the intended purpose) stages. One way of achieving it is
by ensuring that all stages of the project are done in accordance with relevant engineering and
building codes and standards.
1.1.3. Quality
All clients want the project to be delivered to the highest quality level possible. This is
important in getting value for the money used in the project. Quality is needed in all stages of the
project, from start to finish. It can be achieved through use of good quality materials, advanced
construction equipment and tools, qualified personnel, good workmanship and close supervision.
1.1.4. Speed or completion time
Clients always want the project to be completed within the stipulated period or earlier than
planned. Those in construction industry understand that failure to complete a project with
anticipated time has cost implications. This need has to be met in design and construction stages
of the project – complete the designs on time and finish construction activities in accordance
with the program. Other strategies to help complete the project on time include planning for
foreseeable delay conditions (such as bad weather), preventing or minimizing possible delays
and proper planning for material supply and task allocation.
1.1.5. Cost
All clients, regardless of whether from public or private sector, want their projects to be
completed within stipulated budget. They want the contractor to provide accurate estimates at the
start of the project (not underestimation or overestimation) and ensure that all expenditures are
monitored properly and minimized where possible. After design and construction, clients also
want the structure to be easy and cost effective to operate and maintain (consume less water and
energy). This need is important in all stages of the project.
1. Task 1: Client Needs
1.1. Task 1.1: Client needs for construction projects
Clients are very important stakeholders in any construction project because they are the ones
who come up with the idea, specifications and finances of the project. A construction project is
usually considered to have failed if clients’ needs are not met. In this context, needs are basically
desires or requirements of the client in a particular project. The needs of clients are usually the
same regardless of whether they are public or private clients. All other stakeholders (including
contractors, consultants and suppliers) should make efforts to ensure that the needs of clients are
met. Some of these needs include:
1.1.1. Functionality
Functionality is a very crucial need not only to the client but also to the final users of the
structure (Sotech Co., Ltd, 2014). Clients need buildings and structures that can perform the
intended function effectively. This need is usually attained during design stage of the project
where the dimensions, layout and orientation of the structure are decided (Whole Building Desig
Guide Functionl/Operational Committtee, 2016). The need can also be met by ensuring that the
structure is designed and built in accordance with required performance standards.
1.1.2. Safety
This is another essential need of clients for construction projects in both private and public
sectors. Clients want structures built to be safe for use throughout their lifetime. This need is
attained during design (create proper designs), construction (use suitable materials, equipment
and personnel) and operation (use it for the intended purpose) stages. One way of achieving it is
by ensuring that all stages of the project are done in accordance with relevant engineering and
building codes and standards.
1.1.3. Quality
All clients want the project to be delivered to the highest quality level possible. This is
important in getting value for the money used in the project. Quality is needed in all stages of the
project, from start to finish. It can be achieved through use of good quality materials, advanced
construction equipment and tools, qualified personnel, good workmanship and close supervision.
1.1.4. Speed or completion time
Clients always want the project to be completed within the stipulated period or earlier than
planned. Those in construction industry understand that failure to complete a project with
anticipated time has cost implications. This need has to be met in design and construction stages
of the project – complete the designs on time and finish construction activities in accordance
with the program. Other strategies to help complete the project on time include planning for
foreseeable delay conditions (such as bad weather), preventing or minimizing possible delays
and proper planning for material supply and task allocation.
1.1.5. Cost
All clients, regardless of whether from public or private sector, want their projects to be
completed within stipulated budget. They want the contractor to provide accurate estimates at the
start of the project (not underestimation or overestimation) and ensure that all expenditures are
monitored properly and minimized where possible. After design and construction, clients also
want the structure to be easy and cost effective to operate and maintain (consume less water and
energy). This need is important in all stages of the project.
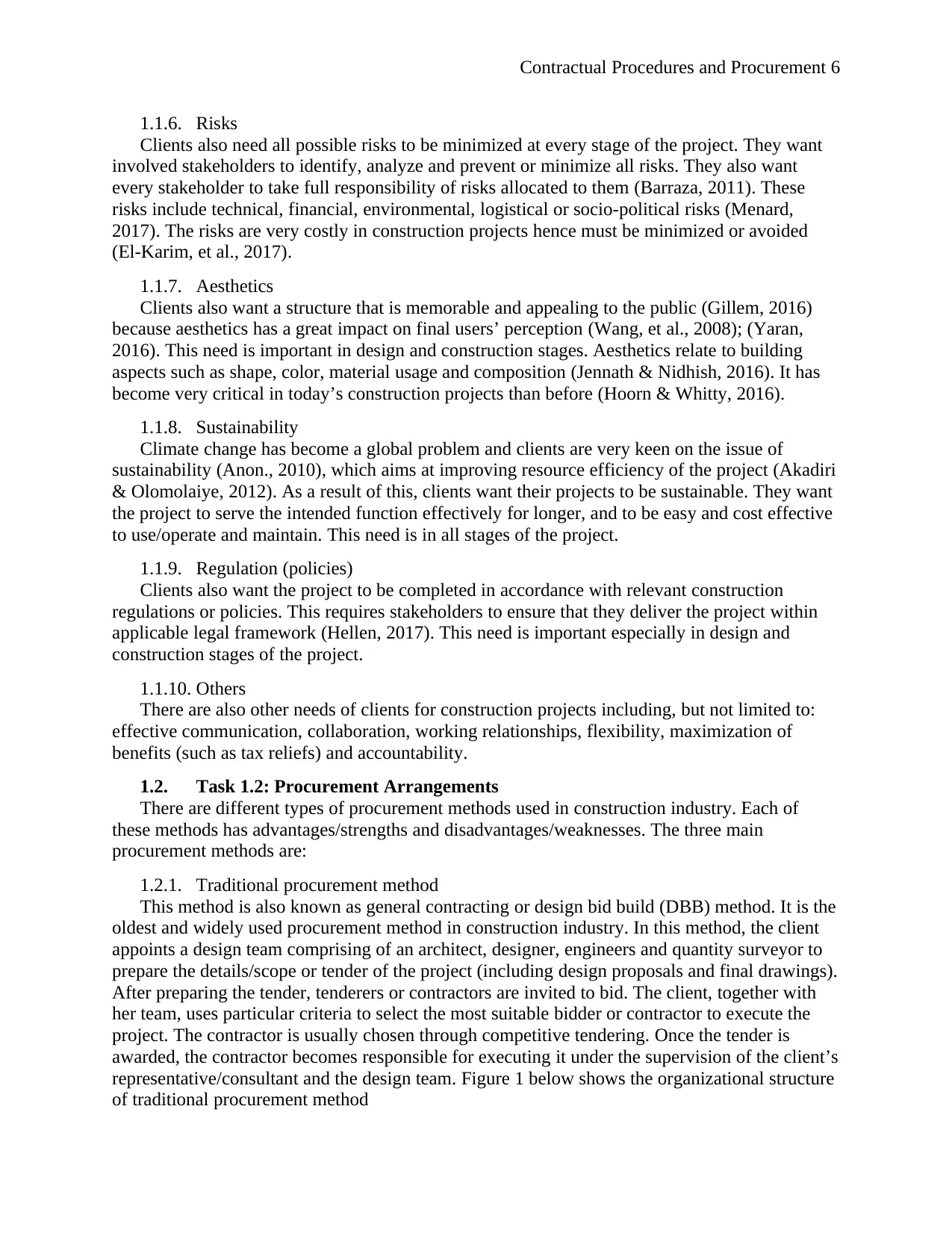
Contractual Procedures and Procurement 6
1.1.6. Risks
Clients also need all possible risks to be minimized at every stage of the project. They want
involved stakeholders to identify, analyze and prevent or minimize all risks. They also want
every stakeholder to take full responsibility of risks allocated to them (Barraza, 2011). These
risks include technical, financial, environmental, logistical or socio-political risks (Menard,
2017). The risks are very costly in construction projects hence must be minimized or avoided
(El-Karim, et al., 2017).
1.1.7. Aesthetics
Clients also want a structure that is memorable and appealing to the public (Gillem, 2016)
because aesthetics has a great impact on final users’ perception (Wang, et al., 2008); (Yaran,
2016). This need is important in design and construction stages. Aesthetics relate to building
aspects such as shape, color, material usage and composition (Jennath & Nidhish, 2016). It has
become very critical in today’s construction projects than before (Hoorn & Whitty, 2016).
1.1.8. Sustainability
Climate change has become a global problem and clients are very keen on the issue of
sustainability (Anon., 2010), which aims at improving resource efficiency of the project (Akadiri
& Olomolaiye, 2012). As a result of this, clients want their projects to be sustainable. They want
the project to serve the intended function effectively for longer, and to be easy and cost effective
to use/operate and maintain. This need is in all stages of the project.
1.1.9. Regulation (policies)
Clients also want the project to be completed in accordance with relevant construction
regulations or policies. This requires stakeholders to ensure that they deliver the project within
applicable legal framework (Hellen, 2017). This need is important especially in design and
construction stages of the project.
1.1.10. Others
There are also other needs of clients for construction projects including, but not limited to:
effective communication, collaboration, working relationships, flexibility, maximization of
benefits (such as tax reliefs) and accountability.
1.2. Task 1.2: Procurement Arrangements
There are different types of procurement methods used in construction industry. Each of
these methods has advantages/strengths and disadvantages/weaknesses. The three main
procurement methods are:
1.2.1. Traditional procurement method
This method is also known as general contracting or design bid build (DBB) method. It is the
oldest and widely used procurement method in construction industry. In this method, the client
appoints a design team comprising of an architect, designer, engineers and quantity surveyor to
prepare the details/scope or tender of the project (including design proposals and final drawings).
After preparing the tender, tenderers or contractors are invited to bid. The client, together with
her team, uses particular criteria to select the most suitable bidder or contractor to execute the
project. The contractor is usually chosen through competitive tendering. Once the tender is
awarded, the contractor becomes responsible for executing it under the supervision of the client’s
representative/consultant and the design team. Figure 1 below shows the organizational structure
of traditional procurement method
1.1.6. Risks
Clients also need all possible risks to be minimized at every stage of the project. They want
involved stakeholders to identify, analyze and prevent or minimize all risks. They also want
every stakeholder to take full responsibility of risks allocated to them (Barraza, 2011). These
risks include technical, financial, environmental, logistical or socio-political risks (Menard,
2017). The risks are very costly in construction projects hence must be minimized or avoided
(El-Karim, et al., 2017).
1.1.7. Aesthetics
Clients also want a structure that is memorable and appealing to the public (Gillem, 2016)
because aesthetics has a great impact on final users’ perception (Wang, et al., 2008); (Yaran,
2016). This need is important in design and construction stages. Aesthetics relate to building
aspects such as shape, color, material usage and composition (Jennath & Nidhish, 2016). It has
become very critical in today’s construction projects than before (Hoorn & Whitty, 2016).
1.1.8. Sustainability
Climate change has become a global problem and clients are very keen on the issue of
sustainability (Anon., 2010), which aims at improving resource efficiency of the project (Akadiri
& Olomolaiye, 2012). As a result of this, clients want their projects to be sustainable. They want
the project to serve the intended function effectively for longer, and to be easy and cost effective
to use/operate and maintain. This need is in all stages of the project.
1.1.9. Regulation (policies)
Clients also want the project to be completed in accordance with relevant construction
regulations or policies. This requires stakeholders to ensure that they deliver the project within
applicable legal framework (Hellen, 2017). This need is important especially in design and
construction stages of the project.
1.1.10. Others
There are also other needs of clients for construction projects including, but not limited to:
effective communication, collaboration, working relationships, flexibility, maximization of
benefits (such as tax reliefs) and accountability.
1.2. Task 1.2: Procurement Arrangements
There are different types of procurement methods used in construction industry. Each of
these methods has advantages/strengths and disadvantages/weaknesses. The three main
procurement methods are:
1.2.1. Traditional procurement method
This method is also known as general contracting or design bid build (DBB) method. It is the
oldest and widely used procurement method in construction industry. In this method, the client
appoints a design team comprising of an architect, designer, engineers and quantity surveyor to
prepare the details/scope or tender of the project (including design proposals and final drawings).
After preparing the tender, tenderers or contractors are invited to bid. The client, together with
her team, uses particular criteria to select the most suitable bidder or contractor to execute the
project. The contractor is usually chosen through competitive tendering. Once the tender is
awarded, the contractor becomes responsible for executing it under the supervision of the client’s
representative/consultant and the design team. Figure 1 below shows the organizational structure
of traditional procurement method
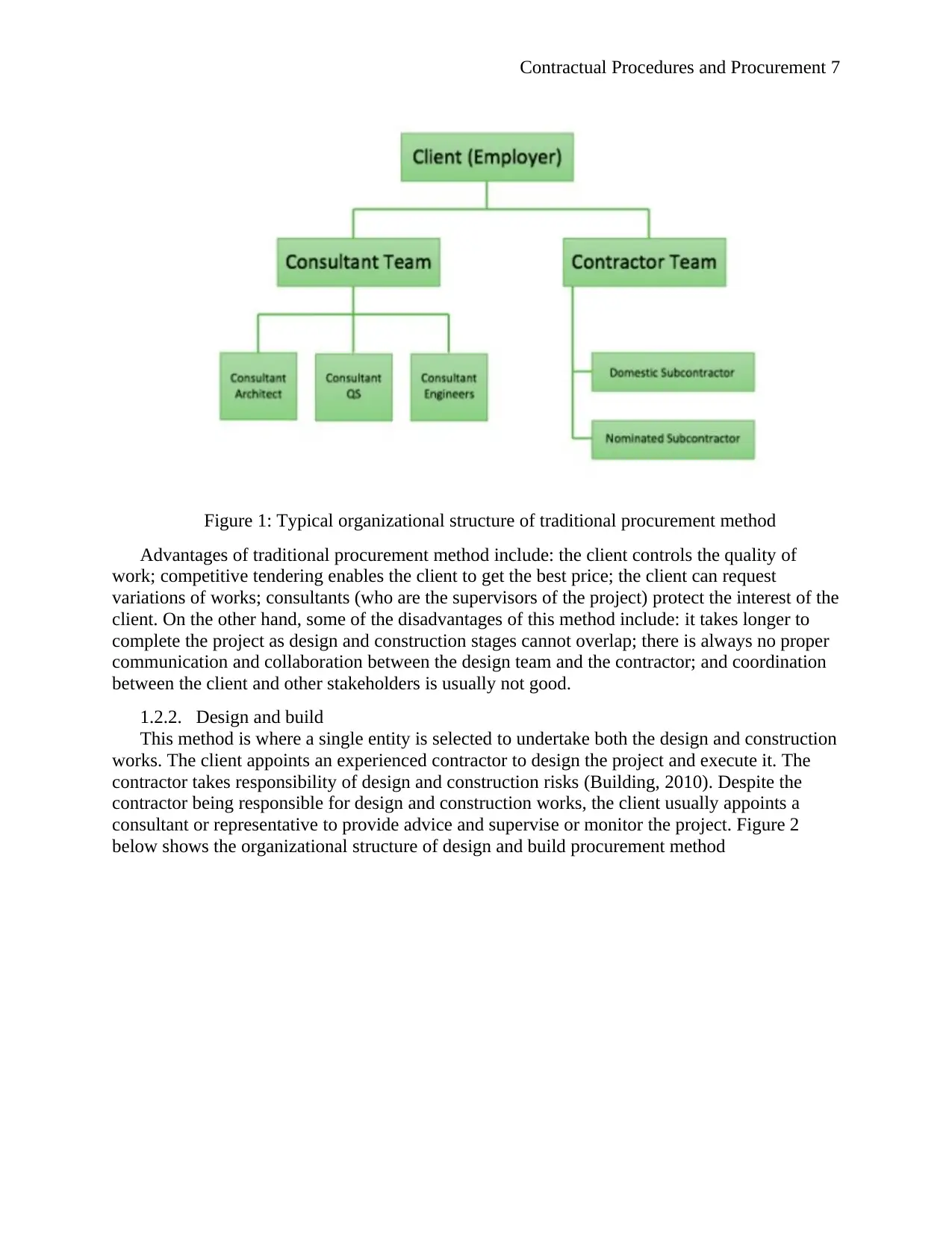
Contractual Procedures and Procurement 7
Figure 1: Typical organizational structure of traditional procurement method
Advantages of traditional procurement method include: the client controls the quality of
work; competitive tendering enables the client to get the best price; the client can request
variations of works; consultants (who are the supervisors of the project) protect the interest of the
client. On the other hand, some of the disadvantages of this method include: it takes longer to
complete the project as design and construction stages cannot overlap; there is always no proper
communication and collaboration between the design team and the contractor; and coordination
between the client and other stakeholders is usually not good.
1.2.2. Design and build
This method is where a single entity is selected to undertake both the design and construction
works. The client appoints an experienced contractor to design the project and execute it. The
contractor takes responsibility of design and construction risks (Building, 2010). Despite the
contractor being responsible for design and construction works, the client usually appoints a
consultant or representative to provide advice and supervise or monitor the project. Figure 2
below shows the organizational structure of design and build procurement method
Figure 1: Typical organizational structure of traditional procurement method
Advantages of traditional procurement method include: the client controls the quality of
work; competitive tendering enables the client to get the best price; the client can request
variations of works; consultants (who are the supervisors of the project) protect the interest of the
client. On the other hand, some of the disadvantages of this method include: it takes longer to
complete the project as design and construction stages cannot overlap; there is always no proper
communication and collaboration between the design team and the contractor; and coordination
between the client and other stakeholders is usually not good.
1.2.2. Design and build
This method is where a single entity is selected to undertake both the design and construction
works. The client appoints an experienced contractor to design the project and execute it. The
contractor takes responsibility of design and construction risks (Building, 2010). Despite the
contractor being responsible for design and construction works, the client usually appoints a
consultant or representative to provide advice and supervise or monitor the project. Figure 2
below shows the organizational structure of design and build procurement method
Paraphrase This Document
Need a fresh take? Get an instant paraphrase of this document with our AI Paraphraser
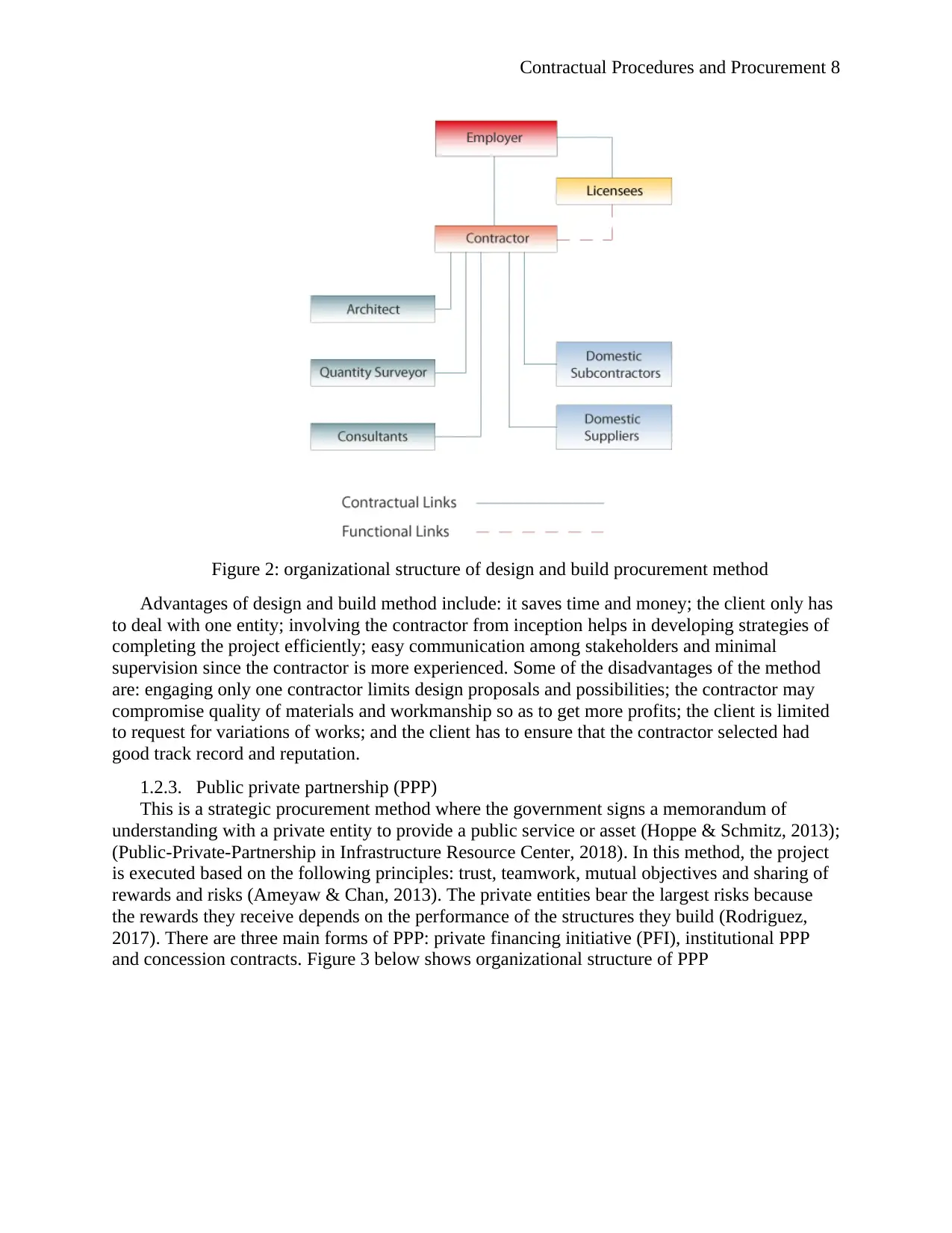
Contractual Procedures and Procurement 8
Figure 2: organizational structure of design and build procurement method
Advantages of design and build method include: it saves time and money; the client only has
to deal with one entity; involving the contractor from inception helps in developing strategies of
completing the project efficiently; easy communication among stakeholders and minimal
supervision since the contractor is more experienced. Some of the disadvantages of the method
are: engaging only one contractor limits design proposals and possibilities; the contractor may
compromise quality of materials and workmanship so as to get more profits; the client is limited
to request for variations of works; and the client has to ensure that the contractor selected had
good track record and reputation.
1.2.3. Public private partnership (PPP)
This is a strategic procurement method where the government signs a memorandum of
understanding with a private entity to provide a public service or asset (Hoppe & Schmitz, 2013);
(Public-Private-Partnership in Infrastructure Resource Center, 2018). In this method, the project
is executed based on the following principles: trust, teamwork, mutual objectives and sharing of
rewards and risks (Ameyaw & Chan, 2013). The private entities bear the largest risks because
the rewards they receive depends on the performance of the structures they build (Rodriguez,
2017). There are three main forms of PPP: private financing initiative (PFI), institutional PPP
and concession contracts. Figure 3 below shows organizational structure of PPP
Figure 2: organizational structure of design and build procurement method
Advantages of design and build method include: it saves time and money; the client only has
to deal with one entity; involving the contractor from inception helps in developing strategies of
completing the project efficiently; easy communication among stakeholders and minimal
supervision since the contractor is more experienced. Some of the disadvantages of the method
are: engaging only one contractor limits design proposals and possibilities; the contractor may
compromise quality of materials and workmanship so as to get more profits; the client is limited
to request for variations of works; and the client has to ensure that the contractor selected had
good track record and reputation.
1.2.3. Public private partnership (PPP)
This is a strategic procurement method where the government signs a memorandum of
understanding with a private entity to provide a public service or asset (Hoppe & Schmitz, 2013);
(Public-Private-Partnership in Infrastructure Resource Center, 2018). In this method, the project
is executed based on the following principles: trust, teamwork, mutual objectives and sharing of
rewards and risks (Ameyaw & Chan, 2013). The private entities bear the largest risks because
the rewards they receive depends on the performance of the structures they build (Rodriguez,
2017). There are three main forms of PPP: private financing initiative (PFI), institutional PPP
and concession contracts. Figure 3 below shows organizational structure of PPP

Contractual Procedures and Procurement 9
Figure 3: Organizational structure of PPP
Some advantages of PPP are: high quality, faster delivery, higher return on investment (ROI)
(Vinogradov, et al., 2014), earlier identification of risks helps in determining the feasibility of the
project’s, the private entity is responsible for the project execution and operational risks; enables
the government to put her resources in other critical socioeconomic projects, reduces
government’s deficits and costs, and greater innovation (Gorey, 2015). Disadvantages of this
procurement method include: it can increase government costs especially when the private entity
has to bear higher risks; low competitiveness, unsteady profits, the government may be
disadvantaged especially if it has no adequate knowledge or experience about the project and
unnecessary delays due to negotiations or political debates (Ismail & Harris, 2014).
