Analysis of Energy Systems in Industrial Cheese Manufacturing
VerifiedAdded on 2023/04/22
|15
|2978
|360
Report
AI Summary
This report offers a comprehensive analysis of energy systems within the cheese manufacturing industry. It begins with an abstract and introduction that outlines the scope and importance of industrial energy management. The core of the report examines five key energy-intensive processes: heat treatment and bacteria reduction, microfiltration, pre-stirring, heating and scalding, and final stirring, detailing their energy requirements. Sankey diagrams are utilized to visually represent energy flows, conversions, and losses within a cheese production facility. The report then explores the potential of renewable energy technologies, such as solar and geothermal energy, and discusses methods for reducing energy costs through bioenergy utilization and industrial heat recovery. Detailed appendices provide supporting data and calculations. The report emphasizes the need for effective energy management to optimize production costs and minimize environmental impact, presenting a practical overview of energy efficiency in the cheese manufacturing process.
Contribute Materials
Your contribution can guide someone’s learning journey. Share your
documents today.
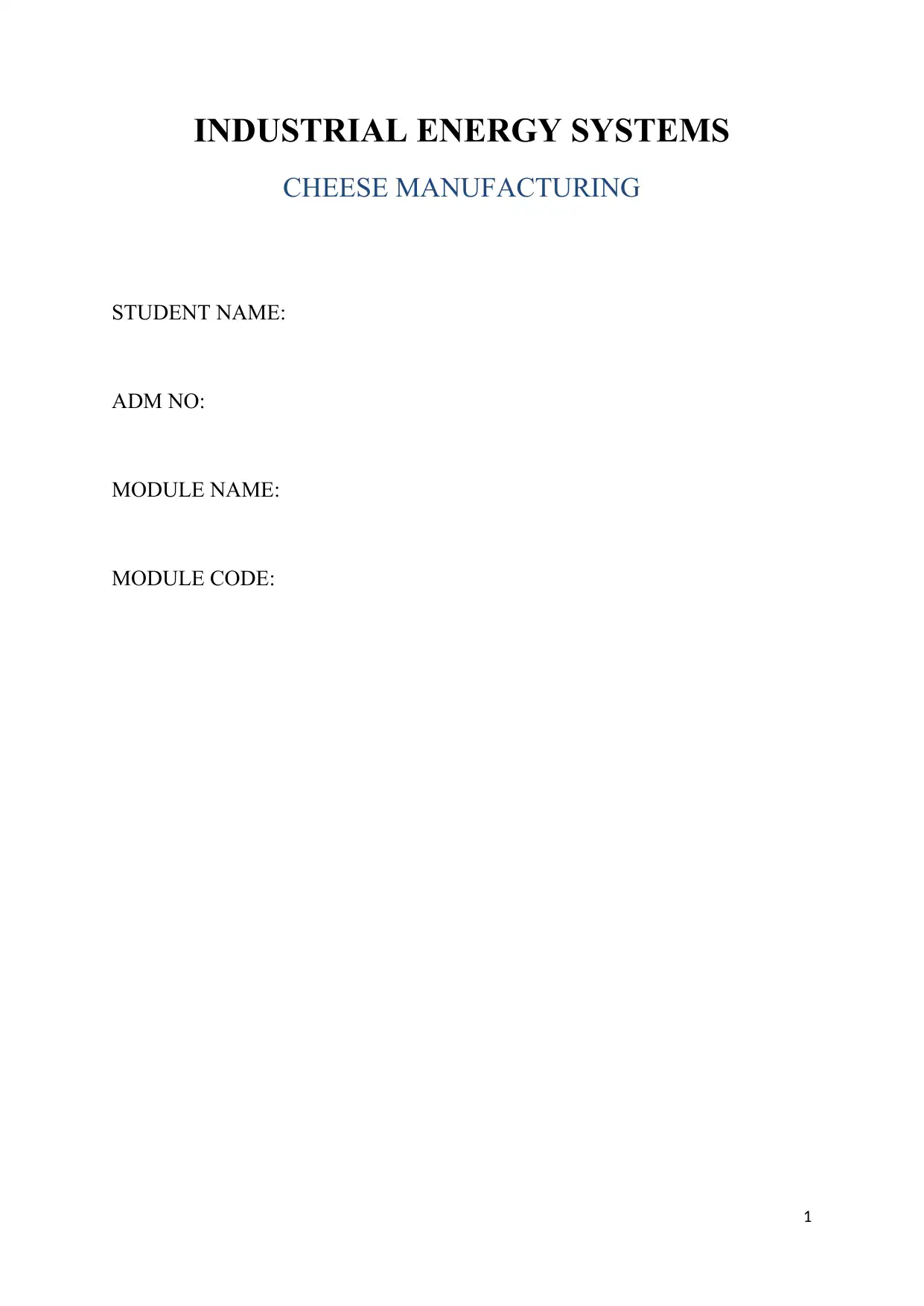
INDUSTRIAL ENERGY SYSTEMS
CHEESE MANUFACTURING
STUDENT NAME:
ADM NO:
MODULE NAME:
MODULE CODE:
1
CHEESE MANUFACTURING
STUDENT NAME:
ADM NO:
MODULE NAME:
MODULE CODE:
1
Secure Best Marks with AI Grader
Need help grading? Try our AI Grader for instant feedback on your assignments.
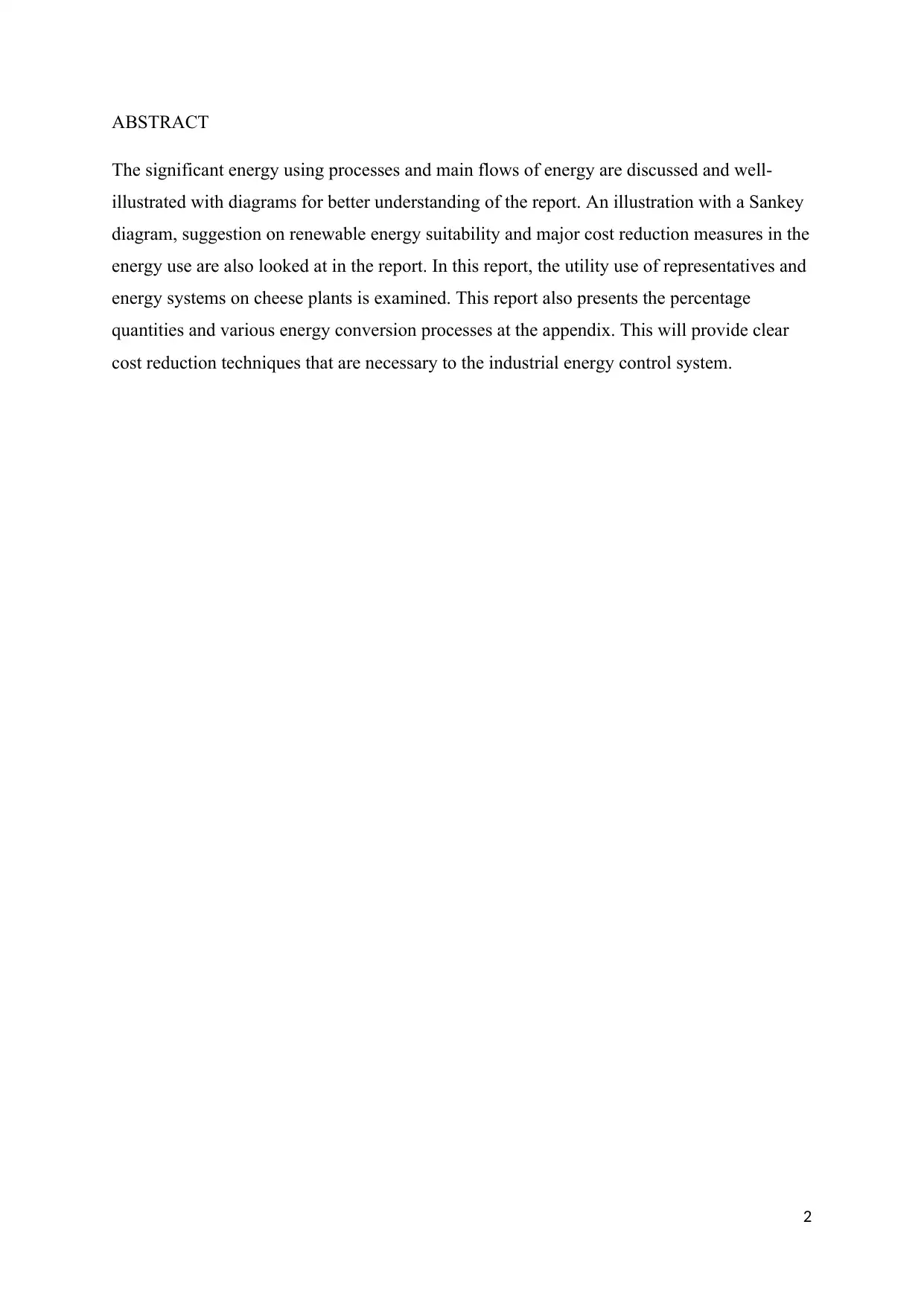
ABSTRACT
The significant energy using processes and main flows of energy are discussed and well-
illustrated with diagrams for better understanding of the report. An illustration with a Sankey
diagram, suggestion on renewable energy suitability and major cost reduction measures in the
energy use are also looked at in the report. In this report, the utility use of representatives and
energy systems on cheese plants is examined. This report also presents the percentage
quantities and various energy conversion processes at the appendix. This will provide clear
cost reduction techniques that are necessary to the industrial energy control system.
2
The significant energy using processes and main flows of energy are discussed and well-
illustrated with diagrams for better understanding of the report. An illustration with a Sankey
diagram, suggestion on renewable energy suitability and major cost reduction measures in the
energy use are also looked at in the report. In this report, the utility use of representatives and
energy systems on cheese plants is examined. This report also presents the percentage
quantities and various energy conversion processes at the appendix. This will provide clear
cost reduction techniques that are necessary to the industrial energy control system.
