Group Assignment: Profitability of Essendon Electronics (BUACC 2613)
VerifiedAdded on  2023/06/05
|10
|2617
|257
Report
AI Summary
This report analyzes the profitability of Essendon Electronics, comparing traditional and Activity-Based Costing (ABC) methods for overhead allocation. The study examines two LCD screen products, Regal and Monarch, manufactured by the company. The report begins by presenting profitability under the traditional method, which allocates overhead based on machine hours. Subsequently, it analyzes profitability using the ABC method, which utilizes cost drivers for various activities. The analysis reveals that the change in overhead allocation significantly impacts the profitability of the two products, with Regal showing a loss under ABC. The report further discusses the rationale behind these profitability changes, addresses comments from Mr. Lockett, and provides recommendations for using ABC, including its benefits, costs, and limitations. The analysis includes detailed cost breakdowns, activity-based costing tables, and a variable cost analysis to support the findings and recommendations.
Contribute Materials
Your contribution can guide someone’s learning journey. Share your
documents today.
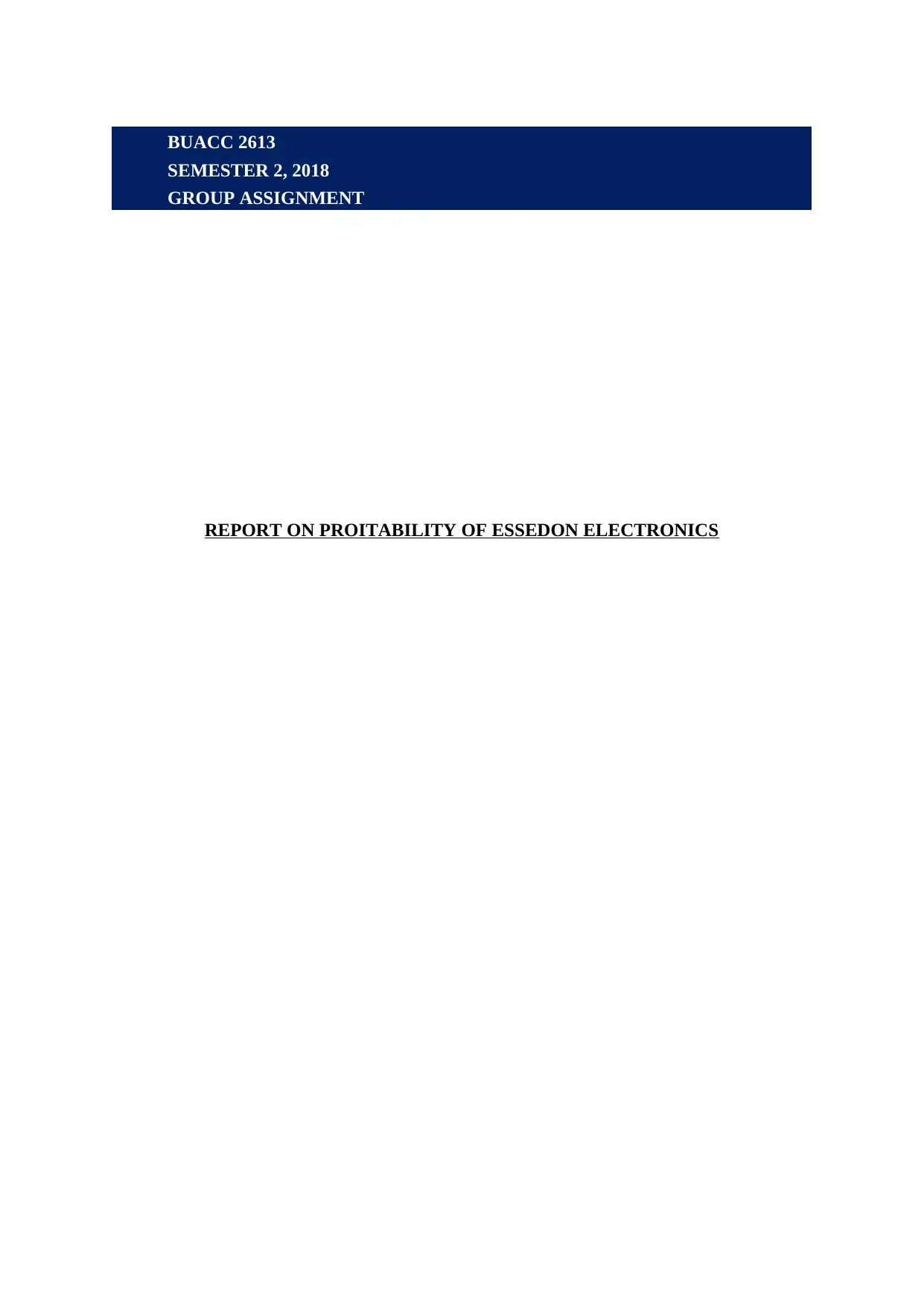
BUACC 2613
SEMESTER 2, 2018
GROUP ASSIGNMENT
REPORT ON PROITABILITY OF ESSEDON ELECTRONICS
SEMESTER 2, 2018
GROUP ASSIGNMENT
REPORT ON PROITABILITY OF ESSEDON ELECTRONICS
Secure Best Marks with AI Grader
Need help grading? Try our AI Grader for instant feedback on your assignments.
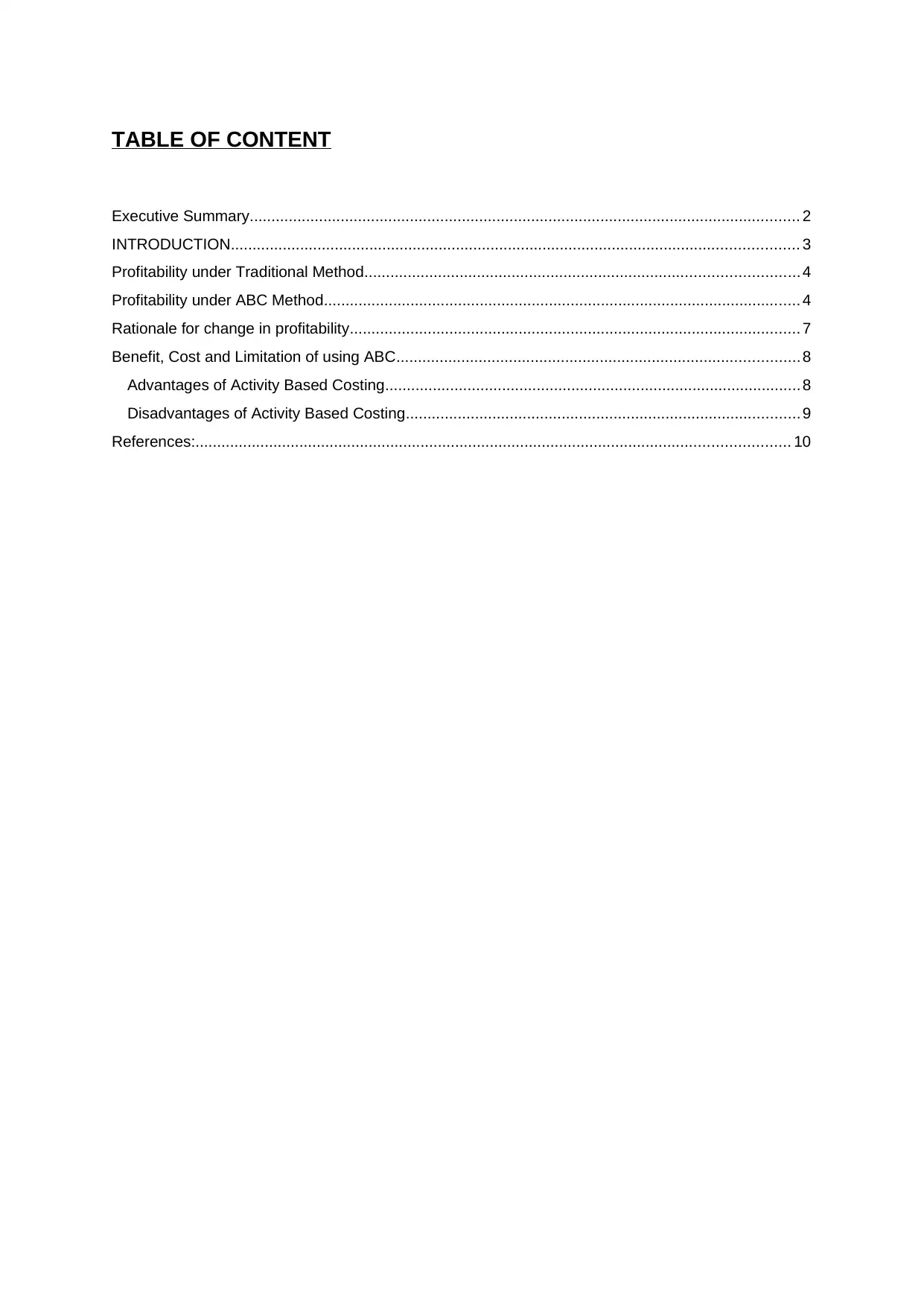
TABLE OF CONTENT
Executive Summary............................................................................................................................... 2
INTRODUCTION................................................................................................................................... 3
Profitability under Traditional Method.................................................................................................... 4
Profitability under ABC Method.............................................................................................................. 4
Rationale for change in profitability........................................................................................................ 7
Benefit, Cost and Limitation of using ABC............................................................................................. 8
Advantages of Activity Based Costing................................................................................................ 8
Disadvantages of Activity Based Costing........................................................................................... 9