Other procurement methods that are becoming common include construction management
and management contracting. The choice of the most suitable procurement method depends on
factors such as cost, financing, speed, quality, risk, ownership of asset, project constraints and
complexity of the project.
1.3. Task 1.3: Contractual arrangements for common forms of contract
Contractual arrangements basically refers to written mutual agreements between parties that
they will individually or jointly execute a project. These arrangements are legally binding. The
choice of suitable contractual arrangement is influenced by factors such as client characteristics
(especially their expertise and experience), complexity of the project and performance level
desired by the client. Most of the contractual arrangements in construction industry are defined
based on how disbursements will be made.
The common forms of contract in construction industry include the following:
1.3.1. Unit price contract
This is a contractual arrangement where all items of the project are counted and their
quantities multiplied by their respective unit prices. The project’ final price is determined by
summing up the product of all the items. This form of contract is suitable in projects where all
items can be accurately determined when preparing the tender.
1.3.2. Lump sum contract
This is a form of contract where the contractor agrees to execute the project works at a fixed
price. It is appropriate in projects where the project’s scope and schedule can be adequately
defined before the start of the project so that the contractor can determine the cost estimate of the
project. This form of contract is also known as fixed price contract.
Figure 3: Organizational structure of PPP
Some advantages of PPP are: high quality, faster delivery, higher return on investment (ROI)
(Vinogradov, et al., 2014), earlier identification of risks helps in determining the feasibility of the
project’s, the private entity is responsible for the project execution and operational risks; enables
the government to put her resources in other critical socioeconomic projects, reduces
government’s deficits and costs, and greater innovation (Gorey, 2015). Disadvantages of this
procurement method include: it can increase government costs especially when the private entity
has to bear higher risks; low competitiveness, unsteady profits, the government may be
disadvantaged especially if it has no adequate knowledge or experience about the project and
unnecessary delays due to negotiations or political debates (Ismail & Harris, 2014).
Other procurement methods that are becoming common include construction management
and management contracting. The choice of the most suitable procurement method depends on
factors such as cost, financing, speed, quality, risk, ownership of asset, project constraints and
complexity of the project.
1.3. Task 1.3: Contractual arrangements for common forms of contract
Contractual arrangements basically refers to written mutual agreements between parties that
they will individually or jointly execute a project. These arrangements are legally binding. The
choice of suitable contractual arrangement is influenced by factors such as client characteristics
(especially their expertise and experience), complexity of the project and performance level
desired by the client. Most of the contractual arrangements in construction industry are defined
based on how disbursements will be made.
The common forms of contract in construction industry include the following:
1.3.1. Unit price contract
This is a contractual arrangement where all items of the project are counted and their
quantities multiplied by their respective unit prices. The project’ final price is determined by
summing up the product of all the items. This form of contract is suitable in projects where all
items can be accurately determined when preparing the tender.
1.3.2. Lump sum contract
This is a form of contract where the contractor agrees to execute the project works at a fixed
price. It is appropriate in projects where the project’s scope and schedule can be adequately
defined before the start of the project so that the contractor can determine the cost estimate of the
project. This form of contract is also known as fixed price contract.
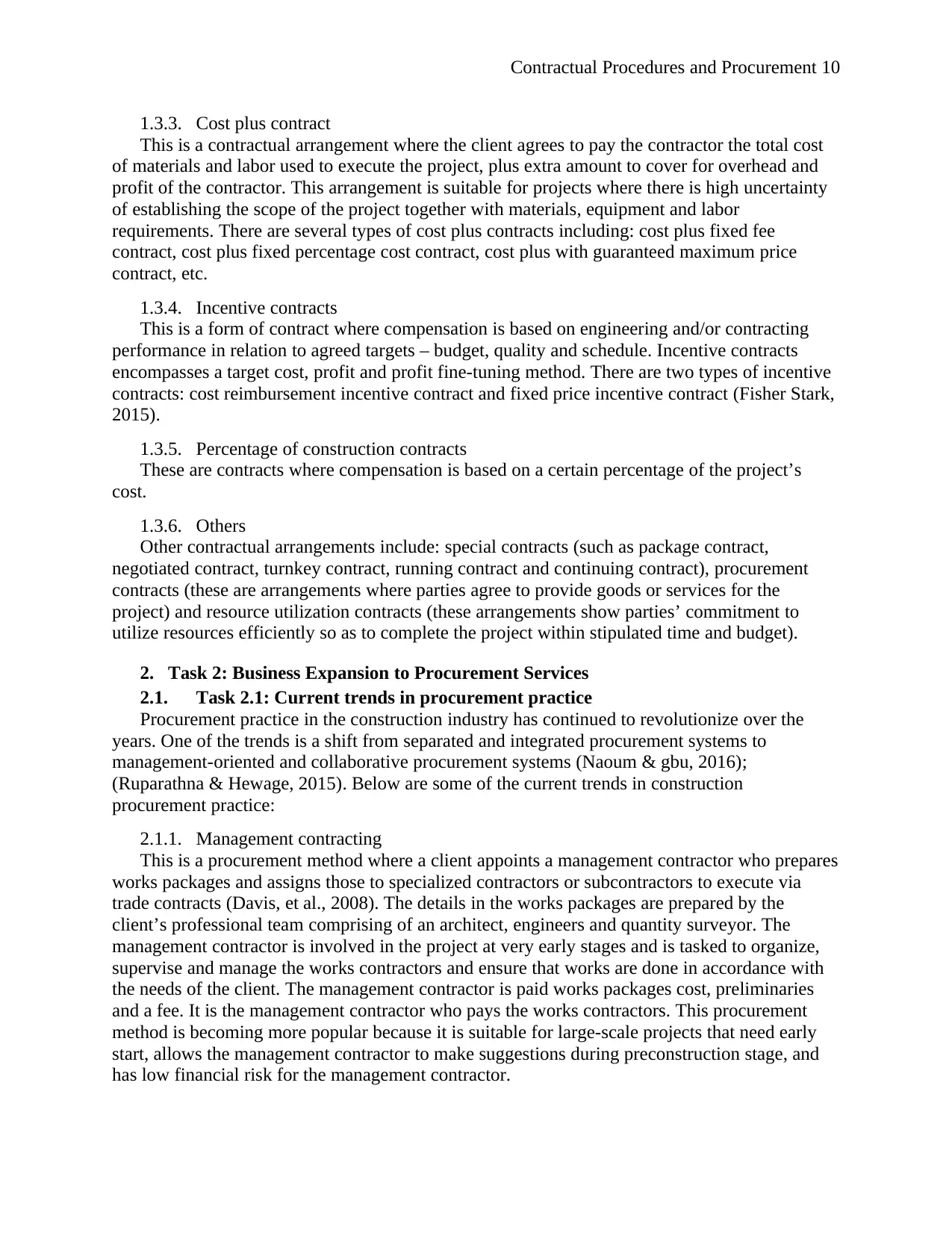
Contractual Procedures and Procurement 10
1.3.3. Cost plus contract
This is a contractual arrangement where the client agrees to pay the contractor the total cost
of materials and labor used to execute the project, plus extra amount to cover for overhead and
profit of the contractor. This arrangement is suitable for projects where there is high uncertainty
of establishing the scope of the project together with materials, equipment and labor
requirements. There are several types of cost plus contracts including: cost plus fixed fee
contract, cost plus fixed percentage cost contract, cost plus with guaranteed maximum price
contract, etc.
1.3.4. Incentive contracts
This is a form of contract where compensation is based on engineering and/or contracting
performance in relation to agreed targets – budget, quality and schedule. Incentive contracts
encompasses a target cost, profit and profit fine-tuning method. There are two types of incentive
contracts: cost reimbursement incentive contract and fixed price incentive contract (Fisher Stark,
2015).
1.3.5. Percentage of construction contracts
These are contracts where compensation is based on a certain percentage of the project’s
cost.
1.3.6. Others
Other contractual arrangements include: special contracts (such as package contract,
negotiated contract, turnkey contract, running contract and continuing contract), procurement
contracts (these are arrangements where parties agree to provide goods or services for the
project) and resource utilization contracts (these arrangements show parties’ commitment to
utilize resources efficiently so as to complete the project within stipulated time and budget).
2. Task 2: Business Expansion to Procurement Services
2.1. Task 2.1: Current trends in procurement practice
Procurement practice in the construction industry has continued to revolutionize over the
years. One of the trends is a shift from separated and integrated procurement systems to
management-oriented and collaborative procurement systems (Naoum & gbu, 2016);
(Ruparathna & Hewage, 2015). Below are some of the current trends in construction
procurement practice:
2.1.1. Management contracting
This is a procurement method where a client appoints a management contractor who prepares
works packages and assigns those to specialized contractors or subcontractors to execute via
trade contracts (Davis, et al., 2008). The details in the works packages are prepared by the
client’s professional team comprising of an architect, engineers and quantity surveyor. The
management contractor is involved in the project at very early stages and is tasked to organize,
supervise and manage the works contractors and ensure that works are done in accordance with
the needs of the client. The management contractor is paid works packages cost, preliminaries
and a fee. It is the management contractor who pays the works contractors. This procurement
method is becoming more popular because it is suitable for large-scale projects that need early
start, allows the management contractor to make suggestions during preconstruction stage, and
has low financial risk for the management contractor.
1.3.3. Cost plus contract
This is a contractual arrangement where the client agrees to pay the contractor the total cost
of materials and labor used to execute the project, plus extra amount to cover for overhead and
profit of the contractor. This arrangement is suitable for projects where there is high uncertainty
of establishing the scope of the project together with materials, equipment and labor
requirements. There are several types of cost plus contracts including: cost plus fixed fee
contract, cost plus fixed percentage cost contract, cost plus with guaranteed maximum price
contract, etc.
1.3.4. Incentive contracts
This is a form of contract where compensation is based on engineering and/or contracting
performance in relation to agreed targets – budget, quality and schedule. Incentive contracts
encompasses a target cost, profit and profit fine-tuning method. There are two types of incentive
contracts: cost reimbursement incentive contract and fixed price incentive contract (Fisher Stark,
2015).
1.3.5. Percentage of construction contracts
These are contracts where compensation is based on a certain percentage of the project’s
cost.
1.3.6. Others
Other contractual arrangements include: special contracts (such as package contract,
negotiated contract, turnkey contract, running contract and continuing contract), procurement
contracts (these are arrangements where parties agree to provide goods or services for the
project) and resource utilization contracts (these arrangements show parties’ commitment to
utilize resources efficiently so as to complete the project within stipulated time and budget).
2. Task 2: Business Expansion to Procurement Services
2.1. Task 2.1: Current trends in procurement practice
Procurement practice in the construction industry has continued to revolutionize over the
years. One of the trends is a shift from separated and integrated procurement systems to
management-oriented and collaborative procurement systems (Naoum & gbu, 2016);
(Ruparathna & Hewage, 2015). Below are some of the current trends in construction
procurement practice:
2.1.1. Management contracting
This is a procurement method where a client appoints a management contractor who prepares
works packages and assigns those to specialized contractors or subcontractors to execute via
trade contracts (Davis, et al., 2008). The details in the works packages are prepared by the
client’s professional team comprising of an architect, engineers and quantity surveyor. The
management contractor is involved in the project at very early stages and is tasked to organize,
supervise and manage the works contractors and ensure that works are done in accordance with
the needs of the client. The management contractor is paid works packages cost, preliminaries
and a fee. It is the management contractor who pays the works contractors. This procurement
method is becoming more popular because it is suitable for large-scale projects that need early
start, allows the management contractor to make suggestions during preconstruction stage, and
has low financial risk for the management contractor.
Secure Best Marks with AI Grader
Need help grading? Try our AI Grader for instant feedback on your assignments.
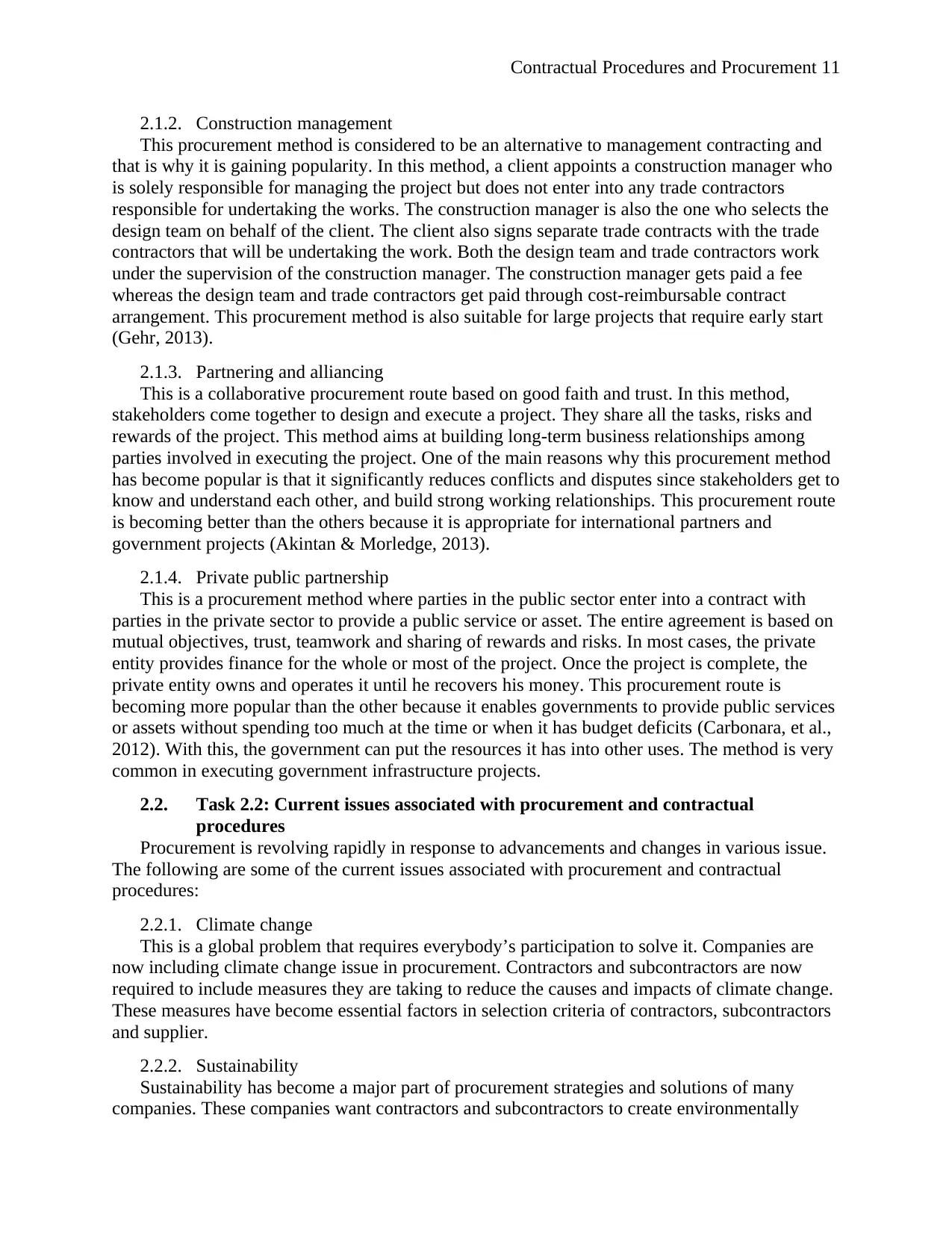
Contractual Procedures and Procurement 11
2.1.2. Construction management
This procurement method is considered to be an alternative to management contracting and
that is why it is gaining popularity. In this method, a client appoints a construction manager who
is solely responsible for managing the project but does not enter into any trade contractors
responsible for undertaking the works. The construction manager is also the one who selects the
design team on behalf of the client. The client also signs separate trade contracts with the trade
contractors that will be undertaking the work. Both the design team and trade contractors work
under the supervision of the construction manager. The construction manager gets paid a fee
whereas the design team and trade contractors get paid through cost-reimbursable contract
arrangement. This procurement method is also suitable for large projects that require early start
(Gehr, 2013).
2.1.3. Partnering and alliancing
This is a collaborative procurement route based on good faith and trust. In this method,
stakeholders come together to design and execute a project. They share all the tasks, risks and
rewards of the project. This method aims at building long-term business relationships among
parties involved in executing the project. One of the main reasons why this procurement method
has become popular is that it significantly reduces conflicts and disputes since stakeholders get to
know and understand each other, and build strong working relationships. This procurement route
is becoming better than the others because it is appropriate for international partners and
government projects (Akintan & Morledge, 2013).
2.1.4. Private public partnership
This is a procurement method where parties in the public sector enter into a contract with
parties in the private sector to provide a public service or asset. The entire agreement is based on
mutual objectives, trust, teamwork and sharing of rewards and risks. In most cases, the private
entity provides finance for the whole or most of the project. Once the project is complete, the
private entity owns and operates it until he recovers his money. This procurement route is
becoming more popular than the other because it enables governments to provide public services
or assets without spending too much at the time or when it has budget deficits (Carbonara, et al.,
2012). With this, the government can put the resources it has into other uses. The method is very
common in executing government infrastructure projects.
2.2. Task 2.2: Current issues associated with procurement and contractual
procedures
Procurement is revolving rapidly in response to advancements and changes in various issue.
The following are some of the current issues associated with procurement and contractual
procedures:
2.2.1. Climate change
This is a global problem that requires everybody’s participation to solve it. Companies are
now including climate change issue in procurement. Contractors and subcontractors are now
required to include measures they are taking to reduce the causes and impacts of climate change.
These measures have become essential factors in selection criteria of contractors, subcontractors
and supplier.
2.2.2. Sustainability
Sustainability has become a major part of procurement strategies and solutions of many
companies. These companies want contractors and subcontractors to create environmentally
2.1.2. Construction management
This procurement method is considered to be an alternative to management contracting and
that is why it is gaining popularity. In this method, a client appoints a construction manager who
is solely responsible for managing the project but does not enter into any trade contractors
responsible for undertaking the works. The construction manager is also the one who selects the
design team on behalf of the client. The client also signs separate trade contracts with the trade
contractors that will be undertaking the work. Both the design team and trade contractors work
under the supervision of the construction manager. The construction manager gets paid a fee
whereas the design team and trade contractors get paid through cost-reimbursable contract
arrangement. This procurement method is also suitable for large projects that require early start
(Gehr, 2013).
2.1.3. Partnering and alliancing
This is a collaborative procurement route based on good faith and trust. In this method,
stakeholders come together to design and execute a project. They share all the tasks, risks and
rewards of the project. This method aims at building long-term business relationships among
parties involved in executing the project. One of the main reasons why this procurement method
has become popular is that it significantly reduces conflicts and disputes since stakeholders get to
know and understand each other, and build strong working relationships. This procurement route
is becoming better than the others because it is appropriate for international partners and
government projects (Akintan & Morledge, 2013).
2.1.4. Private public partnership
This is a procurement method where parties in the public sector enter into a contract with
parties in the private sector to provide a public service or asset. The entire agreement is based on
mutual objectives, trust, teamwork and sharing of rewards and risks. In most cases, the private
entity provides finance for the whole or most of the project. Once the project is complete, the
private entity owns and operates it until he recovers his money. This procurement route is
becoming more popular than the other because it enables governments to provide public services
or assets without spending too much at the time or when it has budget deficits (Carbonara, et al.,
2012). With this, the government can put the resources it has into other uses. The method is very
common in executing government infrastructure projects.
2.2. Task 2.2: Current issues associated with procurement and contractual
procedures
Procurement is revolving rapidly in response to advancements and changes in various issue.
The following are some of the current issues associated with procurement and contractual
procedures:
2.2.1. Climate change
This is a global problem that requires everybody’s participation to solve it. Companies are
now including climate change issue in procurement. Contractors and subcontractors are now
required to include measures they are taking to reduce the causes and impacts of climate change.
These measures have become essential factors in selection criteria of contractors, subcontractors
and supplier.
2.2.2. Sustainability
Sustainability has become a major part of procurement strategies and solutions of many
companies. These companies want contractors and subcontractors to create environmentally

Contractual Procedures and Procurement 12
friendly, economically viable, socially acceptable and sustainable solutions (Naoum & Egbu,
2015). As a result of this, the procurement solutions being offered should include sustainable
development solutions.
2.2.3. Technology
The role of technology in current construction industry cannot be overemphasized.
Technology is being used to make procurement processes faster, cost effective and more efficient
(Weisheng, et al., 2013). Creative procurement strategies including making data-based decisions,
using artificial intelligence and sophisticated analytical tools to select the most suitable
procurement method for each project are backed by technology. Contractors are using
technological tools to select appropriate procurement methods and clients are using these tools to
select the best contractors and supplier.
2.2.4. Lean construction
The need to reduce wastage and conserve the environment has prompted inclusion of lean
construction in procurement practice (Eriksson, 2010). Currently, procurement practice is
inclined towards practices or solutions that improve resource efficiency. During procurement
process, clients are now looking for contractors and suppliers who provide lean construction
solutions so as to reduce cost, improve efficiency and protect the environment.
2.2.5. Building information modelling
This is another important issue in procurement practice today. Building information
modelling (BIM) increases the efficiency of the structure before, during and after it has been
built (Khosrowashahi & Arayici, 2014). Clients now want contractors to incorporate BIM in
their operations so as to increase project efficiency during design, construction and operation
stages.
2.2.6. Ethics
Execution of construction projects involves participation of stakeholders from different
professions and backgrounds. Clients and companies now want to work with individuals who
make ethically sensible decisions. During procurement, it is becoming very difficult for persons
or companies with ethics issue to win tenders.
2.2.7. Risk management
Risks contribute significantly to project failure. This has prompted companies to integrate
risk management in procurement processes. The companies are now making procurement
decisions that have the lowest levels of risks so as to prevent these risks even before the start of
actual construction works.
2.2.8. Transparency
This has also been on the rise especially in relation to eliminating corruption and creating
equal opportunities for everybody. Procurement processes are nowadays done with openness and
honesty. Parties are allowed to ask for any information or clarification they need and the
selection criteria and processes are also open to scrutiny.
2.2.9. Cooperation and collaboration
There is also a rise in cooperation and collaboration among participants during procurement.
Companies are now consulting each other more so as to make the right procurement decisions
friendly, economically viable, socially acceptable and sustainable solutions (Naoum & Egbu,
2015). As a result of this, the procurement solutions being offered should include sustainable
development solutions.
2.2.3. Technology
The role of technology in current construction industry cannot be overemphasized.
Technology is being used to make procurement processes faster, cost effective and more efficient
(Weisheng, et al., 2013). Creative procurement strategies including making data-based decisions,
using artificial intelligence and sophisticated analytical tools to select the most suitable
procurement method for each project are backed by technology. Contractors are using
technological tools to select appropriate procurement methods and clients are using these tools to
select the best contractors and supplier.
2.2.4. Lean construction
The need to reduce wastage and conserve the environment has prompted inclusion of lean
construction in procurement practice (Eriksson, 2010). Currently, procurement practice is
inclined towards practices or solutions that improve resource efficiency. During procurement
process, clients are now looking for contractors and suppliers who provide lean construction
solutions so as to reduce cost, improve efficiency and protect the environment.
2.2.5. Building information modelling
This is another important issue in procurement practice today. Building information
modelling (BIM) increases the efficiency of the structure before, during and after it has been
built (Khosrowashahi & Arayici, 2014). Clients now want contractors to incorporate BIM in
their operations so as to increase project efficiency during design, construction and operation
stages.
2.2.6. Ethics
Execution of construction projects involves participation of stakeholders from different
professions and backgrounds. Clients and companies now want to work with individuals who
make ethically sensible decisions. During procurement, it is becoming very difficult for persons
or companies with ethics issue to win tenders.
