Quality Management for Organisational Excellence: ETC Case Study
VerifiedAdded on 2023/01/09
|10
|3585
|43
Report
AI Summary
This report provides a comprehensive analysis of quality management for organisational excellence, focusing on the case study of the Engineering Tooling Company (ETC). The report begins with an overview of the scenario, detailing ETC's manufacturing operations and challenges. It then explores the development of a company-wide quality improvement strategy, emphasizing the adoption of Total Quality Management (TQM) to enhance product quality and customer satisfaction. The report delves into the benefits and challenges of TQM, and discusses quality assurance processes, including the PDCA cycle. Furthermore, it examines quality control measures and their importance in managing product quality and reducing waste. The report concludes with a discussion on sustaining a culture of quality within the organisation and offers recommendations for ETC to improve its quality management practices. The report aims to provide insights into how ETC can improve its operations and achieve sustainable growth.
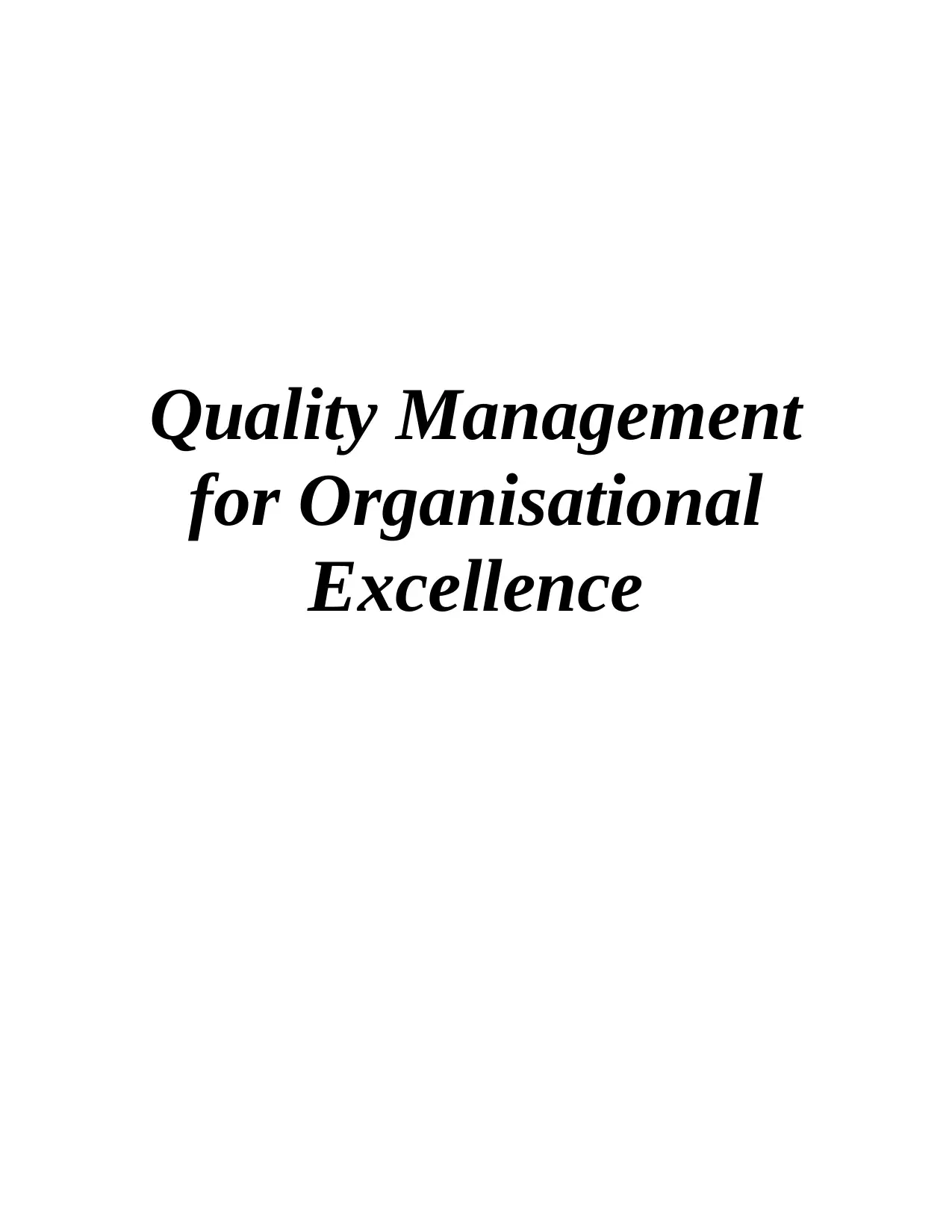
Quality Management
for Organisational
Excellence
for Organisational
Excellence
Paraphrase This Document
Need a fresh take? Get an instant paraphrase of this document with our AI Paraphraser
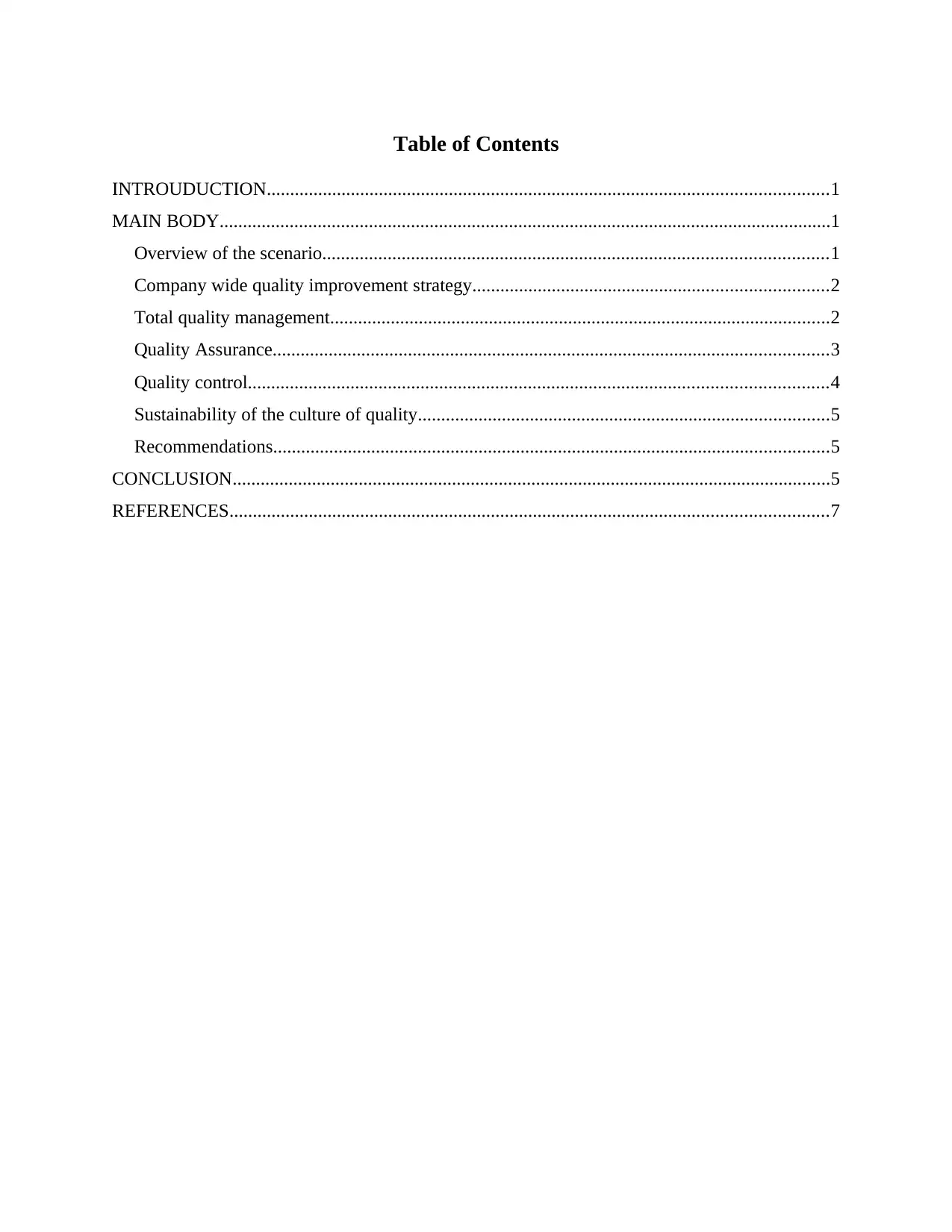
Table of Contents
INTROUDUCTION........................................................................................................................1
MAIN BODY...................................................................................................................................1
Overview of the scenario............................................................................................................1
Company wide quality improvement strategy............................................................................2
Total quality management...........................................................................................................2
Quality Assurance.......................................................................................................................3
Quality control............................................................................................................................4
Sustainability of the culture of quality........................................................................................5
Recommendations.......................................................................................................................5
CONCLUSION................................................................................................................................5
REFERENCES................................................................................................................................7
INTROUDUCTION........................................................................................................................1
MAIN BODY...................................................................................................................................1
Overview of the scenario............................................................................................................1
Company wide quality improvement strategy............................................................................2
Total quality management...........................................................................................................2
Quality Assurance.......................................................................................................................3
Quality control............................................................................................................................4
Sustainability of the culture of quality........................................................................................5
Recommendations.......................................................................................................................5
CONCLUSION................................................................................................................................5
REFERENCES................................................................................................................................7
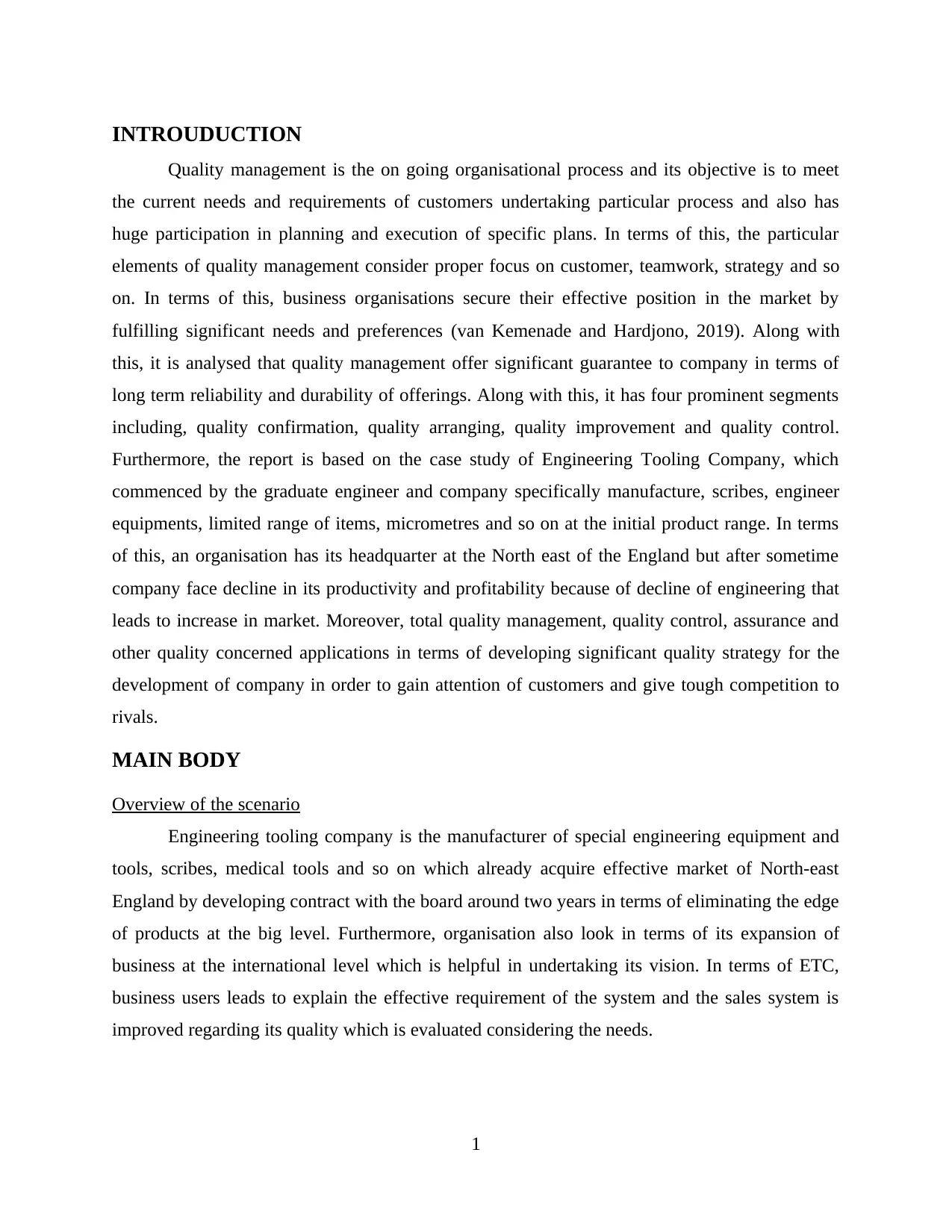
INTROUDUCTION
Quality management is the on going organisational process and its objective is to meet