References:......................................................................................................................................... 10
Executive Summary............................................................................................................................... 2
INTRODUCTION................................................................................................................................... 3
Profitability under Traditional Method.................................................................................................... 4
Profitability under ABC Method.............................................................................................................. 4
Rationale for change in profitability........................................................................................................ 7
Benefit, Cost and Limitation of using ABC............................................................................................. 8
Advantages of Activity Based Costing................................................................................................ 8
Disadvantages of Activity Based Costing........................................................................................... 9
References:......................................................................................................................................... 10
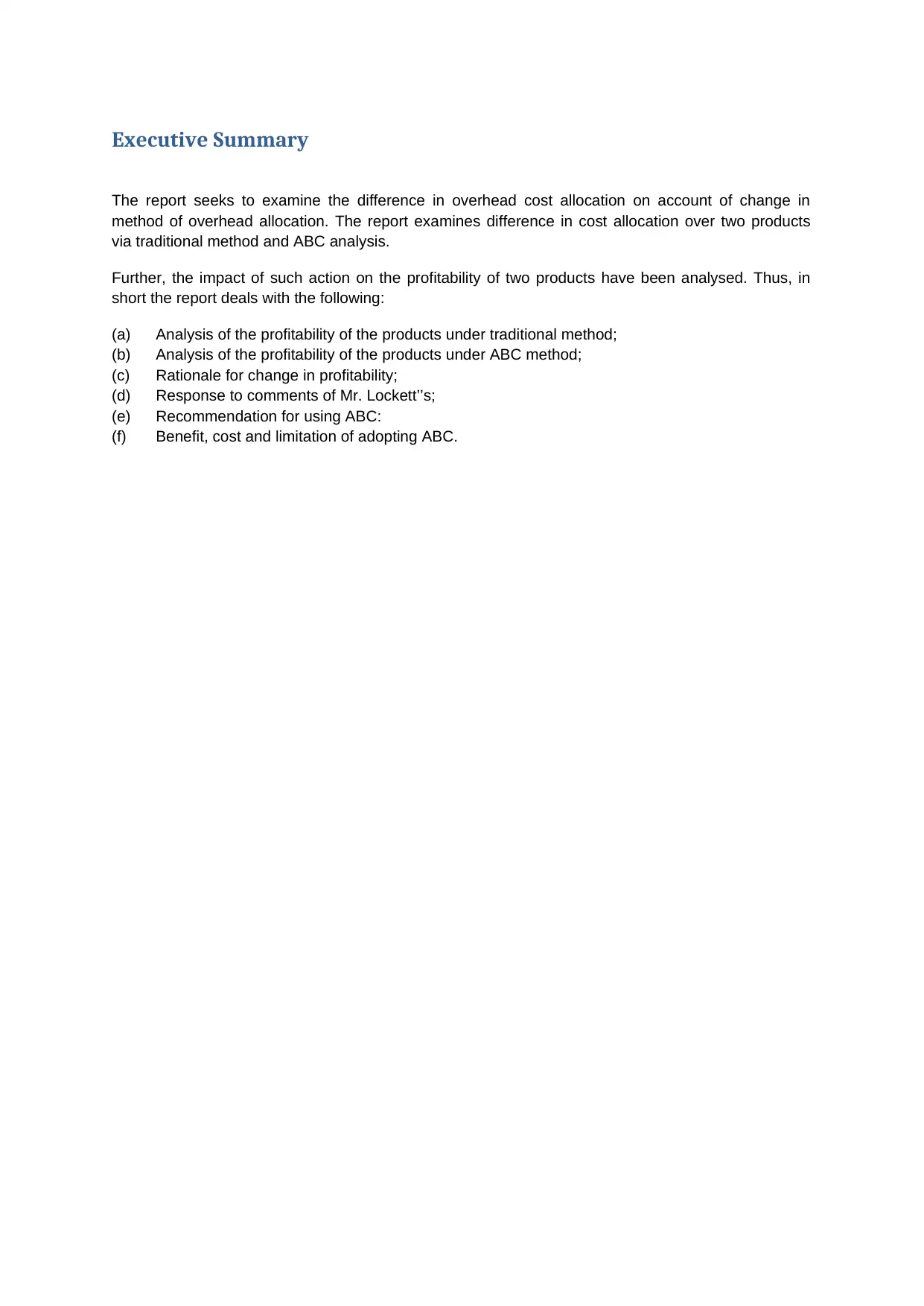
Executive Summary
The report seeks to examine the difference in overhead cost allocation on account of change in
method of overhead allocation. The report examines difference in cost allocation over two products
via traditional method and ABC analysis.
Further, the impact of such action on the profitability of two products have been analysed. Thus, in
short the report deals with the following:
(a) Analysis of the profitability of the products under traditional method;
(b) Analysis of the profitability of the products under ABC method;
(c) Rationale for change in profitability;
(d) Response to comments of Mr. Lockett’’s;
(e) Recommendation for using ABC:
(f) Benefit, cost and limitation of adopting ABC.
The report seeks to examine the difference in overhead cost allocation on account of change in
method of overhead allocation. The report examines difference in cost allocation over two products
via traditional method and ABC analysis.
Further, the impact of such action on the profitability of two products have been analysed. Thus, in
short the report deals with the following:
(a) Analysis of the profitability of the products under traditional method;
(b) Analysis of the profitability of the products under ABC method;
(c) Rationale for change in profitability;
(d) Response to comments of Mr. Lockett’’s;
(e) Recommendation for using ABC:
(f) Benefit, cost and limitation of adopting ABC.
