Report: Ensuring a Safe Workplace - Assessment Task 3
VerifiedAdded on 2019/10/30
|11
|2560
|266
Report
AI Summary
This report, an assessment task, addresses workplace safety for ISS, focusing on hazard identification, risk assessment, and the implementation of a comprehensive WHS management system. It details various workplace hazards, including fire risks, personal injuries from lifting, and exposure ...
Read More
Contribute Materials
Your contribution can guide someone’s learning journey. Share your
documents today.
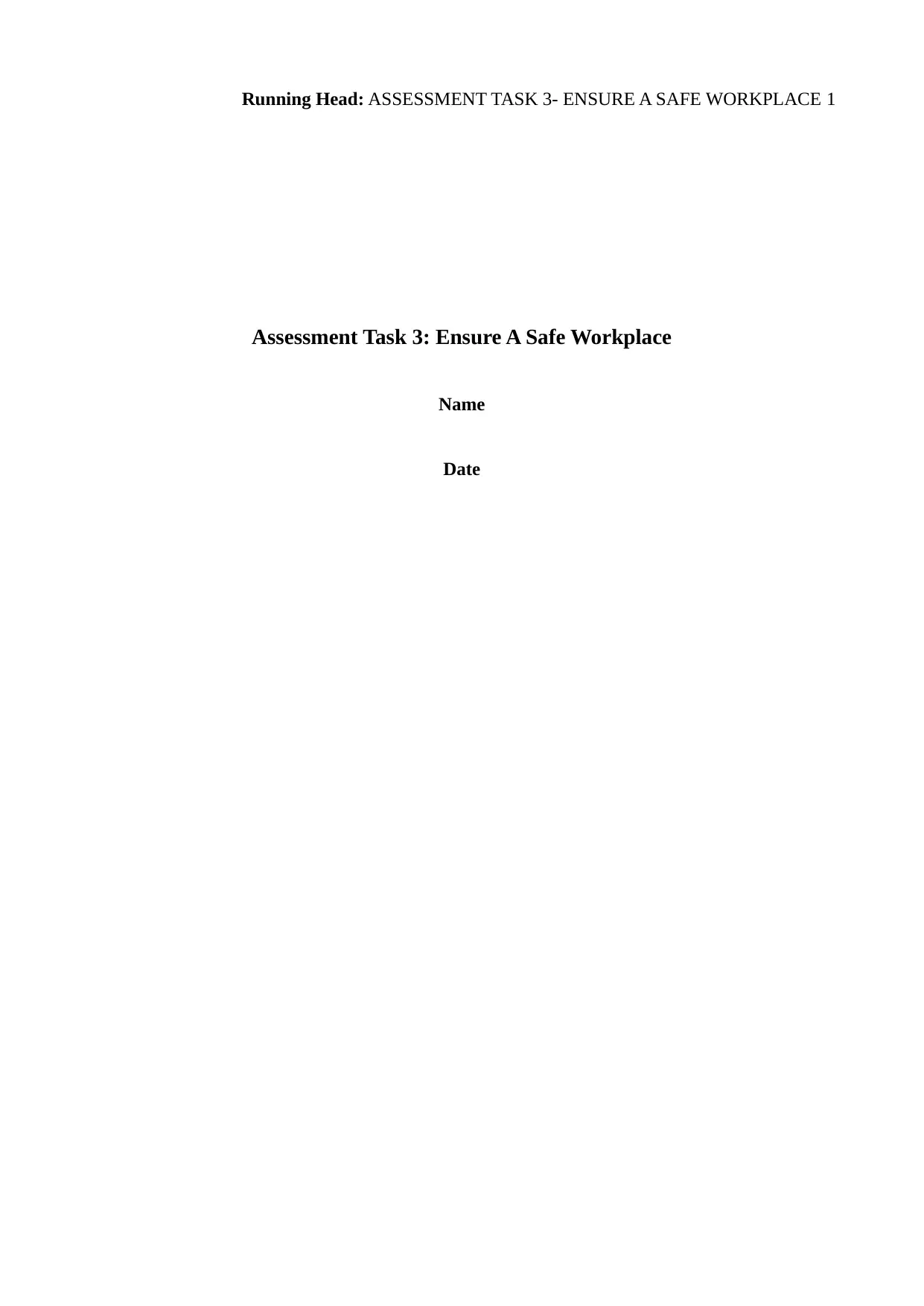
Running Head: ASSESSMENT TASK 3- ENSURE A SAFE WORKPLACE 1
Assessment Task 3: Ensure A Safe Workplace
Name
Date
Assessment Task 3: Ensure A Safe Workplace
Name
Date
Secure Best Marks with AI Grader
Need help grading? Try our AI Grader for instant feedback on your assignments.
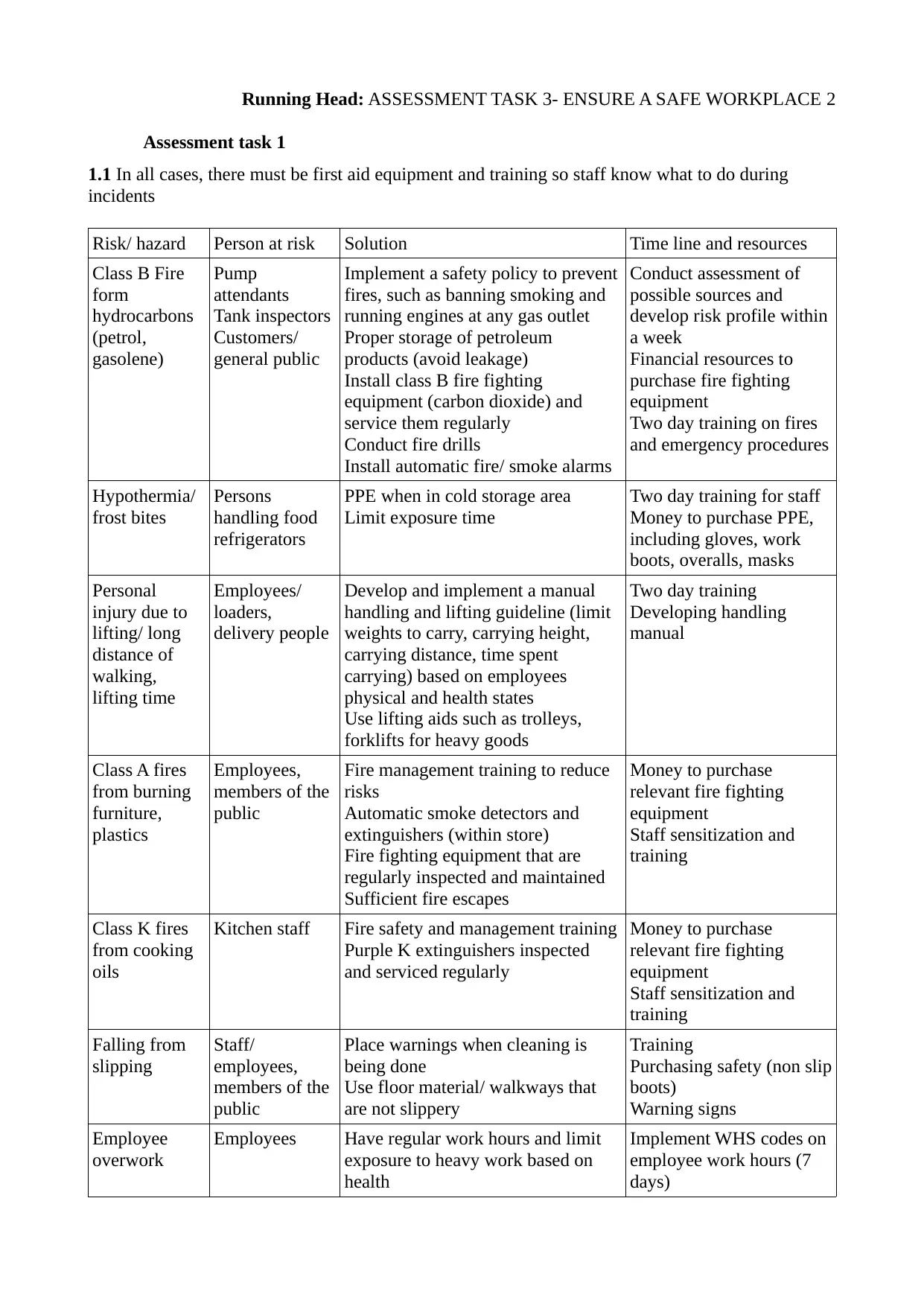
Running Head: ASSESSMENT TASK 3- ENSURE A SAFE WORKPLACE 2
Assessment task 1
1.1 In all cases, there must be first aid equipment and training so staff know what to do during
incidents
Risk/ hazard Person at risk Solution Time line and resources
Class B Fire
form
hydrocarbons
(petrol,
gasolene)
Pump
attendants
Tank inspectors
Customers/
general public
Implement a safety policy to prevent
fires, such as banning smoking and
running engines at any gas outlet
Proper storage of petroleum
products (avoid leakage)
Install class B fire fighting
equipment (carbon dioxide) and
service them regularly
Conduct fire drills
Install automatic fire/ smoke alarms
Conduct assessment of
possible sources and
develop risk profile within
a week
Financial resources to
purchase fire fighting
equipment
Two day training on fires
and emergency procedures
Hypothermia/
frost bites
Persons
handling food
refrigerators
PPE when in cold storage area
Limit exposure time
Two day training for staff
Money to purchase PPE,
including gloves, work
boots, overalls, masks
Personal
injury due to
lifting/ long
distance of
walking,
lifting time
Employees/
loaders,
delivery people
Develop and implement a manual
handling and lifting guideline (limit
weights to carry, carrying height,
carrying distance, time spent
carrying) based on employees
physical and health states
Use lifting aids such as trolleys,
forklifts for heavy goods
Two day training
Developing handling
manual
Class A fires
from burning
furniture,
plastics
Employees,
members of the
public
Fire management training to reduce
risks
Automatic smoke detectors and
extinguishers (within store)
Fire fighting equipment that are
regularly inspected and maintained
Sufficient fire escapes
Money to purchase
relevant fire fighting
equipment
Staff sensitization and
training
Class K fires
from cooking
oils
Kitchen staff Fire safety and management training
Purple K extinguishers inspected
and serviced regularly
Money to purchase
relevant fire fighting
equipment
Staff sensitization and
training
Falling from
slipping
Staff/
employees,
members of the
public
Place warnings when cleaning is
being done
Use floor material/ walkways that
are not slippery
Training
Purchasing safety (non slip
boots)
Warning signs
Employee
overwork
Employees Have regular work hours and limit
exposure to heavy work based on
health
Implement WHS codes on
employee work hours (7
days)
Assessment task 1
1.1 In all cases, there must be first aid equipment and training so staff know what to do during
incidents
Risk/ hazard Person at risk Solution Time line and resources
Class B Fire
form
hydrocarbons
(petrol,
gasolene)
Pump
attendants
Tank inspectors
Customers/
general public
Implement a safety policy to prevent
fires, such as banning smoking and
running engines at any gas outlet
