Costing Analysis: Comparing Traditional and ABC Costing Models
VerifiedAdded on 2021/06/15
|14
|2470
|95
Report
AI Summary
This report provides a comprehensive analysis of costing methods, comparing traditional and activity-based costing (ABC) techniques. It begins with calculations of cost per unit under both methods, followed by income statements for Sewing Easy using each costing system. The analysis highlights the impact of different costing approaches on financial outcomes, including net income and overhead allocation. The report further explores the importance of accurate product costing and differentiates between applied and actual overhead costs. It also discusses the advantages and disadvantages of the ABC model, emphasizing its relevance in modern manufacturing environments. The report concludes with a bibliography of relevant sources.
Contribute Materials
Your contribution can guide someone’s learning journey. Share your
documents today.
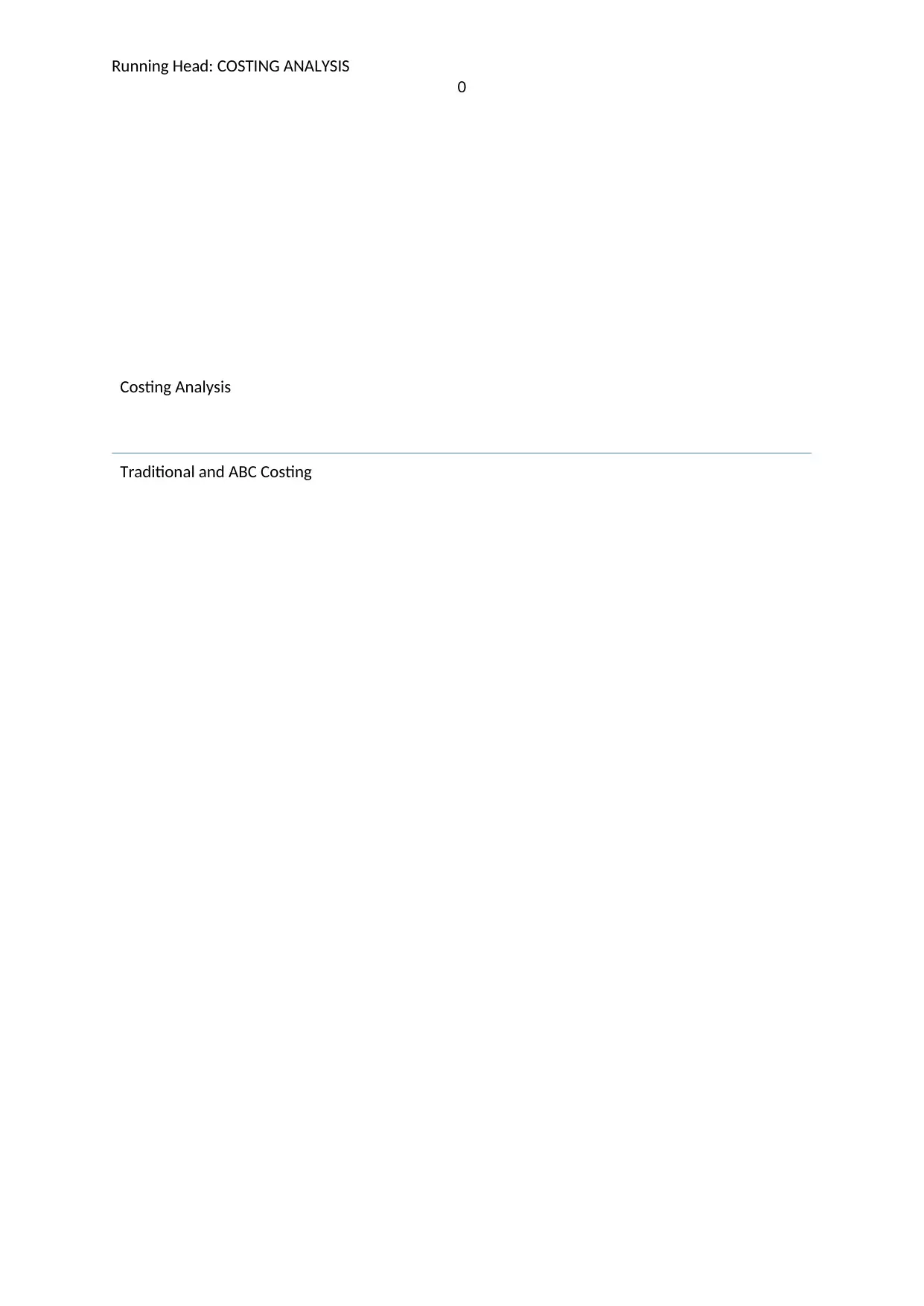
Running Head: COSTING ANALYSIS
0
Costing Analysis
Traditional and ABC Costing
0
Costing Analysis
Traditional and ABC Costing
Secure Best Marks with AI Grader
Need help grading? Try our AI Grader for instant feedback on your assignments.
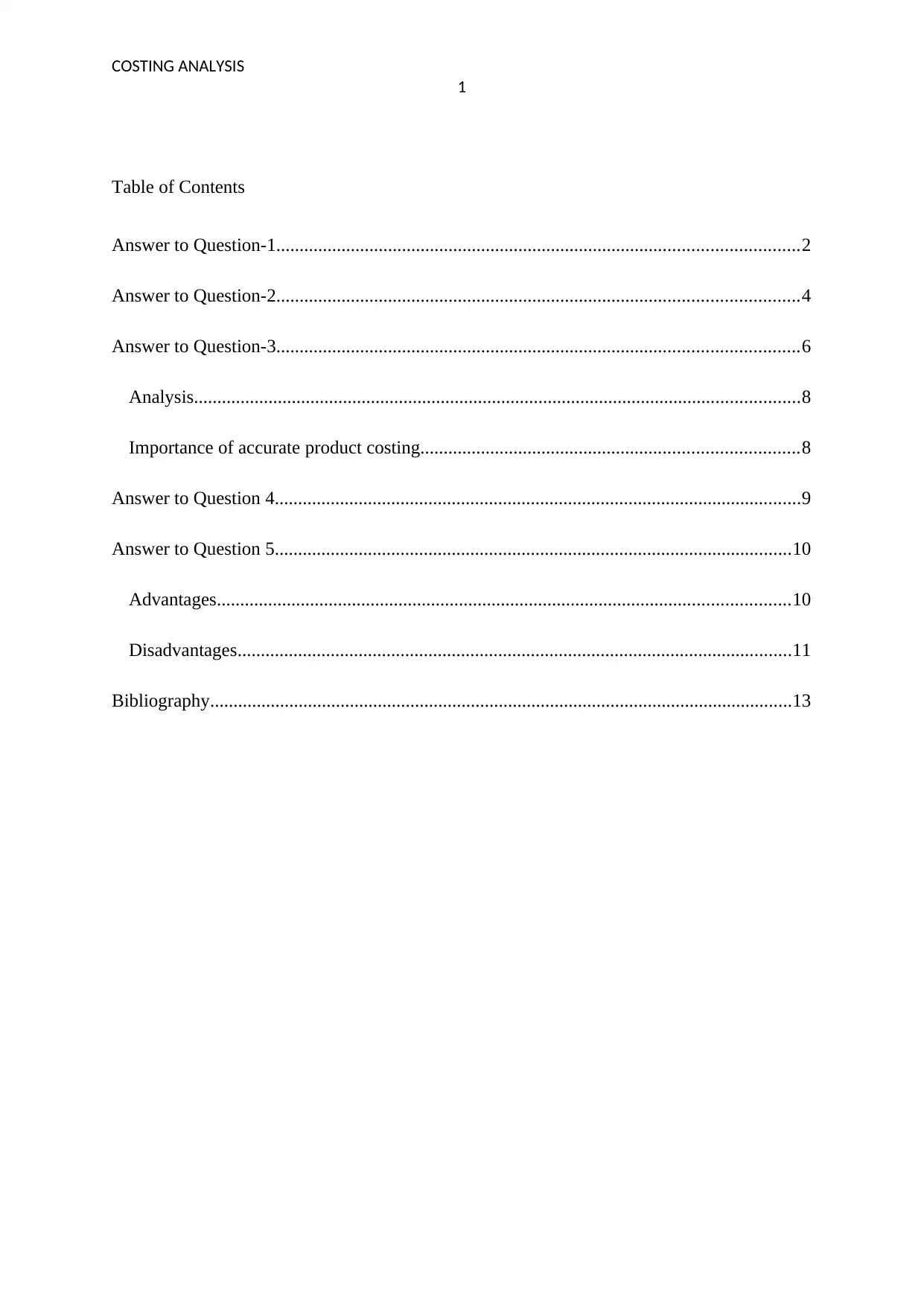
COSTING ANALYSIS
1
Table of Contents
Answer to Question-1................................................................................................................2
Answer to Question-2................................................................................................................4
Answer to Question-3................................................................................................................6
Analysis..................................................................................................................................8
Importance of accurate product costing.................................................................................8
Answer to Question 4.................................................................................................................9
Answer to Question 5...............................................................................................................10
Advantages...........................................................................................................................10
Disadvantages.......................................................................................................................11
Bibliography.............................................................................................................................13
1
Table of Contents
Answer to Question-1................................................................................................................2
Answer to Question-2................................................................................................................4
