BSB51915 - Sustainability and Continuous Improvement Analysis Report
VerifiedAdded on 2022/12/29
|12
|2703
|71
Report
AI Summary
This report delves into the critical relationship between sustainability and continuous improvement within the Australian retail sector, using Coles Supermarkets as a prime example. It explores the competitive nature of the industry and how companies like Coles leverage continuous improvement to gain an edge, particularly in environmental sustainability. The report defines continuous improvement, its lifecycle, and various models and theories, including Kaizen, Total Quality Management, PDCA cycle, Lean Theory, Six Sigma, and the SMAIC model. It proposes the application of the SMAIC model to Coles, focusing on waste reduction and plastic mitigation. The report also outlines continuous improvement strategies, Key Performance Indicators (KPIs), implementation methods, and communication plans necessary for success. Finally, it emphasizes the importance of training, resources, feedback, and evaluation in fostering a culture of continuous improvement, ultimately leading to sustainable operations and competitive advantages within the retail landscape.
Contribute Materials
Your contribution can guide someone’s learning journey. Share your
documents today.
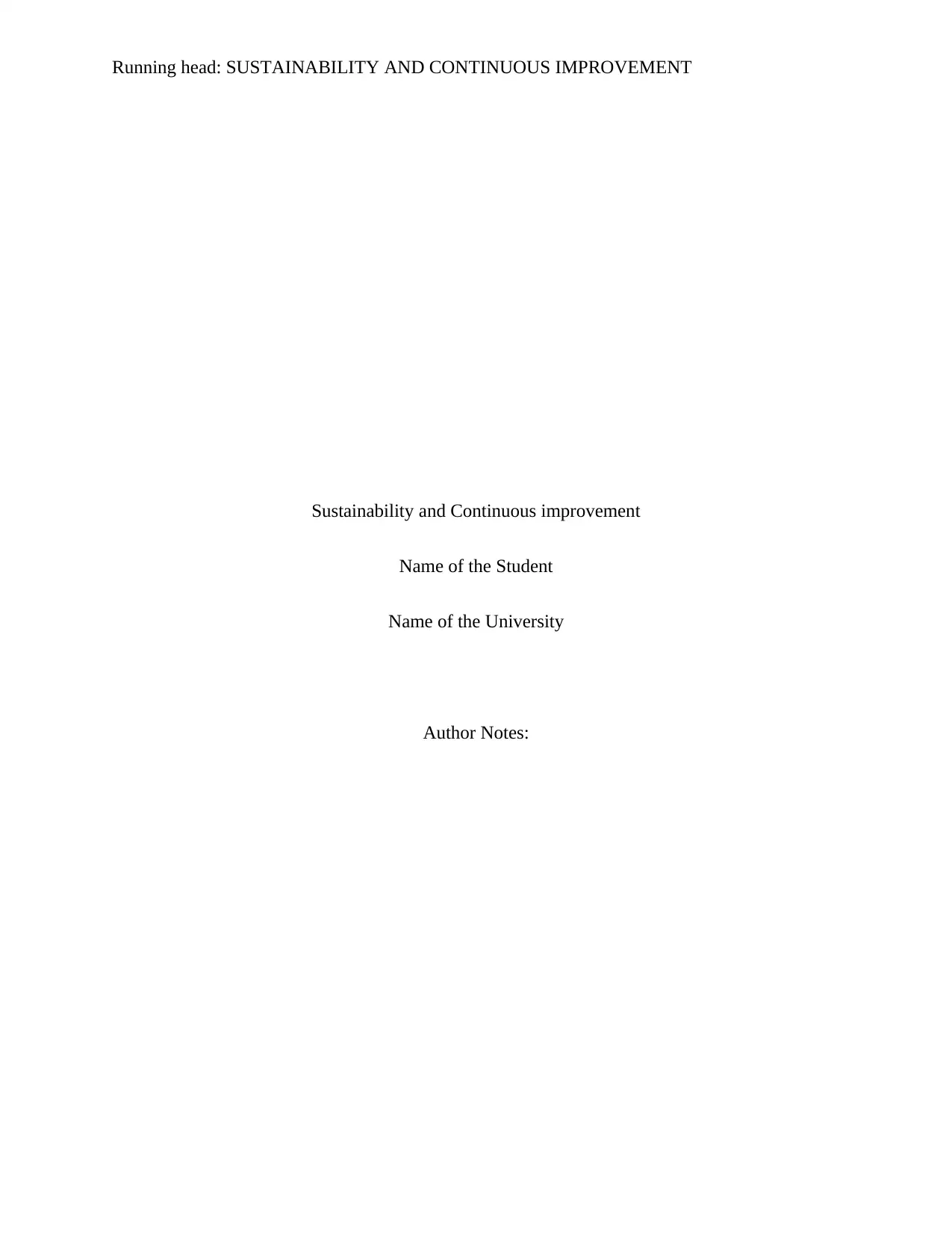
Running head: SUSTAINABILITY AND CONTINUOUS IMPROVEMENT
Sustainability and Continuous improvement
Name of the Student
Name of the University
Author Notes:
Sustainability and Continuous improvement
Name of the Student
Name of the University
Author Notes:
Secure Best Marks with AI Grader
Need help grading? Try our AI Grader for instant feedback on your assignments.
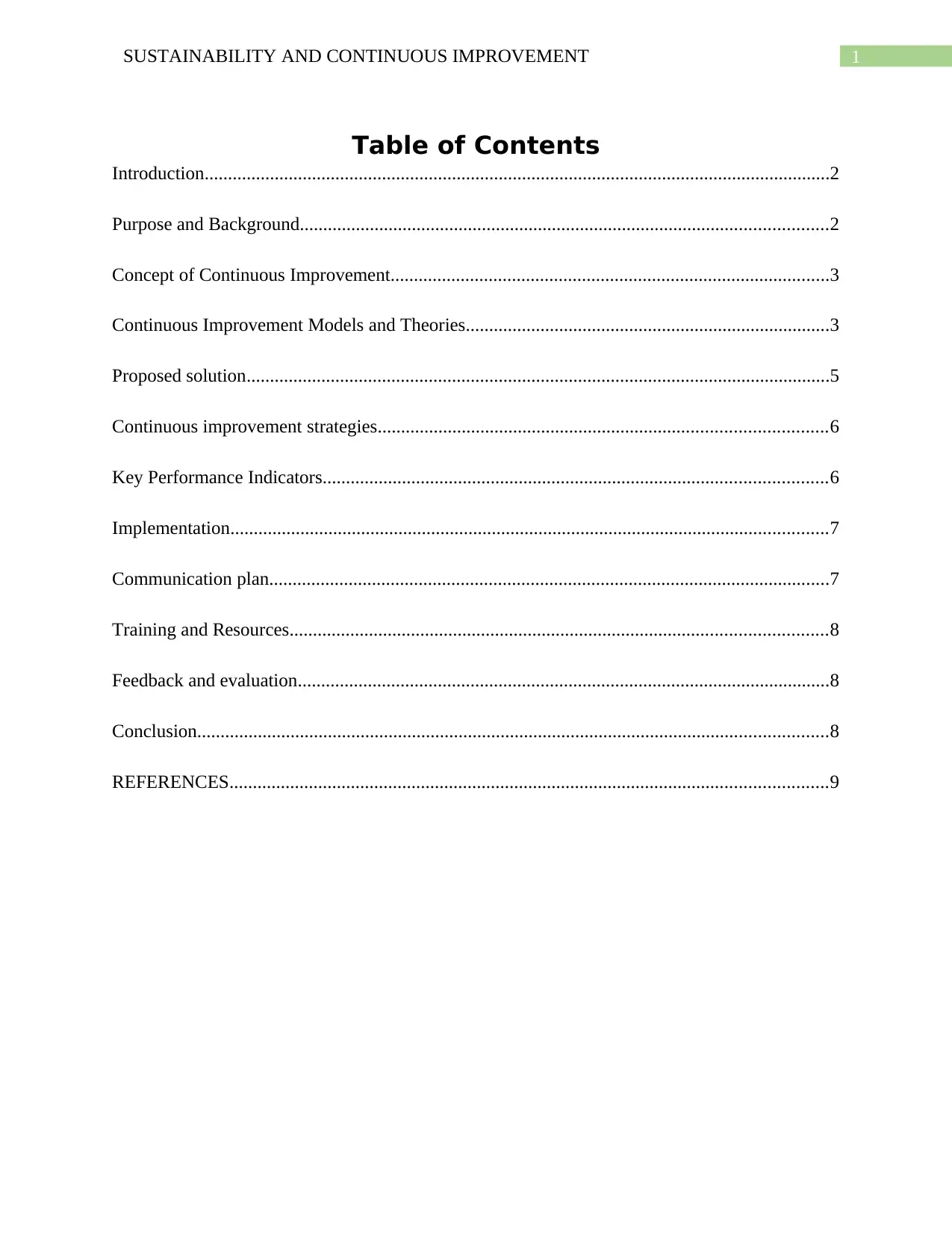
1SUSTAINABILITY AND CONTINUOUS IMPROVEMENT
Table of Contents
Introduction......................................................................................................................................2
Purpose and Background.................................................................................................................2
Concept of Continuous Improvement..............................................................................................3
Continuous Improvement Models and Theories..............................................................................3
Proposed solution.............................................................................................................................5
Continuous improvement strategies................................................................................................6
Key Performance Indicators............................................................................................................6
Implementation................................................................................................................................7
Communication plan........................................................................................................................7
Training and Resources...................................................................................................................8
Feedback and evaluation..................................................................................................................8
Conclusion.......................................................................................................................................8
REFERENCES................................................................................................................................9
Table of Contents
Introduction......................................................................................................................................2
Purpose and Background.................................................................................................................2
Concept of Continuous Improvement..............................................................................................3
Continuous Improvement Models and Theories..............................................................................3
