Engineering Secondary and Finishing Techniques Report - Unit 21
VerifiedAdded on 2023/03/21
|24
|5019
|21
Report
AI Summary
This report provides a detailed overview of engineering secondary and finishing techniques, focusing on surface hardening of steels, assembly techniques, and finishing methods like anodizing and plating. Surface hardening methods, including diffusion techniques such as carburizing, carbonitriding, nitriding, and nitrocarburizing, as well as energy methods like flame and induction hardening, are discussed. The report also covers manual and automated assembly processes, highlighting the use of screwed fasteners, locking devices, and modularity techniques. Furthermore, it examines anodizing and plating methods, detailing their advantages and applications in enhancing metal surface properties. Desklib offers this and many other solved assignments.
Contribute Materials
Your contribution can guide someone’s learning journey. Share your
documents today.
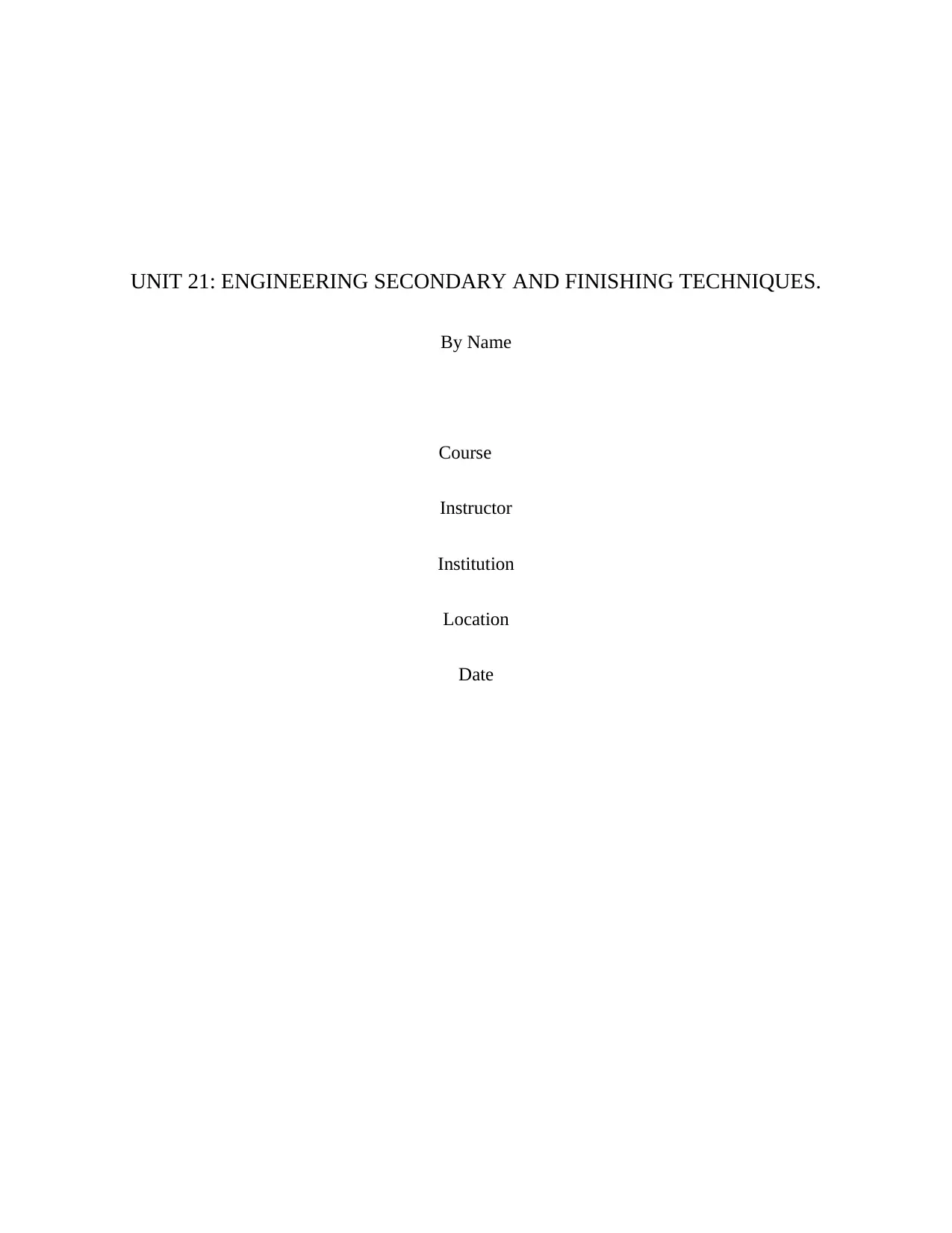
UNIT 21: ENGINEERING SECONDARY AND FINISHING TECHNIQUES.
By Name
Course
Instructor
Institution
Location
Date
By Name
Course
Instructor
Institution
Location
Date
Secure Best Marks with AI Grader
Need help grading? Try our AI Grader for instant feedback on your assignments.
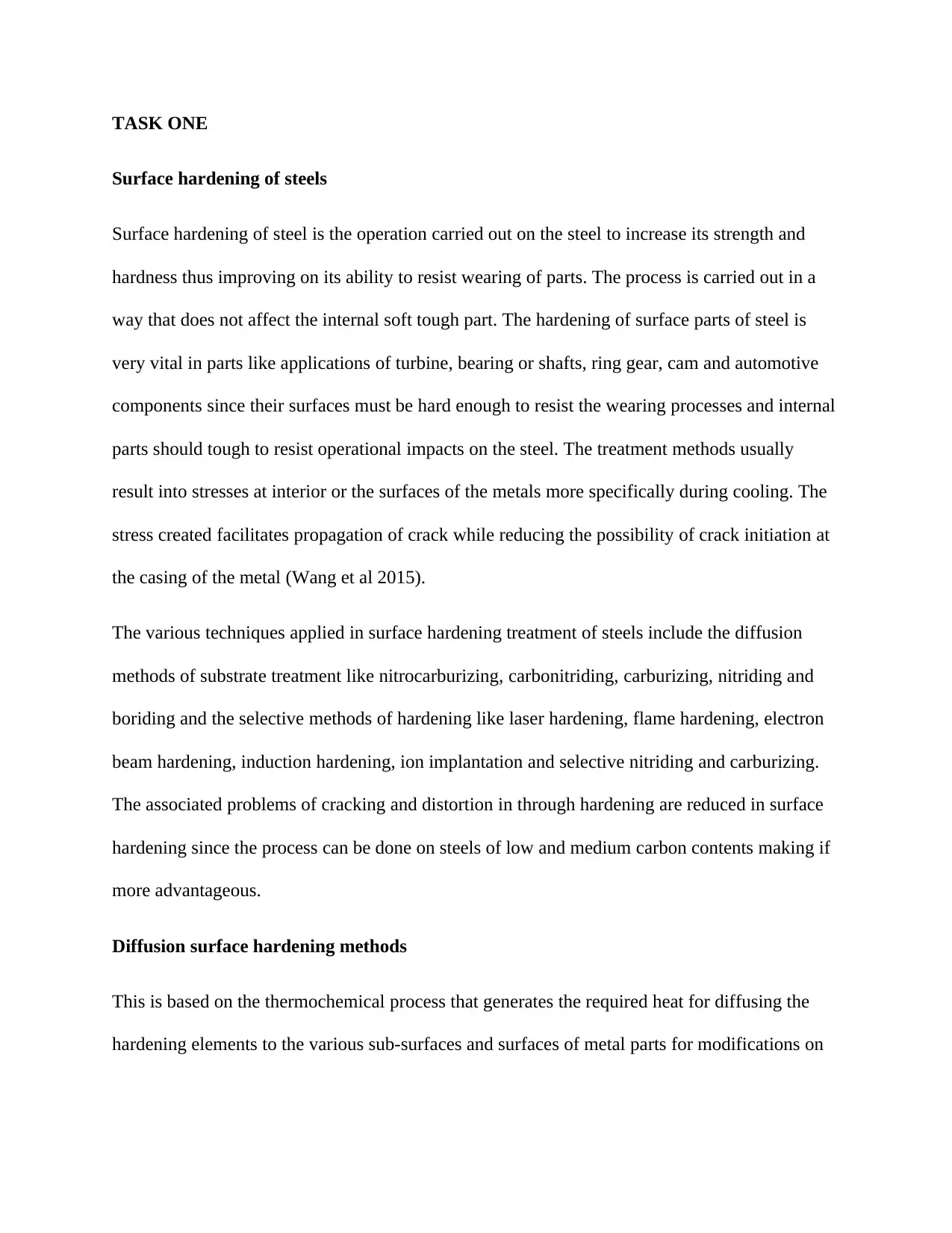
TASK ONE
Surface hardening of steels
Surface hardening of steel is the operation carried out on the steel to increase its strength and
hardness thus improving on its ability to resist wearing of parts. The process is carried out in a
way that does not affect the internal soft tough part. The hardening of surface parts of steel is
very vital in parts like applications of turbine, bearing or shafts, ring gear, cam and automotive
components since their surfaces must be hard enough to resist the wearing processes and internal
parts should tough to resist operational impacts on the steel. The treatment methods usually
result into stresses at interior or the surfaces of the metals more specifically during cooling. The
stress created facilitates propagation of crack while reducing the possibility of crack initiation at
the casing of the metal (Wang et al 2015).
The various techniques applied in surface hardening treatment of steels include the diffusion
methods of substrate treatment like nitrocarburizing, carbonitriding, carburizing, nitriding and
boriding and the selective methods of hardening like laser hardening, flame hardening, electron
beam hardening, induction hardening, ion implantation and selective nitriding and carburizing.
The associated problems of cracking and distortion in through hardening are reduced in surface
hardening since the process can be done on steels of low and medium carbon contents making if
more advantageous.
Diffusion surface hardening methods
This is based on the thermochemical process that generates the required heat for diffusing the
hardening elements to the various sub-surfaces and surfaces of metal parts for modifications on
Surface hardening of steels
Surface hardening of steel is the operation carried out on the steel to increase its strength and
hardness thus improving on its ability to resist wearing of parts. The process is carried out in a
way that does not affect the internal soft tough part. The hardening of surface parts of steel is
very vital in parts like applications of turbine, bearing or shafts, ring gear, cam and automotive
components since their surfaces must be hard enough to resist the wearing processes and internal
parts should tough to resist operational impacts on the steel. The treatment methods usually
result into stresses at interior or the surfaces of the metals more specifically during cooling. The
stress created facilitates propagation of crack while reducing the possibility of crack initiation at
the casing of the metal (Wang et al 2015).
The various techniques applied in surface hardening treatment of steels include the diffusion
methods of substrate treatment like nitrocarburizing, carbonitriding, carburizing, nitriding and
boriding and the selective methods of hardening like laser hardening, flame hardening, electron
beam hardening, induction hardening, ion implantation and selective nitriding and carburizing.
The associated problems of cracking and distortion in through hardening are reduced in surface
hardening since the process can be done on steels of low and medium carbon contents making if
more advantageous.
Diffusion surface hardening methods
This is based on the thermochemical process that generates the required heat for diffusing the
hardening elements to the various sub-surfaces and surfaces of metal parts for modifications on
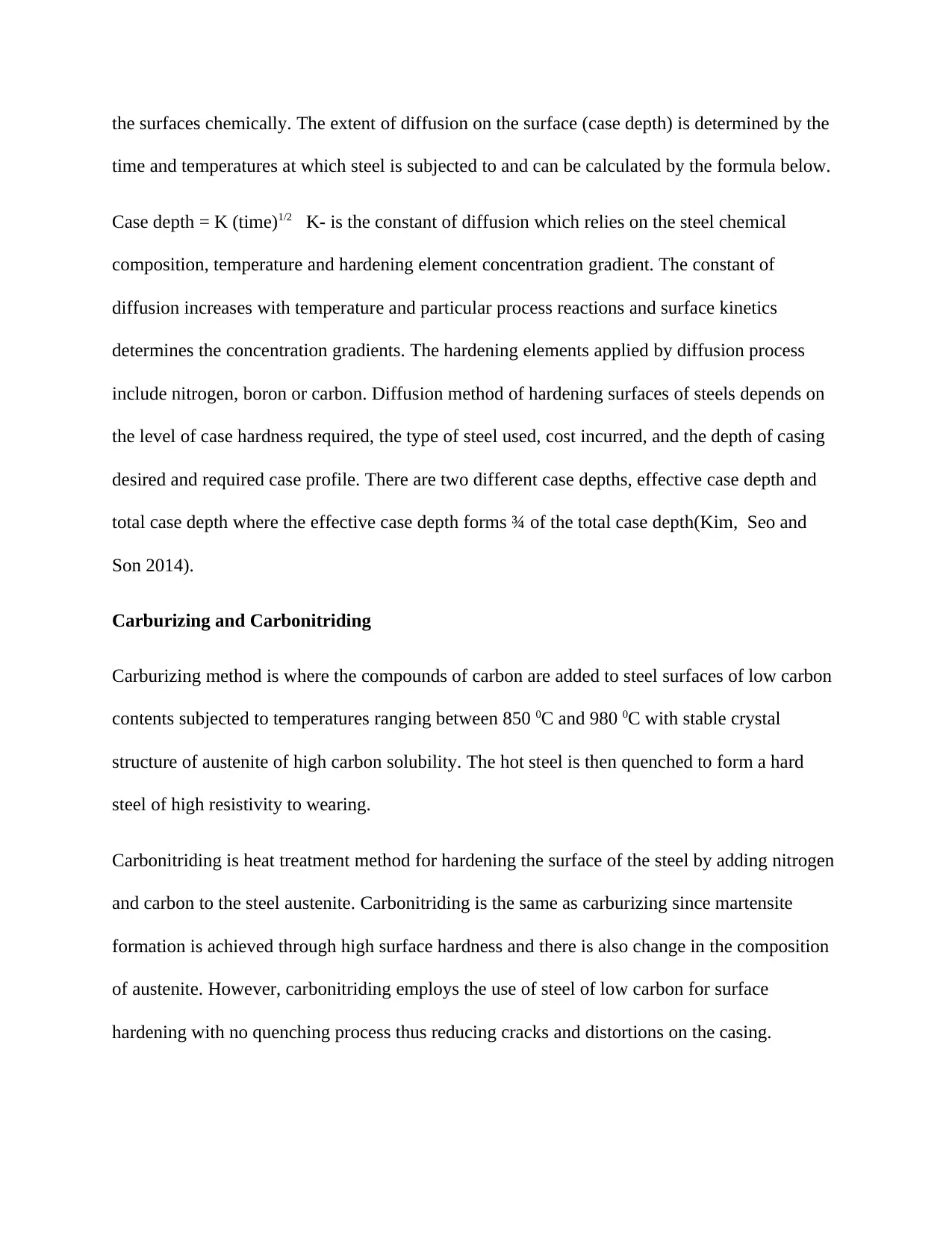
the surfaces chemically. The extent of diffusion on the surface (case depth) is determined by the
time and temperatures at which steel is subjected to and can be calculated by the formula below.
Case depth = K (time)1/2 K- is the constant of diffusion which relies on the steel chemical
composition, temperature and hardening element concentration gradient. The constant of
diffusion increases with temperature and particular process reactions and surface kinetics
determines the concentration gradients. The hardening elements applied by diffusion process
include nitrogen, boron or carbon. Diffusion method of hardening surfaces of steels depends on
the level of case hardness required, the type of steel used, cost incurred, and the depth of casing
desired and required case profile. There are two different case depths, effective case depth and
total case depth where the effective case depth forms ¾ of the total case depth(Kim, Seo and
Son 2014).
Carburizing and Carbonitriding
Carburizing method is where the compounds of carbon are added to steel surfaces of low carbon
contents subjected to temperatures ranging between 850 0C and 980 0C with stable crystal
structure of austenite of high carbon solubility. The hot steel is then quenched to form a hard
steel of high resistivity to wearing.
Carbonitriding is heat treatment method for hardening the surface of the steel by adding nitrogen
and carbon to the steel austenite. Carbonitriding is the same as carburizing since martensite
formation is achieved through high surface hardness and there is also change in the composition
of austenite. However, carbonitriding employs the use of steel of low carbon for surface
hardening with no quenching process thus reducing cracks and distortions on the casing.
time and temperatures at which steel is subjected to and can be calculated by the formula below.
Case depth = K (time)1/2 K- is the constant of diffusion which relies on the steel chemical
composition, temperature and hardening element concentration gradient. The constant of
diffusion increases with temperature and particular process reactions and surface kinetics
determines the concentration gradients. The hardening elements applied by diffusion process
include nitrogen, boron or carbon. Diffusion method of hardening surfaces of steels depends on
the level of case hardness required, the type of steel used, cost incurred, and the depth of casing
desired and required case profile. There are two different case depths, effective case depth and
total case depth where the effective case depth forms ¾ of the total case depth(Kim, Seo and
Son 2014).