the current needs and requirements of customers undertaking particular process and also has
huge participation in planning and execution of specific plans. In terms of this, the particular
elements of quality management consider proper focus on customer, teamwork, strategy and so
on. In terms of this, business organisations secure their effective position in the market by
fulfilling significant needs and preferences (van Kemenade and Hardjono, 2019). Along with
this, it is analysed that quality management offer significant guarantee to company in terms of
long term reliability and durability of offerings. Along with this, it has four prominent segments
including, quality confirmation, quality arranging, quality improvement and quality control.
Furthermore, the report is based on the case study of Engineering Tooling Company, which
commenced by the graduate engineer and company specifically manufacture, scribes, engineer
equipments, limited range of items, micrometres and so on at the initial product range. In terms
of this, an organisation has its headquarter at the North east of the England but after sometime
company face decline in its productivity and profitability because of decline of engineering that
leads to increase in market. Moreover, total quality management, quality control, assurance and
other quality concerned applications in terms of developing significant quality strategy for the
development of company in order to gain attention of customers and give tough competition to
rivals.
MAIN BODY
Overview of the scenario
Engineering tooling company is the manufacturer of special engineering equipment and
tools, scribes, medical tools and so on which already acquire effective market of North-east
England by developing contract with the board around two years in terms of eliminating the edge
of products at the big level. Furthermore, organisation also look in terms of its expansion of
business at the international level which is helpful in undertaking its vision. In terms of ETC,
business users leads to explain the effective requirement of the system and the sales system is
improved regarding its quality which is evaluated considering the needs.
1
Quality management is the on going organisational process and its objective is to meet
the current needs and requirements of customers undertaking particular process and also has
huge participation in planning and execution of specific plans. In terms of this, the particular
elements of quality management consider proper focus on customer, teamwork, strategy and so
on. In terms of this, business organisations secure their effective position in the market by
fulfilling significant needs and preferences (van Kemenade and Hardjono, 2019). Along with
this, it is analysed that quality management offer significant guarantee to company in terms of
long term reliability and durability of offerings. Along with this, it has four prominent segments
including, quality confirmation, quality arranging, quality improvement and quality control.
Furthermore, the report is based on the case study of Engineering Tooling Company, which
commenced by the graduate engineer and company specifically manufacture, scribes, engineer
equipments, limited range of items, micrometres and so on at the initial product range. In terms
of this, an organisation has its headquarter at the North east of the England but after sometime
company face decline in its productivity and profitability because of decline of engineering that
leads to increase in market. Moreover, total quality management, quality control, assurance and
other quality concerned applications in terms of developing significant quality strategy for the
development of company in order to gain attention of customers and give tough competition to
rivals.
MAIN BODY
Overview of the scenario
Engineering tooling company is the manufacturer of special engineering equipment and
tools, scribes, medical tools and so on which already acquire effective market of North-east
England by developing contract with the board around two years in terms of eliminating the edge
of products at the big level. Furthermore, organisation also look in terms of its expansion of
business at the international level which is helpful in undertaking its vision. In terms of ETC,
business users leads to explain the effective requirement of the system and the sales system is
improved regarding its quality which is evaluated considering the needs.
1
⊘ This is a preview!⊘
Do you want full access?
Subscribe today to unlock all pages.

