Evolution of Costing Models: Traditional, ABC, TDABC, and PFABC
VerifiedAdded on 2023/05/27
|12
|7264
|191
Report
AI Summary
This report examines the evolution of costing models, beginning with traditional costing and progressing to Activity Based Costing (ABC), Time Driven Activity Based Costing (TDABC), and Performance Focused Activity Based Costing (PFABC). It highlights the shortcomings of traditional costing, such as the use of a single cost driver and the allocation of overhead costs, which often leads to inaccurate cost prices. The report then introduces ABC, developed to address these issues by allocating costs based on activities. However, it acknowledges the challenges of ABC, including high implementation costs and complexities in data collection. TDABC is then presented as a simplified version of ABC, using time as a cost driver. Finally, the report discusses PFABC, which offers more flexibility in cost allocation by integrating aspects of both ABC and TDABC. The report emphasizes the importance of accurate cost information for managerial decision-making and highlights the ongoing need for costing systems to adapt to changes in technology and business environments.
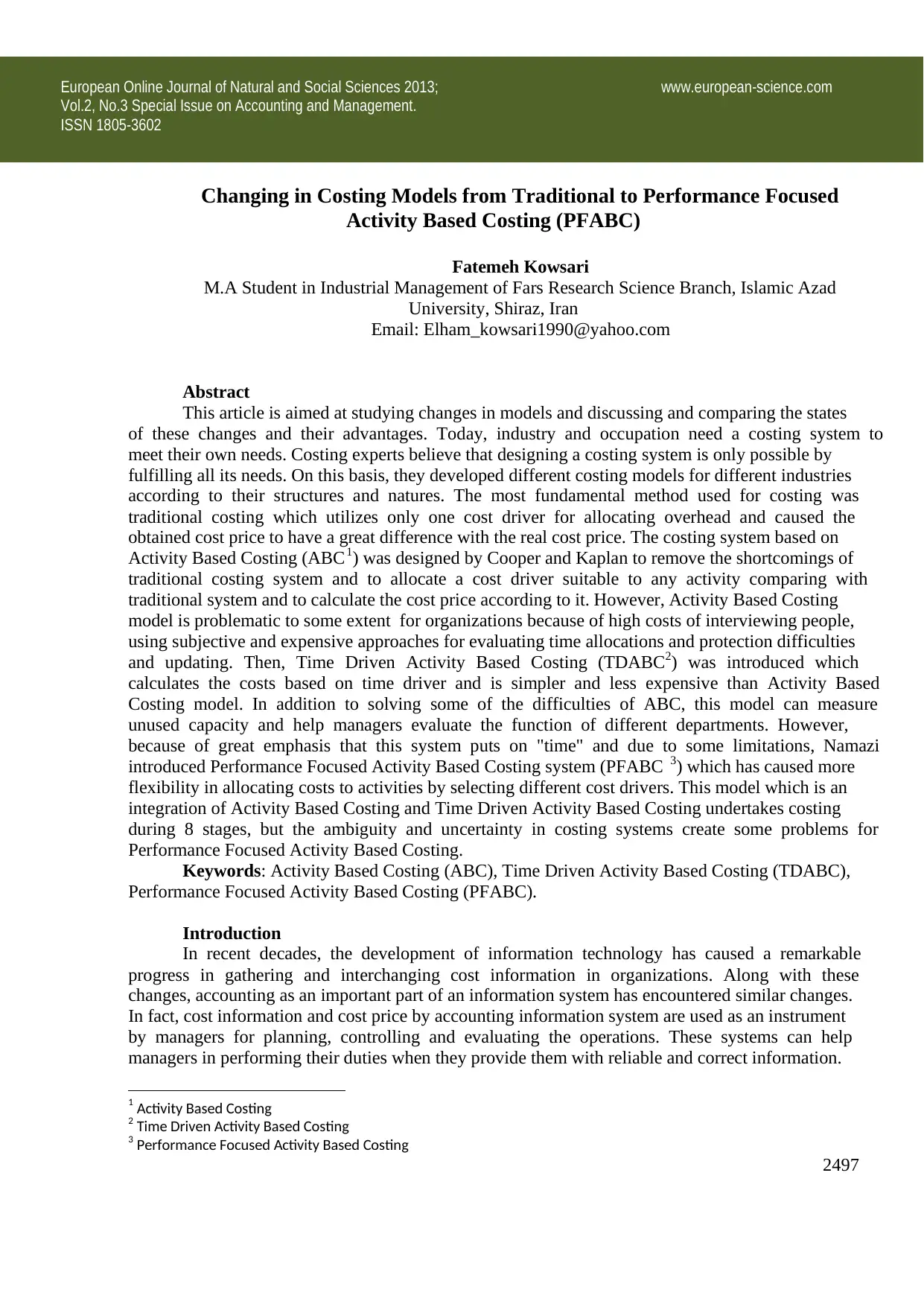
European Online Journal of Natural and Social Sciences 2013; www.european-science.com
Vol.2, No.3 Special Issue on Accounting and Management.
ISSN 1805-3602
2497
Changing in Costing Models from Traditional to Performance Focused
Activity Based Costing (PFABC)
Fatemeh Kowsari
M.A Student in Industrial Management of Fars Research Science Branch, Islamic Azad
University, Shiraz, Iran
Email: Elham_kowsari1990@yahoo.com
Abstract
This article is aimed at studying changes in models and discussing and comparing the states
of these changes and their advantages. Today, industry and occupation need a costing system to
meet their own needs. Costing experts believe that designing a costing system is only possible by
fulfilling all its needs. On this basis, they developed different costing models for different industries
according to their structures and natures. The most fundamental method used for costing was
traditional costing which utilizes only one cost driver for allocating overhead and caused the
obtained cost price to have a great difference with the real cost price. The costing system based on
Activity Based Costing (ABC1) was designed by Cooper and Kaplan to remove the shortcomings of
traditional costing system and to allocate a cost driver suitable to any activity comparing with
traditional system and to calculate the cost price according to it. However, Activity Based Costing
model is problematic to some extent for organizations because of high costs of interviewing people,
using subjective and expensive approaches for evaluating time allocations and protection difficulties
and updating. Then, Time Driven Activity Based Costing (TDABC2) was introduced which
calculates the costs based on time driver and is simpler and less expensive than Activity Based
Costing model. In addition to solving some of the difficulties of ABC, this model can measure
unused capacity and help managers evaluate the function of different departments. However,
because of great emphasis that this system puts on "time" and due to some limitations, Namazi
introduced Performance Focused Activity Based Costing system (PFABC 3) which has caused more
flexibility in allocating costs to activities by selecting different cost drivers. This model which is an
integration of Activity Based Costing and Time Driven Activity Based Costing undertakes costing
during 8 stages, but the ambiguity and uncertainty in costing systems create some problems for
Performance Focused Activity Based Costing.
Keywords: Activity Based Costing (ABC), Time Driven Activity Based Costing (TDABC),
Performance Focused Activity Based Costing (PFABC).
Introduction
In recent decades, the development of information technology has caused a remarkable
progress in gathering and interchanging cost information in organizations. Along with these
changes, accounting as an important part of an information system has encountered similar changes.
In fact, cost information and cost price by accounting information system are used as an instrument
by managers for planning, controlling and evaluating the operations. These systems can help
managers in performing their duties when they provide them with reliable and correct information.
1 Activity Based Costing
2 Time Driven Activity Based Costing
3 Performance Focused Activity Based Costing
Vol.2, No.3 Special Issue on Accounting and Management.
ISSN 1805-3602
2497
Changing in Costing Models from Traditional to Performance Focused
Activity Based Costing (PFABC)
Fatemeh Kowsari
M.A Student in Industrial Management of Fars Research Science Branch, Islamic Azad
University, Shiraz, Iran
Email: Elham_kowsari1990@yahoo.com
Abstract
This article is aimed at studying changes in models and discussing and comparing the states
of these changes and their advantages. Today, industry and occupation need a costing system to
meet their own needs. Costing experts believe that designing a costing system is only possible by
fulfilling all its needs. On this basis, they developed different costing models for different industries
according to their structures and natures. The most fundamental method used for costing was
traditional costing which utilizes only one cost driver for allocating overhead and caused the
obtained cost price to have a great difference with the real cost price. The costing system based on
Activity Based Costing (ABC1) was designed by Cooper and Kaplan to remove the shortcomings of
traditional costing system and to allocate a cost driver suitable to any activity comparing with
traditional system and to calculate the cost price according to it. However, Activity Based Costing
model is problematic to some extent for organizations because of high costs of interviewing people,
using subjective and expensive approaches for evaluating time allocations and protection difficulties
and updating. Then, Time Driven Activity Based Costing (TDABC2) was introduced which
calculates the costs based on time driver and is simpler and less expensive than Activity Based
Costing model. In addition to solving some of the difficulties of ABC, this model can measure
unused capacity and help managers evaluate the function of different departments. However,
because of great emphasis that this system puts on "time" and due to some limitations, Namazi
introduced Performance Focused Activity Based Costing system (PFABC 3) which has caused more
flexibility in allocating costs to activities by selecting different cost drivers. This model which is an
integration of Activity Based Costing and Time Driven Activity Based Costing undertakes costing
during 8 stages, but the ambiguity and uncertainty in costing systems create some problems for
Performance Focused Activity Based Costing.
Keywords: Activity Based Costing (ABC), Time Driven Activity Based Costing (TDABC),
Performance Focused Activity Based Costing (PFABC).
Introduction
In recent decades, the development of information technology has caused a remarkable
progress in gathering and interchanging cost information in organizations. Along with these
changes, accounting as an important part of an information system has encountered similar changes.
In fact, cost information and cost price by accounting information system are used as an instrument
by managers for planning, controlling and evaluating the operations. These systems can help
managers in performing their duties when they provide them with reliable and correct information.
1 Activity Based Costing
2 Time Driven Activity Based Costing
3 Performance Focused Activity Based Costing
Paraphrase This Document
Need a fresh take? Get an instant paraphrase of this document with our AI Paraphraser
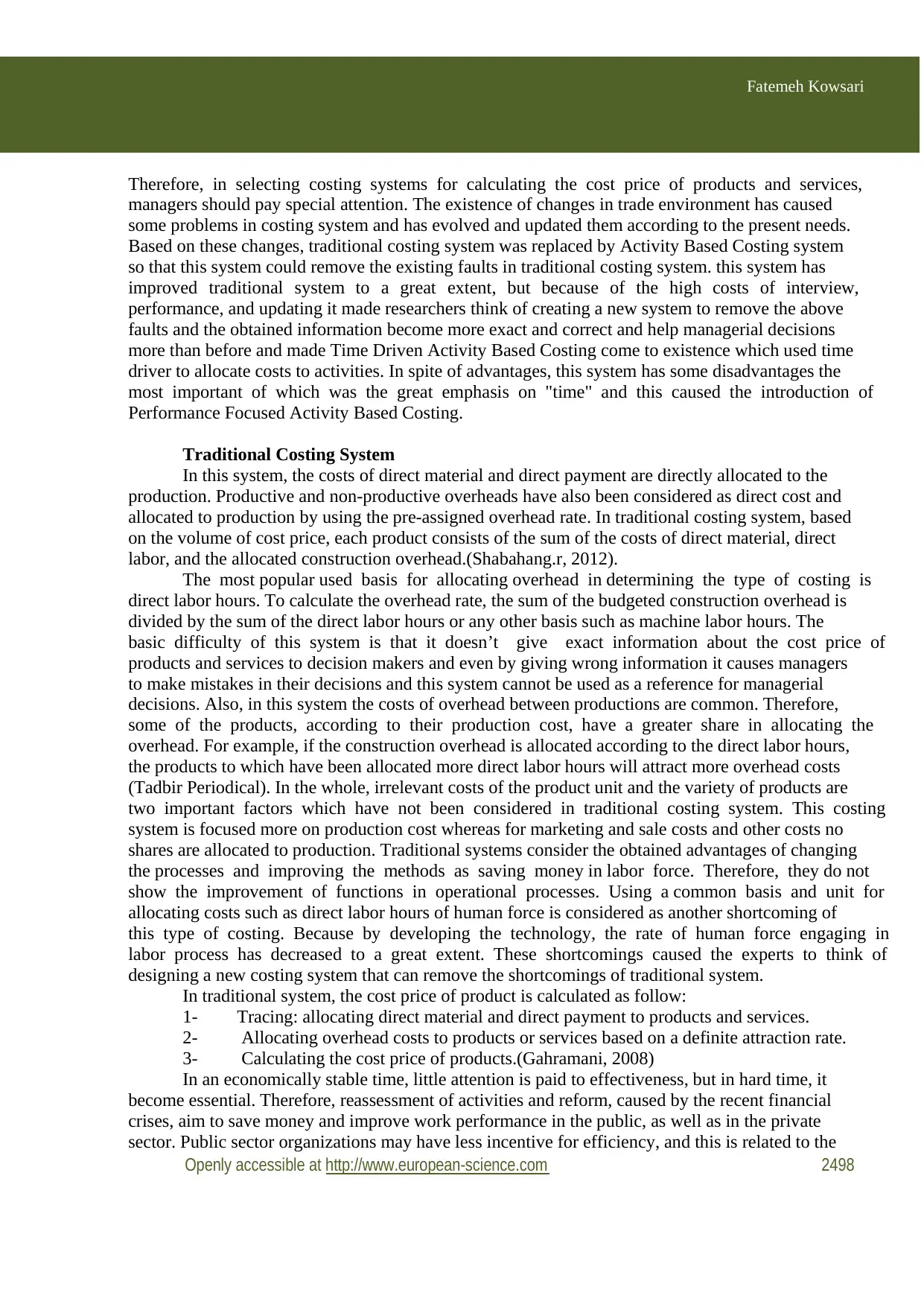
Fatemeh Kowsari
Openly accessible at http://www.european-science.com 2498
Therefore, in selecting costing systems for calculating the cost price of products and services,
managers should pay special attention. The existence of changes in trade environment has caused
some problems in costing system and has evolved and updated them according to the present needs.
