EG7037: Environmental Sustainable Engineering and Logistics Report
VerifiedAdded on 2022/09/10
|12
|4154
|19
Report
AI Summary
This report analyzes the environmental sustainable engineering and logistics aspects of a £340 million shopping center project in Central London. It begins by identifying potential environmental, economic, and historic & cultural issues that could lead to significant costs and delays. The report then explores various renewable energy and sustainable material sources, such as bamboo, timber crete, ferrock, and solar power, evaluating their suitability for the project. It further delves into supply chain management, procurement strategies, and health and safety factors crucial for sustainable construction. Finally, the report examines the role of passive and active systems in minimizing environmental impact, providing a comprehensive overview of sustainable engineering practices in the context of this case study.
Contribute Materials
Your contribution can guide someone’s learning journey. Share your
documents today.
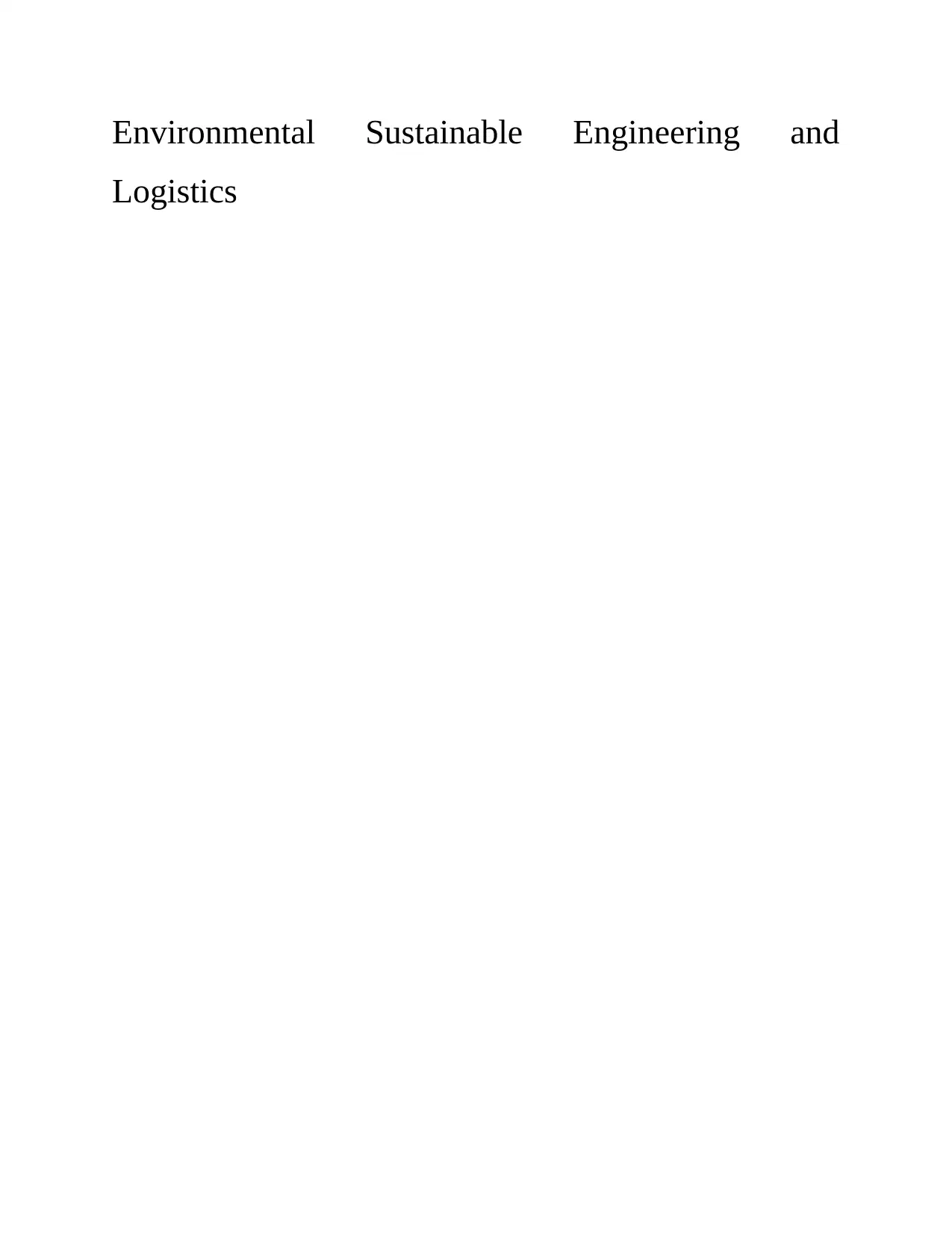
Environmental Sustainable Engineering and
Logistics
Logistics
Secure Best Marks with AI Grader
Need help grading? Try our AI Grader for instant feedback on your assignments.
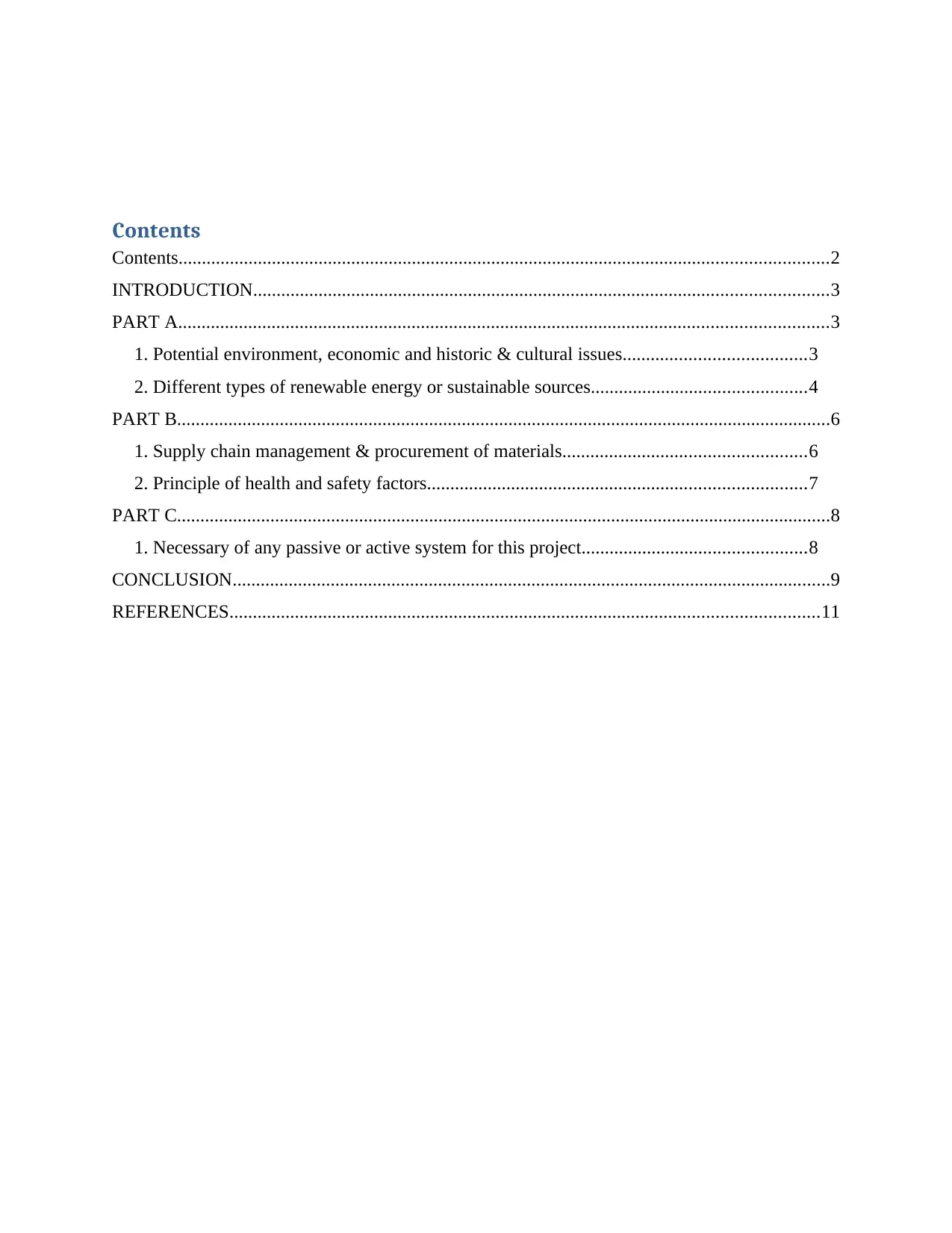
Contents
Contents...........................................................................................................................................2
INTRODUCTION...........................................................................................................................3
PART A...........................................................................................................................................3
1. Potential environment, economic and historic & cultural issues.......................................3
2. Different types of renewable energy or sustainable sources..............................................4
PART B............................................................................................................................................6
1. Supply chain management & procurement of materials....................................................6
2. Principle of health and safety factors.................................................................................7
PART C............................................................................................................................................8
1. Necessary of any passive or active system for this project................................................8
CONCLUSION................................................................................................................................9
REFERENCES..............................................................................................................................11
Contents...........................................................................................................................................2
INTRODUCTION...........................................................................................................................3
PART A...........................................................................................................................................3
1. Potential environment, economic and historic & cultural issues.......................................3
2. Different types of renewable energy or sustainable sources..............................................4
PART B............................................................................................................................................6
1. Supply chain management & procurement of materials....................................................6
2. Principle of health and safety factors.................................................................................7
PART C............................................................................................................................................8
1. Necessary of any passive or active system for this project................................................8
CONCLUSION................................................................................................................................9
REFERENCES..............................................................................................................................11
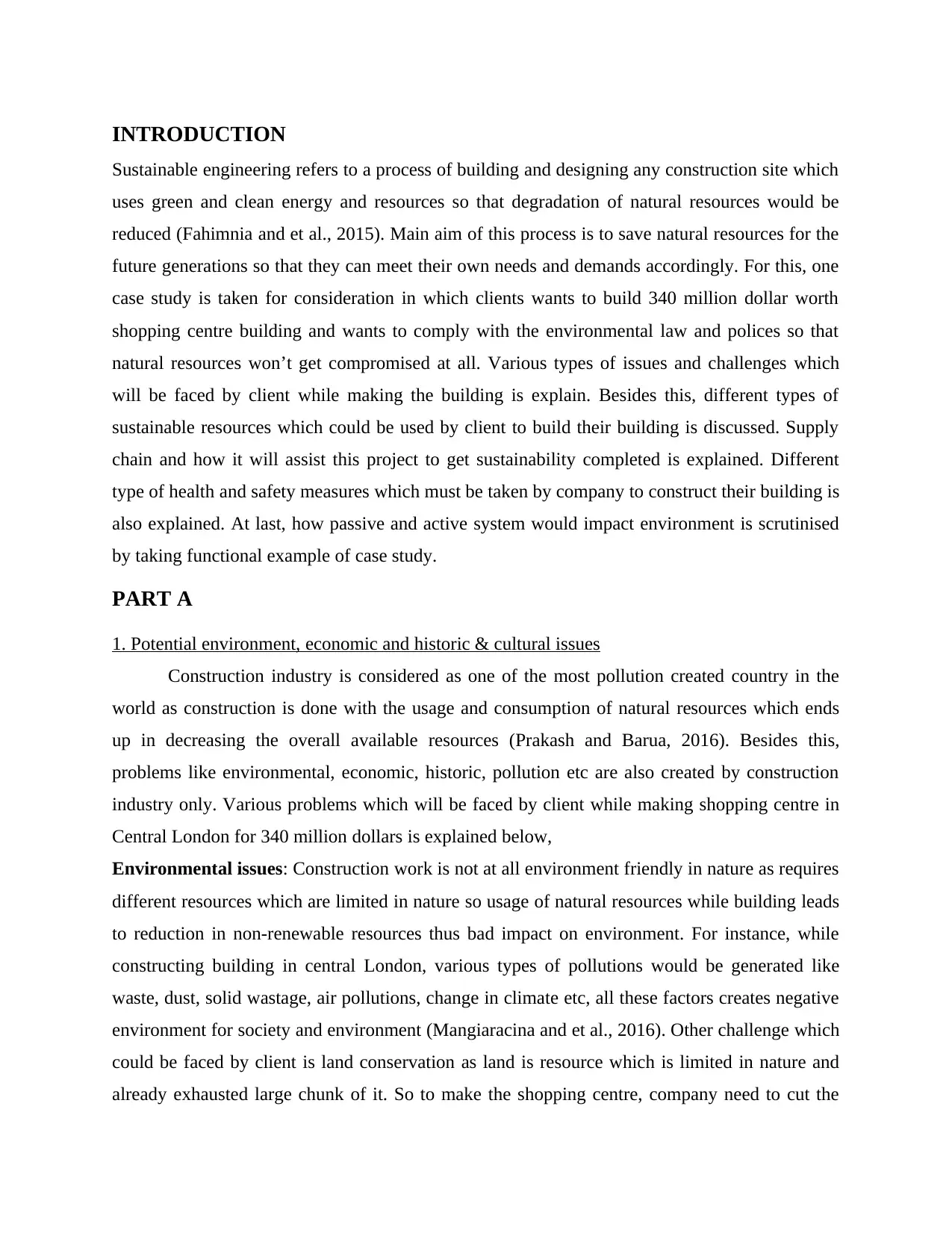
INTRODUCTION
Sustainable engineering refers to a process of building and designing any construction site which
uses green and clean energy and resources so that degradation of natural resources would be
reduced (Fahimnia and et al., 2015). Main aim of this process is to save natural resources for the
future generations so that they can meet their own needs and demands accordingly. For this, one
case study is taken for consideration in which clients wants to build 340 million dollar worth