Proper storage of petroleum
products (avoid leakage)
Install class B fire fighting
equipment (carbon dioxide) and
service them regularly
Conduct fire drills
Install automatic fire/ smoke alarms
Conduct assessment of
possible sources and
develop risk profile within
a week
Financial resources to
purchase fire fighting
equipment
Two day training on fires
and emergency procedures
Hypothermia/
frost bites
Persons
handling food
refrigerators
PPE when in cold storage area
Limit exposure time
Two day training for staff
Money to purchase PPE,
including gloves, work
boots, overalls, masks
Personal
injury due to
lifting/ long
distance of
walking,
lifting time
Employees/
loaders,
delivery people
Develop and implement a manual
handling and lifting guideline (limit
weights to carry, carrying height,
carrying distance, time spent
carrying) based on employees
physical and health states
Use lifting aids such as trolleys,
forklifts for heavy goods
Two day training
Developing handling
manual
Class A fires
from burning
furniture,
plastics
Employees,
members of the
public
Fire management training to reduce
risks
Automatic smoke detectors and
extinguishers (within store)
Fire fighting equipment that are
regularly inspected and maintained
Sufficient fire escapes
Money to purchase
relevant fire fighting
equipment
Staff sensitization and
training
Class K fires
from cooking
oils
Kitchen staff Fire safety and management training
Purple K extinguishers inspected
and serviced regularly
Money to purchase
relevant fire fighting
equipment
Staff sensitization and
training
Falling from
slipping
Staff/
employees,
members of the
public
Place warnings when cleaning is
being done
Use floor material/ walkways that
are not slippery
Training
Purchasing safety (non slip
boots)
Warning signs
Employee
overwork
Employees Have regular work hours and limit
exposure to heavy work based on
health
Implement WHS codes on
employee work hours (7
days)
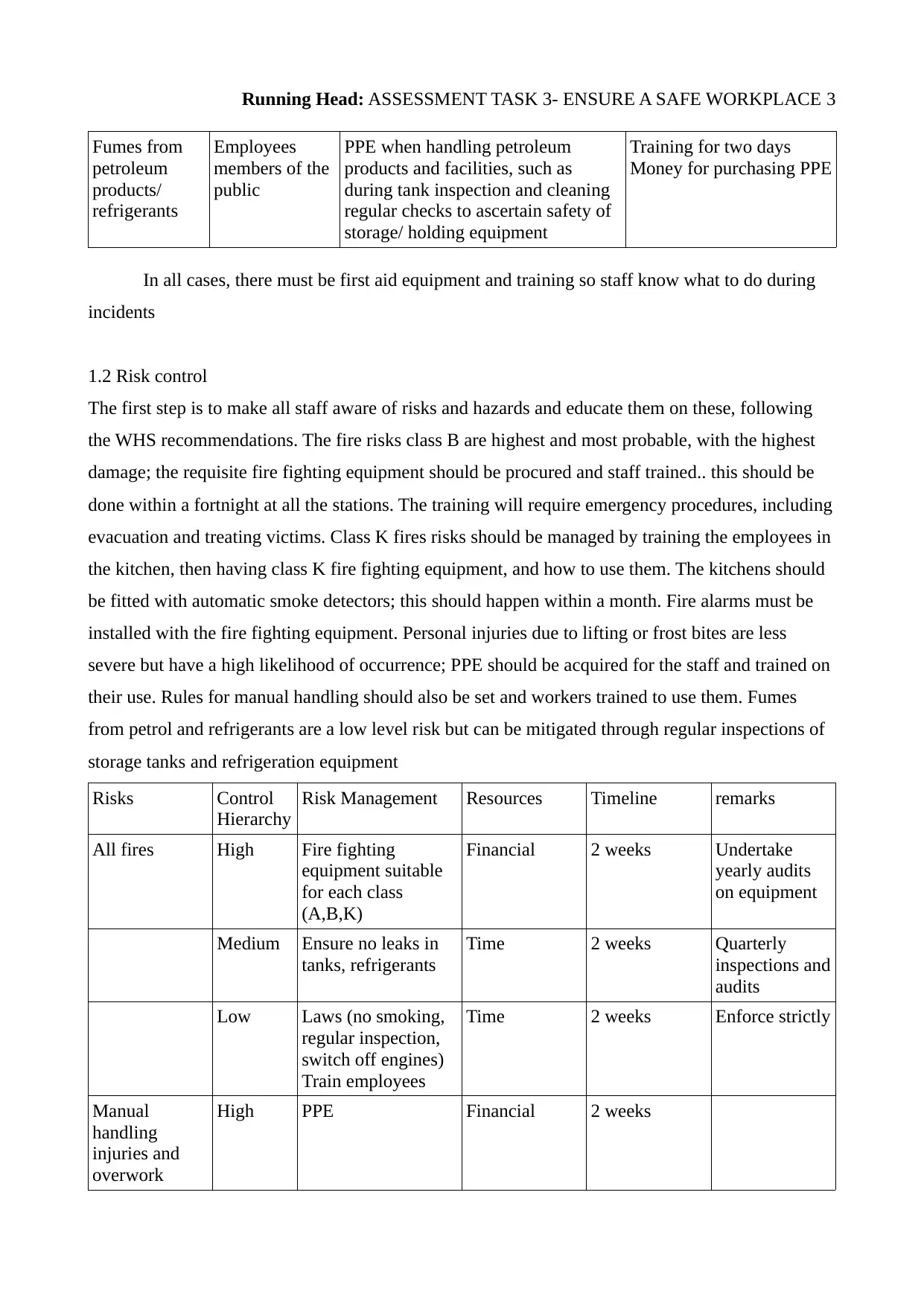
Running Head: ASSESSMENT TASK 3- ENSURE A SAFE WORKPLACE 3
Fumes from
petroleum
products/
refrigerants
Employees
members of the
public
PPE when handling petroleum
products and facilities, such as
during tank inspection and cleaning
regular checks to ascertain safety of
storage/ holding equipment
Training for two days
Money for purchasing PPE
In all cases, there must be first aid equipment and training so staff know what to do during
incidents
1.2 Risk control
The first step is to make all staff aware of risks and hazards and educate them on these, following
the WHS recommendations. The fire risks class B are highest and most probable, with the highest
damage; the requisite fire fighting equipment should be procured and staff trained.. this should be
done within a fortnight at all the stations. The training will require emergency procedures, including
evacuation and treating victims. Class K fires risks should be managed by training the employees in
the kitchen, then having class K fire fighting equipment, and how to use them. The kitchens should
be fitted with automatic smoke detectors; this should happen within a month. Fire alarms must be
installed with the fire fighting equipment. Personal injuries due to lifting or frost bites are less
severe but have a high likelihood of occurrence; PPE should be acquired for the staff and trained on
their use. Rules for manual handling should also be set and workers trained to use them. Fumes
from petrol and refrigerants are a low level risk but can be mitigated through regular inspections of
storage tanks and refrigeration equipment
Risks Control
Hierarchy
Risk Management Resources Timeline remarks
All fires High Fire fighting
equipment suitable
