Comprehensive Analysis of Warehouse Safety Management at Daraz.pk
VerifiedAdded on 2022/01/20
|5
|1604
|92
Report
AI Summary
This report provides a detailed analysis of warehouse safety management at Daraz.pk, a prominent e-commerce platform operating in Pakistan and other South Asian countries. The report examines Daraz.pk's 3PL (Third-Party Logistics) model, which involves separate parties for product sales, procurement, and delivery, and how this impacts warehouse operations. It describes the structure of Daraz.pk's warehouses, including non-bulky and bulky segments, and the processes within each, such as inbound and receiving, inventory and storage, outbound and forwarding, and quality control. The report also highlights the technologies and equipment used in the warehouses, including manual forklifts, palettes, and trolleys, along with the strategic placement of aisles. Furthermore, it discusses the safety measures implemented to mitigate risks, such as guided forklifts, advanced Warehouse Management Systems (WMS), and end barriers, especially in the context of the ongoing pandemic. The report concludes by emphasizing the growing trend of automation and the use of AI in warehouse operations, along with the prospects for future advancements in the industry.
Contribute Materials
Your contribution can guide someone’s learning journey. Share your
documents today.
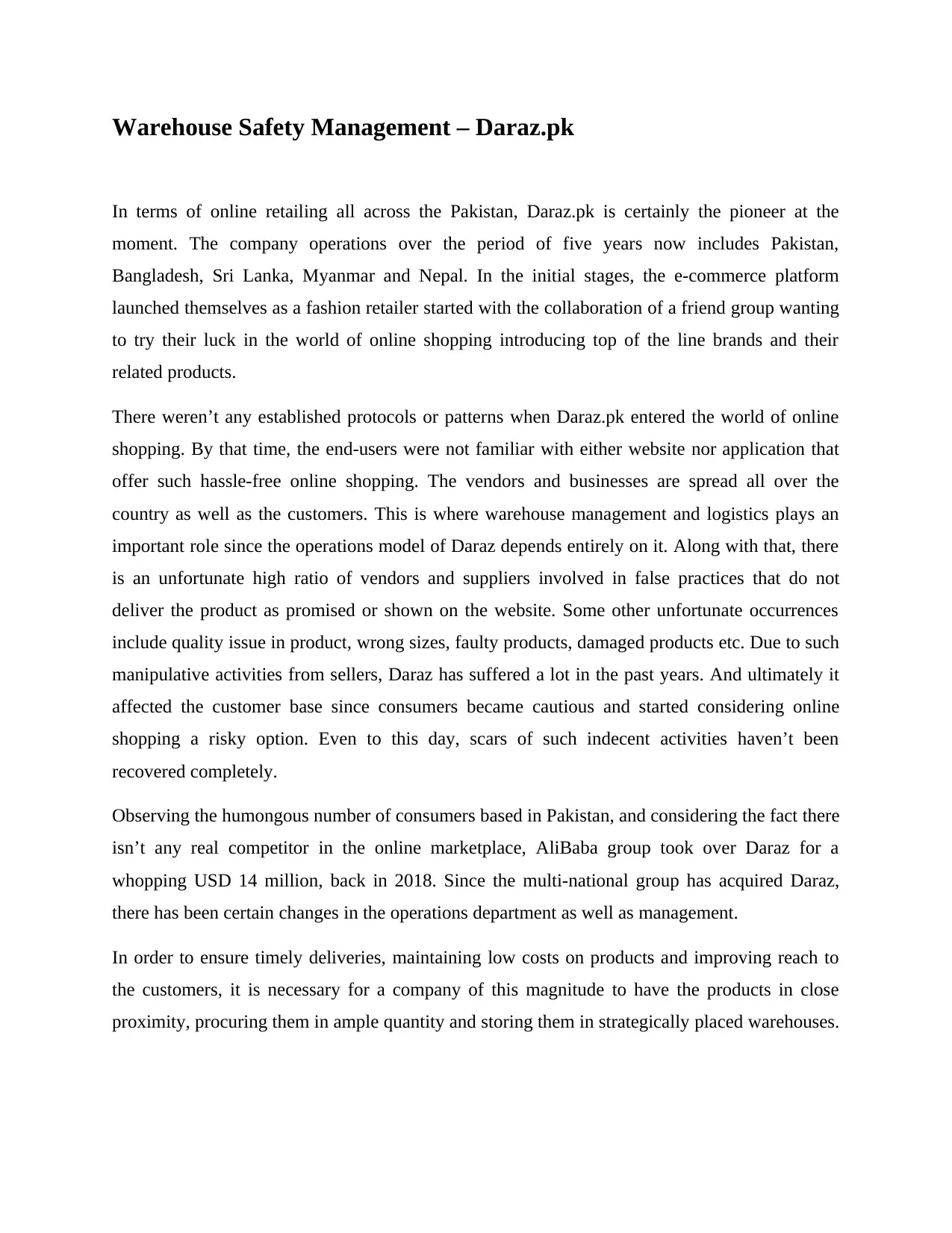
Warehouse Safety Management – Daraz.pk
In terms of online retailing all across the Pakistan, Daraz.pk is certainly the pioneer at the
moment. The company operations over the period of five years now includes Pakistan,
Bangladesh, Sri Lanka, Myanmar and Nepal. In the initial stages, the e-commerce platform
launched themselves as a fashion retailer started with the collaboration of a friend group wanting
to try their luck in the world of online shopping introducing top of the line brands and their
related products.