Trusted by 1+ million students worldwide
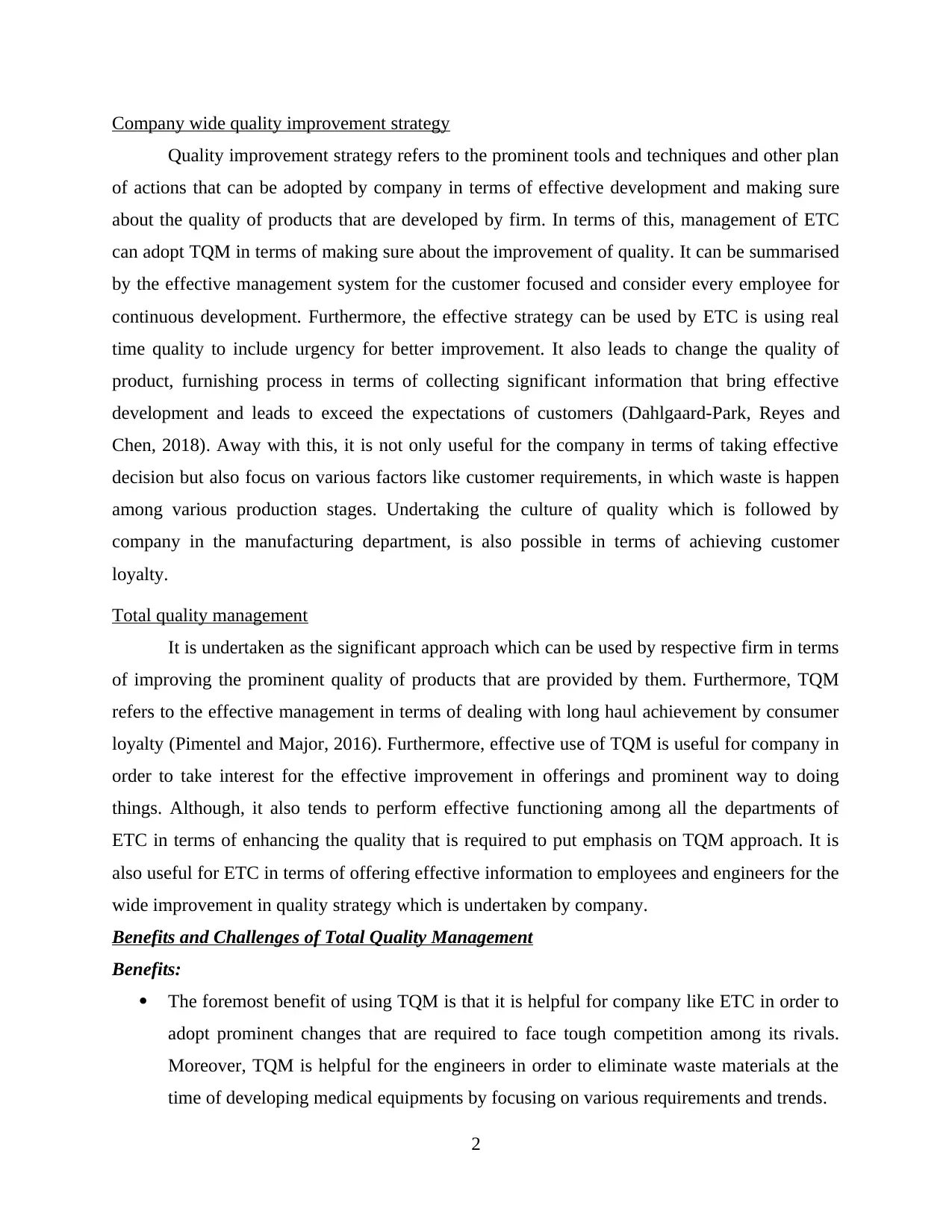
Company wide quality improvement strategy
Quality improvement strategy refers to the prominent tools and techniques and other plan
of actions that can be adopted by company in terms of effective development and making sure
about the quality of products that are developed by firm. In terms of this, management of ETC
can adopt TQM in terms of making sure about the improvement of quality. It can be summarised
by the effective management system for the customer focused and consider every employee for
continuous development. Furthermore, the effective strategy can be used by ETC is using real
time quality to include urgency for better improvement. It also leads to change the quality of
product, furnishing process in terms of collecting significant information that bring effective
development and leads to exceed the expectations of customers (Dahlgaard-Park, Reyes and
Chen, 2018). Away with this, it is not only useful for the company in terms of taking effective
decision but also focus on various factors like customer requirements, in which waste is happen
among various production stages. Undertaking the culture of quality which is followed by
company in the manufacturing department, is also possible in terms of achieving customer
loyalty.
Total quality management
It is undertaken as the significant approach which can be used by respective firm in terms
of improving the prominent quality of products that are provided by them. Furthermore, TQM
refers to the effective management in terms of dealing with long haul achievement by consumer
loyalty (Pimentel and Major, 2016). Furthermore, effective use of TQM is useful for company in
order to take interest for the effective improvement in offerings and prominent way to doing
things. Although, it also tends to perform effective functioning among all the departments of
ETC in terms of enhancing the quality that is required to put emphasis on TQM approach. It is
also useful for ETC in terms of offering effective information to employees and engineers for the
wide improvement in quality strategy which is undertaken by company.
Benefits and Challenges of Total Quality Management
Benefits:
The foremost benefit of using TQM is that it is helpful for company like ETC in order to
adopt prominent changes that are required to face tough competition among its rivals.
Moreover, TQM is helpful for the engineers in order to eliminate waste materials at the
time of developing medical equipments by focusing on various requirements and trends.
2
Quality improvement strategy refers to the prominent tools and techniques and other plan
of actions that can be adopted by company in terms of effective development and making sure
about the quality of products that are developed by firm. In terms of this, management of ETC
can adopt TQM in terms of making sure about the improvement of quality. It can be summarised
by the effective management system for the customer focused and consider every employee for
continuous development. Furthermore, the effective strategy can be used by ETC is using real
time quality to include urgency for better improvement. It also leads to change the quality of
product, furnishing process in terms of collecting significant information that bring effective
development and leads to exceed the expectations of customers (Dahlgaard-Park, Reyes and
Chen, 2018). Away with this, it is not only useful for the company in terms of taking effective
decision but also focus on various factors like customer requirements, in which waste is happen
among various production stages. Undertaking the culture of quality which is followed by
company in the manufacturing department, is also possible in terms of achieving customer
loyalty.
Total quality management
It is undertaken as the significant approach which can be used by respective firm in terms
of improving the prominent quality of products that are provided by them. Furthermore, TQM
refers to the effective management in terms of dealing with long haul achievement by consumer
loyalty (Pimentel and Major, 2016). Furthermore, effective use of TQM is useful for company in
order to take interest for the effective improvement in offerings and prominent way to doing
things. Although, it also tends to perform effective functioning among all the departments of
ETC in terms of enhancing the quality that is required to put emphasis on TQM approach. It is
also useful for ETC in terms of offering effective information to employees and engineers for the
wide improvement in quality strategy which is undertaken by company.
Benefits and Challenges of Total Quality Management
Benefits:
The foremost benefit of using TQM is that it is helpful for company like ETC in order to
adopt prominent changes that are required to face tough competition among its rivals.
Moreover, TQM is helpful for the engineers in order to eliminate waste materials at the
time of developing medical equipments by focusing on various requirements and trends.
2
Paraphrase This Document
Need a fresh take? Get an instant paraphrase of this document with our AI Paraphraser

Along with this, TQM is useful in order to get real time quality data in terms of bringing
urgency for the requirement that should be improved (Nicholas, 2016). Engineering
tooling company also analyse the detailed information that is collected after adopting the
prominent strategy for significant changes.
Challenges:
The prominent absence of secure quality culture depicts threat for the effective protection
from the changes which is hesitant for acknowledging the procedure that make the
variety in terms of existing way of working (Carvalho and et. al., 2019).
Moreover, if effective autocratic style of management is clutches by the higher authority
of the executives of ETC, as it leads to make situation to dread. Moreover, as a result the
workers does not contribute their full potential that corrupts their interest.