for each class
(A,B,K)
Financial 2 weeks Undertake
yearly audits
on equipment
Medium Ensure no leaks in
tanks, refrigerants
Time 2 weeks Quarterly
inspections and
audits
Low Laws (no smoking,
regular inspection,
switch off engines)
Train employees
Time 2 weeks Enforce strictly
Manual
handling
injuries and
overwork
High PPE Financial 2 weeks
Fumes from
petroleum
products/
refrigerants
Employees
members of the
public
PPE when handling petroleum
products and facilities, such as
during tank inspection and cleaning
regular checks to ascertain safety of
storage/ holding equipment
Training for two days
Money for purchasing PPE
In all cases, there must be first aid equipment and training so staff know what to do during
incidents
1.2 Risk control
The first step is to make all staff aware of risks and hazards and educate them on these, following
the WHS recommendations. The fire risks class B are highest and most probable, with the highest
damage; the requisite fire fighting equipment should be procured and staff trained.. this should be
done within a fortnight at all the stations. The training will require emergency procedures, including
evacuation and treating victims. Class K fires risks should be managed by training the employees in
the kitchen, then having class K fire fighting equipment, and how to use them. The kitchens should
be fitted with automatic smoke detectors; this should happen within a month. Fire alarms must be
installed with the fire fighting equipment. Personal injuries due to lifting or frost bites are less
severe but have a high likelihood of occurrence; PPE should be acquired for the staff and trained on
their use. Rules for manual handling should also be set and workers trained to use them. Fumes
from petrol and refrigerants are a low level risk but can be mitigated through regular inspections of
storage tanks and refrigeration equipment
Risks Control
Hierarchy
Risk Management Resources Timeline remarks
All fires High Fire fighting
equipment suitable
for each class
(A,B,K)
Financial 2 weeks Undertake
yearly audits
on equipment
Medium Ensure no leaks in
tanks, refrigerants
Time 2 weeks Quarterly
inspections and
audits
Low Laws (no smoking,
regular inspection,
switch off engines)
Train employees
Time 2 weeks Enforce strictly
Manual
handling
injuries and
overwork
High PPE Financial 2 weeks
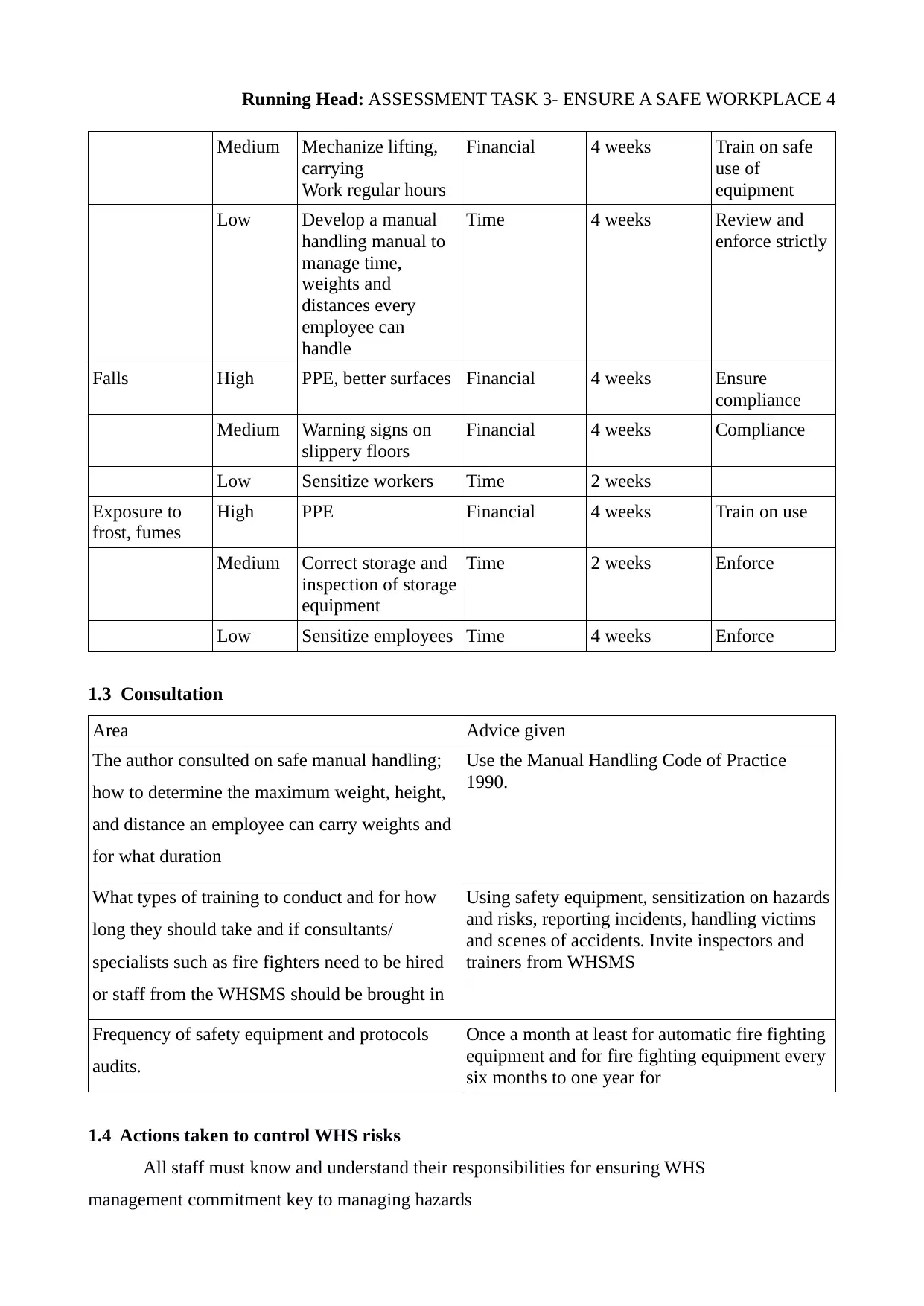
Running Head: ASSESSMENT TASK 3- ENSURE A SAFE WORKPLACE 4
Medium Mechanize lifting,
carrying
Work regular hours
Financial 4 weeks Train on safe
use of
equipment
Low Develop a manual
handling manual to
manage time,
weights and
distances every
employee can
handle
Time 4 weeks Review and
enforce strictly
Falls High PPE, better surfaces Financial 4 weeks Ensure
compliance
Medium Warning signs on
slippery floors
Financial 4 weeks Compliance
Low Sensitize workers Time 2 weeks
Exposure to
frost, fumes
High PPE Financial 4 weeks Train on use
Medium Correct storage and
inspection of storage
equipment
Time 2 weeks Enforce
Low Sensitize employees Time 4 weeks Enforce
1.3 Consultation
Area Advice given
The author consulted on safe manual handling;
how to determine the maximum weight, height,
and distance an employee can carry weights and
for what duration
Use the Manual Handling Code of Practice
1990.
What types of training to conduct and for how
long they should take and if consultants/
specialists such as fire fighters need to be hired
or staff from the WHSMS should be brought in
Using safety equipment, sensitization on hazards
and risks, reporting incidents, handling victims
and scenes of accidents. Invite inspectors and
trainers from WHSMS
Frequency of safety equipment and protocols
audits.