Proposed solution.............................................................................................................................5
Continuous improvement strategies................................................................................................6
Key Performance Indicators............................................................................................................6
Implementation................................................................................................................................7
Communication plan........................................................................................................................7
Training and Resources...................................................................................................................8
Feedback and evaluation..................................................................................................................8
Conclusion.......................................................................................................................................8
REFERENCES................................................................................................................................9
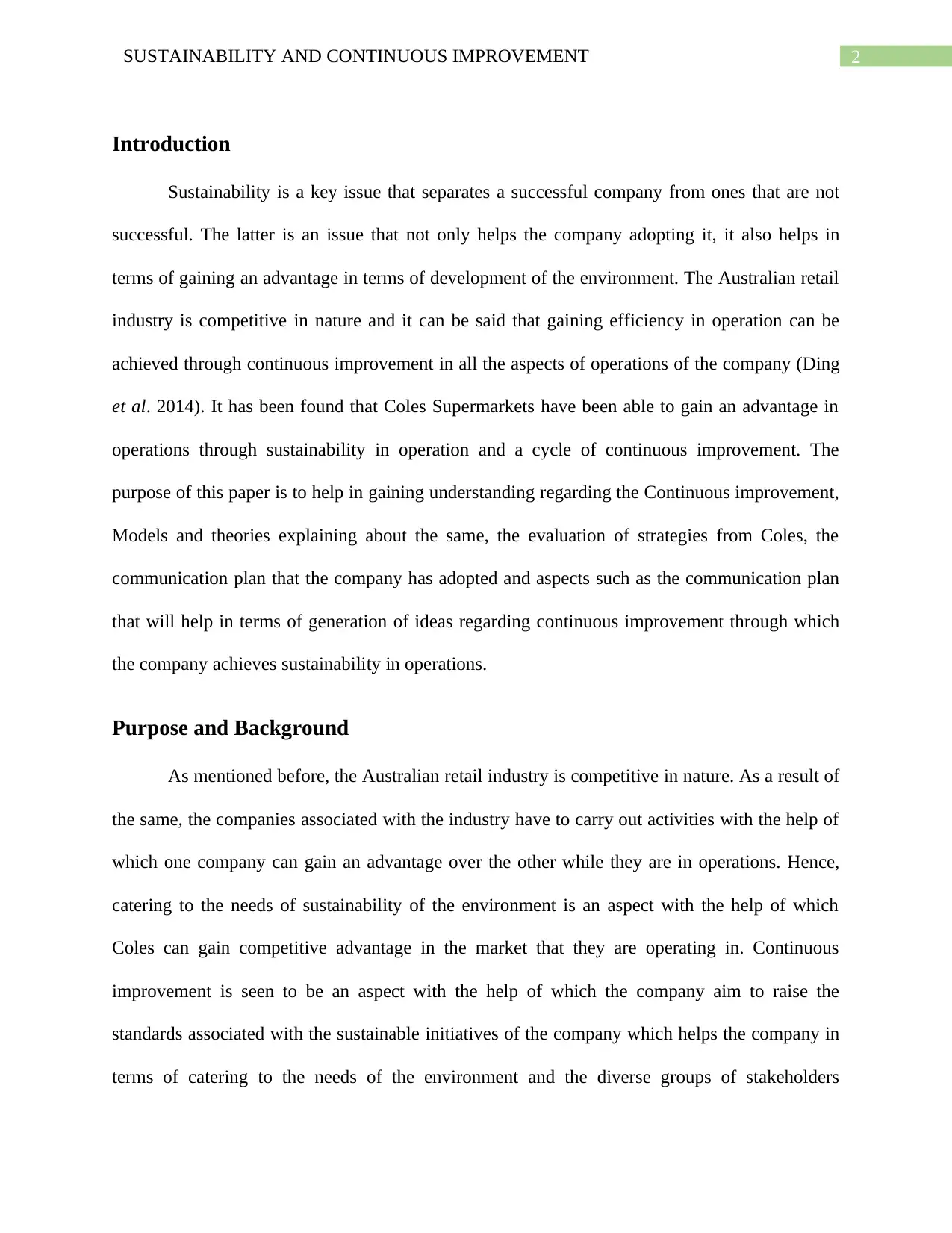
2SUSTAINABILITY AND CONTINUOUS IMPROVEMENT
Introduction
Sustainability is a key issue that separates a successful company from ones that are not
successful. The latter is an issue that not only helps the company adopting it, it also helps in
terms of gaining an advantage in terms of development of the environment. The Australian retail
industry is competitive in nature and it can be said that gaining efficiency in operation can be
achieved through continuous improvement in all the aspects of operations of the company (Ding
et al. 2014). It has been found that Coles Supermarkets have been able to gain an advantage in
operations through sustainability in operation and a cycle of continuous improvement. The
purpose of this paper is to help in gaining understanding regarding the Continuous improvement,
Models and theories explaining about the same, the evaluation of strategies from Coles, the
communication plan that the company has adopted and aspects such as the communication plan
that will help in terms of generation of ideas regarding continuous improvement through which
the company achieves sustainability in operations.
Purpose and Background
As mentioned before, the Australian retail industry is competitive in nature. As a result of
the same, the companies associated with the industry have to carry out activities with the help of
which one company can gain an advantage over the other while they are in operations. Hence,
catering to the needs of sustainability of the environment is an aspect with the help of which
Coles can gain competitive advantage in the market that they are operating in. Continuous
improvement is seen to be an aspect with the help of which the company aim to raise the
standards associated with the sustainable initiatives of the company which helps the company in
terms of catering to the needs of the environment and the diverse groups of stakeholders
Introduction
Sustainability is a key issue that separates a successful company from ones that are not
successful. The latter is an issue that not only helps the company adopting it, it also helps in
terms of gaining an advantage in terms of development of the environment. The Australian retail
industry is competitive in nature and it can be said that gaining efficiency in operation can be
achieved through continuous improvement in all the aspects of operations of the company (Ding
et al. 2014). It has been found that Coles Supermarkets have been able to gain an advantage in
operations through sustainability in operation and a cycle of continuous improvement. The
purpose of this paper is to help in gaining understanding regarding the Continuous improvement,
Models and theories explaining about the same, the evaluation of strategies from Coles, the
communication plan that the company has adopted and aspects such as the communication plan
that will help in terms of generation of ideas regarding continuous improvement through which
the company achieves sustainability in operations.