2
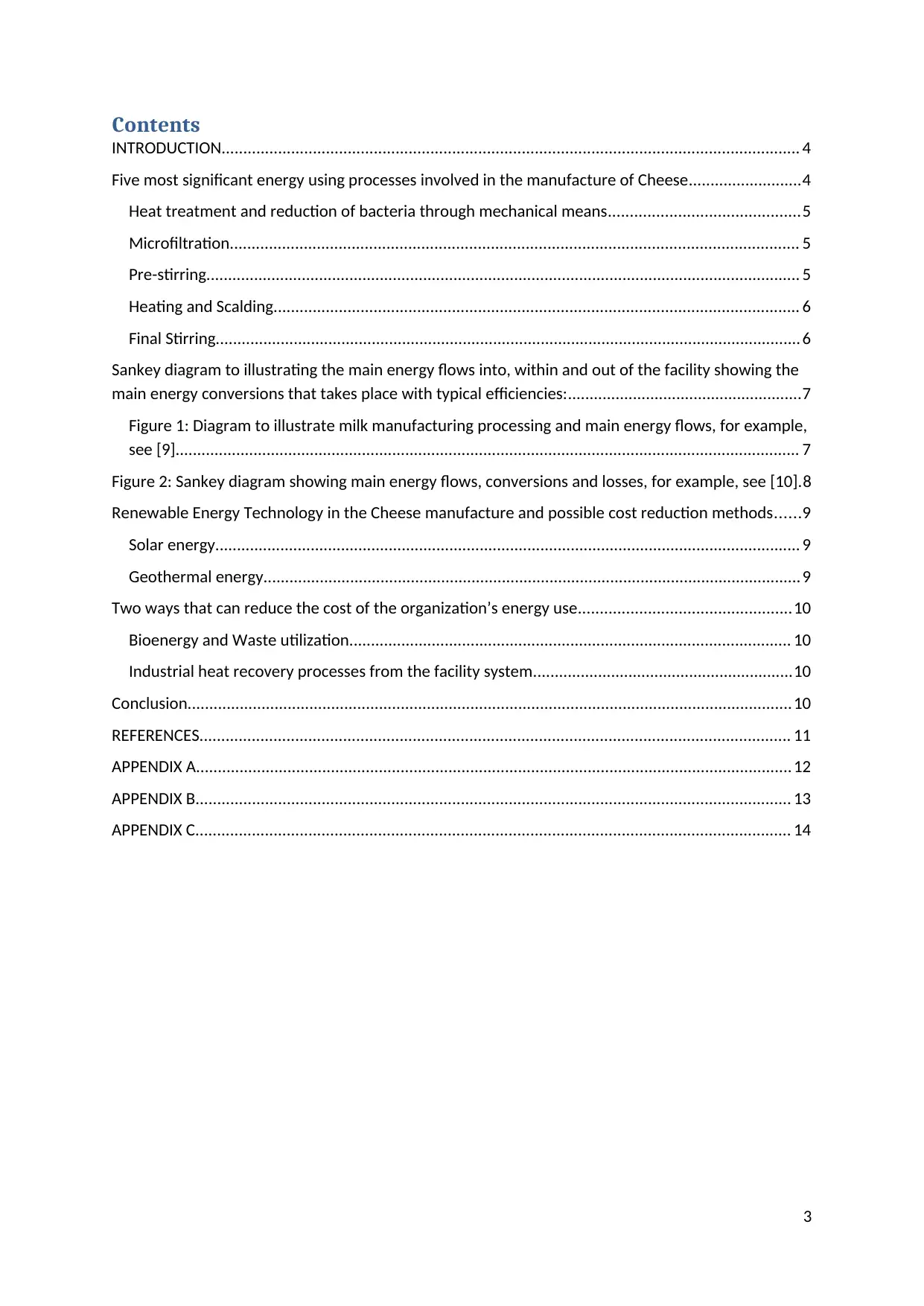
Contents
INTRODUCTION..................................................................................................................................... 4
Five most significant energy using processes involved in the manufacture of Cheese..........................4
Heat treatment and reduction of bacteria through mechanical means............................................5
Microfiltration................................................................................................................................... 5
Pre-stirring......................................................................................................................................... 5
Heating and Scalding......................................................................................................................... 6
Final Stirring....................................................................................................................................... 6
Sankey diagram to illustrating the main energy flows into, within and out of the facility showing the
main energy conversions that takes place with typical efficiencies:......................................................7
Figure 1: Diagram to illustrate milk manufacturing processing and main energy flows, for example,
see [9]................................................................................................................................................ 7
Figure 2: Sankey diagram showing main energy flows, conversions and losses, for example, see [10].8
Renewable Energy Technology in the Cheese manufacture and possible cost reduction methods......9
Solar energy....................................................................................................................................... 9
Geothermal energy............................................................................................................................9
Two ways that can reduce the cost of the organization’s energy use.................................................10
Bioenergy and Waste utilization...................................................................................................... 10
Industrial heat recovery processes from the facility system............................................................10
Conclusion...........................................................................................................................................10
REFERENCES........................................................................................................................................ 11
APPENDIX A......................................................................................................................................... 12
APPENDIX B......................................................................................................................................... 13
APPENDIX C......................................................................................................................................... 14
3
INTRODUCTION..................................................................................................................................... 4
Five most significant energy using processes involved in the manufacture of Cheese..........................4
Heat treatment and reduction of bacteria through mechanical means............................................5
Microfiltration................................................................................................................................... 5
Pre-stirring......................................................................................................................................... 5
Heating and Scalding......................................................................................................................... 6
Final Stirring....................................................................................................................................... 6
Sankey diagram to illustrating the main energy flows into, within and out of the facility showing the
main energy conversions that takes place with typical efficiencies:......................................................7
Figure 1: Diagram to illustrate milk manufacturing processing and main energy flows, for example,
see [9]................................................................................................................................................ 7
Figure 2: Sankey diagram showing main energy flows, conversions and losses, for example, see [10].8
Renewable Energy Technology in the Cheese manufacture and possible cost reduction methods......9
Solar energy....................................................................................................................................... 9
Geothermal energy............................................................................................................................9
Two ways that can reduce the cost of the organization’s energy use.................................................10
Bioenergy and Waste utilization...................................................................................................... 10
Industrial heat recovery processes from the facility system............................................................10
Conclusion...........................................................................................................................................10
REFERENCES........................................................................................................................................ 11
APPENDIX A......................................................................................................................................... 12
APPENDIX B......................................................................................................................................... 13
APPENDIX C......................................................................................................................................... 14
3
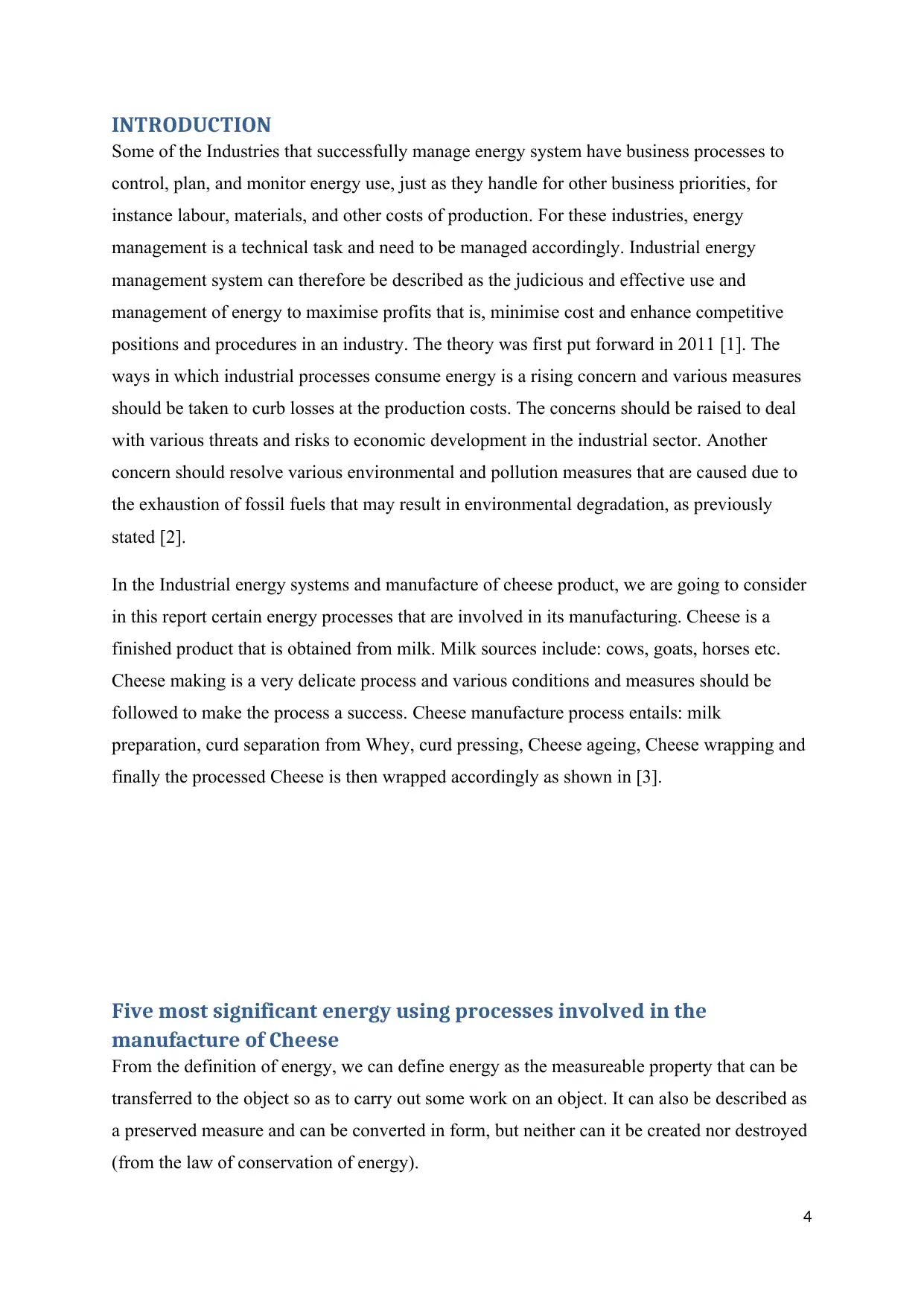
INTRODUCTION
Some of the Industries that successfully manage energy system have business processes to
control, plan, and monitor energy use, just as they handle for other business priorities, for
instance labour, materials, and other costs of production. For these industries, energy
management is a technical task and need to be managed accordingly. Industrial energy
management system can therefore be described as the judicious and effective use and
management of energy to maximise profits that is, minimise cost and enhance competitive
positions and procedures in an industry. The theory was first put forward in 2011 [1]. The
ways in which industrial processes consume energy is a rising concern and various measures
should be taken to curb losses at the production costs. The concerns should be raised to deal
with various threats and risks to economic development in the industrial sector. Another
concern should resolve various environmental and pollution measures that are caused due to
the exhaustion of fossil fuels that may result in environmental degradation, as previously
stated [2].
In the Industrial energy systems and manufacture of cheese product, we are going to consider
in this report certain energy processes that are involved in its manufacturing. Cheese is a
finished product that is obtained from milk. Milk sources include: cows, goats, horses etc.
Cheese making is a very delicate process and various conditions and measures should be
followed to make the process a success. Cheese manufacture process entails: milk
preparation, curd separation from Whey, curd pressing, Cheese ageing, Cheese wrapping and
finally the processed Cheese is then wrapped accordingly as shown in [3].
