ENGR2842: Concrete Mix Design, Casting, and Strength Evaluation
VerifiedAdded on 2023/06/03
|7
|1051
|442
Practical Assignment
AI Summary
This report details a concrete mix design experiment conducted to achieve a target strength of 30 MPa. The process involved designing the mix, performing a slump test to assess workability, and casting the concrete into cylindrical molds. The report includes the quantities of cement, sand, aggregate, and water used, along with the water/cement ratio. The compressive strength of the hardened concrete was tested after 28 days, and the results were compared to the target strength. The report discusses any variations in the results and validates the mix design ratio's ability to achieve the desired compressive strength. This document is available on Desklib, a platform offering a variety of study resources for students.
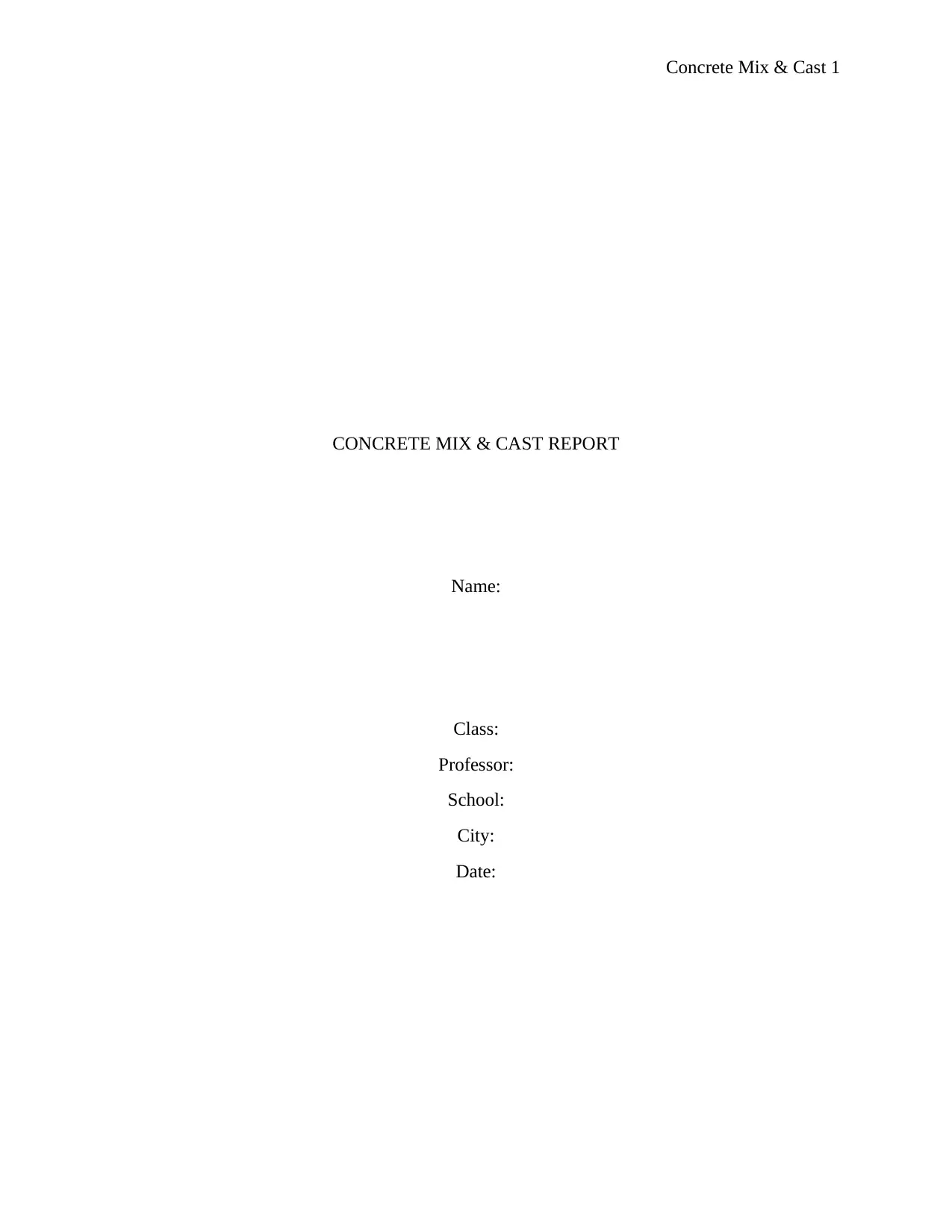
Concrete Mix & Cast 1
CONCRETE MIX & CAST REPORT
Name:
Class:
Professor:
School:
City:
Date:
CONCRETE MIX & CAST REPORT
Name:
Class:
Professor:
School:
City:
Date:
Paraphrase This Document