Once a month at least for automatic fire fighting
equipment and for fire fighting equipment every
six months to one year for
1.4 Actions taken to control WHS risks
All staff must know and understand their responsibilities for ensuring WHS
management commitment key to managing hazards
Medium Mechanize lifting,
carrying
Work regular hours
Financial 4 weeks Train on safe
use of
equipment
Low Develop a manual
handling manual to
manage time,
weights and
distances every
employee can
handle
Time 4 weeks Review and
enforce strictly
Falls High PPE, better surfaces Financial 4 weeks Ensure
compliance
Medium Warning signs on
slippery floors
Financial 4 weeks Compliance
Low Sensitize workers Time 2 weeks
Exposure to
frost, fumes
High PPE Financial 4 weeks Train on use
Medium Correct storage and
inspection of storage
equipment
Time 2 weeks Enforce
Low Sensitize employees Time 4 weeks Enforce
1.3 Consultation
Area Advice given
The author consulted on safe manual handling;
how to determine the maximum weight, height,
and distance an employee can carry weights and
for what duration
Use the Manual Handling Code of Practice
1990.
What types of training to conduct and for how
long they should take and if consultants/
specialists such as fire fighters need to be hired
or staff from the WHSMS should be brought in
Using safety equipment, sensitization on hazards
and risks, reporting incidents, handling victims
and scenes of accidents. Invite inspectors and
trainers from WHSMS
Frequency of safety equipment and protocols
audits.
Once a month at least for automatic fire fighting
equipment and for fire fighting equipment every
six months to one year for
1.4 Actions taken to control WHS risks
All staff must know and understand their responsibilities for ensuring WHS
management commitment key to managing hazards
Secure Best Marks with AI Grader
Need help grading? Try our AI Grader for instant feedback on your assignments.
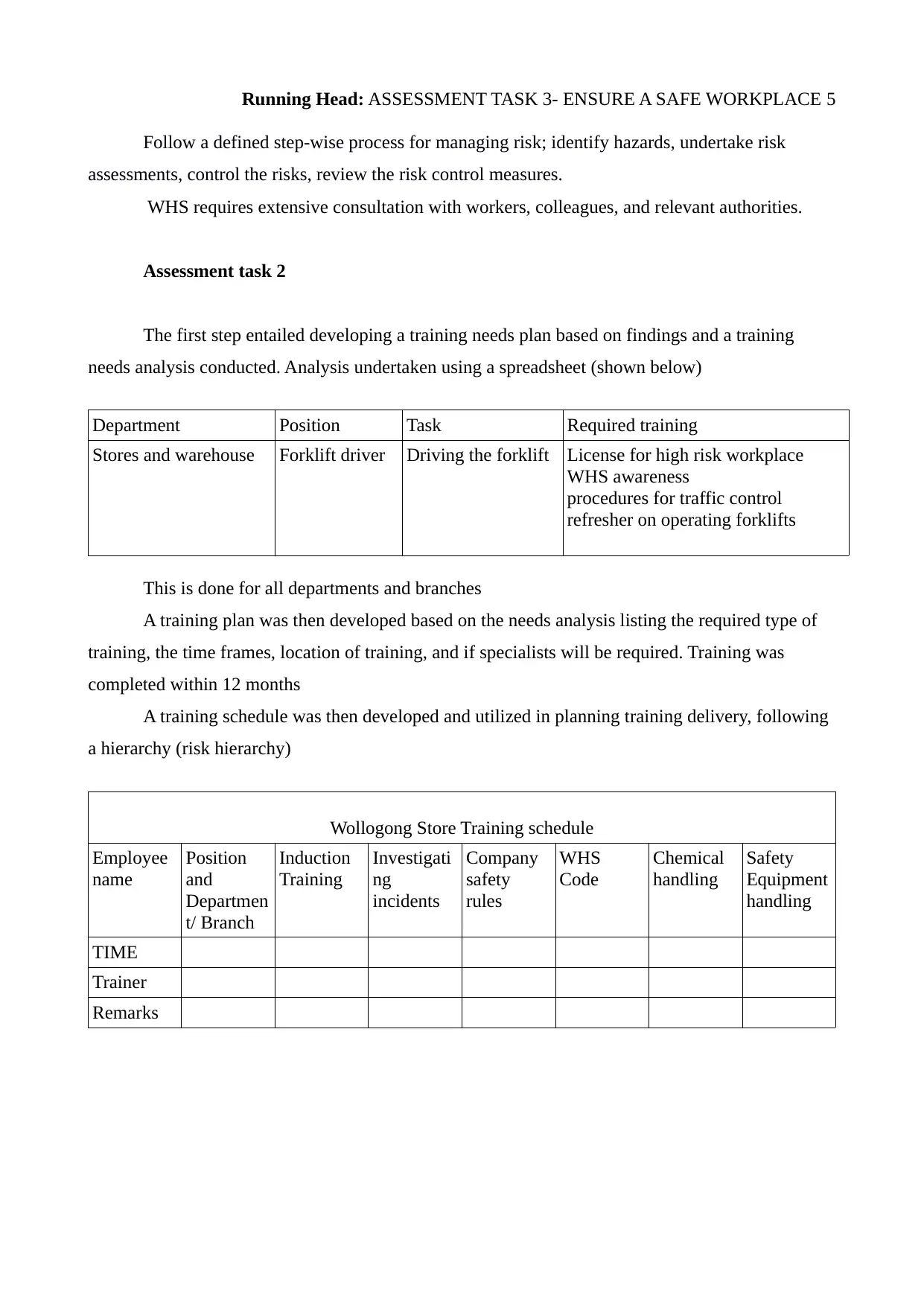
Running Head: ASSESSMENT TASK 3- ENSURE A SAFE WORKPLACE 5
Follow a defined step-wise process for managing risk; identify hazards, undertake risk
assessments, control the risks, review the risk control measures.
WHS requires extensive consultation with workers, colleagues, and relevant authorities.
Assessment task 2
The first step entailed developing a training needs plan based on findings and a training
needs analysis conducted. Analysis undertaken using a spreadsheet (shown below)
Department Position Task Required training
Stores and warehouse Forklift driver Driving the forklift License for high risk workplace
WHS awareness
procedures for traffic control
refresher on operating forklifts
This is done for all departments and branches
A training plan was then developed based on the needs analysis listing the required type of
training, the time frames, location of training, and if specialists will be required. Training was
completed within 12 months
A training schedule was then developed and utilized in planning training delivery, following
a hierarchy (risk hierarchy)
Wollogong Store Training schedule
Employee
name
Position
and
Departmen
t/ Branch
Induction
Training
Investigati
ng
incidents
Company
safety
rules
WHS
Code
Chemical
handling
Safety
Equipment
handling
TIME
Trainer
Remarks
Follow a defined step-wise process for managing risk; identify hazards, undertake risk
assessments, control the risks, review the risk control measures.
WHS requires extensive consultation with workers, colleagues, and relevant authorities.