Five most significant energy using processes involved in the
manufacture of Cheese
From the definition of energy, we can define energy as the measureable property that can be
transferred to the object so as to carry out some work on an object. It can also be described as
a preserved measure and can be converted in form, but neither can it be created nor destroyed
(from the law of conservation of energy).
4
Some of the Industries that successfully manage energy system have business processes to
control, plan, and monitor energy use, just as they handle for other business priorities, for
instance labour, materials, and other costs of production. For these industries, energy
management is a technical task and need to be managed accordingly. Industrial energy
management system can therefore be described as the judicious and effective use and
management of energy to maximise profits that is, minimise cost and enhance competitive
positions and procedures in an industry. The theory was first put forward in 2011 [1]. The
ways in which industrial processes consume energy is a rising concern and various measures
should be taken to curb losses at the production costs. The concerns should be raised to deal
with various threats and risks to economic development in the industrial sector. Another
concern should resolve various environmental and pollution measures that are caused due to
the exhaustion of fossil fuels that may result in environmental degradation, as previously
stated [2].
In the Industrial energy systems and manufacture of cheese product, we are going to consider
in this report certain energy processes that are involved in its manufacturing. Cheese is a
finished product that is obtained from milk. Milk sources include: cows, goats, horses etc.
Cheese making is a very delicate process and various conditions and measures should be
followed to make the process a success. Cheese manufacture process entails: milk
preparation, curd separation from Whey, curd pressing, Cheese ageing, Cheese wrapping and
finally the processed Cheese is then wrapped accordingly as shown in [3].
Five most significant energy using processes involved in the
manufacture of Cheese
From the definition of energy, we can define energy as the measureable property that can be
transferred to the object so as to carry out some work on an object. It can also be described as
a preserved measure and can be converted in form, but neither can it be created nor destroyed
(from the law of conservation of energy).
4
Secure Best Marks with AI Grader
Need help grading? Try our AI Grader for instant feedback on your assignments.
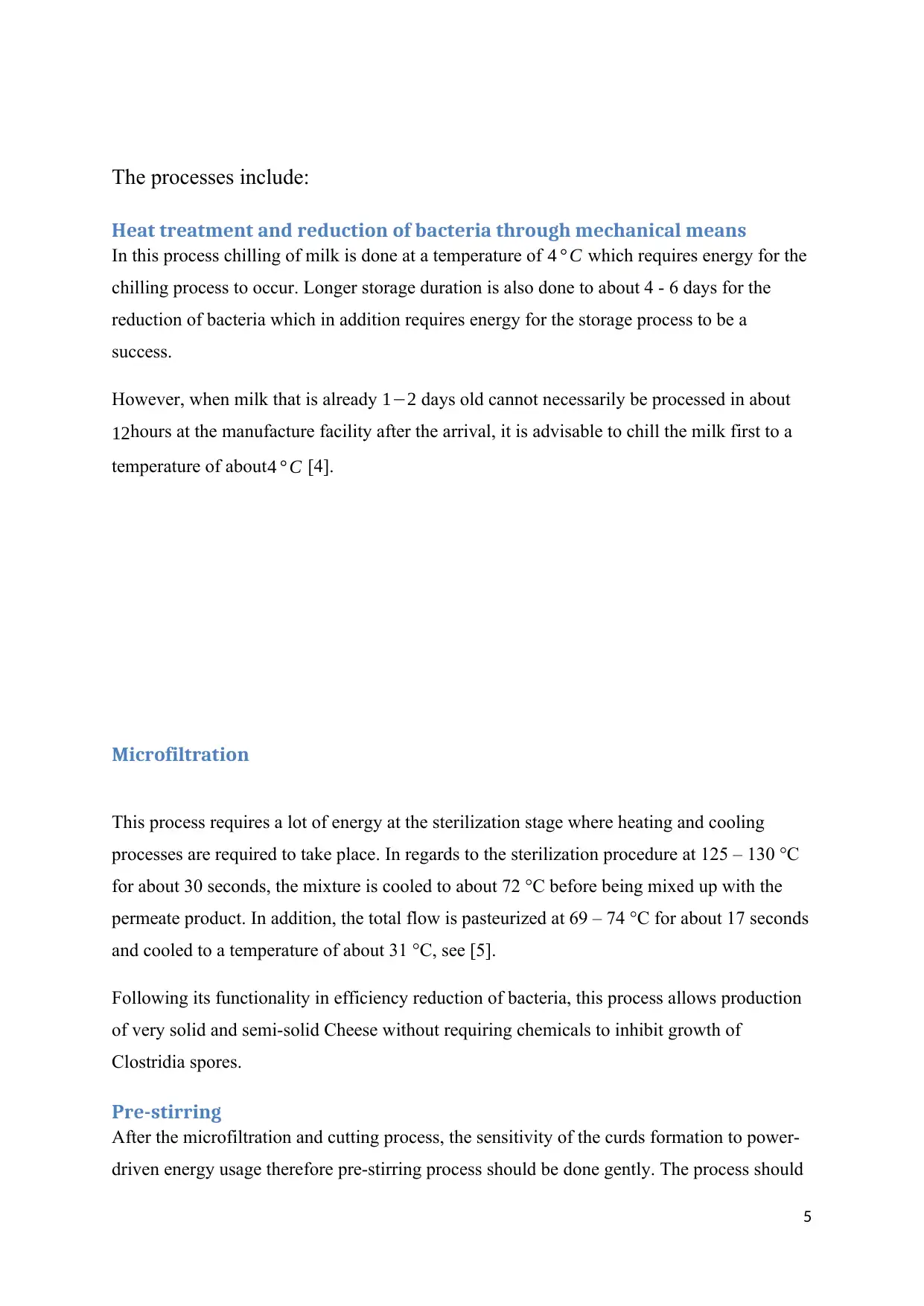
The processes include:
Heat treatment and reduction of bacteria through mechanical means
In this process chilling of milk is done at a temperature of 4 ° C which requires energy for the
chilling process to occur. Longer storage duration is also done to about 4 - 6 days for the
reduction of bacteria which in addition requires energy for the storage process to be a
success.
However, when milk that is already 1−2 days old cannot necessarily be processed in about
12hours at the manufacture facility after the arrival, it is advisable to chill the milk first to a
temperature of about4 ° C [4].
Microfiltration
This process requires a lot of energy at the sterilization stage where heating and cooling
processes are required to take place. In regards to the sterilization procedure at 125 – 130 °C
for about 30 seconds, the mixture is cooled to about 72 °C before being mixed up with the
permeate product. In addition, the total flow is pasteurized at 69 – 74 °C for about 17 seconds
and cooled to a temperature of about 31 °C, see [5].
Following its functionality in efficiency reduction of bacteria, this process allows production
of very solid and semi-solid Cheese without requiring chemicals to inhibit growth of
Clostridia spores.
Pre-stirring
After the microfiltration and cutting process, the sensitivity of the curds formation to power-
driven energy usage therefore pre-stirring process should be done gently. The process should
5
Heat treatment and reduction of bacteria through mechanical means
In this process chilling of milk is done at a temperature of 4 ° C which requires energy for the
chilling process to occur. Longer storage duration is also done to about 4 - 6 days for the
reduction of bacteria which in addition requires energy for the storage process to be a
success.
However, when milk that is already 1−2 days old cannot necessarily be processed in about
12hours at the manufacture facility after the arrival, it is advisable to chill the milk first to a
temperature of about4 ° C [4].
Microfiltration
This process requires a lot of energy at the sterilization stage where heating and cooling
processes are required to take place. In regards to the sterilization procedure at 125 – 130 °C
for about 30 seconds, the mixture is cooled to about 72 °C before being mixed up with the
permeate product. In addition, the total flow is pasteurized at 69 – 74 °C for about 17 seconds
and cooled to a temperature of about 31 °C, see [5].
Following its functionality in efficiency reduction of bacteria, this process allows production
of very solid and semi-solid Cheese without requiring chemicals to inhibit growth of
Clostridia spores.
Pre-stirring
After the microfiltration and cutting process, the sensitivity of the curds formation to power-
driven energy usage therefore pre-stirring process should be done gently. The process should
5
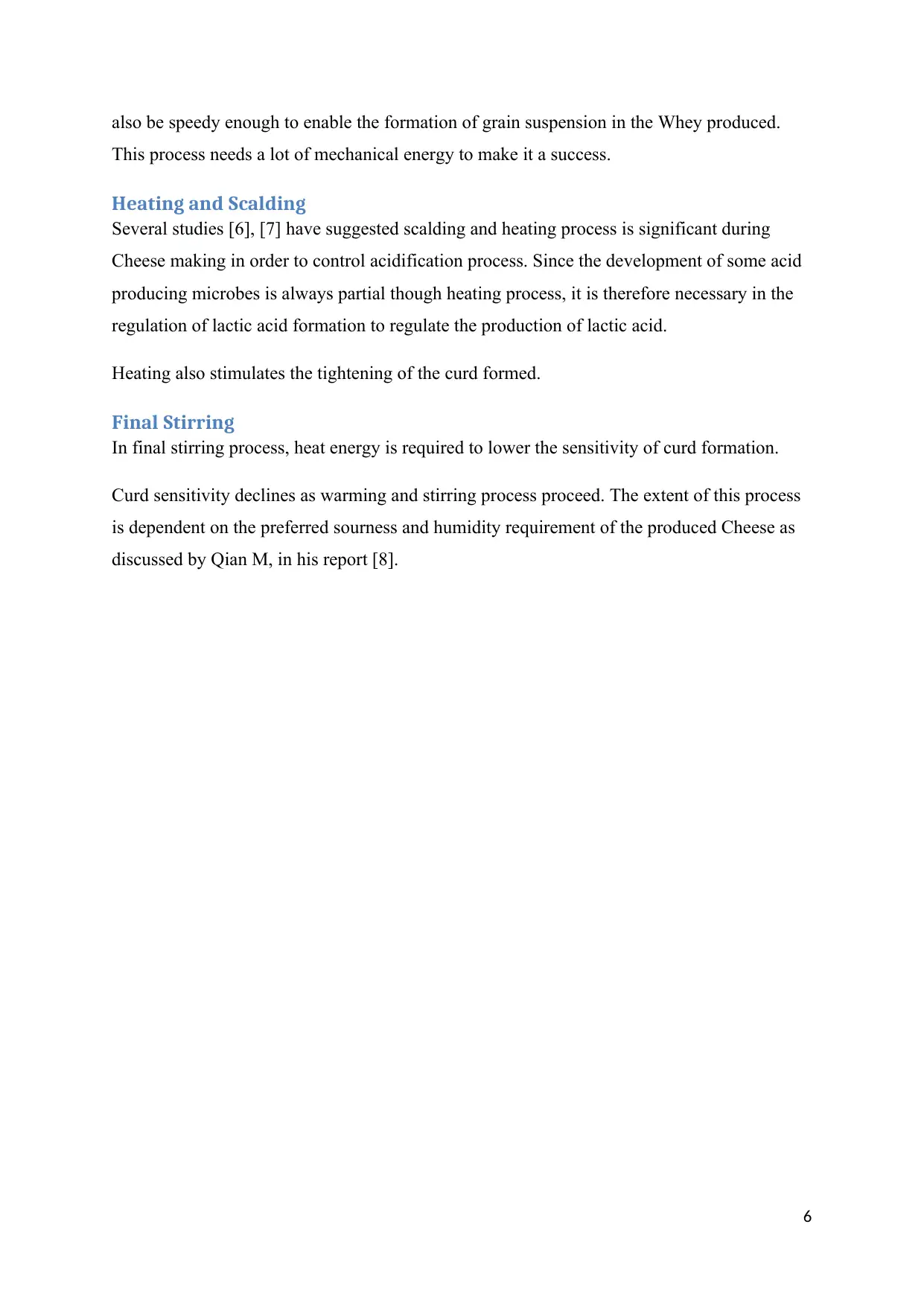
also be speedy enough to enable the formation of grain suspension in the Whey produced.