shopping centre building and wants to comply with the environmental law and polices so that
natural resources won’t get compromised at all. Various types of issues and challenges which
will be faced by client while making the building is explain. Besides this, different types of
sustainable resources which could be used by client to build their building is discussed. Supply
chain and how it will assist this project to get sustainability completed is explained. Different
type of health and safety measures which must be taken by company to construct their building is
also explained. At last, how passive and active system would impact environment is scrutinised
by taking functional example of case study.
PART A
1. Potential environment, economic and historic & cultural issues
Construction industry is considered as one of the most pollution created country in the
world as construction is done with the usage and consumption of natural resources which ends
up in decreasing the overall available resources (Prakash and Barua, 2016). Besides this,
problems like environmental, economic, historic, pollution etc are also created by construction
industry only. Various problems which will be faced by client while making shopping centre in
Central London for 340 million dollars is explained below,
Environmental issues: Construction work is not at all environment friendly in nature as requires
different resources which are limited in nature so usage of natural resources while building leads
to reduction in non-renewable resources thus bad impact on environment. For instance, while
constructing building in central London, various types of pollutions would be generated like
waste, dust, solid wastage, air pollutions, change in climate etc, all these factors creates negative
environment for society and environment (Mangiaracina and et al., 2016). Other challenge which
could be faced by client is land conservation as land is resource which is limited in nature and
already exhausted large chunk of it. So to make the shopping centre, company need to cut the
Sustainable engineering refers to a process of building and designing any construction site which
uses green and clean energy and resources so that degradation of natural resources would be
reduced (Fahimnia and et al., 2015). Main aim of this process is to save natural resources for the
future generations so that they can meet their own needs and demands accordingly. For this, one
case study is taken for consideration in which clients wants to build 340 million dollar worth
shopping centre building and wants to comply with the environmental law and polices so that
natural resources won’t get compromised at all. Various types of issues and challenges which
will be faced by client while making the building is explain. Besides this, different types of
sustainable resources which could be used by client to build their building is discussed. Supply
chain and how it will assist this project to get sustainability completed is explained. Different
type of health and safety measures which must be taken by company to construct their building is
also explained. At last, how passive and active system would impact environment is scrutinised
by taking functional example of case study.
PART A
1. Potential environment, economic and historic & cultural issues
Construction industry is considered as one of the most pollution created country in the
world as construction is done with the usage and consumption of natural resources which ends
up in decreasing the overall available resources (Prakash and Barua, 2016). Besides this,
problems like environmental, economic, historic, pollution etc are also created by construction
industry only. Various problems which will be faced by client while making shopping centre in
Central London for 340 million dollars is explained below,
Environmental issues: Construction work is not at all environment friendly in nature as requires
different resources which are limited in nature so usage of natural resources while building leads
to reduction in non-renewable resources thus bad impact on environment. For instance, while
constructing building in central London, various types of pollutions would be generated like
waste, dust, solid wastage, air pollutions, change in climate etc, all these factors creates negative
environment for society and environment (Mangiaracina and et al., 2016). Other challenge which
could be faced by client is land conservation as land is resource which is limited in nature and
already exhausted large chunk of it. So to make the shopping centre, company need to cut the
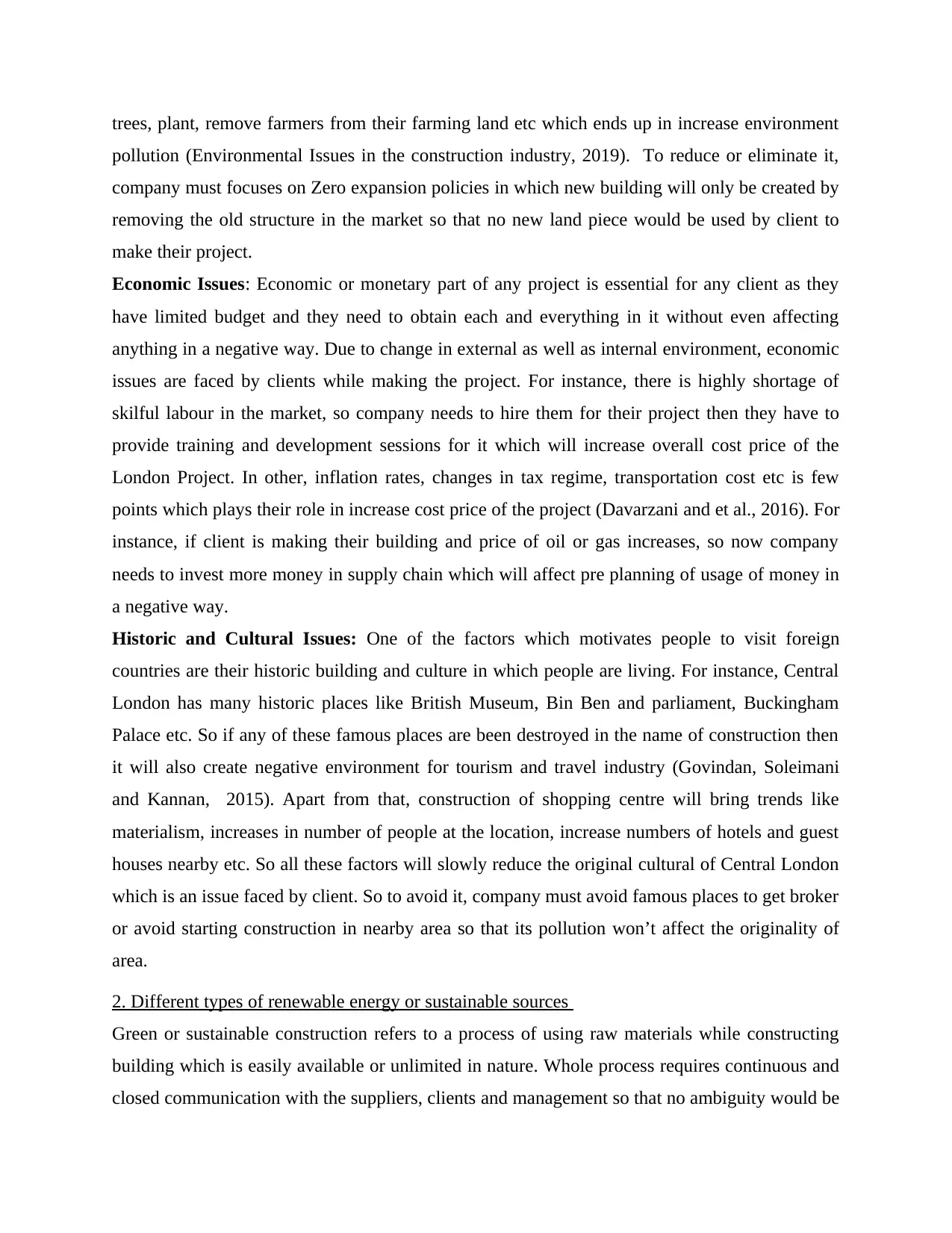
trees, plant, remove farmers from their farming land etc which ends up in increase environment
pollution (Environmental Issues in the construction industry, 2019). To reduce or eliminate it,
company must focuses on Zero expansion policies in which new building will only be created by
removing the old structure in the market so that no new land piece would be used by client to
make their project.