Need a fresh take? Get an instant paraphrase of this document with our AI Paraphraser
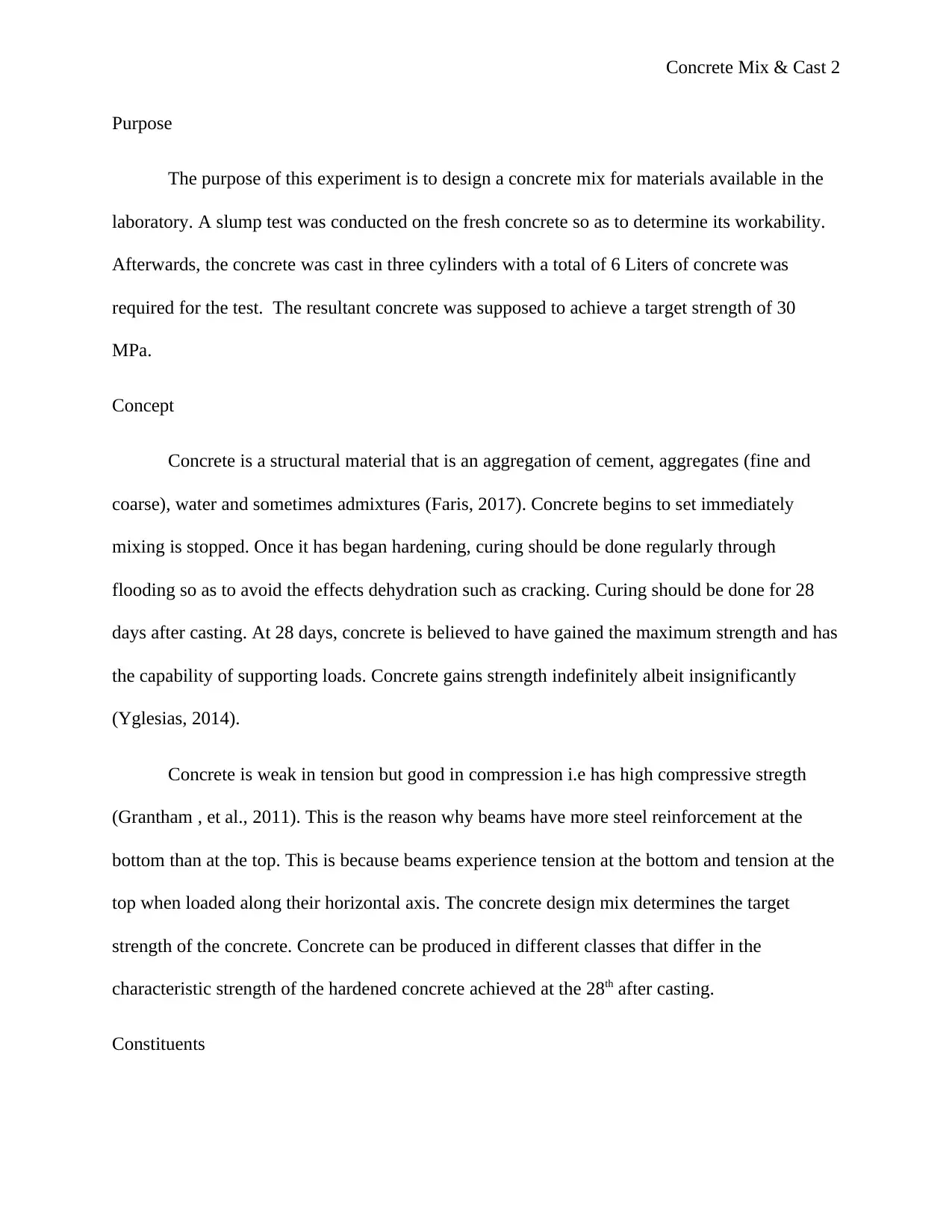
Concrete Mix & Cast 2
Purpose
The purpose of this experiment is to design a concrete mix for materials available in the
laboratory. A slump test was conducted on the fresh concrete so as to determine its workability.
Afterwards, the concrete was cast in three cylinders with a total of 6 Liters of concrete was
required for the test. The resultant concrete was supposed to achieve a target strength of 30
MPa.
Concept
Concrete is a structural material that is an aggregation of cement, aggregates (fine and
coarse), water and sometimes admixtures (Faris, 2017). Concrete begins to set immediately
mixing is stopped. Once it has began hardening, curing should be done regularly through
flooding so as to avoid the effects dehydration such as cracking. Curing should be done for 28
days after casting. At 28 days, concrete is believed to have gained the maximum strength and has
the capability of supporting loads. Concrete gains strength indefinitely albeit insignificantly
(Yglesias, 2014).
