Costing, Variance Analysis, Budgeting and Sensitivity Analysis
VerifiedAdded on  2022/12/28
|10
|2301
|32
Homework Assignment
AI Summary
This assignment solution addresses key concepts in costing and budgeting, providing detailed calculations and analyses. Question 1 explores overhead absorption and activity-based costing, comparing their impacts on product profitability, including calculations for overhead absorption rates, cost per unit, and profit margins. Question 2 delves into variance analysis, calculating material usage, mix, and yield variances, and discussing issues with current variance reporting systems. Finally, Question 3 examines zero-based budgeting (ZBB) and incremental budgeting (IB), comparing their roles in planning and coordination, and discussing the strengths and weaknesses of each approach, offering a comprehensive overview of financial planning and control techniques.
Contribute Materials
Your contribution can guide someone’s learning journey. Share your
documents today.
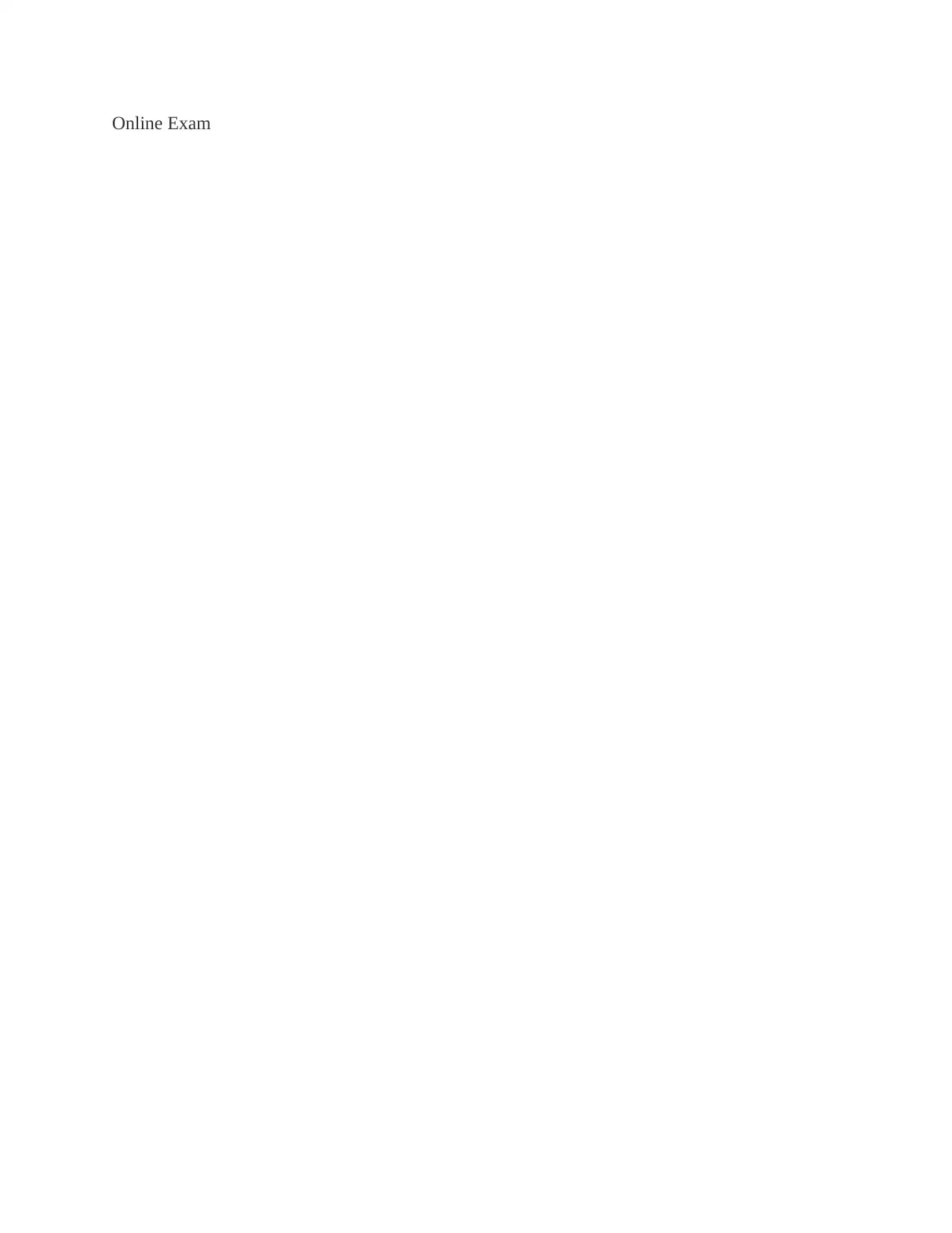
Online Exam
Secure Best Marks with AI Grader
Need help grading? Try our AI Grader for instant feedback on your assignments.
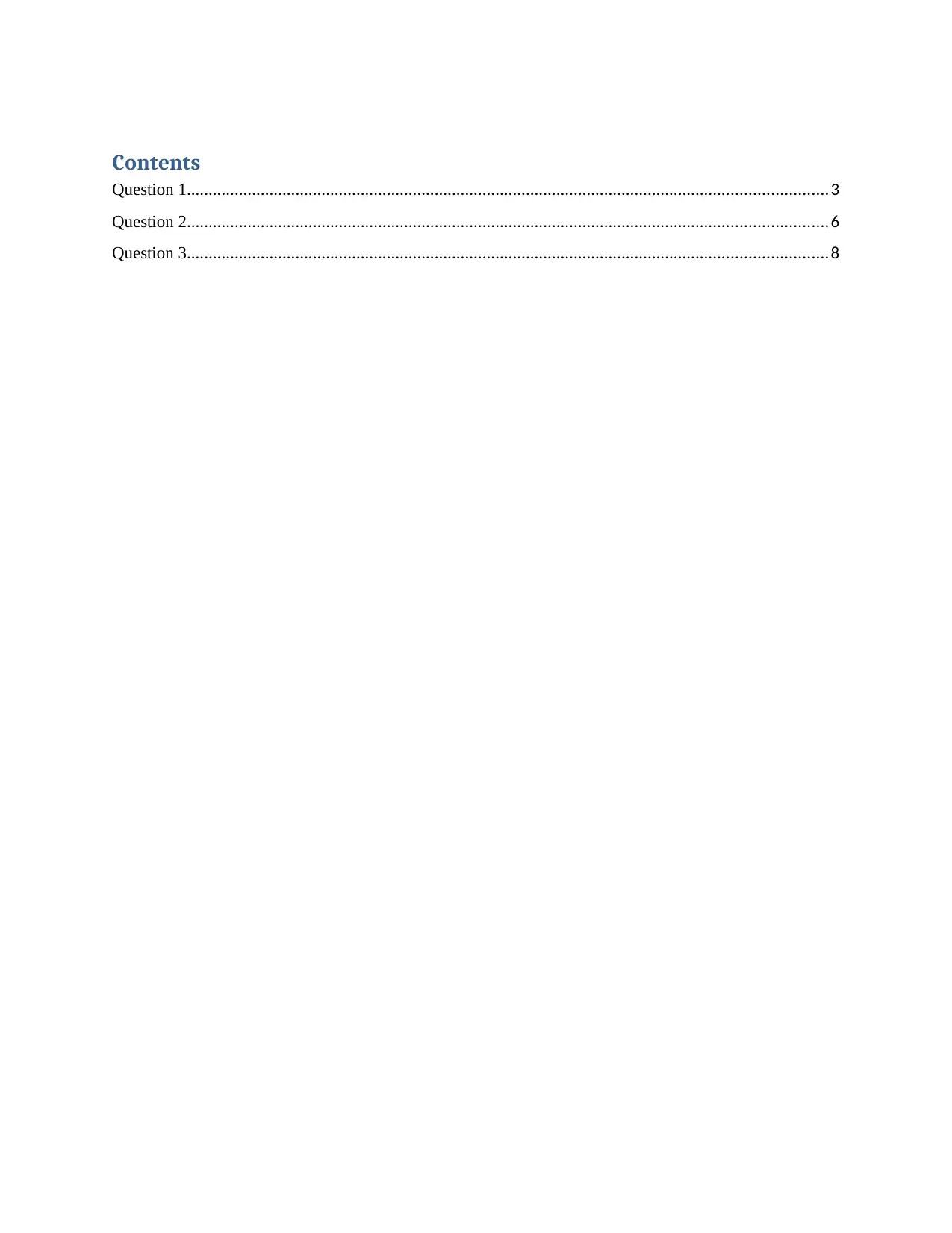
Contents
Question 1...................................................................................................................................................3