There weren’t any established protocols or patterns when Daraz.pk entered the world of online
shopping. By that time, the end-users were not familiar with either website nor application that
offer such hassle-free online shopping. The vendors and businesses are spread all over the
country as well as the customers. This is where warehouse management and logistics plays an
important role since the operations model of Daraz depends entirely on it. Along with that, there
is an unfortunate high ratio of vendors and suppliers involved in false practices that do not
deliver the product as promised or shown on the website. Some other unfortunate occurrences
include quality issue in product, wrong sizes, faulty products, damaged products etc. Due to such
manipulative activities from sellers, Daraz has suffered a lot in the past years. And ultimately it
affected the customer base since consumers became cautious and started considering online
shopping a risky option. Even to this day, scars of such indecent activities haven’t been
recovered completely.
Observing the humongous number of consumers based in Pakistan, and considering the fact there
isn’t any real competitor in the online marketplace, AliBaba group took over Daraz for a
whopping USD 14 million, back in 2018. Since the multi-national group has acquired Daraz,
there has been certain changes in the operations department as well as management.
In order to ensure timely deliveries, maintaining low costs on products and improving reach to
the customers, it is necessary for a company of this magnitude to have the products in close
proximity, procuring them in ample quantity and storing them in strategically placed warehouses.
In terms of online retailing all across the Pakistan, Daraz.pk is certainly the pioneer at the
moment. The company operations over the period of five years now includes Pakistan,
Bangladesh, Sri Lanka, Myanmar and Nepal. In the initial stages, the e-commerce platform
launched themselves as a fashion retailer started with the collaboration of a friend group wanting
to try their luck in the world of online shopping introducing top of the line brands and their
related products.
There weren’t any established protocols or patterns when Daraz.pk entered the world of online
shopping. By that time, the end-users were not familiar with either website nor application that
offer such hassle-free online shopping. The vendors and businesses are spread all over the
country as well as the customers. This is where warehouse management and logistics plays an
important role since the operations model of Daraz depends entirely on it. Along with that, there
is an unfortunate high ratio of vendors and suppliers involved in false practices that do not
deliver the product as promised or shown on the website. Some other unfortunate occurrences
include quality issue in product, wrong sizes, faulty products, damaged products etc. Due to such
manipulative activities from sellers, Daraz has suffered a lot in the past years. And ultimately it
affected the customer base since consumers became cautious and started considering online
shopping a risky option. Even to this day, scars of such indecent activities haven’t been
recovered completely.
Observing the humongous number of consumers based in Pakistan, and considering the fact there
isn’t any real competitor in the online marketplace, AliBaba group took over Daraz for a
whopping USD 14 million, back in 2018. Since the multi-national group has acquired Daraz,
there has been certain changes in the operations department as well as management.
In order to ensure timely deliveries, maintaining low costs on products and improving reach to
the customers, it is necessary for a company of this magnitude to have the products in close
proximity, procuring them in ample quantity and storing them in strategically placed warehouses.
Secure Best Marks with AI Grader
Need help grading? Try our AI Grader for instant feedback on your assignments.
