ENGT5220 Coursework A: Low Impact Manufacturing Report
VerifiedAdded on 2022/08/12
|5
|1932
|19
Report
AI Summary
This report examines the energy consumption within the manufacturing process of cottage cheese, identifying key energy inputs, conversions, and losses. Utilizing Sankey diagrams, the analysis highlights significant energy inefficiencies, with over half the energy lost during production. The report explores the potential of integrating renewable energy technologies, specifically solar energy, to supplement the existing energy demands. It calculates the energy contribution of solar panels, assesses the financial implications of such an investment, and concludes that while complete energy replacement with solar is costly, supplementing the energy mix with renewables is a viable option for improving sustainability and reducing environmental impact. Operational efficiencies are also recommended to ensure more energy savings. The report is based on a coursework assignment for the Faculty of Technology module ENGT5220, focusing on the analysis of industrial energy systems.
Contribute Materials
Your contribution can guide someone’s learning journey. Share your
documents today.
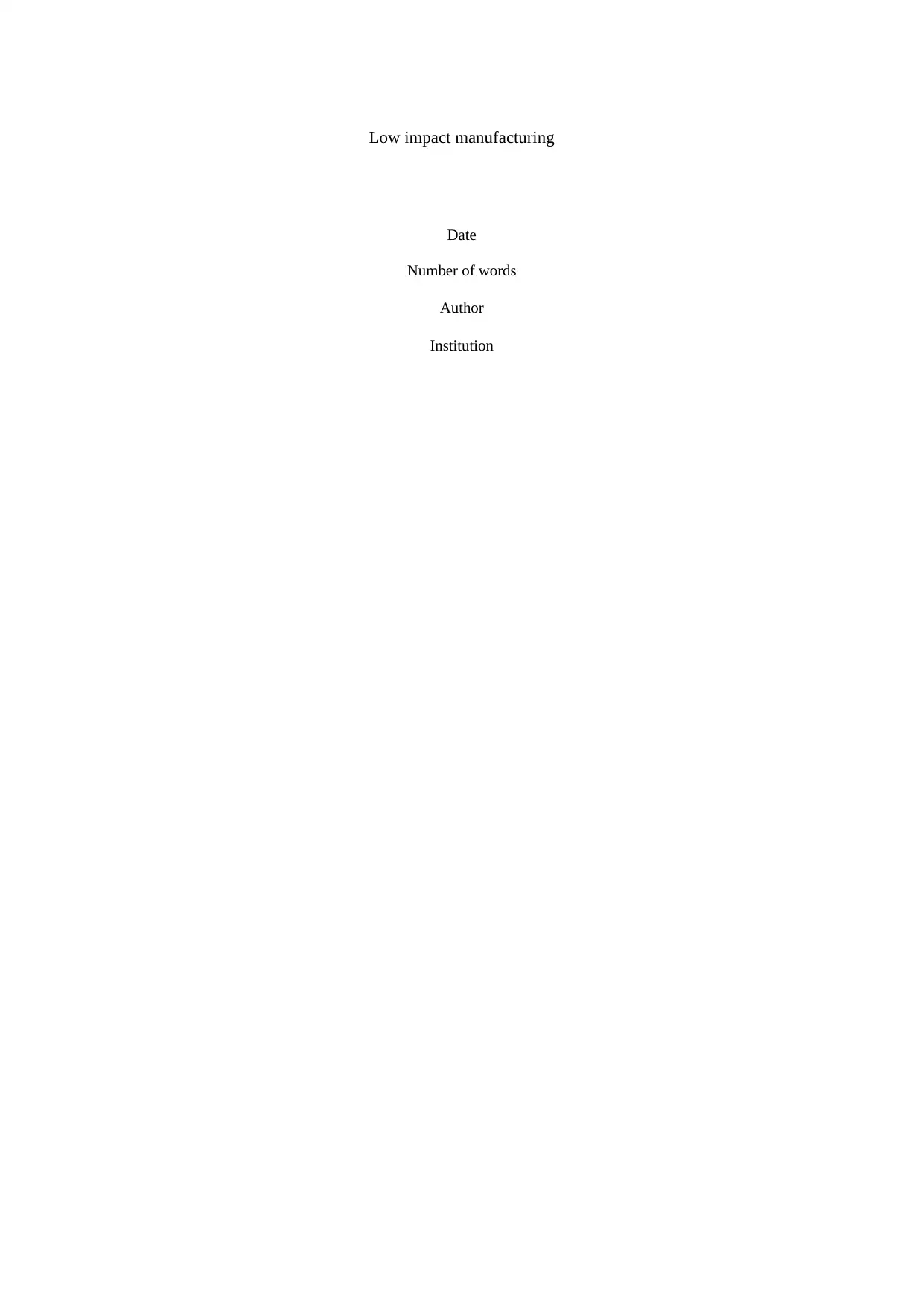
Low impact manufacturing
Date
Number of words
Author
Institution
Date
Number of words
Author
Institution
Secure Best Marks with AI Grader
Need help grading? Try our AI Grader for instant feedback on your assignments.