Answer to Question-3................................................................................................................6
Analysis..................................................................................................................................8
Importance of accurate product costing.................................................................................8
Answer to Question 4.................................................................................................................9
Answer to Question 5...............................................................................................................10
Advantages...........................................................................................................................10
Disadvantages.......................................................................................................................11
Bibliography.............................................................................................................................13
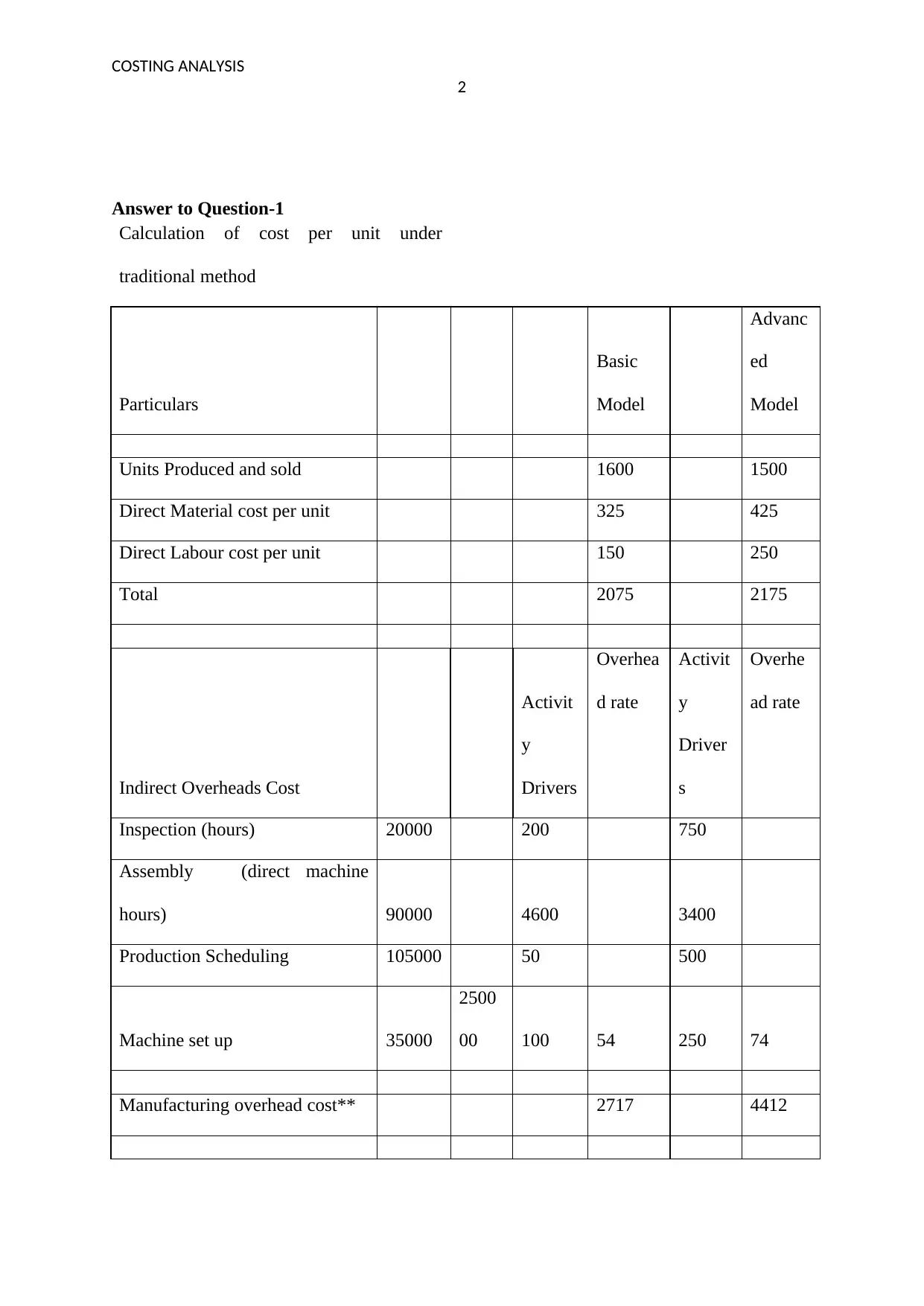
COSTING ANALYSIS
2
Answer to Question-1
Calculation of cost per unit under
traditional method
Particulars
Basic
Model
Advanc
ed
Model
Units Produced and sold 1600 1500
Direct Material cost per unit 325 425
Direct Labour cost per unit 150 250
Total 2075 2175
Indirect Overheads Cost
Activit
y
Drivers
Overhea
d rate
Activit
y
Driver
s
Overhe
ad rate
Inspection (hours) 20000 200 750
Assembly (direct machine
hours) 90000 4600 3400
Production Scheduling 105000 50 500
Machine set up 35000
2500
00 100 54 250 74
Manufacturing overhead cost** 2717 4412
2
Answer to Question-1
Calculation of cost per unit under
traditional method
Particulars
Basic
Model
Advanc
ed
Model
Units Produced and sold 1600 1500
Direct Material cost per unit 325 425
Direct Labour cost per unit 150 250
Total 2075 2175
Indirect Overheads Cost
Activit
y
Drivers
Overhea
d rate
Activit
y
Driver
s
Overhe
ad rate
Inspection (hours) 20000 200 750
Assembly (direct machine
hours) 90000 4600 3400
Production Scheduling 105000 50 500
Machine set up 35000
2500
00 100 54 250 74
Manufacturing overhead cost** 2717 4412
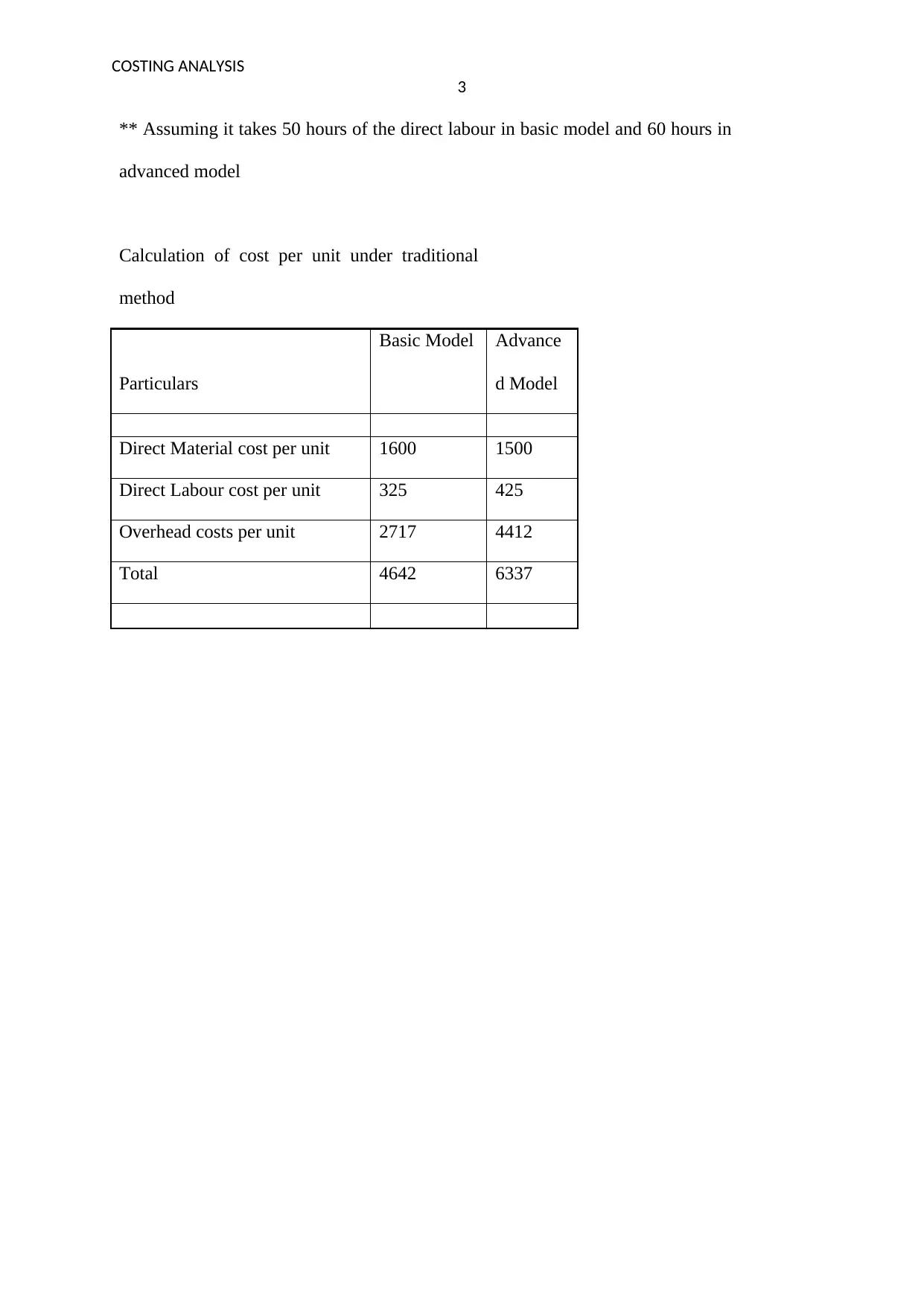
COSTING ANALYSIS
3
** Assuming it takes 50 hours of the direct labour in basic model and 60 hours in
advanced model
Calculation of cost per unit under traditional
method
Particulars
Basic Model Advance
d Model
Direct Material cost per unit 1600 1500
Direct Labour cost per unit 325 425
Overhead costs per unit 2717 4412
Total 4642 6337
3
** Assuming it takes 50 hours of the direct labour in basic model and 60 hours in
advanced model
Calculation of cost per unit under traditional
method
Particulars
Basic Model Advance
d Model
Direct Material cost per unit 1600 1500
Direct Labour cost per unit 325 425
Overhead costs per unit 2717 4412
Total 4642 6337
Secure Best Marks with AI Grader
Need help grading? Try our AI Grader for instant feedback on your assignments.
