Unit 21: Engineering Secondary & Finishing Techniques - Report
VerifiedAdded on 2023/03/21
|10
|1581
|22
Report
AI Summary
This report delves into engineering secondary and finishing techniques, focusing on processes like heat treatment, turning, drilling, and water jetting in manufacturing components such as bolts, brake discs, washers, and caliper assemblies. It further discusses case hardening, a metal surface treatment to enhance durability, and its applications in various industries. The report also addresses the environmental impact of steel production, including air emissions, water contamination, and waste generation, highlighting the hazards and risks associated with these processes. In conclusion, while case hardening improves material surface characteristics, alternative methods like diode laser cladding may offer better control and meet specific surface requirements, emphasizing the importance of selecting appropriate techniques based on material properties and desired outcomes. Desklib offers a range of solved assignments and past papers for students seeking assistance with similar topics.
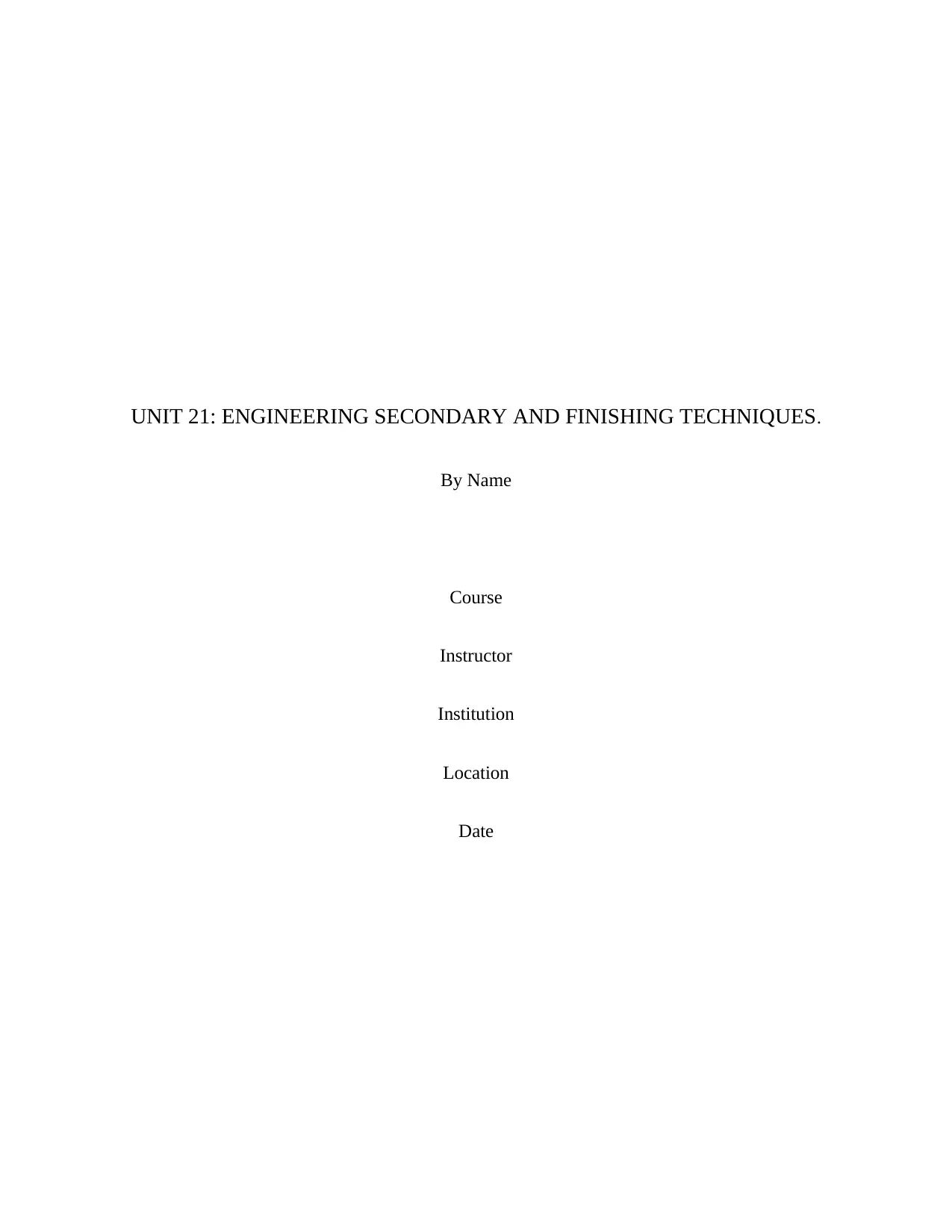
UNIT 21: ENGINEERING SECONDARY AND FINISHING TECHNIQUES.