Based on these changes, traditional costing system was replaced by Activity Based Costing system
so that this system could remove the existing faults in traditional costing system. this system has
improved traditional system to a great extent, but because of the high costs of interview,
performance, and updating it made researchers think of creating a new system to remove the above
faults and the obtained information become more exact and correct and help managerial decisions
more than before and made Time Driven Activity Based Costing come to existence which used time
driver to allocate costs to activities. In spite of advantages, this system has some disadvantages the
most important of which was the great emphasis on "time" and this caused the introduction of
Performance Focused Activity Based Costing.
Traditional Costing System
In this system, the costs of direct material and direct payment are directly allocated to the
production. Productive and non-productive overheads have also been considered as direct cost and
allocated to production by using the pre-assigned overhead rate. In traditional costing system, based
on the volume of cost price, each product consists of the sum of the costs of direct material, direct
labor, and the allocated construction overhead.(Shabahang.r, 2012).
The most popular used basis for allocating overhead in determining the type of costing is
direct labor hours. To calculate the overhead rate, the sum of the budgeted construction overhead is
divided by the sum of the direct labor hours or any other basis such as machine labor hours. The
basic difficulty of this system is that it doesn’t give exact information about the cost price of
products and services to decision makers and even by giving wrong information it causes managers
to make mistakes in their decisions and this system cannot be used as a reference for managerial
decisions. Also, in this system the costs of overhead between productions are common. Therefore,
some of the products, according to their production cost, have a greater share in allocating the
overhead. For example, if the construction overhead is allocated according to the direct labor hours,
the products to which have been allocated more direct labor hours will attract more overhead costs
(Tadbir Periodical). In the whole, irrelevant costs of the product unit and the variety of products are
two important factors which have not been considered in traditional costing system. This costing
system is focused more on production cost whereas for marketing and sale costs and other costs no
shares are allocated to production. Traditional systems consider the obtained advantages of changing
the processes and improving the methods as saving money in labor force. Therefore, they do not
show the improvement of functions in operational processes. Using a common basis and unit for
allocating costs such as direct labor hours of human force is considered as another shortcoming of
this type of costing. Because by developing the technology, the rate of human force engaging in
labor process has decreased to a great extent. These shortcomings caused the experts to think of
designing a new costing system that can remove the shortcomings of traditional system.
In traditional system, the cost price of product is calculated as follow:
1- Tracing: allocating direct material and direct payment to products and services.
2- Allocating overhead costs to products or services based on a definite attraction rate.
3- Calculating the cost price of products.(Gahramani, 2008)
In an economically stable time, little attention is paid to effectiveness, but in hard time, it
become essential. Therefore, reassessment of activities and reform, caused by the recent financial
crises, aim to save money and improve work performance in the public, as well as in the private
sector. Public sector organizations may have less incentive for efficiency, and this is related to the
Openly accessible at http://www.european-science.com 2498
Therefore, in selecting costing systems for calculating the cost price of products and services,
managers should pay special attention. The existence of changes in trade environment has caused
some problems in costing system and has evolved and updated them according to the present needs.
Based on these changes, traditional costing system was replaced by Activity Based Costing system
so that this system could remove the existing faults in traditional costing system. this system has
improved traditional system to a great extent, but because of the high costs of interview,
performance, and updating it made researchers think of creating a new system to remove the above
faults and the obtained information become more exact and correct and help managerial decisions
more than before and made Time Driven Activity Based Costing come to existence which used time
driver to allocate costs to activities. In spite of advantages, this system has some disadvantages the
most important of which was the great emphasis on "time" and this caused the introduction of
Performance Focused Activity Based Costing.
Traditional Costing System
In this system, the costs of direct material and direct payment are directly allocated to the
production. Productive and non-productive overheads have also been considered as direct cost and
allocated to production by using the pre-assigned overhead rate. In traditional costing system, based
on the volume of cost price, each product consists of the sum of the costs of direct material, direct
labor, and the allocated construction overhead.(Shabahang.r, 2012).
The most popular used basis for allocating overhead in determining the type of costing is
direct labor hours. To calculate the overhead rate, the sum of the budgeted construction overhead is
divided by the sum of the direct labor hours or any other basis such as machine labor hours. The
basic difficulty of this system is that it doesn’t give exact information about the cost price of
products and services to decision makers and even by giving wrong information it causes managers
to make mistakes in their decisions and this system cannot be used as a reference for managerial
decisions. Also, in this system the costs of overhead between productions are common. Therefore,
some of the products, according to their production cost, have a greater share in allocating the
overhead. For example, if the construction overhead is allocated according to the direct labor hours,
the products to which have been allocated more direct labor hours will attract more overhead costs
(Tadbir Periodical). In the whole, irrelevant costs of the product unit and the variety of products are
two important factors which have not been considered in traditional costing system. This costing
system is focused more on production cost whereas for marketing and sale costs and other costs no
shares are allocated to production. Traditional systems consider the obtained advantages of changing
the processes and improving the methods as saving money in labor force. Therefore, they do not
show the improvement of functions in operational processes. Using a common basis and unit for
allocating costs such as direct labor hours of human force is considered as another shortcoming of
this type of costing. Because by developing the technology, the rate of human force engaging in
labor process has decreased to a great extent. These shortcomings caused the experts to think of
designing a new costing system that can remove the shortcomings of traditional system.
In traditional system, the cost price of product is calculated as follow:
1- Tracing: allocating direct material and direct payment to products and services.
2- Allocating overhead costs to products or services based on a definite attraction rate.
3- Calculating the cost price of products.(Gahramani, 2008)
In an economically stable time, little attention is paid to effectiveness, but in hard time, it
become essential. Therefore, reassessment of activities and reform, caused by the recent financial
crises, aim to save money and improve work performance in the public, as well as in the private
sector. Public sector organizations may have less incentive for efficiency, and this is related to the
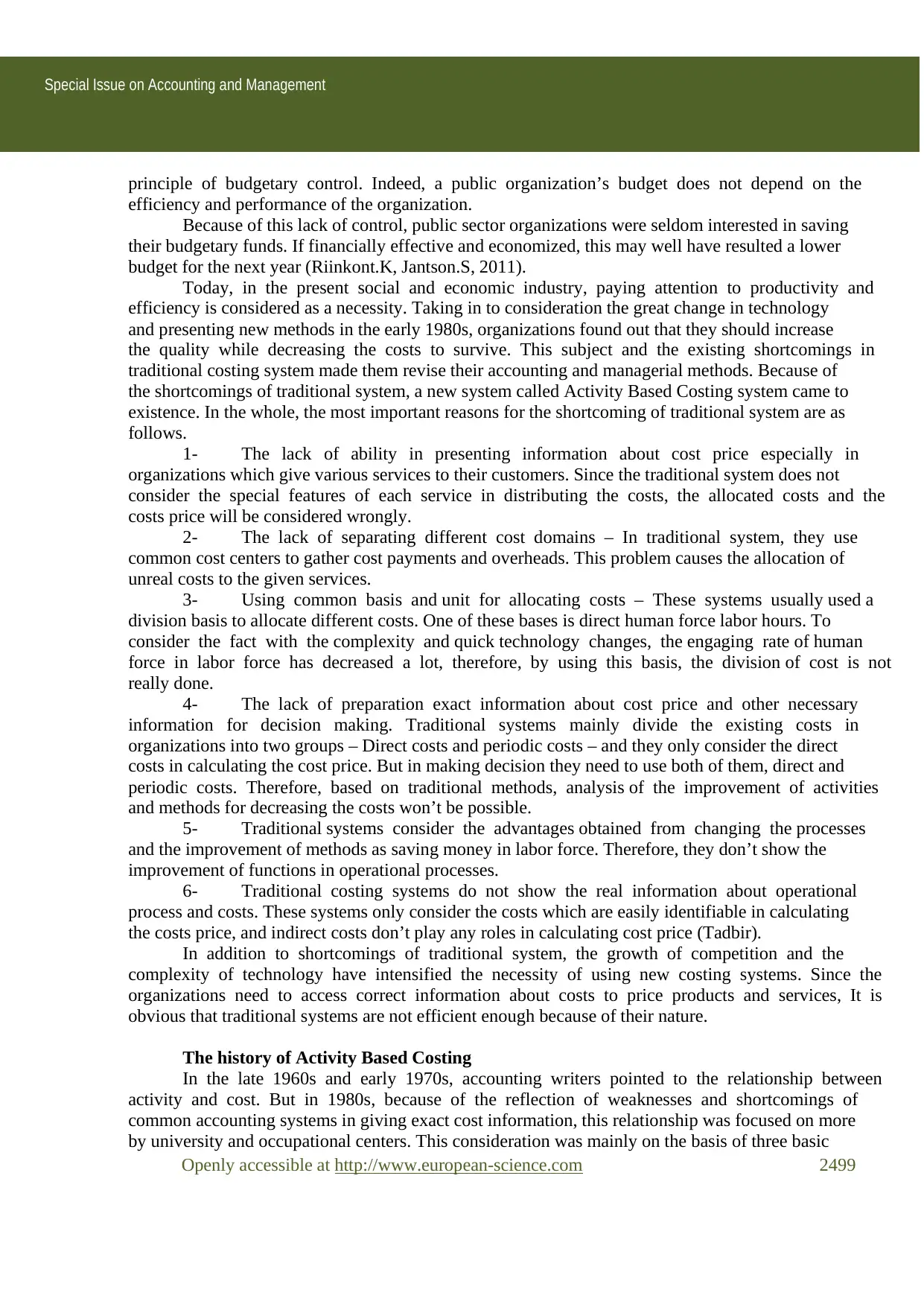
Special Issue on Accounting and Management
Openly accessible at http://www.european-science.com 2499
principle of budgetary control. Indeed, a public organization’s budget does not depend on the
efficiency and performance of the organization.
Because of this lack of control, public sector organizations were seldom interested in saving
their budgetary funds. If financially effective and economized, this may well have resulted a lower
budget for the next year (Riinkont.K, Jantson.S, 2011).
Today, in the present social and economic industry, paying attention to productivity and
efficiency is considered as a necessity. Taking in to consideration the great change in technology
and presenting new methods in the early 1980s, organizations found out that they should increase
the quality while decreasing the costs to survive. This subject and the existing shortcomings in
traditional costing system made them revise their accounting and managerial methods. Because of
the shortcomings of traditional system, a new system called Activity Based Costing system came to
existence. In the whole, the most important reasons for the shortcoming of traditional system are as
follows.
1- The lack of ability in presenting information about cost price especially in
organizations which give various services to their customers. Since the traditional system does not
consider the special features of each service in distributing the costs, the allocated costs and the
costs price will be considered wrongly.
2- The lack of separating different cost domains – In traditional system, they use
common cost centers to gather cost payments and overheads. This problem causes the allocation of
unreal costs to the given services.
3- Using common basis and unit for allocating costs – These systems usually used a
division basis to allocate different costs. One of these bases is direct human force labor hours. To
consider the fact with the complexity and quick technology changes, the engaging rate of human
force in labor force has decreased a lot, therefore, by using this basis, the division of cost is not
really done.
4- The lack of preparation exact information about cost price and other necessary
information for decision making. Traditional systems mainly divide the existing costs in
organizations into two groups – Direct costs and periodic costs – and they only consider the direct
costs in calculating the cost price. But in making decision they need to use both of them, direct and
periodic costs. Therefore, based on traditional methods, analysis of the improvement of activities
and methods for decreasing the costs won’t be possible.
5- Traditional systems consider the advantages obtained from changing the processes
and the improvement of methods as saving money in labor force. Therefore, they don’t show the
improvement of functions in operational processes.
6- Traditional costing systems do not show the real information about operational
process and costs. These systems only consider the costs which are easily identifiable in calculating
the costs price, and indirect costs don’t play any roles in calculating cost price (Tadbir).
In addition to shortcomings of traditional system, the growth of competition and the
complexity of technology have intensified the necessity of using new costing systems. Since the
organizations need to access correct information about costs to price products and services, It is
obvious that traditional systems are not efficient enough because of their nature.
The history of Activity Based Costing
In the late 1960s and early 1970s, accounting writers pointed to the relationship between
activity and cost. But in 1980s, because of the reflection of weaknesses and shortcomings of
common accounting systems in giving exact cost information, this relationship was focused on more
by university and occupational centers. This consideration was mainly on the basis of three basic
Openly accessible at http://www.european-science.com 2499
principle of budgetary control. Indeed, a public organization’s budget does not depend on the
efficiency and performance of the organization.
Because of this lack of control, public sector organizations were seldom interested in saving
their budgetary funds. If financially effective and economized, this may well have resulted a lower
budget for the next year (Riinkont.K, Jantson.S, 2011).
Today, in the present social and economic industry, paying attention to productivity and
efficiency is considered as a necessity. Taking in to consideration the great change in technology
and presenting new methods in the early 1980s, organizations found out that they should increase
the quality while decreasing the costs to survive. This subject and the existing shortcomings in
traditional costing system made them revise their accounting and managerial methods. Because of
the shortcomings of traditional system, a new system called Activity Based Costing system came to
existence. In the whole, the most important reasons for the shortcoming of traditional system are as
follows.
1- The lack of ability in presenting information about cost price especially in
organizations which give various services to their customers. Since the traditional system does not
consider the special features of each service in distributing the costs, the allocated costs and the
costs price will be considered wrongly.
2- The lack of separating different cost domains – In traditional system, they use
common cost centers to gather cost payments and overheads. This problem causes the allocation of
unreal costs to the given services.