Concrete is weak in tension but good in compression i.e has high compressive stregth
(Grantham , et al., 2011). This is the reason why beams have more steel reinforcement at the
bottom than at the top. This is because beams experience tension at the bottom and tension at the
top when loaded along their horizontal axis. The concrete design mix determines the target
strength of the concrete. Concrete can be produced in different classes that differ in the
characteristic strength of the hardened concrete achieved at the 28th after casting.
Constituents
Purpose
The purpose of this experiment is to design a concrete mix for materials available in the
laboratory. A slump test was conducted on the fresh concrete so as to determine its workability.
Afterwards, the concrete was cast in three cylinders with a total of 6 Liters of concrete was
required for the test. The resultant concrete was supposed to achieve a target strength of 30
MPa.
Concept
Concrete is a structural material that is an aggregation of cement, aggregates (fine and
coarse), water and sometimes admixtures (Faris, 2017). Concrete begins to set immediately
mixing is stopped. Once it has began hardening, curing should be done regularly through
flooding so as to avoid the effects dehydration such as cracking. Curing should be done for 28
days after casting. At 28 days, concrete is believed to have gained the maximum strength and has
the capability of supporting loads. Concrete gains strength indefinitely albeit insignificantly
(Yglesias, 2014).
Concrete is weak in tension but good in compression i.e has high compressive stregth
(Grantham , et al., 2011). This is the reason why beams have more steel reinforcement at the
bottom than at the top. This is because beams experience tension at the bottom and tension at the
top when loaded along their horizontal axis. The concrete design mix determines the target
strength of the concrete. Concrete can be produced in different classes that differ in the
characteristic strength of the hardened concrete achieved at the 28th after casting.
Constituents
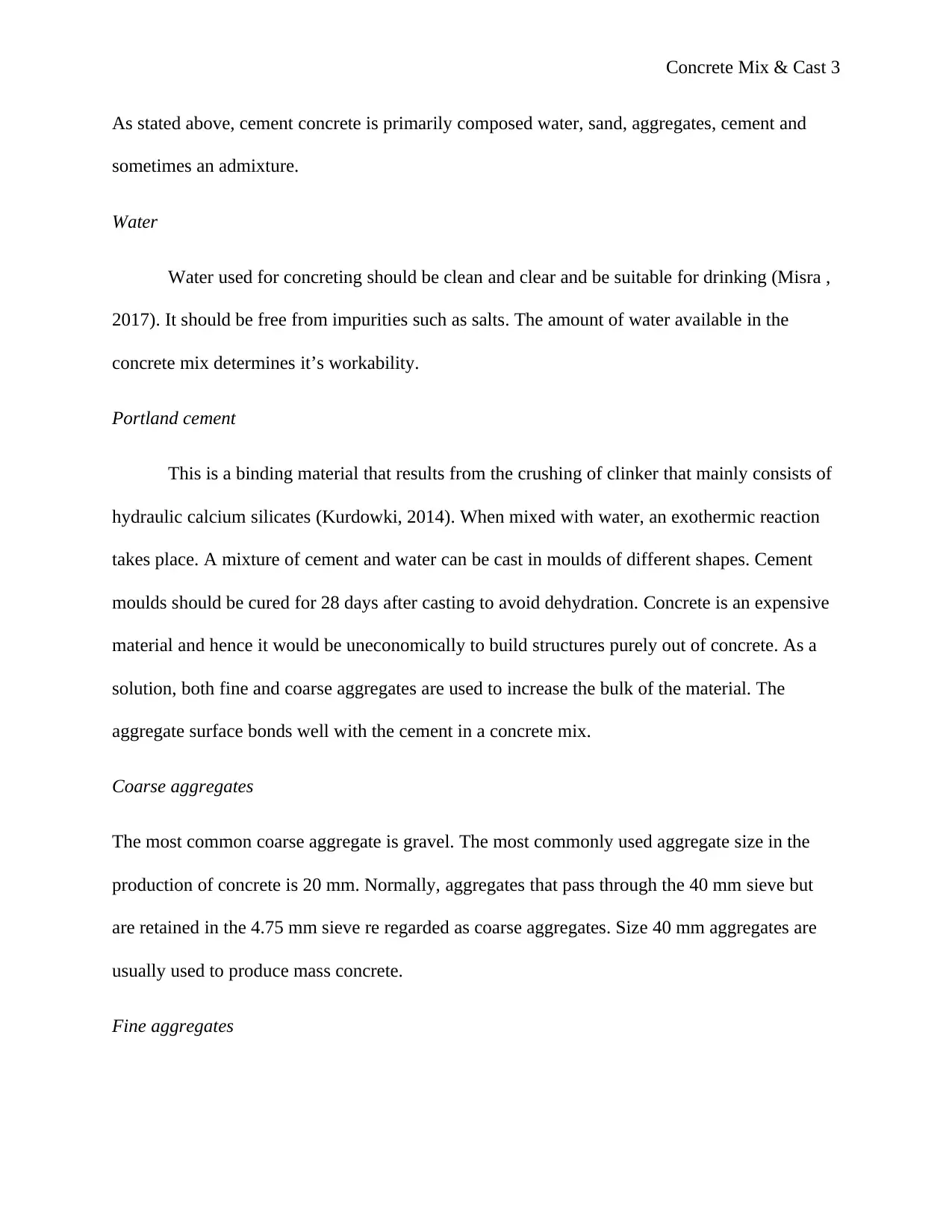
Concrete Mix & Cast 3
As stated above, cement concrete is primarily composed water, sand, aggregates, cement and
sometimes an admixture.