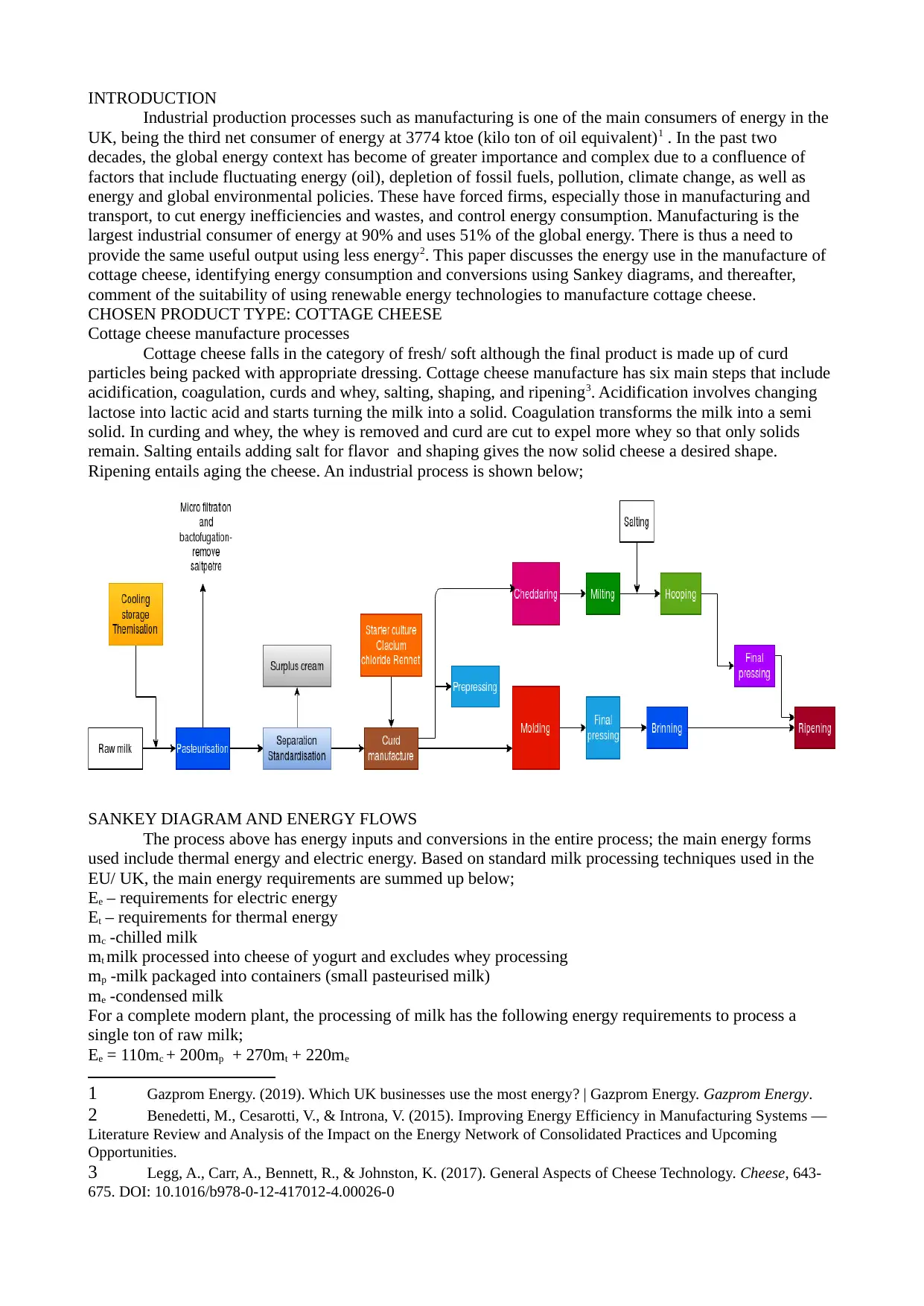
INTRODUCTION
Industrial production processes such as manufacturing is one of the main consumers of energy in the
UK, being the third net consumer of energy at 3774 ktoe (kilo ton of oil equivalent)1 . In the past two
decades, the global energy context has become of greater importance and complex due to a confluence of
factors that include fluctuating energy (oil), depletion of fossil fuels, pollution, climate change, as well as
energy and global environmental policies. These have forced firms, especially those in manufacturing and
transport, to cut energy inefficiencies and wastes, and control energy consumption. Manufacturing is the
largest industrial consumer of energy at 90% and uses 51% of the global energy. There is thus a need to
provide the same useful output using less energy2. This paper discusses the energy use in the manufacture of
cottage cheese, identifying energy consumption and conversions using Sankey diagrams, and thereafter,
comment of the suitability of using renewable energy technologies to manufacture cottage cheese.