3- Using common basis and unit for allocating costs – These systems usually used a
division basis to allocate different costs. One of these bases is direct human force labor hours. To
consider the fact with the complexity and quick technology changes, the engaging rate of human
force in labor force has decreased a lot, therefore, by using this basis, the division of cost is not
really done.
4- The lack of preparation exact information about cost price and other necessary
information for decision making. Traditional systems mainly divide the existing costs in
organizations into two groups – Direct costs and periodic costs – and they only consider the direct
costs in calculating the cost price. But in making decision they need to use both of them, direct and
periodic costs. Therefore, based on traditional methods, analysis of the improvement of activities
and methods for decreasing the costs won’t be possible.
5- Traditional systems consider the advantages obtained from changing the processes
and the improvement of methods as saving money in labor force. Therefore, they don’t show the
improvement of functions in operational processes.
6- Traditional costing systems do not show the real information about operational
process and costs. These systems only consider the costs which are easily identifiable in calculating
the costs price, and indirect costs don’t play any roles in calculating cost price (Tadbir).
In addition to shortcomings of traditional system, the growth of competition and the
complexity of technology have intensified the necessity of using new costing systems. Since the
organizations need to access correct information about costs to price products and services, It is
obvious that traditional systems are not efficient enough because of their nature.
The history of Activity Based Costing
In the late 1960s and early 1970s, accounting writers pointed to the relationship between
activity and cost. But in 1980s, because of the reflection of weaknesses and shortcomings of
common accounting systems in giving exact cost information, this relationship was focused on more
by university and occupational centers. This consideration was mainly on the basis of three basic
You're viewing a preview
Unlock full access by subscribing today!
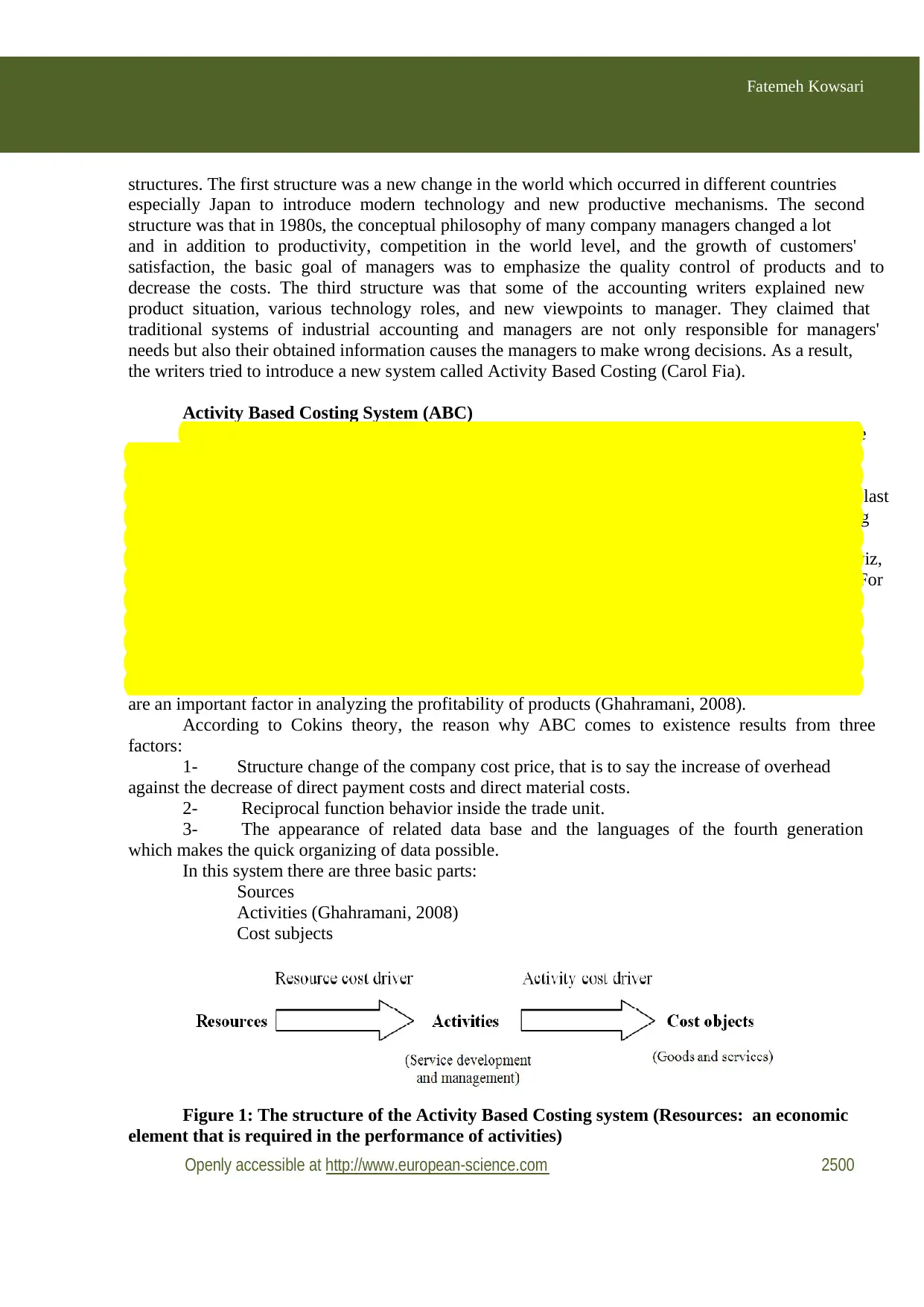
Fatemeh Kowsari
Openly accessible at http://www.european-science.com 2500
structures. The first structure was a new change in the world which occurred in different countries
especially Japan to introduce modern technology and new productive mechanisms. The second
structure was that in 1980s, the conceptual philosophy of many company managers changed a lot
and in addition to productivity, competition in the world level, and the growth of customers'
satisfaction, the basic goal of managers was to emphasize the quality control of products and to
decrease the costs. The third structure was that some of the accounting writers explained new
product situation, various technology roles, and new viewpoints to manager. They claimed that
traditional systems of industrial accounting and managers are not only responsible for managers'
needs but also their obtained information causes the managers to make wrong decisions. As a result,
the writers tried to introduce a new system called Activity Based Costing (Carol Fia).
Activity Based Costing System (ABC)
Cooper and Kaplan along with Johnson (1980) have an important role in reflecting the
shortcomings of management accounting system in giving exact cost information. In 1980s, Cooper
and Kaplan suggested Activity Based Costing for the first time and it was used as a creative
invention. ABC is used as the best known method in management accounting during several last
years. In fact, in response to the need of production sector to face the dissatisfaction of using
traditional costing system, this approach depends on allocating overhead to products. In the whole, it
is not logical to use traditional approach in modern production environment (Alinezhad & Saviz,
2013). Today, most of remarkable costs in producing an item are not related to its volume. For
instance, the costs of engineering, order processing, planning, and quality controlling, or the costs of
delivering the products in time don’t relate to the production volume (Riinkont & Jantson,
2011).Activity Based Costing consist of the ability of measuring real sources used by daily activities
of a company that the obtained information of this kind of costing is considered as supporting the
management decision making. Activities done on the basis of costs related to each of the products
are an important factor in analyzing the profitability of products (Ghahramani, 2008).
According to Cokins theory, the reason why ABC comes to existence results from three
factors:
1- Structure change of the company cost price, that is to say the increase of overhead
against the decrease of direct payment costs and direct material costs.
2- Reciprocal function behavior inside the trade unit.
3- The appearance of related data base and the languages of the fourth generation
which makes the quick organizing of data possible.
In this system there are three basic parts:
Sources
Activities (Ghahramani, 2008)
Cost subjects
Figure 1: The structure of the Activity Based Costing system (Resources: an economic
element that is required in the performance of activities)
Openly accessible at http://www.european-science.com 2500
structures. The first structure was a new change in the world which occurred in different countries
especially Japan to introduce modern technology and new productive mechanisms. The second
structure was that in 1980s, the conceptual philosophy of many company managers changed a lot
and in addition to productivity, competition in the world level, and the growth of customers'
satisfaction, the basic goal of managers was to emphasize the quality control of products and to
decrease the costs. The third structure was that some of the accounting writers explained new
product situation, various technology roles, and new viewpoints to manager. They claimed that
traditional systems of industrial accounting and managers are not only responsible for managers'
needs but also their obtained information causes the managers to make wrong decisions. As a result,
the writers tried to introduce a new system called Activity Based Costing (Carol Fia).
Activity Based Costing System (ABC)
Cooper and Kaplan along with Johnson (1980) have an important role in reflecting the
shortcomings of management accounting system in giving exact cost information. In 1980s, Cooper
and Kaplan suggested Activity Based Costing for the first time and it was used as a creative
invention. ABC is used as the best known method in management accounting during several last
years. In fact, in response to the need of production sector to face the dissatisfaction of using
traditional costing system, this approach depends on allocating overhead to products. In the whole, it
is not logical to use traditional approach in modern production environment (Alinezhad & Saviz,
2013). Today, most of remarkable costs in producing an item are not related to its volume. For
instance, the costs of engineering, order processing, planning, and quality controlling, or the costs of
delivering the products in time don’t relate to the production volume (Riinkont & Jantson,
2011).Activity Based Costing consist of the ability of measuring real sources used by daily activities
of a company that the obtained information of this kind of costing is considered as supporting the
management decision making. Activities done on the basis of costs related to each of the products
are an important factor in analyzing the profitability of products (Ghahramani, 2008).
According to Cokins theory, the reason why ABC comes to existence results from three
factors:
1- Structure change of the company cost price, that is to say the increase of overhead
against the decrease of direct payment costs and direct material costs.
2- Reciprocal function behavior inside the trade unit.
3- The appearance of related data base and the languages of the fourth generation
which makes the quick organizing of data possible.
In this system there are three basic parts:
Sources
Activities (Ghahramani, 2008)
Cost subjects
Figure 1: The structure of the Activity Based Costing system (Resources: an economic
element that is required in the performance of activities)
Paraphrase This Document
Need a fresh take? Get an instant paraphrase of this document with our AI Paraphraser
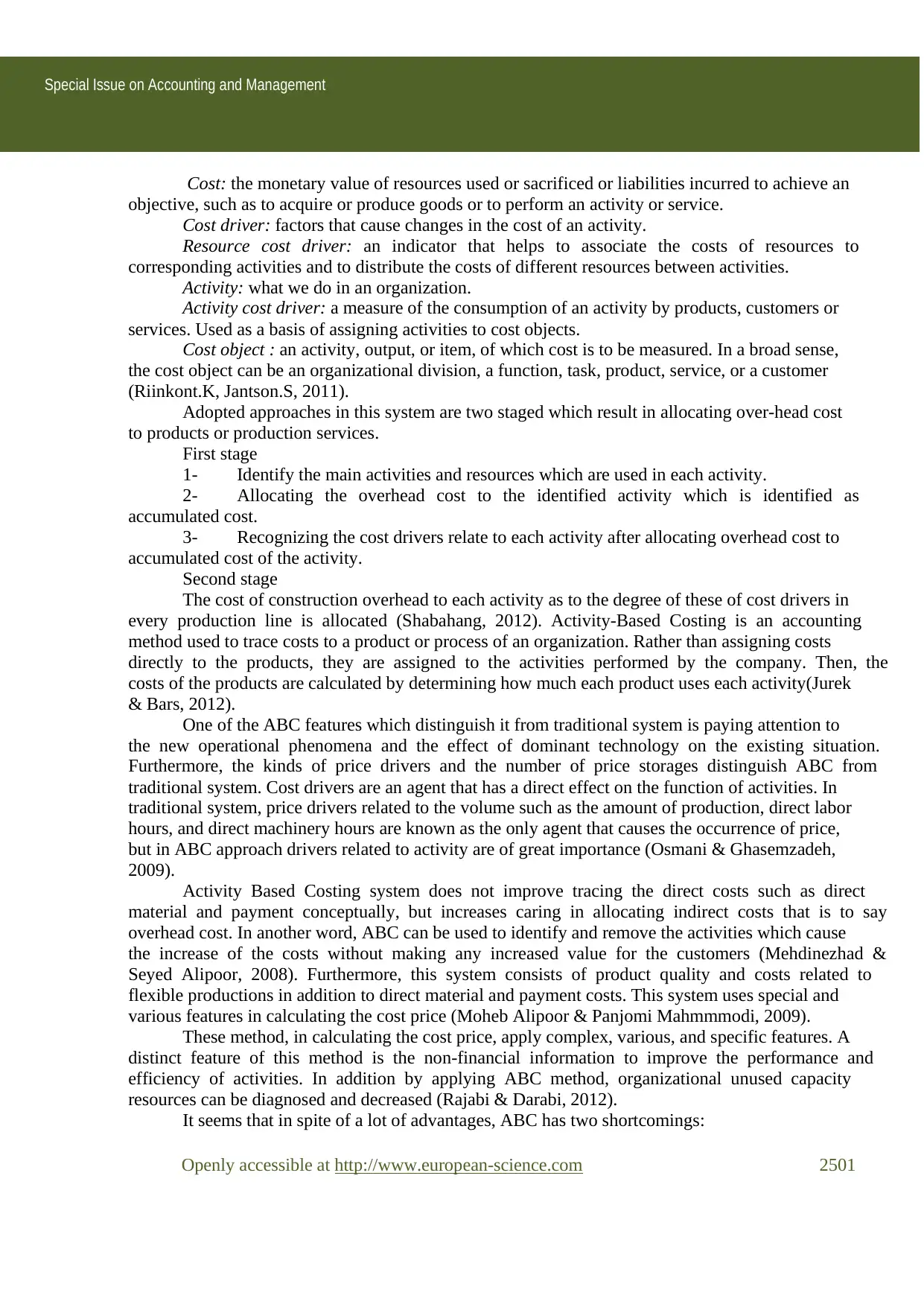
Special Issue on Accounting and Management
Openly accessible at http://www.european-science.com 2501
Cost: the monetary value of resources used or sacrificed or liabilities incurred to achieve an
objective, such as to acquire or produce goods or to perform an activity or service.