Assessment task 2
The first step entailed developing a training needs plan based on findings and a training
needs analysis conducted. Analysis undertaken using a spreadsheet (shown below)
Department Position Task Required training
Stores and warehouse Forklift driver Driving the forklift License for high risk workplace
WHS awareness
procedures for traffic control
refresher on operating forklifts
This is done for all departments and branches
A training plan was then developed based on the needs analysis listing the required type of
training, the time frames, location of training, and if specialists will be required. Training was
completed within 12 months
A training schedule was then developed and utilized in planning training delivery, following
a hierarchy (risk hierarchy)
Wollogong Store Training schedule
Employee
name
Position
and
Departmen
t/ Branch
Induction
Training
Investigati
ng
incidents
Company
safety
rules
WHS
Code
Chemical
handling
Safety
Equipment
handling
TIME
Trainer
Remarks
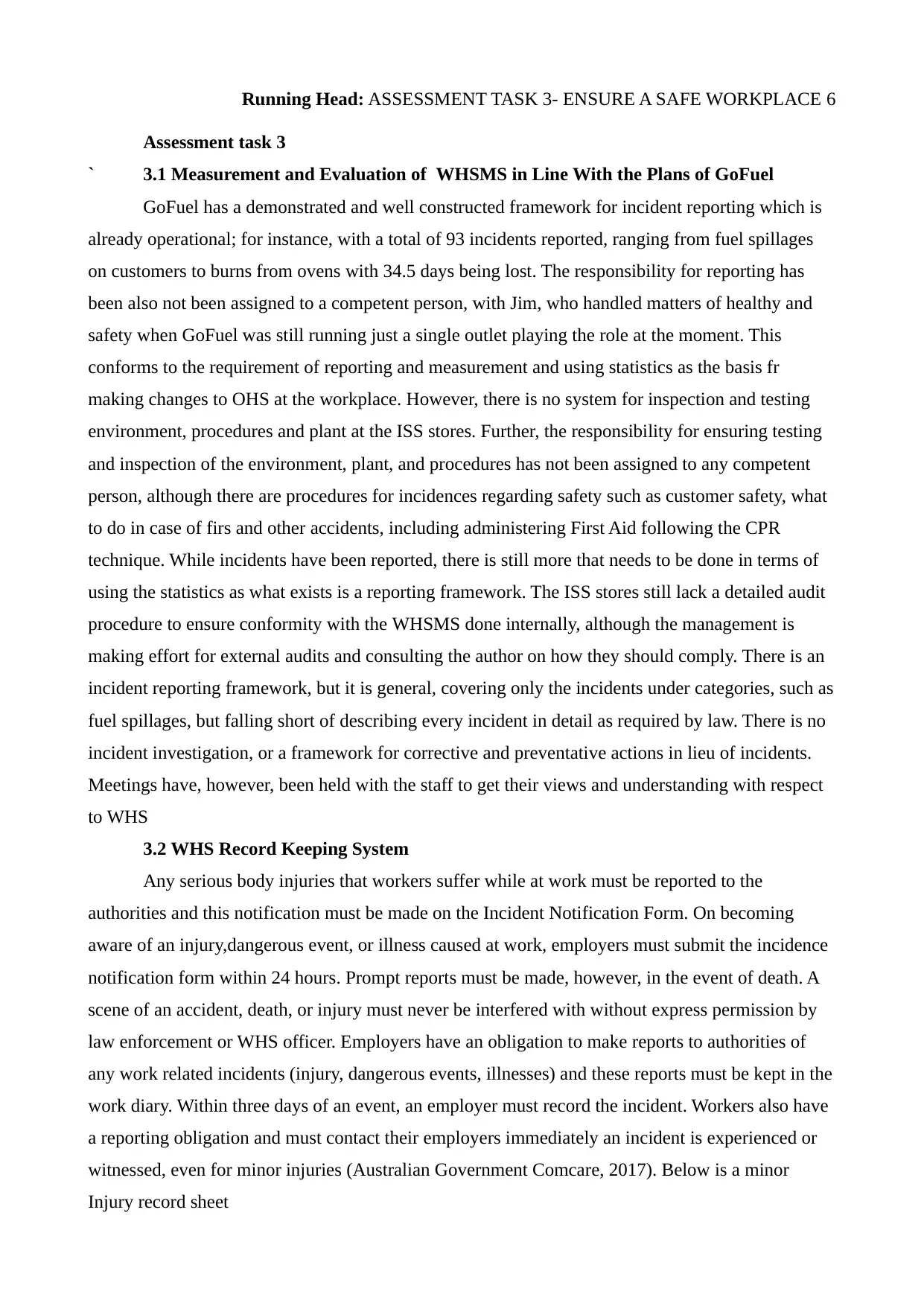
Running Head: ASSESSMENT TASK 3- ENSURE A SAFE WORKPLACE 6
Assessment task 3
` 3.1 Measurement and Evaluation of WHSMS in Line With the Plans of GoFuel
GoFuel has a demonstrated and well constructed framework for incident reporting which is
already operational; for instance, with a total of 93 incidents reported, ranging from fuel spillages
on customers to burns from ovens with 34.5 days being lost. The responsibility for reporting has
been also not been assigned to a competent person, with Jim, who handled matters of healthy and
safety when GoFuel was still running just a single outlet playing the role at the moment. This
conforms to the requirement of reporting and measurement and using statistics as the basis fr
making changes to OHS at the workplace. However, there is no system for inspection and testing
environment, procedures and plant at the ISS stores. Further, the responsibility for ensuring testing
and inspection of the environment, plant, and procedures has not been assigned to any competent
person, although there are procedures for incidences regarding safety such as customer safety, what
to do in case of firs and other accidents, including administering First Aid following the CPR
technique. While incidents have been reported, there is still more that needs to be done in terms of
using the statistics as what exists is a reporting framework. The ISS stores still lack a detailed audit
procedure to ensure conformity with the WHSMS done internally, although the management is
making effort for external audits and consulting the author on how they should comply. There is an
incident reporting framework, but it is general, covering only the incidents under categories, such as
fuel spillages, but falling short of describing every incident in detail as required by law. There is no
incident investigation, or a framework for corrective and preventative actions in lieu of incidents.
Meetings have, however, been held with the staff to get their views and understanding with respect
to WHS
3.2 WHS Record Keeping System
Any serious body injuries that workers suffer while at work must be reported to the
authorities and this notification must be made on the Incident Notification Form. On becoming
aware of an injury,dangerous event, or illness caused at work, employers must submit the incidence
notification form within 24 hours. Prompt reports must be made, however, in the event of death. A
scene of an accident, death, or injury must never be interfered with without express permission by
law enforcement or WHS officer. Employers have an obligation to make reports to authorities of
any work related incidents (injury, dangerous events, illnesses) and these reports must be kept in the
work diary. Within three days of an event, an employer must record the incident. Workers also have
a reporting obligation and must contact their employers immediately an incident is experienced or
witnessed, even for minor injuries (Australian Government Comcare, 2017). Below is a minor
Injury record sheet
Assessment task 3
` 3.1 Measurement and Evaluation of WHSMS in Line With the Plans of GoFuel
GoFuel has a demonstrated and well constructed framework for incident reporting which is
already operational; for instance, with a total of 93 incidents reported, ranging from fuel spillages
on customers to burns from ovens with 34.5 days being lost. The responsibility for reporting has
been also not been assigned to a competent person, with Jim, who handled matters of healthy and
safety when GoFuel was still running just a single outlet playing the role at the moment. This
conforms to the requirement of reporting and measurement and using statistics as the basis fr
making changes to OHS at the workplace. However, there is no system for inspection and testing
environment, procedures and plant at the ISS stores. Further, the responsibility for ensuring testing
and inspection of the environment, plant, and procedures has not been assigned to any competent
person, although there are procedures for incidences regarding safety such as customer safety, what
to do in case of firs and other accidents, including administering First Aid following the CPR
technique. While incidents have been reported, there is still more that needs to be done in terms of
using the statistics as what exists is a reporting framework. The ISS stores still lack a detailed audit
procedure to ensure conformity with the WHSMS done internally, although the management is
making effort for external audits and consulting the author on how they should comply. There is an
incident reporting framework, but it is general, covering only the incidents under categories, such as
fuel spillages, but falling short of describing every incident in detail as required by law. There is no
incident investigation, or a framework for corrective and preventative actions in lieu of incidents.