By Name
Course
Instructor
Institution
Location
Date
By Name
Course
Instructor
Institution
Location
Date
Paraphrase This Document
Need a fresh take? Get an instant paraphrase of this document with our AI Paraphraser
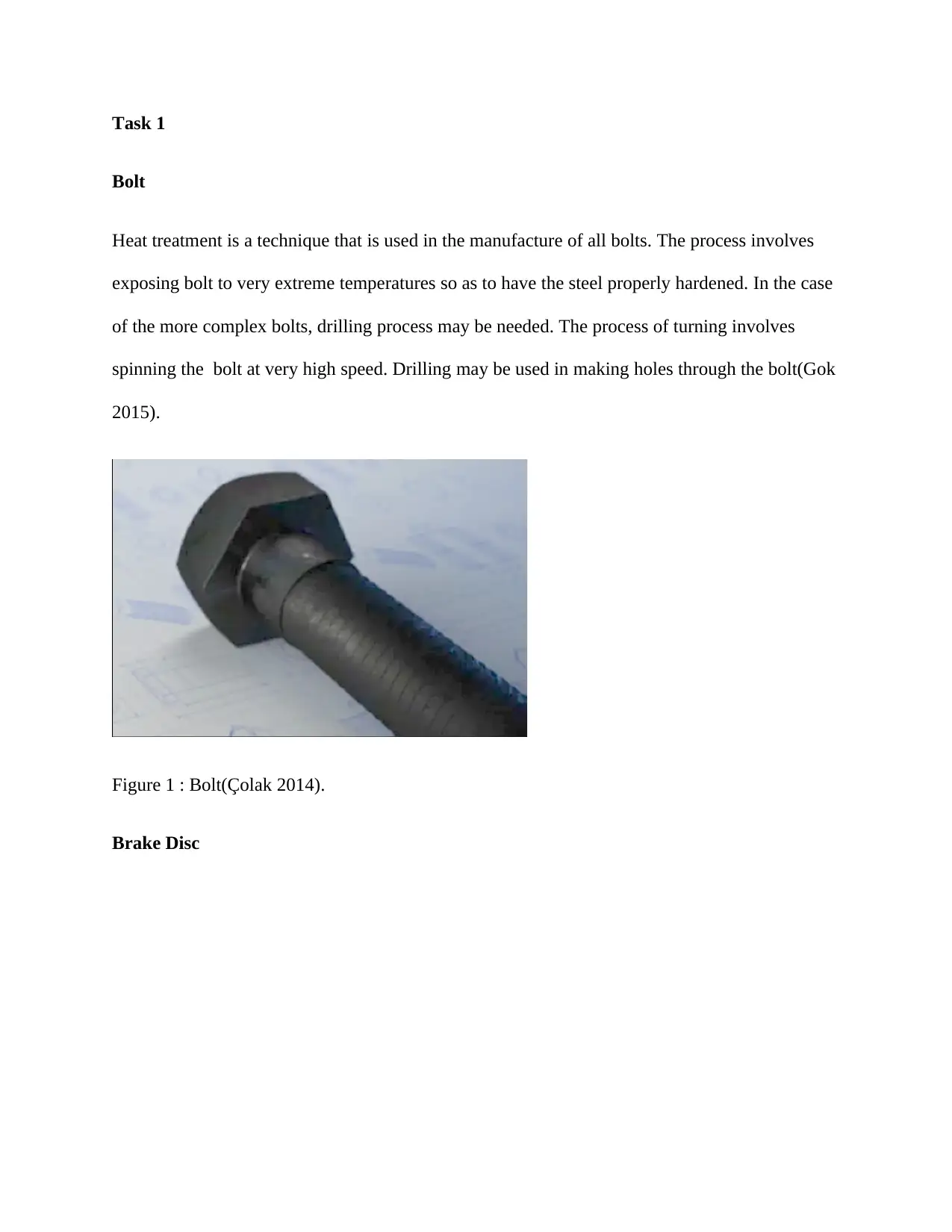
Task 1
Bolt
Heat treatment is a technique that is used in the manufacture of all bolts. The process involves
exposing bolt to very extreme temperatures so as to have the steel properly hardened. In the case
of the more complex bolts, drilling process may be needed. The process of turning involves
spinning the bolt at very high speed. Drilling may be used in making holes through the bolt(Gok
2015).
Figure 1 : Bolt(Çolak 2014).
Brake Disc
Bolt
Heat treatment is a technique that is used in the manufacture of all bolts. The process involves
exposing bolt to very extreme temperatures so as to have the steel properly hardened. In the case
of the more complex bolts, drilling process may be needed. The process of turning involves
spinning the bolt at very high speed. Drilling may be used in making holes through the bolt(Gok
2015).
Figure 1 : Bolt(Çolak 2014).
Brake Disc
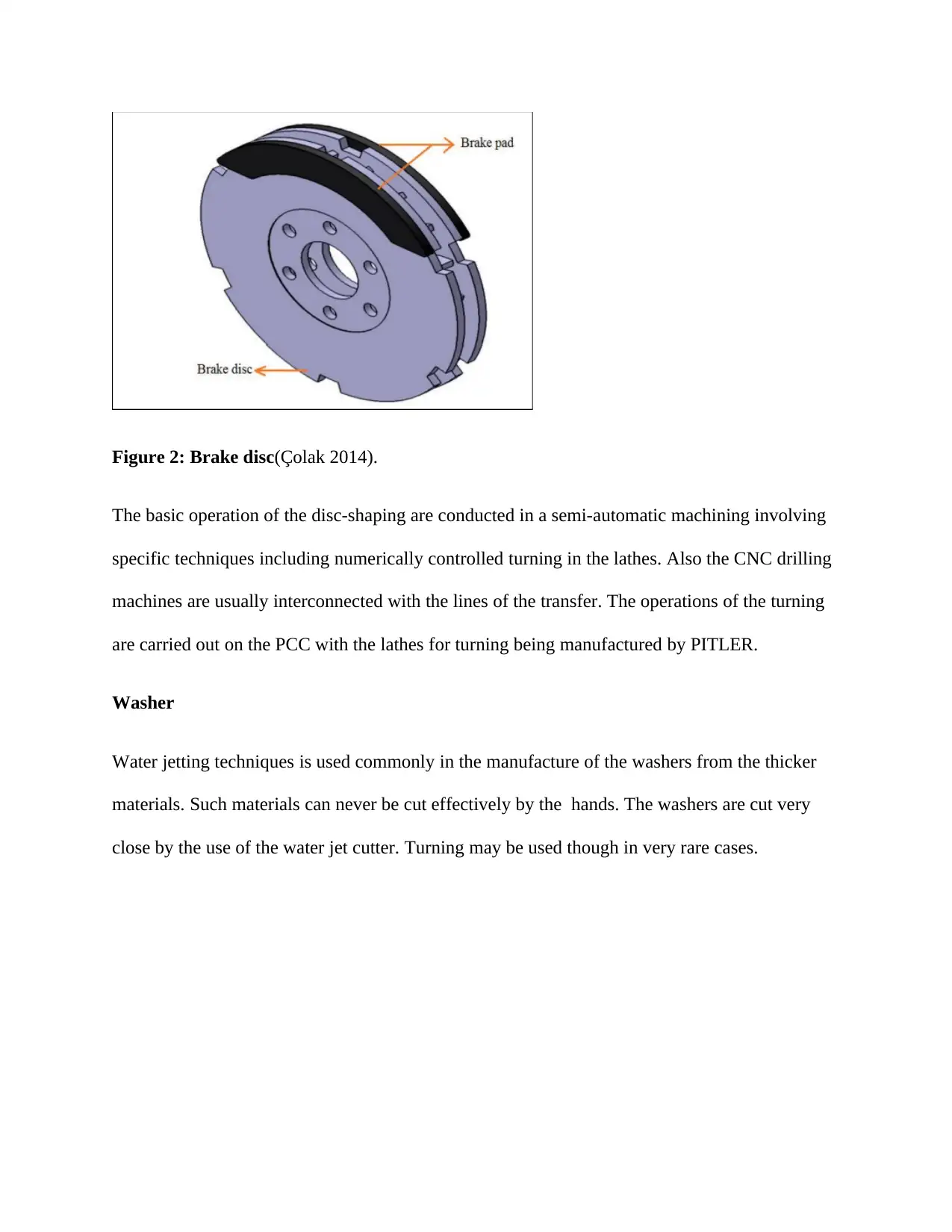
Figure 2: Brake disc(Çolak 2014).