Carburizing and Carbonitriding
Carburizing method is where the compounds of carbon are added to steel surfaces of low carbon
contents subjected to temperatures ranging between 850 0C and 980 0C with stable crystal
structure of austenite of high carbon solubility. The hot steel is then quenched to form a hard
steel of high resistivity to wearing.
Carbonitriding is heat treatment method for hardening the surface of the steel by adding nitrogen
and carbon to the steel austenite. Carbonitriding is the same as carburizing since martensite
formation is achieved through high surface hardness and there is also change in the composition
of austenite. However, carbonitriding employs the use of steel of low carbon for surface
hardening with no quenching process thus reducing cracks and distortions on the casing.
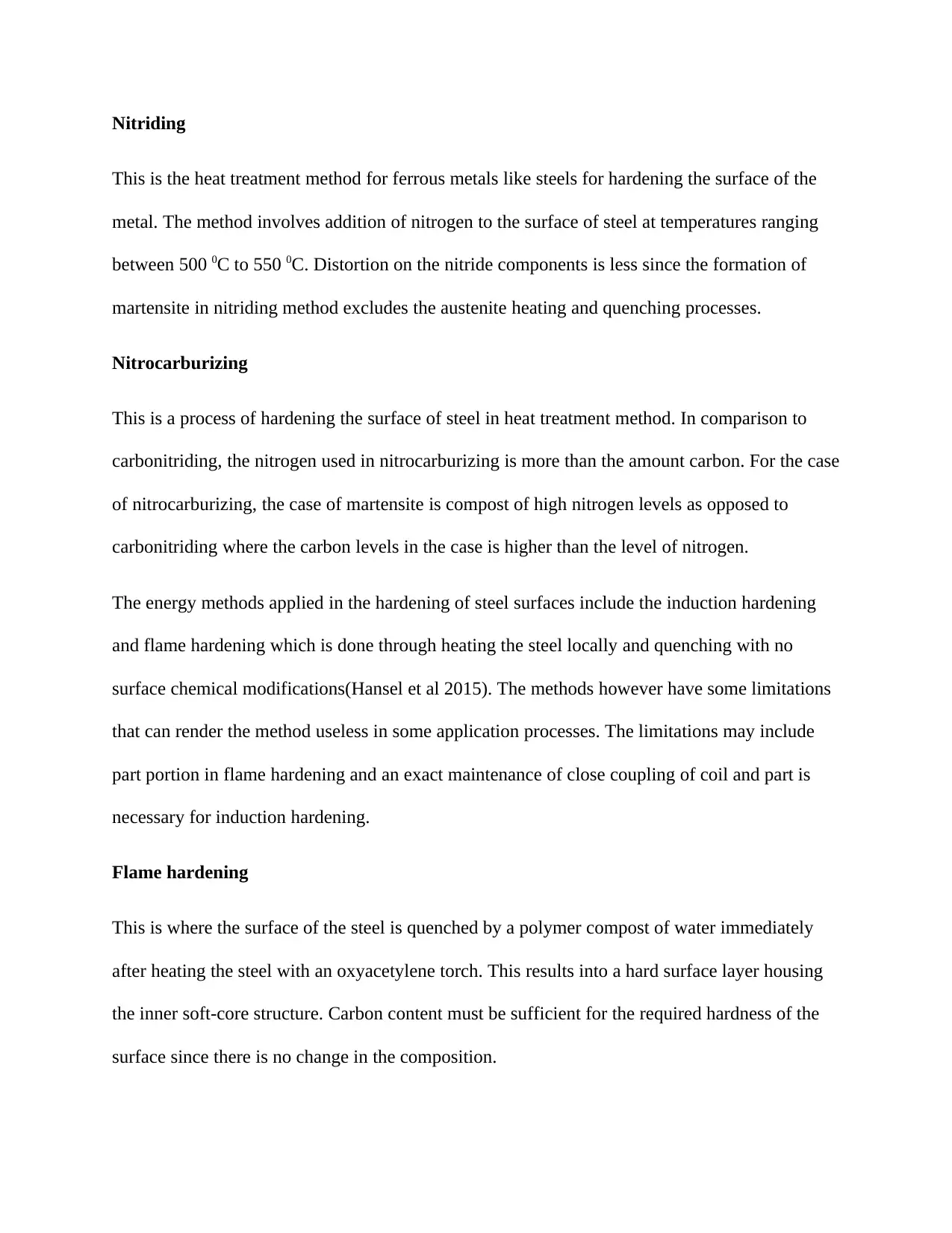
Nitriding
This is the heat treatment method for ferrous metals like steels for hardening the surface of the
metal. The method involves addition of nitrogen to the surface of steel at temperatures ranging
between 500 0C to 550 0C. Distortion on the nitride components is less since the formation of
martensite in nitriding method excludes the austenite heating and quenching processes.
Nitrocarburizing
This is a process of hardening the surface of steel in heat treatment method. In comparison to
carbonitriding, the nitrogen used in nitrocarburizing is more than the amount carbon. For the case
of nitrocarburizing, the case of martensite is compost of high nitrogen levels as opposed to
carbonitriding where the carbon levels in the case is higher than the level of nitrogen.
The energy methods applied in the hardening of steel surfaces include the induction hardening
and flame hardening which is done through heating the steel locally and quenching with no
surface chemical modifications(Hansel et al 2015). The methods however have some limitations
that can render the method useless in some application processes. The limitations may include
part portion in flame hardening and an exact maintenance of close coupling of coil and part is
necessary for induction hardening.
Flame hardening
This is where the surface of the steel is quenched by a polymer compost of water immediately
after heating the steel with an oxyacetylene torch. This results into a hard surface layer housing
the inner soft-core structure. Carbon content must be sufficient for the required hardness of the
surface since there is no change in the composition.
This is the heat treatment method for ferrous metals like steels for hardening the surface of the
metal. The method involves addition of nitrogen to the surface of steel at temperatures ranging
between 500 0C to 550 0C. Distortion on the nitride components is less since the formation of
martensite in nitriding method excludes the austenite heating and quenching processes.
Nitrocarburizing
This is a process of hardening the surface of steel in heat treatment method. In comparison to
carbonitriding, the nitrogen used in nitrocarburizing is more than the amount carbon. For the case
of nitrocarburizing, the case of martensite is compost of high nitrogen levels as opposed to
carbonitriding where the carbon levels in the case is higher than the level of nitrogen.
The energy methods applied in the hardening of steel surfaces include the induction hardening
and flame hardening which is done through heating the steel locally and quenching with no
surface chemical modifications(Hansel et al 2015). The methods however have some limitations
that can render the method useless in some application processes. The limitations may include
part portion in flame hardening and an exact maintenance of close coupling of coil and part is
necessary for induction hardening.
Flame hardening
This is where the surface of the steel is quenched by a polymer compost of water immediately
after heating the steel with an oxyacetylene torch. This results into a hard surface layer housing
the inner soft-core structure. Carbon content must be sufficient for the required hardness of the
surface since there is no change in the composition.
Secure Best Marks with AI Grader
Need help grading? Try our AI Grader for instant feedback on your assignments.
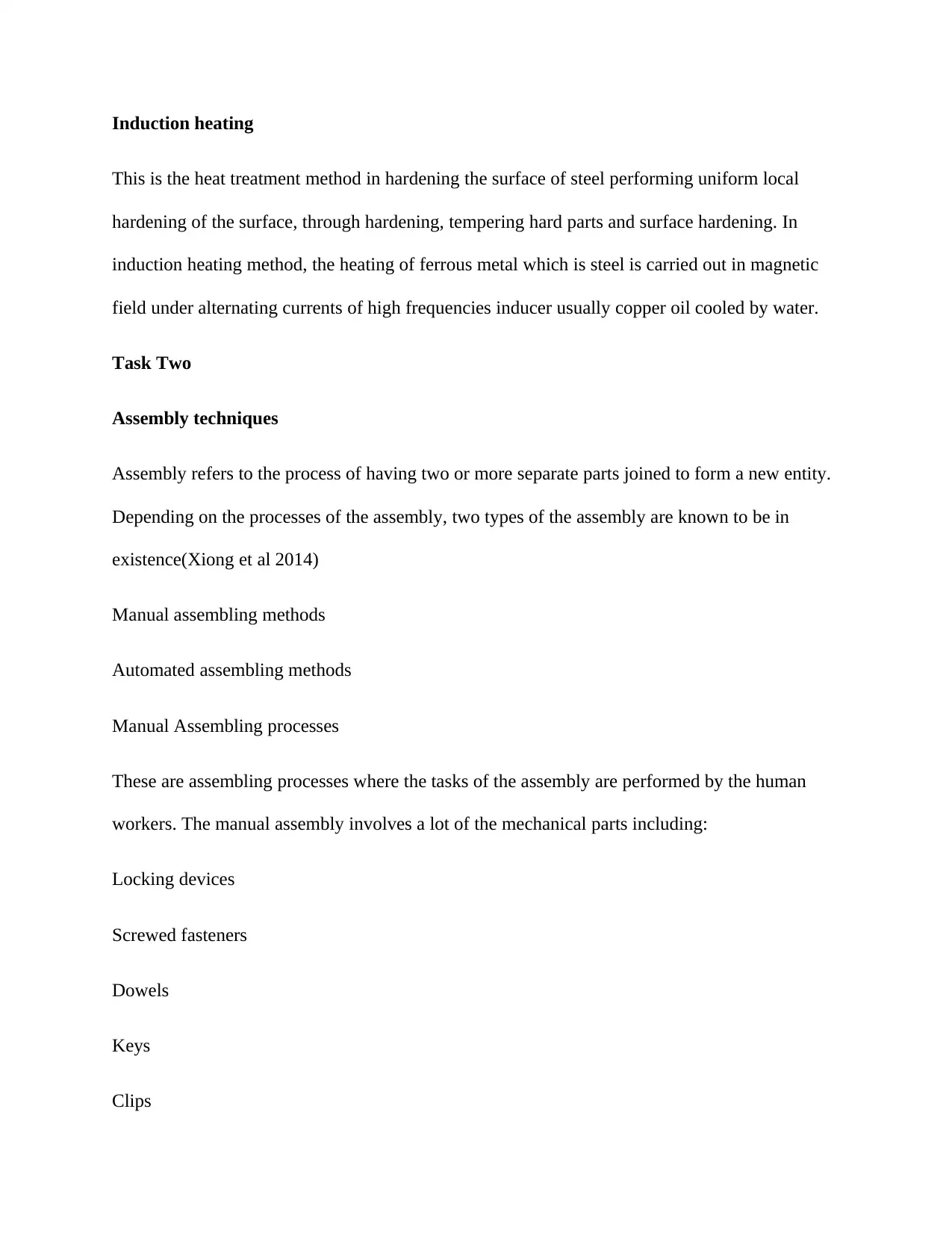
Induction heating
This is the heat treatment method in hardening the surface of steel performing uniform local
hardening of the surface, through hardening, tempering hard parts and surface hardening. In
induction heating method, the heating of ferrous metal which is steel is carried out in magnetic
field under alternating currents of high frequencies inducer usually copper oil cooled by water.
Task Two
Assembly techniques
Assembly refers to the process of having two or more separate parts joined to form a new entity.
Depending on the processes of the assembly, two types of the assembly are known to be in
existence(Xiong et al 2014)
Manual assembling methods
Automated assembling methods
Manual Assembling processes
These are assembling processes where the tasks of the assembly are performed by the human
workers. The manual assembly involves a lot of the mechanical parts including:
Locking devices
Screwed fasteners
Dowels
Keys
Clips
This is the heat treatment method in hardening the surface of steel performing uniform local
hardening of the surface, through hardening, tempering hard parts and surface hardening. In
induction heating method, the heating of ferrous metal which is steel is carried out in magnetic
field under alternating currents of high frequencies inducer usually copper oil cooled by water.
Task Two
Assembly techniques
Assembly refers to the process of having two or more separate parts joined to form a new entity.
Depending on the processes of the assembly, two types of the assembly are known to be in
existence(Xiong et al 2014)
Manual assembling methods
Automated assembling methods
Manual Assembling processes
These are assembling processes where the tasks of the assembly are performed by the human
workers. The manual assembly involves a lot of the mechanical parts including:
Locking devices
Screwed fasteners
Dowels
Keys
Clips
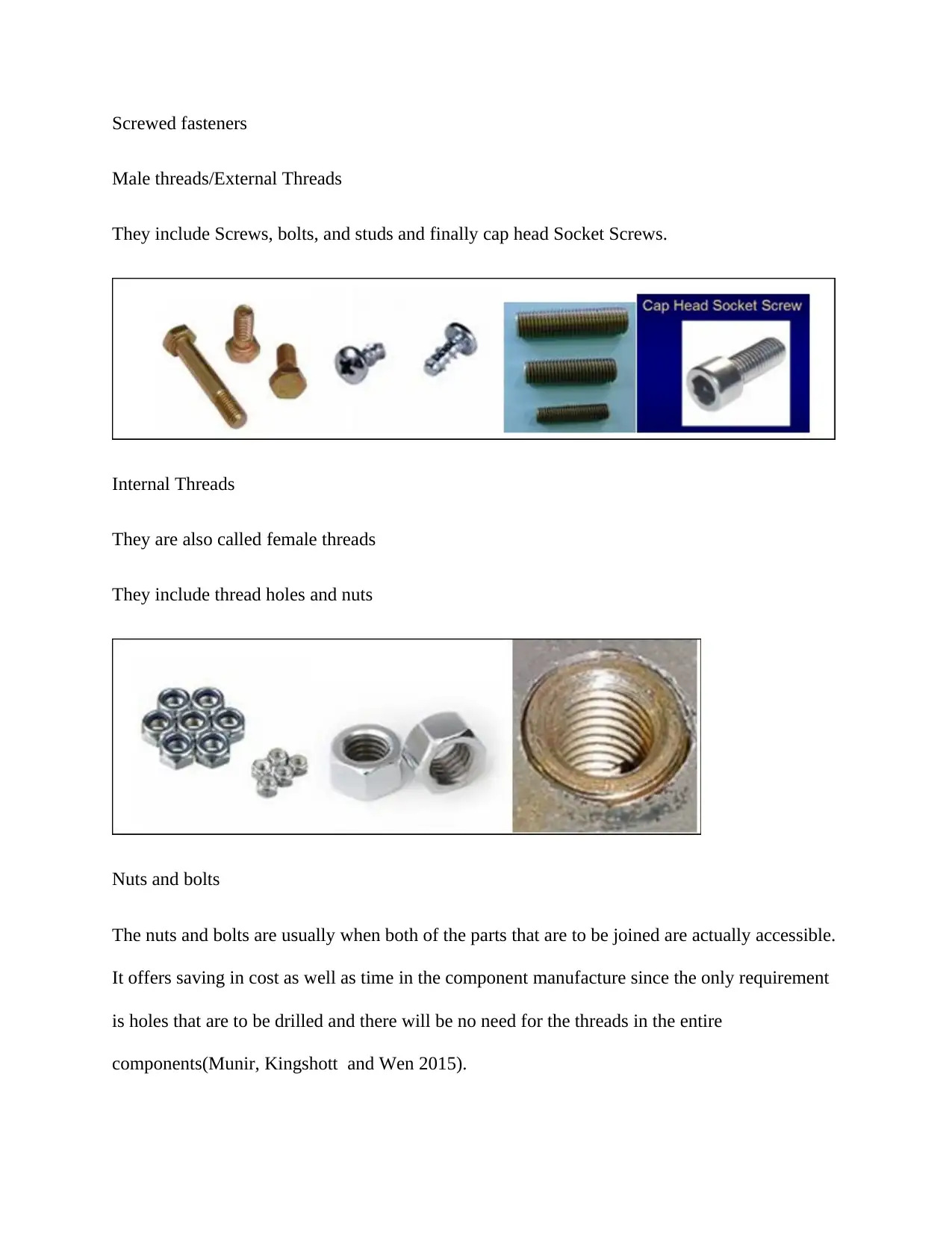
Screwed fasteners
Male threads/External Threads
They include Screws, bolts, and studs and finally cap head Socket Screws.
Internal Threads
They are also called female threads
They include thread holes and nuts
Nuts and bolts
The nuts and bolts are usually when both of the parts that are to be joined are actually accessible.
It offers saving in cost as well as time in the component manufacture since the only requirement
is holes that are to be drilled and there will be no need for the threads in the entire
components(Munir, Kingshott and Wen 2015).
Male threads/External Threads
They include Screws, bolts, and studs and finally cap head Socket Screws.
Internal Threads
They are also called female threads
They include thread holes and nuts
Nuts and bolts
The nuts and bolts are usually when both of the parts that are to be joined are actually accessible.
It offers saving in cost as well as time in the component manufacture since the only requirement
is holes that are to be drilled and there will be no need for the threads in the entire
components(Munir, Kingshott and Wen 2015).