Meetings have, however, been held with the staff to get their views and understanding with respect
to WHS
3.2 WHS Record Keeping System
Any serious body injuries that workers suffer while at work must be reported to the
authorities and this notification must be made on the Incident Notification Form. On becoming
aware of an injury,dangerous event, or illness caused at work, employers must submit the incidence
notification form within 24 hours. Prompt reports must be made, however, in the event of death. A
scene of an accident, death, or injury must never be interfered with without express permission by
law enforcement or WHS officer. Employers have an obligation to make reports to authorities of
any work related incidents (injury, dangerous events, illnesses) and these reports must be kept in the
work diary. Within three days of an event, an employer must record the incident. Workers also have
a reporting obligation and must contact their employers immediately an incident is experienced or
witnessed, even for minor injuries (Australian Government Comcare, 2017). Below is a minor
Injury record sheet
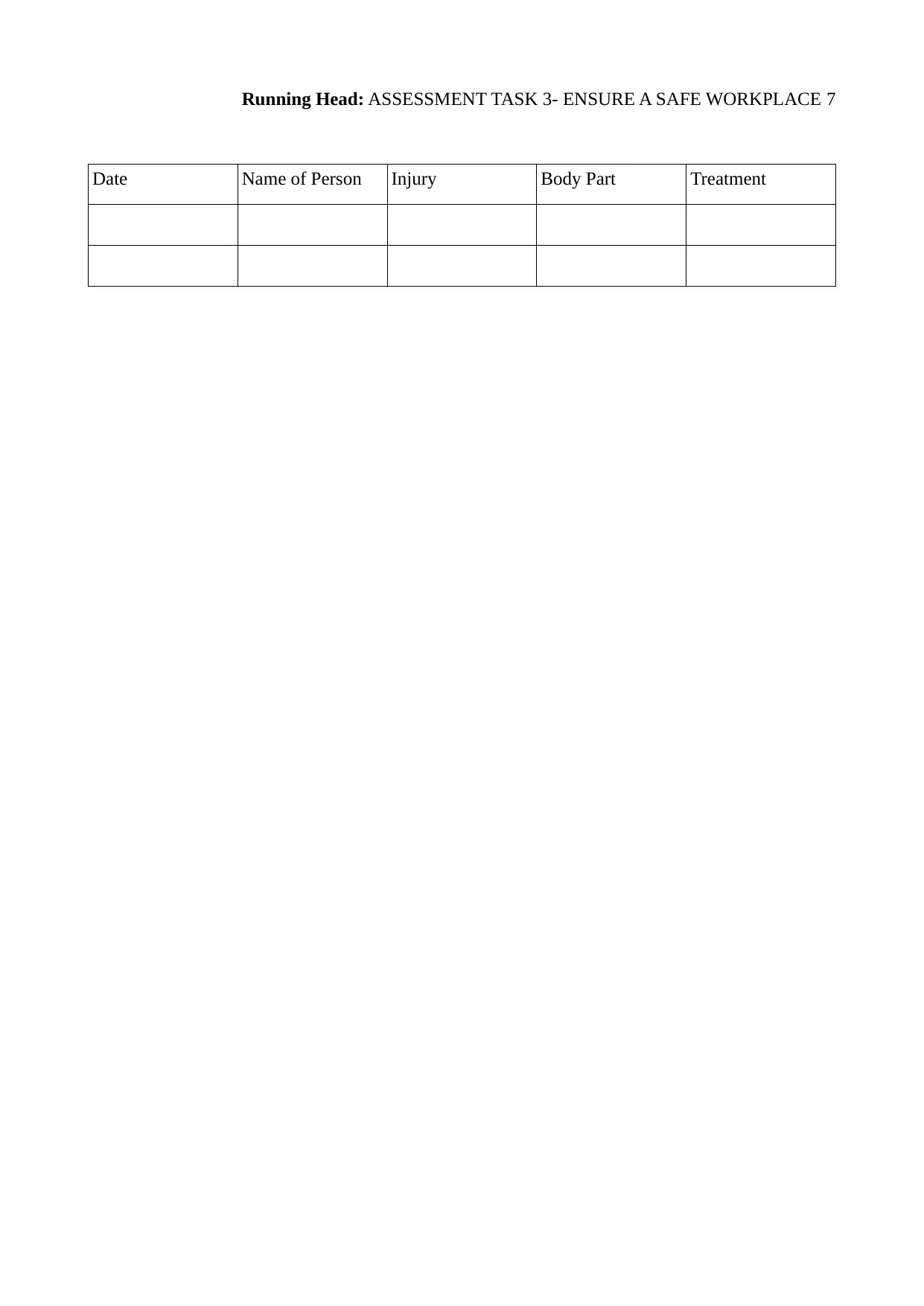
Running Head: ASSESSMENT TASK 3- ENSURE A SAFE WORKPLACE 7
Date Name of Person Injury Body Part Treatment
Date Name of Person Injury Body Part Treatment
Paraphrase This Document
Need a fresh take? Get an instant paraphrase of this document with our AI Paraphraser
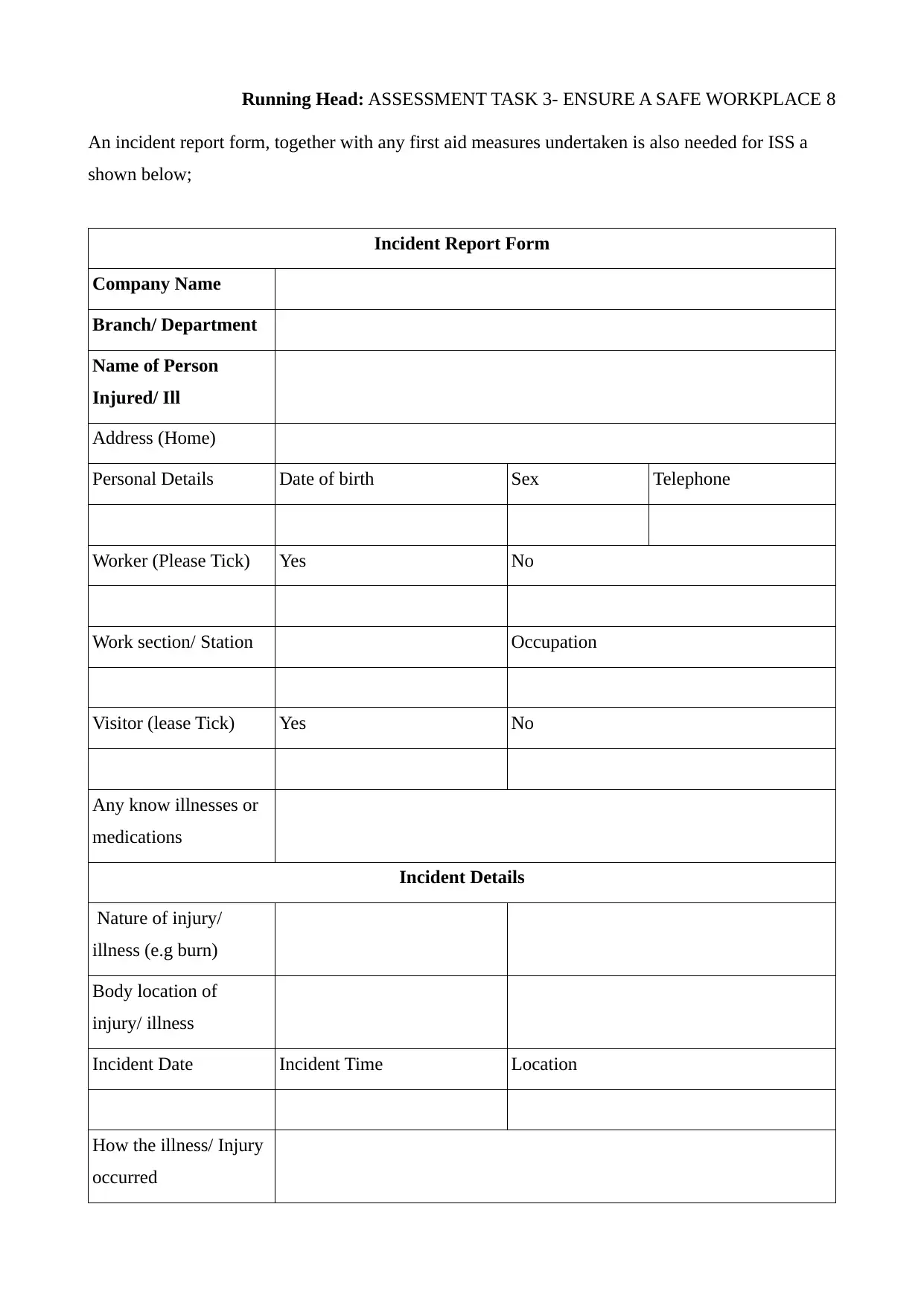
Running Head: ASSESSMENT TASK 3- ENSURE A SAFE WORKPLACE 8
An incident report form, together with any first aid measures undertaken is also needed for ISS a
shown below;
Incident Report Form
Company Name
Branch/ Department
Name of Person
Injured/ Ill
Address (Home)
Personal Details Date of birth Sex Telephone
Worker (Please Tick) Yes No
Work section/ Station Occupation
Visitor (lease Tick) Yes No
Any know illnesses or
medications
Incident Details
Nature of injury/
illness (e.g burn)
Body location of
injury/ illness
Incident Date Incident Time Location
How the illness/ Injury
occurred
An incident report form, together with any first aid measures undertaken is also needed for ISS a
shown below;
Incident Report Form
Company Name
Branch/ Department
Name of Person
Injured/ Ill
Address (Home)
Personal Details Date of birth Sex Telephone
Worker (Please Tick) Yes No
Work section/ Station Occupation
Visitor (lease Tick) Yes No
Any know illnesses or
medications
Incident Details
Nature of injury/
illness (e.g burn)
Body location of
injury/ illness
Incident Date Incident Time Location
How the illness/ Injury
occurred
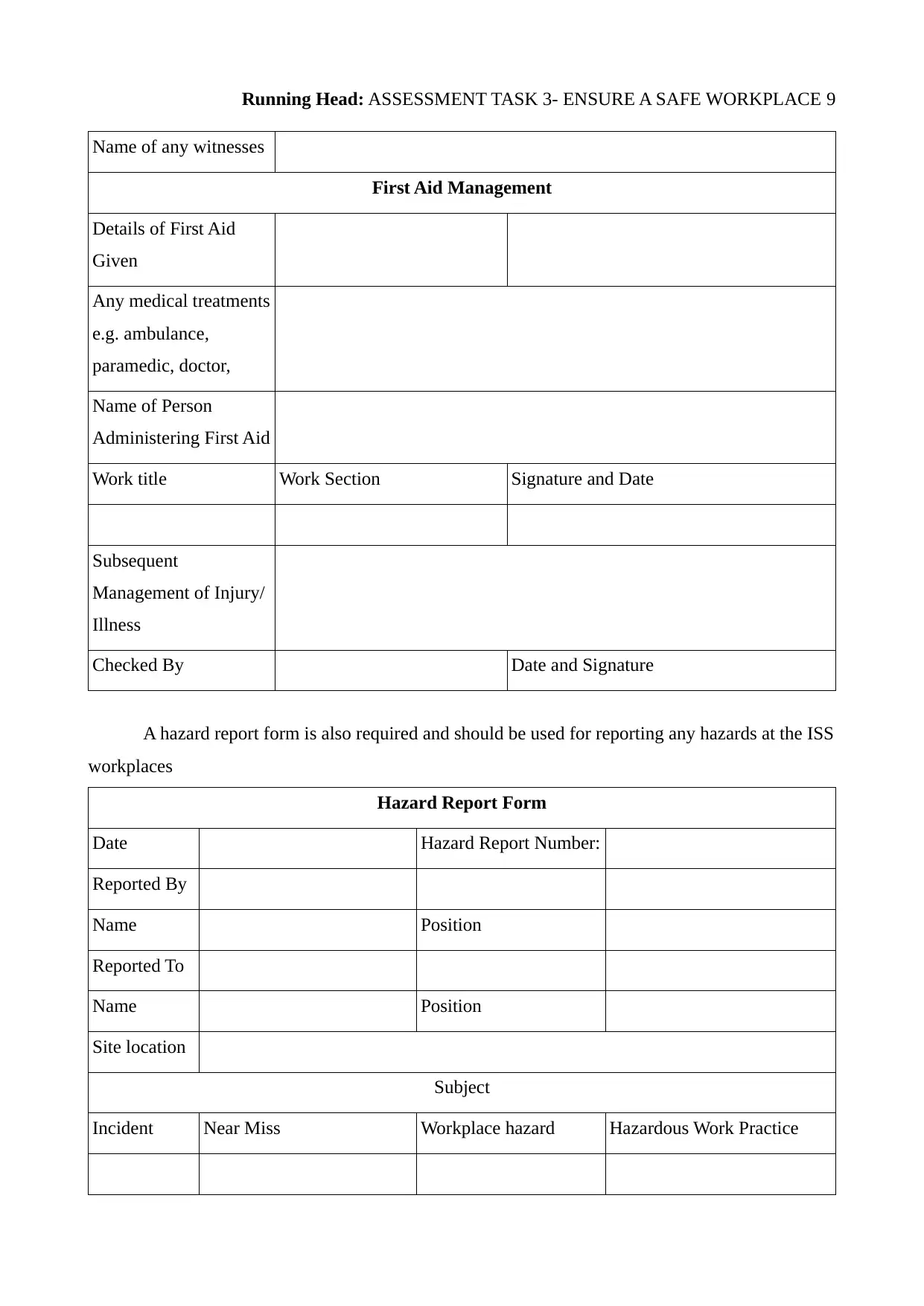