Economic Issues: Economic or monetary part of any project is essential for any client as they
have limited budget and they need to obtain each and everything in it without even affecting
anything in a negative way. Due to change in external as well as internal environment, economic
issues are faced by clients while making the project. For instance, there is highly shortage of
skilful labour in the market, so company needs to hire them for their project then they have to
provide training and development sessions for it which will increase overall cost price of the
London Project. In other, inflation rates, changes in tax regime, transportation cost etc is few
points which plays their role in increase cost price of the project (Davarzani and et al., 2016). For
instance, if client is making their building and price of oil or gas increases, so now company
needs to invest more money in supply chain which will affect pre planning of usage of money in
a negative way.
Historic and Cultural Issues: One of the factors which motivates people to visit foreign
countries are their historic building and culture in which people are living. For instance, Central
London has many historic places like British Museum, Bin Ben and parliament, Buckingham
Palace etc. So if any of these famous places are been destroyed in the name of construction then
it will also create negative environment for tourism and travel industry (Govindan, Soleimani
and Kannan, 2015). Apart from that, construction of shopping centre will bring trends like
materialism, increases in number of people at the location, increase numbers of hotels and guest
houses nearby etc. So all these factors will slowly reduce the original cultural of Central London
which is an issue faced by client. So to avoid it, company must avoid famous places to get broker
or avoid starting construction in nearby area so that its pollution won’t affect the originality of
area.
2. Different types of renewable energy or sustainable sources
Green or sustainable construction refers to a process of using raw materials while constructing
building which is easily available or unlimited in nature. Whole process requires continuous and
closed communication with the suppliers, clients and management so that no ambiguity would be
pollution (Environmental Issues in the construction industry, 2019). To reduce or eliminate it,
company must focuses on Zero expansion policies in which new building will only be created by
removing the old structure in the market so that no new land piece would be used by client to
make their project.
Economic Issues: Economic or monetary part of any project is essential for any client as they
have limited budget and they need to obtain each and everything in it without even affecting
anything in a negative way. Due to change in external as well as internal environment, economic
issues are faced by clients while making the project. For instance, there is highly shortage of
skilful labour in the market, so company needs to hire them for their project then they have to
provide training and development sessions for it which will increase overall cost price of the
London Project. In other, inflation rates, changes in tax regime, transportation cost etc is few
points which plays their role in increase cost price of the project (Davarzani and et al., 2016). For
instance, if client is making their building and price of oil or gas increases, so now company
needs to invest more money in supply chain which will affect pre planning of usage of money in
a negative way.
Historic and Cultural Issues: One of the factors which motivates people to visit foreign
countries are their historic building and culture in which people are living. For instance, Central
London has many historic places like British Museum, Bin Ben and parliament, Buckingham
Palace etc. So if any of these famous places are been destroyed in the name of construction then
it will also create negative environment for tourism and travel industry (Govindan, Soleimani
and Kannan, 2015). Apart from that, construction of shopping centre will bring trends like
materialism, increases in number of people at the location, increase numbers of hotels and guest
houses nearby etc. So all these factors will slowly reduce the original cultural of Central London
which is an issue faced by client. So to avoid it, company must avoid famous places to get broker
or avoid starting construction in nearby area so that its pollution won’t affect the originality of
area.
2. Different types of renewable energy or sustainable sources
Green or sustainable construction refers to a process of using raw materials while constructing
building which is easily available or unlimited in nature. Whole process requires continuous and
closed communication with the suppliers, clients and management so that no ambiguity would be
Secure Best Marks with AI Grader
Need help grading? Try our AI Grader for instant feedback on your assignments.
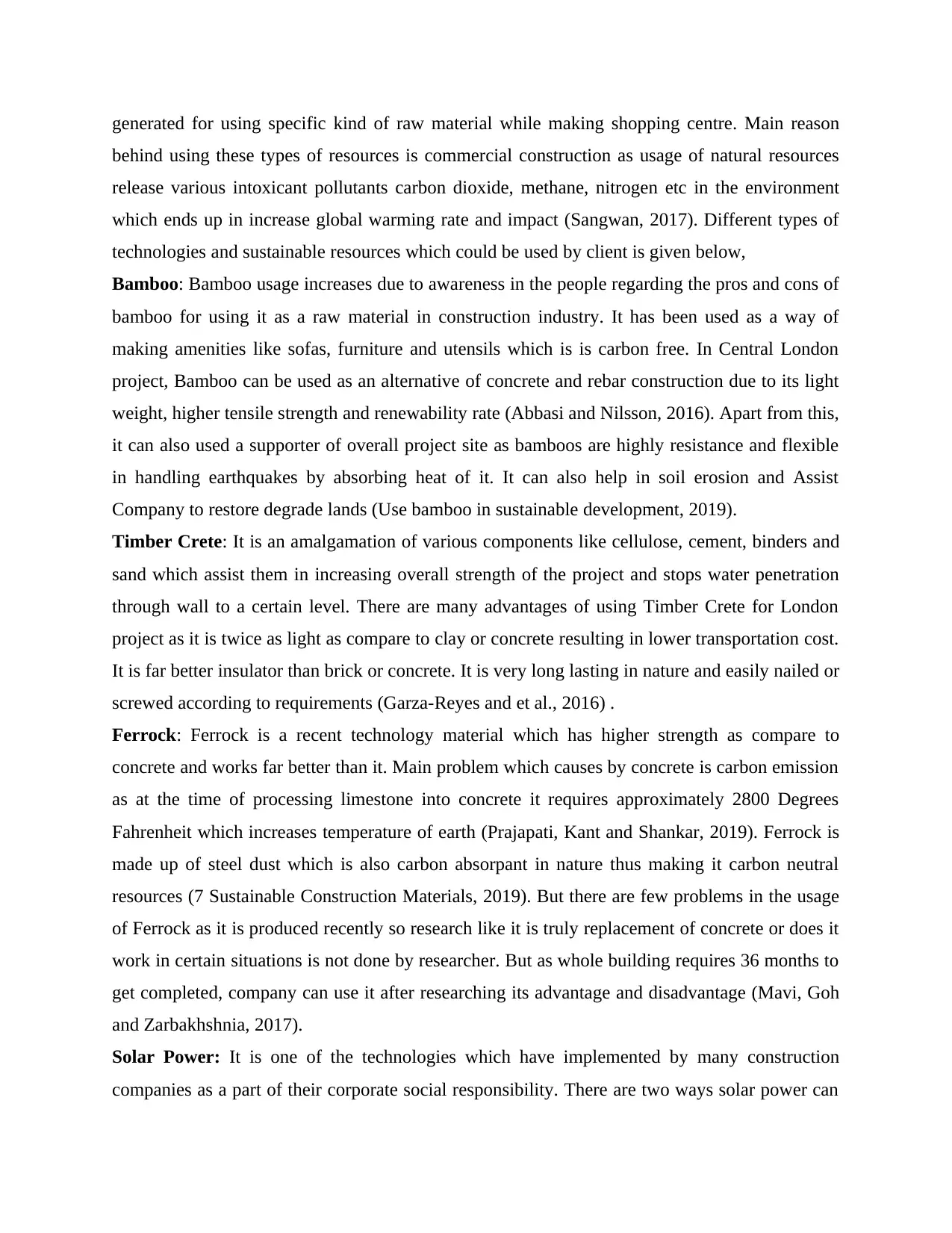
generated for using specific kind of raw material while making shopping centre. Main reason
behind using these types of resources is commercial construction as usage of natural resources
release various intoxicant pollutants carbon dioxide, methane, nitrogen etc in the environment
which ends up in increase global warming rate and impact (Sangwan, 2017). Different types of
technologies and sustainable resources which could be used by client is given below,
Bamboo: Bamboo usage increases due to awareness in the people regarding the pros and cons of
bamboo for using it as a raw material in construction industry. It has been used as a way of
making amenities like sofas, furniture and utensils which is is carbon free. In Central London
project, Bamboo can be used as an alternative of concrete and rebar construction due to its light
weight, higher tensile strength and renewability rate (Abbasi and Nilsson, 2016). Apart from this,
it can also used a supporter of overall project site as bamboos are highly resistance and flexible
in handling earthquakes by absorbing heat of it. It can also help in soil erosion and Assist
Company to restore degrade lands (Use bamboo in sustainable development, 2019).
Timber Crete: It is an amalgamation of various components like cellulose, cement, binders and
sand which assist them in increasing overall strength of the project and stops water penetration
through wall to a certain level. There are many advantages of using Timber Crete for London
project as it is twice as light as compare to clay or concrete resulting in lower transportation cost.
It is far better insulator than brick or concrete. It is very long lasting in nature and easily nailed or
screwed according to requirements (Garza-Reyes and et al., 2016) .
Ferrock: Ferrock is a recent technology material which has higher strength as compare to
concrete and works far better than it. Main problem which causes by concrete is carbon emission
as at the time of processing limestone into concrete it requires approximately 2800 Degrees
Fahrenheit which increases temperature of earth (Prajapati, Kant and Shankar, 2019). Ferrock is
made up of steel dust which is also carbon absorpant in nature thus making it carbon neutral
resources (7 Sustainable Construction Materials, 2019). But there are few problems in the usage
of Ferrock as it is produced recently so research like it is truly replacement of concrete or does it
work in certain situations is not done by researcher. But as whole building requires 36 months to
get completed, company can use it after researching its advantage and disadvantage (Mavi, Goh
and Zarbakhshnia, 2017).
Solar Power: It is one of the technologies which have implemented by many construction
companies as a part of their corporate social responsibility. There are two ways solar power can
behind using these types of resources is commercial construction as usage of natural resources
release various intoxicant pollutants carbon dioxide, methane, nitrogen etc in the environment
which ends up in increase global warming rate and impact (Sangwan, 2017). Different types of
technologies and sustainable resources which could be used by client is given below,
Bamboo: Bamboo usage increases due to awareness in the people regarding the pros and cons of
bamboo for using it as a raw material in construction industry. It has been used as a way of
making amenities like sofas, furniture and utensils which is is carbon free. In Central London
project, Bamboo can be used as an alternative of concrete and rebar construction due to its light
weight, higher tensile strength and renewability rate (Abbasi and Nilsson, 2016). Apart from this,
it can also used a supporter of overall project site as bamboos are highly resistance and flexible
in handling earthquakes by absorbing heat of it. It can also help in soil erosion and Assist
Company to restore degrade lands (Use bamboo in sustainable development, 2019).