Quality Assurance
It refers to the procedure in terms of assuring that the company offer its products and also
offer effective facilities to consumers. Moreover, Quality assurance leads to paradigm for the
effective development of prominent activities in terms of providing the quality products and
services to the targeted audiences. For this, effective development also leads to make sure that
prominent actions are more effective and appropriate as per the quality standards (Androniceanu,
2017). It is prominently acknowledges as the quality assurance in terms of testing as the
management of ETC leads to determine and identify the quality of engineering items. Moreover,
ETC need to create products and services in order to meet the needs and desires of consumers
and also offer high quality products that leads to develop trust for the targeted audiences. Along
with this, the process tends to explain the quality assurance activity and other programs that
helps in protecting commodities before any defect. Moreover, to prominent conduct the quality
assurance, significant approach can be considered as the PDCA cycle and this model is
mentioned as under: Plan: It describe the proper implementation and execution of anything and for this, an
organisation need to plan and develop significant activity which is concerned with
prominent activities and also identify the activities that should need effective way to
deliver the quality of product (Fernandes and et. al., 2017). In terms ETC, at this stage,
the management need to form a plan which is related with selection of prominent
strategies and other tools in regard of achieving goals and objectives.
3
urgency for the requirement that should be improved (Nicholas, 2016). Engineering
tooling company also analyse the detailed information that is collected after adopting the
prominent strategy for significant changes.
Challenges:
The prominent absence of secure quality culture depicts threat for the effective protection
from the changes which is hesitant for acknowledging the procedure that make the
variety in terms of existing way of working (Carvalho and et. al., 2019).
Moreover, if effective autocratic style of management is clutches by the higher authority
of the executives of ETC, as it leads to make situation to dread. Moreover, as a result the
workers does not contribute their full potential that corrupts their interest.
Quality Assurance
It refers to the procedure in terms of assuring that the company offer its products and also
offer effective facilities to consumers. Moreover, Quality assurance leads to paradigm for the
effective development of prominent activities in terms of providing the quality products and
services to the targeted audiences. For this, effective development also leads to make sure that
prominent actions are more effective and appropriate as per the quality standards (Androniceanu,
2017). It is prominently acknowledges as the quality assurance in terms of testing as the
management of ETC leads to determine and identify the quality of engineering items. Moreover,
ETC need to create products and services in order to meet the needs and desires of consumers
and also offer high quality products that leads to develop trust for the targeted audiences. Along
with this, the process tends to explain the quality assurance activity and other programs that
helps in protecting commodities before any defect. Moreover, to prominent conduct the quality
assurance, significant approach can be considered as the PDCA cycle and this model is
mentioned as under: Plan: It describe the proper implementation and execution of anything and for this, an
organisation need to plan and develop significant activity which is concerned with
prominent activities and also identify the activities that should need effective way to
deliver the quality of product (Fernandes and et. al., 2017). In terms ETC, at this stage,
the management need to form a plan which is related with selection of prominent
strategies and other tools in regard of achieving goals and objectives.
3
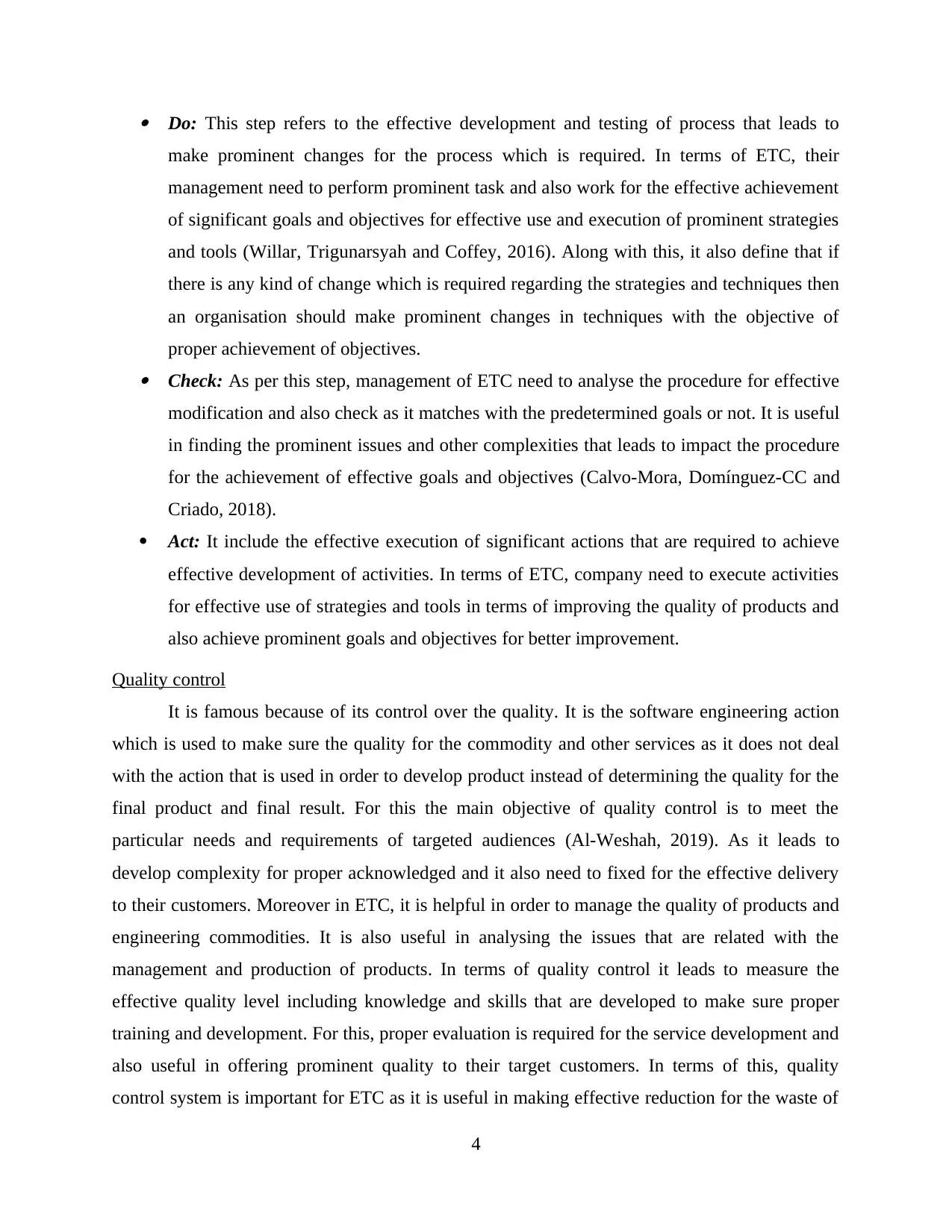
Do: This step refers to the effective development and testing of process that leads to
make prominent changes for the process which is required. In terms of ETC, their
management need to perform prominent task and also work for the effective achievement
of significant goals and objectives for effective use and execution of prominent strategies
and tools (Willar, Trigunarsyah and Coffey, 2016). Along with this, it also define that if
there is any kind of change which is required regarding the strategies and techniques then
an organisation should make prominent changes in techniques with the objective of
proper achievement of objectives. Check: As per this step, management of ETC need to analyse the procedure for effective
modification and also check as it matches with the predetermined goals or not. It is useful
in finding the prominent issues and other complexities that leads to impact the procedure
for the achievement of effective goals and objectives (Calvo-Mora, Domínguez-CC and
Criado, 2018).
Act: It include the effective execution of significant actions that are required to achieve
effective development of activities. In terms of ETC, company need to execute activities
for effective use of strategies and tools in terms of improving the quality of products and
also achieve prominent goals and objectives for better improvement.
Quality control
It is famous because of its control over the quality. It is the software engineering action
which is used to make sure the quality for the commodity and other services as it does not deal
with the action that is used in order to develop product instead of determining the quality for the
final product and final result. For this the main objective of quality control is to meet the
particular needs and requirements of targeted audiences (Al-Weshah, 2019). As it leads to
develop complexity for proper acknowledged and it also need to fixed for the effective delivery
to their customers. Moreover in ETC, it is helpful in order to manage the quality of products and
engineering commodities. It is also useful in analysing the issues that are related with the
management and production of products. In terms of quality control it leads to measure the
effective quality level including knowledge and skills that are developed to make sure proper
training and development. For this, proper evaluation is required for the service development and
also useful in offering prominent quality to their target customers. In terms of this, quality
control system is important for ETC as it is useful in making effective reduction for the waste of
4
make prominent changes for the process which is required. In terms of ETC, their
management need to perform prominent task and also work for the effective achievement
of significant goals and objectives for effective use and execution of prominent strategies
and tools (Willar, Trigunarsyah and Coffey, 2016). Along with this, it also define that if
there is any kind of change which is required regarding the strategies and techniques then
an organisation should make prominent changes in techniques with the objective of
proper achievement of objectives. Check: As per this step, management of ETC need to analyse the procedure for effective
modification and also check as it matches with the predetermined goals or not. It is useful
in finding the prominent issues and other complexities that leads to impact the procedure
for the achievement of effective goals and objectives (Calvo-Mora, Domínguez-CC and
Criado, 2018).