This process needs a lot of mechanical energy to make it a success.
Heating and Scalding
Several studies [6], [7] have suggested scalding and heating process is significant during
Cheese making in order to control acidification process. Since the development of some acid
producing microbes is always partial though heating process, it is therefore necessary in the
regulation of lactic acid formation to regulate the production of lactic acid.
Heating also stimulates the tightening of the curd formed.
Final Stirring
In final stirring process, heat energy is required to lower the sensitivity of curd formation.
Curd sensitivity declines as warming and stirring process proceed. The extent of this process
is dependent on the preferred sourness and humidity requirement of the produced Cheese as
discussed by Qian M, in his report [8].
6
This process needs a lot of mechanical energy to make it a success.
Heating and Scalding
Several studies [6], [7] have suggested scalding and heating process is significant during
Cheese making in order to control acidification process. Since the development of some acid
producing microbes is always partial though heating process, it is therefore necessary in the
regulation of lactic acid formation to regulate the production of lactic acid.
Heating also stimulates the tightening of the curd formed.
Final Stirring
In final stirring process, heat energy is required to lower the sensitivity of curd formation.
Curd sensitivity declines as warming and stirring process proceed. The extent of this process
is dependent on the preferred sourness and humidity requirement of the produced Cheese as
discussed by Qian M, in his report [8].
6
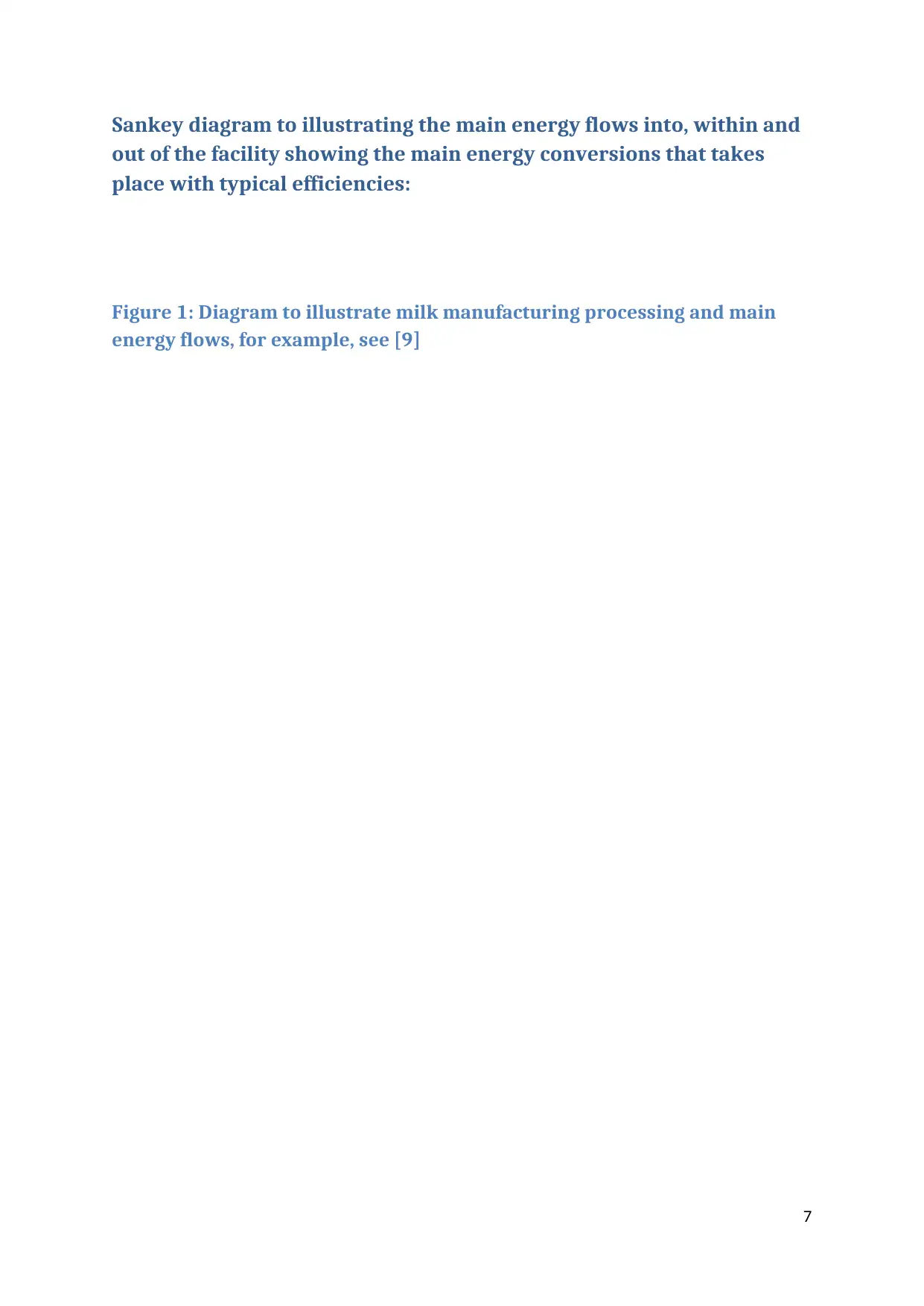
Sankey diagram to illustrating the main energy flows into, within and
out of the facility showing the main energy conversions that takes
place with typical efficiencies:
Figure 1: Diagram to illustrate milk manufacturing processing and main
energy flows, for example, see [9]
7
out of the facility showing the main energy conversions that takes
place with typical efficiencies:
Figure 1: Diagram to illustrate milk manufacturing processing and main
energy flows, for example, see [9]
7
Paraphrase This Document
Need a fresh take? Get an instant paraphrase of this document with our AI Paraphraser
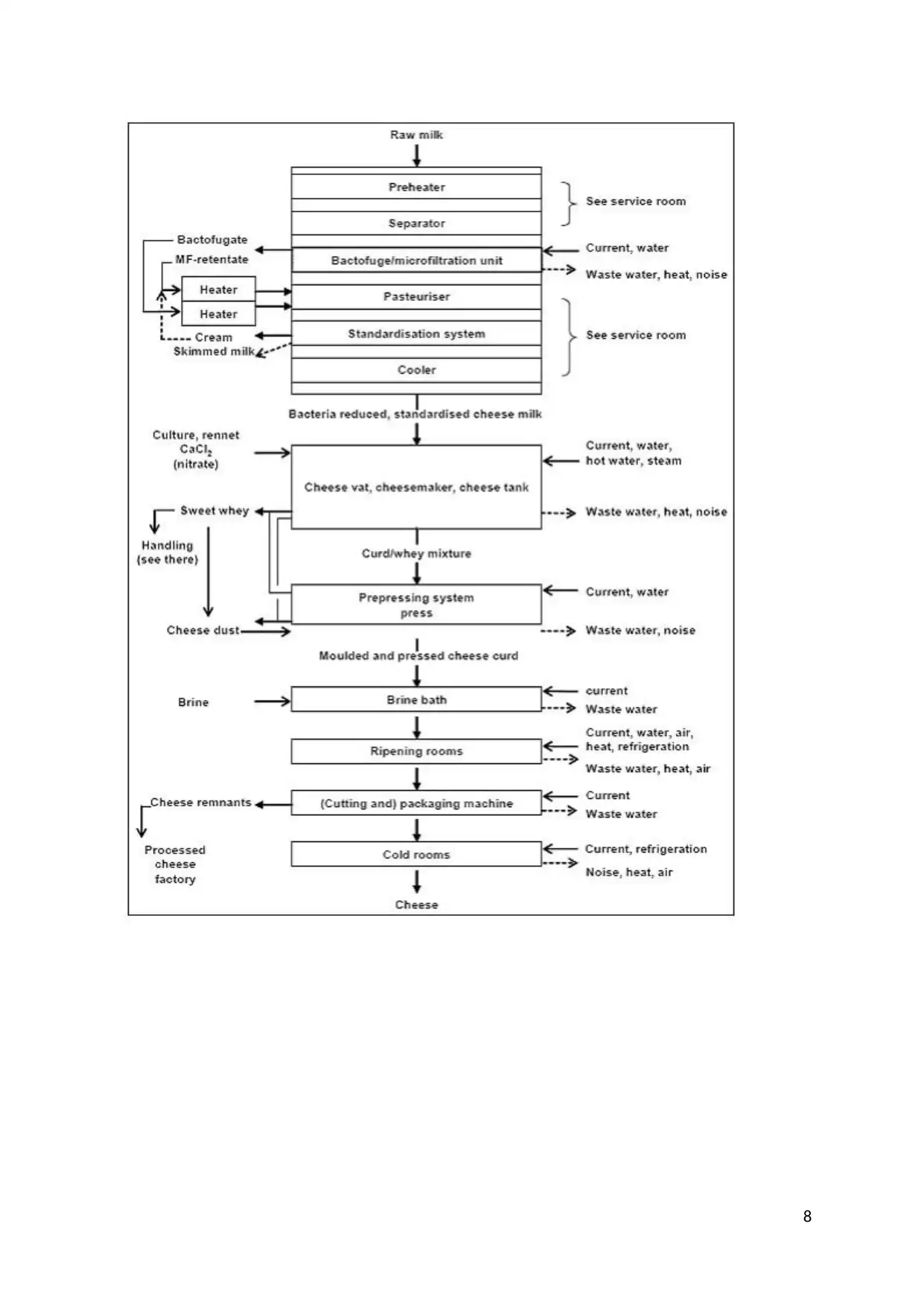
8
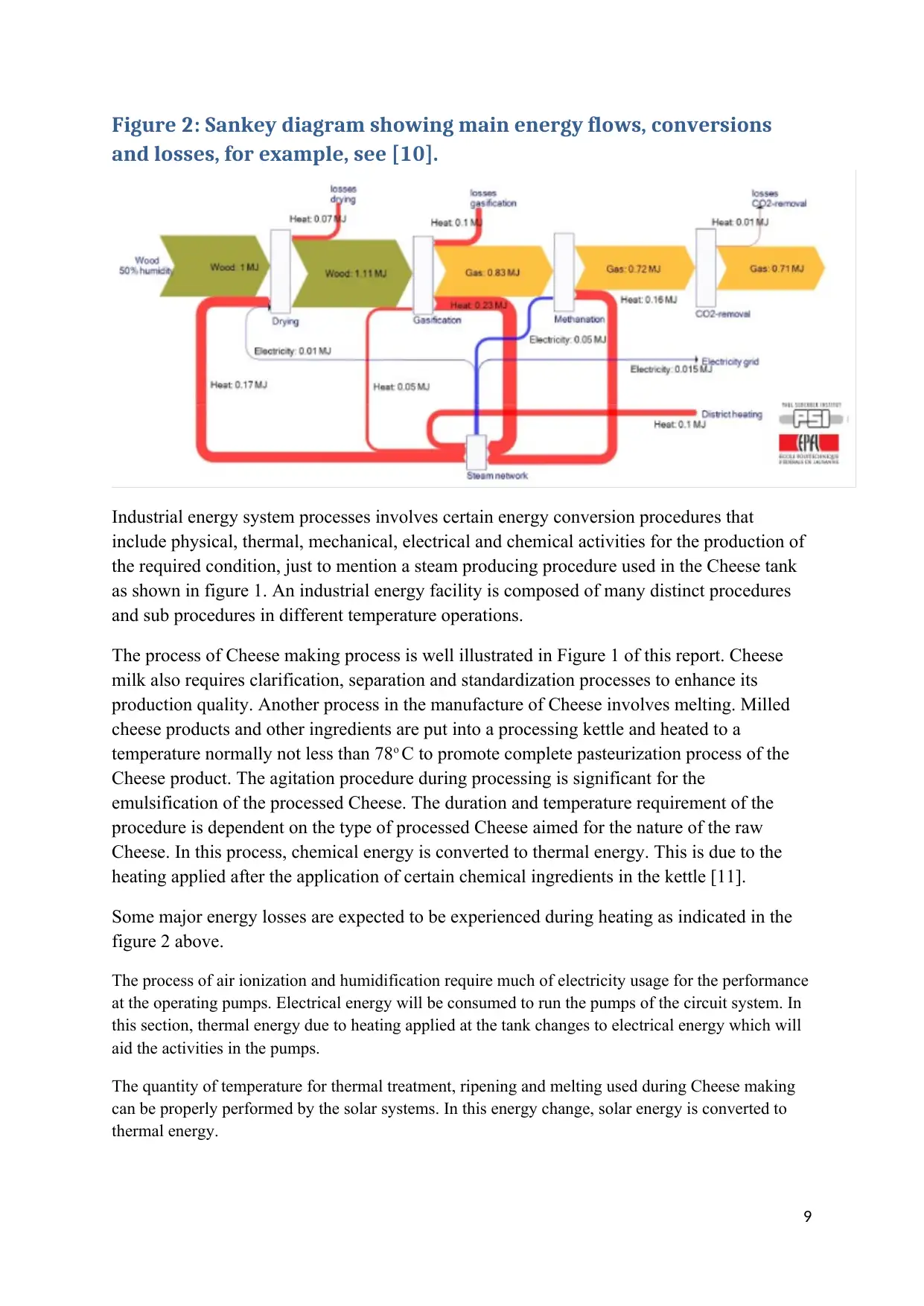
Figure 2: Sankey diagram showing main energy flows, conversions
and losses, for example, see [10].
Industrial energy system processes involves certain energy conversion procedures that
include physical, thermal, mechanical, electrical and chemical activities for the production of
the required condition, just to mention a steam producing procedure used in the Cheese tank
as shown in figure 1. An industrial energy facility is composed of many distinct procedures
and sub procedures in different temperature operations.
The process of Cheese making process is well illustrated in Figure 1 of this report. Cheese
milk also requires clarification, separation and standardization processes to enhance its
production quality. Another process in the manufacture of Cheese involves melting. Milled
cheese products and other ingredients are put into a processing kettle and heated to a
temperature normally not less than 78o C to promote complete pasteurization process of the