2.2.7. Risk management
Risks contribute significantly to project failure. This has prompted companies to integrate
risk management in procurement processes. The companies are now making procurement
decisions that have the lowest levels of risks so as to prevent these risks even before the start of
actual construction works.
2.2.8. Transparency
This has also been on the rise especially in relation to eliminating corruption and creating
equal opportunities for everybody. Procurement processes are nowadays done with openness and
honesty. Parties are allowed to ask for any information or clarification they need and the
selection criteria and processes are also open to scrutiny.
2.2.9. Cooperation and collaboration
There is also a rise in cooperation and collaboration among participants during procurement.
Companies are now consulting each other more so as to make the right procurement decisions
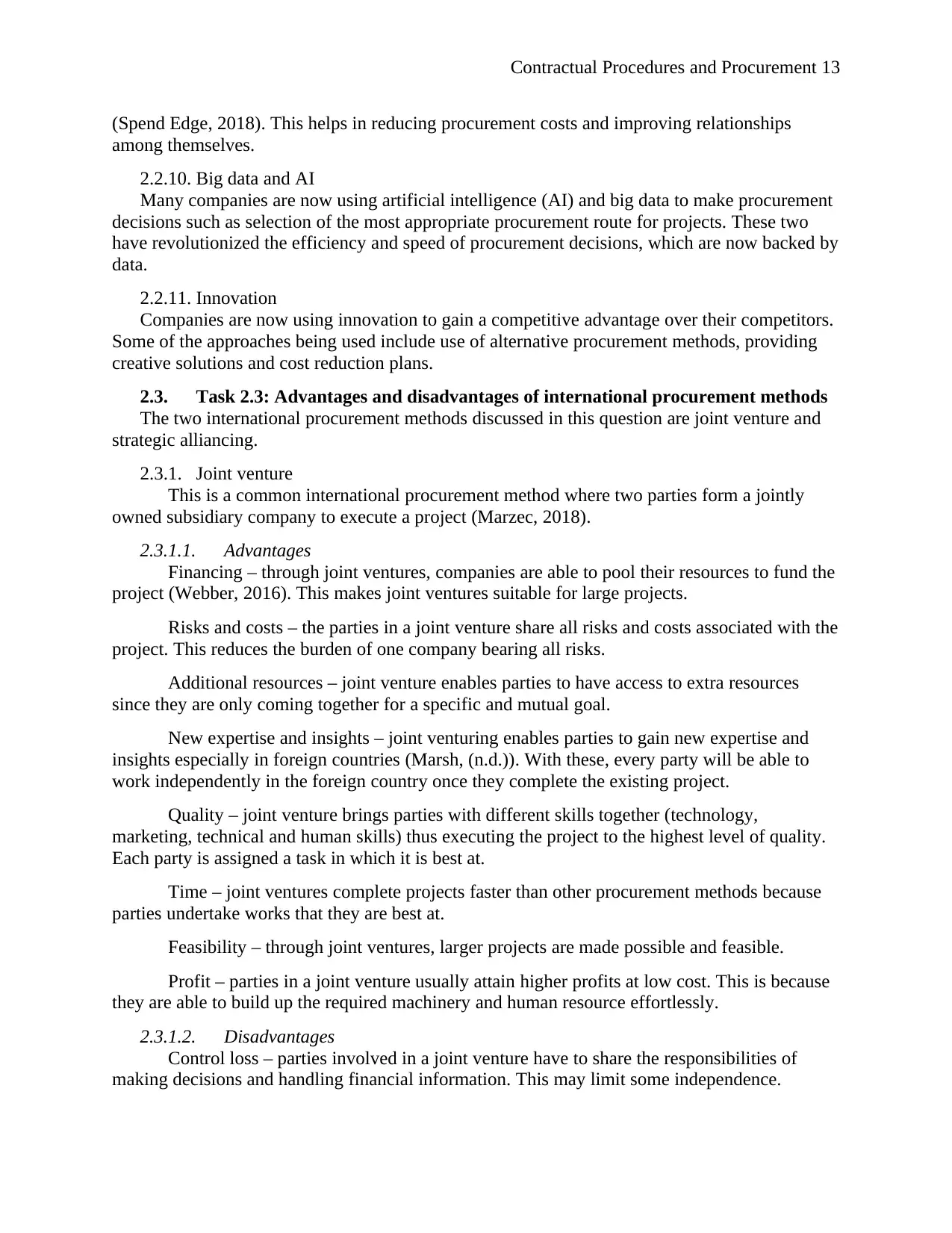
Contractual Procedures and Procurement 13
(Spend Edge, 2018). This helps in reducing procurement costs and improving relationships
among themselves.
2.2.10. Big data and AI
Many companies are now using artificial intelligence (AI) and big data to make procurement
decisions such as selection of the most appropriate procurement route for projects. These two
have revolutionized the efficiency and speed of procurement decisions, which are now backed by
data.
2.2.11. Innovation
Companies are now using innovation to gain a competitive advantage over their competitors.
Some of the approaches being used include use of alternative procurement methods, providing
creative solutions and cost reduction plans.
2.3. Task 2.3: Advantages and disadvantages of international procurement methods
The two international procurement methods discussed in this question are joint venture and
strategic alliancing.
2.3.1. Joint venture
This is a common international procurement method where two parties form a jointly
owned subsidiary company to execute a project (Marzec, 2018).
2.3.1.1. Advantages
Financing – through joint ventures, companies are able to pool their resources to fund the
project (Webber, 2016). This makes joint ventures suitable for large projects.
Risks and costs – the parties in a joint venture share all risks and costs associated with the
project. This reduces the burden of one company bearing all risks.
Additional resources – joint venture enables parties to have access to extra resources
since they are only coming together for a specific and mutual goal.
New expertise and insights – joint venturing enables parties to gain new expertise and
insights especially in foreign countries (Marsh, (n.d.)). With these, every party will be able to
work independently in the foreign country once they complete the existing project.
Quality – joint venture brings parties with different skills together (technology,
marketing, technical and human skills) thus executing the project to the highest level of quality.
Each party is assigned a task in which it is best at.
Time – joint ventures complete projects faster than other procurement methods because
parties undertake works that they are best at.
Feasibility – through joint ventures, larger projects are made possible and feasible.
Profit – parties in a joint venture usually attain higher profits at low cost. This is because
they are able to build up the required machinery and human resource effortlessly.
2.3.1.2. Disadvantages
Control loss – parties involved in a joint venture have to share the responsibilities of
making decisions and handling financial information. This may limit some independence.
(Spend Edge, 2018). This helps in reducing procurement costs and improving relationships
among themselves.
2.2.10. Big data and AI
Many companies are now using artificial intelligence (AI) and big data to make procurement
decisions such as selection of the most appropriate procurement route for projects. These two
have revolutionized the efficiency and speed of procurement decisions, which are now backed by
data.
2.2.11. Innovation
Companies are now using innovation to gain a competitive advantage over their competitors.
Some of the approaches being used include use of alternative procurement methods, providing
creative solutions and cost reduction plans.
2.3. Task 2.3: Advantages and disadvantages of international procurement methods
The two international procurement methods discussed in this question are joint venture and
strategic alliancing.
2.3.1. Joint venture
This is a common international procurement method where two parties form a jointly
owned subsidiary company to execute a project (Marzec, 2018).
2.3.1.1. Advantages
Financing – through joint ventures, companies are able to pool their resources to fund the
project (Webber, 2016). This makes joint ventures suitable for large projects.
Risks and costs – the parties in a joint venture share all risks and costs associated with the
project. This reduces the burden of one company bearing all risks.
Additional resources – joint venture enables parties to have access to extra resources
since they are only coming together for a specific and mutual goal.
New expertise and insights – joint venturing enables parties to gain new expertise and
insights especially in foreign countries (Marsh, (n.d.)). With these, every party will be able to
work independently in the foreign country once they complete the existing project.
Quality – joint venture brings parties with different skills together (technology,
marketing, technical and human skills) thus executing the project to the highest level of quality.
Each party is assigned a task in which it is best at.
Time – joint ventures complete projects faster than other procurement methods because
parties undertake works that they are best at.
Feasibility – through joint ventures, larger projects are made possible and feasible.
Profit – parties in a joint venture usually attain higher profits at low cost. This is because
they are able to build up the required machinery and human resource effortlessly.
2.3.1.2. Disadvantages
Control loss – parties involved in a joint venture have to share the responsibilities of
making decisions and handling financial information. This may limit some independence.
Paraphrase This Document
Need a fresh take? Get an instant paraphrase of this document with our AI Paraphraser
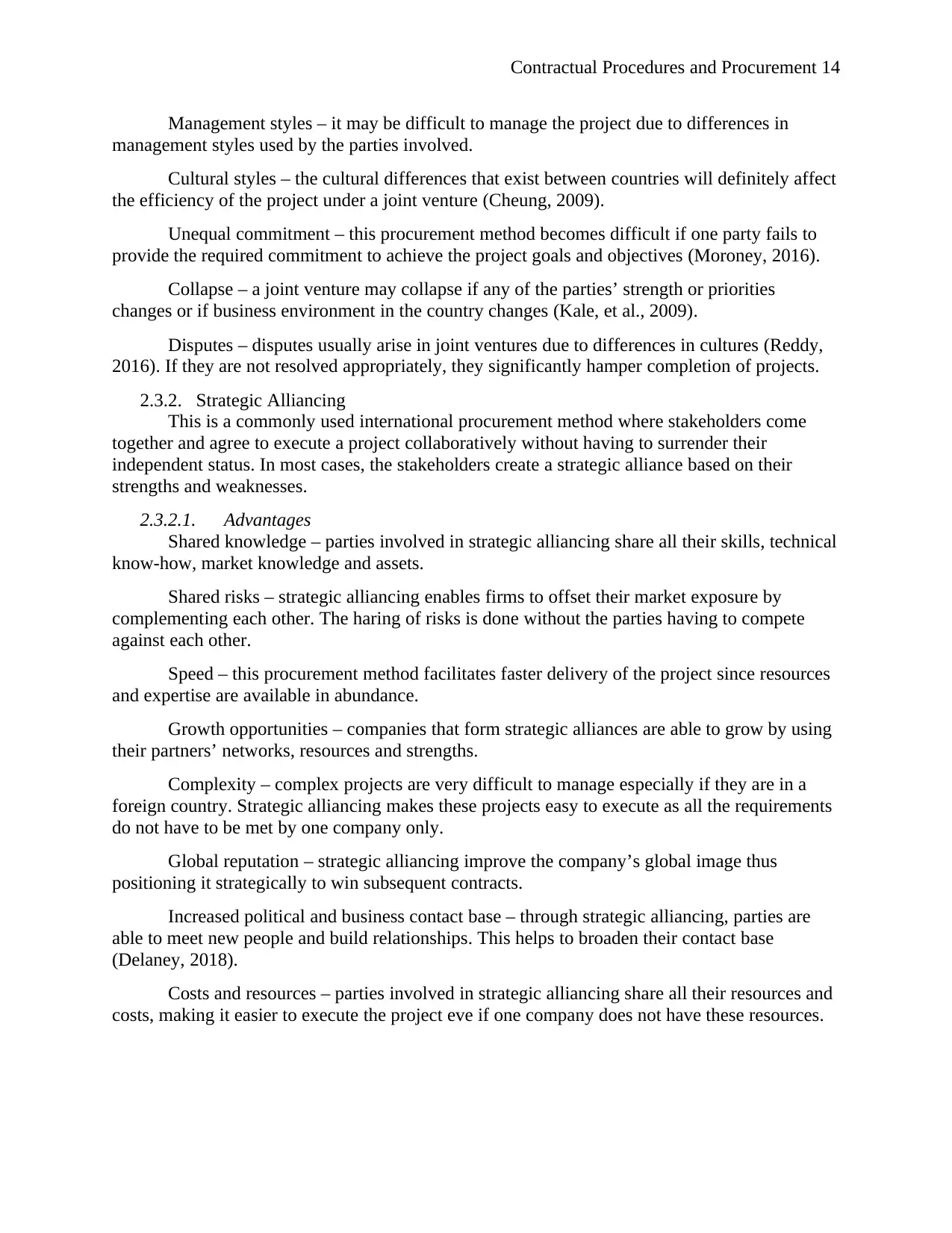
Contractual Procedures and Procurement 14
Management styles – it may be difficult to manage the project due to differences in
management styles used by the parties involved.
Cultural styles – the cultural differences that exist between countries will definitely affect
the efficiency of the project under a joint venture (Cheung, 2009).
Unequal commitment – this procurement method becomes difficult if one party fails to
provide the required commitment to achieve the project goals and objectives (Moroney, 2016).
Collapse – a joint venture may collapse if any of the parties’ strength or priorities
changes or if business environment in the country changes (Kale, et al., 2009).
Disputes – disputes usually arise in joint ventures due to differences in cultures (Reddy,
2016). If they are not resolved appropriately, they significantly hamper completion of projects.
2.3.2. Strategic Alliancing
This is a commonly used international procurement method where stakeholders come
together and agree to execute a project collaboratively without having to surrender their
independent status. In most cases, the stakeholders create a strategic alliance based on their
strengths and weaknesses.
2.3.2.1. Advantages
Shared knowledge – parties involved in strategic alliancing share all their skills, technical
know-how, market knowledge and assets.
Shared risks – strategic alliancing enables firms to offset their market exposure by
complementing each other. The haring of risks is done without the parties having to compete
against each other.
Speed – this procurement method facilitates faster delivery of the project since resources
and expertise are available in abundance.
Growth opportunities – companies that form strategic alliances are able to grow by using
their partners’ networks, resources and strengths.
Complexity – complex projects are very difficult to manage especially if they are in a
foreign country. Strategic alliancing makes these projects easy to execute as all the requirements
do not have to be met by one company only.
Global reputation – strategic alliancing improve the company’s global image thus
positioning it strategically to win subsequent contracts.
Increased political and business contact base – through strategic alliancing, parties are
able to meet new people and build relationships. This helps to broaden their contact base
(Delaney, 2018).
Costs and resources – parties involved in strategic alliancing share all their resources and
costs, making it easier to execute the project eve if one company does not have these resources.
Management styles – it may be difficult to manage the project due to differences in
management styles used by the parties involved.
Cultural styles – the cultural differences that exist between countries will definitely affect
the efficiency of the project under a joint venture (Cheung, 2009).
Unequal commitment – this procurement method becomes difficult if one party fails to
provide the required commitment to achieve the project goals and objectives (Moroney, 2016).
Collapse – a joint venture may collapse if any of the parties’ strength or priorities
changes or if business environment in the country changes (Kale, et al., 2009).
Disputes – disputes usually arise in joint ventures due to differences in cultures (Reddy,
2016). If they are not resolved appropriately, they significantly hamper completion of projects.
2.3.2. Strategic Alliancing
This is a commonly used international procurement method where stakeholders come
together and agree to execute a project collaboratively without having to surrender their
independent status. In most cases, the stakeholders create a strategic alliance based on their
strengths and weaknesses.
2.3.2.1. Advantages
Shared knowledge – parties involved in strategic alliancing share all their skills, technical
know-how, market knowledge and assets.
Shared risks – strategic alliancing enables firms to offset their market exposure by
complementing each other. The haring of risks is done without the parties having to compete
against each other.
Speed – this procurement method facilitates faster delivery of the project since resources
and expertise are available in abundance.
Growth opportunities – companies that form strategic alliances are able to grow by using
their partners’ networks, resources and strengths.
Complexity – complex projects are very difficult to manage especially if they are in a
foreign country. Strategic alliancing makes these projects easy to execute as all the requirements
do not have to be met by one company only.
Global reputation – strategic alliancing improve the company’s global image thus
positioning it strategically to win subsequent contracts.
Increased political and business contact base – through strategic alliancing, parties are
able to meet new people and build relationships. This helps to broaden their contact base
(Delaney, 2018).
Costs and resources – parties involved in strategic alliancing share all their resources and
costs, making it easier to execute the project eve if one company does not have these resources.
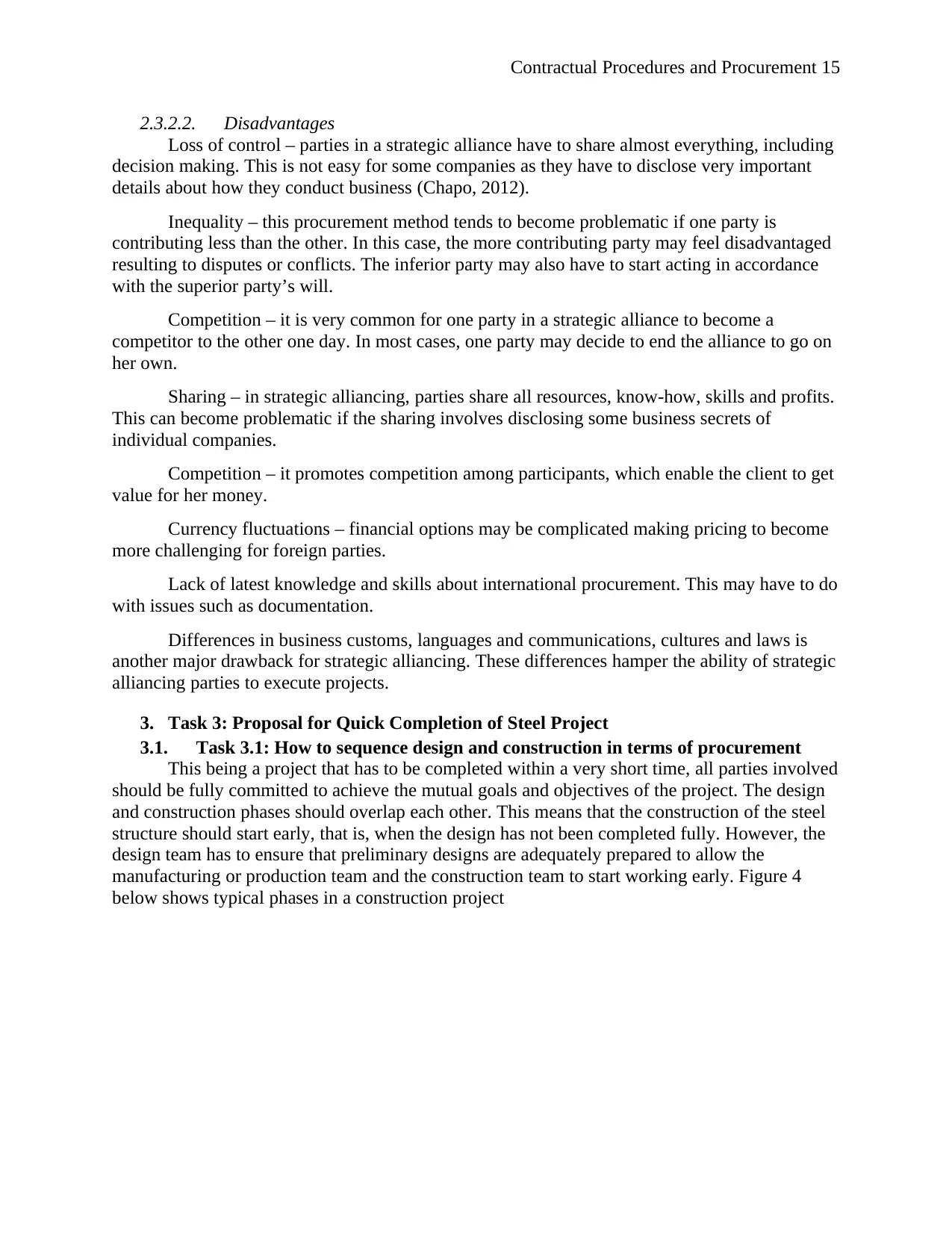
Contractual Procedures and Procurement 15
2.3.2.2. Disadvantages
Loss of control – parties in a strategic alliance have to share almost everything, including
decision making. This is not easy for some companies as they have to disclose very important
details about how they conduct business (Chapo, 2012).
Inequality – this procurement method tends to become problematic if one party is
contributing less than the other. In this case, the more contributing party may feel disadvantaged
resulting to disputes or conflicts. The inferior party may also have to start acting in accordance
with the superior party’s will.
Competition – it is very common for one party in a strategic alliance to become a
competitor to the other one day. In most cases, one party may decide to end the alliance to go on
her own.
Sharing – in strategic alliancing, parties share all resources, know-how, skills and profits.
This can become problematic if the sharing involves disclosing some business secrets of
individual companies.
Competition – it promotes competition among participants, which enable the client to get
value for her money.
Currency fluctuations – financial options may be complicated making pricing to become
more challenging for foreign parties.
Lack of latest knowledge and skills about international procurement. This may have to do
with issues such as documentation.
Differences in business customs, languages and communications, cultures and laws is
another major drawback for strategic alliancing. These differences hamper the ability of strategic
alliancing parties to execute projects.
3. Task 3: Proposal for Quick Completion of Steel Project
3.1. Task 3.1: How to sequence design and construction in terms of procurement
This being a project that has to be completed within a very short time, all parties involved
should be fully committed to achieve the mutual goals and objectives of the project. The design
and construction phases should overlap each other. This means that the construction of the steel
structure should start early, that is, when the design has not been completed fully. However, the
design team has to ensure that preliminary designs are adequately prepared to allow the
manufacturing or production team and the construction team to start working early. Figure 4
below shows typical phases in a construction project
2.3.2.2. Disadvantages
Loss of control – parties in a strategic alliance have to share almost everything, including
decision making. This is not easy for some companies as they have to disclose very important
details about how they conduct business (Chapo, 2012).
Inequality – this procurement method tends to become problematic if one party is
contributing less than the other. In this case, the more contributing party may feel disadvantaged
resulting to disputes or conflicts. The inferior party may also have to start acting in accordance
with the superior party’s will.
Competition – it is very common for one party in a strategic alliance to become a
competitor to the other one day. In most cases, one party may decide to end the alliance to go on
her own.
Sharing – in strategic alliancing, parties share all resources, know-how, skills and profits.
This can become problematic if the sharing involves disclosing some business secrets of
individual companies.
Competition – it promotes competition among participants, which enable the client to get
value for her money.
Currency fluctuations – financial options may be complicated making pricing to become
more challenging for foreign parties.
Lack of latest knowledge and skills about international procurement. This may have to do
with issues such as documentation.
Differences in business customs, languages and communications, cultures and laws is
another major drawback for strategic alliancing. These differences hamper the ability of strategic
alliancing parties to execute projects.
