EMAM511 Finance: Production Cost Analysis of Electrochic Company
VerifiedAdded on 2023/04/24
|19
|4816
|229
Case Study
AI Summary
This case study provides a comprehensive analysis of Electrochic, a company facing challenges in a competitive market. The analysis delves into production costs, comparing traditional costing methods with activity-based costing (ABC). It examines two proposals for cost allocation, evaluating their advantages and disadvantages. Proposal 1 focuses on cost pools for production, marketing, distribution, and administration, while Proposal 2 suggests allocating costs based on operational activities. The study explores the calculation of per-unit production costs and discusses the implications of different costing methods on pricing and profitability. Ultimately, the case study aims to determine the most pertinent costing method for Electrochic, considering factors such as product complexity, overhead costs, and market competition. Desklib offers a wealth of resources for students, including past papers and solved assignments.
Contribute Materials
Your contribution can guide someone’s learning journey. Share your
documents today.

P a g e 1 | 19
PRODUCTION COST
AND
ITS CALCULATION
PRODUCTION COST
AND
ITS CALCULATION
Secure Best Marks with AI Grader
Need help grading? Try our AI Grader for instant feedback on your assignments.

CONTENTS
INTRODUCTION........................................................................................................................3
TRADITIONAL COSTING........................................................................................................4
COST- POOL................................................................................................................................4
MODERN METHOD OF COSTING.........................................................................................4
ACTIVITY- BASED COSTING.............................................................................................4
TRADITIONAL COSTING METHOD VS. ACTIVITY-BASED COSTING METHOD.. .5
HOW IS PRODUCTION COST PER UNIT CALCULATED................................................6
CASE STUDY ANALYSIS..........................................................................................................8
COMPARATIVE ANALYSIS OF THE TWO PROPOSALS................................................9
CONCLUDING THE ANALYSIS........................................................................................10
ADVANTAGES AND DISADVANTAGES OF PROPOSAL 1............................................11
Advantages................................................................................................................................11
Disadvantages...........................................................................................................................11
ADVANTAGES AND DISADVANTAGES OF PROPOSAL 2............................................12
Advantages................................................................................................................................12
Disadvantages...........................................................................................................................12
CONCLUSION...........................................................................................................................13
REFERENCES.............................................................................................................................14
P a g e 2 | 19
INTRODUCTION........................................................................................................................3
TRADITIONAL COSTING........................................................................................................4
COST- POOL................................................................................................................................4
MODERN METHOD OF COSTING.........................................................................................4
ACTIVITY- BASED COSTING.............................................................................................4
TRADITIONAL COSTING METHOD VS. ACTIVITY-BASED COSTING METHOD.. .5
HOW IS PRODUCTION COST PER UNIT CALCULATED................................................6
CASE STUDY ANALYSIS..........................................................................................................8
COMPARATIVE ANALYSIS OF THE TWO PROPOSALS................................................9
CONCLUDING THE ANALYSIS........................................................................................10
ADVANTAGES AND DISADVANTAGES OF PROPOSAL 1............................................11
Advantages................................................................................................................................11
Disadvantages...........................................................................................................................11
ADVANTAGES AND DISADVANTAGES OF PROPOSAL 2............................................12
Advantages................................................................................................................................12
Disadvantages...........................................................................................................................12
CONCLUSION...........................................................................................................................13
REFERENCES.............................................................................................................................14
P a g e 2 | 19

INTRODUCTION
Production costs is a cost that a business incurs while manufacturing any good or providing any
service (HUNDAL, 1997). The cost is related to both the material as well as the labor that is
required to manufacture or produce any product by the manufacturers. The material and labor
required are direct material and direct labor.
Production costs are divided into direct cost and indirect costs. The direct materials required and
direct labor required fall under the direct production cost head. This is due to the reason that
these cost can be traced very easily. For example, the cost of the staff maintenance falls under
this category. These direct cost are fixed costs of the business. They do not change even if there
is a change in the business economy.
On the other hand, indirect production cost is the manufacturing overhead costs because it is
not easy to trace these cost from the point of the product being manufactured. The indirect cost
may or may not be related to the manufacturing of the product but still occurs during the
manufacturing process. The name ‘indirect cost’ itself suggest that these cost are not fixed and
may vary from time to time (Andrade, Pessanha Filho, Espozel, Maia & Qassim, 1999).
P a g e 3 | 19
Production costs is a cost that a business incurs while manufacturing any good or providing any
service (HUNDAL, 1997). The cost is related to both the material as well as the labor that is
required to manufacture or produce any product by the manufacturers. The material and labor
required are direct material and direct labor.
Production costs are divided into direct cost and indirect costs. The direct materials required and
direct labor required fall under the direct production cost head. This is due to the reason that
these cost can be traced very easily. For example, the cost of the staff maintenance falls under
this category. These direct cost are fixed costs of the business. They do not change even if there
is a change in the business economy.
On the other hand, indirect production cost is the manufacturing overhead costs because it is
not easy to trace these cost from the point of the product being manufactured. The indirect cost
may or may not be related to the manufacturing of the product but still occurs during the
manufacturing process. The name ‘indirect cost’ itself suggest that these cost are not fixed and
may vary from time to time (Andrade, Pessanha Filho, Espozel, Maia & Qassim, 1999).
P a g e 3 | 19

