Detailed Design Report: Buck-Boost DC-DC Converter Analysis
VerifiedAdded on 2023/06/15
|35
|7113
|252
Report
AI Summary
This report presents a detailed design of a buck-boost DC-DC converter, a versatile topology combining buck and boost functionalities for voltage regulation. The report covers the converter's operation in both continuous and discontinuous conduction modes, providing in-depth analysis of each. Design specifications, including input voltage range, output voltage, and current requirements, are outlined. The design process encompasses the calculation of the duty cycle, selection of appropriate inductor and capacitor values, determination of maximum switching current, and output voltage setting. Furthermore, the report discusses MOSFET selection criteria for the converter and includes a design evaluation section, explaining the circuit's operation and performance. The design is simulated using Multisim software, and simulation results are presented to validate the design.
Contribute Materials
Your contribution can guide someone’s learning journey. Share your
documents today.
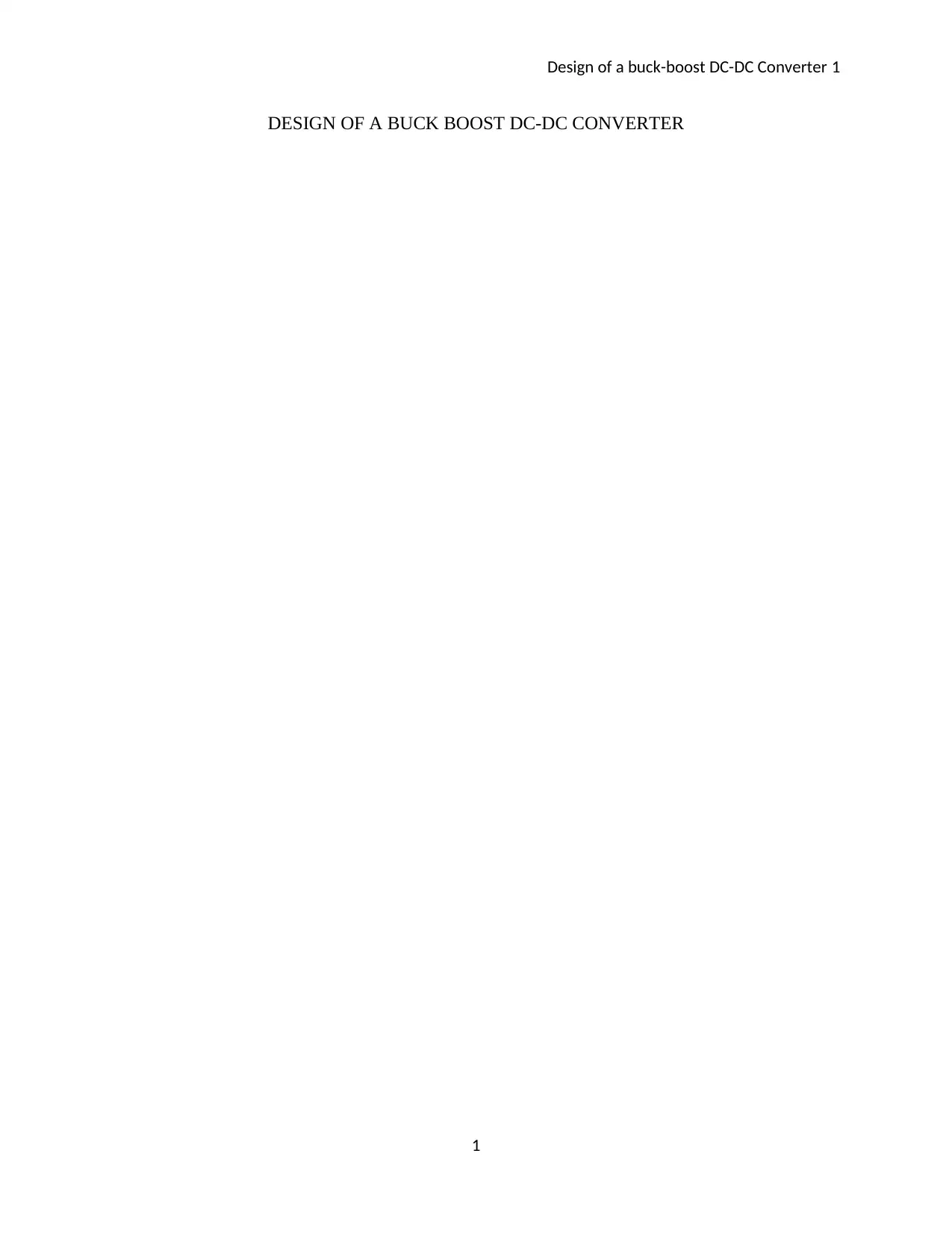
Design of a buck-boost DC-DC Converter 1
DESIGN OF A BUCK BOOST DC-DC CONVERTER
1
DESIGN OF A BUCK BOOST DC-DC CONVERTER
1
Secure Best Marks with AI Grader
Need help grading? Try our AI Grader for instant feedback on your assignments.
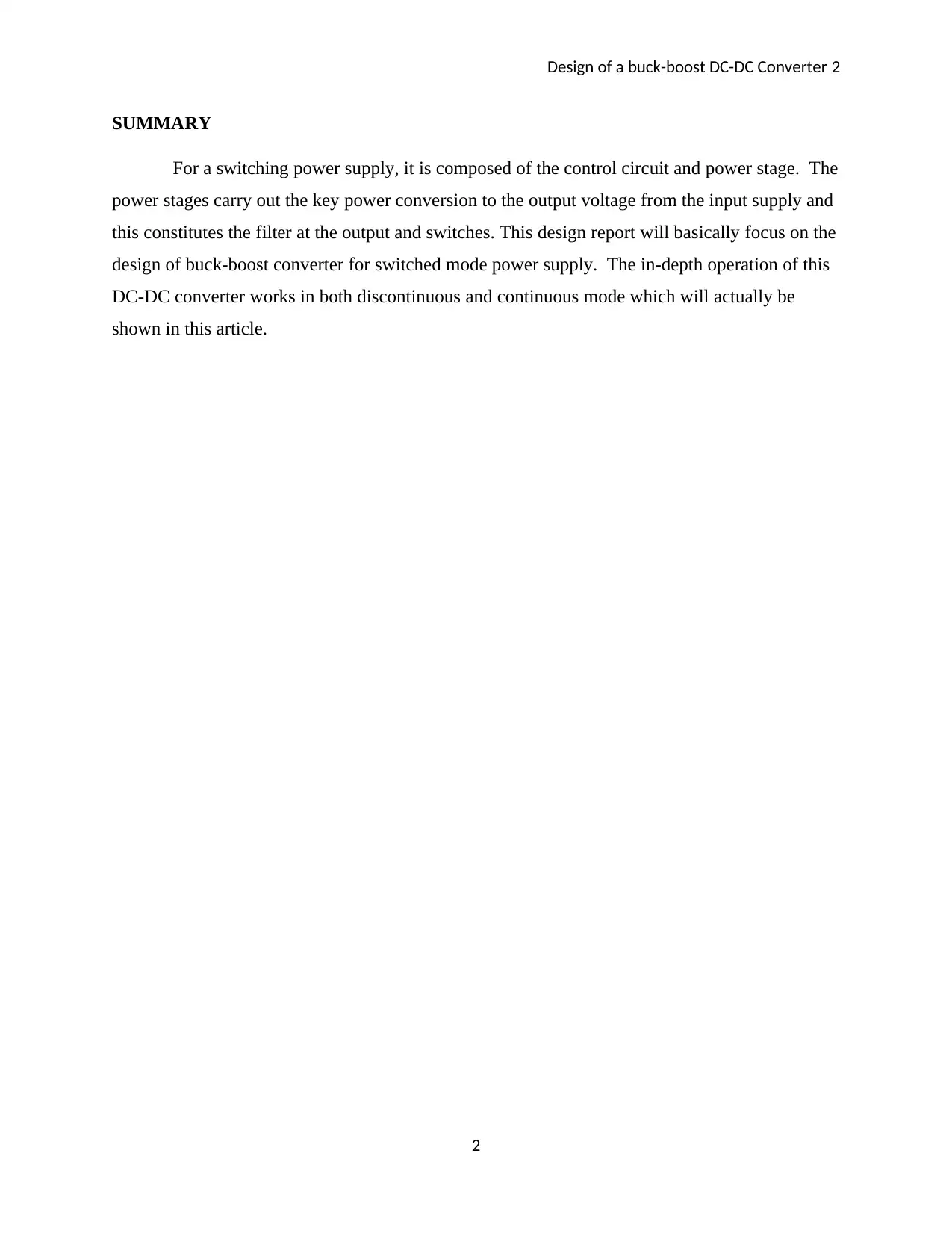
Design of a buck-boost DC-DC Converter 2
SUMMARY
For a switching power supply, it is composed of the control circuit and power stage. The
power stages carry out the key power conversion to the output voltage from the input supply and
this constitutes the filter at the output and switches. This design report will basically focus on the
design of buck-boost converter for switched mode power supply. The in-depth operation of this
DC-DC converter works in both discontinuous and continuous mode which will actually be
shown in this article.
2
SUMMARY
For a switching power supply, it is composed of the control circuit and power stage. The
power stages carry out the key power conversion to the output voltage from the input supply and
this constitutes the filter at the output and switches. This design report will basically focus on the
design of buck-boost converter for switched mode power supply. The in-depth operation of this
DC-DC converter works in both discontinuous and continuous mode which will actually be
shown in this article.
2

Design of a buck-boost DC-DC Converter 3
TABLE OF CONTENTS
ACKNOWLEDGMENTS...............................................................................................................2
SUMMARY.....................................................................................................................................2
INTRODUCTION...........................................................................................................................6
Buck-Boost Converters....................................................................................................................6
Schematic diagram of the buck-boost converter..........................................................................7
Buck-Boost Steady-State Continuous Conduction Mode Analysis...........................................11
Buck-Boost Steady-State discontinuous Conduction Mode Analysis.......................................13
SPECIFICATION..........................................................................................................................14
DESIGN PARAMETERS.............................................................................................................15
DESCRIPTION OF DESIGN........................................................................................................15
Calculation of the Duty Cycle....................................................................................................15
Buck mode.................................................................................................................................16
Boost mode................................................................................................................................16
Selection of input capacitor........................................................................................................17
Selection of output capacitor......................................................................................................17
Inductor Selection......................................................................................................................18
Buck Mode.................................................................................................................................18
Boost mode................................................................................................................................19
Calculation of maximum switching current...............................................................................19
Buck Mode.................................................................................................................................19
Boost Mode................................................................................................................................20
Output voltage setting................................................................................................................ 21
MOSFET selection for the Buck-boost converter......................................................................22
3
TABLE OF CONTENTS
ACKNOWLEDGMENTS...............................................................................................................2
SUMMARY.....................................................................................................................................2
INTRODUCTION...........................................................................................................................6
Buck-Boost Converters....................................................................................................................6
Schematic diagram of the buck-boost converter..........................................................................7
Buck-Boost Steady-State Continuous Conduction Mode Analysis...........................................11
Buck-Boost Steady-State discontinuous Conduction Mode Analysis.......................................13
SPECIFICATION..........................................................................................................................14
DESIGN PARAMETERS.............................................................................................................15
DESCRIPTION OF DESIGN........................................................................................................15
Calculation of the Duty Cycle....................................................................................................15
Buck mode.................................................................................................................................16
Boost mode................................................................................................................................16
Selection of input capacitor........................................................................................................17
Selection of output capacitor......................................................................................................17
Inductor Selection......................................................................................................................18
Buck Mode.................................................................................................................................18
Boost mode................................................................................................................................19
Calculation of maximum switching current...............................................................................19
Buck Mode.................................................................................................................................19
Boost Mode................................................................................................................................20
Output voltage setting................................................................................................................ 21
MOSFET selection for the Buck-boost converter......................................................................22
3