3. Task 3: Proposal for Quick Completion of Steel Project
3.1. Task 3.1: How to sequence design and construction in terms of procurement
This being a project that has to be completed within a very short time, all parties involved
should be fully committed to achieve the mutual goals and objectives of the project. The design
and construction phases should overlap each other. This means that the construction of the steel
structure should start early, that is, when the design has not been completed fully. However, the
design team has to ensure that preliminary designs are adequately prepared to allow the
manufacturing or production team and the construction team to start working early. Figure 4
below shows typical phases in a construction project
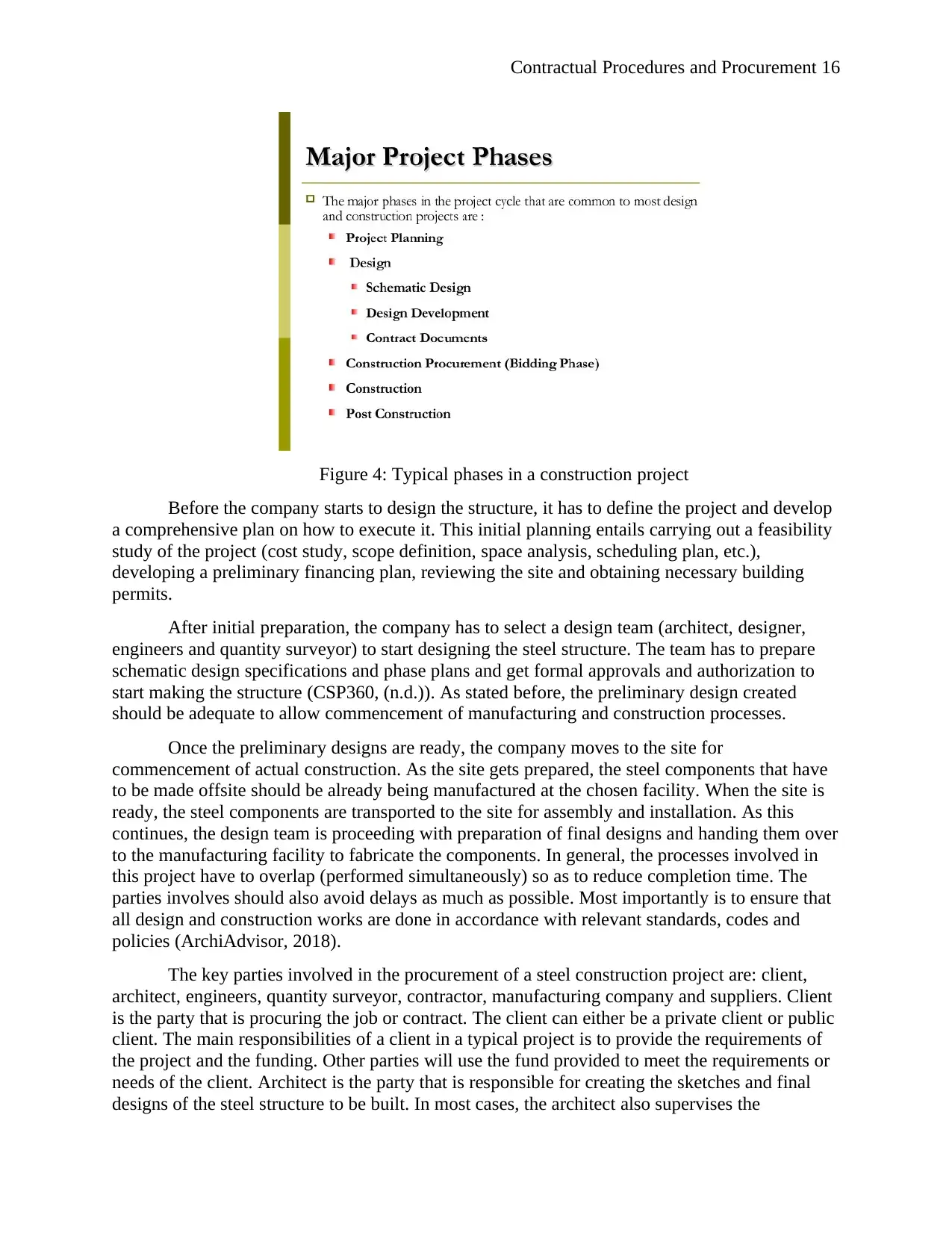
Contractual Procedures and Procurement 16
Figure 4: Typical phases in a construction project
Before the company starts to design the structure, it has to define the project and develop
a comprehensive plan on how to execute it. This initial planning entails carrying out a feasibility
study of the project (cost study, scope definition, space analysis, scheduling plan, etc.),
developing a preliminary financing plan, reviewing the site and obtaining necessary building
permits.
After initial preparation, the company has to select a design team (architect, designer,
engineers and quantity surveyor) to start designing the steel structure. The team has to prepare
schematic design specifications and phase plans and get formal approvals and authorization to
start making the structure (CSP360, (n.d.)). As stated before, the preliminary design created
should be adequate to allow commencement of manufacturing and construction processes.
Once the preliminary designs are ready, the company moves to the site for
commencement of actual construction. As the site gets prepared, the steel components that have
to be made offsite should be already being manufactured at the chosen facility. When the site is
ready, the steel components are transported to the site for assembly and installation. As this
continues, the design team is proceeding with preparation of final designs and handing them over
to the manufacturing facility to fabricate the components. In general, the processes involved in
this project have to overlap (performed simultaneously) so as to reduce completion time. The
parties involves should also avoid delays as much as possible. Most importantly is to ensure that
all design and construction works are done in accordance with relevant standards, codes and
policies (ArchiAdvisor, 2018).
The key parties involved in the procurement of a steel construction project are: client,
architect, engineers, quantity surveyor, contractor, manufacturing company and suppliers. Client
is the party that is procuring the job or contract. The client can either be a private client or public
client. The main responsibilities of a client in a typical project is to provide the requirements of
the project and the funding. Other parties will use the fund provided to meet the requirements or
needs of the client. Architect is the party that is responsible for creating the sketches and final
designs of the steel structure to be built. In most cases, the architect also supervises the
Figure 4: Typical phases in a construction project
Before the company starts to design the structure, it has to define the project and develop
a comprehensive plan on how to execute it. This initial planning entails carrying out a feasibility
study of the project (cost study, scope definition, space analysis, scheduling plan, etc.),
developing a preliminary financing plan, reviewing the site and obtaining necessary building
permits.
After initial preparation, the company has to select a design team (architect, designer,
engineers and quantity surveyor) to start designing the steel structure. The team has to prepare
schematic design specifications and phase plans and get formal approvals and authorization to
start making the structure (CSP360, (n.d.)). As stated before, the preliminary design created
should be adequate to allow commencement of manufacturing and construction processes.
Once the preliminary designs are ready, the company moves to the site for
commencement of actual construction. As the site gets prepared, the steel components that have
to be made offsite should be already being manufactured at the chosen facility. When the site is
ready, the steel components are transported to the site for assembly and installation. As this
continues, the design team is proceeding with preparation of final designs and handing them over
to the manufacturing facility to fabricate the components. In general, the processes involved in
this project have to overlap (performed simultaneously) so as to reduce completion time. The
parties involves should also avoid delays as much as possible. Most importantly is to ensure that
all design and construction works are done in accordance with relevant standards, codes and
policies (ArchiAdvisor, 2018).
The key parties involved in the procurement of a steel construction project are: client,
architect, engineers, quantity surveyor, contractor, manufacturing company and suppliers. Client
is the party that is procuring the job or contract. The client can either be a private client or public
client. The main responsibilities of a client in a typical project is to provide the requirements of
the project and the funding. Other parties will use the fund provided to meet the requirements or
needs of the client. Architect is the party that is responsible for creating the sketches and final
designs of the steel structure to be built. In most cases, the architect also supervises the
Secure Best Marks with AI Grader
Need help grading? Try our AI Grader for instant feedback on your assignments.
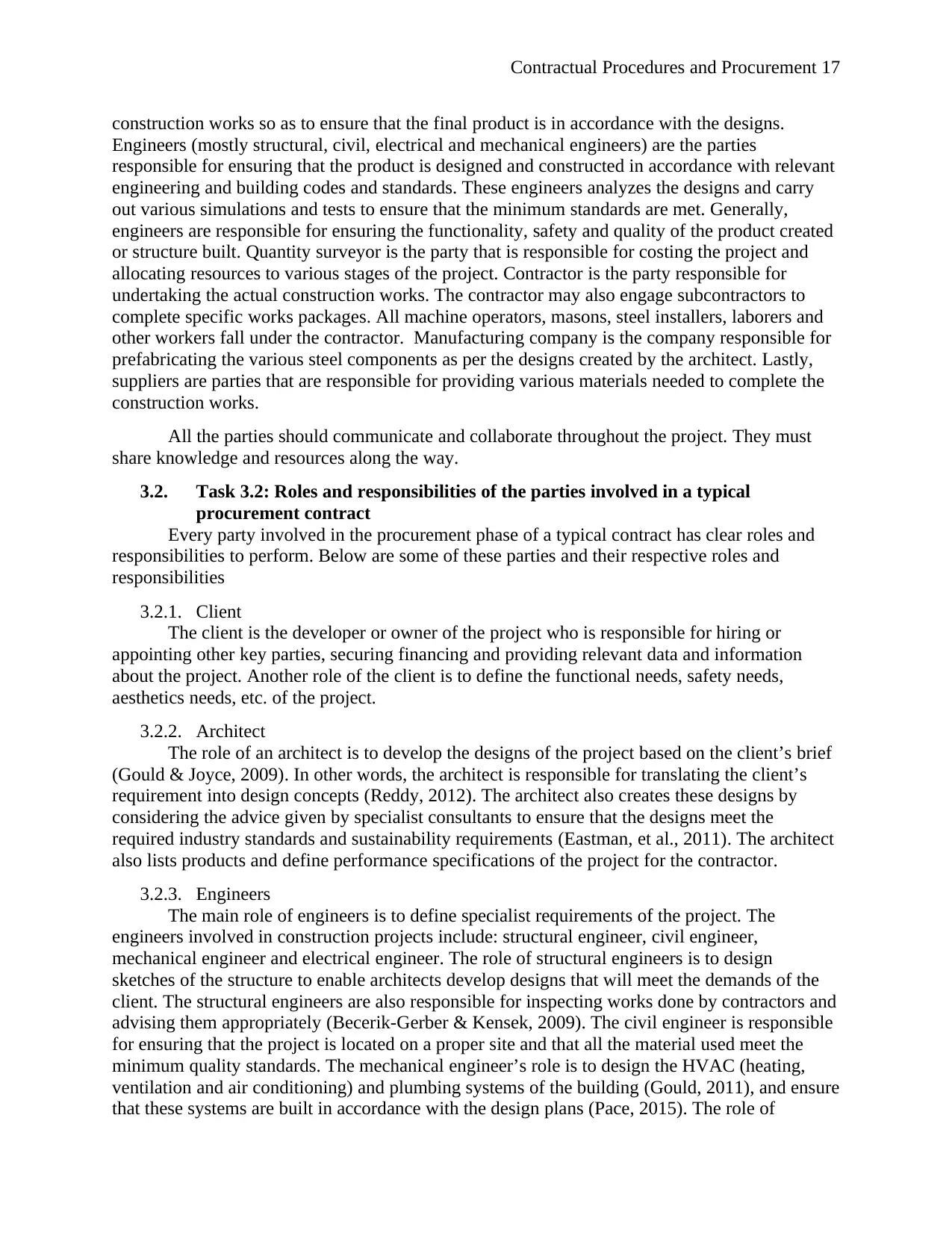
Contractual Procedures and Procurement 17
construction works so as to ensure that the final product is in accordance with the designs.
Engineers (mostly structural, civil, electrical and mechanical engineers) are the parties
responsible for ensuring that the product is designed and constructed in accordance with relevant
engineering and building codes and standards. These engineers analyzes the designs and carry
out various simulations and tests to ensure that the minimum standards are met. Generally,
engineers are responsible for ensuring the functionality, safety and quality of the product created
or structure built. Quantity surveyor is the party that is responsible for costing the project and
allocating resources to various stages of the project. Contractor is the party responsible for
undertaking the actual construction works. The contractor may also engage subcontractors to
complete specific works packages. All machine operators, masons, steel installers, laborers and
other workers fall under the contractor. Manufacturing company is the company responsible for
prefabricating the various steel components as per the designs created by the architect. Lastly,
suppliers are parties that are responsible for providing various materials needed to complete the
construction works.
All the parties should communicate and collaborate throughout the project. They must
share knowledge and resources along the way.
3.2. Task 3.2: Roles and responsibilities of the parties involved in a typical
procurement contract
Every party involved in the procurement phase of a typical contract has clear roles and
responsibilities to perform. Below are some of these parties and their respective roles and
responsibilities
3.2.1. Client
The client is the developer or owner of the project who is responsible for hiring or
appointing other key parties, securing financing and providing relevant data and information
about the project. Another role of the client is to define the functional needs, safety needs,
aesthetics needs, etc. of the project.
3.2.2. Architect
The role of an architect is to develop the designs of the project based on the client’s brief
(Gould & Joyce, 2009). In other words, the architect is responsible for translating the client’s
requirement into design concepts (Reddy, 2012). The architect also creates these designs by
considering the advice given by specialist consultants to ensure that the designs meet the
required industry standards and sustainability requirements (Eastman, et al., 2011). The architect
also lists products and define performance specifications of the project for the contractor.
3.2.3. Engineers
The main role of engineers is to define specialist requirements of the project. The
engineers involved in construction projects include: structural engineer, civil engineer,
mechanical engineer and electrical engineer. The role of structural engineers is to design
sketches of the structure to enable architects develop designs that will meet the demands of the
client. The structural engineers are also responsible for inspecting works done by contractors and
advising them appropriately (Becerik-Gerber & Kensek, 2009). The civil engineer is responsible
for ensuring that the project is located on a proper site and that all the material used meet the
minimum quality standards. The mechanical engineer’s role is to design the HVAC (heating,
ventilation and air conditioning) and plumbing systems of the building (Gould, 2011), and ensure
that these systems are built in accordance with the design plans (Pace, 2015). The role of
construction works so as to ensure that the final product is in accordance with the designs.
Engineers (mostly structural, civil, electrical and mechanical engineers) are the parties
responsible for ensuring that the product is designed and constructed in accordance with relevant
engineering and building codes and standards. These engineers analyzes the designs and carry
out various simulations and tests to ensure that the minimum standards are met. Generally,
engineers are responsible for ensuring the functionality, safety and quality of the product created
or structure built. Quantity surveyor is the party that is responsible for costing the project and
allocating resources to various stages of the project. Contractor is the party responsible for
undertaking the actual construction works. The contractor may also engage subcontractors to
complete specific works packages. All machine operators, masons, steel installers, laborers and
other workers fall under the contractor. Manufacturing company is the company responsible for
prefabricating the various steel components as per the designs created by the architect. Lastly,
suppliers are parties that are responsible for providing various materials needed to complete the
construction works.
All the parties should communicate and collaborate throughout the project. They must
share knowledge and resources along the way.
3.2. Task 3.2: Roles and responsibilities of the parties involved in a typical
procurement contract
Every party involved in the procurement phase of a typical contract has clear roles and
responsibilities to perform. Below are some of these parties and their respective roles and
responsibilities
3.2.1. Client
The client is the developer or owner of the project who is responsible for hiring or
appointing other key parties, securing financing and providing relevant data and information
about the project. Another role of the client is to define the functional needs, safety needs,
aesthetics needs, etc. of the project.
3.2.2. Architect
The role of an architect is to develop the designs of the project based on the client’s brief
(Gould & Joyce, 2009). In other words, the architect is responsible for translating the client’s
requirement into design concepts (Reddy, 2012). The architect also creates these designs by
considering the advice given by specialist consultants to ensure that the designs meet the
required industry standards and sustainability requirements (Eastman, et al., 2011). The architect
also lists products and define performance specifications of the project for the contractor.
3.2.3. Engineers
The main role of engineers is to define specialist requirements of the project. The
engineers involved in construction projects include: structural engineer, civil engineer,
mechanical engineer and electrical engineer. The role of structural engineers is to design
sketches of the structure to enable architects develop designs that will meet the demands of the
client. The structural engineers are also responsible for inspecting works done by contractors and
advising them appropriately (Becerik-Gerber & Kensek, 2009). The civil engineer is responsible
for ensuring that the project is located on a proper site and that all the material used meet the
minimum quality standards. The mechanical engineer’s role is to design the HVAC (heating,
ventilation and air conditioning) and plumbing systems of the building (Gould, 2011), and ensure
that these systems are built in accordance with the design plans (Pace, 2015). The role of
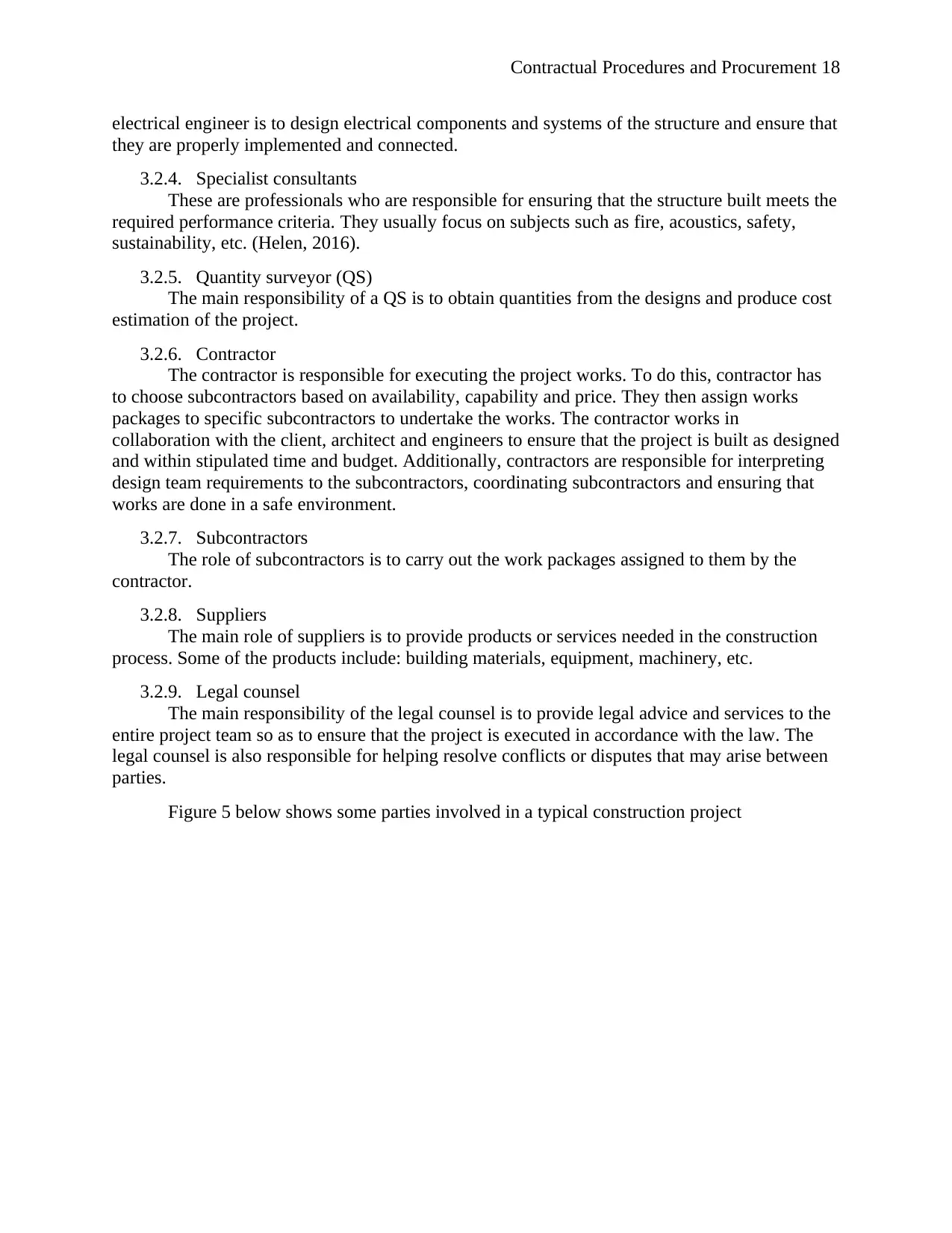
Contractual Procedures and Procurement 18
electrical engineer is to design electrical components and systems of the structure and ensure that
they are properly implemented and connected.
3.2.4. Specialist consultants
These are professionals who are responsible for ensuring that the structure built meets the
required performance criteria. They usually focus on subjects such as fire, acoustics, safety,
sustainability, etc. (Helen, 2016).
3.2.5. Quantity surveyor (QS)
The main responsibility of a QS is to obtain quantities from the designs and produce cost
estimation of the project.
3.2.6. Contractor
The contractor is responsible for executing the project works. To do this, contractor has
to choose subcontractors based on availability, capability and price. They then assign works
packages to specific subcontractors to undertake the works. The contractor works in
collaboration with the client, architect and engineers to ensure that the project is built as designed
and within stipulated time and budget. Additionally, contractors are responsible for interpreting
design team requirements to the subcontractors, coordinating subcontractors and ensuring that
works are done in a safe environment.
3.2.7. Subcontractors
The role of subcontractors is to carry out the work packages assigned to them by the
contractor.
3.2.8. Suppliers
The main role of suppliers is to provide products or services needed in the construction
process. Some of the products include: building materials, equipment, machinery, etc.
3.2.9. Legal counsel
The main responsibility of the legal counsel is to provide legal advice and services to the
entire project team so as to ensure that the project is executed in accordance with the law. The
legal counsel is also responsible for helping resolve conflicts or disputes that may arise between
parties.
Figure 5 below shows some parties involved in a typical construction project
electrical engineer is to design electrical components and systems of the structure and ensure that
they are properly implemented and connected.
3.2.4. Specialist consultants
These are professionals who are responsible for ensuring that the structure built meets the
required performance criteria. They usually focus on subjects such as fire, acoustics, safety,
sustainability, etc. (Helen, 2016).
3.2.5. Quantity surveyor (QS)
The main responsibility of a QS is to obtain quantities from the designs and produce cost
estimation of the project.
3.2.6. Contractor
The contractor is responsible for executing the project works. To do this, contractor has
to choose subcontractors based on availability, capability and price. They then assign works
packages to specific subcontractors to undertake the works. The contractor works in
collaboration with the client, architect and engineers to ensure that the project is built as designed
and within stipulated time and budget. Additionally, contractors are responsible for interpreting
design team requirements to the subcontractors, coordinating subcontractors and ensuring that
works are done in a safe environment.
3.2.7. Subcontractors
The role of subcontractors is to carry out the work packages assigned to them by the
contractor.
3.2.8. Suppliers
The main role of suppliers is to provide products or services needed in the construction
process. Some of the products include: building materials, equipment, machinery, etc.
3.2.9. Legal counsel
The main responsibility of the legal counsel is to provide legal advice and services to the
entire project team so as to ensure that the project is executed in accordance with the law. The
legal counsel is also responsible for helping resolve conflicts or disputes that may arise between
parties.
Figure 5 below shows some parties involved in a typical construction project
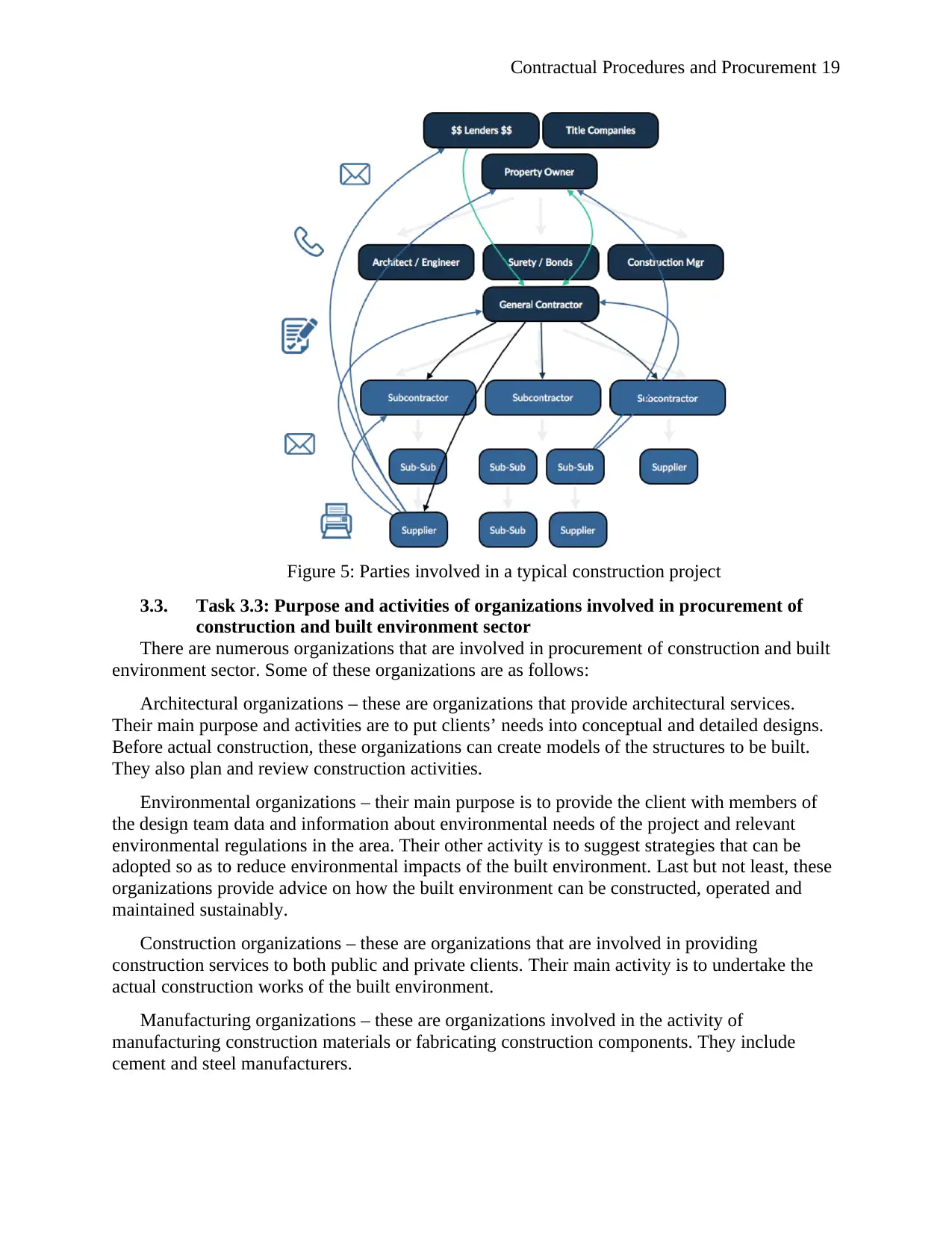
Contractual Procedures and Procurement 19
Figure 5: Parties involved in a typical construction project
3.3. Task 3.3: Purpose and activities of organizations involved in procurement of
construction and built environment sector
There are numerous organizations that are involved in procurement of construction and built
environment sector. Some of these organizations are as follows:
Architectural organizations – these are organizations that provide architectural services.