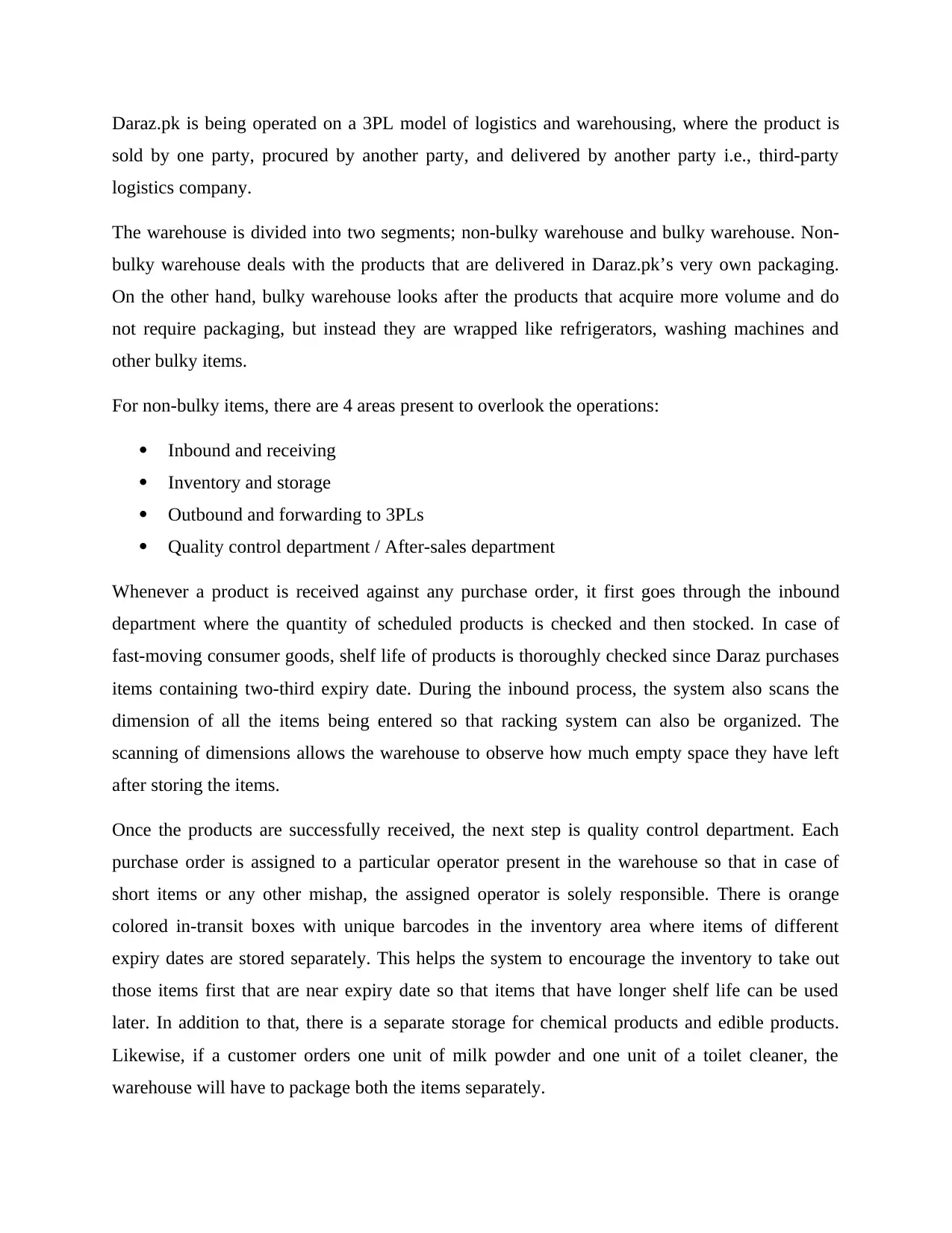
Daraz.pk is being operated on a 3PL model of logistics and warehousing, where the product is
sold by one party, procured by another party, and delivered by another party i.e., third-party
logistics company.
The warehouse is divided into two segments; non-bulky warehouse and bulky warehouse. Non-
bulky warehouse deals with the products that are delivered in Daraz.pk’s very own packaging.
On the other hand, bulky warehouse looks after the products that acquire more volume and do
not require packaging, but instead they are wrapped like refrigerators, washing machines and
other bulky items.