CHOSEN PRODUCT TYPE: COTTAGE CHEESE
Cottage cheese manufacture processes
Cottage cheese falls in the category of fresh/ soft although the final product is made up of curd
particles being packed with appropriate dressing. Cottage cheese manufacture has six main steps that include
acidification, coagulation, curds and whey, salting, shaping, and ripening3. Acidification involves changing
lactose into lactic acid and starts turning the milk into a solid. Coagulation transforms the milk into a semi
solid. In curding and whey, the whey is removed and curd are cut to expel more whey so that only solids
remain. Salting entails adding salt for flavor and shaping gives the now solid cheese a desired shape.
Ripening entails aging the cheese. An industrial process is shown below;
SANKEY DIAGRAM AND ENERGY FLOWS
The process above has energy inputs and conversions in the entire process; the main energy forms
used include thermal energy and electric energy. Based on standard milk processing techniques used in the
EU/ UK, the main energy requirements are summed up below;
Ee – requirements for electric energy
Et – requirements for thermal energy
mc -chilled milk
mt milk processed into cheese of yogurt and excludes whey processing
mp -milk packaged into containers (small pasteurised milk)
me -condensed milk
For a complete modern plant, the processing of milk has the following energy requirements to process a
single ton of raw milk;
Ee = 110mc + 200mp + 270mt + 220me
1 Gazprom Energy. (2019). Which UK businesses use the most energy? | Gazprom Energy. Gazprom Energy.
2 Benedetti, M., Cesarotti, V., & Introna, V. (2015). Improving Energy Efficiency in Manufacturing Systems —
Literature Review and Analysis of the Impact on the Energy Network of Consolidated Practices and Upcoming
Opportunities.
3 Legg, A., Carr, A., Bennett, R., & Johnston, K. (2017). General Aspects of Cheese Technology. Cheese, 643-
675. DOI: 10.1016/b978-0-12-417012-4.00026-0
Industrial production processes such as manufacturing is one of the main consumers of energy in the
UK, being the third net consumer of energy at 3774 ktoe (kilo ton of oil equivalent)1 . In the past two
decades, the global energy context has become of greater importance and complex due to a confluence of
factors that include fluctuating energy (oil), depletion of fossil fuels, pollution, climate change, as well as
energy and global environmental policies. These have forced firms, especially those in manufacturing and
transport, to cut energy inefficiencies and wastes, and control energy consumption. Manufacturing is the
largest industrial consumer of energy at 90% and uses 51% of the global energy. There is thus a need to
provide the same useful output using less energy2. This paper discusses the energy use in the manufacture of
cottage cheese, identifying energy consumption and conversions using Sankey diagrams, and thereafter,
comment of the suitability of using renewable energy technologies to manufacture cottage cheese.
CHOSEN PRODUCT TYPE: COTTAGE CHEESE
Cottage cheese manufacture processes
Cottage cheese falls in the category of fresh/ soft although the final product is made up of curd
particles being packed with appropriate dressing. Cottage cheese manufacture has six main steps that include
acidification, coagulation, curds and whey, salting, shaping, and ripening3. Acidification involves changing
lactose into lactic acid and starts turning the milk into a solid. Coagulation transforms the milk into a semi
solid. In curding and whey, the whey is removed and curd are cut to expel more whey so that only solids
remain. Salting entails adding salt for flavor and shaping gives the now solid cheese a desired shape.
Ripening entails aging the cheese. An industrial process is shown below;
SANKEY DIAGRAM AND ENERGY FLOWS
The process above has energy inputs and conversions in the entire process; the main energy forms
used include thermal energy and electric energy. Based on standard milk processing techniques used in the
EU/ UK, the main energy requirements are summed up below;
Ee – requirements for electric energy
Et – requirements for thermal energy
mc -chilled milk
mt milk processed into cheese of yogurt and excludes whey processing
mp -milk packaged into containers (small pasteurised milk)
me -condensed milk
For a complete modern plant, the processing of milk has the following energy requirements to process a
single ton of raw milk;
Ee = 110mc + 200mp + 270mt + 220me
1 Gazprom Energy. (2019). Which UK businesses use the most energy? | Gazprom Energy. Gazprom Energy.
2 Benedetti, M., Cesarotti, V., & Introna, V. (2015). Improving Energy Efficiency in Manufacturing Systems —
Literature Review and Analysis of the Impact on the Energy Network of Consolidated Practices and Upcoming
Opportunities.