Their main purpose and activities are to put clients’ needs into conceptual and detailed designs.
Before actual construction, these organizations can create models of the structures to be built.
They also plan and review construction activities.
Environmental organizations – their main purpose is to provide the client with members of
the design team data and information about environmental needs of the project and relevant
environmental regulations in the area. Their other activity is to suggest strategies that can be
adopted so as to reduce environmental impacts of the built environment. Last but not least, these
organizations provide advice on how the built environment can be constructed, operated and
maintained sustainably.
Construction organizations – these are organizations that are involved in providing
construction services to both public and private clients. Their main activity is to undertake the
actual construction works of the built environment.
Manufacturing organizations – these are organizations involved in the activity of
manufacturing construction materials or fabricating construction components. They include
cement and steel manufacturers.
Figure 5: Parties involved in a typical construction project
3.3. Task 3.3: Purpose and activities of organizations involved in procurement of
construction and built environment sector
There are numerous organizations that are involved in procurement of construction and built
environment sector. Some of these organizations are as follows:
Architectural organizations – these are organizations that provide architectural services.
Their main purpose and activities are to put clients’ needs into conceptual and detailed designs.
Before actual construction, these organizations can create models of the structures to be built.
They also plan and review construction activities.
Environmental organizations – their main purpose is to provide the client with members of
the design team data and information about environmental needs of the project and relevant
environmental regulations in the area. Their other activity is to suggest strategies that can be
adopted so as to reduce environmental impacts of the built environment. Last but not least, these
organizations provide advice on how the built environment can be constructed, operated and
maintained sustainably.
Construction organizations – these are organizations that are involved in providing
construction services to both public and private clients. Their main activity is to undertake the
actual construction works of the built environment.
Manufacturing organizations – these are organizations involved in the activity of
manufacturing construction materials or fabricating construction components. They include
cement and steel manufacturers.
Paraphrase This Document
Need a fresh take? Get an instant paraphrase of this document with our AI Paraphraser
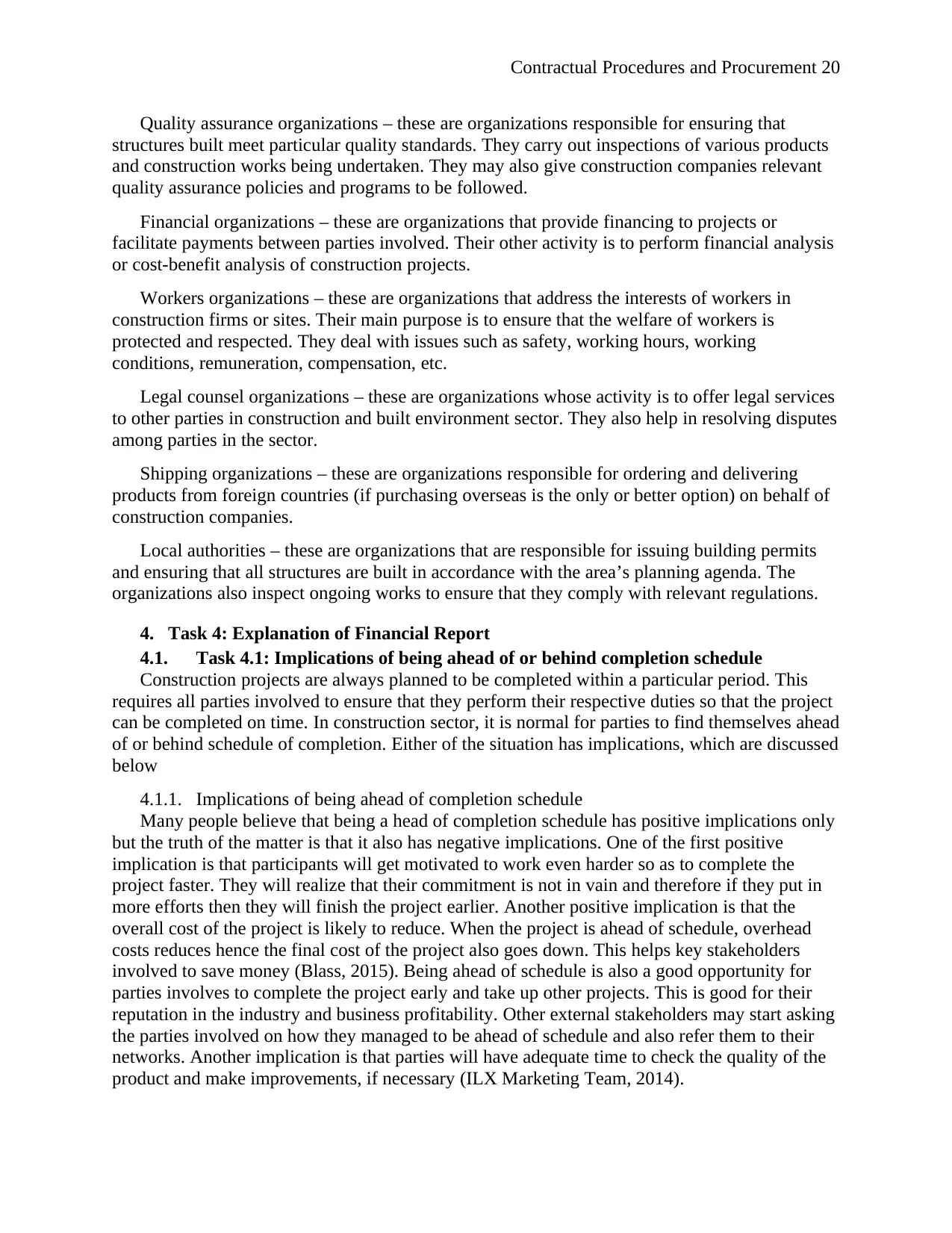
Contractual Procedures and Procurement 20
Quality assurance organizations – these are organizations responsible for ensuring that
structures built meet particular quality standards. They carry out inspections of various products
and construction works being undertaken. They may also give construction companies relevant
quality assurance policies and programs to be followed.
Financial organizations – these are organizations that provide financing to projects or
facilitate payments between parties involved. Their other activity is to perform financial analysis
or cost-benefit analysis of construction projects.
Workers organizations – these are organizations that address the interests of workers in
construction firms or sites. Their main purpose is to ensure that the welfare of workers is
protected and respected. They deal with issues such as safety, working hours, working
conditions, remuneration, compensation, etc.
Legal counsel organizations – these are organizations whose activity is to offer legal services
to other parties in construction and built environment sector. They also help in resolving disputes
among parties in the sector.
Shipping organizations – these are organizations responsible for ordering and delivering
products from foreign countries (if purchasing overseas is the only or better option) on behalf of
construction companies.
Local authorities – these are organizations that are responsible for issuing building permits
and ensuring that all structures are built in accordance with the area’s planning agenda. The
organizations also inspect ongoing works to ensure that they comply with relevant regulations.
4. Task 4: Explanation of Financial Report
4.1. Task 4.1: Implications of being ahead of or behind completion schedule
Construction projects are always planned to be completed within a particular period. This
requires all parties involved to ensure that they perform their respective duties so that the project
can be completed on time. In construction sector, it is normal for parties to find themselves ahead
of or behind schedule of completion. Either of the situation has implications, which are discussed
below
4.1.1. Implications of being ahead of completion schedule
Many people believe that being a head of completion schedule has positive implications only
but the truth of the matter is that it also has negative implications. One of the first positive
implication is that participants will get motivated to work even harder so as to complete the
project faster. They will realize that their commitment is not in vain and therefore if they put in
more efforts then they will finish the project earlier. Another positive implication is that the
overall cost of the project is likely to reduce. When the project is ahead of schedule, overhead
costs reduces hence the final cost of the project also goes down. This helps key stakeholders
involved to save money (Blass, 2015). Being ahead of schedule is also a good opportunity for
parties involves to complete the project early and take up other projects. This is good for their
reputation in the industry and business profitability. Other external stakeholders may start asking
the parties involved on how they managed to be ahead of schedule and also refer them to their
networks. Another implication is that parties will have adequate time to check the quality of the
product and make improvements, if necessary (ILX Marketing Team, 2014).
Quality assurance organizations – these are organizations responsible for ensuring that
structures built meet particular quality standards. They carry out inspections of various products
and construction works being undertaken. They may also give construction companies relevant
quality assurance policies and programs to be followed.
Financial organizations – these are organizations that provide financing to projects or
facilitate payments between parties involved. Their other activity is to perform financial analysis
or cost-benefit analysis of construction projects.
Workers organizations – these are organizations that address the interests of workers in
construction firms or sites. Their main purpose is to ensure that the welfare of workers is
protected and respected. They deal with issues such as safety, working hours, working
conditions, remuneration, compensation, etc.
Legal counsel organizations – these are organizations whose activity is to offer legal services
to other parties in construction and built environment sector. They also help in resolving disputes
among parties in the sector.
Shipping organizations – these are organizations responsible for ordering and delivering
products from foreign countries (if purchasing overseas is the only or better option) on behalf of
construction companies.
Local authorities – these are organizations that are responsible for issuing building permits
and ensuring that all structures are built in accordance with the area’s planning agenda. The
organizations also inspect ongoing works to ensure that they comply with relevant regulations.
4. Task 4: Explanation of Financial Report
4.1. Task 4.1: Implications of being ahead of or behind completion schedule
Construction projects are always planned to be completed within a particular period. This
requires all parties involved to ensure that they perform their respective duties so that the project
can be completed on time. In construction sector, it is normal for parties to find themselves ahead
of or behind schedule of completion. Either of the situation has implications, which are discussed
below
4.1.1. Implications of being ahead of completion schedule
Many people believe that being a head of completion schedule has positive implications only
but the truth of the matter is that it also has negative implications. One of the first positive
implication is that participants will get motivated to work even harder so as to complete the
project faster. They will realize that their commitment is not in vain and therefore if they put in
more efforts then they will finish the project earlier. Another positive implication is that the
overall cost of the project is likely to reduce. When the project is ahead of schedule, overhead
costs reduces hence the final cost of the project also goes down. This helps key stakeholders
involved to save money (Blass, 2015). Being ahead of schedule is also a good opportunity for
parties involves to complete the project early and take up other projects. This is good for their
reputation in the industry and business profitability. Other external stakeholders may start asking
the parties involved on how they managed to be ahead of schedule and also refer them to their
networks. Another implication is that parties will have adequate time to check the quality of the
product and make improvements, if necessary (ILX Marketing Team, 2014).
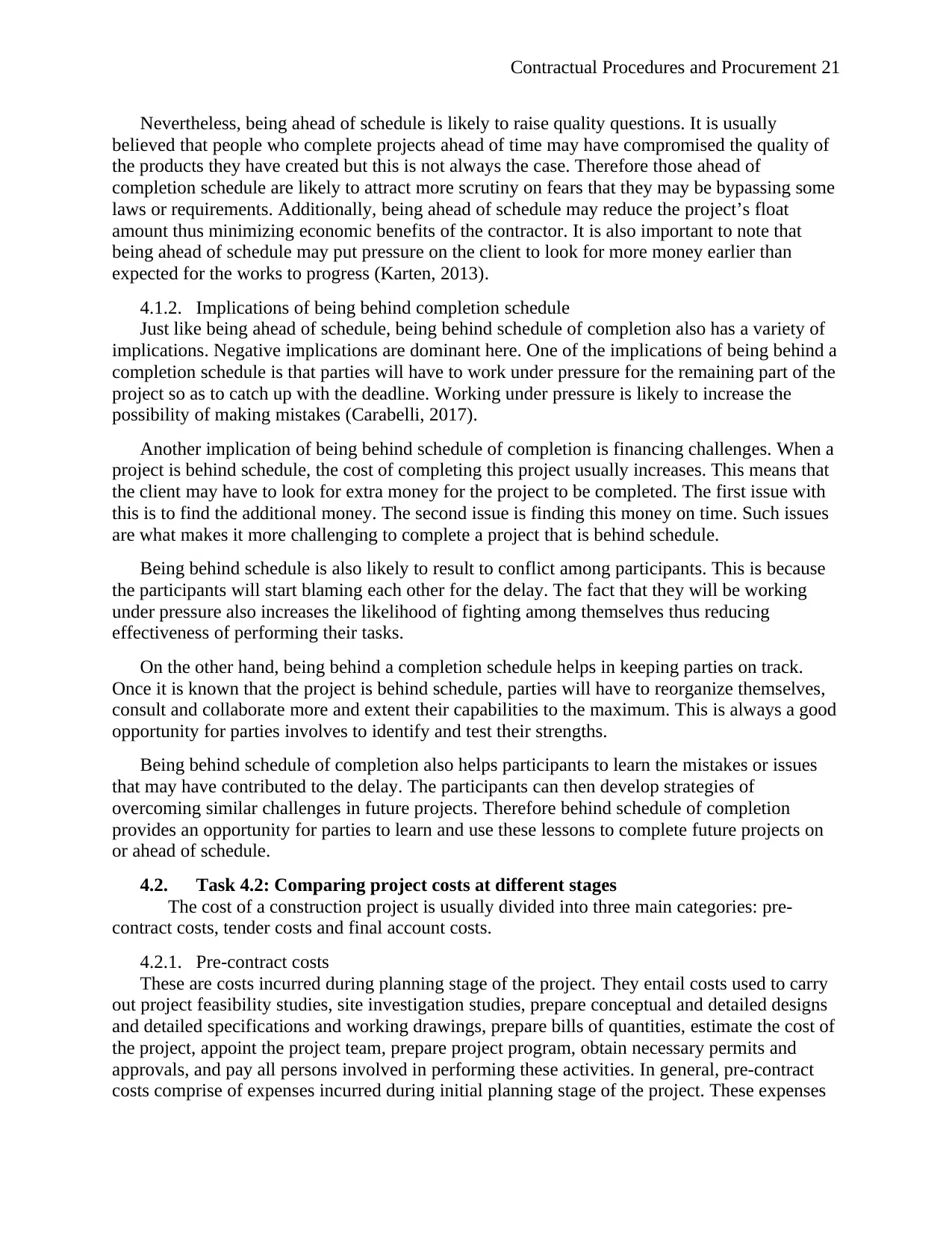
Contractual Procedures and Procurement 21
Nevertheless, being ahead of schedule is likely to raise quality questions. It is usually
believed that people who complete projects ahead of time may have compromised the quality of
the products they have created but this is not always the case. Therefore those ahead of
completion schedule are likely to attract more scrutiny on fears that they may be bypassing some
laws or requirements. Additionally, being ahead of schedule may reduce the project’s float
amount thus minimizing economic benefits of the contractor. It is also important to note that
being ahead of schedule may put pressure on the client to look for more money earlier than
expected for the works to progress (Karten, 2013).
4.1.2. Implications of being behind completion schedule
Just like being ahead of schedule, being behind schedule of completion also has a variety of
implications. Negative implications are dominant here. One of the implications of being behind a
completion schedule is that parties will have to work under pressure for the remaining part of the
project so as to catch up with the deadline. Working under pressure is likely to increase the
possibility of making mistakes (Carabelli, 2017).
Another implication of being behind schedule of completion is financing challenges. When a
project is behind schedule, the cost of completing this project usually increases. This means that
the client may have to look for extra money for the project to be completed. The first issue with
this is to find the additional money. The second issue is finding this money on time. Such issues
are what makes it more challenging to complete a project that is behind schedule.
Being behind schedule is also likely to result to conflict among participants. This is because
the participants will start blaming each other for the delay. The fact that they will be working
under pressure also increases the likelihood of fighting among themselves thus reducing
effectiveness of performing their tasks.
On the other hand, being behind a completion schedule helps in keeping parties on track.
Once it is known that the project is behind schedule, parties will have to reorganize themselves,
consult and collaborate more and extent their capabilities to the maximum. This is always a good
opportunity for parties involves to identify and test their strengths.
Being behind schedule of completion also helps participants to learn the mistakes or issues
that may have contributed to the delay. The participants can then develop strategies of
overcoming similar challenges in future projects. Therefore behind schedule of completion
provides an opportunity for parties to learn and use these lessons to complete future projects on
or ahead of schedule.
4.2. Task 4.2: Comparing project costs at different stages
The cost of a construction project is usually divided into three main categories: pre-
contract costs, tender costs and final account costs.
4.2.1. Pre-contract costs
These are costs incurred during planning stage of the project. They entail costs used to carry
out project feasibility studies, site investigation studies, prepare conceptual and detailed designs
and detailed specifications and working drawings, prepare bills of quantities, estimate the cost of
the project, appoint the project team, prepare project program, obtain necessary permits and
approvals, and pay all persons involved in performing these activities. In general, pre-contract
costs comprise of expenses incurred during initial planning stage of the project. These expenses
Nevertheless, being ahead of schedule is likely to raise quality questions. It is usually
believed that people who complete projects ahead of time may have compromised the quality of
the products they have created but this is not always the case. Therefore those ahead of
completion schedule are likely to attract more scrutiny on fears that they may be bypassing some
laws or requirements. Additionally, being ahead of schedule may reduce the project’s float
amount thus minimizing economic benefits of the contractor. It is also important to note that
being ahead of schedule may put pressure on the client to look for more money earlier than
expected for the works to progress (Karten, 2013).
4.1.2. Implications of being behind completion schedule
Just like being ahead of schedule, being behind schedule of completion also has a variety of
implications. Negative implications are dominant here. One of the implications of being behind a
completion schedule is that parties will have to work under pressure for the remaining part of the
project so as to catch up with the deadline. Working under pressure is likely to increase the
possibility of making mistakes (Carabelli, 2017).
Another implication of being behind schedule of completion is financing challenges. When a
project is behind schedule, the cost of completing this project usually increases. This means that
the client may have to look for extra money for the project to be completed. The first issue with
this is to find the additional money. The second issue is finding this money on time. Such issues
are what makes it more challenging to complete a project that is behind schedule.
Being behind schedule is also likely to result to conflict among participants. This is because
the participants will start blaming each other for the delay. The fact that they will be working
under pressure also increases the likelihood of fighting among themselves thus reducing
effectiveness of performing their tasks.
On the other hand, being behind a completion schedule helps in keeping parties on track.
Once it is known that the project is behind schedule, parties will have to reorganize themselves,
consult and collaborate more and extent their capabilities to the maximum. This is always a good
opportunity for parties involves to identify and test their strengths.
Being behind schedule of completion also helps participants to learn the mistakes or issues
that may have contributed to the delay. The participants can then develop strategies of
overcoming similar challenges in future projects. Therefore behind schedule of completion
provides an opportunity for parties to learn and use these lessons to complete future projects on
or ahead of schedule.
4.2. Task 4.2: Comparing project costs at different stages
The cost of a construction project is usually divided into three main categories: pre-
contract costs, tender costs and final account costs.
4.2.1. Pre-contract costs
These are costs incurred during planning stage of the project. They entail costs used to carry
out project feasibility studies, site investigation studies, prepare conceptual and detailed designs
and detailed specifications and working drawings, prepare bills of quantities, estimate the cost of
the project, appoint the project team, prepare project program, obtain necessary permits and
approvals, and pay all persons involved in performing these activities. In general, pre-contract
costs comprise of expenses incurred during initial planning stage of the project. These expenses
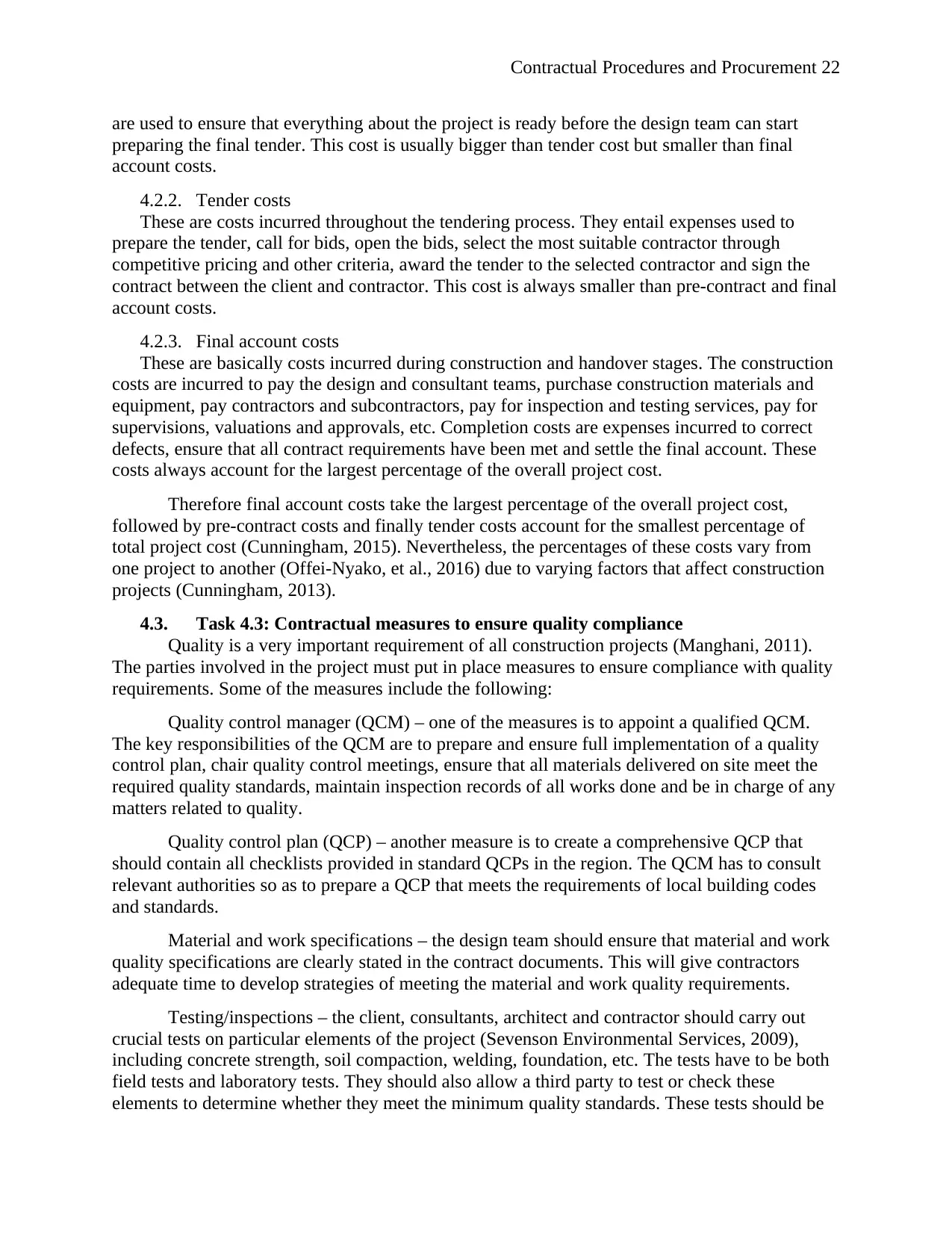
Contractual Procedures and Procurement 22
are used to ensure that everything about the project is ready before the design team can start
preparing the final tender. This cost is usually bigger than tender cost but smaller than final
account costs.