Design of a buck-boost DC-DC Converter 4
Design evaluation.......................................................................................................................24
Explanation of the operation of the above design..................................................................24
DISCUSSION…………………………………………………………………………………... 26
CONCLUSION…………………………………………………………………………………. 28
REFERENCES…………………………………………………………………………………. 29
APPENDICES…………………………………………………………………………………. 30
4
Design evaluation.......................................................................................................................24
Explanation of the operation of the above design..................................................................24
DISCUSSION…………………………………………………………………………………... 26
CONCLUSION…………………………………………………………………………………. 28
REFERENCES…………………………………………………………………………………. 29
APPENDICES…………………………………………………………………………………. 30
4
Secure Best Marks with AI Grader
Need help grading? Try our AI Grader for instant feedback on your assignments.
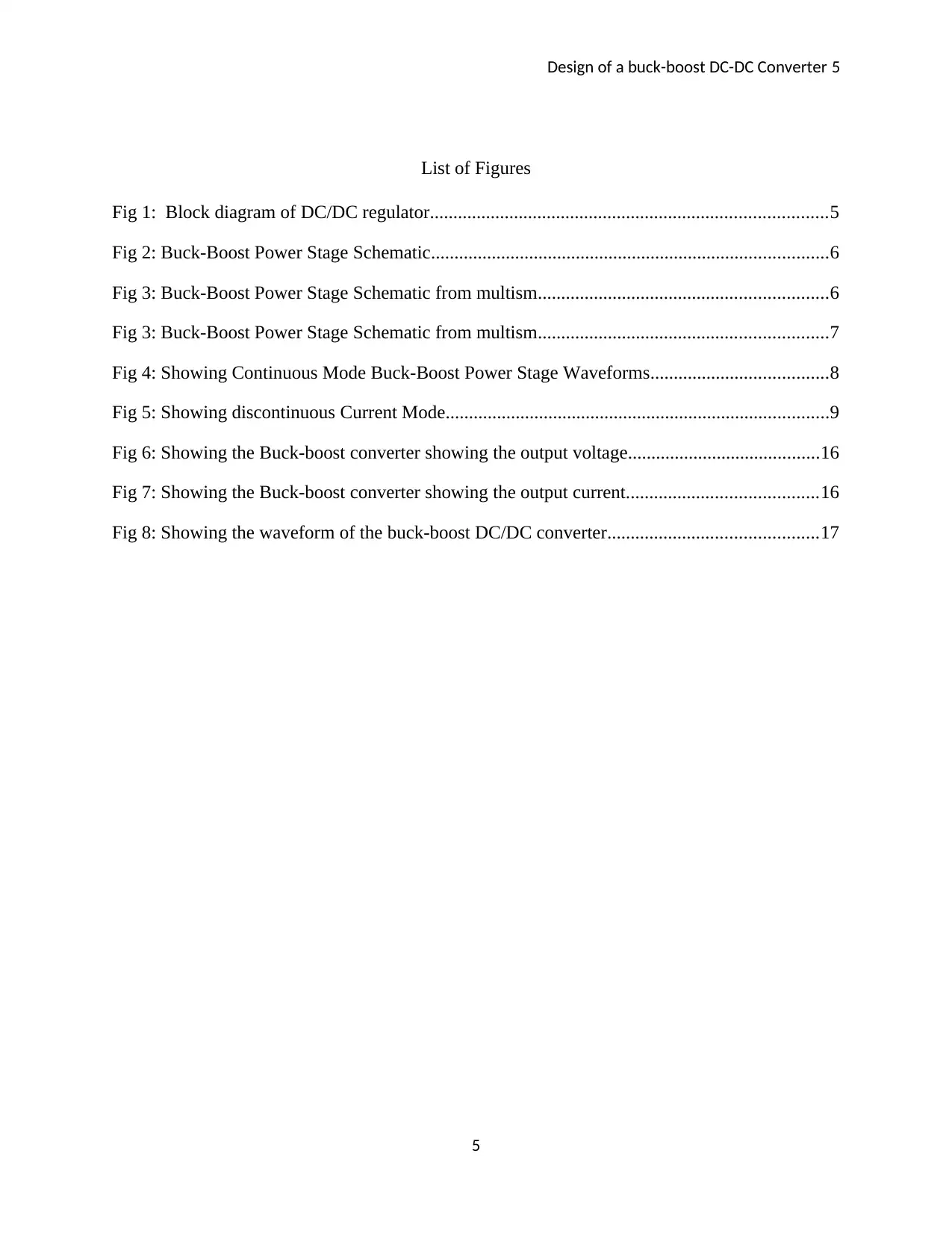
Design of a buck-boost DC-DC Converter 5
List of Figures
Fig 1: Block diagram of DC/DC regulator.....................................................................................5
Fig 2: Buck-Boost Power Stage Schematic.....................................................................................6
Fig 3: Buck-Boost Power Stage Schematic from multism..............................................................6
Fig 3: Buck-Boost Power Stage Schematic from multism..............................................................7
Fig 4: Showing Continuous Mode Buck-Boost Power Stage Waveforms......................................8
Fig 5: Showing discontinuous Current Mode..................................................................................9
Fig 6: Showing the Buck-boost converter showing the output voltage.........................................16
Fig 7: Showing the Buck-boost converter showing the output current.........................................16
Fig 8: Showing the waveform of the buck-boost DC/DC converter.............................................17
5
List of Figures
Fig 1: Block diagram of DC/DC regulator.....................................................................................5
Fig 2: Buck-Boost Power Stage Schematic.....................................................................................6
Fig 3: Buck-Boost Power Stage Schematic from multism..............................................................6
Fig 3: Buck-Boost Power Stage Schematic from multism..............................................................7
Fig 4: Showing Continuous Mode Buck-Boost Power Stage Waveforms......................................8
Fig 5: Showing discontinuous Current Mode..................................................................................9
Fig 6: Showing the Buck-boost converter showing the output voltage.........................................16
Fig 7: Showing the Buck-boost converter showing the output current.........................................16
Fig 8: Showing the waveform of the buck-boost DC/DC converter.............................................17
5
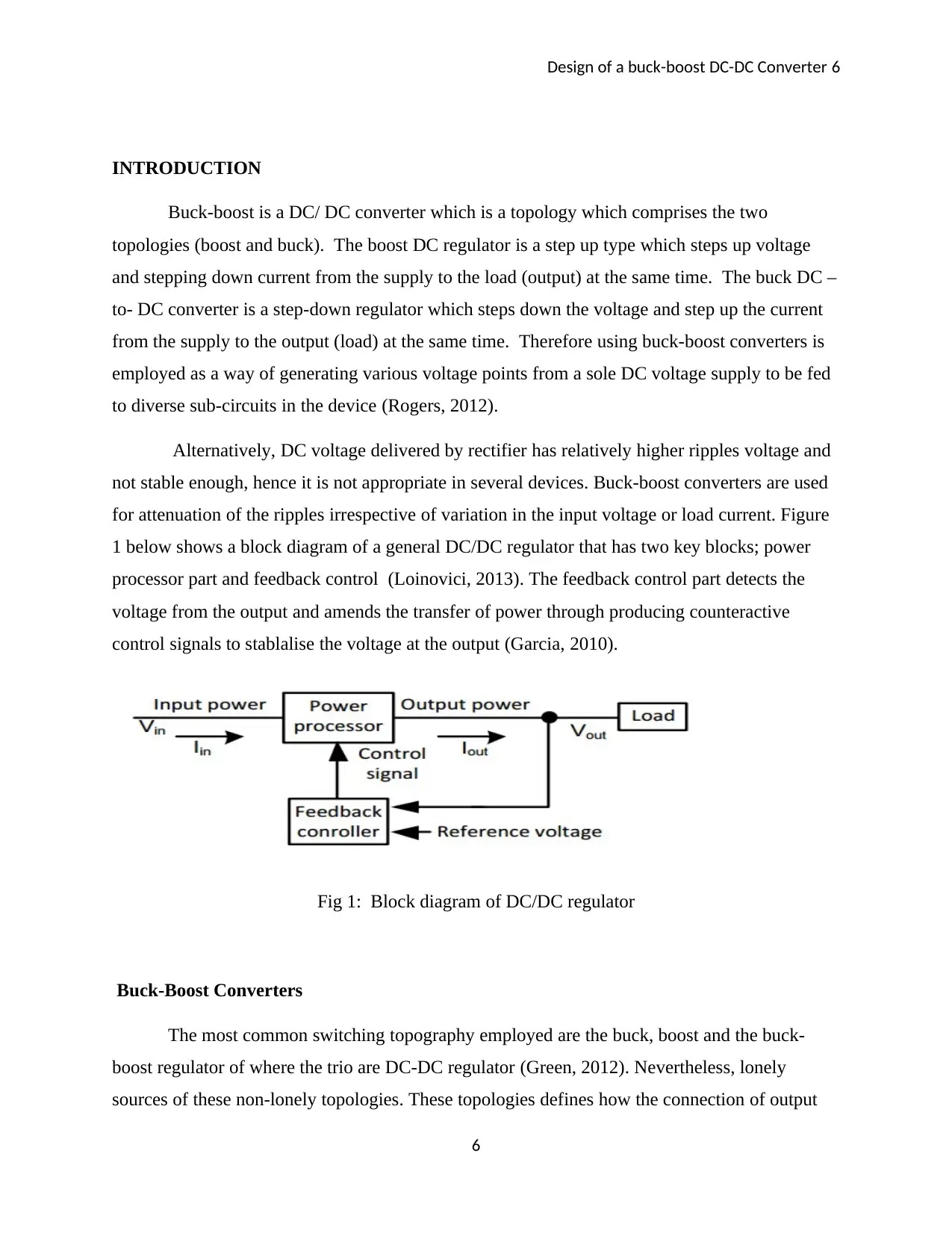
Design of a buck-boost DC-DC Converter 6
INTRODUCTION
Buck-boost is a DC/ DC converter which is a topology which comprises the two
topologies (boost and buck). The boost DC regulator is a step up type which steps up voltage
and stepping down current from the supply to the load (output) at the same time. The buck DC –
to- DC converter is a step-down regulator which steps down the voltage and step up the current
from the supply to the output (load) at the same time. Therefore using buck-boost converters is
employed as a way of generating various voltage points from a sole DC voltage supply to be fed
to diverse sub-circuits in the device (Rogers, 2012).
Alternatively, DC voltage delivered by rectifier has relatively higher ripples voltage and
not stable enough, hence it is not appropriate in several devices. Buck-boost converters are used
for attenuation of the ripples irrespective of variation in the input voltage or load current. Figure
1 below shows a block diagram of a general DC/DC regulator that has two key blocks; power
processor part and feedback control (Loinovici, 2013). The feedback control part detects the
voltage from the output and amends the transfer of power through producing counteractive
control signals to stablalise the voltage at the output (Garcia, 2010).
Fig 1: Block diagram of DC/DC regulator
Buck-Boost Converters
The most common switching topography employed are the buck, boost and the buck-
boost regulator of where the trio are DC-DC regulator (Green, 2012). Nevertheless, lonely
sources of these non-lonely topologies. These topologies defines how the connection of output
6
INTRODUCTION
Buck-boost is a DC/ DC converter which is a topology which comprises the two
topologies (boost and buck). The boost DC regulator is a step up type which steps up voltage
and stepping down current from the supply to the load (output) at the same time. The buck DC –
to- DC converter is a step-down regulator which steps down the voltage and step up the current
from the supply to the output (load) at the same time. Therefore using buck-boost converters is
employed as a way of generating various voltage points from a sole DC voltage supply to be fed
to diverse sub-circuits in the device (Rogers, 2012).
Alternatively, DC voltage delivered by rectifier has relatively higher ripples voltage and
not stable enough, hence it is not appropriate in several devices. Buck-boost converters are used
for attenuation of the ripples irrespective of variation in the input voltage or load current. Figure
1 below shows a block diagram of a general DC/DC regulator that has two key blocks; power
processor part and feedback control (Loinovici, 2013). The feedback control part detects the
voltage from the output and amends the transfer of power through producing counteractive
control signals to stablalise the voltage at the output (Garcia, 2010).
Fig 1: Block diagram of DC/DC regulator
Buck-Boost Converters
The most common switching topography employed are the buck, boost and the buck-
boost regulator of where the trio are DC-DC regulator (Green, 2012). Nevertheless, lonely
sources of these non-lonely topologies. These topologies defines how the connection of output
6
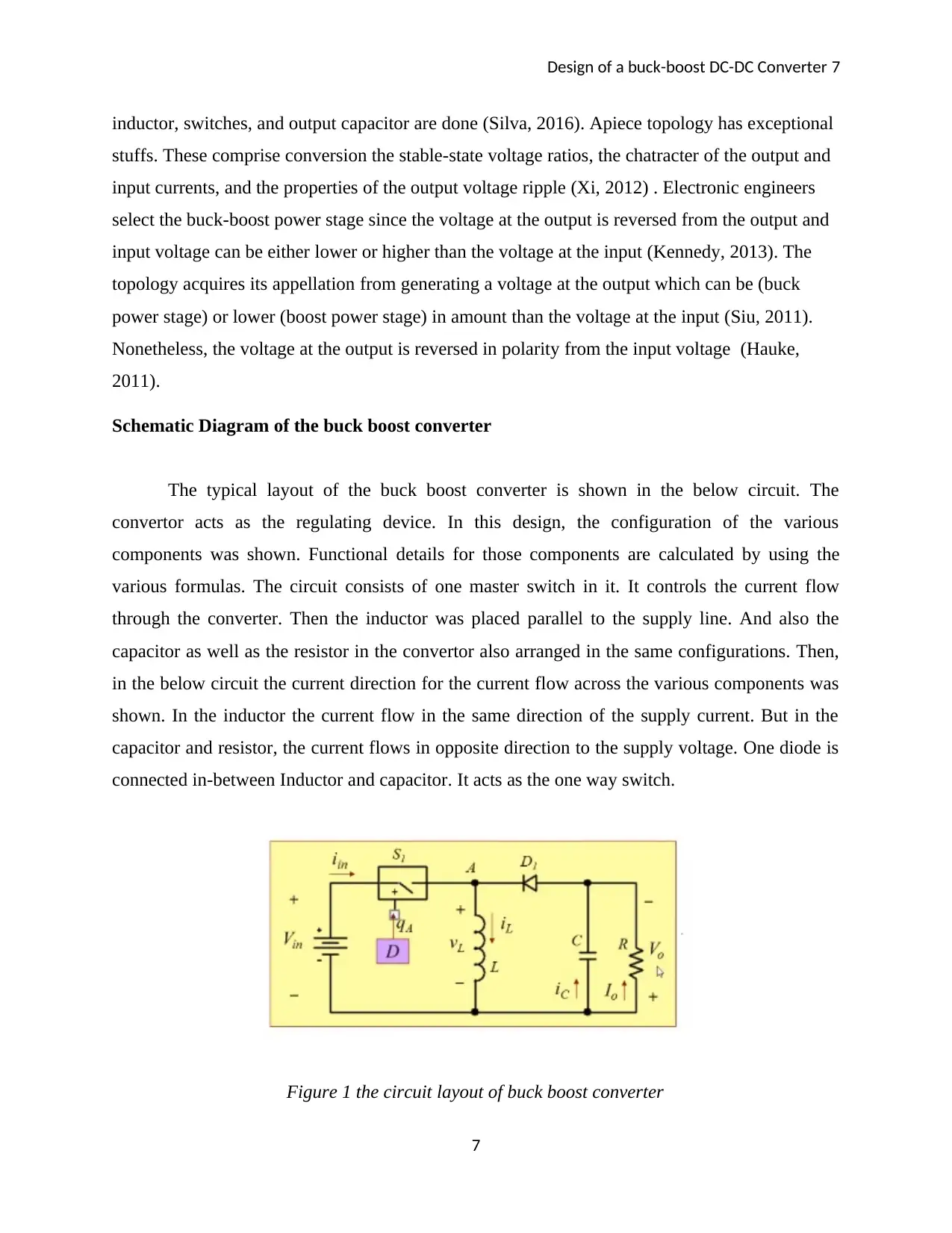
Design of a buck-boost DC-DC Converter 7
inductor, switches, and output capacitor are done (Silva, 2016). Apiece topology has exceptional
stuffs. These comprise conversion the stable-state voltage ratios, the chatracter of the output and
input currents, and the properties of the output voltage ripple (Xi, 2012) . Electronic engineers
select the buck-boost power stage since the voltage at the output is reversed from the output and
input voltage can be either lower or higher than the voltage at the input (Kennedy, 2013). The
topology acquires its appellation from generating a voltage at the output which can be (buck
power stage) or lower (boost power stage) in amount than the voltage at the input (Siu, 2011).
Nonetheless, the voltage at the output is reversed in polarity from the input voltage (Hauke,
2011).
Schematic Diagram of the buck boost converter
The typical layout of the buck boost converter is shown in the below circuit. The
convertor acts as the regulating device. In this design, the configuration of the various
components was shown. Functional details for those components are calculated by using the
various formulas. The circuit consists of one master switch in it. It controls the current flow
through the converter. Then the inductor was placed parallel to the supply line. And also the
capacitor as well as the resistor in the convertor also arranged in the same configurations. Then,
in the below circuit the current direction for the current flow across the various components was
shown. In the inductor the current flow in the same direction of the supply current. But in the
capacitor and resistor, the current flows in opposite direction to the supply voltage. One diode is
connected in-between Inductor and capacitor. It acts as the one way switch.
Figure 1 the circuit layout of buck boost converter
7
inductor, switches, and output capacitor are done (Silva, 2016). Apiece topology has exceptional
stuffs. These comprise conversion the stable-state voltage ratios, the chatracter of the output and
input currents, and the properties of the output voltage ripple (Xi, 2012) . Electronic engineers
select the buck-boost power stage since the voltage at the output is reversed from the output and
input voltage can be either lower or higher than the voltage at the input (Kennedy, 2013). The
topology acquires its appellation from generating a voltage at the output which can be (buck
power stage) or lower (boost power stage) in amount than the voltage at the input (Siu, 2011).
Nonetheless, the voltage at the output is reversed in polarity from the input voltage (Hauke,
2011).
Schematic Diagram of the buck boost converter
The typical layout of the buck boost converter is shown in the below circuit. The
convertor acts as the regulating device. In this design, the configuration of the various
components was shown. Functional details for those components are calculated by using the
various formulas. The circuit consists of one master switch in it. It controls the current flow
through the converter. Then the inductor was placed parallel to the supply line. And also the
capacitor as well as the resistor in the convertor also arranged in the same configurations. Then,
in the below circuit the current direction for the current flow across the various components was
shown. In the inductor the current flow in the same direction of the supply current. But in the
capacitor and resistor, the current flows in opposite direction to the supply voltage. One diode is
connected in-between Inductor and capacitor. It acts as the one way switch.
Figure 1 the circuit layout of buck boost converter
7
Paraphrase This Document
Need a fresh take? Get an instant paraphrase of this document with our AI Paraphraser