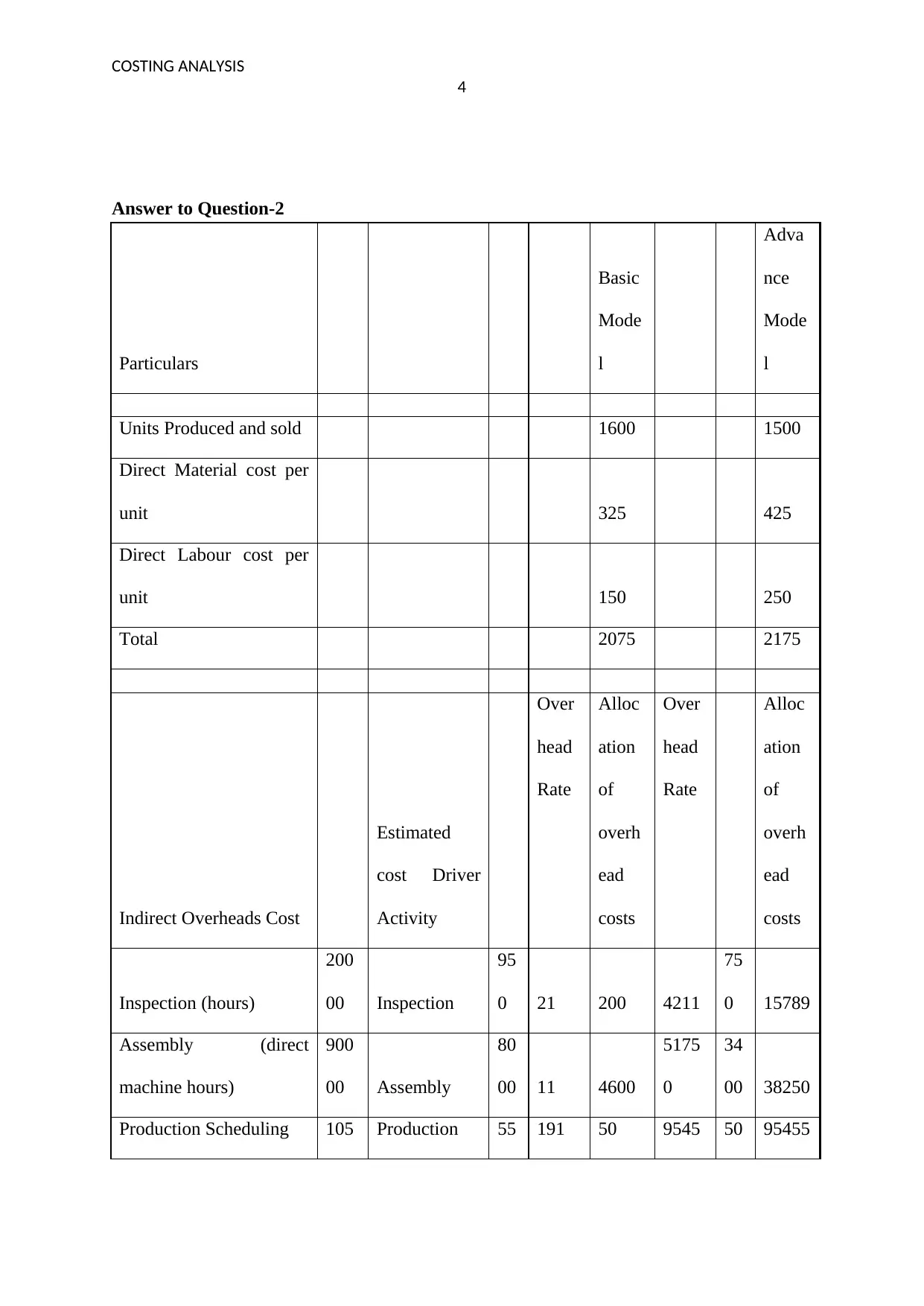
COSTING ANALYSIS
4
Answer to Question-2
Particulars
Basic
Mode
l
Adva
nce
Mode
l
Units Produced and sold 1600 1500
Direct Material cost per
unit 325 425
Direct Labour cost per
unit 150 250
Total 2075 2175
Indirect Overheads Cost
Estimated
cost Driver
Activity
Over
head
Rate
Alloc
ation
of
overh
ead
costs
Over
head
Rate
Alloc
ation
of
overh
ead
costs
Inspection (hours)
200
00 Inspection
95
0 21 200 4211
75
0 15789
Assembly (direct
machine hours)
900
00 Assembly
80
00 11 4600
5175
0
34
00 38250
Production Scheduling 105 Production 55 191 50 9545 50 95455
4
Answer to Question-2
Particulars
Basic
Mode
l
Adva
nce
Mode
l
Units Produced and sold 1600 1500
Direct Material cost per
unit 325 425
Direct Labour cost per
unit 150 250
Total 2075 2175
Indirect Overheads Cost
Estimated
cost Driver
Activity
Over
head
Rate
Alloc
ation
of
overh
ead
costs
Over
head
Rate
Alloc
ation
of
overh
ead
costs
Inspection (hours)
200
00 Inspection
95
0 21 200 4211
75
0 15789
Assembly (direct
machine hours)
900
00 Assembly
80
00 11 4600
5175
0
34
00 38250
Production Scheduling 105 Production 55 191 50 9545 50 95455
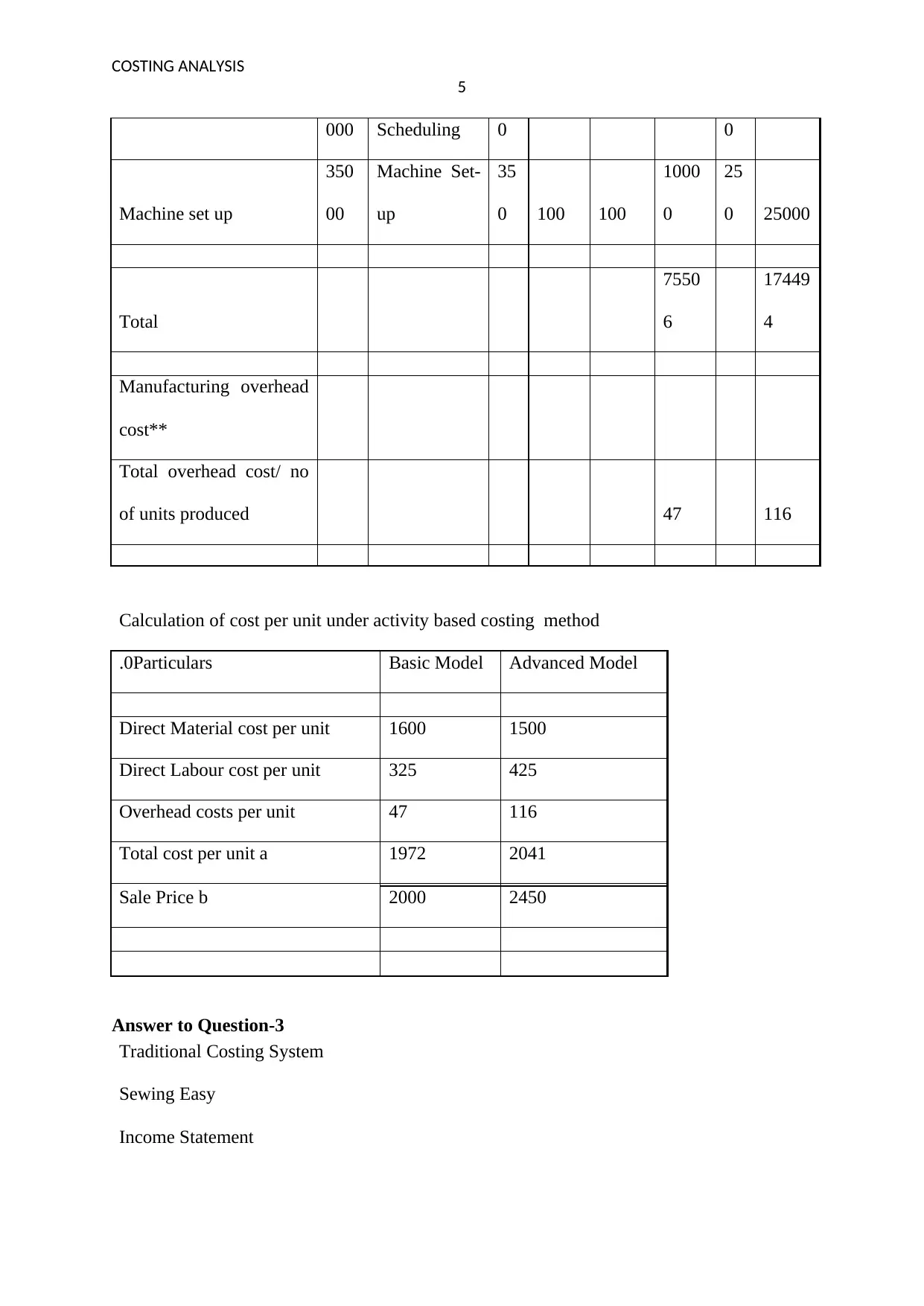
COSTING ANALYSIS
5
000 Scheduling 0 0
Machine set up
350
00
Machine Set-
up
35
0 100 100
1000
0
25
0 25000
Total
7550
6
17449
4
Manufacturing overhead
cost**
Total overhead cost/ no
of units produced 47 116
Calculation of cost per unit under activity based costing method
.0Particulars Basic Model Advanced Model
Direct Material cost per unit 1600 1500
Direct Labour cost per unit 325 425
Overhead costs per unit 47 116
Total cost per unit a 1972 2041
Sale Price b 2000 2450
Answer to Question-3
Traditional Costing System
Sewing Easy
Income Statement
5
000 Scheduling 0 0
Machine set up
350
00
Machine Set-
up
35
0 100 100
1000
0
25
0 25000
Total
7550
6
17449
4
Manufacturing overhead
cost**
Total overhead cost/ no
of units produced 47 116
Calculation of cost per unit under activity based costing method
.0Particulars Basic Model Advanced Model
Direct Material cost per unit 1600 1500
Direct Labour cost per unit 325 425
Overhead costs per unit 47 116
Total cost per unit a 1972 2041
Sale Price b 2000 2450
Answer to Question-3
Traditional Costing System
Sewing Easy
Income Statement
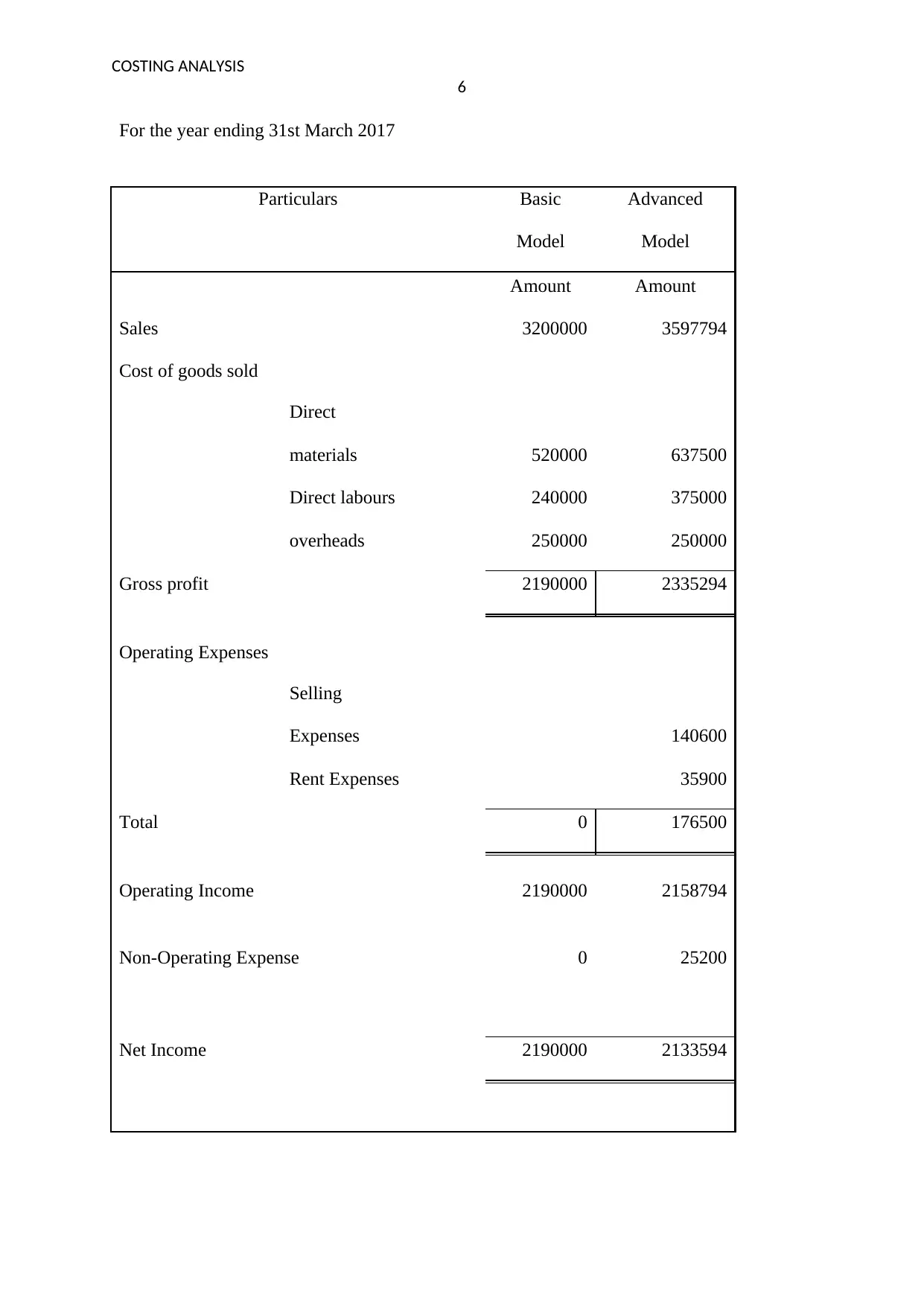
COSTING ANALYSIS
6
For the year ending 31st March 2017
Particulars Basic
Model
Advanced
Model
Amount Amount
Sales 3200000 3597794
Cost of goods sold
Direct
materials 520000 637500
Direct labours 240000 375000
overheads 250000 250000
Gross profit 2190000 2335294
Operating Expenses
Selling
Expenses 140600
Rent Expenses 35900
Total 0 176500
Operating Income 2190000 2158794
Non-Operating Expense 0 25200
Net Income 2190000 2133594
6
For the year ending 31st March 2017
Particulars Basic
Model
Advanced
Model
Amount Amount
Sales 3200000 3597794
Cost of goods sold
Direct
materials 520000 637500
Direct labours 240000 375000
overheads 250000 250000