The basic operation of the disc-shaping are conducted in a semi-automatic machining involving
specific techniques including numerically controlled turning in the lathes. Also the CNC drilling
machines are usually interconnected with the lines of the transfer. The operations of the turning
are carried out on the PCC with the lathes for turning being manufactured by PITLER.
Washer
Water jetting techniques is used commonly in the manufacture of the washers from the thicker
materials. Such materials can never be cut effectively by the hands. The washers are cut very
close by the use of the water jet cutter. Turning may be used though in very rare cases.
The basic operation of the disc-shaping are conducted in a semi-automatic machining involving
specific techniques including numerically controlled turning in the lathes. Also the CNC drilling
machines are usually interconnected with the lines of the transfer. The operations of the turning
are carried out on the PCC with the lathes for turning being manufactured by PITLER.
Washer
Water jetting techniques is used commonly in the manufacture of the washers from the thicker
materials. Such materials can never be cut effectively by the hands. The washers are cut very
close by the use of the water jet cutter. Turning may be used though in very rare cases.
⊘ This is a preview!⊘
Do you want full access?
Subscribe today to unlock all pages.

Trusted by 1+ million students worldwide
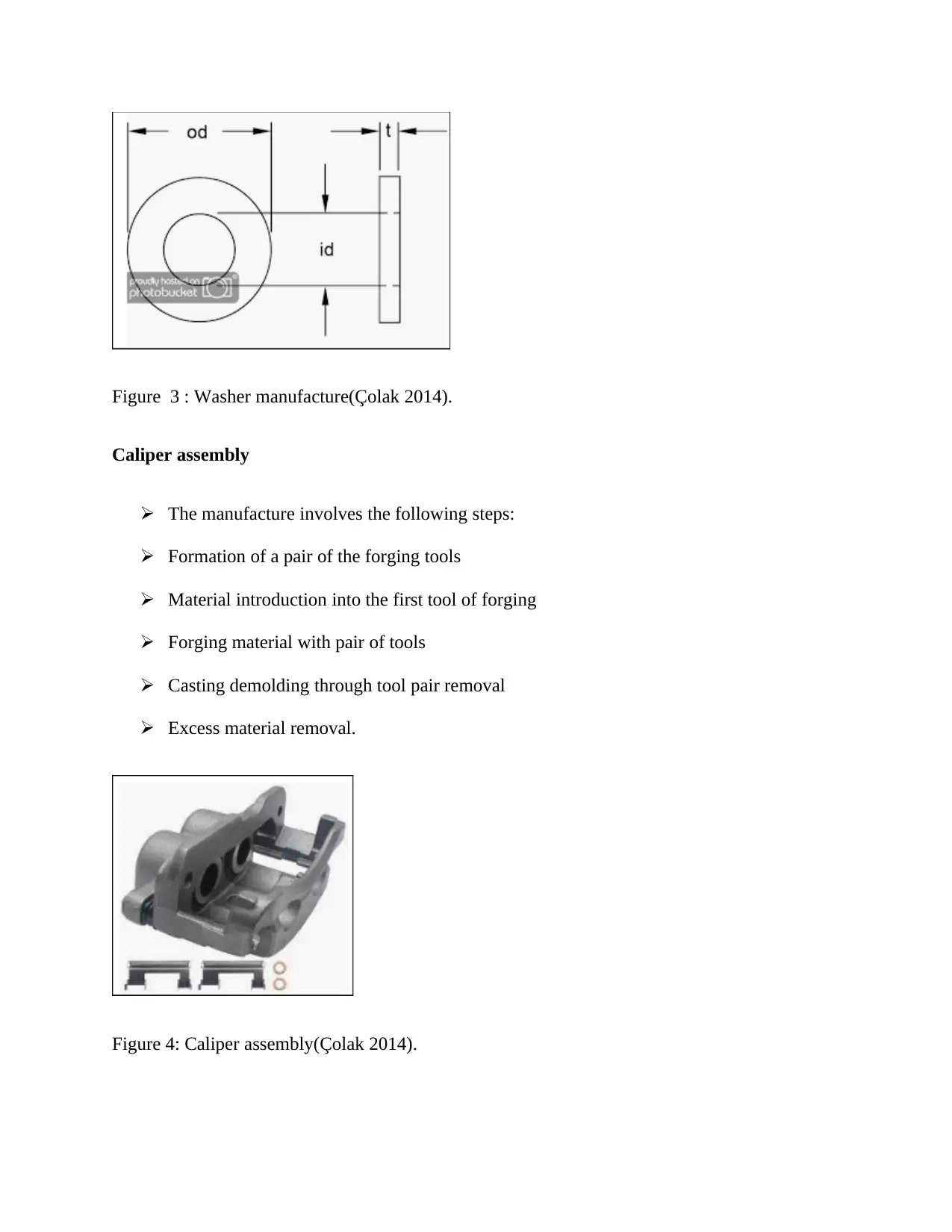
Figure 3 : Washer manufacture(Çolak 2014).
Caliper assembly
The manufacture involves the following steps:
Formation of a pair of the forging tools
Material introduction into the first tool of forging
Forging material with pair of tools
Casting demolding through tool pair removal
Excess material removal.
Figure 4: Caliper assembly(Çolak 2014).
Caliper assembly
The manufacture involves the following steps:
Formation of a pair of the forging tools
Material introduction into the first tool of forging
Forging material with pair of tools
Casting demolding through tool pair removal
Excess material removal.
Figure 4: Caliper assembly(Çolak 2014).