3 Legg, A., Carr, A., Bennett, R., & Johnston, K. (2017). General Aspects of Cheese Technology. Cheese, 643-
675. DOI: 10.1016/b978-0-12-417012-4.00026-0
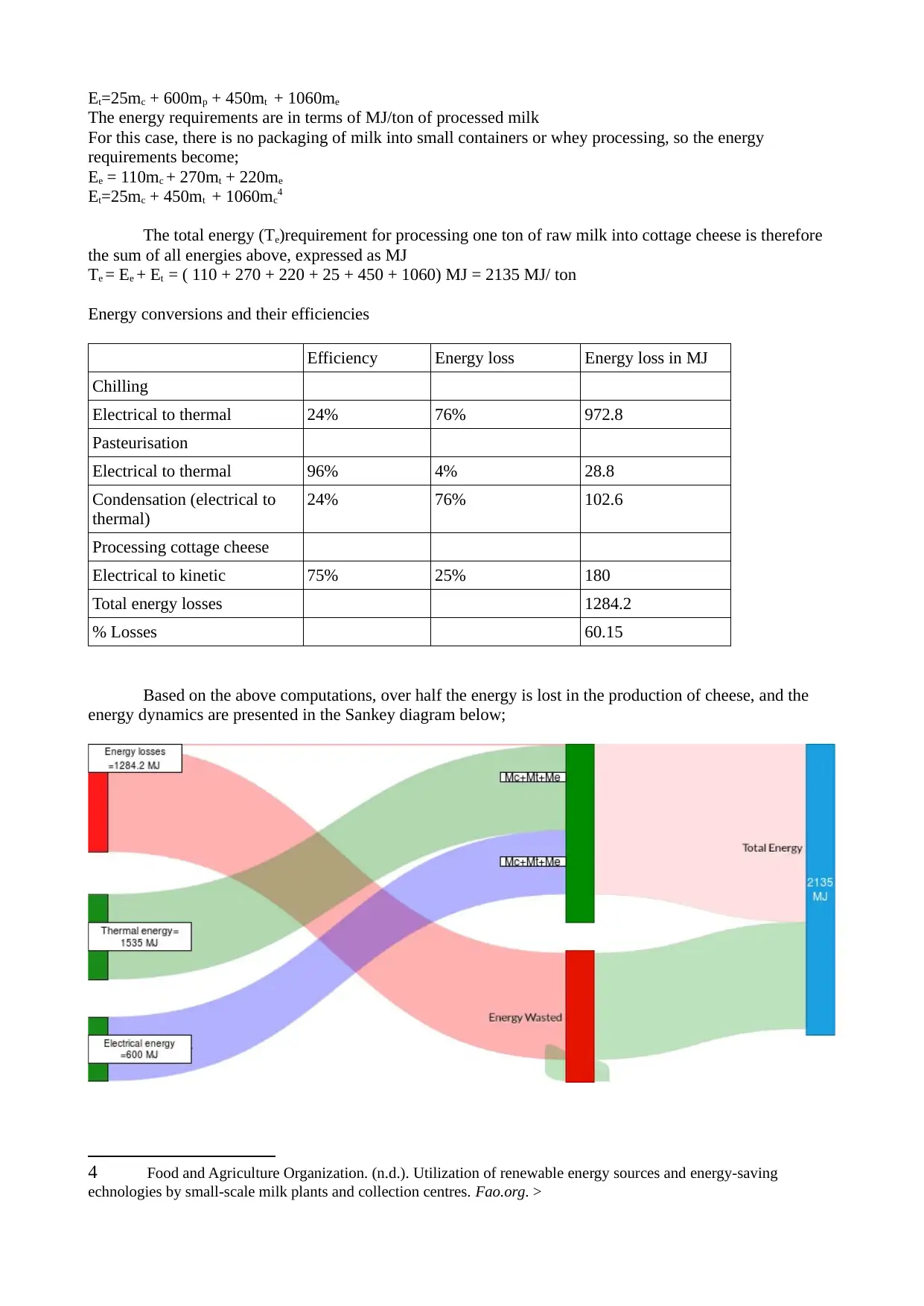
Et=25mc + 600mp + 450mt + 1060me
The energy requirements are in terms of MJ/ton of processed milk
For this case, there is no packaging of milk into small containers or whey processing, so the energy
requirements become;
Ee = 110mc + 270mt + 220me
Et=25mc + 450mt + 1060mc4
The total energy (Te)requirement for processing one ton of raw milk into cottage cheese is therefore
the sum of all energies above, expressed as MJ
Te = Ee + Et = ( 110 + 270 + 220 + 25 + 450 + 1060) MJ = 2135 MJ/ ton
Energy conversions and their efficiencies
Efficiency Energy loss Energy loss in MJ
Chilling
Electrical to thermal 24% 76% 972.8
Pasteurisation
Electrical to thermal 96% 4% 28.8
Condensation (electrical to
thermal)
24% 76% 102.6
Processing cottage cheese
Electrical to kinetic 75% 25% 180
Total energy losses 1284.2
% Losses 60.15
Based on the above computations, over half the energy is lost in the production of cheese, and the
energy dynamics are presented in the Sankey diagram below;
4 Food and Agriculture Organization. (n.d.). Utilization of renewable energy sources and energy-saving
echnologies by small-scale milk plants and collection centres. Fao.org. >
The energy requirements are in terms of MJ/ton of processed milk
For this case, there is no packaging of milk into small containers or whey processing, so the energy
requirements become;
Ee = 110mc + 270mt + 220me
Et=25mc + 450mt + 1060mc4
The total energy (Te)requirement for processing one ton of raw milk into cottage cheese is therefore
the sum of all energies above, expressed as MJ
Te = Ee + Et = ( 110 + 270 + 220 + 25 + 450 + 1060) MJ = 2135 MJ/ ton
Energy conversions and their efficiencies
Efficiency Energy loss Energy loss in MJ
Chilling
Electrical to thermal 24% 76% 972.8
Pasteurisation
Electrical to thermal 96% 4% 28.8
Condensation (electrical to
thermal)
24% 76% 102.6
Processing cottage cheese
Electrical to kinetic 75% 25% 180
Total energy losses 1284.2
% Losses 60.15
Based on the above computations, over half the energy is lost in the production of cheese, and the
energy dynamics are presented in the Sankey diagram below;