Purpose and Background
As mentioned before, the Australian retail industry is competitive in nature. As a result of
the same, the companies associated with the industry have to carry out activities with the help of
which one company can gain an advantage over the other while they are in operations. Hence,
catering to the needs of sustainability of the environment is an aspect with the help of which
Coles can gain competitive advantage in the market that they are operating in. Continuous
improvement is seen to be an aspect with the help of which the company aim to raise the
standards associated with the sustainable initiatives of the company which helps the company in
terms of catering to the needs of the environment and the diverse groups of stakeholders
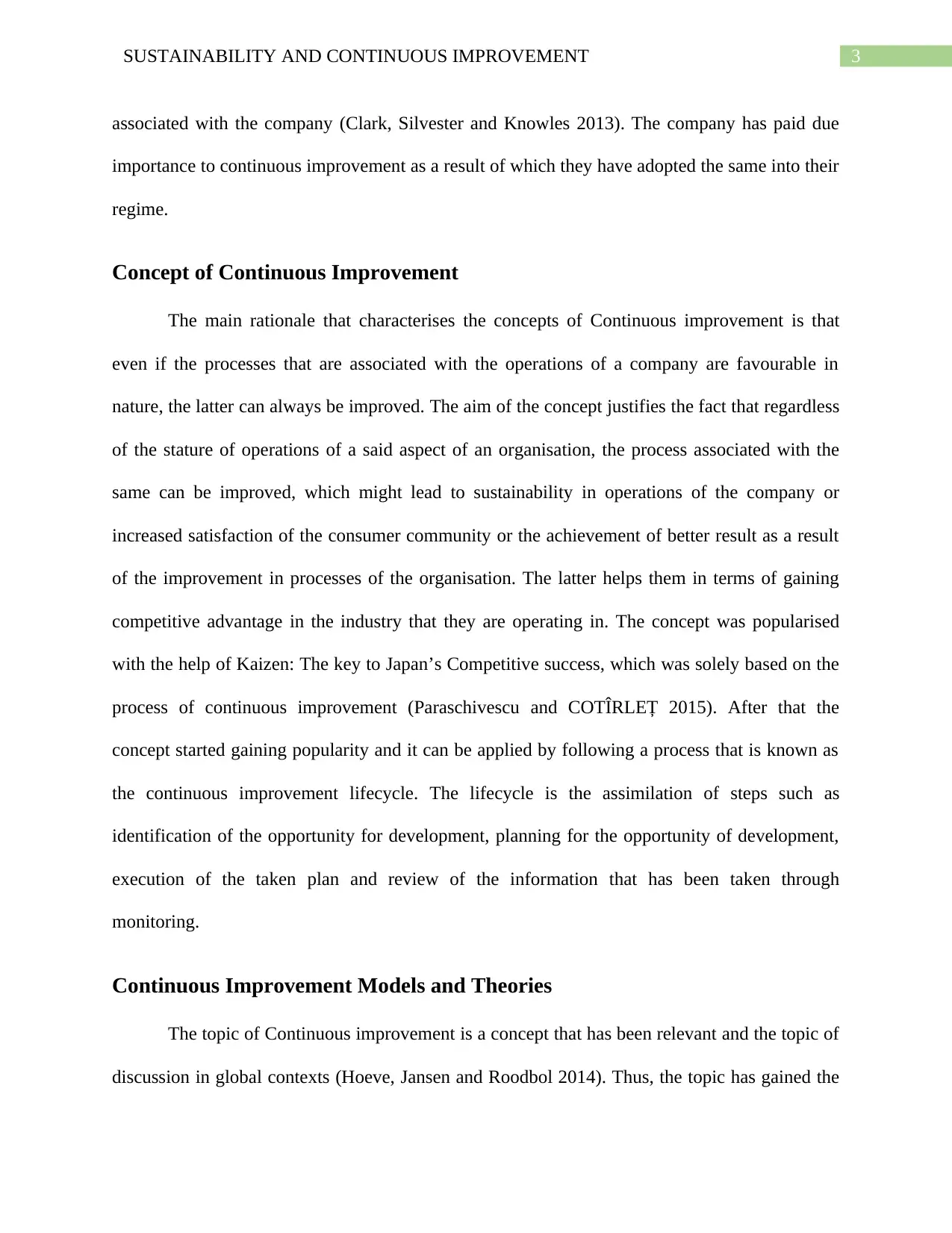
3SUSTAINABILITY AND CONTINUOUS IMPROVEMENT
associated with the company (Clark, Silvester and Knowles 2013). The company has paid due
importance to continuous improvement as a result of which they have adopted the same into their
regime.
Concept of Continuous Improvement
The main rationale that characterises the concepts of Continuous improvement is that
even if the processes that are associated with the operations of a company are favourable in
nature, the latter can always be improved. The aim of the concept justifies the fact that regardless
of the stature of operations of a said aspect of an organisation, the process associated with the
same can be improved, which might lead to sustainability in operations of the company or
increased satisfaction of the consumer community or the achievement of better result as a result
of the improvement in processes of the organisation. The latter helps them in terms of gaining
competitive advantage in the industry that they are operating in. The concept was popularised
with the help of Kaizen: The key to Japan’s Competitive success, which was solely based on the
process of continuous improvement (Paraschivescu and COTÎRLEȚ 2015). After that the
concept started gaining popularity and it can be applied by following a process that is known as
the continuous improvement lifecycle. The lifecycle is the assimilation of steps such as
identification of the opportunity for development, planning for the opportunity of development,
execution of the taken plan and review of the information that has been taken through
monitoring.
Continuous Improvement Models and Theories
The topic of Continuous improvement is a concept that has been relevant and the topic of
discussion in global contexts (Hoeve, Jansen and Roodbol 2014). Thus, the topic has gained the
associated with the company (Clark, Silvester and Knowles 2013). The company has paid due
importance to continuous improvement as a result of which they have adopted the same into their
regime.
Concept of Continuous Improvement
The main rationale that characterises the concepts of Continuous improvement is that
even if the processes that are associated with the operations of a company are favourable in
nature, the latter can always be improved. The aim of the concept justifies the fact that regardless
of the stature of operations of a said aspect of an organisation, the process associated with the
same can be improved, which might lead to sustainability in operations of the company or
increased satisfaction of the consumer community or the achievement of better result as a result
of the improvement in processes of the organisation. The latter helps them in terms of gaining
competitive advantage in the industry that they are operating in. The concept was popularised
with the help of Kaizen: The key to Japan’s Competitive success, which was solely based on the
process of continuous improvement (Paraschivescu and COTÎRLEȚ 2015). After that the
concept started gaining popularity and it can be applied by following a process that is known as
the continuous improvement lifecycle. The lifecycle is the assimilation of steps such as
identification of the opportunity for development, planning for the opportunity of development,
execution of the taken plan and review of the information that has been taken through
monitoring.
Continuous Improvement Models and Theories
The topic of Continuous improvement is a concept that has been relevant and the topic of
discussion in global contexts (Hoeve, Jansen and Roodbol 2014). Thus, the topic has gained the
Secure Best Marks with AI Grader
Need help grading? Try our AI Grader for instant feedback on your assignments.

4SUSTAINABILITY AND CONTINUOUS IMPROVEMENT
attentions of various scholars and educational institutes who have carried out extensive research
on the same. The research that has been carried out by the scholars and the institutions has
resulted in the development of concepts inside of the concepts of the process of continuous
improvement. Furthermore, there have been development of various theories catering to the
process of continuous improvement. Following are some theories and models associated to the
latter;
Kaizen Theory: The Kaizen theory is based on the importance of commitments and cooperation
that helps in terms different approaches to management of the process of change or transition in
the processes of the organisation (Coimbra 2013). According to the theory, the process of
continuous improvement is based on an idea regarding the development of positive changes that
are based on miniature ideas.
Total Quality Management: It is a perspective of management that is characterised by the
culture in an organisation where the employees and the management of the organisation
constantly seel methods through which they can improve irrespective of the current nature of
operations of the organisation (Sallis 2014).
PDCA Cycle: PDCA stands for Plan Do Check and Act. It is a model that is based on the cycle
of continuous improvement and is an iterative approach that concerns continuous improvement
of products and services, and people (Matsuo and Nakahara 2013). The latter has been able to
establish its place in the modern day management activities that is considered to be lean in
nature.
Lean Theory: This is a theory catering to continuous improvement in an organisation by the
maintaining a minimum amount of wastage in operation (Arfmann and Barbe 2014). It is a
attentions of various scholars and educational institutes who have carried out extensive research
on the same. The research that has been carried out by the scholars and the institutions has
resulted in the development of concepts inside of the concepts of the process of continuous
improvement. Furthermore, there have been development of various theories catering to the
process of continuous improvement. Following are some theories and models associated to the
latter;
Kaizen Theory: The Kaizen theory is based on the importance of commitments and cooperation
that helps in terms different approaches to management of the process of change or transition in
the processes of the organisation (Coimbra 2013). According to the theory, the process of
continuous improvement is based on an idea regarding the development of positive changes that
are based on miniature ideas.
Total Quality Management: It is a perspective of management that is characterised by the
culture in an organisation where the employees and the management of the organisation
constantly seel methods through which they can improve irrespective of the current nature of
operations of the organisation (Sallis 2014).