TRADITIONAL COSTING
The traditional method of costing refers to costs incurred by the production overhead
distributed to the products manufactured. In the traditional method the indirect costs incurred in
the factory is allocated to items produced in the factory based on the volume, for example the
number of units of production, the direct labour hours or the machine hours of production, etc.
(Huang, 2018). In our discussions, we will use machine hours. Traditional costing techniques
include standard costing, accountability, marginal costing, etc.
If only machine hours is used for allocating the overhead production to products produced, the
machine hours will only become the overhead production’s primary cause. Earlier this may have
been reasonable or, sufficient for the Company's external financial statement. However, in the
recent years the manufacturing overhead has been driven or caused by a number of other
factors.
COST- POOL
A cost pool is an individual cost grouping, usually by department or service center. Costs are
then allocated from the cost pool (Mastilak, 2011). The maintenance costs, for example, are
collected in a cost pool and then allocated to departments using their services.
A cost pool of activities is a collection of all costs related with the performance of a specific
business task, such as the production of a specific product (Bragg & Bragg, 2019). By pooling
or by assembling all the expenses or the costs accumulated in a given task, a precise and in-
depth evaluation of all the cost of the given task can be done in a easier way.
P a g e 4 | 19
The traditional method of costing refers to costs incurred by the production overhead
distributed to the products manufactured. In the traditional method the indirect costs incurred in
the factory is allocated to items produced in the factory based on the volume, for example the
number of units of production, the direct labour hours or the machine hours of production, etc.
(Huang, 2018). In our discussions, we will use machine hours. Traditional costing techniques
include standard costing, accountability, marginal costing, etc.
If only machine hours is used for allocating the overhead production to products produced, the
machine hours will only become the overhead production’s primary cause. Earlier this may have
been reasonable or, sufficient for the Company's external financial statement. However, in the
recent years the manufacturing overhead has been driven or caused by a number of other
factors.
COST- POOL
A cost pool is an individual cost grouping, usually by department or service center. Costs are
then allocated from the cost pool (Mastilak, 2011). The maintenance costs, for example, are
collected in a cost pool and then allocated to departments using their services.
A cost pool of activities is a collection of all costs related with the performance of a specific
business task, such as the production of a specific product (Bragg & Bragg, 2019). By pooling
or by assembling all the expenses or the costs accumulated in a given task, a precise and in-
depth evaluation of all the cost of the given task can be done in a easier way.
P a g e 4 | 19
Secure Best Marks with AI Grader
Need help grading? Try our AI Grader for instant feedback on your assignments.

MODERN METHOD OF COSTING
In addition to its traditional techniques, recent developments in cost accounting represent
development in the field of cost accounting. The modern costing techniques include: Pareto
Analysis, ABC (Activity based Costing), Customer Profitability Analysis, Just-In-Time
(JIT), Back Flush Accounting, Target Costing, etc.
ACTIVITY- BASED COSTING
Activity Based Costing system (ABC system) was planned, formed and brought into action so
as to rectify the shortages and insufficiencies of the costing systems used traditional. The ABC
system need to primarily focus on providing a fair and accurate cost apportionment and product
profitability evaluation. Costing based on activities i.e. Activity-Based Costing (ABC) is a
general method for determination of costs of production. ABC defines production as a variety of
activities and allocates costs for each activity. Activity based costing (ABC) allots the cost of
overhead manufacturing to the products in a more reasonable way than the traditional way of
machine-hour apportionment of costs (Bukh, 1997). Activity based costing initially allocates
costs to activities that are the real cause of overhead. The costs of these activities are only then
allocated to products that actually require the activities. Activity-based costing recognizes that
special engineering, special tests, machine installations and others are cost-causing activities —
causing the company to consume its resources (Collins, 1991). The company calculates the cost
of the resources used in each of these activities under ABC.
Activity-based costing has become more importance and exceedingly used in recent years
because (1) costs of overhead productions have increased to a great extent, (2) costs of overhead
production does not correlate with production machine hours or direct labor hours, (3) product
range and customer demand diversity have increased, and (4) some of the products are
manufactured in large quantities, while some of the other products are manufactured in small
quantities (Shim & Siegel, 2000).
The benefits of ABC costs are (Reyhanoglu, 2004):
P a g e 5 | 19
In addition to its traditional techniques, recent developments in cost accounting represent
development in the field of cost accounting. The modern costing techniques include: Pareto
Analysis, ABC (Activity based Costing), Customer Profitability Analysis, Just-In-Time
(JIT), Back Flush Accounting, Target Costing, etc.
ACTIVITY- BASED COSTING
Activity Based Costing system (ABC system) was planned, formed and brought into action so
as to rectify the shortages and insufficiencies of the costing systems used traditional. The ABC
system need to primarily focus on providing a fair and accurate cost apportionment and product
profitability evaluation. Costing based on activities i.e. Activity-Based Costing (ABC) is a
general method for determination of costs of production. ABC defines production as a variety of
activities and allocates costs for each activity. Activity based costing (ABC) allots the cost of
overhead manufacturing to the products in a more reasonable way than the traditional way of
machine-hour apportionment of costs (Bukh, 1997). Activity based costing initially allocates
costs to activities that are the real cause of overhead. The costs of these activities are only then
allocated to products that actually require the activities. Activity-based costing recognizes that
special engineering, special tests, machine installations and others are cost-causing activities —
causing the company to consume its resources (Collins, 1991). The company calculates the cost
of the resources used in each of these activities under ABC.
Activity-based costing has become more importance and exceedingly used in recent years
because (1) costs of overhead productions have increased to a great extent, (2) costs of overhead
production does not correlate with production machine hours or direct labor hours, (3) product
range and customer demand diversity have increased, and (4) some of the products are
manufactured in large quantities, while some of the other products are manufactured in small
quantities (Shim & Siegel, 2000).
The benefits of ABC costs are (Reyhanoglu, 2004):
P a g e 5 | 19

1. Helps to recognise the most profitable customers, profitable products and profitable
channels.
2. Determine the true contributors and financial performance detractors.
3. Cost, profit and requirements of resource associated with changes are predicted
accurately in case the business wants to modify or change its production volumes,
organizational structure and resource costs. Easily identify the main reasons of poor
performance in the financial statements.
4. Tracks costs of activities and work processes
5. Cost intelligence equipment managers to drive improvements
6. Facilitate a better marketing mix
7. Increase customer negotiating power
8. Improved product positioning
TRADITIONAL COSTING METHOD VS. ACTIVITY-BASED
COSTING METHOD
The major dilemma faced by many manufacturers is the choice of costing systems. ABC system
of costing or activity based costing differs from traditional methods of costing. Traditional costs
are product-based and time-consuming. Product-based costs include materials, labor and
overhead, while sales, general costs and administration are included during the period. For each
accounting period, these are charged against revenue (Troxel, 1989). According to some
managers, allotting these costs to manufacturing products can give distorted or inaccurate
estimations, particularly if a factory produces a variety of different products. However,
traditional costs and ABC would generate similar estimates of product costs for a company with
a single product. The factors indicating that ABC costs must be implemented are:
1. On the basis of volume and complexity of manufacturing the line of product differ
prominently
2. There are numerous, diverse product lines requiring different levels of support services;
P a g e 6 | 19
channels.
2. Determine the true contributors and financial performance detractors.
3. Cost, profit and requirements of resource associated with changes are predicted
accurately in case the business wants to modify or change its production volumes,
organizational structure and resource costs. Easily identify the main reasons of poor
performance in the financial statements.
4. Tracks costs of activities and work processes
5. Cost intelligence equipment managers to drive improvements
6. Facilitate a better marketing mix
7. Increase customer negotiating power
8. Improved product positioning
TRADITIONAL COSTING METHOD VS. ACTIVITY-BASED
COSTING METHOD
The major dilemma faced by many manufacturers is the choice of costing systems. ABC system
of costing or activity based costing differs from traditional methods of costing. Traditional costs
are product-based and time-consuming. Product-based costs include materials, labor and
overhead, while sales, general costs and administration are included during the period. For each
accounting period, these are charged against revenue (Troxel, 1989). According to some
managers, allotting these costs to manufacturing products can give distorted or inaccurate
estimations, particularly if a factory produces a variety of different products. However,
traditional costs and ABC would generate similar estimates of product costs for a company with
a single product. The factors indicating that ABC costs must be implemented are:
1. On the basis of volume and complexity of manufacturing the line of product differ
prominently
2. There are numerous, diverse product lines requiring different levels of support services;
P a g e 6 | 19