Timber Crete: It is an amalgamation of various components like cellulose, cement, binders and
sand which assist them in increasing overall strength of the project and stops water penetration
through wall to a certain level. There are many advantages of using Timber Crete for London
project as it is twice as light as compare to clay or concrete resulting in lower transportation cost.
It is far better insulator than brick or concrete. It is very long lasting in nature and easily nailed or
screwed according to requirements (Garza-Reyes and et al., 2016) .
Ferrock: Ferrock is a recent technology material which has higher strength as compare to
concrete and works far better than it. Main problem which causes by concrete is carbon emission
as at the time of processing limestone into concrete it requires approximately 2800 Degrees
Fahrenheit which increases temperature of earth (Prajapati, Kant and Shankar, 2019). Ferrock is
made up of steel dust which is also carbon absorpant in nature thus making it carbon neutral
resources (7 Sustainable Construction Materials, 2019). But there are few problems in the usage
of Ferrock as it is produced recently so research like it is truly replacement of concrete or does it
work in certain situations is not done by researcher. But as whole building requires 36 months to
get completed, company can use it after researching its advantage and disadvantage (Mavi, Goh
and Zarbakhshnia, 2017).
Solar Power: It is one of the technologies which have implemented by many construction
companies as a part of their corporate social responsibility. There are two ways solar power can
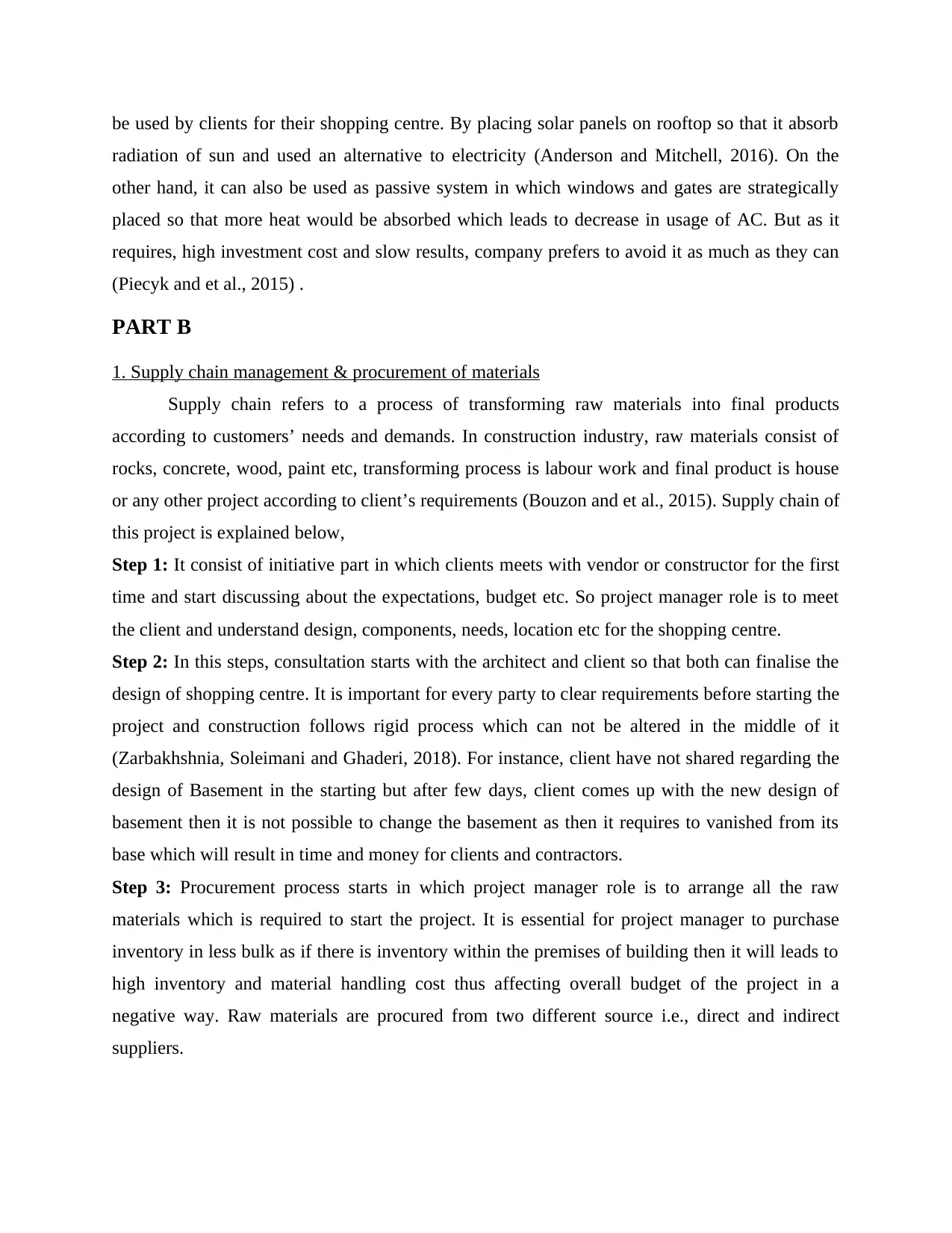
be used by clients for their shopping centre. By placing solar panels on rooftop so that it absorb
radiation of sun and used an alternative to electricity (Anderson and Mitchell, 2016). On the
other hand, it can also be used as passive system in which windows and gates are strategically
placed so that more heat would be absorbed which leads to decrease in usage of AC. But as it
requires, high investment cost and slow results, company prefers to avoid it as much as they can
(Piecyk and et al., 2015) .
PART B
1. Supply chain management & procurement of materials
Supply chain refers to a process of transforming raw materials into final products
according to customers’ needs and demands. In construction industry, raw materials consist of
rocks, concrete, wood, paint etc, transforming process is labour work and final product is house
or any other project according to client’s requirements (Bouzon and et al., 2015). Supply chain of
this project is explained below,
Step 1: It consist of initiative part in which clients meets with vendor or constructor for the first
time and start discussing about the expectations, budget etc. So project manager role is to meet
the client and understand design, components, needs, location etc for the shopping centre.
Step 2: In this steps, consultation starts with the architect and client so that both can finalise the
design of shopping centre. It is important for every party to clear requirements before starting the
project and construction follows rigid process which can not be altered in the middle of it
(Zarbakhshnia, Soleimani and Ghaderi, 2018). For instance, client have not shared regarding the
design of Basement in the starting but after few days, client comes up with the new design of
basement then it is not possible to change the basement as then it requires to vanished from its
base which will result in time and money for clients and contractors.
Step 3: Procurement process starts in which project manager role is to arrange all the raw
materials which is required to start the project. It is essential for project manager to purchase
inventory in less bulk as if there is inventory within the premises of building then it will leads to
high inventory and material handling cost thus affecting overall budget of the project in a
negative way. Raw materials are procured from two different source i.e., direct and indirect
suppliers.
radiation of sun and used an alternative to electricity (Anderson and Mitchell, 2016). On the
other hand, it can also be used as passive system in which windows and gates are strategically
placed so that more heat would be absorbed which leads to decrease in usage of AC. But as it
requires, high investment cost and slow results, company prefers to avoid it as much as they can
(Piecyk and et al., 2015) .
PART B
1. Supply chain management & procurement of materials
Supply chain refers to a process of transforming raw materials into final products
according to customers’ needs and demands. In construction industry, raw materials consist of
rocks, concrete, wood, paint etc, transforming process is labour work and final product is house
or any other project according to client’s requirements (Bouzon and et al., 2015). Supply chain of
this project is explained below,
Step 1: It consist of initiative part in which clients meets with vendor or constructor for the first
time and start discussing about the expectations, budget etc. So project manager role is to meet
the client and understand design, components, needs, location etc for the shopping centre.
Step 2: In this steps, consultation starts with the architect and client so that both can finalise the
design of shopping centre. It is important for every party to clear requirements before starting the
project and construction follows rigid process which can not be altered in the middle of it
(Zarbakhshnia, Soleimani and Ghaderi, 2018). For instance, client have not shared regarding the
design of Basement in the starting but after few days, client comes up with the new design of
basement then it is not possible to change the basement as then it requires to vanished from its
base which will result in time and money for clients and contractors.
Step 3: Procurement process starts in which project manager role is to arrange all the raw
materials which is required to start the project. It is essential for project manager to purchase
inventory in less bulk as if there is inventory within the premises of building then it will leads to
high inventory and material handling cost thus affecting overall budget of the project in a
negative way. Raw materials are procured from two different source i.e., direct and indirect
suppliers.
