UGB262 Quality Management: Engineering Tooling Company Report
VerifiedAdded on 2023/04/22
|13
|4050
|341
Report
AI Summary
This report provides a comprehensive quality improvement strategy for the Engineering Tooling Company (ETC), addressing the challenges posed by globalization and declining engineering in the North East of England. As a Quality Manager, the report focuses on implementing a strategy encompassing Total Quality Management (TQM), Quality Assurance, and Quality Control. The TQM strategy emphasizes teamwork, customer focus, quality measurement, and communication. Quality Assurance involves timely inspections and adherence to ISO 9000 standards. Quality Control includes physical tests, inspections, and a focus on creating a quality culture through competent hiring, defined processes, and employee training. The report further highlights the importance of sustaining a quality culture through customer focus, open communication, employee involvement, and continuous improvement, ultimately aiming for long-term success and customer satisfaction. This report (UGB262) is available on Desklib, along with other solved assignments and study resources.
Contribute Materials
Your contribution can guide someone’s learning journey. Share your
documents today.
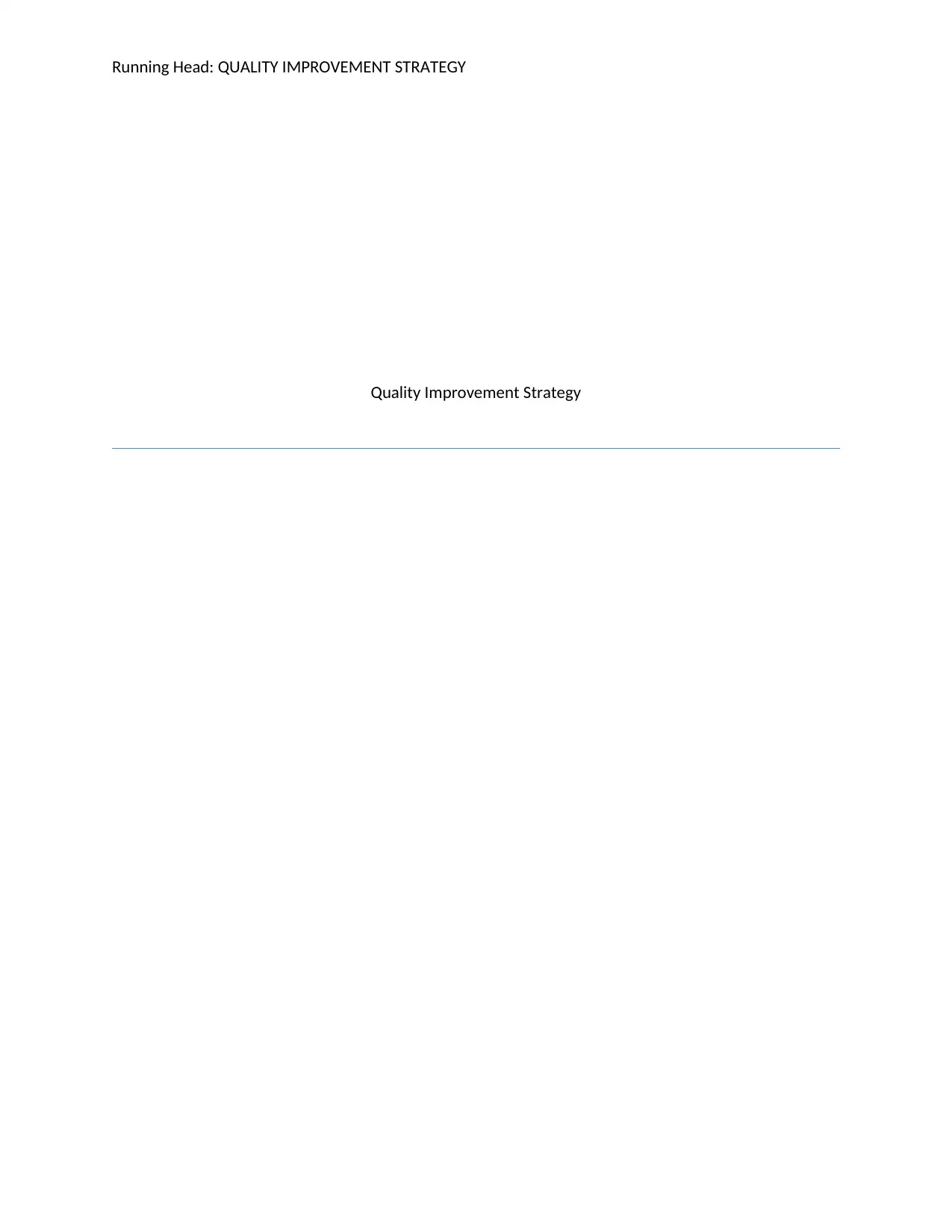
Running Head: QUALITY IMPROVEMENT STRATEGY
Quality Improvement Strategy
Quality Improvement Strategy
Secure Best Marks with AI Grader
Need help grading? Try our AI Grader for instant feedback on your assignments.
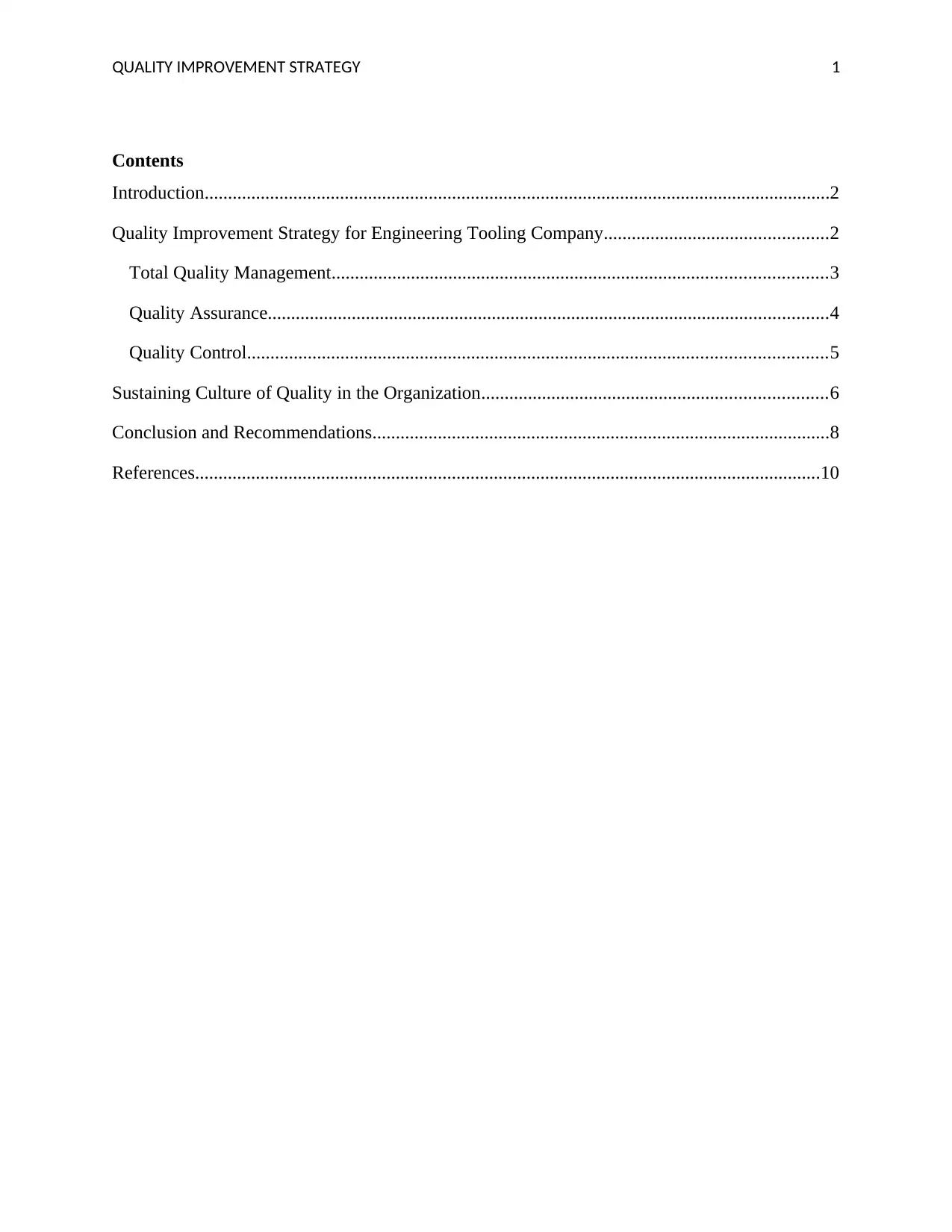
QUALITY IMPROVEMENT STRATEGY 1
Contents
Introduction......................................................................................................................................2
Quality Improvement Strategy for Engineering Tooling Company................................................2
Total Quality Management..........................................................................................................3
Quality Assurance........................................................................................................................4
Quality Control............................................................................................................................5
Sustaining Culture of Quality in the Organization..........................................................................6
Conclusion and Recommendations..................................................................................................8
References......................................................................................................................................10
Contents
Introduction......................................................................................................................................2
Quality Improvement Strategy for Engineering Tooling Company................................................2
Total Quality Management..........................................................................................................3
Quality Assurance........................................................................................................................4
Quality Control............................................................................................................................5
Sustaining Culture of Quality in the Organization..........................................................................6
Conclusion and Recommendations..................................................................................................8
References......................................................................................................................................10
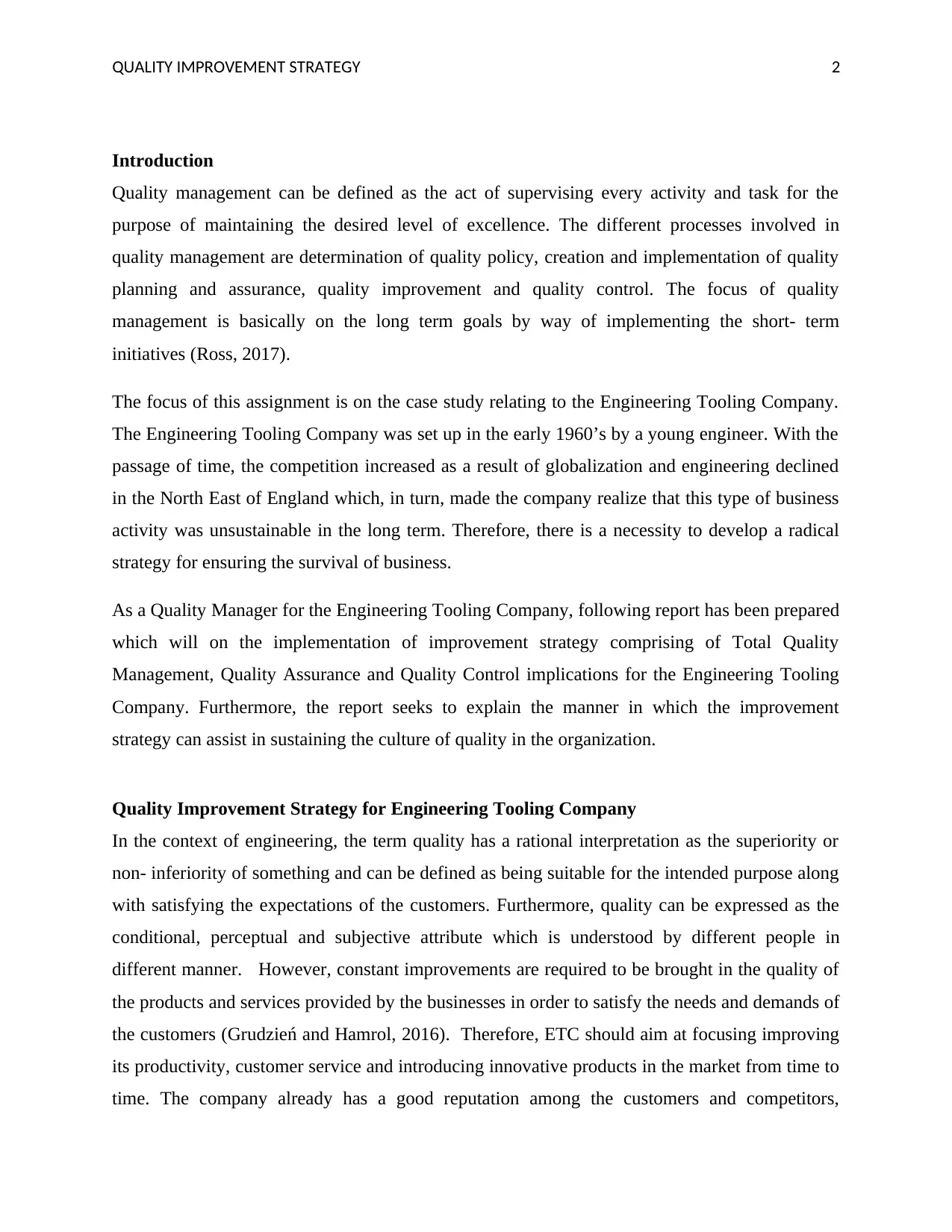
QUALITY IMPROVEMENT STRATEGY 2
Introduction
Quality management can be defined as the act of supervising every activity and task for the
purpose of maintaining the desired level of excellence. The different processes involved in
quality management are determination of quality policy, creation and implementation of quality
planning and assurance, quality improvement and quality control. The focus of quality
management is basically on the long term goals by way of implementing the short- term
initiatives (Ross, 2017).