3. Overhead costs represent a considerable part of total costs;
4. the production process or the amount of products greatly changed– such as, from production
which is labour-intensive to a production which is capital- intensive due to automation;
Activity-based costing is precise and better than traditional costs. The ABC cost method is used
when the overhead of the company is high and there are a large number of different products
(Baines, 1992). Inaccuracy or errors are most unwanted because the competitors set the
competitive rates based on the market. Due to this heavy and rigid competition, a highly reliable
and accurate cost management method is required.
Traditional accounting costs use a single overhead pool and can not calculate the true cost. The
cost of the objects is randomly allocated based on working hours or machine hours, etc. ABC
costs include identifiable parts of products or labor while Traditional costing system
accumulates costs, wages and pays, devaluations, etc. arbitrarily (Mishra & Vaysman, 2001).
Smaller target costs, based on activities, are calculated using the ABC system. The ABC system
is beneficial because it helps to make the decision-making process simple and clarifies and
focuses the management concepts. It also helps to evaluate performance and sets such standards
which will be helpful to the managers to compare their information.
In the Traditional Cost Accounting System, the company determines the cost of production after
the products have been produced whereas in the target or Activity Based Accounting System,
the value or cost of the product is determined on the basis of customer feedback and pocket
range (RUAN & ZHOU, 2017). The ABC system helps the company to determine whether to
lower or raise the activities cost to grab the consumers. The ABC system also helps in keeping
up with the competitors without sacrificing the quality and the quantity of the products.
The advantage of ABC system is that it links the cost of production more directly (Maingi,
2013). This is achieved by eliminating the dissimilarity between product and time-based
costing. In addition, ABC does not allocate unused capacity costs for products. Under method of
traditional costing, a part of the cost of purchase could be allocated to a product regardless of
the actual purchasing activity. ABC would like to evaluate a product’s actual purchasing
activity. Furthermore, unused capacity could also be allocated to a product and its costs could be
distorted.
P a g e 7 | 19
4. the production process or the amount of products greatly changed– such as, from production
which is labour-intensive to a production which is capital- intensive due to automation;
Activity-based costing is precise and better than traditional costs. The ABC cost method is used
when the overhead of the company is high and there are a large number of different products
(Baines, 1992). Inaccuracy or errors are most unwanted because the competitors set the
competitive rates based on the market. Due to this heavy and rigid competition, a highly reliable
and accurate cost management method is required.
Traditional accounting costs use a single overhead pool and can not calculate the true cost. The
cost of the objects is randomly allocated based on working hours or machine hours, etc. ABC
costs include identifiable parts of products or labor while Traditional costing system
accumulates costs, wages and pays, devaluations, etc. arbitrarily (Mishra & Vaysman, 2001).
Smaller target costs, based on activities, are calculated using the ABC system. The ABC system
is beneficial because it helps to make the decision-making process simple and clarifies and
focuses the management concepts. It also helps to evaluate performance and sets such standards
which will be helpful to the managers to compare their information.
In the Traditional Cost Accounting System, the company determines the cost of production after
the products have been produced whereas in the target or Activity Based Accounting System,
the value or cost of the product is determined on the basis of customer feedback and pocket
range (RUAN & ZHOU, 2017). The ABC system helps the company to determine whether to
lower or raise the activities cost to grab the consumers. The ABC system also helps in keeping
up with the competitors without sacrificing the quality and the quantity of the products.
The advantage of ABC system is that it links the cost of production more directly (Maingi,
2013). This is achieved by eliminating the dissimilarity between product and time-based
costing. In addition, ABC does not allocate unused capacity costs for products. Under method of
traditional costing, a part of the cost of purchase could be allocated to a product regardless of
the actual purchasing activity. ABC would like to evaluate a product’s actual purchasing
activity. Furthermore, unused capacity could also be allocated to a product and its costs could be
distorted.
P a g e 7 | 19
Paraphrase This Document
Need a fresh take? Get an instant paraphrase of this document with our AI Paraphraser

P a g e 8 | 19

HOW IS PRODUCTION COST PER UNIT CALCULATED
After calculating the cost of production, the per unit production cost can be calculated. To
calculate the per unit cost of production, the amount is divided by the number of units of
products produced in the given period of time. The sale price must match, if not exceed, the cost
per unit. Only if then sale prices exceed the cost per unit, it will be resulting in profits. If the sale
prices are below the cost per unit, it will result as loss for the business. If the latter takes places
i.e. cost of production per unit exceeds the sale price, meaning the firm incurs a loss in
production, producers may temporarily or permanently terminate production of the products.
P a g e 9 | 19
After calculating the cost of production, the per unit production cost can be calculated. To
calculate the per unit cost of production, the amount is divided by the number of units of
products produced in the given period of time. The sale price must match, if not exceed, the cost
per unit. Only if then sale prices exceed the cost per unit, it will be resulting in profits. If the sale
prices are below the cost per unit, it will result as loss for the business. If the latter takes places
i.e. cost of production per unit exceeds the sale price, meaning the firm incurs a loss in
production, producers may temporarily or permanently terminate production of the products.
P a g e 9 | 19