Question 2...................................................................................................................................................6
Question 3...................................................................................................................................................8
Question 1...................................................................................................................................................3
Question 2...................................................................................................................................................6
Question 3...................................................................................................................................................8
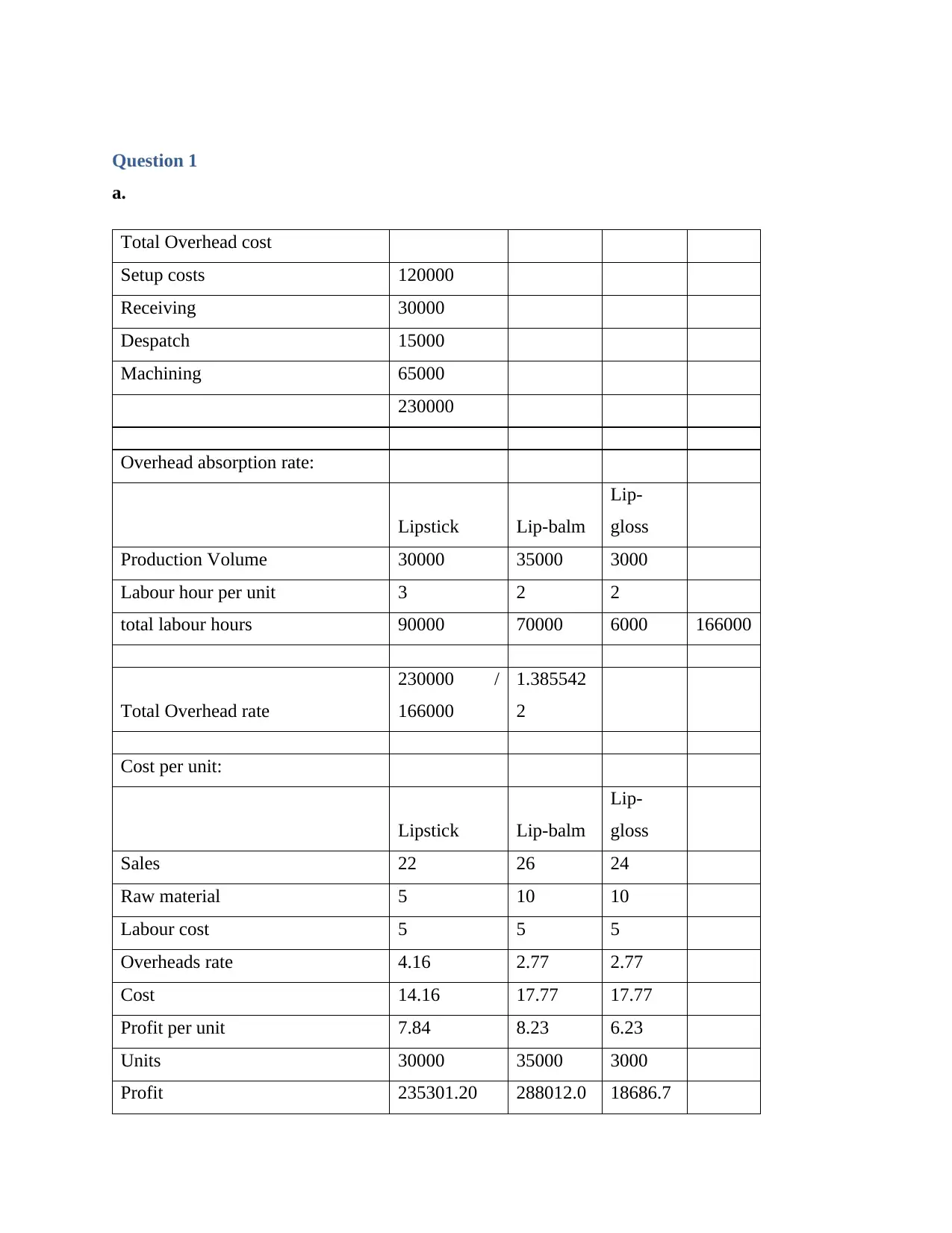
Question 1
a.
Total Overhead cost
Setup costs 120000
Receiving 30000
Despatch 15000
Machining 65000
230000
Overhead absorption rate:
Lipstick Lip-balm
Lip-
gloss
Production Volume 30000 35000 3000
Labour hour per unit 3 2 2
total labour hours 90000 70000 6000 166000
Total Overhead rate
230000 /
166000
1.385542
2
Cost per unit:
Lipstick Lip-balm
Lip-
gloss
Sales 22 26 24
Raw material 5 10 10
Labour cost 5 5 5
Overheads rate 4.16 2.77 2.77
Cost 14.16 17.77 17.77
Profit per unit 7.84 8.23 6.23
Units 30000 35000 3000
Profit 235301.20 288012.0 18686.7
a.