Cheese product. The agitation procedure during processing is significant for the
emulsification of the processed Cheese. The duration and temperature requirement of the
procedure is dependent on the type of processed Cheese aimed for the nature of the raw
Cheese. In this process, chemical energy is converted to thermal energy. This is due to the
heating applied after the application of certain chemical ingredients in the kettle [11].
Some major energy losses are expected to be experienced during heating as indicated in the
figure 2 above.
The process of air ionization and humidification require much of electricity usage for the performance
at the operating pumps. Electrical energy will be consumed to run the pumps of the circuit system. In
this section, thermal energy due to heating applied at the tank changes to electrical energy which will
aid the activities in the pumps.
The quantity of temperature for thermal treatment, ripening and melting used during Cheese making
can be properly performed by the solar systems. In this energy change, solar energy is converted to
thermal energy.
9
and losses, for example, see [10].
Industrial energy system processes involves certain energy conversion procedures that
include physical, thermal, mechanical, electrical and chemical activities for the production of
the required condition, just to mention a steam producing procedure used in the Cheese tank
as shown in figure 1. An industrial energy facility is composed of many distinct procedures
and sub procedures in different temperature operations.
The process of Cheese making process is well illustrated in Figure 1 of this report. Cheese
milk also requires clarification, separation and standardization processes to enhance its
production quality. Another process in the manufacture of Cheese involves melting. Milled
cheese products and other ingredients are put into a processing kettle and heated to a
temperature normally not less than 78o C to promote complete pasteurization process of the
Cheese product. The agitation procedure during processing is significant for the
emulsification of the processed Cheese. The duration and temperature requirement of the
procedure is dependent on the type of processed Cheese aimed for the nature of the raw
Cheese. In this process, chemical energy is converted to thermal energy. This is due to the
heating applied after the application of certain chemical ingredients in the kettle [11].
Some major energy losses are expected to be experienced during heating as indicated in the
figure 2 above.
The process of air ionization and humidification require much of electricity usage for the performance
at the operating pumps. Electrical energy will be consumed to run the pumps of the circuit system. In
this section, thermal energy due to heating applied at the tank changes to electrical energy which will
aid the activities in the pumps.
The quantity of temperature for thermal treatment, ripening and melting used during Cheese making
can be properly performed by the solar systems. In this energy change, solar energy is converted to
thermal energy.
9
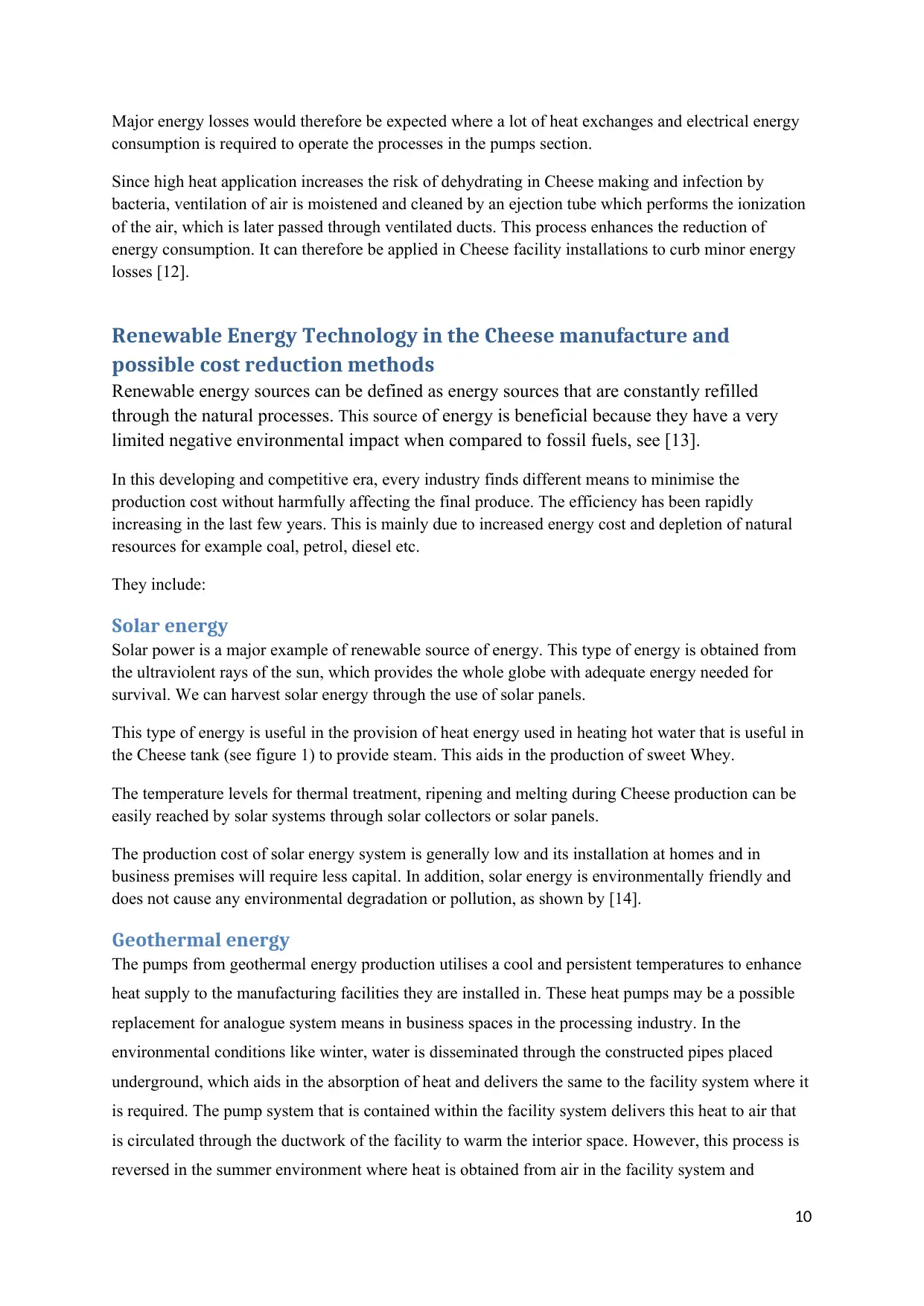
Major energy losses would therefore be expected where a lot of heat exchanges and electrical energy
consumption is required to operate the processes in the pumps section.