CASE STUDY ANALYSIS
In the given case study, the company Electrochic have a gradually maturing stage of production
for their product line of Chip Pans. During this time, the company decides to expand its business
and bring two new product lines ―Iron and Robot mixers. Now the irons have a tough
competitive market where as the Robot Mixers have less competition. The competitors for irons
are reducing their prices.
To manufacture Chip Pans 8 components are required. To manufacture Irons 5 components are
required. And Robot mixers are the most complex of all the 3 products and requires the
maximum amount of components.
In a scenario like this, where the competitors are lowering their prices everyday in order to earn
more, there seems to be a worrying issue for Mr. Bigshot, the CEO of Electrochic. He calls for a
meeting to take view points of Mr. Check, the control manager, Mr. Cost Cut, Production
Manager and Mr. Total Sum, the Sales Manager.
During the meeting, a detailed discussion is done on how the rival firms are lowering their
prices so drastically. Also a serious discussion on what the Electrochic should do so as to
overcome losses and make profit.
Here, Mr. Check suggests that the company should split up into various cost pools such as
production, marketing & distribution and administration. Production includes assembling,
finished products and maintenance. And each activity in these pools should be dealt in a way to
makes the situation advantageous for the business. Thus, Mr. Check suggest the proposal 1 to
Mr. Bigshot.
In this proposal 1, the Irons prove to be doing well, the Robot Mixers work excellently but the
Chip Pans make a huge fall. So it is better to concentrate on Robot mixers as per the meeting.
On the other hand, Mr. Total Sum makes a new suggestion. The suggestion is to allocate the
costs of each product according to their operations such as reception and handling of
components, packaging and delivery of products, maintenance, transportation, etc. Since the
P a g e 10 | 19
In the given case study, the company Electrochic have a gradually maturing stage of production
for their product line of Chip Pans. During this time, the company decides to expand its business
and bring two new product lines ―Iron and Robot mixers. Now the irons have a tough
competitive market where as the Robot Mixers have less competition. The competitors for irons
are reducing their prices.
To manufacture Chip Pans 8 components are required. To manufacture Irons 5 components are
required. And Robot mixers are the most complex of all the 3 products and requires the
maximum amount of components.
In a scenario like this, where the competitors are lowering their prices everyday in order to earn
more, there seems to be a worrying issue for Mr. Bigshot, the CEO of Electrochic. He calls for a
meeting to take view points of Mr. Check, the control manager, Mr. Cost Cut, Production
Manager and Mr. Total Sum, the Sales Manager.
During the meeting, a detailed discussion is done on how the rival firms are lowering their
prices so drastically. Also a serious discussion on what the Electrochic should do so as to
overcome losses and make profit.
Here, Mr. Check suggests that the company should split up into various cost pools such as
production, marketing & distribution and administration. Production includes assembling,
finished products and maintenance. And each activity in these pools should be dealt in a way to
makes the situation advantageous for the business. Thus, Mr. Check suggest the proposal 1 to
Mr. Bigshot.
In this proposal 1, the Irons prove to be doing well, the Robot Mixers work excellently but the
Chip Pans make a huge fall. So it is better to concentrate on Robot mixers as per the meeting.
On the other hand, Mr. Total Sum makes a new suggestion. The suggestion is to allocate the
costs of each product according to their operations such as reception and handling of
components, packaging and delivery of products, maintenance, transportation, etc. Since the
P a g e 10 | 19
Secure Best Marks with AI Grader
Need help grading? Try our AI Grader for instant feedback on your assignments.

products are dependent on each of the operations, so each operational cost must be included.
This is the ABC analysis or the Activity-based costing Analysis.
Mr. Total Sum suggests proposal 2 which envolves a detailed analysis of all the fixed costs
involed in the production of each of the 3 products.
COMPARATIVE ANALYSIS OF THE TWO PROPOSALS
The cost price and the marginal units of the three products ― Chip Pans, Irons, and Robot
Mixers have been calculated. An analysis of the calculation is as follows:
There was a production of 10000 chip pans, 20000 irons and 6000 domestic appliances
produced in batches of 2, 6 and 12 respectively on a monthly basis as given in appendix 1.
Selling price per unit of each of the three products were € 50, €55 and €90 and turnover was
€500000, € 1100000 and €540000 respectively for Chip pans, Irons and Robot mixers for a
month. This analysis show that even though the selling price per unit is highest for Robot
mixers, the highest turnover is earned from Iron since the number of units produced is highest
for Iron.
Again, the direct material costs as given in appendix 1 are 16, 8 and 20 and direct labor costs as
calculated by adding the labor hour per unit batch and labor hour per unit finished and
multiplying the sum with labor hour rate are 6.28, 12.60 and 12.80 respectively for the three
products Chip pans, Irons and Robot Mixers. The direct total cost calculated by adding direct
material cost and direct labor cost are € 22.28, €20.60 and €32.80 respectively for Chip Pans,
Irons and Robot Mixers.
The total contributions of for Chip Pans, Irons and Robot Mixers are € 277200, € 688000 and €
343200 respectively. And the contribution per unit is 27.72, 34.40 and 57.20 respectively.
These are the direct costs of production. They do not change even if there is a change in the
indirect costs.
For proposal 1, it is seen that, the maintenance cost of machines have been distributed amongst
production assembling and production finishing. The total indirect cost of Chip Pans is €
P a g e 11 | 19
This is the ABC analysis or the Activity-based costing Analysis.
Mr. Total Sum suggests proposal 2 which envolves a detailed analysis of all the fixed costs
involed in the production of each of the 3 products.
COMPARATIVE ANALYSIS OF THE TWO PROPOSALS
The cost price and the marginal units of the three products ― Chip Pans, Irons, and Robot
Mixers have been calculated. An analysis of the calculation is as follows:
There was a production of 10000 chip pans, 20000 irons and 6000 domestic appliances
produced in batches of 2, 6 and 12 respectively on a monthly basis as given in appendix 1.
Selling price per unit of each of the three products were € 50, €55 and €90 and turnover was
€500000, € 1100000 and €540000 respectively for Chip pans, Irons and Robot mixers for a
month. This analysis show that even though the selling price per unit is highest for Robot
mixers, the highest turnover is earned from Iron since the number of units produced is highest
for Iron.
Again, the direct material costs as given in appendix 1 are 16, 8 and 20 and direct labor costs as
calculated by adding the labor hour per unit batch and labor hour per unit finished and
multiplying the sum with labor hour rate are 6.28, 12.60 and 12.80 respectively for the three
products Chip pans, Irons and Robot Mixers. The direct total cost calculated by adding direct
material cost and direct labor cost are € 22.28, €20.60 and €32.80 respectively for Chip Pans,
Irons and Robot Mixers.
The total contributions of for Chip Pans, Irons and Robot Mixers are € 277200, € 688000 and €
343200 respectively. And the contribution per unit is 27.72, 34.40 and 57.20 respectively.
These are the direct costs of production. They do not change even if there is a change in the
indirect costs.
For proposal 1, it is seen that, the maintenance cost of machines have been distributed amongst
production assembling and production finishing. The total indirect cost of Chip Pans is €
P a g e 11 | 19