Total Overhead cost
Setup costs 120000
Receiving 30000
Despatch 15000
Machining 65000
230000
Overhead absorption rate:
Lipstick Lip-balm
Lip-
gloss
Production Volume 30000 35000 3000
Labour hour per unit 3 2 2
total labour hours 90000 70000 6000 166000
Total Overhead rate
230000 /
166000
1.385542
2
Cost per unit:
Lipstick Lip-balm
Lip-
gloss
Sales 22 26 24
Raw material 5 10 10
Labour cost 5 5 5
Overheads rate 4.16 2.77 2.77
Cost 14.16 17.77 17.77
Profit per unit 7.84 8.23 6.23
Units 30000 35000 3000
Profit 235301.20 288012.0 18686.7
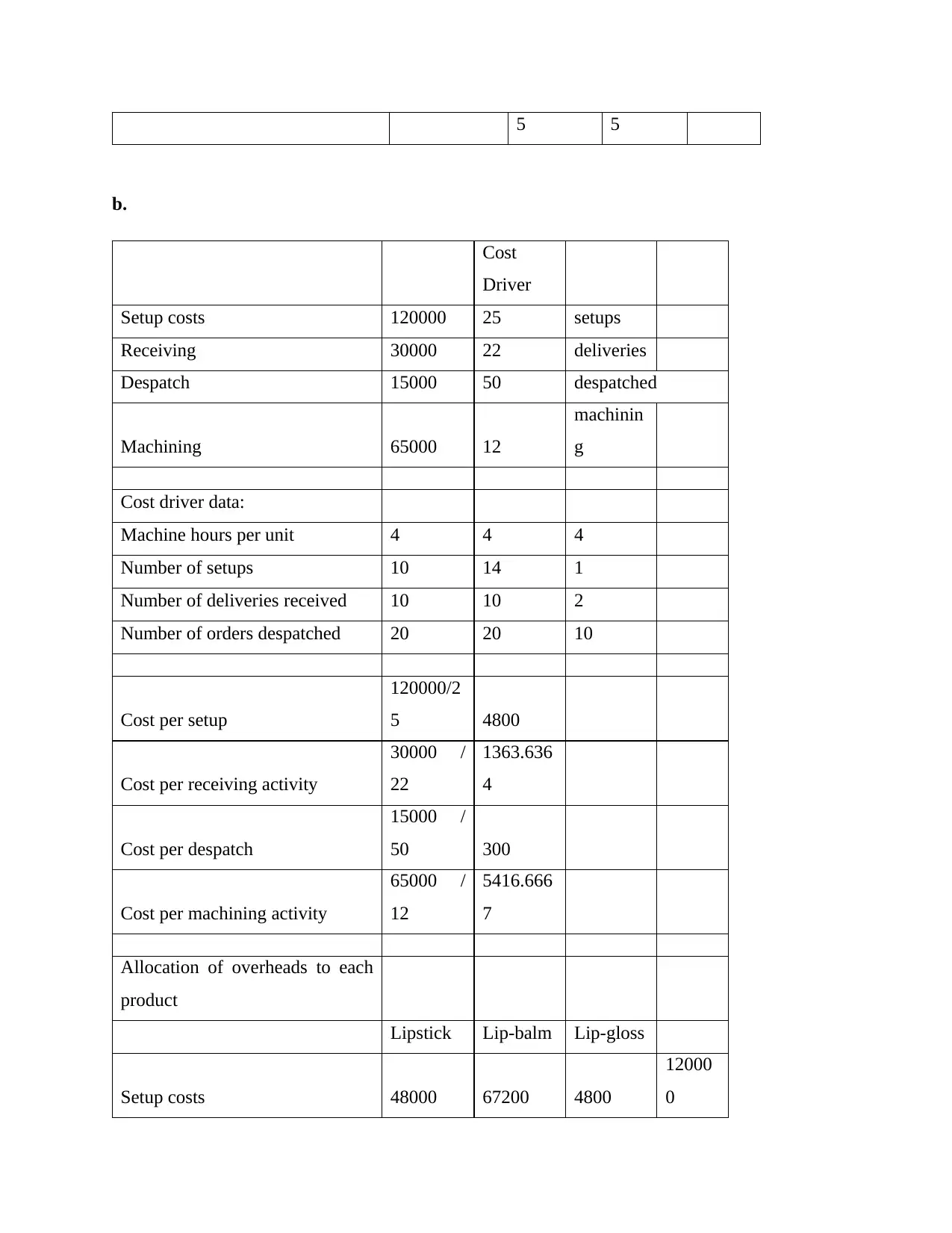
5 5
b.
Cost
Driver
Setup costs 120000 25 setups
Receiving 30000 22 deliveries
Despatch 15000 50 despatched
Machining 65000 12
machinin
g
Cost driver data:
Machine hours per unit 4 4 4
Number of setups 10 14 1
Number of deliveries received 10 10 2
Number of orders despatched 20 20 10
Cost per setup
120000/2
5 4800
Cost per receiving activity
30000 /
22
1363.636
4
Cost per despatch
15000 /
50 300
Cost per machining activity
65000 /
12
5416.666
7
Allocation of overheads to each
product
Lipstick Lip-balm Lip-gloss
Setup costs 48000 67200 4800
12000
0
b.
Cost
Driver
Setup costs 120000 25 setups
Receiving 30000 22 deliveries
Despatch 15000 50 despatched
Machining 65000 12
machinin
g
Cost driver data:
Machine hours per unit 4 4 4
Number of setups 10 14 1
Number of deliveries received 10 10 2
Number of orders despatched 20 20 10
Cost per setup
120000/2
5 4800
Cost per receiving activity
30000 /
22
1363.636
4
Cost per despatch
15000 /
50 300
Cost per machining activity
65000 /
12
5416.666
7
Allocation of overheads to each
product
Lipstick Lip-balm Lip-gloss
Setup costs 48000 67200 4800
12000
0
Secure Best Marks with AI Grader
Need help grading? Try our AI Grader for instant feedback on your assignments.
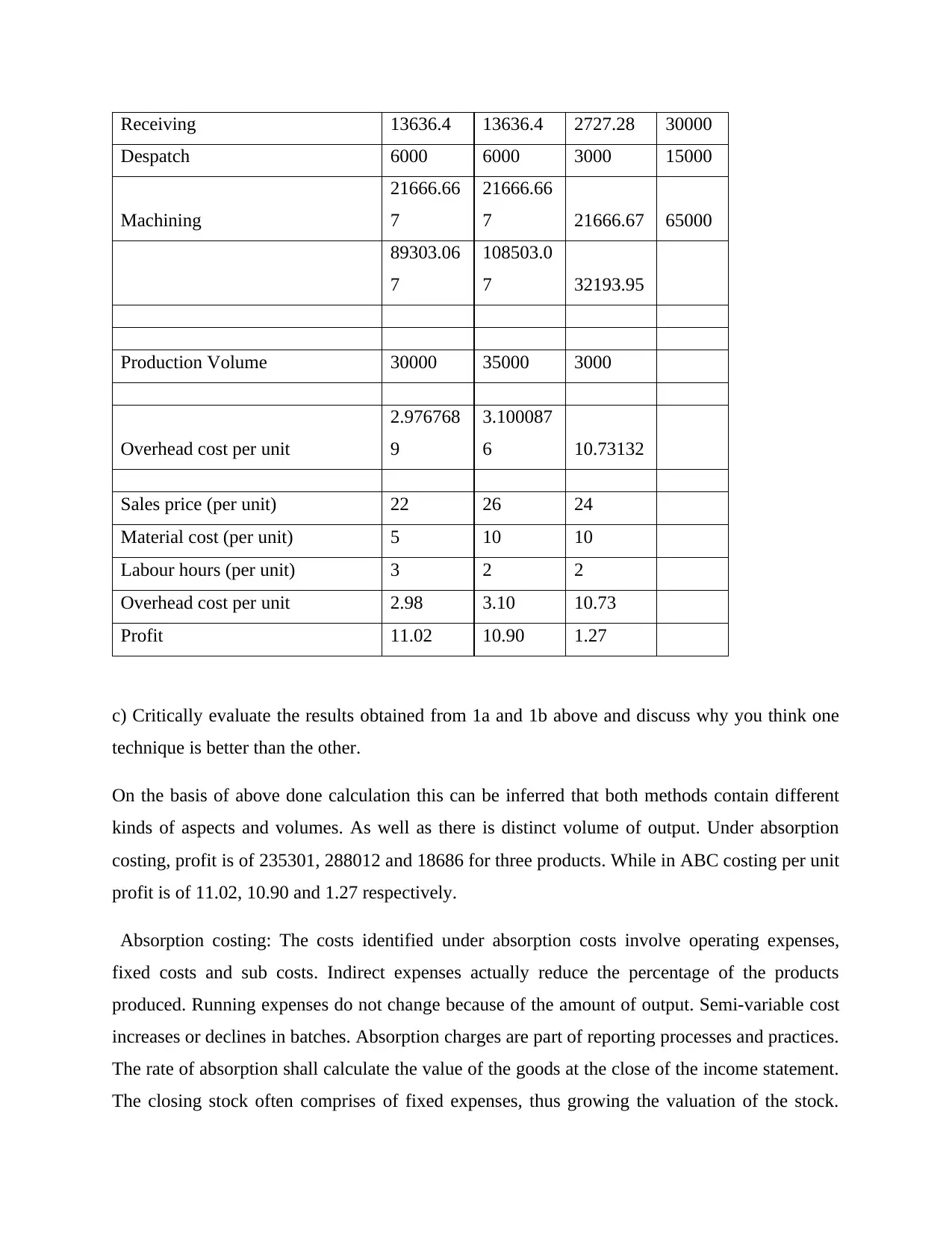
Receiving 13636.4 13636.4 2727.28 30000
Despatch 6000 6000 3000 15000
Machining
21666.66
7
21666.66
7 21666.67 65000
89303.06
7
108503.0
7 32193.95
Production Volume 30000 35000 3000
Overhead cost per unit
2.976768
9
3.100087
6 10.73132
Sales price (per unit) 22 26 24
Material cost (per unit) 5 10 10
Labour hours (per unit) 3 2 2
Overhead cost per unit 2.98 3.10 10.73
Profit 11.02 10.90 1.27
c) Critically evaluate the results obtained from 1a and 1b above and discuss why you think one
technique is better than the other.