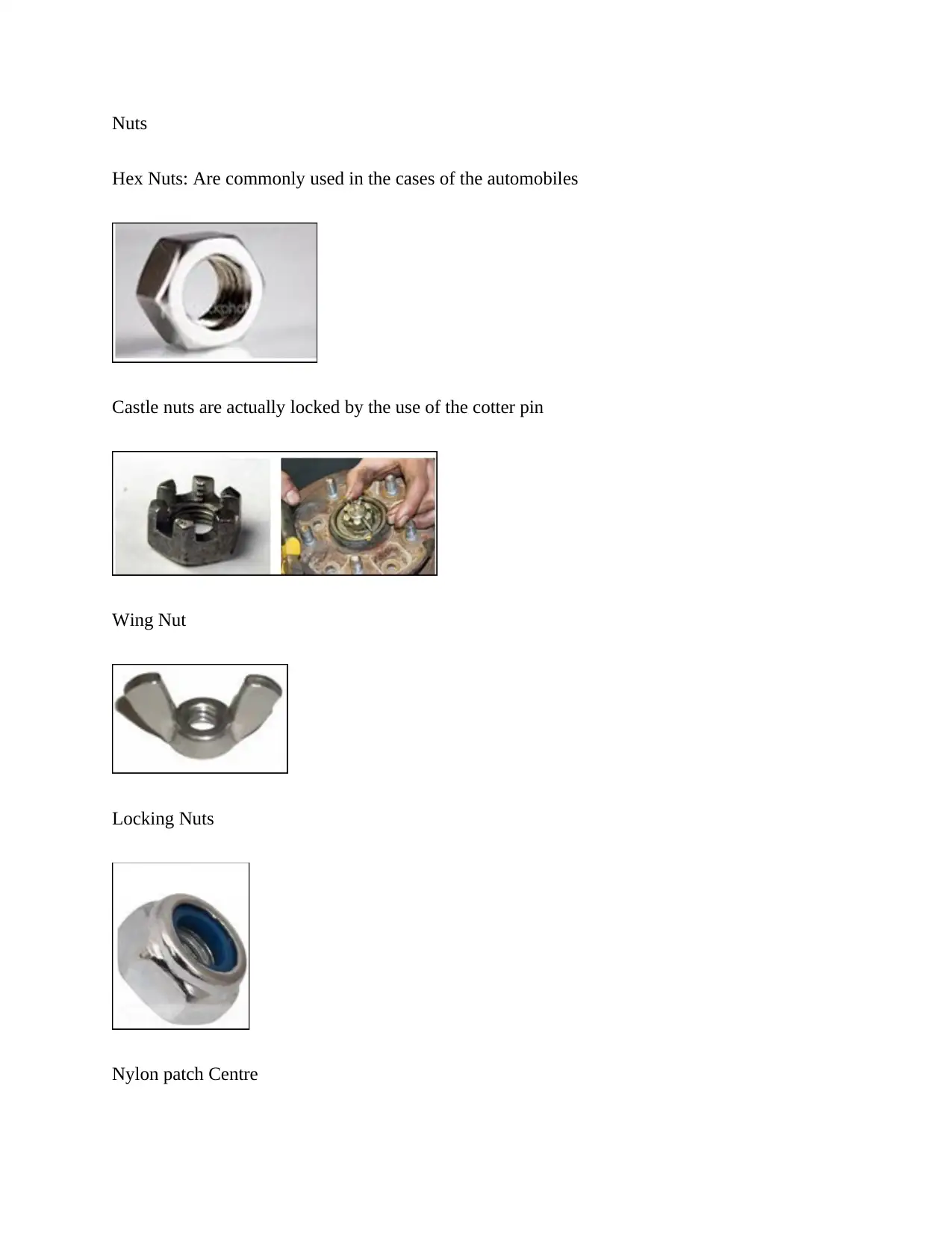
Nuts
Hex Nuts: Are commonly used in the cases of the automobiles
Castle nuts are actually locked by the use of the cotter pin
Wing Nut
Locking Nuts
Nylon patch Centre
Hex Nuts: Are commonly used in the cases of the automobiles
Castle nuts are actually locked by the use of the cotter pin
Wing Nut
Locking Nuts
Nylon patch Centre
Paraphrase This Document
Need a fresh take? Get an instant paraphrase of this document with our AI Paraphraser
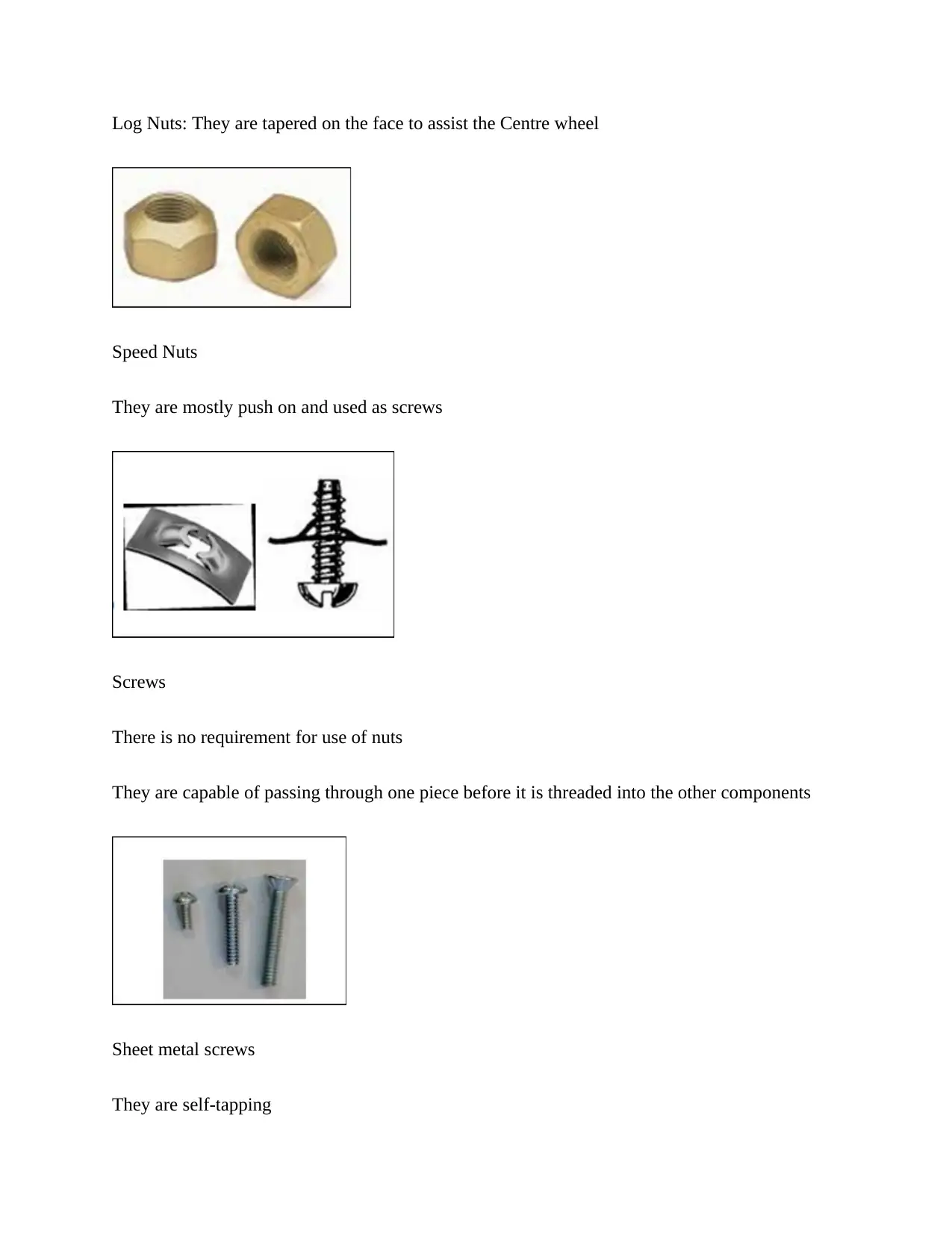
Log Nuts: They are tapered on the face to assist the Centre wheel
Speed Nuts
They are mostly push on and used as screws
Screws
There is no requirement for use of nuts
They are capable of passing through one piece before it is threaded into the other components
Sheet metal screws
They are self-tapping
Speed Nuts
They are mostly push on and used as screws
Screws
There is no requirement for use of nuts
They are capable of passing through one piece before it is threaded into the other components
Sheet metal screws
They are self-tapping
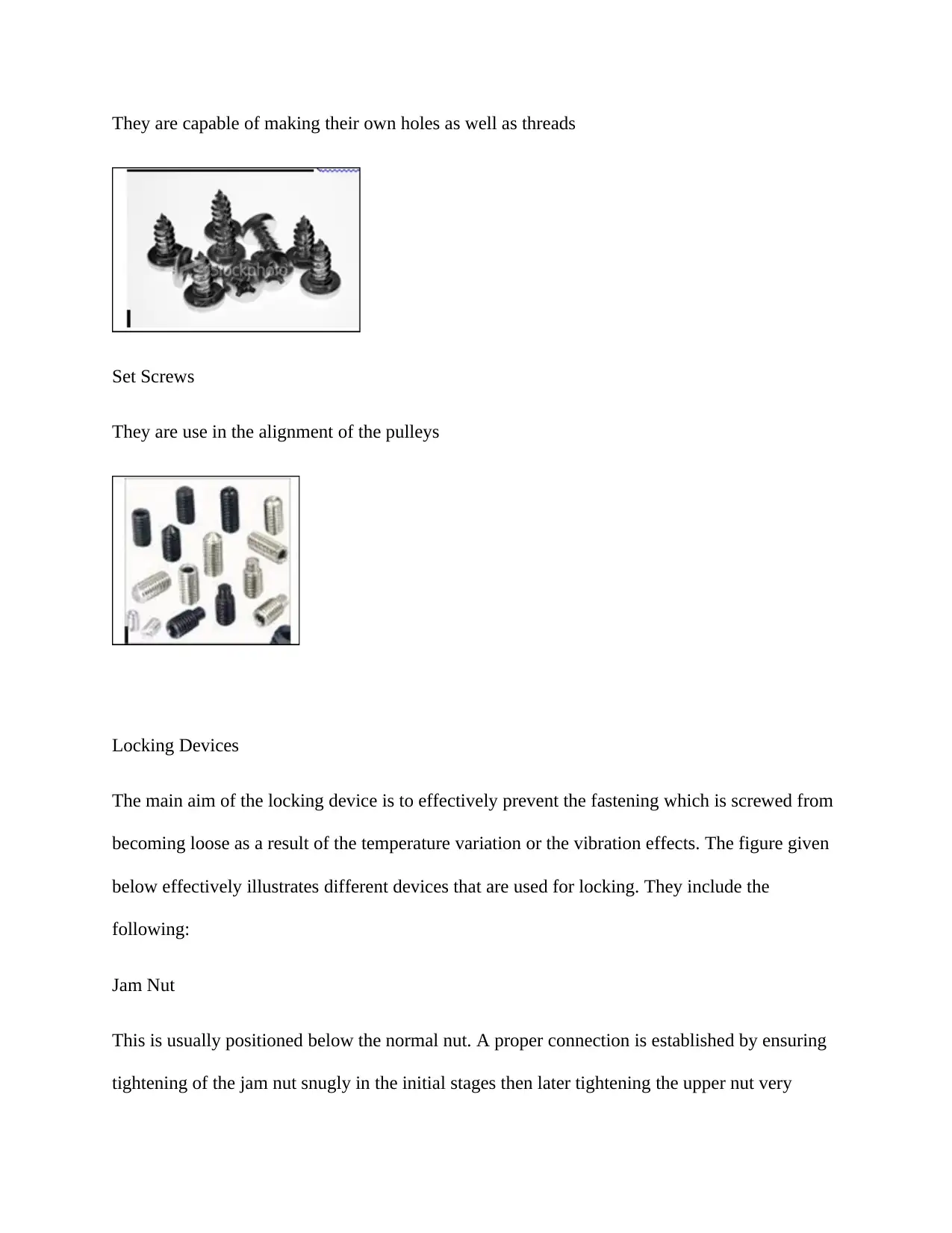
They are capable of making their own holes as well as threads
Set Screws
They are use in the alignment of the pulleys
Locking Devices
The main aim of the locking device is to effectively prevent the fastening which is screwed from
becoming loose as a result of the temperature variation or the vibration effects. The figure given
below effectively illustrates different devices that are used for locking. They include the
following:
Jam Nut
This is usually positioned below the normal nut. A proper connection is established by ensuring
tightening of the jam nut snugly in the initial stages then later tightening the upper nut very
Set Screws
They are use in the alignment of the pulleys
Locking Devices
The main aim of the locking device is to effectively prevent the fastening which is screwed from
becoming loose as a result of the temperature variation or the vibration effects. The figure given
below effectively illustrates different devices that are used for locking. They include the
following:
Jam Nut
This is usually positioned below the normal nut. A proper connection is established by ensuring
tightening of the jam nut snugly in the initial stages then later tightening the upper nut very
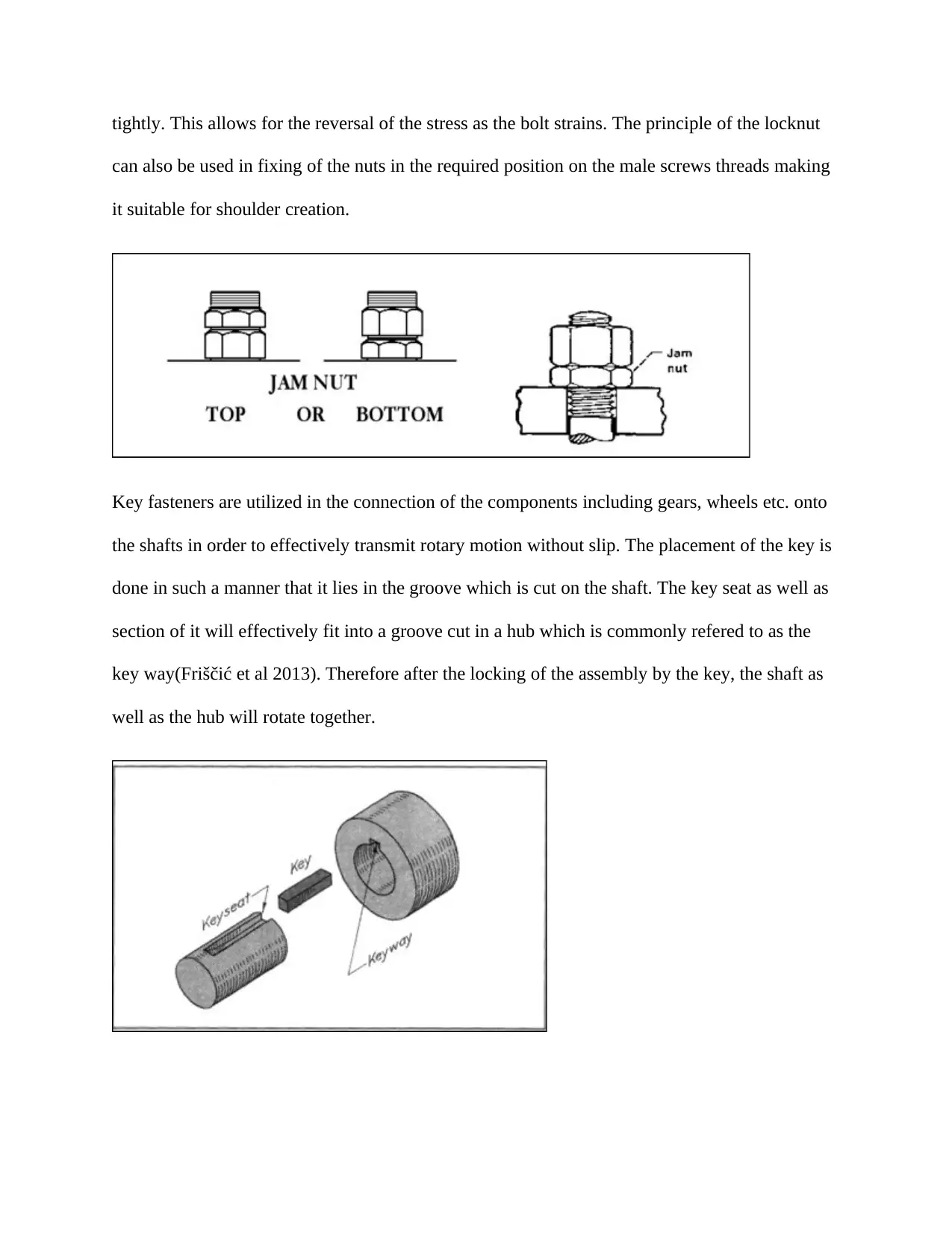
tightly. This allows for the reversal of the stress as the bolt strains. The principle of the locknut
can also be used in fixing of the nuts in the required position on the male screws threads making
it suitable for shoulder creation.