The focus of this assignment is on the case study relating to the Engineering Tooling Company.
The Engineering Tooling Company was set up in the early 1960’s by a young engineer. With the
passage of time, the competition increased as a result of globalization and engineering declined
in the North East of England which, in turn, made the company realize that this type of business
activity was unsustainable in the long term. Therefore, there is a necessity to develop a radical
strategy for ensuring the survival of business.
As a Quality Manager for the Engineering Tooling Company, following report has been prepared
which will on the implementation of improvement strategy comprising of Total Quality
Management, Quality Assurance and Quality Control implications for the Engineering Tooling
Company. Furthermore, the report seeks to explain the manner in which the improvement
strategy can assist in sustaining the culture of quality in the organization.
Quality Improvement Strategy for Engineering Tooling Company
In the context of engineering, the term quality has a rational interpretation as the superiority or
non- inferiority of something and can be defined as being suitable for the intended purpose along
with satisfying the expectations of the customers. Furthermore, quality can be expressed as the
conditional, perceptual and subjective attribute which is understood by different people in
different manner. However, constant improvements are required to be brought in the quality of
the products and services provided by the businesses in order to satisfy the needs and demands of
the customers (Grudzień and Hamrol, 2016). Therefore, ETC should aim at focusing improving
its productivity, customer service and introducing innovative products in the market from time to
time. The company already has a good reputation among the customers and competitors,
Introduction
Quality management can be defined as the act of supervising every activity and task for the
purpose of maintaining the desired level of excellence. The different processes involved in
quality management are determination of quality policy, creation and implementation of quality
planning and assurance, quality improvement and quality control. The focus of quality
management is basically on the long term goals by way of implementing the short- term
initiatives (Ross, 2017).
The focus of this assignment is on the case study relating to the Engineering Tooling Company.
The Engineering Tooling Company was set up in the early 1960’s by a young engineer. With the
passage of time, the competition increased as a result of globalization and engineering declined
in the North East of England which, in turn, made the company realize that this type of business
activity was unsustainable in the long term. Therefore, there is a necessity to develop a radical
strategy for ensuring the survival of business.
As a Quality Manager for the Engineering Tooling Company, following report has been prepared
which will on the implementation of improvement strategy comprising of Total Quality
Management, Quality Assurance and Quality Control implications for the Engineering Tooling
Company. Furthermore, the report seeks to explain the manner in which the improvement
strategy can assist in sustaining the culture of quality in the organization.
Quality Improvement Strategy for Engineering Tooling Company
In the context of engineering, the term quality has a rational interpretation as the superiority or
non- inferiority of something and can be defined as being suitable for the intended purpose along
with satisfying the expectations of the customers. Furthermore, quality can be expressed as the
conditional, perceptual and subjective attribute which is understood by different people in
different manner. However, constant improvements are required to be brought in the quality of
the products and services provided by the businesses in order to satisfy the needs and demands of
the customers (Grudzień and Hamrol, 2016). Therefore, ETC should aim at focusing improving
its productivity, customer service and introducing innovative products in the market from time to
time. The company already has a good reputation among the customers and competitors,
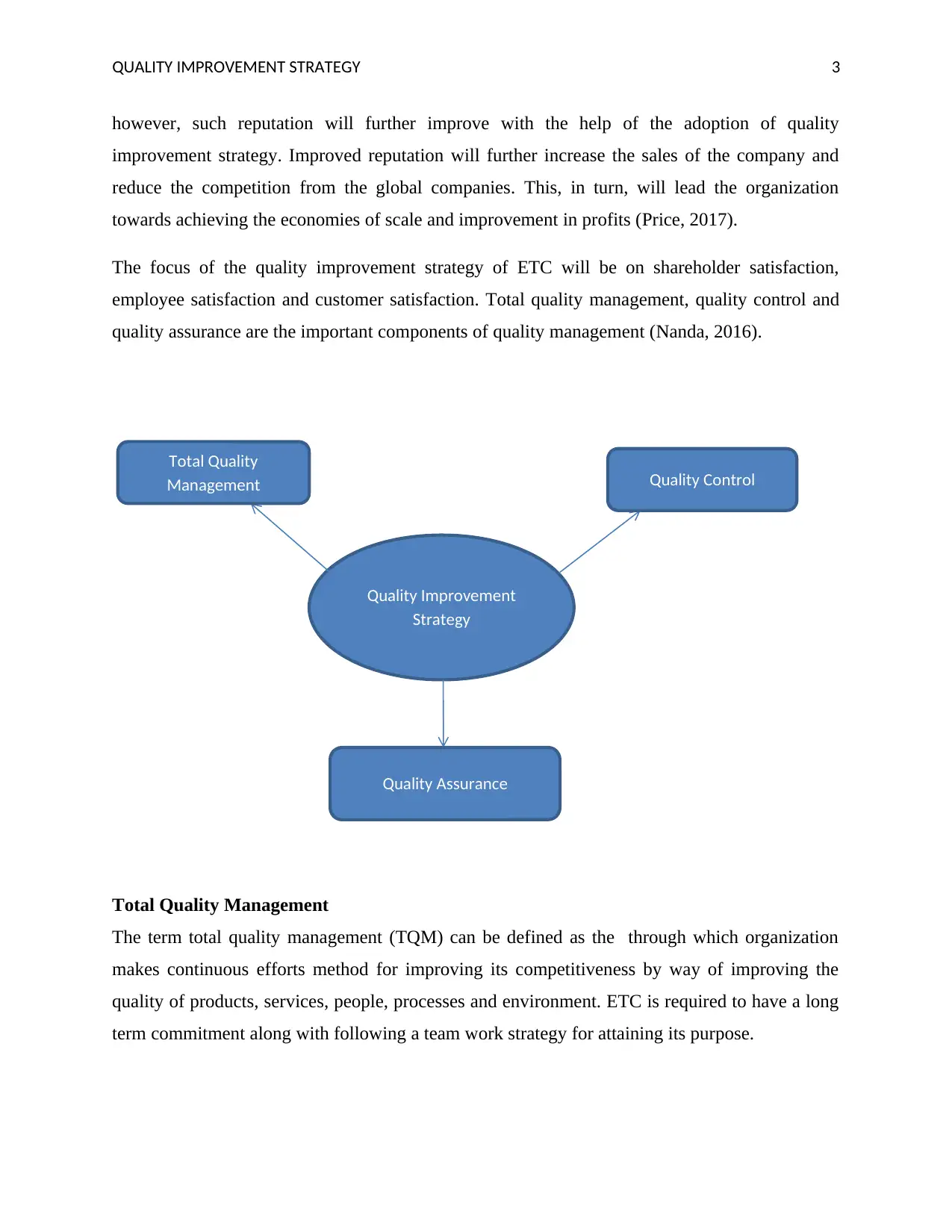
QUALITY IMPROVEMENT STRATEGY 3
however, such reputation will further improve with the help of the adoption of quality
improvement strategy. Improved reputation will further increase the sales of the company and
reduce the competition from the global companies. This, in turn, will lead the organization
towards achieving the economies of scale and improvement in profits (Price, 2017).
The focus of the quality improvement strategy of ETC will be on shareholder satisfaction,
employee satisfaction and customer satisfaction. Total quality management, quality control and
quality assurance are the important components of quality management (Nanda, 2016).
Total Quality Management
The term total quality management (TQM) can be defined as the through which organization
makes continuous efforts method for improving its competitiveness by way of improving the
quality of products, services, people, processes and environment. ETC is required to have a long
term commitment along with following a team work strategy for attaining its purpose.
Quality Improvement
Strategy
Total Quality
Management Quality Control
Quality Assurance
however, such reputation will further improve with the help of the adoption of quality
improvement strategy. Improved reputation will further increase the sales of the company and
reduce the competition from the global companies. This, in turn, will lead the organization
towards achieving the economies of scale and improvement in profits (Price, 2017).
The focus of the quality improvement strategy of ETC will be on shareholder satisfaction,
employee satisfaction and customer satisfaction. Total quality management, quality control and
quality assurance are the important components of quality management (Nanda, 2016).