304765.06, the total indirect cost of Irons is € 345230.77 and the total indirect cost of Robot
Mixers is € 329004.17.
The total indirect cost per unit is 30.48 for Chip Pans, 17.26 for Irons and 54.83 for Robot
mixers.
Whereas, for proposal 2, the total indirect cost of chip Pans is € 236159.42, the total indirect
cost of € 272318.97 and total indirect cost of Robot Mixers is € 470521.61.
Per unit total indirect cost of proposal 2 is 23.62 for Chip pans, 13.62 for Irons and 78.42 for
Robot mixers.
The profits for each proposal is calculated by subtracting the total indirect cost from
contribution.
The total profits (loses) found out for proposal 1 are € 27565.06 (loss) for Chip pans, €
342769.23 for Irons, and € 14195.83 for Robot Mixers. And the total profits (loses) calculated
for proposal 2 are € 41040.58, € 415681.03 and € 127321.61 (loss) for Chip Pans, Irons and
Robot Mixers respectively.
The profit per unit is calculated by subtracting the total indirect cost per unit from the
contribution per unit.
The Chip Pans have a loss per unit of € 2.76 in proposal 1 and a gain of €4.10 in proposal 2. The
Irons have a gain of € 17.14 in proposal 1 and a gain of €20.78 in proposal 2. And the Robot
mixers have a gain of € 2.37 in proposal 1 but a loss of € 21.22 in proposal 2.
Now by comparing the total profits of the two proposals, it can be seen that, for the first product
i.e. Chip Pans there is a loss of € 27565.06 if proposal 1 is taken into consideration whereas
there is a huge gain of € 41040.58 if proposal 2 is chosen. Similarly, a loss of 2.76 per unit is
going to incur in proposal 1 and a gain of 4.10 per unit if proposal 2 is chosen. Thus, proposal 2
is far better than proposal 1 since it gives a profit to the company Electrochic and proposal 2
gives a loss. For the second product i.e. for Iron, proposal 1 makes a profit of € 342769.23 and
proposal 2 makes a profit of € 415681.03. Similarly, if per unit profit or loss is considered then
proposal 2 makes more profit than proposal 1. Therefore again, proposal 2 is a better option to
choose since it makes more profit for the company Electrochic. Lastly, for the product Robot
P a g e 12 | 19
Mixers is € 329004.17.
The total indirect cost per unit is 30.48 for Chip Pans, 17.26 for Irons and 54.83 for Robot
mixers.
Whereas, for proposal 2, the total indirect cost of chip Pans is € 236159.42, the total indirect
cost of € 272318.97 and total indirect cost of Robot Mixers is € 470521.61.
Per unit total indirect cost of proposal 2 is 23.62 for Chip pans, 13.62 for Irons and 78.42 for
Robot mixers.
The profits for each proposal is calculated by subtracting the total indirect cost from
contribution.
The total profits (loses) found out for proposal 1 are € 27565.06 (loss) for Chip pans, €
342769.23 for Irons, and € 14195.83 for Robot Mixers. And the total profits (loses) calculated
for proposal 2 are € 41040.58, € 415681.03 and € 127321.61 (loss) for Chip Pans, Irons and
Robot Mixers respectively.
The profit per unit is calculated by subtracting the total indirect cost per unit from the
contribution per unit.
The Chip Pans have a loss per unit of € 2.76 in proposal 1 and a gain of €4.10 in proposal 2. The
Irons have a gain of € 17.14 in proposal 1 and a gain of €20.78 in proposal 2. And the Robot
mixers have a gain of € 2.37 in proposal 1 but a loss of € 21.22 in proposal 2.
Now by comparing the total profits of the two proposals, it can be seen that, for the first product
i.e. Chip Pans there is a loss of € 27565.06 if proposal 1 is taken into consideration whereas
there is a huge gain of € 41040.58 if proposal 2 is chosen. Similarly, a loss of 2.76 per unit is
going to incur in proposal 1 and a gain of 4.10 per unit if proposal 2 is chosen. Thus, proposal 2
is far better than proposal 1 since it gives a profit to the company Electrochic and proposal 2
gives a loss. For the second product i.e. for Iron, proposal 1 makes a profit of € 342769.23 and
proposal 2 makes a profit of € 415681.03. Similarly, if per unit profit or loss is considered then
proposal 2 makes more profit than proposal 1. Therefore again, proposal 2 is a better option to
choose since it makes more profit for the company Electrochic. Lastly, for the product Robot
P a g e 12 | 19