Water
Water used for concreting should be clean and clear and be suitable for drinking (Misra ,
2017). It should be free from impurities such as salts. The amount of water available in the
concrete mix determines it’s workability.
Portland cement
This is a binding material that results from the crushing of clinker that mainly consists of
hydraulic calcium silicates (Kurdowki, 2014). When mixed with water, an exothermic reaction
takes place. A mixture of cement and water can be cast in moulds of different shapes. Cement
moulds should be cured for 28 days after casting to avoid dehydration. Concrete is an expensive
material and hence it would be uneconomically to build structures purely out of concrete. As a
solution, both fine and coarse aggregates are used to increase the bulk of the material. The
aggregate surface bonds well with the cement in a concrete mix.
Coarse aggregates
The most common coarse aggregate is gravel. The most commonly used aggregate size in the
production of concrete is 20 mm. Normally, aggregates that pass through the 40 mm sieve but
are retained in the 4.75 mm sieve re regarded as coarse aggregates. Size 40 mm aggregates are
usually used to produce mass concrete.
Fine aggregates
As stated above, cement concrete is primarily composed water, sand, aggregates, cement and
sometimes an admixture.
Water
Water used for concreting should be clean and clear and be suitable for drinking (Misra ,
2017). It should be free from impurities such as salts. The amount of water available in the
concrete mix determines it’s workability.
Portland cement
This is a binding material that results from the crushing of clinker that mainly consists of
hydraulic calcium silicates (Kurdowki, 2014). When mixed with water, an exothermic reaction
takes place. A mixture of cement and water can be cast in moulds of different shapes. Cement
moulds should be cured for 28 days after casting to avoid dehydration. Concrete is an expensive