Total Quality Management
The term total quality management (TQM) can be defined as the through which organization
makes continuous efforts method for improving its competitiveness by way of improving the
quality of products, services, people, processes and environment. ETC is required to have a long
term commitment along with following a team work strategy for attaining its purpose.
Quality Improvement
Strategy
Total Quality
Management Quality Control
Quality Assurance
Secure Best Marks with AI Grader
Need help grading? Try our AI Grader for instant feedback on your assignments.
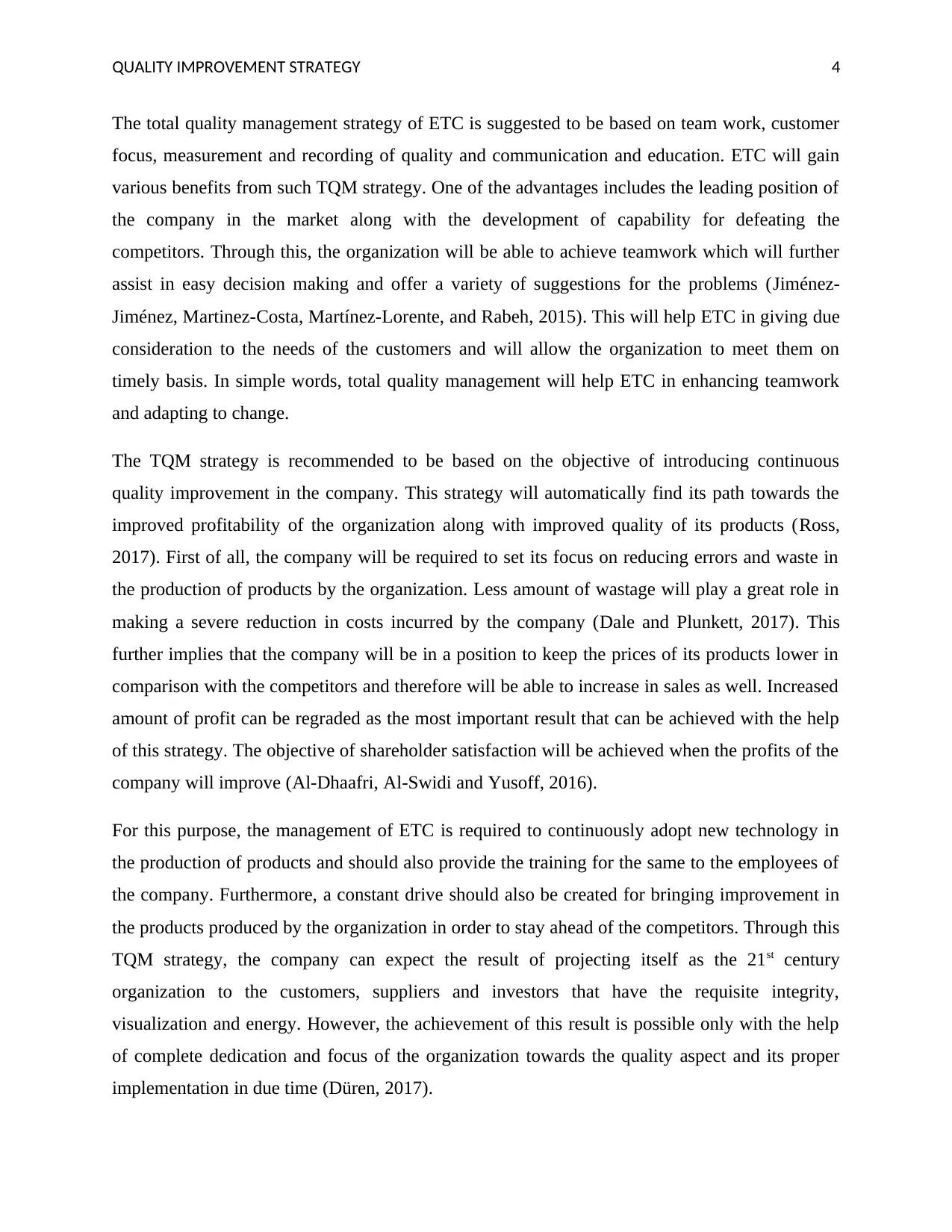
QUALITY IMPROVEMENT STRATEGY 4
The total quality management strategy of ETC is suggested to be based on team work, customer
focus, measurement and recording of quality and communication and education. ETC will gain
various benefits from such TQM strategy. One of the advantages includes the leading position of
the company in the market along with the development of capability for defeating the
competitors. Through this, the organization will be able to achieve teamwork which will further
assist in easy decision making and offer a variety of suggestions for the problems (Jiménez-
Jiménez, Martinez-Costa, Martínez-Lorente, and Rabeh, 2015). This will help ETC in giving due
consideration to the needs of the customers and will allow the organization to meet them on
timely basis. In simple words, total quality management will help ETC in enhancing teamwork
and adapting to change.
The TQM strategy is recommended to be based on the objective of introducing continuous
quality improvement in the company. This strategy will automatically find its path towards the
improved profitability of the organization along with improved quality of its products (Ross,
2017). First of all, the company will be required to set its focus on reducing errors and waste in
the production of products by the organization. Less amount of wastage will play a great role in
making a severe reduction in costs incurred by the company (Dale and Plunkett, 2017). This
further implies that the company will be in a position to keep the prices of its products lower in
comparison with the competitors and therefore will be able to increase in sales as well. Increased
amount of profit can be regraded as the most important result that can be achieved with the help
of this strategy. The objective of shareholder satisfaction will be achieved when the profits of the
company will improve (Al-Dhaafri, Al-Swidi and Yusoff, 2016).
For this purpose, the management of ETC is required to continuously adopt new technology in
the production of products and should also provide the training for the same to the employees of
the company. Furthermore, a constant drive should also be created for bringing improvement in
the products produced by the organization in order to stay ahead of the competitors. Through this
TQM strategy, the company can expect the result of projecting itself as the 21st century
organization to the customers, suppliers and investors that have the requisite integrity,
visualization and energy. However, the achievement of this result is possible only with the help
of complete dedication and focus of the organization towards the quality aspect and its proper
implementation in due time (Düren, 2017).
The total quality management strategy of ETC is suggested to be based on team work, customer
focus, measurement and recording of quality and communication and education. ETC will gain
various benefits from such TQM strategy. One of the advantages includes the leading position of
the company in the market along with the development of capability for defeating the
competitors. Through this, the organization will be able to achieve teamwork which will further
assist in easy decision making and offer a variety of suggestions for the problems (Jiménez-
Jiménez, Martinez-Costa, Martínez-Lorente, and Rabeh, 2015). This will help ETC in giving due
consideration to the needs of the customers and will allow the organization to meet them on
timely basis. In simple words, total quality management will help ETC in enhancing teamwork
and adapting to change.
The TQM strategy is recommended to be based on the objective of introducing continuous
quality improvement in the company. This strategy will automatically find its path towards the
improved profitability of the organization along with improved quality of its products (Ross,
2017). First of all, the company will be required to set its focus on reducing errors and waste in
the production of products by the organization. Less amount of wastage will play a great role in
making a severe reduction in costs incurred by the company (Dale and Plunkett, 2017). This
further implies that the company will be in a position to keep the prices of its products lower in
comparison with the competitors and therefore will be able to increase in sales as well. Increased
amount of profit can be regraded as the most important result that can be achieved with the help
of this strategy. The objective of shareholder satisfaction will be achieved when the profits of the
company will improve (Al-Dhaafri, Al-Swidi and Yusoff, 2016).
For this purpose, the management of ETC is required to continuously adopt new technology in
the production of products and should also provide the training for the same to the employees of
the company. Furthermore, a constant drive should also be created for bringing improvement in
the products produced by the organization in order to stay ahead of the competitors. Through this
TQM strategy, the company can expect the result of projecting itself as the 21st century
organization to the customers, suppliers and investors that have the requisite integrity,
visualization and energy. However, the achievement of this result is possible only with the help
of complete dedication and focus of the organization towards the quality aspect and its proper
implementation in due time (Düren, 2017).
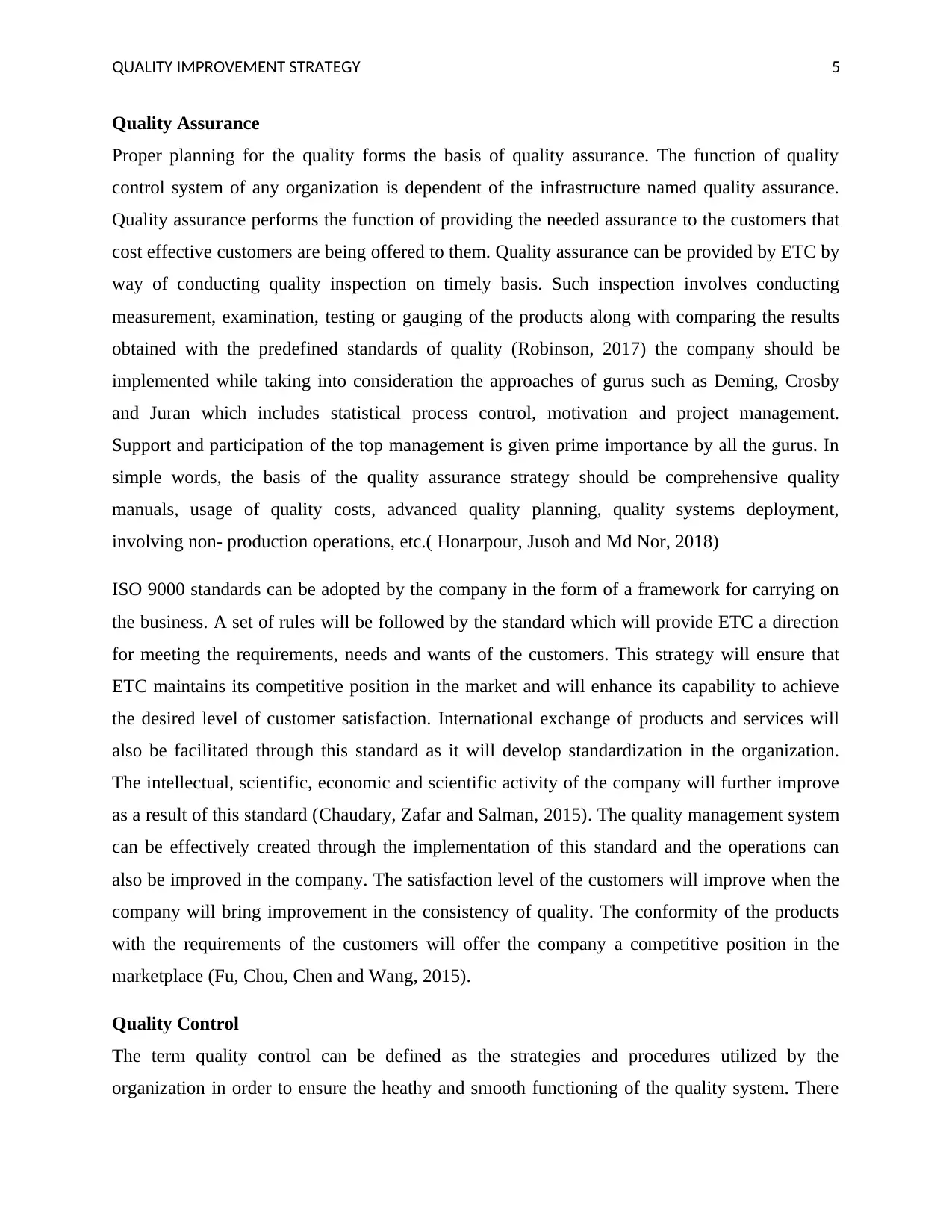
QUALITY IMPROVEMENT STRATEGY 5
Quality Assurance
Proper planning for the quality forms the basis of quality assurance. The function of quality
control system of any organization is dependent of the infrastructure named quality assurance.