Cost driver: factors that cause changes in the cost of an activity.
Resource cost driver: an indicator that helps to associate the costs of resources to
corresponding activities and to distribute the costs of different resources between activities.
Activity: what we do in an organization.
Activity cost driver: a measure of the consumption of an activity by products, customers or
services. Used as a basis of assigning activities to cost objects.
Cost object : an activity, output, or item, of which cost is to be measured. In a broad sense,
the cost object can be an organizational division, a function, task, product, service, or a customer
(Riinkont.K, Jantson.S, 2011).
Adopted approaches in this system are two staged which result in allocating over-head cost
to products or production services.
First stage
1- Identify the main activities and resources which are used in each activity.
2- Allocating the overhead cost to the identified activity which is identified as
accumulated cost.
3- Recognizing the cost drivers relate to each activity after allocating overhead cost to
accumulated cost of the activity.
Second stage
The cost of construction overhead to each activity as to the degree of these of cost drivers in
every production line is allocated (Shabahang, 2012). Activity-Based Costing is an accounting
method used to trace costs to a product or process of an organization. Rather than assigning costs
directly to the products, they are assigned to the activities performed by the company. Then, the
costs of the products are calculated by determining how much each product uses each activity(Jurek
& Bars, 2012).
One of the ABC features which distinguish it from traditional system is paying attention to
the new operational phenomena and the effect of dominant technology on the existing situation.
Furthermore, the kinds of price drivers and the number of price storages distinguish ABC from
traditional system. Cost drivers are an agent that has a direct effect on the function of activities. In
traditional system, price drivers related to the volume such as the amount of production, direct labor
hours, and direct machinery hours are known as the only agent that causes the occurrence of price,
but in ABC approach drivers related to activity are of great importance (Osmani & Ghasemzadeh,
2009).
Activity Based Costing system does not improve tracing the direct costs such as direct
material and payment conceptually, but increases caring in allocating indirect costs that is to say
overhead cost. In another word, ABC can be used to identify and remove the activities which cause
the increase of the costs without making any increased value for the customers (Mehdinezhad &
Seyed Alipoor, 2008). Furthermore, this system consists of product quality and costs related to
flexible productions in addition to direct material and payment costs. This system uses special and
various features in calculating the cost price (Moheb Alipoor & Panjomi Mahmmmodi, 2009).
These method, in calculating the cost price, apply complex, various, and specific features. A
distinct feature of this method is the non-financial information to improve the performance and
efficiency of activities. In addition by applying ABC method, organizational unused capacity
resources can be diagnosed and decreased (Rajabi & Darabi, 2012).
It seems that in spite of a lot of advantages, ABC has two shortcomings:
Openly accessible at http://www.european-science.com 2501
Cost: the monetary value of resources used or sacrificed or liabilities incurred to achieve an
objective, such as to acquire or produce goods or to perform an activity or service.
Cost driver: factors that cause changes in the cost of an activity.
Resource cost driver: an indicator that helps to associate the costs of resources to
corresponding activities and to distribute the costs of different resources between activities.
Activity: what we do in an organization.
Activity cost driver: a measure of the consumption of an activity by products, customers or
services. Used as a basis of assigning activities to cost objects.
Cost object : an activity, output, or item, of which cost is to be measured. In a broad sense,
the cost object can be an organizational division, a function, task, product, service, or a customer
(Riinkont.K, Jantson.S, 2011).
Adopted approaches in this system are two staged which result in allocating over-head cost
to products or production services.
First stage
1- Identify the main activities and resources which are used in each activity.
2- Allocating the overhead cost to the identified activity which is identified as
accumulated cost.
3- Recognizing the cost drivers relate to each activity after allocating overhead cost to
accumulated cost of the activity.
Second stage
The cost of construction overhead to each activity as to the degree of these of cost drivers in
every production line is allocated (Shabahang, 2012). Activity-Based Costing is an accounting
method used to trace costs to a product or process of an organization. Rather than assigning costs
directly to the products, they are assigned to the activities performed by the company. Then, the
costs of the products are calculated by determining how much each product uses each activity(Jurek
& Bars, 2012).
One of the ABC features which distinguish it from traditional system is paying attention to
the new operational phenomena and the effect of dominant technology on the existing situation.
Furthermore, the kinds of price drivers and the number of price storages distinguish ABC from
traditional system. Cost drivers are an agent that has a direct effect on the function of activities. In
traditional system, price drivers related to the volume such as the amount of production, direct labor
hours, and direct machinery hours are known as the only agent that causes the occurrence of price,
but in ABC approach drivers related to activity are of great importance (Osmani & Ghasemzadeh,
2009).
Activity Based Costing system does not improve tracing the direct costs such as direct
material and payment conceptually, but increases caring in allocating indirect costs that is to say
overhead cost. In another word, ABC can be used to identify and remove the activities which cause
the increase of the costs without making any increased value for the customers (Mehdinezhad &
Seyed Alipoor, 2008). Furthermore, this system consists of product quality and costs related to
flexible productions in addition to direct material and payment costs. This system uses special and
various features in calculating the cost price (Moheb Alipoor & Panjomi Mahmmmodi, 2009).
These method, in calculating the cost price, apply complex, various, and specific features. A
distinct feature of this method is the non-financial information to improve the performance and
efficiency of activities. In addition by applying ABC method, organizational unused capacity
resources can be diagnosed and decreased (Rajabi & Darabi, 2012).
It seems that in spite of a lot of advantages, ABC has two shortcomings:
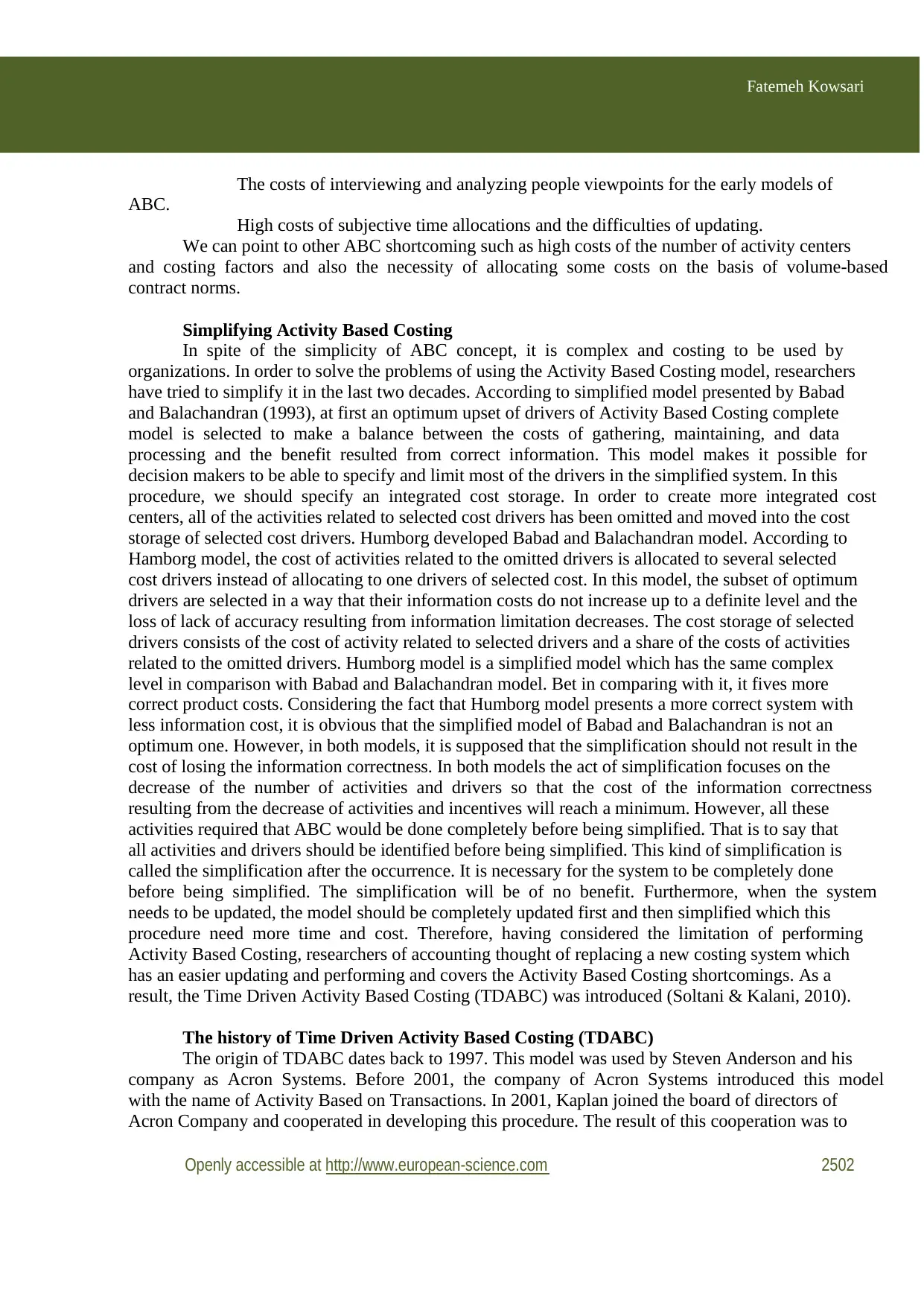
Fatemeh Kowsari
Openly accessible at http://www.european-science.com 2502
The costs of interviewing and analyzing people viewpoints for the early models of
ABC.
High costs of subjective time allocations and the difficulties of updating.
We can point to other ABC shortcoming such as high costs of the number of activity centers
and costing factors and also the necessity of allocating some costs on the basis of volume-based
contract norms.
Simplifying Activity Based Costing
In spite of the simplicity of ABC concept, it is complex and costing to be used by
organizations. In order to solve the problems of using the Activity Based Costing model, researchers
have tried to simplify it in the last two decades. According to simplified model presented by Babad
and Balachandran (1993), at first an optimum upset of drivers of Activity Based Costing complete
model is selected to make a balance between the costs of gathering, maintaining, and data
processing and the benefit resulted from correct information. This model makes it possible for
decision makers to be able to specify and limit most of the drivers in the simplified system. In this
procedure, we should specify an integrated cost storage. In order to create more integrated cost
centers, all of the activities related to selected cost drivers has been omitted and moved into the cost
storage of selected cost drivers. Humborg developed Babad and Balachandran model. According to
Hamborg model, the cost of activities related to the omitted drivers is allocated to several selected
cost drivers instead of allocating to one drivers of selected cost. In this model, the subset of optimum
drivers are selected in a way that their information costs do not increase up to a definite level and the
loss of lack of accuracy resulting from information limitation decreases. The cost storage of selected
drivers consists of the cost of activity related to selected drivers and a share of the costs of activities
related to the omitted drivers. Humborg model is a simplified model which has the same complex
level in comparison with Babad and Balachandran model. Bet in comparing with it, it fives more
correct product costs. Considering the fact that Humborg model presents a more correct system with
less information cost, it is obvious that the simplified model of Babad and Balachandran is not an
optimum one. However, in both models, it is supposed that the simplification should not result in the
cost of losing the information correctness. In both models the act of simplification focuses on the
decrease of the number of activities and drivers so that the cost of the information correctness
resulting from the decrease of activities and incentives will reach a minimum. However, all these
activities required that ABC would be done completely before being simplified. That is to say that
all activities and drivers should be identified before being simplified. This kind of simplification is
called the simplification after the occurrence. It is necessary for the system to be completely done
before being simplified. The simplification will be of no benefit. Furthermore, when the system
needs to be updated, the model should be completely updated first and then simplified which this
procedure need more time and cost. Therefore, having considered the limitation of performing
Activity Based Costing, researchers of accounting thought of replacing a new costing system which
has an easier updating and performing and covers the Activity Based Costing shortcomings. As a
result, the Time Driven Activity Based Costing (TDABC) was introduced (Soltani & Kalani, 2010).
The history of Time Driven Activity Based Costing (TDABC)
The origin of TDABC dates back to 1997. This model was used by Steven Anderson and his
company as Acron Systems. Before 2001, the company of Acron Systems introduced this model
with the name of Activity Based on Transactions. In 2001, Kaplan joined the board of directors of
Acron Company and cooperated in developing this procedure. The result of this cooperation was to
Openly accessible at http://www.european-science.com 2502
The costs of interviewing and analyzing people viewpoints for the early models of
ABC.
High costs of subjective time allocations and the difficulties of updating.
We can point to other ABC shortcoming such as high costs of the number of activity centers
and costing factors and also the necessity of allocating some costs on the basis of volume-based
contract norms.