On the basis of above done calculation this can be inferred that both methods contain different
kinds of aspects and volumes. As well as there is distinct volume of output. Under absorption
costing, profit is of 235301, 288012 and 18686 for three products. While in ABC costing per unit
profit is of 11.02, 10.90 and 1.27 respectively.
Absorption costing: The costs identified under absorption costs involve operating expenses,
fixed costs and sub costs. Indirect expenses actually reduce the percentage of the products
produced. Running expenses do not change because of the amount of output. Semi-variable cost
increases or declines in batches. Absorption charges are part of reporting processes and practices.
The rate of absorption shall calculate the value of the goods at the close of the income statement.
The closing stock often comprises of fixed expenses, thus growing the valuation of the stock.
Despatch 6000 6000 3000 15000
Machining
21666.66
7
21666.66
7 21666.67 65000
89303.06
7
108503.0
7 32193.95
Production Volume 30000 35000 3000
Overhead cost per unit
2.976768
9
3.100087
6 10.73132
Sales price (per unit) 22 26 24
Material cost (per unit) 5 10 10
Labour hours (per unit) 3 2 2
Overhead cost per unit 2.98 3.10 10.73
Profit 11.02 10.90 1.27
c) Critically evaluate the results obtained from 1a and 1b above and discuss why you think one
technique is better than the other.
On the basis of above done calculation this can be inferred that both methods contain different
kinds of aspects and volumes. As well as there is distinct volume of output. Under absorption
costing, profit is of 235301, 288012 and 18686 for three products. While in ABC costing per unit
profit is of 11.02, 10.90 and 1.27 respectively.
Absorption costing: The costs identified under absorption costs involve operating expenses,
fixed costs and sub costs. Indirect expenses actually reduce the percentage of the products
produced. Running expenses do not change because of the amount of output. Semi-variable cost
increases or declines in batches. Absorption charges are part of reporting processes and practices.
The rate of absorption shall calculate the value of the goods at the close of the income statement.
The closing stock often comprises of fixed expenses, thus growing the valuation of the stock.
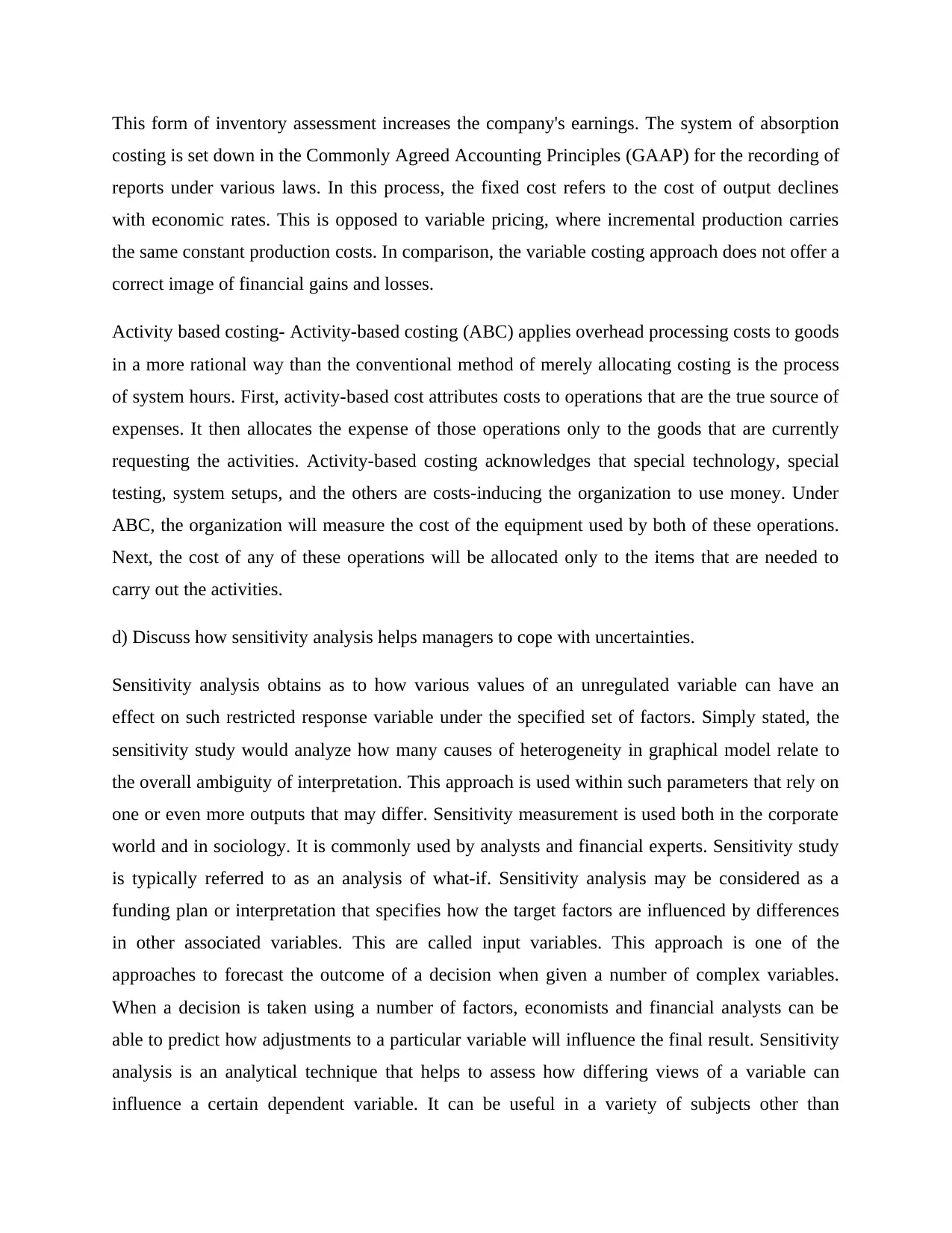
This form of inventory assessment increases the company's earnings. The system of absorption
costing is set down in the Commonly Agreed Accounting Principles (GAAP) for the recording of
reports under various laws. In this process, the fixed cost refers to the cost of output declines
with economic rates. This is opposed to variable pricing, where incremental production carries
the same constant production costs. In comparison, the variable costing approach does not offer a
correct image of financial gains and losses.
Activity based costing- Activity-based costing (ABC) applies overhead processing costs to goods
in a more rational way than the conventional method of merely allocating costing is the process
of system hours. First, activity-based cost attributes costs to operations that are the true source of
expenses. It then allocates the expense of those operations only to the goods that are currently
requesting the activities. Activity-based costing acknowledges that special technology, special
testing, system setups, and the others are costs-inducing the organization to use money. Under
ABC, the organization will measure the cost of the equipment used by both of these operations.