Design of a buck-boost DC-DC Converter 8
Switch closed state
When the switch is closed, then the current will not flow directly to the diode. The
current first flows through the inductor L, then to the capacitor C, and Resistor R. In this stage
the diode is in reverse biased state. The current through the inductor is represented as iL, the
current through the capacitor is iC, and the output current Io is measured across resistor R. The
input voltage is represented as Vin and Output voltage is represented as Vo. When the switch is
in ON condition, the inductor voltage equals to the Input voltage. Then the energy is stored in an
Inductor gets increases. Then the capacitor maintains the constant voltage.
Here, q= 1 switch –ON = Diode Reverse biased.
Figure 2 the circuit in closed switch state
Switch open state
The below figure consists of a closed switch circuit of the buck-boost converter. When
the switch is in OFF condition, the inductor voltage equals to the negative value of Output
voltage. Then the energy is stored in an Inductor gets decreases. Then the capacitor maintains
the constant voltage. In the open state of the switch, the current flows through the Inductor,
capacitor, and resistor. The flow of current is shown in below circuit. In this stage, the diode is
forward biased.
Here q=0 switch – off = Diode forward biased
8
Switch closed state
When the switch is closed, then the current will not flow directly to the diode. The
current first flows through the inductor L, then to the capacitor C, and Resistor R. In this stage
the diode is in reverse biased state. The current through the inductor is represented as iL, the
current through the capacitor is iC, and the output current Io is measured across resistor R. The
input voltage is represented as Vin and Output voltage is represented as Vo. When the switch is
in ON condition, the inductor voltage equals to the Input voltage. Then the energy is stored in an
Inductor gets increases. Then the capacitor maintains the constant voltage.
Here, q= 1 switch –ON = Diode Reverse biased.
Figure 2 the circuit in closed switch state
Switch open state
The below figure consists of a closed switch circuit of the buck-boost converter. When
the switch is in OFF condition, the inductor voltage equals to the negative value of Output
voltage. Then the energy is stored in an Inductor gets decreases. Then the capacitor maintains
the constant voltage. In the open state of the switch, the current flows through the Inductor,
capacitor, and resistor. The flow of current is shown in below circuit. In this stage, the diode is
forward biased.
Here q=0 switch – off = Diode forward biased
8
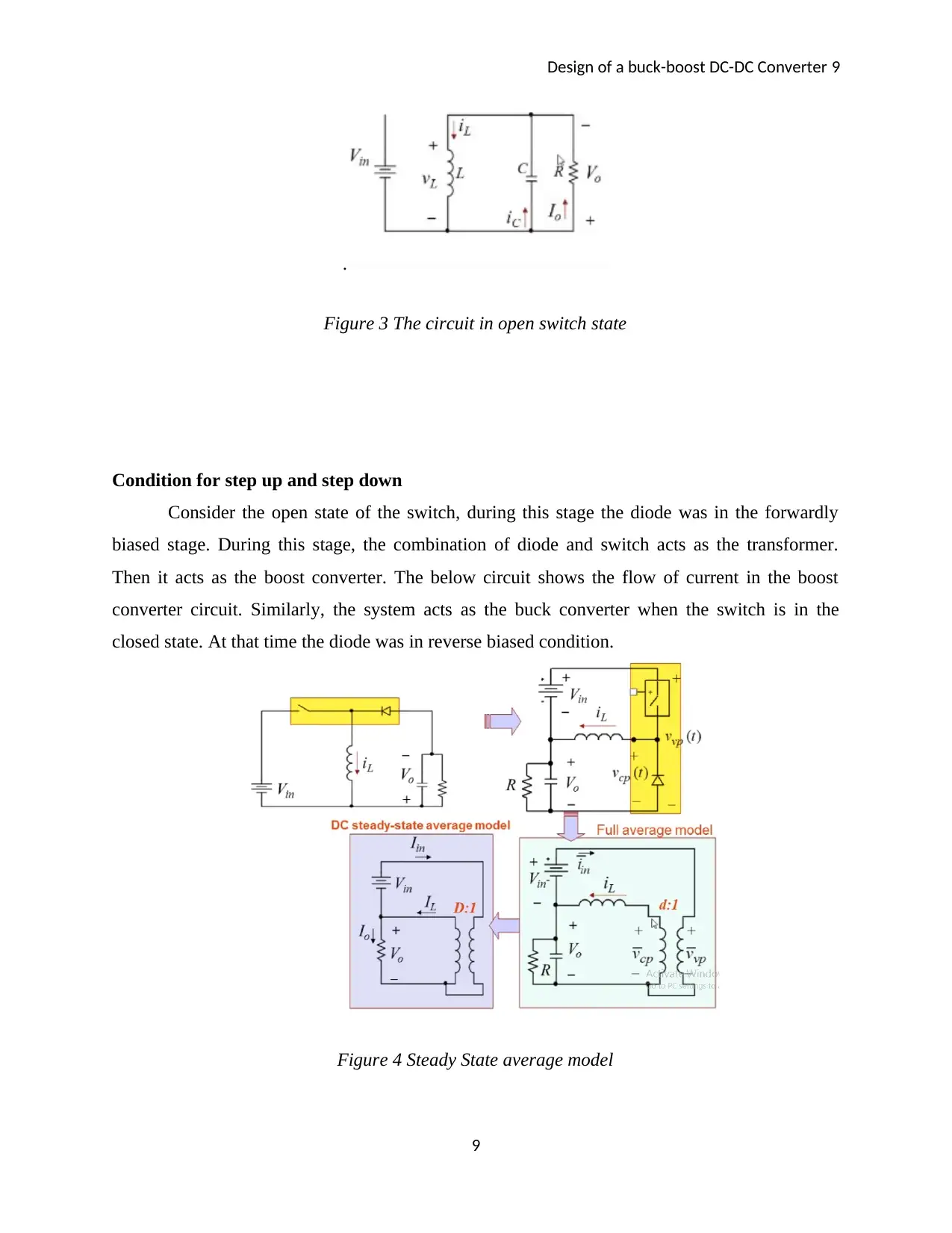
Design of a buck-boost DC-DC Converter 9
.
Figure 3 The circuit in open switch state
Condition for step up and step down
Consider the open state of the switch, during this stage the diode was in the forwardly
biased stage. During this stage, the combination of diode and switch acts as the transformer.
Then it acts as the boost converter. The below circuit shows the flow of current in the boost
converter circuit. Similarly, the system acts as the buck converter when the switch is in the
closed state. At that time the diode was in reverse biased condition.
Figure 4 Steady State average model
9
.
Figure 3 The circuit in open switch state
Condition for step up and step down
Consider the open state of the switch, during this stage the diode was in the forwardly
biased stage. During this stage, the combination of diode and switch acts as the transformer.
Then it acts as the boost converter. The below circuit shows the flow of current in the boost
converter circuit. Similarly, the system acts as the buck converter when the switch is in the
closed state. At that time the diode was in reverse biased condition.
Figure 4 Steady State average model
9