4.2.2. Tender costs
These are costs incurred throughout the tendering process. They entail expenses used to
prepare the tender, call for bids, open the bids, select the most suitable contractor through
competitive pricing and other criteria, award the tender to the selected contractor and sign the
contract between the client and contractor. This cost is always smaller than pre-contract and final
account costs.
4.2.3. Final account costs
These are basically costs incurred during construction and handover stages. The construction
costs are incurred to pay the design and consultant teams, purchase construction materials and
equipment, pay contractors and subcontractors, pay for inspection and testing services, pay for
supervisions, valuations and approvals, etc. Completion costs are expenses incurred to correct
defects, ensure that all contract requirements have been met and settle the final account. These
costs always account for the largest percentage of the overall project cost.
Therefore final account costs take the largest percentage of the overall project cost,
followed by pre-contract costs and finally tender costs account for the smallest percentage of
total project cost (Cunningham, 2015). Nevertheless, the percentages of these costs vary from
one project to another (Offei-Nyako, et al., 2016) due to varying factors that affect construction
projects (Cunningham, 2013).
4.3. Task 4.3: Contractual measures to ensure quality compliance
Quality is a very important requirement of all construction projects (Manghani, 2011).
The parties involved in the project must put in place measures to ensure compliance with quality
requirements. Some of the measures include the following:
Quality control manager (QCM) – one of the measures is to appoint a qualified QCM.
The key responsibilities of the QCM are to prepare and ensure full implementation of a quality
control plan, chair quality control meetings, ensure that all materials delivered on site meet the
required quality standards, maintain inspection records of all works done and be in charge of any
matters related to quality.
Quality control plan (QCP) – another measure is to create a comprehensive QCP that
should contain all checklists provided in standard QCPs in the region. The QCM has to consult
relevant authorities so as to prepare a QCP that meets the requirements of local building codes
and standards.
Material and work specifications – the design team should ensure that material and work
quality specifications are clearly stated in the contract documents. This will give contractors
adequate time to develop strategies of meeting the material and work quality requirements.
Testing/inspections – the client, consultants, architect and contractor should carry out
crucial tests on particular elements of the project (Sevenson Environmental Services, 2009),
including concrete strength, soil compaction, welding, foundation, etc. The tests have to be both
field tests and laboratory tests. They should also allow a third party to test or check these
elements to determine whether they meet the minimum quality standards. These tests should be
are used to ensure that everything about the project is ready before the design team can start
preparing the final tender. This cost is usually bigger than tender cost but smaller than final
account costs.
4.2.2. Tender costs
These are costs incurred throughout the tendering process. They entail expenses used to
prepare the tender, call for bids, open the bids, select the most suitable contractor through
competitive pricing and other criteria, award the tender to the selected contractor and sign the
contract between the client and contractor. This cost is always smaller than pre-contract and final
account costs.
4.2.3. Final account costs
These are basically costs incurred during construction and handover stages. The construction
costs are incurred to pay the design and consultant teams, purchase construction materials and
equipment, pay contractors and subcontractors, pay for inspection and testing services, pay for
supervisions, valuations and approvals, etc. Completion costs are expenses incurred to correct
defects, ensure that all contract requirements have been met and settle the final account. These
costs always account for the largest percentage of the overall project cost.
Therefore final account costs take the largest percentage of the overall project cost,
followed by pre-contract costs and finally tender costs account for the smallest percentage of
total project cost (Cunningham, 2015). Nevertheless, the percentages of these costs vary from
one project to another (Offei-Nyako, et al., 2016) due to varying factors that affect construction
projects (Cunningham, 2013).
4.3. Task 4.3: Contractual measures to ensure quality compliance
Quality is a very important requirement of all construction projects (Manghani, 2011).
The parties involved in the project must put in place measures to ensure compliance with quality
requirements. Some of the measures include the following:
Quality control manager (QCM) – one of the measures is to appoint a qualified QCM.
The key responsibilities of the QCM are to prepare and ensure full implementation of a quality
control plan, chair quality control meetings, ensure that all materials delivered on site meet the
required quality standards, maintain inspection records of all works done and be in charge of any
matters related to quality.
Quality control plan (QCP) – another measure is to create a comprehensive QCP that
should contain all checklists provided in standard QCPs in the region. The QCM has to consult
relevant authorities so as to prepare a QCP that meets the requirements of local building codes
and standards.
Material and work specifications – the design team should ensure that material and work
quality specifications are clearly stated in the contract documents. This will give contractors
adequate time to develop strategies of meeting the material and work quality requirements.
Testing/inspections – the client, consultants, architect and contractor should carry out
crucial tests on particular elements of the project (Sevenson Environmental Services, 2009),
including concrete strength, soil compaction, welding, foundation, etc. The tests have to be both
field tests and laboratory tests. They should also allow a third party to test or check these
elements to determine whether they meet the minimum quality standards. These tests should be
Secure Best Marks with AI Grader
Need help grading? Try our AI Grader for instant feedback on your assignments.
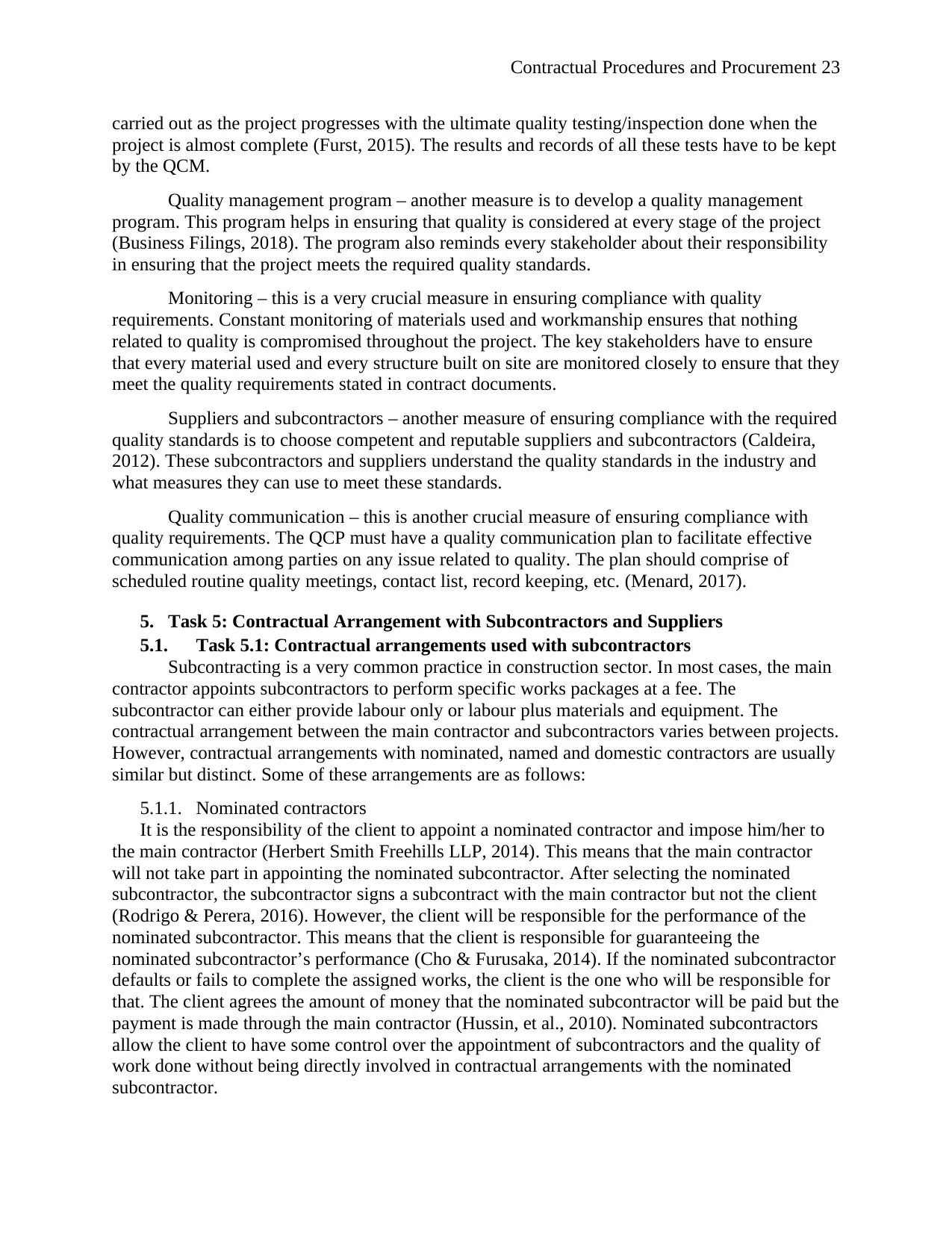
Contractual Procedures and Procurement 23
carried out as the project progresses with the ultimate quality testing/inspection done when the
project is almost complete (Furst, 2015). The results and records of all these tests have to be kept
by the QCM.
Quality management program – another measure is to develop a quality management
program. This program helps in ensuring that quality is considered at every stage of the project
(Business Filings, 2018). The program also reminds every stakeholder about their responsibility
in ensuring that the project meets the required quality standards.
Monitoring – this is a very crucial measure in ensuring compliance with quality
requirements. Constant monitoring of materials used and workmanship ensures that nothing
related to quality is compromised throughout the project. The key stakeholders have to ensure
that every material used and every structure built on site are monitored closely to ensure that they
meet the quality requirements stated in contract documents.
Suppliers and subcontractors – another measure of ensuring compliance with the required
quality standards is to choose competent and reputable suppliers and subcontractors (Caldeira,
2012). These subcontractors and suppliers understand the quality standards in the industry and
what measures they can use to meet these standards.
Quality communication – this is another crucial measure of ensuring compliance with
quality requirements. The QCP must have a quality communication plan to facilitate effective
communication among parties on any issue related to quality. The plan should comprise of
scheduled routine quality meetings, contact list, record keeping, etc. (Menard, 2017).
5. Task 5: Contractual Arrangement with Subcontractors and Suppliers
5.1. Task 5.1: Contractual arrangements used with subcontractors
Subcontracting is a very common practice in construction sector. In most cases, the main
contractor appoints subcontractors to perform specific works packages at a fee. The
subcontractor can either provide labour only or labour plus materials and equipment. The
contractual arrangement between the main contractor and subcontractors varies between projects.
However, contractual arrangements with nominated, named and domestic contractors are usually
similar but distinct. Some of these arrangements are as follows:
5.1.1. Nominated contractors
It is the responsibility of the client to appoint a nominated contractor and impose him/her to
the main contractor (Herbert Smith Freehills LLP, 2014). This means that the main contractor
will not take part in appointing the nominated subcontractor. After selecting the nominated
subcontractor, the subcontractor signs a subcontract with the main contractor but not the client
(Rodrigo & Perera, 2016). However, the client will be responsible for the performance of the
nominated subcontractor. This means that the client is responsible for guaranteeing the
nominated subcontractor’s performance (Cho & Furusaka, 2014). If the nominated subcontractor
defaults or fails to complete the assigned works, the client is the one who will be responsible for
that. The client agrees the amount of money that the nominated subcontractor will be paid but the
payment is made through the main contractor (Hussin, et al., 2010). Nominated subcontractors
allow the client to have some control over the appointment of subcontractors and the quality of
work done without being directly involved in contractual arrangements with the nominated
subcontractor.
carried out as the project progresses with the ultimate quality testing/inspection done when the
project is almost complete (Furst, 2015). The results and records of all these tests have to be kept
by the QCM.
Quality management program – another measure is to develop a quality management
program. This program helps in ensuring that quality is considered at every stage of the project
(Business Filings, 2018). The program also reminds every stakeholder about their responsibility
in ensuring that the project meets the required quality standards.
Monitoring – this is a very crucial measure in ensuring compliance with quality
requirements. Constant monitoring of materials used and workmanship ensures that nothing
related to quality is compromised throughout the project. The key stakeholders have to ensure
that every material used and every structure built on site are monitored closely to ensure that they
meet the quality requirements stated in contract documents.
Suppliers and subcontractors – another measure of ensuring compliance with the required
quality standards is to choose competent and reputable suppliers and subcontractors (Caldeira,
2012). These subcontractors and suppliers understand the quality standards in the industry and
what measures they can use to meet these standards.
Quality communication – this is another crucial measure of ensuring compliance with
quality requirements. The QCP must have a quality communication plan to facilitate effective
communication among parties on any issue related to quality. The plan should comprise of
scheduled routine quality meetings, contact list, record keeping, etc. (Menard, 2017).
5. Task 5: Contractual Arrangement with Subcontractors and Suppliers
5.1. Task 5.1: Contractual arrangements used with subcontractors
Subcontracting is a very common practice in construction sector. In most cases, the main
contractor appoints subcontractors to perform specific works packages at a fee. The
subcontractor can either provide labour only or labour plus materials and equipment. The
contractual arrangement between the main contractor and subcontractors varies between projects.
However, contractual arrangements with nominated, named and domestic contractors are usually
similar but distinct. Some of these arrangements are as follows:
5.1.1. Nominated contractors
It is the responsibility of the client to appoint a nominated contractor and impose him/her to
the main contractor (Herbert Smith Freehills LLP, 2014). This means that the main contractor
will not take part in appointing the nominated subcontractor. After selecting the nominated
subcontractor, the subcontractor signs a subcontract with the main contractor but not the client
(Rodrigo & Perera, 2016). However, the client will be responsible for the performance of the
nominated subcontractor. This means that the client is responsible for guaranteeing the
nominated subcontractor’s performance (Cho & Furusaka, 2014). If the nominated subcontractor
defaults or fails to complete the assigned works, the client is the one who will be responsible for
that. The client agrees the amount of money that the nominated subcontractor will be paid but the
payment is made through the main contractor (Hussin, et al., 2010). Nominated subcontractors
allow the client to have some control over the appointment of subcontractors and the quality of
work done without being directly involved in contractual arrangements with the nominated
subcontractor.
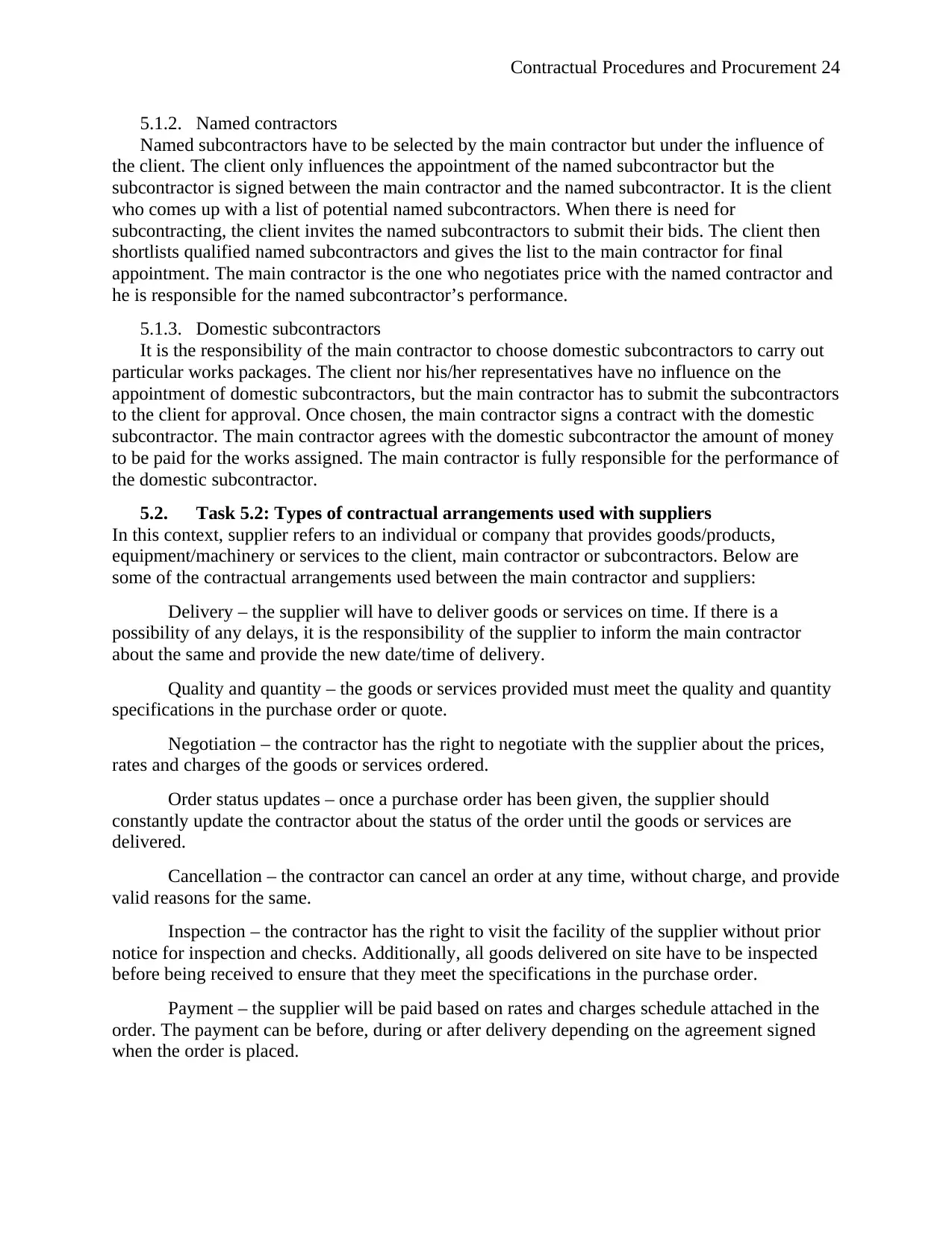
Contractual Procedures and Procurement 24
5.1.2. Named contractors
Named subcontractors have to be selected by the main contractor but under the influence of
the client. The client only influences the appointment of the named subcontractor but the
subcontractor is signed between the main contractor and the named subcontractor. It is the client
who comes up with a list of potential named subcontractors. When there is need for
subcontracting, the client invites the named subcontractors to submit their bids. The client then
shortlists qualified named subcontractors and gives the list to the main contractor for final
appointment. The main contractor is the one who negotiates price with the named contractor and
he is responsible for the named subcontractor’s performance.
5.1.3. Domestic subcontractors
It is the responsibility of the main contractor to choose domestic subcontractors to carry out
particular works packages. The client nor his/her representatives have no influence on the
appointment of domestic subcontractors, but the main contractor has to submit the subcontractors
to the client for approval. Once chosen, the main contractor signs a contract with the domestic
subcontractor. The main contractor agrees with the domestic subcontractor the amount of money
to be paid for the works assigned. The main contractor is fully responsible for the performance of
the domestic subcontractor.
5.2. Task 5.2: Types of contractual arrangements used with suppliers
In this context, supplier refers to an individual or company that provides goods/products,
equipment/machinery or services to the client, main contractor or subcontractors. Below are
some of the contractual arrangements used between the main contractor and suppliers:
Delivery – the supplier will have to deliver goods or services on time. If there is a
possibility of any delays, it is the responsibility of the supplier to inform the main contractor
about the same and provide the new date/time of delivery.
Quality and quantity – the goods or services provided must meet the quality and quantity
specifications in the purchase order or quote.
Negotiation – the contractor has the right to negotiate with the supplier about the prices,
rates and charges of the goods or services ordered.
Order status updates – once a purchase order has been given, the supplier should
constantly update the contractor about the status of the order until the goods or services are
delivered.
Cancellation – the contractor can cancel an order at any time, without charge, and provide
valid reasons for the same.
Inspection – the contractor has the right to visit the facility of the supplier without prior
notice for inspection and checks. Additionally, all goods delivered on site have to be inspected
before being received to ensure that they meet the specifications in the purchase order.
Payment – the supplier will be paid based on rates and charges schedule attached in the
order. The payment can be before, during or after delivery depending on the agreement signed
when the order is placed.
5.1.2. Named contractors
Named subcontractors have to be selected by the main contractor but under the influence of
the client. The client only influences the appointment of the named subcontractor but the
subcontractor is signed between the main contractor and the named subcontractor. It is the client
who comes up with a list of potential named subcontractors. When there is need for
subcontracting, the client invites the named subcontractors to submit their bids. The client then
shortlists qualified named subcontractors and gives the list to the main contractor for final
appointment. The main contractor is the one who negotiates price with the named contractor and
he is responsible for the named subcontractor’s performance.
5.1.3. Domestic subcontractors
It is the responsibility of the main contractor to choose domestic subcontractors to carry out
particular works packages. The client nor his/her representatives have no influence on the
appointment of domestic subcontractors, but the main contractor has to submit the subcontractors
to the client for approval. Once chosen, the main contractor signs a contract with the domestic
subcontractor. The main contractor agrees with the domestic subcontractor the amount of money
to be paid for the works assigned. The main contractor is fully responsible for the performance of
the domestic subcontractor.
5.2. Task 5.2: Types of contractual arrangements used with suppliers
In this context, supplier refers to an individual or company that provides goods/products,
equipment/machinery or services to the client, main contractor or subcontractors. Below are
some of the contractual arrangements used between the main contractor and suppliers:
Delivery – the supplier will have to deliver goods or services on time. If there is a
possibility of any delays, it is the responsibility of the supplier to inform the main contractor
about the same and provide the new date/time of delivery.
Quality and quantity – the goods or services provided must meet the quality and quantity
specifications in the purchase order or quote.
Negotiation – the contractor has the right to negotiate with the supplier about the prices,
rates and charges of the goods or services ordered.
Order status updates – once a purchase order has been given, the supplier should
constantly update the contractor about the status of the order until the goods or services are
delivered.
Cancellation – the contractor can cancel an order at any time, without charge, and provide
valid reasons for the same.
Inspection – the contractor has the right to visit the facility of the supplier without prior
notice for inspection and checks. Additionally, all goods delivered on site have to be inspected
before being received to ensure that they meet the specifications in the purchase order.
Payment – the supplier will be paid based on rates and charges schedule attached in the
order. The payment can be before, during or after delivery depending on the agreement signed
when the order is placed.