Key fasteners are utilized in the connection of the components including gears, wheels etc. onto
the shafts in order to effectively transmit rotary motion without slip. The placement of the key is
done in such a manner that it lies in the groove which is cut on the shaft. The key seat as well as
section of it will effectively fit into a groove cut in a hub which is commonly refered to as the
key way(Friščić et al 2013). Therefore after the locking of the assembly by the key, the shaft as
well as the hub will rotate together.
can also be used in fixing of the nuts in the required position on the male screws threads making
it suitable for shoulder creation.
Key fasteners are utilized in the connection of the components including gears, wheels etc. onto
the shafts in order to effectively transmit rotary motion without slip. The placement of the key is
done in such a manner that it lies in the groove which is cut on the shaft. The key seat as well as
section of it will effectively fit into a groove cut in a hub which is commonly refered to as the
key way(Friščić et al 2013). Therefore after the locking of the assembly by the key, the shaft as
well as the hub will rotate together.
Secure Best Marks with AI Grader
Need help grading? Try our AI Grader for instant feedback on your assignments.
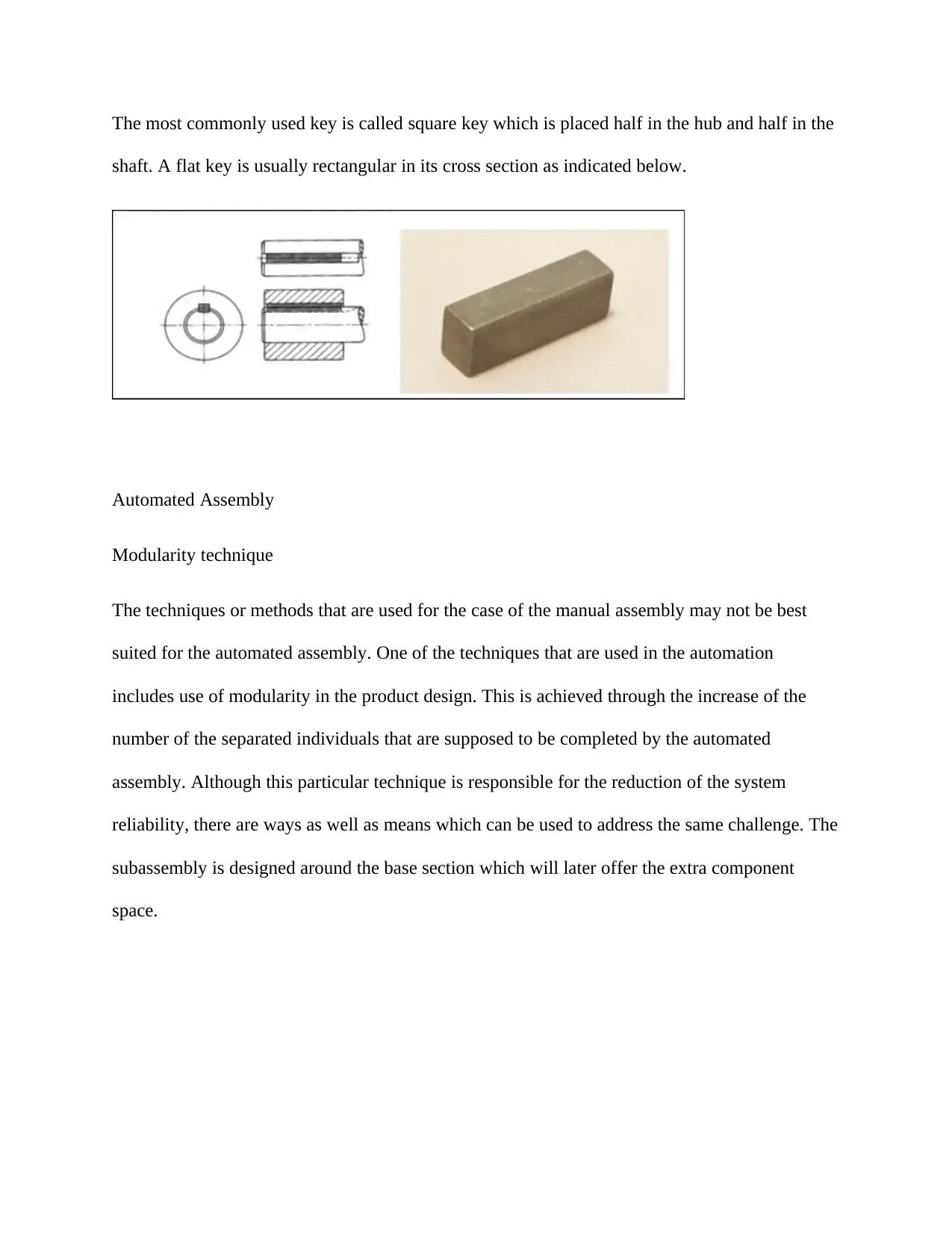
The most commonly used key is called square key which is placed half in the hub and half in the
shaft. A flat key is usually rectangular in its cross section as indicated below.
Automated Assembly
Modularity technique
The techniques or methods that are used for the case of the manual assembly may not be best
suited for the automated assembly. One of the techniques that are used in the automation
includes use of modularity in the product design. This is achieved through the increase of the
number of the separated individuals that are supposed to be completed by the automated
assembly. Although this particular technique is responsible for the reduction of the system
reliability, there are ways as well as means which can be used to address the same challenge. The
subassembly is designed around the base section which will later offer the extra component
space.
shaft. A flat key is usually rectangular in its cross section as indicated below.
Automated Assembly
Modularity technique
The techniques or methods that are used for the case of the manual assembly may not be best
suited for the automated assembly. One of the techniques that are used in the automation
includes use of modularity in the product design. This is achieved through the increase of the
number of the separated individuals that are supposed to be completed by the automated
assembly. Although this particular technique is responsible for the reduction of the system
reliability, there are ways as well as means which can be used to address the same challenge. The
subassembly is designed around the base section which will later offer the extra component
space.
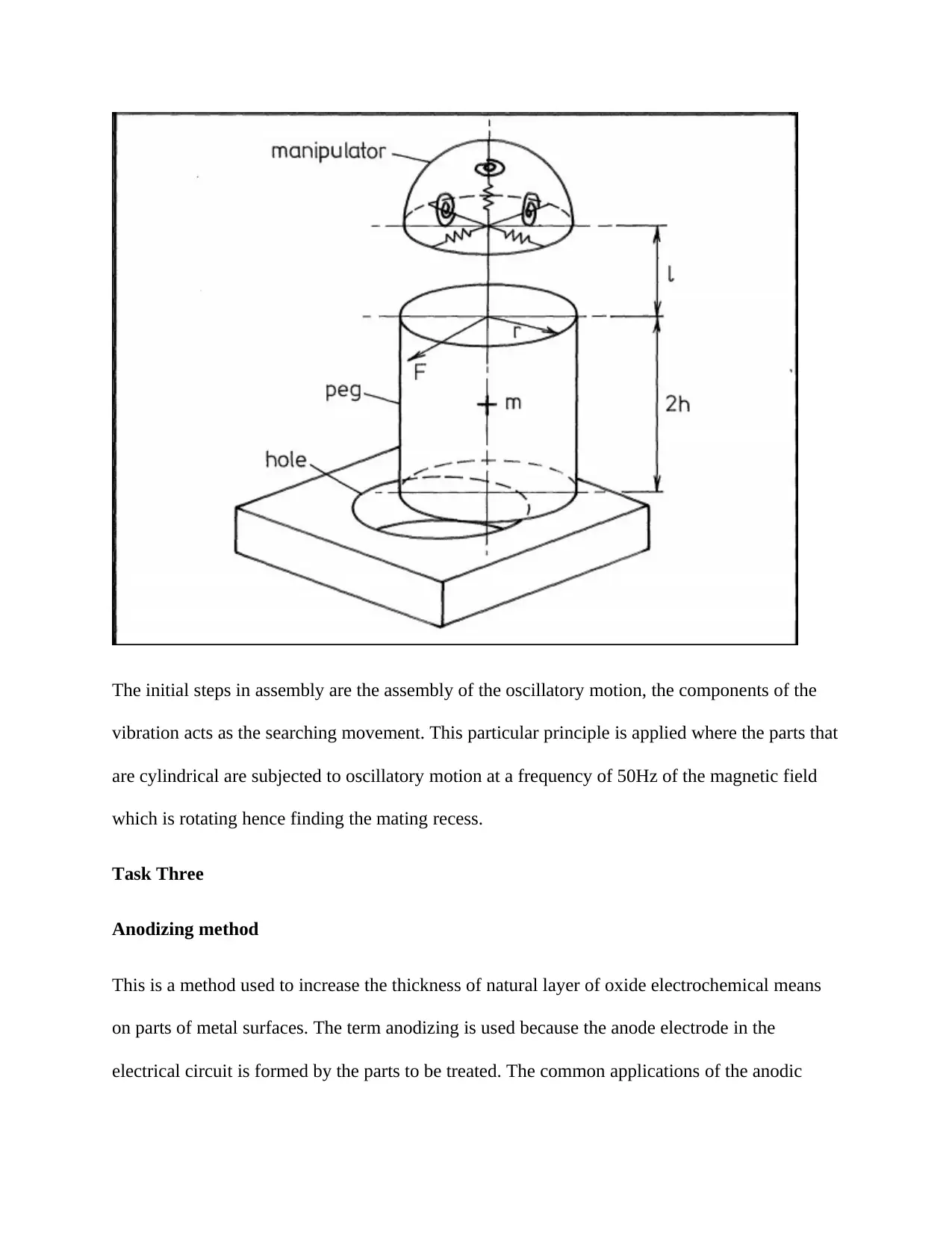
The initial steps in assembly are the assembly of the oscillatory motion, the components of the
vibration acts as the searching movement. This particular principle is applied where the parts that
are cylindrical are subjected to oscillatory motion at a frequency of 50Hz of the magnetic field
which is rotating hence finding the mating recess.
Task Three
Anodizing method
This is a method used to increase the thickness of natural layer of oxide electrochemical means
on parts of metal surfaces. The term anodizing is used because the anode electrode in the
electrical circuit is formed by the parts to be treated. The common applications of the anodic
vibration acts as the searching movement. This particular principle is applied where the parts that
are cylindrical are subjected to oscillatory motion at a frequency of 50Hz of the magnetic field
which is rotating hence finding the mating recess.
Task Three
Anodizing method
This is a method used to increase the thickness of natural layer of oxide electrochemical means
on parts of metal surfaces. The term anodizing is used because the anode electrode in the
electrical circuit is formed by the parts to be treated. The common applications of the anodic
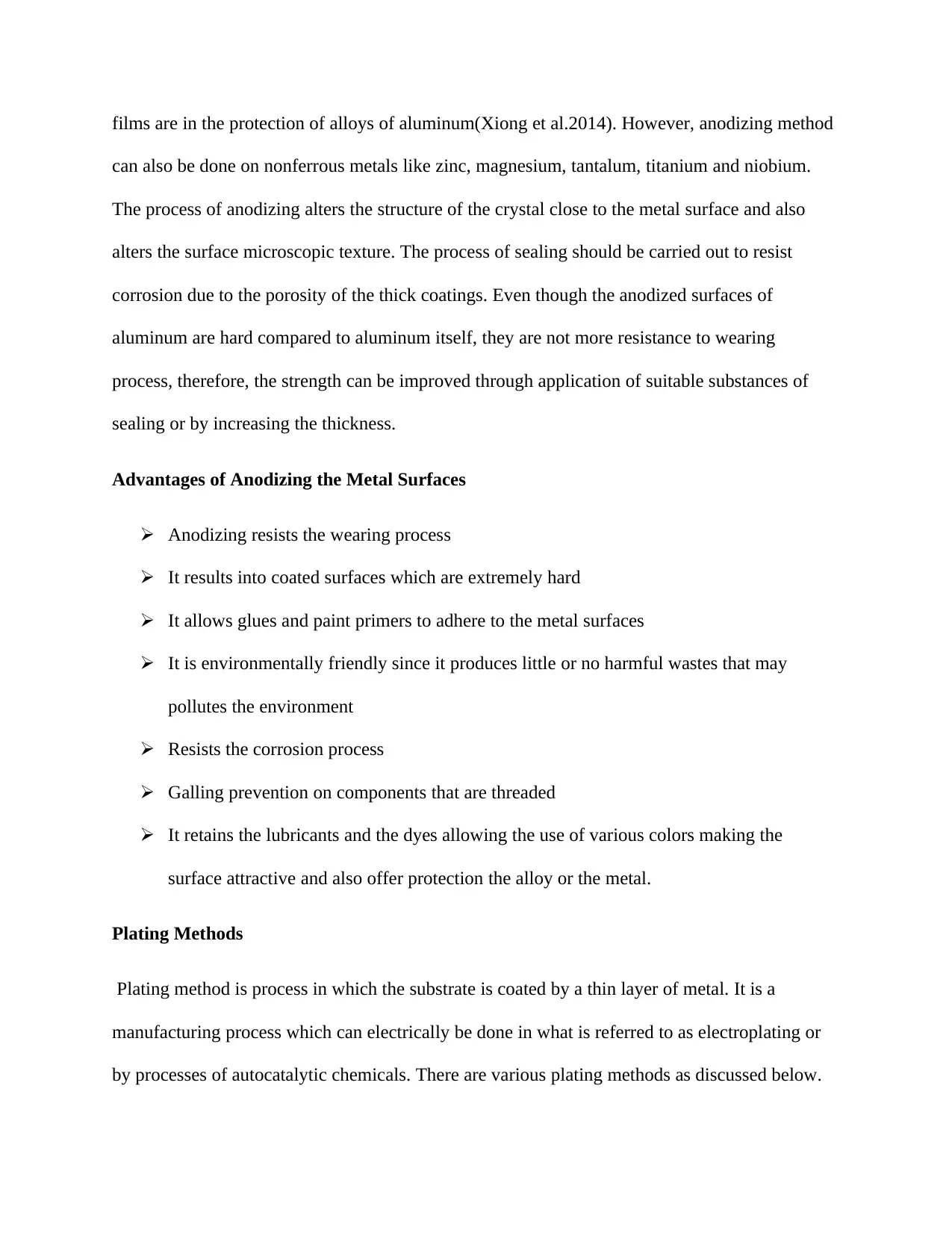
films are in the protection of alloys of aluminum(Xiong et al.2014). However, anodizing method
can also be done on nonferrous metals like zinc, magnesium, tantalum, titanium and niobium.
The process of anodizing alters the structure of the crystal close to the metal surface and also
alters the surface microscopic texture. The process of sealing should be carried out to resist
corrosion due to the porosity of the thick coatings. Even though the anodized surfaces of
aluminum are hard compared to aluminum itself, they are not more resistance to wearing
process, therefore, the strength can be improved through application of suitable substances of
sealing or by increasing the thickness.
Advantages of Anodizing the Metal Surfaces
Anodizing resists the wearing process
It results into coated surfaces which are extremely hard
It allows glues and paint primers to adhere to the metal surfaces
It is environmentally friendly since it produces little or no harmful wastes that may
pollutes the environment
Resists the corrosion process
Galling prevention on components that are threaded
It retains the lubricants and the dyes allowing the use of various colors making the
surface attractive and also offer protection the alloy or the metal.
Plating Methods
Plating method is process in which the substrate is coated by a thin layer of metal. It is a
manufacturing process which can electrically be done in what is referred to as electroplating or
by processes of autocatalytic chemicals. There are various plating methods as discussed below.
can also be done on nonferrous metals like zinc, magnesium, tantalum, titanium and niobium.
The process of anodizing alters the structure of the crystal close to the metal surface and also
alters the surface microscopic texture. The process of sealing should be carried out to resist
corrosion due to the porosity of the thick coatings. Even though the anodized surfaces of
aluminum are hard compared to aluminum itself, they are not more resistance to wearing
process, therefore, the strength can be improved through application of suitable substances of
sealing or by increasing the thickness.
Advantages of Anodizing the Metal Surfaces
Anodizing resists the wearing process
It results into coated surfaces which are extremely hard
It allows glues and paint primers to adhere to the metal surfaces
It is environmentally friendly since it produces little or no harmful wastes that may
pollutes the environment
Resists the corrosion process
Galling prevention on components that are threaded
It retains the lubricants and the dyes allowing the use of various colors making the
surface attractive and also offer protection the alloy or the metal.
Plating Methods
Plating method is process in which the substrate is coated by a thin layer of metal. It is a
manufacturing process which can electrically be done in what is referred to as electroplating or
by processes of autocatalytic chemicals. There are various plating methods as discussed below.