For non-bulky items, there are 4 areas present to overlook the operations:
Inbound and receiving
Inventory and storage
Outbound and forwarding to 3PLs
Quality control department / After-sales department
Whenever a product is received against any purchase order, it first goes through the inbound
department where the quantity of scheduled products is checked and then stocked. In case of
fast-moving consumer goods, shelf life of products is thoroughly checked since Daraz purchases
items containing two-third expiry date. During the inbound process, the system also scans the
dimension of all the items being entered so that racking system can also be organized. The
scanning of dimensions allows the warehouse to observe how much empty space they have left
after storing the items.
Once the products are successfully received, the next step is quality control department. Each
purchase order is assigned to a particular operator present in the warehouse so that in case of
short items or any other mishap, the assigned operator is solely responsible. There is orange
colored in-transit boxes with unique barcodes in the inventory area where items of different
expiry dates are stored separately. This helps the system to encourage the inventory to take out
those items first that are near expiry date so that items that have longer shelf life can be used
later. In addition to that, there is a separate storage for chemical products and edible products.
Likewise, if a customer orders one unit of milk powder and one unit of a toilet cleaner, the
warehouse will have to package both the items separately.
sold by one party, procured by another party, and delivered by another party i.e., third-party
logistics company.
The warehouse is divided into two segments; non-bulky warehouse and bulky warehouse. Non-
bulky warehouse deals with the products that are delivered in Daraz.pk’s very own packaging.
On the other hand, bulky warehouse looks after the products that acquire more volume and do
not require packaging, but instead they are wrapped like refrigerators, washing machines and
other bulky items.
For non-bulky items, there are 4 areas present to overlook the operations:
Inbound and receiving
Inventory and storage
Outbound and forwarding to 3PLs
Quality control department / After-sales department
Whenever a product is received against any purchase order, it first goes through the inbound
department where the quantity of scheduled products is checked and then stocked. In case of
fast-moving consumer goods, shelf life of products is thoroughly checked since Daraz purchases
items containing two-third expiry date. During the inbound process, the system also scans the
dimension of all the items being entered so that racking system can also be organized. The
scanning of dimensions allows the warehouse to observe how much empty space they have left
after storing the items.
Once the products are successfully received, the next step is quality control department. Each
purchase order is assigned to a particular operator present in the warehouse so that in case of
short items or any other mishap, the assigned operator is solely responsible. There is orange