Mixers, proposal 1 makes a profit of € 14195.83 and proposal 2 makes a loss of € 127321.61.
Similarly again, per unit profit is earned in proposal 1 and a per unit loss in proposal 2. Thus, in
case of Robot Mixers it is seen that proposal 1 is a better option than proposal 2 since proposal 2
makes a huge loss for the business.
CONCLUDING THE ANALYSIS
This analysis show that both the methods have very different findings. The finding of proposal 1
do not match with the finding of proposal 2. We know that the contribution is same for both the
proposals. The change takes place in the fixed cost or the indirect cost.
In the given analysis we can see that proposal 1 only considers 3 heads― production, Sale and
Administration while analysing its profit whereas proposal 2 divides its analysis into many
heads such as―contact the supplier, handle components, plan and control, assemble, finish,
packaging, transport, organise promotion, service follow-up, etc. proposal 2 is Activity Based
Analysis or ABC analysis. This ABC analysis is a more in-depth analysis and it is more
appropriate to follow this analysis for any business. It shows a more detailed evaluation of all its
expenses.
To explain, we can see that as per proposal 1, Robot Mixers make the higher profit of € 2.37 per
unit compared to chip pans which make a loss of € 2.76 per unit. But at the same time, if we
compare this to proposal 2, we will find that, robot mixers incurs much higher expenses in items
like handle components, transport and customer service follow-up which should make the
expenses of Robot mixers rise. But this do not happen in proposal 1 because proposal 1 do not
consider these expenses. Thus, it is legal and eligible to say that proposal 1 is far behind the
actual scenario of expenses and profit. For this reason, proposal 2 is more appropriate compared
to proposal one. In proposal 2, robot mixers make a loss while chip pans make profit for the
business.
Again, we know that the labour rate per hour is equal for all the 3 products. Therefore, it is
practical to consider that same quality labours is employed for each department and each
product. Now considering proposal 2, it is evident that due to a higher rate of indirect expenses
the product is making losses. Thus it is more intelligent to stop the production line of Robot
Mixers and invest the time and labour for the production of a more profitable product i.e. Iron.
P a g e 13 | 19
Similarly again, per unit profit is earned in proposal 1 and a per unit loss in proposal 2. Thus, in
case of Robot Mixers it is seen that proposal 1 is a better option than proposal 2 since proposal 2
makes a huge loss for the business.
CONCLUDING THE ANALYSIS
This analysis show that both the methods have very different findings. The finding of proposal 1
do not match with the finding of proposal 2. We know that the contribution is same for both the
proposals. The change takes place in the fixed cost or the indirect cost.
In the given analysis we can see that proposal 1 only considers 3 heads― production, Sale and
Administration while analysing its profit whereas proposal 2 divides its analysis into many
heads such as―contact the supplier, handle components, plan and control, assemble, finish,
packaging, transport, organise promotion, service follow-up, etc. proposal 2 is Activity Based
Analysis or ABC analysis. This ABC analysis is a more in-depth analysis and it is more
appropriate to follow this analysis for any business. It shows a more detailed evaluation of all its
expenses.
To explain, we can see that as per proposal 1, Robot Mixers make the higher profit of € 2.37 per
unit compared to chip pans which make a loss of € 2.76 per unit. But at the same time, if we
compare this to proposal 2, we will find that, robot mixers incurs much higher expenses in items
like handle components, transport and customer service follow-up which should make the
expenses of Robot mixers rise. But this do not happen in proposal 1 because proposal 1 do not
consider these expenses. Thus, it is legal and eligible to say that proposal 1 is far behind the
actual scenario of expenses and profit. For this reason, proposal 2 is more appropriate compared
to proposal one. In proposal 2, robot mixers make a loss while chip pans make profit for the
business.
Again, we know that the labour rate per hour is equal for all the 3 products. Therefore, it is
practical to consider that same quality labours is employed for each department and each
product. Now considering proposal 2, it is evident that due to a higher rate of indirect expenses
the product is making losses. Thus it is more intelligent to stop the production line of Robot
Mixers and invest the time and labour for the production of a more profitable product i.e. Iron.
P a g e 13 | 19
Paraphrase This Document
Need a fresh take? Get an instant paraphrase of this document with our AI Paraphraser
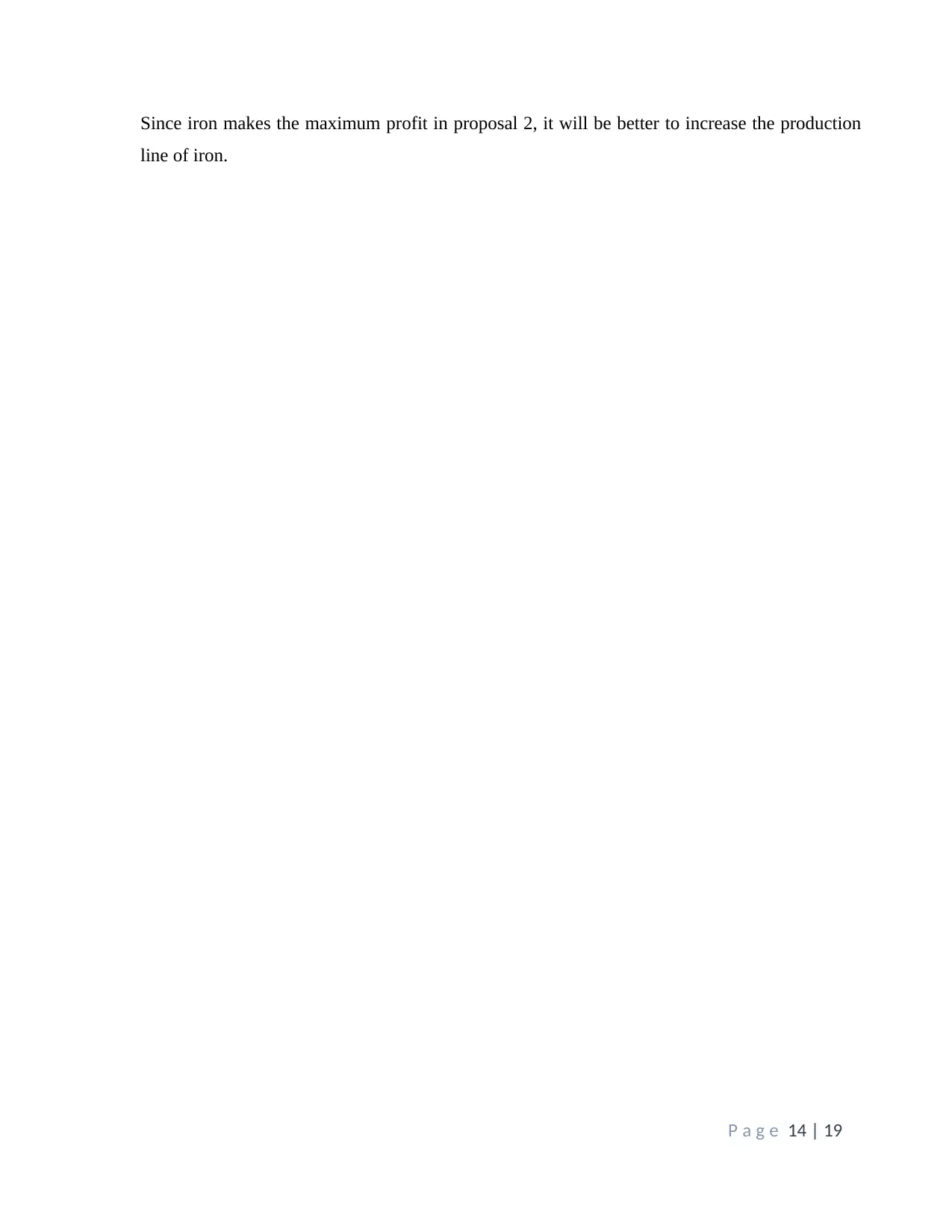
Since iron makes the maximum profit in proposal 2, it will be better to increase the production
line of iron.
P a g e 14 | 19
line of iron.
P a g e 14 | 19