Paraphrase This Document
Need a fresh take? Get an instant paraphrase of this document with our AI Paraphraser
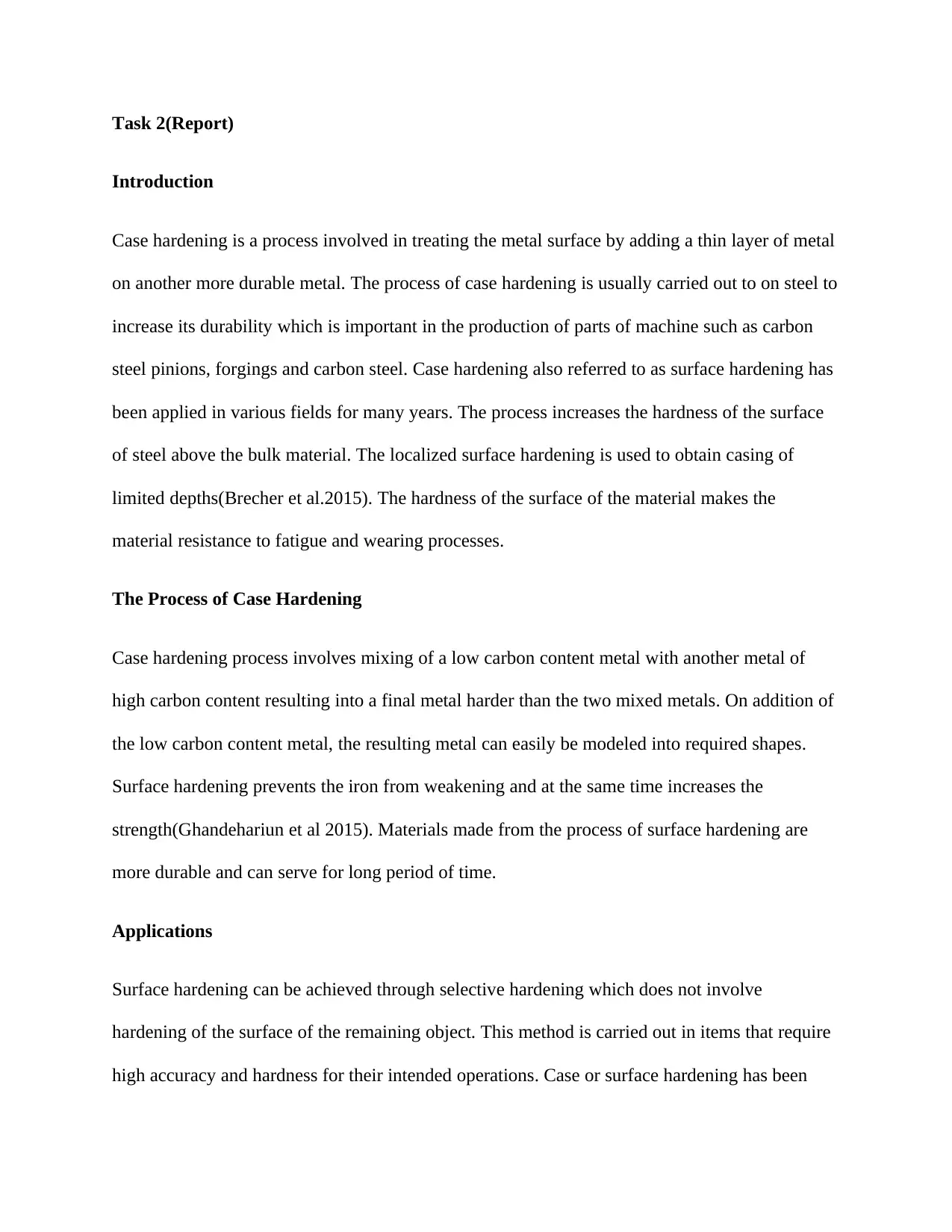
Task 2(Report)
Introduction
Case hardening is a process involved in treating the metal surface by adding a thin layer of metal
on another more durable metal. The process of case hardening is usually carried out to on steel to
increase its durability which is important in the production of parts of machine such as carbon
steel pinions, forgings and carbon steel. Case hardening also referred to as surface hardening has
been applied in various fields for many years. The process increases the hardness of the surface
of steel above the bulk material. The localized surface hardening is used to obtain casing of
limited depths(Brecher et al.2015). The hardness of the surface of the material makes the
material resistance to fatigue and wearing processes.
The Process of Case Hardening
Case hardening process involves mixing of a low carbon content metal with another metal of
high carbon content resulting into a final metal harder than the two mixed metals. On addition of
the low carbon content metal, the resulting metal can easily be modeled into required shapes.
Surface hardening prevents the iron from weakening and at the same time increases the
strength(Ghandehariun et al 2015). Materials made from the process of surface hardening are
more durable and can serve for long period of time.
Applications
Surface hardening can be achieved through selective hardening which does not involve
hardening of the surface of the remaining object. This method is carried out in items that require
high accuracy and hardness for their intended operations. Case or surface hardening has been
Introduction
Case hardening is a process involved in treating the metal surface by adding a thin layer of metal
on another more durable metal. The process of case hardening is usually carried out to on steel to
increase its durability which is important in the production of parts of machine such as carbon
steel pinions, forgings and carbon steel. Case hardening also referred to as surface hardening has
been applied in various fields for many years. The process increases the hardness of the surface
of steel above the bulk material. The localized surface hardening is used to obtain casing of
limited depths(Brecher et al.2015). The hardness of the surface of the material makes the
material resistance to fatigue and wearing processes.
The Process of Case Hardening
Case hardening process involves mixing of a low carbon content metal with another metal of
high carbon content resulting into a final metal harder than the two mixed metals. On addition of
the low carbon content metal, the resulting metal can easily be modeled into required shapes.
Surface hardening prevents the iron from weakening and at the same time increases the
strength(Ghandehariun et al 2015). Materials made from the process of surface hardening are
more durable and can serve for long period of time.
Applications
Surface hardening can be achieved through selective hardening which does not involve
hardening of the surface of the remaining object. This method is carried out in items that require
high accuracy and hardness for their intended operations. Case or surface hardening has been
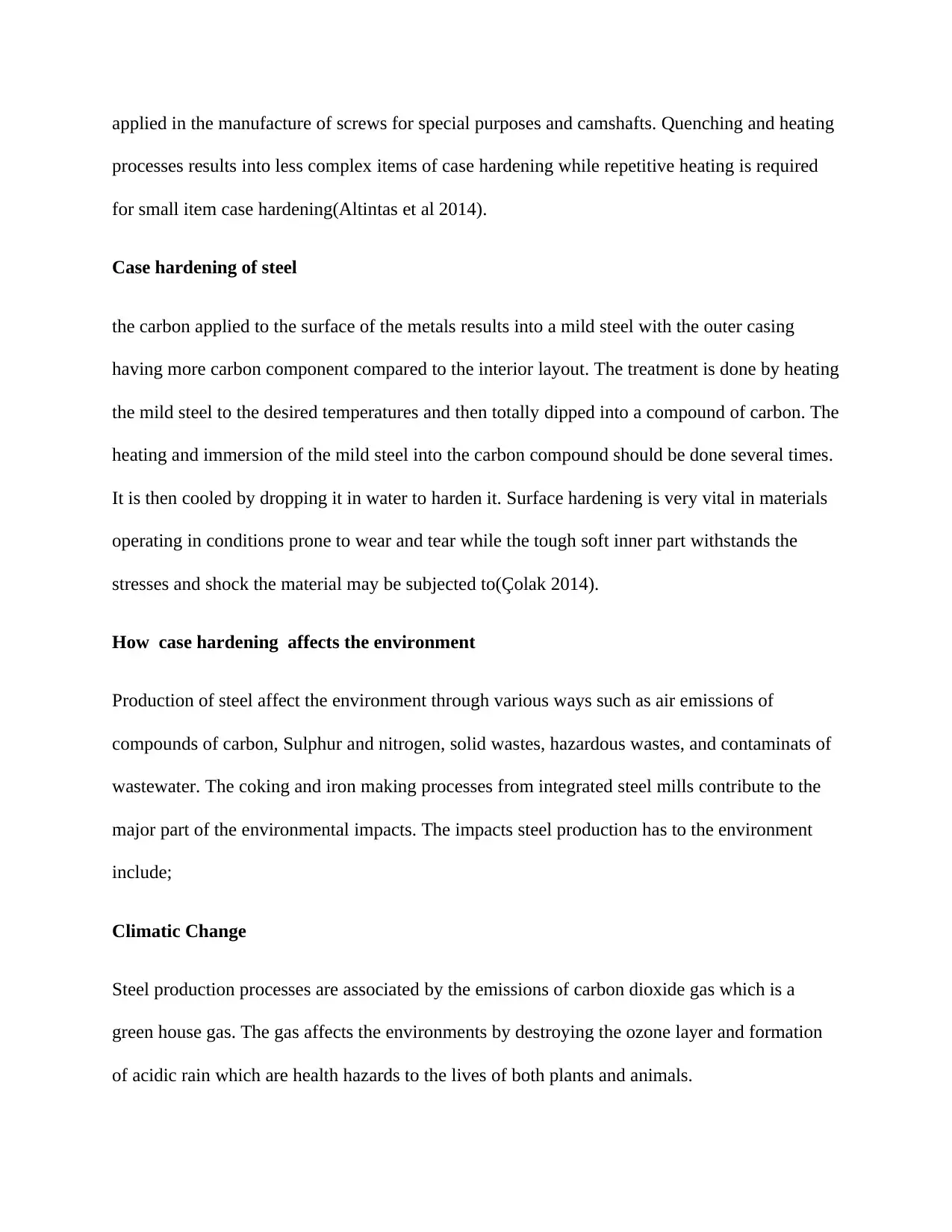
applied in the manufacture of screws for special purposes and camshafts. Quenching and heating