colored in-transit boxes with unique barcodes in the inventory area where items of different
expiry dates are stored separately. This helps the system to encourage the inventory to take out
those items first that are near expiry date so that items that have longer shelf life can be used
later. In addition to that, there is a separate storage for chemical products and edible products.
Likewise, if a customer orders one unit of milk powder and one unit of a toilet cleaner, the
warehouse will have to package both the items separately.
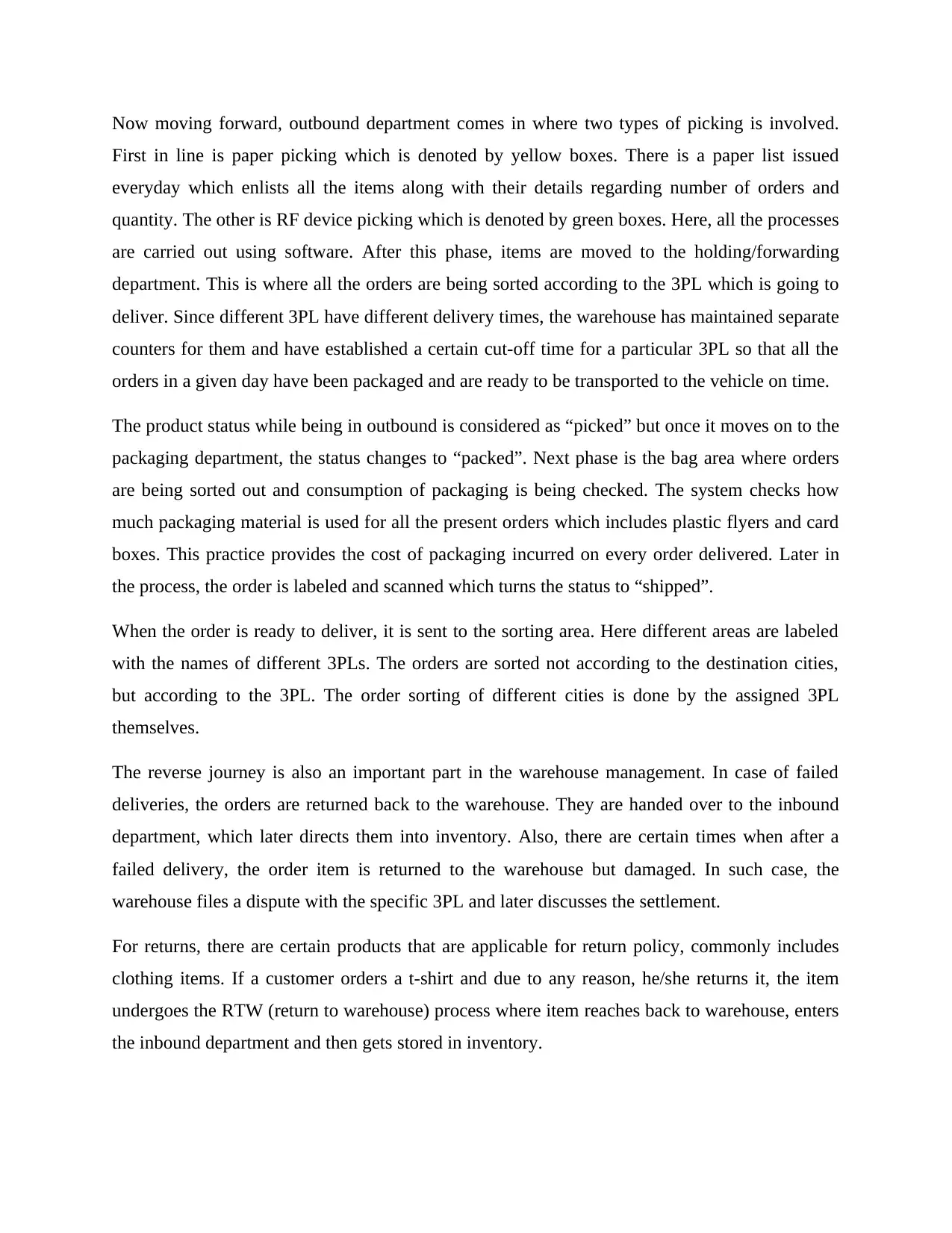
Now moving forward, outbound department comes in where two types of picking is involved.
First in line is paper picking which is denoted by yellow boxes. There is a paper list issued
everyday which enlists all the items along with their details regarding number of orders and
quantity. The other is RF device picking which is denoted by green boxes. Here, all the processes
are carried out using software. After this phase, items are moved to the holding/forwarding
department. This is where all the orders are being sorted according to the 3PL which is going to
deliver. Since different 3PL have different delivery times, the warehouse has maintained separate
counters for them and have established a certain cut-off time for a particular 3PL so that all the
orders in a given day have been packaged and are ready to be transported to the vehicle on time.
The product status while being in outbound is considered as “picked” but once it moves on to the
packaging department, the status changes to “packed”. Next phase is the bag area where orders
are being sorted out and consumption of packaging is being checked. The system checks how
much packaging material is used for all the present orders which includes plastic flyers and card
boxes. This practice provides the cost of packaging incurred on every order delivered. Later in
the process, the order is labeled and scanned which turns the status to “shipped”.
When the order is ready to deliver, it is sent to the sorting area. Here different areas are labeled
with the names of different 3PLs. The orders are sorted not according to the destination cities,
but according to the 3PL. The order sorting of different cities is done by the assigned 3PL
themselves.
The reverse journey is also an important part in the warehouse management. In case of failed
deliveries, the orders are returned back to the warehouse. They are handed over to the inbound
department, which later directs them into inventory. Also, there are certain times when after a
failed delivery, the order item is returned to the warehouse but damaged. In such case, the
warehouse files a dispute with the specific 3PL and later discusses the settlement.
For returns, there are certain products that are applicable for return policy, commonly includes
clothing items. If a customer orders a t-shirt and due to any reason, he/she returns it, the item
undergoes the RTW (return to warehouse) process where item reaches back to warehouse, enters
the inbound department and then gets stored in inventory.