Gross profit 2190000 2335294
Operating Expenses
Selling
Expenses 140600
Rent Expenses 35900
Total 0 176500
Operating Income 2190000 2158794
Non-Operating Expense 0 25200
Net Income 2190000 2133594
Paraphrase This Document
Need a fresh take? Get an instant paraphrase of this document with our AI Paraphraser
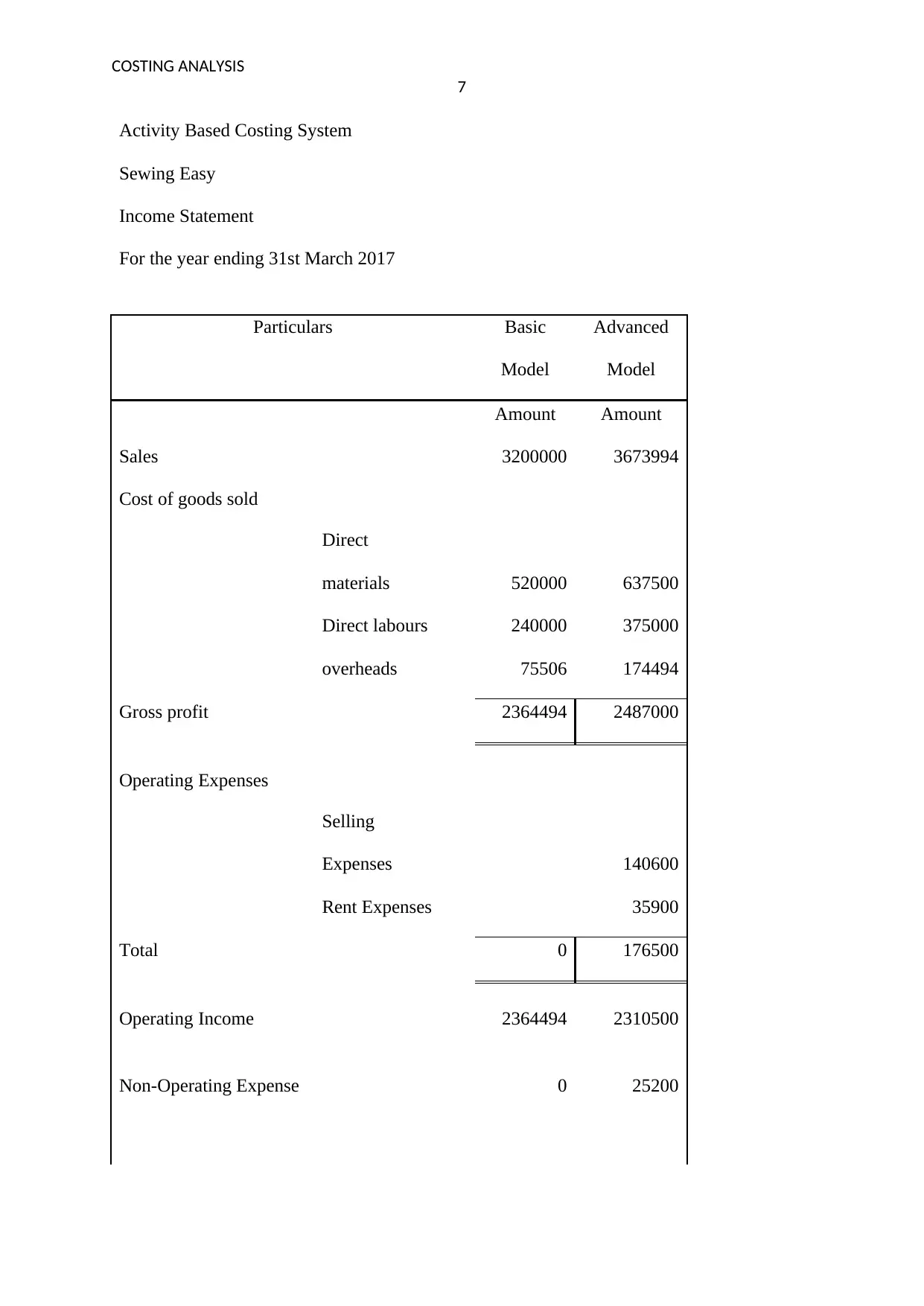
COSTING ANALYSIS
7
Activity Based Costing System
Sewing Easy
Income Statement
For the year ending 31st March 2017
Particulars Basic
Model
Advanced
Model
Amount Amount
Sales 3200000 3673994
Cost of goods sold
Direct
materials 520000 637500
Direct labours 240000 375000
overheads 75506 174494
Gross profit 2364494 2487000
Operating Expenses
Selling
Expenses 140600
Rent Expenses 35900
Total 0 176500
Operating Income 2364494 2310500
Non-Operating Expense 0 25200
7
Activity Based Costing System
Sewing Easy
Income Statement
For the year ending 31st March 2017
Particulars Basic
Model
Advanced
Model
Amount Amount
Sales 3200000 3673994
Cost of goods sold
Direct
materials 520000 637500
Direct labours 240000 375000
overheads 75506 174494
Gross profit 2364494 2487000
Operating Expenses
Selling
Expenses 140600
Rent Expenses 35900
Total 0 176500
Operating Income 2364494 2310500
Non-Operating Expense 0 25200
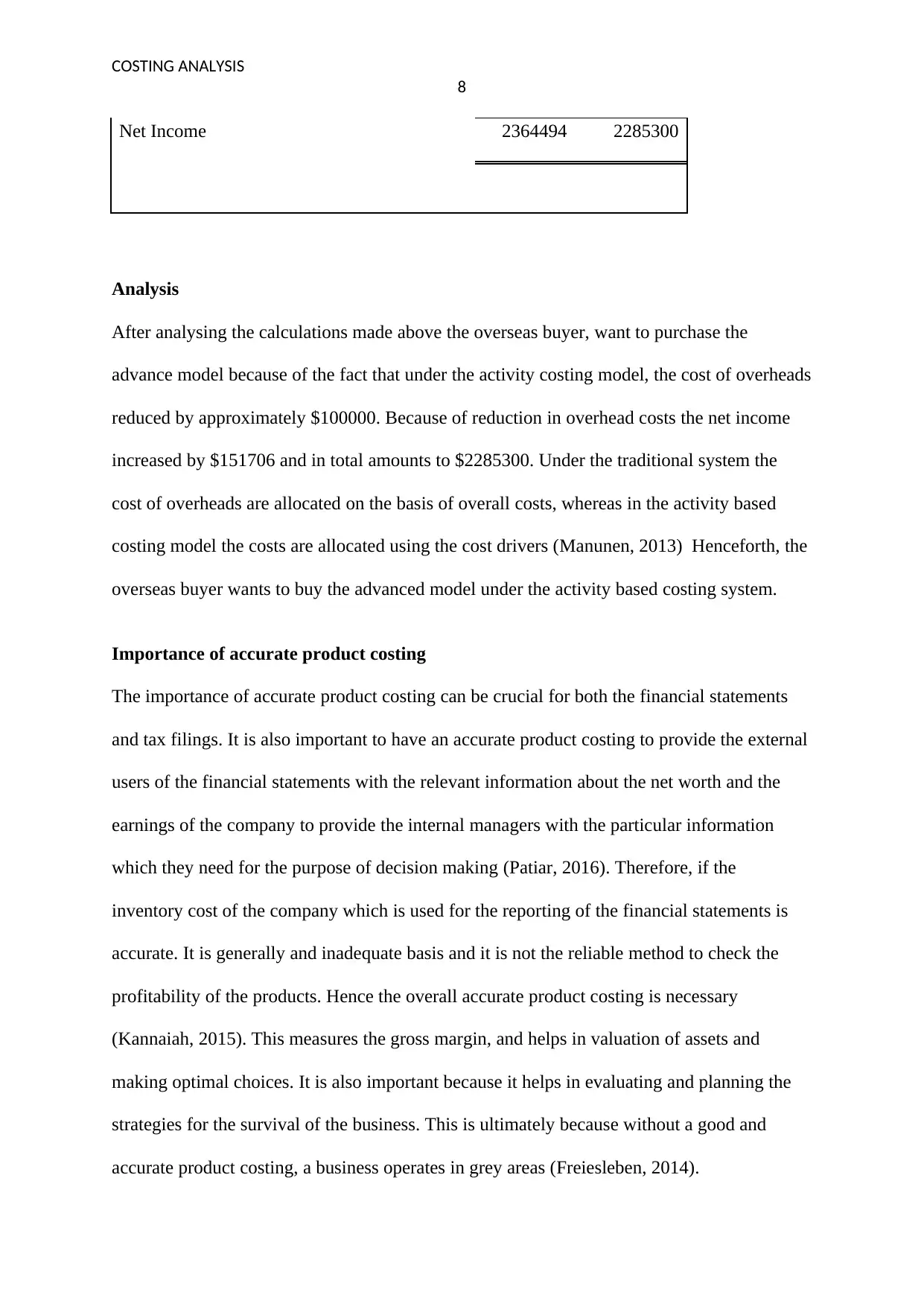
COSTING ANALYSIS
8
Net Income 2364494 2285300
Analysis
After analysing the calculations made above the overseas buyer, want to purchase the
advance model because of the fact that under the activity costing model, the cost of overheads
reduced by approximately $100000. Because of reduction in overhead costs the net income
increased by $151706 and in total amounts to $2285300. Under the traditional system the
cost of overheads are allocated on the basis of overall costs, whereas in the activity based
costing model the costs are allocated using the cost drivers (Manunen, 2013) Henceforth, the
overseas buyer wants to buy the advanced model under the activity based costing system.
Importance of accurate product costing
The importance of accurate product costing can be crucial for both the financial statements
and tax filings. It is also important to have an accurate product costing to provide the external
users of the financial statements with the relevant information about the net worth and the
earnings of the company to provide the internal managers with the particular information
which they need for the purpose of decision making (Patiar, 2016). Therefore, if the
inventory cost of the company which is used for the reporting of the financial statements is
accurate. It is generally and inadequate basis and it is not the reliable method to check the
profitability of the products. Hence the overall accurate product costing is necessary
(Kannaiah, 2015). This measures the gross margin, and helps in valuation of assets and
making optimal choices. It is also important because it helps in evaluating and planning the
strategies for the survival of the business. This is ultimately because without a good and