Paraphrase This Document
Need a fresh take? Get an instant paraphrase of this document with our AI Paraphraser
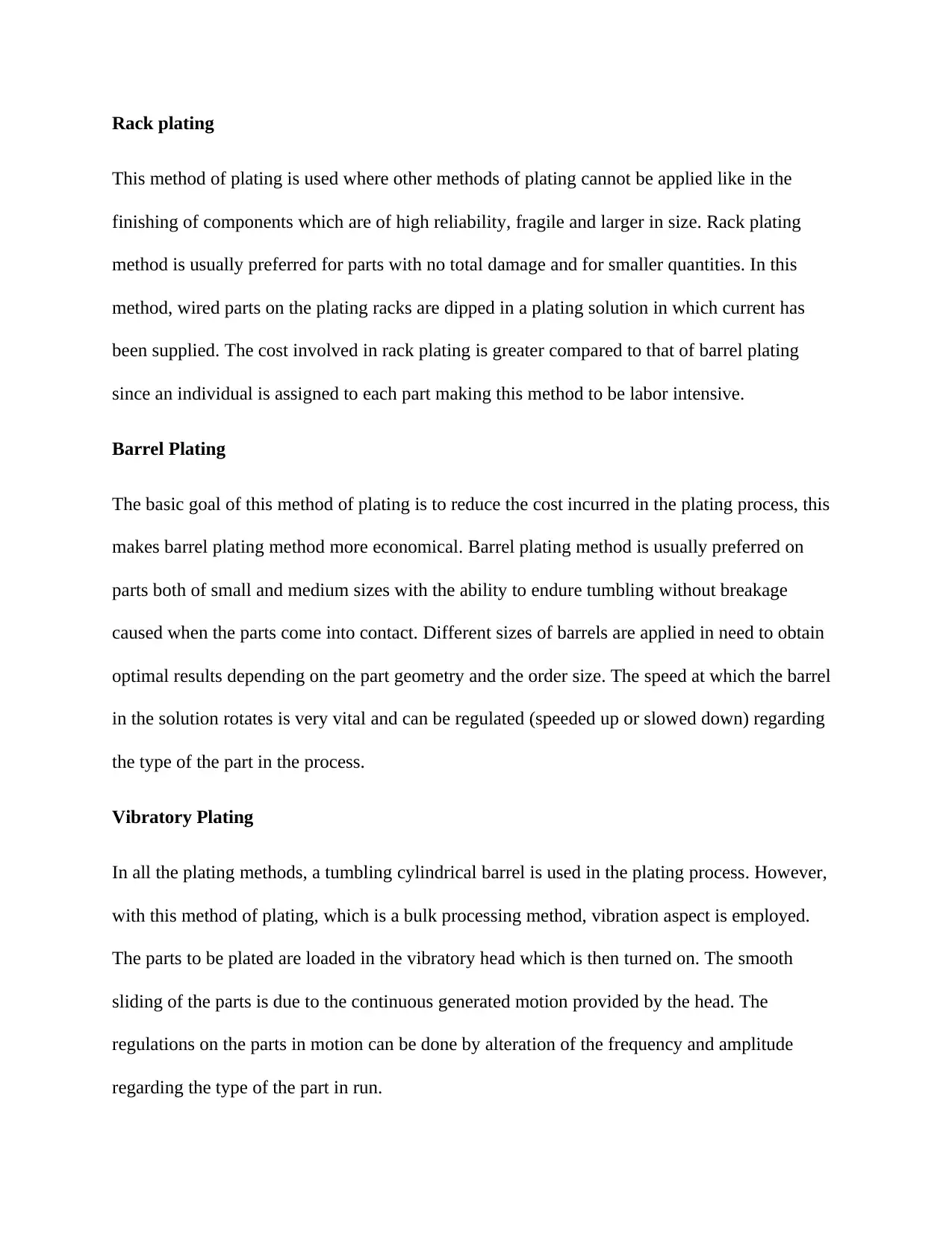
Rack plating
This method of plating is used where other methods of plating cannot be applied like in the
finishing of components which are of high reliability, fragile and larger in size. Rack plating
method is usually preferred for parts with no total damage and for smaller quantities. In this
method, wired parts on the plating racks are dipped in a plating solution in which current has
been supplied. The cost involved in rack plating is greater compared to that of barrel plating
since an individual is assigned to each part making this method to be labor intensive.
Barrel Plating
The basic goal of this method of plating is to reduce the cost incurred in the plating process, this
makes barrel plating method more economical. Barrel plating method is usually preferred on
parts both of small and medium sizes with the ability to endure tumbling without breakage
caused when the parts come into contact. Different sizes of barrels are applied in need to obtain
optimal results depending on the part geometry and the order size. The speed at which the barrel
in the solution rotates is very vital and can be regulated (speeded up or slowed down) regarding
the type of the part in the process.
Vibratory Plating
In all the plating methods, a tumbling cylindrical barrel is used in the plating process. However,
with this method of plating, which is a bulk processing method, vibration aspect is employed.
The parts to be plated are loaded in the vibratory head which is then turned on. The smooth
sliding of the parts is due to the continuous generated motion provided by the head. The
regulations on the parts in motion can be done by alteration of the frequency and amplitude
regarding the type of the part in run.
This method of plating is used where other methods of plating cannot be applied like in the
finishing of components which are of high reliability, fragile and larger in size. Rack plating
method is usually preferred for parts with no total damage and for smaller quantities. In this
method, wired parts on the plating racks are dipped in a plating solution in which current has
been supplied. The cost involved in rack plating is greater compared to that of barrel plating
since an individual is assigned to each part making this method to be labor intensive.
Barrel Plating
The basic goal of this method of plating is to reduce the cost incurred in the plating process, this
makes barrel plating method more economical. Barrel plating method is usually preferred on
parts both of small and medium sizes with the ability to endure tumbling without breakage
caused when the parts come into contact. Different sizes of barrels are applied in need to obtain
optimal results depending on the part geometry and the order size. The speed at which the barrel
in the solution rotates is very vital and can be regulated (speeded up or slowed down) regarding
the type of the part in the process.
Vibratory Plating
In all the plating methods, a tumbling cylindrical barrel is used in the plating process. However,
with this method of plating, which is a bulk processing method, vibration aspect is employed.
The parts to be plated are loaded in the vibratory head which is then turned on. The smooth
sliding of the parts is due to the continuous generated motion provided by the head. The
regulations on the parts in motion can be done by alteration of the frequency and amplitude
regarding the type of the part in run.
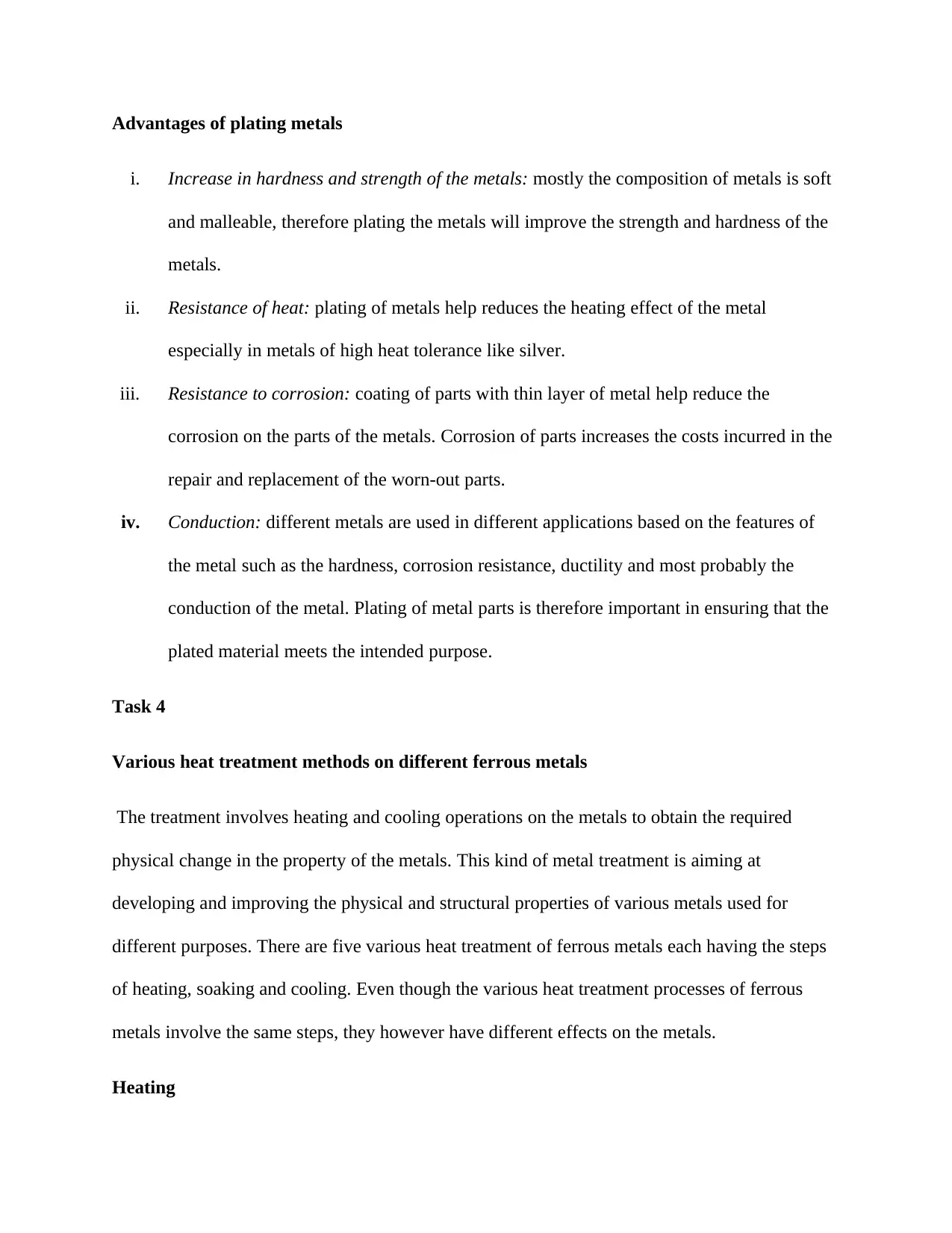
Advantages of plating metals
i. Increase in hardness and strength of the metals: mostly the composition of metals is soft
and malleable, therefore plating the metals will improve the strength and hardness of the
metals.
ii. Resistance of heat: plating of metals help reduces the heating effect of the metal
especially in metals of high heat tolerance like silver.
iii. Resistance to corrosion: coating of parts with thin layer of metal help reduce the
corrosion on the parts of the metals. Corrosion of parts increases the costs incurred in the
repair and replacement of the worn-out parts.
iv. Conduction: different metals are used in different applications based on the features of
the metal such as the hardness, corrosion resistance, ductility and most probably the
conduction of the metal. Plating of metal parts is therefore important in ensuring that the
plated material meets the intended purpose.
Task 4
Various heat treatment methods on different ferrous metals
The treatment involves heating and cooling operations on the metals to obtain the required
physical change in the property of the metals. This kind of metal treatment is aiming at
developing and improving the physical and structural properties of various metals used for
different purposes. There are five various heat treatment of ferrous metals each having the steps
of heating, soaking and cooling. Even though the various heat treatment processes of ferrous
metals involve the same steps, they however have different effects on the metals.
Heating
i. Increase in hardness and strength of the metals: mostly the composition of metals is soft
and malleable, therefore plating the metals will improve the strength and hardness of the
metals.
ii. Resistance of heat: plating of metals help reduces the heating effect of the metal
especially in metals of high heat tolerance like silver.
iii. Resistance to corrosion: coating of parts with thin layer of metal help reduce the
corrosion on the parts of the metals. Corrosion of parts increases the costs incurred in the
repair and replacement of the worn-out parts.
iv. Conduction: different metals are used in different applications based on the features of
the metal such as the hardness, corrosion resistance, ductility and most probably the
conduction of the metal. Plating of metal parts is therefore important in ensuring that the
plated material meets the intended purpose.
Task 4
Various heat treatment methods on different ferrous metals
The treatment involves heating and cooling operations on the metals to obtain the required
physical change in the property of the metals. This kind of metal treatment is aiming at
developing and improving the physical and structural properties of various metals used for
different purposes. There are five various heat treatment of ferrous metals each having the steps
of heating, soaking and cooling. Even though the various heat treatment processes of ferrous
metals involve the same steps, they however have different effects on the metals.
Heating
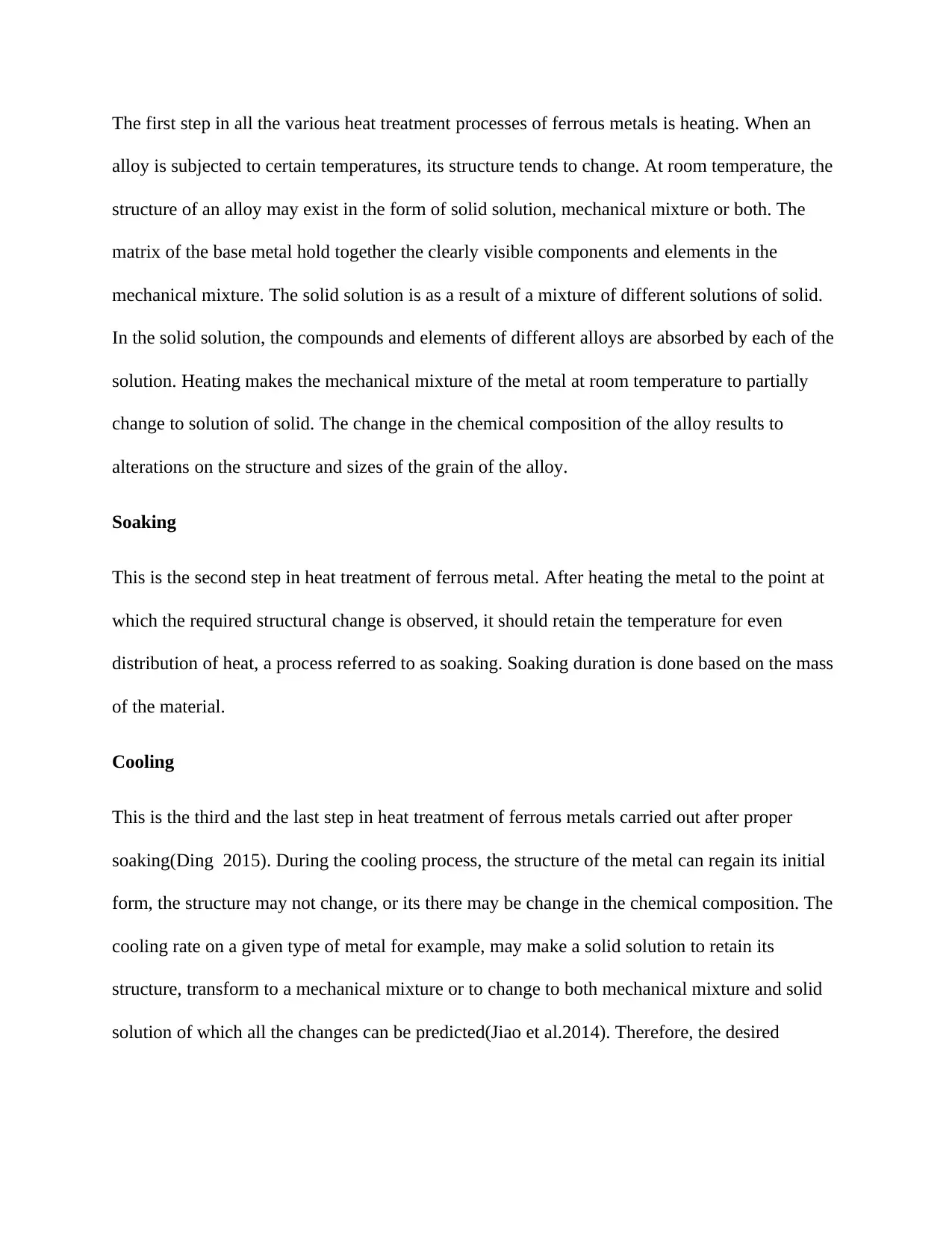
The first step in all the various heat treatment processes of ferrous metals is heating. When an
alloy is subjected to certain temperatures, its structure tends to change. At room temperature, the
structure of an alloy may exist in the form of solid solution, mechanical mixture or both. The
matrix of the base metal hold together the clearly visible components and elements in the
mechanical mixture. The solid solution is as a result of a mixture of different solutions of solid.
In the solid solution, the compounds and elements of different alloys are absorbed by each of the
solution. Heating makes the mechanical mixture of the metal at room temperature to partially
change to solution of solid. The change in the chemical composition of the alloy results to
alterations on the structure and sizes of the grain of the alloy.
Soaking
This is the second step in heat treatment of ferrous metal. After heating the metal to the point at
which the required structural change is observed, it should retain the temperature for even
distribution of heat, a process referred to as soaking. Soaking duration is done based on the mass
of the material.