Quality assurance performs the function of providing the needed assurance to the customers that
cost effective customers are being offered to them. Quality assurance can be provided by ETC by
way of conducting quality inspection on timely basis. Such inspection involves conducting
measurement, examination, testing or gauging of the products along with comparing the results
obtained with the predefined standards of quality (Robinson, 2017) the company should be
implemented while taking into consideration the approaches of gurus such as Deming, Crosby
and Juran which includes statistical process control, motivation and project management.
Support and participation of the top management is given prime importance by all the gurus. In
simple words, the basis of the quality assurance strategy should be comprehensive quality
manuals, usage of quality costs, advanced quality planning, quality systems deployment,
involving non- production operations, etc.( Honarpour, Jusoh and Md Nor, 2018)
ISO 9000 standards can be adopted by the company in the form of a framework for carrying on
the business. A set of rules will be followed by the standard which will provide ETC a direction
for meeting the requirements, needs and wants of the customers. This strategy will ensure that
ETC maintains its competitive position in the market and will enhance its capability to achieve
the desired level of customer satisfaction. International exchange of products and services will
also be facilitated through this standard as it will develop standardization in the organization.
The intellectual, scientific, economic and scientific activity of the company will further improve
as a result of this standard (Chaudary, Zafar and Salman, 2015). The quality management system
can be effectively created through the implementation of this standard and the operations can
also be improved in the company. The satisfaction level of the customers will improve when the
company will bring improvement in the consistency of quality. The conformity of the products
with the requirements of the customers will offer the company a competitive position in the
marketplace (Fu, Chou, Chen and Wang, 2015).
Quality Control
The term quality control can be defined as the strategies and procedures utilized by the
organization in order to ensure the heathy and smooth functioning of the quality system. There
Quality Assurance
Proper planning for the quality forms the basis of quality assurance. The function of quality
control system of any organization is dependent of the infrastructure named quality assurance.
Quality assurance performs the function of providing the needed assurance to the customers that
cost effective customers are being offered to them. Quality assurance can be provided by ETC by
way of conducting quality inspection on timely basis. Such inspection involves conducting
measurement, examination, testing or gauging of the products along with comparing the results
obtained with the predefined standards of quality (Robinson, 2017) the company should be
implemented while taking into consideration the approaches of gurus such as Deming, Crosby
and Juran which includes statistical process control, motivation and project management.
Support and participation of the top management is given prime importance by all the gurus. In
simple words, the basis of the quality assurance strategy should be comprehensive quality
manuals, usage of quality costs, advanced quality planning, quality systems deployment,
involving non- production operations, etc.( Honarpour, Jusoh and Md Nor, 2018)
ISO 9000 standards can be adopted by the company in the form of a framework for carrying on
the business. A set of rules will be followed by the standard which will provide ETC a direction
for meeting the requirements, needs and wants of the customers. This strategy will ensure that
ETC maintains its competitive position in the market and will enhance its capability to achieve
the desired level of customer satisfaction. International exchange of products and services will
also be facilitated through this standard as it will develop standardization in the organization.
The intellectual, scientific, economic and scientific activity of the company will further improve
as a result of this standard (Chaudary, Zafar and Salman, 2015). The quality management system
can be effectively created through the implementation of this standard and the operations can
also be improved in the company. The satisfaction level of the customers will improve when the
company will bring improvement in the consistency of quality. The conformity of the products
with the requirements of the customers will offer the company a competitive position in the
marketplace (Fu, Chou, Chen and Wang, 2015).
Quality Control
The term quality control can be defined as the strategies and procedures utilized by the
organization in order to ensure the heathy and smooth functioning of the quality system. There
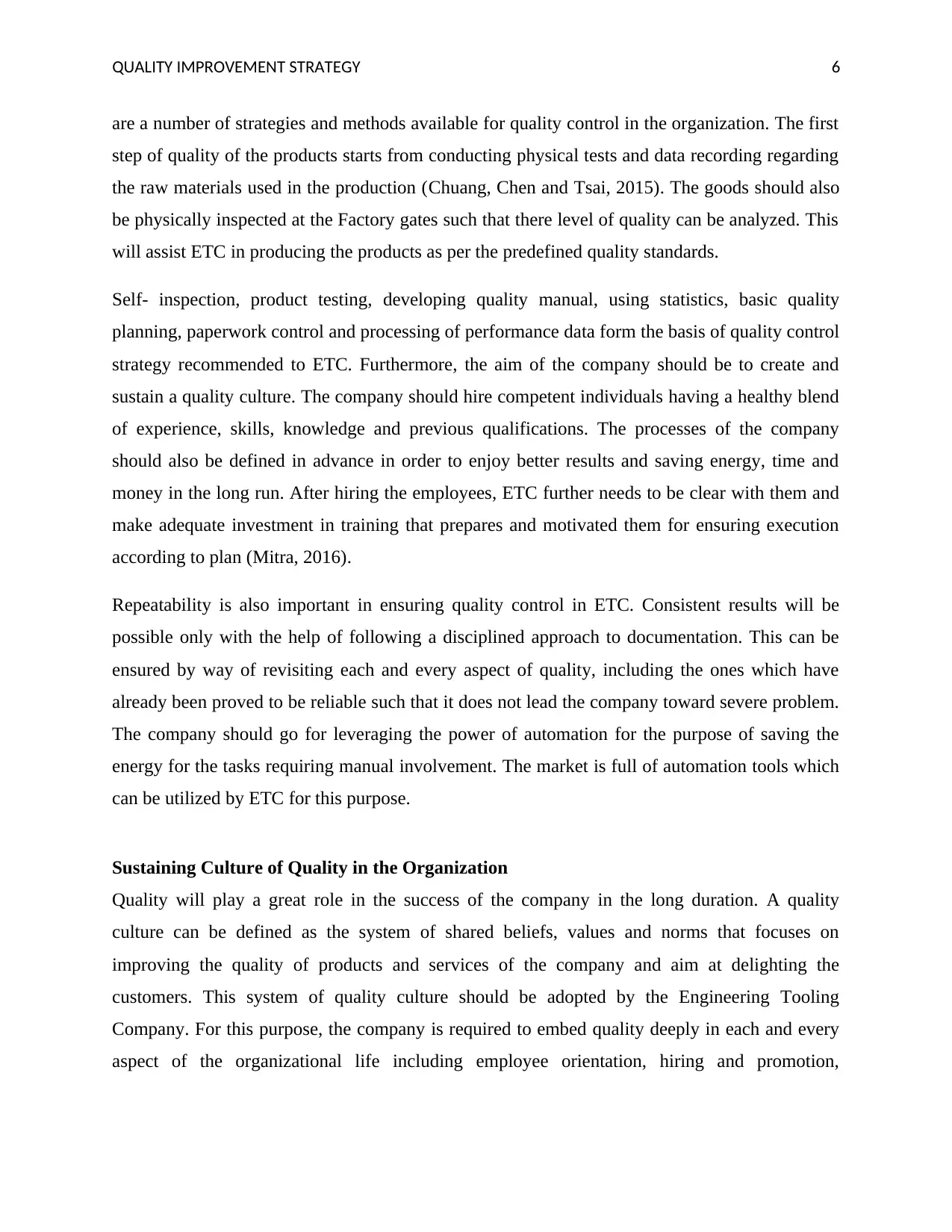
QUALITY IMPROVEMENT STRATEGY 6
are a number of strategies and methods available for quality control in the organization. The first
step of quality of the products starts from conducting physical tests and data recording regarding
the raw materials used in the production (Chuang, Chen and Tsai, 2015). The goods should also
be physically inspected at the Factory gates such that there level of quality can be analyzed. This
will assist ETC in producing the products as per the predefined quality standards.
Self- inspection, product testing, developing quality manual, using statistics, basic quality
planning, paperwork control and processing of performance data form the basis of quality control
strategy recommended to ETC. Furthermore, the aim of the company should be to create and
sustain a quality culture. The company should hire competent individuals having a healthy blend
of experience, skills, knowledge and previous qualifications. The processes of the company
should also be defined in advance in order to enjoy better results and saving energy, time and
money in the long run. After hiring the employees, ETC further needs to be clear with them and
make adequate investment in training that prepares and motivated them for ensuring execution
according to plan (Mitra, 2016).
Repeatability is also important in ensuring quality control in ETC. Consistent results will be
possible only with the help of following a disciplined approach to documentation. This can be
ensured by way of revisiting each and every aspect of quality, including the ones which have
already been proved to be reliable such that it does not lead the company toward severe problem.
The company should go for leveraging the power of automation for the purpose of saving the
energy for the tasks requiring manual involvement. The market is full of automation tools which
can be utilized by ETC for this purpose.
Sustaining Culture of Quality in the Organization
Quality will play a great role in the success of the company in the long duration. A quality
culture can be defined as the system of shared beliefs, values and norms that focuses on
improving the quality of products and services of the company and aim at delighting the
customers. This system of quality culture should be adopted by the Engineering Tooling
Company. For this purpose, the company is required to embed quality deeply in each and every
aspect of the organizational life including employee orientation, hiring and promotion,
are a number of strategies and methods available for quality control in the organization. The first
step of quality of the products starts from conducting physical tests and data recording regarding
the raw materials used in the production (Chuang, Chen and Tsai, 2015). The goods should also
be physically inspected at the Factory gates such that there level of quality can be analyzed. This
will assist ETC in producing the products as per the predefined quality standards.