ADVANTAGES AND DISADVANTAGES OF PROPOSAL 1
The proposal 1 is based on the traditional cost accounting system. This method is based on cost
driving activities. The advantages and disadvantages of proposal 1 is as follows:
Advantages
1. Proposal 1 is a very simple method. It does not include an in-depth calculation.
Therefore, it is very simple and easier to understand for any one.
2. It does not have any complicated calculations to determine the average overhead rate.
Thus, it is a cheaper approach. It has very few calculations to do.
Disadvantages
1. Since, Proposal 1 uses very limited segregation and thus the accuracy is not high. It does
not consider the actual expenses that occur. Any expenses that is not anticipated earlier
is not considered in this approach .
2. Many indirect cost occurring under this system is not considered. It is a very limited
approach.
3. Proposal 1 is a way too simple method which does not satisfy the requirements of a
business.
4. This proposal does not consider any of the non- manufacturing expenses.
5.
P a g e 15 | 19
The proposal 1 is based on the traditional cost accounting system. This method is based on cost
driving activities. The advantages and disadvantages of proposal 1 is as follows:
Advantages
1. Proposal 1 is a very simple method. It does not include an in-depth calculation.
Therefore, it is very simple and easier to understand for any one.
2. It does not have any complicated calculations to determine the average overhead rate.
Thus, it is a cheaper approach. It has very few calculations to do.
Disadvantages
1. Since, Proposal 1 uses very limited segregation and thus the accuracy is not high. It does
not consider the actual expenses that occur. Any expenses that is not anticipated earlier
is not considered in this approach .
2. Many indirect cost occurring under this system is not considered. It is a very limited
approach.
3. Proposal 1 is a way too simple method which does not satisfy the requirements of a
business.
4. This proposal does not consider any of the non- manufacturing expenses.
5.
P a g e 15 | 19

ADVANTAGES AND DISADVANTAGES OF PROPOSAL 2
Proposal 2 is a more segregated approach towards the calculation of profit. This method is
known as the ACTIVITY- BASED COSTING (ABC). The advantages and disadvantages of
using proposal 2 is as follows:
Advantages
1. In this proposal, a more detailed segregation has been done of all the indirect expenses
of the business. It is a more transparent method of calculating (Editor, 2019).
2. In proposal 2, all the accounting for the cost are done in accordance to production. Thus,
it helps to identify all the costs and expenses in a better way
3. This is a more accurate method. The Electrochic company will have a more accurate
knowledge of where they are heading with proposal 2 unlike proposal 1.
4. Proposal 2 is better for Electrochic since it produces more than one kind of products.
The costing will be more accurate with the help of ABC costing
Disadvantages
1. Since proposal 2 uses ABC costing which is a more detailed analysis, the method is
quite complicated and difficult.
2. Proposal 2 is also a costly method compared to proposal 1 since it requires a complete
breakdown of each individual components
3. The data interpretation in proposal 2 differs from the data interpretation of proposal 1.
4.
P a g e 16 | 19
Proposal 2 is a more segregated approach towards the calculation of profit. This method is
known as the ACTIVITY- BASED COSTING (ABC). The advantages and disadvantages of
using proposal 2 is as follows:
Advantages
1. In this proposal, a more detailed segregation has been done of all the indirect expenses
of the business. It is a more transparent method of calculating (Editor, 2019).
2. In proposal 2, all the accounting for the cost are done in accordance to production. Thus,
it helps to identify all the costs and expenses in a better way
3. This is a more accurate method. The Electrochic company will have a more accurate
knowledge of where they are heading with proposal 2 unlike proposal 1.
4. Proposal 2 is better for Electrochic since it produces more than one kind of products.
The costing will be more accurate with the help of ABC costing
Disadvantages
1. Since proposal 2 uses ABC costing which is a more detailed analysis, the method is
quite complicated and difficult.
2. Proposal 2 is also a costly method compared to proposal 1 since it requires a complete
breakdown of each individual components
3. The data interpretation in proposal 2 differs from the data interpretation of proposal 1.
4.
P a g e 16 | 19
Secure Best Marks with AI Grader
Need help grading? Try our AI Grader for instant feedback on your assignments.

CONCLUSION
After the detailed analysis of proposal 1 and proposal 2, it is clear both the methods have certain
advantages and certain flaws. The proposal 2 is a more accurate method to use in place where
there is more than one kind of product being manufactured (Editor, 2019). This is because in
these cases the calculation is not simple and accuracy is a very crucial part of the calculation.
Proposal 2 does and in-depth analysis considering each activity. In proposal 1, very limited
components of production is taken into consideration. Therefore, accuracy may or may not be
present. Yet, proposal 1 will take a much lesser time compared to proposal 2. Even though ABC
costing is costly yet it will provide better information. In the long run ABC costing i.e. proposal
2 will help the business to make profit and do better than its competitor firms.
Finally, Electrochic Company should go for proposal 2 since the calculations are more
appropriate and accurate. This proposal will help the business earn higher profits in the long run.
P a g e 17 | 19
After the detailed analysis of proposal 1 and proposal 2, it is clear both the methods have certain
advantages and certain flaws. The proposal 2 is a more accurate method to use in place where
there is more than one kind of product being manufactured (Editor, 2019). This is because in
these cases the calculation is not simple and accuracy is a very crucial part of the calculation.
Proposal 2 does and in-depth analysis considering each activity. In proposal 1, very limited
components of production is taken into consideration. Therefore, accuracy may or may not be
present. Yet, proposal 1 will take a much lesser time compared to proposal 2. Even though ABC
costing is costly yet it will provide better information. In the long run ABC costing i.e. proposal
2 will help the business to make profit and do better than its competitor firms.
Finally, Electrochic Company should go for proposal 2 since the calculations are more
appropriate and accurate. This proposal will help the business earn higher profits in the long run.
P a g e 17 | 19