Design of a buck-boost DC-DC Converter 10
Schematic representation of a basic Buck Boost Converter
The basic configuration of buck boost converter is shown in below diagram. In which the
switches are acts as MOSFET(Metal Oxide Semiconductor Field Efffect transistor). It consists of
one inductor,two capacitors and four switches.This kind of converters reduce size of the solution
and the difficulty of the solution tends to become easy.
Figure 5 Schematic layout of basic Buck Boost converter
Power stage parameters of Buck Boost converter
The important parameters used to calculate the power stage are in the following:
1. Maximum output current (Iout)
2. Range of input voltage (Vin min and Vin max)
3. Desired output voltage (Vout)
The above-mentioned parameters are needed to calculate the analysis of buck-boost
converter.Buck-boost converter was built with the help of Integrator circuit. For calculation
purpose, some constant parameters are taken from the datasheet. The power stage can be
calculated easily after the four parameters are obtained.
When the above figure two was drawn in the multism the below circuit diagram is obtained.
10
Schematic representation of a basic Buck Boost Converter
The basic configuration of buck boost converter is shown in below diagram. In which the
switches are acts as MOSFET(Metal Oxide Semiconductor Field Efffect transistor). It consists of
one inductor,two capacitors and four switches.This kind of converters reduce size of the solution
and the difficulty of the solution tends to become easy.
Figure 5 Schematic layout of basic Buck Boost converter
Power stage parameters of Buck Boost converter
The important parameters used to calculate the power stage are in the following:
1. Maximum output current (Iout)
2. Range of input voltage (Vin min and Vin max)
3. Desired output voltage (Vout)
The above-mentioned parameters are needed to calculate the analysis of buck-boost
converter.Buck-boost converter was built with the help of Integrator circuit. For calculation
purpose, some constant parameters are taken from the datasheet. The power stage can be
calculated easily after the four parameters are obtained.
When the above figure two was drawn in the multism the below circuit diagram is obtained.
10
Secure Best Marks with AI Grader
Need help grading? Try our AI Grader for instant feedback on your assignments.

Design of a buck-boost DC-DC Converter 11
Fig 3: Buck-Boost Power Stage Schematic from multism
Fig 3: Buck-Boost Power Stage Schematic from multism
The output voltage must be kept stable, irrespective of vicissitudes in the input voltage/load
current (James, 2013). This is achieved by building a feedback circuit which vicissitudes the
converter control input in such a way that the difference between output voltage and anticipated
reference value must be minimalized.
Buck-Boost Steady-State Continuous Conduction Mode Analysis
The time for the switching to be in ON state is given as
TON = D × TS . . . . . . . . . . . . . . . . . . . . . . . . . . . . . . . . . . . . . . . . . . . . . . . . . . . . . . . . . . . . 1
11
Fig 3: Buck-Boost Power Stage Schematic from multism
Fig 3: Buck-Boost Power Stage Schematic from multism
The output voltage must be kept stable, irrespective of vicissitudes in the input voltage/load
current (James, 2013). This is achieved by building a feedback circuit which vicissitudes the
converter control input in such a way that the difference between output voltage and anticipated
reference value must be minimalized.
Buck-Boost Steady-State Continuous Conduction Mode Analysis
The time for the switching to be in ON state is given as
TON = D × TS . . . . . . . . . . . . . . . . . . . . . . . . . . . . . . . . . . . . . . . . . . . . . . . . . . . . . . . . . . . . 1
11

Design of a buck-boost DC-DC Converter 12
Where D is the duty cycle
The time for the switching to be in ON state is known as TOFF. Because there are only two
states per switching cycle for continuous conduction mode (Nteilele, 2012). TOFF will be given
by the following equation
TOFF = (1−D) × TS . . . . . . . . . . . . . . . . . . . . . . . . . . . . . . . . . . . . . . . . . . . . . . . . . . . . . . . . . . . . 2
Where (1−D) is known as called D’.
And the summation of TON and TOFF is known as the settling time.
And the graphs for the TON and TOFF are shown in the following figures
12
Where D is the duty cycle
The time for the switching to be in ON state is known as TOFF. Because there are only two
states per switching cycle for continuous conduction mode (Nteilele, 2012). TOFF will be given
by the following equation
TOFF = (1−D) × TS . . . . . . . . . . . . . . . . . . . . . . . . . . . . . . . . . . . . . . . . . . . . . . . . . . . . . . . . . . . . 2
Where (1−D) is known as called D’.
And the summation of TON and TOFF is known as the settling time.
And the graphs for the TON and TOFF are shown in the following figures
12

Design of a buck-boost DC-DC Converter 13
Fig 4: Showing Continuous Mode Buck-Boost Power Stage Waveforms
Buck-Boost Steady-State discontinuous Conduction Mode Analysis
The discontinuous state power stage frequency reaction is rather dissimilar to the continuous one
Likewise, the relationship between the input and output is quite different and is illustrated in the
waveforms below.
13
Fig 4: Showing Continuous Mode Buck-Boost Power Stage Waveforms
Buck-Boost Steady-State discontinuous Conduction Mode Analysis
The discontinuous state power stage frequency reaction is rather dissimilar to the continuous one
Likewise, the relationship between the input and output is quite different and is illustrated in the
waveforms below.
13
Paraphrase This Document
Need a fresh take? Get an instant paraphrase of this document with our AI Paraphraser

Design of a buck-boost DC-DC Converter 14
Fig 5: Showing discontinuous Current Mode
SPECIFICATION
The design of a Buck-Boost Converter operates in continuous conduction mode with
voltage control proficient of acquiescent DC input voltage and availing a 3.3V output at a
maximum of 3 A loads. This design needs to have a feedback control to standardize the output
voltage to a required value (John, 2013). The design of the buck-boost converter is done and
built in a multism software it will is run and the output waves are displayed. During the design,
some ideal electronic components for power supplies like inductors, capacitors, and load are
employed at the development stage.
And the design should contain the following contents.
i. The basic configuration of Buck-Boost converter.
ii. System requirements (Parameters of power stage)
a. Input Voltage range Vinmin and Vinmax
b. Nominal output Voltage Vout
c. Maximum output current Iout
iii. Duty cycle.
iv. Inductor selection for Buck-boost mode.
v. Maximum switch current.
14
Fig 5: Showing discontinuous Current Mode
SPECIFICATION
The design of a Buck-Boost Converter operates in continuous conduction mode with
voltage control proficient of acquiescent DC input voltage and availing a 3.3V output at a
maximum of 3 A loads. This design needs to have a feedback control to standardize the output
voltage to a required value (John, 2013). The design of the buck-boost converter is done and
built in a multism software it will is run and the output waves are displayed. During the design,
some ideal electronic components for power supplies like inductors, capacitors, and load are
employed at the development stage.
And the design should contain the following contents.
i. The basic configuration of Buck-Boost converter.
ii. System requirements (Parameters of power stage)
a. Input Voltage range Vinmin and Vinmax
b. Nominal output Voltage Vout
c. Maximum output current Iout
iii. Duty cycle.
iv. Inductor selection for Buck-boost mode.
v. Maximum switch current.
14