PDCA Cycle: PDCA stands for Plan Do Check and Act. It is a model that is based on the cycle
of continuous improvement and is an iterative approach that concerns continuous improvement
of products and services, and people (Matsuo and Nakahara 2013). The latter has been able to
establish its place in the modern day management activities that is considered to be lean in
nature.
Lean Theory: This is a theory catering to continuous improvement in an organisation by the
maintaining a minimum amount of wastage in operation (Arfmann and Barbe 2014). It is a
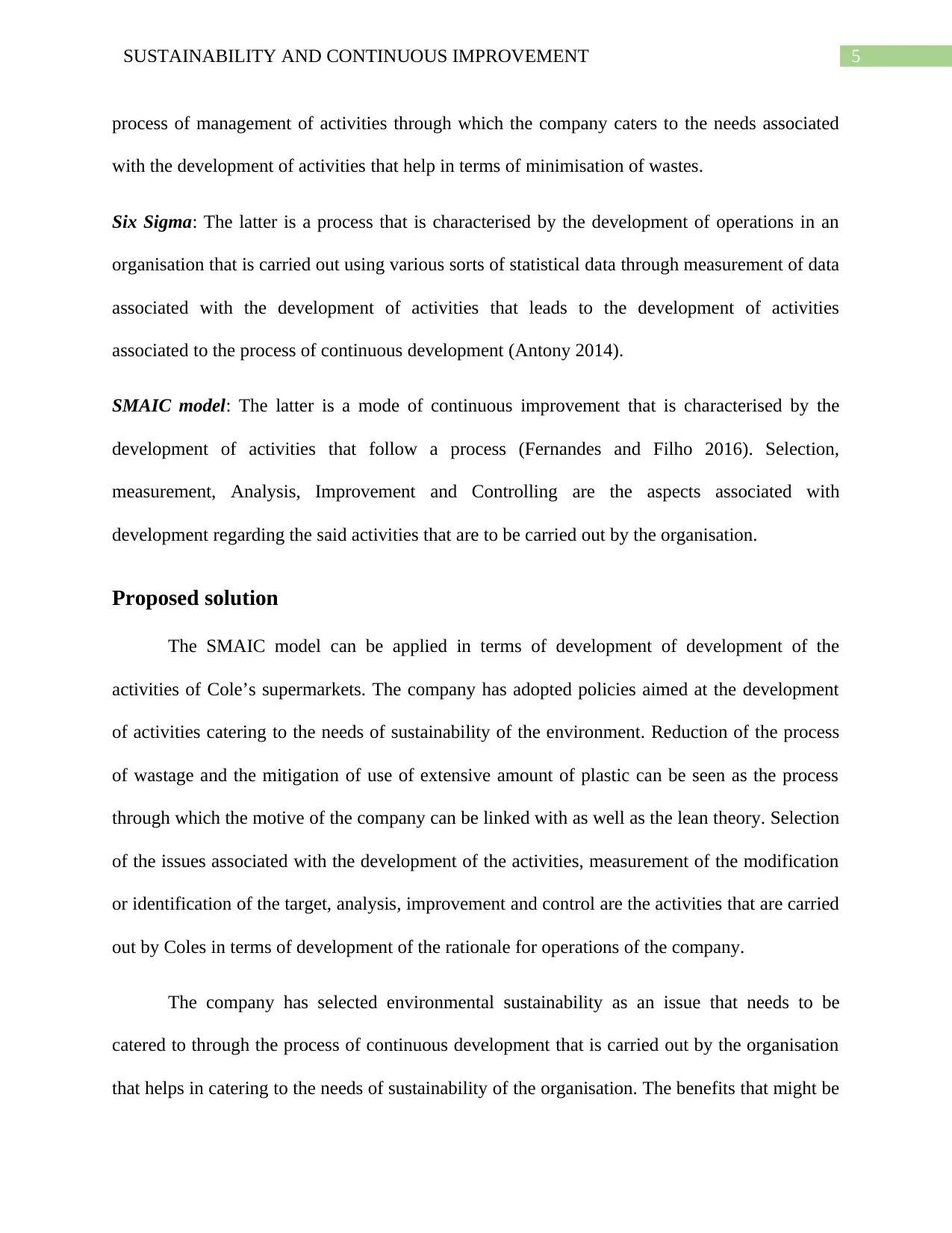
5SUSTAINABILITY AND CONTINUOUS IMPROVEMENT
process of management of activities through which the company caters to the needs associated
with the development of activities that help in terms of minimisation of wastes.
Six Sigma: The latter is a process that is characterised by the development of operations in an
organisation that is carried out using various sorts of statistical data through measurement of data
associated with the development of activities that leads to the development of activities
associated to the process of continuous development (Antony 2014).
SMAIC model: The latter is a mode of continuous improvement that is characterised by the
development of activities that follow a process (Fernandes and Filho 2016). Selection,
measurement, Analysis, Improvement and Controlling are the aspects associated with
development regarding the said activities that are to be carried out by the organisation.
Proposed solution
The SMAIC model can be applied in terms of development of development of the
activities of Cole’s supermarkets. The company has adopted policies aimed at the development
of activities catering to the needs of sustainability of the environment. Reduction of the process
of wastage and the mitigation of use of extensive amount of plastic can be seen as the process
through which the motive of the company can be linked with as well as the lean theory. Selection
of the issues associated with the development of the activities, measurement of the modification
or identification of the target, analysis, improvement and control are the activities that are carried
out by Coles in terms of development of the rationale for operations of the company.
The company has selected environmental sustainability as an issue that needs to be
catered to through the process of continuous development that is carried out by the organisation
that helps in catering to the needs of sustainability of the organisation. The benefits that might be
process of management of activities through which the company caters to the needs associated
with the development of activities that help in terms of minimisation of wastes.
Six Sigma: The latter is a process that is characterised by the development of operations in an
organisation that is carried out using various sorts of statistical data through measurement of data
associated with the development of activities that leads to the development of activities
associated to the process of continuous development (Antony 2014).
SMAIC model: The latter is a mode of continuous improvement that is characterised by the
development of activities that follow a process (Fernandes and Filho 2016). Selection,
measurement, Analysis, Improvement and Controlling are the aspects associated with
development regarding the said activities that are to be carried out by the organisation.
Proposed solution
The SMAIC model can be applied in terms of development of development of the
activities of Cole’s supermarkets. The company has adopted policies aimed at the development
of activities catering to the needs of sustainability of the environment. Reduction of the process
of wastage and the mitigation of use of extensive amount of plastic can be seen as the process
through which the motive of the company can be linked with as well as the lean theory. Selection
of the issues associated with the development of the activities, measurement of the modification
or identification of the target, analysis, improvement and control are the activities that are carried
out by Coles in terms of development of the rationale for operations of the company.