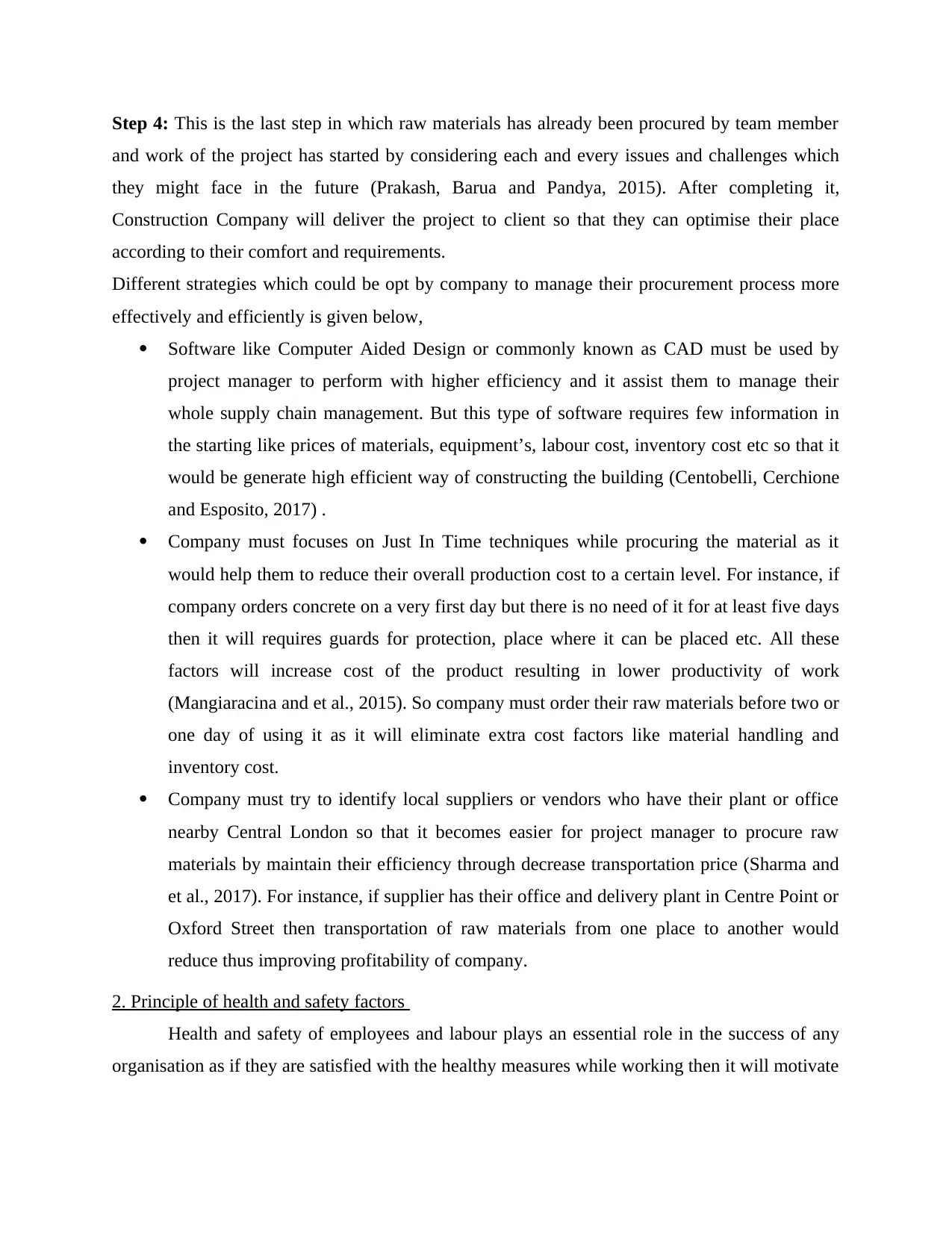
Step 4: This is the last step in which raw materials has already been procured by team member
and work of the project has started by considering each and every issues and challenges which
they might face in the future (Prakash, Barua and Pandya, 2015). After completing it,
Construction Company will deliver the project to client so that they can optimise their place
according to their comfort and requirements.
Different strategies which could be opt by company to manage their procurement process more
effectively and efficiently is given below,
Software like Computer Aided Design or commonly known as CAD must be used by
project manager to perform with higher efficiency and it assist them to manage their
whole supply chain management. But this type of software requires few information in
the starting like prices of materials, equipment’s, labour cost, inventory cost etc so that it
would be generate high efficient way of constructing the building (Centobelli, Cerchione
and Esposito, 2017) .
Company must focuses on Just In Time techniques while procuring the material as it
would help them to reduce their overall production cost to a certain level. For instance, if
company orders concrete on a very first day but there is no need of it for at least five days
then it will requires guards for protection, place where it can be placed etc. All these
factors will increase cost of the product resulting in lower productivity of work
(Mangiaracina and et al., 2015). So company must order their raw materials before two or
one day of using it as it will eliminate extra cost factors like material handling and
inventory cost.
Company must try to identify local suppliers or vendors who have their plant or office
nearby Central London so that it becomes easier for project manager to procure raw
materials by maintain their efficiency through decrease transportation price (Sharma and
et al., 2017). For instance, if supplier has their office and delivery plant in Centre Point or
Oxford Street then transportation of raw materials from one place to another would
reduce thus improving profitability of company.
2. Principle of health and safety factors
Health and safety of employees and labour plays an essential role in the success of any
organisation as if they are satisfied with the healthy measures while working then it will motivate
and work of the project has started by considering each and every issues and challenges which
they might face in the future (Prakash, Barua and Pandya, 2015). After completing it,
Construction Company will deliver the project to client so that they can optimise their place
according to their comfort and requirements.
Different strategies which could be opt by company to manage their procurement process more
effectively and efficiently is given below,
Software like Computer Aided Design or commonly known as CAD must be used by
project manager to perform with higher efficiency and it assist them to manage their
whole supply chain management. But this type of software requires few information in
the starting like prices of materials, equipment’s, labour cost, inventory cost etc so that it
would be generate high efficient way of constructing the building (Centobelli, Cerchione
and Esposito, 2017) .
Company must focuses on Just In Time techniques while procuring the material as it
would help them to reduce their overall production cost to a certain level. For instance, if
company orders concrete on a very first day but there is no need of it for at least five days
then it will requires guards for protection, place where it can be placed etc. All these
factors will increase cost of the product resulting in lower productivity of work
(Mangiaracina and et al., 2015). So company must order their raw materials before two or
one day of using it as it will eliminate extra cost factors like material handling and
inventory cost.
Company must try to identify local suppliers or vendors who have their plant or office
nearby Central London so that it becomes easier for project manager to procure raw
materials by maintain their efficiency through decrease transportation price (Sharma and
et al., 2017). For instance, if supplier has their office and delivery plant in Centre Point or
Oxford Street then transportation of raw materials from one place to another would
reduce thus improving profitability of company.
2. Principle of health and safety factors
Health and safety of employees and labour plays an essential role in the success of any
organisation as if they are satisfied with the healthy measures while working then it will motivate
Paraphrase This Document
Need a fresh take? Get an instant paraphrase of this document with our AI Paraphraser
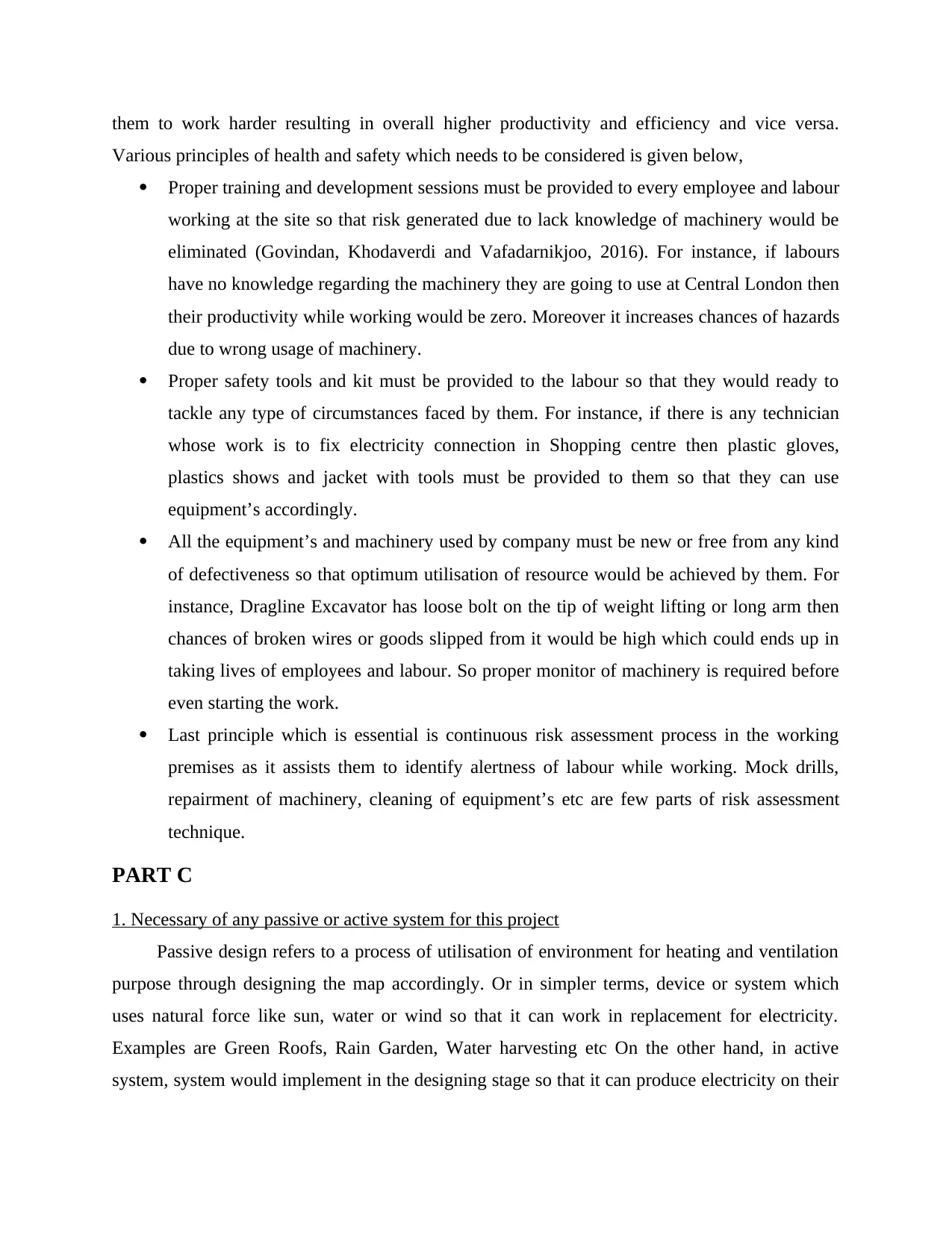
them to work harder resulting in overall higher productivity and efficiency and vice versa.
Various principles of health and safety which needs to be considered is given below,
Proper training and development sessions must be provided to every employee and labour
working at the site so that risk generated due to lack knowledge of machinery would be
eliminated (Govindan, Khodaverdi and Vafadarnikjoo, 2016). For instance, if labours
have no knowledge regarding the machinery they are going to use at Central London then
their productivity while working would be zero. Moreover it increases chances of hazards
due to wrong usage of machinery.
Proper safety tools and kit must be provided to the labour so that they would ready to
tackle any type of circumstances faced by them. For instance, if there is any technician
whose work is to fix electricity connection in Shopping centre then plastic gloves,
plastics shows and jacket with tools must be provided to them so that they can use
equipment’s accordingly.
All the equipment’s and machinery used by company must be new or free from any kind
of defectiveness so that optimum utilisation of resource would be achieved by them. For
instance, Dragline Excavator has loose bolt on the tip of weight lifting or long arm then
chances of broken wires or goods slipped from it would be high which could ends up in
taking lives of employees and labour. So proper monitor of machinery is required before
even starting the work.