Design of a buck-boost DC-DC Converter 15
vi. Output voltage setting.
vii. Input and output capacitor selection.
DESIGN PARAMETERS
For a perfect design according to the design, the following design specifications are given as
below.
1. Input Voltage Range: 1.8 V to 5.5 V
2. Fixed and Adjustable Output Voltage Options from 1.2 V to 5.5 V
3. Up to 96% Efficiency
4. 3-A Output Current at 3.3 V in Step Down Mode (VIN = 3.6 V to 5.5 V)
5. More than 2-A Output Current at 3.3 V in Boost Mode (VIN > 2.5 V)
6. Switching Frequency (Min) (kHz) : 2200
7. Switching Frequency (Max) (kHz) : 2600
8. Ripple current is 25% to 40%
9. Ripple voltage is 30-40mV
The above-mentioned parameters are needed to calculate the analysis of buck-boost
converter.Buck-boost converter was built with the help of Integrator circuit. For calculation
purpose, some constant parameters are taken from the datasheet. The power stage can be
calculated easily after the four parameters are obtained.
DESCRIPTION OF DESIGN
Calculation of the Duty Cycle
The duty cycle is obtained for each of the two operating modes i.e buck mode and boost mode.
Duty cycle is used to calculate the performance of a buck boost converter in a particular time
period. Duty cycle is calculated separately for buck and boost modes. The duty cycle calculation
needs the output voltage, efficiency and the minimum and maximum range of input voltage.
Maximum value of duty cycle is obtained for boost mode. Minimum value of duty cycle is
obtained for buck mode. The condition for the duty cycle value for the buck boost converter or
any other devices will always be less than 1 and non- negative.
15
vi. Output voltage setting.
vii. Input and output capacitor selection.
DESIGN PARAMETERS
For a perfect design according to the design, the following design specifications are given as
below.
1. Input Voltage Range: 1.8 V to 5.5 V
2. Fixed and Adjustable Output Voltage Options from 1.2 V to 5.5 V
3. Up to 96% Efficiency
4. 3-A Output Current at 3.3 V in Step Down Mode (VIN = 3.6 V to 5.5 V)
5. More than 2-A Output Current at 3.3 V in Boost Mode (VIN > 2.5 V)
6. Switching Frequency (Min) (kHz) : 2200
7. Switching Frequency (Max) (kHz) : 2600
8. Ripple current is 25% to 40%
9. Ripple voltage is 30-40mV
The above-mentioned parameters are needed to calculate the analysis of buck-boost
converter.Buck-boost converter was built with the help of Integrator circuit. For calculation
purpose, some constant parameters are taken from the datasheet. The power stage can be
calculated easily after the four parameters are obtained.
DESCRIPTION OF DESIGN
Calculation of the Duty Cycle
The duty cycle is obtained for each of the two operating modes i.e buck mode and boost mode.
Duty cycle is used to calculate the performance of a buck boost converter in a particular time
period. Duty cycle is calculated separately for buck and boost modes. The duty cycle calculation
needs the output voltage, efficiency and the minimum and maximum range of input voltage.
Maximum value of duty cycle is obtained for boost mode. Minimum value of duty cycle is
obtained for buck mode. The condition for the duty cycle value for the buck boost converter or
any other devices will always be less than 1 and non- negative.
15

Design of a buck-boost DC-DC Converter 16
Where,
η - Estimated efficiency at obtained Iout, Vin and Vout
Dboost - Boost mode - duty cycle
Dbuck - Buck mode - duty cycle
Vout - Desired output voltage
Vin min -Minimum input voltage
Vin max -Maximum input voltage
Buck mode
For the Dbuck, the following equation is employed in the calculation. The value of inductance is
calculated by using the below formula for Buck mode in Buck boost converter.
Dbuck = VOUT × η
VIN MAX
. . . . . . . . . . . . . . . . . . . . . . . . . . . . . . . . . . . . . . . . . . . . . . . . . . . . . . . . . . . . . . 3
Where; VOUT is the output voltage, η is the efficiency which in this design specification is
given as 96 % VIN MAX is the maximum input voltage (Mouhadjer, 2012).
Dbuck = 1.2× 0.96
5.5 = 0.209
The estimation value for the inductor ripple current is in the range from 20% to 40% of the
output current, or 0.2 < Kind < 0.4.
Boost mode
For the Dboost the following equation is employed in the calculation. The inductance for boost
mode in buck – boost converter is found by using the below formula.
16
Where,
η - Estimated efficiency at obtained Iout, Vin and Vout
Dboost - Boost mode - duty cycle
Dbuck - Buck mode - duty cycle
Vout - Desired output voltage
Vin min -Minimum input voltage
Vin max -Maximum input voltage
Buck mode
For the Dbuck, the following equation is employed in the calculation. The value of inductance is
calculated by using the below formula for Buck mode in Buck boost converter.
Dbuck = VOUT × η
VIN MAX
. . . . . . . . . . . . . . . . . . . . . . . . . . . . . . . . . . . . . . . . . . . . . . . . . . . . . . . . . . . . . . 3
Where; VOUT is the output voltage, η is the efficiency which in this design specification is
given as 96 % VIN MAX is the maximum input voltage (Mouhadjer, 2012).
Dbuck = 1.2× 0.96
5.5 = 0.209
The estimation value for the inductor ripple current is in the range from 20% to 40% of the
output current, or 0.2 < Kind < 0.4.
Boost mode
For the Dboost the following equation is employed in the calculation. The inductance for boost
mode in buck – boost converter is found by using the below formula.
16
Secure Best Marks with AI Grader
Need help grading? Try our AI Grader for instant feedback on your assignments.

Design of a buck-boost DC-DC Converter 17
Dboost = 1- VIN MIN ×η
VOUT MAX . . . . . . . . . . . . . . . . . . . . . . . . . . . . . . . . . . . . . . . . . . . . . . . . . . . . . . . . .
.4
Dboost = 1- 1.8× 0.96
5.5 = 1- 0.31
Dboost = 0.68
The estimated value of the inductor ripple current is from 20% to 40% of the output current or it
would be 0.2 < Kind < 0.4.
Selection of input capacitor
To advance transient behaviour of the regulator of the total supplied power to the circuit. This
design will operate best at minimum input capacitor of 20μF (Tanzawa, 2015).
There are three parameters involved in the selection of input capacitor. They are,
1) Rated voltage- It must be higher than maximum input voltage.
2) Rated ripple current- It must be greater than maximum input ripple current occurring in IC
input.
3) DC bias and temperature characteristics when using ceramic capacitors.
The instability of the input voltage occurs due to the requirement of peak current in switching
power supply. To stabilize this input voltage, the input capacitor value is needed. The capacitor
value should be minimum value. It is given in the datasheet.
The capacitors of ceramic type with low ESR value are good choice to use and the dielectric
material should be five times better than the actual resistor. Or else due to temperature and dc
bias the capacitor loses its capacitance during its operation. The value of the input capacitance
will be increased when the more noise occurs in the input voltage.
Selection of output capacitor
The selection of the output capacitor is obtained from the following equation 5. Three parameters
are important when selecting the input capacitors. They are listed below.
1) Rated voltage
2) Rated ripple current
3) ESR (Equivalent Series Resistance)
17
Dboost = 1- VIN MIN ×η
VOUT MAX . . . . . . . . . . . . . . . . . . . . . . . . . . . . . . . . . . . . . . . . . . . . . . . . . . . . . . . . .
.4
Dboost = 1- 1.8× 0.96
5.5 = 1- 0.31
Dboost = 0.68
The estimated value of the inductor ripple current is from 20% to 40% of the output current or it
would be 0.2 < Kind < 0.4.
Selection of input capacitor
To advance transient behaviour of the regulator of the total supplied power to the circuit. This
design will operate best at minimum input capacitor of 20μF (Tanzawa, 2015).
There are three parameters involved in the selection of input capacitor. They are,
1) Rated voltage- It must be higher than maximum input voltage.
2) Rated ripple current- It must be greater than maximum input ripple current occurring in IC
input.
3) DC bias and temperature characteristics when using ceramic capacitors.
The instability of the input voltage occurs due to the requirement of peak current in switching
power supply. To stabilize this input voltage, the input capacitor value is needed. The capacitor
value should be minimum value. It is given in the datasheet.
The capacitors of ceramic type with low ESR value are good choice to use and the dielectric
material should be five times better than the actual resistor. Or else due to temperature and dc
bias the capacitor loses its capacitance during its operation. The value of the input capacitance
will be increased when the more noise occurs in the input voltage.
Selection of output capacitor
The selection of the output capacitor is obtained from the following equation 5. Three parameters
are important when selecting the input capacitors. They are listed below.
1) Rated voltage
2) Rated ripple current
3) ESR (Equivalent Series Resistance)
17

Design of a buck-boost DC-DC Converter 18
To minimize the ripple current in the output voltage, low ESR value capacitors are used. The
ceramic capacitors are the best choice when the dielectric material is five times better than the
actual resistors.
The compensated values of the converters should keep the recommended values as the same ratio
of L x C. Or else the Inductor and Capacitor values should be assumed as per the requirements.
The externally compensated converters use the solution that satisfies both the boost and buck
modes in buck boost converter. The first step is to find the minimum output capacitance value
for buck and boost mode of the converter. Then select the output capacitance value which is
greater than both minimum value of output capacitance for buck and boost mode (Marasco,
2012).
Minimum Output Capacitor = Kind × IOUT
8 × Fsw ×Vout ripple . . . . . . . . . . . . . . . . . . . . . . . . . . . . . . . . . . . .
. . 5
Where,
Fsw - Switching frequency of the converter in buck mode
Voutripple - Ripple value of the output voltage
Iout - Output current
Kind - The coefficient which represents the value of the inductor ripple current
By substituting the values in above formula we get,
C = 0.4 ×3
8 ×260000 ×0.004
C= 1.4422μF
Inductor Selection
The datasheet is used to give the range of values for inductor. The inductor value should be
taken in that range alone. The maximum output current occurs when the value of inductor is
high. In this stage the reduced value of the ripple current is obtained. The value of inductance is
decreases because of the increasing value of the peak current. The low value of the current leads
to the size of the solution for inductor selection will be low. The high value of inductor leads to
high value of current.
18
To minimize the ripple current in the output voltage, low ESR value capacitors are used. The
ceramic capacitors are the best choice when the dielectric material is five times better than the
actual resistors.
The compensated values of the converters should keep the recommended values as the same ratio
of L x C. Or else the Inductor and Capacitor values should be assumed as per the requirements.
The externally compensated converters use the solution that satisfies both the boost and buck
modes in buck boost converter. The first step is to find the minimum output capacitance value
for buck and boost mode of the converter. Then select the output capacitance value which is
greater than both minimum value of output capacitance for buck and boost mode (Marasco,
2012).
Minimum Output Capacitor = Kind × IOUT
8 × Fsw ×Vout ripple . . . . . . . . . . . . . . . . . . . . . . . . . . . . . . . . . . . .
. . 5
Where,
Fsw - Switching frequency of the converter in buck mode
Voutripple - Ripple value of the output voltage
Iout - Output current
Kind - The coefficient which represents the value of the inductor ripple current
By substituting the values in above formula we get,
C = 0.4 ×3
8 ×260000 ×0.004
C= 1.4422μF
Inductor Selection
The datasheet is used to give the range of values for inductor. The inductor value should be
taken in that range alone. The maximum output current occurs when the value of inductor is
high. In this stage the reduced value of the ripple current is obtained. The value of inductance is
decreases because of the increasing value of the peak current. The low value of the current leads
to the size of the solution for inductor selection will be low. The high value of inductor leads to
high value of current.
18

Design of a buck-boost DC-DC Converter 19
The inductor to be selected should be satisfied for both Buck and Boost conditions.The value of
the inductor is selected from the highest result from the highest result obtained after calculation
in the below equations.
Buck Mode
The value of inductance is calculated by using the below formula for Buck mode in Buck boost
converter.
L> VOUT ×(VIN MAX−VOUT )
Kind × Fsw ×VinMax × Iout
Where,
Fsw - Switching frequency of the converter in buck mode
Vout - Output voltage
Iout - Output current
Vinmax - Input maximum Voltage
Kind - The coefficient which represents the value of the inductor ripple current.
By substituting the values in the above formula we get,
L> 5.5 ×(5.5−1.2)
0.4 ×260000 ×5.5 ×3
L> 5.5 × 4,3
1716000
L> 23.65
1716000
L> 0.000013782
Boost mode
The inductance for boost mode in buck – boost converter is found by using the below formula.
L> ( Vout−Vin Min ) ×Vinmin2
Fsw × Kind × Iout ×Vout2
Where,
Fsw - Switching frequency of the converter
Vout - Output voltage
19
The inductor to be selected should be satisfied for both Buck and Boost conditions.The value of
the inductor is selected from the highest result from the highest result obtained after calculation
in the below equations.
Buck Mode
The value of inductance is calculated by using the below formula for Buck mode in Buck boost
converter.
L> VOUT ×(VIN MAX−VOUT )
Kind × Fsw ×VinMax × Iout
Where,
Fsw - Switching frequency of the converter in buck mode
Vout - Output voltage
Iout - Output current
Vinmax - Input maximum Voltage
Kind - The coefficient which represents the value of the inductor ripple current.
By substituting the values in the above formula we get,
L> 5.5 ×(5.5−1.2)
0.4 ×260000 ×5.5 ×3
L> 5.5 × 4,3
1716000
L> 23.65
1716000
L> 0.000013782
Boost mode
The inductance for boost mode in buck – boost converter is found by using the below formula.
L> ( Vout−Vin Min ) ×Vinmin2
Fsw × Kind × Iout ×Vout2
Where,
Fsw - Switching frequency of the converter
Vout - Output voltage
19
Paraphrase This Document
Need a fresh take? Get an instant paraphrase of this document with our AI Paraphraser