Self- inspection, product testing, developing quality manual, using statistics, basic quality
planning, paperwork control and processing of performance data form the basis of quality control
strategy recommended to ETC. Furthermore, the aim of the company should be to create and
sustain a quality culture. The company should hire competent individuals having a healthy blend
of experience, skills, knowledge and previous qualifications. The processes of the company
should also be defined in advance in order to enjoy better results and saving energy, time and
money in the long run. After hiring the employees, ETC further needs to be clear with them and
make adequate investment in training that prepares and motivated them for ensuring execution
according to plan (Mitra, 2016).
Repeatability is also important in ensuring quality control in ETC. Consistent results will be
possible only with the help of following a disciplined approach to documentation. This can be
ensured by way of revisiting each and every aspect of quality, including the ones which have
already been proved to be reliable such that it does not lead the company toward severe problem.
The company should go for leveraging the power of automation for the purpose of saving the
energy for the tasks requiring manual involvement. The market is full of automation tools which
can be utilized by ETC for this purpose.
Sustaining Culture of Quality in the Organization
Quality will play a great role in the success of the company in the long duration. A quality
culture can be defined as the system of shared beliefs, values and norms that focuses on
improving the quality of products and services of the company and aim at delighting the
customers. This system of quality culture should be adopted by the Engineering Tooling
Company. For this purpose, the company is required to embed quality deeply in each and every
aspect of the organizational life including employee orientation, hiring and promotion,
Paraphrase This Document
Need a fresh take? Get an instant paraphrase of this document with our AI Paraphraser
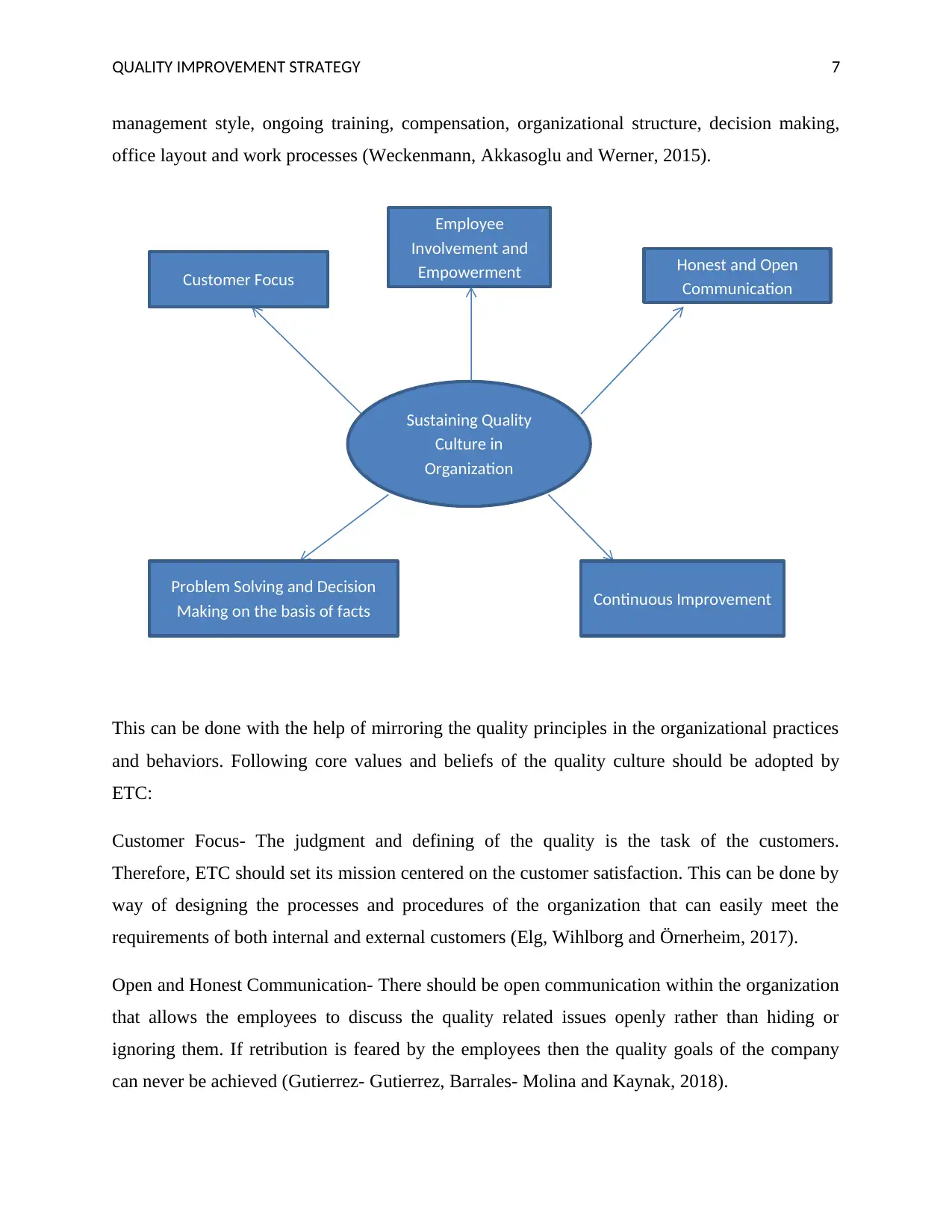
QUALITY IMPROVEMENT STRATEGY 7
management style, ongoing training, compensation, organizational structure, decision making,
office layout and work processes (Weckenmann, Akkasoglu and Werner, 2015).
This can be done with the help of mirroring the quality principles in the organizational practices
and behaviors. Following core values and beliefs of the quality culture should be adopted by
ETC:
Customer Focus- The judgment and defining of the quality is the task of the customers.
Therefore, ETC should set its mission centered on the customer satisfaction. This can be done by
way of designing the processes and procedures of the organization that can easily meet the
requirements of both internal and external customers (Elg, Wihlborg and Örnerheim, 2017).
Open and Honest Communication- There should be open communication within the organization
that allows the employees to discuss the quality related issues openly rather than hiding or
ignoring them. If retribution is feared by the employees then the quality goals of the company
can never be achieved (Gutierrez- Gutierrez, Barrales- Molina and Kaynak, 2018).
Sustaining Quality
Culture in
Organization
Customer Focus Honest and Open
Communication
Employee
Involvement and
Empowerment
Problem Solving and Decision
Making on the basis of facts Continuous Improvement
management style, ongoing training, compensation, organizational structure, decision making,
office layout and work processes (Weckenmann, Akkasoglu and Werner, 2015).
This can be done with the help of mirroring the quality principles in the organizational practices
and behaviors. Following core values and beliefs of the quality culture should be adopted by
ETC:
Customer Focus- The judgment and defining of the quality is the task of the customers.
Therefore, ETC should set its mission centered on the customer satisfaction. This can be done by
way of designing the processes and procedures of the organization that can easily meet the
requirements of both internal and external customers (Elg, Wihlborg and Örnerheim, 2017).
Open and Honest Communication- There should be open communication within the organization
that allows the employees to discuss the quality related issues openly rather than hiding or
ignoring them. If retribution is feared by the employees then the quality goals of the company
can never be achieved (Gutierrez- Gutierrez, Barrales- Molina and Kaynak, 2018).
Sustaining Quality
Culture in
Organization
Customer Focus Honest and Open
Communication
Employee
Involvement and
Empowerment
Problem Solving and Decision
Making on the basis of facts Continuous Improvement
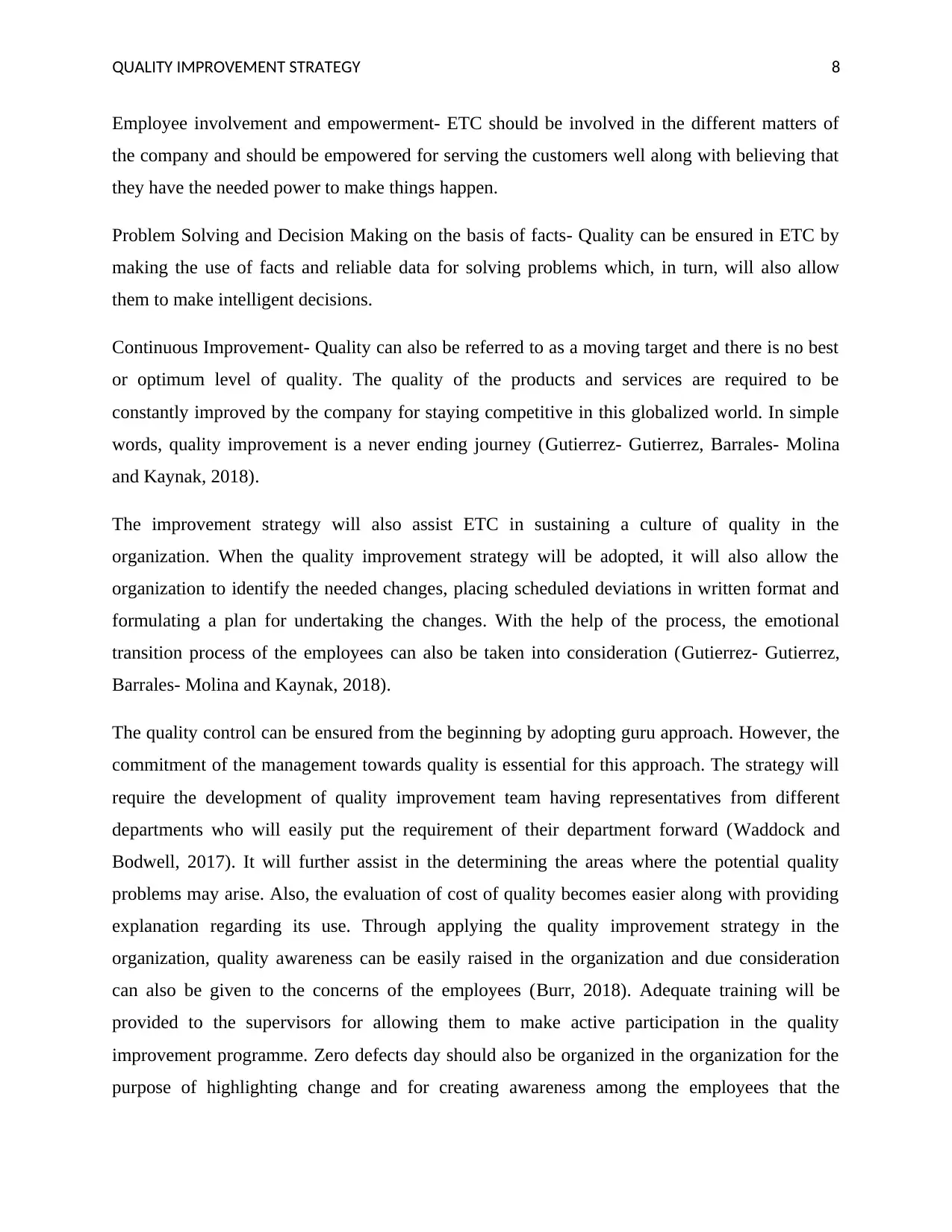
QUALITY IMPROVEMENT STRATEGY 8
Employee involvement and empowerment- ETC should be involved in the different matters of
the company and should be empowered for serving the customers well along with believing that
they have the needed power to make things happen.