processes results into less complex items of case hardening while repetitive heating is required
for small item case hardening(Altintas et al 2014).
Case hardening of steel
the carbon applied to the surface of the metals results into a mild steel with the outer casing
having more carbon component compared to the interior layout. The treatment is done by heating
the mild steel to the desired temperatures and then totally dipped into a compound of carbon. The
heating and immersion of the mild steel into the carbon compound should be done several times.
It is then cooled by dropping it in water to harden it. Surface hardening is very vital in materials
operating in conditions prone to wear and tear while the tough soft inner part withstands the
stresses and shock the material may be subjected to(Çolak 2014).
How case hardening affects the environment
Production of steel affect the environment through various ways such as air emissions of
compounds of carbon, Sulphur and nitrogen, solid wastes, hazardous wastes, and contaminats of
wastewater. The coking and iron making processes from integrated steel mills contribute to the
major part of the environmental impacts. The impacts steel production has to the environment
include;
Climatic Change
Steel production processes are associated by the emissions of carbon dioxide gas which is a
green house gas. The gas affects the environments by destroying the ozone layer and formation
of acidic rain which are health hazards to the lives of both plants and animals.
processes results into less complex items of case hardening while repetitive heating is required
for small item case hardening(Altintas et al 2014).
Case hardening of steel
the carbon applied to the surface of the metals results into a mild steel with the outer casing
having more carbon component compared to the interior layout. The treatment is done by heating
the mild steel to the desired temperatures and then totally dipped into a compound of carbon. The
heating and immersion of the mild steel into the carbon compound should be done several times.
It is then cooled by dropping it in water to harden it. Surface hardening is very vital in materials
operating in conditions prone to wear and tear while the tough soft inner part withstands the
stresses and shock the material may be subjected to(Çolak 2014).
How case hardening affects the environment
Production of steel affect the environment through various ways such as air emissions of
compounds of carbon, Sulphur and nitrogen, solid wastes, hazardous wastes, and contaminats of
wastewater. The coking and iron making processes from integrated steel mills contribute to the
major part of the environmental impacts. The impacts steel production has to the environment
include;
Climatic Change
Steel production processes are associated by the emissions of carbon dioxide gas which is a
green house gas. The gas affects the environments by destroying the ozone layer and formation
of acidic rain which are health hazards to the lives of both plants and animals.
⊘ This is a preview!⊘
Do you want full access?
Subscribe today to unlock all pages.

Trusted by 1+ million students worldwide
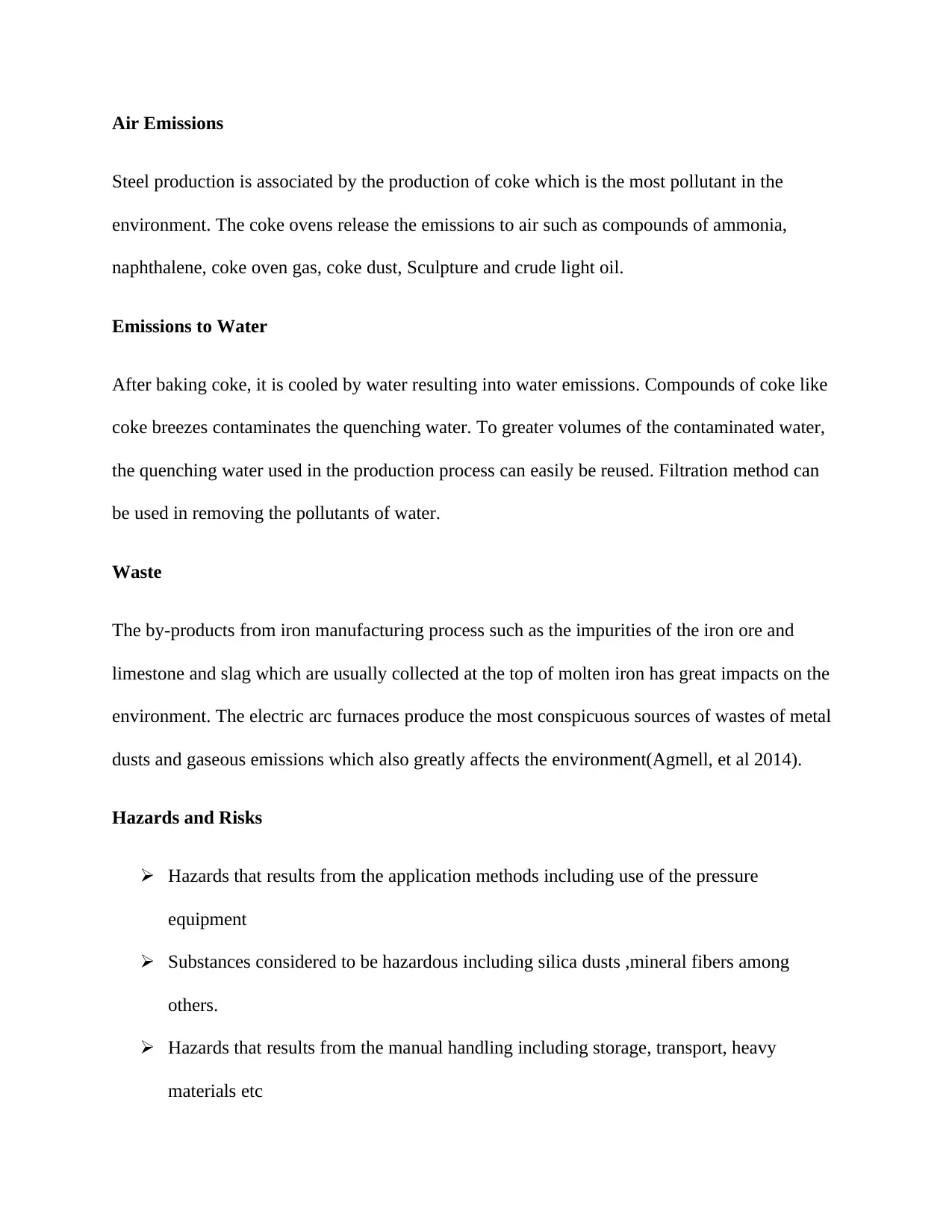
Air Emissions
Steel production is associated by the production of coke which is the most pollutant in the
environment. The coke ovens release the emissions to air such as compounds of ammonia,
naphthalene, coke oven gas, coke dust, Sculpture and crude light oil.