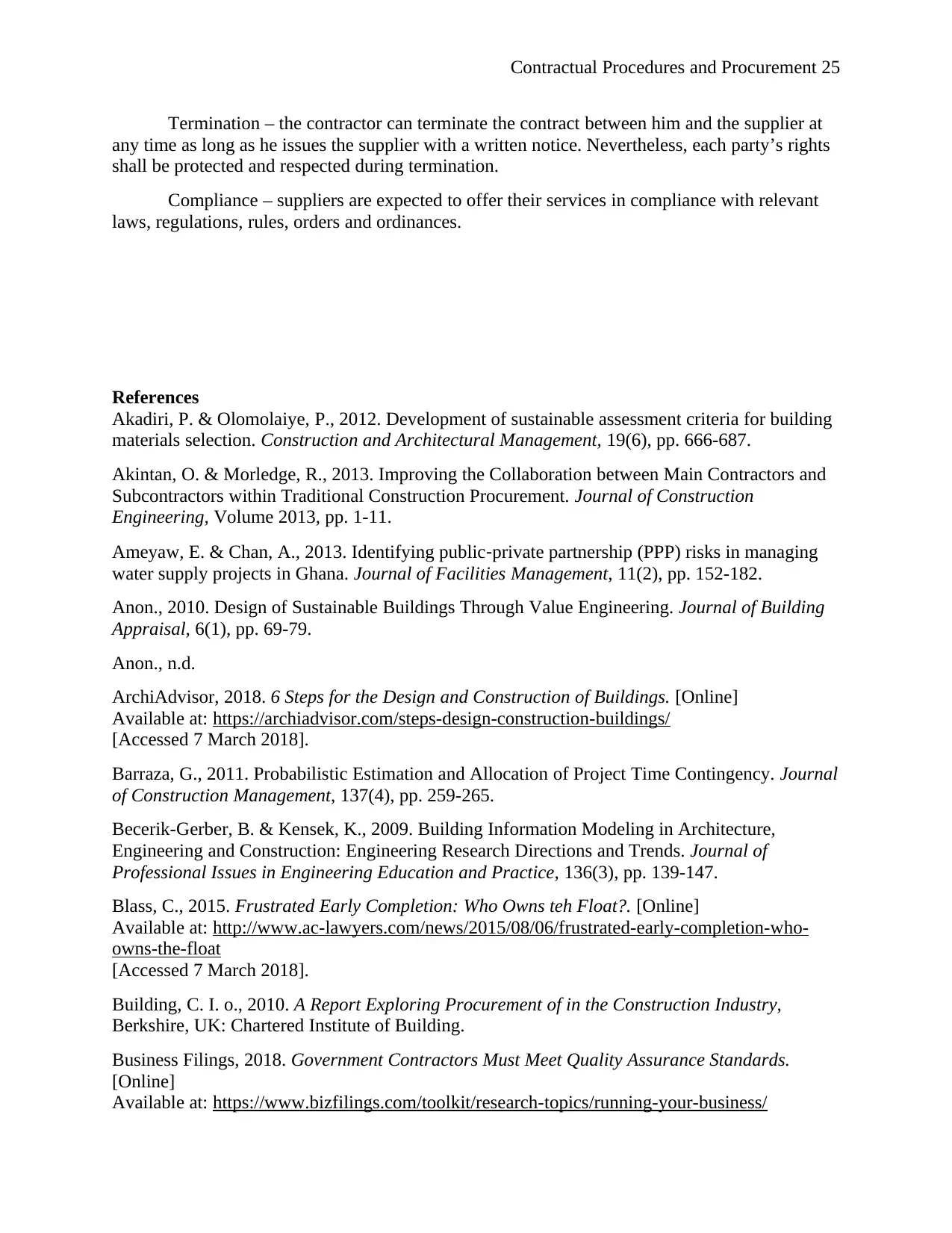
Contractual Procedures and Procurement 25
Termination – the contractor can terminate the contract between him and the supplier at
any time as long as he issues the supplier with a written notice. Nevertheless, each party’s rights
shall be protected and respected during termination.
Compliance – suppliers are expected to offer their services in compliance with relevant
laws, regulations, rules, orders and ordinances.
References
Akadiri, P. & Olomolaiye, P., 2012. Development of sustainable assessment criteria for building
materials selection. Construction and Architectural Management, 19(6), pp. 666-687.
Akintan, O. & Morledge, R., 2013. Improving the Collaboration between Main Contractors and
Subcontractors within Traditional Construction Procurement. Journal of Construction
Engineering, Volume 2013, pp. 1-11.
Ameyaw, E. & Chan, A., 2013. Identifying public‐private partnership (PPP) risks in managing
water supply projects in Ghana. Journal of Facilities Management, 11(2), pp. 152-182.
Anon., 2010. Design of Sustainable Buildings Through Value Engineering. Journal of Building
Appraisal, 6(1), pp. 69-79.
Anon., n.d.
ArchiAdvisor, 2018. 6 Steps for the Design and Construction of Buildings. [Online]
Available at: https://archiadvisor.com/steps-design-construction-buildings/
[Accessed 7 March 2018].
Barraza, G., 2011. Probabilistic Estimation and Allocation of Project Time Contingency. Journal
of Construction Management, 137(4), pp. 259-265.
Becerik-Gerber, B. & Kensek, K., 2009. Building Information Modeling in Architecture,
Engineering and Construction: Engineering Research Directions and Trends. Journal of
Professional Issues in Engineering Education and Practice, 136(3), pp. 139-147.
Blass, C., 2015. Frustrated Early Completion: Who Owns teh Float?. [Online]
Available at: http://www.ac-lawyers.com/news/2015/08/06/frustrated-early-completion-who-
owns-the-float
[Accessed 7 March 2018].
Building, C. I. o., 2010. A Report Exploring Procurement of in the Construction Industry,
Berkshire, UK: Chartered Institute of Building.
Business Filings, 2018. Government Contractors Must Meet Quality Assurance Standards.
[Online]
Available at: https://www.bizfilings.com/toolkit/research-topics/running-your-business/
Termination – the contractor can terminate the contract between him and the supplier at
any time as long as he issues the supplier with a written notice. Nevertheless, each party’s rights
shall be protected and respected during termination.
Compliance – suppliers are expected to offer their services in compliance with relevant
laws, regulations, rules, orders and ordinances.
References
Akadiri, P. & Olomolaiye, P., 2012. Development of sustainable assessment criteria for building
materials selection. Construction and Architectural Management, 19(6), pp. 666-687.
Akintan, O. & Morledge, R., 2013. Improving the Collaboration between Main Contractors and
Subcontractors within Traditional Construction Procurement. Journal of Construction
Engineering, Volume 2013, pp. 1-11.
Ameyaw, E. & Chan, A., 2013. Identifying public‐private partnership (PPP) risks in managing
water supply projects in Ghana. Journal of Facilities Management, 11(2), pp. 152-182.
Anon., 2010. Design of Sustainable Buildings Through Value Engineering. Journal of Building
Appraisal, 6(1), pp. 69-79.
Anon., n.d.
ArchiAdvisor, 2018. 6 Steps for the Design and Construction of Buildings. [Online]
Available at: https://archiadvisor.com/steps-design-construction-buildings/
[Accessed 7 March 2018].
Barraza, G., 2011. Probabilistic Estimation and Allocation of Project Time Contingency. Journal
of Construction Management, 137(4), pp. 259-265.
Becerik-Gerber, B. & Kensek, K., 2009. Building Information Modeling in Architecture,
Engineering and Construction: Engineering Research Directions and Trends. Journal of
Professional Issues in Engineering Education and Practice, 136(3), pp. 139-147.
Blass, C., 2015. Frustrated Early Completion: Who Owns teh Float?. [Online]
Available at: http://www.ac-lawyers.com/news/2015/08/06/frustrated-early-completion-who-
owns-the-float
[Accessed 7 March 2018].
Building, C. I. o., 2010. A Report Exploring Procurement of in the Construction Industry,
Berkshire, UK: Chartered Institute of Building.
Business Filings, 2018. Government Contractors Must Meet Quality Assurance Standards.
[Online]
Available at: https://www.bizfilings.com/toolkit/research-topics/running-your-business/
Paraphrase This Document
Need a fresh take? Get an instant paraphrase of this document with our AI Paraphraser
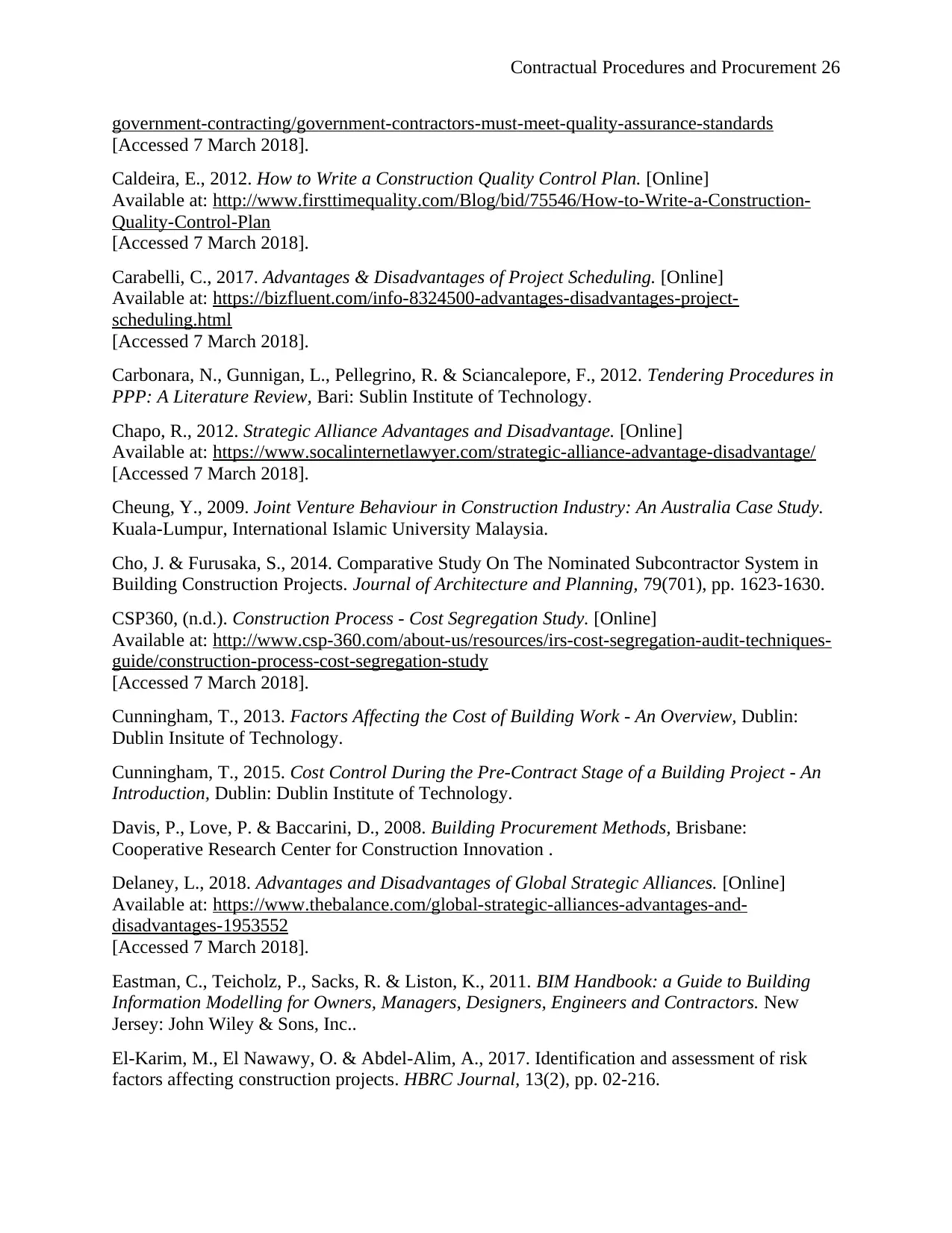
Contractual Procedures and Procurement 26
government-contracting/government-contractors-must-meet-quality-assurance-standards
[Accessed 7 March 2018].
Caldeira, E., 2012. How to Write a Construction Quality Control Plan. [Online]
Available at: http://www.firsttimequality.com/Blog/bid/75546/How-to-Write-a-Construction-
Quality-Control-Plan
[Accessed 7 March 2018].
Carabelli, C., 2017. Advantages & Disadvantages of Project Scheduling. [Online]
Available at: https://bizfluent.com/info-8324500-advantages-disadvantages-project-
scheduling.html
[Accessed 7 March 2018].
Carbonara, N., Gunnigan, L., Pellegrino, R. & Sciancalepore, F., 2012. Tendering Procedures in
PPP: A Literature Review, Bari: Sublin Institute of Technology.
Chapo, R., 2012. Strategic Alliance Advantages and Disadvantage. [Online]
Available at: https://www.socalinternetlawyer.com/strategic-alliance-advantage-disadvantage/
[Accessed 7 March 2018].
Cheung, Y., 2009. Joint Venture Behaviour in Construction Industry: An Australia Case Study.
Kuala-Lumpur, International Islamic University Malaysia.
Cho, J. & Furusaka, S., 2014. Comparative Study On The Nominated Subcontractor System in
Building Construction Projects. Journal of Architecture and Planning, 79(701), pp. 1623-1630.
CSP360, (n.d.). Construction Process - Cost Segregation Study. [Online]
Available at: http://www.csp-360.com/about-us/resources/irs-cost-segregation-audit-techniques-
guide/construction-process-cost-segregation-study
[Accessed 7 March 2018].
Cunningham, T., 2013. Factors Affecting the Cost of Building Work - An Overview, Dublin:
Dublin Insitute of Technology.
Cunningham, T., 2015. Cost Control During the Pre-Contract Stage of a Building Project - An
Introduction, Dublin: Dublin Institute of Technology.
Davis, P., Love, P. & Baccarini, D., 2008. Building Procurement Methods, Brisbane:
Cooperative Research Center for Construction Innovation .
Delaney, L., 2018. Advantages and Disadvantages of Global Strategic Alliances. [Online]
Available at: https://www.thebalance.com/global-strategic-alliances-advantages-and-
disadvantages-1953552
[Accessed 7 March 2018].
Eastman, C., Teicholz, P., Sacks, R. & Liston, K., 2011. BIM Handbook: a Guide to Building
Information Modelling for Owners, Managers, Designers, Engineers and Contractors. New
Jersey: John Wiley & Sons, Inc..
El-Karim, M., El Nawawy, O. & Abdel-Alim, A., 2017. Identification and assessment of risk
factors affecting construction projects. HBRC Journal, 13(2), pp. 02-216.
government-contracting/government-contractors-must-meet-quality-assurance-standards
[Accessed 7 March 2018].
Caldeira, E., 2012. How to Write a Construction Quality Control Plan. [Online]
Available at: http://www.firsttimequality.com/Blog/bid/75546/How-to-Write-a-Construction-
Quality-Control-Plan
[Accessed 7 March 2018].
Carabelli, C., 2017. Advantages & Disadvantages of Project Scheduling. [Online]
Available at: https://bizfluent.com/info-8324500-advantages-disadvantages-project-
scheduling.html
[Accessed 7 March 2018].
Carbonara, N., Gunnigan, L., Pellegrino, R. & Sciancalepore, F., 2012. Tendering Procedures in
PPP: A Literature Review, Bari: Sublin Institute of Technology.
Chapo, R., 2012. Strategic Alliance Advantages and Disadvantage. [Online]
Available at: https://www.socalinternetlawyer.com/strategic-alliance-advantage-disadvantage/
[Accessed 7 March 2018].
Cheung, Y., 2009. Joint Venture Behaviour in Construction Industry: An Australia Case Study.
Kuala-Lumpur, International Islamic University Malaysia.
Cho, J. & Furusaka, S., 2014. Comparative Study On The Nominated Subcontractor System in
Building Construction Projects. Journal of Architecture and Planning, 79(701), pp. 1623-1630.
CSP360, (n.d.). Construction Process - Cost Segregation Study. [Online]
Available at: http://www.csp-360.com/about-us/resources/irs-cost-segregation-audit-techniques-
guide/construction-process-cost-segregation-study
[Accessed 7 March 2018].
Cunningham, T., 2013. Factors Affecting the Cost of Building Work - An Overview, Dublin:
Dublin Insitute of Technology.
Cunningham, T., 2015. Cost Control During the Pre-Contract Stage of a Building Project - An
Introduction, Dublin: Dublin Institute of Technology.
Davis, P., Love, P. & Baccarini, D., 2008. Building Procurement Methods, Brisbane:
Cooperative Research Center for Construction Innovation .
Delaney, L., 2018. Advantages and Disadvantages of Global Strategic Alliances. [Online]
Available at: https://www.thebalance.com/global-strategic-alliances-advantages-and-
disadvantages-1953552
[Accessed 7 March 2018].
Eastman, C., Teicholz, P., Sacks, R. & Liston, K., 2011. BIM Handbook: a Guide to Building
Information Modelling for Owners, Managers, Designers, Engineers and Contractors. New
Jersey: John Wiley & Sons, Inc..
El-Karim, M., El Nawawy, O. & Abdel-Alim, A., 2017. Identification and assessment of risk
factors affecting construction projects. HBRC Journal, 13(2), pp. 02-216.
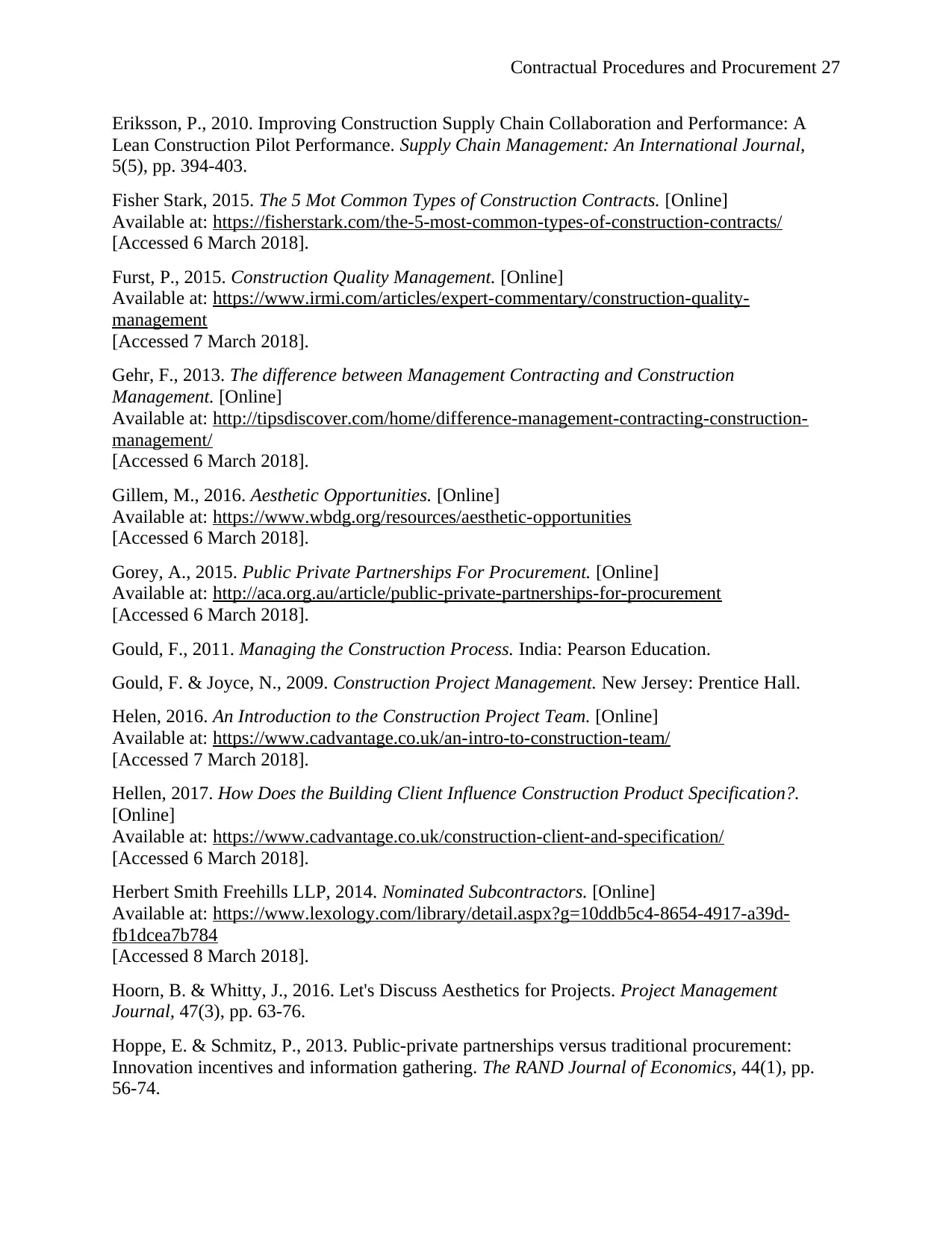
Contractual Procedures and Procurement 27
Eriksson, P., 2010. Improving Construction Supply Chain Collaboration and Performance: A
Lean Construction Pilot Performance. Supply Chain Management: An International Journal,
5(5), pp. 394-403.
Fisher Stark, 2015. The 5 Mot Common Types of Construction Contracts. [Online]
Available at: https://fisherstark.com/the-5-most-common-types-of-construction-contracts/
[Accessed 6 March 2018].
Furst, P., 2015. Construction Quality Management. [Online]
Available at: https://www.irmi.com/articles/expert-commentary/construction-quality-
management
[Accessed 7 March 2018].
Gehr, F., 2013. The difference between Management Contracting and Construction
Management. [Online]
Available at: http://tipsdiscover.com/home/difference-management-contracting-construction-
management/
[Accessed 6 March 2018].
Gillem, M., 2016. Aesthetic Opportunities. [Online]
Available at: https://www.wbdg.org/resources/aesthetic-opportunities
[Accessed 6 March 2018].
Gorey, A., 2015. Public Private Partnerships For Procurement. [Online]
Available at: http://aca.org.au/article/public-private-partnerships-for-procurement
[Accessed 6 March 2018].
Gould, F., 2011. Managing the Construction Process. India: Pearson Education.
Gould, F. & Joyce, N., 2009. Construction Project Management. New Jersey: Prentice Hall.
Helen, 2016. An Introduction to the Construction Project Team. [Online]
Available at: https://www.cadvantage.co.uk/an-intro-to-construction-team/
[Accessed 7 March 2018].
Hellen, 2017. How Does the Building Client Influence Construction Product Specification?.
[Online]
Available at: https://www.cadvantage.co.uk/construction-client-and-specification/
[Accessed 6 March 2018].
Herbert Smith Freehills LLP, 2014. Nominated Subcontractors. [Online]
Available at: https://www.lexology.com/library/detail.aspx?g=10ddb5c4-8654-4917-a39d-
fb1dcea7b784
[Accessed 8 March 2018].
Hoorn, B. & Whitty, J., 2016. Let's Discuss Aesthetics for Projects. Project Management
Journal, 47(3), pp. 63-76.
Hoppe, E. & Schmitz, P., 2013. Public-private partnerships versus traditional procurement:
Innovation incentives and information gathering. The RAND Journal of Economics, 44(1), pp.
56-74.
Eriksson, P., 2010. Improving Construction Supply Chain Collaboration and Performance: A
Lean Construction Pilot Performance. Supply Chain Management: An International Journal,
5(5), pp. 394-403.
Fisher Stark, 2015. The 5 Mot Common Types of Construction Contracts. [Online]
Available at: https://fisherstark.com/the-5-most-common-types-of-construction-contracts/
[Accessed 6 March 2018].
Furst, P., 2015. Construction Quality Management. [Online]
Available at: https://www.irmi.com/articles/expert-commentary/construction-quality-
management
[Accessed 7 March 2018].
Gehr, F., 2013. The difference between Management Contracting and Construction
Management. [Online]
Available at: http://tipsdiscover.com/home/difference-management-contracting-construction-
management/
[Accessed 6 March 2018].
Gillem, M., 2016. Aesthetic Opportunities. [Online]
Available at: https://www.wbdg.org/resources/aesthetic-opportunities
[Accessed 6 March 2018].
Gorey, A., 2015. Public Private Partnerships For Procurement. [Online]
Available at: http://aca.org.au/article/public-private-partnerships-for-procurement
[Accessed 6 March 2018].
Gould, F., 2011. Managing the Construction Process. India: Pearson Education.
Gould, F. & Joyce, N., 2009. Construction Project Management. New Jersey: Prentice Hall.
Helen, 2016. An Introduction to the Construction Project Team. [Online]
Available at: https://www.cadvantage.co.uk/an-intro-to-construction-team/
[Accessed 7 March 2018].
Hellen, 2017. How Does the Building Client Influence Construction Product Specification?.
[Online]
Available at: https://www.cadvantage.co.uk/construction-client-and-specification/
[Accessed 6 March 2018].
Herbert Smith Freehills LLP, 2014. Nominated Subcontractors. [Online]
Available at: https://www.lexology.com/library/detail.aspx?g=10ddb5c4-8654-4917-a39d-
fb1dcea7b784
[Accessed 8 March 2018].
Hoorn, B. & Whitty, J., 2016. Let's Discuss Aesthetics for Projects. Project Management
Journal, 47(3), pp. 63-76.
Hoppe, E. & Schmitz, P., 2013. Public-private partnerships versus traditional procurement:
Innovation incentives and information gathering. The RAND Journal of Economics, 44(1), pp.
56-74.