Act: It include the effective execution of significant actions that are required to achieve
effective development of activities. In terms of ETC, company need to execute activities
for effective use of strategies and tools in terms of improving the quality of products and
also achieve prominent goals and objectives for better improvement.
Quality control
It is famous because of its control over the quality. It is the software engineering action
which is used to make sure the quality for the commodity and other services as it does not deal
with the action that is used in order to develop product instead of determining the quality for the
final product and final result. For this the main objective of quality control is to meet the
particular needs and requirements of targeted audiences (Al-Weshah, 2019). As it leads to
develop complexity for proper acknowledged and it also need to fixed for the effective delivery
to their customers. Moreover in ETC, it is helpful in order to manage the quality of products and
engineering commodities. It is also useful in analysing the issues that are related with the
management and production of products. In terms of quality control it leads to measure the
effective quality level including knowledge and skills that are developed to make sure proper
training and development. For this, proper evaluation is required for the service development and
also useful in offering prominent quality to their target customers. In terms of this, quality
control system is important for ETC as it is useful in making effective reduction for the waste of
4
⊘ This is a preview!⊘
Do you want full access?
Subscribe today to unlock all pages.

Trusted by 1+ million students worldwide
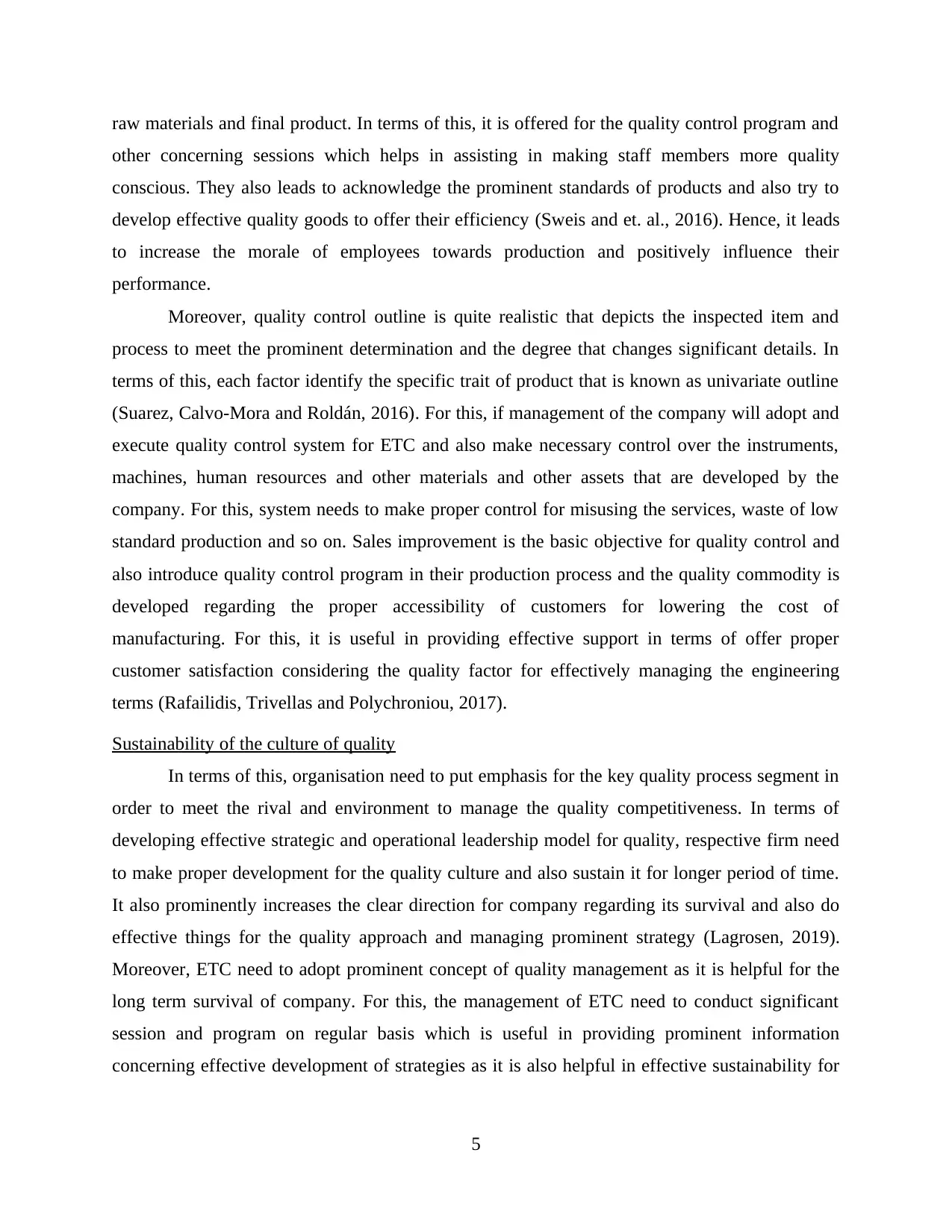
raw materials and final product. In terms of this, it is offered for the quality control program and
other concerning sessions which helps in assisting in making staff members more quality
conscious. They also leads to acknowledge the prominent standards of products and also try to
develop effective quality goods to offer their efficiency (Sweis and et. al., 2016). Hence, it leads
to increase the morale of employees towards production and positively influence their
performance.
Moreover, quality control outline is quite realistic that depicts the inspected item and
process to meet the prominent determination and the degree that changes significant details. In
terms of this, each factor identify the specific trait of product that is known as univariate outline
(Suarez, Calvo-Mora and Roldán, 2016). For this, if management of the company will adopt and
execute quality control system for ETC and also make necessary control over the instruments,
machines, human resources and other materials and other assets that are developed by the
company. For this, system needs to make proper control for misusing the services, waste of low
standard production and so on. Sales improvement is the basic objective for quality control and
also introduce quality control program in their production process and the quality commodity is
developed regarding the proper accessibility of customers for lowering the cost of
manufacturing. For this, it is useful in providing effective support in terms of offer proper
customer satisfaction considering the quality factor for effectively managing the engineering
terms (Rafailidis, Trivellas and Polychroniou, 2017).
Sustainability of the culture of quality
In terms of this, organisation need to put emphasis for the key quality process segment in
order to meet the rival and environment to manage the quality competitiveness. In terms of
developing effective strategic and operational leadership model for quality, respective firm need
to make proper development for the quality culture and also sustain it for longer period of time.
It also prominently increases the clear direction for company regarding its survival and also do
effective things for the quality approach and managing prominent strategy (Lagrosen, 2019).
Moreover, ETC need to adopt prominent concept of quality management as it is helpful for the
long term survival of company. For this, the management of ETC need to conduct significant
session and program on regular basis which is useful in providing prominent information
concerning effective development of strategies as it is also helpful in effective sustainability for
5
other concerning sessions which helps in assisting in making staff members more quality
conscious. They also leads to acknowledge the prominent standards of products and also try to
develop effective quality goods to offer their efficiency (Sweis and et. al., 2016). Hence, it leads
to increase the morale of employees towards production and positively influence their
performance.
Moreover, quality control outline is quite realistic that depicts the inspected item and
process to meet the prominent determination and the degree that changes significant details. In
terms of this, each factor identify the specific trait of product that is known as univariate outline
(Suarez, Calvo-Mora and Roldán, 2016). For this, if management of the company will adopt and
execute quality control system for ETC and also make necessary control over the instruments,
machines, human resources and other materials and other assets that are developed by the
company. For this, system needs to make proper control for misusing the services, waste of low
standard production and so on. Sales improvement is the basic objective for quality control and
also introduce quality control program in their production process and the quality commodity is
developed regarding the proper accessibility of customers for lowering the cost of
manufacturing. For this, it is useful in providing effective support in terms of offer proper
customer satisfaction considering the quality factor for effectively managing the engineering
terms (Rafailidis, Trivellas and Polychroniou, 2017).