Design of a buck-boost DC-DC Converter 20
Vinmin - Input minimum Voltage
Kind - The coefficient which represents the value of the inductor ripple current
Iout - Maximum value of output current
By substituting the values in the above formula we get,
L> ( 5.51 .8 ) ×5.52
260000× 0.4 ×3 × 5.52
L> 111.925
9438000
L> 0.000011858
Therefore the maximum value between the two is selected and that is
L>13.783μH
Thus 15μH is selected
Calculation of maximum switching current
For the calculation of the maximum switching current, both the buck mode and the boost mode
are employed. And the maximum value of the two is selected (Alvandpour, 2016). The
maximum switching current gives the value of current for which the switch of the circuit remains
in open state. Due to this the switching process takes place in the buck boost converter.
Maximum switching current is calculated for both buck and boost mode.
Buck Mode
In the buck mode, the maximum switch current is when the input voltage is at its maximum.
The maximum switching current is obtained from the below equation,
Isw Max = ∆ Imax
2 +Iout . . . . . . . . . . . . . . . . . . . . . . . . . . . . . . . . . . . . . . . . . . . . . . . . . . . . . . . . .
6
Where,
Iout - Output current
ΔImax - Maximum value of the ripple current
Isw max - Maximum value of switch current
20
Vinmin - Input minimum Voltage
Kind - The coefficient which represents the value of the inductor ripple current
Iout - Maximum value of output current
By substituting the values in the above formula we get,
L> ( 5.51 .8 ) ×5.52
260000× 0.4 ×3 × 5.52
L> 111.925
9438000
L> 0.000011858
Therefore the maximum value between the two is selected and that is
L>13.783μH
Thus 15μH is selected
Calculation of maximum switching current
For the calculation of the maximum switching current, both the buck mode and the boost mode
are employed. And the maximum value of the two is selected (Alvandpour, 2016). The
maximum switching current gives the value of current for which the switch of the circuit remains
in open state. Due to this the switching process takes place in the buck boost converter.
Maximum switching current is calculated for both buck and boost mode.
Buck Mode
In the buck mode, the maximum switch current is when the input voltage is at its maximum.
The maximum switching current is obtained from the below equation,
Isw Max = ∆ Imax
2 +Iout . . . . . . . . . . . . . . . . . . . . . . . . . . . . . . . . . . . . . . . . . . . . . . . . . . . . . . . . .
6
Where,
Iout - Output current
ΔImax - Maximum value of the ripple current
Isw max - Maximum value of switch current
20

Design of a buck-boost DC-DC Converter 21
But the value of ∆ Imax is obtained from the below equation 5
∆ Imax= ( Vin Max −Vout ) × Dbuck
Fsw × L . . . . . . . . . . . . . . . . . . . . . . . . . . . . . . . . . . . . . . . . . . . . . . . . . .
. . 7
Where,
Vin max - Maximum value of the input voltage (for buck mode-5.5V
Vout - Output voltage
Dbuck - Minimum duty cycle for buck mode
L - Inductor value
Fsw - Switching frequency of the converter
Before calculating the other values, it has to be verifying that the converter can deliver the
maximum current which is greater than Iout or not. The output transient response is used for the
selection of the output capacitor and the steady state ripple is not used to select the output
capacitor. The deviation in the output voltage occurs according to the need of increased or
decreased value of inductor output current. The output capacitance value is calculated by using
the following formula. It is calculated for the maximum peak value caused by the removal of the
current which is at load.
By substituting the values in the above formula we get,
∆ Imax= ( 5.5−1.8 ) ×0.209
260000× 15 μH
∆ Imax= 3.7× 0.209
260000× 0.000015
∆ Imax= 0.7733
3.9 = 0.1983
Therefore from equation 4 above, we can obtain the maximum switching current (Safari, 2012).
Isw Max = 0.1983
2 +3
Isw Max = 3.09915
Boost Mode
21
But the value of ∆ Imax is obtained from the below equation 5
∆ Imax= ( Vin Max −Vout ) × Dbuck
Fsw × L . . . . . . . . . . . . . . . . . . . . . . . . . . . . . . . . . . . . . . . . . . . . . . . . . .
. . 7
Where,
Vin max - Maximum value of the input voltage (for buck mode-5.5V
Vout - Output voltage
Dbuck - Minimum duty cycle for buck mode
L - Inductor value
Fsw - Switching frequency of the converter
Before calculating the other values, it has to be verifying that the converter can deliver the
maximum current which is greater than Iout or not. The output transient response is used for the
selection of the output capacitor and the steady state ripple is not used to select the output
capacitor. The deviation in the output voltage occurs according to the need of increased or
decreased value of inductor output current. The output capacitance value is calculated by using
the following formula. It is calculated for the maximum peak value caused by the removal of the
current which is at load.
By substituting the values in the above formula we get,
∆ Imax= ( 5.5−1.8 ) ×0.209
260000× 15 μH
∆ Imax= 3.7× 0.209
260000× 0.000015
∆ Imax= 0.7733
3.9 = 0.1983
Therefore from equation 4 above, we can obtain the maximum switching current (Safari, 2012).
Isw Max = 0.1983
2 +3
Isw Max = 3.09915
Boost Mode
21

Design of a buck-boost DC-DC Converter 22
In the boost mode, the maximum value for switch current is calculated when the input voltage is
at its minimum value.
Isw Max = ∆ Imax
2 + Iout
1−Dboost
. . . . . . . . . . . . . . . . . . . . . . . . . . . . . . . . . . . . . . . . . . . . . . . . . . . . . 8
Where,
Iout - Output current
ΔImax - Maximum value of the Inductor ripple current
Isw max – Maximum value of switching current
Dboost - Boost mode duty cycle
And the value of ∆ Imax is obtained by the following equation
∆ Imax= Vin Min × Dboost
Fsw × L
Where,
Vout - Output voltage
Vin min – Minimum value of input voltage
Fsw - The converter switching frequency
Dboost - Boost mode duty cycle
L - Value of the Inductor
By substituting the values in the above formula we get,
∆ Imax= 1.8× 0.68
260000× 0.000015
∆ Imax= 1.224
3.9 = 0.3138
Isw Max = 0.3138
2 + 3
0.32
Isw Max = 0.1569+9.375
Isw Max = 9.5319
Thus Isw Max is selected as 9.5319.
22
In the boost mode, the maximum value for switch current is calculated when the input voltage is
at its minimum value.
Isw Max = ∆ Imax
2 + Iout
1−Dboost
. . . . . . . . . . . . . . . . . . . . . . . . . . . . . . . . . . . . . . . . . . . . . . . . . . . . . 8
Where,
Iout - Output current
ΔImax - Maximum value of the Inductor ripple current
Isw max – Maximum value of switching current
Dboost - Boost mode duty cycle
And the value of ∆ Imax is obtained by the following equation
∆ Imax= Vin Min × Dboost
Fsw × L
Where,
Vout - Output voltage
Vin min – Minimum value of input voltage
Fsw - The converter switching frequency
Dboost - Boost mode duty cycle
L - Value of the Inductor
By substituting the values in the above formula we get,
∆ Imax= 1.8× 0.68
260000× 0.000015
∆ Imax= 1.224
3.9 = 0.3138
Isw Max = 0.3138
2 + 3
0.32
Isw Max = 0.1569+9.375
Isw Max = 9.5319
Thus Isw Max is selected as 9.5319.
22
Secure Best Marks with AI Grader
Need help grading? Try our AI Grader for instant feedback on your assignments.

Design of a buck-boost DC-DC Converter 23
Output Voltage Setting
There are two types in output voltage of buck – boost converters. They are internal and
external voltages. The internal voltages are fixed voltages. The external voltages are adjustable
voltages. The Vout is represented for the internal type of voltages and the Vfb is represented for
the external type of voltages. The voltage divider which is in external is not used in the voltage
which is in the internal. But external voltage divider is used in external voltage type. Feedback
circuits which is used in buck boost converters of external output voltage type is shown below.
Figure 6 Voltage divider circuit
The voltage divider can be calculated with feedback bias current and feedback voltage (Vfb).
The current through the resistive divider (IR1/2) must be at least 100 times the size of the
feedback bias current (IFB)
Where,
IR1/2 - Resistive divider current
IFB - Feedback bias current from datasheet.
Here, the calculations are used to find the value of the resistors (R1 and R2)
23
Output Voltage Setting
There are two types in output voltage of buck – boost converters. They are internal and
external voltages. The internal voltages are fixed voltages. The external voltages are adjustable
voltages. The Vout is represented for the internal type of voltages and the Vfb is represented for
the external type of voltages. The voltage divider which is in external is not used in the voltage
which is in the internal. But external voltage divider is used in external voltage type. Feedback
circuits which is used in buck boost converters of external output voltage type is shown below.
Figure 6 Voltage divider circuit
The voltage divider can be calculated with feedback bias current and feedback voltage (Vfb).
The current through the resistive divider (IR1/2) must be at least 100 times the size of the
feedback bias current (IFB)
Where,
IR1/2 - Resistive divider current
IFB - Feedback bias current from datasheet.
Here, the calculations are used to find the value of the resistors (R1 and R2)
23

Design of a buck-boost DC-DC Converter 24
Where,
R1, R2 - Value of resistors in resistive divider
Vfb - Voltage at the feedback circuit
IR1/2 - Current through the resistive divider to GND
Vout - Output voltage
MOSFET selection for the Buck boost converter
Input voltage is given as 5.5 (max input from the specification)
Maximum output current is given as 3A (from design specification)
Duty cycle is 0.68 (max duty cycle from calculation)
Trise= Tfall = 50 ns (selected for a perfect operation of the MOSFET)
Fsw = 2600kHz
Rds = 0.02ῼ (selected for a perfect operation of the switching device)
Conduction Power= ID2×Rds×D
Conduction Power= 32×0.02×0.68
Conduction Power= 0.1224 Watts
Switching Power = (V× ½ID) ×( Ton +Toff)× Fsw + ( Coss×V2×Fsw)
Switching Power = ( 5.5 ×½×3)× (50ns +50ns )× 260000 + ( 890pF×5.52×260000)
Switching Power = (8.25× 0.0000001×260000) + (0.0069999)
Switching Power= 0.2145+0.006999
Switching Power =0.2215 watts
Total power for the switching device is hence given as
24
Where,
R1, R2 - Value of resistors in resistive divider
Vfb - Voltage at the feedback circuit
IR1/2 - Current through the resistive divider to GND
Vout - Output voltage
MOSFET selection for the Buck boost converter
Input voltage is given as 5.5 (max input from the specification)
Maximum output current is given as 3A (from design specification)
Duty cycle is 0.68 (max duty cycle from calculation)
Trise= Tfall = 50 ns (selected for a perfect operation of the MOSFET)
Fsw = 2600kHz
Rds = 0.02ῼ (selected for a perfect operation of the switching device)
Conduction Power= ID2×Rds×D
Conduction Power= 32×0.02×0.68
Conduction Power= 0.1224 Watts
Switching Power = (V× ½ID) ×( Ton +Toff)× Fsw + ( Coss×V2×Fsw)
Switching Power = ( 5.5 ×½×3)× (50ns +50ns )× 260000 + ( 890pF×5.52×260000)
Switching Power = (8.25× 0.0000001×260000) + (0.0069999)
Switching Power= 0.2145+0.006999
Switching Power =0.2215 watts
Total power for the switching device is hence given as
24