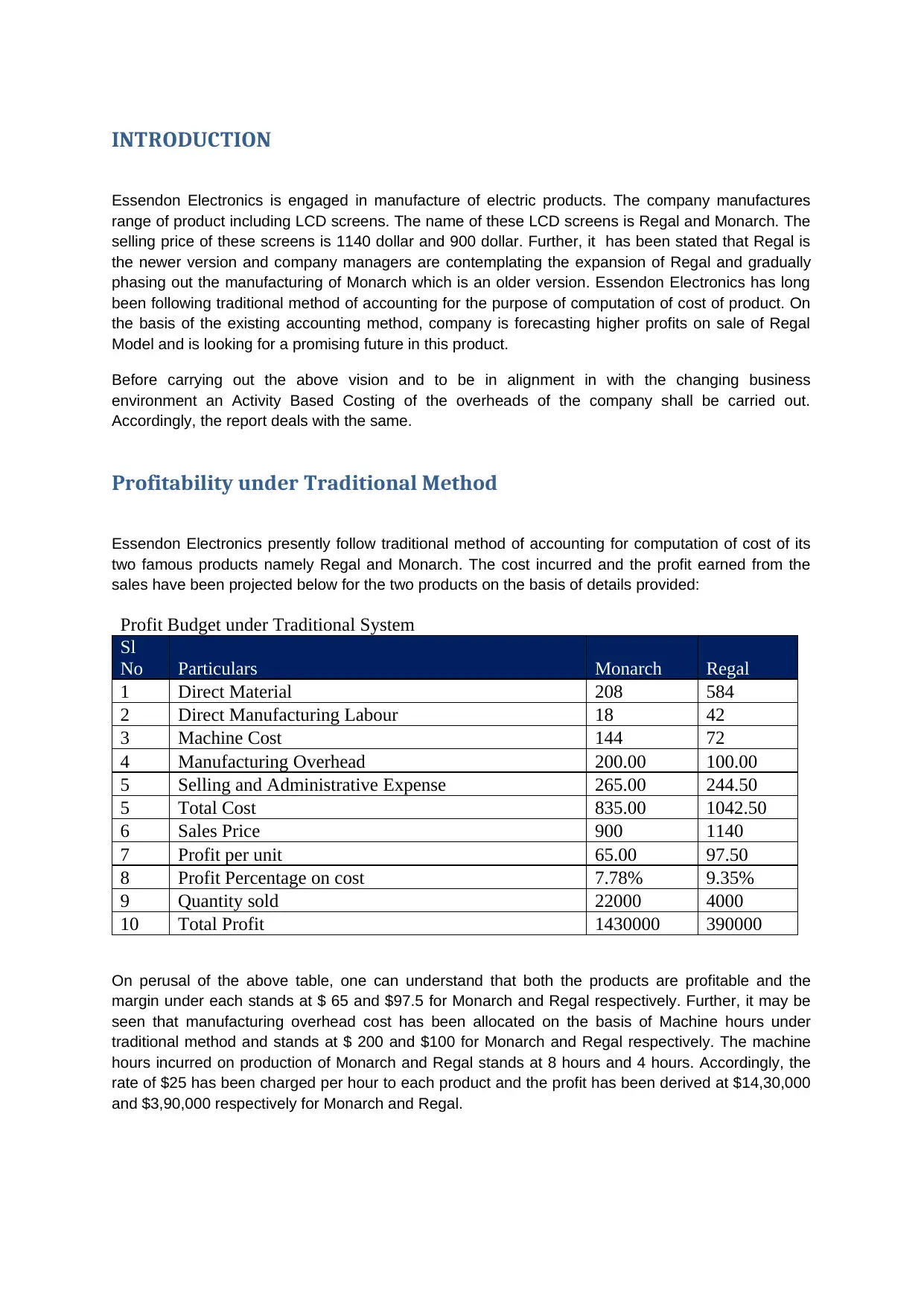
INTRODUCTION
Essendon Electronics is engaged in manufacture of electric products. The company manufactures
range of product including LCD screens. The name of these LCD screens is Regal and Monarch. The
selling price of these screens is 1140 dollar and 900 dollar. Further, it has been stated that Regal is
the newer version and company managers are contemplating the expansion of Regal and gradually
phasing out the manufacturing of Monarch which is an older version. Essendon Electronics has long
been following traditional method of accounting for the purpose of computation of cost of product. On
the basis of the existing accounting method, company is forecasting higher profits on sale of Regal
Model and is looking for a promising future in this product.
Before carrying out the above vision and to be in alignment in with the changing business
environment an Activity Based Costing of the overheads of the company shall be carried out.
Accordingly, the report deals with the same.
Profitability under Traditional Method
Essendon Electronics presently follow traditional method of accounting for computation of cost of its
two famous products namely Regal and Monarch. The cost incurred and the profit earned from the
sales have been projected below for the two products on the basis of details provided:
Profit Budget under Traditional System
Sl
No Particulars Monarch Regal
1 Direct Material 208 584
2 Direct Manufacturing Labour 18 42
3 Machine Cost 144 72
4 Manufacturing Overhead 200.00 100.00
5 Selling and Administrative Expense 265.00 244.50
5 Total Cost 835.00 1042.50
6 Sales Price 900 1140
7 Profit per unit 65.00 97.50
8 Profit Percentage on cost 7.78% 9.35%
9 Quantity sold 22000 4000
10 Total Profit 1430000 390000
On perusal of the above table, one can understand that both the products are profitable and the
margin under each stands at $ 65 and $97.5 for Monarch and Regal respectively. Further, it may be
seen that manufacturing overhead cost has been allocated on the basis of Machine hours under
traditional method and stands at $ 200 and $100 for Monarch and Regal respectively. The machine
hours incurred on production of Monarch and Regal stands at 8 hours and 4 hours. Accordingly, the
rate of $25 has been charged per hour to each product and the profit has been derived at $14,30,000
and $3,90,000 respectively for Monarch and Regal.
Essendon Electronics is engaged in manufacture of electric products. The company manufactures
range of product including LCD screens. The name of these LCD screens is Regal and Monarch. The
selling price of these screens is 1140 dollar and 900 dollar. Further, it has been stated that Regal is
the newer version and company managers are contemplating the expansion of Regal and gradually
phasing out the manufacturing of Monarch which is an older version. Essendon Electronics has long
been following traditional method of accounting for the purpose of computation of cost of product. On
the basis of the existing accounting method, company is forecasting higher profits on sale of Regal
Model and is looking for a promising future in this product.
Before carrying out the above vision and to be in alignment in with the changing business
environment an Activity Based Costing of the overheads of the company shall be carried out.
Accordingly, the report deals with the same.
Profitability under Traditional Method
Essendon Electronics presently follow traditional method of accounting for computation of cost of its
two famous products namely Regal and Monarch. The cost incurred and the profit earned from the
sales have been projected below for the two products on the basis of details provided:
Profit Budget under Traditional System
Sl
No Particulars Monarch Regal
1 Direct Material 208 584
2 Direct Manufacturing Labour 18 42
3 Machine Cost 144 72
4 Manufacturing Overhead 200.00 100.00
5 Selling and Administrative Expense 265.00 244.50
5 Total Cost 835.00 1042.50
6 Sales Price 900 1140
7 Profit per unit 65.00 97.50
8 Profit Percentage on cost 7.78% 9.35%
9 Quantity sold 22000 4000
10 Total Profit 1430000 390000
On perusal of the above table, one can understand that both the products are profitable and the
margin under each stands at $ 65 and $97.5 for Monarch and Regal respectively. Further, it may be
seen that manufacturing overhead cost has been allocated on the basis of Machine hours under
traditional method and stands at $ 200 and $100 for Monarch and Regal respectively. The machine
hours incurred on production of Monarch and Regal stands at 8 hours and 4 hours. Accordingly, the
rate of $25 has been charged per hour to each product and the profit has been derived at $14,30,000
and $3,90,000 respectively for Monarch and Regal.
Secure Best Marks with AI Grader
Need help grading? Try our AI Grader for instant feedback on your assignments.