Simplifying Activity Based Costing
In spite of the simplicity of ABC concept, it is complex and costing to be used by
organizations. In order to solve the problems of using the Activity Based Costing model, researchers
have tried to simplify it in the last two decades. According to simplified model presented by Babad
and Balachandran (1993), at first an optimum upset of drivers of Activity Based Costing complete
model is selected to make a balance between the costs of gathering, maintaining, and data
processing and the benefit resulted from correct information. This model makes it possible for
decision makers to be able to specify and limit most of the drivers in the simplified system. In this
procedure, we should specify an integrated cost storage. In order to create more integrated cost
centers, all of the activities related to selected cost drivers has been omitted and moved into the cost
storage of selected cost drivers. Humborg developed Babad and Balachandran model. According to
Hamborg model, the cost of activities related to the omitted drivers is allocated to several selected
cost drivers instead of allocating to one drivers of selected cost. In this model, the subset of optimum
drivers are selected in a way that their information costs do not increase up to a definite level and the
loss of lack of accuracy resulting from information limitation decreases. The cost storage of selected
drivers consists of the cost of activity related to selected drivers and a share of the costs of activities
related to the omitted drivers. Humborg model is a simplified model which has the same complex
level in comparison with Babad and Balachandran model. Bet in comparing with it, it fives more
correct product costs. Considering the fact that Humborg model presents a more correct system with
less information cost, it is obvious that the simplified model of Babad and Balachandran is not an
optimum one. However, in both models, it is supposed that the simplification should not result in the
cost of losing the information correctness. In both models the act of simplification focuses on the
decrease of the number of activities and drivers so that the cost of the information correctness
resulting from the decrease of activities and incentives will reach a minimum. However, all these
activities required that ABC would be done completely before being simplified. That is to say that
all activities and drivers should be identified before being simplified. This kind of simplification is
called the simplification after the occurrence. It is necessary for the system to be completely done
before being simplified. The simplification will be of no benefit. Furthermore, when the system
needs to be updated, the model should be completely updated first and then simplified which this
procedure need more time and cost. Therefore, having considered the limitation of performing
Activity Based Costing, researchers of accounting thought of replacing a new costing system which
has an easier updating and performing and covers the Activity Based Costing shortcomings. As a
result, the Time Driven Activity Based Costing (TDABC) was introduced (Soltani & Kalani, 2010).
The history of Time Driven Activity Based Costing (TDABC)
The origin of TDABC dates back to 1997. This model was used by Steven Anderson and his
company as Acron Systems. Before 2001, the company of Acron Systems introduced this model
with the name of Activity Based on Transactions. In 2001, Kaplan joined the board of directors of
Acron Company and cooperated in developing this procedure. The result of this cooperation was to
You're viewing a preview
Unlock full access by subscribing today!
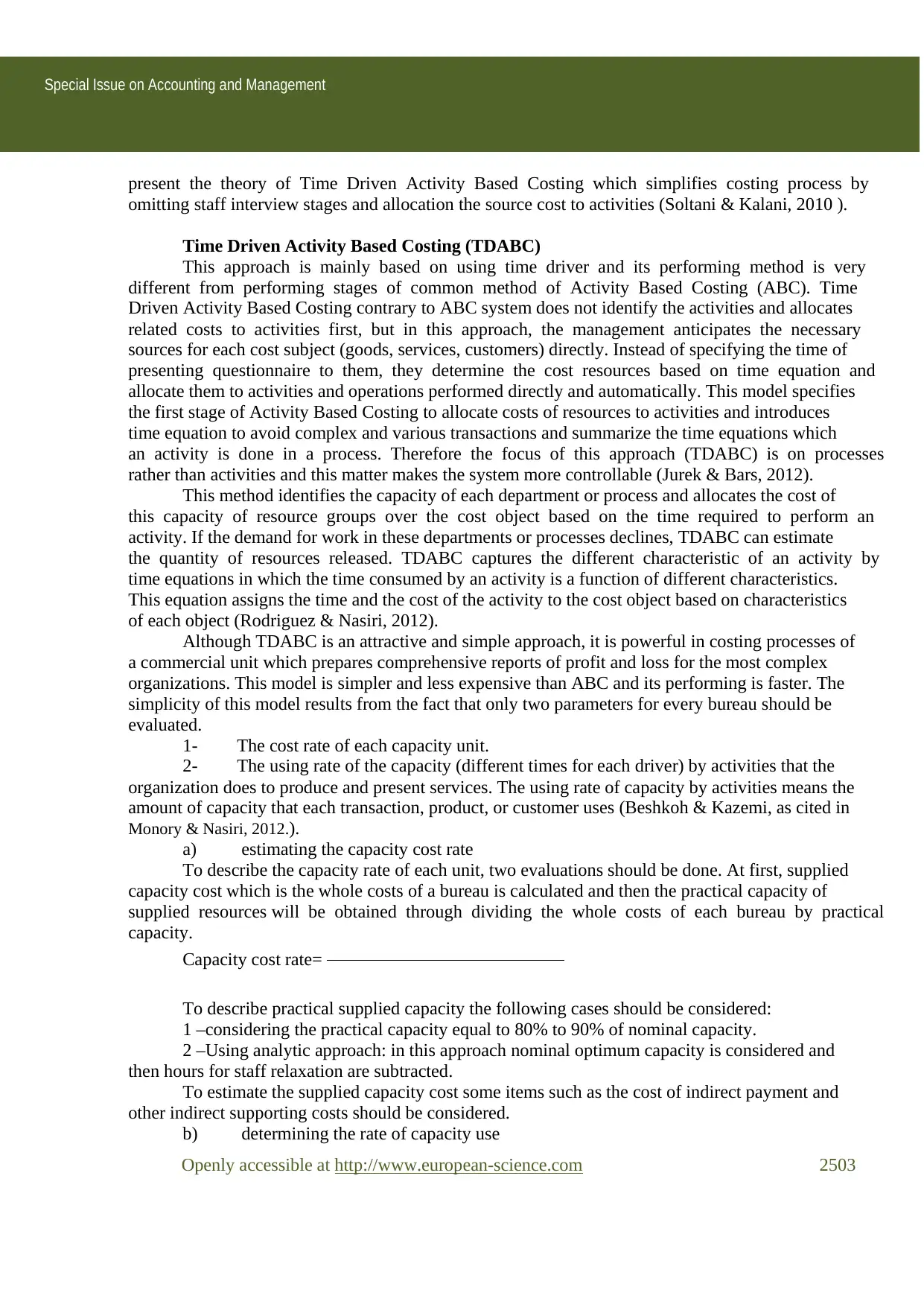
Special Issue on Accounting and Management
Openly accessible at http://www.european-science.com 2503
present the theory of Time Driven Activity Based Costing which simplifies costing process by
omitting staff interview stages and allocation the source cost to activities (Soltani & Kalani, 2010 ).
Time Driven Activity Based Costing (TDABC)
This approach is mainly based on using time driver and its performing method is very
different from performing stages of common method of Activity Based Costing (ABC). Time
Driven Activity Based Costing contrary to ABC system does not identify the activities and allocates
related costs to activities first, but in this approach, the management anticipates the necessary
sources for each cost subject (goods, services, customers) directly. Instead of specifying the time of
presenting questionnaire to them, they determine the cost resources based on time equation and
allocate them to activities and operations performed directly and automatically. This model specifies
the first stage of Activity Based Costing to allocate costs of resources to activities and introduces
time equation to avoid complex and various transactions and summarize the time equations which
an activity is done in a process. Therefore the focus of this approach (TDABC) is on processes
rather than activities and this matter makes the system more controllable (Jurek & Bars, 2012).
This method identifies the capacity of each department or process and allocates the cost of
this capacity of resource groups over the cost object based on the time required to perform an
activity. If the demand for work in these departments or processes declines, TDABC can estimate
the quantity of resources released. TDABC captures the different characteristic of an activity by
time equations in which the time consumed by an activity is a function of different characteristics.
This equation assigns the time and the cost of the activity to the cost object based on characteristics
of each object (Rodriguez & Nasiri, 2012).
Although TDABC is an attractive and simple approach, it is powerful in costing processes of
a commercial unit which prepares comprehensive reports of profit and loss for the most complex
organizations. This model is simpler and less expensive than ABC and its performing is faster. The
simplicity of this model results from the fact that only two parameters for every bureau should be
evaluated.
1- The cost rate of each capacity unit.
2- The using rate of the capacity (different times for each driver) by activities that the
organization does to produce and present services. The using rate of capacity by activities means the
amount of capacity that each transaction, product, or customer uses (Beshkoh & Kazemi, as cited in
Monory & Nasiri, 2012.).
a) estimating the capacity cost rate
To describe the capacity rate of each unit, two evaluations should be done. At first, supplied
capacity cost which is the whole costs of a bureau is calculated and then the practical capacity of
supplied resources will be obtained through dividing the whole costs of each bureau by practical
capacity.
Capacity cost rate=
To describe practical supplied capacity the following cases should be considered:
1 –considering the practical capacity equal to 80% to 90% of nominal capacity.
2 –Using analytic approach: in this approach nominal optimum capacity is considered and
then hours for staff relaxation are subtracted.
To estimate the supplied capacity cost some items such as the cost of indirect payment and
other indirect supporting costs should be considered.
b) determining the rate of capacity use
Openly accessible at http://www.european-science.com 2503
present the theory of Time Driven Activity Based Costing which simplifies costing process by
omitting staff interview stages and allocation the source cost to activities (Soltani & Kalani, 2010 ).
Time Driven Activity Based Costing (TDABC)
This approach is mainly based on using time driver and its performing method is very
different from performing stages of common method of Activity Based Costing (ABC). Time
Driven Activity Based Costing contrary to ABC system does not identify the activities and allocates
related costs to activities first, but in this approach, the management anticipates the necessary
sources for each cost subject (goods, services, customers) directly. Instead of specifying the time of
presenting questionnaire to them, they determine the cost resources based on time equation and
allocate them to activities and operations performed directly and automatically. This model specifies
the first stage of Activity Based Costing to allocate costs of resources to activities and introduces
time equation to avoid complex and various transactions and summarize the time equations which
an activity is done in a process. Therefore the focus of this approach (TDABC) is on processes
rather than activities and this matter makes the system more controllable (Jurek & Bars, 2012).
This method identifies the capacity of each department or process and allocates the cost of
this capacity of resource groups over the cost object based on the time required to perform an
activity. If the demand for work in these departments or processes declines, TDABC can estimate
the quantity of resources released. TDABC captures the different characteristic of an activity by
time equations in which the time consumed by an activity is a function of different characteristics.
This equation assigns the time and the cost of the activity to the cost object based on characteristics
of each object (Rodriguez & Nasiri, 2012).
Although TDABC is an attractive and simple approach, it is powerful in costing processes of
a commercial unit which prepares comprehensive reports of profit and loss for the most complex
organizations. This model is simpler and less expensive than ABC and its performing is faster. The
simplicity of this model results from the fact that only two parameters for every bureau should be
evaluated.
1- The cost rate of each capacity unit.
2- The using rate of the capacity (different times for each driver) by activities that the
organization does to produce and present services. The using rate of capacity by activities means the
amount of capacity that each transaction, product, or customer uses (Beshkoh & Kazemi, as cited in
Monory & Nasiri, 2012.).
a) estimating the capacity cost rate
To describe the capacity rate of each unit, two evaluations should be done. At first, supplied
capacity cost which is the whole costs of a bureau is calculated and then the practical capacity of
supplied resources will be obtained through dividing the whole costs of each bureau by practical
capacity.
Capacity cost rate=
To describe practical supplied capacity the following cases should be considered:
1 –considering the practical capacity equal to 80% to 90% of nominal capacity.
2 –Using analytic approach: in this approach nominal optimum capacity is considered and
then hours for staff relaxation are subtracted.
To estimate the supplied capacity cost some items such as the cost of indirect payment and
other indirect supporting costs should be considered.
b) determining the rate of capacity use
Paraphrase This Document
Need a fresh take? Get an instant paraphrase of this document with our AI Paraphraser
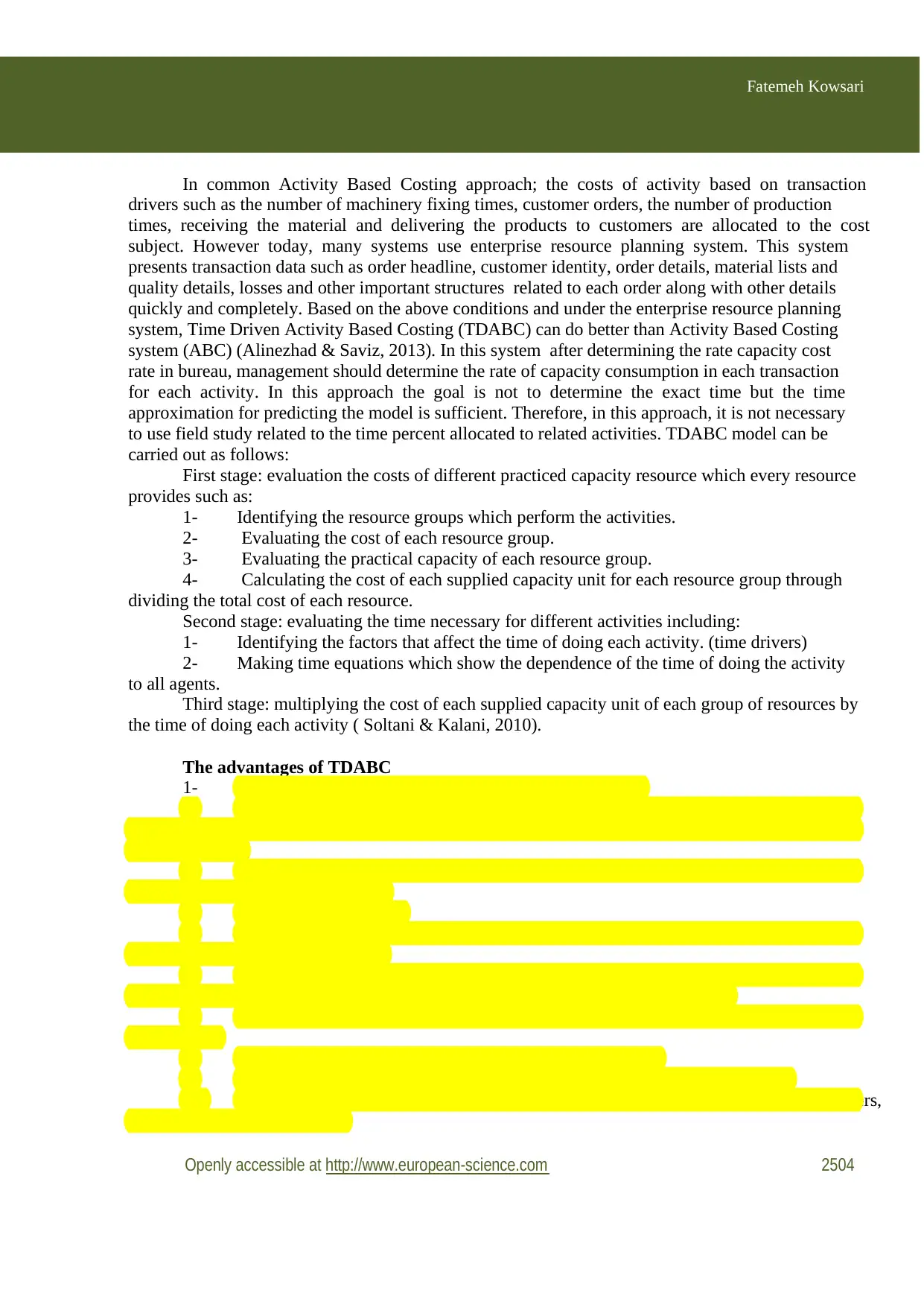
Fatemeh Kowsari
Openly accessible at http://www.european-science.com 2504
In common Activity Based Costing approach; the costs of activity based on transaction
drivers such as the number of machinery fixing times, customer orders, the number of production
times, receiving the material and delivering the products to customers are allocated to the cost
subject. However today, many systems use enterprise resource planning system. This system
presents transaction data such as order headline, customer identity, order details, material lists and
quality details, losses and other important structures related to each order along with other details
quickly and completely. Based on the above conditions and under the enterprise resource planning
system, Time Driven Activity Based Costing (TDABC) can do better than Activity Based Costing
system (ABC) (Alinezhad & Saviz, 2013). In this system after determining the rate capacity cost
rate in bureau, management should determine the rate of capacity consumption in each transaction
for each activity. In this approach the goal is not to determine the exact time but the time
approximation for predicting the model is sufficient. Therefore, in this approach, it is not necessary
to use field study related to the time percent allocated to related activities. TDABC model can be
carried out as follows:
First stage: evaluation the costs of different practiced capacity resource which every resource
provides such as:
1- Identifying the resource groups which perform the activities.