Next, the cost of any of these operations will be allocated only to the items that are needed to
carry out the activities.
d) Discuss how sensitivity analysis helps managers to cope with uncertainties.
Sensitivity analysis obtains as to how various values of an unregulated variable can have an
effect on such restricted response variable under the specified set of factors. Simply stated, the
sensitivity study would analyze how many causes of heterogeneity in graphical model relate to
the overall ambiguity of interpretation. This approach is used within such parameters that rely on
one or even more outputs that may differ. Sensitivity measurement is used both in the corporate
world and in sociology. It is commonly used by analysts and financial experts. Sensitivity study
is typically referred to as an analysis of what-if. Sensitivity analysis may be considered as a
funding plan or interpretation that specifies how the target factors are influenced by differences
in other associated variables. This are called input variables. This approach is one of the
approaches to forecast the outcome of a decision when given a number of complex variables.
When a decision is taken using a number of factors, economists and financial analysts can be
able to predict how adjustments to a particular variable will influence the final result. Sensitivity
analysis is an analytical technique that helps to assess how differing views of a variable can
influence a certain dependent variable. It can be useful in a variety of subjects other than
costing is set down in the Commonly Agreed Accounting Principles (GAAP) for the recording of
reports under various laws. In this process, the fixed cost refers to the cost of output declines
with economic rates. This is opposed to variable pricing, where incremental production carries
the same constant production costs. In comparison, the variable costing approach does not offer a
correct image of financial gains and losses.
Activity based costing- Activity-based costing (ABC) applies overhead processing costs to goods
in a more rational way than the conventional method of merely allocating costing is the process
of system hours. First, activity-based cost attributes costs to operations that are the true source of
expenses. It then allocates the expense of those operations only to the goods that are currently
requesting the activities. Activity-based costing acknowledges that special technology, special
testing, system setups, and the others are costs-inducing the organization to use money. Under
ABC, the organization will measure the cost of the equipment used by both of these operations.
Next, the cost of any of these operations will be allocated only to the items that are needed to
carry out the activities.
d) Discuss how sensitivity analysis helps managers to cope with uncertainties.
Sensitivity analysis obtains as to how various values of an unregulated variable can have an
effect on such restricted response variable under the specified set of factors. Simply stated, the
sensitivity study would analyze how many causes of heterogeneity in graphical model relate to
the overall ambiguity of interpretation. This approach is used within such parameters that rely on
one or even more outputs that may differ. Sensitivity measurement is used both in the corporate
world and in sociology. It is commonly used by analysts and financial experts. Sensitivity study
is typically referred to as an analysis of what-if. Sensitivity analysis may be considered as a
funding plan or interpretation that specifies how the target factors are influenced by differences
in other associated variables. This are called input variables. This approach is one of the
approaches to forecast the outcome of a decision when given a number of complex variables.
When a decision is taken using a number of factors, economists and financial analysts can be
able to predict how adjustments to a particular variable will influence the final result. Sensitivity
analysis is an analytical technique that helps to assess how differing views of a variable can
influence a certain dependent variable. It can be useful in a variety of subjects other than
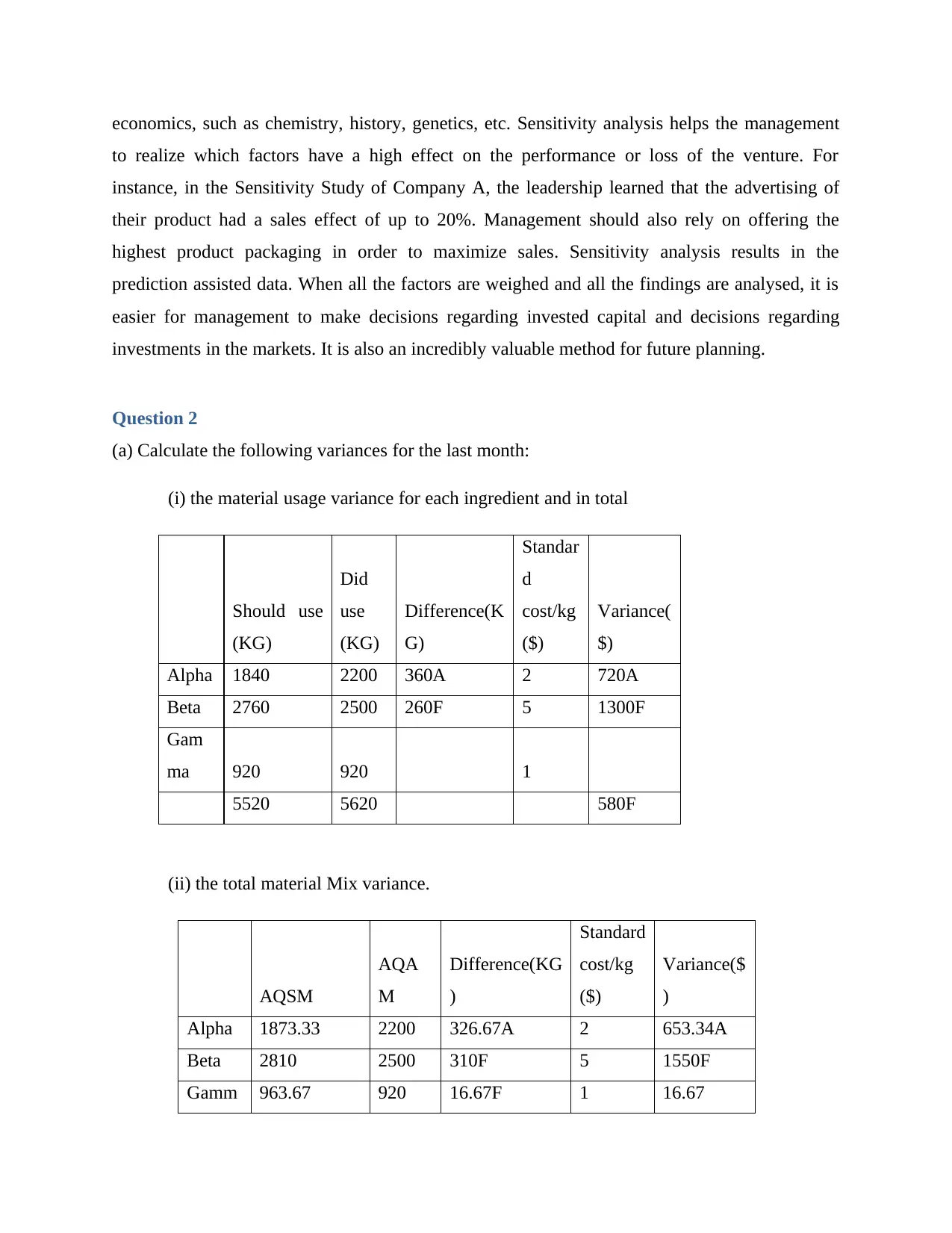
economics, such as chemistry, history, genetics, etc. Sensitivity analysis helps the management
to realize which factors have a high effect on the performance or loss of the venture. For
instance, in the Sensitivity Study of Company A, the leadership learned that the advertising of
their product had a sales effect of up to 20%. Management should also rely on offering the
highest product packaging in order to maximize sales. Sensitivity analysis results in the
prediction assisted data. When all the factors are weighed and all the findings are analysed, it is
easier for management to make decisions regarding invested capital and decisions regarding
investments in the markets. It is also an incredibly valuable method for future planning.