accurate product costing, a business operates in grey areas (Freiesleben, 2014).
8
Net Income 2364494 2285300
Analysis
After analysing the calculations made above the overseas buyer, want to purchase the
advance model because of the fact that under the activity costing model, the cost of overheads
reduced by approximately $100000. Because of reduction in overhead costs the net income
increased by $151706 and in total amounts to $2285300. Under the traditional system the
cost of overheads are allocated on the basis of overall costs, whereas in the activity based
costing model the costs are allocated using the cost drivers (Manunen, 2013) Henceforth, the
overseas buyer wants to buy the advanced model under the activity based costing system.
Importance of accurate product costing
The importance of accurate product costing can be crucial for both the financial statements
and tax filings. It is also important to have an accurate product costing to provide the external
users of the financial statements with the relevant information about the net worth and the
earnings of the company to provide the internal managers with the particular information
which they need for the purpose of decision making (Patiar, 2016). Therefore, if the
inventory cost of the company which is used for the reporting of the financial statements is
accurate. It is generally and inadequate basis and it is not the reliable method to check the
profitability of the products. Hence the overall accurate product costing is necessary
(Kannaiah, 2015). This measures the gross margin, and helps in valuation of assets and
making optimal choices. It is also important because it helps in evaluating and planning the
strategies for the survival of the business. This is ultimately because without a good and
accurate product costing, a business operates in grey areas (Freiesleben, 2014).

COSTING ANALYSIS
9
Answer to Question 4
The primary difference between the applied and the actual overhead is that the former one is
arrived during and after a certain period of time while the later one is arrived before a certain
period of time. In terms of accounting overheads generally refers to the manufacturing costs
which are of indirect nature. These are those manufacturing costs which are other than the
direct materials and direct labours. The actual overheads can be derived from the
manufacturing costs that actually occur and a record of the same can be kept (Tsai, 2016).
These also include the costs of electricity, water, rent, property tax, depreciation,
maintenance.
A company generally do not incur the costs of overheads uniformly. For example the cost of
heat during the winter is generally high as compared to summers. However, when the
discussion is regarding the allocation of the costs this purpose is not served fully. They are
useful for the purpose of the inventory and also in determining the profitability of the
business.