Since high heat application increases the risk of dehydrating in Cheese making and infection by
bacteria, ventilation of air is moistened and cleaned by an ejection tube which performs the ionization
of the air, which is later passed through ventilated ducts. This process enhances the reduction of
energy consumption. It can therefore be applied in Cheese facility installations to curb minor energy
losses [12].
Renewable Energy Technology in the Cheese manufacture and
possible cost reduction methods
Renewable energy sources can be defined as energy sources that are constantly refilled
through the natural processes. This source of energy is beneficial because they have a very
limited negative environmental impact when compared to fossil fuels, see [13].
In this developing and competitive era, every industry finds different means to minimise the
production cost without harmfully affecting the final produce. The efficiency has been rapidly
increasing in the last few years. This is mainly due to increased energy cost and depletion of natural
resources for example coal, petrol, diesel etc.
They include:
Solar energy
Solar power is a major example of renewable source of energy. This type of energy is obtained from
the ultraviolent rays of the sun, which provides the whole globe with adequate energy needed for
survival. We can harvest solar energy through the use of solar panels.
This type of energy is useful in the provision of heat energy used in heating hot water that is useful in
the Cheese tank (see figure 1) to provide steam. This aids in the production of sweet Whey.
The temperature levels for thermal treatment, ripening and melting during Cheese production can be
easily reached by solar systems through solar collectors or solar panels.
The production cost of solar energy system is generally low and its installation at homes and in
business premises will require less capital. In addition, solar energy is environmentally friendly and
does not cause any environmental degradation or pollution, as shown by [14].
Geothermal energy
The pumps from geothermal energy production utilises a cool and persistent temperatures to enhance
heat supply to the manufacturing facilities they are installed in. These heat pumps may be a possible
replacement for analogue system means in business spaces in the processing industry. In the
environmental conditions like winter, water is disseminated through the constructed pipes placed
underground, which aids in the absorption of heat and delivers the same to the facility system where it
is required. The pump system that is contained within the facility system delivers this heat to air that
is circulated through the ductwork of the facility to warm the interior space. However, this process is
reversed in the summer environment where heat is obtained from air in the facility system and
10
consumption is required to operate the processes in the pumps section.
Since high heat application increases the risk of dehydrating in Cheese making and infection by
bacteria, ventilation of air is moistened and cleaned by an ejection tube which performs the ionization
of the air, which is later passed through ventilated ducts. This process enhances the reduction of
energy consumption. It can therefore be applied in Cheese facility installations to curb minor energy
losses [12].
Renewable Energy Technology in the Cheese manufacture and
possible cost reduction methods
Renewable energy sources can be defined as energy sources that are constantly refilled
through the natural processes. This source of energy is beneficial because they have a very
limited negative environmental impact when compared to fossil fuels, see [13].
In this developing and competitive era, every industry finds different means to minimise the
production cost without harmfully affecting the final produce. The efficiency has been rapidly
increasing in the last few years. This is mainly due to increased energy cost and depletion of natural
resources for example coal, petrol, diesel etc.
They include:
Solar energy
Solar power is a major example of renewable source of energy. This type of energy is obtained from
the ultraviolent rays of the sun, which provides the whole globe with adequate energy needed for
survival. We can harvest solar energy through the use of solar panels.
This type of energy is useful in the provision of heat energy used in heating hot water that is useful in
the Cheese tank (see figure 1) to provide steam. This aids in the production of sweet Whey.
The temperature levels for thermal treatment, ripening and melting during Cheese production can be
easily reached by solar systems through solar collectors or solar panels.
The production cost of solar energy system is generally low and its installation at homes and in
business premises will require less capital. In addition, solar energy is environmentally friendly and
does not cause any environmental degradation or pollution, as shown by [14].
Geothermal energy
The pumps from geothermal energy production utilises a cool and persistent temperatures to enhance
heat supply to the manufacturing facilities they are installed in. These heat pumps may be a possible
replacement for analogue system means in business spaces in the processing industry. In the
environmental conditions like winter, water is disseminated through the constructed pipes placed
underground, which aids in the absorption of heat and delivers the same to the facility system where it
is required. The pump system that is contained within the facility system delivers this heat to air that
is circulated through the ductwork of the facility to warm the interior space. However, this process is
reversed in the summer environment where heat is obtained from air in the facility system and
10
Secure Best Marks with AI Grader
Need help grading? Try our AI Grader for instant feedback on your assignments.
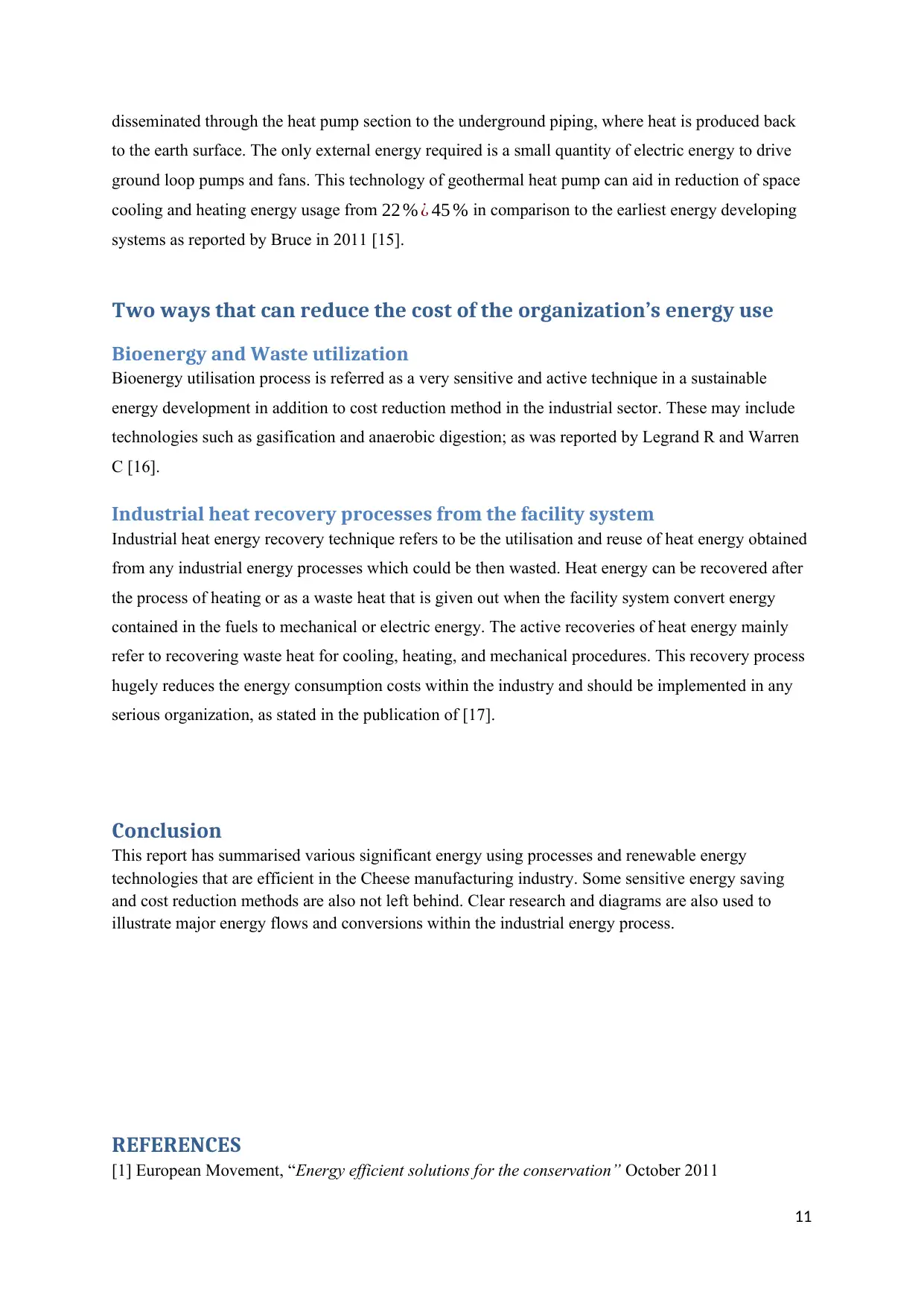
disseminated through the heat pump section to the underground piping, where heat is produced back
to the earth surface. The only external energy required is a small quantity of electric energy to drive
ground loop pumps and fans. This technology of geothermal heat pump can aid in reduction of space
cooling and heating energy usage from 22 % ¿ 45 % in comparison to the earliest energy developing
systems as reported by Bruce in 2011 [15].
Two ways that can reduce the cost of the organization’s energy use
Bioenergy and Waste utilization
Bioenergy utilisation process is referred as a very sensitive and active technique in a sustainable
energy development in addition to cost reduction method in the industrial sector. These may include
technologies such as gasification and anaerobic digestion; as was reported by Legrand R and Warren
C [16].
Industrial heat recovery processes from the facility system
Industrial heat energy recovery technique refers to be the utilisation and reuse of heat energy obtained
from any industrial energy processes which could be then wasted. Heat energy can be recovered after
the process of heating or as a waste heat that is given out when the facility system convert energy
contained in the fuels to mechanical or electric energy. The active recoveries of heat energy mainly
refer to recovering waste heat for cooling, heating, and mechanical procedures. This recovery process
hugely reduces the energy consumption costs within the industry and should be implemented in any
serious organization, as stated in the publication of [17].
Conclusion
This report has summarised various significant energy using processes and renewable energy
technologies that are efficient in the Cheese manufacturing industry. Some sensitive energy saving
and cost reduction methods are also not left behind. Clear research and diagrams are also used to
illustrate major energy flows and conversions within the industrial energy process.
REFERENCES
[1] European Movement, “Energy efficient solutions for the conservation” October 2011
11
to the earth surface. The only external energy required is a small quantity of electric energy to drive
ground loop pumps and fans. This technology of geothermal heat pump can aid in reduction of space
cooling and heating energy usage from 22 % ¿ 45 % in comparison to the earliest energy developing
systems as reported by Bruce in 2011 [15].
Two ways that can reduce the cost of the organization’s energy use
Bioenergy and Waste utilization
Bioenergy utilisation process is referred as a very sensitive and active technique in a sustainable
energy development in addition to cost reduction method in the industrial sector. These may include
technologies such as gasification and anaerobic digestion; as was reported by Legrand R and Warren
C [16].
Industrial heat recovery processes from the facility system
Industrial heat energy recovery technique refers to be the utilisation and reuse of heat energy obtained
from any industrial energy processes which could be then wasted. Heat energy can be recovered after
the process of heating or as a waste heat that is given out when the facility system convert energy
contained in the fuels to mechanical or electric energy. The active recoveries of heat energy mainly
refer to recovering waste heat for cooling, heating, and mechanical procedures. This recovery process
hugely reduces the energy consumption costs within the industry and should be implemented in any
serious organization, as stated in the publication of [17].