Emissions to Water
After baking coke, it is cooled by water resulting into water emissions. Compounds of coke like
coke breezes contaminates the quenching water. To greater volumes of the contaminated water,
the quenching water used in the production process can easily be reused. Filtration method can
be used in removing the pollutants of water.
Waste
The by-products from iron manufacturing process such as the impurities of the iron ore and
limestone and slag which are usually collected at the top of molten iron has great impacts on the
environment. The electric arc furnaces produce the most conspicuous sources of wastes of metal
dusts and gaseous emissions which also greatly affects the environment(Agmell, et al 2014).
Hazards and Risks
Hazards that results from the application methods including use of the pressure
equipment
Substances considered to be hazardous including silica dusts ,mineral fibers among
others.
Hazards that results from the manual handling including storage, transport, heavy
materials etc
Steel production is associated by the production of coke which is the most pollutant in the
environment. The coke ovens release the emissions to air such as compounds of ammonia,
naphthalene, coke oven gas, coke dust, Sculpture and crude light oil.
Emissions to Water
After baking coke, it is cooled by water resulting into water emissions. Compounds of coke like
coke breezes contaminates the quenching water. To greater volumes of the contaminated water,
the quenching water used in the production process can easily be reused. Filtration method can
be used in removing the pollutants of water.
Waste
The by-products from iron manufacturing process such as the impurities of the iron ore and
limestone and slag which are usually collected at the top of molten iron has great impacts on the
environment. The electric arc furnaces produce the most conspicuous sources of wastes of metal
dusts and gaseous emissions which also greatly affects the environment(Agmell, et al 2014).
Hazards and Risks
Hazards that results from the application methods including use of the pressure
equipment
Substances considered to be hazardous including silica dusts ,mineral fibers among
others.
Hazards that results from the manual handling including storage, transport, heavy
materials etc
Paraphrase This Document
Need a fresh take? Get an instant paraphrase of this document with our AI Paraphraser
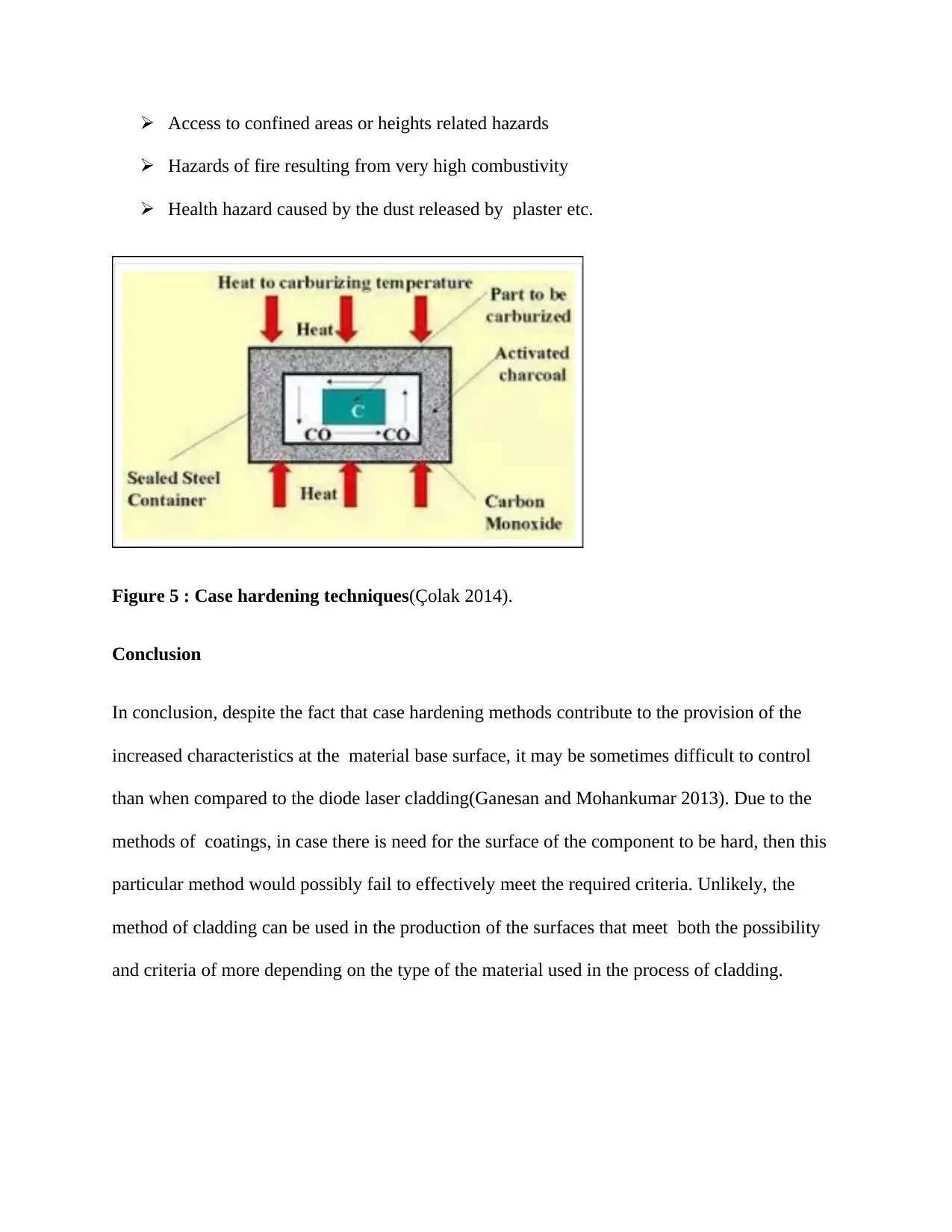
Access to confined areas or heights related hazards
Hazards of fire resulting from very high combustivity
Health hazard caused by the dust released by plaster etc.