Problem Solving and Decision Making on the basis of facts- Quality can be ensured in ETC by
making the use of facts and reliable data for solving problems which, in turn, will also allow
them to make intelligent decisions.
Continuous Improvement- Quality can also be referred to as a moving target and there is no best
or optimum level of quality. The quality of the products and services are required to be
constantly improved by the company for staying competitive in this globalized world. In simple
words, quality improvement is a never ending journey (Gutierrez- Gutierrez, Barrales- Molina
and Kaynak, 2018).
The improvement strategy will also assist ETC in sustaining a culture of quality in the
organization. When the quality improvement strategy will be adopted, it will also allow the
organization to identify the needed changes, placing scheduled deviations in written format and
formulating a plan for undertaking the changes. With the help of the process, the emotional
transition process of the employees can also be taken into consideration (Gutierrez- Gutierrez,
Barrales- Molina and Kaynak, 2018).
The quality control can be ensured from the beginning by adopting guru approach. However, the
commitment of the management towards quality is essential for this approach. The strategy will
require the development of quality improvement team having representatives from different
departments who will easily put the requirement of their department forward (Waddock and
Bodwell, 2017). It will further assist in the determining the areas where the potential quality
problems may arise. Also, the evaluation of cost of quality becomes easier along with providing
explanation regarding its use. Through applying the quality improvement strategy in the
organization, quality awareness can be easily raised in the organization and due consideration
can also be given to the concerns of the employees (Burr, 2018). Adequate training will be
provided to the supervisors for allowing them to make active participation in the quality
improvement programme. Zero defects day should also be organized in the organization for the
purpose of highlighting change and for creating awareness among the employees that the
Employee involvement and empowerment- ETC should be involved in the different matters of
the company and should be empowered for serving the customers well along with believing that
they have the needed power to make things happen.
Problem Solving and Decision Making on the basis of facts- Quality can be ensured in ETC by
making the use of facts and reliable data for solving problems which, in turn, will also allow
them to make intelligent decisions.
Continuous Improvement- Quality can also be referred to as a moving target and there is no best
or optimum level of quality. The quality of the products and services are required to be
constantly improved by the company for staying competitive in this globalized world. In simple
words, quality improvement is a never ending journey (Gutierrez- Gutierrez, Barrales- Molina
and Kaynak, 2018).
The improvement strategy will also assist ETC in sustaining a culture of quality in the
organization. When the quality improvement strategy will be adopted, it will also allow the
organization to identify the needed changes, placing scheduled deviations in written format and
formulating a plan for undertaking the changes. With the help of the process, the emotional
transition process of the employees can also be taken into consideration (Gutierrez- Gutierrez,
Barrales- Molina and Kaynak, 2018).
The quality control can be ensured from the beginning by adopting guru approach. However, the
commitment of the management towards quality is essential for this approach. The strategy will
require the development of quality improvement team having representatives from different
departments who will easily put the requirement of their department forward (Waddock and
Bodwell, 2017). It will further assist in the determining the areas where the potential quality
problems may arise. Also, the evaluation of cost of quality becomes easier along with providing
explanation regarding its use. Through applying the quality improvement strategy in the
organization, quality awareness can be easily raised in the organization and due consideration
can also be given to the concerns of the employees (Burr, 2018). Adequate training will be
provided to the supervisors for allowing them to make active participation in the quality
improvement programme. Zero defects day should also be organized in the organization for the
purpose of highlighting change and for creating awareness among the employees that the
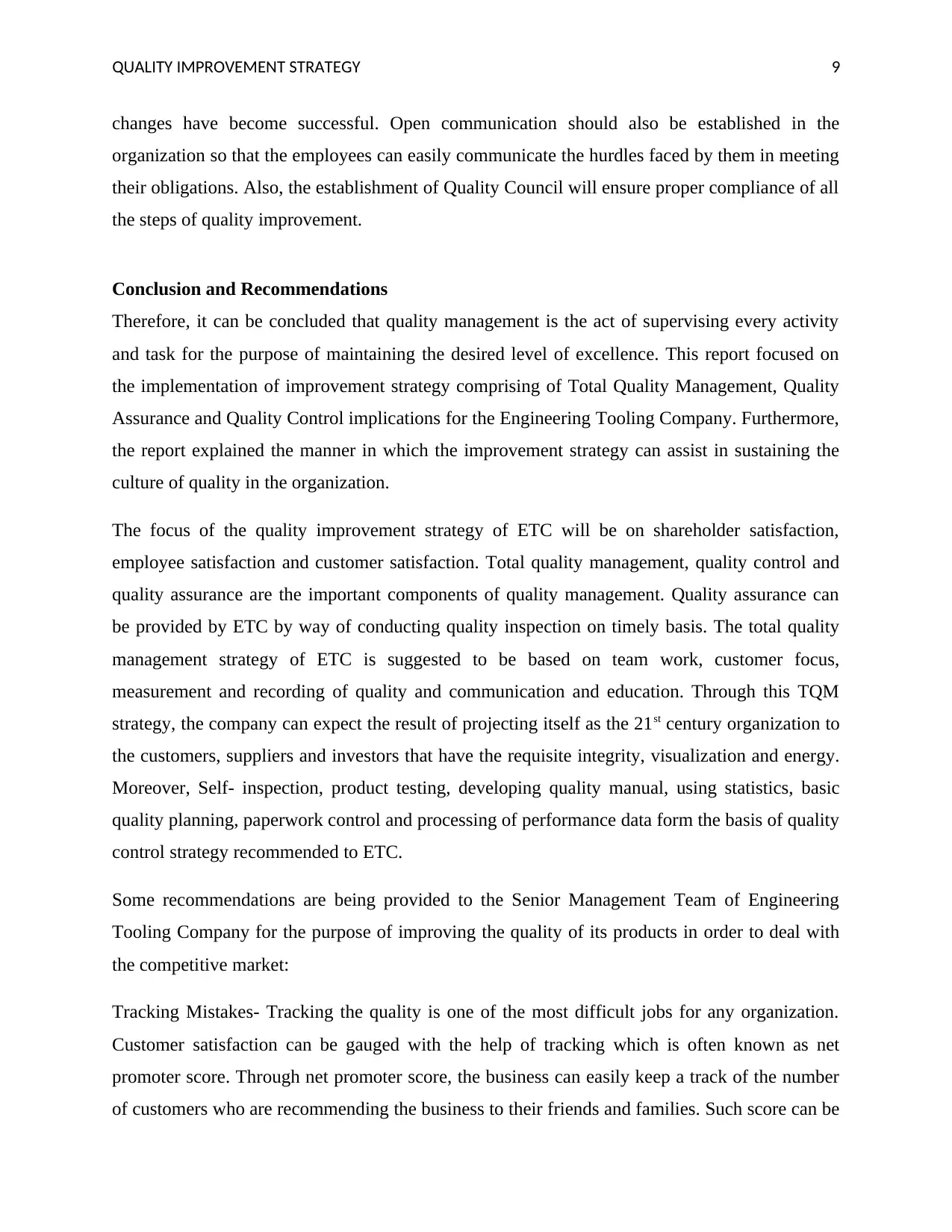
QUALITY IMPROVEMENT STRATEGY 9
changes have become successful. Open communication should also be established in the
organization so that the employees can easily communicate the hurdles faced by them in meeting
their obligations. Also, the establishment of Quality Council will ensure proper compliance of all
the steps of quality improvement.
Conclusion and Recommendations
Therefore, it can be concluded that quality management is the act of supervising every activity
and task for the purpose of maintaining the desired level of excellence. This report focused on
the implementation of improvement strategy comprising of Total Quality Management, Quality
Assurance and Quality Control implications for the Engineering Tooling Company. Furthermore,
the report explained the manner in which the improvement strategy can assist in sustaining the
culture of quality in the organization.
The focus of the quality improvement strategy of ETC will be on shareholder satisfaction,
employee satisfaction and customer satisfaction. Total quality management, quality control and
quality assurance are the important components of quality management. Quality assurance can
be provided by ETC by way of conducting quality inspection on timely basis. The total quality
management strategy of ETC is suggested to be based on team work, customer focus,
measurement and recording of quality and communication and education. Through this TQM
strategy, the company can expect the result of projecting itself as the 21st century organization to
the customers, suppliers and investors that have the requisite integrity, visualization and energy.
Moreover, Self- inspection, product testing, developing quality manual, using statistics, basic
quality planning, paperwork control and processing of performance data form the basis of quality
control strategy recommended to ETC.
Some recommendations are being provided to the Senior Management Team of Engineering
Tooling Company for the purpose of improving the quality of its products in order to deal with
the competitive market:
Tracking Mistakes- Tracking the quality is one of the most difficult jobs for any organization.
Customer satisfaction can be gauged with the help of tracking which is often known as net
promoter score. Through net promoter score, the business can easily keep a track of the number
of customers who are recommending the business to their friends and families. Such score can be
changes have become successful. Open communication should also be established in the
organization so that the employees can easily communicate the hurdles faced by them in meeting
their obligations. Also, the establishment of Quality Council will ensure proper compliance of all
the steps of quality improvement.
Conclusion and Recommendations
Therefore, it can be concluded that quality management is the act of supervising every activity
and task for the purpose of maintaining the desired level of excellence. This report focused on
the implementation of improvement strategy comprising of Total Quality Management, Quality
Assurance and Quality Control implications for the Engineering Tooling Company. Furthermore,
the report explained the manner in which the improvement strategy can assist in sustaining the
culture of quality in the organization.
The focus of the quality improvement strategy of ETC will be on shareholder satisfaction,
employee satisfaction and customer satisfaction. Total quality management, quality control and
quality assurance are the important components of quality management. Quality assurance can
be provided by ETC by way of conducting quality inspection on timely basis. The total quality
management strategy of ETC is suggested to be based on team work, customer focus,
measurement and recording of quality and communication and education. Through this TQM
strategy, the company can expect the result of projecting itself as the 21st century organization to
the customers, suppliers and investors that have the requisite integrity, visualization and energy.
Moreover, Self- inspection, product testing, developing quality manual, using statistics, basic
quality planning, paperwork control and processing of performance data form the basis of quality
control strategy recommended to ETC.
Some recommendations are being provided to the Senior Management Team of Engineering
Tooling Company for the purpose of improving the quality of its products in order to deal with
the competitive market:
Tracking Mistakes- Tracking the quality is one of the most difficult jobs for any organization.