The applied overhead refers to the manufacturing costs of the indirect nature that have been
allocated to the manufactured goods. Manufactured overheads are generally allocated on the
basis of the annual over rate (Gracanin, Buchmeister and Lalic, 2014).
If too much of overhead is applied to the jobs the overhead is considered as over applied
whereas if the overhead costs are applied little, it is called as under applied. An over applied
overhead cost occurs when the cost of goods sold are inclusive of too much of overhead and
vice versa in the case of under applied overhead. An account called “Factory overhead” is
created and credited to reflect the application in the work in progress method.
How to deal with over/undervalued applied overhead.
First the amount may be carried forward to the next period’s account.
9
Answer to Question 4
The primary difference between the applied and the actual overhead is that the former one is
arrived during and after a certain period of time while the later one is arrived before a certain
period of time. In terms of accounting overheads generally refers to the manufacturing costs
which are of indirect nature. These are those manufacturing costs which are other than the
direct materials and direct labours. The actual overheads can be derived from the
manufacturing costs that actually occur and a record of the same can be kept (Tsai, 2016).
These also include the costs of electricity, water, rent, property tax, depreciation,
maintenance.
A company generally do not incur the costs of overheads uniformly. For example the cost of
heat during the winter is generally high as compared to summers. However, when the
discussion is regarding the allocation of the costs this purpose is not served fully. They are
useful for the purpose of the inventory and also in determining the profitability of the
business.
The applied overhead refers to the manufacturing costs of the indirect nature that have been
allocated to the manufactured goods. Manufactured overheads are generally allocated on the
basis of the annual over rate (Gracanin, Buchmeister and Lalic, 2014).
If too much of overhead is applied to the jobs the overhead is considered as over applied
whereas if the overhead costs are applied little, it is called as under applied. An over applied
overhead cost occurs when the cost of goods sold are inclusive of too much of overhead and
vice versa in the case of under applied overhead. An account called “Factory overhead” is
created and credited to reflect the application in the work in progress method.
How to deal with over/undervalued applied overhead.
First the amount may be carried forward to the next period’s account.
Secure Best Marks with AI Grader
Need help grading? Try our AI Grader for instant feedback on your assignments.
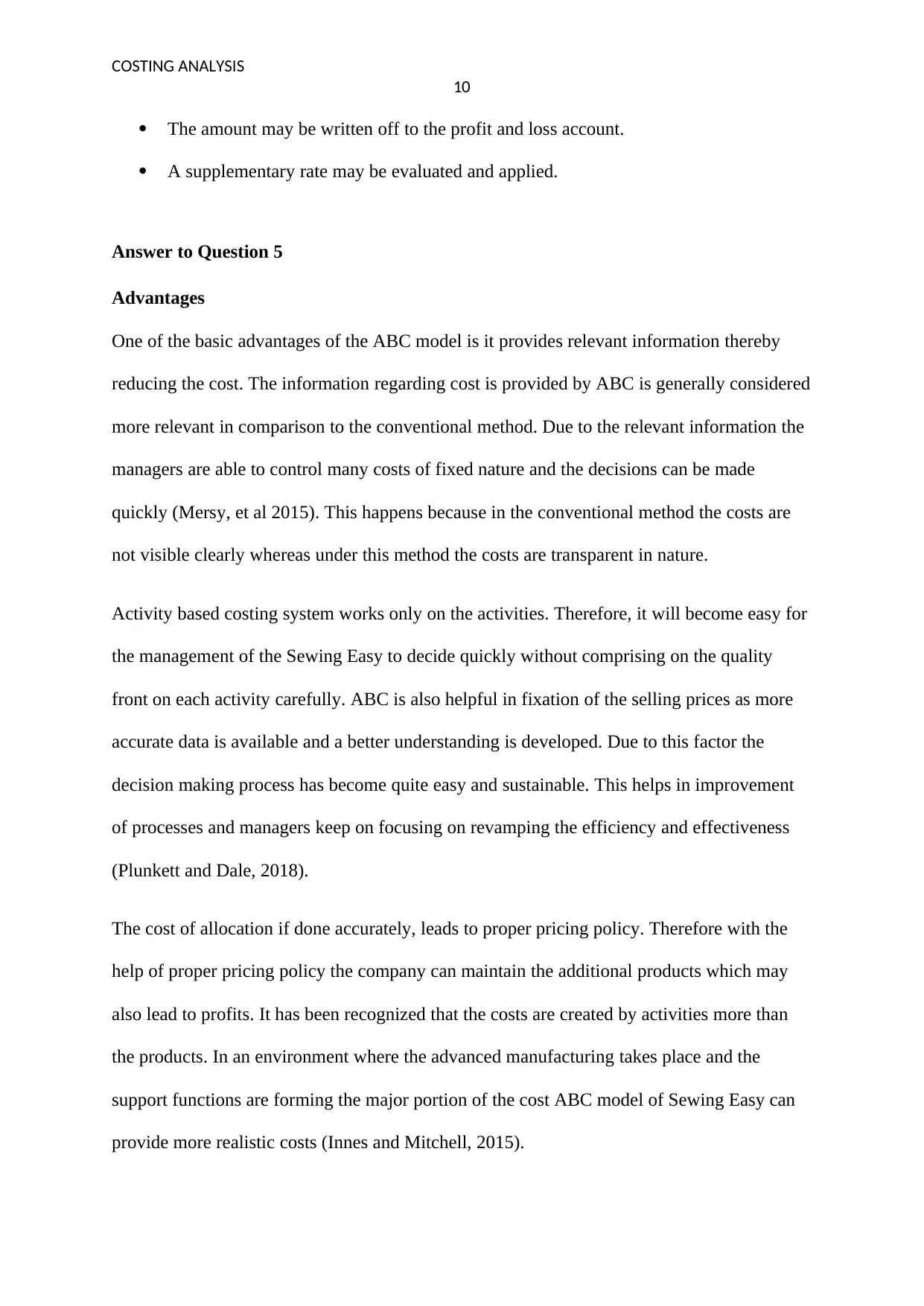
COSTING ANALYSIS
10
The amount may be written off to the profit and loss account.
A supplementary rate may be evaluated and applied.
Answer to Question 5
Advantages
One of the basic advantages of the ABC model is it provides relevant information thereby
reducing the cost. The information regarding cost is provided by ABC is generally considered
more relevant in comparison to the conventional method. Due to the relevant information the
managers are able to control many costs of fixed nature and the decisions can be made
quickly (Mersy, et al 2015). This happens because in the conventional method the costs are
not visible clearly whereas under this method the costs are transparent in nature.
Activity based costing system works only on the activities. Therefore, it will become easy for
the management of the Sewing Easy to decide quickly without comprising on the quality
front on each activity carefully. ABC is also helpful in fixation of the selling prices as more
accurate data is available and a better understanding is developed. Due to this factor the
decision making process has become quite easy and sustainable. This helps in improvement
of processes and managers keep on focusing on revamping the efficiency and effectiveness
(Plunkett and Dale, 2018).
The cost of allocation if done accurately, leads to proper pricing policy. Therefore with the
help of proper pricing policy the company can maintain the additional products which may
also lead to profits. It has been recognized that the costs are created by activities more than
the products. In an environment where the advanced manufacturing takes place and the
support functions are forming the major portion of the cost ABC model of Sewing Easy can
provide more realistic costs (Innes and Mitchell, 2015).
10
The amount may be written off to the profit and loss account.
A supplementary rate may be evaluated and applied.
Answer to Question 5
Advantages
One of the basic advantages of the ABC model is it provides relevant information thereby
reducing the cost. The information regarding cost is provided by ABC is generally considered
more relevant in comparison to the conventional method. Due to the relevant information the
managers are able to control many costs of fixed nature and the decisions can be made
quickly (Mersy, et al 2015). This happens because in the conventional method the costs are
not visible clearly whereas under this method the costs are transparent in nature.
Activity based costing system works only on the activities. Therefore, it will become easy for
the management of the Sewing Easy to decide quickly without comprising on the quality
front on each activity carefully. ABC is also helpful in fixation of the selling prices as more
accurate data is available and a better understanding is developed. Due to this factor the
decision making process has become quite easy and sustainable. This helps in improvement
of processes and managers keep on focusing on revamping the efficiency and effectiveness
(Plunkett and Dale, 2018).
The cost of allocation if done accurately, leads to proper pricing policy. Therefore with the
help of proper pricing policy the company can maintain the additional products which may
also lead to profits. It has been recognized that the costs are created by activities more than
the products. In an environment where the advanced manufacturing takes place and the
support functions are forming the major portion of the cost ABC model of Sewing Easy can
provide more realistic costs (Innes and Mitchell, 2015).