Last principle which is essential is continuous risk assessment process in the working
premises as it assists them to identify alertness of labour while working. Mock drills,
repairment of machinery, cleaning of equipment’s etc are few parts of risk assessment
technique.
PART C
1. Necessary of any passive or active system for this project
Passive design refers to a process of utilisation of environment for heating and ventilation
purpose through designing the map accordingly. Or in simpler terms, device or system which
uses natural force like sun, water or wind so that it can work in replacement for electricity.
Examples are Green Roofs, Rain Garden, Water harvesting etc On the other hand, in active
system, system would implement in the designing stage so that it can produce electricity on their
Various principles of health and safety which needs to be considered is given below,
Proper training and development sessions must be provided to every employee and labour
working at the site so that risk generated due to lack knowledge of machinery would be
eliminated (Govindan, Khodaverdi and Vafadarnikjoo, 2016). For instance, if labours
have no knowledge regarding the machinery they are going to use at Central London then
their productivity while working would be zero. Moreover it increases chances of hazards
due to wrong usage of machinery.
Proper safety tools and kit must be provided to the labour so that they would ready to
tackle any type of circumstances faced by them. For instance, if there is any technician
whose work is to fix electricity connection in Shopping centre then plastic gloves,
plastics shows and jacket with tools must be provided to them so that they can use
equipment’s accordingly.
All the equipment’s and machinery used by company must be new or free from any kind
of defectiveness so that optimum utilisation of resource would be achieved by them. For
instance, Dragline Excavator has loose bolt on the tip of weight lifting or long arm then
chances of broken wires or goods slipped from it would be high which could ends up in
taking lives of employees and labour. So proper monitor of machinery is required before
even starting the work.
Last principle which is essential is continuous risk assessment process in the working
premises as it assists them to identify alertness of labour while working. Mock drills,
repairment of machinery, cleaning of equipment’s etc are few parts of risk assessment
technique.
PART C
1. Necessary of any passive or active system for this project
Passive design refers to a process of utilisation of environment for heating and ventilation
purpose through designing the map accordingly. Or in simpler terms, device or system which
uses natural force like sun, water or wind so that it can work in replacement for electricity.
Examples are Green Roofs, Rain Garden, Water harvesting etc On the other hand, in active
system, system would implement in the designing stage so that it can produce electricity on their
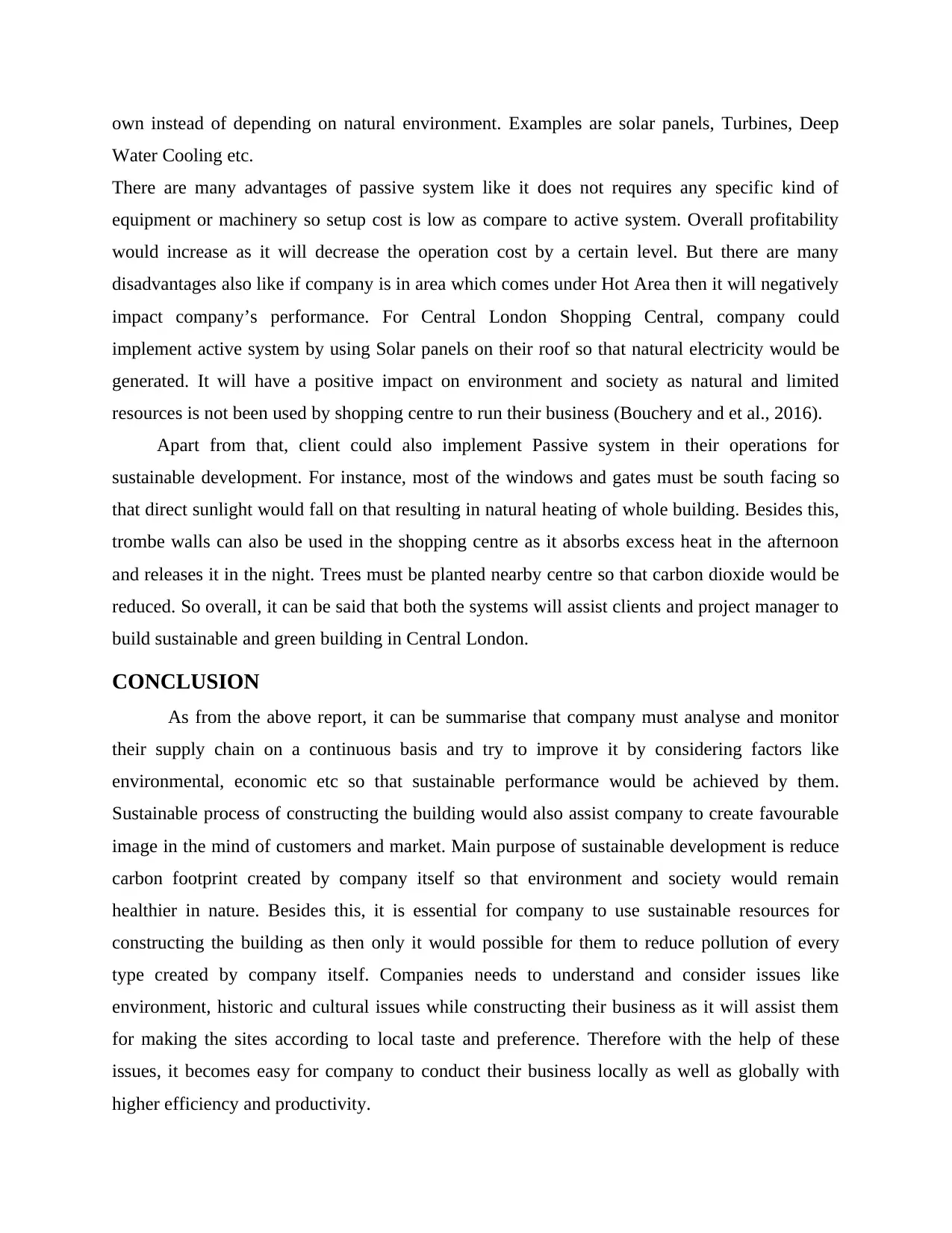
own instead of depending on natural environment. Examples are solar panels, Turbines, Deep
Water Cooling etc.
There are many advantages of passive system like it does not requires any specific kind of
equipment or machinery so setup cost is low as compare to active system. Overall profitability
would increase as it will decrease the operation cost by a certain level. But there are many
disadvantages also like if company is in area which comes under Hot Area then it will negatively
impact company’s performance. For Central London Shopping Central, company could
implement active system by using Solar panels on their roof so that natural electricity would be
generated. It will have a positive impact on environment and society as natural and limited
resources is not been used by shopping centre to run their business (Bouchery and et al., 2016).
Apart from that, client could also implement Passive system in their operations for
sustainable development. For instance, most of the windows and gates must be south facing so
that direct sunlight would fall on that resulting in natural heating of whole building. Besides this,
trombe walls can also be used in the shopping centre as it absorbs excess heat in the afternoon
and releases it in the night. Trees must be planted nearby centre so that carbon dioxide would be
reduced. So overall, it can be said that both the systems will assist clients and project manager to
build sustainable and green building in Central London.
CONCLUSION
As from the above report, it can be summarise that company must analyse and monitor
their supply chain on a continuous basis and try to improve it by considering factors like
environmental, economic etc so that sustainable performance would be achieved by them.
Sustainable process of constructing the building would also assist company to create favourable
image in the mind of customers and market. Main purpose of sustainable development is reduce
carbon footprint created by company itself so that environment and society would remain
healthier in nature. Besides this, it is essential for company to use sustainable resources for
constructing the building as then only it would possible for them to reduce pollution of every
type created by company itself. Companies needs to understand and consider issues like
environment, historic and cultural issues while constructing their business as it will assist them
for making the sites according to local taste and preference. Therefore with the help of these
issues, it becomes easy for company to conduct their business locally as well as globally with
higher efficiency and productivity.
Water Cooling etc.
There are many advantages of passive system like it does not requires any specific kind of
equipment or machinery so setup cost is low as compare to active system. Overall profitability
would increase as it will decrease the operation cost by a certain level. But there are many
disadvantages also like if company is in area which comes under Hot Area then it will negatively
impact company’s performance. For Central London Shopping Central, company could
implement active system by using Solar panels on their roof so that natural electricity would be
generated. It will have a positive impact on environment and society as natural and limited
resources is not been used by shopping centre to run their business (Bouchery and et al., 2016).
Apart from that, client could also implement Passive system in their operations for
sustainable development. For instance, most of the windows and gates must be south facing so
that direct sunlight would fall on that resulting in natural heating of whole building. Besides this,
trombe walls can also be used in the shopping centre as it absorbs excess heat in the afternoon
and releases it in the night. Trees must be planted nearby centre so that carbon dioxide would be
reduced. So overall, it can be said that both the systems will assist clients and project manager to
build sustainable and green building in Central London.
CONCLUSION
As from the above report, it can be summarise that company must analyse and monitor
their supply chain on a continuous basis and try to improve it by considering factors like
environmental, economic etc so that sustainable performance would be achieved by them.
Sustainable process of constructing the building would also assist company to create favourable
image in the mind of customers and market. Main purpose of sustainable development is reduce
carbon footprint created by company itself so that environment and society would remain
healthier in nature. Besides this, it is essential for company to use sustainable resources for
constructing the building as then only it would possible for them to reduce pollution of every
type created by company itself. Companies needs to understand and consider issues like
environment, historic and cultural issues while constructing their business as it will assist them
for making the sites according to local taste and preference. Therefore with the help of these
issues, it becomes easy for company to conduct their business locally as well as globally with
higher efficiency and productivity.