First in line is paper picking which is denoted by yellow boxes. There is a paper list issued
everyday which enlists all the items along with their details regarding number of orders and
quantity. The other is RF device picking which is denoted by green boxes. Here, all the processes
are carried out using software. After this phase, items are moved to the holding/forwarding
department. This is where all the orders are being sorted according to the 3PL which is going to
deliver. Since different 3PL have different delivery times, the warehouse has maintained separate
counters for them and have established a certain cut-off time for a particular 3PL so that all the
orders in a given day have been packaged and are ready to be transported to the vehicle on time.
The product status while being in outbound is considered as “picked” but once it moves on to the
packaging department, the status changes to “packed”. Next phase is the bag area where orders
are being sorted out and consumption of packaging is being checked. The system checks how
much packaging material is used for all the present orders which includes plastic flyers and card
boxes. This practice provides the cost of packaging incurred on every order delivered. Later in
the process, the order is labeled and scanned which turns the status to “shipped”.
When the order is ready to deliver, it is sent to the sorting area. Here different areas are labeled
with the names of different 3PLs. The orders are sorted not according to the destination cities,
but according to the 3PL. The order sorting of different cities is done by the assigned 3PL
themselves.
The reverse journey is also an important part in the warehouse management. In case of failed
deliveries, the orders are returned back to the warehouse. They are handed over to the inbound
department, which later directs them into inventory. Also, there are certain times when after a
failed delivery, the order item is returned to the warehouse but damaged. In such case, the
warehouse files a dispute with the specific 3PL and later discusses the settlement.
For returns, there are certain products that are applicable for return policy, commonly includes
clothing items. If a customer orders a t-shirt and due to any reason, he/she returns it, the item
undergoes the RTW (return to warehouse) process where item reaches back to warehouse, enters
the inbound department and then gets stored in inventory.
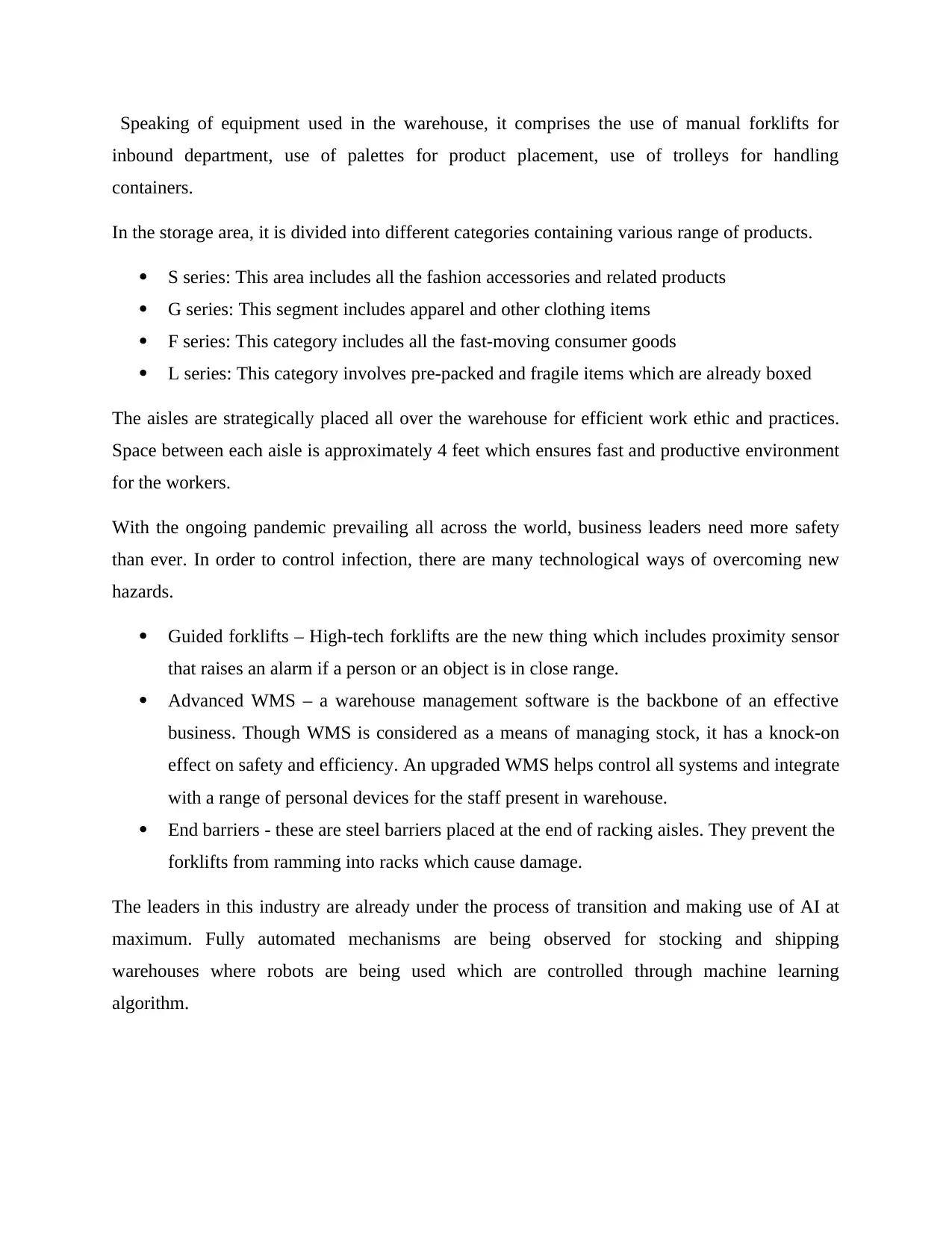
Speaking of equipment used in the warehouse, it comprises the use of manual forklifts for
inbound department, use of palettes for product placement, use of trolleys for handling
containers.
In the storage area, it is divided into different categories containing various range of products.
S series: This area includes all the fashion accessories and related products
G series: This segment includes apparel and other clothing items
F series: This category includes all the fast-moving consumer goods
L series: This category involves pre-packed and fragile items which are already boxed
The aisles are strategically placed all over the warehouse for efficient work ethic and practices.