Design of a buck-boost DC-DC Converter 25
P total = 0.2215+0.1224
P total = 0.3438995 watts
P channel device will hence be selected to simplify the gate drive circuitry for the MOSFET
(switching device) (Elision, 2011).
After perfectly conducted the design of the buck-boost DC/DC converter the specifications and
the calculations obtained were used to draw the Converter in the multism and the circuit diagram
is shown as in figures below. The switches were also replaced with the switching devices
( MOSFET)
Fig 6: Showing the Buck-boost converter showing the output voltage
25
P total = 0.2215+0.1224
P total = 0.3438995 watts
P channel device will hence be selected to simplify the gate drive circuitry for the MOSFET
(switching device) (Elision, 2011).
After perfectly conducted the design of the buck-boost DC/DC converter the specifications and
the calculations obtained were used to draw the Converter in the multism and the circuit diagram
is shown as in figures below. The switches were also replaced with the switching devices
( MOSFET)
Fig 6: Showing the Buck-boost converter showing the output voltage
25
Paraphrase This Document
Need a fresh take? Get an instant paraphrase of this document with our AI Paraphraser

Design of a buck-boost DC-DC Converter 26
Fig 7: Showing the Buck-boost converter showing the output current.
Fig 8: Showing the waveform of the buck-boost DC/DC converter
Design evaluation
After the design of the converter, the waveforms are shown above fully qualifies the above
design of the converter (Ang, 2015). For a better design of the converter, the value of the input
voltage VIN and the output voltage VOUT. The duty cycle between the two operating modes
(buck and boost) should be nearly equal. And this will be achieved by giving the VOUT a higher
value and a relatively higher value of the operating efficiency of about 99%.
Explanation of the operation of the above design.
The DC converter operates in two operation modes i.e the
1. The Continuous conduction mode.
Here, the current via the inductor does not go to, In this mode, there are some cases which will
enable us to understand best the operation of the above design (Lenk, 2013).
Case a : WHEN SWITCHES ARE ON
26
Fig 7: Showing the Buck-boost converter showing the output current.
Fig 8: Showing the waveform of the buck-boost DC/DC converter
Design evaluation
After the design of the converter, the waveforms are shown above fully qualifies the above
design of the converter (Ang, 2015). For a better design of the converter, the value of the input
voltage VIN and the output voltage VOUT. The duty cycle between the two operating modes
(buck and boost) should be nearly equal. And this will be achieved by giving the VOUT a higher
value and a relatively higher value of the operating efficiency of about 99%.
Explanation of the operation of the above design.
The DC converter operates in two operation modes i.e the
1. The Continuous conduction mode.
Here, the current via the inductor does not go to, In this mode, there are some cases which will
enable us to understand best the operation of the above design (Lenk, 2013).
Case a : WHEN SWITCHES ARE ON
26

Design of a buck-boost DC-DC Converter 27
During the time the switch is ON (ton) , the MOSFET will operates as open circuit thus the
current will not flow from input to output direction. At this time the inductor will charge and the
inductor current increase and the current via the inductor is obtained as below (Basso, 2014);
. . . . . . . . . . . . . . . . . . . . . . . . . . . . . . . . . . . . . . . . . . . . . . . . 9
Assume the previous to the opening of the switches the inductor current I’L off. Because the
input voltage is constant which is illustrated by the following equations
. . . . . . . . . . . . . . . . . . . . . . . . . . . . . . . . . . . . . . .10
Assuming the switch is open for ton seconds
(given by D*Ts) where D is the duty cycle and the Ts is the switching time (Williams, 2011).
The current via the inductor after switching on the switching device.
IL, on = (1/L) *Vin*D*Ts + I’L, on . . . . . . . . . . . . . . . . . . . . . . . . . . . . . . . . . . . . . . . . . . . . . . . . 11
Case b
The inductor will discharges via the MOSFET and Assuming the erstwhile to the closing of
switch the inductor current is I’’L, off. The current via the inductor can be obtained as below;
. . . . . . . . . . . . . . . . . . . . . . . . . . . . . . . . . . . . . . . . 12
The current through the inductor at the end of switch
I’’’L, off = -(1/L) *Vout*(1-D)*Ts + I’’L, off . . . . . . . . . . . . . . . . . . . . . . . . . . . . . . . . . . . . . . . .13
2. Discontinuous conduction mode
When converter operated in discontinuous mode the inductor will drain its stored energy entirely
before completion of switching cycle (Emadi, 2017).
. . . . . . . . . . . . . . . . . . . . . . . . . . . . . . . . . . . . . . . . . . . . . . . . . 14
27
During the time the switch is ON (ton) , the MOSFET will operates as open circuit thus the
current will not flow from input to output direction. At this time the inductor will charge and the
inductor current increase and the current via the inductor is obtained as below (Basso, 2014);
. . . . . . . . . . . . . . . . . . . . . . . . . . . . . . . . . . . . . . . . . . . . . . . . 9
Assume the previous to the opening of the switches the inductor current I’L off. Because the
input voltage is constant which is illustrated by the following equations
. . . . . . . . . . . . . . . . . . . . . . . . . . . . . . . . . . . . . . .10
Assuming the switch is open for ton seconds
(given by D*Ts) where D is the duty cycle and the Ts is the switching time (Williams, 2011).
The current via the inductor after switching on the switching device.
IL, on = (1/L) *Vin*D*Ts + I’L, on . . . . . . . . . . . . . . . . . . . . . . . . . . . . . . . . . . . . . . . . . . . . . . . . 11
Case b
The inductor will discharges via the MOSFET and Assuming the erstwhile to the closing of
switch the inductor current is I’’L, off. The current via the inductor can be obtained as below;
. . . . . . . . . . . . . . . . . . . . . . . . . . . . . . . . . . . . . . . . 12
The current through the inductor at the end of switch
I’’’L, off = -(1/L) *Vout*(1-D)*Ts + I’’L, off . . . . . . . . . . . . . . . . . . . . . . . . . . . . . . . . . . . . . . . .13
2. Discontinuous conduction mode
When converter operated in discontinuous mode the inductor will drain its stored energy entirely
before completion of switching cycle (Emadi, 2017).
. . . . . . . . . . . . . . . . . . . . . . . . . . . . . . . . . . . . . . . . . . . . . . . . . 14
27

Design of a buck-boost DC-DC Converter 28
The waveforms obtained from the multism indicates the period for which the switch is on TON
and off TOFF.
DISCUSSION
In this stage the various merits and demerits of the developed buck boost converter
design was discussed below.
Advantages of boost converter
Buck-boost converter is a type of converter that can able to increase or decrease the input
voltage.
There are some advantages of the boost converter are there. They are:
The input current is continuous.
The construction of control and drive circuit is easy.
The control of the circuit is easy due to the positive output voltage.
Output voltage is higher than input voltage.
Easy to filter and meet electromagnetic interference requirements.
Capable of giving higher boost than buck-boost converter.
The cost of these type of converters is less when compared to other converters.
The performance in the buck-boost is almost similar to other converters which are high-
cost converters.
The voltage for the step up and step down performances are always in the minimum
component count. Whereas in the other converters like Cuk, zeta is the count of a double
component.
The other major advantages of buck-boost converters are it can handle a large amount of
current as an output. It has very low thermal dissipation and hence produces very less
amount of heat energy. It always produces higher energy.And inverting and
buck/boosting are other major advantages.
Disadvantages of boost converter:
28
The waveforms obtained from the multism indicates the period for which the switch is on TON
and off TOFF.
DISCUSSION
In this stage the various merits and demerits of the developed buck boost converter
design was discussed below.
Advantages of boost converter
Buck-boost converter is a type of converter that can able to increase or decrease the input
voltage.
There are some advantages of the boost converter are there. They are:
The input current is continuous.
The construction of control and drive circuit is easy.
The control of the circuit is easy due to the positive output voltage.
Output voltage is higher than input voltage.
Easy to filter and meet electromagnetic interference requirements.
Capable of giving higher boost than buck-boost converter.
The cost of these type of converters is less when compared to other converters.
The performance in the buck-boost is almost similar to other converters which are high-
cost converters.
The voltage for the step up and step down performances are always in the minimum
component count. Whereas in the other converters like Cuk, zeta is the count of a double
component.
The other major advantages of buck-boost converters are it can handle a large amount of
current as an output. It has very low thermal dissipation and hence produces very less
amount of heat energy. It always produces higher energy.And inverting and
buck/boosting are other major advantages.
Disadvantages of boost converter:
28
Secure Best Marks with AI Grader
Need help grading? Try our AI Grader for instant feedback on your assignments.

Design of a buck-boost DC-DC Converter 29
The charging current of the output capacitor is discontinuous.
Efficiency is poor for high gain.
Cannot provide a large limit of maximum power point tracking.
There is no isolation from input and output.
Difficult to control.
To reduce ripple voltage large output capacitor is needed.
Due to presence of right half zero in CCM boost converter, there will be a slower
transient response and difficult feedback loop compensation.
The design of the buck-boost converter has a very complicated one.
The count parts in this converter are very high.
The major disadvantages of this converter are switch noise and ripple exist.
The other disadvantages are sensing complexity.
Controlling the buck-boost converters are difficult because of the transfer functions.
The power supply for the semiconductors is very complex because it supplies the current
through only the gate drivers.
Advantages of buck converter:
Buck converter is simple and it is not needed more than one power switch.
In the converter, the buck regulator has the efficiency level at ninety percent.
The cost for the converter is low. And also the size of the buck converter is also low.
It has the huge tolerance for line voltage variation. It is used to step down the voltage
from the input to the output.
And it seems to be easy for the implementation. It has the low noise at the output of this
converter. It has the low price level at high powers.
It has the compact ability in the design. Feedback got easily by using this converter.
Disadvantages of buck converter:
It also had some disadvantages. It has the transient response as slow.
The input filter is always needed. And it needs the huge output ripple.
29
The charging current of the output capacitor is discontinuous.
Efficiency is poor for high gain.
Cannot provide a large limit of maximum power point tracking.
There is no isolation from input and output.
Difficult to control.
To reduce ripple voltage large output capacitor is needed.
Due to presence of right half zero in CCM boost converter, there will be a slower
transient response and difficult feedback loop compensation.
The design of the buck-boost converter has a very complicated one.
The count parts in this converter are very high.
The major disadvantages of this converter are switch noise and ripple exist.
The other disadvantages are sensing complexity.
Controlling the buck-boost converters are difficult because of the transfer functions.
The power supply for the semiconductors is very complex because it supplies the current
through only the gate drivers.
Advantages of buck converter:
Buck converter is simple and it is not needed more than one power switch.
In the converter, the buck regulator has the efficiency level at ninety percent.
The cost for the converter is low. And also the size of the buck converter is also low.
It has the huge tolerance for line voltage variation. It is used to step down the voltage
from the input to the output.
And it seems to be easy for the implementation. It has the low noise at the output of this
converter. It has the low price level at high powers.
It has the compact ability in the design. Feedback got easily by using this converter.
Disadvantages of buck converter:
It also had some disadvantages. It has the transient response as slow.
The input filter is always needed. And it needs the huge output ripple.
29