Question 2
(a) Calculate the following variances for the last month:
(i) the material usage variance for each ingredient and in total
Should use
(KG)
Did
use
(KG)
Difference(K
G)
Standar
d
cost/kg
($)
Variance(
$)
Alpha 1840 2200 360A 2 720A
Beta 2760 2500 260F 5 1300F
Gam
ma 920 920 1
5520 5620 580F
(ii) the total material Mix variance.
AQSM
AQA
M
Difference(KG
)
Standard
cost/kg
($)
Variance($
)
Alpha 1873.33 2200 326.67A 2 653.34A
Beta 2810 2500 310F 5 1550F
Gamm 963.67 920 16.67F 1 16.67
to realize which factors have a high effect on the performance or loss of the venture. For
instance, in the Sensitivity Study of Company A, the leadership learned that the advertising of
their product had a sales effect of up to 20%. Management should also rely on offering the
highest product packaging in order to maximize sales. Sensitivity analysis results in the
prediction assisted data. When all the factors are weighed and all the findings are analysed, it is
easier for management to make decisions regarding invested capital and decisions regarding
investments in the markets. It is also an incredibly valuable method for future planning.
Question 2
(a) Calculate the following variances for the last month:
(i) the material usage variance for each ingredient and in total
Should use
(KG)
Did
use
(KG)
Difference(K
G)
Standar
d
cost/kg
($)
Variance(
$)
Alpha 1840 2200 360A 2 720A
Beta 2760 2500 260F 5 1300F
Gam
ma 920 920 1
5520 5620 580F
(ii) the total material Mix variance.
AQSM
AQA
M
Difference(KG
)
Standard
cost/kg
($)
Variance($
)
Alpha 1873.33 2200 326.67A 2 653.34A
Beta 2810 2500 310F 5 1550F
Gamm 963.67 920 16.67F 1 16.67
Paraphrase This Document
Need a fresh take? Get an instant paraphrase of this document with our AI Paraphraser
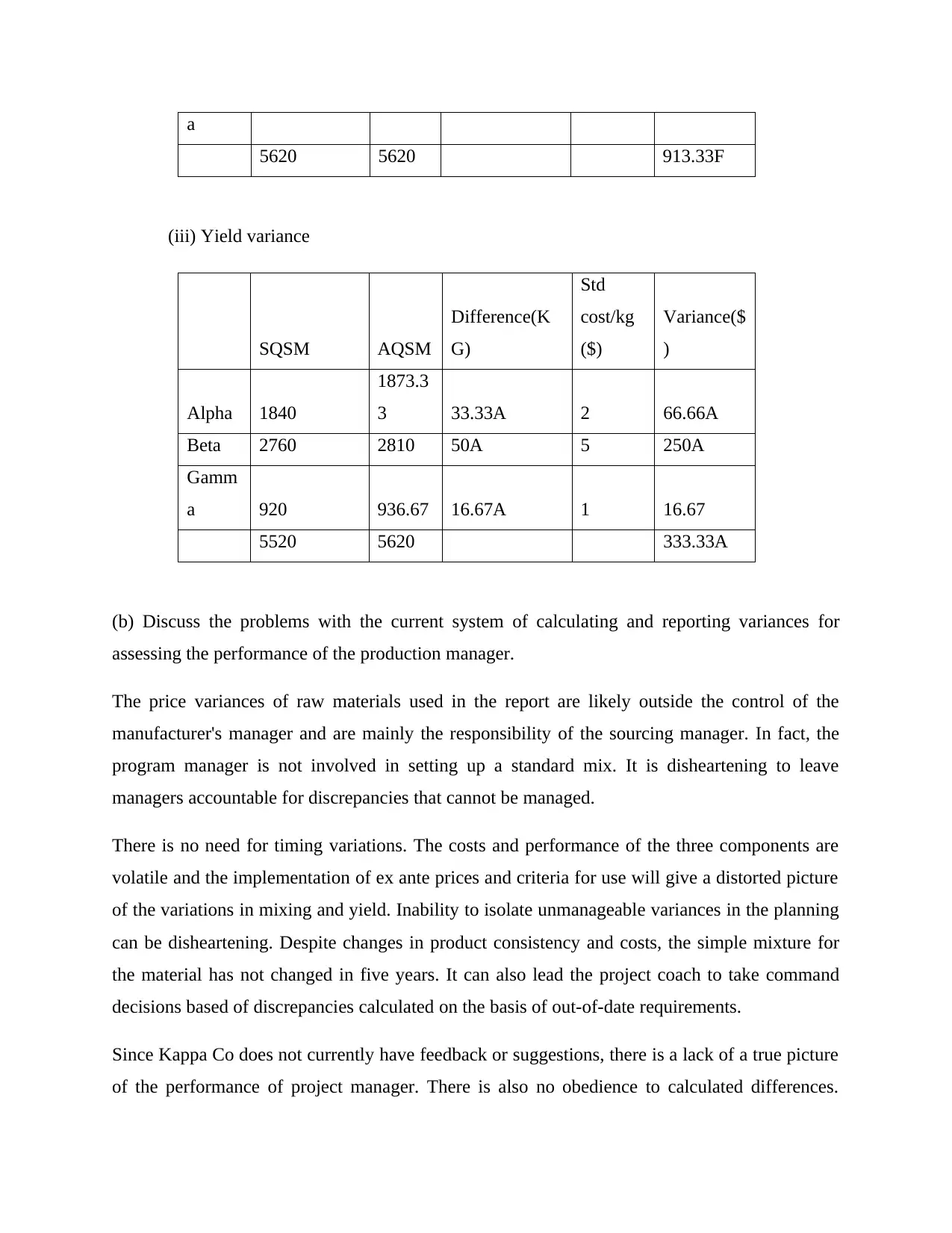
a
5620 5620 913.33F
(iii) Yield variance
SQSM AQSM
Difference(K
G)
Std
cost/kg
($)
Variance($
)
Alpha 1840
1873.3
3 33.33A 2 66.66A
Beta 2760 2810 50A 5 250A
Gamm
a 920 936.67 16.67A 1 16.67
5520 5620 333.33A
(b) Discuss the problems with the current system of calculating and reporting variances for
assessing the performance of the production manager.
The price variances of raw materials used in the report are likely outside the control of the
manufacturer's manager and are mainly the responsibility of the sourcing manager. In fact, the
program manager is not involved in setting up a standard mix. It is disheartening to leave
managers accountable for discrepancies that cannot be managed.
There is no need for timing variations. The costs and performance of the three components are
volatile and the implementation of ex ante prices and criteria for use will give a distorted picture
of the variations in mixing and yield. Inability to isolate unmanageable variances in the planning
can be disheartening. Despite changes in product consistency and costs, the simple mixture for
the material has not changed in five years. It can also lead the project coach to take command
decisions based of discrepancies calculated on the basis of out-of-date requirements.
Since Kappa Co does not currently have feedback or suggestions, there is a lack of a true picture
of the performance of project manager. There is also no obedience to calculated differences.
5620 5620 913.33F
(iii) Yield variance
SQSM AQSM
Difference(K
G)
Std
cost/kg
($)
Variance($
)
Alpha 1840
1873.3
3 33.33A 2 66.66A
Beta 2760 2810 50A 5 250A
Gamm
a 920 936.67 16.67A 1 16.67
5520 5620 333.33A
(b) Discuss the problems with the current system of calculating and reporting variances for
assessing the performance of the production manager.
The price variances of raw materials used in the report are likely outside the control of the
manufacturer's manager and are mainly the responsibility of the sourcing manager. In fact, the
program manager is not involved in setting up a standard mix. It is disheartening to leave
managers accountable for discrepancies that cannot be managed.