Sustainability of the culture of quality
In terms of this, organisation need to put emphasis for the key quality process segment in
order to meet the rival and environment to manage the quality competitiveness. In terms of
developing effective strategic and operational leadership model for quality, respective firm need
to make proper development for the quality culture and also sustain it for longer period of time.
It also prominently increases the clear direction for company regarding its survival and also do
effective things for the quality approach and managing prominent strategy (Lagrosen, 2019).
Moreover, ETC need to adopt prominent concept of quality management as it is helpful for the
long term survival of company. For this, the management of ETC need to conduct significant
session and program on regular basis which is useful in providing prominent information
concerning effective development of strategies as it is also helpful in effective sustainability for
5
Paraphrase This Document
Need a fresh take? Get an instant paraphrase of this document with our AI Paraphraser
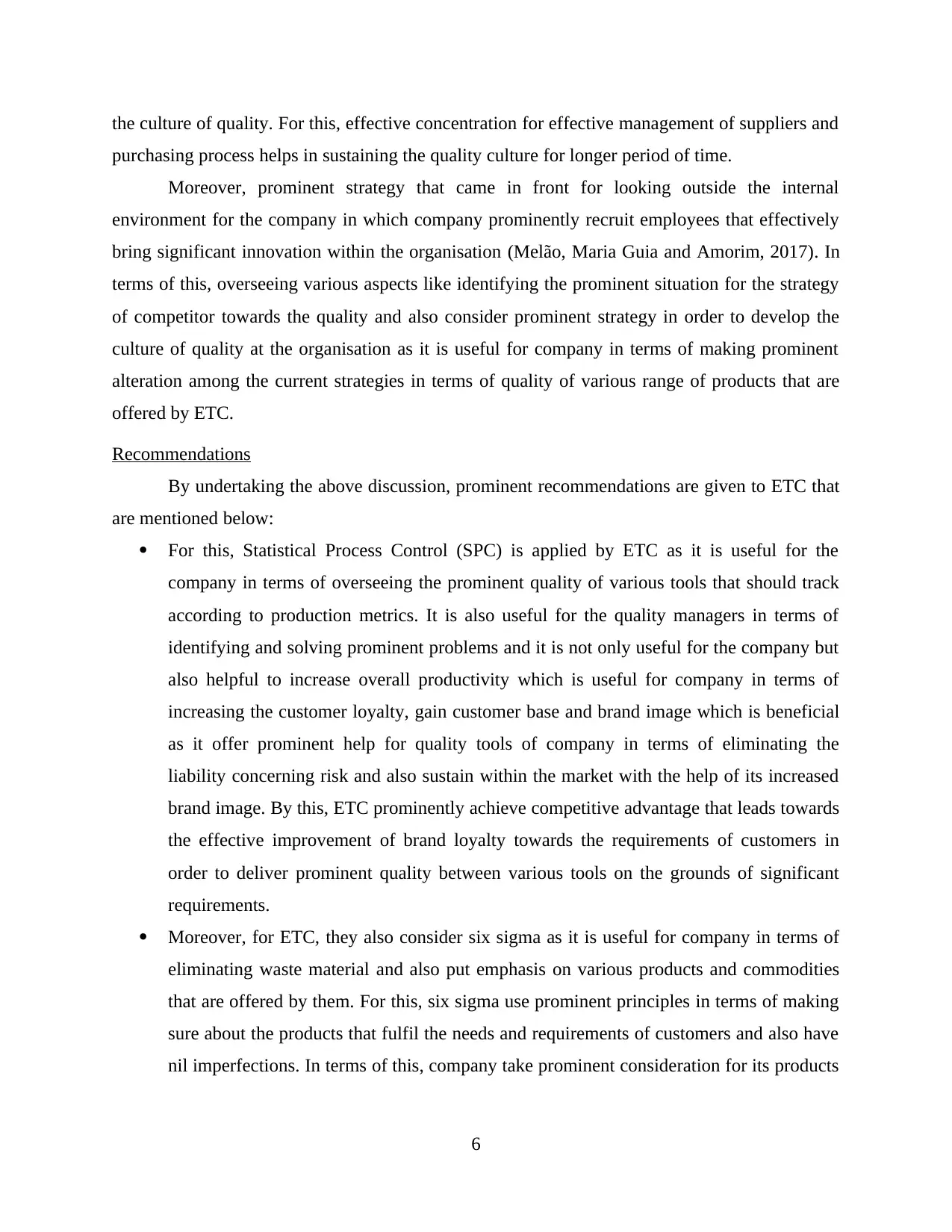
the culture of quality. For this, effective concentration for effective management of suppliers and
purchasing process helps in sustaining the quality culture for longer period of time.
Moreover, prominent strategy that came in front for looking outside the internal
environment for the company in which company prominently recruit employees that effectively
bring significant innovation within the organisation (Melão, Maria Guia and Amorim, 2017). In
terms of this, overseeing various aspects like identifying the prominent situation for the strategy
of competitor towards the quality and also consider prominent strategy in order to develop the
culture of quality at the organisation as it is useful for company in terms of making prominent
alteration among the current strategies in terms of quality of various range of products that are
offered by ETC.
Recommendations
By undertaking the above discussion, prominent recommendations are given to ETC that
are mentioned below:
For this, Statistical Process Control (SPC) is applied by ETC as it is useful for the
company in terms of overseeing the prominent quality of various tools that should track
according to production metrics. It is also useful for the quality managers in terms of
identifying and solving prominent problems and it is not only useful for the company but
also helpful to increase overall productivity which is useful for company in terms of
increasing the customer loyalty, gain customer base and brand image which is beneficial
as it offer prominent help for quality tools of company in terms of eliminating the
liability concerning risk and also sustain within the market with the help of its increased
brand image. By this, ETC prominently achieve competitive advantage that leads towards
the effective improvement of brand loyalty towards the requirements of customers in
order to deliver prominent quality between various tools on the grounds of significant
requirements.
Moreover, for ETC, they also consider six sigma as it is useful for company in terms of
eliminating waste material and also put emphasis on various products and commodities
that are offered by them. For this, six sigma use prominent principles in terms of making
sure about the products that fulfil the needs and requirements of customers and also have
nil imperfections. In terms of this, company take prominent consideration for its products
6
purchasing process helps in sustaining the quality culture for longer period of time.
Moreover, prominent strategy that came in front for looking outside the internal
environment for the company in which company prominently recruit employees that effectively
bring significant innovation within the organisation (Melão, Maria Guia and Amorim, 2017). In
terms of this, overseeing various aspects like identifying the prominent situation for the strategy
of competitor towards the quality and also consider prominent strategy in order to develop the
culture of quality at the organisation as it is useful for company in terms of making prominent
alteration among the current strategies in terms of quality of various range of products that are
offered by ETC.
Recommendations
By undertaking the above discussion, prominent recommendations are given to ETC that
are mentioned below:
For this, Statistical Process Control (SPC) is applied by ETC as it is useful for the
company in terms of overseeing the prominent quality of various tools that should track
according to production metrics. It is also useful for the quality managers in terms of
identifying and solving prominent problems and it is not only useful for the company but
also helpful to increase overall productivity which is useful for company in terms of
increasing the customer loyalty, gain customer base and brand image which is beneficial
as it offer prominent help for quality tools of company in terms of eliminating the
liability concerning risk and also sustain within the market with the help of its increased
brand image. By this, ETC prominently achieve competitive advantage that leads towards
the effective improvement of brand loyalty towards the requirements of customers in
order to deliver prominent quality between various tools on the grounds of significant
requirements.