Cooling
This is the third and the last step in heat treatment of ferrous metals carried out after proper
soaking(Ding 2015). During the cooling process, the structure of the metal can regain its initial
form, the structure may not change, or its there may be change in the chemical composition. The
cooling rate on a given type of metal for example, may make a solid solution to retain its
structure, transform to a mechanical mixture or to change to both mechanical mixture and solid
solution of which all the changes can be predicted(Jiao et al.2014). Therefore, the desired
alloy is subjected to certain temperatures, its structure tends to change. At room temperature, the
structure of an alloy may exist in the form of solid solution, mechanical mixture or both. The
matrix of the base metal hold together the clearly visible components and elements in the
mechanical mixture. The solid solution is as a result of a mixture of different solutions of solid.
In the solid solution, the compounds and elements of different alloys are absorbed by each of the
solution. Heating makes the mechanical mixture of the metal at room temperature to partially
change to solution of solid. The change in the chemical composition of the alloy results to
alterations on the structure and sizes of the grain of the alloy.
Soaking
This is the second step in heat treatment of ferrous metal. After heating the metal to the point at
which the required structural change is observed, it should retain the temperature for even
distribution of heat, a process referred to as soaking. Soaking duration is done based on the mass
of the material.
Cooling
This is the third and the last step in heat treatment of ferrous metals carried out after proper
soaking(Ding 2015). During the cooling process, the structure of the metal can regain its initial
form, the structure may not change, or its there may be change in the chemical composition. The
cooling rate on a given type of metal for example, may make a solid solution to retain its
structure, transform to a mechanical mixture or to change to both mechanical mixture and solid
solution of which all the changes can be predicted(Jiao et al.2014). Therefore, the desired
Secure Best Marks with AI Grader
Need help grading? Try our AI Grader for instant feedback on your assignments.
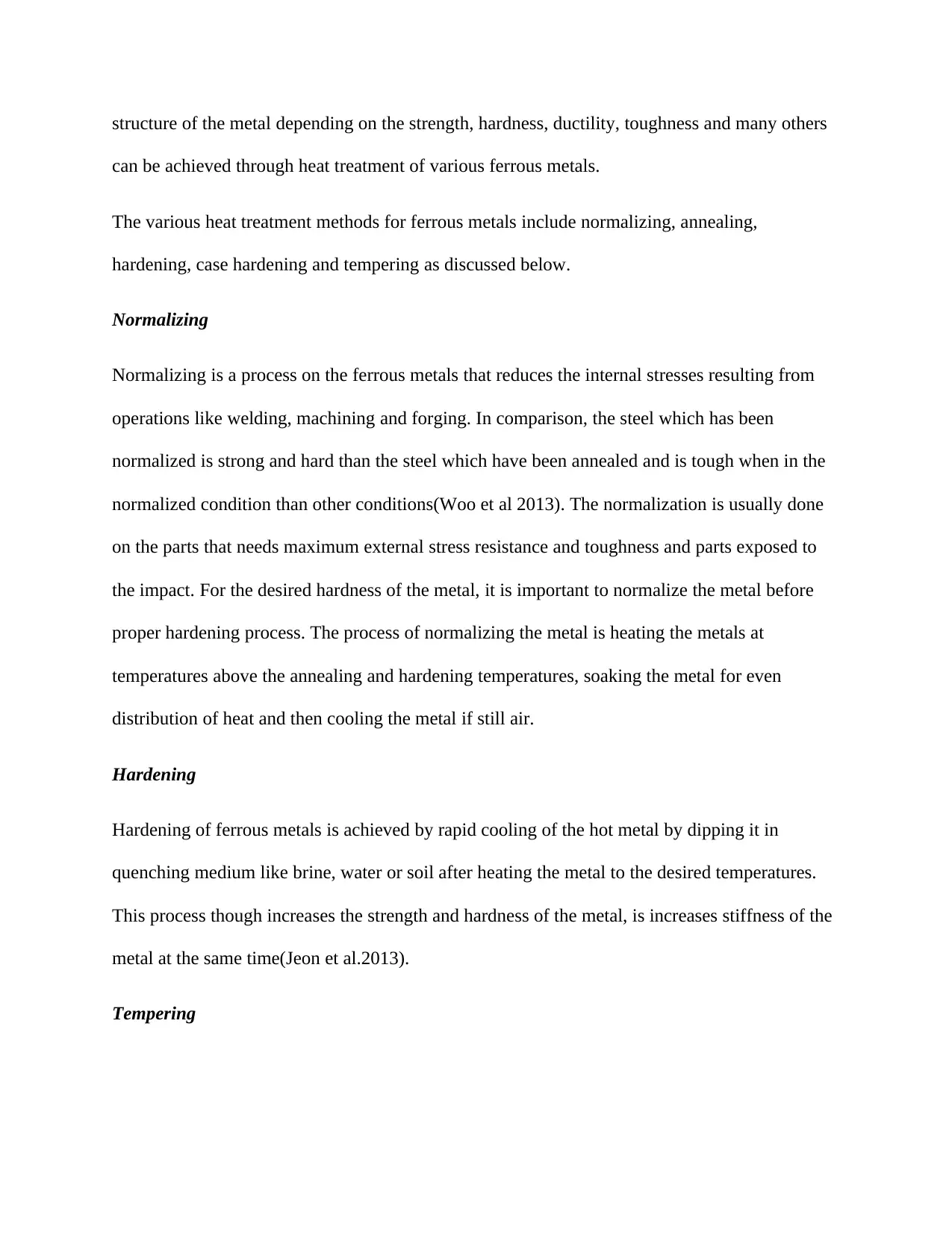
structure of the metal depending on the strength, hardness, ductility, toughness and many others
can be achieved through heat treatment of various ferrous metals.
The various heat treatment methods for ferrous metals include normalizing, annealing,
hardening, case hardening and tempering as discussed below.
Normalizing
Normalizing is a process on the ferrous metals that reduces the internal stresses resulting from
operations like welding, machining and forging. In comparison, the steel which has been
normalized is strong and hard than the steel which have been annealed and is tough when in the
normalized condition than other conditions(Woo et al 2013). The normalization is usually done
on the parts that needs maximum external stress resistance and toughness and parts exposed to
the impact. For the desired hardness of the metal, it is important to normalize the metal before
proper hardening process. The process of normalizing the metal is heating the metals at
temperatures above the annealing and hardening temperatures, soaking the metal for even
distribution of heat and then cooling the metal if still air.
Hardening
Hardening of ferrous metals is achieved by rapid cooling of the hot metal by dipping it in
quenching medium like brine, water or soil after heating the metal to the desired temperatures.
This process though increases the strength and hardness of the metal, is increases stiffness of the
metal at the same time(Jeon et al.2013).
Tempering
can be achieved through heat treatment of various ferrous metals.
The various heat treatment methods for ferrous metals include normalizing, annealing,
hardening, case hardening and tempering as discussed below.
Normalizing
Normalizing is a process on the ferrous metals that reduces the internal stresses resulting from
operations like welding, machining and forging. In comparison, the steel which has been
normalized is strong and hard than the steel which have been annealed and is tough when in the
normalized condition than other conditions(Woo et al 2013). The normalization is usually done
on the parts that needs maximum external stress resistance and toughness and parts exposed to
the impact. For the desired hardness of the metal, it is important to normalize the metal before
proper hardening process. The process of normalizing the metal is heating the metals at
temperatures above the annealing and hardening temperatures, soaking the metal for even
distribution of heat and then cooling the metal if still air.
Hardening
Hardening of ferrous metals is achieved by rapid cooling of the hot metal by dipping it in
quenching medium like brine, water or soil after heating the metal to the desired temperatures.
This process though increases the strength and hardness of the metal, is increases stiffness of the
metal at the same time(Jeon et al.2013).
Tempering
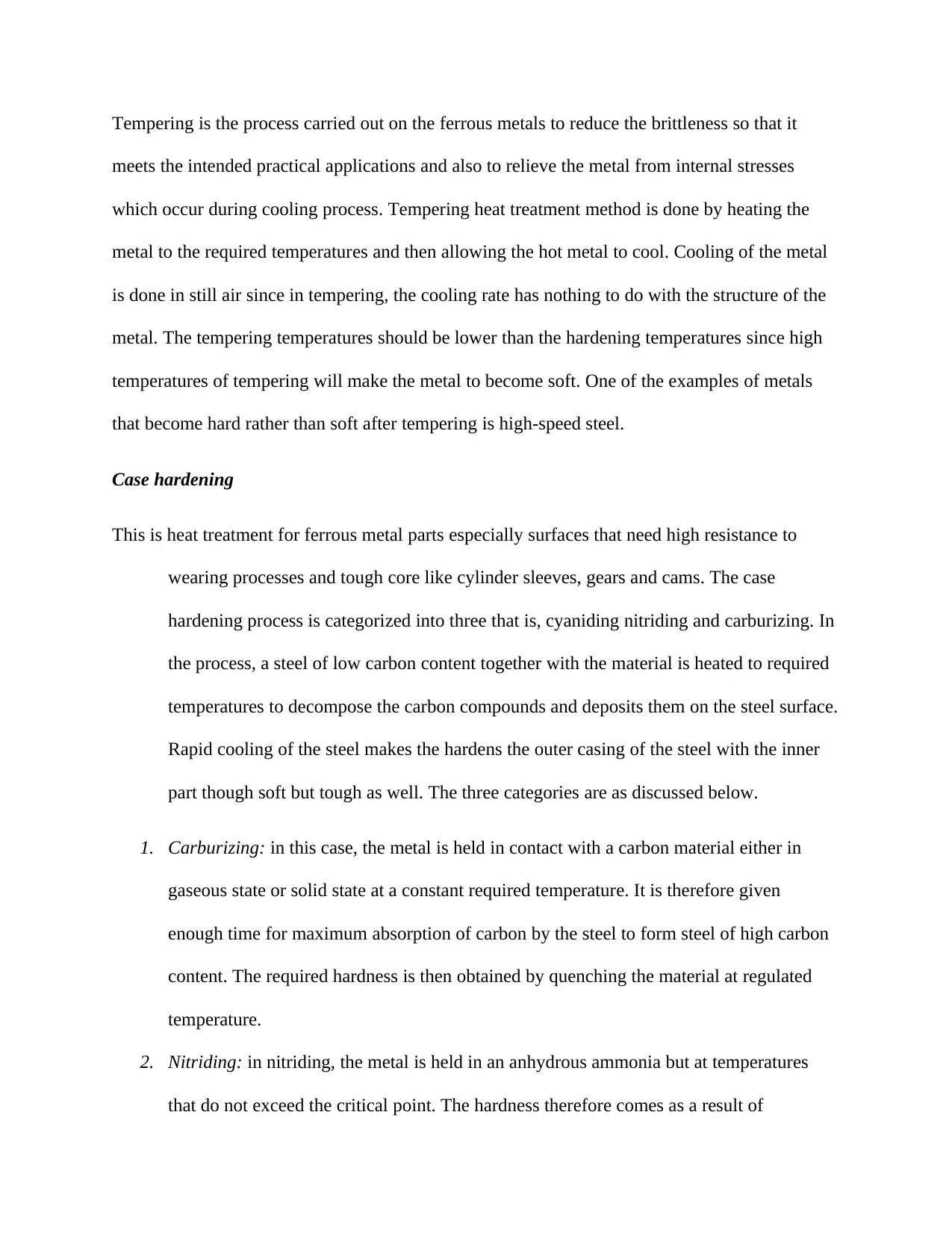
Tempering is the process carried out on the ferrous metals to reduce the brittleness so that it
meets the intended practical applications and also to relieve the metal from internal stresses
which occur during cooling process. Tempering heat treatment method is done by heating the
metal to the required temperatures and then allowing the hot metal to cool. Cooling of the metal
is done in still air since in tempering, the cooling rate has nothing to do with the structure of the
metal. The tempering temperatures should be lower than the hardening temperatures since high
temperatures of tempering will make the metal to become soft. One of the examples of metals
that become hard rather than soft after tempering is high-speed steel.
Case hardening
This is heat treatment for ferrous metal parts especially surfaces that need high resistance to
wearing processes and tough core like cylinder sleeves, gears and cams. The case
hardening process is categorized into three that is, cyaniding nitriding and carburizing. In
the process, a steel of low carbon content together with the material is heated to required
temperatures to decompose the carbon compounds and deposits them on the steel surface.
Rapid cooling of the steel makes the hardens the outer casing of the steel with the inner
part though soft but tough as well. The three categories are as discussed below.
1. Carburizing: in this case, the metal is held in contact with a carbon material either in
gaseous state or solid state at a constant required temperature. It is therefore given
enough time for maximum absorption of carbon by the steel to form steel of high carbon
content. The required hardness is then obtained by quenching the material at regulated
temperature.
2. Nitriding: in nitriding, the metal is held in an anhydrous ammonia but at temperatures
that do not exceed the critical point. The hardness therefore comes as a result of
meets the intended practical applications and also to relieve the metal from internal stresses
which occur during cooling process. Tempering heat treatment method is done by heating the
metal to the required temperatures and then allowing the hot metal to cool. Cooling of the metal
is done in still air since in tempering, the cooling rate has nothing to do with the structure of the
metal. The tempering temperatures should be lower than the hardening temperatures since high
temperatures of tempering will make the metal to become soft. One of the examples of metals
that become hard rather than soft after tempering is high-speed steel.
Case hardening
This is heat treatment for ferrous metal parts especially surfaces that need high resistance to
wearing processes and tough core like cylinder sleeves, gears and cams. The case
hardening process is categorized into three that is, cyaniding nitriding and carburizing. In
the process, a steel of low carbon content together with the material is heated to required
temperatures to decompose the carbon compounds and deposits them on the steel surface.
Rapid cooling of the steel makes the hardens the outer casing of the steel with the inner
part though soft but tough as well. The three categories are as discussed below.
1. Carburizing: in this case, the metal is held in contact with a carbon material either in
gaseous state or solid state at a constant required temperature. It is therefore given
enough time for maximum absorption of carbon by the steel to form steel of high carbon
content. The required hardness is then obtained by quenching the material at regulated
temperature.
2. Nitriding: in nitriding, the metal is held in an anhydrous ammonia but at temperatures
that do not exceed the critical point. The hardness therefore comes as a result of
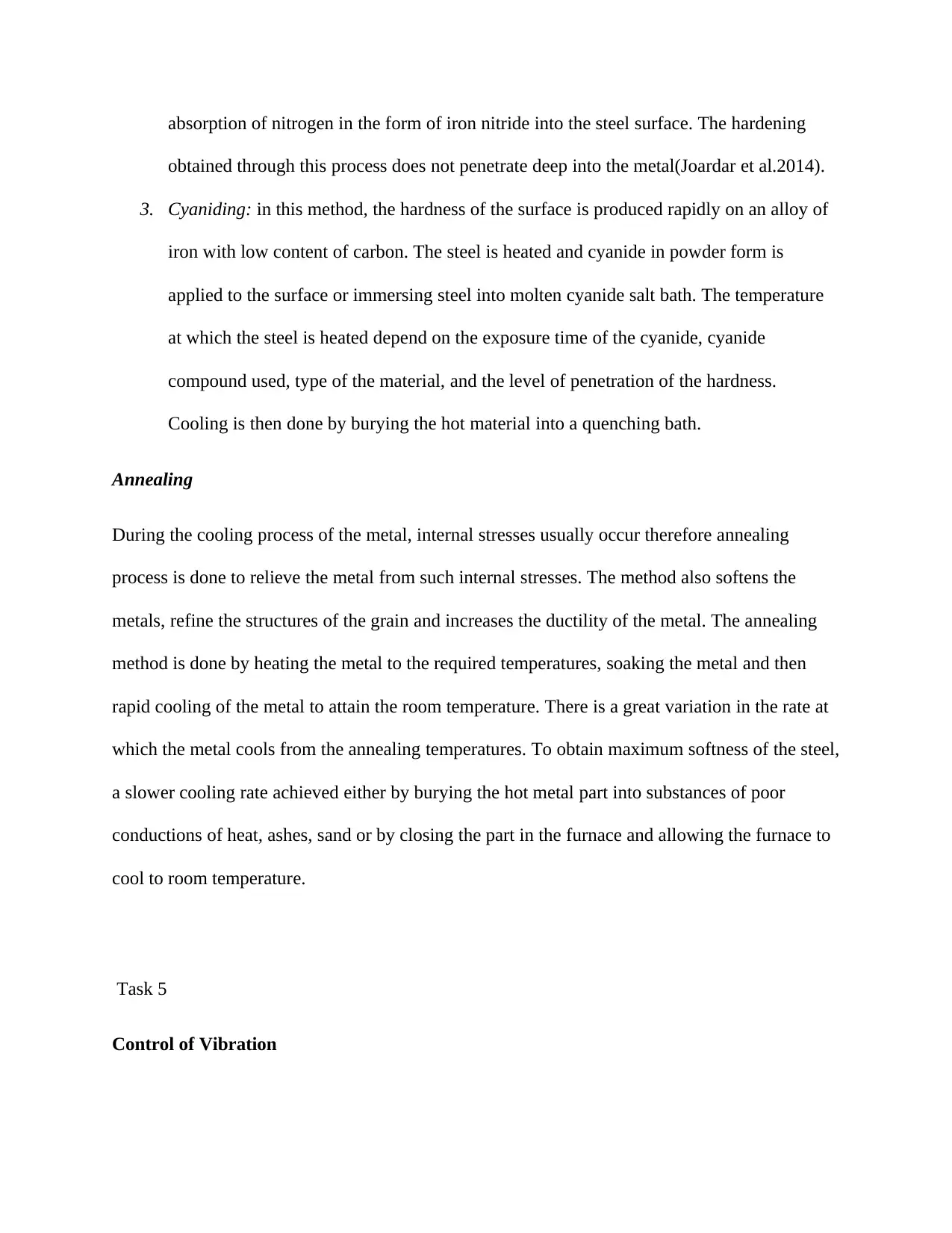
absorption of nitrogen in the form of iron nitride into the steel surface. The hardening
obtained through this process does not penetrate deep into the metal(Joardar et al.2014).