There is no need for timing variations. The costs and performance of the three components are
volatile and the implementation of ex ante prices and criteria for use will give a distorted picture
of the variations in mixing and yield. Inability to isolate unmanageable variances in the planning
can be disheartening. Despite changes in product consistency and costs, the simple mixture for
the material has not changed in five years. It can also lead the project coach to take command
decisions based of discrepancies calculated on the basis of out-of-date requirements.
Since Kappa Co does not currently have feedback or suggestions, there is a lack of a true picture
of the performance of project manager. There is also no obedience to calculated differences.
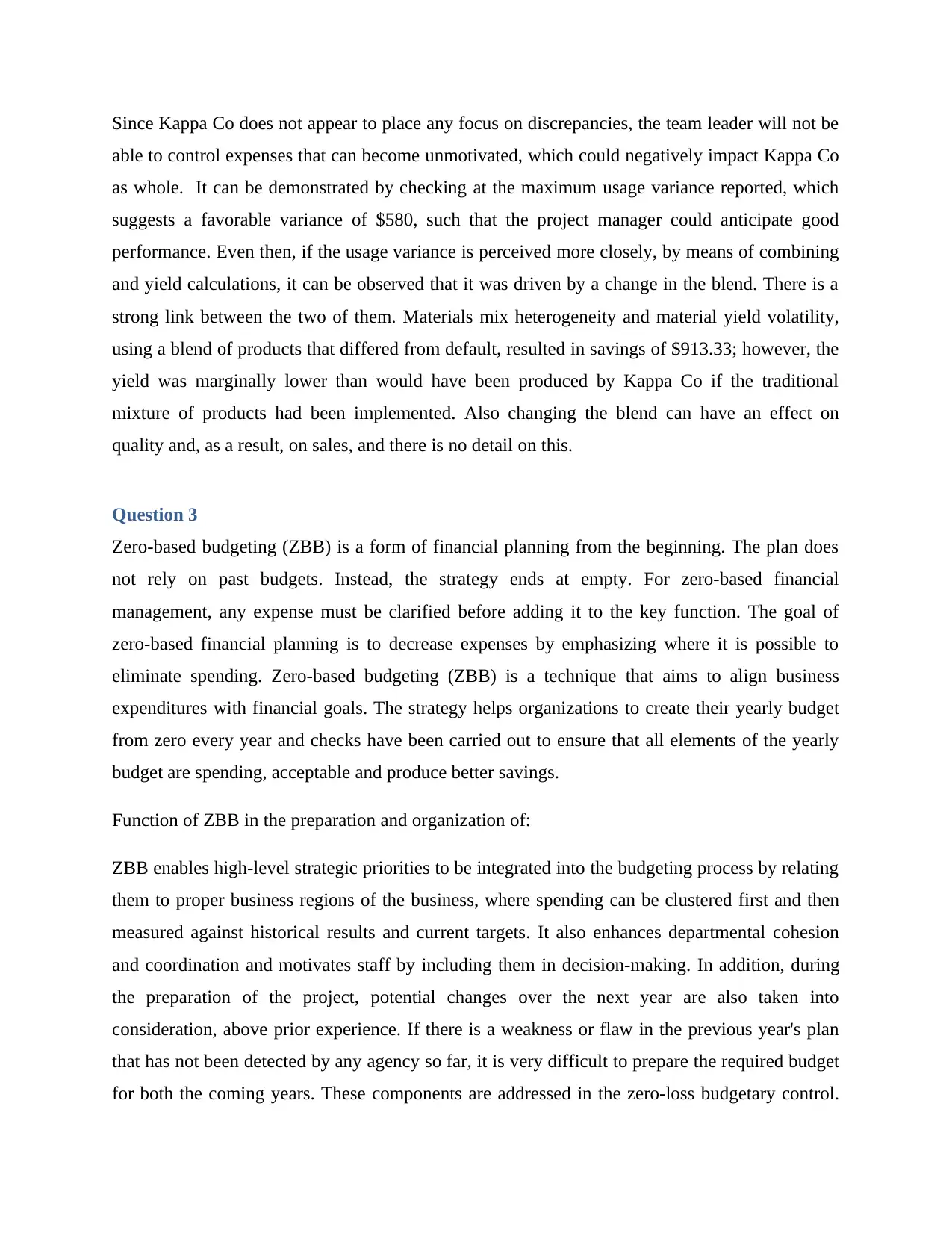
Since Kappa Co does not appear to place any focus on discrepancies, the team leader will not be
able to control expenses that can become unmotivated, which could negatively impact Kappa Co
as whole. It can be demonstrated by checking at the maximum usage variance reported, which
suggests a favorable variance of $580, such that the project manager could anticipate good
performance. Even then, if the usage variance is perceived more closely, by means of combining
and yield calculations, it can be observed that it was driven by a change in the blend. There is a
strong link between the two of them. Materials mix heterogeneity and material yield volatility,
using a blend of products that differed from default, resulted in savings of $913.33; however, the
yield was marginally lower than would have been produced by Kappa Co if the traditional
mixture of products had been implemented. Also changing the blend can have an effect on
quality and, as a result, on sales, and there is no detail on this.
Question 3
Zero-based budgeting (ZBB) is a form of financial planning from the beginning. The plan does
not rely on past budgets. Instead, the strategy ends at empty. For zero-based financial
management, any expense must be clarified before adding it to the key function. The goal of
zero-based financial planning is to decrease expenses by emphasizing where it is possible to
eliminate spending. Zero-based budgeting (ZBB) is a technique that aims to align business
expenditures with financial goals. The strategy helps organizations to create their yearly budget
from zero every year and checks have been carried out to ensure that all elements of the yearly
budget are spending, acceptable and produce better savings.
Function of ZBB in the preparation and organization of:
ZBB enables high-level strategic priorities to be integrated into the budgeting process by relating
them to proper business regions of the business, where spending can be clustered first and then
measured against historical results and current targets. It also enhances departmental cohesion
and coordination and motivates staff by including them in decision-making. In addition, during
the preparation of the project, potential changes over the next year are also taken into
consideration, above prior experience. If there is a weakness or flaw in the previous year's plan
that has not been detected by any agency so far, it is very difficult to prepare the required budget
for both the coming years. These components are addressed in the zero-loss budgetary control.
able to control expenses that can become unmotivated, which could negatively impact Kappa Co
as whole. It can be demonstrated by checking at the maximum usage variance reported, which
suggests a favorable variance of $580, such that the project manager could anticipate good
performance. Even then, if the usage variance is perceived more closely, by means of combining
and yield calculations, it can be observed that it was driven by a change in the blend. There is a
strong link between the two of them. Materials mix heterogeneity and material yield volatility,
using a blend of products that differed from default, resulted in savings of $913.33; however, the
yield was marginally lower than would have been produced by Kappa Co if the traditional
mixture of products had been implemented. Also changing the blend can have an effect on
quality and, as a result, on sales, and there is no detail on this.
Question 3
Zero-based budgeting (ZBB) is a form of financial planning from the beginning. The plan does
not rely on past budgets. Instead, the strategy ends at empty. For zero-based financial
management, any expense must be clarified before adding it to the key function. The goal of
zero-based financial planning is to decrease expenses by emphasizing where it is possible to
eliminate spending. Zero-based budgeting (ZBB) is a technique that aims to align business
expenditures with financial goals. The strategy helps organizations to create their yearly budget
from zero every year and checks have been carried out to ensure that all elements of the yearly
budget are spending, acceptable and produce better savings.