Conclusion
This report has summarised various significant energy using processes and renewable energy
technologies that are efficient in the Cheese manufacturing industry. Some sensitive energy saving
and cost reduction methods are also not left behind. Clear research and diagrams are also used to
illustrate major energy flows and conversions within the industrial energy process.
REFERENCES
[1] European Movement, “Energy efficient solutions for the conservation” October 2011
11
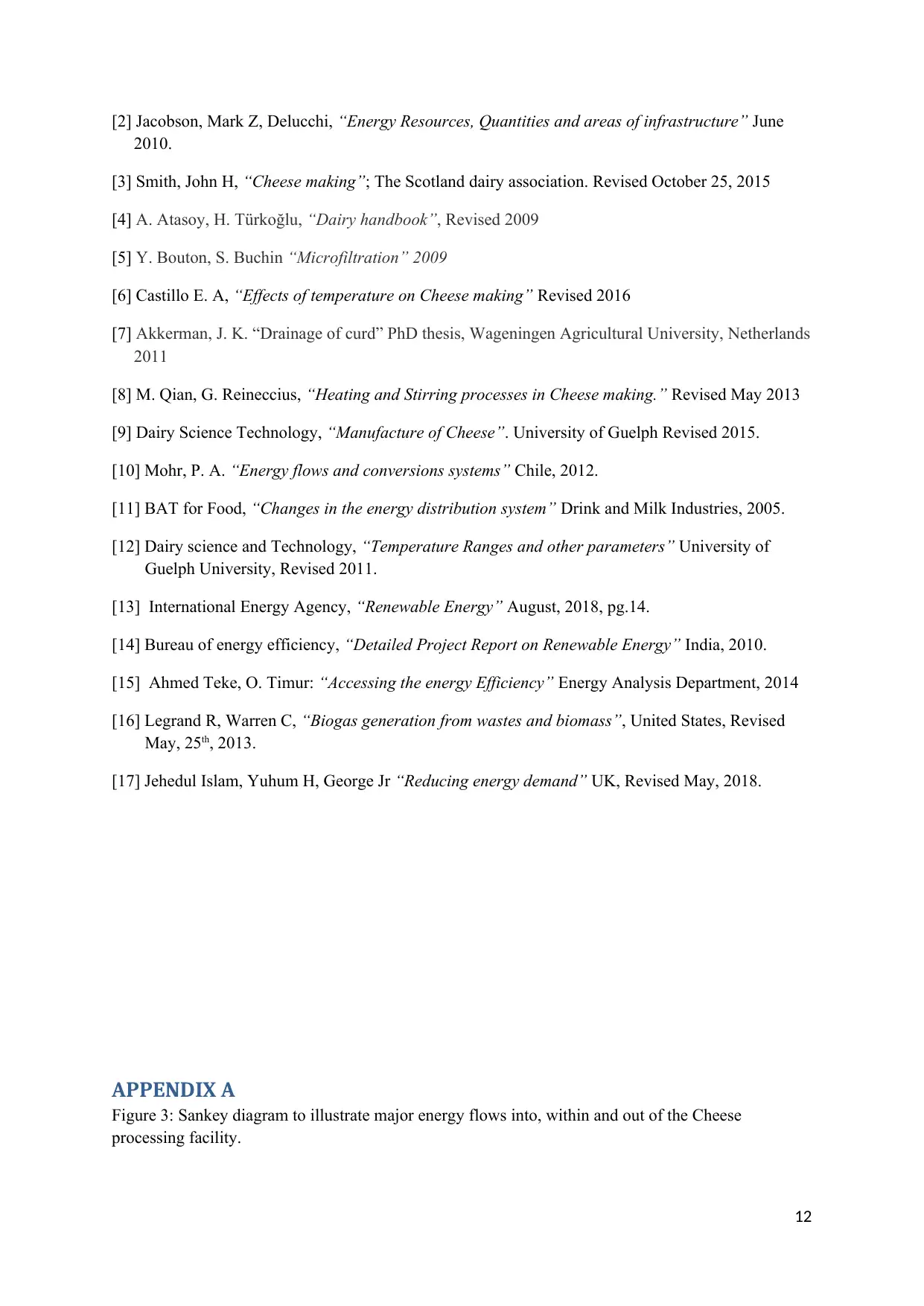
[2] Jacobson, Mark Z, Delucchi, “Energy Resources, Quantities and areas of infrastructure” June
2010.
[3] Smith, John H, “Cheese making”; The Scotland dairy association. Revised October 25, 2015
[4] A. Atasoy, H. Türkoğlu, “Dairy handbook”, Revised 2009
[5] Y. Bouton, S. Buchin “Microfiltration” 2009
[6] Castillo E. A, “Effects of temperature on Cheese making” Revised 2016
[7] Akkerman, J. K. “Drainage of curd” PhD thesis, Wageningen Agricultural University, Netherlands
2011
[8] M. Qian, G. Reineccius, “Heating and Stirring processes in Cheese making.” Revised May 2013
[9] Dairy Science Technology, “Manufacture of Cheese”. University of Guelph Revised 2015.
[10] Mohr, P. A. “Energy flows and conversions systems” Chile, 2012.
[11] BAT for Food, “Changes in the energy distribution system” Drink and Milk Industries, 2005.
[12] Dairy science and Technology, “Temperature Ranges and other parameters” University of
Guelph University, Revised 2011.
[13] International Energy Agency, “Renewable Energy” August, 2018, pg.14.
[14] Bureau of energy efficiency, “Detailed Project Report on Renewable Energy” India, 2010.
[15] Ahmed Teke, O. Timur: “Accessing the energy Efficiency” Energy Analysis Department, 2014
[16] Legrand R, Warren C, “Biogas generation from wastes and biomass”, United States, Revised
May, 25th, 2013.
[17] Jehedul Islam, Yuhum H, George Jr “Reducing energy demand” UK, Revised May, 2018.
APPENDIX A
Figure 3: Sankey diagram to illustrate major energy flows into, within and out of the Cheese
processing facility.
12
2010.
[3] Smith, John H, “Cheese making”; The Scotland dairy association. Revised October 25, 2015
[4] A. Atasoy, H. Türkoğlu, “Dairy handbook”, Revised 2009
[5] Y. Bouton, S. Buchin “Microfiltration” 2009
[6] Castillo E. A, “Effects of temperature on Cheese making” Revised 2016
[7] Akkerman, J. K. “Drainage of curd” PhD thesis, Wageningen Agricultural University, Netherlands
2011
[8] M. Qian, G. Reineccius, “Heating and Stirring processes in Cheese making.” Revised May 2013
[9] Dairy Science Technology, “Manufacture of Cheese”. University of Guelph Revised 2015.
[10] Mohr, P. A. “Energy flows and conversions systems” Chile, 2012.
[11] BAT for Food, “Changes in the energy distribution system” Drink and Milk Industries, 2005.
[12] Dairy science and Technology, “Temperature Ranges and other parameters” University of
Guelph University, Revised 2011.
[13] International Energy Agency, “Renewable Energy” August, 2018, pg.14.
[14] Bureau of energy efficiency, “Detailed Project Report on Renewable Energy” India, 2010.
[15] Ahmed Teke, O. Timur: “Accessing the energy Efficiency” Energy Analysis Department, 2014
[16] Legrand R, Warren C, “Biogas generation from wastes and biomass”, United States, Revised
May, 25th, 2013.
[17] Jehedul Islam, Yuhum H, George Jr “Reducing energy demand” UK, Revised May, 2018.
APPENDIX A
Figure 3: Sankey diagram to illustrate major energy flows into, within and out of the Cheese
processing facility.
12
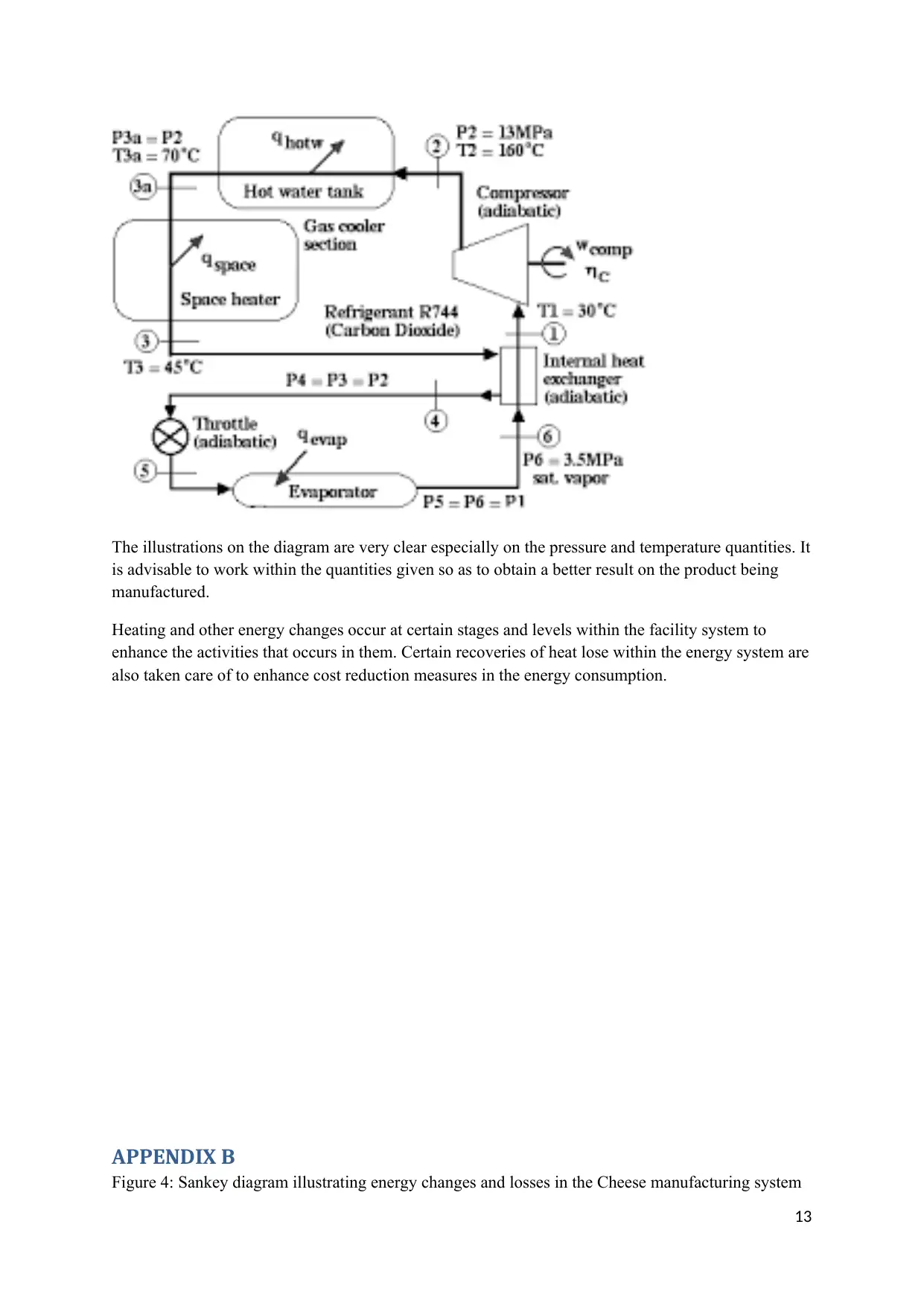
The illustrations on the diagram are very clear especially on the pressure and temperature quantities. It
is advisable to work within the quantities given so as to obtain a better result on the product being
manufactured.