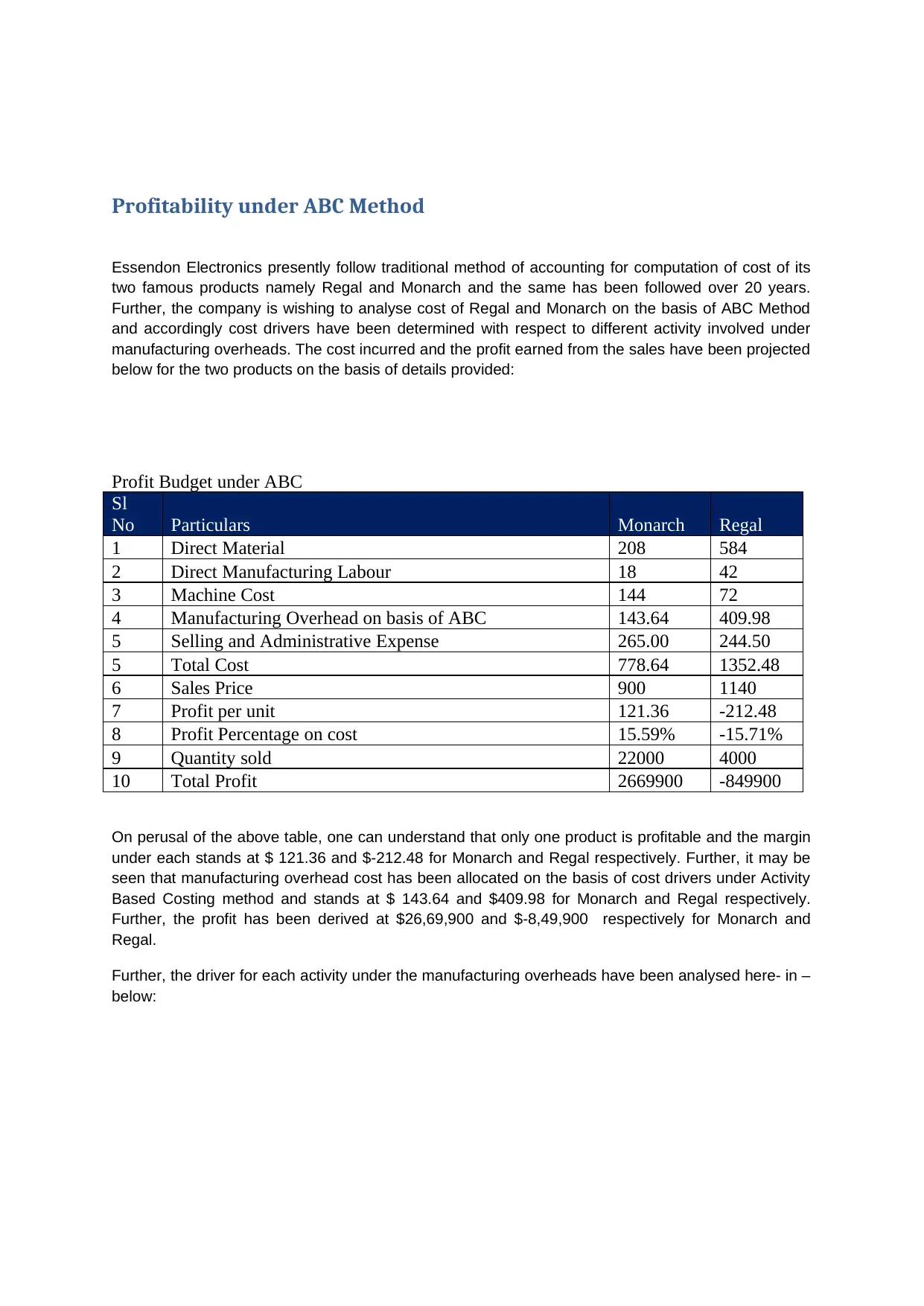
Profitability under ABC Method
Essendon Electronics presently follow traditional method of accounting for computation of cost of its
two famous products namely Regal and Monarch and the same has been followed over 20 years.
Further, the company is wishing to analyse cost of Regal and Monarch on the basis of ABC Method
and accordingly cost drivers have been determined with respect to different activity involved under
manufacturing overheads. The cost incurred and the profit earned from the sales have been projected
below for the two products on the basis of details provided:
Profit Budget under ABC
Sl
No Particulars Monarch Regal
1 Direct Material 208 584
2 Direct Manufacturing Labour 18 42
3 Machine Cost 144 72
4 Manufacturing Overhead on basis of ABC 143.64 409.98
5 Selling and Administrative Expense 265.00 244.50
5 Total Cost 778.64 1352.48
6 Sales Price 900 1140
7 Profit per unit 121.36 -212.48
8 Profit Percentage on cost 15.59% -15.71%
9 Quantity sold 22000 4000
10 Total Profit 2669900 -849900
On perusal of the above table, one can understand that only one product is profitable and the margin
under each stands at $ 121.36 and $-212.48 for Monarch and Regal respectively. Further, it may be
seen that manufacturing overhead cost has been allocated on the basis of cost drivers under Activity
Based Costing method and stands at $ 143.64 and $409.98 for Monarch and Regal respectively.
Further, the profit has been derived at $26,69,900 and $-8,49,900 respectively for Monarch and
Regal.
Further, the driver for each activity under the manufacturing overheads have been analysed here- in –
below:
Essendon Electronics presently follow traditional method of accounting for computation of cost of its
two famous products namely Regal and Monarch and the same has been followed over 20 years.
Further, the company is wishing to analyse cost of Regal and Monarch on the basis of ABC Method
and accordingly cost drivers have been determined with respect to different activity involved under
manufacturing overheads. The cost incurred and the profit earned from the sales have been projected
below for the two products on the basis of details provided:
Profit Budget under ABC
Sl
No Particulars Monarch Regal
1 Direct Material 208 584
2 Direct Manufacturing Labour 18 42
3 Machine Cost 144 72
4 Manufacturing Overhead on basis of ABC 143.64 409.98
5 Selling and Administrative Expense 265.00 244.50
5 Total Cost 778.64 1352.48
6 Sales Price 900 1140
7 Profit per unit 121.36 -212.48
8 Profit Percentage on cost 15.59% -15.71%
9 Quantity sold 22000 4000
10 Total Profit 2669900 -849900
On perusal of the above table, one can understand that only one product is profitable and the margin
under each stands at $ 121.36 and $-212.48 for Monarch and Regal respectively. Further, it may be
seen that manufacturing overhead cost has been allocated on the basis of cost drivers under Activity
Based Costing method and stands at $ 143.64 and $409.98 for Monarch and Regal respectively.
Further, the profit has been derived at $26,69,900 and $-8,49,900 respectively for Monarch and
Regal.
Further, the driver for each activity under the manufacturing overheads have been analysed here- in –
below:
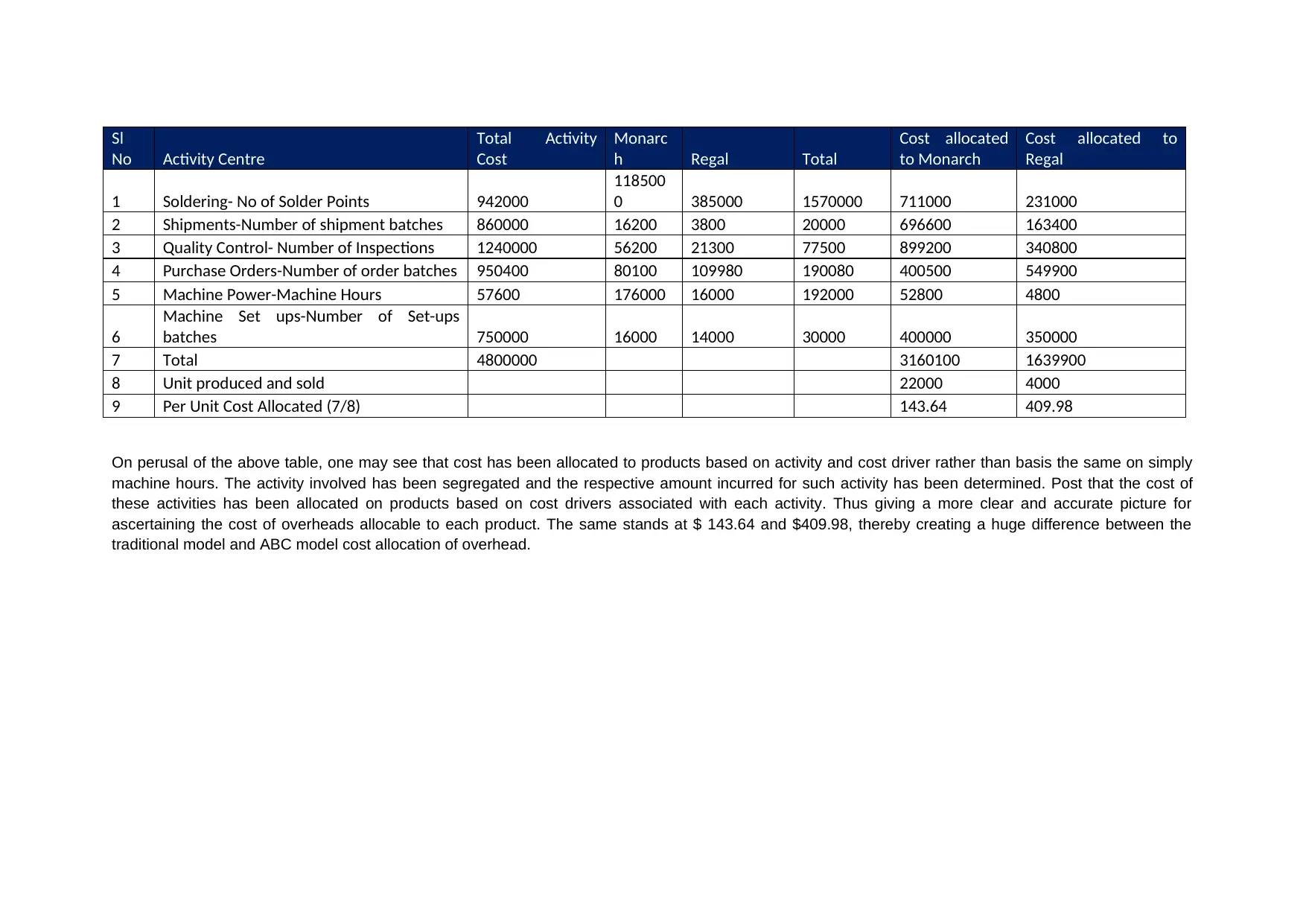
Sl
No Activity Centre
Total Activity
Cost
Monarc
h Regal Total
Cost allocated
to Monarch
Cost allocated to
Regal
1 Soldering- No of Solder Points 942000
118500
0 385000 1570000 711000 231000
2 Shipments-Number of shipment batches 860000 16200 3800 20000 696600 163400
3 Quality Control- Number of Inspections 1240000 56200 21300 77500 899200 340800
4 Purchase Orders-Number of order batches 950400 80100 109980 190080 400500 549900
5 Machine Power-Machine Hours 57600 176000 16000 192000 52800 4800
6
Machine Set ups-Number of Set-ups
batches 750000 16000 14000 30000 400000 350000
7 Total 4800000 3160100 1639900
8 Unit produced and sold 22000 4000
9 Per Unit Cost Allocated (7/8) 143.64 409.98
On perusal of the above table, one may see that cost has been allocated to products based on activity and cost driver rather than basis the same on simply
machine hours. The activity involved has been segregated and the respective amount incurred for such activity has been determined. Post that the cost of
these activities has been allocated on products based on cost drivers associated with each activity. Thus giving a more clear and accurate picture for
ascertaining the cost of overheads allocable to each product. The same stands at $ 143.64 and $409.98, thereby creating a huge difference between the
traditional model and ABC model cost allocation of overhead.