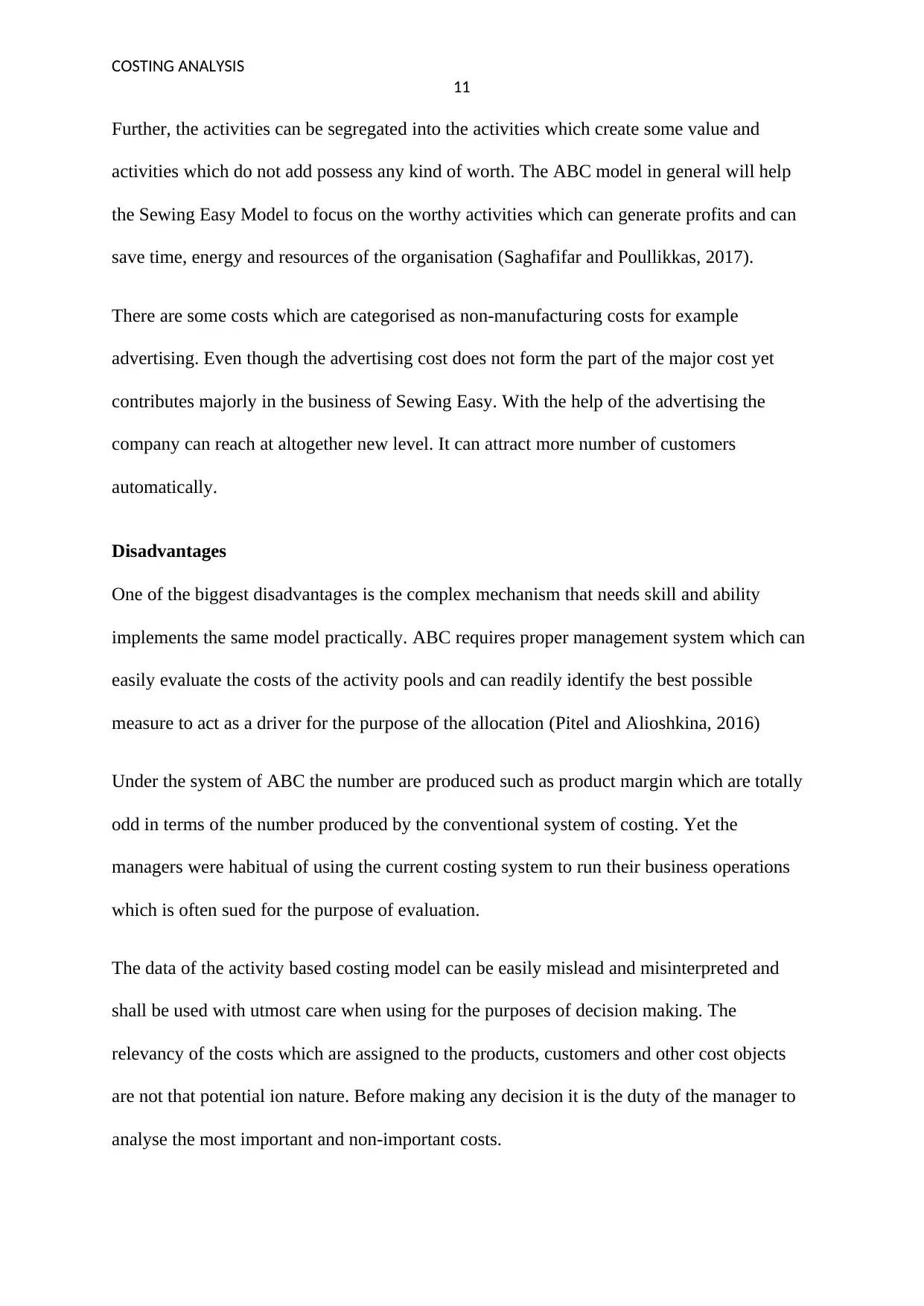
COSTING ANALYSIS
11
Further, the activities can be segregated into the activities which create some value and
activities which do not add possess any kind of worth. The ABC model in general will help
the Sewing Easy Model to focus on the worthy activities which can generate profits and can
save time, energy and resources of the organisation (Saghafifar and Poullikkas, 2017).
There are some costs which are categorised as non-manufacturing costs for example
advertising. Even though the advertising cost does not form the part of the major cost yet
contributes majorly in the business of Sewing Easy. With the help of the advertising the
company can reach at altogether new level. It can attract more number of customers
automatically.
Disadvantages
One of the biggest disadvantages is the complex mechanism that needs skill and ability
implements the same model practically. ABC requires proper management system which can
easily evaluate the costs of the activity pools and can readily identify the best possible
measure to act as a driver for the purpose of the allocation (Pitel and Alioshkina, 2016)
Under the system of ABC the number are produced such as product margin which are totally
odd in terms of the number produced by the conventional system of costing. Yet the
managers were habitual of using the current costing system to run their business operations
which is often sued for the purpose of evaluation.
The data of the activity based costing model can be easily mislead and misinterpreted and
shall be used with utmost care when using for the purposes of decision making. The
relevancy of the costs which are assigned to the products, customers and other cost objects
are not that potential ion nature. Before making any decision it is the duty of the manager to
analyse the most important and non-important costs.
11
Further, the activities can be segregated into the activities which create some value and
activities which do not add possess any kind of worth. The ABC model in general will help
the Sewing Easy Model to focus on the worthy activities which can generate profits and can
save time, energy and resources of the organisation (Saghafifar and Poullikkas, 2017).
There are some costs which are categorised as non-manufacturing costs for example
advertising. Even though the advertising cost does not form the part of the major cost yet
contributes majorly in the business of Sewing Easy. With the help of the advertising the
company can reach at altogether new level. It can attract more number of customers
automatically.
Disadvantages
One of the biggest disadvantages is the complex mechanism that needs skill and ability
implements the same model practically. ABC requires proper management system which can
easily evaluate the costs of the activity pools and can readily identify the best possible
measure to act as a driver for the purpose of the allocation (Pitel and Alioshkina, 2016)
Under the system of ABC the number are produced such as product margin which are totally
odd in terms of the number produced by the conventional system of costing. Yet the
managers were habitual of using the current costing system to run their business operations
which is often sued for the purpose of evaluation.
The data of the activity based costing model can be easily mislead and misinterpreted and
shall be used with utmost care when using for the purposes of decision making. The
relevancy of the costs which are assigned to the products, customers and other cost objects
are not that potential ion nature. Before making any decision it is the duty of the manager to
analyse the most important and non-important costs.
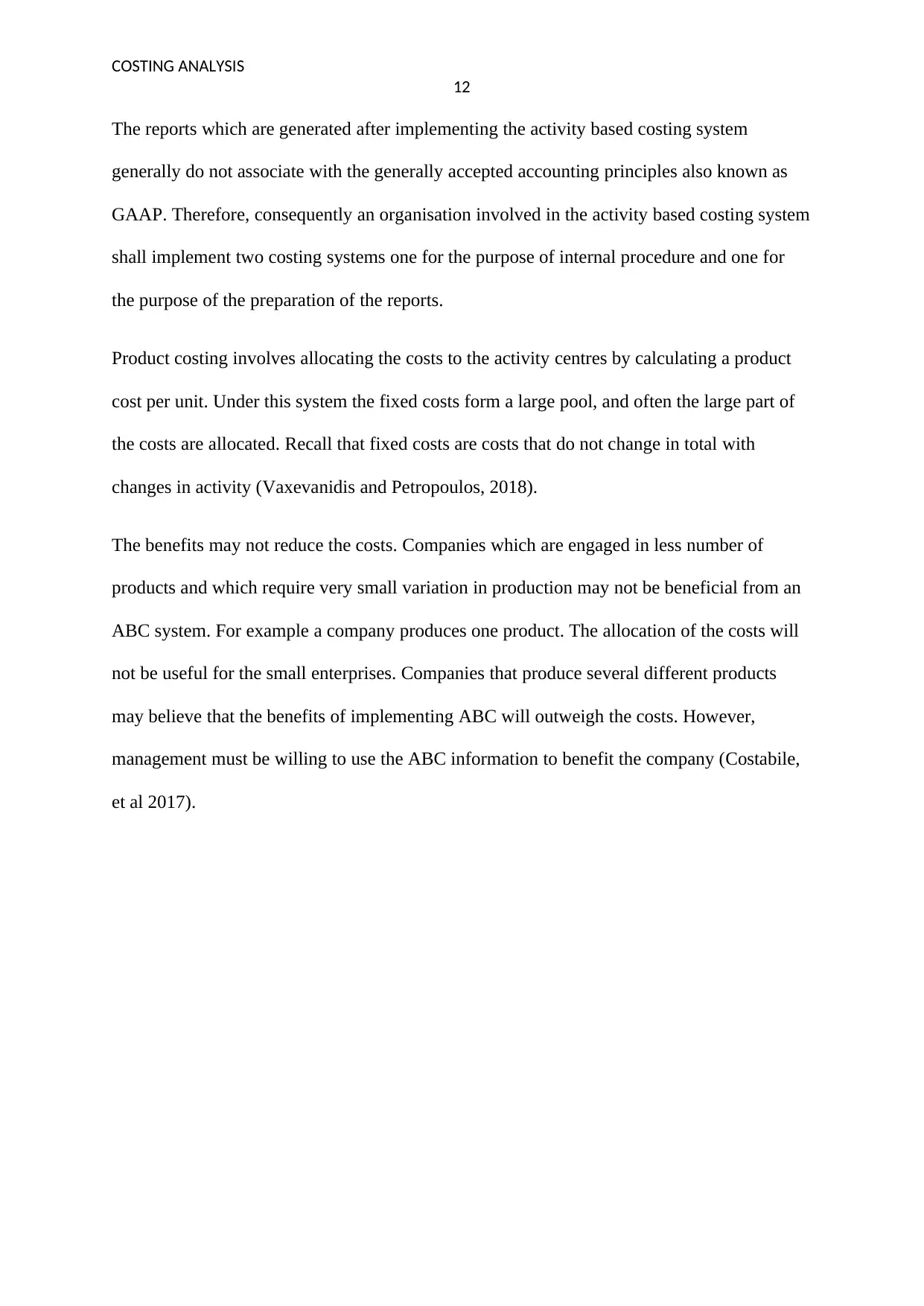
COSTING ANALYSIS
12
The reports which are generated after implementing the activity based costing system
generally do not associate with the generally accepted accounting principles also known as
GAAP. Therefore, consequently an organisation involved in the activity based costing system
shall implement two costing systems one for the purpose of internal procedure and one for
the purpose of the preparation of the reports.