Moreover, for ETC, they also consider six sigma as it is useful for company in terms of
eliminating waste material and also put emphasis on various products and commodities
that are offered by them. For this, six sigma use prominent principles in terms of making
sure about the products that fulfil the needs and requirements of customers and also have
nil imperfections. In terms of this, company take prominent consideration for its products
6
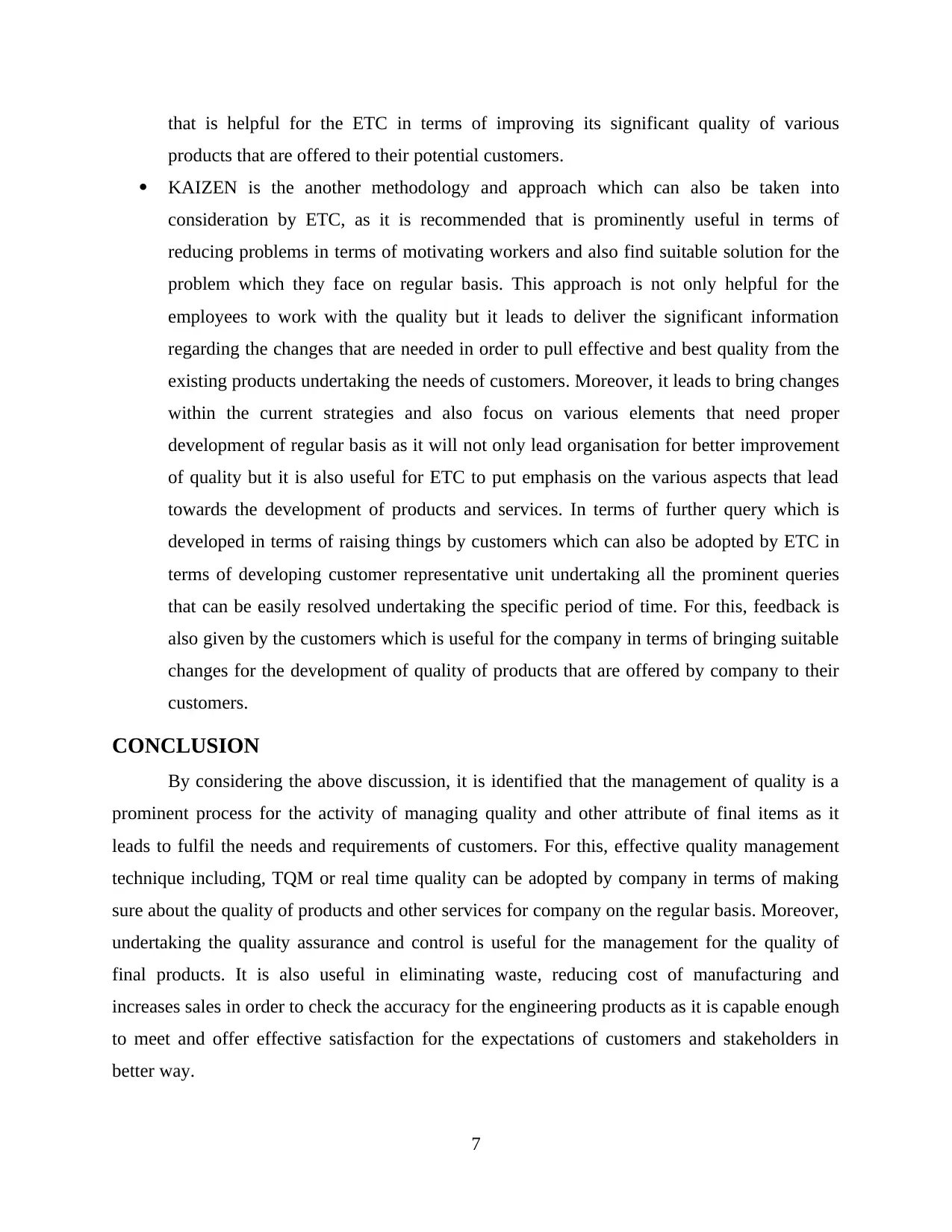
that is helpful for the ETC in terms of improving its significant quality of various
products that are offered to their potential customers.
KAIZEN is the another methodology and approach which can also be taken into
consideration by ETC, as it is recommended that is prominently useful in terms of
reducing problems in terms of motivating workers and also find suitable solution for the
problem which they face on regular basis. This approach is not only helpful for the
employees to work with the quality but it leads to deliver the significant information
regarding the changes that are needed in order to pull effective and best quality from the
existing products undertaking the needs of customers. Moreover, it leads to bring changes
within the current strategies and also focus on various elements that need proper
development of regular basis as it will not only lead organisation for better improvement
of quality but it is also useful for ETC to put emphasis on the various aspects that lead
towards the development of products and services. In terms of further query which is
developed in terms of raising things by customers which can also be adopted by ETC in
terms of developing customer representative unit undertaking all the prominent queries
that can be easily resolved undertaking the specific period of time. For this, feedback is
also given by the customers which is useful for the company in terms of bringing suitable
changes for the development of quality of products that are offered by company to their
customers.
CONCLUSION
By considering the above discussion, it is identified that the management of quality is a
prominent process for the activity of managing quality and other attribute of final items as it
leads to fulfil the needs and requirements of customers. For this, effective quality management
technique including, TQM or real time quality can be adopted by company in terms of making
sure about the quality of products and other services for company on the regular basis. Moreover,
undertaking the quality assurance and control is useful for the management for the quality of
final products. It is also useful in eliminating waste, reducing cost of manufacturing and
increases sales in order to check the accuracy for the engineering products as it is capable enough
to meet and offer effective satisfaction for the expectations of customers and stakeholders in
better way.
7
products that are offered to their potential customers.
KAIZEN is the another methodology and approach which can also be taken into
consideration by ETC, as it is recommended that is prominently useful in terms of
reducing problems in terms of motivating workers and also find suitable solution for the
problem which they face on regular basis. This approach is not only helpful for the
employees to work with the quality but it leads to deliver the significant information
regarding the changes that are needed in order to pull effective and best quality from the
existing products undertaking the needs of customers. Moreover, it leads to bring changes
within the current strategies and also focus on various elements that need proper
development of regular basis as it will not only lead organisation for better improvement
of quality but it is also useful for ETC to put emphasis on the various aspects that lead
towards the development of products and services. In terms of further query which is
developed in terms of raising things by customers which can also be adopted by ETC in
terms of developing customer representative unit undertaking all the prominent queries
that can be easily resolved undertaking the specific period of time. For this, feedback is
also given by the customers which is useful for the company in terms of bringing suitable
changes for the development of quality of products that are offered by company to their
customers.
CONCLUSION
By considering the above discussion, it is identified that the management of quality is a
prominent process for the activity of managing quality and other attribute of final items as it
leads to fulfil the needs and requirements of customers. For this, effective quality management
technique including, TQM or real time quality can be adopted by company in terms of making
sure about the quality of products and other services for company on the regular basis. Moreover,
undertaking the quality assurance and control is useful for the management for the quality of
final products. It is also useful in eliminating waste, reducing cost of manufacturing and
increases sales in order to check the accuracy for the engineering products as it is capable enough
to meet and offer effective satisfaction for the expectations of customers and stakeholders in
better way.
7
⊘ This is a preview!⊘
Do you want full access?
Subscribe today to unlock all pages.