4 Food and Agriculture Organization. (n.d.). Utilization of renewable energy sources and energy-saving
echnologies by small-scale milk plants and collection centres. Fao.org. >
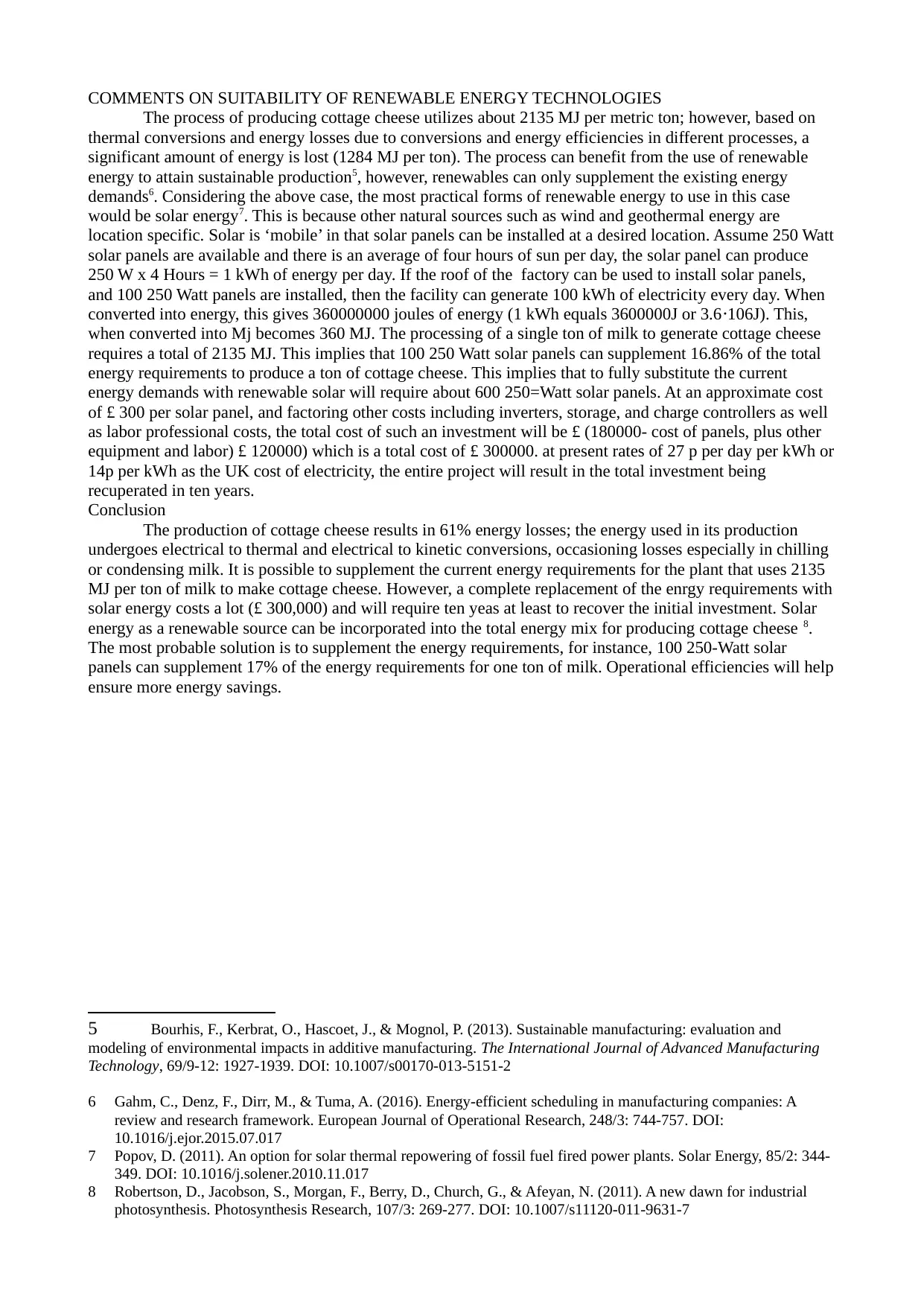
COMMENTS ON SUITABILITY OF RENEWABLE ENERGY TECHNOLOGIES
The process of producing cottage cheese utilizes about 2135 MJ per metric ton; however, based on
thermal conversions and energy losses due to conversions and energy efficiencies in different processes, a
significant amount of energy is lost (1284 MJ per ton). The process can benefit from the use of renewable
energy to attain sustainable production5, however, renewables can only supplement the existing energy
demands6. Considering the above case, the most practical forms of renewable energy to use in this case
would be solar energy7. This is because other natural sources such as wind and geothermal energy are
location specific. Solar is ‘mobile’ in that solar panels can be installed at a desired location. Assume 250 Watt
solar panels are available and there is an average of four hours of sun per day, the solar panel can produce
250 W x 4 Hours = 1 kWh of energy per day. If the roof of the factory can be used to install solar panels,
and 100 250 Watt panels are installed, then the facility can generate 100 kWh of electricity every day. When
converted into energy, this gives 360000000 joules of energy (1 kWh equals 3600000J or 3.6 106J). This,⋅
when converted into Mj becomes 360 MJ. The processing of a single ton of milk to generate cottage cheese
requires a total of 2135 MJ. This implies that 100 250 Watt solar panels can supplement 16.86% of the total
energy requirements to produce a ton of cottage cheese. This implies that to fully substitute the current
energy demands with renewable solar will require about 600 250=Watt solar panels. At an approximate cost
of £ 300 per solar panel, and factoring other costs including inverters, storage, and charge controllers as well
as labor professional costs, the total cost of such an investment will be £ (180000- cost of panels, plus other
equipment and labor) £ 120000) which is a total cost of £ 300000. at present rates of 27 p per day per kWh or
14p per kWh as the UK cost of electricity, the entire project will result in the total investment being
recuperated in ten years.