2- Evaluating the cost of each resource group.
3- Evaluating the practical capacity of each resource group.
4- Calculating the cost of each supplied capacity unit for each resource group through
dividing the total cost of each resource.
Second stage: evaluating the time necessary for different activities including:
1- Identifying the factors that affect the time of doing each activity. (time drivers)
2- Making time equations which show the dependence of the time of doing the activity
to all agents.
Third stage: multiplying the cost of each supplied capacity unit of each group of resources by
the time of doing each activity ( Soltani & Kalani, 2010).
The advantages of TDABC
1- Constructing an exact model is made quicker and easier.
2- Having a good conforming with the data which are available in enterprise resource
planning system. This (matter) makes the system more dynamic and at the same time less dependent
on human force.
3- It moves the cost to activities and order by using the characteristics of orders,
processes, suppliers, and customers.
4- It can be used monthly.
5- It creates transparency in using the capacity and proficiency of processes that is to
say it determines the extra capacity.
6- It anticipates thee demand rate of necessary resources and provides the possible
budgeting for capacity resources based the anticipated order rate for the companies.
7- It conforms to the existing model using software and technology of information
banks easily.
8- It’s possible to maintain a quick and less expensive model.
9- It provides clear information for users in identifying the difficulty originally.
10- It’s used in every industry or company with different complexity about customers,
products, units, and processes.
Openly accessible at http://www.european-science.com 2504
In common Activity Based Costing approach; the costs of activity based on transaction
drivers such as the number of machinery fixing times, customer orders, the number of production
times, receiving the material and delivering the products to customers are allocated to the cost
subject. However today, many systems use enterprise resource planning system. This system
presents transaction data such as order headline, customer identity, order details, material lists and
quality details, losses and other important structures related to each order along with other details
quickly and completely. Based on the above conditions and under the enterprise resource planning
system, Time Driven Activity Based Costing (TDABC) can do better than Activity Based Costing
system (ABC) (Alinezhad & Saviz, 2013). In this system after determining the rate capacity cost
rate in bureau, management should determine the rate of capacity consumption in each transaction
for each activity. In this approach the goal is not to determine the exact time but the time
approximation for predicting the model is sufficient. Therefore, in this approach, it is not necessary
to use field study related to the time percent allocated to related activities. TDABC model can be
carried out as follows:
First stage: evaluation the costs of different practiced capacity resource which every resource
provides such as:
1- Identifying the resource groups which perform the activities.
2- Evaluating the cost of each resource group.
3- Evaluating the practical capacity of each resource group.
4- Calculating the cost of each supplied capacity unit for each resource group through
dividing the total cost of each resource.
Second stage: evaluating the time necessary for different activities including:
1- Identifying the factors that affect the time of doing each activity. (time drivers)
2- Making time equations which show the dependence of the time of doing the activity
to all agents.
Third stage: multiplying the cost of each supplied capacity unit of each group of resources by
the time of doing each activity ( Soltani & Kalani, 2010).
The advantages of TDABC
1- Constructing an exact model is made quicker and easier.
2- Having a good conforming with the data which are available in enterprise resource
planning system. This (matter) makes the system more dynamic and at the same time less dependent
on human force.
3- It moves the cost to activities and order by using the characteristics of orders,
processes, suppliers, and customers.
4- It can be used monthly.
5- It creates transparency in using the capacity and proficiency of processes that is to
say it determines the extra capacity.
6- It anticipates thee demand rate of necessary resources and provides the possible
budgeting for capacity resources based the anticipated order rate for the companies.
7- It conforms to the existing model using software and technology of information
banks easily.
8- It’s possible to maintain a quick and less expensive model.
9- It provides clear information for users in identifying the difficulty originally.
10- It’s used in every industry or company with different complexity about customers,
products, units, and processes.
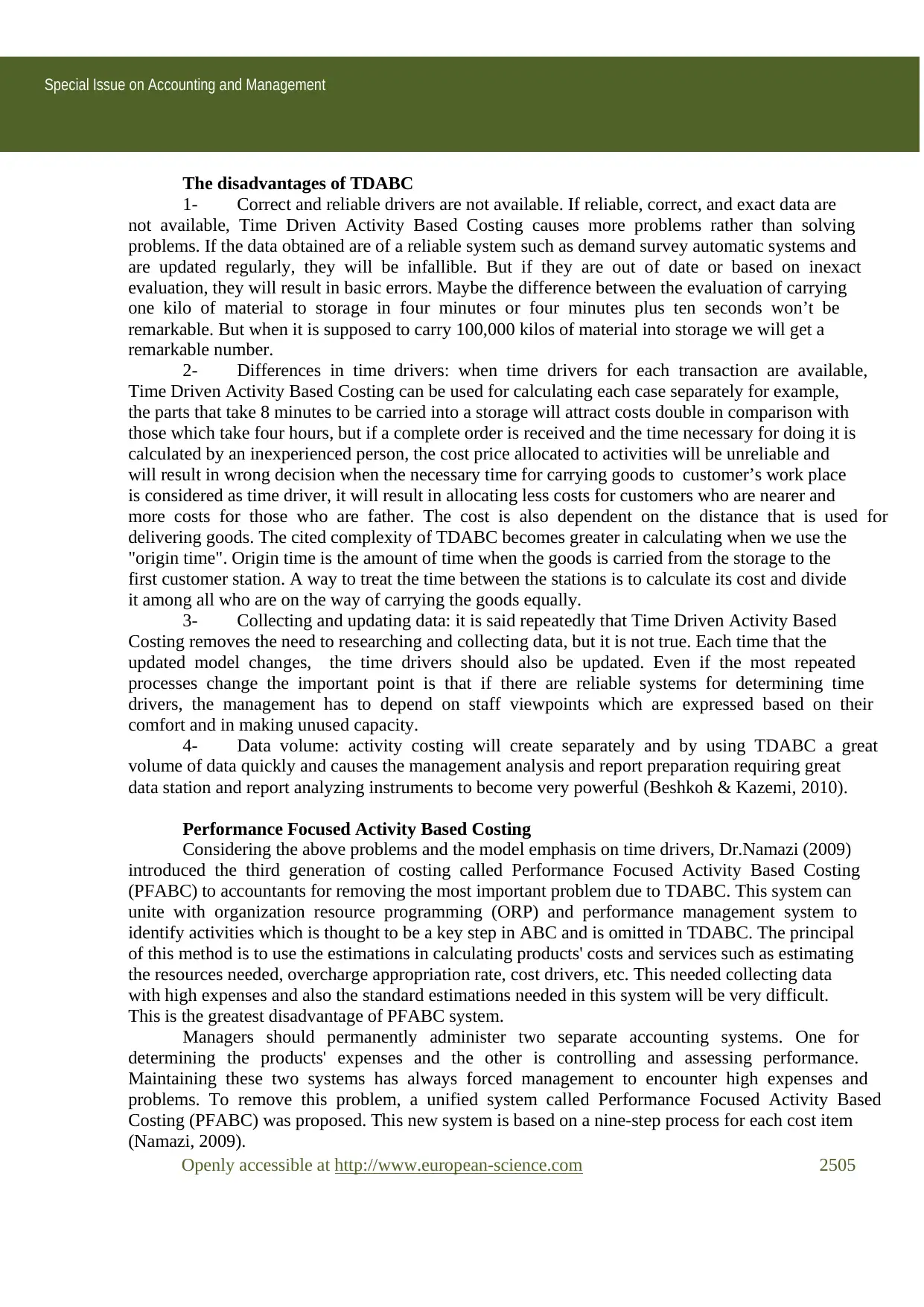
Special Issue on Accounting and Management
Openly accessible at http://www.european-science.com 2505
The disadvantages of TDABC
1- Correct and reliable drivers are not available. If reliable, correct, and exact data are
not available, Time Driven Activity Based Costing causes more problems rather than solving
problems. If the data obtained are of a reliable system such as demand survey automatic systems and
are updated regularly, they will be infallible. But if they are out of date or based on inexact
evaluation, they will result in basic errors. Maybe the difference between the evaluation of carrying
one kilo of material to storage in four minutes or four minutes plus ten seconds won’t be
remarkable. But when it is supposed to carry 100,000 kilos of material into storage we will get a
remarkable number.
2- Differences in time drivers: when time drivers for each transaction are available,
Time Driven Activity Based Costing can be used for calculating each case separately for example,
the parts that take 8 minutes to be carried into a storage will attract costs double in comparison with
those which take four hours, but if a complete order is received and the time necessary for doing it is
calculated by an inexperienced person, the cost price allocated to activities will be unreliable and
will result in wrong decision when the necessary time for carrying goods to customer’s work place
is considered as time driver, it will result in allocating less costs for customers who are nearer and
more costs for those who are father. The cost is also dependent on the distance that is used for
delivering goods. The cited complexity of TDABC becomes greater in calculating when we use the
"origin time". Origin time is the amount of time when the goods is carried from the storage to the
first customer station. A way to treat the time between the stations is to calculate its cost and divide
it among all who are on the way of carrying the goods equally.
3- Collecting and updating data: it is said repeatedly that Time Driven Activity Based
Costing removes the need to researching and collecting data, but it is not true. Each time that the
updated model changes, the time drivers should also be updated. Even if the most repeated
processes change the important point is that if there are reliable systems for determining time
drivers, the management has to depend on staff viewpoints which are expressed based on their
comfort and in making unused capacity.
4- Data volume: activity costing will create separately and by using TDABC a great
volume of data quickly and causes the management analysis and report preparation requiring great
data station and report analyzing instruments to become very powerful (Beshkoh & Kazemi, 2010).
Performance Focused Activity Based Costing
Considering the above problems and the model emphasis on time drivers, Dr.Namazi (2009)
introduced the third generation of costing called Performance Focused Activity Based Costing
(PFABC) to accountants for removing the most important problem due to TDABC. This system can
unite with organization resource programming (ORP) and performance management system to
identify activities which is thought to be a key step in ABC and is omitted in TDABC. The principal
of this method is to use the estimations in calculating products' costs and services such as estimating
the resources needed, overcharge appropriation rate, cost drivers, etc. This needed collecting data
with high expenses and also the standard estimations needed in this system will be very difficult.
This is the greatest disadvantage of PFABC system.
Managers should permanently administer two separate accounting systems. One for
determining the products' expenses and the other is controlling and assessing performance.
Maintaining these two systems has always forced management to encounter high expenses and
problems. To remove this problem, a unified system called Performance Focused Activity Based
Costing (PFABC) was proposed. This new system is based on a nine-step process for each cost item
(Namazi, 2009).
Openly accessible at http://www.european-science.com 2505
The disadvantages of TDABC
1- Correct and reliable drivers are not available. If reliable, correct, and exact data are
not available, Time Driven Activity Based Costing causes more problems rather than solving
problems. If the data obtained are of a reliable system such as demand survey automatic systems and
are updated regularly, they will be infallible. But if they are out of date or based on inexact
evaluation, they will result in basic errors. Maybe the difference between the evaluation of carrying
one kilo of material to storage in four minutes or four minutes plus ten seconds won’t be
remarkable. But when it is supposed to carry 100,000 kilos of material into storage we will get a
remarkable number.
2- Differences in time drivers: when time drivers for each transaction are available,
Time Driven Activity Based Costing can be used for calculating each case separately for example,
the parts that take 8 minutes to be carried into a storage will attract costs double in comparison with
those which take four hours, but if a complete order is received and the time necessary for doing it is
calculated by an inexperienced person, the cost price allocated to activities will be unreliable and
will result in wrong decision when the necessary time for carrying goods to customer’s work place
is considered as time driver, it will result in allocating less costs for customers who are nearer and
more costs for those who are father. The cost is also dependent on the distance that is used for
delivering goods. The cited complexity of TDABC becomes greater in calculating when we use the
"origin time". Origin time is the amount of time when the goods is carried from the storage to the
first customer station. A way to treat the time between the stations is to calculate its cost and divide
it among all who are on the way of carrying the goods equally.