material and hence it would be uneconomically to build structures purely out of concrete. As a
solution, both fine and coarse aggregates are used to increase the bulk of the material. The
aggregate surface bonds well with the cement in a concrete mix.
Coarse aggregates
The most common coarse aggregate is gravel. The most commonly used aggregate size in the
production of concrete is 20 mm. Normally, aggregates that pass through the 40 mm sieve but
are retained in the 4.75 mm sieve re regarded as coarse aggregates. Size 40 mm aggregates are
usually used to produce mass concrete.
Fine aggregates
⊘ This is a preview!⊘
Do you want full access?
Subscribe today to unlock all pages.

Trusted by 1+ million students worldwide
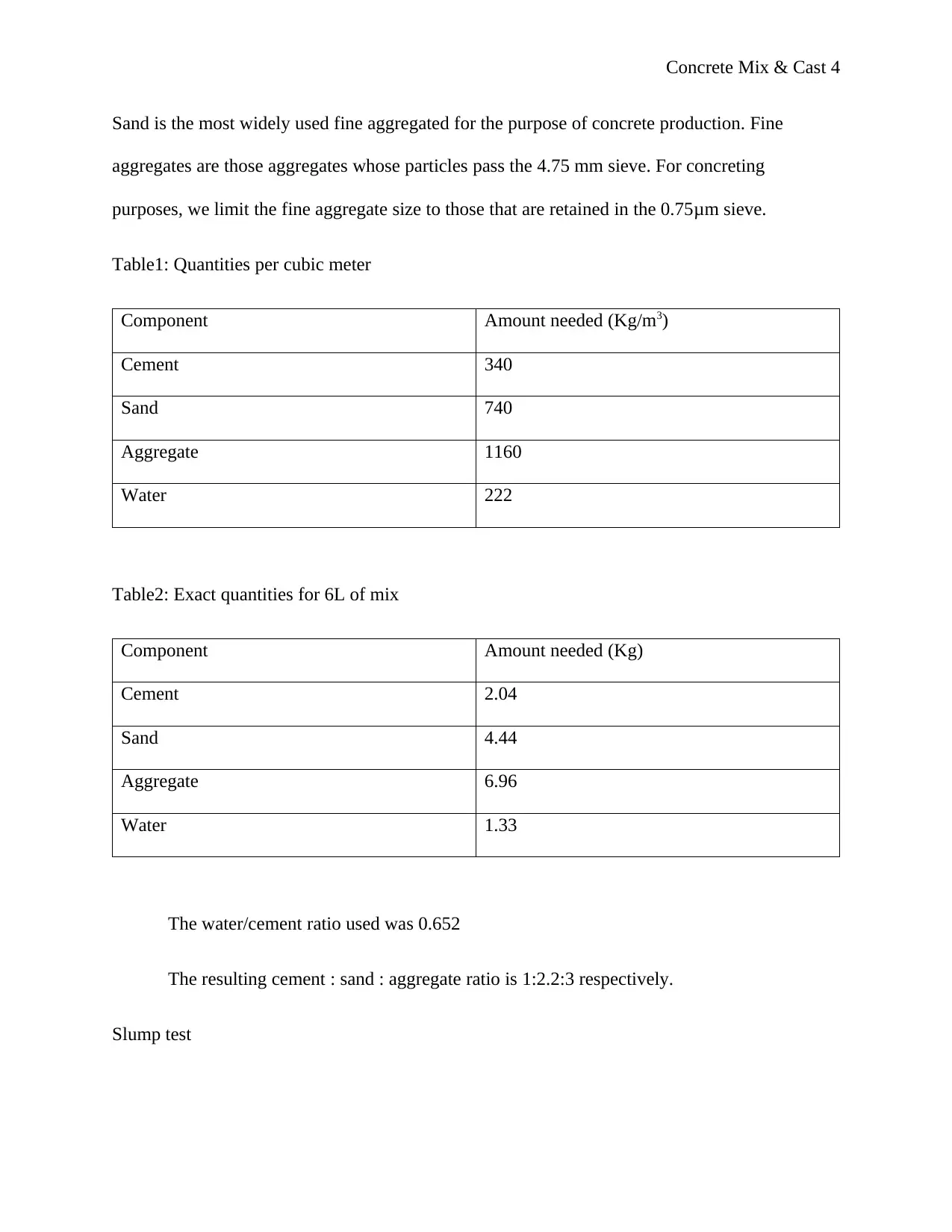
Concrete Mix & Cast 4
Sand is the most widely used fine aggregated for the purpose of concrete production. Fine
aggregates are those aggregates whose particles pass the 4.75 mm sieve. For concreting
purposes, we limit the fine aggregate size to those that are retained in the 0.75μm sieve.
Table1: Quantities per cubic meter
Component Amount needed (Kg/m3)
Cement 340
Sand 740
Aggregate 1160
Water 222
Table2: Exact quantities for 6L of mix
Component Amount needed (Kg)
Cement 2.04
Sand 4.44
Aggregate 6.96
Water 1.33
The water/cement ratio used was 0.652
The resulting cement : sand : aggregate ratio is 1:2.2:3 respectively.
Slump test
Sand is the most widely used fine aggregated for the purpose of concrete production. Fine
aggregates are those aggregates whose particles pass the 4.75 mm sieve. For concreting
purposes, we limit the fine aggregate size to those that are retained in the 0.75μm sieve.
Table1: Quantities per cubic meter
Component Amount needed (Kg/m3)
Cement 340
Sand 740
Aggregate 1160
Water 222
Table2: Exact quantities for 6L of mix
Component Amount needed (Kg)
Cement 2.04
Sand 4.44
Aggregate 6.96
Water 1.33
The water/cement ratio used was 0.652
The resulting cement : sand : aggregate ratio is 1:2.2:3 respectively.