Product costing involves allocating the costs to the activity centres by calculating a product
cost per unit. Under this system the fixed costs form a large pool, and often the large part of
the costs are allocated. Recall that fixed costs are costs that do not change in total with
changes in activity (Vaxevanidis and Petropoulos, 2018).
The benefits may not reduce the costs. Companies which are engaged in less number of
products and which require very small variation in production may not be beneficial from an
ABC system. For example a company produces one product. The allocation of the costs will
not be useful for the small enterprises. Companies that produce several different products
may believe that the benefits of implementing ABC will outweigh the costs. However,
management must be willing to use the ABC information to benefit the company (Costabile,
et al 2017).
12
The reports which are generated after implementing the activity based costing system
generally do not associate with the generally accepted accounting principles also known as
GAAP. Therefore, consequently an organisation involved in the activity based costing system
shall implement two costing systems one for the purpose of internal procedure and one for
the purpose of the preparation of the reports.
Product costing involves allocating the costs to the activity centres by calculating a product
cost per unit. Under this system the fixed costs form a large pool, and often the large part of
the costs are allocated. Recall that fixed costs are costs that do not change in total with
changes in activity (Vaxevanidis and Petropoulos, 2018).
The benefits may not reduce the costs. Companies which are engaged in less number of
products and which require very small variation in production may not be beneficial from an
ABC system. For example a company produces one product. The allocation of the costs will
not be useful for the small enterprises. Companies that produce several different products
may believe that the benefits of implementing ABC will outweigh the costs. However,
management must be willing to use the ABC information to benefit the company (Costabile,
et al 2017).
Paraphrase This Document
Need a fresh take? Get an instant paraphrase of this document with our AI Paraphraser
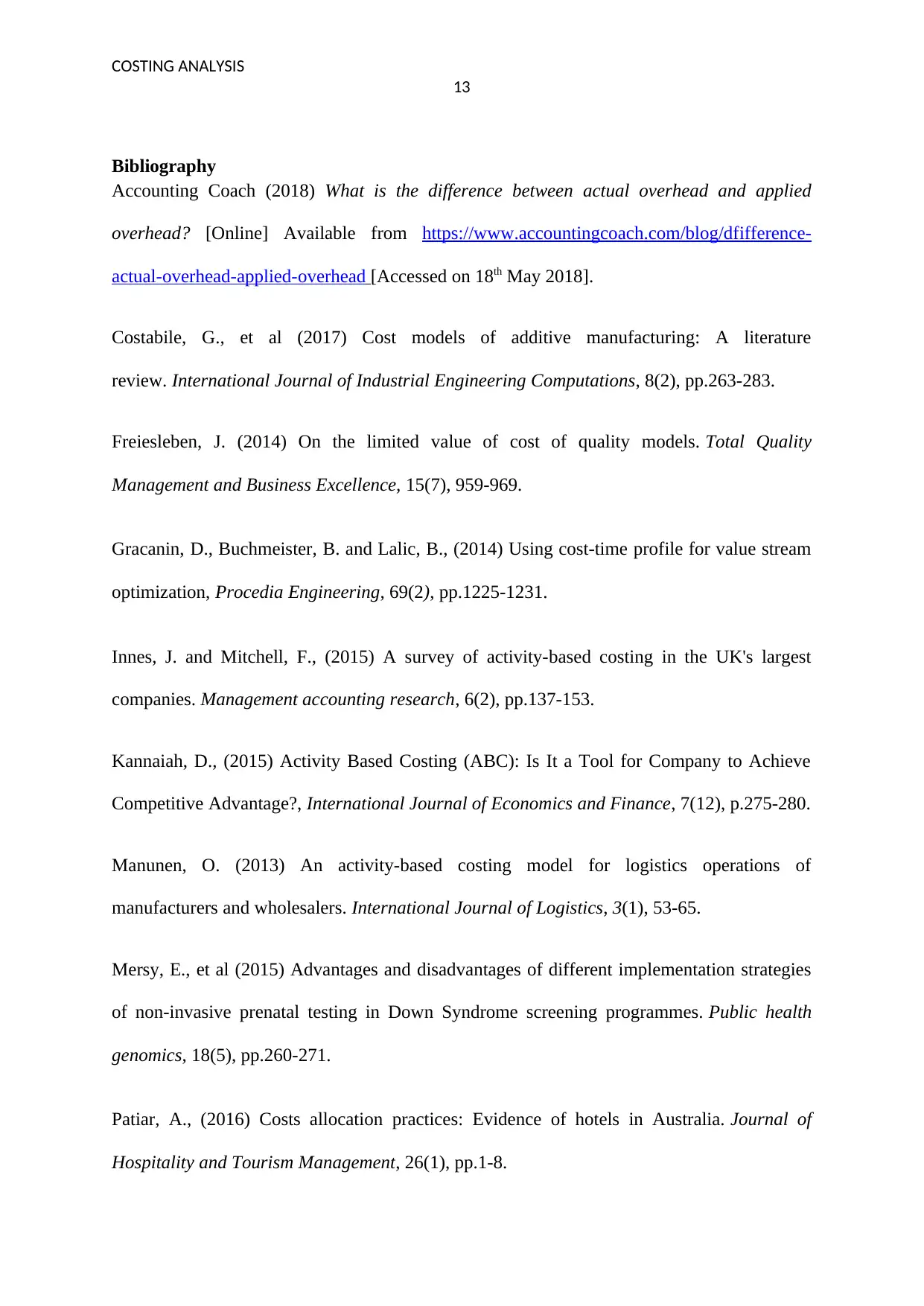
COSTING ANALYSIS
13
Bibliography
Accounting Coach (2018) What is the difference between actual overhead and applied
overhead? [Online] Available from https://www.accountingcoach.com/blog/dfifference-
actual-overhead-applied-overhead [Accessed on 18th May 2018].
Costabile, G., et al (2017) Cost models of additive manufacturing: A literature
review. International Journal of Industrial Engineering Computations, 8(2), pp.263-283.
Freiesleben, J. (2014) On the limited value of cost of quality models. Total Quality
Management and Business Excellence, 15(7), 959-969.
Gracanin, D., Buchmeister, B. and Lalic, B., (2014) Using cost-time profile for value stream
optimization, Procedia Engineering, 69(2), pp.1225-1231.
Innes, J. and Mitchell, F., (2015) A survey of activity-based costing in the UK's largest
companies. Management accounting research, 6(2), pp.137-153.
Kannaiah, D., (2015) Activity Based Costing (ABC): Is It a Tool for Company to Achieve
Competitive Advantage?, International Journal of Economics and Finance, 7(12), p.275-280.
Manunen, O. (2013) An activity-based costing model for logistics operations of
manufacturers and wholesalers. International Journal of Logistics, 3(1), 53-65.
Mersy, E., et al (2015) Advantages and disadvantages of different implementation strategies
of non-invasive prenatal testing in Down Syndrome screening programmes. Public health
genomics, 18(5), pp.260-271.
Patiar, A., (2016) Costs allocation practices: Evidence of hotels in Australia. Journal of
Hospitality and Tourism Management, 26(1), pp.1-8.
13
Bibliography
Accounting Coach (2018) What is the difference between actual overhead and applied
overhead? [Online] Available from https://www.accountingcoach.com/blog/dfifference-
actual-overhead-applied-overhead [Accessed on 18th May 2018].
Costabile, G., et al (2017) Cost models of additive manufacturing: A literature
review. International Journal of Industrial Engineering Computations, 8(2), pp.263-283.
Freiesleben, J. (2014) On the limited value of cost of quality models. Total Quality
Management and Business Excellence, 15(7), 959-969.
Gracanin, D., Buchmeister, B. and Lalic, B., (2014) Using cost-time profile for value stream
optimization, Procedia Engineering, 69(2), pp.1225-1231.
Innes, J. and Mitchell, F., (2015) A survey of activity-based costing in the UK's largest
companies. Management accounting research, 6(2), pp.137-153.
Kannaiah, D., (2015) Activity Based Costing (ABC): Is It a Tool for Company to Achieve
Competitive Advantage?, International Journal of Economics and Finance, 7(12), p.275-280.
Manunen, O. (2013) An activity-based costing model for logistics operations of
manufacturers and wholesalers. International Journal of Logistics, 3(1), 53-65.
Mersy, E., et al (2015) Advantages and disadvantages of different implementation strategies
of non-invasive prenatal testing in Down Syndrome screening programmes. Public health
genomics, 18(5), pp.260-271.
Patiar, A., (2016) Costs allocation practices: Evidence of hotels in Australia. Journal of
Hospitality and Tourism Management, 26(1), pp.1-8.
1 out of 14
Related Documents

Your All-in-One AI-Powered Toolkit for Academic Success.
+13062052269
info@desklib.com
Available 24*7 on WhatsApp / Email
Unlock your academic potential
© 2024 | Zucol Services PVT LTD | All rights reserved.