Figure 5 : Case hardening techniques(Çolak 2014).
Conclusion
In conclusion, despite the fact that case hardening methods contribute to the provision of the
increased characteristics at the material base surface, it may be sometimes difficult to control
than when compared to the diode laser cladding(Ganesan and Mohankumar 2013). Due to the
methods of coatings, in case there is need for the surface of the component to be hard, then this
particular method would possibly fail to effectively meet the required criteria. Unlikely, the
method of cladding can be used in the production of the surfaces that meet both the possibility
and criteria of more depending on the type of the material used in the process of cladding.
Hazards of fire resulting from very high combustivity
Health hazard caused by the dust released by plaster etc.
Figure 5 : Case hardening techniques(Çolak 2014).
Conclusion
In conclusion, despite the fact that case hardening methods contribute to the provision of the
increased characteristics at the material base surface, it may be sometimes difficult to control
than when compared to the diode laser cladding(Ganesan and Mohankumar 2013). Due to the
methods of coatings, in case there is need for the surface of the component to be hard, then this
particular method would possibly fail to effectively meet the required criteria. Unlikely, the
method of cladding can be used in the production of the surfaces that meet both the possibility
and criteria of more depending on the type of the material used in the process of cladding.
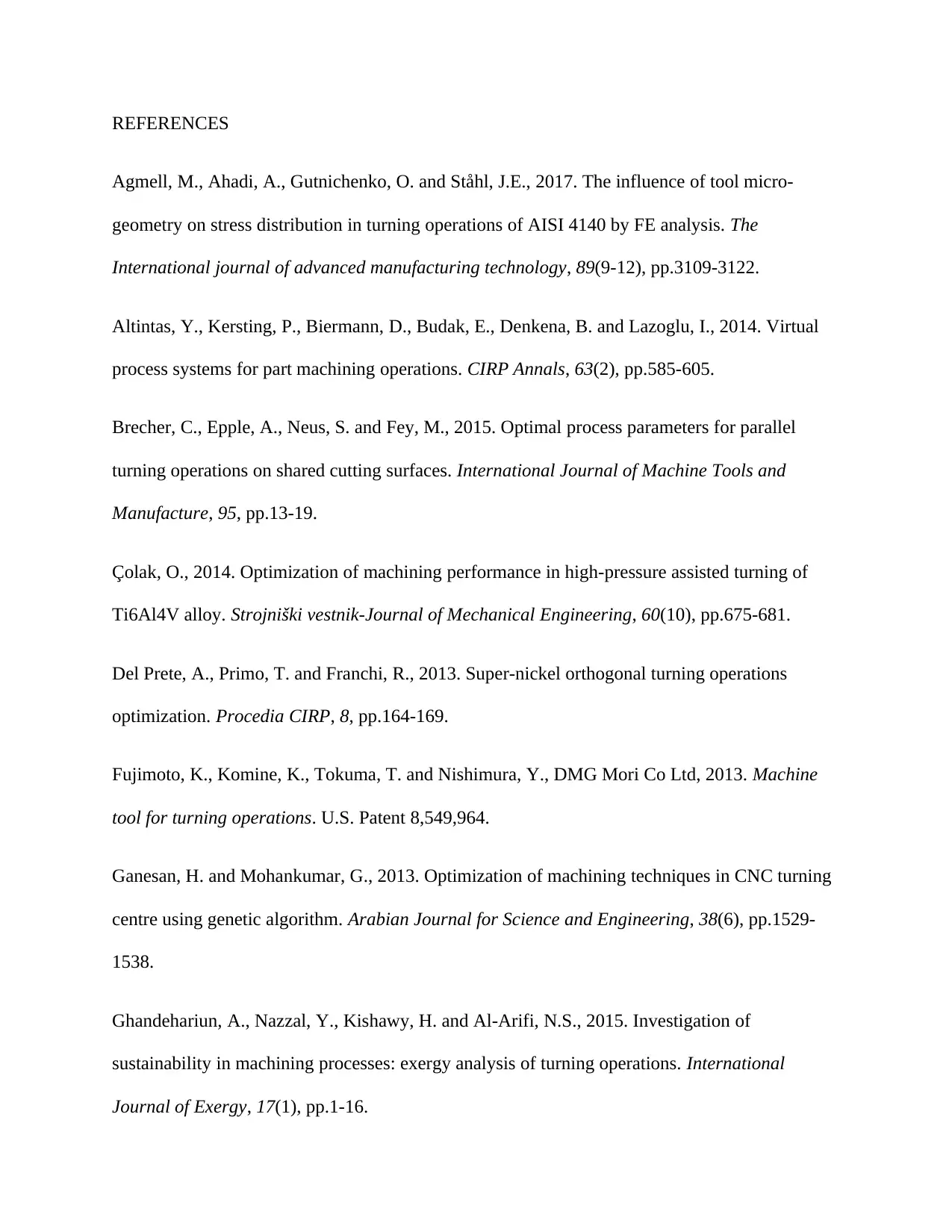
REFERENCES
Agmell, M., Ahadi, A., Gutnichenko, O. and Ståhl, J.E., 2017. The influence of tool micro-
geometry on stress distribution in turning operations of AISI 4140 by FE analysis. The
International journal of advanced manufacturing technology, 89(9-12), pp.3109-3122.
Altintas, Y., Kersting, P., Biermann, D., Budak, E., Denkena, B. and Lazoglu, I., 2014. Virtual
process systems for part machining operations. CIRP Annals, 63(2), pp.585-605.
Brecher, C., Epple, A., Neus, S. and Fey, M., 2015. Optimal process parameters for parallel
turning operations on shared cutting surfaces. International Journal of Machine Tools and
Manufacture, 95, pp.13-19.
Çolak, O., 2014. Optimization of machining performance in high-pressure assisted turning of
Ti6Al4V alloy. Strojniški vestnik-Journal of Mechanical Engineering, 60(10), pp.675-681.