The company has selected environmental sustainability as an issue that needs to be
catered to through the process of continuous development that is carried out by the organisation
that helps in catering to the needs of sustainability of the organisation. The benefits that might be
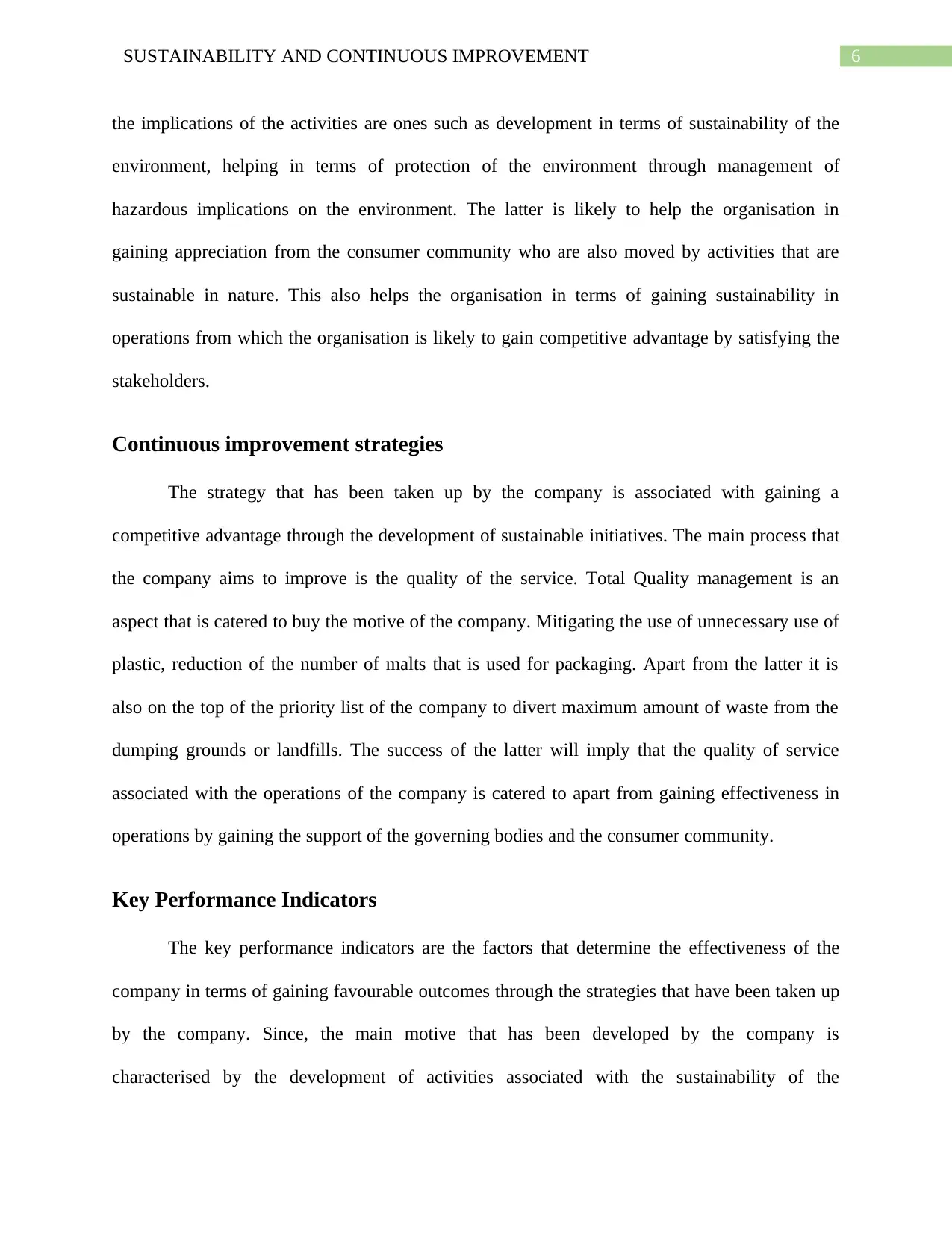
6SUSTAINABILITY AND CONTINUOUS IMPROVEMENT
the implications of the activities are ones such as development in terms of sustainability of the
environment, helping in terms of protection of the environment through management of
hazardous implications on the environment. The latter is likely to help the organisation in
gaining appreciation from the consumer community who are also moved by activities that are
sustainable in nature. This also helps the organisation in terms of gaining sustainability in
operations from which the organisation is likely to gain competitive advantage by satisfying the
stakeholders.
Continuous improvement strategies
The strategy that has been taken up by the company is associated with gaining a
competitive advantage through the development of sustainable initiatives. The main process that
the company aims to improve is the quality of the service. Total Quality management is an
aspect that is catered to buy the motive of the company. Mitigating the use of unnecessary use of
plastic, reduction of the number of malts that is used for packaging. Apart from the latter it is
also on the top of the priority list of the company to divert maximum amount of waste from the
dumping grounds or landfills. The success of the latter will imply that the quality of service
associated with the operations of the company is catered to apart from gaining effectiveness in
operations by gaining the support of the governing bodies and the consumer community.
Key Performance Indicators
The key performance indicators are the factors that determine the effectiveness of the
company in terms of gaining favourable outcomes through the strategies that have been taken up
by the company. Since, the main motive that has been developed by the company is
characterised by the development of activities associated with the sustainability of the
the implications of the activities are ones such as development in terms of sustainability of the
environment, helping in terms of protection of the environment through management of
hazardous implications on the environment. The latter is likely to help the organisation in
gaining appreciation from the consumer community who are also moved by activities that are
sustainable in nature. This also helps the organisation in terms of gaining sustainability in
operations from which the organisation is likely to gain competitive advantage by satisfying the
stakeholders.
Continuous improvement strategies
The strategy that has been taken up by the company is associated with gaining a
competitive advantage through the development of sustainable initiatives. The main process that
the company aims to improve is the quality of the service. Total Quality management is an
aspect that is catered to buy the motive of the company. Mitigating the use of unnecessary use of
plastic, reduction of the number of malts that is used for packaging. Apart from the latter it is
also on the top of the priority list of the company to divert maximum amount of waste from the
dumping grounds or landfills. The success of the latter will imply that the quality of service
associated with the operations of the company is catered to apart from gaining effectiveness in
operations by gaining the support of the governing bodies and the consumer community.
Key Performance Indicators
The key performance indicators are the factors that determine the effectiveness of the
company in terms of gaining favourable outcomes through the strategies that have been taken up
by the company. Since, the main motive that has been developed by the company is
characterised by the development of activities associated with the sustainability of the
Paraphrase This Document
Need a fresh take? Get an instant paraphrase of this document with our AI Paraphraser
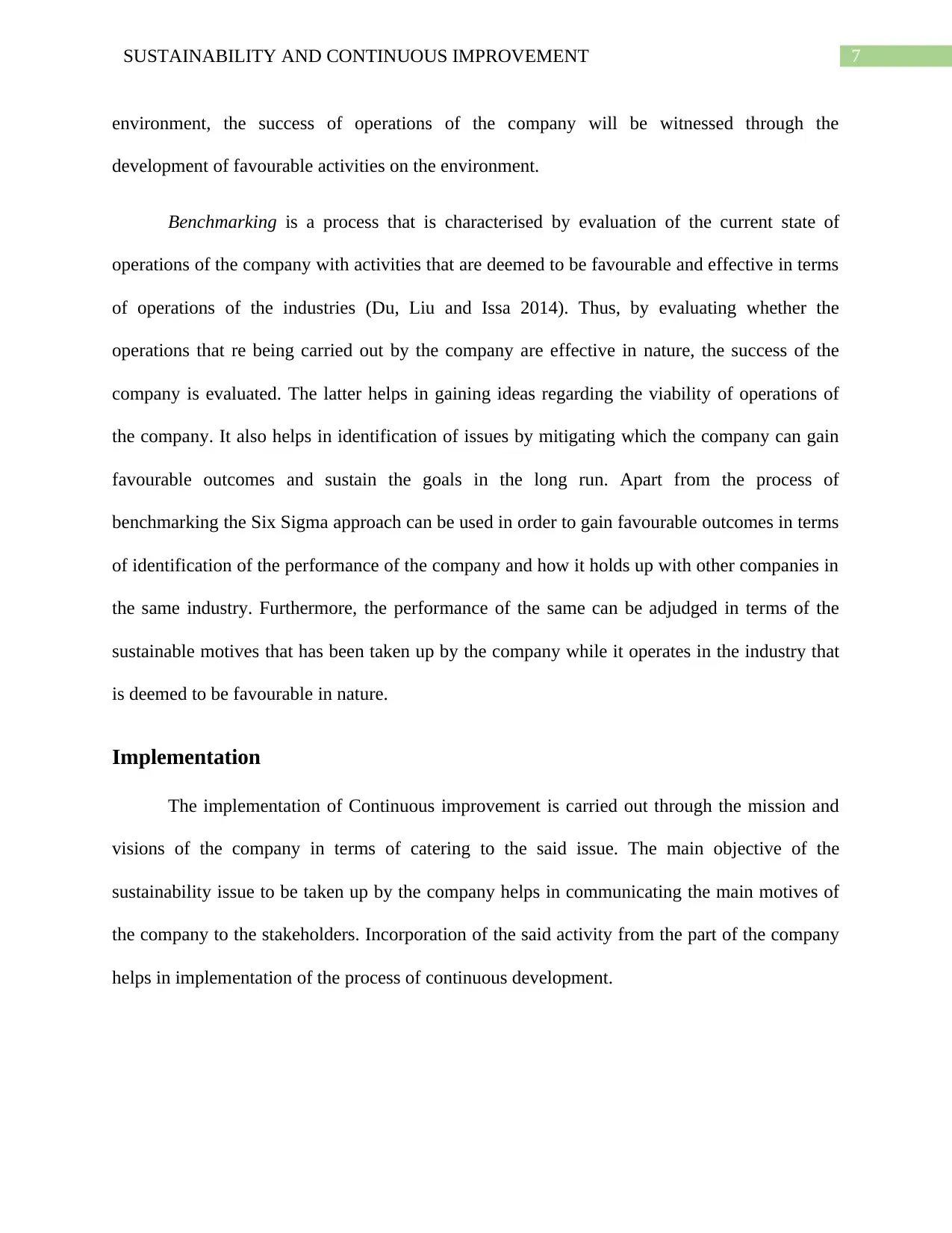
7SUSTAINABILITY AND CONTINUOUS IMPROVEMENT
environment, the success of operations of the company will be witnessed through the
development of favourable activities on the environment.