Design of a buck-boost DC-DC Converter 30
It has not isolation between the input and output. And the ground is not safe. The voltage
of the converter is not increased in the step-down process.
The output appearance should be dependent on the frequency of power line.
In the inductance, it has flux density level at the huge rate. And it needed a huge peak
current in the semi-conductors.
30
It has not isolation between the input and output. And the ground is not safe. The voltage
of the converter is not increased in the step-down process.
The output appearance should be dependent on the frequency of power line.
In the inductance, it has flux density level at the huge rate. And it needed a huge peak
current in the semi-conductors.
30

Design of a buck-boost DC-DC Converter 31
CONCLUSION
In this project, the detailed study about the various types of DC/DC converters and regulators
were completed. Various design methodologies involved in the process of developing the buck-
boost converter was studied. Based on the knowledge acquired by the study carried out the
conceptual design for the buck-boost converters are developed. The developed design critically
analyzed to analyses the performance characteristics of the buck-boost converter. Initially, the
various calculations of various elements for the buck booster converters were completed. Based
on the calculations, the various elements for the buck-boost converters were selected. Then the
schematic layout for the buck-boost converters was developed. Then the manually developed
results are regenerated using the computer. For that the Multisim software package was used. At
first, the schematic layout of the buck-boost converter was developed. Then the value for the
various components present in the buck-boost converter was assigned in the multisim software
package. Then the circuit was simulated using the same software itself. The developed design
satisfies the various critical parameters. Based on the critical analysis carried out on the
developed design of the buck and boost converter that is clear the developed design performs
well. The simulation shows that the developed design gives the results similar to the values
required for the buck-boost converter.
31
CONCLUSION
In this project, the detailed study about the various types of DC/DC converters and regulators
were completed. Various design methodologies involved in the process of developing the buck-
boost converter was studied. Based on the knowledge acquired by the study carried out the
conceptual design for the buck-boost converters are developed. The developed design critically
analyzed to analyses the performance characteristics of the buck-boost converter. Initially, the
various calculations of various elements for the buck booster converters were completed. Based
on the calculations, the various elements for the buck-boost converters were selected. Then the
schematic layout for the buck-boost converters was developed. Then the manually developed
results are regenerated using the computer. For that the Multisim software package was used. At
first, the schematic layout of the buck-boost converter was developed. Then the value for the
various components present in the buck-boost converter was assigned in the multisim software
package. Then the circuit was simulated using the same software itself. The developed design
satisfies the various critical parameters. Based on the critical analysis carried out on the
developed design of the buck and boost converter that is clear the developed design performs
well. The simulation shows that the developed design gives the results similar to the values
required for the buck-boost converter.
31
Paraphrase This Document
Need a fresh take? Get an instant paraphrase of this document with our AI Paraphraser

Design of a buck-boost DC-DC Converter 32
REFERENCES
Alvandpour, A., 2016. Buck-boost Converter Design Issues. 2nd ed. Colorado: CRC.
Ang, S., 2015. Power switching Converter. 2nd ed. Manchester: CRC press.
Basso, C., 2014. Switch-Mode Power Supplies. 2nd ed. Amsterdam: McGraw Hill Professional.
Elision, C., 2011. Designing a boost switching regulator. 2nd ed. London: CRC.
Emadi, A., 2017. Integrated Power Electronic Converters. 1st ed. Hull: CRC.
Garcia, M. P., 2010. INTEGRATED DESIGN & CONTROL OF A BUCK-BOOST
CONVERTER. 3rd ed. Hull: CRC.
Green, M., 2012. Design Calculations for Buck-Boost Converters. 3rd ed. Florida: Texas
Instruments.
Hauke, B., 2011. Basic Calculation of a Boost Converter's Power Stage. 1st ed. Florida: Texas
Instruments.
James, G., 2013. Designing and modulation of the DC-DC buck-boost Converter. 3rd ed. Hull:
CRC.
john, E., 2013. Fundamental of Power electronics. 2nd ed. Chicago: Springer.
Kennedy, M., 2013. Pulse - width modulated DC-DC power converter. 2nd ed. Ottawa: CRC.
Lenk, J., 2013. Simplified Design of witching Power Supplies. 3rd ed. Hawaii: Elsevier.
Voinovich, A., 2013. Power Electronics and Energy Conversion System of the switching
converter. 2nd ed. Chicago: Wiley.
Marasco, K., 2012. How to Apply DC-to-DC Buck-boost converter successfully. 2nd ed.
Chicago: Adventure works.
Mouhadjer, S., 2012. Comprehensive and field study to design a buck-boost converter for
photovoltaic systems. 1st ed. Colorado: Springer.
Steele, J., 2012. Basic Calculation of a Boost Converter's Power Stage. 2nd ed. Hawaii: CRC.
32
REFERENCES
Alvandpour, A., 2016. Buck-boost Converter Design Issues. 2nd ed. Colorado: CRC.
Ang, S., 2015. Power switching Converter. 2nd ed. Manchester: CRC press.
Basso, C., 2014. Switch-Mode Power Supplies. 2nd ed. Amsterdam: McGraw Hill Professional.
Elision, C., 2011. Designing a boost switching regulator. 2nd ed. London: CRC.
Emadi, A., 2017. Integrated Power Electronic Converters. 1st ed. Hull: CRC.
Garcia, M. P., 2010. INTEGRATED DESIGN & CONTROL OF A BUCK-BOOST
CONVERTER. 3rd ed. Hull: CRC.
Green, M., 2012. Design Calculations for Buck-Boost Converters. 3rd ed. Florida: Texas
Instruments.
Hauke, B., 2011. Basic Calculation of a Boost Converter's Power Stage. 1st ed. Florida: Texas
Instruments.
James, G., 2013. Designing and modulation of the DC-DC buck-boost Converter. 3rd ed. Hull:
CRC.
john, E., 2013. Fundamental of Power electronics. 2nd ed. Chicago: Springer.
Kennedy, M., 2013. Pulse - width modulated DC-DC power converter. 2nd ed. Ottawa: CRC.
Lenk, J., 2013. Simplified Design of witching Power Supplies. 3rd ed. Hawaii: Elsevier.
Voinovich, A., 2013. Power Electronics and Energy Conversion System of the switching
converter. 2nd ed. Chicago: Wiley.
Marasco, K., 2012. How to Apply DC-to-DC Buck-boost converter successfully. 2nd ed.
Chicago: Adventure works.
Mouhadjer, S., 2012. Comprehensive and field study to design a buck-boost converter for
photovoltaic systems. 1st ed. Colorado: Springer.
Steele, J., 2012. Basic Calculation of a Boost Converter's Power Stage. 2nd ed. Hawaii: CRC.
32

Design of a buck-boost DC-DC Converter 33
Rogers, E., 2012. Understanding Buck-Boost Power Stages in Switch Mode. 2nd ed. Washington
DC: Texas Instruments.
Safari, N., 2012. Design of a DC/DC buck converter for ultra-low power applications in 65nm
CMOS Process. 3rd ed. Stoke: CRC.
Silva, R., 2016. Control Design Technology in Power Electronics Devices. 2nd ed. Hawaii:
Springer.
Siu, K., 2011. P F C bo os t c on v er ter d esi in gu I d e. 1st ed. Hull: Infineon press.
Tanzawa, T., 2015. calculations and the designs of the DC-Dc converter. 2nd ed. Athens : CRC.
Williams, J., 2011. Analog Circuit Design. 2nd ed. Berlin: Elsevier .
Xi, F., 2012. Design of DC-DC Converters. 2nd ed. Beijing: Monolithic Power Systems Inc.
33
Rogers, E., 2012. Understanding Buck-Boost Power Stages in Switch Mode. 2nd ed. Washington
DC: Texas Instruments.
Safari, N., 2012. Design of a DC/DC buck converter for ultra-low power applications in 65nm
CMOS Process. 3rd ed. Stoke: CRC.
Silva, R., 2016. Control Design Technology in Power Electronics Devices. 2nd ed. Hawaii:
Springer.
Siu, K., 2011. P F C bo os t c on v er ter d esi in gu I d e. 1st ed. Hull: Infineon press.
Tanzawa, T., 2015. calculations and the designs of the DC-Dc converter. 2nd ed. Athens : CRC.
Williams, J., 2011. Analog Circuit Design. 2nd ed. Berlin: Elsevier .
Xi, F., 2012. Design of DC-DC Converters. 2nd ed. Beijing: Monolithic Power Systems Inc.
33

Design of a buck-boost DC-DC Converter 34
APPENDICES
1. Time taken to switch off the switching devive (MOSFET) is given by
TOFF = (1−D) × TS
2. Duty cycle of the buck mode is obtained by the following equation
Dbuck = VOUT × η
VIN MAX
3. Duty cycle of the boost mode is obtained by the following equation
Dboost = 1- VIN MIN ×η
VOUT MAX
4. The selection of the output capacitor is obtained from the following equation
Minimum Output Capacitor = Kind × IOUT
8 × Fsw ×Vout ripple
5. The value of the inductor is selected from the highest result from the highest result
obtained after calculation in the below equations.
a. Buck Mode
L> VOUT ×(VIN MAX−VOUT )
Kind × Fsw ×VinMax × Iout
b. L> ( Vout−Vin Min ) ×Vinmin2
Fsw × Kind × Iout ×Vout2
6. The maximum switching current is obtained from the below equation,
34
APPENDICES
1. Time taken to switch off the switching devive (MOSFET) is given by
TOFF = (1−D) × TS
2. Duty cycle of the buck mode is obtained by the following equation
Dbuck = VOUT × η
VIN MAX
3. Duty cycle of the boost mode is obtained by the following equation
Dboost = 1- VIN MIN ×η
VOUT MAX
4. The selection of the output capacitor is obtained from the following equation
Minimum Output Capacitor = Kind × IOUT
8 × Fsw ×Vout ripple
5. The value of the inductor is selected from the highest result from the highest result
obtained after calculation in the below equations.
a. Buck Mode
L> VOUT ×(VIN MAX−VOUT )
Kind × Fsw ×VinMax × Iout
b. L> ( Vout−Vin Min ) ×Vinmin2
Fsw × Kind × Iout ×Vout2
6. The maximum switching current is obtained from the below equation,
34
Secure Best Marks with AI Grader
Need help grading? Try our AI Grader for instant feedback on your assignments.

Design of a buck-boost DC-DC Converter 35
a. Buck mode
Isw Max = ∆ Imax
2 +Iout
b. Boost
Isw Max = ∆ Imax
2 + Iout
1−D boost
7. The Conduction Power for the MOSFET is obtained by the following equation
ID2×Rds×D
8. Switching Power of the switching device MOSFET is given by the below equation
(V× ½ID) ×( Ton +Toff)× Fsw + ( Coss×V2×Fsw)
35
a. Buck mode
Isw Max = ∆ Imax
2 +Iout
b. Boost
Isw Max = ∆ Imax
2 + Iout
1−D boost
7. The Conduction Power for the MOSFET is obtained by the following equation
ID2×Rds×D
8. Switching Power of the switching device MOSFET is given by the below equation
(V× ½ID) ×( Ton +Toff)× Fsw + ( Coss×V2×Fsw)
35
1 out of 35
Related Documents

Your All-in-One AI-Powered Toolkit for Academic Success.
+13062052269
info@desklib.com
Available 24*7 on WhatsApp / Email
Unlock your academic potential
© 2024 | Zucol Services PVT LTD | All rights reserved.