Space between each aisle is approximately 4 feet which ensures fast and productive environment
for the workers.
With the ongoing pandemic prevailing all across the world, business leaders need more safety
than ever. In order to control infection, there are many technological ways of overcoming new
hazards.
Guided forklifts – High-tech forklifts are the new thing which includes proximity sensor
that raises an alarm if a person or an object is in close range.
Advanced WMS – a warehouse management software is the backbone of an effective
business. Though WMS is considered as a means of managing stock, it has a knock-on
effect on safety and efficiency. An upgraded WMS helps control all systems and integrate
with a range of personal devices for the staff present in warehouse.
End barriers - these are steel barriers placed at the end of racking aisles. They prevent the
forklifts from ramming into racks which cause damage.
The leaders in this industry are already under the process of transition and making use of AI at
maximum. Fully automated mechanisms are being observed for stocking and shipping
warehouses where robots are being used which are controlled through machine learning
algorithm.
inbound department, use of palettes for product placement, use of trolleys for handling
containers.
In the storage area, it is divided into different categories containing various range of products.
S series: This area includes all the fashion accessories and related products
G series: This segment includes apparel and other clothing items
F series: This category includes all the fast-moving consumer goods
L series: This category involves pre-packed and fragile items which are already boxed
The aisles are strategically placed all over the warehouse for efficient work ethic and practices.
Space between each aisle is approximately 4 feet which ensures fast and productive environment
for the workers.
With the ongoing pandemic prevailing all across the world, business leaders need more safety
than ever. In order to control infection, there are many technological ways of overcoming new
hazards.
Guided forklifts – High-tech forklifts are the new thing which includes proximity sensor
that raises an alarm if a person or an object is in close range.
Advanced WMS – a warehouse management software is the backbone of an effective
business. Though WMS is considered as a means of managing stock, it has a knock-on
effect on safety and efficiency. An upgraded WMS helps control all systems and integrate
with a range of personal devices for the staff present in warehouse.
End barriers - these are steel barriers placed at the end of racking aisles. They prevent the
forklifts from ramming into racks which cause damage.
The leaders in this industry are already under the process of transition and making use of AI at
maximum. Fully automated mechanisms are being observed for stocking and shipping
warehouses where robots are being used which are controlled through machine learning
algorithm.
Secure Best Marks with AI Grader
Need help grading? Try our AI Grader for instant feedback on your assignments.