Trusted by 1+ million students worldwide
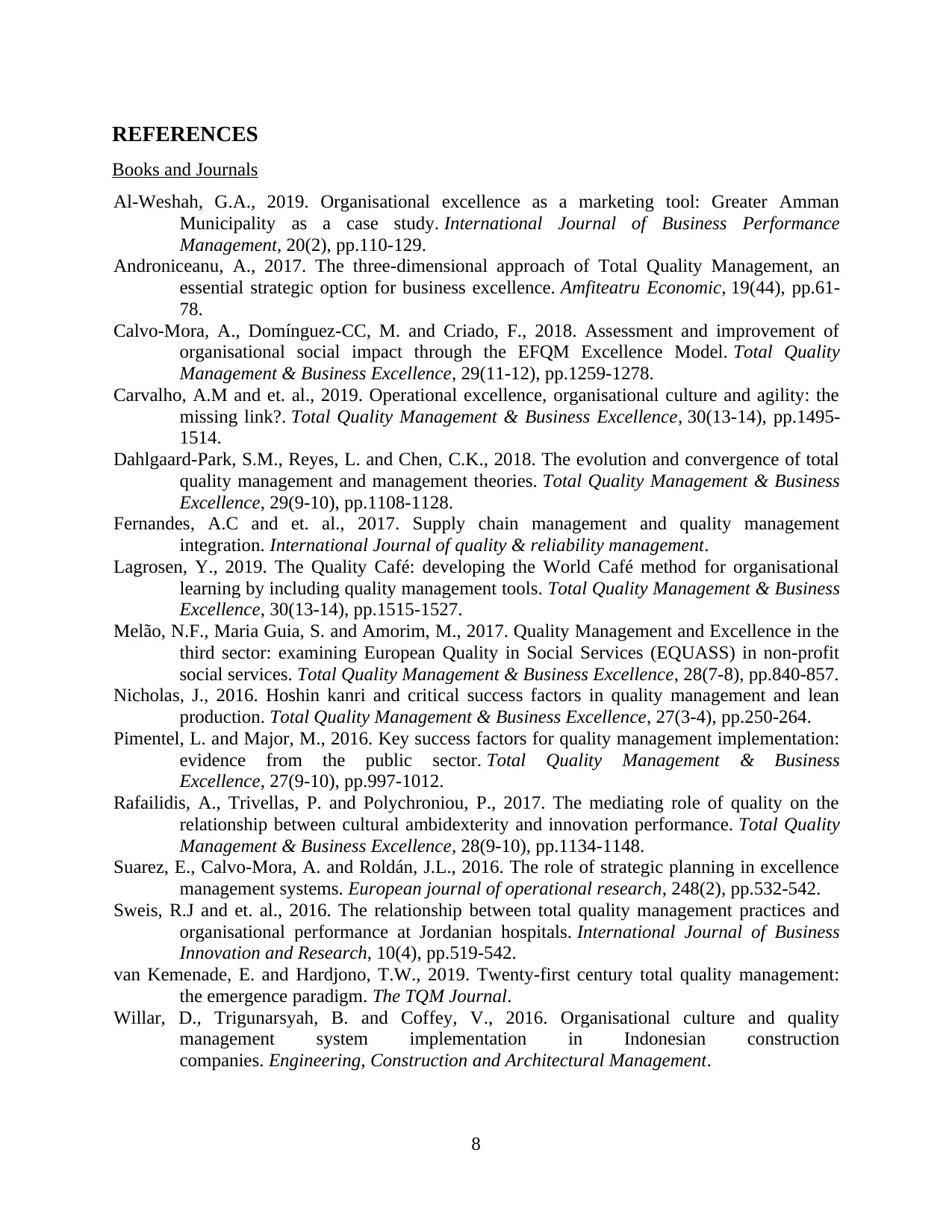
REFERENCES
Books and Journals
Al-Weshah, G.A., 2019. Organisational excellence as a marketing tool: Greater Amman
Municipality as a case study. International Journal of Business Performance
Management, 20(2), pp.110-129.
Androniceanu, A., 2017. The three-dimensional approach of Total Quality Management, an
essential strategic option for business excellence. Amfiteatru Economic, 19(44), pp.61-
78.
Calvo-Mora, A., Domínguez-CC, M. and Criado, F., 2018. Assessment and improvement of
organisational social impact through the EFQM Excellence Model. Total Quality
Management & Business Excellence, 29(11-12), pp.1259-1278.
Carvalho, A.M and et. al., 2019. Operational excellence, organisational culture and agility: the
missing link?. Total Quality Management & Business Excellence, 30(13-14), pp.1495-
1514.
Dahlgaard-Park, S.M., Reyes, L. and Chen, C.K., 2018. The evolution and convergence of total
quality management and management theories. Total Quality Management & Business
Excellence, 29(9-10), pp.1108-1128.
Fernandes, A.C and et. al., 2017. Supply chain management and quality management
integration. International Journal of quality & reliability management.
Lagrosen, Y., 2019. The Quality Café: developing the World Café method for organisational
learning by including quality management tools. Total Quality Management & Business
Excellence, 30(13-14), pp.1515-1527.
Melão, N.F., Maria Guia, S. and Amorim, M., 2017. Quality Management and Excellence in the
third sector: examining European Quality in Social Services (EQUASS) in non-profit
social services. Total Quality Management & Business Excellence, 28(7-8), pp.840-857.
Nicholas, J., 2016. Hoshin kanri and critical success factors in quality management and lean
production. Total Quality Management & Business Excellence, 27(3-4), pp.250-264.
Pimentel, L. and Major, M., 2016. Key success factors for quality management implementation:
evidence from the public sector. Total Quality Management & Business
Excellence, 27(9-10), pp.997-1012.
Rafailidis, A., Trivellas, P. and Polychroniou, P., 2017. The mediating role of quality on the
relationship between cultural ambidexterity and innovation performance. Total Quality
Management & Business Excellence, 28(9-10), pp.1134-1148.
Suarez, E., Calvo-Mora, A. and Roldán, J.L., 2016. The role of strategic planning in excellence
management systems. European journal of operational research, 248(2), pp.532-542.
Sweis, R.J and et. al., 2016. The relationship between total quality management practices and
organisational performance at Jordanian hospitals. International Journal of Business
Innovation and Research, 10(4), pp.519-542.
van Kemenade, E. and Hardjono, T.W., 2019. Twenty-first century total quality management:
the emergence paradigm. The TQM Journal.
Willar, D., Trigunarsyah, B. and Coffey, V., 2016. Organisational culture and quality
management system implementation in Indonesian construction
companies. Engineering, Construction and Architectural Management.
8
Books and Journals
Al-Weshah, G.A., 2019. Organisational excellence as a marketing tool: Greater Amman
Municipality as a case study. International Journal of Business Performance
Management, 20(2), pp.110-129.
Androniceanu, A., 2017. The three-dimensional approach of Total Quality Management, an
essential strategic option for business excellence. Amfiteatru Economic, 19(44), pp.61-
78.
Calvo-Mora, A., Domínguez-CC, M. and Criado, F., 2018. Assessment and improvement of
organisational social impact through the EFQM Excellence Model. Total Quality
Management & Business Excellence, 29(11-12), pp.1259-1278.
Carvalho, A.M and et. al., 2019. Operational excellence, organisational culture and agility: the
missing link?. Total Quality Management & Business Excellence, 30(13-14), pp.1495-
1514.
Dahlgaard-Park, S.M., Reyes, L. and Chen, C.K., 2018. The evolution and convergence of total
quality management and management theories. Total Quality Management & Business
Excellence, 29(9-10), pp.1108-1128.
Fernandes, A.C and et. al., 2017. Supply chain management and quality management
integration. International Journal of quality & reliability management.
Lagrosen, Y., 2019. The Quality Café: developing the World Café method for organisational
learning by including quality management tools. Total Quality Management & Business
Excellence, 30(13-14), pp.1515-1527.
Melão, N.F., Maria Guia, S. and Amorim, M., 2017. Quality Management and Excellence in the
third sector: examining European Quality in Social Services (EQUASS) in non-profit
social services. Total Quality Management & Business Excellence, 28(7-8), pp.840-857.
Nicholas, J., 2016. Hoshin kanri and critical success factors in quality management and lean
production. Total Quality Management & Business Excellence, 27(3-4), pp.250-264.
Pimentel, L. and Major, M., 2016. Key success factors for quality management implementation:
evidence from the public sector. Total Quality Management & Business
Excellence, 27(9-10), pp.997-1012.
Rafailidis, A., Trivellas, P. and Polychroniou, P., 2017. The mediating role of quality on the
relationship between cultural ambidexterity and innovation performance. Total Quality
Management & Business Excellence, 28(9-10), pp.1134-1148.
Suarez, E., Calvo-Mora, A. and Roldán, J.L., 2016. The role of strategic planning in excellence
management systems. European journal of operational research, 248(2), pp.532-542.
Sweis, R.J and et. al., 2016. The relationship between total quality management practices and
organisational performance at Jordanian hospitals. International Journal of Business
Innovation and Research, 10(4), pp.519-542.
van Kemenade, E. and Hardjono, T.W., 2019. Twenty-first century total quality management:
the emergence paradigm. The TQM Journal.
Willar, D., Trigunarsyah, B. and Coffey, V., 2016. Organisational culture and quality
management system implementation in Indonesian construction
companies. Engineering, Construction and Architectural Management.
8
1 out of 10
Related Documents

Your All-in-One AI-Powered Toolkit for Academic Success.
+13062052269
info@desklib.com
Available 24*7 on WhatsApp / Email
Unlock your academic potential
Copyright © 2020–2025 A2Z Services. All Rights Reserved. Developed and managed by ZUCOL.