REFERENCES
Andrade, M., Pessanha Filho, R., Espozel, A., Maia, L., & Qassim, R. (1999). Activity-based
costing for production learning. International Journal Of Production Economics, 62(3),
175-180. doi: 10.1016/s0925-5273(97)00136-9
Baines, A. (1992). Activity‐based costing. Work Study, 41(2), 12-13. doi:
10.1108/eum0000000002664
Bragg, S., & Bragg, S. (2019). Cost pool. Retrieved from
https://www.accountingtools.com/articles/2017/5/4/cost-pool
Bukh, P. (1997). Activity based costing. Aarhus: Department of Management, University of
Aarhus.
Collins, F. (1991). Implementing activity based costing. New York, N.Y.: Executive Enterprises
Publications.
Editor, C. (2019). 8 Pros and Cons of Activity Based Costing | Green Garage. Retrieved from
https://greengarageblog.org/8-pros-and-cons-of-activity-based-costing
Huang, Q. (2018). Skylar, Inc.: Traditional Cost System vs. Activity-Based Cost System – A
Managerial Accounting Case Study. Applied Finance And Accounting, 4(2), 55. doi:
10.11114/afa.v4i2.3496
HUNDAL, M. (1997). Product Costing: A Comparison of Conventional and Activity-based
Costing Methods. Journal Of Engineering Design, 8(1), 91-103. doi:
10.1080/09544829708907954
Maingi, J. (2013). Advantages & disadvantages of activity based costing with reference to.
[Place of publication not identified]: Grin Verlag.
Mastilak, M. (2011). Cost Pool Classification and Judgment Performance. The Accounting
Review, 86(5), 1709-1729. doi: 10.2308/accr-10103
P a g e 18 | 19
Andrade, M., Pessanha Filho, R., Espozel, A., Maia, L., & Qassim, R. (1999). Activity-based
costing for production learning. International Journal Of Production Economics, 62(3),
175-180. doi: 10.1016/s0925-5273(97)00136-9
Baines, A. (1992). Activity‐based costing. Work Study, 41(2), 12-13. doi:
10.1108/eum0000000002664
Bragg, S., & Bragg, S. (2019). Cost pool. Retrieved from
https://www.accountingtools.com/articles/2017/5/4/cost-pool
Bukh, P. (1997). Activity based costing. Aarhus: Department of Management, University of
Aarhus.
Collins, F. (1991). Implementing activity based costing. New York, N.Y.: Executive Enterprises
Publications.
Editor, C. (2019). 8 Pros and Cons of Activity Based Costing | Green Garage. Retrieved from
https://greengarageblog.org/8-pros-and-cons-of-activity-based-costing
Huang, Q. (2018). Skylar, Inc.: Traditional Cost System vs. Activity-Based Cost System – A
Managerial Accounting Case Study. Applied Finance And Accounting, 4(2), 55. doi:
10.11114/afa.v4i2.3496
HUNDAL, M. (1997). Product Costing: A Comparison of Conventional and Activity-based
Costing Methods. Journal Of Engineering Design, 8(1), 91-103. doi:
10.1080/09544829708907954
Maingi, J. (2013). Advantages & disadvantages of activity based costing with reference to.
[Place of publication not identified]: Grin Verlag.
Mastilak, M. (2011). Cost Pool Classification and Judgment Performance. The Accounting
Review, 86(5), 1709-1729. doi: 10.2308/accr-10103
P a g e 18 | 19

Mishra, B., & Vaysman, I. (2001). Cost-System Choice and Incentives-Traditional vs. Activity-
Based Costing. Journal Of Accounting Research, 39(3), 619-641. doi: 10.1111/1475-
679x.00031
Page, D. (2000). Activity-Based Costing (ABC) in Operations Management. Dearborn: Society
of Manufacturing Engineers.
Reyhanoglu, M. (2004). Activity-Based Costing System Advantages and Disadvantages. SSRN
Electronic Journal. doi: 10.2139/ssrn.644561
RUAN, Y., & ZHOU, L. (2017). The Research on Management Accounting Tools—Based on
the Comparison Between Activity-based Costing and Traditional Costing. Destech
Transactions On Engineering And Technology Research, (amsm). doi:
10.12783/dtetr/amsm2017/14848
Shim, J., & Siegel, J. (2000). Modern cost management & analysis. Hauppauge, N.Y.: Barron's
Educational Series.
Troxel, R. (1989). Activity based costing. Dearborn, Mich.: Society of Manufacturing
Engineers.
P a g e 19 | 19
Based Costing. Journal Of Accounting Research, 39(3), 619-641. doi: 10.1111/1475-
679x.00031
Page, D. (2000). Activity-Based Costing (ABC) in Operations Management. Dearborn: Society
of Manufacturing Engineers.
Reyhanoglu, M. (2004). Activity-Based Costing System Advantages and Disadvantages. SSRN
Electronic Journal. doi: 10.2139/ssrn.644561
RUAN, Y., & ZHOU, L. (2017). The Research on Management Accounting Tools—Based on
the Comparison Between Activity-based Costing and Traditional Costing. Destech
Transactions On Engineering And Technology Research, (amsm). doi:
10.12783/dtetr/amsm2017/14848
Shim, J., & Siegel, J. (2000). Modern cost management & analysis. Hauppauge, N.Y.: Barron's
Educational Series.
Troxel, R. (1989). Activity based costing. Dearborn, Mich.: Society of Manufacturing
Engineers.
P a g e 19 | 19
1 out of 19
Related Documents

Your All-in-One AI-Powered Toolkit for Academic Success.
+13062052269
info@desklib.com
Available 24*7 on WhatsApp / Email
Unlock your academic potential
© 2024 | Zucol Services PVT LTD | All rights reserved.