Slump test
Paraphrase This Document
Need a fresh take? Get an instant paraphrase of this document with our AI Paraphraser
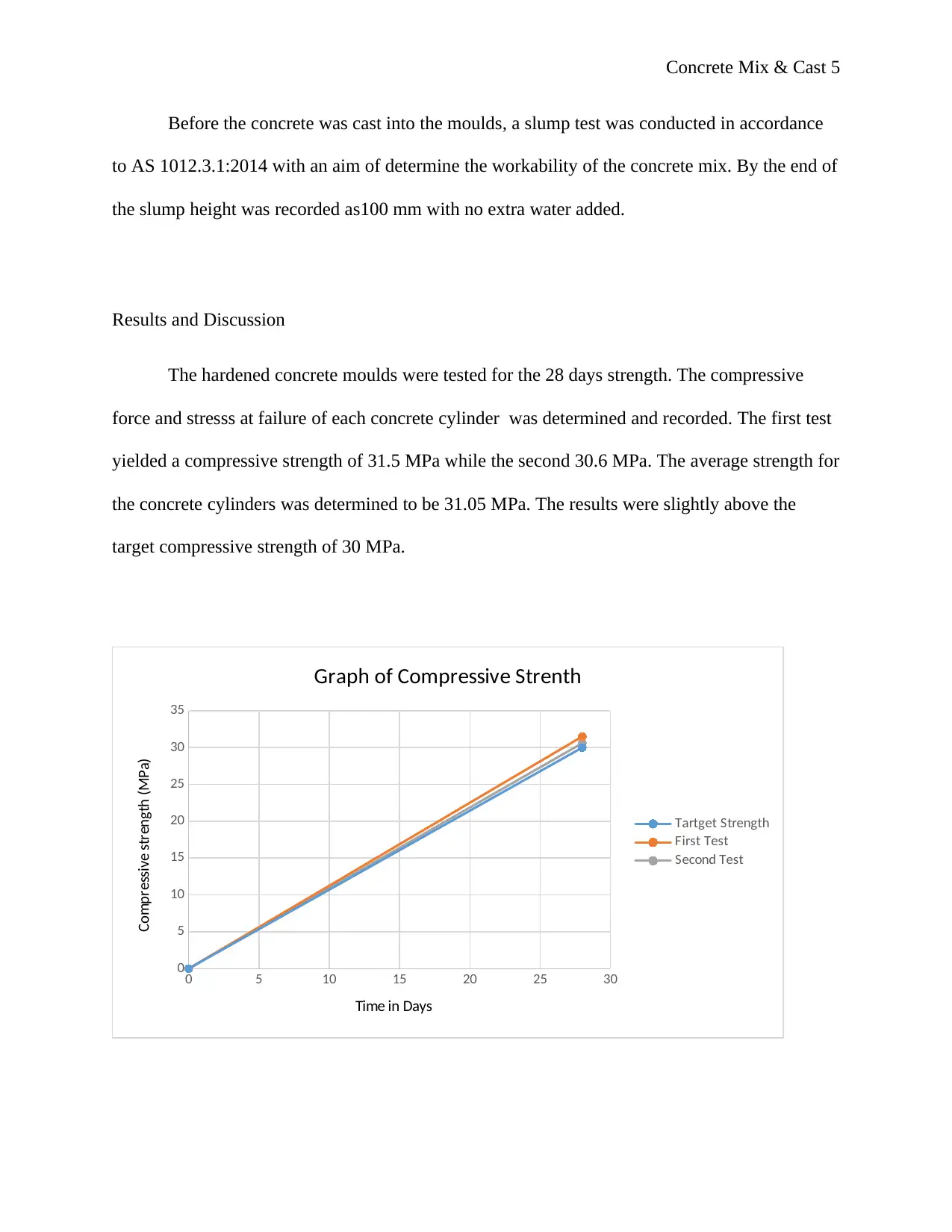
Concrete Mix & Cast 5
Before the concrete was cast into the moulds, a slump test was conducted in accordance
to AS 1012.3.1:2014 with an aim of determine the workability of the concrete mix. By the end of
the slump height was recorded as100 mm with no extra water added.
Results and Discussion
The hardened concrete moulds were tested for the 28 days strength. The compressive
force and stresss at failure of each concrete cylinder was determined and recorded. The first test
yielded a compressive strength of 31.5 MPa while the second 30.6 MPa. The average strength for
the concrete cylinders was determined to be 31.05 MPa. The results were slightly above the
target compressive strength of 30 MPa.
0 5 10 15 20 25 30
0
5
10
15
20
25
30
35
Graph of Compressive Strenth
Tartget Strength
First Test
Second Test
Time in Days
Compressive strength (MPa)
Before the concrete was cast into the moulds, a slump test was conducted in accordance
to AS 1012.3.1:2014 with an aim of determine the workability of the concrete mix. By the end of
the slump height was recorded as100 mm with no extra water added.
Results and Discussion
The hardened concrete moulds were tested for the 28 days strength. The compressive
force and stresss at failure of each concrete cylinder was determined and recorded. The first test
yielded a compressive strength of 31.5 MPa while the second 30.6 MPa. The average strength for
the concrete cylinders was determined to be 31.05 MPa. The results were slightly above the
target compressive strength of 30 MPa.