3. Cyaniding: in this method, the hardness of the surface is produced rapidly on an alloy of
iron with low content of carbon. The steel is heated and cyanide in powder form is
applied to the surface or immersing steel into molten cyanide salt bath. The temperature
at which the steel is heated depend on the exposure time of the cyanide, cyanide
compound used, type of the material, and the level of penetration of the hardness.
Cooling is then done by burying the hot material into a quenching bath.
Annealing
During the cooling process of the metal, internal stresses usually occur therefore annealing
process is done to relieve the metal from such internal stresses. The method also softens the
metals, refine the structures of the grain and increases the ductility of the metal. The annealing
method is done by heating the metal to the required temperatures, soaking the metal and then
rapid cooling of the metal to attain the room temperature. There is a great variation in the rate at
which the metal cools from the annealing temperatures. To obtain maximum softness of the steel,
a slower cooling rate achieved either by burying the hot metal part into substances of poor
conductions of heat, ashes, sand or by closing the part in the furnace and allowing the furnace to
cool to room temperature.
Task 5
Control of Vibration
obtained through this process does not penetrate deep into the metal(Joardar et al.2014).
3. Cyaniding: in this method, the hardness of the surface is produced rapidly on an alloy of
iron with low content of carbon. The steel is heated and cyanide in powder form is
applied to the surface or immersing steel into molten cyanide salt bath. The temperature
at which the steel is heated depend on the exposure time of the cyanide, cyanide
compound used, type of the material, and the level of penetration of the hardness.
Cooling is then done by burying the hot material into a quenching bath.
Annealing
During the cooling process of the metal, internal stresses usually occur therefore annealing
process is done to relieve the metal from such internal stresses. The method also softens the
metals, refine the structures of the grain and increases the ductility of the metal. The annealing
method is done by heating the metal to the required temperatures, soaking the metal and then
rapid cooling of the metal to attain the room temperature. There is a great variation in the rate at
which the metal cools from the annealing temperatures. To obtain maximum softness of the steel,
a slower cooling rate achieved either by burying the hot metal part into substances of poor
conductions of heat, ashes, sand or by closing the part in the furnace and allowing the furnace to
cool to room temperature.
Task 5
Control of Vibration
Paraphrase This Document
Need a fresh take? Get an instant paraphrase of this document with our AI Paraphraser
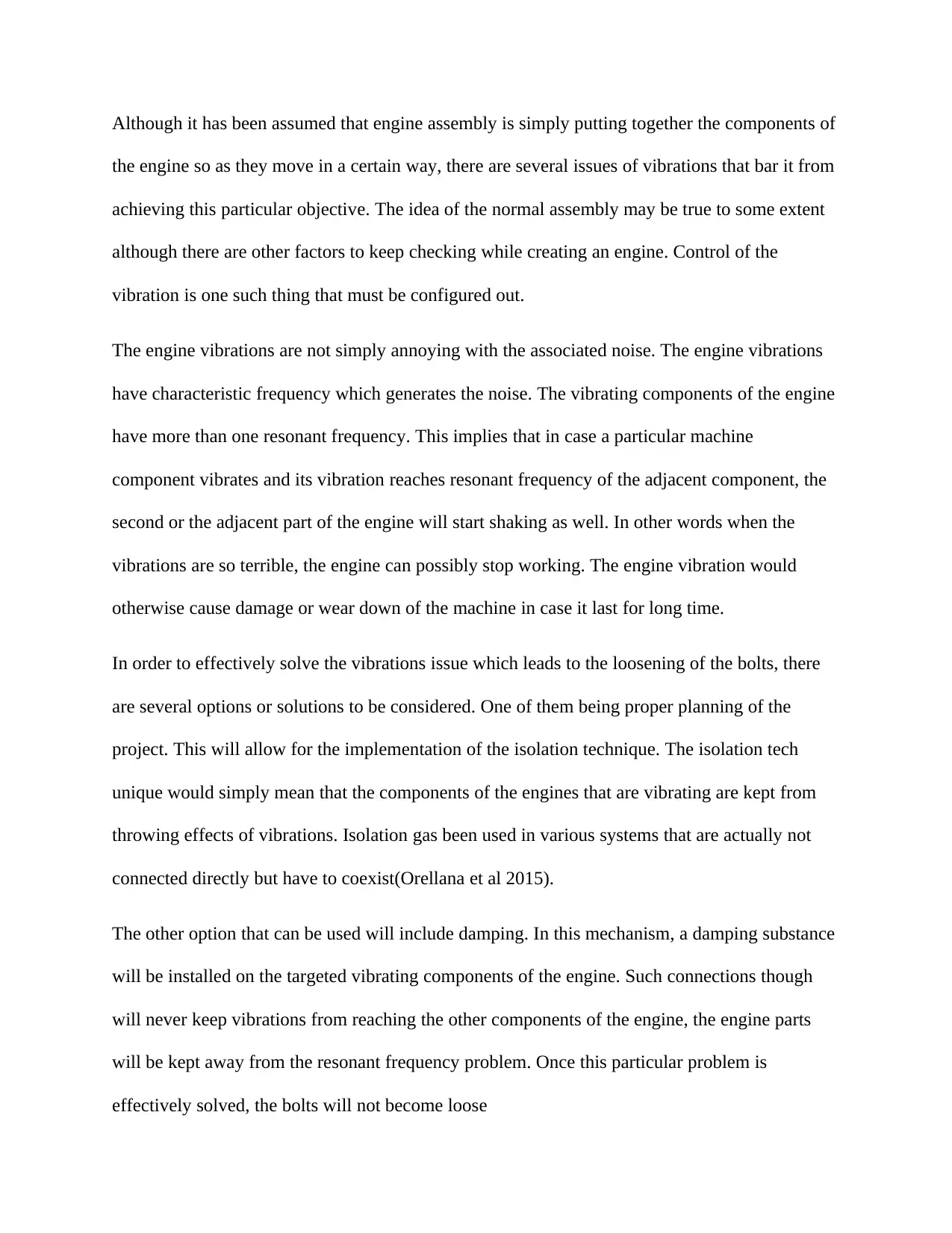
Although it has been assumed that engine assembly is simply putting together the components of
the engine so as they move in a certain way, there are several issues of vibrations that bar it from
achieving this particular objective. The idea of the normal assembly may be true to some extent
although there are other factors to keep checking while creating an engine. Control of the
vibration is one such thing that must be configured out.
The engine vibrations are not simply annoying with the associated noise. The engine vibrations
have characteristic frequency which generates the noise. The vibrating components of the engine
have more than one resonant frequency. This implies that in case a particular machine
component vibrates and its vibration reaches resonant frequency of the adjacent component, the
second or the adjacent part of the engine will start shaking as well. In other words when the
vibrations are so terrible, the engine can possibly stop working. The engine vibration would
otherwise cause damage or wear down of the machine in case it last for long time.
In order to effectively solve the vibrations issue which leads to the loosening of the bolts, there
are several options or solutions to be considered. One of them being proper planning of the
project. This will allow for the implementation of the isolation technique. The isolation tech
unique would simply mean that the components of the engines that are vibrating are kept from
throwing effects of vibrations. Isolation gas been used in various systems that are actually not
connected directly but have to coexist(Orellana et al 2015).
The other option that can be used will include damping. In this mechanism, a damping substance
will be installed on the targeted vibrating components of the engine. Such connections though
will never keep vibrations from reaching the other components of the engine, the engine parts
will be kept away from the resonant frequency problem. Once this particular problem is
effectively solved, the bolts will not become loose
the engine so as they move in a certain way, there are several issues of vibrations that bar it from
achieving this particular objective. The idea of the normal assembly may be true to some extent
although there are other factors to keep checking while creating an engine. Control of the
vibration is one such thing that must be configured out.
The engine vibrations are not simply annoying with the associated noise. The engine vibrations
have characteristic frequency which generates the noise. The vibrating components of the engine
have more than one resonant frequency. This implies that in case a particular machine
component vibrates and its vibration reaches resonant frequency of the adjacent component, the
second or the adjacent part of the engine will start shaking as well. In other words when the
vibrations are so terrible, the engine can possibly stop working. The engine vibration would
otherwise cause damage or wear down of the machine in case it last for long time.
In order to effectively solve the vibrations issue which leads to the loosening of the bolts, there
are several options or solutions to be considered. One of them being proper planning of the
project. This will allow for the implementation of the isolation technique. The isolation tech
unique would simply mean that the components of the engines that are vibrating are kept from
throwing effects of vibrations. Isolation gas been used in various systems that are actually not
connected directly but have to coexist(Orellana et al 2015).
The other option that can be used will include damping. In this mechanism, a damping substance
will be installed on the targeted vibrating components of the engine. Such connections though
will never keep vibrations from reaching the other components of the engine, the engine parts
will be kept away from the resonant frequency problem. Once this particular problem is
effectively solved, the bolts will not become loose
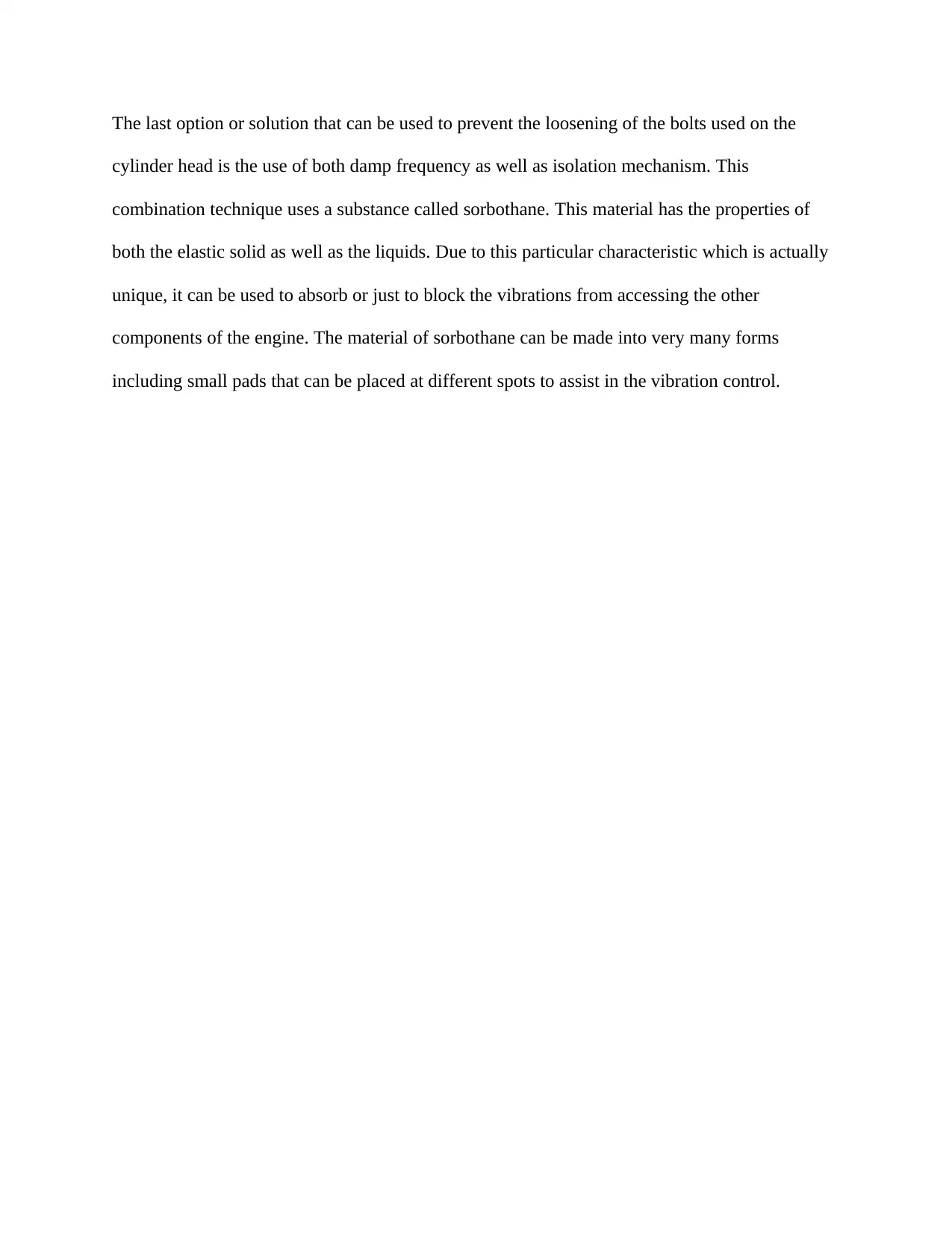
The last option or solution that can be used to prevent the loosening of the bolts used on the
cylinder head is the use of both damp frequency as well as isolation mechanism. This
combination technique uses a substance called sorbothane. This material has the properties of
both the elastic solid as well as the liquids. Due to this particular characteristic which is actually
unique, it can be used to absorb or just to block the vibrations from accessing the other
components of the engine. The material of sorbothane can be made into very many forms
including small pads that can be placed at different spots to assist in the vibration control.
cylinder head is the use of both damp frequency as well as isolation mechanism. This
combination technique uses a substance called sorbothane. This material has the properties of
both the elastic solid as well as the liquids. Due to this particular characteristic which is actually
unique, it can be used to absorb or just to block the vibrations from accessing the other
components of the engine. The material of sorbothane can be made into very many forms
including small pads that can be placed at different spots to assist in the vibration control.
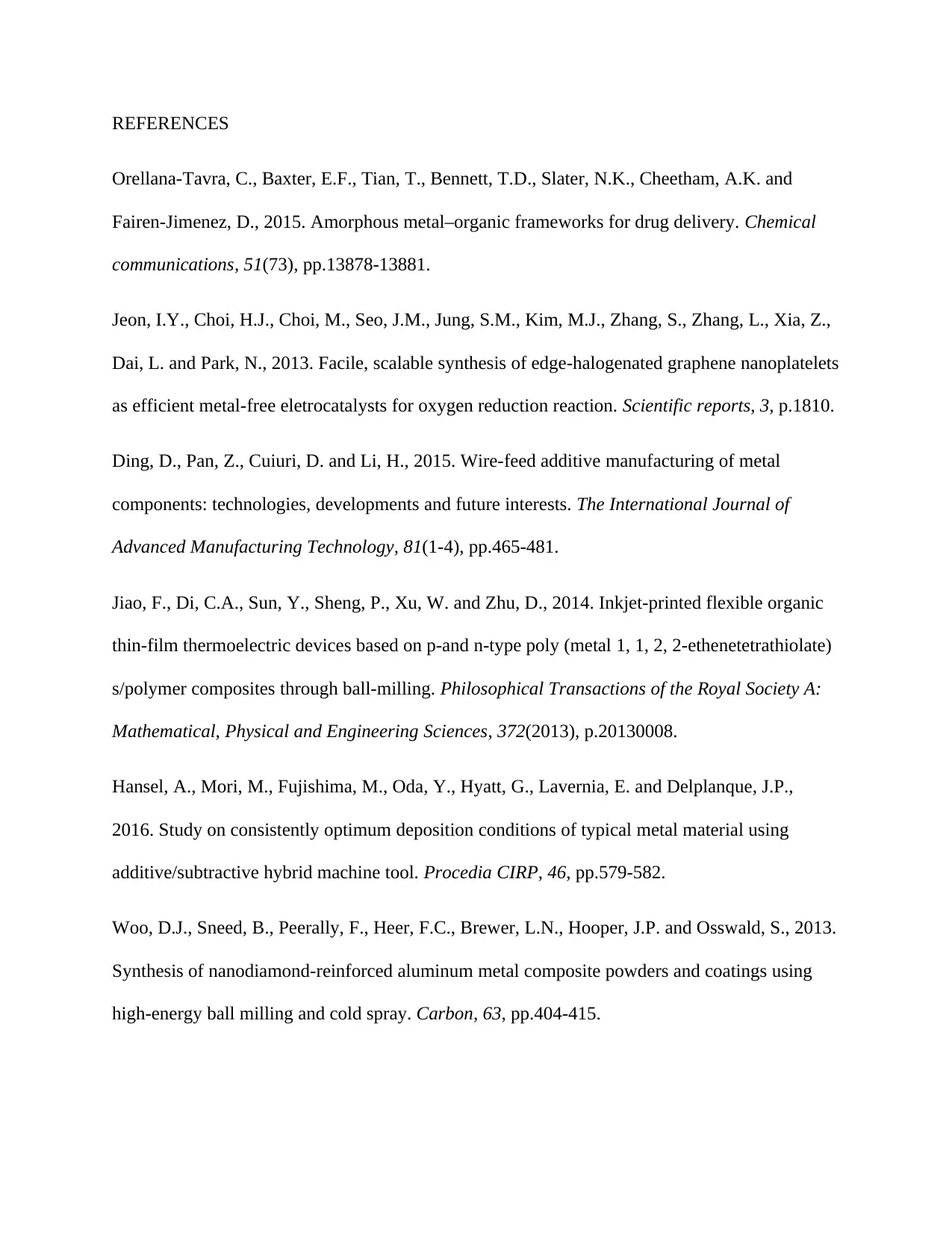
REFERENCES
Orellana-Tavra, C., Baxter, E.F., Tian, T., Bennett, T.D., Slater, N.K., Cheetham, A.K. and
Fairen-Jimenez, D., 2015. Amorphous metal–organic frameworks for drug delivery. Chemical
communications, 51(73), pp.13878-13881.