Conclusion
The production of cottage cheese results in 61% energy losses; the energy used in its production
undergoes electrical to thermal and electrical to kinetic conversions, occasioning losses especially in chilling
or condensing milk. It is possible to supplement the current energy requirements for the plant that uses 2135
MJ per ton of milk to make cottage cheese. However, a complete replacement of the enrgy requirements with
solar energy costs a lot (£ 300,000) and will require ten yeas at least to recover the initial investment. Solar
energy as a renewable source can be incorporated into the total energy mix for producing cottage cheese 8.
The most probable solution is to supplement the energy requirements, for instance, 100 250-Watt solar
panels can supplement 17% of the energy requirements for one ton of milk. Operational efficiencies will help
ensure more energy savings.
5 Bourhis, F., Kerbrat, O., Hascoet, J., & Mognol, P. (2013). Sustainable manufacturing: evaluation and
modeling of environmental impacts in additive manufacturing. The International Journal of Advanced Manufacturing
Technology, 69/9-12: 1927-1939. DOI: 10.1007/s00170-013-5151-2
6 Gahm, C., Denz, F., Dirr, M., & Tuma, A. (2016). Energy-efficient scheduling in manufacturing companies: A
review and research framework. European Journal of Operational Research, 248/3: 744-757. DOI:
10.1016/j.ejor.2015.07.017
7 Popov, D. (2011). An option for solar thermal repowering of fossil fuel fired power plants. Solar Energy, 85/2: 344-
349. DOI: 10.1016/j.solener.2010.11.017
8 Robertson, D., Jacobson, S., Morgan, F., Berry, D., Church, G., & Afeyan, N. (2011). A new dawn for industrial
photosynthesis. Photosynthesis Research, 107/3: 269-277. DOI: 10.1007/s11120-011-9631-7
The process of producing cottage cheese utilizes about 2135 MJ per metric ton; however, based on
thermal conversions and energy losses due to conversions and energy efficiencies in different processes, a
significant amount of energy is lost (1284 MJ per ton). The process can benefit from the use of renewable
energy to attain sustainable production5, however, renewables can only supplement the existing energy
demands6. Considering the above case, the most practical forms of renewable energy to use in this case
would be solar energy7. This is because other natural sources such as wind and geothermal energy are
location specific. Solar is ‘mobile’ in that solar panels can be installed at a desired location. Assume 250 Watt
solar panels are available and there is an average of four hours of sun per day, the solar panel can produce
250 W x 4 Hours = 1 kWh of energy per day. If the roof of the factory can be used to install solar panels,
and 100 250 Watt panels are installed, then the facility can generate 100 kWh of electricity every day. When
converted into energy, this gives 360000000 joules of energy (1 kWh equals 3600000J or 3.6 106J). This,⋅
when converted into Mj becomes 360 MJ. The processing of a single ton of milk to generate cottage cheese
requires a total of 2135 MJ. This implies that 100 250 Watt solar panels can supplement 16.86% of the total
energy requirements to produce a ton of cottage cheese. This implies that to fully substitute the current
energy demands with renewable solar will require about 600 250=Watt solar panels. At an approximate cost
of £ 300 per solar panel, and factoring other costs including inverters, storage, and charge controllers as well
as labor professional costs, the total cost of such an investment will be £ (180000- cost of panels, plus other
equipment and labor) £ 120000) which is a total cost of £ 300000. at present rates of 27 p per day per kWh or
14p per kWh as the UK cost of electricity, the entire project will result in the total investment being
recuperated in ten years.
Conclusion
The production of cottage cheese results in 61% energy losses; the energy used in its production
undergoes electrical to thermal and electrical to kinetic conversions, occasioning losses especially in chilling
or condensing milk. It is possible to supplement the current energy requirements for the plant that uses 2135
MJ per ton of milk to make cottage cheese. However, a complete replacement of the enrgy requirements with
solar energy costs a lot (£ 300,000) and will require ten yeas at least to recover the initial investment. Solar
energy as a renewable source can be incorporated into the total energy mix for producing cottage cheese 8.