0 5 10 15 20 25 30
0
5
10
15
20
25
30
35
Graph of Compressive Strenth
Tartget Strength
First Test
Second Test
Time in Days
Compressive strength (MPa)
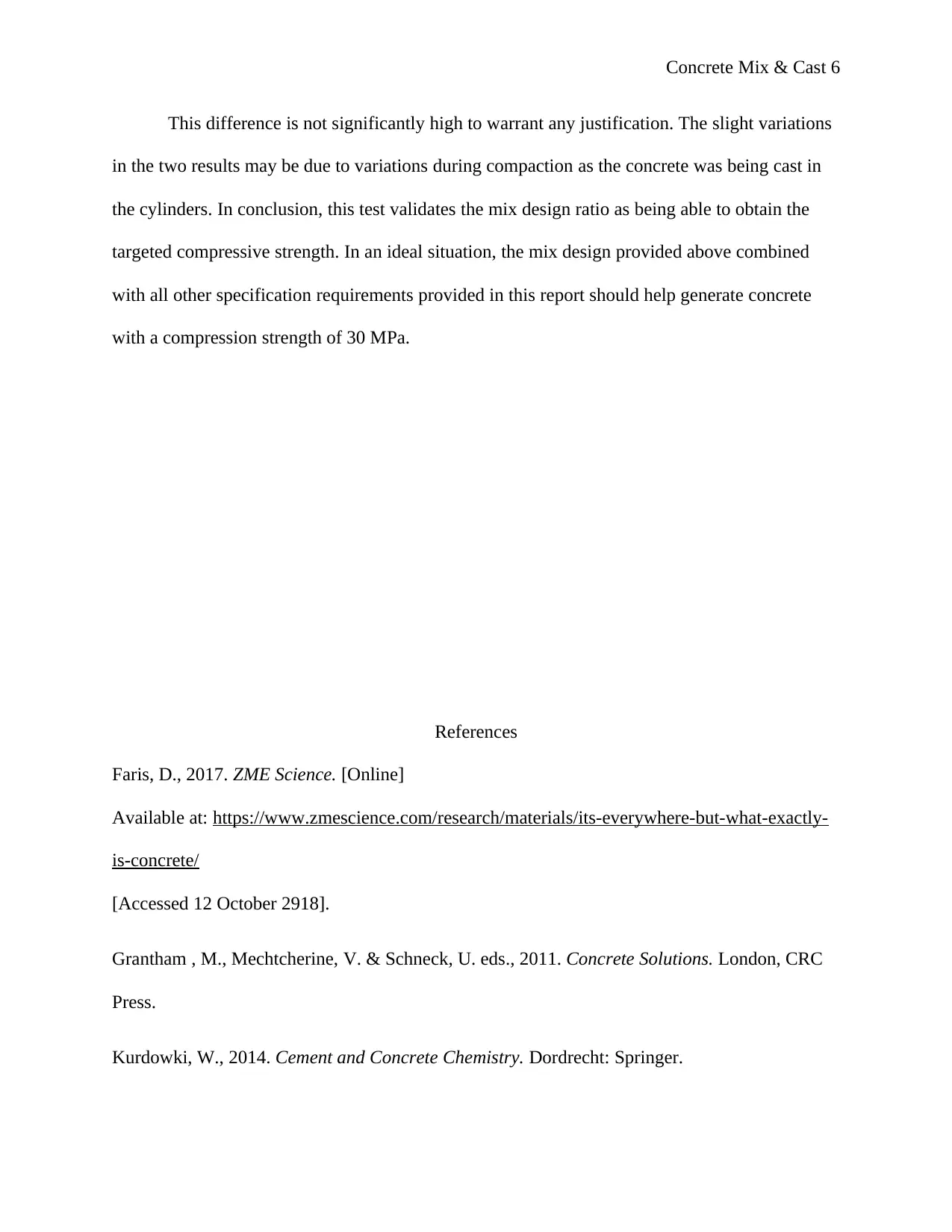
Concrete Mix & Cast 6
This difference is not significantly high to warrant any justification. The slight variations
in the two results may be due to variations during compaction as the concrete was being cast in
the cylinders. In conclusion, this test validates the mix design ratio as being able to obtain the
targeted compressive strength. In an ideal situation, the mix design provided above combined
with all other specification requirements provided in this report should help generate concrete
with a compression strength of 30 MPa.
References
Faris, D., 2017. ZME Science. [Online]
Available at: https://www.zmescience.com/research/materials/its-everywhere-but-what-exactly-
is-concrete/
[Accessed 12 October 2918].
Grantham , M., Mechtcherine, V. & Schneck, U. eds., 2011. Concrete Solutions. London, CRC
Press.
Kurdowki, W., 2014. Cement and Concrete Chemistry. Dordrecht: Springer.
This difference is not significantly high to warrant any justification. The slight variations
in the two results may be due to variations during compaction as the concrete was being cast in
the cylinders. In conclusion, this test validates the mix design ratio as being able to obtain the
targeted compressive strength. In an ideal situation, the mix design provided above combined
with all other specification requirements provided in this report should help generate concrete
with a compression strength of 30 MPa.
References
Faris, D., 2017. ZME Science. [Online]
Available at: https://www.zmescience.com/research/materials/its-everywhere-but-what-exactly-
is-concrete/
[Accessed 12 October 2918].