Running Head: ASSESSMENT TASK 3- ENSURE A SAFE WORKPLACE 9
Name of any witnesses
First Aid Management
Details of First Aid
Given
Any medical treatments
e.g. ambulance,
paramedic, doctor,
Name of Person
Administering First Aid
Work title Work Section Signature and Date
Subsequent
Management of Injury/
Illness
Checked By Date and Signature
A hazard report form is also required and should be used for reporting any hazards at the ISS
workplaces
Hazard Report Form
Date Hazard Report Number:
Reported By
Name Position
Reported To
Name Position
Site location
Subject
Incident Near Miss Workplace hazard Hazardous Work Practice
Name of any witnesses
First Aid Management
Details of First Aid
Given
Any medical treatments
e.g. ambulance,
paramedic, doctor,
Name of Person
Administering First Aid
Work title Work Section Signature and Date
Subsequent
Management of Injury/
Illness
Checked By Date and Signature
A hazard report form is also required and should be used for reporting any hazards at the ISS
workplaces
Hazard Report Form
Date Hazard Report Number:
Reported By
Name Position
Reported To
Name Position
Site location
Subject
Incident Near Miss Workplace hazard Hazardous Work Practice
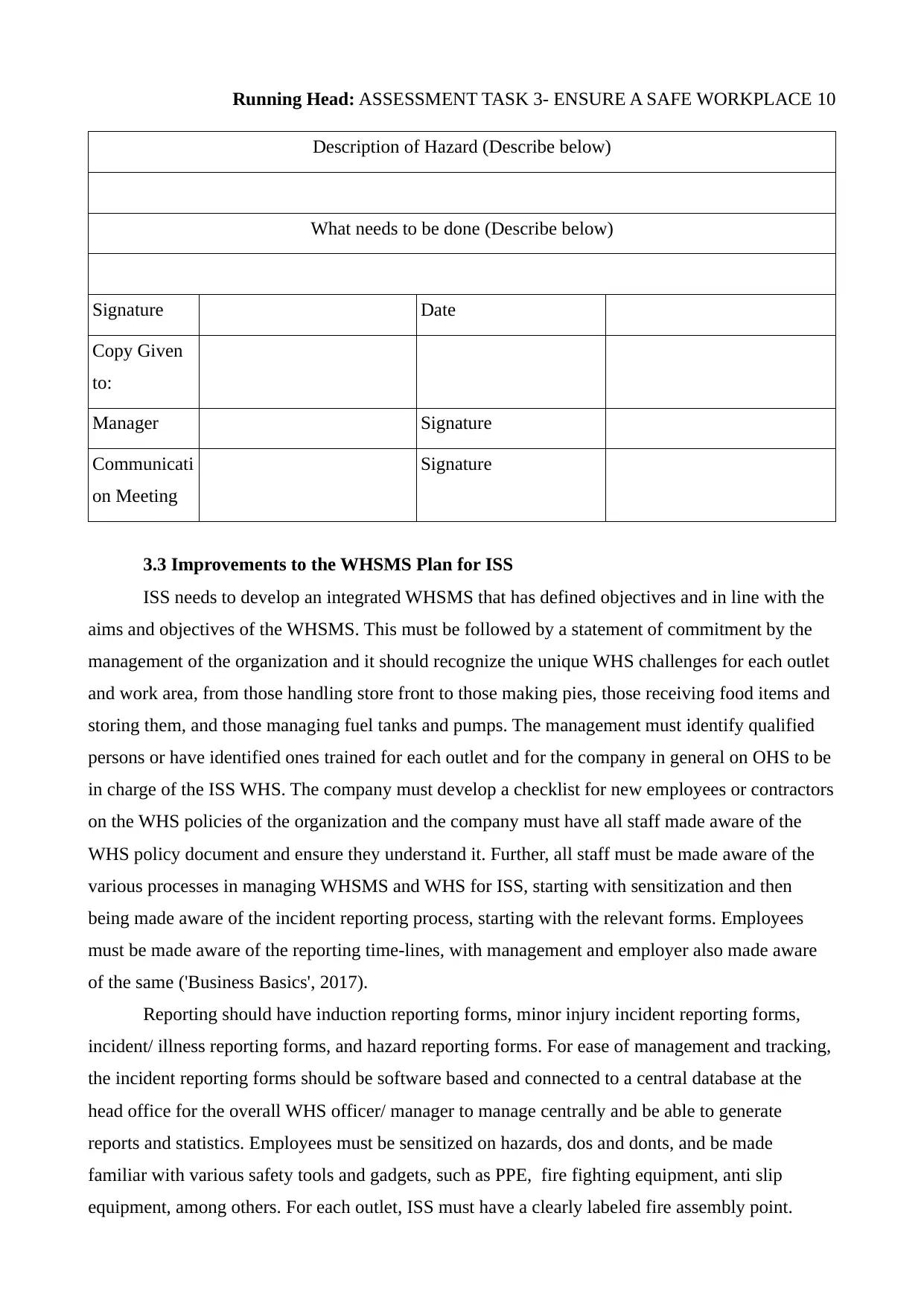
Running Head: ASSESSMENT TASK 3- ENSURE A SAFE WORKPLACE 10
Description of Hazard (Describe below)
What needs to be done (Describe below)
Signature Date
Copy Given
to:
Manager Signature
Communicati
on Meeting
Signature
3.3 Improvements to the WHSMS Plan for ISS
ISS needs to develop an integrated WHSMS that has defined objectives and in line with the
aims and objectives of the WHSMS. This must be followed by a statement of commitment by the
management of the organization and it should recognize the unique WHS challenges for each outlet
and work area, from those handling store front to those making pies, those receiving food items and
storing them, and those managing fuel tanks and pumps. The management must identify qualified
persons or have identified ones trained for each outlet and for the company in general on OHS to be
in charge of the ISS WHS. The company must develop a checklist for new employees or contractors
on the WHS policies of the organization and the company must have all staff made aware of the
WHS policy document and ensure they understand it. Further, all staff must be made aware of the
various processes in managing WHSMS and WHS for ISS, starting with sensitization and then
being made aware of the incident reporting process, starting with the relevant forms. Employees
must be made aware of the reporting time-lines, with management and employer also made aware
of the same ('Business Basics', 2017).