Del Prete, A., Primo, T. and Franchi, R., 2013. Super-nickel orthogonal turning operations
optimization. Procedia CIRP, 8, pp.164-169.
Fujimoto, K., Komine, K., Tokuma, T. and Nishimura, Y., DMG Mori Co Ltd, 2013. Machine
tool for turning operations. U.S. Patent 8,549,964.
Ganesan, H. and Mohankumar, G., 2013. Optimization of machining techniques in CNC turning
centre using genetic algorithm. Arabian Journal for Science and Engineering, 38(6), pp.1529-
1538.
Ghandehariun, A., Nazzal, Y., Kishawy, H. and Al-Arifi, N.S., 2015. Investigation of
sustainability in machining processes: exergy analysis of turning operations. International
Journal of Exergy, 17(1), pp.1-16.
Agmell, M., Ahadi, A., Gutnichenko, O. and Ståhl, J.E., 2017. The influence of tool micro-
geometry on stress distribution in turning operations of AISI 4140 by FE analysis. The
International journal of advanced manufacturing technology, 89(9-12), pp.3109-3122.
Altintas, Y., Kersting, P., Biermann, D., Budak, E., Denkena, B. and Lazoglu, I., 2014. Virtual
process systems for part machining operations. CIRP Annals, 63(2), pp.585-605.
Brecher, C., Epple, A., Neus, S. and Fey, M., 2015. Optimal process parameters for parallel
turning operations on shared cutting surfaces. International Journal of Machine Tools and
Manufacture, 95, pp.13-19.
Çolak, O., 2014. Optimization of machining performance in high-pressure assisted turning of
Ti6Al4V alloy. Strojniški vestnik-Journal of Mechanical Engineering, 60(10), pp.675-681.
Del Prete, A., Primo, T. and Franchi, R., 2013. Super-nickel orthogonal turning operations
optimization. Procedia CIRP, 8, pp.164-169.
Fujimoto, K., Komine, K., Tokuma, T. and Nishimura, Y., DMG Mori Co Ltd, 2013. Machine
tool for turning operations. U.S. Patent 8,549,964.
Ganesan, H. and Mohankumar, G., 2013. Optimization of machining techniques in CNC turning
centre using genetic algorithm. Arabian Journal for Science and Engineering, 38(6), pp.1529-
1538.
Ghandehariun, A., Nazzal, Y., Kishawy, H. and Al-Arifi, N.S., 2015. Investigation of
sustainability in machining processes: exergy analysis of turning operations. International
Journal of Exergy, 17(1), pp.1-16.
⊘ This is a preview!⊘
Do you want full access?
Subscribe today to unlock all pages.

Trusted by 1+ million students worldwide
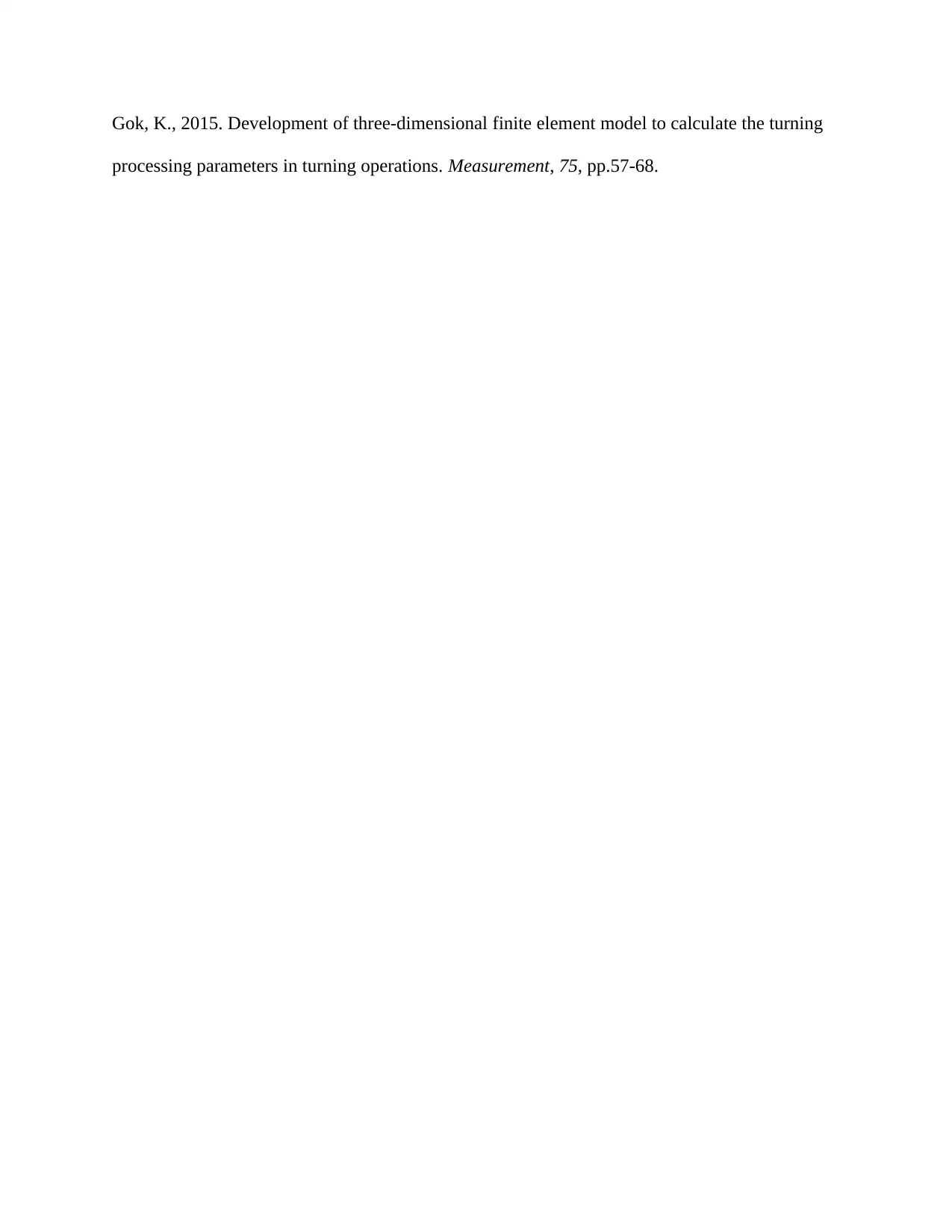
Gok, K., 2015. Development of three-dimensional finite element model to calculate the turning
processing parameters in turning operations. Measurement, 75, pp.57-68.
processing parameters in turning operations. Measurement, 75, pp.57-68.
1 out of 10