No Activity Centre
Total Activity
Cost
Monarc
h Regal Total
Cost allocated
to Monarch
Cost allocated to
Regal
1 Soldering- No of Solder Points 942000
118500
0 385000 1570000 711000 231000
2 Shipments-Number of shipment batches 860000 16200 3800 20000 696600 163400
3 Quality Control- Number of Inspections 1240000 56200 21300 77500 899200 340800
4 Purchase Orders-Number of order batches 950400 80100 109980 190080 400500 549900
5 Machine Power-Machine Hours 57600 176000 16000 192000 52800 4800
6
Machine Set ups-Number of Set-ups
batches 750000 16000 14000 30000 400000 350000
7 Total 4800000 3160100 1639900
8 Unit produced and sold 22000 4000
9 Per Unit Cost Allocated (7/8) 143.64 409.98
On perusal of the above table, one may see that cost has been allocated to products based on activity and cost driver rather than basis the same on simply
machine hours. The activity involved has been segregated and the respective amount incurred for such activity has been determined. Post that the cost of
these activities has been allocated on products based on cost drivers associated with each activity. Thus giving a more clear and accurate picture for
ascertaining the cost of overheads allocable to each product. The same stands at $ 143.64 and $409.98, thereby creating a huge difference between the
traditional model and ABC model cost allocation of overhead.
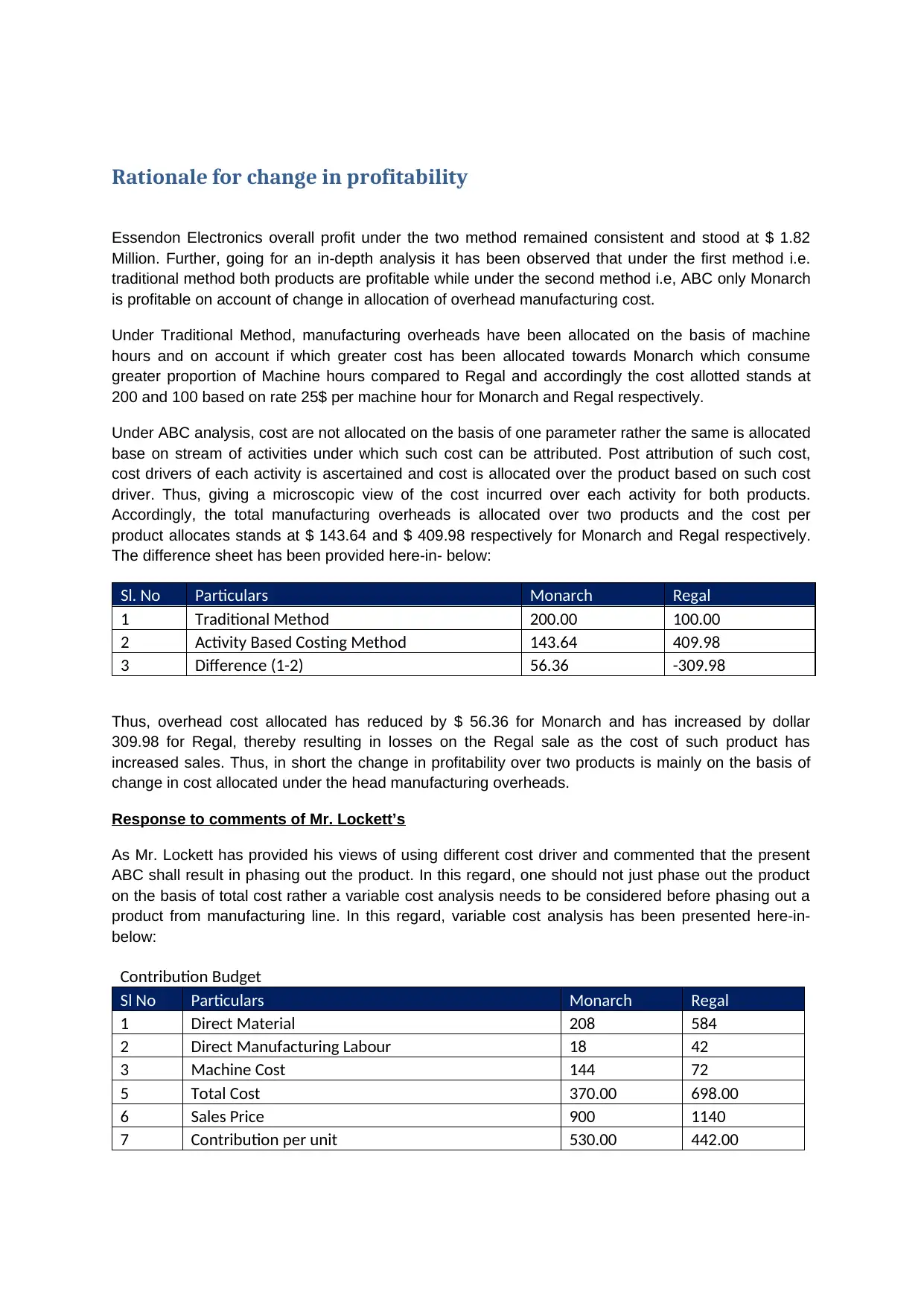
Rationale for change in profitability
Essendon Electronics overall profit under the two method remained consistent and stood at $ 1.82
Million. Further, going for an in-depth analysis it has been observed that under the first method i.e.
traditional method both products are profitable while under the second method i.e, ABC only Monarch
is profitable on account of change in allocation of overhead manufacturing cost.
Under Traditional Method, manufacturing overheads have been allocated on the basis of machine
hours and on account if which greater cost has been allocated towards Monarch which consume
greater proportion of Machine hours compared to Regal and accordingly the cost allotted stands at
200 and 100 based on rate 25$ per machine hour for Monarch and Regal respectively.
Under ABC analysis, cost are not allocated on the basis of one parameter rather the same is allocated
base on stream of activities under which such cost can be attributed. Post attribution of such cost,
cost drivers of each activity is ascertained and cost is allocated over the product based on such cost
driver. Thus, giving a microscopic view of the cost incurred over each activity for both products.
Accordingly, the total manufacturing overheads is allocated over two products and the cost per
product allocates stands at $ 143.64 and $ 409.98 respectively for Monarch and Regal respectively.