3- Collecting and updating data: it is said repeatedly that Time Driven Activity Based
Costing removes the need to researching and collecting data, but it is not true. Each time that the
updated model changes, the time drivers should also be updated. Even if the most repeated
processes change the important point is that if there are reliable systems for determining time
drivers, the management has to depend on staff viewpoints which are expressed based on their
comfort and in making unused capacity.
4- Data volume: activity costing will create separately and by using TDABC a great
volume of data quickly and causes the management analysis and report preparation requiring great
data station and report analyzing instruments to become very powerful (Beshkoh & Kazemi, 2010).
Performance Focused Activity Based Costing
Considering the above problems and the model emphasis on time drivers, Dr.Namazi (2009)
introduced the third generation of costing called Performance Focused Activity Based Costing
(PFABC) to accountants for removing the most important problem due to TDABC. This system can
unite with organization resource programming (ORP) and performance management system to
identify activities which is thought to be a key step in ABC and is omitted in TDABC. The principal
of this method is to use the estimations in calculating products' costs and services such as estimating
the resources needed, overcharge appropriation rate, cost drivers, etc. This needed collecting data
with high expenses and also the standard estimations needed in this system will be very difficult.
This is the greatest disadvantage of PFABC system.
Managers should permanently administer two separate accounting systems. One for
determining the products' expenses and the other is controlling and assessing performance.
Maintaining these two systems has always forced management to encounter high expenses and
problems. To remove this problem, a unified system called Performance Focused Activity Based
Costing (PFABC) was proposed. This new system is based on a nine-step process for each cost item
(Namazi, 2009).
You're viewing a preview
Unlock full access by subscribing today!
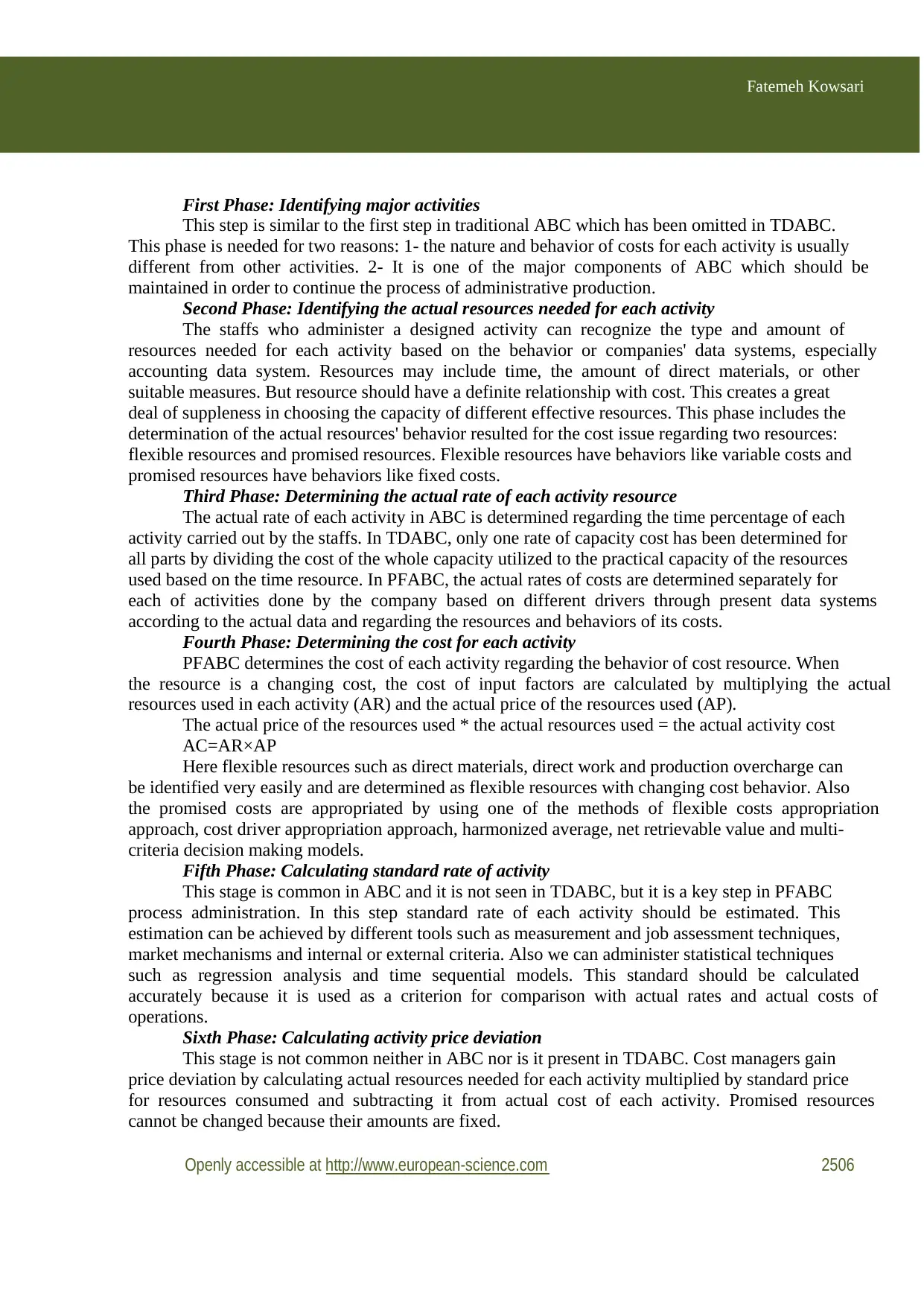
Fatemeh Kowsari
Openly accessible at http://www.european-science.com 2506
First Phase: Identifying major activities
This step is similar to the first step in traditional ABC which has been omitted in TDABC.
This phase is needed for two reasons: 1- the nature and behavior of costs for each activity is usually
different from other activities. 2- It is one of the major components of ABC which should be
maintained in order to continue the process of administrative production.
Second Phase: Identifying the actual resources needed for each activity
The staffs who administer a designed activity can recognize the type and amount of
resources needed for each activity based on the behavior or companies' data systems, especially
accounting data system. Resources may include time, the amount of direct materials, or other
suitable measures. But resource should have a definite relationship with cost. This creates a great
deal of suppleness in choosing the capacity of different effective resources. This phase includes the
determination of the actual resources' behavior resulted for the cost issue regarding two resources:
flexible resources and promised resources. Flexible resources have behaviors like variable costs and
promised resources have behaviors like fixed costs.
Third Phase: Determining the actual rate of each activity resource
The actual rate of each activity in ABC is determined regarding the time percentage of each
activity carried out by the staffs. In TDABC, only one rate of capacity cost has been determined for
all parts by dividing the cost of the whole capacity utilized to the practical capacity of the resources
used based on the time resource. In PFABC, the actual rates of costs are determined separately for
each of activities done by the company based on different drivers through present data systems
according to the actual data and regarding the resources and behaviors of its costs.
Fourth Phase: Determining the cost for each activity
PFABC determines the cost of each activity regarding the behavior of cost resource. When
the resource is a changing cost, the cost of input factors are calculated by multiplying the actual
resources used in each activity (AR) and the actual price of the resources used (AP).
The actual price of the resources used * the actual resources used = the actual activity cost
AC=AR×AP
Here flexible resources such as direct materials, direct work and production overcharge can
be identified very easily and are determined as flexible resources with changing cost behavior. Also
the promised costs are appropriated by using one of the methods of flexible costs appropriation
approach, cost driver appropriation approach, harmonized average, net retrievable value and multi-
criteria decision making models.
Fifth Phase: Calculating standard rate of activity
This stage is common in ABC and it is not seen in TDABC, but it is a key step in PFABC
process administration. In this step standard rate of each activity should be estimated. This
estimation can be achieved by different tools such as measurement and job assessment techniques,
market mechanisms and internal or external criteria. Also we can administer statistical techniques
such as regression analysis and time sequential models. This standard should be calculated
accurately because it is used as a criterion for comparison with actual rates and actual costs of
operations.
Sixth Phase: Calculating activity price deviation
This stage is not common neither in ABC nor is it present in TDABC. Cost managers gain
price deviation by calculating actual resources needed for each activity multiplied by standard price
for resources consumed and subtracting it from actual cost of each activity. Promised resources
cannot be changed because their amounts are fixed.
Openly accessible at http://www.european-science.com 2506
First Phase: Identifying major activities
This step is similar to the first step in traditional ABC which has been omitted in TDABC.
This phase is needed for two reasons: 1- the nature and behavior of costs for each activity is usually
different from other activities. 2- It is one of the major components of ABC which should be
maintained in order to continue the process of administrative production.
Second Phase: Identifying the actual resources needed for each activity
The staffs who administer a designed activity can recognize the type and amount of
resources needed for each activity based on the behavior or companies' data systems, especially
accounting data system. Resources may include time, the amount of direct materials, or other
suitable measures. But resource should have a definite relationship with cost. This creates a great
deal of suppleness in choosing the capacity of different effective resources. This phase includes the
determination of the actual resources' behavior resulted for the cost issue regarding two resources:
flexible resources and promised resources. Flexible resources have behaviors like variable costs and
promised resources have behaviors like fixed costs.
Third Phase: Determining the actual rate of each activity resource
The actual rate of each activity in ABC is determined regarding the time percentage of each
activity carried out by the staffs. In TDABC, only one rate of capacity cost has been determined for
all parts by dividing the cost of the whole capacity utilized to the practical capacity of the resources
used based on the time resource. In PFABC, the actual rates of costs are determined separately for
each of activities done by the company based on different drivers through present data systems
according to the actual data and regarding the resources and behaviors of its costs.
Fourth Phase: Determining the cost for each activity
PFABC determines the cost of each activity regarding the behavior of cost resource. When
the resource is a changing cost, the cost of input factors are calculated by multiplying the actual
resources used in each activity (AR) and the actual price of the resources used (AP).
The actual price of the resources used * the actual resources used = the actual activity cost
AC=AR×AP
Here flexible resources such as direct materials, direct work and production overcharge can
be identified very easily and are determined as flexible resources with changing cost behavior. Also
the promised costs are appropriated by using one of the methods of flexible costs appropriation
approach, cost driver appropriation approach, harmonized average, net retrievable value and multi-
criteria decision making models.
Fifth Phase: Calculating standard rate of activity
This stage is common in ABC and it is not seen in TDABC, but it is a key step in PFABC
process administration. In this step standard rate of each activity should be estimated. This
estimation can be achieved by different tools such as measurement and job assessment techniques,
market mechanisms and internal or external criteria. Also we can administer statistical techniques
such as regression analysis and time sequential models. This standard should be calculated
accurately because it is used as a criterion for comparison with actual rates and actual costs of
operations.
Sixth Phase: Calculating activity price deviation
This stage is not common neither in ABC nor is it present in TDABC. Cost managers gain
price deviation by calculating actual resources needed for each activity multiplied by standard price
for resources consumed and subtracting it from actual cost of each activity. Promised resources
cannot be changed because their amounts are fixed.
Paraphrase This Document
Need a fresh take? Get an instant paraphrase of this document with our AI Paraphraser
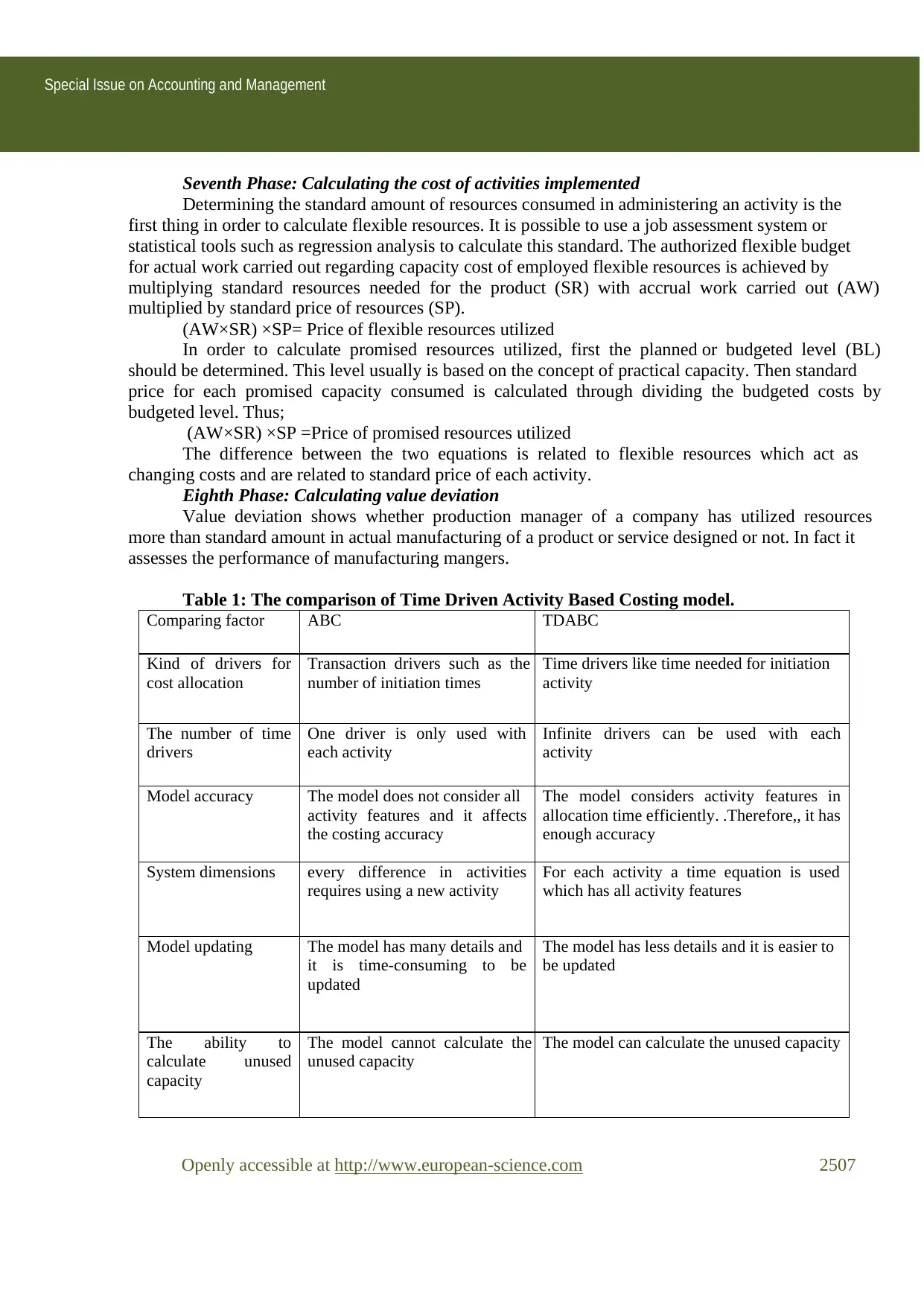
Special Issue on Accounting and Management
Openly accessible at http://www.european-science.com 2507
Seventh Phase: Calculating the cost of activities implemented
Determining the standard amount of resources consumed in administering an activity is the
first thing in order to calculate flexible resources. It is possible to use a job assessment system or
statistical tools such as regression analysis to calculate this standard. The authorized flexible budget
for actual work carried out regarding capacity cost of employed flexible resources is achieved by
multiplying standard resources needed for the product (SR) with accrual work carried out (AW)
multiplied by standard price of resources (SP).