Reporting should have induction reporting forms, minor injury incident reporting forms,
incident/ illness reporting forms, and hazard reporting forms. For ease of management and tracking,
the incident reporting forms should be software based and connected to a central database at the
head office for the overall WHS officer/ manager to manage centrally and be able to generate
reports and statistics. Employees must be sensitized on hazards, dos and donts, and be made
familiar with various safety tools and gadgets, such as PPE, fire fighting equipment, anti slip
equipment, among others. For each outlet, ISS must have a clearly labeled fire assembly point.
Description of Hazard (Describe below)
What needs to be done (Describe below)
Signature Date
Copy Given
to:
Manager Signature
Communicati
on Meeting
Signature
3.3 Improvements to the WHSMS Plan for ISS
ISS needs to develop an integrated WHSMS that has defined objectives and in line with the
aims and objectives of the WHSMS. This must be followed by a statement of commitment by the
management of the organization and it should recognize the unique WHS challenges for each outlet
and work area, from those handling store front to those making pies, those receiving food items and
storing them, and those managing fuel tanks and pumps. The management must identify qualified
persons or have identified ones trained for each outlet and for the company in general on OHS to be
in charge of the ISS WHS. The company must develop a checklist for new employees or contractors
on the WHS policies of the organization and the company must have all staff made aware of the
WHS policy document and ensure they understand it. Further, all staff must be made aware of the
various processes in managing WHSMS and WHS for ISS, starting with sensitization and then
being made aware of the incident reporting process, starting with the relevant forms. Employees
must be made aware of the reporting time-lines, with management and employer also made aware
of the same ('Business Basics', 2017).
Reporting should have induction reporting forms, minor injury incident reporting forms,
incident/ illness reporting forms, and hazard reporting forms. For ease of management and tracking,
the incident reporting forms should be software based and connected to a central database at the
head office for the overall WHS officer/ manager to manage centrally and be able to generate
reports and statistics. Employees must be sensitized on hazards, dos and donts, and be made
familiar with various safety tools and gadgets, such as PPE, fire fighting equipment, anti slip
equipment, among others. For each outlet, ISS must have a clearly labeled fire assembly point.
Secure Best Marks with AI Grader
Need help grading? Try our AI Grader for instant feedback on your assignments.
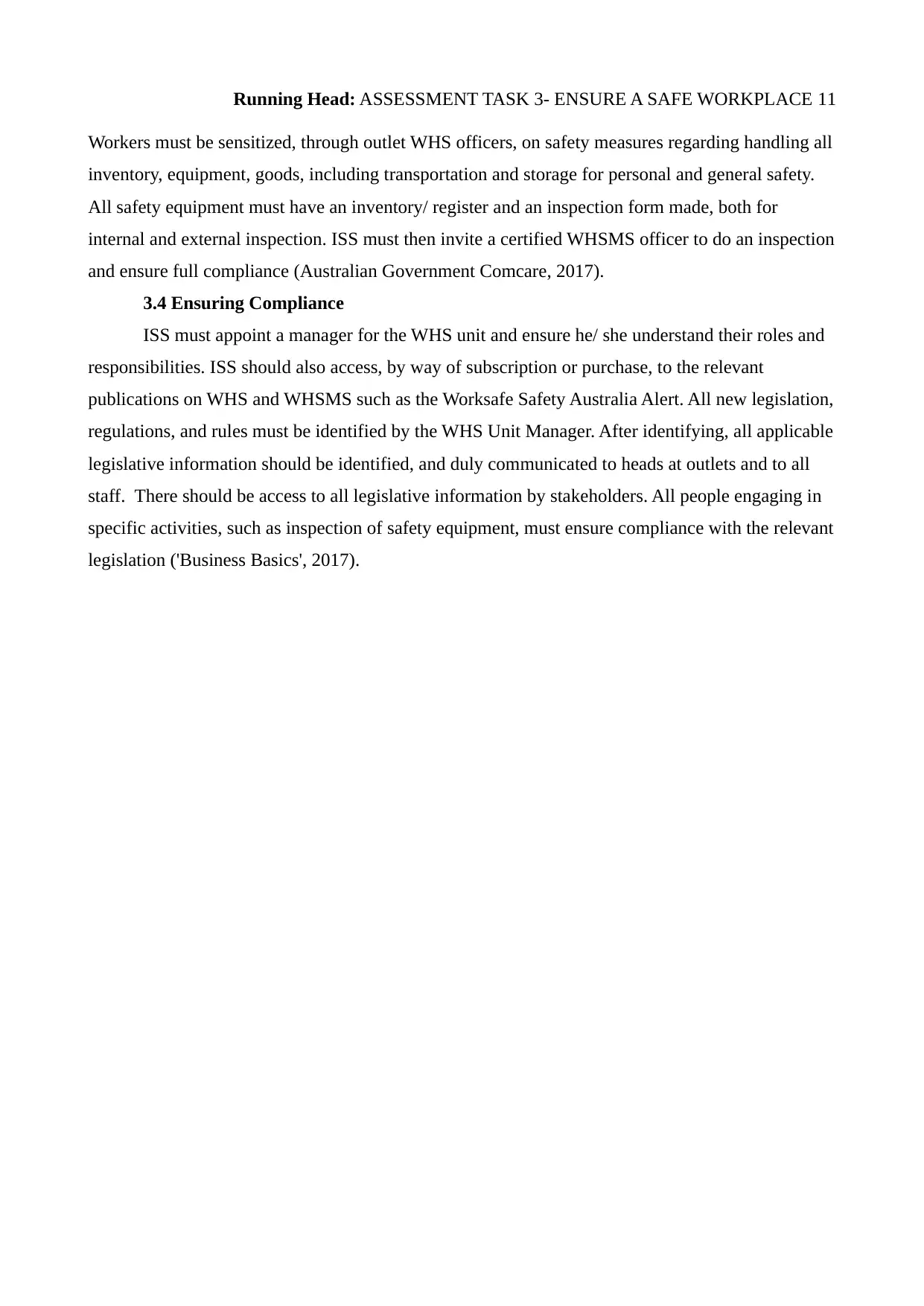
Running Head: ASSESSMENT TASK 3- ENSURE A SAFE WORKPLACE 11
Workers must be sensitized, through outlet WHS officers, on safety measures regarding handling all
inventory, equipment, goods, including transportation and storage for personal and general safety.
All safety equipment must have an inventory/ register and an inspection form made, both for
internal and external inspection. ISS must then invite a certified WHSMS officer to do an inspection
and ensure full compliance (Australian Government Comcare, 2017).
3.4 Ensuring Compliance
ISS must appoint a manager for the WHS unit and ensure he/ she understand their roles and
responsibilities. ISS should also access, by way of subscription or purchase, to the relevant
publications on WHS and WHSMS such as the Worksafe Safety Australia Alert. All new legislation,
regulations, and rules must be identified by the WHS Unit Manager. After identifying, all applicable
legislative information should be identified, and duly communicated to heads at outlets and to all
staff. There should be access to all legislative information by stakeholders. All people engaging in
specific activities, such as inspection of safety equipment, must ensure compliance with the relevant
legislation ('Business Basics', 2017).
Workers must be sensitized, through outlet WHS officers, on safety measures regarding handling all
inventory, equipment, goods, including transportation and storage for personal and general safety.
All safety equipment must have an inventory/ register and an inspection form made, both for
internal and external inspection. ISS must then invite a certified WHSMS officer to do an inspection
and ensure full compliance (Australian Government Comcare, 2017).
3.4 Ensuring Compliance
ISS must appoint a manager for the WHS unit and ensure he/ she understand their roles and
responsibilities. ISS should also access, by way of subscription or purchase, to the relevant
publications on WHS and WHSMS such as the Worksafe Safety Australia Alert. All new legislation,
regulations, and rules must be identified by the WHS Unit Manager. After identifying, all applicable
legislative information should be identified, and duly communicated to heads at outlets and to all
staff. There should be access to all legislative information by stakeholders. All people engaging in
specific activities, such as inspection of safety equipment, must ensure compliance with the relevant
legislation ('Business Basics', 2017).
1 out of 11

Your All-in-One AI-Powered Toolkit for Academic Success.
+13062052269
info@desklib.com
Available 24*7 on WhatsApp / Email
Unlock your academic potential
© 2024 | Zucol Services PVT LTD | All rights reserved.