Benchmarking is a process that is characterised by evaluation of the current state of
operations of the company with activities that are deemed to be favourable and effective in terms
of operations of the industries (Du, Liu and Issa 2014). Thus, by evaluating whether the
operations that re being carried out by the company are effective in nature, the success of the
company is evaluated. The latter helps in gaining ideas regarding the viability of operations of
the company. It also helps in identification of issues by mitigating which the company can gain
favourable outcomes and sustain the goals in the long run. Apart from the process of
benchmarking the Six Sigma approach can be used in order to gain favourable outcomes in terms
of identification of the performance of the company and how it holds up with other companies in
the same industry. Furthermore, the performance of the same can be adjudged in terms of the
sustainable motives that has been taken up by the company while it operates in the industry that
is deemed to be favourable in nature.
Implementation
The implementation of Continuous improvement is carried out through the mission and
visions of the company in terms of catering to the said issue. The main objective of the
sustainability issue to be taken up by the company helps in communicating the main motives of
the company to the stakeholders. Incorporation of the said activity from the part of the company
helps in implementation of the process of continuous development.
environment, the success of operations of the company will be witnessed through the
development of favourable activities on the environment.
Benchmarking is a process that is characterised by evaluation of the current state of
operations of the company with activities that are deemed to be favourable and effective in terms
of operations of the industries (Du, Liu and Issa 2014). Thus, by evaluating whether the
operations that re being carried out by the company are effective in nature, the success of the
company is evaluated. The latter helps in gaining ideas regarding the viability of operations of
the company. It also helps in identification of issues by mitigating which the company can gain
favourable outcomes and sustain the goals in the long run. Apart from the process of
benchmarking the Six Sigma approach can be used in order to gain favourable outcomes in terms
of identification of the performance of the company and how it holds up with other companies in
the same industry. Furthermore, the performance of the same can be adjudged in terms of the
sustainable motives that has been taken up by the company while it operates in the industry that
is deemed to be favourable in nature.
Implementation
The implementation of Continuous improvement is carried out through the mission and
visions of the company in terms of catering to the said issue. The main objective of the
sustainability issue to be taken up by the company helps in communicating the main motives of
the company to the stakeholders. Incorporation of the said activity from the part of the company
helps in implementation of the process of continuous development.
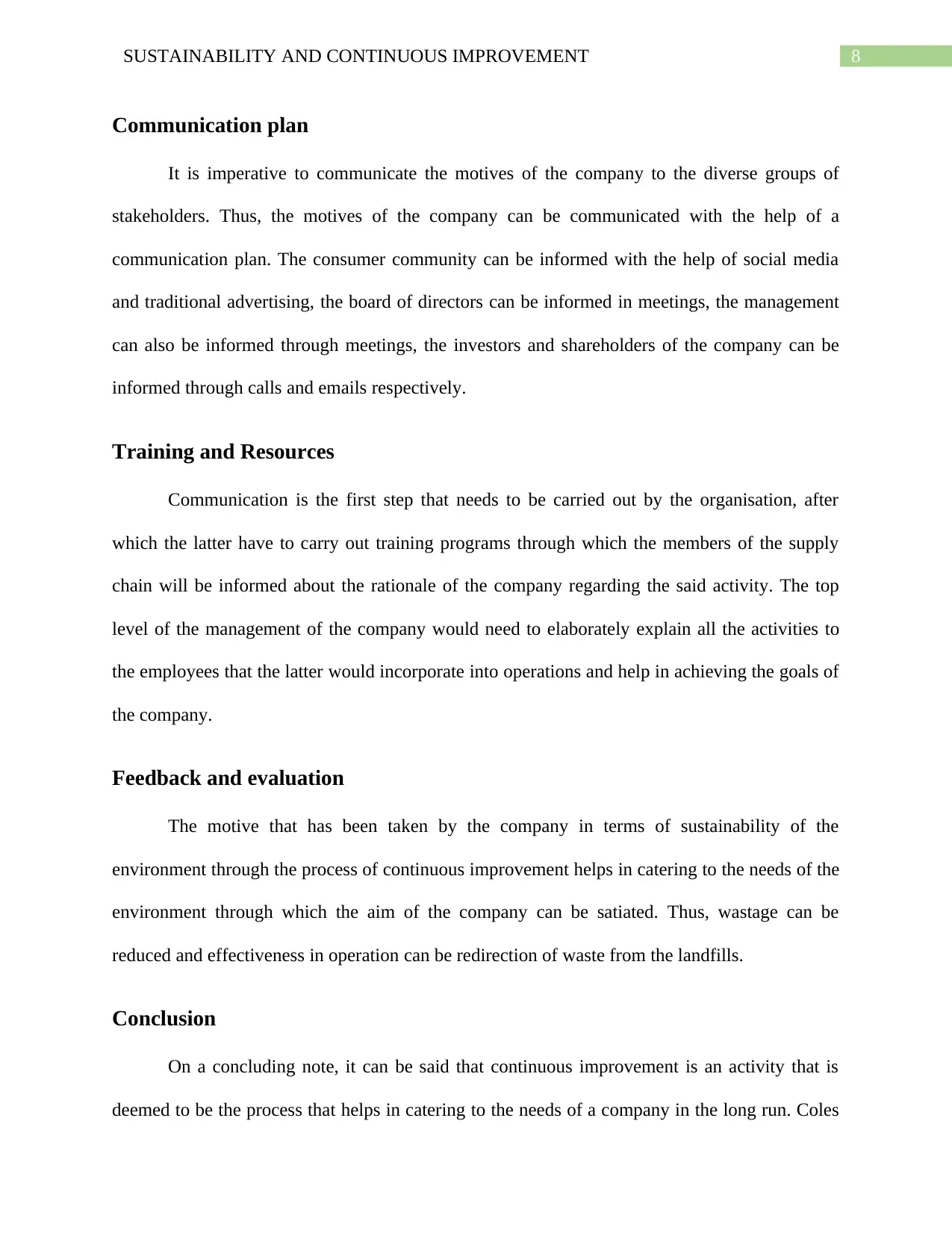
8SUSTAINABILITY AND CONTINUOUS IMPROVEMENT
Communication plan
It is imperative to communicate the motives of the company to the diverse groups of
stakeholders. Thus, the motives of the company can be communicated with the help of a
communication plan. The consumer community can be informed with the help of social media
and traditional advertising, the board of directors can be informed in meetings, the management
can also be informed through meetings, the investors and shareholders of the company can be
informed through calls and emails respectively.
Training and Resources
Communication is the first step that needs to be carried out by the organisation, after
which the latter have to carry out training programs through which the members of the supply
chain will be informed about the rationale of the company regarding the said activity. The top
level of the management of the company would need to elaborately explain all the activities to
the employees that the latter would incorporate into operations and help in achieving the goals of
the company.
Feedback and evaluation
The motive that has been taken by the company in terms of sustainability of the
environment through the process of continuous improvement helps in catering to the needs of the
environment through which the aim of the company can be satiated. Thus, wastage can be
reduced and effectiveness in operation can be redirection of waste from the landfills.
Conclusion
On a concluding note, it can be said that continuous improvement is an activity that is
deemed to be the process that helps in catering to the needs of a company in the long run. Coles
Communication plan
It is imperative to communicate the motives of the company to the diverse groups of
stakeholders. Thus, the motives of the company can be communicated with the help of a
communication plan. The consumer community can be informed with the help of social media
and traditional advertising, the board of directors can be informed in meetings, the management
can also be informed through meetings, the investors and shareholders of the company can be
informed through calls and emails respectively.
Training and Resources
Communication is the first step that needs to be carried out by the organisation, after
which the latter have to carry out training programs through which the members of the supply
chain will be informed about the rationale of the company regarding the said activity. The top
level of the management of the company would need to elaborately explain all the activities to
the employees that the latter would incorporate into operations and help in achieving the goals of
the company.
Feedback and evaluation
The motive that has been taken by the company in terms of sustainability of the
environment through the process of continuous improvement helps in catering to the needs of the
environment through which the aim of the company can be satiated. Thus, wastage can be
reduced and effectiveness in operation can be redirection of waste from the landfills.