The most probable solution is to supplement the energy requirements, for instance, 100 250-Watt solar
panels can supplement 17% of the energy requirements for one ton of milk. Operational efficiencies will help
ensure more energy savings.
5 Bourhis, F., Kerbrat, O., Hascoet, J., & Mognol, P. (2013). Sustainable manufacturing: evaluation and
modeling of environmental impacts in additive manufacturing. The International Journal of Advanced Manufacturing
Technology, 69/9-12: 1927-1939. DOI: 10.1007/s00170-013-5151-2
6 Gahm, C., Denz, F., Dirr, M., & Tuma, A. (2016). Energy-efficient scheduling in manufacturing companies: A
review and research framework. European Journal of Operational Research, 248/3: 744-757. DOI:
10.1016/j.ejor.2015.07.017
7 Popov, D. (2011). An option for solar thermal repowering of fossil fuel fired power plants. Solar Energy, 85/2: 344-
349. DOI: 10.1016/j.solener.2010.11.017
8 Robertson, D., Jacobson, S., Morgan, F., Berry, D., Church, G., & Afeyan, N. (2011). A new dawn for industrial
photosynthesis. Photosynthesis Research, 107/3: 269-277. DOI: 10.1007/s11120-011-9631-7
Secure Best Marks with AI Grader
Need help grading? Try our AI Grader for instant feedback on your assignments.
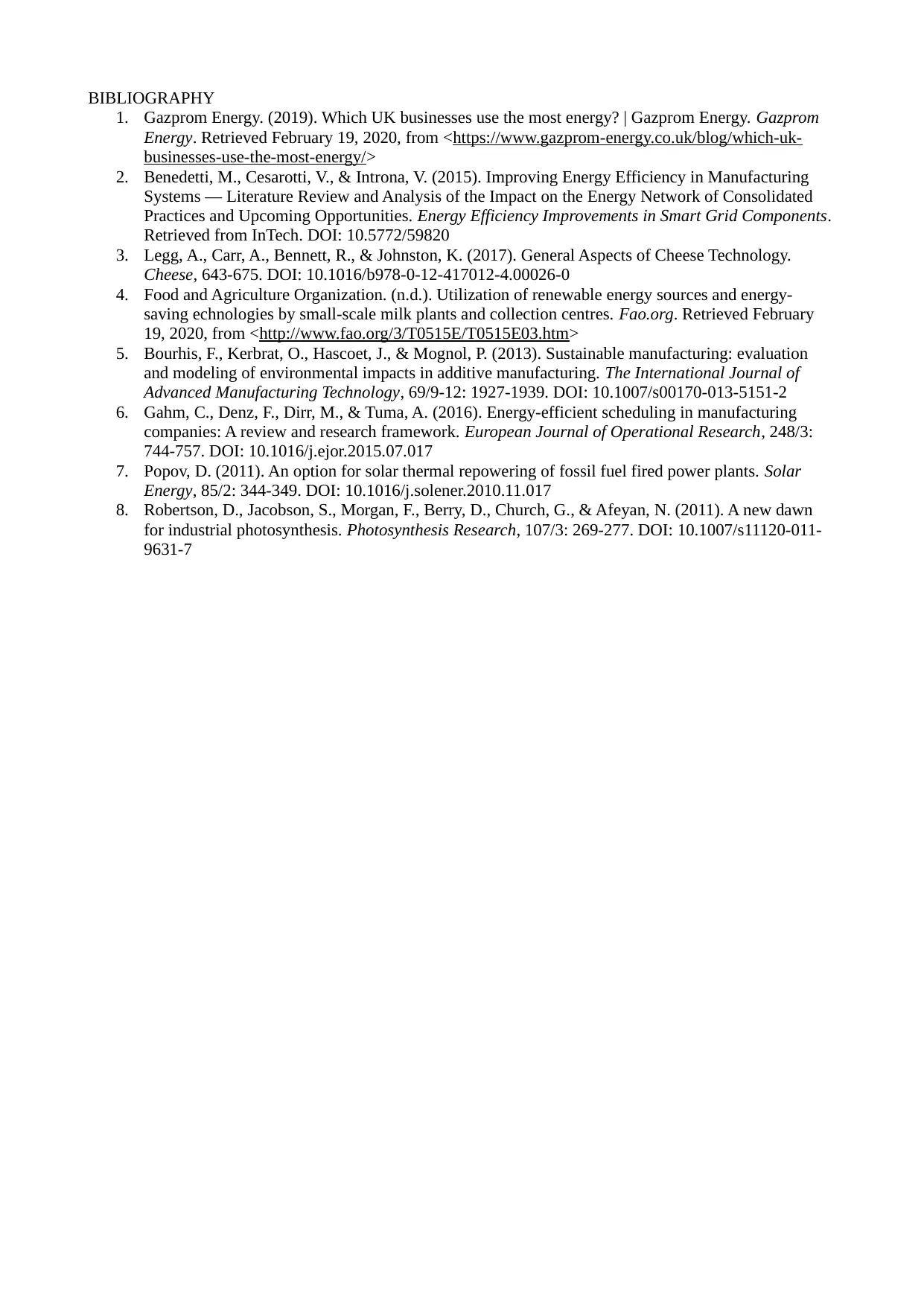
BIBLIOGRAPHY
1. Gazprom Energy. (2019). Which UK businesses use the most energy? | Gazprom Energy. Gazprom
Energy. Retrieved February 19, 2020, from <https://www.gazprom-energy.co.uk/blog/which-uk-
businesses-use-the-most-energy/>
2. Benedetti, M., Cesarotti, V., & Introna, V. (2015). Improving Energy Efficiency in Manufacturing
Systems — Literature Review and Analysis of the Impact on the Energy Network of Consolidated
Practices and Upcoming Opportunities. Energy Efficiency Improvements in Smart Grid Components.