The difference sheet has been provided here-in- below:
Sl. No Particulars Monarch Regal
1 Traditional Method 200.00 100.00
2 Activity Based Costing Method 143.64 409.98
3 Difference (1-2) 56.36 -309.98
Thus, overhead cost allocated has reduced by $ 56.36 for Monarch and has increased by dollar
309.98 for Regal, thereby resulting in losses on the Regal sale as the cost of such product has
increased sales. Thus, in short the change in profitability over two products is mainly on the basis of
change in cost allocated under the head manufacturing overheads.
Response to comments of Mr. Lockett’s
As Mr. Lockett has provided his views of using different cost driver and commented that the present
ABC shall result in phasing out the product. In this regard, one should not just phase out the product
on the basis of total cost rather a variable cost analysis needs to be considered before phasing out a
product from manufacturing line. In this regard, variable cost analysis has been presented here-in-
below:
Contribution Budget
Sl No Particulars Monarch Regal
1 Direct Material 208 584
2 Direct Manufacturing Labour 18 42
3 Machine Cost 144 72
5 Total Cost 370.00 698.00
6 Sales Price 900 1140
7 Contribution per unit 530.00 442.00
Essendon Electronics overall profit under the two method remained consistent and stood at $ 1.82
Million. Further, going for an in-depth analysis it has been observed that under the first method i.e.
traditional method both products are profitable while under the second method i.e, ABC only Monarch
is profitable on account of change in allocation of overhead manufacturing cost.
Under Traditional Method, manufacturing overheads have been allocated on the basis of machine
hours and on account if which greater cost has been allocated towards Monarch which consume
greater proportion of Machine hours compared to Regal and accordingly the cost allotted stands at
200 and 100 based on rate 25$ per machine hour for Monarch and Regal respectively.
Under ABC analysis, cost are not allocated on the basis of one parameter rather the same is allocated
base on stream of activities under which such cost can be attributed. Post attribution of such cost,
cost drivers of each activity is ascertained and cost is allocated over the product based on such cost
driver. Thus, giving a microscopic view of the cost incurred over each activity for both products.
Accordingly, the total manufacturing overheads is allocated over two products and the cost per
product allocates stands at $ 143.64 and $ 409.98 respectively for Monarch and Regal respectively.
The difference sheet has been provided here-in- below:
Sl. No Particulars Monarch Regal
1 Traditional Method 200.00 100.00
2 Activity Based Costing Method 143.64 409.98
3 Difference (1-2) 56.36 -309.98
Thus, overhead cost allocated has reduced by $ 56.36 for Monarch and has increased by dollar
309.98 for Regal, thereby resulting in losses on the Regal sale as the cost of such product has
increased sales. Thus, in short the change in profitability over two products is mainly on the basis of
change in cost allocated under the head manufacturing overheads.
Response to comments of Mr. Lockett’s
As Mr. Lockett has provided his views of using different cost driver and commented that the present
ABC shall result in phasing out the product. In this regard, one should not just phase out the product
on the basis of total cost rather a variable cost analysis needs to be considered before phasing out a
product from manufacturing line. In this regard, variable cost analysis has been presented here-in-
below:
Contribution Budget
Sl No Particulars Monarch Regal
1 Direct Material 208 584
2 Direct Manufacturing Labour 18 42
3 Machine Cost 144 72
5 Total Cost 370.00 698.00
6 Sales Price 900 1140
7 Contribution per unit 530.00 442.00
Paraphrase This Document
Need a fresh take? Get an instant paraphrase of this document with our AI Paraphraser
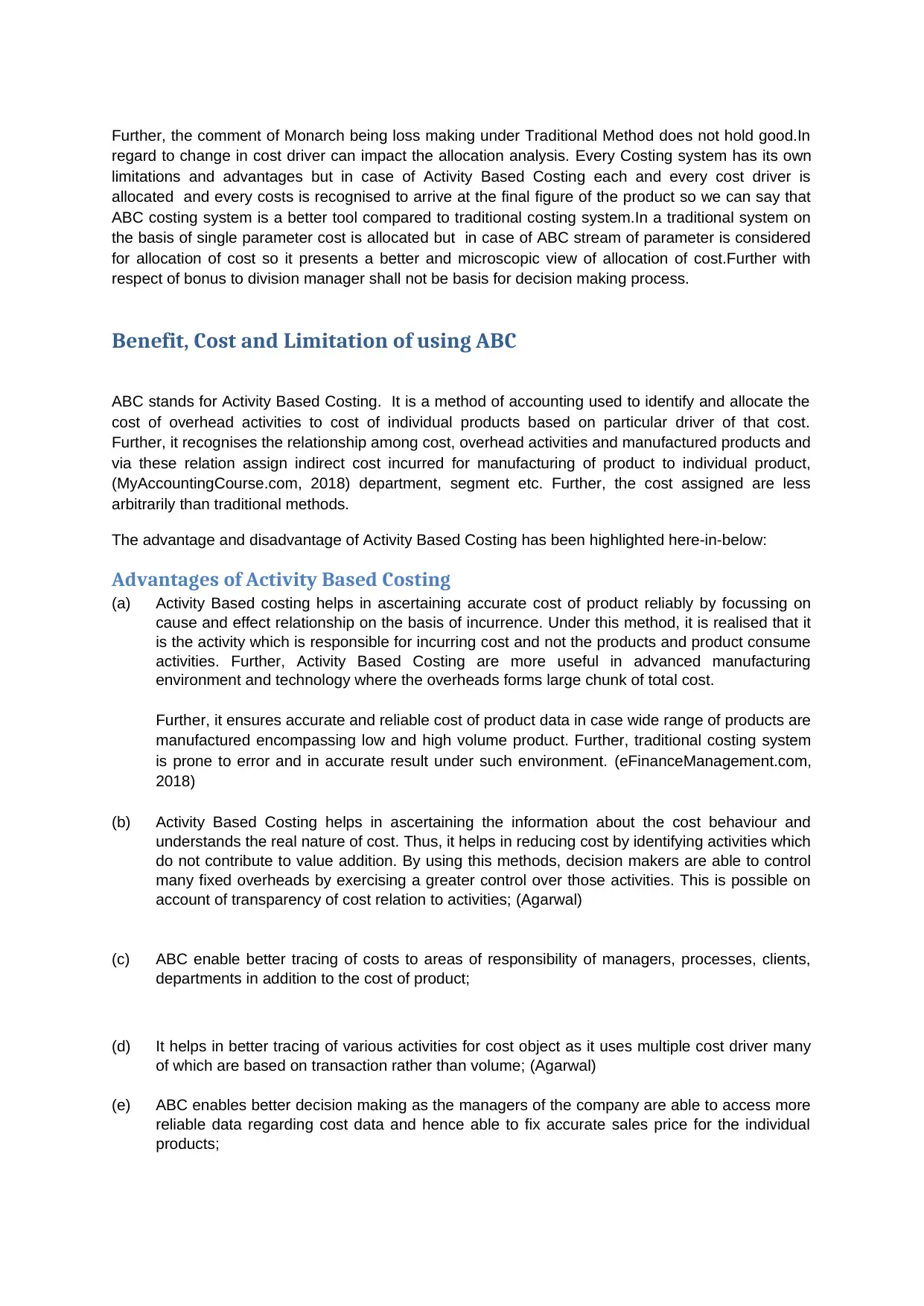
Further, the comment of Monarch being loss making under Traditional Method does not hold good.In
regard to change in cost driver can impact the allocation analysis. Every Costing system has its own
limitations and advantages but in case of Activity Based Costing each and every cost driver is
allocated and every costs is recognised to arrive at the final figure of the product so we can say that
ABC costing system is a better tool compared to traditional costing system.In a traditional system on
the basis of single parameter cost is allocated but in case of ABC stream of parameter is considered
for allocation of cost so it presents a better and microscopic view of allocation of cost.Further with
respect of bonus to division manager shall not be basis for decision making process.
Benefit, Cost and Limitation of using ABC
ABC stands for Activity Based Costing. It is a method of accounting used to identify and allocate the
cost of overhead activities to cost of individual products based on particular driver of that cost.
Further, it recognises the relationship among cost, overhead activities and manufactured products and
via these relation assign indirect cost incurred for manufacturing of product to individual product,
(MyAccountingCourse.com, 2018) department, segment etc. Further, the cost assigned are less
arbitrarily than traditional methods.