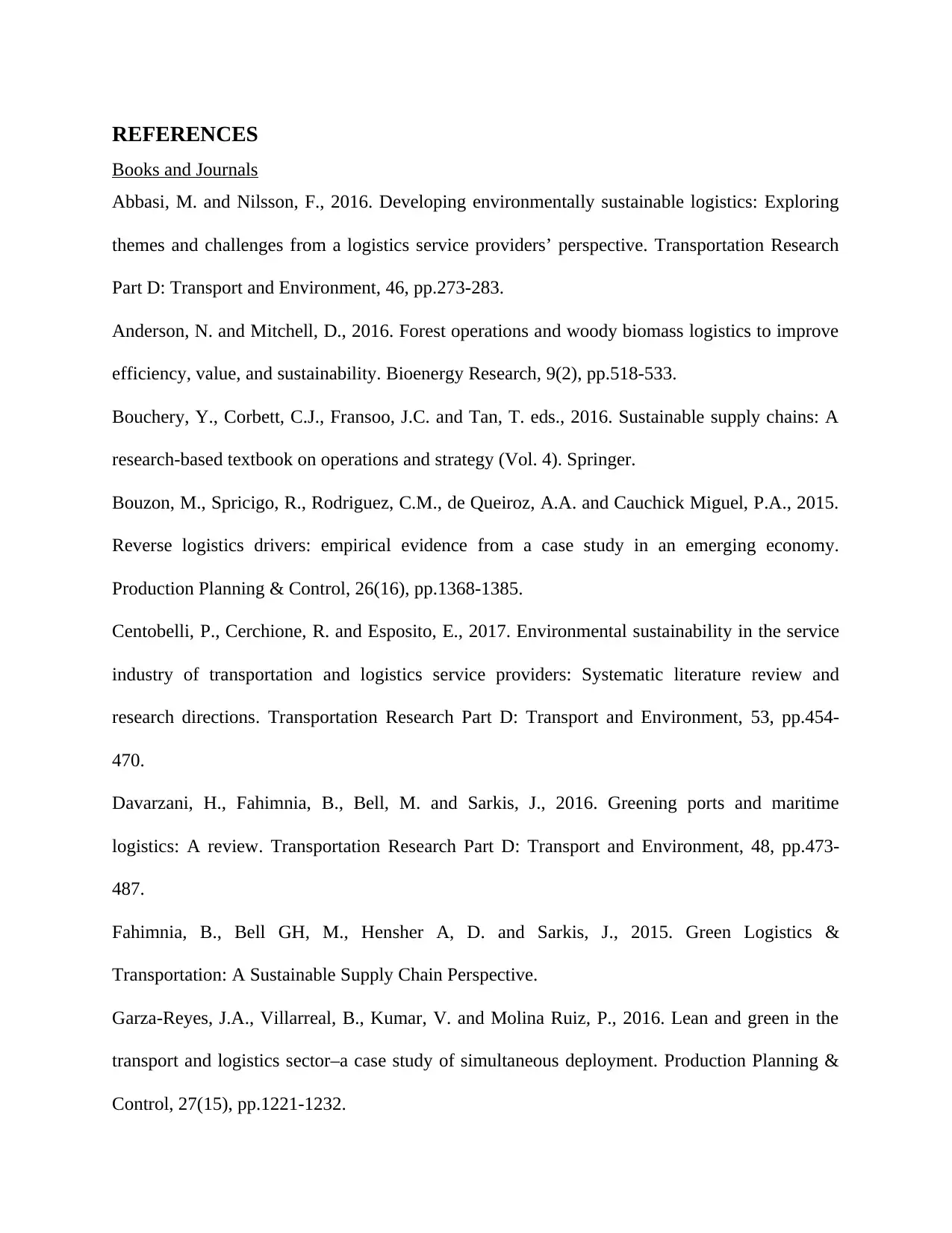
REFERENCES
Books and Journals
Abbasi, M. and Nilsson, F., 2016. Developing environmentally sustainable logistics: Exploring
themes and challenges from a logistics service providers’ perspective. Transportation Research
Part D: Transport and Environment, 46, pp.273-283.
Anderson, N. and Mitchell, D., 2016. Forest operations and woody biomass logistics to improve
efficiency, value, and sustainability. Bioenergy Research, 9(2), pp.518-533.
Bouchery, Y., Corbett, C.J., Fransoo, J.C. and Tan, T. eds., 2016. Sustainable supply chains: A
research-based textbook on operations and strategy (Vol. 4). Springer.
Bouzon, M., Spricigo, R., Rodriguez, C.M., de Queiroz, A.A. and Cauchick Miguel, P.A., 2015.
Reverse logistics drivers: empirical evidence from a case study in an emerging economy.
Production Planning & Control, 26(16), pp.1368-1385.
Centobelli, P., Cerchione, R. and Esposito, E., 2017. Environmental sustainability in the service
industry of transportation and logistics service providers: Systematic literature review and
research directions. Transportation Research Part D: Transport and Environment, 53, pp.454-
470.
Davarzani, H., Fahimnia, B., Bell, M. and Sarkis, J., 2016. Greening ports and maritime
logistics: A review. Transportation Research Part D: Transport and Environment, 48, pp.473-
487.
Fahimnia, B., Bell GH, M., Hensher A, D. and Sarkis, J., 2015. Green Logistics &
Transportation: A Sustainable Supply Chain Perspective.
Garza-Reyes, J.A., Villarreal, B., Kumar, V. and Molina Ruiz, P., 2016. Lean and green in the
transport and logistics sector–a case study of simultaneous deployment. Production Planning &
Control, 27(15), pp.1221-1232.
Books and Journals
Abbasi, M. and Nilsson, F., 2016. Developing environmentally sustainable logistics: Exploring
themes and challenges from a logistics service providers’ perspective. Transportation Research
Part D: Transport and Environment, 46, pp.273-283.
Anderson, N. and Mitchell, D., 2016. Forest operations and woody biomass logistics to improve
efficiency, value, and sustainability. Bioenergy Research, 9(2), pp.518-533.
Bouchery, Y., Corbett, C.J., Fransoo, J.C. and Tan, T. eds., 2016. Sustainable supply chains: A
research-based textbook on operations and strategy (Vol. 4). Springer.
Bouzon, M., Spricigo, R., Rodriguez, C.M., de Queiroz, A.A. and Cauchick Miguel, P.A., 2015.
Reverse logistics drivers: empirical evidence from a case study in an emerging economy.
Production Planning & Control, 26(16), pp.1368-1385.
Centobelli, P., Cerchione, R. and Esposito, E., 2017. Environmental sustainability in the service
industry of transportation and logistics service providers: Systematic literature review and
research directions. Transportation Research Part D: Transport and Environment, 53, pp.454-
470.
Davarzani, H., Fahimnia, B., Bell, M. and Sarkis, J., 2016. Greening ports and maritime
logistics: A review. Transportation Research Part D: Transport and Environment, 48, pp.473-
487.
Fahimnia, B., Bell GH, M., Hensher A, D. and Sarkis, J., 2015. Green Logistics &
Transportation: A Sustainable Supply Chain Perspective.
Garza-Reyes, J.A., Villarreal, B., Kumar, V. and Molina Ruiz, P., 2016. Lean and green in the
transport and logistics sector–a case study of simultaneous deployment. Production Planning &
Control, 27(15), pp.1221-1232.
Secure Best Marks with AI Grader
Need help grading? Try our AI Grader for instant feedback on your assignments.
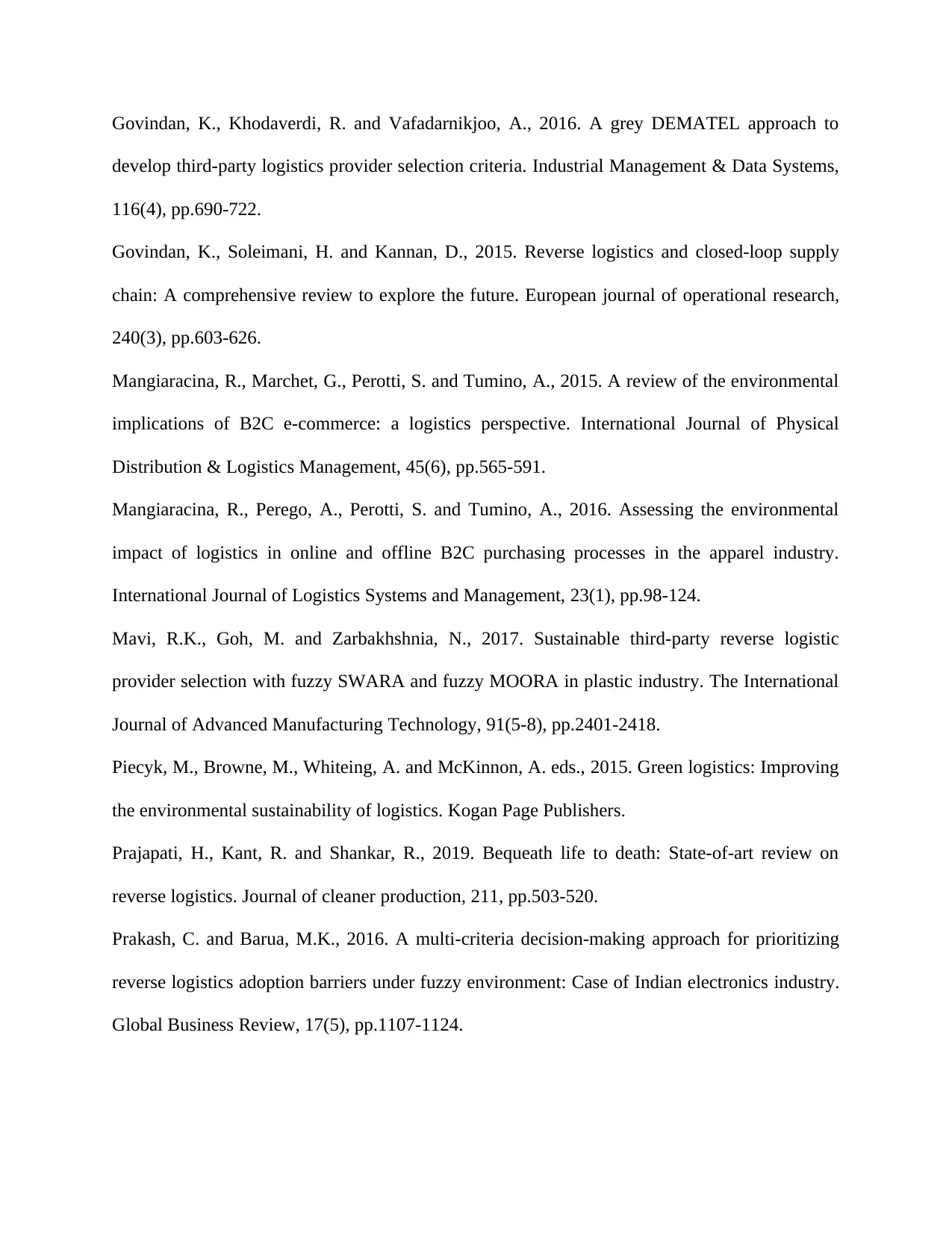
Govindan, K., Khodaverdi, R. and Vafadarnikjoo, A., 2016. A grey DEMATEL approach to
develop third-party logistics provider selection criteria. Industrial Management & Data Systems,
116(4), pp.690-722.