(AW×SR) ×SP= Price of flexible resources utilized
In order to calculate promised resources utilized, first the planned or budgeted level (BL)
should be determined. This level usually is based on the concept of practical capacity. Then standard
price for each promised capacity consumed is calculated through dividing the budgeted costs by
budgeted level. Thus;
(AW×SR) ×SP =Price of promised resources utilized
The difference between the two equations is related to flexible resources which act as
changing costs and are related to standard price of each activity.
Eighth Phase: Calculating value deviation
Value deviation shows whether production manager of a company has utilized resources
more than standard amount in actual manufacturing of a product or service designed or not. In fact it
assesses the performance of manufacturing mangers.
Table 1: The comparison of Time Driven Activity Based Costing model.
TDABCABCComparing factor
Time drivers like time needed for initiation
activity
Transaction drivers such as the
number of initiation times
Kind of drivers for
cost allocation
Infinite drivers can be used with each
activity
One driver is only used with
each activity
The number of time
drivers
The model considers activity features in
allocation time efficiently. .Therefore,, it has
enough accuracy
The model does not consider all
activity features and it affects
the costing accuracy
Model accuracy
For each activity a time equation is used
which has all activity features
every difference in activities
requires using a new activity
System dimensions
The model has less details and it is easier to
be updated
The model has many details and
it is time-consuming to be
updated
Model updating
The model can calculate the unused capacityThe model cannot calculate the
unused capacity
The ability to
calculate unused
capacity
Openly accessible at http://www.european-science.com 2507
Seventh Phase: Calculating the cost of activities implemented
Determining the standard amount of resources consumed in administering an activity is the
first thing in order to calculate flexible resources. It is possible to use a job assessment system or
statistical tools such as regression analysis to calculate this standard. The authorized flexible budget
for actual work carried out regarding capacity cost of employed flexible resources is achieved by
multiplying standard resources needed for the product (SR) with accrual work carried out (AW)
multiplied by standard price of resources (SP).
(AW×SR) ×SP= Price of flexible resources utilized
In order to calculate promised resources utilized, first the planned or budgeted level (BL)
should be determined. This level usually is based on the concept of practical capacity. Then standard
price for each promised capacity consumed is calculated through dividing the budgeted costs by
budgeted level. Thus;
(AW×SR) ×SP =Price of promised resources utilized
The difference between the two equations is related to flexible resources which act as
changing costs and are related to standard price of each activity.
Eighth Phase: Calculating value deviation
Value deviation shows whether production manager of a company has utilized resources
more than standard amount in actual manufacturing of a product or service designed or not. In fact it
assesses the performance of manufacturing mangers.
Table 1: The comparison of Time Driven Activity Based Costing model.
TDABCABCComparing factor
Time drivers like time needed for initiation
activity
Transaction drivers such as the
number of initiation times
Kind of drivers for
cost allocation
Infinite drivers can be used with each
activity
One driver is only used with
each activity
The number of time
drivers
The model considers activity features in
allocation time efficiently. .Therefore,, it has
enough accuracy
The model does not consider all
activity features and it affects
the costing accuracy
Model accuracy
For each activity a time equation is used
which has all activity features
every difference in activities
requires using a new activity
System dimensions
The model has less details and it is easier to
be updated
The model has many details and
it is time-consuming to be
updated
Model updating
The model can calculate the unused capacityThe model cannot calculate the
unused capacity
The ability to
calculate unused
capacity
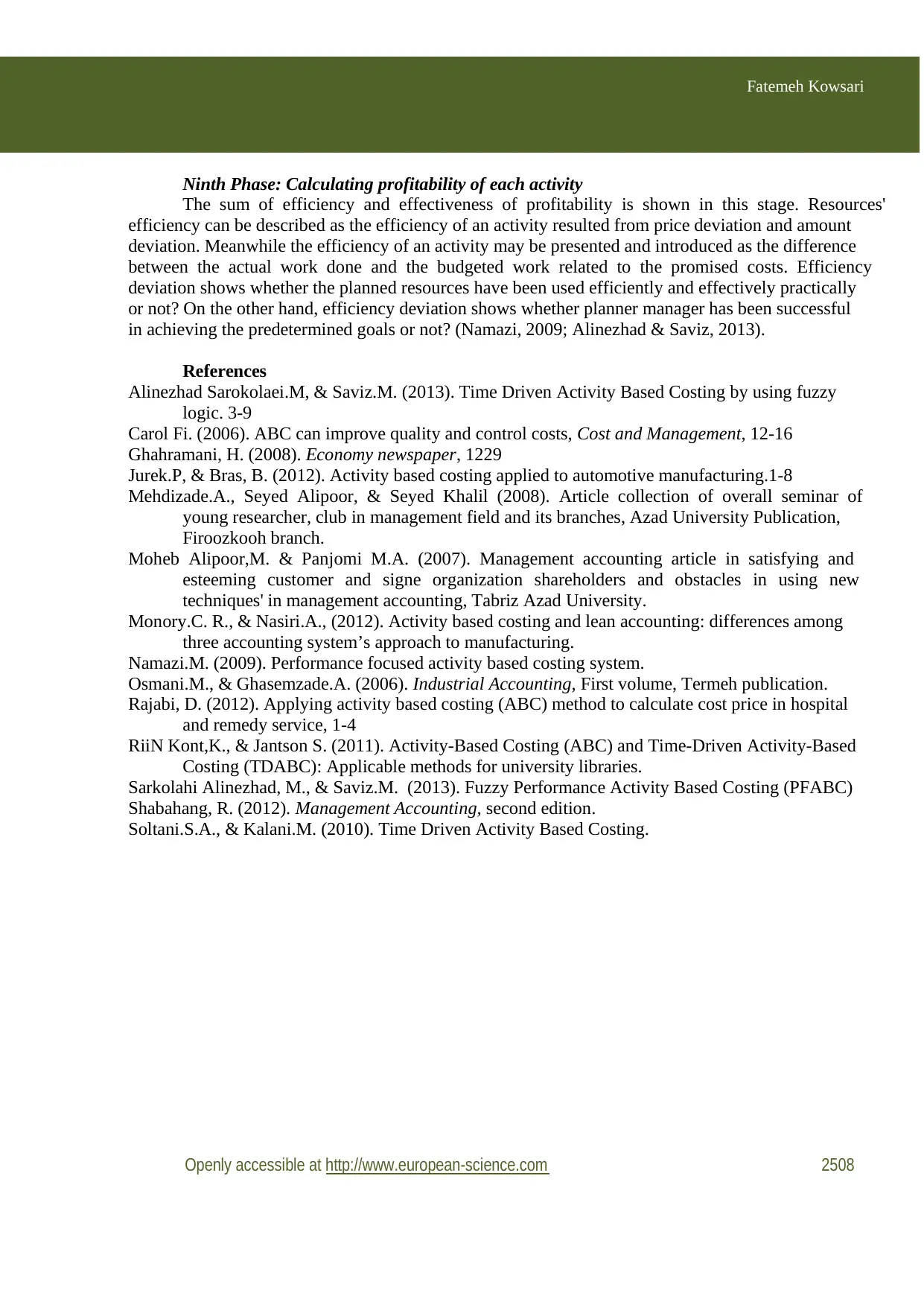
Fatemeh Kowsari
Openly accessible at http://www.european-science.com 2508
Ninth Phase: Calculating profitability of each activity
The sum of efficiency and effectiveness of profitability is shown in this stage. Resources'
efficiency can be described as the efficiency of an activity resulted from price deviation and amount
deviation. Meanwhile the efficiency of an activity may be presented and introduced as the difference
between the actual work done and the budgeted work related to the promised costs. Efficiency
deviation shows whether the planned resources have been used efficiently and effectively practically
or not? On the other hand, efficiency deviation shows whether planner manager has been successful
in achieving the predetermined goals or not? (Namazi, 2009; Alinezhad & Saviz, 2013).
References
Alinezhad Sarokolaei.M, & Saviz.M. (2013). Time Driven Activity Based Costing by using fuzzy
logic. 3-9
Carol Fi. (2006). ABC can improve quality and control costs, Cost and Management, 12-16
Ghahramani, H. (2008). Economy newspaper, 1229
Jurek.P, & Bras, B. (2012). Activity based costing applied to automotive manufacturing.1-8
Mehdizade.A., Seyed Alipoor, & Seyed Khalil (2008). Article collection of overall seminar of
young researcher, club in management field and its branches, Azad University Publication,
Firoozkooh branch.
Moheb Alipoor,M. & Panjomi M.A. (2007). Management accounting article in satisfying and
esteeming customer and signe organization shareholders and obstacles in using new
techniques' in management accounting, Tabriz Azad University.
Monory.C. R., & Nasiri.A., (2012). Activity based costing and lean accounting: differences among
three accounting system’s approach to manufacturing.
Namazi.M. (2009). Performance focused activity based costing system.
Osmani.M., & Ghasemzade.A. (2006). Industrial Accounting, First volume, Termeh publication.
Rajabi, D. (2012). Applying activity based costing (ABC) method to calculate cost price in hospital
and remedy service, 1-4
RiiN Kont,K., & Jantson S. (2011). Activity-Based Costing (ABC) and Time-Driven Activity-Based
Costing (TDABC): Applicable methods for university libraries.
Sarkolahi Alinezhad, M., & Saviz.M. (2013). Fuzzy Performance Activity Based Costing (PFABC)
Shabahang, R. (2012). Management Accounting, second edition.
Soltani.S.A., & Kalani.M. (2010). Time Driven Activity Based Costing.
Openly accessible at http://www.european-science.com 2508
Ninth Phase: Calculating profitability of each activity
The sum of efficiency and effectiveness of profitability is shown in this stage. Resources'
efficiency can be described as the efficiency of an activity resulted from price deviation and amount
deviation. Meanwhile the efficiency of an activity may be presented and introduced as the difference
between the actual work done and the budgeted work related to the promised costs. Efficiency
deviation shows whether the planned resources have been used efficiently and effectively practically
or not? On the other hand, efficiency deviation shows whether planner manager has been successful
in achieving the predetermined goals or not? (Namazi, 2009; Alinezhad & Saviz, 2013).
References
Alinezhad Sarokolaei.M, & Saviz.M. (2013). Time Driven Activity Based Costing by using fuzzy
logic. 3-9
Carol Fi. (2006). ABC can improve quality and control costs, Cost and Management, 12-16
Ghahramani, H. (2008). Economy newspaper, 1229
Jurek.P, & Bras, B. (2012). Activity based costing applied to automotive manufacturing.1-8
Mehdizade.A., Seyed Alipoor, & Seyed Khalil (2008). Article collection of overall seminar of
young researcher, club in management field and its branches, Azad University Publication,
Firoozkooh branch.
Moheb Alipoor,M. & Panjomi M.A. (2007). Management accounting article in satisfying and
esteeming customer and signe organization shareholders and obstacles in using new
techniques' in management accounting, Tabriz Azad University.
Monory.C. R., & Nasiri.A., (2012). Activity based costing and lean accounting: differences among
three accounting system’s approach to manufacturing.
Namazi.M. (2009). Performance focused activity based costing system.
Osmani.M., & Ghasemzade.A. (2006). Industrial Accounting, First volume, Termeh publication.
Rajabi, D. (2012). Applying activity based costing (ABC) method to calculate cost price in hospital
and remedy service, 1-4
RiiN Kont,K., & Jantson S. (2011). Activity-Based Costing (ABC) and Time-Driven Activity-Based
Costing (TDABC): Applicable methods for university libraries.
Sarkolahi Alinezhad, M., & Saviz.M. (2013). Fuzzy Performance Activity Based Costing (PFABC)
Shabahang, R. (2012). Management Accounting, second edition.
Soltani.S.A., & Kalani.M. (2010). Time Driven Activity Based Costing.
You're viewing a preview
Unlock full access by subscribing today!
1 out of 12
Related Documents

Your All-in-One AI-Powered Toolkit for Academic Success.
+13062052269
info@desklib.com
Available 24*7 on WhatsApp / Email
Unlock your academic potential
© 2024 | Zucol Services PVT LTD | All rights reserved.