Conclusion
On a concluding note, it can be said that continuous improvement is an activity that is
deemed to be the process that helps in catering to the needs of a company in the long run. Coles
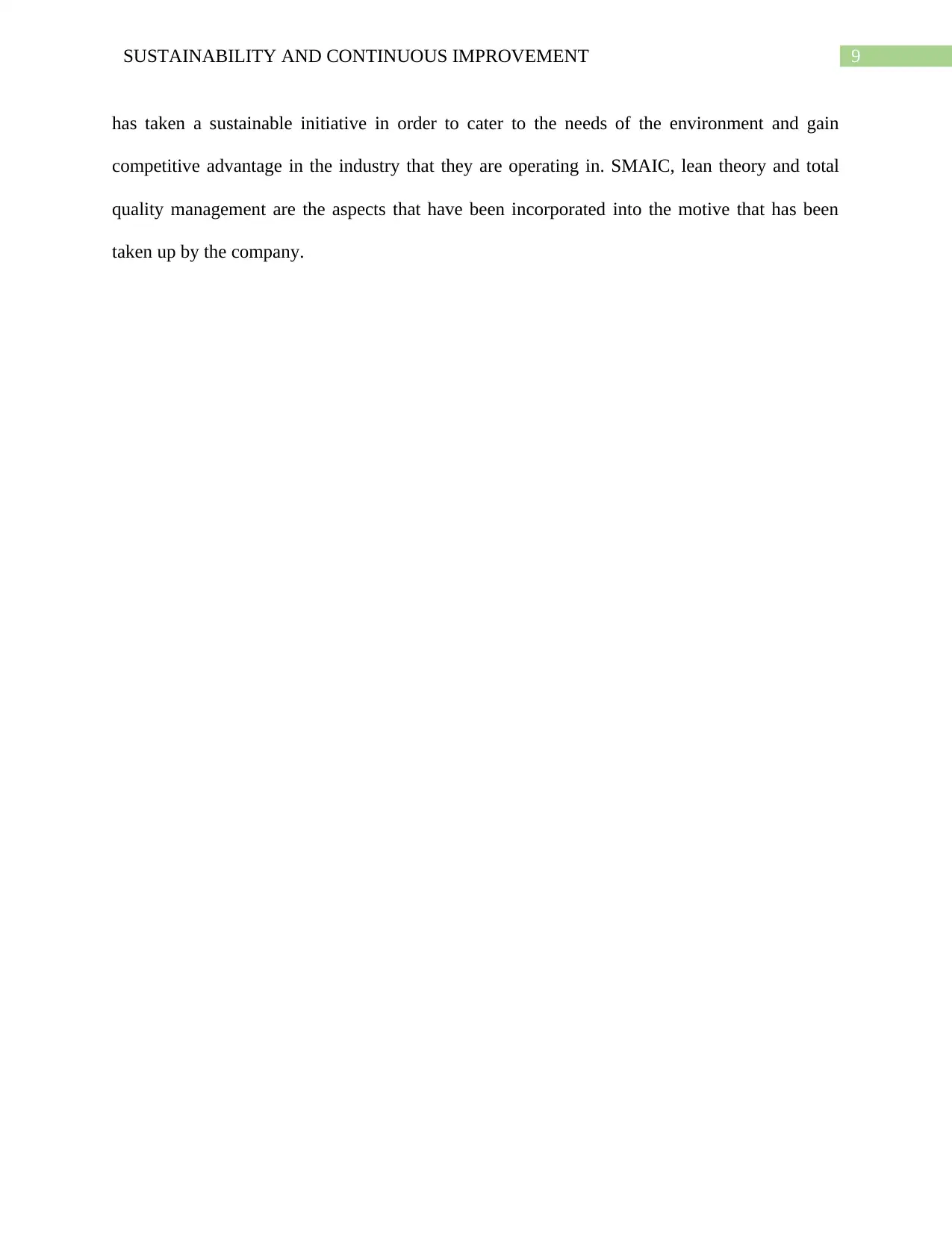
9SUSTAINABILITY AND CONTINUOUS IMPROVEMENT
has taken a sustainable initiative in order to cater to the needs of the environment and gain
competitive advantage in the industry that they are operating in. SMAIC, lean theory and total
quality management are the aspects that have been incorporated into the motive that has been
taken up by the company.
has taken a sustainable initiative in order to cater to the needs of the environment and gain
competitive advantage in the industry that they are operating in. SMAIC, lean theory and total
quality management are the aspects that have been incorporated into the motive that has been
taken up by the company.
Secure Best Marks with AI Grader
Need help grading? Try our AI Grader for instant feedback on your assignments.
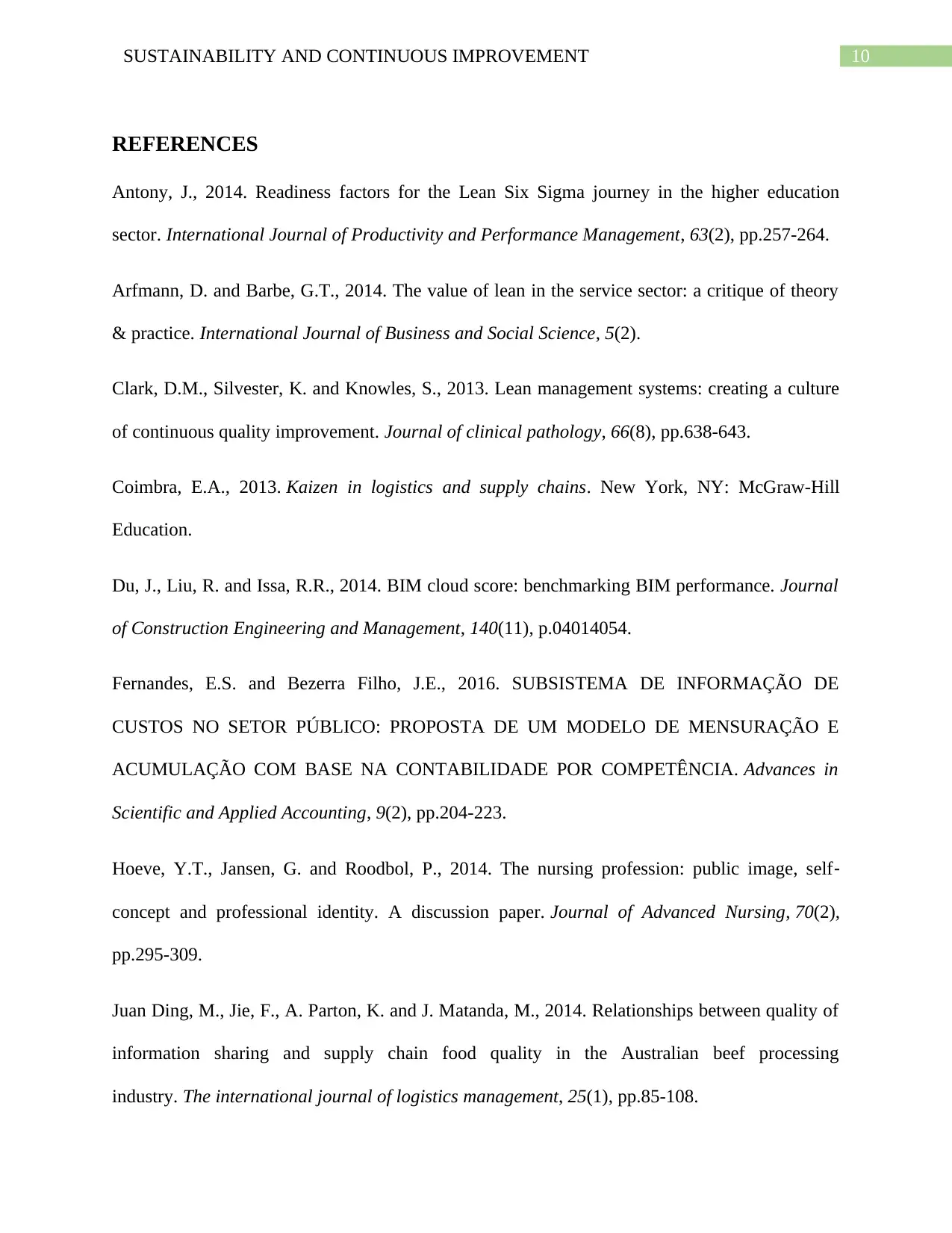
10SUSTAINABILITY AND CONTINUOUS IMPROVEMENT
REFERENCES
Antony, J., 2014. Readiness factors for the Lean Six Sigma journey in the higher education
sector. International Journal of Productivity and Performance Management, 63(2), pp.257-264.