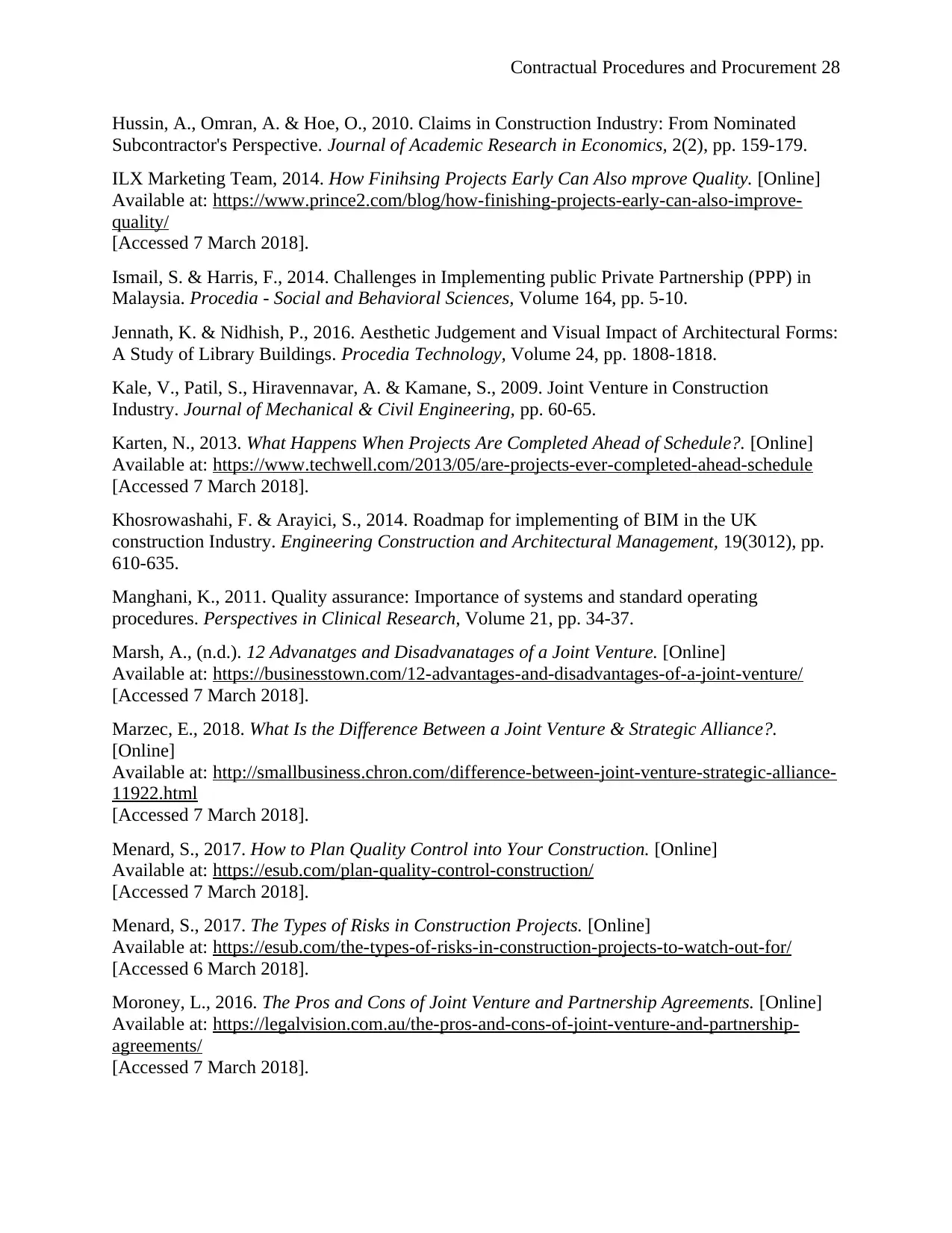
Contractual Procedures and Procurement 28
Hussin, A., Omran, A. & Hoe, O., 2010. Claims in Construction Industry: From Nominated
Subcontractor's Perspective. Journal of Academic Research in Economics, 2(2), pp. 159-179.
ILX Marketing Team, 2014. How Finihsing Projects Early Can Also mprove Quality. [Online]
Available at: https://www.prince2.com/blog/how-finishing-projects-early-can-also-improve-
quality/
[Accessed 7 March 2018].
Ismail, S. & Harris, F., 2014. Challenges in Implementing public Private Partnership (PPP) in
Malaysia. Procedia - Social and Behavioral Sciences, Volume 164, pp. 5-10.
Jennath, K. & Nidhish, P., 2016. Aesthetic Judgement and Visual Impact of Architectural Forms:
A Study of Library Buildings. Procedia Technology, Volume 24, pp. 1808-1818.
Kale, V., Patil, S., Hiravennavar, A. & Kamane, S., 2009. Joint Venture in Construction
Industry. Journal of Mechanical & Civil Engineering, pp. 60-65.
Karten, N., 2013. What Happens When Projects Are Completed Ahead of Schedule?. [Online]
Available at: https://www.techwell.com/2013/05/are-projects-ever-completed-ahead-schedule
[Accessed 7 March 2018].
Khosrowashahi, F. & Arayici, S., 2014. Roadmap for implementing of BIM in the UK
construction Industry. Engineering Construction and Architectural Management, 19(3012), pp.
610-635.
Manghani, K., 2011. Quality assurance: Importance of systems and standard operating
procedures. Perspectives in Clinical Research, Volume 21, pp. 34-37.
Marsh, A., (n.d.). 12 Advanatges and Disadvanatages of a Joint Venture. [Online]
Available at: https://businesstown.com/12-advantages-and-disadvantages-of-a-joint-venture/
[Accessed 7 March 2018].
Marzec, E., 2018. What Is the Difference Between a Joint Venture & Strategic Alliance?.
[Online]
Available at: http://smallbusiness.chron.com/difference-between-joint-venture-strategic-alliance-
11922.html
[Accessed 7 March 2018].
Menard, S., 2017. How to Plan Quality Control into Your Construction. [Online]
Available at: https://esub.com/plan-quality-control-construction/
[Accessed 7 March 2018].
Menard, S., 2017. The Types of Risks in Construction Projects. [Online]
Available at: https://esub.com/the-types-of-risks-in-construction-projects-to-watch-out-for/
[Accessed 6 March 2018].
Moroney, L., 2016. The Pros and Cons of Joint Venture and Partnership Agreements. [Online]
Available at: https://legalvision.com.au/the-pros-and-cons-of-joint-venture-and-partnership-
agreements/
[Accessed 7 March 2018].
Hussin, A., Omran, A. & Hoe, O., 2010. Claims in Construction Industry: From Nominated
Subcontractor's Perspective. Journal of Academic Research in Economics, 2(2), pp. 159-179.
ILX Marketing Team, 2014. How Finihsing Projects Early Can Also mprove Quality. [Online]
Available at: https://www.prince2.com/blog/how-finishing-projects-early-can-also-improve-
quality/
[Accessed 7 March 2018].
Ismail, S. & Harris, F., 2014. Challenges in Implementing public Private Partnership (PPP) in
Malaysia. Procedia - Social and Behavioral Sciences, Volume 164, pp. 5-10.
Jennath, K. & Nidhish, P., 2016. Aesthetic Judgement and Visual Impact of Architectural Forms:
A Study of Library Buildings. Procedia Technology, Volume 24, pp. 1808-1818.
Kale, V., Patil, S., Hiravennavar, A. & Kamane, S., 2009. Joint Venture in Construction
Industry. Journal of Mechanical & Civil Engineering, pp. 60-65.
Karten, N., 2013. What Happens When Projects Are Completed Ahead of Schedule?. [Online]
Available at: https://www.techwell.com/2013/05/are-projects-ever-completed-ahead-schedule
[Accessed 7 March 2018].
Khosrowashahi, F. & Arayici, S., 2014. Roadmap for implementing of BIM in the UK
construction Industry. Engineering Construction and Architectural Management, 19(3012), pp.
610-635.
Manghani, K., 2011. Quality assurance: Importance of systems and standard operating
procedures. Perspectives in Clinical Research, Volume 21, pp. 34-37.
Marsh, A., (n.d.). 12 Advanatges and Disadvanatages of a Joint Venture. [Online]
Available at: https://businesstown.com/12-advantages-and-disadvantages-of-a-joint-venture/
[Accessed 7 March 2018].
Marzec, E., 2018. What Is the Difference Between a Joint Venture & Strategic Alliance?.
[Online]
Available at: http://smallbusiness.chron.com/difference-between-joint-venture-strategic-alliance-
11922.html
[Accessed 7 March 2018].
Menard, S., 2017. How to Plan Quality Control into Your Construction. [Online]
Available at: https://esub.com/plan-quality-control-construction/
[Accessed 7 March 2018].
Menard, S., 2017. The Types of Risks in Construction Projects. [Online]
Available at: https://esub.com/the-types-of-risks-in-construction-projects-to-watch-out-for/
[Accessed 6 March 2018].
Moroney, L., 2016. The Pros and Cons of Joint Venture and Partnership Agreements. [Online]
Available at: https://legalvision.com.au/the-pros-and-cons-of-joint-venture-and-partnership-
agreements/
[Accessed 7 March 2018].
Secure Best Marks with AI Grader
Need help grading? Try our AI Grader for instant feedback on your assignments.
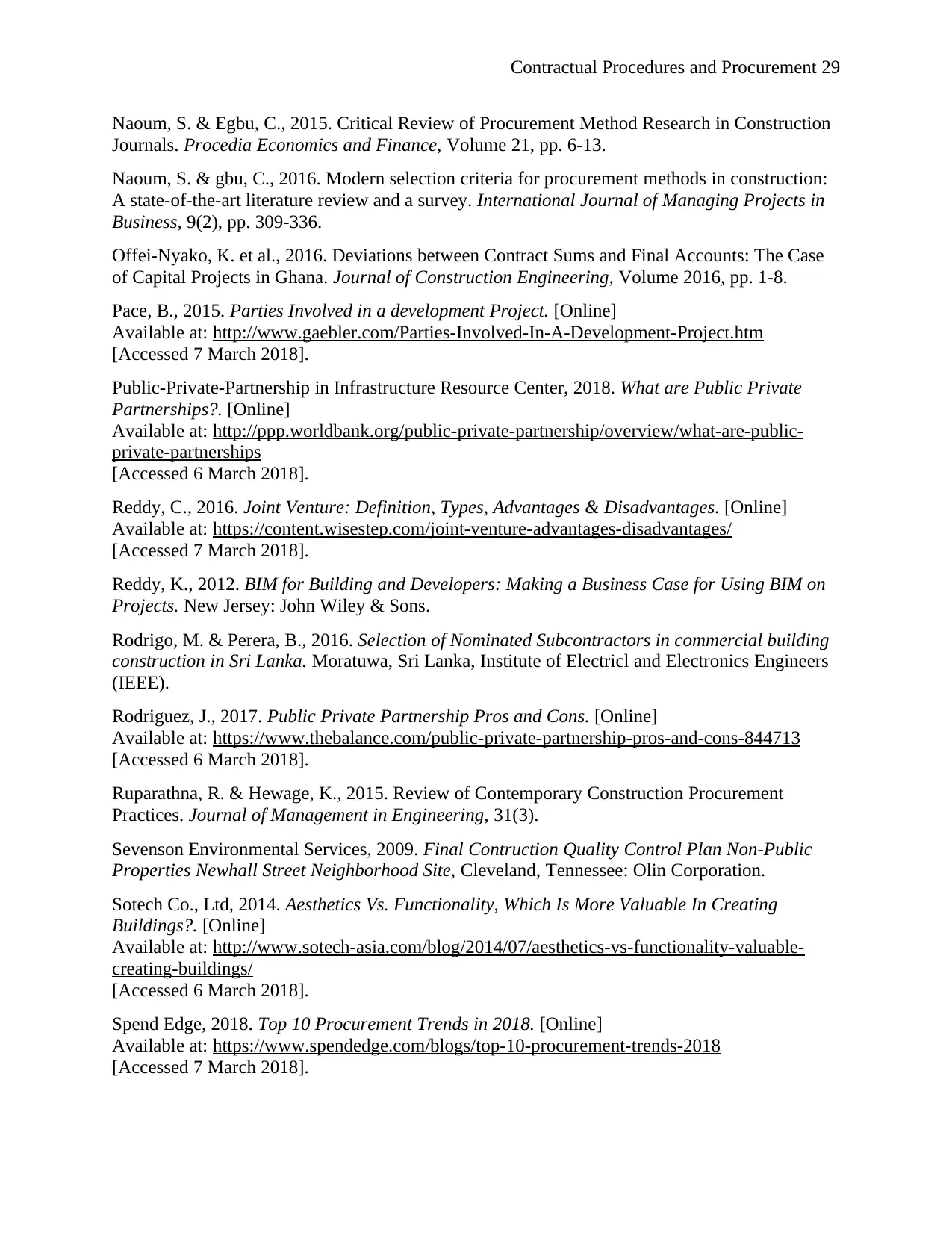
Contractual Procedures and Procurement 29
Naoum, S. & Egbu, C., 2015. Critical Review of Procurement Method Research in Construction
Journals. Procedia Economics and Finance, Volume 21, pp. 6-13.
Naoum, S. & gbu, C., 2016. Modern selection criteria for procurement methods in construction:
A state-of-the-art literature review and a survey. International Journal of Managing Projects in
Business, 9(2), pp. 309-336.
Offei-Nyako, K. et al., 2016. Deviations between Contract Sums and Final Accounts: The Case
of Capital Projects in Ghana. Journal of Construction Engineering, Volume 2016, pp. 1-8.
Pace, B., 2015. Parties Involved in a development Project. [Online]
Available at: http://www.gaebler.com/Parties-Involved-In-A-Development-Project.htm
[Accessed 7 March 2018].
Public-Private-Partnership in Infrastructure Resource Center, 2018. What are Public Private
Partnerships?. [Online]
Available at: http://ppp.worldbank.org/public-private-partnership/overview/what-are-public-
private-partnerships
[Accessed 6 March 2018].
Reddy, C., 2016. Joint Venture: Definition, Types, Advantages & Disadvantages. [Online]
Available at: https://content.wisestep.com/joint-venture-advantages-disadvantages/
[Accessed 7 March 2018].
Reddy, K., 2012. BIM for Building and Developers: Making a Business Case for Using BIM on
Projects. New Jersey: John Wiley & Sons.
Rodrigo, M. & Perera, B., 2016. Selection of Nominated Subcontractors in commercial building
construction in Sri Lanka. Moratuwa, Sri Lanka, Institute of Electricl and Electronics Engineers
(IEEE).
Rodriguez, J., 2017. Public Private Partnership Pros and Cons. [Online]
Available at: https://www.thebalance.com/public-private-partnership-pros-and-cons-844713
[Accessed 6 March 2018].
Ruparathna, R. & Hewage, K., 2015. Review of Contemporary Construction Procurement
Practices. Journal of Management in Engineering, 31(3).
Sevenson Environmental Services, 2009. Final Contruction Quality Control Plan Non-Public
Properties Newhall Street Neighborhood Site, Cleveland, Tennessee: Olin Corporation.
Sotech Co., Ltd, 2014. Aesthetics Vs. Functionality, Which Is More Valuable In Creating
Buildings?. [Online]
Available at: http://www.sotech-asia.com/blog/2014/07/aesthetics-vs-functionality-valuable-
creating-buildings/
[Accessed 6 March 2018].
Spend Edge, 2018. Top 10 Procurement Trends in 2018. [Online]
Available at: https://www.spendedge.com/blogs/top-10-procurement-trends-2018
[Accessed 7 March 2018].
Naoum, S. & Egbu, C., 2015. Critical Review of Procurement Method Research in Construction
Journals. Procedia Economics and Finance, Volume 21, pp. 6-13.
Naoum, S. & gbu, C., 2016. Modern selection criteria for procurement methods in construction:
A state-of-the-art literature review and a survey. International Journal of Managing Projects in
Business, 9(2), pp. 309-336.
Offei-Nyako, K. et al., 2016. Deviations between Contract Sums and Final Accounts: The Case
of Capital Projects in Ghana. Journal of Construction Engineering, Volume 2016, pp. 1-8.
Pace, B., 2015. Parties Involved in a development Project. [Online]
Available at: http://www.gaebler.com/Parties-Involved-In-A-Development-Project.htm
[Accessed 7 March 2018].
Public-Private-Partnership in Infrastructure Resource Center, 2018. What are Public Private
Partnerships?. [Online]
Available at: http://ppp.worldbank.org/public-private-partnership/overview/what-are-public-
private-partnerships
[Accessed 6 March 2018].
Reddy, C., 2016. Joint Venture: Definition, Types, Advantages & Disadvantages. [Online]
Available at: https://content.wisestep.com/joint-venture-advantages-disadvantages/
[Accessed 7 March 2018].
Reddy, K., 2012. BIM for Building and Developers: Making a Business Case for Using BIM on
Projects. New Jersey: John Wiley & Sons.
Rodrigo, M. & Perera, B., 2016. Selection of Nominated Subcontractors in commercial building
construction in Sri Lanka. Moratuwa, Sri Lanka, Institute of Electricl and Electronics Engineers
(IEEE).
Rodriguez, J., 2017. Public Private Partnership Pros and Cons. [Online]
Available at: https://www.thebalance.com/public-private-partnership-pros-and-cons-844713
[Accessed 6 March 2018].
Ruparathna, R. & Hewage, K., 2015. Review of Contemporary Construction Procurement
Practices. Journal of Management in Engineering, 31(3).
Sevenson Environmental Services, 2009. Final Contruction Quality Control Plan Non-Public
Properties Newhall Street Neighborhood Site, Cleveland, Tennessee: Olin Corporation.
Sotech Co., Ltd, 2014. Aesthetics Vs. Functionality, Which Is More Valuable In Creating
Buildings?. [Online]
Available at: http://www.sotech-asia.com/blog/2014/07/aesthetics-vs-functionality-valuable-
creating-buildings/
[Accessed 6 March 2018].
Spend Edge, 2018. Top 10 Procurement Trends in 2018. [Online]
Available at: https://www.spendedge.com/blogs/top-10-procurement-trends-2018
[Accessed 7 March 2018].
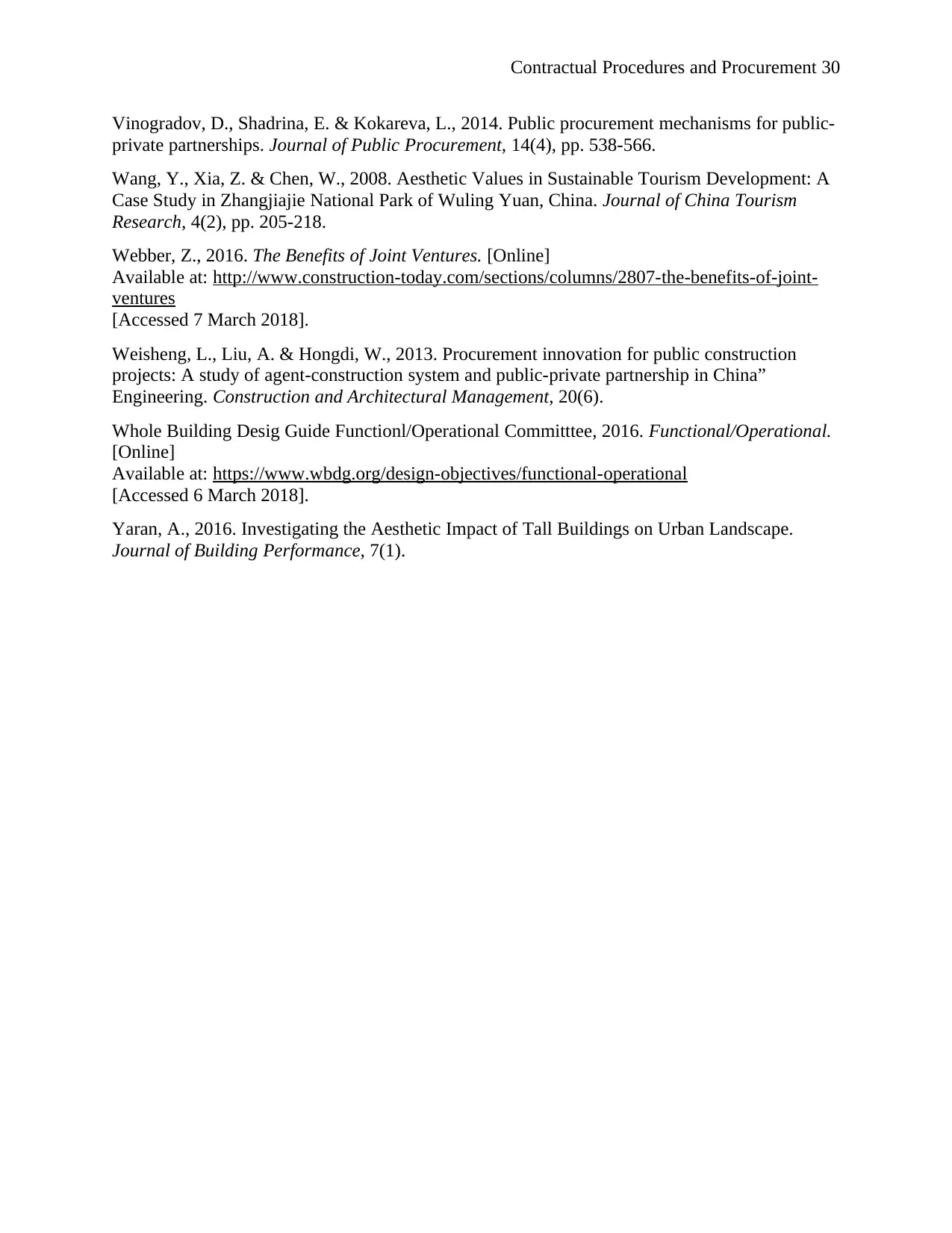
Contractual Procedures and Procurement 30
Vinogradov, D., Shadrina, E. & Kokareva, L., 2014. Public procurement mechanisms for public-
private partnerships. Journal of Public Procurement, 14(4), pp. 538-566.
Wang, Y., Xia, Z. & Chen, W., 2008. Aesthetic Values in Sustainable Tourism Development: A
Case Study in Zhangjiajie National Park of Wuling Yuan, China. Journal of China Tourism
Research, 4(2), pp. 205-218.
Webber, Z., 2016. The Benefits of Joint Ventures. [Online]
Available at: http://www.construction-today.com/sections/columns/2807-the-benefits-of-joint-
ventures
[Accessed 7 March 2018].
Weisheng, L., Liu, A. & Hongdi, W., 2013. Procurement innovation for public construction
projects: A study of agent-construction system and public-private partnership in China”
Engineering. Construction and Architectural Management, 20(6).
Whole Building Desig Guide Functionl/Operational Committtee, 2016. Functional/Operational.
[Online]
Available at: https://www.wbdg.org/design-objectives/functional-operational
[Accessed 6 March 2018].
Yaran, A., 2016. Investigating the Aesthetic Impact of Tall Buildings on Urban Landscape.
Journal of Building Performance, 7(1).
Vinogradov, D., Shadrina, E. & Kokareva, L., 2014. Public procurement mechanisms for public-
private partnerships. Journal of Public Procurement, 14(4), pp. 538-566.
Wang, Y., Xia, Z. & Chen, W., 2008. Aesthetic Values in Sustainable Tourism Development: A
Case Study in Zhangjiajie National Park of Wuling Yuan, China. Journal of China Tourism
Research, 4(2), pp. 205-218.
Webber, Z., 2016. The Benefits of Joint Ventures. [Online]
Available at: http://www.construction-today.com/sections/columns/2807-the-benefits-of-joint-
ventures
[Accessed 7 March 2018].
Weisheng, L., Liu, A. & Hongdi, W., 2013. Procurement innovation for public construction
projects: A study of agent-construction system and public-private partnership in China”
Engineering. Construction and Architectural Management, 20(6).
Whole Building Desig Guide Functionl/Operational Committtee, 2016. Functional/Operational.
[Online]
Available at: https://www.wbdg.org/design-objectives/functional-operational
[Accessed 6 March 2018].
Yaran, A., 2016. Investigating the Aesthetic Impact of Tall Buildings on Urban Landscape.
Journal of Building Performance, 7(1).
1 out of 30
Related Documents

Your All-in-One AI-Powered Toolkit for Academic Success.
+13062052269
info@desklib.com
Available 24*7 on WhatsApp / Email
Unlock your academic potential
© 2024 | Zucol Services PVT LTD | All rights reserved.