Function of ZBB in the preparation and organization of:
ZBB enables high-level strategic priorities to be integrated into the budgeting process by relating
them to proper business regions of the business, where spending can be clustered first and then
measured against historical results and current targets. It also enhances departmental cohesion
and coordination and motivates staff by including them in decision-making. In addition, during
the preparation of the project, potential changes over the next year are also taken into
consideration, above prior experience. If there is a weakness or flaw in the previous year's plan
that has not been detected by any agency so far, it is very difficult to prepare the required budget
for both the coming years. These components are addressed in the zero-loss budgetary control.
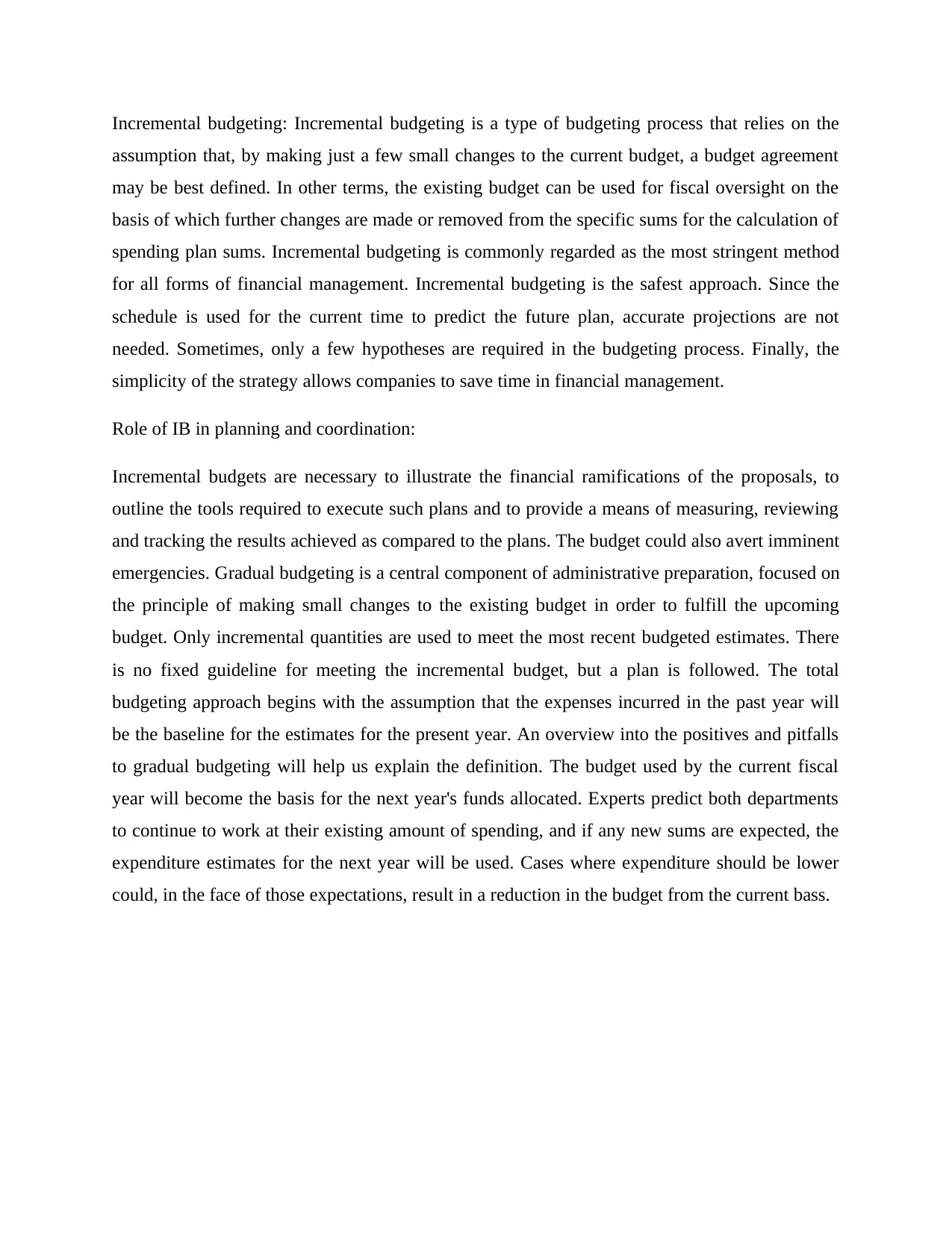
Incremental budgeting: Incremental budgeting is a type of budgeting process that relies on the
assumption that, by making just a few small changes to the current budget, a budget agreement
may be best defined. In other terms, the existing budget can be used for fiscal oversight on the
basis of which further changes are made or removed from the specific sums for the calculation of
spending plan sums. Incremental budgeting is commonly regarded as the most stringent method
for all forms of financial management. Incremental budgeting is the safest approach. Since the
schedule is used for the current time to predict the future plan, accurate projections are not
needed. Sometimes, only a few hypotheses are required in the budgeting process. Finally, the
simplicity of the strategy allows companies to save time in financial management.
Role of IB in planning and coordination:
Incremental budgets are necessary to illustrate the financial ramifications of the proposals, to
outline the tools required to execute such plans and to provide a means of measuring, reviewing
and tracking the results achieved as compared to the plans. The budget could also avert imminent
emergencies. Gradual budgeting is a central component of administrative preparation, focused on
the principle of making small changes to the existing budget in order to fulfill the upcoming
budget. Only incremental quantities are used to meet the most recent budgeted estimates. There
is no fixed guideline for meeting the incremental budget, but a plan is followed. The total
budgeting approach begins with the assumption that the expenses incurred in the past year will
be the baseline for the estimates for the present year. An overview into the positives and pitfalls
to gradual budgeting will help us explain the definition. The budget used by the current fiscal
year will become the basis for the next year's funds allocated. Experts predict both departments
to continue to work at their existing amount of spending, and if any new sums are expected, the
expenditure estimates for the next year will be used. Cases where expenditure should be lower
could, in the face of those expectations, result in a reduction in the budget from the current bass.
assumption that, by making just a few small changes to the current budget, a budget agreement
may be best defined. In other terms, the existing budget can be used for fiscal oversight on the
basis of which further changes are made or removed from the specific sums for the calculation of
spending plan sums. Incremental budgeting is commonly regarded as the most stringent method
for all forms of financial management. Incremental budgeting is the safest approach. Since the
schedule is used for the current time to predict the future plan, accurate projections are not
needed. Sometimes, only a few hypotheses are required in the budgeting process. Finally, the
simplicity of the strategy allows companies to save time in financial management.
Role of IB in planning and coordination:
Incremental budgets are necessary to illustrate the financial ramifications of the proposals, to
outline the tools required to execute such plans and to provide a means of measuring, reviewing
and tracking the results achieved as compared to the plans. The budget could also avert imminent
emergencies. Gradual budgeting is a central component of administrative preparation, focused on
the principle of making small changes to the existing budget in order to fulfill the upcoming
budget. Only incremental quantities are used to meet the most recent budgeted estimates. There
is no fixed guideline for meeting the incremental budget, but a plan is followed. The total
budgeting approach begins with the assumption that the expenses incurred in the past year will
be the baseline for the estimates for the present year. An overview into the positives and pitfalls
to gradual budgeting will help us explain the definition. The budget used by the current fiscal
year will become the basis for the next year's funds allocated. Experts predict both departments
to continue to work at their existing amount of spending, and if any new sums are expected, the
expenditure estimates for the next year will be used. Cases where expenditure should be lower
could, in the face of those expectations, result in a reduction in the budget from the current bass.
1 out of 10
Related Documents

Your All-in-One AI-Powered Toolkit for Academic Success.
 +13062052269
info@desklib.com
Available 24*7 on WhatsApp / Email
Unlock your academic potential
© 2024  |  Zucol Services PVT LTD  |  All rights reserved.