Retrieved from InTech. DOI: 10.5772/59820
3. Legg, A., Carr, A., Bennett, R., & Johnston, K. (2017). General Aspects of Cheese Technology.
Cheese, 643-675. DOI: 10.1016/b978-0-12-417012-4.00026-0
4. Food and Agriculture Organization. (n.d.). Utilization of renewable energy sources and energy-
saving echnologies by small-scale milk plants and collection centres. Fao.org. Retrieved February
19, 2020, from <http://www.fao.org/3/T0515E/T0515E03.htm>
5. Bourhis, F., Kerbrat, O., Hascoet, J., & Mognol, P. (2013). Sustainable manufacturing: evaluation
and modeling of environmental impacts in additive manufacturing. The International Journal of
Advanced Manufacturing Technology, 69/9-12: 1927-1939. DOI: 10.1007/s00170-013-5151-2
6. Gahm, C., Denz, F., Dirr, M., & Tuma, A. (2016). Energy-efficient scheduling in manufacturing
companies: A review and research framework. European Journal of Operational Research, 248/3:
744-757. DOI: 10.1016/j.ejor.2015.07.017
7. Popov, D. (2011). An option for solar thermal repowering of fossil fuel fired power plants. Solar
Energy, 85/2: 344-349. DOI: 10.1016/j.solener.2010.11.017
8. Robertson, D., Jacobson, S., Morgan, F., Berry, D., Church, G., & Afeyan, N. (2011). A new dawn
for industrial photosynthesis. Photosynthesis Research, 107/3: 269-277. DOI: 10.1007/s11120-011-
9631-7
1. Gazprom Energy. (2019). Which UK businesses use the most energy? | Gazprom Energy. Gazprom
Energy. Retrieved February 19, 2020, from <https://www.gazprom-energy.co.uk/blog/which-uk-
businesses-use-the-most-energy/>
2. Benedetti, M., Cesarotti, V., & Introna, V. (2015). Improving Energy Efficiency in Manufacturing
Systems — Literature Review and Analysis of the Impact on the Energy Network of Consolidated
Practices and Upcoming Opportunities. Energy Efficiency Improvements in Smart Grid Components.
Retrieved from InTech. DOI: 10.5772/59820
3. Legg, A., Carr, A., Bennett, R., & Johnston, K. (2017). General Aspects of Cheese Technology.
Cheese, 643-675. DOI: 10.1016/b978-0-12-417012-4.00026-0
4. Food and Agriculture Organization. (n.d.). Utilization of renewable energy sources and energy-
saving echnologies by small-scale milk plants and collection centres. Fao.org. Retrieved February
19, 2020, from <http://www.fao.org/3/T0515E/T0515E03.htm>
5. Bourhis, F., Kerbrat, O., Hascoet, J., & Mognol, P. (2013). Sustainable manufacturing: evaluation
and modeling of environmental impacts in additive manufacturing. The International Journal of
Advanced Manufacturing Technology, 69/9-12: 1927-1939. DOI: 10.1007/s00170-013-5151-2
6. Gahm, C., Denz, F., Dirr, M., & Tuma, A. (2016). Energy-efficient scheduling in manufacturing
companies: A review and research framework. European Journal of Operational Research, 248/3:
744-757. DOI: 10.1016/j.ejor.2015.07.017
7. Popov, D. (2011). An option for solar thermal repowering of fossil fuel fired power plants. Solar
Energy, 85/2: 344-349. DOI: 10.1016/j.solener.2010.11.017
8. Robertson, D., Jacobson, S., Morgan, F., Berry, D., Church, G., & Afeyan, N. (2011). A new dawn
for industrial photosynthesis. Photosynthesis Research, 107/3: 269-277. DOI: 10.1007/s11120-011-
9631-7
1 out of 5

Your All-in-One AI-Powered Toolkit for Academic Success.
+13062052269
info@desklib.com
Available 24*7 on WhatsApp / Email
Unlock your academic potential
© 2024 | Zucol Services PVT LTD | All rights reserved.