Customer satisfaction can be gauged with the help of tracking which is often known as net
promoter score. Through net promoter score, the business can easily keep a track of the number
of customers who are recommending the business to their friends and families. Such score can be
Secure Best Marks with AI Grader
Need help grading? Try our AI Grader for instant feedback on your assignments.
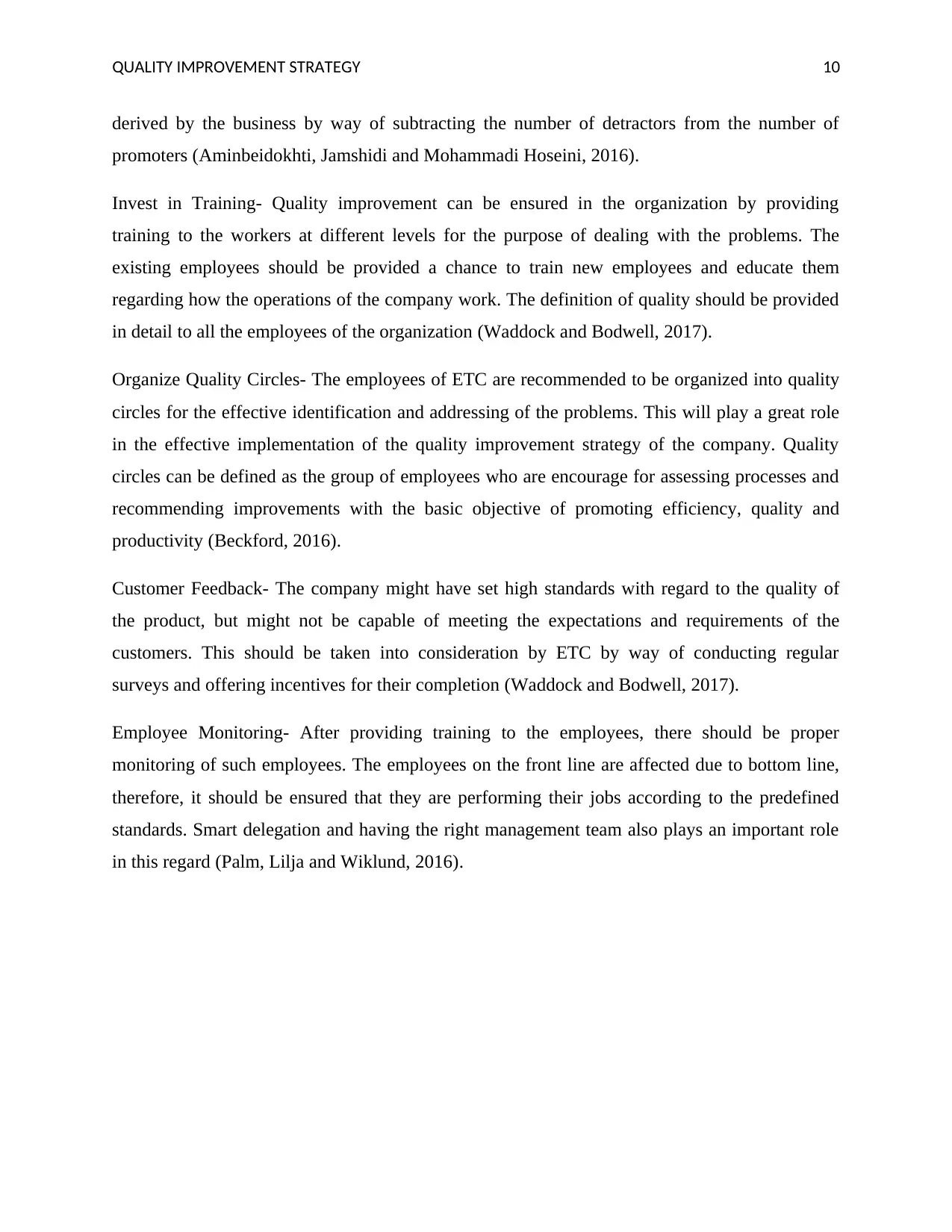
QUALITY IMPROVEMENT STRATEGY 10
derived by the business by way of subtracting the number of detractors from the number of
promoters (Aminbeidokhti, Jamshidi and Mohammadi Hoseini, 2016).
Invest in Training- Quality improvement can be ensured in the organization by providing
training to the workers at different levels for the purpose of dealing with the problems. The
existing employees should be provided a chance to train new employees and educate them
regarding how the operations of the company work. The definition of quality should be provided
in detail to all the employees of the organization (Waddock and Bodwell, 2017).
Organize Quality Circles- The employees of ETC are recommended to be organized into quality
circles for the effective identification and addressing of the problems. This will play a great role
in the effective implementation of the quality improvement strategy of the company. Quality
circles can be defined as the group of employees who are encourage for assessing processes and
recommending improvements with the basic objective of promoting efficiency, quality and
productivity (Beckford, 2016).
Customer Feedback- The company might have set high standards with regard to the quality of
the product, but might not be capable of meeting the expectations and requirements of the
customers. This should be taken into consideration by ETC by way of conducting regular
surveys and offering incentives for their completion (Waddock and Bodwell, 2017).
Employee Monitoring- After providing training to the employees, there should be proper
monitoring of such employees. The employees on the front line are affected due to bottom line,
therefore, it should be ensured that they are performing their jobs according to the predefined
standards. Smart delegation and having the right management team also plays an important role
in this regard (Palm, Lilja and Wiklund, 2016).
derived by the business by way of subtracting the number of detractors from the number of
promoters (Aminbeidokhti, Jamshidi and Mohammadi Hoseini, 2016).
Invest in Training- Quality improvement can be ensured in the organization by providing
training to the workers at different levels for the purpose of dealing with the problems. The
existing employees should be provided a chance to train new employees and educate them
regarding how the operations of the company work. The definition of quality should be provided
in detail to all the employees of the organization (Waddock and Bodwell, 2017).
Organize Quality Circles- The employees of ETC are recommended to be organized into quality
circles for the effective identification and addressing of the problems. This will play a great role
in the effective implementation of the quality improvement strategy of the company. Quality
circles can be defined as the group of employees who are encourage for assessing processes and
recommending improvements with the basic objective of promoting efficiency, quality and
productivity (Beckford, 2016).
Customer Feedback- The company might have set high standards with regard to the quality of
the product, but might not be capable of meeting the expectations and requirements of the
customers. This should be taken into consideration by ETC by way of conducting regular
surveys and offering incentives for their completion (Waddock and Bodwell, 2017).
Employee Monitoring- After providing training to the employees, there should be proper
monitoring of such employees. The employees on the front line are affected due to bottom line,
therefore, it should be ensured that they are performing their jobs according to the predefined
standards. Smart delegation and having the right management team also plays an important role
in this regard (Palm, Lilja and Wiklund, 2016).
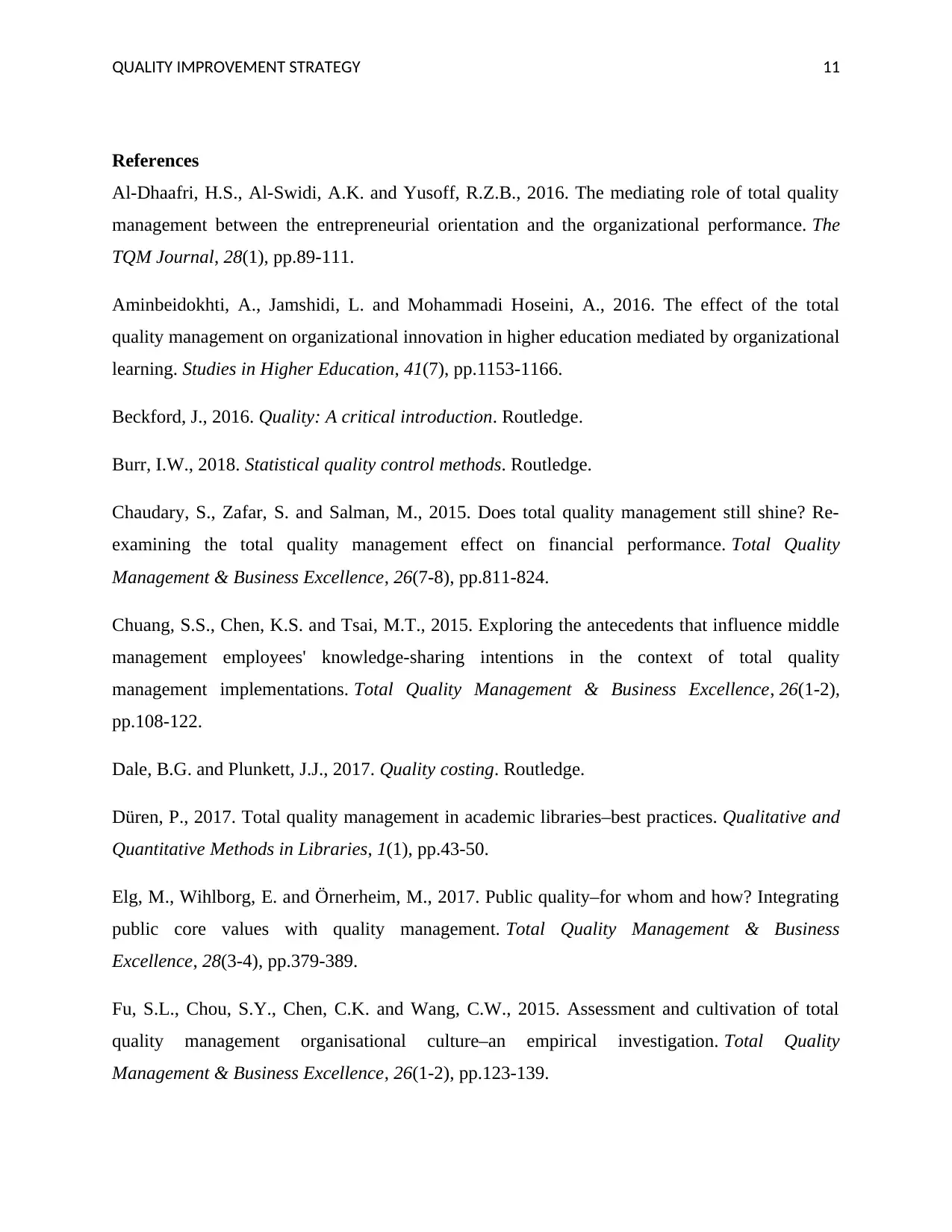
QUALITY IMPROVEMENT STRATEGY 11
References
Al-Dhaafri, H.S., Al-Swidi, A.K. and Yusoff, R.Z.B., 2016. The mediating role of total quality
management between the entrepreneurial orientation and the organizational performance. The
TQM Journal, 28(1), pp.89-111.