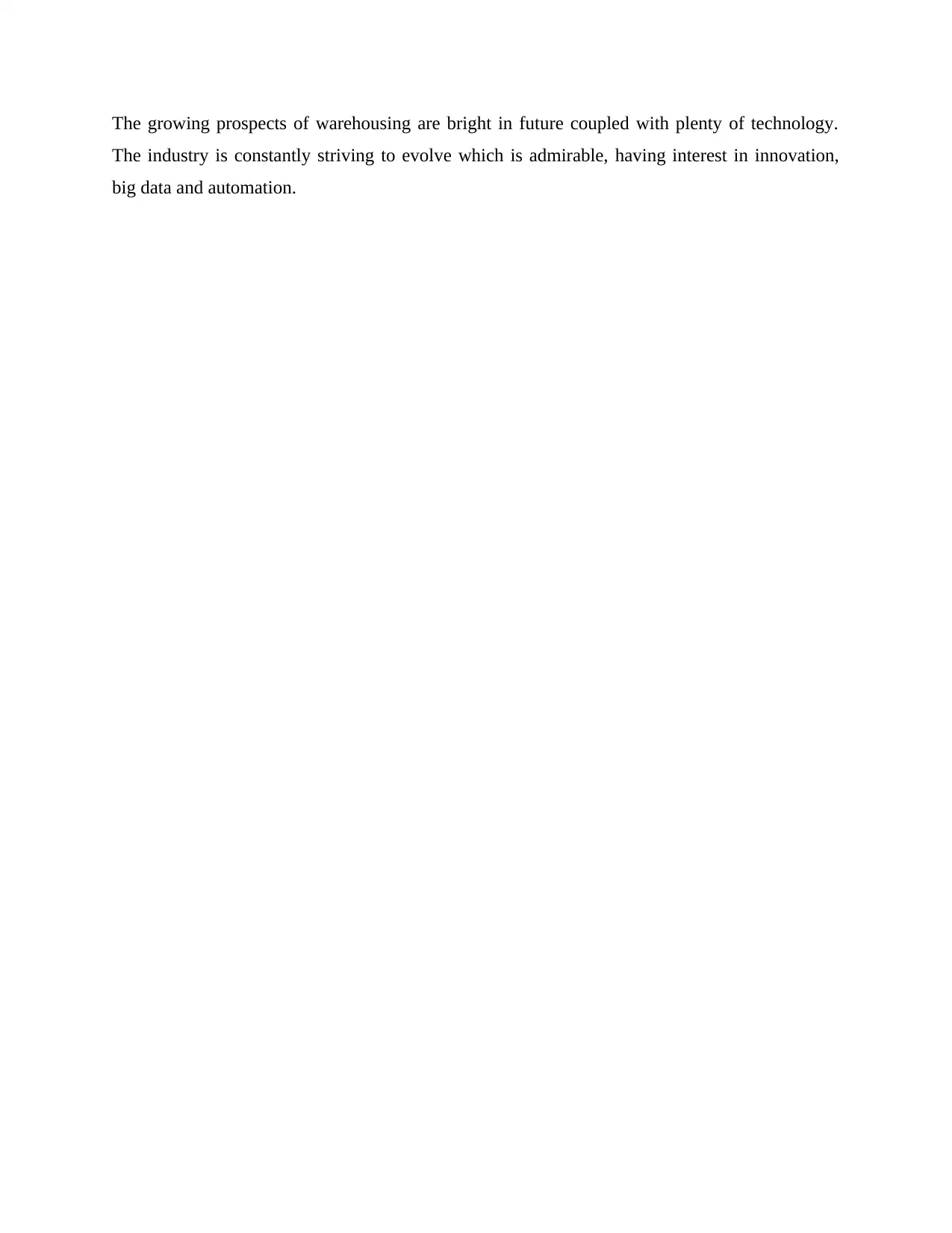
The growing prospects of warehousing are bright in future coupled with plenty of technology.
The industry is constantly striving to evolve which is admirable, having interest in innovation,
big data and automation.
The industry is constantly striving to evolve which is admirable, having interest in innovation,
big data and automation.
1 out of 5

Your All-in-One AI-Powered Toolkit for Academic Success.
+13062052269
info@desklib.com
Available 24*7 on WhatsApp / Email
Unlock your academic potential
© 2024 | Zucol Services PVT LTD | All rights reserved.