Grantham , M., Mechtcherine, V. & Schneck, U. eds., 2011. Concrete Solutions. London, CRC
Press.
Kurdowki, W., 2014. Cement and Concrete Chemistry. Dordrecht: Springer.
⊘ This is a preview!⊘
Do you want full access?
Subscribe today to unlock all pages.

Trusted by 1+ million students worldwide
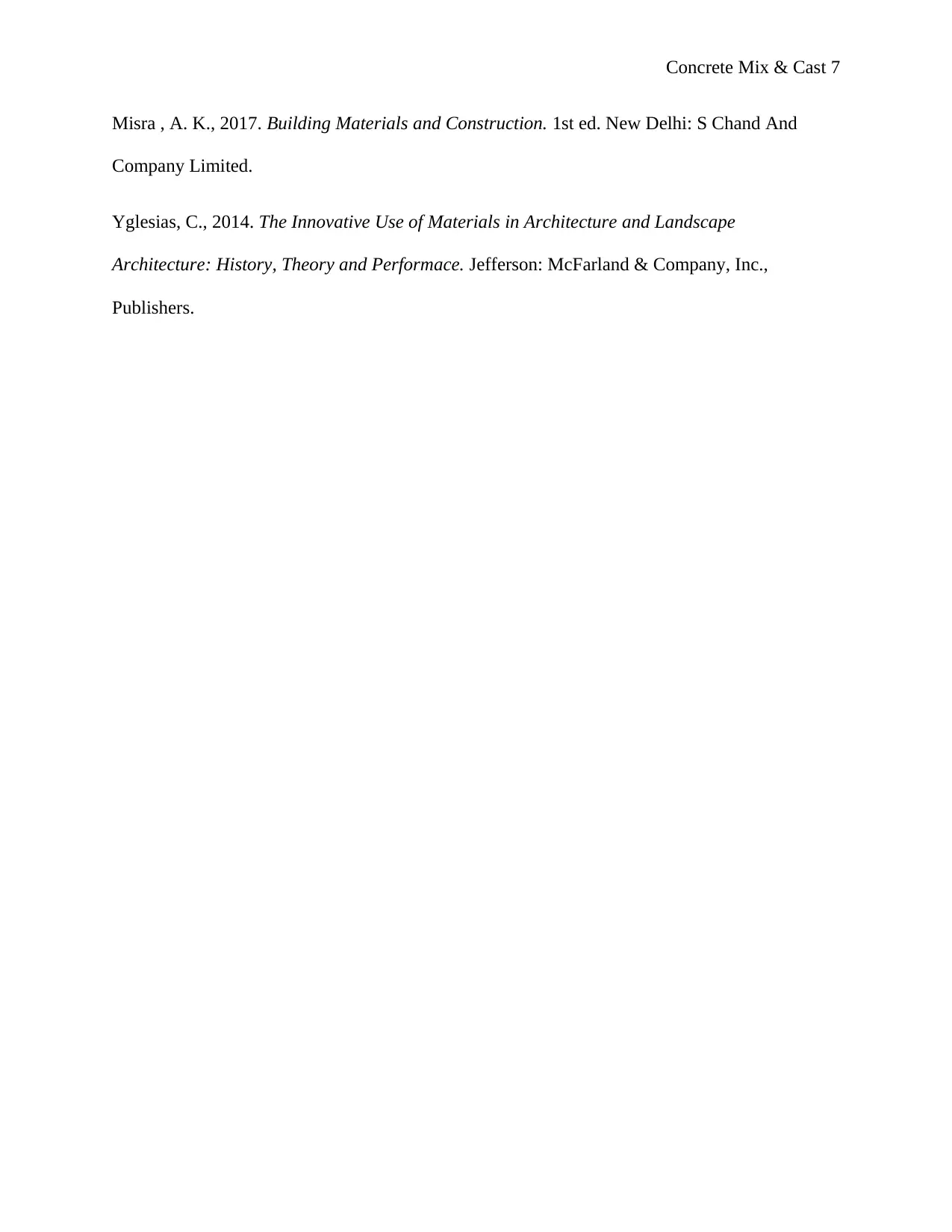
Concrete Mix & Cast 7
Misra , A. K., 2017. Building Materials and Construction. 1st ed. New Delhi: S Chand And
Company Limited.
Yglesias, C., 2014. The Innovative Use of Materials in Architecture and Landscape
Architecture: History, Theory and Performace. Jefferson: McFarland & Company, Inc.,
Publishers.
Misra , A. K., 2017. Building Materials and Construction. 1st ed. New Delhi: S Chand And
Company Limited.
Yglesias, C., 2014. The Innovative Use of Materials in Architecture and Landscape
Architecture: History, Theory and Performace. Jefferson: McFarland & Company, Inc.,
Publishers.
1 out of 7