The advantage and disadvantage of Activity Based Costing has been highlighted here-in-below:
Advantages of Activity Based Costing
(a) Activity Based costing helps in ascertaining accurate cost of product reliably by focussing on
cause and effect relationship on the basis of incurrence. Under this method, it is realised that it
is the activity which is responsible for incurring cost and not the products and product consume
activities. Further, Activity Based Costing are more useful in advanced manufacturing
environment and technology where the overheads forms large chunk of total cost.
Further, it ensures accurate and reliable cost of product data in case wide range of products are
manufactured encompassing low and high volume product. Further, traditional costing system
is prone to error and in accurate result under such environment. (eFinanceManagement.com,
2018)
(b) Activity Based Costing helps in ascertaining the information about the cost behaviour and
understands the real nature of cost. Thus, it helps in reducing cost by identifying activities which
do not contribute to value addition. By using this methods, decision makers are able to control
many fixed overheads by exercising a greater control over those activities. This is possible on
account of transparency of cost relation to activities; (Agarwal)
(c) ABC enable better tracing of costs to areas of responsibility of managers, processes, clients,
departments in addition to the cost of product;
(d) It helps in better tracing of various activities for cost object as it uses multiple cost driver many
of which are based on transaction rather than volume; (Agarwal)
(e) ABC enables better decision making as the managers of the company are able to access more
reliable data regarding cost data and hence able to fix accurate sales price for the individual
products;
regard to change in cost driver can impact the allocation analysis. Every Costing system has its own
limitations and advantages but in case of Activity Based Costing each and every cost driver is
allocated and every costs is recognised to arrive at the final figure of the product so we can say that
ABC costing system is a better tool compared to traditional costing system.In a traditional system on
the basis of single parameter cost is allocated but in case of ABC stream of parameter is considered
for allocation of cost so it presents a better and microscopic view of allocation of cost.Further with
respect of bonus to division manager shall not be basis for decision making process.
Benefit, Cost and Limitation of using ABC
ABC stands for Activity Based Costing. It is a method of accounting used to identify and allocate the
cost of overhead activities to cost of individual products based on particular driver of that cost.
Further, it recognises the relationship among cost, overhead activities and manufactured products and
via these relation assign indirect cost incurred for manufacturing of product to individual product,
(MyAccountingCourse.com, 2018) department, segment etc. Further, the cost assigned are less
arbitrarily than traditional methods.
The advantage and disadvantage of Activity Based Costing has been highlighted here-in-below:
Advantages of Activity Based Costing
(a) Activity Based costing helps in ascertaining accurate cost of product reliably by focussing on
cause and effect relationship on the basis of incurrence. Under this method, it is realised that it
is the activity which is responsible for incurring cost and not the products and product consume
activities. Further, Activity Based Costing are more useful in advanced manufacturing
environment and technology where the overheads forms large chunk of total cost.
Further, it ensures accurate and reliable cost of product data in case wide range of products are
manufactured encompassing low and high volume product. Further, traditional costing system
is prone to error and in accurate result under such environment. (eFinanceManagement.com,
2018)
(b) Activity Based Costing helps in ascertaining the information about the cost behaviour and
understands the real nature of cost. Thus, it helps in reducing cost by identifying activities which
do not contribute to value addition. By using this methods, decision makers are able to control
many fixed overheads by exercising a greater control over those activities. This is possible on
account of transparency of cost relation to activities; (Agarwal)
(c) ABC enable better tracing of costs to areas of responsibility of managers, processes, clients,
departments in addition to the cost of product;
(d) It helps in better tracing of various activities for cost object as it uses multiple cost driver many
of which are based on transaction rather than volume; (Agarwal)
(e) ABC enables better decision making as the managers of the company are able to access more
reliable data regarding cost data and hence able to fix accurate sales price for the individual
products;
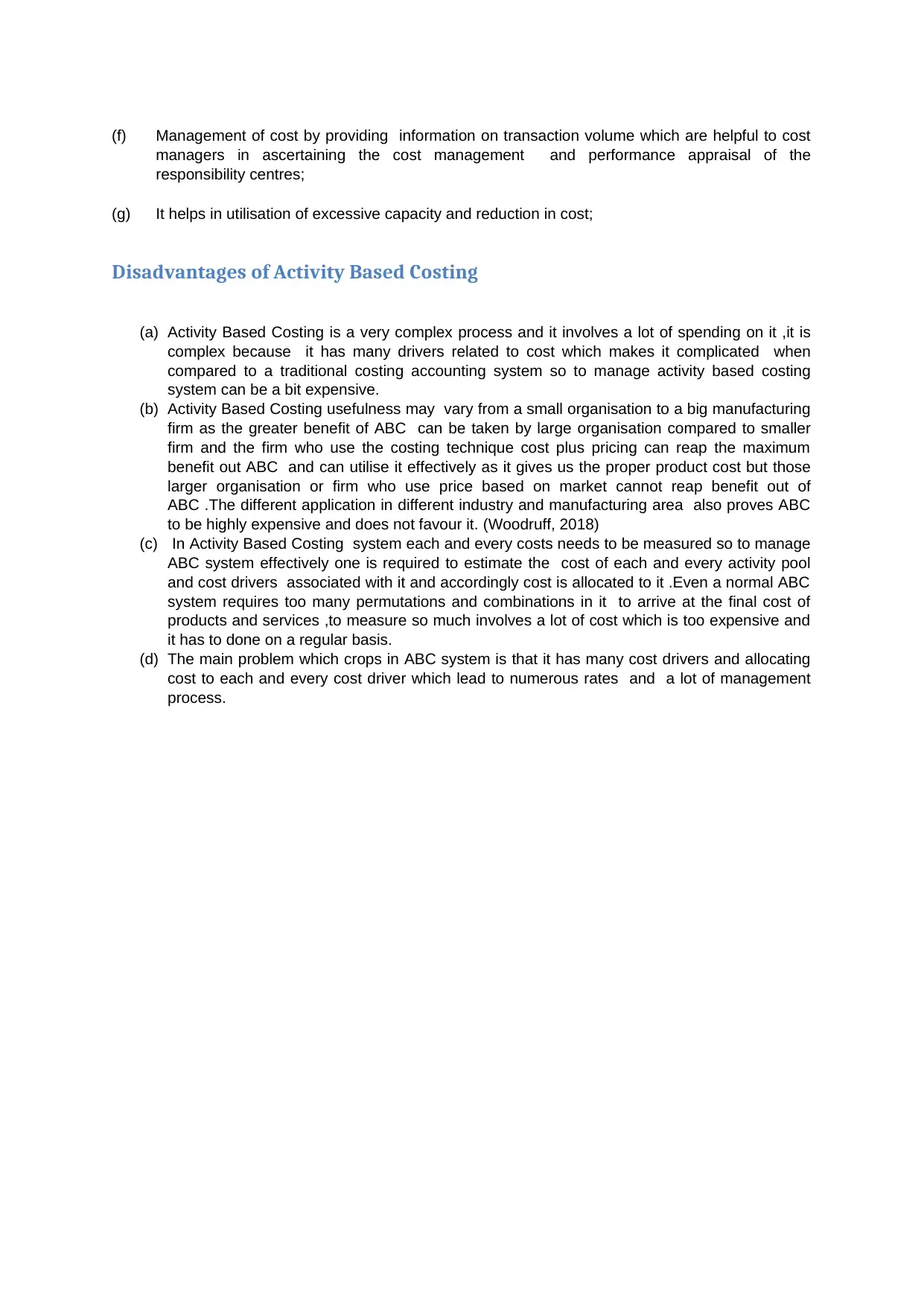
(f) Management of cost by providing information on transaction volume which are helpful to cost
managers in ascertaining the cost management and performance appraisal of the
responsibility centres;
(g) It helps in utilisation of excessive capacity and reduction in cost;
Disadvantages of Activity Based Costing
(a) Activity Based Costing is a very complex process and it involves a lot of spending on it ,it is
complex because it has many drivers related to cost which makes it complicated when
compared to a traditional costing accounting system so to manage activity based costing
system can be a bit expensive.