Jeon, I.Y., Choi, H.J., Choi, M., Seo, J.M., Jung, S.M., Kim, M.J., Zhang, S., Zhang, L., Xia, Z.,
Dai, L. and Park, N., 2013. Facile, scalable synthesis of edge-halogenated graphene nanoplatelets
as efficient metal-free eletrocatalysts for oxygen reduction reaction. Scientific reports, 3, p.1810.
Ding, D., Pan, Z., Cuiuri, D. and Li, H., 2015. Wire-feed additive manufacturing of metal
components: technologies, developments and future interests. The International Journal of
Advanced Manufacturing Technology, 81(1-4), pp.465-481.
Jiao, F., Di, C.A., Sun, Y., Sheng, P., Xu, W. and Zhu, D., 2014. Inkjet-printed flexible organic
thin-film thermoelectric devices based on p-and n-type poly (metal 1, 1, 2, 2-ethenetetrathiolate)
s/polymer composites through ball-milling. Philosophical Transactions of the Royal Society A:
Mathematical, Physical and Engineering Sciences, 372(2013), p.20130008.
Hansel, A., Mori, M., Fujishima, M., Oda, Y., Hyatt, G., Lavernia, E. and Delplanque, J.P.,
2016. Study on consistently optimum deposition conditions of typical metal material using
additive/subtractive hybrid machine tool. Procedia CIRP, 46, pp.579-582.
Woo, D.J., Sneed, B., Peerally, F., Heer, F.C., Brewer, L.N., Hooper, J.P. and Osswald, S., 2013.
Synthesis of nanodiamond-reinforced aluminum metal composite powders and coatings using
high-energy ball milling and cold spray. Carbon, 63, pp.404-415.
Orellana-Tavra, C., Baxter, E.F., Tian, T., Bennett, T.D., Slater, N.K., Cheetham, A.K. and
Fairen-Jimenez, D., 2015. Amorphous metal–organic frameworks for drug delivery. Chemical
communications, 51(73), pp.13878-13881.
Jeon, I.Y., Choi, H.J., Choi, M., Seo, J.M., Jung, S.M., Kim, M.J., Zhang, S., Zhang, L., Xia, Z.,
Dai, L. and Park, N., 2013. Facile, scalable synthesis of edge-halogenated graphene nanoplatelets
as efficient metal-free eletrocatalysts for oxygen reduction reaction. Scientific reports, 3, p.1810.
Ding, D., Pan, Z., Cuiuri, D. and Li, H., 2015. Wire-feed additive manufacturing of metal
components: technologies, developments and future interests. The International Journal of
Advanced Manufacturing Technology, 81(1-4), pp.465-481.
Jiao, F., Di, C.A., Sun, Y., Sheng, P., Xu, W. and Zhu, D., 2014. Inkjet-printed flexible organic
thin-film thermoelectric devices based on p-and n-type poly (metal 1, 1, 2, 2-ethenetetrathiolate)
s/polymer composites through ball-milling. Philosophical Transactions of the Royal Society A:
Mathematical, Physical and Engineering Sciences, 372(2013), p.20130008.
Hansel, A., Mori, M., Fujishima, M., Oda, Y., Hyatt, G., Lavernia, E. and Delplanque, J.P.,
2016. Study on consistently optimum deposition conditions of typical metal material using
additive/subtractive hybrid machine tool. Procedia CIRP, 46, pp.579-582.
Woo, D.J., Sneed, B., Peerally, F., Heer, F.C., Brewer, L.N., Hooper, J.P. and Osswald, S., 2013.
Synthesis of nanodiamond-reinforced aluminum metal composite powders and coatings using
high-energy ball milling and cold spray. Carbon, 63, pp.404-415.
Secure Best Marks with AI Grader
Need help grading? Try our AI Grader for instant feedback on your assignments.
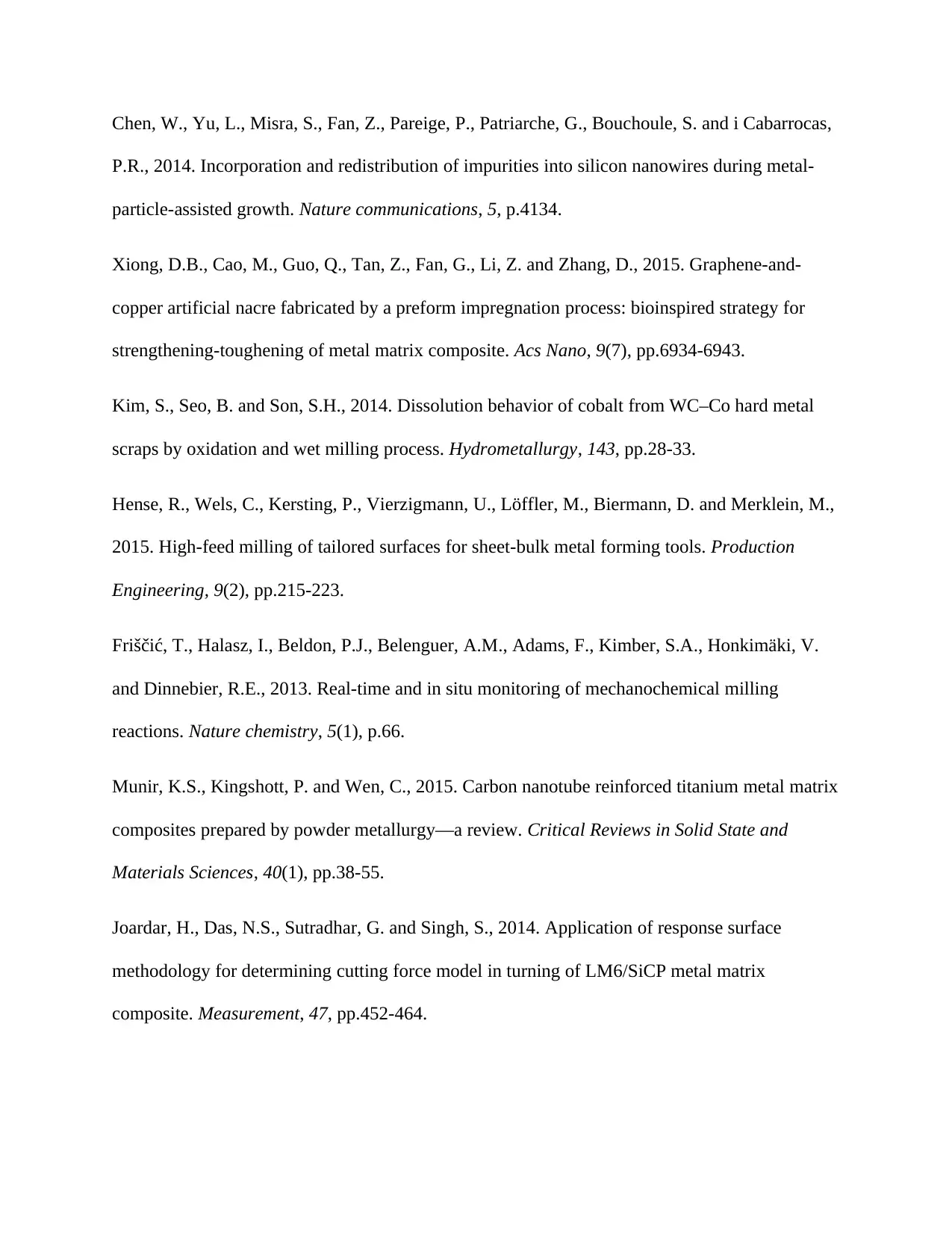
Chen, W., Yu, L., Misra, S., Fan, Z., Pareige, P., Patriarche, G., Bouchoule, S. and i Cabarrocas,
P.R., 2014. Incorporation and redistribution of impurities into silicon nanowires during metal-
particle-assisted growth. Nature communications, 5, p.4134.
Xiong, D.B., Cao, M., Guo, Q., Tan, Z., Fan, G., Li, Z. and Zhang, D., 2015. Graphene-and-
copper artificial nacre fabricated by a preform impregnation process: bioinspired strategy for
strengthening-toughening of metal matrix composite. Acs Nano, 9(7), pp.6934-6943.
Kim, S., Seo, B. and Son, S.H., 2014. Dissolution behavior of cobalt from WC–Co hard metal
scraps by oxidation and wet milling process. Hydrometallurgy, 143, pp.28-33.
Hense, R., Wels, C., Kersting, P., Vierzigmann, U., Löffler, M., Biermann, D. and Merklein, M.,
2015. High-feed milling of tailored surfaces for sheet-bulk metal forming tools. Production
Engineering, 9(2), pp.215-223.
Friščić, T., Halasz, I., Beldon, P.J., Belenguer, A.M., Adams, F., Kimber, S.A., Honkimäki, V.
and Dinnebier, R.E., 2013. Real-time and in situ monitoring of mechanochemical milling
reactions. Nature chemistry, 5(1), p.66.
Munir, K.S., Kingshott, P. and Wen, C., 2015. Carbon nanotube reinforced titanium metal matrix
composites prepared by powder metallurgy—a review. Critical Reviews in Solid State and
Materials Sciences, 40(1), pp.38-55.
Joardar, H., Das, N.S., Sutradhar, G. and Singh, S., 2014. Application of response surface
methodology for determining cutting force model in turning of LM6/SiCP metal matrix
composite. Measurement, 47, pp.452-464.
P.R., 2014. Incorporation and redistribution of impurities into silicon nanowires during metal-
particle-assisted growth. Nature communications, 5, p.4134.
Xiong, D.B., Cao, M., Guo, Q., Tan, Z., Fan, G., Li, Z. and Zhang, D., 2015. Graphene-and-
copper artificial nacre fabricated by a preform impregnation process: bioinspired strategy for
strengthening-toughening of metal matrix composite. Acs Nano, 9(7), pp.6934-6943.
Kim, S., Seo, B. and Son, S.H., 2014. Dissolution behavior of cobalt from WC–Co hard metal
scraps by oxidation and wet milling process. Hydrometallurgy, 143, pp.28-33.
Hense, R., Wels, C., Kersting, P., Vierzigmann, U., Löffler, M., Biermann, D. and Merklein, M.,
2015. High-feed milling of tailored surfaces for sheet-bulk metal forming tools. Production
Engineering, 9(2), pp.215-223.
Friščić, T., Halasz, I., Beldon, P.J., Belenguer, A.M., Adams, F., Kimber, S.A., Honkimäki, V.
and Dinnebier, R.E., 2013. Real-time and in situ monitoring of mechanochemical milling
reactions. Nature chemistry, 5(1), p.66.
Munir, K.S., Kingshott, P. and Wen, C., 2015. Carbon nanotube reinforced titanium metal matrix
composites prepared by powder metallurgy—a review. Critical Reviews in Solid State and
Materials Sciences, 40(1), pp.38-55.
Joardar, H., Das, N.S., Sutradhar, G. and Singh, S., 2014. Application of response surface
methodology for determining cutting force model in turning of LM6/SiCP metal matrix
composite. Measurement, 47, pp.452-464.
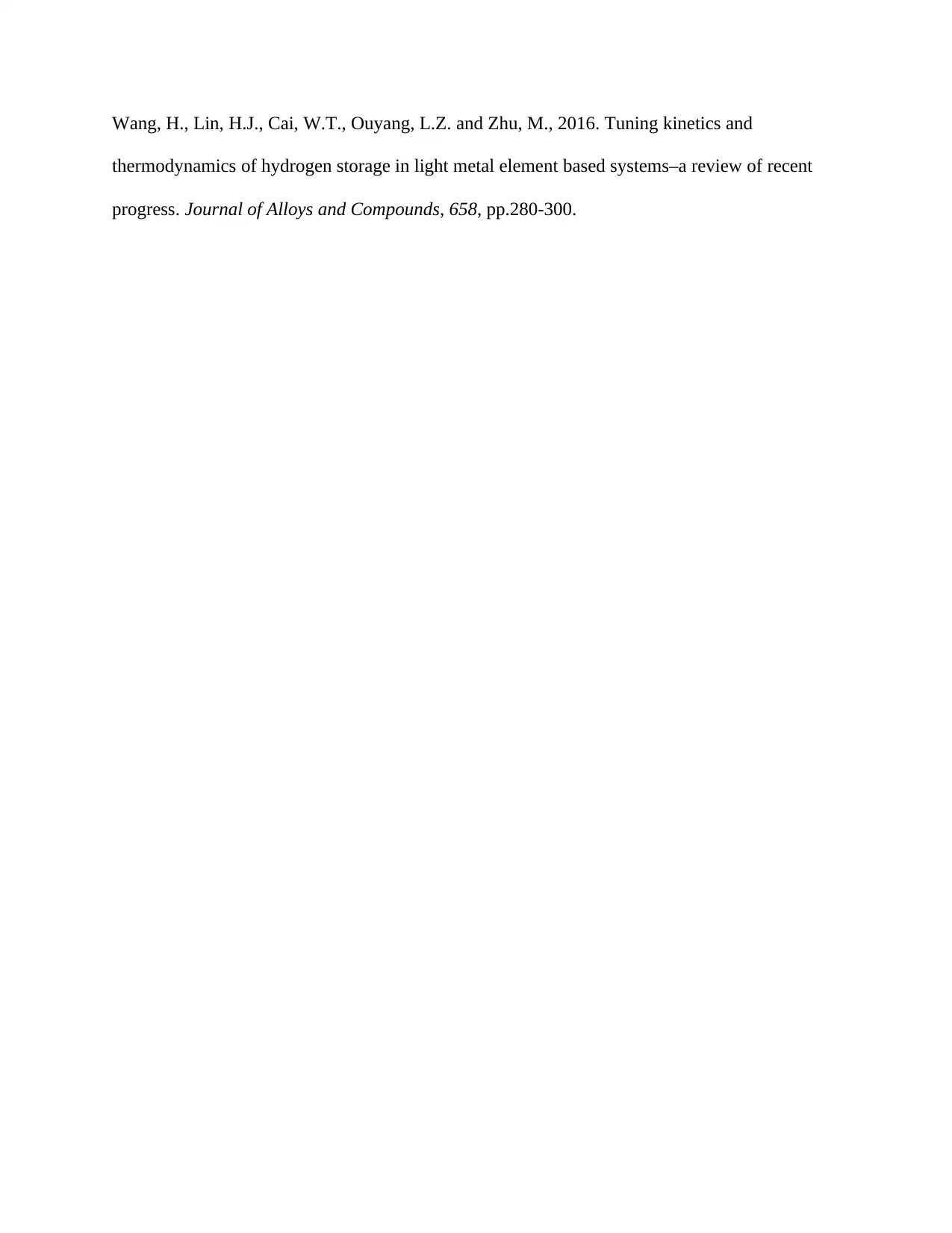
Wang, H., Lin, H.J., Cai, W.T., Ouyang, L.Z. and Zhu, M., 2016. Tuning kinetics and
thermodynamics of hydrogen storage in light metal element based systems–a review of recent
progress. Journal of Alloys and Compounds, 658, pp.280-300.
thermodynamics of hydrogen storage in light metal element based systems–a review of recent
progress. Journal of Alloys and Compounds, 658, pp.280-300.
1 out of 24
Related Documents

Your All-in-One AI-Powered Toolkit for Academic Success.
+13062052269
info@desklib.com
Available 24*7 on WhatsApp / Email
Unlock your academic potential
© 2024 | Zucol Services PVT LTD | All rights reserved.