Arfmann, D. and Barbe, G.T., 2014. The value of lean in the service sector: a critique of theory
& practice. International Journal of Business and Social Science, 5(2).
Clark, D.M., Silvester, K. and Knowles, S., 2013. Lean management systems: creating a culture
of continuous quality improvement. Journal of clinical pathology, 66(8), pp.638-643.
Coimbra, E.A., 2013. Kaizen in logistics and supply chains. New York, NY: McGraw-Hill
Education.
Du, J., Liu, R. and Issa, R.R., 2014. BIM cloud score: benchmarking BIM performance. Journal
of Construction Engineering and Management, 140(11), p.04014054.
Fernandes, E.S. and Bezerra Filho, J.E., 2016. SUBSISTEMA DE INFORMAÇÃO DE
CUSTOS NO SETOR PÚBLICO: PROPOSTA DE UM MODELO DE MENSURAÇÃO E
ACUMULAÇÃO COM BASE NA CONTABILIDADE POR COMPETÊNCIA. Advances in
Scientific and Applied Accounting, 9(2), pp.204-223.
Hoeve, Y.T., Jansen, G. and Roodbol, P., 2014. The nursing profession: public image, self‐
concept and professional identity. A discussion paper. Journal of Advanced Nursing, 70(2),
pp.295-309.
Juan Ding, M., Jie, F., A. Parton, K. and J. Matanda, M., 2014. Relationships between quality of
information sharing and supply chain food quality in the Australian beef processing
industry. The international journal of logistics management, 25(1), pp.85-108.
REFERENCES
Antony, J., 2014. Readiness factors for the Lean Six Sigma journey in the higher education
sector. International Journal of Productivity and Performance Management, 63(2), pp.257-264.
Arfmann, D. and Barbe, G.T., 2014. The value of lean in the service sector: a critique of theory
& practice. International Journal of Business and Social Science, 5(2).
Clark, D.M., Silvester, K. and Knowles, S., 2013. Lean management systems: creating a culture
of continuous quality improvement. Journal of clinical pathology, 66(8), pp.638-643.
Coimbra, E.A., 2013. Kaizen in logistics and supply chains. New York, NY: McGraw-Hill
Education.
Du, J., Liu, R. and Issa, R.R., 2014. BIM cloud score: benchmarking BIM performance. Journal
of Construction Engineering and Management, 140(11), p.04014054.
Fernandes, E.S. and Bezerra Filho, J.E., 2016. SUBSISTEMA DE INFORMAÇÃO DE
CUSTOS NO SETOR PÚBLICO: PROPOSTA DE UM MODELO DE MENSURAÇÃO E
ACUMULAÇÃO COM BASE NA CONTABILIDADE POR COMPETÊNCIA. Advances in
Scientific and Applied Accounting, 9(2), pp.204-223.
Hoeve, Y.T., Jansen, G. and Roodbol, P., 2014. The nursing profession: public image, self‐
concept and professional identity. A discussion paper. Journal of Advanced Nursing, 70(2),
pp.295-309.
Juan Ding, M., Jie, F., A. Parton, K. and J. Matanda, M., 2014. Relationships between quality of
information sharing and supply chain food quality in the Australian beef processing
industry. The international journal of logistics management, 25(1), pp.85-108.
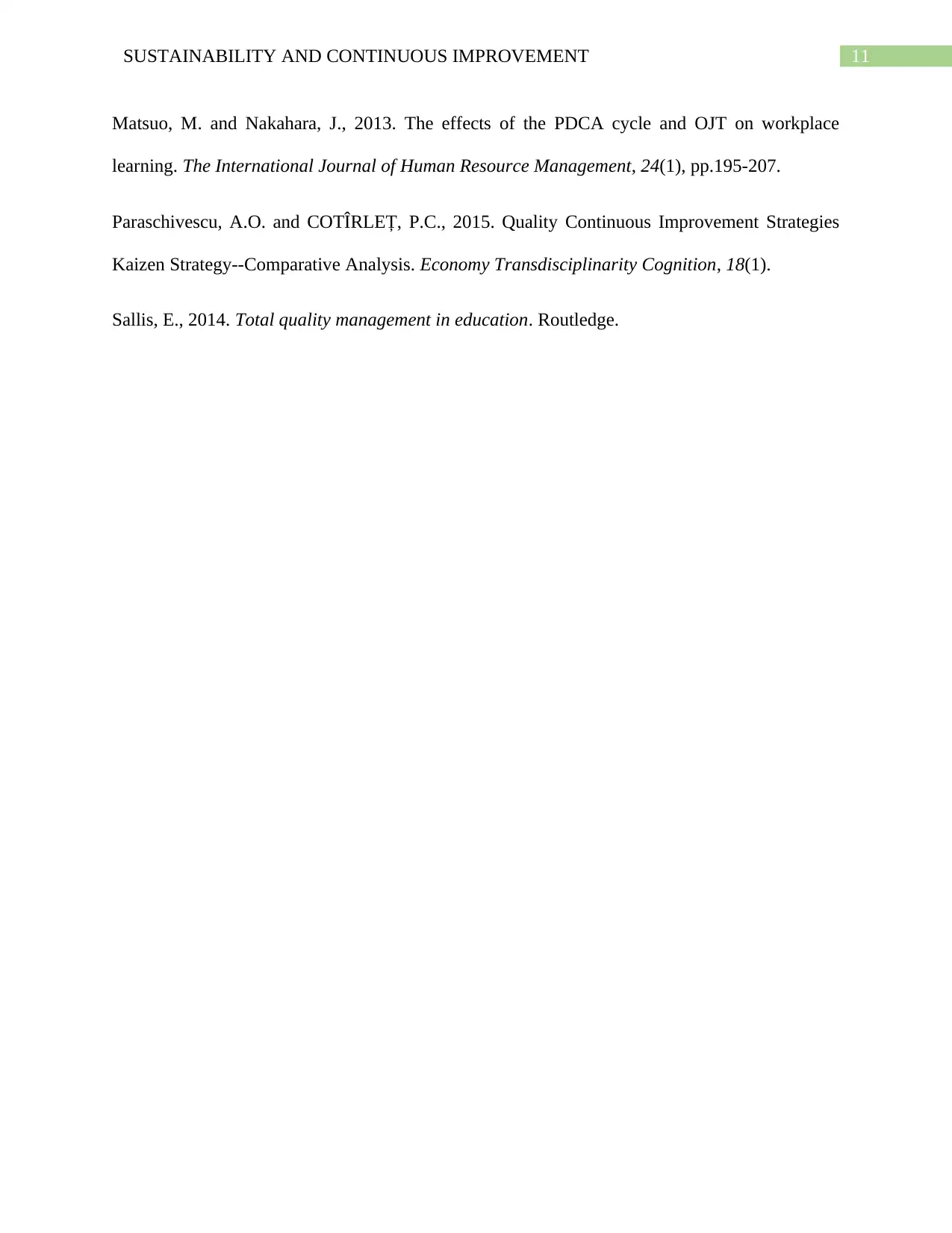
11SUSTAINABILITY AND CONTINUOUS IMPROVEMENT
Matsuo, M. and Nakahara, J., 2013. The effects of the PDCA cycle and OJT on workplace
learning. The International Journal of Human Resource Management, 24(1), pp.195-207.
Paraschivescu, A.O. and COTÎRLEȚ, P.C., 2015. Quality Continuous Improvement Strategies
Kaizen Strategy--Comparative Analysis. Economy Transdisciplinarity Cognition, 18(1).
Sallis, E., 2014. Total quality management in education. Routledge.
Matsuo, M. and Nakahara, J., 2013. The effects of the PDCA cycle and OJT on workplace
learning. The International Journal of Human Resource Management, 24(1), pp.195-207.
Paraschivescu, A.O. and COTÎRLEȚ, P.C., 2015. Quality Continuous Improvement Strategies
Kaizen Strategy--Comparative Analysis. Economy Transdisciplinarity Cognition, 18(1).
Sallis, E., 2014. Total quality management in education. Routledge.
1 out of 12
Related Documents

Your All-in-One AI-Powered Toolkit for Academic Success.
+13062052269
info@desklib.com
Available 24*7 on WhatsApp / Email
Unlock your academic potential
© 2024 | Zucol Services PVT LTD | All rights reserved.