(b) Activity Based Costing usefulness may vary from a small organisation to a big manufacturing
firm as the greater benefit of ABC can be taken by large organisation compared to smaller
firm and the firm who use the costing technique cost plus pricing can reap the maximum
benefit out ABC and can utilise it effectively as it gives us the proper product cost but those
larger organisation or firm who use price based on market cannot reap benefit out of
ABC .The different application in different industry and manufacturing area also proves ABC
to be highly expensive and does not favour it. (Woodruff, 2018)
(c) In Activity Based Costing system each and every costs needs to be measured so to manage
ABC system effectively one is required to estimate the cost of each and every activity pool
and cost drivers associated with it and accordingly cost is allocated to it .Even a normal ABC
system requires too many permutations and combinations in it to arrive at the final cost of
products and services ,to measure so much involves a lot of cost which is too expensive and
it has to done on a regular basis.
(d) The main problem which crops in ABC system is that it has many cost drivers and allocating
cost to each and every cost driver which lead to numerous rates and a lot of management
process.
managers in ascertaining the cost management and performance appraisal of the
responsibility centres;
(g) It helps in utilisation of excessive capacity and reduction in cost;
Disadvantages of Activity Based Costing
(a) Activity Based Costing is a very complex process and it involves a lot of spending on it ,it is
complex because it has many drivers related to cost which makes it complicated when
compared to a traditional costing accounting system so to manage activity based costing
system can be a bit expensive.
(b) Activity Based Costing usefulness may vary from a small organisation to a big manufacturing
firm as the greater benefit of ABC can be taken by large organisation compared to smaller
firm and the firm who use the costing technique cost plus pricing can reap the maximum
benefit out ABC and can utilise it effectively as it gives us the proper product cost but those
larger organisation or firm who use price based on market cannot reap benefit out of
ABC .The different application in different industry and manufacturing area also proves ABC
to be highly expensive and does not favour it. (Woodruff, 2018)
(c) In Activity Based Costing system each and every costs needs to be measured so to manage
ABC system effectively one is required to estimate the cost of each and every activity pool
and cost drivers associated with it and accordingly cost is allocated to it .Even a normal ABC
system requires too many permutations and combinations in it to arrive at the final cost of
products and services ,to measure so much involves a lot of cost which is too expensive and
it has to done on a regular basis.
(d) The main problem which crops in ABC system is that it has many cost drivers and allocating
cost to each and every cost driver which lead to numerous rates and a lot of management
process.
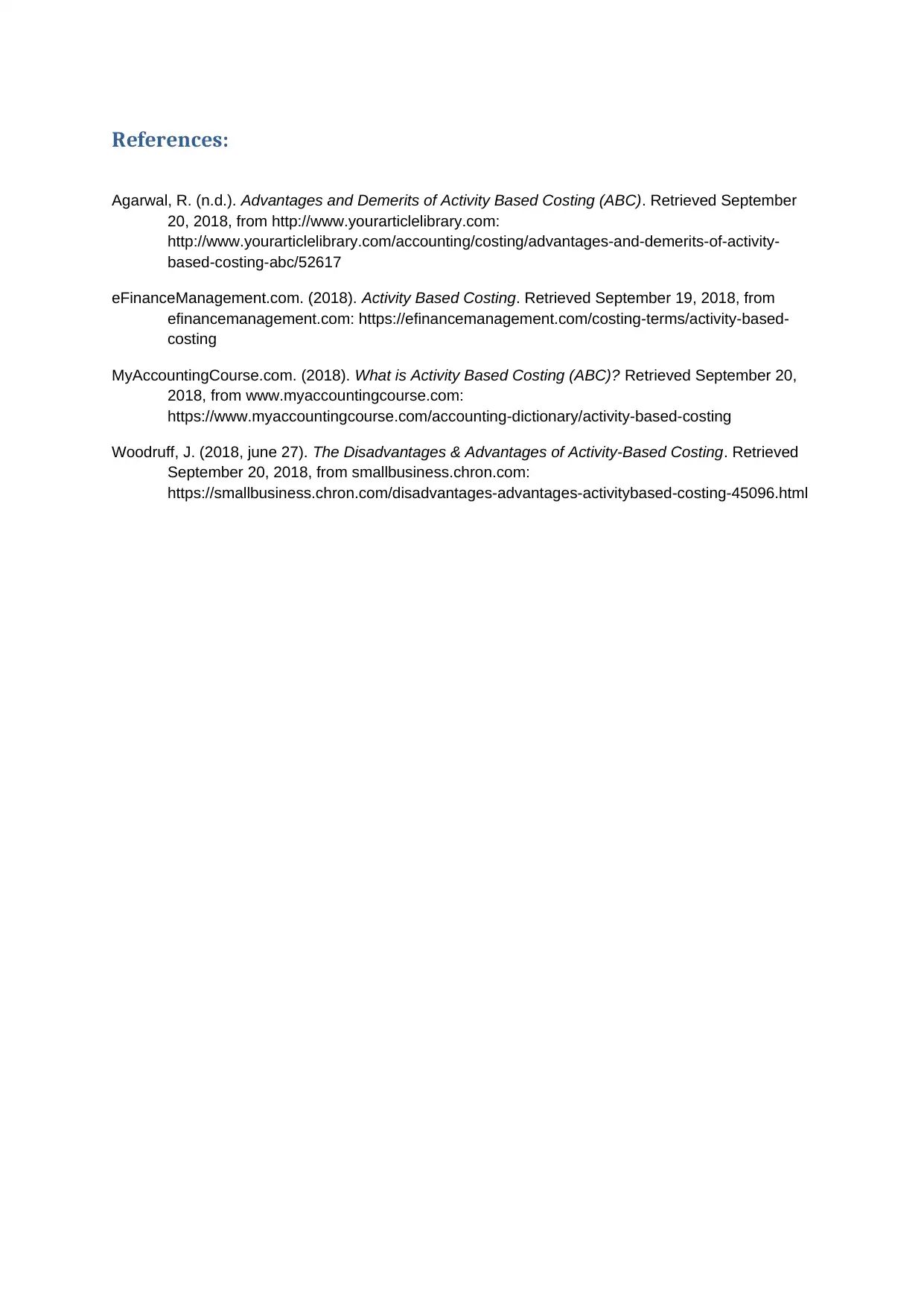
References:
Agarwal, R. (n.d.). Advantages and Demerits of Activity Based Costing (ABC). Retrieved September
20, 2018, from http://www.yourarticlelibrary.com:
http://www.yourarticlelibrary.com/accounting/costing/advantages-and-demerits-of-activity-
based-costing-abc/52617
eFinanceManagement.com. (2018). Activity Based Costing. Retrieved September 19, 2018, from
efinancemanagement.com: https://efinancemanagement.com/costing-terms/activity-based-
costing
MyAccountingCourse.com. (2018). What is Activity Based Costing (ABC)? Retrieved September 20,
2018, from www.myaccountingcourse.com:
https://www.myaccountingcourse.com/accounting-dictionary/activity-based-costing
Woodruff, J. (2018, june 27). The Disadvantages & Advantages of Activity-Based Costing. Retrieved
September 20, 2018, from smallbusiness.chron.com:
https://smallbusiness.chron.com/disadvantages-advantages-activitybased-costing-45096.html
Agarwal, R. (n.d.). Advantages and Demerits of Activity Based Costing (ABC). Retrieved September
20, 2018, from http://www.yourarticlelibrary.com:
http://www.yourarticlelibrary.com/accounting/costing/advantages-and-demerits-of-activity-
based-costing-abc/52617
eFinanceManagement.com. (2018). Activity Based Costing. Retrieved September 19, 2018, from
efinancemanagement.com: https://efinancemanagement.com/costing-terms/activity-based-
costing
MyAccountingCourse.com. (2018). What is Activity Based Costing (ABC)? Retrieved September 20,
2018, from www.myaccountingcourse.com:
https://www.myaccountingcourse.com/accounting-dictionary/activity-based-costing
Woodruff, J. (2018, june 27). The Disadvantages & Advantages of Activity-Based Costing. Retrieved
September 20, 2018, from smallbusiness.chron.com:
https://smallbusiness.chron.com/disadvantages-advantages-activitybased-costing-45096.html
1 out of 10
Related Documents

Your All-in-One AI-Powered Toolkit for Academic Success.
 +13062052269
info@desklib.com
Available 24*7 on WhatsApp / Email
Unlock your academic potential
© 2024  |  Zucol Services PVT LTD  |  All rights reserved.