Govindan, K., Soleimani, H. and Kannan, D., 2015. Reverse logistics and closed-loop supply
chain: A comprehensive review to explore the future. European journal of operational research,
240(3), pp.603-626.
Mangiaracina, R., Marchet, G., Perotti, S. and Tumino, A., 2015. A review of the environmental
implications of B2C e-commerce: a logistics perspective. International Journal of Physical
Distribution & Logistics Management, 45(6), pp.565-591.
Mangiaracina, R., Perego, A., Perotti, S. and Tumino, A., 2016. Assessing the environmental
impact of logistics in online and offline B2C purchasing processes in the apparel industry.
International Journal of Logistics Systems and Management, 23(1), pp.98-124.
Mavi, R.K., Goh, M. and Zarbakhshnia, N., 2017. Sustainable third-party reverse logistic
provider selection with fuzzy SWARA and fuzzy MOORA in plastic industry. The International
Journal of Advanced Manufacturing Technology, 91(5-8), pp.2401-2418.
Piecyk, M., Browne, M., Whiteing, A. and McKinnon, A. eds., 2015. Green logistics: Improving
the environmental sustainability of logistics. Kogan Page Publishers.
Prajapati, H., Kant, R. and Shankar, R., 2019. Bequeath life to death: State-of-art review on
reverse logistics. Journal of cleaner production, 211, pp.503-520.
Prakash, C. and Barua, M.K., 2016. A multi-criteria decision-making approach for prioritizing
reverse logistics adoption barriers under fuzzy environment: Case of Indian electronics industry.
Global Business Review, 17(5), pp.1107-1124.
develop third-party logistics provider selection criteria. Industrial Management & Data Systems,
116(4), pp.690-722.
Govindan, K., Soleimani, H. and Kannan, D., 2015. Reverse logistics and closed-loop supply
chain: A comprehensive review to explore the future. European journal of operational research,
240(3), pp.603-626.
Mangiaracina, R., Marchet, G., Perotti, S. and Tumino, A., 2015. A review of the environmental
implications of B2C e-commerce: a logistics perspective. International Journal of Physical
Distribution & Logistics Management, 45(6), pp.565-591.
Mangiaracina, R., Perego, A., Perotti, S. and Tumino, A., 2016. Assessing the environmental
impact of logistics in online and offline B2C purchasing processes in the apparel industry.
International Journal of Logistics Systems and Management, 23(1), pp.98-124.
Mavi, R.K., Goh, M. and Zarbakhshnia, N., 2017. Sustainable third-party reverse logistic
provider selection with fuzzy SWARA and fuzzy MOORA in plastic industry. The International
Journal of Advanced Manufacturing Technology, 91(5-8), pp.2401-2418.
Piecyk, M., Browne, M., Whiteing, A. and McKinnon, A. eds., 2015. Green logistics: Improving
the environmental sustainability of logistics. Kogan Page Publishers.
Prajapati, H., Kant, R. and Shankar, R., 2019. Bequeath life to death: State-of-art review on
reverse logistics. Journal of cleaner production, 211, pp.503-520.
Prakash, C. and Barua, M.K., 2016. A multi-criteria decision-making approach for prioritizing
reverse logistics adoption barriers under fuzzy environment: Case of Indian electronics industry.
Global Business Review, 17(5), pp.1107-1124.
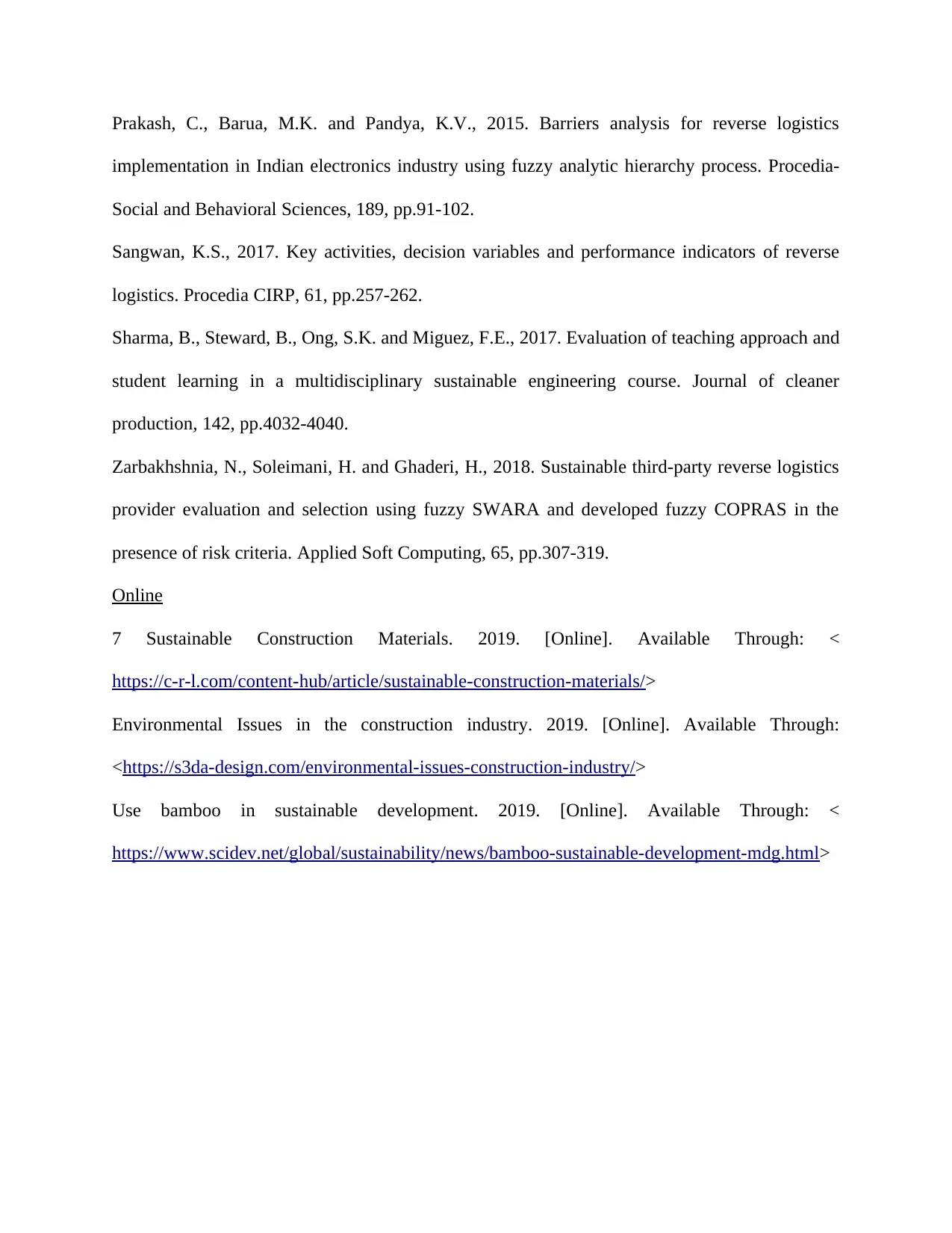
Prakash, C., Barua, M.K. and Pandya, K.V., 2015. Barriers analysis for reverse logistics
implementation in Indian electronics industry using fuzzy analytic hierarchy process. Procedia-
Social and Behavioral Sciences, 189, pp.91-102.
Sangwan, K.S., 2017. Key activities, decision variables and performance indicators of reverse
logistics. Procedia CIRP, 61, pp.257-262.
Sharma, B., Steward, B., Ong, S.K. and Miguez, F.E., 2017. Evaluation of teaching approach and
student learning in a multidisciplinary sustainable engineering course. Journal of cleaner
production, 142, pp.4032-4040.
Zarbakhshnia, N., Soleimani, H. and Ghaderi, H., 2018. Sustainable third-party reverse logistics
provider evaluation and selection using fuzzy SWARA and developed fuzzy COPRAS in the
presence of risk criteria. Applied Soft Computing, 65, pp.307-319.
Online
7 Sustainable Construction Materials. 2019. [Online]. Available Through: <
https://c-r-l.com/content-hub/article/sustainable-construction-materials/>
Environmental Issues in the construction industry. 2019. [Online]. Available Through:
<https://s3da-design.com/environmental-issues-construction-industry/>
Use bamboo in sustainable development. 2019. [Online]. Available Through: <
https://www.scidev.net/global/sustainability/news/bamboo-sustainable-development-mdg.html>
implementation in Indian electronics industry using fuzzy analytic hierarchy process. Procedia-
Social and Behavioral Sciences, 189, pp.91-102.
Sangwan, K.S., 2017. Key activities, decision variables and performance indicators of reverse
logistics. Procedia CIRP, 61, pp.257-262.
Sharma, B., Steward, B., Ong, S.K. and Miguez, F.E., 2017. Evaluation of teaching approach and
student learning in a multidisciplinary sustainable engineering course. Journal of cleaner
production, 142, pp.4032-4040.
Zarbakhshnia, N., Soleimani, H. and Ghaderi, H., 2018. Sustainable third-party reverse logistics
provider evaluation and selection using fuzzy SWARA and developed fuzzy COPRAS in the
presence of risk criteria. Applied Soft Computing, 65, pp.307-319.
Online
7 Sustainable Construction Materials. 2019. [Online]. Available Through: <
https://c-r-l.com/content-hub/article/sustainable-construction-materials/>
Environmental Issues in the construction industry. 2019. [Online]. Available Through:
<https://s3da-design.com/environmental-issues-construction-industry/>
Use bamboo in sustainable development. 2019. [Online]. Available Through: <
https://www.scidev.net/global/sustainability/news/bamboo-sustainable-development-mdg.html>
1 out of 12
Related Documents

Your All-in-One AI-Powered Toolkit for Academic Success.
+13062052269
info@desklib.com
Available 24*7 on WhatsApp / Email
Unlock your academic potential
© 2024 | Zucol Services PVT LTD | All rights reserved.