Aminbeidokhti, A., Jamshidi, L. and Mohammadi Hoseini, A., 2016. The effect of the total
quality management on organizational innovation in higher education mediated by organizational
learning. Studies in Higher Education, 41(7), pp.1153-1166.
Beckford, J., 2016. Quality: A critical introduction. Routledge.
Burr, I.W., 2018. Statistical quality control methods. Routledge.
Chaudary, S., Zafar, S. and Salman, M., 2015. Does total quality management still shine? Re-
examining the total quality management effect on financial performance. Total Quality
Management & Business Excellence, 26(7-8), pp.811-824.
Chuang, S.S., Chen, K.S. and Tsai, M.T., 2015. Exploring the antecedents that influence middle
management employees' knowledge-sharing intentions in the context of total quality
management implementations. Total Quality Management & Business Excellence, 26(1-2),
pp.108-122.
Dale, B.G. and Plunkett, J.J., 2017. Quality costing. Routledge.
Düren, P., 2017. Total quality management in academic libraries–best practices. Qualitative and
Quantitative Methods in Libraries, 1(1), pp.43-50.
Elg, M., Wihlborg, E. and Örnerheim, M., 2017. Public quality–for whom and how? Integrating
public core values with quality management. Total Quality Management & Business
Excellence, 28(3-4), pp.379-389.
Fu, S.L., Chou, S.Y., Chen, C.K. and Wang, C.W., 2015. Assessment and cultivation of total
quality management organisational culture–an empirical investigation. Total Quality
Management & Business Excellence, 26(1-2), pp.123-139.
References
Al-Dhaafri, H.S., Al-Swidi, A.K. and Yusoff, R.Z.B., 2016. The mediating role of total quality
management between the entrepreneurial orientation and the organizational performance. The
TQM Journal, 28(1), pp.89-111.
Aminbeidokhti, A., Jamshidi, L. and Mohammadi Hoseini, A., 2016. The effect of the total
quality management on organizational innovation in higher education mediated by organizational
learning. Studies in Higher Education, 41(7), pp.1153-1166.
Beckford, J., 2016. Quality: A critical introduction. Routledge.
Burr, I.W., 2018. Statistical quality control methods. Routledge.
Chaudary, S., Zafar, S. and Salman, M., 2015. Does total quality management still shine? Re-
examining the total quality management effect on financial performance. Total Quality
Management & Business Excellence, 26(7-8), pp.811-824.
Chuang, S.S., Chen, K.S. and Tsai, M.T., 2015. Exploring the antecedents that influence middle
management employees' knowledge-sharing intentions in the context of total quality
management implementations. Total Quality Management & Business Excellence, 26(1-2),
pp.108-122.
Dale, B.G. and Plunkett, J.J., 2017. Quality costing. Routledge.
Düren, P., 2017. Total quality management in academic libraries–best practices. Qualitative and
Quantitative Methods in Libraries, 1(1), pp.43-50.
Elg, M., Wihlborg, E. and Örnerheim, M., 2017. Public quality–for whom and how? Integrating
public core values with quality management. Total Quality Management & Business
Excellence, 28(3-4), pp.379-389.
Fu, S.L., Chou, S.Y., Chen, C.K. and Wang, C.W., 2015. Assessment and cultivation of total
quality management organisational culture–an empirical investigation. Total Quality
Management & Business Excellence, 26(1-2), pp.123-139.
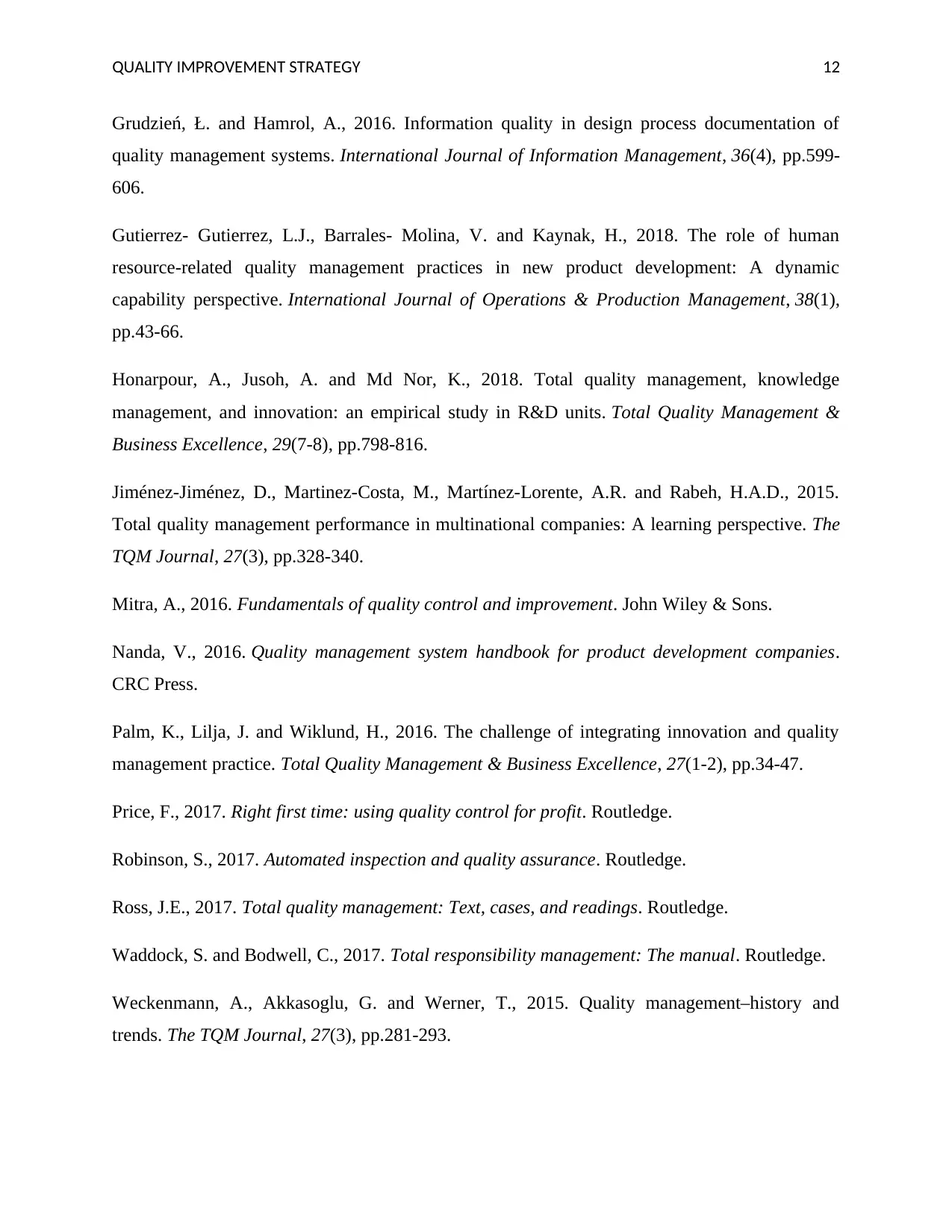
QUALITY IMPROVEMENT STRATEGY 12
Grudzień, Ł. and Hamrol, A., 2016. Information quality in design process documentation of
quality management systems. International Journal of Information Management, 36(4), pp.599-
606.
Gutierrez- Gutierrez, L.J., Barrales- Molina, V. and Kaynak, H., 2018. The role of human
resource-related quality management practices in new product development: A dynamic
capability perspective. International Journal of Operations & Production Management, 38(1),
pp.43-66.
Honarpour, A., Jusoh, A. and Md Nor, K., 2018. Total quality management, knowledge
management, and innovation: an empirical study in R&D units. Total Quality Management &
Business Excellence, 29(7-8), pp.798-816.
Jiménez-Jiménez, D., Martinez-Costa, M., Martínez-Lorente, A.R. and Rabeh, H.A.D., 2015.
Total quality management performance in multinational companies: A learning perspective. The
TQM Journal, 27(3), pp.328-340.
Mitra, A., 2016. Fundamentals of quality control and improvement. John Wiley & Sons.
Nanda, V., 2016. Quality management system handbook for product development companies.
CRC Press.
Palm, K., Lilja, J. and Wiklund, H., 2016. The challenge of integrating innovation and quality
management practice. Total Quality Management & Business Excellence, 27(1-2), pp.34-47.
Price, F., 2017. Right first time: using quality control for profit. Routledge.
Robinson, S., 2017. Automated inspection and quality assurance. Routledge.
Ross, J.E., 2017. Total quality management: Text, cases, and readings. Routledge.
Waddock, S. and Bodwell, C., 2017. Total responsibility management: The manual. Routledge.
Weckenmann, A., Akkasoglu, G. and Werner, T., 2015. Quality management–history and
trends. The TQM Journal, 27(3), pp.281-293.
Grudzień, Ł. and Hamrol, A., 2016. Information quality in design process documentation of
quality management systems. International Journal of Information Management, 36(4), pp.599-
606.
Gutierrez- Gutierrez, L.J., Barrales- Molina, V. and Kaynak, H., 2018. The role of human
resource-related quality management practices in new product development: A dynamic
capability perspective. International Journal of Operations & Production Management, 38(1),
pp.43-66.
Honarpour, A., Jusoh, A. and Md Nor, K., 2018. Total quality management, knowledge
management, and innovation: an empirical study in R&D units. Total Quality Management &
Business Excellence, 29(7-8), pp.798-816.
Jiménez-Jiménez, D., Martinez-Costa, M., Martínez-Lorente, A.R. and Rabeh, H.A.D., 2015.
Total quality management performance in multinational companies: A learning perspective. The
TQM Journal, 27(3), pp.328-340.
Mitra, A., 2016. Fundamentals of quality control and improvement. John Wiley & Sons.
Nanda, V., 2016. Quality management system handbook for product development companies.
CRC Press.
Palm, K., Lilja, J. and Wiklund, H., 2016. The challenge of integrating innovation and quality
management practice. Total Quality Management & Business Excellence, 27(1-2), pp.34-47.
Price, F., 2017. Right first time: using quality control for profit. Routledge.
Robinson, S., 2017. Automated inspection and quality assurance. Routledge.
Ross, J.E., 2017. Total quality management: Text, cases, and readings. Routledge.
Waddock, S. and Bodwell, C., 2017. Total responsibility management: The manual. Routledge.
Weckenmann, A., Akkasoglu, G. and Werner, T., 2015. Quality management–history and
trends. The TQM Journal, 27(3), pp.281-293.
1 out of 13
Related Documents

Your All-in-One AI-Powered Toolkit for Academic Success.
+13062052269
info@desklib.com
Available 24*7 on WhatsApp / Email
Unlock your academic potential
© 2024 | Zucol Services PVT LTD | All rights reserved.