Heating and other energy changes occur at certain stages and levels within the facility system to
enhance the activities that occurs in them. Certain recoveries of heat lose within the energy system are
also taken care of to enhance cost reduction measures in the energy consumption.
APPENDIX B
Figure 4: Sankey diagram illustrating energy changes and losses in the Cheese manufacturing system
13
is advisable to work within the quantities given so as to obtain a better result on the product being
manufactured.
Heating and other energy changes occur at certain stages and levels within the facility system to
enhance the activities that occurs in them. Certain recoveries of heat lose within the energy system are
also taken care of to enhance cost reduction measures in the energy consumption.
APPENDIX B
Figure 4: Sankey diagram illustrating energy changes and losses in the Cheese manufacturing system
13
Paraphrase This Document
Need a fresh take? Get an instant paraphrase of this document with our AI Paraphraser
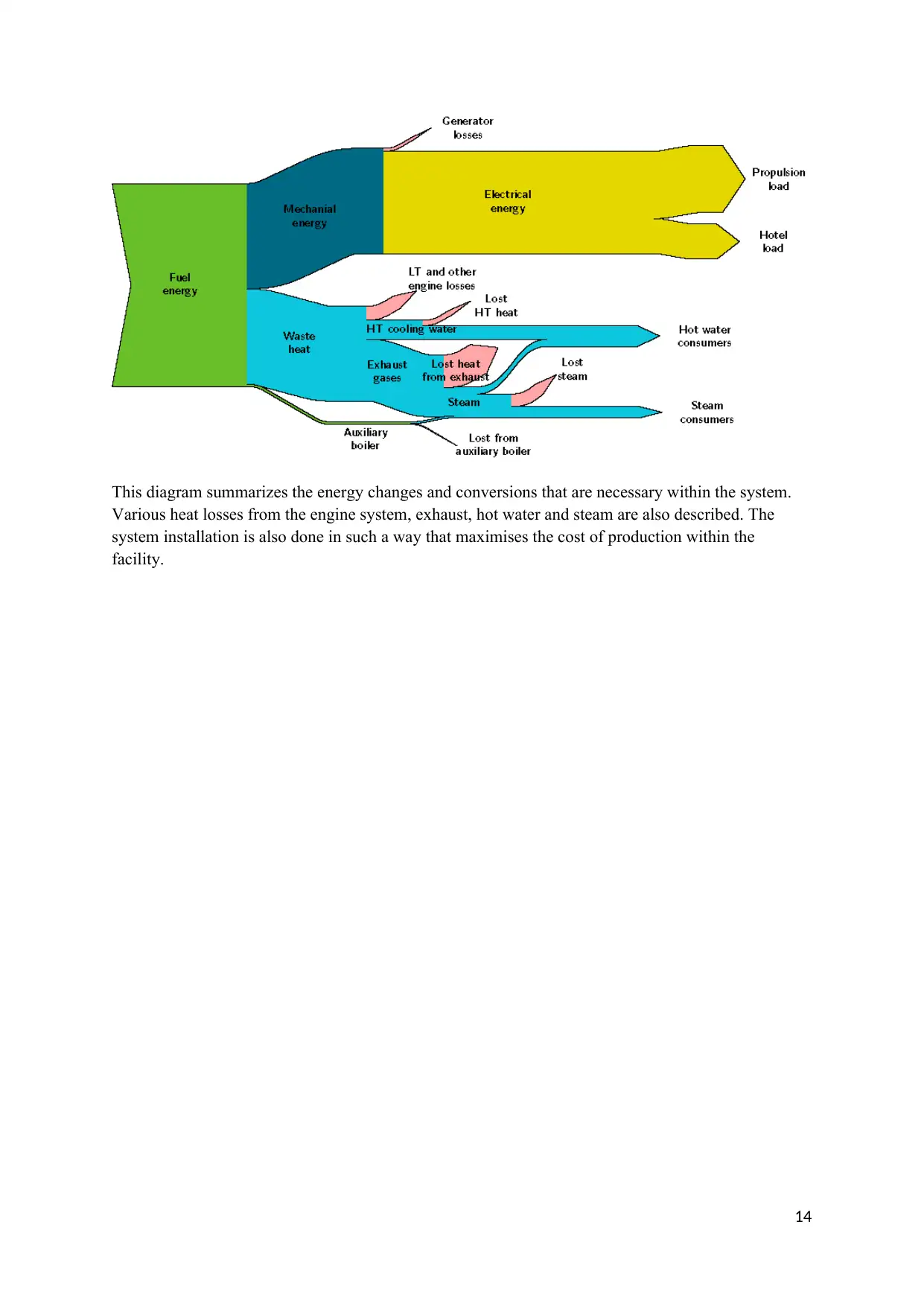
This diagram summarizes the energy changes and conversions that are necessary within the system.
Various heat losses from the engine system, exhaust, hot water and steam are also described. The
system installation is also done in such a way that maximises the cost of production within the
facility.
14
Various heat losses from the engine system, exhaust, hot water and steam are also described. The
system installation is also done in such a way that maximises the cost of production within the
facility.
14
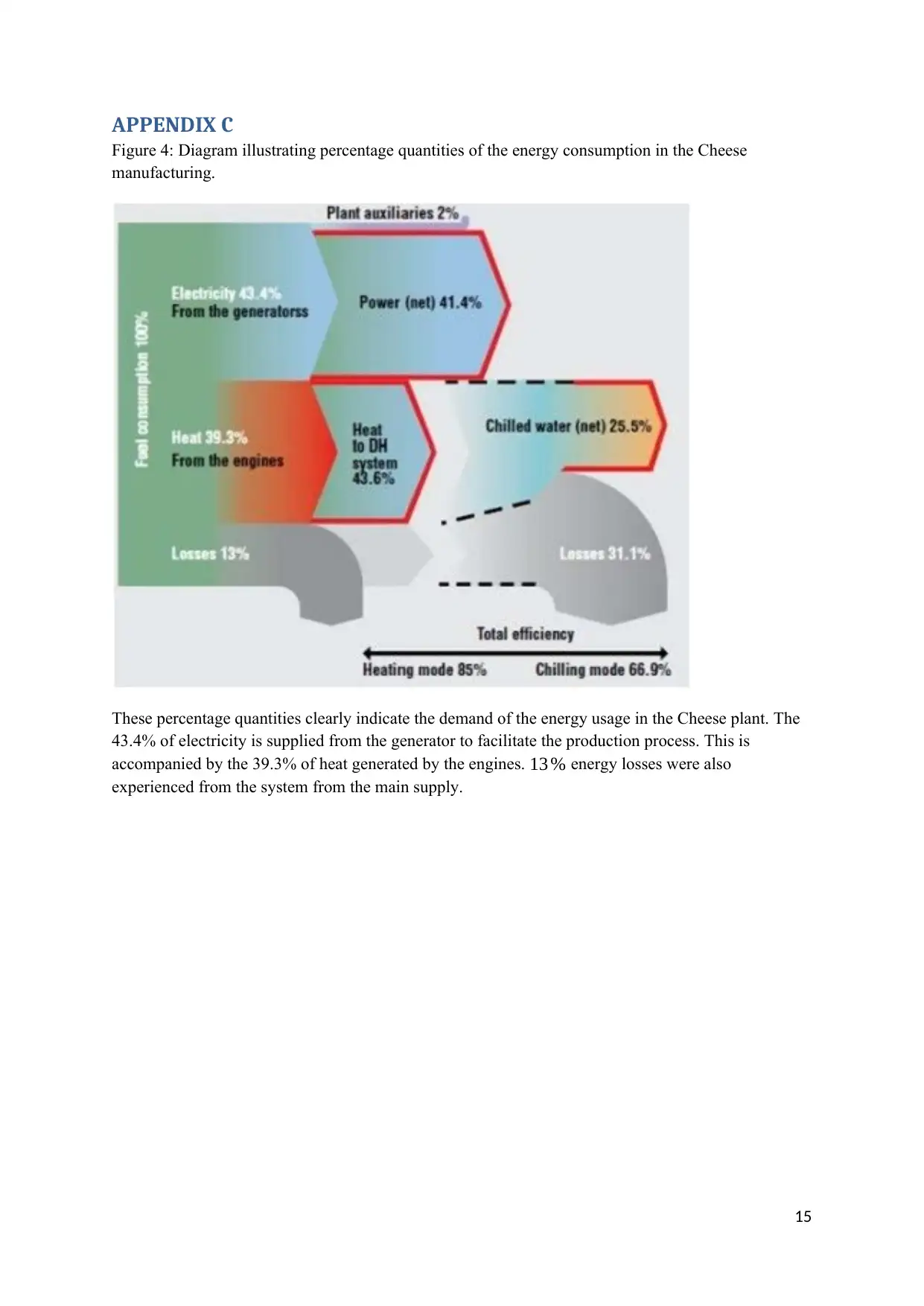
APPENDIX C
Figure 4: Diagram illustrating percentage quantities of the energy consumption in the Cheese
manufacturing.
These percentage quantities clearly indicate the demand of the energy usage in the Cheese plant. The
43.4% of electricity is supplied from the generator to facilitate the production process. This is
accompanied by the 39.3% of heat generated by the engines. 13 % energy losses were also
experienced from the system from the main supply.
15
Figure 4: Diagram illustrating percentage quantities of the energy consumption in the Cheese
manufacturing.
These percentage quantities clearly indicate the demand of the energy usage in the Cheese plant. The
43.4% of electricity is supplied from the generator to facilitate the production process. This is
accompanied by the 39.3% of heat generated by the engines. 13 % energy losses were also
experienced from the system from the main supply.
15
1 out of 15
Related Documents

Your All-in-One AI-Powered Toolkit for Academic Success.
+13062052269
info@desklib.com
Available 24*7 on WhatsApp / Email
Unlock your academic potential
© 2024 | Zucol Services PVT LTD | All rights reserved.